MESH Management Review May 2007 2007 Eaton Corporation
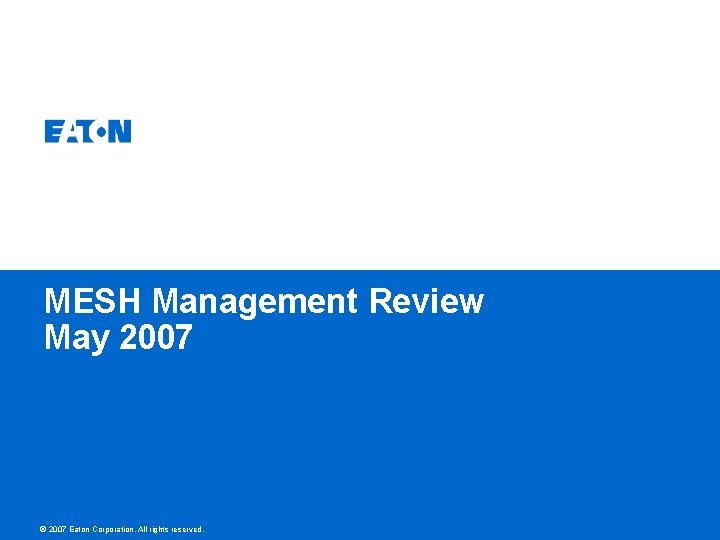
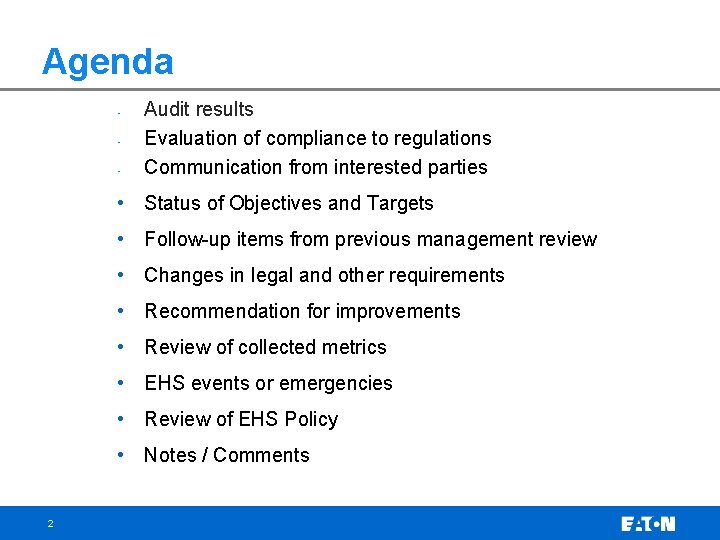
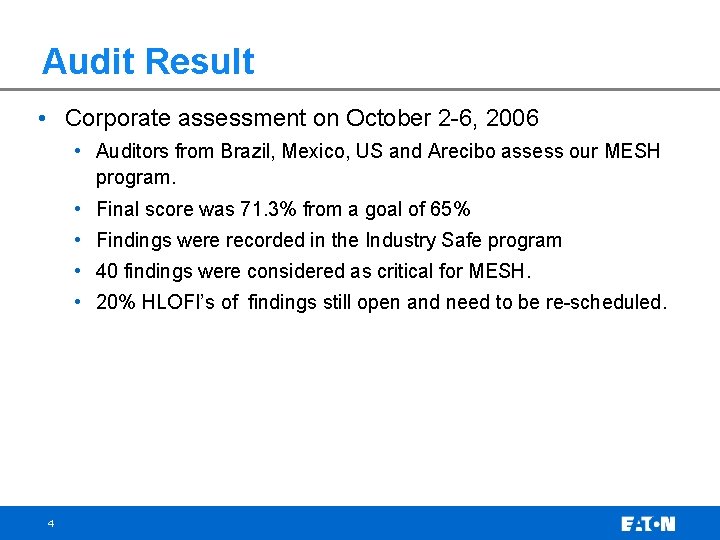
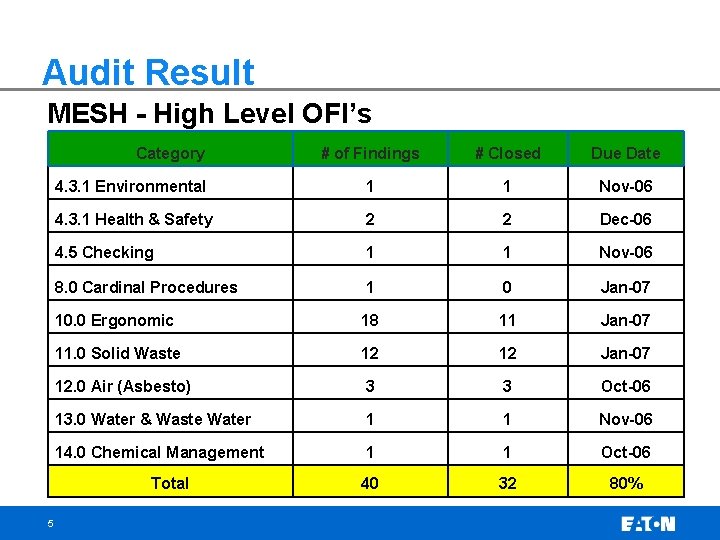
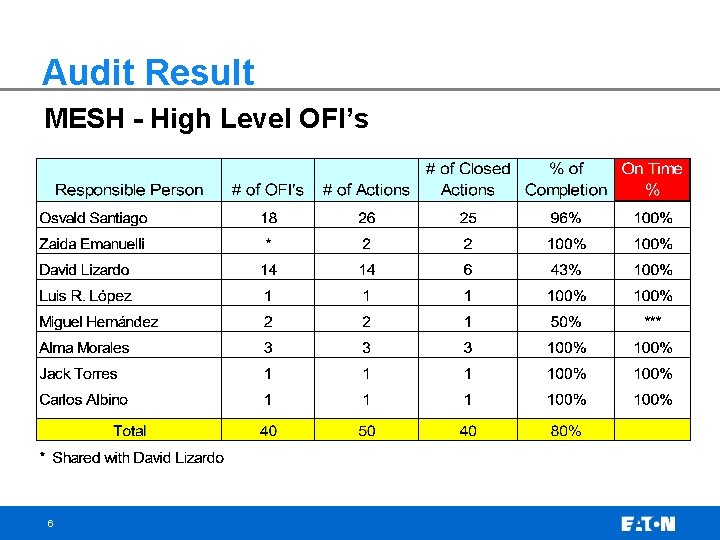
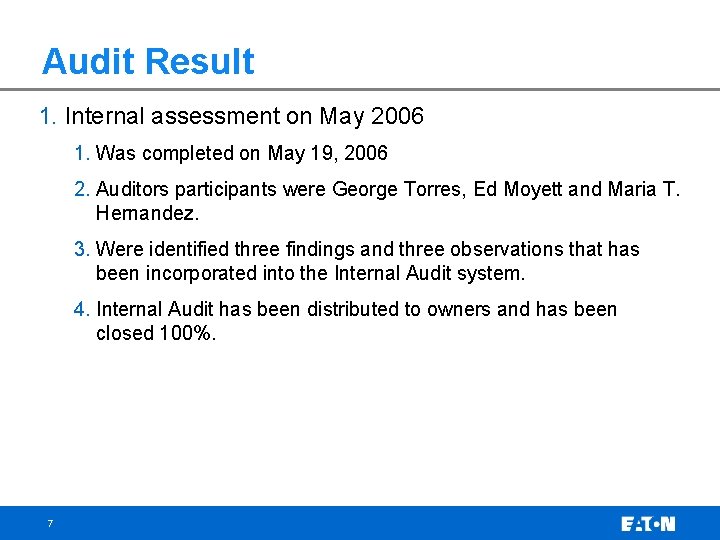
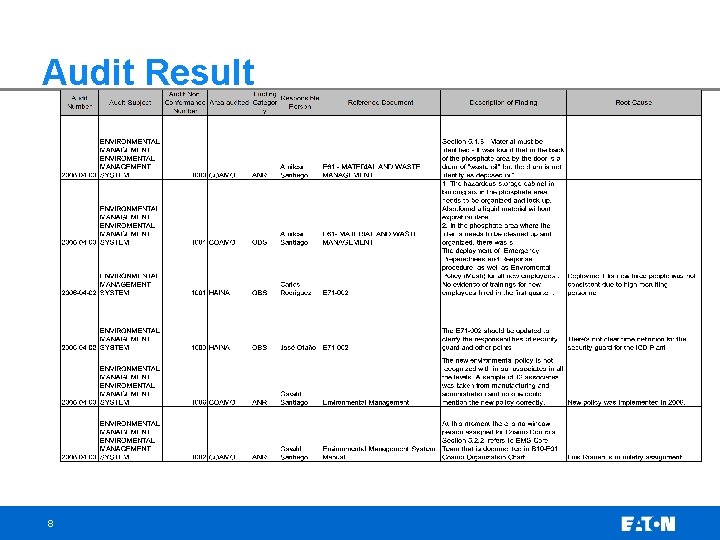
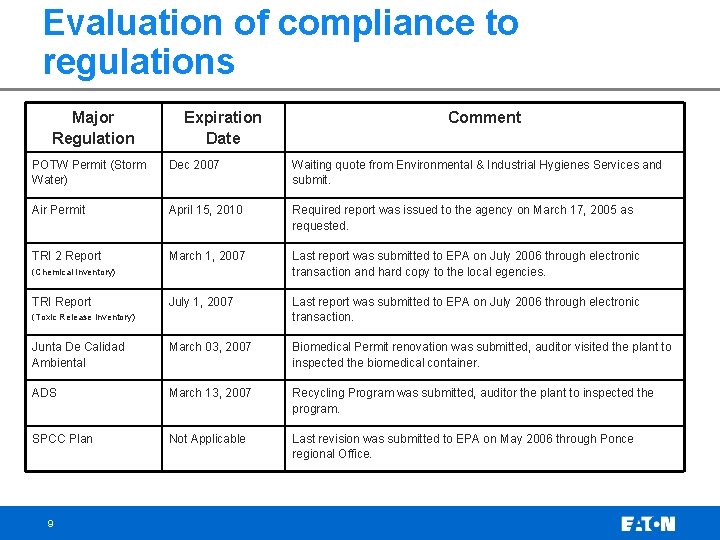
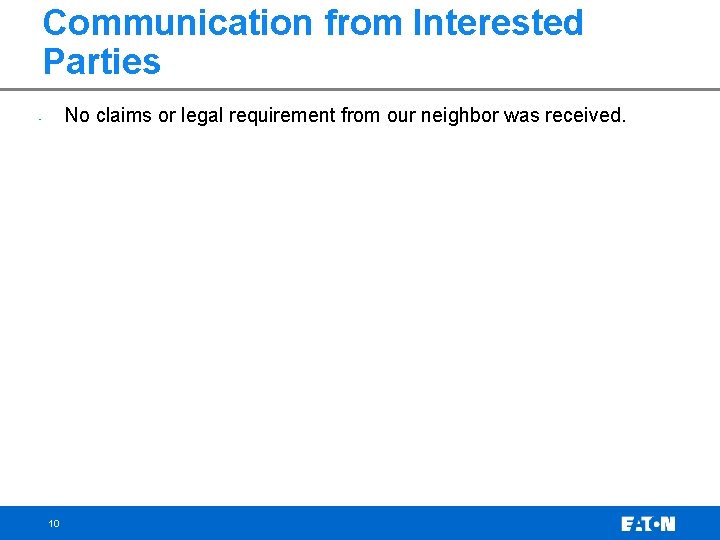
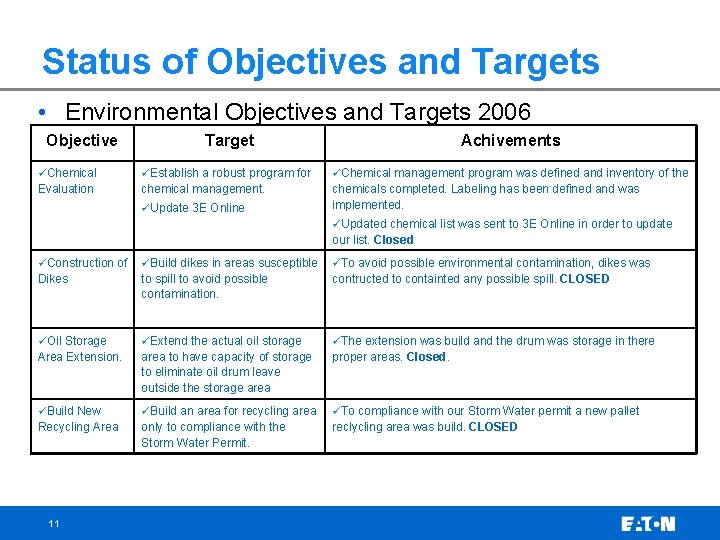
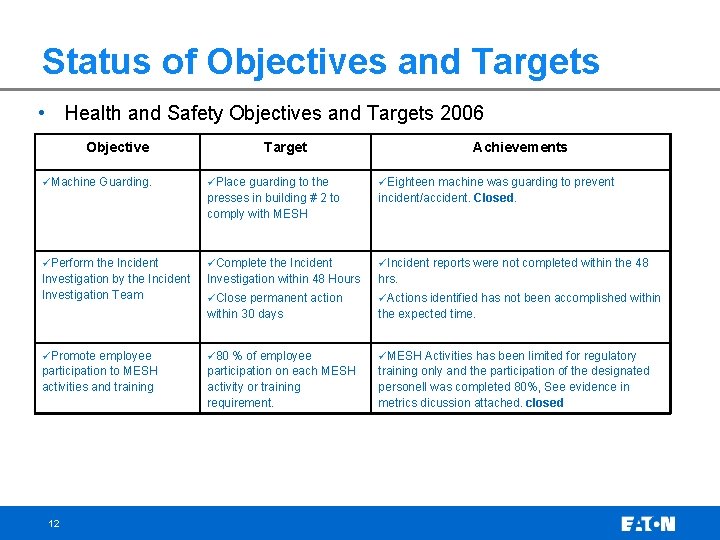

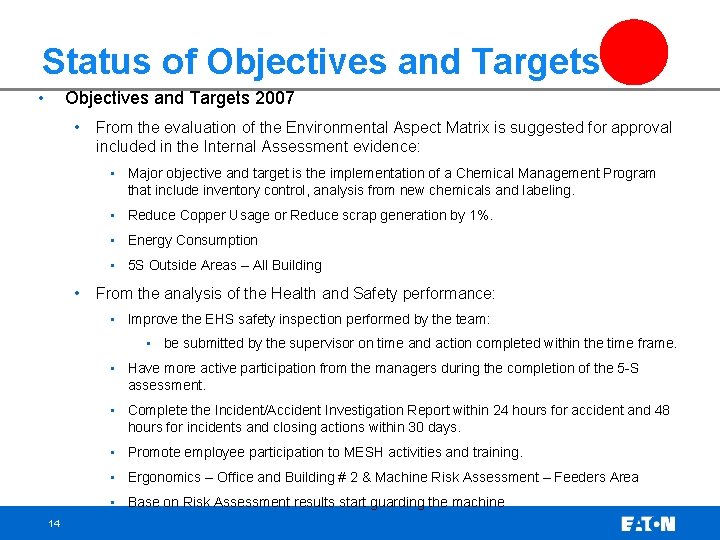
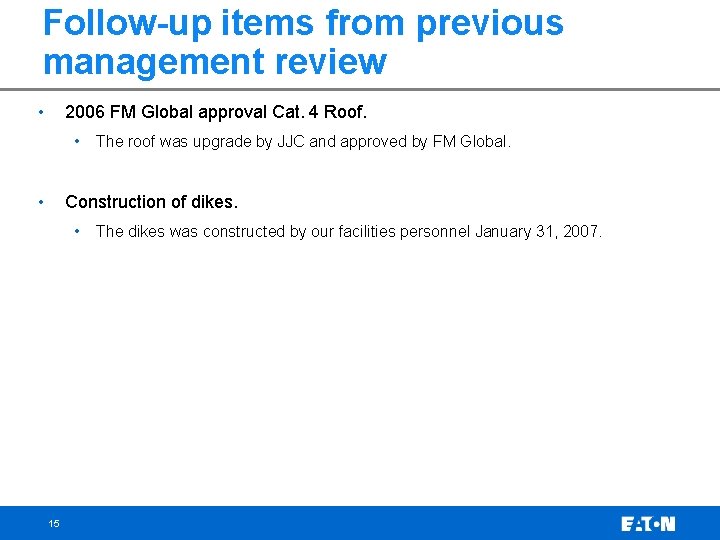
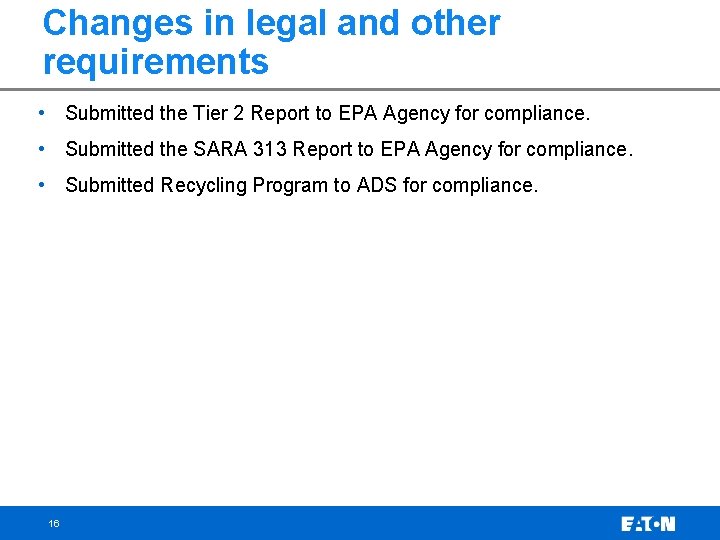
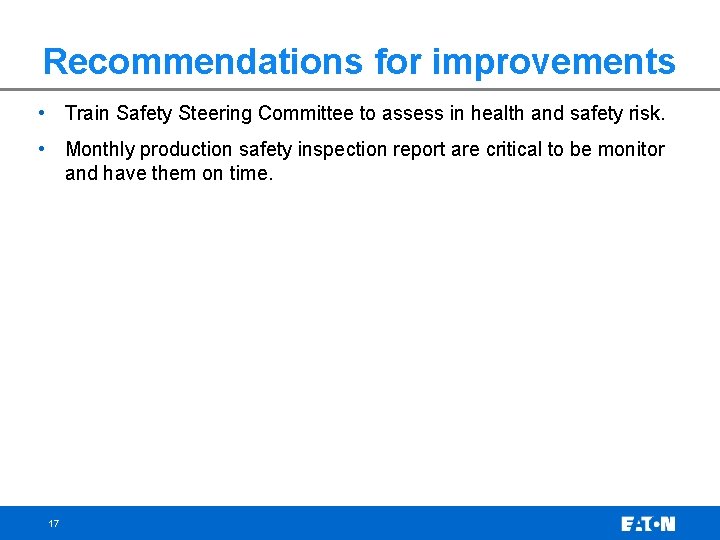
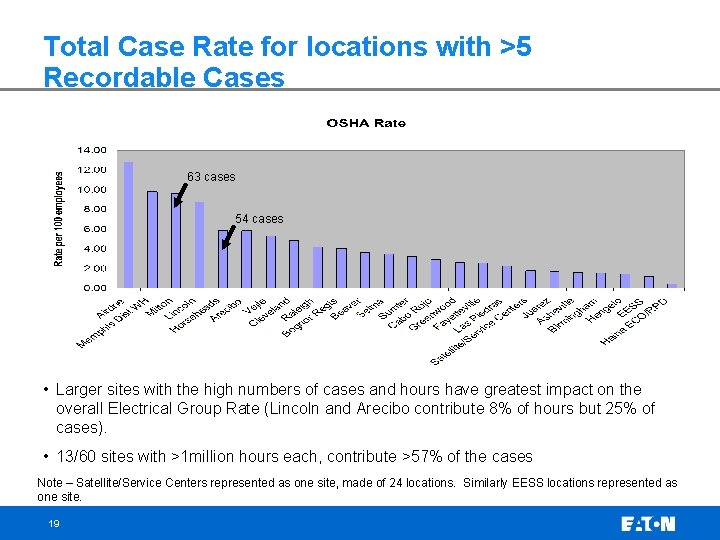
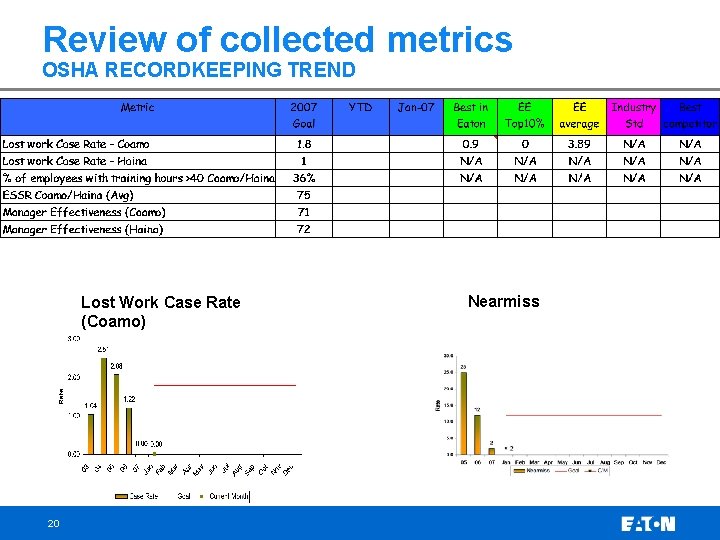
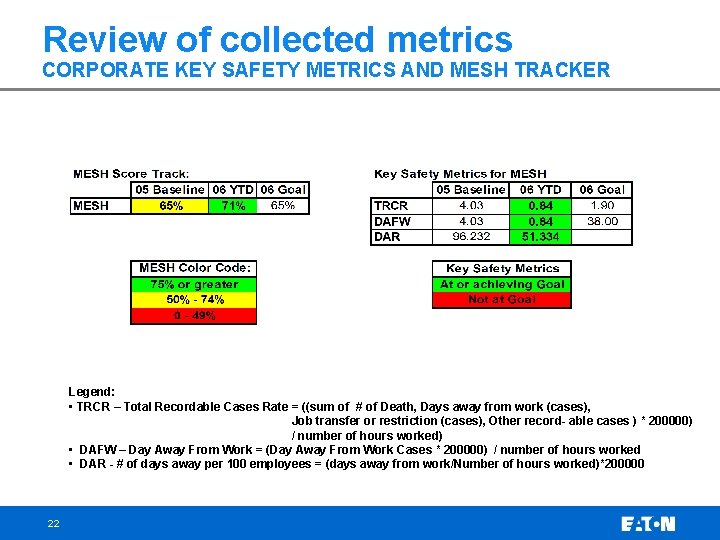
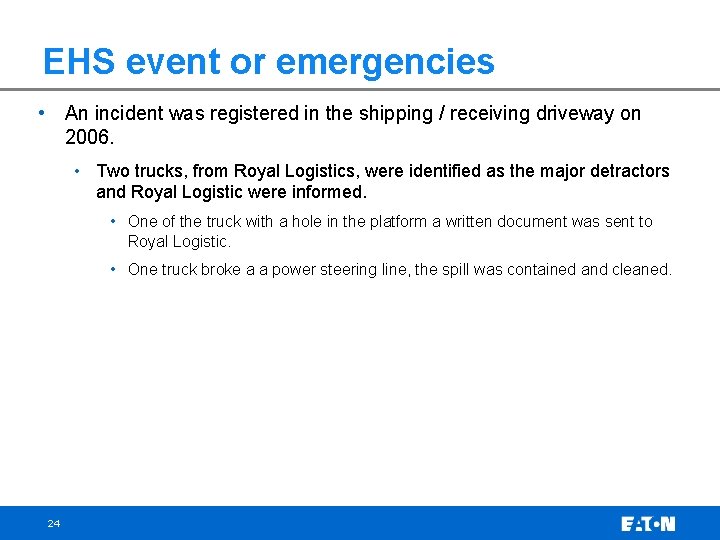
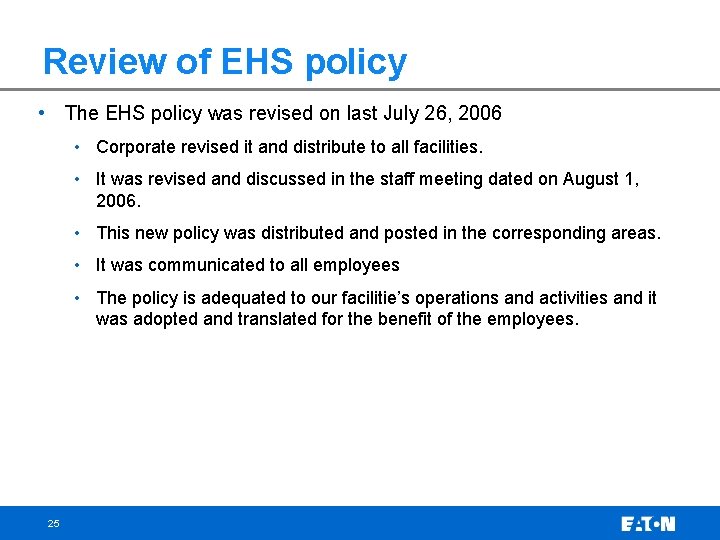
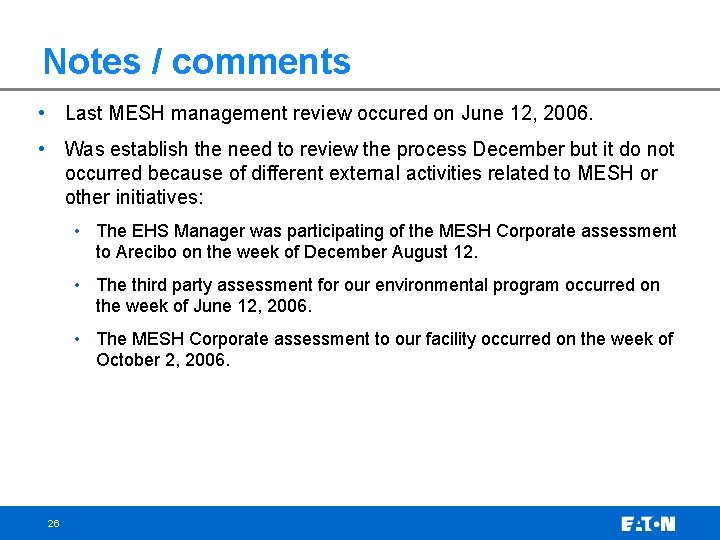
- Slides: 22
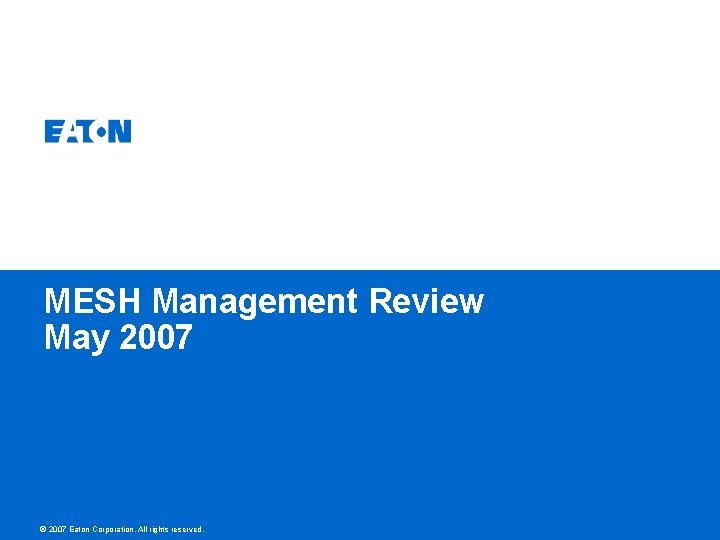
MESH Management Review May 2007 © 2007 Eaton Corporation. All rights reserved.
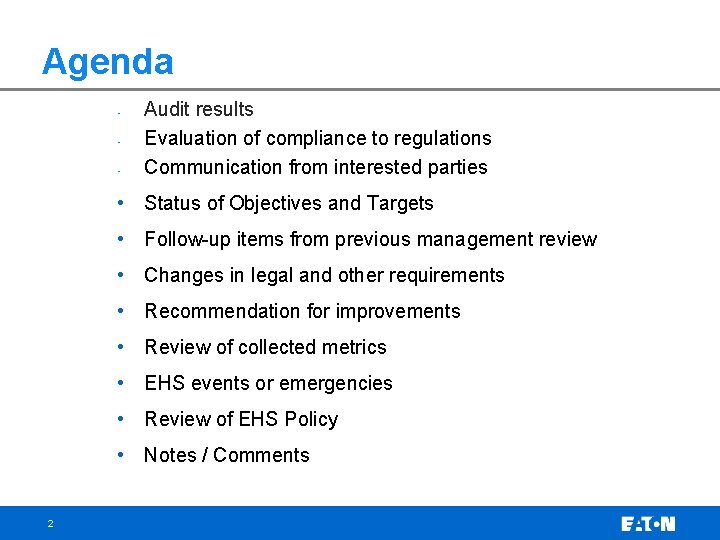
Agenda • • • Audit results Evaluation of compliance to regulations Communication from interested parties • Status of Objectives and Targets • Follow-up items from previous management review • Changes in legal and other requirements • Recommendation for improvements • Review of collected metrics • EHS events or emergencies • Review of EHS Policy • Notes / Comments 2
