Multidisciplinary Senior Design Rochester Institute of Technology DresserRand
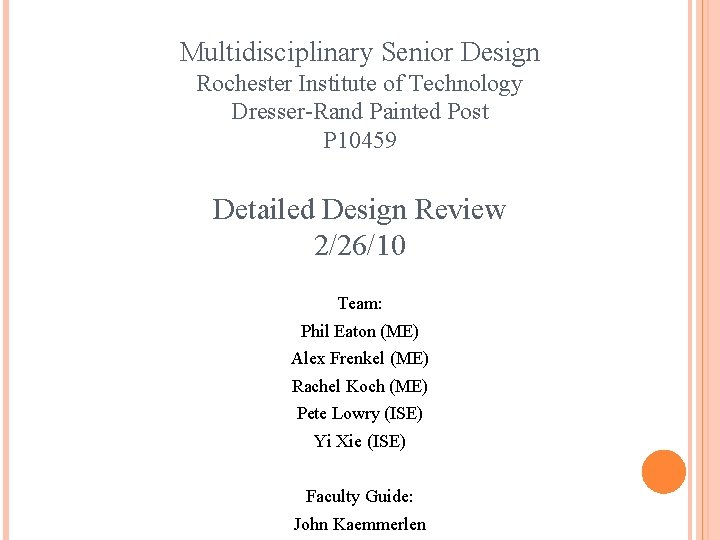
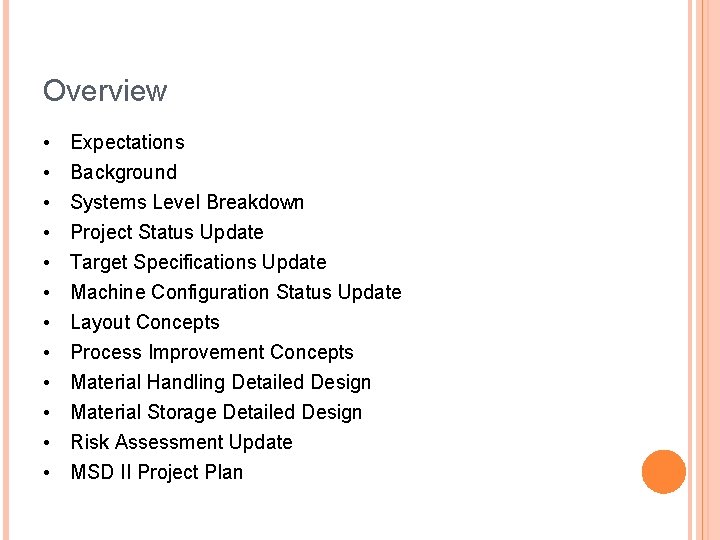
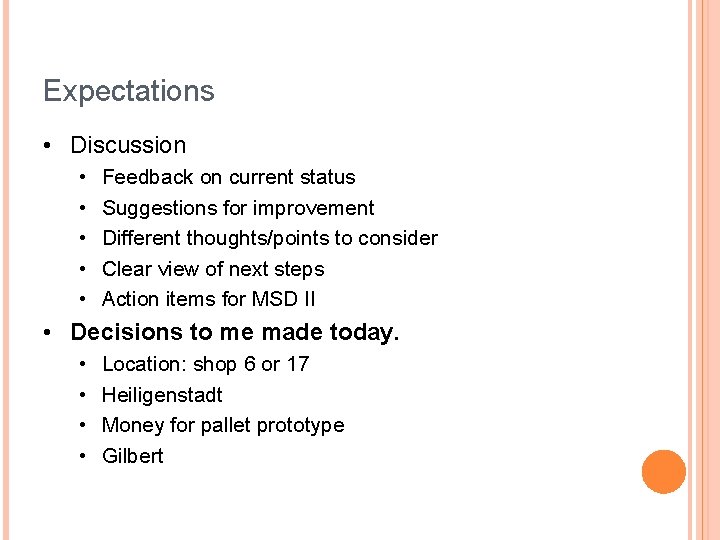
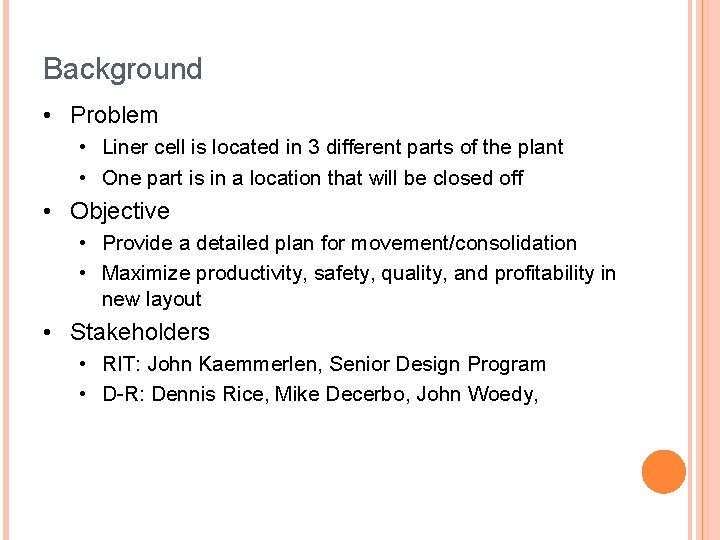
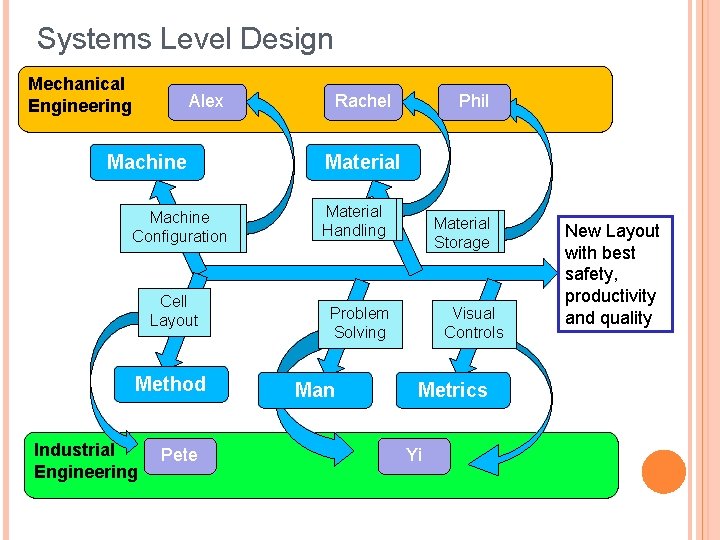
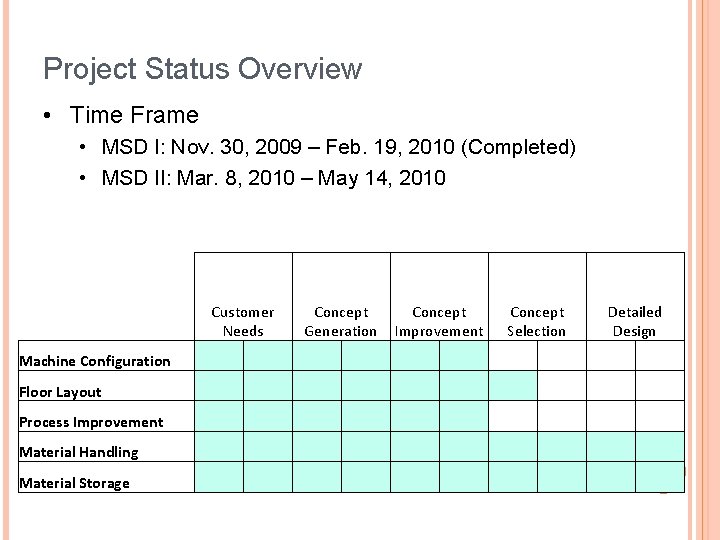
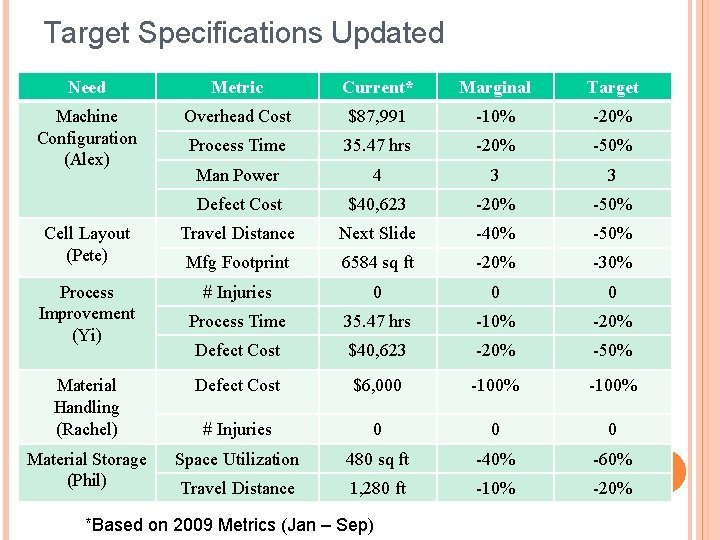
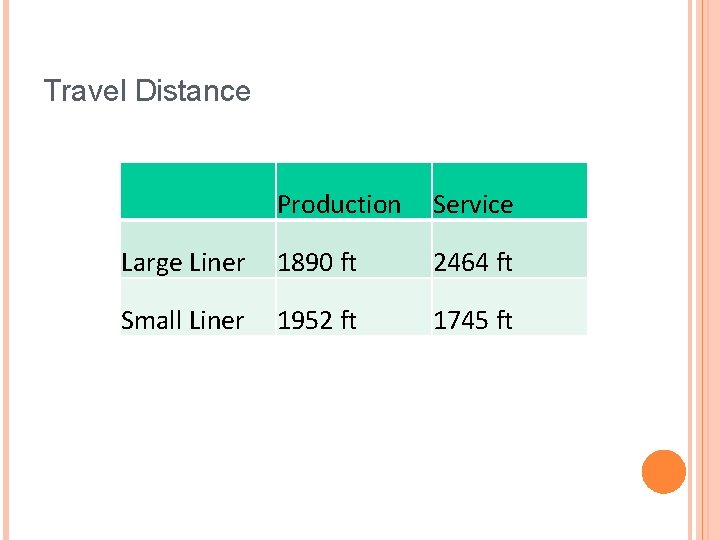
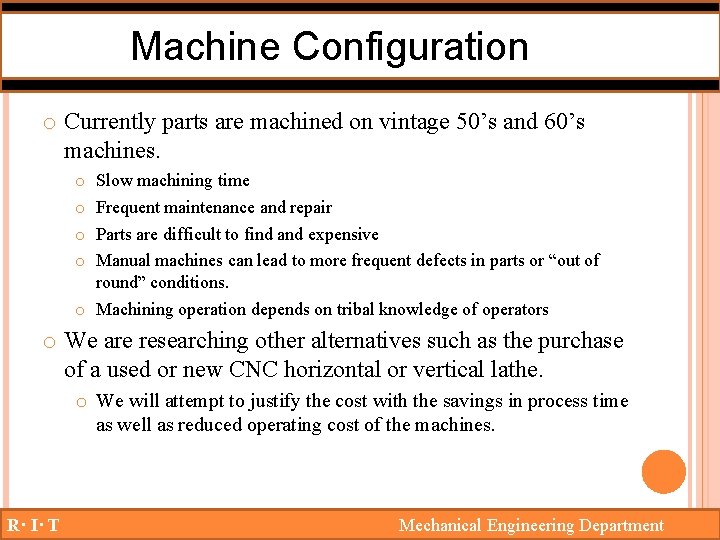
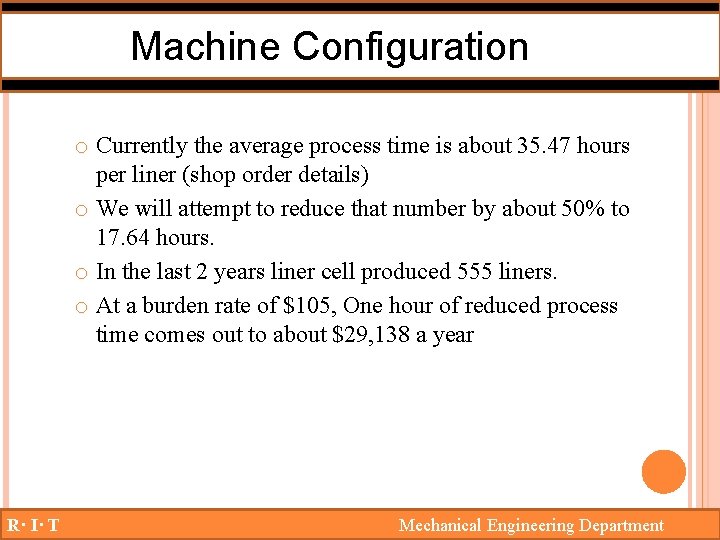
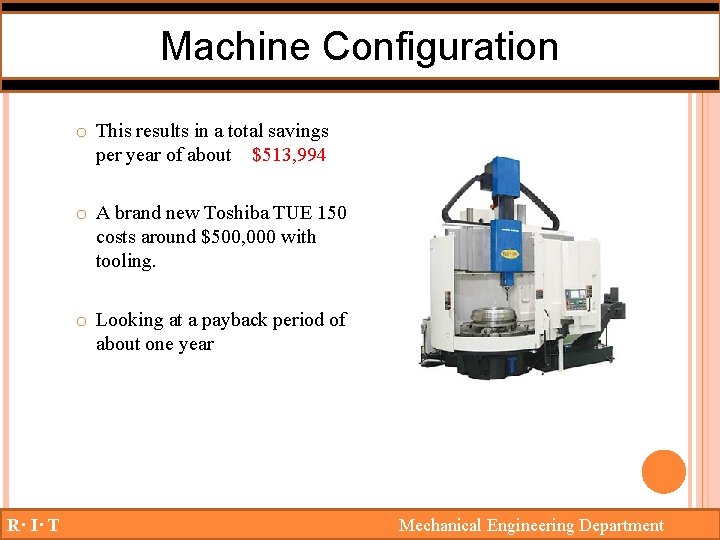
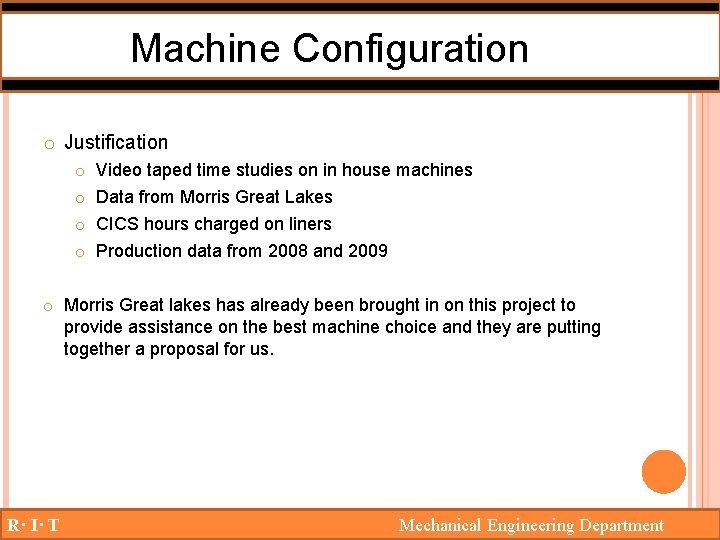
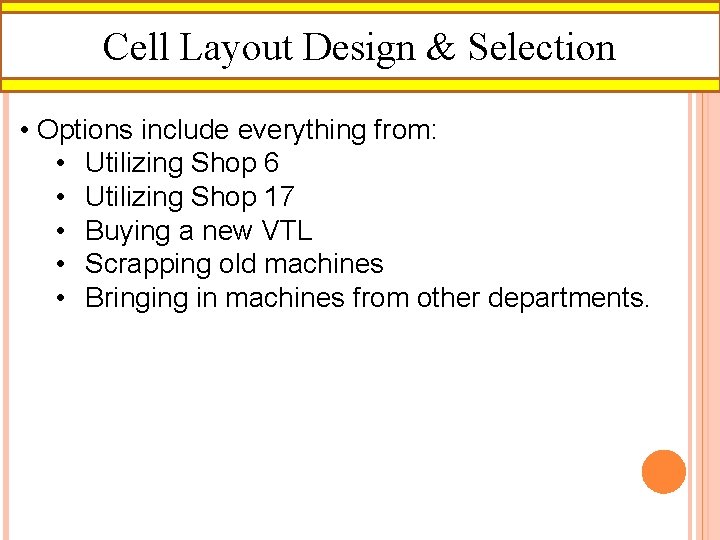
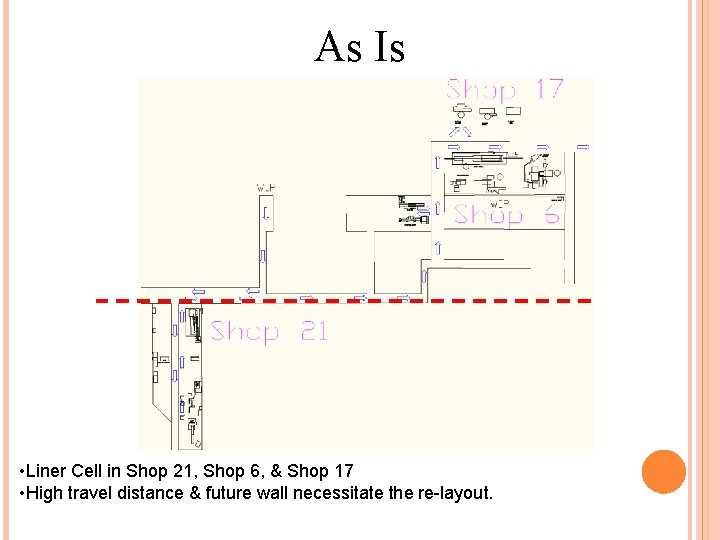
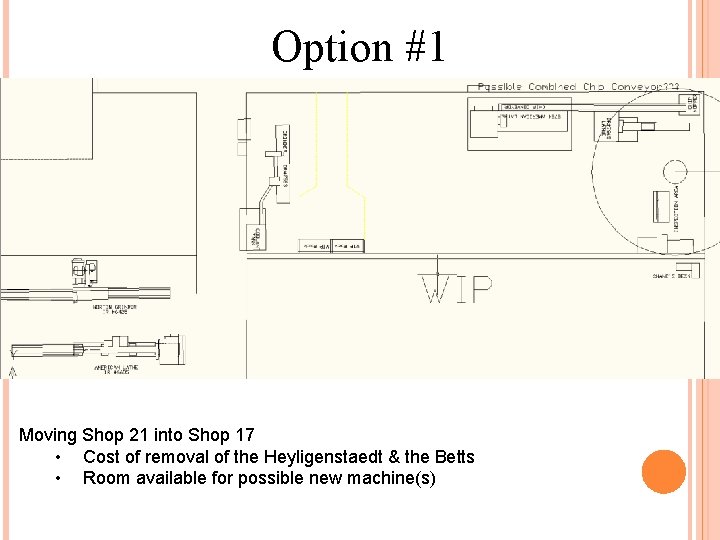
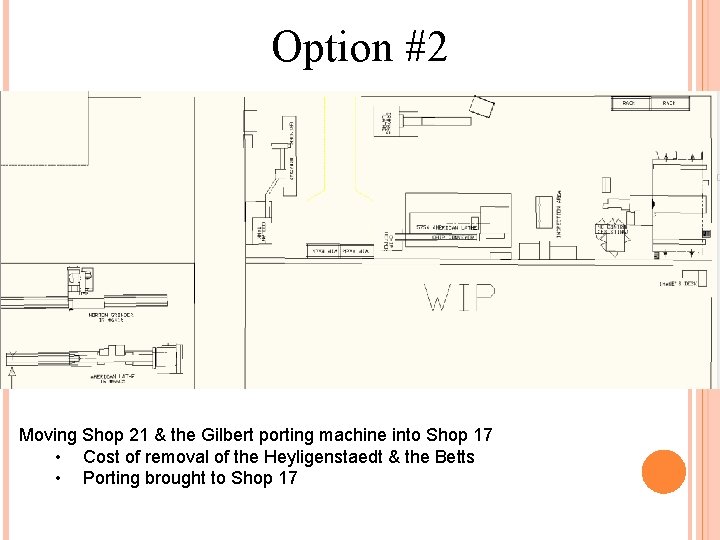
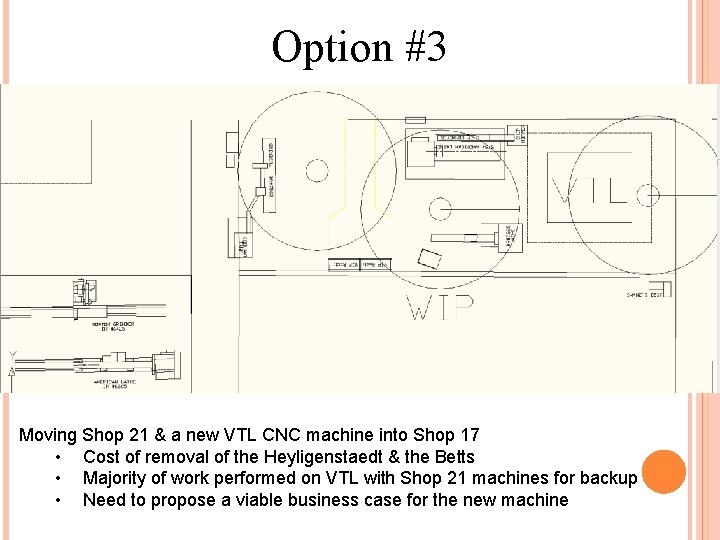
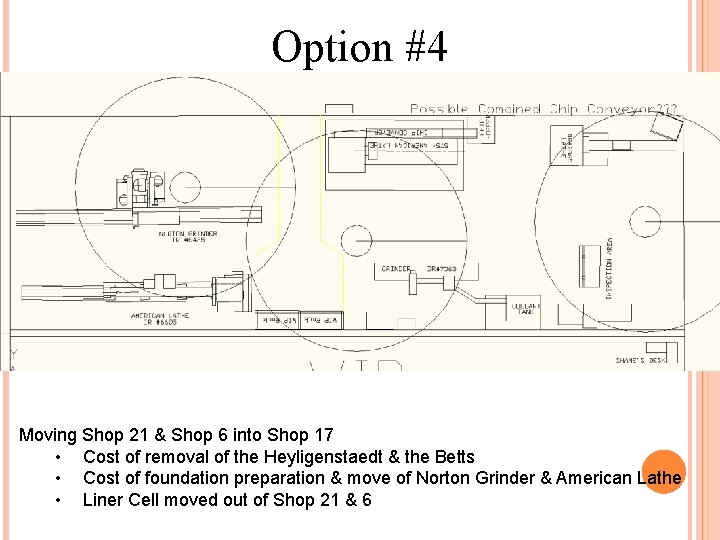
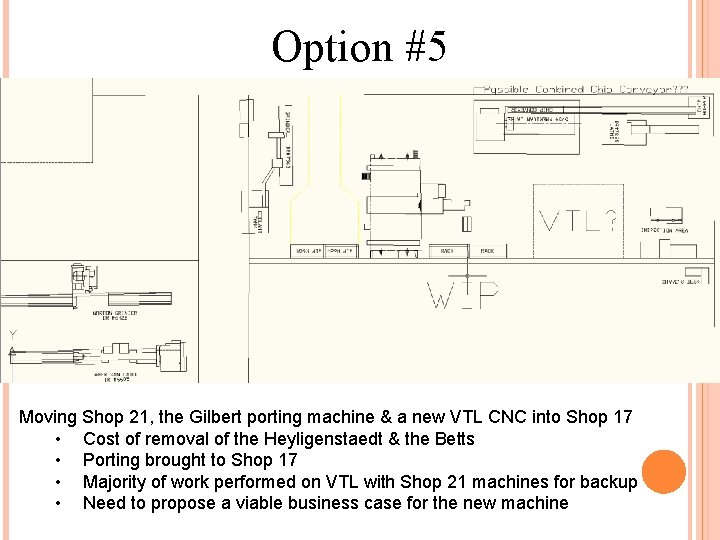
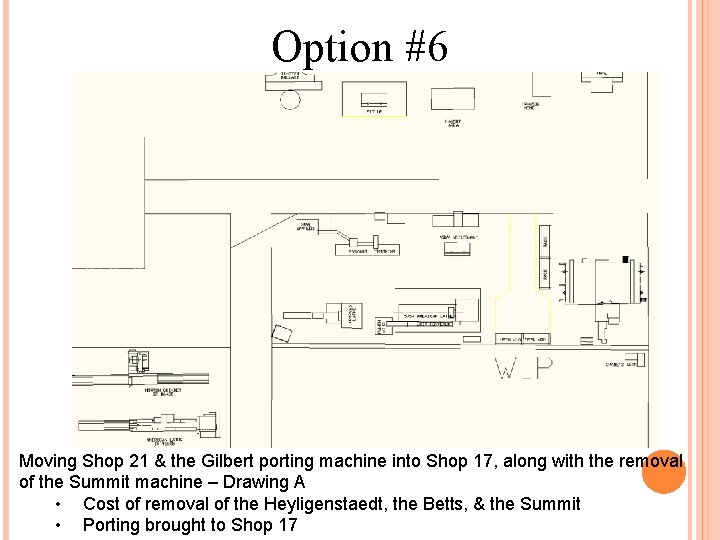
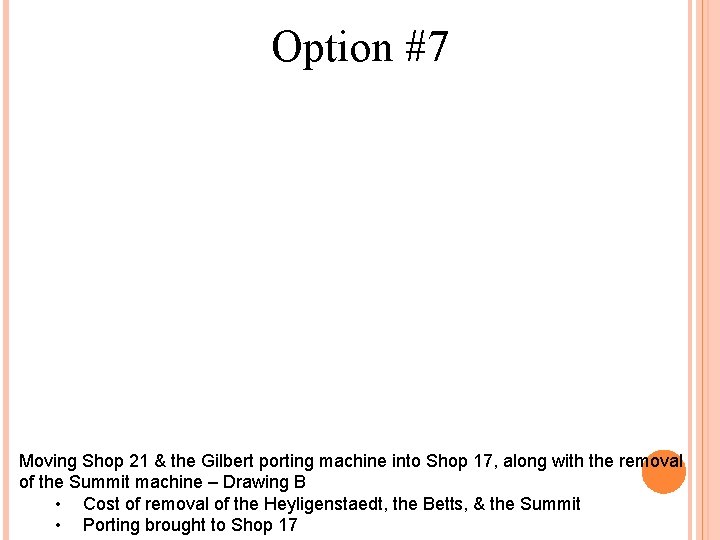
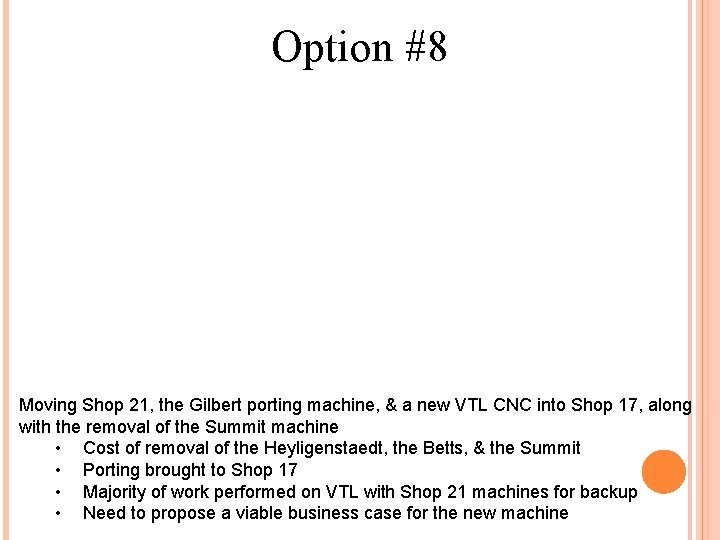
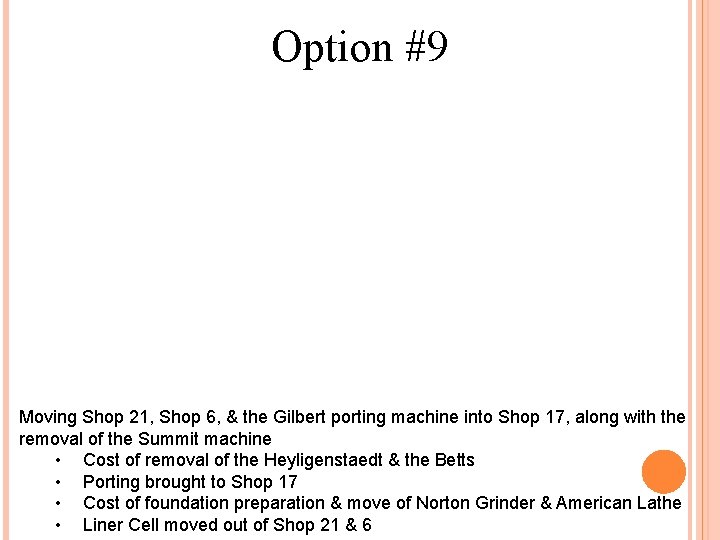
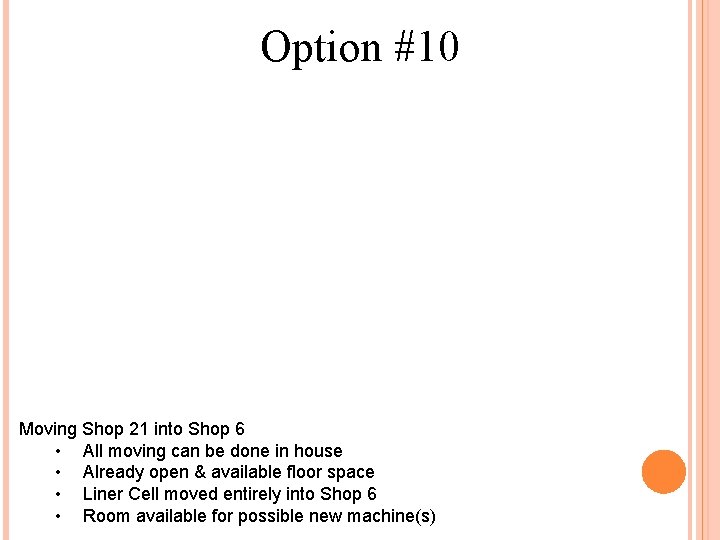
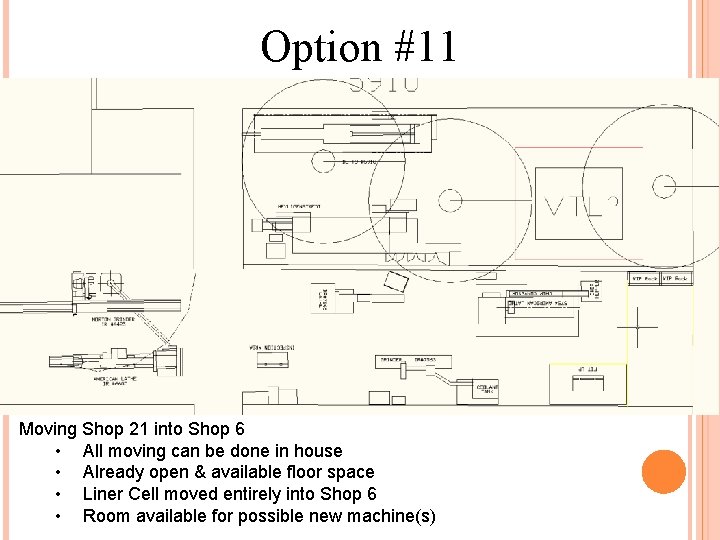
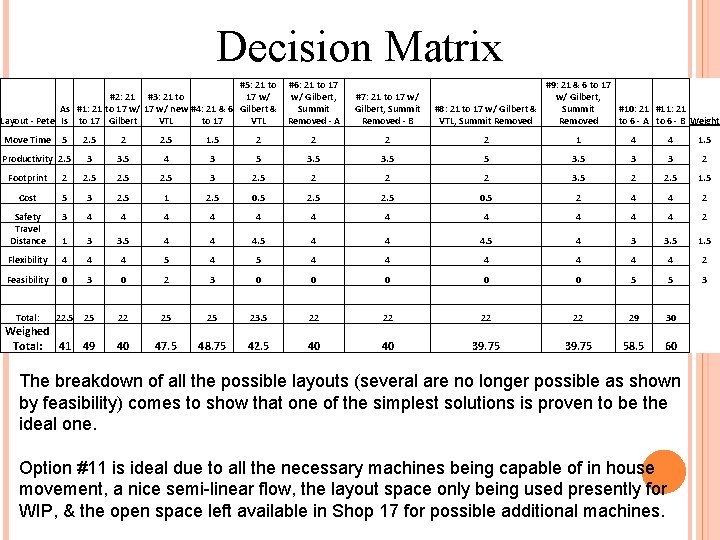
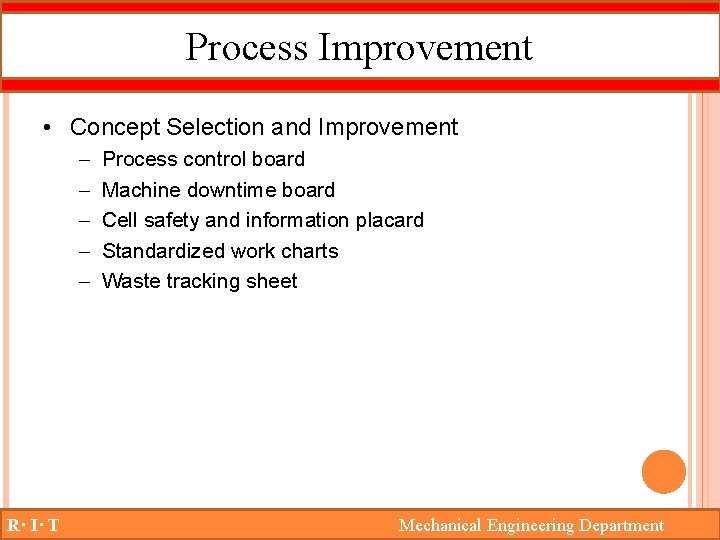
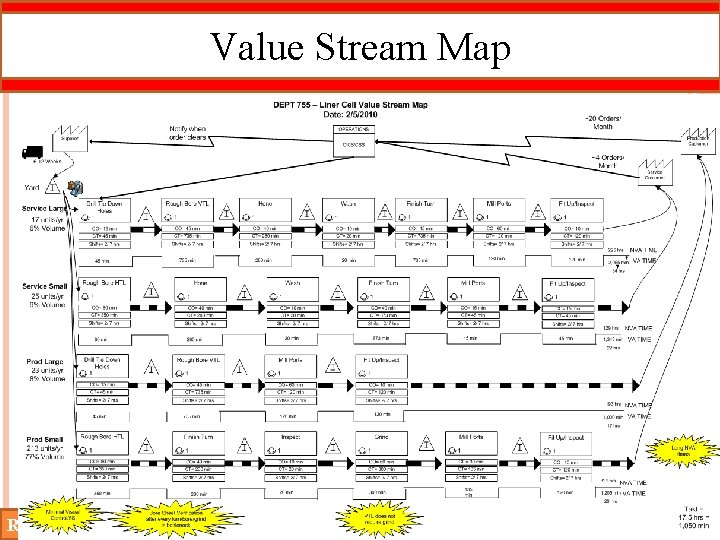
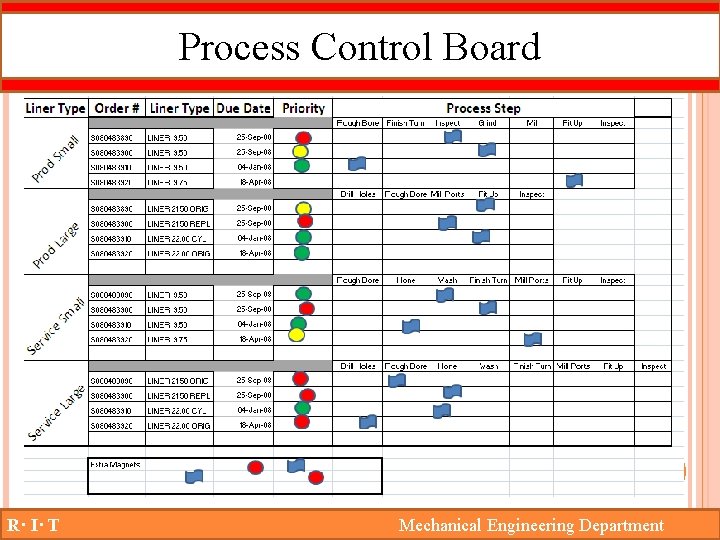
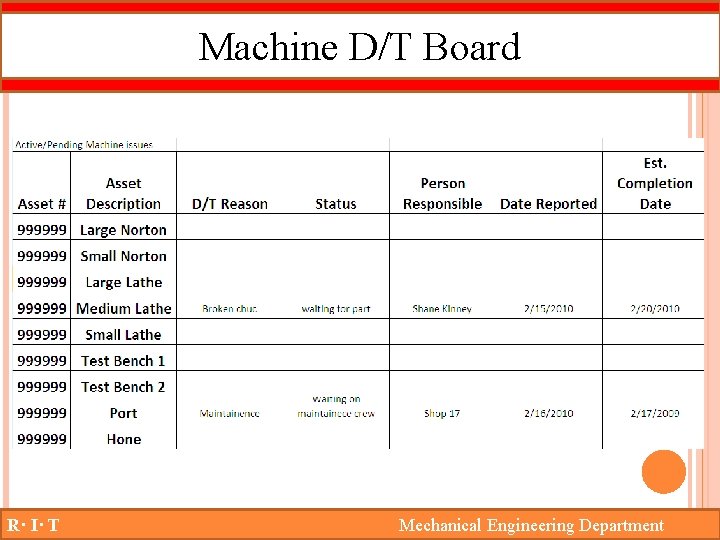
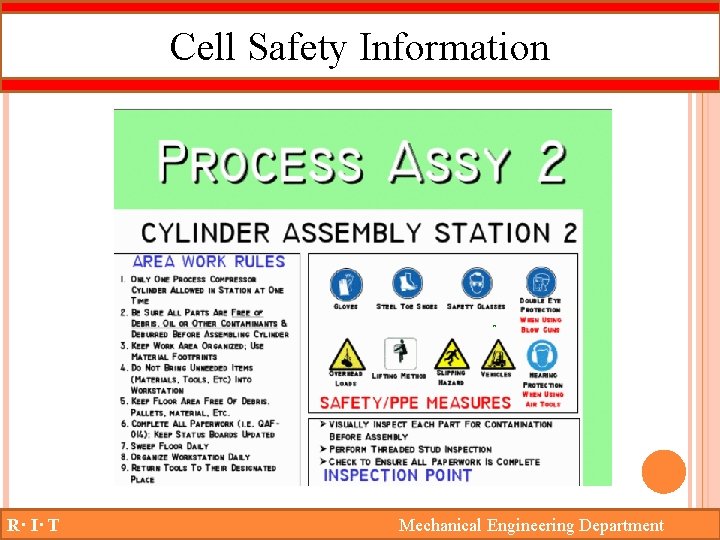
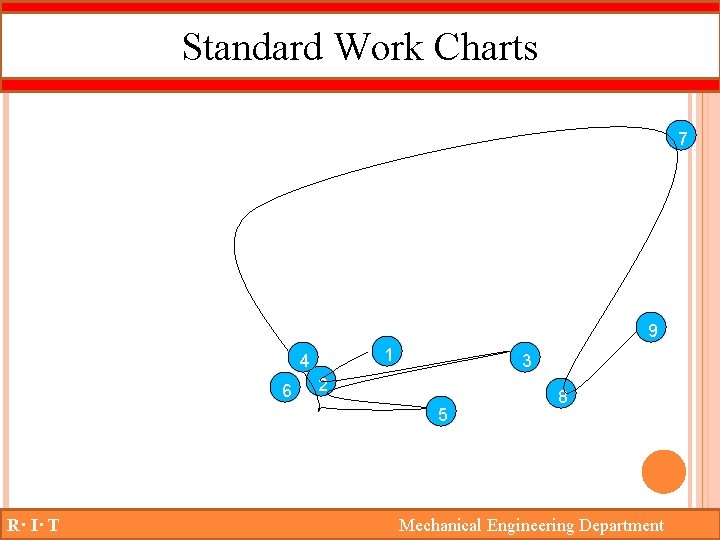
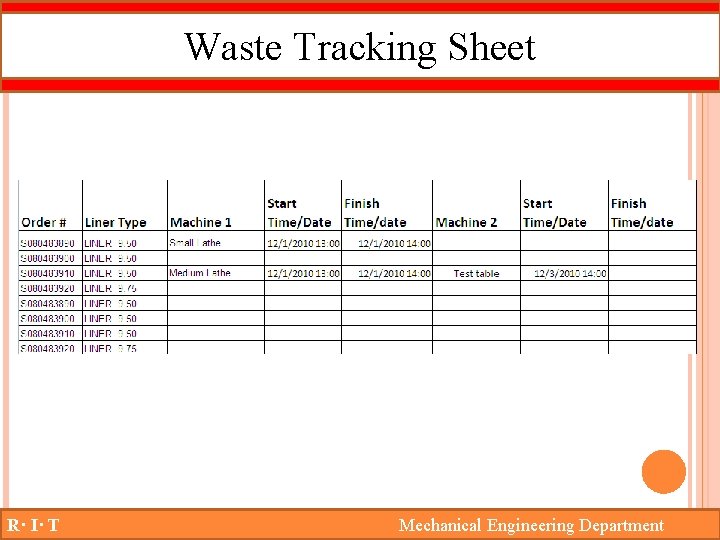
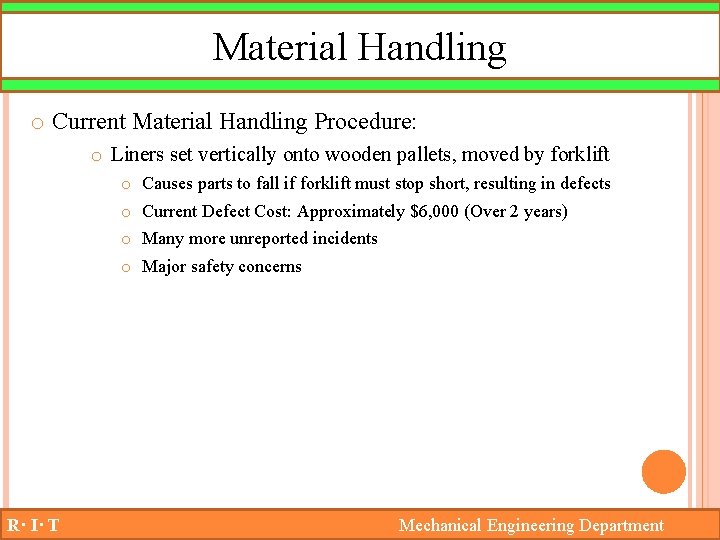
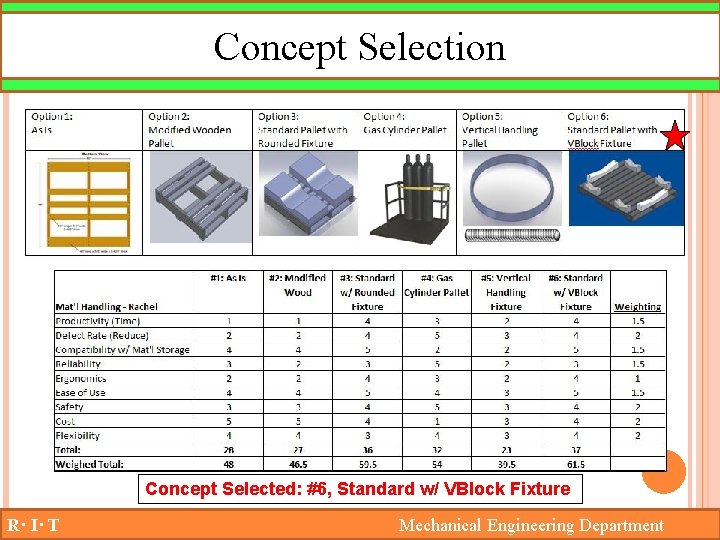
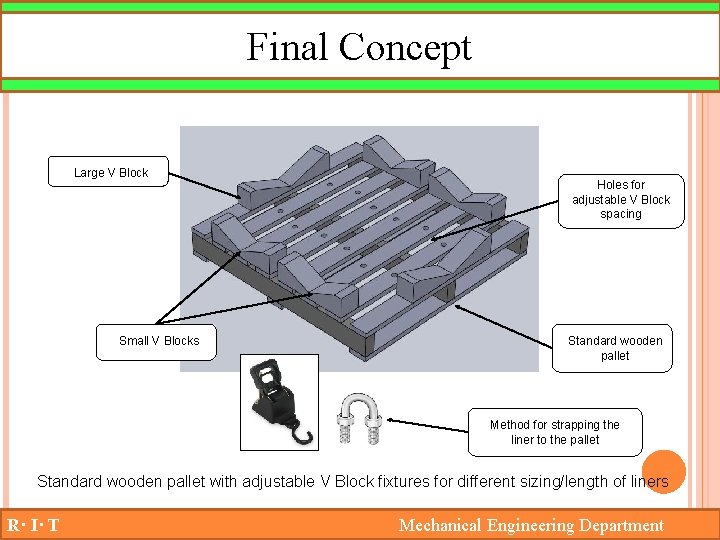
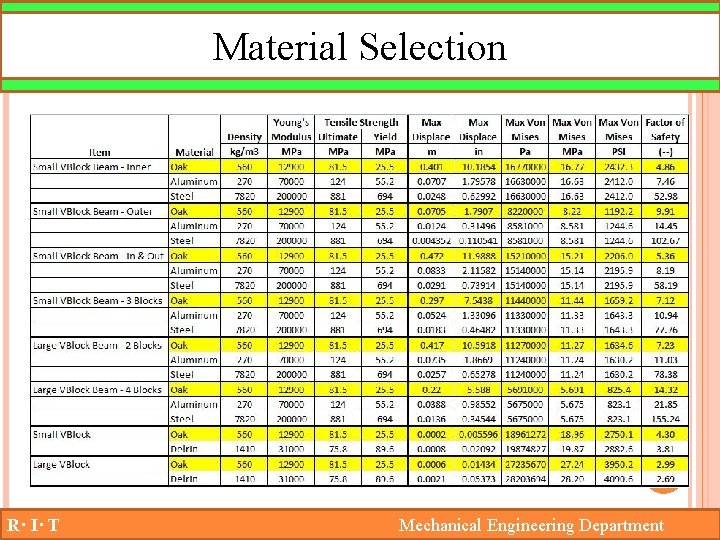
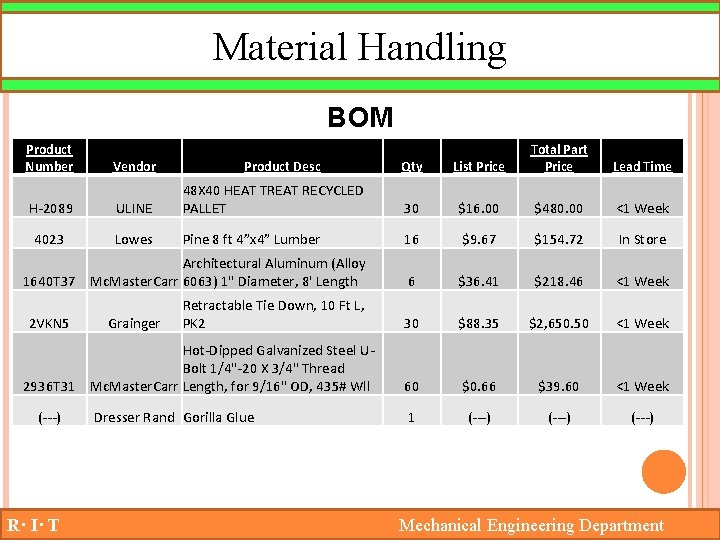
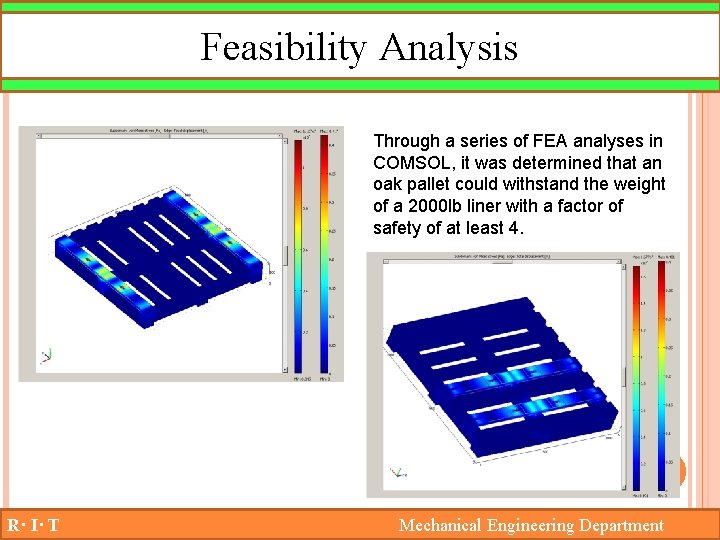
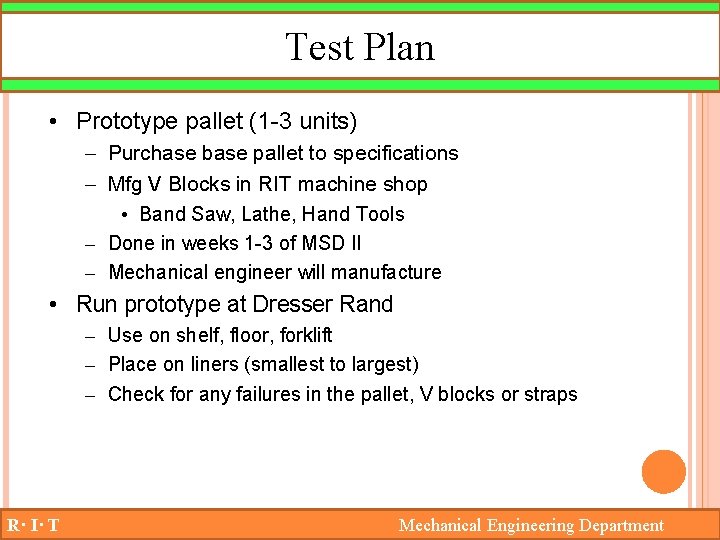
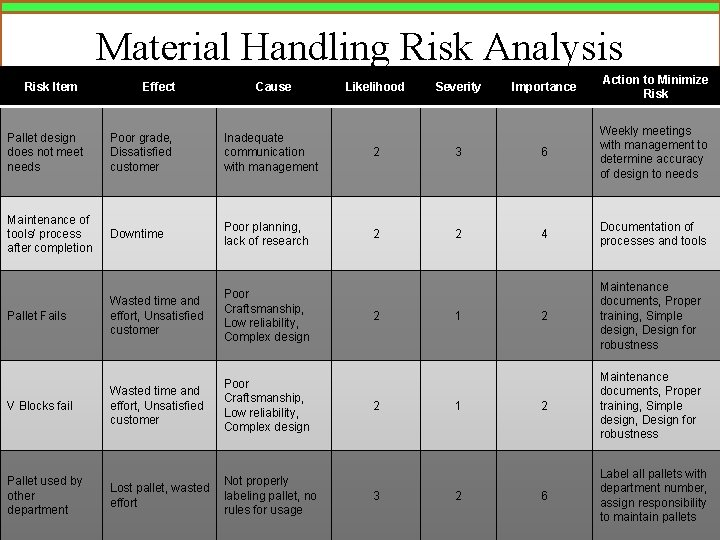
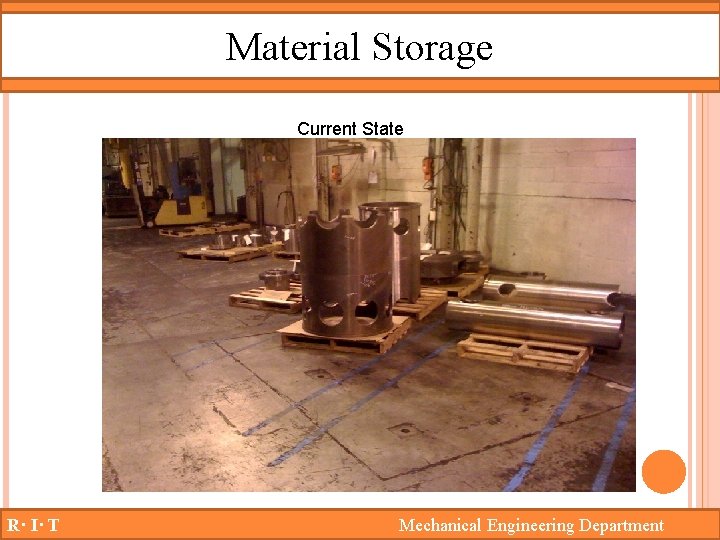
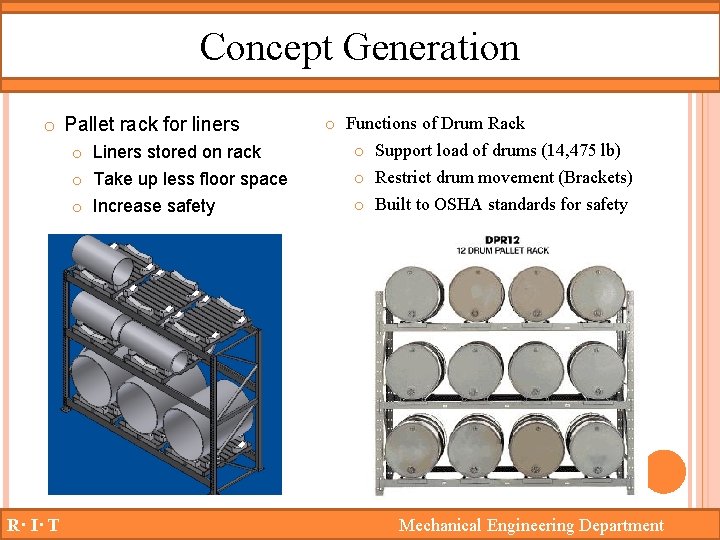
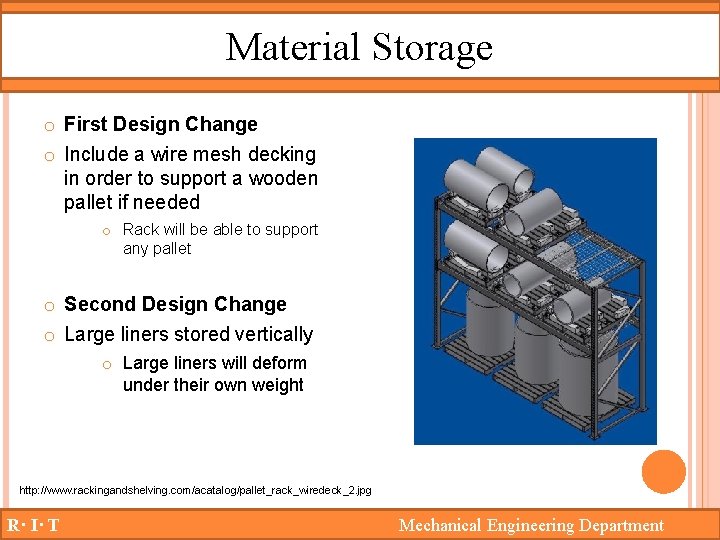
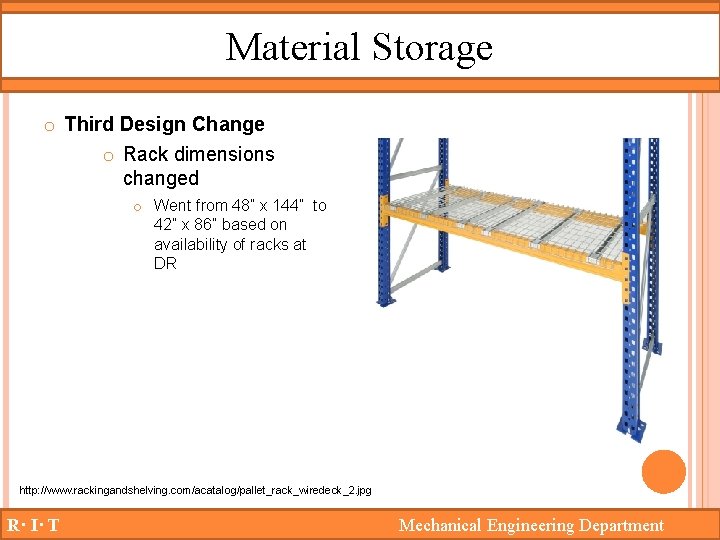
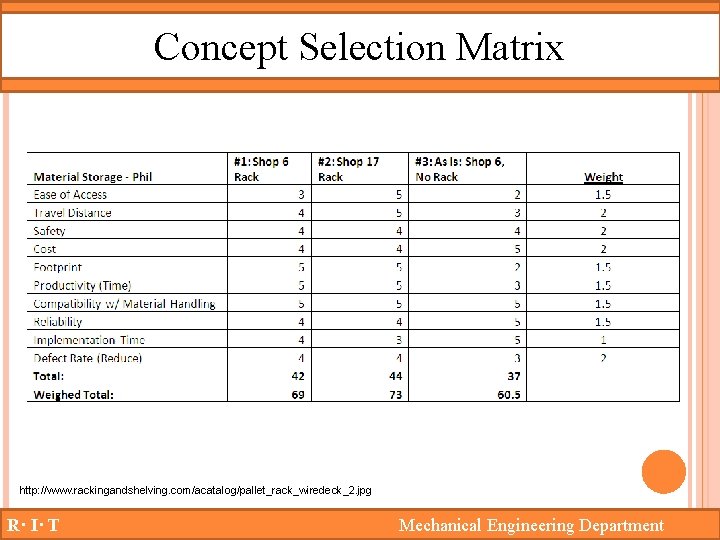
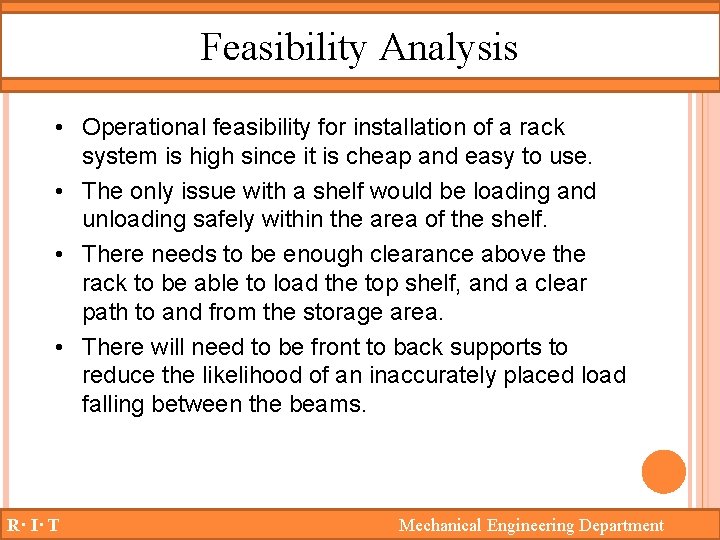
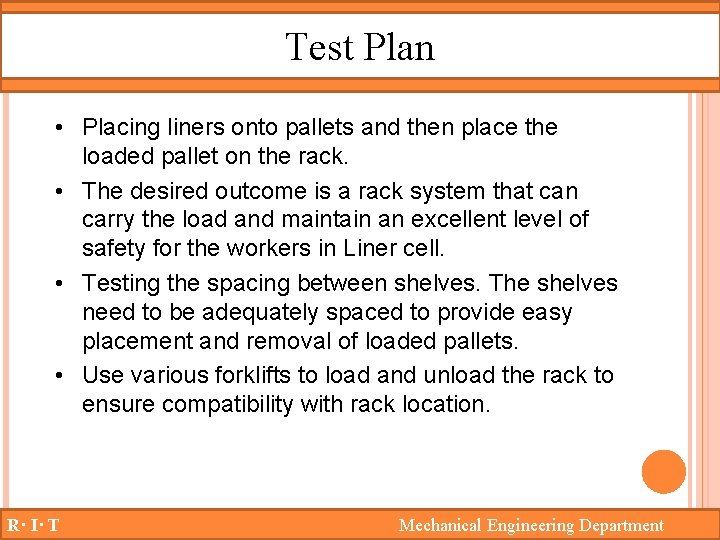
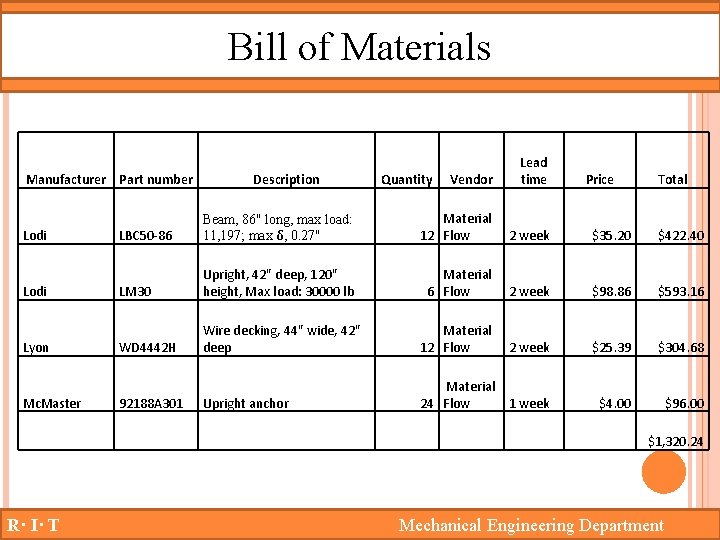
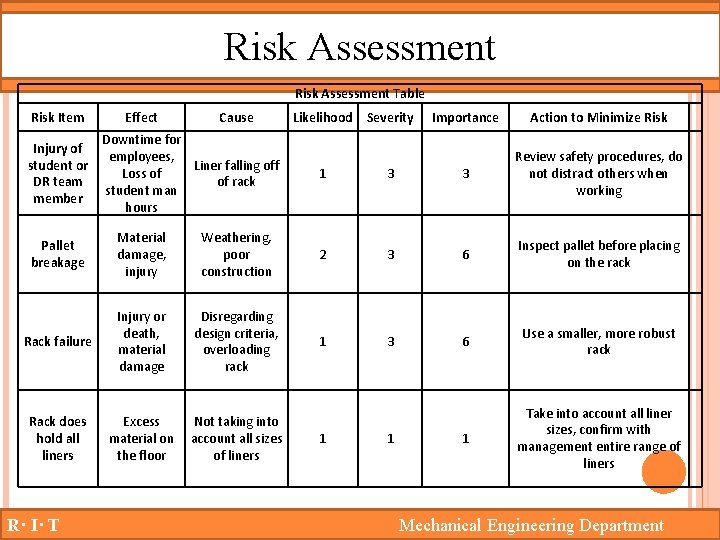
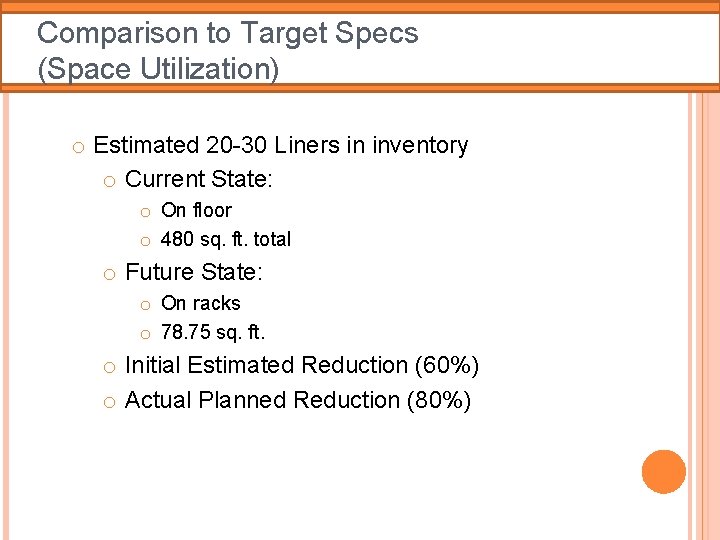
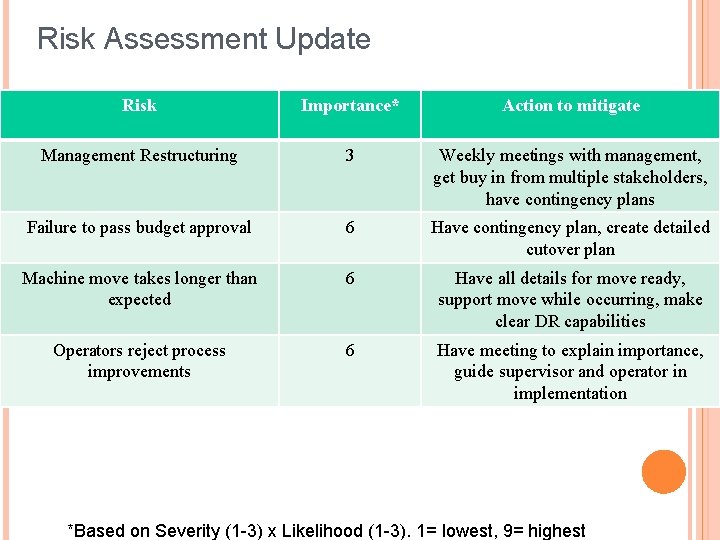
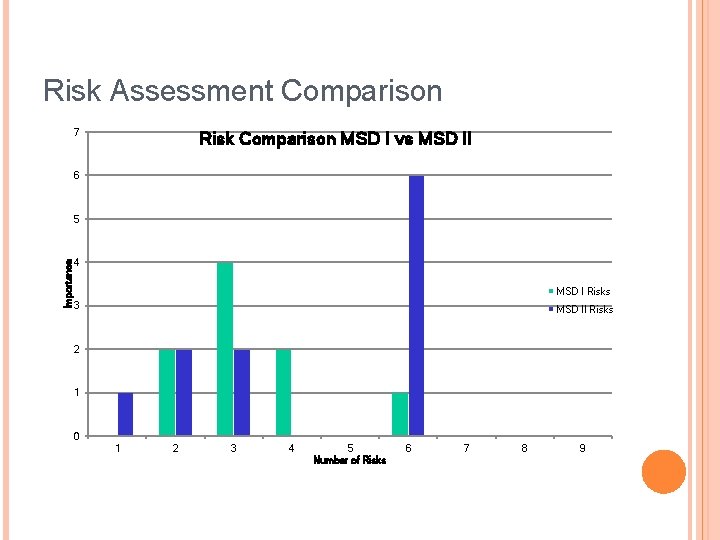
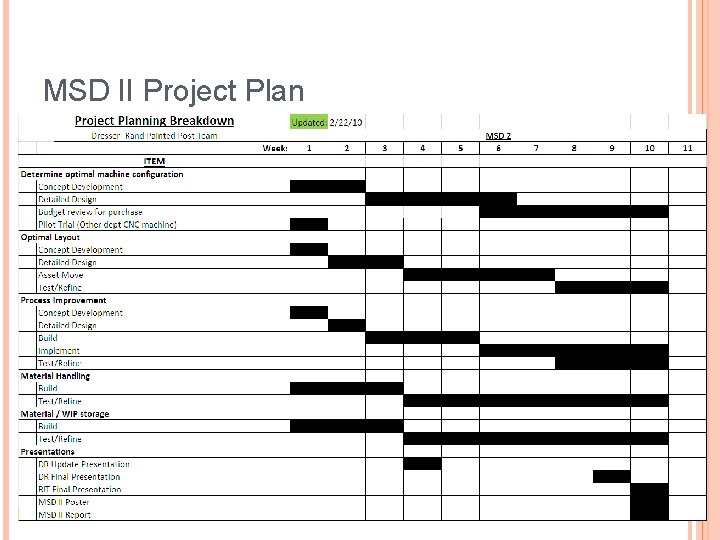
- Slides: 54
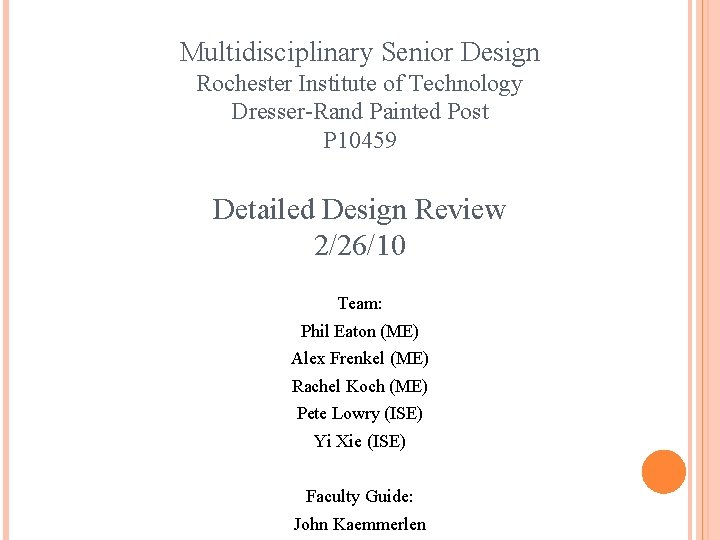
Multidisciplinary Senior Design Rochester Institute of Technology Dresser-Rand Painted Post P 10459 Detailed Design Review 2/26/10 Team: Phil Eaton (ME) Alex Frenkel (ME) Rachel Koch (ME) Pete Lowry (ISE) Yi Xie (ISE) Faculty Guide: John Kaemmerlen
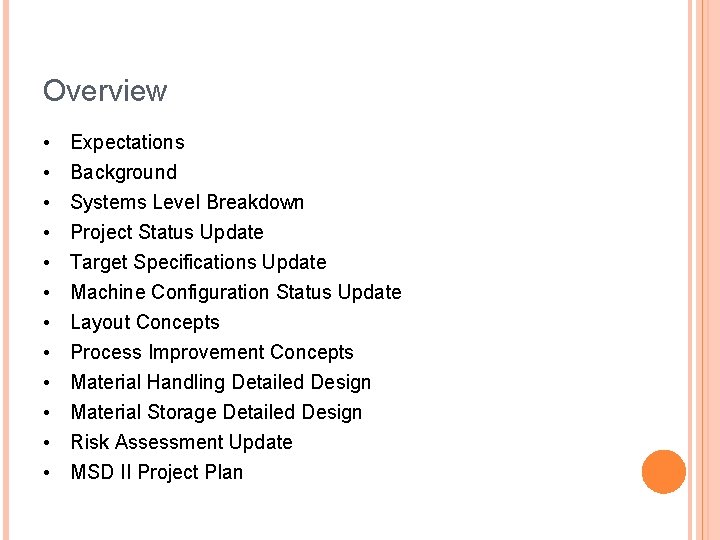
Overview • • • Expectations Background Systems Level Breakdown Project Status Update Target Specifications Update Machine Configuration Status Update Layout Concepts Process Improvement Concepts Material Handling Detailed Design Material Storage Detailed Design Risk Assessment Update MSD II Project Plan
