Liquid Penetrant Testing Non Destructive Testing Methods to
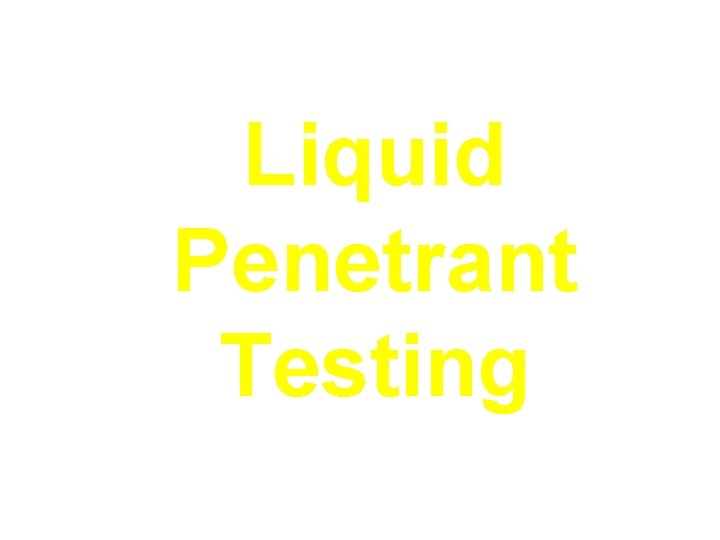
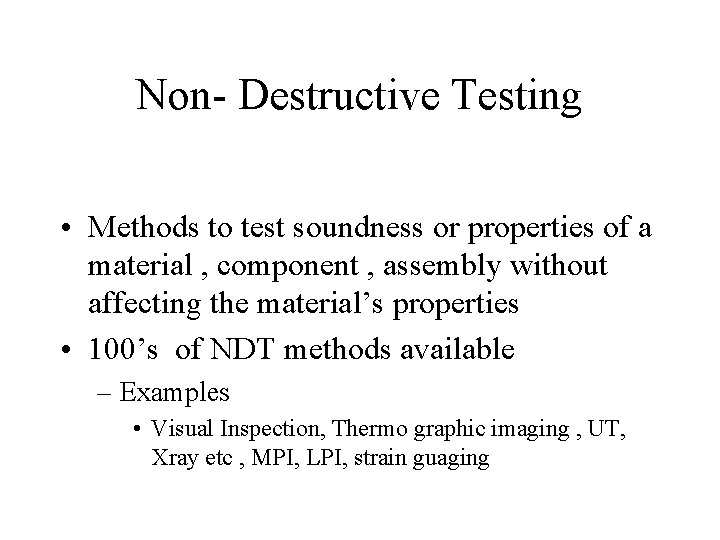
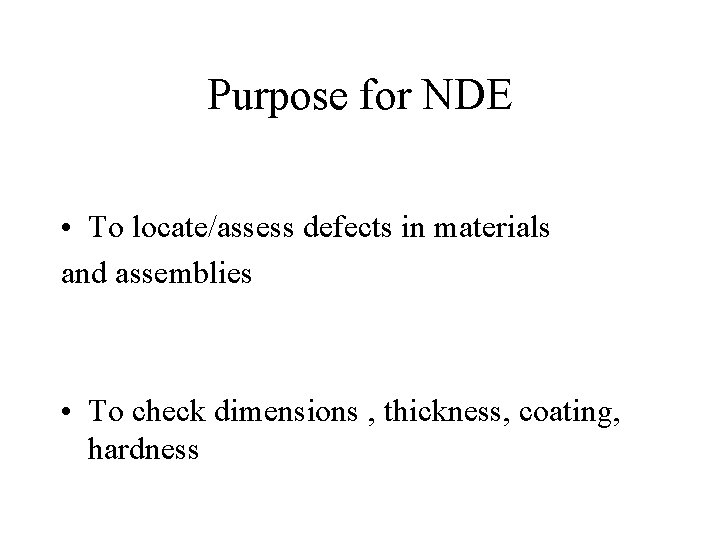
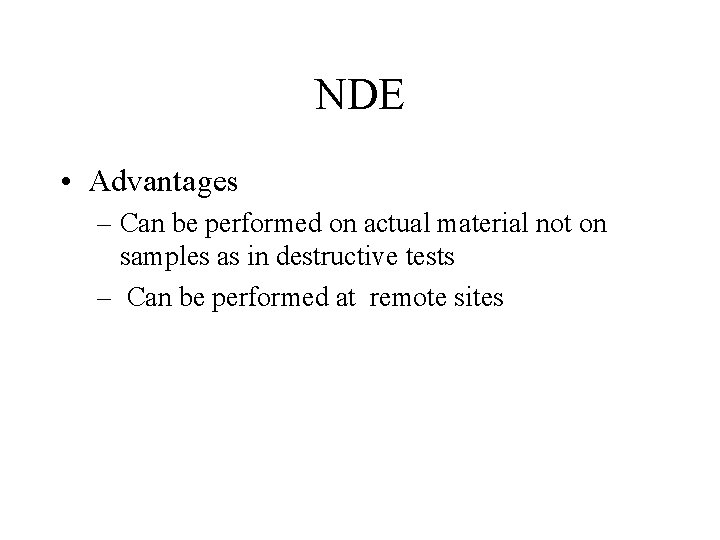
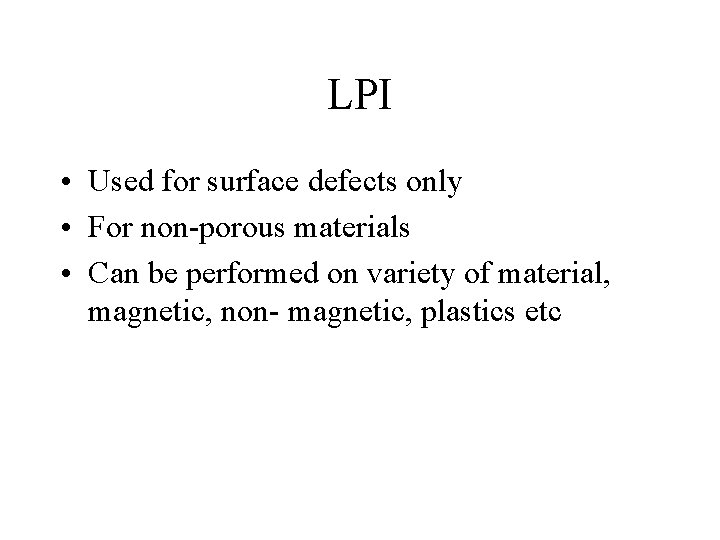
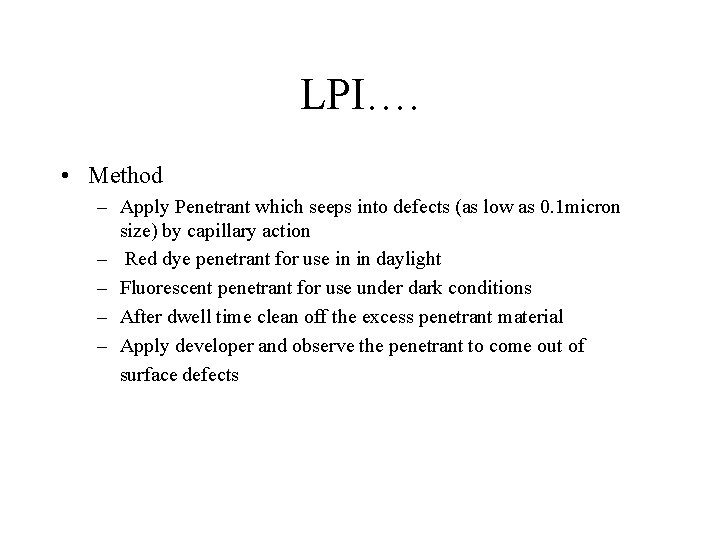
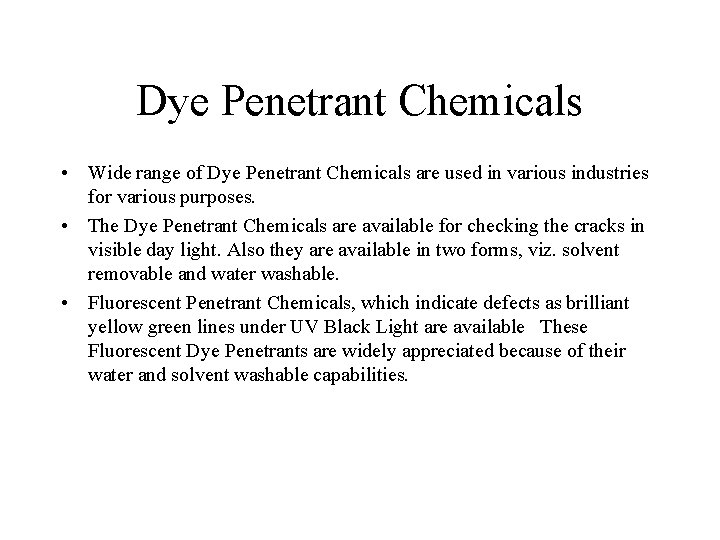
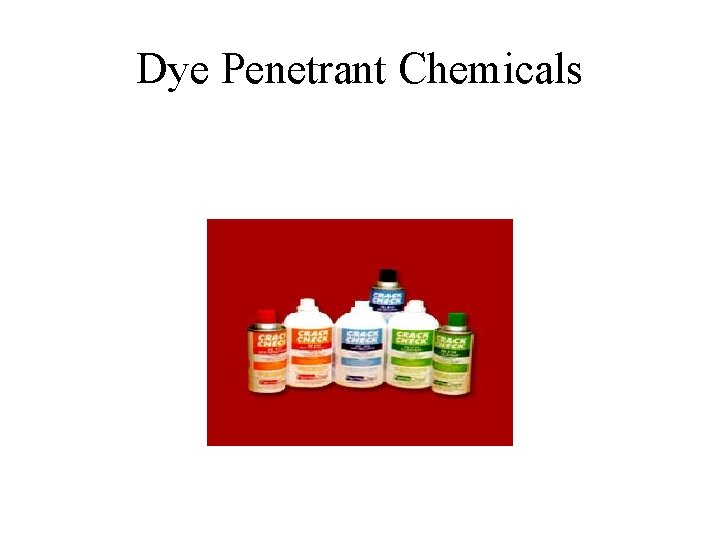
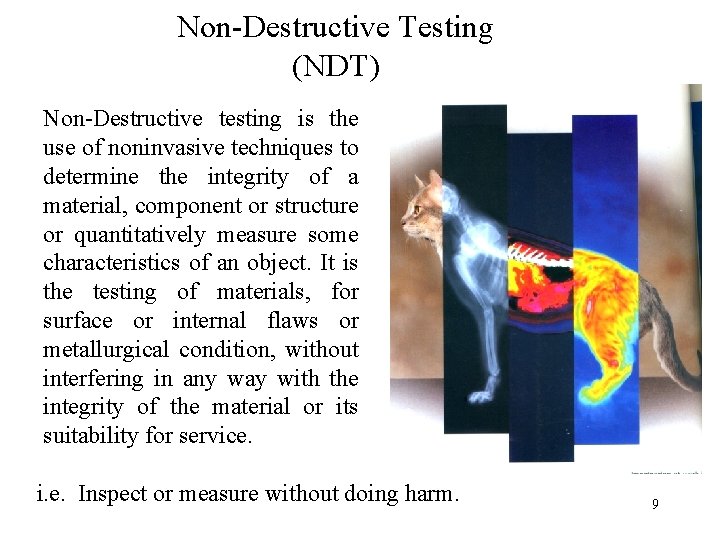
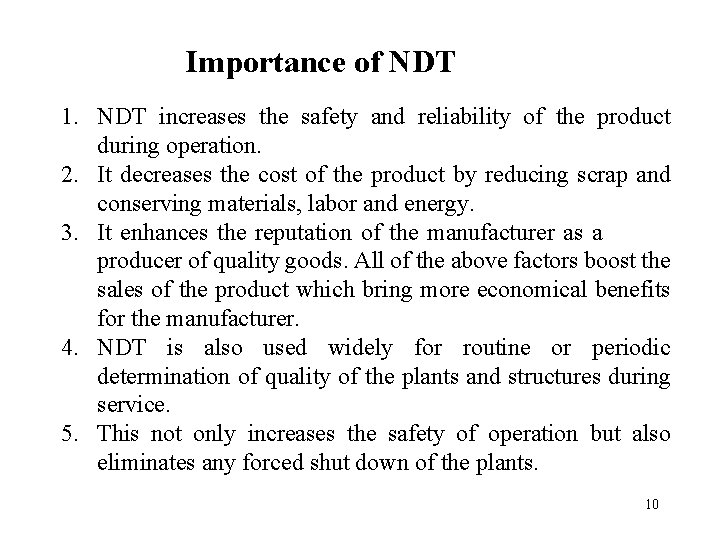
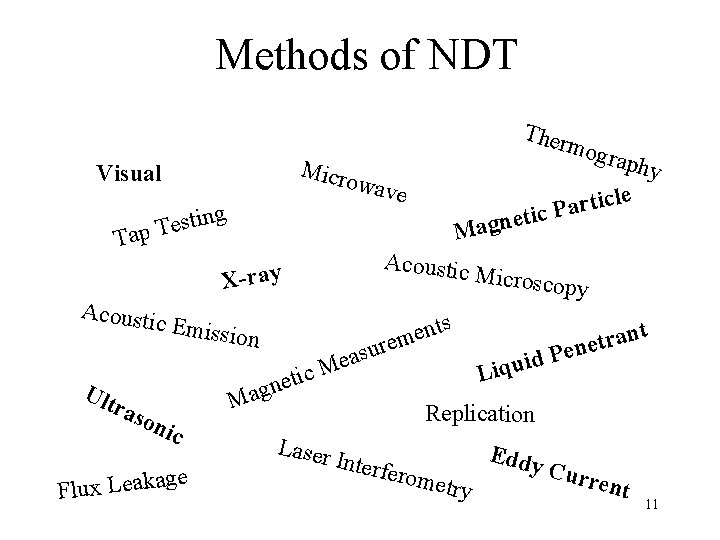
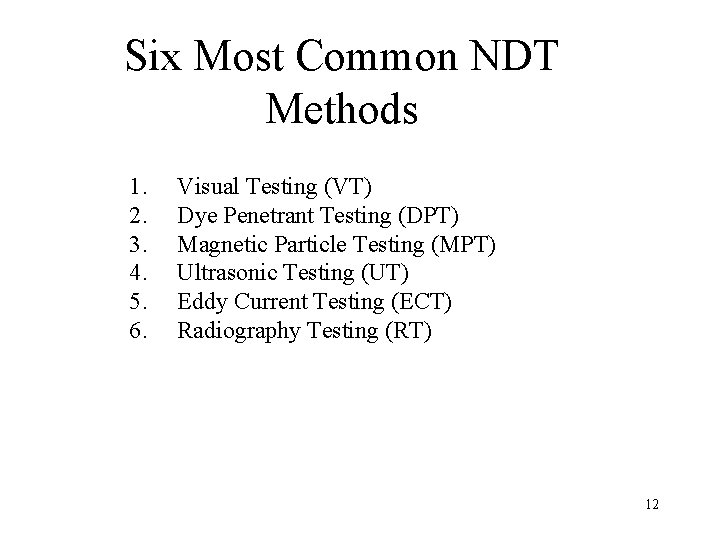
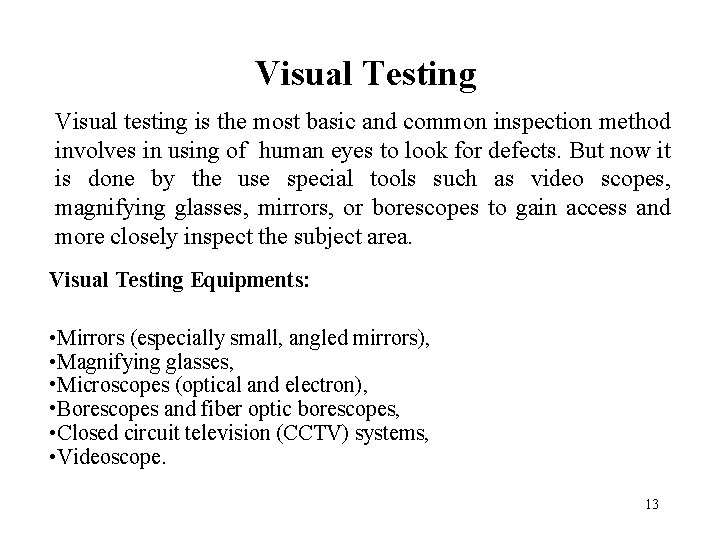
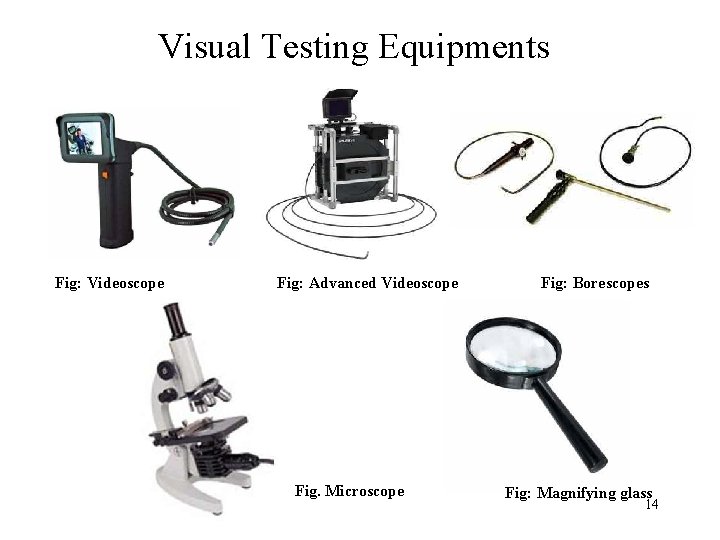
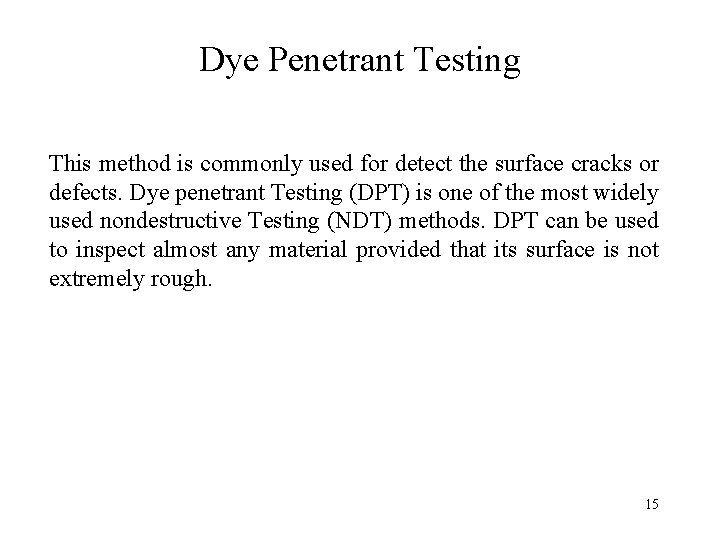
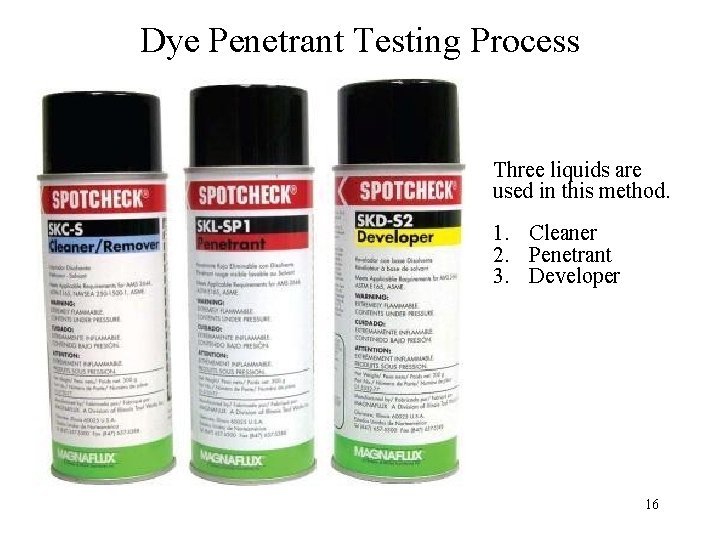
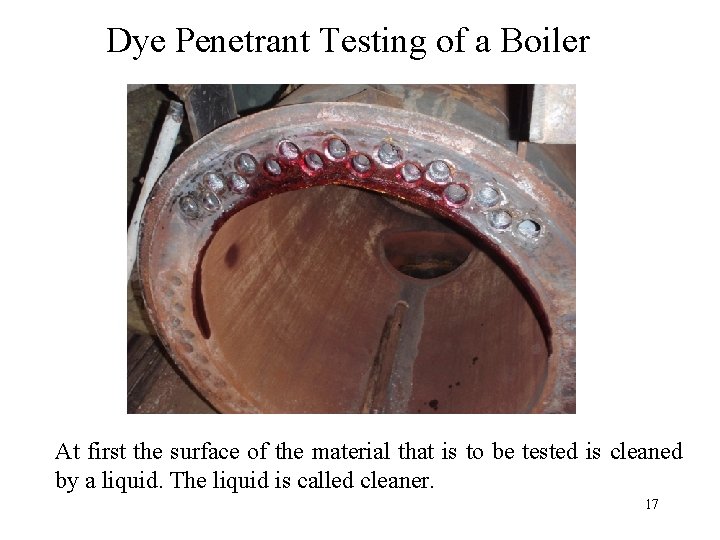
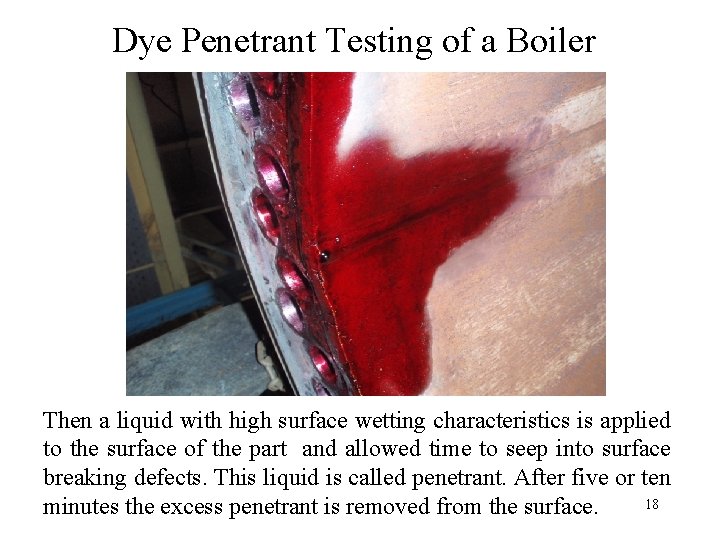
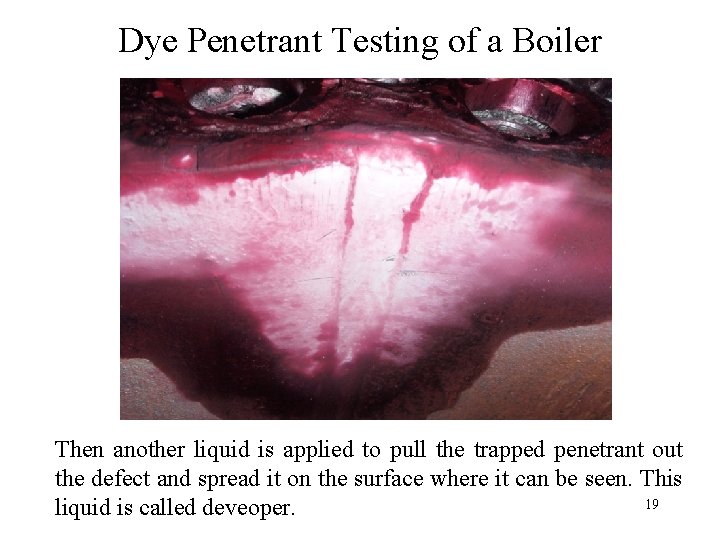
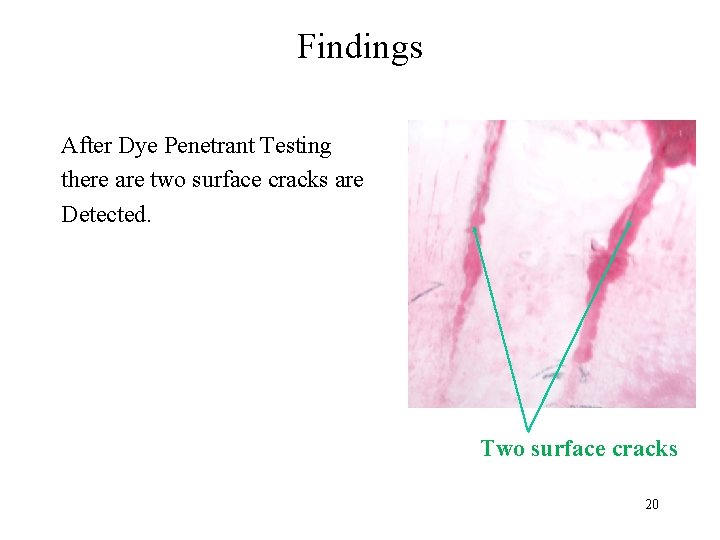
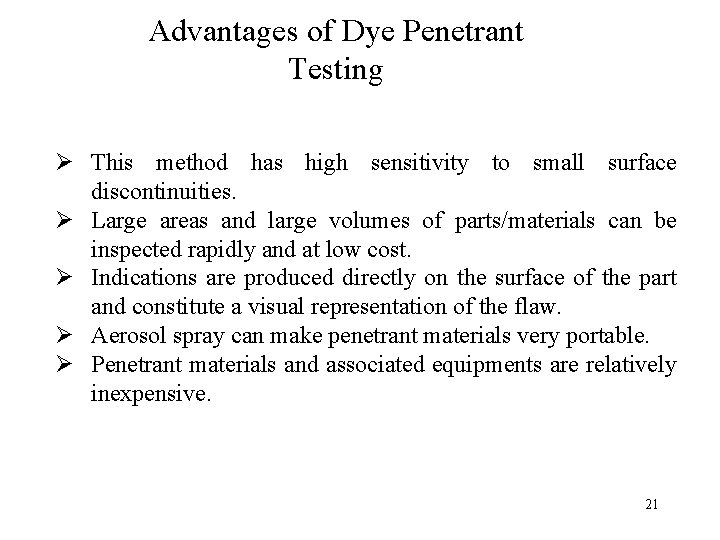
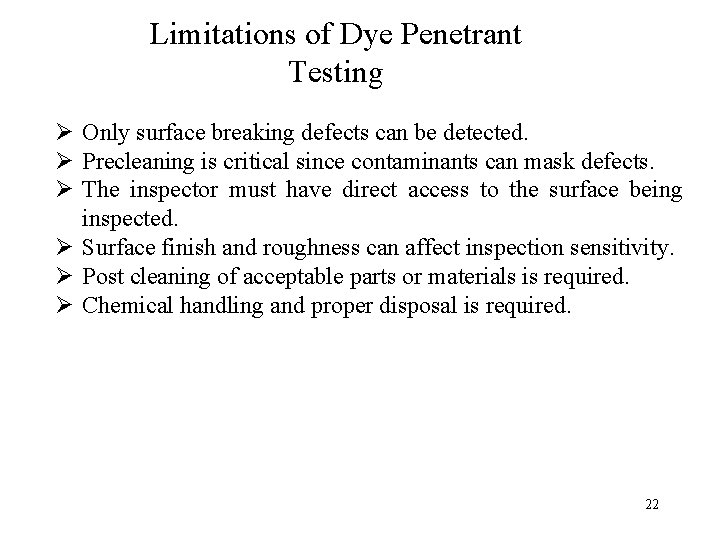
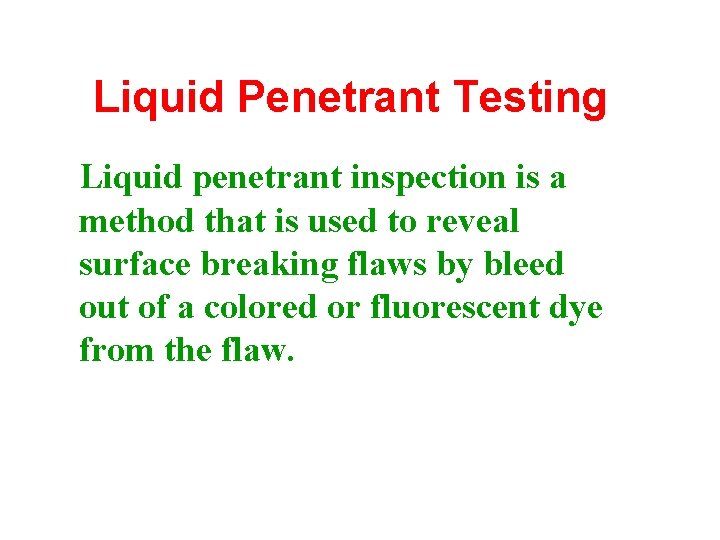
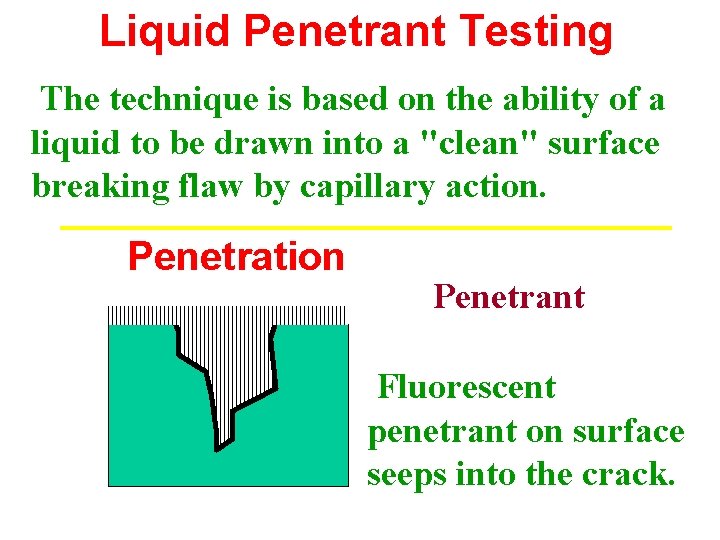
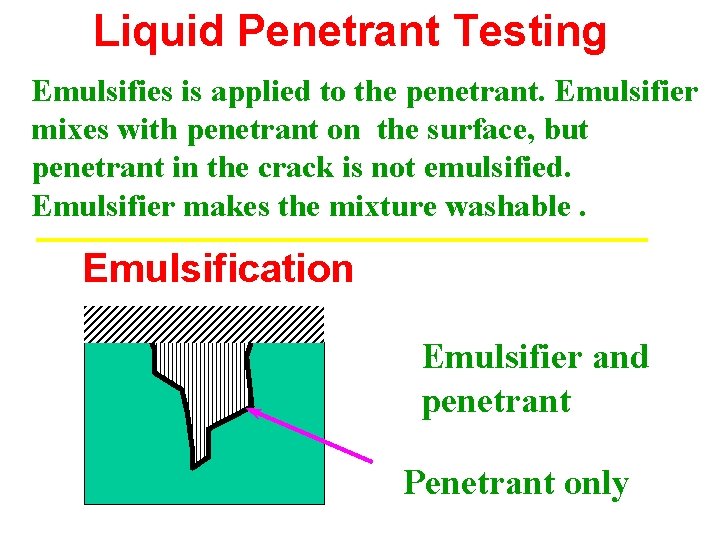
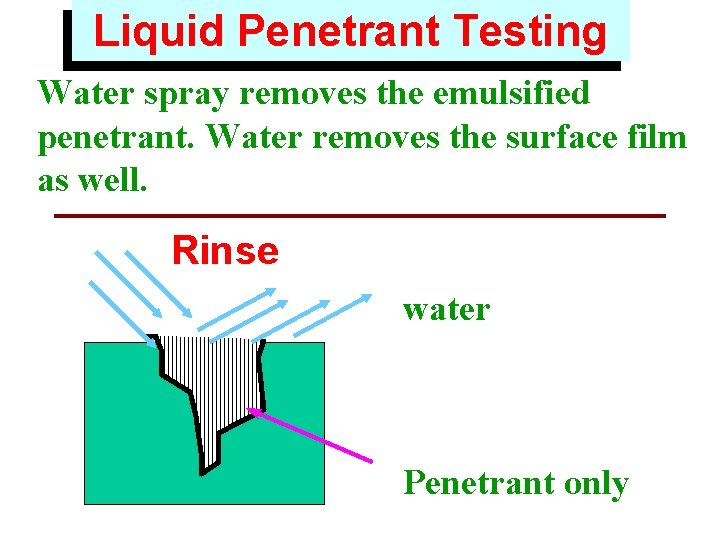
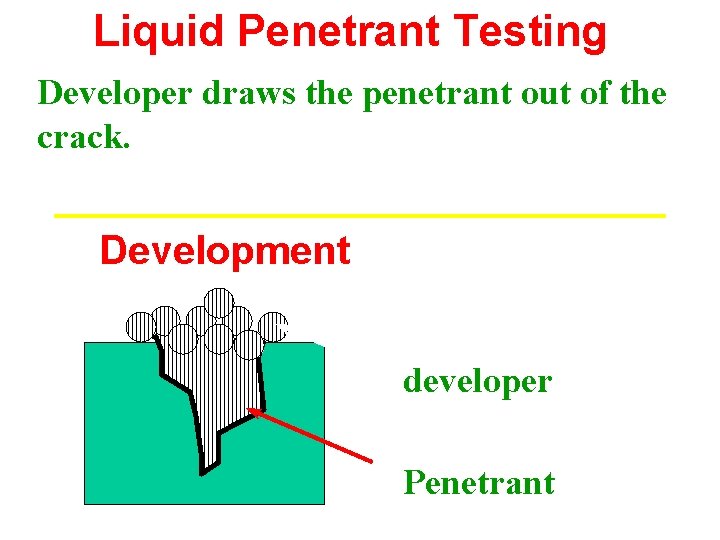
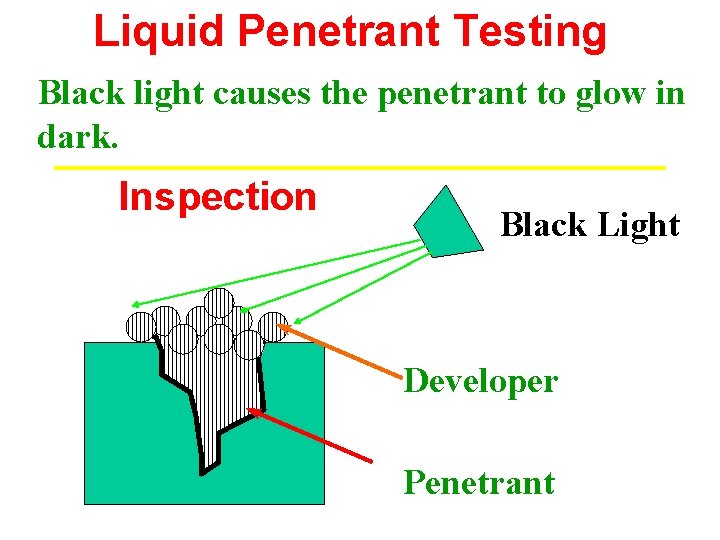