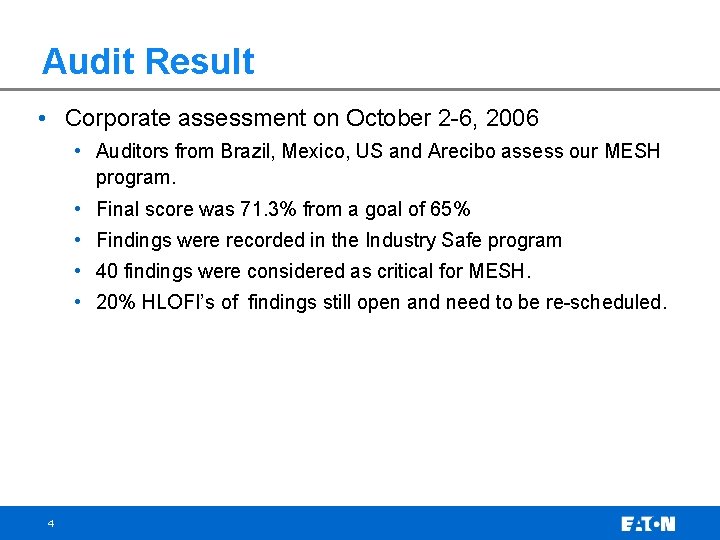
Audit Result • Corporate assessment on October 2 -6, 2006 • Auditors from Brazil, Mexico, US and Arecibo assess our MESH program. • Final score was 71. 3% from a goal of 65% • Findings were recorded in the Industry Safe program • 40 findings were considered as critical for MESH. • 20% HLOFI’s of findings still open and need to be re-scheduled. 4
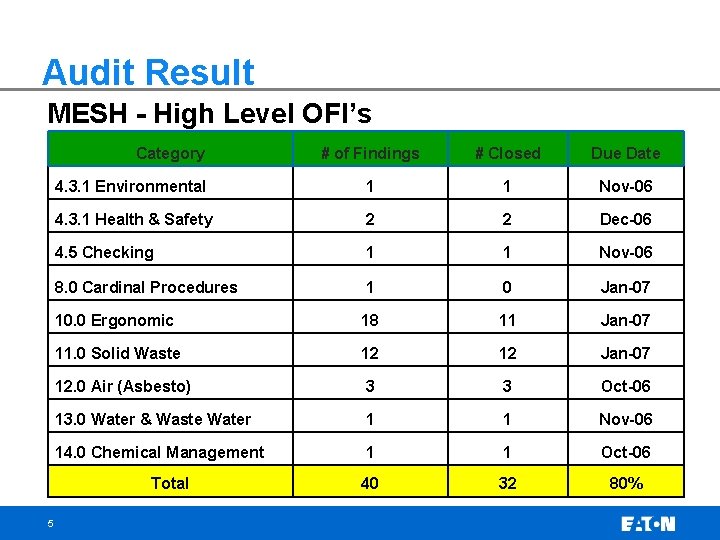
Audit Result MESH - High Level OFI’s Category # of Findings # Closed Due Date 4. 3. 1 Environmental 1 1 Nov-06 4. 3. 1 Health & Safety 2 2 Dec-06 4. 5 Checking 1 1 Nov-06 8. 0 Cardinal Procedures 1 0 Jan-07 10. 0 Ergonomic 18 11 Jan-07 11. 0 Solid Waste 12 12 Jan-07 12. 0 Air (Asbesto) 3 3 Oct-06 13. 0 Water & Waste Water 1 1 Nov-06 14. 0 Chemical Management 1 1 Oct-06 40 32 80% Total 5
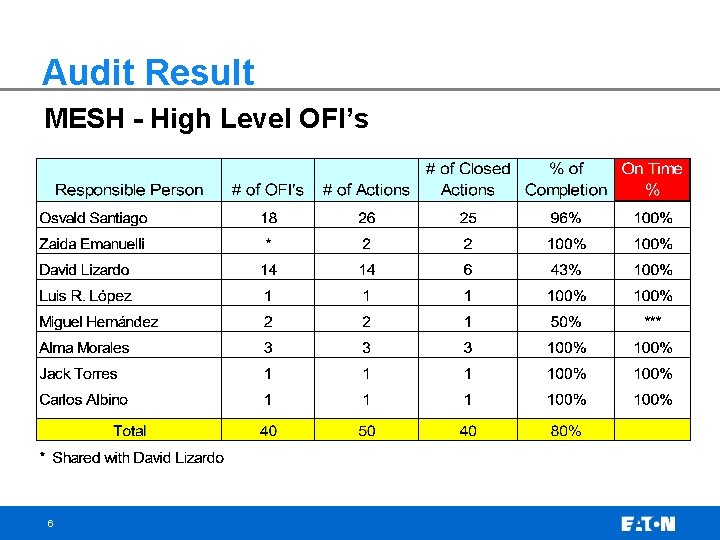
Audit Result MESH - High Level OFI’s 6
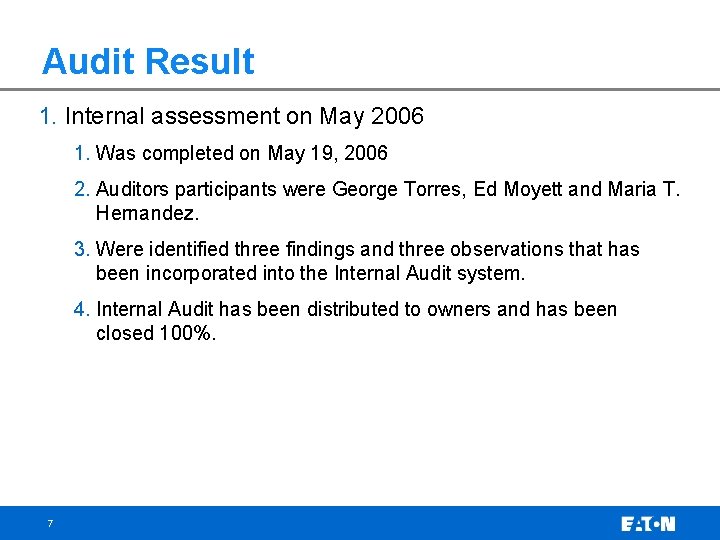
Audit Result 1. Internal assessment on May 2006 1. Was completed on May 19, 2006 2. Auditors participants were George Torres, Ed Moyett and Maria T. Hernandez. 3. Were identified three findings and three observations that has been incorporated into the Internal Audit system. 4. Internal Audit has been distributed to owners and has been closed 100%. 7
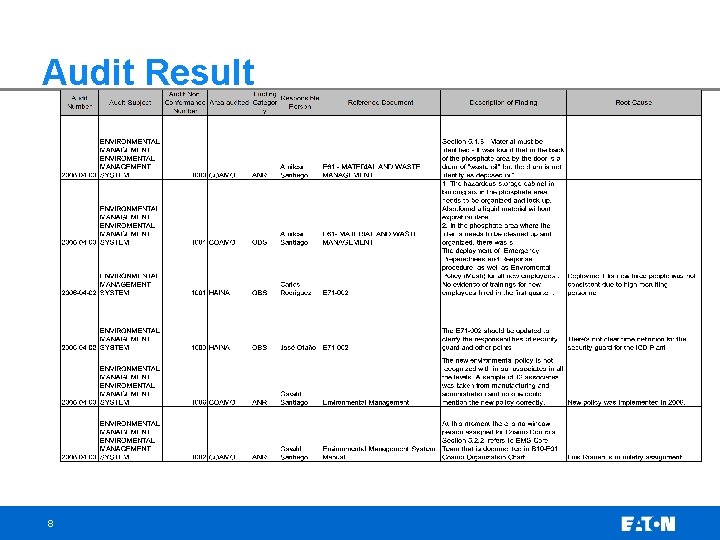
Audit Result 8
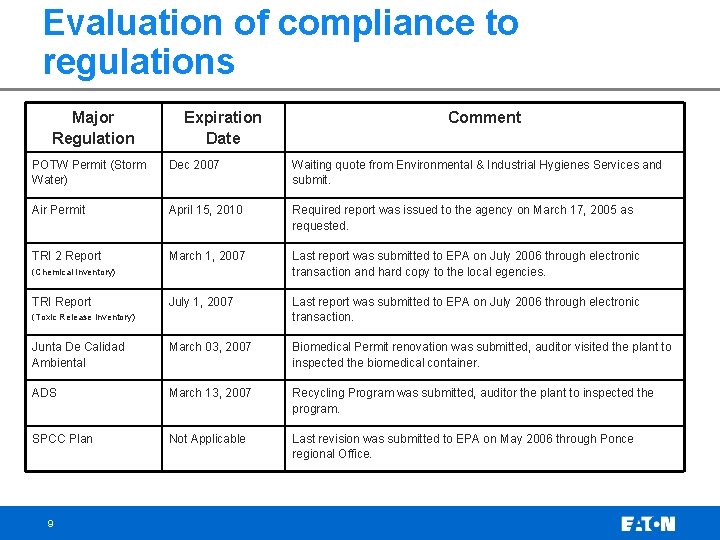
