Nigerian Academy of Engineering June 2013 Some Engineering
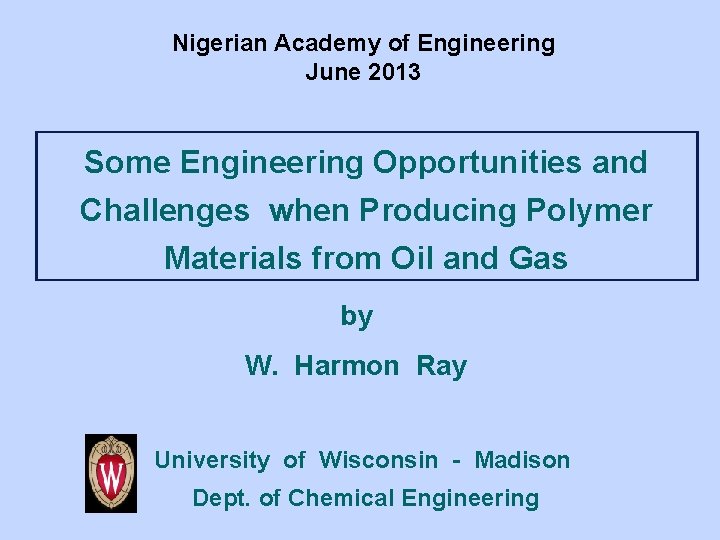
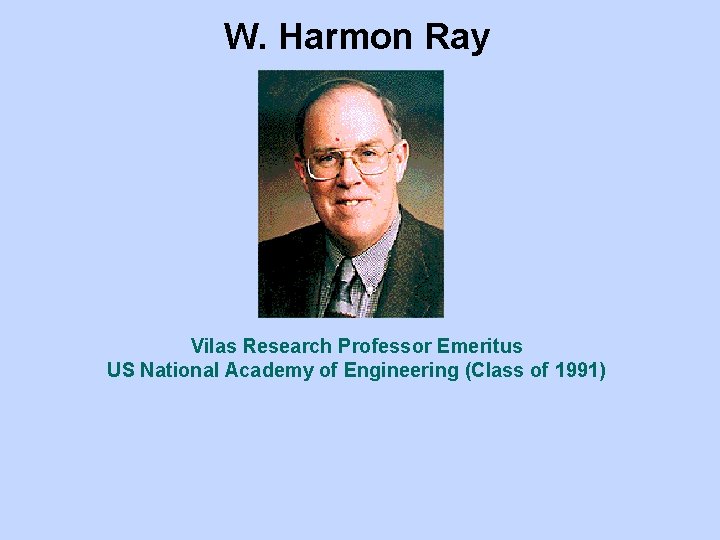
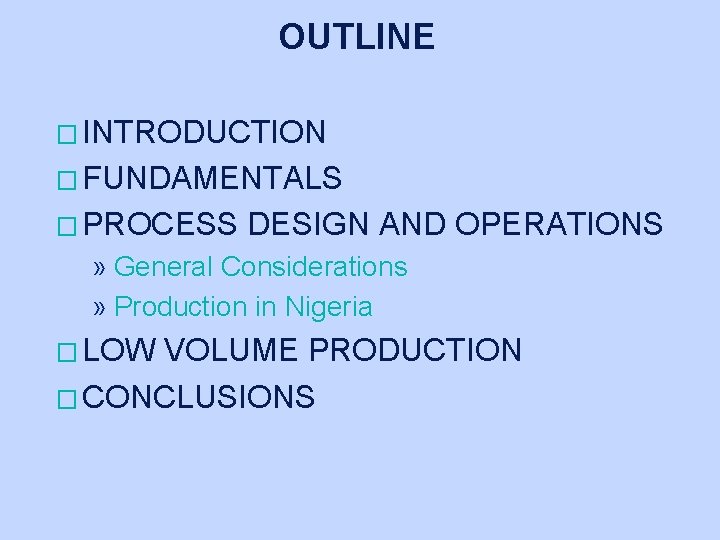
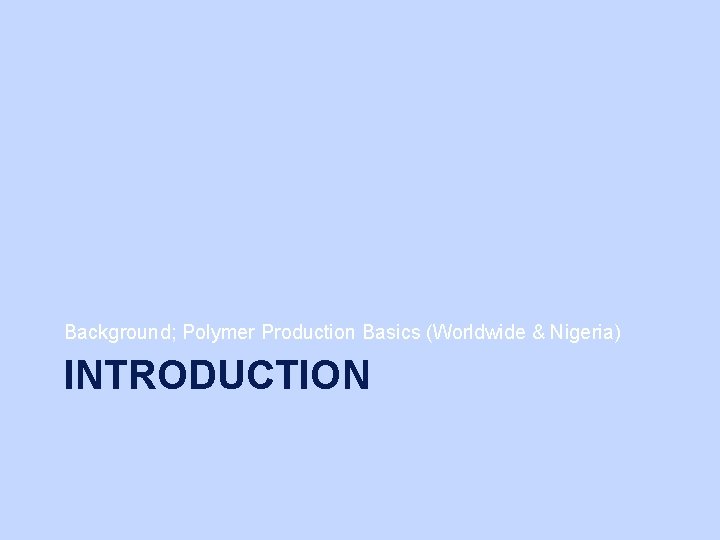
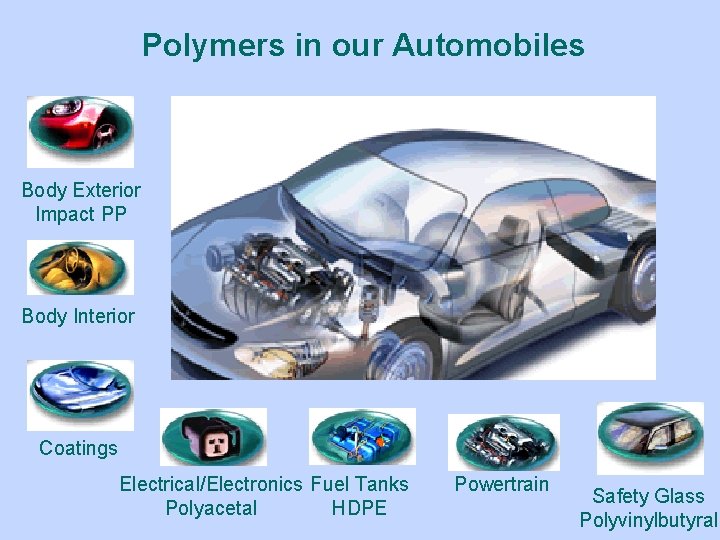
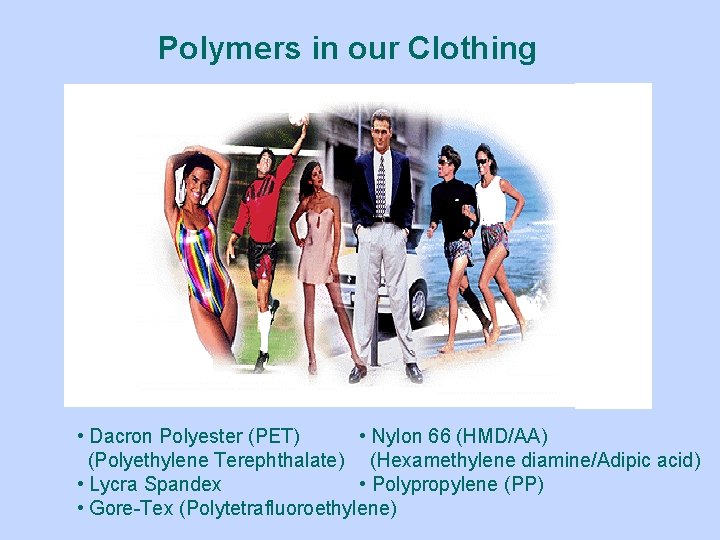
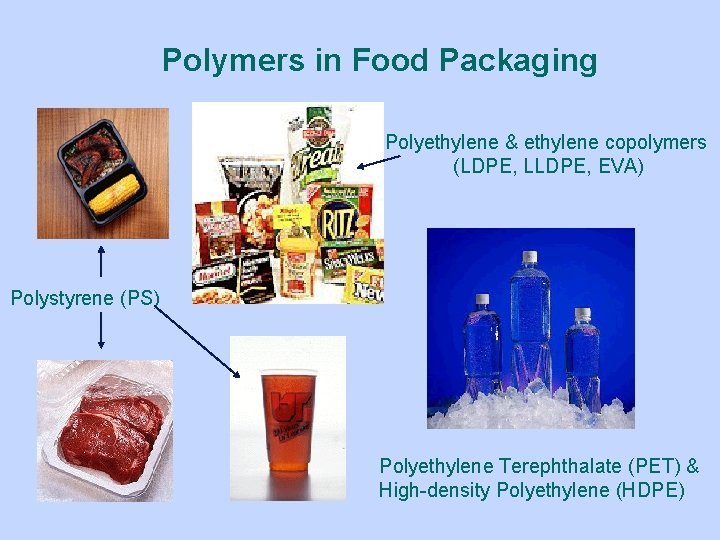
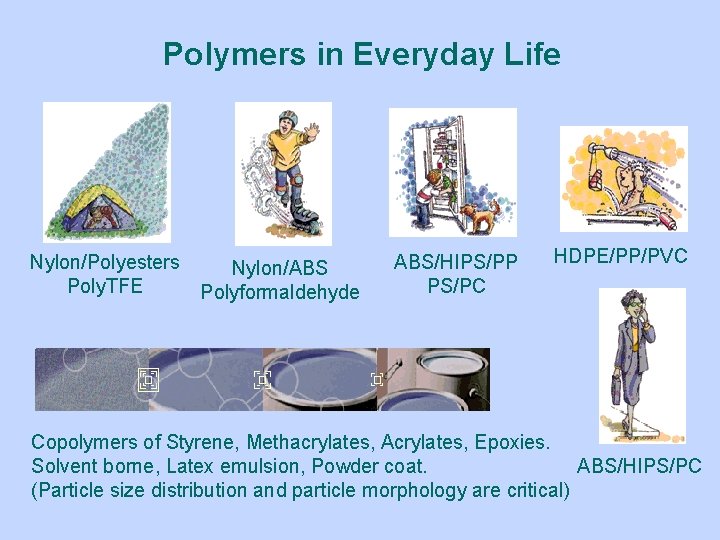
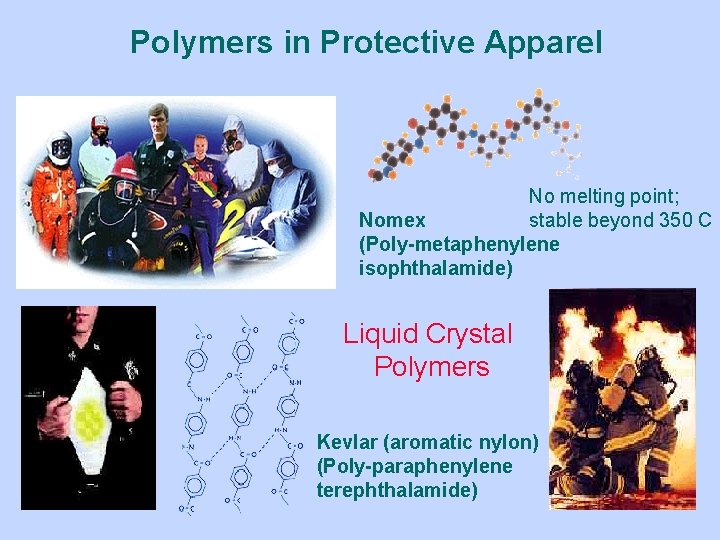
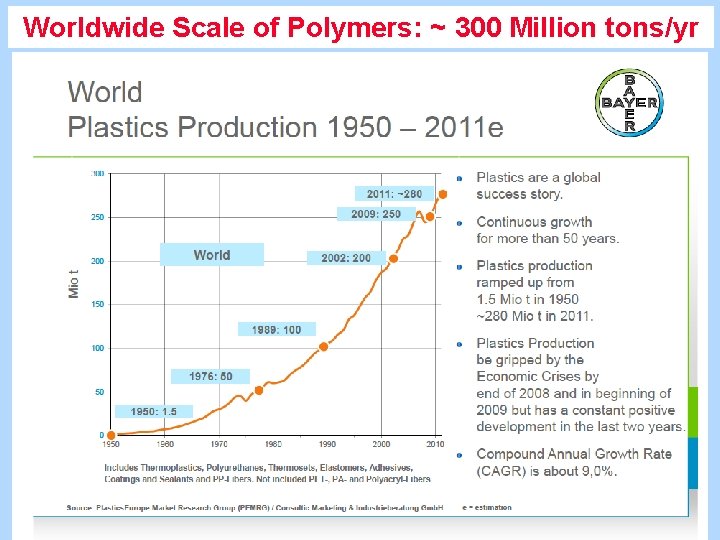
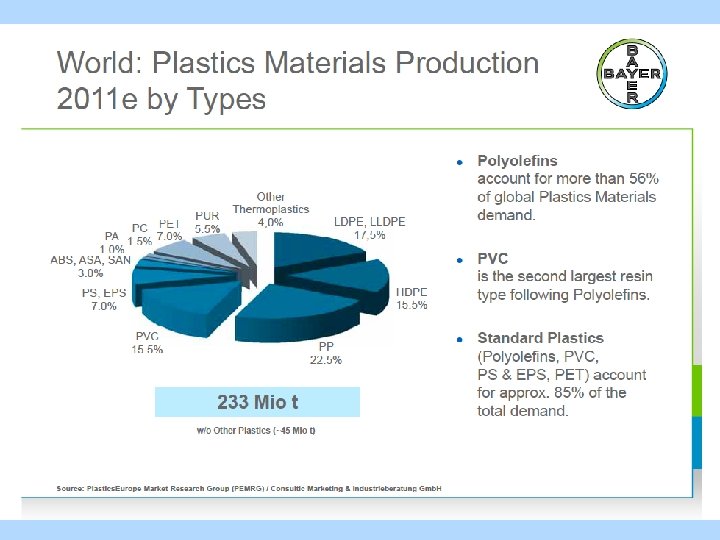
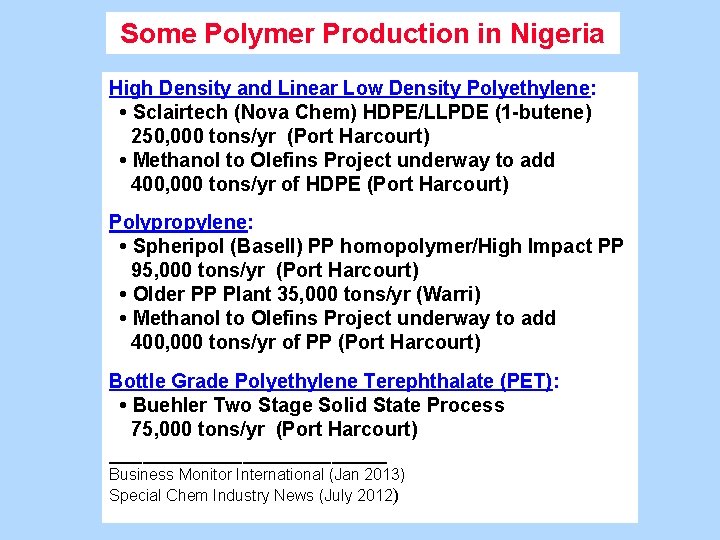
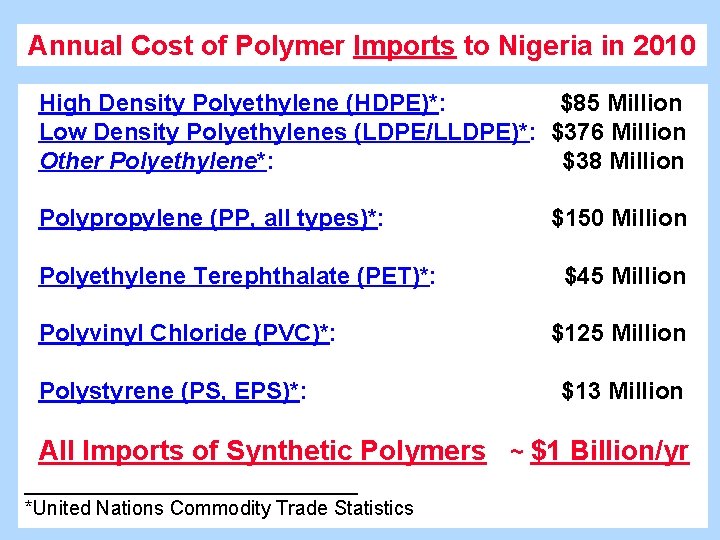
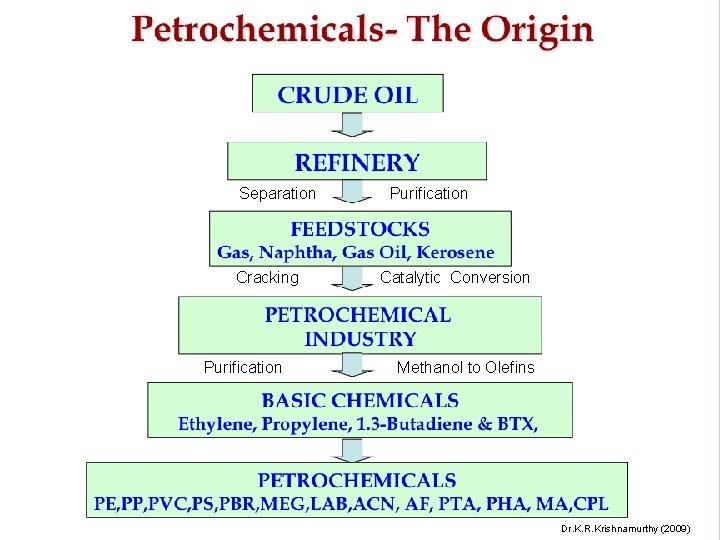
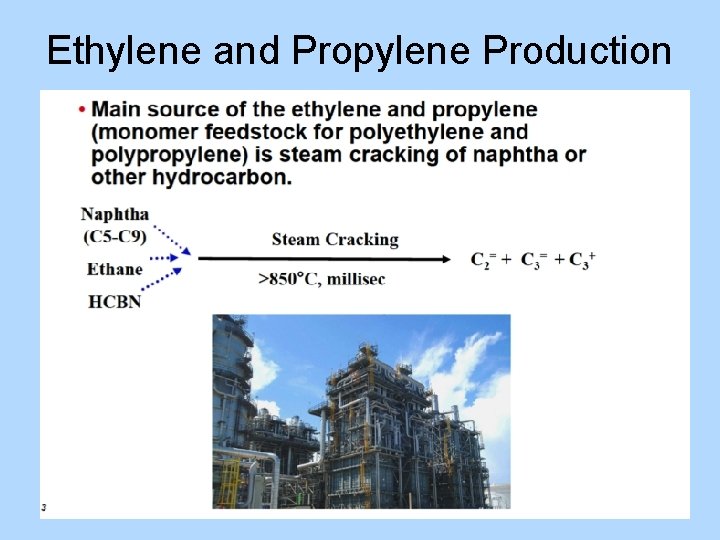
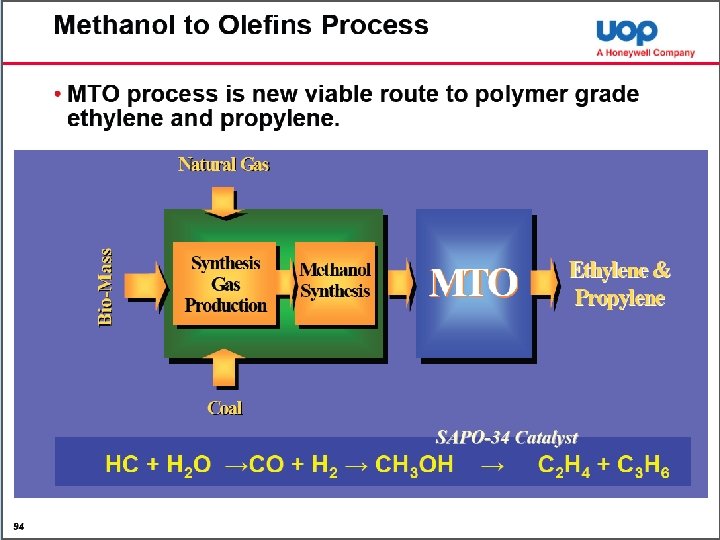
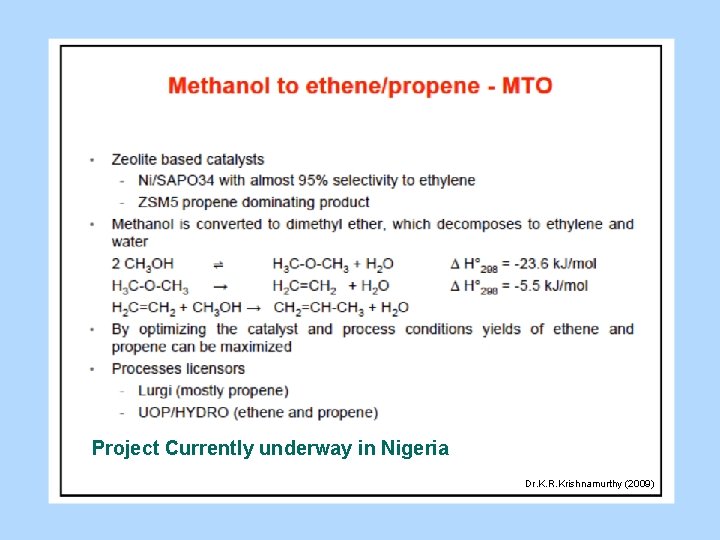
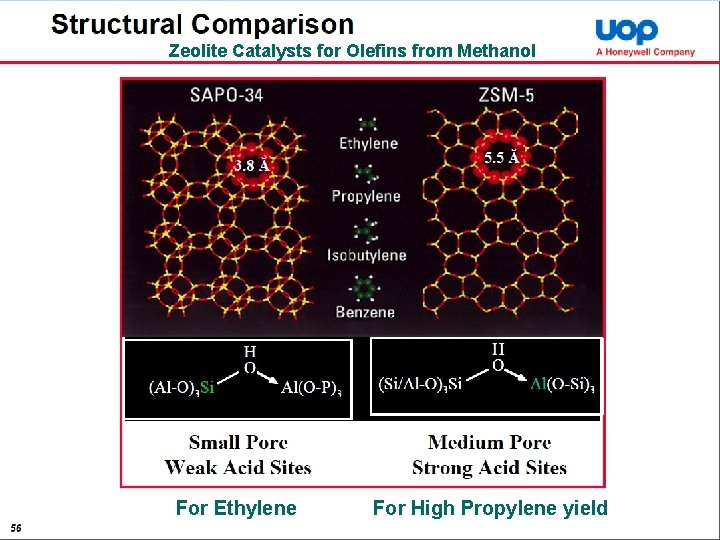
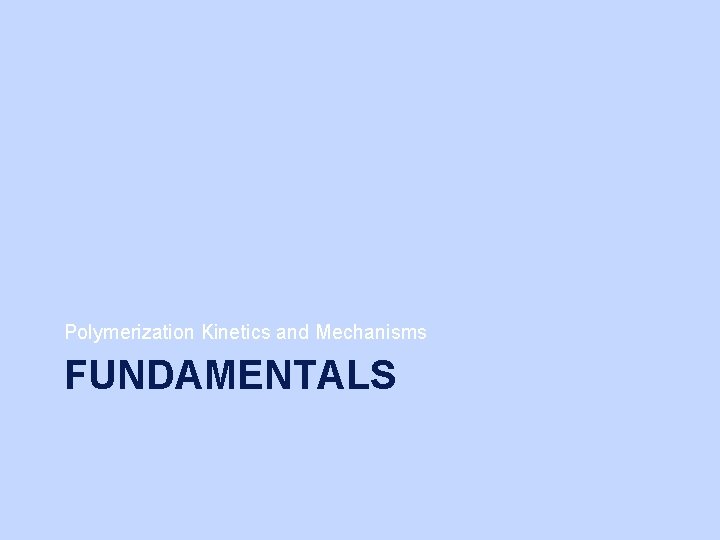
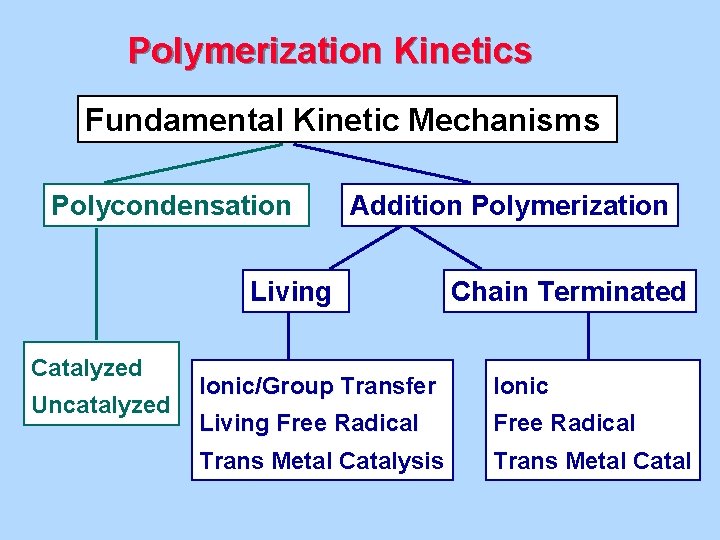
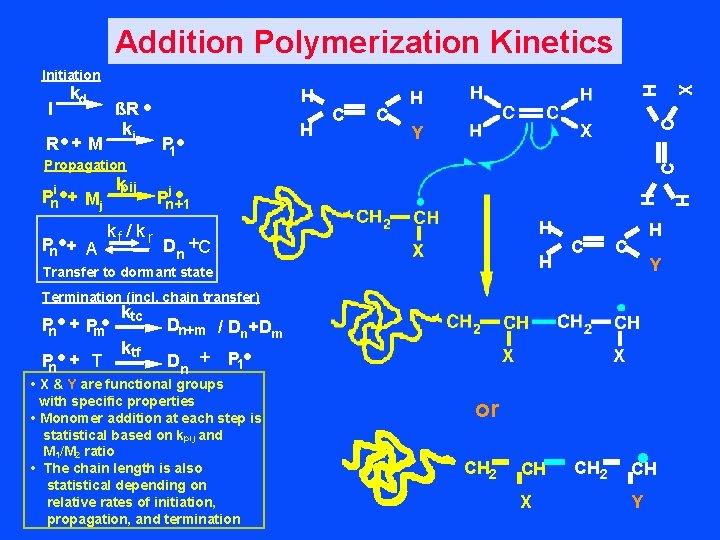
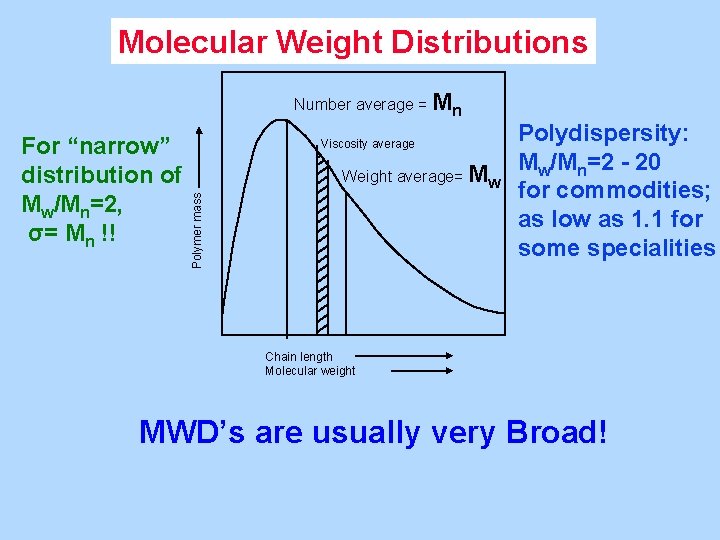
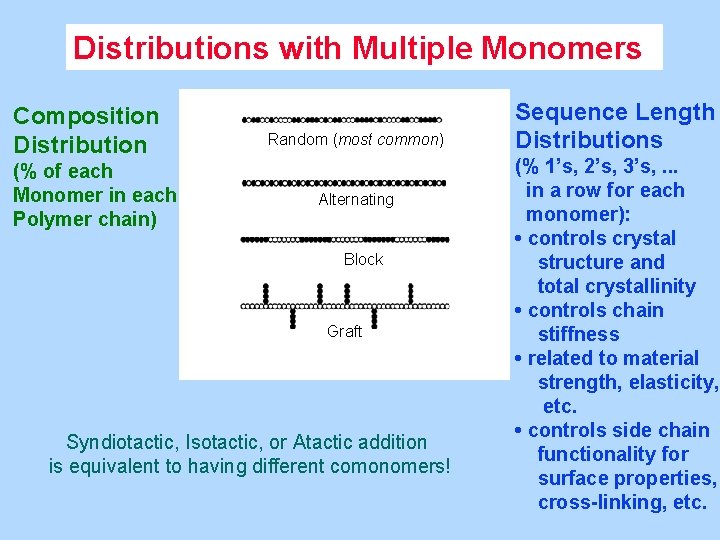

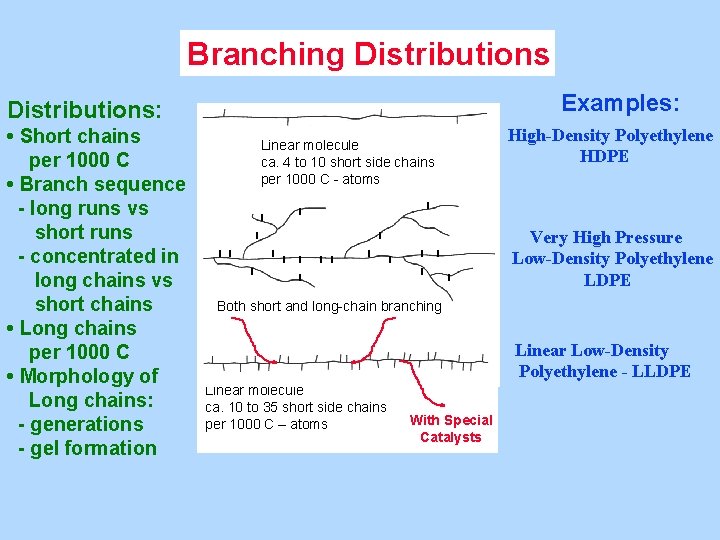
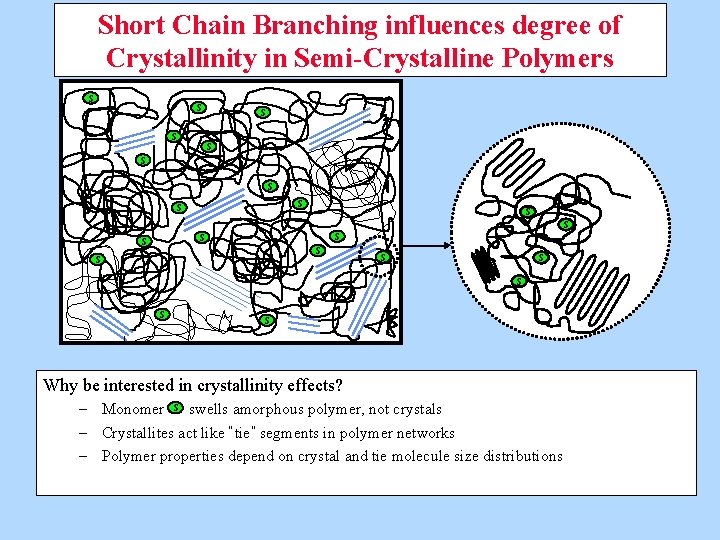
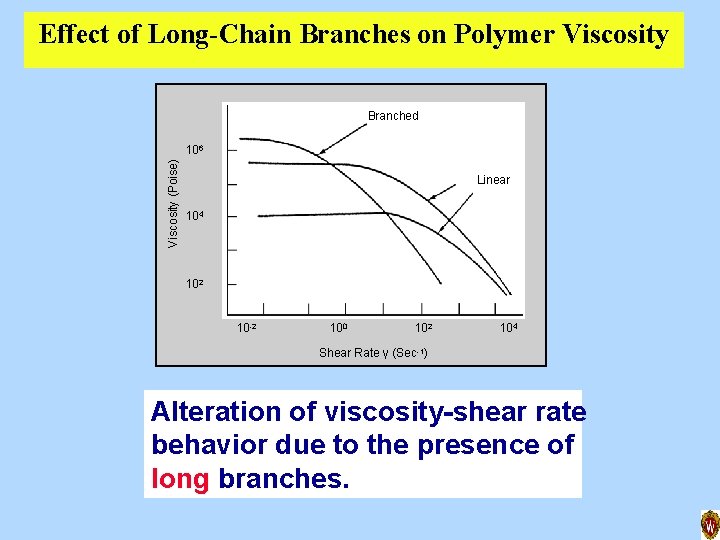
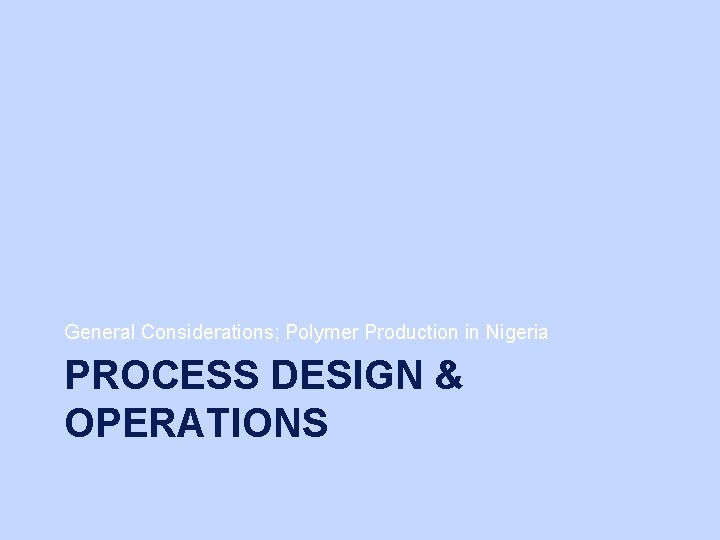
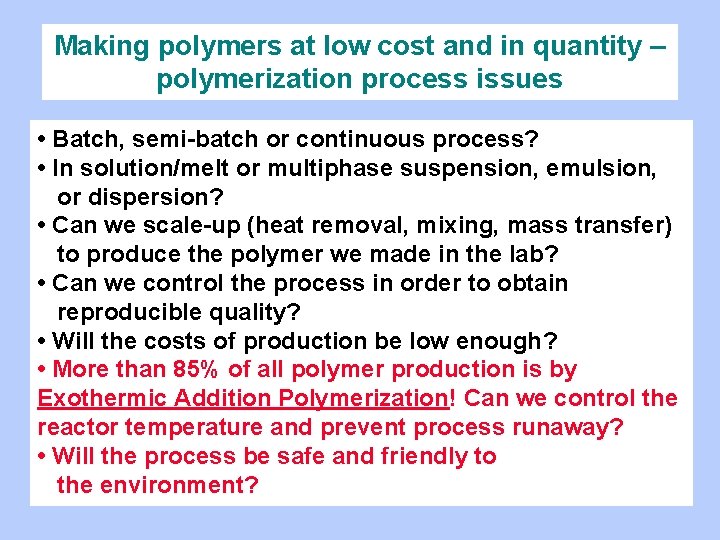
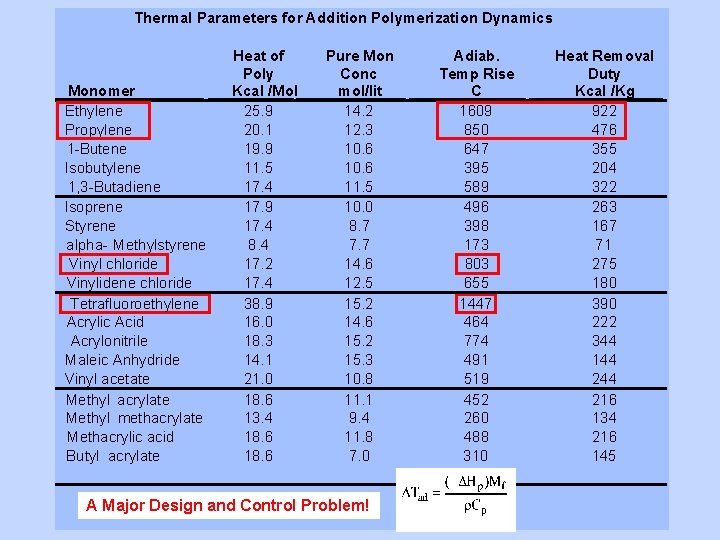
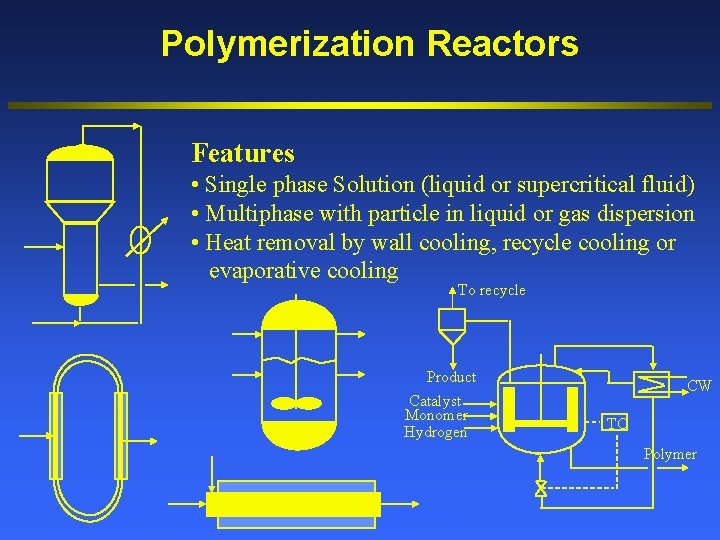
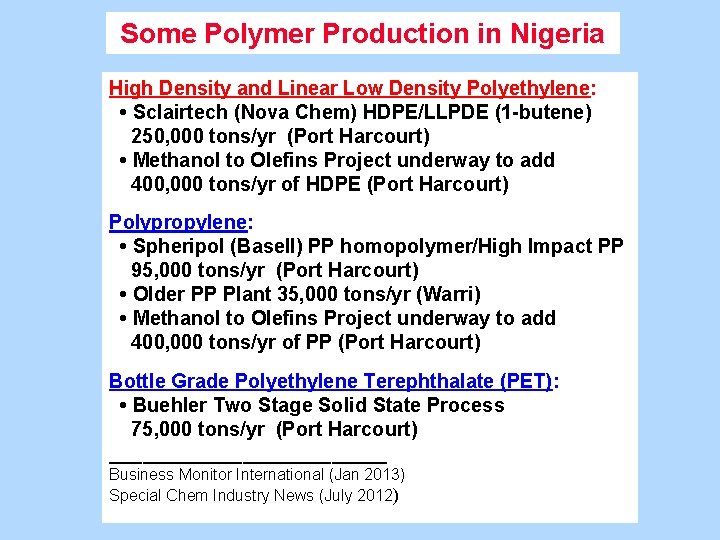
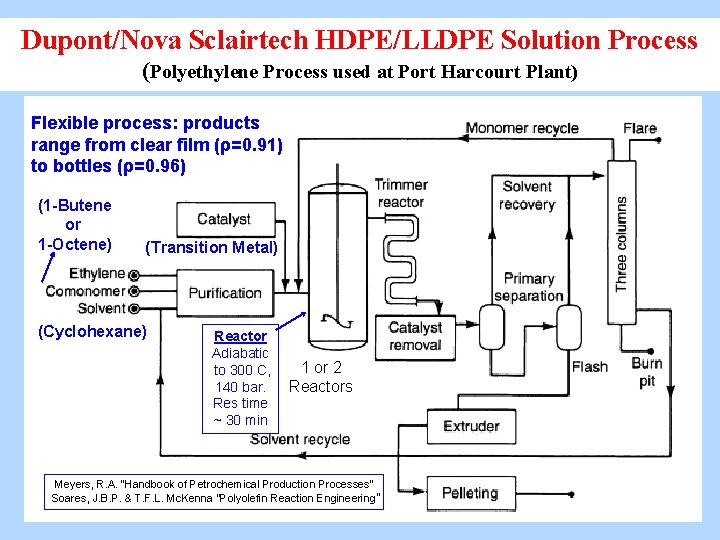
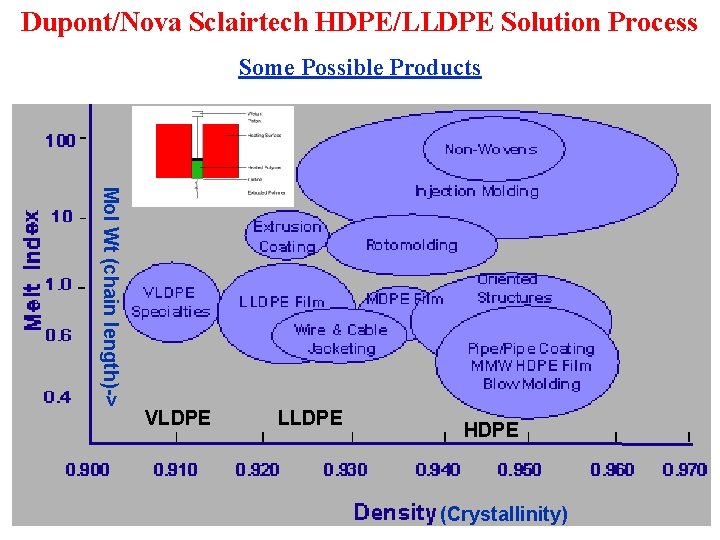
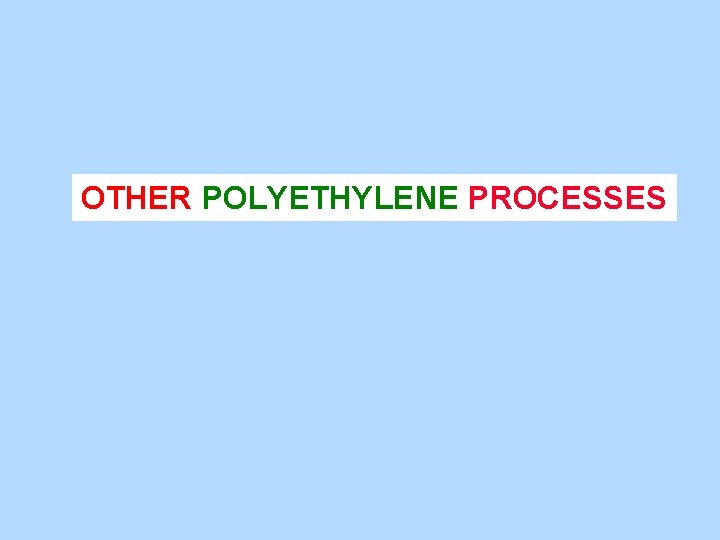
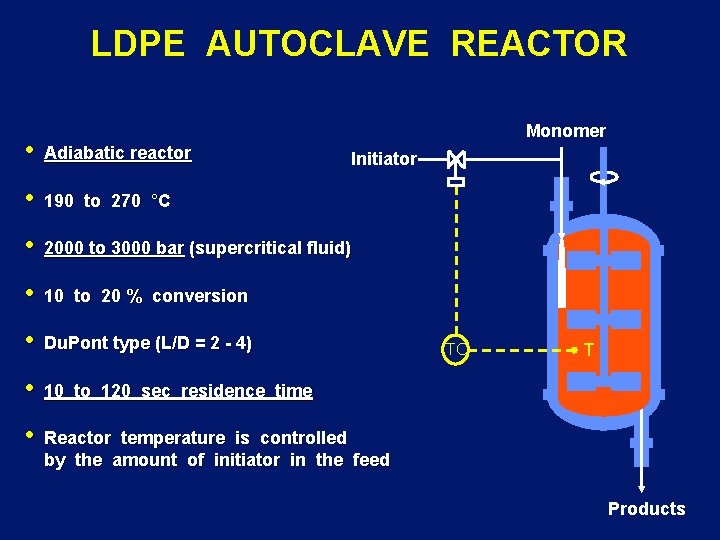
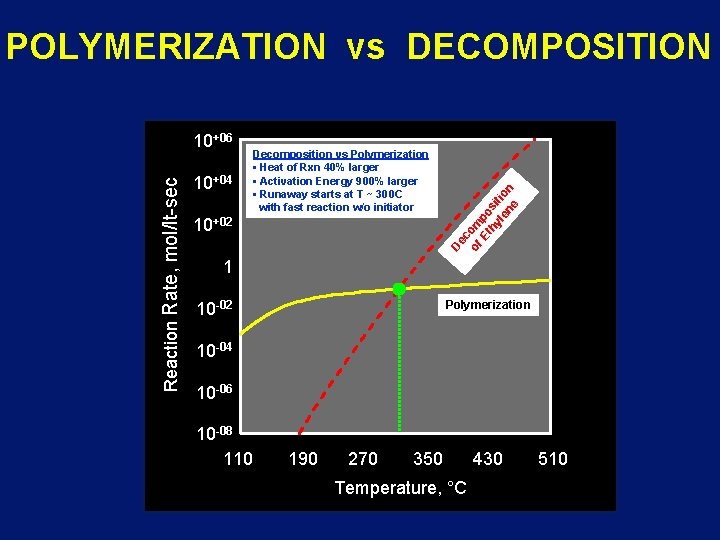
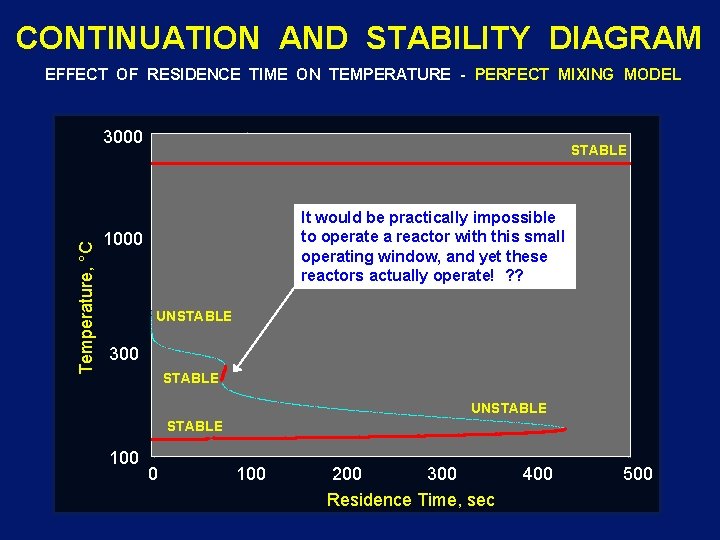
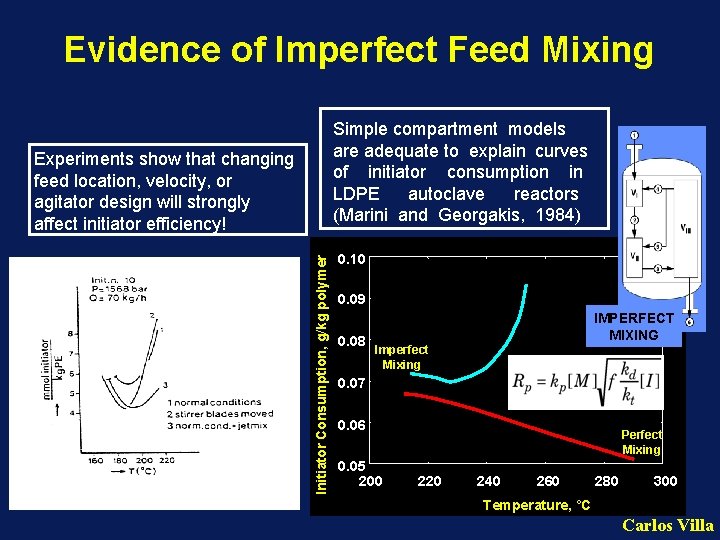
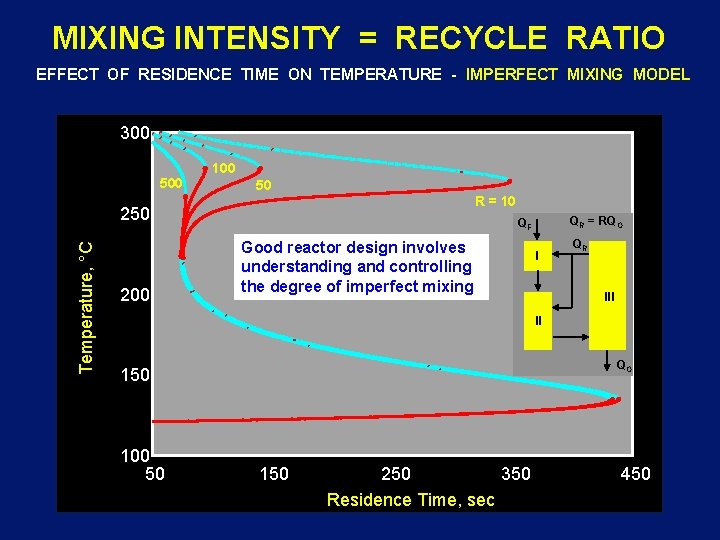
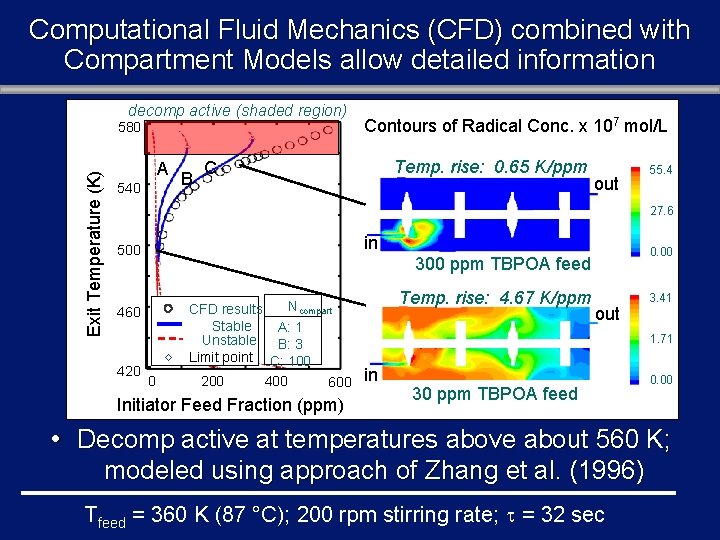
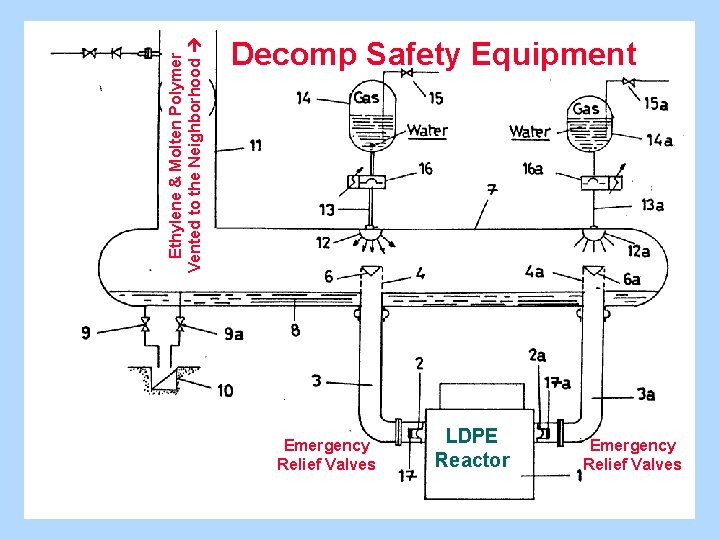
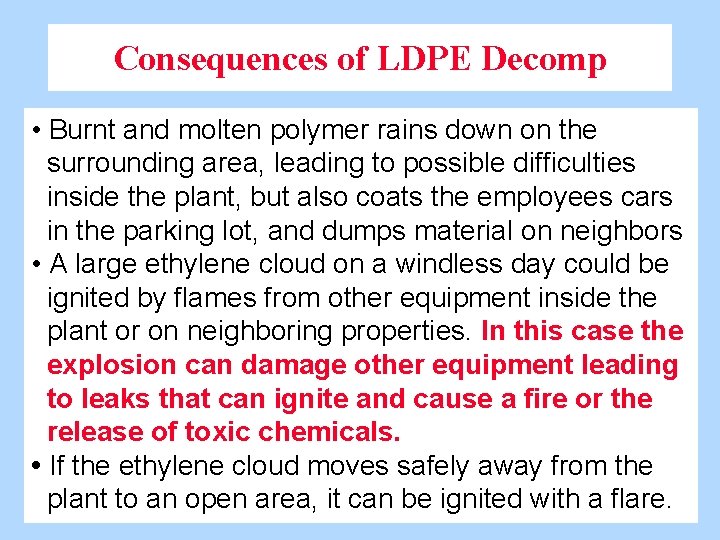
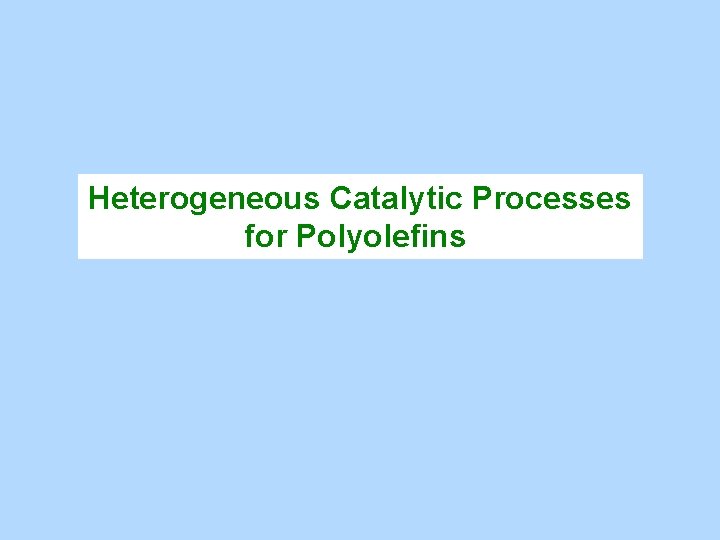
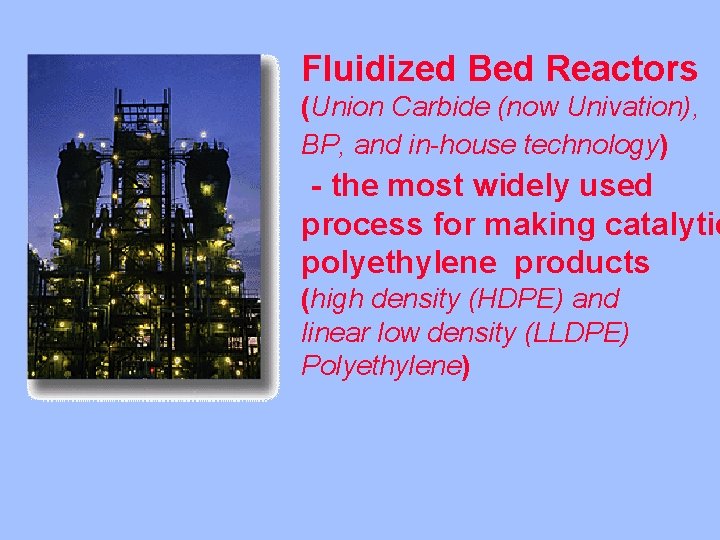
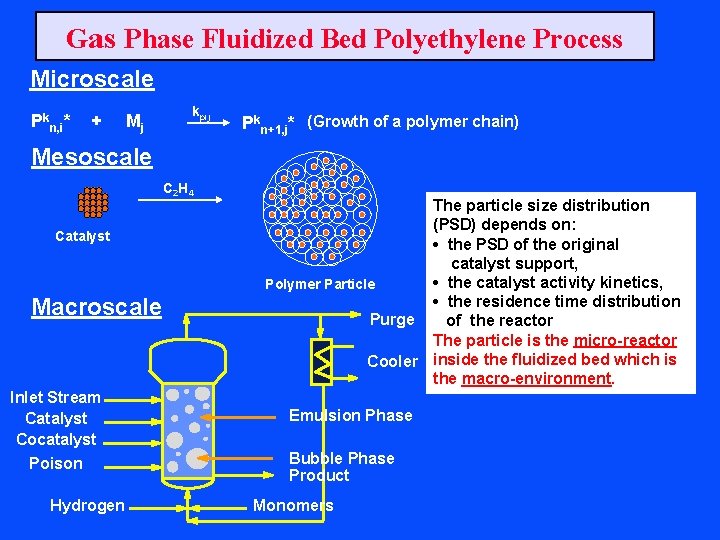
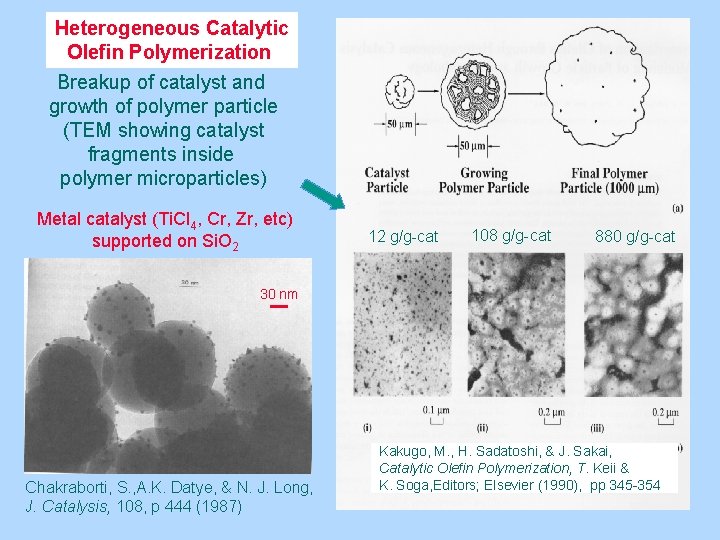
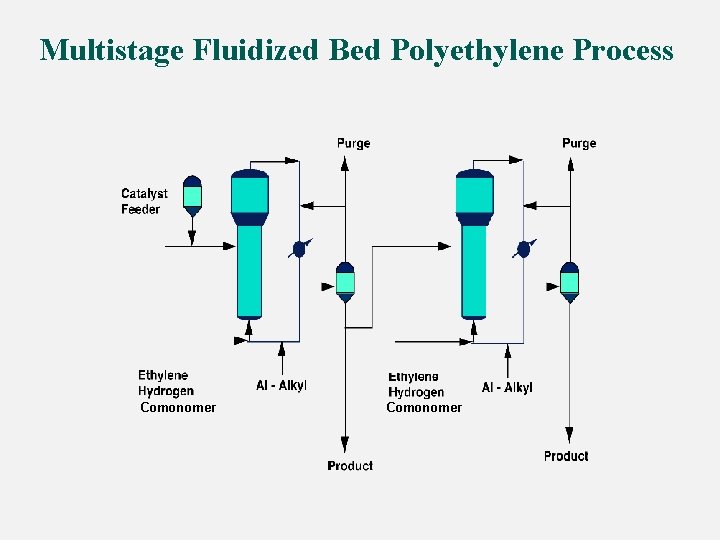
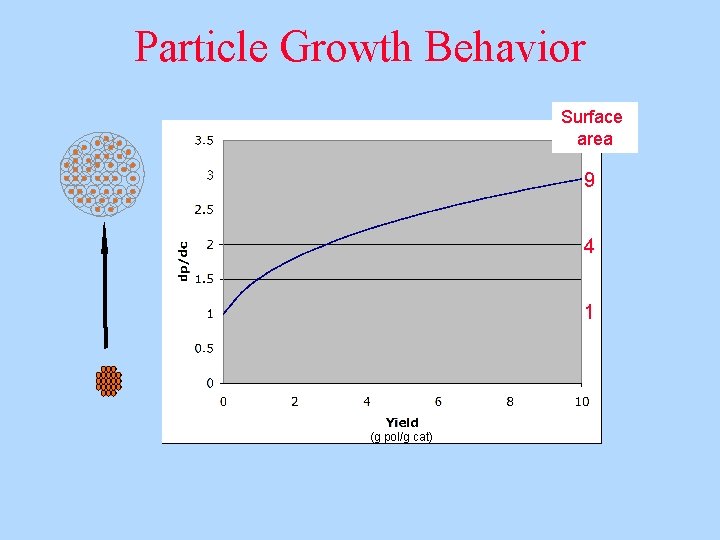
![Fluidized Bed Particle Temperatures Temperature difference DT [C] Melted Quasi-steady state particle temperature, fully Fluidized Bed Particle Temperatures Temperature difference DT [C] Melted Quasi-steady state particle temperature, fully](https://slidetodoc.com/presentation_image/529806be0ef6f944551970577fc32074/image-50.jpg)
