Model Persediaan Khusus SI 403 Riset Operasi Suryo
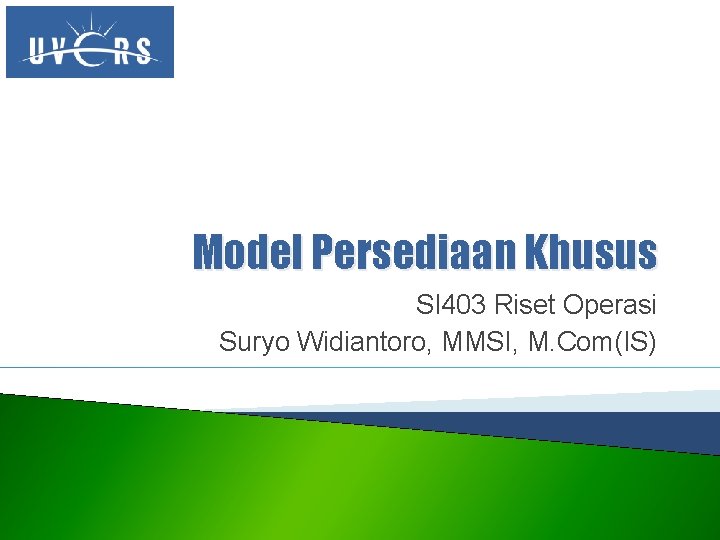
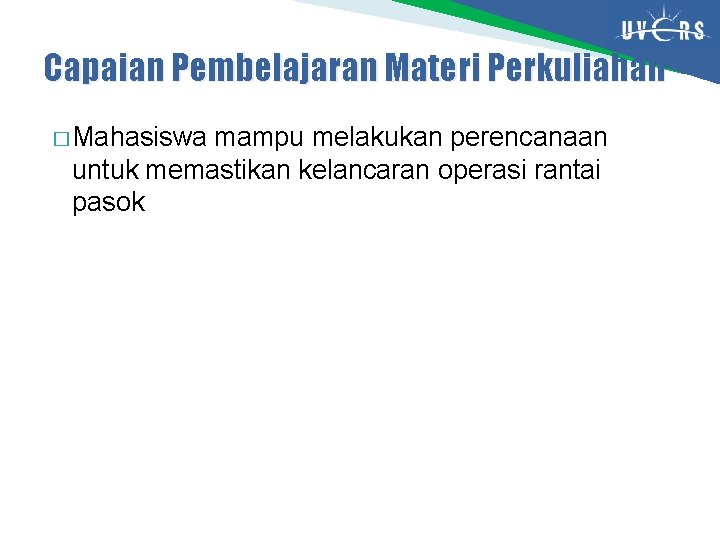

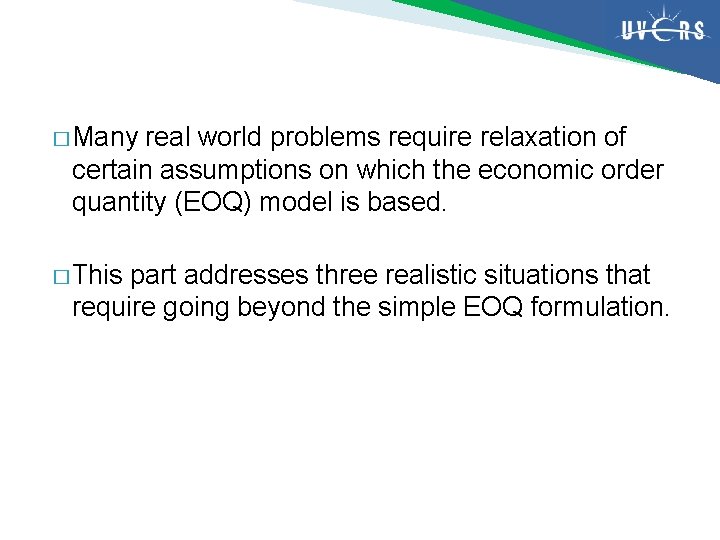
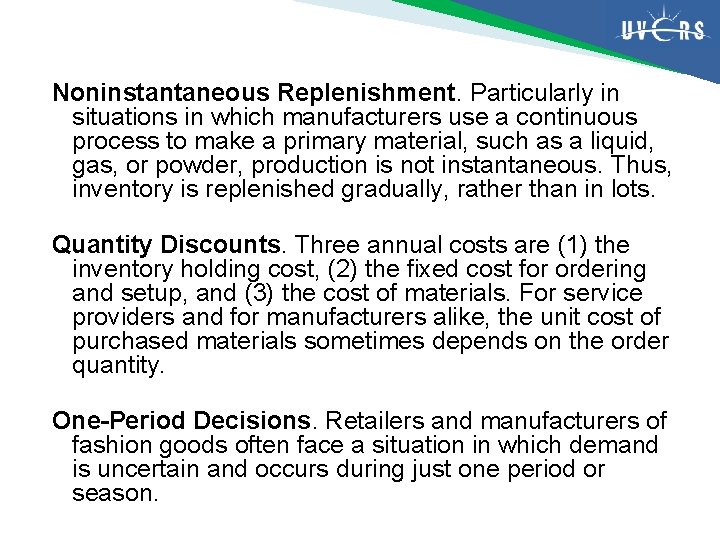
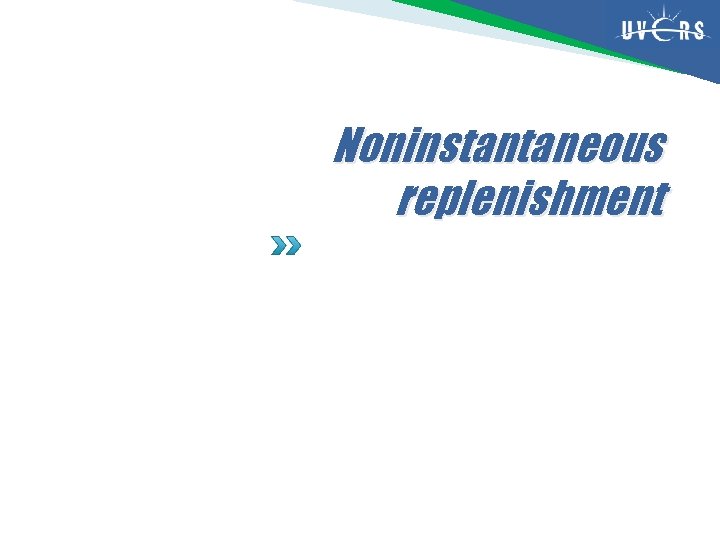
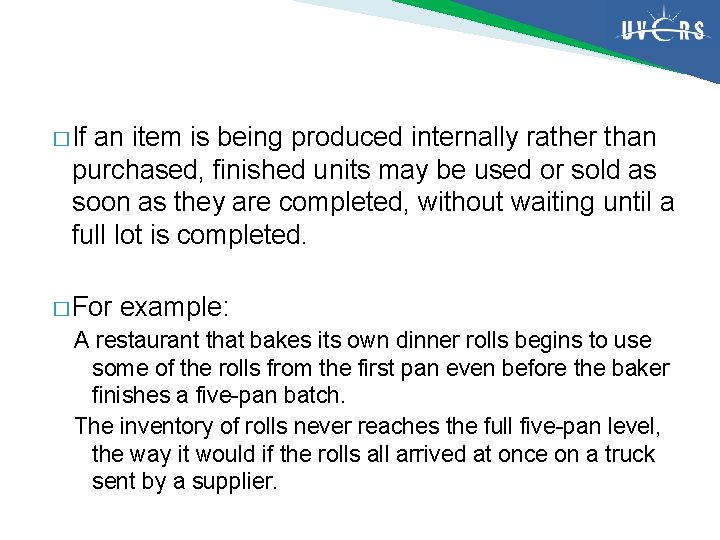
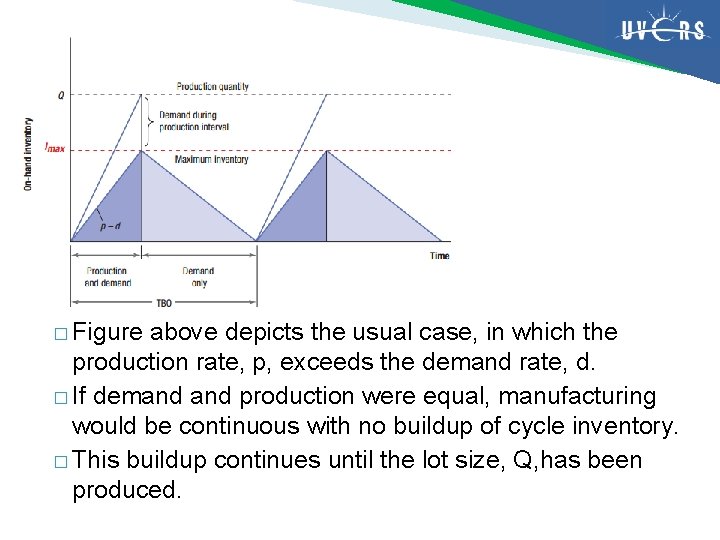
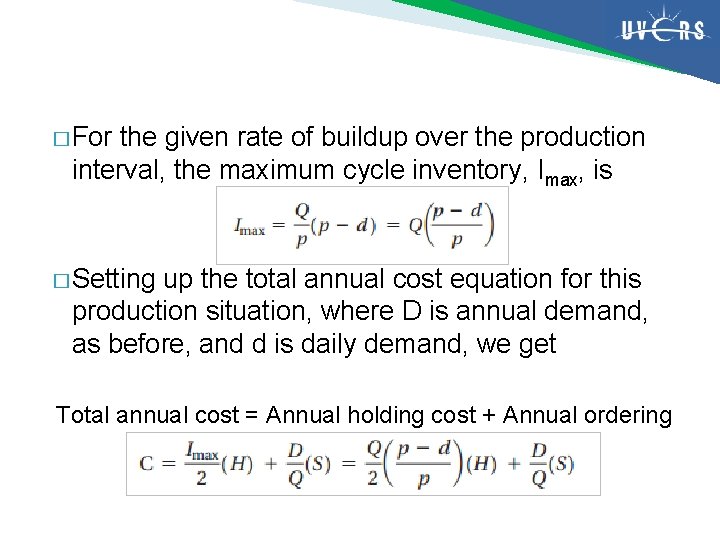
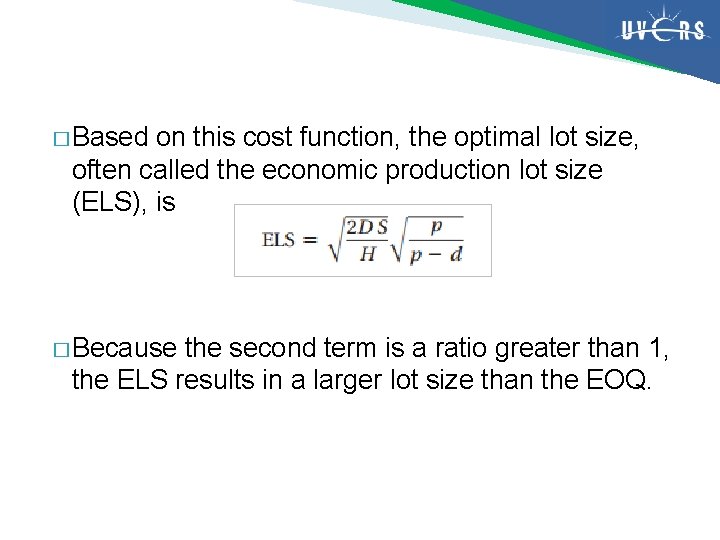

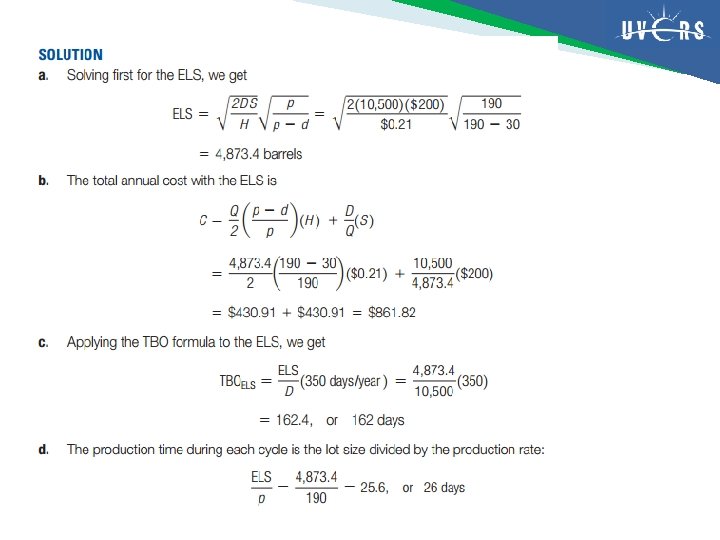
