Circuit Master CFA 1000 Introduction Crimp Force Analysis
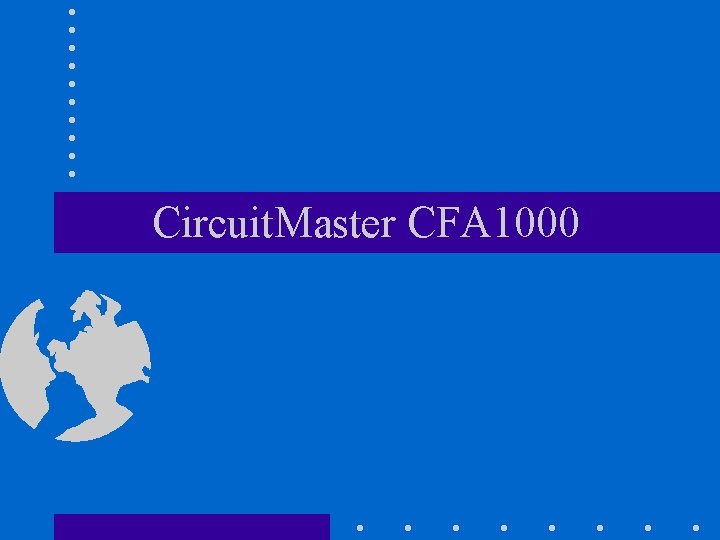
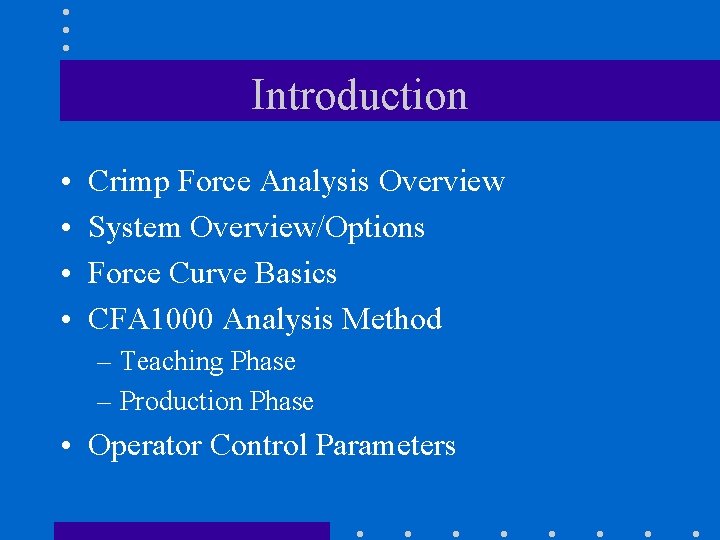
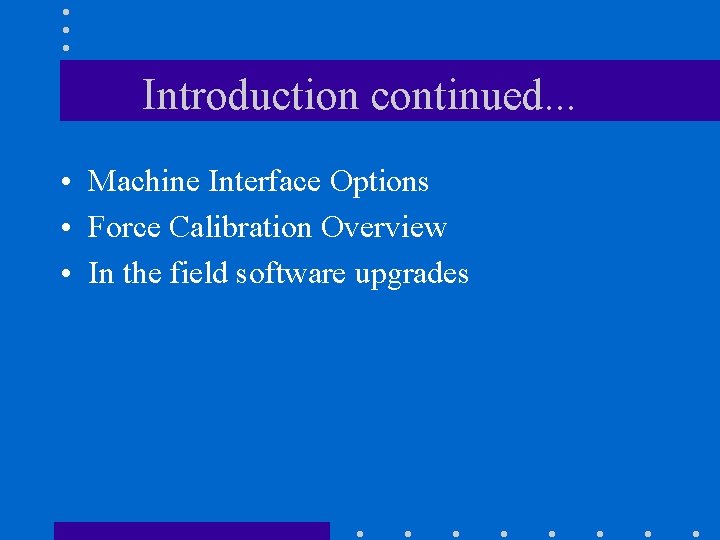
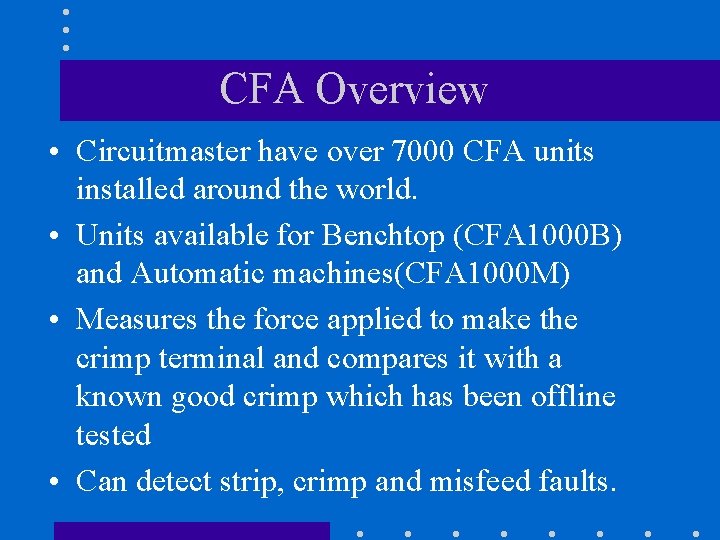
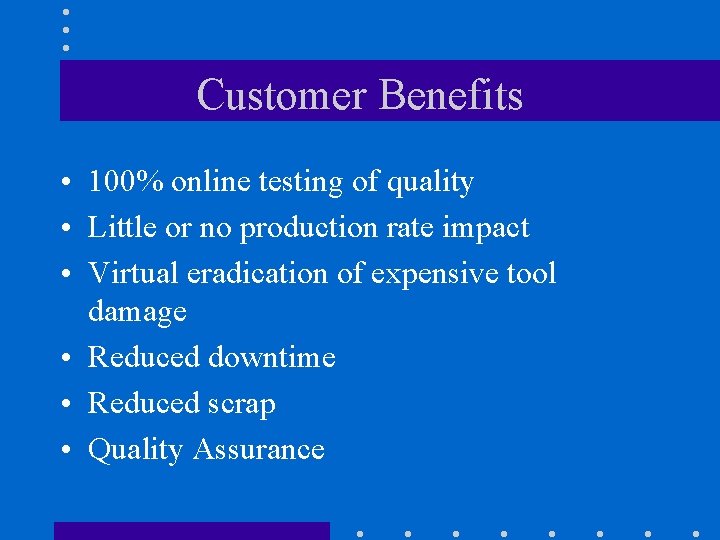
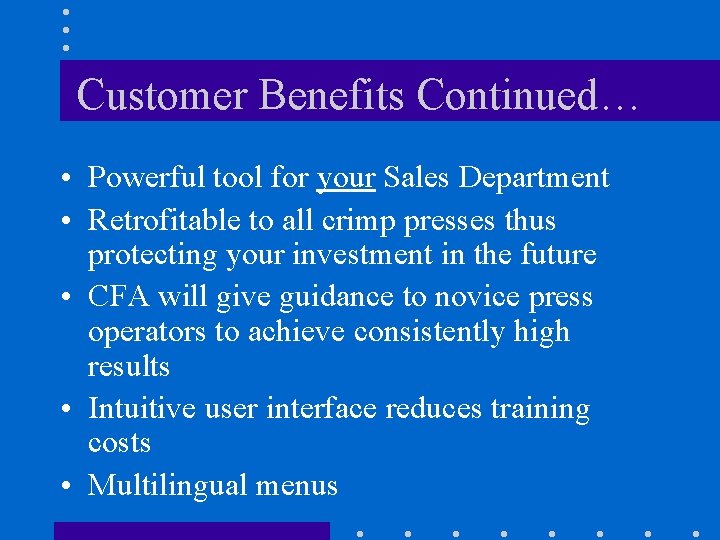
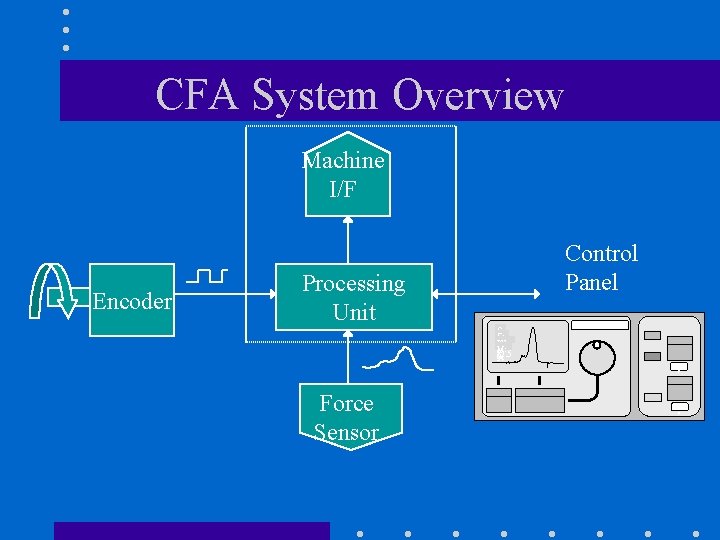
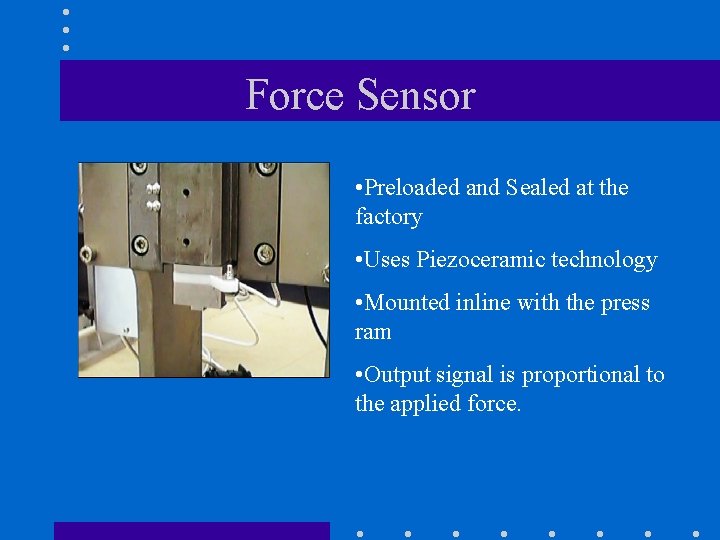
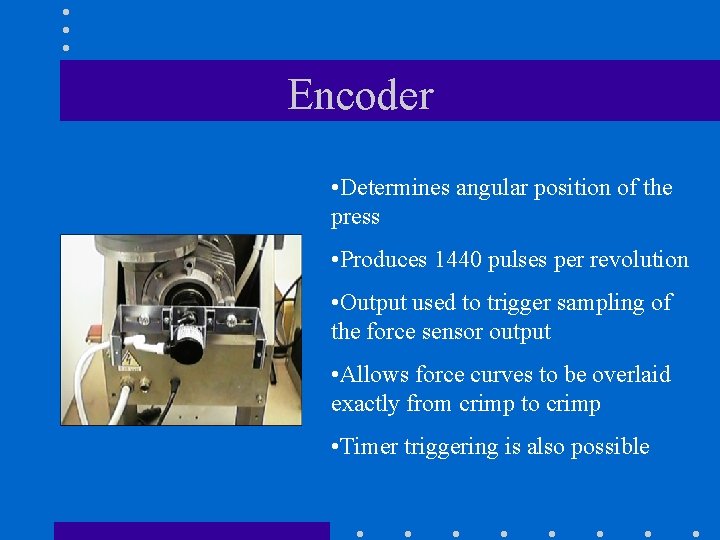
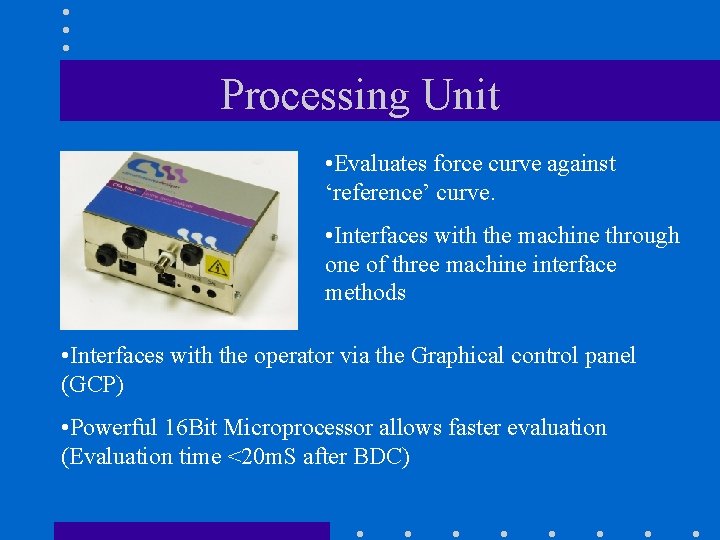
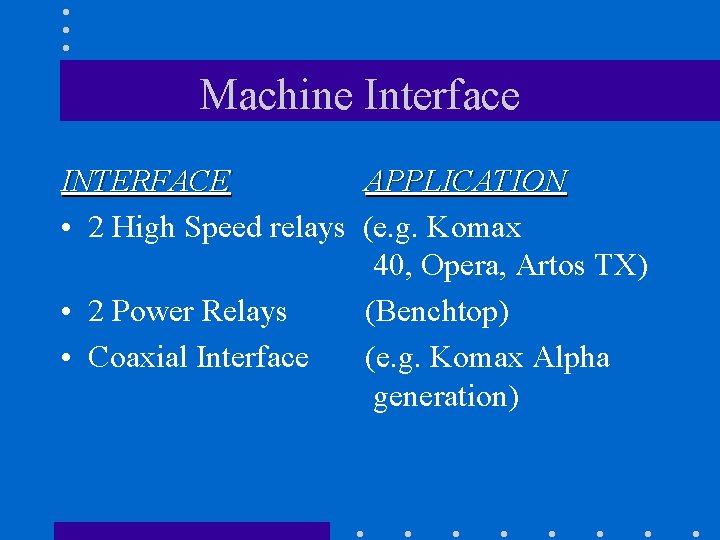
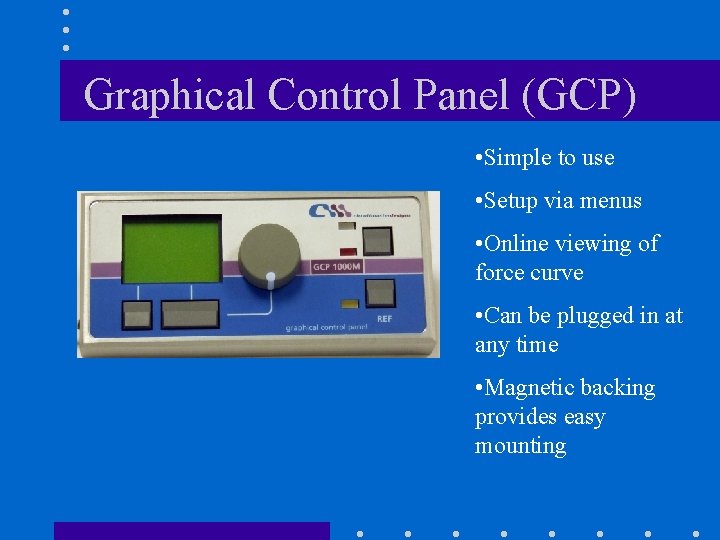
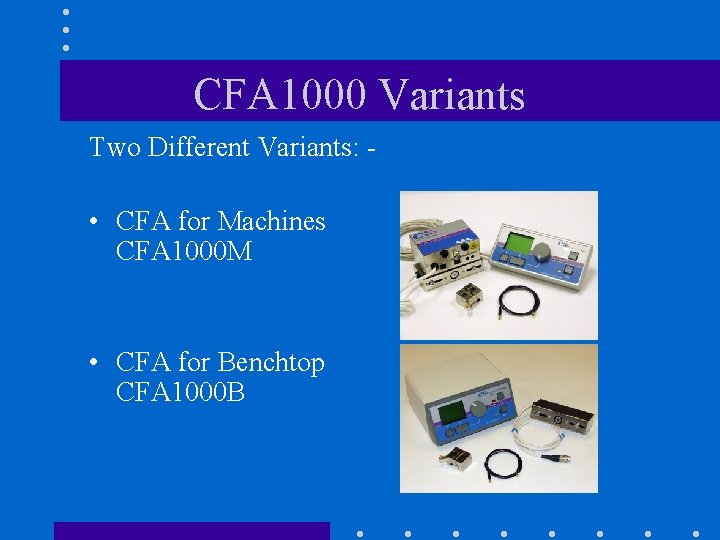
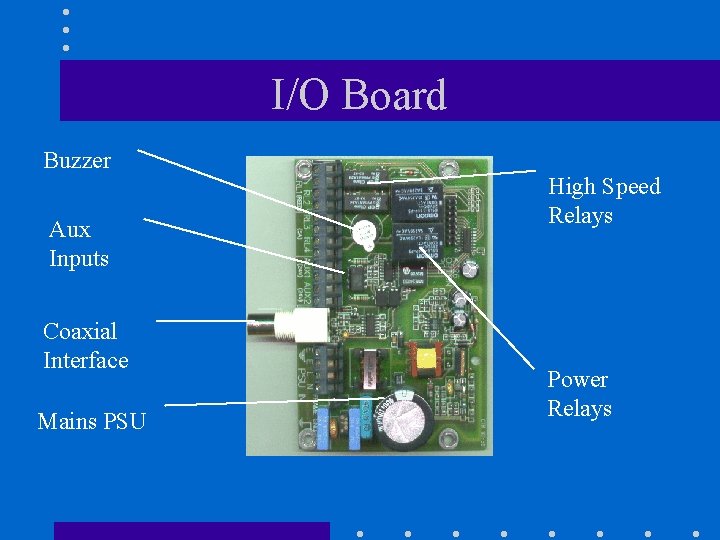
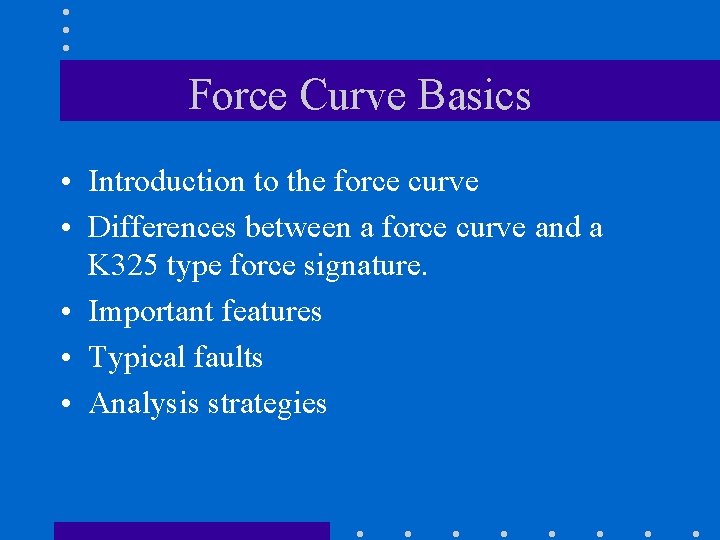
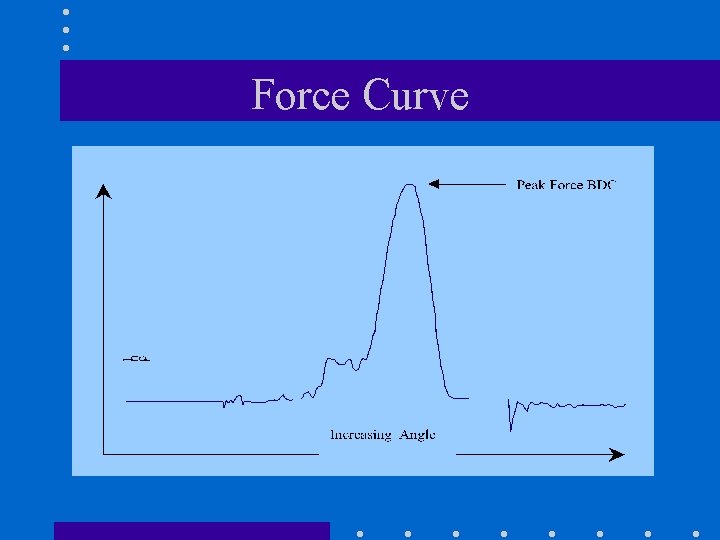
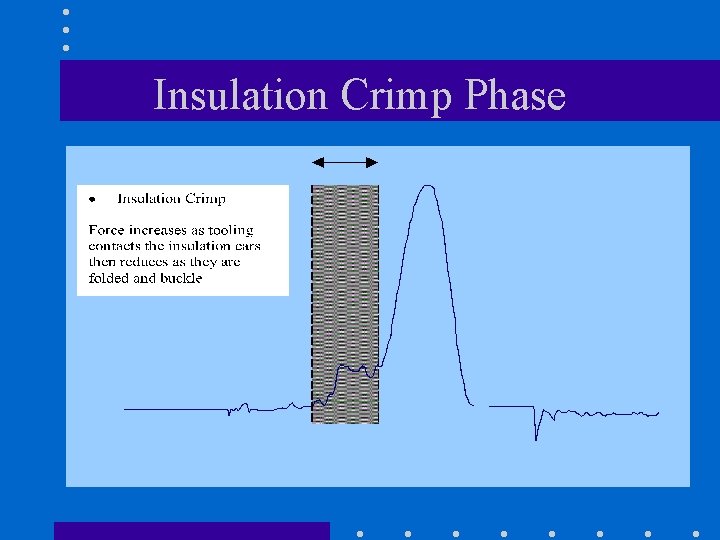