Evaluation of compliance to regulations Major Regulation Expiration Date Comment POTW Permit (Storm Water) Dec 2007 Waiting quote from Environmental & Industrial Hygienes Services and submit. Air Permit April 15, 2010 Required report was issued to the agency on March 17, 2005 as requested. TRI 2 Report March 1, 2007 Last report was submitted to EPA on July 2006 through electronic transaction and hard copy to the local egencies. July 1, 2007 Last report was submitted to EPA on July 2006 through electronic transaction. Junta De Calidad Ambiental March 03, 2007 Biomedical Permit renovation was submitted, auditor visited the plant to inspected the biomedical container. ADS March 13, 2007 Recycling Program was submitted, auditor the plant to inspected the program. SPCC Plan Not Applicable Last revision was submitted to EPA on May 2006 through Ponce regional Office. (Chemical Inventory) TRI Report (Toxic Release Inventory) 9
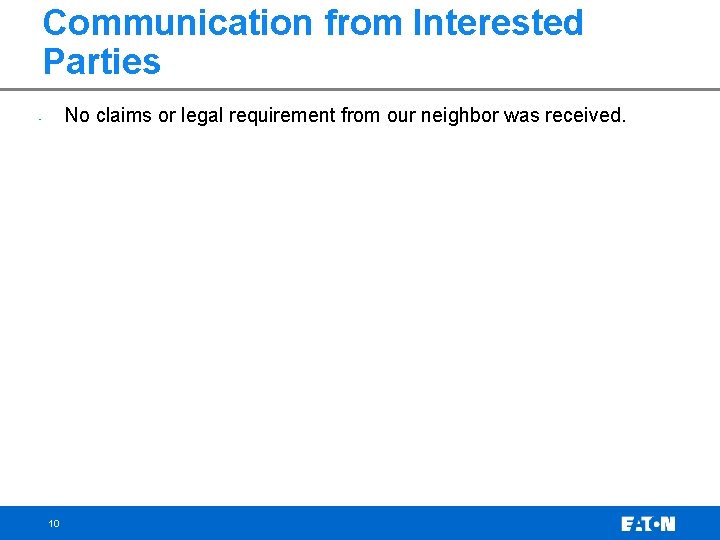
Communication from Interested Parties No claims or legal requirement from our neighbor was received. • 10
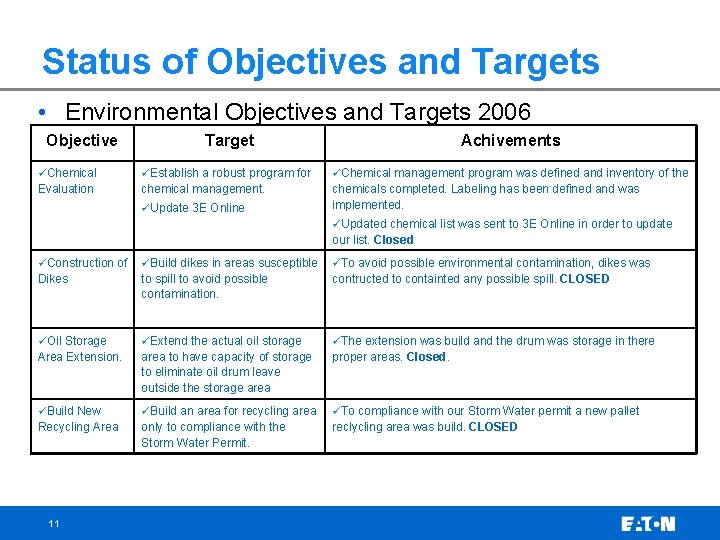
Status of Objectives and Targets • Environmental Objectives and Targets 2006 Objective Target Achivements üChemical üEstablish a robust program for üChemical management program was defined and inventory of the Evaluation chemical management. chemicals completed. Labeling has been defined and was implemented. üUpdate 3 E Online üUpdated chemical list was sent to 3 