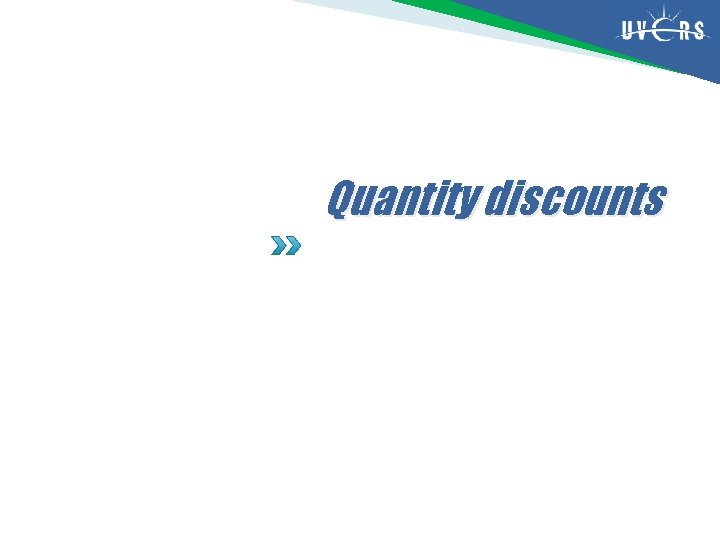
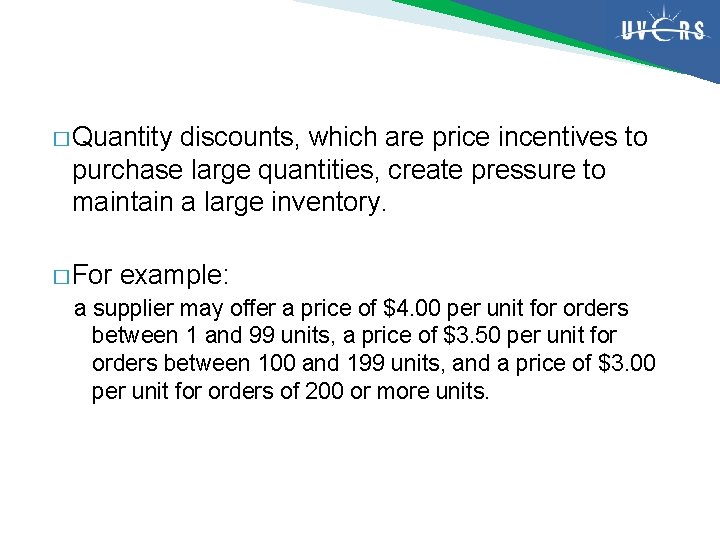
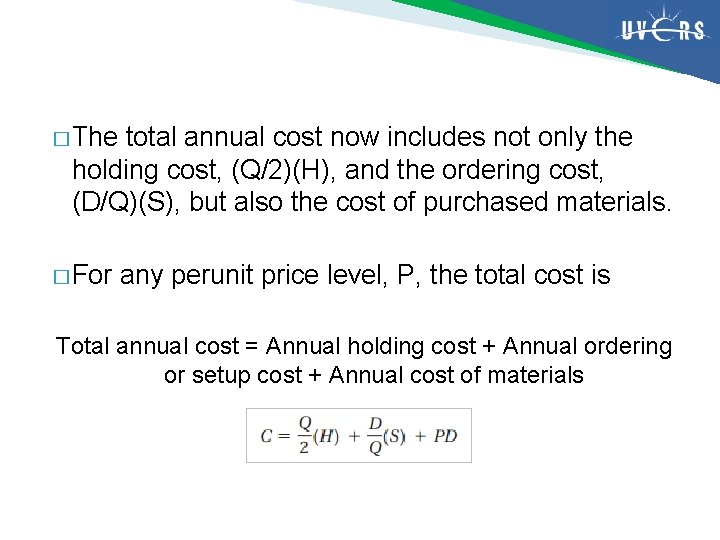
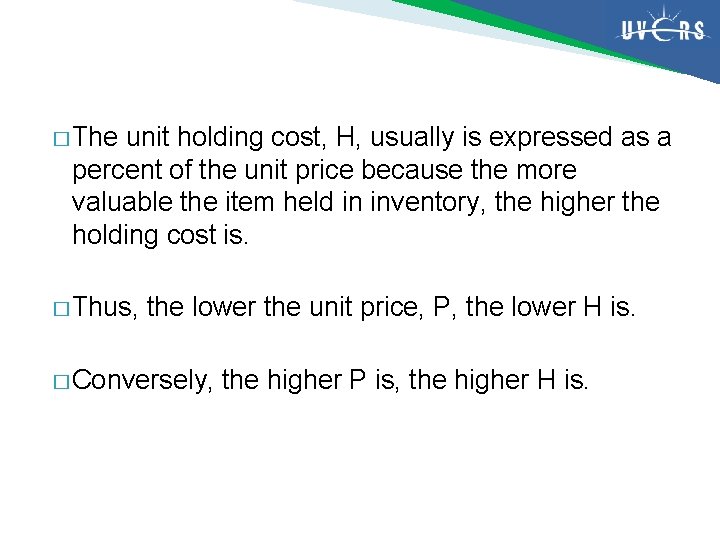
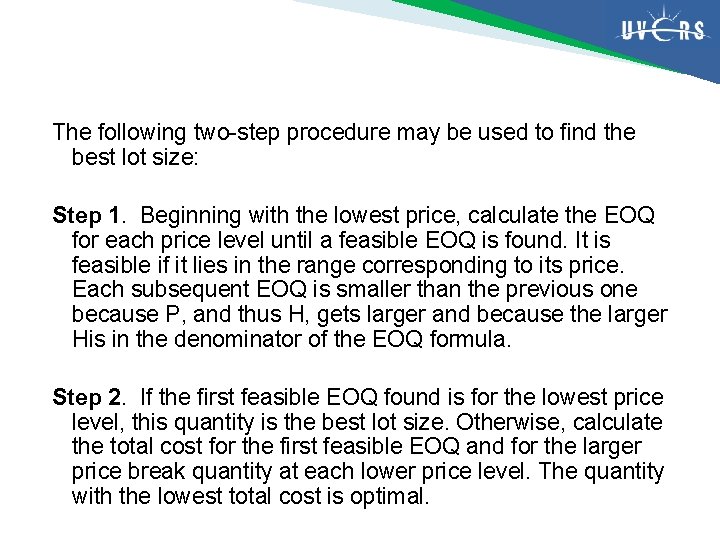
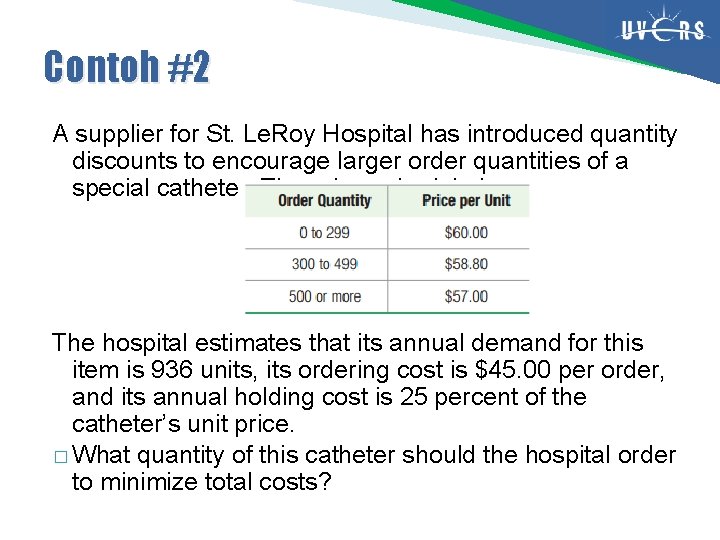
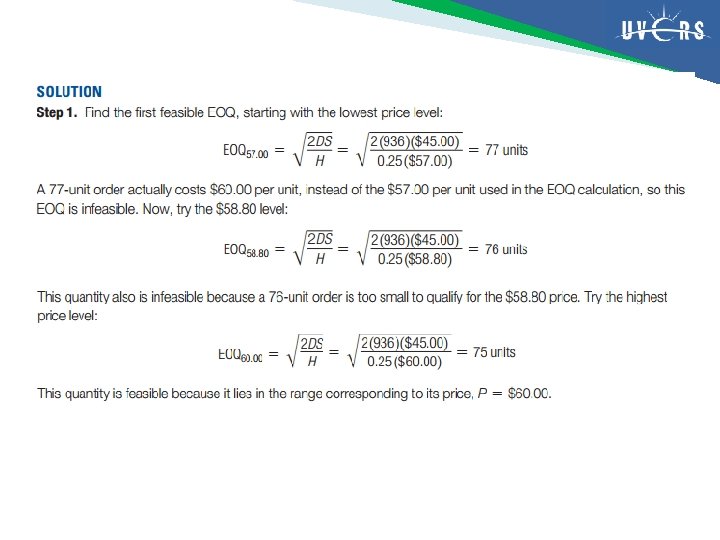
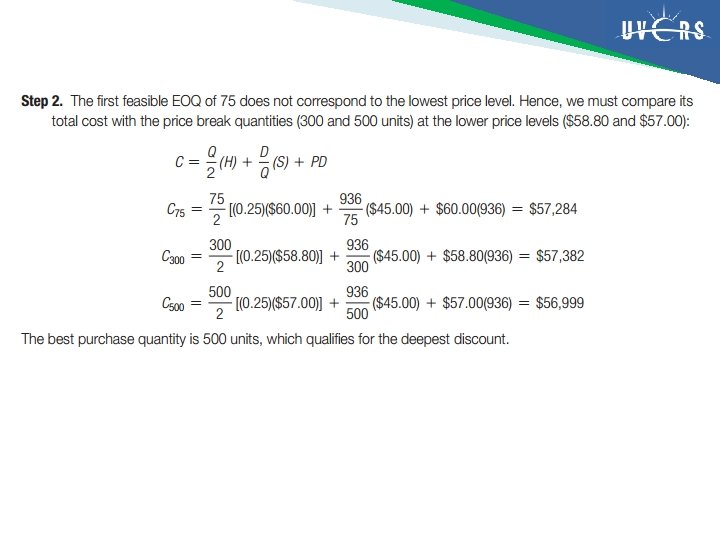
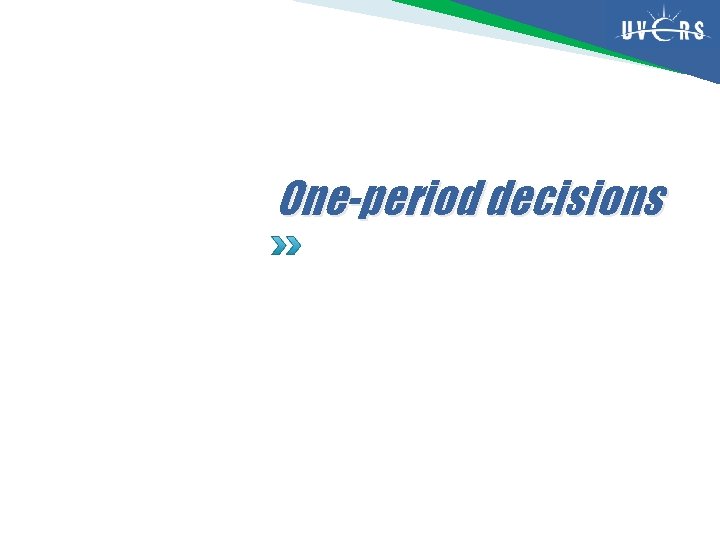
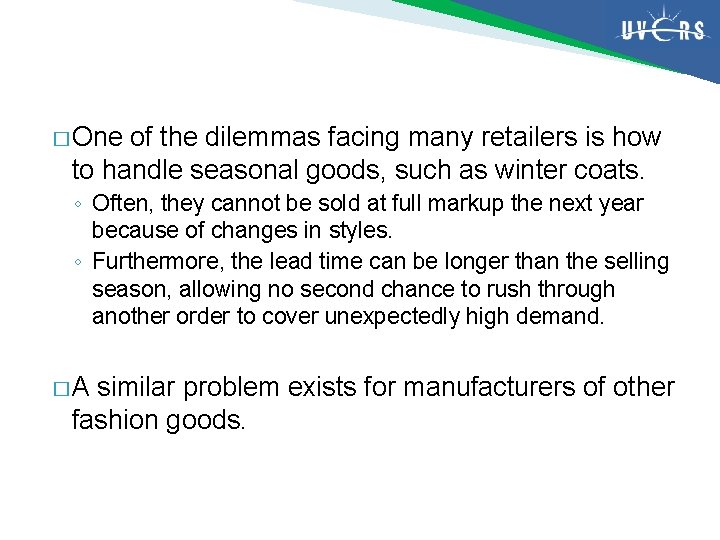
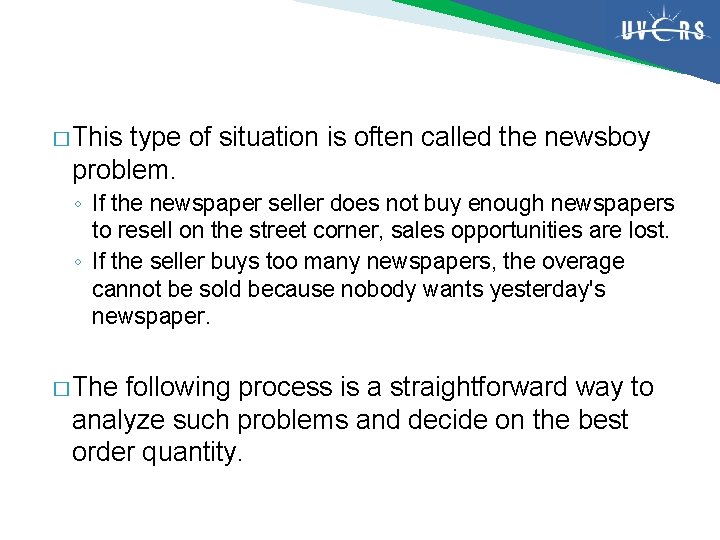
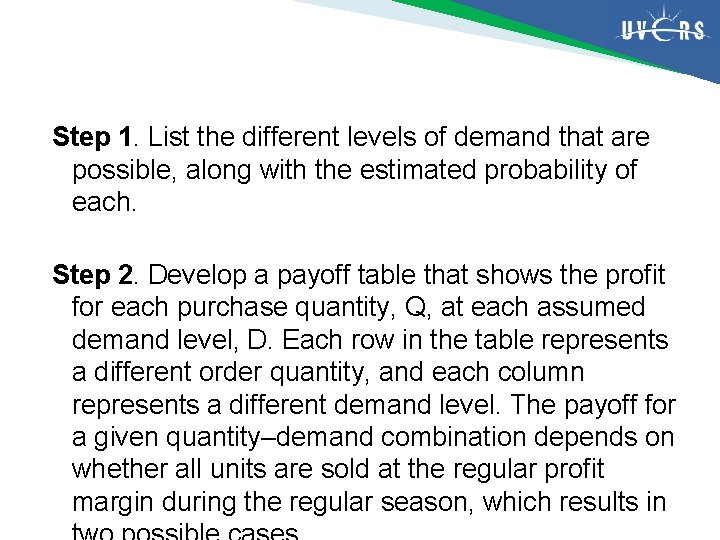