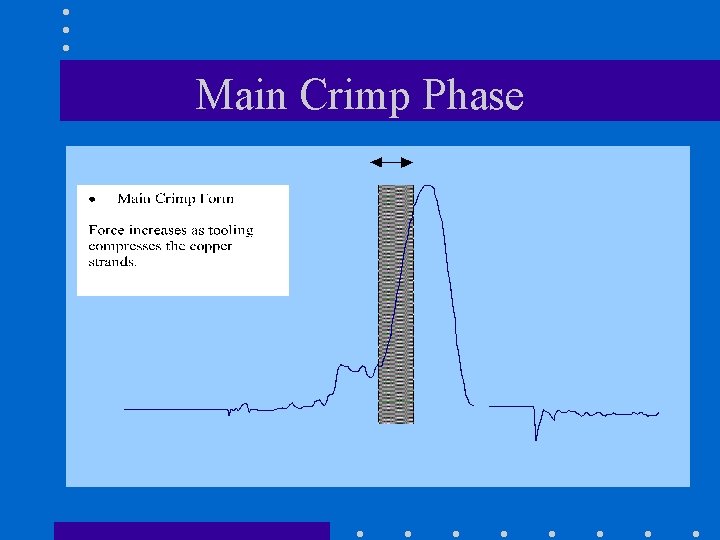
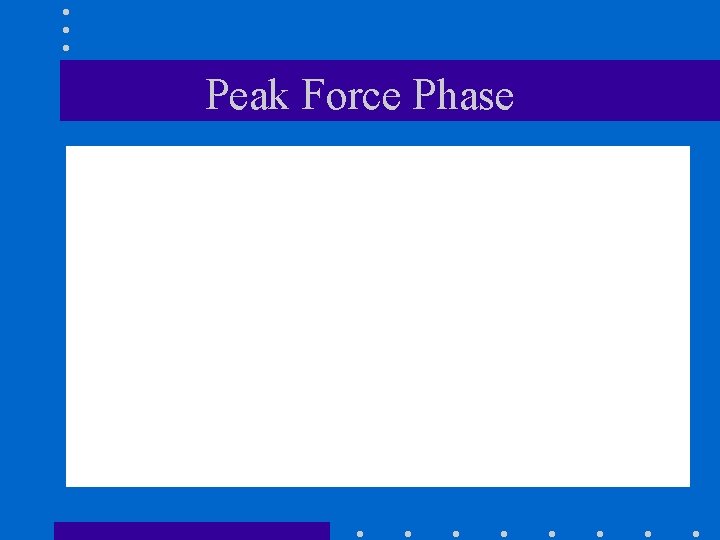
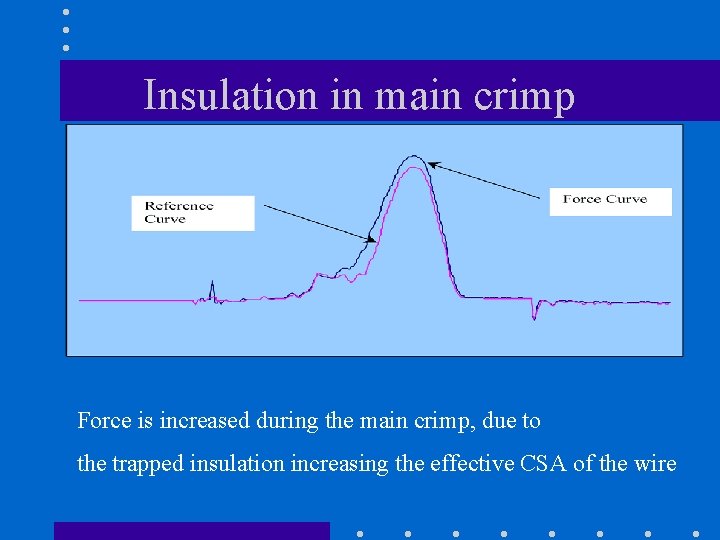
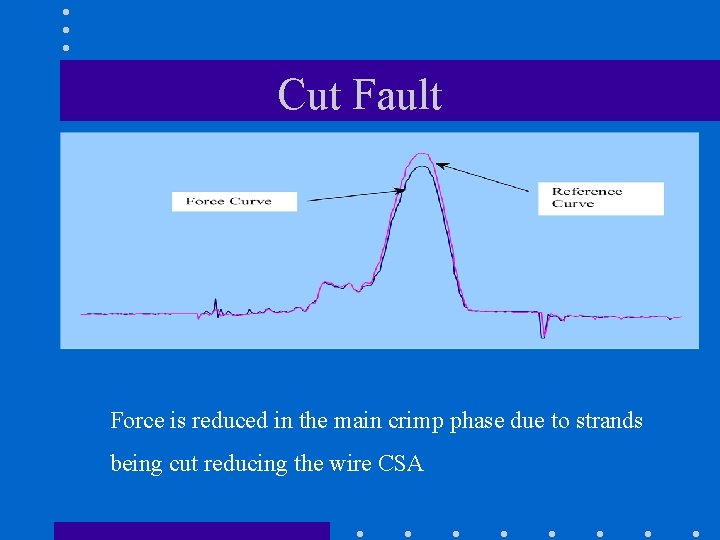
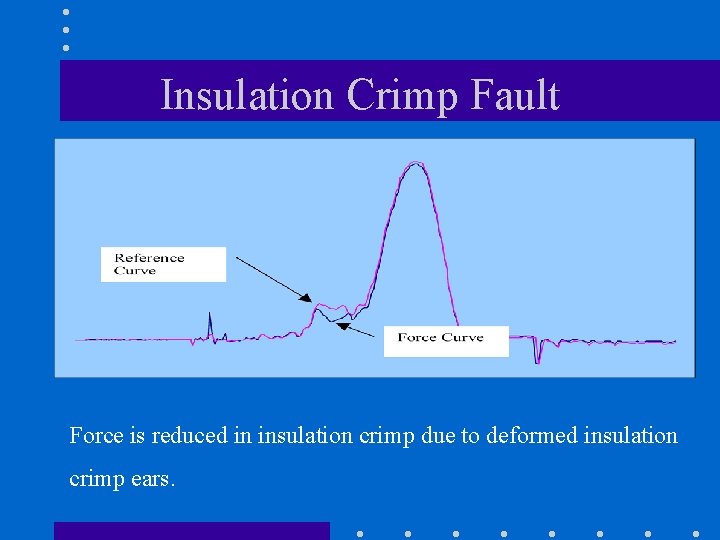
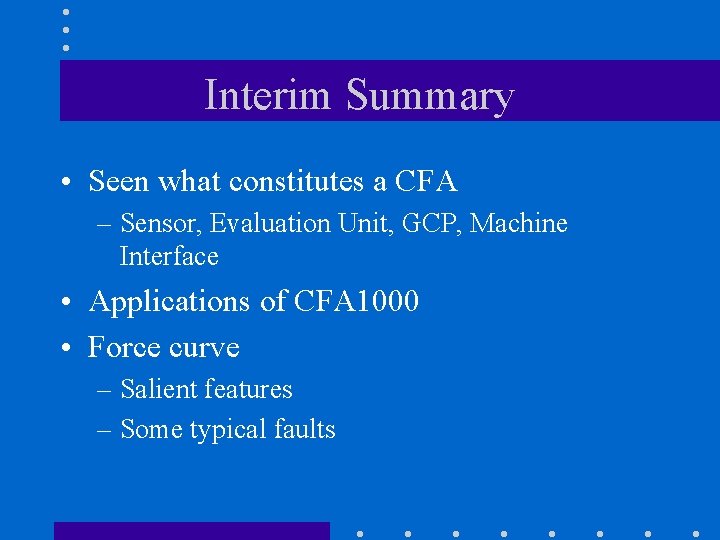
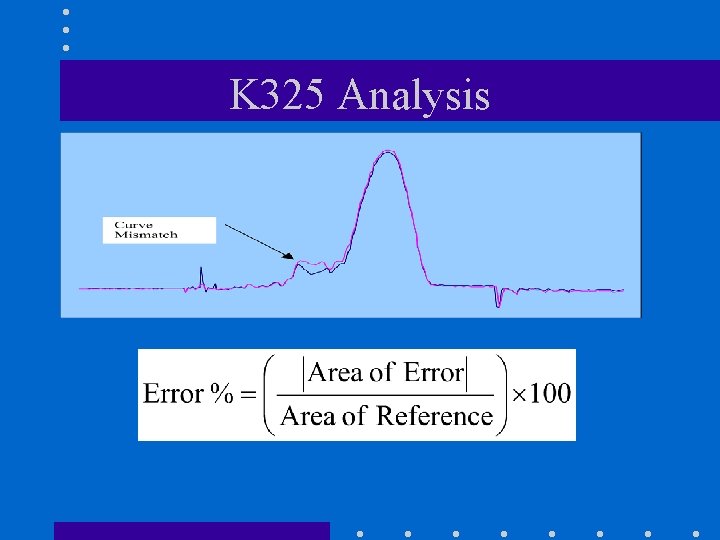
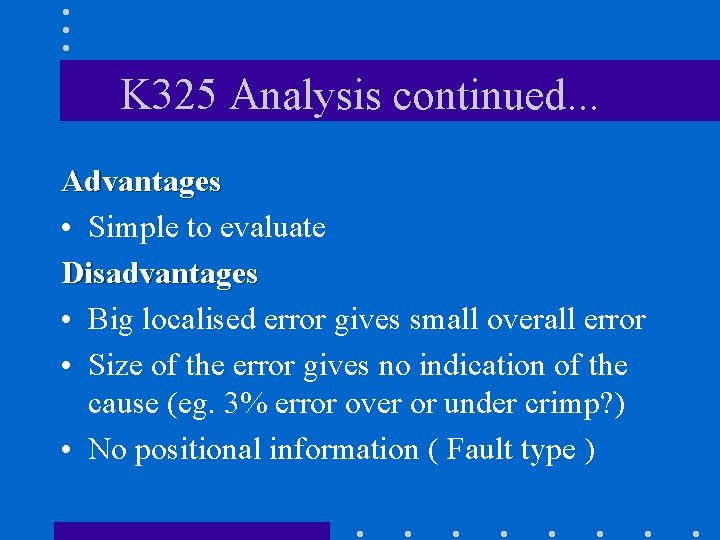
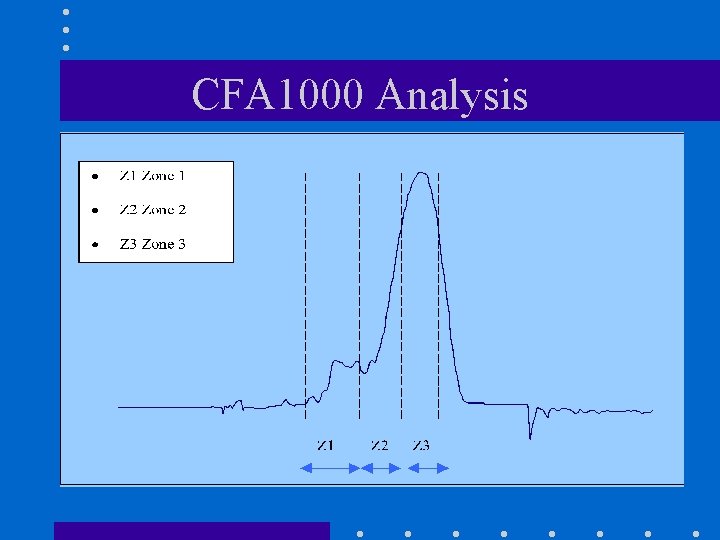
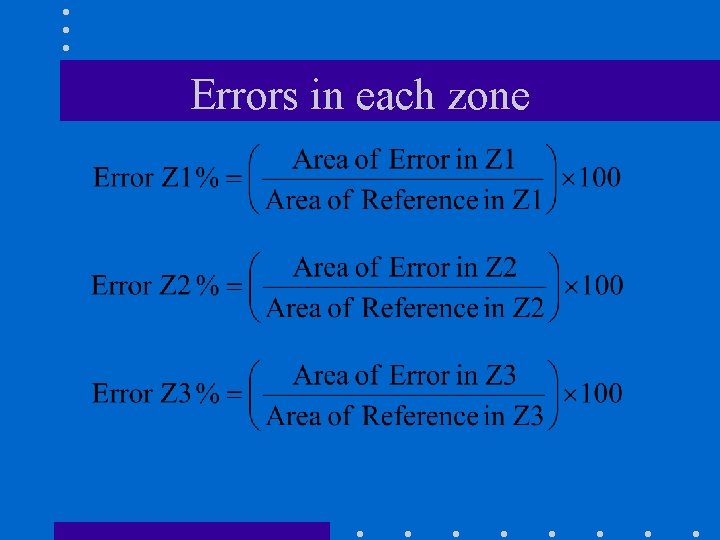
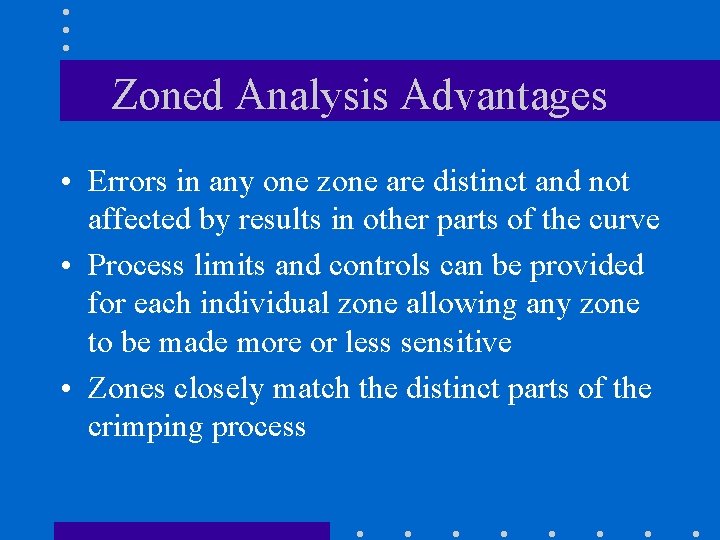
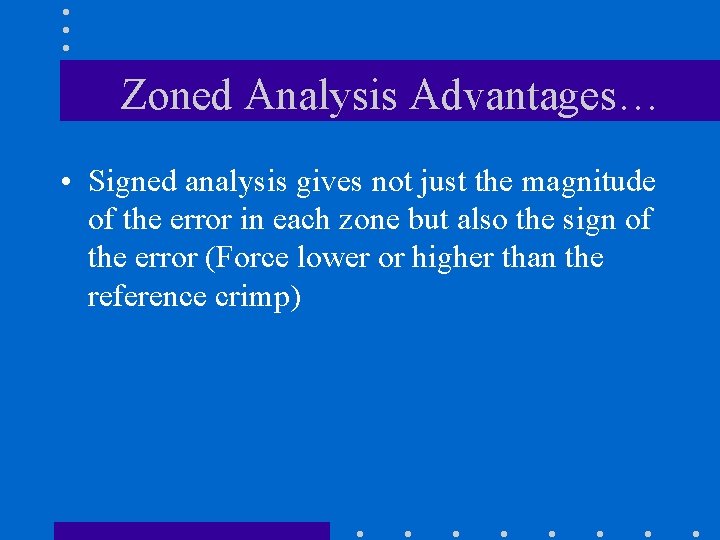
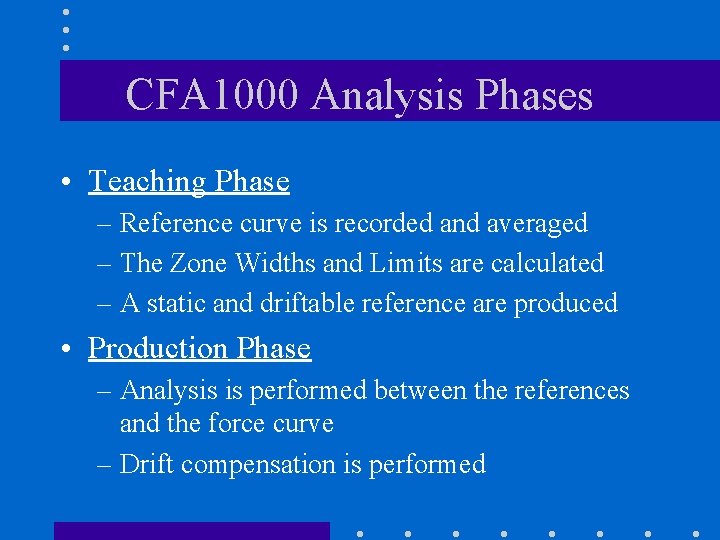
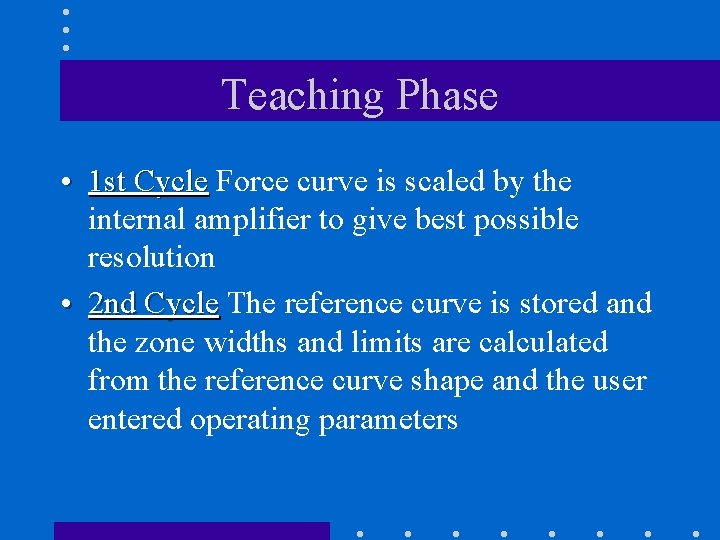
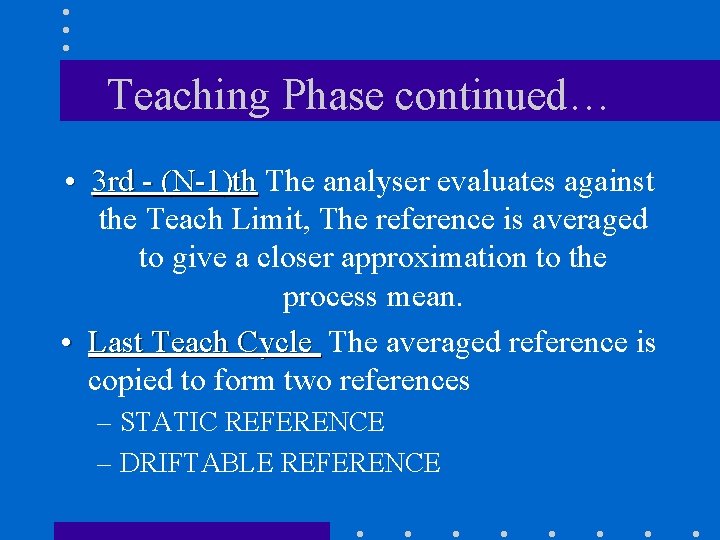
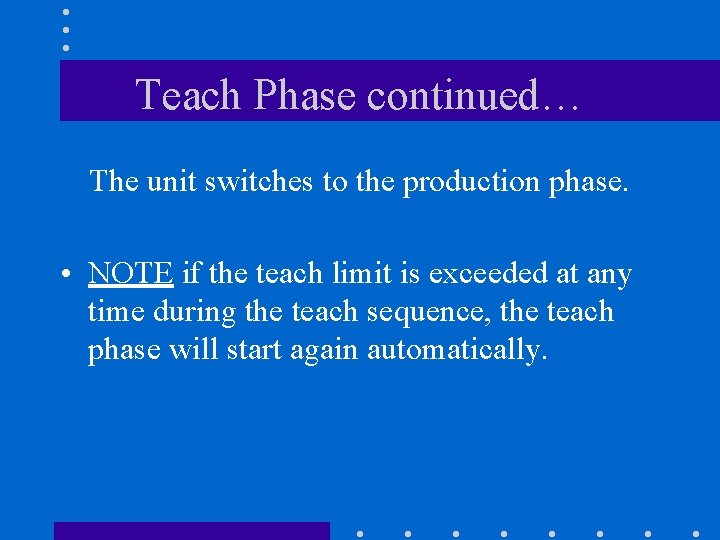
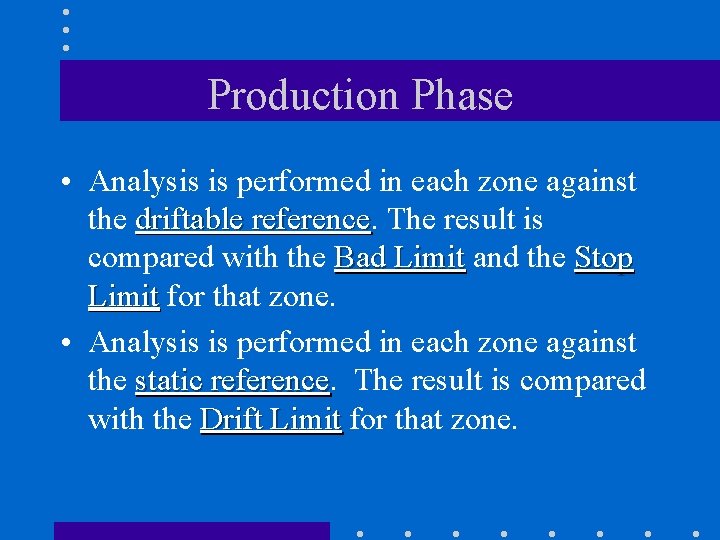