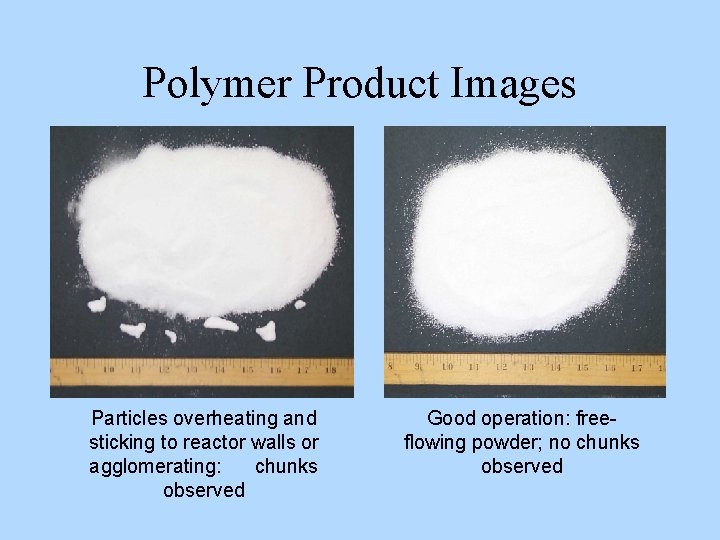
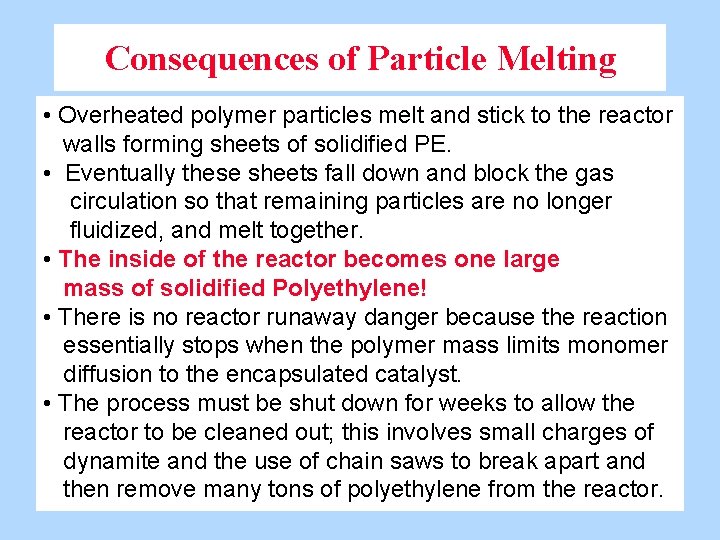
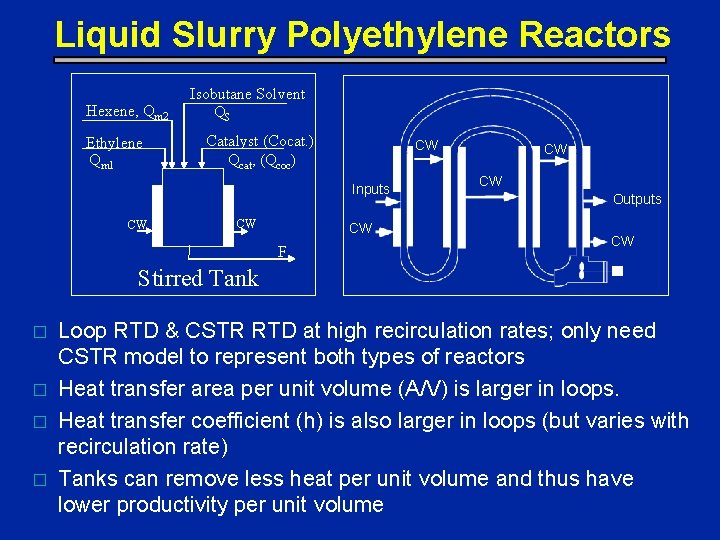
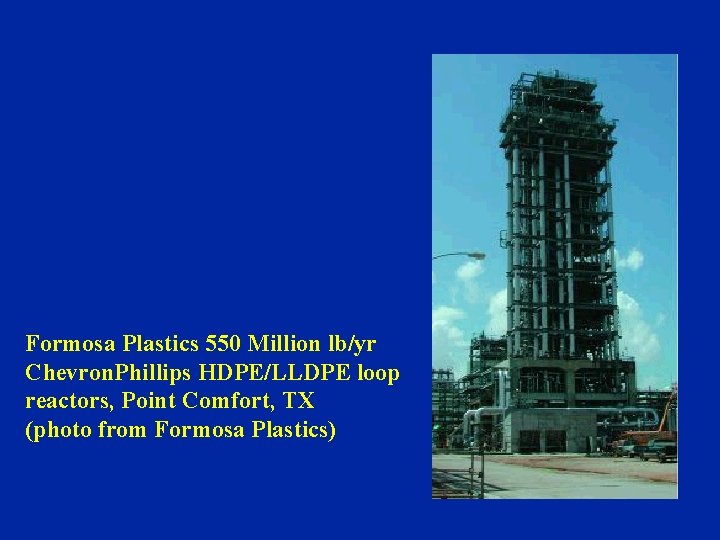
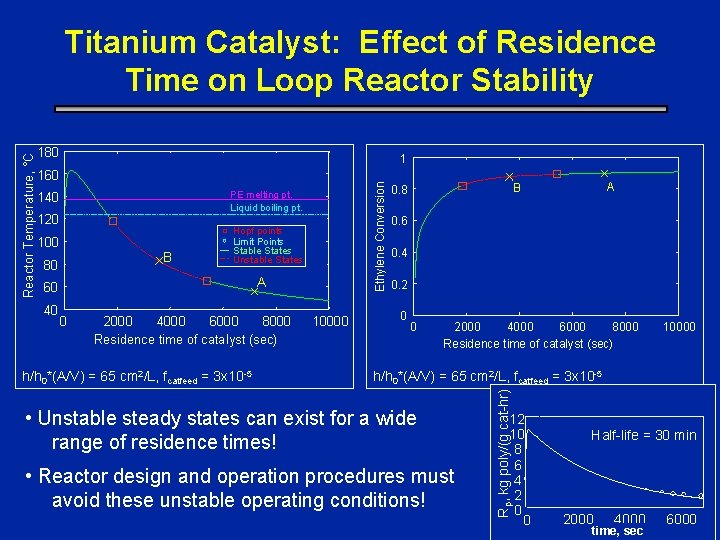
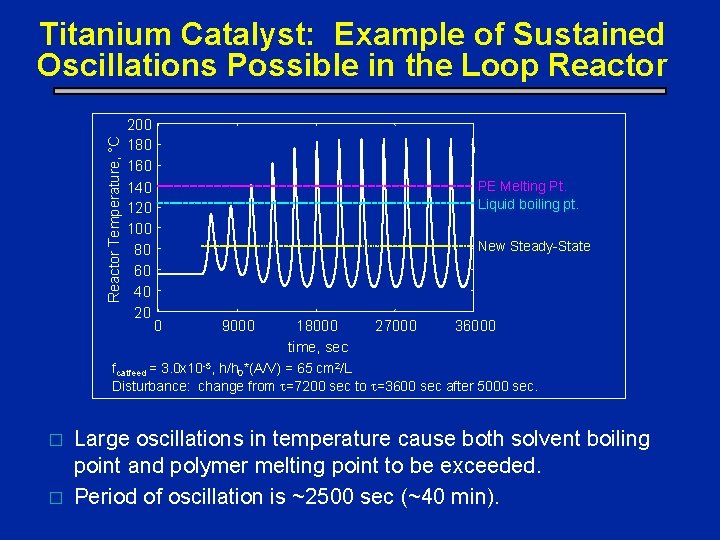
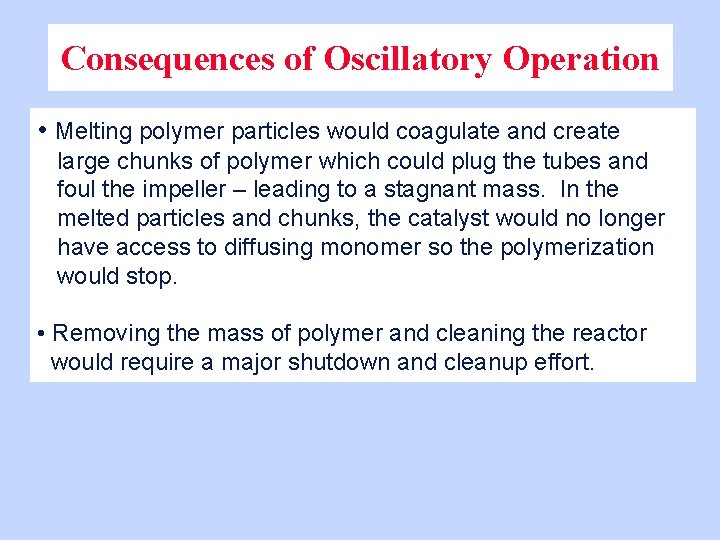
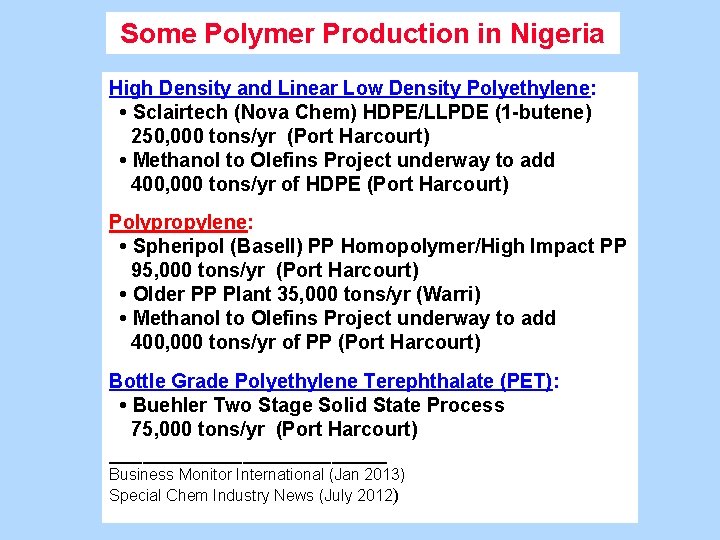
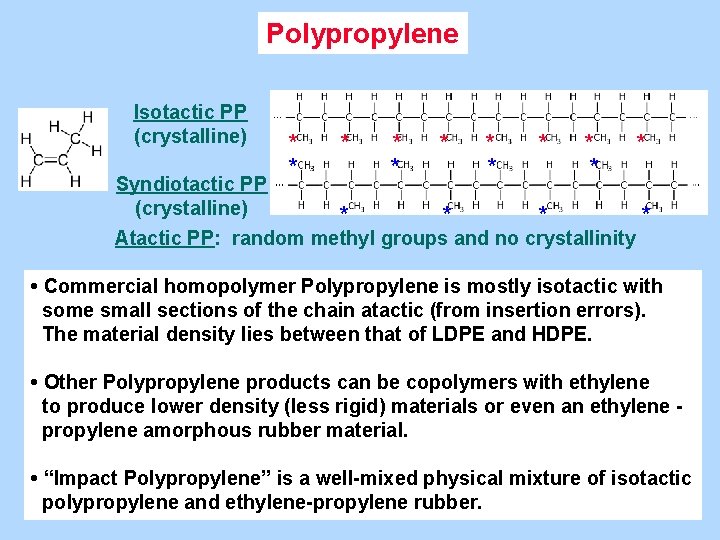
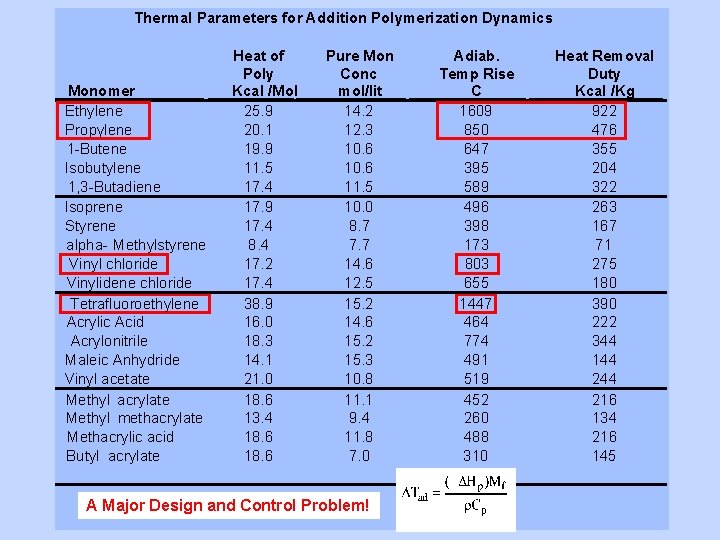
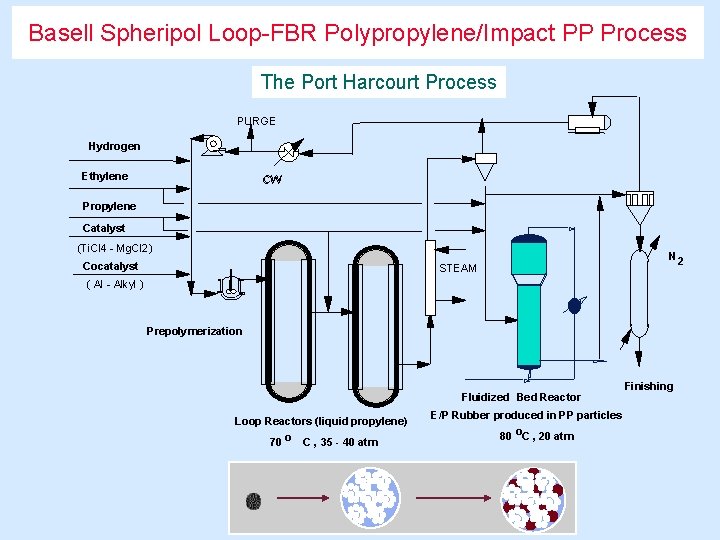
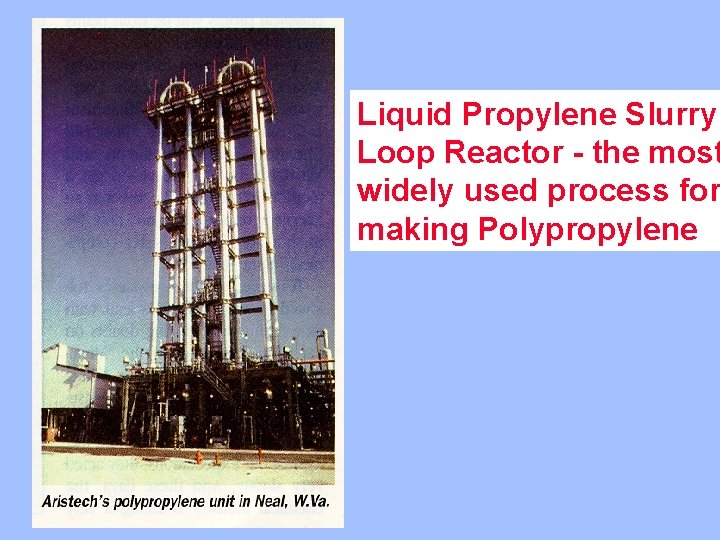
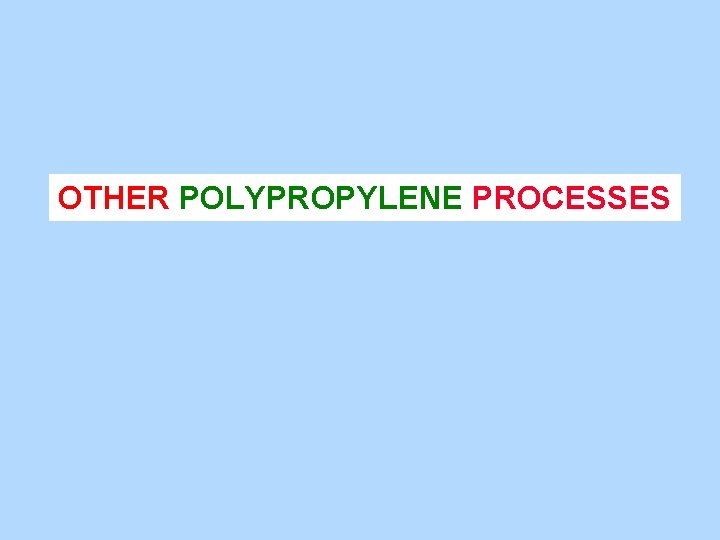
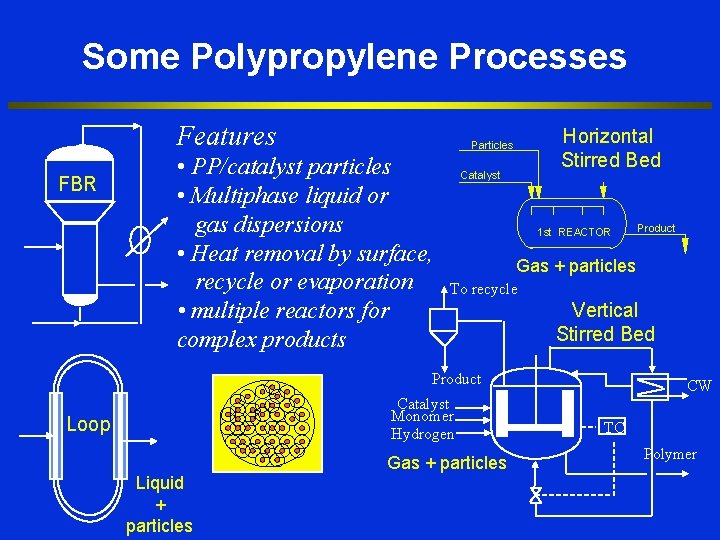
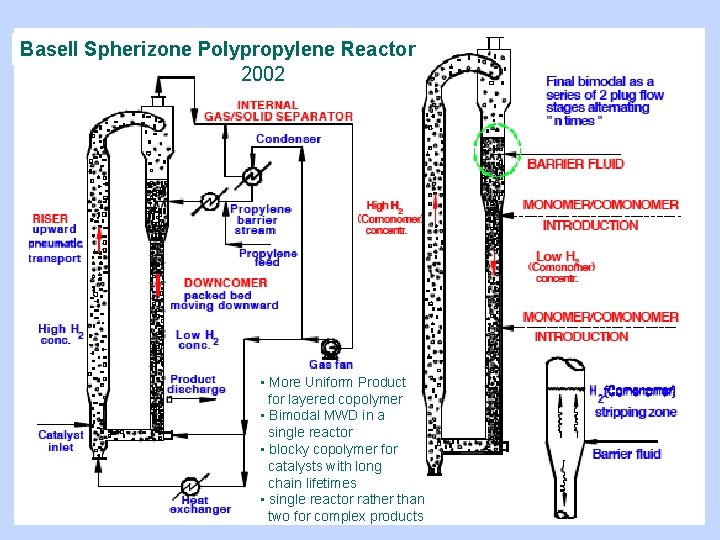
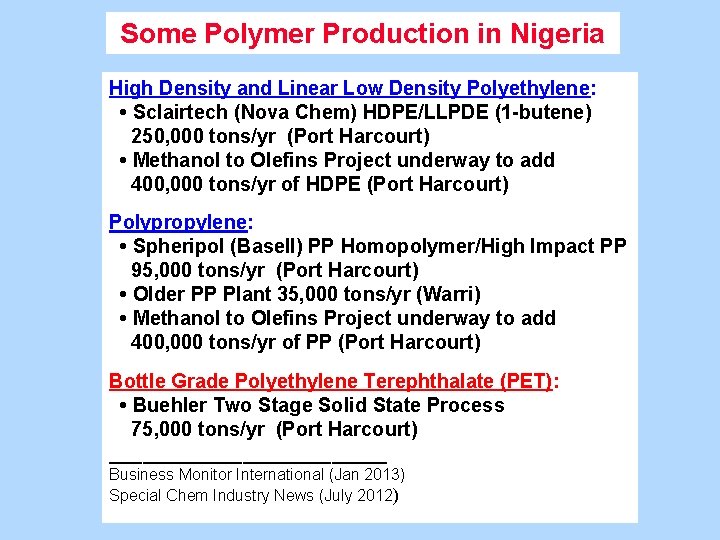
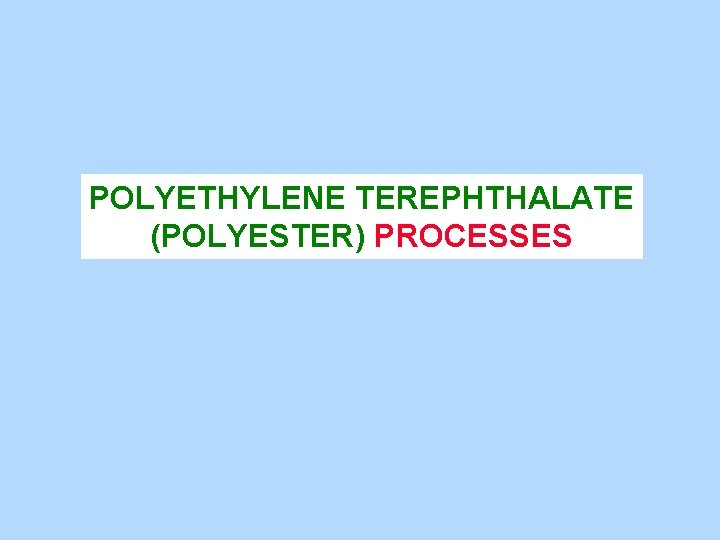
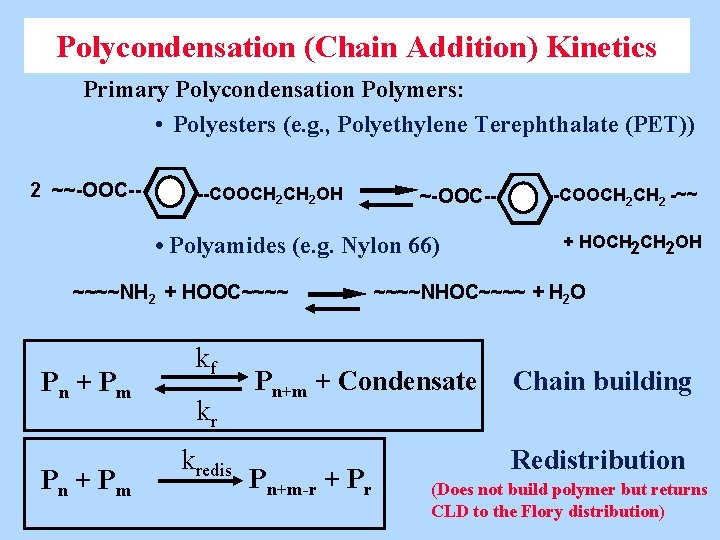
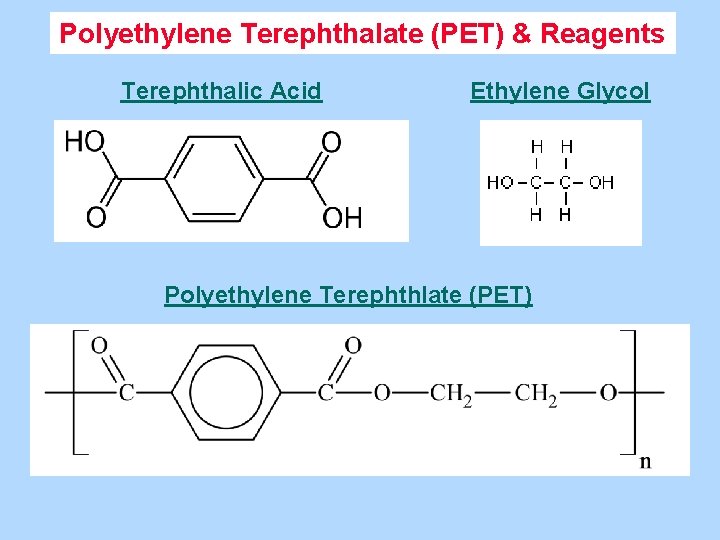

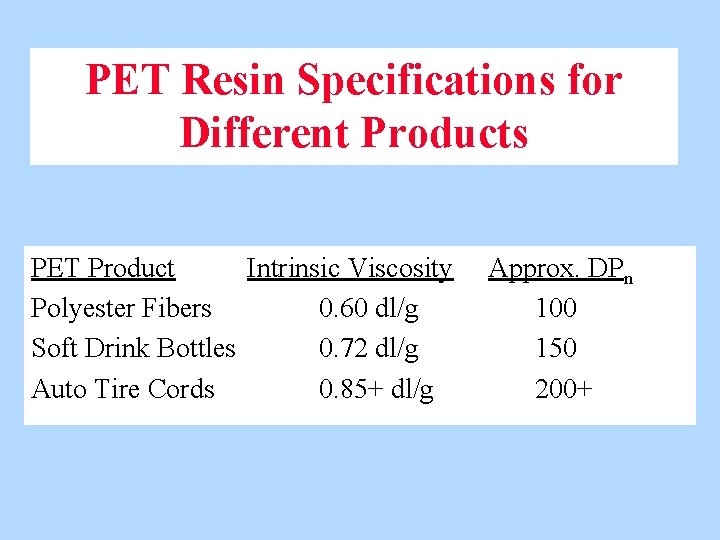
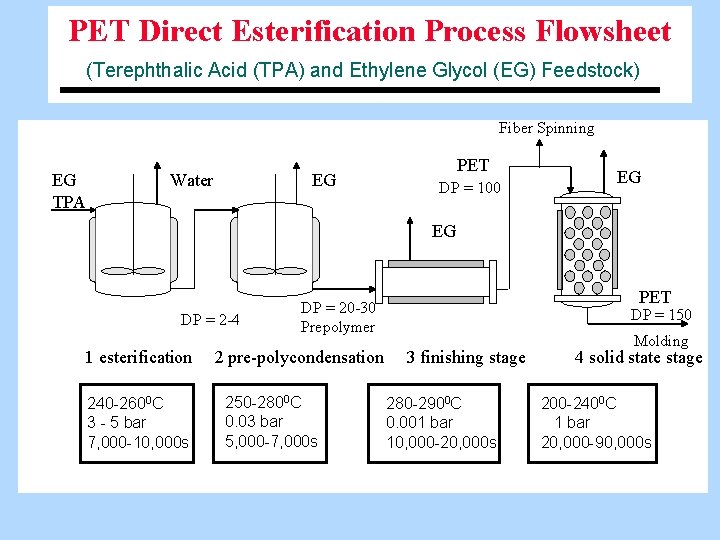
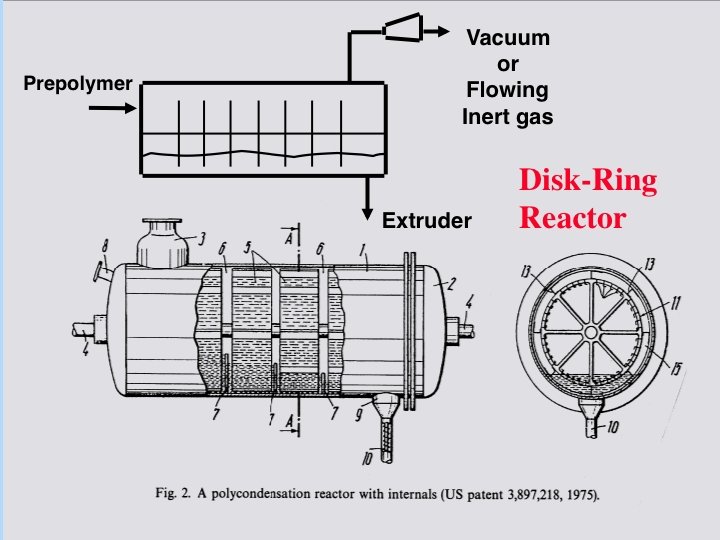
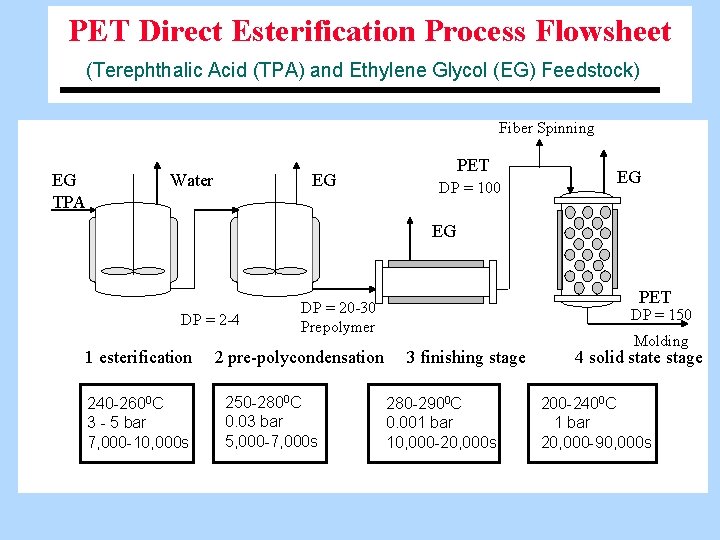
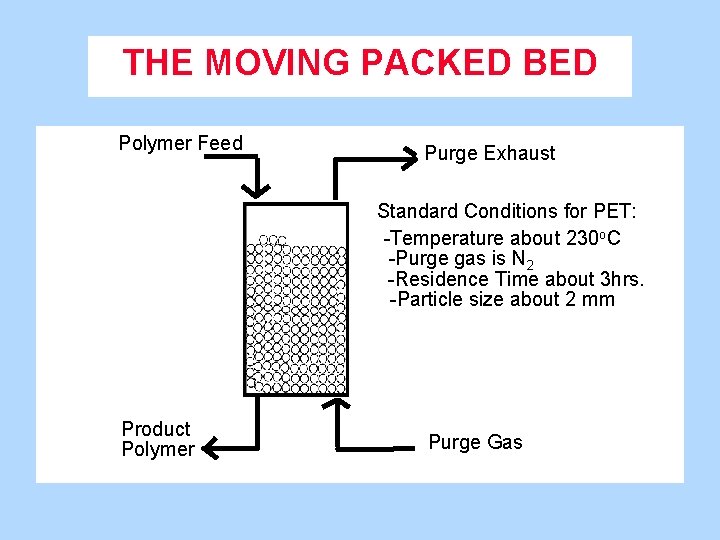
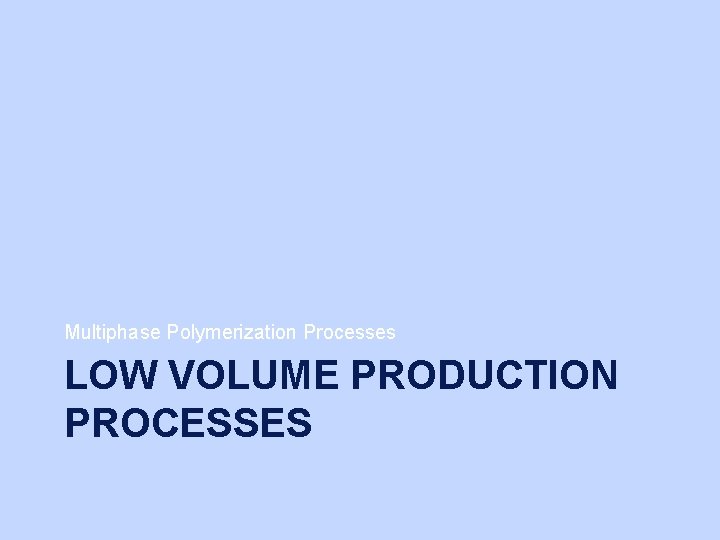
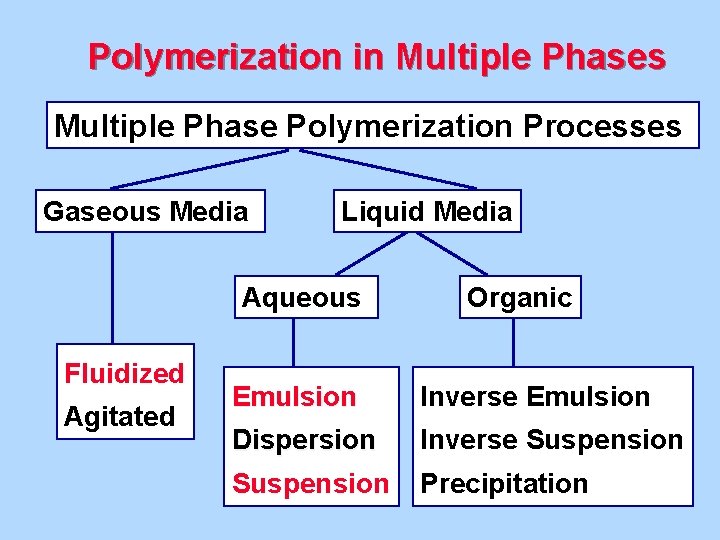
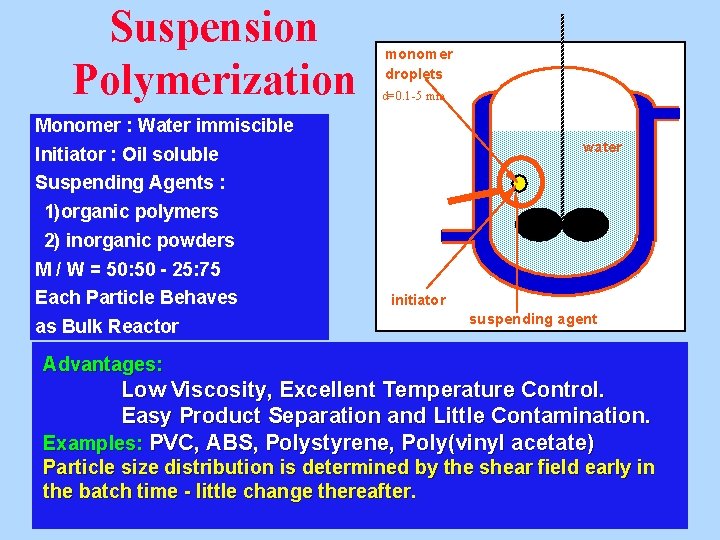
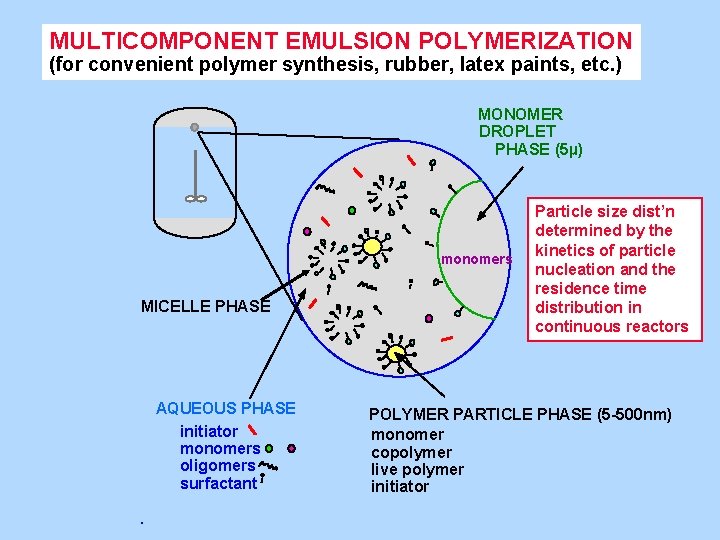

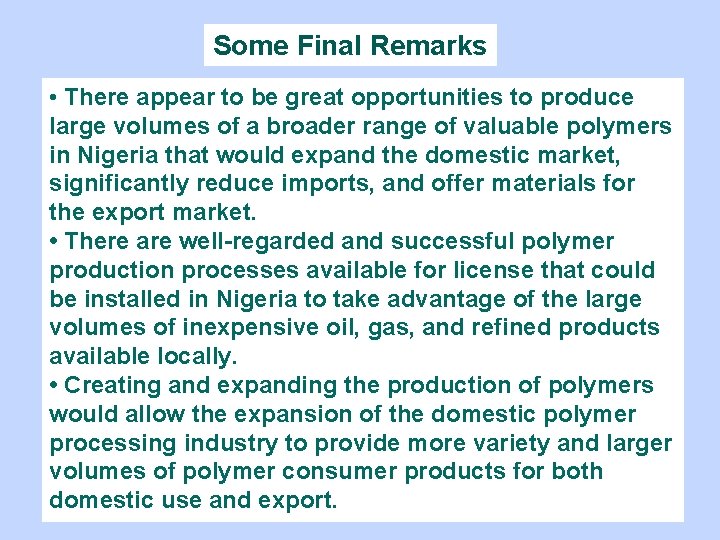
- Slides: 81
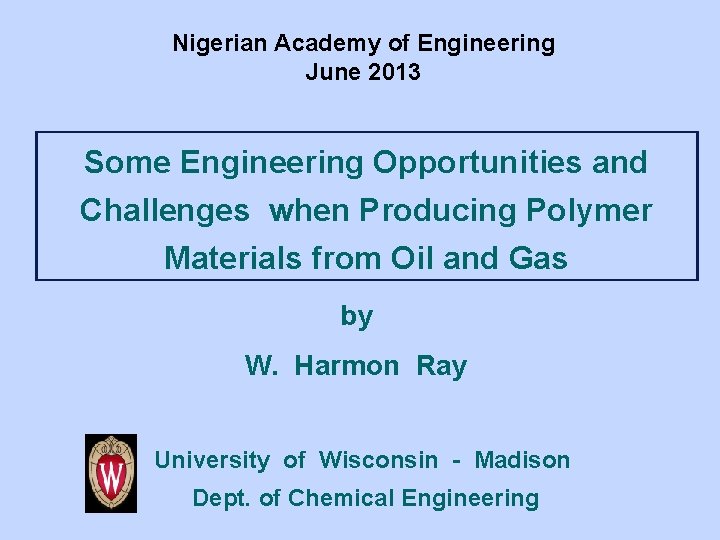
Nigerian Academy of Engineering June 2013 Some Engineering Opportunities and Challenges when Producing Polymer Materials from Oil and Gas by W. Harmon Ray University of Wisconsin - Madison Dept. of Chemical Engineering
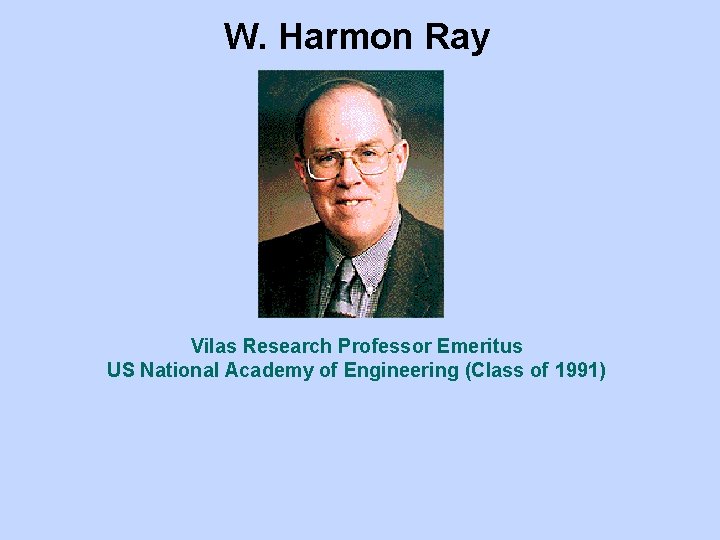
W. Harmon Ray Vilas Research Professor Emeritus US National Academy of Engineering (Class of 1991)
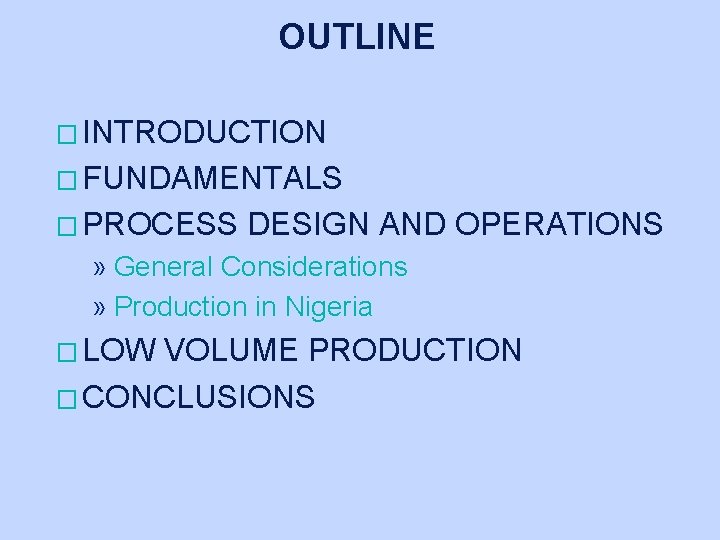
OUTLINE � INTRODUCTION � FUNDAMENTALS � PROCESS DESIGN AND OPERATIONS » General Considerations » Production in Nigeria � LOW VOLUME PRODUCTION � CONCLUSIONS
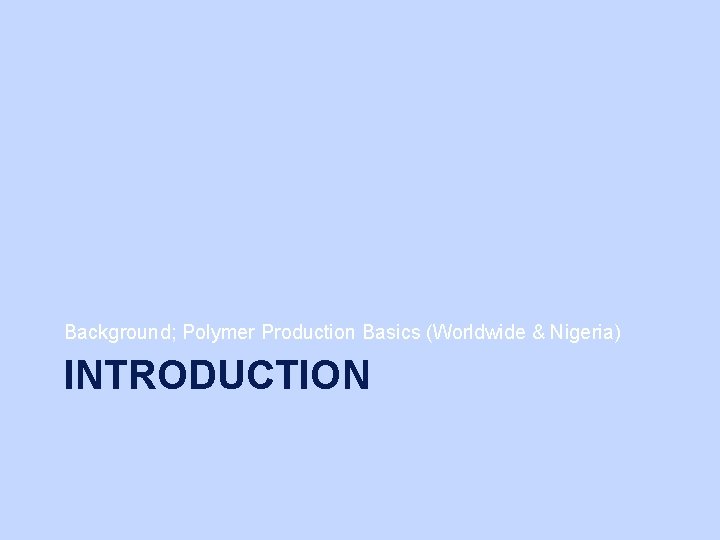
Background; Polymer Production Basics (Worldwide & Nigeria) INTRODUCTION
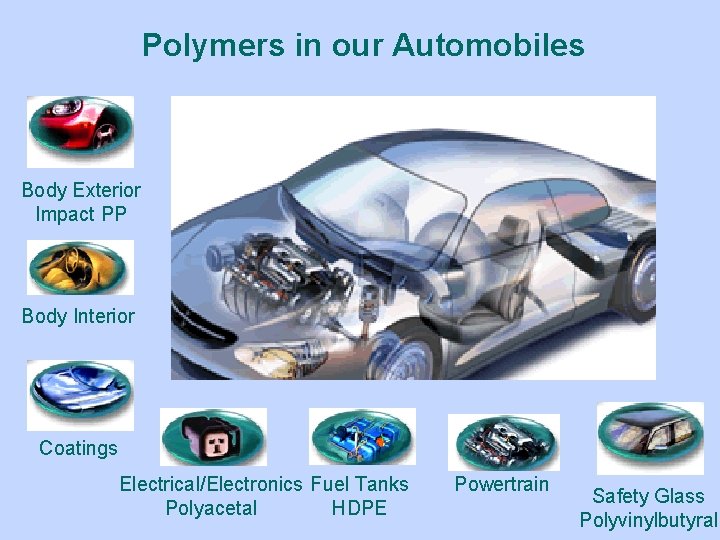
Polymers in our Automobiles Body Exterior Impact PP Body Interior Coatings Electrical/Electronics Fuel Tanks Polyacetal HDPE Powertrain Safety Glass Polyvinylbutyral
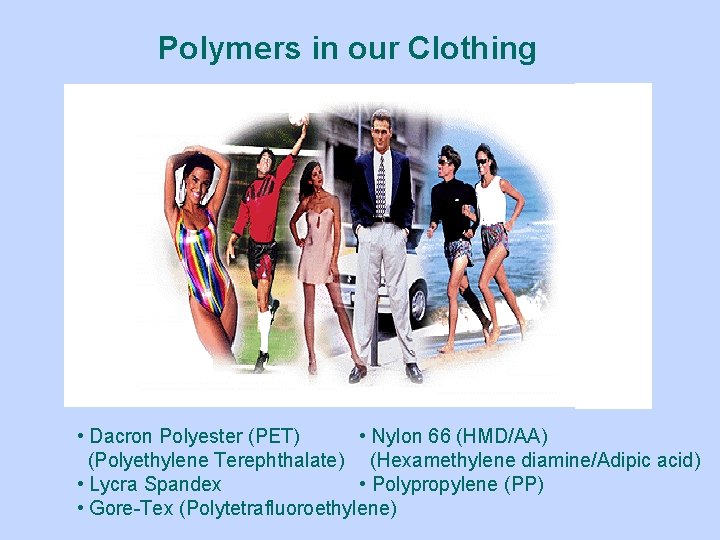
Polymers in our Clothing • Dacron Polyester (PET) • Nylon 66 (HMD/AA) (Polyethylene Terephthalate) (Hexamethylene diamine/Adipic acid) • Lycra Spandex • Polypropylene (PP) • Gore-Tex (Polytetrafluoroethylene)