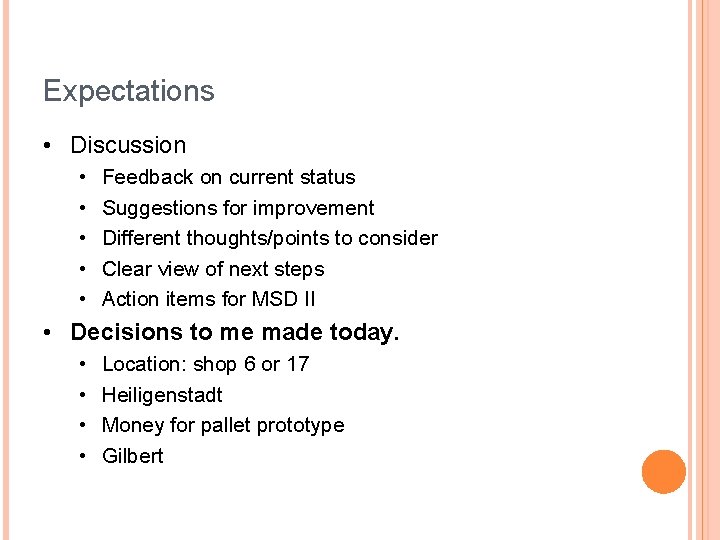
Expectations • Discussion • • • Feedback on current status Suggestions for improvement Different thoughts/points to consider Clear view of next steps Action items for MSD II • Decisions to me made today. • • Location: shop 6 or 17 Heiligenstadt Money for pallet prototype Gilbert
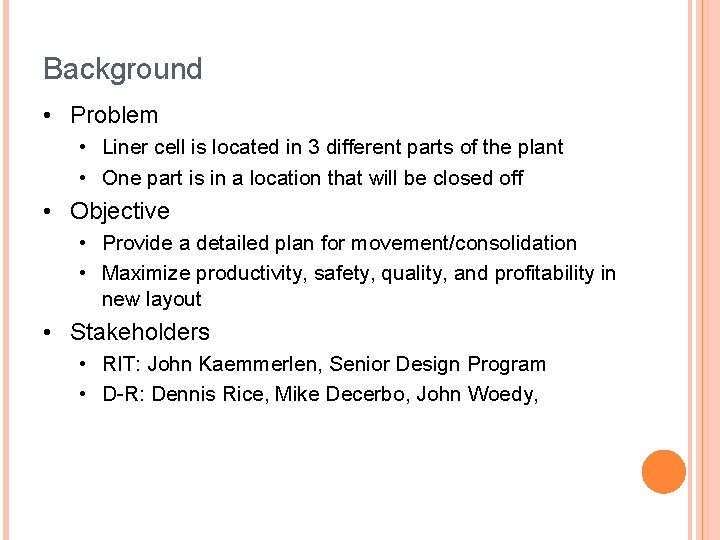
Background • Problem • Liner cell is located in 3 different parts of the plant • One part is in a location that will be closed off • Objective • Provide a detailed plan for movement/consolidation • Maximize productivity, safety, quality, and profitability in new layout • Stakeholders • RIT: John Kaemmerlen, Senior Design Program • D-R: Dennis Rice, Mike Decerbo, John Woedy,
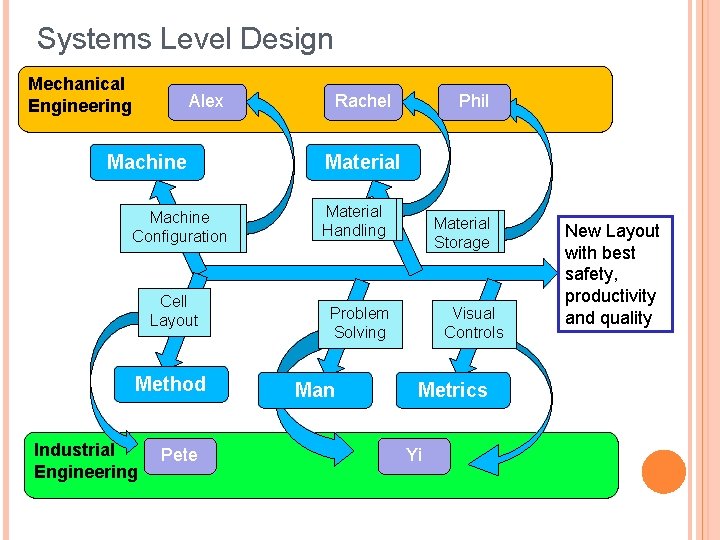
Systems Level Design Mechanical Engineering Alex Machine Configuration Cell Layout Method Industrial Engineering Pete Rachel Phil Material Handling Material Storage Problem Solving Man Visual Controls Metrics Yi New Layout with best safety, productivity and quality
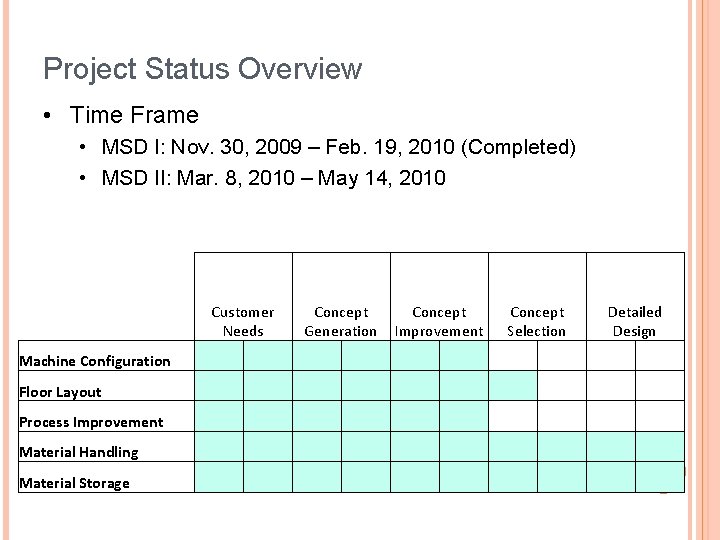
Project Status Overview • Time Frame • MSD I: Nov. 30, 2009 – Feb. 19, 2010 (Completed) • MSD II: Mar. 8, 2010 – May 14, 2010 Customer Needs Concept Generation Concept Improvement Concept Selection Detailed Design Machine Configuration Floor Layout Process Improvement Material Handling Material Storage
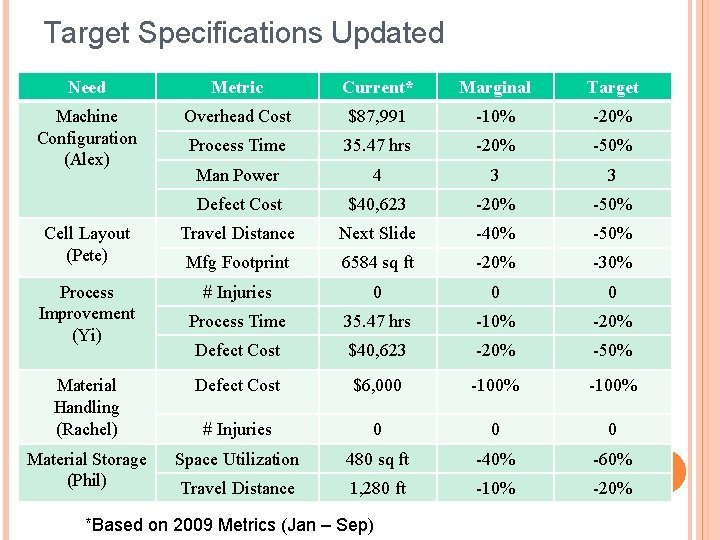
Target Specifications Updated Need Metric Current* Marginal Target Machine Configuration (Alex) Overhead Cost $87, 991 -10% -20% Process Time 35. 47 hrs -20% -50% Man Power 4 3 3 Defect Cost $40, 623 -20% -50% Cell Layout (Pete) Travel Distance Next Slide -40% -50% Mfg Footprint 6584 sq ft -20% -30% Process Improvement (Yi) # Injuries 0 0 0 Process Time 35. 47 hrs -10% -20% Defect Cost $40, 623 -20% -50% Material Handling (Rachel) Defect Cost $6, 000 -100% # Injuries 0 0 0 Material Storage (Phil) Space Utilization 480 sq ft -40% -60% Travel Distance 1, 280 ft -10% -20% *Based on 2009 Metrics (Jan – Sep)
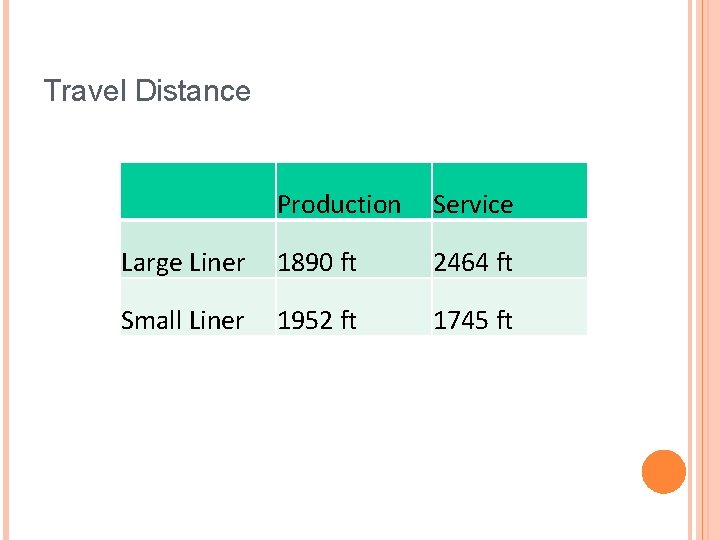
Travel Distance Production Service Large Liner 1890 ft 2464 ft Small Liner 1952 ft 1745 ft
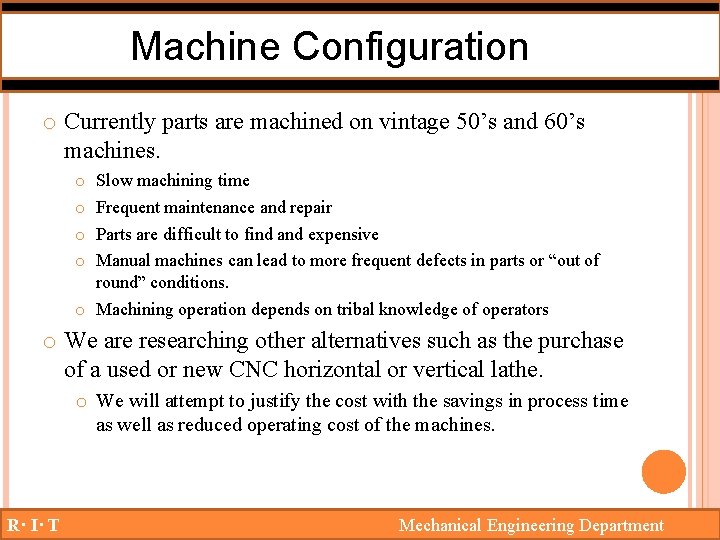
Machine Configuration o Currently parts are machined on vintage 50’s and 60’s machines. Slow machining time Frequent maintenance and repair Parts are difficult to find and expensive Manual machines can lead to more frequent defects in parts or “out of round” conditions. o Machining operation depends on tribal knowledge of operators o o o We are researching other alternatives such as the purchase of a used or new CNC horizontal or vertical lathe. o We will attempt to justify the cost with the savings in process time as well as reduced operating cost of the machines. R· I· T Mechanical Engineering Department
