Hydrogen Direct Injection Technology Challenges and Opportunities NHA
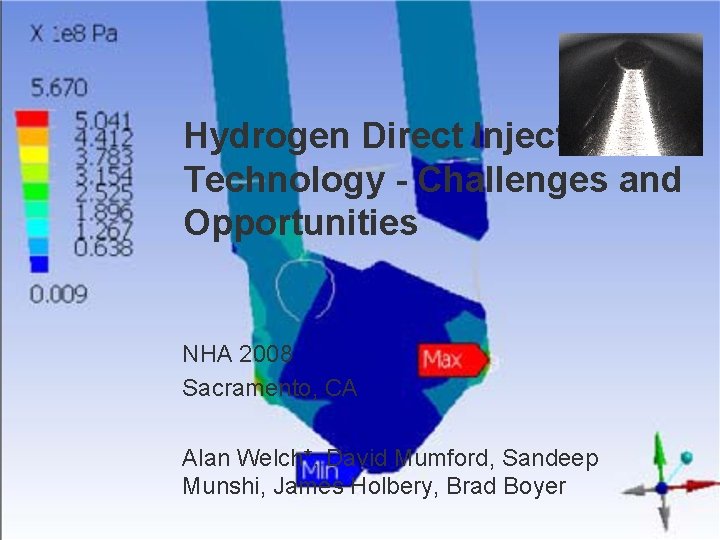
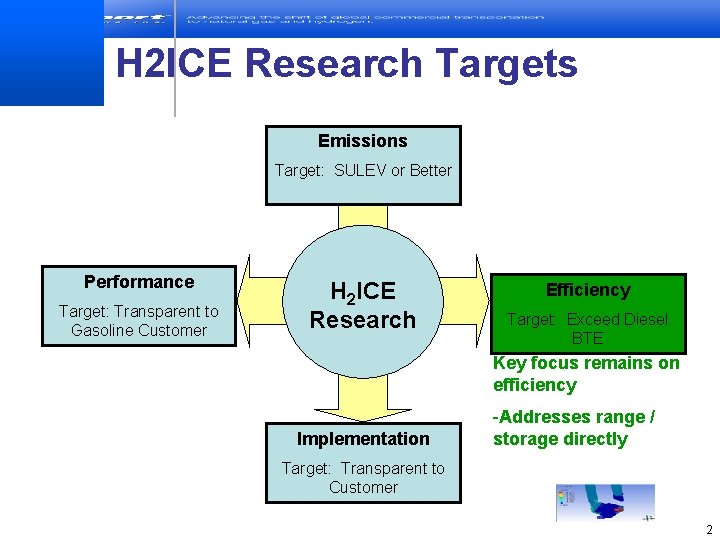
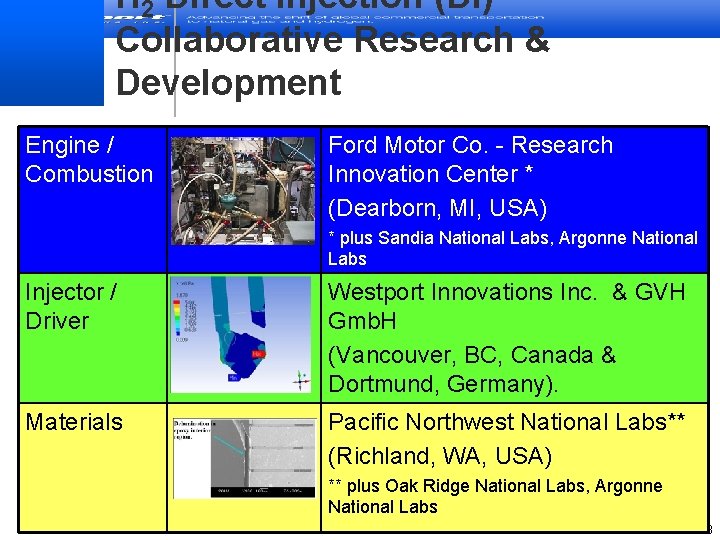
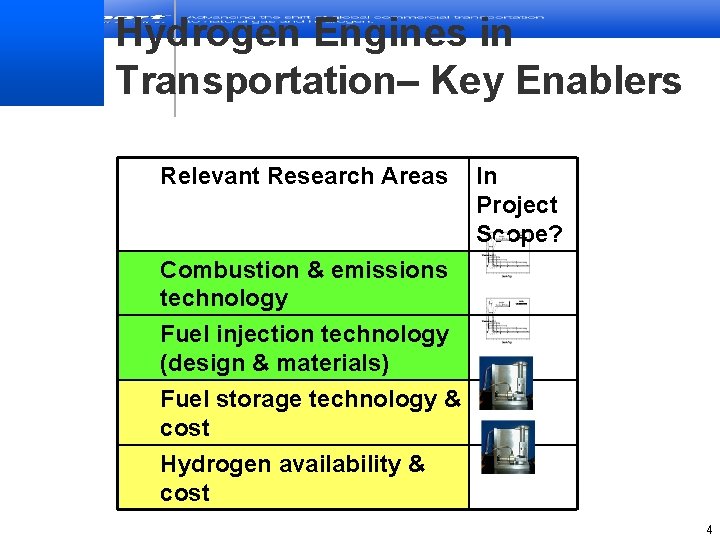
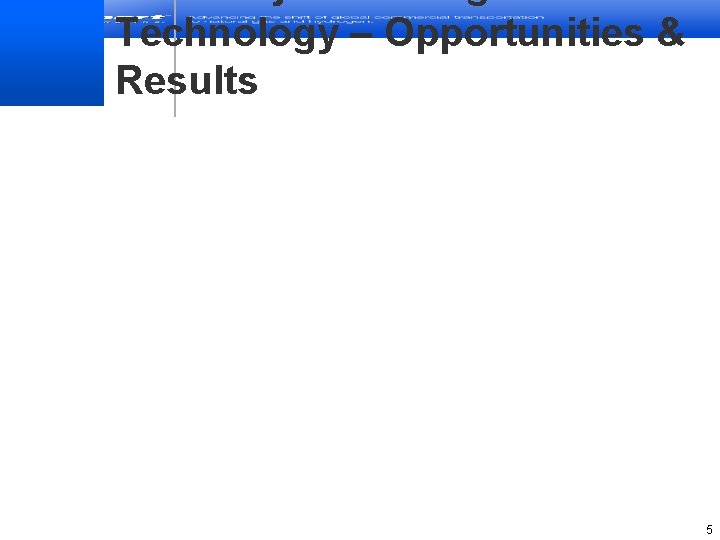
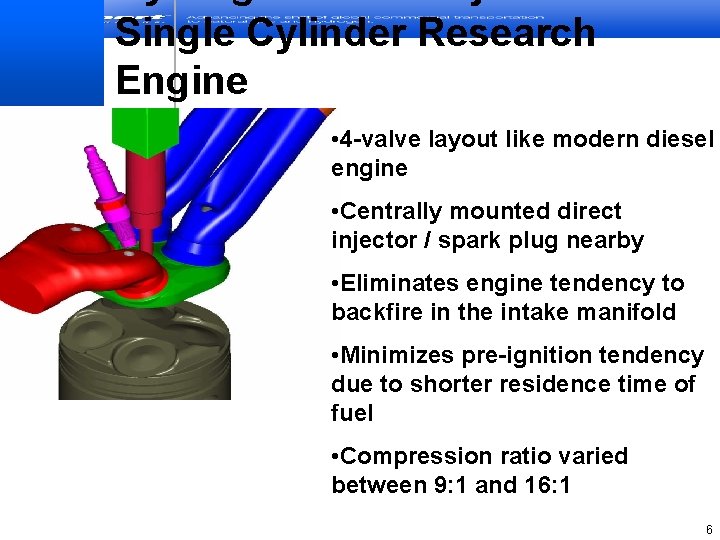
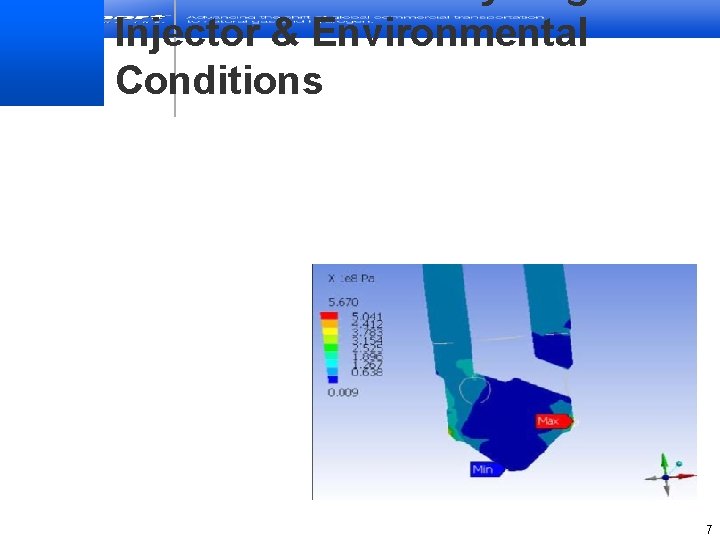

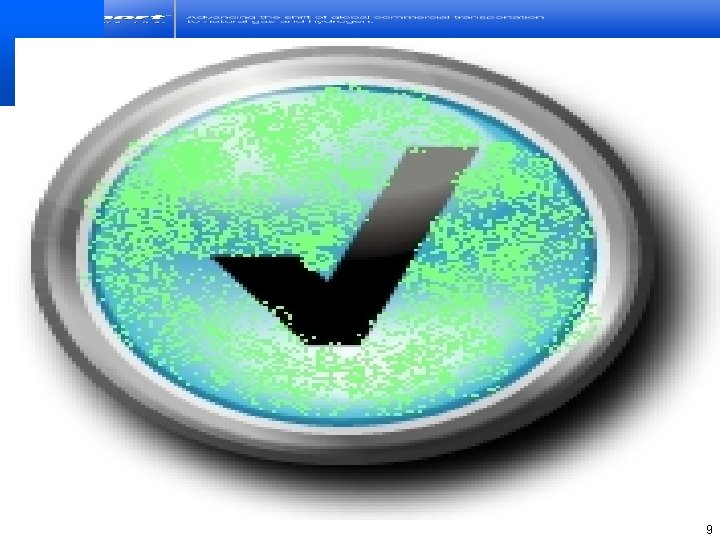
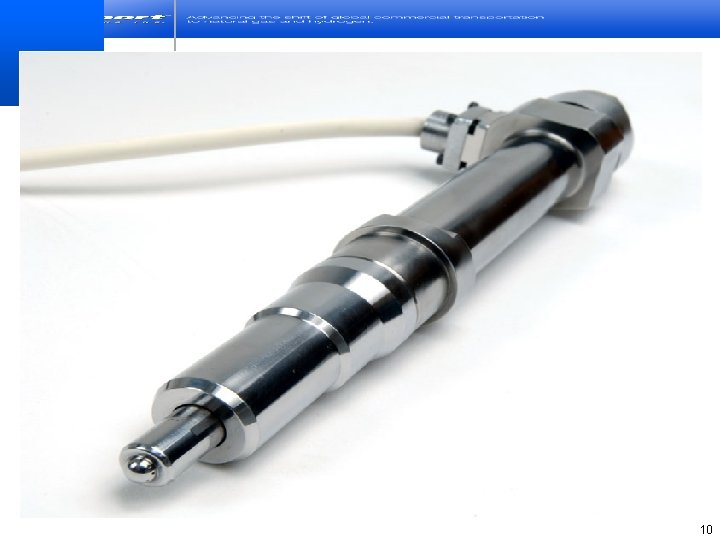
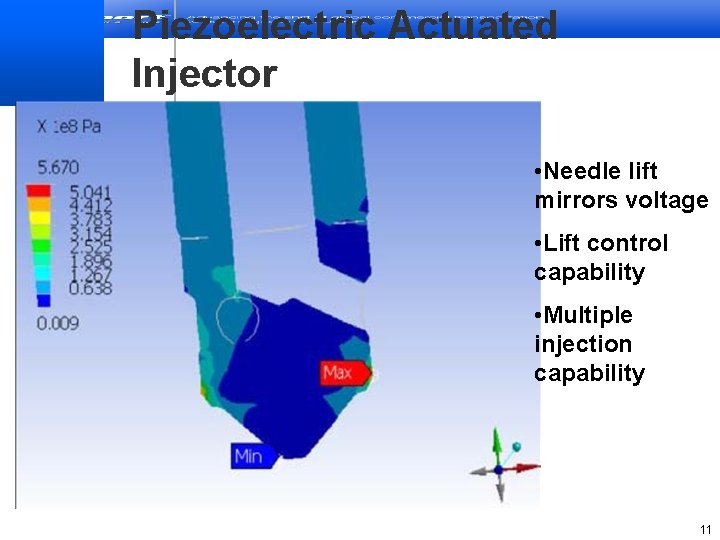
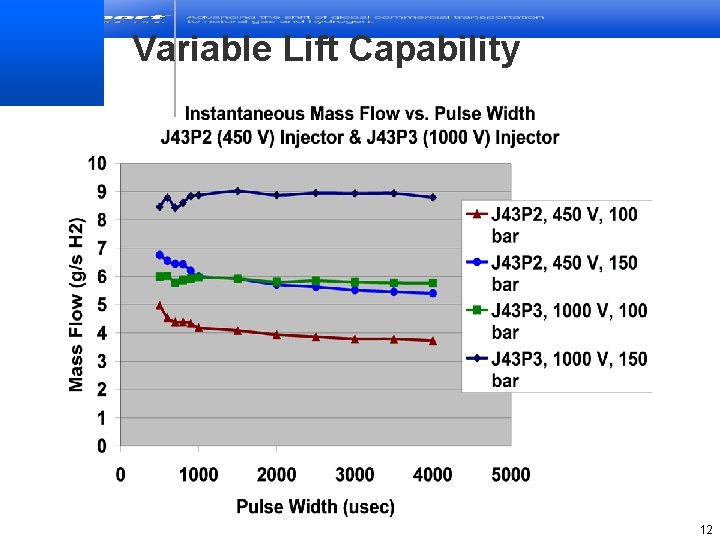
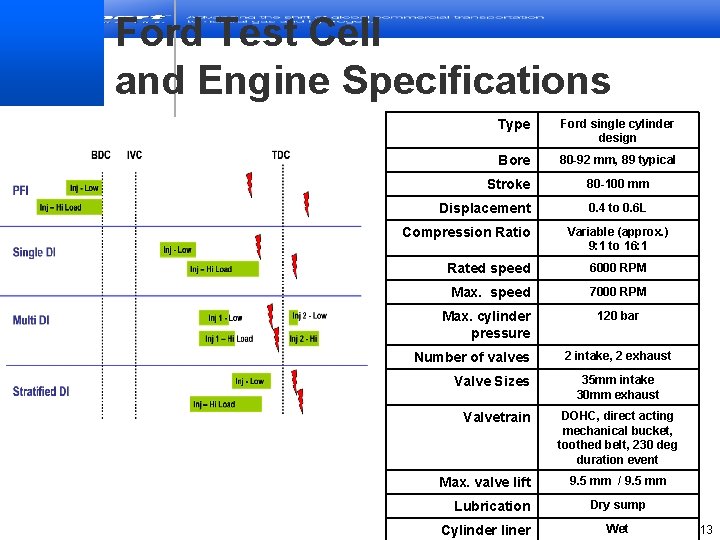
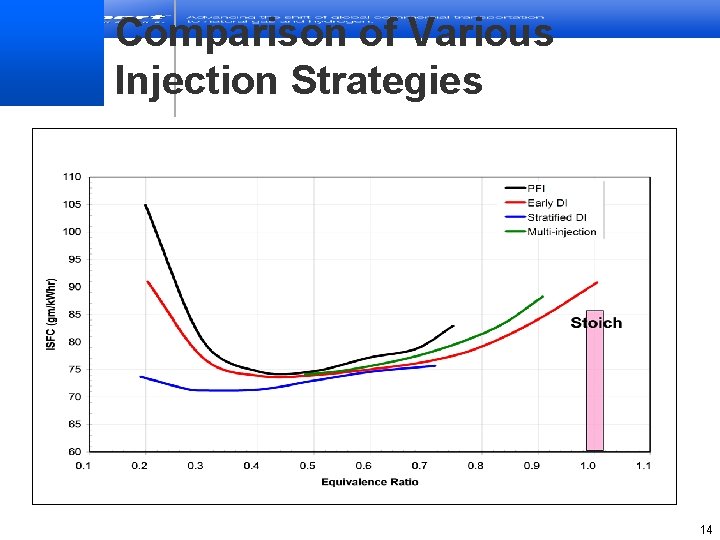
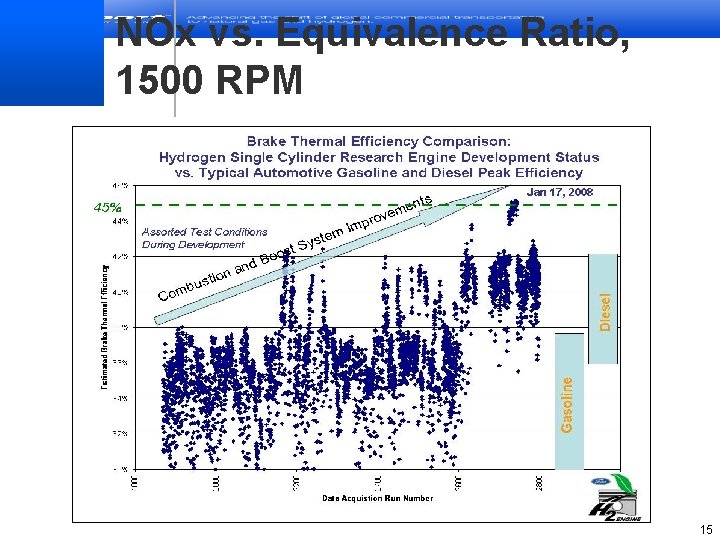
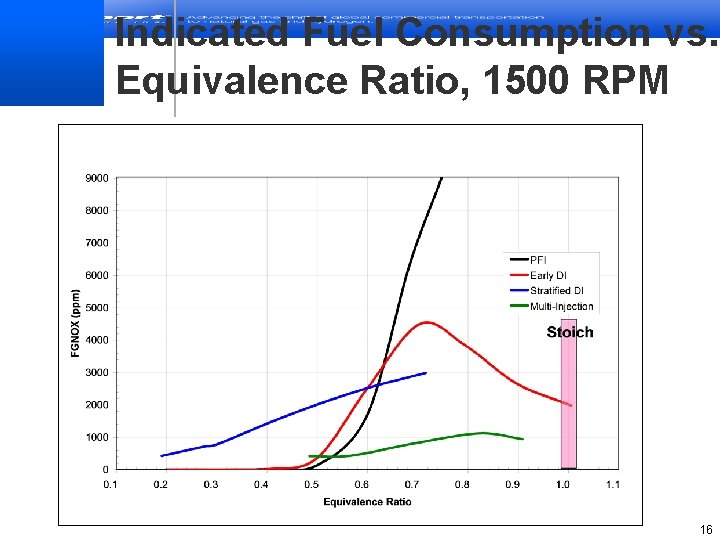
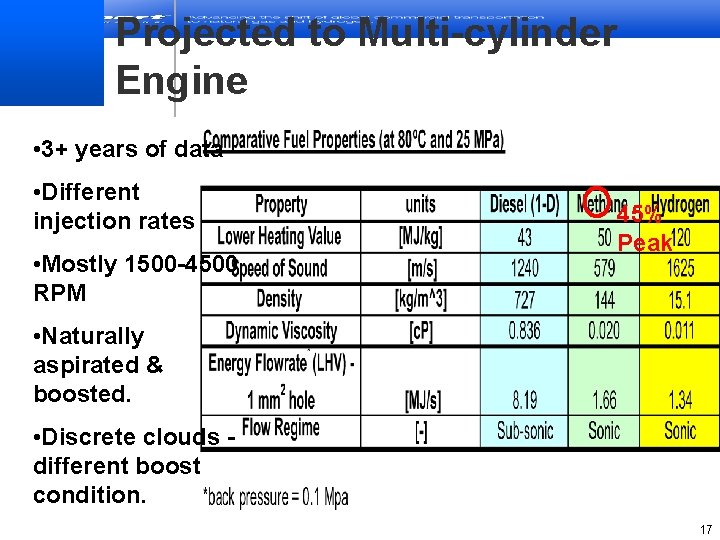
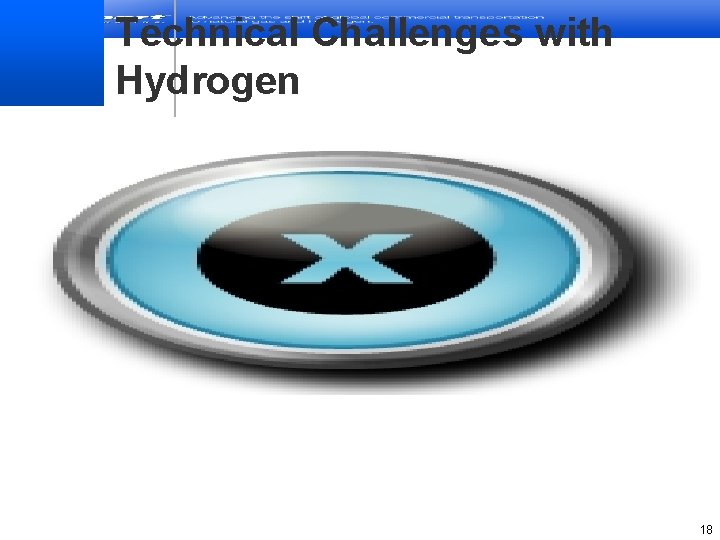
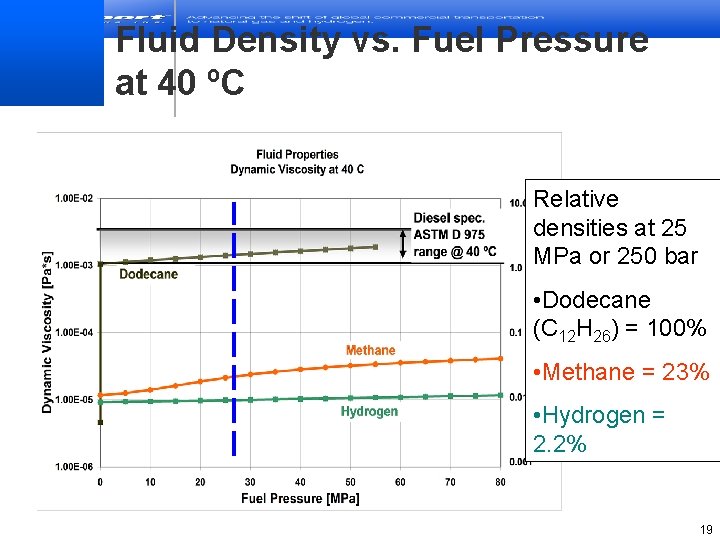
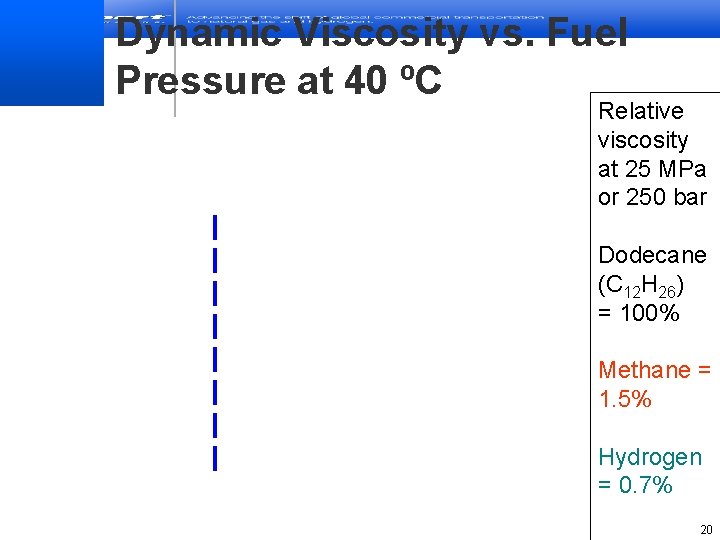
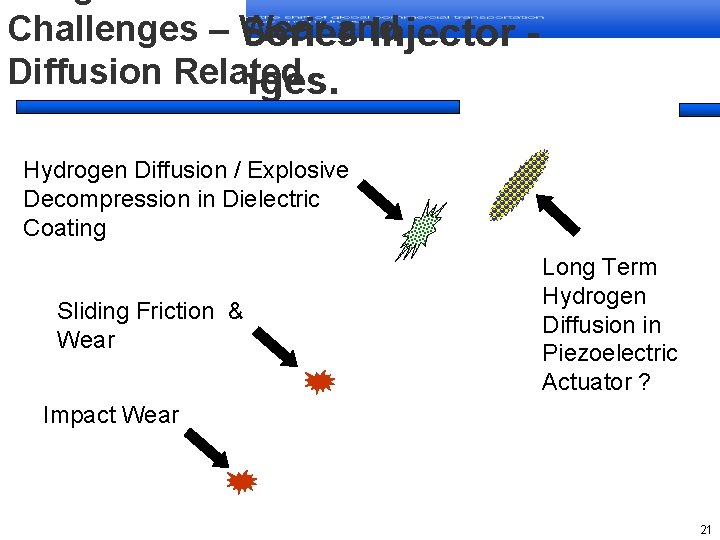
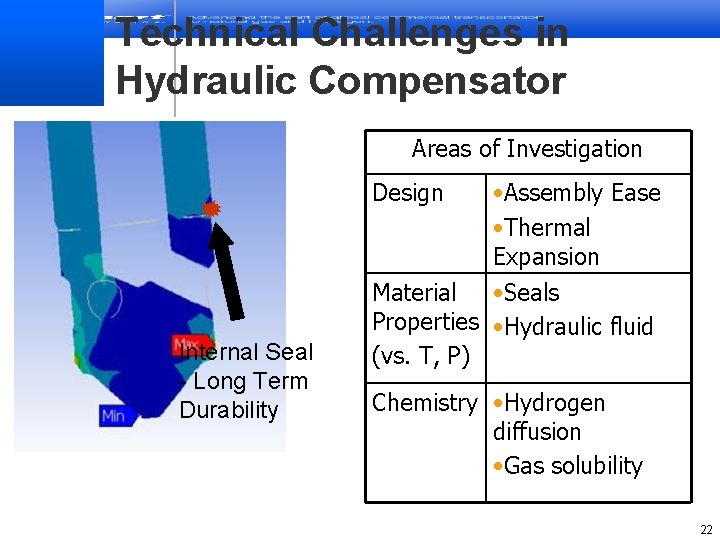
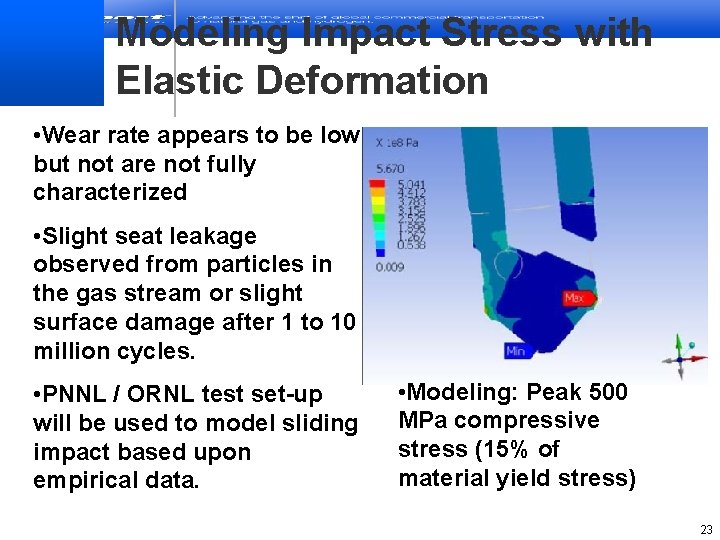
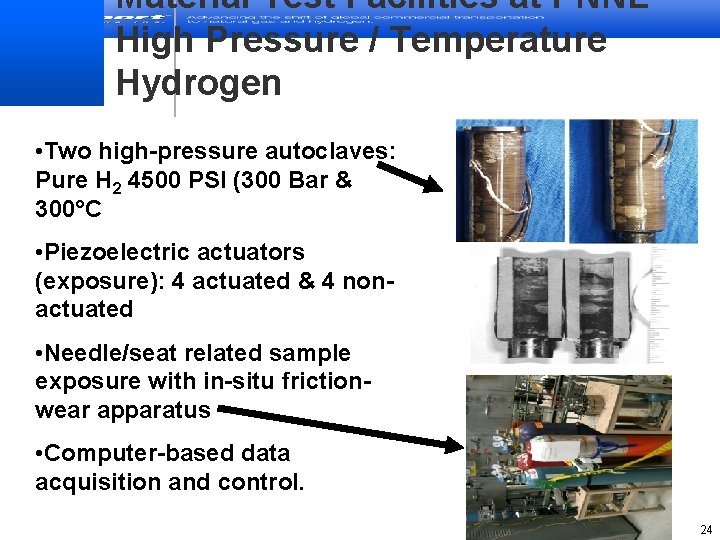
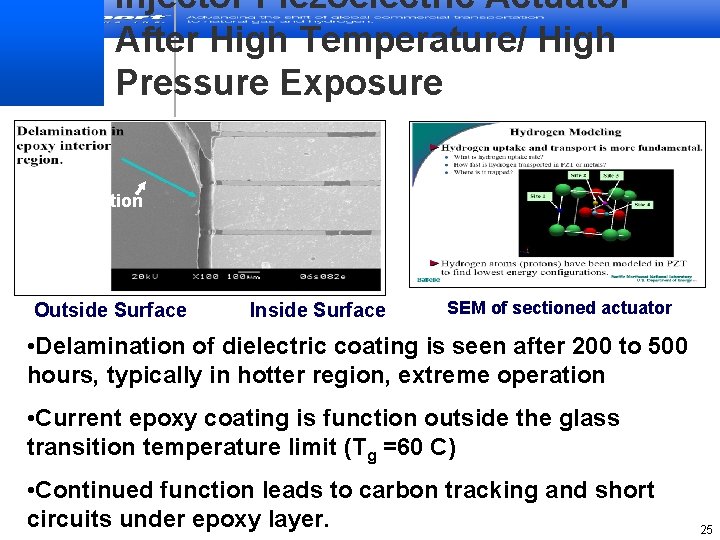
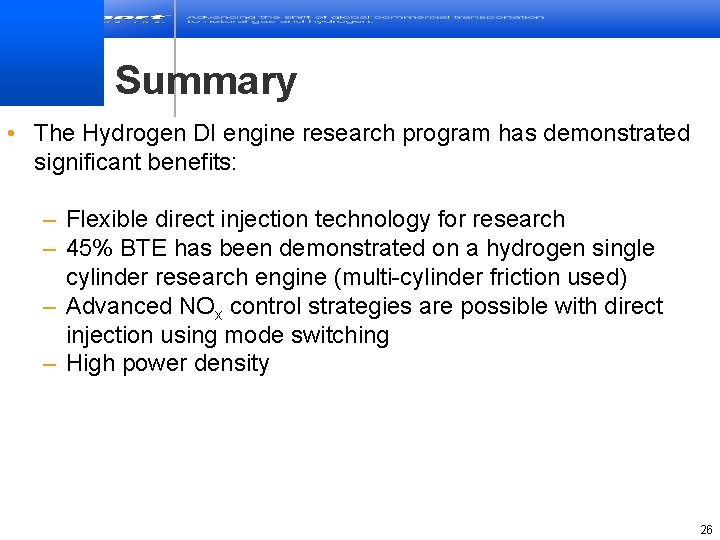
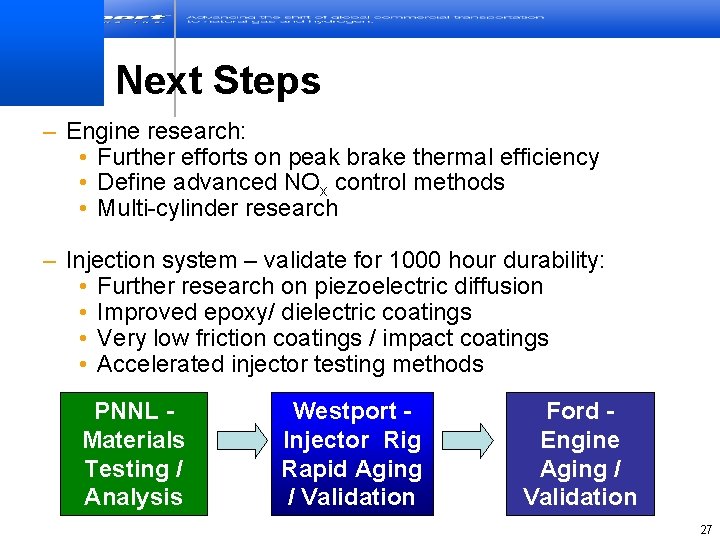
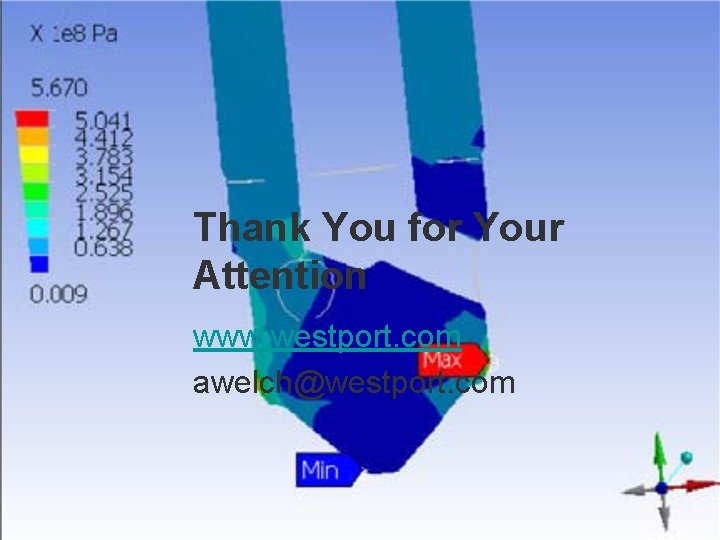
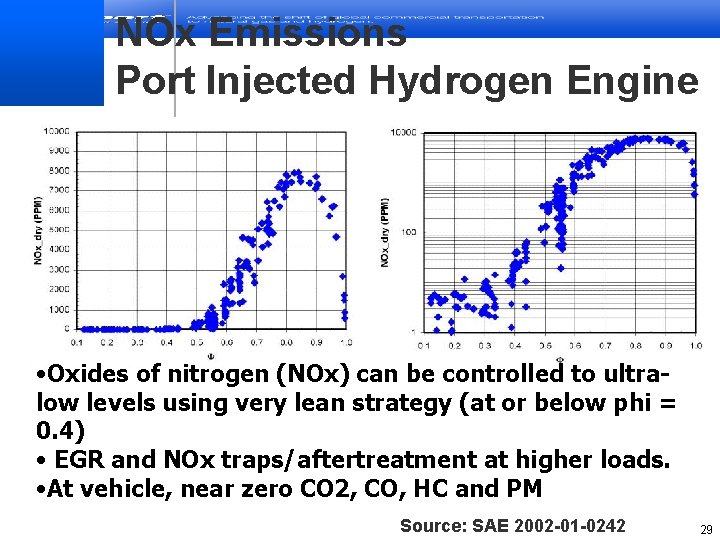
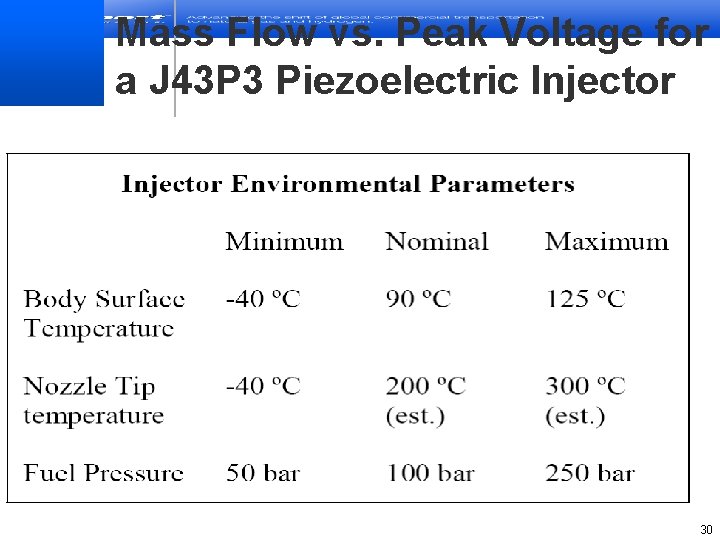
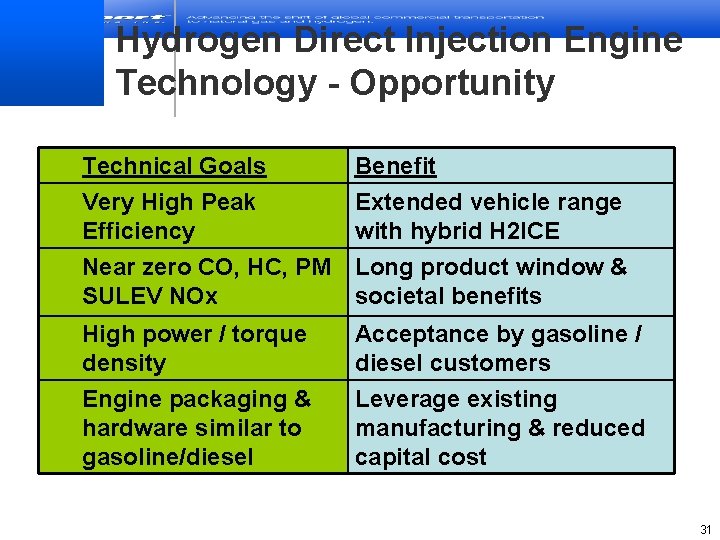
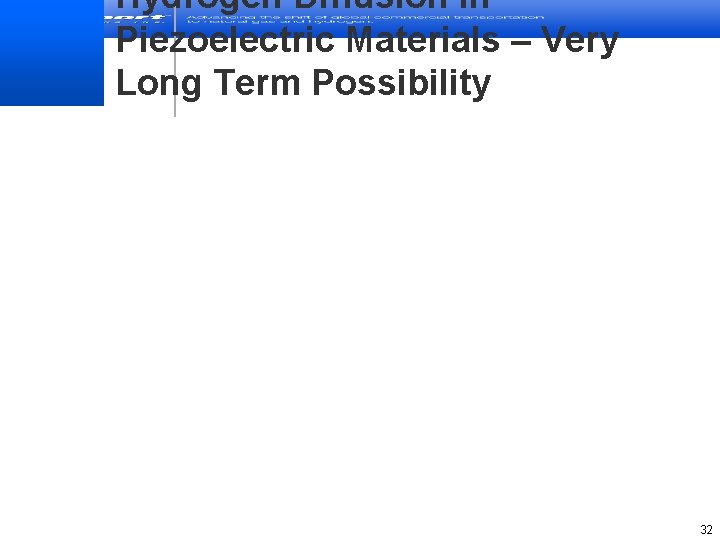