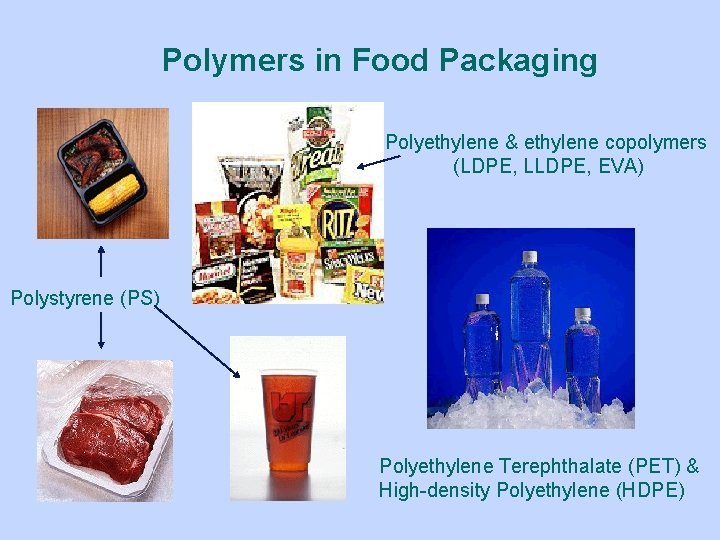
Polymers in Food Packaging Polyethylene & ethylene copolymers (LDPE, LLDPE, EVA) Polystyrene (PS) Polyethylene Terephthalate (PET) & High-density Polyethylene (HDPE)
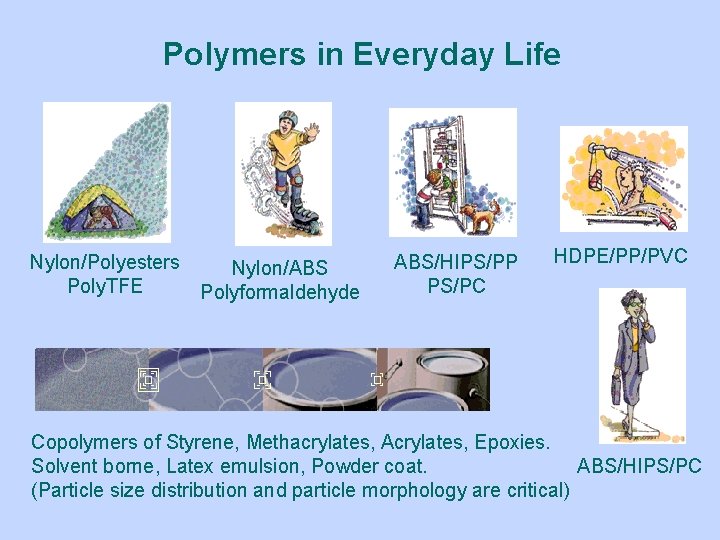
Polymers in Everyday Life Nylon/Polyesters Poly. TFE Nylon/ABS Polyformaldehyde ABS/HIPS/PP PS/PC HDPE/PP/PVC Copolymers of Styrene, Methacrylates, Acrylates, Epoxies. ABS/HIPS/PC Solvent borne, Latex emulsion, Powder coat. (Particle size distribution and particle morphology are critical)
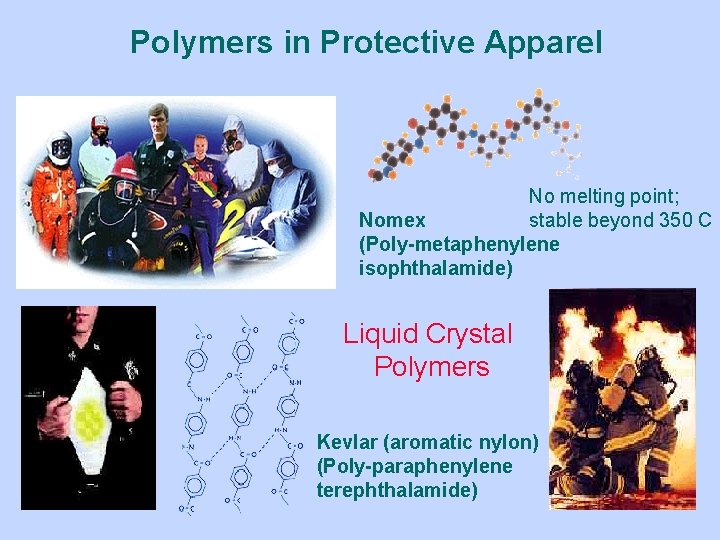
Polymers in Protective Apparel No melting point; Nomex stable beyond 350 C (Poly-metaphenylene isophthalamide) Liquid Crystal Polymers Kevlar (aromatic nylon) (Poly-paraphenylene terephthalamide)
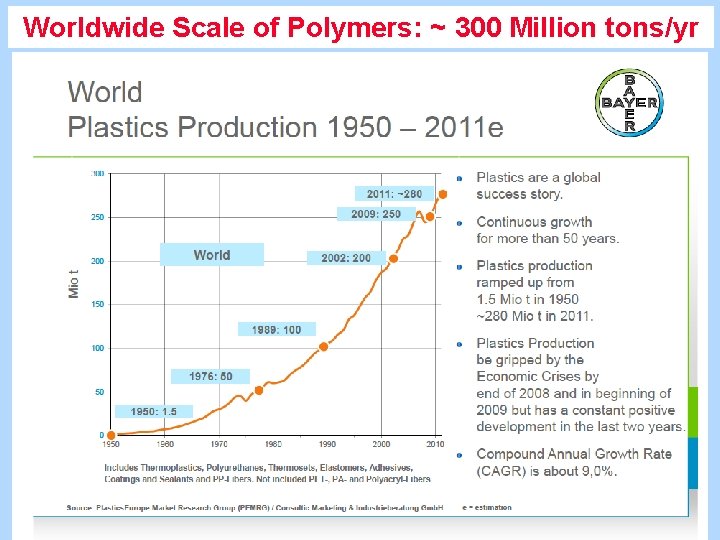
Worldwide Scale of Polymers: ~ 300 Million tons/yr
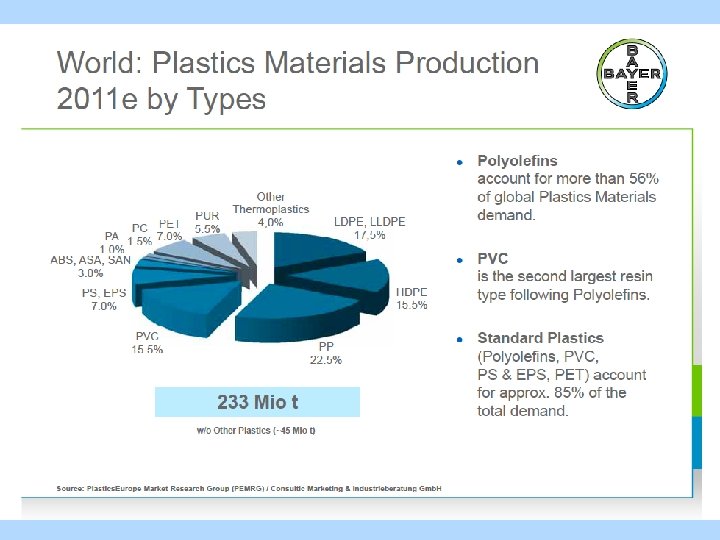
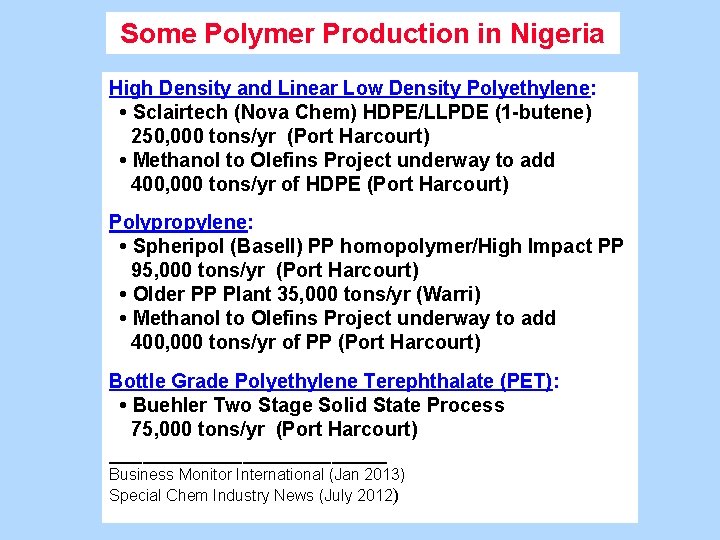
Some Polymer Production in Nigeria High Density and Linear Low Density Polyethylene: • Sclairtech (Nova Chem) HDPE/LLPDE (1 -butene) 250, 000 tons/yr (Port Harcourt) • Methanol to Olefins Project underway to add 400, 000 tons/yr of HDPE (Port Harcourt) Polypropylene: • Spheripol (Basell) PP homopolymer/High Impact PP 95, 000 tons/yr (Port Harcourt) • Older PP Plant 35, 000 tons/yr (Warri) • Methanol to Olefins Project underway to add 400, 000 tons/yr of PP (Port Harcourt) Bottle Grade Polyethylene Terephthalate (PET): • Buehler Two Stage Solid State Process 75, 000 tons/yr (Port Harcourt) _____________ Business Monitor International (Jan 2013) Special Chem Industry News (July 2012)
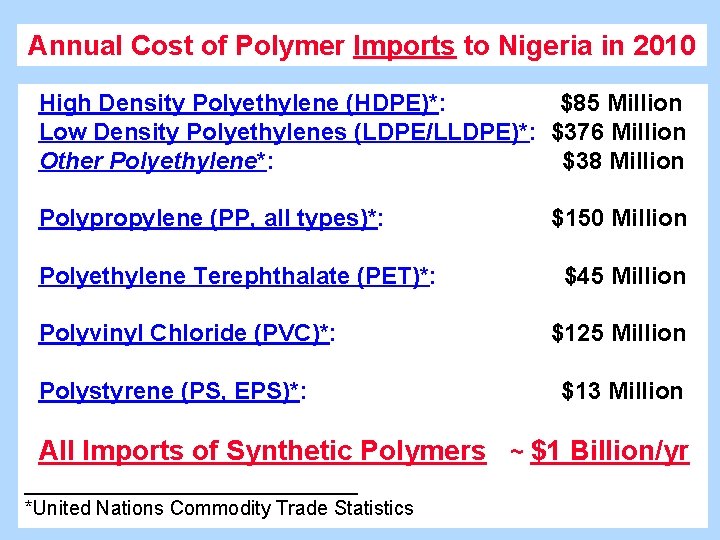
Annual Cost of Polymer Imports to Nigeria in 2010 High Density Polyethylene (HDPE)*: $85 Million Low Density Polyethylenes (LDPE/LLDPE)*: $376 Million Other Polyethylene*: $38 Million Polypropylene (PP, all types)*: $150 Million Polyethylene Terephthalate (PET)*: $45 Million Polyvinyl Chloride (PVC)*: $125 Million Polystyrene (PS, EPS)*: $13 Million All Imports of Synthetic Polymers ~ $1 Billion/yr _____________ *United Nations Commodity Trade Statistics
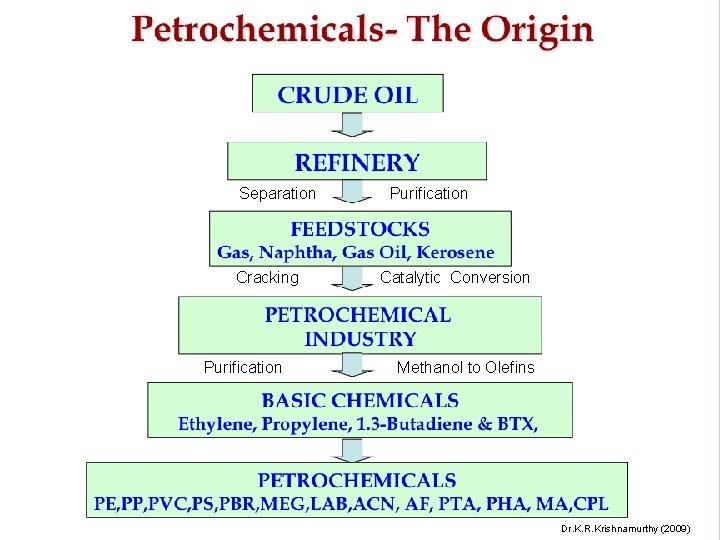
Separation Cracking Purification Catalytic Conversion Methanol to Olefins Dr. K. R. Krishnamurthy (2009)
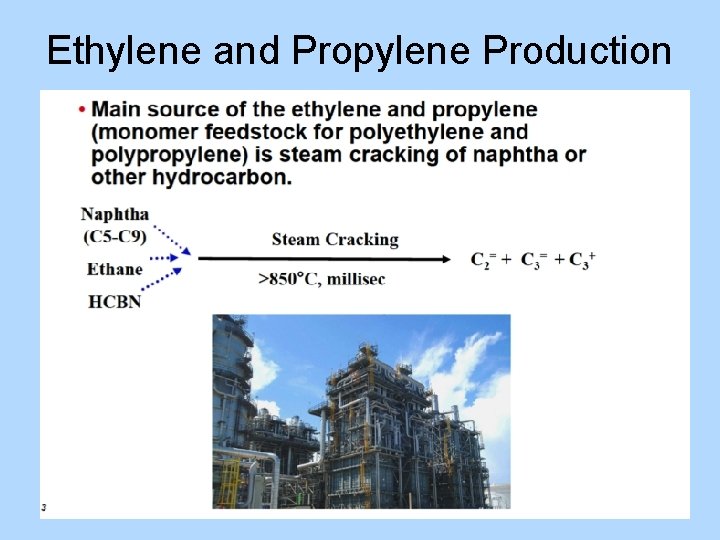
