DPT 213 MANUFACTURING PROCESS II UNIVERSITI MALAYSIA PERLIS
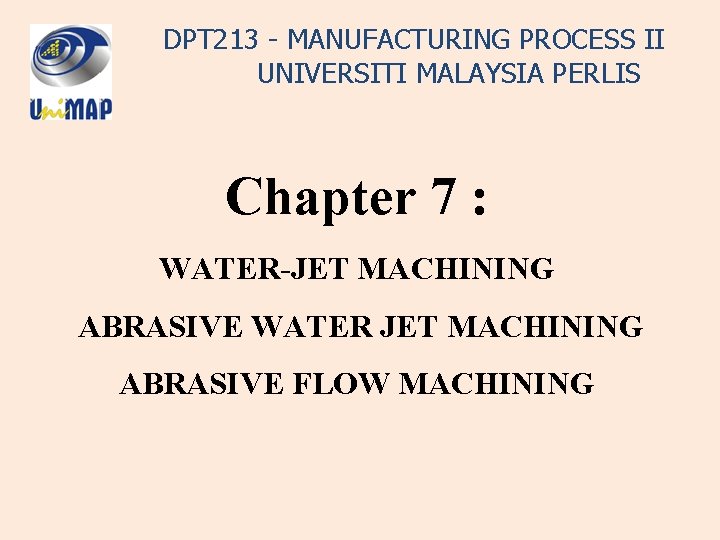
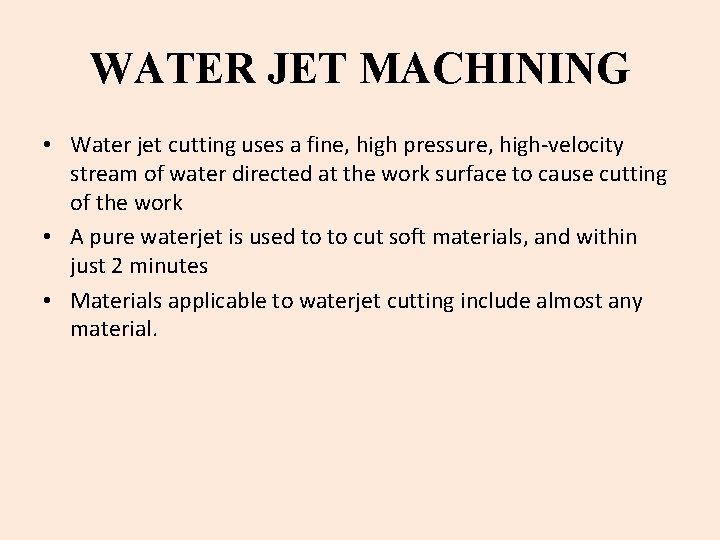
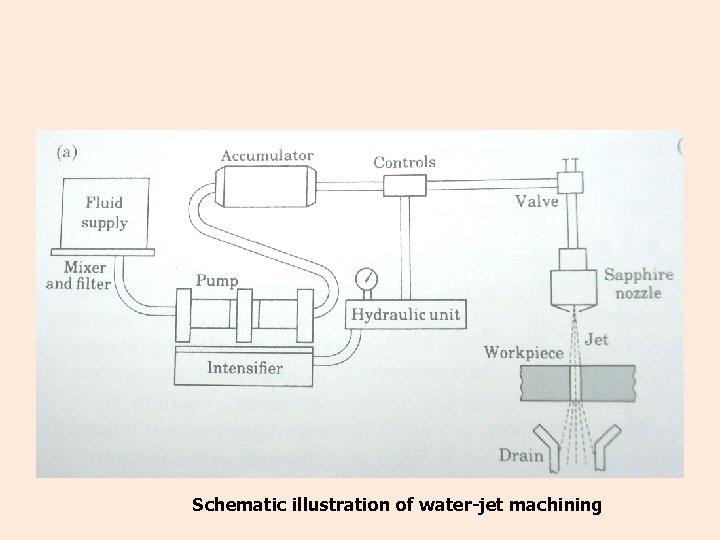
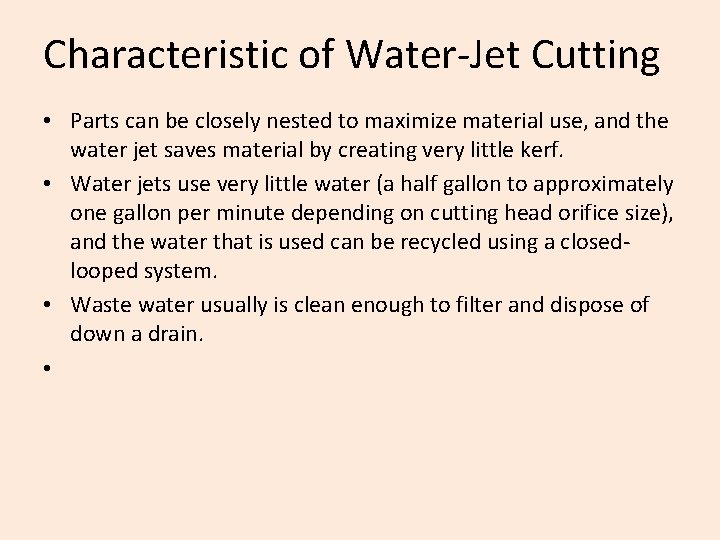
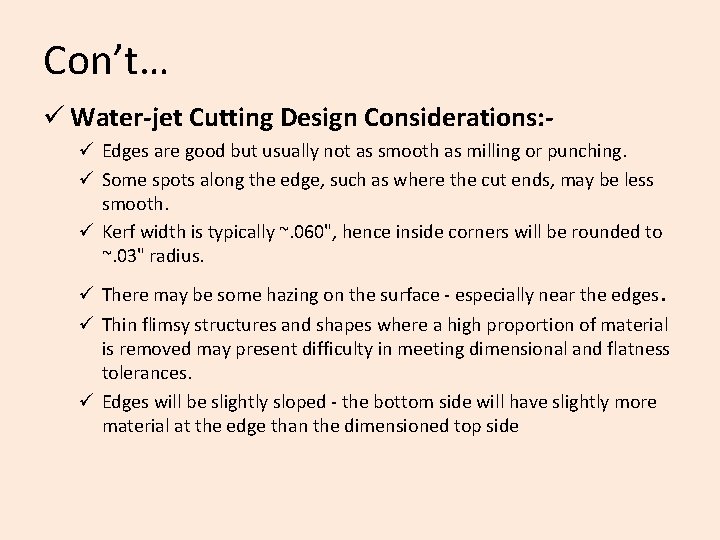
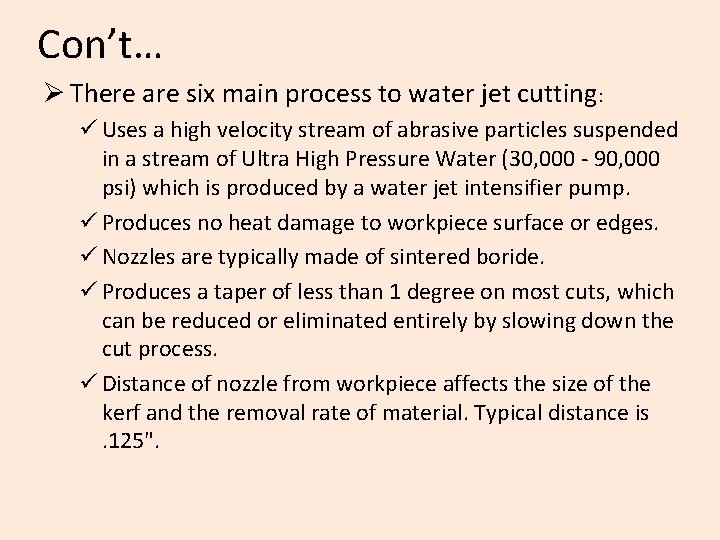