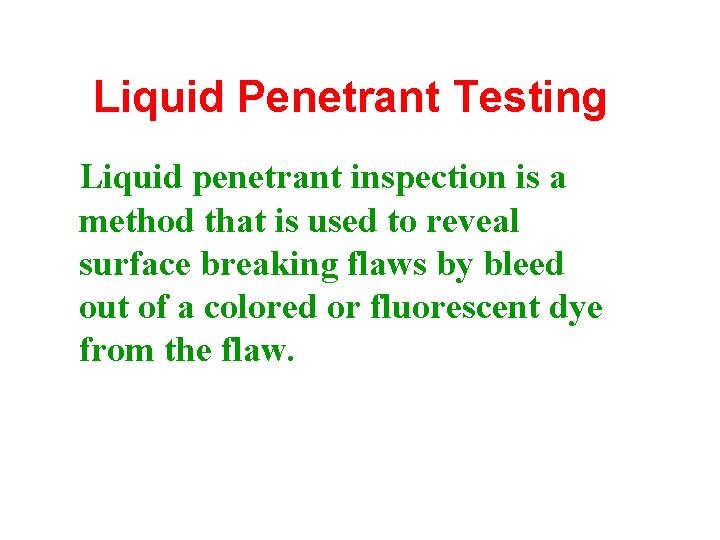
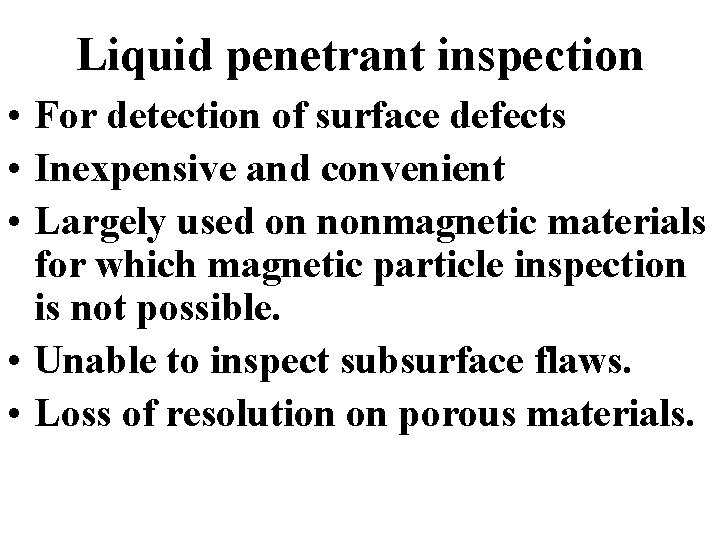
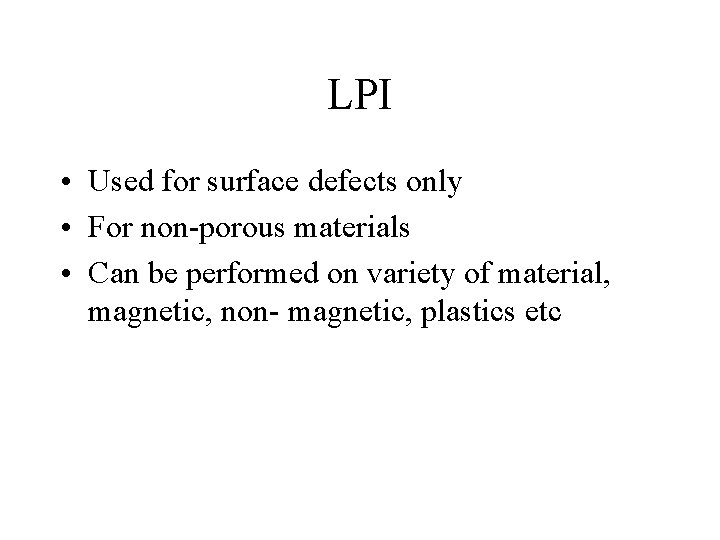
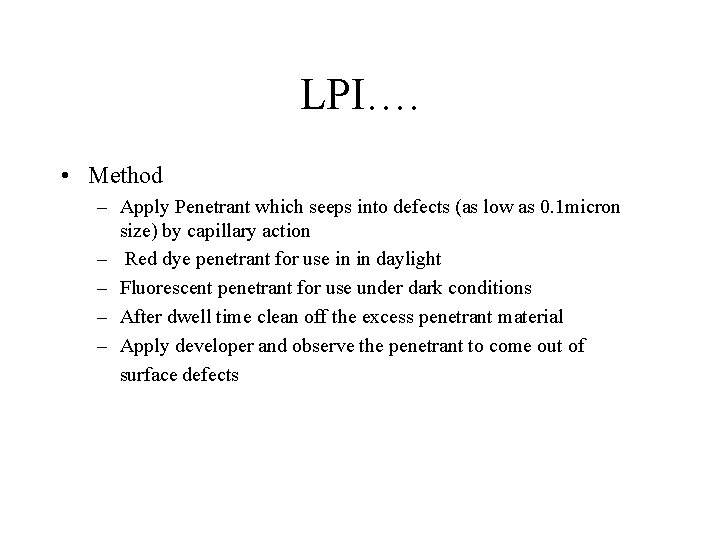
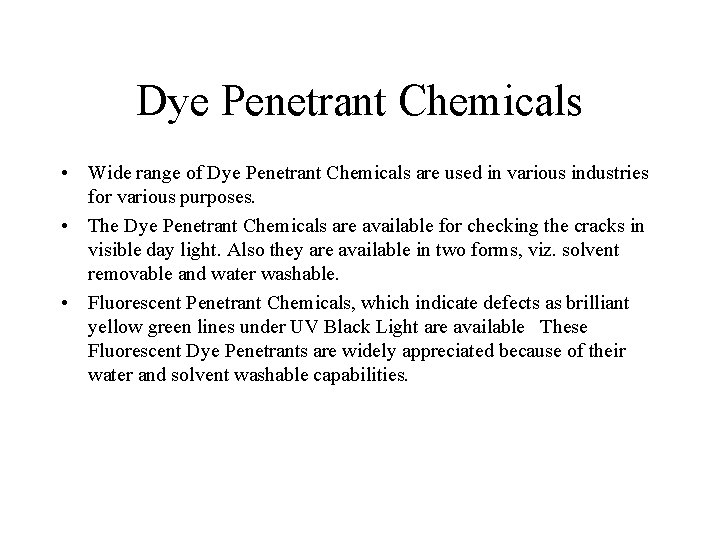
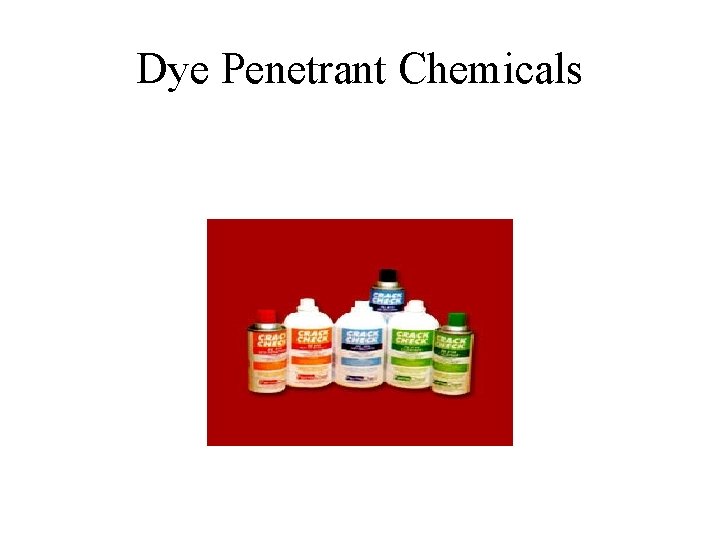
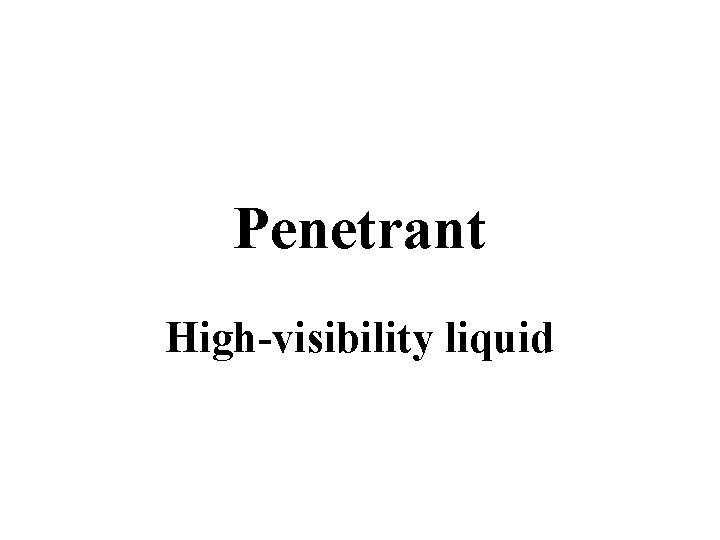
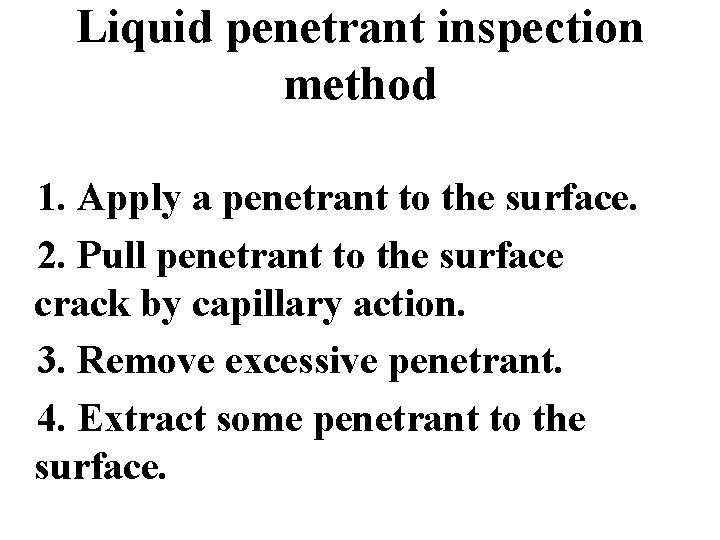
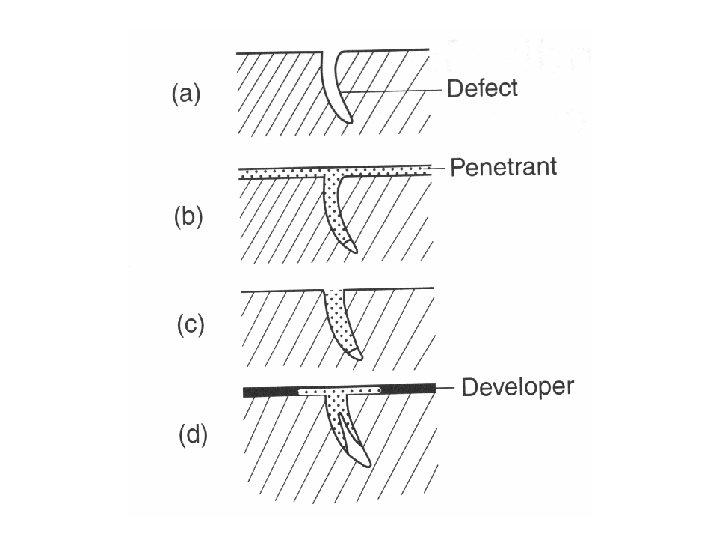
- Slides: 37
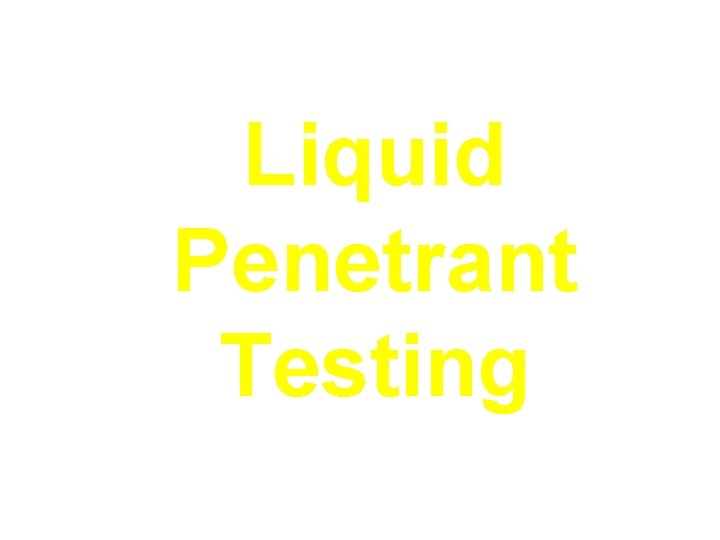
Liquid Penetrant Testing
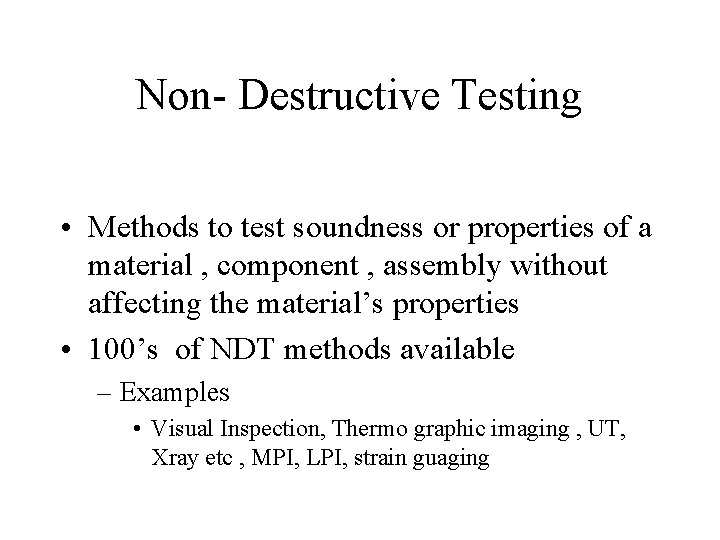
Non- Destructive Testing • Methods to test soundness or properties of a material , component , assembly without affecting the material’s properties • 100’s of NDT methods available – Examples • Visual Inspection, Thermo graphic imaging , UT, Xray etc , MPI, LPI, strain guaging
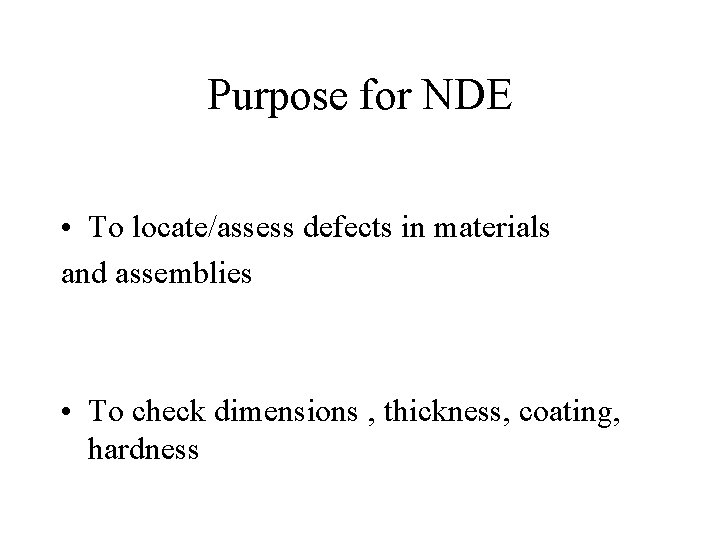
Purpose for NDE • To locate/assess defects in materials and assemblies • To check dimensions , thickness, coating, hardness
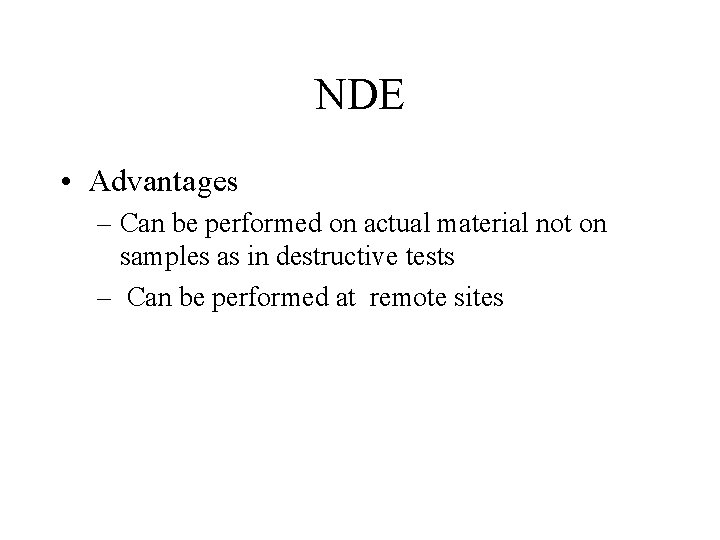
NDE • Advantages – Can be performed on actual material not on samples as in destructive tests – Can be performed at remote sites
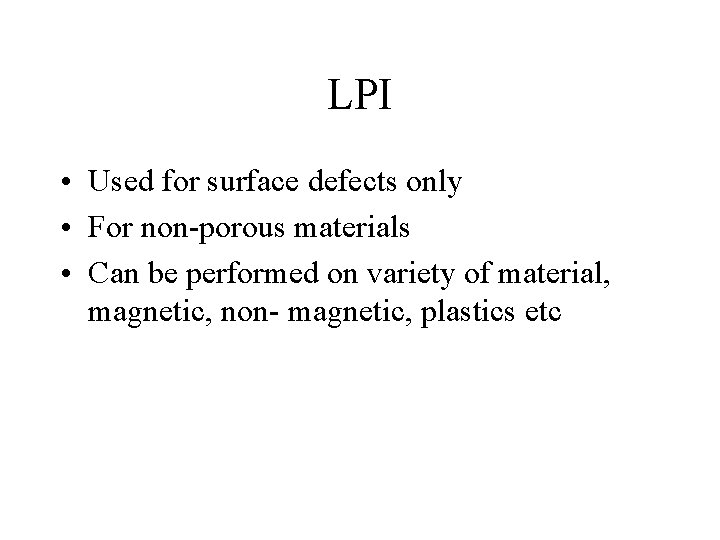
