L Applying Lean Six Sigma Methodology and Metrics
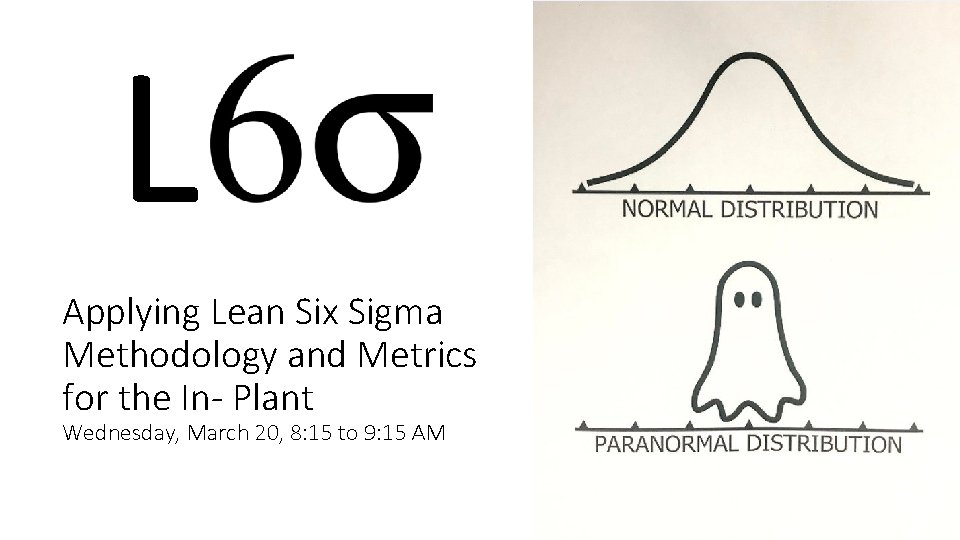
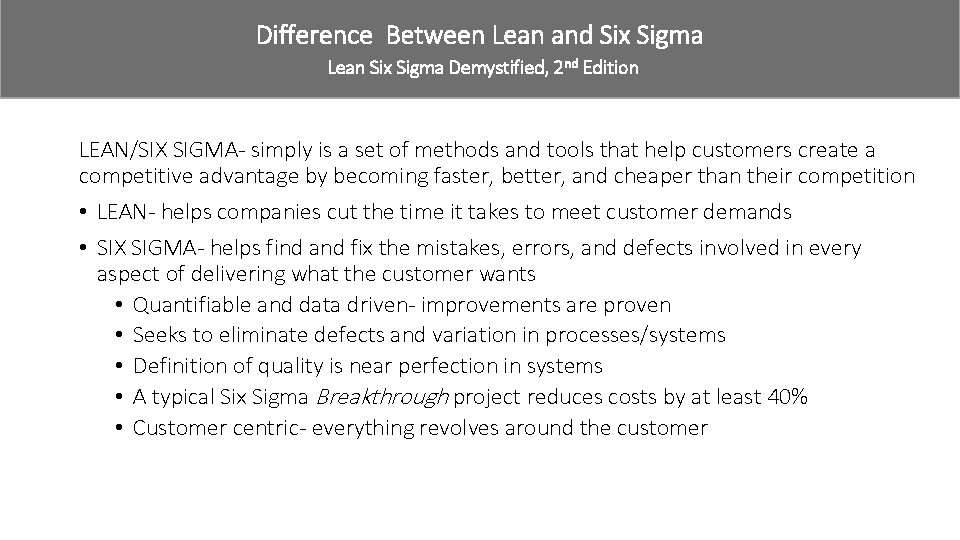
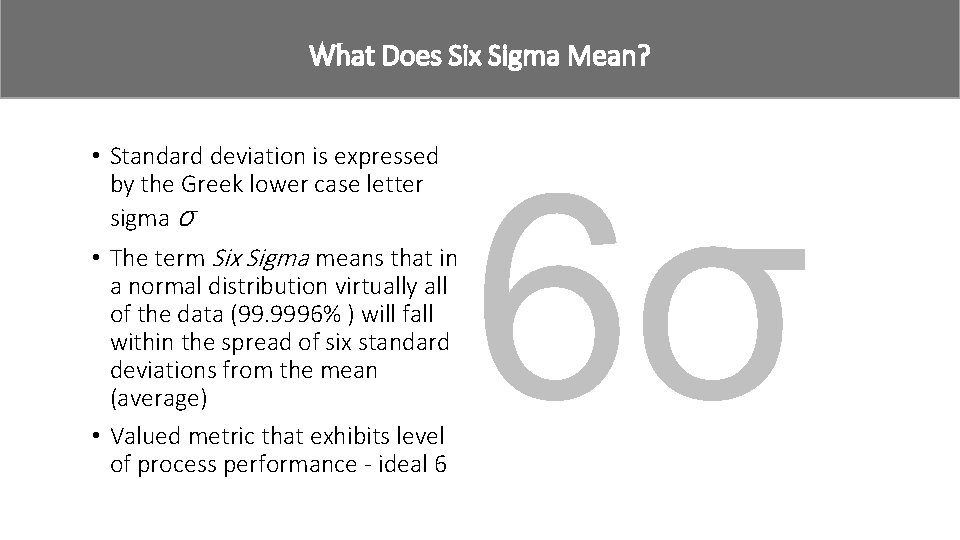
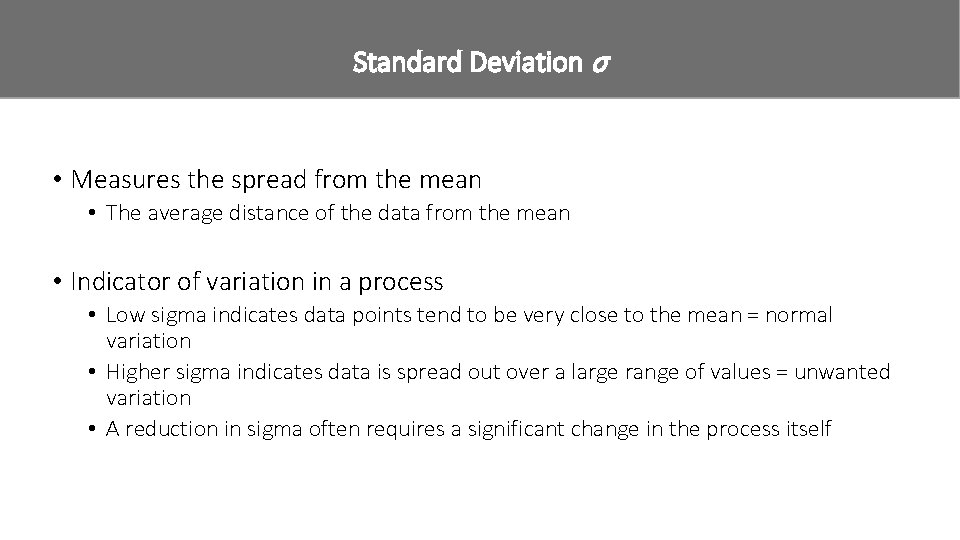
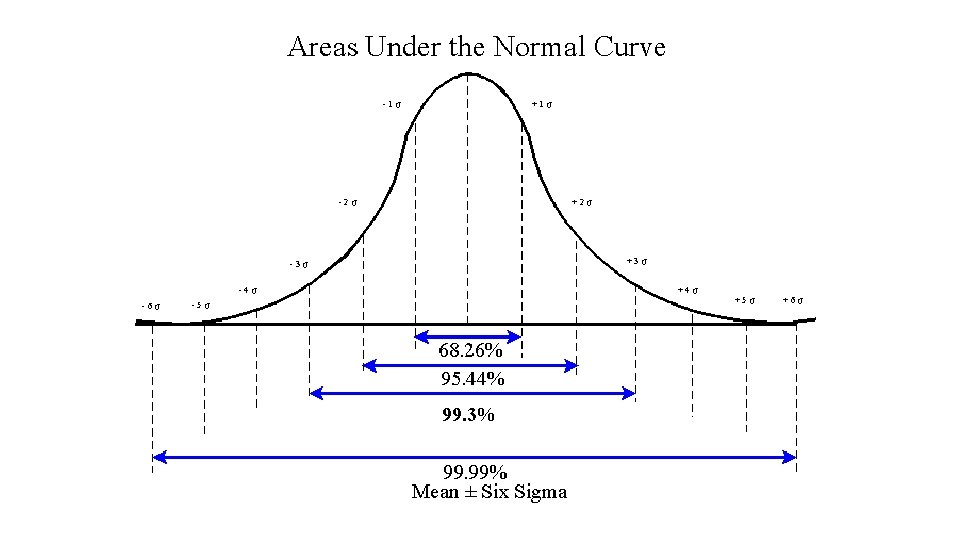
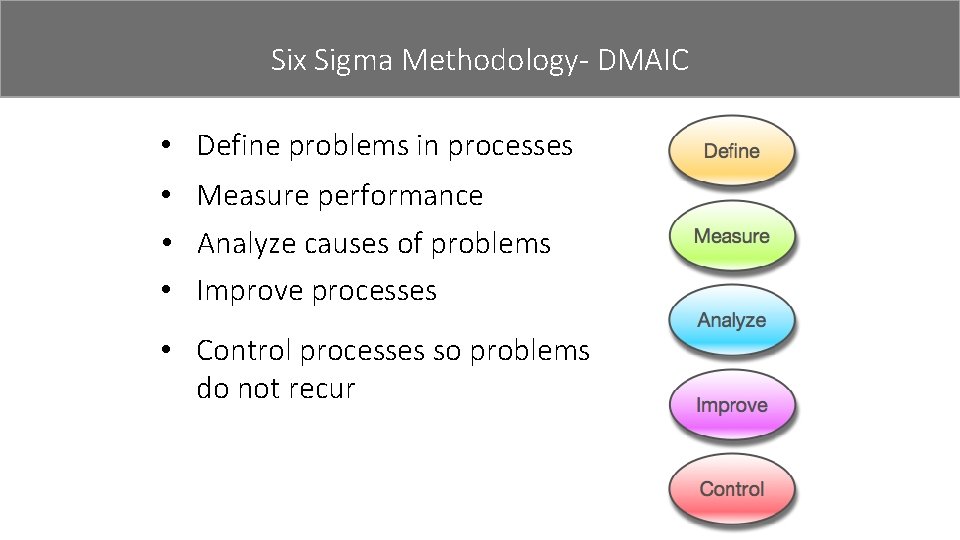
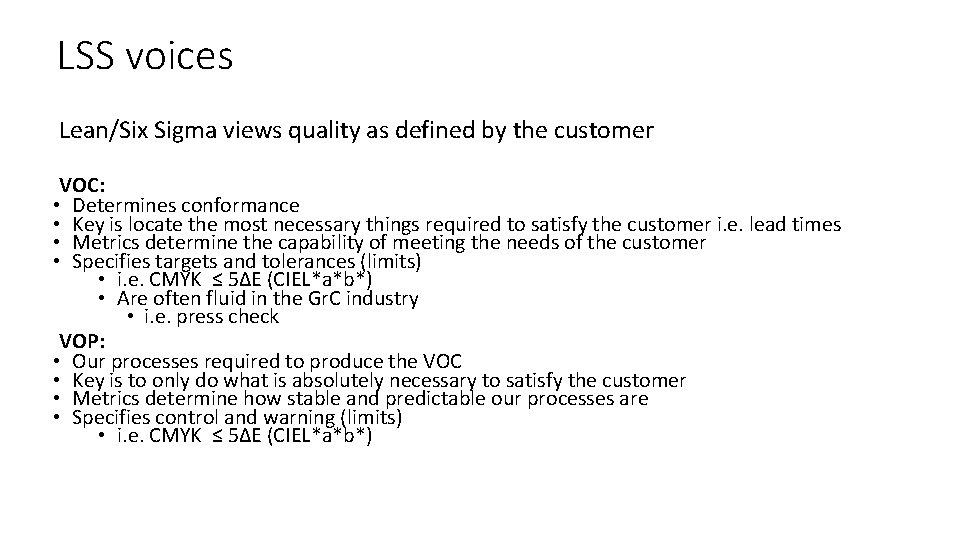
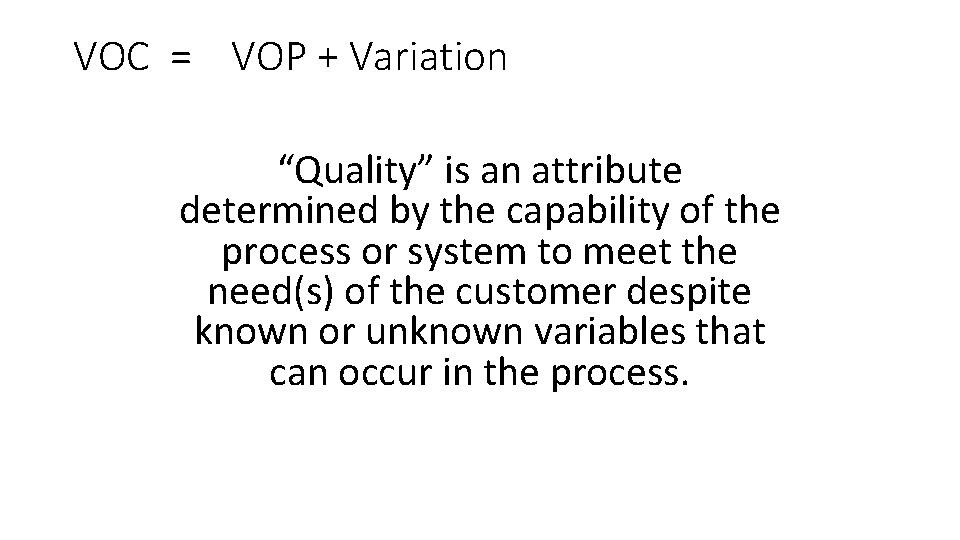
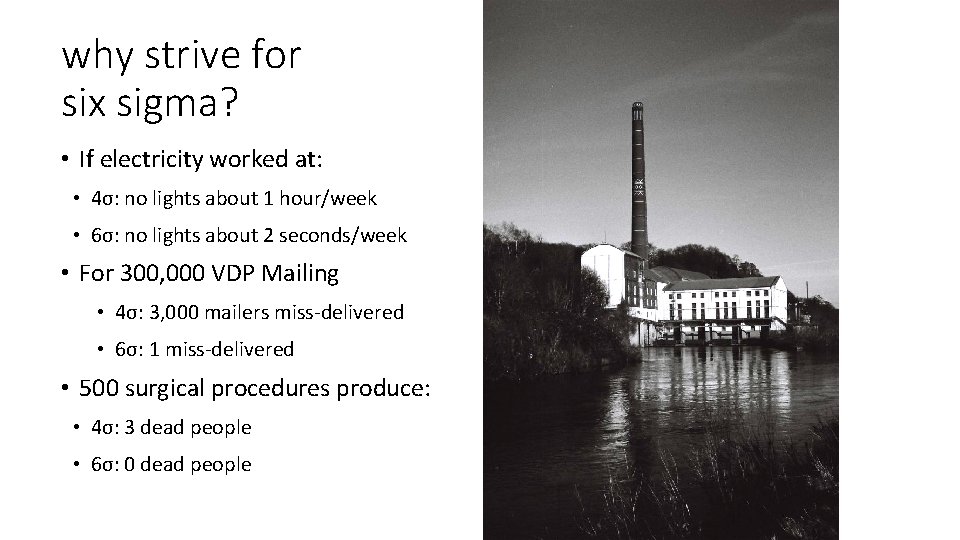
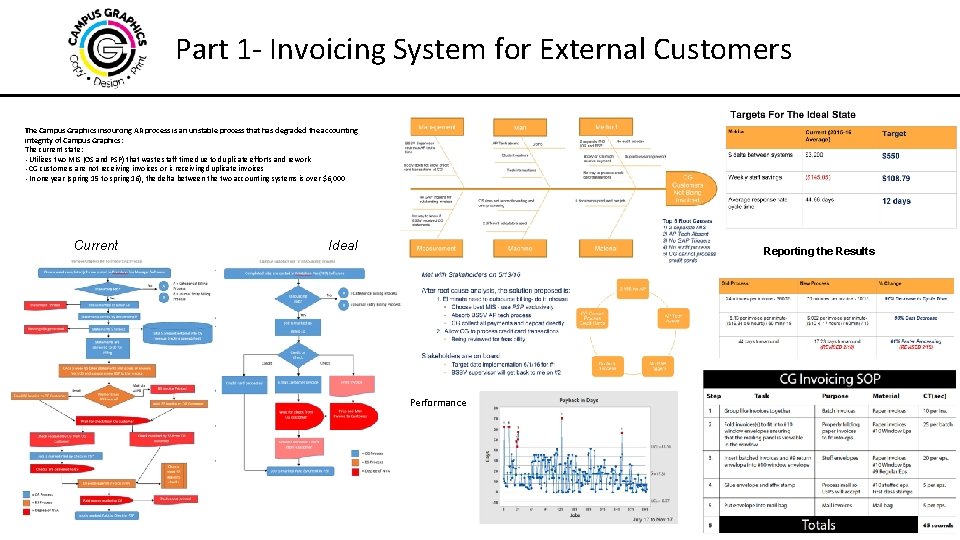
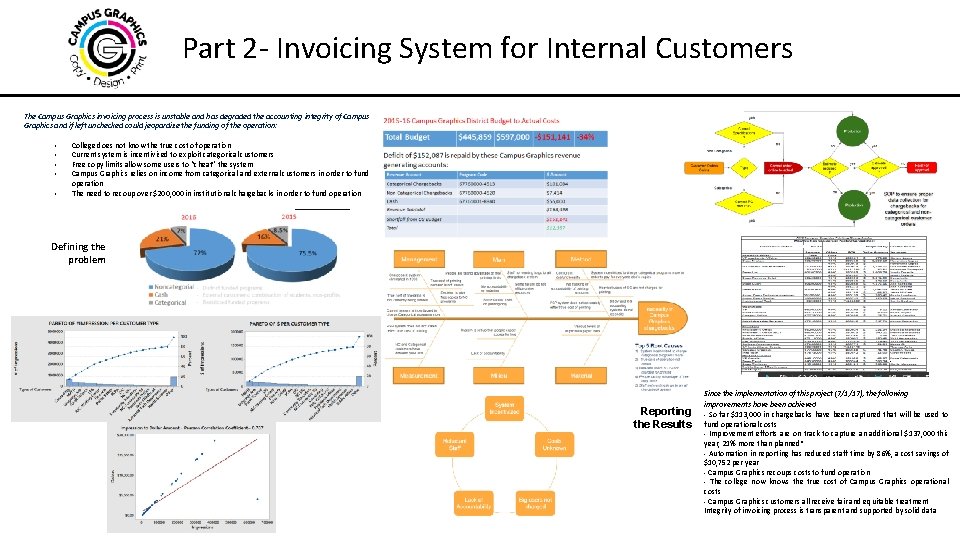
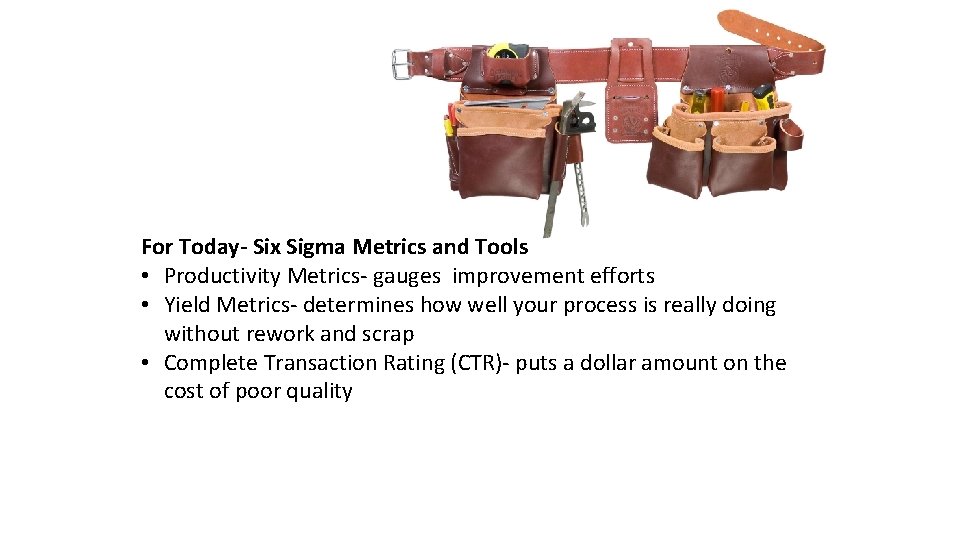
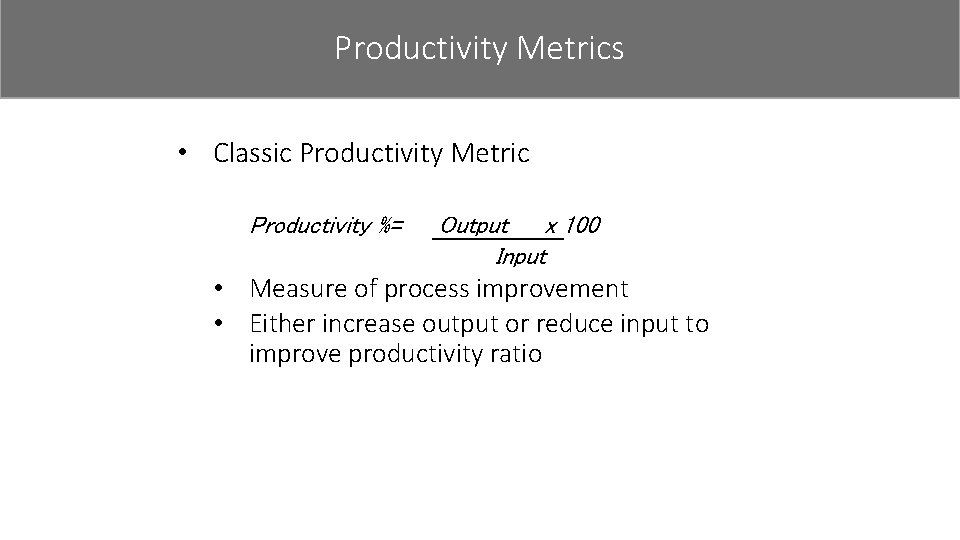
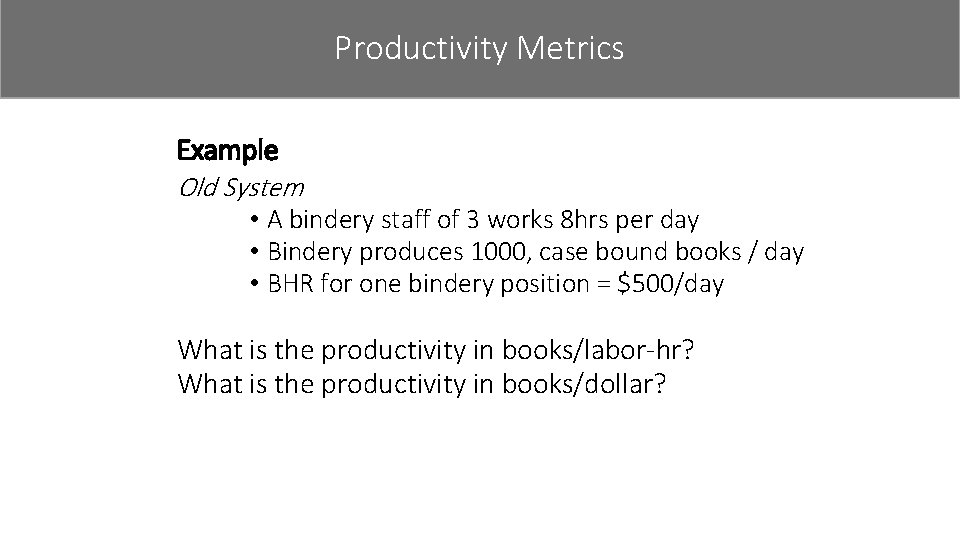
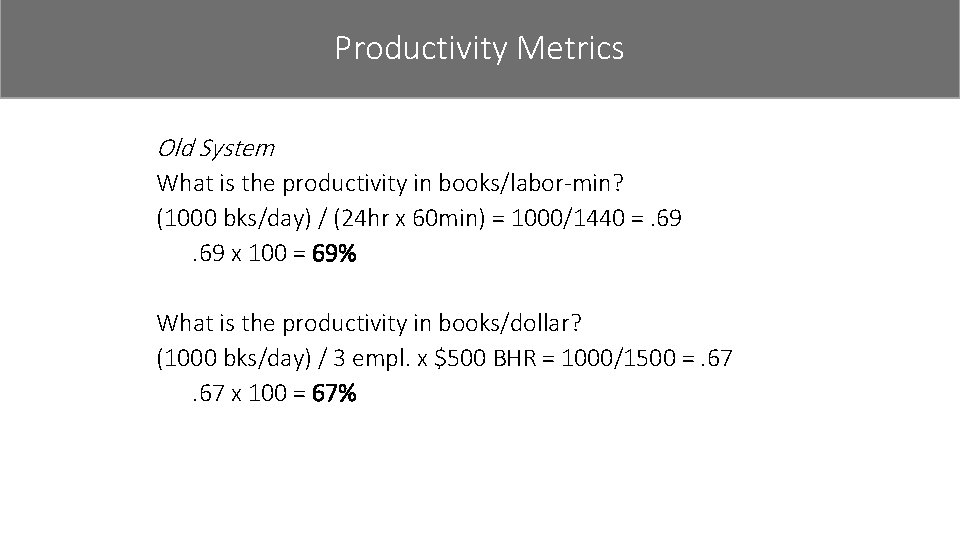
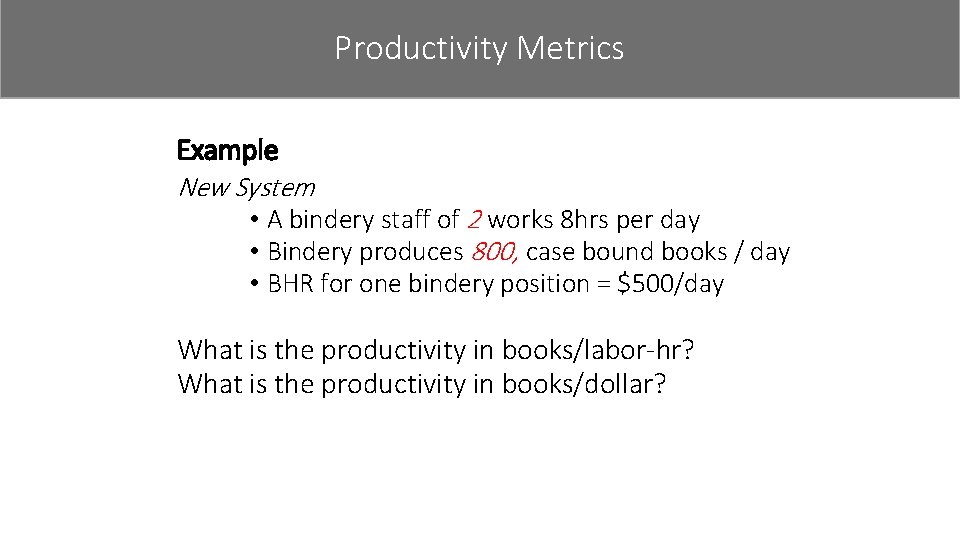
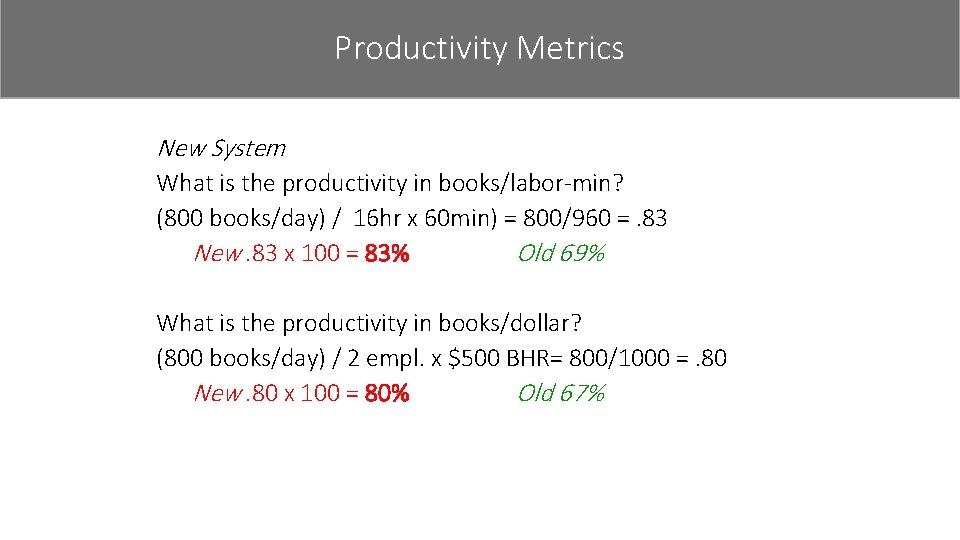
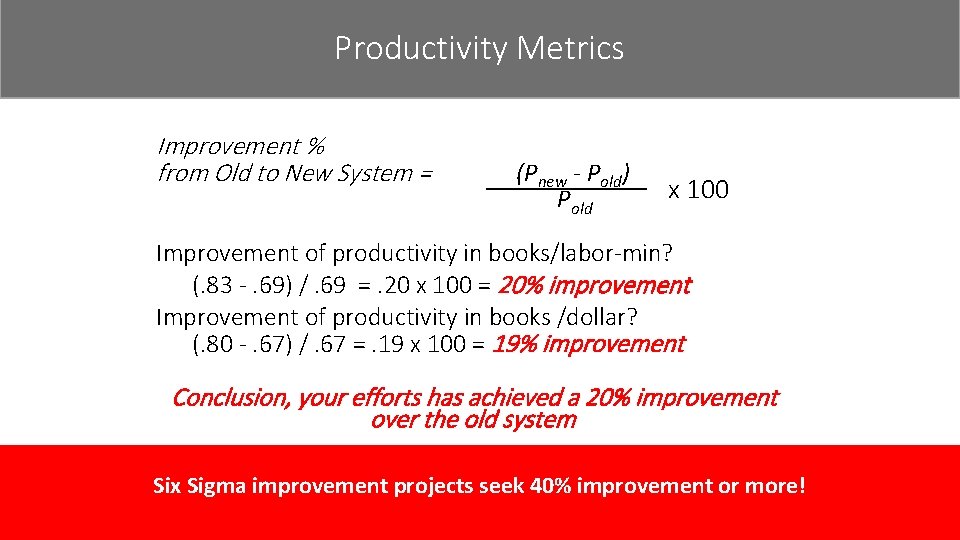
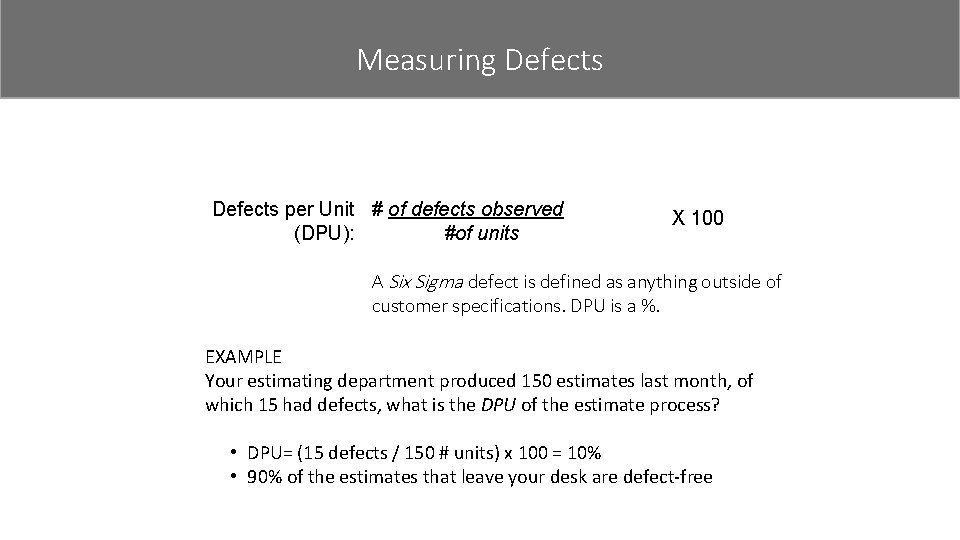
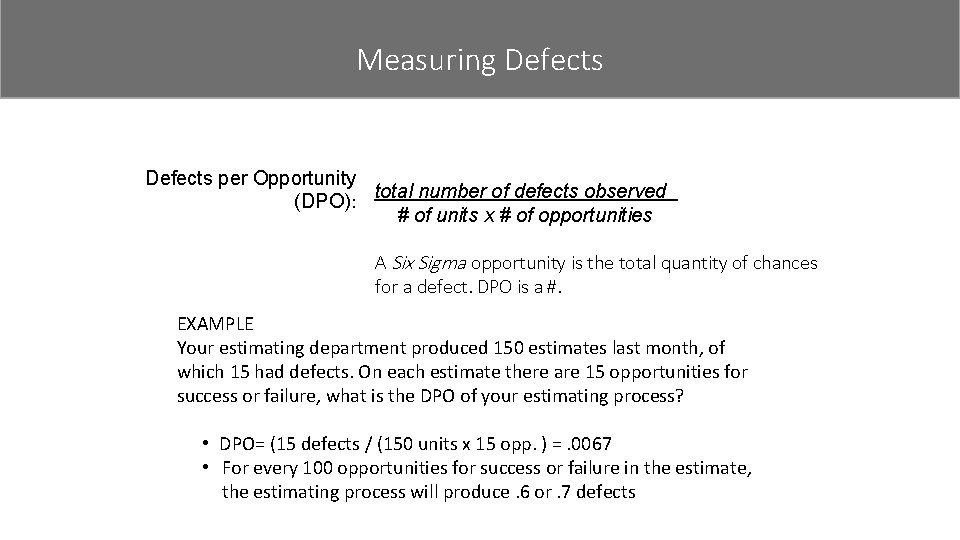
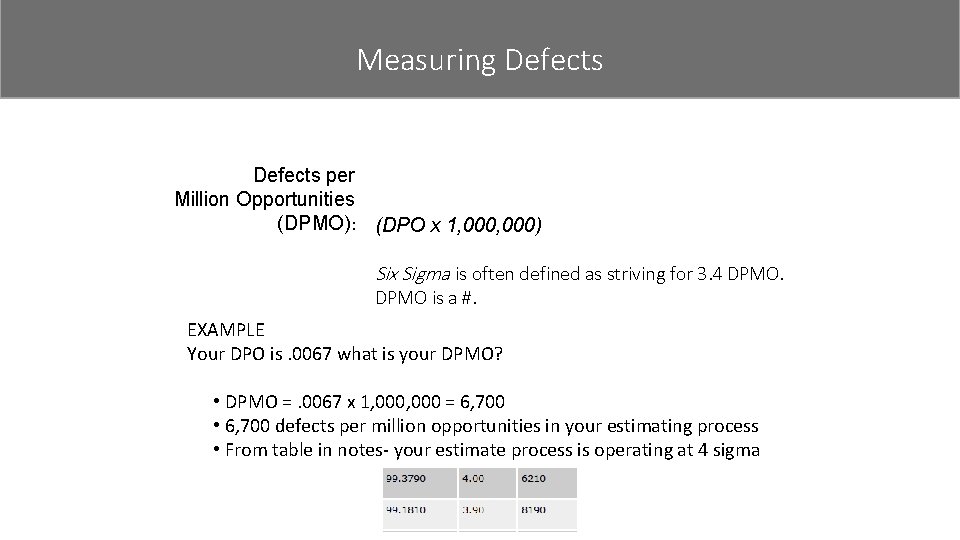
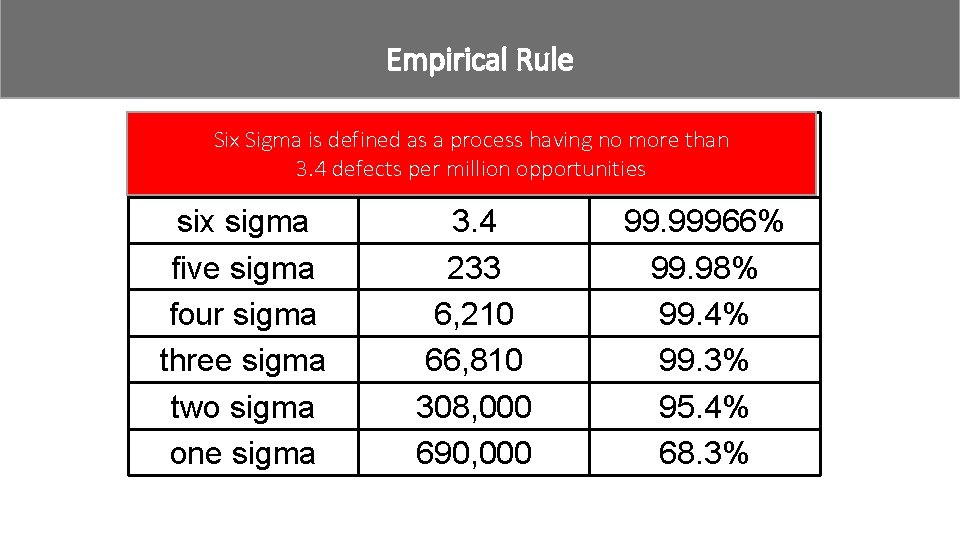
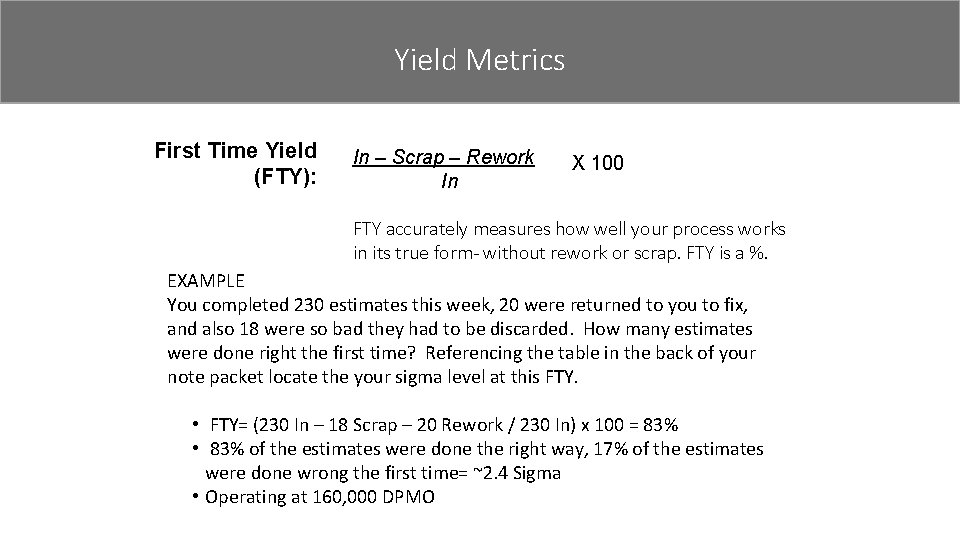
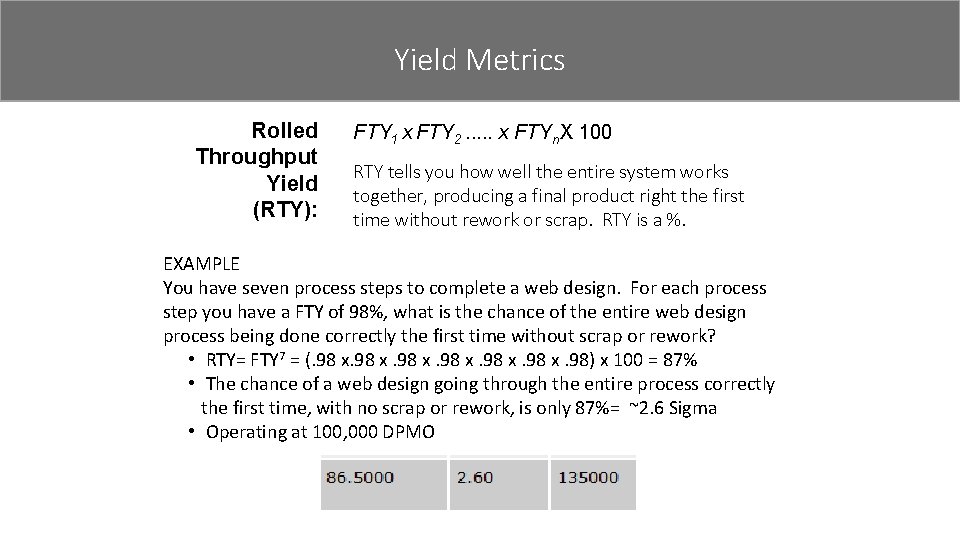
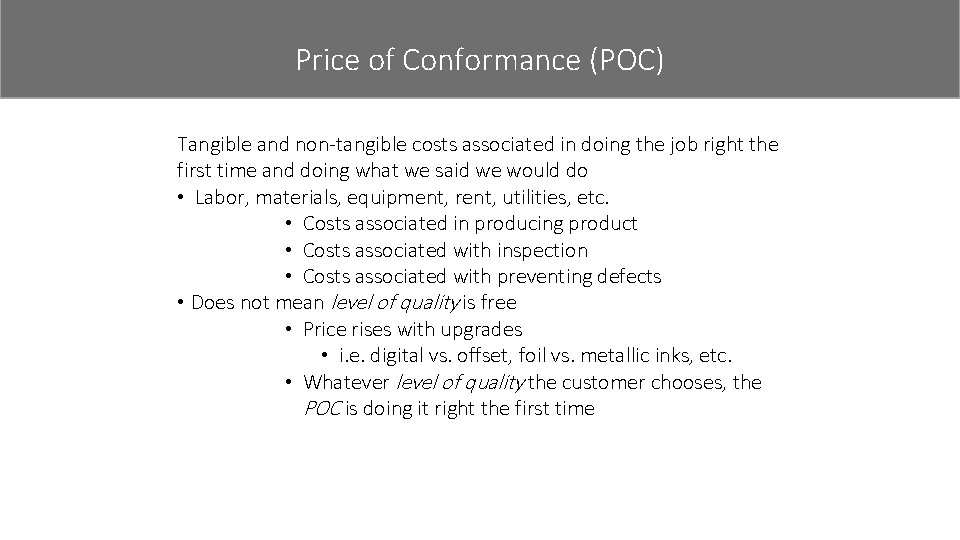
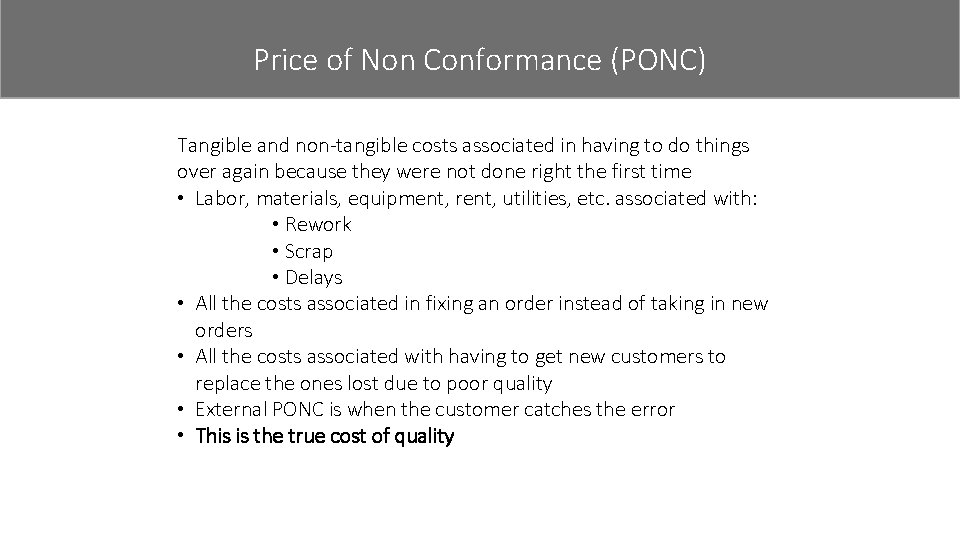
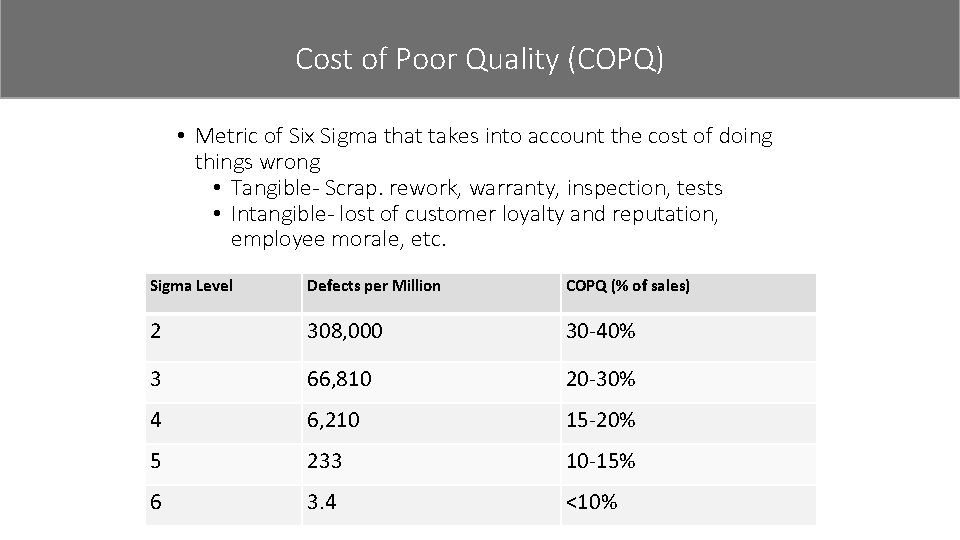
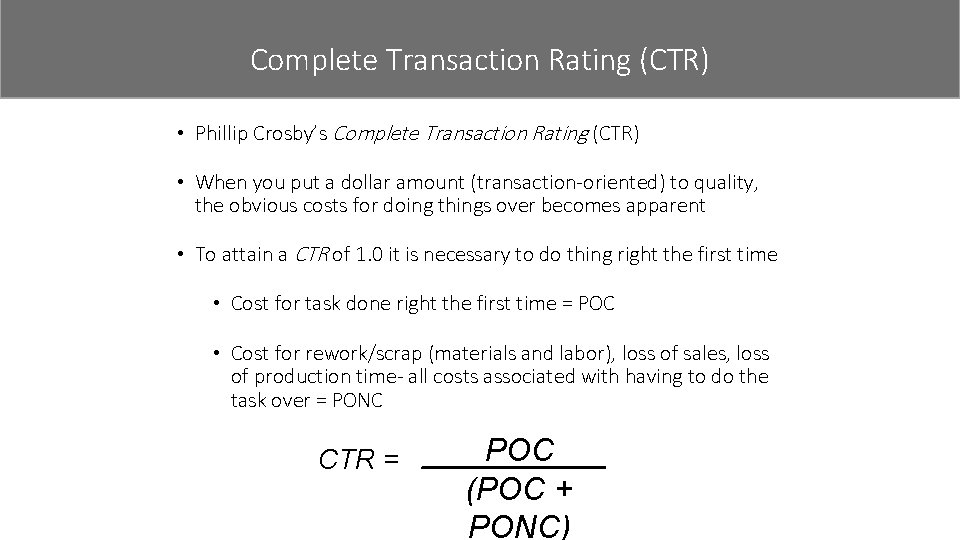
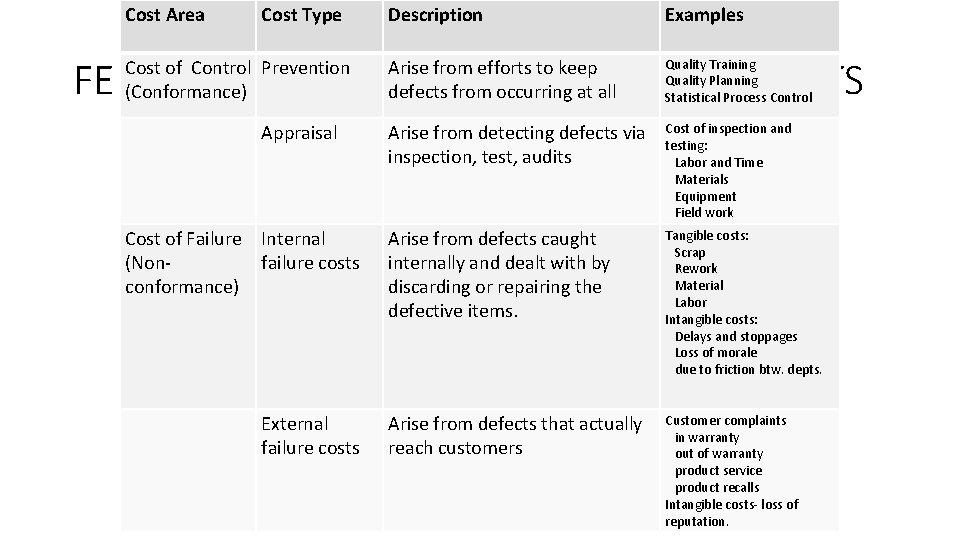
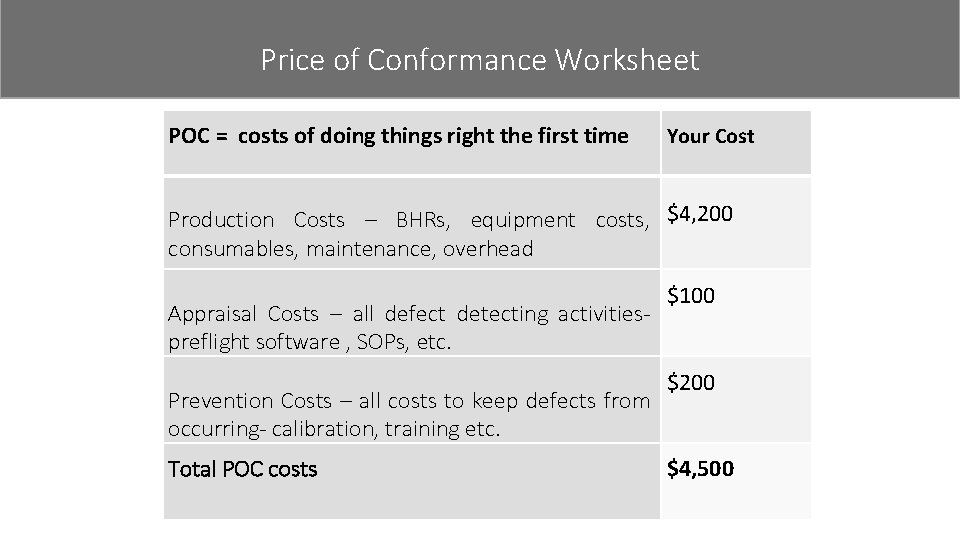
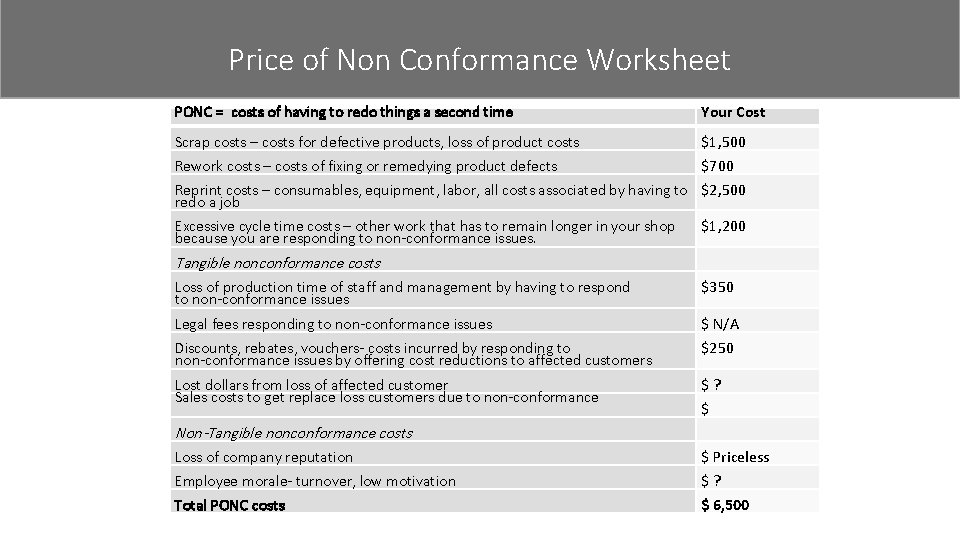
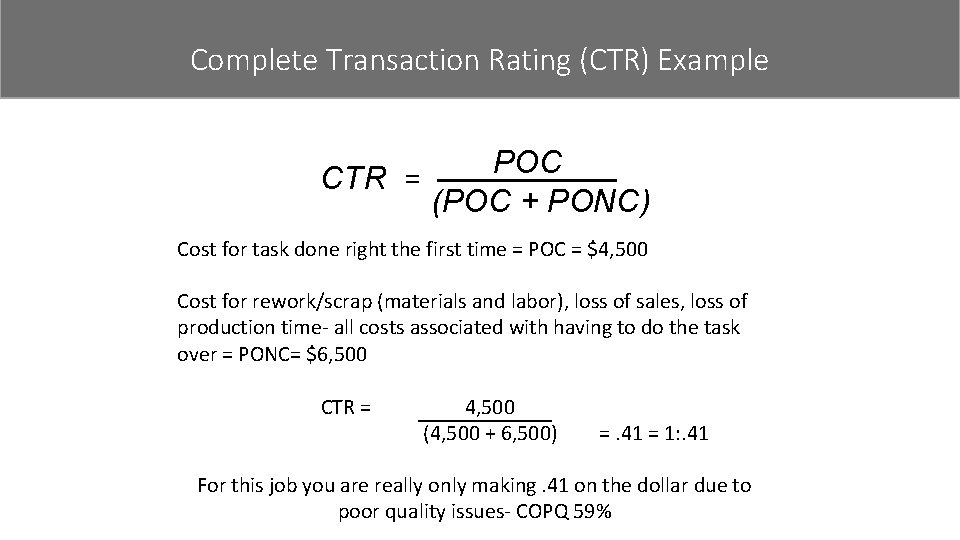
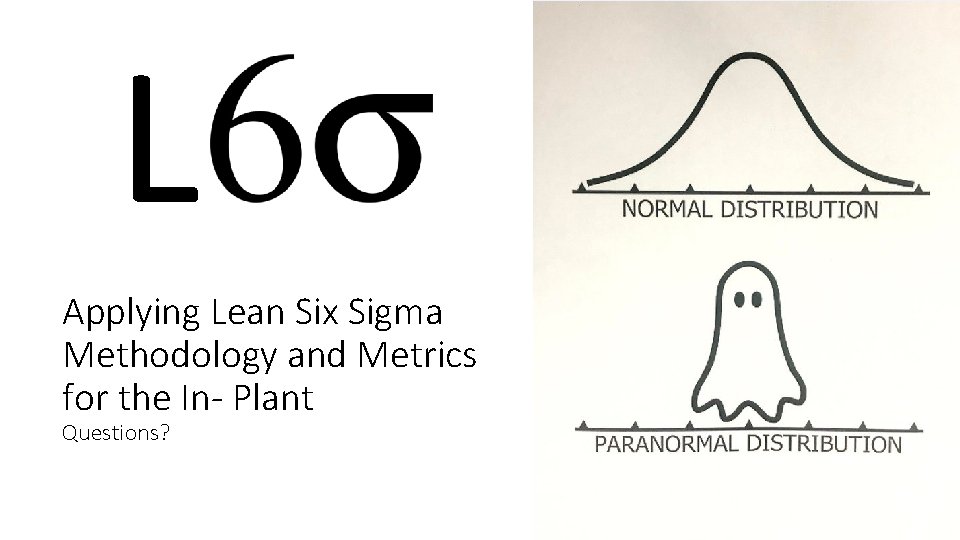
- Slides: 33
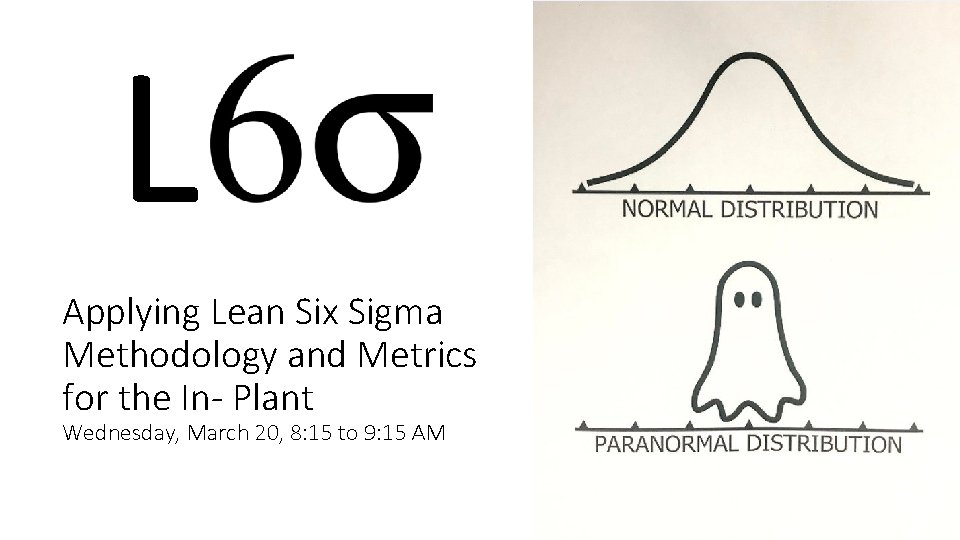
