Integrating a Lego Simulation into a LeanSix Sigma
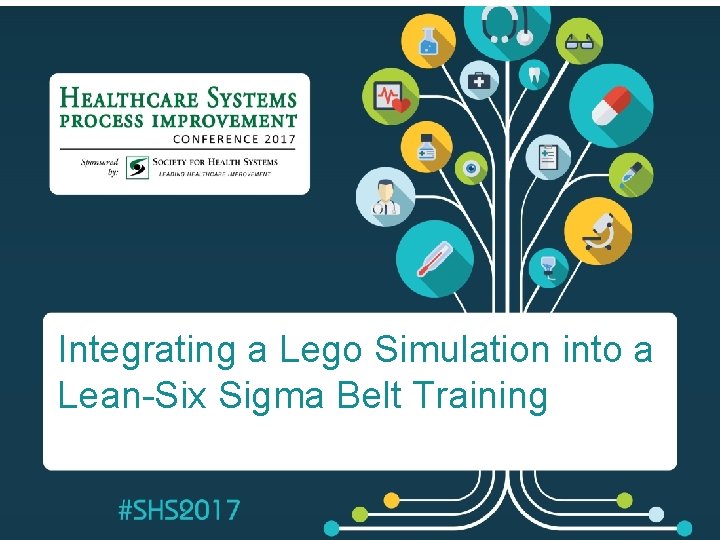
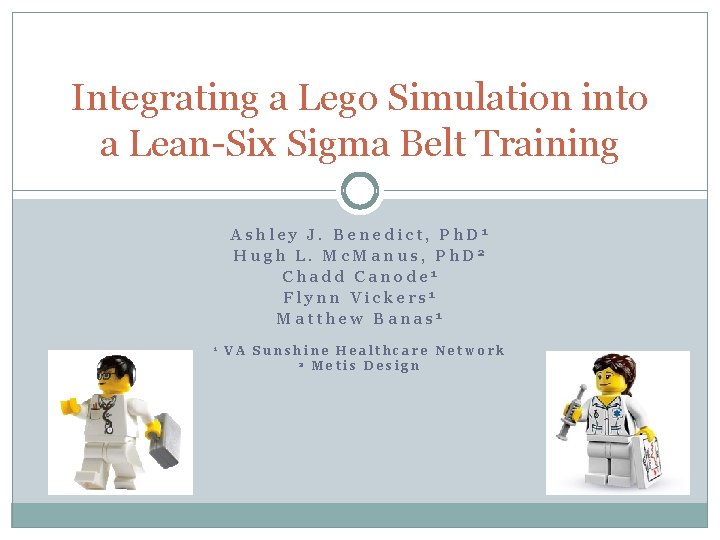
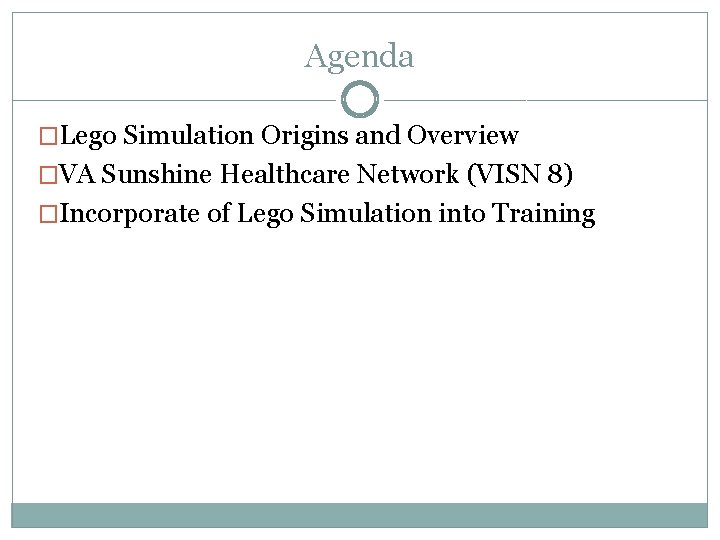
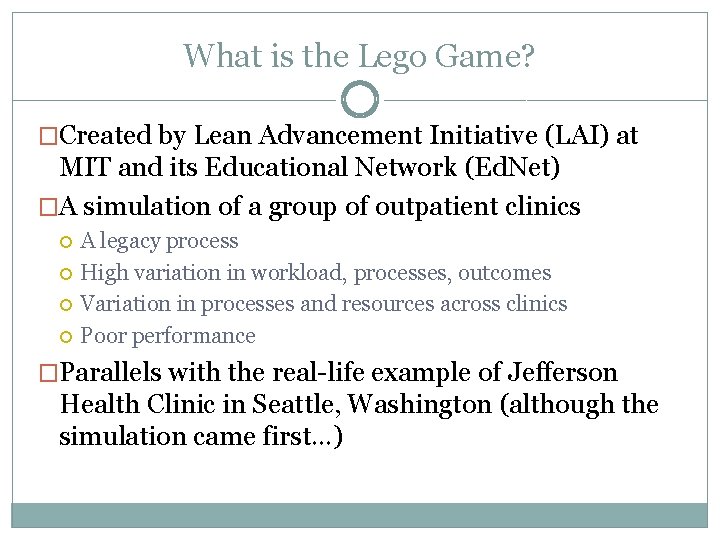
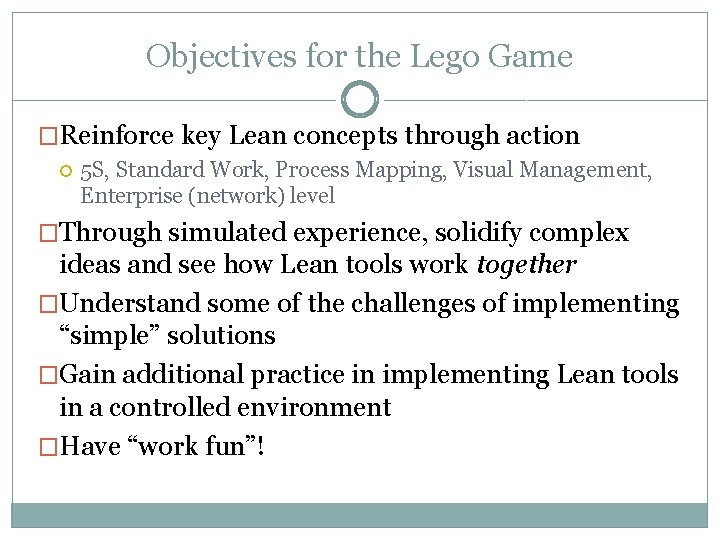
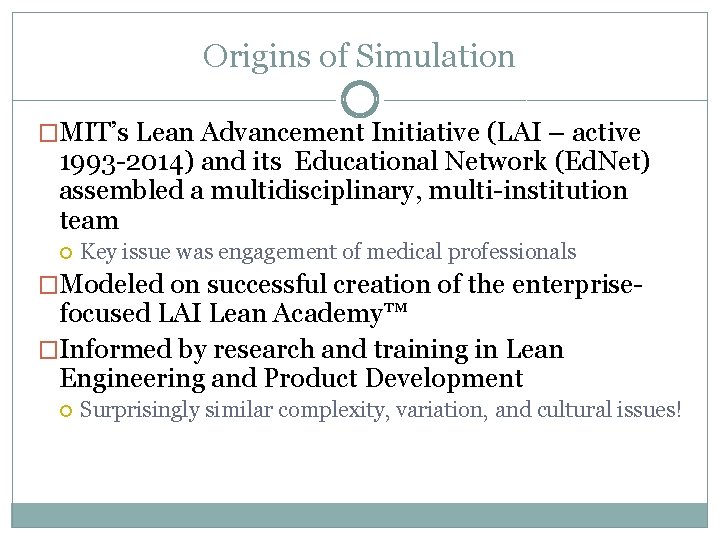
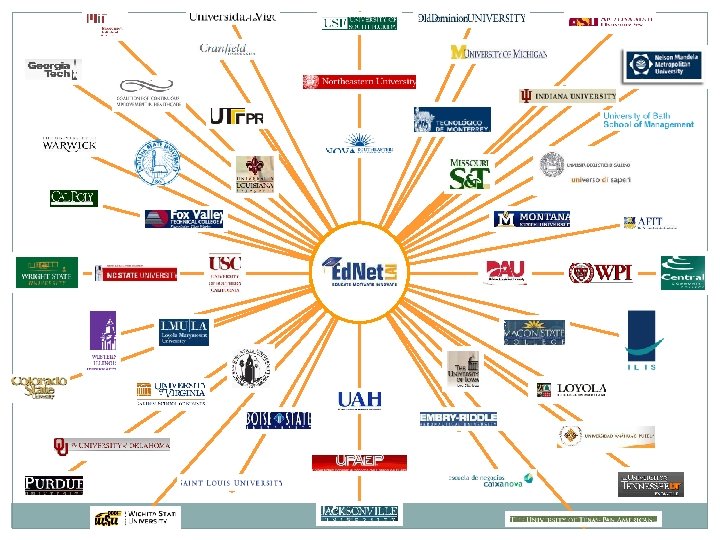
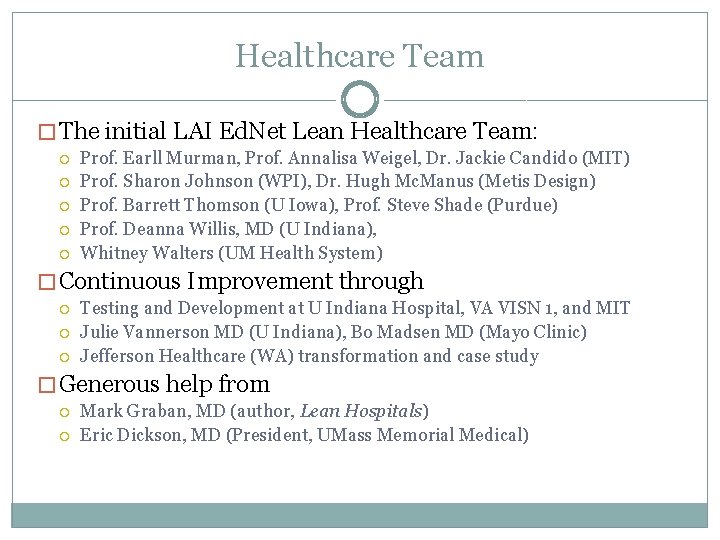
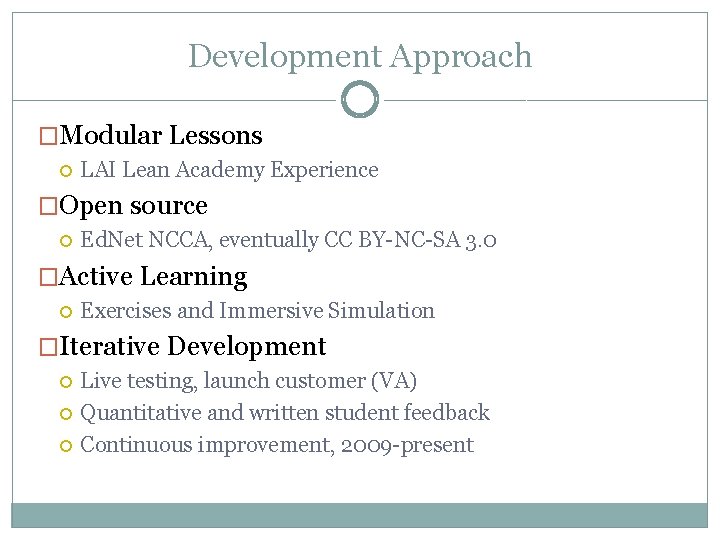
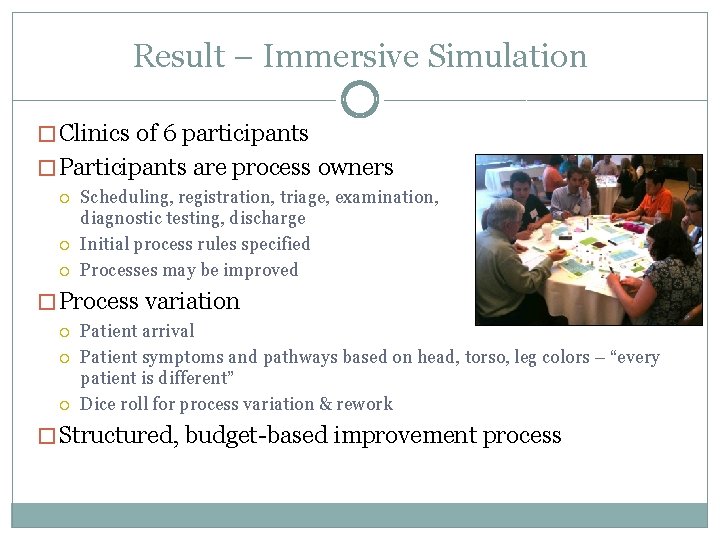
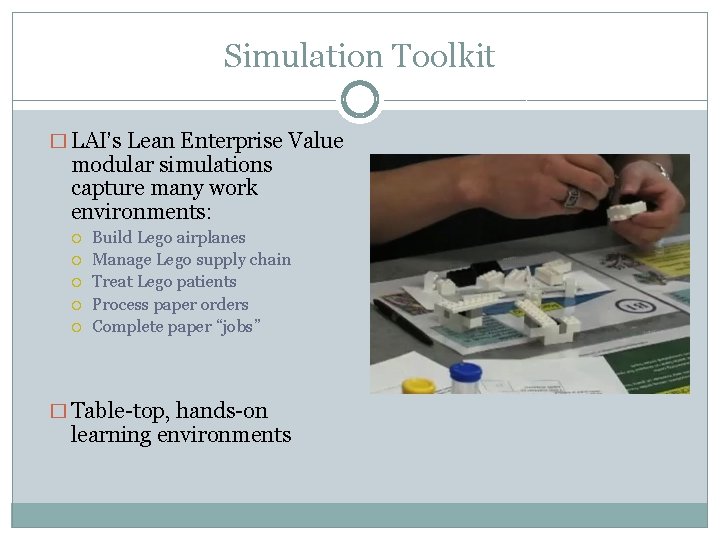
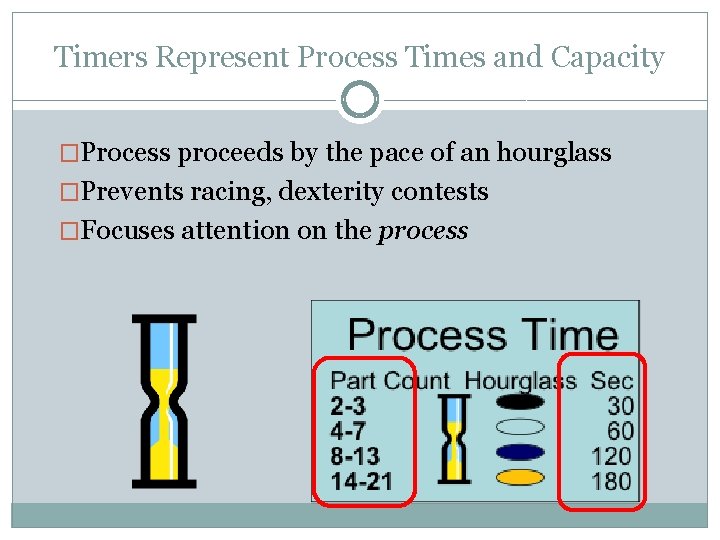
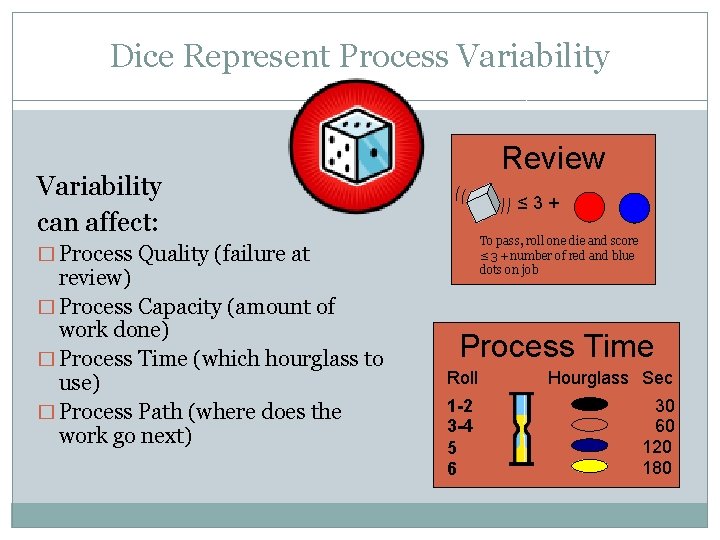
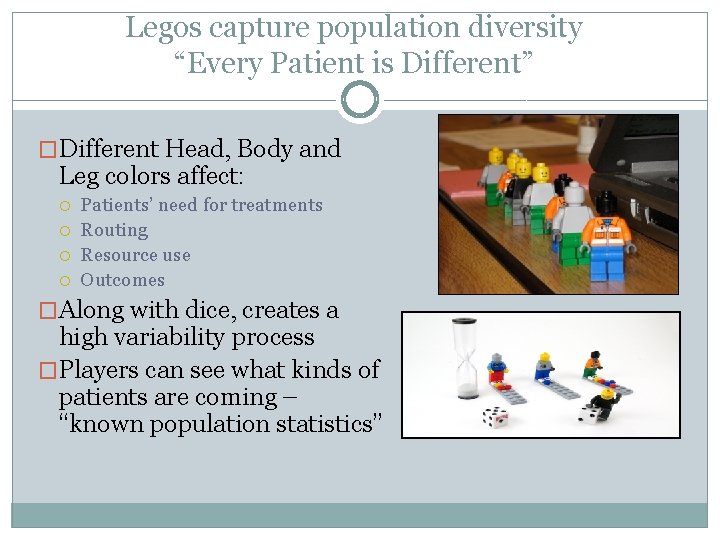
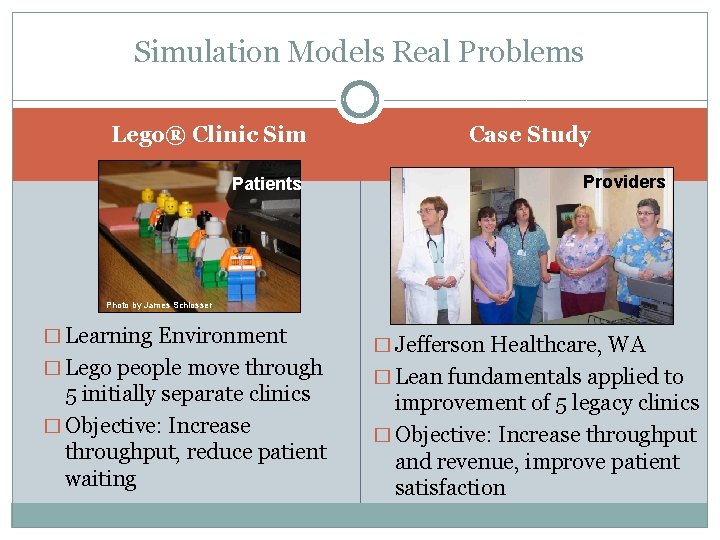
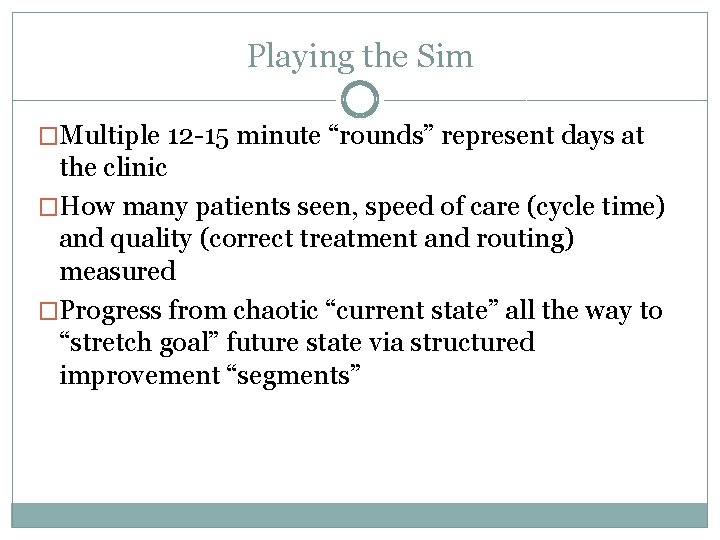
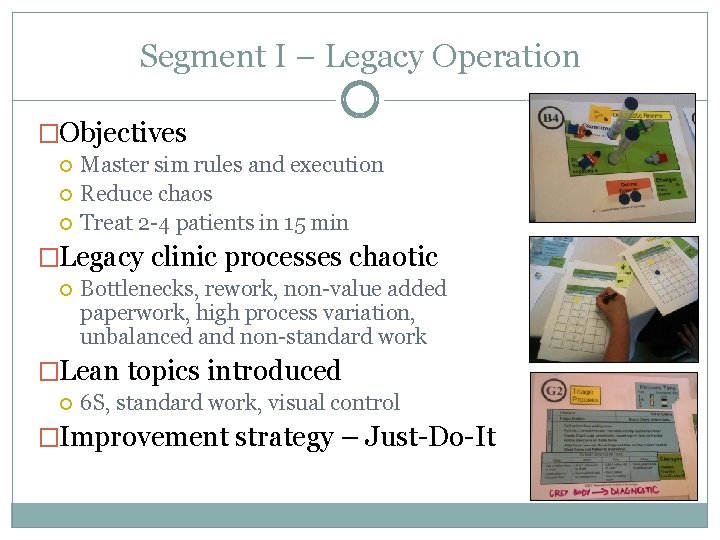
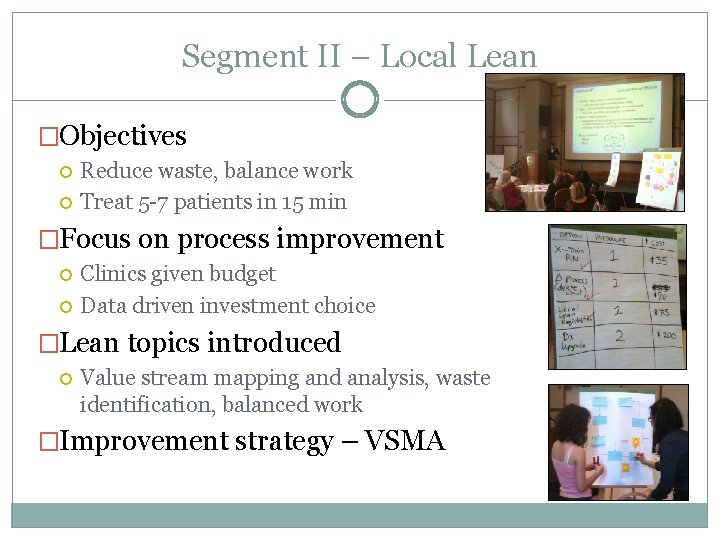
