Resource Planning Chapter 16 Copyright 2013 Pearson Education
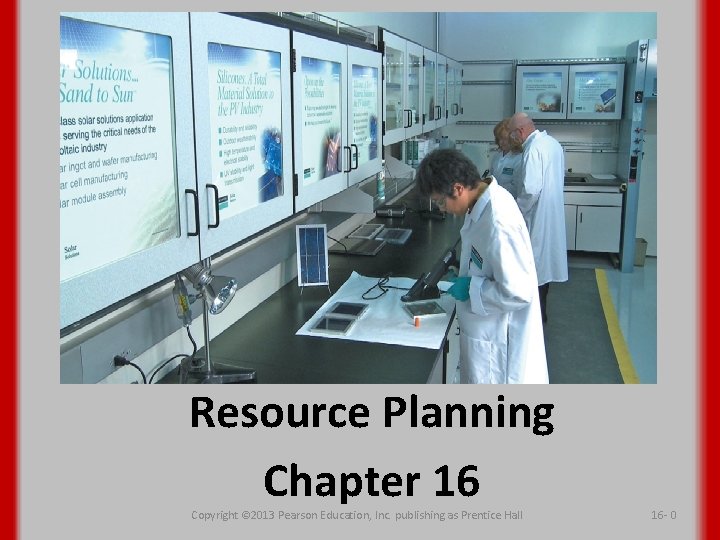
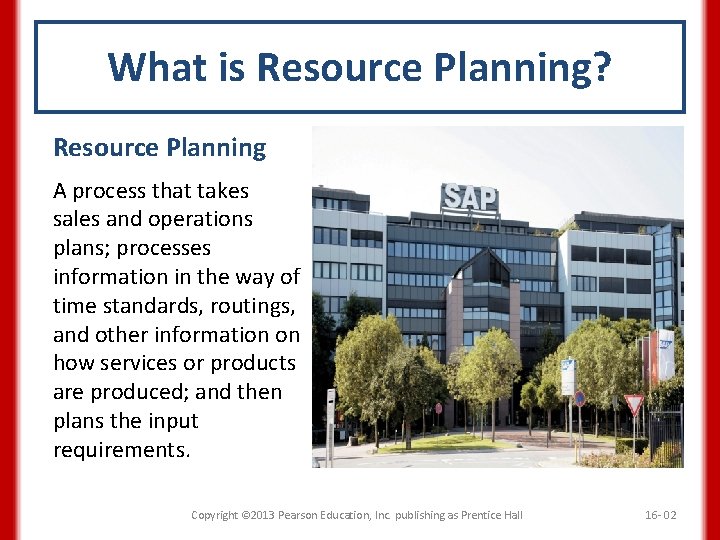
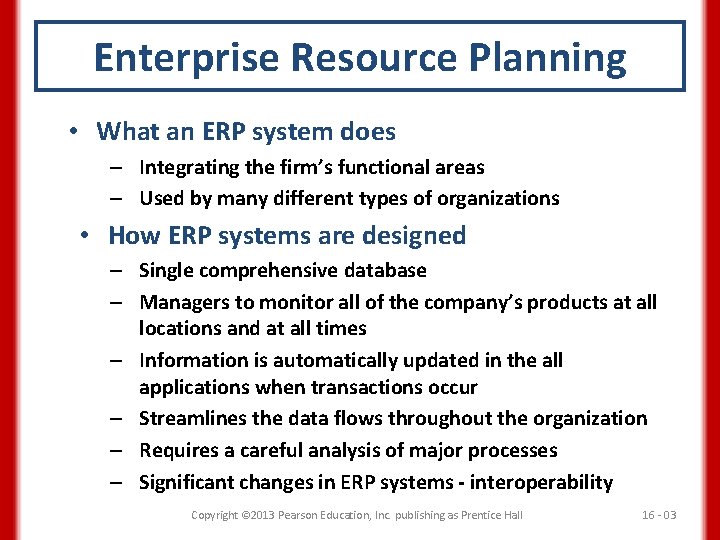
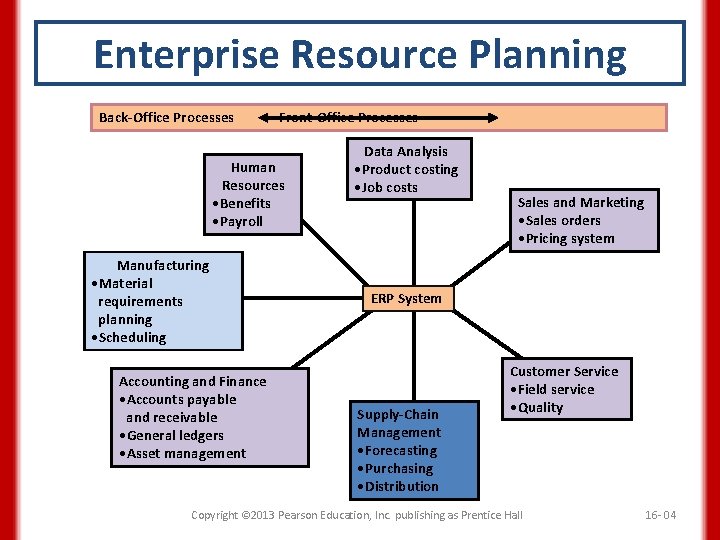
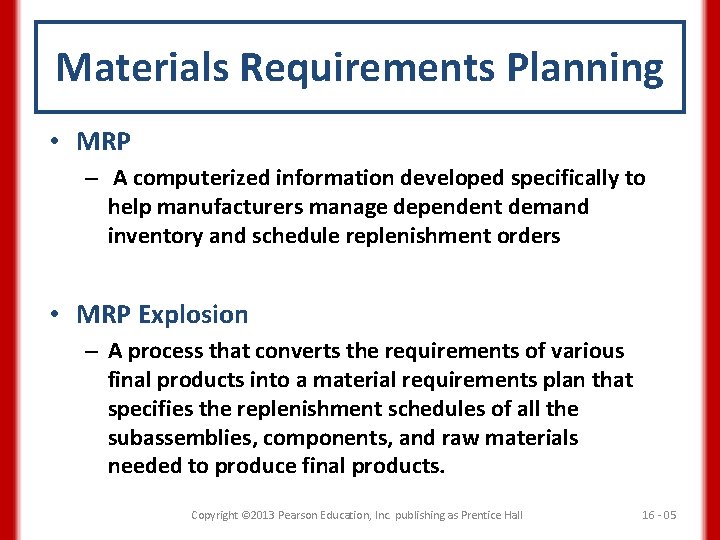
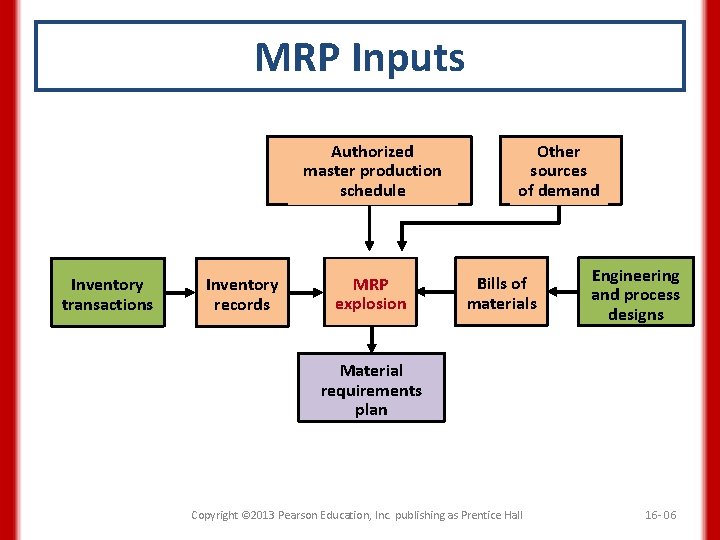
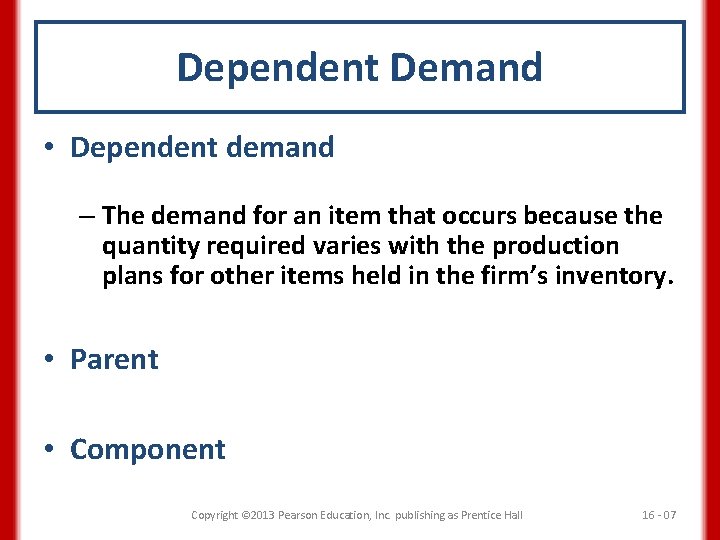

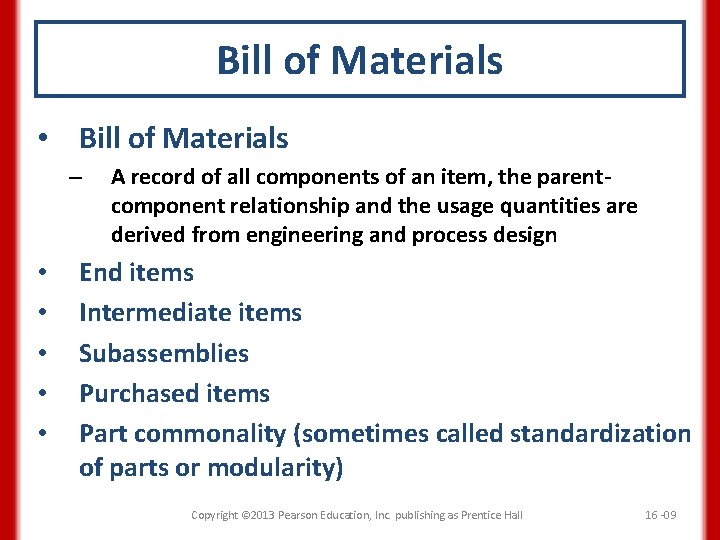
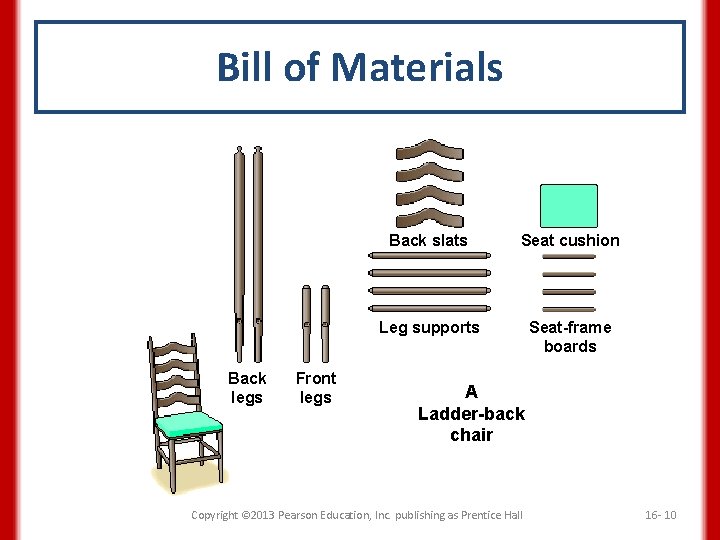
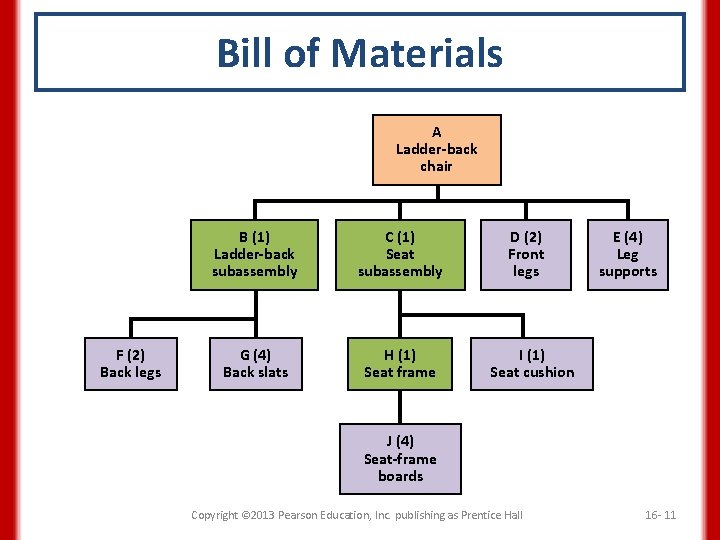
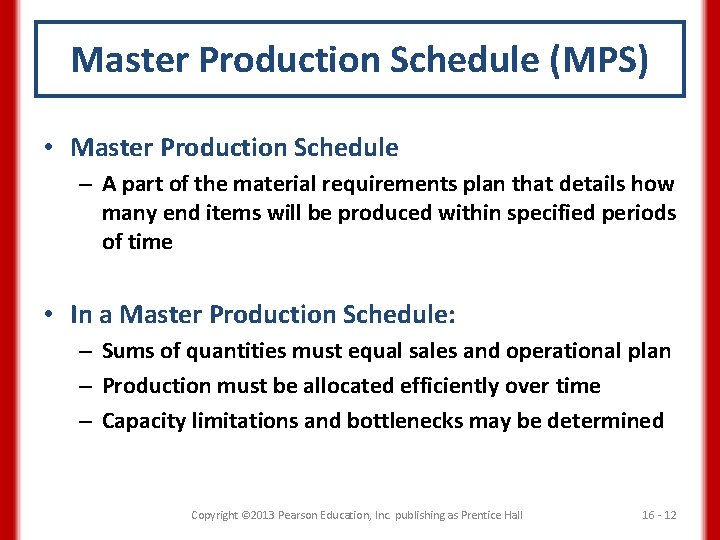
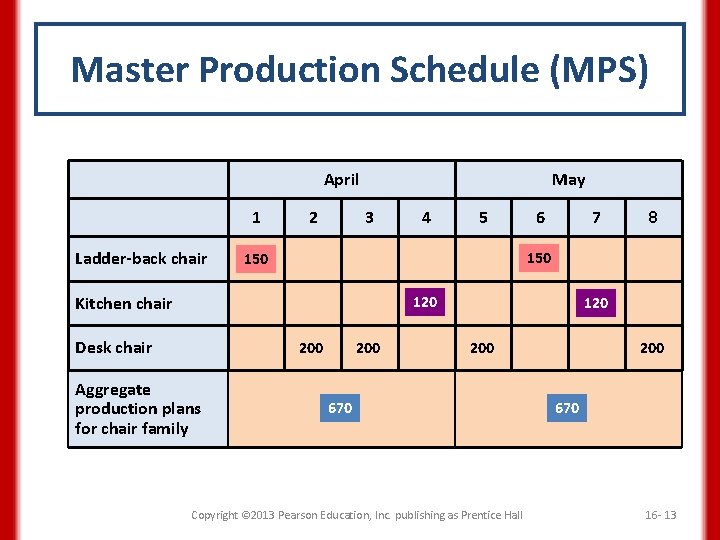
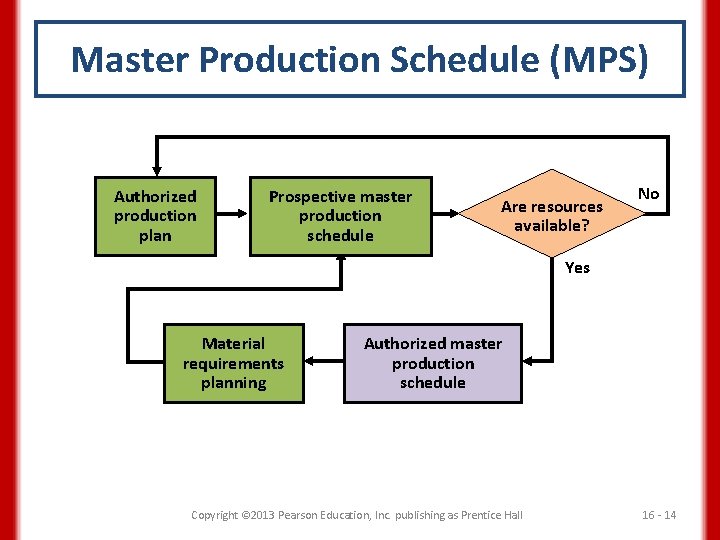
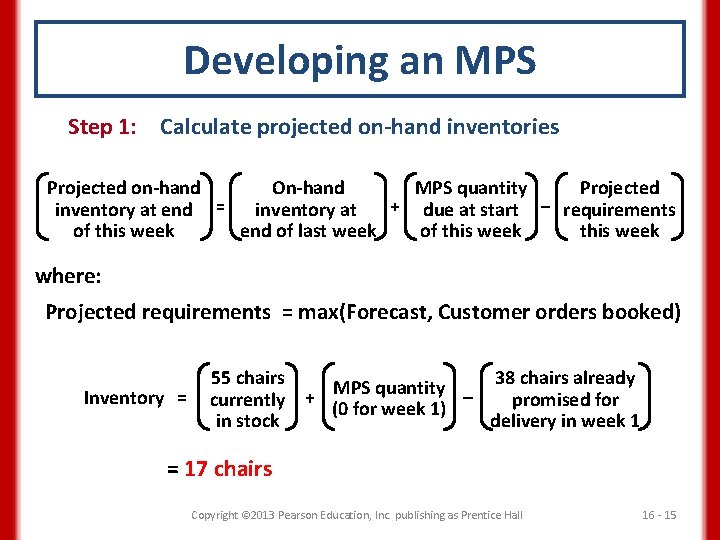
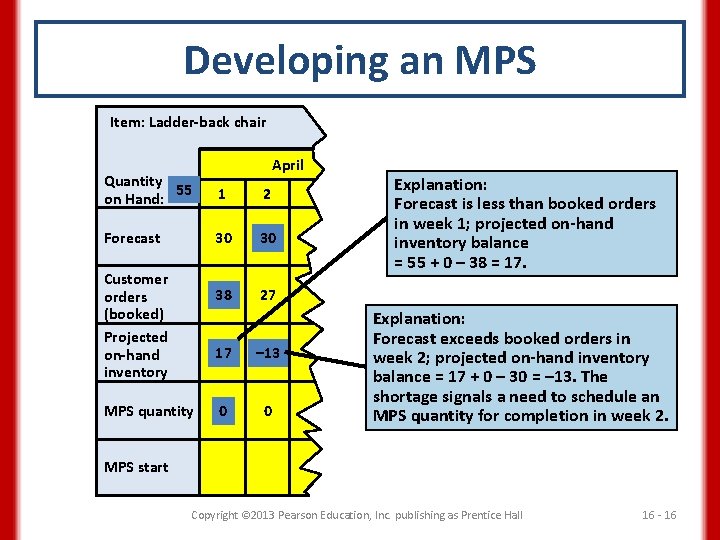
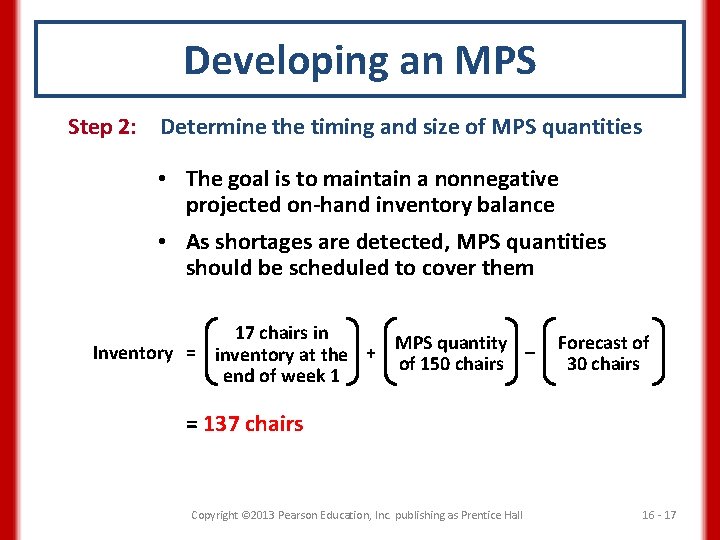
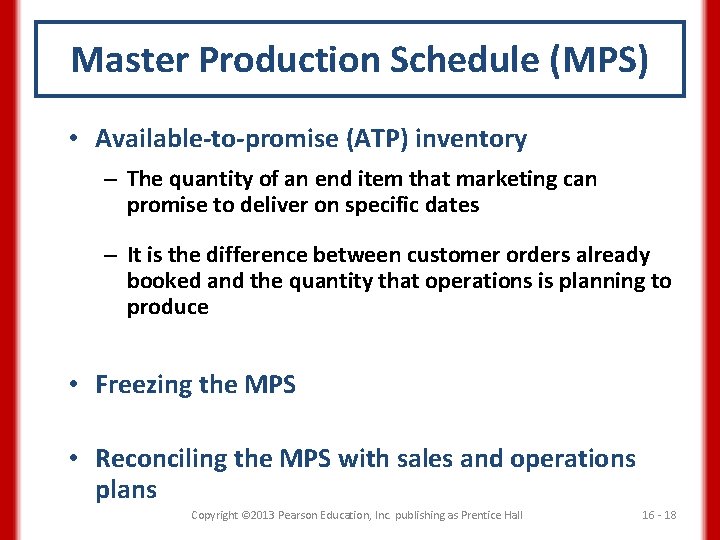
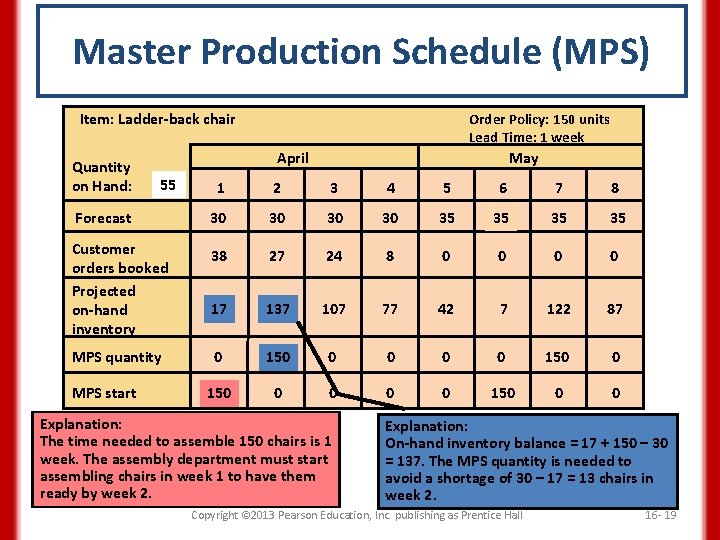
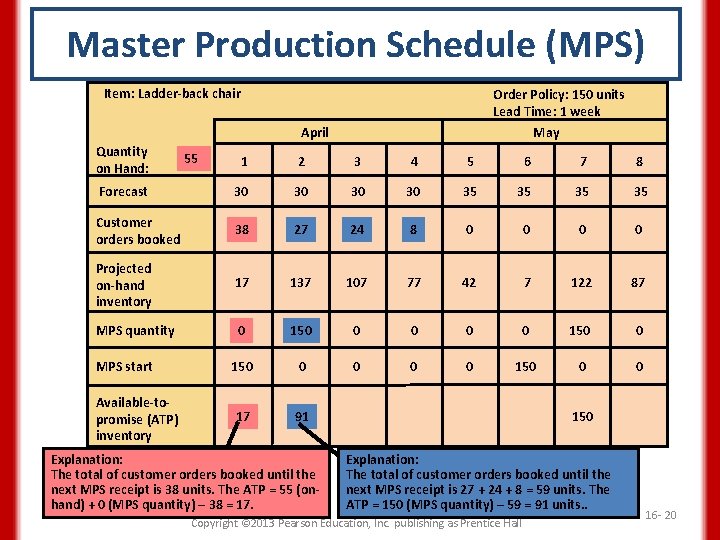
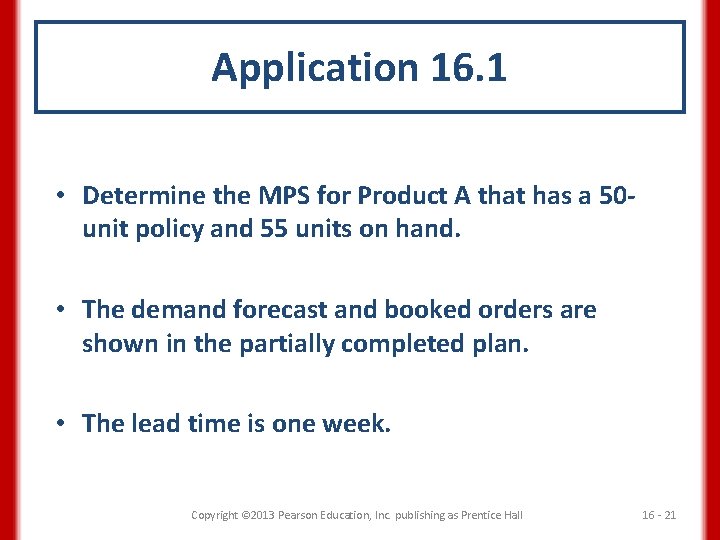
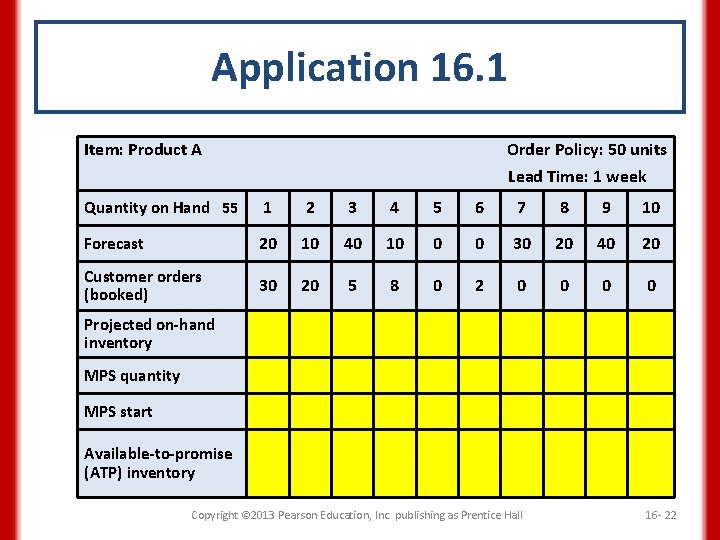
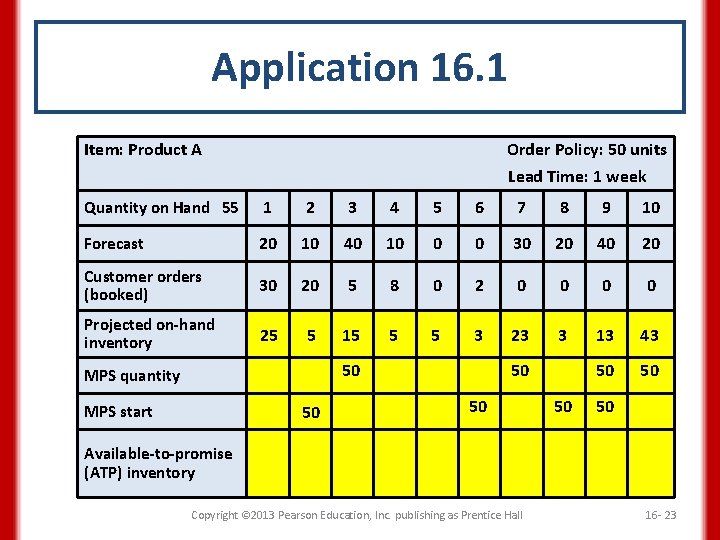
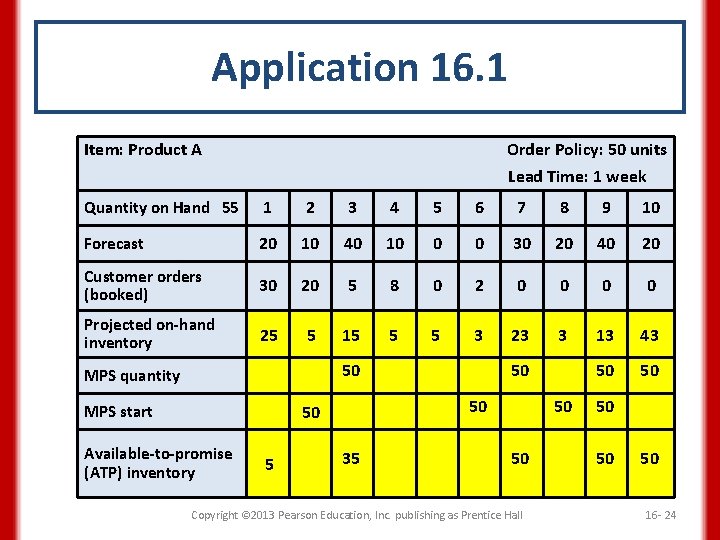
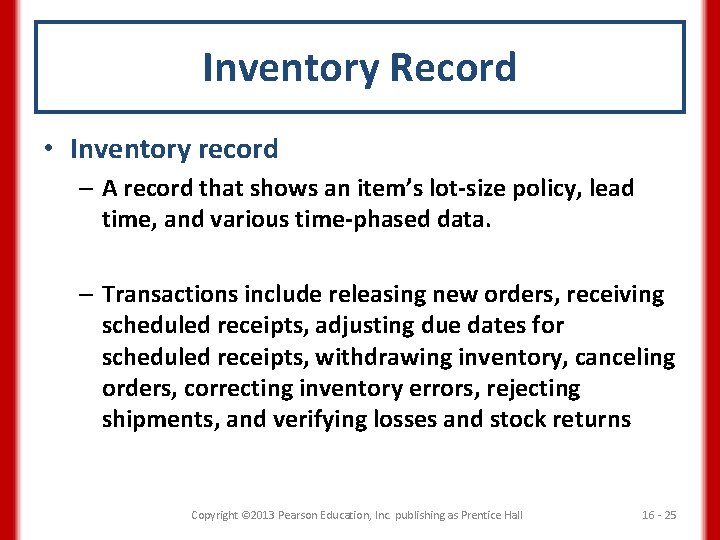
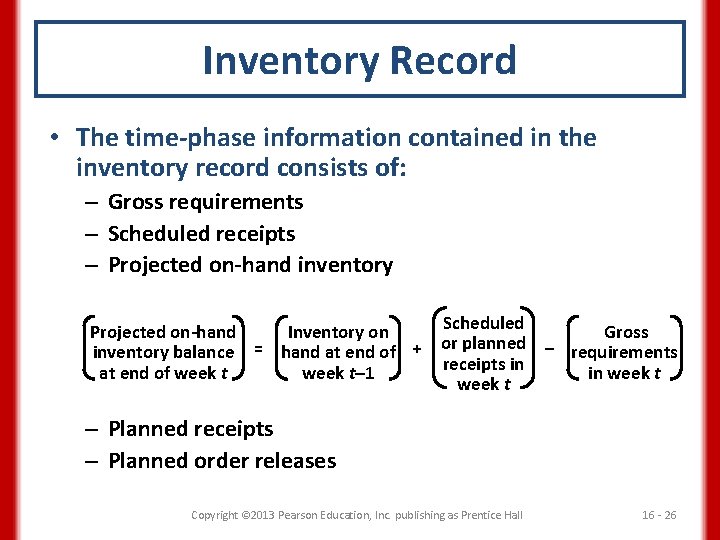
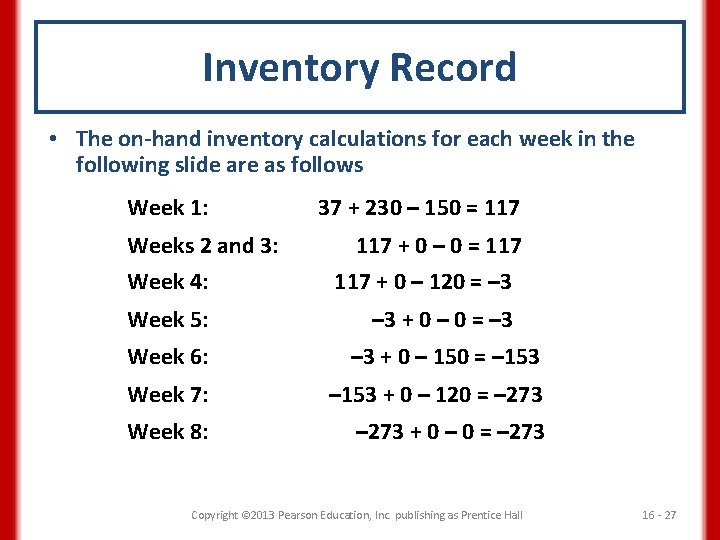

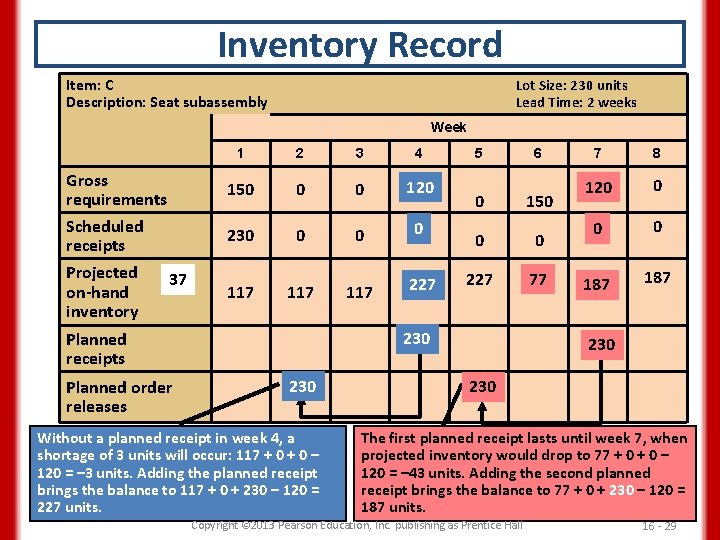
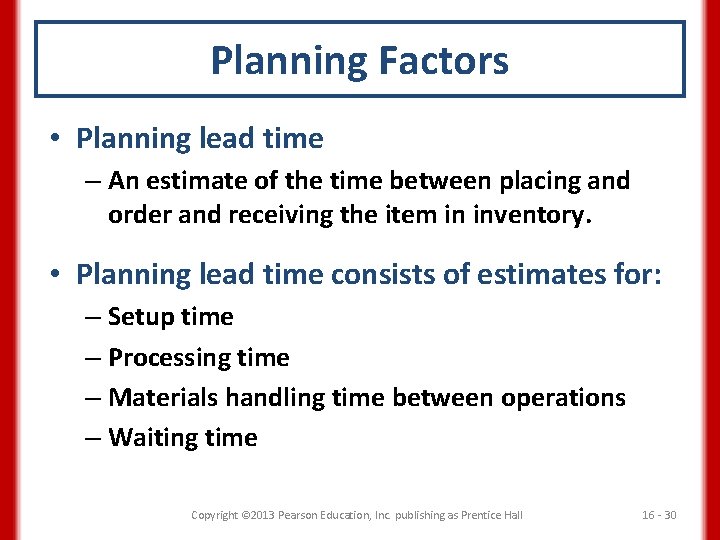
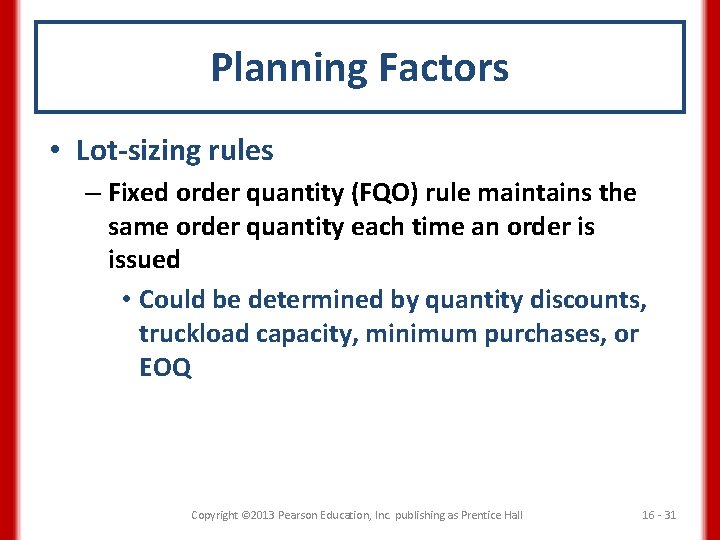
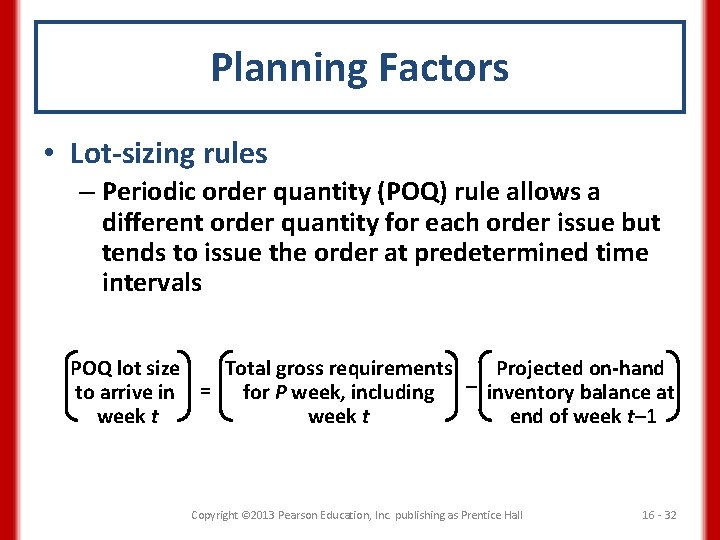
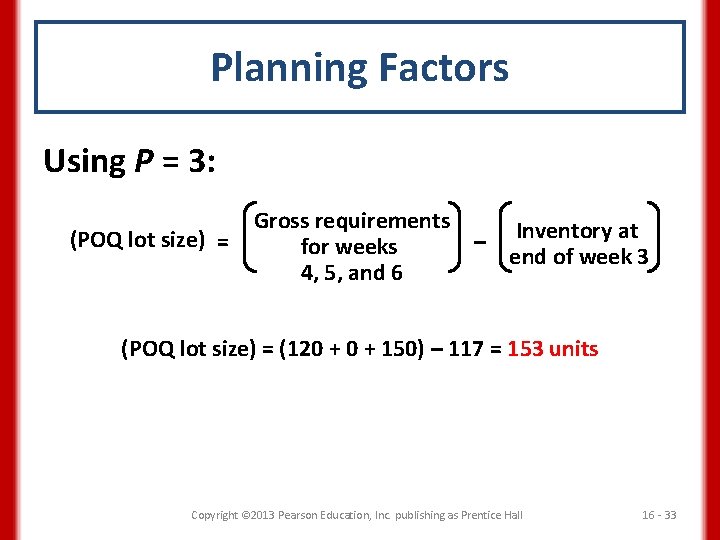
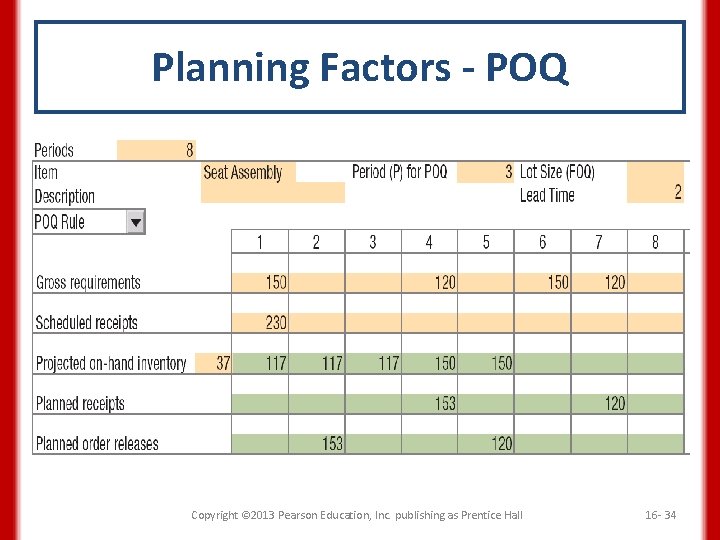
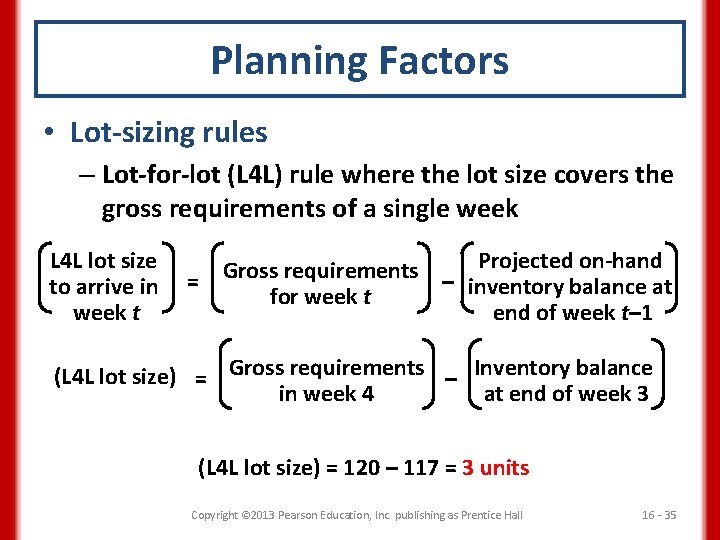

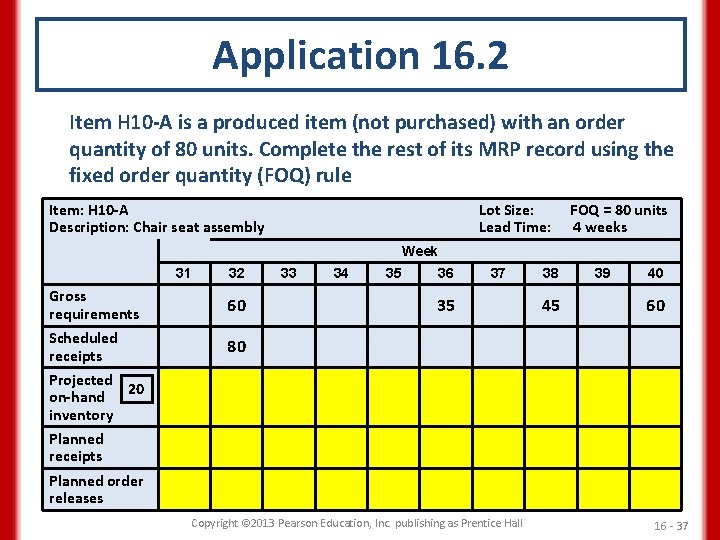
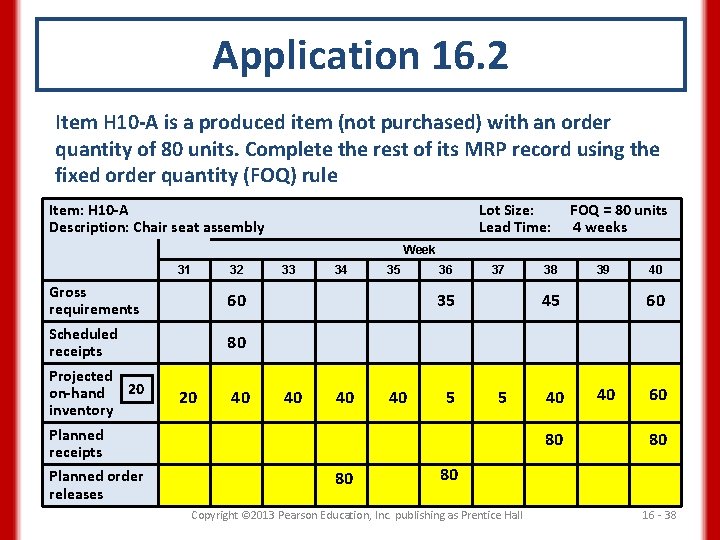
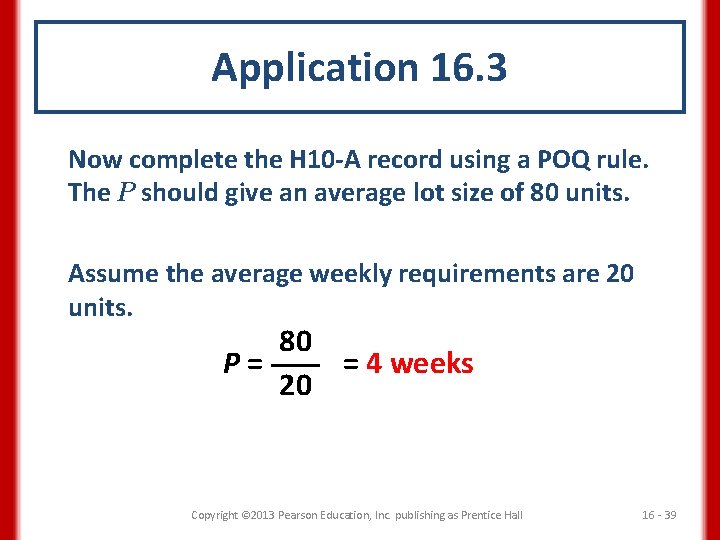
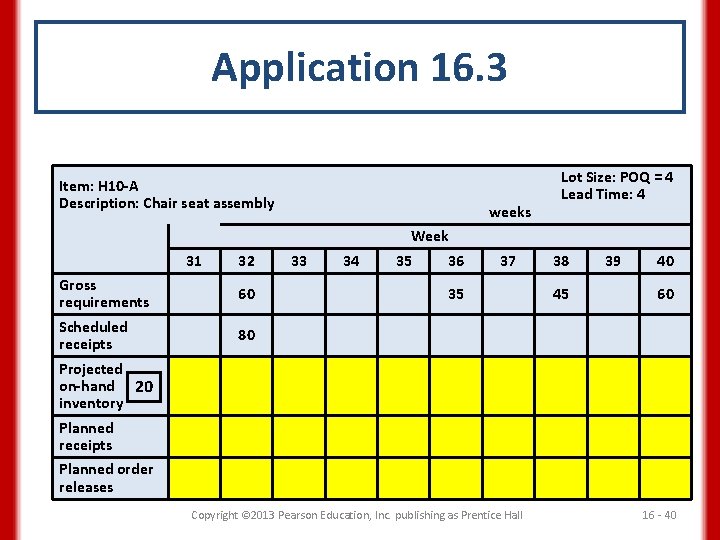
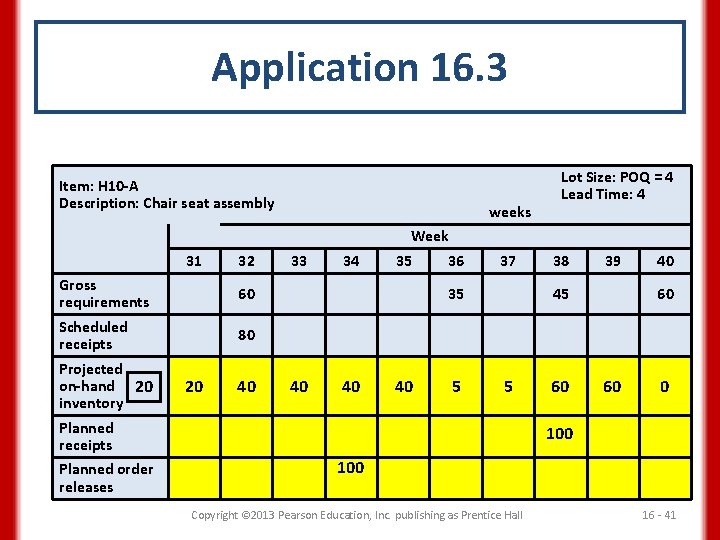
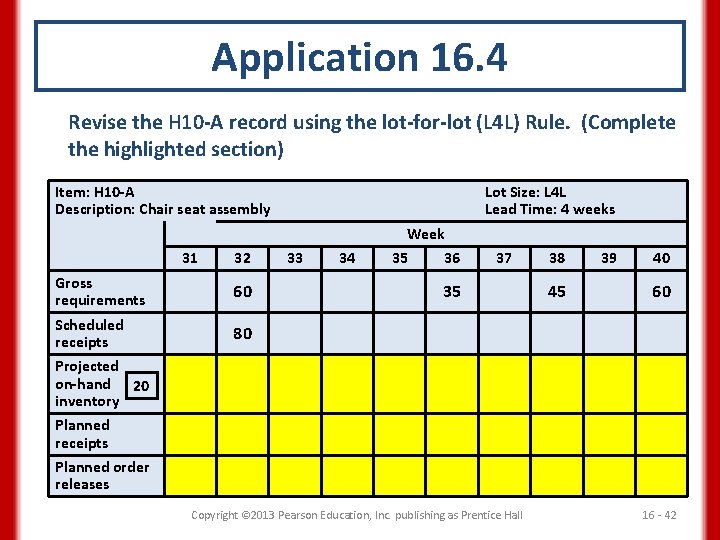
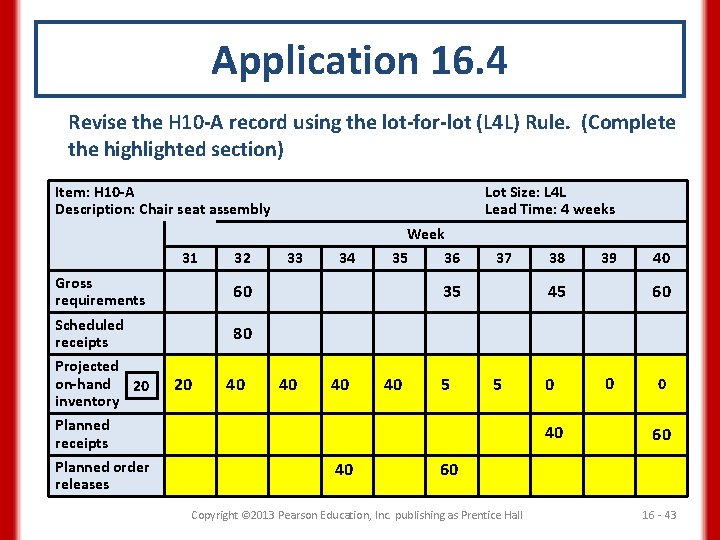
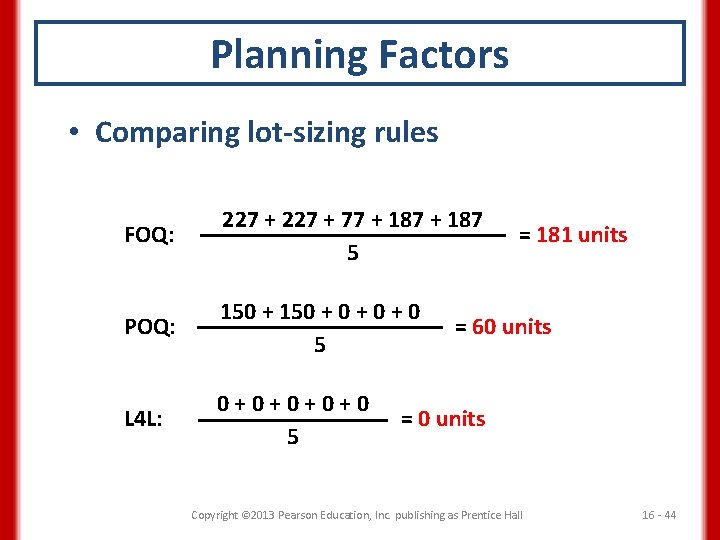
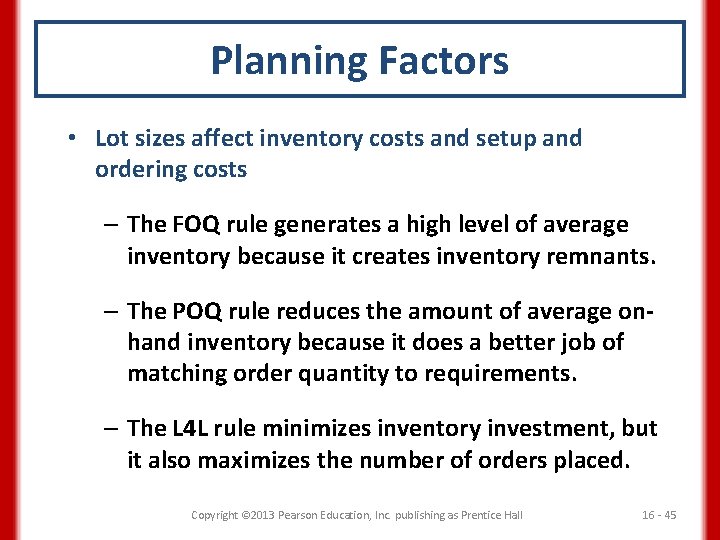
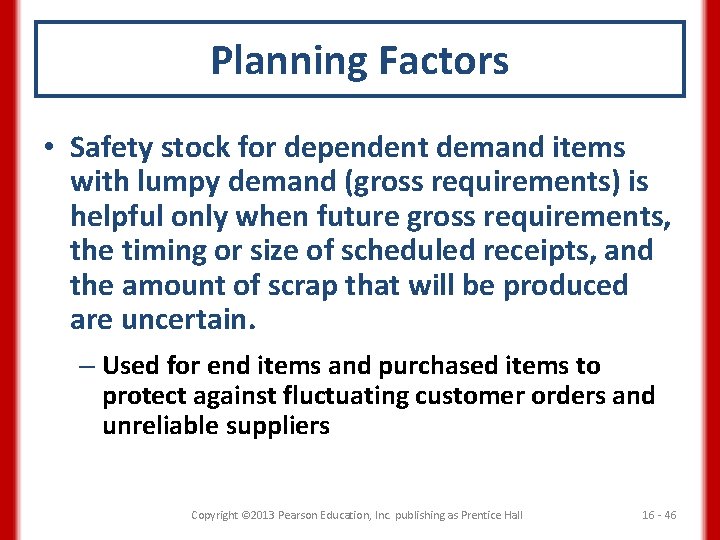
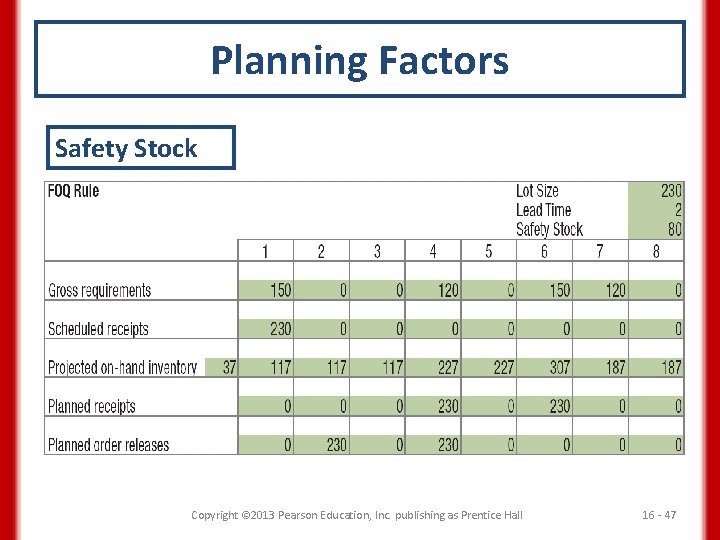
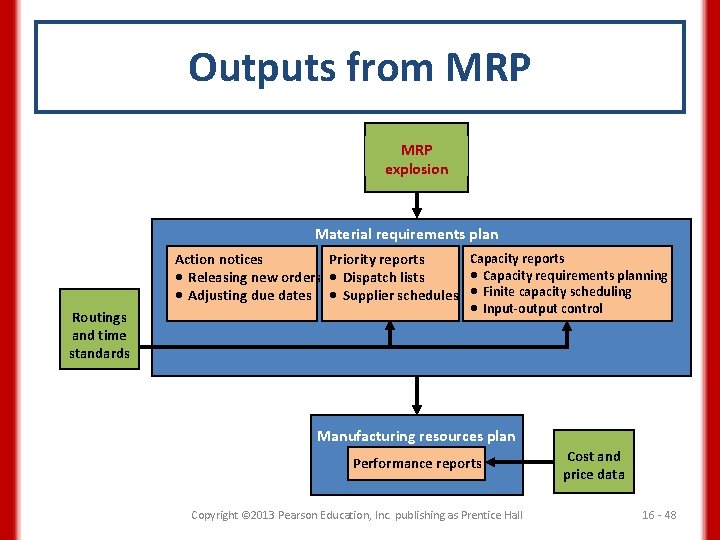
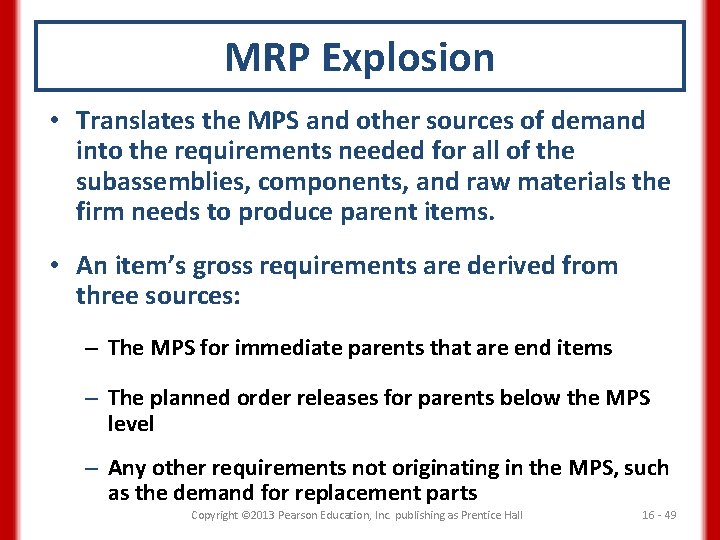
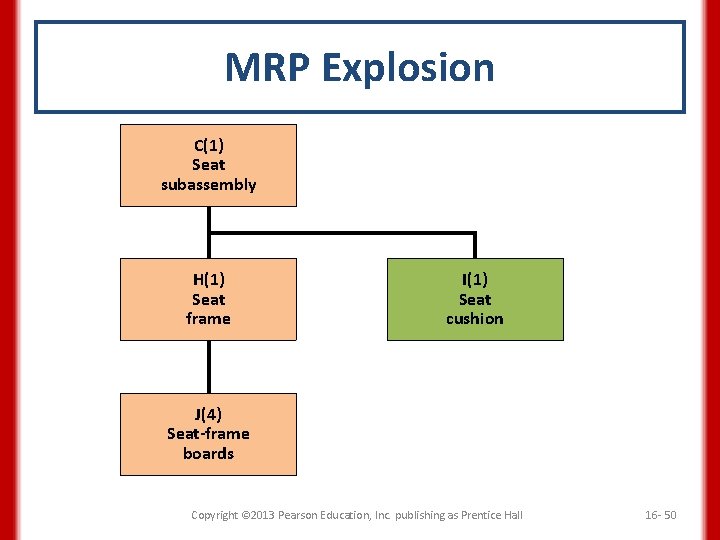
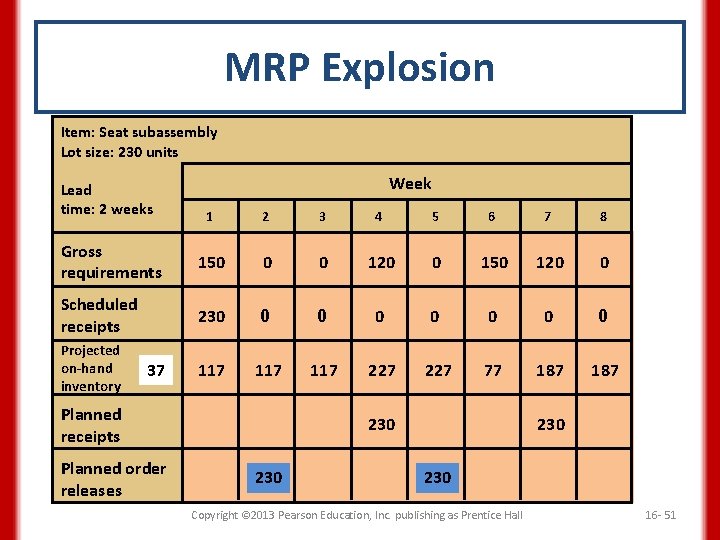
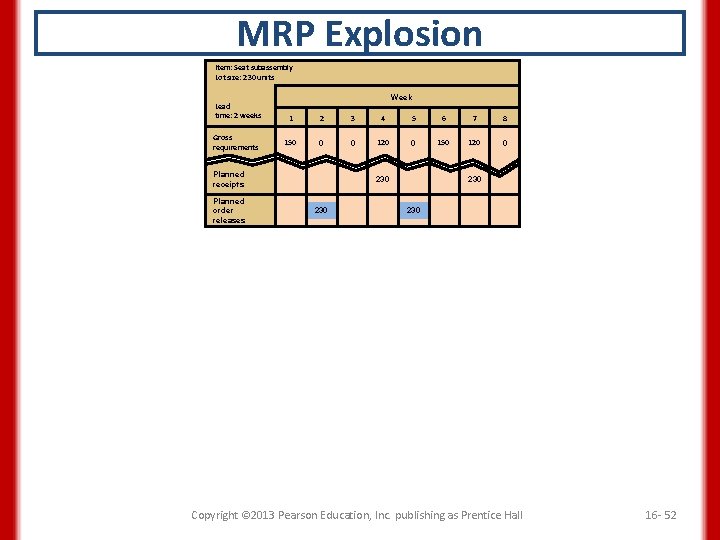
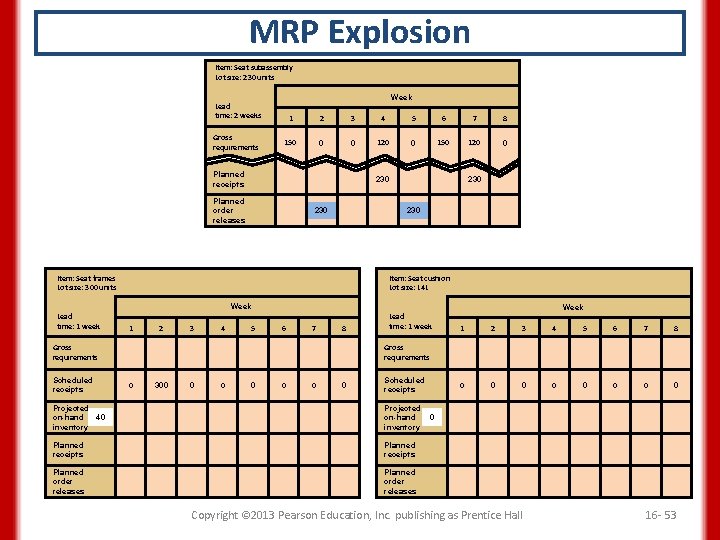
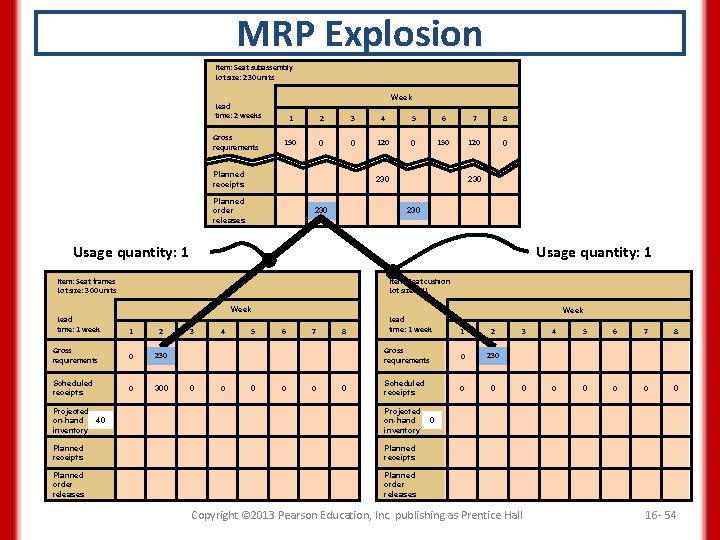
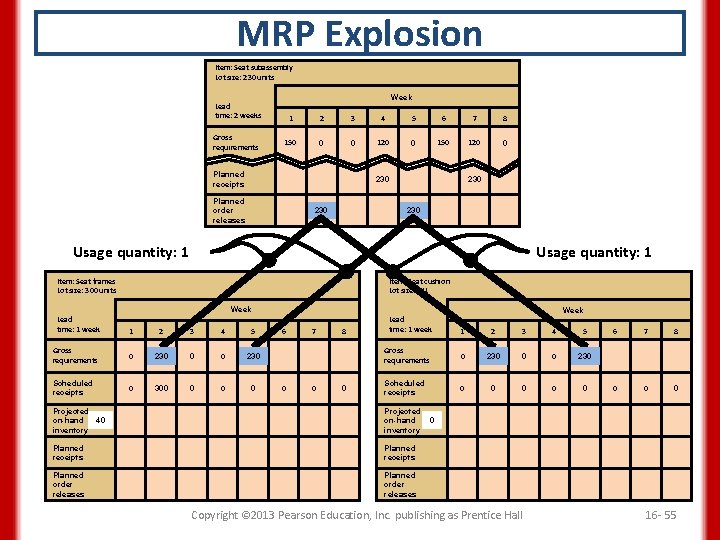
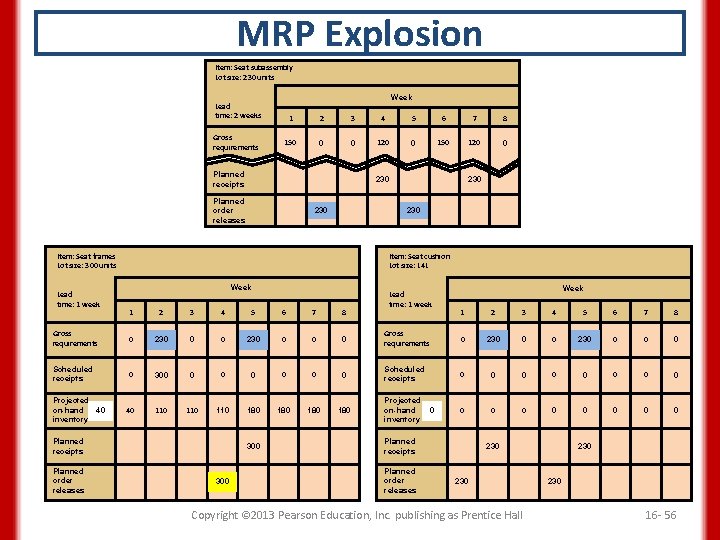
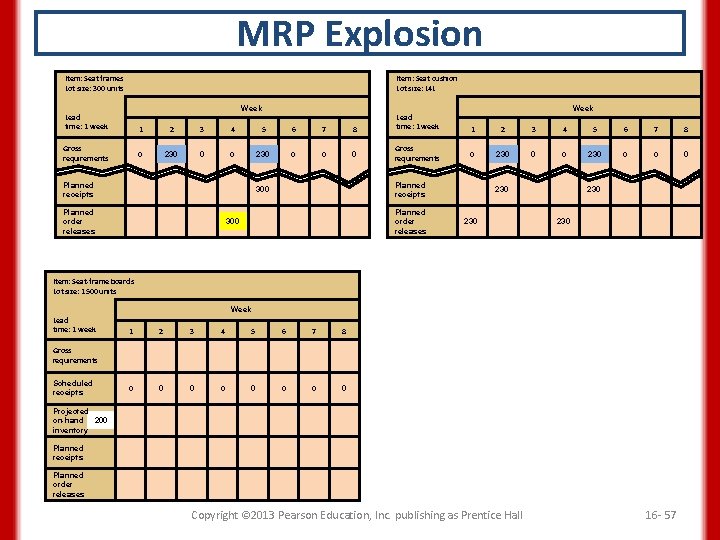
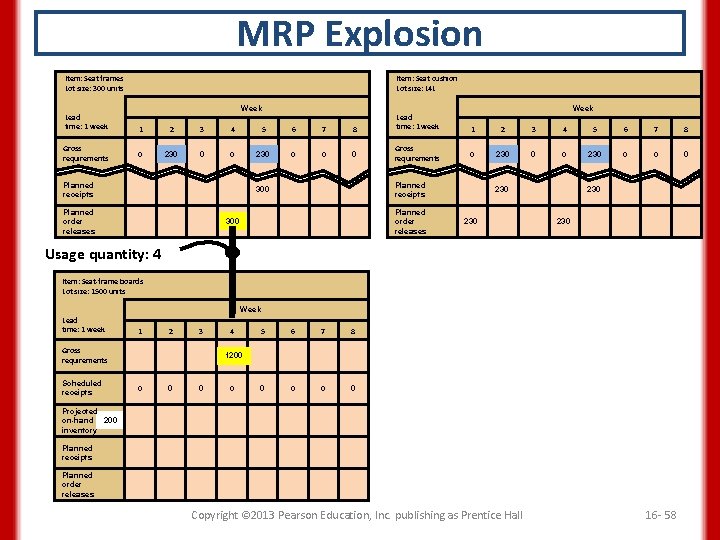
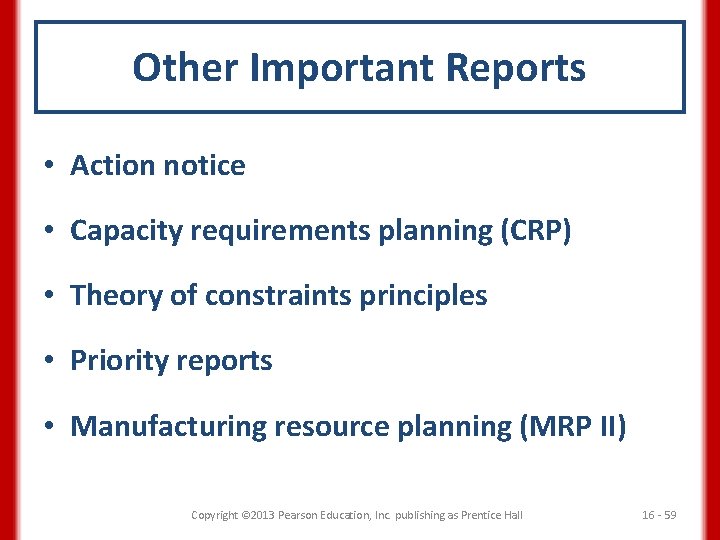
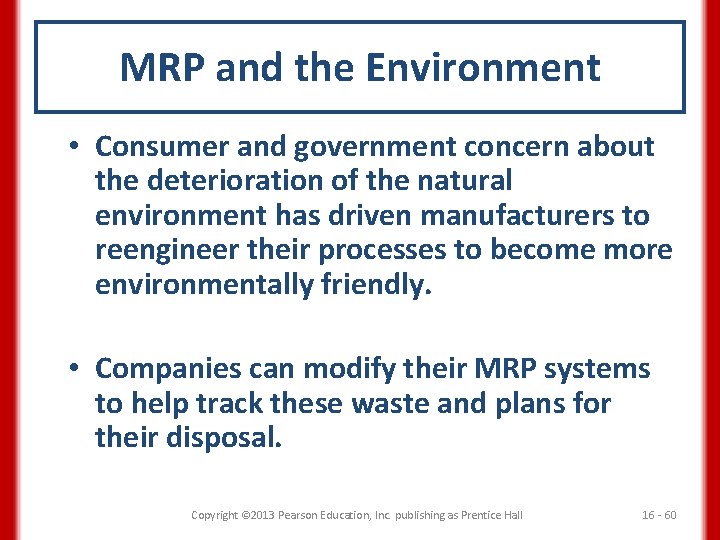
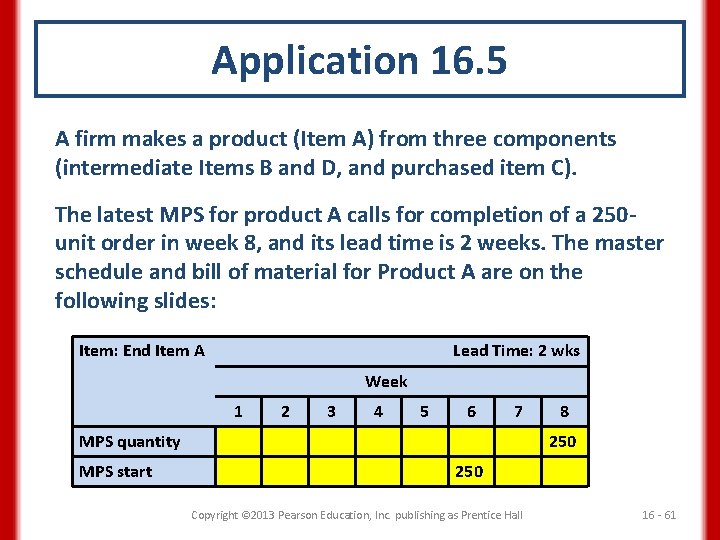
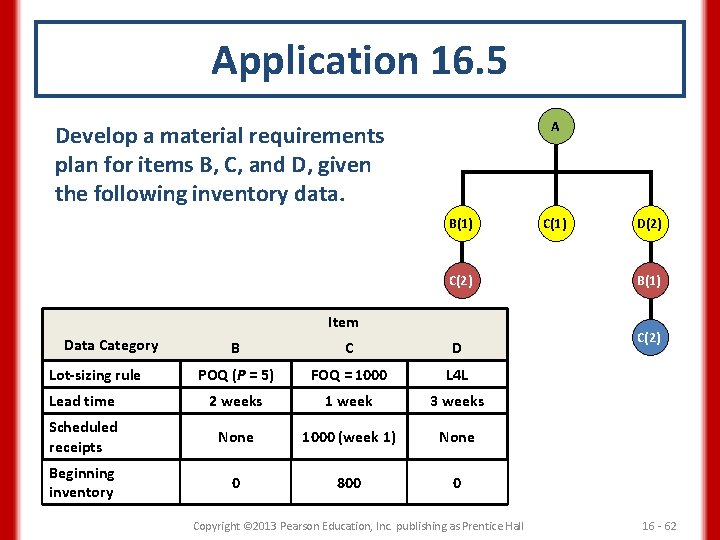
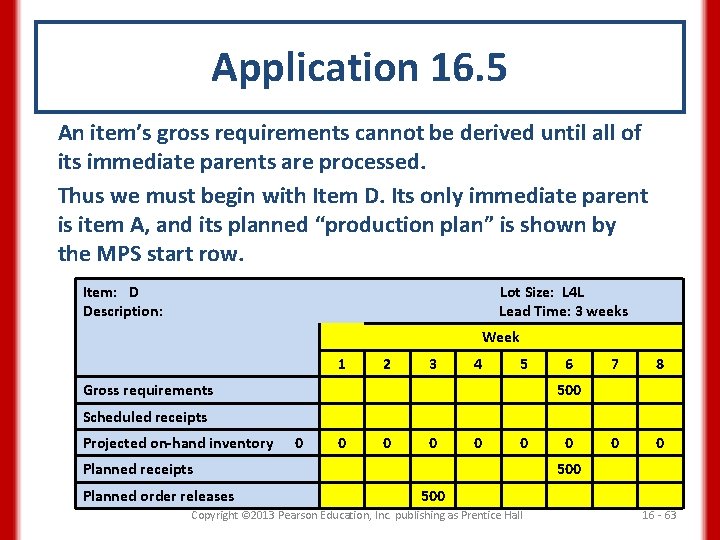
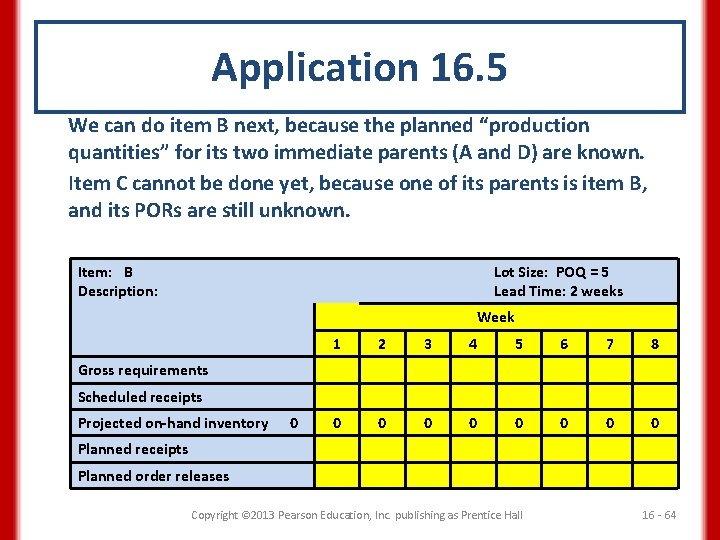
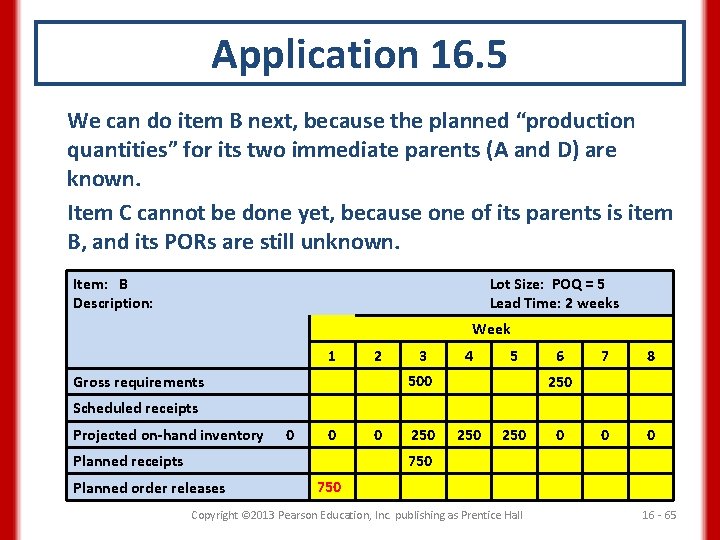
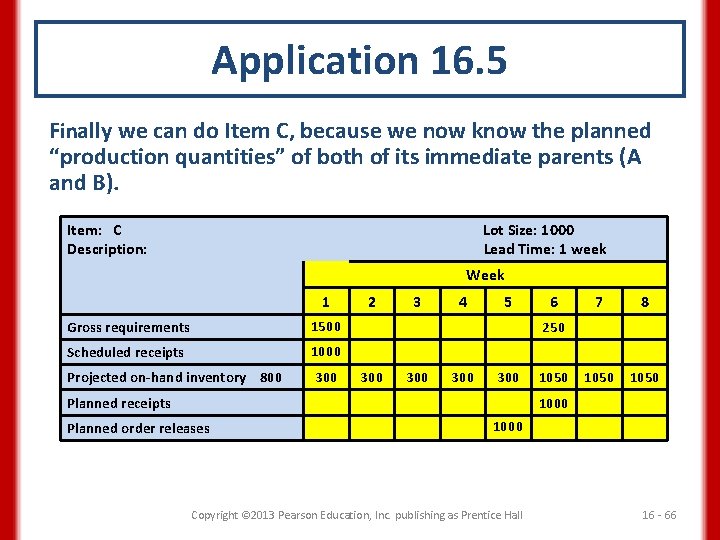
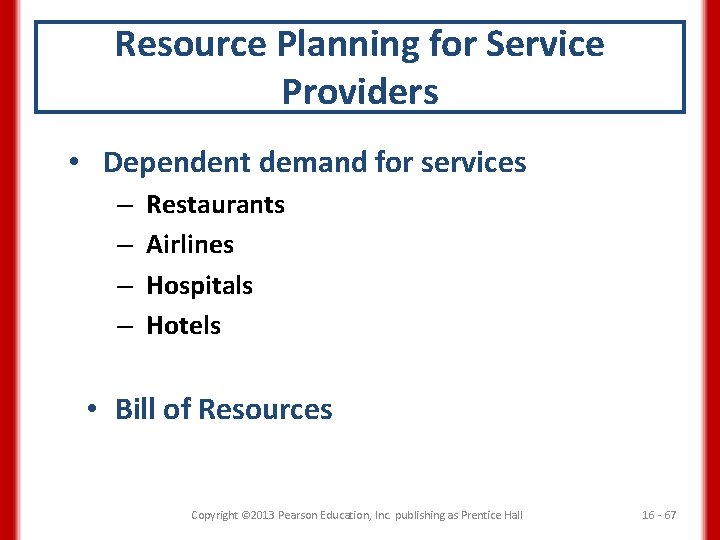
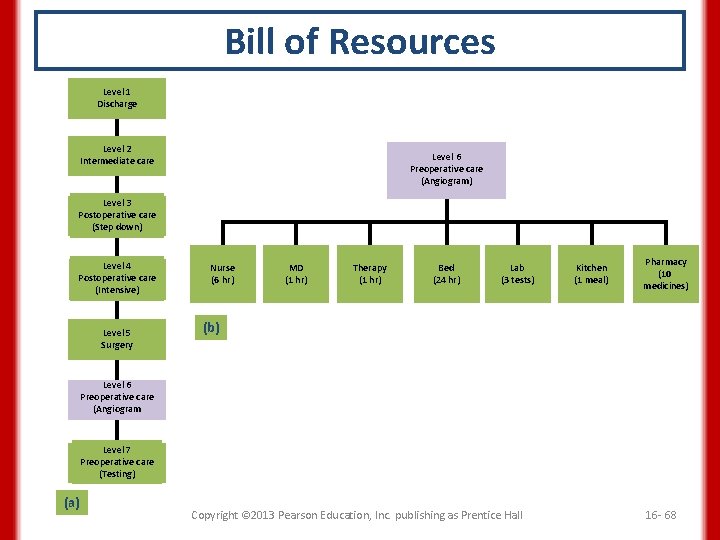
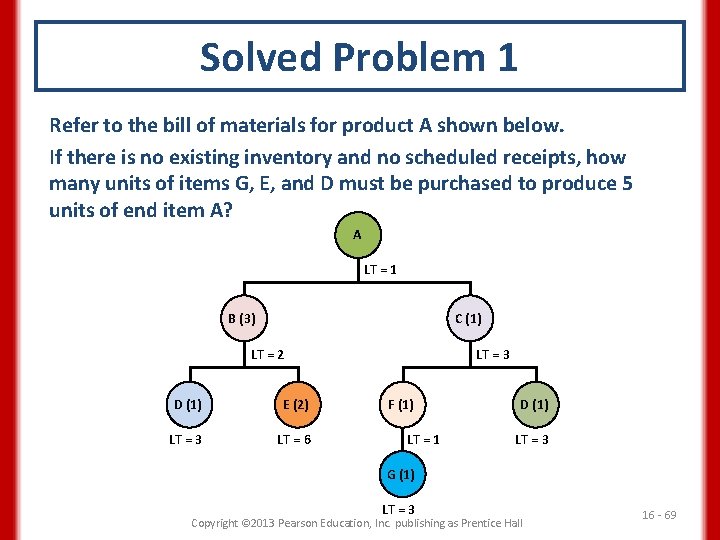
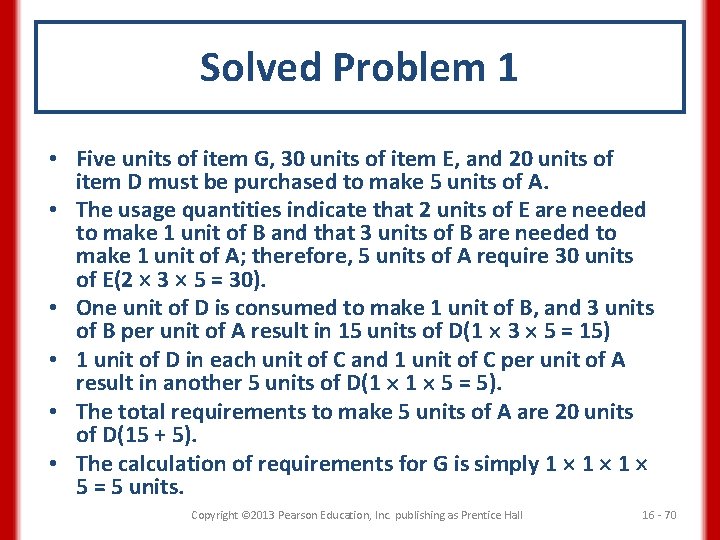

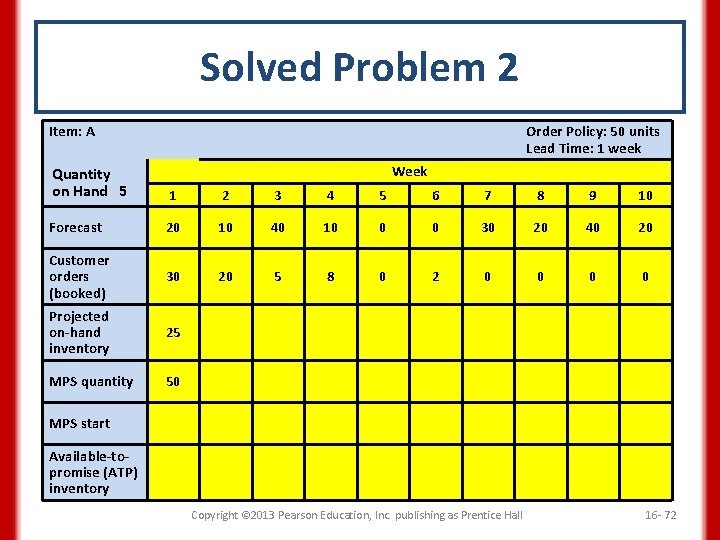
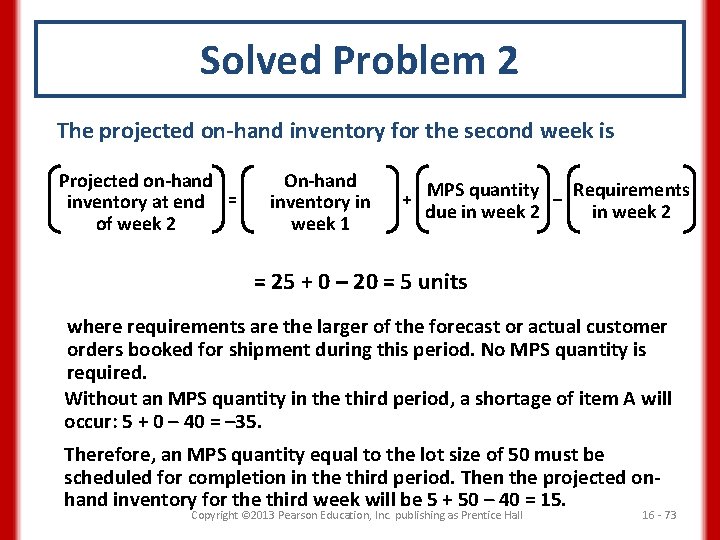
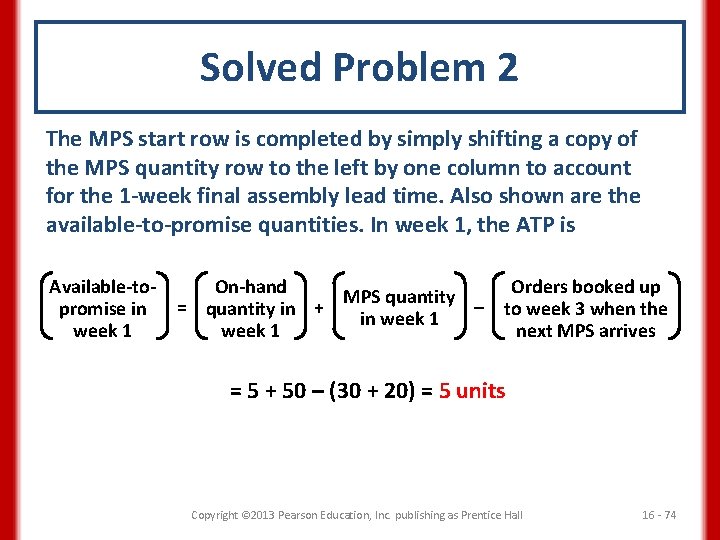
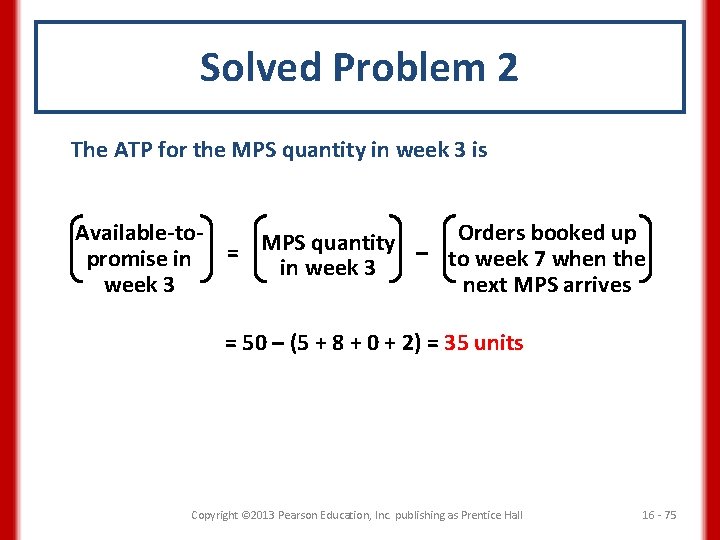
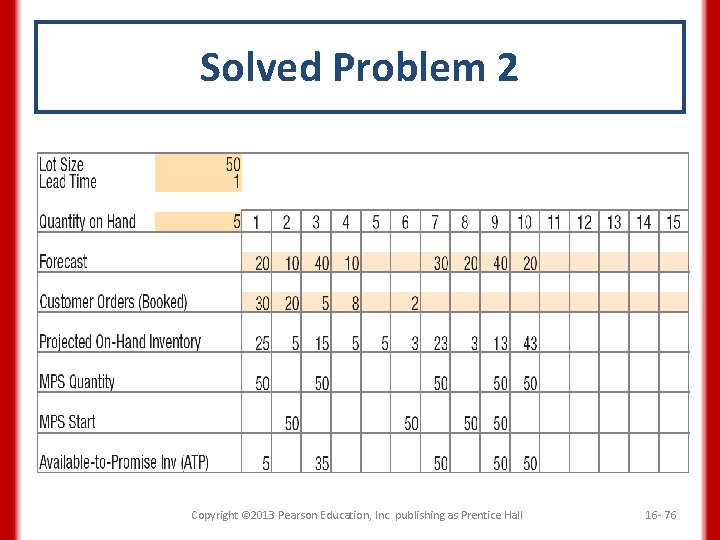
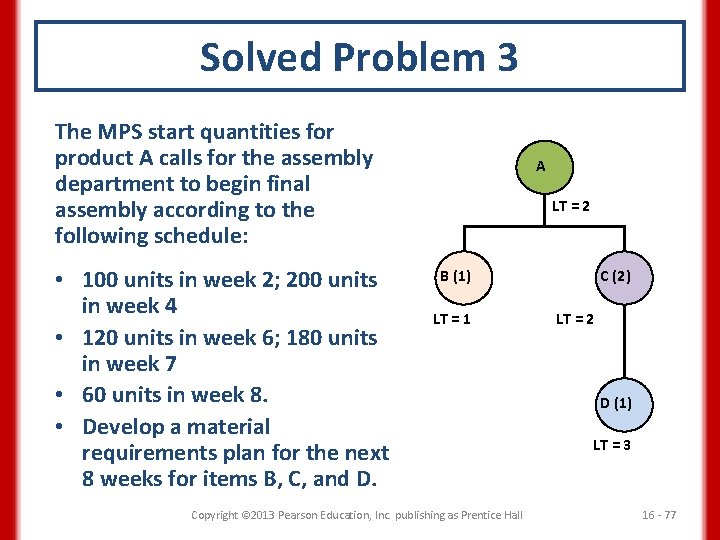
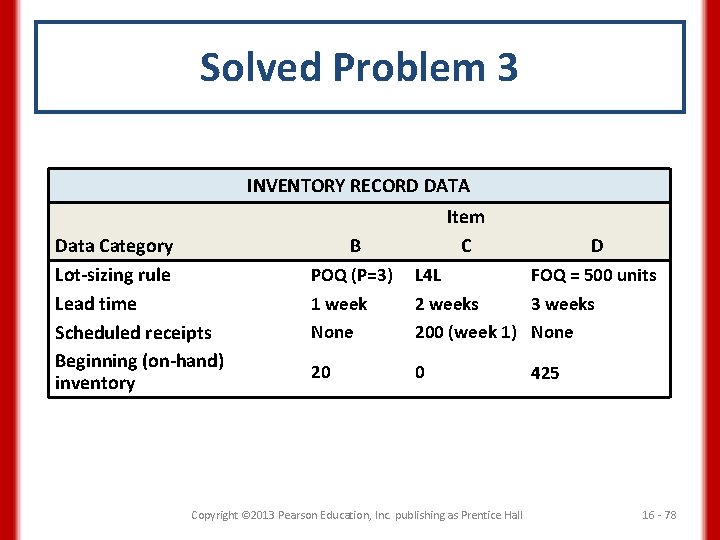
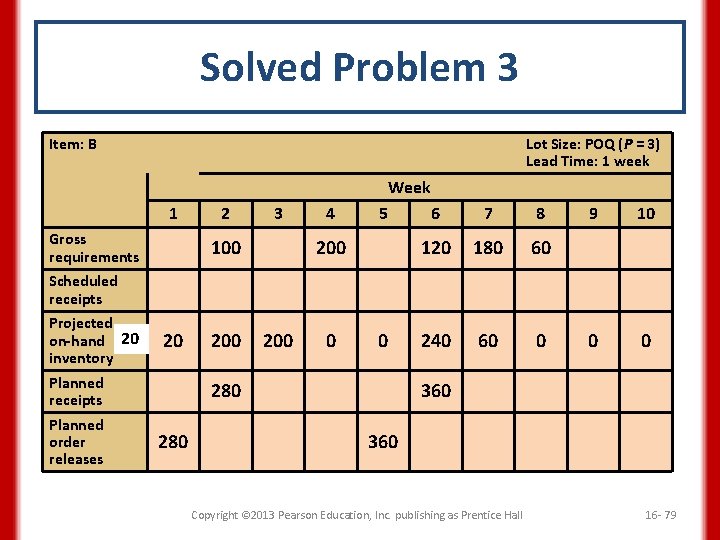
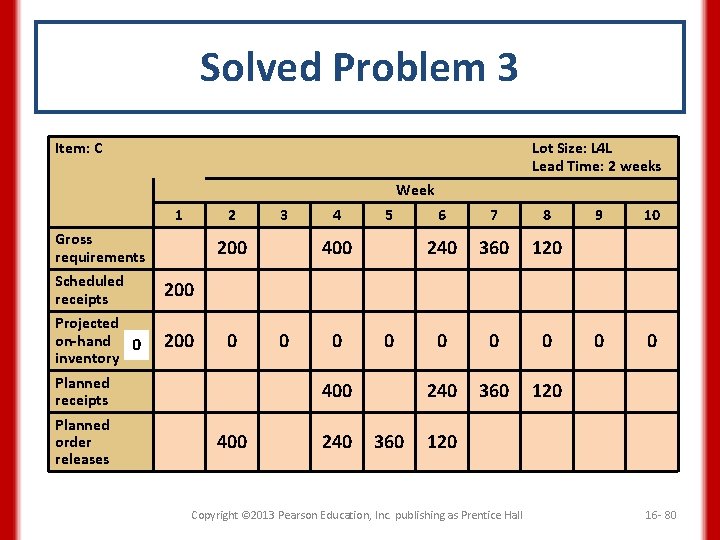
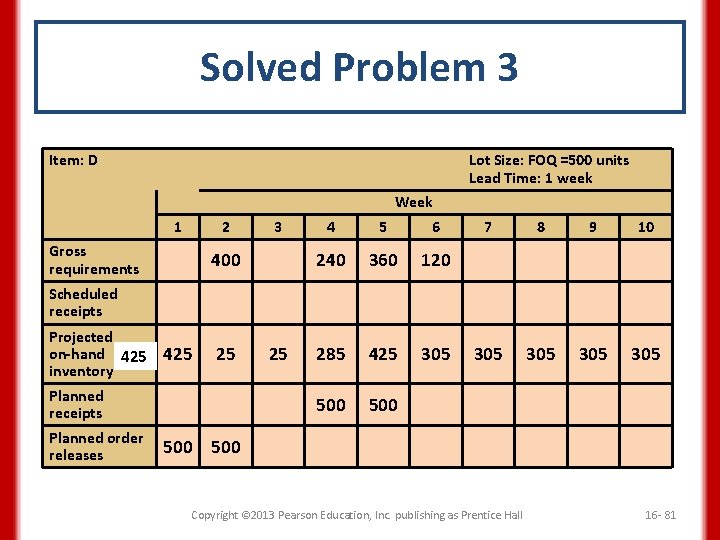
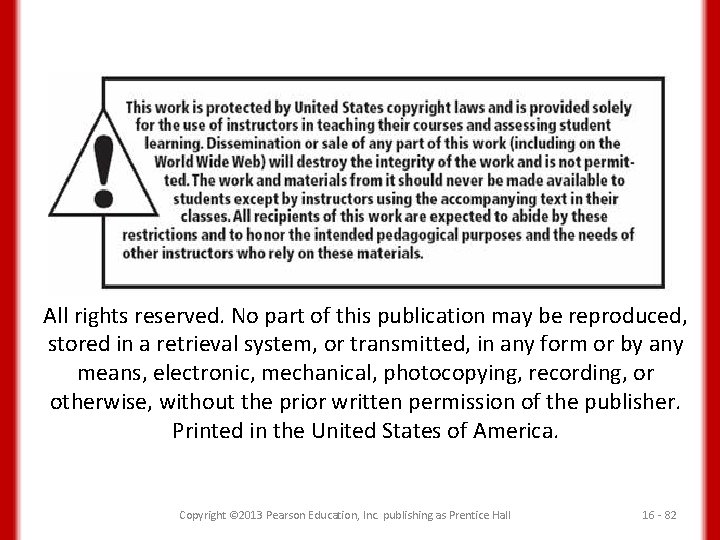
- Slides: 82
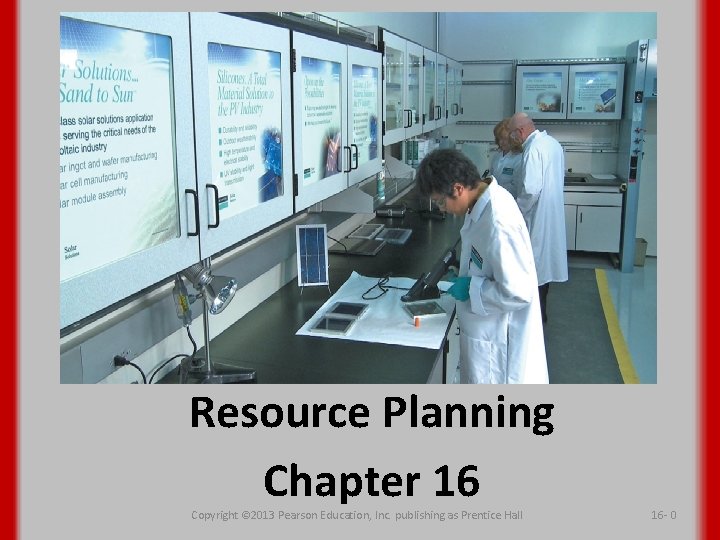
Resource Planning Chapter 16 Copyright © 2013 Pearson Education, Inc. publishing as Prentice Hall 16 - 0
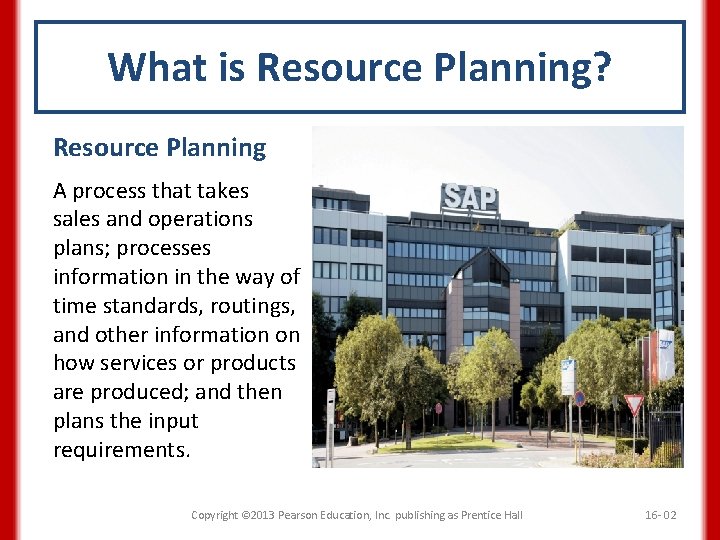
What is Resource Planning? Resource Planning A process that takes sales and operations plans; processes information in the way of time standards, routings, and other information on how services or products are produced; and then plans the input requirements. Copyright © 2013 Pearson Education, Inc. publishing as Prentice Hall 16 - 02
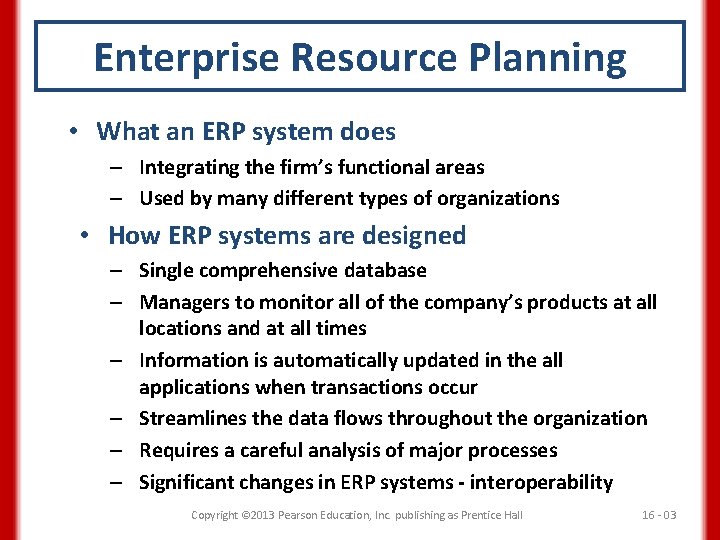
Enterprise Resource Planning • What an ERP system does – Integrating the firm’s functional areas – Used by many different types of organizations • How ERP systems are designed – Single comprehensive database – Managers to monitor all of the company’s products at all locations and at all times – Information is automatically updated in the all applications when transactions occur – Streamlines the data flows throughout the organization – Requires a careful analysis of major processes – Significant changes in ERP systems - interoperability Copyright © 2013 Pearson Education, Inc. publishing as Prentice Hall 16 - 03
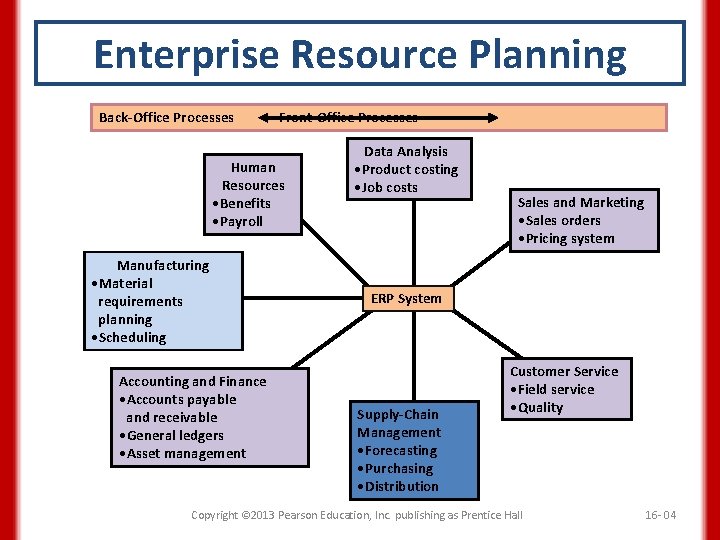
Enterprise Resource Planning Back-Office Processes Front-Office Processes Human Resources • Benefits • Payroll Manufacturing • Material requirements planning • Scheduling Accounting and Finance • Accounts payable and receivable • General ledgers • Asset management Data Analysis • Product costing • Job costs Sales and Marketing • Sales orders • Pricing system ERP System Supply-Chain Management • Forecasting • Purchasing • Distribution Customer Service • Field service • Quality Copyright © 2013 Pearson Education, Inc. publishing as Prentice Hall 16 - 04
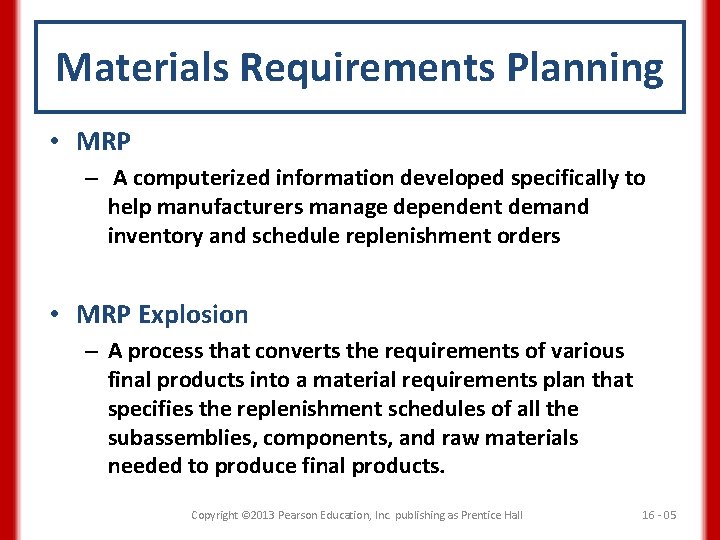
Materials Requirements Planning • MRP – A computerized information developed specifically to help manufacturers manage dependent demand inventory and schedule replenishment orders • MRP Explosion – A process that converts the requirements of various final products into a material requirements plan that specifies the replenishment schedules of all the subassemblies, components, and raw materials needed to produce final products. Copyright © 2013 Pearson Education, Inc. publishing as Prentice Hall 16 - 05
