MANUFACTURING PROCESS 1 DPT 110 MATERIAL SELECTION CO
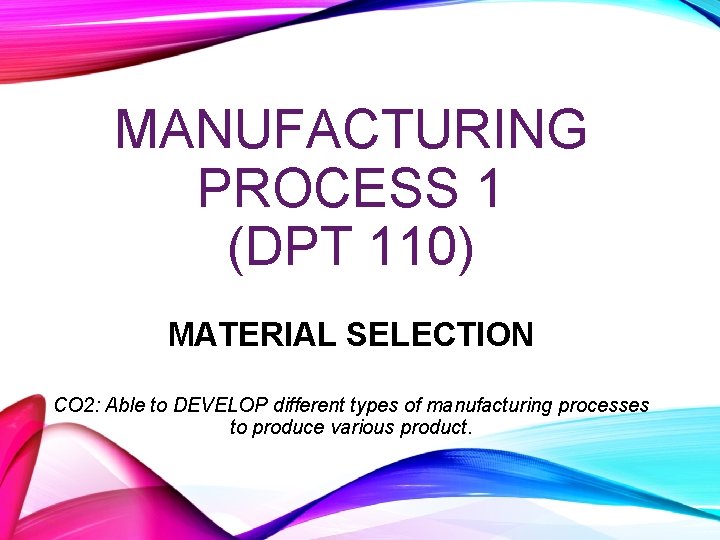
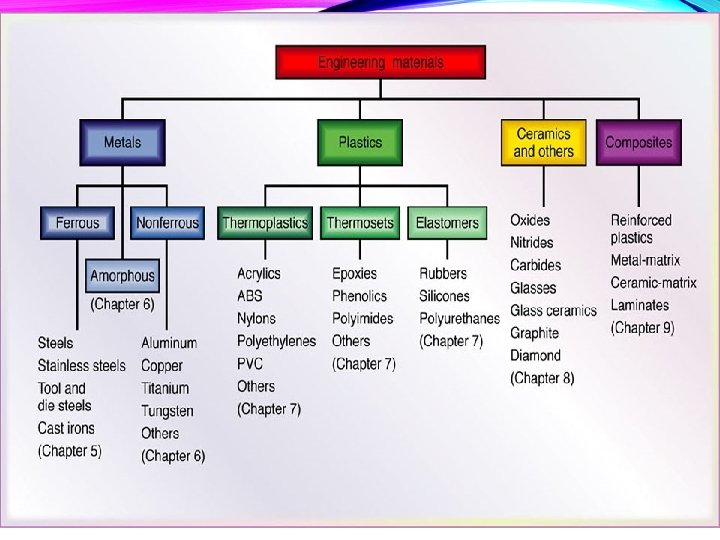
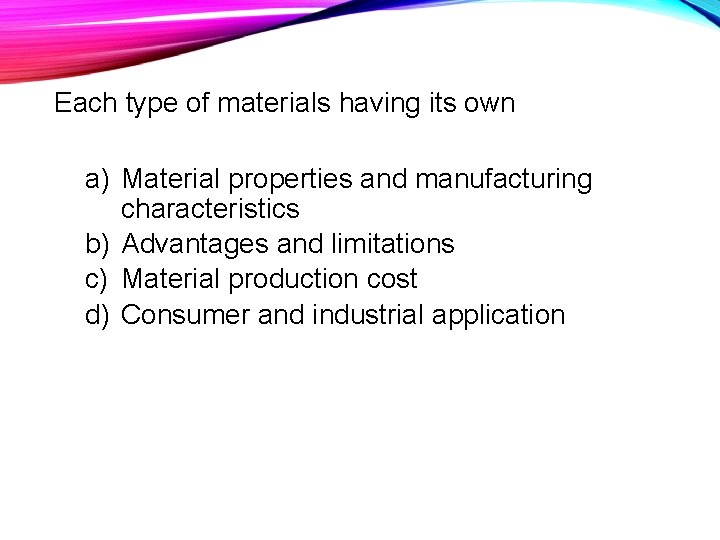
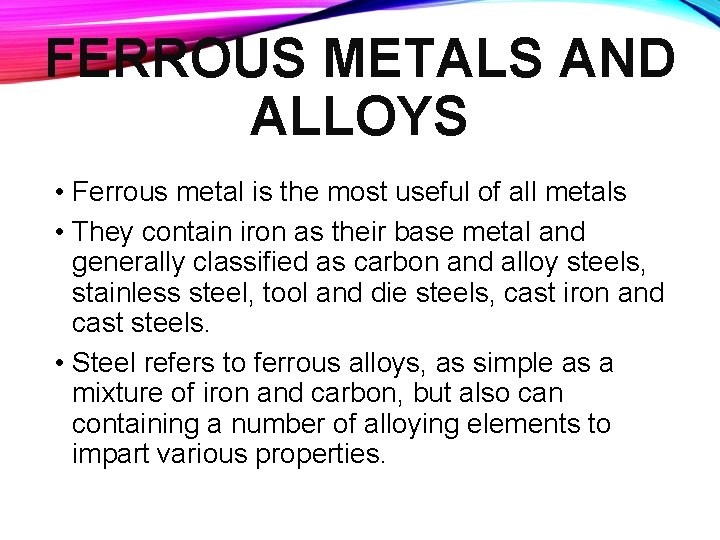
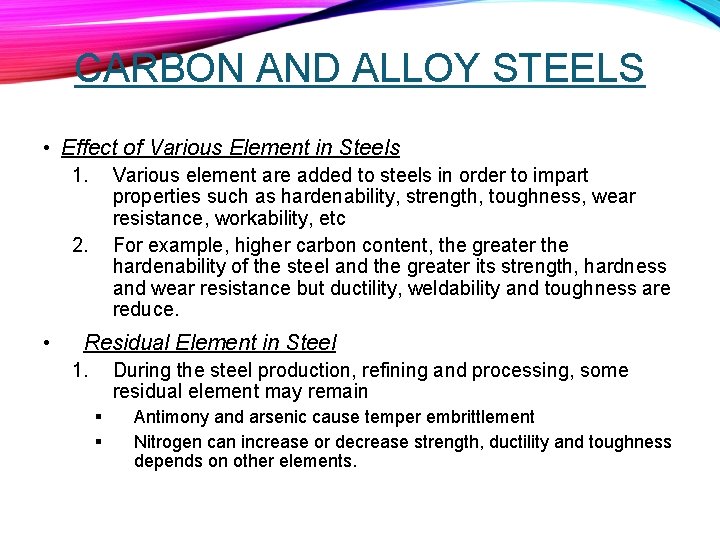
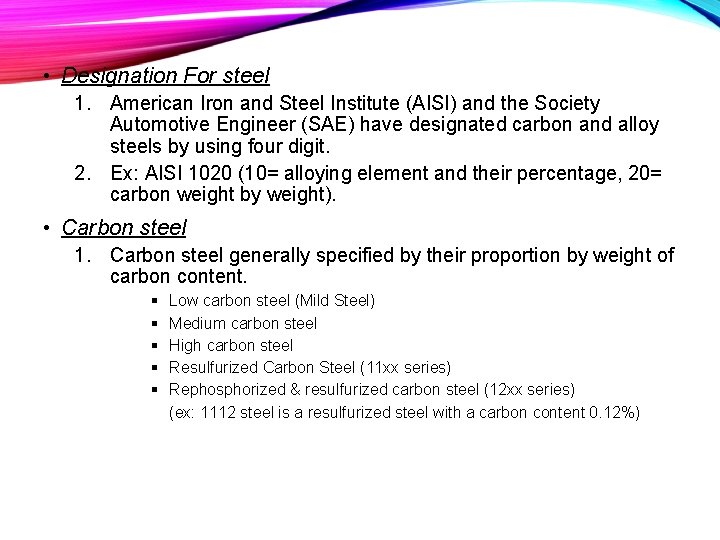
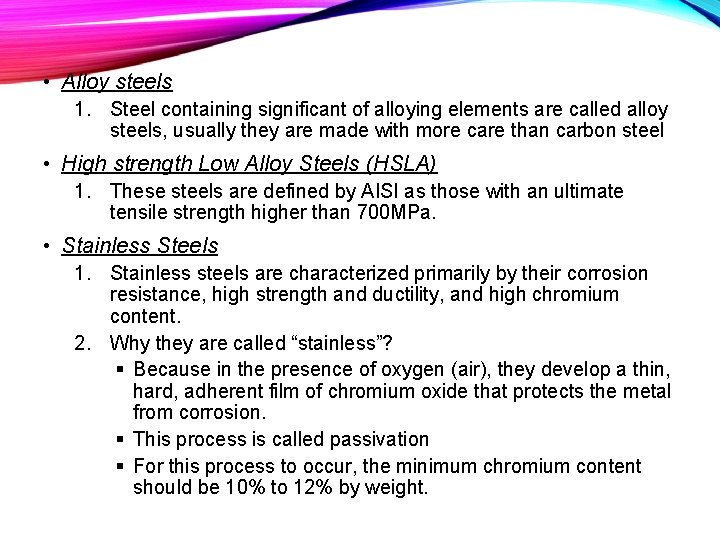
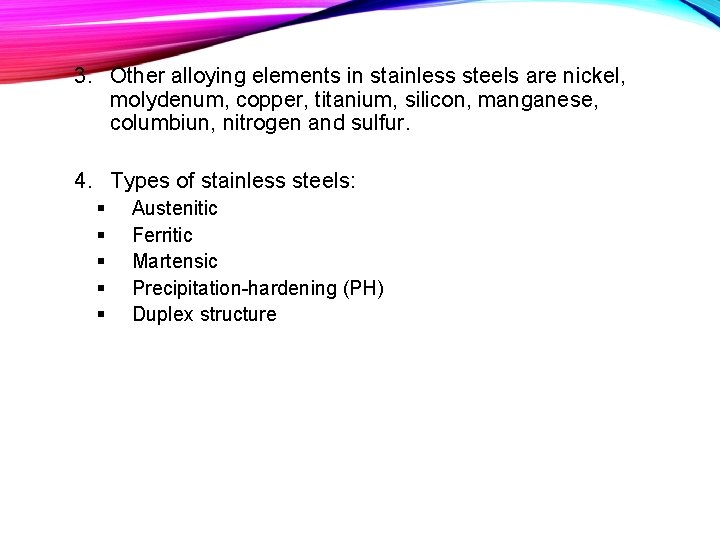
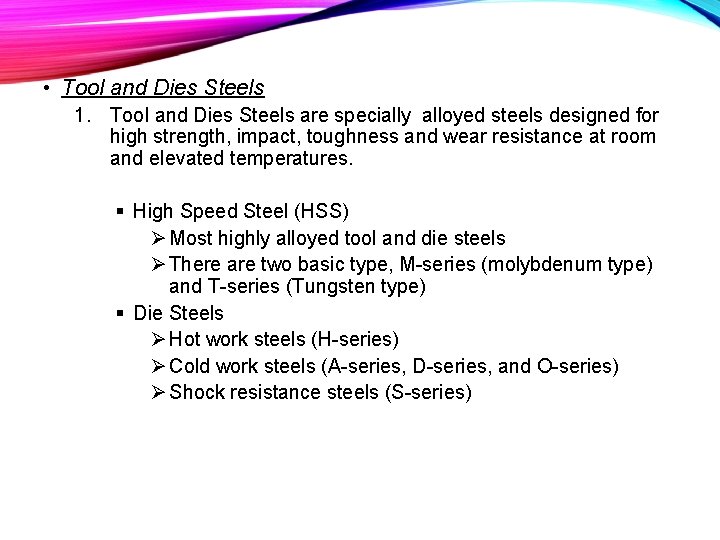
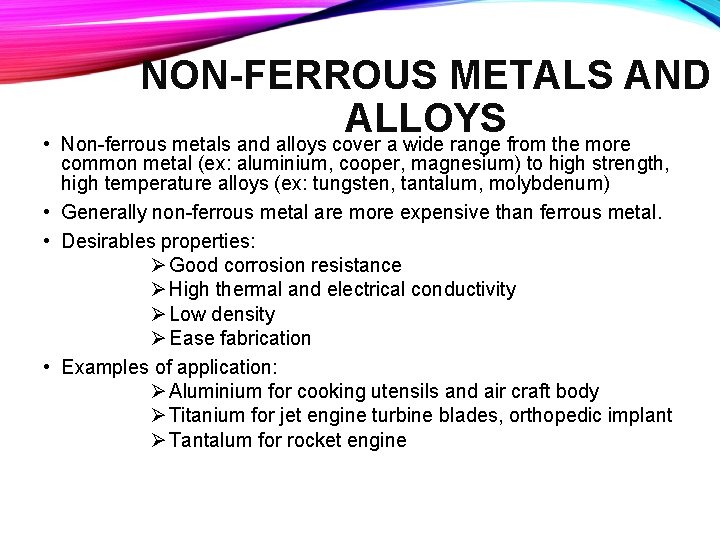
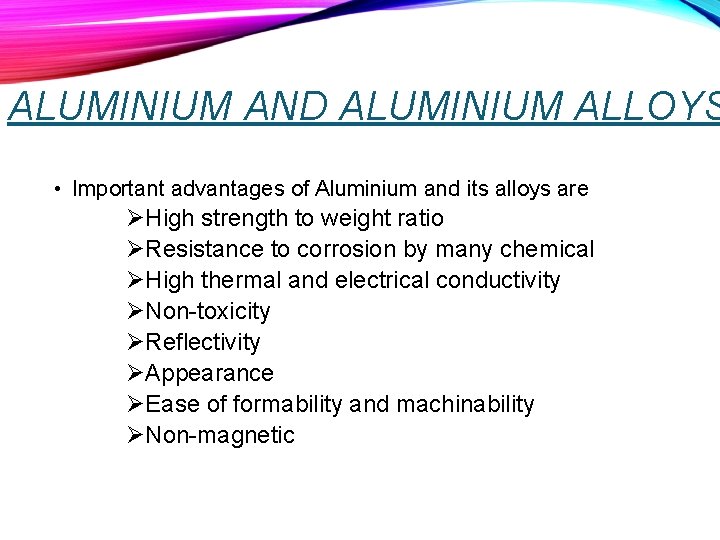
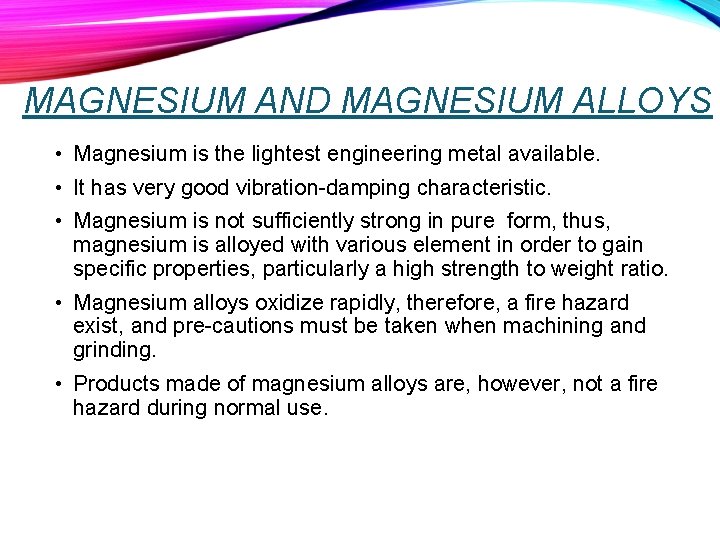
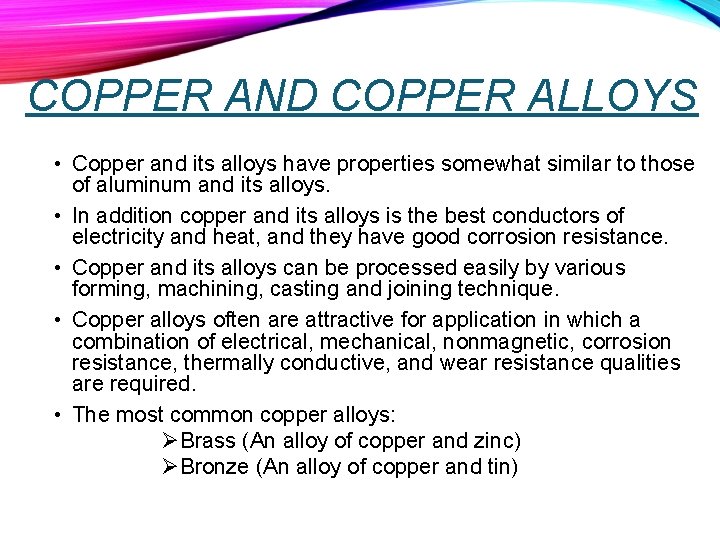
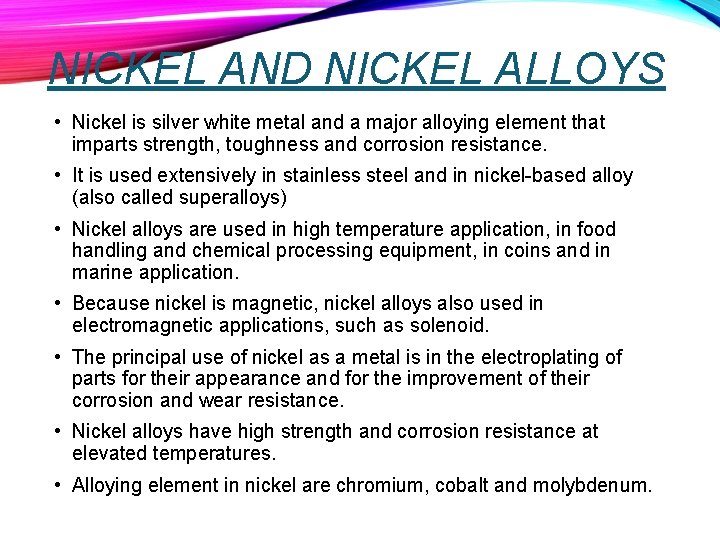
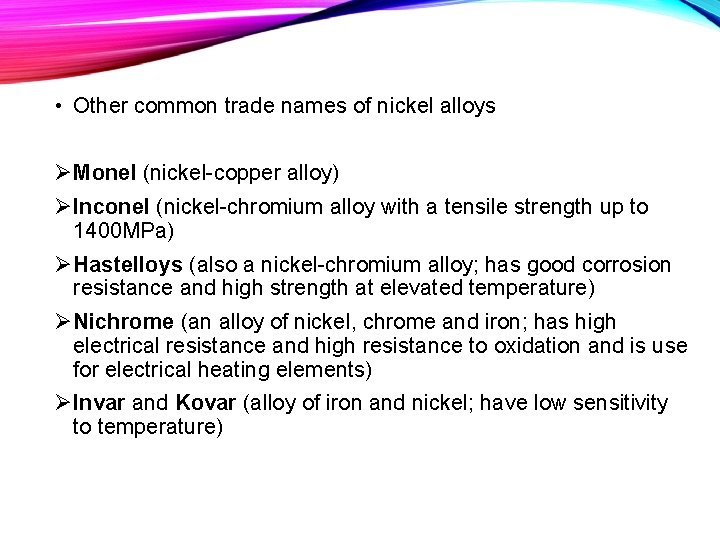
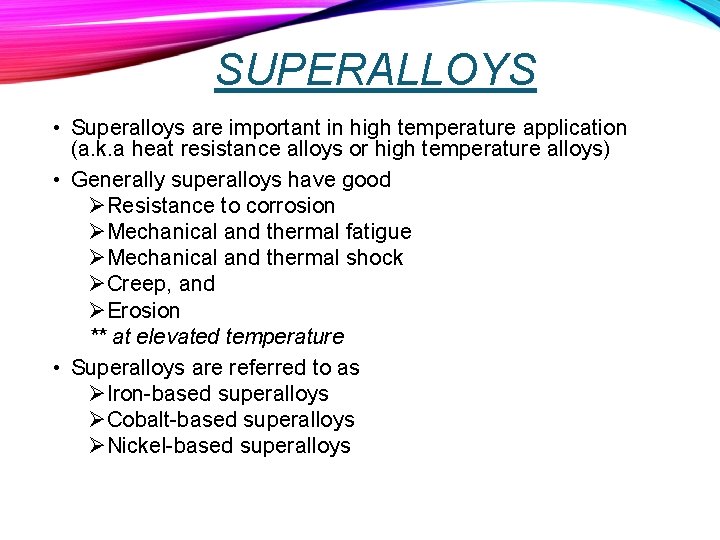
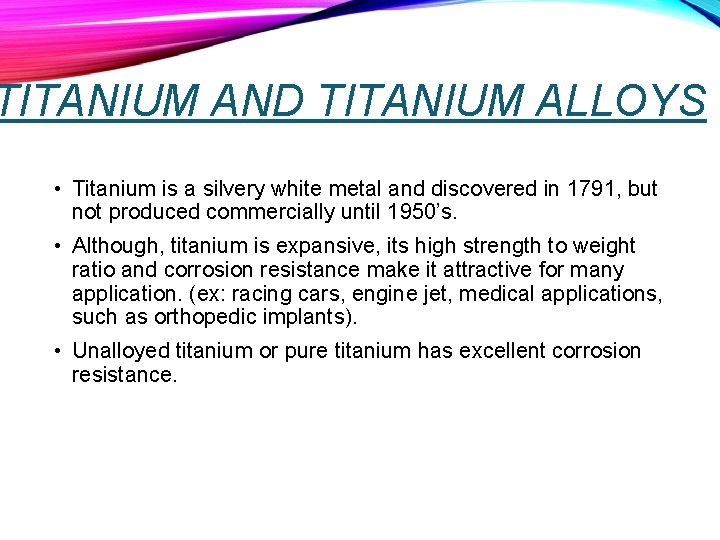
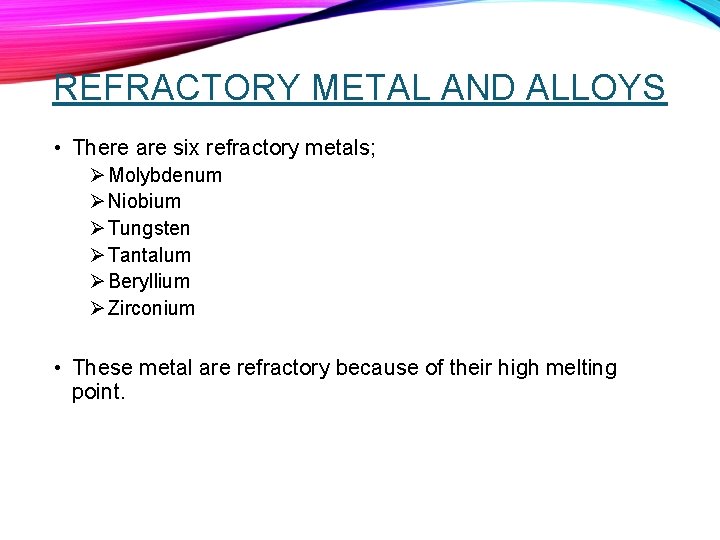
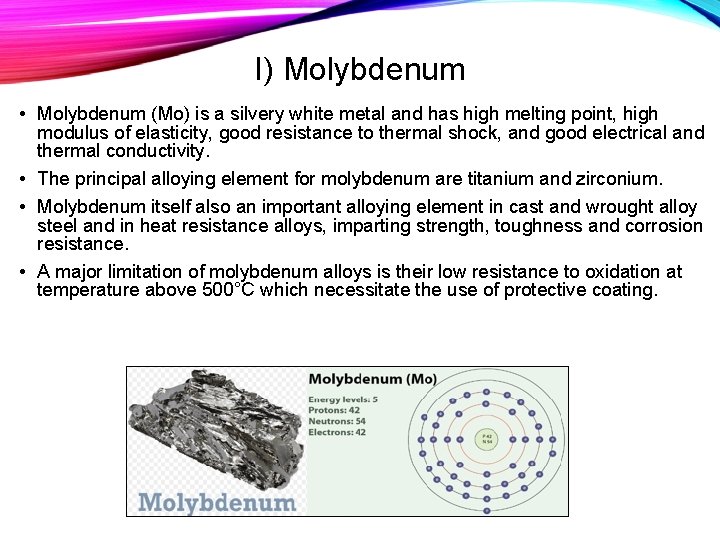