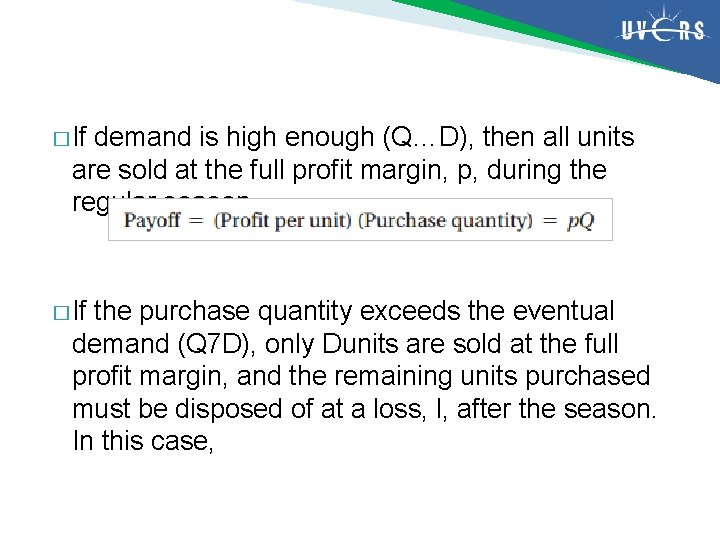
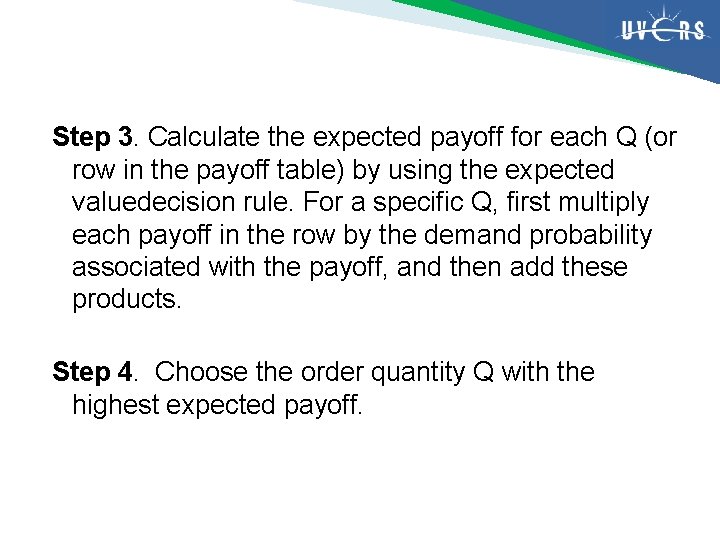
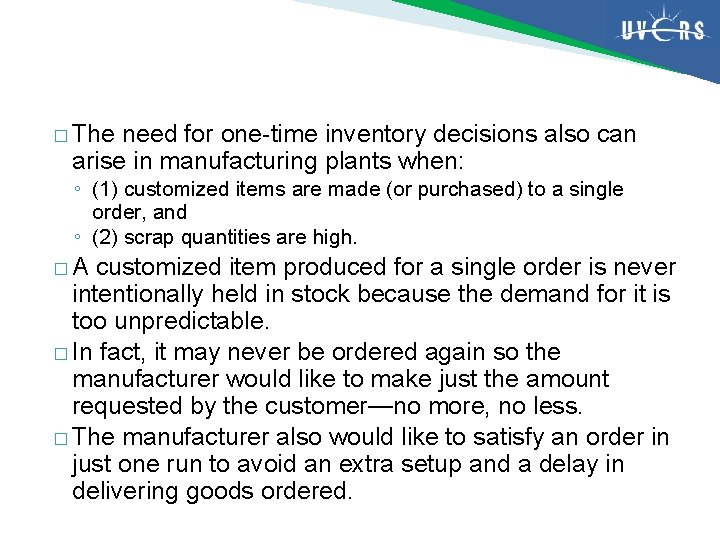
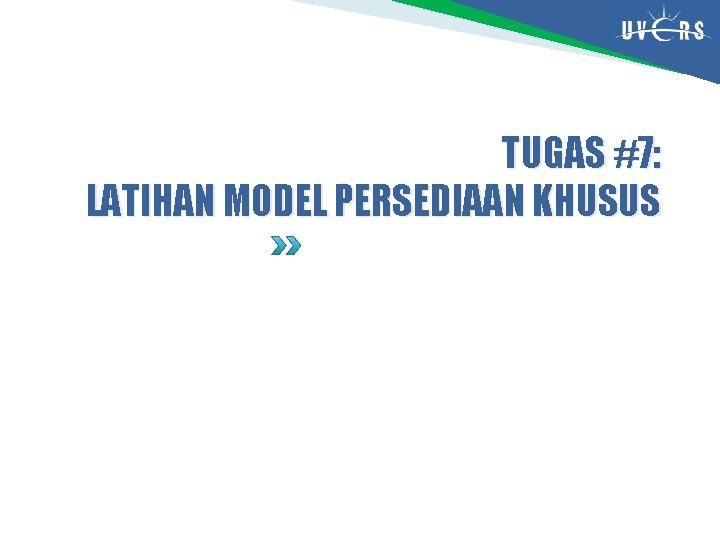
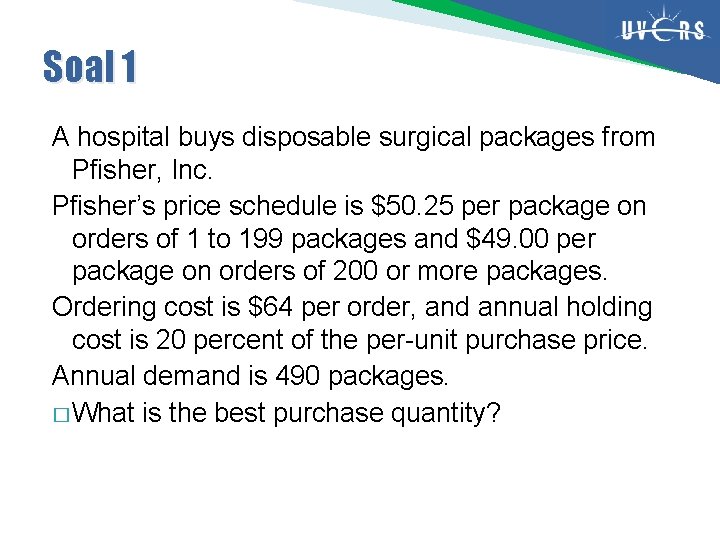
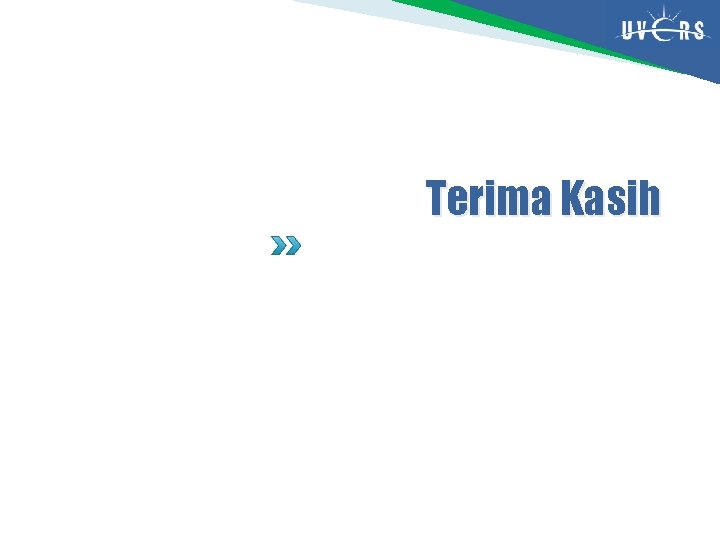
- Slides: 30
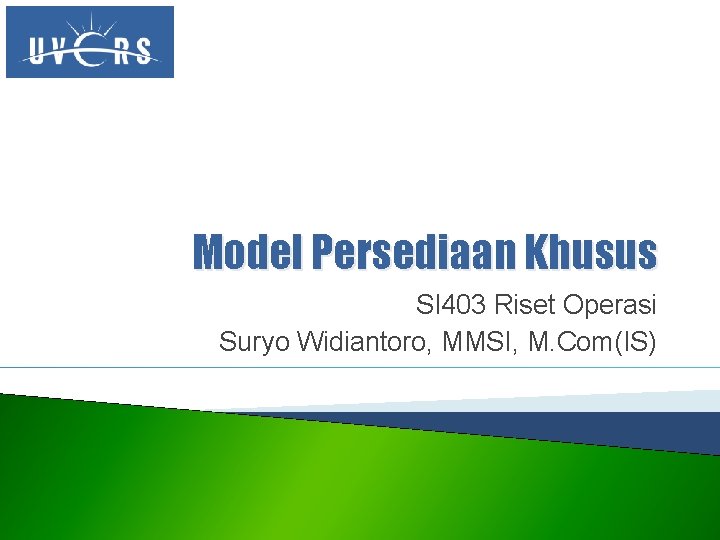
Model Persediaan Khusus SI 403 Riset Operasi Suryo Widiantoro, MMSI, M. Com(IS)
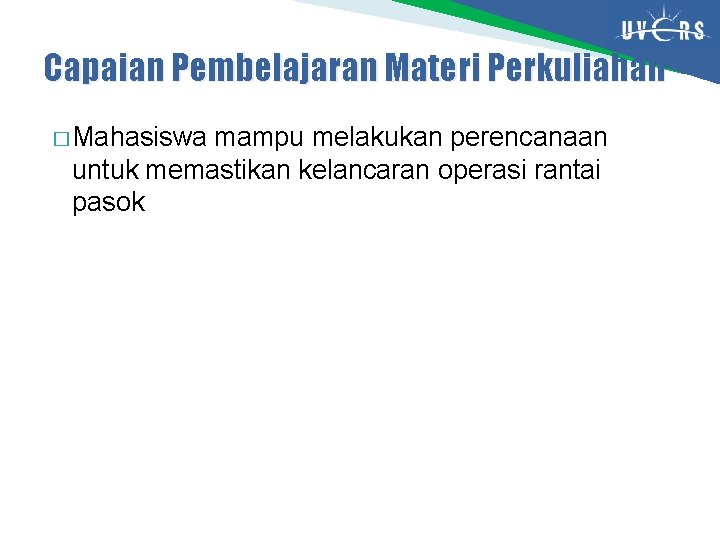
