Lean Production Lean Manufacturing Odchudzona produkcja Strategia Lean
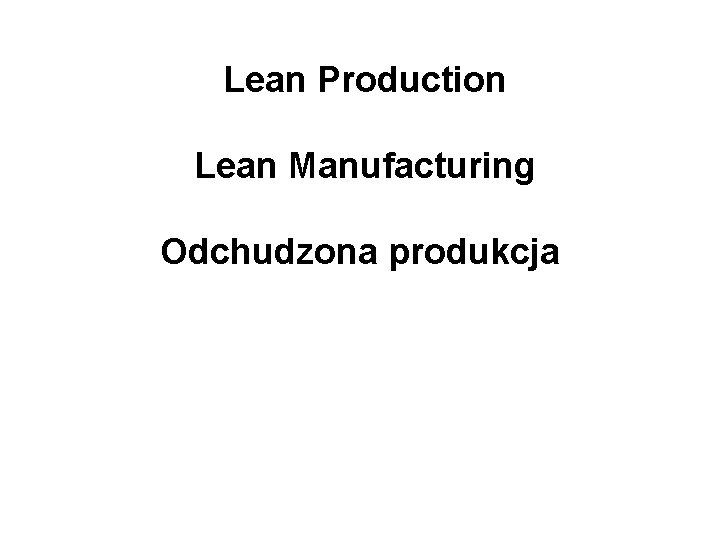
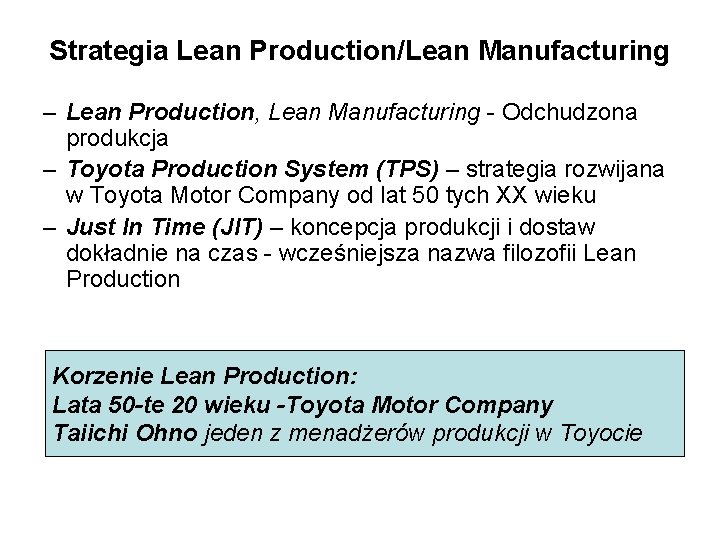
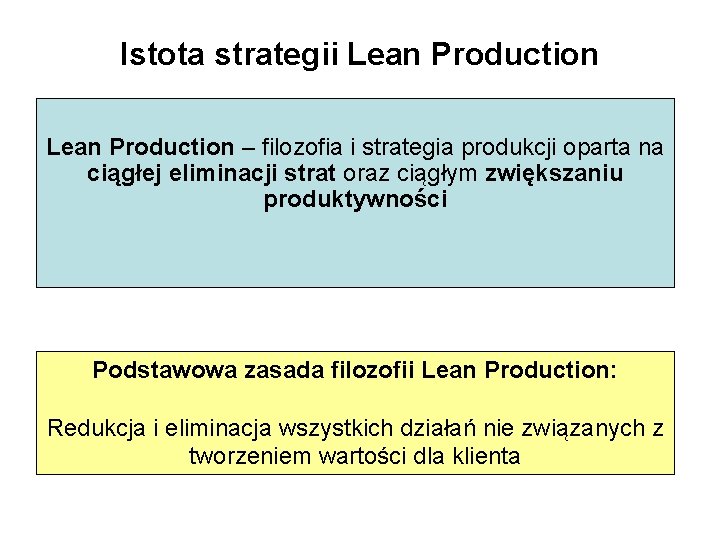
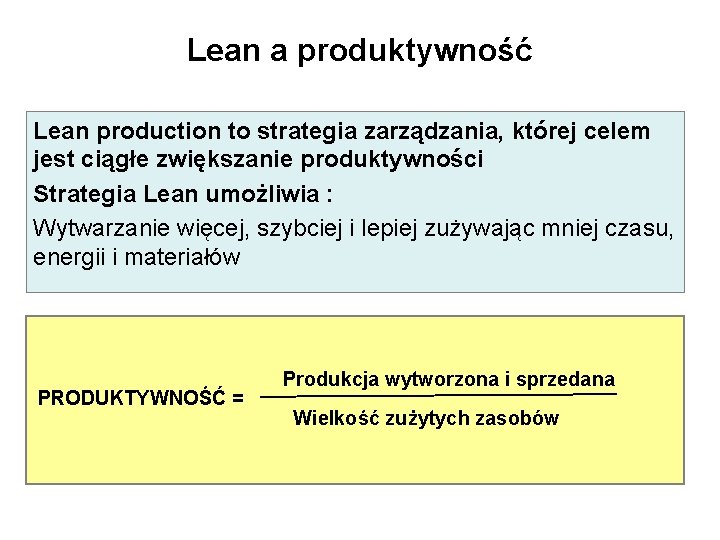
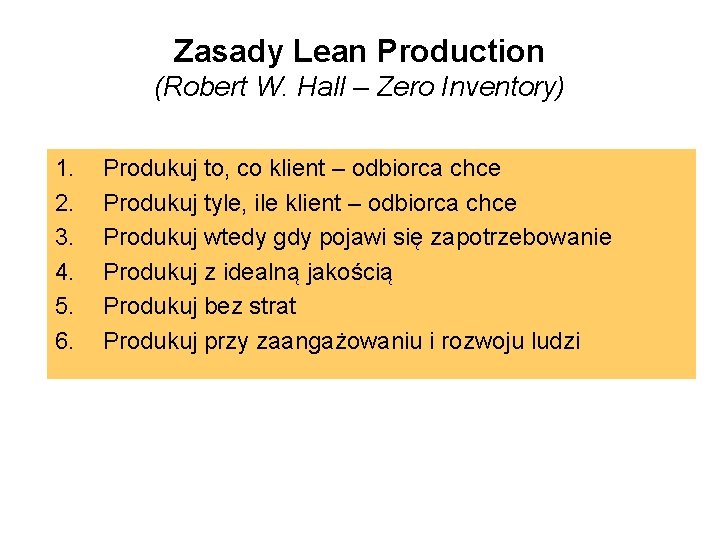
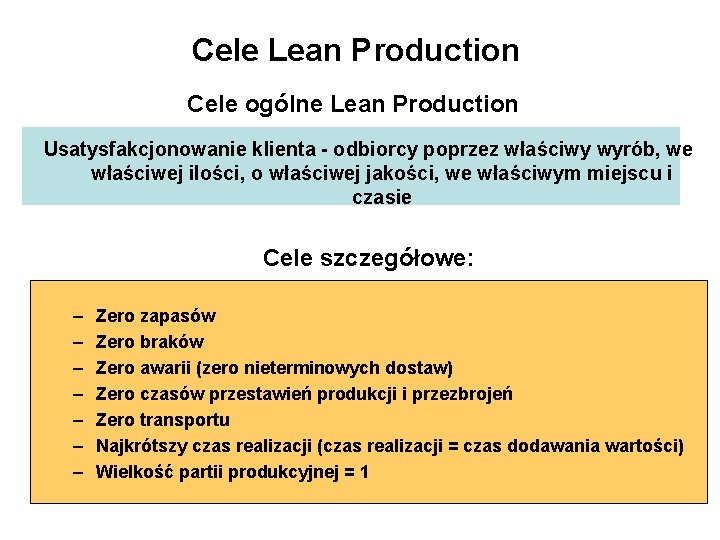

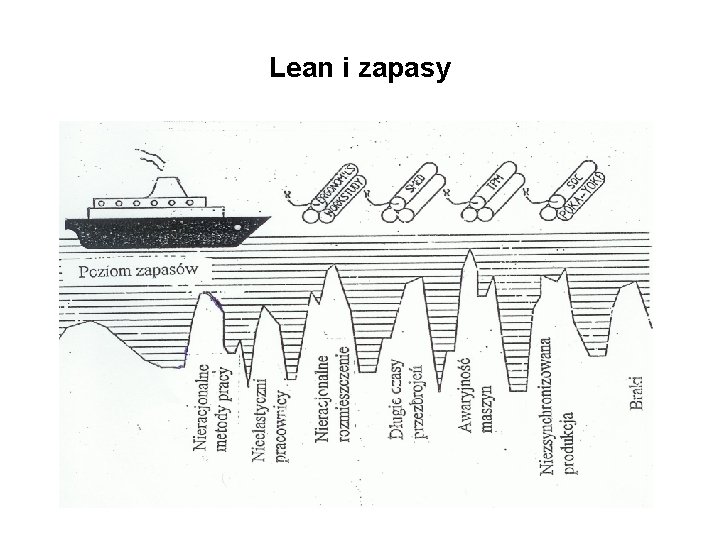
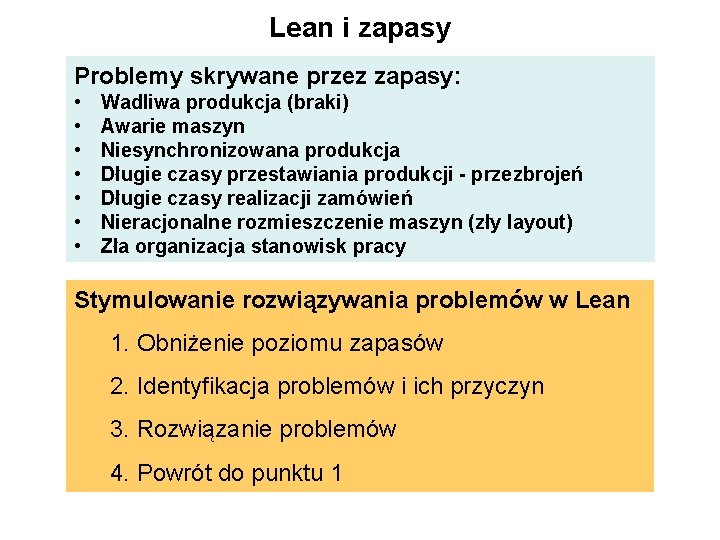
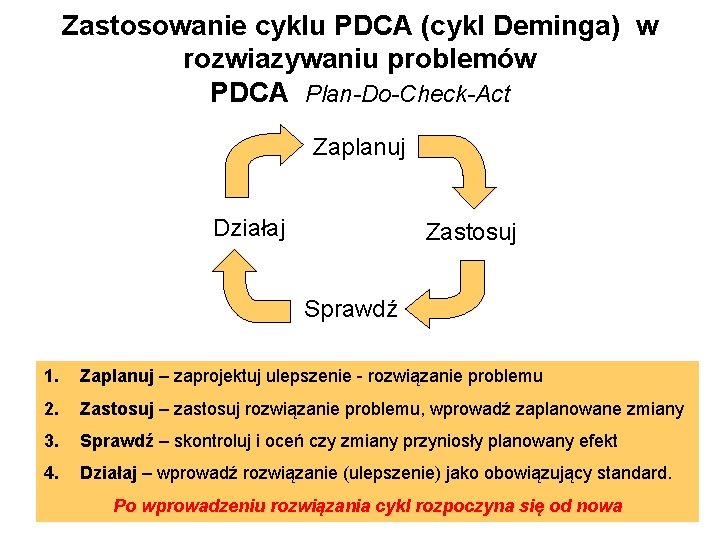
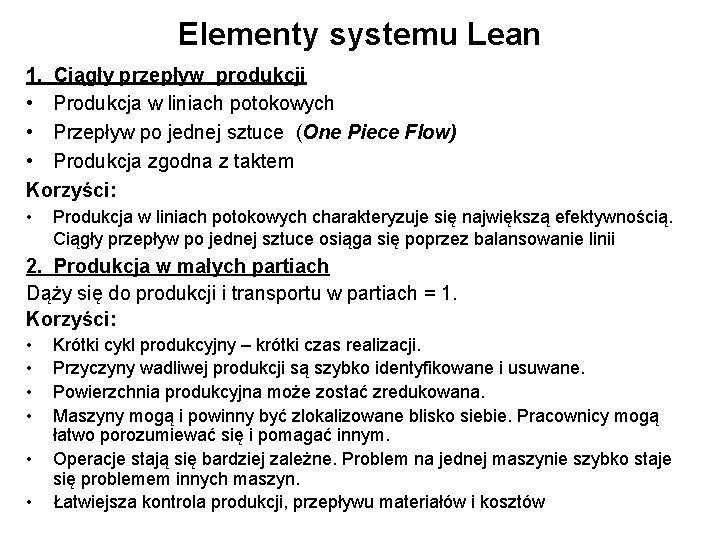
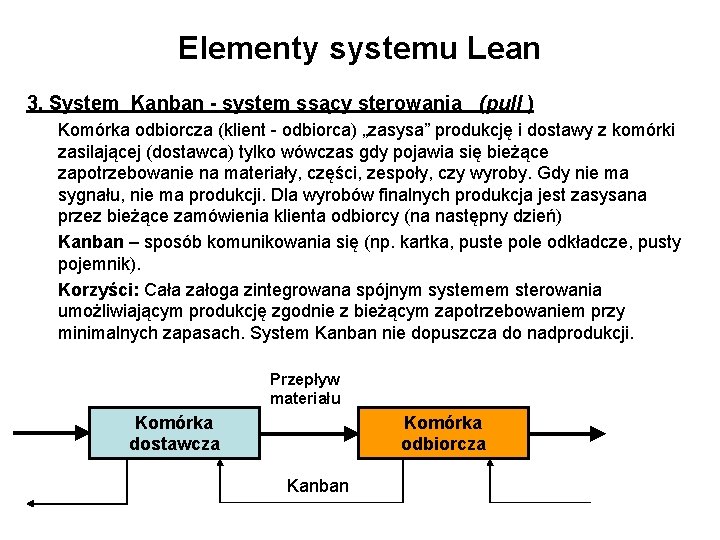
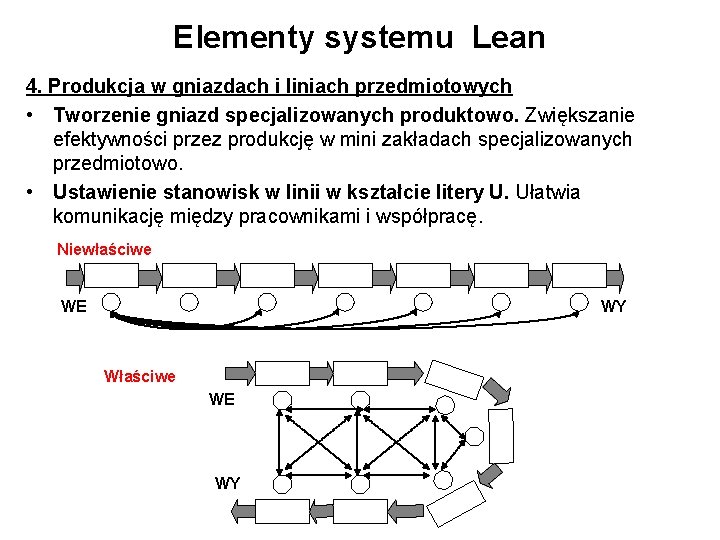
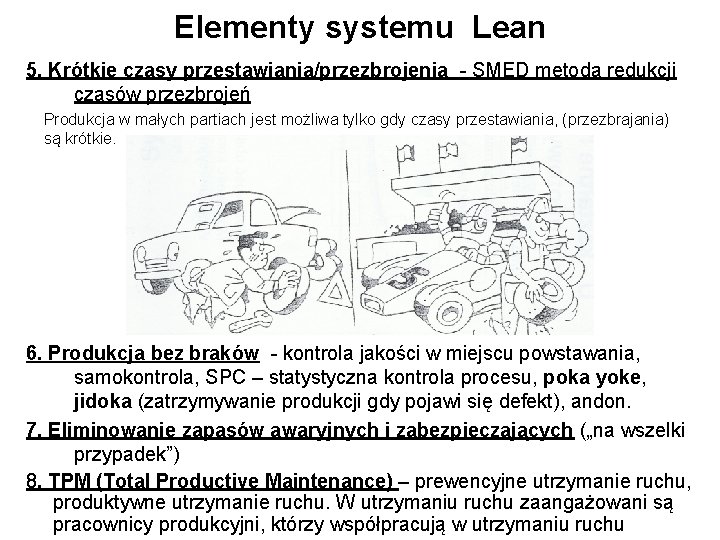
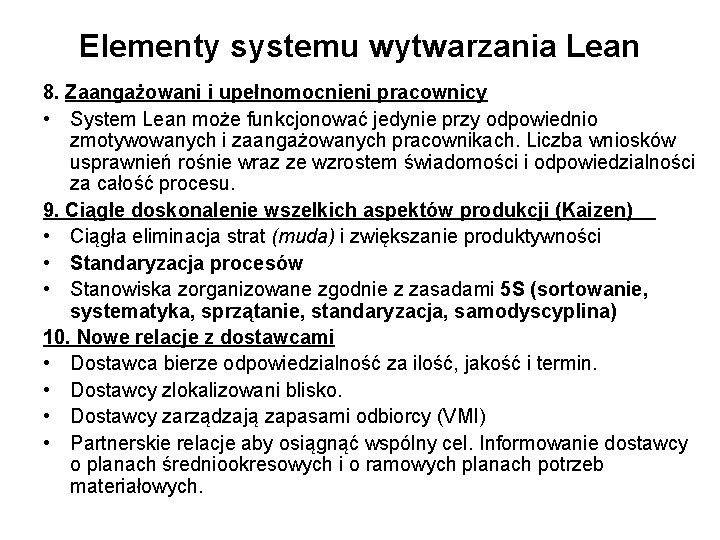
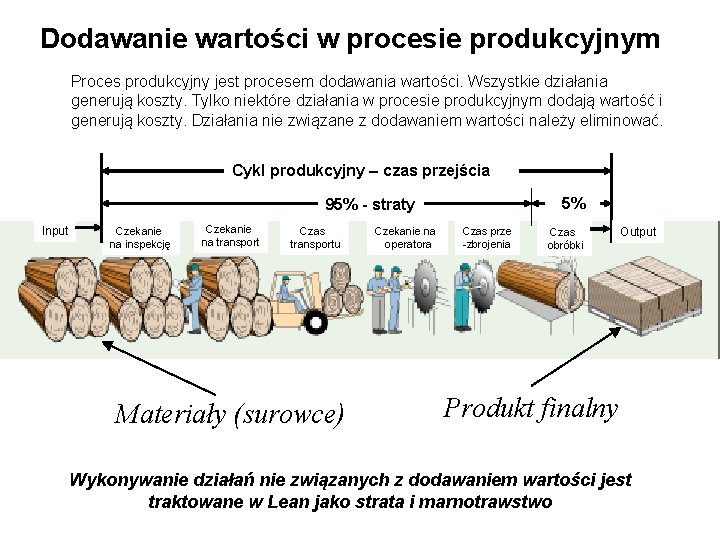
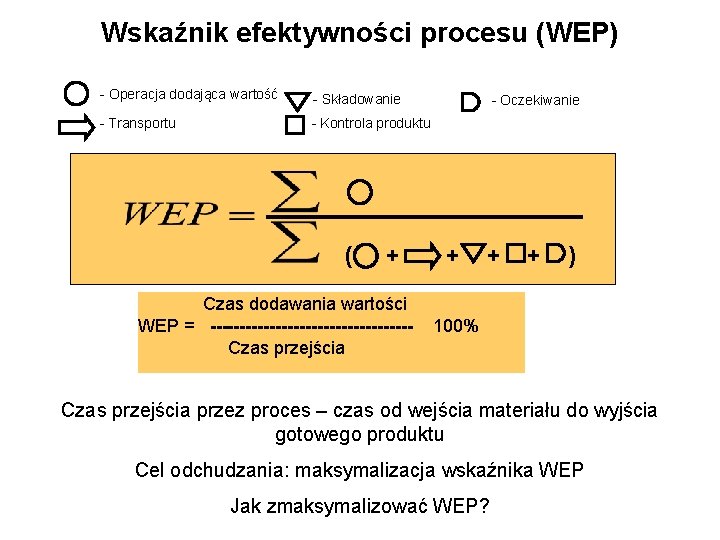
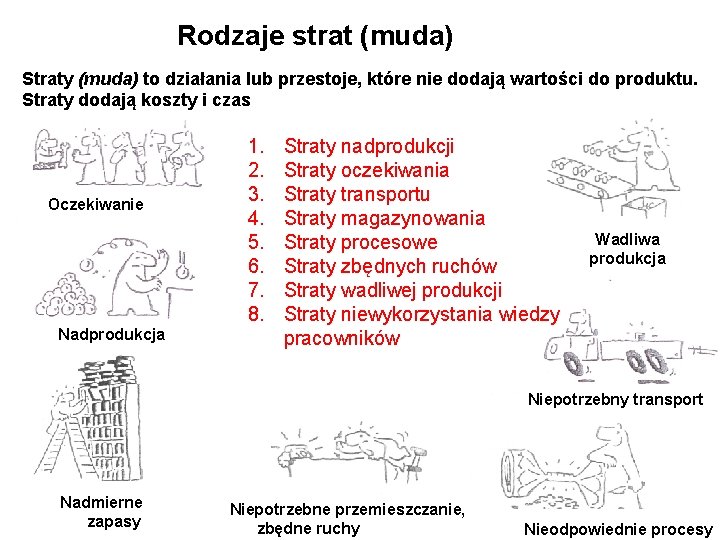
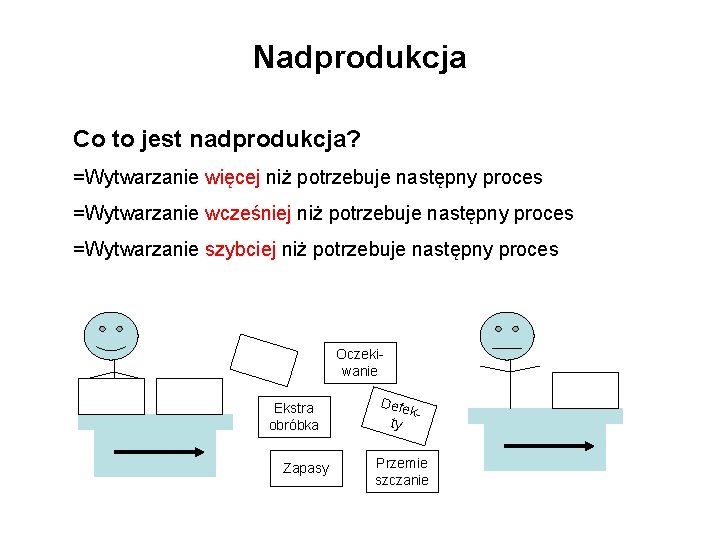
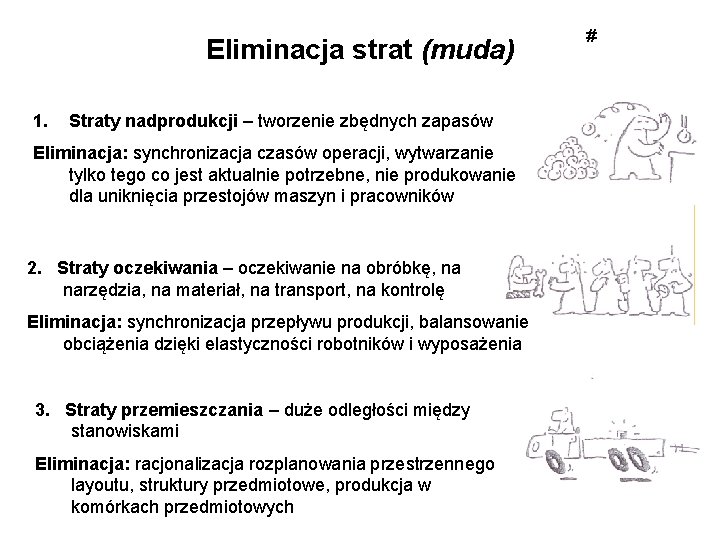
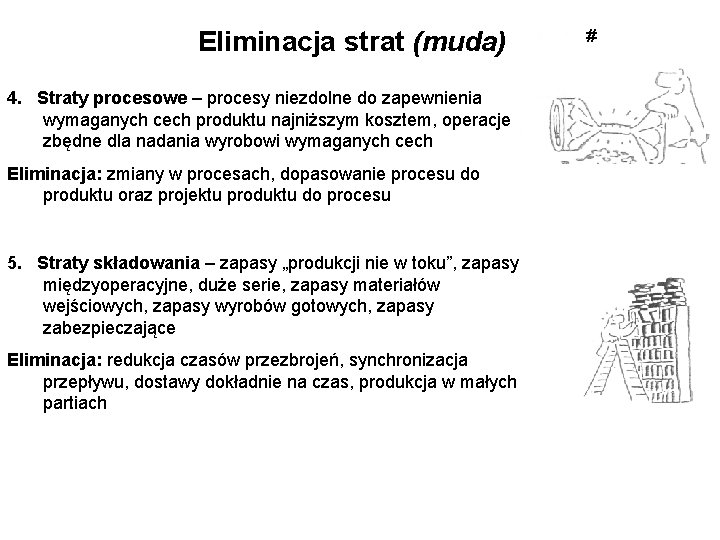
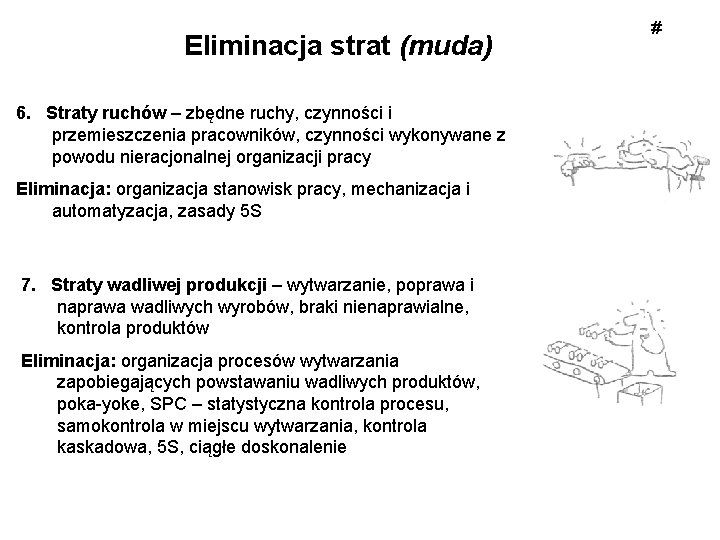
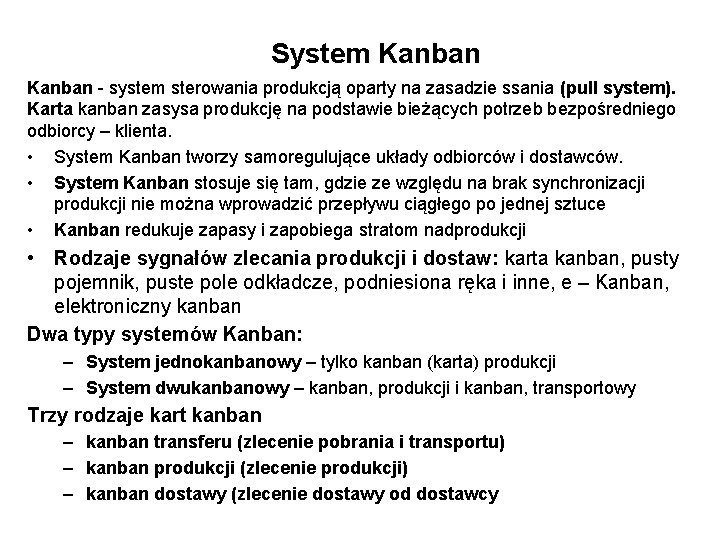
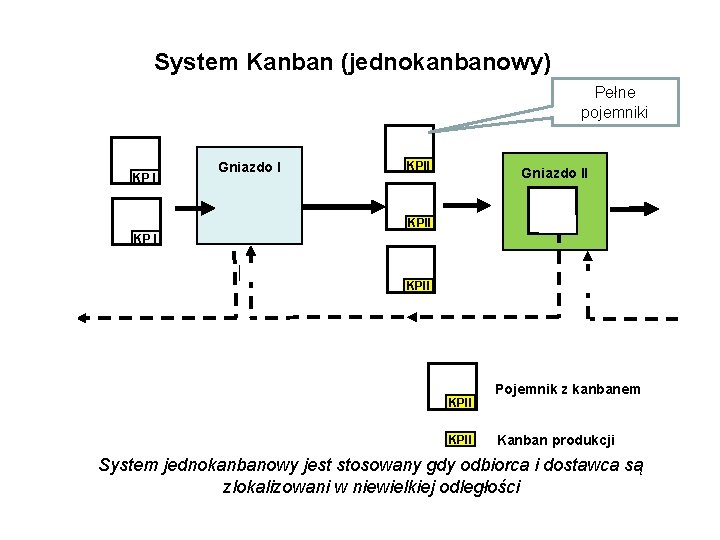
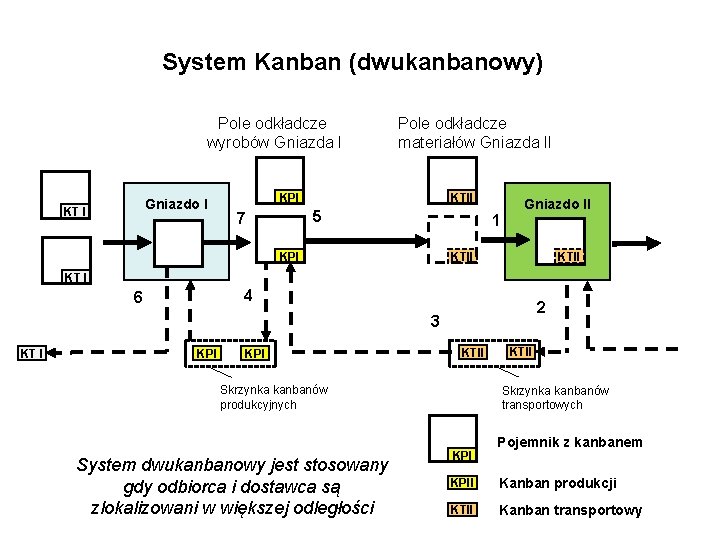
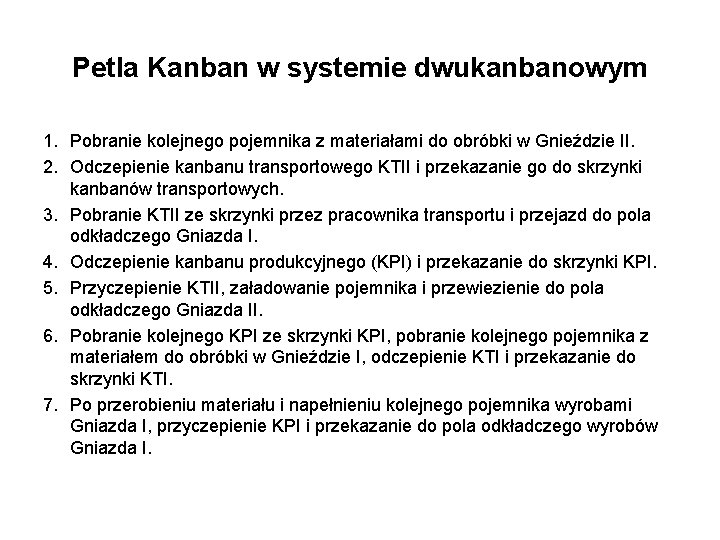
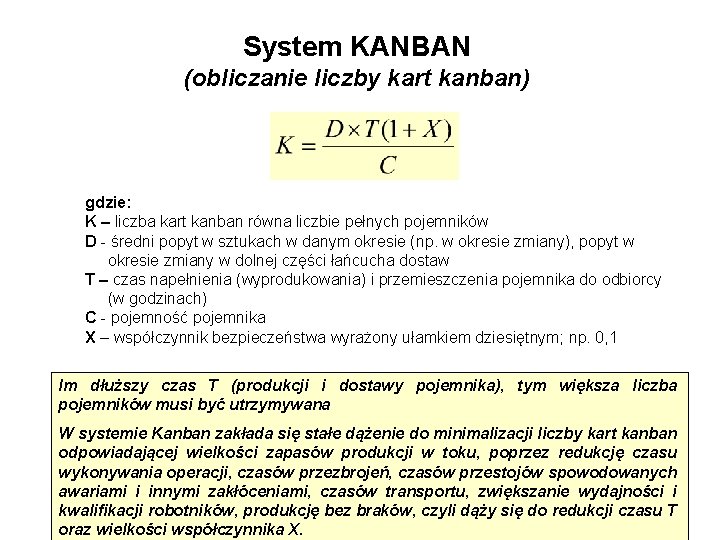
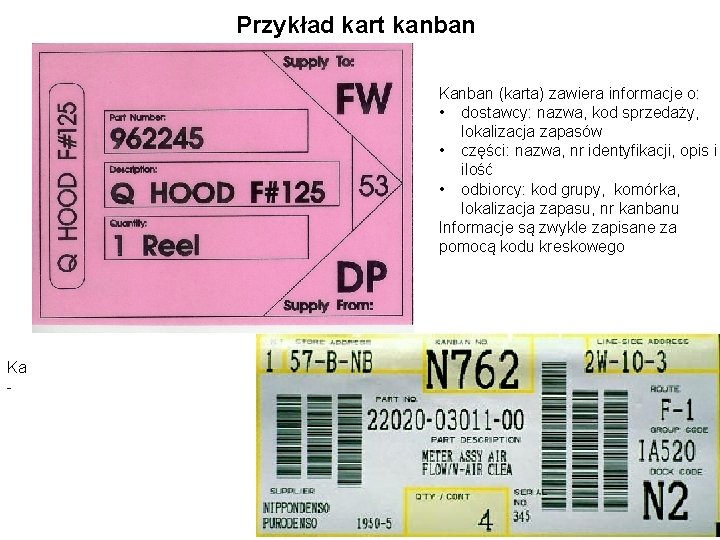
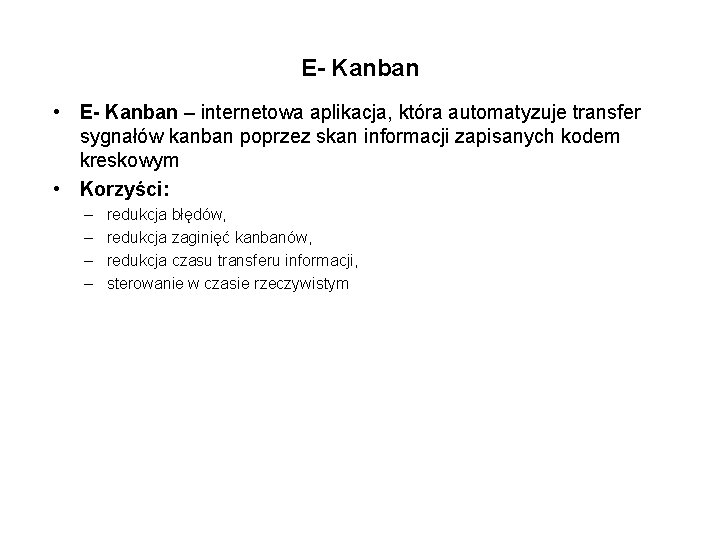
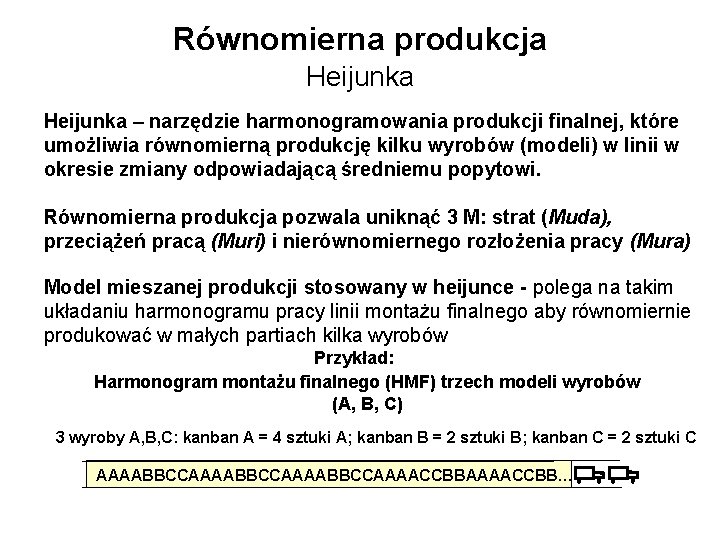
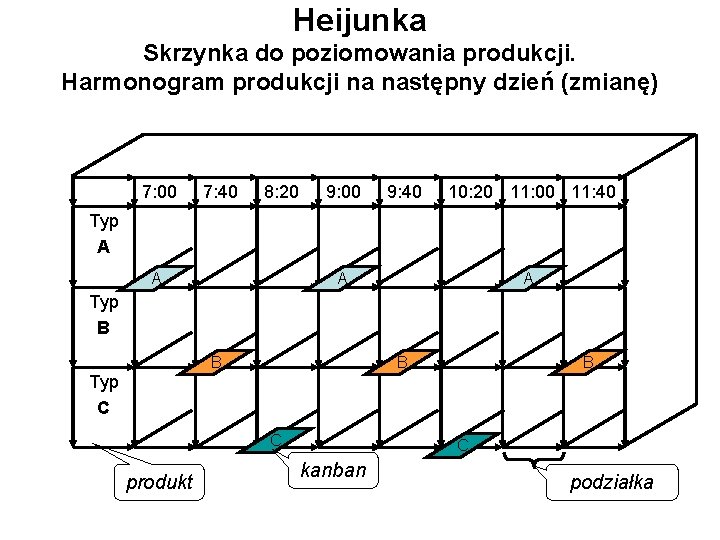
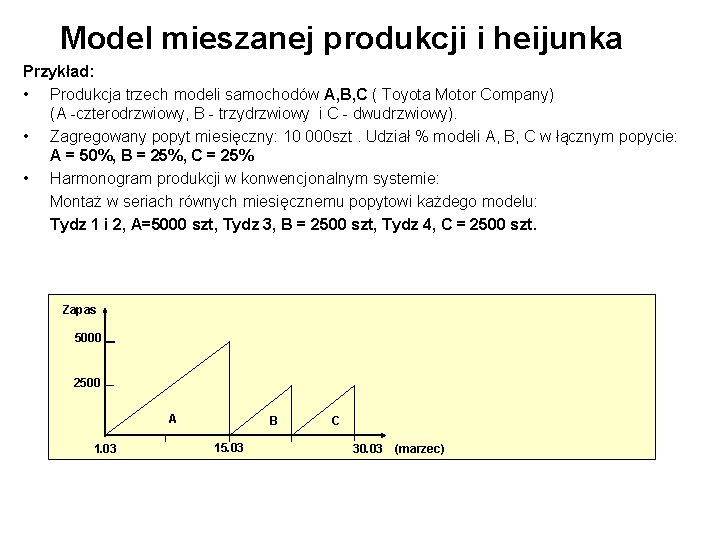
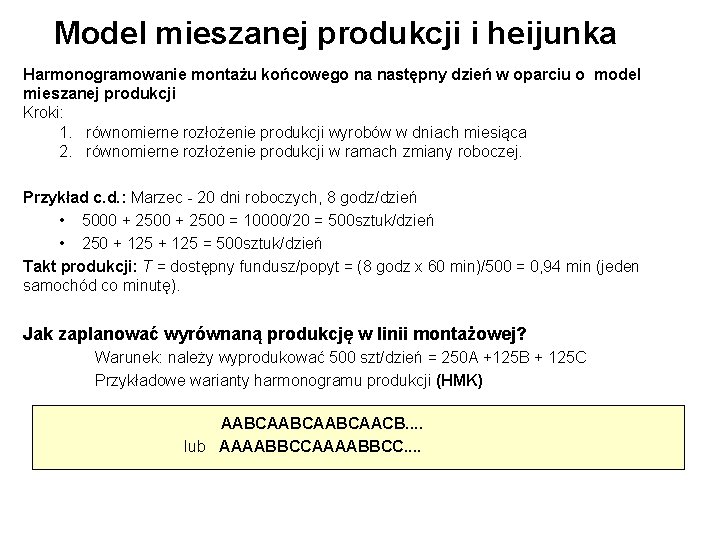
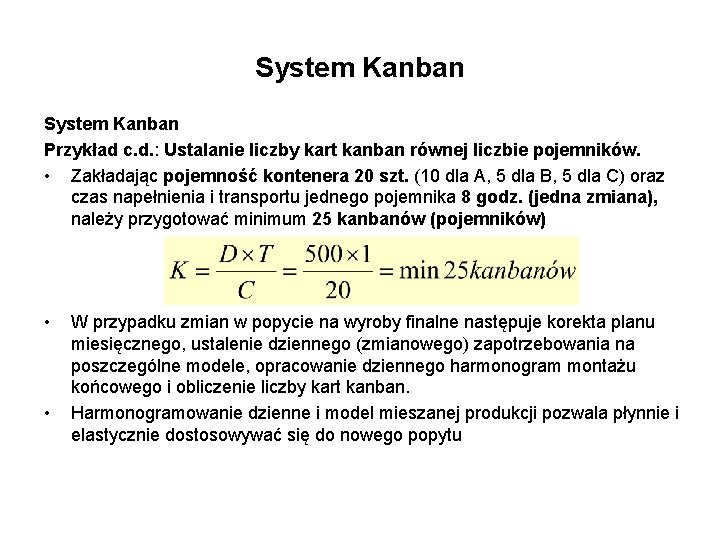
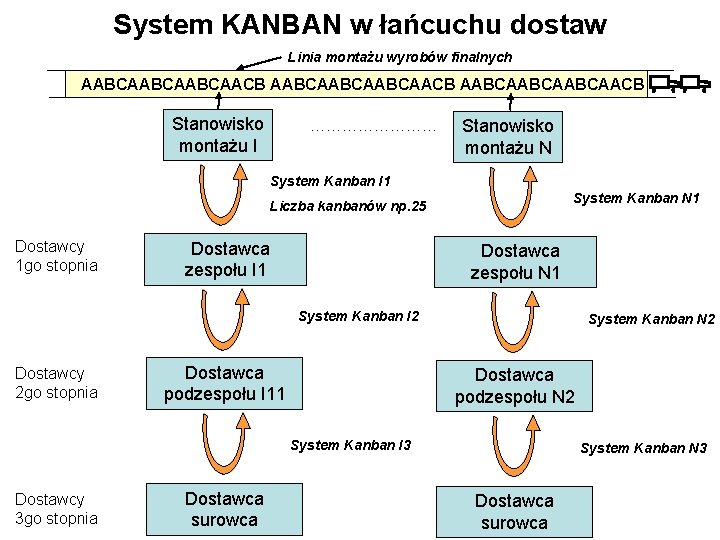
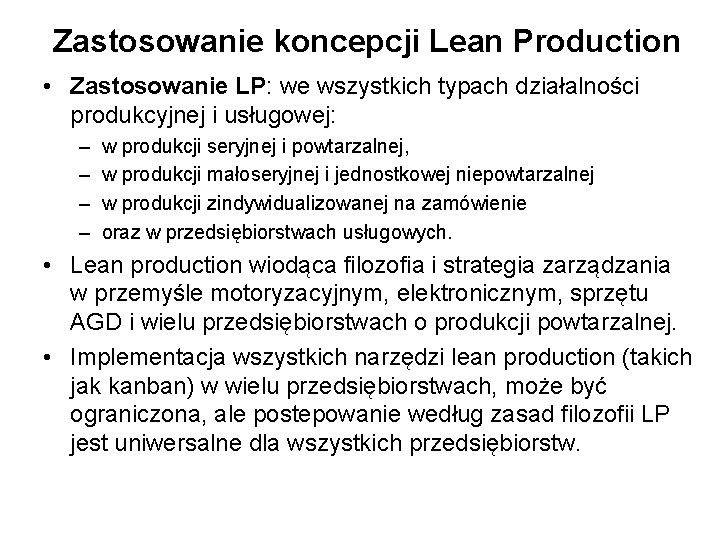
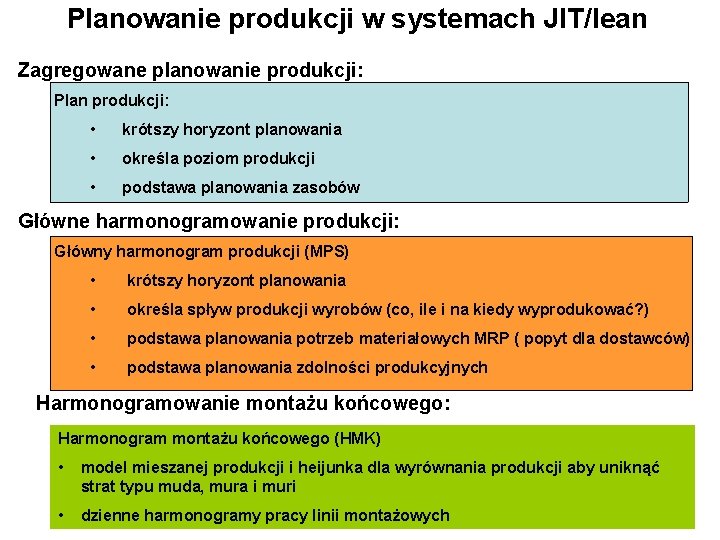
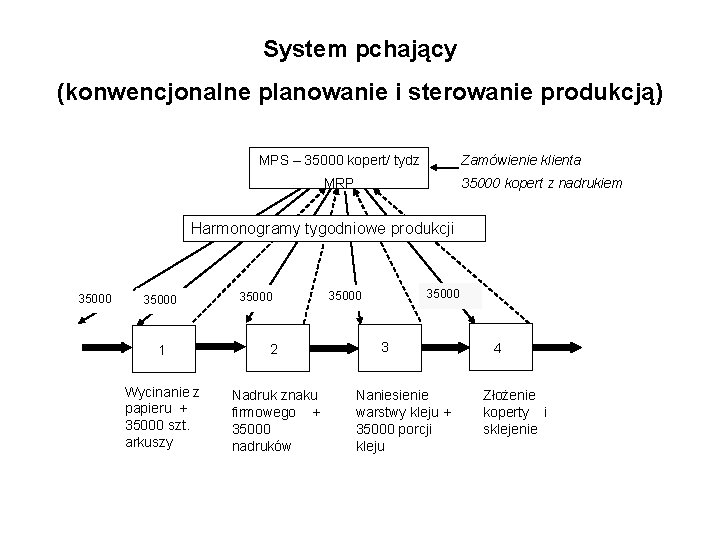
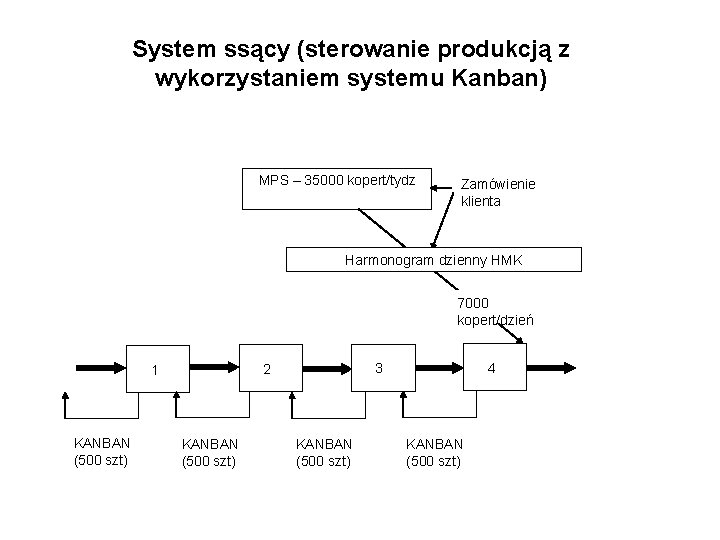
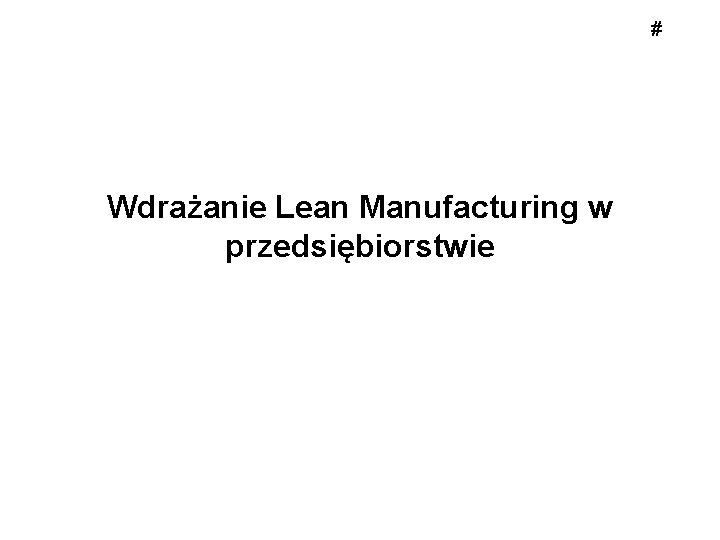
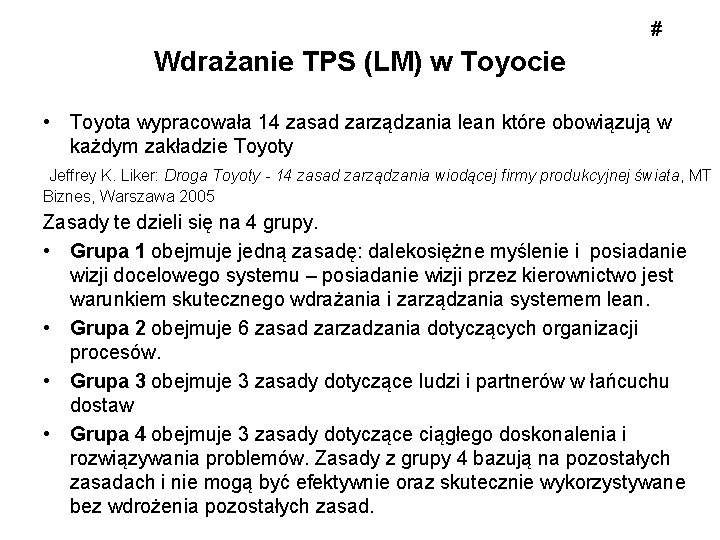
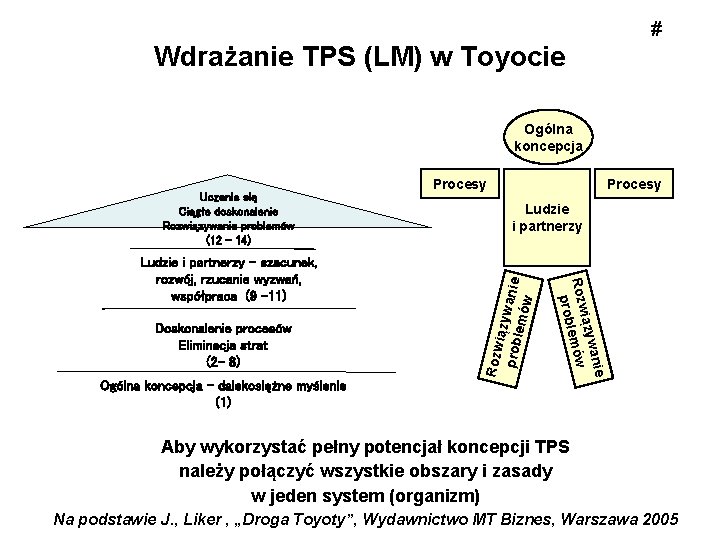
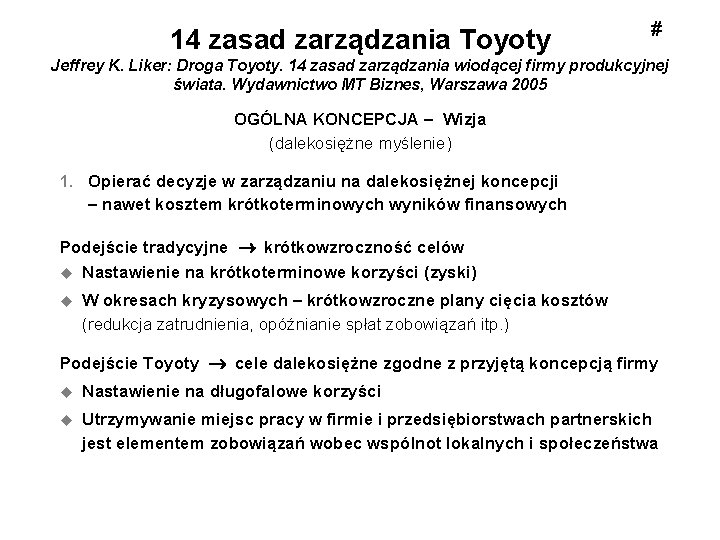
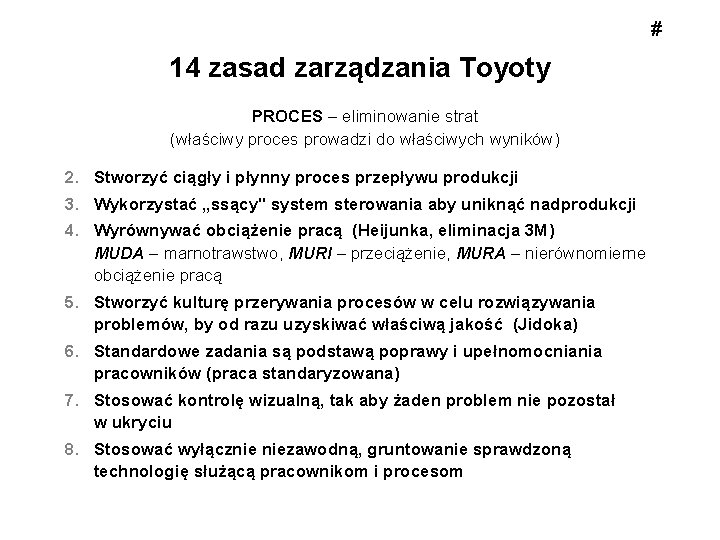
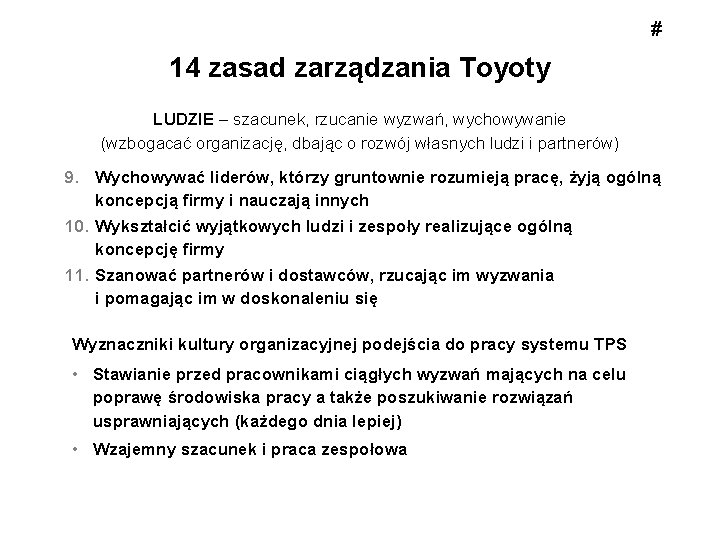
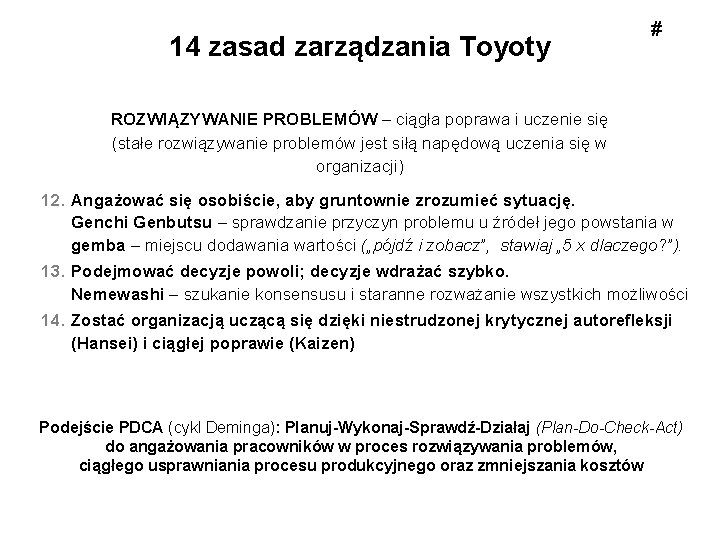
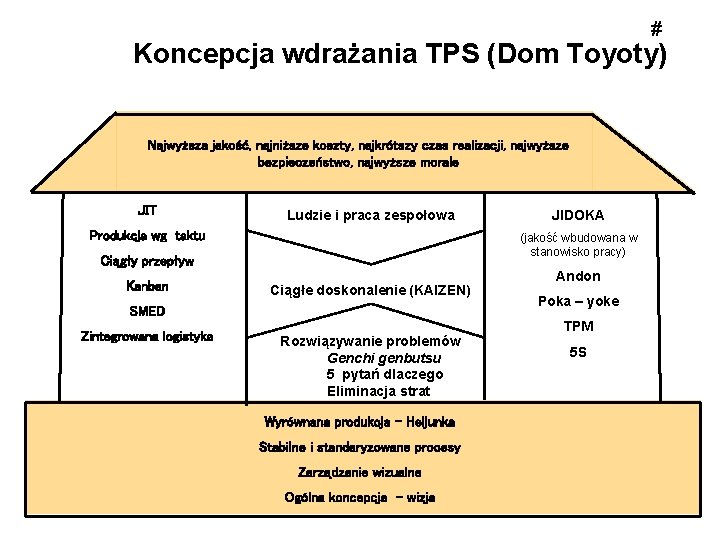
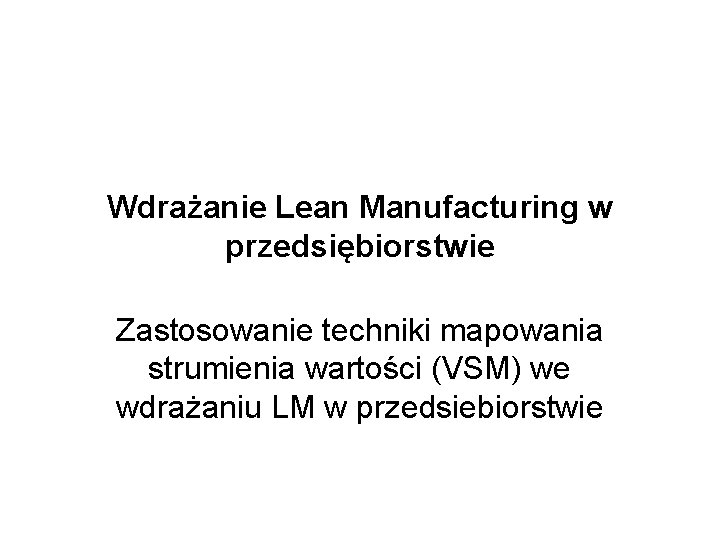
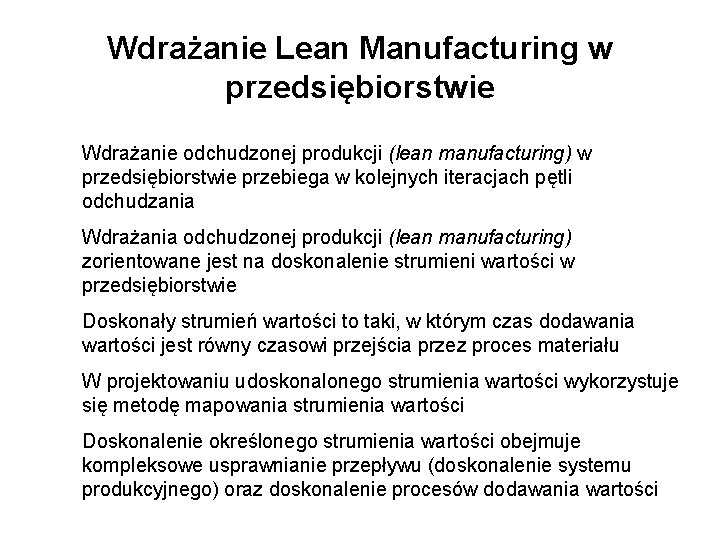
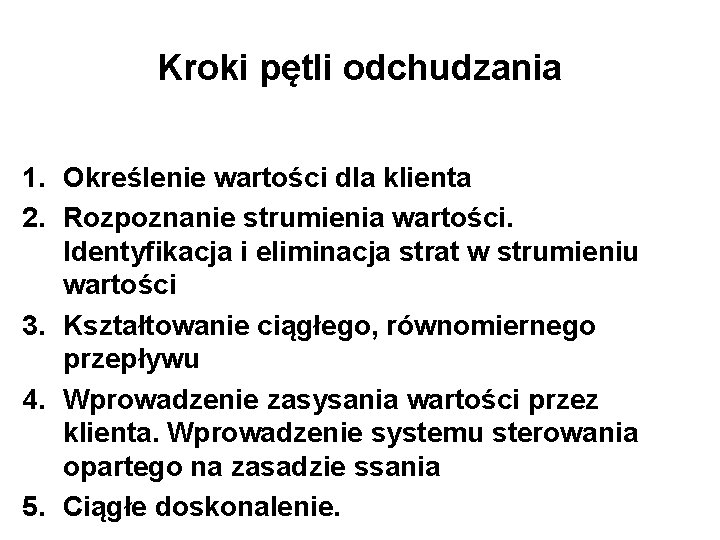
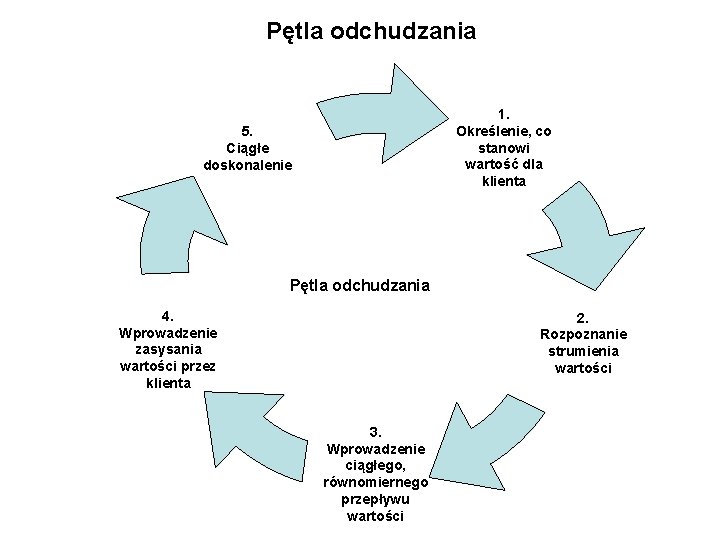
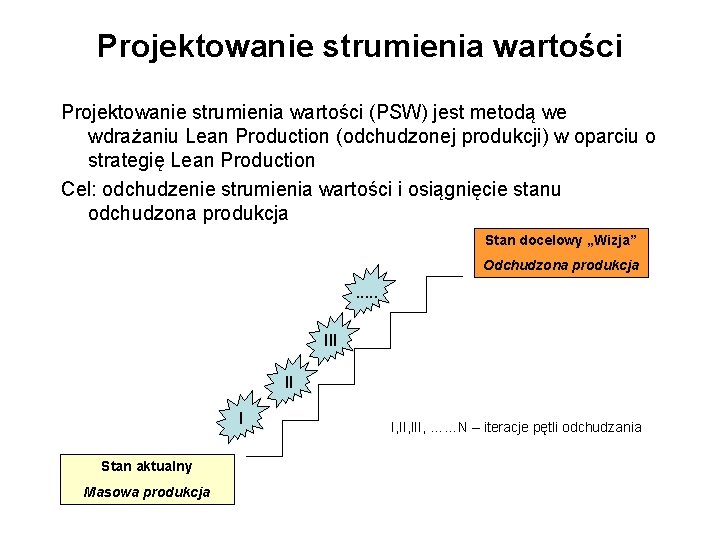
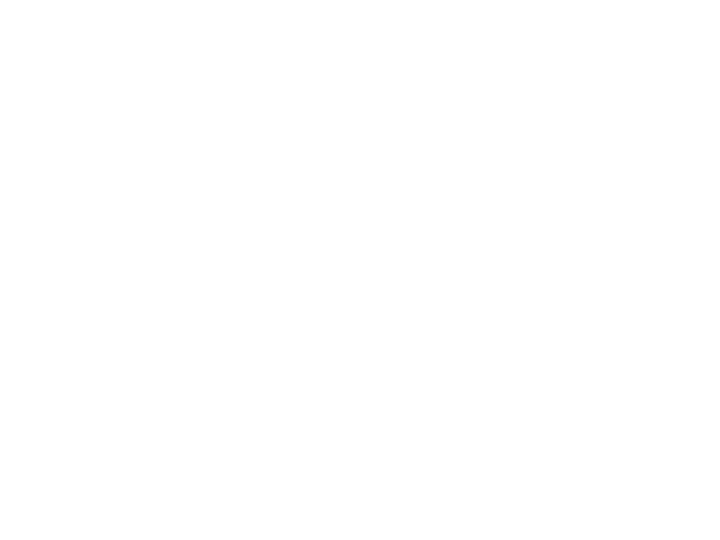
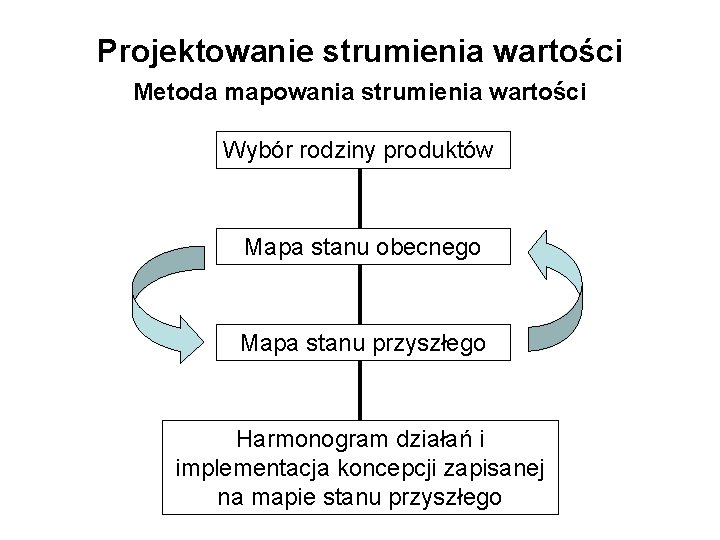
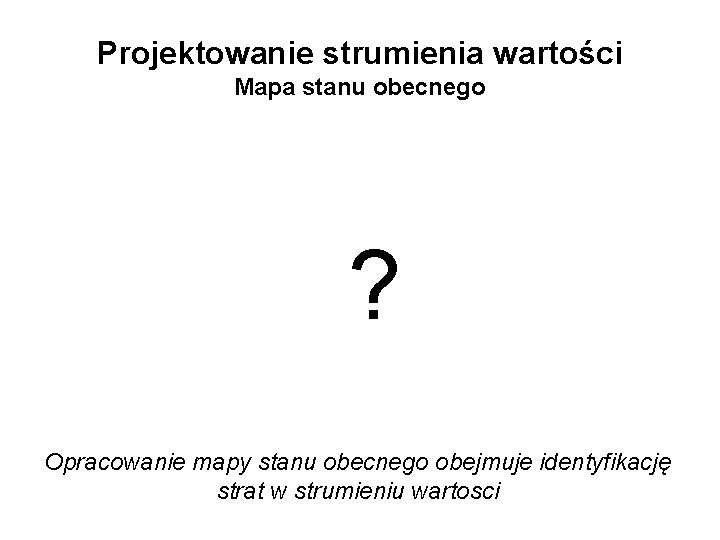
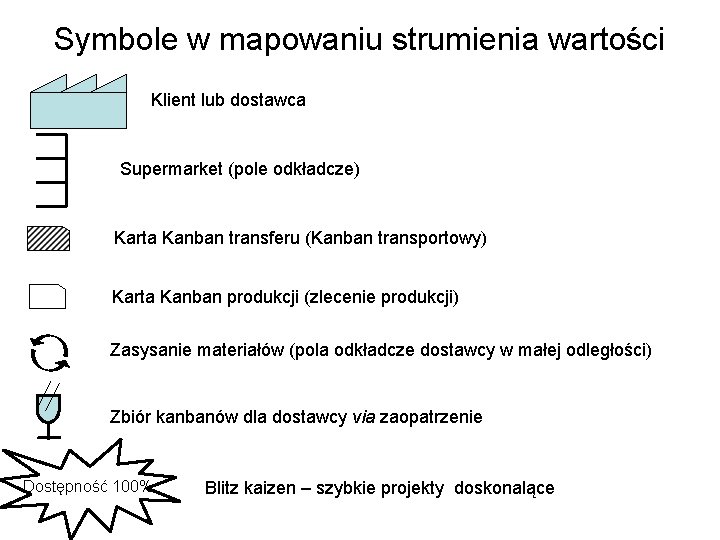
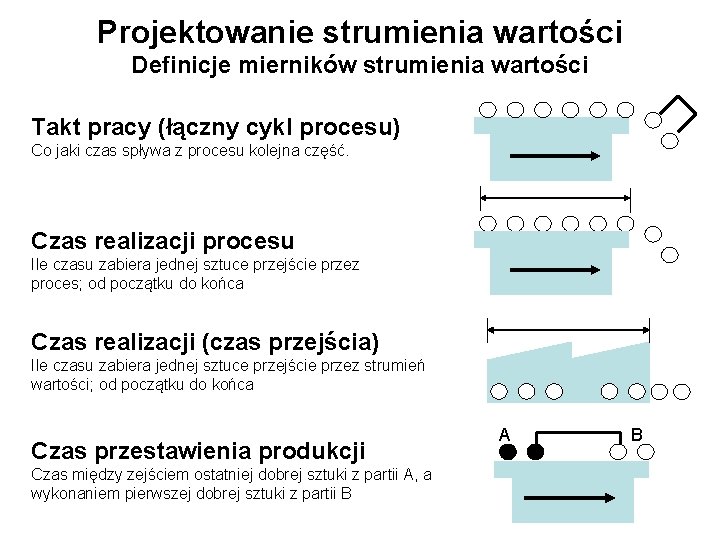
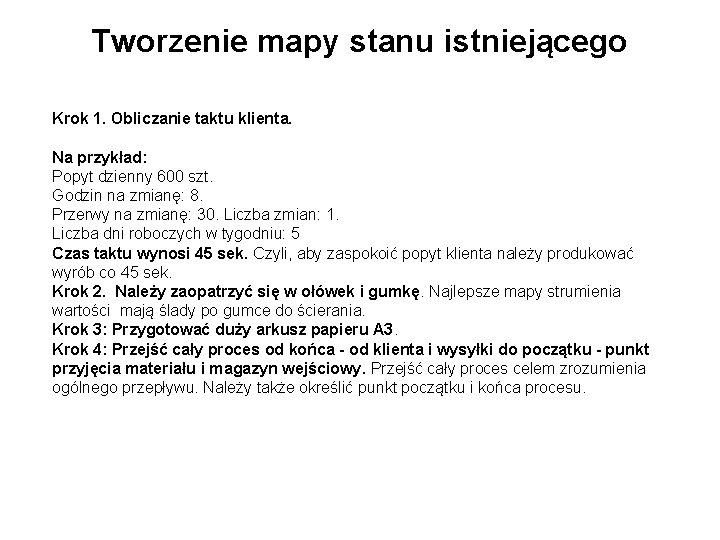
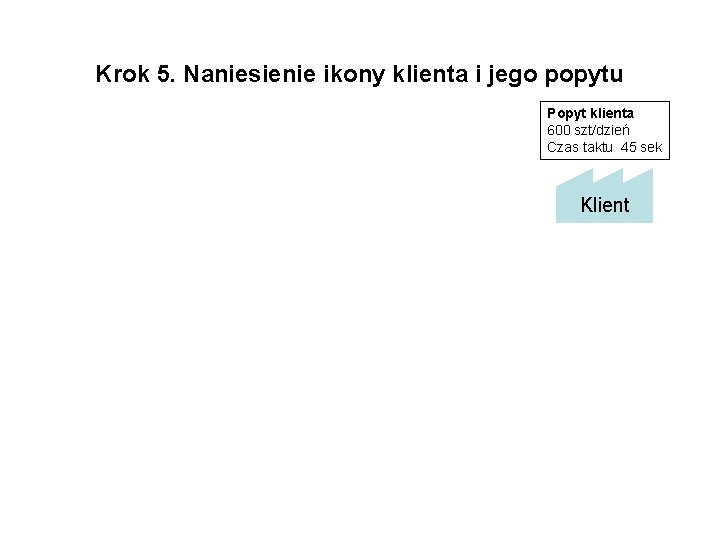
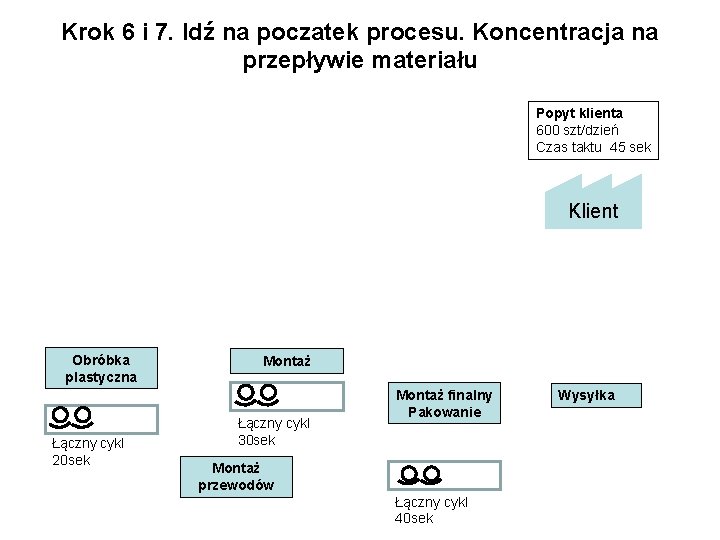
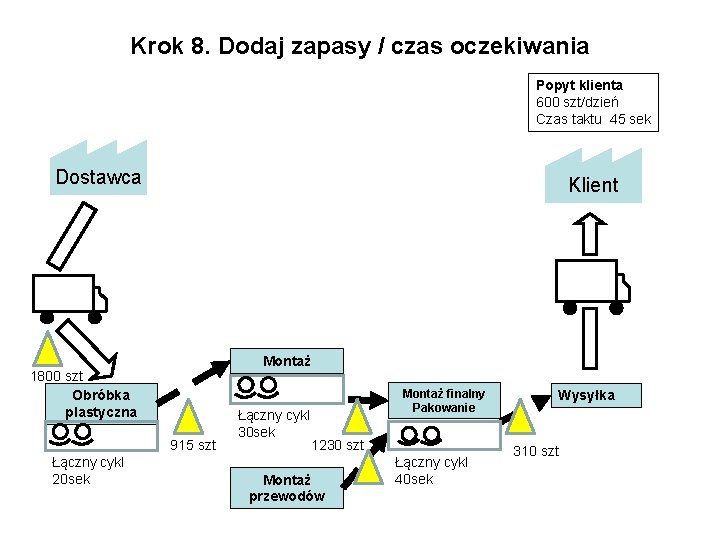
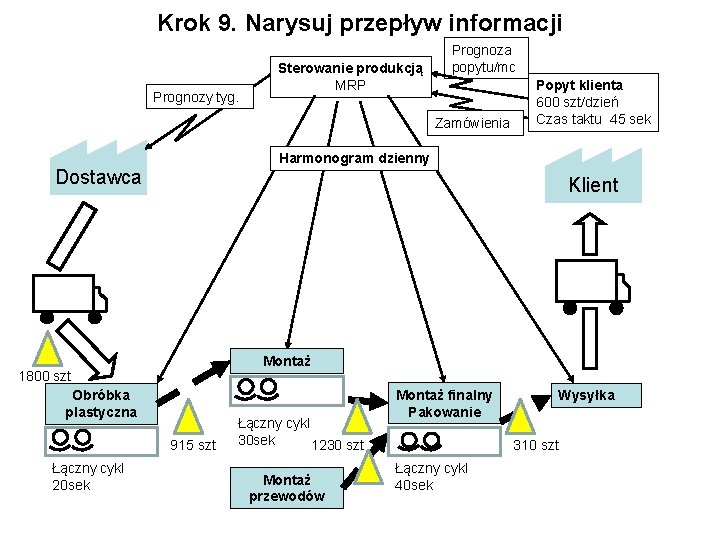
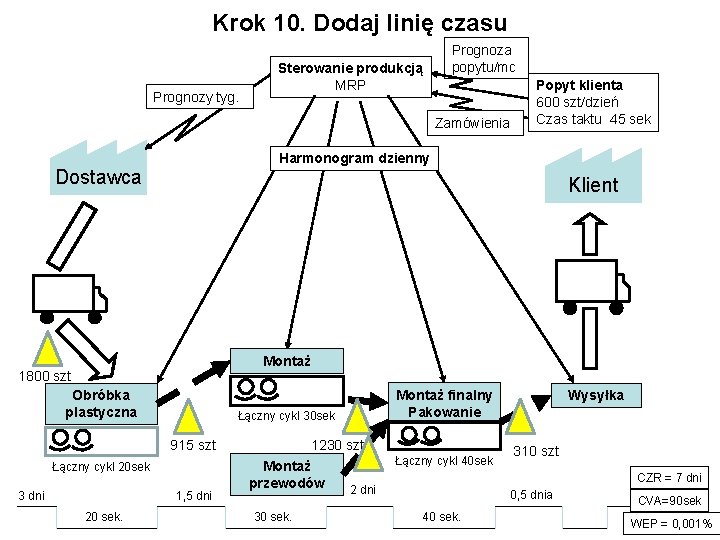
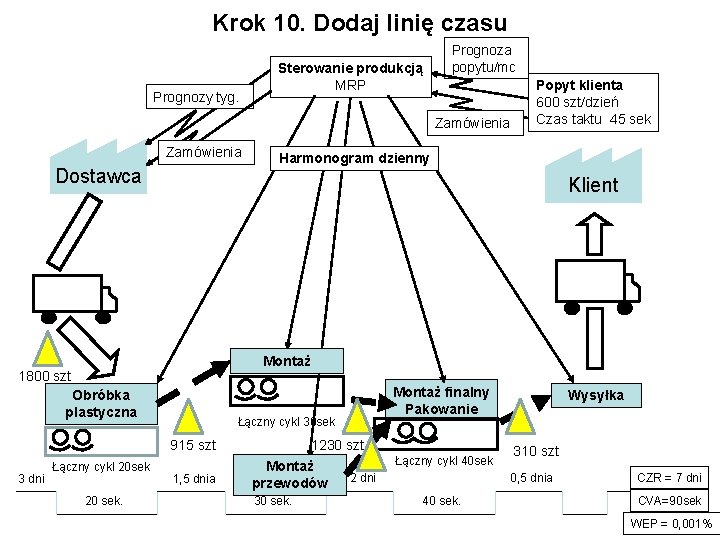
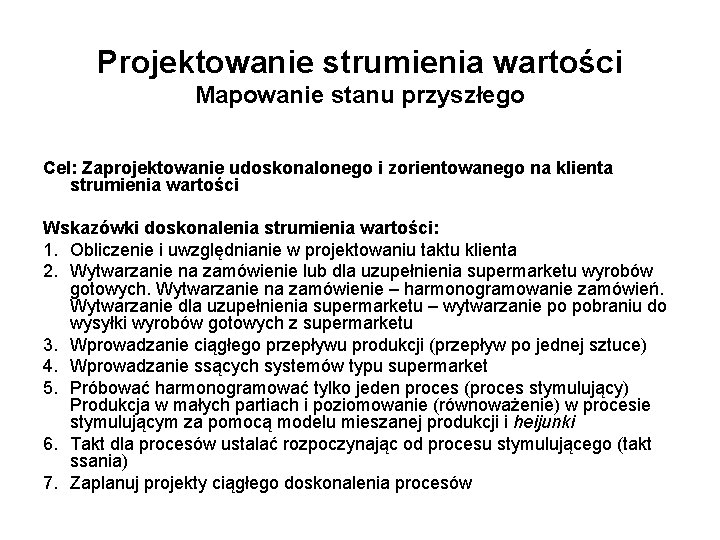