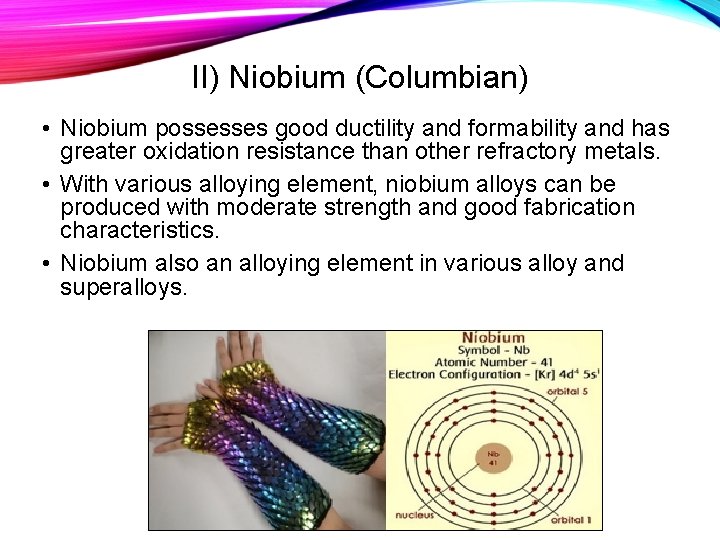
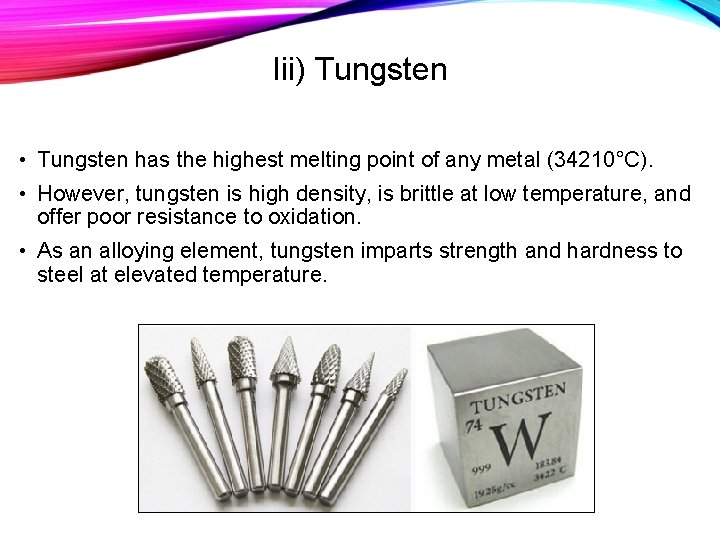
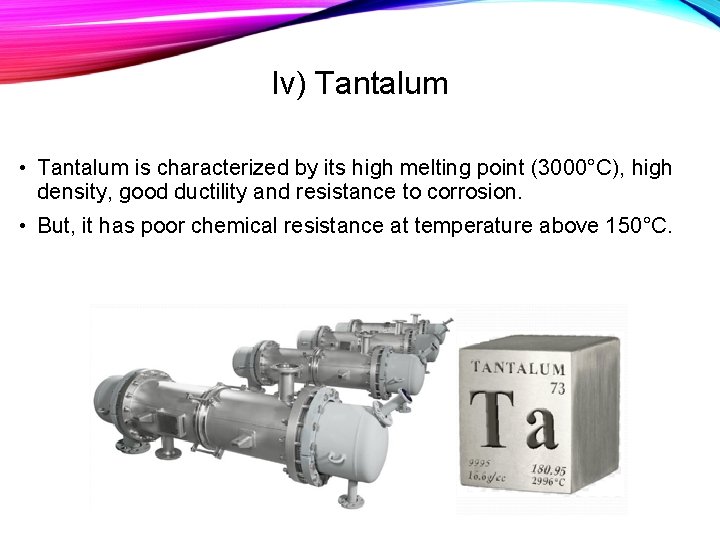
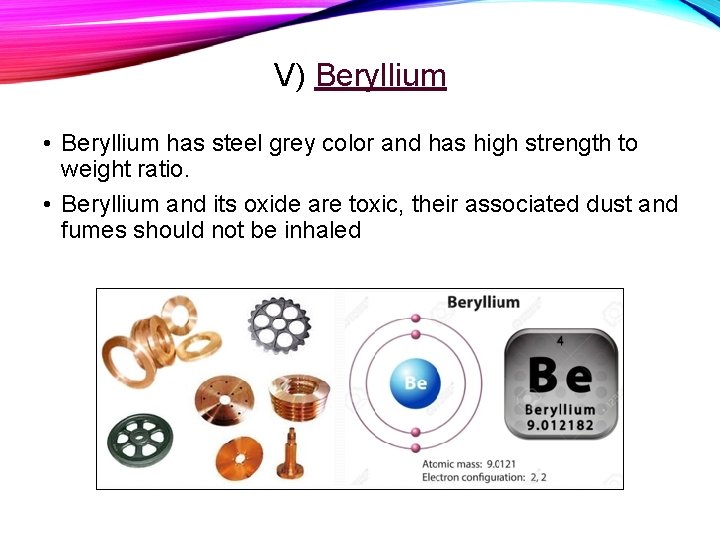
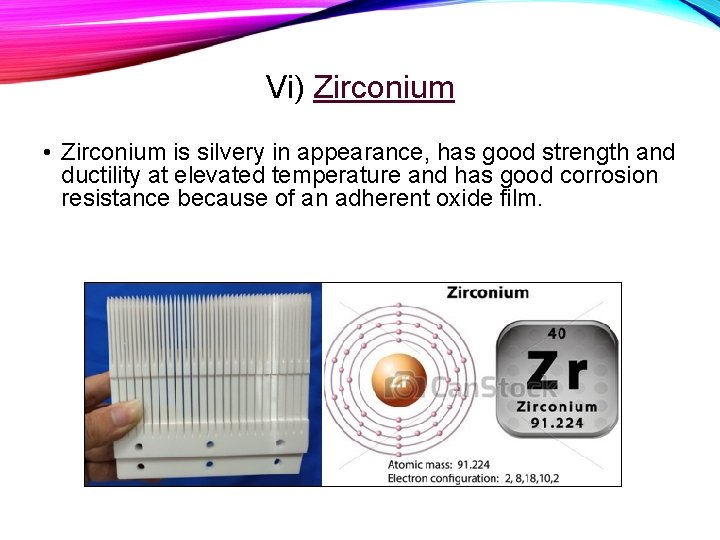
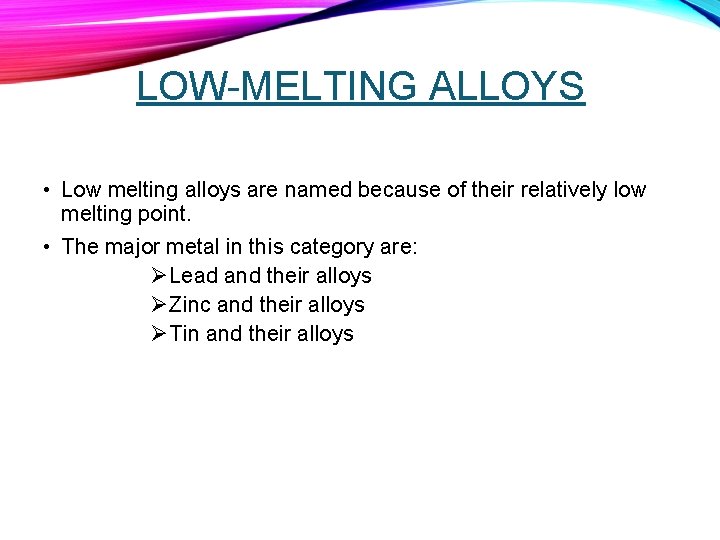
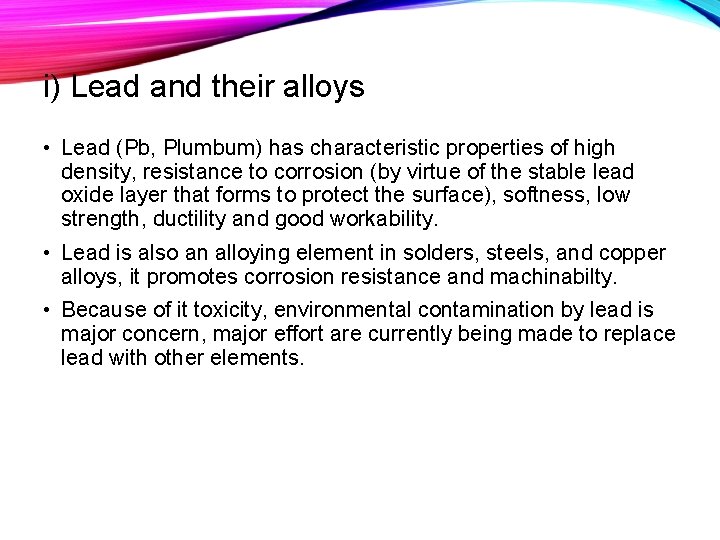
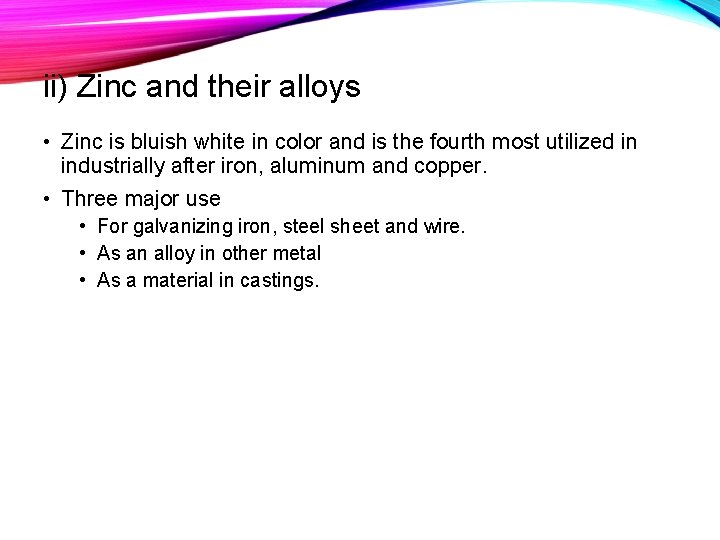
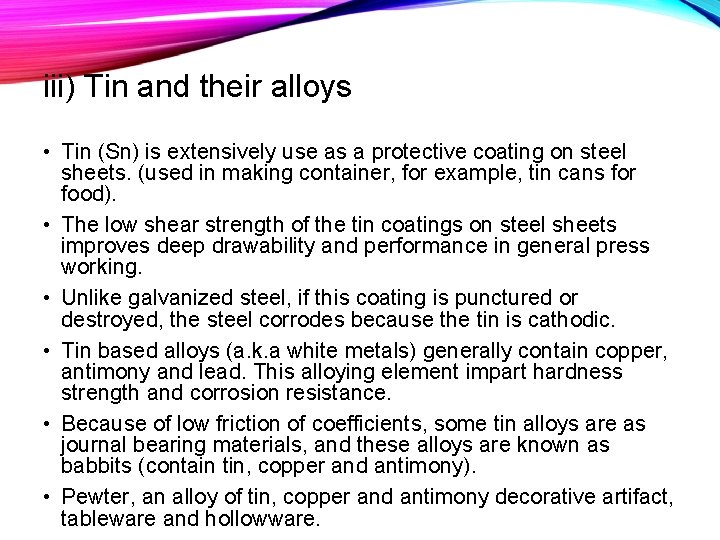
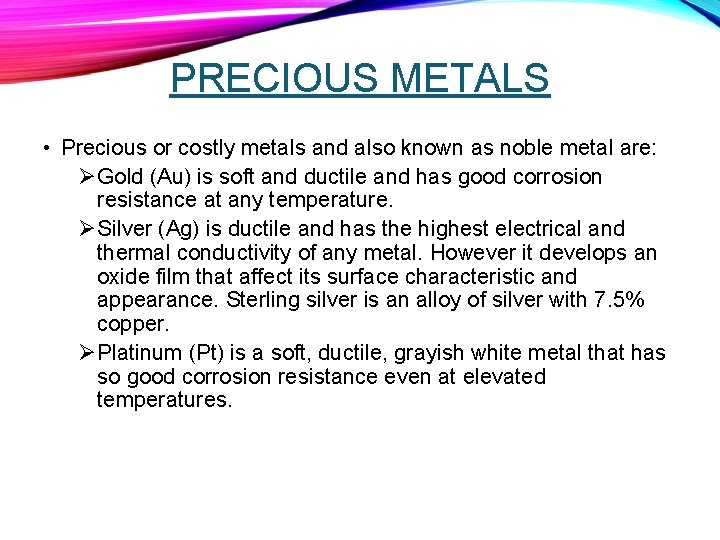
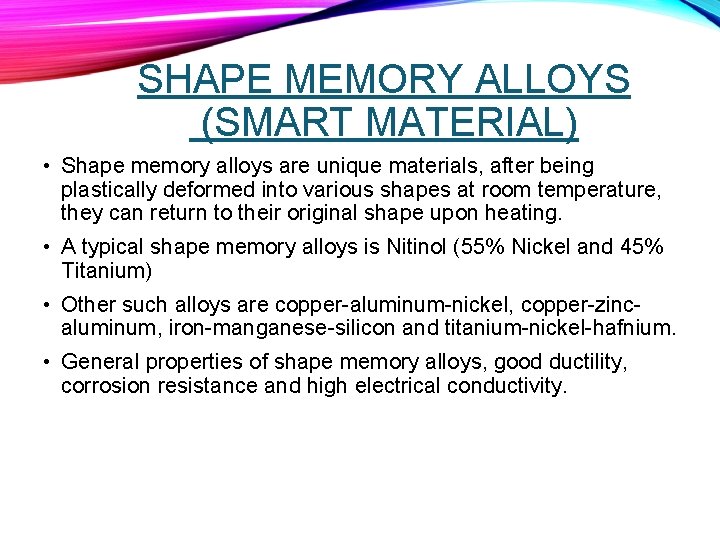
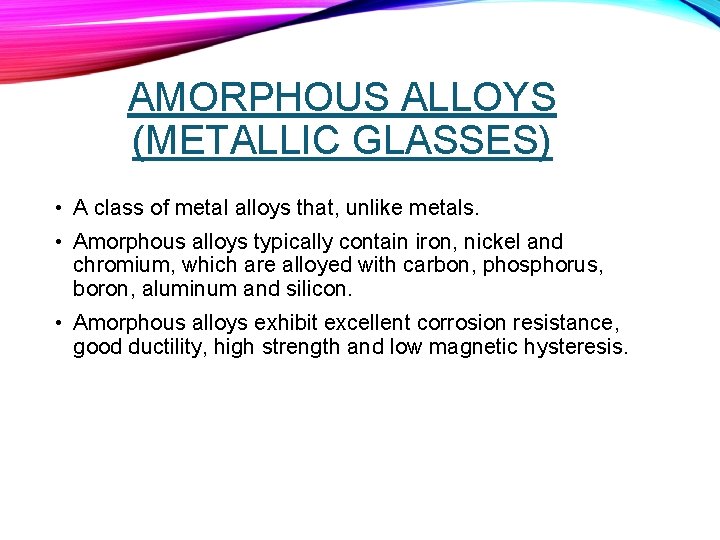

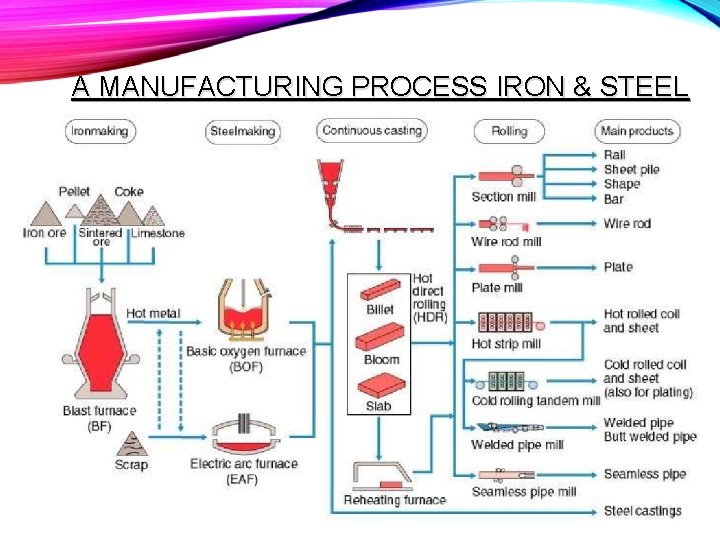
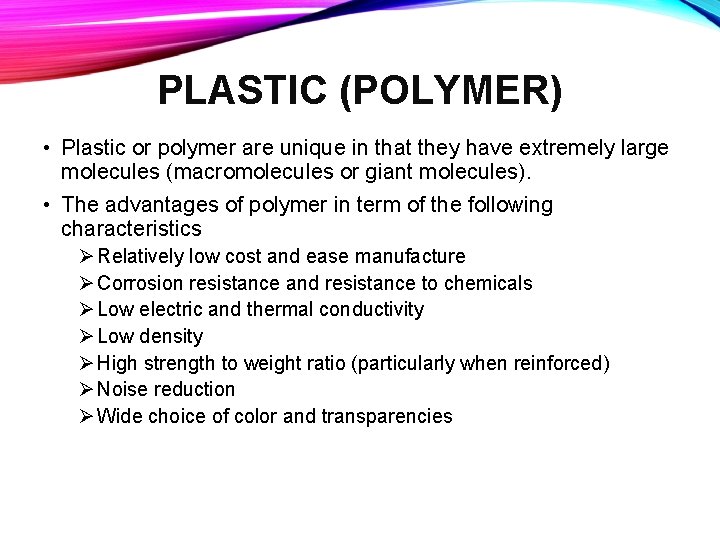
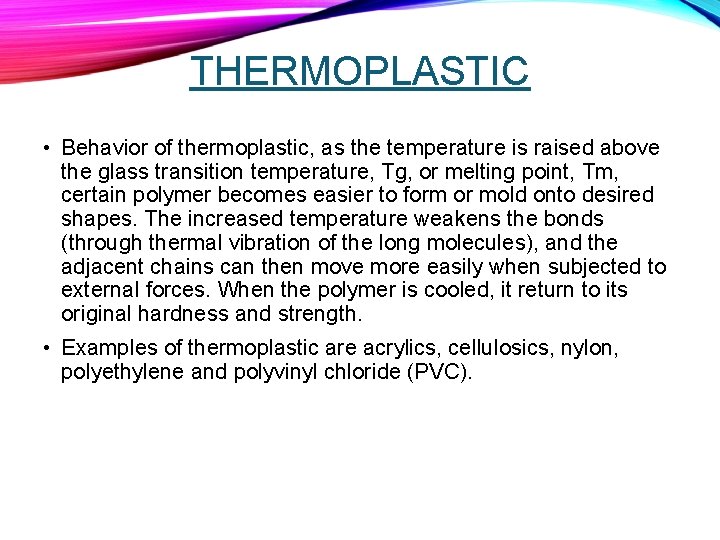
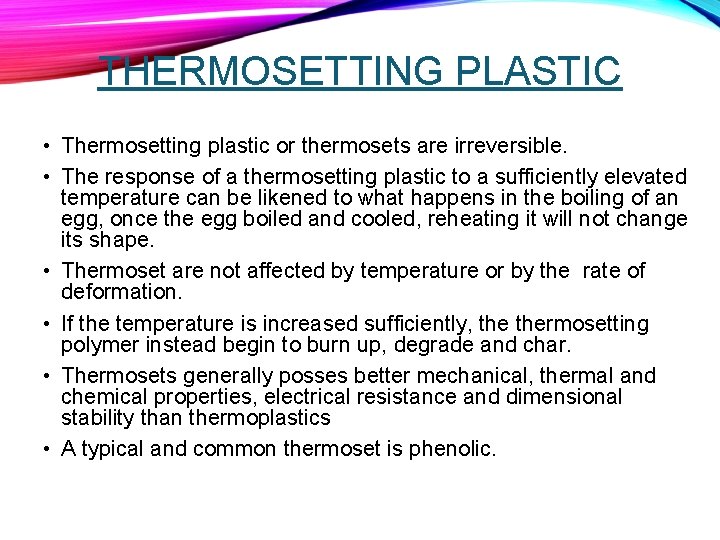

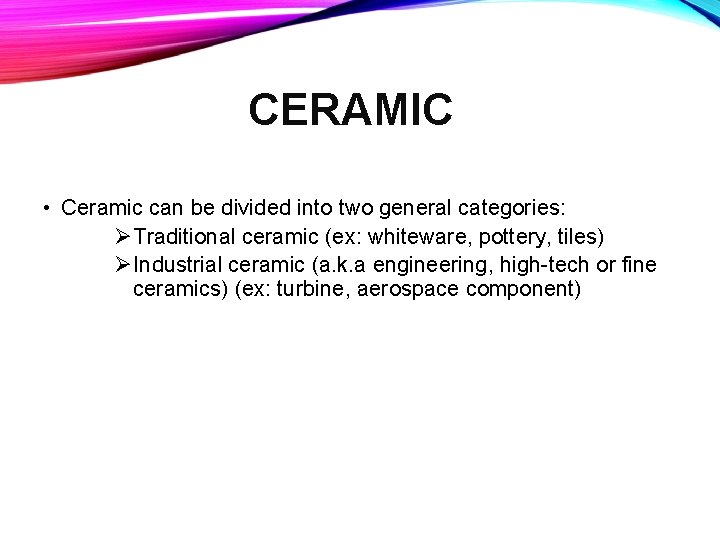
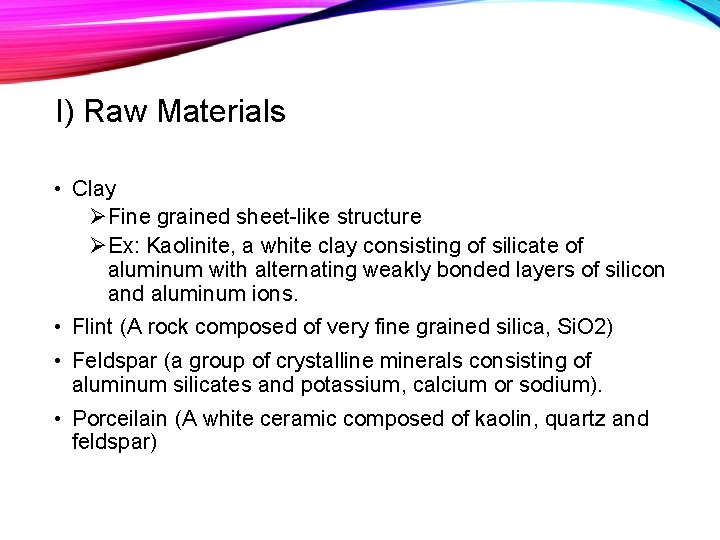
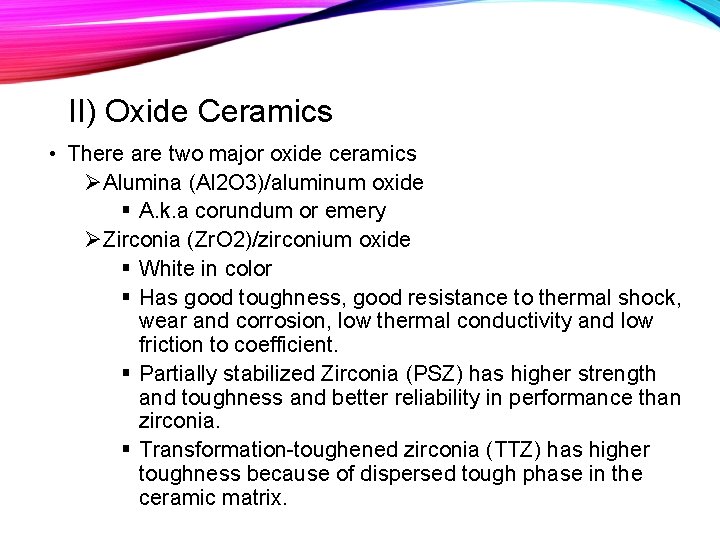
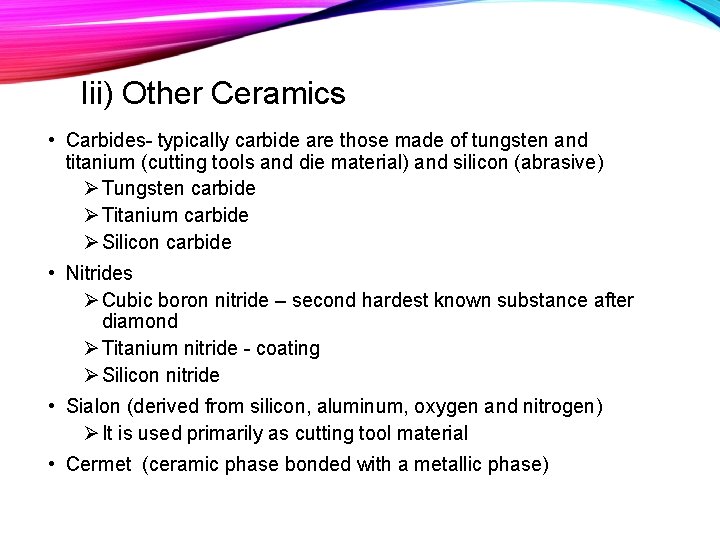
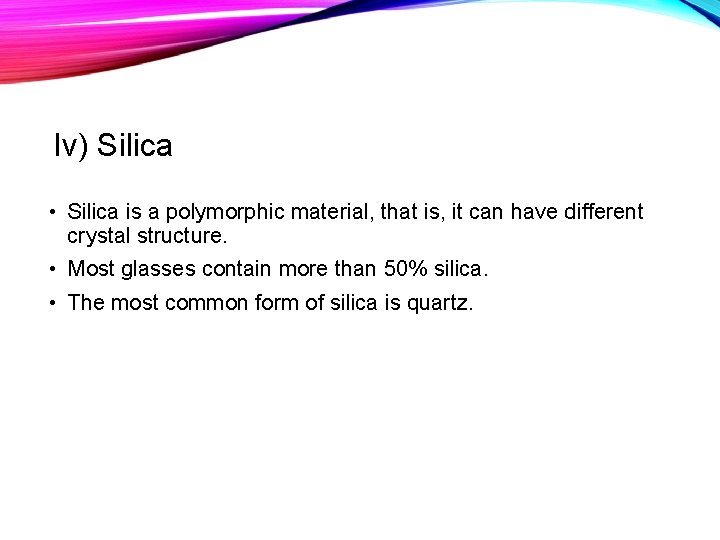
