Lean Manufacturing Dr Chander Arora Main Goals of
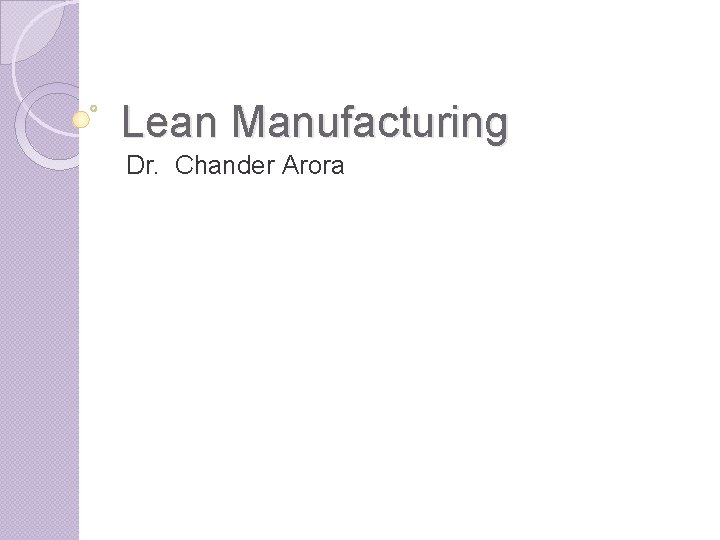
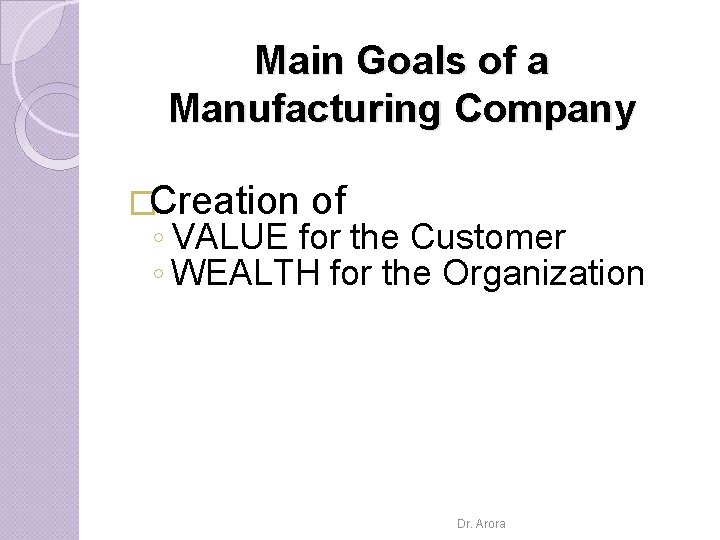
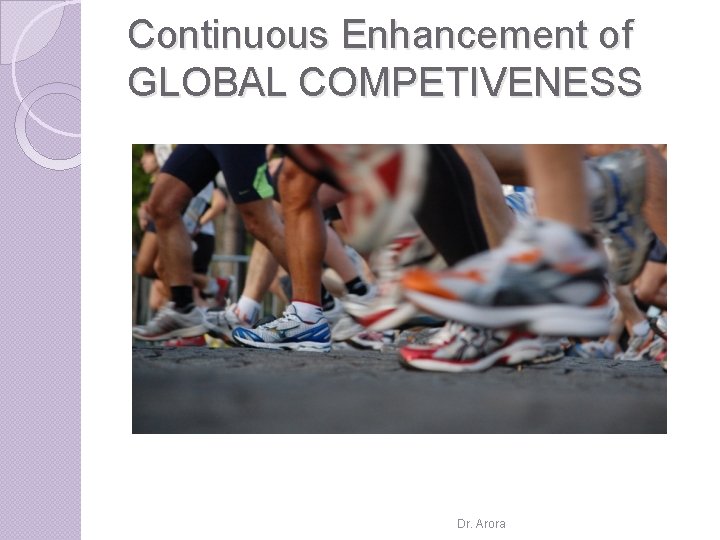
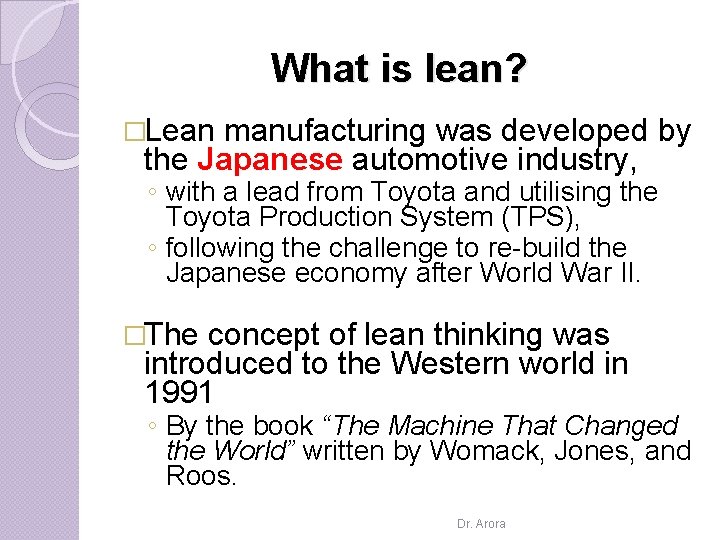
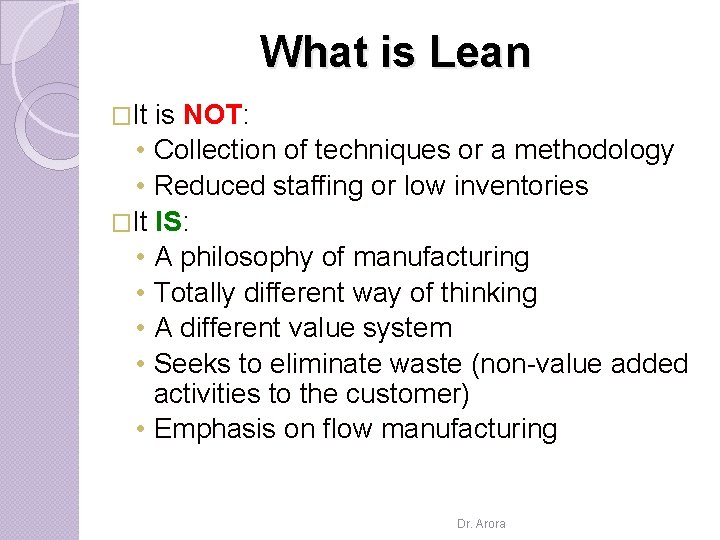

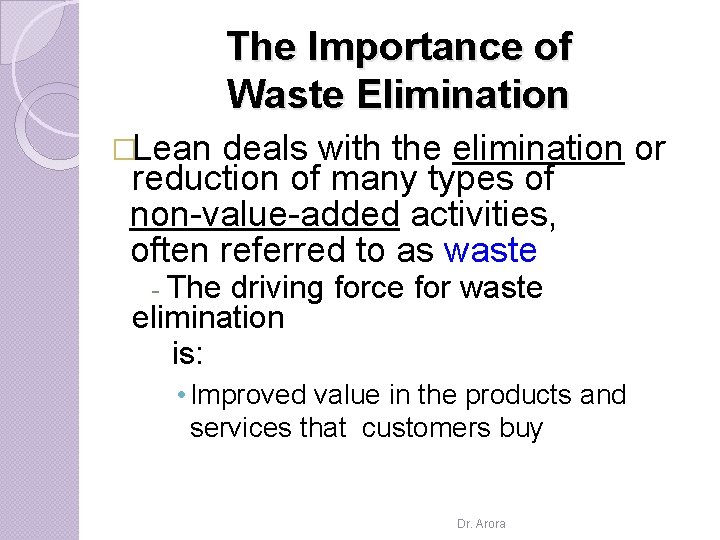
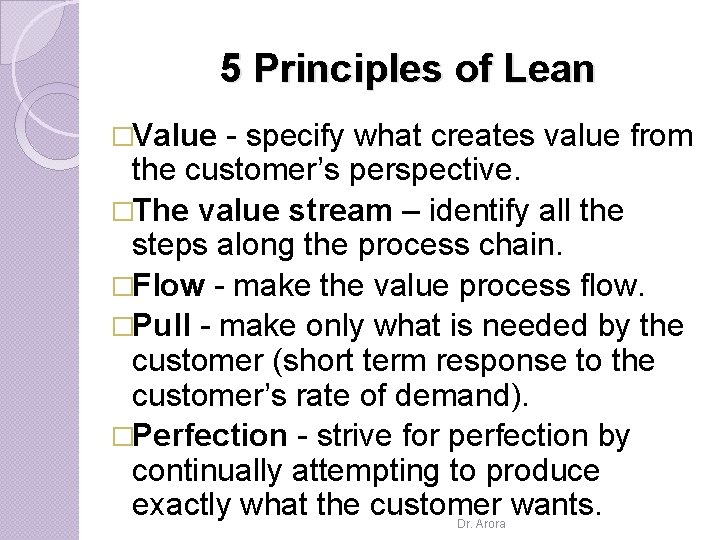
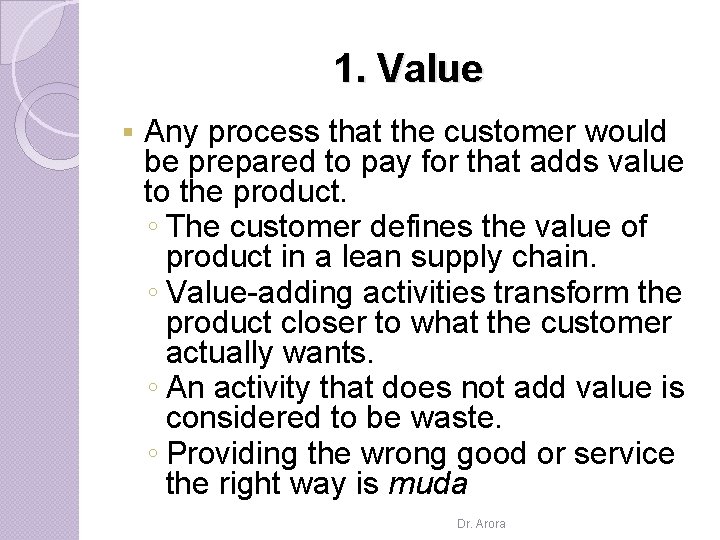
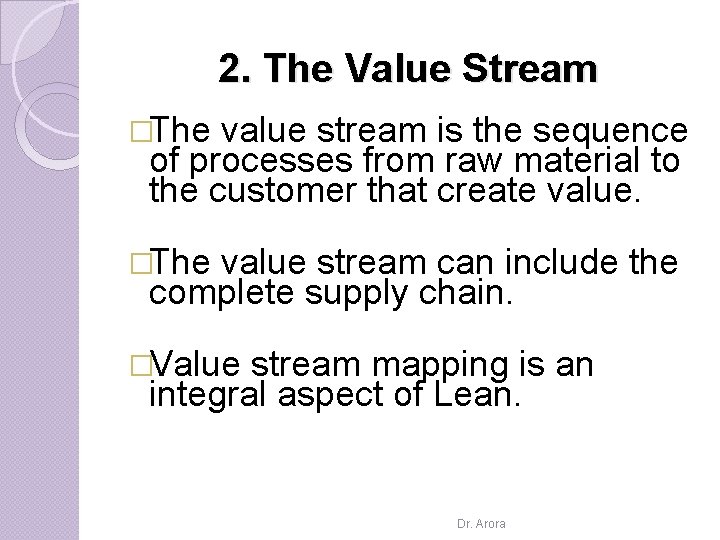
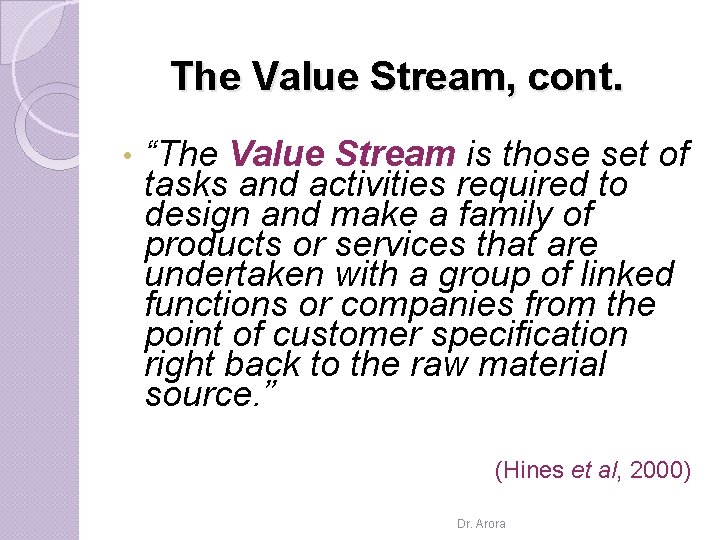
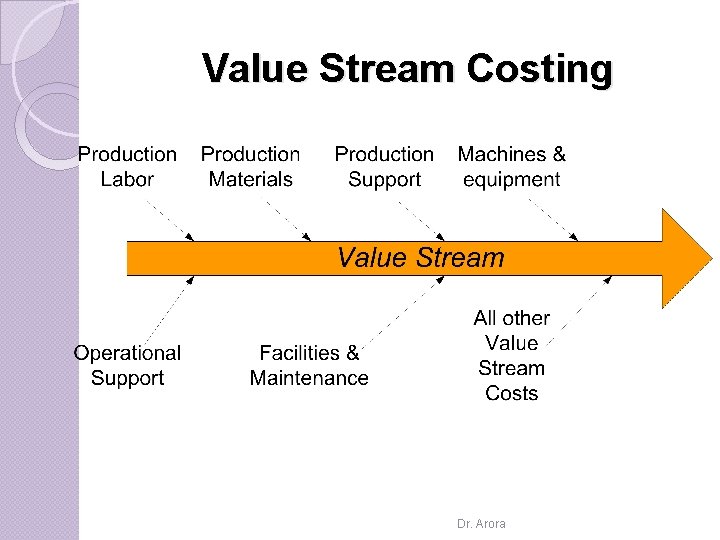
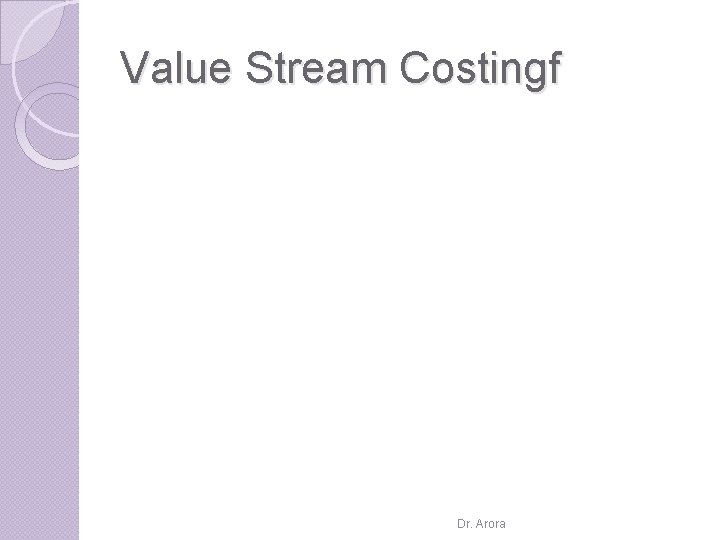
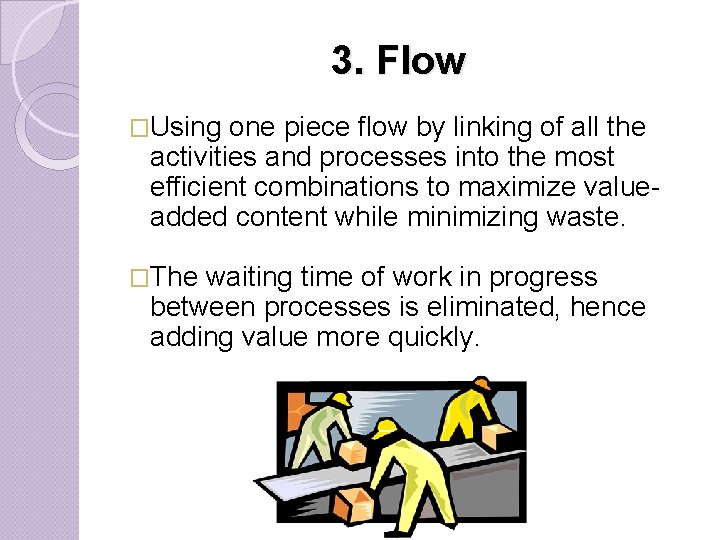
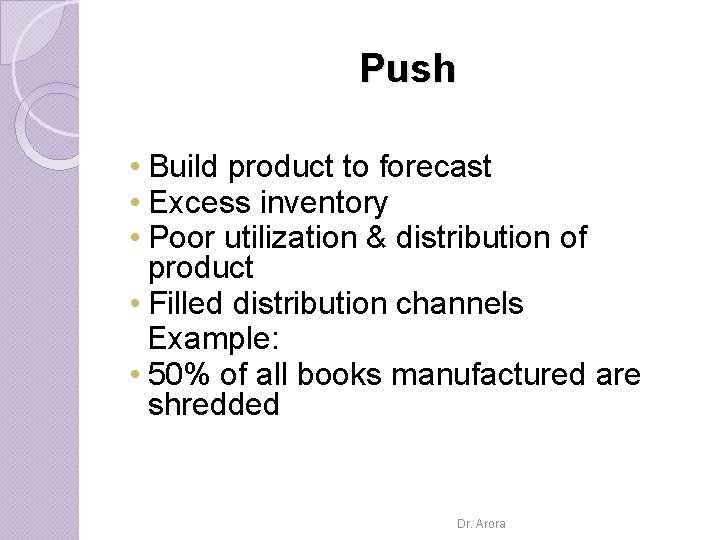
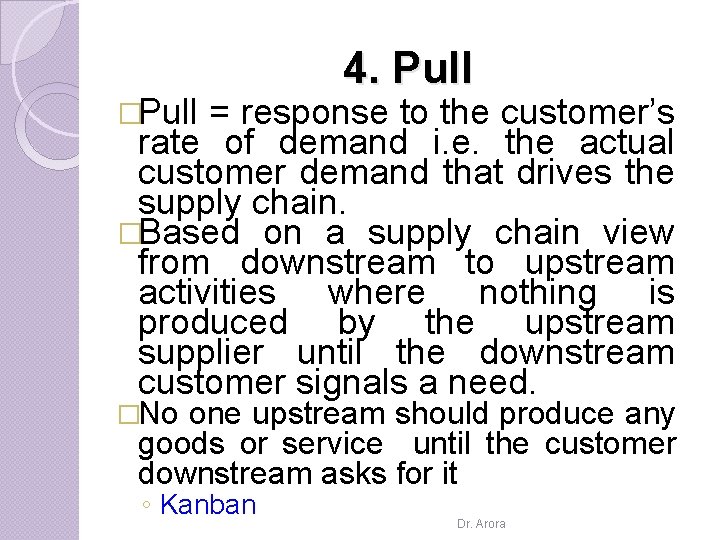
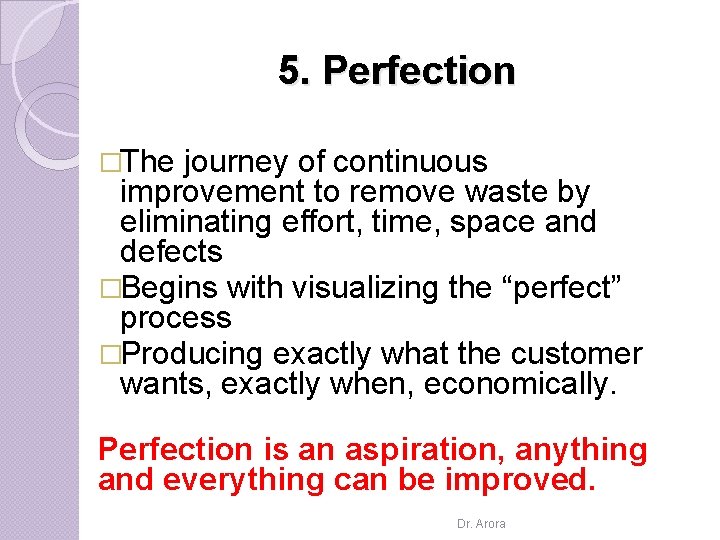
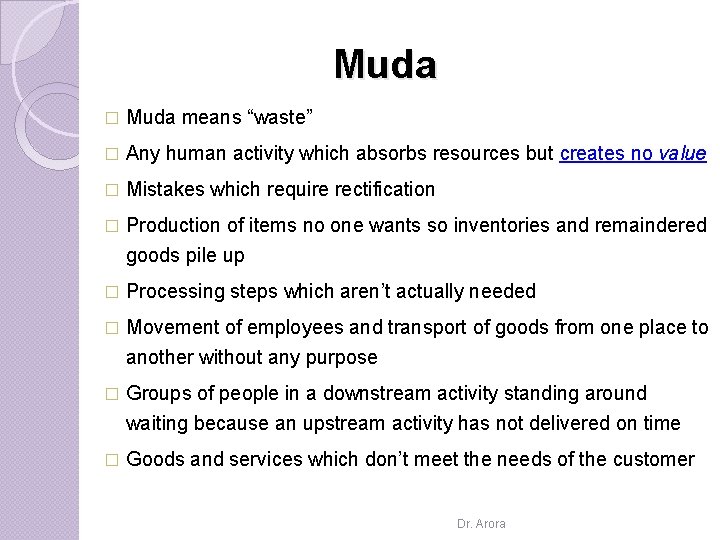
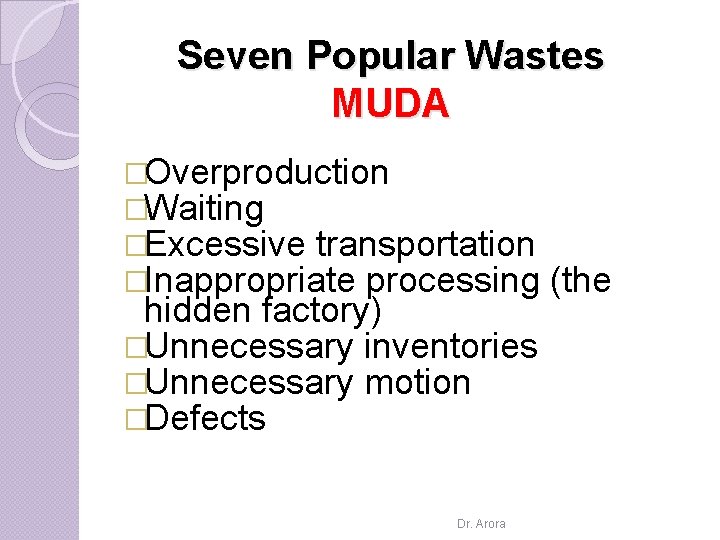
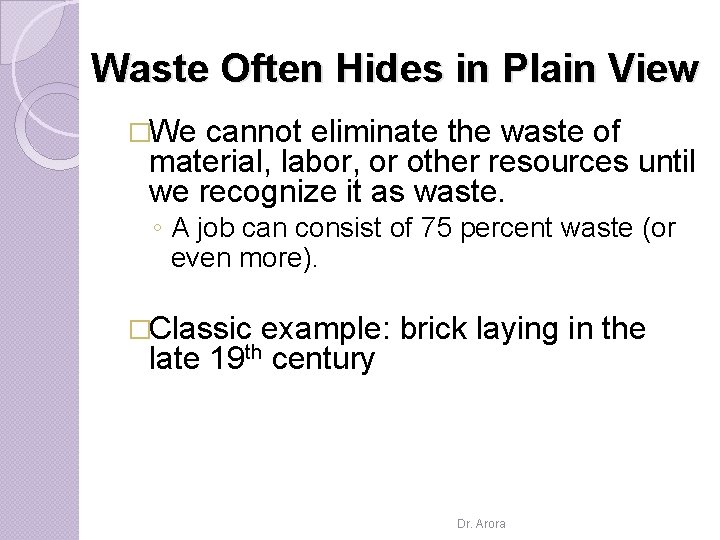
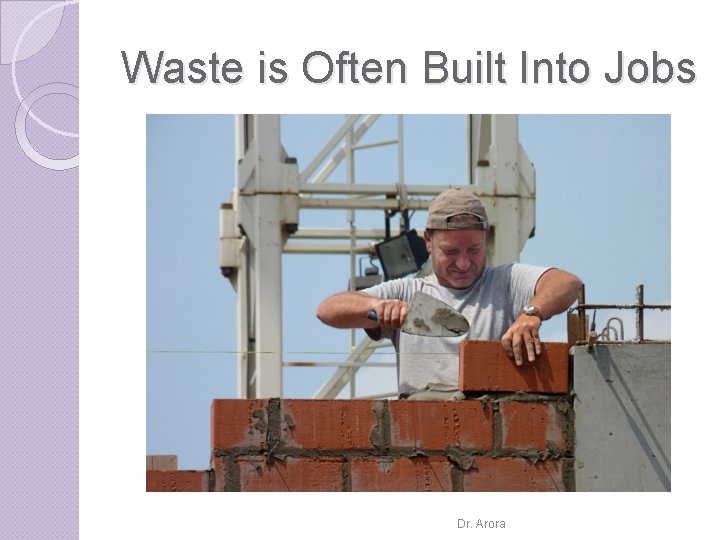
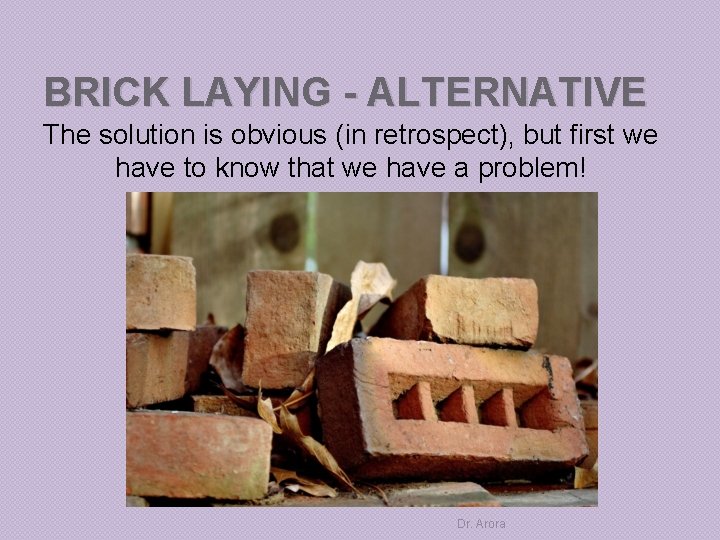
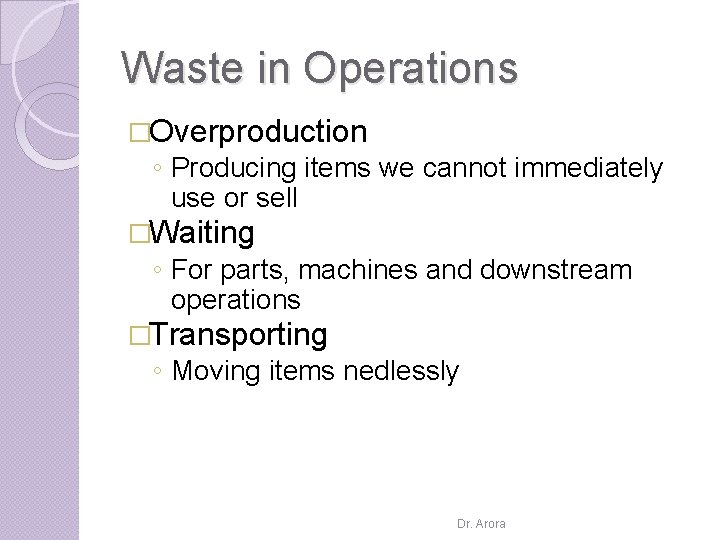
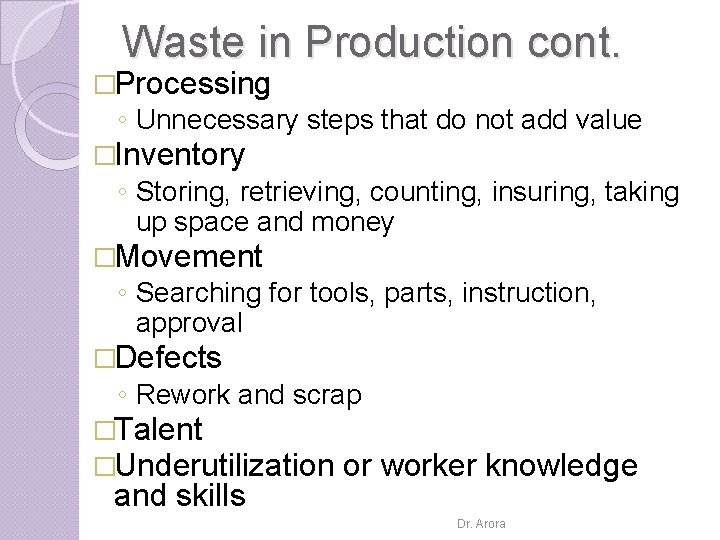
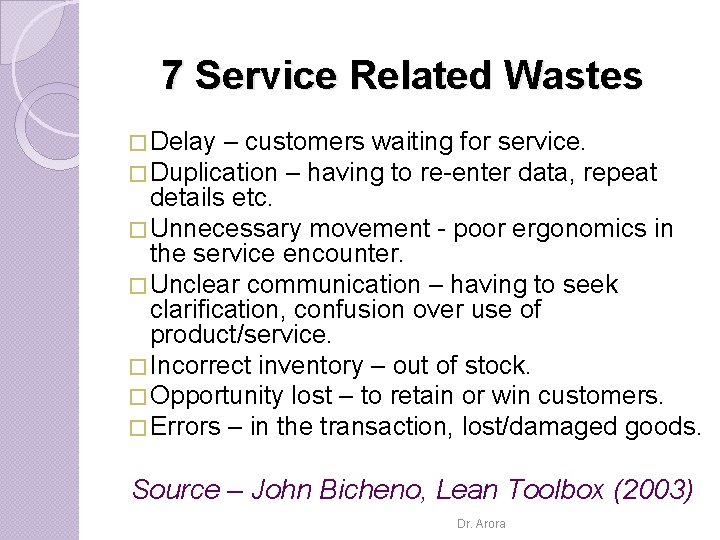
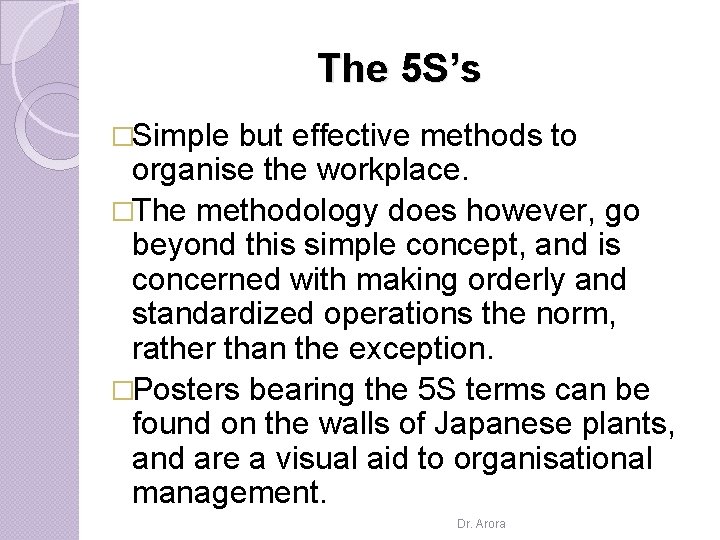