E Online in order to update our list. Closed üConstruction of üBuild dikes in areas susceptible üTo avoid possible environmental contamination, dikes was Dikes to spill to avoid possible contamination. contructed to containted any possible spill. CLOSED üOil Storage üExtend the actual oil storage üThe extension was build and the drum was storage in there Area Extension. area to have capacity of storage to eliminate oil drum leave outside the storage area proper areas. Closed. üBuild New üBuild an area for recycling area üTo compliance with our Storm Water permit a new pallet Recycling Area only to compliance with the Storm Water Permit. reclycling area was build. CLOSED 11
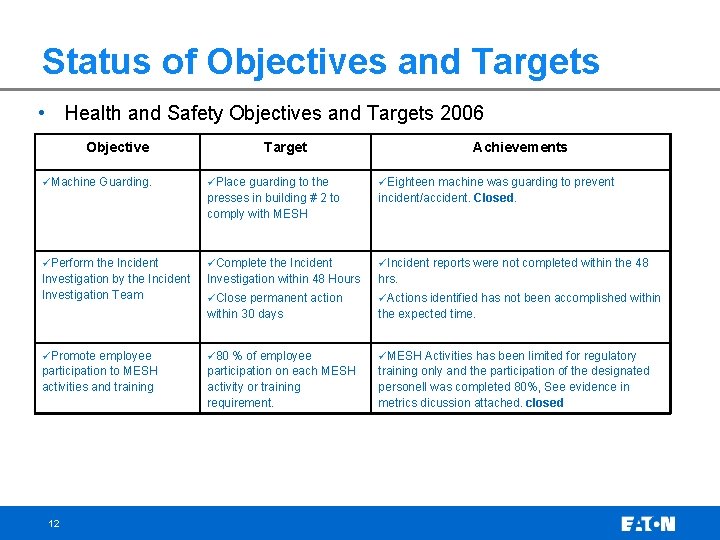
Status of Objectives and Targets • Health and Safety Objectives and Targets 2006 Objective üMachine Guarding. Target Achievements üPlace guarding to the üEighteen machine was guarding to prevent presses in building # 2 to comply with MESH incident/accident. Closed. üPerform the Incident üComplete the Incident üIncident reports were not completed within the 48 Investigation by the Incident Investigation Team Investigation within 48 Hours hrs. üClose permanent action üActions identified has not been accomplished within 30 days the expected time. üPromote employee ü 80 % of employee üMESH Activities has been limited for regulatory participation to MESH activities and training participation on each MESH activity or training requirement. training only and the participation of the designated personell was completed 80%, See evidence in metrics dicussion attached. closed 12