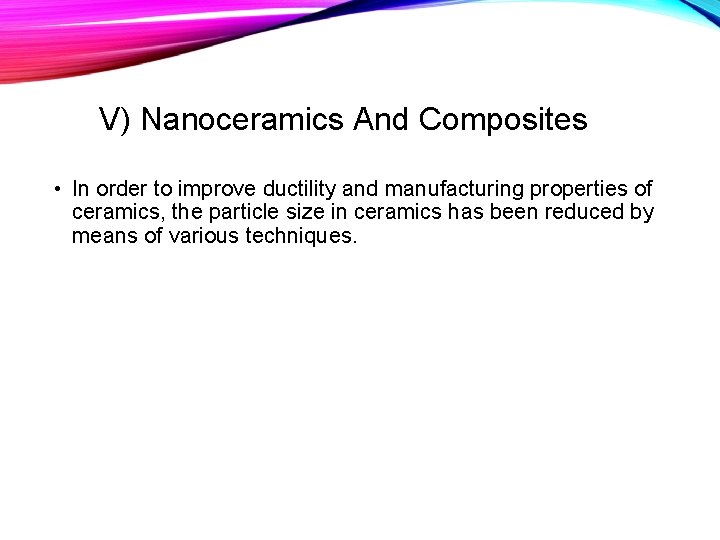
- Slides: 43
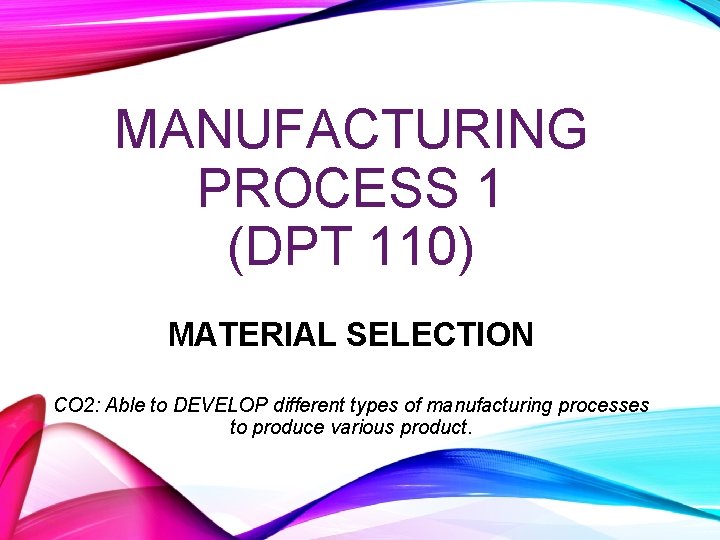
MANUFACTURING PROCESS 1 (DPT 110) MATERIAL SELECTION CO 2: Able to DEVELOP different types of manufacturing processes to produce various product.
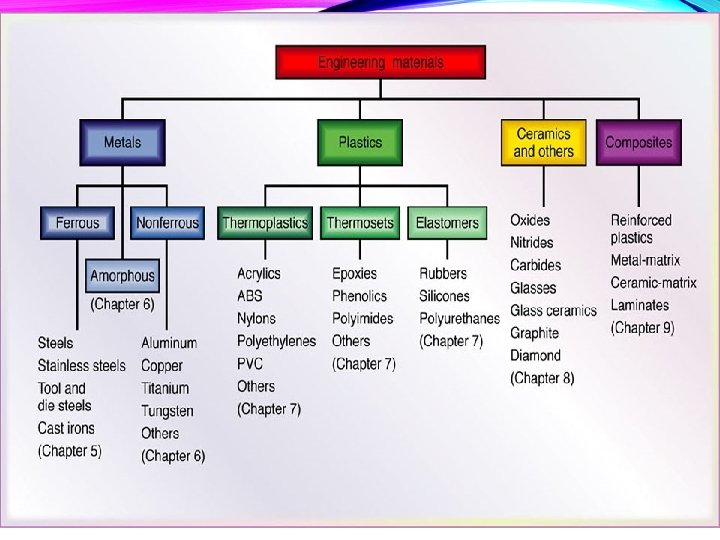
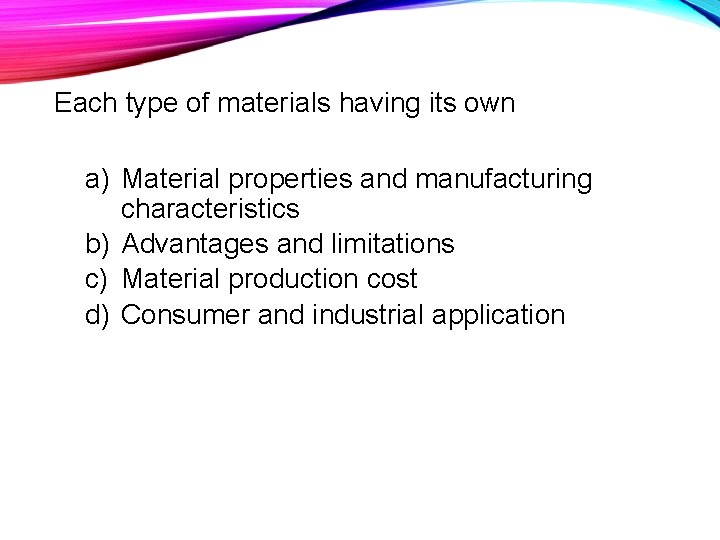
Each type of materials having its own a) Material properties and manufacturing characteristics b) Advantages and limitations c) Material production cost d) Consumer and industrial application
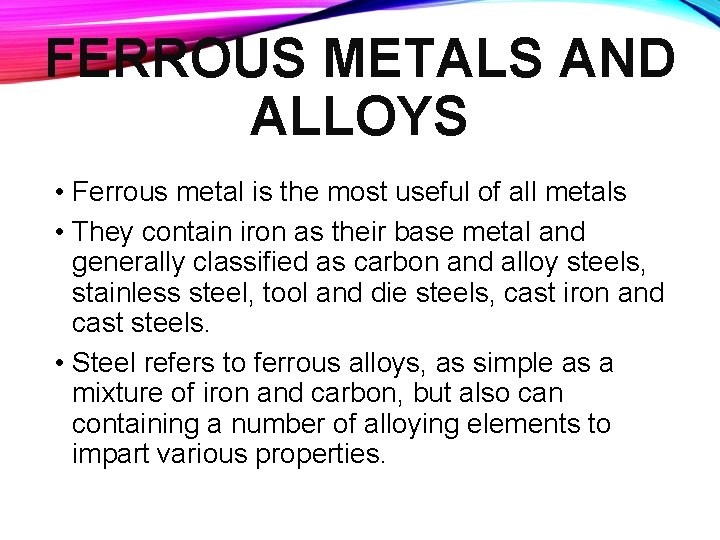
FERROUS METALS AND ALLOYS • Ferrous metal is the most useful of all metals • They contain iron as their base metal and generally classified as carbon and alloy steels, stainless steel, tool and die steels, cast iron and cast steels. • Steel refers to ferrous