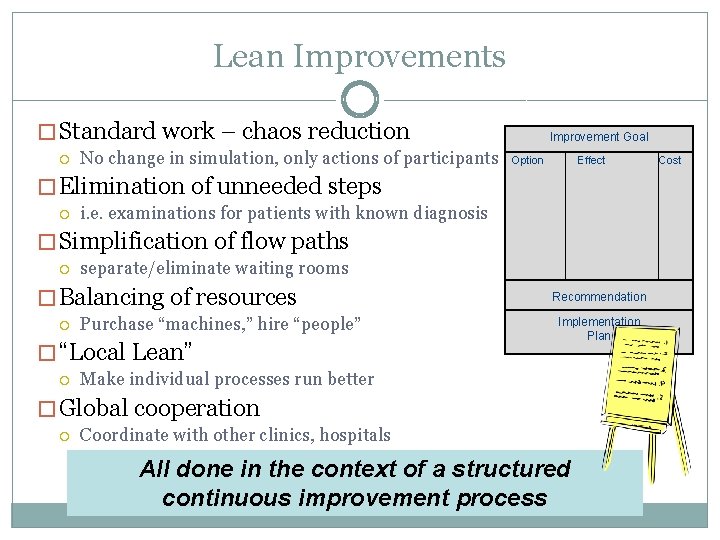
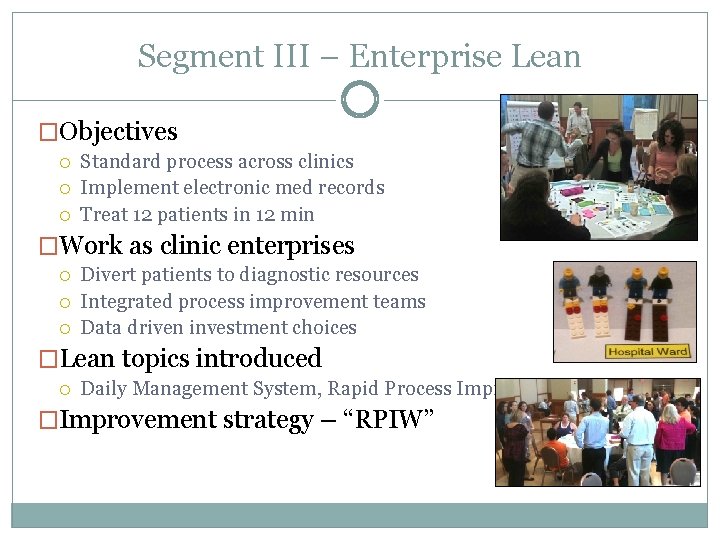
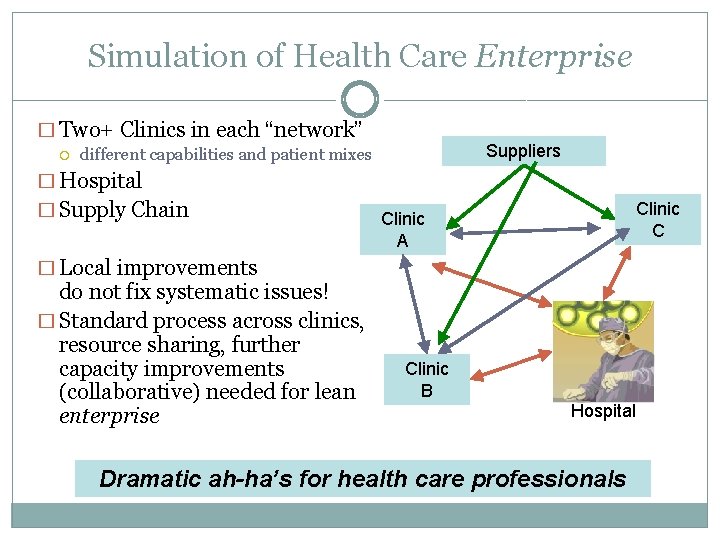
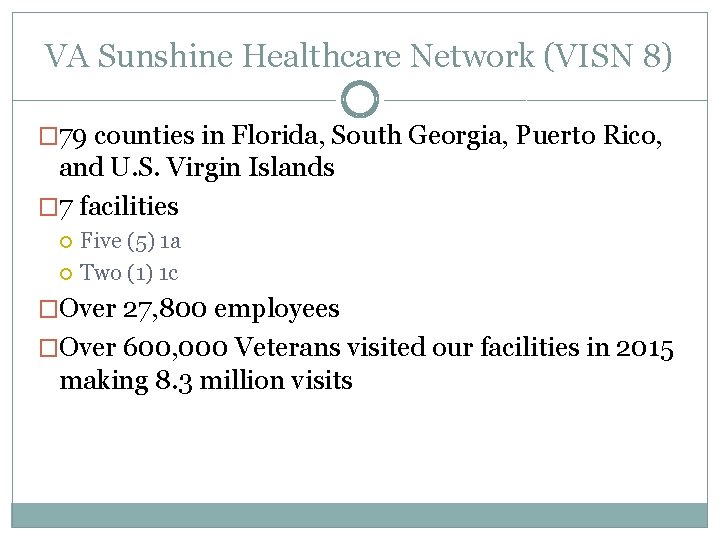
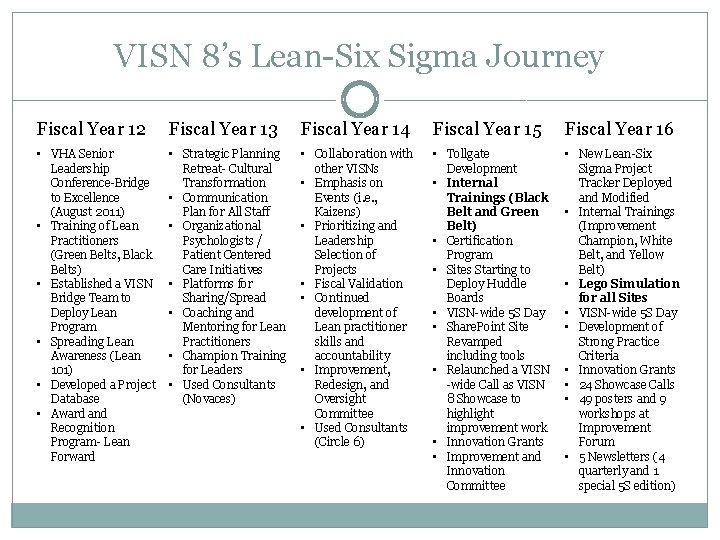
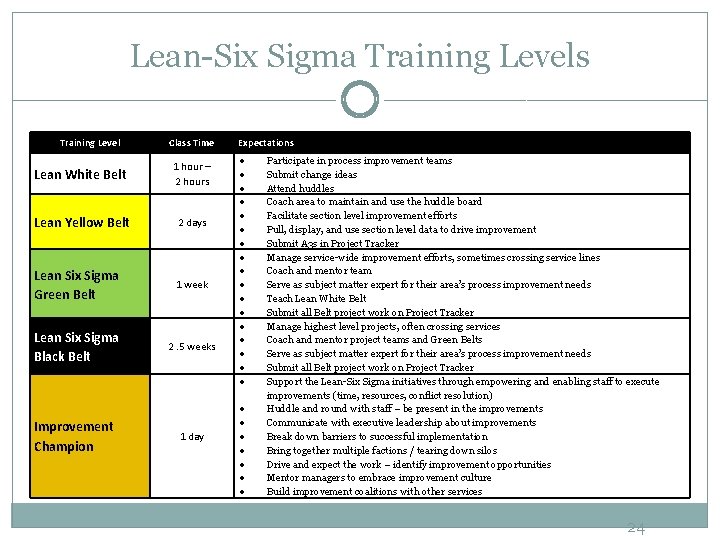
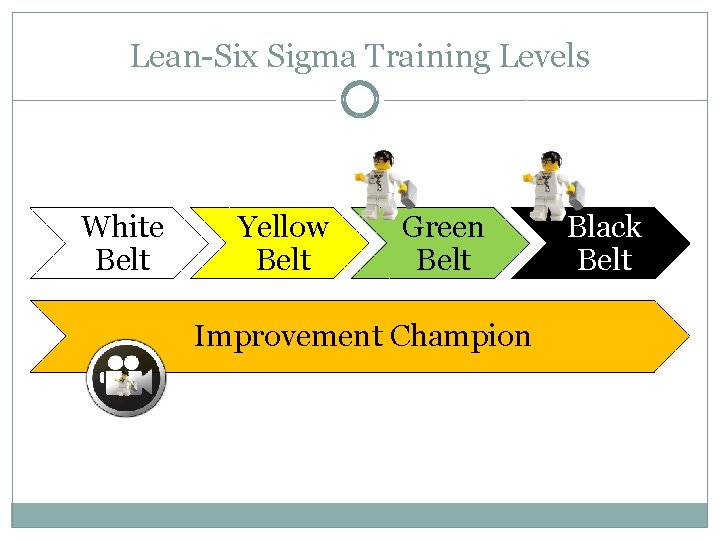
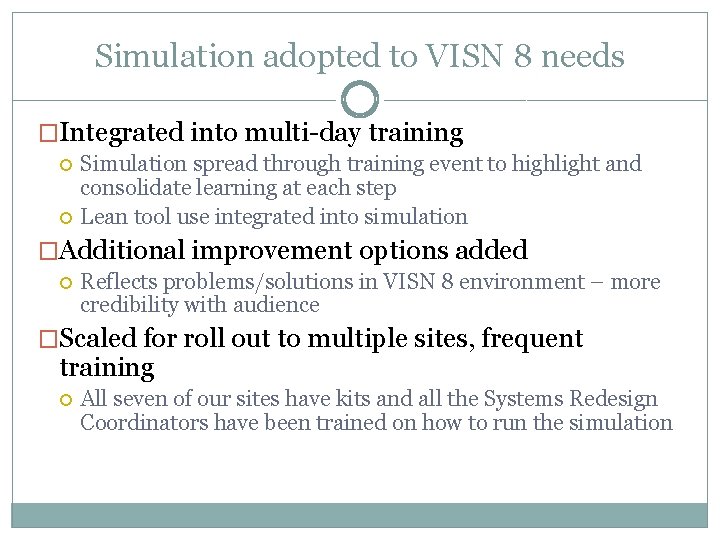
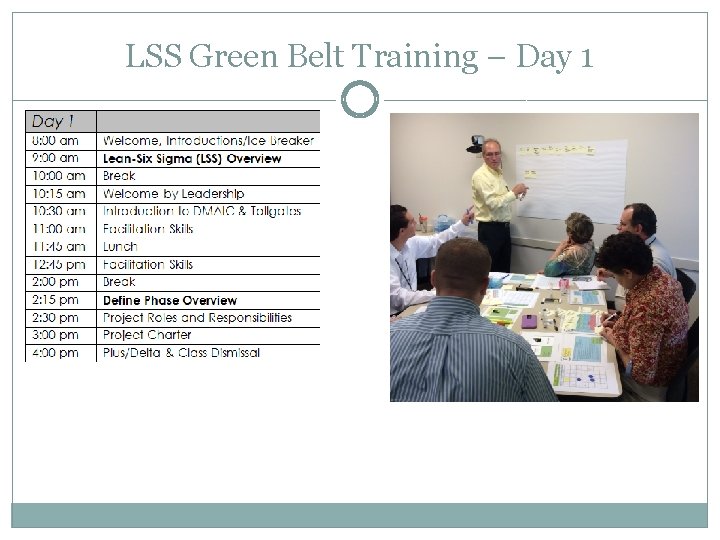
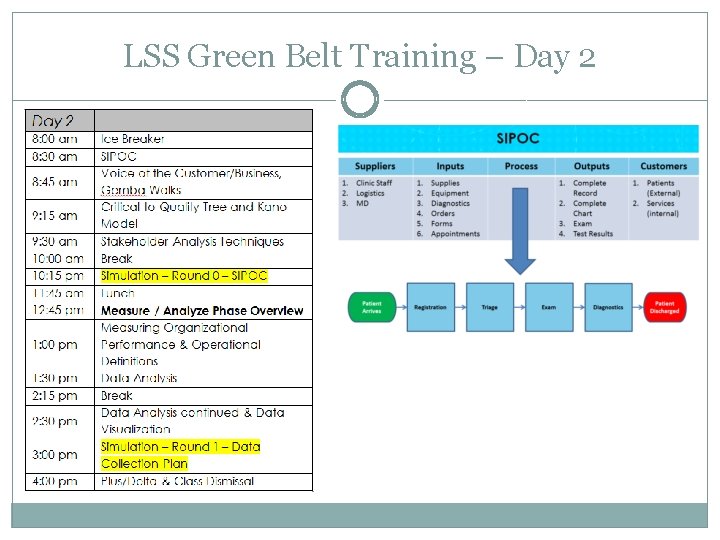
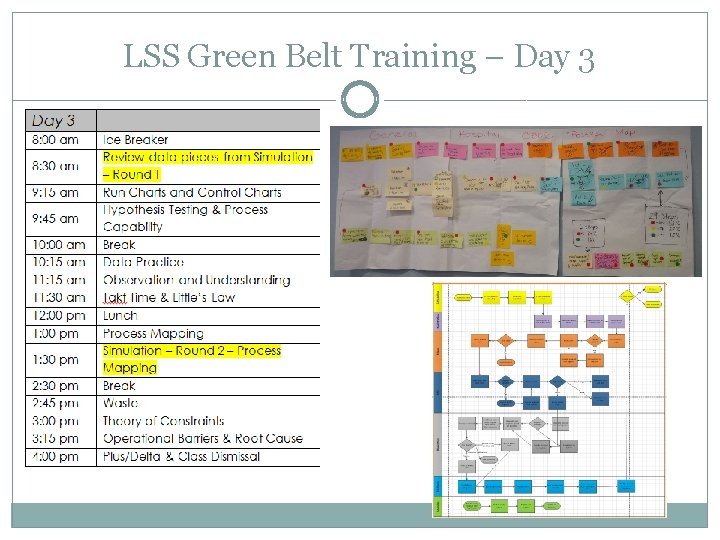
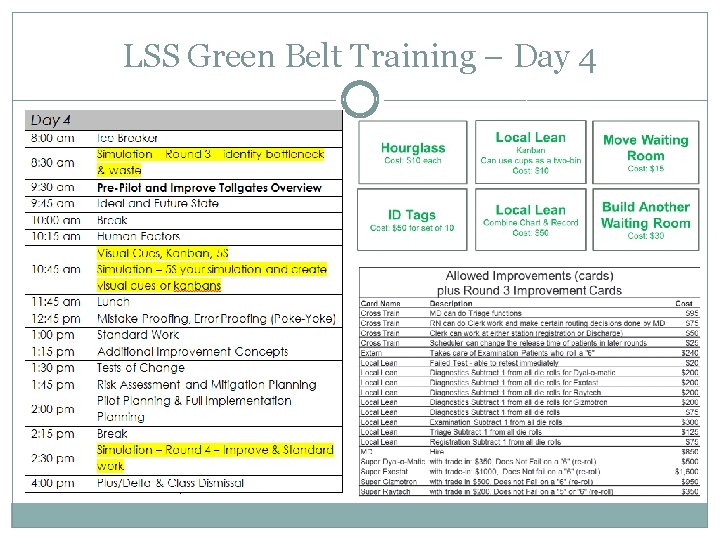
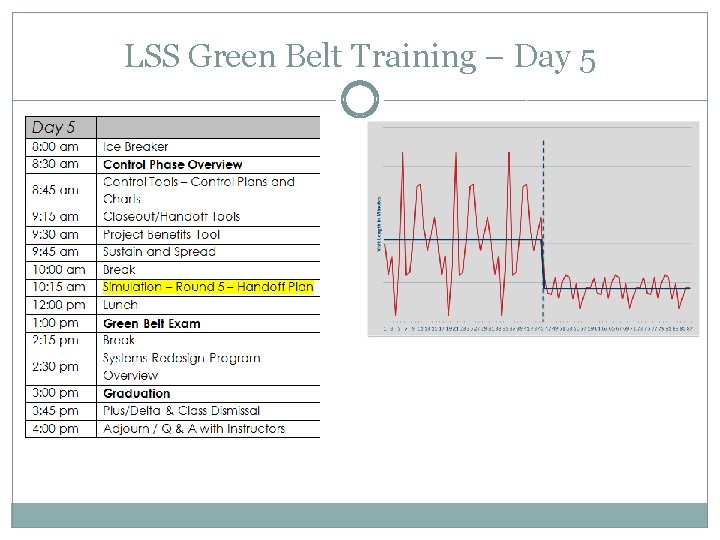
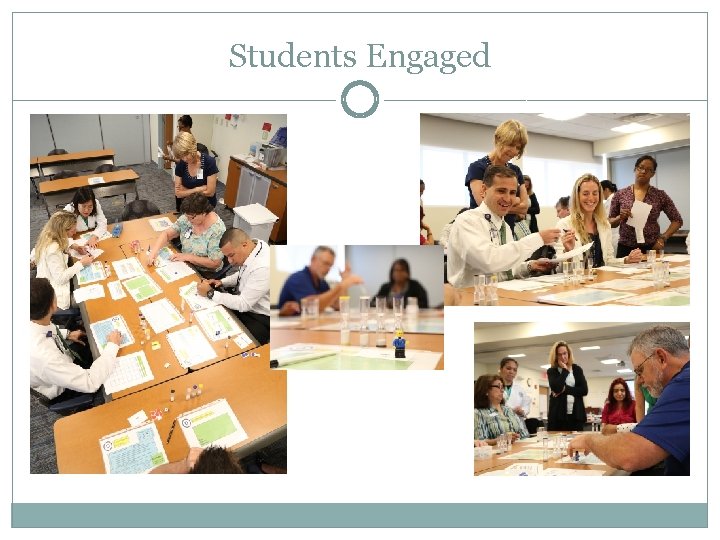
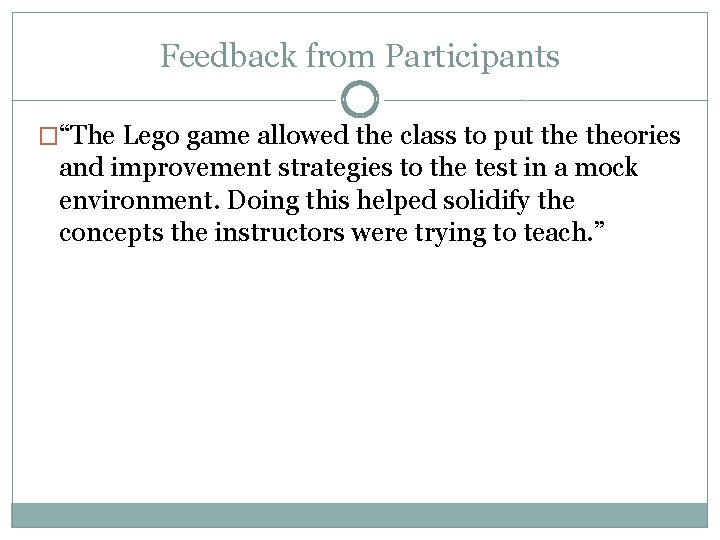
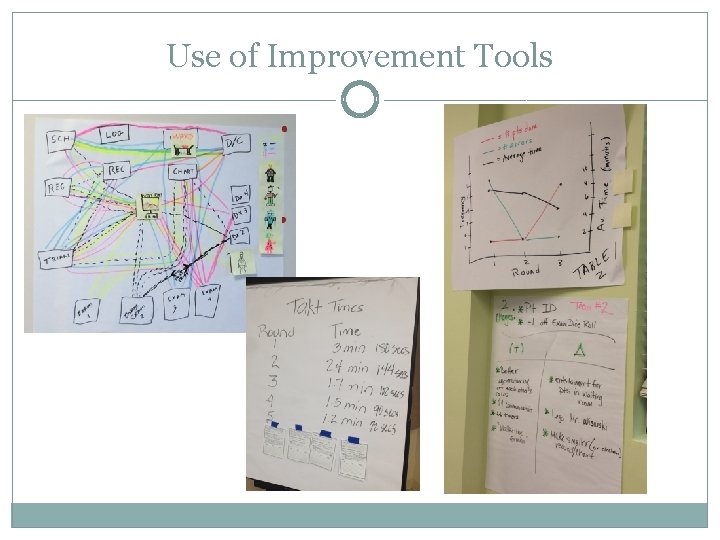

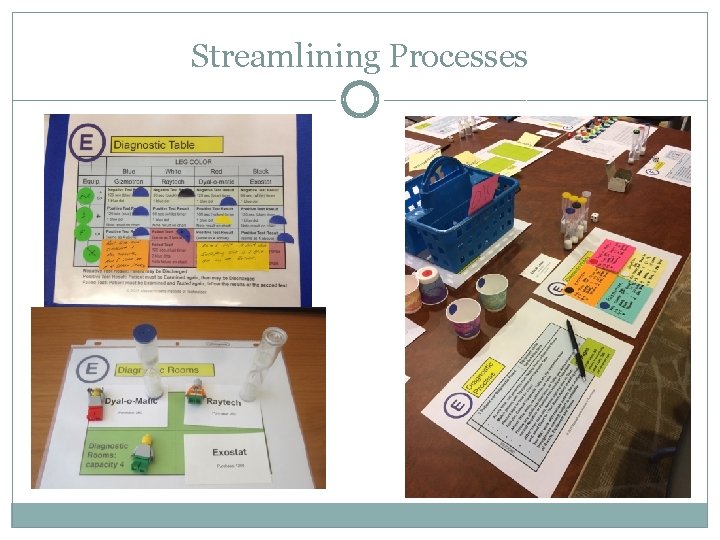
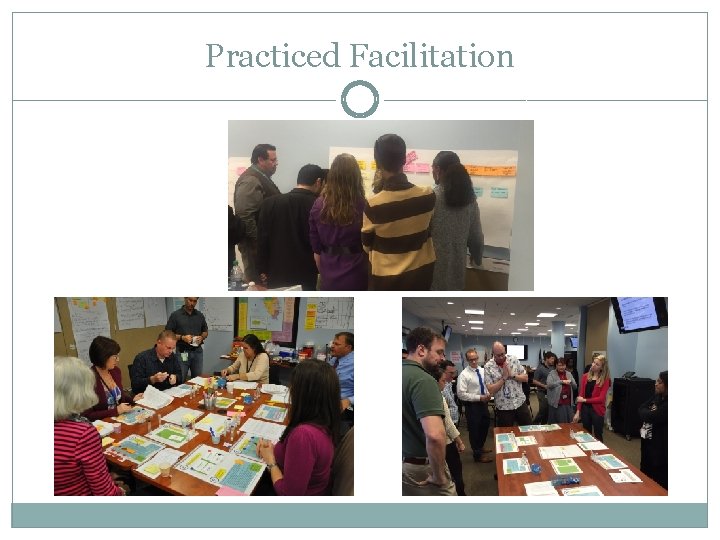

