Topic 1 2 Refrigeration Cycle 1 Carnot Refrigeration
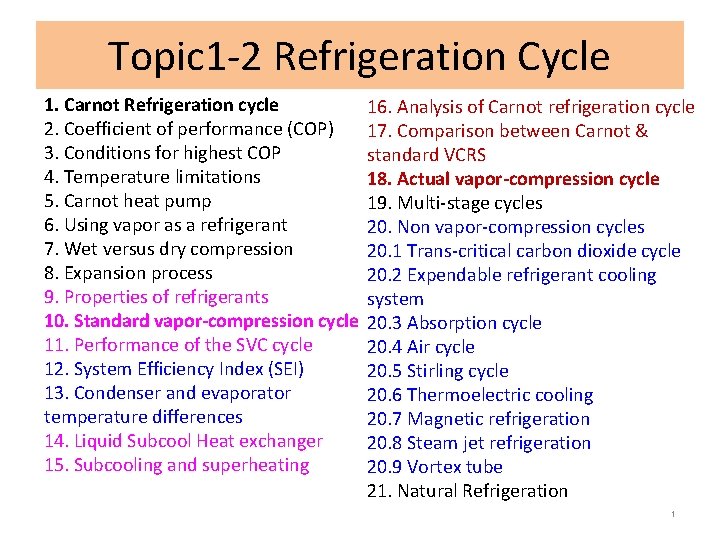
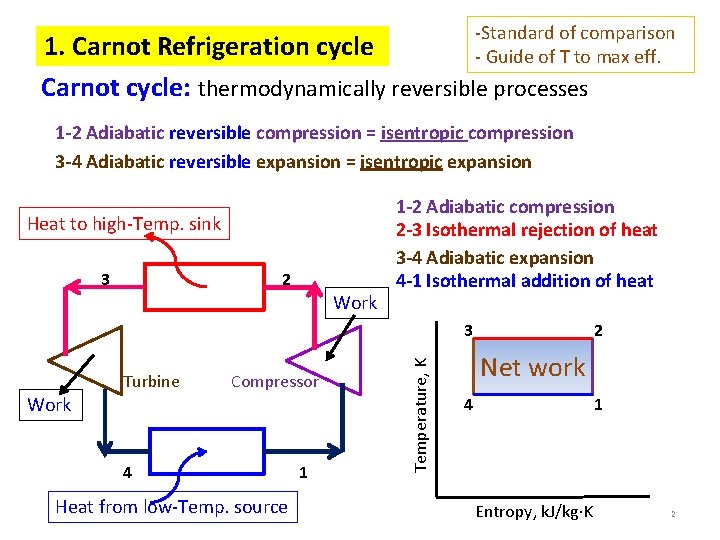
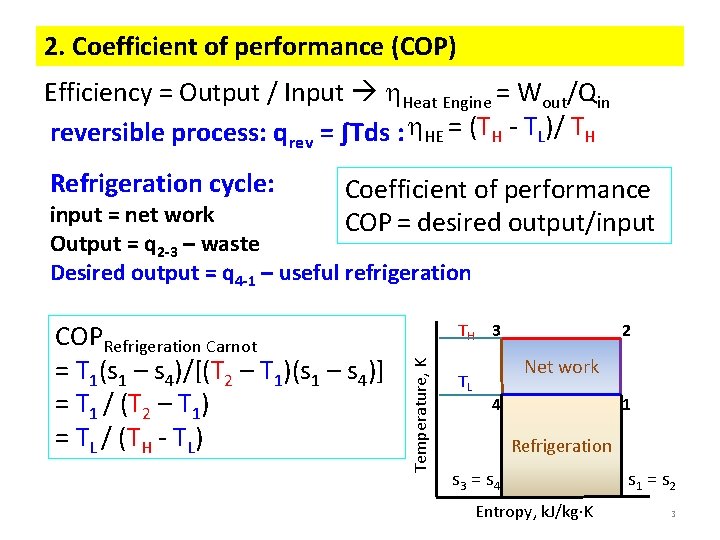
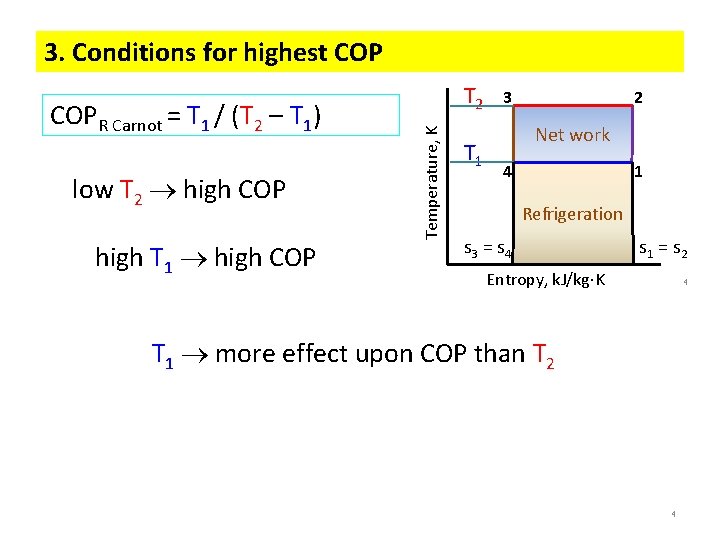
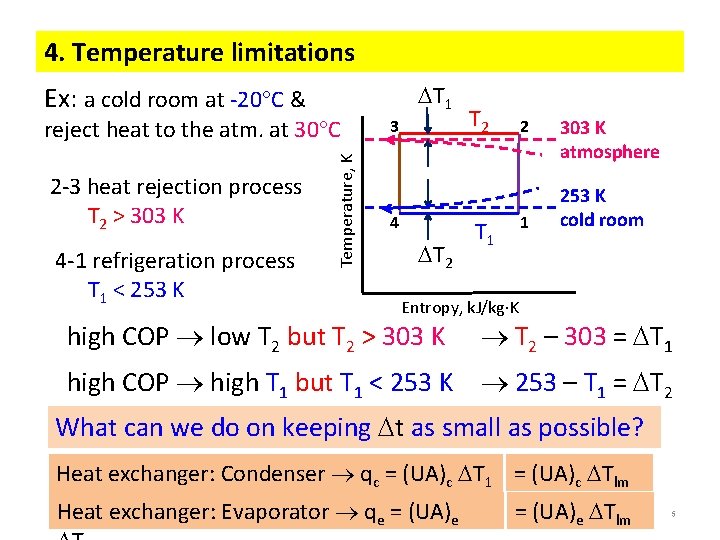
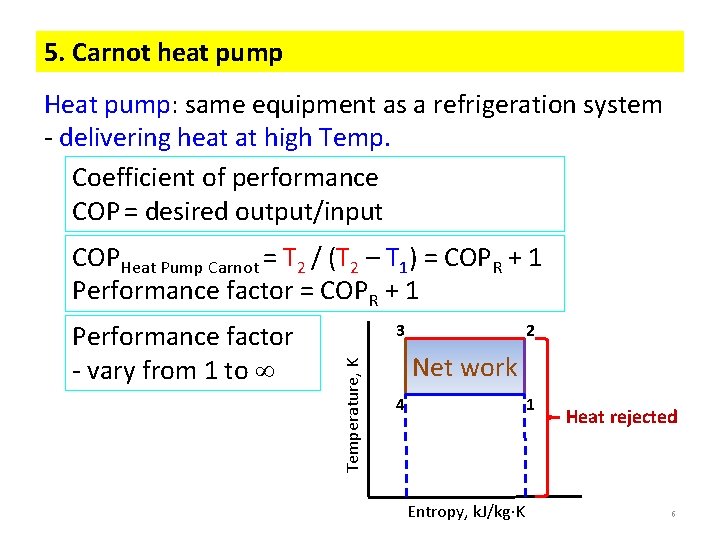

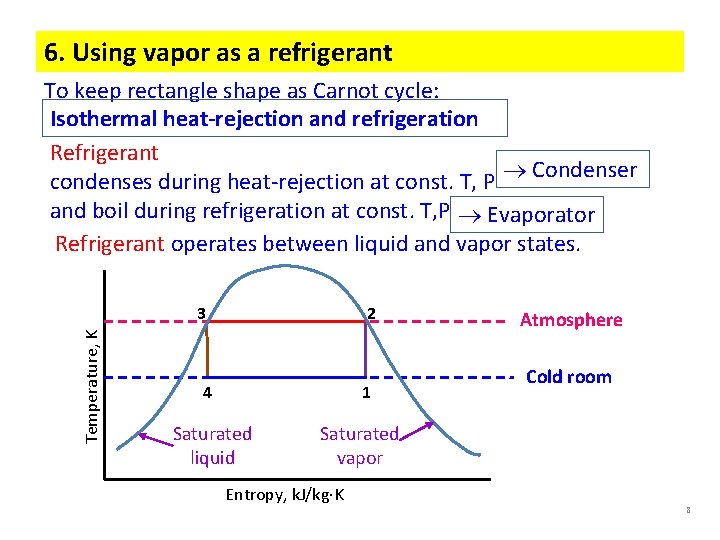
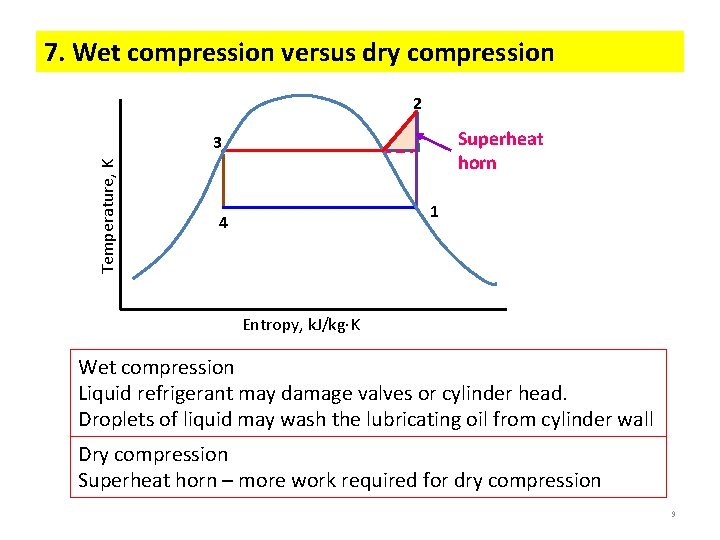
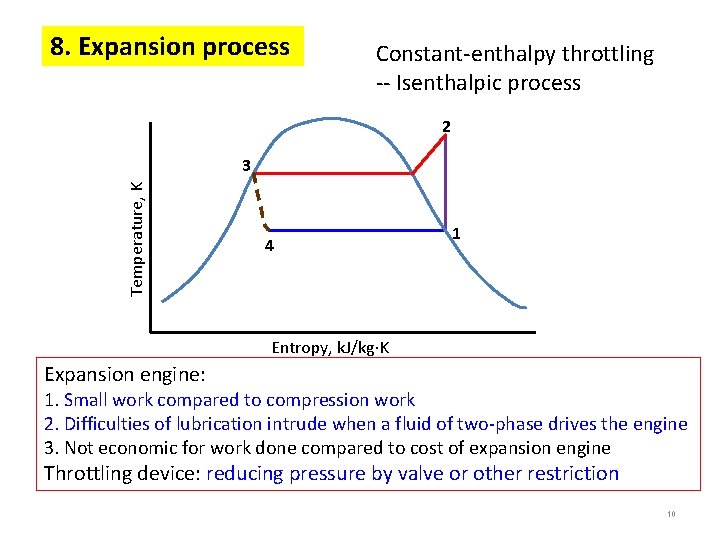
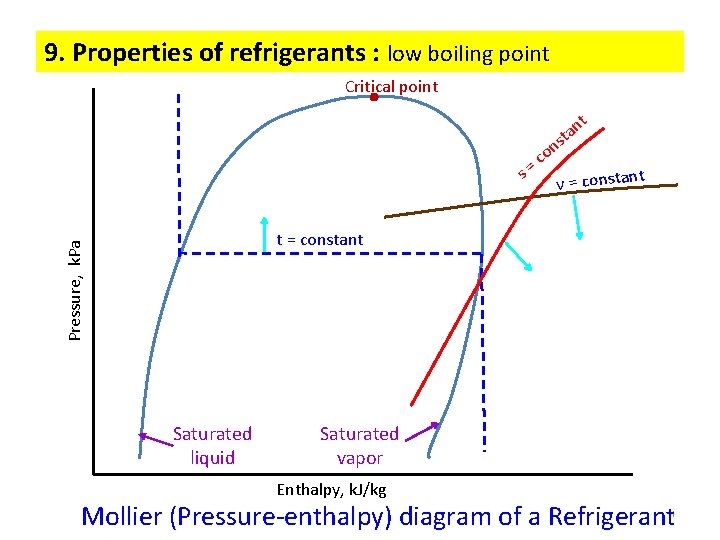
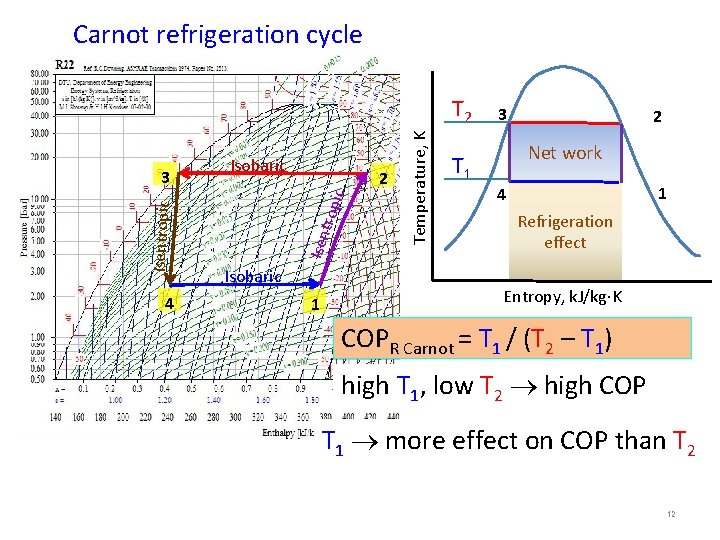
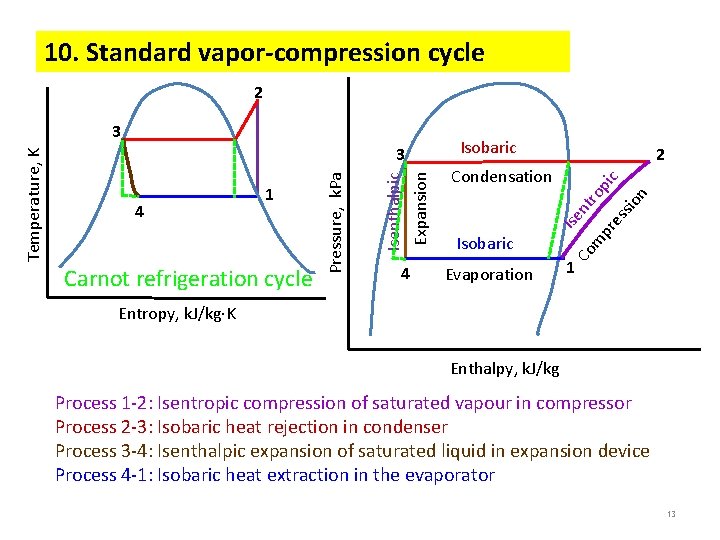
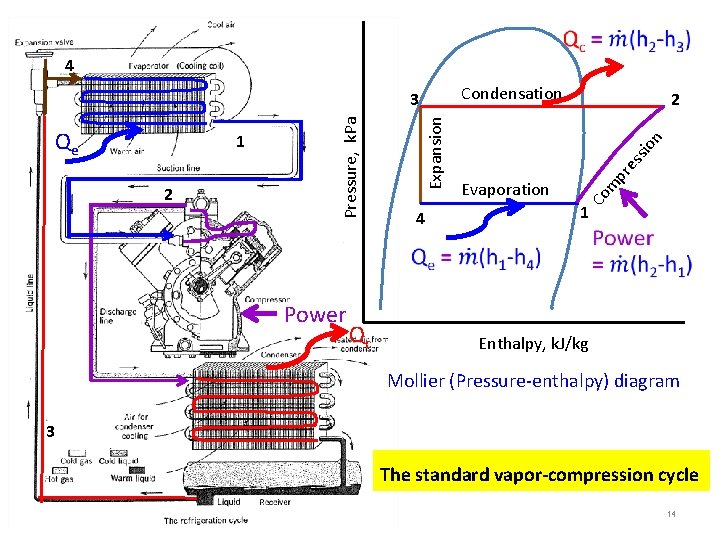
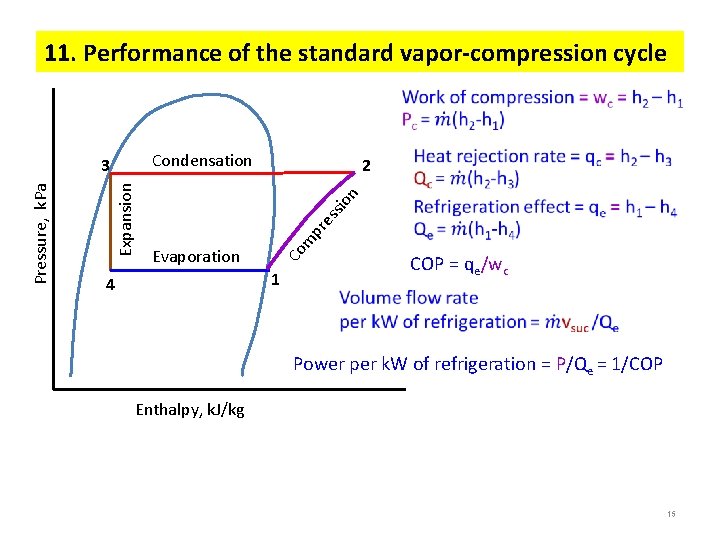
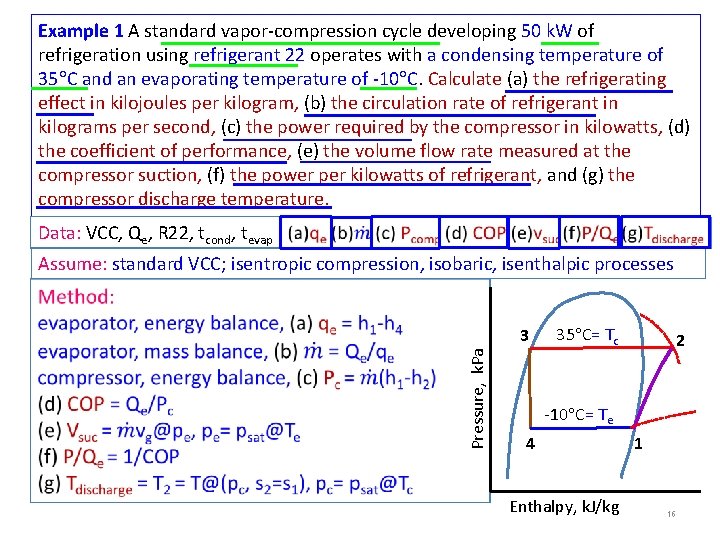
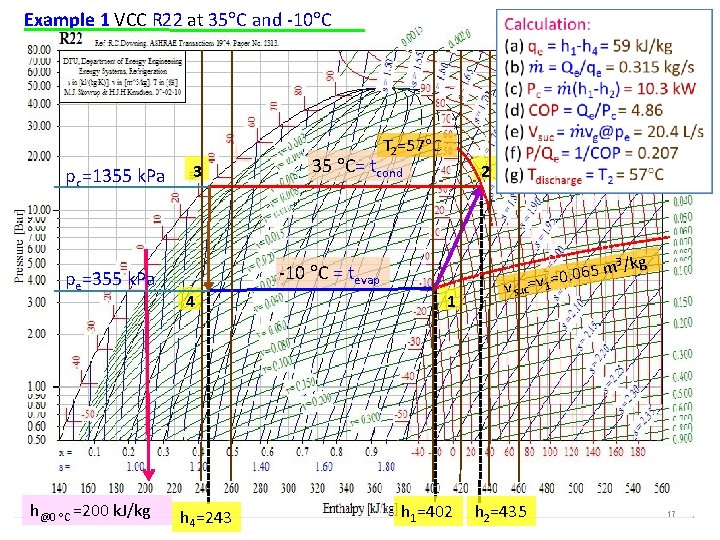
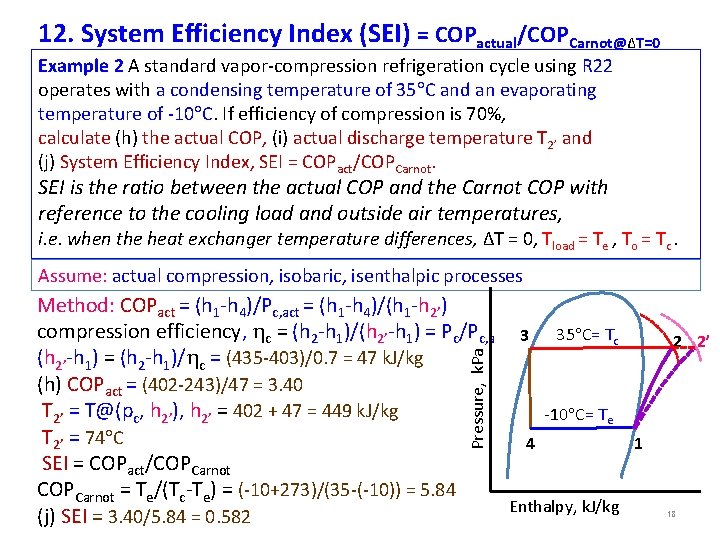
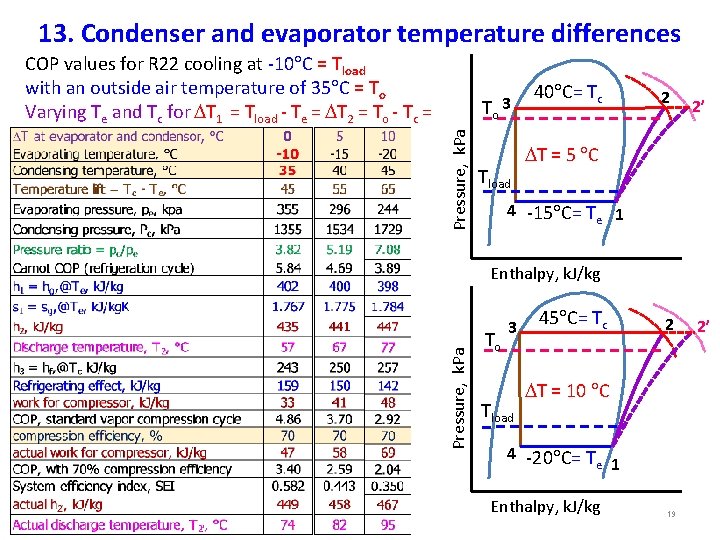
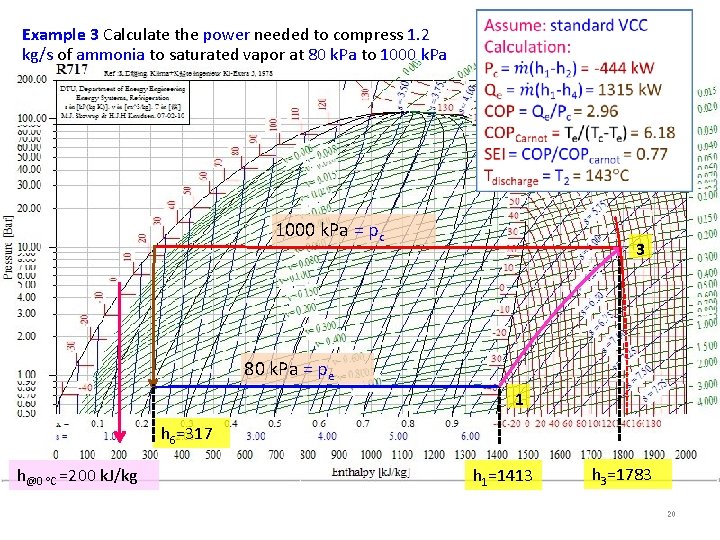
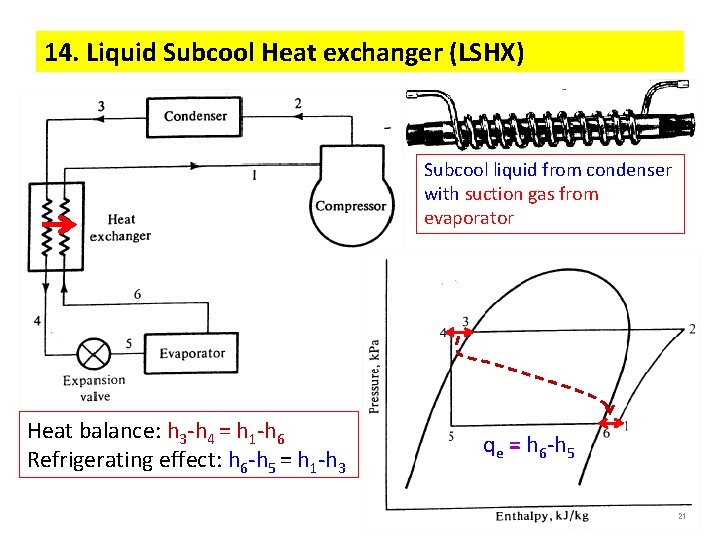
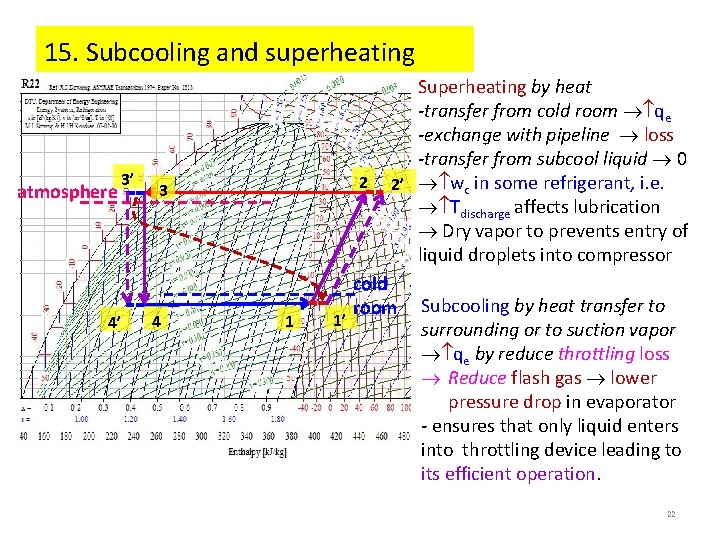
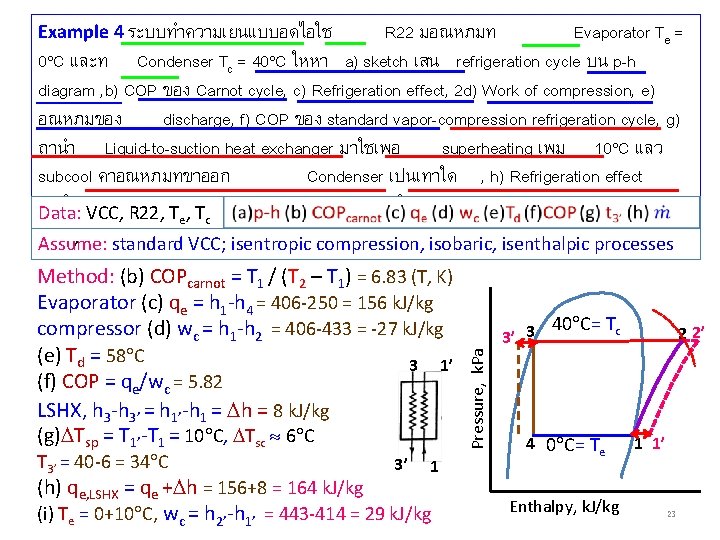
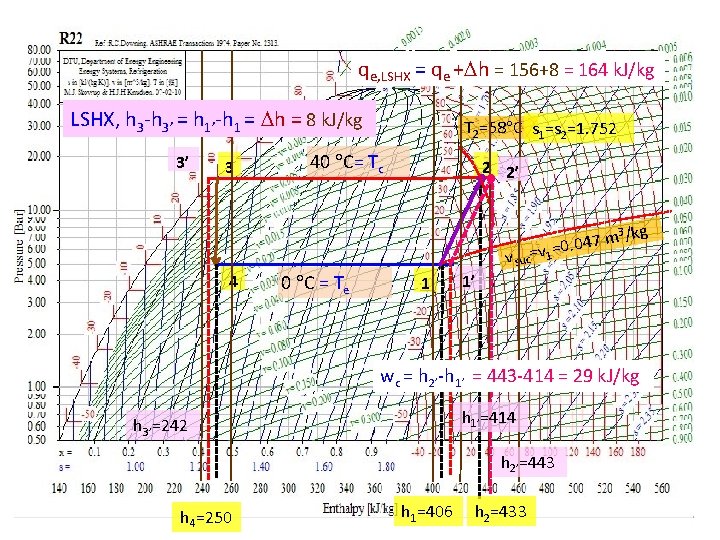
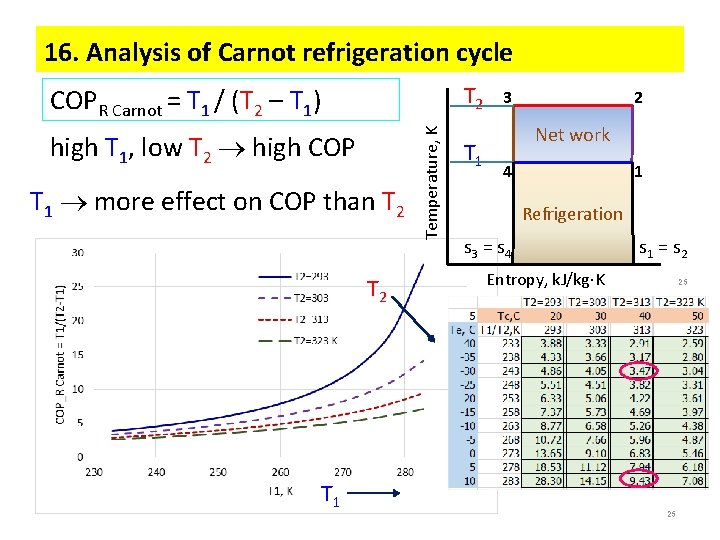
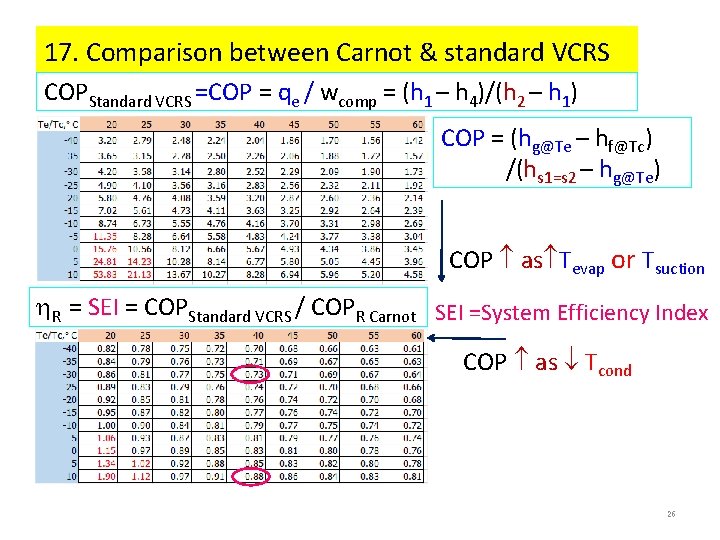
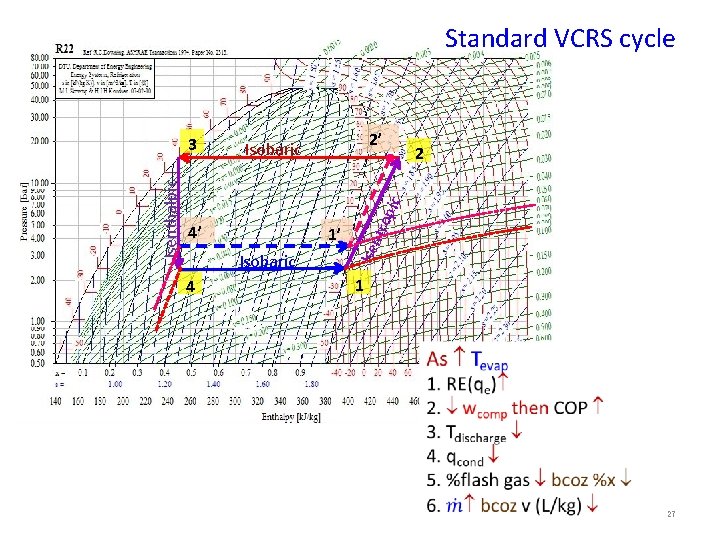
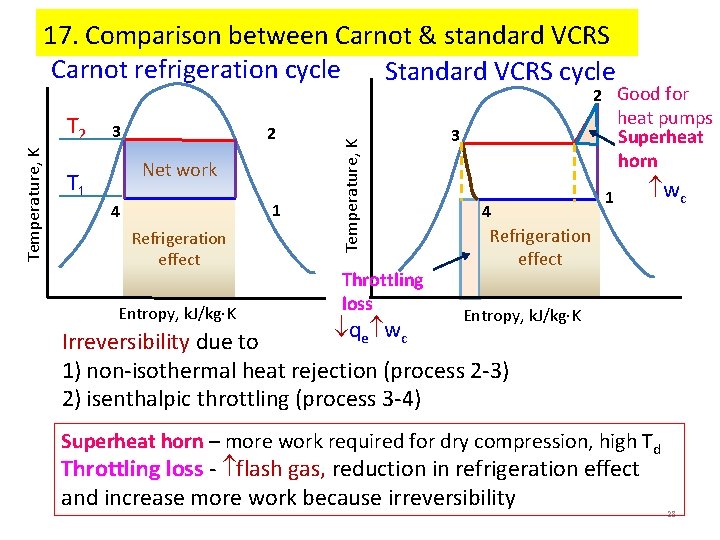
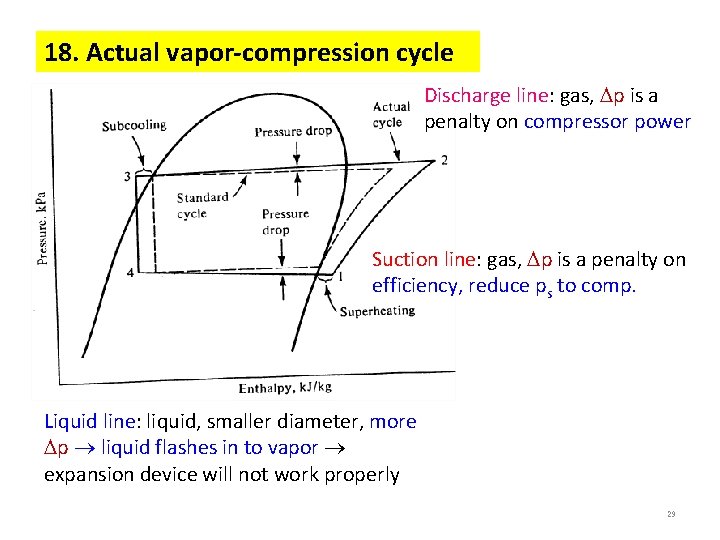
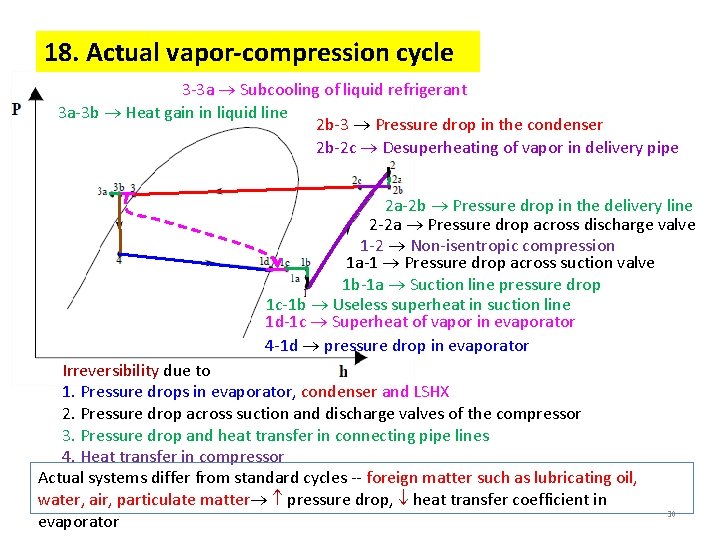
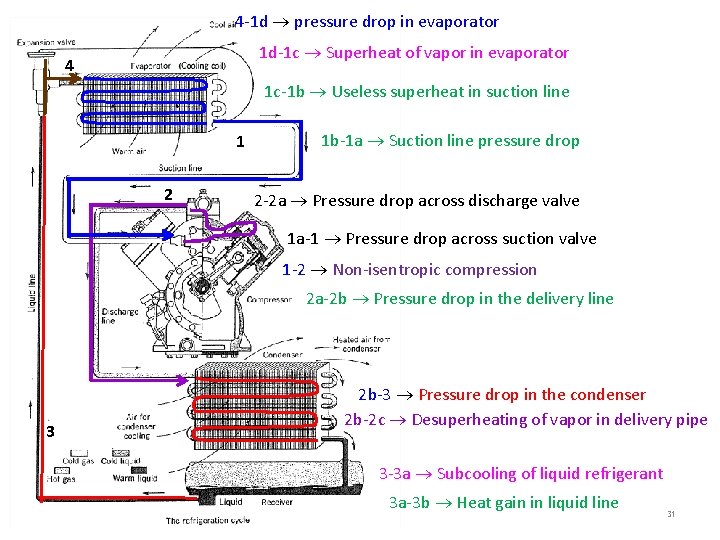
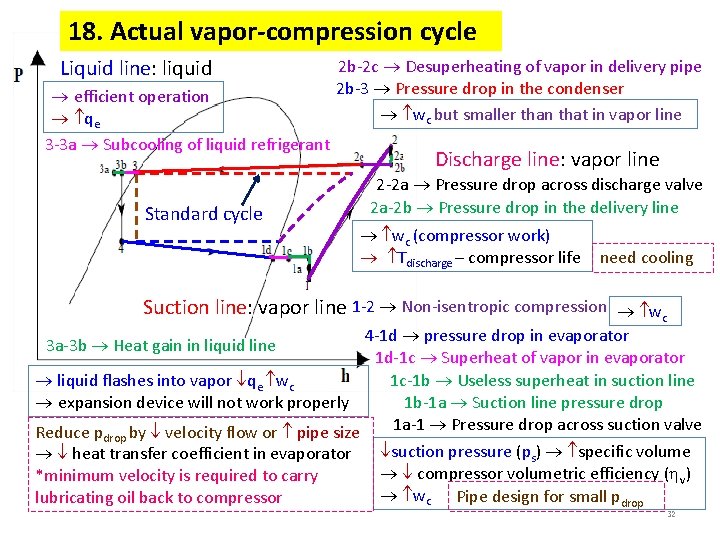
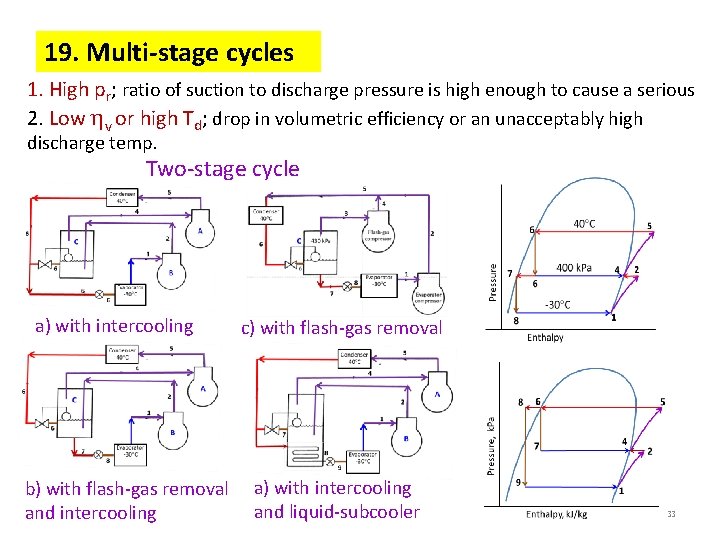
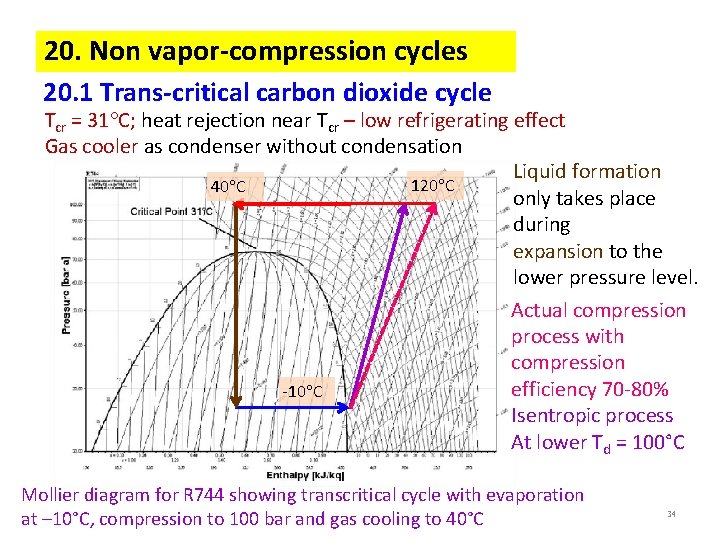
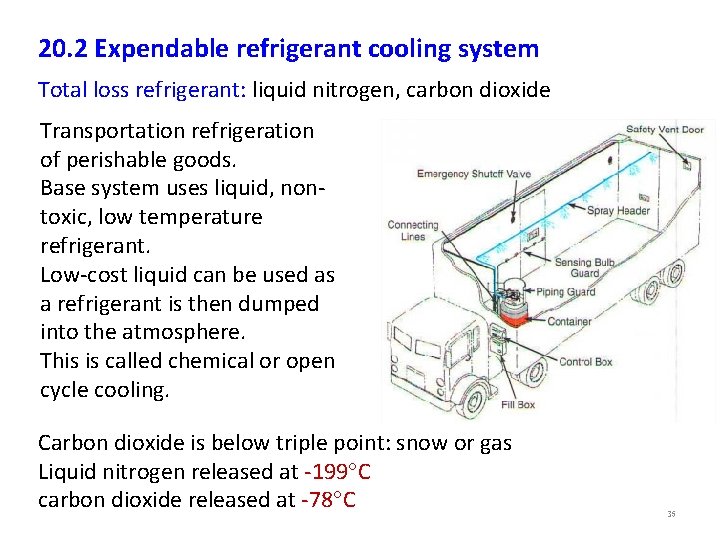
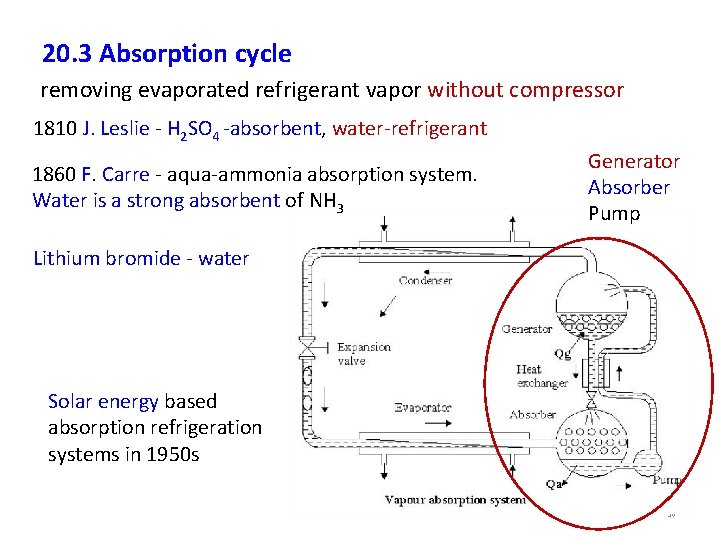
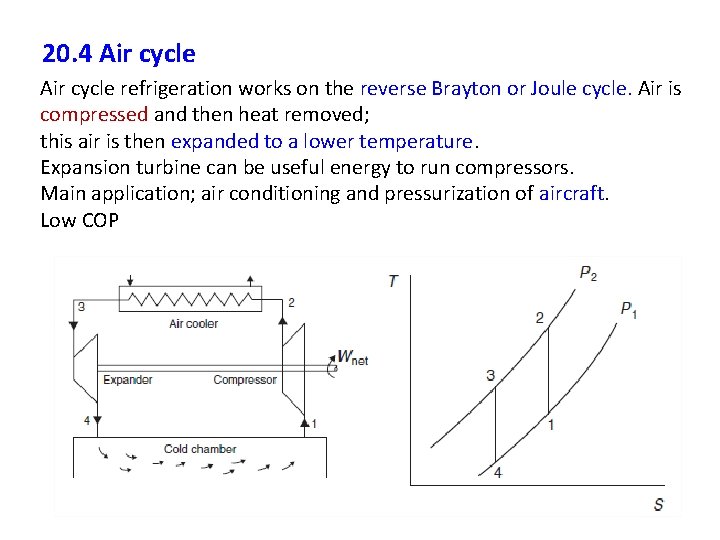
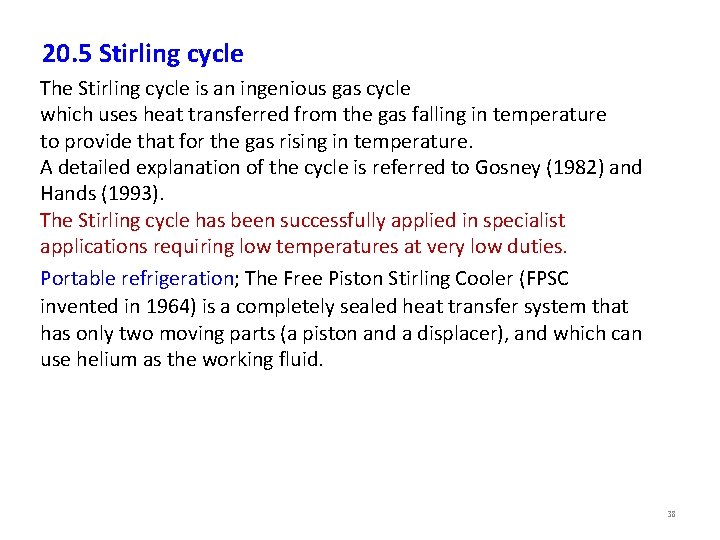
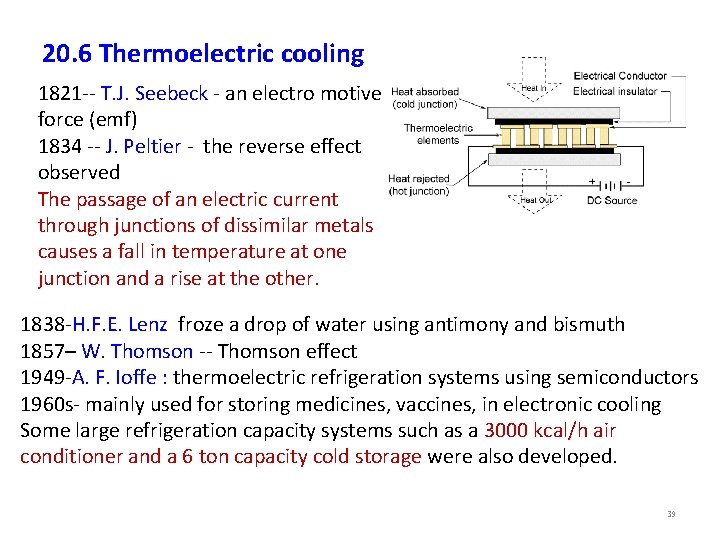
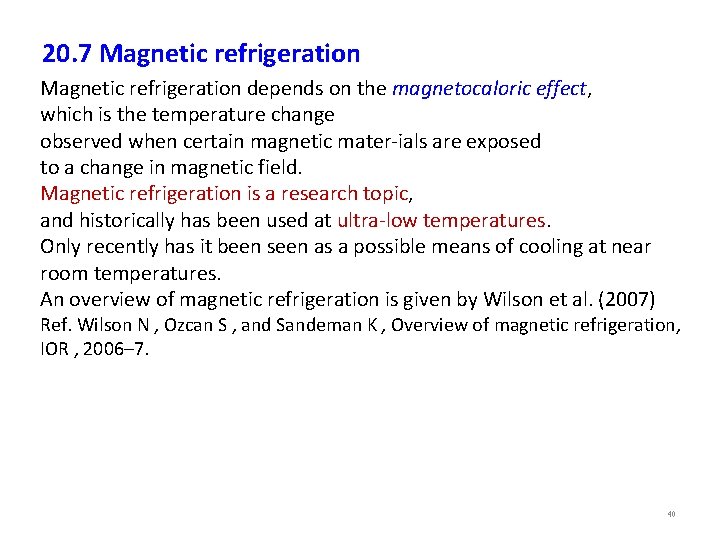
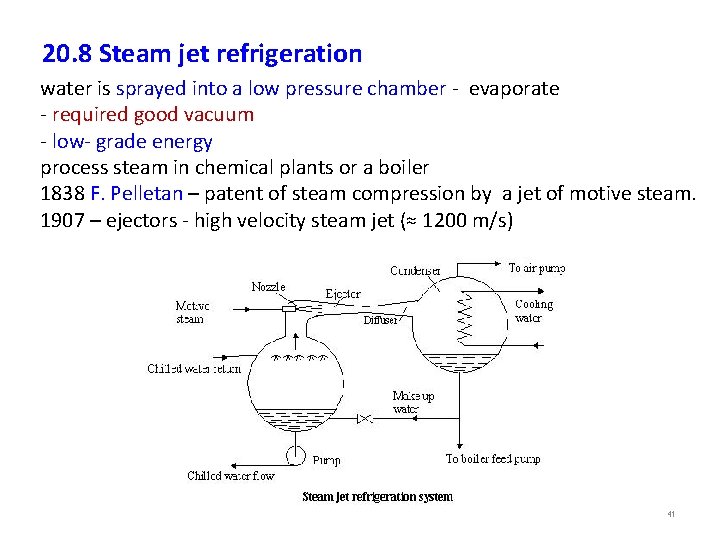
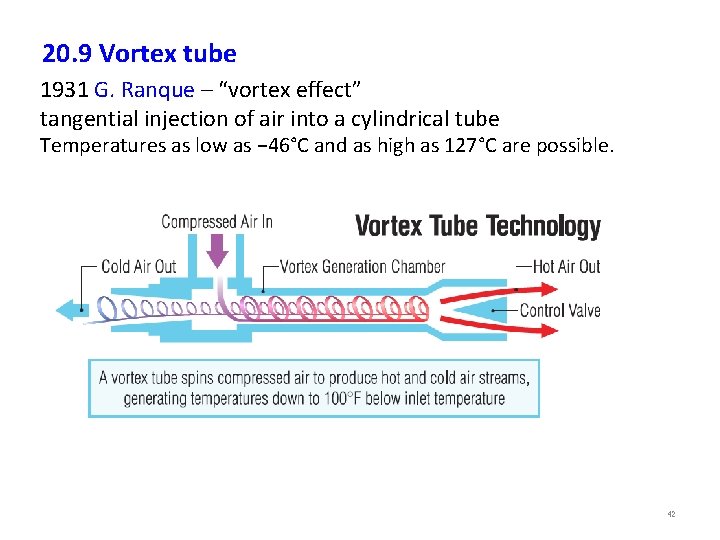
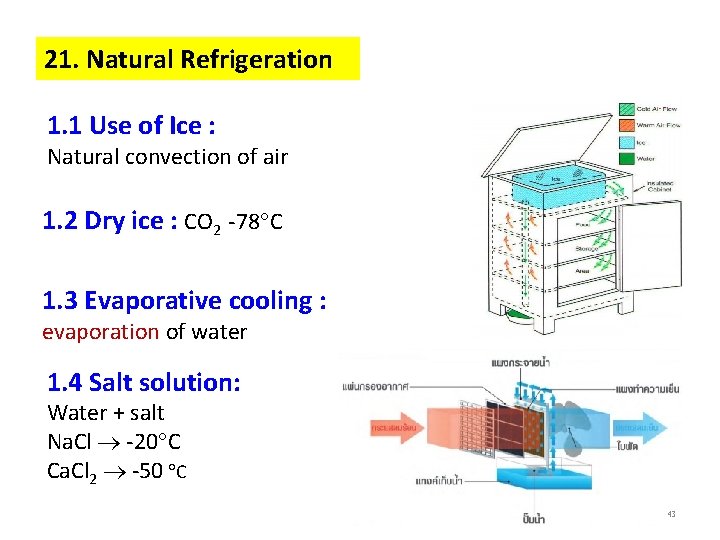
- Slides: 43
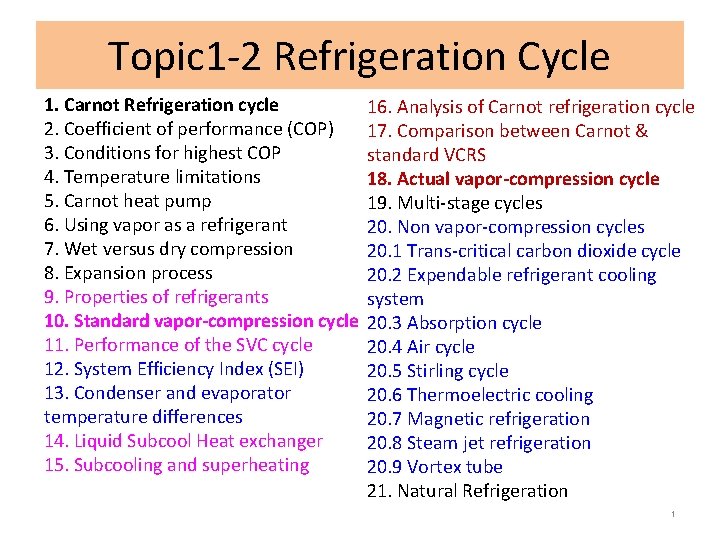
Topic 1 -2 Refrigeration Cycle 1. Carnot Refrigeration cycle 2. Coefficient of performance (COP) 3. Conditions for highest COP 4. Temperature limitations 5. Carnot heat pump 6. Using vapor as a refrigerant 7. Wet versus dry compression 8. Expansion process 9. Properties of refrigerants 10. Standard vapor-compression cycle 11. Performance of the SVC cycle 12. System Efficiency Index (SEI) 13. Condenser and evaporator temperature differences 14. Liquid Subcool Heat exchanger 15. Subcooling and superheating 16. Analysis of Carnot refrigeration cycle 17. Comparison between Carnot & standard VCRS 18. Actual vapor-compression cycle 19. Multi-stage cycles 20. Non vapor-compression cycles 20. 1 Trans-critical carbon dioxide cycle 20. 2 Expendable refrigerant cooling system 20. 3 Absorption cycle 20. 4 Air cycle 20. 5 Stirling cycle 20. 6 Thermoelectric cooling 20. 7 Magnetic refrigeration 20. 8 Steam jet refrigeration 20. 9 Vortex tube 21. Natural Refrigeration 1
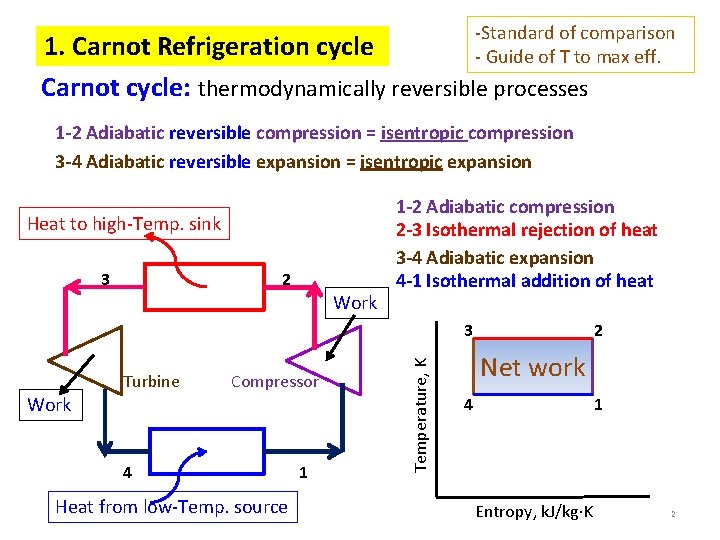