alloys, as simple as a mixture of iron and carbon, but also can containing a number of alloying elements to impart various properties.
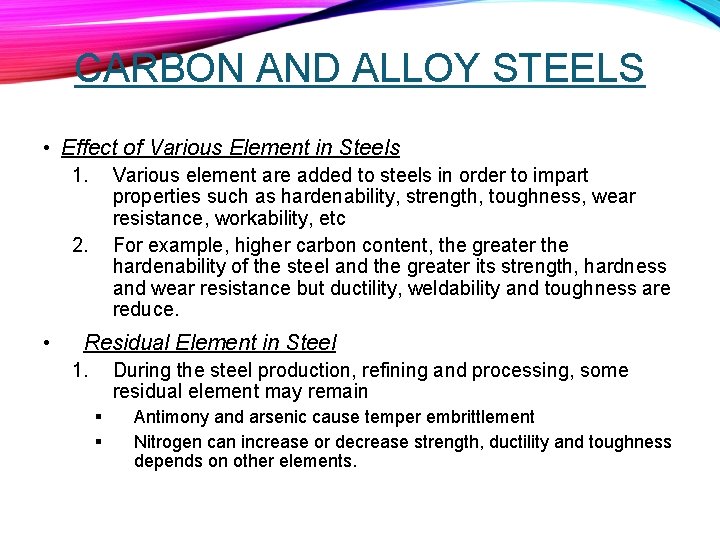
CARBON AND ALLOY STEELS • Effect of Various Element in Steels 1. Various element are added to steels in order to impart properties such as hardenability, strength, toughness, wear resistance, workability, etc For example, higher carbon content, the greater the hardenability of the steel and the greater its strength, hardness and wear resistance but ductility, weldability and toughness are reduce. 2. • Residual Element in Steel 1. During the steel production, refining and processing, some residual element may remain § § Antimony and arsenic cause temper embrittlement Nitrogen can increase or decrease strength, ductility and toughness depends on other elements.