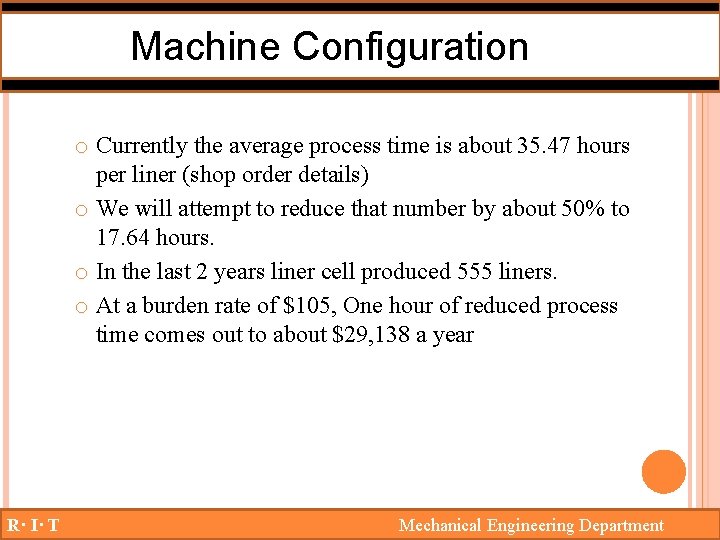
Machine Configuration o Currently the average process time is about 35. 47 hours per liner (shop order details) o We will attempt to reduce that number by about 50% to 17. 64 hours. o In the last 2 years liner cell produced 555 liners. o At a burden rate of $105, One hour of reduced process time comes out to about $29, 138 a year R· I· T Mechanical Engineering Department
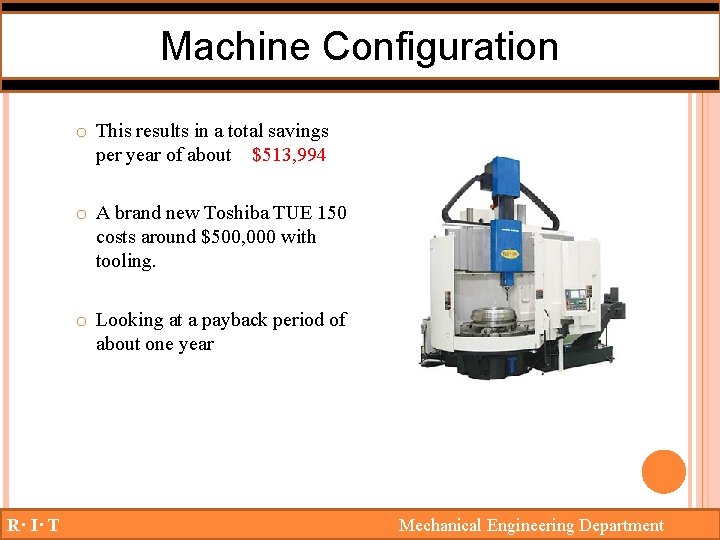
Machine Configuration o This results in a total savings per year of about $513, 994 o A brand new Toshiba TUE 150 costs around $500, 000 with tooling. o Looking at a payback period of about one year R· I· T Mechanical Engineering Department
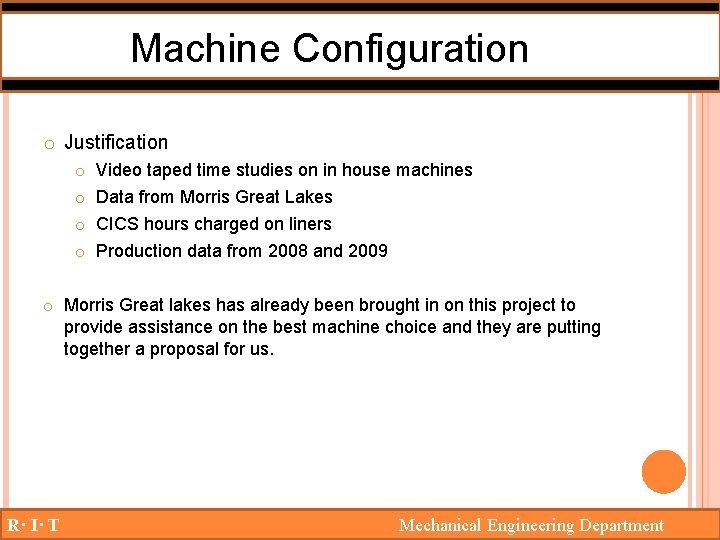
Machine Configuration o Justification o o Video taped time studies on in house machines Data from Morris Great Lakes CICS hours charged on liners Production data from 2008 and 2009 o Morris Great lakes has already been brought in on this project to provide assistance on the best machine choice and they are putting together a proposal for us. R· I· T Mechanical Engineering Department
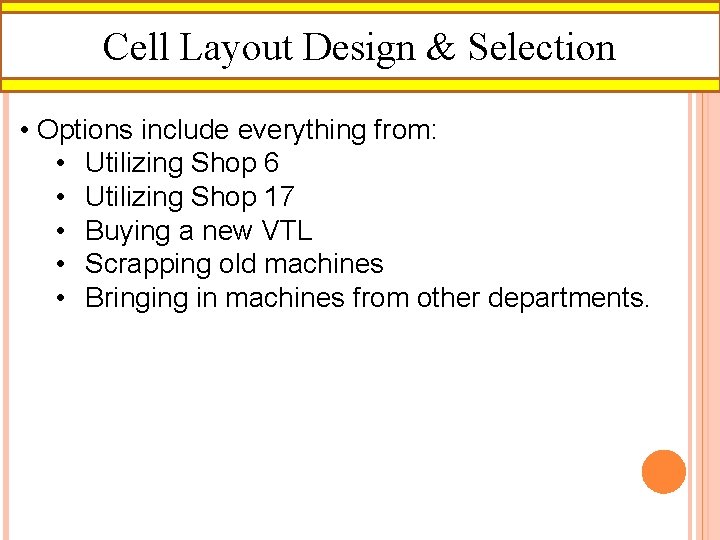
Cell Layout Design & Selection • Options include everything from: • Utilizing Shop 6 • Utilizing Shop 17 • Buying a new VTL • Scrapping old machines • Bringing in machines from other departments.
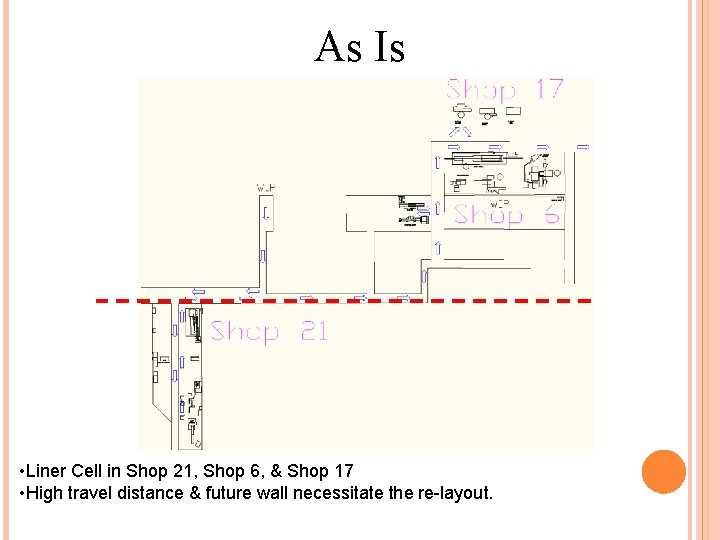
As Is • Liner Cell in Shop 21, Shop 6, & Shop 17 • High travel distance & future wall necessitate the re-layout.
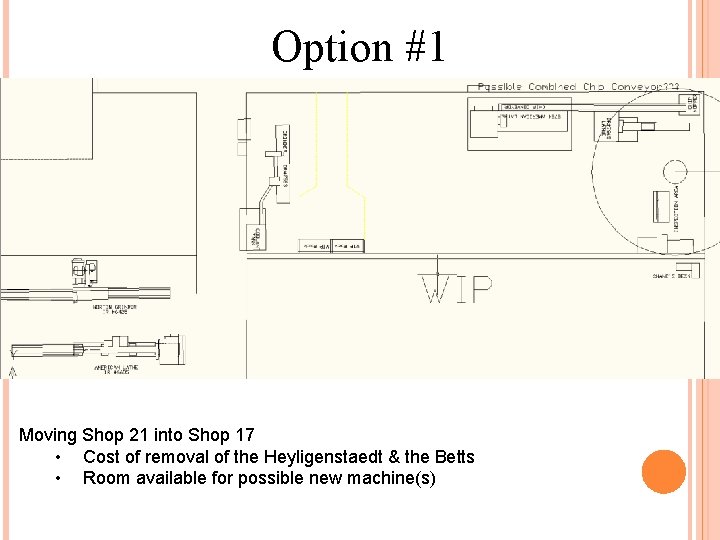
Option #1 Moving Shop 21 into Shop 17 • Cost of removal of the Heyligenstaedt & the Betts • Room available for possible new machine(s)
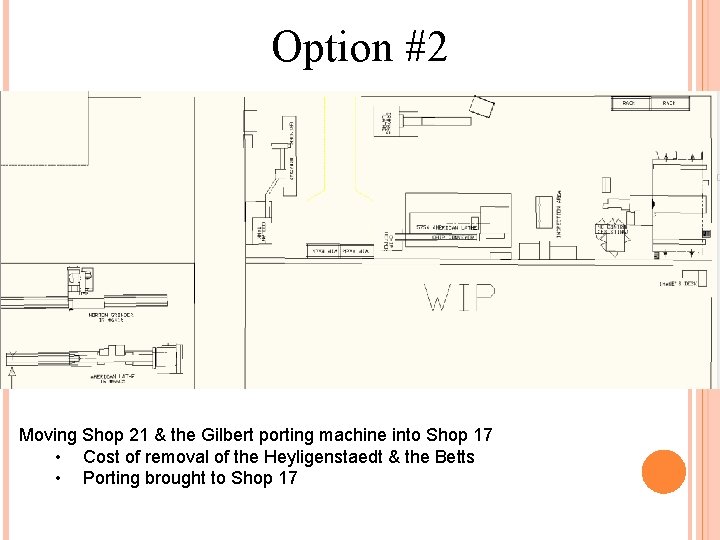
Option #2 Moving Shop 21 & the Gilbert porting machine into Shop 17 • Cost of removal of the Heyligenstaedt & the Betts • Porting brought to Shop 17
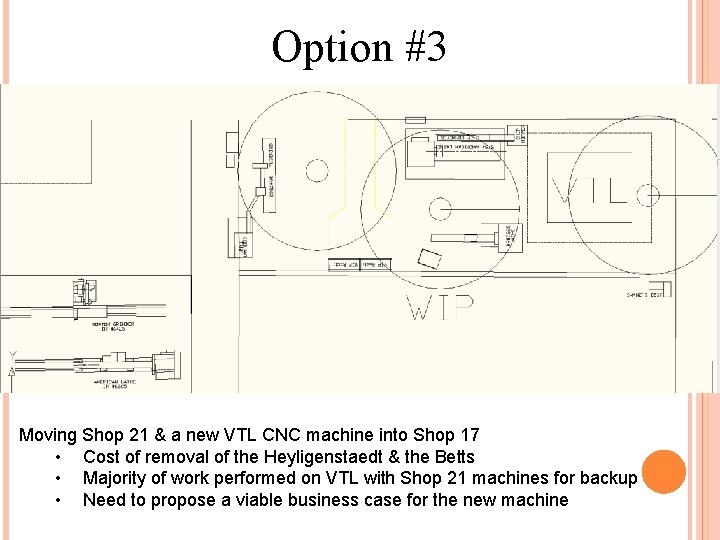
Option #3 Moving Shop 21 & a new VTL CNC machine into Shop 17 • Cost of removal of the Heyligenstaedt & the Betts • Majority of work performed on VTL with Shop 21 machines for backup • Need to propose a viable business case for the new machine
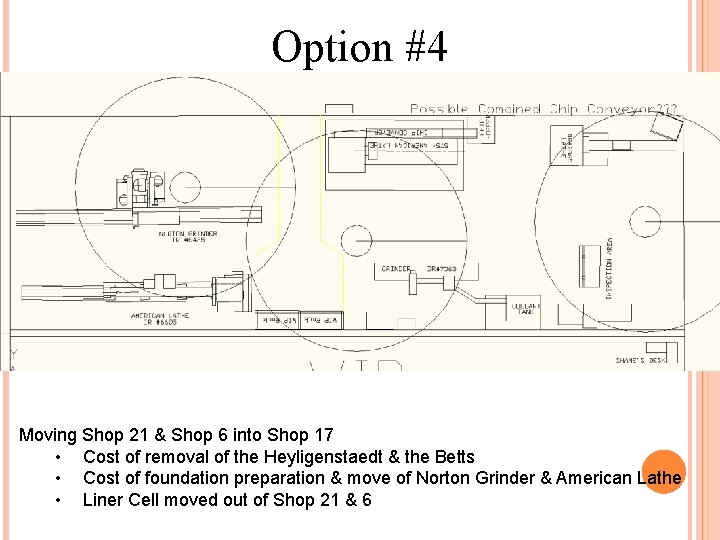
Option #4 Moving Shop 21 & Shop 6 into Shop 17 • Cost of removal of the Heyligenstaedt & the Betts • Cost of foundation preparation & move of Norton Grinder & American Lathe • Liner Cell moved out of Shop 21 & 6
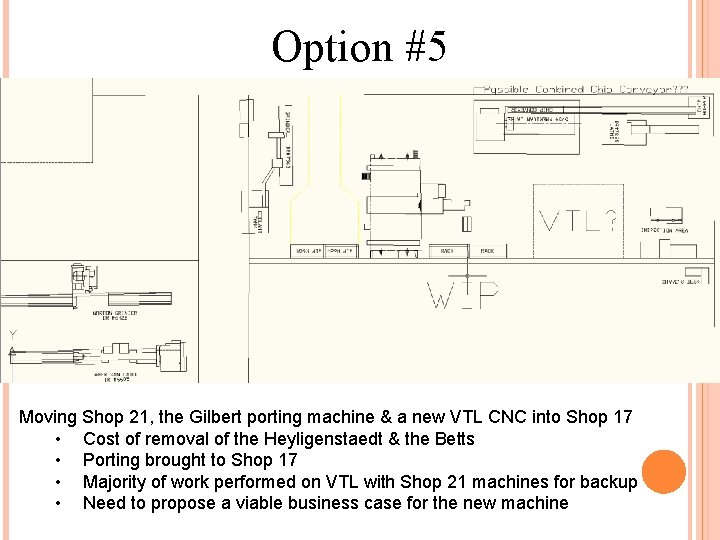
Option #5 Moving Shop 21, the Gilbert porting machine & a new VTL CNC into Shop 17 • Cost of removal of the Heyligenstaedt & the Betts • Porting brought to Shop 17 • Majority of work performed on VTL with Shop 21 machines for backup • Need to propose a viable business case for the new machine