LPI • Used for surface defects only • For non-porous materials • Can be performed on variety of material, magnetic, non- magnetic, plastics etc
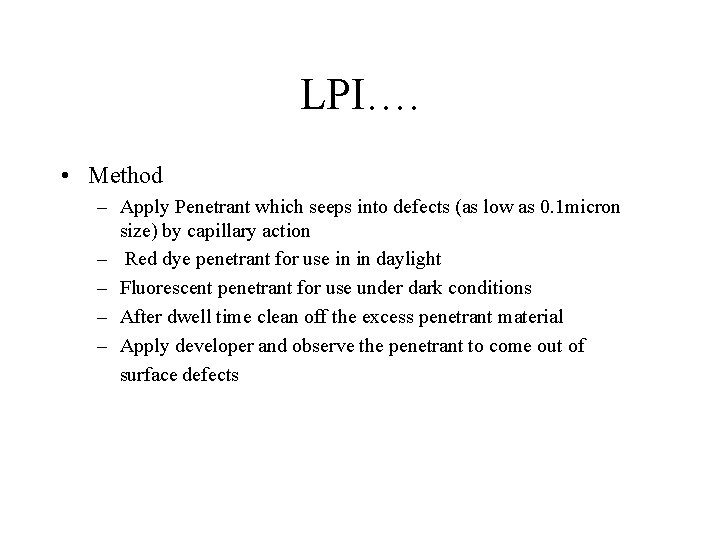
LPI…. • Method – Apply Penetrant which seeps into defects (as low as 0. 1 micron size) by capillary action – Red dye penetrant for use in in daylight – Fluorescent penetrant for use under dark conditions – After dwell time clean off the excess penetrant material – Apply developer and observe the penetrant to come out of surface defects
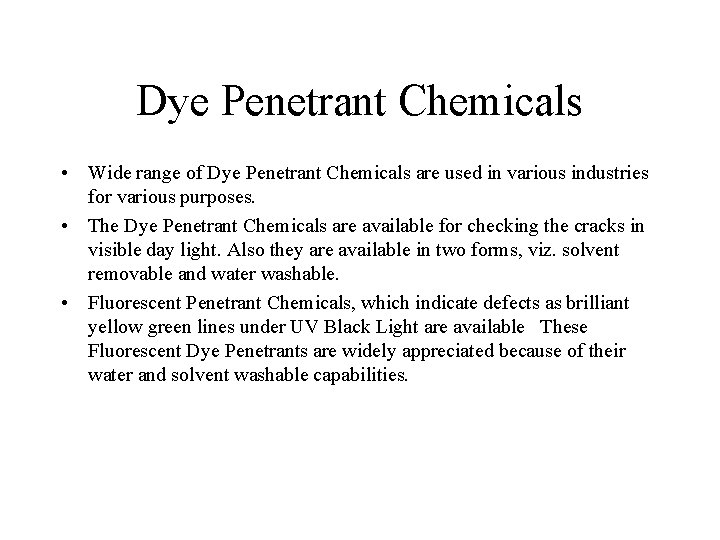
Dye Penetrant Chemicals • Wide range of Dye Penetrant Chemicals are used in various industries for various purposes. • The Dye Penetrant Chemicals are available for checking the cracks in visible day light. Also they are available in two forms, viz. solvent removable and water washable. • Fluorescent Penetrant Chemicals, which indicate defects as brilliant yellow green lines under UV Black Light are available These Fluorescent Dye Penetrants are widely appreciated because of their water and solvent washable capabilities.
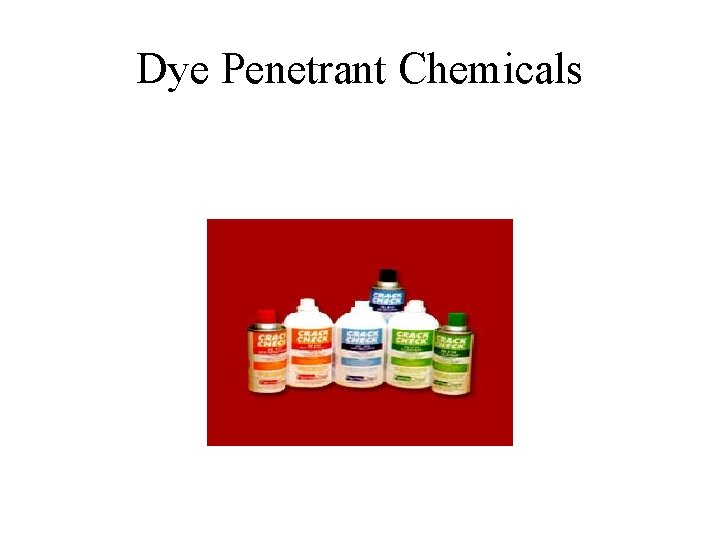
Dye Penetrant Chemicals
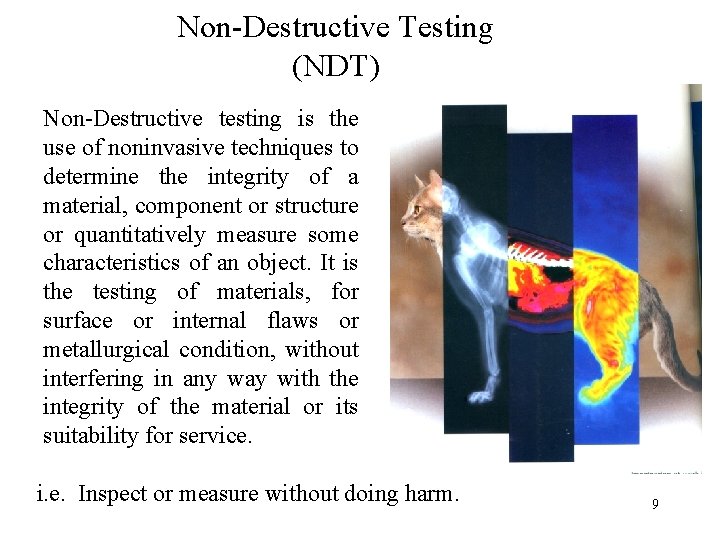