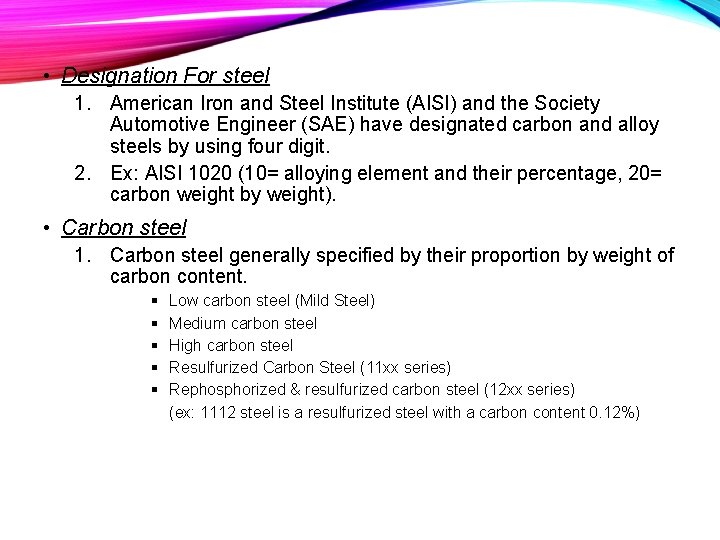
• Designation For steel 1. American Iron and Steel Institute (AISI) and the Society Automotive Engineer (SAE) have designated carbon and alloy steels by using four digit. 2. Ex: AISI 1020 (10= alloying element and their percentage, 20= carbon weight by weight). • Carbon steel 1. Carbon steel generally specified by their proportion by weight of carbon content. § § § Low carbon steel (Mild Steel) Medium carbon steel High carbon steel Resulfurized Carbon Steel (11 xx series) Rephosphorized & resulfurized carbon steel (12 xx series) (ex: 1112 steel is a resulfurized steel with a carbon content 0. 12%)
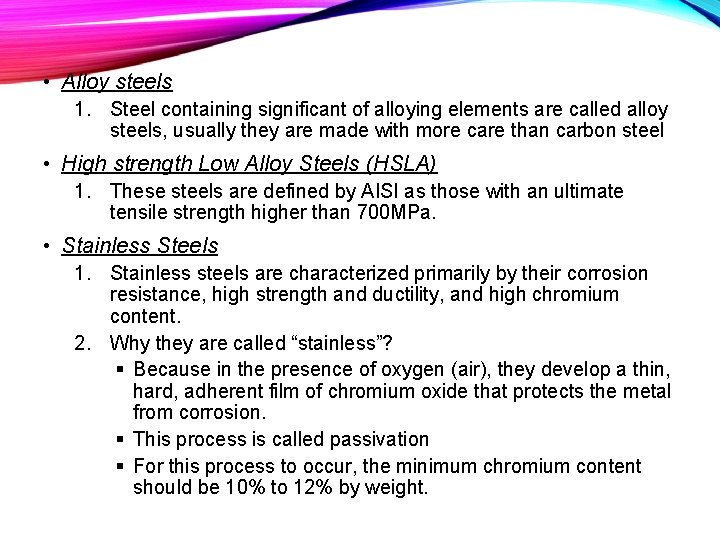
• Alloy steels 1. Steel containing significant of alloying elements are called alloy steels, usually they are made with more care than carbon steel • High strength Low Alloy Steels (HSLA) 1. These steels are defined by AISI as those with an ultimate tensile strength higher than 700 MPa. • Stainless Steels 1. Stainless steels are characterized primarily by their corrosion resistance, high strength and ductility, and high chromium content. 2. Why they are called “stainless”? § Because in the presence of oxygen (air), they develop a thin, hard, adherent film of chromium oxide that protects the metal from corrosion. § This process is called passivation § For this process to occur, the minimum chromium content should be 10% to 12% by weight.
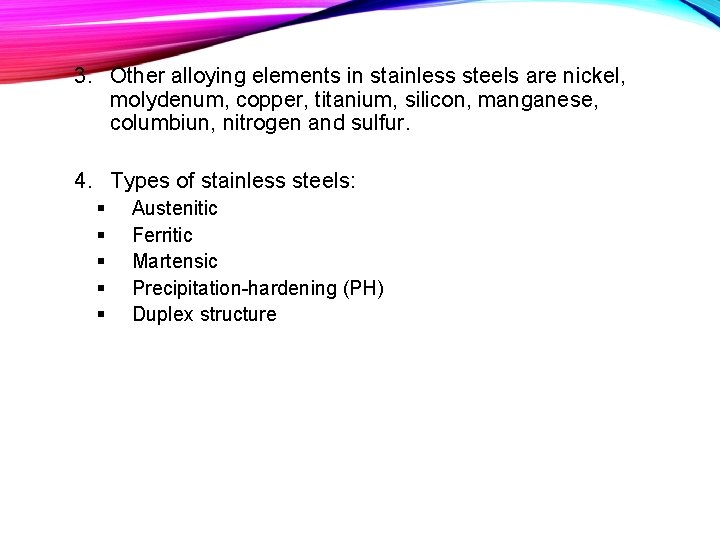
3. Other alloying elements in stainless steels are nickel, molydenum, copper, titanium, silicon, manganese, columbiun, nitrogen and sulfur. 4. Types of stainless steels: § § § Austenitic Ferritic Martensic Precipitation-hardening (PH) Duplex structure
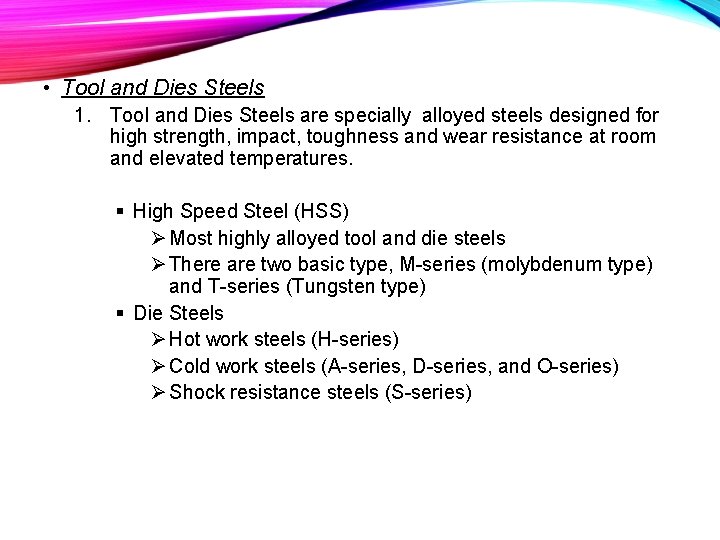
• Tool and Dies Steels 1. Tool and Dies Steels are specially alloyed steels designed for high strength, impact, toughness and wear resistance at room and elevated temperatures. § High Speed Steel (HSS) Ø Most highly alloyed tool and die steels Ø There are two basic type, M-series (molybdenum type) and T-series (Tungsten type) § Die Steels Ø Hot work steels (H-series) Ø Cold work steels (A-series, D-series, and O-series) Ø Shock resistance steels (S-series)
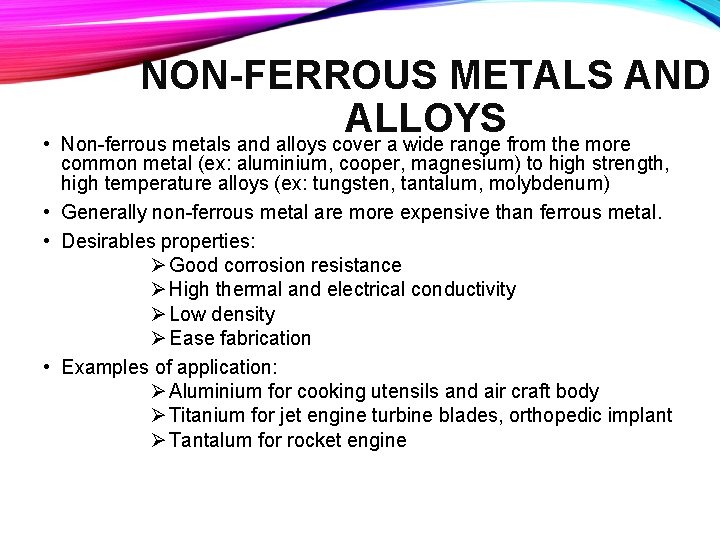
NON-FERROUS METALS AND ALLOYS • Non-ferrous metals and alloys cover a wide range from the more common metal (ex: aluminium, cooper, magnesium) to high strength, high temperature alloys (ex: tungsten, tantalum, molybdenum) • Generally non-ferrous metal are more expensive than ferrous metal. • Desirables properties: Ø Good corrosion resistance Ø High thermal and electrical conductivity Ø Low density Ø Ease fabrication • Examples of application: Ø Aluminium for cooking utensils and air craft body Ø Titanium for jet engine turbine blades, orthopedic implant Ø Tantalum for rocket engine
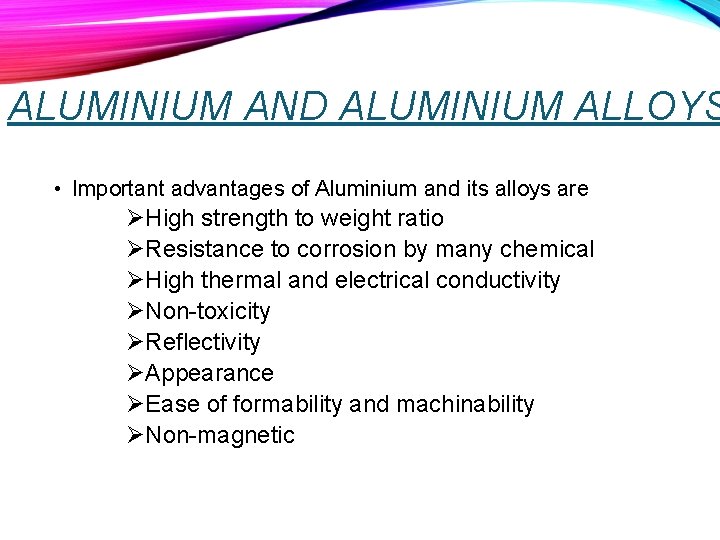
ALUMINIUM AND ALUMINIUM ALLOYS • Important advantages of Aluminium and its alloys are ØHigh strength to weight ratio ØResistance to corrosion by many chemical ØHigh thermal and electrical conductivity ØNon-toxicity ØReflectivity ØAppearance ØEase of formability and machinability ØNon-magnetic
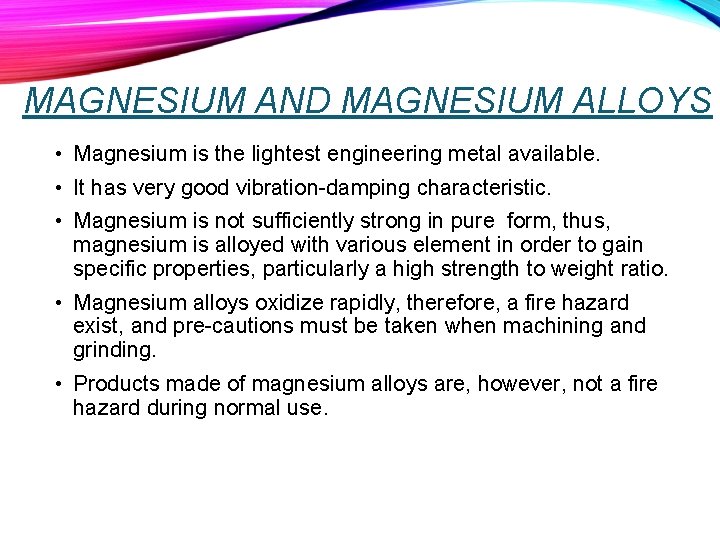
MAGNESIUM AND MAGNESIUM ALLOYS • Magnesium is the lightest engineering metal available. • It has very good vibration-damping characteristic. • Magnesium is not sufficiently strong in pure form, thus, magnesium is alloyed with various element in order to gain specific properties, particularly a high strength to weight ratio. • Magnesium alloys oxidize rapidly, therefore, a fire hazard exist, and pre-cautions must be taken when machining and grinding. • Products made of magnesium alloys are, however, not a fire hazard during normal use.
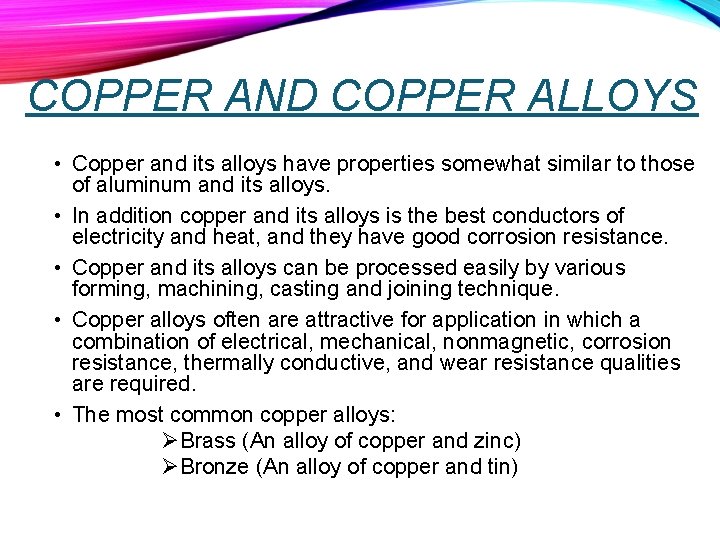
COPPER AND COPPER ALLOYS • Copper and its alloys have properties somewhat similar to those of aluminum and its alloys. • In addition copper and its alloys is the best conductors of electricity and heat, and they have good corrosion resistance. • Copper and its alloys can be processed easily by various forming, machining, casting and joining technique. • Copper alloys often are attractive for application in which a combination of electrical, mechanical, nonmagnetic, corrosion resistance, thermally conductive, and wear resistance qualities are required. • The most common copper alloys: ØBrass (An alloy of copper and zinc) ØBronze (An alloy of copper and tin)
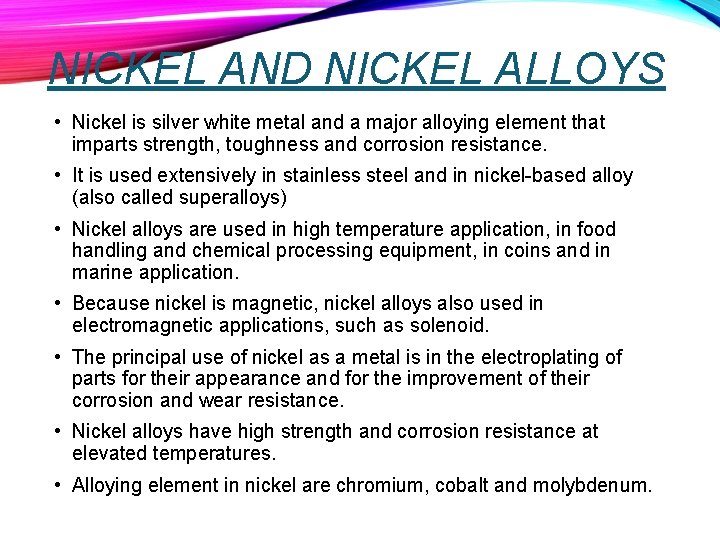
NICKEL AND NICKEL ALLOYS • Nickel is silver white metal and a major alloying element that imparts strength, toughness and corrosion resistance. • It is used extensively in stainless steel and in nickel-based alloy (also called superalloys) • Nickel alloys are used in high temperature application, in food handling and chemical processing equipment, in coins and in marine application. • Because nickel is magnetic, nickel alloys also used in electromagnetic applications, such as solenoid. • The principal use of nickel as a metal is in the electroplating of parts for their appearance and for the improvement of their corrosion and wear resistance. • Nickel alloys have high strength and corrosion resistance at elevated temperatures. • Alloying element in nickel are chromium, cobalt and molybdenum.