Capaian Pembelajaran Materi Perkuliahan � Mahasiswa mampu melakukan perencanaan untuk memastikan kelancaran operasi rantai pasok

Topik Bahasan 1. 2. 3. Noninstantaneous replenishment Quantity discounts One-period decisions
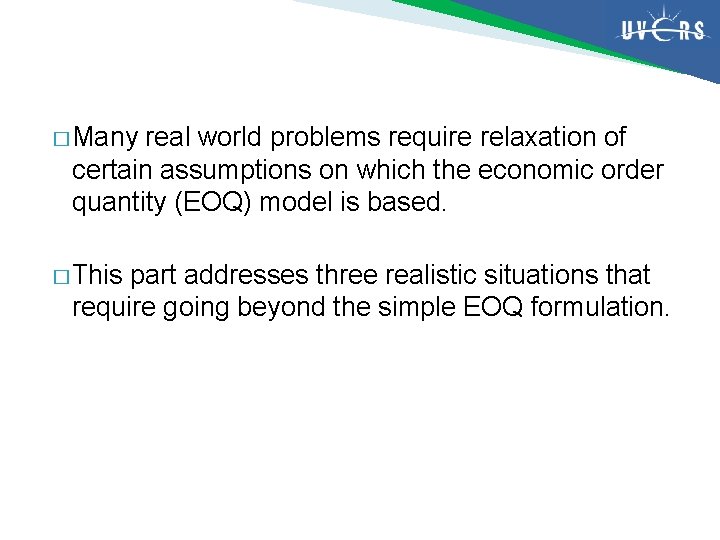
� Many real world problems require relaxation of certain assumptions on which the economic order quantity (EOQ) model is based. � This part addresses three realistic situations that require going beyond the simple EOQ formulation.