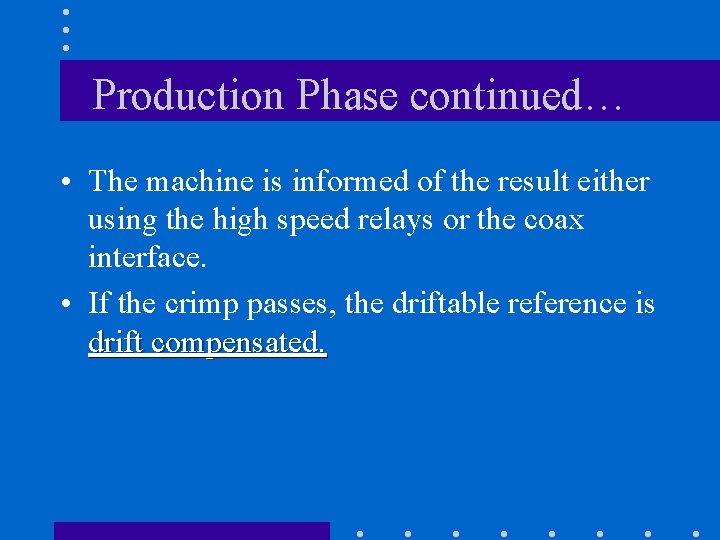
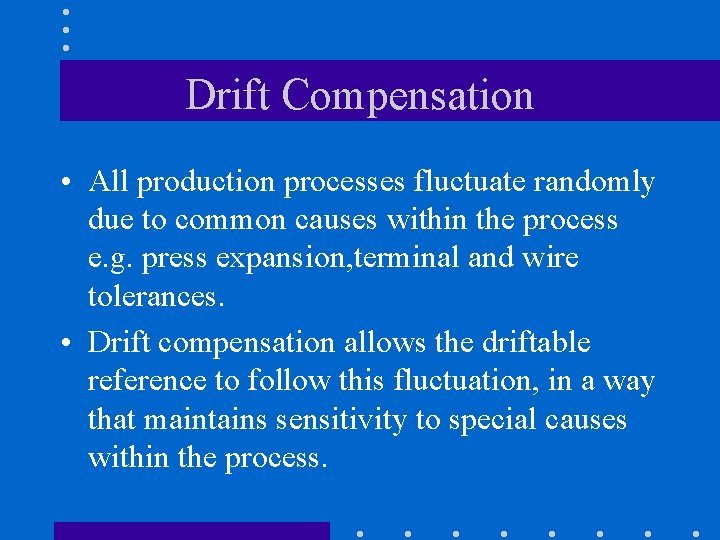
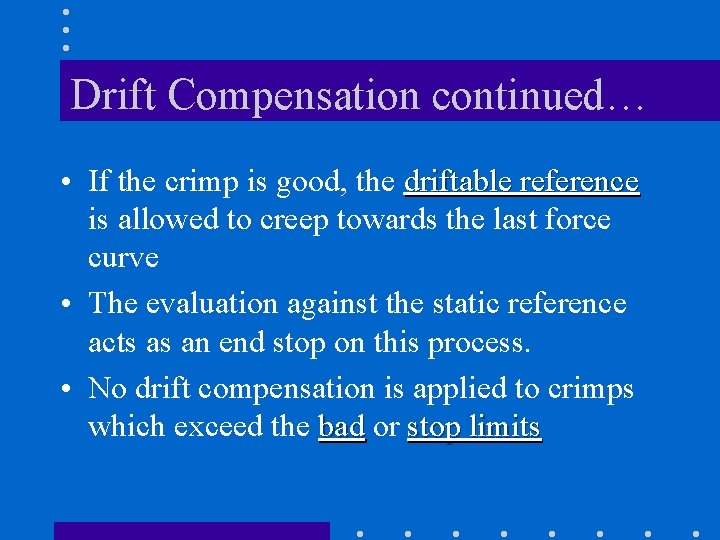
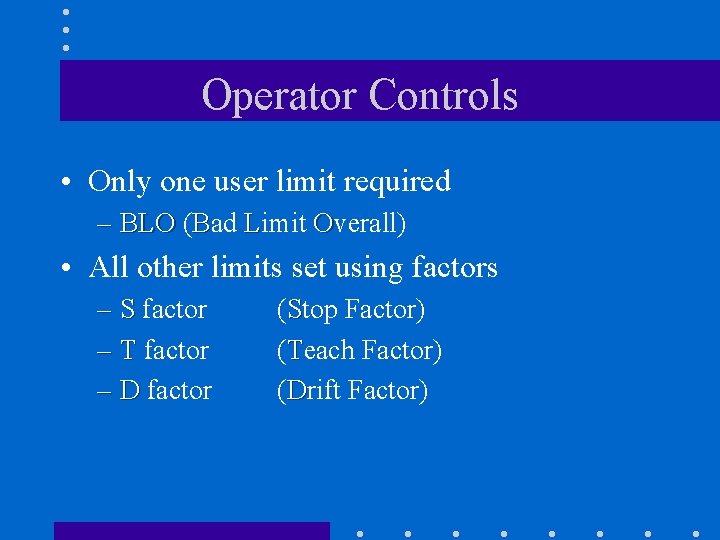
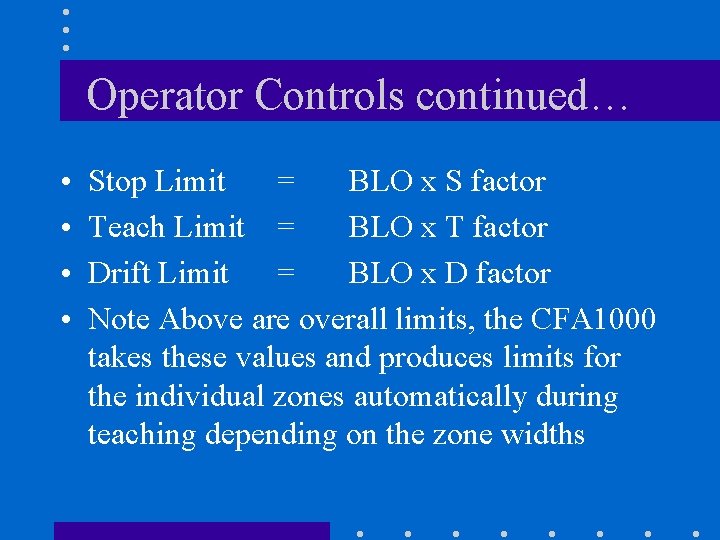
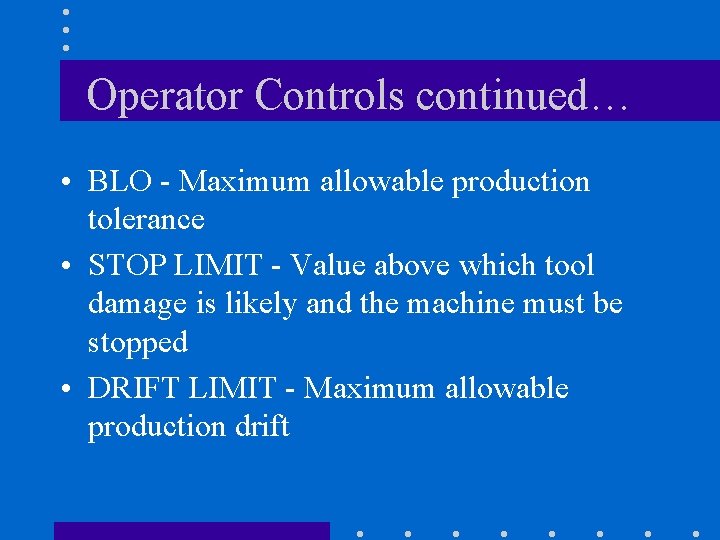
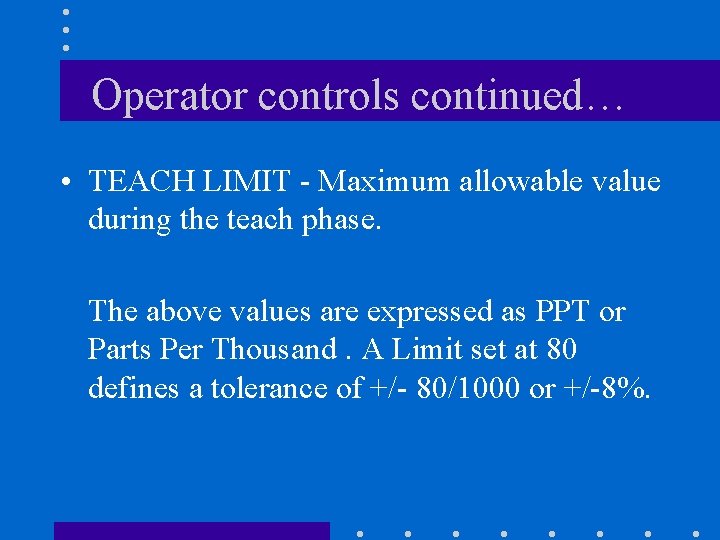
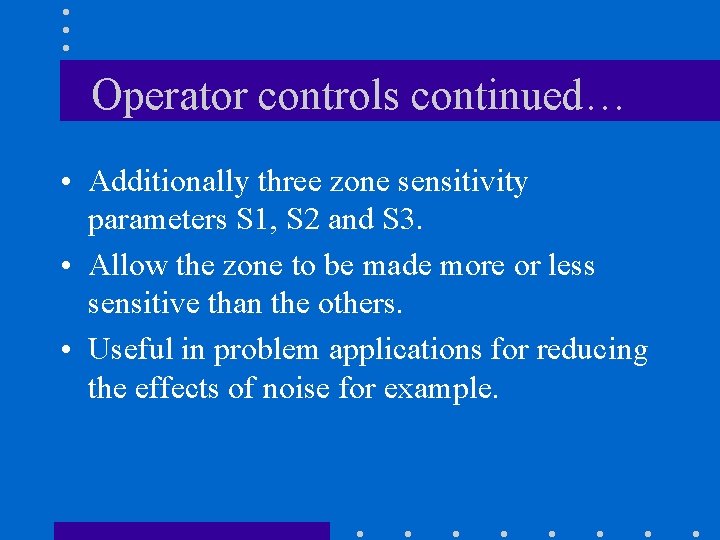
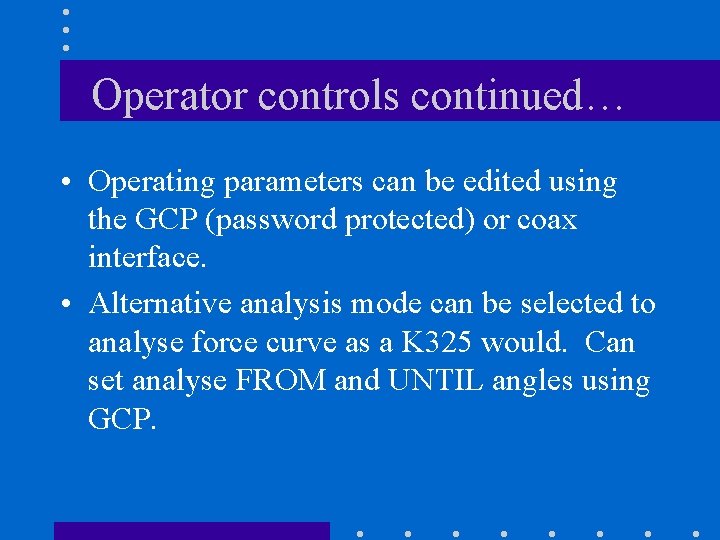
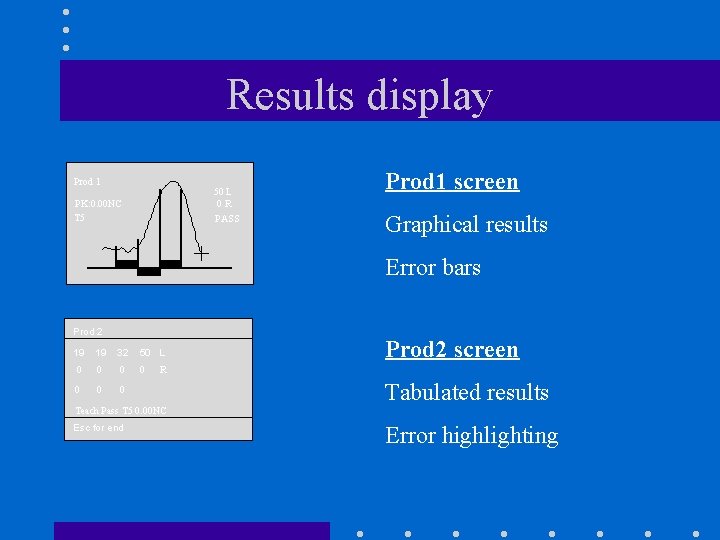
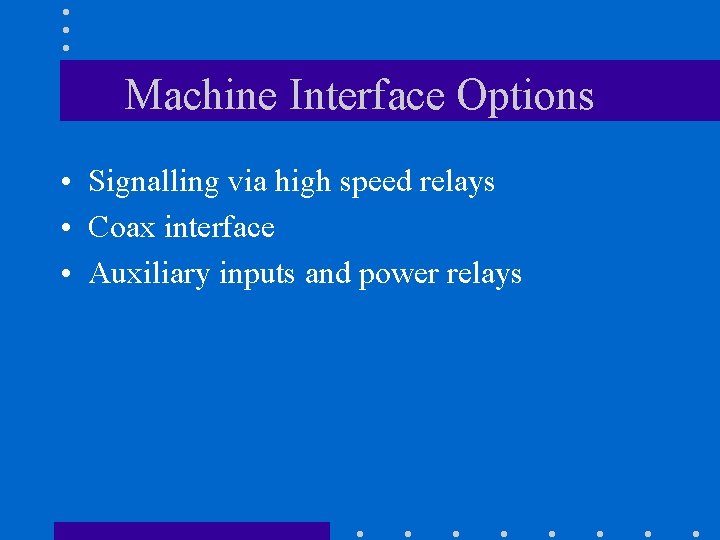
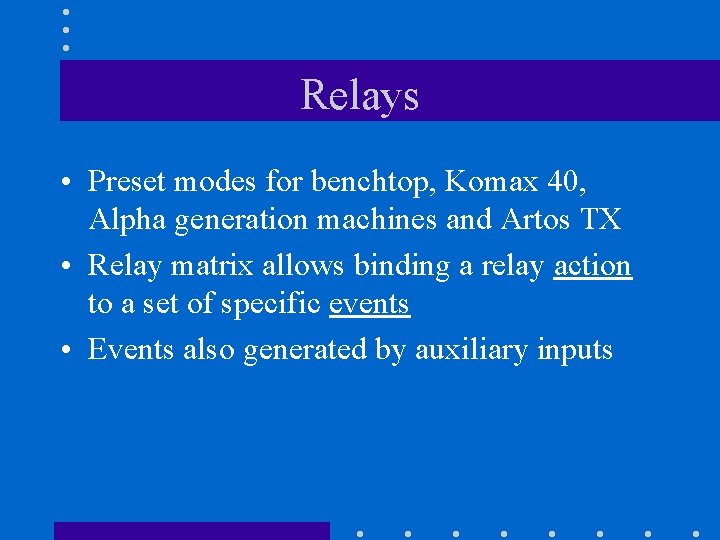
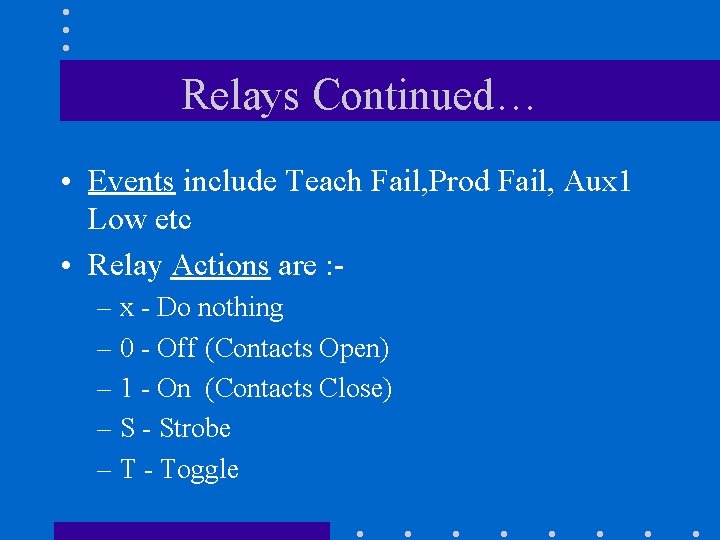
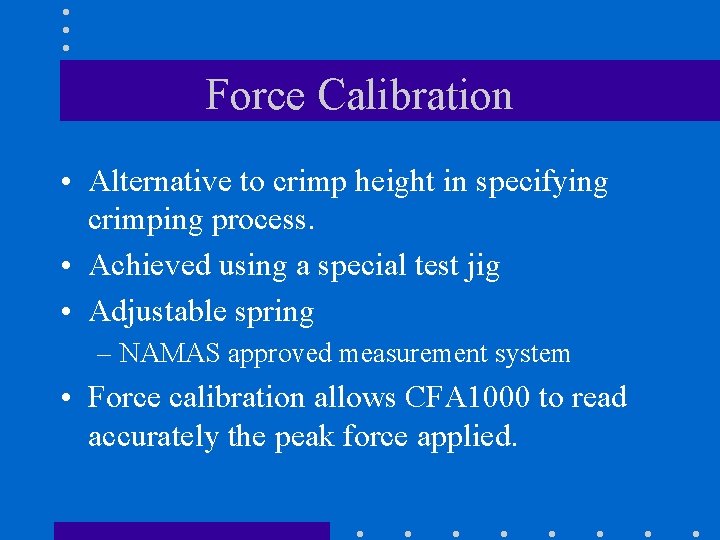
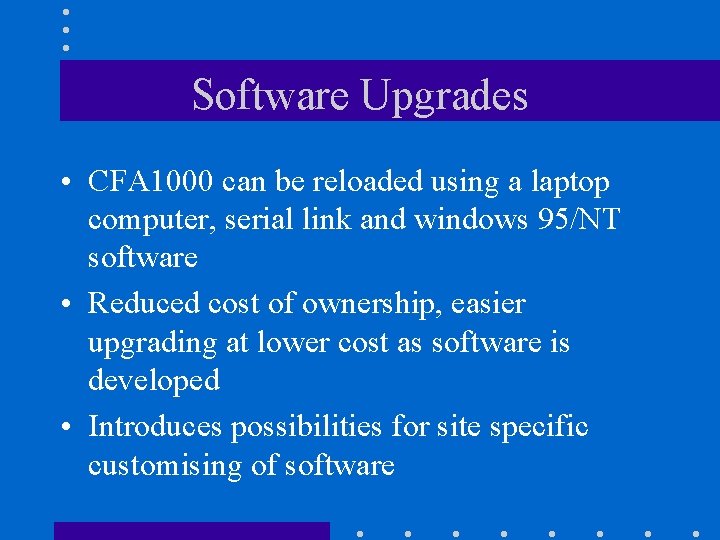
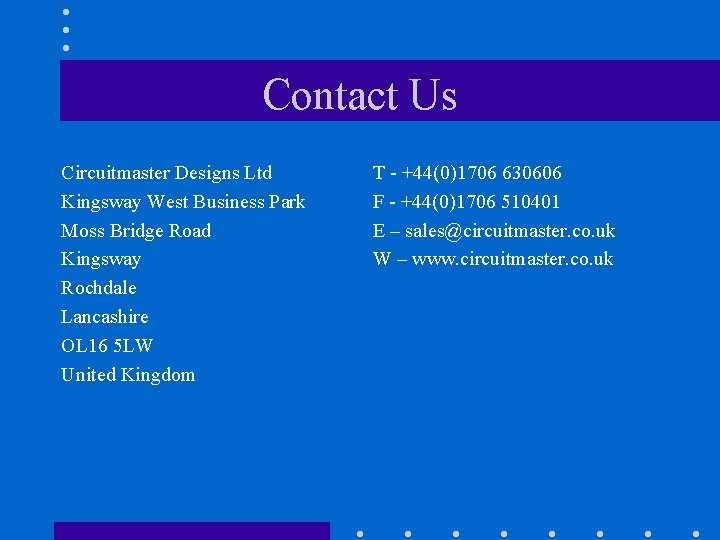
- Slides: 50
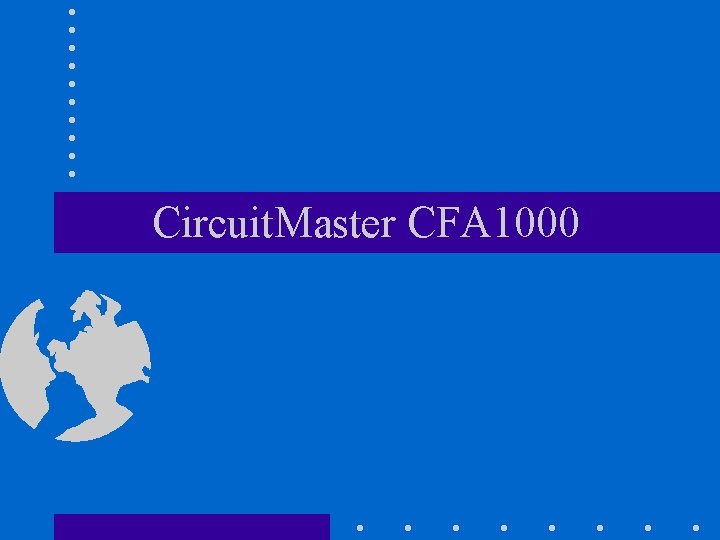
Circuit. Master CFA 1000