-Standard of comparison - Guide of T to max eff. 1. Carnot Refrigeration cycle Carnot cycle: thermodynamically reversible processes 1 -2 Adiabatic reversible compression = isentropic compression 3 -4 Adiabatic reversible expansion = isentropic expansion Heat to high-Temp. sink 3 2 Work 1 -2 Adiabatic compression 2 -3 Isothermal rejection of heat 3 -4 Adiabatic expansion 4 -1 Isothermal addition of heat Turbine Compressor Work 4 Heat from low-Temp. source 1 Temperature, K 3 2 Net work 4 1 Entropy, k. J/kg K 2
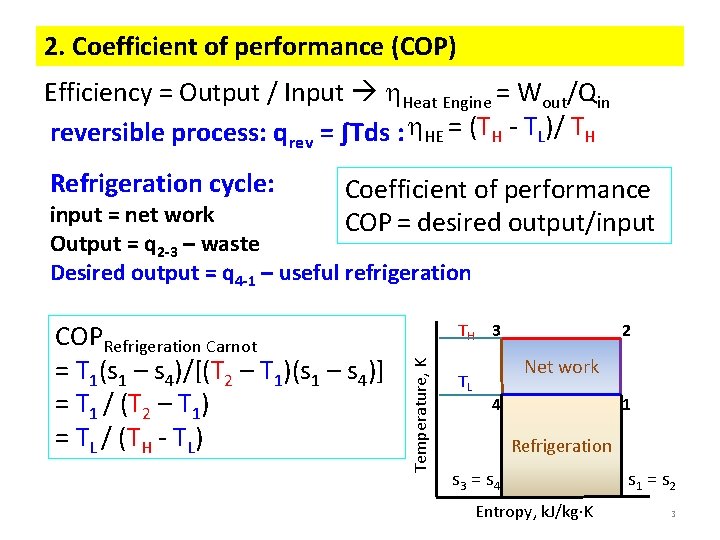
2. Coefficient of performance (COP) Efficiency = Output / Input Heat Engine = Wout/Qin reversible process: qrev = ∫Tds : HE = (TH - TL)/ TH Refrigeration cycle: Coefficient of performance COP = desired output/input = net work Output = q 2 -3 – waste Desired output = q 4 -1 – useful refrigeration TH 3 Temperature, K COPRefrigeration Carnot = T 1(s 1 – s 4)/[(T 2 – T 1)(s 1 – s 4)] = T 1 / (T 2 – T 1) = TL / (TH - TL) TL 2 Net work 4 1 Refrigeration s 3 = s 4 Entropy, k. J/kg K s 1 = s 2 3
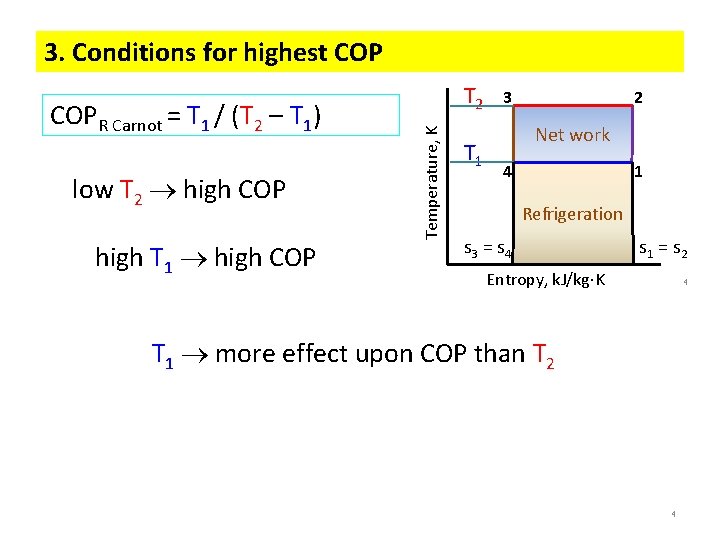
3. Conditions for highest COP low T 2 high COP high T 1 high COP Temperature, K COPR Carnot = T 1 / (T 2 – T 1) T 2 T 1 3 2 Net work 4 1 Refrigeration s 3 = s 4 s 1 = s 2 Entropy, k. J/kg K 4 T 1 more effect upon COP than T 2 4
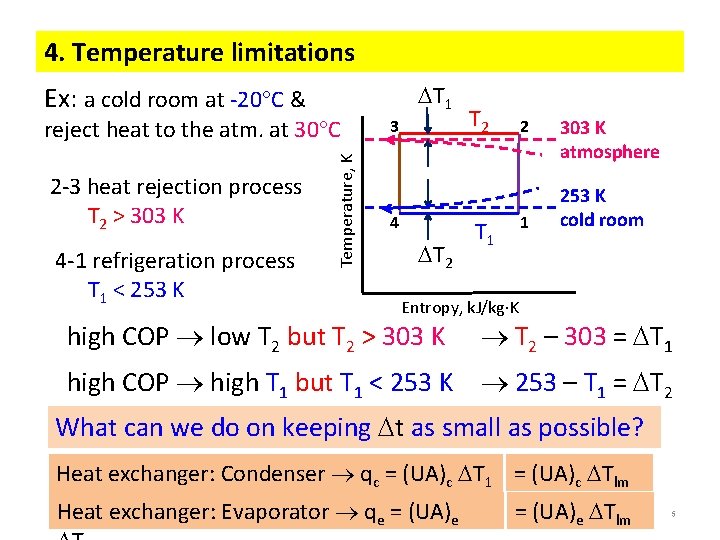
4. Temperature limitations T 1 Ex: a cold room at -20 C & 2 -3 heat rejection process T 2 > 303 K 4 -1 refrigeration process T 1 < 253 K Temperature, K reject heat to the atm. at 30 C 3 4 T 2 2 1 T 1 303 K atmosphere 253 K cold room Entropy, k. J/kg K high COP low T 2 but T 2 > 303 K T 2 – 303 = T 1 high COP high T 1 but T 1 < 253 K 253 – T 1 = T 2 What can we do on keeping t as small as possible? Heat exchanger: Condenser qc = (UA)c T 1 = (UA)c Tlm Heat exchanger: Evaporator qe = (UA)e Tlm 5
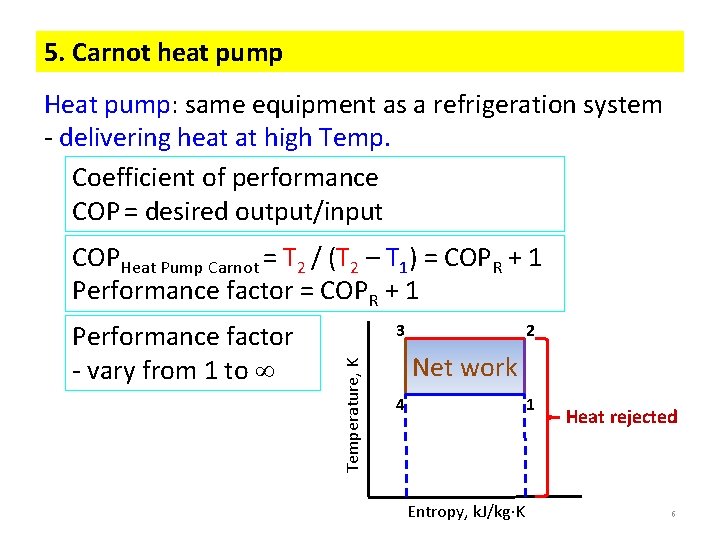
5. Carnot heat pump Heat pump: same equipment as a refrigeration system - delivering heat at high Temp. Coefficient of performance COP = desired output/input COPHeat Pump Carnot = T 2 / (T 2 – T 1) = COPR + 1 Performance factor = COPR + 1 3 Temperature, K Performance factor - vary from 1 to 2 Net work 4 1 Entropy, k. J/kg K Heat rejected 6

6. Using vapor as a refrigerant Refrigerant: gas, i. e. air Different from Carnot cycle by area x and y Temperature, K 2 -3 constant-pressure heating 4 -1 constant-pressure cooling x 3 area x and y decrease COP 4 y 2 Atmosphere 1 Cold room Entropy, k. J/kg K 7
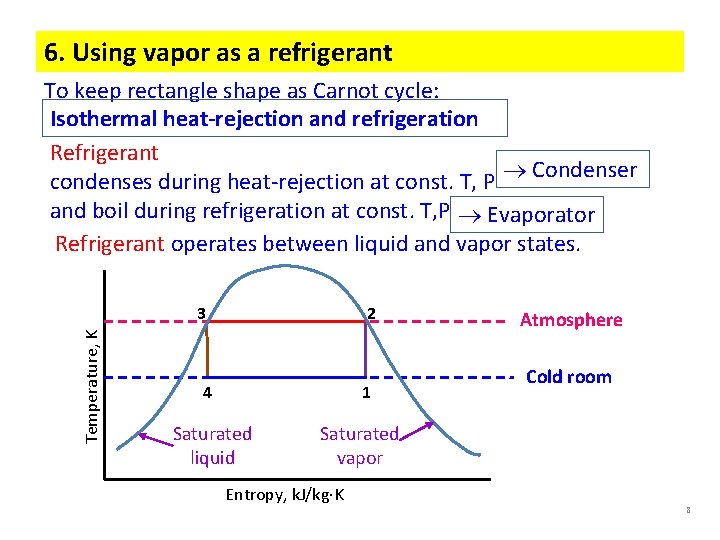
6. Using vapor as a refrigerant To keep rectangle shape as Carnot cycle: Isothermal heat-rejection and refrigeration Refrigerant condenses during heat-rejection at const. T, P Condenser and boil during refrigeration at const. T, P Evaporator Refrigerant operates between liquid and vapor states. Temperature, K 3 2 4 1 Saturated liquid Atmosphere Cold room Saturated vapor Entropy, k. J/kg K 8
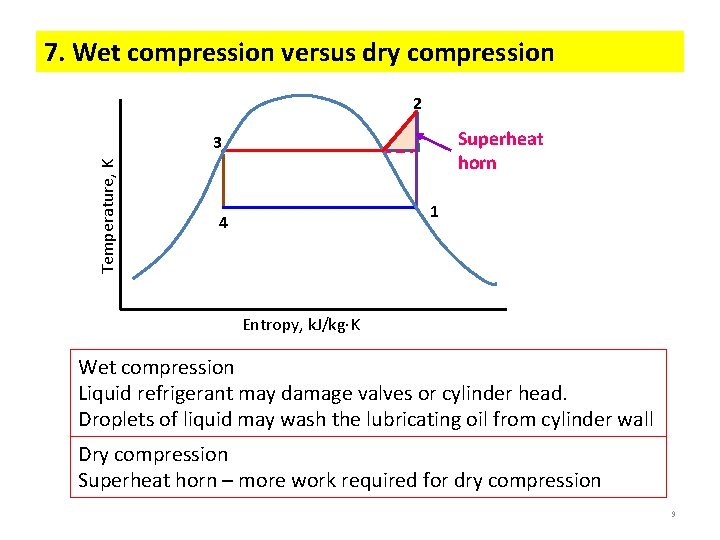