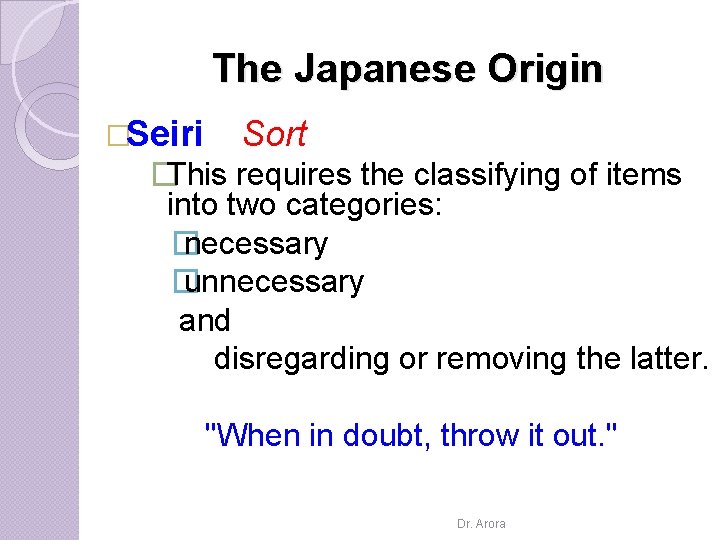
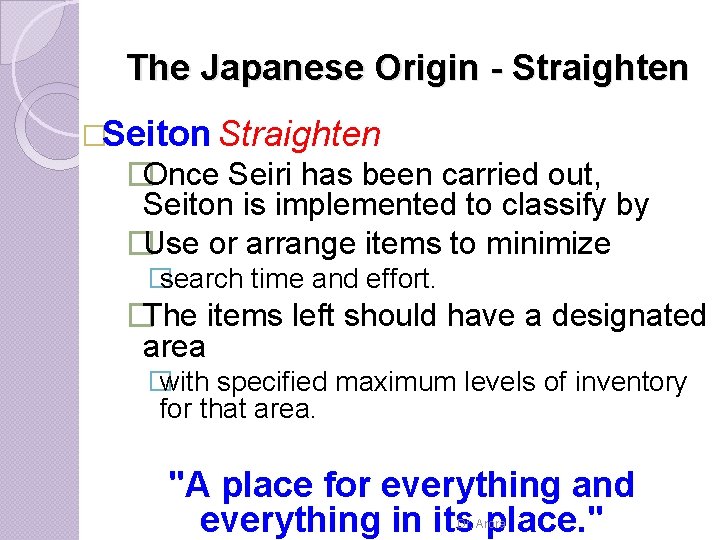
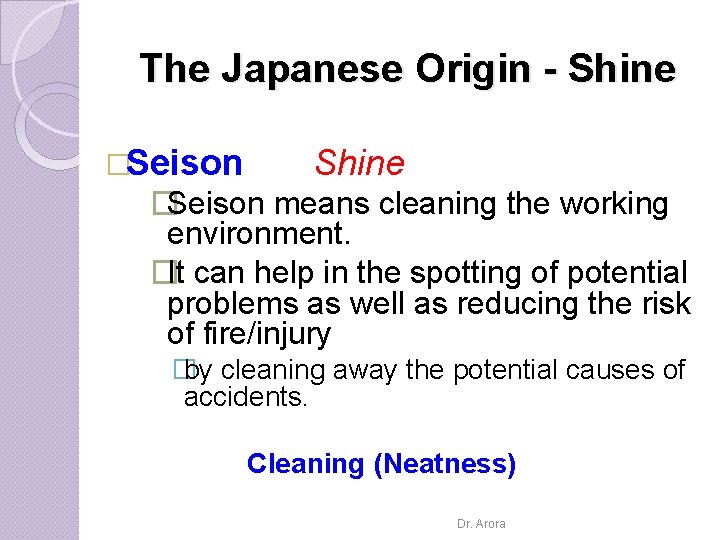
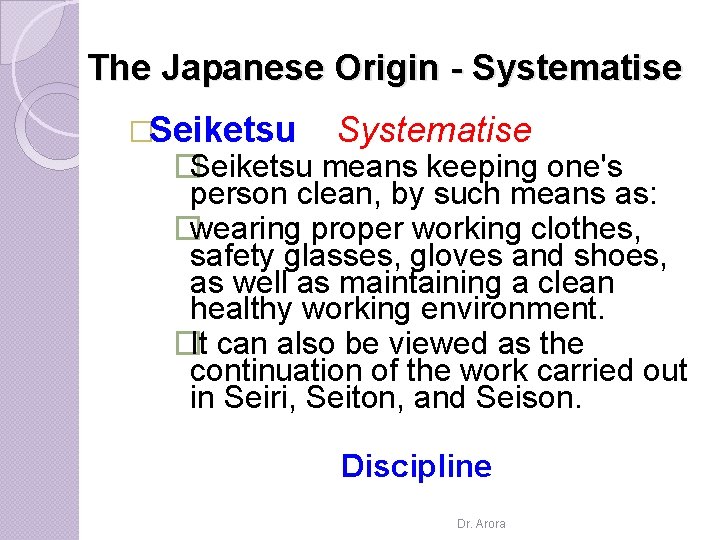
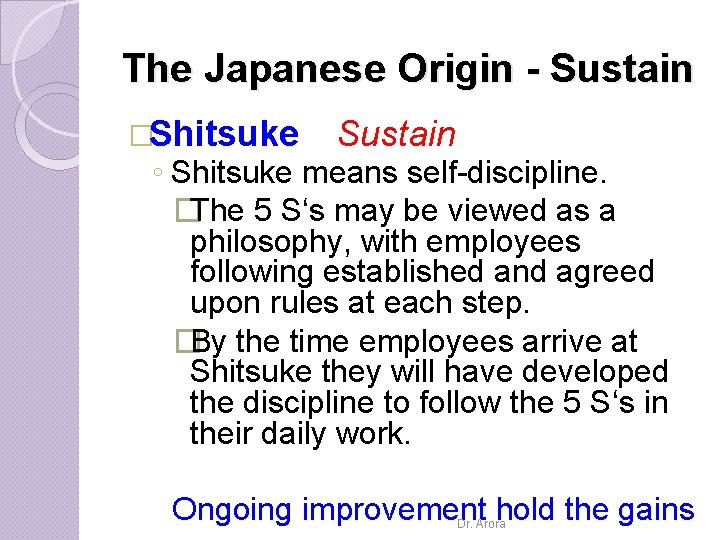
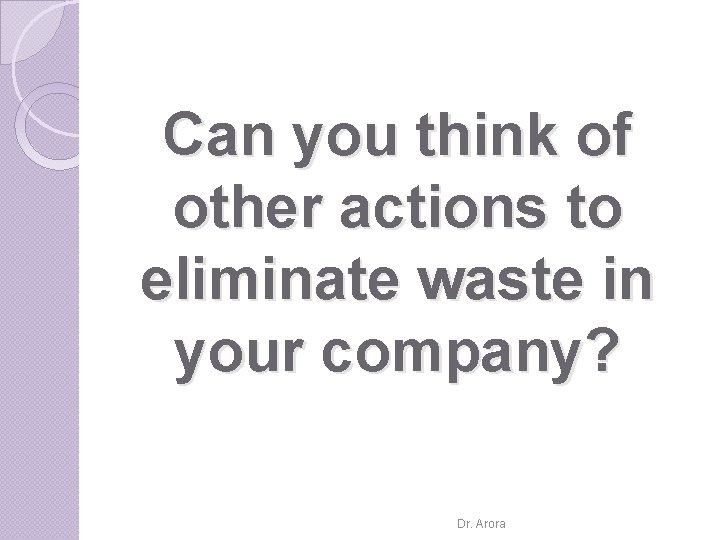
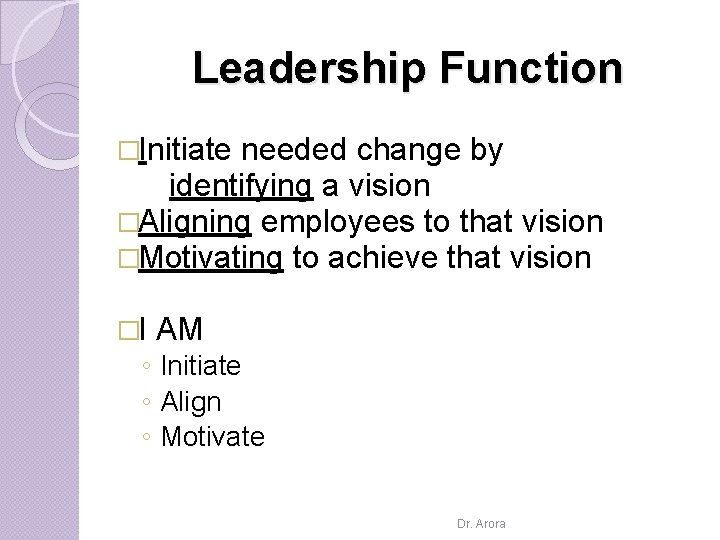
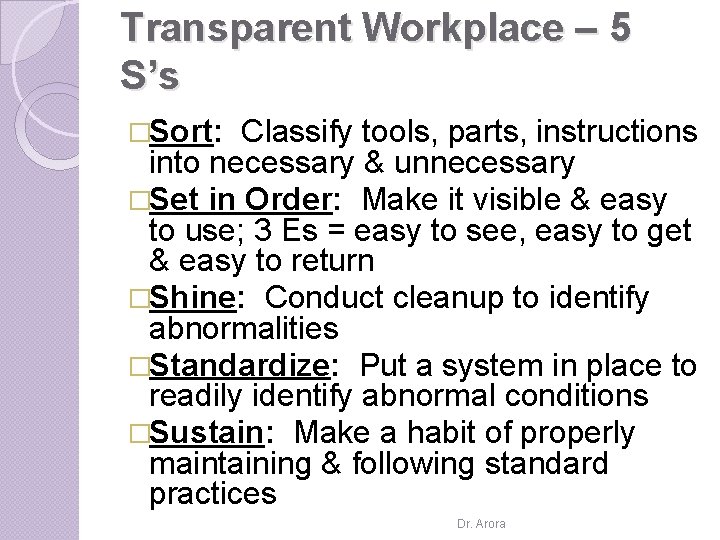
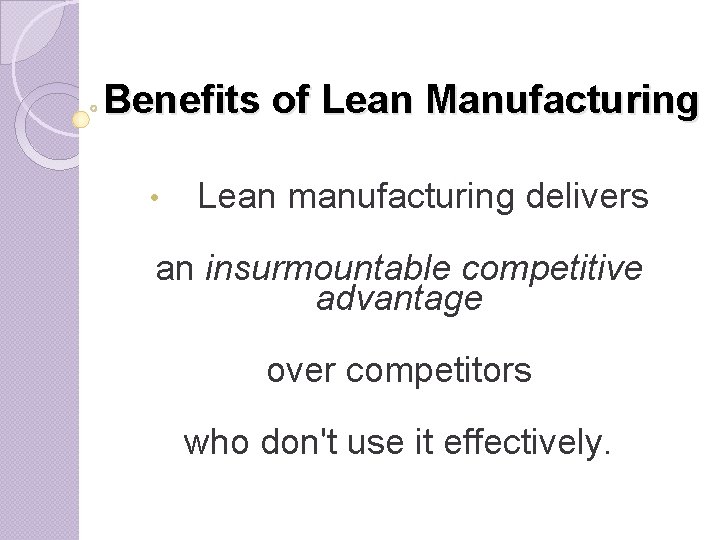
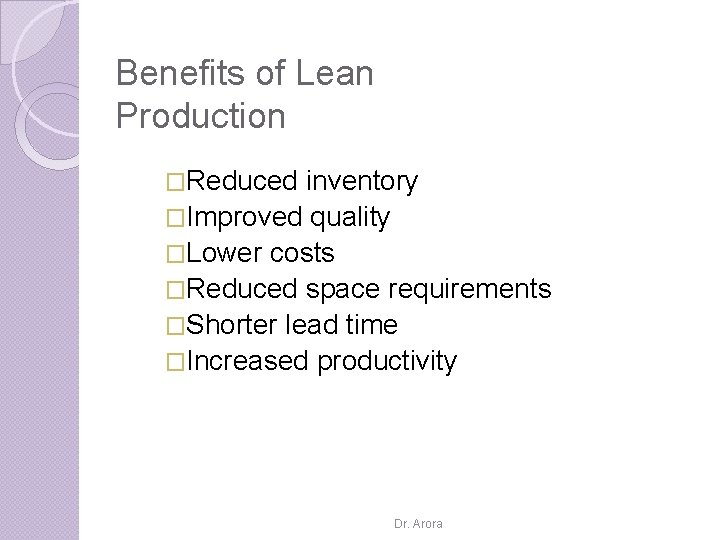
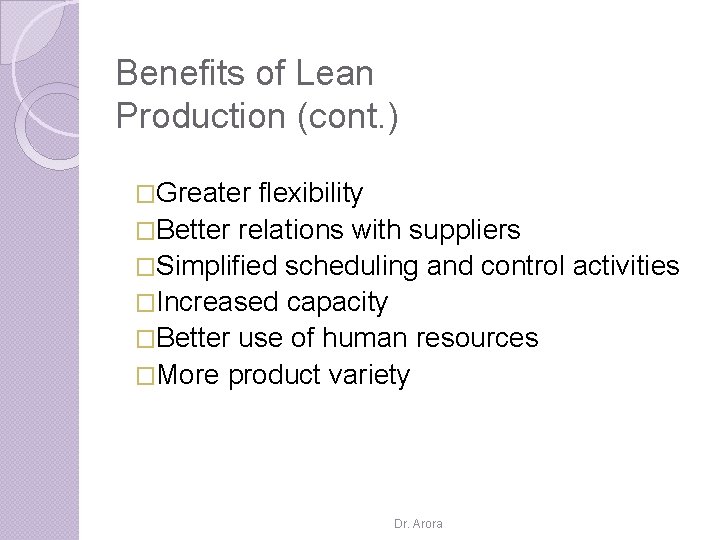
- Slides: 37
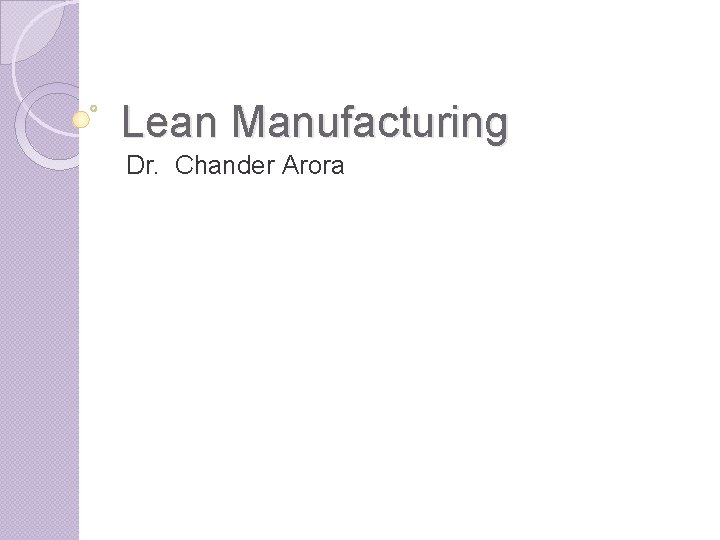
Lean Manufacturing Dr. Chander Arora
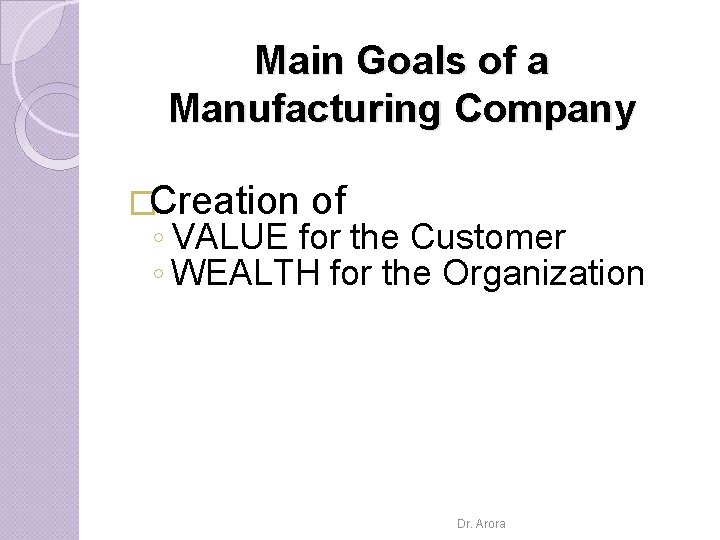
Main Goals of a Manufacturing Company �Creation of ◦ VALUE for the Customer ◦ WEALTH for the Organization Dr. Arora
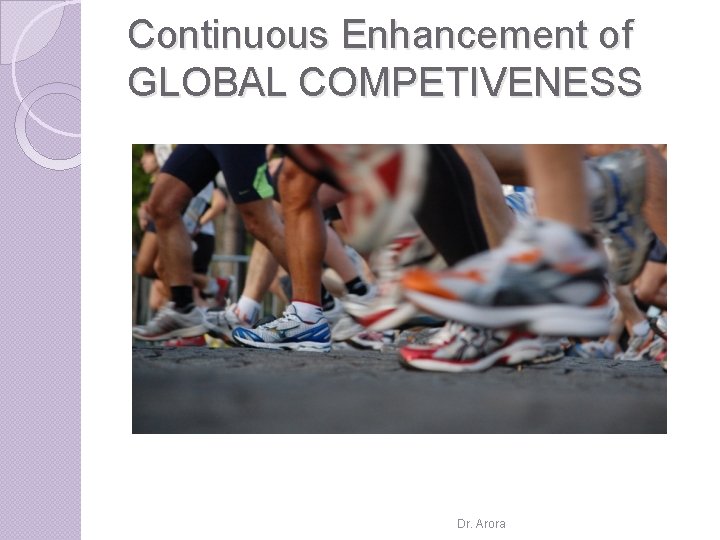
Continuous Enhancement of GLOBAL COMPETIVENESS Dr. Arora
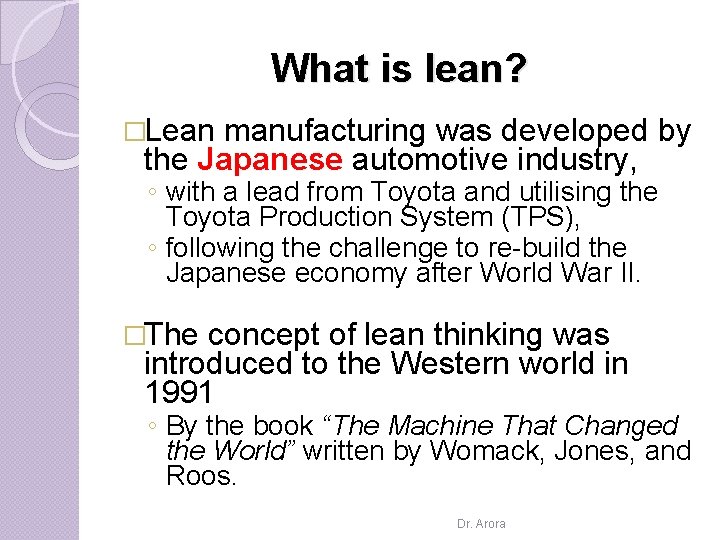
What is lean? �Lean manufacturing was developed by the Japanese automotive industry, ◦ with a lead from Toyota and utilising the Toyota Production System (TPS), ◦ following the challenge to re-build the Japanese economy