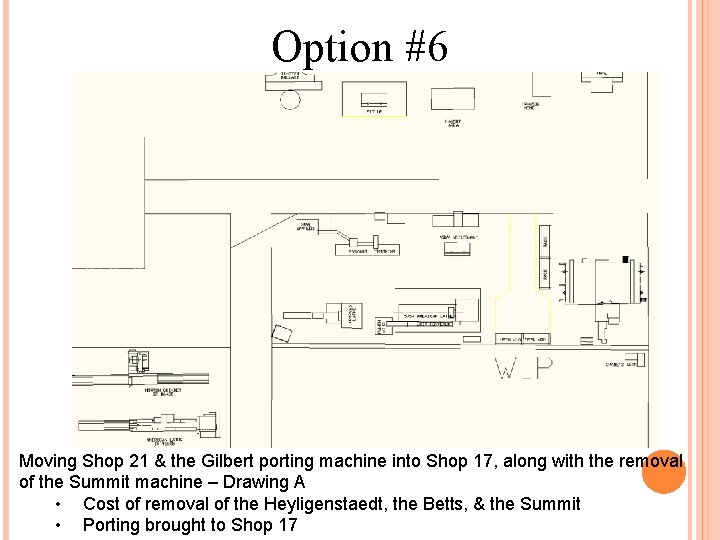
Option #6 Moving Shop 21 & the Gilbert porting machine into Shop 17, along with the removal of the Summit machine – Drawing A • Cost of removal of the Heyligenstaedt, the Betts, & the Summit • Porting brought to Shop 17
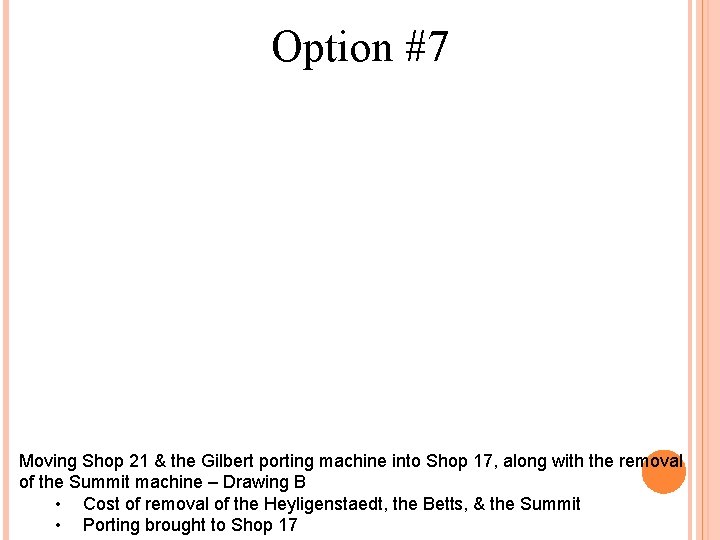
Option #7 Moving Shop 21 & the Gilbert porting machine into Shop 17, along with the removal of the Summit machine – Drawing B • Cost of removal of the Heyligenstaedt, the Betts, & the Summit • Porting brought to Shop 17
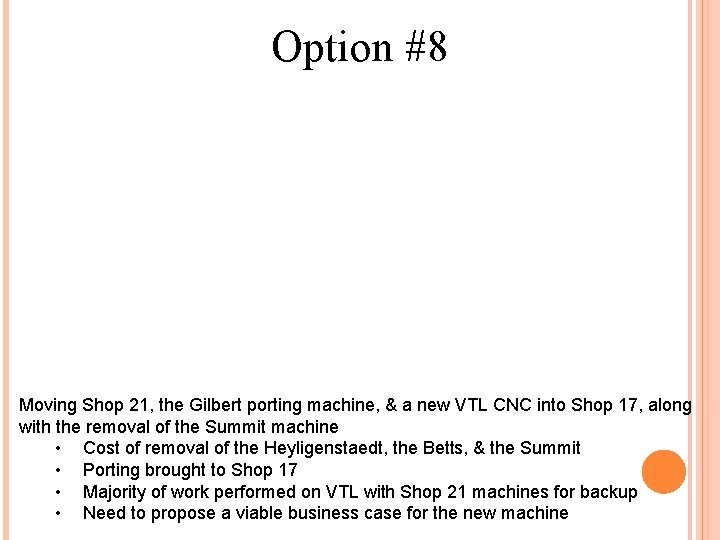
Option #8 Moving Shop 21, the Gilbert porting machine, & a new VTL CNC into Shop 17, along with the removal of the Summit machine • Cost of removal of the Heyligenstaedt, the Betts, & the Summit • Porting brought to Shop 17 • Majority of work performed on VTL with Shop 21 machines for backup • Need to propose a viable business case for the new machine
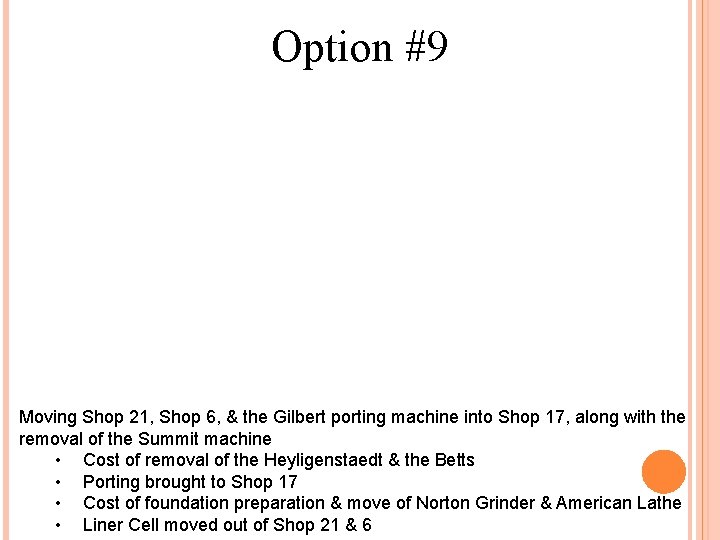
Option #9 Moving Shop 21, Shop 6, & the Gilbert porting machine into Shop 17, along with the removal of the Summit machine • Cost of removal of the Heyligenstaedt & the Betts • Porting brought to Shop 17 • Cost of foundation preparation & move of Norton Grinder & American Lathe • Liner Cell moved out of Shop 21 & 6
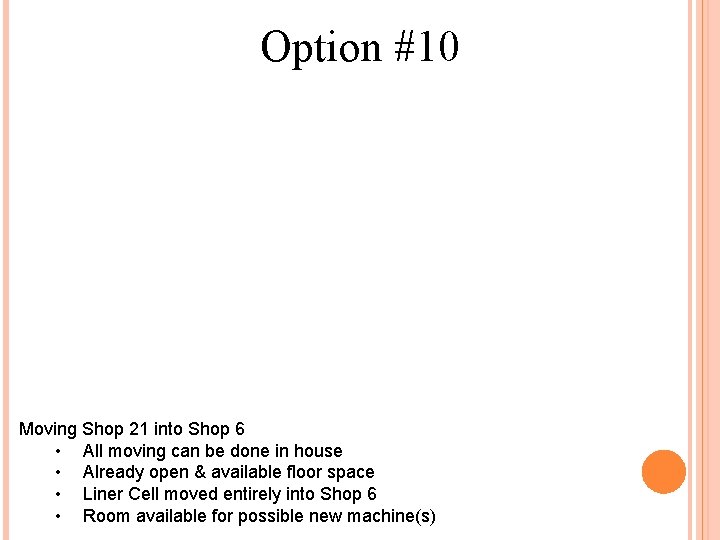
Option #10 Moving Shop 21 into Shop 6 • All moving can be done in house • Already open & available floor space • Liner Cell moved entirely into Shop 6 • Room available for possible new machine(s)
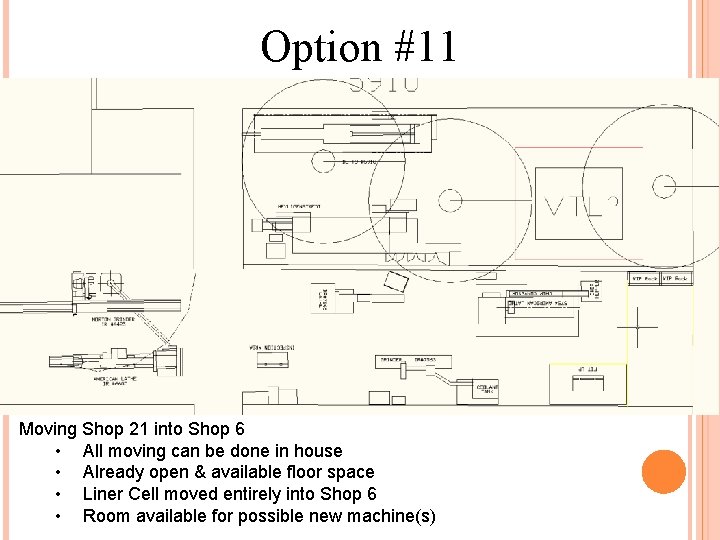
Option #11 Moving Shop 21 into Shop 6 • All moving can be done in house • Already open & available floor space • Liner Cell moved entirely into Shop 6 • Room available for possible new machine(s)
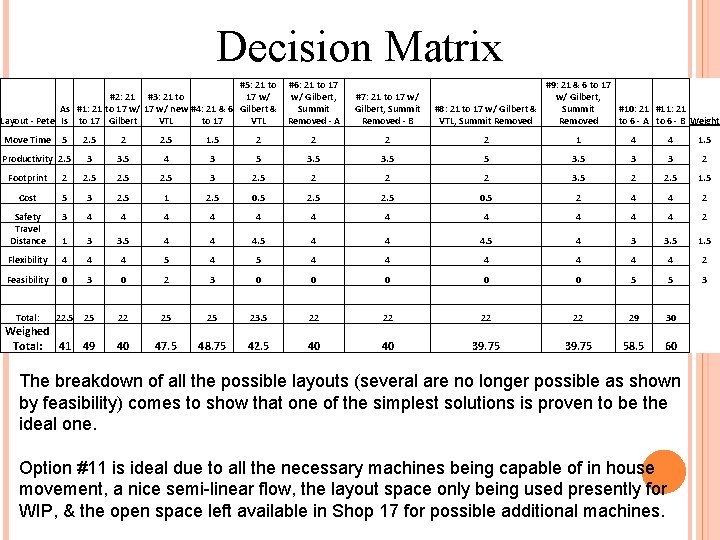
Decision Matrix #5: 21 to #6: 21 to 17 #2: 21 #3: 21 to 17 w/ w/ Gilbert, As #1: 21 to 17 w/ new #4: 21 & 6 Gilbert & Summit Layout - Pete Is to 17 Gilbert VTL to 17 VTL Removed - A Move Time 5 Productivity 2. 5 #7: 21 to 17 w/ Gilbert, Summit Removed - B #9: 21 & 6 to 17 w/ Gilbert, #8: 21 to 17 w/ Gilbert & Summit #10: 21 #11: 21 VTL, Summit Removed to 6 - A to 6 - B Weight 2. 5 2 2. 5 1. 5 2 2 1 4 4 1. 5 3 3. 5 4 3 5 3 3 2 Footprint 2 2. 5 3 2. 5 2 2 2 3. 5 2 2. 5 1. 5 Cost 5 3 2. 5 1 2. 5 0. 5 2 4 4 2 Safety Travel Distance 3 4 4 4 2 1 3 3. 5 4 4 4. 5 4 3 3. 5 1. 5 Flexibility 4 4 4 5 4 4 4 2 Feasibility 0 3 0 2 3 0 0 0 5 5 3 Total: 22. 5 25 22 25 25 23. 5 22 22 29 30 49 40 47. 5 48. 75 42. 5 40 40 39. 75 58. 5 60 Weighed Total: 41 The breakdown of all the possible layouts (several are no longer possible as shown by feasibility) comes to show that one of the simplest solutions is proven to be the ideal one. Option #11 is ideal due to all the necessary machines being capable of in house movement, a nice semi-linear flow, the layout space only being used presently for WIP, & the open space left available in Shop 17 for possible additional machines.