7. Wet compression versus dry compression 2 Superheat horn Temperature, K 3 1 4 Entropy, k. J/kg K Wet compression Liquid refrigerant may damage valves or cylinder head. Droplets of liquid may wash the lubricating oil from cylinder wall Dry compression Superheat horn – more work required for dry compression 9
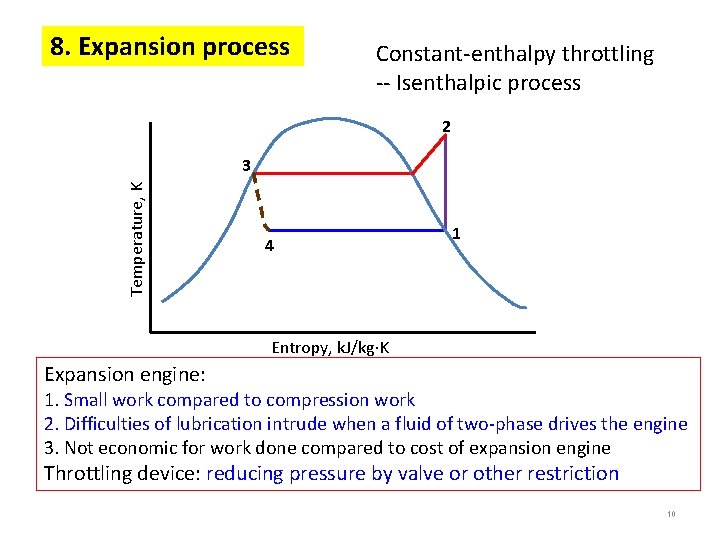
8. Expansion process Constant-enthalpy throttling -- Isenthalpic process 2 Temperature, K 3 4 1 Entropy, k. J/kg K Expansion engine: 1. Small work compared to compression work 2. Difficulties of lubrication intrude when a fluid of two-phase drives the engine 3. Not economic for work done compared to cost of expansion engine Throttling device: reducing pressure by valve or other restriction 10
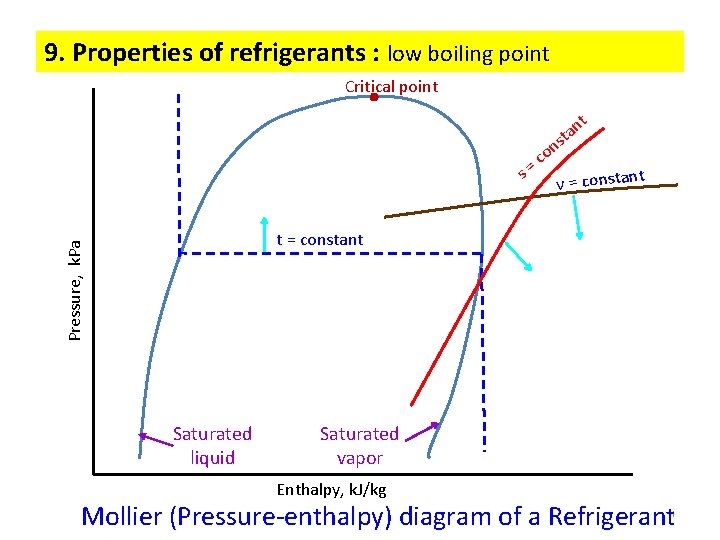
9. Properties of refrigerants : low boiling point Critical point t s o c = n sta n t v = constan Pressure, k. Pa t = constant Saturated liquid Saturated vapor Enthalpy, k. J/kg Mollier (Pressure-enthalpy) diagram of a Refrigerant 11
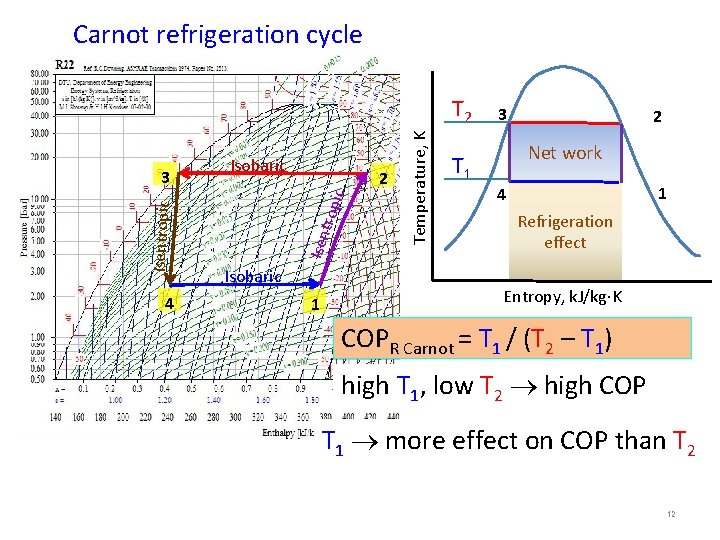
Carnot refrigeration cycle 4 trop ic 2 Isentropic 3 Isobaric 1 Temperature, K T 2 T 1 3 2 Net work 1 4 Refrigeration effect Entropy, k. J/kg K COPR Carnot = T 1 / (T 2 – T 1) high T 1, low T 2 high COP T 1 more effect on COP than T 2 12
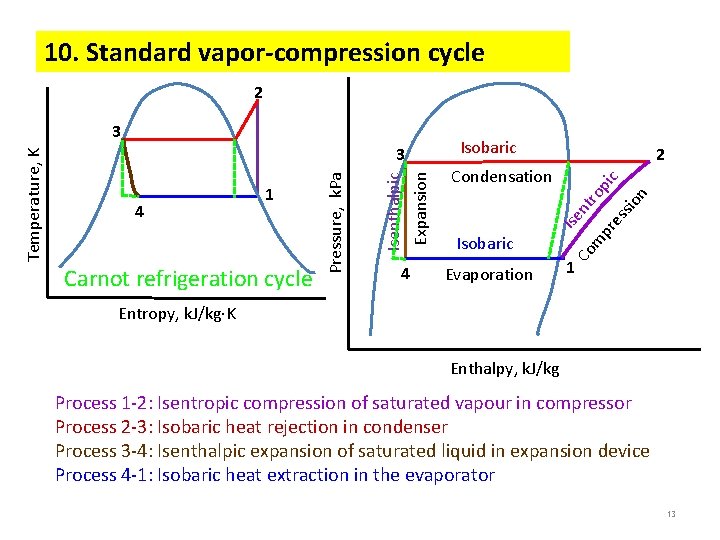
10. Standard vapor-compression cycle 2 Carnot refrigeration cycle 2 Evaporation n io ss m Isobaric pr e nt ro pi c Condensation Co 4 Isobaric Ise 4 1 Isenthalpic Expansion 3 Pressure, k. Pa Temperature, K 3 1 Entropy, k. J/kg K Enthalpy, k. J/kg Process 1 -2: Isentropic compression of saturated vapour in compressor Process 2 -3: Isobaric heat rejection in condenser Process 3 -4: Isenthalpic expansion of saturated liquid in expansion device Process 4 -1: Isobaric heat extraction in the evaporator 13
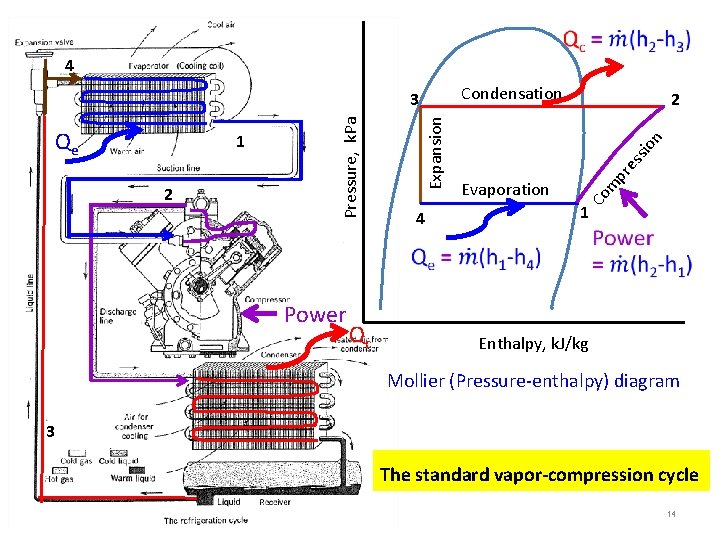
4 Condensation Power Qc 4 n io ss pr e Evaporation m 2 2 Co 1 Expansion Qe Pressure, k. Pa 3 1 Enthalpy, k. J/kg Mollier (Pressure-enthalpy) diagram 3 The standard vapor-compression cycle 14
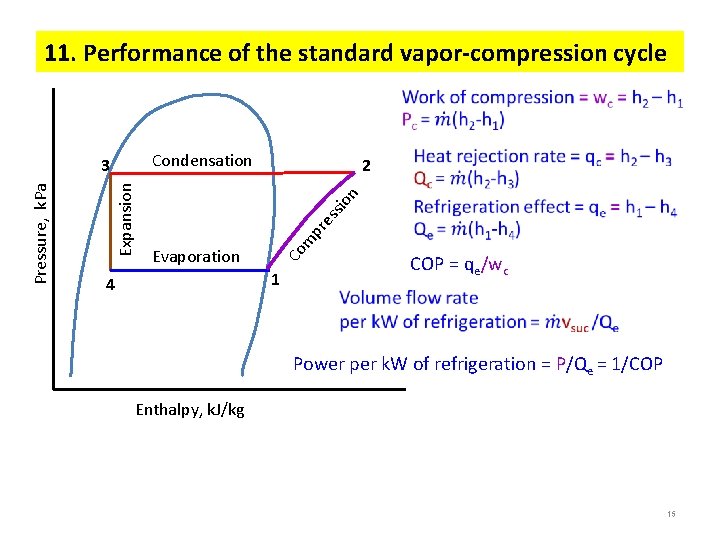
11. Performance of the standard vapor-compression cycle Condensation Evaporation m pr es sio n 2 Co Expansion Pressure, k. Pa 3 1 4 COP = qe/wc Power per k. W of refrigeration = P/Qe = 1/COP Enthalpy, k. J/kg 15
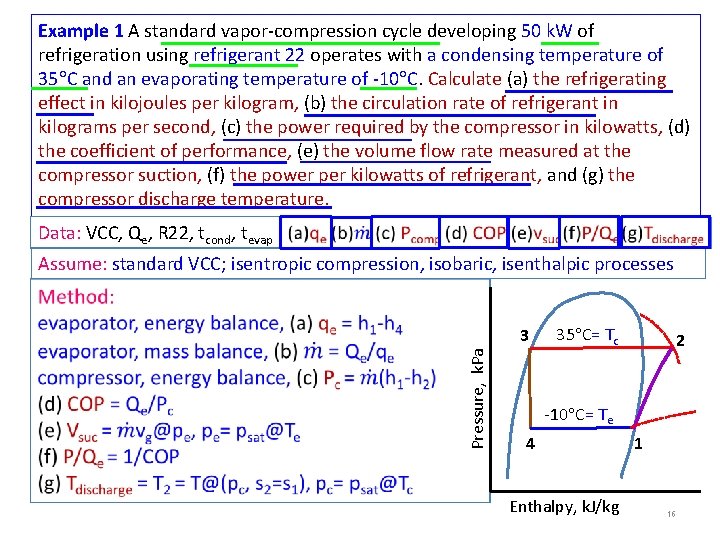
Example 1 A standard vapor-compression cycle developing 50 k. W of refrigeration using refrigerant 22 operates with a condensing temperature of 35 C and an evaporating temperature of -10 C. Calculate (a) the refrigerating effect in kilojoules per kilogram, (b) the circulation rate of refrigerant in kilograms per second, (c) the power required by the compressor in kilowatts, (d) the coefficient of performance, (e) the volume flow rate measured at the compressor suction, (f) the power per kilowatts of refrigerant, and (g) the compressor discharge temperature. Data: VCC, Qe, R 22, tcond, tevap Assume: standard VCC; isentropic compression, isobaric, isenthalpic processes Pressure, k. Pa 3 35 C= Tc 2 -10 C= Te 4 Enthalpy, k. J/kg 1 16
