OnSite Hydrogen Production From HighPressure Liquids NHA Hydrogen
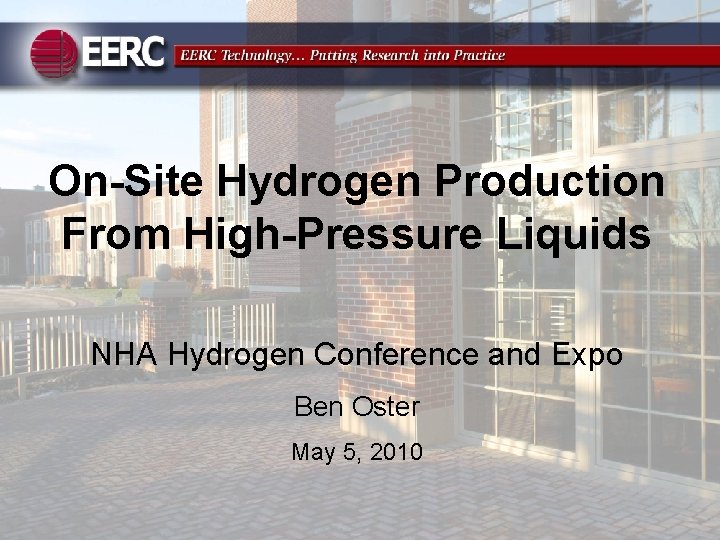
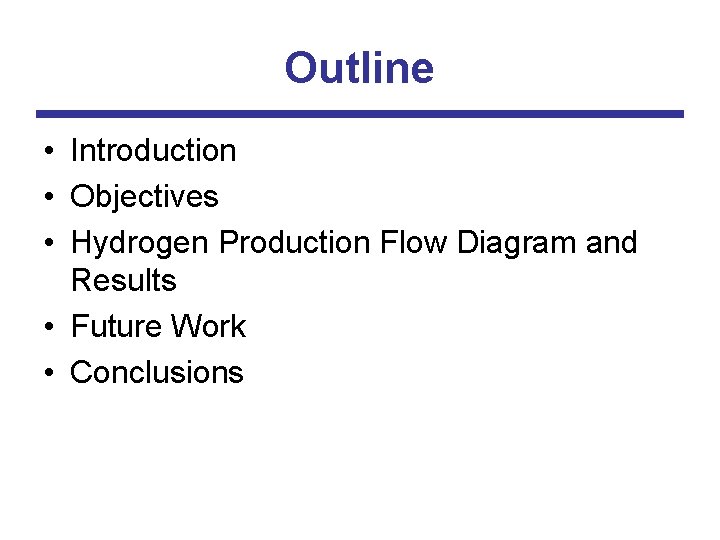
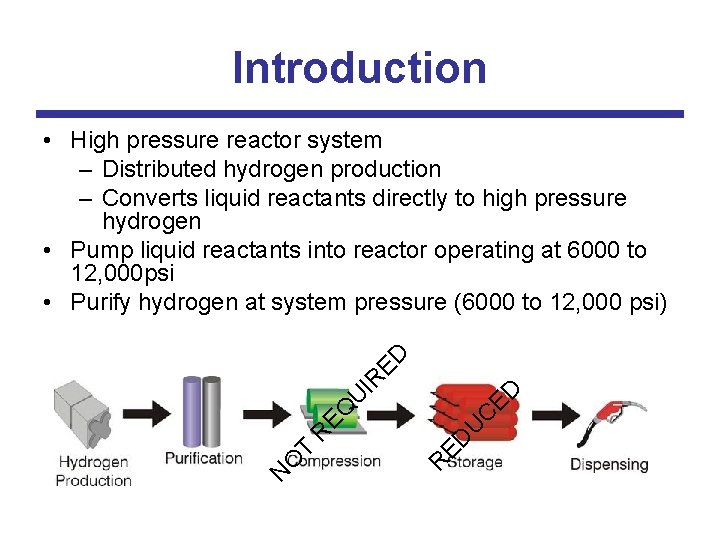