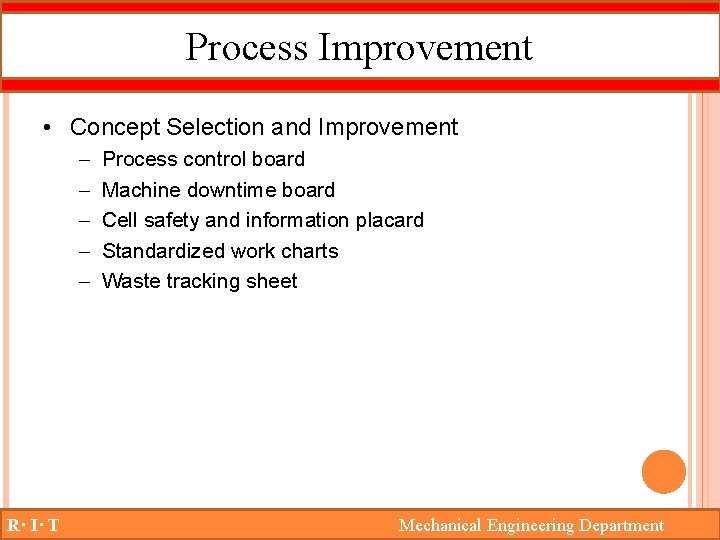
Process Improvement • Concept Selection and Improvement – – – R· I· T Process control board Machine downtime board Cell safety and information placard Standardized work charts Waste tracking sheet Mechanical Engineering Department
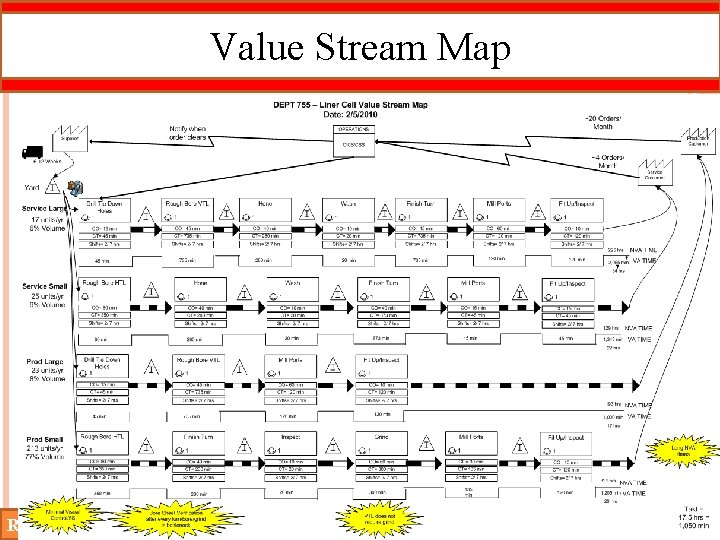
Value Stream Map R· I· T Mechanical Engineering Department
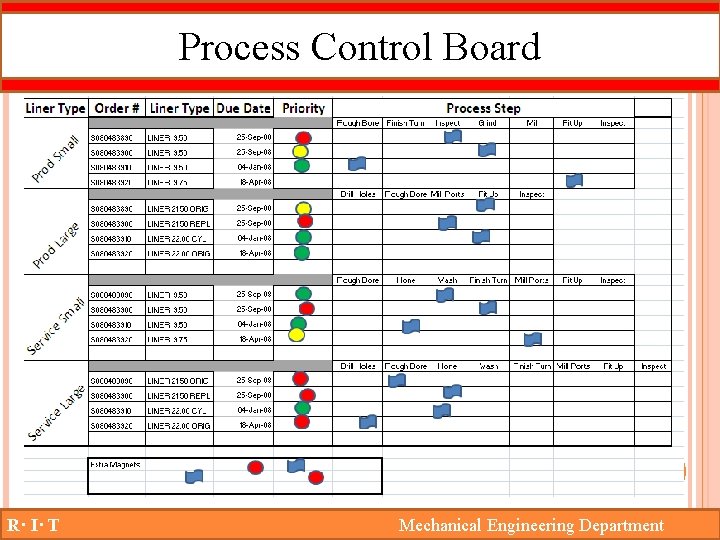
Process Control Board R· I· T Mechanical Engineering Department
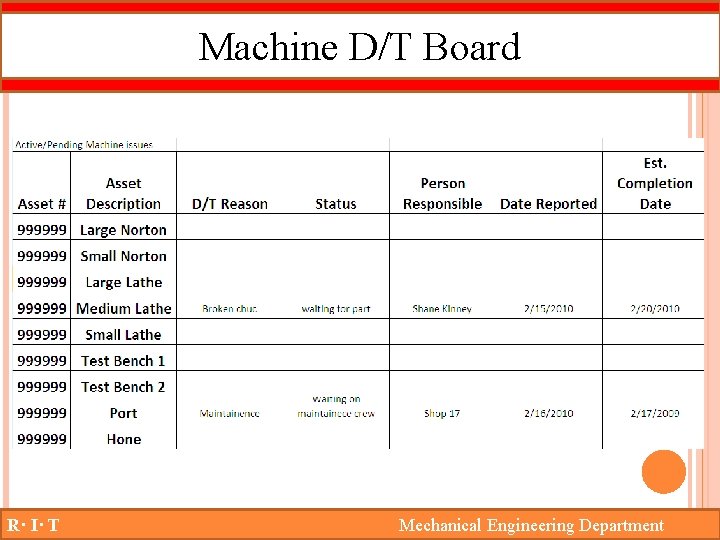
Machine D/T Board R· I· T Mechanical Engineering Department
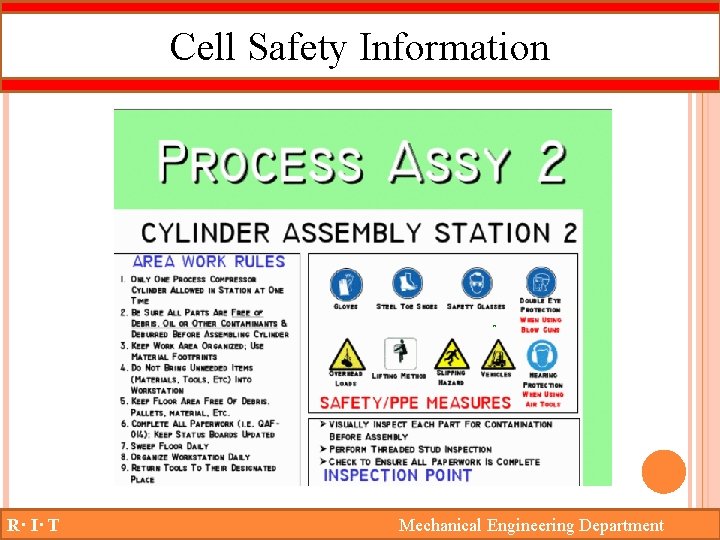
Cell Safety Information R· I· T Mechanical Engineering Department
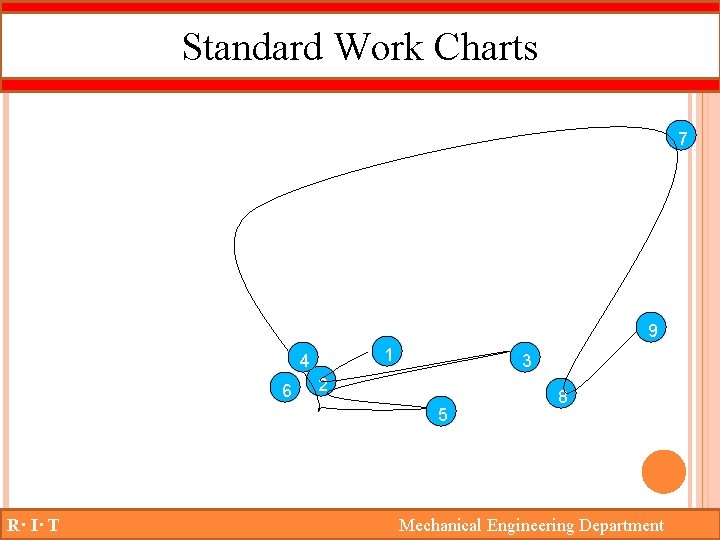
Standard Work Charts 7 9 1 4 6 3 2 5 R· I· T 8 Mechanical Engineering Department
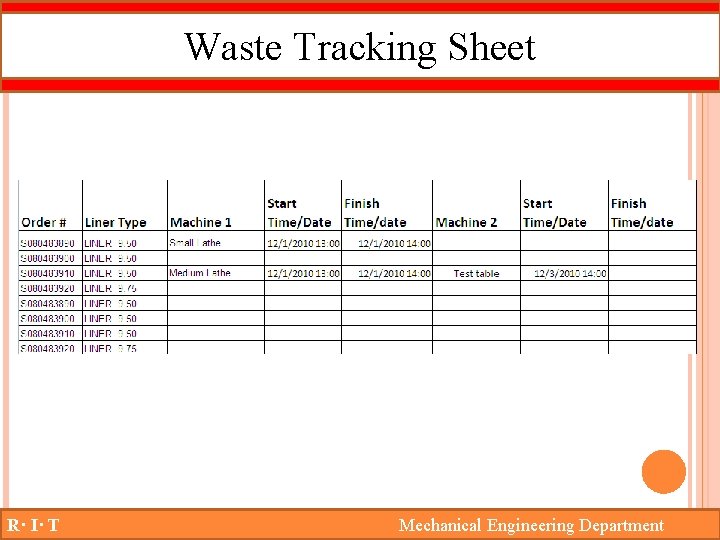
Waste Tracking Sheet R· I· T Mechanical Engineering Department
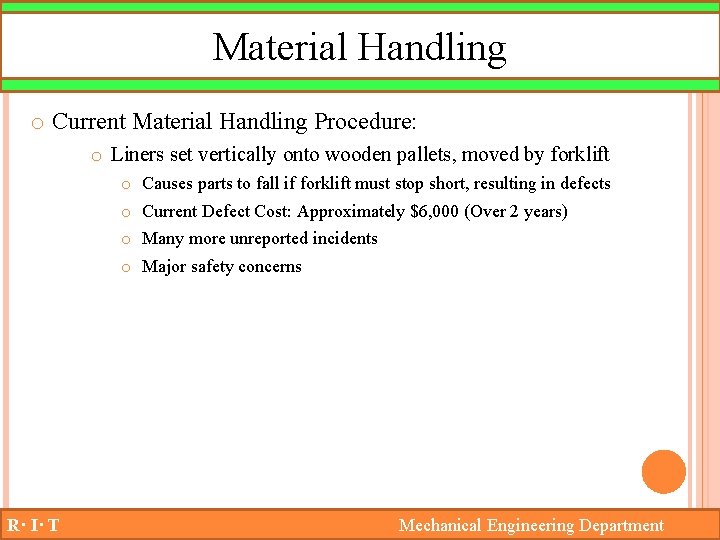
Material Handling o Current Material Handling Procedure: o Liners set vertically onto wooden pallets, moved by forklift o o R· I· T Causes parts to fall if forklift must stop short, resulting in defects Current Defect Cost: Approximately $6, 000 (Over 2 years) Many more unreported incidents Major safety concerns Mechanical Engineering Department
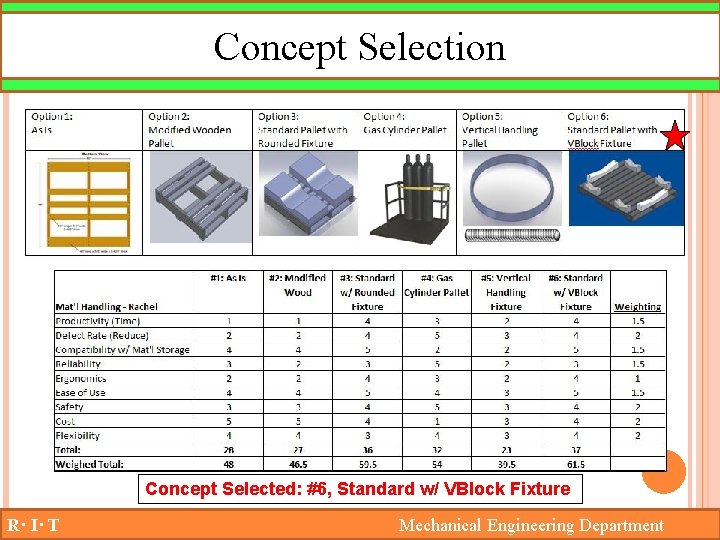
Concept Selection Concept Selected: #6, Standard w/ VBlock Fixture R· I· T Mechanical Engineering Department
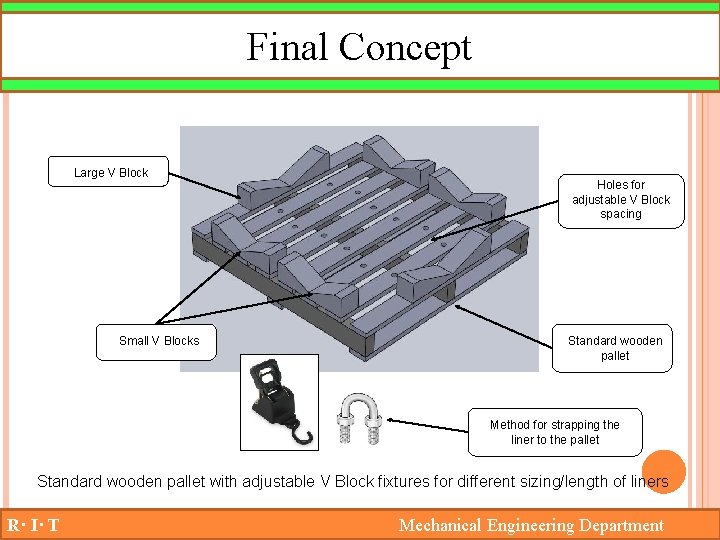
Final Concept Large V Block Small V Blocks Holes for adjustable V Block spacing Standard wooden pallet Method for strapping the liner to the pallet Standard wooden pallet with adjustable V Block fixtures for different sizing/length of liners R· I· T Mechanical Engineering Department
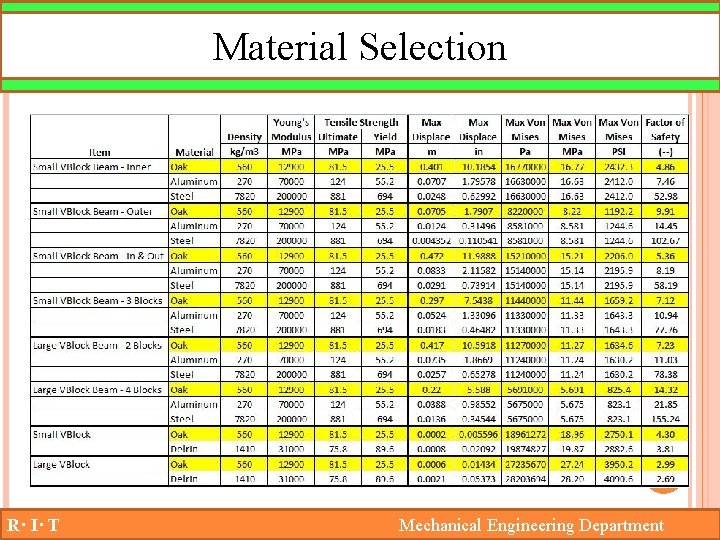
Material Selection R· I· T Mechanical Engineering Department
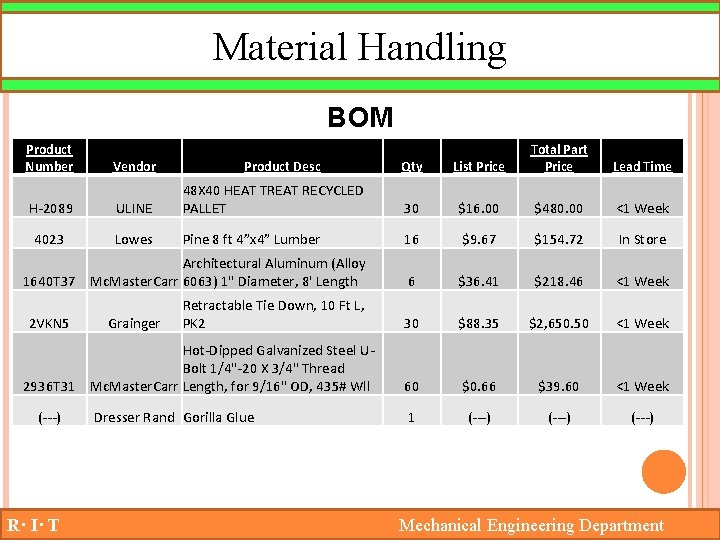
Material Handling BOM Product Number Qty List Price Total Part Price 30 $16. 00 $480. 00 <1 Week 16 $9. 67 $154. 72 In Store Architectural Aluminum (Alloy 1640 T 37 Mc. Master. Carr 6063) 1" Diameter, 8' Length 6 $36. 41 $218. 46 <1 Week Retractable Tie Down, 10 Ft L, PK 2 30 $88. 35 $2, 650. 50 <1 Week 60 $0. 66 $39. 60 <1 Week 1 (---) Vendor Product Desc H-2089 ULINE 48 X 40 HEAT TREAT RECYCLED PALLET 4023 Lowes Pine 8 ft 4”x 4” Lumber 2 VKN 5 Grainger Hot-Dipped Galvanized Steel UBolt 1/4"-20 X 3/4" Thread 2936 T 31 Mc. Master. Carr Length, for 9/16" OD, 435# Wll (---) R· I· T Dresser Rand Gorilla Glue Lead Time Mechanical Engineering Department