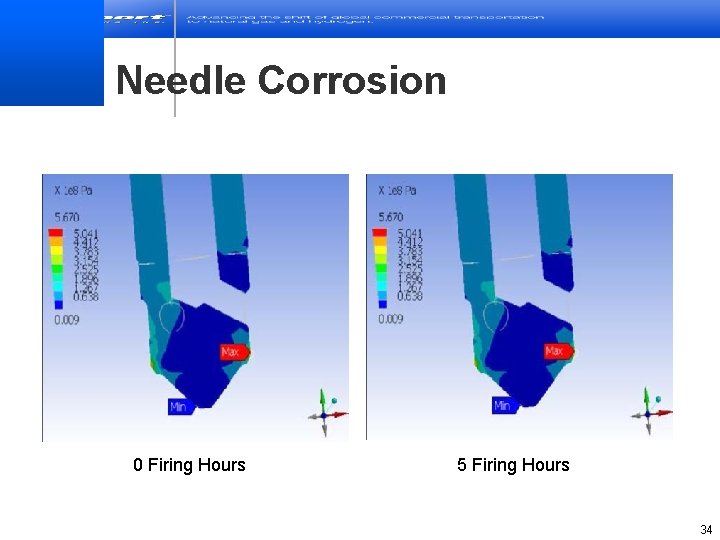
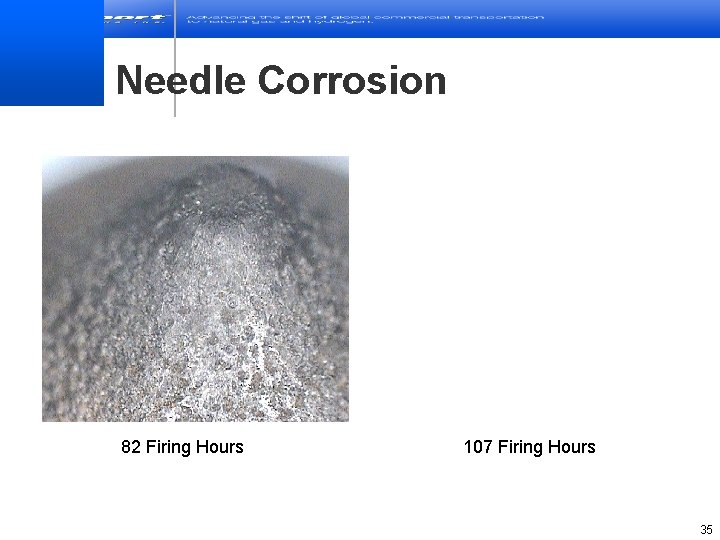
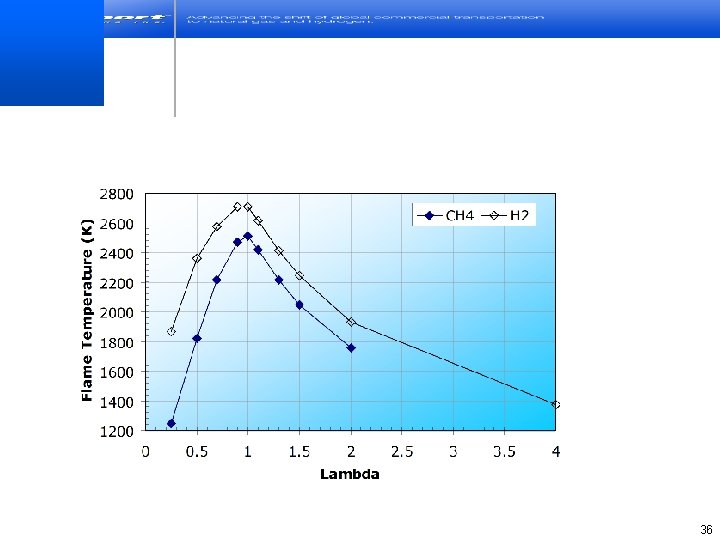
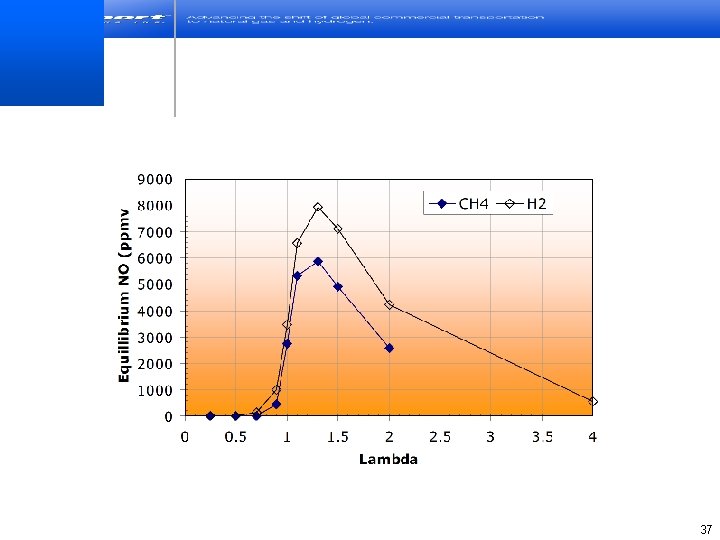
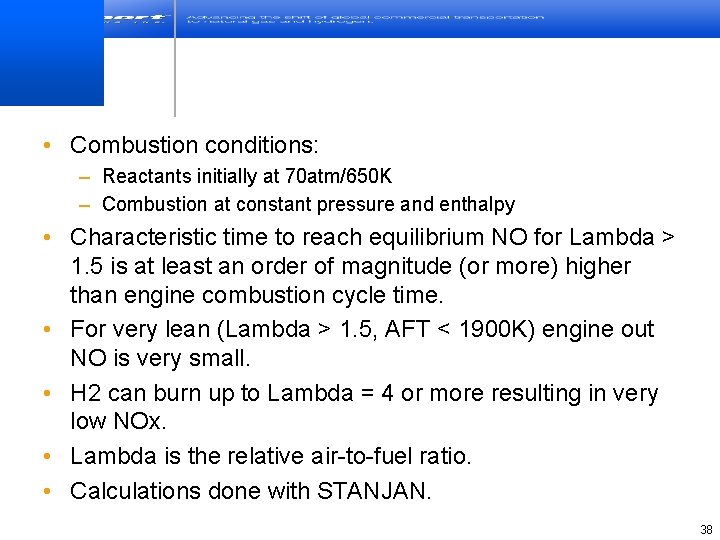
- Slides: 37
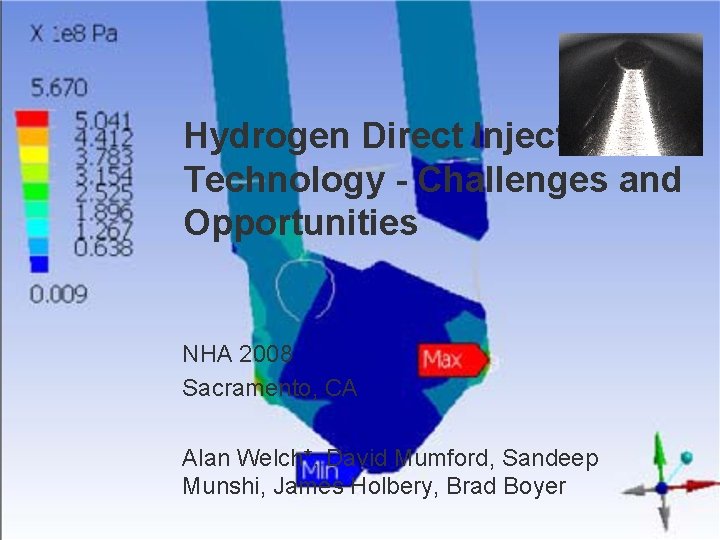
Hydrogen Direct Injection Technology - Challenges and Opportunities NHA 2008 Sacramento, CA Alan Welch*, David Mumford, Sandeep Munshi, James Holbery, Brad Boyer
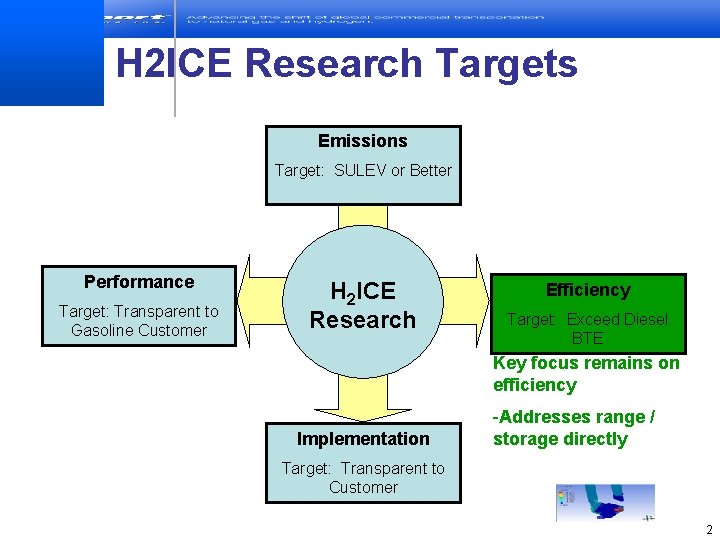
H 2 ICE Research Targets Emissions Target: SULEV or Better Performance Target: Transparent to Gasoline Customer H 2 ICE Research Efficiency Target: Exceed Diesel BTE Key focus remains on efficiency Implementation -Addresses range / storage directly Target: Transparent to Customer 2
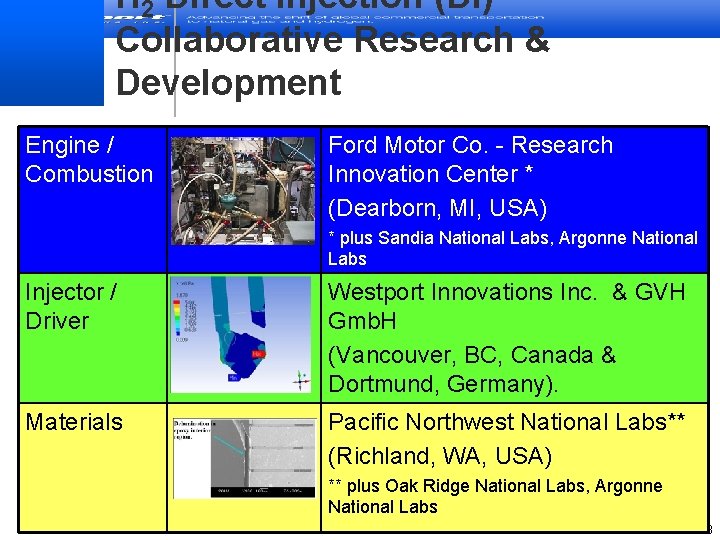
H 2 Direct Injection (DI) Collaborative Research & Development Engine / Combustion Ford Motor Co. - Research Innovation Center * (Dearborn, MI, USA) * plus Sandia National Labs, Argonne National Labs Injector / Driver Westport Innovations Inc. & GVH Gmb. H (Vancouver, BC, Canada & Dortmund, Germany). Materials Pacific Northwest National Labs** (Richland, WA, USA) ** plus Oak Ridge National Labs, Argonne National Labs 3
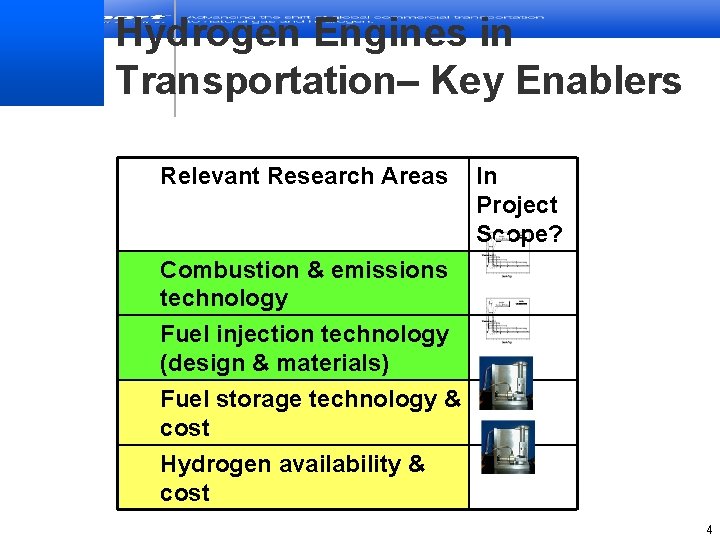
Hydrogen Engines in Transportation– Key Enablers Relevant Research Areas In Project Scope? Combustion & emissions technology Fuel injection technology (design & materials) Fuel storage technology & cost Hydrogen availability & cost 4