Non-Destructive Testing (NDT) Non-Destructive testing is the use of noninvasive techniques to determine the integrity of a material, component or structure or quantitatively measure some characteristics of an object. It is the testing of materials, for surface or internal flaws or metallurgical condition, without interfering in any way with the integrity of the material or its suitability for service. i. e. Inspect or measure without doing harm. 9
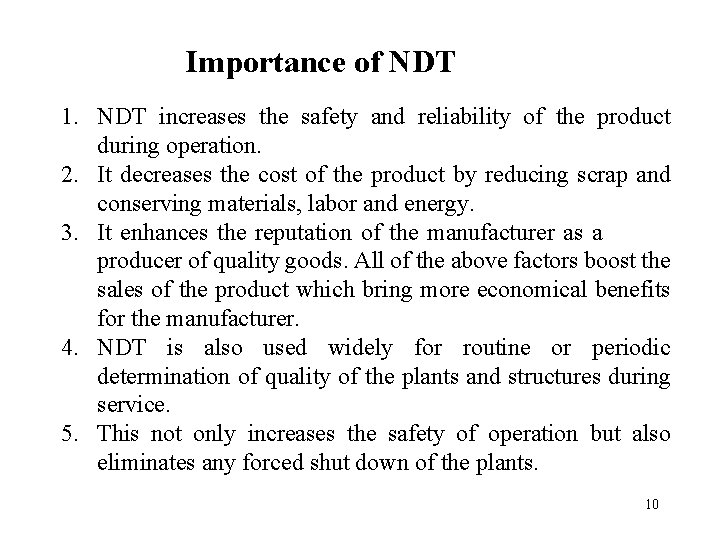
Importance of NDT 1. NDT increases the safety and reliability of the product during operation. 2. It decreases the cost of the product by reducing scrap and conserving materials, labor and energy. 3. It enhances the reputation of the manufacturer as a producer of quality goods. All of the above factors boost the sales of the product which bring more economical benefits for the manufacturer. 4. NDT is also used widely for routine or periodic determination of quality of the plants and structures during service. 5. This not only increases the safety of operation but also eliminates any forced shut down of the plants. 10
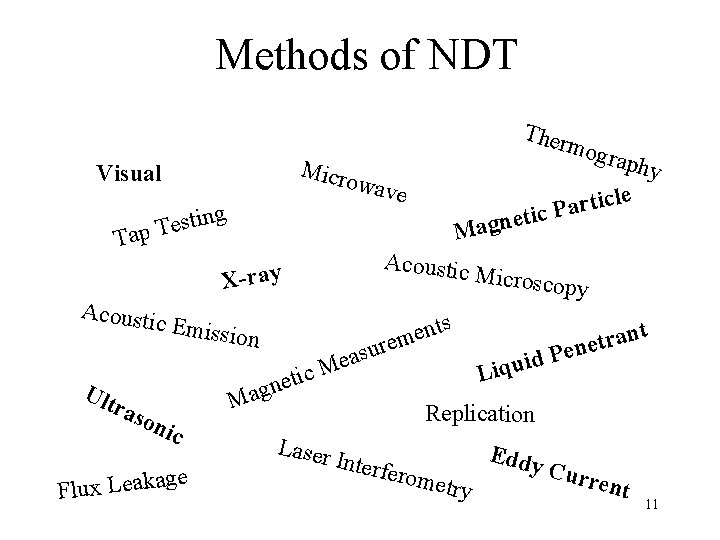