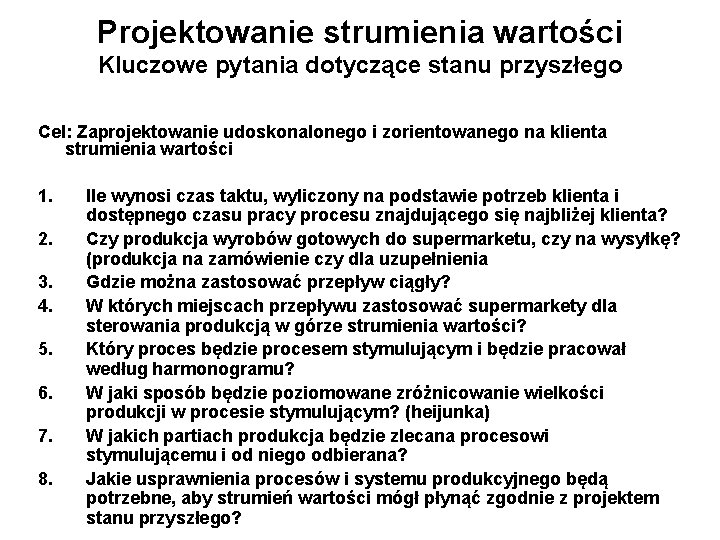
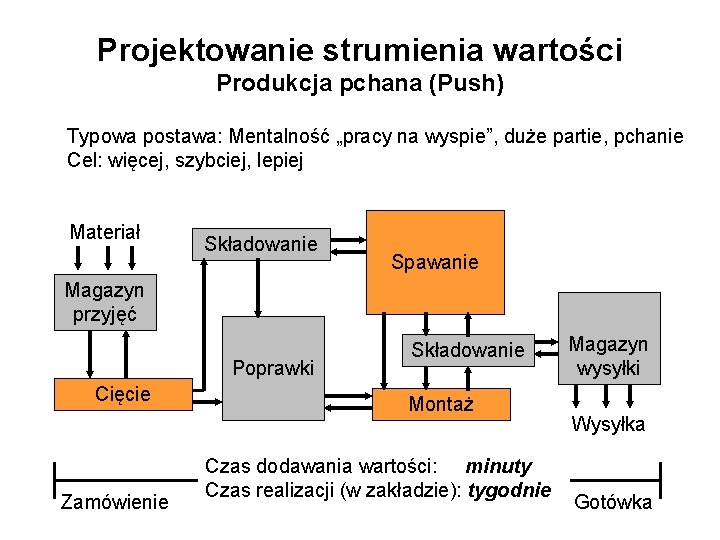
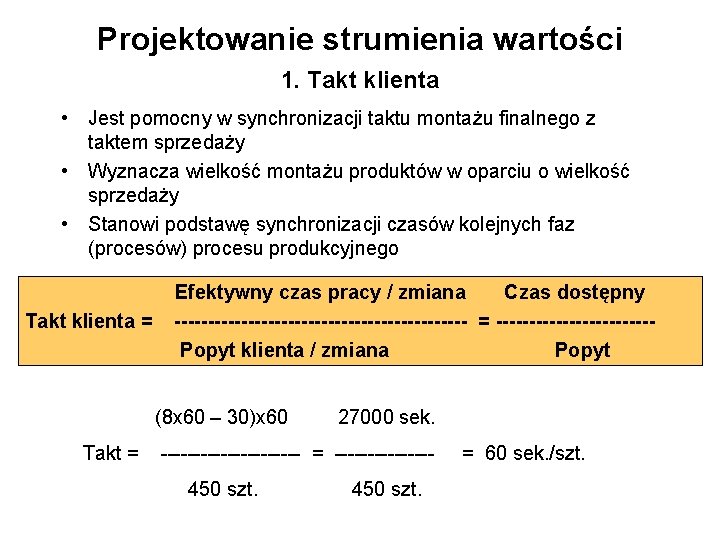
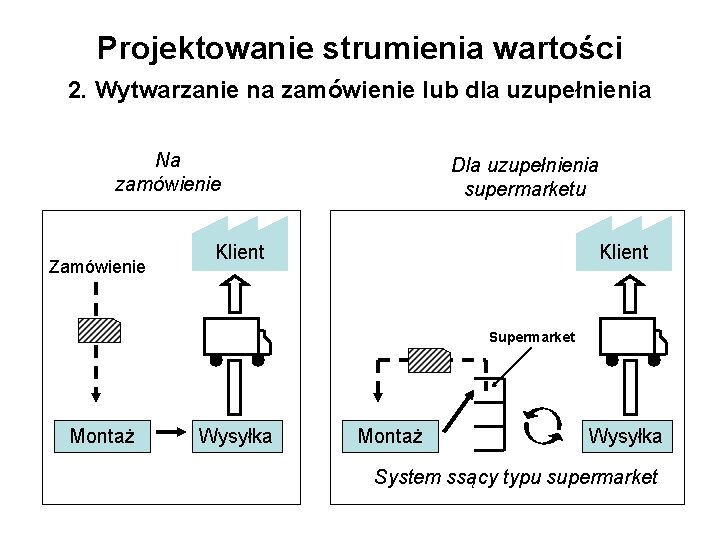
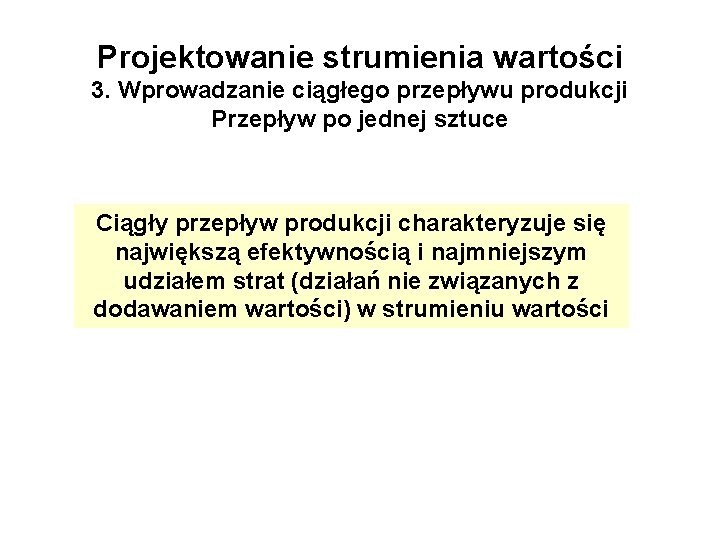
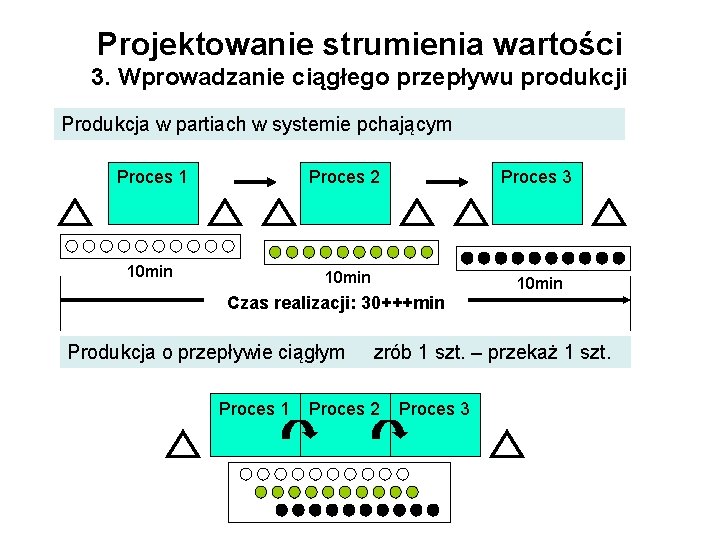
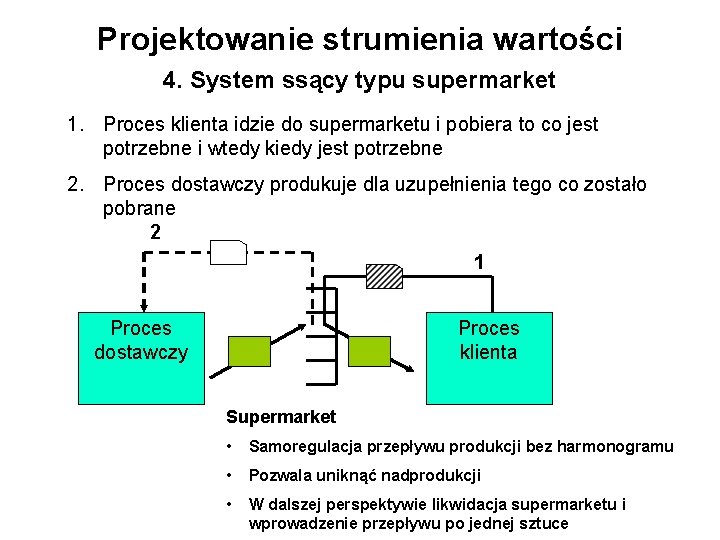
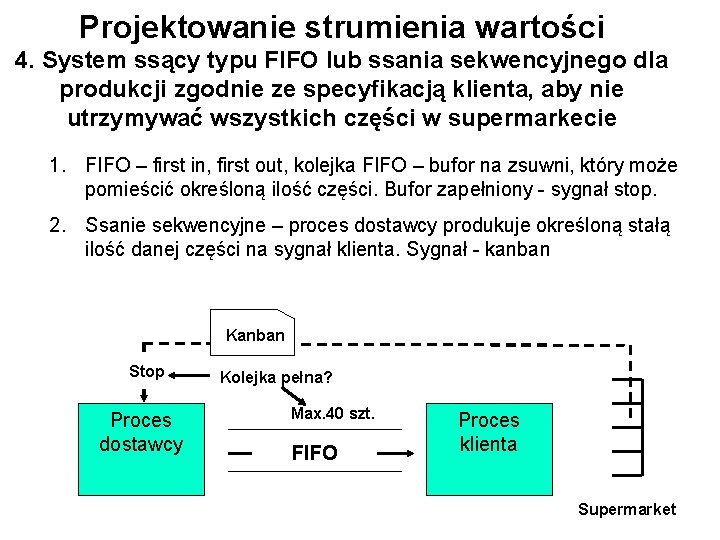
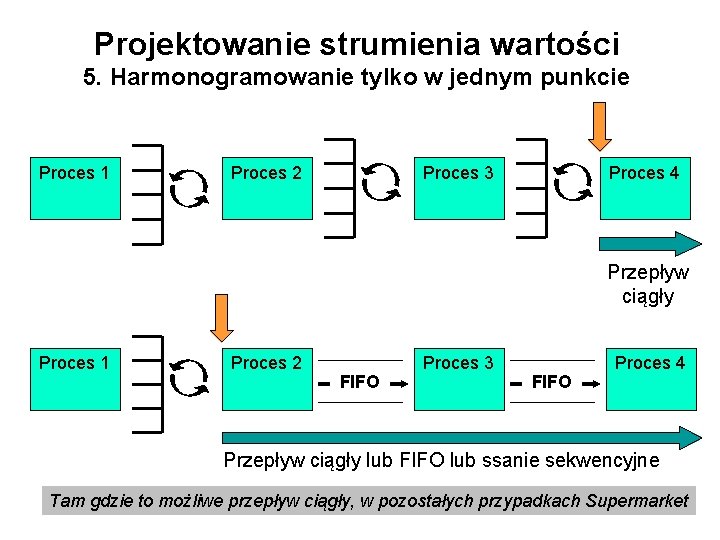
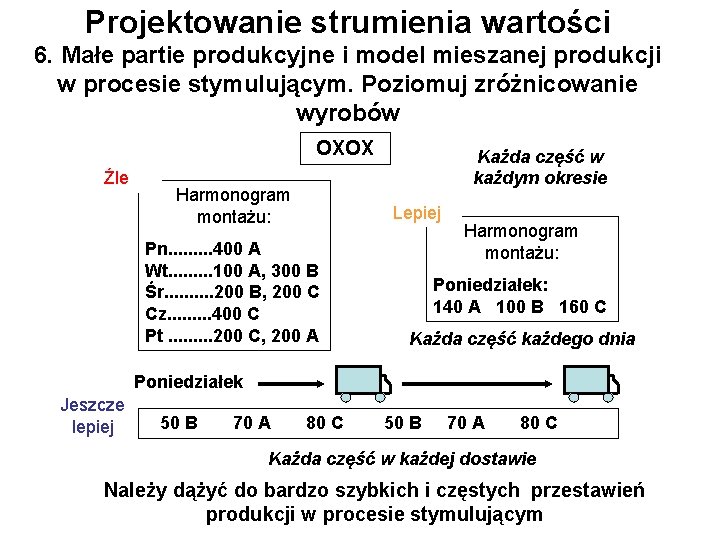
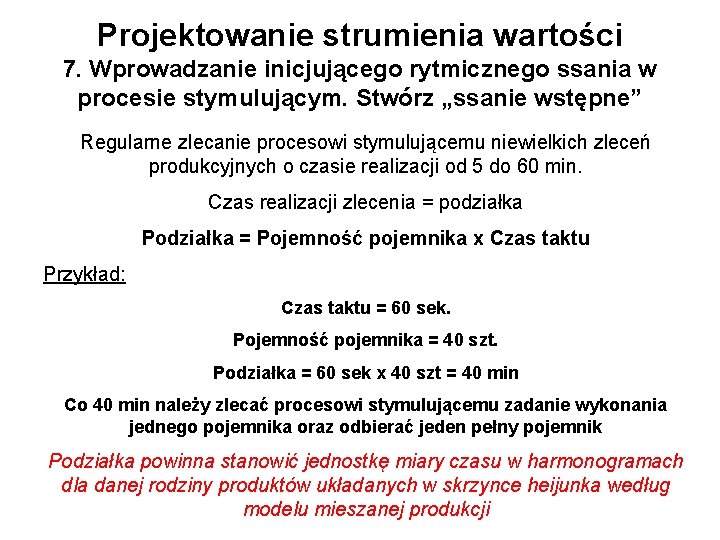
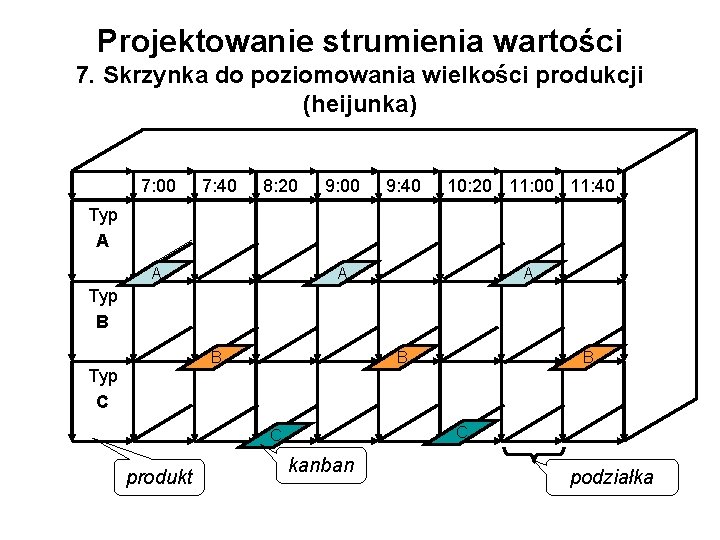
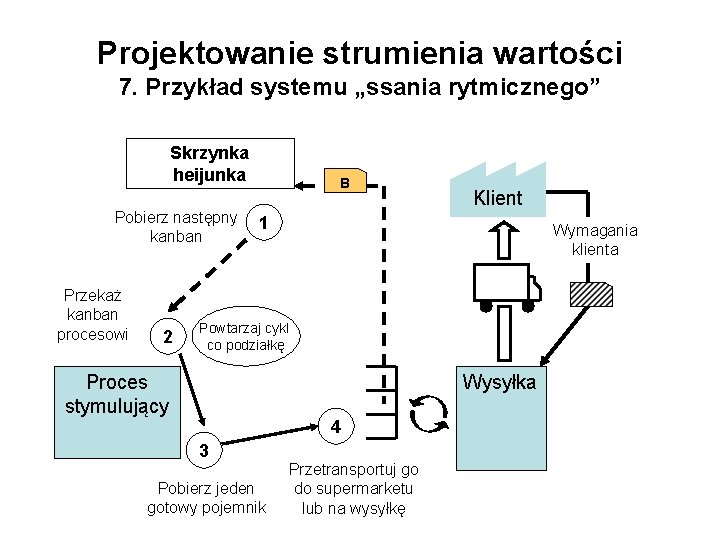
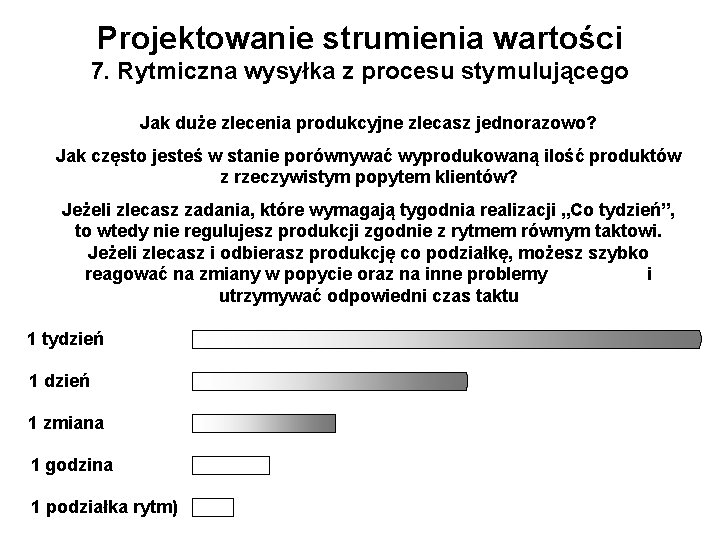
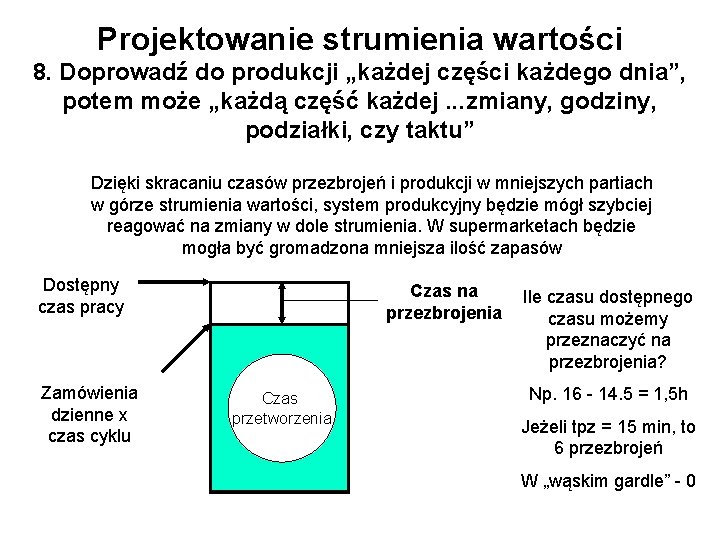
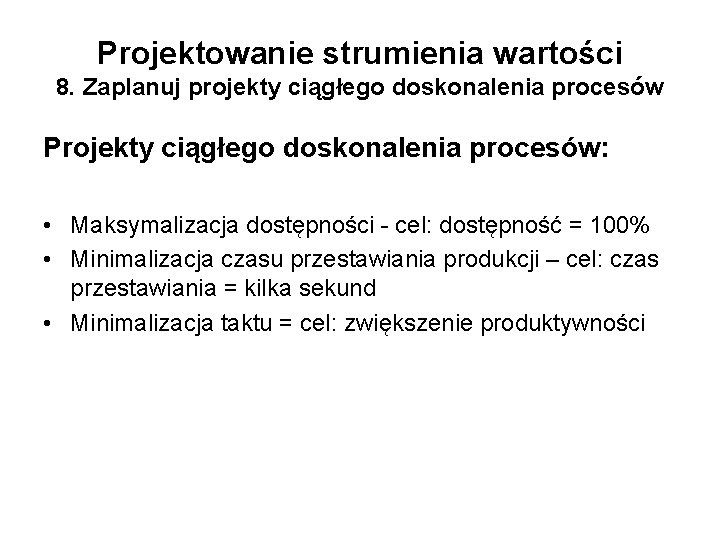
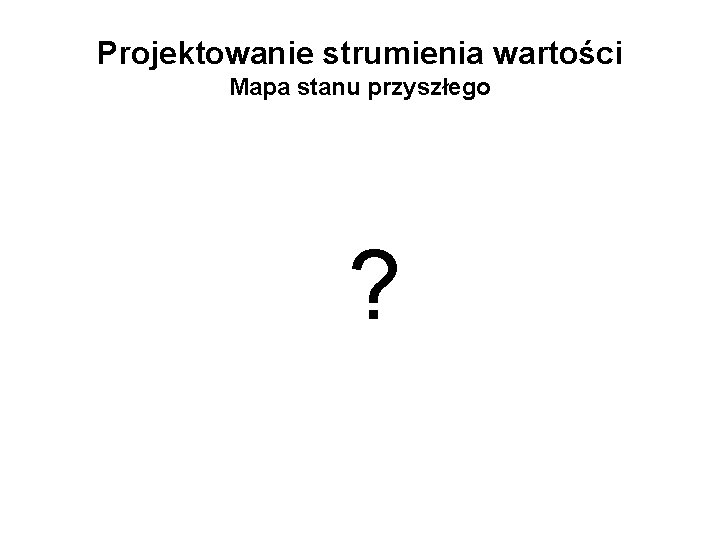
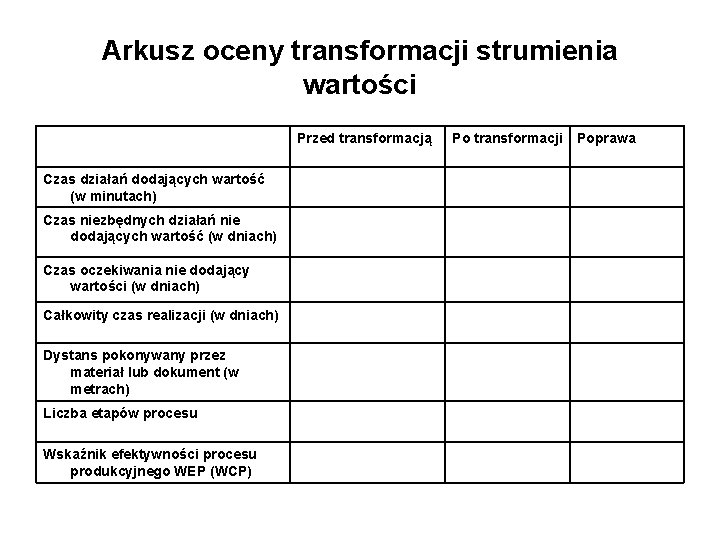
- Slides: 83
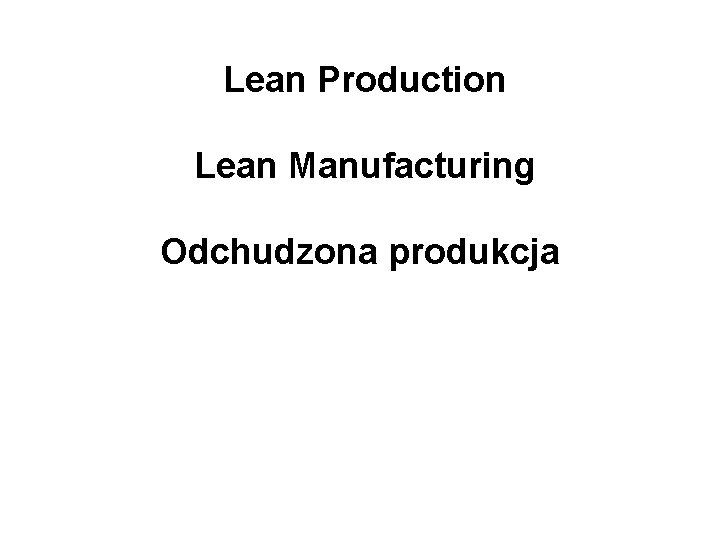
Lean Production Lean Manufacturing Odchudzona produkcja
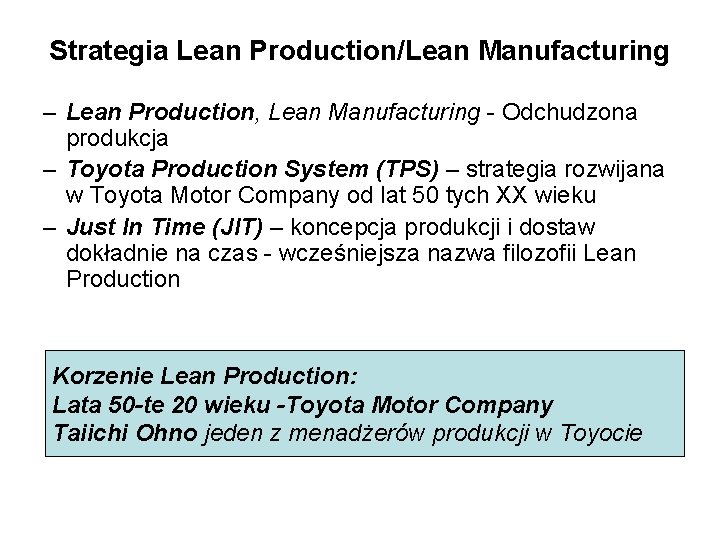
Strategia Lean Production/Lean Manufacturing – Lean Production, Lean Manufacturing - Odchudzona produkcja – Toyota Production System (TPS) – strategia rozwijana w Toyota Motor Company od lat 50 tych XX wieku – Just In Time (JIT) – koncepcja produkcji i dostaw dokładnie na czas - wcześniejsza nazwa filozofii Lean Production Korzenie Lean Production: Lata 50 -te 20 wieku -Toyota Motor Company Taiichi Ohno jeden z menadżerów produkcji w Toyocie
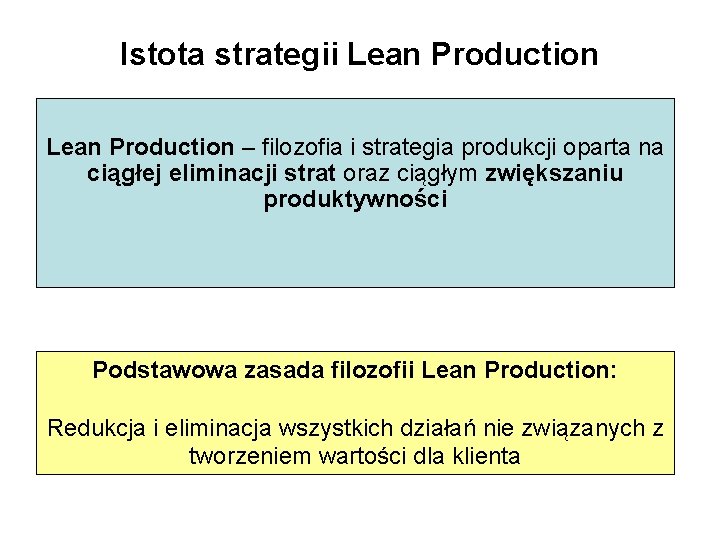
Istota strategii Lean Production – filozofia i strategia produkcji oparta na ciągłej eliminacji strat oraz ciągłym zwiększaniu produktywności Podstawowa zasada filozofii Lean Production: Redukcja i eliminacja wszystkich działań nie związanych z tworzeniem wartości dla klienta
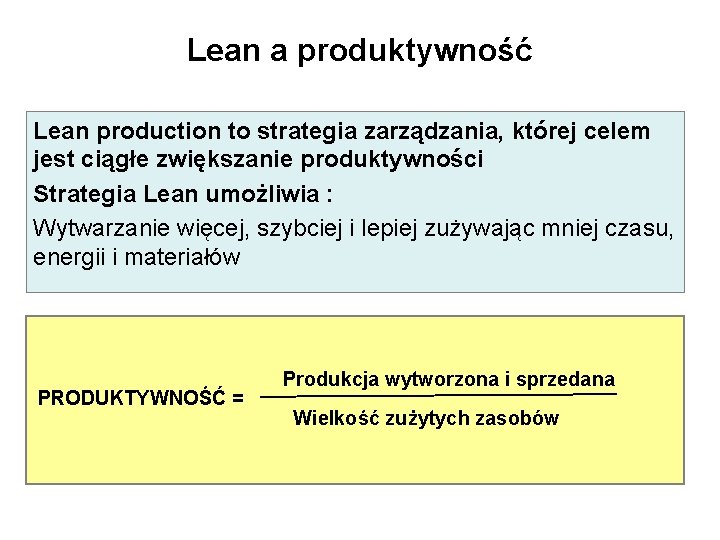
Lean a produktywność Lean production to strategia zarządzania, której celem jest ciągłe zwiększanie produktywności Strategia Lean umożliwia : Wytwarzanie więcej, szybciej i lepiej zużywając mniej czasu, energii i materiałów PRODUKTYWNOŚĆ = Produkcja wytworzona i sprzedana Wielkość zużytych zasobów
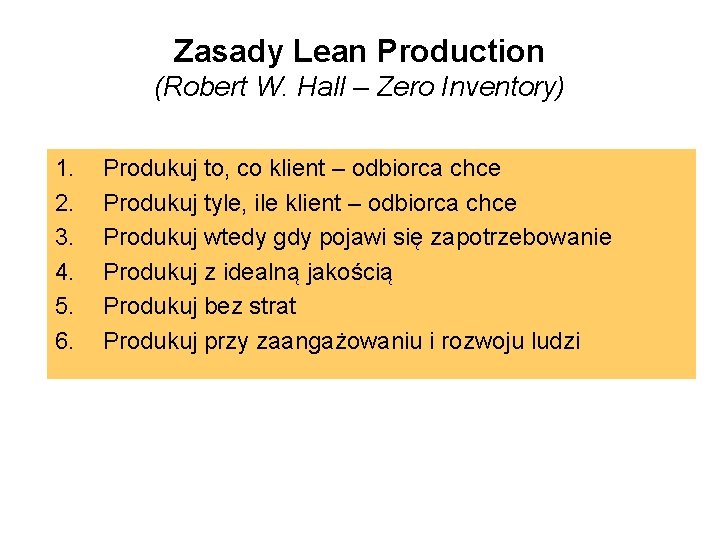
Zasady Lean Production (Robert W. Hall – Zero Inventory) 1. 2. 3. 4. 5. 6. Produkuj to, co klient – odbiorca chce Produkuj tyle, ile klient – odbiorca chce Produkuj wtedy gdy pojawi się zapotrzebowanie Produkuj z idealną jakością Produkuj bez strat Produkuj przy zaangażowaniu i rozwoju ludzi
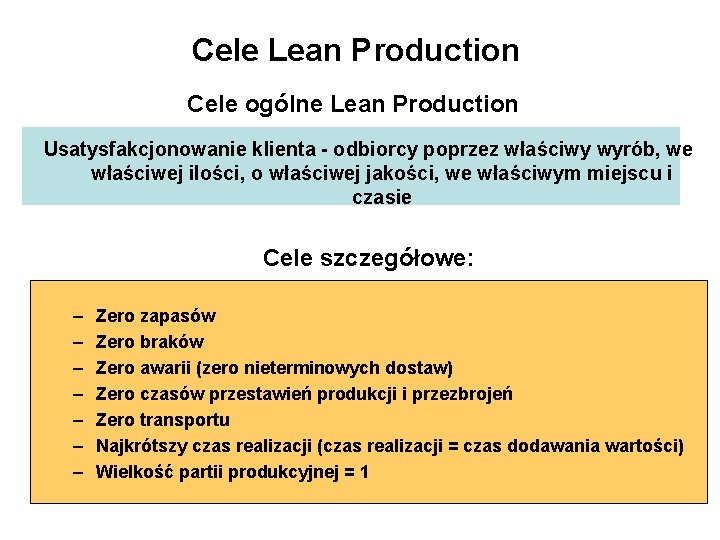
Cele Lean Production Cele ogólne Lean Production Usatysfakcjonowanie klienta - odbiorcy poprzez właściwy wyrób, we właściwej ilości, o właściwej jakości, we właściwym miejscu i czasie Cele szczegółowe: – – – – Zero zapasów Zero braków Zero awarii (zero nieterminowych dostaw) Zero czasów przestawień produkcji i przezbrojeń Zero transportu Najkrótszy czas realizacji (czas realizacji = czas dodawania wartości) Wielkość partii produkcyjnej = 1