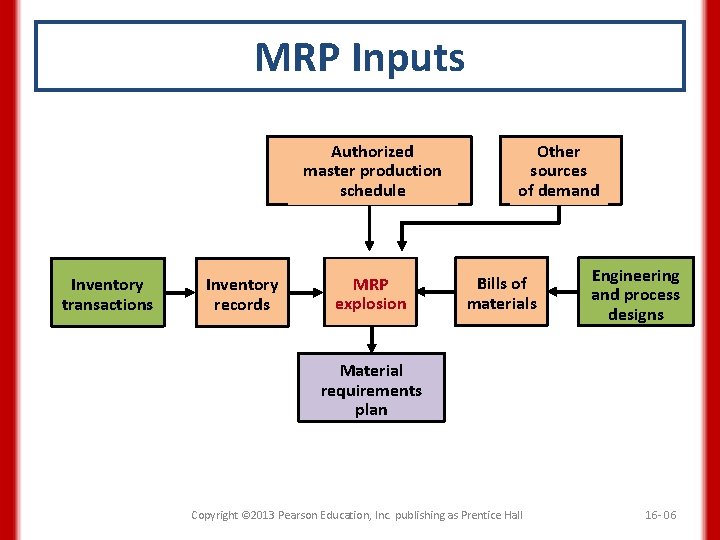
MRP Inputs Authorized master production schedule Inventory transactions Inventory records MRP explosion Other sources of demand Bills of materials Engineering and process designs Material requirements plan Copyright © 2013 Pearson Education, Inc. publishing as Prentice Hall 16 - 06
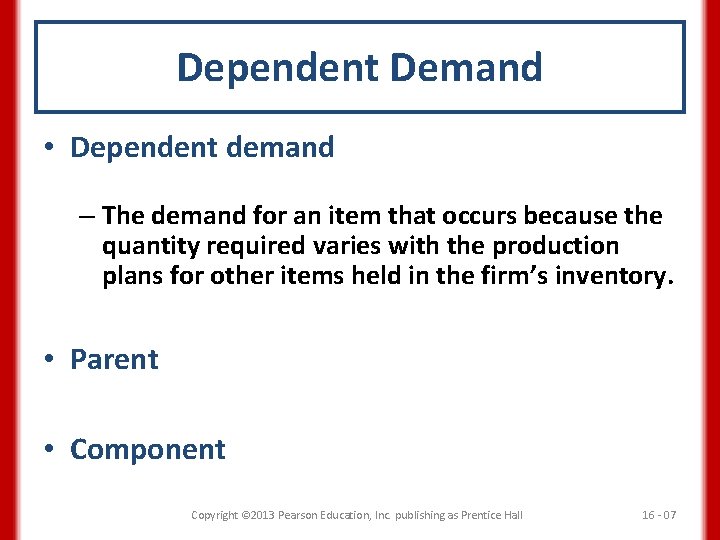
Dependent Demand • Dependent demand – The demand for an item that occurs because the quantity required varies with the production plans for other items held in the firm’s inventory. • Parent • Component Copyright © 2013 Pearson Education, Inc. publishing as Prentice Hall 16 - 07

Demand Patterns 2000 – Order 1000 on day 3 1500 – Rims Bicycles 1500 – Order 1000 on day 8 1000 – 500 – Reorder point 0 | 1 | | | Day | 5 | (a) Parent inventory | | 10 0 | 1 | | | Day | 5 | | | 10 (b) Component demand Copyright © 2013 Pearson Education, Inc. publishing as Prentice Hall 16 - 08
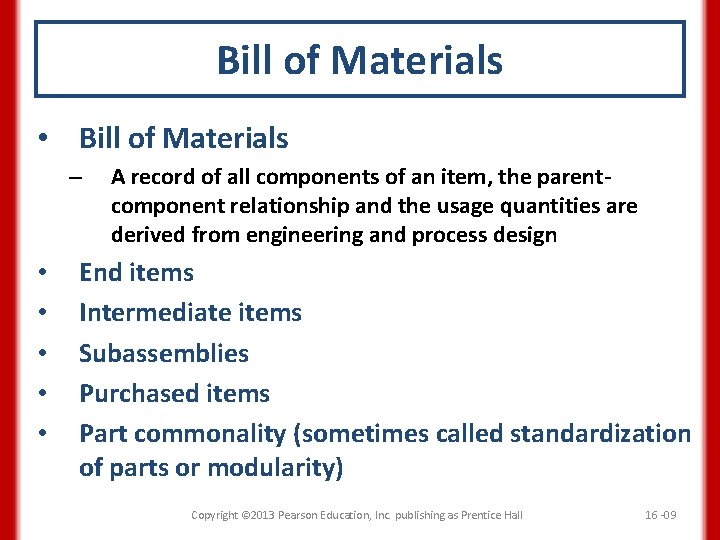
Bill of Materials • Bill of Materials – • • • A record of all components of an item, the parentcomponent relationship and the usage quantities are derived from engineering and process design End items Intermediate items Subassemblies Purchased items Part commonality (sometimes called standardization of parts or modularity) Copyright © 2013 Pearson Education, Inc. publishing as Prentice Hall 16 -09
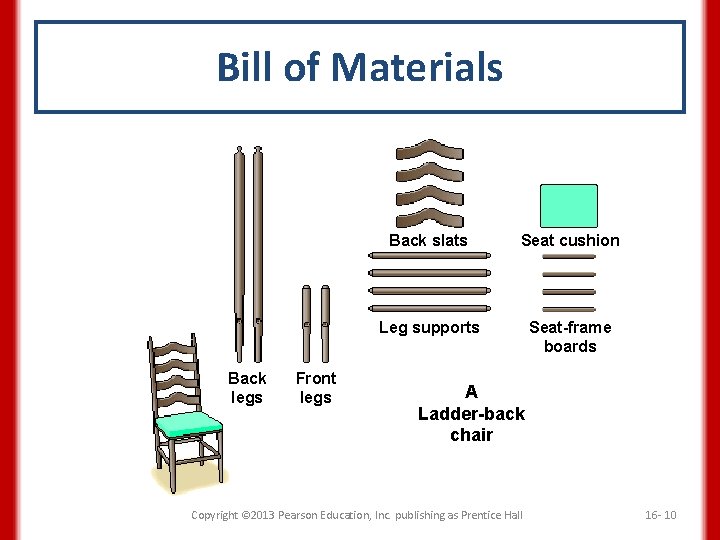
Bill of Materials Back legs Front legs Back slats Seat cushion Leg supports Seat-frame boards A Ladder-back chair Copyright © 2013 Pearson Education, Inc. publishing as Prentice Hall 16 - 10
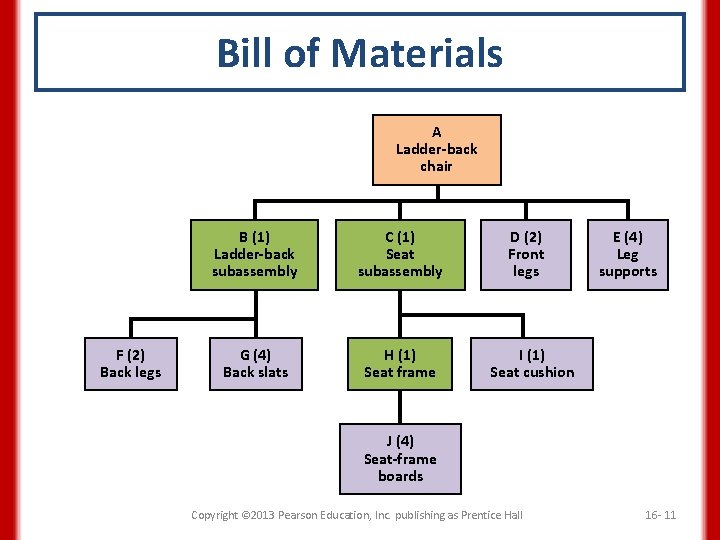
Bill of Materials A Ladder-back chair F (2) Back legs B (1) Ladder-back subassembly C (1) Seat subassembly G (4) Back slats H (1) Seat frame D (2) Front legs E (4) Leg supports I (1) Seat cushion J (4) Seat-frame boards Copyright © 2013 Pearson Education, Inc. publishing as Prentice Hall 16 - 11
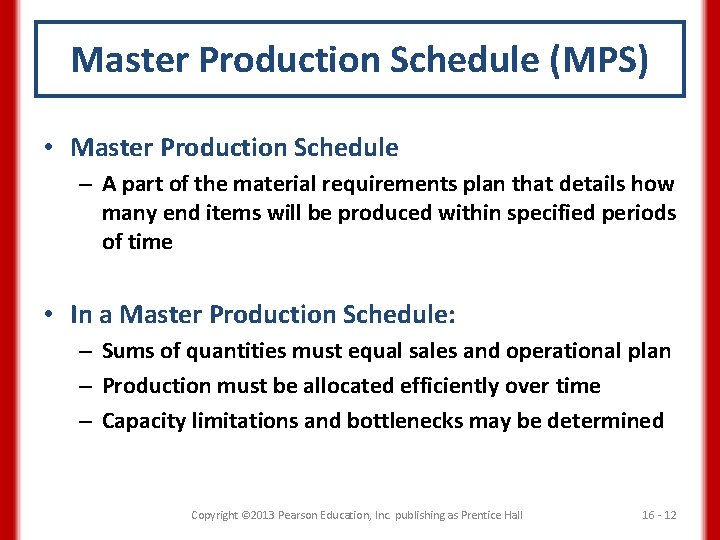
Master Production Schedule (MPS) • Master Production Schedule – A part of the material requirements plan that details how many end items will be produced within specified periods of time • In a Master Production Schedule: – Sums of quantities must equal sales and operational plan – Production must be allocated efficiently over time – Capacity limitations and bottlenecks may be determined Copyright © 2013 Pearson Education, Inc. publishing as Prentice Hall 16 - 12
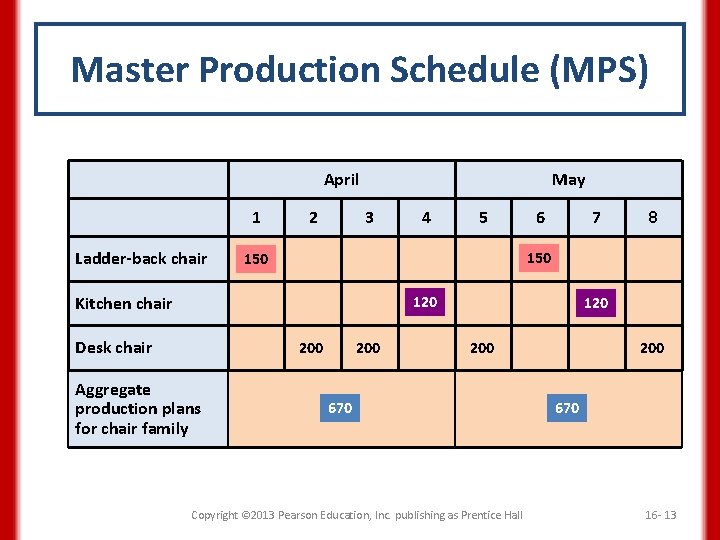
Master Production Schedule (MPS) April 1 Ladder-back chair 2 May 3 4 5 6 7 150 Kitchen chair 120 Desk chair 200 Aggregate production plans for chair family 8 200 120 200 670 Copyright © 2013 Pearson Education, Inc. publishing as Prentice Hall 200 670 16 - 13
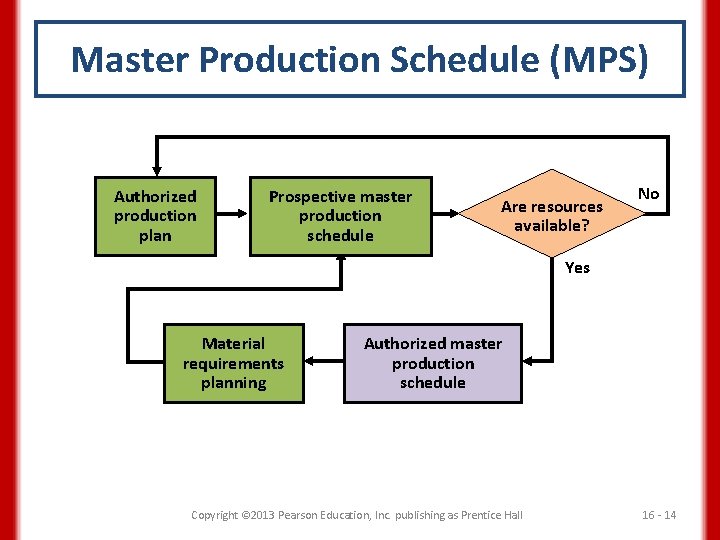
Master Production Schedule (MPS) Authorized production plan Prospective master production schedule Are resources available? No Yes Material requirements planning Authorized master production schedule Copyright © 2013 Pearson Education, Inc. publishing as Prentice Hall 16 - 14
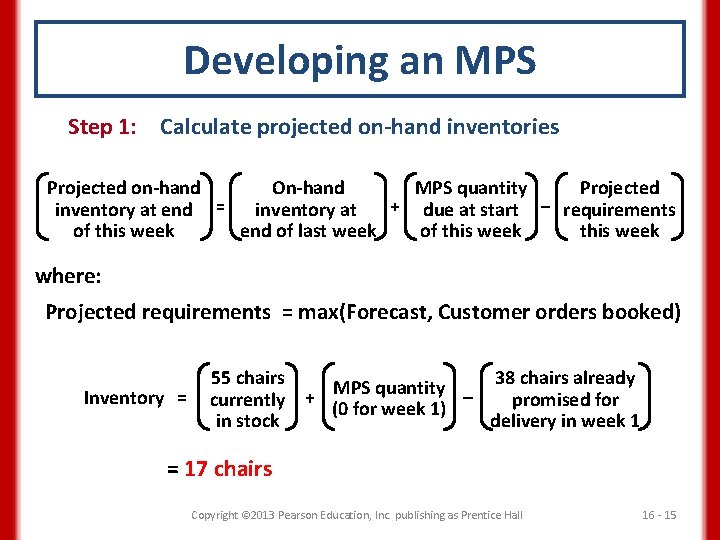
Developing an MPS Step 1: Calculate projected on-hand inventories Projected on-hand Projected MPS quantity On-hand + due at start – requirements inventory at end = inventory at of this week end of last week where: Projected requirements = max(Forecast, Customer orders booked) Inventory = 38 chairs already 55 chairs MPS quantity promised for currently + (0 for week 1) – delivery in week 1 in stock = 17 chairs Copyright © 2013 Pearson Education, Inc. publishing as Prentice Hall 16 - 15
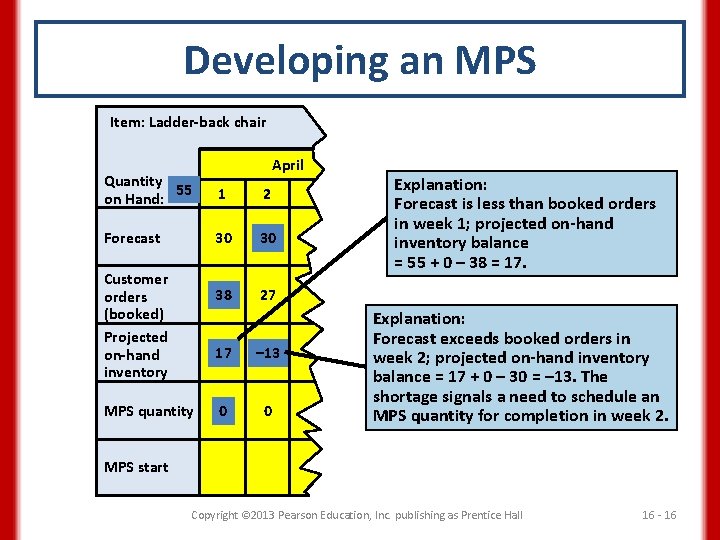
Developing an MPS Item: Ladder-back chair April Quantity 55 on Hand: 1 2 Forecast 30 30 38 27 Customer orders (booked) Projected on-hand inventory MPS quantity 17 – 13 0 0 Explanation: Forecast is less than booked orders in week 1; projected on-hand inventory balance = 55 + 0 – 38 = 17. Explanation: Forecast exceeds booked orders in week 2; projected on-hand inventory balance = 17 + 0 – 30 = – 13. The shortage signals a need to schedule an MPS quantity for completion in week 2. MPS start Copyright © 2013 Pearson Education, Inc. publishing as Prentice Hall 16 - 16
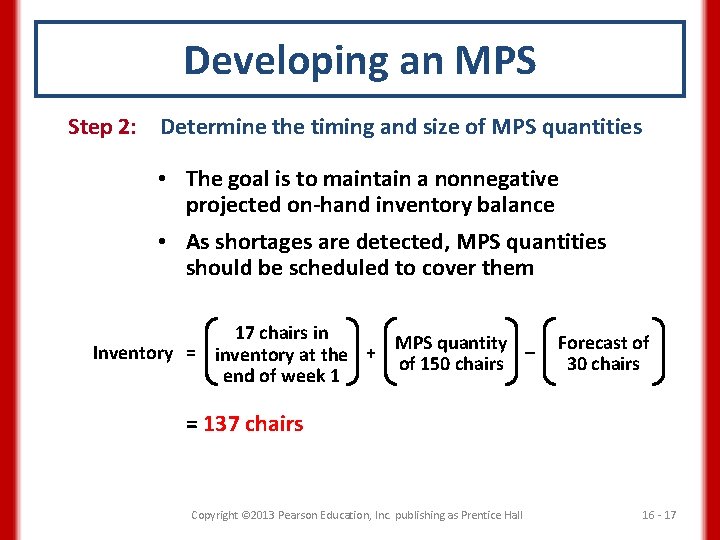
Developing an MPS Step 2: Determine the timing and size of MPS quantities • The goal is to maintain a nonnegative projected on-hand inventory balance • As shortages are detected, MPS quantities should be scheduled to cover them 17 chairs in Inventory = inventory at the + MPS quantity – of 150 chairs end of week 1 Forecast of 30 chairs = 137 chairs Copyright © 2013 Pearson Education, Inc. publishing as Prentice Hall 16 - 17
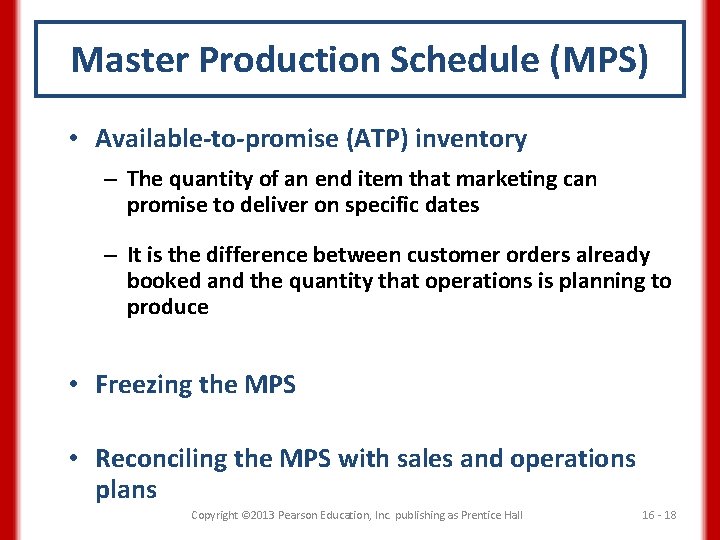
Master Production Schedule (MPS) • Available-to-promise (ATP) inventory – The quantity of an end item that marketing can promise to deliver on specific dates – It is the difference between customer orders already booked and the quantity that operations is planning to produce • Freezing the MPS • Reconciling the MPS with sales and operations plans Copyright © 2013 Pearson Education, Inc. publishing as Prentice Hall 16 - 18