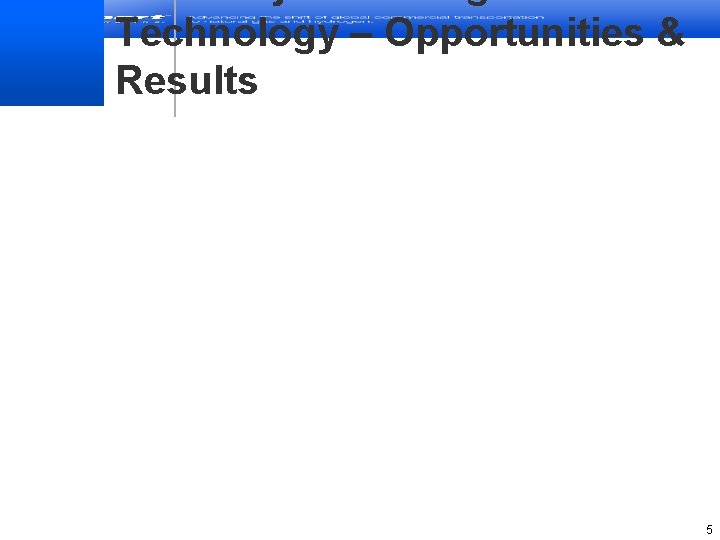
Technology – Opportunities & Results 5
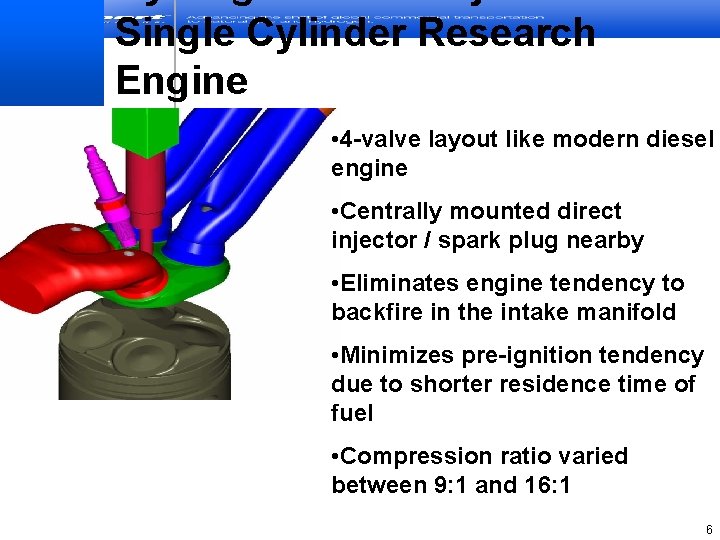
Single Cylinder Research Engine • 4 -valve layout like modern diesel engine • Centrally mounted direct injector / spark plug nearby • Eliminates engine tendency to backfire in the intake manifold • Minimizes pre-ignition tendency due to shorter residence time of fuel • Compression ratio varied between 9: 1 and 16: 1 6
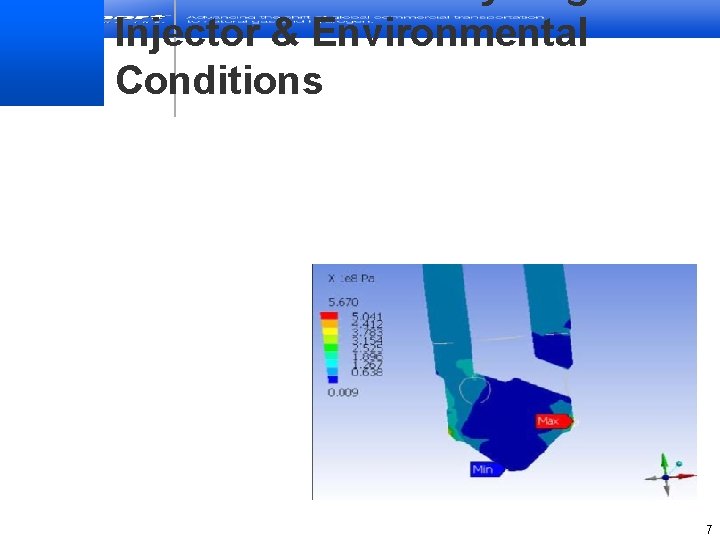
Injector & Environmental Conditions 7

J 43 Px Injector Animation 8
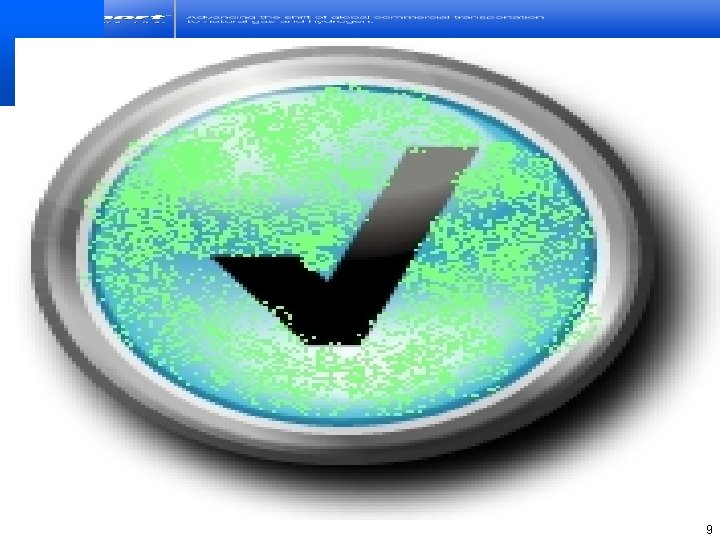
9
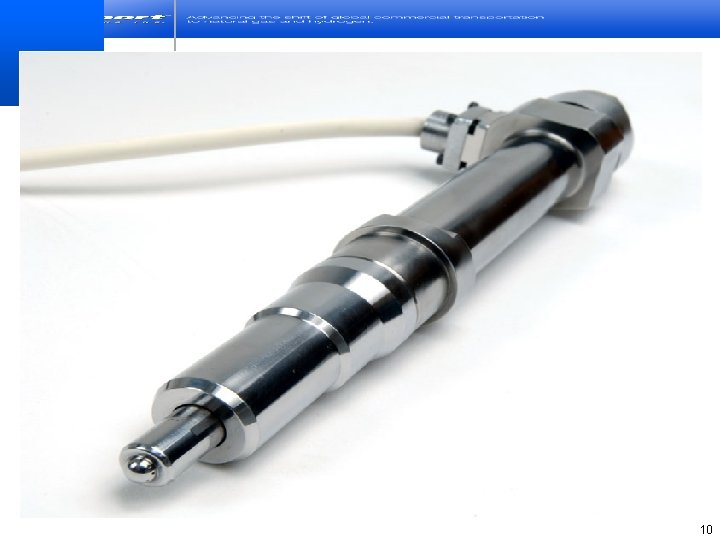
10
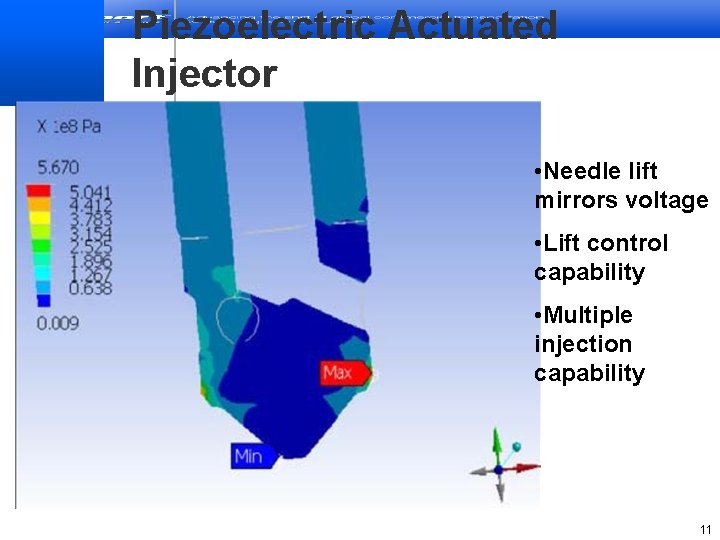
Piezoelectric Actuated Injector • Needle lift mirrors voltage • Lift control capability • Multiple injection capability 11
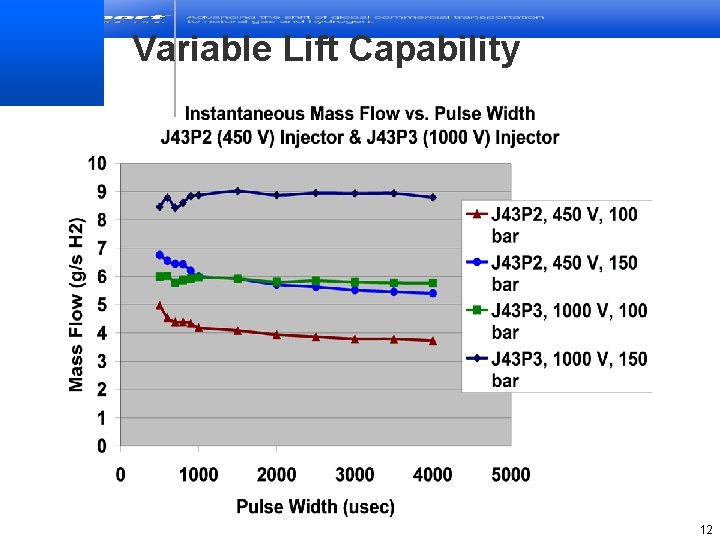
Variable Lift Capability 12
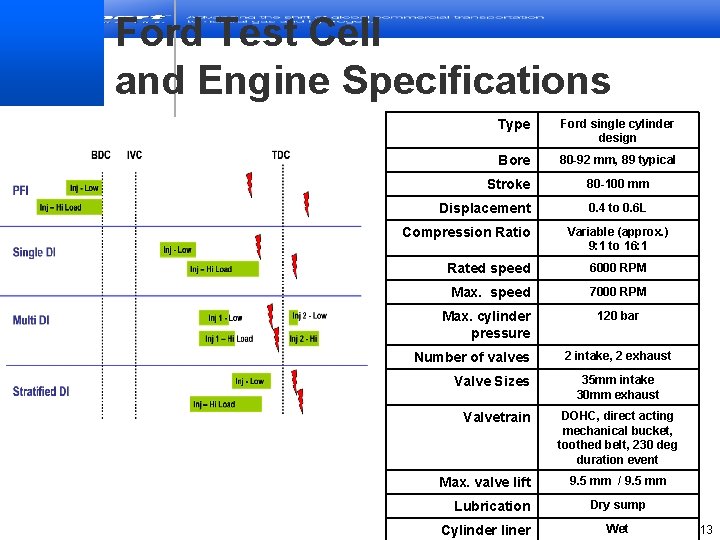
Ford Test Cell and Engine Specifications Type Ford single cylinder design Bore 80 -92 mm, 89 typical Stroke 80 -100 mm Displacement 0. 4 to 0. 6 L Compression Ratio Variable (approx. ) 9: 1 to 16: 1 Rated speed 6000 RPM Max. speed 7000 RPM Max. cylinder pressure Number of valves Valve Sizes Valvetrain Max. valve lift Lubrication Cylinder liner 120 bar 2 intake, 2 exhaust 35 mm intake 30 mm exhaust DOHC, direct acting mechanical bucket, toothed belt, 230 deg duration event 9. 5 mm / 9. 5 mm Dry sump Wet 13