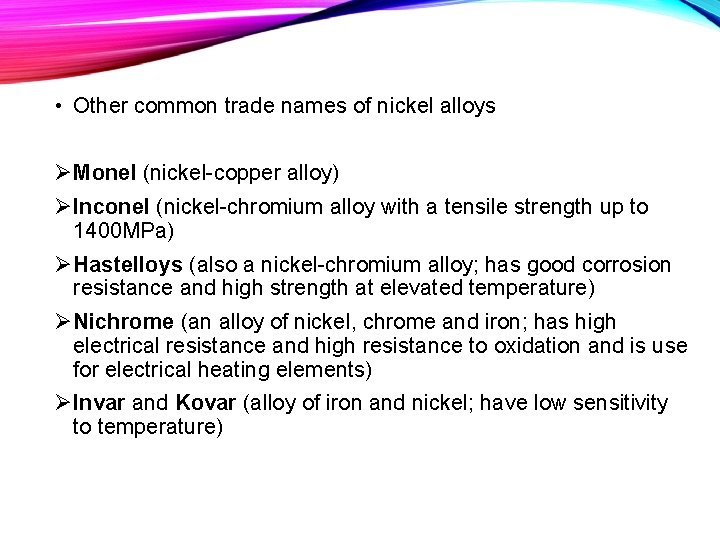
• Other common trade names of nickel alloys ØMonel (nickel-copper alloy) ØInconel (nickel-chromium alloy with a tensile strength up to 1400 MPa) ØHastelloys (also a nickel-chromium alloy; has good corrosion resistance and high strength at elevated temperature) ØNichrome (an alloy of nickel, chrome and iron; has high electrical resistance and high resistance to oxidation and is use for electrical heating elements) ØInvar and Kovar (alloy of iron and nickel; have low sensitivity to temperature)
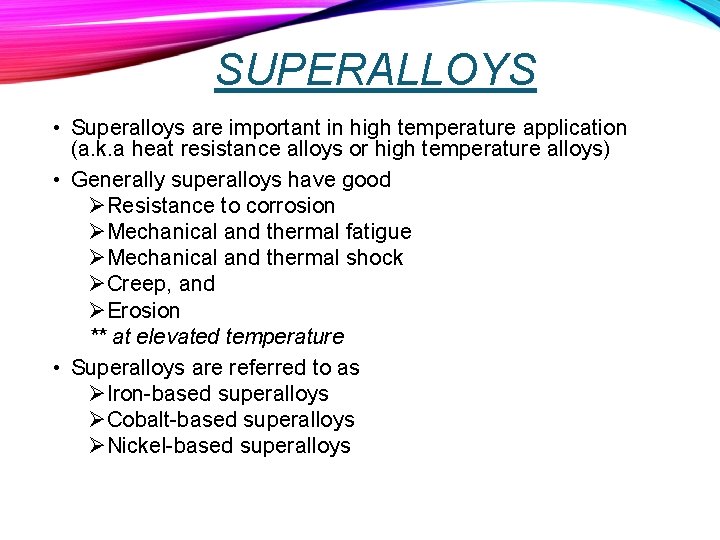
SUPERALLOYS • Superalloys are important in high temperature application (a. k. a heat resistance alloys or high temperature alloys) • Generally superalloys have good ØResistance to corrosion ØMechanical and thermal fatigue ØMechanical and thermal shock ØCreep, and ØErosion ** at elevated temperature • Superalloys are referred to as ØIron-based superalloys ØCobalt-based superalloys ØNickel-based superalloys
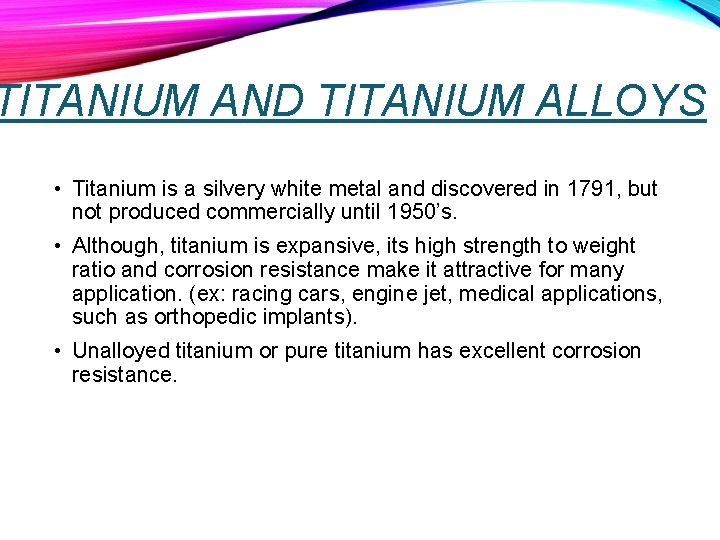
TITANIUM AND TITANIUM ALLOYS • Titanium is a silvery white metal and discovered in 1791, but not produced commercially until 1950’s. • Although, titanium is expansive, its high strength to weight ratio and corrosion resistance make it attractive for many application. (ex: racing cars, engine jet, medical applications, such as orthopedic implants). • Unalloyed titanium or pure titanium has excellent corrosion resistance.
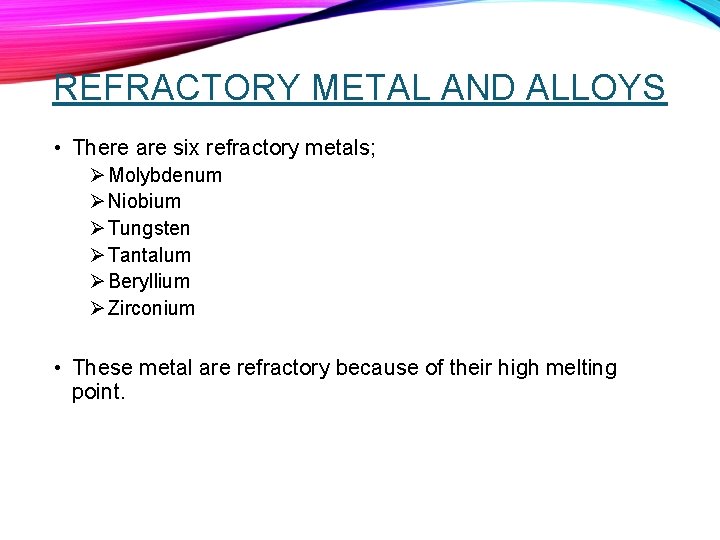
REFRACTORY METAL AND ALLOYS • There are six refractory metals; Ø Molybdenum Ø Niobium Ø Tungsten Ø Tantalum Ø Beryllium Ø Zirconium • These metal are refractory because of their high melting point.
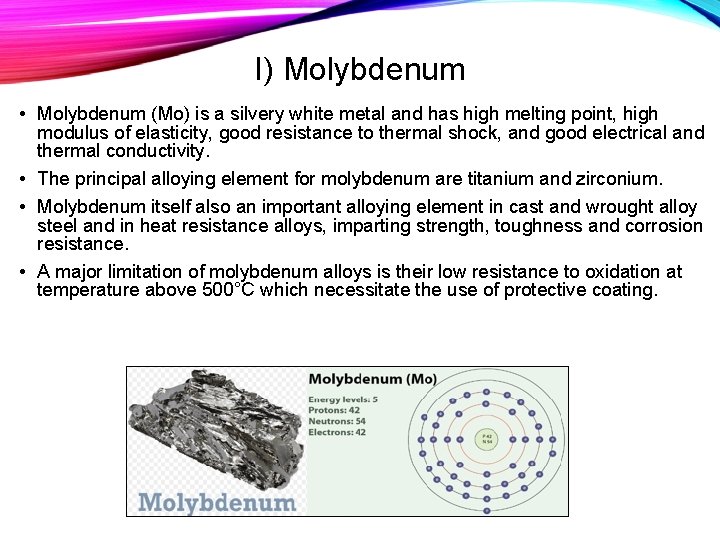
I) Molybdenum • Molybdenum (Mo) is a silvery white metal and has high melting point, high modulus of elasticity, good resistance to thermal shock, and good electrical and thermal conductivity. • The principal alloying element for molybdenum are titanium and zirconium. • Molybdenum itself also an important alloying element in cast and wrought alloy steel and in heat resistance alloys, imparting strength, toughness and corrosion resistance. • A major limitation of molybdenum alloys is their low resistance to oxidation at temperature above 500°C which necessitate the use of protective coating.
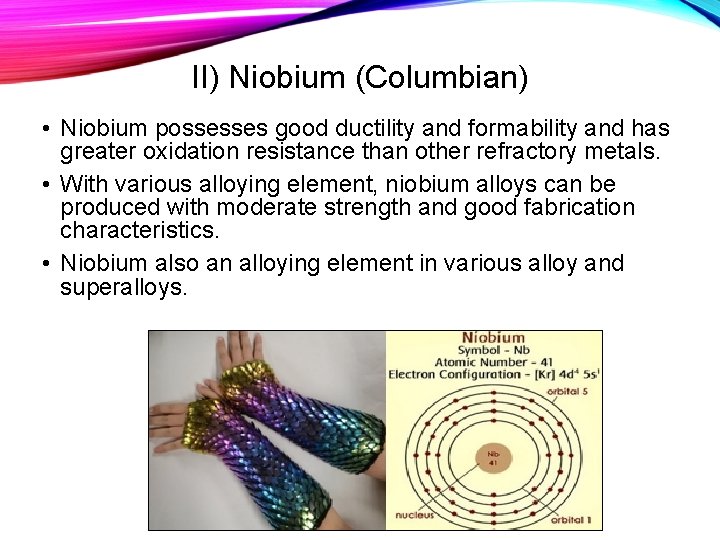
II) Niobium (Columbian) • Niobium possesses good ductility and formability and has greater oxidation resistance than other refractory metals. • With various alloying element, niobium alloys can be produced with moderate strength and good fabrication characteristics. • Niobium also an alloying element in various alloy and superalloys.
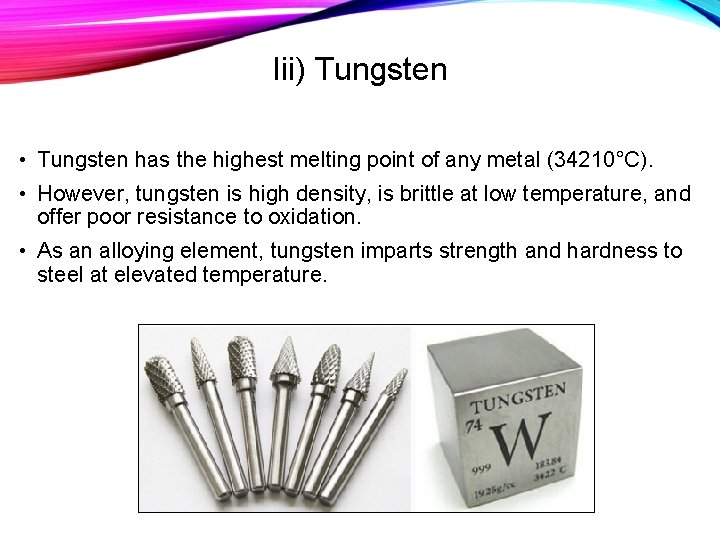
Iii) Tungsten • Tungsten has the highest melting point of any metal (34210°C). • However, tungsten is high density, is brittle at low temperature, and offer poor resistance to oxidation. • As an alloying element, tungsten imparts strength and hardness to steel at elevated temperature.
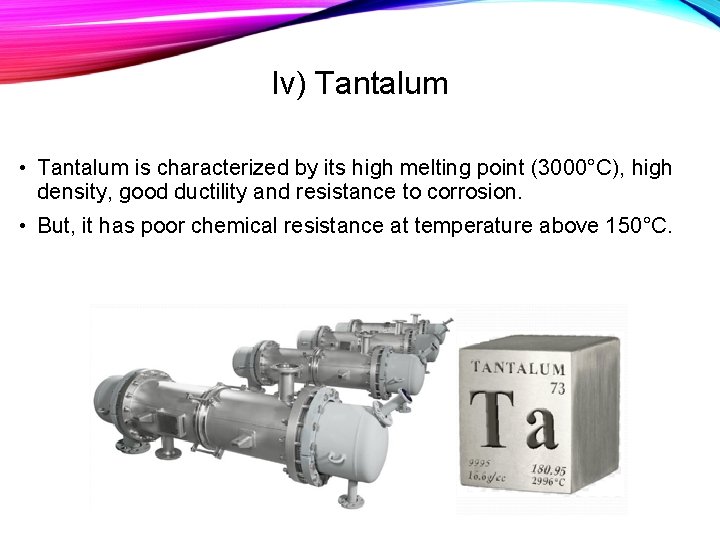
Iv) Tantalum • Tantalum is characterized by its high melting point (3000°C), high density, good ductility and resistance to corrosion. • But, it has poor chemical resistance at temperature above 150°C.
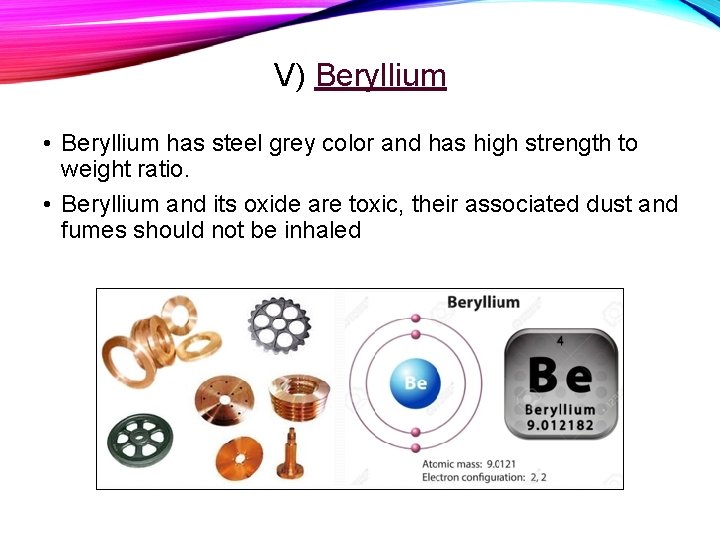
V) Beryllium • Beryllium has steel grey color and has high strength to weight ratio. • Beryllium and its oxide are toxic, their associated dust and fumes should not be inhaled
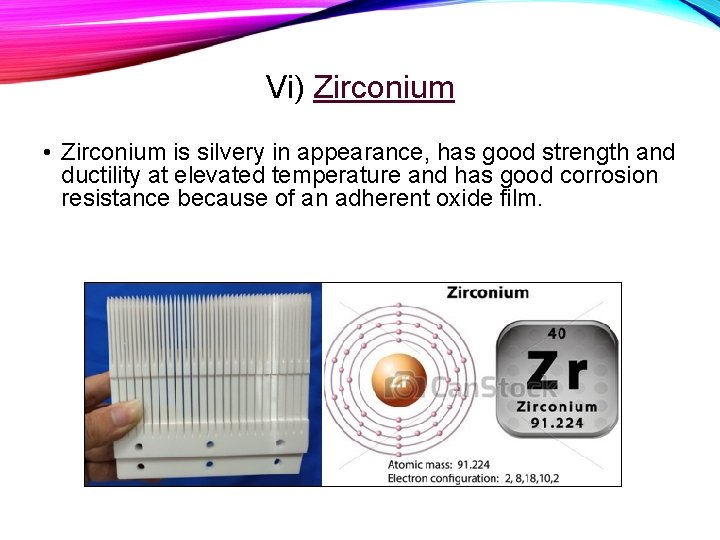
Vi) Zirconium • Zirconium is silvery in appearance, has good strength and ductility at elevated temperature and has good corrosion resistance because of an adherent oxide film.