Methods of NDT wave g n i t s e p. T Ta Acousti c Emiss ts n e em ion c oni c ge Flux Leaka i t e n ag r u s a Me M Laser phy article P c i t e n Mag Acoustic X-ray ras mog ra Micro Visual Ult Ther Microsco py t n a r t ene P d i u Liq Replication Interf erome try Eddy Curr ent 11
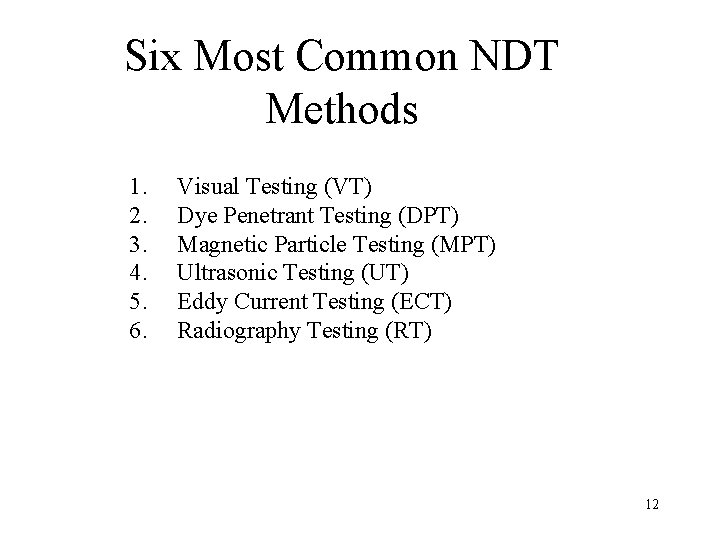
Six Most Common NDT Methods 1. 2. 3. 4. 5. 6. Visual Testing (VT) Dye Penetrant Testing (DPT) Magnetic Particle Testing (MPT) Ultrasonic Testing (UT) Eddy Current Testing (ECT) Radiography Testing (RT) 12
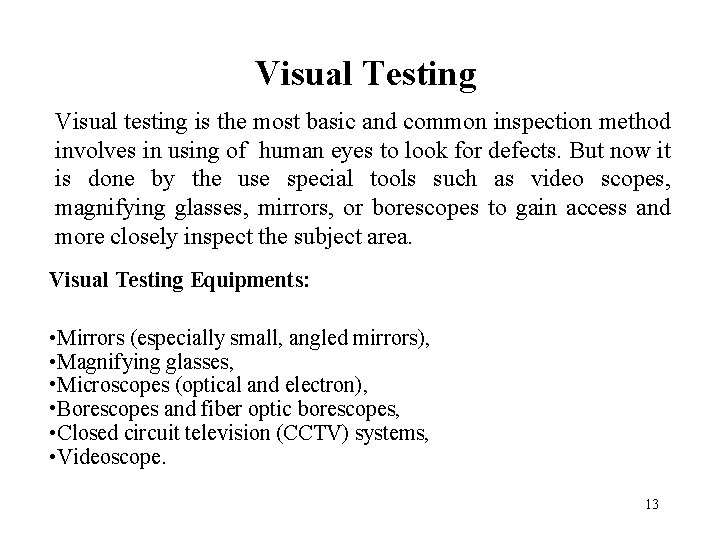
Visual Testing Visual testing is the most basic and common inspection method involves in using of human eyes to look for defects. But now it is done by the use special tools such as video scopes, magnifying glasses, mirrors, or borescopes to gain access and more closely inspect the subject area. Visual Testing Equipments: • Mirrors (especially small, angled mirrors), • Magnifying glasses, • Microscopes (optical and electron), • Borescopes and fiber optic borescopes, • Closed circuit television (CCTV) systems, • Videoscope. 13
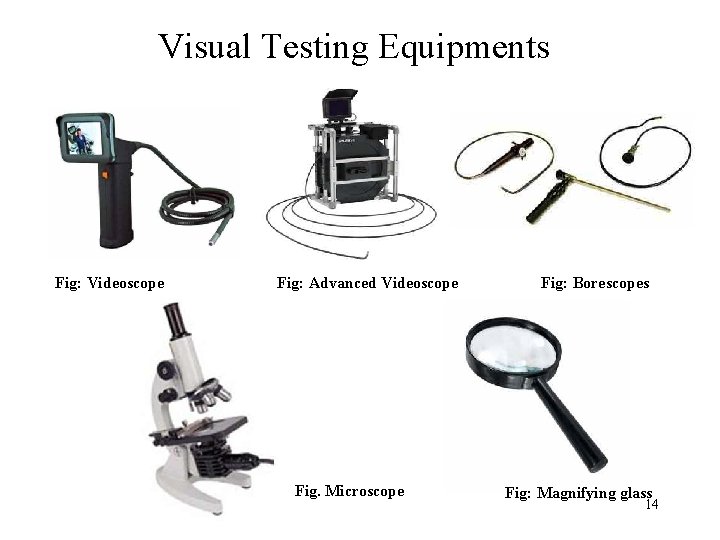
Visual Testing Equipments Fig: Videoscope Fig: Advanced Videoscope Fig. Microscope Fig: Borescopes Fig: Magnifying glass 14
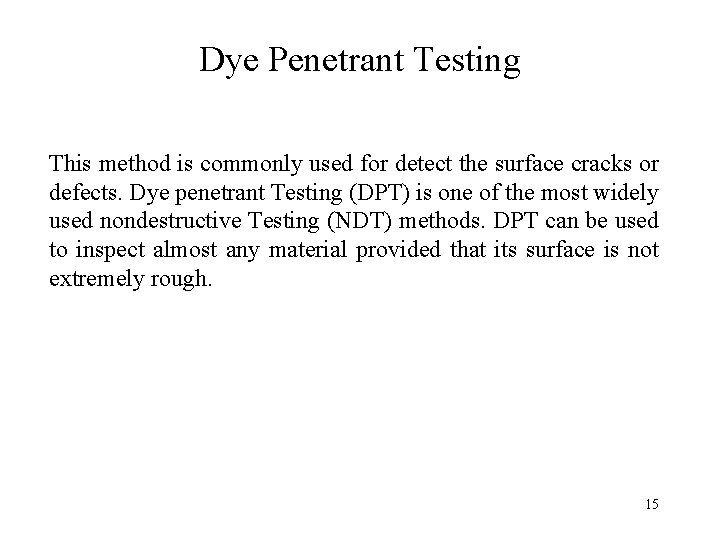