after World War II. �The concept of lean thinking was introduced to the Western world in 1991 ◦ By the book “The Machine That Changed the World” written by Womack, Jones, and Roos. Dr. Arora
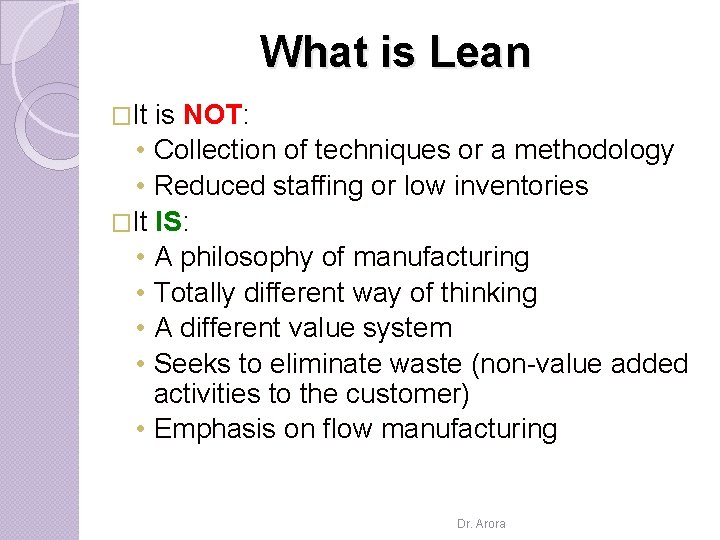
What is Lean �It is NOT: • Collection of techniques or a methodology • Reduced staffing or low inventories �It IS: • A philosophy of manufacturing • Totally different way of thinking • A different value system • Seeks to eliminate waste (non-value added activities to the customer) • Emphasis on flow manufacturing Dr. Arora

Lean Characteristics � Focus is on the improvement of resource utilization: ― Equipment setup time reduced ― Scheduled machine maintenance ― Orderly, clean workplace ― Pull production being used ― Inventory control ― Factory layout in work cell arrangement by products ― Active error elimination ― Improved quality, etc. Dr. Arora
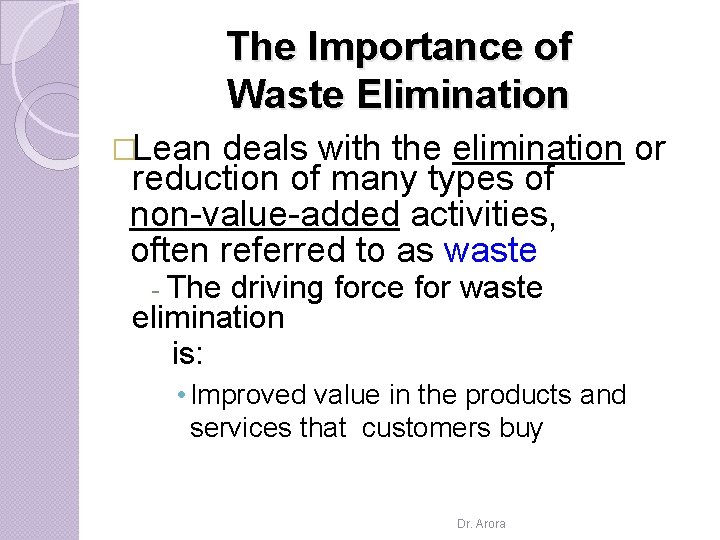