L Applying Lean Six Sigma Methodology and Metrics for the In- Plant Wednesday, March 20, 8: 15 to 9: 15 AM
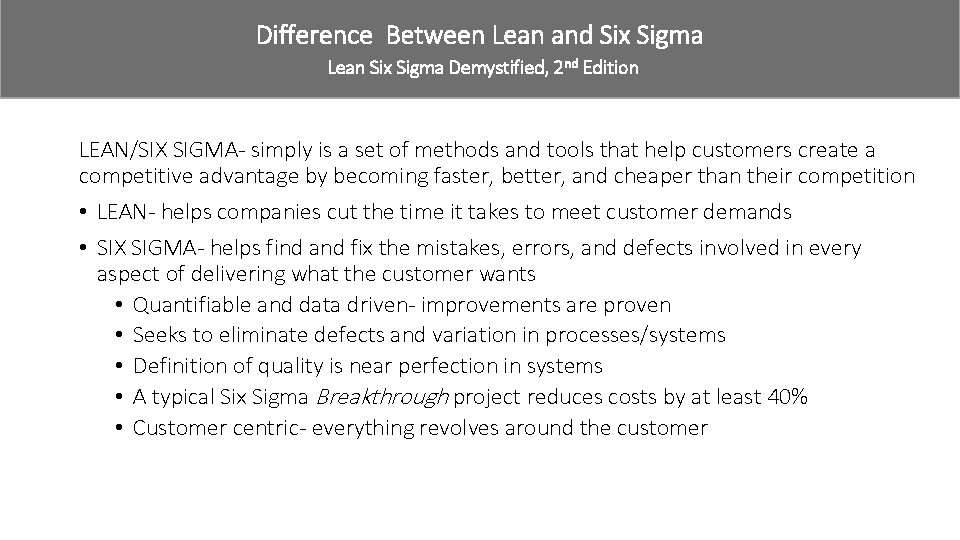
Difference Between Lean and Six Sigma Lean Six Sigma Demystified, 2 nd Edition LEAN/SIX SIGMA- simply is a set of methods and tools that help customers create a competitive advantage by becoming faster, better, and cheaper than their competition • LEAN- helps companies cut the time it takes to meet customer demands • SIX SIGMA- helps find and fix the mistakes, errors, and defects involved in every aspect of delivering what the customer wants • Quantifiable and data driven- improvements are proven • Seeks to eliminate defects and variation in processes/systems • Definition of quality is near perfection in systems • A typical Six Sigma Breakthrough project reduces costs by at least 40% • Customer centric- everything revolves around the customer
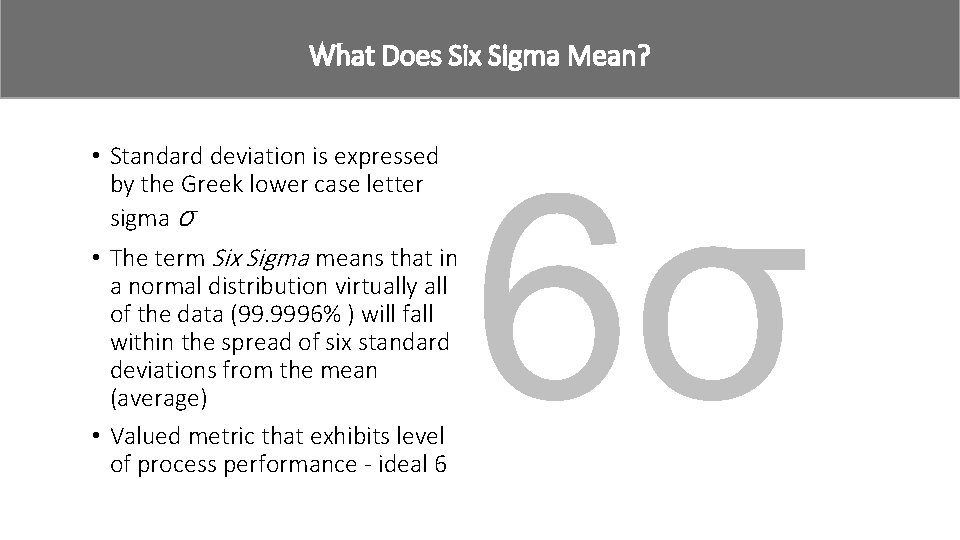
why strive for What Does Six Sigma Mean? six sigma? • Standard deviation is expressed by the Greek lower case letter sigma σ • The term Six Sigma means that in a normal distribution virtually all of the data (99. 9996% ) will fall within the spread of six standard deviations from the mean (average) • Valued metric that exhibits level of process performance - ideal 6 6σ
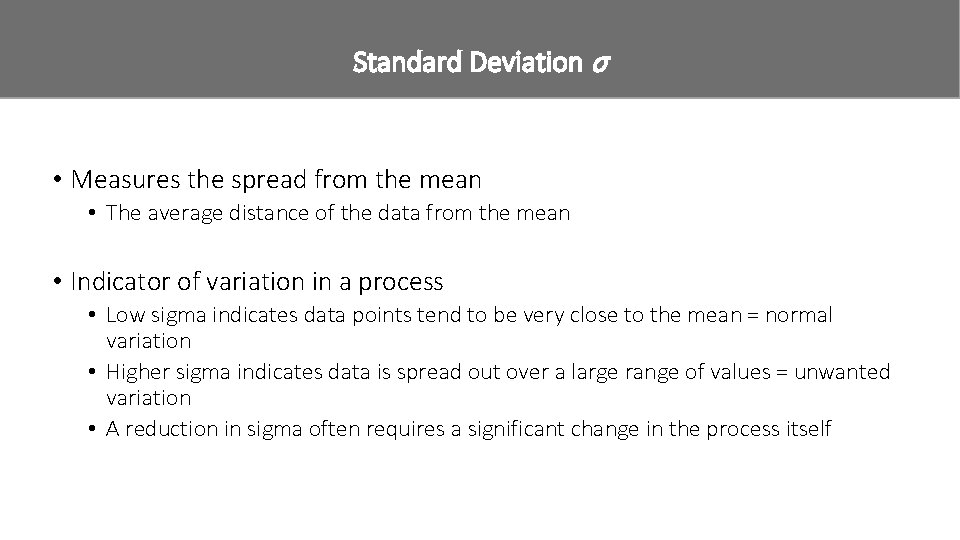