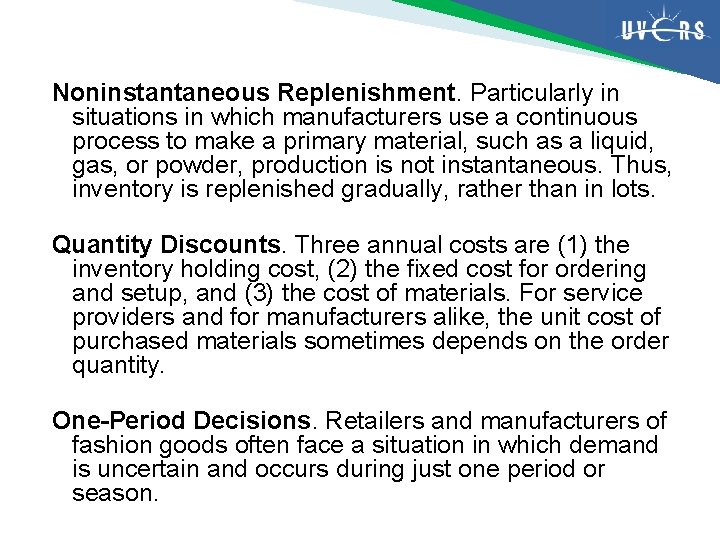
Noninstantaneous Replenishment. Particularly in situations in which manufacturers use a continuous process to make a primary material, such as a liquid, gas, or powder, production is not instantaneous. Thus, inventory is replenished gradually, rather than in lots. Quantity Discounts. Three annual costs are (1) the inventory holding cost, (2) the fixed cost for ordering and setup, and (3) the cost of materials. For service providers and for manufacturers alike, the unit cost of purchased materials sometimes depends on the order quantity. One-Period Decisions. Retailers and manufacturers of fashion goods often face a situation in which demand is uncertain and occurs during just one period or season.
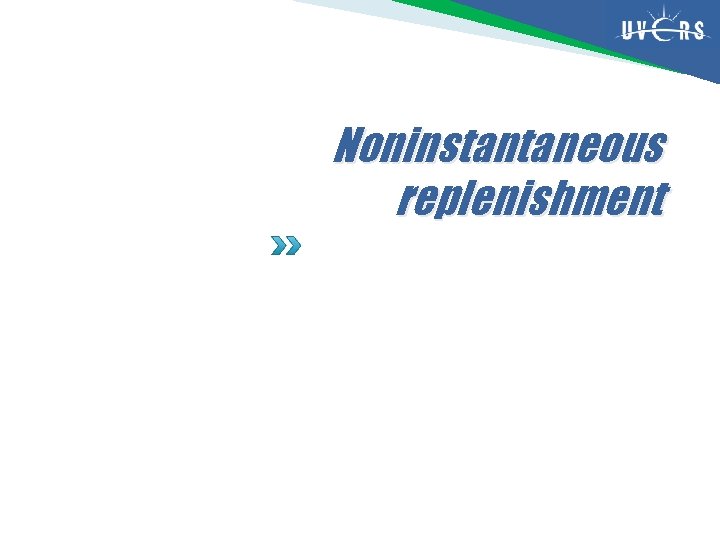
Noninstantaneous replenishment
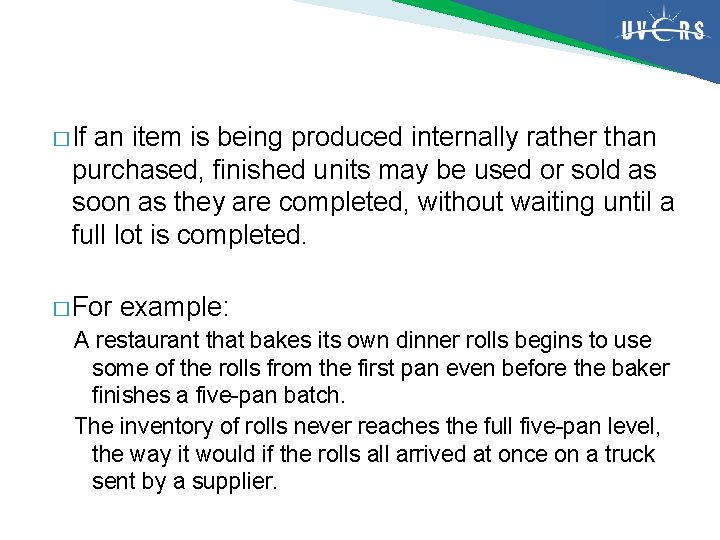
� If an item is being produced internally rather than purchased, finished units may be used or sold as soon as they are completed, without waiting until a full lot is completed. � For example: A restaurant that bakes its own dinner rolls begins to use some of the rolls from the first pan even before the baker finishes a five-pan batch. The inventory of rolls never reaches the full five-pan level, the way it would if the rolls all arrived at once on a truck sent by a supplier.
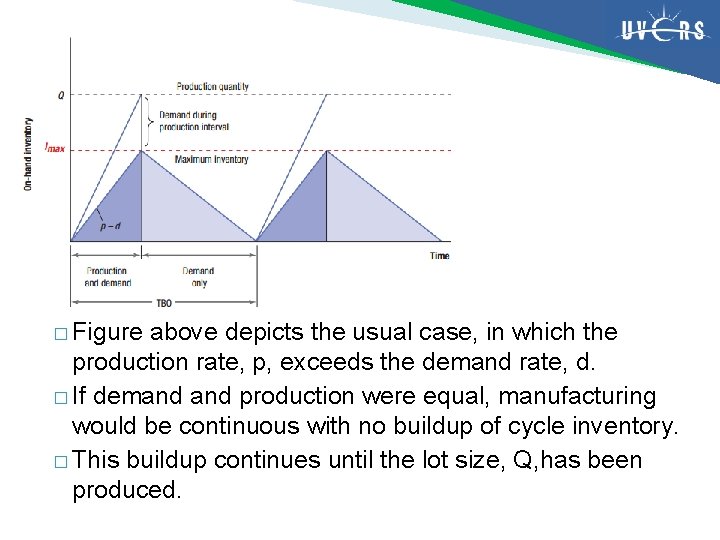
� Figure above depicts the usual case, in which the production rate, p, exceeds the demand rate, d. � If demand production were equal, manufacturing would be continuous with no buildup of cycle inventory. � This buildup continues until the lot size, Q, has been produced.
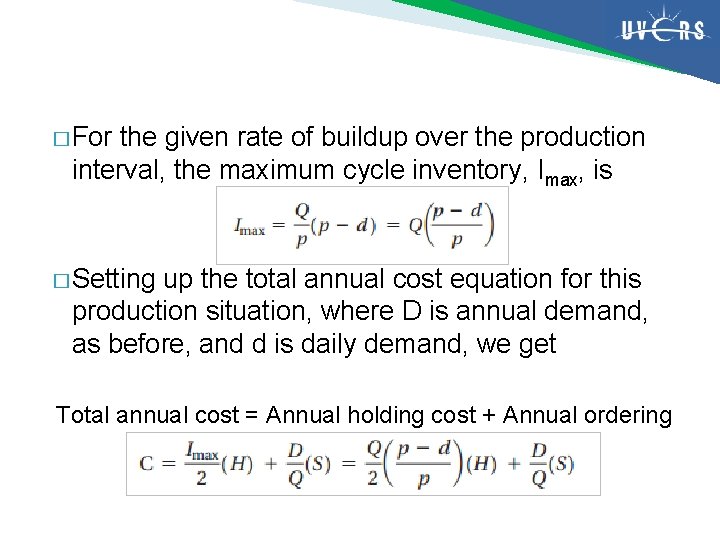
� For the given rate of buildup over the production interval, the maximum cycle inventory, Imax, is � Setting up the total annual cost equation for this production situation, where D is annual demand, as before, and d is daily demand, we get Total annual cost = Annual holding cost + Annual ordering or setup cost
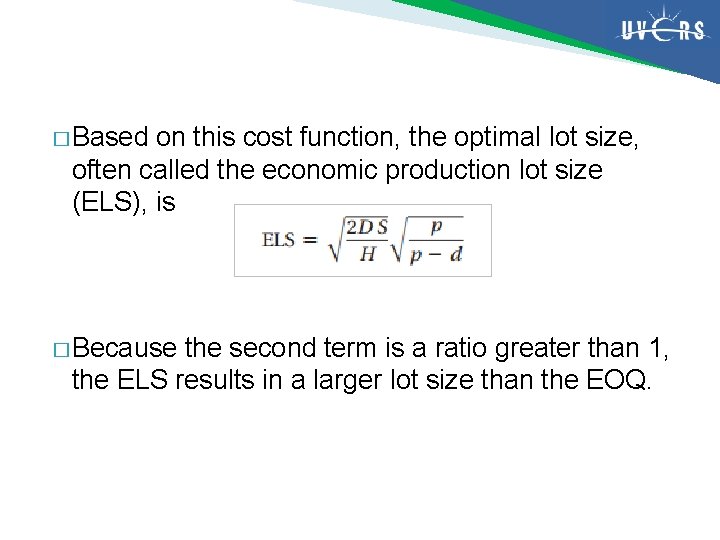
� Based on this cost function, the optimal lot size, often called the economic production lot size (ELS), is � Because the second term is a ratio greater than 1, the ELS results in a larger lot size than the EOQ.