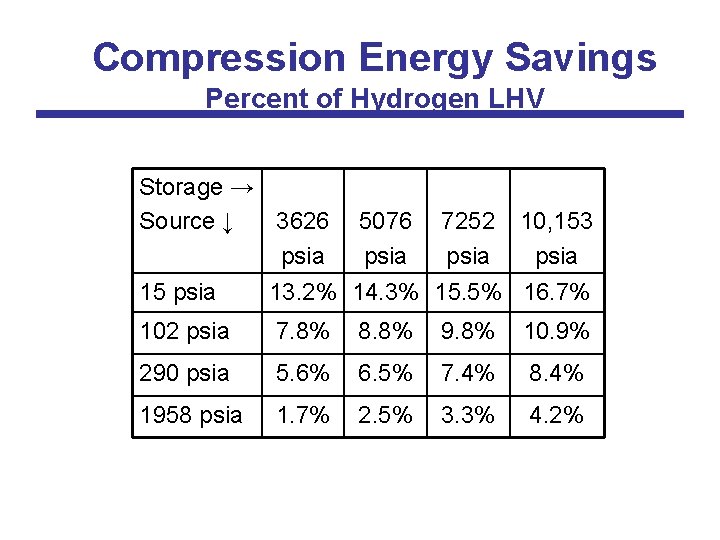
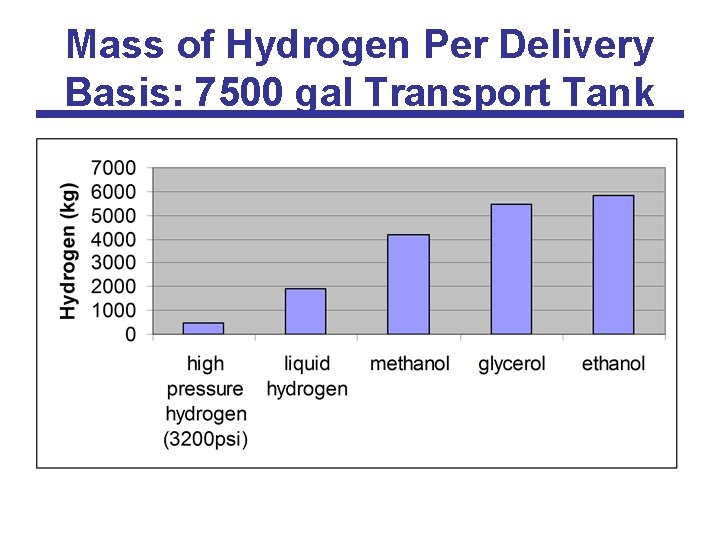
![Hydrogen Pipeline Challenges • Least expensive way to transport large amounts of hydrogen [1] Hydrogen