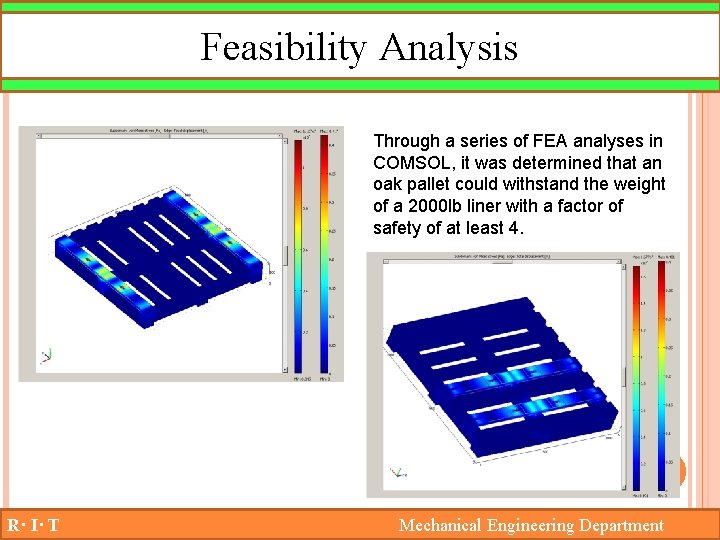
Feasibility Analysis Through a series of FEA analyses in COMSOL, it was determined that an oak pallet could withstand the weight of a 2000 lb liner with a factor of safety of at least 4. R· I· T Mechanical Engineering Department
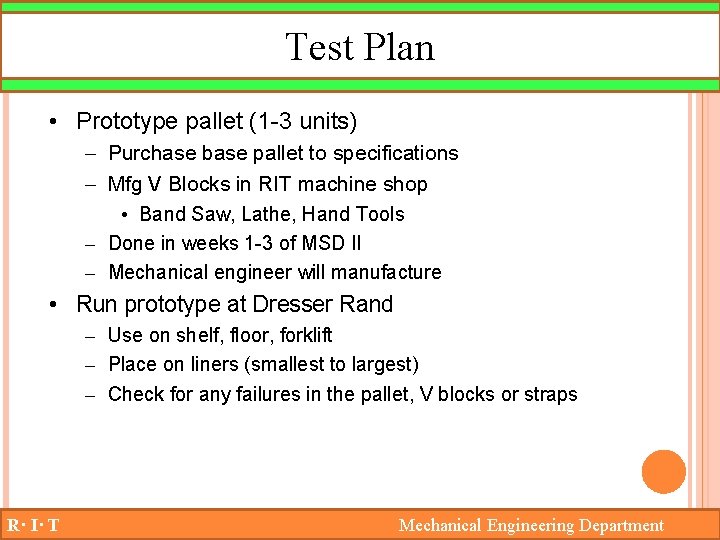
Test Plan • Prototype pallet (1 -3 units) – Purchase base pallet to specifications – Mfg V Blocks in RIT machine shop • Band Saw, Lathe, Hand Tools – Done in weeks 1 -3 of MSD II – Mechanical engineer will manufacture • Run prototype at Dresser Rand – Use on shelf, floor, forklift – Place on liners (smallest to largest) – Check for any failures in the pallet, V blocks or straps R· I· T Mechanical Engineering Department
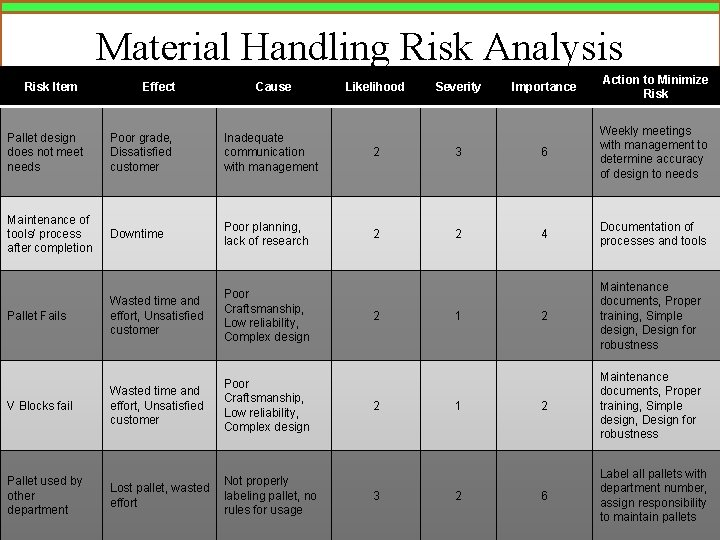
Material Handling Risk Analysis Risk Item Effect Cause Likelihood Severity Importance Action to Minimize Risk Pallet design does not meet needs Poor grade, Dissatisfied customer Inadequate communication with management 2 3 6 Weekly meetings with management to determine accuracy of design to needs Maintenance of tools/ process after completion Downtime Poor planning, lack of research 2 2 4 Documentation of processes and tools Pallet Fails Wasted time and effort, Unsatisfied customer Poor Craftsmanship, Low reliability, Complex design 2 Maintenance documents, Proper training, Simple design, Design for robustness V Blocks fail Wasted time and effort, Unsatisfied customer Poor Craftsmanship, Low reliability, Complex design 2 Maintenance documents, Proper training, Simple design, Design for robustness Lost pallet, wasted effort Not properly labeling pallet, no rules for usage 6 Label all pallets with department number, assign responsibility to maintain pallets Pallet used by other department R· I· T 2 2 3 1 1 2 Mechanical Engineering Department
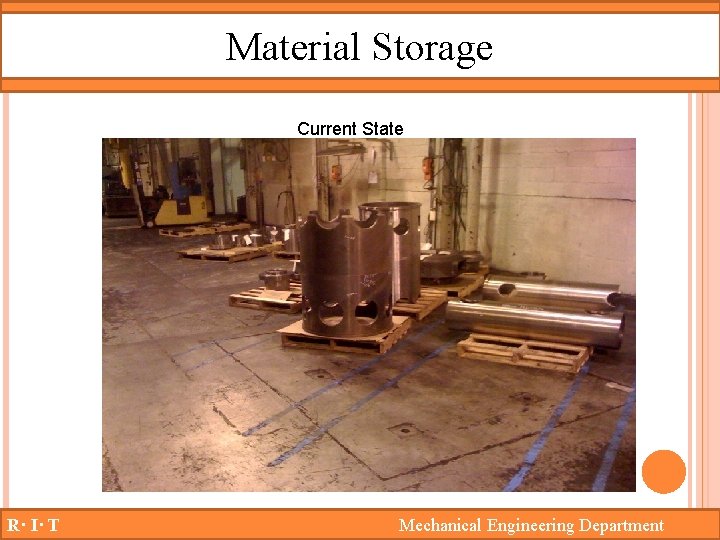
Material Storage Current State R· I· T Mechanical Engineering Department
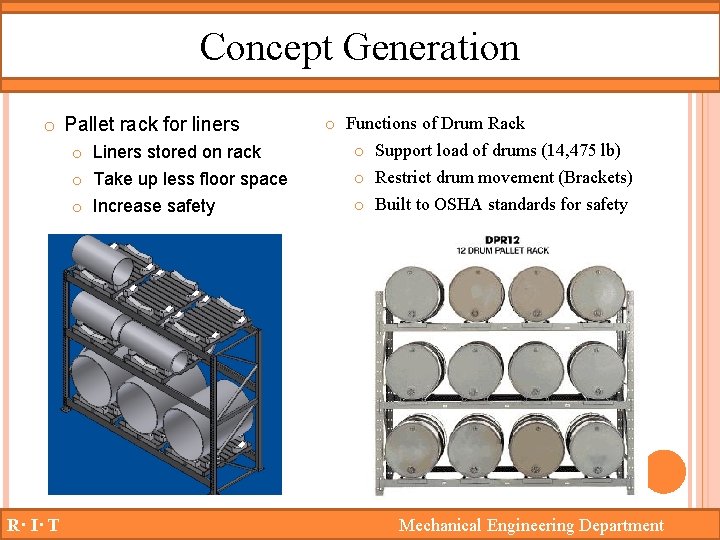
Concept Generation o Pallet rack for liners o Liners stored on rack o Take up less floor space o Increase safety R· I· T o Functions of Drum Rack o Support load of drums (14, 475 lb) o Restrict drum movement (Brackets) o Built to OSHA standards for safety Mechanical Engineering Department
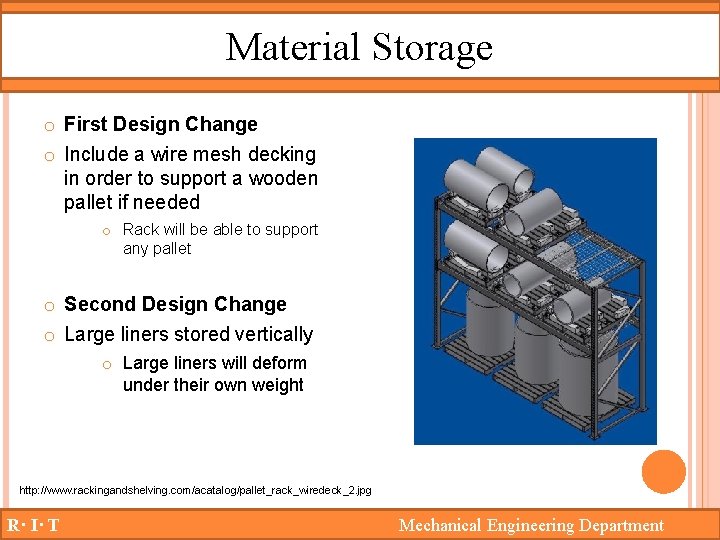
Material Storage o First Design Change o Include a wire mesh decking in order to support a wooden pallet if needed o Rack will be able to support any pallet o Second Design Change o Large liners stored vertically o Large liners will deform under their own weight http: //www. rackingandshelving. com/acatalog/pallet_rack_wiredeck_2. jpg R· I· T Mechanical Engineering Department
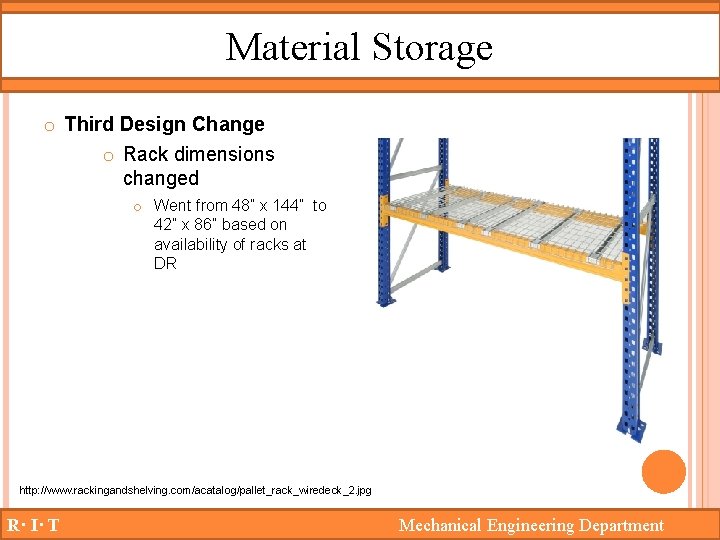