The Importance of Waste Elimination �Lean deals with the elimination or reduction of many types of non-value-added activities, often referred to as waste - The driving force for waste elimination is: • Improved value in the products and services that customers buy Dr. Arora
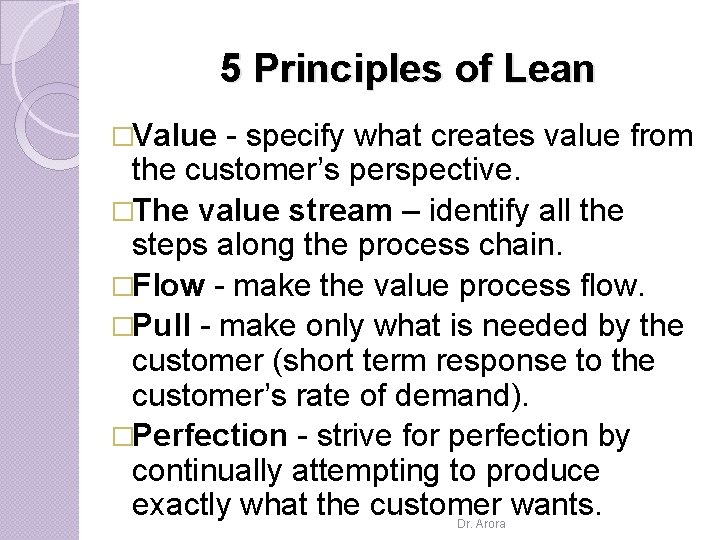
5 Principles of Lean �Value - specify what creates value from the customer’s perspective. �The value stream – identify all the steps along the process chain. �Flow - make the value process flow. �Pull - make only what is needed by the customer (short term response to the customer’s rate of demand). �Perfection - strive for perfection by continually attempting to produce exactly what the customer wants. Dr. Arora
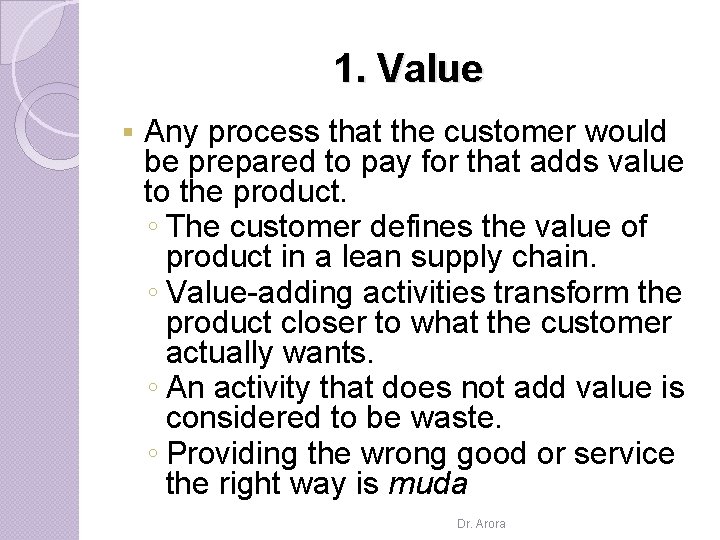
1. Value § Any process that the customer would be prepared to pay for that adds value to the product. ◦ The customer defines the value of product in a lean supply chain. ◦ Value-adding activities transform the product closer to what the customer actually wants. ◦ An activity that does not add value is considered to be waste. ◦ Providing the wrong good or service the right way is muda Dr. Arora
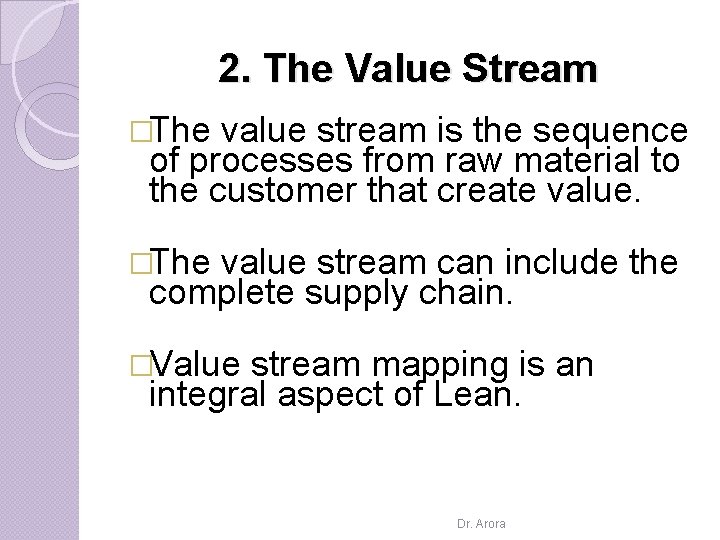