Standard Deviation σ • Measures the spread from the mean • The average distance of the data from the mean • Indicator of variation in a process • Low sigma indicates data points tend to be very close to the mean = normal variation • Higher sigma indicates data is spread out over a large range of values = unwanted variation • A reduction in sigma often requires a significant change in the process itself
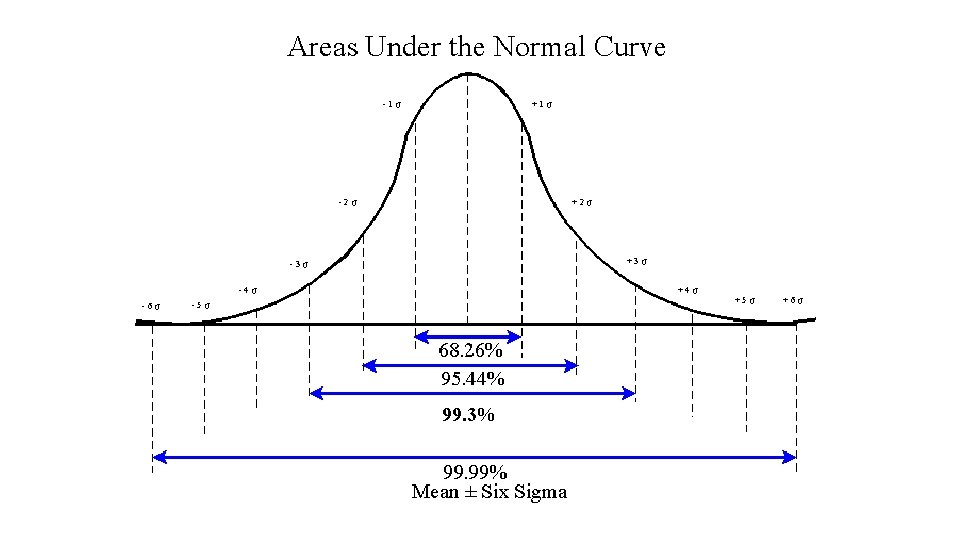
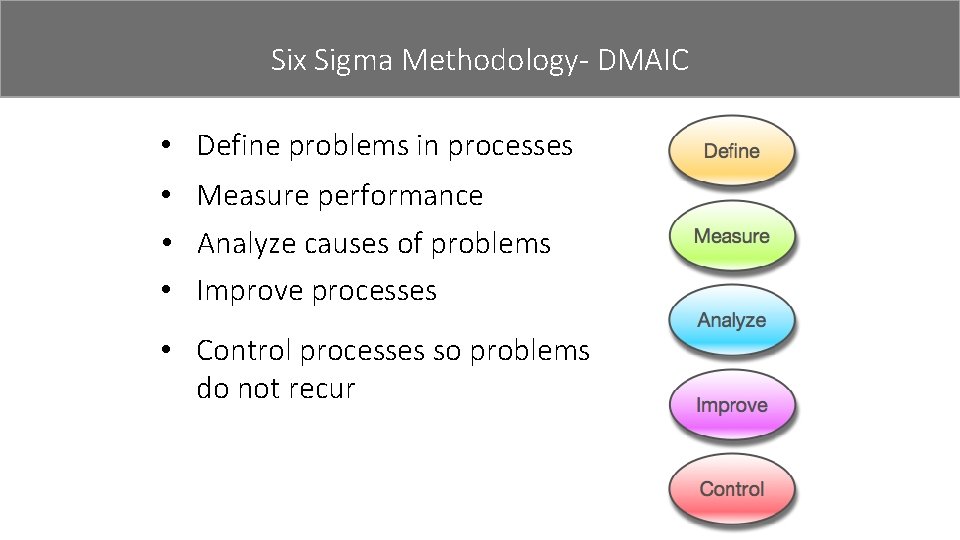
Six Sigma Methodology- DMAIC • Define problems in processes • Measure performance • Analyze causes of problems • Improve processes • Control processes so problems do not recur
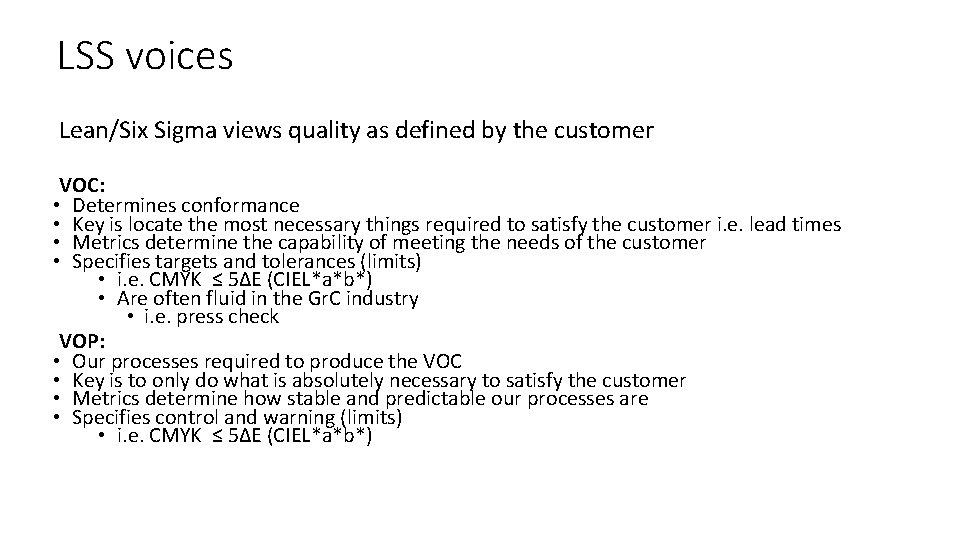
LSS voices • Lean/Six Sigma views quality as defined by the customer • VOC: • Determines conformance • Key is locate the most necessary things required to satisfy the customer i. e. lead times • Metrics determine the capability of meeting the needs of the customer • Specifies targets and tolerances (limits) • i. e. CMYK ≤ 5∆E (CIEL*a*b*) • Are often fluid in the Gr. C industry • i. e. press check • VOP: • Our processes required to produce the VOC • Key is to only do what is absolutely necessary to satisfy the customer • Metrics determine how stable and predictable our processes are • Specifies control and warning (limits) • i. e. CMYK ≤ 5∆E (CIEL*a*b*)
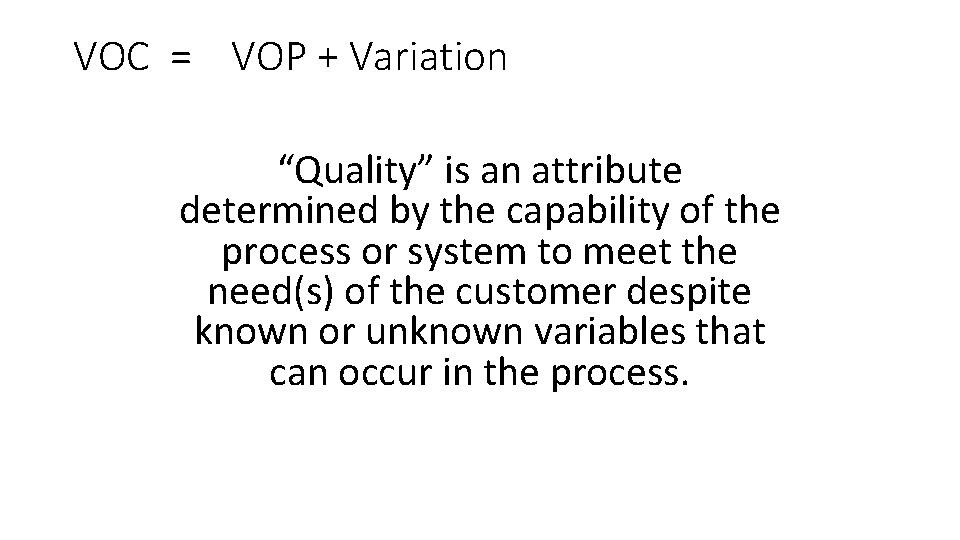
VOC = VOP + Variation “Quality” is an attribute determined by the capability of the process or system to meet the need(s) of the customer despite known or unknown variables that can occur in the process.