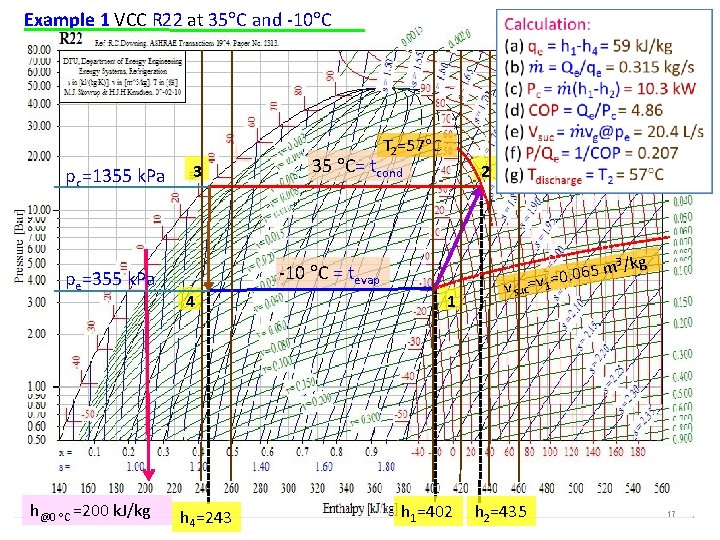
Example 1 VCC R 22 at 35 C and -10 C T 2=57 C pc=1355 k. Pa pe=355 k. Pa h@0 C =200 k. J/kg 3 35 C= tcond 2 -10 C = tevap 4 h 4=243 1 h 1=402 3 /kg m 5 6 0. 0 v suc=v 1= h 2=435 17
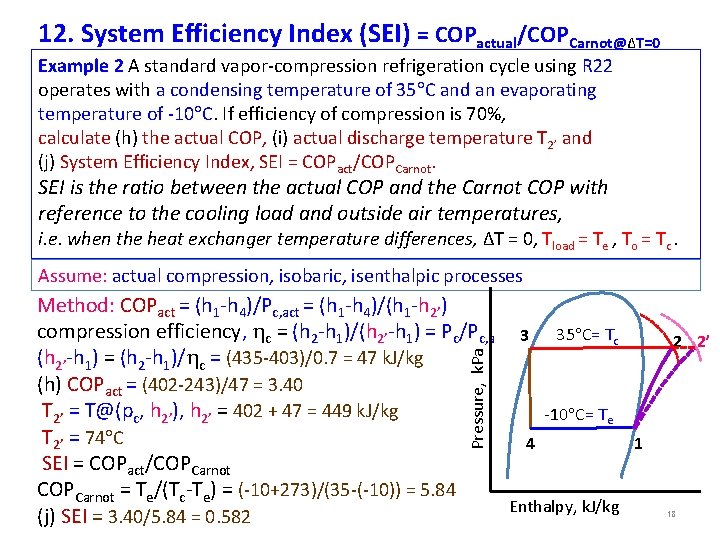
12. System Efficiency Index (SEI) = COPactual/COPCarnot@ΔT=0 Example 2 A standard vapor-compression refrigeration cycle using R 22 operates with a condensing temperature of 35 C and an evaporating temperature of -10 C. If efficiency of compression is 70%, calculate (h) the actual COP, (i) actual discharge temperature T 2’ and (j) System Efficiency Index, SEI = COPact/COPCarnot. SEI is the ratio between the actual COP and the Carnot COP with reference to the cooling load and outside air temperatures, i. e. when the heat exchanger temperature differences, ΔT = 0, Tload = Te , To = Tc. Assume: actual compression, isobaric, isenthalpic processes Pressure, k. Pa Method: COPact = (h 1 -h 4)/Pc, act = (h 1 -h 4)/(h 1 -h 2’) compression efficiency, c = (h 2 -h 1)/(h 2’-h 1) = Pc/Pc, a 3 35 C= Tc (h 2’-h 1) = (h 2 -h 1)/ c = (435 -403)/0. 7 = 47 k. J/kg (h) COPact = (402 -243)/47 = 3. 40 T 2’ = T@(pc, h 2’), h 2’ = 402 + 47 = 449 k. J/kg -10 C= Te T 2’ = 74 C 4 1 SEI = COPact/COPCarnot = Te/(Tc-Te) = (-10+273)/(35 -(-10)) = 5. 84 Enthalpy, k. J/kg (j) SEI = 3. 40/5. 84 = 0. 582 2 2’ 18
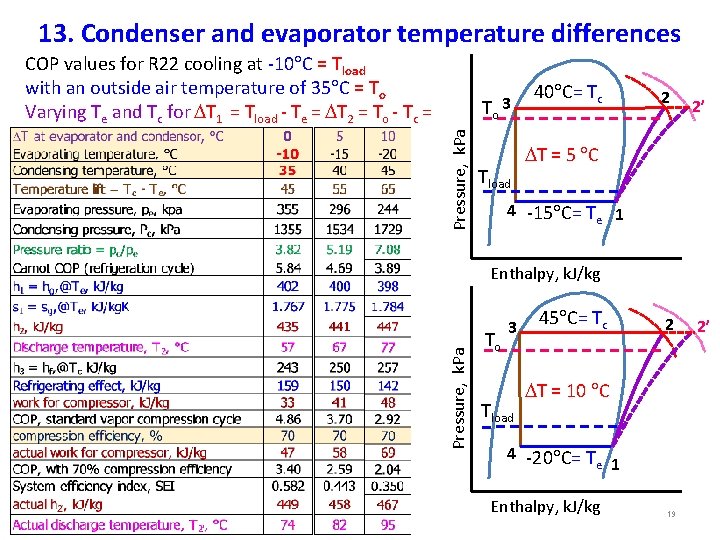
13. Condenser and evaporator temperature differences Pressure, k. Pa To 3 Tload 40 C= Tc 2 2’ T = 5 C 4 -15 C= Te 1 Enthalpy, k. J/kg Pressure, k. Pa COP values for R 22 cooling at -10 C = Tload with an outside air temperature of 35 C = To Varying Te and Tc for T 1 = Tload - Te = T 2 = To - Tc = T To 3 Tload 45 C= Tc T = 10 C 4 -20 C= T e 1 Enthalpy, k. J/kg 19
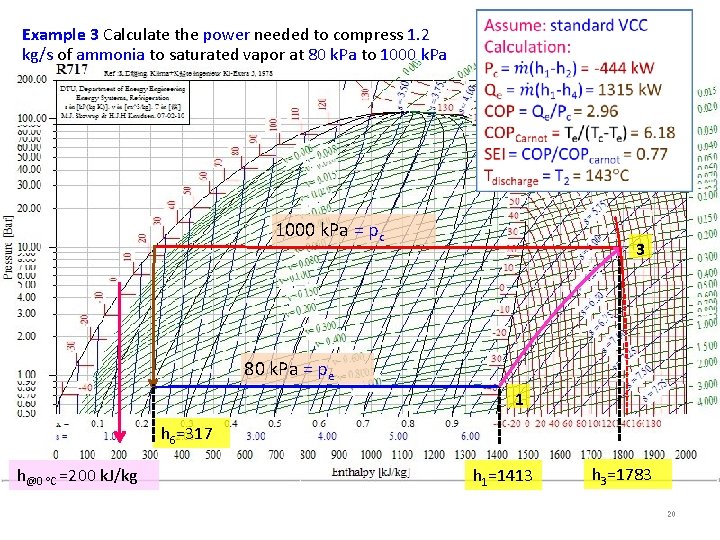
Example 3 Calculate the power needed to compress 1. 2 kg/s of ammonia to saturated vapor at 80 k. Pa to 1000 k. Pa = pc 3 80 k. Pa = pe 1 h 6=317 h@0 C =200 k. J/kg h 1=1413 h 3=1783 20
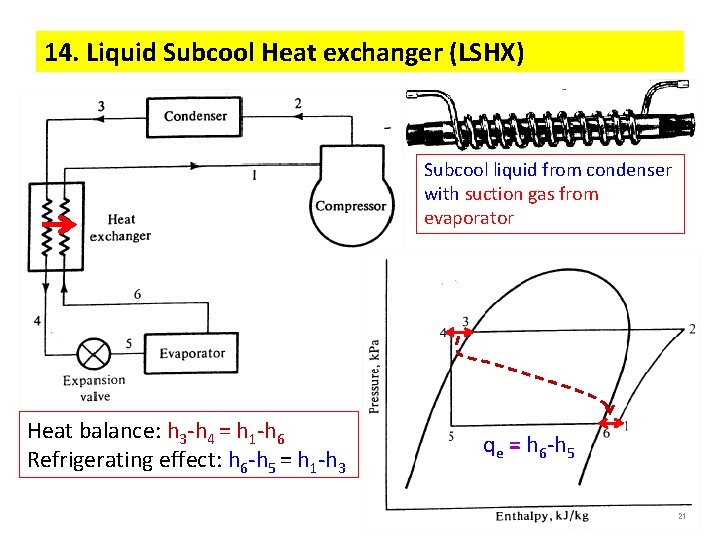
14. Liquid Subcool Heat exchanger (LSHX) Subcool liquid from condenser with suction gas from evaporator Heat balance: h 3 -h 4 = h 1 -h 6 Refrigerating effect: h 6 -h 5 = h 1 -h 3 qe = h 6 -h 5 21 21
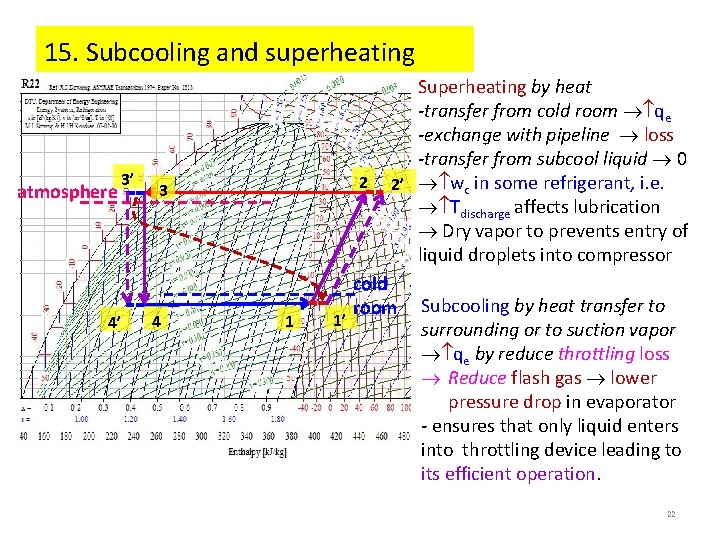
15. Subcooling and superheating atmosphere 3’ 4’ 2 3 4 1 1’ Superheating by heat -transfer from cold room qe -exchange with pipeline loss -transfer from subcool liquid 0 2’ wc in some refrigerant, i. e. Tdischarge affects lubrication Dry vapor to prevents entry of liquid droplets into compressor cold room Subcooling by heat transfer to surrounding or to suction vapor qe by reduce throttling loss Reduce flash gas lower pressure drop in evaporator - ensures that only liquid enters into throttling device leading to its efficient operation. 22