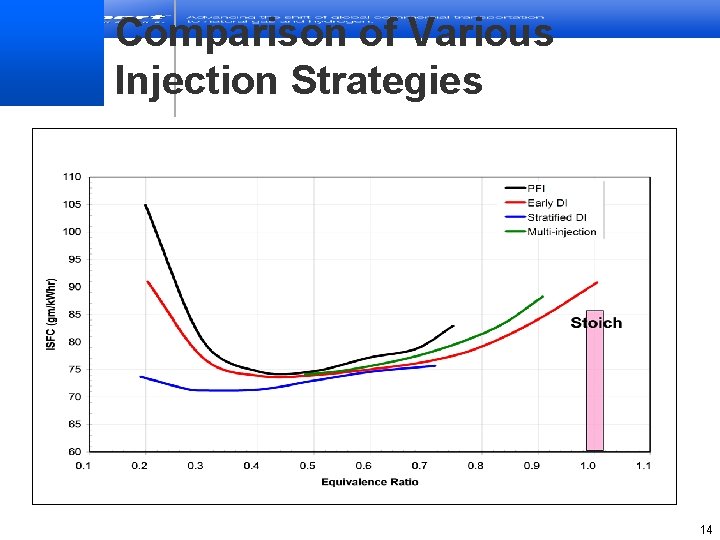
Comparison of Various Injection Strategies 14
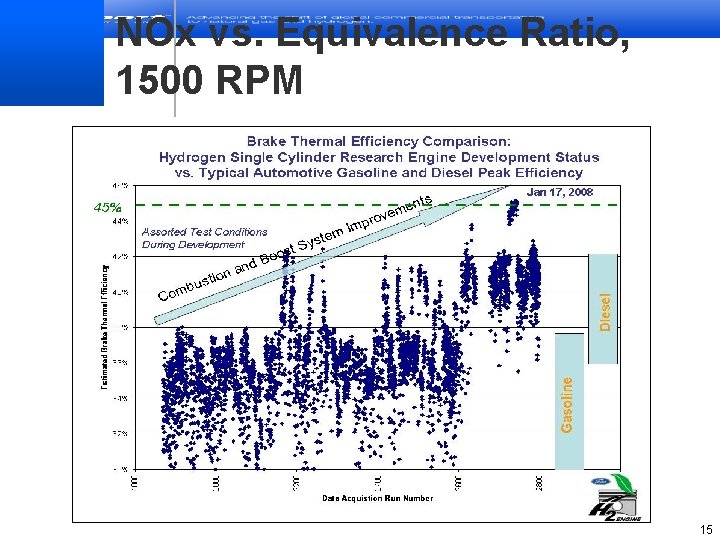
NOx vs. Equivalence Ratio, 1500 RPM 15
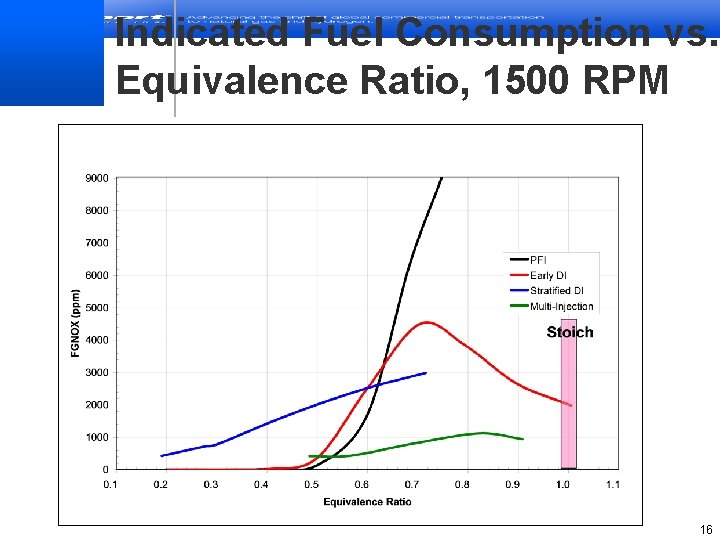
Indicated Fuel Consumption vs. Equivalence Ratio, 1500 RPM 16
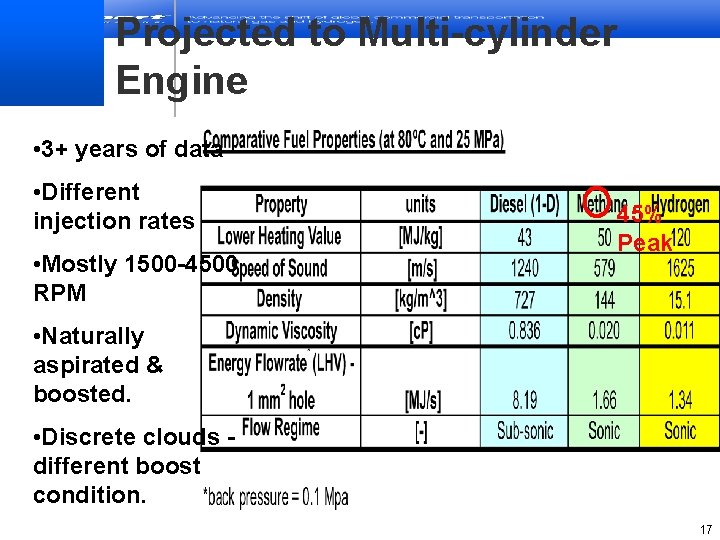
Projected to Multi-cylinder Engine • 3+ years of data • Different injection rates • Mostly 1500 -4500 RPM 45% Peak • Naturally aspirated & boosted. • Discrete clouds different boost condition. 17
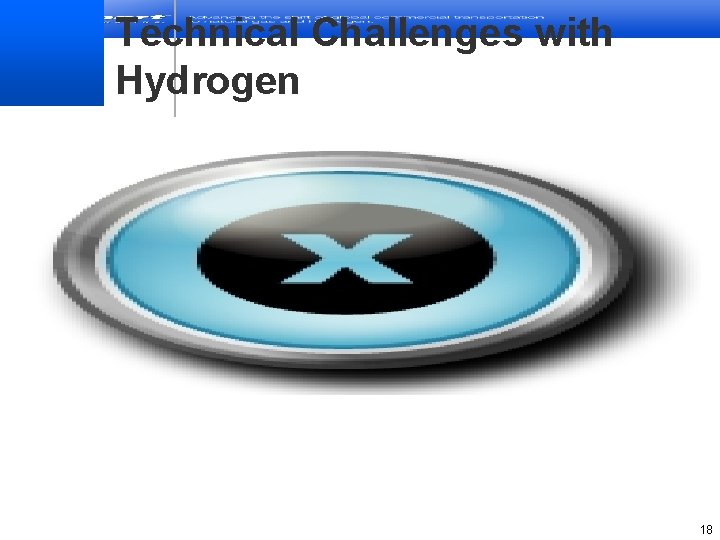
Technical Challenges with Hydrogen 18
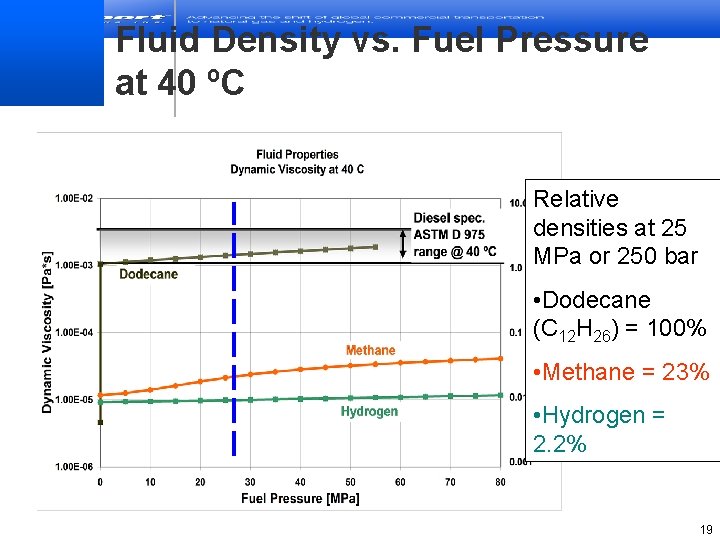
Fluid Density vs. Fuel Pressure at 40 ºC Relative densities at 25 MPa or 250 bar • Dodecane (C 12 H 26) = 100% • Methane = 23% • Hydrogen = 2. 2% 19
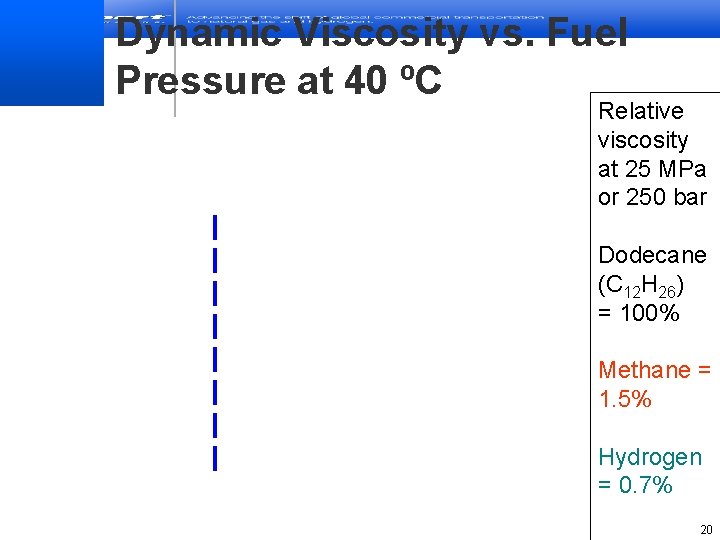
Dynamic Viscosity vs. Fuel Pressure at 40 ºC Relative viscosity at 25 MPa or 250 bar Dodecane (C 12 H 26) = 100% Methane = 1. 5% Hydrogen = 0. 7% 20
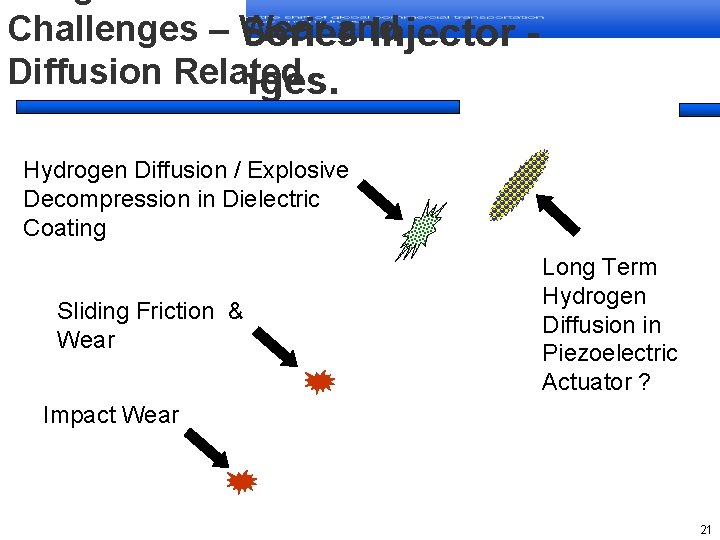
Challenges and J 43 px– Wear Series Injector Diffusion Related Challenges. Hydrogen Diffusion / Explosive Decompression in Dielectric Coating Sliding Friction & Wear Long Term Hydrogen Diffusion in Piezoelectric Actuator ? Impact Wear 21