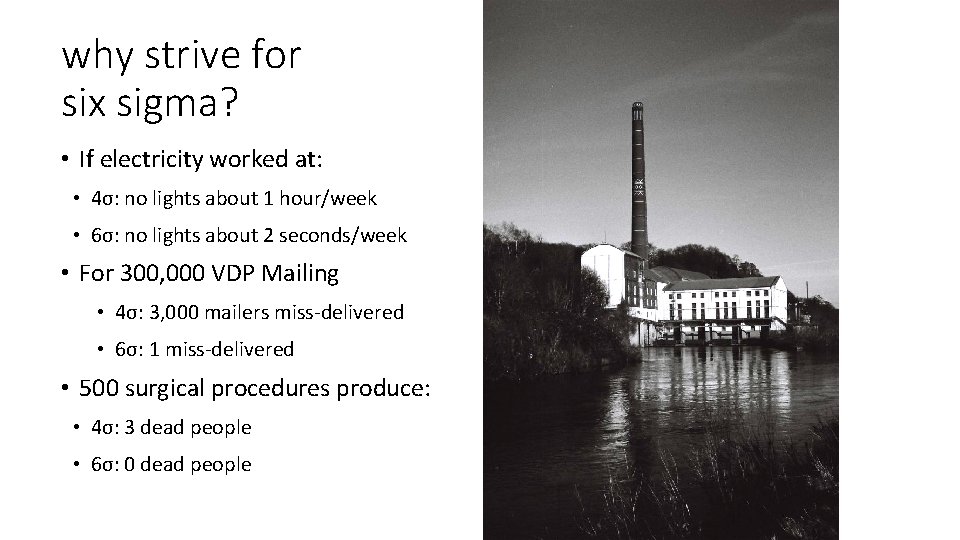
why strive for six sigma? • If electricity worked at: • 4σ: no lights about 1 hour/week • 6σ: no lights about 2 seconds/week • For 300, 000 VDP Mailing • 4σ: 3, 000 mailers miss-delivered • 6σ: 1 miss-delivered • 500 surgical procedures produce: • 4σ: 3 dead people • 6σ: 0 dead people
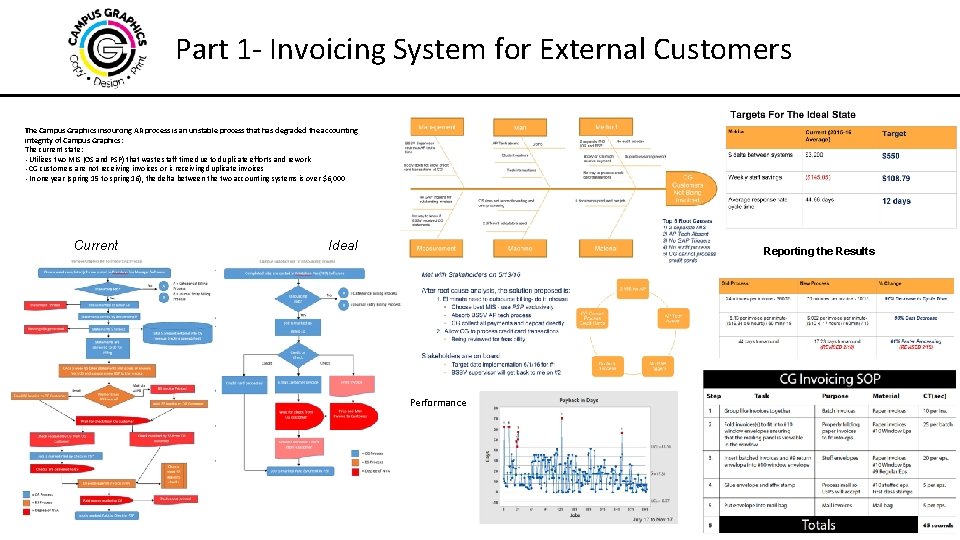
Part 1 - Invoicing System for External Customers The Campus Graphics insourcing AR process is an unstable process that has degraded the accounting integrity of Campus Graphics: The current state: · Utilizes two MIS (OS and PSP) that waste staff time due to duplicate efforts and rework · CG customers are not receiving invoices or is receiving duplicate invoices · In one year (spring 15 to spring 16), the delta between the two accounting systems is over $6, 000 Current Ideal Reporting the Results Performance
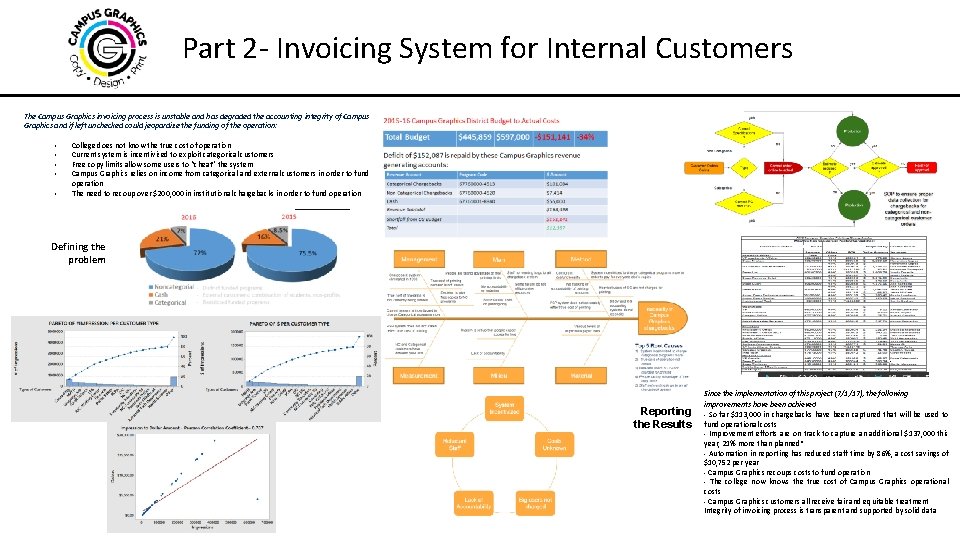
Part 2 - Invoicing System for Internal Customers The Campus Graphics invoicing process is unstable and has degraded the accounting integrity of Campus Graphics and if left unchecked could jeopardize the funding of the operation: • • • College does not know the true cost of operation Current system is incentivized to exploit categorical customers Free copy limits allow some users to “cheat” the system Campus Graphics relies on income from categorical and external customers in order to fund operation The need to recoup over $200, 000 in institutional chargebacks