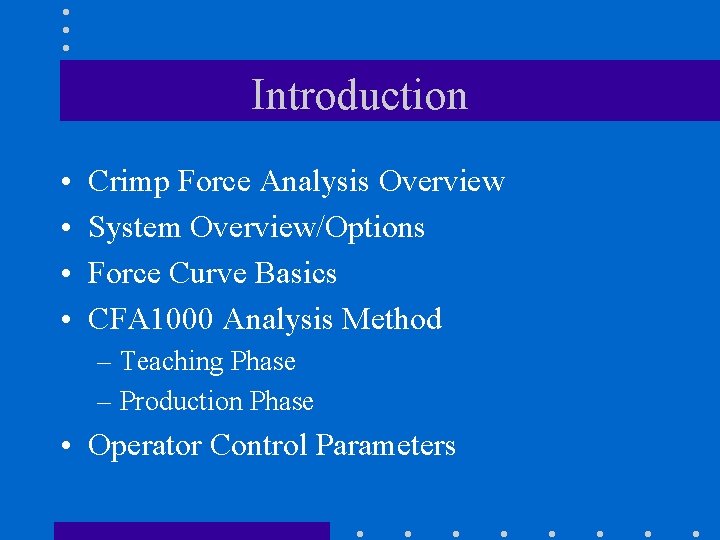
Introduction • • Crimp Force Analysis Overview System Overview/Options Force Curve Basics CFA 1000 Analysis Method – Teaching Phase – Production Phase • Operator Control Parameters
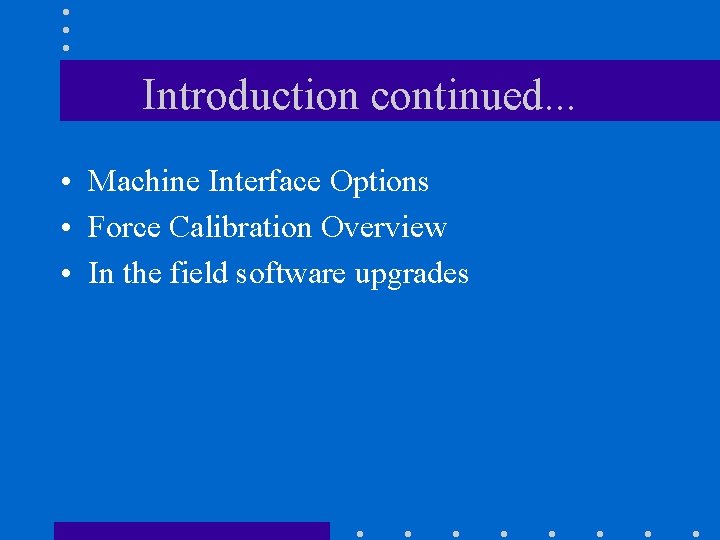
Introduction continued. . . • Machine Interface Options • Force Calibration Overview • In the field software upgrades
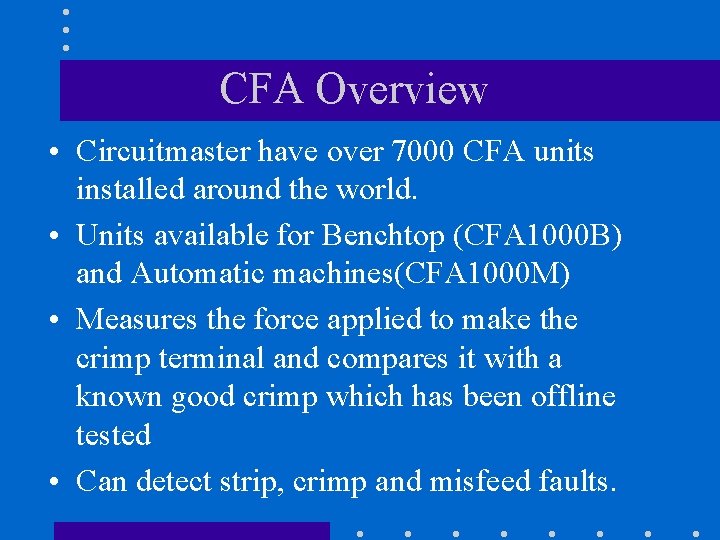
CFA Overview • Circuitmaster have over 7000 CFA units installed around the world. • Units available for Benchtop (CFA 1000 B) and Automatic machines(CFA 1000 M) • Measures the force applied to make the crimp terminal and compares it with a known good crimp which has been offline tested • Can detect strip, crimp and misfeed faults.