Ethylene and Propylene Production
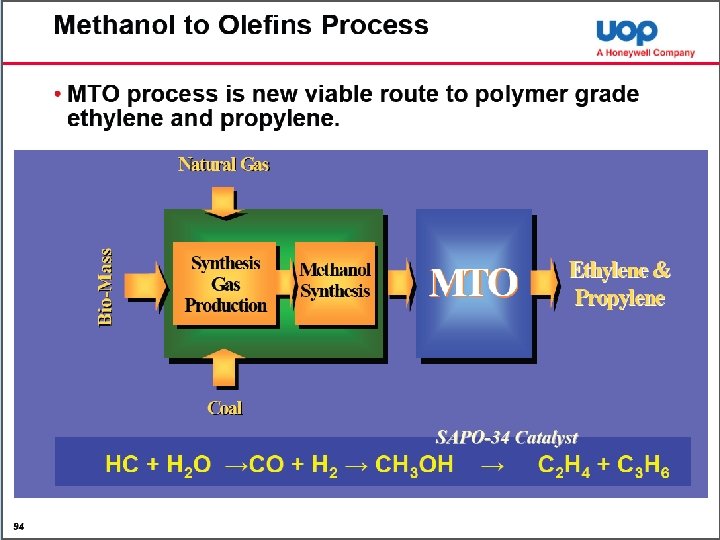
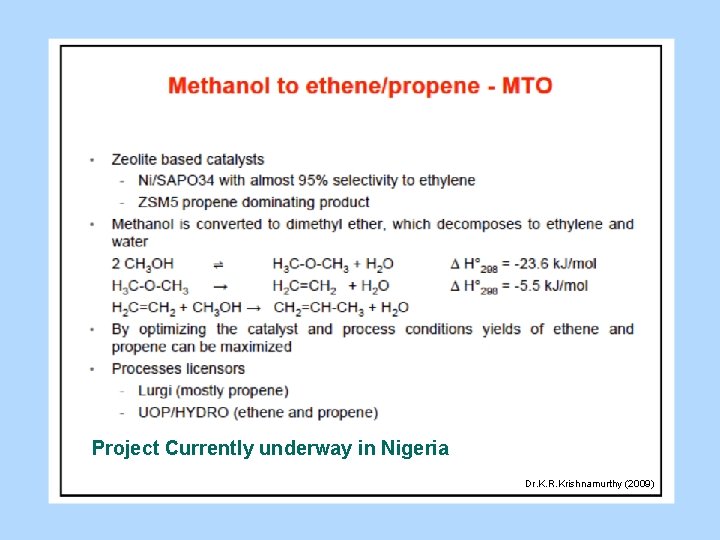
Project Currently underway in Nigeria Dr. K. R. Krishnamurthy (2009)
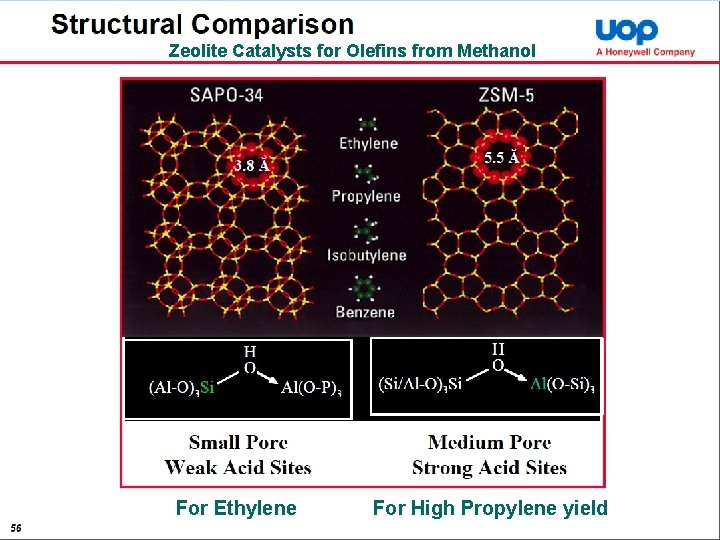
Zeolite Catalysts for Olefins from Methanol For Ethylene For High Propylene yield
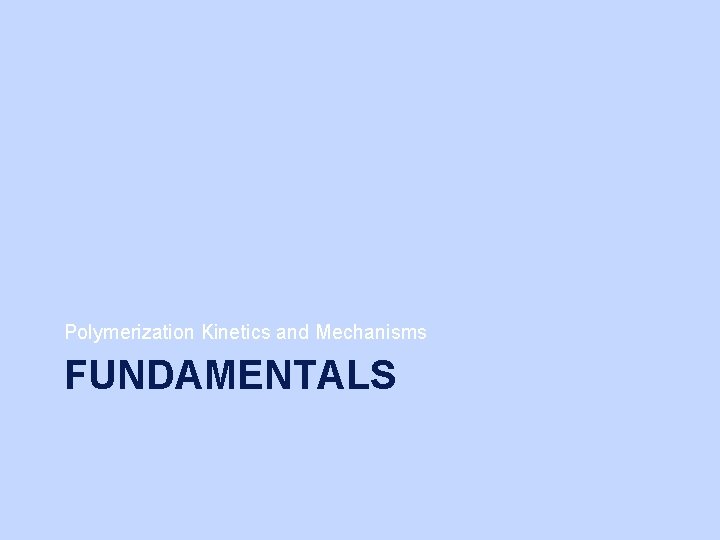
Polymerization Kinetics and Mechanisms FUNDAMENTALS
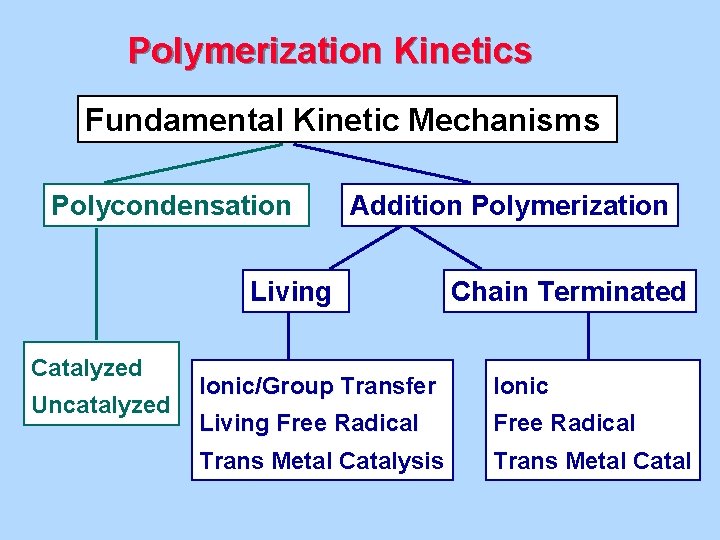
Polymerization Kinetics Fundamental Kinetic Mechanisms Polycondensation Addition Polymerization Living Catalyzed Uncatalyzed Chain Terminated Ionic/Group Transfer Ionic Living Free Radical Trans Metal Catalysis Trans Metal Catal
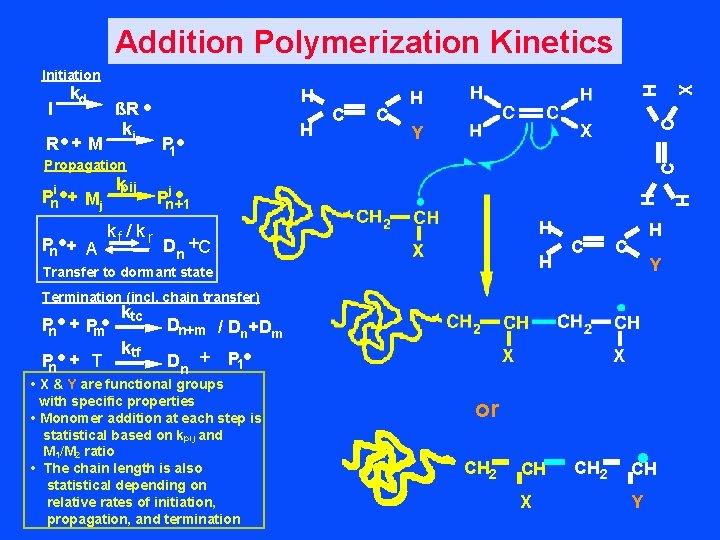
Addition Polymerization Kinetics Pni • + Mj kpij Pn • + A kf / k r C Y j • Pn+1 H Dn +C H Transfer to dormant state C H C Y Termination (incl. chain transfer) ktc Pn + Pm Dn+m / Dn+Dm • • Pn • + T k tf Dn + P 1 • • X & Y are functional groups with specific properties • Monomer addition at each step is statistical based on kpij and M 1/M 2 ratio • The chain length is also statistical depending on relative rates of initiation, propagation, and termination or CH 2 CH X CH 2 • CH Y X H Propagation H P 1 • C H C R • + M H C ßR • ki H I kd H Initiation
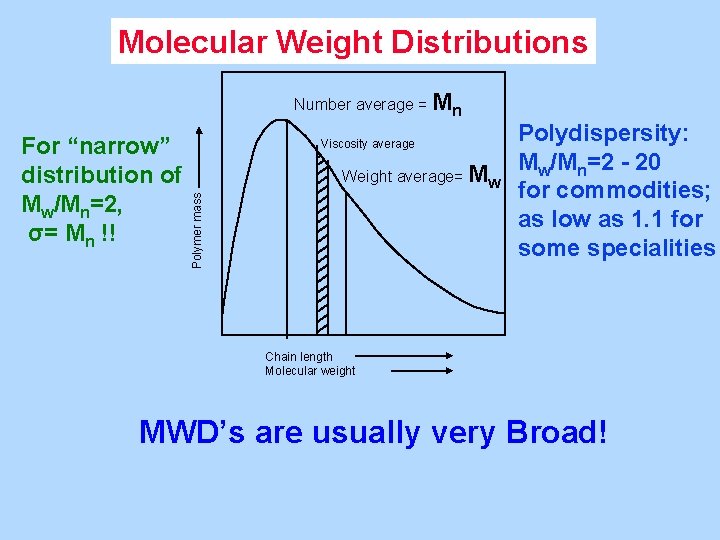
Molecular Weight Distributions Number average = Mn Viscosity average Weight average= Mw Polymer mass For “narrow” distribution of Mw/Mn=2, σ= Mn !! Polydispersity: Mw/Mn=2 - 20 for commodities; as low as 1. 1 for some specialities Chain length Molecular weight MWD’s are usually very Broad!
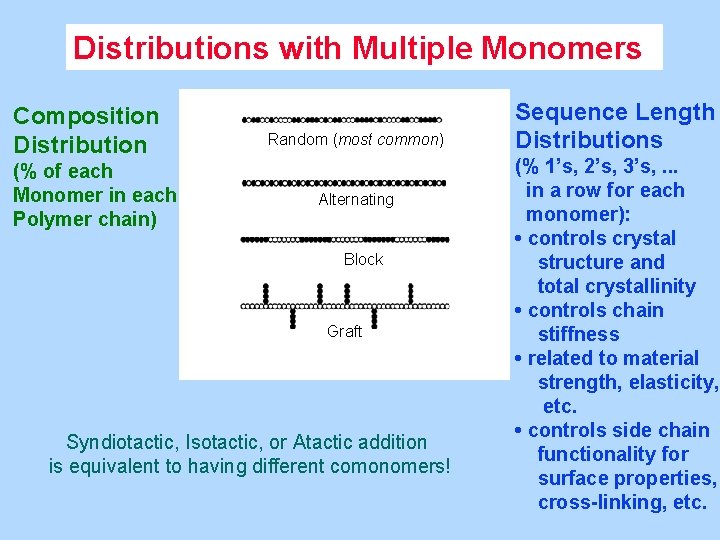
Distributions with Multiple Monomers Composition Distribution (% of each Monomer in each Polymer chain) Random (most common) Alternating Block Graft Syndiotactic, Isotactic, or Atactic addition is equivalent to having different comonomers! Sequence Length Distributions (% 1’s, 2’s, 3’s, . . . in a row for each monomer): • controls crystal structure and total crystallinity • controls chain stiffness • related to material strength, elasticity, etc. • controls side chain functionality for surface properties, cross-linking, etc.