in order to fund operation Defining the problem Reporting the Results Since the implementation of this project (7/1/17), the following improvements have been achieved - So far $113, 000 in chargebacks have been captured that will be used to fund operational costs - Improvement efforts are on track to capture an additional $137, 000 this year, 21% more than planned* - Automation in reporting has reduced staff time by 86%, a cost savings of $10, 752 per year - Campus Graphics recoups costs to fund operation - The college now knows the true cost of Campus Graphics operational costs - Campus Graphics customers all receive fair and equitable treatment Integrity of invoicing process is transparent and supported by solid data
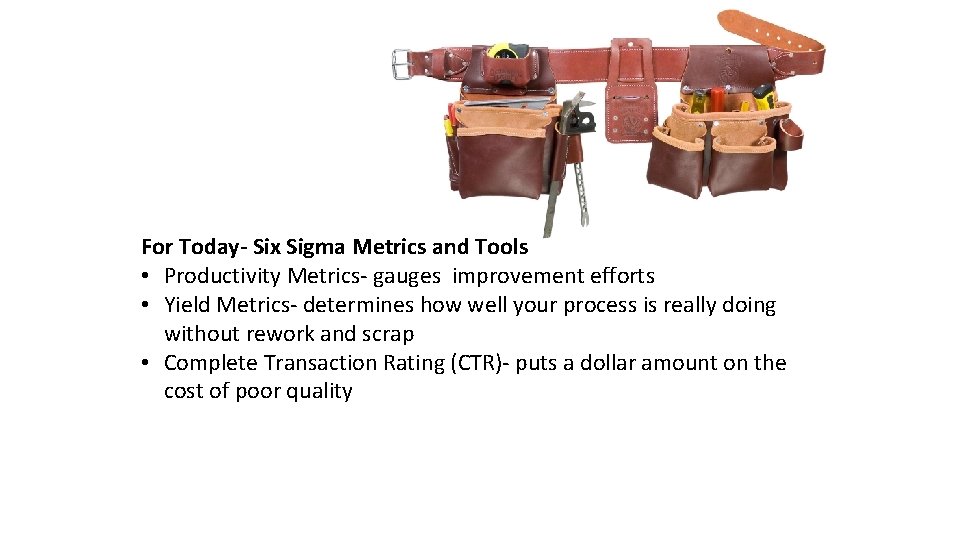
Six Sigma Tool Belt For Today- Six Sigma Metrics and Tools • Productivity Metrics- gauges improvement efforts • Yield Metrics- determines how well your process is really doing without rework and scrap • Complete Transaction Rating (CTR)- puts a dollar amount on the cost of poor quality
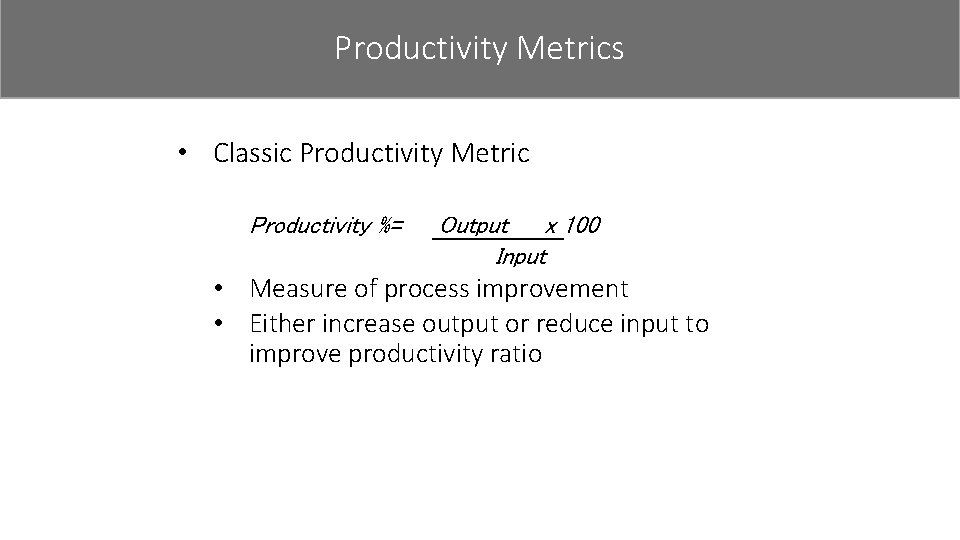
Productivity Metrics • Classic Productivity Metric Productivity %= Output x 100 Input • Measure of process improvement • Either increase output or reduce input to improve productivity ratio
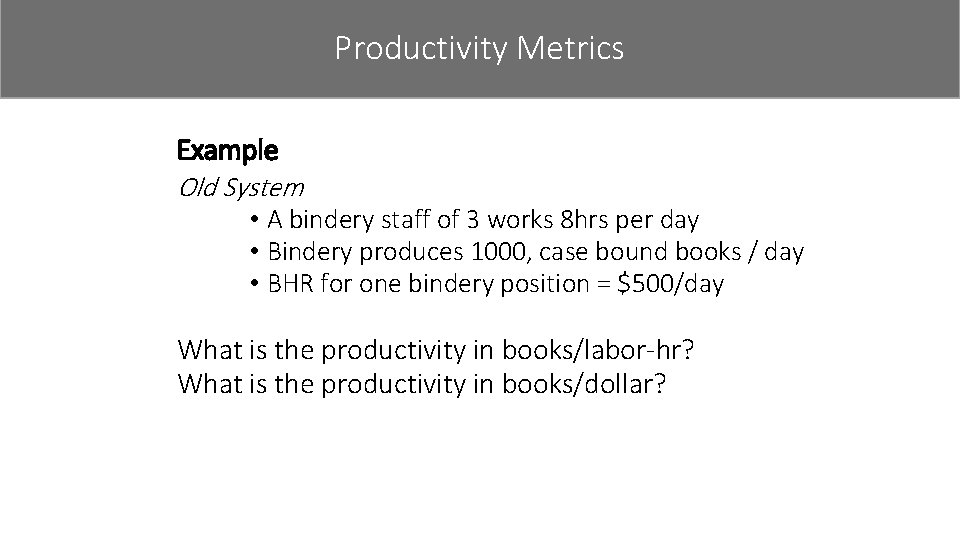
Productivity Metrics Example Old System • A bindery staff of 3 works 8 hrs per day • Bindery produces 1000, case bound books / day • BHR for one bindery position = $500/day What is the productivity in books/labor-hr? What is the productivity in books/dollar?