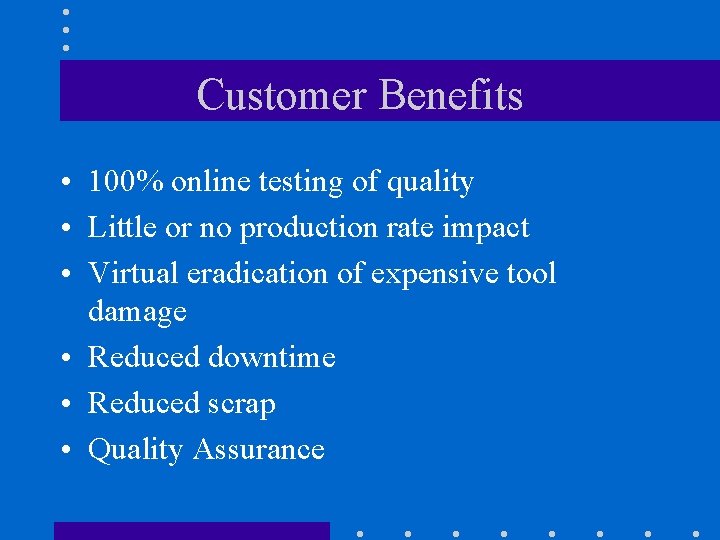
Customer Benefits • 100% online testing of quality • Little or no production rate impact • Virtual eradication of expensive tool damage • Reduced downtime • Reduced scrap • Quality Assurance
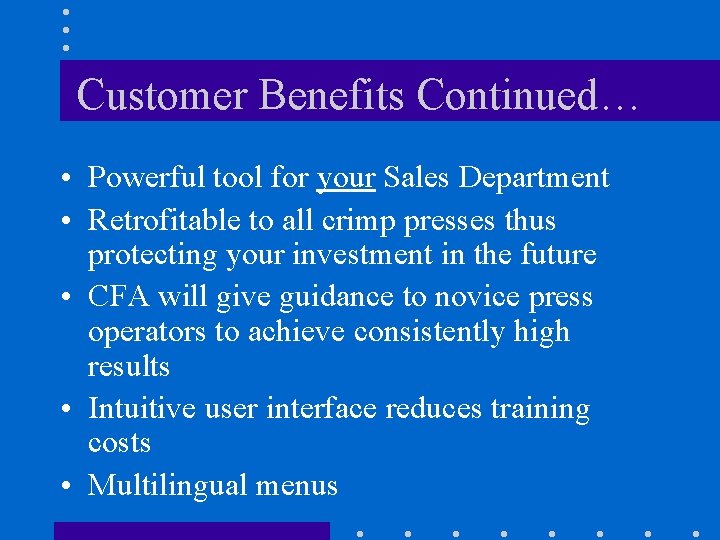
Customer Benefits Continued… • Powerful tool for your Sales Department • Retrofitable to all crimp presses thus protecting your investment in the future • CFA will give guidance to novice press operators to achieve consistently high results • Intuitive user interface reduces training costs • Multilingual menus
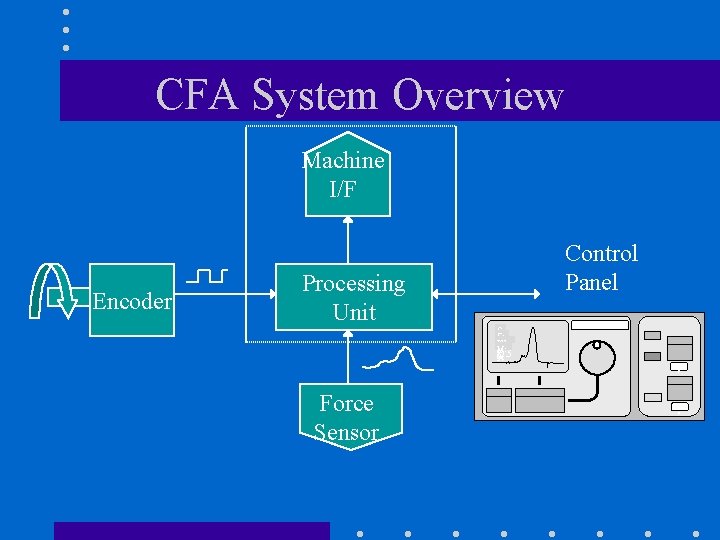
CFA System Overview Machine I/F Encoder Control Panel Processing Unit S E: : 3 PK: 12 M: 0 12. 5 0 34 Circuitmaster CFA 1000 CL R Force Sensor RE F
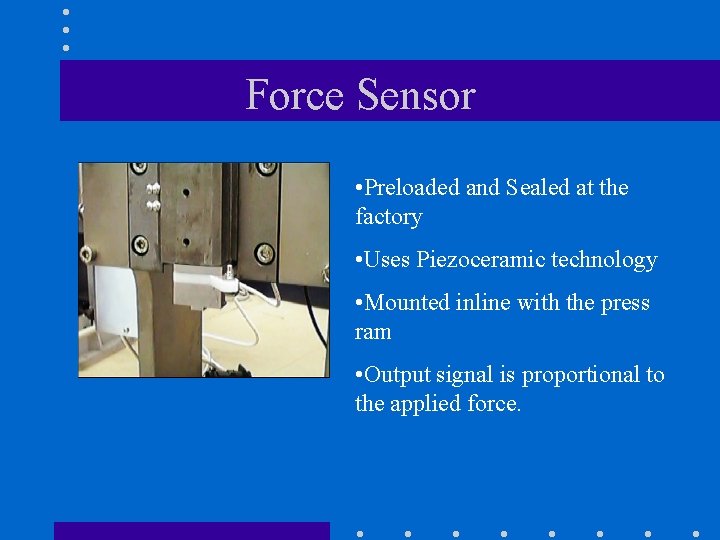
Force Sensor • Preloaded and Sealed at the factory • Uses Piezoceramic technology • Mounted inline with the press ram • Output signal is proportional to the applied force.
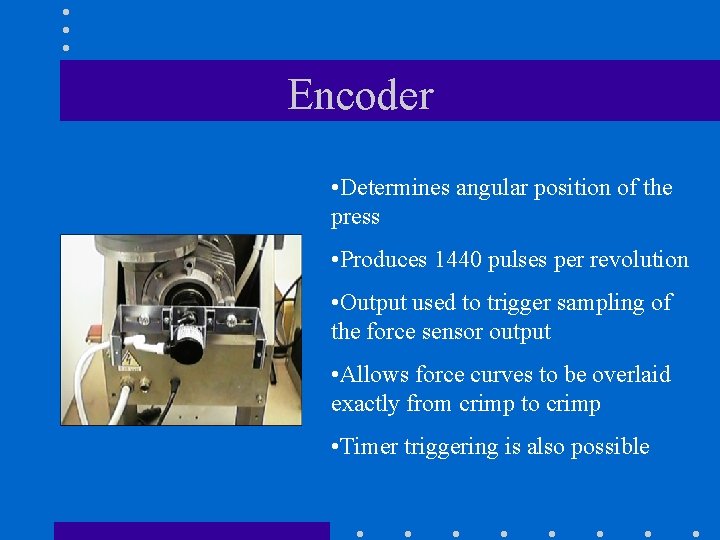
Encoder • Determines angular position of the press • Produces 1440 pulses per revolution • Output used to trigger sampling of the force sensor output • Allows force curves to be overlaid exactly from crimp to crimp • Timer triggering is also possible
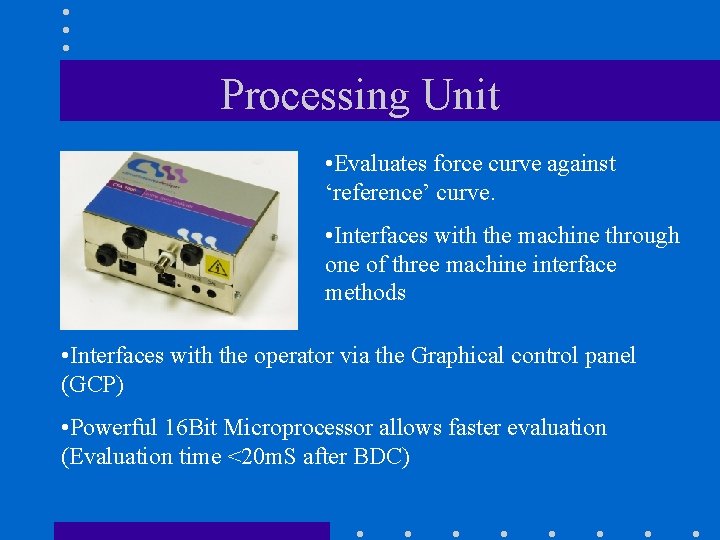
Processing Unit • Evaluates force curve against ‘reference’ curve. • Interfaces with the machine through one of three machine interface methods • Interfaces with the operator via the Graphical control panel (GCP) • Powerful 16 Bit Microprocessor allows faster evaluation (Evaluation time <20 m. S after BDC)
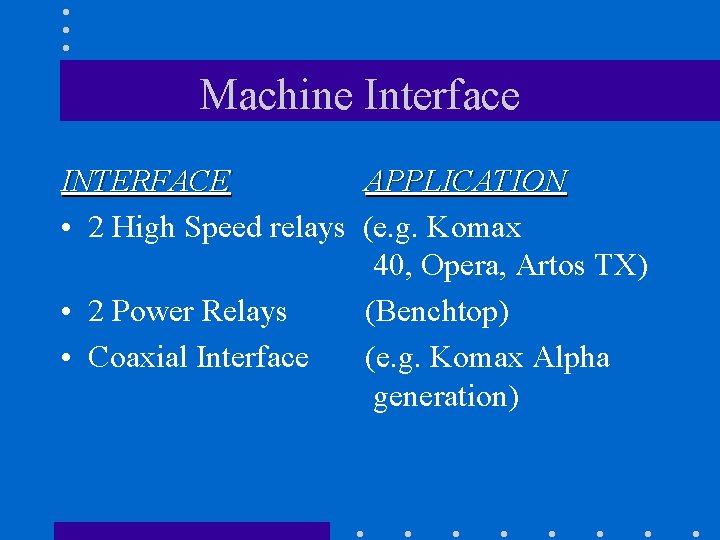
Machine Interface INTERFACE APPLICATION • 2 High Speed relays (e. g. Komax 40, Opera, Artos TX) • 2 Power Relays (Benchtop) • Coaxial Interface (e. g. Komax Alpha generation)
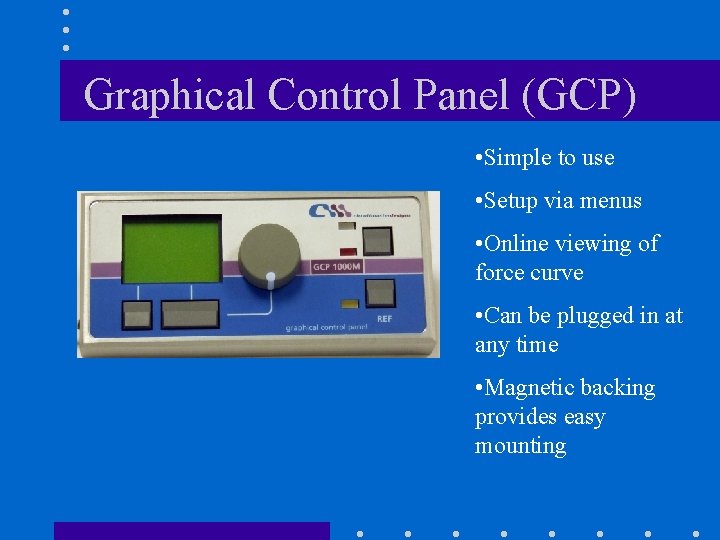
Graphical Control Panel (GCP) • Simple to use • Setup via menus • Online viewing of force curve • Can be plugged in at any time • Magnetic backing provides easy mounting
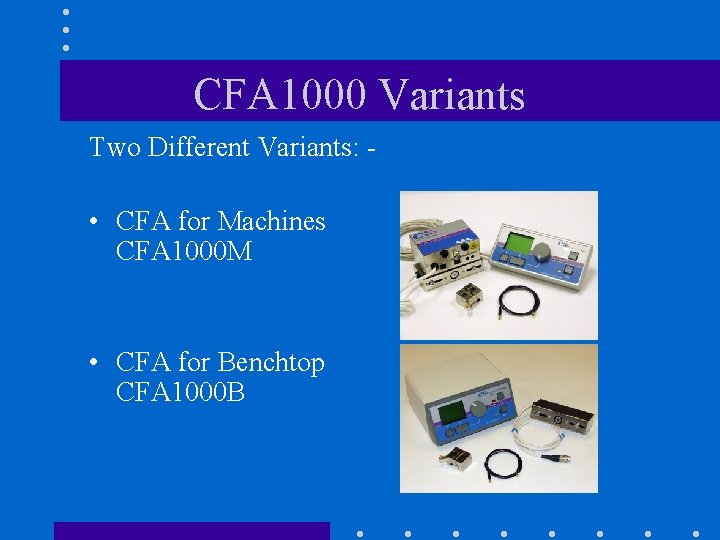
CFA 1000 Variants Two Different Variants: - • CFA for Machines CFA 1000 M • CFA for Benchtop CFA 1000 B
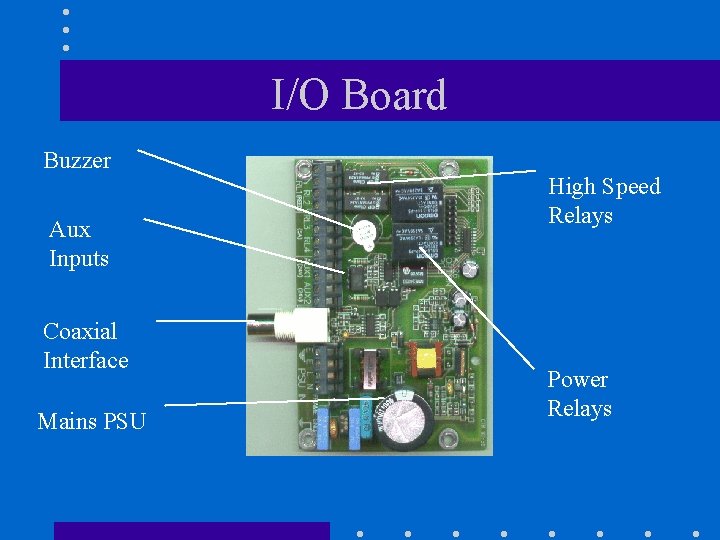
I/O Board Buzzer Aux Inputs Coaxial Interface Mains PSU High Speed Relays Power Relays
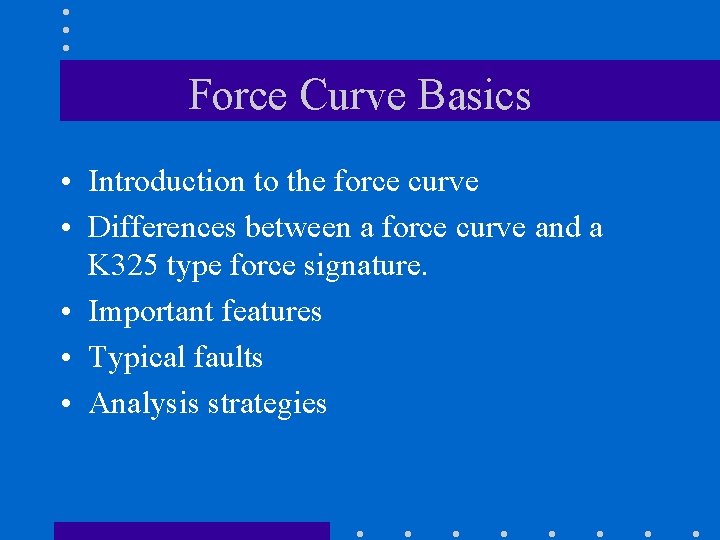
Force Curve Basics • Introduction to the force curve • Differences between a force curve and a K 325 type force signature. • Important features • Typical faults • Analysis strategies
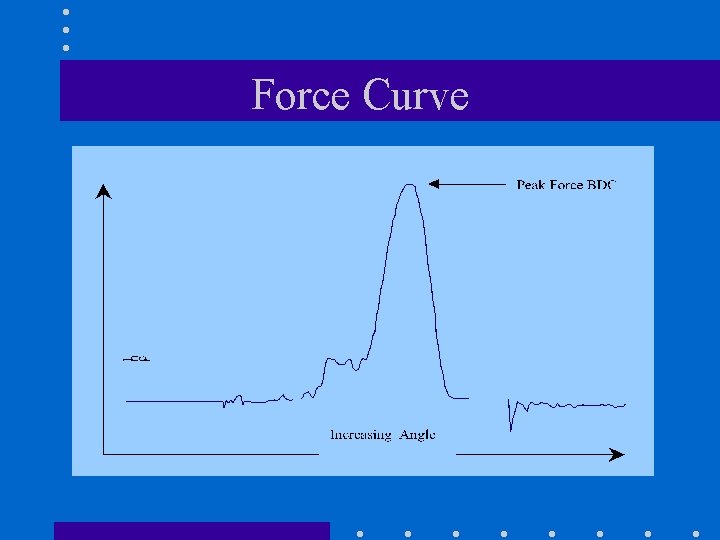
Force Curve
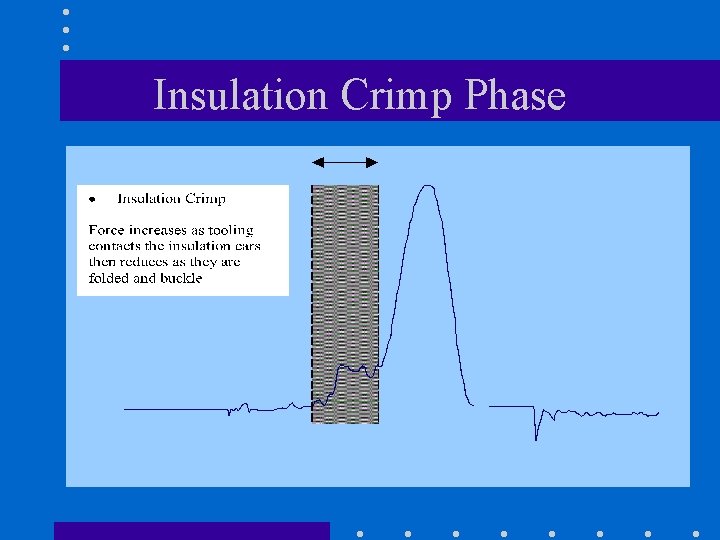
Insulation Crimp Phase