Lean i zapasy Zapasy są złem! Zapasy są jak opium, im więcej ich masz tym więcej ich chcesz 1. Zapasy kosztują – – – Koszty utrzymywania infrastruktury magazynowej, koszty powierzchni magazynowej i produkcyjnej Koszty utrzymywania zapasów Koszty zamrożenia środków obrotowych w zapasach 2. Zapasy skrywają problemy – – Rozwiązując problemy eliminuje się powód utrzymywania zapasów Uwolnione pieniądze można zainwestować w dalsze doskonalenie procesów i rozwiązanie problemów
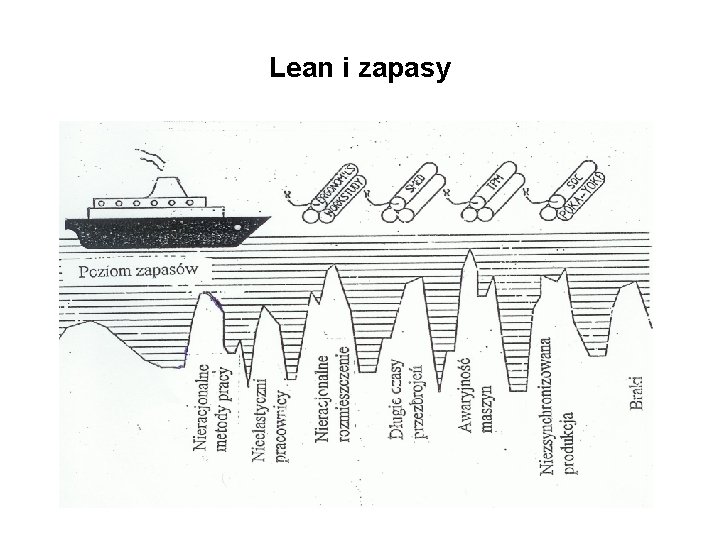
Lean i zapasy
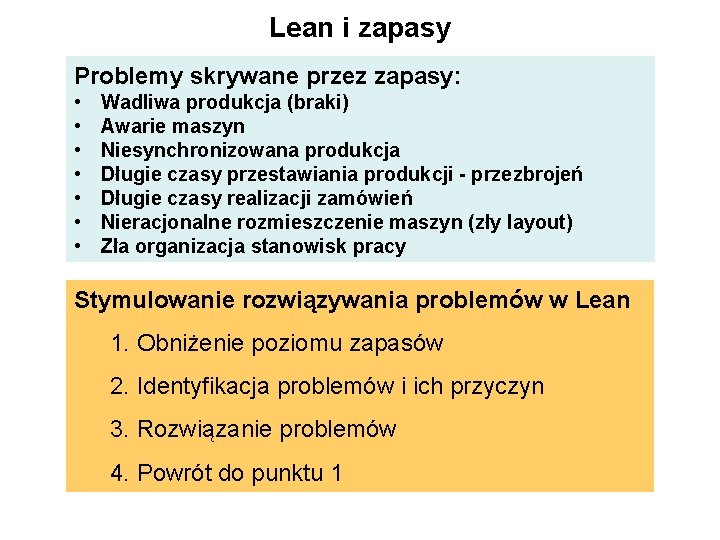
Lean i zapasy Problemy skrywane przez zapasy: • • Wadliwa produkcja (braki) Awarie maszyn Niesynchronizowana produkcja Długie czasy przestawiania produkcji - przezbrojeń Długie czasy realizacji zamówień Nieracjonalne rozmieszczenie maszyn (zły layout) Zła organizacja stanowisk pracy Stymulowanie rozwiązywania problemów w Lean 1. Obniżenie poziomu zapasów 2. Identyfikacja problemów i ich przyczyn 3. Rozwiązanie problemów 4. Powrót do punktu 1
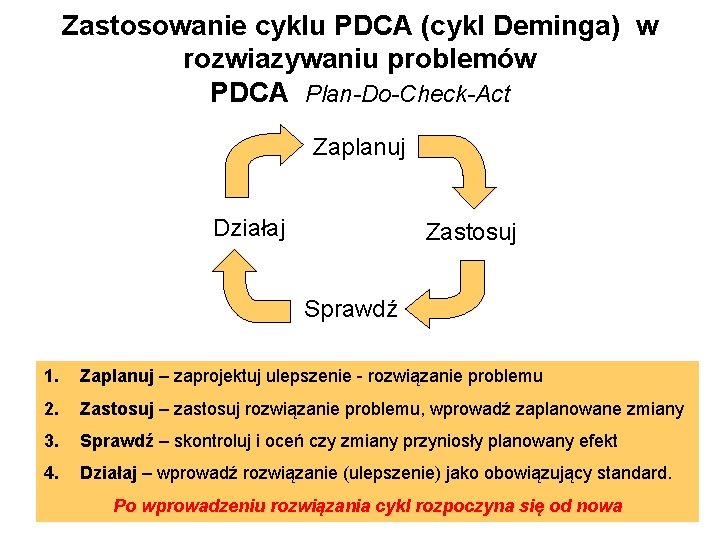
Zastosowanie cyklu PDCA (cykl Deminga) w rozwiazywaniu problemów PDCA Plan-Do-Check-Act Zaplanuj Działaj Zastosuj Sprawdź 1. Zaplanuj – zaprojektuj ulepszenie - rozwiązanie problemu 2. Zastosuj – zastosuj rozwiązanie problemu, wprowadź zaplanowane zmiany 3. Sprawdź – skontroluj i oceń czy zmiany przyniosły planowany efekt 4. Działaj – wprowadź rozwiązanie (ulepszenie) jako obowiązujący standard. Po wprowadzeniu rozwiązania cykl rozpoczyna się od nowa
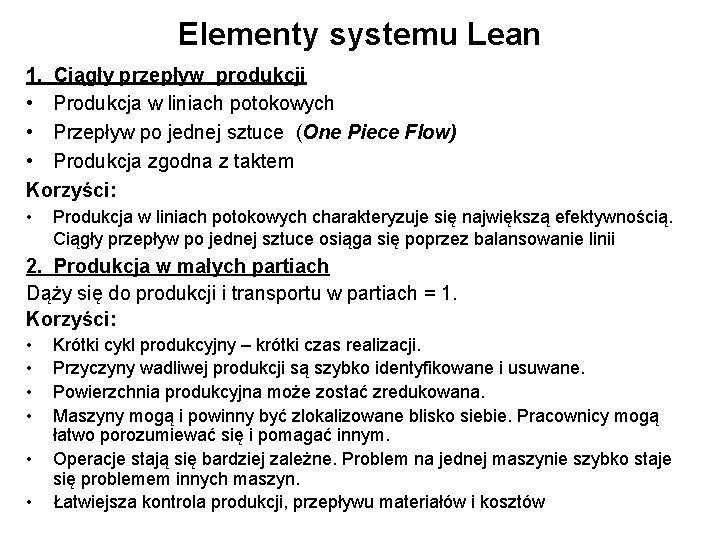
Elementy systemu Lean 1. Ciągły przepływ produkcji • Produkcja w liniach potokowych • Przepływ po jednej sztuce (One Piece Flow) • Produkcja zgodna z taktem Korzyści: • Produkcja w liniach potokowych charakteryzuje się największą efektywnością. Ciągły przepływ po jednej sztuce osiąga się poprzez balansowanie linii 2. Produkcja w małych partiach Dąży się do produkcji i transportu w partiach = 1. Korzyści: • • • Krótki cykl produkcyjny – krótki czas realizacji. Przyczyny wadliwej produkcji są szybko identyfikowane i usuwane. Powierzchnia produkcyjna może zostać zredukowana. Maszyny mogą i powinny być zlokalizowane blisko siebie. Pracownicy mogą łatwo porozumiewać się i pomagać innym. Operacje stają się bardziej zależne. Problem na jednej maszynie szybko staje się problemem innych maszyn. Łatwiejsza kontrola produkcji, przepływu materiałów i kosztów
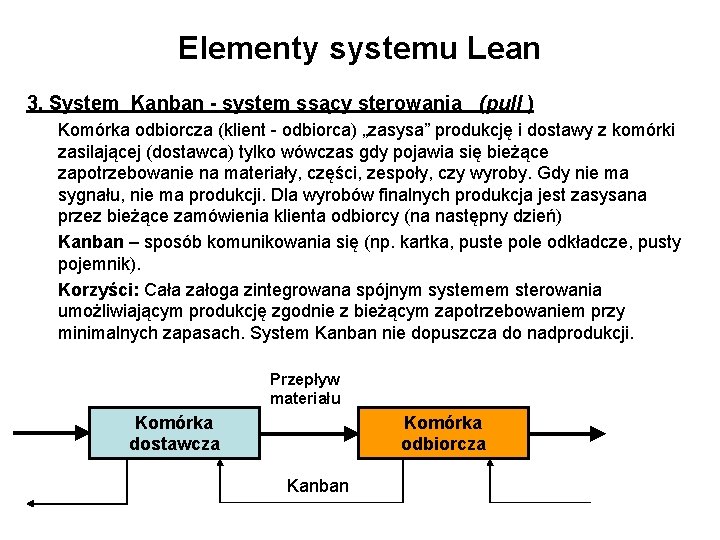