Pipeline Challenges • Least expensive way to transport large amounts of hydrogen [1]](https://slidetodoc.com/presentation_image_h2/881d591719b9309cd6b7039a7cf5c801/image-6.jpg)
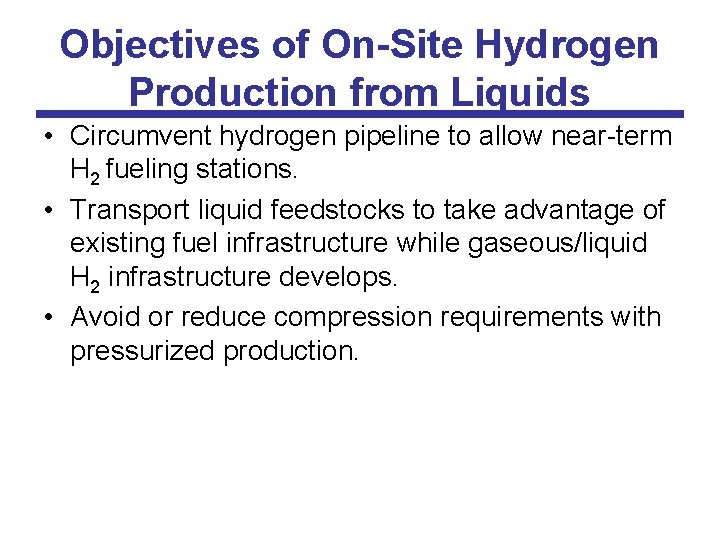
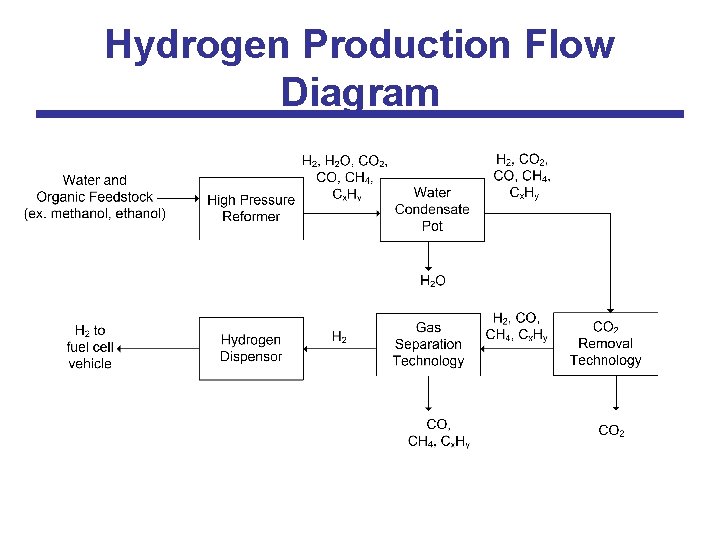
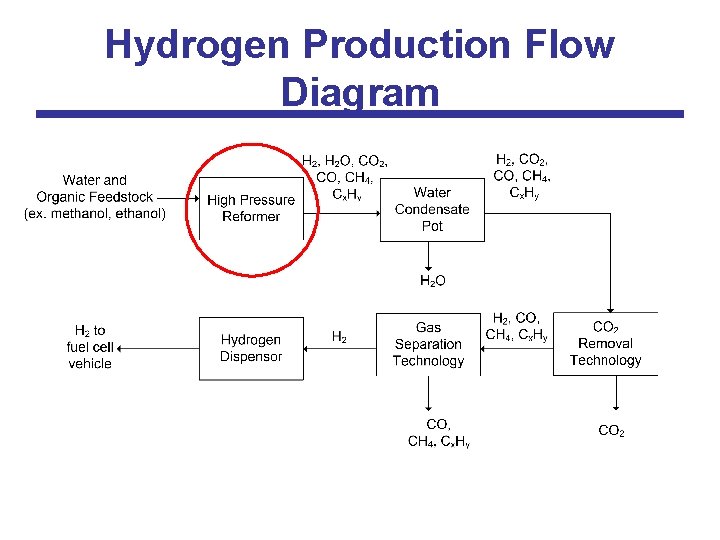
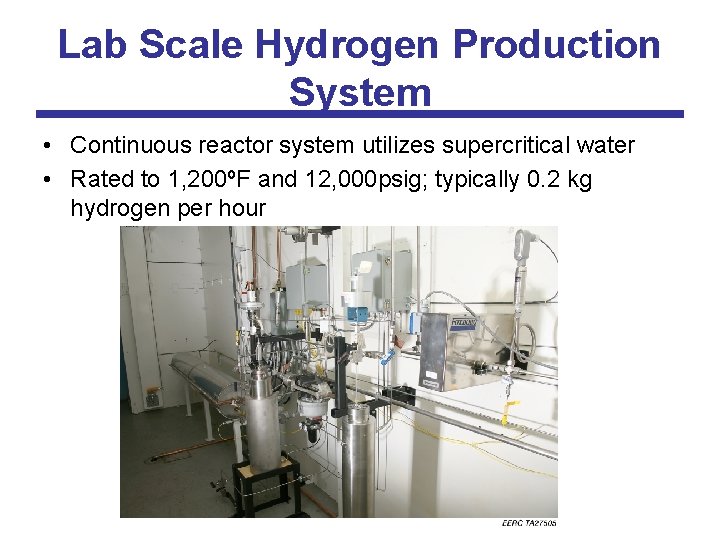

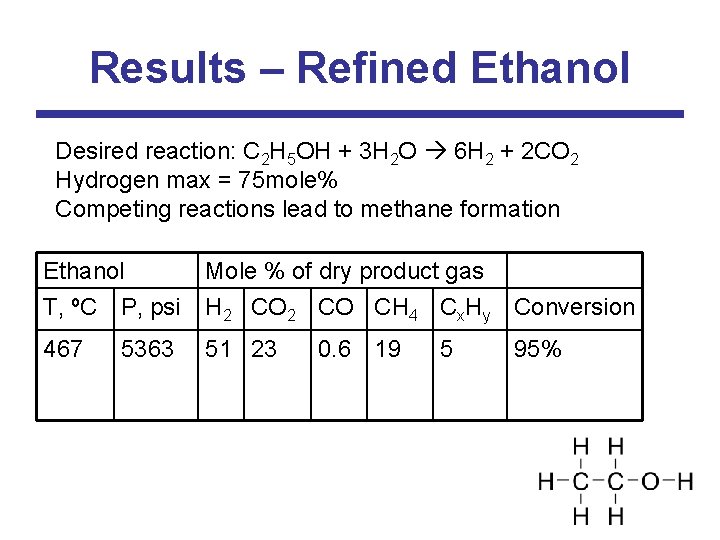