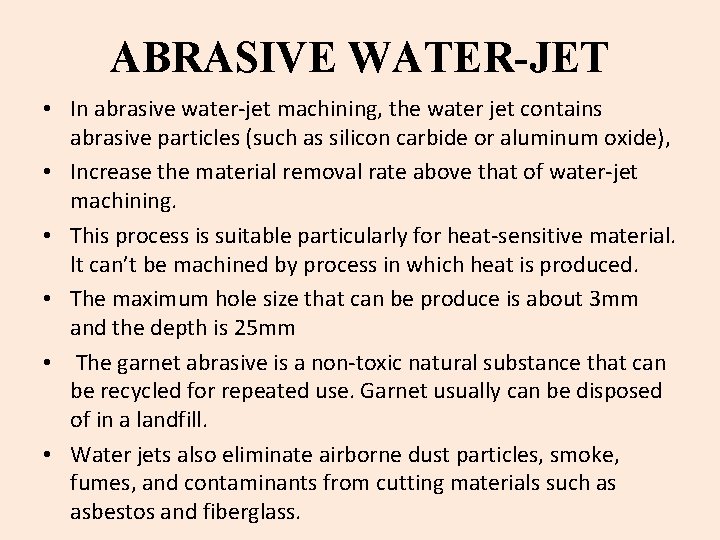
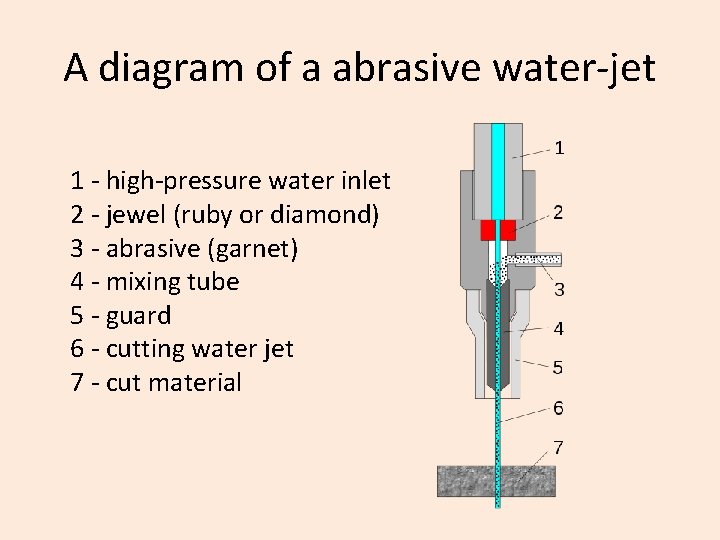
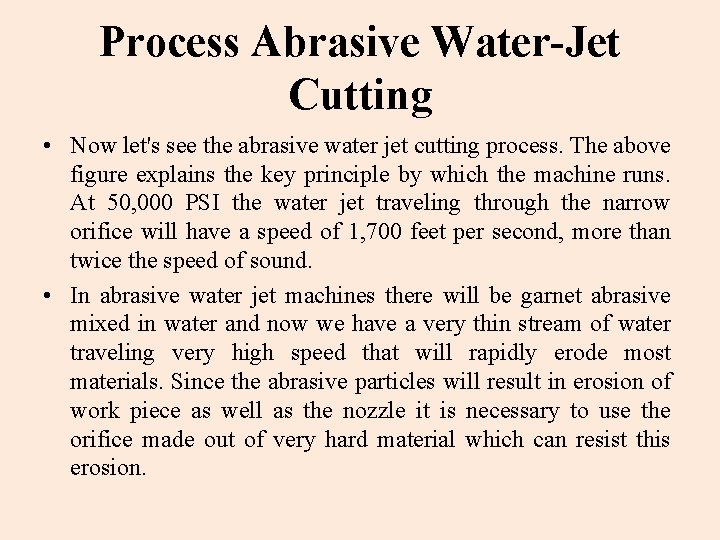
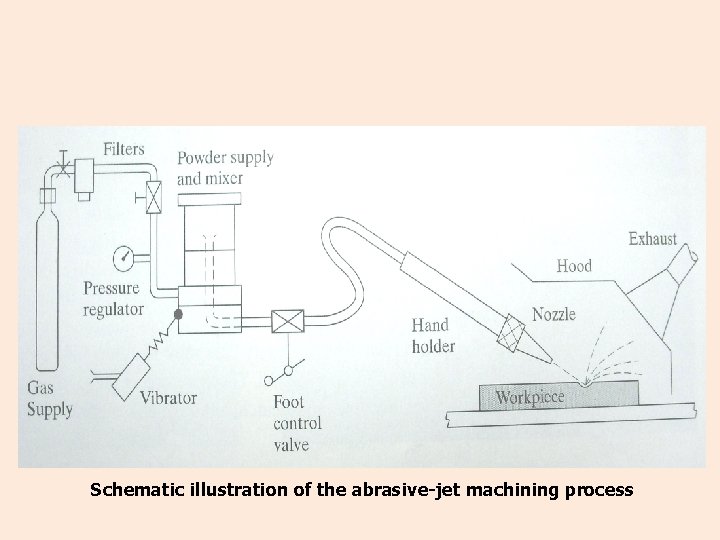
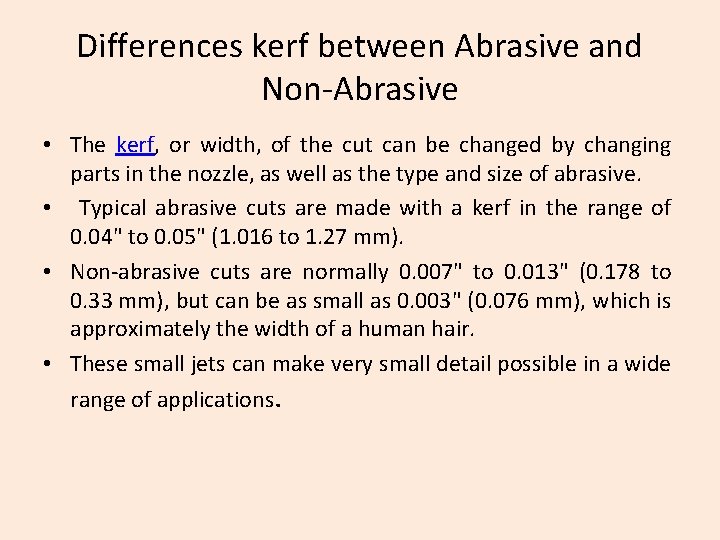
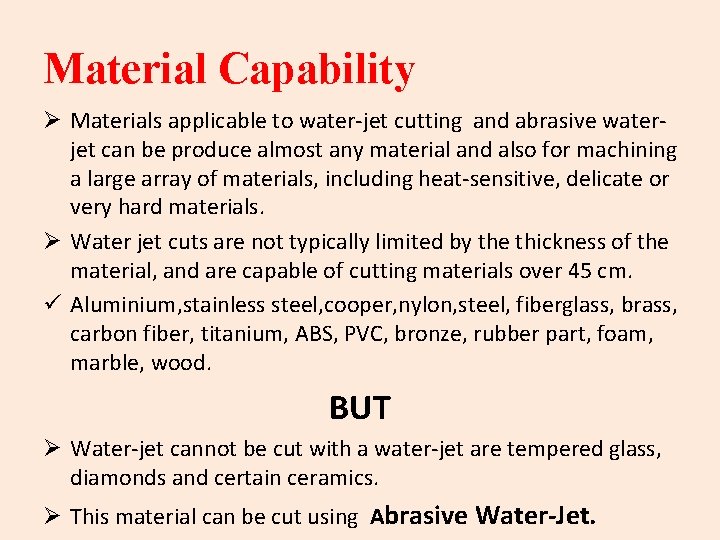
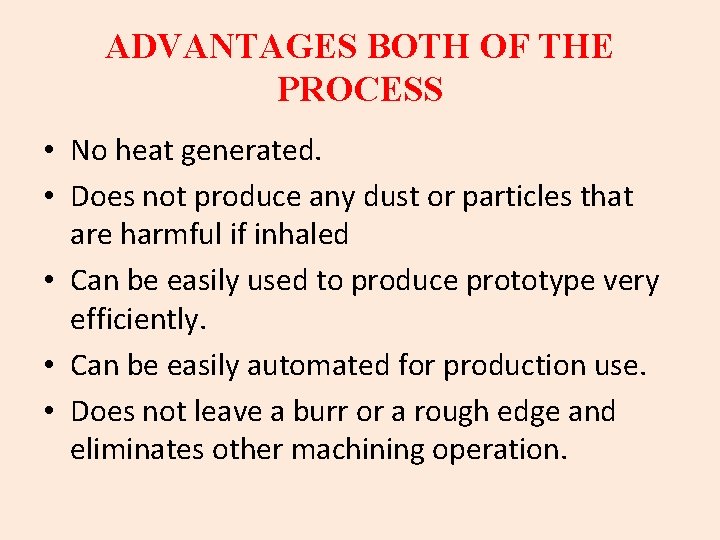

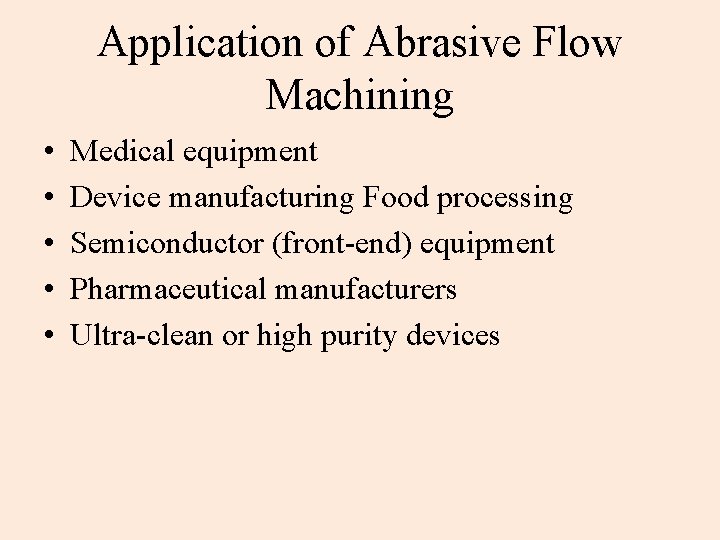