Elementy systemu Lean 3. System Kanban - system ssący sterowania (pull ) Komórka odbiorcza (klient - odbiorca) „zasysa” produkcję i dostawy z komórki zasilającej (dostawca) tylko wówczas gdy pojawia się bieżące zapotrzebowanie na materiały, części, zespoły, czy wyroby. Gdy nie ma sygnału, nie ma produkcji. Dla wyrobów finalnych produkcja jest zasysana przez bieżące zamówienia klienta odbiorcy (na następny dzień) Kanban – sposób komunikowania się (np. kartka, puste pole odkładcze, pusty pojemnik). Korzyści: Cała załoga zintegrowana spójnym systemem sterowania umożliwiającym produkcję zgodnie z bieżącym zapotrzebowaniem przy minimalnych zapasach. System Kanban nie dopuszcza do nadprodukcji. Przepływ materiału Komórka dostawcza Komórka odbiorcza Kanban
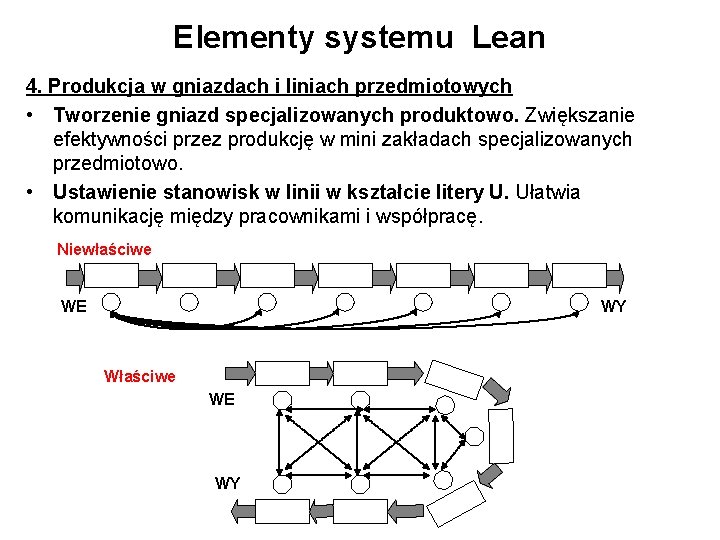
Elementy systemu Lean 4. Produkcja w gniazdach i liniach przedmiotowych • Tworzenie gniazd specjalizowanych produktowo. Zwiększanie efektywności przez produkcję w mini zakładach specjalizowanych przedmiotowo. • Ustawienie stanowisk w linii w kształcie litery U. Ułatwia komunikację między pracownikami i współpracę. Niewłaściwe WE WY Właściwe WE WY
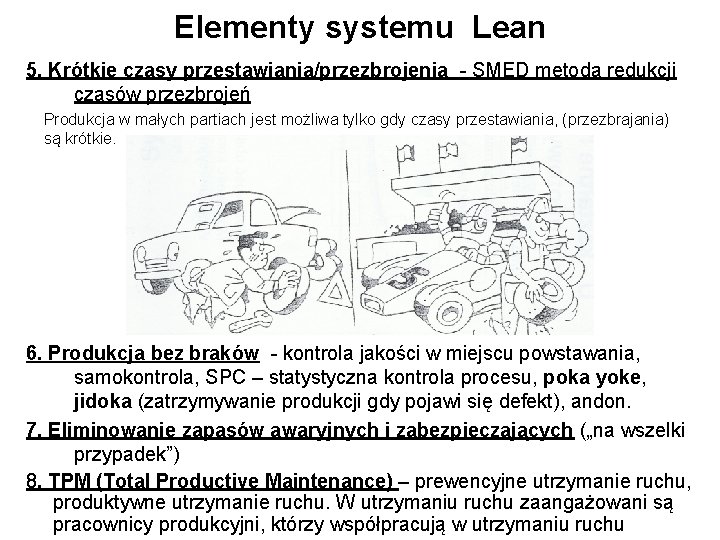
Elementy systemu Lean 5. Krótkie czasy przestawiania/przezbrojenia - SMED metoda redukcji czasów przezbrojeń Produkcja w małych partiach jest możliwa tylko gdy czasy przestawiania, (przezbrajania) są krótkie. 6. Produkcja bez braków - kontrola jakości w miejscu powstawania, samokontrola, SPC – statystyczna kontrola procesu, poka yoke, jidoka (zatrzymywanie produkcji gdy pojawi się defekt), andon. 7. Eliminowanie zapasów awaryjnych i zabezpieczających („na wszelki przypadek”) 8. TPM (Total Productive Maintenance) – prewencyjne utrzymanie ruchu, produktywne utrzymanie ruchu. W utrzymaniu ruchu zaangażowani są pracownicy produkcyjni, którzy współpracują w utrzymaniu ruchu
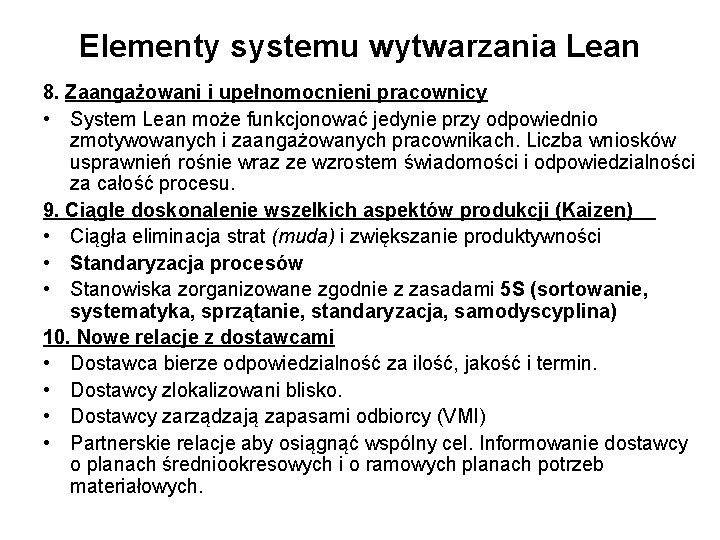
Elementy systemu wytwarzania Lean 8. Zaangażowani i upełnomocnieni pracownicy • System Lean może funkcjonować jedynie przy odpowiednio zmotywowanych i zaangażowanych pracownikach. Liczba wniosków usprawnień rośnie wraz ze wzrostem świadomości i odpowiedzialności za całość procesu. 9. Ciągłe doskonalenie wszelkich aspektów produkcji (Kaizen) • Ciągła eliminacja strat (muda) i zwiększanie produktywności • Standaryzacja procesów • Stanowiska zorganizowane zgodnie z zasadami 5 S (sortowanie, systematyka, sprzątanie, standaryzacja, samodyscyplina) 10. Nowe relacje z dostawcami • Dostawca bierze odpowiedzialność za ilość, jakość i termin. • Dostawcy zlokalizowani blisko. • Dostawcy zarządzają zapasami odbiorcy (VMI) • Partnerskie relacje aby osiągnąć wspólny cel. Informowanie dostawcy o planach średniookresowych i o ramowych planach potrzeb materiałowych.