Status of Objectives and Targets 2006 OTMP - Coamo Ro. HS - directive to restrict lead in solders and other chemicals. Recycling - Batteries • • Actual Objectives ** Storm Waters - 0 Contamination - OK Pallets - 10 % Reusable Actual New Compressed Air - Improve 15 % Coamo = $200 year Energy Conservation -. 12% as CGS Phosphate Waste Water Control –. 126 as CGS Aluminum, Metals, Cardboard, and Plastic Recycling • • 13 Process Water Treatment - Evaporator System -. 126% as CGS Thermoplastic Regrind & RTP for PB Products – Cost Saving - $5, 265. 00 as May
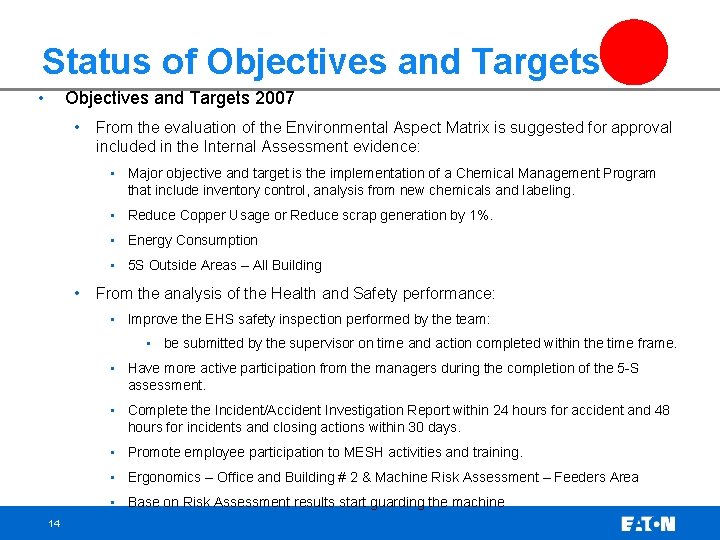
Status of Objectives and Targets • Objectives and Targets 2007 • From the evaluation of the Environmental Aspect Matrix is suggested for approval included in the Internal Assessment evidence: • Major objective and target is the implementation of a Chemical Management Program that include inventory control, analysis from new chemicals and labeling. • Reduce Copper Usage or Reduce scrap generation by 1%. • Energy Consumption • 5 S Outside Areas – All Building • From the analysis of the Health and Safety performance: • Improve the EHS safety inspection performed by the team: • be submitted by the supervisor on time and action completed within the time frame. • Have more active