Material Storage o Third Design Change o Rack dimensions changed o Went from 48” x 144” to 42” x 86” based on availability of racks at DR http: //www. rackingandshelving. com/acatalog/pallet_rack_wiredeck_2. jpg R· I· T Mechanical Engineering Department
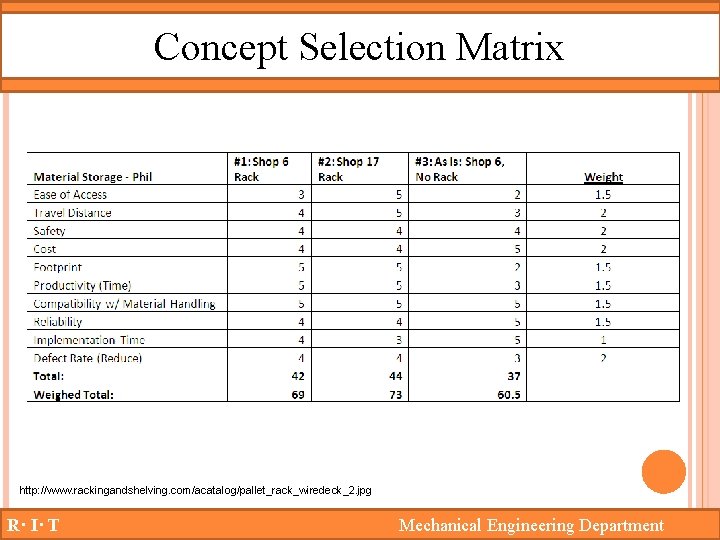
Concept Selection Matrix http: //www. rackingandshelving. com/acatalog/pallet_rack_wiredeck_2. jpg R· I· T Mechanical Engineering Department
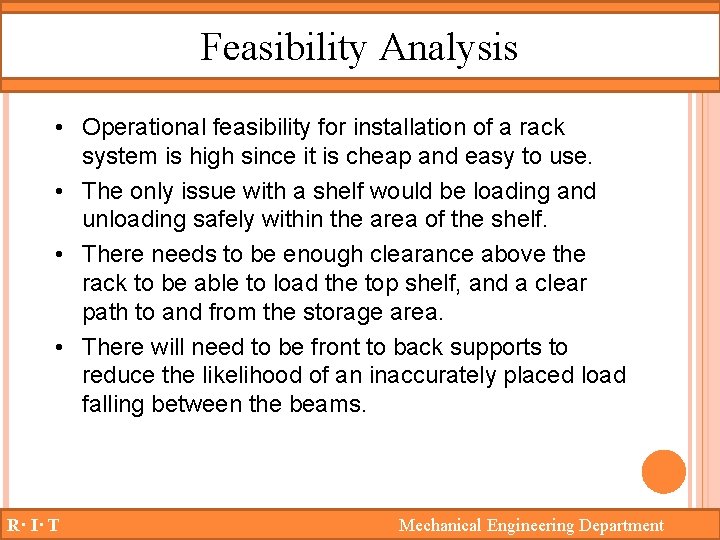
Feasibility Analysis • Operational feasibility for installation of a rack system is high since it is cheap and easy to use. • The only issue with a shelf would be loading and unloading safely within the area of the shelf. • There needs to be enough clearance above the rack to be able to load the top shelf, and a clear path to and from the storage area. • There will need to be front to back supports to reduce the likelihood of an inaccurately placed load falling between the beams. R· I· T Mechanical Engineering Department
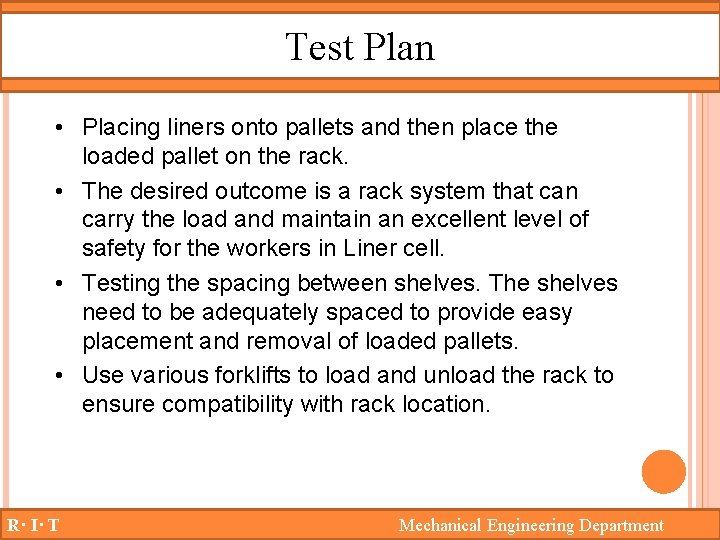
Test Plan • Placing liners onto pallets and then place the loaded pallet on the rack. • The desired outcome is a rack system that can carry the load and maintain an excellent level of safety for the workers in Liner cell. • Testing the spacing between shelves. The shelves need to be adequately spaced to provide easy placement and removal of loaded pallets. • Use various forklifts to load and unload the rack to ensure compatibility with rack location. R· I· T Mechanical Engineering Department
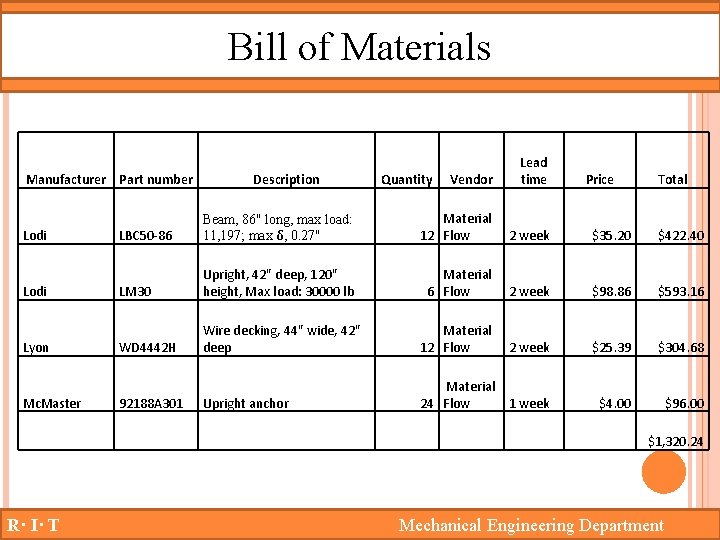
Bill of Materials Vendor Lead time LBC 50 -86 Beam, 86" long, max load: 11, 197; max δ, 0. 27" Material 12 Flow 2 week $35. 20 $422. 40 LM 30 Upright, 42" deep, 120" height, Max load: 30000 lb Material 6 Flow 2 week $98. 86 $593. 16 WD 4442 H Wire decking, 44" wide, 42" deep Material 12 Flow 2 week $25. 39 $304. 68 Material 24 Flow 1 week $4. 00 $96. 00 Manufacturer Part number Lodi Lyon Description Mc. Master 92188 A 301 Upright anchor R· I· T Quantity Price Total $1, 320. 24 Mechanical Engineering Department
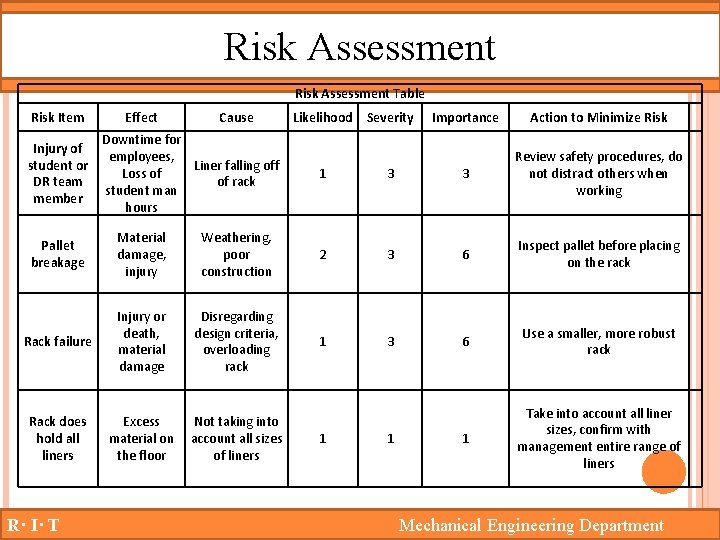
Risk Assessment Table Risk Item Injury of student or DR team member Effect Cause Downtime for employees, Liner falling off Loss of of rack student man hours Likelihood Severity Importance Action to Minimize Risk 1 3 3 Review safety procedures, do not distract others when working Pallet breakage Material damage, injury Weathering, poor construction 2 3 6 Inspect pallet before placing on the rack Rack failure Injury or death, material damage Disregarding design criteria, overloading rack 1 3 6 Use a smaller, more robust rack 1 Take into account all liner sizes, confirm with management entire range of liners Rack does hold all liners R· I· T Excess Not taking into material on account all sizes the floor of liners 1 1 Mechanical Engineering Department