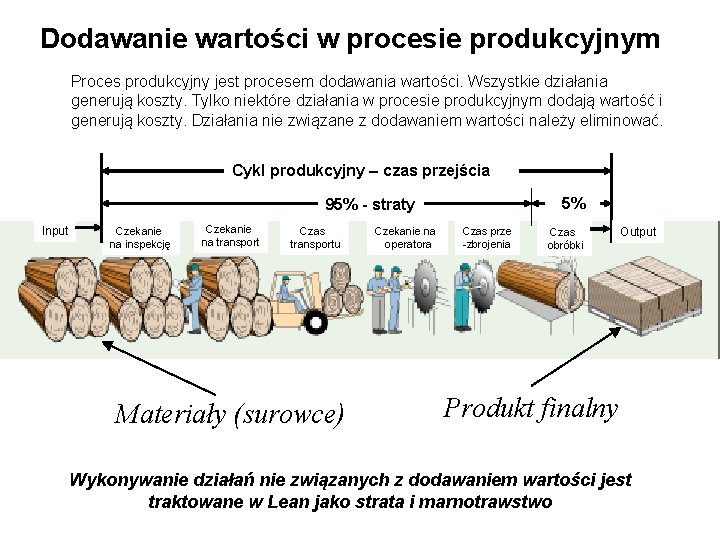
Dodawanie wartości w procesie produkcyjnym Proces produkcyjny jest procesem dodawania wartości. Wszystkie działania generują koszty. Tylko niektóre działania w procesie produkcyjnym dodają wartość i generują koszty. Działania nie związane z dodawaniem wartości należy eliminować. Cykl produkcyjny – czas przejścia 5% 95% - straty Input Czekanie na inspekcję Czekanie na transport Czas transportu Materiały (surowce) Czekanie na operatora Czas prze -zbrojenia Czas obróbki Output Produkt finalny Wykonywanie działań nie związanych z dodawaniem wartości jest traktowane w Lean jako strata i marnotrawstwo
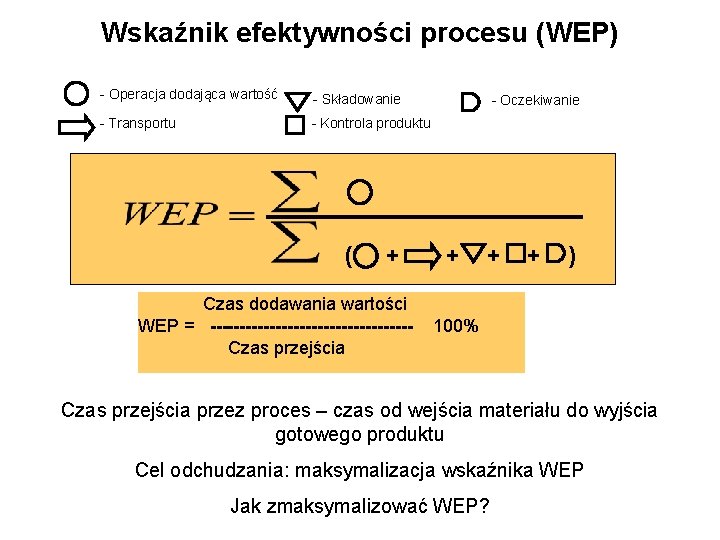
Wskaźnik efektywności procesu (WEP) - Operacja dodająca wartość - Składowanie - Transportu - Kontrola produktu ( + Czas dodawania wartości WEP = -----------------Czas przejścia - Oczekiwanie + + + ) 100% Czas przejścia przez proces – czas od wejścia materiału do wyjścia gotowego produktu Cel odchudzania: maksymalizacja wskaźnika WEP Jak zmaksymalizować WEP?
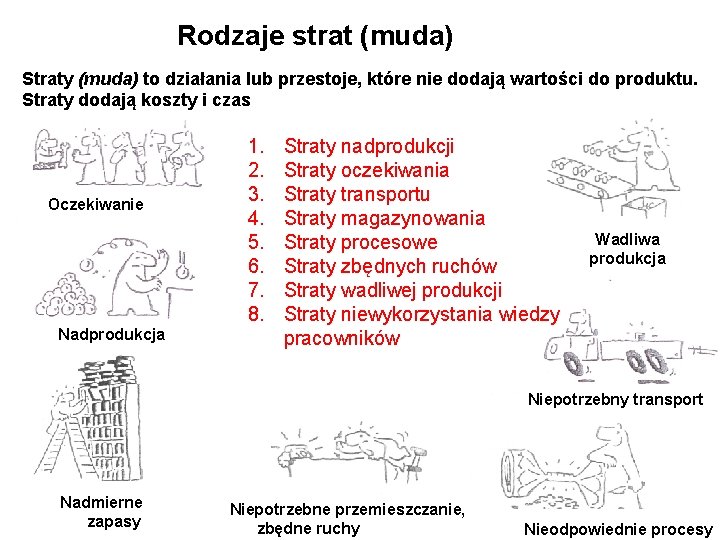
Rodzaje strat (muda) Straty (muda) to działania lub przestoje, które nie dodają wartości do produktu. Straty dodają koszty i czas Oczekiwanie Nadprodukcja 1. 2. 3. 4. 5. 6. 7. 8. Straty nadprodukcji Straty oczekiwania Straty transportu Straty magazynowania Straty procesowe Straty zbędnych ruchów Straty wadliwej produkcji Straty niewykorzystania wiedzy pracowników Wadliwa produkcja Niepotrzebny transport Nadmierne zapasy Niepotrzebne przemieszczanie, zbędne ruchy Nieodpowiednie procesy
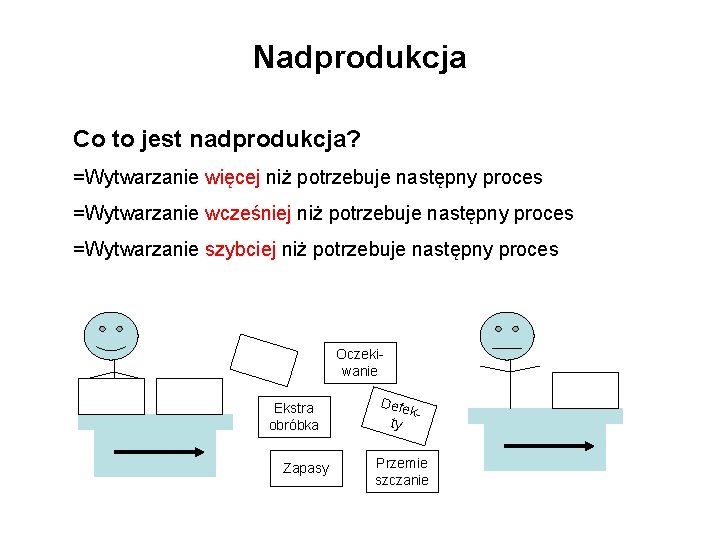
Nadprodukcja Co to jest nadprodukcja? =Wytwarzanie więcej niż potrzebuje następny proces =Wytwarzanie wcześniej niż potrzebuje następny proces =Wytwarzanie szybciej niż potrzebuje następny proces Oczekiwanie Ekstra obróbka Zapasy Defe kty Przemie szczanie
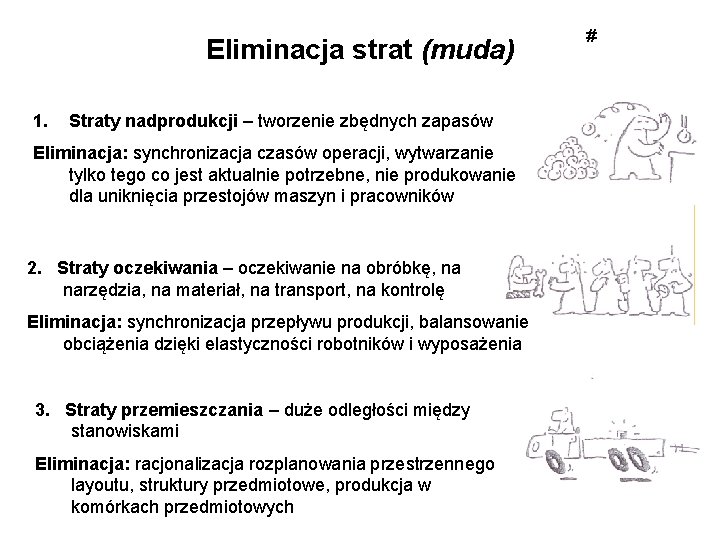
Eliminacja strat (muda) 1. Straty nadprodukcji – tworzenie zbędnych zapasów Eliminacja: synchronizacja czasów operacji, wytwarzanie tylko tego co jest aktualnie potrzebne, nie produkowanie dla uniknięcia przestojów maszyn i pracowników 2. Straty oczekiwania – oczekiwanie na obróbkę, na narzędzia, na materiał, na transport, na kontrolę Eliminacja: synchronizacja przepływu produkcji, balansowanie obciążenia dzięki elastyczności robotników i wyposażenia 3. Straty przemieszczania – duże odległości między stanowiskami Eliminacja: racjonalizacja rozplanowania przestrzennego layoutu, struktury przedmiotowe, produkcja w komórkach przedmiotowych #
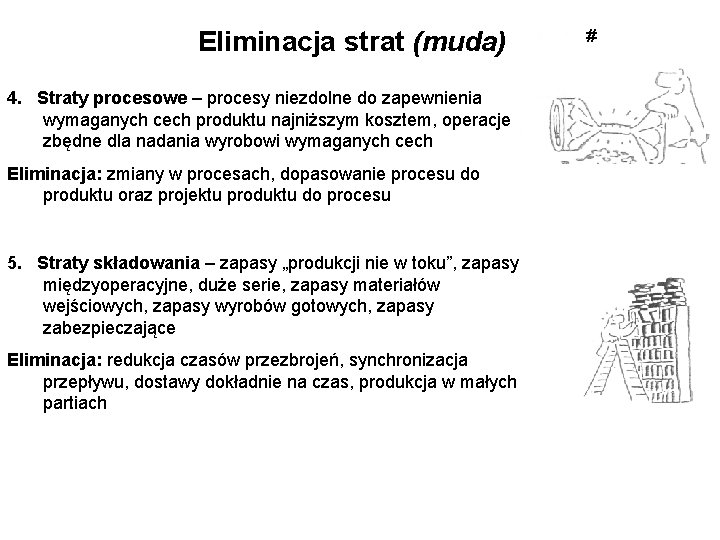
Eliminacja strat (muda) 4. Straty procesowe – procesy niezdolne do zapewnienia wymaganych cech produktu najniższym kosztem, operacje zbędne dla nadania wyrobowi wymaganych cech Eliminacja: zmiany w procesach, dopasowanie procesu do produktu oraz projektu produktu do procesu 5. Straty składowania – zapasy „produkcji nie w toku”, zapasy międzyoperacyjne, duże serie, zapasy materiałów wejściowych, zapasy wyrobów gotowych, zapasy zabezpieczające Eliminacja: redukcja czasów przezbrojeń, synchronizacja przepływu, dostawy dokładnie na czas, produkcja w małych partiach #
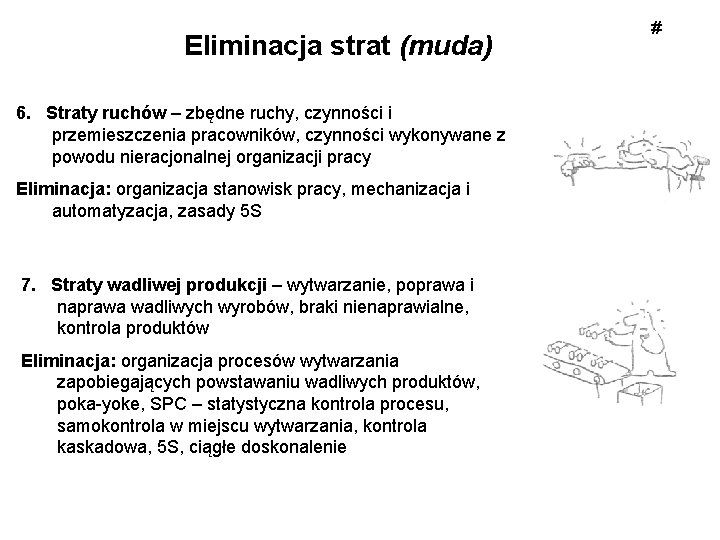
Eliminacja strat (muda) 6. Straty ruchów – zbędne ruchy, czynności i przemieszczenia pracowników, czynności wykonywane z powodu nieracjonalnej organizacji pracy Eliminacja: organizacja stanowisk pracy, mechanizacja i automatyzacja, zasady 5 S 7. Straty wadliwej produkcji – wytwarzanie, poprawa i naprawa wadliwych wyrobów, braki nienaprawialne, kontrola produktów Eliminacja: organizacja procesów wytwarzania zapobiegających powstawaniu wadliwych produktów, poka-yoke, SPC – statystyczna kontrola procesu, samokontrola w miejscu wytwarzania, kontrola kaskadowa, 5 S, ciągłe doskonalenie #
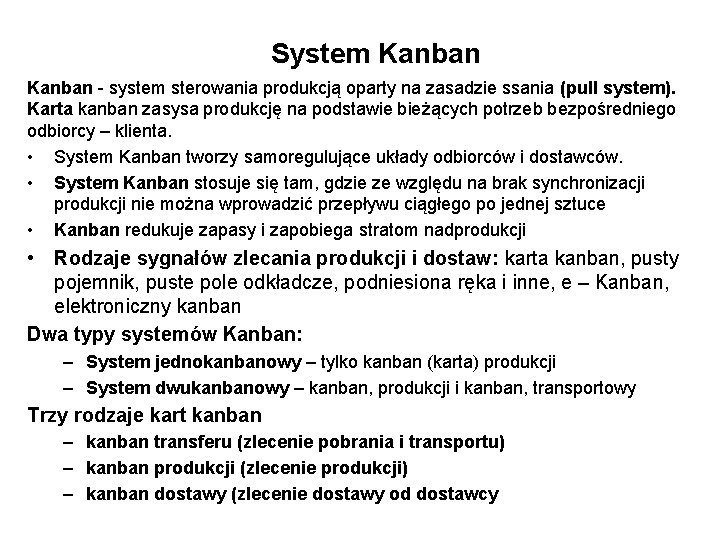
System Kanban - system sterowania produkcją oparty na zasadzie ssania (pull system). Karta kanban zasysa produkcję na podstawie bieżących potrzeb bezpośredniego odbiorcy – klienta. • System Kanban tworzy samoregulujące układy odbiorców i dostawców. • System Kanban stosuje się tam, gdzie ze względu na brak synchronizacji produkcji nie można wprowadzić przepływu ciągłego po jednej sztuce • Kanban redukuje zapasy i zapobiega stratom nadprodukcji • Rodzaje sygnałów zlecania produkcji i dostaw: karta kanban, pusty pojemnik, puste pole odkładcze, podniesiona ręka i inne, e – Kanban, elektroniczny kanban Dwa typy systemów Kanban: – System jednokanbanowy – tylko kanban (karta) produkcji – System dwukanbanowy – kanban, produkcji i kanban, transportowy Trzy rodzaje kart kanban – kanban transferu (zlecenie pobrania i transportu) – kanban produkcji (zlecenie produkcji) – kanban dostawy (zlecenie dostawy od dostawcy
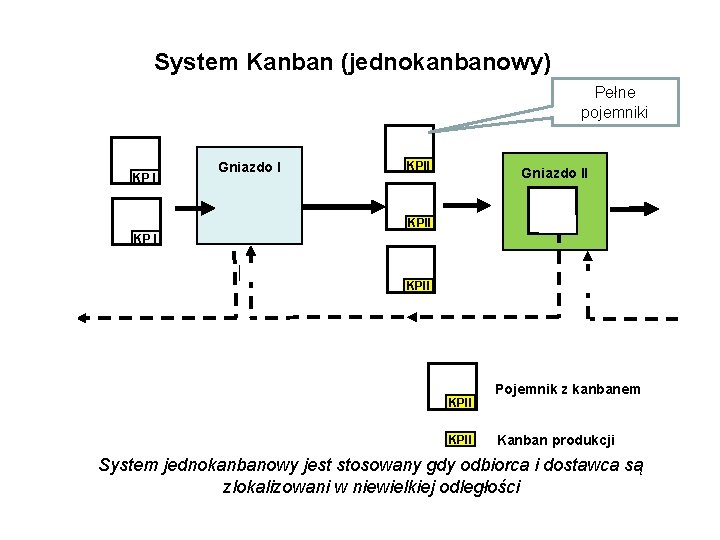
System Kanban (jednokanbanowy) Pełne pojemniki KP I KP KP II Gniazdo I KPII Gniazdo II KPII KP I KPII Pojemnik z kanbanem Kanban produkcji System jednokanbanowy jest stosowany gdy odbiorca i dostawca są zlokalizowani w niewielkiej odległości
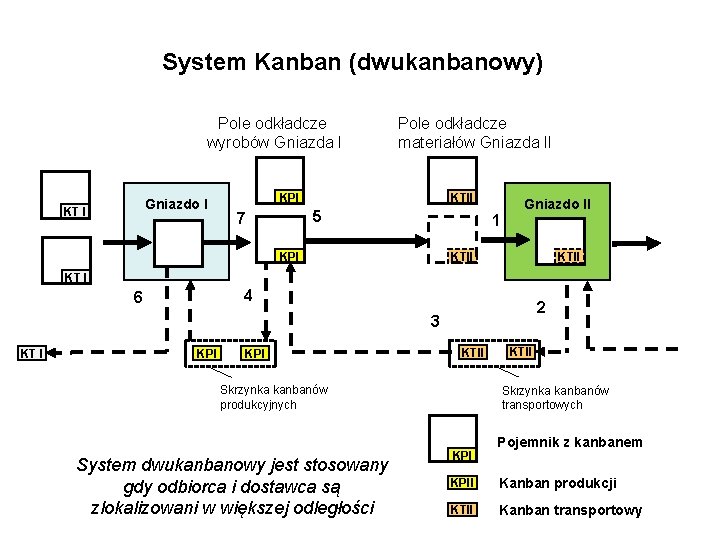
System Kanban (dwukanbanowy) Pole odkładcze wyrobów Gniazda I Gniazdo I KT I Pole odkładcze materiałów Gniazda II KPI KTII 5 7 1 KPI Gniazdo II KTII KT I 4 6 2 3 KT I KPI KTII Skrzynka kanbanów produkcyjnych System dwukanbanowy jest stosowany gdy odbiorca i dostawca są zlokalizowani w większej odległości KTII Skrzynka kanbanów transportowych KPI Pojemnik z kanbanem KPII Kanban produkcji KTII Kanban transportowy
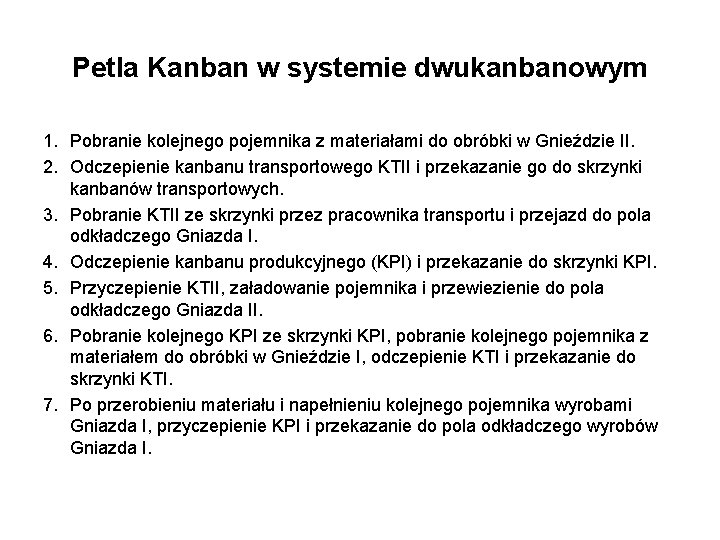
Petla Kanban w systemie dwukanbanowym 1. Pobranie kolejnego pojemnika z materiałami do obróbki w Gnieździe II. 2. Odczepienie kanbanu transportowego KTII i przekazanie go do skrzynki kanbanów transportowych. 3. Pobranie KTII ze skrzynki przez pracownika transportu i przejazd do pola odkładczego Gniazda I. 4. Odczepienie kanbanu produkcyjnego (KPI) i przekazanie do skrzynki KPI. 5. Przyczepienie KTII, załadowanie pojemnika i przewiezienie do pola odkładczego Gniazda II. 6. Pobranie kolejnego KPI ze skrzynki KPI, pobranie kolejnego pojemnika z materiałem do obróbki w Gnieździe I, odczepienie KTI i przekazanie do skrzynki KTI. 7. Po przerobieniu materiału i napełnieniu kolejnego pojemnika wyrobami Gniazda I, przyczepienie KPI i przekazanie do pola odkładczego wyrobów Gniazda I.
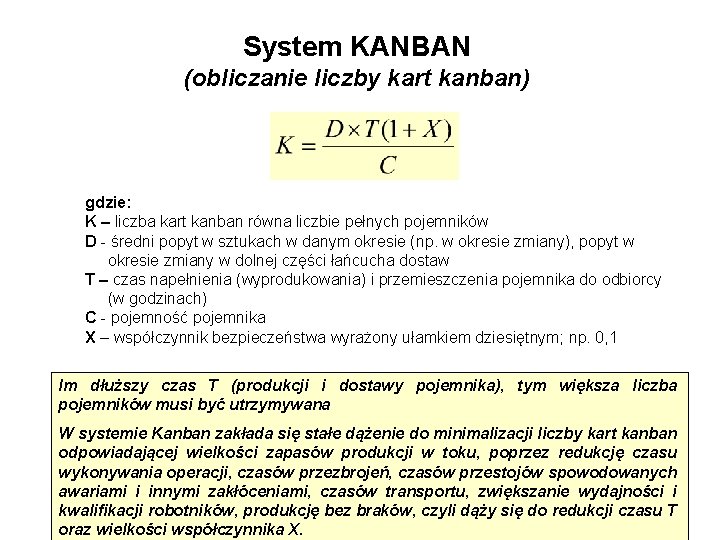
System KANBAN (obliczanie liczby kart kanban) gdzie: K – liczba kart kanban równa liczbie pełnych pojemników D - średni popyt w sztukach w danym okresie (np. w okresie zmiany), popyt w okresie zmiany w dolnej części łańcucha dostaw T – czas napełnienia (wyprodukowania) i przemieszczenia pojemnika do odbiorcy (w godzinach) C - pojemność pojemnika X – współczynnik bezpieczeństwa wyrażony ułamkiem dziesiętnym; np. 0, 1 Im dłuższy czas T (produkcji i dostawy pojemnika), tym większa liczba pojemników musi być utrzymywana W systemie Kanban zakłada się stałe dążenie do minimalizacji liczby kart kanban odpowiadającej wielkości zapasów produkcji w toku, poprzez redukcję czasu wykonywania operacji, czasów przezbrojeń, czasów przestojów spowodowanych awariami i innymi zakłóceniami, czasów transportu, zwiększanie wydajności i kwalifikacji robotników, produkcję bez braków, czyli dąży się do redukcji czasu T oraz wielkości współczynnika X.
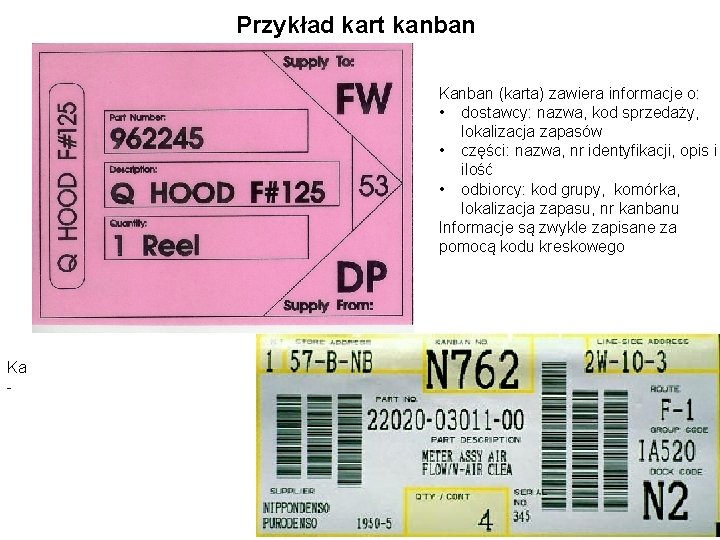
Przykład kart kanban Kanban (karta) zawiera informacje o: • dostawcy: nazwa, kod sprzedaży, lokalizacja zapasów • części: nazwa, nr identyfikacji, opis i ilość • odbiorcy: kod grupy, komórka, lokalizacja zapasu, nr kanbanu Informacje są zwykle zapisane za pomocą kodu kreskowego Ka -
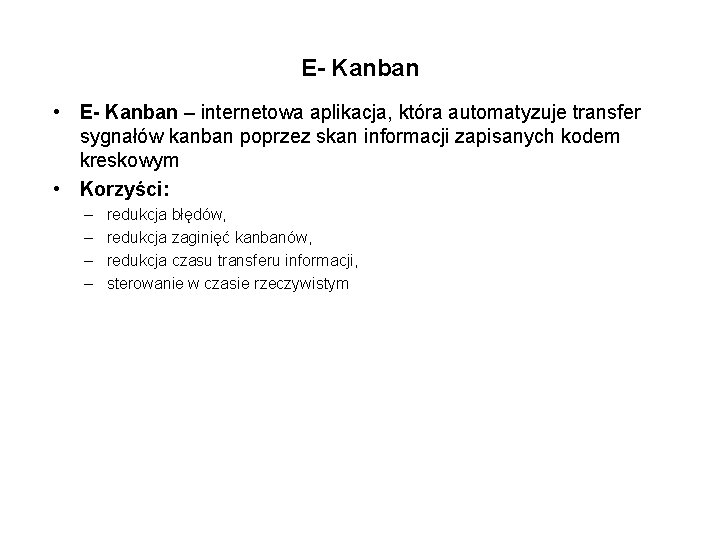
E- Kanban • E- Kanban – internetowa aplikacja, która automatyzuje transfer sygnałów kanban poprzez skan informacji zapisanych kodem kreskowym • Korzyści: – – redukcja błędów, redukcja zaginięć kanbanów, redukcja czasu transferu informacji, sterowanie w czasie rzeczywistym
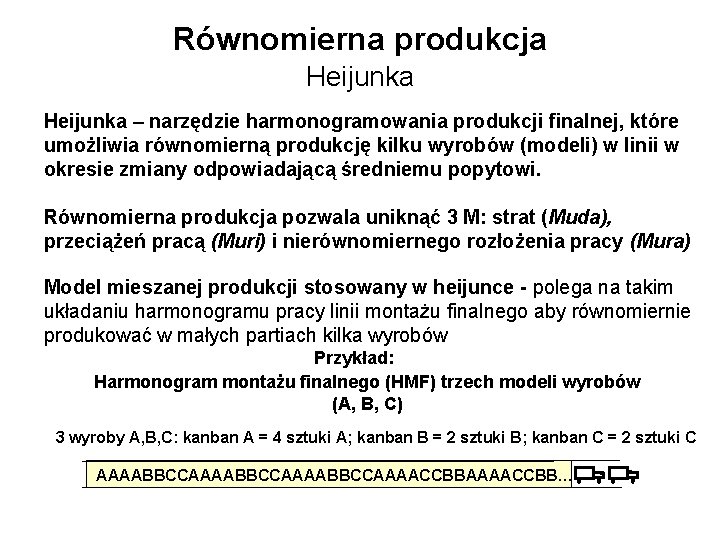
Równomierna produkcja Heijunka – narzędzie harmonogramowania produkcji finalnej, które umożliwia równomierną produkcję kilku wyrobów (modeli) w linii w okresie zmiany odpowiadającą średniemu popytowi. Równomierna produkcja pozwala uniknąć 3 M: strat (Muda), przeciążeń pracą (Muri) i nierównomiernego rozłożenia pracy (Mura) Model mieszanej produkcji stosowany w heijunce - polega na takim układaniu harmonogramu pracy linii montażu finalnego aby równomiernie produkować w małych partiach kilka wyrobów Przykład: Harmonogram montażu finalnego (HMF) trzech modeli wyrobów (A, B, C) 3 wyroby A, B, C: kanban A = 4 sztuki A; kanban B = 2 sztuki B; kanban C = 2 sztuki C AAAABBCCAAAABBCCAAAACCBB…
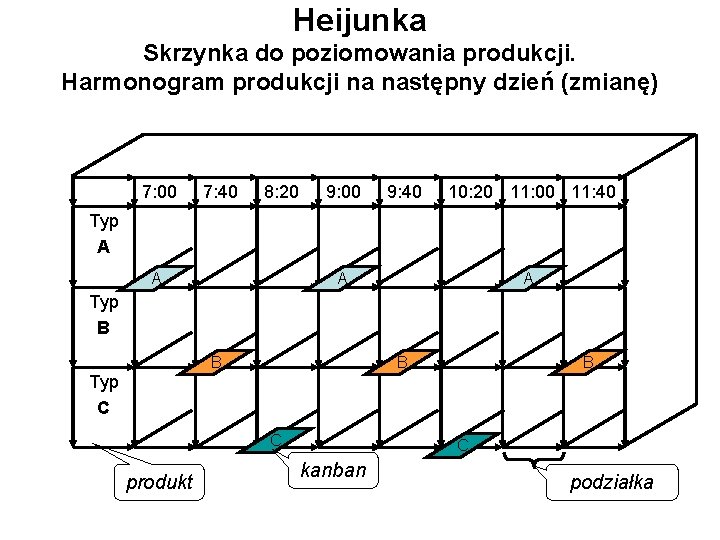
Heijunka Skrzynka do poziomowania produkcji. Harmonogram produkcji na następny dzień (zmianę) 7: 00 7: 40 8: 20 9: 00 9: 40 10: 20 11: 00 11: 40 Typ A A Typ B B Typ C C produkt C kanban podziałka
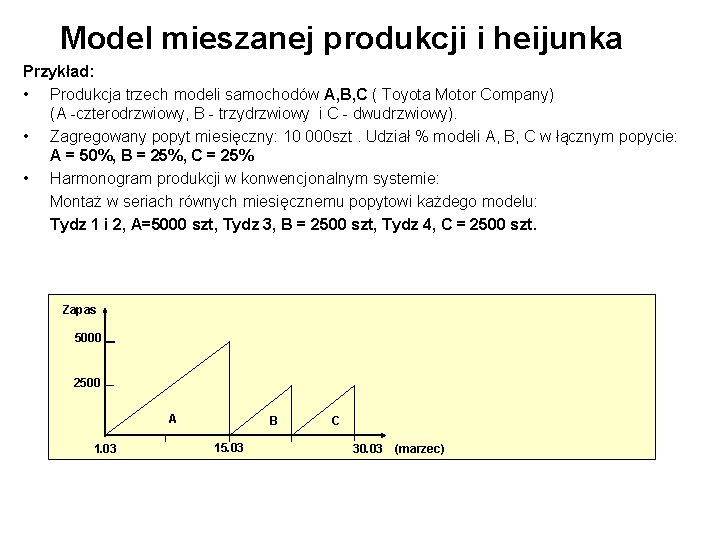
Model mieszanej produkcji i heijunka Przykład: • Produkcja trzech modeli samochodów A, B, C ( Toyota Motor Company) (A -czterodrzwiowy, B - trzydrzwiowy i C - dwudrzwiowy). • Zagregowany popyt miesięczny: 10 000 szt. Udział % modeli A, B, C w łącznym popycie: A = 50%, B = 25%, C = 25% • Harmonogram produkcji w konwencjonalnym systemie: Montaż w seriach równych miesięcznemu popytowi każdego modelu: Tydz 1 i 2, A=5000 szt, Tydz 3, B = 2500 szt, Tydz 4, C = 2500 szt. Zapas 5000 2500 A 1. 03 B 15. 03 C 30. 03 (marzec)
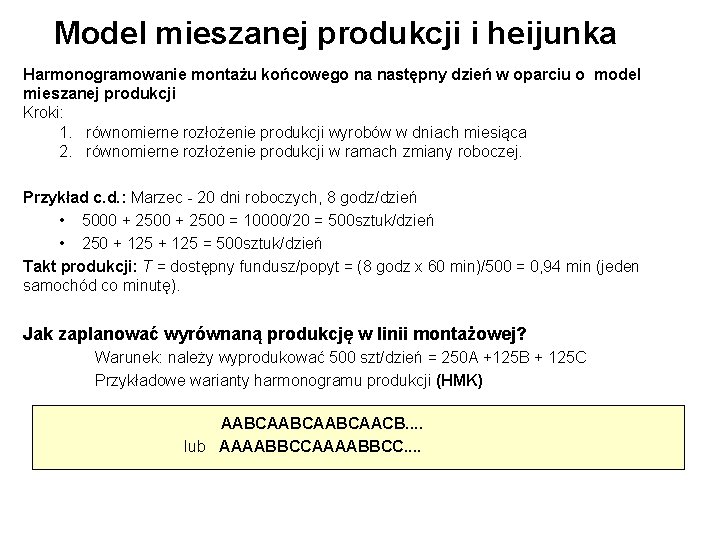
Model mieszanej produkcji i heijunka Harmonogramowanie montażu końcowego na następny dzień w oparciu o model mieszanej produkcji Kroki: 1. równomierne rozłożenie produkcji wyrobów w dniach miesiąca 2. równomierne rozłożenie produkcji w ramach zmiany roboczej. Przykład c. d. : Marzec - 20 dni roboczych, 8 godz/dzień • 5000 + 2500 = 10000/20 = 500 sztuk/dzień • 250 + 125 = 500 sztuk/dzień Takt produkcji: T = dostępny fundusz/popyt = (8 godz x 60 min)/500 = 0, 94 min (jeden samochód co minutę). Jak zaplanować wyrównaną produkcję w linii montażowej? Warunek: należy wyprodukować 500 szt/dzień = 250 A +125 B + 125 C Przykładowe warianty harmonogramu produkcji (HMK) AABCAABCAACB. . lub AAAABBCC. .