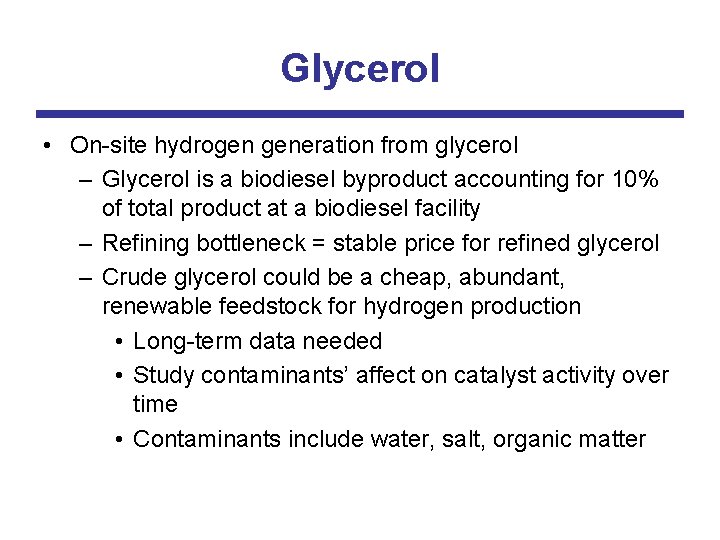
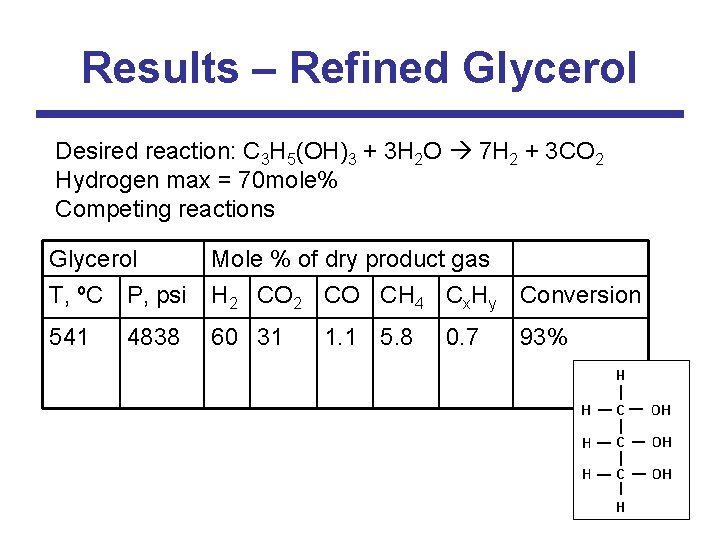

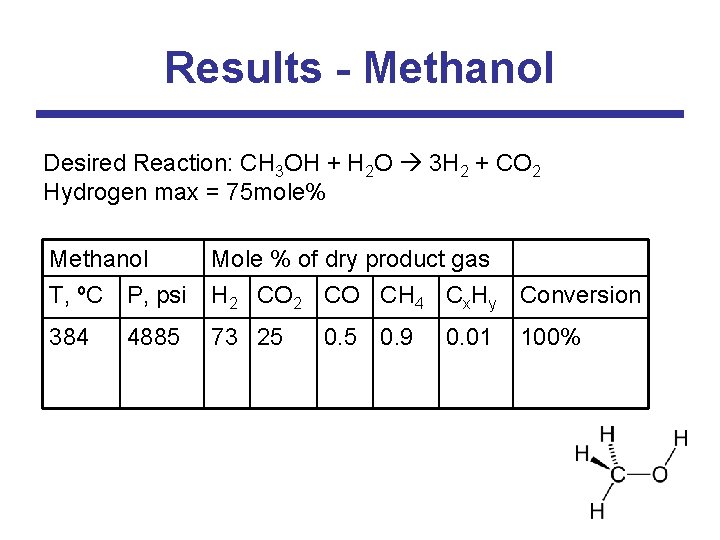
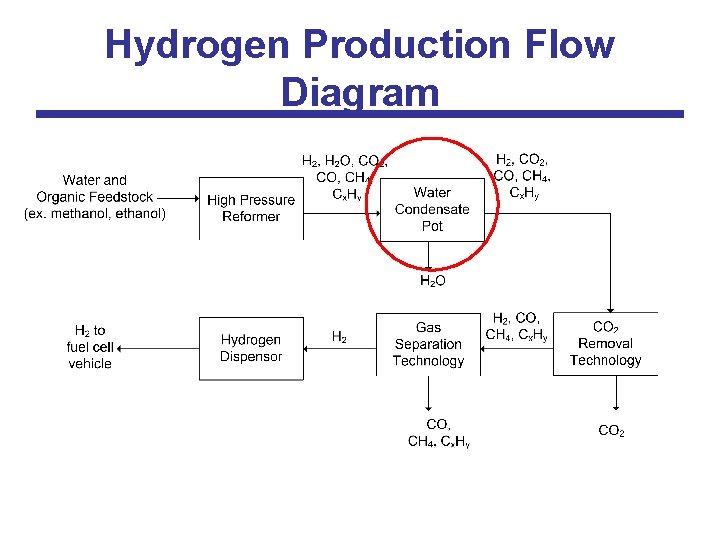