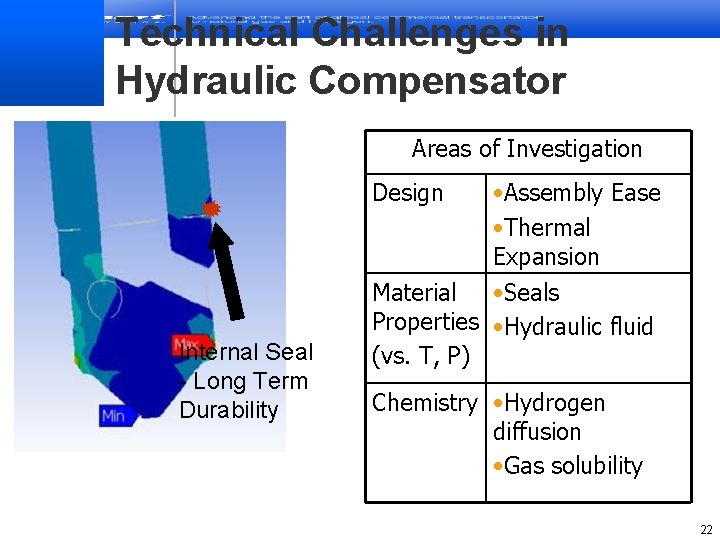
Technical Challenges in Hydraulic Compensator Areas of Investigation • Assembly Ease • Thermal Expansion Material • Seals Properties • Hydraulic fluid (vs. T, P) Design Internal Seal - Long Term Durability Chemistry • Hydrogen diffusion • Gas solubility 22
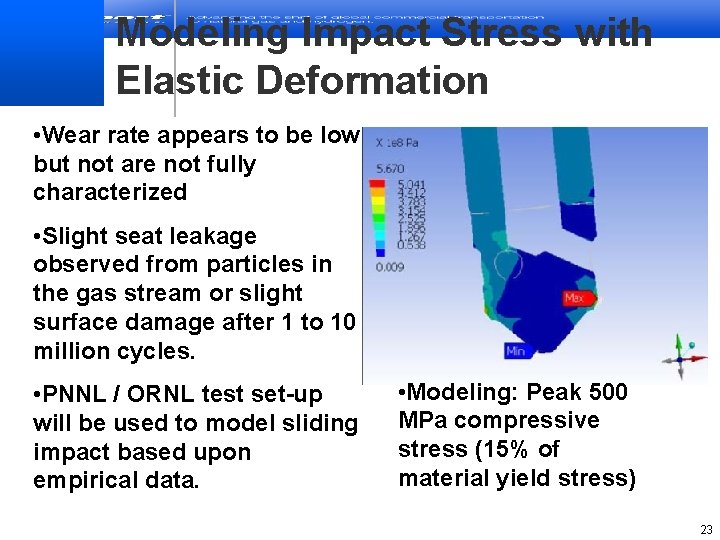
Modeling Impact Stress with Elastic Deformation • Wear rate appears to be low but not are not fully characterized • Slight seat leakage observed from particles in the gas stream or slight surface damage after 1 to 10 million cycles. • PNNL / ORNL test set-up will be used to model sliding impact based upon empirical data. • Modeling: Peak 500 MPa compressive stress (15% of material yield stress) 23
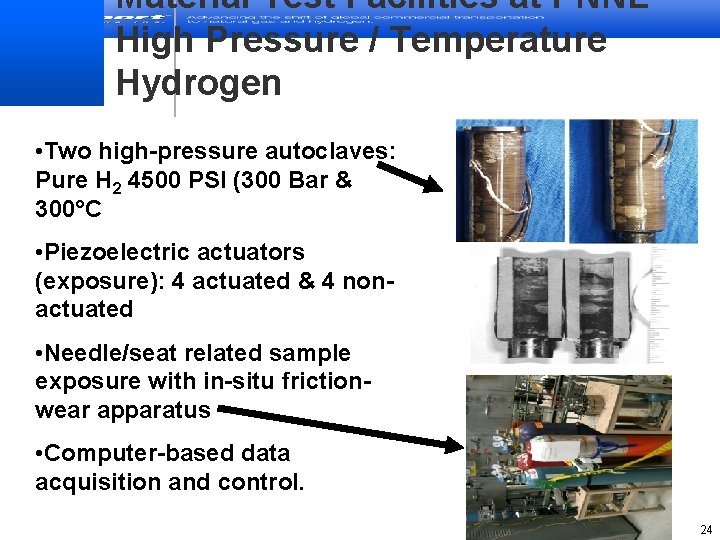
Material Test Facilities at PNNL High Pressure / Temperature Hydrogen • Two high-pressure autoclaves: Pure H 2 4500 PSI (300 Bar & 300°C • Piezoelectric actuators (exposure): 4 actuated & 4 nonactuated • Needle/seat related sample exposure with in-situ frictionwear apparatus • Computer-based data acquisition and control. 24
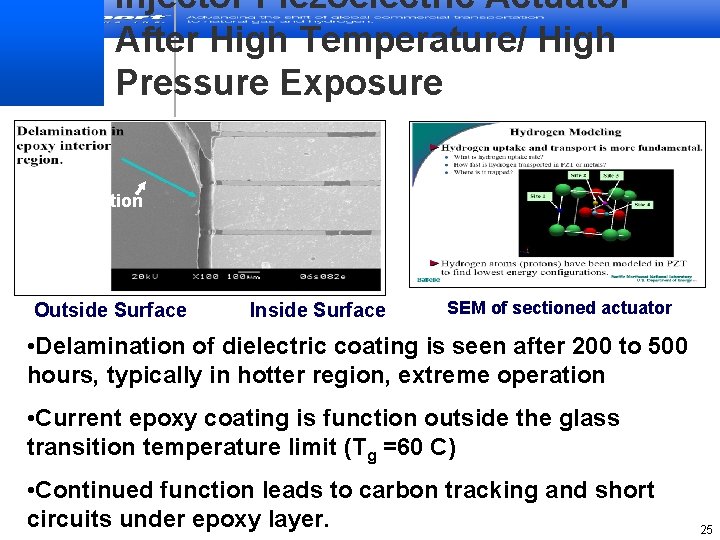
