Process Mapping SIPOC Six Sigma Foundations Continuous Improvement
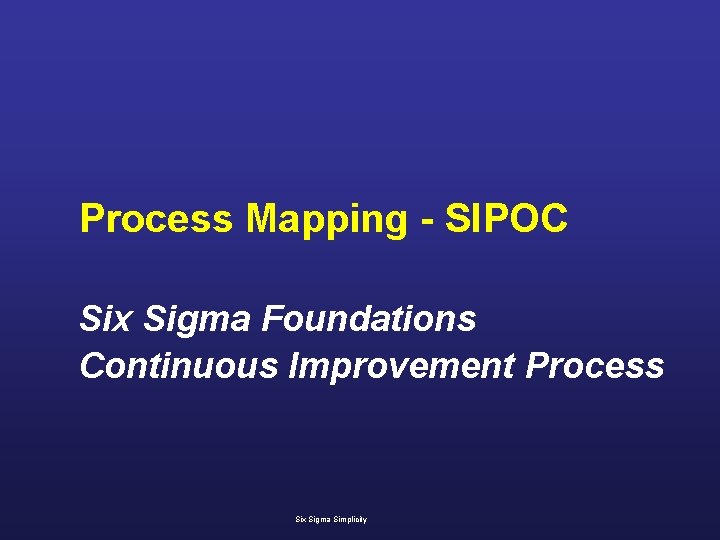
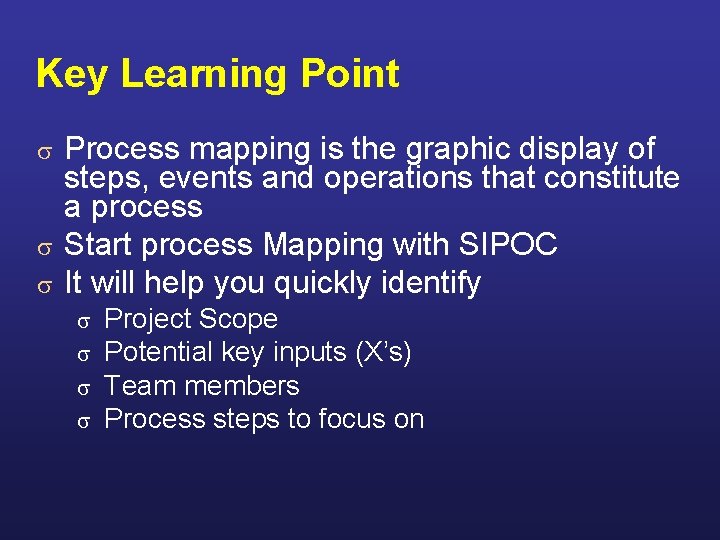
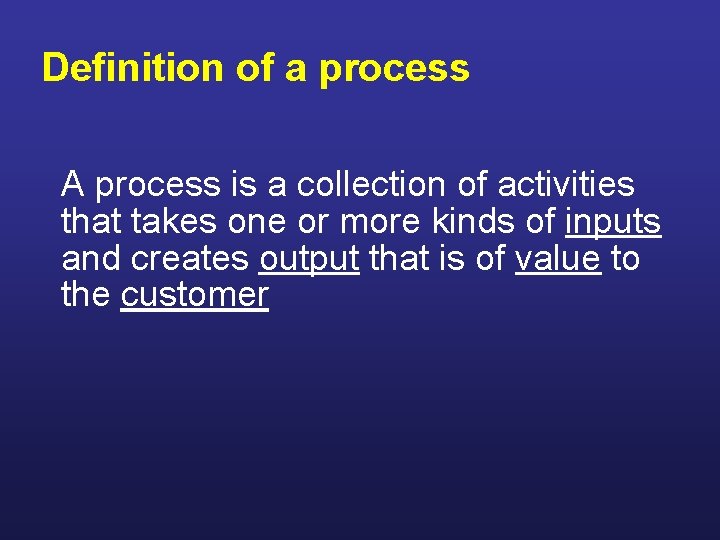
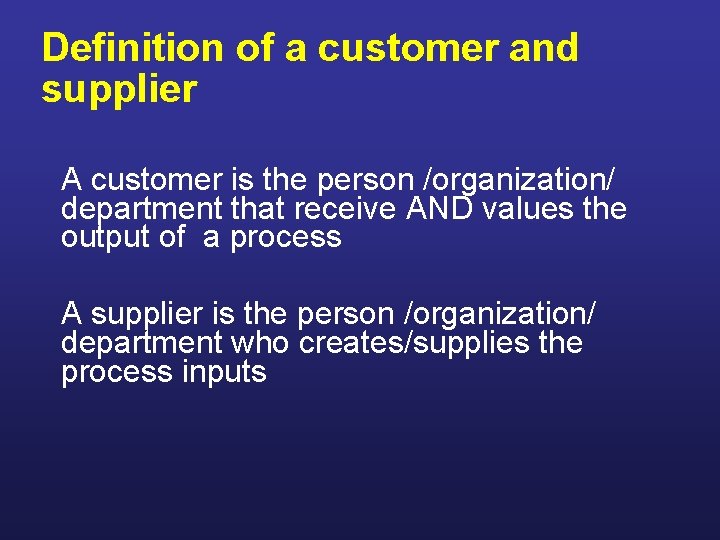
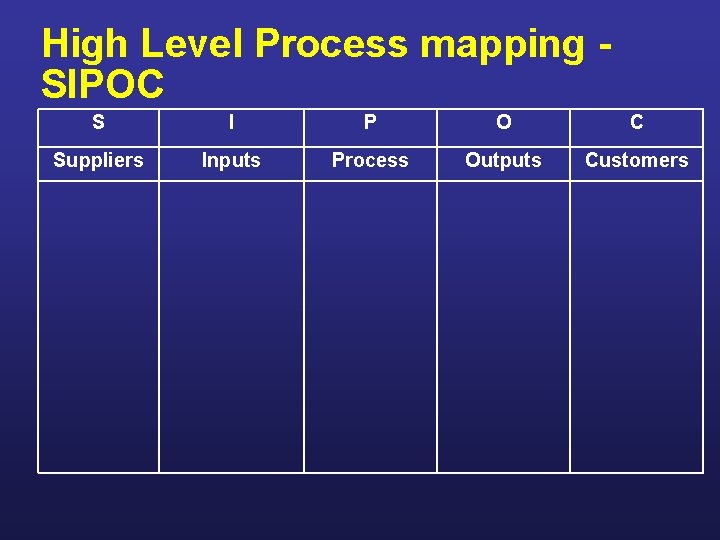
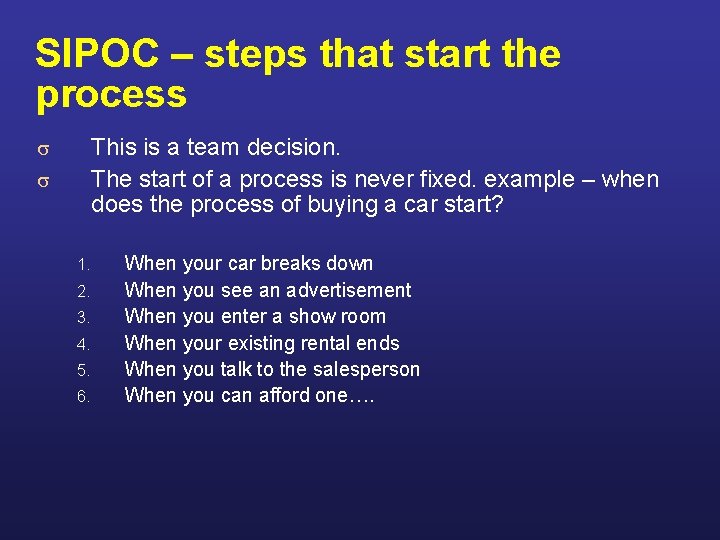
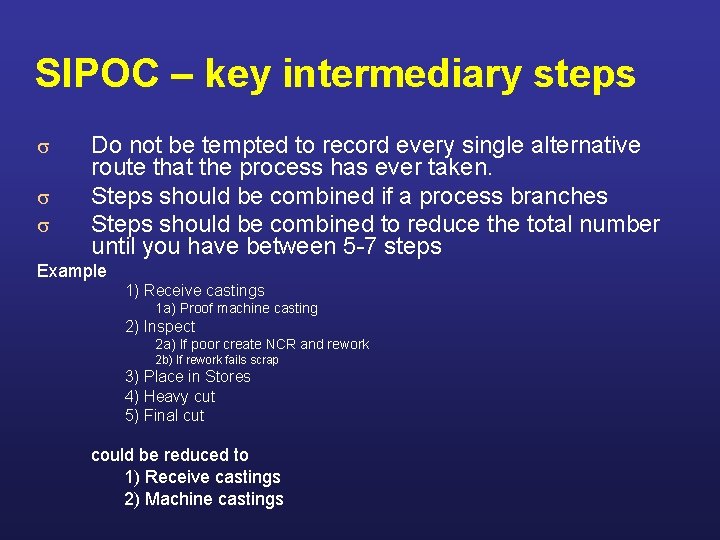