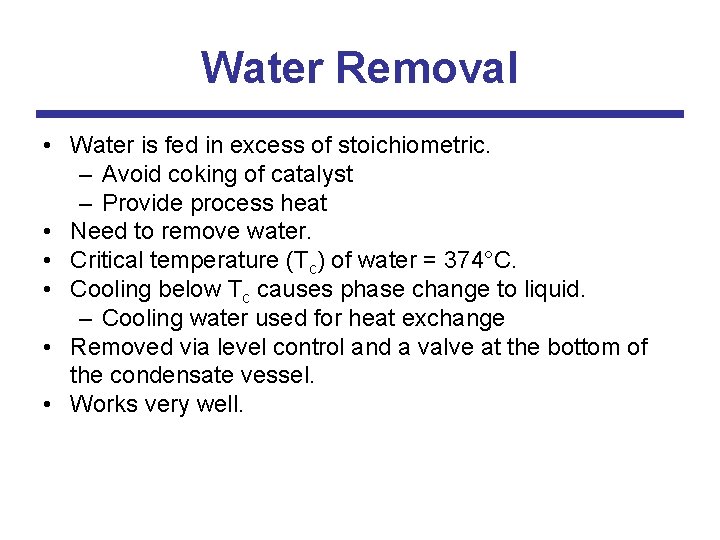
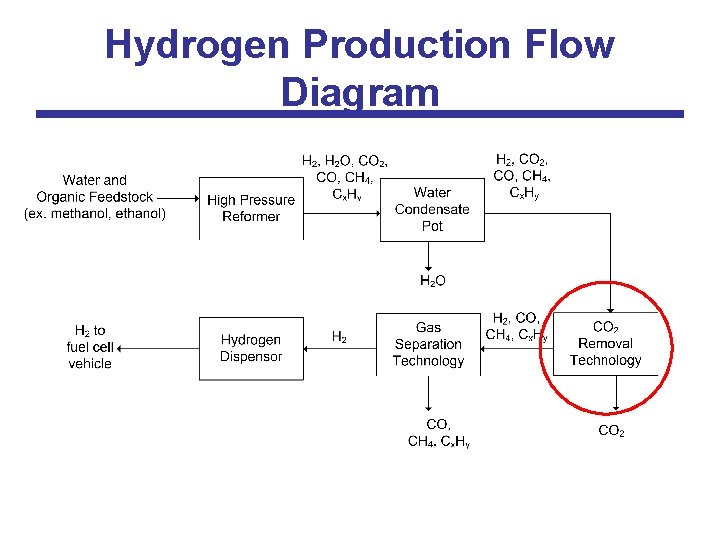
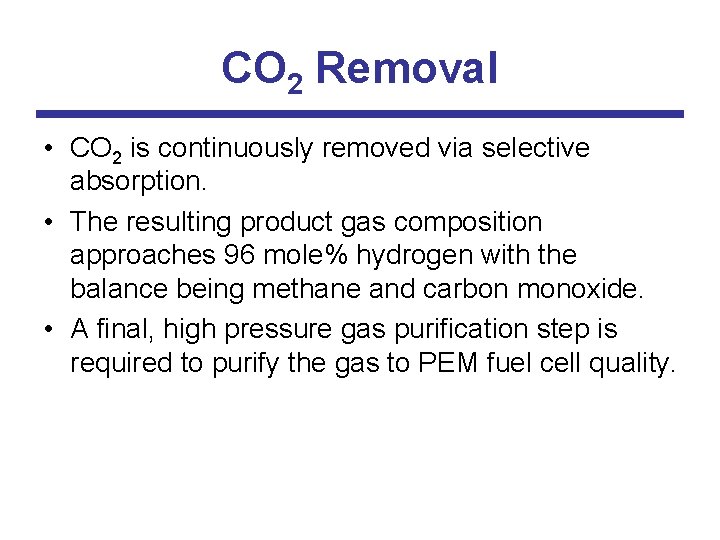
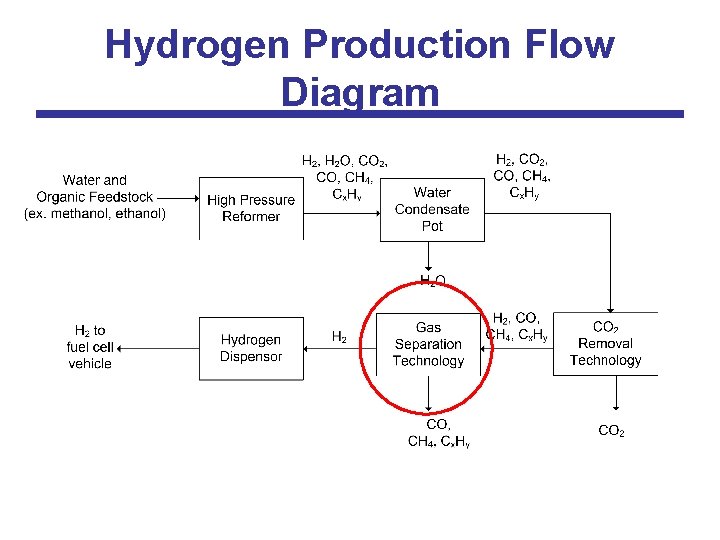
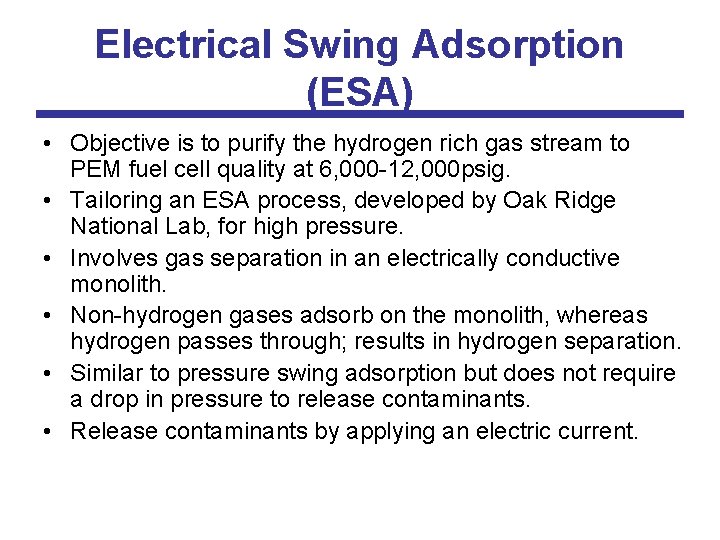