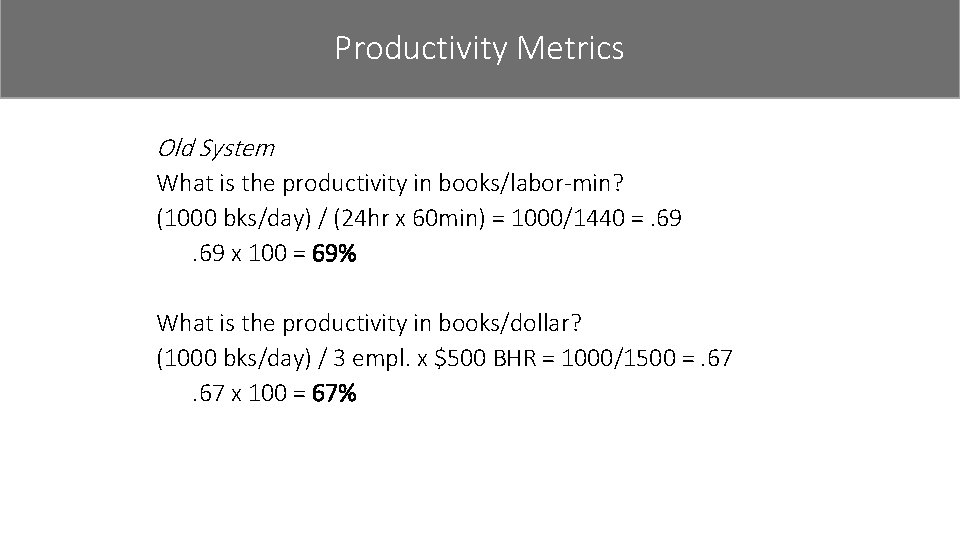
Productivity Metrics Old System What is the productivity in books/labor-min? (1000 bks/day) / (24 hr x 60 min) = 1000/1440 =. 69 x 100 = 69% What is the productivity in books/dollar? (1000 bks/day) / 3 empl. x $500 BHR = 1000/1500 =. 67 x 100 = 67%
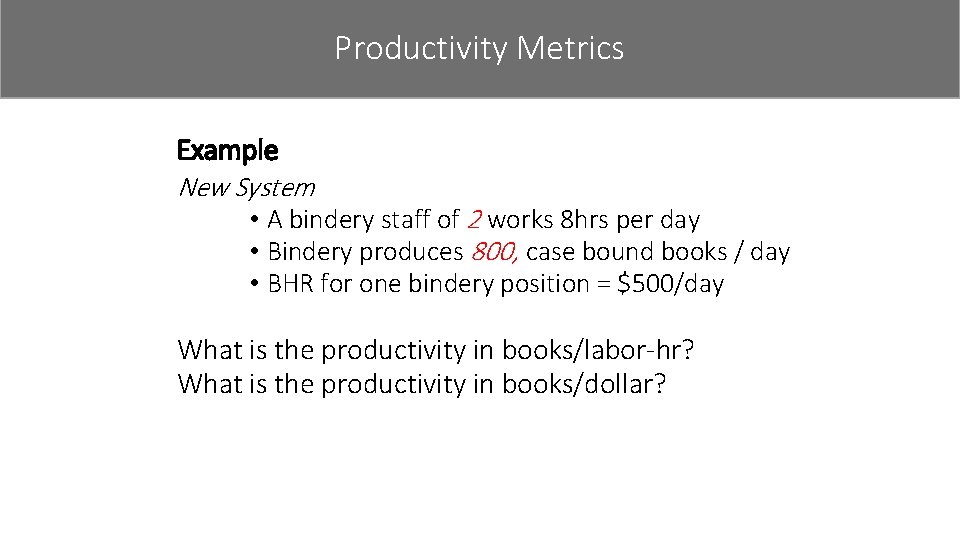
Productivity Metrics Example New System • A bindery staff of 2 works 8 hrs per day • Bindery produces 800, case bound books / day • BHR for one bindery position = $500/day What is the productivity in books/labor-hr? What is the productivity in books/dollar?
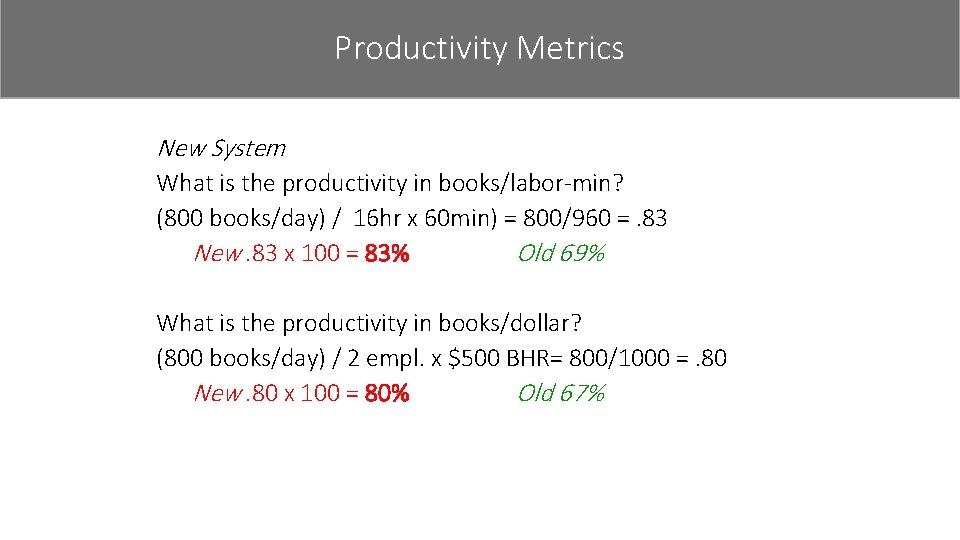
Productivity Metrics New System What is the productivity in books/labor-min? (800 books/day) / 16 hr x 60 min) = 800/960 =. 83 New. 83 x 100 = 83% Old 69% What is the productivity in books/dollar? (800 books/day) / 2 empl. x $500 BHR= 800/1000 =. 80 New. 80 x 100 = 80% Old 67%
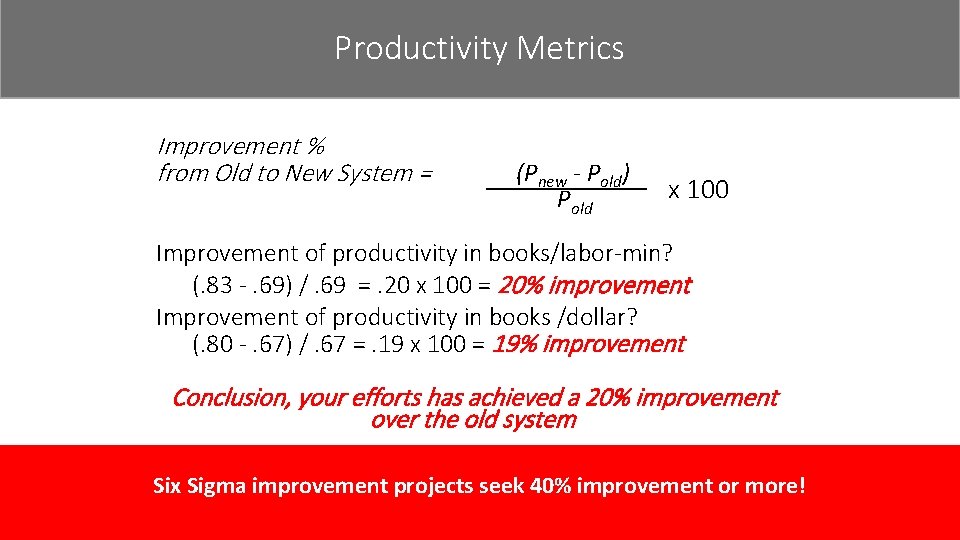
Productivity Metrics Improvement % from Old to New System = (Pnew - Pold) Pold x 100 Improvement of productivity in books/labor-min? (. 83 -. 69) /. 69 =. 20 x 100 = 20% improvement Improvement of productivity in books /dollar? (. 80 -. 67) /. 67 =. 19 x 100 = 19% improvement Conclusion, your efforts has achieved a 20% improvement over the old system Six Sigma improvement projects seek 40% improvement or more!