Contoh #1 A plant manager of a chemical plant must determine the lot size for a particular chemical that has a steady demand of 30 barrels per day. The production rate is 190 barrels per day, annual demand is 10, 500 barrels, setup cost is $200, annual holding cost is $0. 21 per barrel, and the plant operates 350 days per year. � a) Determine the economic production lot size (ELS). � b) Determine the total annual setup and inventory holding cost for this item. � c) Determine the time between orders (TBO), or cycle length, for the ELS. � d) Determine the production time per lot.
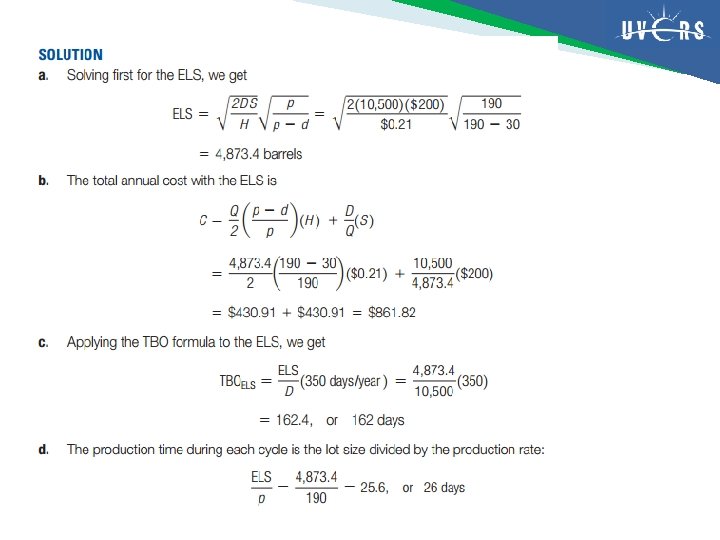
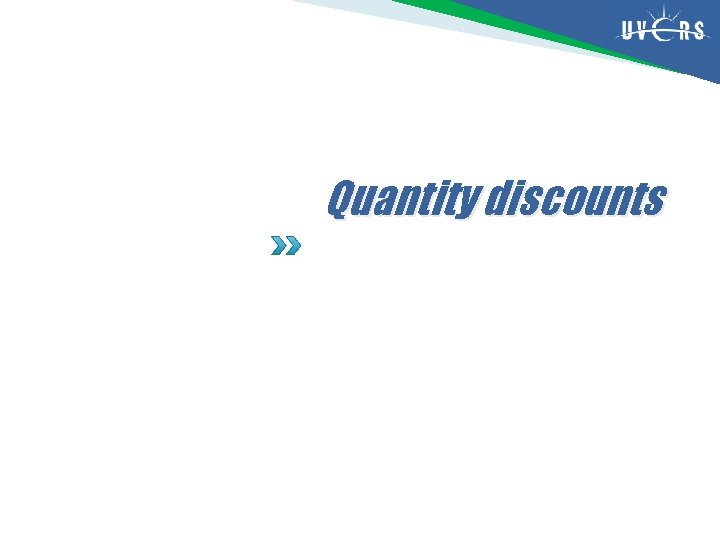
Quantity discounts
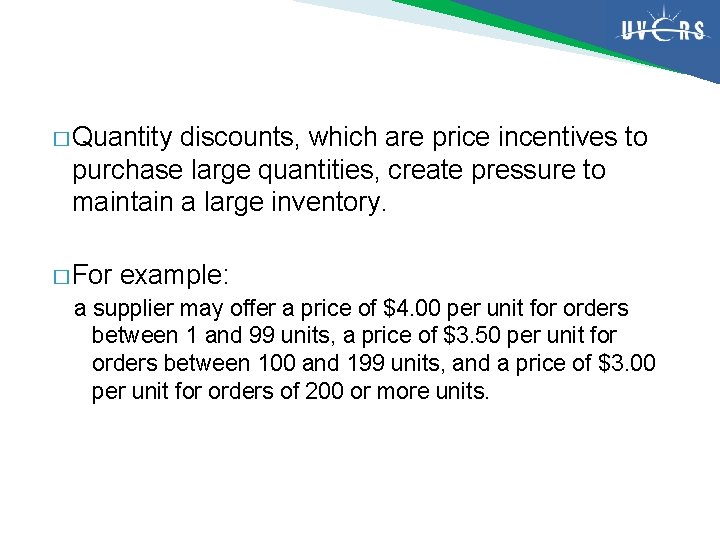
� Quantity discounts, which are price incentives to purchase large quantities, create pressure to maintain a large inventory. � For example: a supplier may offer a price of $4. 00 per unit for orders between 1 and 99 units, a price of $3. 50 per unit for orders between 100 and 199 units, and a price of $3. 00 per unit for orders of 200 or more units.
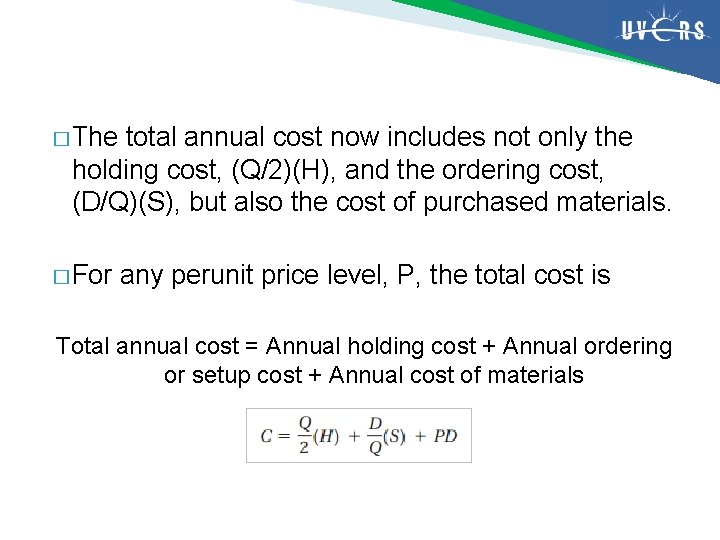
� The total annual cost now includes not only the holding cost, (Q/2)(H), and the ordering cost, (D/Q)(S), but also the cost of purchased materials. � For any perunit price level, P, the total cost is Total annual cost = Annual holding cost + Annual ordering or setup cost + Annual cost of materials
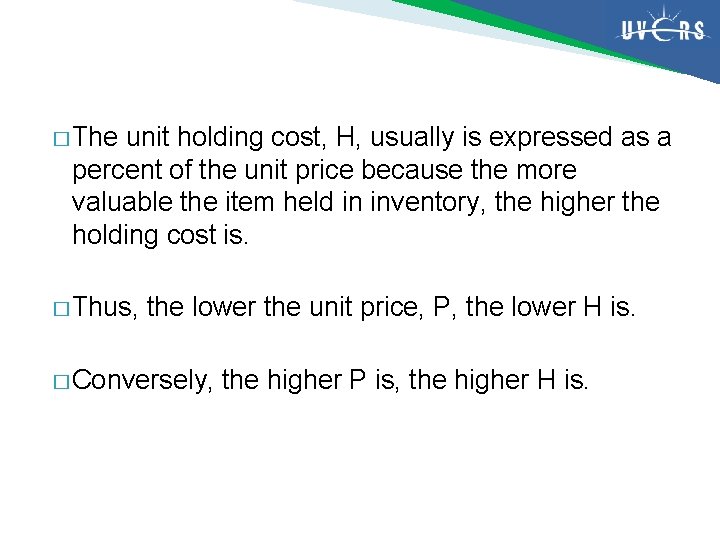
� The unit holding cost, H, usually is expressed as a percent of the unit price because the more valuable the item held in inventory, the higher the holding cost is. � Thus, the lower the unit price, P, the lower H is. � Conversely, the higher P is, the higher H is.
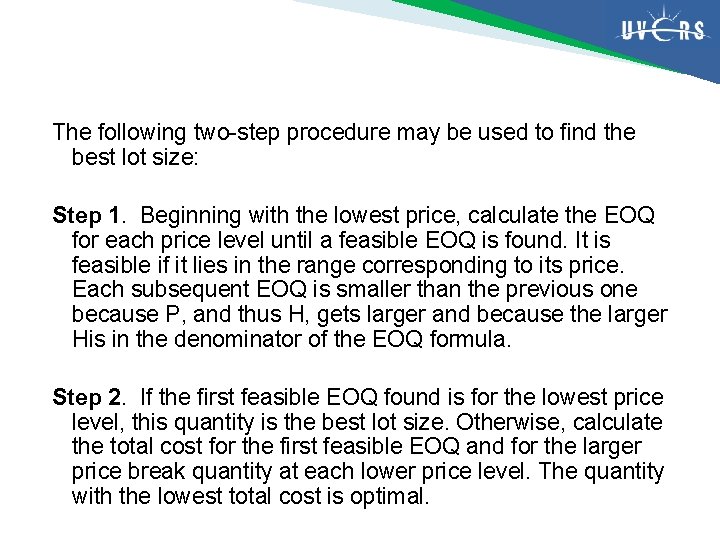
The following two-step procedure may be used to find the best lot size: Step 1. Beginning with the lowest price, calculate the EOQ for each price level until a feasible EOQ is found. It is feasible if it lies in the range corresponding to its price. Each subsequent EOQ is smaller than the previous one because P, and thus H, gets larger and because the larger His in the denominator of the EOQ formula. Step 2. If the first feasible EOQ found is for the lowest price level, this quantity is the best lot size. Otherwise, calculate the total cost for the first feasible EOQ and for the larger price break quantity at each lower price level. The quantity with the lowest total cost is optimal.