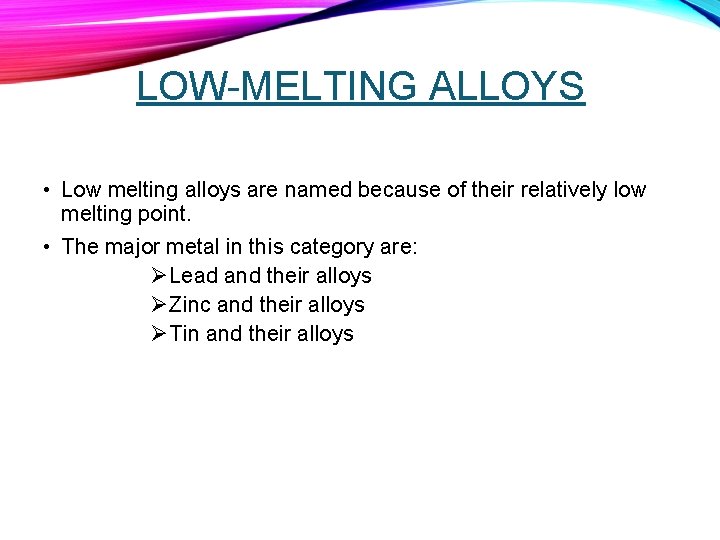
LOW-MELTING ALLOYS • Low melting alloys are named because of their relatively low melting point. • The major metal in this category are: ØLead and their alloys ØZinc and their alloys ØTin and their alloys
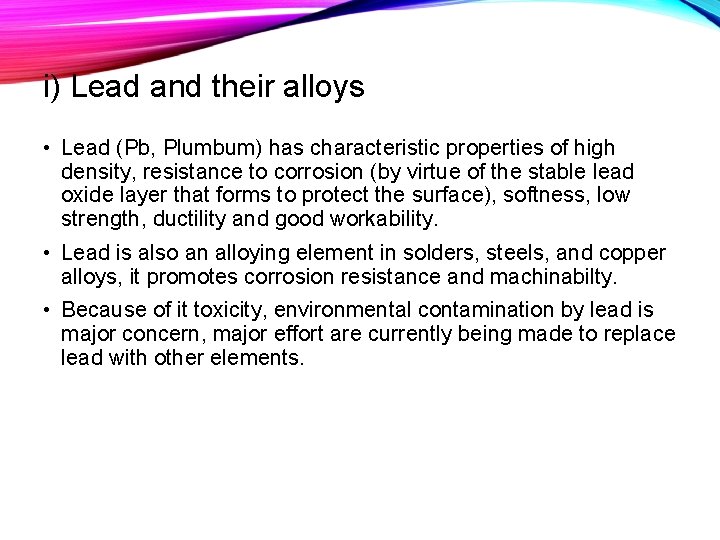
i) Lead and their alloys • Lead (Pb, Plumbum) has characteristic properties of high density, resistance to corrosion (by virtue of the stable lead oxide layer that forms to protect the surface), softness, low strength, ductility and good workability. • Lead is also an alloying element in solders, steels, and copper alloys, it promotes corrosion resistance and machinabilty. • Because of it toxicity, environmental contamination by lead is major concern, major effort are currently being made to replace lead with other elements.
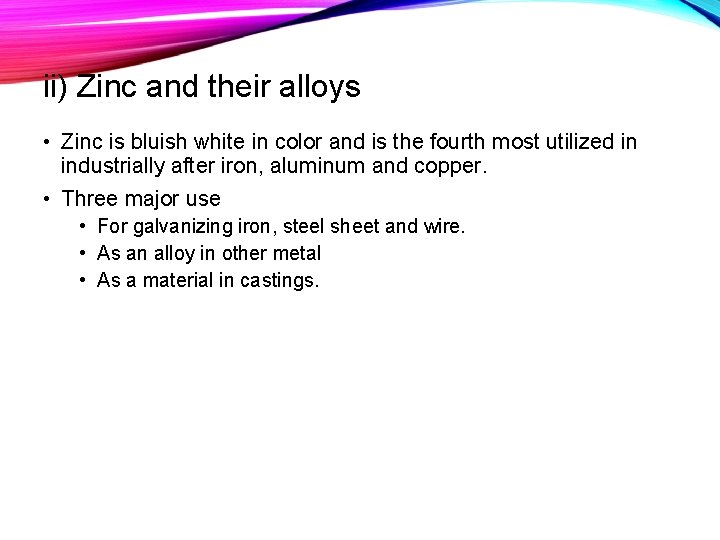
ii) Zinc and their alloys • Zinc is bluish white in color and is the fourth most utilized in industrially after iron, aluminum and copper. • Three major use • For galvanizing iron, steel sheet and wire. • As an alloy in other metal • As a material in castings.
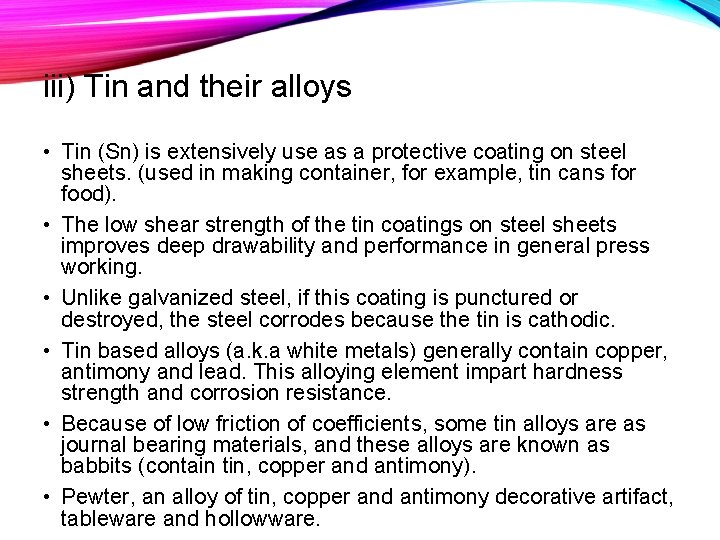
iii) Tin and their alloys • Tin (Sn) is extensively use as a protective coating on steel sheets. (used in making container, for example, tin cans for food). • The low shear strength of the tin coatings on steel sheets improves deep drawability and performance in general press working. • Unlike galvanized steel, if this coating is punctured or destroyed, the steel corrodes because the tin is cathodic. • Tin based alloys (a. k. a white metals) generally contain copper, antimony and lead. This alloying element impart hardness strength and corrosion resistance. • Because of low friction of coefficients, some tin alloys are as journal bearing materials, and these alloys are known as babbits (contain tin, copper and antimony). • Pewter, an alloy of tin, copper and antimony decorative artifact, tableware and hollowware.
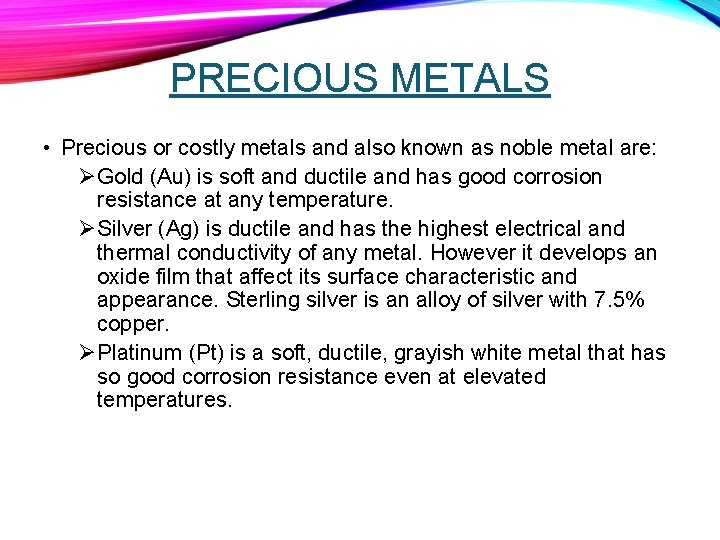
PRECIOUS METALS • Precious or costly metals and also known as noble metal are: ØGold (Au) is soft and ductile and has good corrosion resistance at any temperature. ØSilver (Ag) is ductile and has the highest electrical and thermal conductivity of any metal. However it develops an oxide film that affect its surface characteristic and appearance. Sterling silver is an alloy of silver with 7. 5% copper. ØPlatinum (Pt) is a soft, ductile, grayish white metal that has so good corrosion resistance even at elevated temperatures.
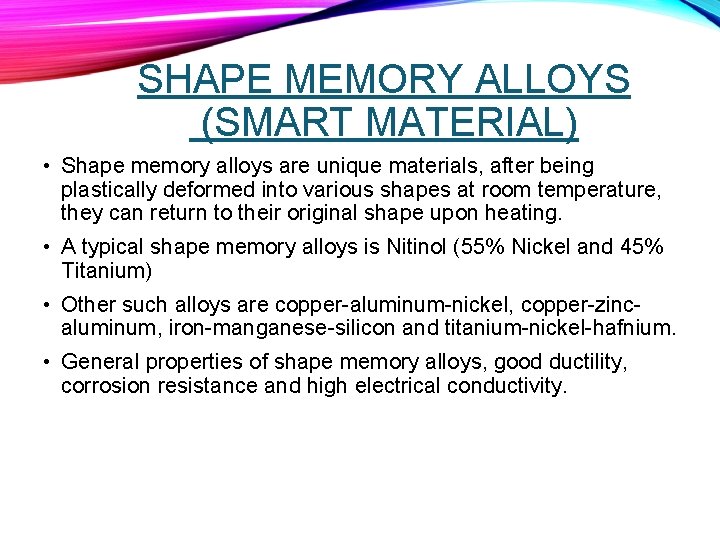
SHAPE MEMORY ALLOYS (SMART MATERIAL) • Shape memory alloys are unique materials, after being plastically deformed into various shapes at room temperature, they can return to their original shape upon heating. • A typical shape memory alloys is Nitinol (55% Nickel and 45% Titanium) • Other such alloys are copper-aluminum-nickel, copper-zincaluminum, iron-manganese-silicon and titanium-nickel-hafnium. • General properties of shape memory alloys, good ductility, corrosion resistance and high electrical conductivity.
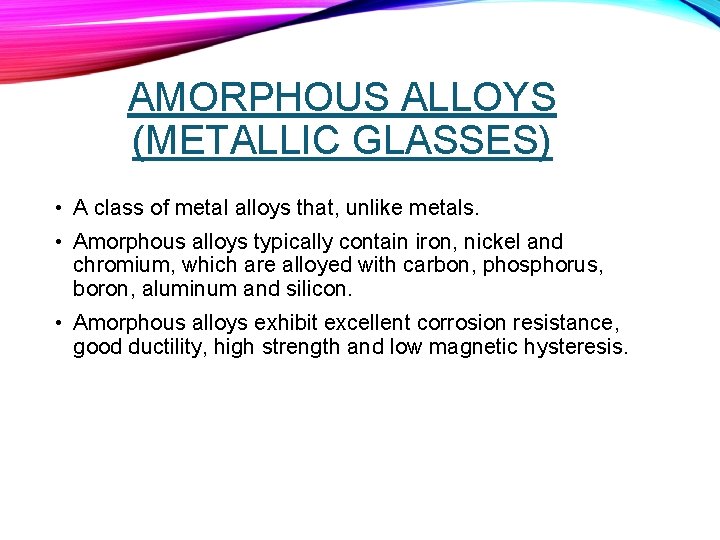
AMORPHOUS ALLOYS (METALLIC GLASSES) • A class of metal alloys that, unlike metals. • Amorphous alloys typically contain iron, nickel and chromium, which are alloyed with carbon, phosphorus, boron, aluminum and silicon. • Amorphous alloys exhibit excellent corrosion resistance, good ductility, high strength and low magnetic hysteresis.

METAL FOAMS • Metal foam are material structures where the metal consists of only 5 to 20% of the structure’s volume. • Usually made of aluminum alloys (but also of titanium, tantalum, and others). • Metal foam have unique combinations of strength to density and stiffness to density ratios, although this ratios are not as high as the base metal themselves. • Metal foam are very lightweight and thus attractive materials for aerospace application.
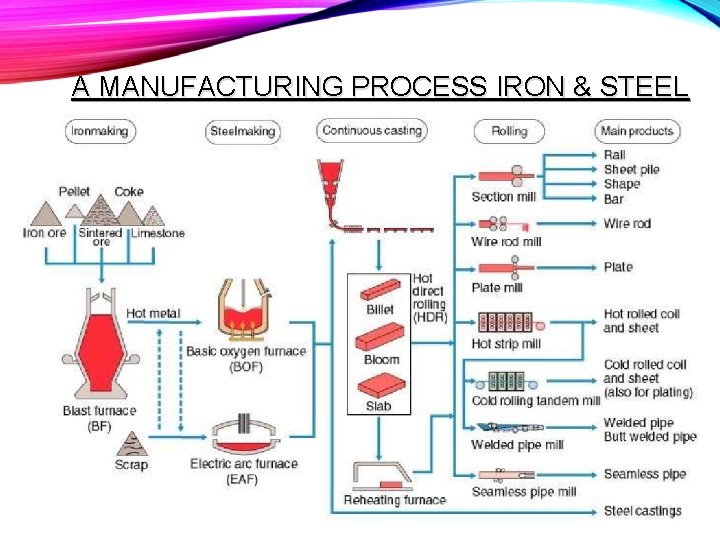
A MANUFACTURING PROCESS IRON & STEEL
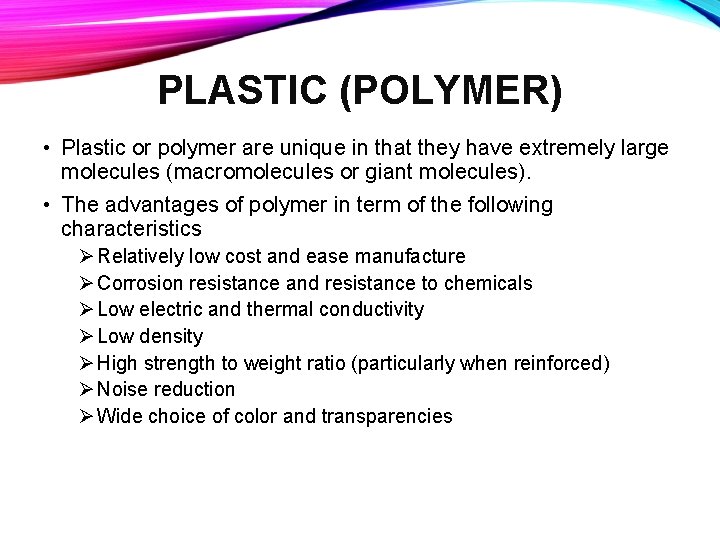
PLASTIC (POLYMER) • Plastic or polymer are unique in that they have extremely large molecules (macromolecules or giant molecules). • The advantages of polymer in term of the following characteristics Ø Relatively low cost and ease manufacture Ø Corrosion resistance and resistance to chemicals Ø Low electric and thermal conductivity Ø Low density Ø High strength to weight ratio (particularly when reinforced) Ø Noise reduction Ø Wide choice of color and transparencies
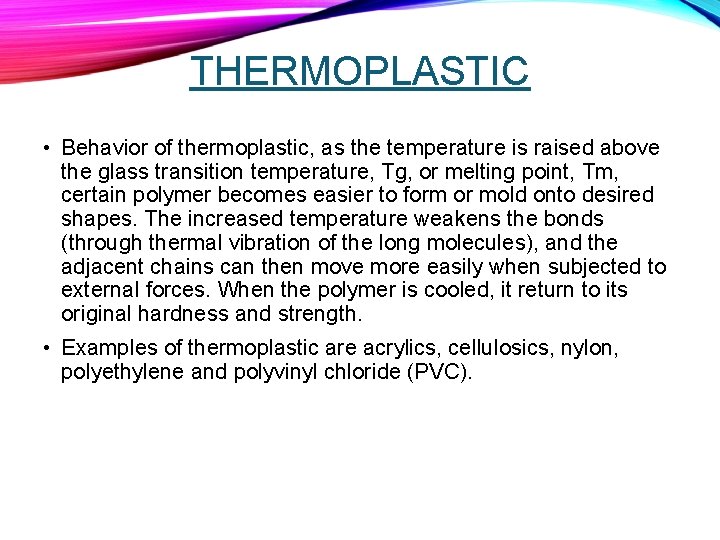
THERMOPLASTIC • Behavior of thermoplastic, as the temperature is raised above the glass transition temperature, Tg, or melting point, Tm, certain polymer becomes easier to form or mold onto desired shapes. The increased temperature weakens the bonds (through thermal vibration of the long molecules), and the adjacent chains can then move more easily when subjected to external forces. When the polymer is cooled, it return to its original hardness and strength. • Examples of thermoplastic are acrylics, cellulosics, nylon, polyethylene and polyvinyl chloride (PVC).