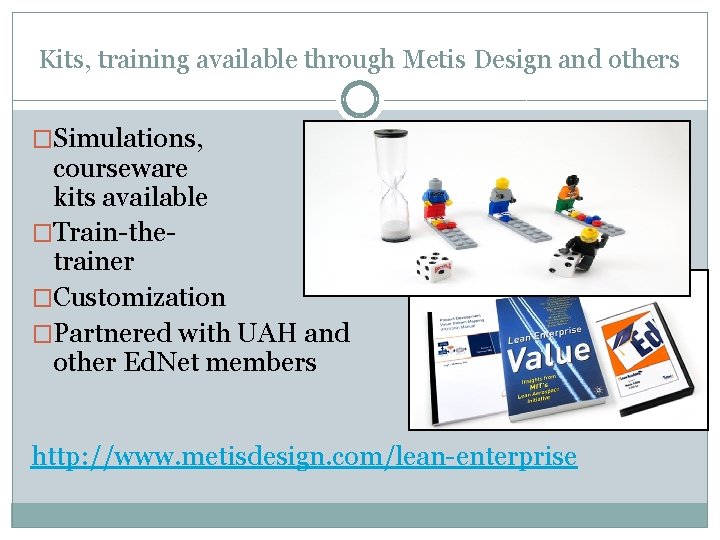
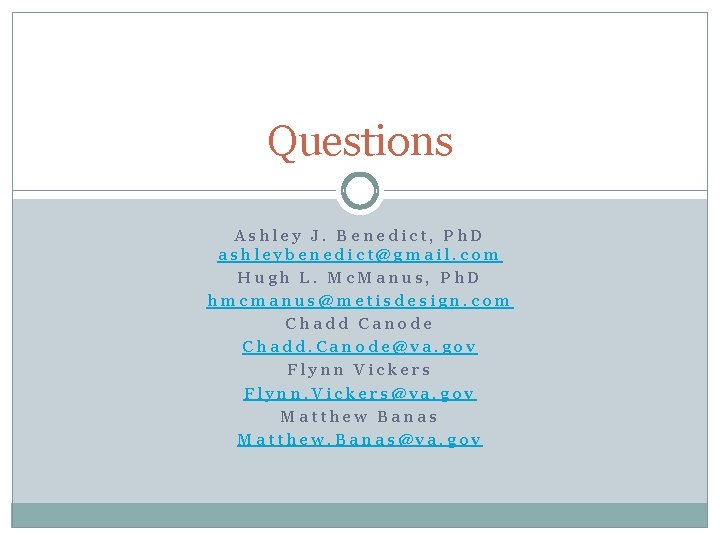
- Slides: 40
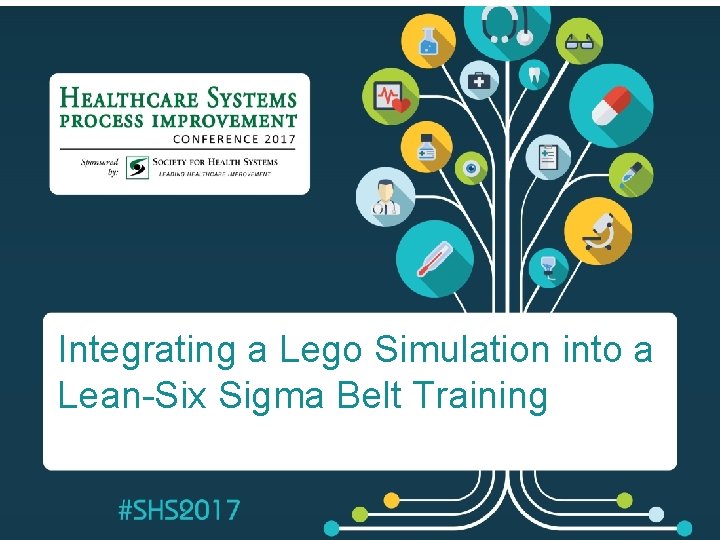
Integrating a Lego Simulation into a Lean-Six Sigma Belt Training
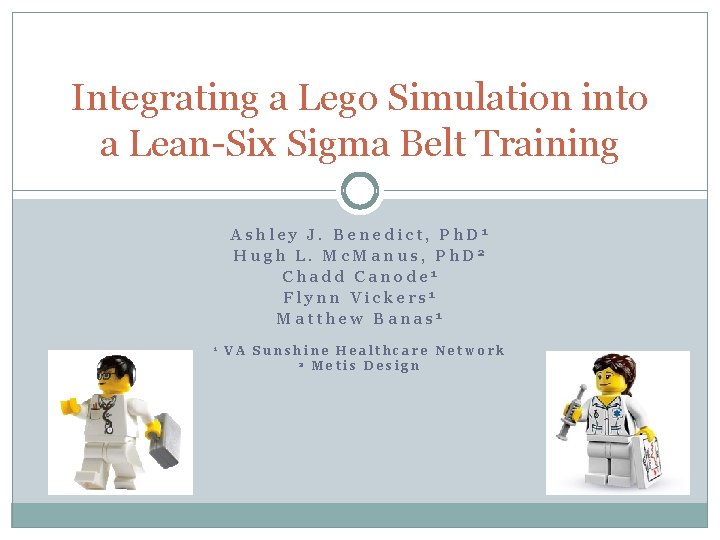
Integrating a Lego Simulation into a Lean-Six Sigma Belt Training Ashley J. Benedict, Ph. D 1 Hugh L. Mc. Manus, Ph. D 2 Chadd Canode 1 Flynn Vickers 1 Matthew Banas 1 1 VA Sunshine Healthcare Network 2 Metis Design
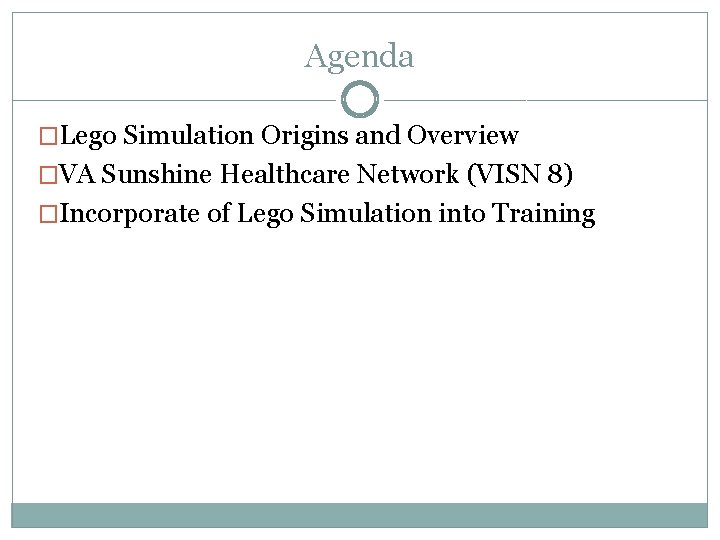
Agenda �Lego Simulation Origins and Overview �VA Sunshine Healthcare Network (VISN 8) �Incorporate of Lego Simulation into Training
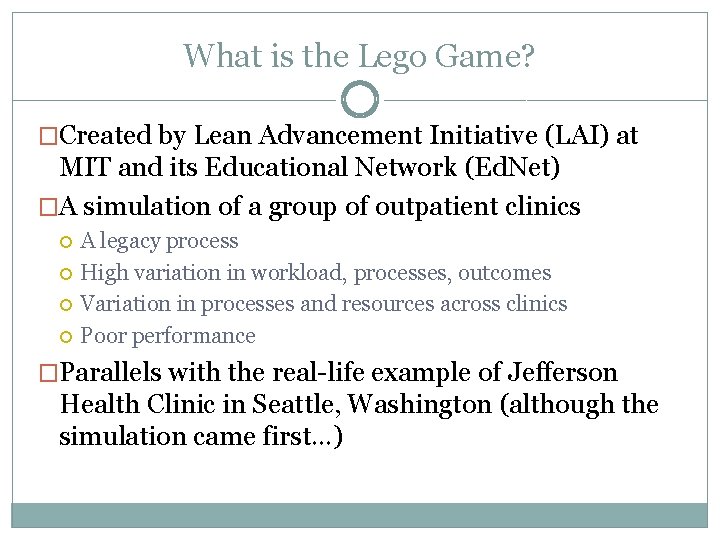