2. The Value Stream �The value stream is the sequence of processes from raw material to the customer that create value. �The value stream can include the complete supply chain. �Value stream mapping is an integral aspect of Lean. Dr. Arora
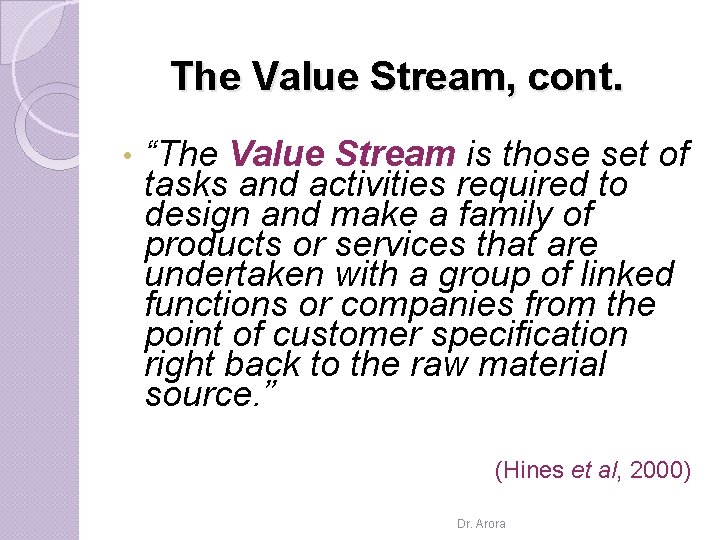
The Value Stream, cont. • “The Value Stream is those set of tasks and activities required to design and make a family of products or services that are undertaken with a group of linked functions or companies from the point of customer specification right back to the raw material source. ” (Hines et al, 2000) Dr. Arora
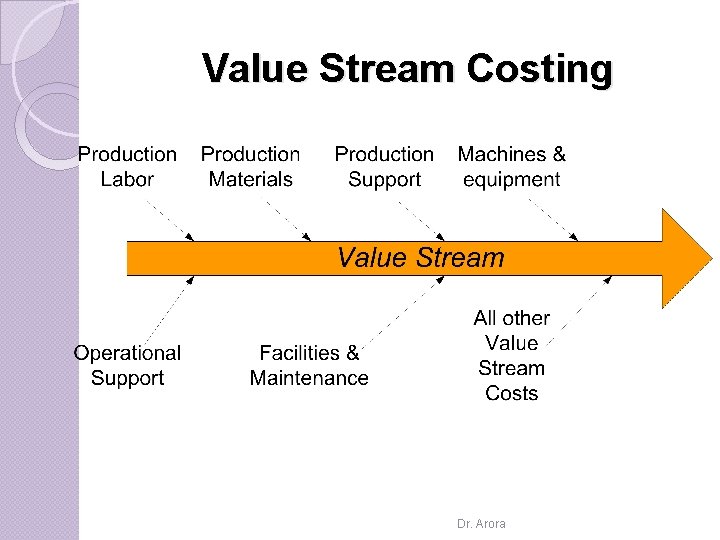
Value Stream Costing Dr. Arora
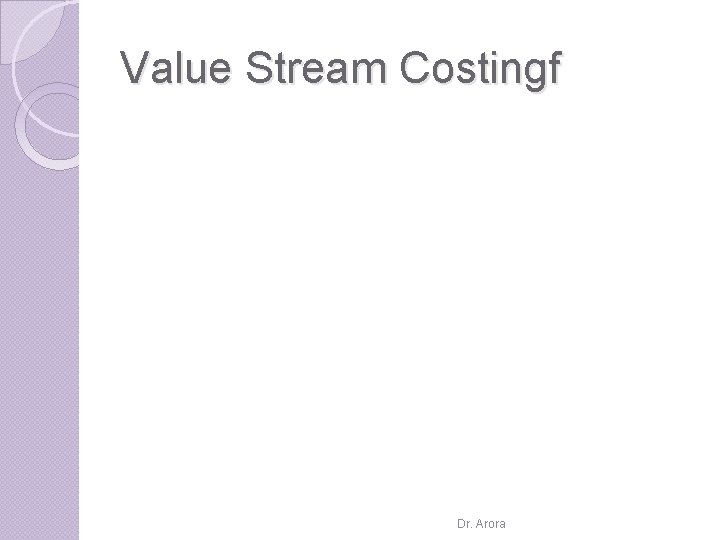
Value Stream Costingf Dr. Arora
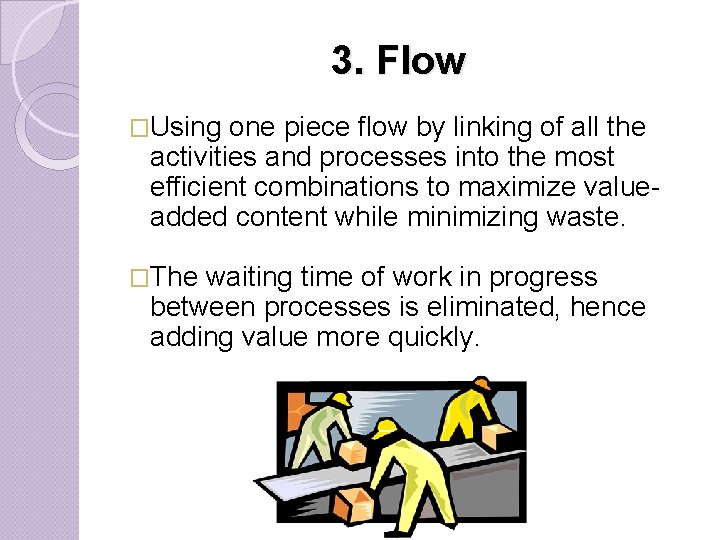
3. Flow �Using one piece flow by linking of all the activities and processes into the most efficient combinations to maximize valueadded content while minimizing waste. �The waiting time of work in progress between processes is eliminated, hence adding value more quickly.