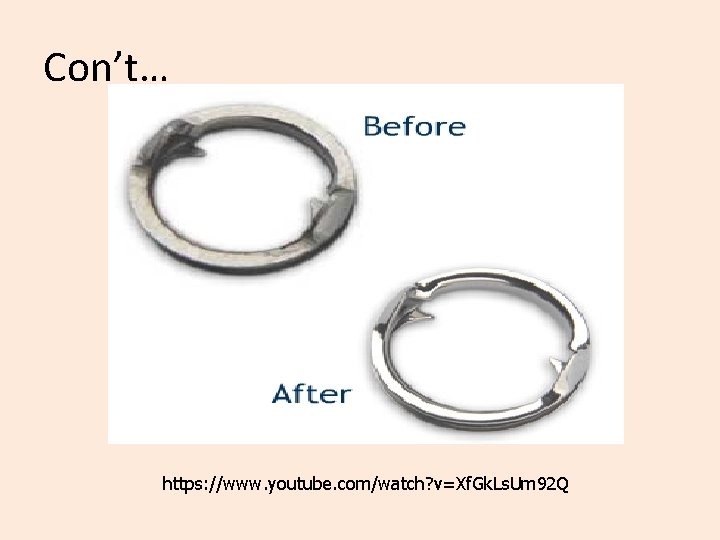
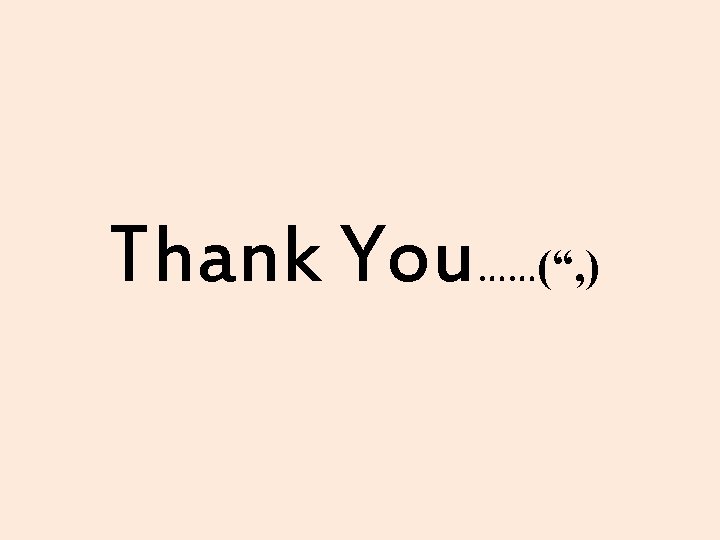
- Slides: 17
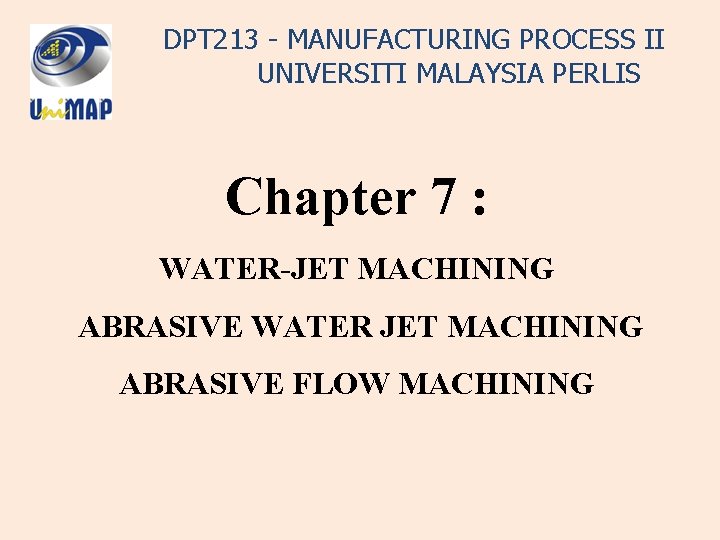
DPT 213 - MANUFACTURING PROCESS II UNIVERSITI MALAYSIA PERLIS Chapter 7 : WATER-JET MACHINING ABRASIVE WATER JET MACHINING ABRASIVE FLOW MACHINING
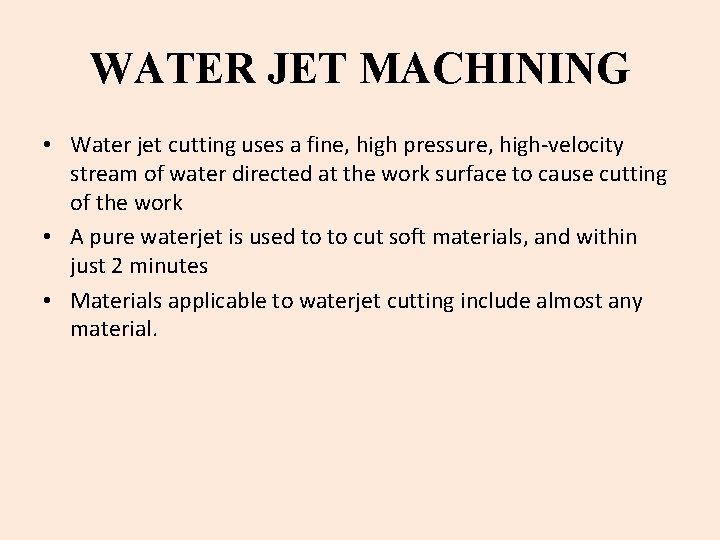
WATER JET MACHINING • Water jet cutting uses a fine, high pressure, high-velocity stream of water directed at the work surface to cause cutting of the work • A pure waterjet is used to to cut soft materials, and within just 2 minutes • Materials applicable to waterjet cutting include almost any material.