What is the Lego Game? �Created by Lean Advancement Initiative (LAI) at MIT and its Educational Network (Ed. Net) �A simulation of a group of outpatient clinics A legacy process High variation in workload, processes, outcomes Variation in processes and resources across clinics Poor performance �Parallels with the real-life example of Jefferson Health Clinic in Seattle, Washington (although the simulation came first…)
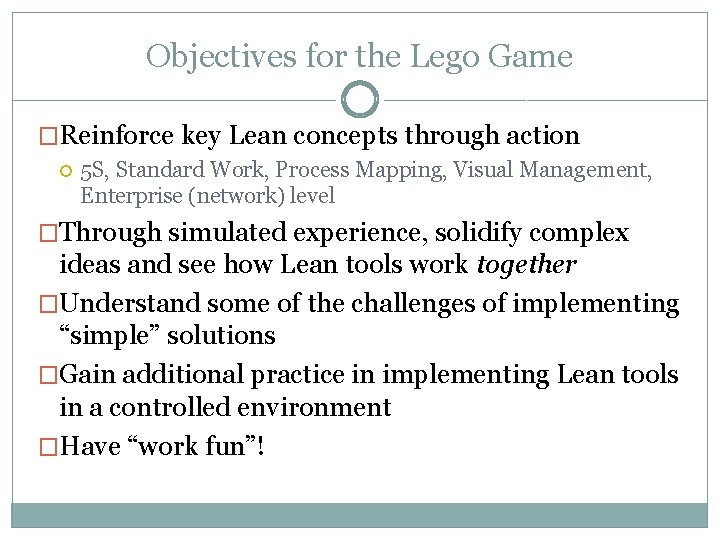
Objectives for the Lego Game �Reinforce key Lean concepts through action 5 S, Standard Work, Process Mapping, Visual Management, Enterprise (network) level �Through simulated experience, solidify complex ideas and see how Lean tools work together �Understand some of the challenges of implementing “simple” solutions �Gain additional practice in implementing Lean tools in a controlled environment �Have “work fun”!