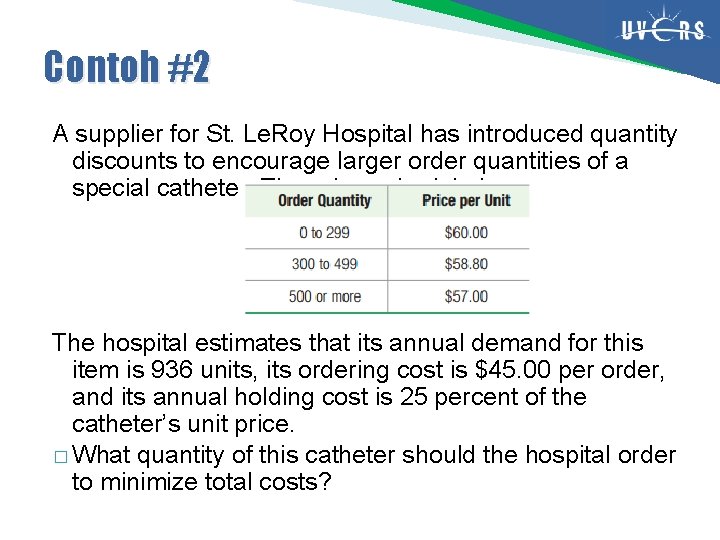
Contoh #2 A supplier for St. Le. Roy Hospital has introduced quantity discounts to encourage larger order quantities of a special catheter. The price schedule is The hospital estimates that its annual demand for this item is 936 units, its ordering cost is $45. 00 per order, and its annual holding cost is 25 percent of the catheter’s unit price. � What quantity of this catheter should the hospital order to minimize total costs?
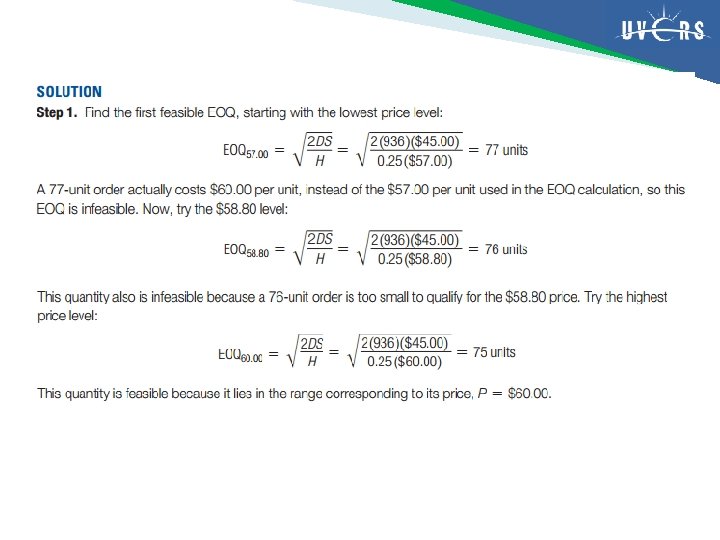
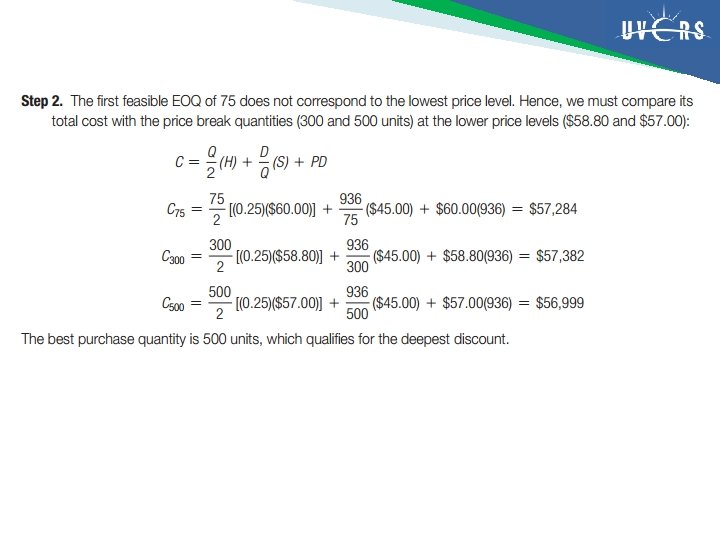
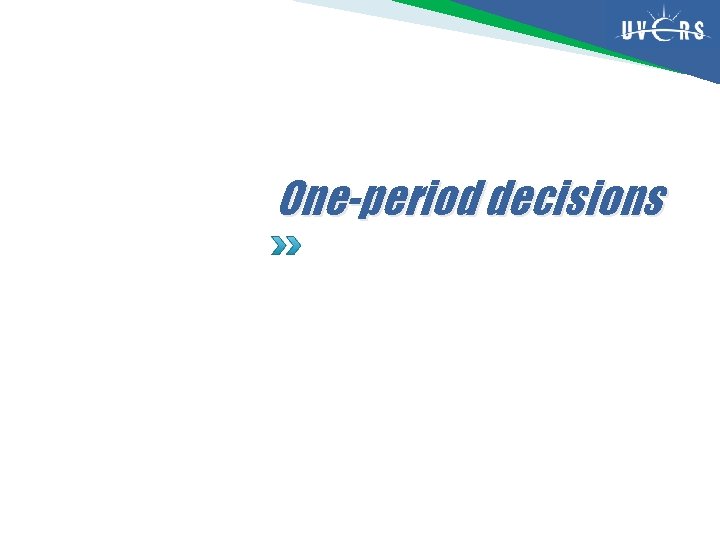
One-period decisions
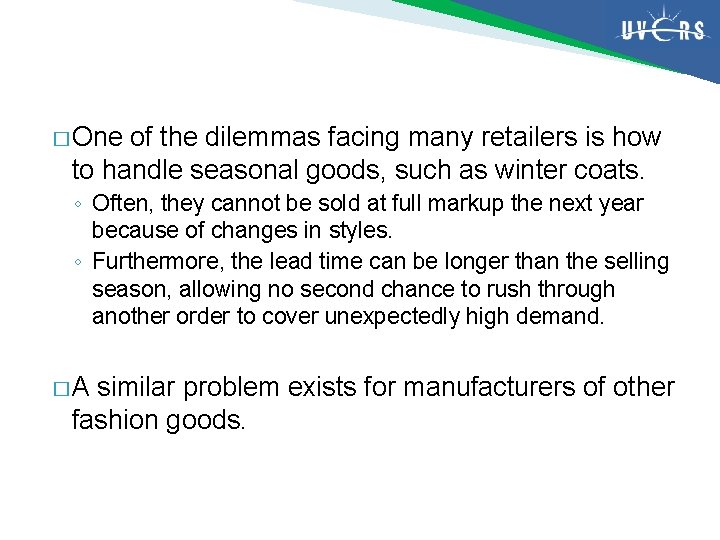
� One of the dilemmas facing many retailers is how to handle seasonal goods, such as winter coats. ◦ Often, they cannot be sold at full markup the next year because of changes in styles. ◦ Furthermore, the lead time can be longer than the selling season, allowing no second chance to rush through another order to cover unexpectedly high demand. �A similar problem exists for manufacturers of other fashion goods.
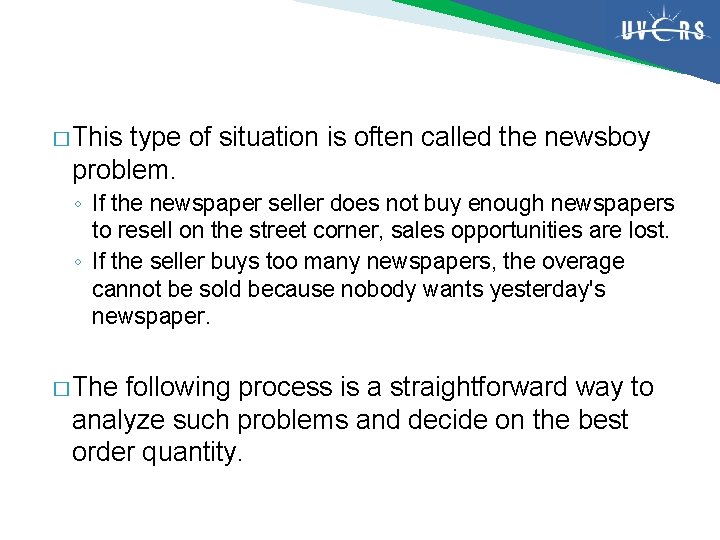
� This type of situation is often called the newsboy problem. ◦ If the newspaper seller does not buy enough newspapers to resell on the street corner, sales opportunities are lost. ◦ If the seller buys too many newspapers, the overage cannot be sold because nobody wants yesterday's newspaper. � The following process is a straightforward way to analyze such problems and decide on the best order quantity.