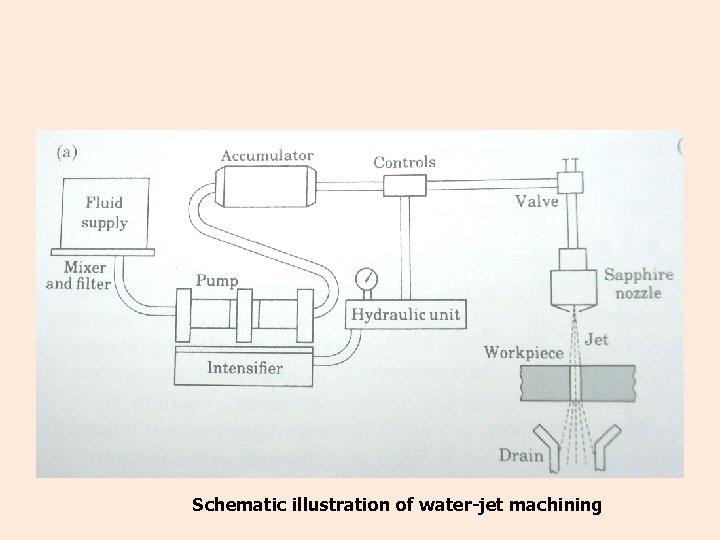
Schematic illustration of water-jet machining
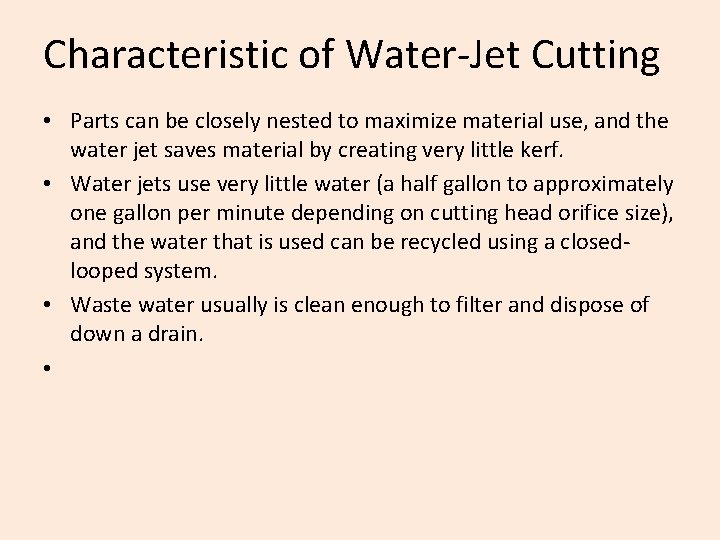
Characteristic of Water-Jet Cutting • Parts can be closely nested to maximize material use, and the water jet saves material by creating very little kerf. • Water jets use very little water (a half gallon to approximately one gallon per minute depending on cutting head orifice size), and the water that is used can be recycled using a closedlooped system. • Waste water usually is clean enough to filter and dispose of down a drain. •
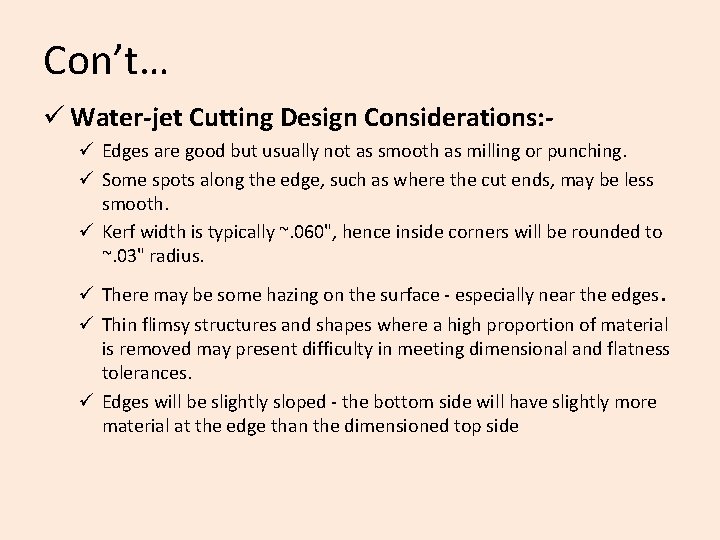
Con’t… ü Water-jet Cutting Design Considerations: ü Edges are good but usually not as smooth as milling or punching. ü Some spots along the edge, such as where the cut ends, may be less smooth. ü Kerf width is typically ~. 060", hence inside corners will be rounded to ~. 03" radius. ü There may be some hazing on the surface - especially near the edges. ü Thin flimsy structures and shapes where a high proportion of material is removed may present difficulty in meeting dimensional and flatness tolerances. ü Edges will be slightly sloped - the bottom side will have slightly more material at the edge than the dimensioned top side
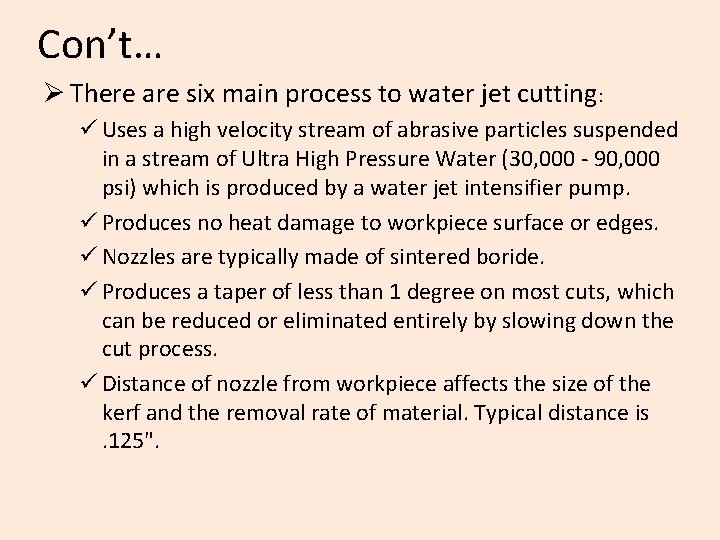
Con’t… Ø There are six main process to water jet cutting: ü Uses a high velocity stream of abrasive particles suspended in a stream of Ultra High Pressure Water (30, 000 - 90, 000 psi) which is produced by a water jet intensifier pump. ü Produces no heat damage to workpiece surface or edges. ü Nozzles are typically made of sintered boride. ü Produces a taper of less than 1 degree on most cuts, which can be reduced or eliminated entirely by slowing down the cut process. ü Distance of nozzle from workpiece affects the size of the kerf and the removal rate of material. Typical distance is . 125".