Dye Penetrant Testing This method is commonly used for detect the surface cracks or defects. Dye penetrant Testing (DPT) is one of the most widely used nondestructive Testing (NDT) methods. DPT can be used to inspect almost any material provided that its surface is not extremely rough. 15
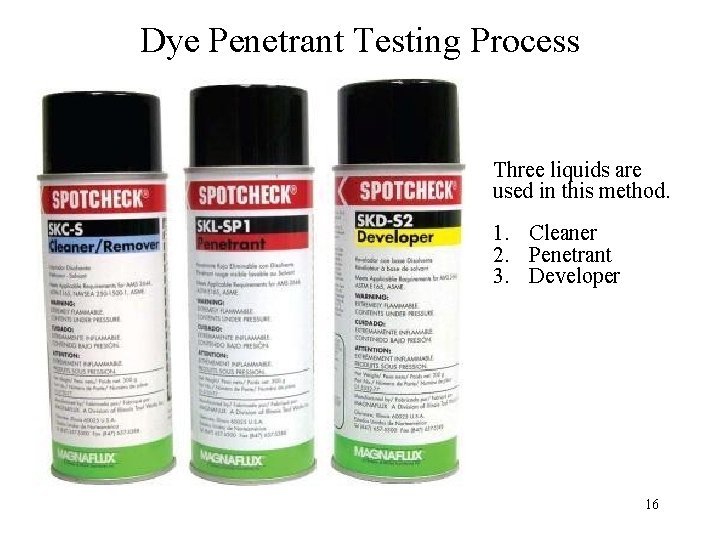
Dye Penetrant Testing Process Three liquids are used in this method. 1. Cleaner 2. Penetrant 3. Developer 16
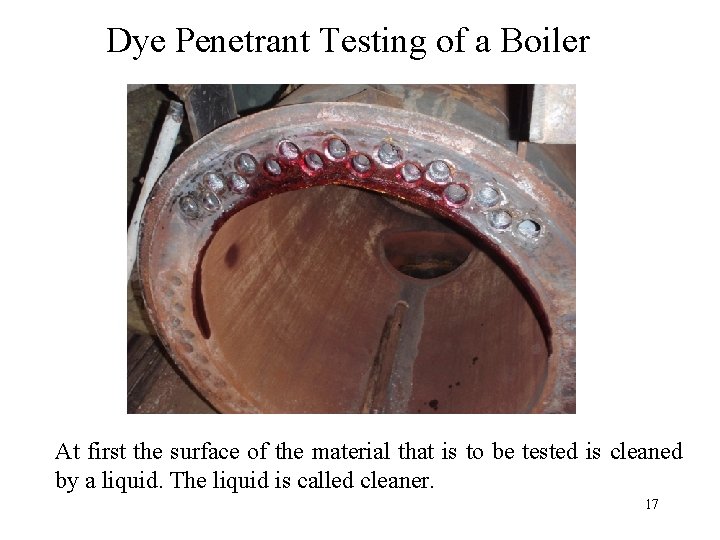
Dye Penetrant Testing of a Boiler At first the surface of the material that is to be tested is cleaned by a liquid. The liquid is called cleaner. 17
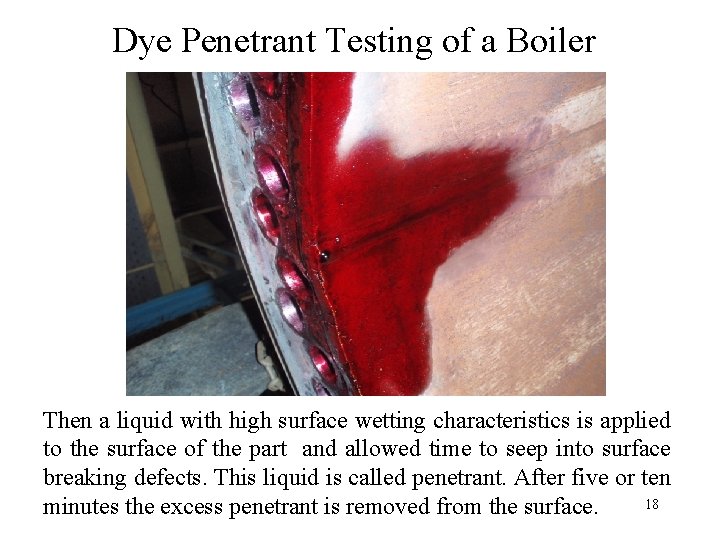
Dye Penetrant Testing of a Boiler Then a liquid with high surface wetting characteristics is applied to the surface of the part and allowed time to seep into surface breaking defects. This liquid is called penetrant. After five or ten 18 minutes the excess penetrant is removed from the surface.
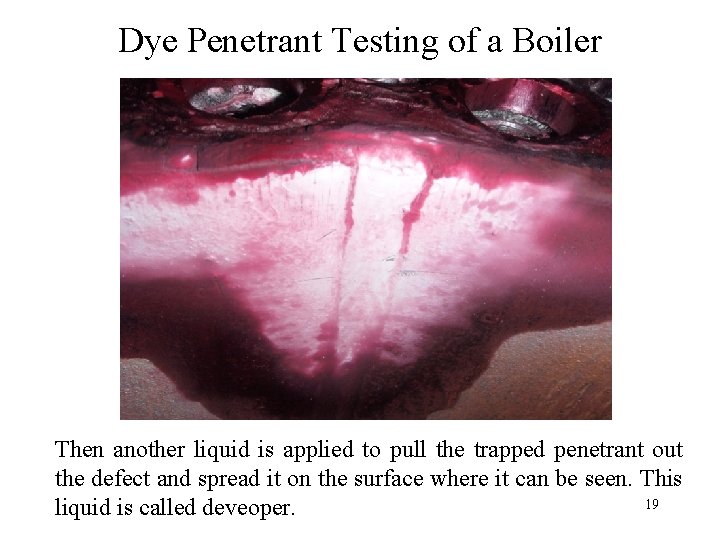
Dye Penetrant Testing of a Boiler Then another liquid is applied to pull the trapped penetrant out the defect and spread it on the surface where it can be seen. This 19 liquid is called deveoper.