Key to control of Polyethylene properties --> Branching Ethylene Unbranched Polyethylene (rare) Short-chain Branched PE Short and Long-chain Branched PE LDPE HDPE & LLDPE • For high pressure LDPE, short and long-chain branches are formed naturally and are controlled by reaction conditions (temperature and pressure). • For HDPE and LLDPE, short-chain branches are formed by copolymerization with α-olefins such as butene, hexene, or octene. No long-chain branching occurs except with special catalysts allowing polymer chains to be inserted.
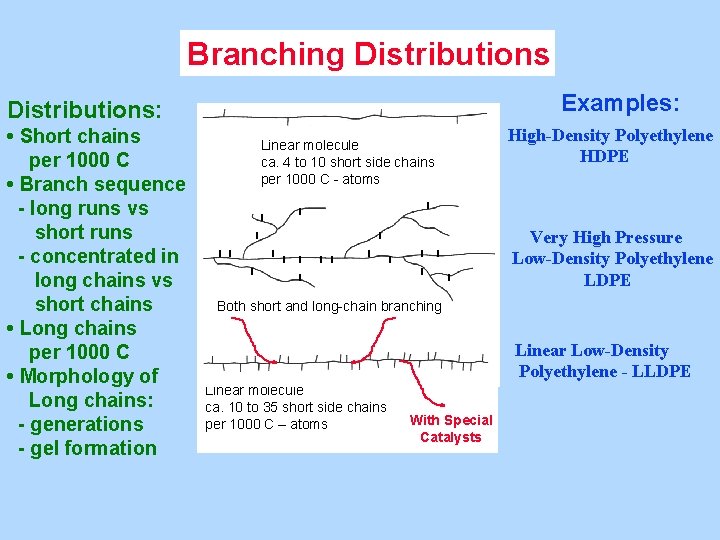
Branching Distributions Examples: Distributions: • Short chains per 1000 C • Branch sequence - long runs vs short runs - concentrated in long chains vs short chains • Long chains per 1000 C • Morphology of Long chains: - generations - gel formation Linear molecule ca. 4 to 10 short side chains per 1000 C - atoms High-Density Polyethylene HDPE Very High Pressure Low-Density Polyethylene LDPE Both short and long-chain branching Linear Low-Density Polyethylene - LLDPE Linear molecule ca. 10 to 35 short side chains per 1000 C – atoms With Special Catalysts
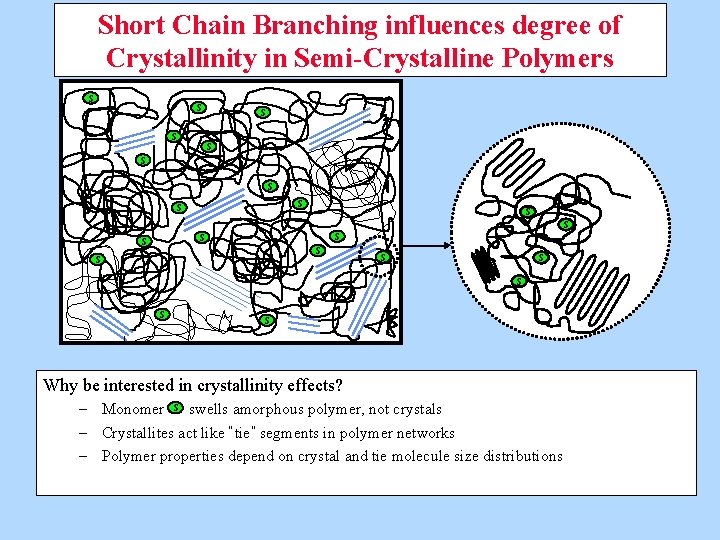
Short Chain Branching influences degree of Crystallinity in Semi-Crystalline Polymers S S S S S S Why be interested in crystallinity effects? – Monomer S swells amorphous polymer, not crystals – Crystallites act like “tie” segments in polymer networks – Polymer properties depend on crystal and tie molecule size distributions
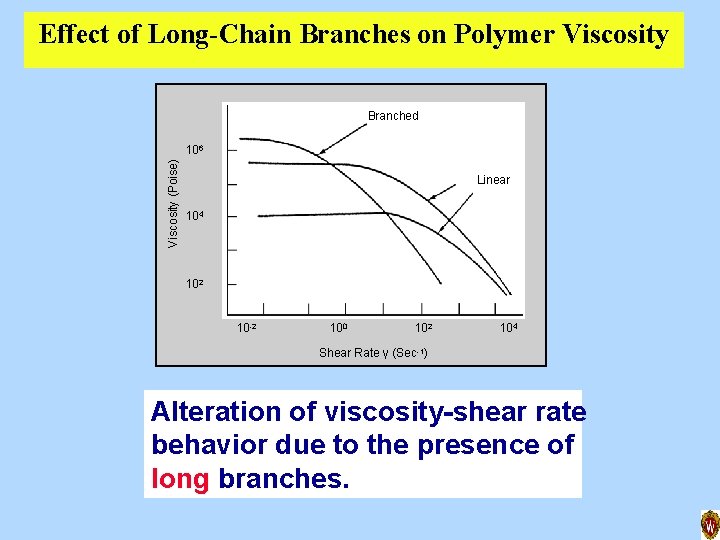
Effect of Long-Chain Branches on Polymer Viscosity Branched Viscosity (Poise) 106 Linear 104 102 10 -2 100 102 104 Shear Rate γ (Sec-1) Alteration of viscosity-shear rate behavior due to the presence of long branches.
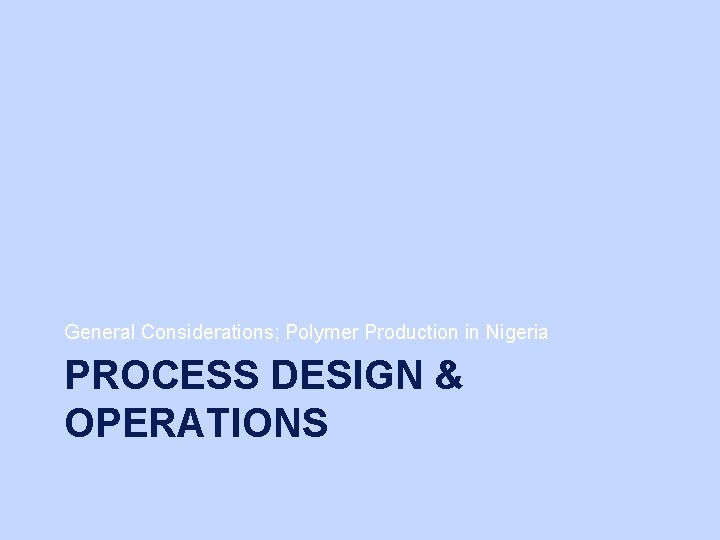
General Considerations; Polymer Production in Nigeria PROCESS DESIGN & OPERATIONS
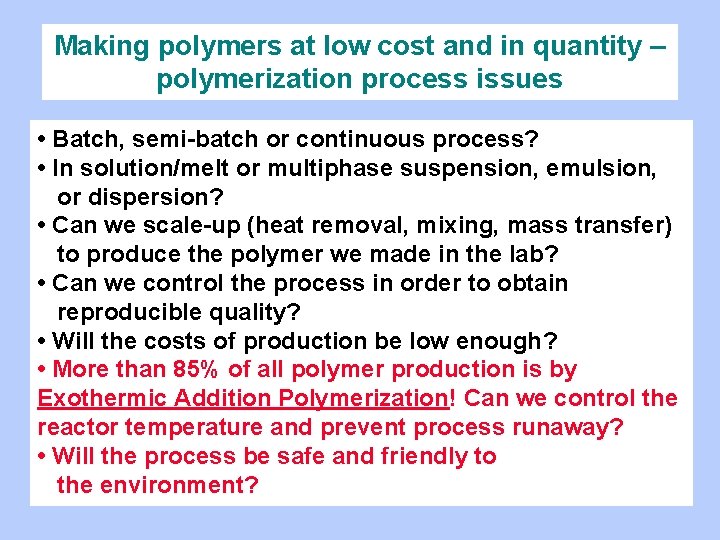
Making polymers at low cost and in quantity – polymerization process issues • Batch, semi-batch or continuous process? • In solution/melt or multiphase suspension, emulsion, or dispersion? • Can we scale-up (heat removal, mixing, mass transfer) to produce the polymer we made in the lab? • Can we control the process in order to obtain reproducible quality? • Will the costs of production be low enough? • More than 85% of all polymer production is by Exothermic Addition Polymerization! Can we control the reactor temperature and prevent process runaway? • Will the process be safe and friendly to the environment?