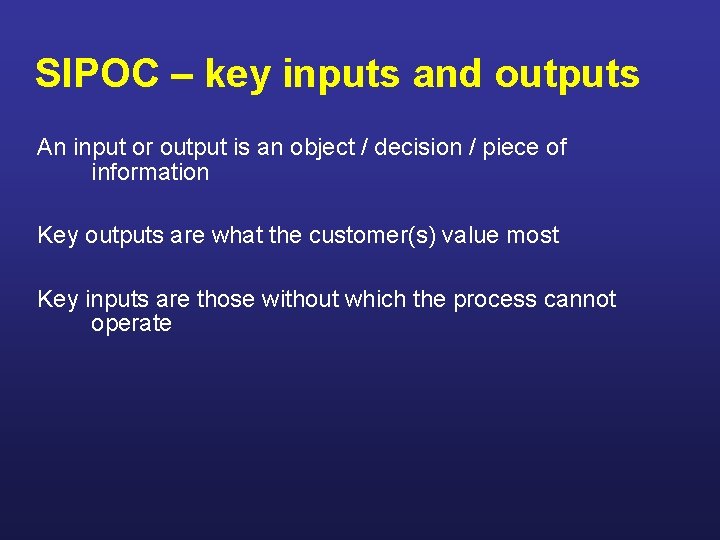
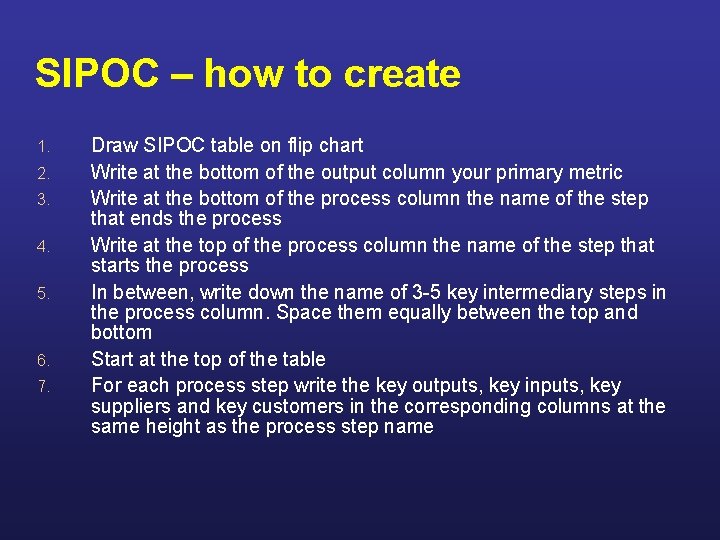
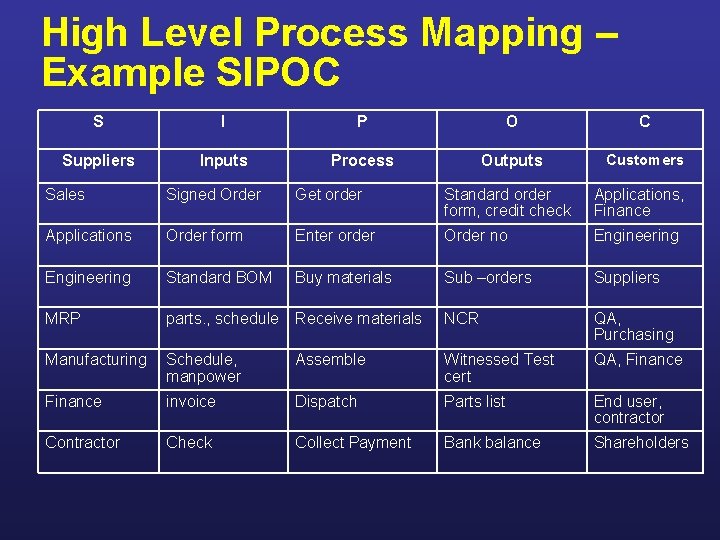
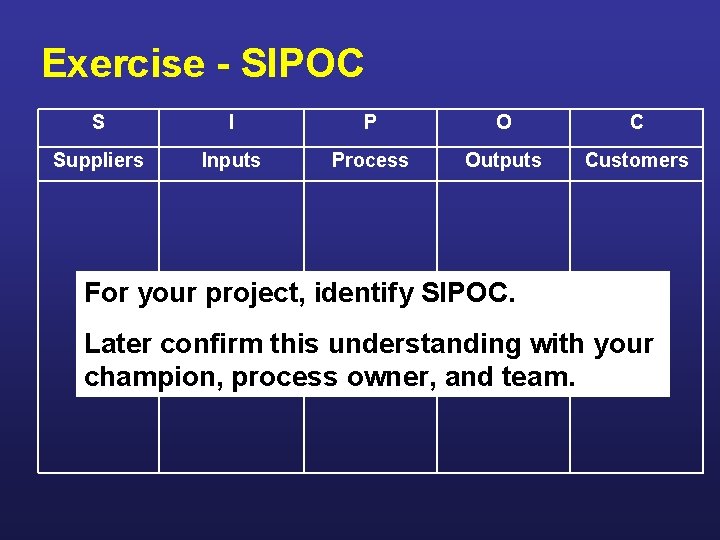
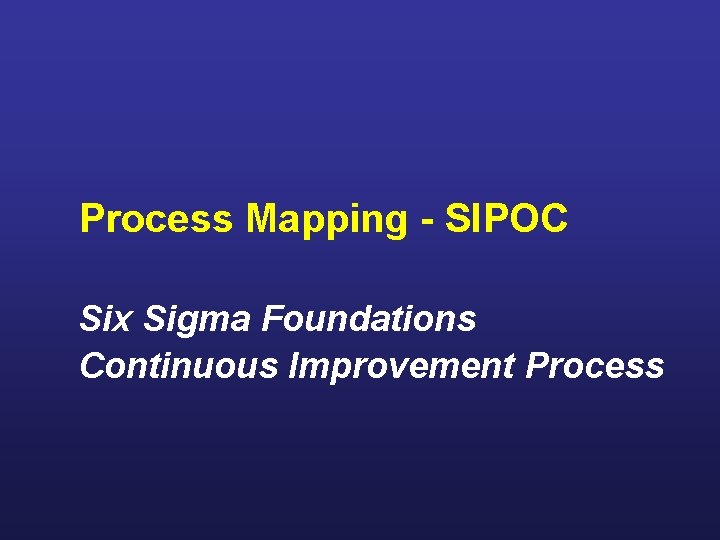
- Slides: 12
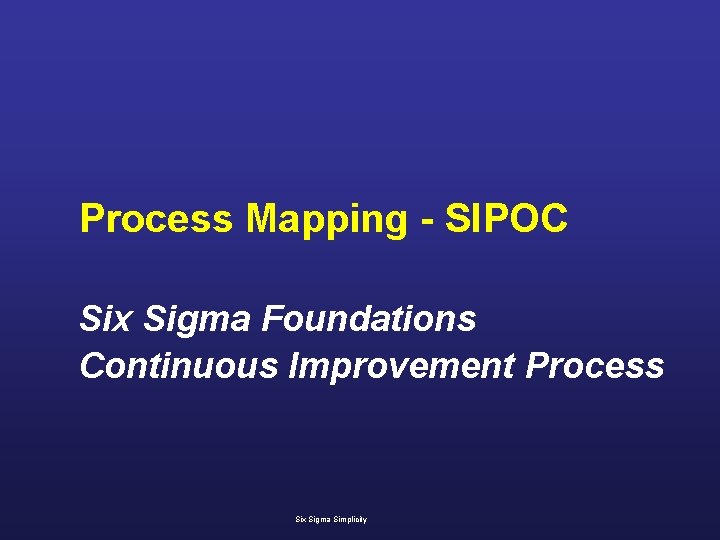
Process Mapping - SIPOC Six Sigma Foundations Continuous Improvement Process Six Sigma Simplicity