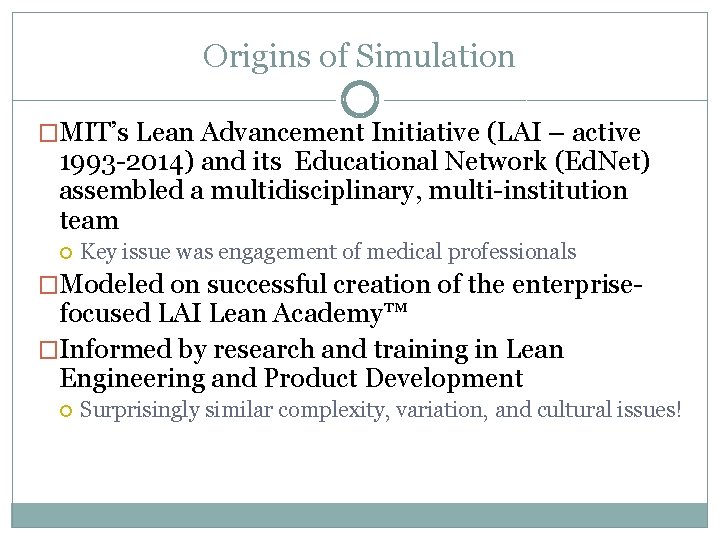
Origins of Simulation �MIT’s Lean Advancement Initiative (LAI – active 1993 -2014) and its Educational Network (Ed. Net) assembled a multidisciplinary, multi-institution team Key issue was engagement of medical professionals �Modeled on successful creation of the enterprise- focused LAI Lean Academy™ �Informed by research and training in Lean Engineering and Product Development Surprisingly similar complexity, variation, and cultural issues!
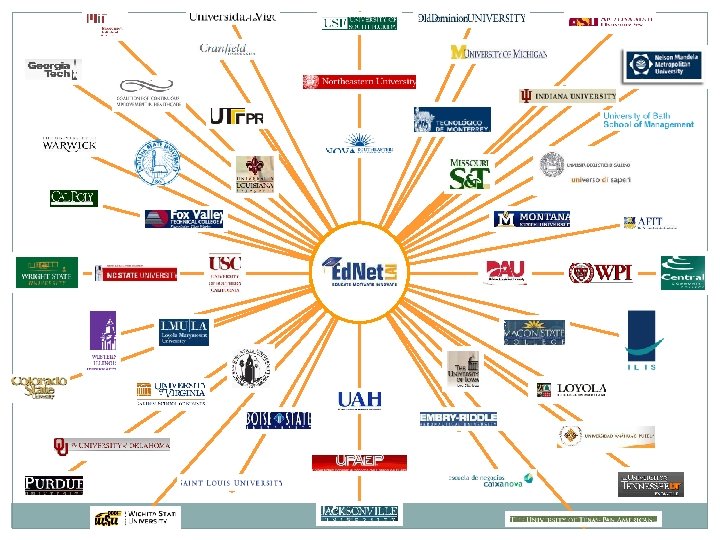
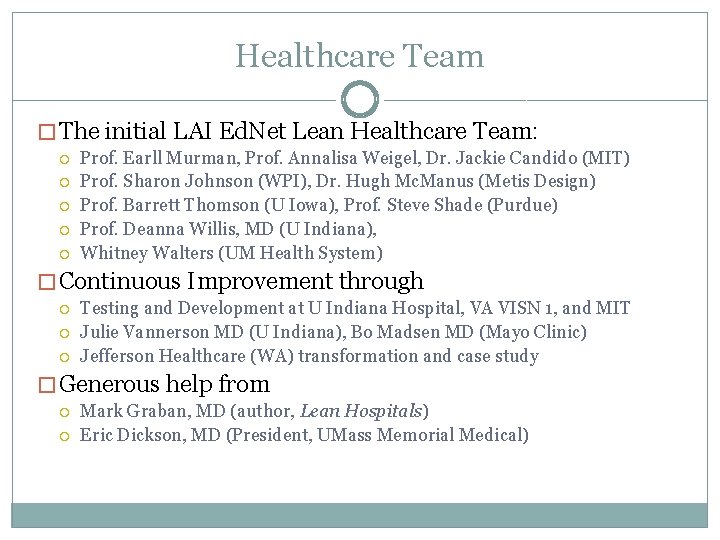
Healthcare Team � The initial LAI Ed. Net Lean Healthcare Team: Prof. Earll Murman, Prof. Annalisa Weigel, Dr. Jackie Candido (MIT) Prof. Sharon Johnson (WPI), Dr. Hugh Mc. Manus (Metis Design) Prof. Barrett Thomson (U Iowa), Prof. Steve Shade (Purdue) Prof. Deanna Willis, MD (U Indiana), Whitney Walters (UM Health System) � Continuous Improvement through Testing and Development at U Indiana Hospital, VA VISN 1, and MIT Julie Vannerson MD (U Indiana), Bo Madsen MD (Mayo Clinic) Jefferson Healthcare (WA) transformation and case study � Generous help from Mark Graban, MD (author, Lean Hospitals) Eric Dickson, MD (President, UMass Memorial Medical)
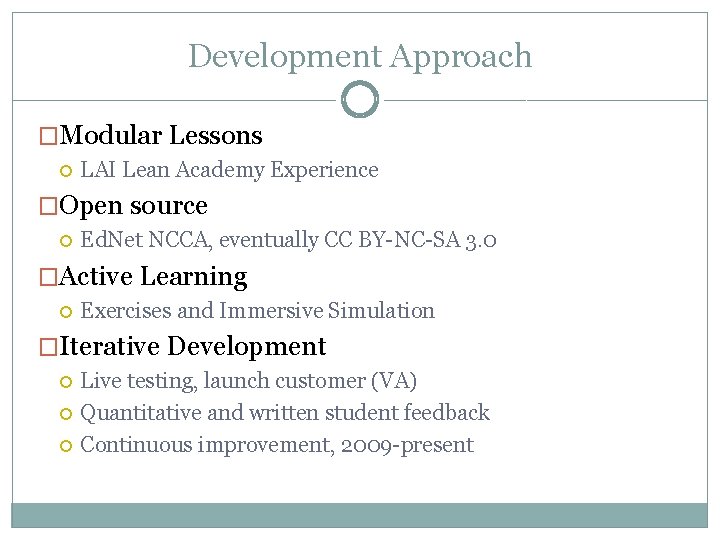
Development Approach �Modular Lessons LAI Lean Academy Experience �Open source Ed. Net NCCA, eventually CC BY-NC-SA 3. 0 �Active Learning Exercises and Immersive Simulation �Iterative Development Live testing, launch customer (VA) Quantitative and written student feedback Continuous improvement, 2009 -present
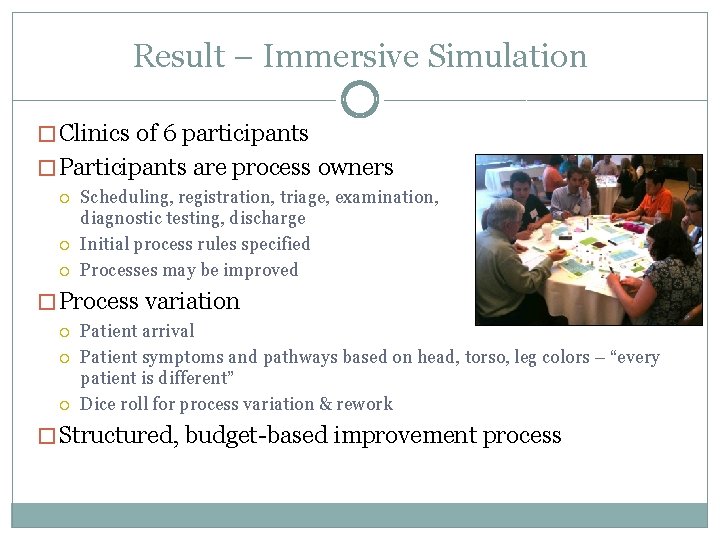
Result – Immersive Simulation � Clinics of 6 participants � Participants are process owners Scheduling, registration, triage, examination, diagnostic testing, discharge Initial process rules specified Processes may be improved � Process variation Patient arrival Patient symptoms and pathways based on head, torso, leg colors – “every patient is different” Dice roll for process variation & rework � Structured, budget-based improvement process
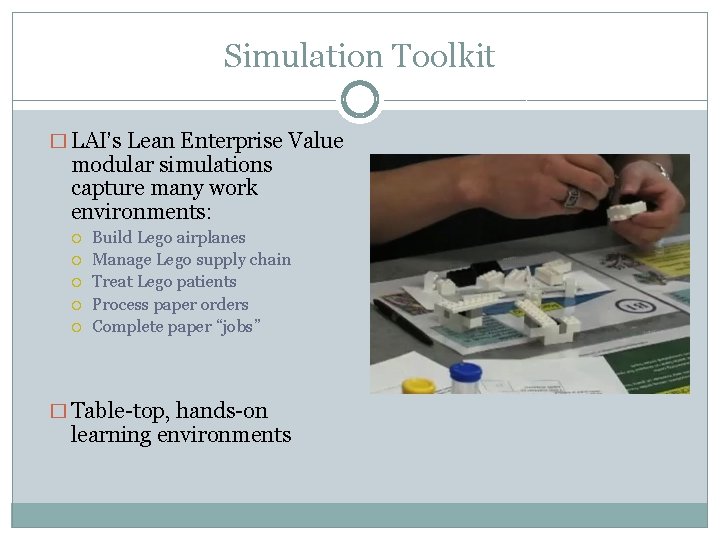
Simulation Toolkit � LAI’s Lean Enterprise Value modular simulations capture many work environments: Build Lego airplanes Manage Lego supply chain Treat Lego patients Process paper orders Complete paper “jobs” � Table-top, hands-on learning environments
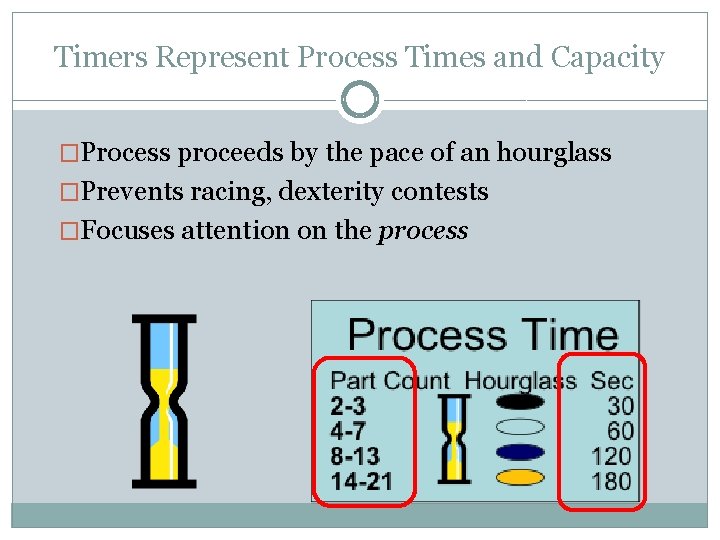
Timers Represent Process Times and Capacity �Process proceeds by the pace of an hourglass �Prevents racing, dexterity contests �Focuses attention on the process
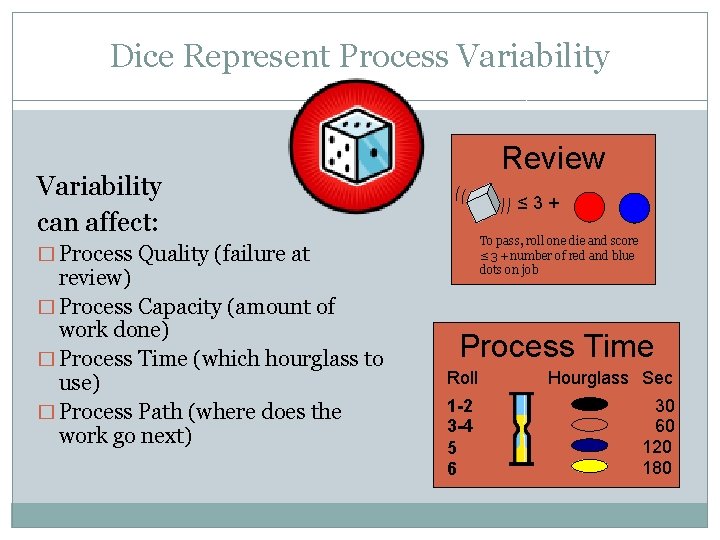
Dice Represent Process Variability Review Variability can affect: ≤ 3+ To pass, roll one die and score ≤ 3 + number of red and blue dots on job � Process Quality (failure at review) � Process Capacity (amount of work done) � Process Time (which hourglass to use) � Process Path (where does the work go next) Process Time Roll Hourglass Sec 1 -2 3 -4 5 6 30 60 120 180
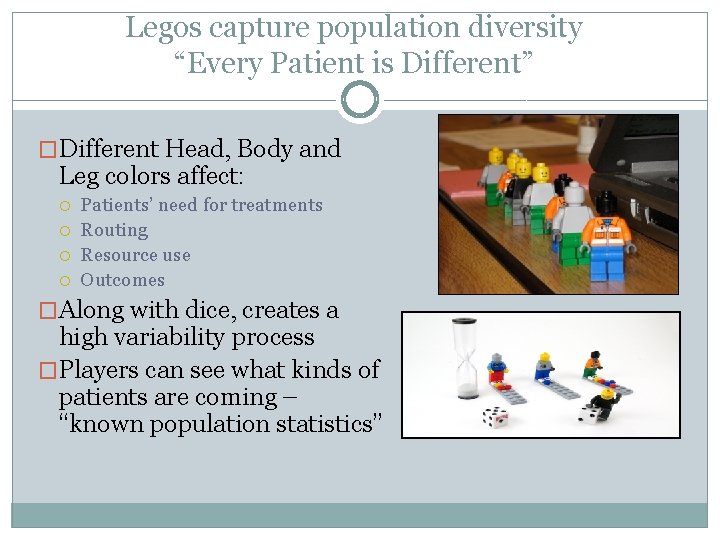
Legos capture population diversity “Every Patient is Different” �Different Head, Body and Leg colors affect: Patients’ need for treatments Routing Resource use Outcomes �Along with dice, creates a high variability process �Players can see what kinds of patients are coming – “known population statistics”
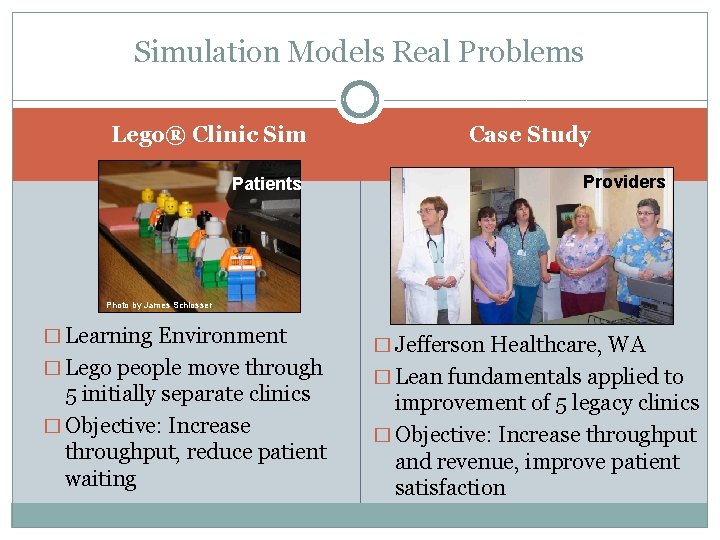