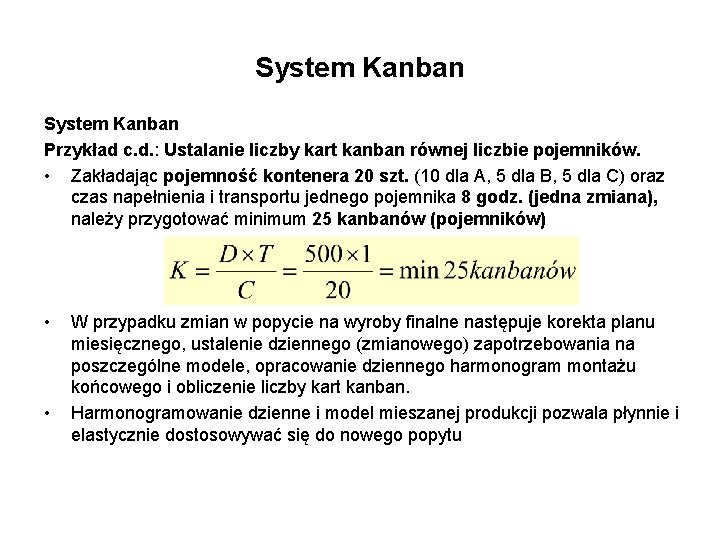
System Kanban Przykład c. d. : Ustalanie liczby kart kanban równej liczbie pojemników. • Zakładając pojemność kontenera 20 szt. (10 dla A, 5 dla B, 5 dla C) oraz czas napełnienia i transportu jednego pojemnika 8 godz. (jedna zmiana), należy przygotować minimum 25 kanbanów (pojemników) • • W przypadku zmian w popycie na wyroby finalne następuje korekta planu miesięcznego, ustalenie dziennego (zmianowego) zapotrzebowania na poszczególne modele, opracowanie dziennego harmonogram montażu końcowego i obliczenie liczby kart kanban. Harmonogramowanie dzienne i model mieszanej produkcji pozwala płynnie i elastycznie dostosowywać się do nowego popytu
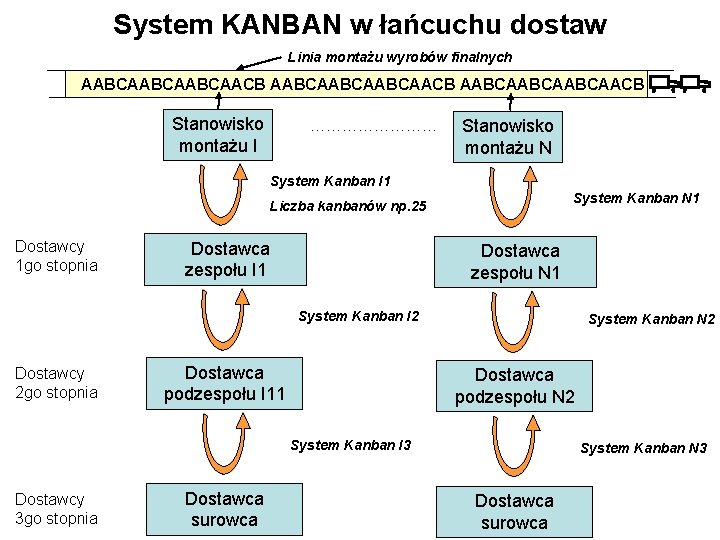
System KANBAN w łańcuchu dostaw Linia montażu wyrobów finalnych AABCAABCAABCAACB Stanowisko montażu I ………… Stanowisko montażu N System Kanban I 1 System Kanban N 1 Liczba kanbanów np. 25 Dostawcy 1 go stopnia Dostawca zespołu I 1 Dostawca zespołu N 1 System Kanban I 2 Dostawcy 2 go stopnia Dostawca podzespołu I 11 System Kanban N 2 Dostawca podzespołu N 2 System Kanban I 3 Dostawcy 3 go stopnia Dostawca surowca System Kanban N 3 Dostawca surowca
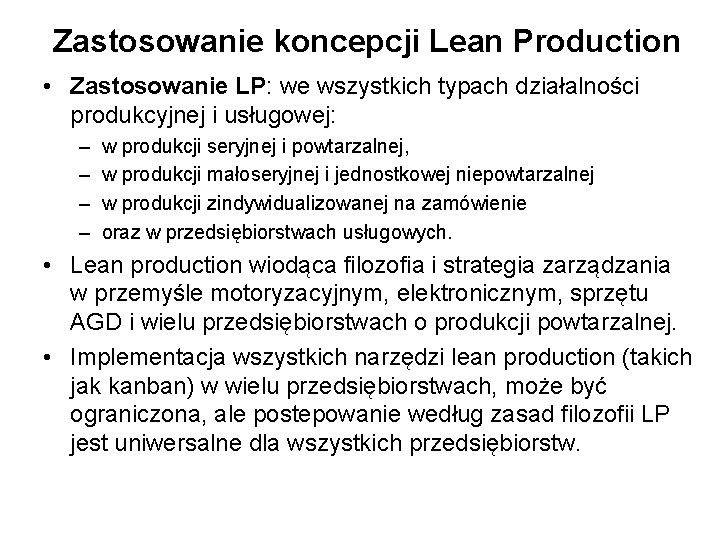
Zastosowanie koncepcji Lean Production • Zastosowanie LP: we wszystkich typach działalności produkcyjnej i usługowej: – – w produkcji seryjnej i powtarzalnej, w produkcji małoseryjnej i jednostkowej niepowtarzalnej w produkcji zindywidualizowanej na zamówienie oraz w przedsiębiorstwach usługowych. • Lean production wiodąca filozofia i strategia zarządzania w przemyśle motoryzacyjnym, elektronicznym, sprzętu AGD i wielu przedsiębiorstwach o produkcji powtarzalnej. • Implementacja wszystkich narzędzi lean production (takich jak kanban) w wielu przedsiębiorstwach, może być ograniczona, ale postepowanie według zasad filozofii LP jest uniwersalne dla wszystkich przedsiębiorstw.
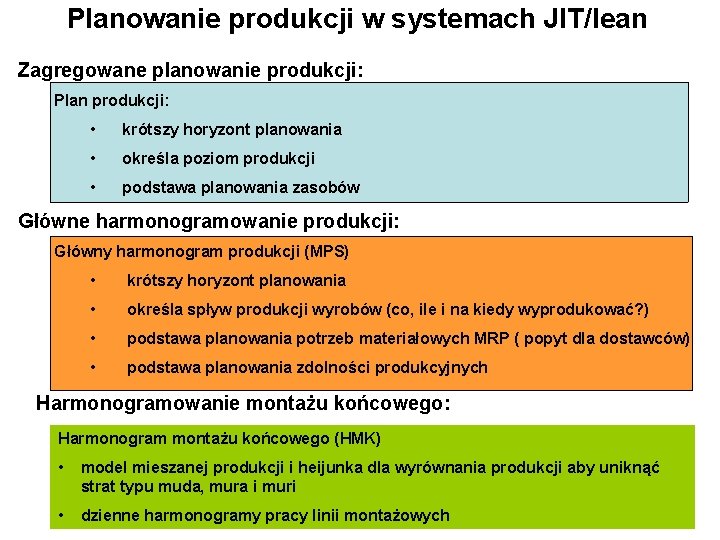
Planowanie produkcji w systemach JIT/lean Zagregowane planowanie produkcji: Plan produkcji: • krótszy horyzont planowania • określa poziom produkcji • podstawa planowania zasobów Główne harmonogramowanie produkcji: Główny harmonogram produkcji (MPS) • krótszy horyzont planowania • określa spływ produkcji wyrobów (co, ile i na kiedy wyprodukować? ) • podstawa planowania potrzeb materiałowych MRP ( popyt dla dostawców) • podstawa planowania zdolności produkcyjnych Harmonogramowanie montażu końcowego: Harmonogram montażu końcowego (HMK) • model mieszanej produkcji i heijunka dla wyrównania produkcji aby uniknąć strat typu muda, mura i muri • dzienne harmonogramy pracy linii montażowych
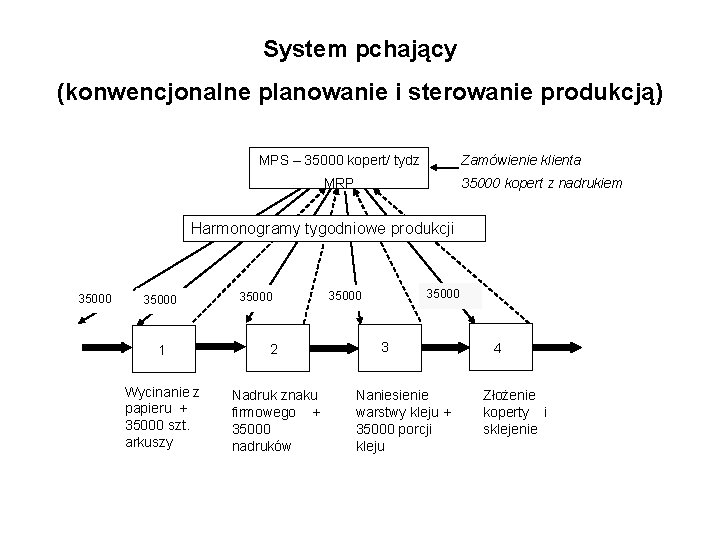
System pchający (konwencjonalne planowanie i sterowanie produkcją) Zamówienie klienta MPS – 35000 kopert/ tydz 35000 kopert z nadrukiem MRP Harmonogramy tygodniowe produkcji 35000 1 2 Wycinanie z papieru + 35000 szt. arkuszy Nadruk znaku firmowego + 35000 nadruków 35000 3 Naniesienie warstwy kleju + 35000 porcji kleju 4 Złożenie koperty i sklejenie
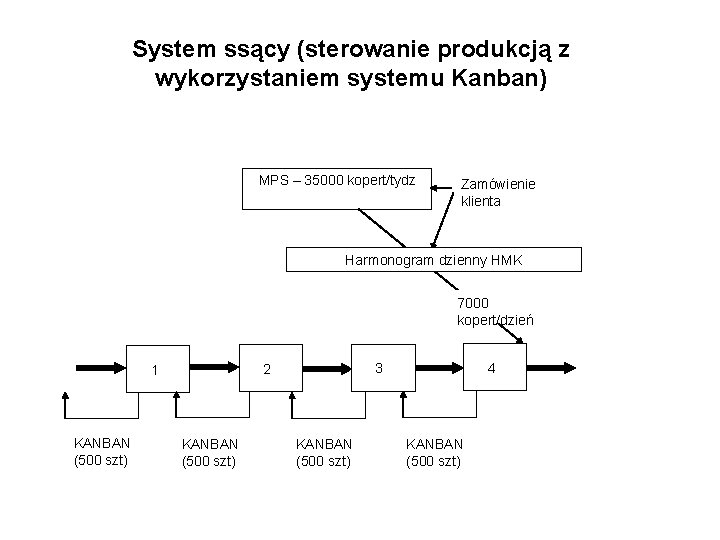
System ssący (sterowanie produkcją z wykorzystaniem systemu Kanban) MPS – 35000 kopert/tydz Zamówienie klienta Harmonogram dzienny HMK 7000 kopert/dzień KANBAN (500 szt) 3 2 1 KANBAN (500 szt) 4 KANBAN (500 szt)
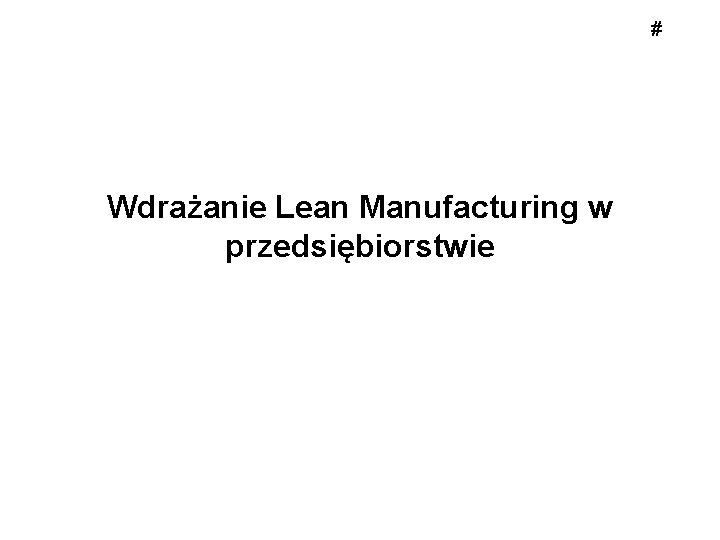
# Wdrażanie Lean Manufacturing w przedsiębiorstwie
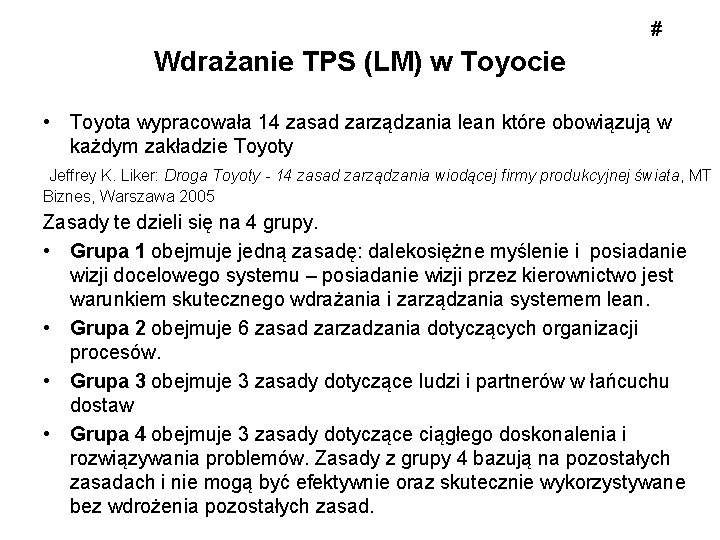
# Wdrażanie TPS (LM) w Toyocie • Toyota wypracowała 14 zasad zarządzania lean które obowiązują w każdym zakładzie Toyoty Jeffrey K. Liker: Droga Toyoty - 14 zasad zarządzania wiodącej firmy produkcyjnej świata, MT Biznes, Warszawa 2005 Zasady te dzieli się na 4 grupy. • Grupa 1 obejmuje jedną zasadę: dalekosiężne myślenie i posiadanie wizji docelowego systemu – posiadanie wizji przez kierownictwo jest warunkiem skutecznego wdrażania i zarządzania systemem lean. • Grupa 2 obejmuje 6 zasad zarzadzania dotyczących organizacji procesów. • Grupa 3 obejmuje 3 zasady dotyczące ludzi i partnerów w łańcuchu dostaw • Grupa 4 obejmuje 3 zasady dotyczące ciągłego doskonalenia i rozwiązywania problemów. Zasady z grupy 4 bazują na pozostałych zasadach i nie mogą być efektywnie oraz skutecznie wykorzystywane bez wdrożenia pozostałych zasad.
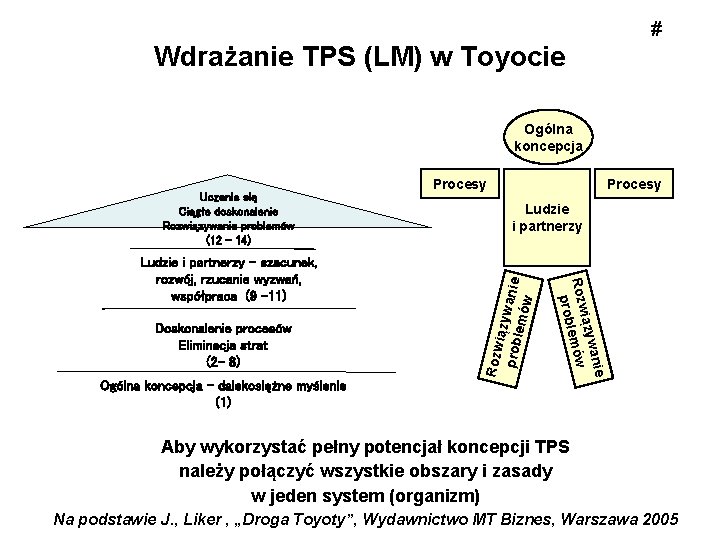
# Wdrażanie TPS (LM) w Toyocie Ogólna koncepcja Doskonalenie procesów Eliminacja strat (2 - 8) Procesy Ludzie i partnerzy anie iązyw Rozw lemów prob Ludzie i partnerzy – szacunek, rozwój, rzucanie wyzwań, współpraca (9 – 11) Procesy Rozw iąz prob ywanie lemó w Uczenie się Ciągłe doskonalenie Rozwiązywanie problemów (12 – 14) Ogólna koncepcja – dalekosiężne myślenie (1) Aby wykorzystać pełny potencjał koncepcji TPS należy połączyć wszystkie obszary i zasady w jeden system (organizm) Na podstawie J. , Liker , „Droga Toyoty”, Wydawnictwo MT Biznes, Warszawa 2005
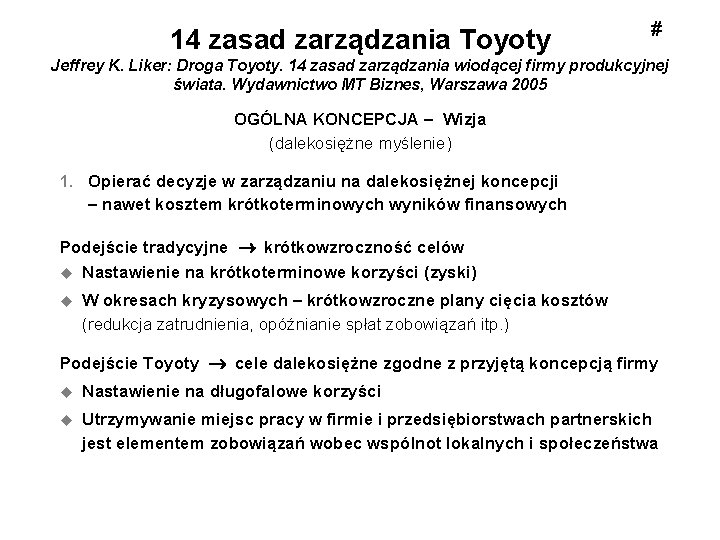
14 zasad zarządzania Toyoty # Jeffrey K. Liker: Droga Toyoty. 14 zasad zarządzania wiodącej firmy produkcyjnej świata. Wydawnictwo MT Biznes, Warszawa 2005 OGÓLNA KONCEPCJA – Wizja (dalekosiężne myślenie) 1. Opierać decyzje w zarządzaniu na dalekosiężnej koncepcji – nawet kosztem krótkoterminowych wyników finansowych Podejście tradycyjne krótkowzroczność celów u Nastawienie na krótkoterminowe korzyści (zyski) u W okresach kryzysowych – krótkowzroczne plany cięcia kosztów (redukcja zatrudnienia, opóźnianie spłat zobowiązań itp. ) Podejście Toyoty cele dalekosiężne zgodne z przyjętą koncepcją firmy u Nastawienie na długofalowe korzyści u Utrzymywanie miejsc pracy w firmie i przedsiębiorstwach partnerskich jest elementem zobowiązań wobec wspólnot lokalnych i społeczeństwa
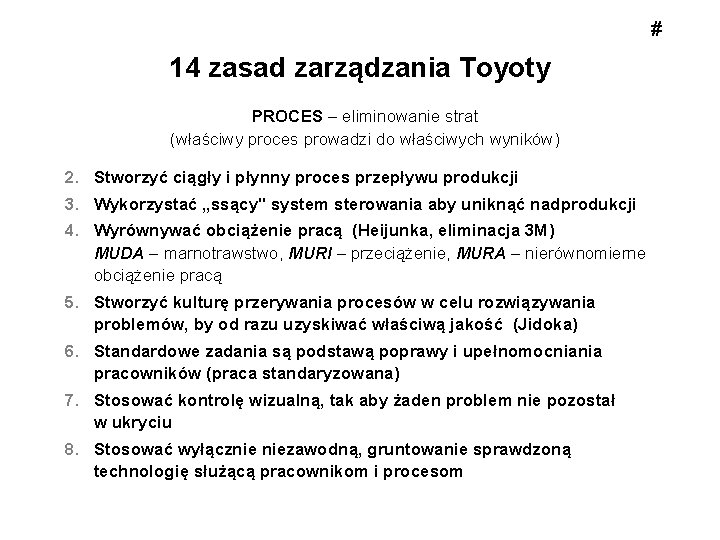
# 14 zasad zarządzania Toyoty PROCES – eliminowanie strat (właściwy proces prowadzi do właściwych wyników) 2. Stworzyć ciągły i płynny proces przepływu produkcji 3. Wykorzystać „ssący" system sterowania aby uniknąć nadprodukcji 4. Wyrównywać obciążenie pracą (Heijunka, eliminacja 3 M) MUDA – marnotrawstwo, MURI – przeciążenie, MURA – nierównomierne obciążenie pracą 5. Stworzyć kulturę przerywania procesów w celu rozwiązywania problemów, by od razu uzyskiwać właściwą jakość (Jidoka) 6. Standardowe zadania są podstawą poprawy i upełnomocniania pracowników (praca standaryzowana) 7. Stosować kontrolę wizualną, tak aby żaden problem nie pozostał w ukryciu 8. Stosować wyłącznie niezawodną, gruntowanie sprawdzoną technologię służącą pracownikom i procesom
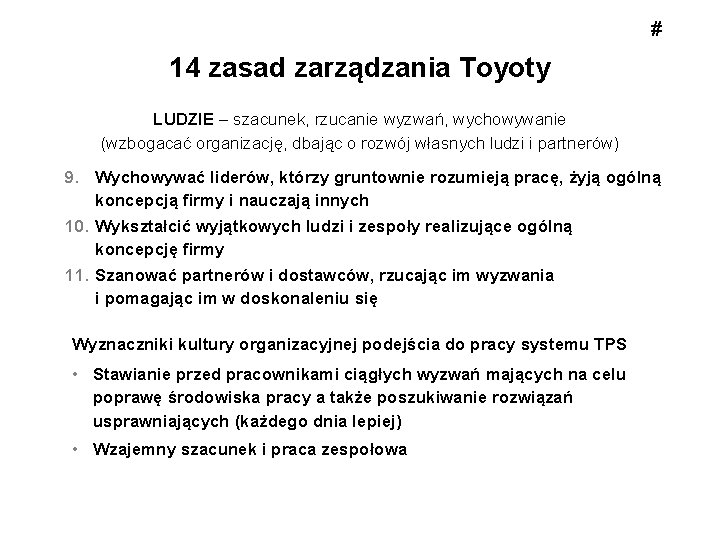
# 14 zasad zarządzania Toyoty LUDZIE – szacunek, rzucanie wyzwań, wychowywanie (wzbogacać organizację, dbając o rozwój własnych ludzi i partnerów) 9. Wychowywać liderów, którzy gruntownie rozumieją pracę, żyją ogólną koncepcją firmy i nauczają innych 10. Wykształcić wyjątkowych ludzi i zespoły realizujące ogólną koncepcję firmy 11. Szanować partnerów i dostawców, rzucając im wyzwania i pomagając im w doskonaleniu się Wyznaczniki kultury organizacyjnej podejścia do pracy systemu TPS • Stawianie przed pracownikami ciągłych wyzwań mających na celu poprawę środowiska pracy a także poszukiwanie rozwiązań usprawniających (każdego dnia lepiej) • Wzajemny szacunek i praca zespołowa
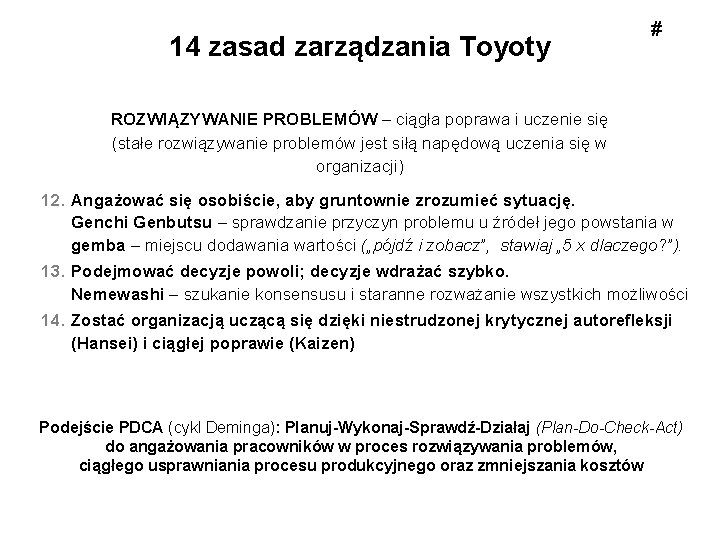
14 zasad zarządzania Toyoty # ROZWIĄZYWANIE PROBLEMÓW – ciągła poprawa i uczenie się (stałe rozwiązywanie problemów jest siłą napędową uczenia się w organizacji) 12. Angażować się osobiście, aby gruntownie zrozumieć sytuację. Genchi Genbutsu – sprawdzanie przyczyn problemu u źródeł jego powstania w gemba – miejscu dodawania wartości („pójdź i zobacz”, stawiaj „ 5 x dlaczego? ”). 13. Podejmować decyzje powoli; decyzje wdrażać szybko. Nemewashi – szukanie konsensusu i staranne rozważanie wszystkich możliwości 14. Zostać organizacją uczącą się dzięki niestrudzonej krytycznej autorefleksji (Hansei) i ciągłej poprawie (Kaizen) Podejście PDCA (cykl Deminga): Planuj-Wykonaj-Sprawdź-Działaj (Plan-Do-Check-Act) do angażowania pracowników w proces rozwiązywania problemów, ciągłego usprawniania procesu produkcyjnego oraz zmniejszania kosztów
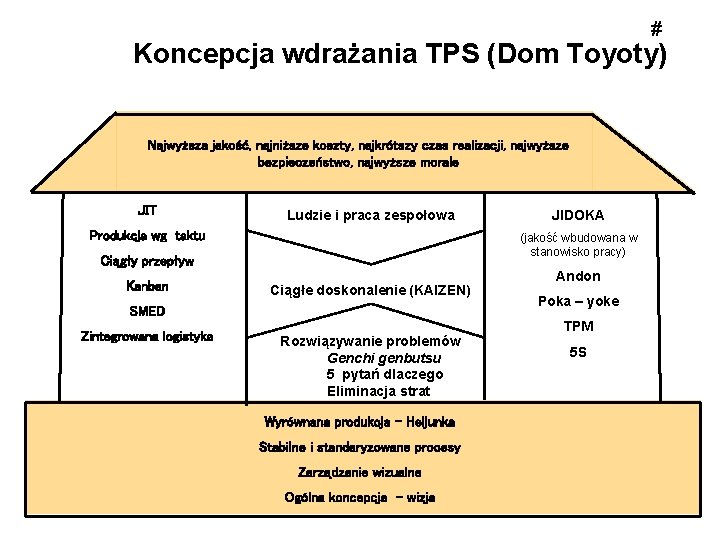
# Koncepcja wdrażania TPS (Dom Toyoty) Najwyższa jakość, najniższe koszty, najkrótszy czas realizacji, najwyższe bezpieczeństwo, najwyższe morale JIT Ludzie i praca zespołowa Produkcja wg taktu (jakość wbudowana w stanowisko pracy) Ciągły przepływ Kanban Ciągłe doskonalenie (KAIZEN) SMED Zintegrowana logistyka JIDOKA Rozwiązywanie problemów Genchi genbutsu 5 pytań dlaczego Eliminacja strat Wyrównana produkcja - Heijunka Stabilne i standaryzowane procesy Zarządzanie wizualne Ogólna koncepcja - wizja Andon Poka – yoke TPM 5 S
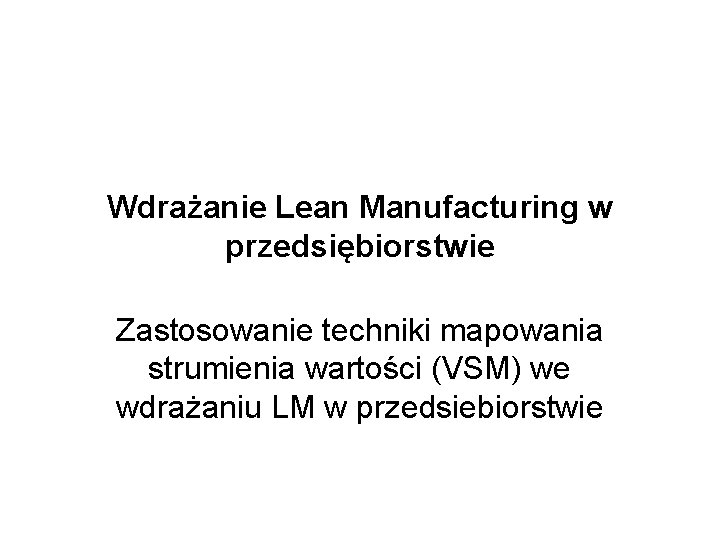
Wdrażanie Lean Manufacturing w przedsiębiorstwie Zastosowanie techniki mapowania strumienia wartości (VSM) we wdrażaniu LM w przedsiebiorstwie
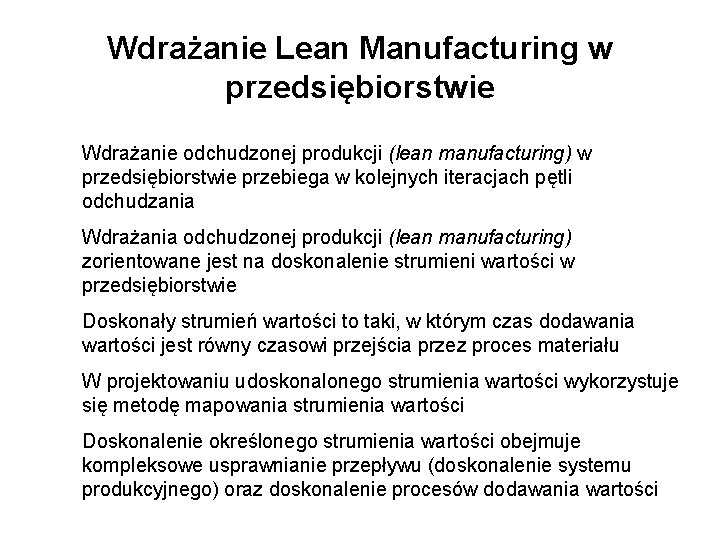
Wdrażanie Lean Manufacturing w przedsiębiorstwie Wdrażanie odchudzonej produkcji (lean manufacturing) w przedsiębiorstwie przebiega w kolejnych iteracjach pętli odchudzania Wdrażania odchudzonej produkcji (lean manufacturing) zorientowane jest na doskonalenie strumieni wartości w przedsiębiorstwie Doskonały strumień wartości to taki, w którym czas dodawania wartości jest równy czasowi przejścia przez proces materiału W projektowaniu udoskonalonego strumienia wartości wykorzystuje się metodę mapowania strumienia wartości Doskonalenie określonego strumienia wartości obejmuje kompleksowe usprawnianie przepływu (doskonalenie systemu produkcyjnego) oraz doskonalenie procesów dodawania wartości
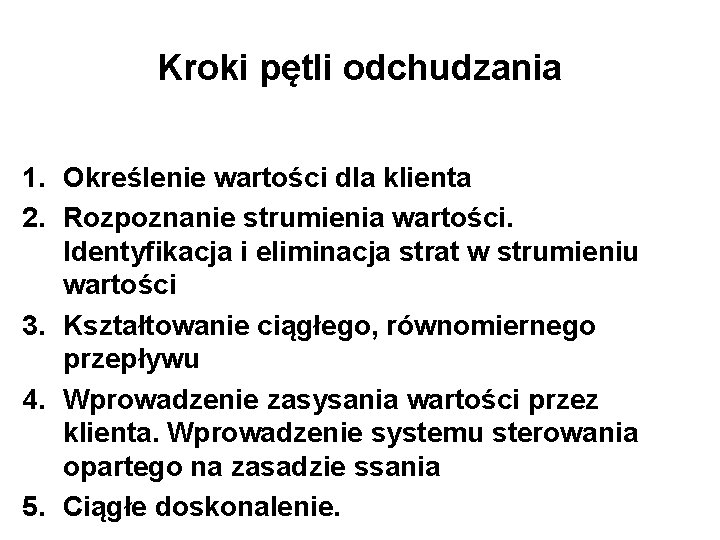
Kroki pętli odchudzania 1. Określenie wartości dla klienta 2. Rozpoznanie strumienia wartości. Identyfikacja i eliminacja strat w strumieniu wartości 3. Kształtowanie ciągłego, równomiernego przepływu 4. Wprowadzenie zasysania wartości przez klienta. Wprowadzenie systemu sterowania opartego na zasadzie ssania 5. Ciągłe doskonalenie.