Injector Piezoelectric Actuator After High Temperature/ High Pressure Exposure Delamination Outside Surface Inside Surface SEM of sectioned actuator • Delamination of dielectric coating is seen after 200 to 500 hours, typically in hotter region, extreme operation • Current epoxy coating is function outside the glass transition temperature limit (Tg =60 C) • Continued function leads to carbon tracking and short circuits under epoxy layer. 25
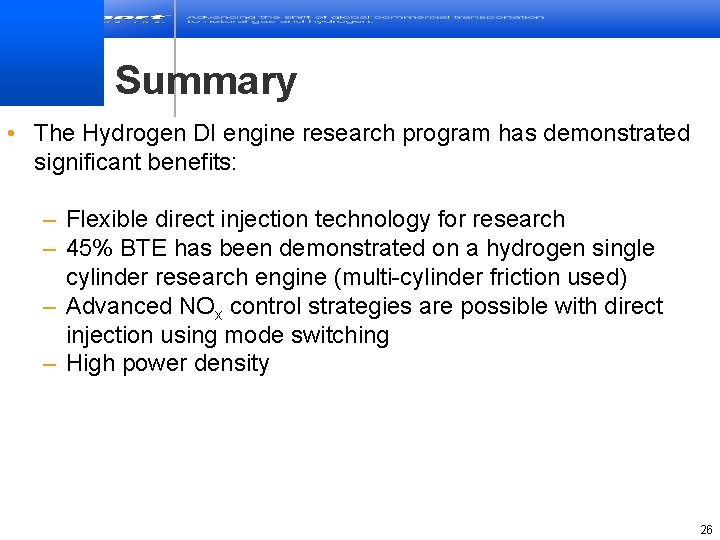
Summary • The Hydrogen DI engine research program has demonstrated significant benefits: – Flexible direct injection technology for research – 45% BTE has been demonstrated on a hydrogen single cylinder research engine (multi-cylinder friction used) – Advanced NOx control strategies are possible with direct injection using mode switching – High power density 26
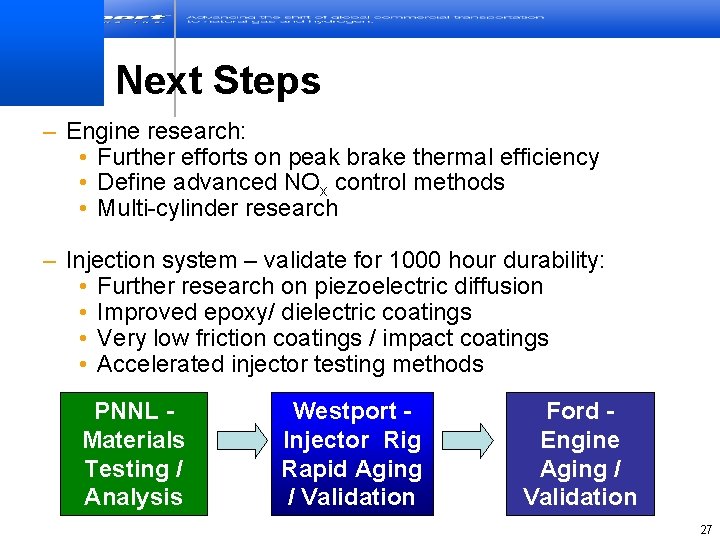
Next Steps – Engine research: • Further efforts on peak brake thermal efficiency • Define advanced NOx control methods • Multi-cylinder research – Injection system – validate for 1000 hour durability: • Further research on piezoelectric diffusion • Improved epoxy/ dielectric coatings • Very low friction coatings / impact coatings • Accelerated injector testing methods PNNL Materials Testing / Analysis Westport Injector Rig Rapid Aging / Validation Ford Engine Aging / Validation 27
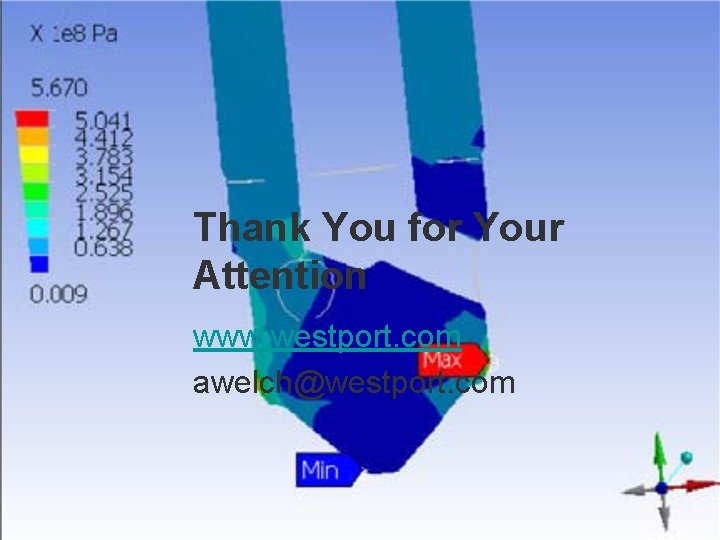
Thank You for Your Attention www. westport. com awelch@westport. com