participation from the managers during the completion of the 5 -S assessment. • Complete the Incident/Accident Investigation Report within 24 hours for accident and 48 hours for incidents and closing actions within 30 days. • Promote employee participation to MESH activities and training. • Ergonomics – Office and Building # 2 & Machine Risk Assessment – Feeders Area • Base on Risk Assessment results start guarding the machine 14
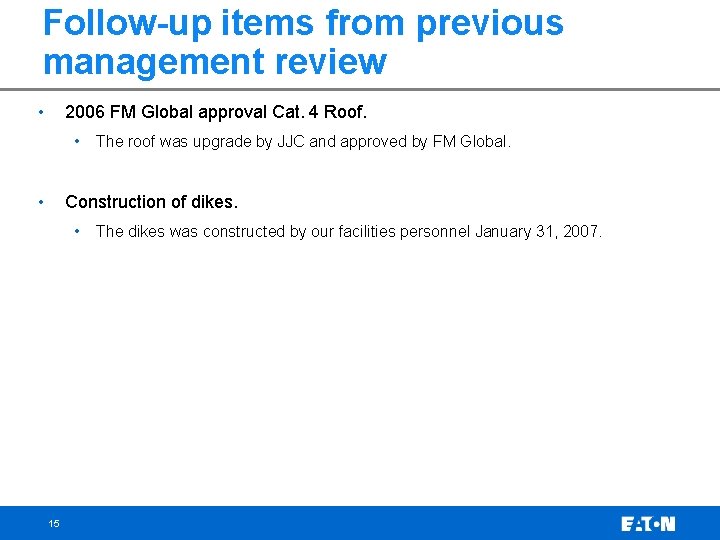
Follow-up items from previous management review • 2006 FM Global approval Cat. 4 Roof. • • The roof was upgrade by JJC and approved by FM Global. Construction of dikes. • 15 The dikes was constructed by our facilities personnel January 31, 2007.
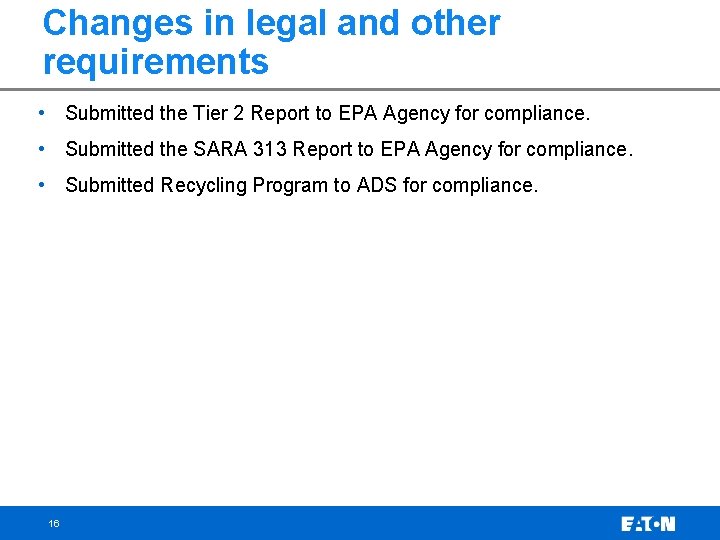
Changes in legal and other requirements • Submitted the Tier 2 Report to EPA Agency for compliance. • Submitted the SARA 313 Report to EPA Agency for compliance. • Submitted Recycling Program to ADS for compliance. 16
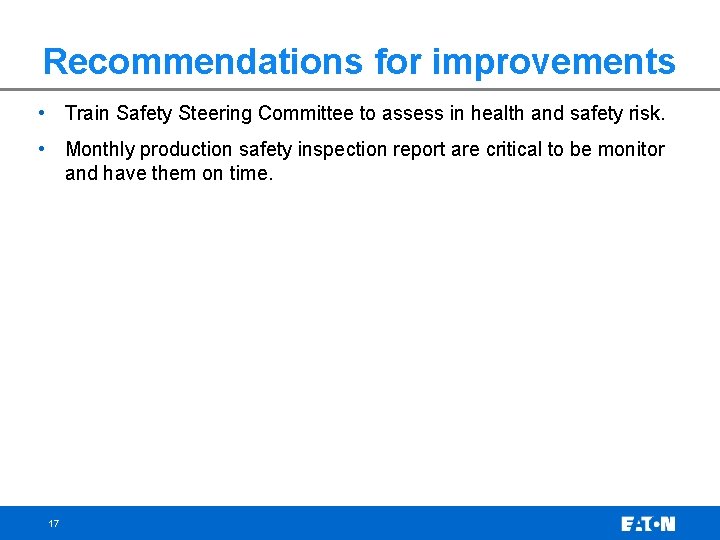
Recommendations for improvements • Train Safety Steering Committee to assess in health and safety risk. • Monthly production safety inspection report are critical to be monitor and have them on time. 17
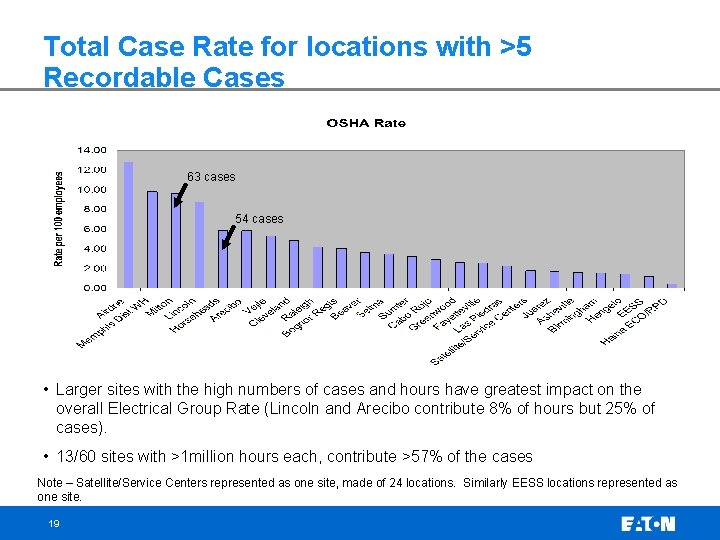