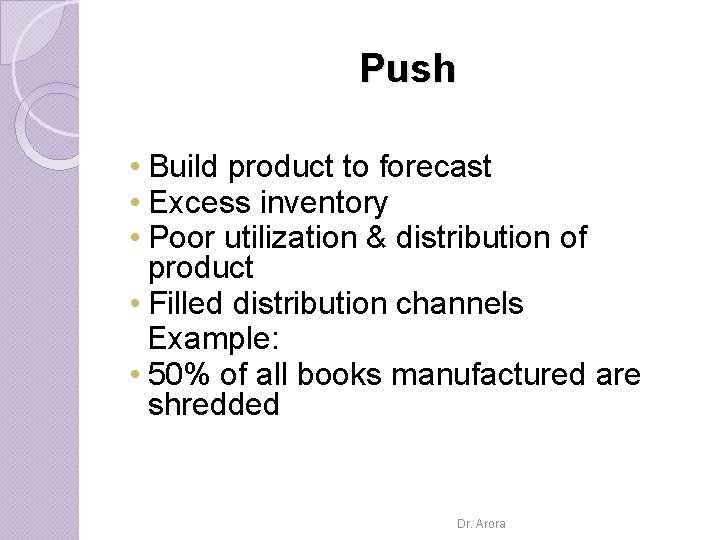
Push • Build product to forecast • Excess inventory • Poor utilization & distribution of product • Filled distribution channels Example: • 50% of all books manufactured are shredded Dr. Arora
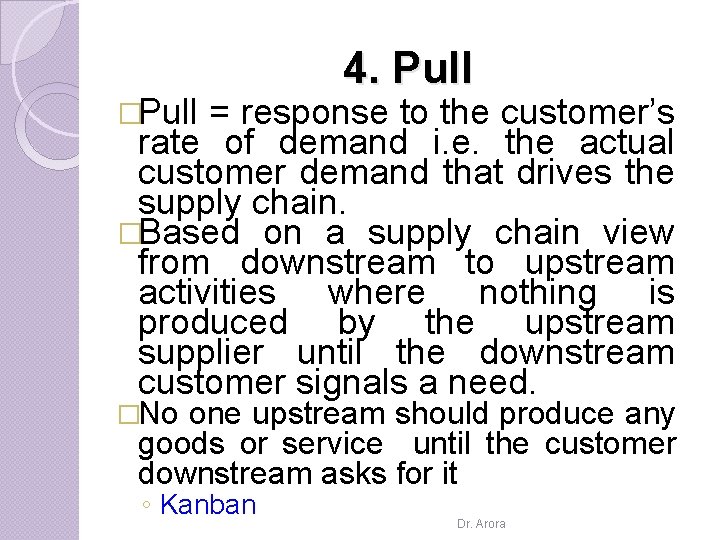
�Pull 4. Pull = response to the customer’s rate of demand i. e. the actual customer demand that drives the supply chain. �Based on a supply chain view from downstream to upstream activities where nothing is produced by the upstream supplier until the downstream customer signals a need. �No one upstream should produce any goods or service until the customer downstream asks for it ◦ Kanban Dr. Arora
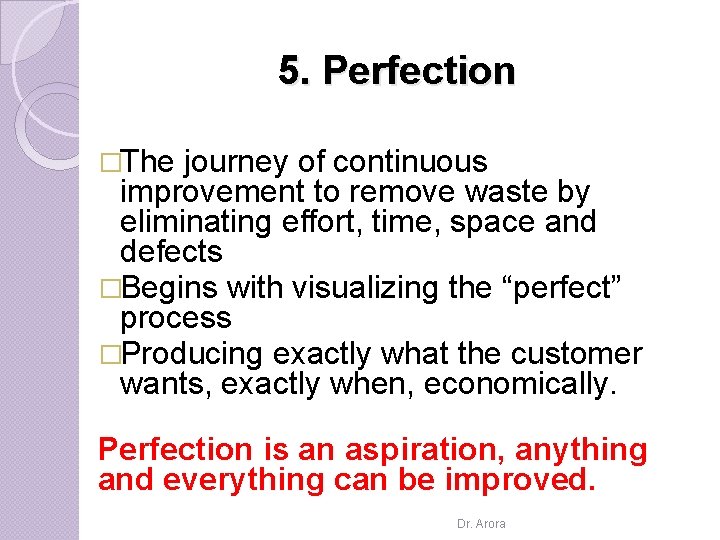
5. Perfection �The journey of continuous improvement to remove waste by eliminating effort, time, space and defects �Begins with visualizing the “perfect” process �Producing exactly what the customer wants, exactly when, economically. Perfection is an aspiration, anything and everything can be improved. Dr. Arora
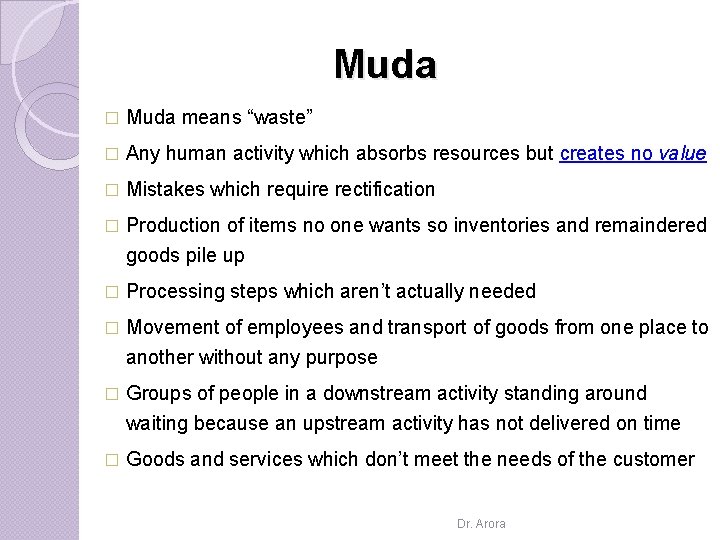
Muda � Muda means “waste” � Any human activity which absorbs resources but creates no value � Mistakes which require rectification � Production of items no one wants so inventories and remaindered goods pile up � Processing steps which aren’t actually needed � Movement of employees and transport of goods from one place to another without any purpose � Groups of people in a downstream activity standing around waiting because an upstream activity has not delivered on time � Goods and services which don’t meet the needs of the customer Dr. Arora
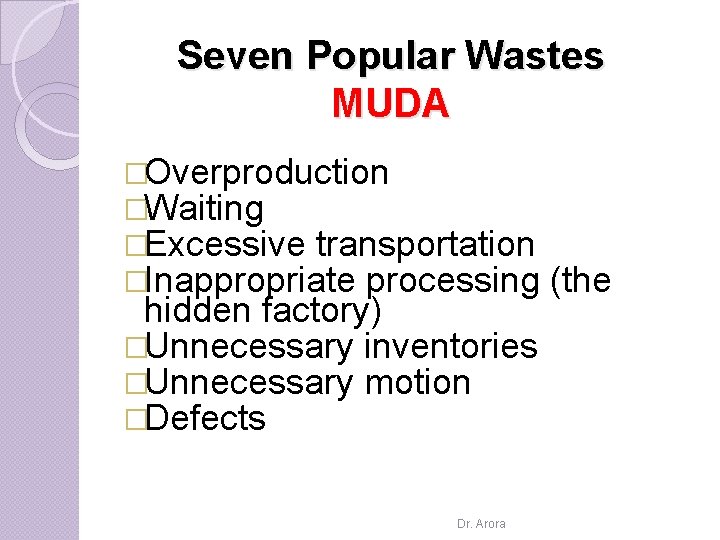
Seven Popular Wastes MUDA �Overproduction �Waiting �Excessive transportation �Inappropriate processing hidden factory) �Unnecessary inventories �Unnecessary motion �Defects Dr. Arora (the
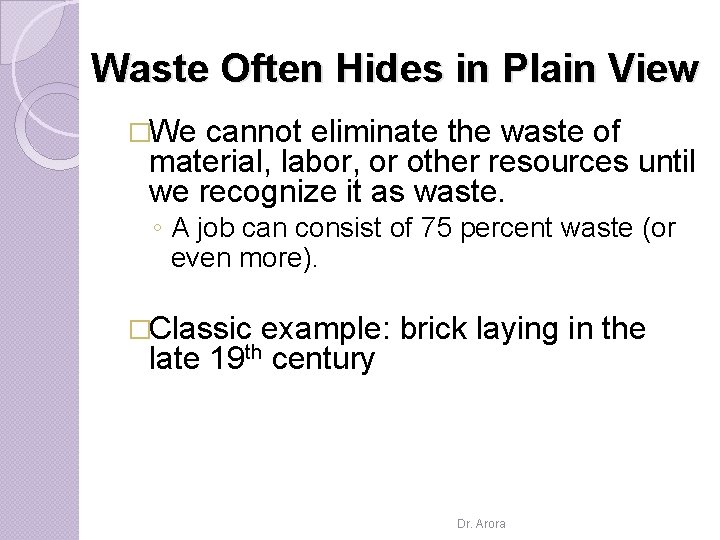
Waste Often Hides in Plain View �We cannot eliminate the waste of material, labor, or other resources until we recognize it as waste. ◦ A job can consist of 75 percent waste (or even more). �Classic example: brick laying in the late 19 th century Dr. Arora
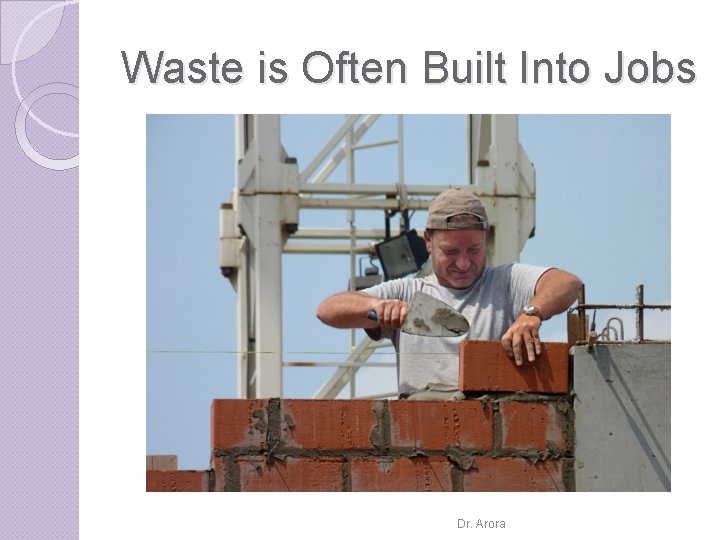
Waste is Often Built Into Jobs Dr. Arora
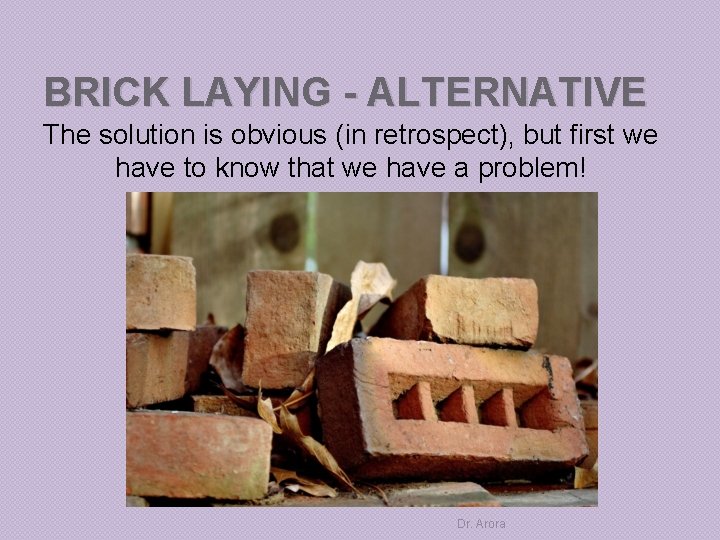
BRICK LAYING - ALTERNATIVE The solution is obvious (in retrospect), but first we have to know that we have a problem! Dr. Arora
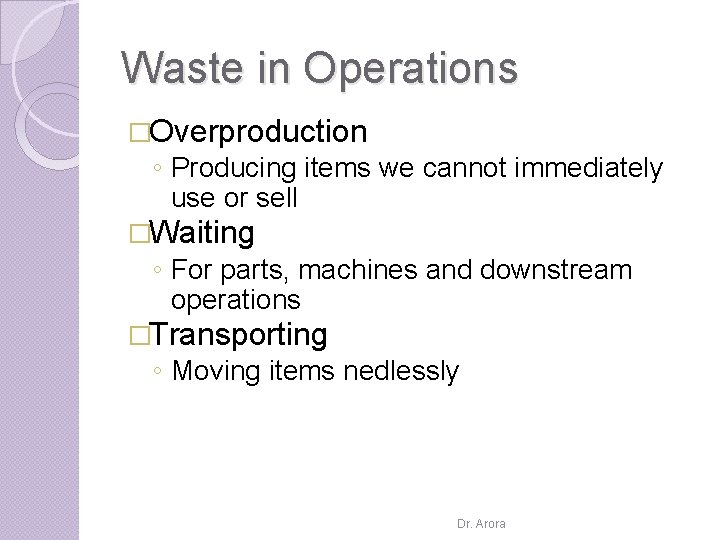
Waste in Operations �Overproduction ◦ Producing items we cannot immediately use or sell �Waiting ◦ For parts, machines and downstream operations �Transporting ◦ Moving items nedlessly Dr. Arora
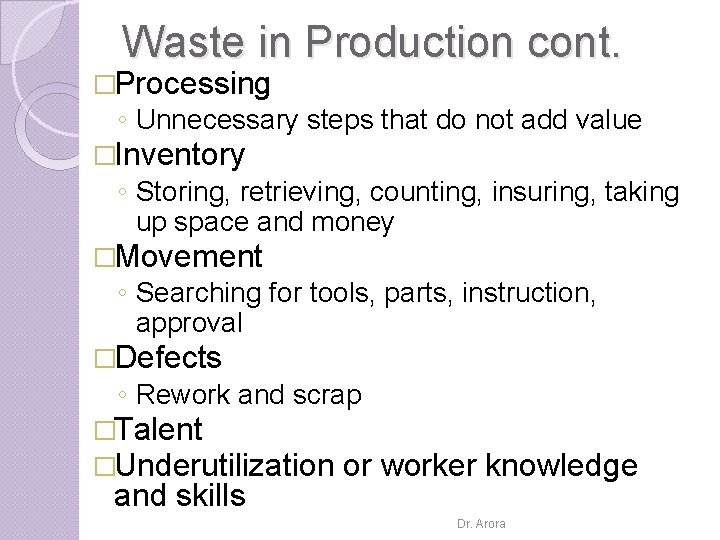