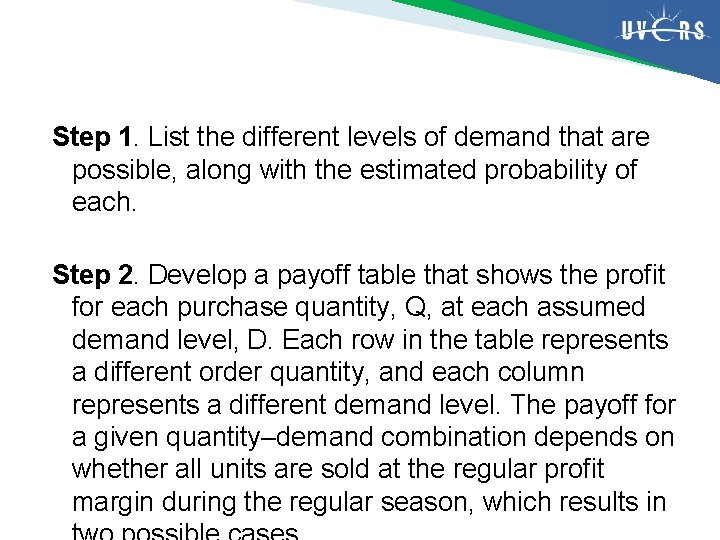
Step 1. List the different levels of demand that are possible, along with the estimated probability of each. Step 2. Develop a payoff table that shows the profit for each purchase quantity, Q, at each assumed demand level, D. Each row in the table represents a different order quantity, and each column represents a different demand level. The payoff for a given quantity–demand combination depends on whether all units are sold at the regular profit margin during the regular season, which results in
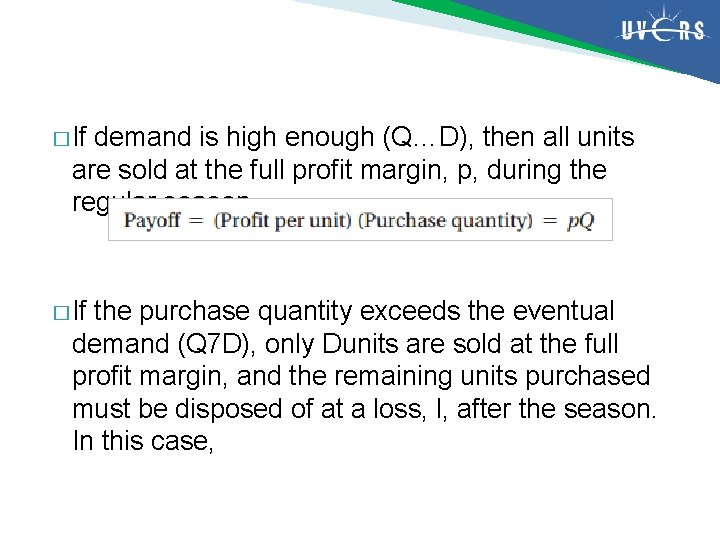
� If demand is high enough (Q…D), then all units are sold at the full profit margin, p, during the regular season � If the purchase quantity exceeds the eventual demand (Q 7 D), only Dunits are sold at the full profit margin, and the remaining units purchased must be disposed of at a loss, l, after the season. In this case,
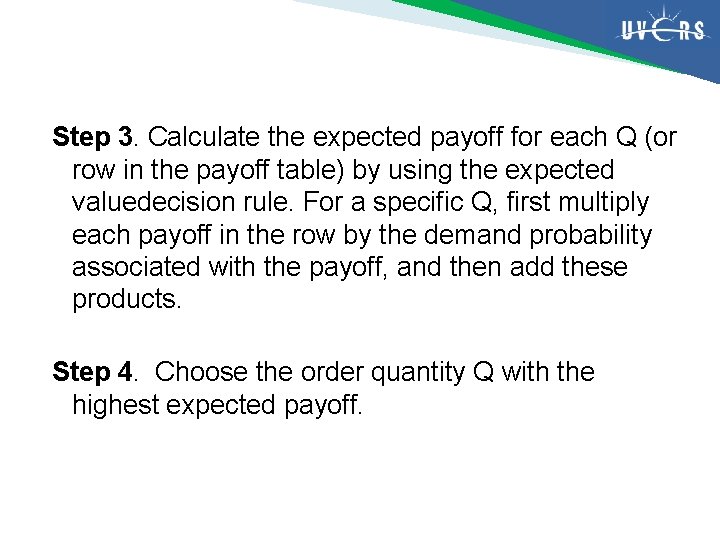
Step 3. Calculate the expected payoff for each Q (or row in the payoff table) by using the expected valuedecision rule. For a specific Q, first multiply each payoff in the row by the demand probability associated with the payoff, and then add these products. Step 4. Choose the order quantity Q with the highest expected payoff.
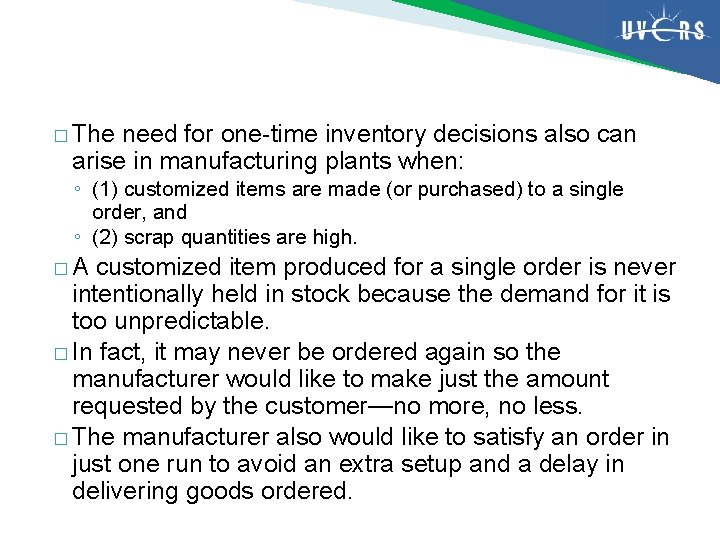
� The need for one-time inventory decisions also can arise in manufacturing plants when: ◦ (1) customized items are made (or purchased) to a single order, and ◦ (2) scrap quantities are high. �A customized item produced for a single order is never intentionally held in stock because the demand for it is too unpredictable. � In fact, it may never be ordered again so the manufacturer would like to make just the amount requested by the customer—no more, no less. � The manufacturer also would like to satisfy an order in just one run to avoid an extra setup and a delay in delivering goods ordered.
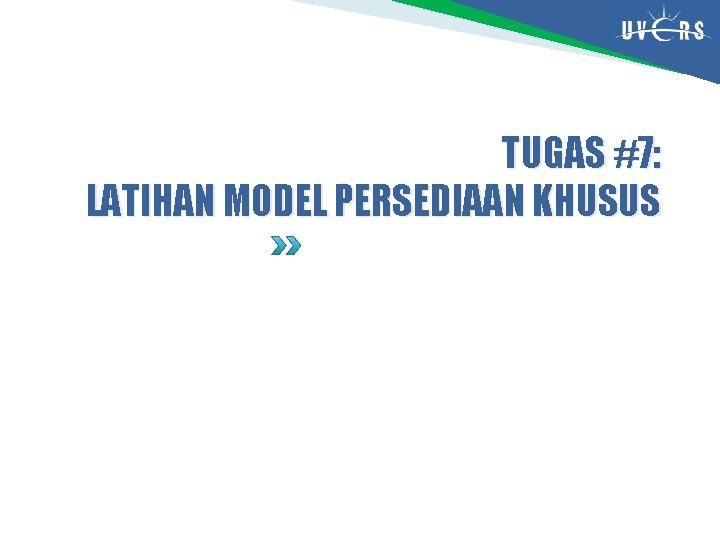
TUGAS #7: LATIHAN MODEL PERSEDIAAN KHUSUS
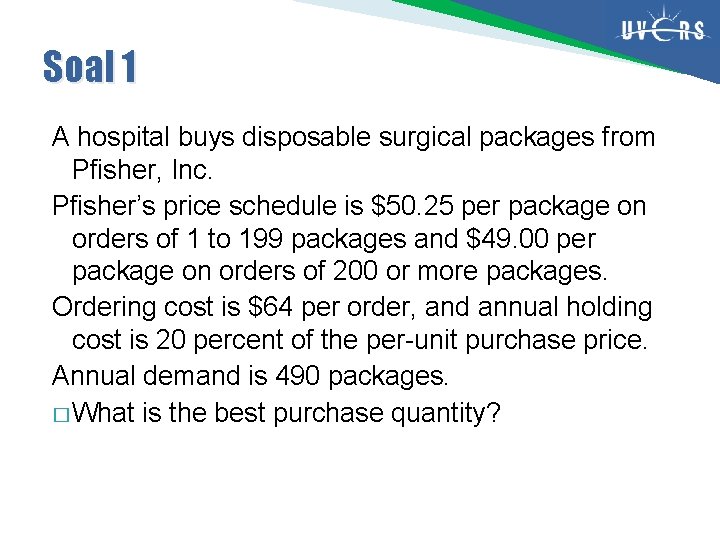
Soal 1 A hospital buys disposable surgical packages from Pfisher, Inc. Pfisher’s price schedule is $50. 25 per package on orders of 1 to 199 packages and $49. 00 per package on orders of 200 or more packages. Ordering cost is $64 per order, and annual holding cost is 20 percent of the per-unit purchase price. Annual demand is 490 packages. � What is the best purchase quantity?
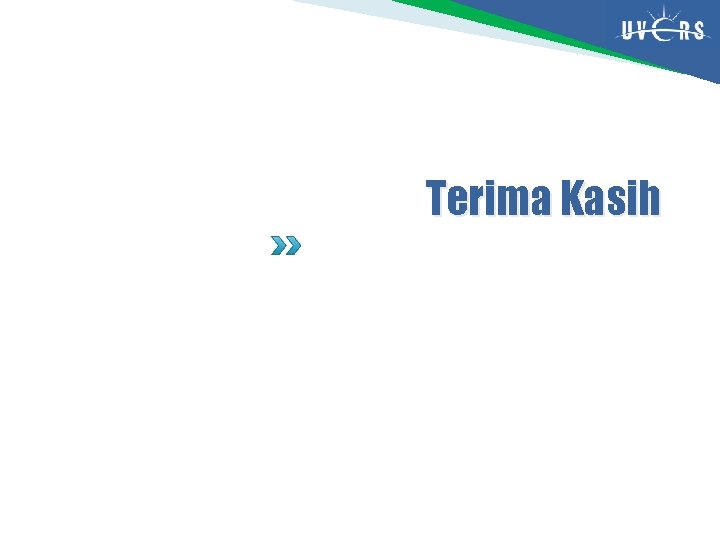
Terima Kasih
Contoh soal riset operasi model persediaan
Model jaringan riset operasi
Materi riset operasi
Hidangan kesempatan khusus untuk acara adat istiadat
Riset operasi
Ruang lingkup riset operasi pdf
Konsep dualitas
Kelemahan riset operasi
Teori antrian
Contoh penggunaan riset operasi dalam pekerjaan
Masalah penugasan riset operasi
Contoh soal assignment
Metode modi
Kelemahan riset operasi
Teori permainan riset operasi
Jawaban soal pt bakery
Riset operasi metode transportasi
Big m
Riset operasi
Metode big m riset operasi
Operations research and supply chain
Definisi riset operasi
Teori antrian riset operasi
Teori antrian riset operasi
Review materi adalah
Pengertian riset operasi
Cse 403
Po 403
Voltage classification
Envirobond 403
Direct coding in computer graphics