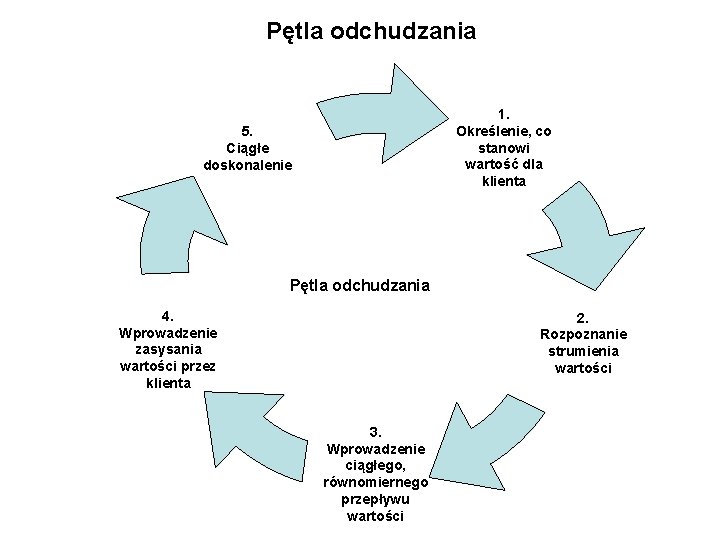
Pętla odchudzania 1. Określenie, co stanowi wartość dla klienta 5. Ciągłe doskonalenie Pętla odchudzania 4. Wprowadzenie zasysania wartości przez klienta 2. Rozpoznanie strumienia wartości 3. Wprowadzenie ciągłego, równomiernego przepływu wartości
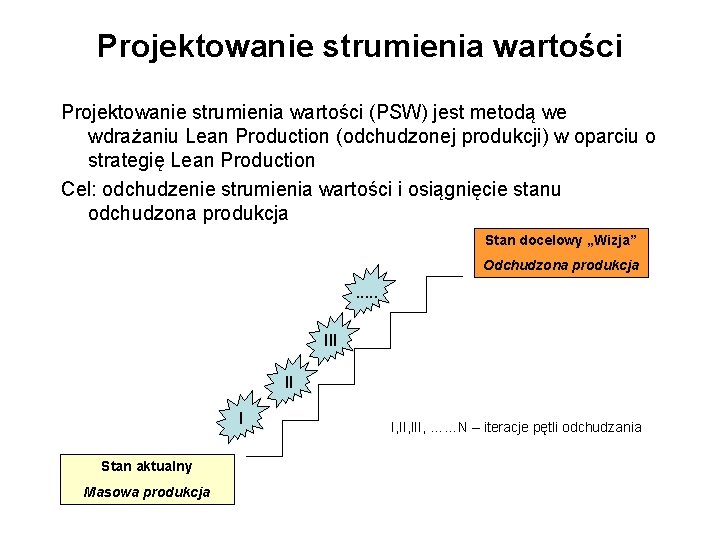
Projektowanie strumienia wartości (PSW) jest metodą we wdrażaniu Lean Production (odchudzonej produkcji) w oparciu o strategię Lean Production Cel: odchudzenie strumienia wartości i osiągnięcie stanu odchudzona produkcja Stan docelowy „Wizja” Odchudzona produkcja . . . III II I Stan aktualny Masowa produkcja I, III, ……N – iteracje pętli odchudzania
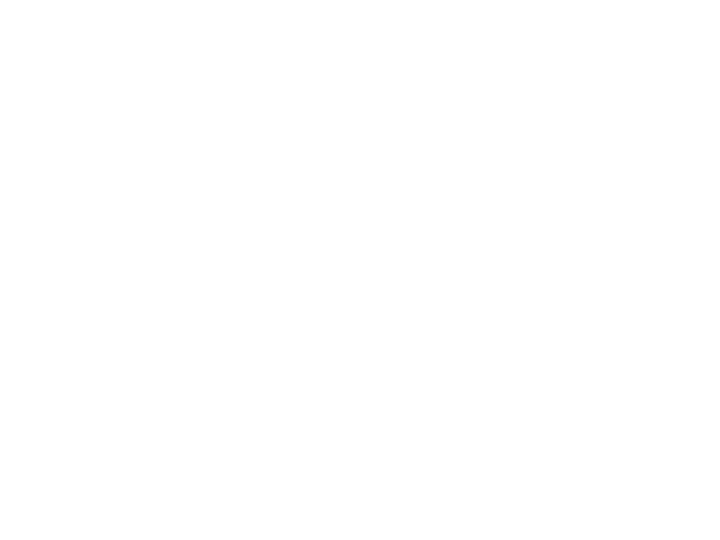
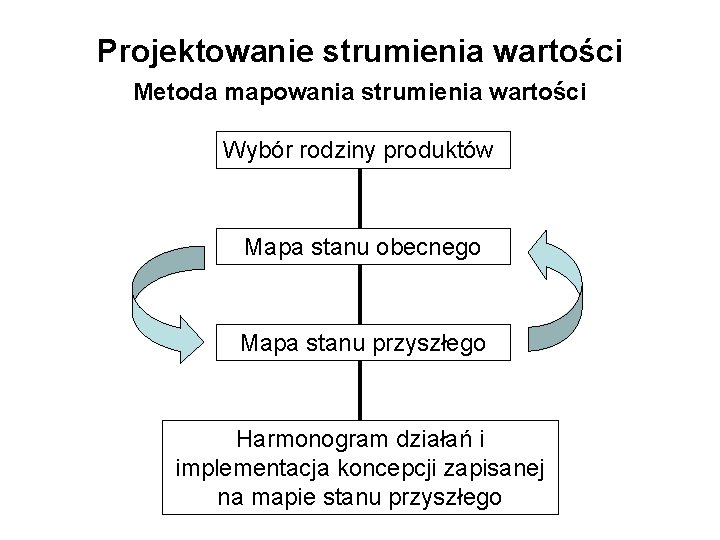
Projektowanie strumienia wartości Metoda mapowania strumienia wartości Wybór rodziny produktów Mapa stanu obecnego Mapa stanu przyszłego Harmonogram działań i implementacja koncepcji zapisanej na mapie stanu przyszłego
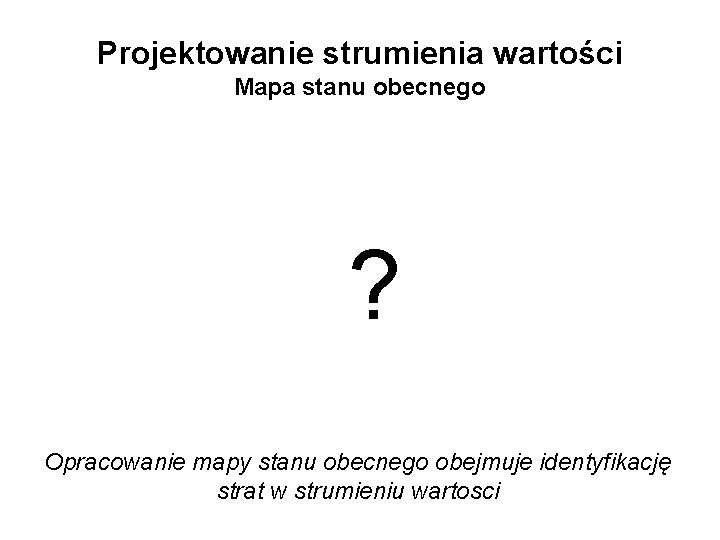
Projektowanie strumienia wartości Mapa stanu obecnego ? Opracowanie mapy stanu obecnego obejmuje identyfikację strat w strumieniu wartosci
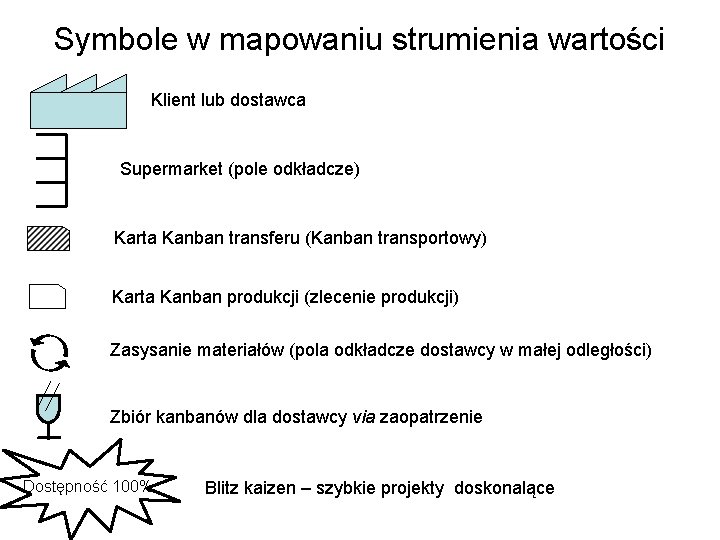
Symbole w mapowaniu strumienia wartości Klient lub dostawca Supermarket (pole odkładcze) Karta Kanban transferu (Kanban transportowy) Karta Kanban produkcji (zlecenie produkcji) Zasysanie materiałów (pola odkładcze dostawcy w małej odległości) Zbiór kanbanów dla dostawcy via zaopatrzenie Dostępność 100% Blitz kaizen – szybkie projekty doskonalące
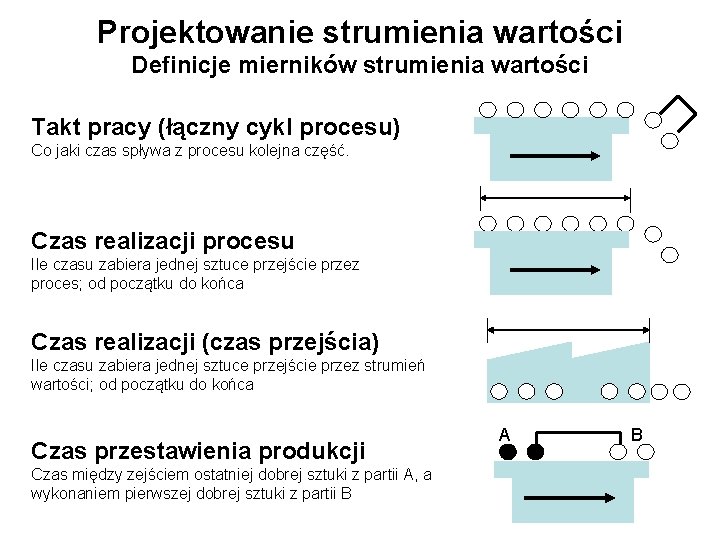
Projektowanie strumienia wartości Definicje mierników strumienia wartości Takt pracy (łączny cykl procesu) Co jaki czas spływa z procesu kolejna część. Czas realizacji procesu Ile czasu zabiera jednej sztuce przejście przez proces; od początku do końca Czas realizacji (czas przejścia) Ile czasu zabiera jednej sztuce przejście przez strumień wartości; od początku do końca Czas przestawienia produkcji Czas między zejściem ostatniej dobrej sztuki z partii A, a wykonaniem pierwszej dobrej sztuki z partii B A B
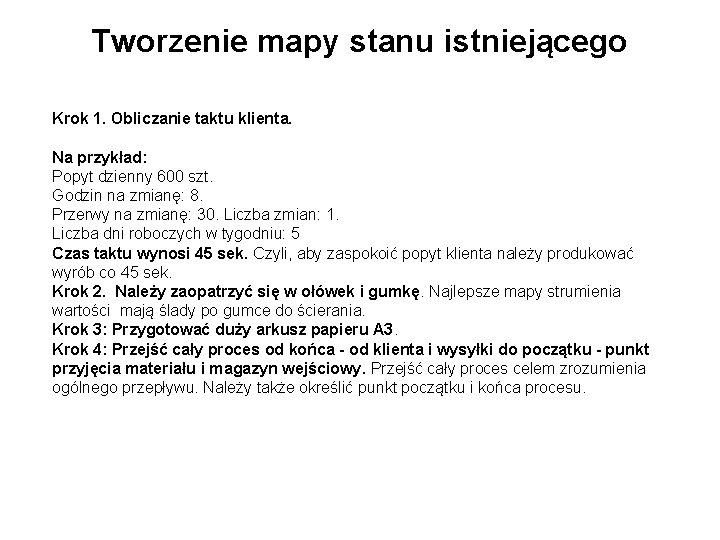
Tworzenie mapy stanu istniejącego Krok 1. Obliczanie taktu klienta. Na przykład: Popyt dzienny 600 szt. Godzin na zmianę: 8. Przerwy na zmianę: 30. Liczba zmian: 1. Liczba dni roboczych w tygodniu: 5 Czas taktu wynosi 45 sek. Czyli, aby zaspokoić popyt klienta należy produkować wyrób co 45 sek. Krok 2. Należy zaopatrzyć się w ołówek i gumkę. Najlepsze mapy strumienia wartości mają ślady po gumce do ścierania. Krok 3: Przygotować duży arkusz papieru A 3. Krok 4: Przejść cały proces od końca - od klienta i wysyłki do początku - punkt przyjęcia materiału i magazyn wejściowy. Przejść cały proces celem zrozumienia ogólnego przepływu. Należy także określić punkt początku i końca procesu.
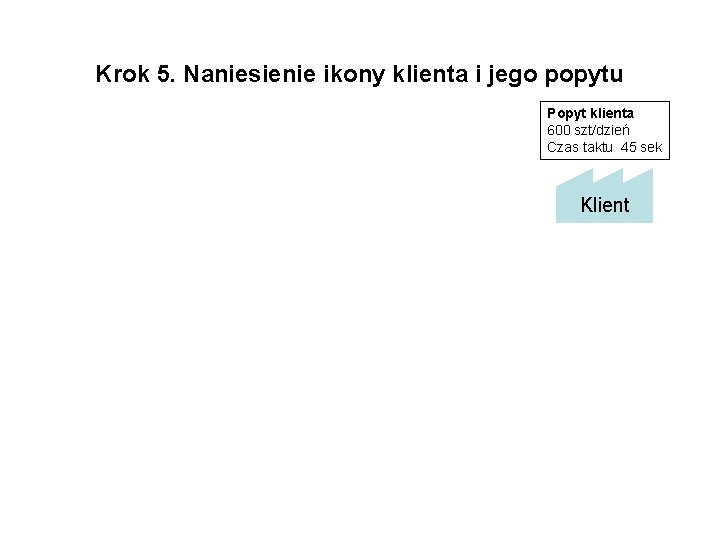
Krok 5. Naniesienie ikony klienta i jego popytu Popyt klienta 600 szt/dzień Czas taktu 45 sek Klient
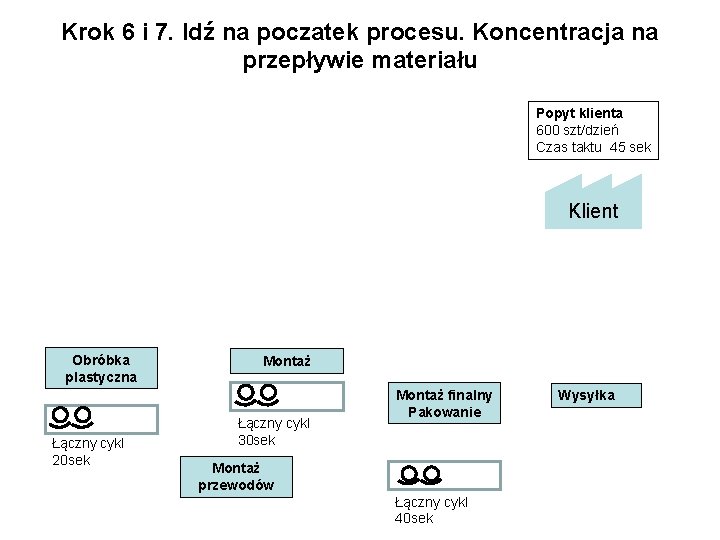
Krok 6 i 7. Idź na poczatek procesu. Koncentracja na przepływie materiału Popyt klienta 600 szt/dzień Czas taktu 45 sek Klient Obróbka plastyczna Łączny cykl 20 sek Montaż Łączny cykl 30 sek Montaż finalny Pakowanie Montaż przewodów Łączny cykl 40 sek Wysyłka
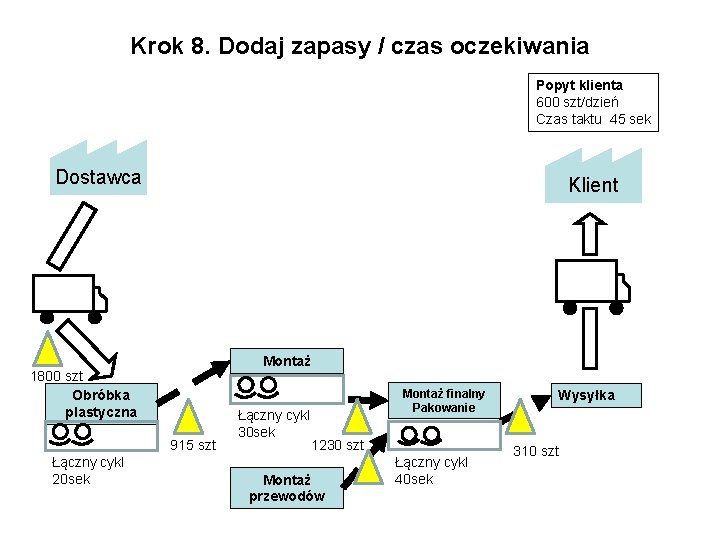
Krok 8. Dodaj zapasy / czas oczekiwania Popyt klienta 600 szt/dzień Czas taktu 45 sek Dostawca Klient Montaż 1800 szt Obróbka plastyczna 915 szt Łączny cykl 20 sek Łączny cykl 30 sek Montaż finalny Pakowanie 1230 szt Montaż przewodów Łączny cykl 40 sek Wysyłka 310 szt
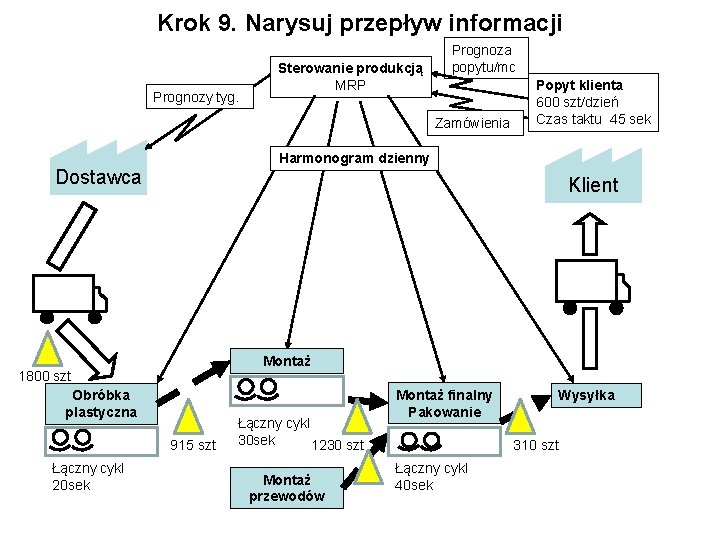
Krok 9. Narysuj przepływ informacji Prognozy tyg. Sterowanie produkcją MRP Prognoza popytu/mc Zamówienia Harmonogram dzienny Dostawca Klient Montaż 1800 szt Obróbka plastyczna 915 szt Łączny cykl 20 sek Popyt klienta 600 szt/dzień Czas taktu 45 sek Łączny cykl 30 sek 1230 szt Montaż przewodów Montaż finalny Pakowanie Wysyłka 310 szt Łączny cykl 40 sek
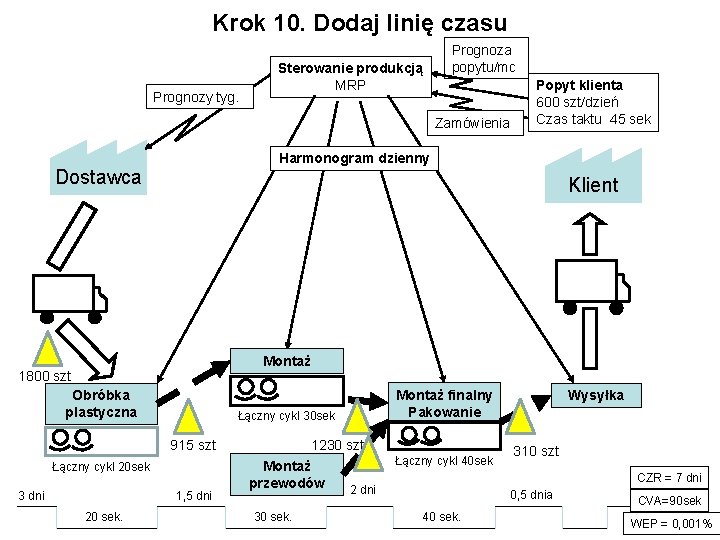
Krok 10. Dodaj linię czasu Prognozy tyg. Sterowanie produkcją MRP Prognoza popytu/mc Zamówienia Popyt klienta 600 szt/dzień Czas taktu 45 sek Harmonogram dzienny Dostawca Klient Montaż 1800 szt Obróbka plastyczna Łączny cykl 30 sek 915 szt Łączny cykl 20 sek 3 dni 1, 5 dni 20 sek. 1230 szt Montaż przewodów 2 dni 30 sek. Montaż finalny Pakowanie Łączny cykl 40 sek Wysyłka 310 szt CZR = 7 dni 0, 5 dnia 40 sek. CVA=90 sek WEP = 0, 001%
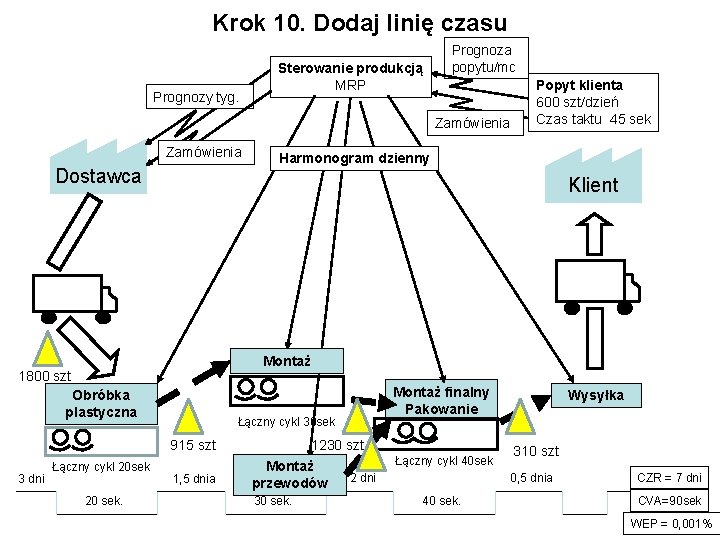
Krok 10. Dodaj linię czasu Prognozy tyg. Sterowanie produkcją MRP Prognoza popytu/mc Zamówienia Dostawca Harmonogram dzienny Klient Montaż 1800 szt Obróbka plastyczna Łączny cykl 30 sek 915 szt 3 dni Popyt klienta 600 szt/dzień Czas taktu 45 sek Łączny cykl 20 sek 20 sek. 1, 5 dnia 1230 szt Montaż 2 dni przewodów 30 sek. Montaż finalny Pakowanie Łączny cykl 40 sek Wysyłka 310 szt 0, 5 dnia 40 sek. CZR = 7 dni CVA=90 sek WEP = 0, 001%
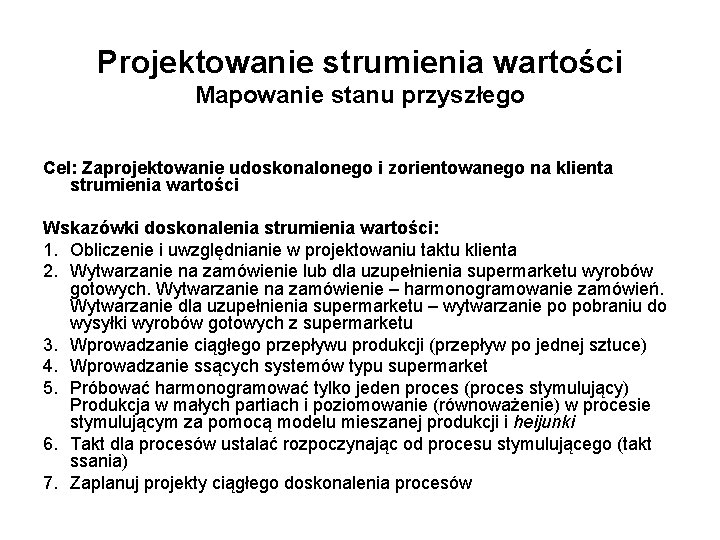
Projektowanie strumienia wartości Mapowanie stanu przyszłego Cel: Zaprojektowanie udoskonalonego i zorientowanego na klienta strumienia wartości Wskazówki doskonalenia strumienia wartości: 1. Obliczenie i uwzględnianie w projektowaniu taktu klienta 2. Wytwarzanie na zamówienie lub dla uzupełnienia supermarketu wyrobów gotowych. Wytwarzanie na zamówienie – harmonogramowanie zamówień. Wytwarzanie dla uzupełnienia supermarketu – wytwarzanie po pobraniu do wysyłki wyrobów gotowych z supermarketu 3. Wprowadzanie ciągłego przepływu produkcji (przepływ po jednej sztuce) 4. Wprowadzanie ssących systemów typu supermarket 5. Próbować harmonogramować tylko jeden proces (proces stymulujący) Produkcja w małych partiach i poziomowanie (równoważenie) w procesie stymulującym za pomocą modelu mieszanej produkcji i heijunki 6. Takt dla procesów ustalać rozpoczynając od procesu stymulującego (takt ssania) 7. Zaplanuj projekty ciągłego doskonalenia procesów
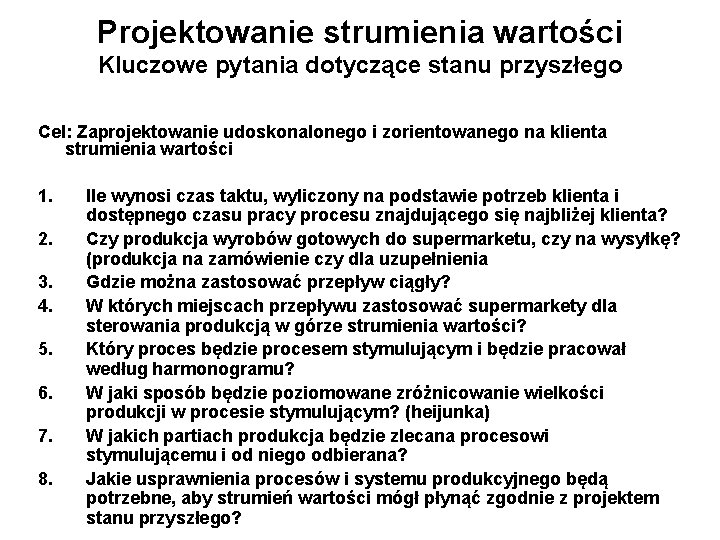
Projektowanie strumienia wartości Kluczowe pytania dotyczące stanu przyszłego Cel: Zaprojektowanie udoskonalonego i zorientowanego na klienta strumienia wartości 1. 2. 3. 4. 5. 6. 7. 8. Ile wynosi czas taktu, wyliczony na podstawie potrzeb klienta i dostępnego czasu pracy procesu znajdującego się najbliżej klienta? Czy produkcja wyrobów gotowych do supermarketu, czy na wysyłkę? (produkcja na zamówienie czy dla uzupełnienia Gdzie można zastosować przepływ ciągły? W których miejscach przepływu zastosować supermarkety dla sterowania produkcją w górze strumienia wartości? Który proces będzie procesem stymulującym i będzie pracował według harmonogramu? W jaki sposób będzie poziomowane zróżnicowanie wielkości produkcji w procesie stymulującym? (heijunka) W jakich partiach produkcja będzie zlecana procesowi stymulującemu i od niego odbierana? Jakie usprawnienia procesów i systemu produkcyjnego będą potrzebne, aby strumień wartości mógł płynąć zgodnie z projektem stanu przyszłego?