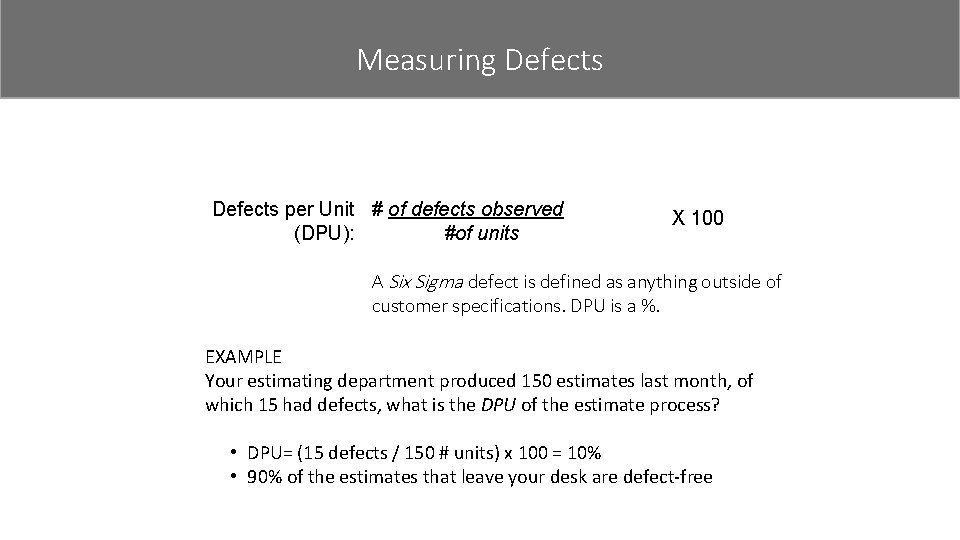
Measuring Defects measure defects Defects per Unit # of defects observed (DPU): #of units X 100 A Six Sigma defect is defined as anything outside of customer specifications. DPU is a %. EXAMPLE Your estimating department produced 150 estimates last month, of which 15 had defects, what is the DPU of the estimate process? • DPU= (15 defects / 150 # units) x 100 = 10% • 90% of the estimates that leave your desk are defect-free
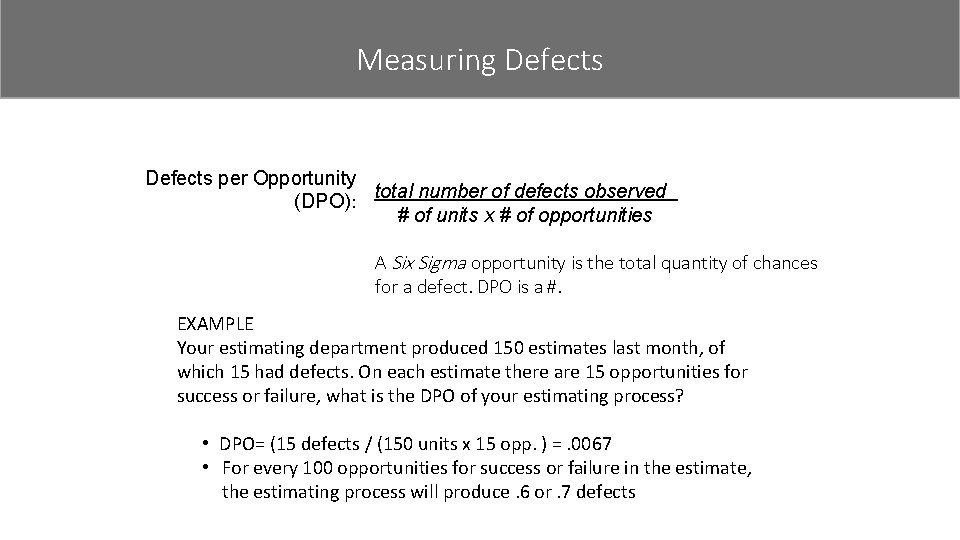
Measuring Defects measure defects Defects per Opportunity total number of defects observed (DPO): # of units x # of opportunities A Six Sigma opportunity is the total quantity of chances for a defect. DPO is a #. EXAMPLE Your estimating department produced 150 estimates last month, of which 15 had defects. On each estimate there are 15 opportunities for success or failure, what is the DPO of your estimating process? • DPO= (15 defects / (150 units x 15 opp. ) =. 0067 • For every 100 opportunities for success or failure in the estimate, the estimating process will produce. 6 or. 7 defects
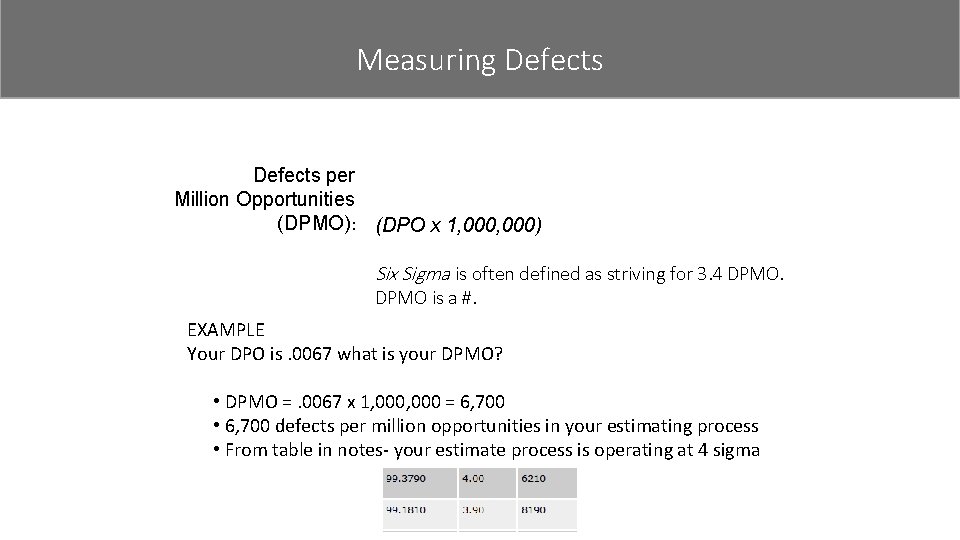
Measuring Defects measure defects Defects per Million Opportunities (DPMO): (DPO x 1, 000) Six Sigma is often defined as striving for 3. 4 DPMO is a #. EXAMPLE Your DPO is. 0067 what is your DPMO? • DPMO =. 0067 x 1, 000 = 6, 700 • 6, 700 defects per million opportunities in your estimating process • From table in notes- your estimate process is operating at 4 sigma
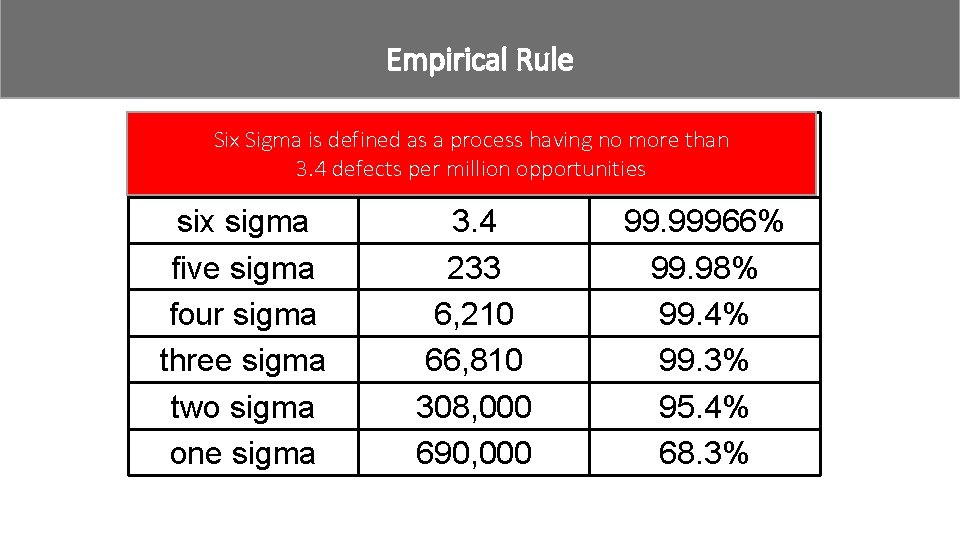
Empirical Rule per Six Sigma is defineddefects as a process having no moreyield than sigma 3. 4 defects per million opportunities million percentage six sigma five sigma four sigma three sigma two sigma one sigma 3. 4 233 6, 210 66, 810 308, 000 690, 000 99. 99966% 99. 98% 99. 4% 99. 3% 95. 4% 68. 3%
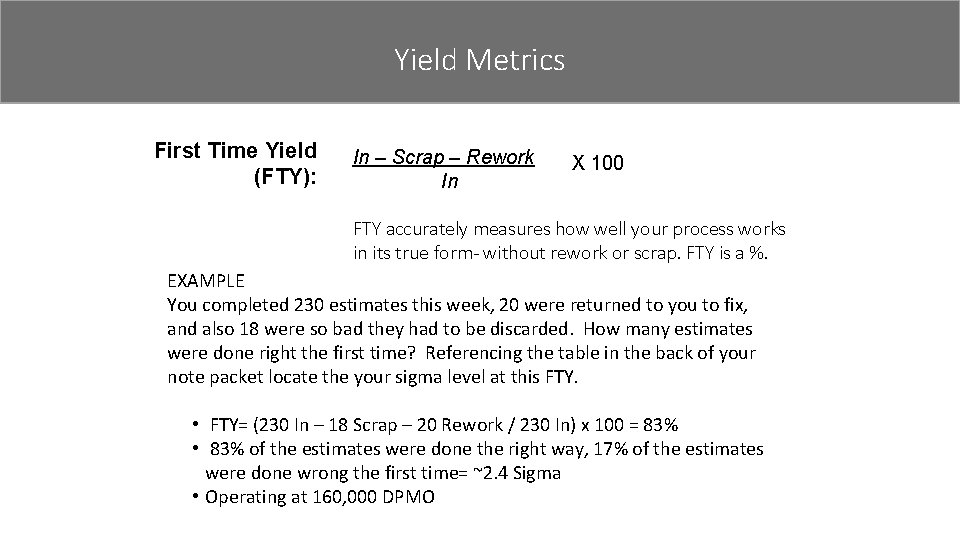
Yield Metrics First Time Yield (FTY): In – Scrap – Rework In X 100 FTY accurately measures how well your process works in its true form- without rework or scrap. FTY is a %. EXAMPLE You completed 230 estimates this week, 20 were returned to you to fix, and also 18 were so bad they had to be discarded. How many estimates were done right the first time? Referencing the table in the back of your note packet locate the your sigma level at this FTY. • FTY= (230 In – 18 Scrap – 20 Rework / 230 In) x 100 = 83% • 83% of the estimates were done the right way, 17% of the estimates were done wrong the first time= ~2. 4 Sigma • Operating at 160, 000 DPMO
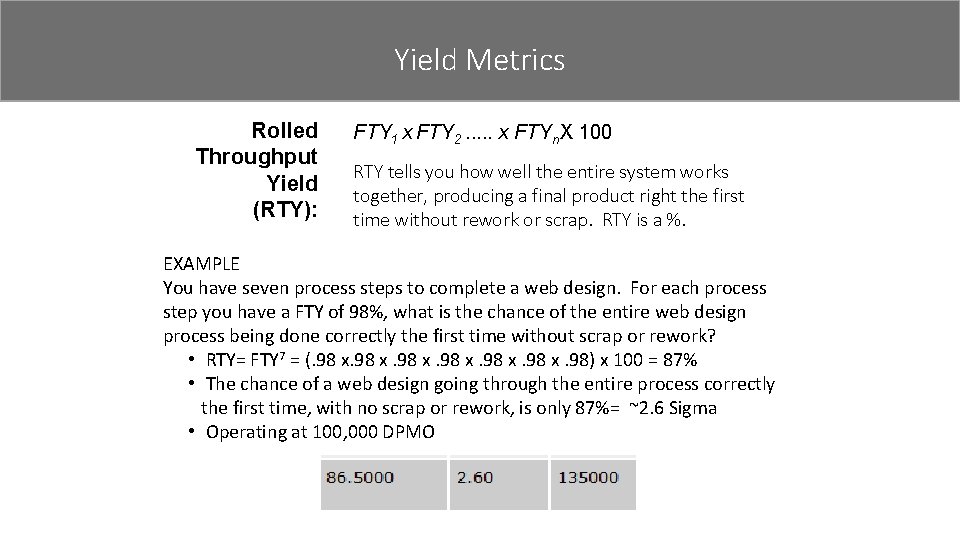
Yield Metrics Rolled Throughput Yield (RTY): FTY 1 x FTY 2. . . x FTYn X 100 RTY tells you how well the entire system works together, producing a final product right the first time without rework or scrap. RTY is a %. EXAMPLE You have seven process steps to complete a web design. For each process step you have a FTY of 98%, what is the chance of the entire web design process being done correctly the first time without scrap or rework? • RTY= FTY 7 = (. 98 x. 98) x 100 = 87% • The chance of a web design going through the entire process correctly the first time, with no scrap or rework, is only 87%= ~2. 6 Sigma • Operating at 100, 000 DPMO
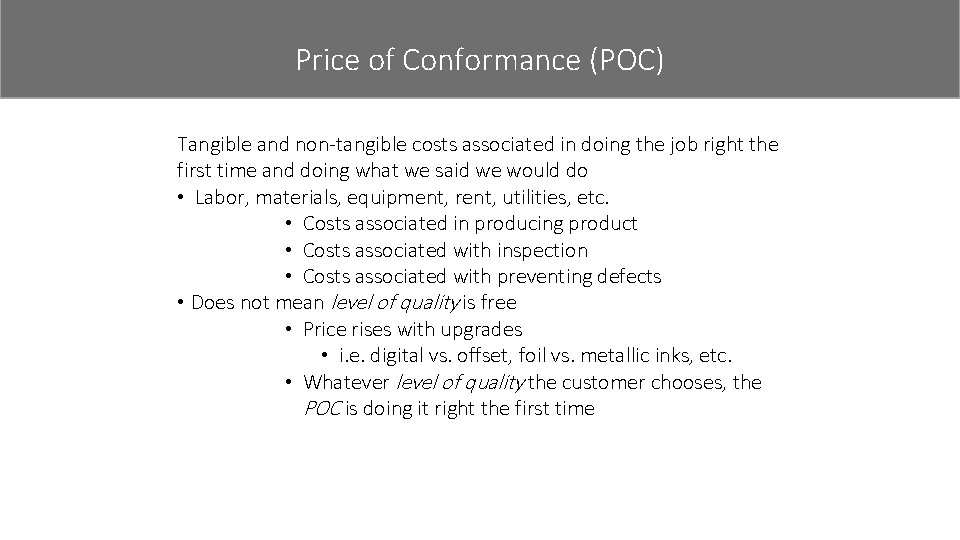
Price of Conformance (POC) Tangible and non-tangible costs associated in doing the job right the first time and doing what we said we would do • Labor, materials, equipment, rent, utilities, etc. • Costs associated in producing product • Costs associated with inspection • Costs associated with preventing defects • Does not mean level of quality is free • Price rises with upgrades • i. e. digital vs. offset, foil vs. metallic inks, etc. • Whatever level of quality the customer chooses, the POC is doing it right the first time
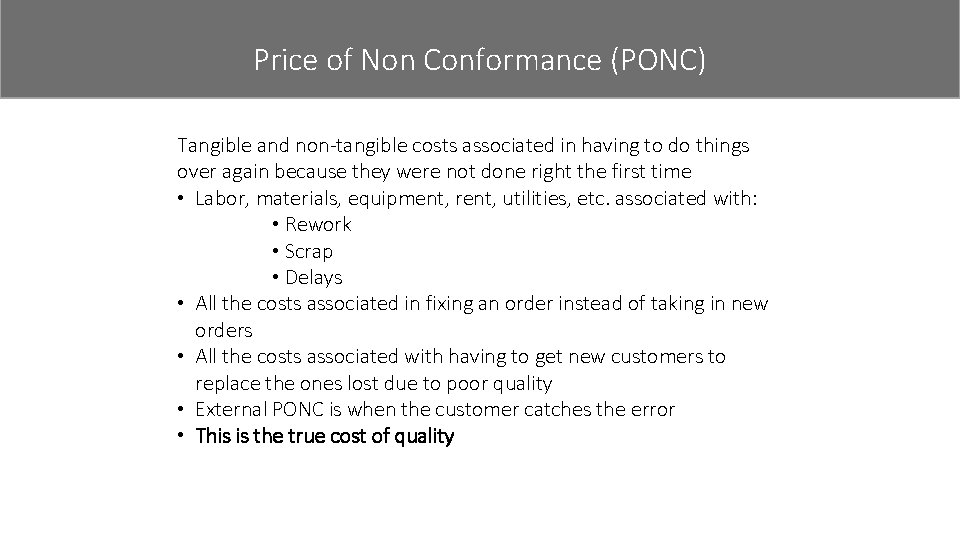
Price of Non Conformance (PONC) Tangible and non-tangible costs associated in having to do things over again because they were not done right the first time • Labor, materials, equipment, rent, utilities, etc. associated with: • Rework • Scrap • Delays • All the costs associated in fixing an order instead of taking in new orders • All the costs associated with having to get new customers to replace the ones lost due to poor quality • External PONC is when the customer catches the error • This is the true cost of quality
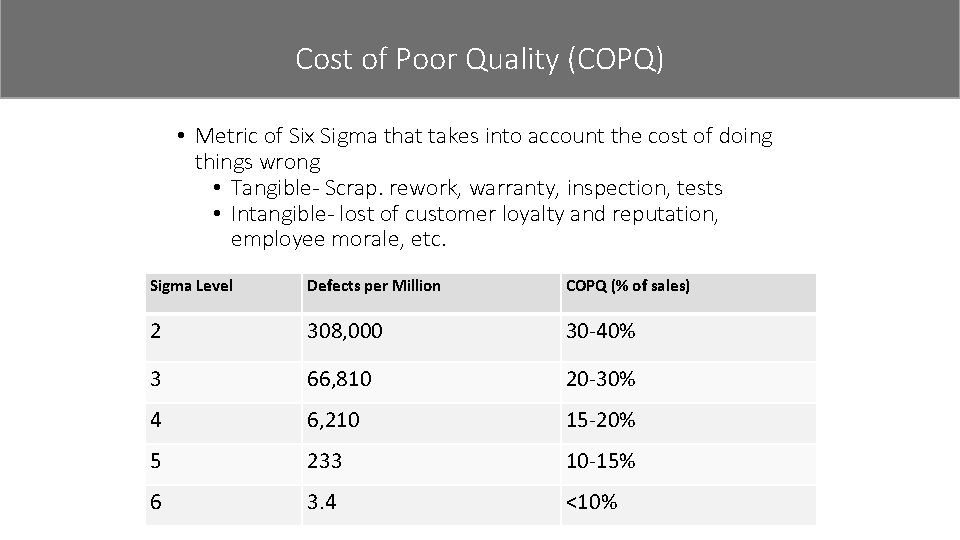
Cost of Poor Quality (COPQ) • Metric of Six Sigma that takes into account the cost of doing things wrong • Tangible- Scrap. rework, warranty, inspection, tests • Intangible- lost of customer loyalty and reputation, employee morale, etc. Sigma Level Defects per Million COPQ (% of sales) 2 308, 000 30 -40% 3 66, 810 20 -30% 4 6, 210 15 -20% 5 233 10 -15% 6 3. 4 <10%