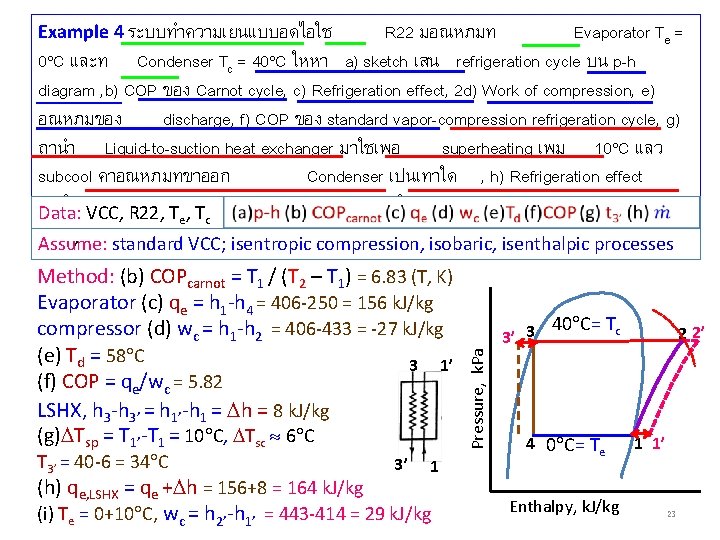
Example 4 ระบบทำความเยนแบบอดไอใช R 22 มอณหภมท Evaporator Te = 0 C และท Condenser Tc = 40 C ใหหา a) sketch เสน refrigeration cycle บน p-h diagram , b) COP ของ Carnot cycle, c) Refrigeration effect, 2 d) Work of compression, e) อณหภมของ discharge, f) COP ของ standard vapor-compression refrigeration cycle, g) ถานำ Liquid-to-suction heat exchanger มาใชเพอ superheating เพม 10 C แลว subcool คาอณหภมทขาออก Condenser เปนเทาใด , h) Refrigeration effect เมอใช VCC, LSHX Data: R 22, Tและ , Ti) Work of compression เมอใช e c Method: (b) COPcarnot = T 1 / (T 2 – T 1) = 6. 83 (T, K) Evaporator (c) qe = h 1 -h 4 = 406 -250 = 156 k. J/kg compressor (d) wc = h 1 -h 2 = 406 -433 = -27 k. J/kg (e) Td = 58 C 3 1’ (f) COP = qe/wc = 5. 82 LSHX, h 3 -h 3’ = h 1’-h 1 = h = 8 k. J/kg (g) Tsp = T 1’-T 1 = 10 C, Tsc 6 C T 3’ = 40 -6 = 34 C 3’ 1 (h) qe, LSHX = qe + h = 156+8 = 164 k. J/kg (i) Te = 0+10 C, wc = h 2’-h 1’ = 443 -414 = 29 k. J/kg Pressure, k. Pa , Assume: standard VCC; isentropic compression, isobaric, isenthalpic processes 40 C= Tc 3’ 3 4 0 C= Te Enthalpy, k. J/kg 2 2’ 1 1’ 23
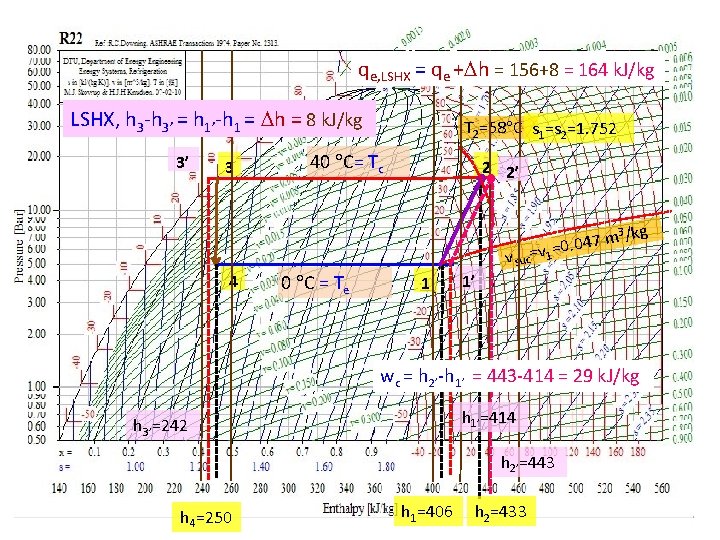
qe, LSHX = qe + h = 156+8 = 164 k. J/kg LSHX, h 3 -h 3’ = h 1’-h 1 = h = 8 k. J/kg 3’ 3 T 2=58 C s 1=s 2=1. 752 40 C= Tc 2 2’ 3 /kg 47 m =v 1=0. 0 v suc 4 0 C = Te 1 1’ wc = h 2’-h 1’ = 443 -414 = 29 k. J/kg h 1’=414 h 3’=242 h 2’=443 h 4=250 h 1=406 h 2=433
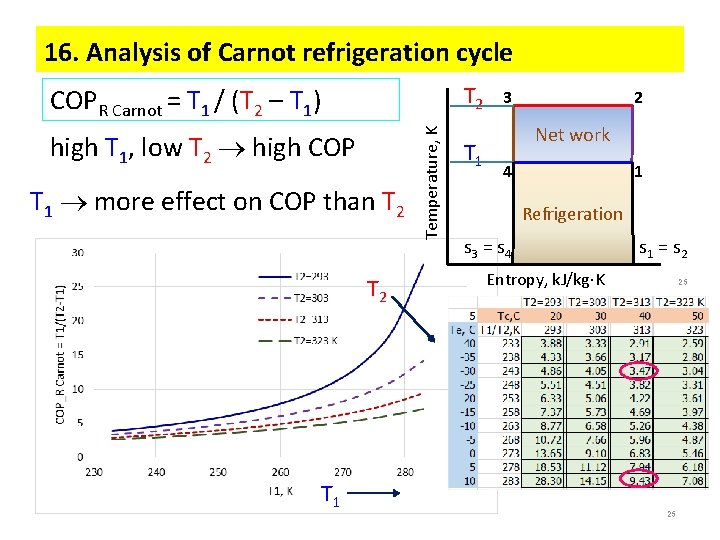
16. Analysis of Carnot refrigeration cycle T 2 high T 1, low T 2 high COP T 1 more effect on COP than T 2 T 1 Temperature, K COPR Carnot = T 1 / (T 2 – T 1) T 1 3 2 Net work 4 1 Refrigeration s 3 = s 4 s 1 = s 2 Entropy, k. J/kg K 25 25
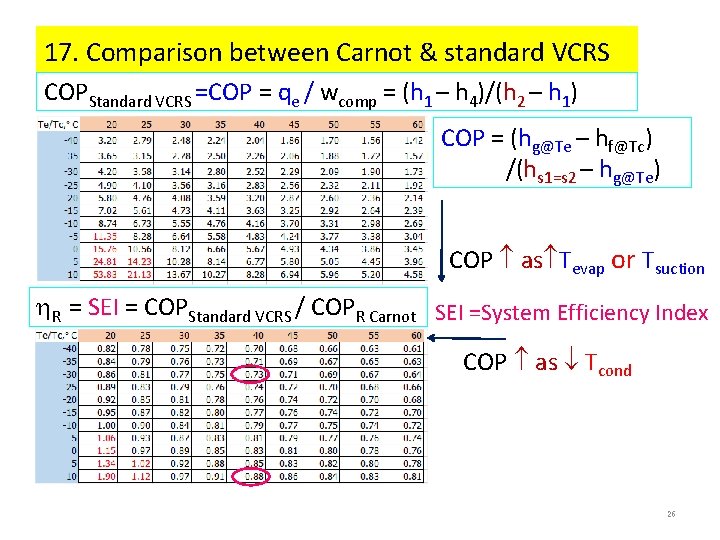
17. Comparison between Carnot & standard VCRS COPStandard VCRS =COP = qe / wcomp = (h 1 – h 4)/(h 2 – h 1) COP = (hg@Te – hf@Tc) /(hs 1=s 2 – hg@Te) COP as Tevap or Tsuction R = SEI = COPStandard VCRS / COPR Carnot SEI =System Efficiency Index COP as Tcond 26
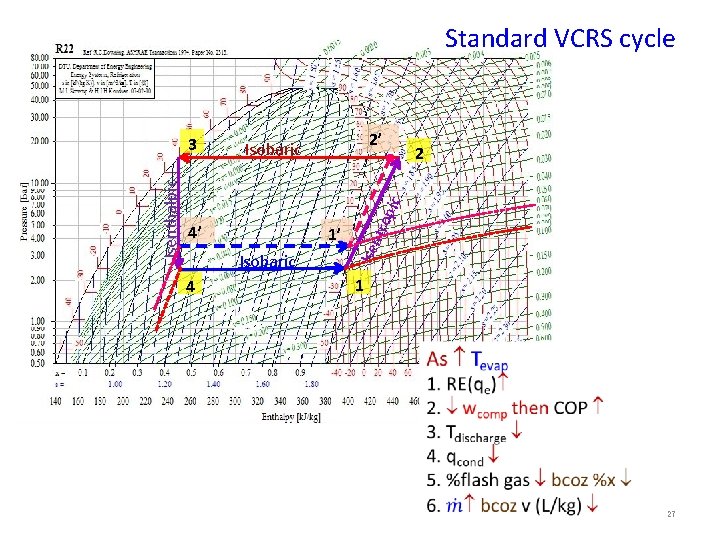
Standard VCRS cycle 2’ 2 4’ 1’ Isobaric 4 tro p ic Isobaric Isenthalpic 3 1 27
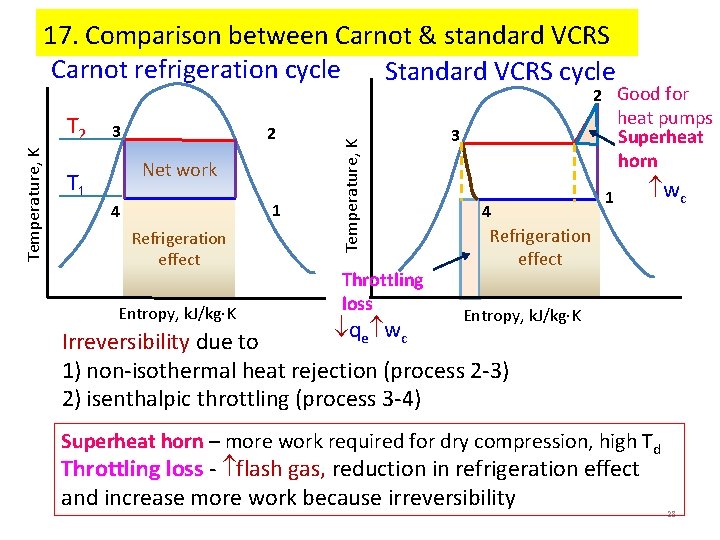
17. Comparison between Carnot & standard VCRS Carnot refrigeration cycle Standard VCRS cycle Temperature, K T 2 T 1 3 2 Net work 1 4 Refrigeration effect Entropy, k. J/kg K Temperature, K 2 Good for Throttling loss heat pumps Superheat horn 3 4 1 wc Refrigeration effect Entropy, k. J/kg K qe wc Irreversibility due to 1) non-isothermal heat rejection (process 2 -3) 2) isenthalpic throttling (process 3 -4) Superheat horn – more work required for dry compression, high Td Throttling loss - flash gas, reduction in refrigeration effect and increase more work because irreversibility 28
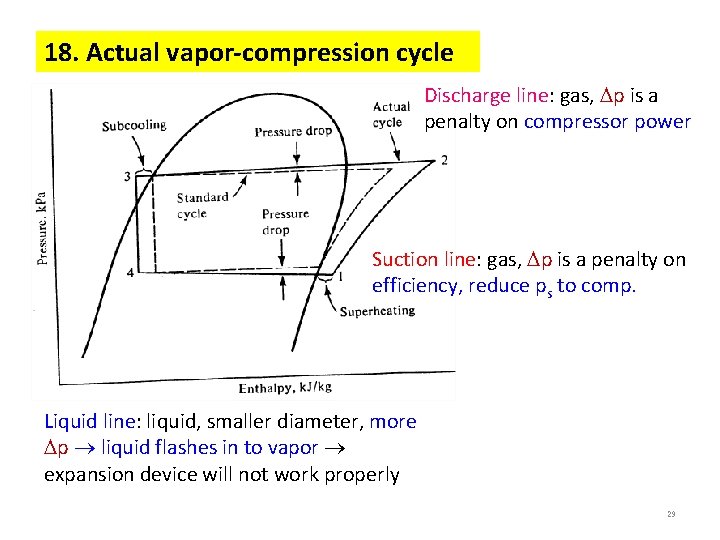