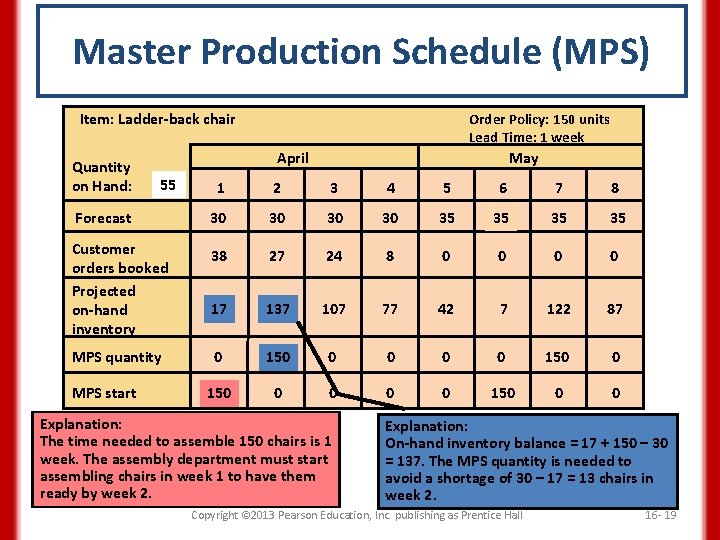
Master Production Schedule (MPS) Item: Ladder-back chair Quantity on Hand: Order Policy: 150 units Lead Time: 1 week April 55 May 1 2 3 4 5 6 7 8 Forecast 30 30 35 35 Customer orders booked Projected on-hand inventory 38 27 24 8 0 0 17 137 107 77 42 7 122 87 MPS quantity 0 150 0 0 0 0 150 0 0 MPS start Explanation: The time needed to assemble 150 chairs is 1 week. The assembly department must start assembling chairs in week 1 to have them ready by week 2. Explanation: On-hand inventory balance = 17 + 150 – 30 = 137. The MPS quantity is needed to avoid a shortage of 30 – 17 = 13 chairs in week 2. Copyright © 2013 Pearson Education, Inc. publishing as Prentice Hall 16 - 19
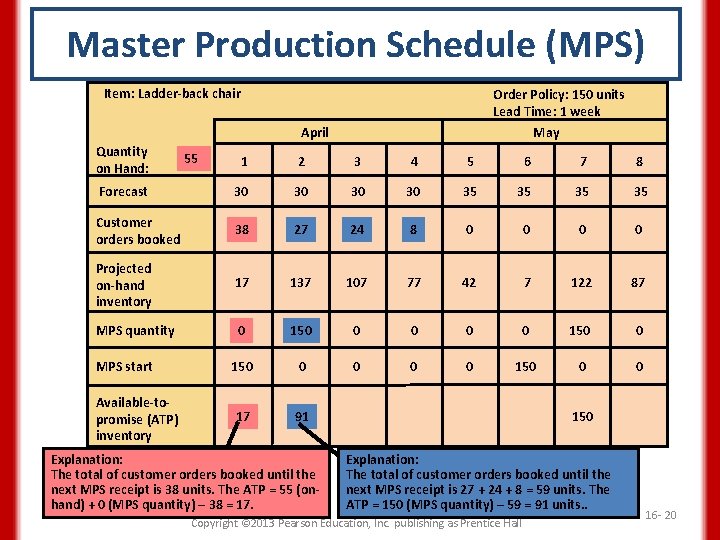
Master Production Schedule (MPS) Item: Ladder-back chair Order Policy: 150 units Lead Time: 1 week April Quantity on Hand: 55 May 1 2 3 4 5 6 7 8 Forecast 30 30 35 35 Customer orders booked 38 27 24 8 0 0 Projected on-hand inventory 17 137 107 77 42 7 122 87 MPS quantity 0 150 0 0 0 0 150 0 0 17 91 MPS start Available-topromise (ATP) inventory Explanation: The total of customer orders booked until the next MPS receipt is 38 units. The ATP = 55 (onhand) + 0 (MPS quantity) – 38 = 17. 150 Explanation: The total of customer orders booked until the next MPS receipt is 27 + 24 + 8 = 59 units. The ATP = 150 (MPS quantity) – 59 = 91 units. . Copyright © 2013 Pearson Education, Inc. publishing as Prentice Hall 16 - 20
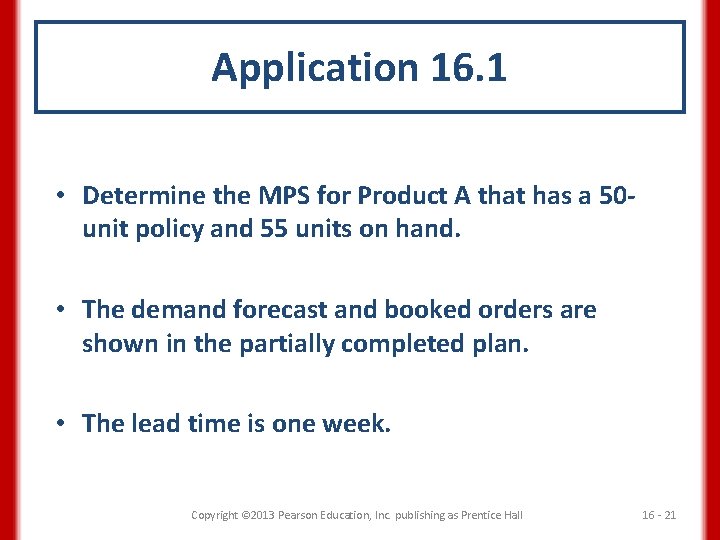
Application 16. 1 • Determine the MPS for Product A that has a 50 unit policy and 55 units on hand. • The demand forecast and booked orders are shown in the partially completed plan. • The lead time is one week. Copyright © 2013 Pearson Education, Inc. publishing as Prentice Hall 16 - 21
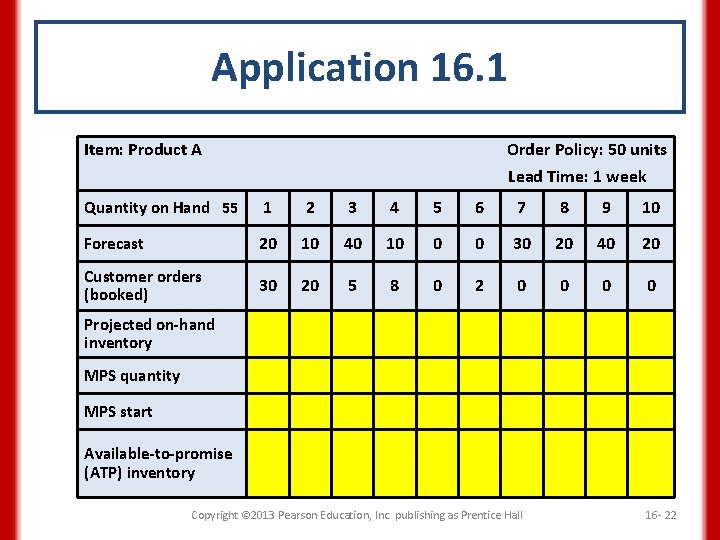
Application 16. 1 Item: Product A Order Policy: 50 units Lead Time: 1 week Quantity on Hand 55 1 2 3 4 5 6 7 8 9 10 Forecast 20 10 40 10 0 0 30 20 40 20 Customer orders (booked) 30 20 5 8 0 2 0 0 Projected on-hand inventory MPS quantity MPS start Available-to-promise (ATP) inventory Copyright © 2013 Pearson Education, Inc. publishing as Prentice Hall 16 - 22
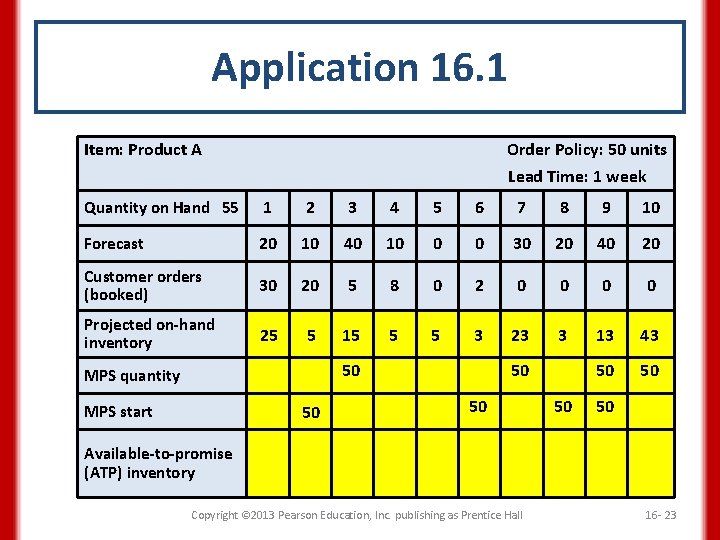
Application 16. 1 Item: Product A Order Policy: 50 units Lead Time: 1 week Quantity on Hand 55 1 2 3 4 5 6 7 8 9 10 Forecast 20 10 40 10 0 0 30 20 40 20 Customer orders (booked) 30 20 5 8 0 2 0 0 Projected on-hand inventory 25 5 15 5 5 3 23 3 13 43 50 50 50 MPS quantity 50 MPS start 50 50 Available-to-promise (ATP) inventory Copyright © 2013 Pearson Education, Inc. publishing as Prentice Hall 16 - 23
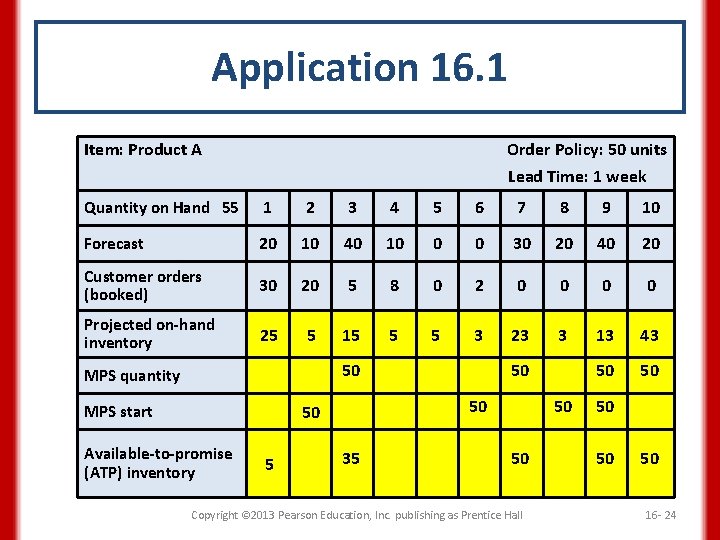
Application 16. 1 Item: Product A Order Policy: 50 units Lead Time: 1 week Quantity on Hand 55 1 2 3 4 5 6 7 8 9 10 Forecast 20 10 40 10 0 0 30 20 40 20 Customer orders (booked) 30 20 5 8 0 2 0 0 Projected on-hand inventory 25 5 15 5 5 3 23 3 13 43 50 50 50 MPS quantity 50 50 MPS start Available-to-promise (ATP) inventory 5 50 35 50 50 Copyright © 2013 Pearson Education, Inc. publishing as Prentice Hall 50 50 50 16 - 24
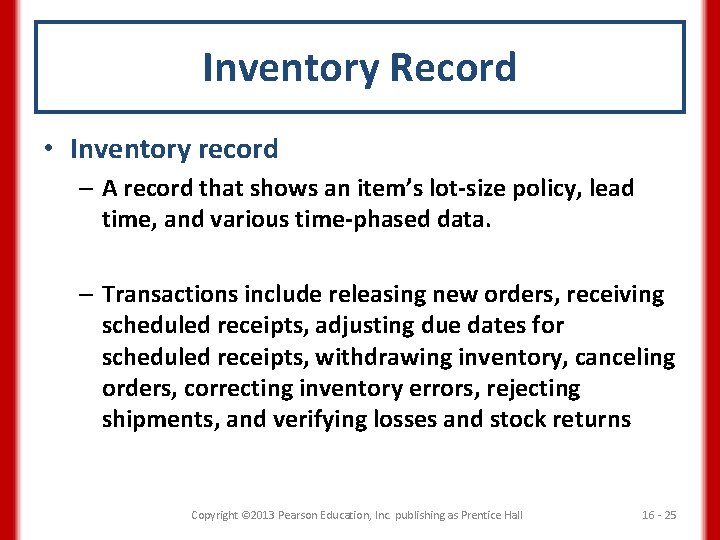
Inventory Record • Inventory record – A record that shows an item’s lot-size policy, lead time, and various time-phased data. – Transactions include releasing new orders, receiving scheduled receipts, adjusting due dates for scheduled receipts, withdrawing inventory, canceling orders, correcting inventory errors, rejecting shipments, and verifying losses and stock returns Copyright © 2013 Pearson Education, Inc. publishing as Prentice Hall 16 - 25
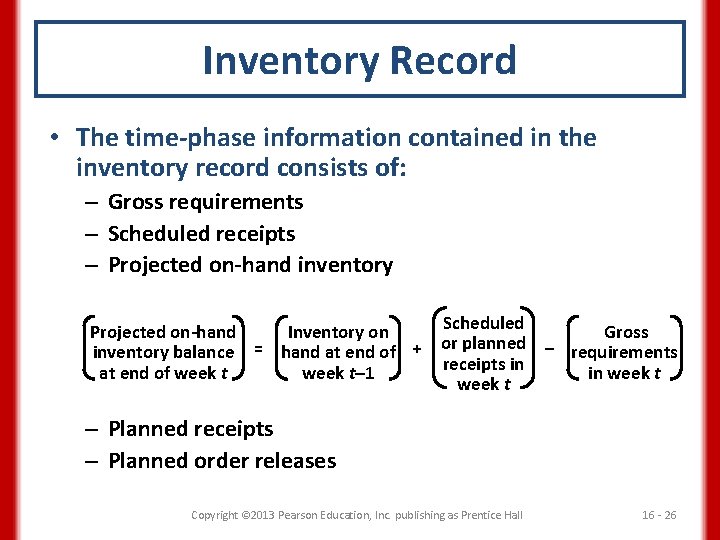
Inventory Record • The time-phase information contained in the inventory record consists of: – Gross requirements – Scheduled receipts – Projected on-hand inventory Projected on-hand Inventory on inventory balance = hand at end of + at end of week t– 1 Scheduled Gross or planned – requirements receipts in in week t – Planned receipts – Planned order releases Copyright © 2013 Pearson Education, Inc. publishing as Prentice Hall 16 - 26
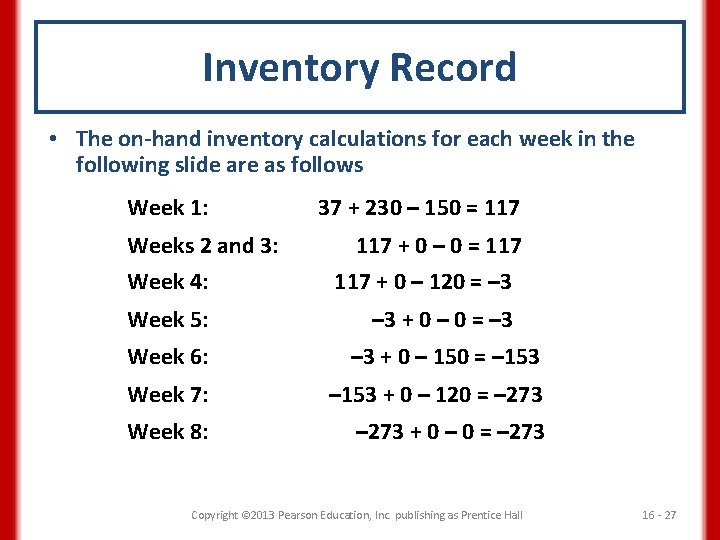
Inventory Record • The on-hand inventory calculations for each week in the following slide are as follows Week 1: Weeks 2 and 3: Week 4: 37 + 230 – 150 = 117 117 + 0 – 120 = – 3 Week 5: – 3 + 0 – 0 = – 3 Week 6: – 3 + 0 – 150 = – 153 Week 7: – 153 + 0 – 120 = – 273 Week 8: – 273 + 0 – 0 = – 273 Copyright © 2013 Pearson Education, Inc. publishing as Prentice Hall 16 - 27

Inventory Record Item: C Description: Seat subassembly Lot Size: 230 units Lead Time: 2 weeks Week Gross requirements Scheduled receipts Projected 37 on-hand inventory Planned receipts 1 2 3 4 5 6 7 8 150 0 0 120 0 150 120 0 230 0 0 0 117 117 – 3 – 153 – 273 Planned order releases Explanation: Gross requirements are the total demand for the two chairs. Projected on-hand inventory in week 1 is 37 + 230 – 150 = 117 units. Copyright © 2013 Pearson Education, Inc. publishing as Prentice Hall 16 - 28
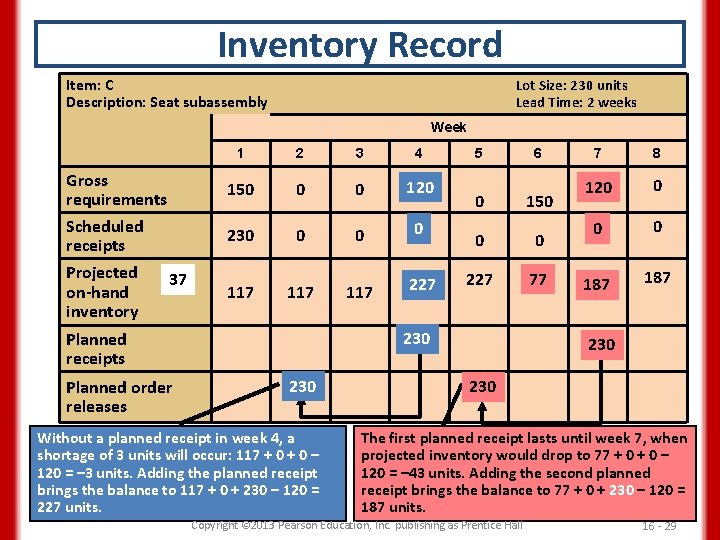