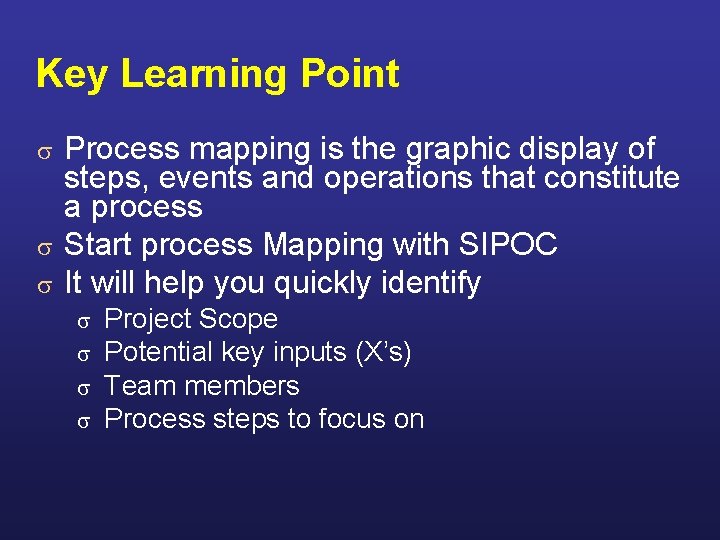
Key Learning Point Process mapping is the graphic display of steps, events and operations that constitute a process s Start process Mapping with SIPOC s It will help you quickly identify s s s Project Scope Potential key inputs (X’s) Team members Process steps to focus on