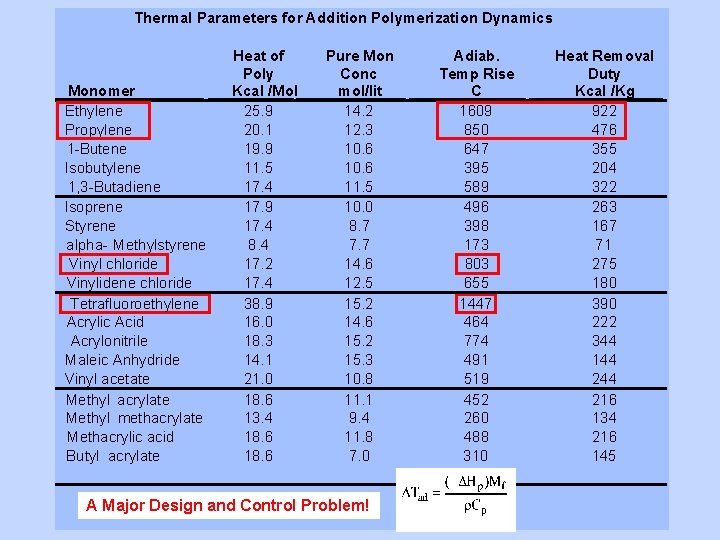
Thermal Parameters for Addition Polymerization Dynamics Monomer Ethylene Propylene 1 -Butene Isobutylene 1, 3 -Butadiene Isoprene Styrene alpha- Methylstyrene Vinyl chloride Vinylidene chloride Tetrafluoroethylene Acrylic Acid Acrylonitrile Maleic Anhydride Vinyl acetate Methyl acrylate Methyl methacrylate Methacrylic acid Butyl acrylate Heat of Poly Kcal /Mol 25. 9 20. 1 19. 9 11. 5 17. 4 17. 9 17. 4 8. 4 17. 2 17. 4 38. 9 16. 0 18. 3 14. 1 21. 0 18. 6 13. 4 18. 6 Pure Mon Conc mol/lit 14. 2 12. 3 10. 6 11. 5 10. 0 8. 7 7. 7 14. 6 12. 5 15. 2 14. 6 15. 2 15. 3 10. 8 11. 1 9. 4 11. 8 7. 0 A Major Design and Control Problem! Adiab. Temp Rise C 1609 850 647 395 589 496 398 173 803 655 1447 464 774 491 519 452 260 488 310 Heat Removal Duty Kcal /Kg 922 476 355 204 322 263 167 71 275 180 390 222 344 144 216 134 216 145
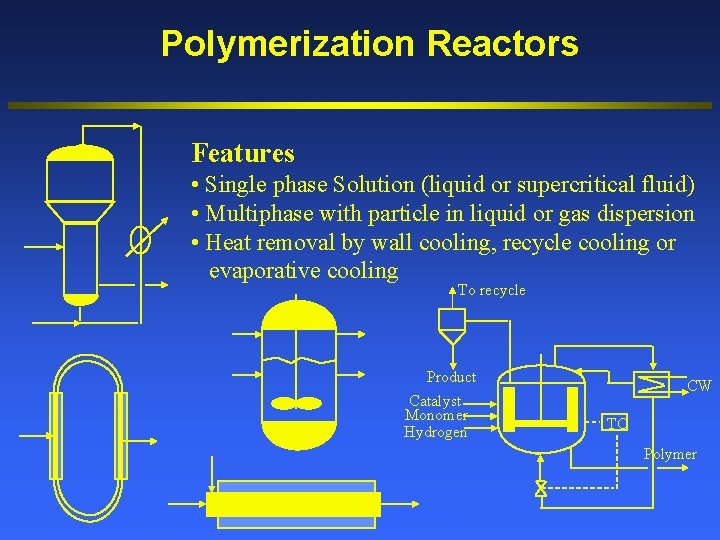
Polymerization Reactors Features • Single phase Solution (liquid or supercritical fluid) • Multiphase with particle in liquid or gas dispersion • Heat removal by wall cooling, recycle cooling or evaporative cooling To recycle Product Catalyst Monomer Hydrogen CW TC Polymer
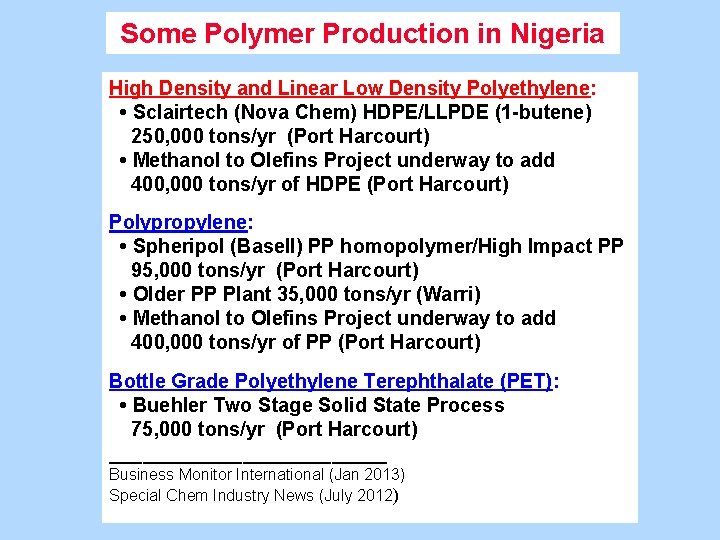
Some Polymer Production in Nigeria High Density and Linear Low Density Polyethylene: • Sclairtech (Nova Chem) HDPE/LLPDE (1 -butene) 250, 000 tons/yr (Port Harcourt) • Methanol to Olefins Project underway to add 400, 000 tons/yr of HDPE (Port Harcourt) Polypropylene: • Spheripol (Basell) PP homopolymer/High Impact PP 95, 000 tons/yr (Port Harcourt) • Older PP Plant 35, 000 tons/yr (Warri) • Methanol to Olefins Project underway to add 400, 000 tons/yr of PP (Port Harcourt) Bottle Grade Polyethylene Terephthalate (PET): • Buehler Two Stage Solid State Process 75, 000 tons/yr (Port Harcourt) _____________ Business Monitor International (Jan 2013) Special Chem Industry News (July 2012)
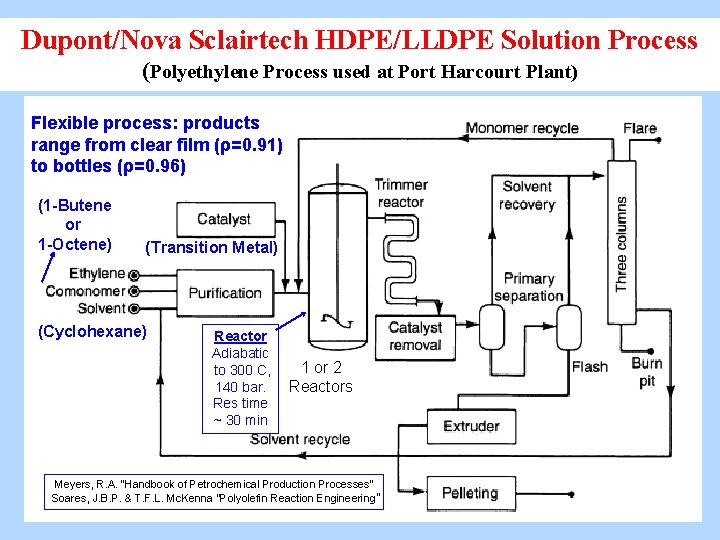
Dupont/Nova Sclairtech HDPE/LLDPE Solution Process (Polyethylene Process used at Port Harcourt Plant) Flexible process: products range from clear film (ρ=0. 91) to bottles (ρ=0. 96) (1 -Butene or 1 -Octene) (Transition Metal) (Cyclohexane) Reactor Adiabatic to 300 C, 140 bar. Res time ~ 30 min 1 or 2 Reactors Meyers, R. A. “Handbook of Petrochemical Production Processes” Soares, J. B. P. & T. F. L. Mc. Kenna “Polyolefin Reaction Engineering”
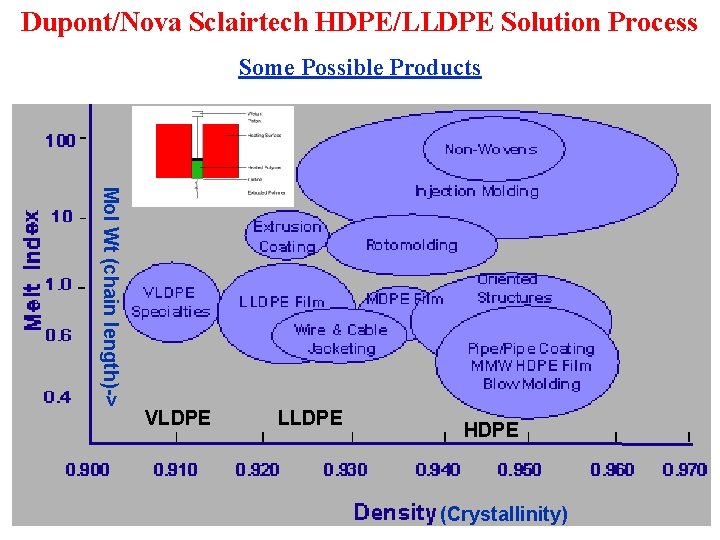
Dupont/Nova Sclairtech HDPE/LLDPE Solution Process Some Possible Products Mol Wt (chain length)-> VLDPE LLDPE HDPE (Crystallinity)
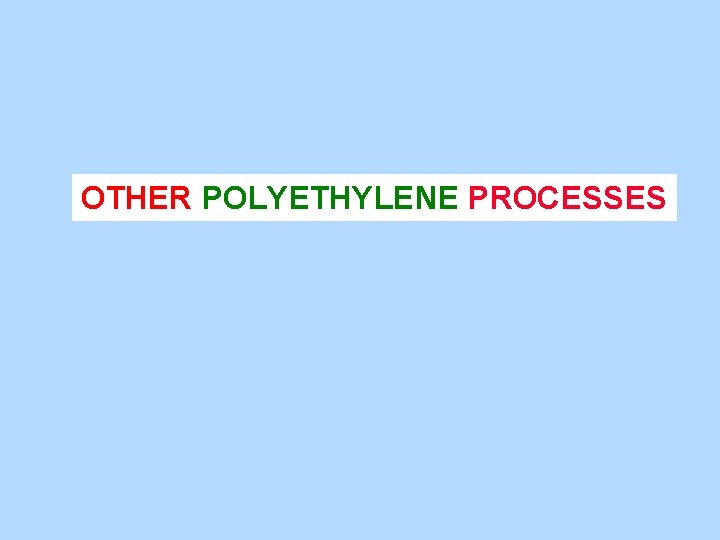
OTHER POLYETHYLENE PROCESSES
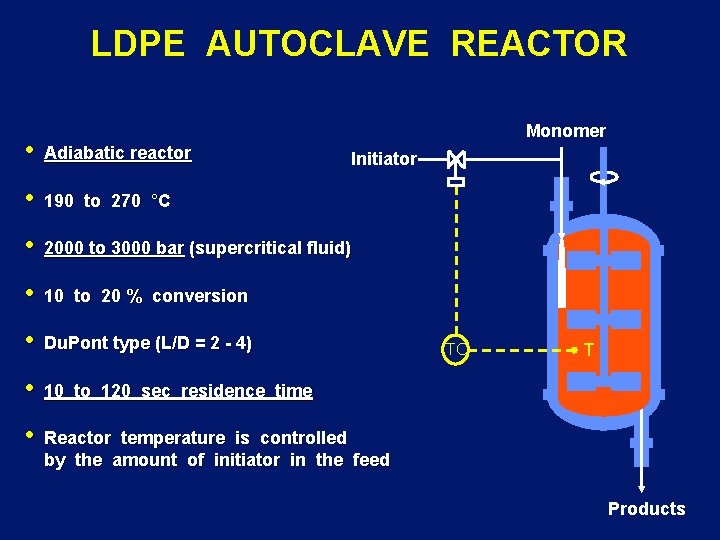
LDPE AUTOCLAVE REACTOR • Monomer Adiabatic reactor Initiator • 190 to 270 °C • 2000 to 3000 bar (supercritical fluid) • 10 to 20 % conversion • Du. Pont type (L/D = 2 - 4) TC T • 10 to 120 sec residence time • Reactor temperature is controlled by the amount of initiator in the feed Products
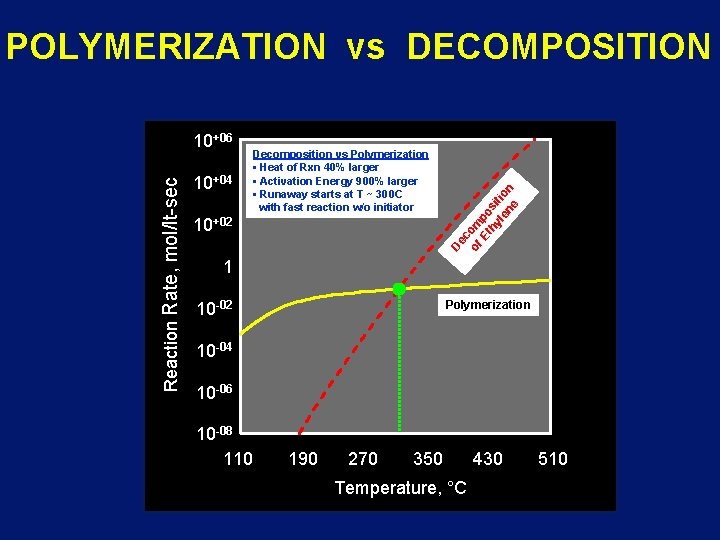
Reaction Rate, mol/lt-sec 10+06 10+04 Decomposition vs Polymerization • Heat of Rxn 40% larger • Activation Energy 900% larger • Runaway starts at T ~ 300 C with fast reaction w/o initiator 10+02 De c o om f E p th os yl iti en on e POLYMERIZATION vs DECOMPOSITION 1 Polymerization 10 -02 10 -04 10 -06 10 -08 110 190 270 350 Temperature, °C 430 510
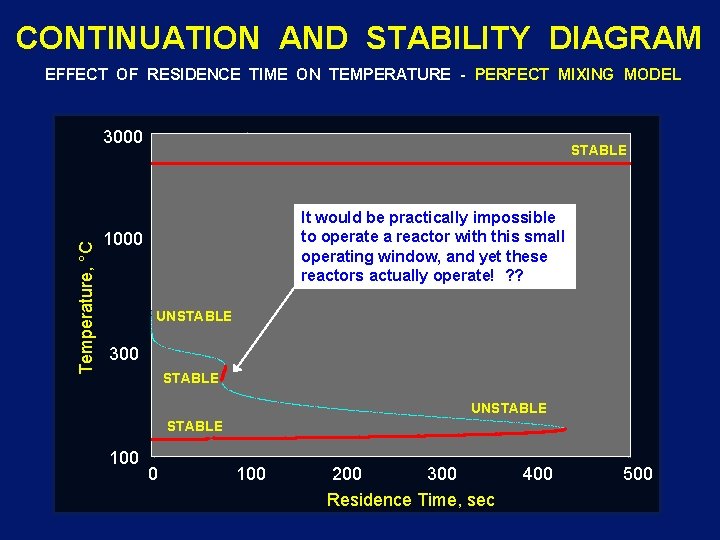
CONTINUATION AND STABILITY DIAGRAM EFFECT OF RESIDENCE TIME ON TEMPERATURE - PERFECT MIXING MODEL Temperature, °C 3000 STABLE It would be practically impossible to operate a reactor with this small operating window, and yet these reactors actually operate! ? ? 1000 UNSTABLE 300 STABLE UNSTABLE 100 0 100 200 300 Residence Time, sec 400 500
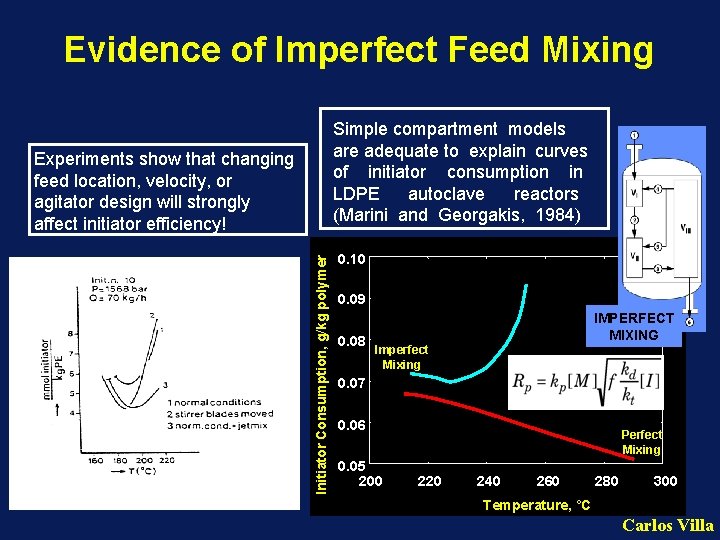
Evidence of Imperfect Feed Mixing Simple compartment models are adequate to explain curves of initiator consumption in LDPE autoclave reactors (Marini and Georgakis, 1984) van der Molen et al. (1982) Initiator Consumption, g/kg polymer Experiments show that changing feed location, velocity, or agitator design will strongly affect initiator efficiency! 0. 10 0. 09 0. 08 IMPERFECT MIXING Imperfect Mixing 0. 07 0. 06 0. 05 200 Perfect Mixing 220 240 260 280 300 Temperature, °C Carlos Villa
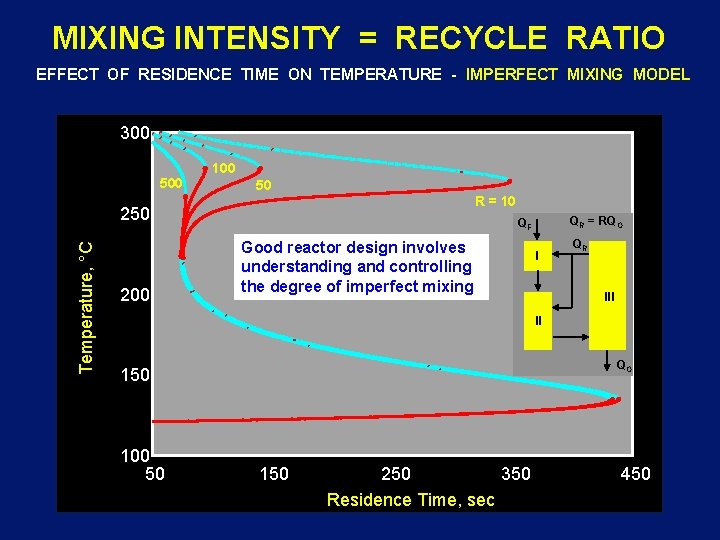
MIXING INTENSITY = RECYCLE RATIO EFFECT OF RESIDENCE TIME ON TEMPERATURE - IMPERFECT MIXING MODEL 300 500 100 50 R = 10 Temperature, °C 250 200 QR = RQO QF Good reactor design involves understanding and controlling the degree of imperfect mixing I Q R III II QO 150 100 50 150 250 350 Residence Time, sec 450
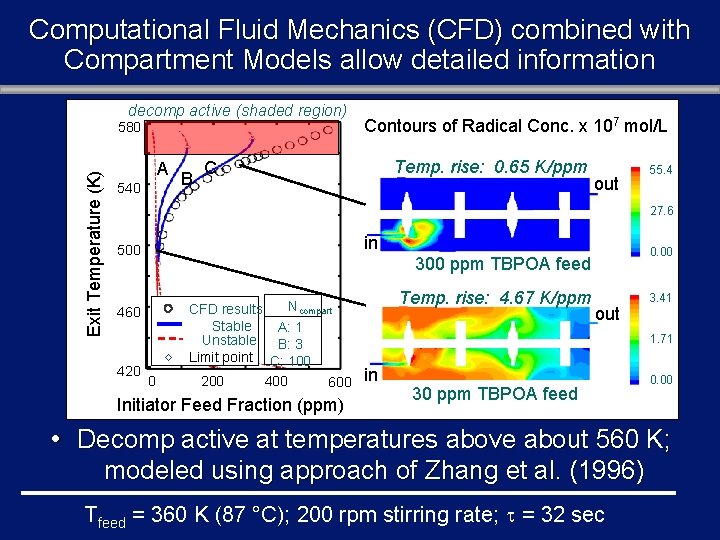
Computational Fluid Mechanics (CFD) combined with Compartment Models allow detailed information decomp active (shaded region) Exit Temperature (K) 580 A 540 B Contours of Radical Conc. x 107 mol/L Temp. rise: 0. 65 K/ppm C out 55. 4 27. 6 in 500 300 ppm TBPOA feed 460 420 0. 00 0 Ncompart CFD results Stable A: 1 Unstable B: 3 Limit point C: 100 400 200 600 Initiator Feed Fraction (ppm) Temp. rise: 4. 67 K/ppm out 3. 41 1. 71 in 30 ppm TBPOA feed 0. 00 • Decomp active at temperatures above about 560 K; modeled using approach of Zhang et al. (1996) Tfeed = 360 K (87 °C); 200 rpm stirring rate; t = 32 sec
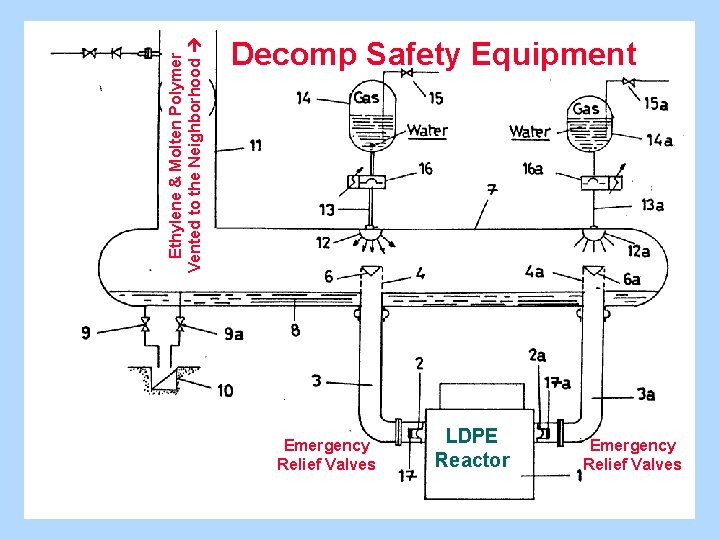
Ethylene & Molten Polymer Vented to the Neighborhood Decomp Safety Equipment Title Emergency Relief Valves LDPE Reactor Emergency Relief Valves
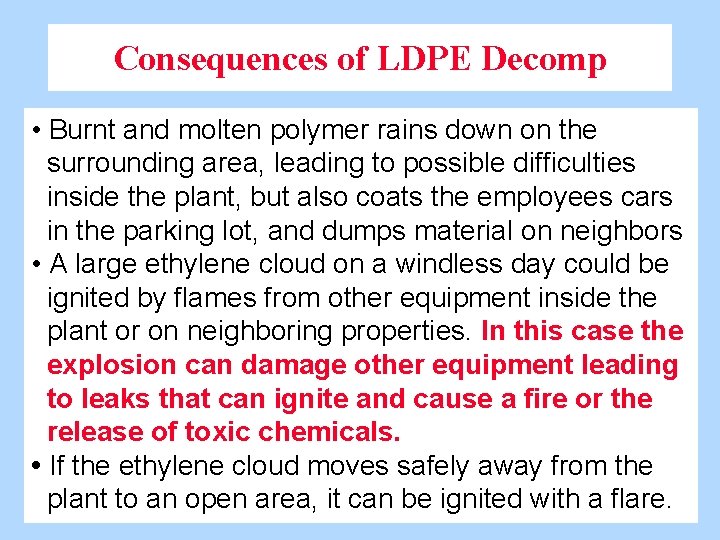
Consequences of LDPE Decomp • Burnt and molten polymer rains down on the surrounding area, leading to possible difficulties inside the plant, but also coats the employees cars in the parking lot, and dumps material on neighbors • A large ethylene cloud on a windless day could be ignited by flames from other equipment inside the plant or on neighboring properties. In this case the explosion can damage other equipment leading to leaks that can ignite and cause a fire or the release of toxic chemicals. • If the ethylene cloud moves safely away from the plant to an open area, it can be ignited with a flare.