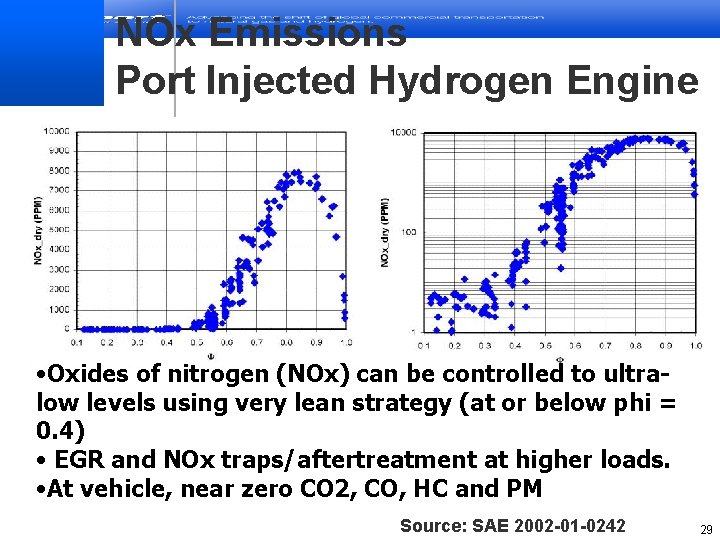
NOx Emissions Port Injected Hydrogen Engine • Oxides of nitrogen (NOx) can be controlled to ultralow levels using very lean strategy (at or below phi = 0. 4) • EGR and NOx traps/aftertreatment at higher loads. • At vehicle, near zero CO 2, CO, HC and PM Source: SAE 2002 -01 -0242 29
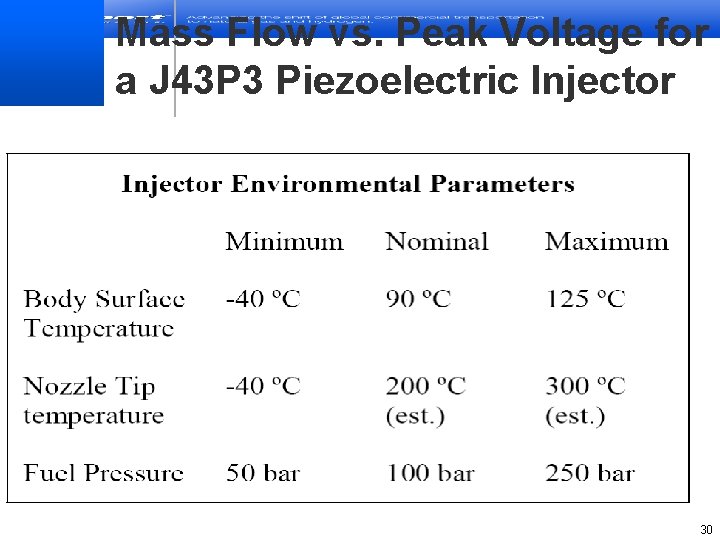
Mass Flow vs. Peak Voltage for a J 43 P 3 Piezoelectric Injector 30
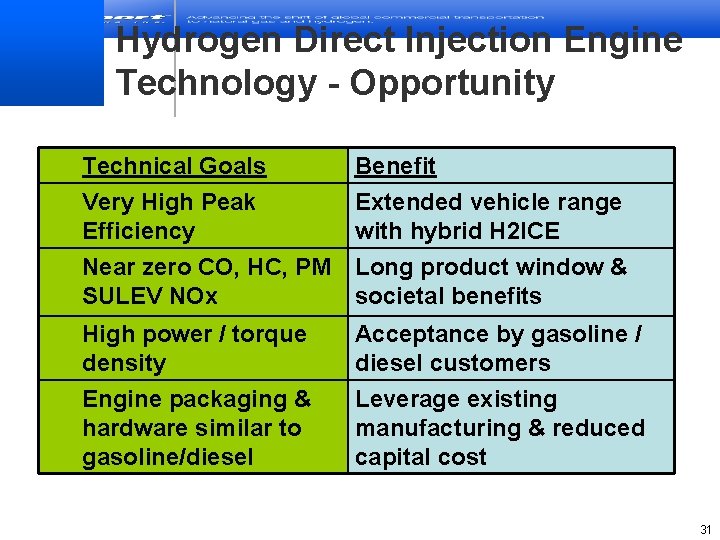
Hydrogen Direct Injection Engine Technology - Opportunity Technical Goals Very High Peak Efficiency Benefit Extended vehicle range with hybrid H 2 ICE Near zero CO, HC, PM Long product window & SULEV NOx societal benefits High power / torque density Engine packaging & hardware similar to gasoline/diesel Acceptance by gasoline / diesel customers Leverage existing manufacturing & reduced capital cost 31
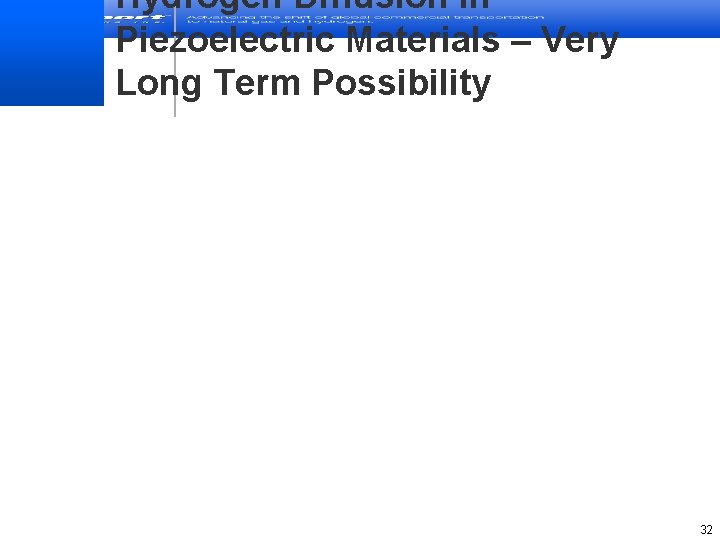
Hydrogen Diffusion in Piezoelectric Materials – Very Long Term Possibility 32
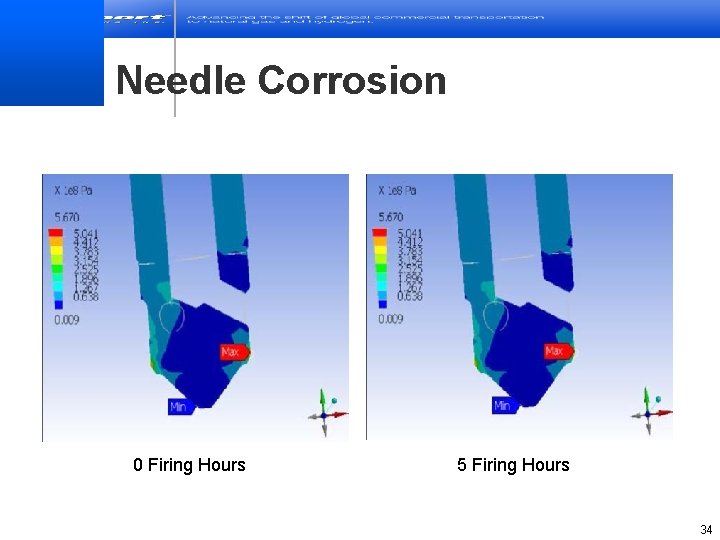
Needle Corrosion 0 Firing Hours 5 Firing Hours 34
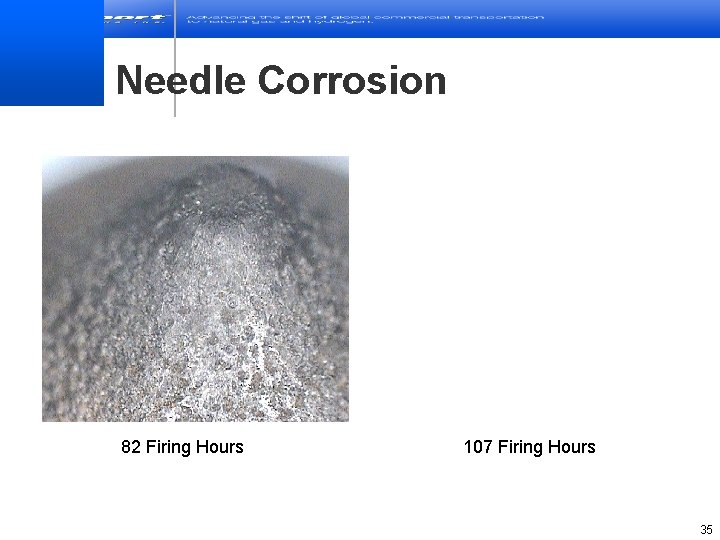
Needle Corrosion 82 Firing Hours 107 Firing Hours 35
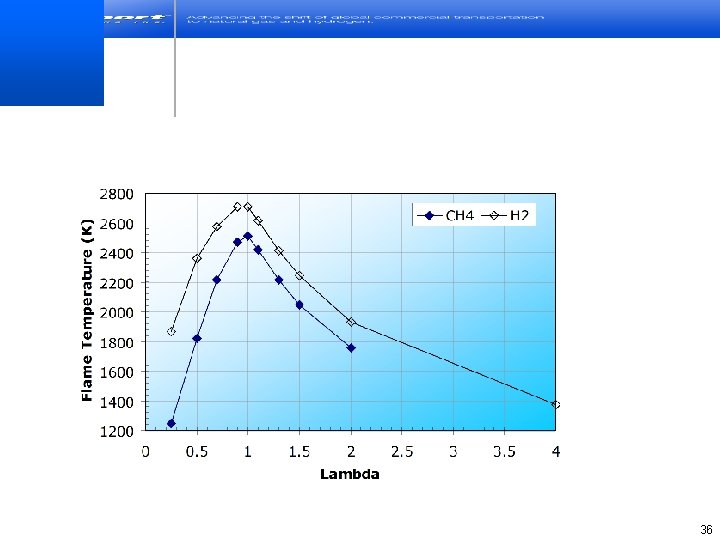
36
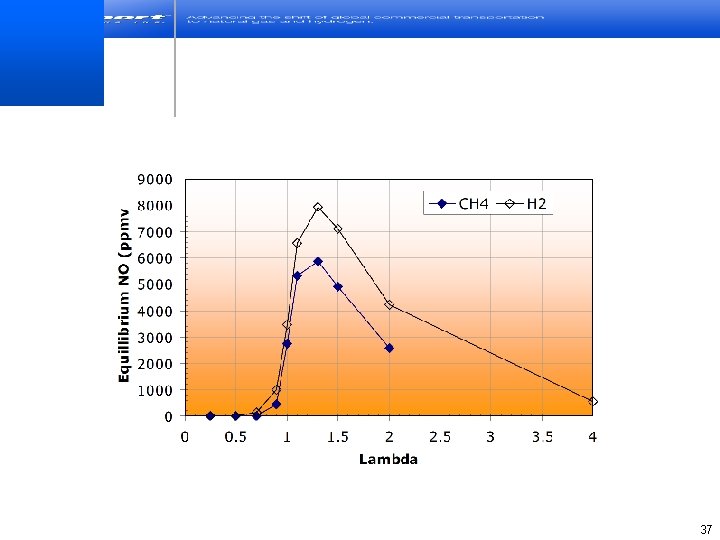
37
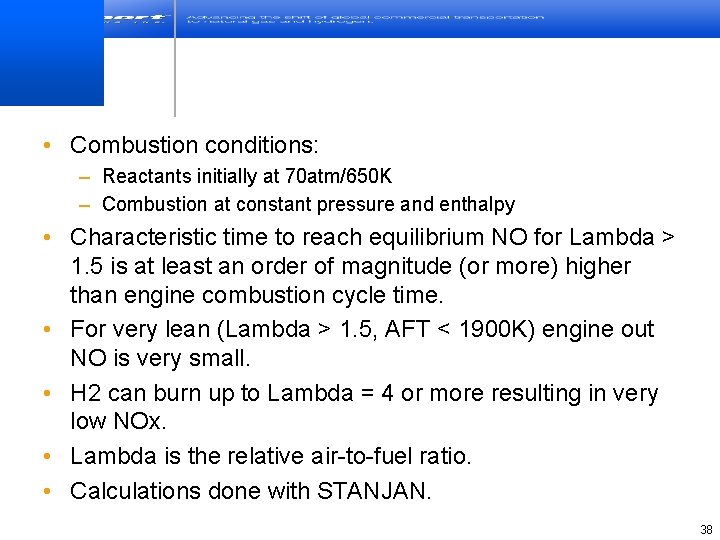