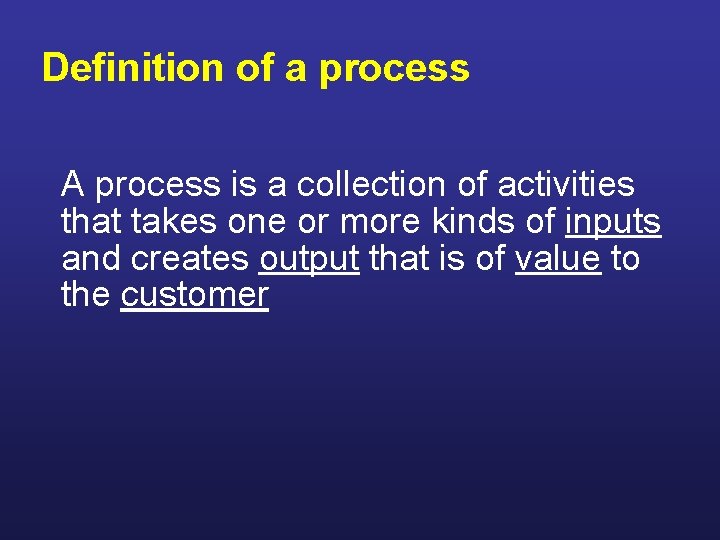
Definition of a process A process is a collection of activities that takes one or more kinds of inputs and creates output that is of value to the customer
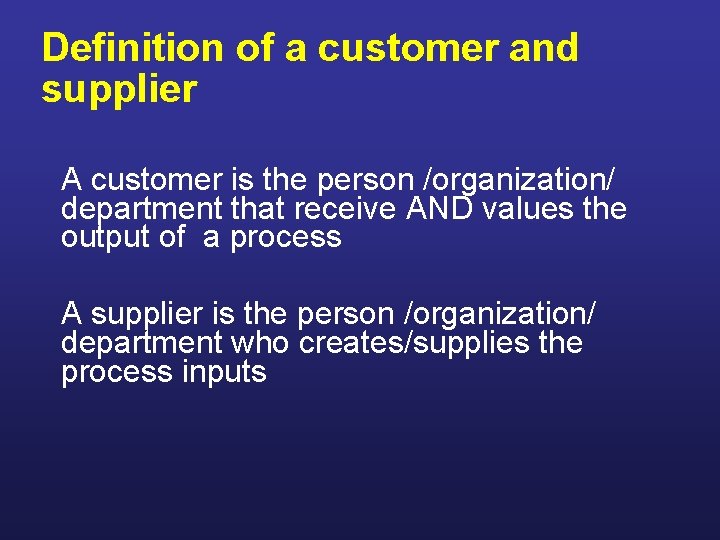
Definition of a customer and supplier A customer is the person /organization/ department that receive AND values the output of a process A supplier is the person /organization/ department who creates/supplies the process inputs
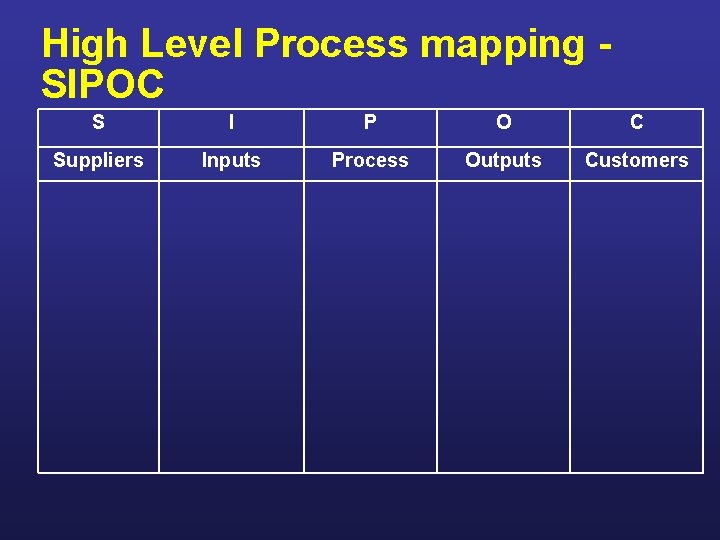
High Level Process mapping SIPOC S I P O C Suppliers Inputs Process Outputs Customers
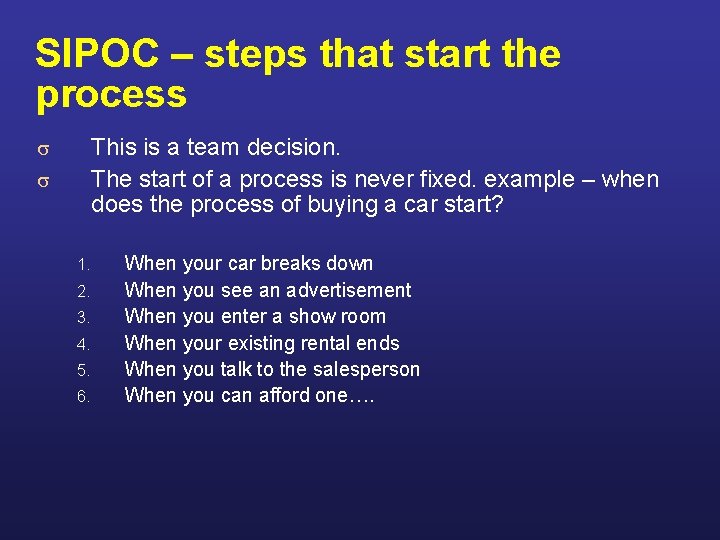
SIPOC – steps that start the process This is a team decision. The start of a process is never fixed. example – when does the process of buying a car start? s s 1. 2. 3. 4. 5. 6. When your car breaks down When you see an advertisement When you enter a show room When your existing rental ends When you talk to the salesperson When you can afford one….