Total Case Rate for locations with >5 Recordable Cases 63 cases 54 cases • Larger sites with the high numbers of cases and hours have greatest impact on the overall Electrical Group Rate (Lincoln and Arecibo contribute 8% of hours but 25% of cases). • 13/60 sites with >1 million hours each, contribute >57% of the cases Note – Satellite/Service Centers represented as one site, made of 24 locations. Similarly EESS locations represented as one site. 19
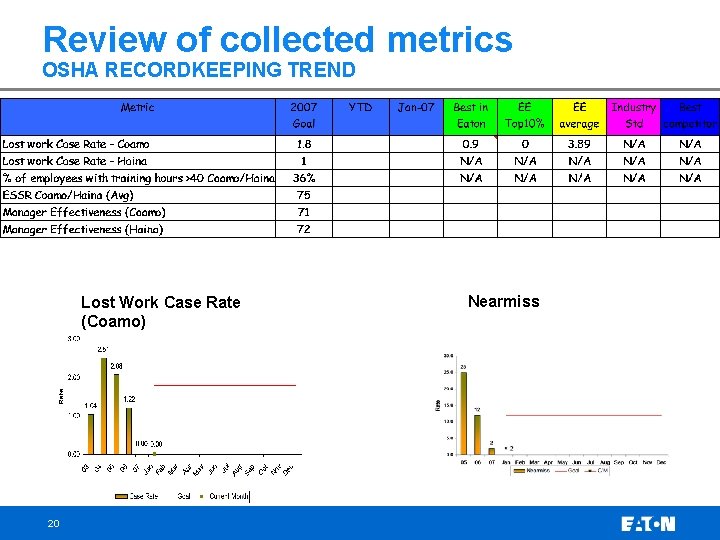
Review of collected metrics OSHA RECORDKEEPING TREND Lost Work Case Rate (Coamo) 20 Nearmiss
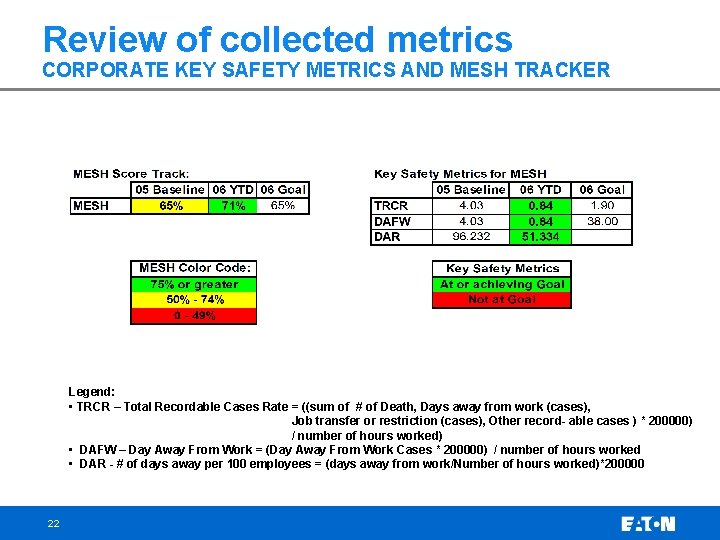
Review of collected metrics CORPORATE KEY SAFETY METRICS AND MESH TRACKER Legend: • TRCR – Total Recordable Cases Rate = ((sum of # of Death, Days away from work (cases), Job transfer or restriction (cases), Other record- able cases ) * 200000) / number of hours worked) • DAFW – Day Away From Work = (Day Away From Work Cases * 200000) / number of hours worked • DAR - # of days away per 100 employees = (days away from work/Number of hours worked)*200000 22
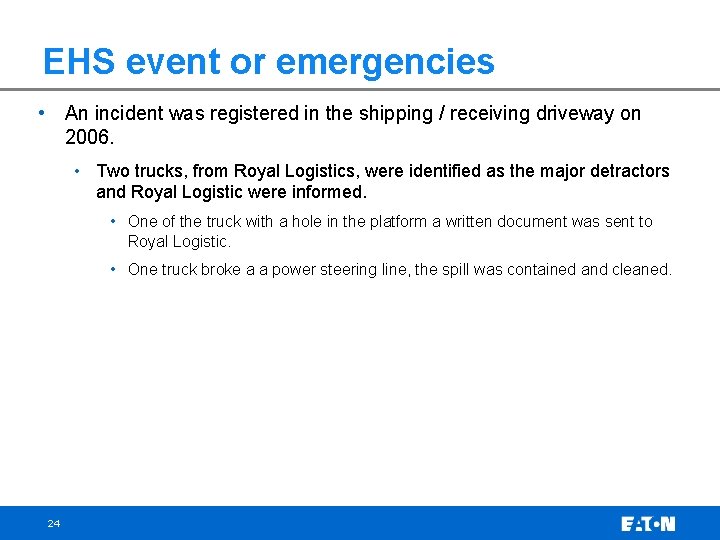
EHS event or emergencies • An incident was registered in the shipping / receiving driveway on 2006. • Two trucks, from Royal Logistics, were identified as the major detractors and Royal Logistic were informed. • One of the truck with a hole in the platform a written document was sent to Royal Logistic. • One truck broke a a power steering line, the spill was contained and cleaned. 24
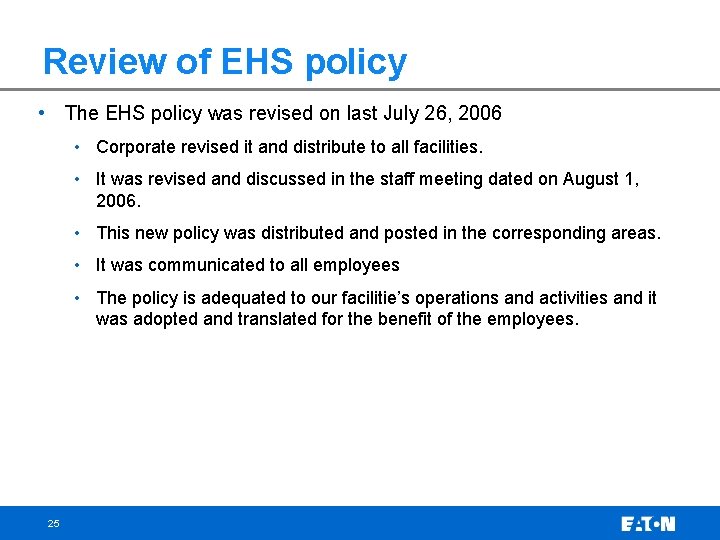