18. Actual vapor-compression cycle Discharge line: gas, p is a penalty on compressor power Suction line: gas, p is a penalty on efficiency, reduce ps to comp. Liquid line: liquid, smaller diameter, more p liquid flashes in to vapor expansion device will not work properly 29
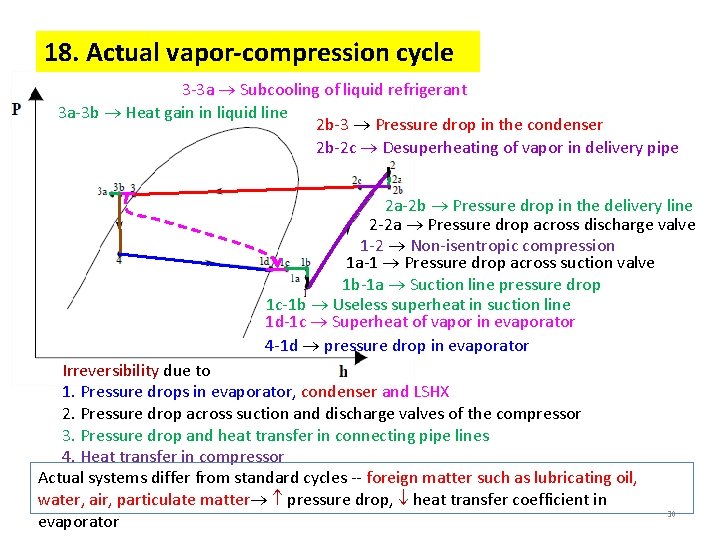
18. Actual vapor-compression cycle 3 -3 a Subcooling of liquid refrigerant 3 a-3 b Heat gain in liquid line 2 b-3 Pressure drop in the condenser 2 b-2 c Desuperheating of vapor in delivery pipe 2 a-2 b Pressure drop in the delivery line 2 -2 a Pressure drop across discharge valve 1 -2 Non-isentropic compression 1 a-1 Pressure drop across suction valve 1 b-1 a Suction line pressure drop 1 c-1 b Useless superheat in suction line 1 d-1 c Superheat of vapor in evaporator 4 -1 d pressure drop in evaporator Irreversibility due to 1. Pressure drops in evaporator, condenser and LSHX 2. Pressure drop across suction and discharge valves of the compressor 3. Pressure drop and heat transfer in connecting pipe lines 4. Heat transfer in compressor Actual systems differ from standard cycles -- foreign matter such as lubricating oil, water, air, particulate matter pressure drop, heat transfer coefficient in evaporator 30
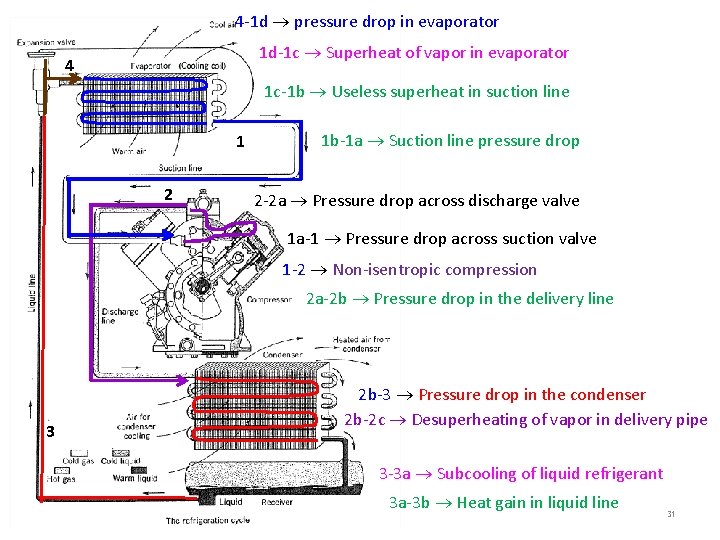
4 -1 d pressure drop in evaporator 1 d-1 c Superheat of vapor in evaporator 4 1 c-1 b Useless superheat in suction line 1 2 1 b-1 a Suction line pressure drop 2 -2 a Pressure drop across discharge valve 1 a-1 Pressure drop across suction valve 1 -2 Non-isentropic compression 2 a-2 b Pressure drop in the delivery line 3 2 b-3 Pressure drop in the condenser 2 b-2 c Desuperheating of vapor in delivery pipe 3 -3 a Subcooling of liquid refrigerant 3 a-3 b Heat gain in liquid line 31
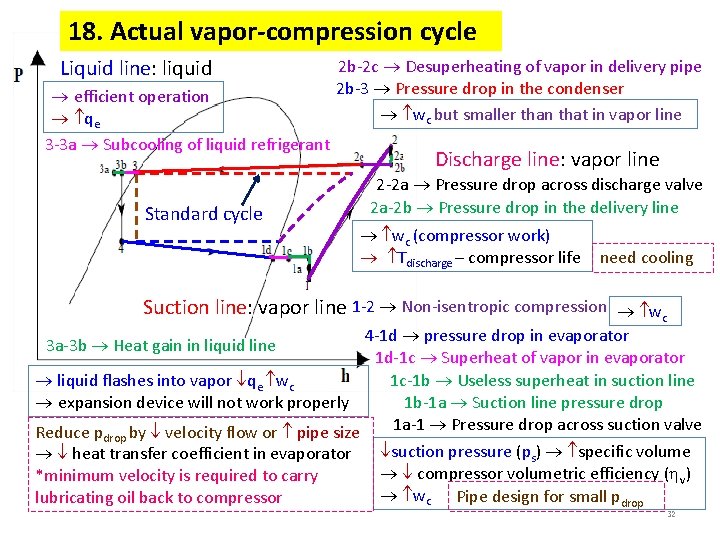
18. Actual vapor-compression cycle Liquid line: liquid efficient operation qe 3 -3 a Subcooling of liquid refrigerant 2 b-2 c Desuperheating of vapor in delivery pipe 2 b-3 Pressure drop in the condenser wc but smaller than that in vapor line Standard cycle Discharge line: vapor line 2 -2 a Pressure drop across discharge valve 2 a-2 b Pressure drop in the delivery line wc (compressor work) Tdischarge – compressor life need cooling Suction line: vapor line 1 -2 Non-isentropic compression wc 4 -1 d pressure drop in evaporator 1 d-1 c Superheat of vapor in evaporator 1 c-1 b Useless superheat in suction line liquid flashes into vapor qe wc expansion device will not work properly 1 b-1 a Suction line pressure drop 1 a-1 Pressure drop across suction valve Reduce p by velocity flow or pipe size 3 a-3 b Heat gain in liquid line drop heat transfer coefficient in evaporator *minimum velocity is required to carry lubricating oil back to compressor suction pressure (ps) specific volume compressor volumetric efficiency ( v) wc Pipe design for small pdrop 32
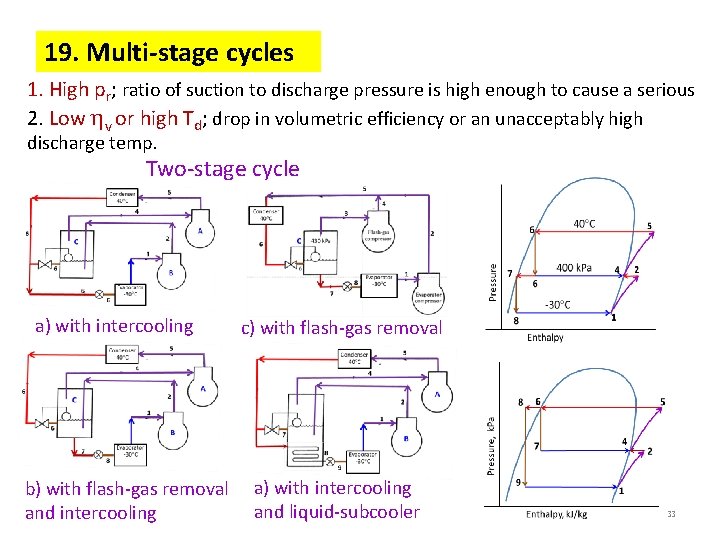