Simulation Models Real Problems Lego® Clinic Sim Patients Case Study Providers Photo by James Schlosser � Learning Environment � Lego people move through 5 initially separate clinics � Objective: Increase throughput, reduce patient waiting � Jefferson Healthcare, WA � Lean fundamentals applied to improvement of 5 legacy clinics � Objective: Increase throughput and revenue, improve patient satisfaction
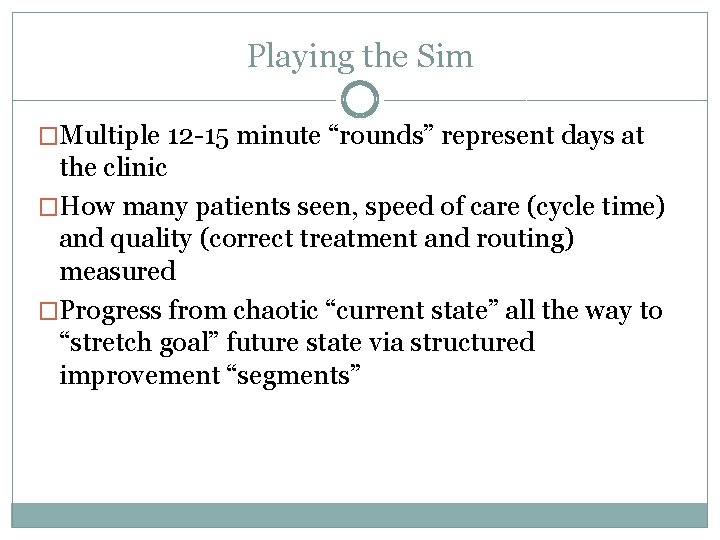
Playing the Sim �Multiple 12 -15 minute “rounds” represent days at the clinic �How many patients seen, speed of care (cycle time) and quality (correct treatment and routing) measured �Progress from chaotic “current state” all the way to “stretch goal” future state via structured improvement “segments”
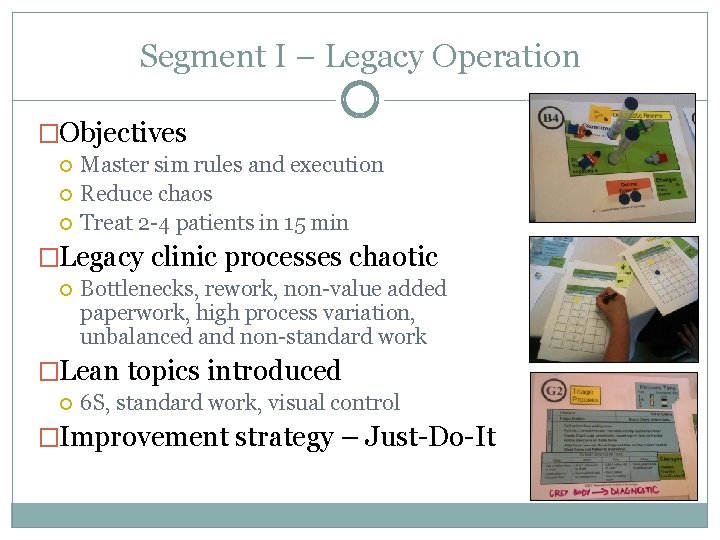
Segment I – Legacy Operation �Objectives Master sim rules and execution Reduce chaos Treat 2 -4 patients in 15 min �Legacy clinic processes chaotic Bottlenecks, rework, non-value added paperwork, high process variation, unbalanced and non-standard work �Lean topics introduced 6 S, standard work, visual control �Improvement strategy – Just-Do-It
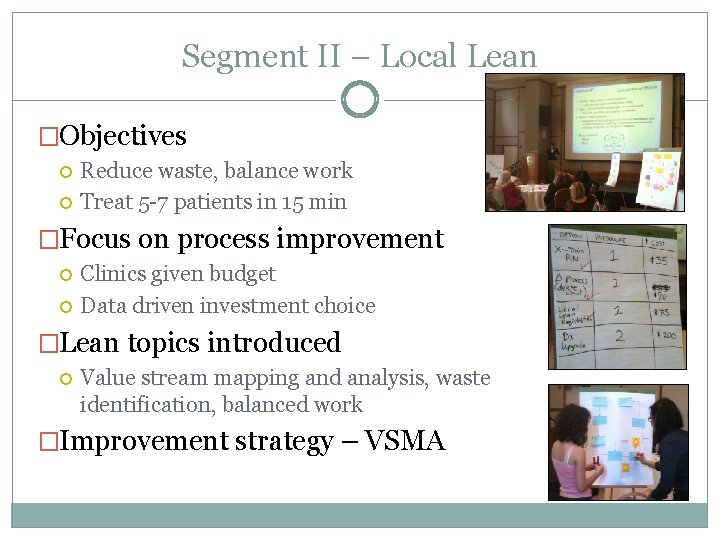
Segment II – Local Lean �Objectives Reduce waste, balance work Treat 5 -7 patients in 15 min �Focus on process improvement Clinics given budget Data driven investment choice �Lean topics introduced Value stream mapping and analysis, waste identification, balanced work �Improvement strategy – VSMA
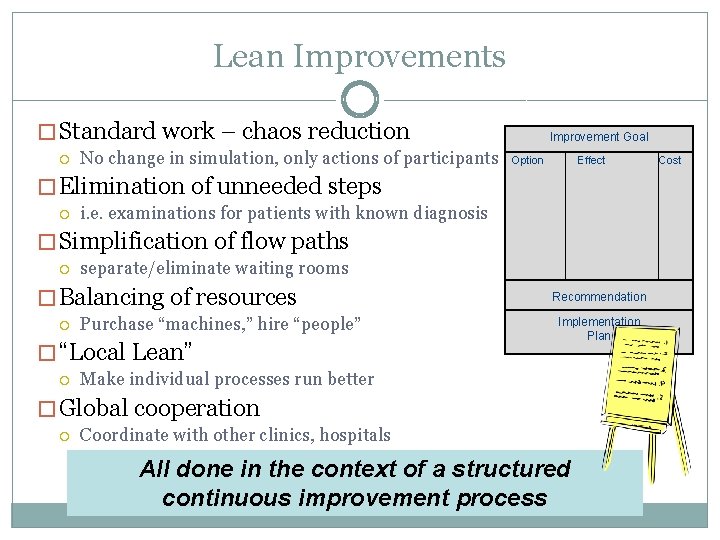
Lean Improvements � Standard work – chaos reduction No change in simulation, only actions of participants Improvement Goal Option Effect � Elimination of unneeded steps i. e. examinations for patients with known diagnosis � Simplification of flow paths separate/eliminate waiting rooms � Balancing of resources Purchase “machines, ” hire “people” � “Local Lean” Recommendation Implementation Plan Make individual processes run better � Global cooperation Coordinate with other clinics, hospitals All done in the context of a structured continuous improvement process Cost
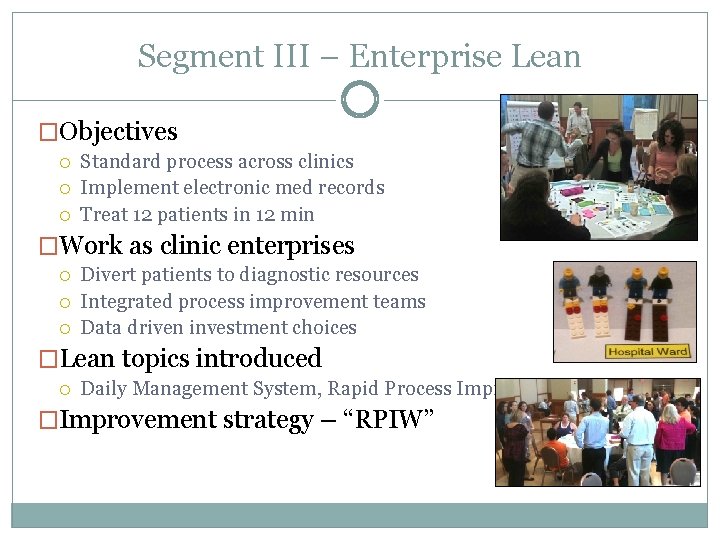
Segment III – Enterprise Lean �Objectives Standard process across clinics Implement electronic med records Treat 12 patients in 12 min �Work as clinic enterprises Divert patients to diagnostic resources Integrated process improvement teams Data driven investment choices �Lean topics introduced Daily Management System, Rapid Process Improvement Workshops �Improvement strategy – “RPIW”
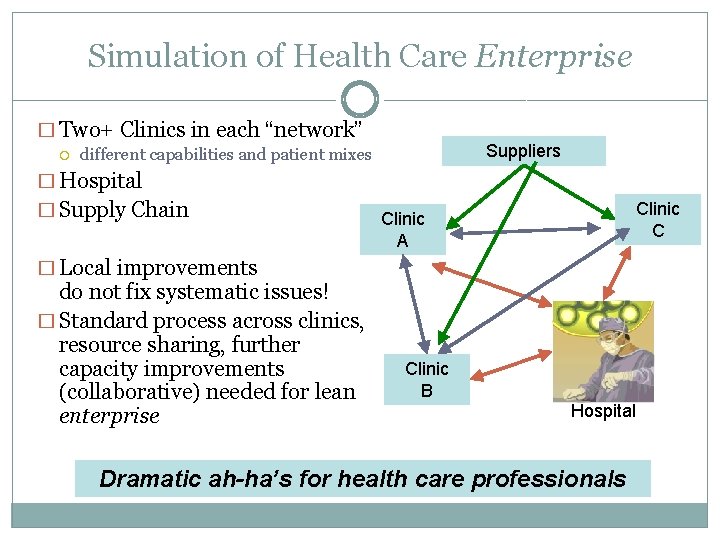
Simulation of Health Care Enterprise � Two+ Clinics in each “network” Suppliers different capabilities and patient mixes � Hospital � Supply Chain Clinic C Clinic A � Local improvements do not fix systematic issues! � Standard process across clinics, resource sharing, further capacity improvements (collaborative) needed for lean enterprise Clinic B Hospital Dramatic ah-ha’s for health care professionals
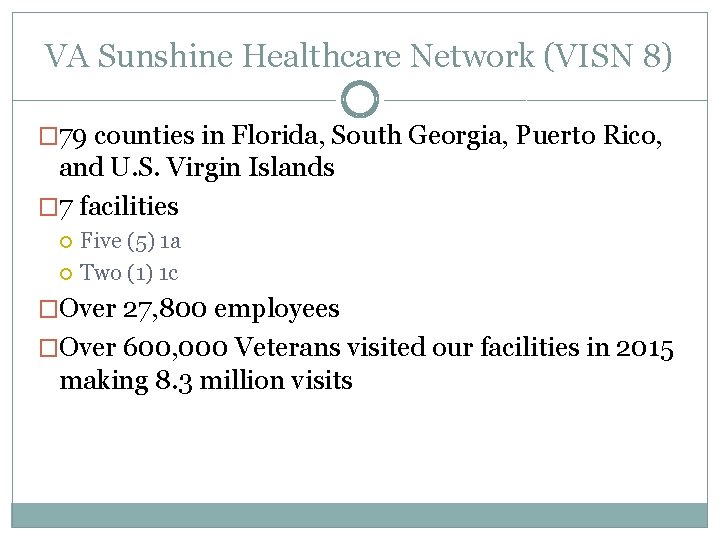
VA Sunshine Healthcare Network (VISN 8) � 79 counties in Florida, South Georgia, Puerto Rico, and U. S. Virgin Islands � 7 facilities Five (5) 1 a Two (1) 1 c �Over 27, 800 employees �Over 600, 000 Veterans visited our facilities in 2015 making 8. 3 million visits
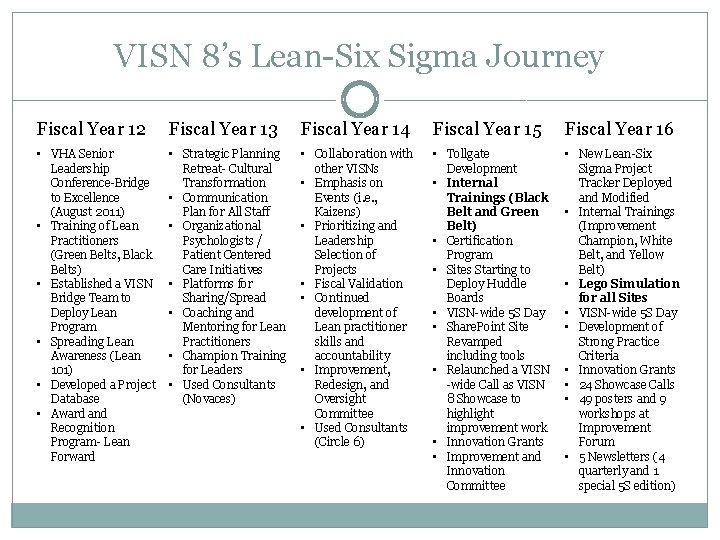