Review of EHS policy • The EHS policy was revised on last July 26, 2006 • Corporate revised it and distribute to all facilities. • It was revised and discussed in the staff meeting dated on August 1, 2006. • This new policy was distributed and posted in the corresponding areas. • It was communicated to all employees • The policy is adequated to our facilitie’s operations and activities and it was adopted and translated for the benefit of the employees. 25
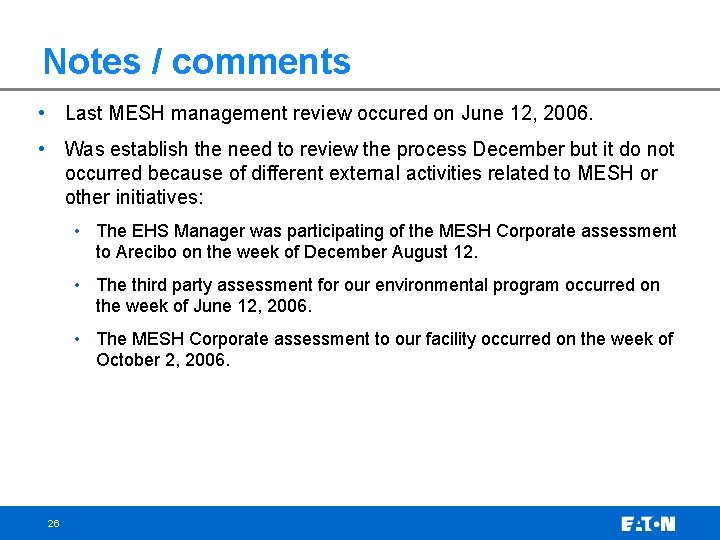
Notes / comments • Last MESH management review occured on June 12, 2006. • Was establish the need to review the process December but it do not occurred because of different external activities related to MESH or other initiatives: • The EHS Manager was participating of the MESH Corporate assessment to Arecibo on the week of December August 12. • The third party assessment for our environmental program occurred on the week of June 12, 2006. • The MESH Corporate assessment to our facility occurred on the week of October 2, 2006. 26
Sliding mesh vs constant mesh
Wisper eaton
Mrs spring fragrance summary
Eaton true sine wave inverter controller
Eaton vance wholesaler map
Eaton hydraulics uk
Eaton iq analyzer
Eaton controls division
E-star eaton
Eaton
Eaton business system
Eaton arc flash relay
Eaton true sine wave inverter
Eaton supplier portal
Eaton ltd havant
Lipe clutch vs eaton
Power xpert 900
Dr koco eaton
Miastenia que es
Eaton arc flash handbook
Eaton park elementary
Vr eaton high school map
Koco eaton