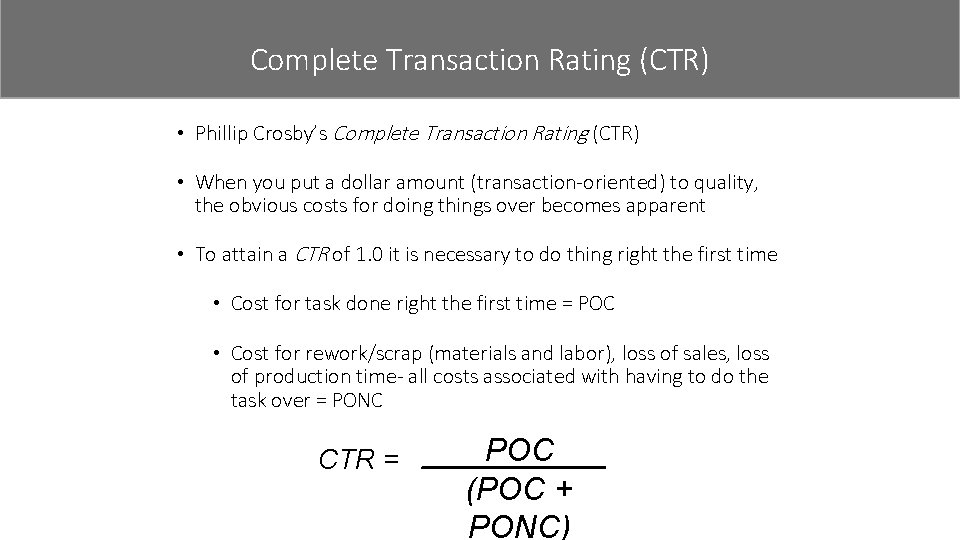
Complete Transaction Rating (CTR) • Phillip Crosby’s Complete Transaction Rating (CTR) • When you put a dollar amount (transaction-oriented) to quality, the obvious costs for doing things over becomes apparent • To attain a CTR of 1. 0 it is necessary to do thing right the first time • Cost for task done right the first time = POC • Cost for rework/scrap (materials and labor), loss of sales, loss of production time- all costs associated with having to do the task over = PONC CTR = POC (POC + PONC)
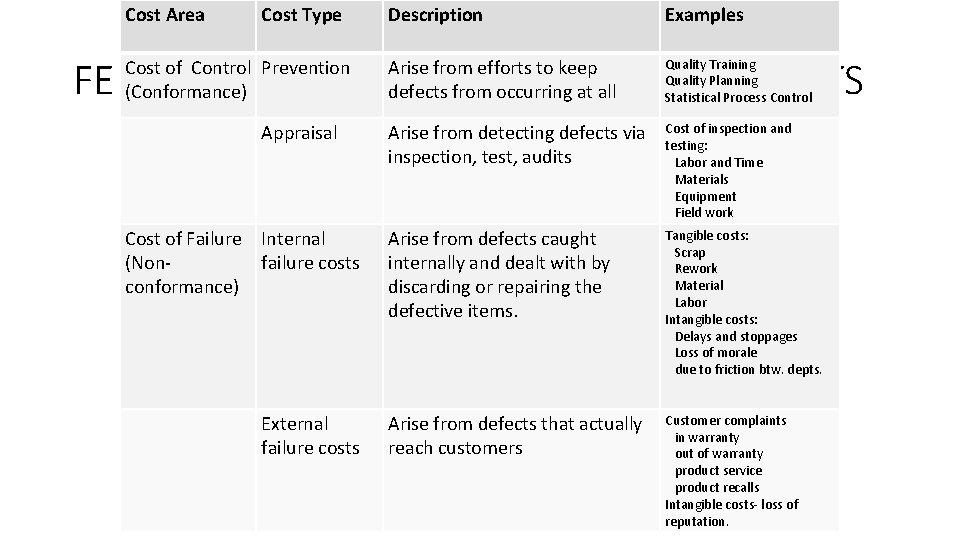
Cost Area Cost Type Description Examples FEIGENBAUM - QUANTIFING QUALITY COSTS Cost of Control Prevention (Conformance) Appraisal Cost of Failure Internal (Nonfailure costs conformance) External failure costs Arise from efforts to keep defects from occurring at all Quality Training Quality Planning Statistical Process Control Arise from detecting defects via inspection, test, audits Cost of inspection and testing: Labor and Time Materials Equipment Field work Arise from defects caught internally and dealt with by discarding or repairing the defective items. Tangible costs: Scrap Rework Material Labor Intangible costs: Delays and stoppages Loss of morale due to friction btw. depts. Arise from defects that actually reach customers Customer complaints in warranty out of warranty product service product recalls Intangible costs- loss of reputation.
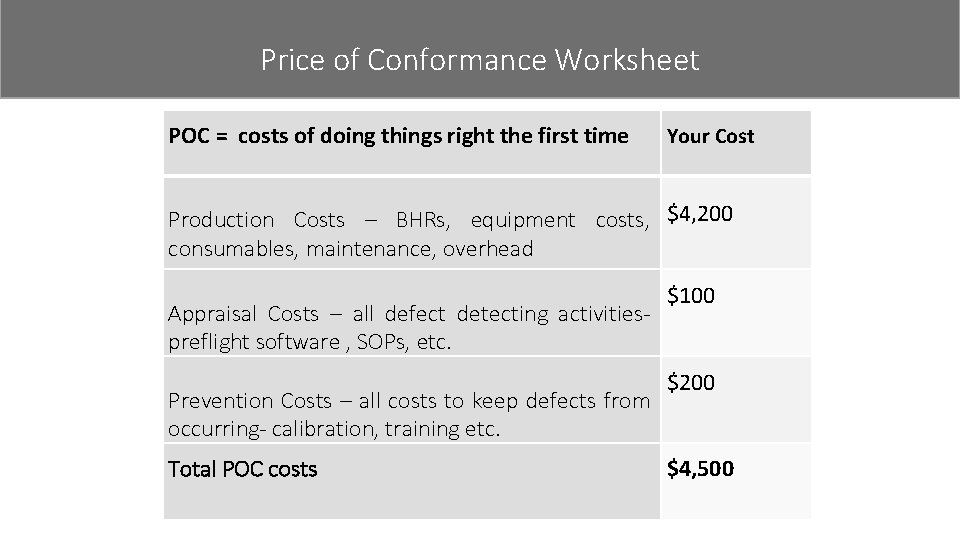
Price of Conformance Worksheet Figure 10 - POC and PONC worksheet POC = costs of doing things right the first time Your Cost Production Costs – BHRs, equipment costs, $4, 200 consumables, maintenance, overhead Appraisal Costs – all defect detecting activitiespreflight software , SOPs, etc. Prevention Costs – all costs to keep defects from occurring- calibration, training etc. Total POC costs $100 $200 $4, 500
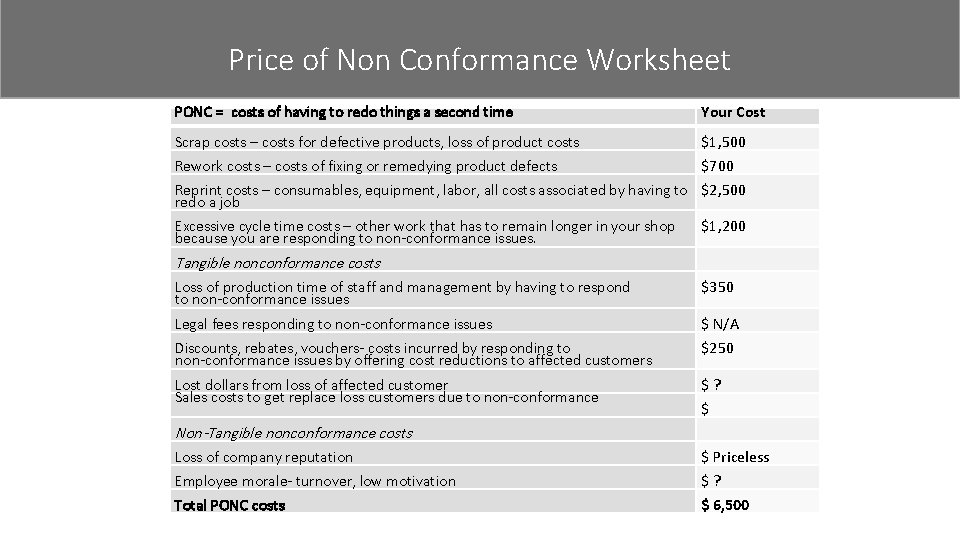
Price of Non Conformance Worksheet Figure 10 - POC and PONC worksheet PONC = costs of having to redo things a second time Your Cost Scrap costs – costs for defective products, loss of product costs Rework costs – costs of fixing or remedying product defects Reprint costs – consumables, equipment, labor, all costs associated by having to redo a job Excessive cycle time costs – other work that has to remain longer in your shop because you are responding to non-conformance issues. $1, 500 $700 $2, 500 $1, 200 Tangible nonconformance costs Loss of production time of staff and management by having to respond to non-conformance issues $350 Legal fees responding to non-conformance issues Discounts, rebates, vouchers- costs incurred by responding to non-conformance issues by offering cost reductions to affected customers $ N/A $250 Lost dollars from loss of affected customer Sales costs to get replace loss customers due to non-conformance $? $ Non-Tangible nonconformance costs Loss of company reputation Employee morale- turnover, low motivation Total PONC costs $ Priceless $? $ 6, 500
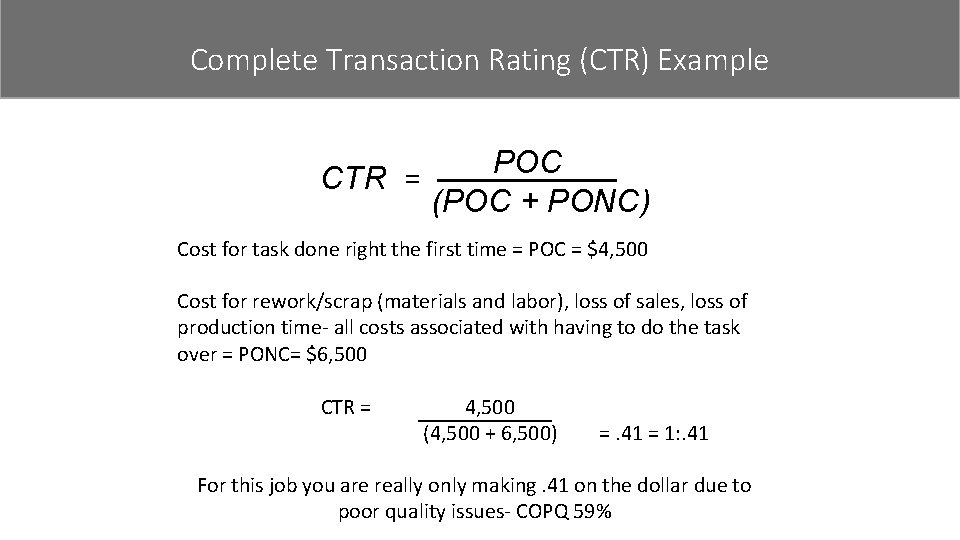
Complete Transaction Rating (CTR) Example POC CTR = (POC + PONC) Cost for task done right the first time = POC = $4, 500 Cost for rework/scrap (materials and labor), loss of sales, loss of production time- all costs associated with having to do the task over = PONC= $6, 500 CTR = 4, 500 (4, 500 + 6, 500) =. 41 = 1: . 41 For this job you are really only making. 41 on the dollar due to poor quality issues- COPQ 59%
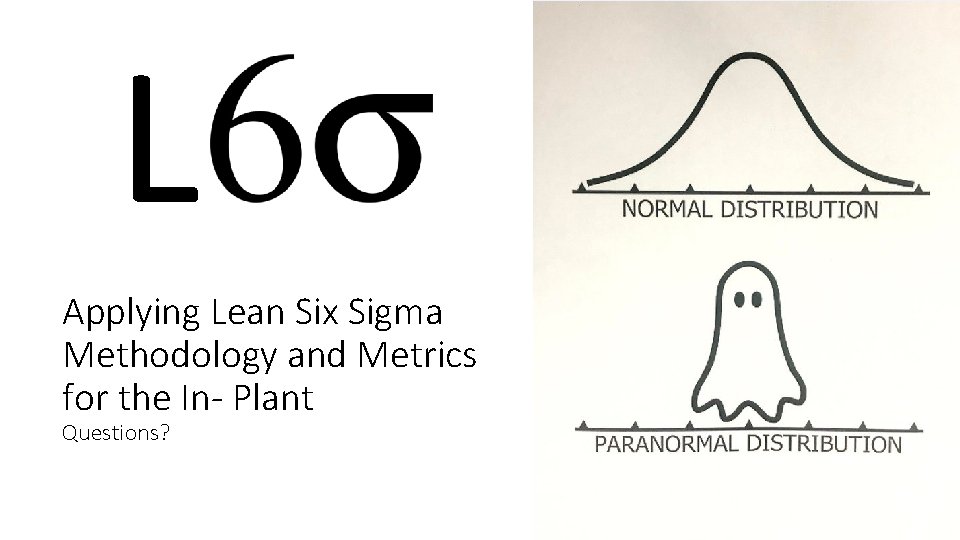
L Applying Lean Six Sigma Methodology and Metrics for the In- Plant Questions?
A socratic approach to lean six sigma
Six sigma forum
Yellow belt dmaic
6 sigma project charter
Human resources six sigma
Navy lean six sigma
Lean six sigma nedir
Sigma simplicity
Formation lean ceinture blanche
Lean six sigma simulation games
Control plan lean six sigma
Six sigma foundations
Project storyboard six sigma
Six sigma foundations download
A key concept of quality control is that all work products
Lean canvas vorlage
Sigma gamma rho march of dimes
Vcom white coat ceremony
Vcom white coat ceremony
Poka yoke
Lean six
Cmmi six sigma
Pilot plan template six sigma
Tollgate definition
Statapult exercise instructions
Six sigma qualtec
Six sigma kpov
Mse six sigma
Six sigma belts hierarchy
Probability symbols cheat sheet
Msa attribute study kappa xls
Six sigma project presentation
Dmaic problem solving
Mse six sigma