• Combustion conditions: – Reactants initially at 70 atm/650 K – Combustion at constant pressure and enthalpy • Characteristic time to reach equilibrium NO for Lambda > 1. 5 is at least an order of magnitude (or more) higher than engine combustion cycle time. • For very lean (Lambda > 1. 5, AFT < 1900 K) engine out NO is very small. • H 2 can burn up to Lambda = 4 or more resulting in very low NOx. • Lambda is the relative air-to-fuel ratio. • Calculations done with STANJAN. 38
Five opportunities in media and information
Greater bay area opportunities and challenges
Gas injection technology
Broadband technology opportunities program
L m p f i system uses
Ltlt pasteurization diagram
Bớt đầu thì bé nhất nhà
Các cơ quan trong bộ máy nhà nước
Dừng chân nghỉ lại nha trang
Design thking
Lưỡi cày đồng
Nhà tôi ở hà nội cách hồ gươm không xa
đi nhà trẻ các bạn ơi cùng vui chơi
Bài tập về nhà
Chuỗi cung ứng của th true milk
O'hen ri
đề tài ngày nhà giáo việt nam 20 tháng 11
Bài tập về nhà
Bài tập về nhà
Tìm số
Anh cút ra khỏi nhà tôi ngay nói giảm nói tránh
Bài tập về nhà
Nhà hình xoắn ở dưới ao
Bài tập về nhà
Bài tập về nhà
Tôi vui mừng tiến bước về nhà cha
Bài tập về nhà
Bác hàng xóm sang chúc tết chỉ có em ở nhà
Bài tập về nhà
Một nhà thơ chân chính
Bài tập về nhà
Nha organizational chart
Fcclainc
Fccla symbol
Nhà nguyễn thành lập
Bài tập về nhà
Tuấn và hải ở cạnh nhà nhau
Vì sao cá sấu mời khỉ đến chơi nhà