19. Multi-stage cycles 1. High pr; ratio of suction to discharge pressure is high enough to cause a serious 2. Low v or high Td; drop in volumetric efficiency or an unacceptably high discharge temp. Two-stage cycle a) with intercooling b) with flash-gas removal and intercooling c) with flash-gas removal a) with intercooling and liquid-subcooler 33
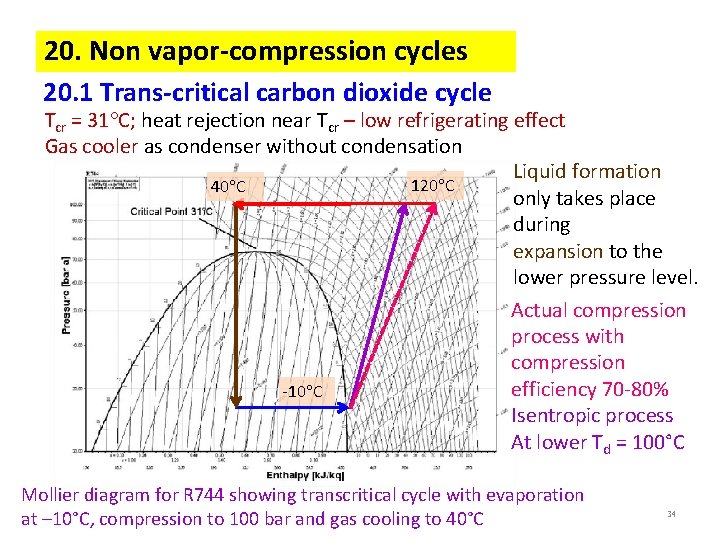
20. Non vapor-compression cycles 20. 1 Trans-critical carbon dioxide cycle Tcr = 31 C; heat rejection near Tcr – low refrigerating effect Gas cooler as condenser without condensation Liquid formation 120 C 40 C only takes place during expansion to the lower pressure level. Actual compression process with compression efficiency 70 -80% -10 C Isentropic process At lower Td = 100°C Mollier diagram for R 744 showing transcritical cycle with evaporation at – 10°C, compression to 100 bar and gas cooling to 40°C 34
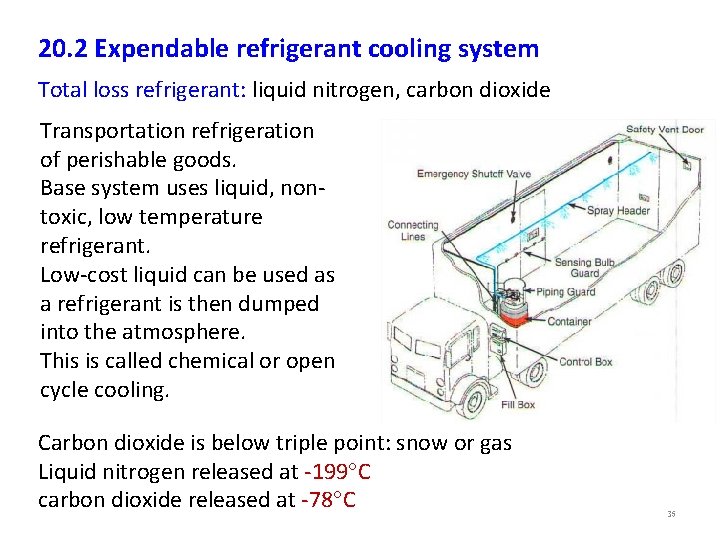
20. 2 Expendable refrigerant cooling system Total loss refrigerant: liquid nitrogen, carbon dioxide Transportation refrigeration of perishable goods. Base system uses liquid, nontoxic, low temperature refrigerant. Low-cost liquid can be used as a refrigerant is then dumped into the atmosphere. This is called chemical or open cycle cooling. Carbon dioxide is below triple point: snow or gas Liquid nitrogen released at -199 C carbon dioxide released at -78 C 35
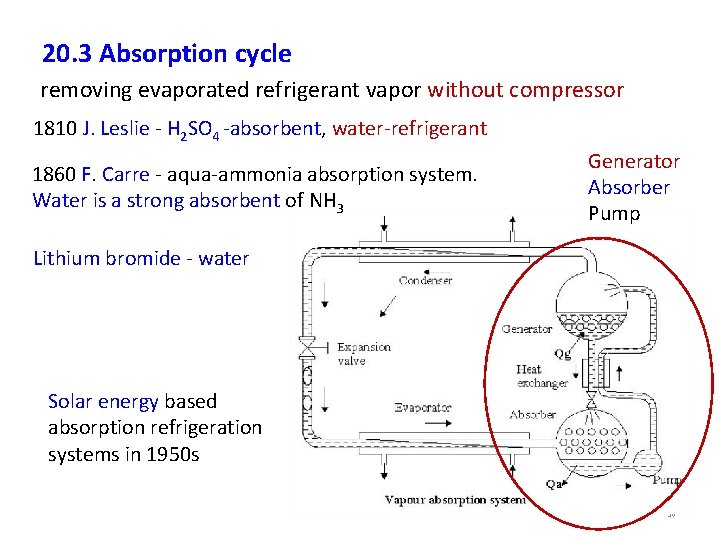
20. 3 Absorption cycle removing evaporated refrigerant vapor without compressor 1810 J. Leslie - H 2 SO 4 -absorbent, water-refrigerant 1860 F. Carre - aqua-ammonia absorption system. Water is a strong absorbent of NH 3 Generator Absorber Pump Lithium bromide - water Solar energy based absorption refrigeration systems in 1950 s 36
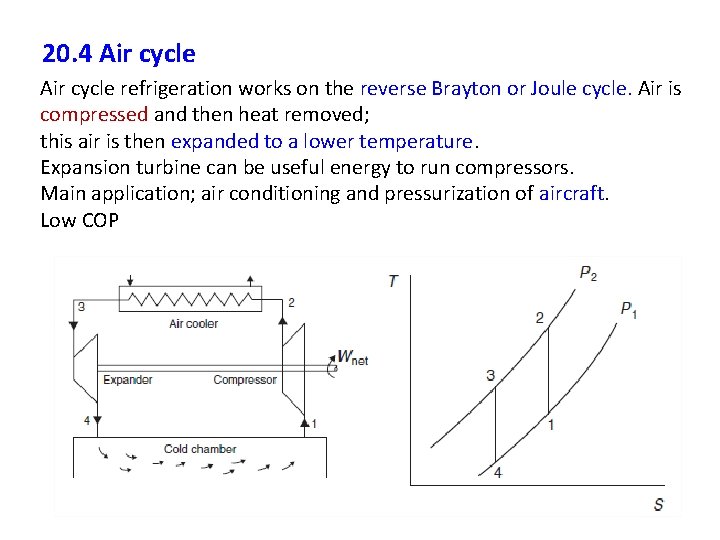
20. 4 Air cycle refrigeration works on the reverse Brayton or Joule cycle. Air is compressed and then heat removed; this air is then expanded to a lower temperature. Expansion turbine can be useful energy to run compressors. Main application; air conditioning and pressurization of aircraft. Low COP 37
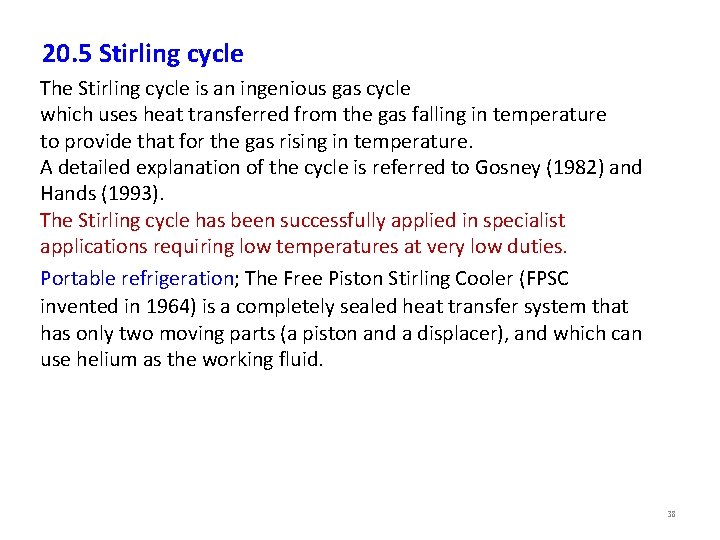
20. 5 Stirling cycle The Stirling cycle is an ingenious gas cycle which uses heat transferred from the gas falling in temperature to provide that for the gas rising in temperature. A detailed explanation of the cycle is referred to Gosney (1982) and Hands (1993). The Stirling cycle has been successfully applied in specialist applications requiring low temperatures at very low duties. Portable refrigeration; The Free Piston Stirling Cooler (FPSC invented in 1964) is a completely sealed heat transfer system that has only two moving parts (a piston and a displacer), and which can use helium as the working fluid. 38
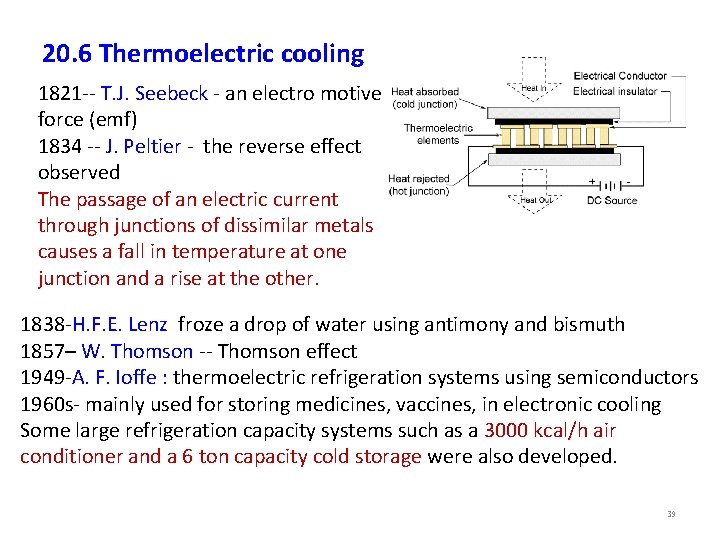