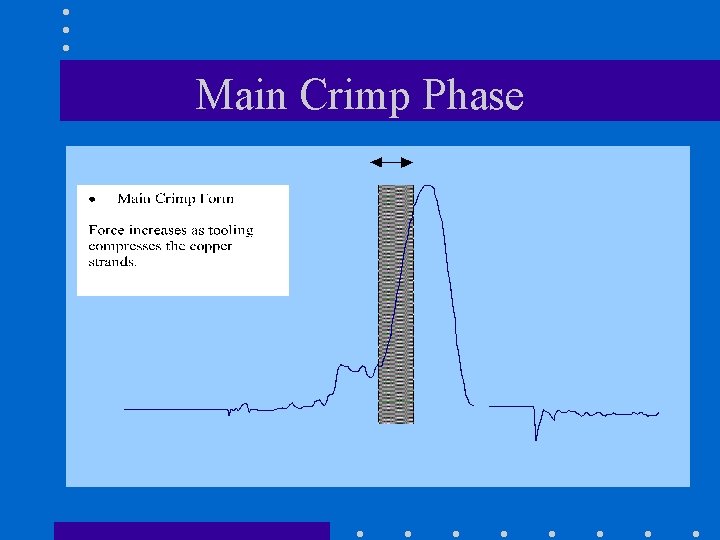
Main Crimp Phase
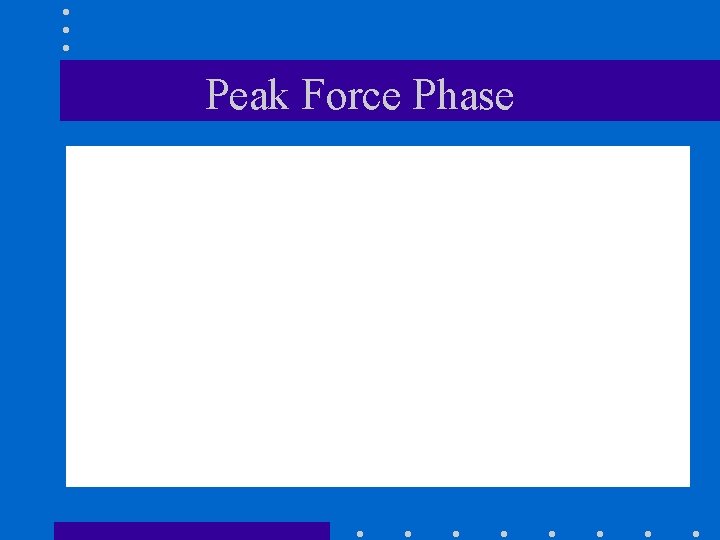
Peak Force Phase
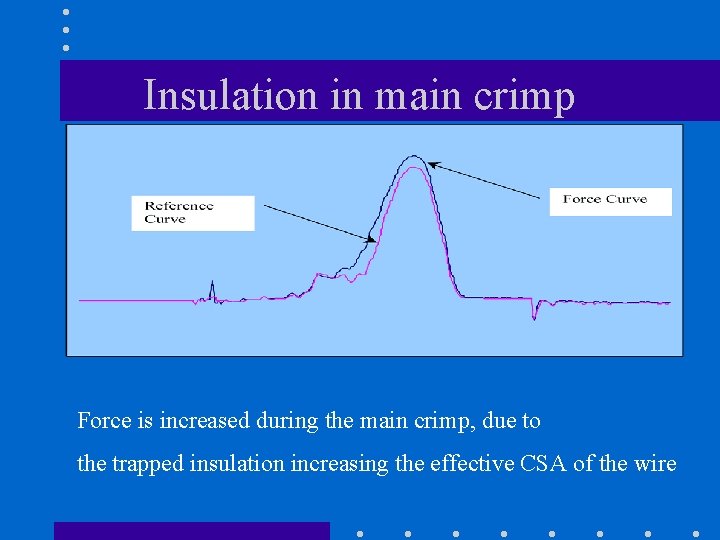
Insulation in main crimp Force is increased during the main crimp, due to the trapped insulation increasing the effective CSA of the wire
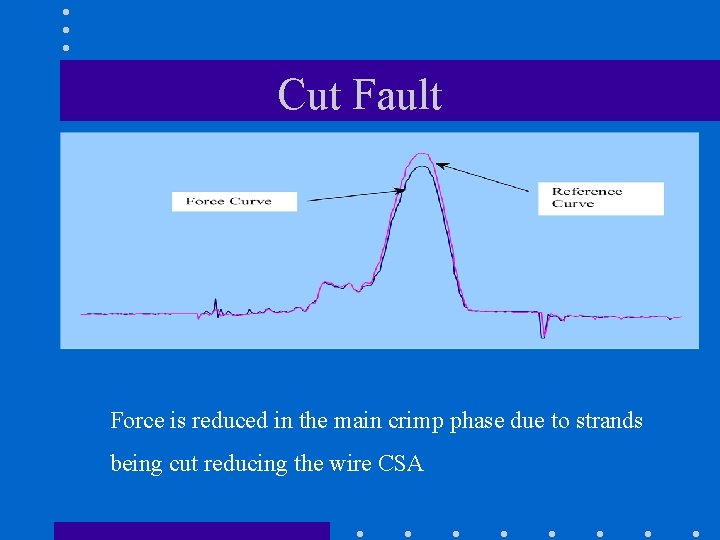
Cut Fault Force is reduced in the main crimp phase due to strands being cut reducing the wire CSA
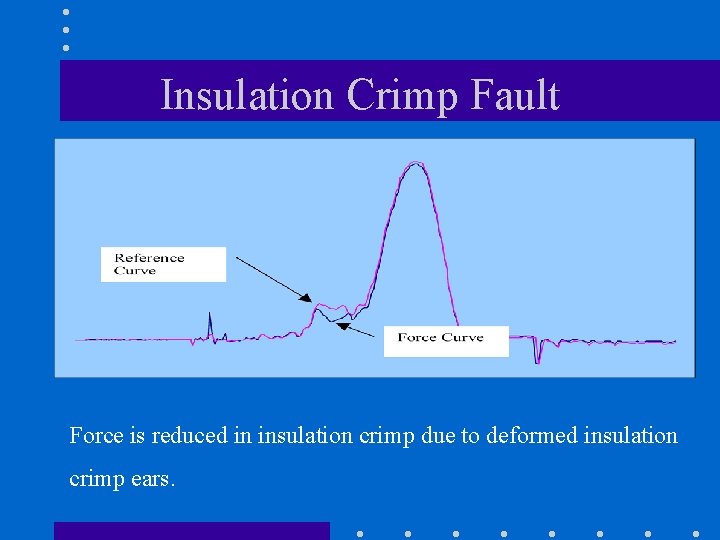
Insulation Crimp Fault Force is reduced in insulation crimp due to deformed insulation crimp ears.
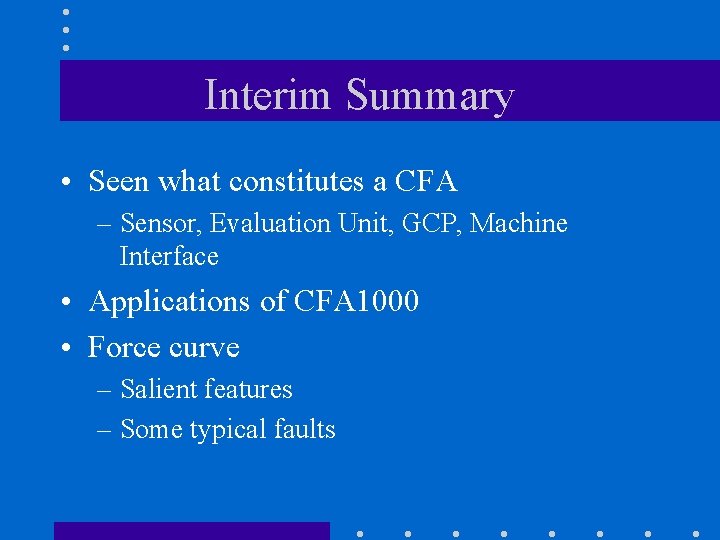
Interim Summary • Seen what constitutes a CFA – Sensor, Evaluation Unit, GCP, Machine Interface • Applications of CFA 1000 • Force curve – Salient features – Some typical faults
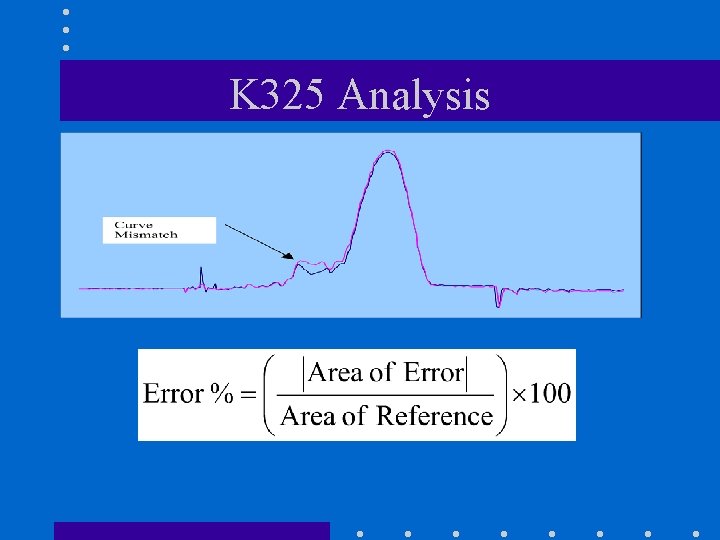
K 325 Analysis
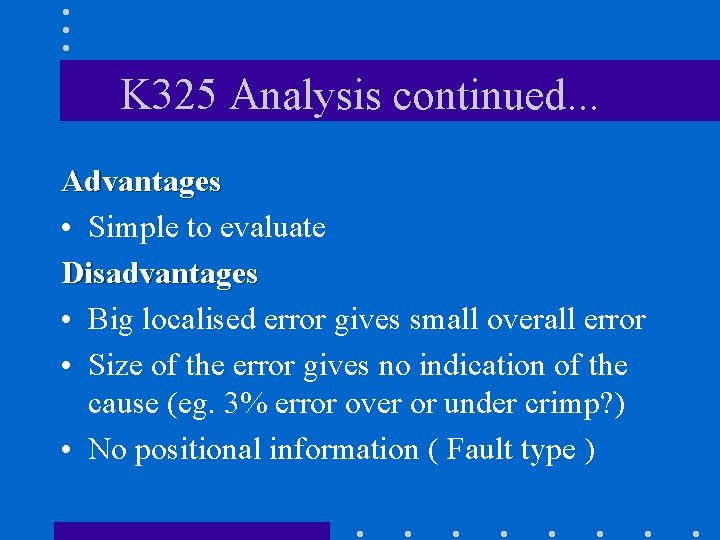
K 325 Analysis continued. . . Advantages • Simple to evaluate Disadvantages • Big localised error gives small overall error • Size of the error gives no indication of the cause (eg. 3% error over or under crimp? ) • No positional information ( Fault type )
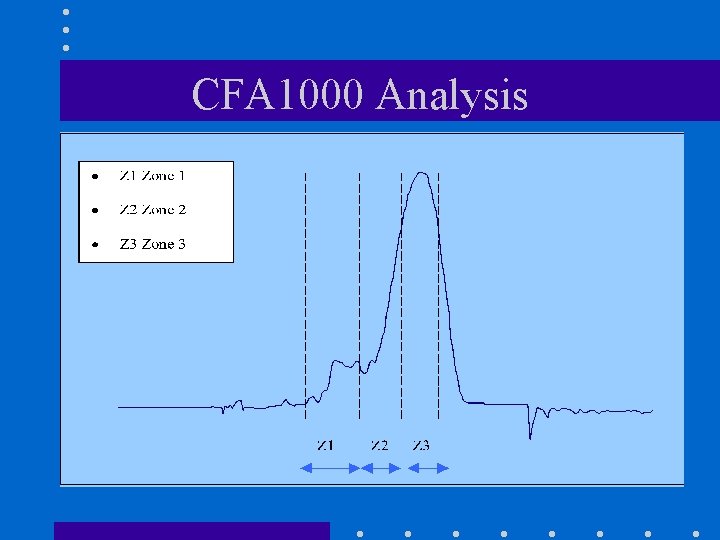
CFA 1000 Analysis
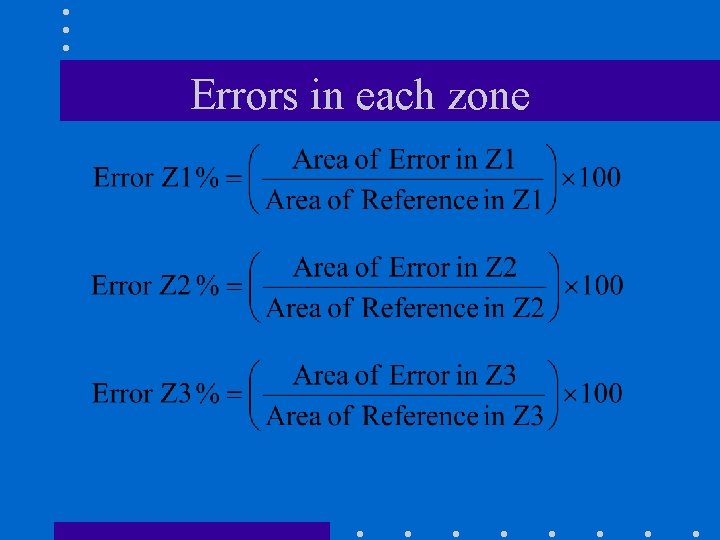
Errors in each zone
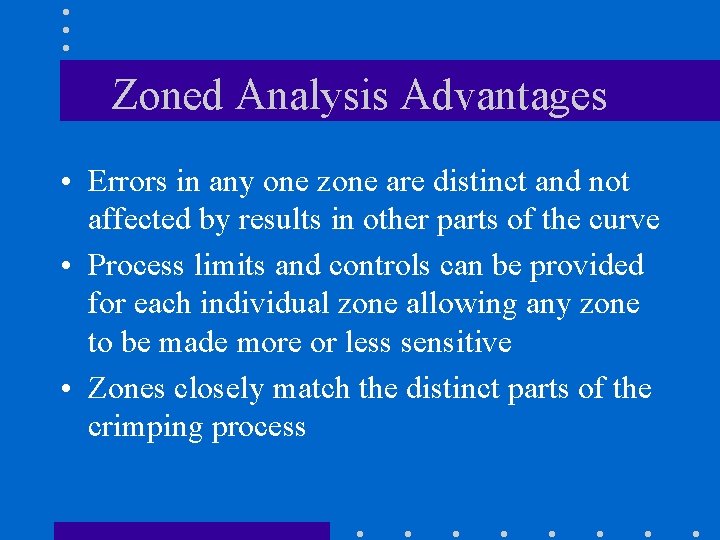
Zoned Analysis Advantages • Errors in any one zone are distinct and not affected by results in other parts of the curve • Process limits and controls can be provided for each individual zone allowing any zone to be made more or less sensitive • Zones closely match the distinct parts of the crimping process
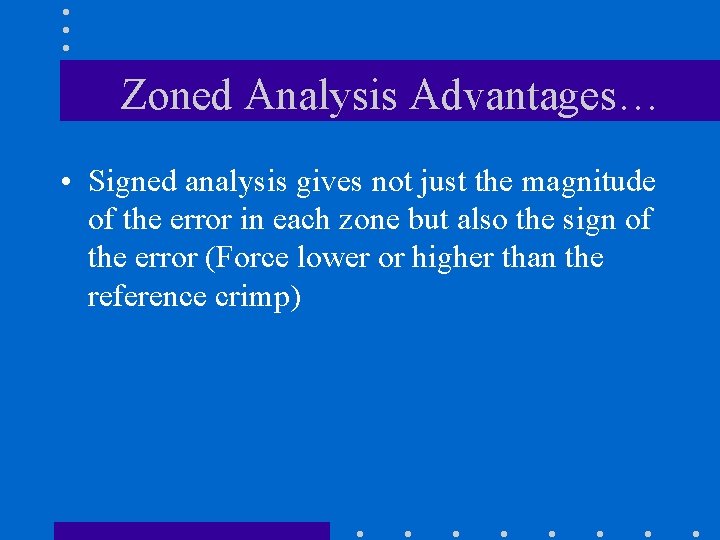
Zoned Analysis Advantages… • Signed analysis gives not just the magnitude of the error in each zone but also the sign of the error (Force lower or higher than the reference crimp)
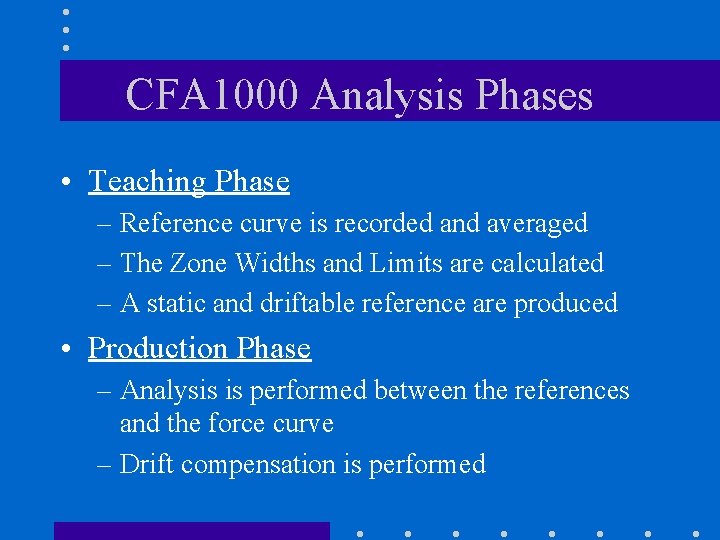
CFA 1000 Analysis Phases • Teaching Phase – Reference curve is recorded and averaged – The Zone Widths and Limits are calculated – A static and driftable reference are produced • Production Phase – Analysis is performed between the references and the force curve – Drift compensation is performed
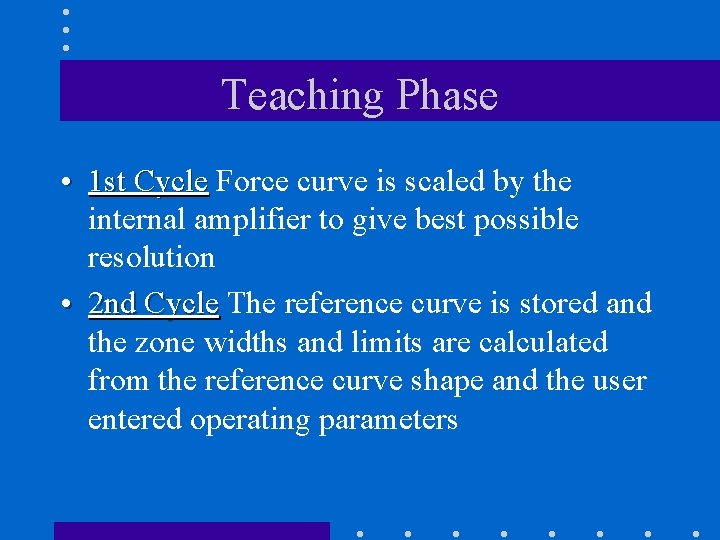
Teaching Phase • 1 st Cycle Force curve is scaled by the internal amplifier to give best possible resolution • 2 nd Cycle The reference curve is stored and the zone widths and limits are calculated from the reference curve shape and the user entered operating parameters
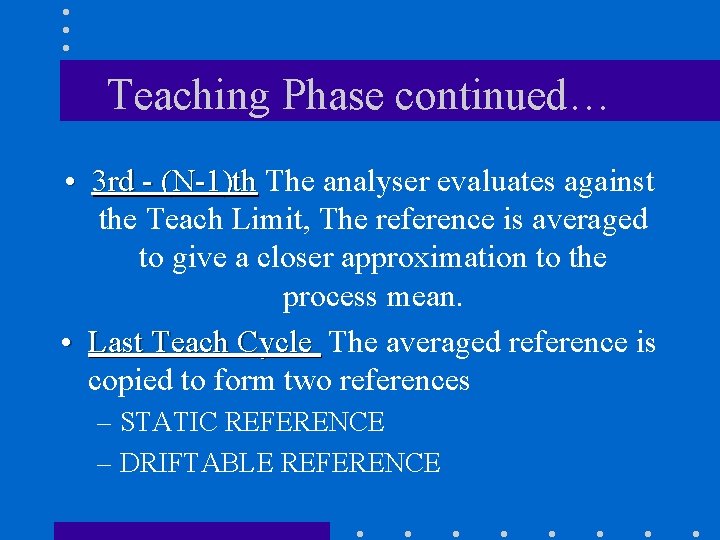
Teaching Phase continued… • 3 rd - (N-1)th The analyser evaluates against the Teach Limit, The reference is averaged to give a closer approximation to the process mean. • Last Teach Cycle The averaged reference is copied to form two references – STATIC REFERENCE – DRIFTABLE REFERENCE