Inventory Record Item: C Description: Seat subassembly Lot Size: 230 units Lead Time: 2 weeks Week Gross requirements Scheduled receipts Projected on-hand inventory 37 1 2 3 4 150 0 0 120 230 0 117 227 117 230 Without a planned receipt in week 4, a shortage of 3 units will occur: 117 + 0 – 120 = – 3 units. Adding the planned receipt brings the balance to 117 + 0 + 230 – 120 = 227 units. 6 0 150 0 0 227 77 230 Planned receipts Planned order releases 5 7 8 120 0 187 230 The first planned receipt lasts until week 7, when projected inventory would drop to 77 + 0 – 120 = – 43 units. Adding the second planned receipt brings the balance to 77 + 0 + 230 – 120 = 187 units. Copyright © 2013 Pearson Education, Inc. publishing as Prentice Hall 16 - 29
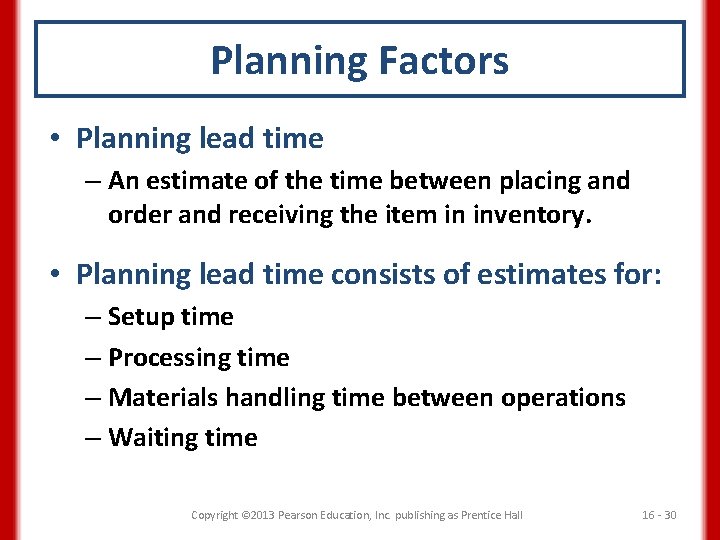
Planning Factors • Planning lead time – An estimate of the time between placing and order and receiving the item in inventory. • Planning lead time consists of estimates for: – Setup time – Processing time – Materials handling time between operations – Waiting time Copyright © 2013 Pearson Education, Inc. publishing as Prentice Hall 16 - 30
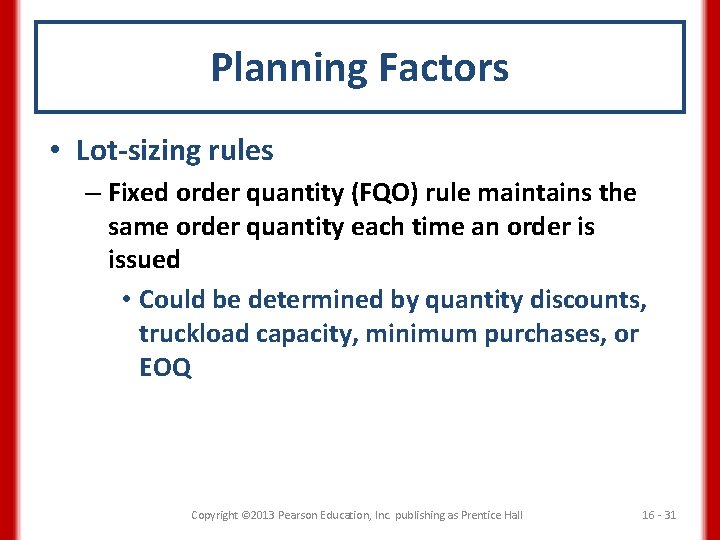
Planning Factors • Lot-sizing rules – Fixed order quantity (FQO) rule maintains the same order quantity each time an order is issued • Could be determined by quantity discounts, truckload capacity, minimum purchases, or EOQ Copyright © 2013 Pearson Education, Inc. publishing as Prentice Hall 16 - 31
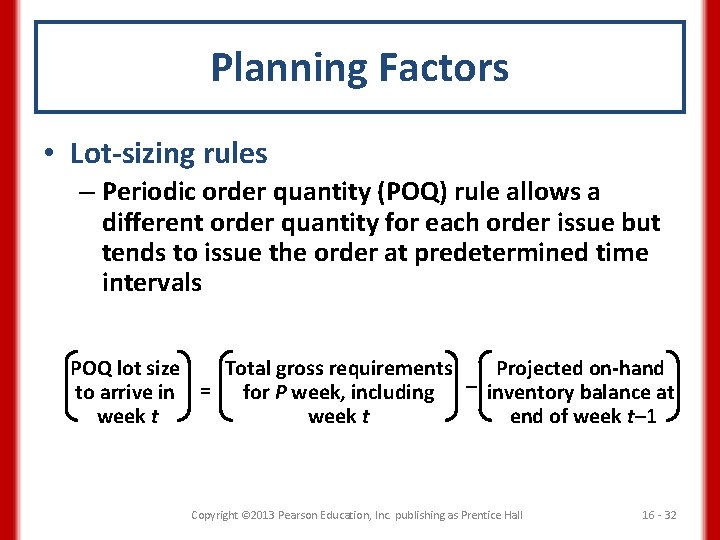
Planning Factors • Lot-sizing rules – Periodic order quantity (POQ) rule allows a different order quantity for each order issue but tends to issue the order at predetermined time intervals POQ lot size Total gross requirements Projected on-hand to arrive in = for P week, including – inventory balance at week t end of week t– 1 Copyright © 2013 Pearson Education, Inc. publishing as Prentice Hall 16 - 32
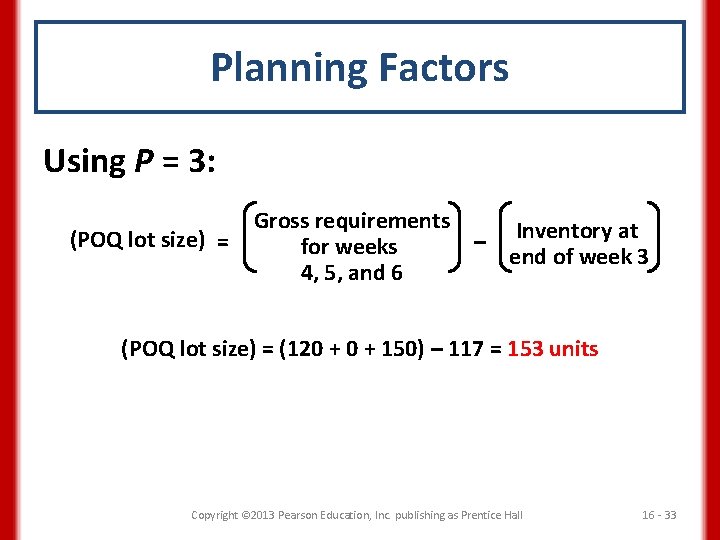
Planning Factors Using P = 3: (POQ lot size) = Gross requirements Inventory at – for weeks end of week 3 4, 5, and 6 (POQ lot size) = (120 + 150) – 117 = 153 units Copyright © 2013 Pearson Education, Inc. publishing as Prentice Hall 16 - 33
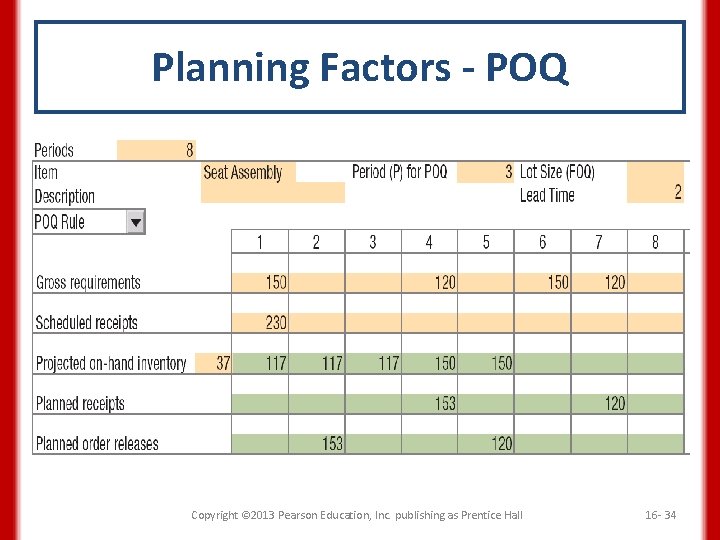
Planning Factors - POQ Copyright © 2013 Pearson Education, Inc. publishing as Prentice Hall 16 - 34
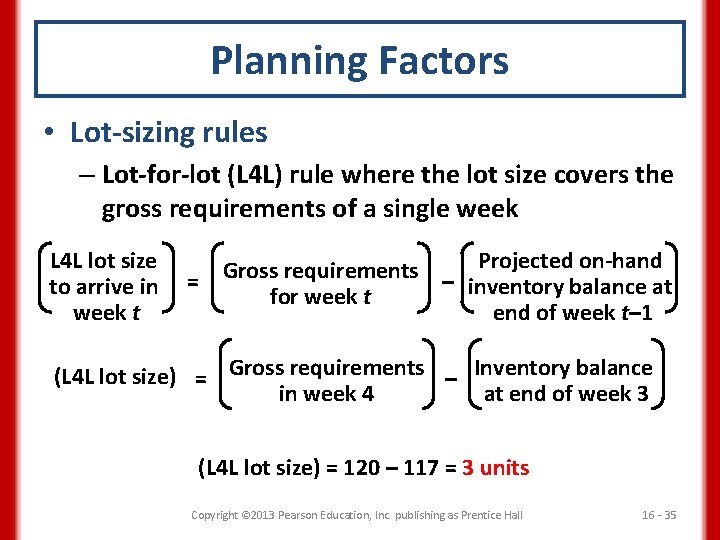
Planning Factors • Lot-sizing rules – Lot-for-lot (L 4 L) rule where the lot size covers the gross requirements of a single week L 4 L lot size to arrive in week t = Gross requirements – Projected on-hand inventory balance at for week t end of week t– 1 (L 4 L lot size) = Gross requirements – Inventory balance in week 4 at end of week 3 (L 4 L lot size) = 120 – 117 = 3 units Copyright © 2013 Pearson Education, Inc. publishing as Prentice Hall 16 - 35

Planning Factors – L 4 L Copyright © 2013 Pearson Education, Inc. publishing as Prentice Hall 16 - 36
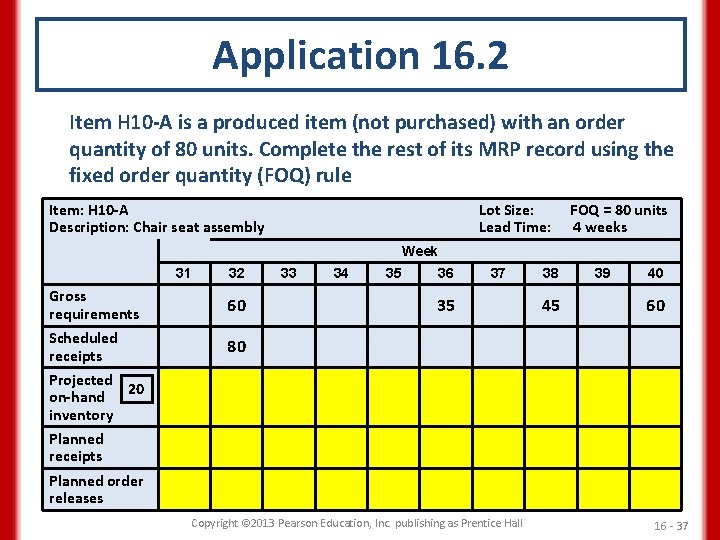
Application 16. 2 Item H 10 -A is a produced item (not purchased) with an order quantity of 80 units. Complete the rest of its MRP record using the fixed order quantity (FOQ) rule Item: H 10 -A Description: Chair seat assembly Lot Size: Lead Time: FOQ = 80 units 4 weeks Week 31 32 Gross requirements 60 Scheduled receipts 80 33 34 35 36 37 35 38 45 39 40 60 Projected 20 on-hand inventory Planned receipts Planned order releases Copyright © 2013 Pearson Education, Inc. publishing as Prentice Hall 16 - 37
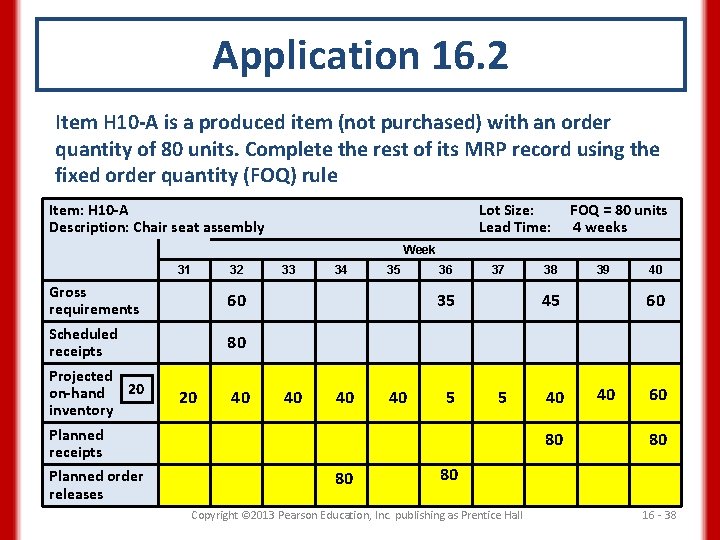
Application 16. 2 Item H 10 -A is a produced item (not purchased) with an order quantity of 80 units. Complete the rest of its MRP record using the fixed order quantity (FOQ) rule Item: H 10 -A Description: Chair seat assembly Lot Size: Lead Time: FOQ = 80 units 4 weeks Week 31 32 Gross requirements 60 Scheduled receipts 80 Projected on-hand 20 inventory 20 40 33 34 35 36 37 35 40 40 40 5 5 40 80 80 39 45 Planned receipts Planned order releases 38 40 60 80 80 Copyright © 2013 Pearson Education, Inc. publishing as Prentice Hall 16 - 38
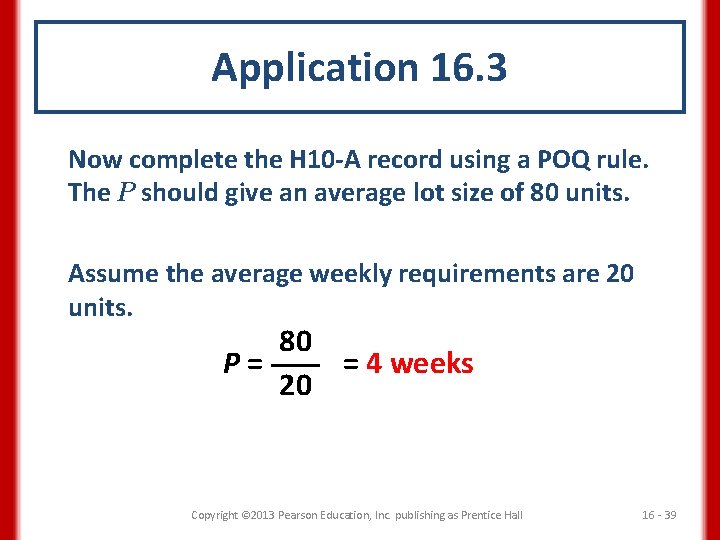
Application 16. 3 Now complete the H 10 -A record using a POQ rule. The P should give an average lot size of 80 units. Assume the average weekly requirements are 20 units. 80 P= = 4 weeks 20 Copyright © 2013 Pearson Education, Inc. publishing as Prentice Hall 16 - 39
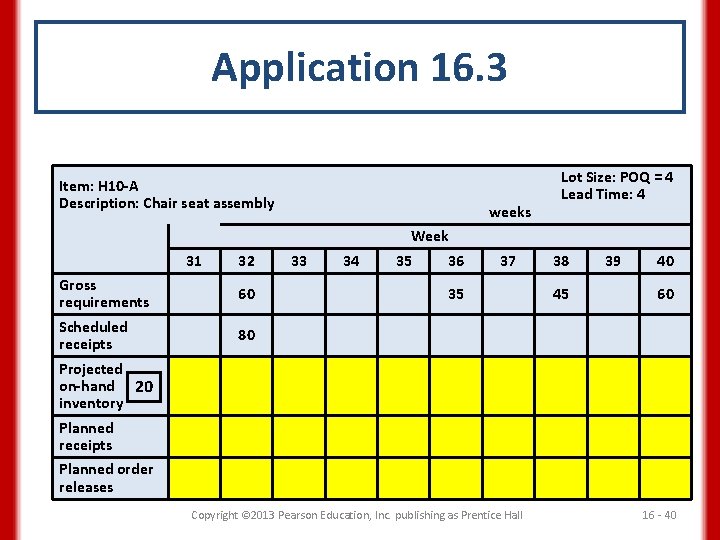
Application 16. 3 Item: H 10 -A Description: Chair seat assembly weeks Lot Size: POQ = 4 Lead Time: 4 Week 31 32 Gross requirements 60 Scheduled receipts 80 33 34 35 36 37 35 38 45 39 40 60 Projected on-hand 20 inventory Planned receipts Planned order releases Copyright © 2013 Pearson Education, Inc. publishing as Prentice Hall 16 - 40
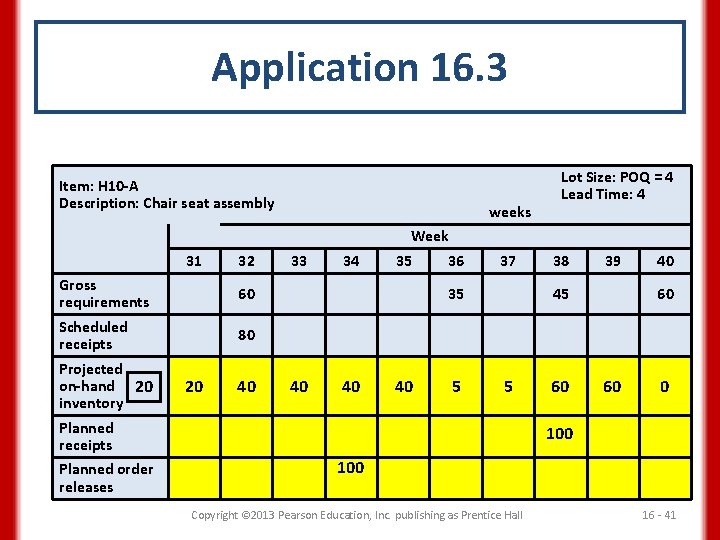
Application 16. 3 Item: H 10 -A Description: Chair seat assembly weeks Lot Size: POQ = 4 Lead Time: 4 Week 31 32 Gross requirements 60 Scheduled receipts 80 Projected on-hand 20 inventory 20 40 33 34 35 36 37 35 40 40 40 5 39 45 5 Planned receipts Planned order releases 38 60 40 60 60 0 100 Copyright © 2013 Pearson Education, Inc. publishing as Prentice Hall 16 - 41
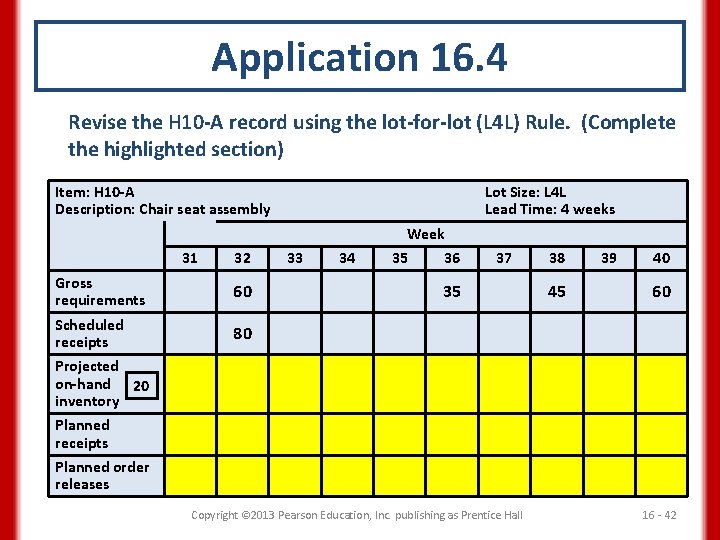
Application 16. 4 Revise the H 10 -A record using the lot-for-lot (L 4 L) Rule. (Complete the highlighted section) Item: H 10 -A Description: Chair seat assembly Lot Size: L 4 L Lead Time: 4 weeks Week 31 32 Gross requirements 60 Scheduled receipts 80 33 34 35 36 37 35 38 45 39 40 60 Projected on-hand 20 inventory Planned receipts Planned order releases Copyright © 2013 Pearson Education, Inc. publishing as Prentice Hall 16 - 42
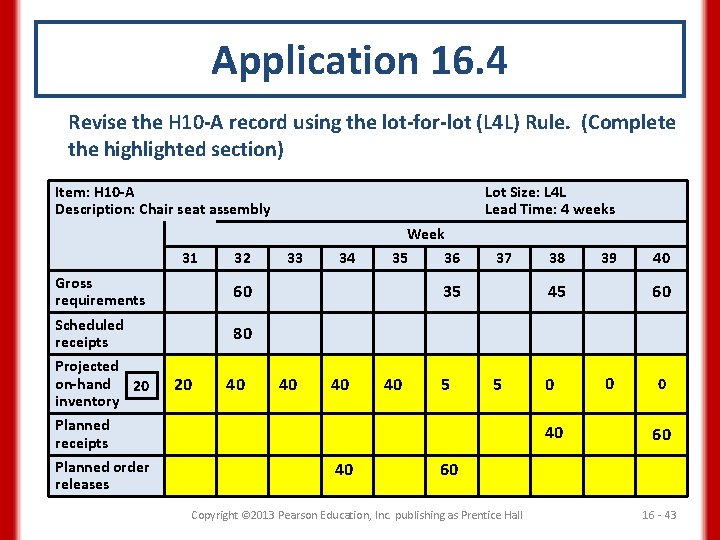