20. 6 Thermoelectric cooling 1821 -- T. J. Seebeck - an electro motive force (emf) 1834 -- J. Peltier - the reverse effect observed The passage of an electric current through junctions of dissimilar metals causes a fall in temperature at one junction and a rise at the other. 1838 -H. F. E. Lenz froze a drop of water using antimony and bismuth 1857– W. Thomson -- Thomson effect 1949 -A. F. Ioffe : thermoelectric refrigeration systems using semiconductors 1960 s- mainly used for storing medicines, vaccines, in electronic cooling Some large refrigeration capacity systems such as a 3000 kcal/h air conditioner and a 6 ton capacity cold storage were also developed. 39
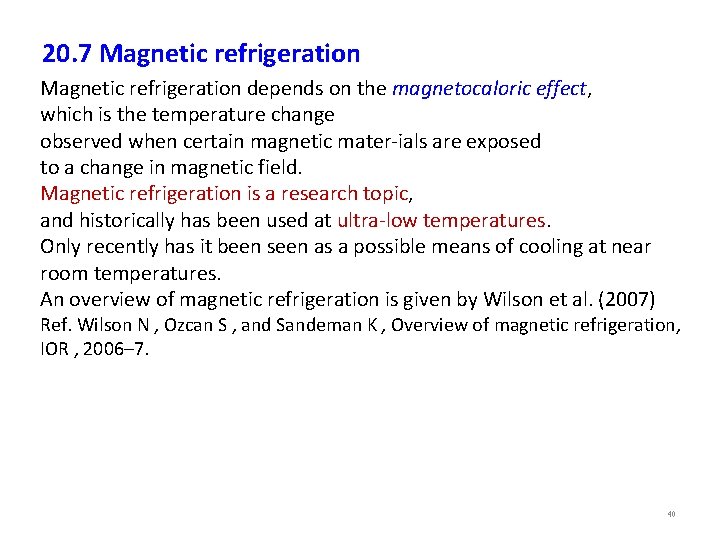
20. 7 Magnetic refrigeration depends on the magnetocaloric effect, which is the temperature change observed when certain magnetic mater-ials are exposed to a change in magnetic field. Magnetic refrigeration is a research topic, and historically has been used at ultra-low temperatures. Only recently has it been seen as a possible means of cooling at near room temperatures. An overview of magnetic refrigeration is given by Wilson et al. (2007) Ref. Wilson N , Ozcan S , and Sandeman K , Overview of magnetic refrigeration, IOR , 2006– 7. 40
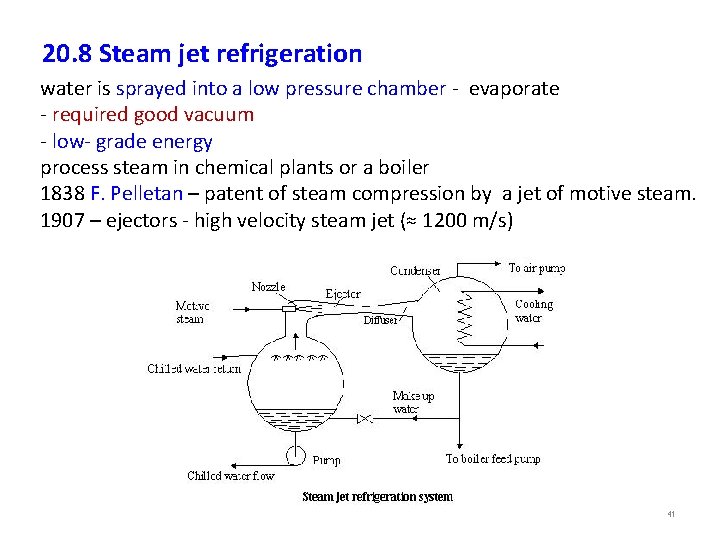
20. 8 Steam jet refrigeration water is sprayed into a low pressure chamber - evaporate - required good vacuum - low- grade energy process steam in chemical plants or a boiler 1838 F. Pelletan – patent of steam compression by a jet of motive steam. 1907 – ejectors - high velocity steam jet (≈ 1200 m/s) 41
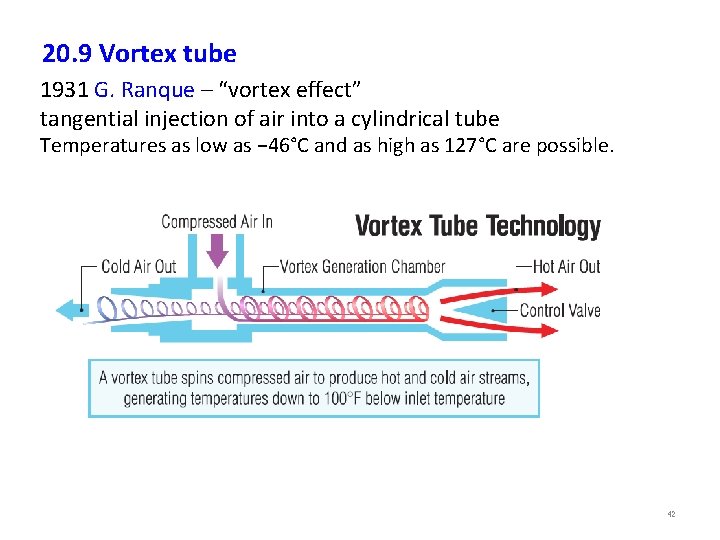
20. 9 Vortex tube 1931 G. Ranque – “vortex effect” tangential injection of air into a cylindrical tube Temperatures as low as − 46°C and as high as 127°C are possible. 42
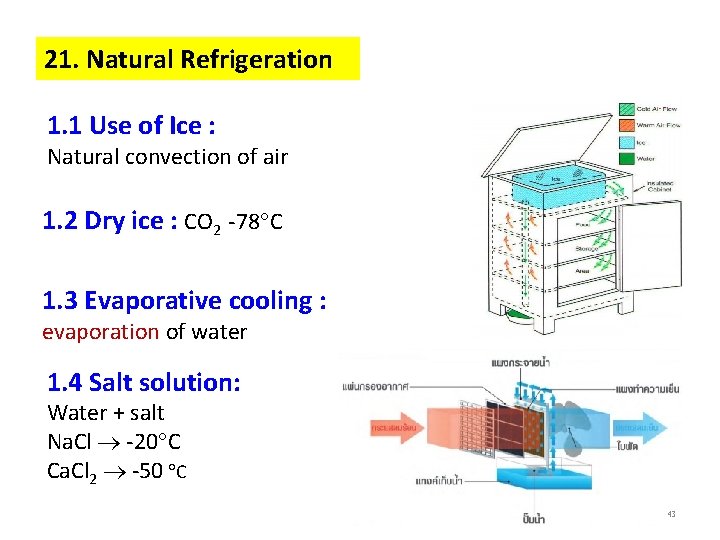
21. Natural Refrigeration 1. 1 Use of Ice : Natural convection of air 1. 2 Dry ice : CO 2 -78 C 1. 3 Evaporative cooling : evaporation of water 1. 4 Salt solution: Water + salt Na. Cl -20 C Ca. Cl 2 -50 C 43
Carnot efficiency
Carnot cycle definition
Reverse carnot cycle
Cycle carnot
Carnot cycle
Cycle carnot
Hurricane carnot engine
Carnot engine animation
Carnot cycle efficiency depends upon
Entropy of diamond
Refrigeration and air conditioning cycle
Reversed carnot cycle
Carnot vapor power cycle
Refrigeration process
Cop of refrigerator
Refrigeration t-s diagram
Adsorption system
Bell coleman cycle process
Matlab refrigeration cycle
Example of specific topic
Narrowed down topic examples
Trabajo neto ciclo de carnot
Thermodinamika
Macchina monoterma
Rendimento in fisica
Carnot cykel
Carnot körfolyamat
Secondo principio della termodinamica
Carnot virkningsgrad
Eficiencia de carnot
Una maquina de carnot absorbe 1200 cal
Trasformazioni termodinamiche zanichelli
Kelvin planck ifadesi
Expansão adiabática
Teorema de carnot ou lei dos cossenos
Ciclo de carnot
Ciclo de carnot
Ciclo de carnot
Ciclo ideal de carnot
Borda carnot
Carnot inverso
Carnot
Inhomogenitás
Carnot engine