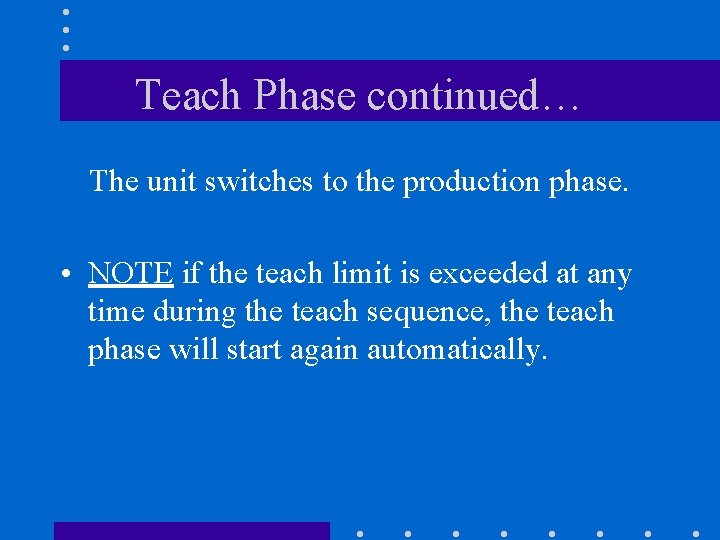
Teach Phase continued… The unit switches to the production phase. • NOTE if the teach limit is exceeded at any time during the teach sequence, the teach phase will start again automatically.
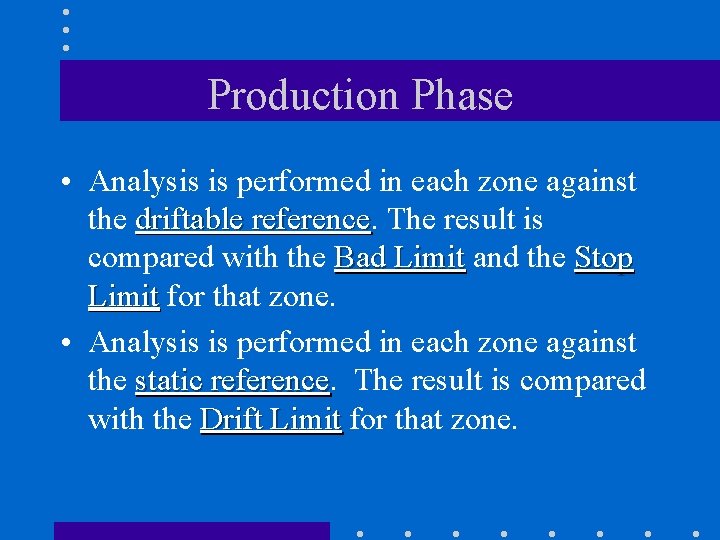
Production Phase • Analysis is performed in each zone against the driftable reference The result is compared with the Bad Limit and the Stop Limit for that zone. • Analysis is performed in each zone against the static reference The result is compared with the Drift Limit for that zone.
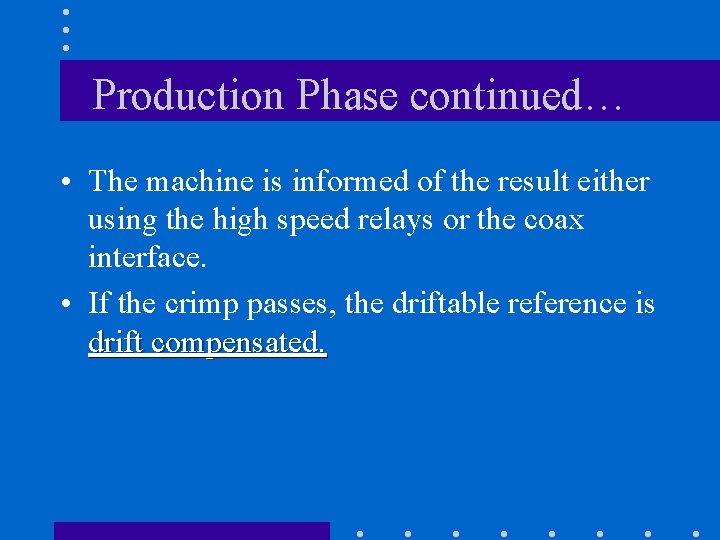
Production Phase continued… • The machine is informed of the result either using the high speed relays or the coax interface. • If the crimp passes, the driftable reference is drift compensated.
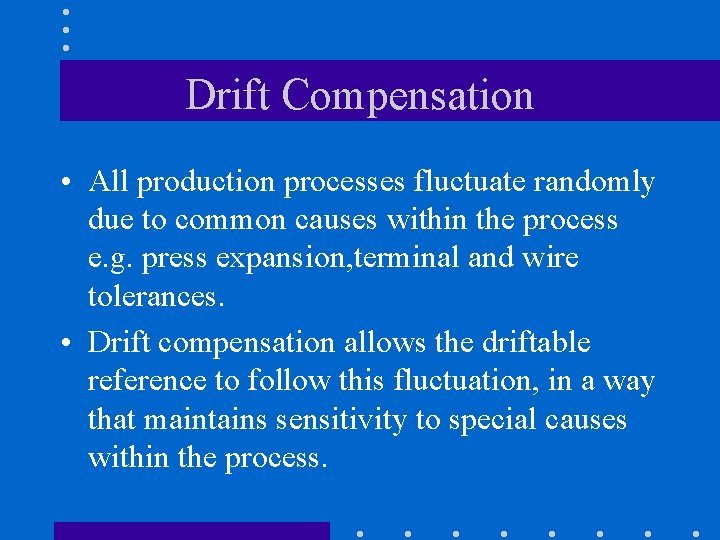
Drift Compensation • All production processes fluctuate randomly due to common causes within the process e. g. press expansion, terminal and wire tolerances. • Drift compensation allows the driftable reference to follow this fluctuation, in a way that maintains sensitivity to special causes within the process.
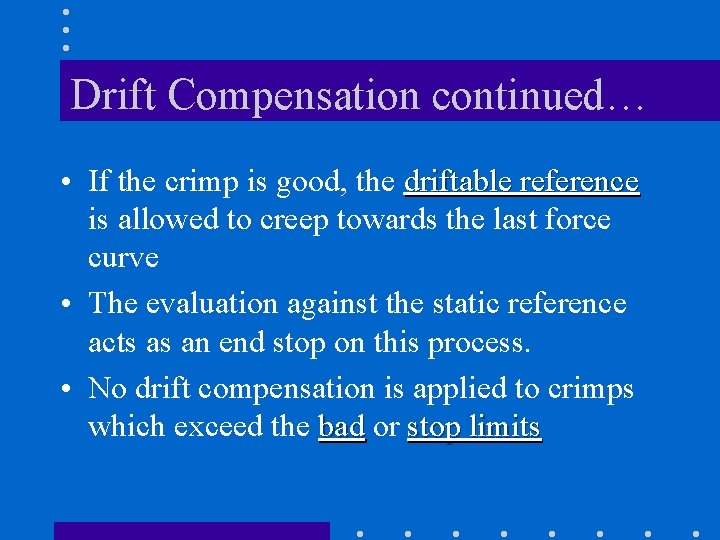
Drift Compensation continued… • If the crimp is good, the driftable reference is allowed to creep towards the last force curve • The evaluation against the static reference acts as an end stop on this process. • No drift compensation is applied to crimps which exceed the bad or stop limits
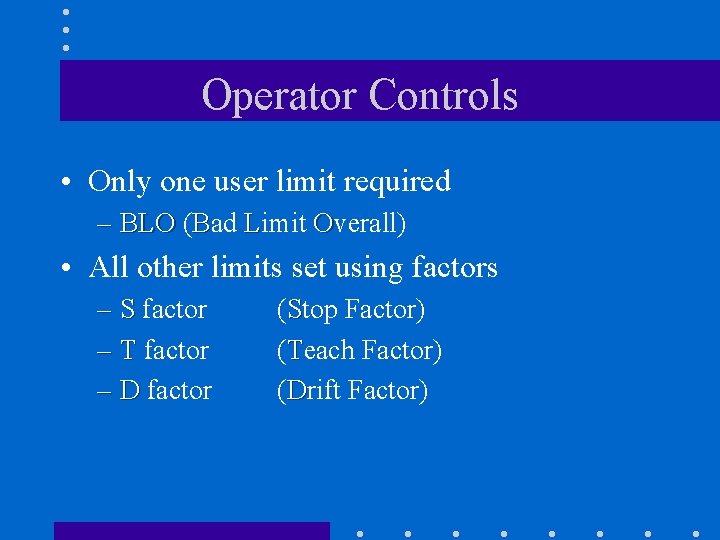
Operator Controls • Only one user limit required – BLO (Bad Limit Overall) • All other limits set using factors – S factor – T factor – D factor (Stop Factor) (Teach Factor) (Drift Factor)
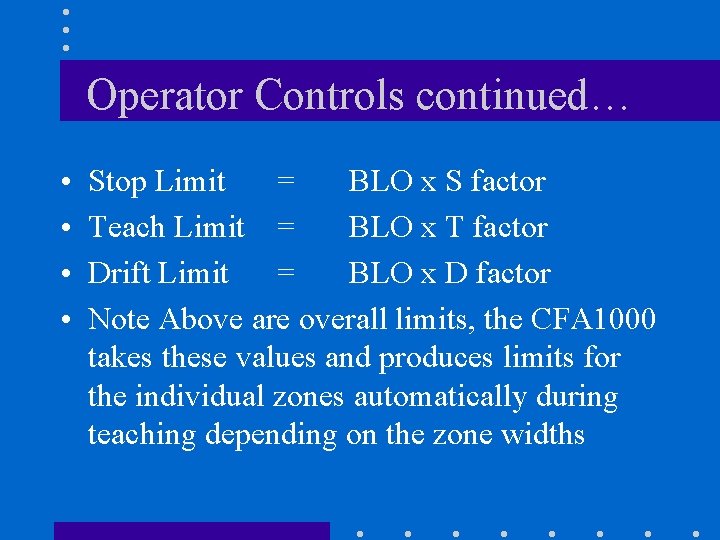
Operator Controls continued… • • Stop Limit = BLO x S factor Teach Limit = BLO x T factor Drift Limit = BLO x D factor Note Above are overall limits, the CFA 1000 takes these values and produces limits for the individual zones automatically during teaching depending on the zone widths
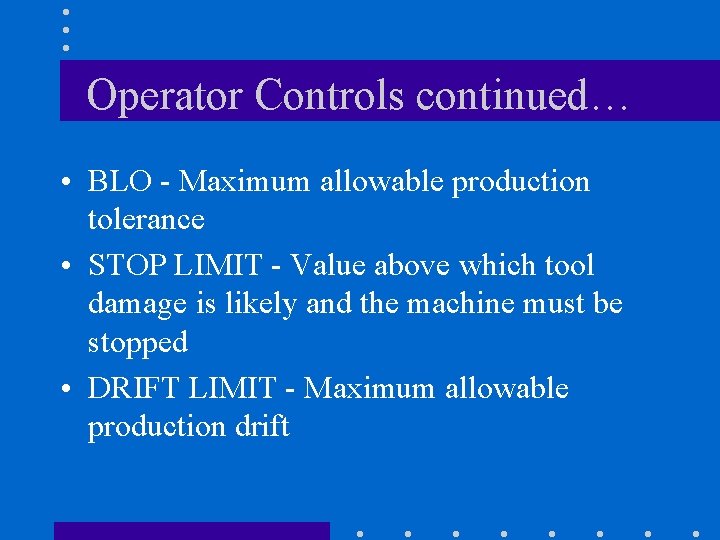
Operator Controls continued… • BLO - Maximum allowable production tolerance • STOP LIMIT - Value above which tool damage is likely and the machine must be stopped • DRIFT LIMIT - Maximum allowable production drift
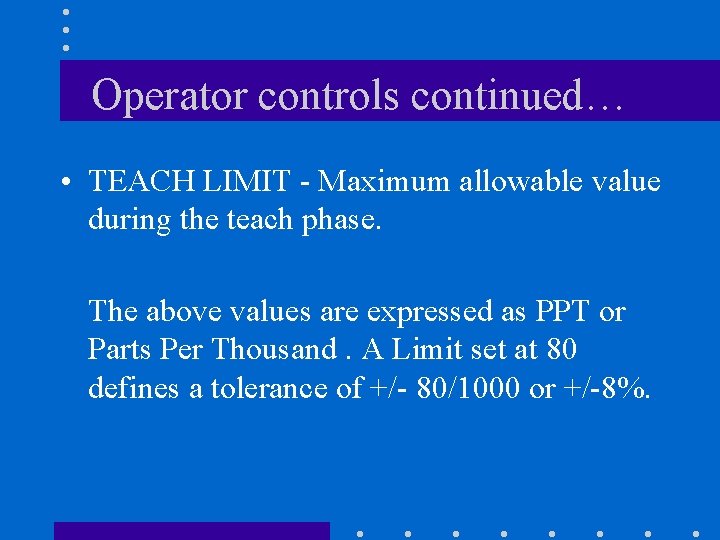
Operator controls continued… • TEACH LIMIT - Maximum allowable value during the teach phase. The above values are expressed as PPT or Parts Per Thousand. A Limit set at 80 defines a tolerance of +/- 80/1000 or +/-8%.