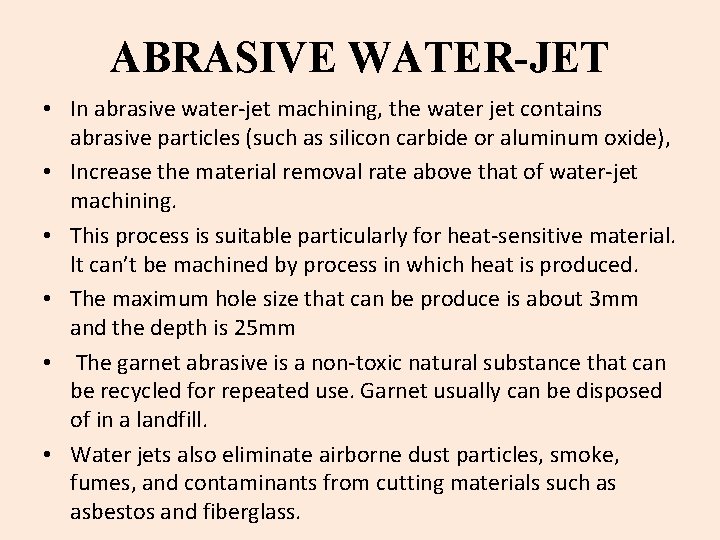
ABRASIVE WATER-JET • In abrasive water-jet machining, the water jet contains abrasive particles (such as silicon carbide or aluminum oxide), • Increase the material removal rate above that of water-jet machining. • This process is suitable particularly for heat-sensitive material. lt can’t be machined by process in which heat is produced. • The maximum hole size that can be produce is about 3 mm and the depth is 25 mm • The garnet abrasive is a non-toxic natural substance that can be recycled for repeated use. Garnet usually can be disposed of in a landfill. • Water jets also eliminate airborne dust particles, smoke, fumes, and contaminants from cutting materials such as asbestos and fiberglass.
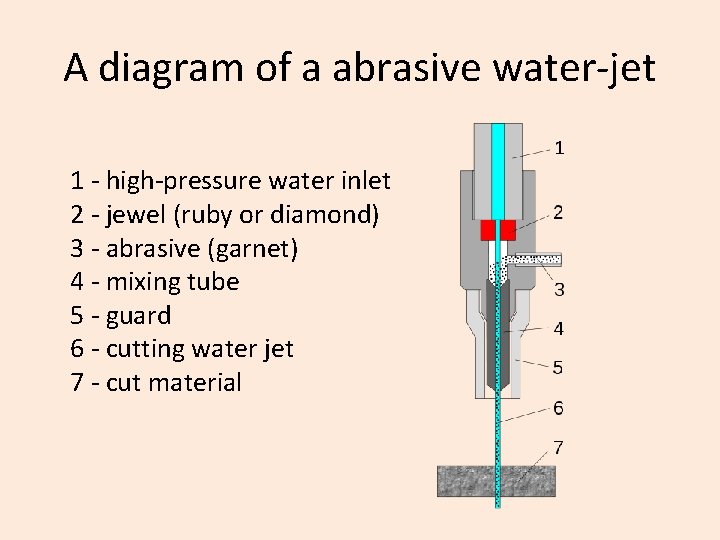
A diagram of a abrasive water-jet 1 - high-pressure water inlet 2 - jewel (ruby or diamond) 3 - abrasive (garnet) 4 - mixing tube 5 - guard 6 - cutting water jet 7 - cut material
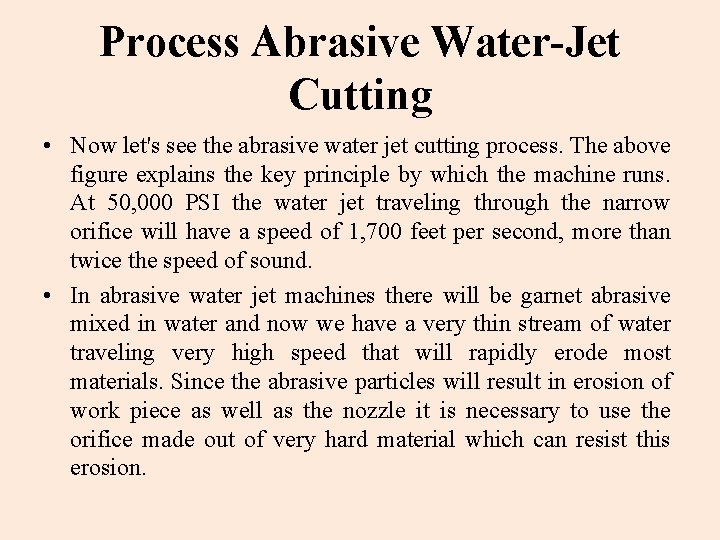
Process Abrasive Water-Jet Cutting • Now let's see the abrasive water jet cutting process. The above figure explains the key principle by which the machine runs. At 50, 000 PSI the water jet traveling through the narrow orifice will have a speed of 1, 700 feet per second, more than twice the speed of sound. • In abrasive water jet machines there will be garnet abrasive mixed in water and now we have a very thin stream of water traveling very high speed that will rapidly erode most materials. Since the abrasive particles will result in erosion of work piece as well as the nozzle it is necessary to use the orifice made out of very hard material which can resist this erosion.