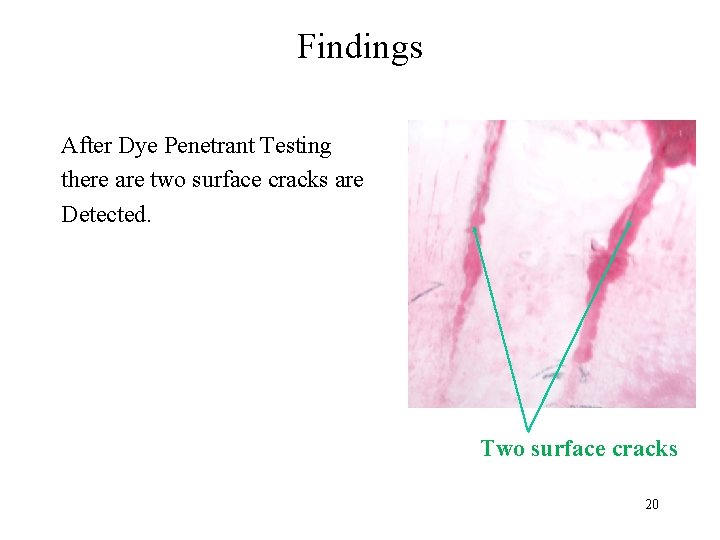
Findings After Dye Penetrant Testing there are two surface cracks are Detected. Two surface cracks 20
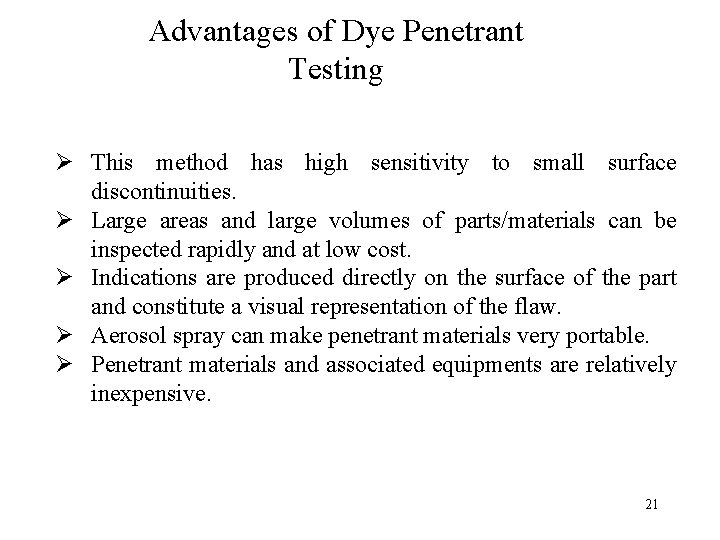
Advantages of Dye Penetrant Testing Ø This method has high sensitivity to small surface discontinuities. Ø Large areas and large volumes of parts/materials can be inspected rapidly and at low cost. Ø Indications are produced directly on the surface of the part and constitute a visual representation of the flaw. Ø Aerosol spray can make penetrant materials very portable. Ø Penetrant materials and associated equipments are relatively inexpensive. 21
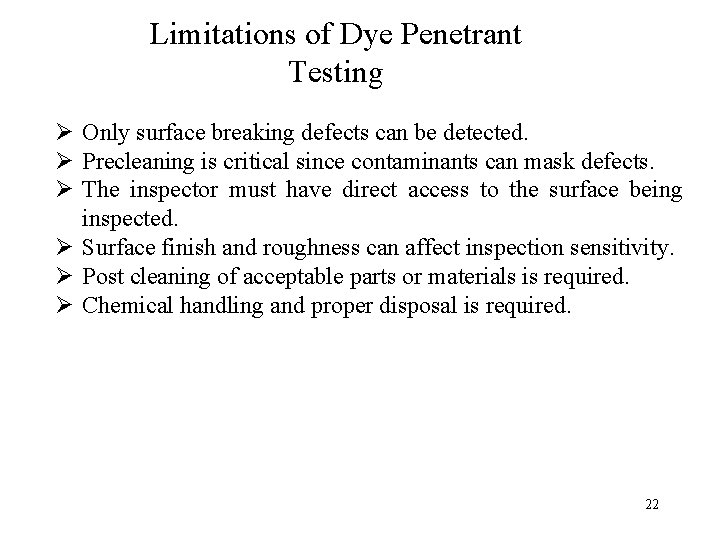
Limitations of Dye Penetrant Testing Ø Only surface breaking defects can be detected. Ø Precleaning is critical since contaminants can mask defects. Ø The inspector must have direct access to the surface being inspected. Ø Surface finish and roughness can affect inspection sensitivity. Ø Post cleaning of acceptable parts or materials is required. Ø Chemical handling and proper disposal is required. 22
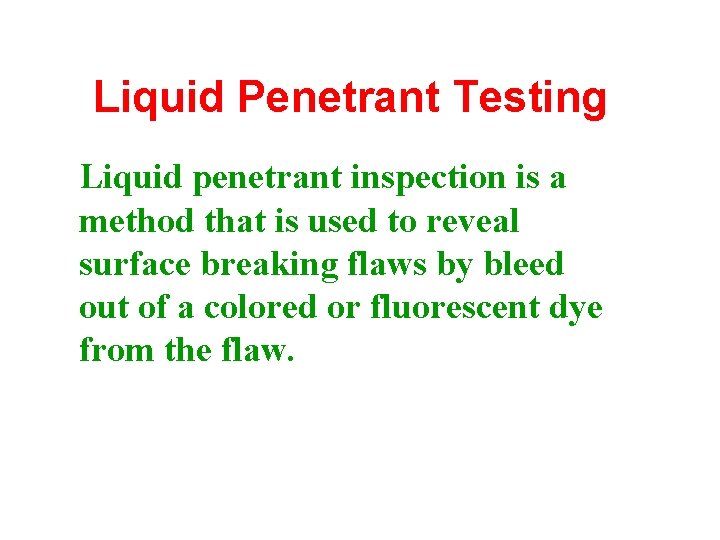
Liquid Penetrant Testing Liquid penetrant inspection is a method that is used to reveal surface breaking flaws by bleed out of a colored or fluorescent dye from the flaw.
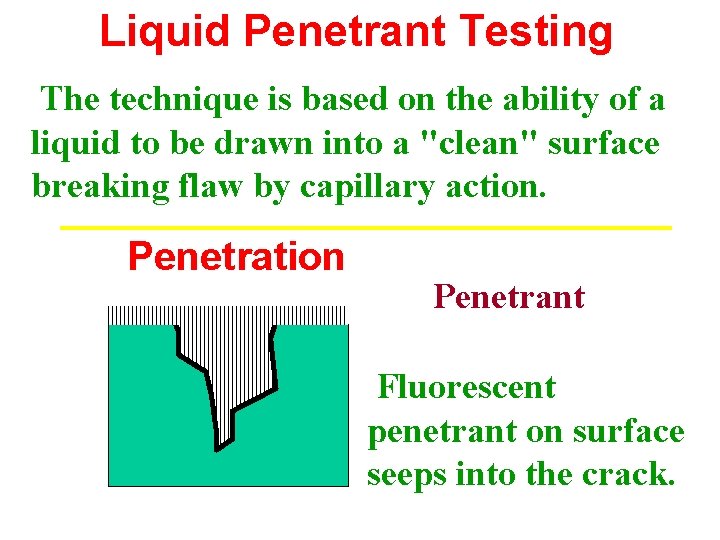
Liquid Penetrant Testing The technique is based on the ability of a liquid to be drawn into a "clean" surface breaking flaw by capillary action. Penetration Penetrant Fluorescent penetrant on surface seeps into the crack.
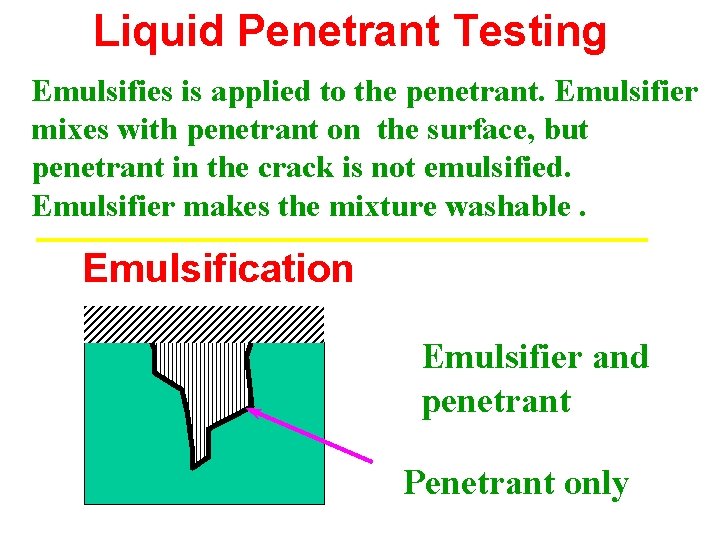
Liquid Penetrant Testing Emulsifies is applied to the penetrant. Emulsifier mixes with penetrant on the surface, but penetrant in the crack is not emulsified. Emulsifier makes the mixture washable. Emulsification Emulsifier and penetrant Penetrant only
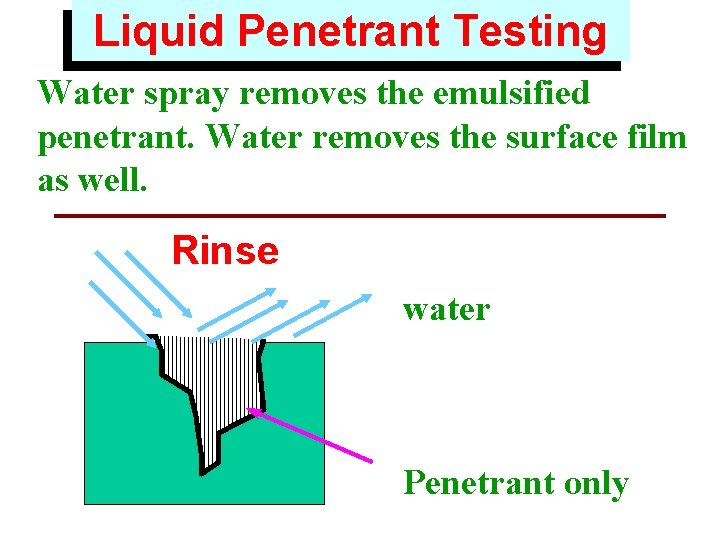
Liquid Penetrant Testing Water spray removes the emulsified penetrant. Water removes the surface film as well. Rinse water Penetrant only
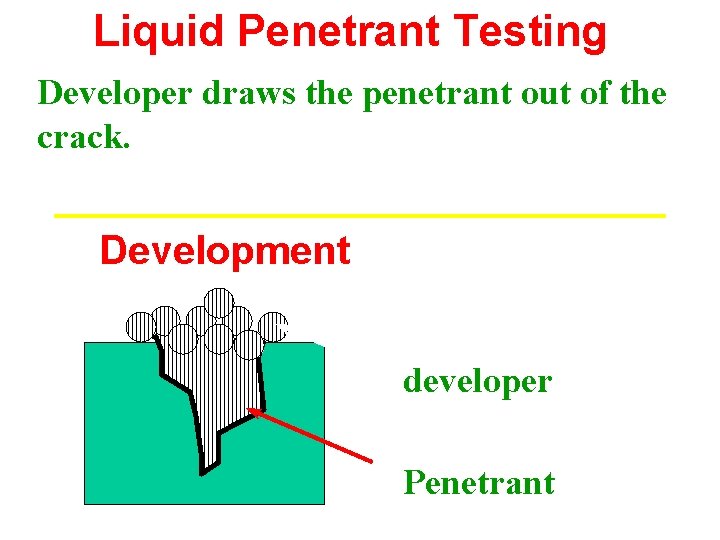
Liquid Penetrant Testing Developer draws the penetrant out of the crack. Development developer Penetrant
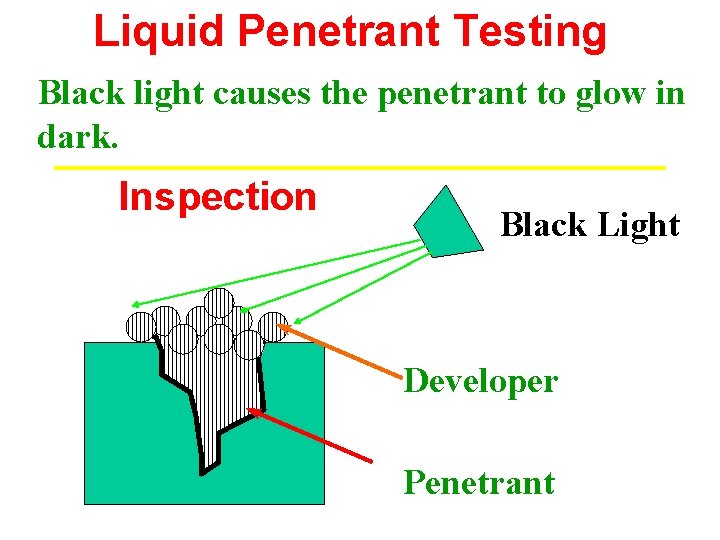
Liquid Penetrant Testing Black light causes the penetrant to glow in dark. Inspection Black Light Developer Penetrant
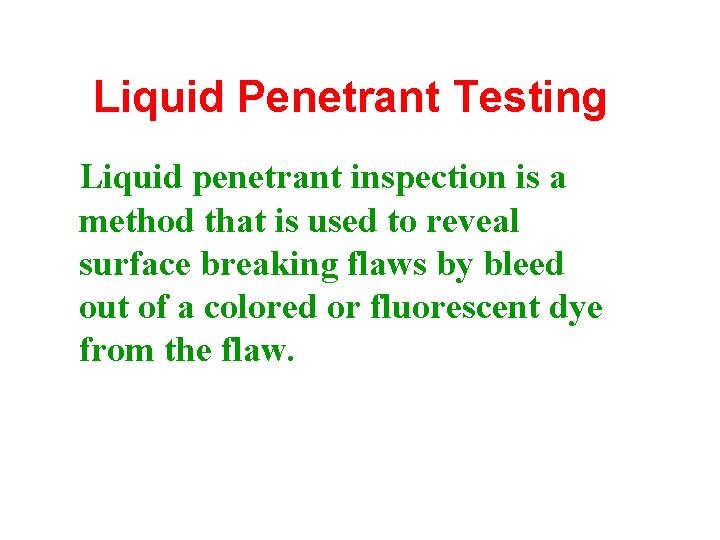
Liquid Penetrant Testing Liquid penetrant inspection is a method that is used to reveal surface breaking flaws by bleed out of a colored or fluorescent dye from the flaw.