VISN 8’s Lean-Six Sigma Journey Fiscal Year 12 Fiscal Year 13 Fiscal Year 14 Fiscal Year 15 Fiscal Year 16 • VHA Senior Leadership Conference-Bridge to Excellence (August 2011) • Training of Lean Practitioners (Green Belts, Black Belts) • Established a VISN Bridge Team to Deploy Lean Program • Spreading Lean Awareness (Lean 101) • Developed a Project Database • Award and Recognition Program- Lean Forward • Strategic Planning Retreat- Cultural Transformation • Communication Plan for All Staff • Organizational Psychologists / Patient Centered Care Initiatives • Platforms for Sharing/Spread • Coaching and Mentoring for Lean Practitioners • Champion Training for Leaders • Used Consultants (Novaces) • Collaboration with other VISNs • Emphasis on Events (i. e. , Kaizens) • Prioritizing and Leadership Selection of Projects • Fiscal Validation • Continued development of Lean practitioner skills and accountability • Improvement, Redesign, and Oversight Committee • Used Consultants (Circle 6) • Tollgate Development • Internal Trainings (Black Belt and Green Belt) • Certification Program • Sites Starting to Deploy Huddle Boards • VISN-wide 5 S Day • Share. Point Site Revamped including tools • Relaunched a VISN -wide Call as VISN 8 Showcase to highlight improvement work • Innovation Grants • Improvement and Innovation Committee • New Lean-Six Sigma Project Tracker Deployed and Modified • Internal Trainings (Improvement Champion, White Belt, and Yellow Belt) • Lego Simulation for all Sites • VISN-wide 5 S Day • Development of Strong Practice Criteria • Innovation Grants • 24 Showcase Calls • 49 posters and 9 workshops at Improvement Forum • 5 Newsletters (4 quarterly and 1 special 5 S edition)
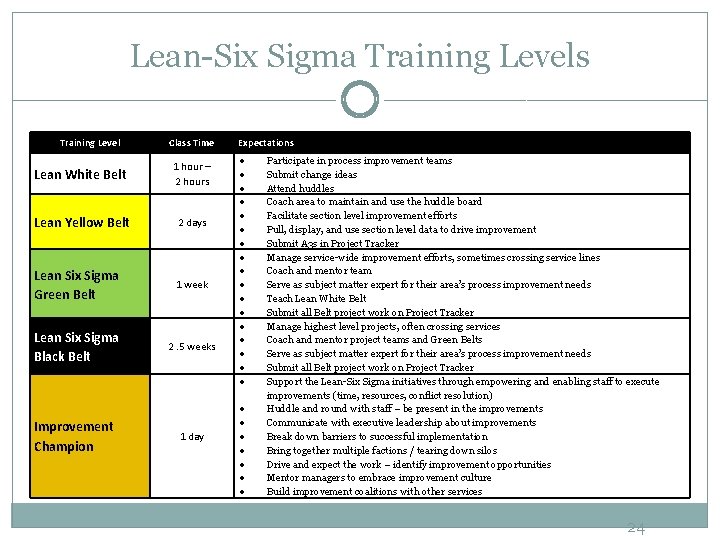
Lean-Six Sigma Training Levels Training Level Class Time Lean White Belt 1 hour – 2 hours Lean Yellow Belt 2 days Lean Six Sigma Green Belt 1 week Lean Six Sigma Black Belt 2. 5 weeks Improvement Champion 1 day Expectations Participate in process improvement teams Submit change ideas Attend huddles Coach area to maintain and use the huddle board Facilitate section level improvement efforts Pull, display, and use section level data to drive improvement Submit A 3 s in Project Tracker Manage service-wide improvement efforts, sometimes crossing service lines Coach and mentor team Serve as subject matter expert for their area’s process improvement needs Teach Lean White Belt Submit all Belt project work on Project Tracker Manage highest level projects, often crossing services Coach and mentor project teams and Green Belts Serve as subject matter expert for their area’s process improvement needs Submit all Belt project work on Project Tracker Support the Lean-Six Sigma initiatives through empowering and enabling staff to execute improvements (time, resources, conflict resolution) Huddle and round with staff – be present in the improvements Communicate with executive leadership about improvements Break down barriers to successful implementation Bring together multiple factions / tearing down silos Drive and expect the work – identify improvement opportunities Mentor managers to embrace improvement culture Build improvement coalitions with other services 24
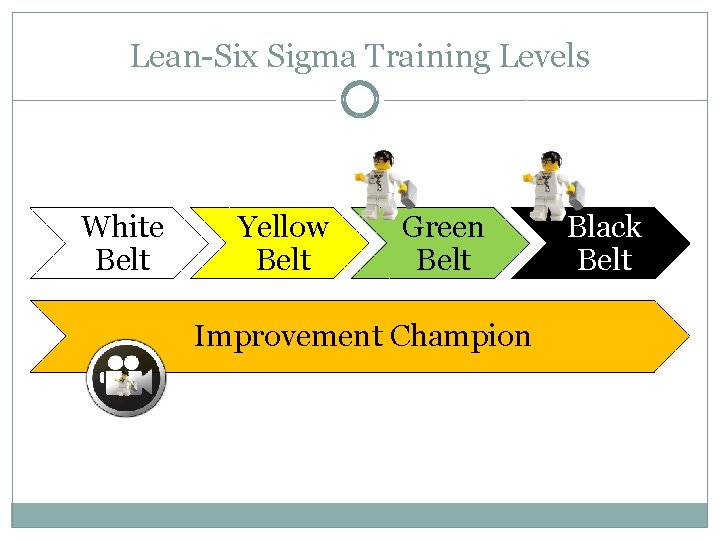
Lean-Six Sigma Training Levels White Belt Yellow Belt Green Belt Improvement Champion Black Belt
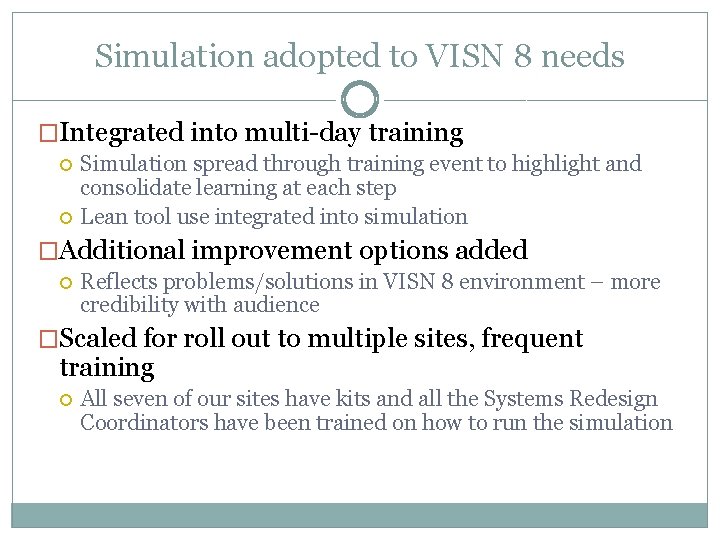