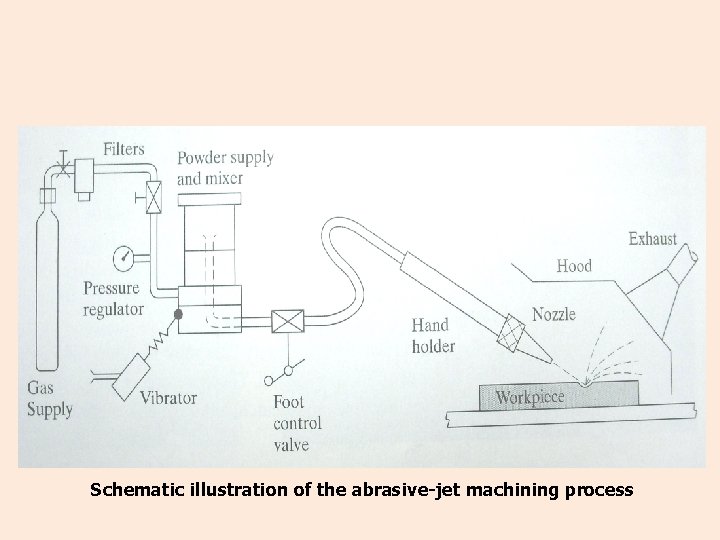
Schematic illustration of the abrasive-jet machining process
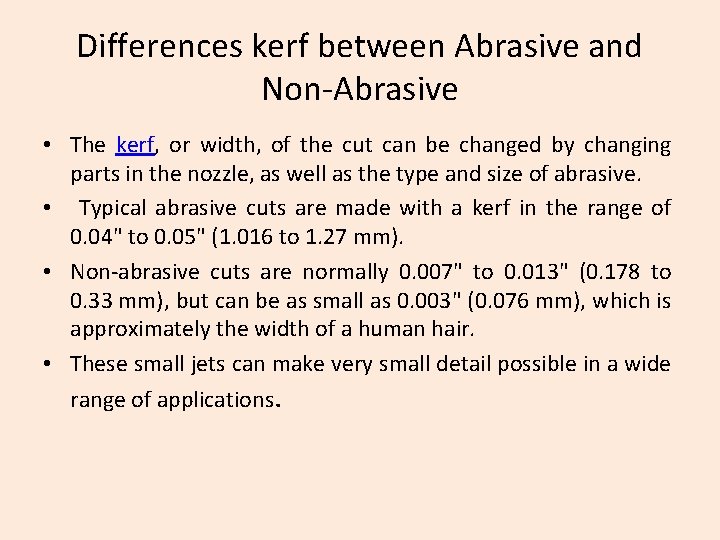
Differences kerf between Abrasive and Non-Abrasive • The kerf, or width, of the cut can be changed by changing parts in the nozzle, as well as the type and size of abrasive. • Typical abrasive cuts are made with a kerf in the range of 0. 04" to 0. 05" (1. 016 to 1. 27 mm). • Non-abrasive cuts are normally 0. 007" to 0. 013" (0. 178 to 0. 33 mm), but can be as small as 0. 003" (0. 076 mm), which is approximately the width of a human hair. • These small jets can make very small detail possible in a wide range of applications.
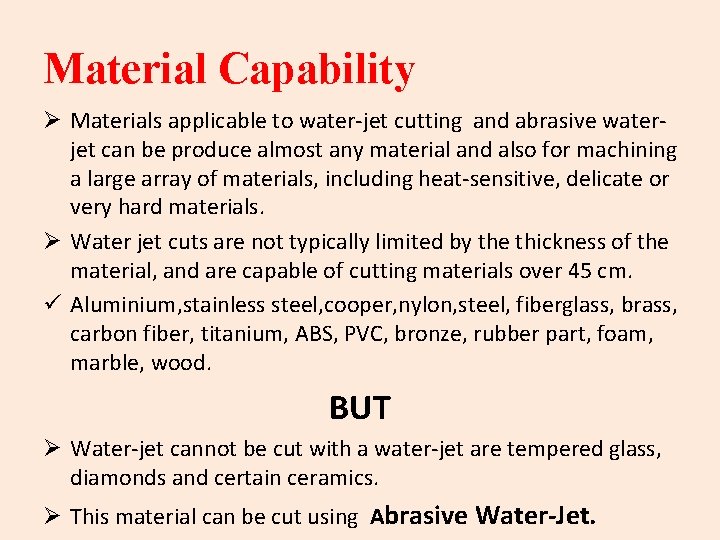
Material Capability Ø Materials applicable to water-jet cutting and abrasive waterjet can be produce almost any material and also for machining a large array of materials, including heat-sensitive, delicate or very hard materials. Ø Water jet cuts are not typically limited by the thickness of the material, and are capable of cutting materials over 45 cm. ü Aluminium, stainless steel, cooper, nylon, steel, fiberglass, brass, carbon fiber, titanium, ABS, PVC, bronze, rubber part, foam, marble, wood. BUT Ø Water-jet cannot be cut with a water-jet are tempered glass, diamonds and certain ceramics. Ø This material can be cut using Abrasive Water-Jet.