Waste in Production cont. �Processing ◦ Unnecessary steps that do not add value �Inventory ◦ Storing, retrieving, counting, insuring, taking up space and money �Movement ◦ Searching for tools, parts, instruction, approval �Defects ◦ Rework and scrap �Talent �Underutilization and skills or worker knowledge Dr. Arora
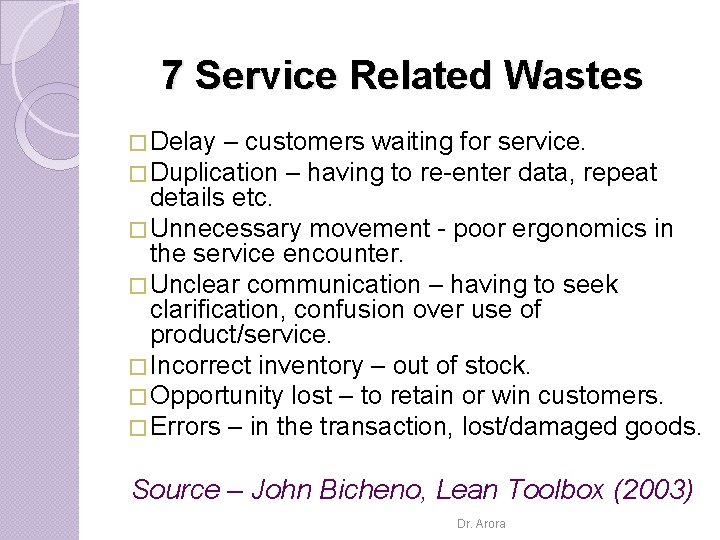
7 Service Related Wastes � Delay – customers waiting for service. � Duplication – having to re-enter data, repeat details etc. � Unnecessary movement - poor ergonomics in the service encounter. � Unclear communication – having to seek clarification, confusion over use of product/service. � Incorrect inventory – out of stock. � Opportunity lost – to retain or win customers. � Errors – in the transaction, lost/damaged goods. Source – John Bicheno, Lean Toolbox (2003) Dr. Arora
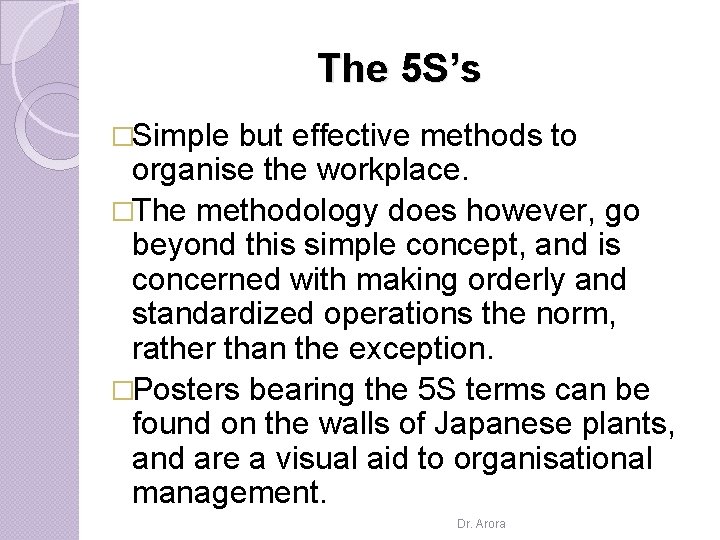
The 5 S’s �Simple but effective methods to organise the workplace. �The methodology does however, go beyond this simple concept, and is concerned with making orderly and standardized operations the norm, rather than the exception. �Posters bearing the 5 S terms can be found on the walls of Japanese plants, and are a visual aid to organisational management. Dr. Arora
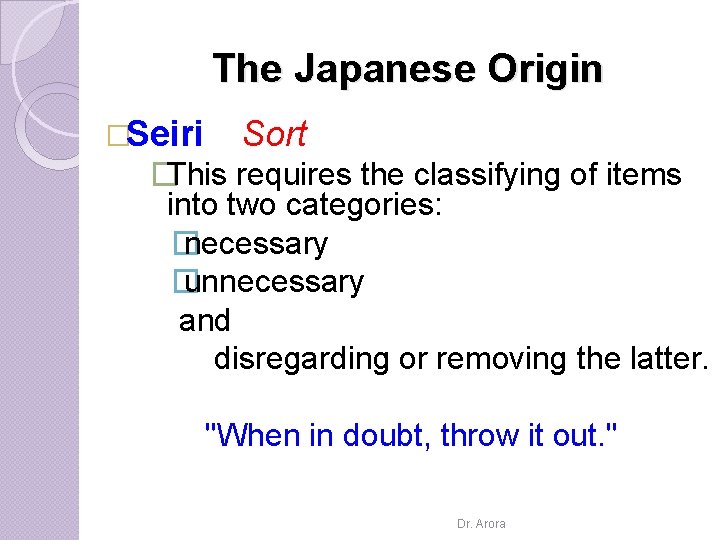
The Japanese Origin �Seiri Sort �This requires the classifying of items into two categories: � necessary � unnecessary and disregarding or removing the latter. "When in doubt, throw it out. " Dr. Arora
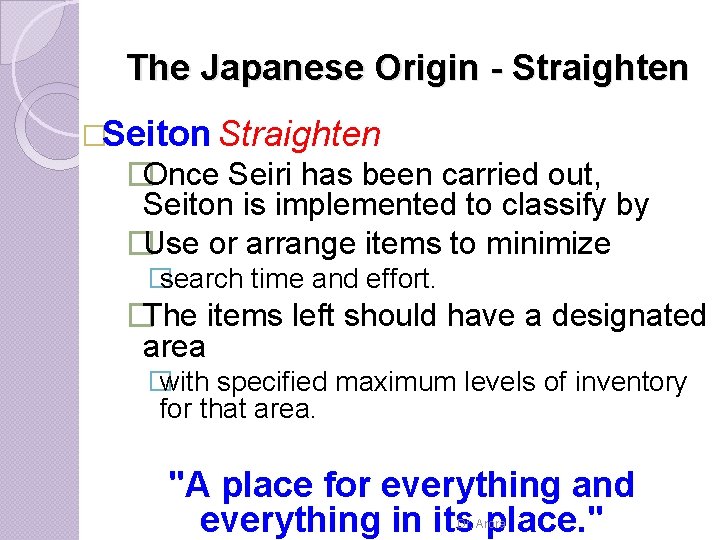
The Japanese Origin - Straighten �Seiton Straighten �Once Seiri has been carried out, Seiton is implemented to classify by �Use or arrange items to minimize � search time and effort. �The items left should have a designated area � with specified maximum levels of inventory for that area. "A place for everything and everything in its place. " Dr. Arora
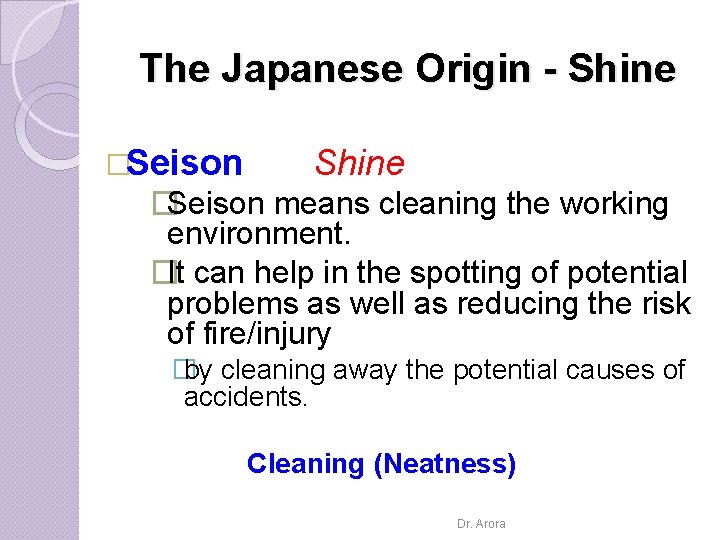
The Japanese Origin - Shine �Seison means cleaning the working environment. �It can help in the spotting of potential problems as well as reducing the risk of fire/injury � by cleaning away the potential causes of accidents. Cleaning (Neatness) Dr. Arora
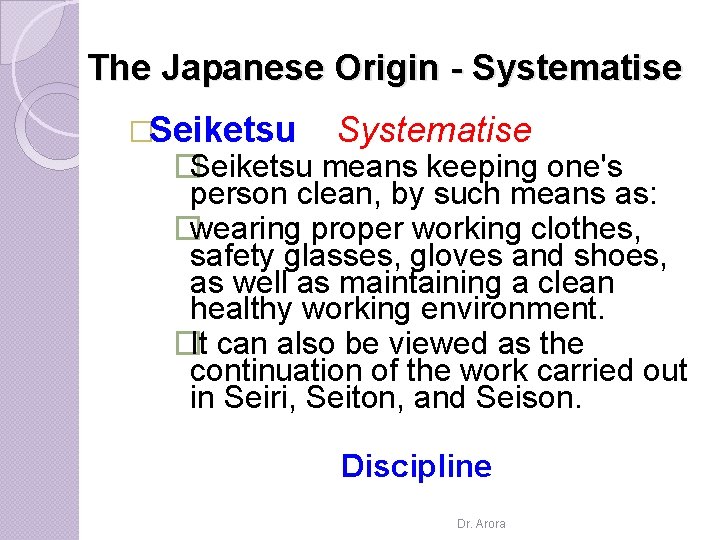
The Japanese Origin - Systematise �Seiketsu means keeping one's person clean, by such means as: �wearing proper working clothes, safety glasses, gloves and shoes, as well as maintaining a clean healthy working environment. �It can also be viewed as the continuation of the work carried out in Seiri, Seiton, and Seison. Discipline Dr. Arora
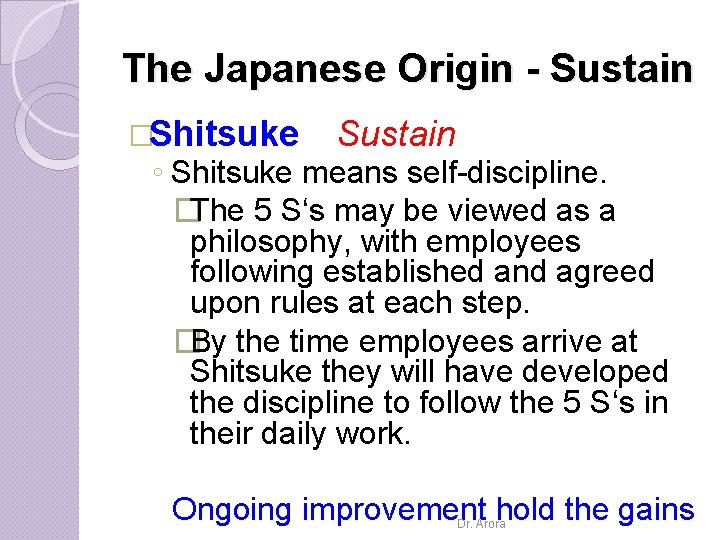