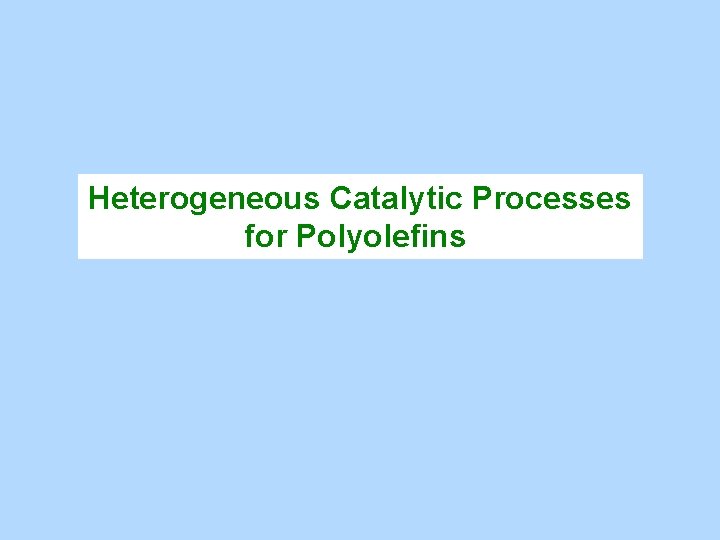
Heterogeneous Catalytic Processes for Polyolefins
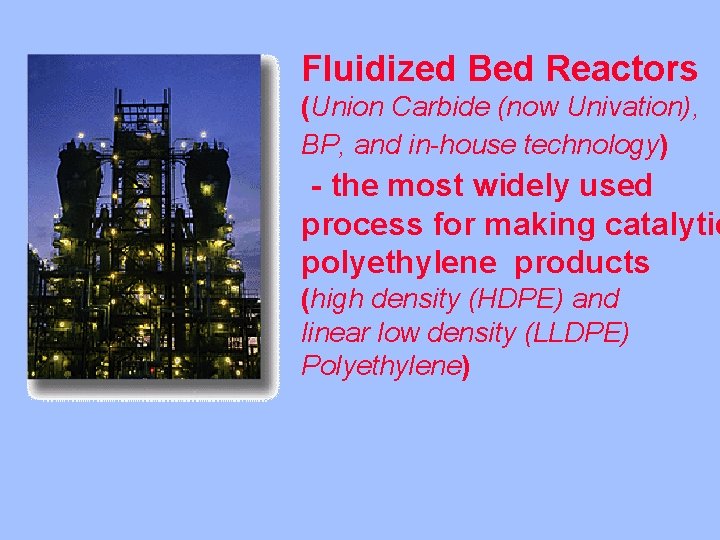
Fluidized Bed Reactors (Union Carbide (now Univation), BP, and in-house technology) - the most widely used process for making catalytic polyethylene products (high density (HDPE) and linear low density (LLDPE) Polyethylene)
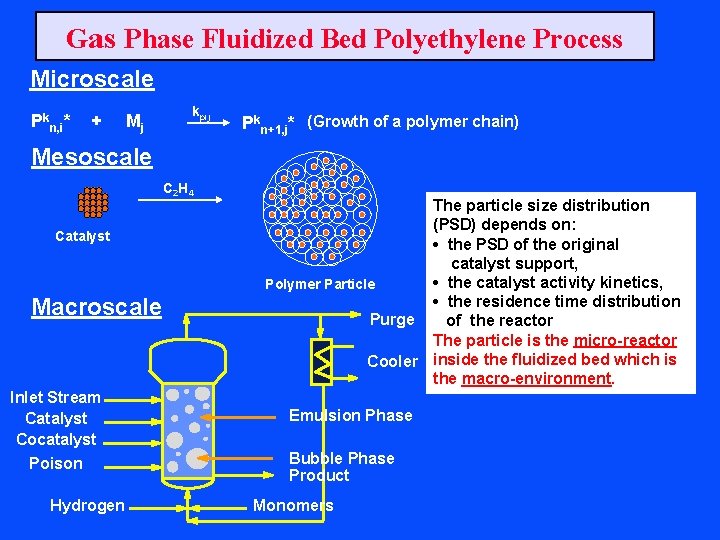
Gas Phase Fluidized Bed Polyethylene Process Microscale Pkn, i* + Mj kpij Pkn+1, j* (Growth of a polymer chain) Mesoscale C 2 H 4 Catalyst Macroscale Inlet Stream Catalyst Cocatalyst Poison Hydrogen The particle size distribution (PSD) depends on: • the PSD of the original catalyst support, • the catalyst activity kinetics, Polymer Particle • the residence time distribution Purge of the reactor The particle is the micro-reactor Cooler inside the fluidized bed which is the macro-environment. Emulsion Phase Bubble Phase Product Monomers
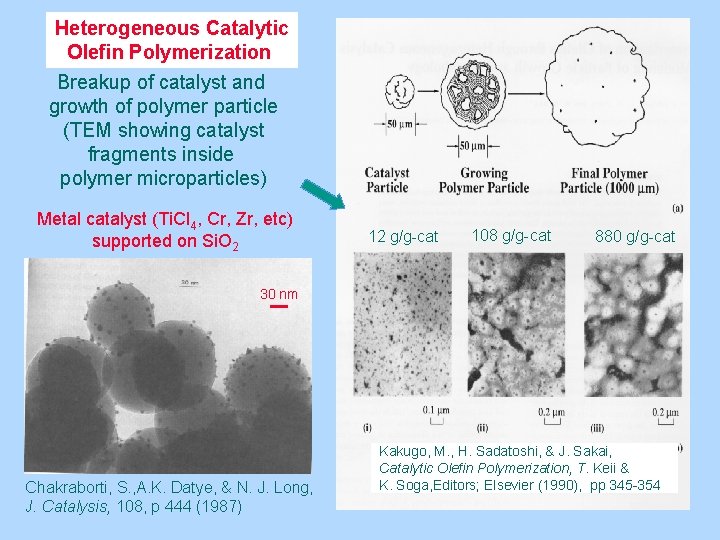
Heterogeneous Catalytic Olefin Polymerization Breakup of catalyst and growth of polymer particle (TEM showing catalyst fragments inside polymer microparticles) Metal catalyst (Ti. Cl 4, Cr, Zr, etc) supported on Si. O 2 12 g/g-cat 108 g/g-cat 880 g/g-cat 30 nm Chakraborti, S. , A. K. Datye, & N. J. Long, J. Catalysis, 108, p 444 (1987) Kakugo, M. , H. Sadatoshi, & J. Sakai, Catalytic Olefin Polymerization, T. Keii & K. Soga, Editors; Elsevier (1990), pp 345 -354
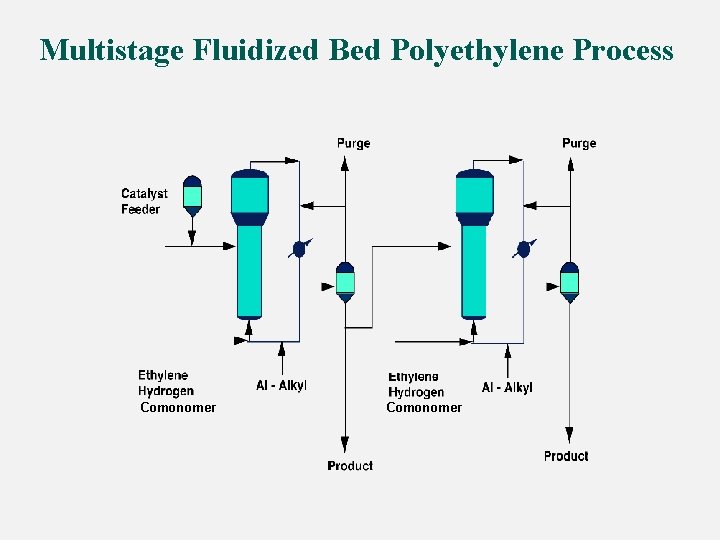
Multistage Fluidized Bed Polyethylene Process Comonomer
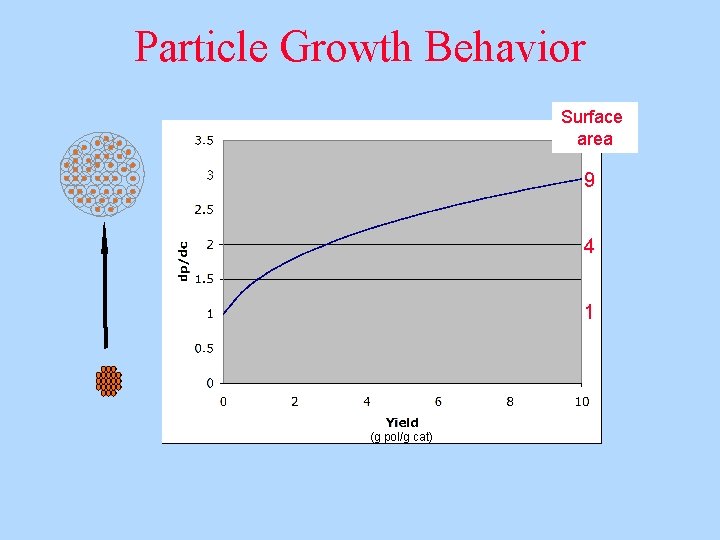
Particle Growth Behavior Surface area 9 4 1 (g pol/g cat)
![Fluidized Bed Particle Temperatures Temperature difference DT C Melted Quasisteady state particle temperature fully Fluidized Bed Particle Temperatures Temperature difference DT [C] Melted Quasi-steady state particle temperature, fully](https://slidetodoc.com/presentation_image/529806be0ef6f944551970577fc32074/image-50.jpg)
Fluidized Bed Particle Temperatures Temperature difference DT [C] Melted Quasi-steady state particle temperature, fully activated Direct injection, fast activation Dynamic particle temperature 15 C temp rise Prepolymerization or slow activation dpmin dcat Particle diameter d. P [mm] Sticky particles adhere to the reactor wall and attract more particles. After some buildup, the polymer sheets on the wall fall down and disrupt the fluidization, causing the entire polymer bed to melt.
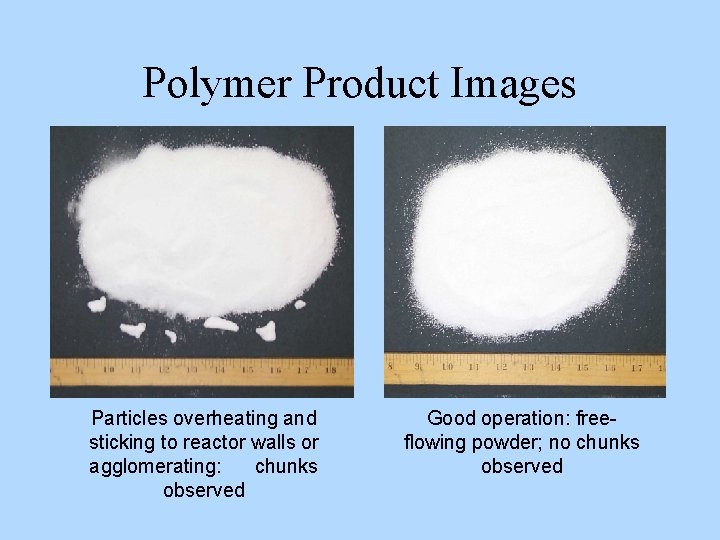
Polymer Product Images Particles overheating and sticking to reactor walls or agglomerating: chunks observed Good operation: freeflowing powder; no chunks observed
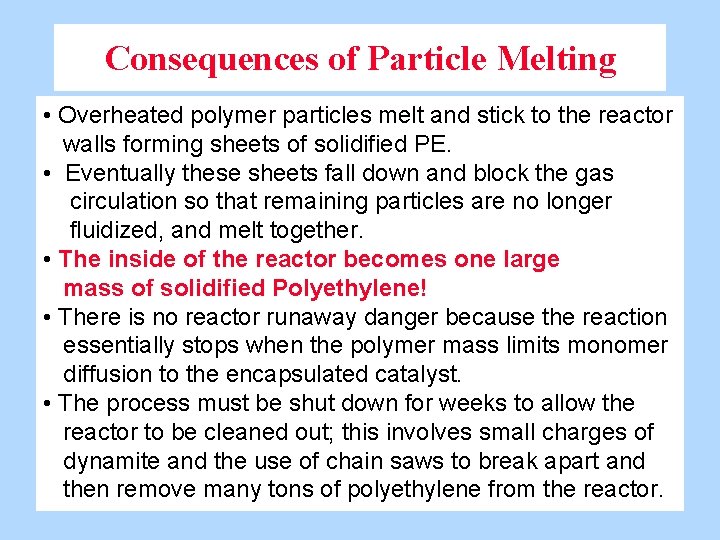
Consequences of Particle Melting • Overheated polymer particles melt and stick to the reactor walls forming sheets of solidified PE. • Eventually these sheets fall down and block the gas circulation so that remaining particles are no longer fluidized, and melt together. • The inside of the reactor becomes one large mass of solidified Polyethylene! • There is no reactor runaway danger because the reaction essentially stops when the polymer mass limits monomer diffusion to the encapsulated catalyst. • The process must be shut down for weeks to allow the reactor to be cleaned out; this involves small charges of dynamite and the use of chain saws to break apart and then remove many tons of polyethylene from the reactor.
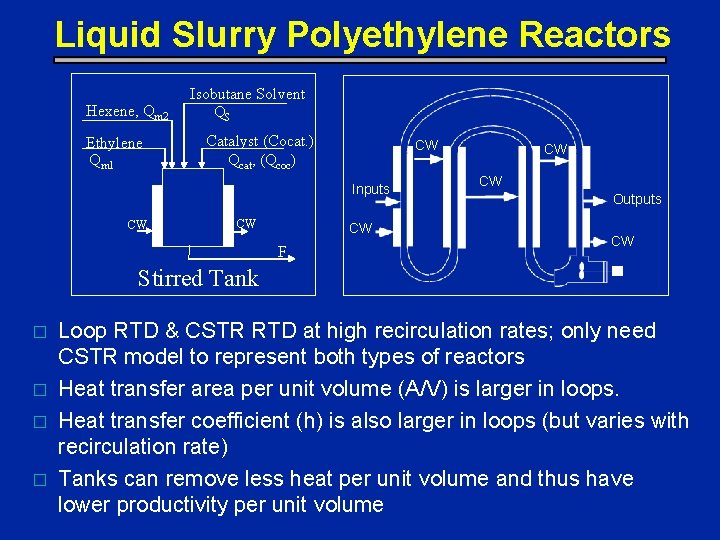
Liquid Slurry Polyethylene Reactors Hexene, Qm 2 Ethylene Qm 1 Isobutane Solvent QS Catalyst (Cocat. ) Qcat, (Qcoc) CW Inputs CW CW CW F CW CW Outputs CW Stirred Tank � � Loop RTD & CSTR RTD at high recirculation rates; only need CSTR model to represent both types of reactors Heat transfer area per unit volume (A/V) is larger in loops. Heat transfer coefficient (h) is also larger in loops (but varies with recirculation rate) Tanks can remove less heat per unit volume and thus have lower productivity per unit volume
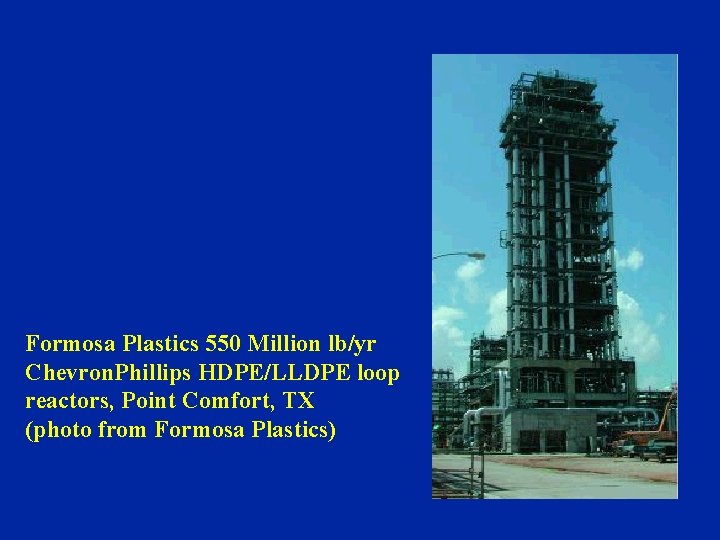
Formosa Plastics 550 Million lb/yr Chevron. Phillips HDPE/LLDPE loop reactors, Point Comfort, TX (photo from Formosa Plastics)
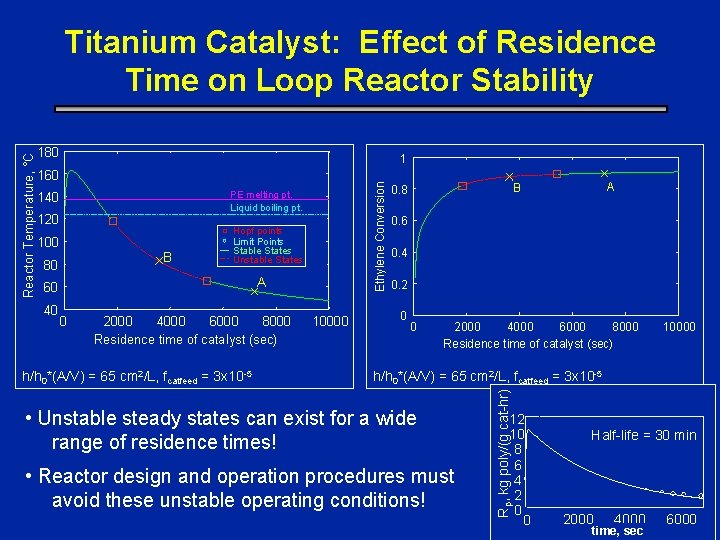
180 1 PE melting pt. Liquid boiling pt. 140 120 100 B 80 Hopf points Limit Points Stable States Unstable States A 60 40 0 2000 4000 6000 8000 Residence time of catalyst (sec) h/h 0*(A/V) = 65 cm 2/L, fcatfeed = 3 x 10 -5 10000 A B 0. 8 0. 6 0. 4 0. 2 0 0 2000 4000 6000 8000 Residence time of catalyst (sec) 10000 h/h 0*(A/V) = 65 cm 2/L, fcatfeed = 3 x 10 -5 • Unstable steady states can exist for a wide range of residence times! • Reactor design and operation procedures must avoid these unstable operating conditions! Rp, kg poly/(g cat-hr) 160 Ethylene Conversion Reactor Temperature, °C Titanium Catalyst: Effect of Residence Time on Loop Reactor Stability 12 10 8 6 4 2 0 0 Half-life = 30 min 2000 4000 time, sec 6000
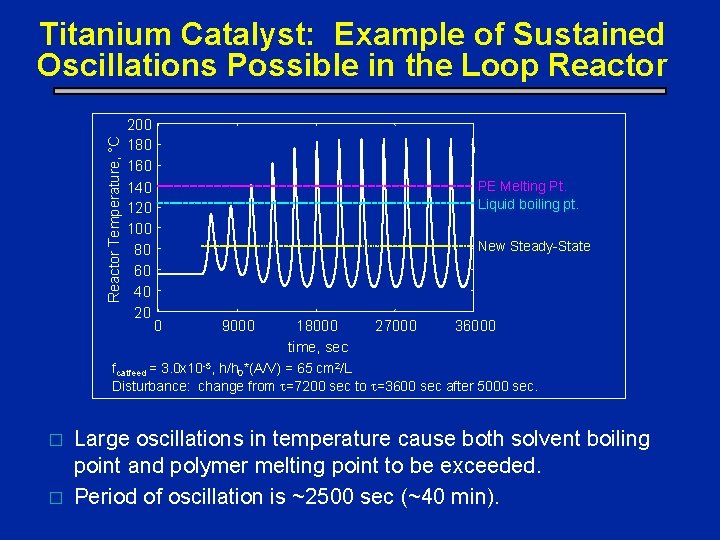
Reactor Temperature, °C Titanium Catalyst: Example of Sustained Oscillations Possible in the Loop Reactor 200 180 160 140 120 100 80 60 40 20 PE Melting Pt. Liquid boiling pt. New Steady-State 0 9000 18000 time, sec 27000 36000 fcatfeed = 3. 0 x 10 -5, h/h 0*(A/V) = 65 cm 2/L Disturbance: change from t=7200 sec to t=3600 sec after 5000 sec. � � Large oscillations in temperature cause both solvent boiling point and polymer melting point to be exceeded. Period of oscillation is ~2500 sec (~40 min).
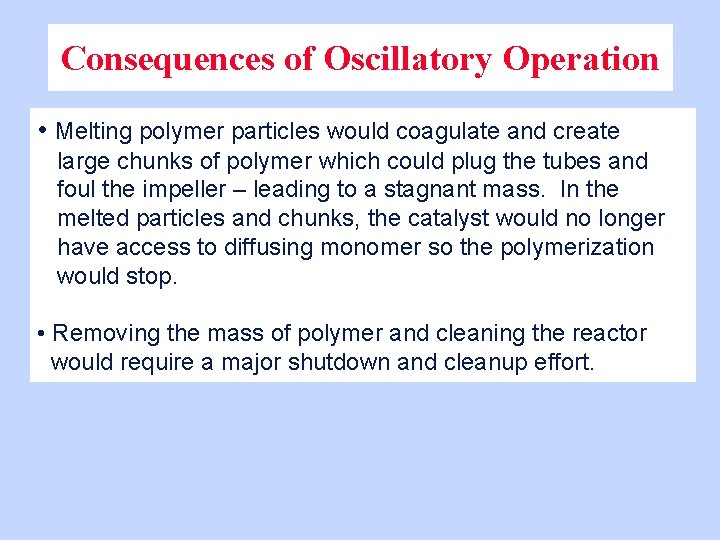
Consequences of Oscillatory Operation • Melting polymer particles would coagulate and create large chunks of polymer which could plug the tubes and foul the impeller – leading to a stagnant mass. In the melted particles and chunks, the catalyst would no longer have access to diffusing monomer so the polymerization would stop. • Removing the mass of polymer and cleaning the reactor would require a major shutdown and cleanup effort.
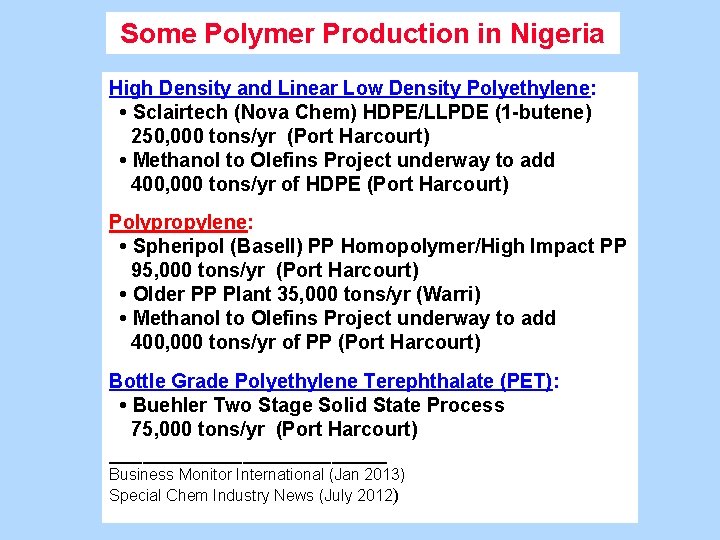
Some Polymer Production in Nigeria High Density and Linear Low Density Polyethylene: • Sclairtech (Nova Chem) HDPE/LLPDE (1 -butene) 250, 000 tons/yr (Port Harcourt) • Methanol to Olefins Project underway to add 400, 000 tons/yr of HDPE (Port Harcourt) Polypropylene: • Spheripol (Basell) PP Homopolymer/High Impact PP 95, 000 tons/yr (Port Harcourt) • Older PP Plant 35, 000 tons/yr (Warri) • Methanol to Olefins Project underway to add 400, 000 tons/yr of PP (Port Harcourt) Bottle Grade Polyethylene Terephthalate (PET): • Buehler Two Stage Solid State Process 75, 000 tons/yr (Port Harcourt) _____________ Business Monitor International (Jan 2013) Special Chem Industry News (July 2012)
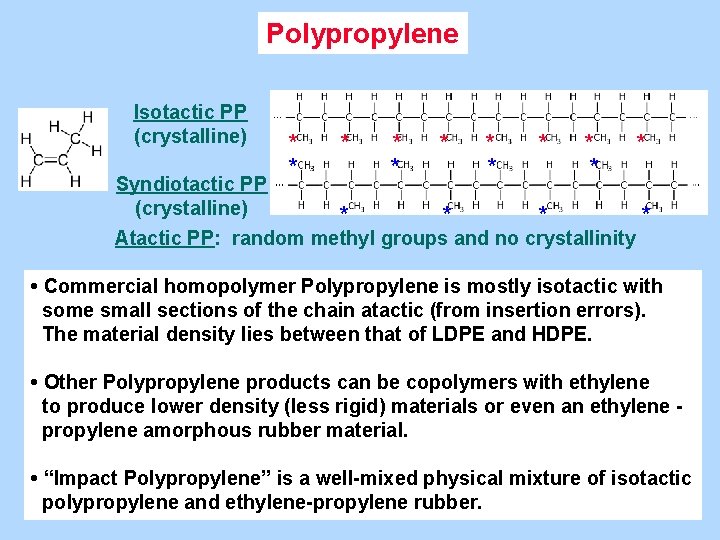
Polypropylene Isotactic PP (crystalline) * * * Syndiotactic PP (crystalline) * * Atactic PP: random methyl groups and no crystallinity • Commercial homopolymer Polypropylene is mostly isotactic with some small sections of the chain atactic (from insertion errors). The material density lies between that of LDPE and HDPE. • Other Polypropylene products can be copolymers with ethylene to produce lower density (less rigid) materials or even an ethylene propylene amorphous rubber material. • “Impact Polypropylene” is a well-mixed physical mixture of isotactic polypropylene and ethylene-propylene rubber.