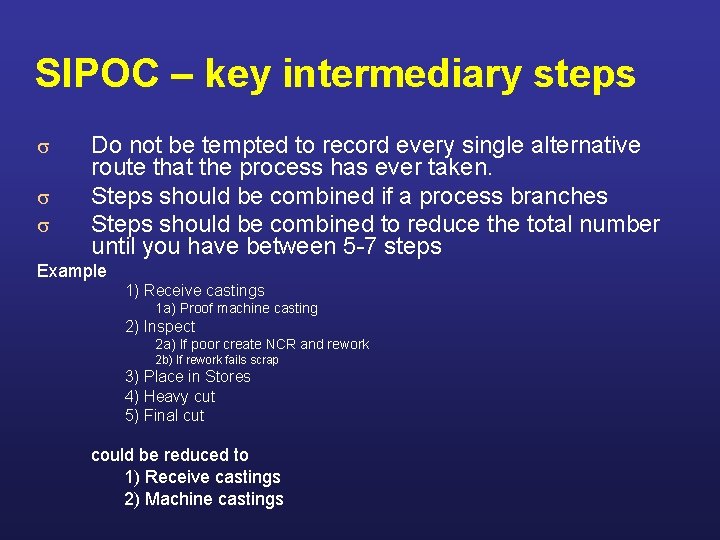
SIPOC – key intermediary steps s Do not be tempted to record every single alternative route that the process has ever taken. Steps should be combined if a process branches Steps should be combined to reduce the total number until you have between 5 -7 steps Example 1) Receive castings 1 a) Proof machine casting 2) Inspect 2 a) If poor create NCR and rework 2 b) If rework fails scrap 3) Place in Stores 4) Heavy cut 5) Final cut could be reduced to 1) Receive castings 2) Machine castings
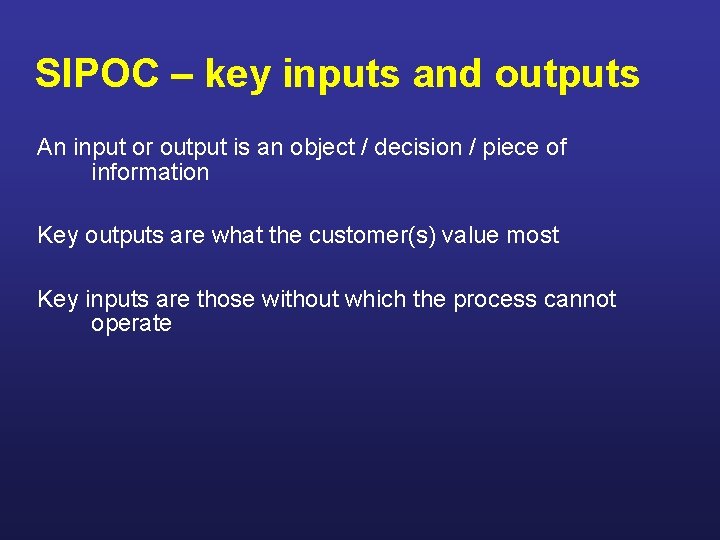
SIPOC – key inputs and outputs An input or output is an object / decision / piece of information Key outputs are what the customer(s) value most Key inputs are those without which the process cannot operate
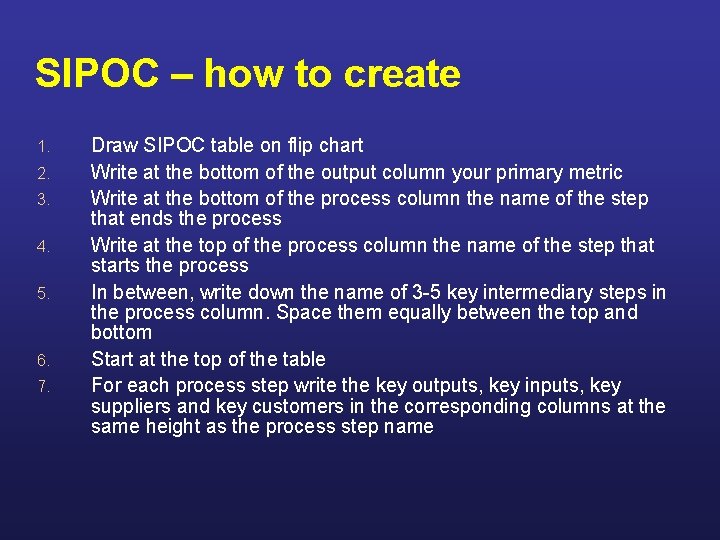
SIPOC – how to create 1. 2. 3. 4. 5. 6. 7. Draw SIPOC table on flip chart Write at the bottom of the output column your primary metric Write at the bottom of the process column the name of the step that ends the process Write at the top of the process column the name of the step that starts the process In between, write down the name of 3 -5 key