Application 16. 4 Revise the H 10 -A record using the lot-for-lot (L 4 L) Rule. (Complete the highlighted section) Item: H 10 -A Description: Chair seat assembly Lot Size: L 4 L Lead Time: 4 weeks Week 31 32 Gross requirements 60 Scheduled receipts 80 Projected on-hand 20 inventory 20 40 33 34 35 36 37 35 40 40 40 5 5 0 40 40 39 45 Planned receipts Planned order releases 38 40 60 0 0 60 60 Copyright © 2013 Pearson Education, Inc. publishing as Prentice Hall 16 - 43
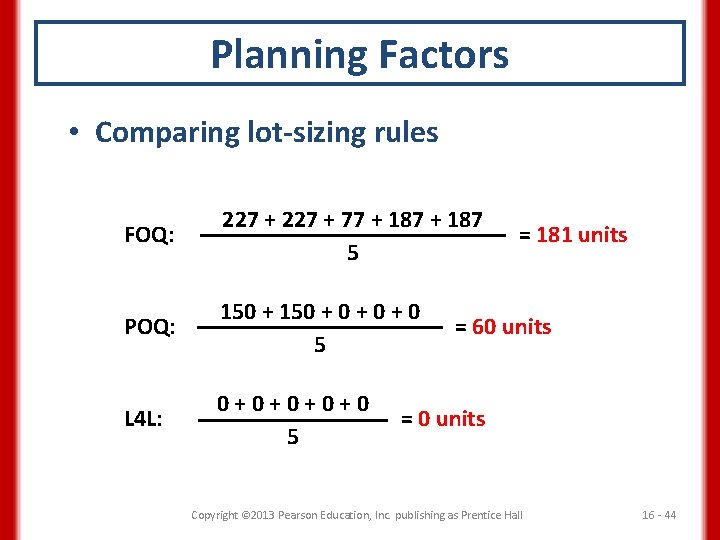
Planning Factors • Comparing lot-sizing rules FOQ: 227 + 77 + 187 5 POQ: 150 + 0 + 0 5 L 4 L: 0+0+0 5 = 181 units = 60 units = 0 units Copyright © 2013 Pearson Education, Inc. publishing as Prentice Hall 16 - 44
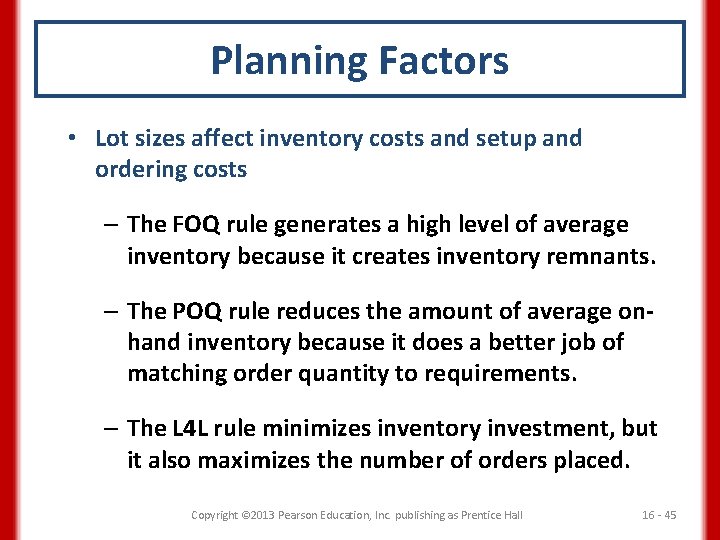
Planning Factors • Lot sizes affect inventory costs and setup and ordering costs – The FOQ rule generates a high level of average inventory because it creates inventory remnants. – The POQ rule reduces the amount of average onhand inventory because it does a better job of matching order quantity to requirements. – The L 4 L rule minimizes inventory investment, but it also maximizes the number of orders placed. Copyright © 2013 Pearson Education, Inc. publishing as Prentice Hall 16 - 45
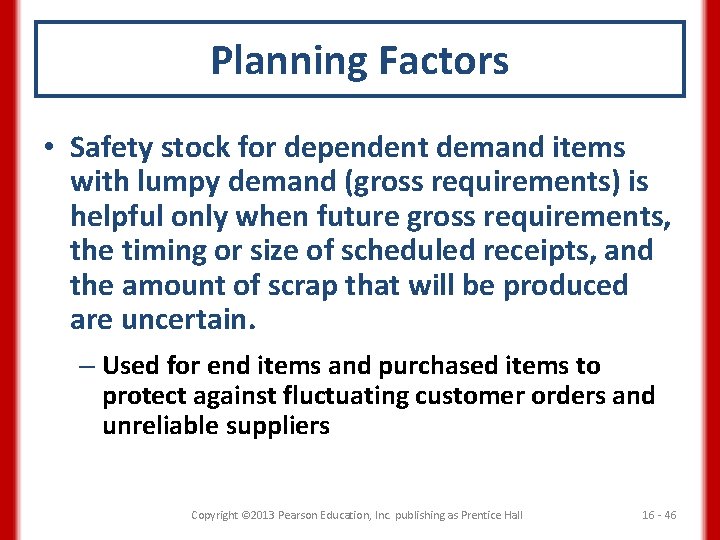
Planning Factors • Safety stock for dependent demand items with lumpy demand (gross requirements) is helpful only when future gross requirements, the timing or size of scheduled receipts, and the amount of scrap that will be produced are uncertain. – Used for end items and purchased items to protect against fluctuating customer orders and unreliable suppliers Copyright © 2013 Pearson Education, Inc. publishing as Prentice Hall 16 - 46
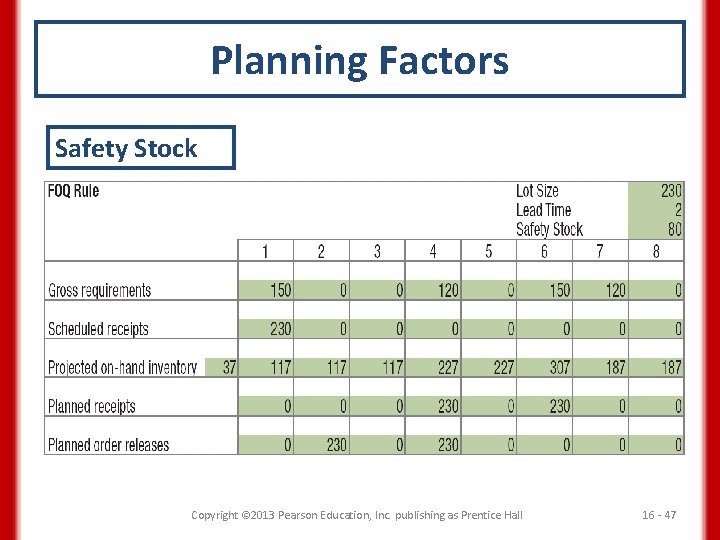
Planning Factors Safety Stock Copyright © 2013 Pearson Education, Inc. publishing as Prentice Hall 16 - 47
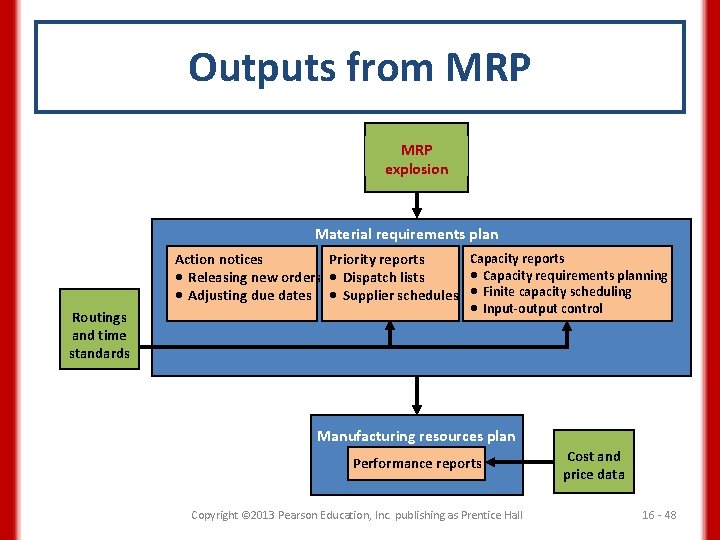
Outputs from MRP explosion Material requirements plan Capacity reports Action notices Priority reports · Capacity requirements planning · Releasing new orders · Dispatch lists · Adjusting due dates · Supplier schedules · Finite capacity scheduling Routings and time standards · Input-output control Manufacturing resources plan Performance reports Copyright © 2013 Pearson Education, Inc. publishing as Prentice Hall Cost and price data 16 - 48
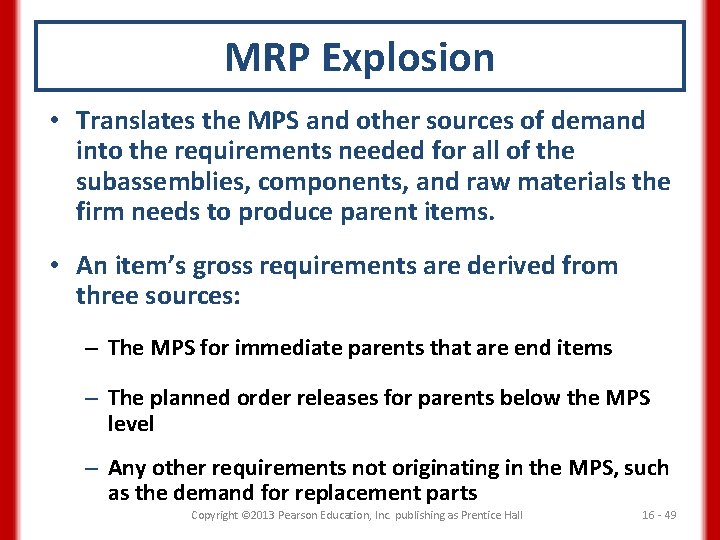
MRP Explosion • Translates the MPS and other sources of demand into the requirements needed for all of the subassemblies, components, and raw materials the firm needs to produce parent items. • An item’s gross requirements are derived from three sources: – The MPS for immediate parents that are end items – The planned order releases for parents below the MPS level – Any other requirements not originating in the MPS, such as the demand for replacement parts Copyright © 2013 Pearson Education, Inc. publishing as Prentice Hall 16 - 49
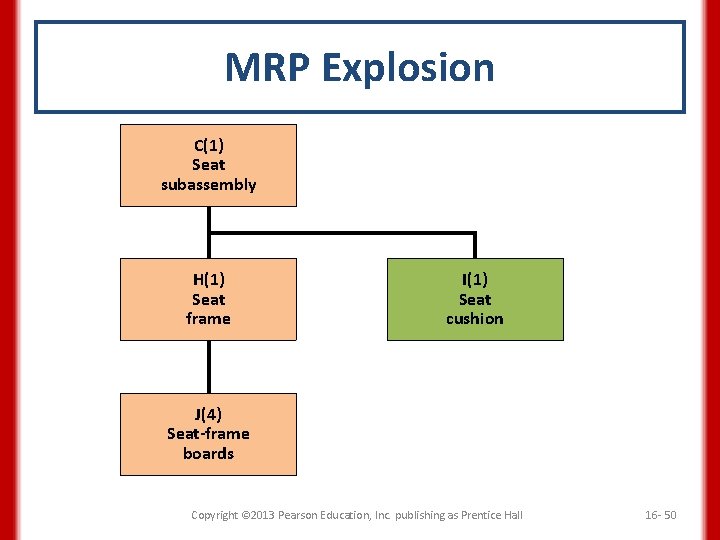
MRP Explosion C(1) Seat subassembly H(1) Seat frame I(1) Seat cushion J(4) Seat-frame boards Copyright © 2013 Pearson Education, Inc. publishing as Prentice Hall 16 - 50
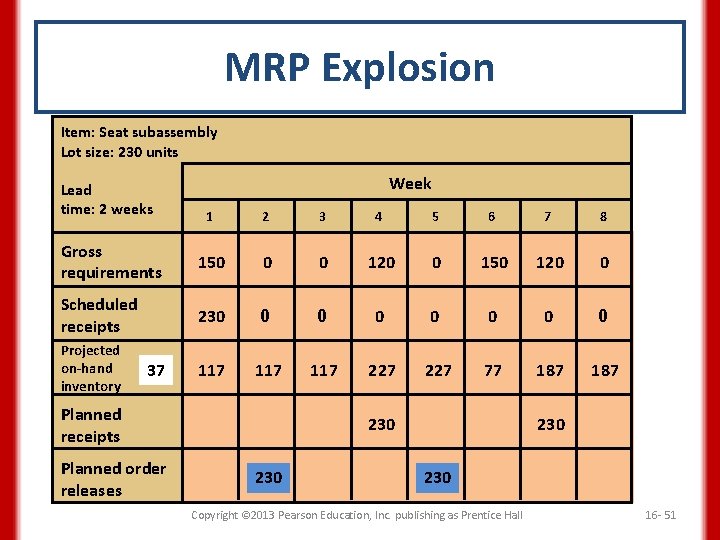
MRP Explosion Item: Seat subassembly Lot size: 230 units Lead time: 2 weeks Week 1 2 3 4 5 6 7 8 Gross requirements 150 0 0 120 0 150 120 0 Scheduled receipts 230 0 0 0 117 117 227 77 187 Projected on-hand inventory 37 Planned receipts Planned order releases 230 230 Copyright © 2013 Pearson Education, Inc. publishing as Prentice Hall 16 - 51
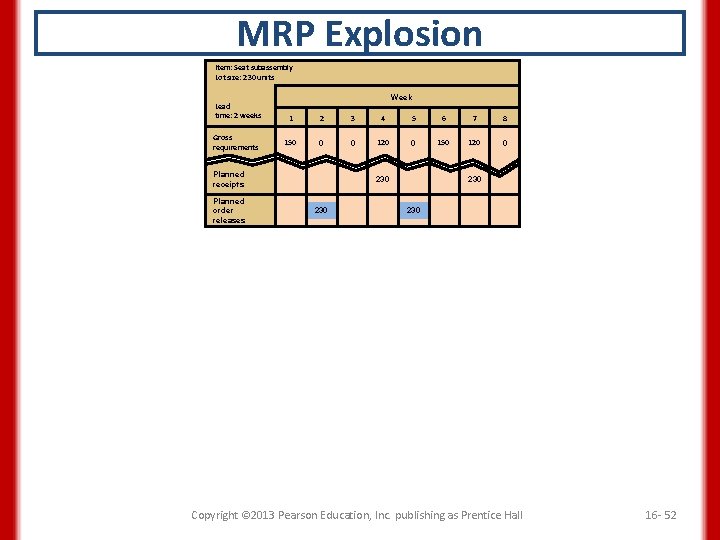
MRP Explosion Item: Seat subassembly Lot size: 230 units Lead time: 2 weeks Gross requirements Week 1 2 3 4 5 6 7 8 150 0 0 120 0 150 120 0 Planned receipts Planned order releases 230 230 Copyright © 2013 Pearson Education, Inc. publishing as Prentice Hall 16 - 52
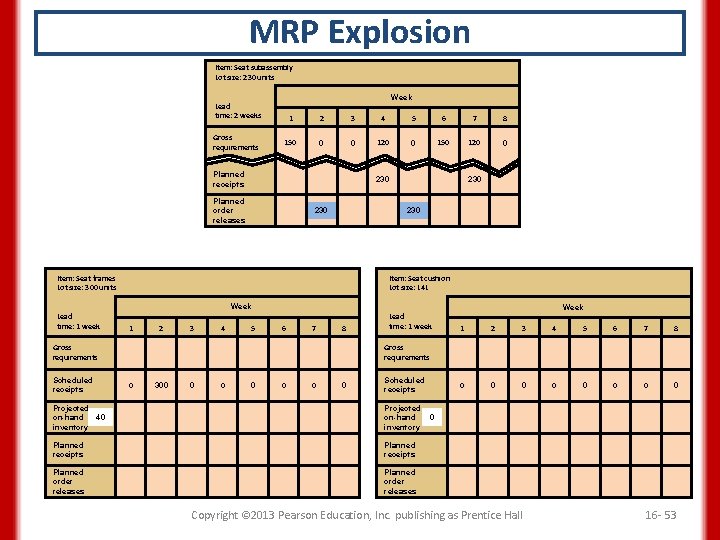
MRP Explosion Item: Seat subassembly Lot size: 230 units Week Lead time: 2 weeks Gross requirements 1 2 3 4 5 6 7 8 150 0 0 120 0 150 120 0 Planned receipts 230 Planned order releases 230 230 Item: Seat frames Lot size: 300 units Item: Seat cushion Lot size: L 4 L Week Lead time: 1 week 1 2 3 4 5 6 7 8 Gross requirements Scheduled receipts Lead time: 1 week Week 1 2 3 4 5 6 7 8 0 0 0 0 Gross requirements 0 300 0 0 0 Scheduled receipts Projected on-hand 40 inventory Projected on-hand inventory Planned receipts Planned order releases 0 Copyright © 2013 Pearson Education, Inc. publishing as Prentice Hall 16 - 53
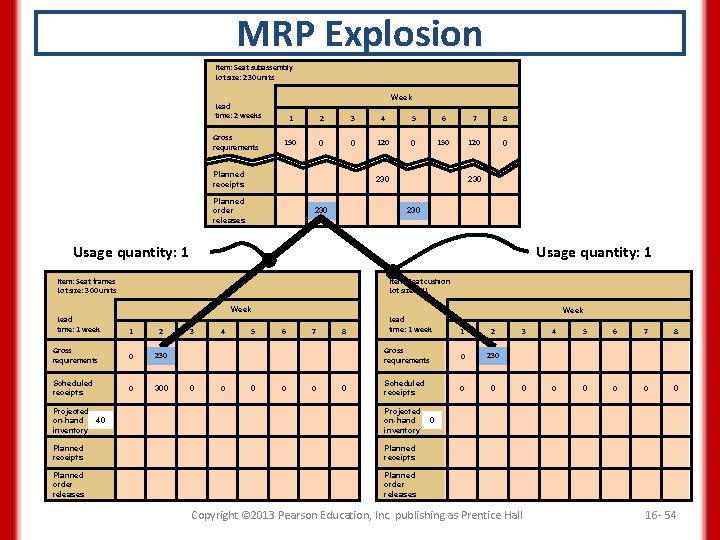
MRP Explosion Item: Seat subassembly Lot size: 230 units Week Lead time: 2 weeks Gross requirements 1 2 3 4 5 6 7 8 150 0 0 120 0 150 120 0 Planned receipts 230 Planned order releases 230 230 Usage quantity: 1 Item: Seat frames Lot size: 300 units Item: Seat cushion Lot size: L 4 L Week Lead time: 1 week 1 2 Gross requirements 0 230 Scheduled receipts 0 300 3 0 4 0 5 0 6 0 7 0 8 0 Lead time: 1 week Week 1 2 Gross requirements 0 230 Scheduled receipts 0 0 Projected on-hand 40 inventory Projected on-hand inventory Planned receipts Planned order releases 3 4 5 6 7 8 0 0 0 0 Copyright © 2013 Pearson Education, Inc. publishing as Prentice Hall 16 - 54
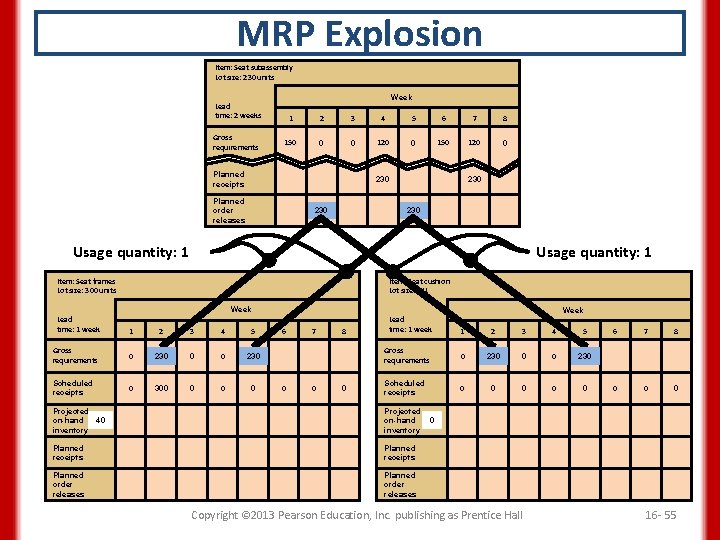