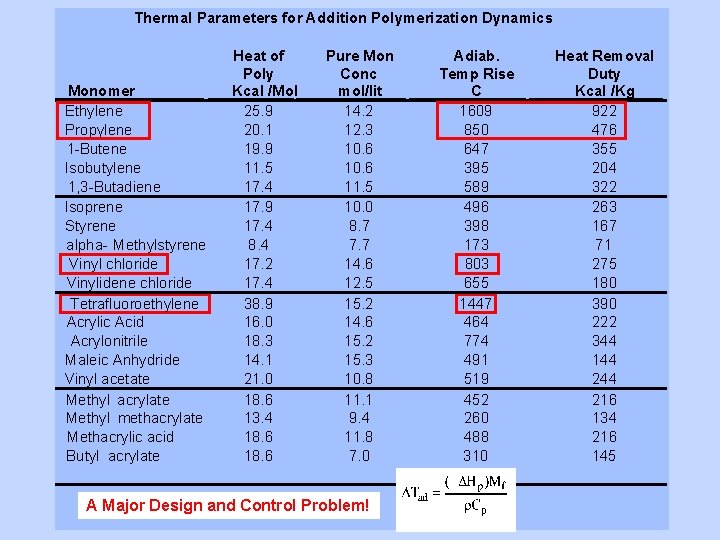
Thermal Parameters for Addition Polymerization Dynamics Monomer Ethylene Propylene 1 -Butene Isobutylene 1, 3 -Butadiene Isoprene Styrene alpha- Methylstyrene Vinyl chloride Vinylidene chloride Tetrafluoroethylene Acrylic Acid Acrylonitrile Maleic Anhydride Vinyl acetate Methyl acrylate Methyl methacrylate Methacrylic acid Butyl acrylate Heat of Poly Kcal /Mol 25. 9 20. 1 19. 9 11. 5 17. 4 17. 9 17. 4 8. 4 17. 2 17. 4 38. 9 16. 0 18. 3 14. 1 21. 0 18. 6 13. 4 18. 6 Pure Mon Conc mol/lit 14. 2 12. 3 10. 6 11. 5 10. 0 8. 7 7. 7 14. 6 12. 5 15. 2 14. 6 15. 2 15. 3 10. 8 11. 1 9. 4 11. 8 7. 0 A Major Design and Control Problem! Adiab. Temp Rise C 1609 850 647 395 589 496 398 173 803 655 1447 464 774 491 519 452 260 488 310 Heat Removal Duty Kcal /Kg 922 476 355 204 322 263 167 71 275 180 390 222 344 144 216 134 216 145
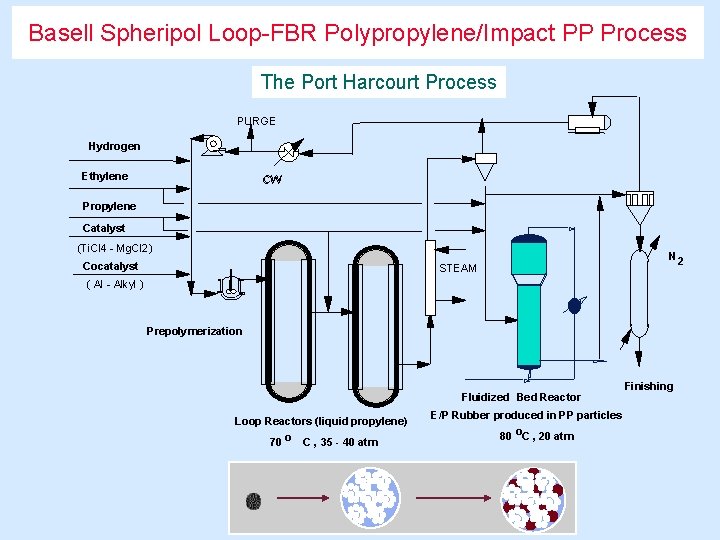
Basell Spheripol Loop-FBR Polypropylene/Impact PP Process The Port Harcourt Process PURGE Hydrogen Ethylene CW Propylene Catalyst (Ti. Cl 4 - Mg. Cl 2) Cocatalyst N 2 STEAM ( Al - Alkyl ) Prepolymerization Fluidized Bed Reactor Loop Reactors (liquid propylene) 70 o C , 35 - 40 atm Finishing E/P Rubber produced in PP particles o 80 C , 20 atm
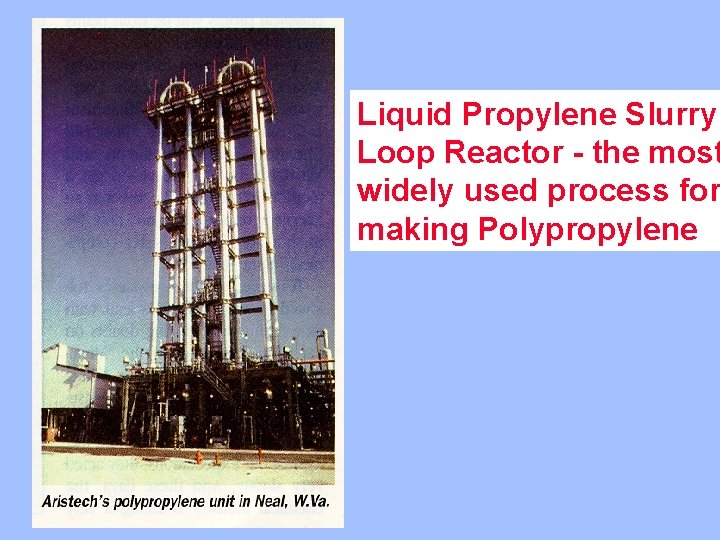
Liquid Propylene Slurry Loop Reactor - the most widely used process for making Polypropylene
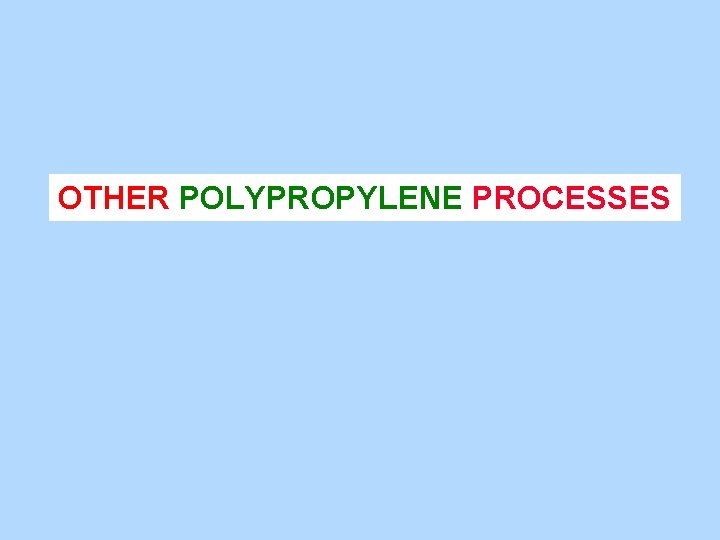
OTHER POLYPROPYLENE PROCESSES
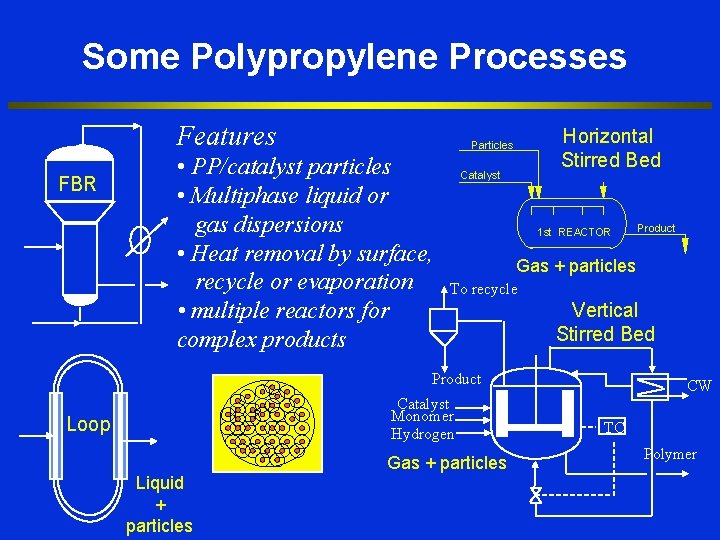
Some Polypropylene Processes Features FBR Horizontal Stirred Bed Particles • PP/catalyst particles • Multiphase liquid or gas dispersions • Heat removal by surface, recycle or evaporation • multiple reactors for complex products Catalyst 1 st REACTOR Gas + particles To recycle Vertical Stirred Bed Product Catalyst Monomer Hydrogen Loop Liquid + particles Product Gas + particles CW TC Polymer
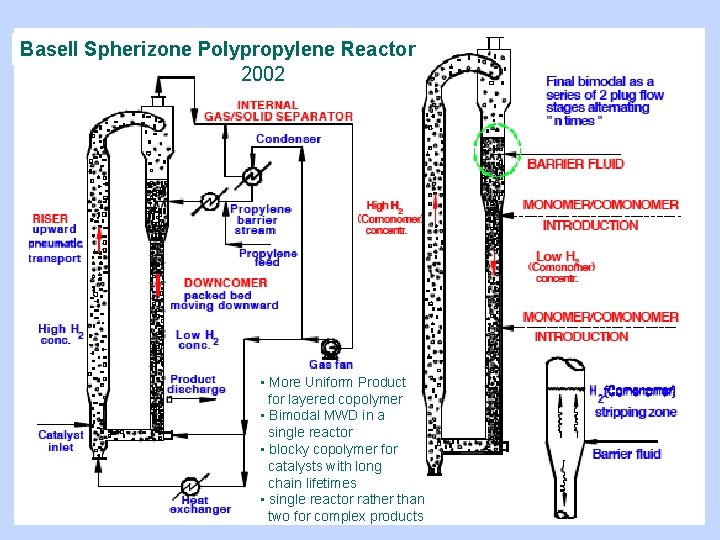
Basell Spherizone Polypropylene Reactor 2002 • More Uniform Product for layered copolymer • Bimodal MWD in a single reactor • blocky copolymer for catalysts with long chain lifetimes • single reactor rather than two for complex products
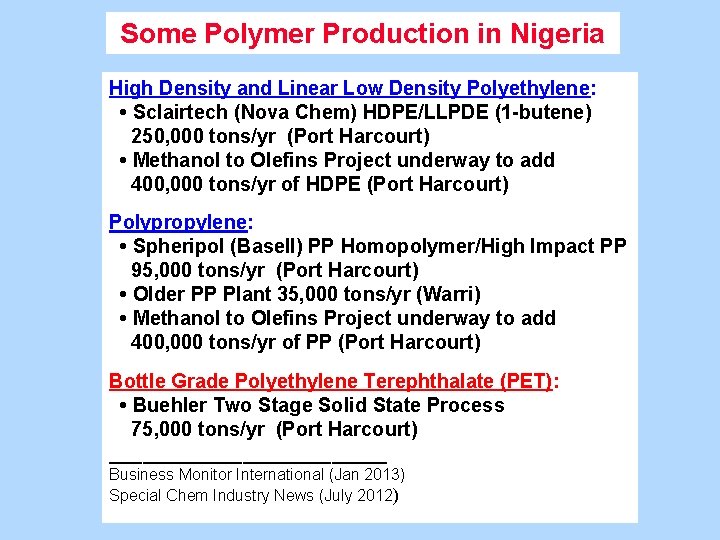
Some Polymer Production in Nigeria High Density and Linear Low Density Polyethylene: • Sclairtech (Nova Chem) HDPE/LLPDE (1 -butene) 250, 000 tons/yr (Port Harcourt) • Methanol to Olefins Project underway to add 400, 000 tons/yr of HDPE (Port Harcourt) Polypropylene: • Spheripol (Basell) PP Homopolymer/High Impact PP 95, 000 tons/yr (Port Harcourt) • Older PP Plant 35, 000 tons/yr (Warri) • Methanol to Olefins Project underway to add 400, 000 tons/yr of PP (Port Harcourt) Bottle Grade Polyethylene Terephthalate (PET): • Buehler Two Stage Solid State Process 75, 000 tons/yr (Port Harcourt) _____________ Business Monitor International (Jan 2013) Special Chem Industry News (July 2012)
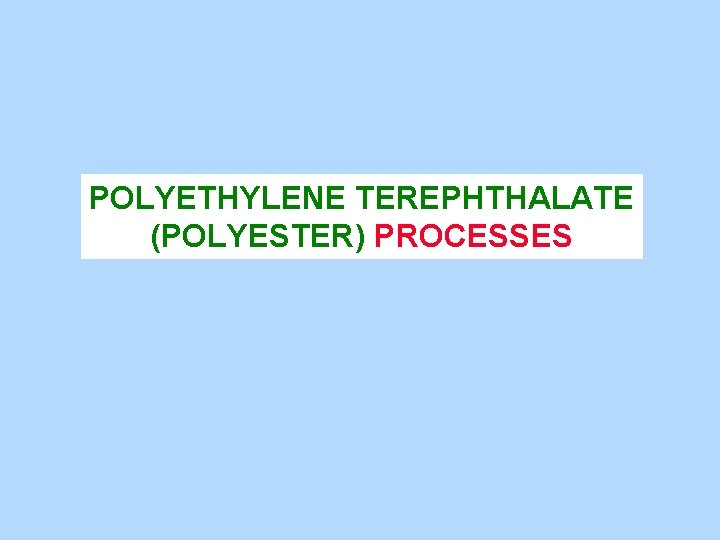
POLYETHYLENE TEREPHTHALATE (POLYESTER) PROCESSES
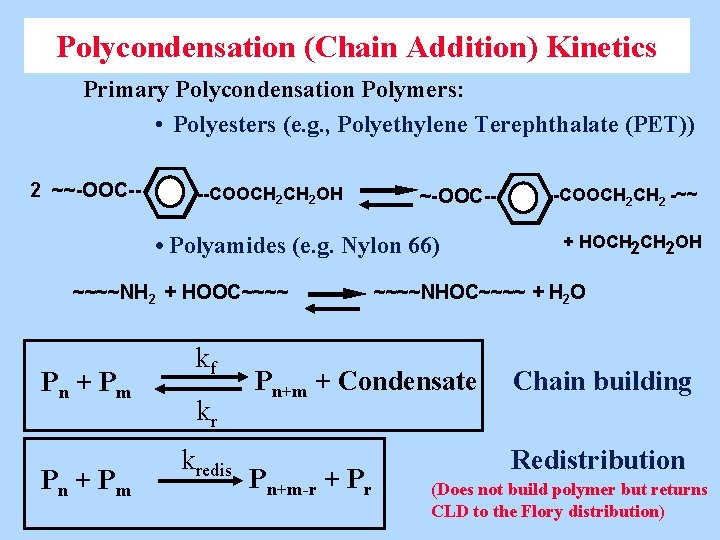
Polycondensation (Chain Addition) Kinetics Primary Polycondensation Polymers: • Polyesters (e. g. , Polyethylene Terephthalate (PET)) 2 ~~-OOC-- --COOCH 2 OH ~-OOC-- • Polyamides (e. g. Nylon 66) ~~~~NH 2 + HOOC~~~~ Pn + P m kf kr kredis + HOCH 2 OH ~~~~NHOC~~~~ + H 2 O Pn+m + Condensate Pn+m-r + Pr --COOCH 2 -~~ Chain building Redistribution (Does not build polymer but returns CLD to the Flory distribution)
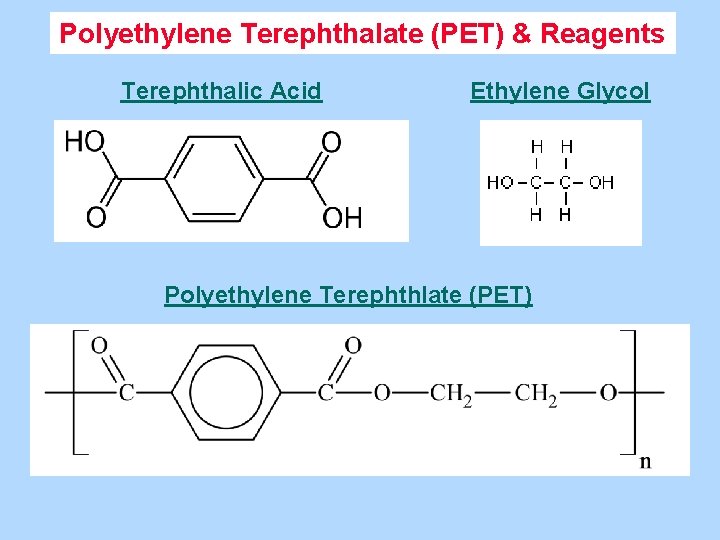
Polyethylene Terephthalate (PET) & Reagents Terephthalic Acid Ethylene Glycol Polyethylene Terephthlate (PET)

Molecular Weight & Chain Length Distributions - Polycondensation (polyester, polyamide, epoxy, polycarbonate, etc. ) For many condensation polymers equilibrium limitations allow only very short chains in a closed system without condensate removal Polycondensation (growth) Redistribution (CLD adjustment) • Reactions occur only between polymer molecules; a “living” polymerization. • Strong equilibrium limitation, so condensate is removed to allow continued chain growth. Degree of Polymerization Usually measured by GPC or Intrinsic Viscosity (IV)
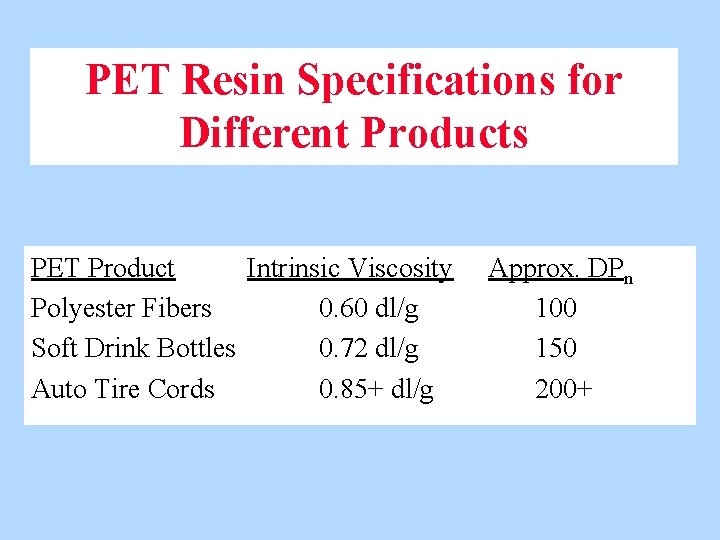
PET Resin Specifications for Different Products PET Product Intrinsic Viscosity Polyester Fibers 0. 60 dl/g Soft Drink Bottles 0. 72 dl/g Auto Tire Cords 0. 85+ dl/g Approx. DPn 100 150 200+
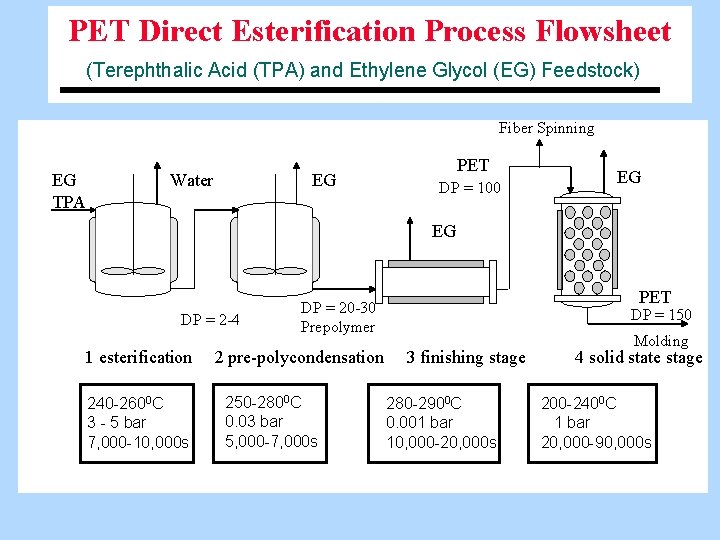
PET Direct Esterification Process Flowsheet (Terephthalic Acid (TPA) and Ethylene Glycol (EG) Feedstock) Fiber Spinning EG TPA Water EG PET DP = 100 EG EG DP = 2 -4 1 esterification 240 -2600 C 3 - 5 bar 7, 000 -10, 000 s PET DP = 20 -30 Prepolymer 2 pre-polycondensation 250 -2800 C 0. 03 bar 5, 000 -7, 000 s DP = 150 3 finishing stage 280 -2900 C 0. 001 bar 10, 000 -20, 000 s Molding 4 solid state stage 200 -2400 C 1 bar 20, 000 -90, 000 s
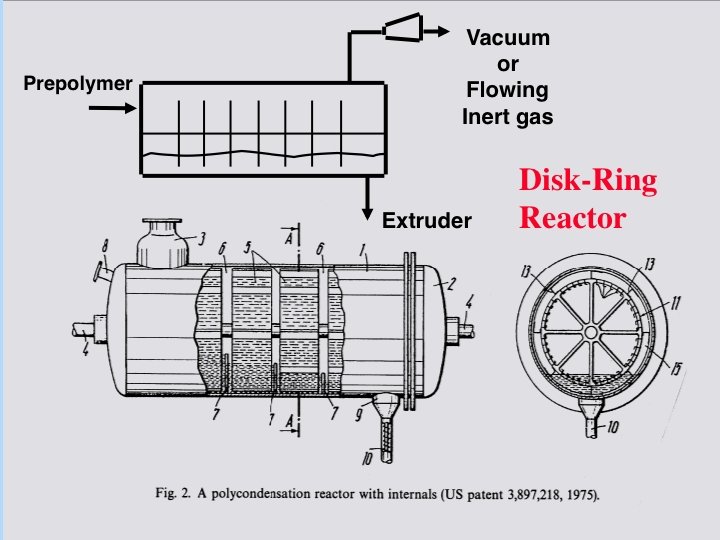
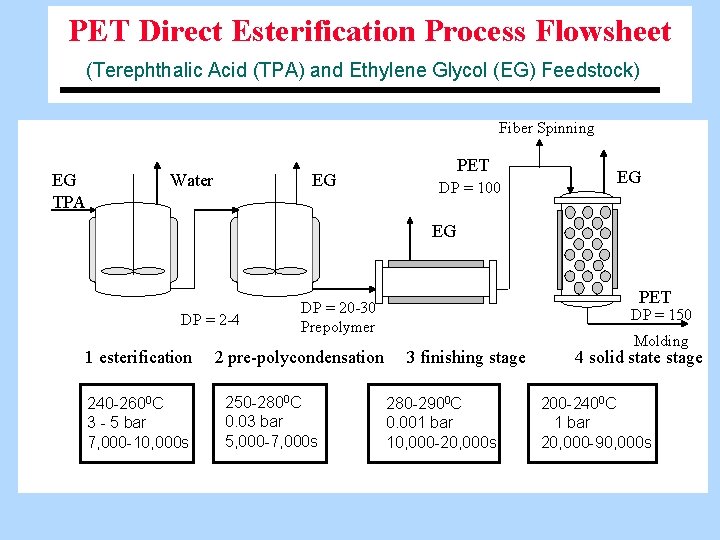
PET Direct Esterification Process Flowsheet (Terephthalic Acid (TPA) and Ethylene Glycol (EG) Feedstock) Fiber Spinning EG TPA Water EG PET DP = 100 EG EG DP = 2 -4 1 esterification 240 -2600 C 3 - 5 bar 7, 000 -10, 000 s PET DP = 20 -30 Prepolymer 2 pre-polycondensation 250 -2800 C 0. 03 bar 5, 000 -7, 000 s DP = 150 3 finishing stage 280 -2900 C 0. 001 bar 10, 000 -20, 000 s Molding 4 solid state stage 200 -2400 C 1 bar 20, 000 -90, 000 s
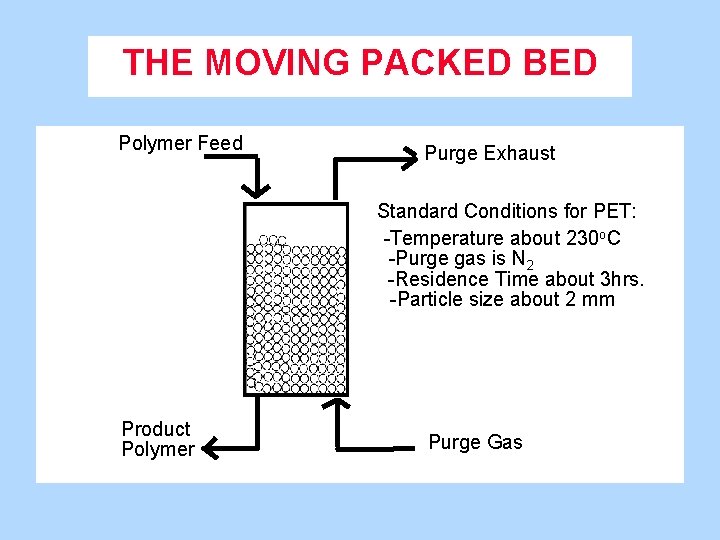
THE MOVING PACKED BED Polymer Feed Purge Exhaust Standard Conditions for PET: -Temperature about 230 o. C -Purge gas is N 2 -Residence Time about 3 hrs. -Particle size about 2 mm Product Polymer Purge Gas
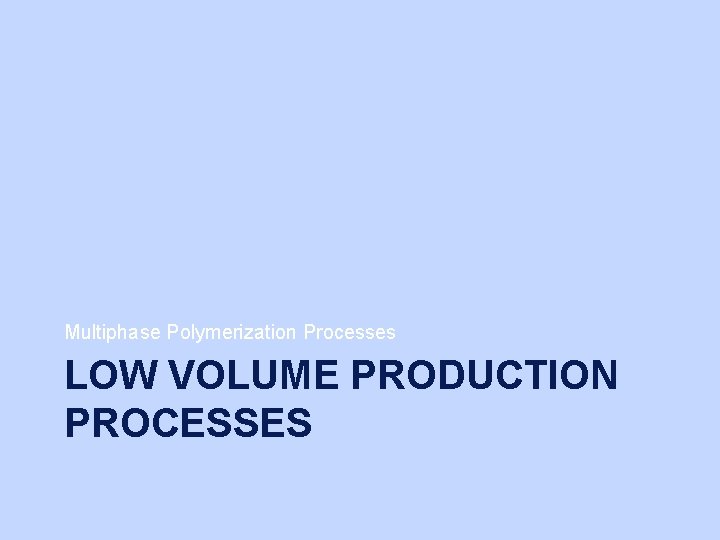
Multiphase Polymerization Processes LOW VOLUME PRODUCTION PROCESSES
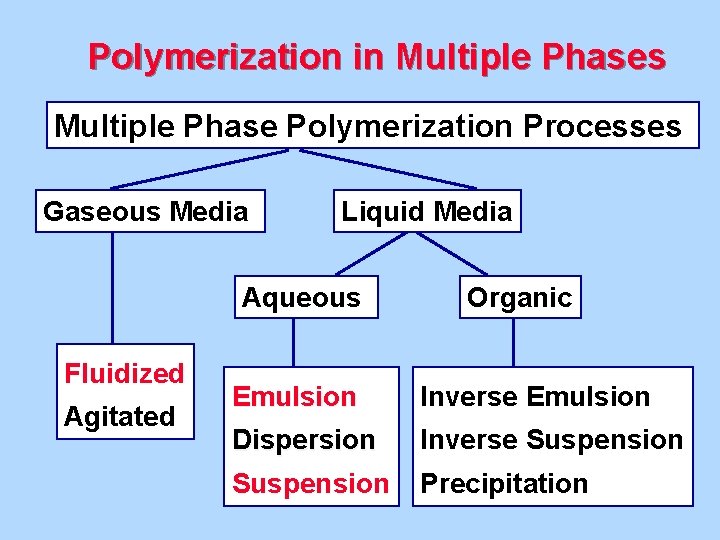
Polymerization in Multiple Phases Multiple Phase Polymerization Processes Gaseous Media Liquid Media Aqueous Fluidized Agitated Organic Emulsion Inverse Emulsion Dispersion Inverse Suspension Precipitation
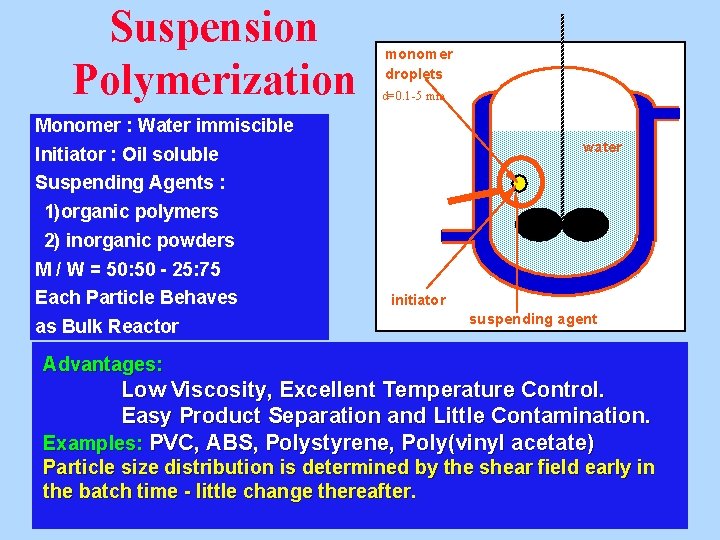
Suspension Polymerization monomer droplets d=0. 1 -5 mm Monomer : Water immiscible water Initiator : Oil soluble Suspending Agents : 1)organic polymers 2) inorganic powders M / W = 50: 50 - 25: 75 Each Particle Behaves as Bulk Reactor initiator suspending agent Advantages: Low Viscosity, Excellent Temperature Control. Easy Product Separation and Little Contamination. Examples: PVC, ABS, Polystyrene, Poly(vinyl acetate) Particle size distribution is determined by the shear field early in the batch time - little change thereafter.
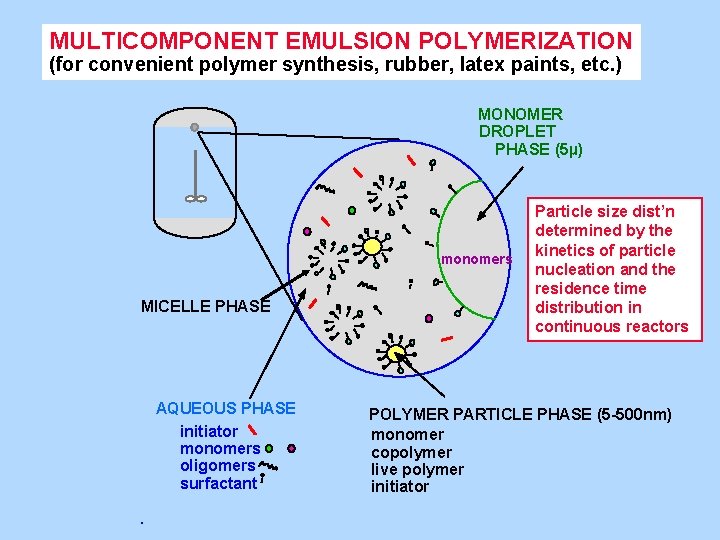
MULTICOMPONENT EMULSION POLYMERIZATION (for convenient polymer synthesis, rubber, latex paints, etc. ) MONOMER DROPLET PHASE (5µ) monomers MICELLE PHASE AQUEOUS PHASE initiator monomers oligomers surfactant Particle size dist’n determined by the kinetics of particle nucleation and the residence time distribution in continuous reactors POLYMER PARTICLE PHASE (5 -500 nm) monomer copolymer live polymer initiator

Final Remarks; Going on From Here CONCLUSIONS
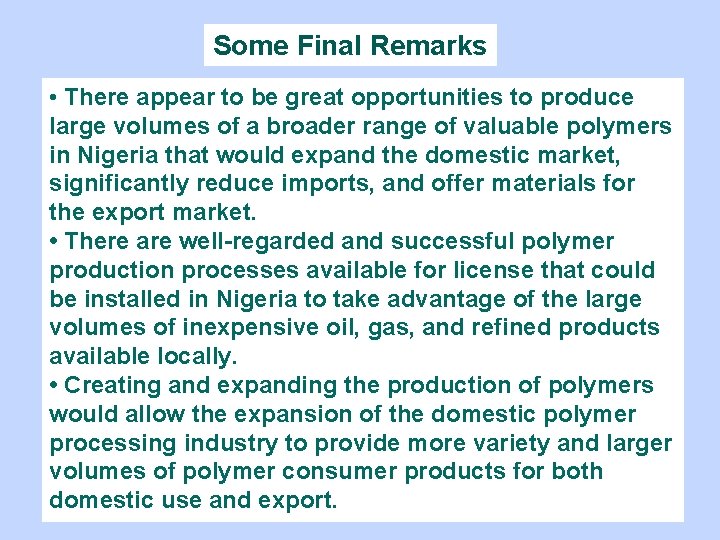
Some Final Remarks • There appear to be great opportunities to produce large volumes of a broader range of valuable polymers in Nigeria that would expand the domestic market, significantly reduce imports, and offer materials for the export market. • There are well-regarded and successful polymer production processes available for license that could be installed in Nigeria to take advantage of the large volumes of inexpensive oil, gas, and refined products available locally. • Creating and expanding the production of polymers would allow the expansion of the domestic polymer processing industry to provide more variety and larger volumes of polymer consumer products for both domestic use and export.
Nigerian academy of engineering
Norjan pinta ala
Nigeria folk tales
Nnnxxx
Nigerian musical instruments
History of son
Nigerian deserts
"unity trust" -nigeria -nigerian -bancorp
They say it only takes a little faith
Sometimes you win some
Cake countable or uncountable noun
Contact forces
Fire and ice diamante poem
Some say the world will end in fire some say in ice
Some may trust in horses
Royal academy of engineering
John jay science and engineering academy
Scope of engineering ethics
Define web engineering
30 days has september april june and november
Spanish flacs exam 2018 answers
June 2007 physics regents
June 2005 calendar
When your child leaves home poem
Good morning 1 june
Lottery in june corn be heavy soon irony
Danswer
Welcome june blessings
English paper 1 june 2021
Grade 7 life orientation test
Good morning welcome june
June 21 2019 geometry regents answers
Checkpoint
Cxc results 2018 may/june date
French music awards
Lenore hetrick photo
June cheetah wegener
Symbolism in the lottery
June canavan foundation
Liz owns stock in nar
19.06.2008 nasa
January 2017 chemistry regents answers
Irpwm 2020
June 20 2008
Simplicissimus cartoon june 1919 analysis
June's journey
Simplissimus 3 june 1919
Flacs checkpoint b spanish exam june 2014 answers
Summary period: june 2021 poem
The map shows that allied forces
A proper noun
Drink before june 2012
June too soon july stand by
Vfpms
The cause of rizal first sorrow
June 22 to july 22
June 6 1944
Workshop expectations
June 15 1215
June preschool newsletter
June 23
Confined placental mosaicism
June f
June safety tips
June 23
June july august
Nysedregents
Prayer for june
Holy june
Companies in june
1 june children's day
Lake june head start
Dr june james
Network weaver
Milton glaser biography
Ward 34 ninewells
2019 june calendar
Kse 1995
Lembar pengesahan dokumen 1 kurikulum 2013
Tutorial access 2013
Quran in word 2013
Brs 2013