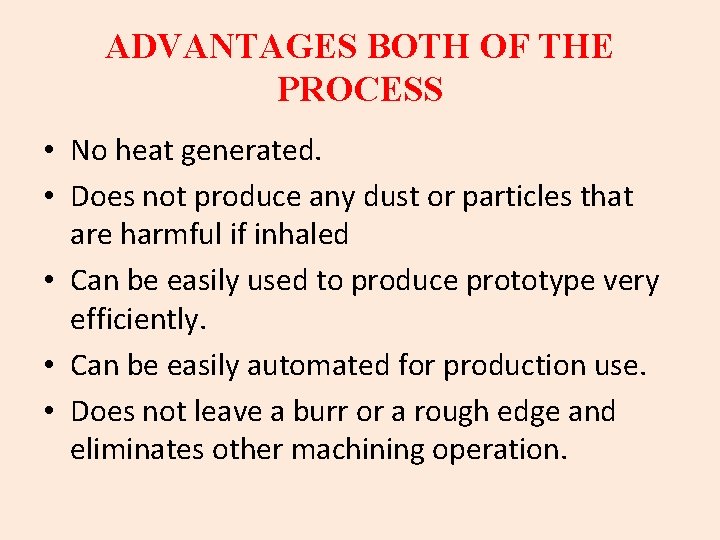
ADVANTAGES BOTH OF THE PROCESS • No heat generated. • Does not produce any dust or particles that are harmful if inhaled • Can be easily used to produce prototype very efficiently. • Can be easily automated for production use. • Does not leave a burr or a rough edge and eliminates other machining operation.

ABRASIVE FLOW MACHINING • Abrasive flow machining is a process using a liquid polymer and an abrasive which can polish any geometric cavity or hard to reach area. This works well for any deep hole or cavity that is hard to polish with solid materials. • When complex geometric cavities need polishing this is where the abrasive flow process shines. In this field we specialize in hi pressure machining of small holes. We have used this process for our wire guide products, fuel injector nozzles, dies, hi pressure gas sensors and more
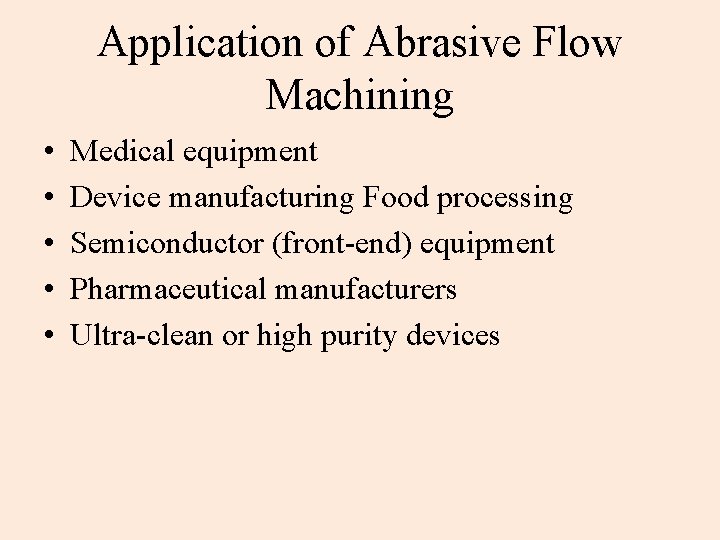
Application of Abrasive Flow Machining • • • Medical equipment Device manufacturing Food processing Semiconductor (front-end) equipment Pharmaceutical manufacturers Ultra-clean or high purity devices
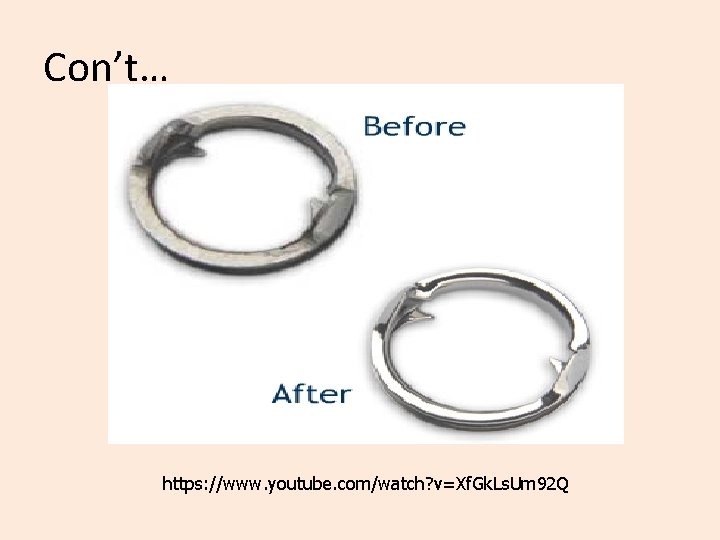
Con’t… https: //www. youtube. com/watch? v=Xf. Gk. Ls. Um 92 Q
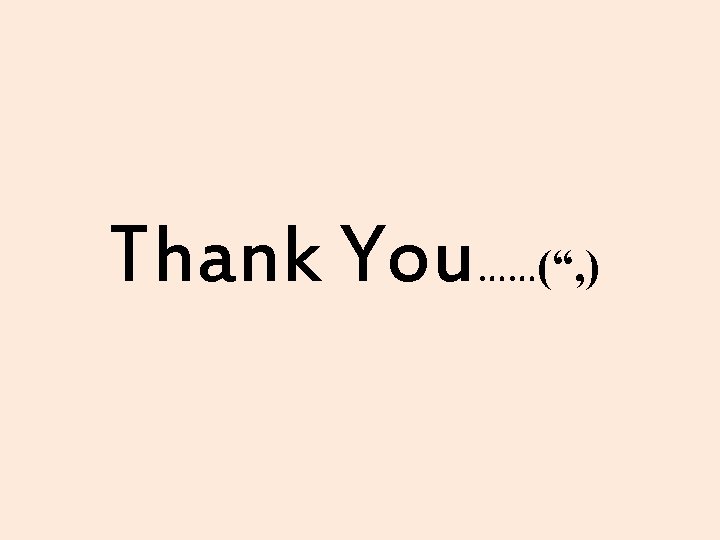
Thank You……(“, )
Perkhidmatan psikiatri di malaysia
Universiti putra malaysia
Maksud slt
Skim perkhidmatan pensyarah universiti
Universiti teknologi mara akta 173
Contoh ayat bagi tatarias
Importance of ndt
Dpt psychology
Dpt 110
Dpt 110
Dpt psychology
For unsaturated air the value of dpt is
Vcu dpt
Manufacturing cost vs non manufacturing cost
Job costing vs process costing
Uncontrollable cost example
Manufacturing cost vs non manufacturing cost
Additive manufacturing steps