Simulation adopted to VISN 8 needs �Integrated into multi-day training Simulation spread through training event to highlight and consolidate learning at each step Lean tool use integrated into simulation �Additional improvement options added Reflects problems/solutions in VISN 8 environment – more credibility with audience �Scaled for roll out to multiple sites, frequent training All seven of our sites have kits and all the Systems Redesign Coordinators have been trained on how to run the simulation
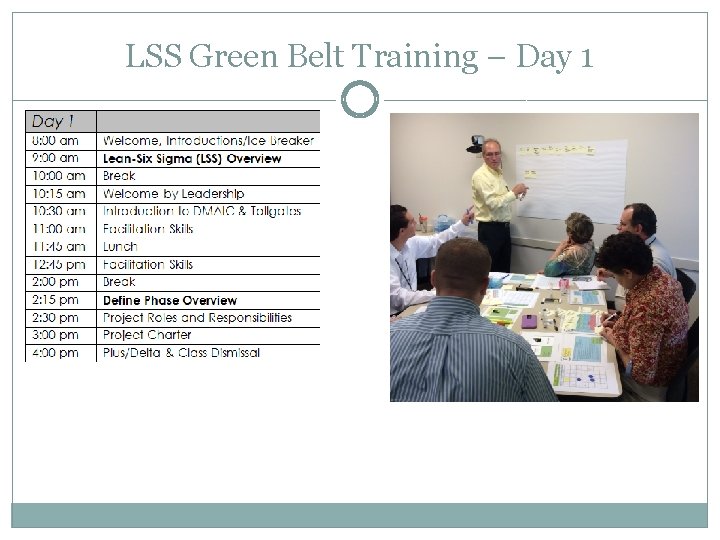
LSS Green Belt Training – Day 1
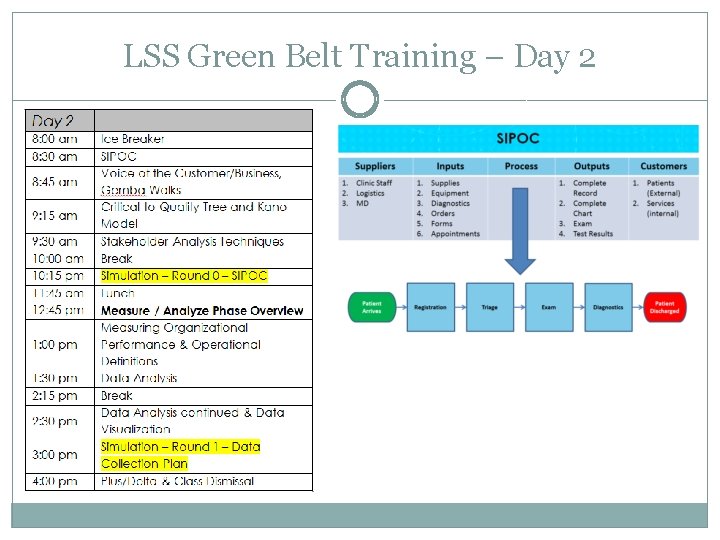
LSS Green Belt Training – Day 2
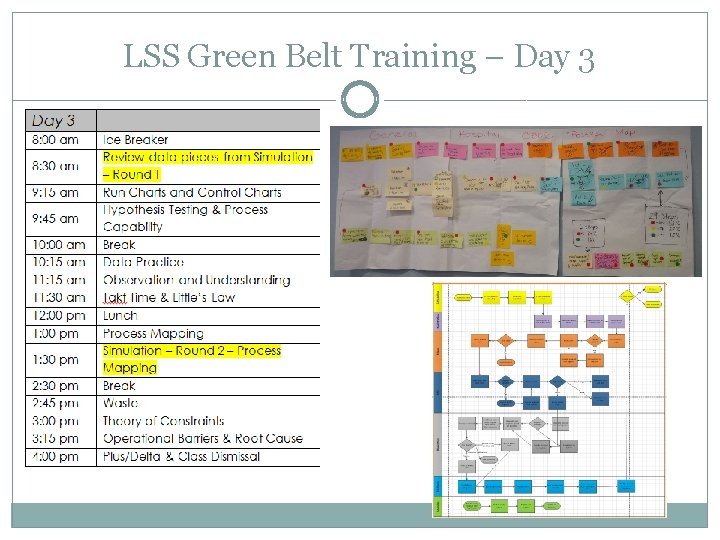
LSS Green Belt Training – Day 3
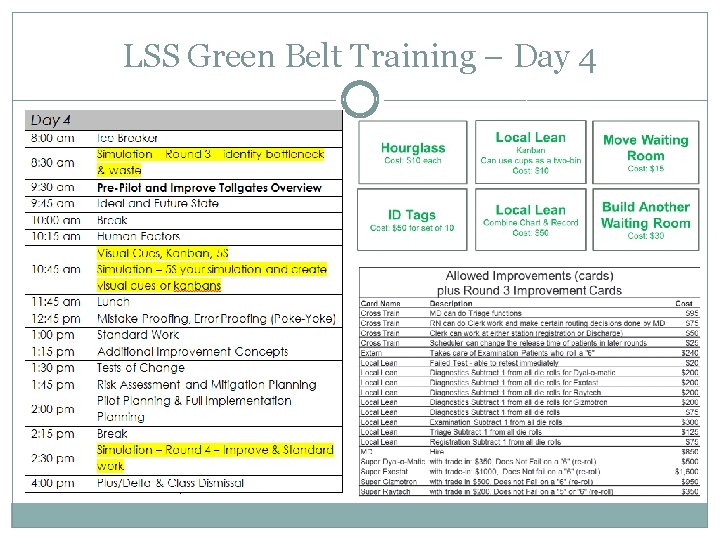
LSS Green Belt Training – Day 4
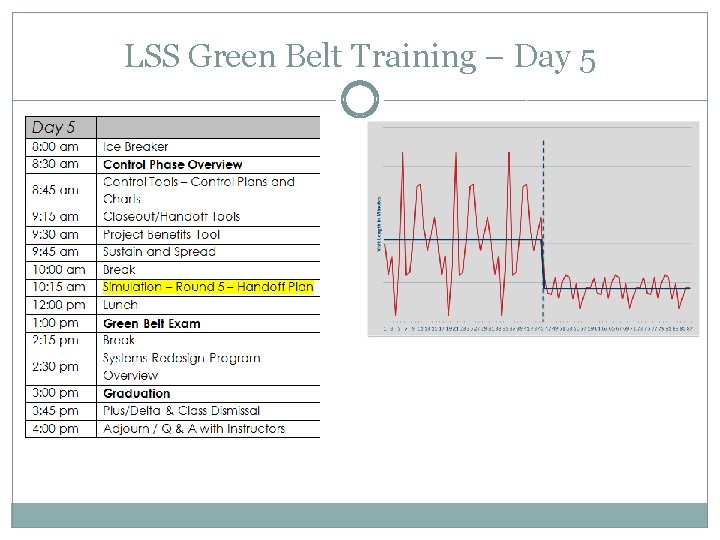
LSS Green Belt Training – Day 5
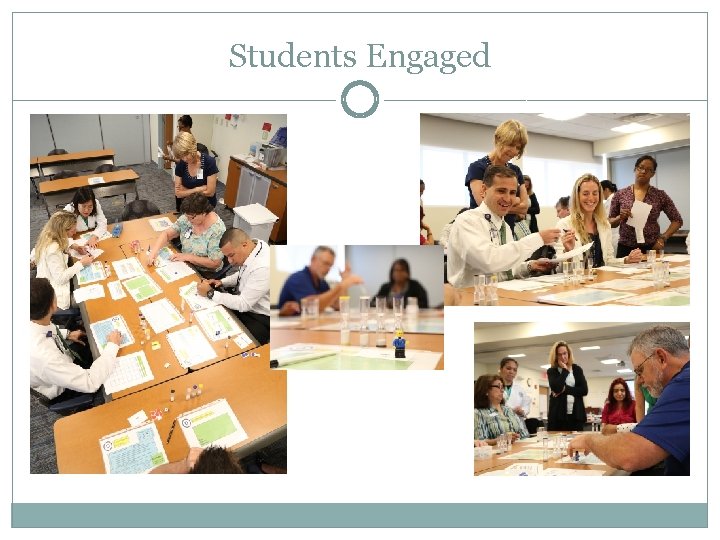
Students Engaged
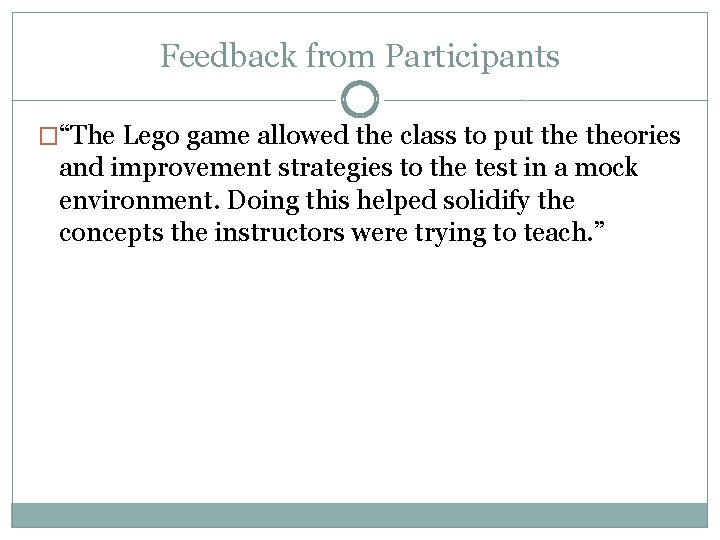
Feedback from Participants �“The Lego game allowed the class to put theories and improvement strategies to the test in a mock environment. Doing this helped solidify the concepts the instructors were trying to teach. ”
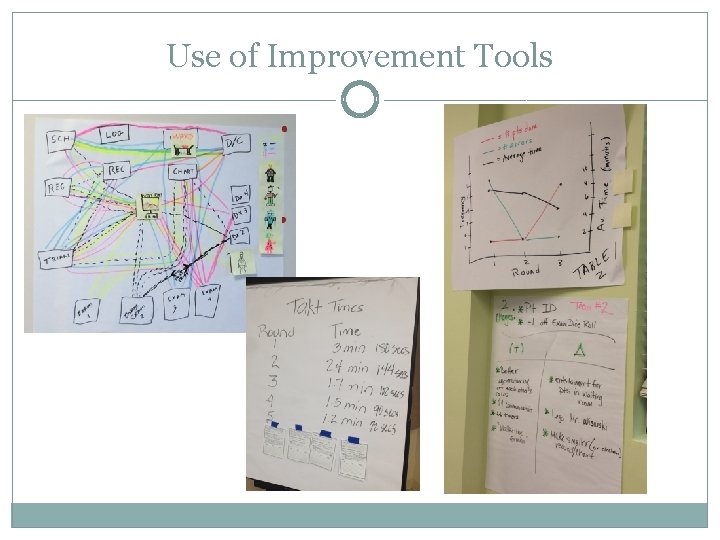
Use of Improvement Tools

Visual Management
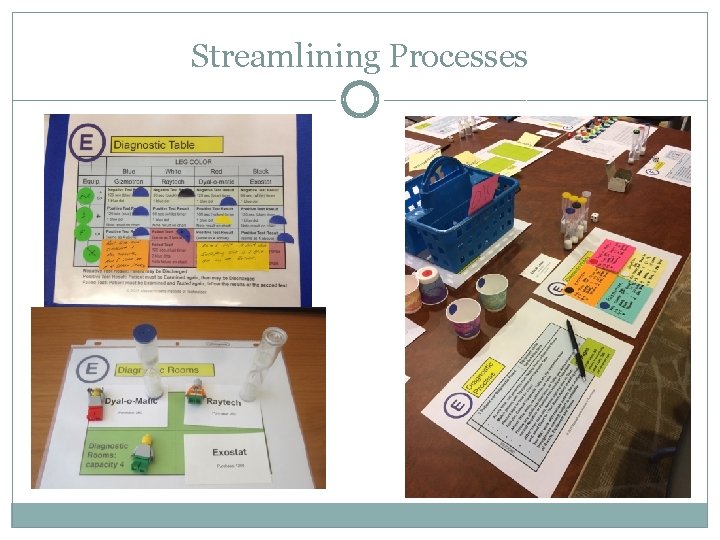
Streamlining Processes
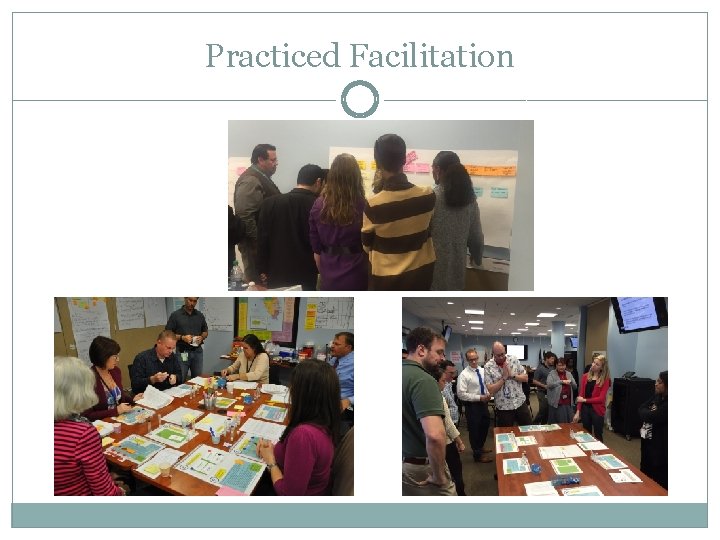
Practiced Facilitation

Summary �Over 400 of our Lean-Six Sigma belts have used the Lego during their training. �The Lego Simulation is an interactive and fun way to engage students with Lean-Six Sigma tools. �Students can practice improvement skills with hands-on, real-time feedback. �Failure is encouraged and expected during the Lego Simulation.
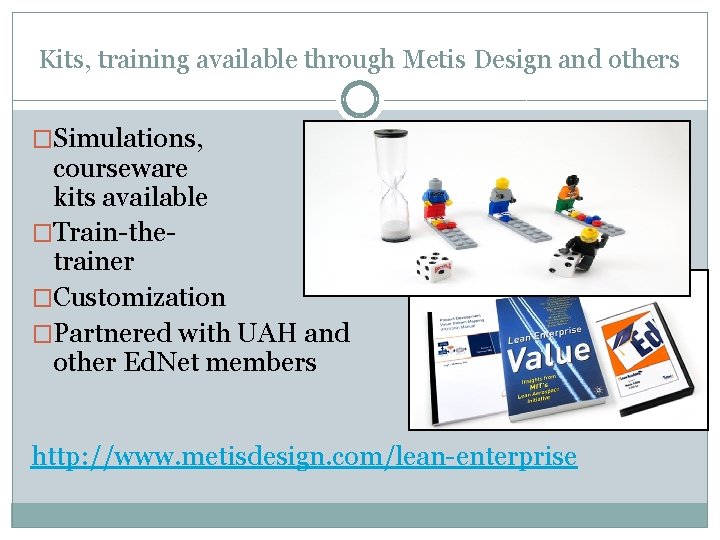
Kits, training available through Metis Design and others �Simulations, courseware kits available �Train-thetrainer �Customization �Partnered with UAH and other Ed. Net members http: //www. metisdesign. com/lean-enterprise
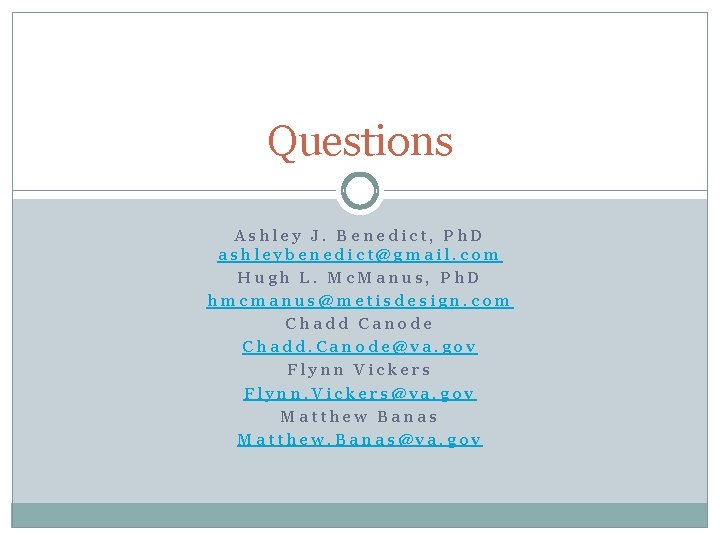
Questions Ashley J. Benedict, Ph. D ashleybenedict@gmail. com Hugh L. Mc. Manus, Ph. D hmcmanus@metisdesign. com Chadd Canode Chadd. Canode@va. gov Flynn Vickers Flynn. Vickers@va. gov Matthew Banas Matthew. Banas@va. gov
Lai lean academy
Signal phrases
Integrating sources into your writing
Vcom white coat ceremony
Edward via college of osteopathic medicine auburn
Integrating concepts in biology
Integrating classification and association rule mining
Composite function integration
Integrating quotes
Integrating marketing communication to build brand equity
Integrating sel and pbis
Blending quotations
Embedded quotes mla examples
Integration by parts meaning
Strategic management internal assessment
Microsoft dynamics 365 plm
Integrating factor
Integrating factor of differential equation
Integrating strategy and culture in internal assessment
Integrating public health and primary care
Longitudinal fissure
Integrating business perspectives
Knapps relational model
Integration of partial differential equation
Middle level integration
Integrating qualitative and quantitative methods
First order ode
Exact differential equation integrating factor
Conscious marketing vs csr
Integrating factor method
Integrating science and social studies
Integrating factor
Integrating factor formula
Tactical communication skills
Process indicators enable software project manager to
Integrating type dvm
Lego blm
Lego cad software
Lego engagement
Pretotyping
Automatic lego sorter