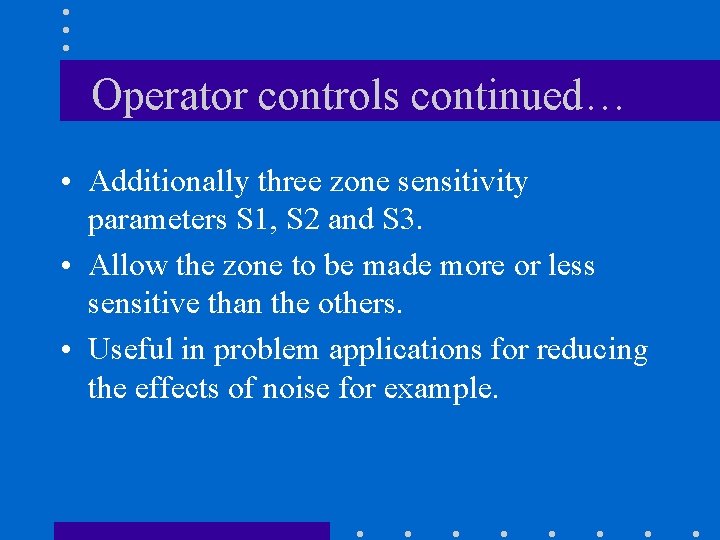
Operator controls continued… • Additionally three zone sensitivity parameters S 1, S 2 and S 3. • Allow the zone to be made more or less sensitive than the others. • Useful in problem applications for reducing the effects of noise for example.
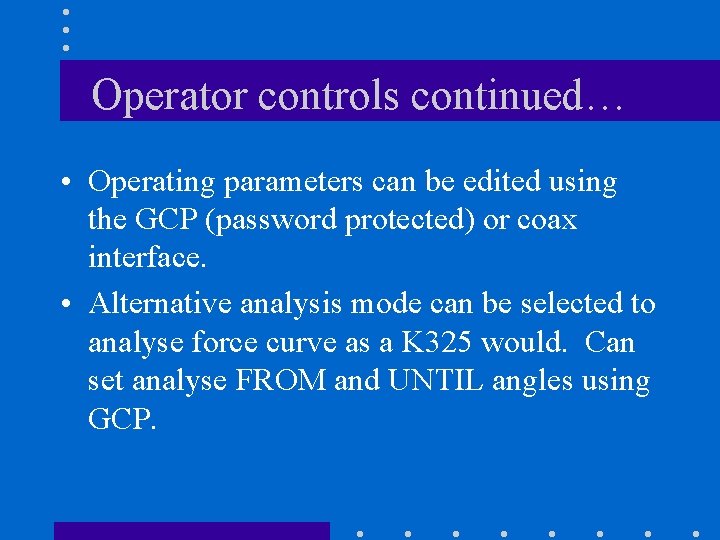
Operator controls continued… • Operating parameters can be edited using the GCP (password protected) or coax interface. • Alternative analysis mode can be selected to analyse force curve as a K 325 would. Can set analyse FROM and UNTIL angles using GCP.
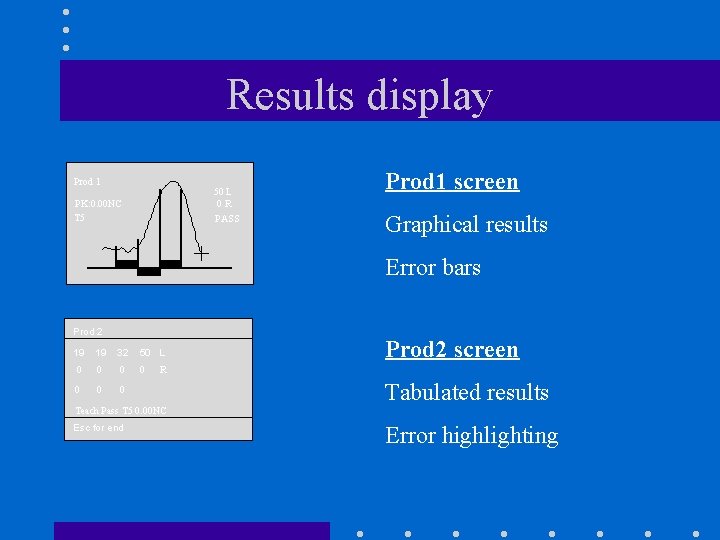
Results display Prod 1 50 L 0 R PK: 0. 00 NC T 5 PASS Prod 1 screen Graphical results Error bars Prod 2 19 19 32 50 L 0 0 0 0 R Teach Pass T 5 0. 00 NC Esc for end Prod 2 screen Tabulated results Error highlighting
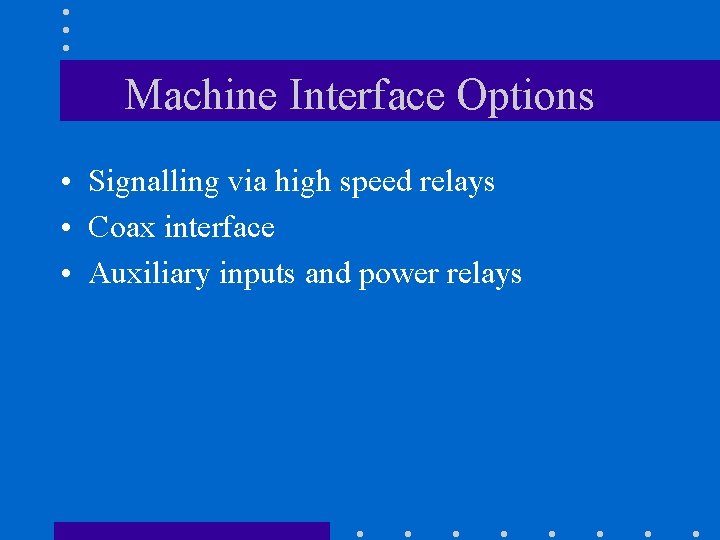
Machine Interface Options • Signalling via high speed relays • Coax interface • Auxiliary inputs and power relays
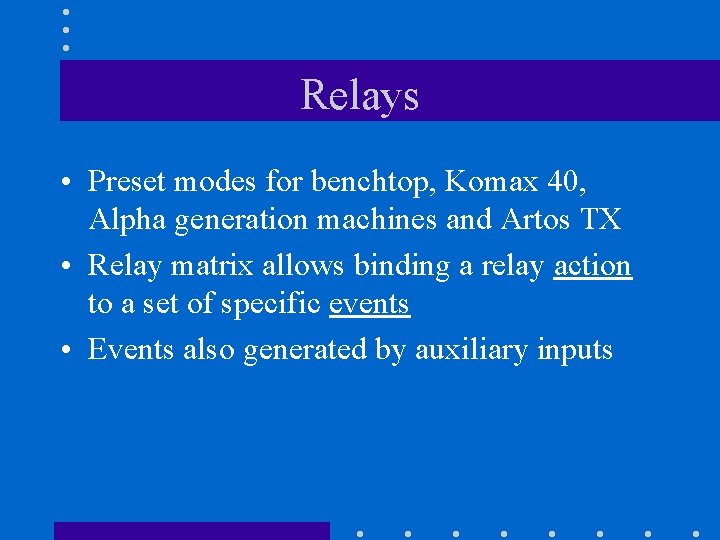
Relays • Preset modes for benchtop, Komax 40, Alpha generation machines and Artos TX • Relay matrix allows binding a relay action to a set of specific events • Events also generated by auxiliary inputs
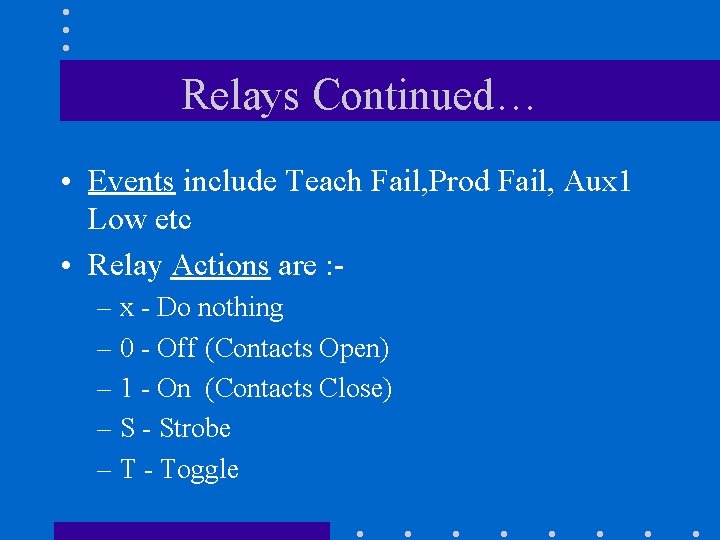
Relays Continued… • Events include Teach Fail, Prod Fail, Aux 1 Low etc • Relay Actions are : – x - Do nothing – 0 - Off (Contacts Open) – 1 - On (Contacts Close) – S - Strobe – T - Toggle
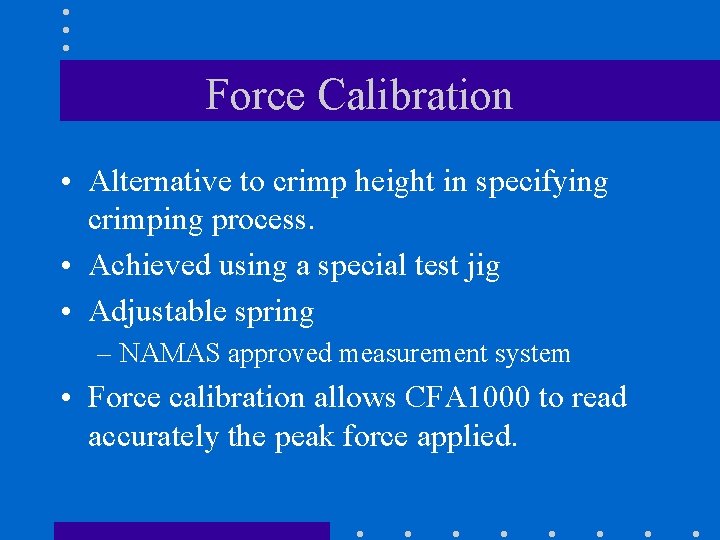
Force Calibration • Alternative to crimp height in specifying crimping process. • Achieved using a special test jig • Adjustable spring – NAMAS approved measurement system • Force calibration allows CFA 1000 to read accurately the peak force applied.
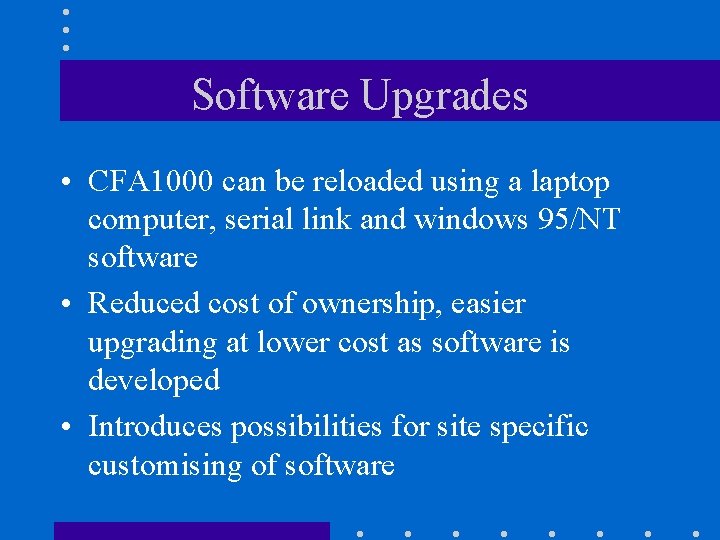
Software Upgrades • CFA 1000 can be reloaded using a laptop computer, serial link and windows 95/NT software • Reduced cost of ownership, easier upgrading at lower cost as software is developed • Introduces possibilities for site specific customising of software
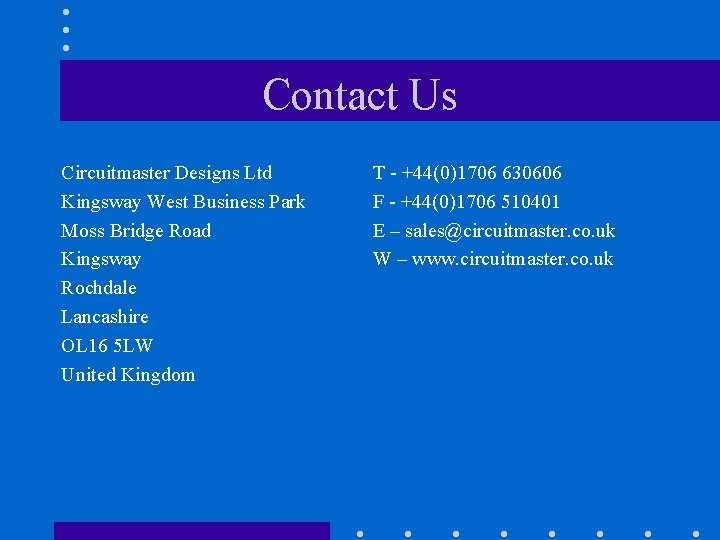
Contact Us Circuitmaster Designs Ltd Kingsway West Business Park Moss Bridge Road Kingsway Rochdale Lancashire OL 16 5 LW United Kingdom T - +44(0)1706 630606 F - +44(0)1706 510401 E – sales@circuitmaster. co. uk W – www. circuitmaster. co. uk
Mastercfa
Crimp and bruges formula
Series vs parallel
Type of circuits
Parallel circuit circuit construction kit
Capacitor series parallel
What is an incomplete circuit
What is short circuit
Venn diagram of climate and weather
Diagram of circulatory system
Advantages of parallel circuits over series circuits
Hamiltonian circuit examples
Cfa climate
Mouvement panafricain de rejet du franc cfa
Cfa essas
Cfa probiz
Tropical humid climate
Skokan 2017 online
Cfa contact
Cfa mn
Cfa institute
Cfa research challenge report template
Cfa los command words
Dorothy jacks cfa aas
Cfa code 3
Cfa resource
Cfa society pittsburgh
Cfa institute esg intergation
Cfa esg integration
Cfa institute españa
Cfa austin
Cfa vs efa
Cfa+recyclage aerosol
Icfa restauration
Confirmatory factor analysis mplus
Cfa south africa
Treasury inflation protected securities cfa
Cfa research challenge rules
Ciia vs cfa
Nathan ronen
Cfa cyprus
Supranational bonds cfa
Aktutor.in mcq
Cfa society czech republic
Cfa cbt results
Cfa lecturer handbook
Paul gainford
Cfa command words
Cfa research challenge rules
Contact vs field forces
Which arrow below represents the direction of acceleration