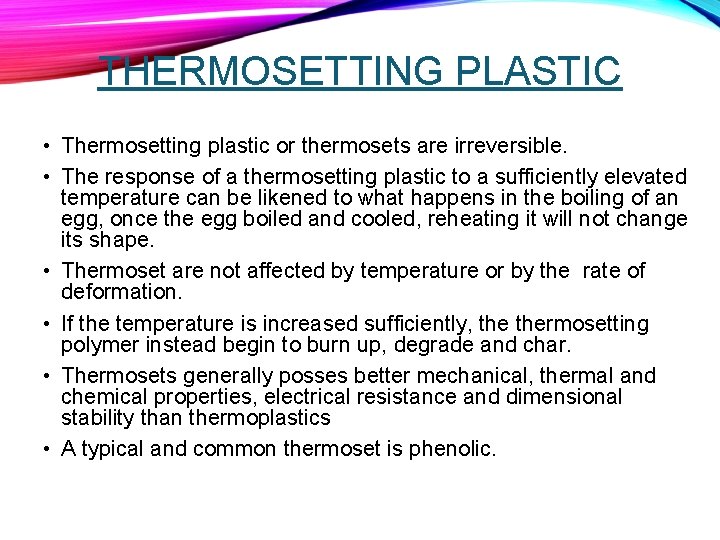
THERMOSETTING PLASTIC • Thermosetting plastic or thermosets are irreversible. • The response of a thermosetting plastic to a sufficiently elevated temperature can be likened to what happens in the boiling of an egg, once the egg boiled and cooled, reheating it will not change its shape. • Thermoset are not affected by temperature or by the rate of deformation. • If the temperature is increased sufficiently, thermosetting polymer instead begin to burn up, degrade and char. • Thermosets generally posses better mechanical, thermal and chemical properties, electrical resistance and dimensional stability than thermoplastics • A typical and common thermoset is phenolic.

ELASTOMER • Elastomer has an ability to undergo large elastic deformation without rupture; also they are soft and have a low elastic modulus. • Elastomer and rubber often are used interchangeable. Elastomer is defined as being capable of recovering substantially in shape and size after load has been remove, while rubber is defined as being capable recovering from large deformation quickly. • Hardness of elastomer can be measure using durometer.
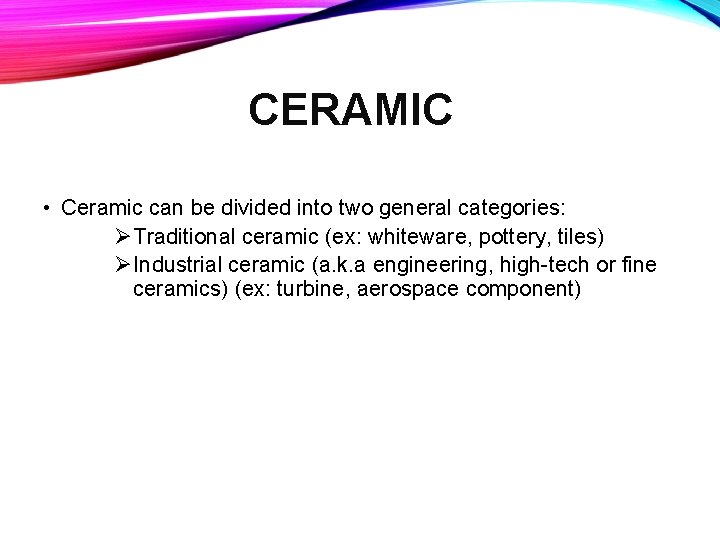
CERAMIC • Ceramic can be divided into two general categories: ØTraditional ceramic (ex: whiteware, pottery, tiles) ØIndustrial ceramic (a. k. a engineering, high-tech or fine ceramics) (ex: turbine, aerospace component)
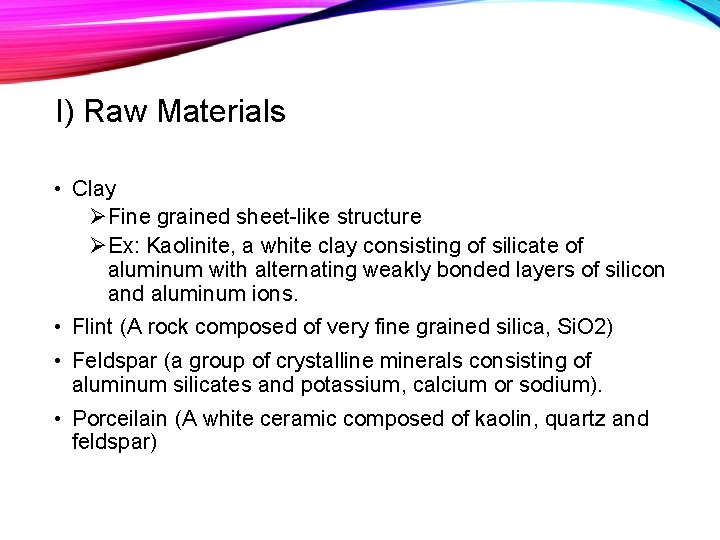
I) Raw Materials • Clay ØFine grained sheet-like structure ØEx: Kaolinite, a white clay consisting of silicate of aluminum with alternating weakly bonded layers of silicon and aluminum ions. • Flint (A rock composed of very fine grained silica, Si. O 2) • Feldspar (a group of crystalline minerals consisting of aluminum silicates and potassium, calcium or sodium). • Porceilain (A white ceramic composed of kaolin, quartz and feldspar)
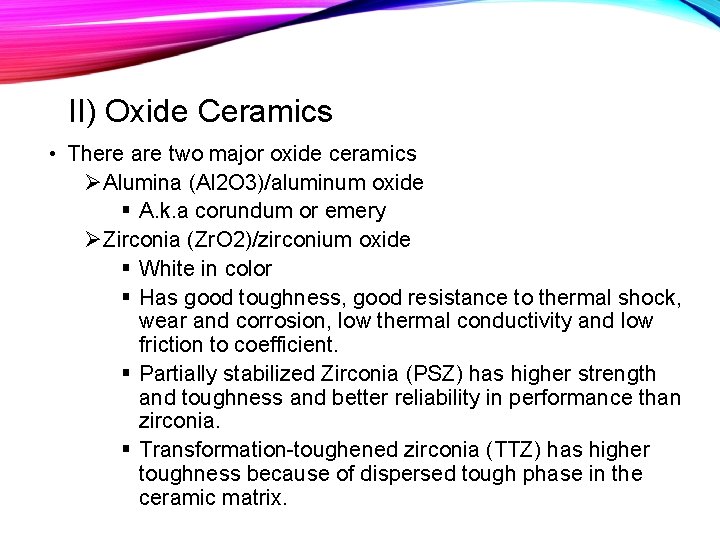
II) Oxide Ceramics • There are two major oxide ceramics ØAlumina (Al 2 O 3)/aluminum oxide § A. k. a corundum or emery ØZirconia (Zr. O 2)/zirconium oxide § White in color § Has good toughness, good resistance to thermal shock, wear and corrosion, low thermal conductivity and low friction to coefficient. § Partially stabilized Zirconia (PSZ) has higher strength and toughness and better reliability in performance than zirconia. § Transformation-toughened zirconia (TTZ) has higher toughness because of dispersed tough phase in the ceramic matrix.
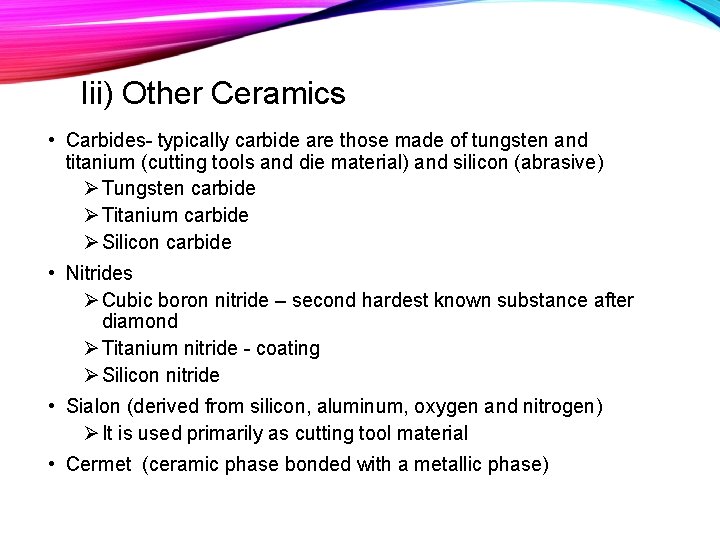
Iii) Other Ceramics • Carbides- typically carbide are those made of tungsten and titanium (cutting tools and die material) and silicon (abrasive) Ø Tungsten carbide Ø Titanium carbide Ø Silicon carbide • Nitrides Ø Cubic boron nitride – second hardest known substance after diamond Ø Titanium nitride - coating Ø Silicon nitride • Sialon (derived from silicon, aluminum, oxygen and nitrogen) Ø It is used primarily as cutting tool material • Cermet (ceramic phase bonded with a metallic phase)
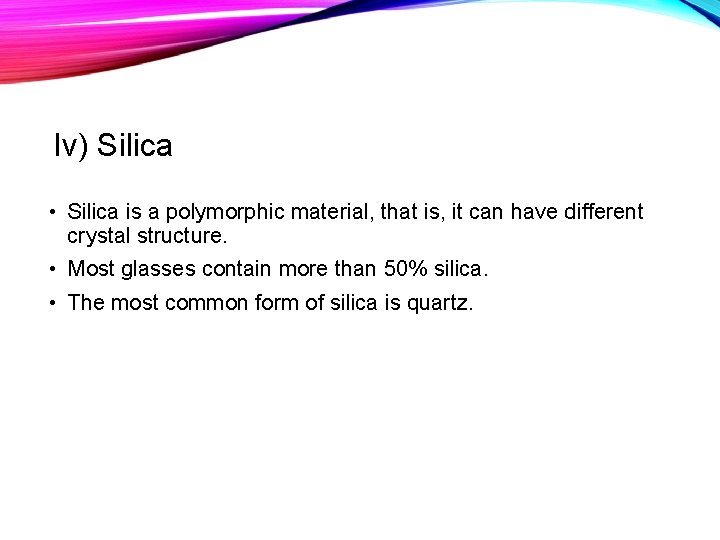
Iv) Silica • Silica is a polymorphic material, that is, it can have different crystal structure. • Most glasses contain more than 50% silica. • The most common form of silica is quartz.
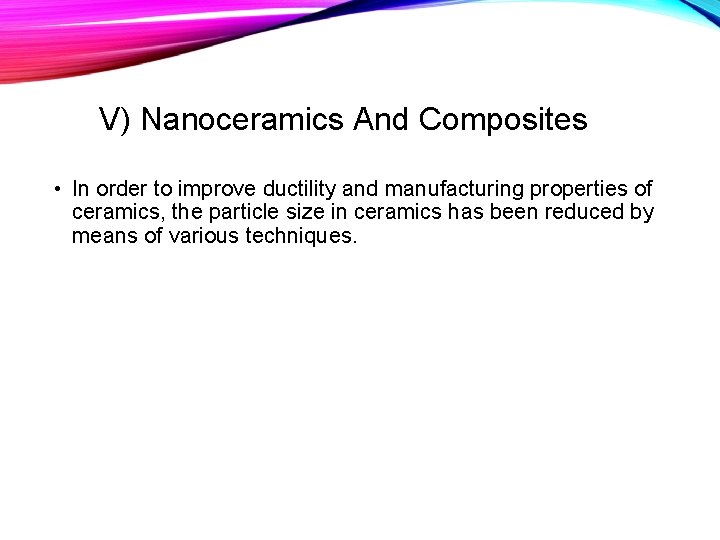
V) Nanoceramics And Composites • In order to improve ductility and manufacturing properties of ceramics, the particle size in ceramics has been reduced by means of various techniques.
Dpt 110
Dpt 110
Vignette mutuelle 110/110
011 101 110
Dpt test procedure
Dpt psychology
Dpt psychology
The psychrometry is study of
Vcu dpt
Manufacturing cost vs non manufacturing cost
Job costing definition
Cost concept and classification
Manufacturing cost vs non manufacturing cost
Additive manufacturing steps
Manufacturing property of a material
Balancing selection vs stabilizing selection
Similarities
K selection r selection
Natural selection vs artificial selection
Difference between continuous and discontinuous variation
Example of sexual selection
K selection r selection
Natural selection vs artificial selection
Two way selection and multiway selection in c
Multiway selection in c
Mass selection and pure line selection
370hr dielectric constant
Single phase alloy
Material selection risks
Gdt symbol
Standard costing and variance analysis formulas
Popular culture example
Refers to the knowledge language values customs
All groups create norms to enforce their cultural values.
The useful
Plate process of soft gelatin capsules
Manufacturing process of polyester
Types of fasteners ppt
Shaping with rack cutter
In production process
Flow chart of cheese production
Chiselling process
Nature of manufacturing process
Tyre manufacturing process