MRP Explosion Item: Seat subassembly Lot size: 230 units Week Lead time: 2 weeks Gross requirements 1 2 3 4 5 6 7 8 150 0 0 120 0 150 120 0 Planned receipts 230 Planned order releases 230 230 Usage quantity: 1 Item: Seat frames Lot size: 300 units Item: Seat cushion Lot size: L 4 L Week Lead time: 1 week 1 2 3 4 5 Gross requirements 0 230 0 0 230 Scheduled receipts 0 300 0 6 0 7 0 8 0 Lead time: 1 week Week 1 2 3 4 5 Gross requirements 0 230 0 0 230 Scheduled receipts 0 0 0 Projected on-hand 40 inventory Projected on-hand inventory Planned receipts Planned order releases 6 7 8 0 0 Copyright © 2013 Pearson Education, Inc. publishing as Prentice Hall 16 - 55
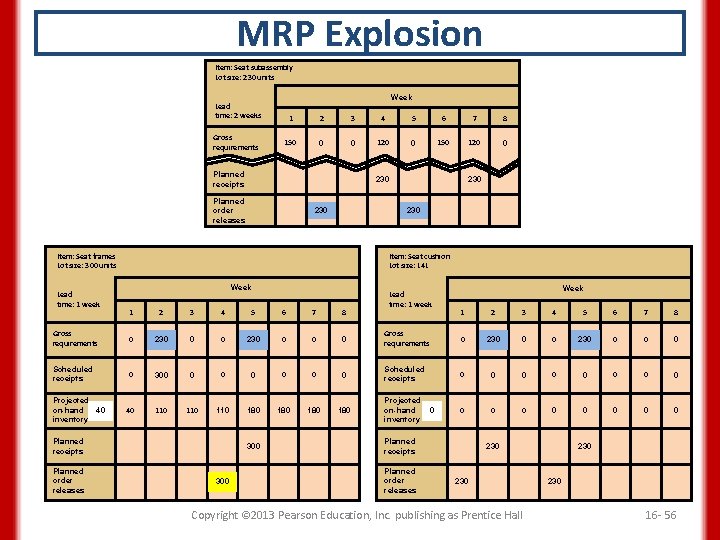
MRP Explosion Item: Seat subassembly Lot size: 230 units Week Lead time: 2 weeks Gross requirements 1 2 3 4 5 6 7 8 150 0 0 120 0 150 120 0 Planned receipts 230 Planned order releases 230 Item: Seat frames Lot size: 300 units Lead time: 1 week Item: Seat cushion Lot size: L 4 L Week 1 2 3 4 5 6 7 8 Gross requirements 0 230 0 0 0 Scheduled receipts 0 300 0 0 Projected on-hand 40 inventory 40 110 110 180 180 Planned receipts Planned order releases 230 300 Lead time: 1 week Week 1 2 3 4 5 6 7 8 Gross requirements 0 230 0 0 0 0 Scheduled receipts 0 0 0 0 180 Projected on-hand inventory 0 0 0 0 0 Planned receipts Planned order releases 230 Copyright © 2013 Pearson Education, Inc. publishing as Prentice Hall 230 16 - 56
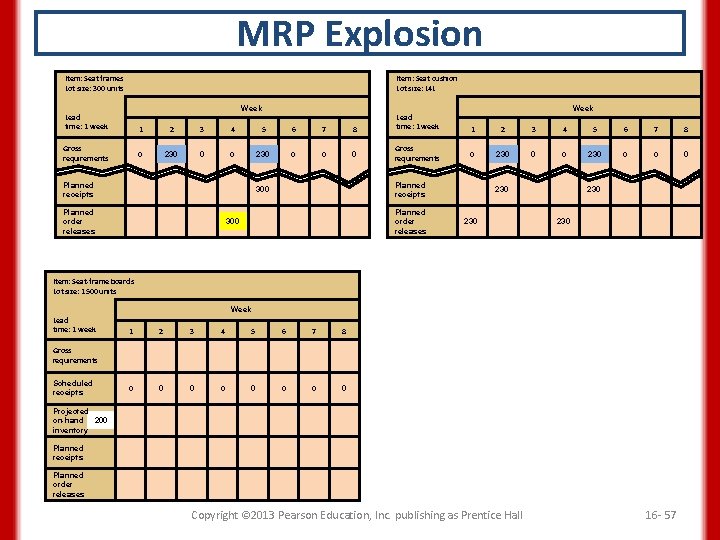
MRP Explosion Item: Seat frames Lot size: 300 units Item: Seat cushion Lot size: L 4 L Week Lead time: 1 week 1 2 3 4 5 6 7 8 Gross requirements 0 230 0 0 0 Planned receipts 300 Planned order releases Week Lead time: 1 week Planned order releases 300 230 230 Item: Seat-frame boards Lot size: 1500 units Week Lead time: 1 week 1 2 3 4 5 6 7 8 0 0 0 0 Gross requirements Scheduled receipts Projected on-hand 200 inventory Planned receipts Planned order releases Copyright © 2013 Pearson Education, Inc. publishing as Prentice Hall 16 - 57
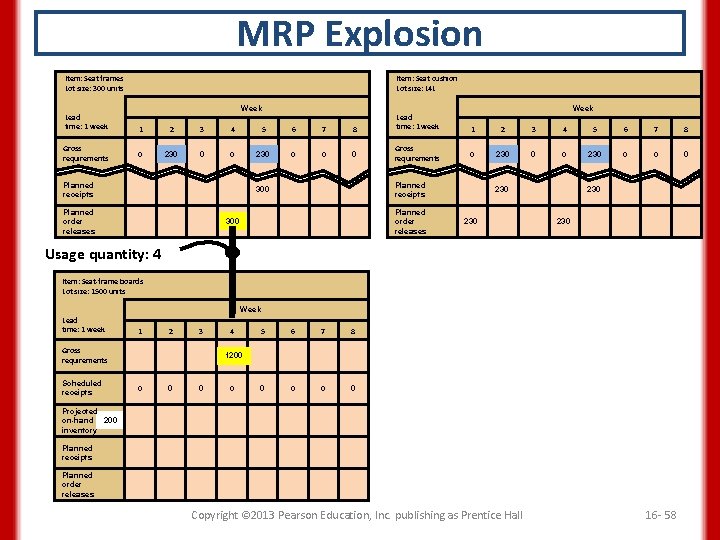
MRP Explosion Item: Seat frames Lot size: 300 units Item: Seat cushion Lot size: L 4 L Week Lead time: 1 week 1 2 3 4 5 6 7 8 Gross requirements 0 230 0 0 0 Planned receipts 300 Planned order releases Week Lead time: 1 week Planned order releases 300 230 230 Usage quantity: 4 Item: Seat-frame boards Lot size: 1500 units Week Lead time: 1 week 1 2 3 Gross requirements Scheduled receipts 4 5 6 7 8 0 0 1200 0 0 Projected on-hand 200 inventory Planned receipts Planned order releases Copyright © 2013 Pearson Education, Inc. publishing as Prentice Hall 16 - 58
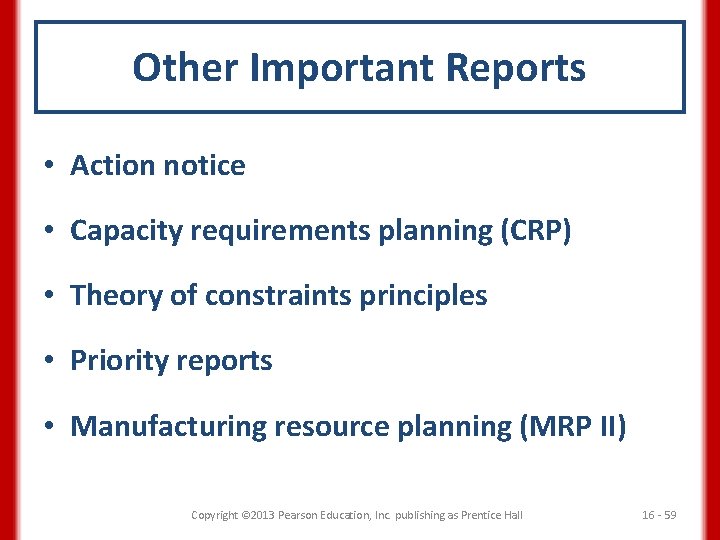
Other Important Reports • Action notice • Capacity requirements planning (CRP) • Theory of constraints principles • Priority reports • Manufacturing resource planning (MRP II) Copyright © 2013 Pearson Education, Inc. publishing as Prentice Hall 16 - 59
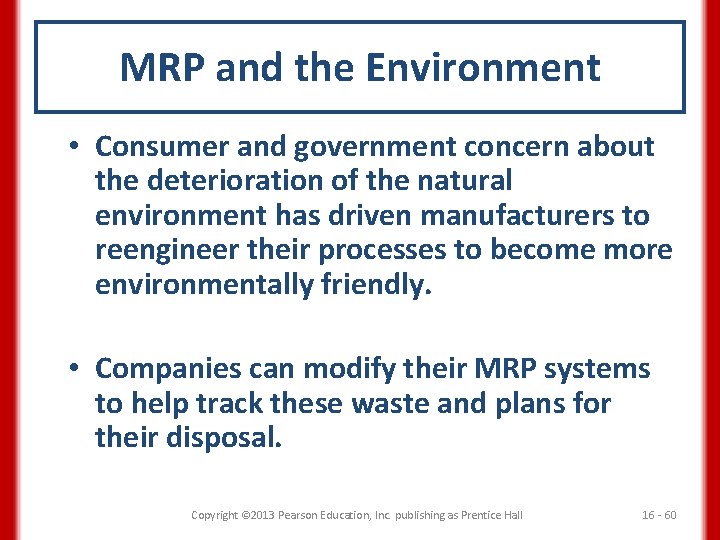
MRP and the Environment • Consumer and government concern about the deterioration of the natural environment has driven manufacturers to reengineer their processes to become more environmentally friendly. • Companies can modify their MRP systems to help track these waste and plans for their disposal. Copyright © 2013 Pearson Education, Inc. publishing as Prentice Hall 16 - 60
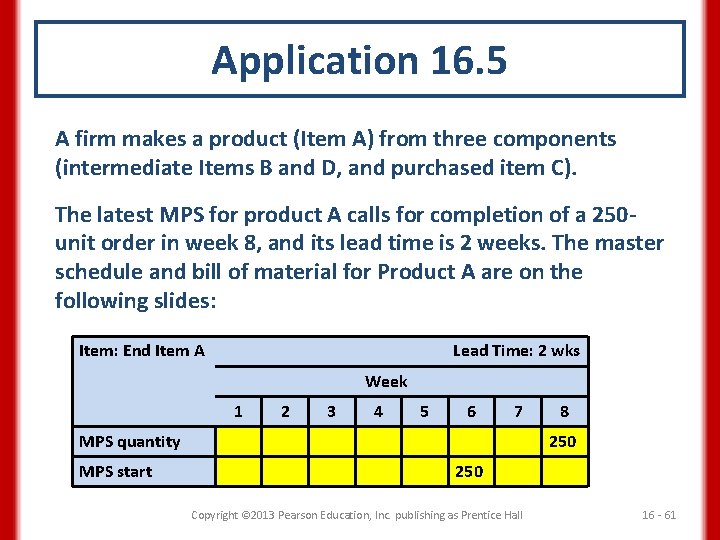
Application 16. 5 A firm makes a product (Item A) from three components (intermediate Items B and D, and purchased item C). The latest MPS for product A calls for completion of a 250 unit order in week 8, and its lead time is 2 weeks. The master schedule and bill of material for Product A are on the following slides: Item: End Item A Lead Time: 2 wks Week 1 2 3 4 5 6 7 MPS quantity MPS start 8 250 Copyright © 2013 Pearson Education, Inc. publishing as Prentice Hall 16 - 61
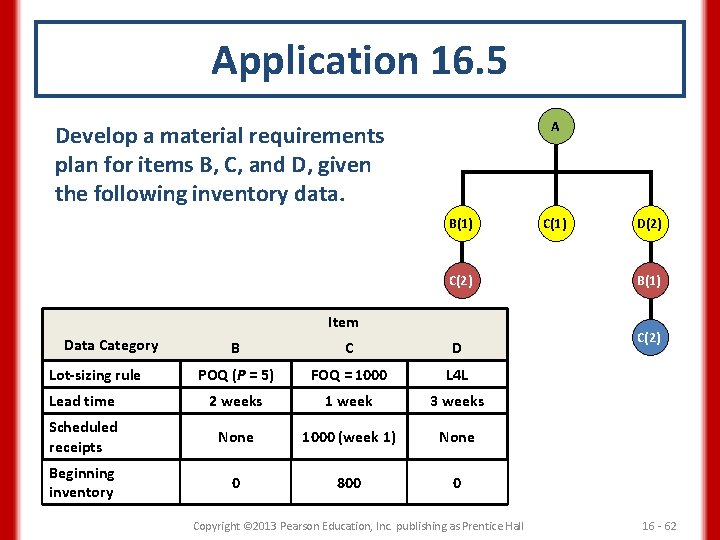
Application 16. 5 A Develop a material requirements plan for items B, C, and D, given the following inventory data. B(1) C(2) Item Data Category B C D POQ (P = 5) FOQ = 1000 L 4 L Lead time 2 weeks 1 week 3 weeks Scheduled receipts None 1000 (week 1) None Beginning inventory 0 800 0 Lot-sizing rule Copyright © 2013 Pearson Education, Inc. publishing as Prentice Hall C(1) D(2) B(1) C(2) 16 - 62
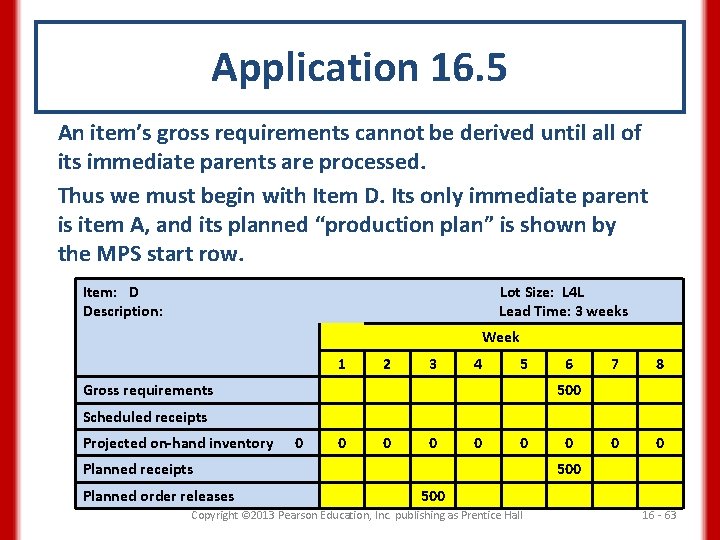
Application 16. 5 An item’s gross requirements cannot be derived until all of its immediate parents are processed. Thus we must begin with Item D. Its only immediate parent is item A, and its planned “production plan” is shown by the MPS start row. Item: D Description: Lot Size: L 4 L Lead Time: 3 weeks Week 1 2 3 4 5 Gross requirements 6 7 8 0 0 500 Scheduled receipts Projected on-hand inventory 0 0 0 Planned receipts Planned order releases 0 500 Copyright © 2013 Pearson Education, Inc. publishing as Prentice Hall 16 - 63
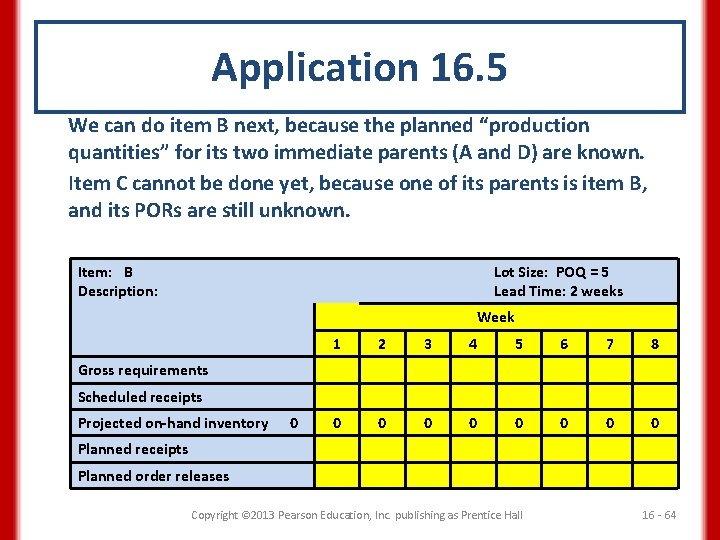
Application 16. 5 We can do item B next, because the planned “production quantities” for its two immediate parents (A and D) are known. Item C cannot be done yet, because one of its parents is item B, and its PORs are still unknown. Item: B Description: Lot Size: POQ = 5 Lead Time: 2 weeks Week 1 2 3 4 5 6 7 8 0 0 0 0 Gross requirements Scheduled receipts Projected on-hand inventory 0 Planned receipts Planned order releases Copyright © 2013 Pearson Education, Inc. publishing as Prentice Hall 16 - 64
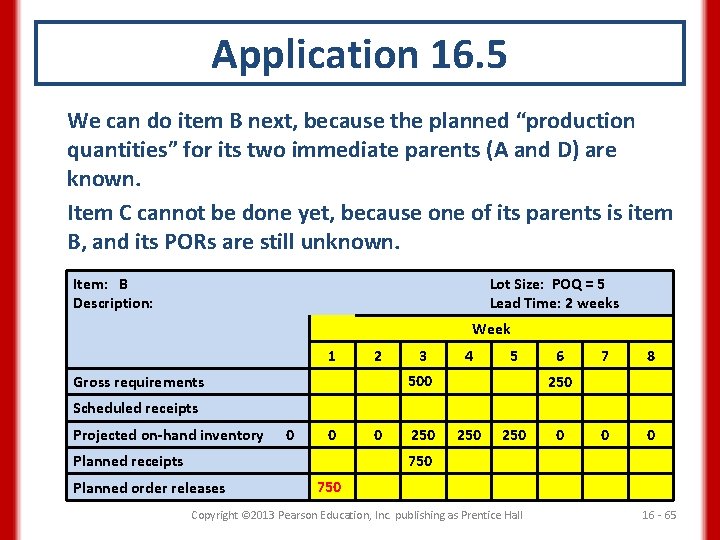