intermediary steps in the process column. Space them equally between the top and bottom Start at the top of the table For each process step write the key outputs, key inputs, key suppliers and key customers in the corresponding columns at the same height as the process step name
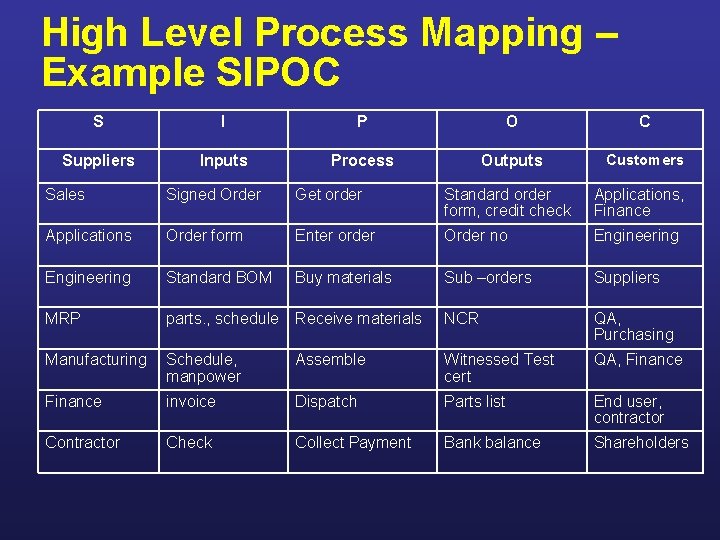
High Level Process Mapping – Example SIPOC S I P O C Suppliers Inputs Process Outputs Customers Sales Signed Order Get order Standard order form, credit check Applications, Finance Applications Order form Enter order Order no Engineering Standard BOM Buy materials Sub –orders Suppliers MRP parts. , schedule Receive materials NCR QA, Purchasing Manufacturing Schedule, manpower Assemble Witnessed Test cert QA, Finance invoice Dispatch Parts list End user, contractor Check Collect Payment Bank balance Shareholders
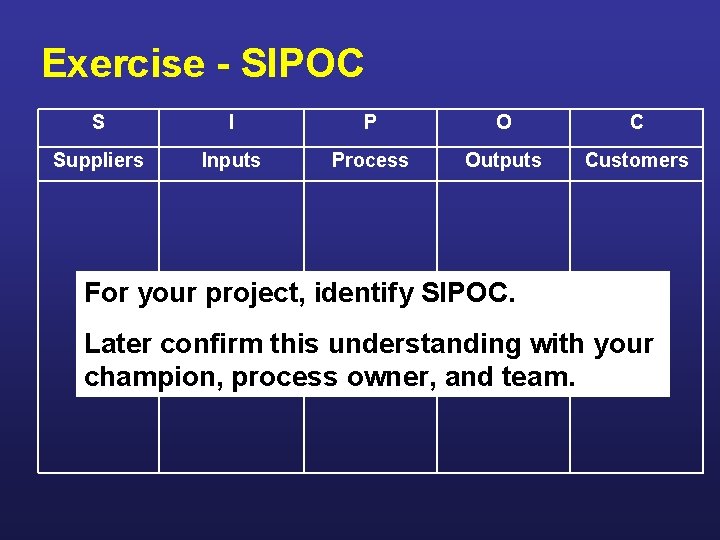
Exercise - SIPOC S I P O C Suppliers Inputs Process Outputs Customers For your project, identify SIPOC. Later confirm this understanding with your champion, process owner, and team.
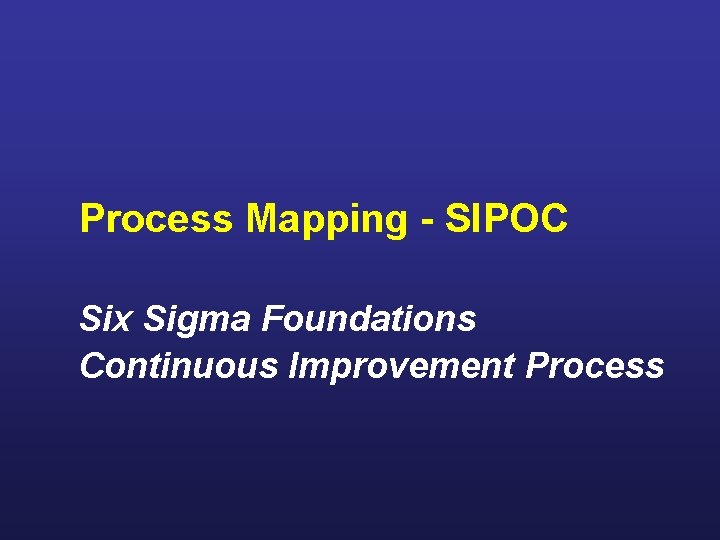
Process Mapping - SIPOC Six Sigma Foundations Continuous Improvement Process