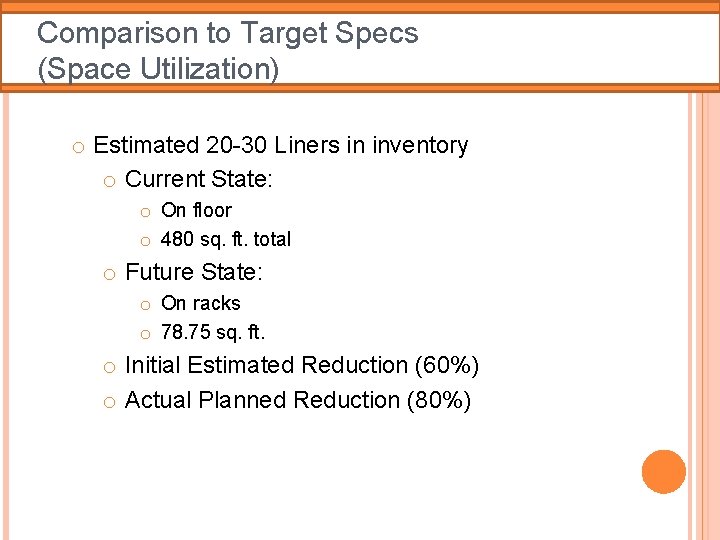
Comparison to Target Specs (Space Utilization) o Estimated 20 -30 Liners in inventory o Current State: o On floor o 480 sq. ft. total o Future State: o On racks o 78. 75 sq. ft. o Initial Estimated Reduction (60%) o Actual Planned Reduction (80%)
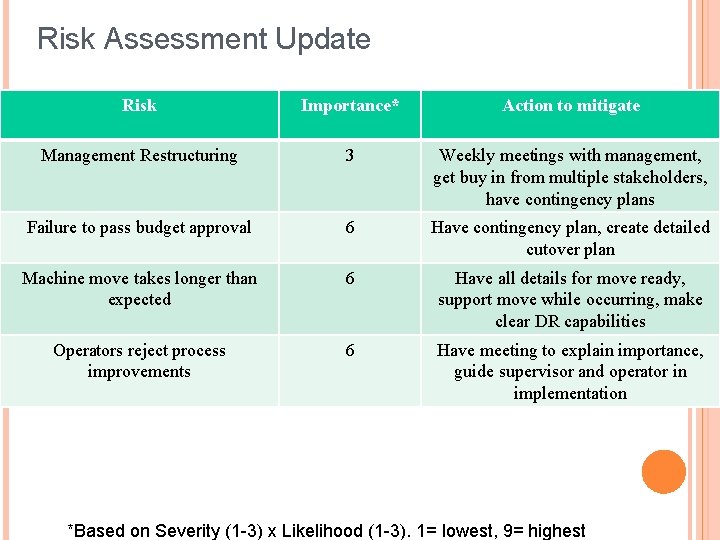
Risk Assessment Update Risk Importance* Action to mitigate Management Restructuring 3 Weekly meetings with management, get buy in from multiple stakeholders, have contingency plans Failure to pass budget approval 6 Have contingency plan, create detailed cutover plan Machine move takes longer than expected 6 Have all details for move ready, support move while occurring, make clear DR capabilities Operators reject process improvements 6 Have meeting to explain importance, guide supervisor and operator in implementation *Based on Severity (1 -3) x Likelihood (1 -3). 1= lowest, 9= highest
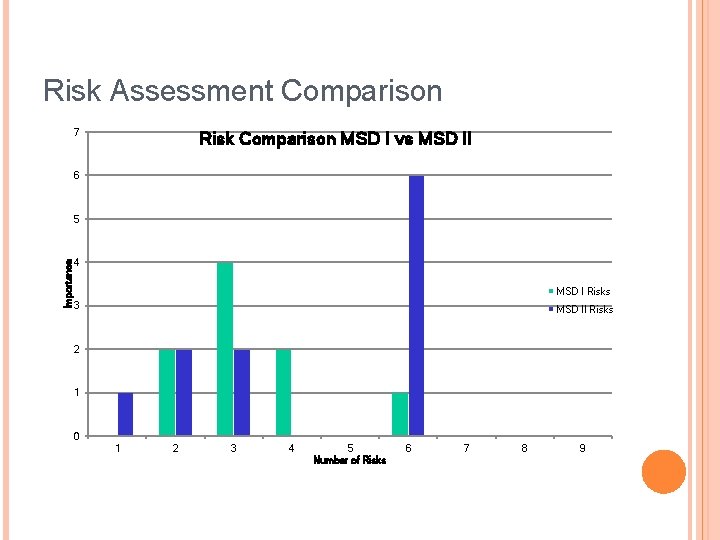
Risk Assessment Comparison 7 Risk Comparison MSD I vs MSD II 6 Importance 5 4 MSD I Risks 3 MSD II Risks 2 1 0 1 2 3 4 5 Number of Risks 6 7 8 9
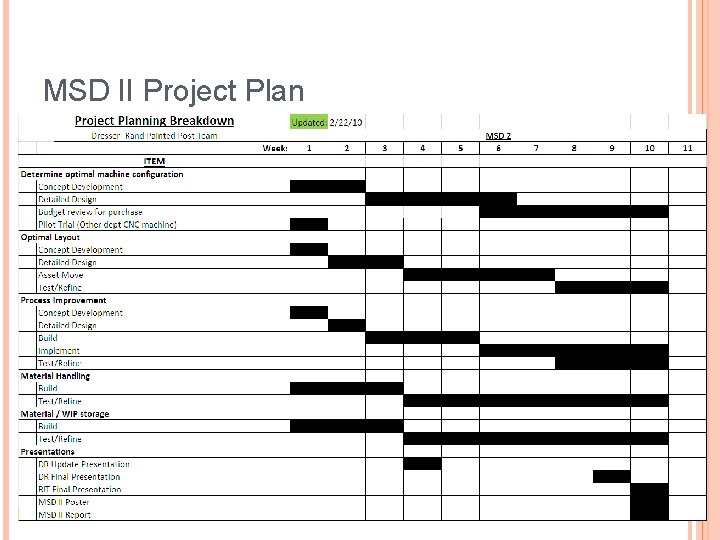
MSD II Project Plan
Multidisciplinary nature of environmental studies;
Reflection on multidisciplinary team
Multidisciplinary
Multidisciplinary vs interdisciplinary
Interdisciplinary design curriculum
Multidisciplinary nature of environmental studies ppt
Multidisciplinary software development team
Conflict in multidisciplinary teams
Multisectoral and multidisciplinary
Interdisciplinary multidisciplinary transdisciplinary
Multidisciplinary studies epcc
Dr. fernando cosio rochester mn
Edra rochester
Lattimore hall university of rochester
Sinantec
Mbhs moodle
Eastman business park
Daniel stefankovic
Rochester first time home buyer
Mesulid şurup
Rochester kriterleri
Rochester kriterleri
University of rochester care network
Rochester golf carts
Csc 161 rochester
Avalanche photodiode
The rochester cloak
Martin rochester
Rochester and rutherford hall
Early childhood screening rochester mn
Travin hazelrigg
Método rochester
Criterios de rochester
Rochester and rutherford hall
Rochester philatelic association
Orpa rochester
Rochester and rutherford
City of rochester water bureau
Ucf senior design
Linda milor
Ncsu csc senior design
Ee senior design project ideas
Calc institute of technology
Vidhyadeep institute of engineering and technology
Waterford kamhlaba vacancies
Unist application fee
Assistive technology implementation plan
Masdar institute of science and technology
Madhav institute of technology and science
Ense grenoble
Hqsa
De lin institute of technology
Dbs institute of technology
Materials technology institute
Bms institute of technology & management