Application 16. 5 We can do item B next, because the planned “production quantities” for its two immediate parents (A and D) are known. Item C cannot be done yet, because one of its parents is item B, and its PORs are still unknown. Item: B Description: Lot Size: POQ = 5 Lead Time: 2 weeks Week 1 2 3 4 5 500 Gross requirements 6 7 8 0 0 250 Scheduled receipts Projected on-hand inventory 0 0 0 250 250 0 750 Planned receipts Planned order releases 750 Copyright © 2013 Pearson Education, Inc. publishing as Prentice Hall 16 - 65
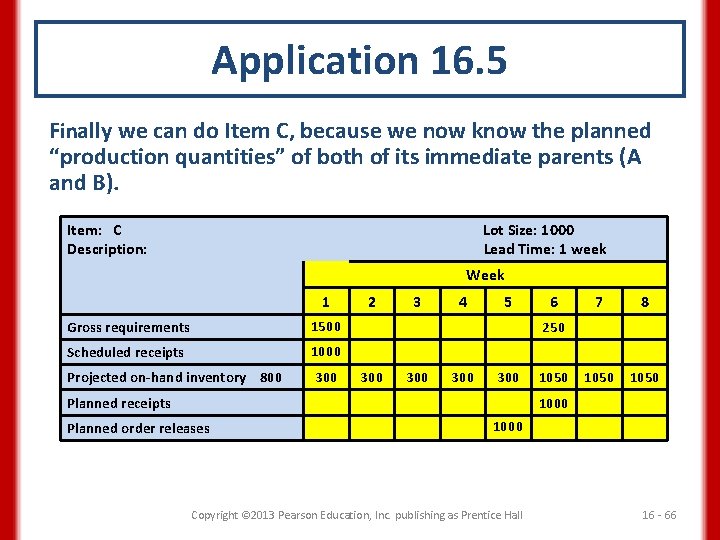
Application 16. 5 Finally we can do Item C, because we now know the planned “production quantities” of both of its immediate parents (A and B). Item: C Description: Lot Size: 1000 Lead Time: 1 week Week 1 Gross requirements 1500 Scheduled receipts 1000 Projected on-hand inventory 800 300 2 3 4 5 6 7 8 1050 250 300 300 Planned receipts 1050 1000 Planned order releases 1000 Copyright © 2013 Pearson Education, Inc. publishing as Prentice Hall 16 - 66
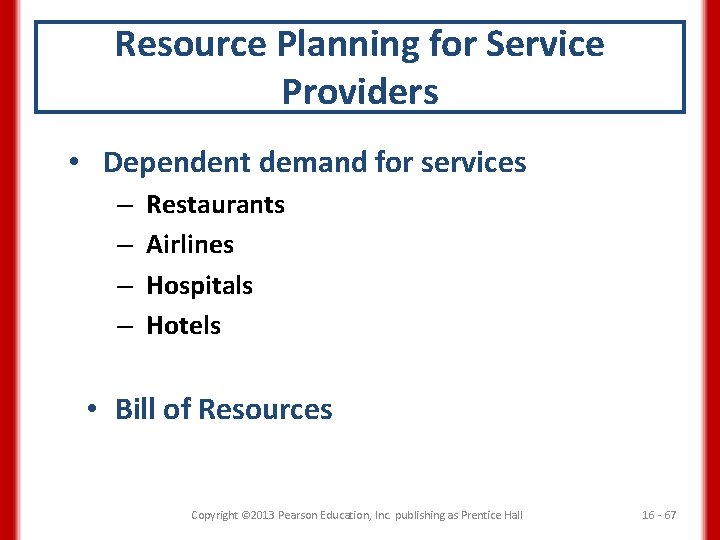
Resource Planning for Service Providers • Dependent demand for services – – Restaurants Airlines Hospitals Hotels • Bill of Resources Copyright © 2013 Pearson Education, Inc. publishing as Prentice Hall 16 - 67
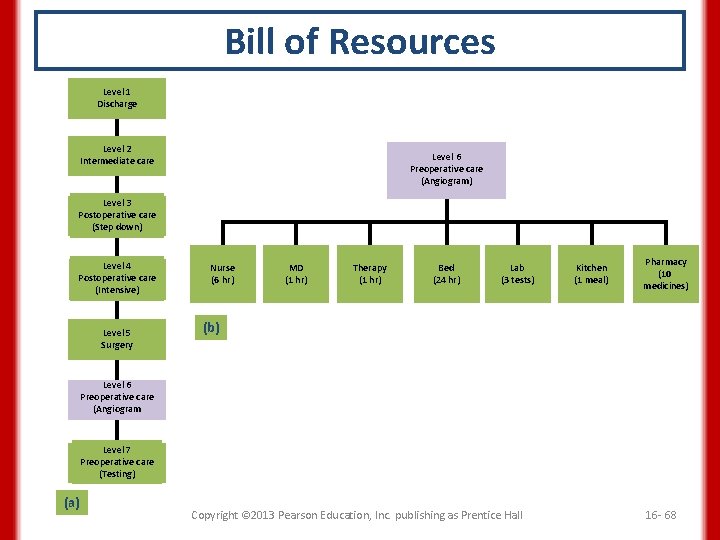
Bill of Resources Level 1 Discharge Level 2 Intermediate care Level 6 Preoperative care (Angiogram) Level 3 Postoperative care (Step down) Level 4 Postoperative care (Intensive) Level 5 Surgery Nurse (6 hr) MD (1 hr) Therapy (1 hr) Bed (24 hr) Lab (3 tests) Kitchen (1 meal) Pharmacy (10 medicines) (b) Level 6 Preoperative care (Angiogram Level 7 Preoperative care (Testing) (a) Copyright © 2013 Pearson Education, Inc. publishing as Prentice Hall 16 - 68
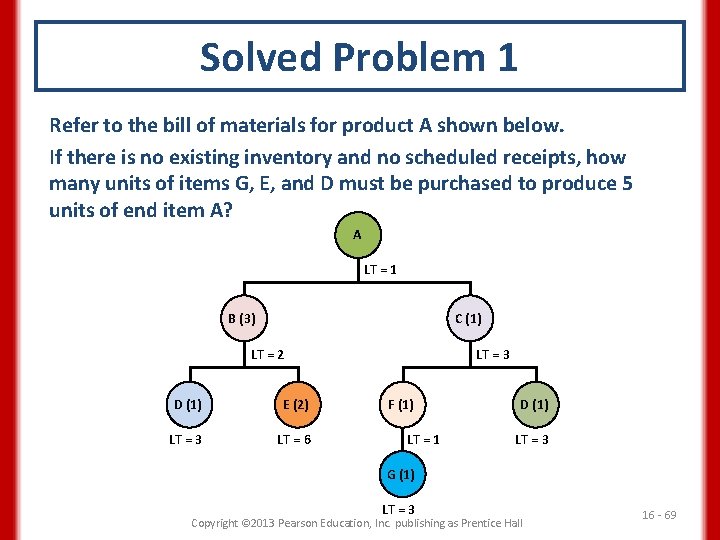
Solved Problem 1 Refer to the bill of materials for product A shown below. If there is no existing inventory and no scheduled receipts, how many units of items G, E, and D must be purchased to produce 5 units of end item A? A LT = 1 B (3) C (1) LT = 2 D (1) E (2) LT = 3 LT = 6 LT = 3 F (1) LT = 1 D (1) LT = 3 G (1) LT = 3 Copyright © 2013 Pearson Education, Inc. publishing as Prentice Hall 16 - 69
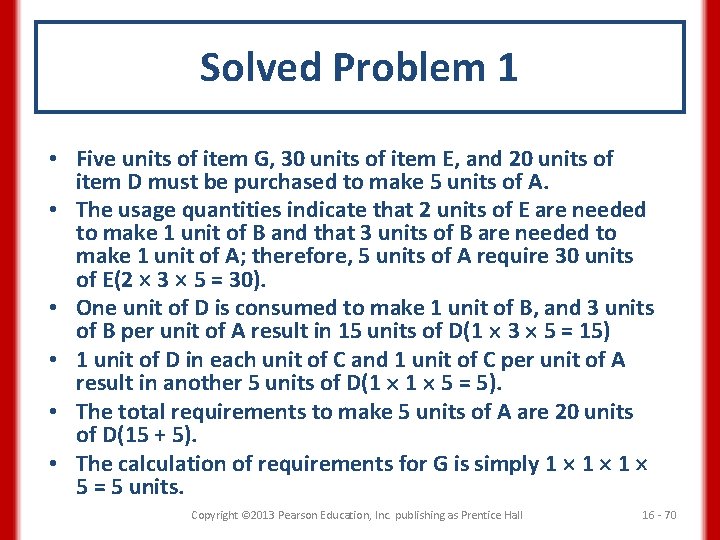
Solved Problem 1 • Five units of item G, 30 units of item E, and 20 units of item D must be purchased to make 5 units of A. • The usage quantities indicate that 2 units of E are needed to make 1 unit of B and that 3 units of B are needed to make 1 unit of A; therefore, 5 units of A require 30 units of E(2 3 5 = 30). • One unit of D is consumed to make 1 unit of B, and 3 units of B per unit of A result in 15 units of D(1 3 5 = 15) • 1 unit of D in each unit of C and 1 unit of C per unit of A result in another 5 units of D(1 1 5 = 5). • The total requirements to make 5 units of A are 20 units of D(15 + 5). • The calculation of requirements for G is simply 1 1 1 5 = 5 units. Copyright © 2013 Pearson Education, Inc. publishing as Prentice Hall 16 - 70

Solved Problem 2 • The order policy is to produce end item A in lots of 50 units. • Complete the projected on-hand inventory and MPS quantity rows. • Then complete the MPS start row by offsetting the MPS quantities for the final assembly lead time. • Finally, compute the available-to-promise inventory for item A. • If in week 1 a customer requests a new order for 30 units of item A, when is the earliest date the entire order could be shipped? Copyright © 2013 Pearson Education, Inc. publishing as Prentice Hall 16 - 71
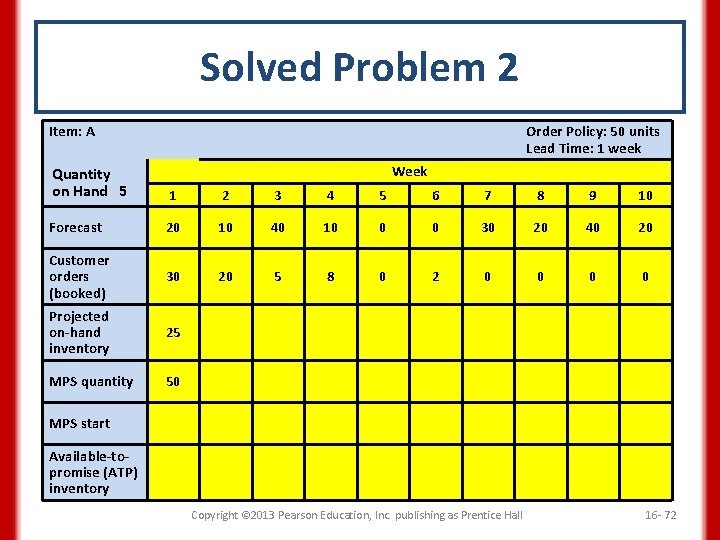
Solved Problem 2 Item: A Order Policy: 50 units Lead Time: 1 week Week Quantity on Hand 5 1 2 3 4 5 6 7 8 9 10 Forecast 20 10 40 10 0 0 30 20 40 20 Customer orders (booked) 30 20 5 8 0 2 0 0 Projected on-hand inventory 25 MPS quantity 50 MPS start Available-topromise (ATP) inventory Copyright © 2013 Pearson Education, Inc. publishing as Prentice Hall 16 - 72
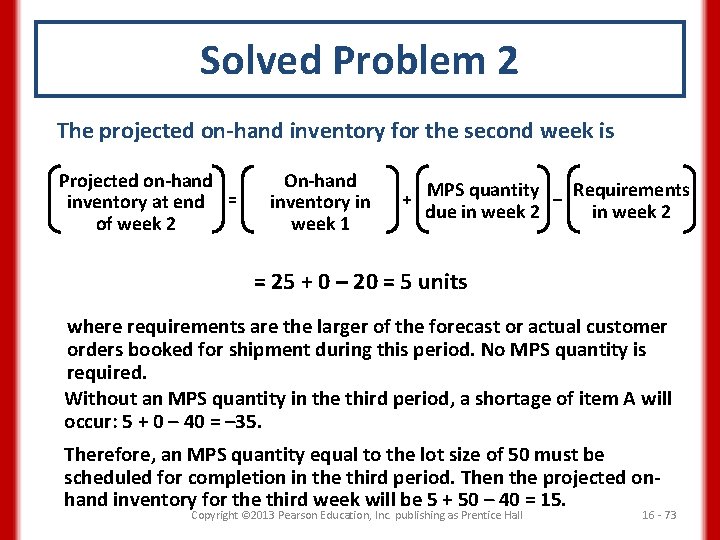
Solved Problem 2 The projected on-hand inventory for the second week is Projected on-hand inventory at end = of week 2 On-hand inventory in week 1 + MPS quantity – Requirements due in week 2 = 25 + 0 – 20 = 5 units where requirements are the larger of the forecast or actual customer orders booked for shipment during this period. No MPS quantity is required. Without an MPS quantity in the third period, a shortage of item A will occur: 5 + 0 – 40 = – 35. Therefore, an MPS quantity equal to the lot size of 50 must be scheduled for completion in the third period. Then the projected onhand inventory for the third week will be 5 + 50 – 40 = 15. Copyright © 2013 Pearson Education, Inc. publishing as Prentice Hall 16 - 73
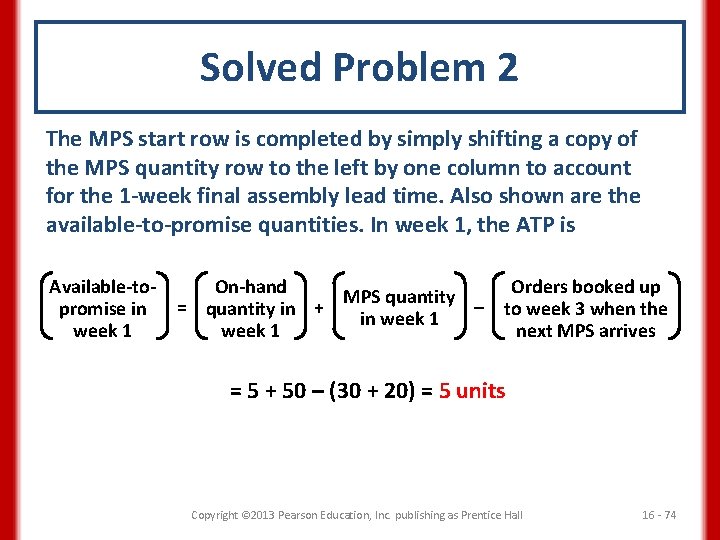
Solved Problem 2 The MPS start row is completed by simply shifting a copy of the MPS quantity row to the left by one column to account for the 1 -week final assembly lead time. Also shown are the available-to-promise quantities. In week 1, the ATP is Available-topromise in week 1 On-hand Orders booked up MPS quantity = quantity in + – to week 3 when the in week 1 next MPS arrives = 5 + 50 – (30 + 20) = 5 units Copyright © 2013 Pearson Education, Inc. publishing as Prentice Hall 16 - 74
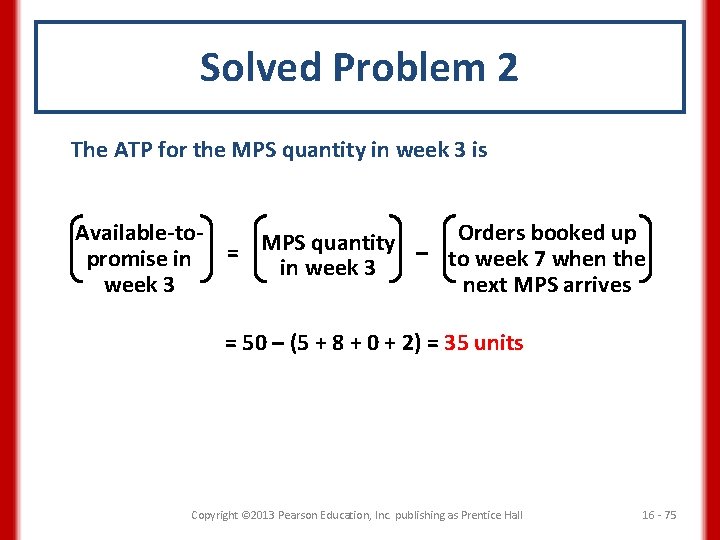
Solved Problem 2 The ATP for the MPS quantity in week 3 is Available-to. Orders booked up MPS quantity – to week 7 when the promise in = in week 3 next MPS arrives = 50 – (5 + 8 + 0 + 2) = 35 units Copyright © 2013 Pearson Education, Inc. publishing as Prentice Hall 16 - 75