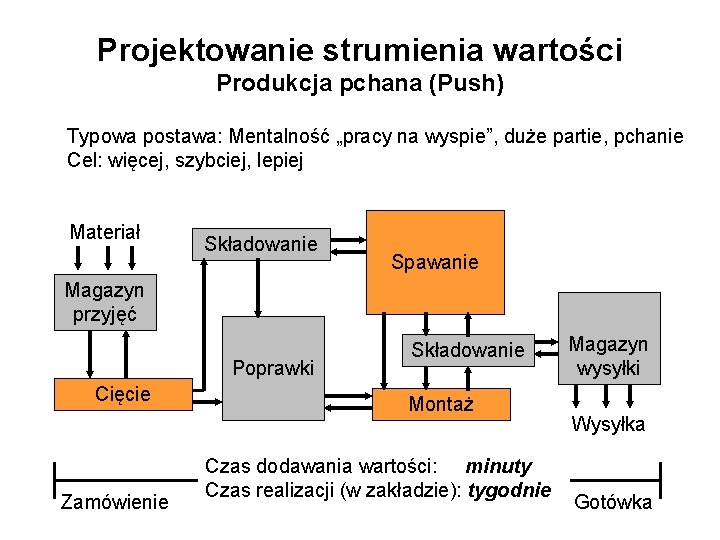
Projektowanie strumienia wartości Produkcja pchana (Push) Typowa postawa: Mentalność „pracy na wyspie”, duże partie, pchanie Cel: więcej, szybciej, lepiej Materiał Składowanie Spawanie Magazyn przyjęć Poprawki Cięcie Zamówienie Składowanie Montaż Czas dodawania wartości: minuty Czas realizacji (w zakładzie): tygodnie Magazyn wysyłki Wysyłka Gotówka
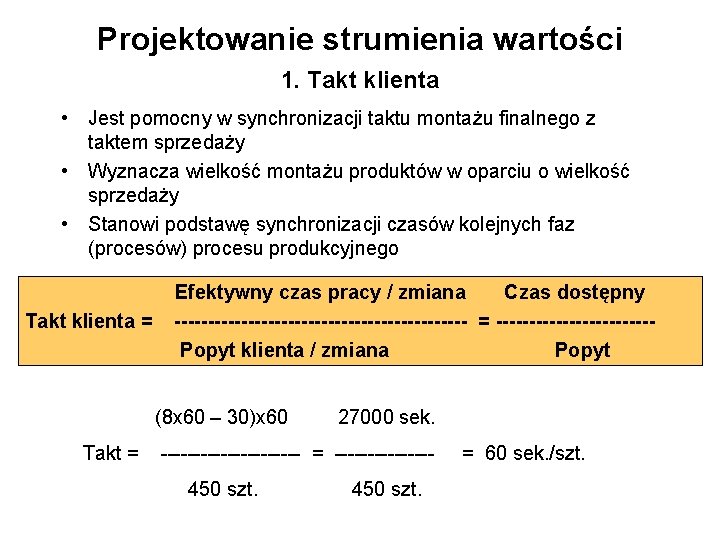
Projektowanie strumienia wartości 1. Takt klienta • Jest pomocny w synchronizacji taktu montażu finalnego z taktem sprzedaży • Wyznacza wielkość montażu produktów w oparciu o wielkość sprzedaży • Stanowi podstawę synchronizacji czasów kolejnych faz (procesów) procesu produkcyjnego Takt klienta = Efektywny czas pracy / zmiana Czas dostępny ---------------------- = ------------Popyt klienta / zmiana Popyt (8 x 60 – 30)x 60 Takt = 27000 sek. ----------- = -------450 szt. = 60 sek. /szt.
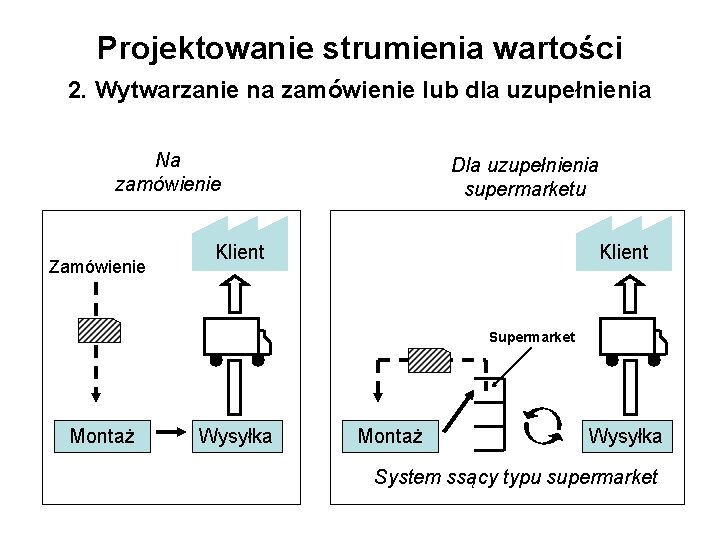
Projektowanie strumienia wartości 2. Wytwarzanie na zamówienie lub dla uzupełnienia Na zamówienie Zamówienie Dla uzupełnienia supermarketu Klient Supermarket Montaż Wysyłka System ssący typu supermarket
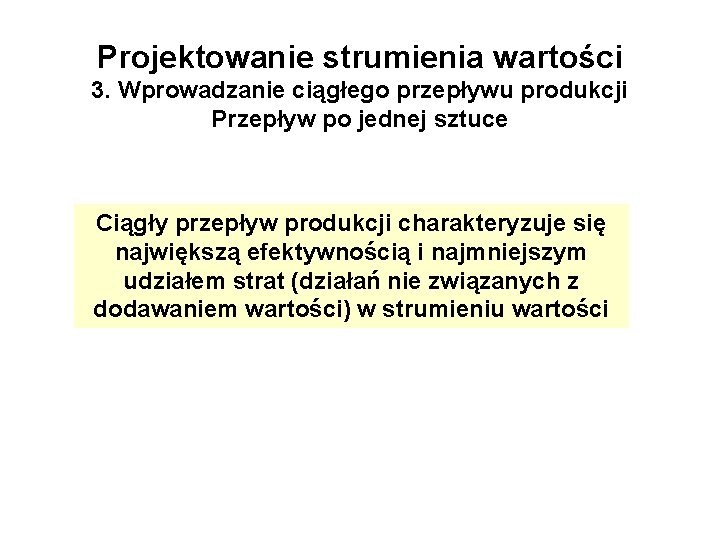
Projektowanie strumienia wartości 3. Wprowadzanie ciągłego przepływu produkcji Przepływ po jednej sztuce Ciągły przepływ produkcji charakteryzuje się największą efektywnością i najmniejszym udziałem strat (działań nie związanych z dodawaniem wartości) w strumieniu wartości
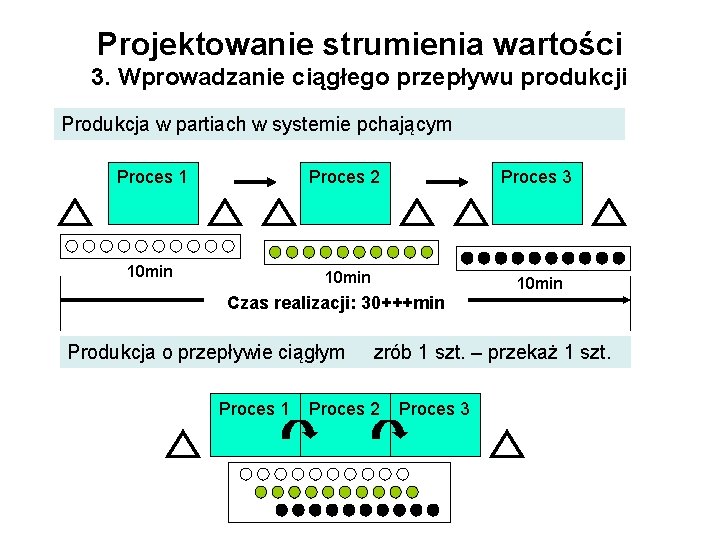
Projektowanie strumienia wartości 3. Wprowadzanie ciągłego przepływu produkcji Produkcja w partiach w systemie pchającym Proces 1 Proces 2 Proces 3 10 min Czas realizacji: 30+++min Produkcja o przepływie ciągłym Proces 1 zrób 1 szt. – przekaż 1 szt. Proces 2 Proces 3
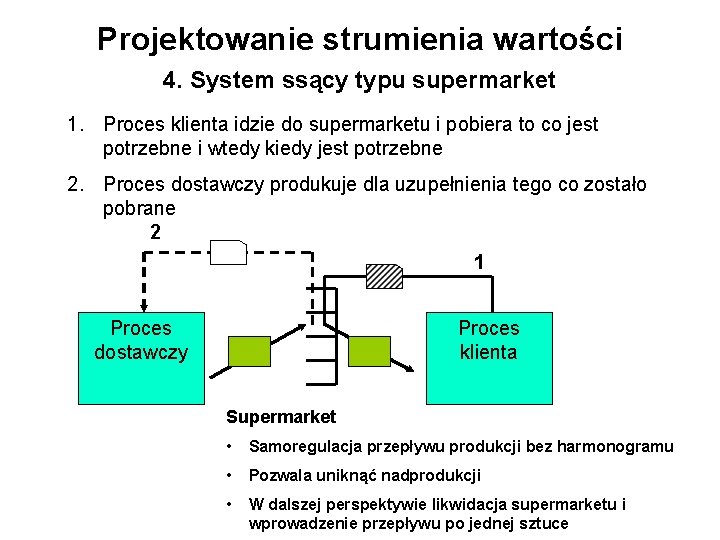
Projektowanie strumienia wartości 4. System ssący typu supermarket 1. Proces klienta idzie do supermarketu i pobiera to co jest potrzebne i wtedy kiedy jest potrzebne 2. Proces dostawczy produkuje dla uzupełnienia tego co zostało pobrane 2 1 Proces dostawczy Proces klienta Supermarket • Samoregulacja przepływu produkcji bez harmonogramu • Pozwala uniknąć nadprodukcji • W dalszej perspektywie likwidacja supermarketu i wprowadzenie przepływu po jednej sztuce
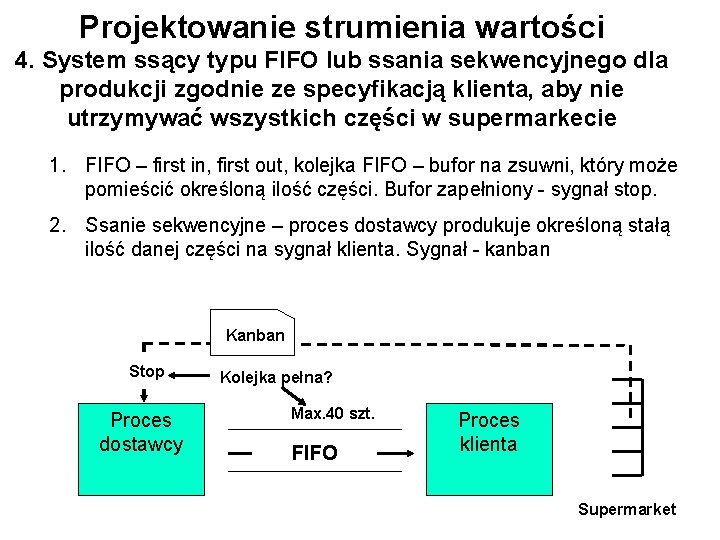
Projektowanie strumienia wartości 4. System ssący typu FIFO lub ssania sekwencyjnego dla produkcji zgodnie ze specyfikacją klienta, aby nie utrzymywać wszystkich części w supermarkecie 1. FIFO – first in, first out, kolejka FIFO – bufor na zsuwni, który może pomieścić określoną ilość części. Bufor zapełniony - sygnał stop. 2. Ssanie sekwencyjne – proces dostawcy produkuje określoną stałą ilość danej części na sygnał klienta. Sygnał - kanban Kanban Stop Proces dostawcy Kolejka pełna? Max. 40 szt. FIFO Proces klienta Supermarket
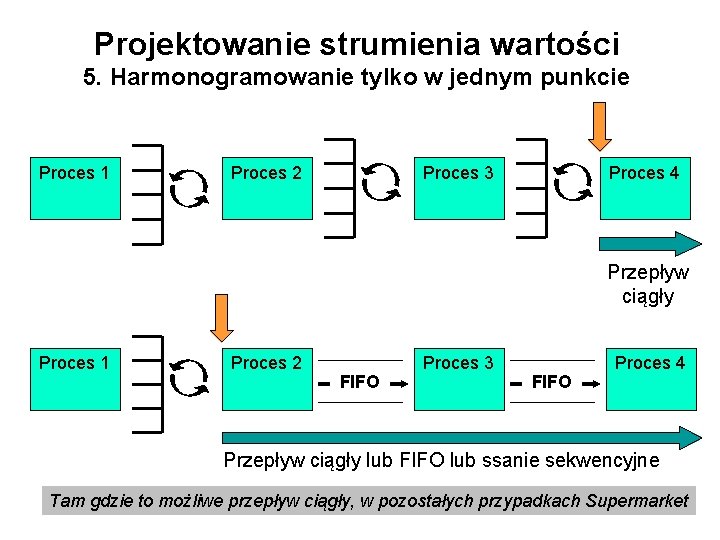
Projektowanie strumienia wartości 5. Harmonogramowanie tylko w jednym punkcie Proces 1 Proces 2 Proces 3 Proces 4 Przepływ ciągły Proces 1 Proces 2 FIFO Proces 3 FIFO Proces 4 Przepływ ciągły lub FIFO lub ssanie sekwencyjne Tam gdzie to możliwe przepływ ciągły, w pozostałych przypadkach Supermarket
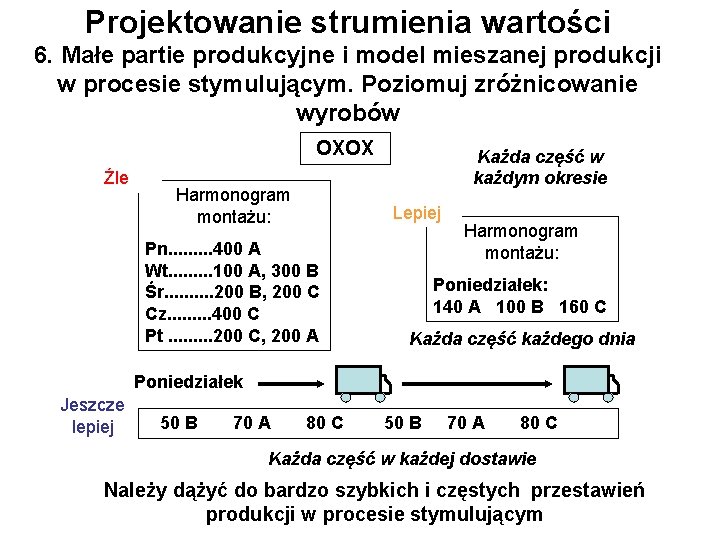
Projektowanie strumienia wartości 6. Małe partie produkcyjne i model mieszanej produkcji w procesie stymulującym. Poziomuj zróżnicowanie wyrobów OXOX Źle Harmonogram montażu: Każda część w każdym okresie Lepiej Pn. . 400 A Wt. . 100 A, 300 B Śr. . 200 B, 200 C Cz. . 400 C Pt. . 200 C, 200 A Harmonogram montażu: Poniedziałek: 140 A 100 B 160 C Każda część każdego dnia Poniedziałek Jeszcze lepiej 50 B 70 A 80 C Każda część w każdej dostawie Należy dążyć do bardzo szybkich i częstych przestawień produkcji w procesie stymulującym
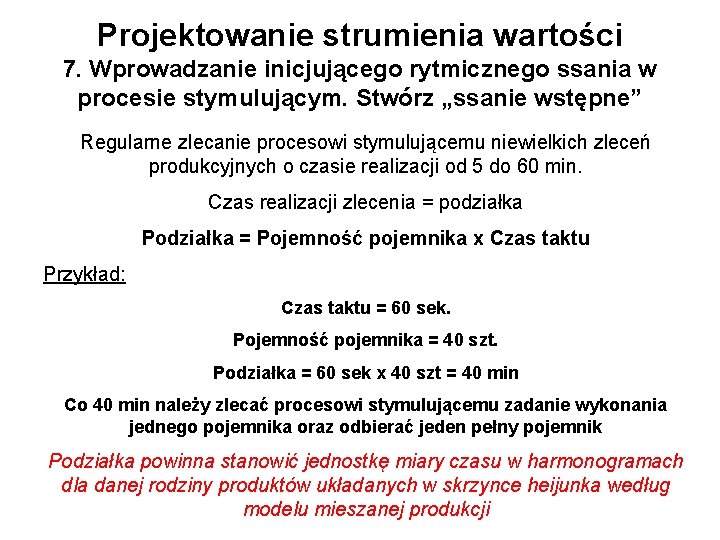
Projektowanie strumienia wartości 7. Wprowadzanie inicjującego rytmicznego ssania w procesie stymulującym. Stwórz „ssanie wstępne” Regularne zlecanie procesowi stymulującemu niewielkich zleceń produkcyjnych o czasie realizacji od 5 do 60 min. Czas realizacji zlecenia = podziałka Podziałka = Pojemność pojemnika x Czas taktu Przykład: Czas taktu = 60 sek. Pojemność pojemnika = 40 szt. Podziałka = 60 sek x 40 szt = 40 min Co 40 min należy zlecać procesowi stymulującemu zadanie wykonania jednego pojemnika oraz odbierać jeden pełny pojemnik Podziałka powinna stanowić jednostkę miary czasu w harmonogramach dla danej rodziny produktów układanych w skrzynce heijunka według modelu mieszanej produkcji
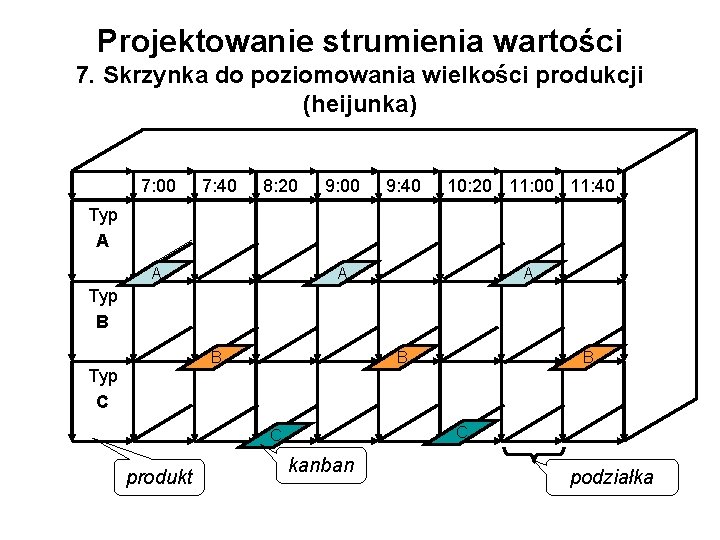
Projektowanie strumienia wartości 7. Skrzynka do poziomowania wielkości produkcji (heijunka) 7: 00 7: 40 8: 20 9: 00 9: 40 10: 20 11: 00 11: 40 Typ A A Typ B B Typ C B C C produkt B kanban podziałka
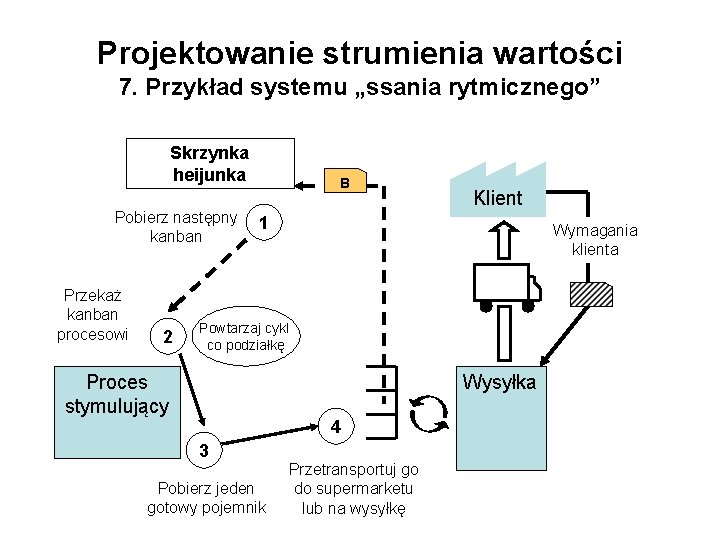
Projektowanie strumienia wartości 7. Przykład systemu „ssania rytmicznego” Skrzynka heijunka Pobierz następny kanban Przekaż kanban procesowi 2 B Klient 1 Wymagania klienta Powtarzaj cykl co podziałkę Proces stymulujący Wysyłka 4 3 Pobierz jeden gotowy pojemnik Przetransportuj go do supermarketu lub na wysyłkę
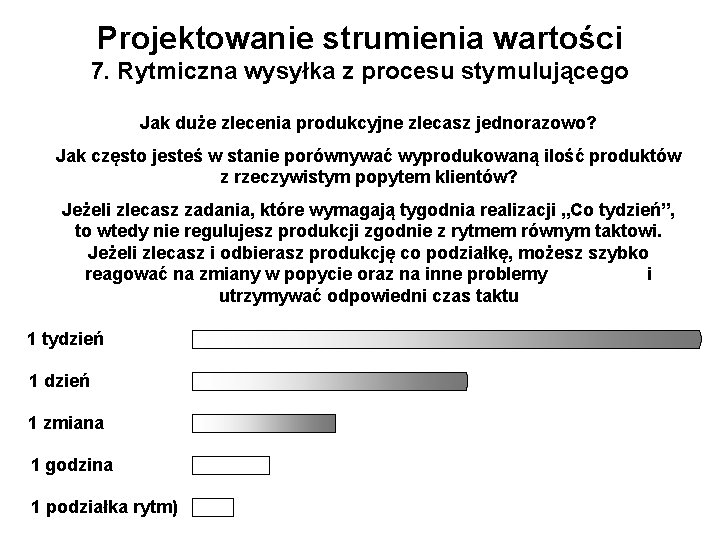
Projektowanie strumienia wartości 7. Rytmiczna wysyłka z procesu stymulującego Jak duże zlecenia produkcyjne zlecasz jednorazowo? Jak często jesteś w stanie porównywać wyprodukowaną ilość produktów z rzeczywistym popytem klientów? Jeżeli zlecasz zadania, które wymagają tygodnia realizacji „Co tydzień”, to wtedy nie regulujesz produkcji zgodnie z rytmem równym taktowi. Jeżeli zlecasz i odbierasz produkcję co podziałkę, możesz szybko reagować na zmiany w popycie oraz na inne problemy i utrzymywać odpowiedni czas taktu 1 tydzień 1 zmiana 1 godzina 1 podziałka rytm)
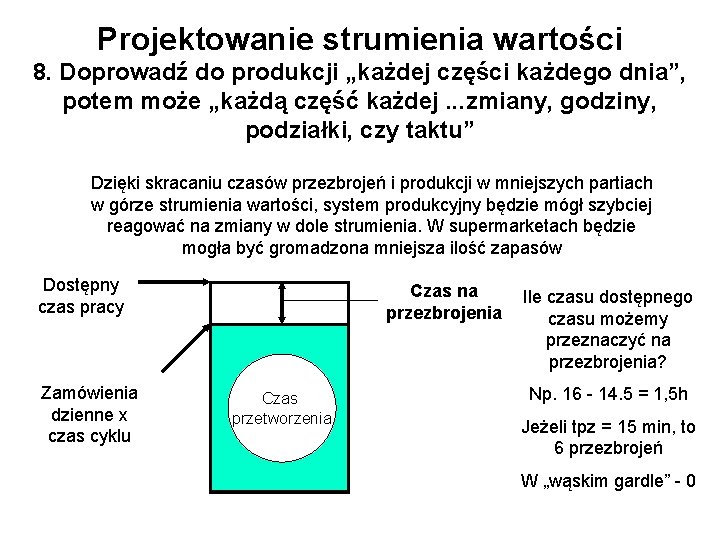
Projektowanie strumienia wartości 8. Doprowadź do produkcji „każdej części każdego dnia”, potem może „każdą część każdej. . . zmiany, godziny, podziałki, czy taktu” Dzięki skracaniu czasów przezbrojeń i produkcji w mniejszych partiach w górze strumienia wartości, system produkcyjny będzie mógł szybciej reagować na zmiany w dole strumienia. W supermarketach będzie mogła być gromadzona mniejsza ilość zapasów Dostępny czas pracy Zamówienia dzienne x czas cyklu Czas na przezbrojenia Czas przetworzenia Ile czasu dostępnego czasu możemy przeznaczyć na przezbrojenia? Np. 16 - 14. 5 = 1, 5 h Jeżeli tpz = 15 min, to 6 przezbrojeń W „wąskim gardle” - 0
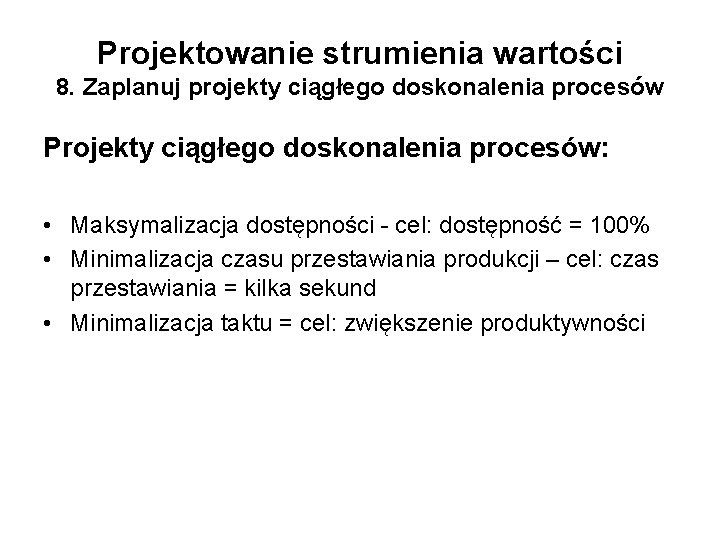
Projektowanie strumienia wartości 8. Zaplanuj projekty ciągłego doskonalenia procesów Projekty ciągłego doskonalenia procesów: • Maksymalizacja dostępności - cel: dostępność = 100% • Minimalizacja czasu przestawiania produkcji – cel: czas przestawiania = kilka sekund • Minimalizacja taktu = cel: zwiększenie produktywności
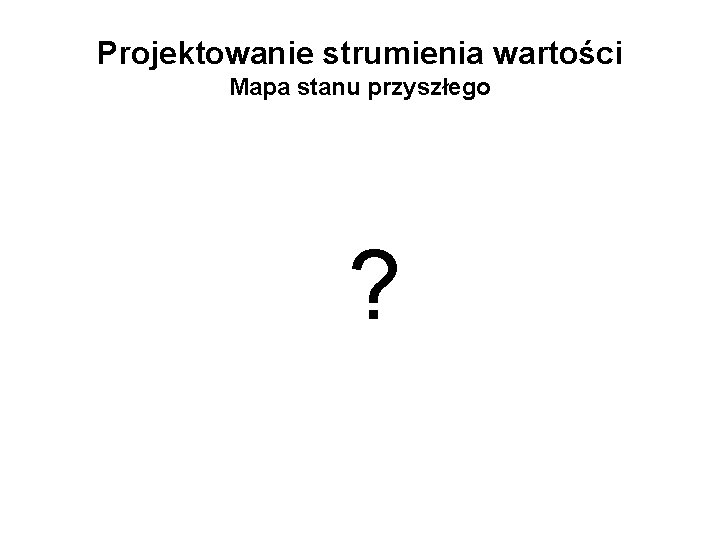
Projektowanie strumienia wartości Mapa stanu przyszłego ?
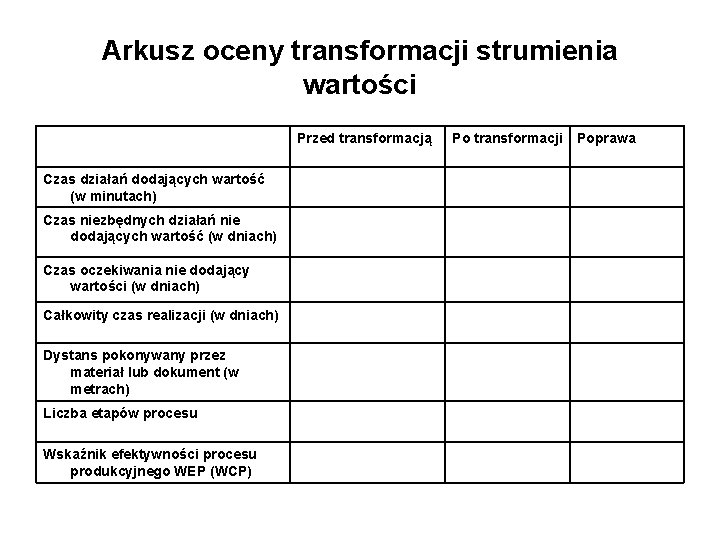
Arkusz oceny transformacji strumienia wartości Przed transformacją Czas działań dodających wartość (w minutach) Czas niezbędnych działań nie dodających wartość (w dniach) Czas oczekiwania nie dodający wartości (w dniach) Całkowity czas realizacji (w dniach) Dystans pokonywany przez materiał lub dokument (w metrach) Liczba etapów procesu Wskaźnik efektywności procesu produkcyjnego WEP (WCP) Po transformacji Poprawa