The Japanese Origin - Sustain �Shitsuke Sustain ◦ Shitsuke means self-discipline. �The 5 S‘s may be viewed as a philosophy, with employees following established and agreed upon rules at each step. �By the time employees arrive at Shitsuke they will have developed the discipline to follow the 5 S‘s in their daily work. Ongoing improvement hold the gains Dr. Arora
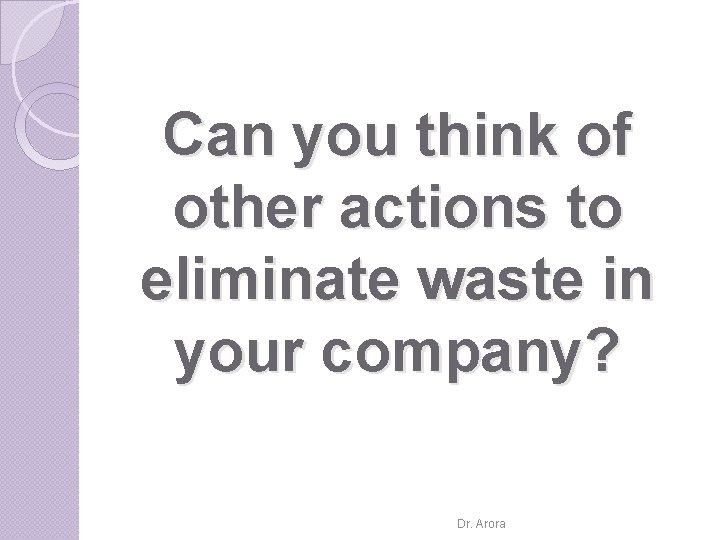
Can you think of other actions to eliminate waste in your company? Dr. Arora
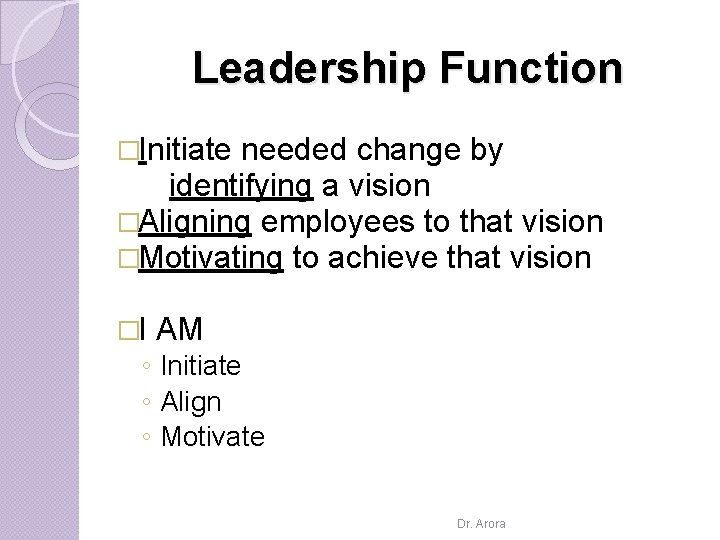
Leadership Function �Initiate needed change by identifying a vision �Aligning employees to that vision �Motivating to achieve that vision �I AM ◦ Initiate ◦ Align ◦ Motivate Dr. Arora
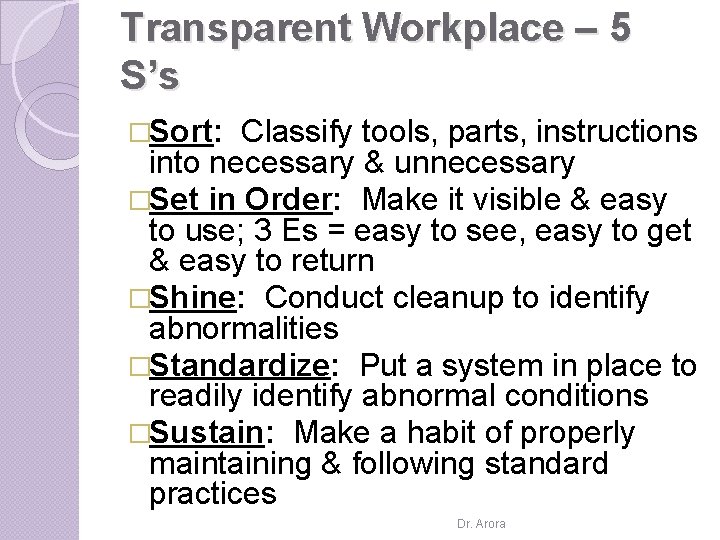
Transparent Workplace – 5 S’s �Sort: Classify tools, parts, instructions into necessary & unnecessary �Set in Order: Make it visible & easy to use; 3 Es = easy to see, easy to get & easy to return �Shine: Conduct cleanup to identify abnormalities �Standardize: Put a system in place to readily identify abnormal conditions �Sustain: Make a habit of properly maintaining & following standard practices Dr. Arora
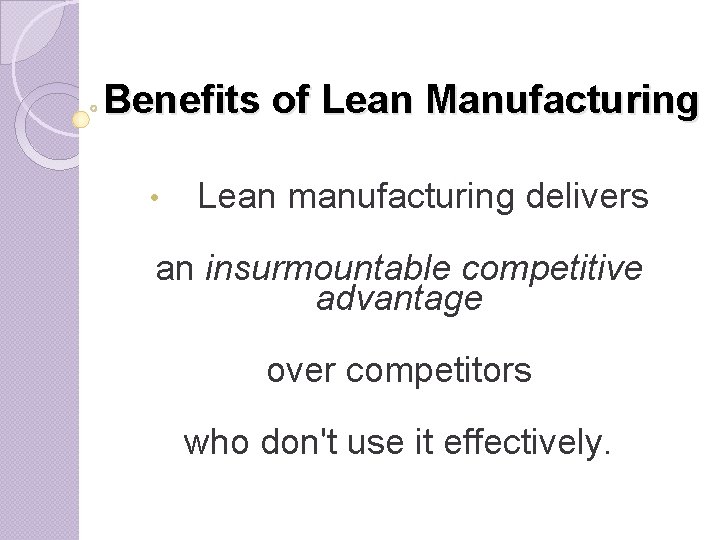
Benefits of Lean Manufacturing • Lean manufacturing delivers an insurmountable competitive advantage over competitors who don't use it effectively.
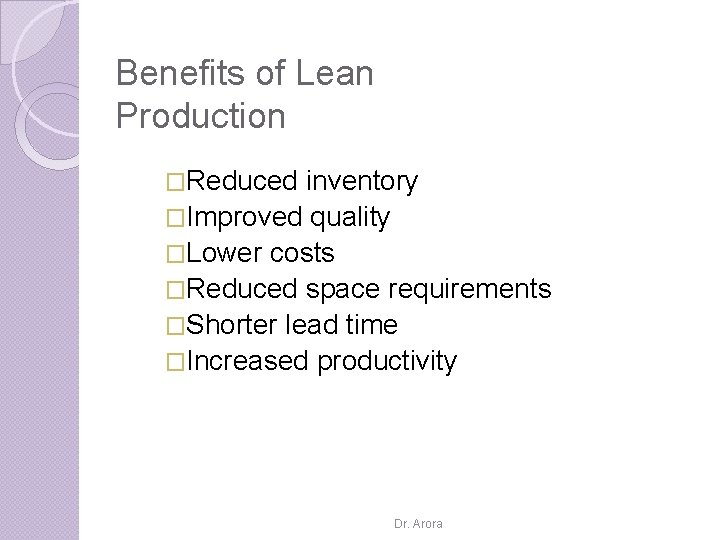
Benefits of Lean Production �Reduced inventory �Improved quality �Lower costs �Reduced space requirements �Shorter lead time �Increased productivity Dr. Arora
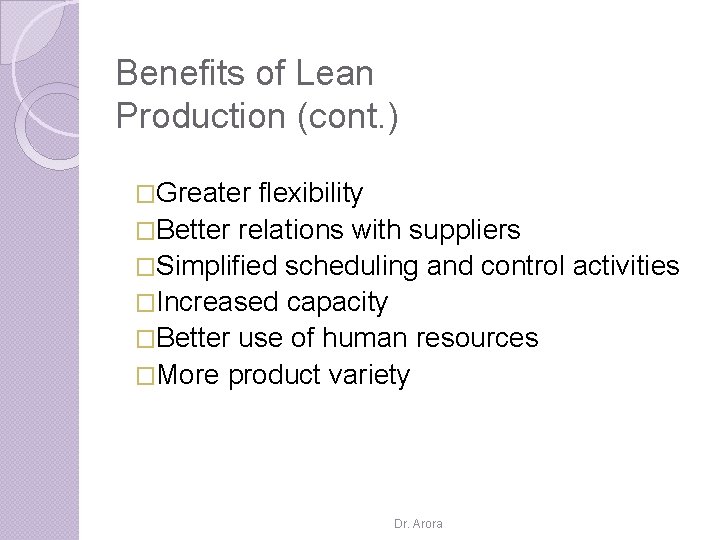
Benefits of Lean Production (cont. ) �Greater flexibility �Better relations with suppliers �Simplified scheduling and control activities �Increased capacity �Better use of human resources �More product variety Dr. Arora
Anaerobes
Strategic goals tactical goals operational goals
Strategic goals tactical goals operational goals
Chander dhall
Visual factory lean manufacturing
7 fő veszteség
Poka-yoke
Lean manufacturing
Jit lean manufacturing
Lean manufacturing definition
Heijunka przykład
Obeya significado
Dynamics 365 lean manufacturing
Lean manufacturing consultancy
Metodologia layout
Batonnage production
Cip lean manufacturing
Housekeeping lean manufacturing
Lean manufacturing malaga
Karta kanban
Decd
Lean manufacturing competitiveness scheme
Jit operations management
One piece flow
Leader standard work training
Lean manufacturing definition
Manufacturing cost vs non manufacturing cost
Manufacturing cost vs non manufacturing cost
Manufacturing cost vs non manufacturing cost
Job costing vs. process costing
Additive manufacturing steps
Anish arora osu
Filippo software
Anish arora osu
Genification
Anish arora
äo 月天
Green marketing meaning