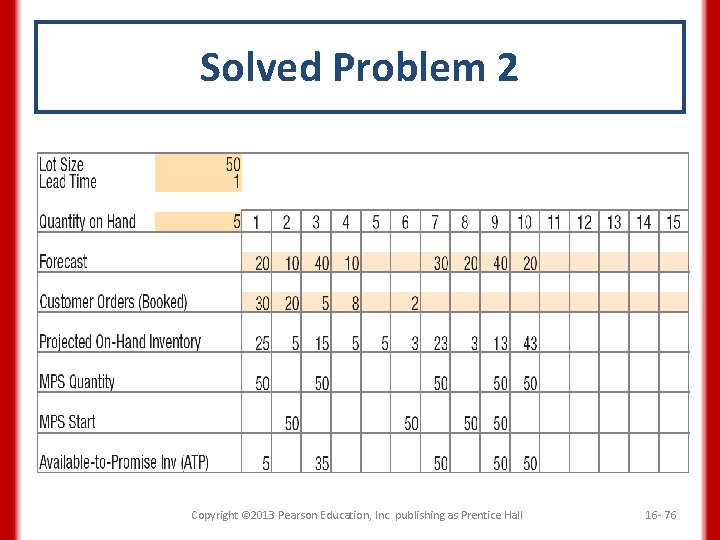
Solved Problem 2 Copyright © 2013 Pearson Education, Inc. publishing as Prentice Hall 16 - 76
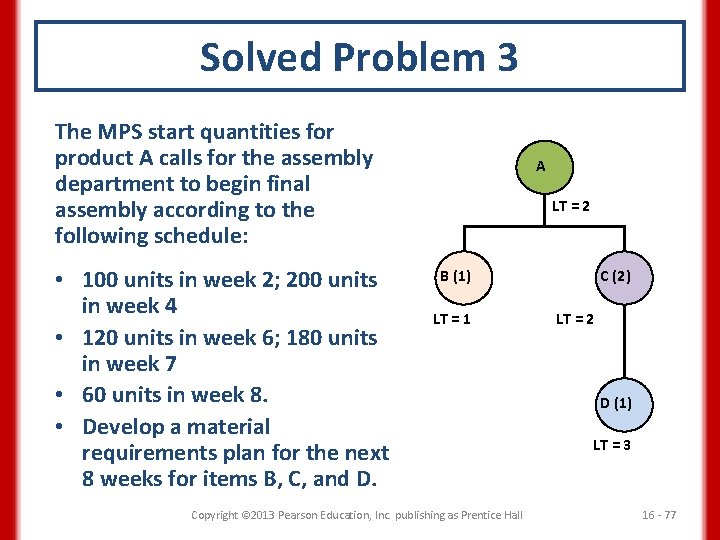
Solved Problem 3 The MPS start quantities for product A calls for the assembly department to begin final assembly according to the following schedule: • 100 units in week 2; 200 units in week 4 • 120 units in week 6; 180 units in week 7 • 60 units in week 8. • Develop a material requirements plan for the next 8 weeks for items B, C, and D. A LT = 2 B (1) LT = 1 Copyright © 2013 Pearson Education, Inc. publishing as Prentice Hall C (2) LT = 2 D (1) LT = 3 16 - 77
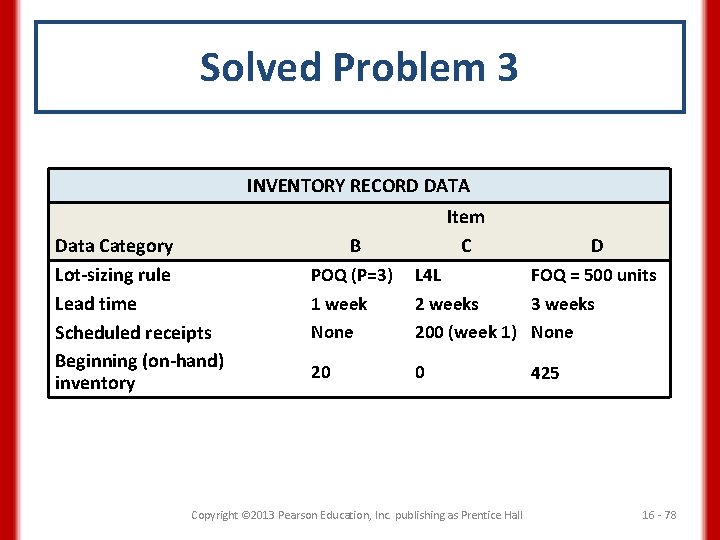
Solved Problem 3 INVENTORY RECORD DATA Data Category Lot-sizing rule Lead time Scheduled receipts Beginning (on-hand) inventory Item C B D POQ (P=3) L 4 L FOQ = 500 units 1 week 2 weeks 3 weeks None 200 (week 1) None 20 0 Copyright © 2013 Pearson Education, Inc. publishing as Prentice Hall 425 16 - 78
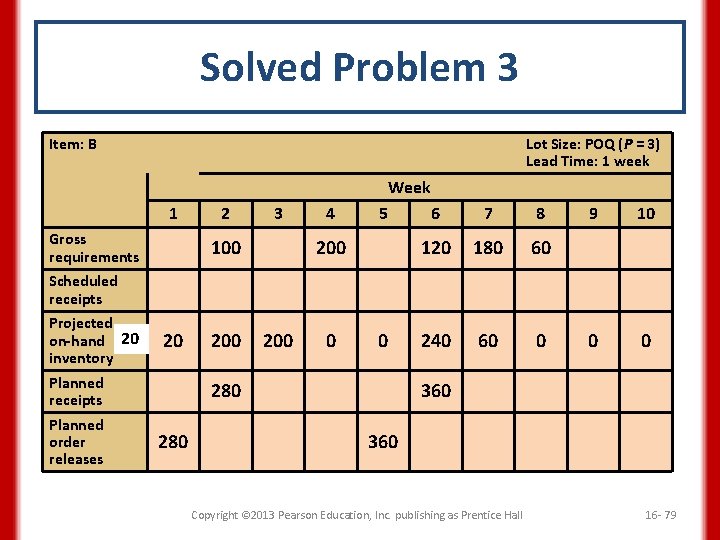
Solved Problem 3 Item: B Lot Size: POQ (P = 3) Lead Time: 1 week Week 1 Gross requirements 2 3 100 4 5 200 6 7 8 120 180 60 240 60 0 9 10 0 0 Scheduled receipts Projected on-hand 20 inventory 20 Planned receipts Planned order releases 200 0 0 280 360 Copyright © 2013 Pearson Education, Inc. publishing as Prentice Hall 16 - 79
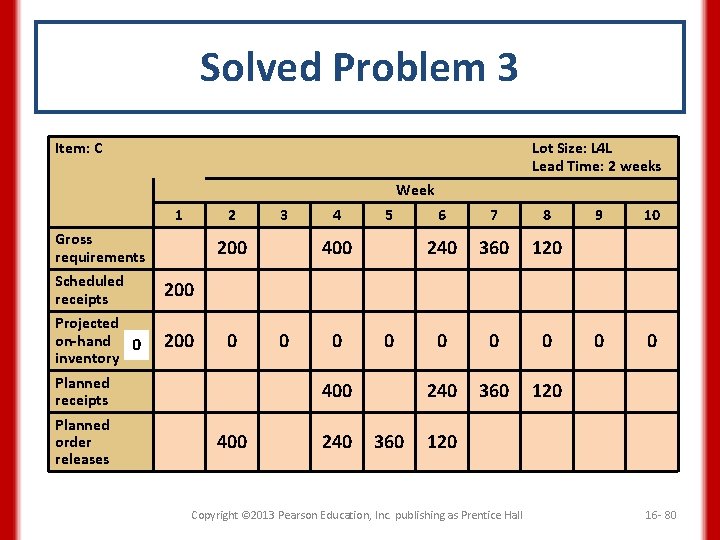
Solved Problem 3 Item: C Lot Size: L 4 L Lead Time: 2 weeks Week 1 2 Gross requirements 200 Scheduled receipts 200 Projected on-hand 0 inventory 200 0 Planned receipts Planned order releases 3 4 5 400 0 400 240 360 6 7 8 240 360 120 0 240 360 120 9 10 0 0 120 Copyright © 2013 Pearson Education, Inc. publishing as Prentice Hall 16 - 80
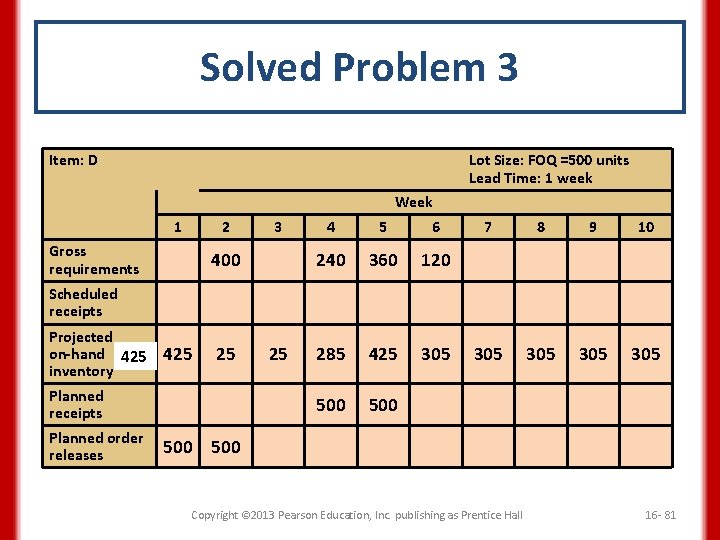
Solved Problem 3 Item: D Lot Size: FOQ =500 units Lead Time: 1 week Week 1 2 Gross requirements 3 400 4 5 6 240 360 120 285 425 305 500 7 8 9 10 305 305 Scheduled receipts Projected on-hand 425 inventory 425 25 Planned receipts Planned order releases 500 25 500 Copyright © 2013 Pearson Education, Inc. publishing as Prentice Hall 16 - 81
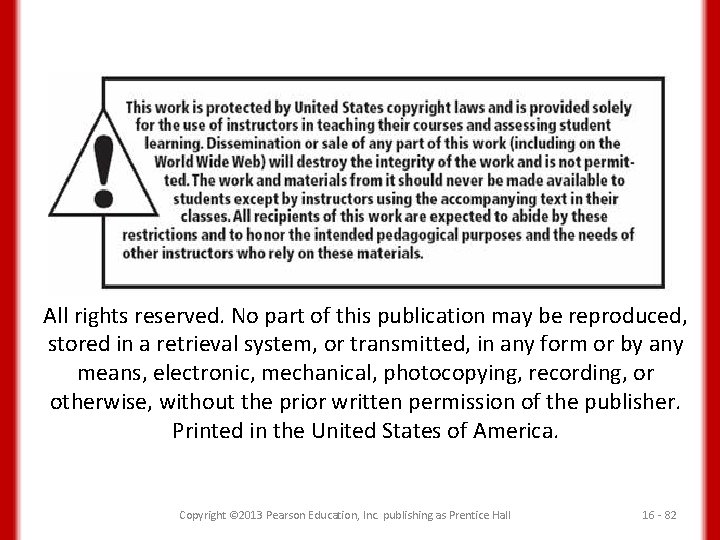
All rights reserved. No part of this publication may be reproduced, stored in a retrieval system, or transmitted, in any form or by any means, electronic, mechanical, photocopying, recording, or otherwise, without the prior written permission of the publisher. Printed in the United States of America. Copyright © 2013 Pearson Education, Inc. publishing as Prentice Hall 16 - 82
2013 pearson education inc
2013 pearson education inc
2013 pearson education inc. answers
2013 pearson education inc
2013 pearson education inc
2013 pearson education inc
2013 pearson education inc
2013 pearson education inc
2013 pearson education inc
2013 pearson education inc
2013 pearson education inc. answers
Employee testing and selection
2013 pearson education inc
2013 pearson education inc
2017 pearson education inc
2017 pearson education inc
2010 pearson education inc
2009 pearson education inc
2018 pearson education inc
2014 pearson education inc
Copyright 2010 pearson education inc
Copyright 2010 pearson education inc
Copyright by pearson education inc. answers
Copyright 2003 pearson education inc
Copyright 2009 pearson education inc
2015 pearson education inc
Copyright 2010 pearson education inc
Copyright 2010 pearson education inc
Copyright 2010 pearson education inc
2010 pearson education inc
Copyright 2010 pearson education inc
Copyright 2010 pearson education inc
Copyright 2010 pearson education inc
Copyright 2009 pearson education inc
2009 pearson education inc
Copyright 2009 pearson education inc
2009 pearson education inc
Copyright pearson education inc
Pearson education, inc. publishing as prentice hall
2011 pearson education inc
Pearson education inc publishing as pearson prentice hall
Pearson 2012
2008 pearson prentice hall inc
Mbti personal impact report
Copyright 2005 pearson prentice hall inc
Chapter 5 human resource planning and recruitment
Resource allocation vs resource leveling
Perbedaan resource loading dan resource levelling
Pearson vue ceo
Educational pearson pearson times
Pakistan education statistics 2013
Enhanced basic education act of 2013
Managerial judgement technique in hrm example
Resource and cost planning
Enterprise resource planning example
Example of short term human resources
Human resource planning means
Hrp meaning and definition
Resource forecasting meaning
Steps of human resource planning
Hrm final exam questions
Factors affecting human resource management
Enterprise resource planning overview
Application of enterprise resource planning
Concepts in enterprise resource planning
Supply forecasting techniques in hrp
Cayenta customer relationship management
Material requirements planning
Enterprise resource planning tradução
Induction in human resource management
Swot analysis of hr manager
Geister meaning
Pengertian erp system
Enterprise resource planning mary sumner
Concepts in enterprise resource planning
Wbs human resource management
Human resource planning model ppt
Creating highly talented personnel
Definition of planning
Core and extended erp components
Contemporary management ppt
Resource and talent planning
Resource loading definition