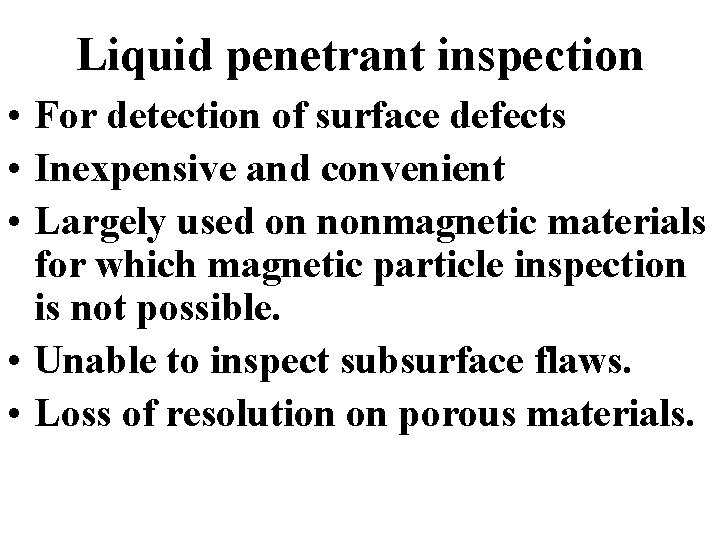
Liquid penetrant inspection • For detection of surface defects • Inexpensive and convenient • Largely used on nonmagnetic materials for which magnetic particle inspection is not possible. • Unable to inspect subsurface flaws. • Loss of resolution on porous materials.
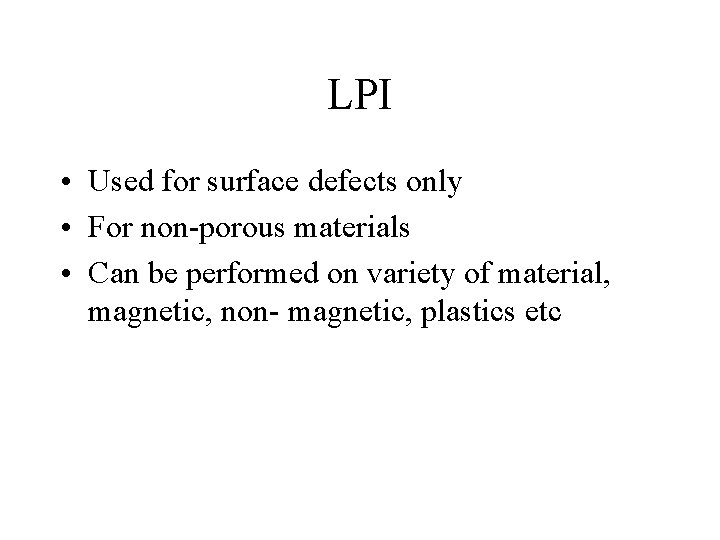
LPI • Used for surface defects only • For non-porous materials • Can be performed on variety of material, magnetic, non- magnetic, plastics etc
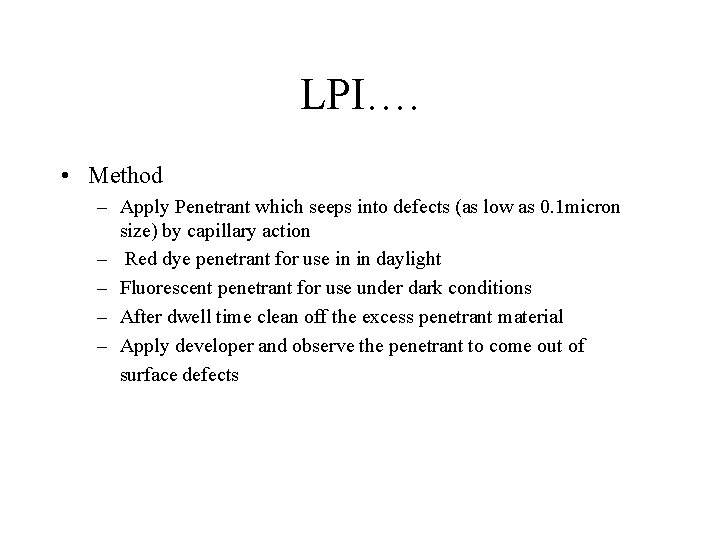
LPI…. • Method – Apply Penetrant which seeps into defects (as low as 0. 1 micron size) by capillary action – Red dye penetrant for use in in daylight – Fluorescent penetrant for use under dark conditions – After dwell time clean off the excess penetrant material – Apply developer and observe the penetrant to come out of surface defects
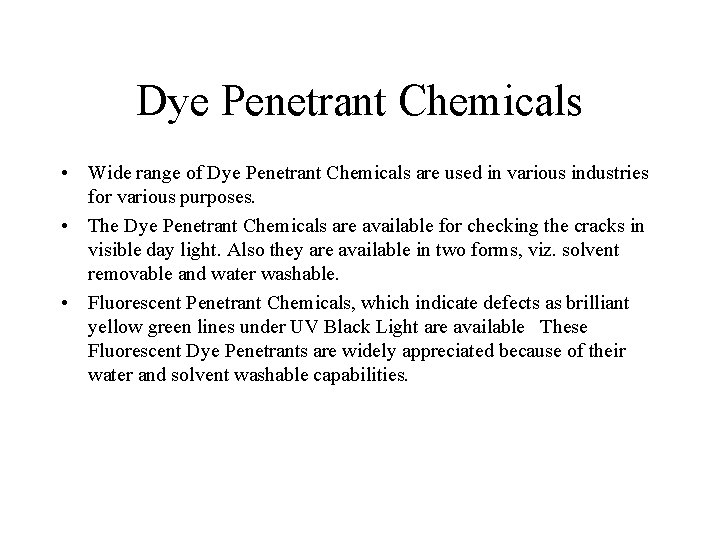
Dye Penetrant Chemicals • Wide range of Dye Penetrant Chemicals are used in various industries for various purposes. • The Dye Penetrant Chemicals are available for checking the cracks in visible day light. Also they are available in two forms, viz. solvent removable and water washable. • Fluorescent Penetrant Chemicals, which indicate defects as brilliant yellow green lines under UV Black Light are available These Fluorescent Dye Penetrants are widely appreciated because of their water and solvent washable capabilities.
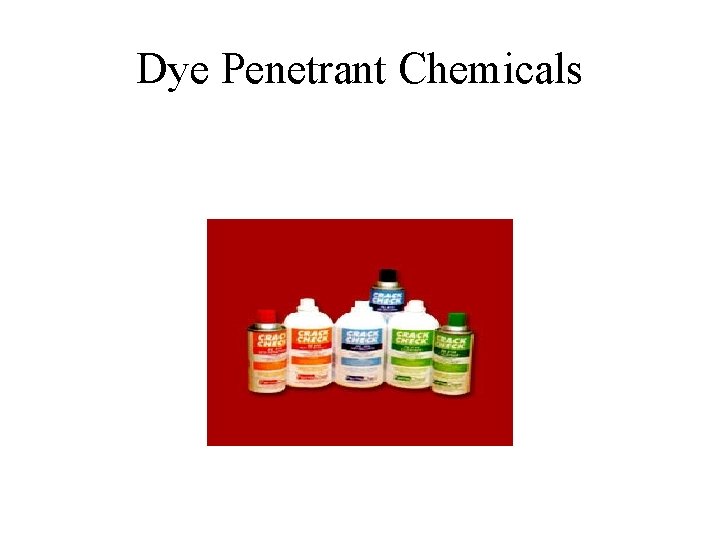
Dye Penetrant Chemicals
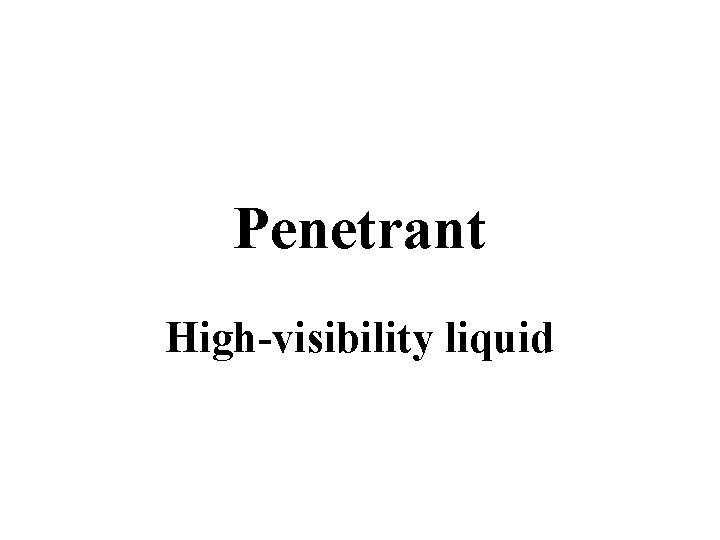
Penetrant High-visibility liquid
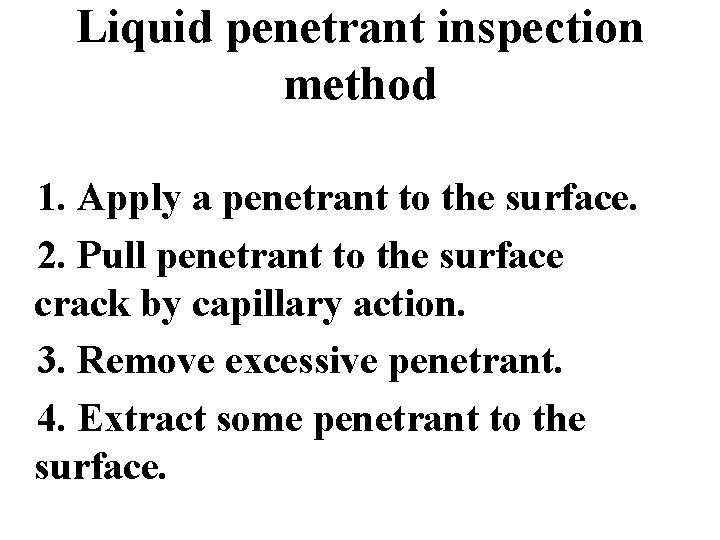
Liquid penetrant inspection method 1. Apply a penetrant to the surface. 2. Pull penetrant to the surface crack by capillary action. 3. Remove excessive penetrant. 4. Extract some penetrant to the surface.
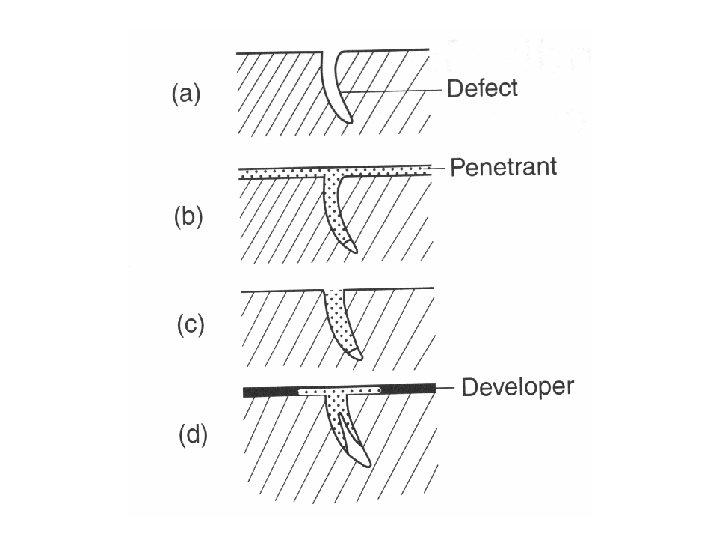
Importance of ndt
Destructive weld testing
Red penetrant
Ndt definition
Characteristics of penetrant
Destructive testing
Functional analysis reverse engineering
Pure liquid dielectrics example
Liquid liquid extraction diagram
Veux-tu briser du péché le pouvoir parole
Inlay wax pattern fabrication
Venn diagram states of matter
Liquid ammonia as non aqueous solvent
Liquid so2 as a non aqueous solvent
Tdd testing private methods
Adc testing methods
Fiber testing methods
Dac testing methods
Pole balance test of generator rotor
Rso generator test
Generator rotor winding resistance test
Sterilization by mechanical methods
Sterile
Which joint is permanent types
Financial motivators
Padilla
Pride is destructive
Constructive and destructive conflict
Are river valleys constructive or destructive
Constructive vs destructive interference
Destructive criticism
Feather destructive behavior
Flash distillation principle
Couples in the great gatsby
Conflict with others
Constructive force example
Constructive and destructive forces 5th grade
What is constructive forces