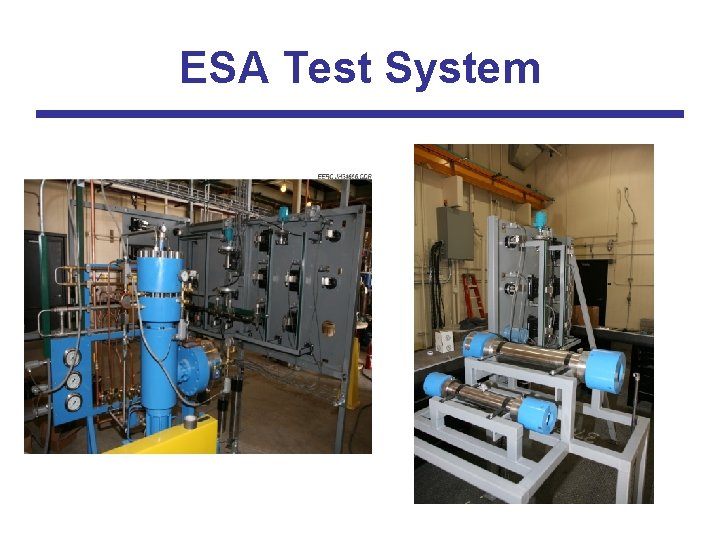
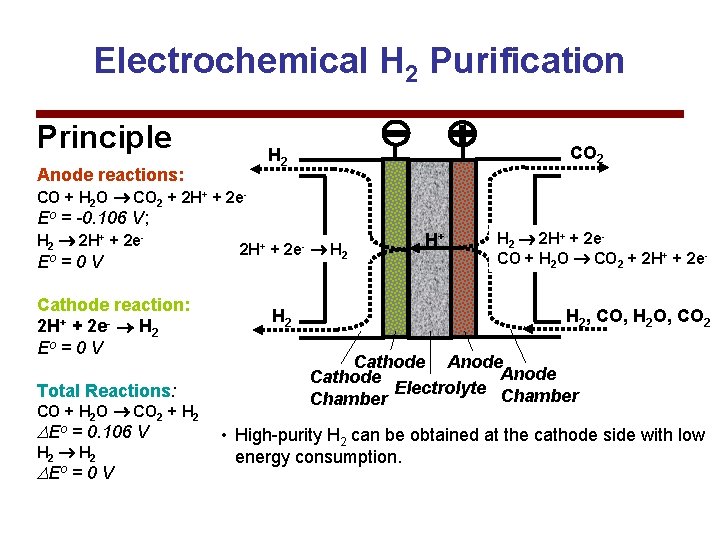
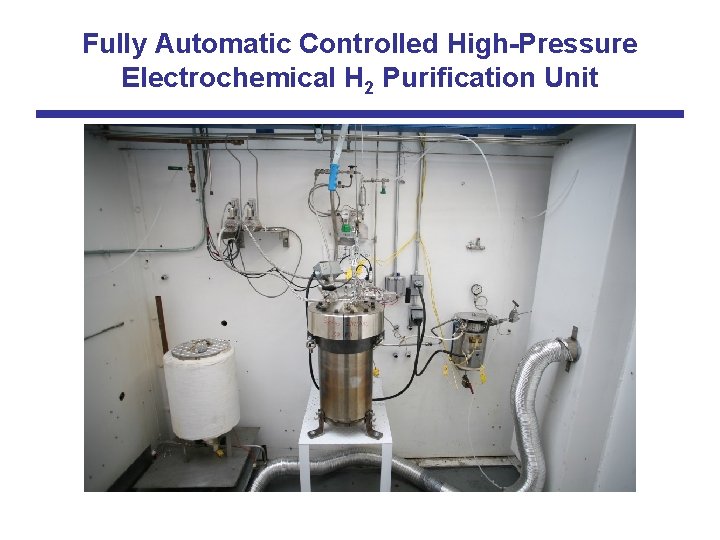
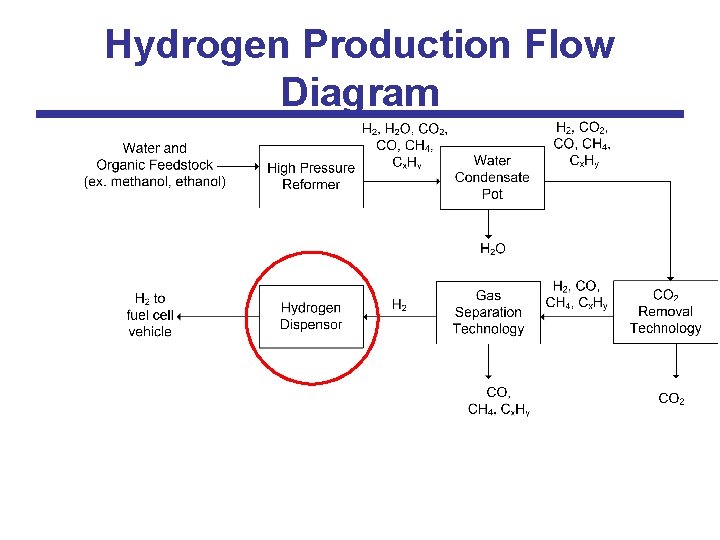

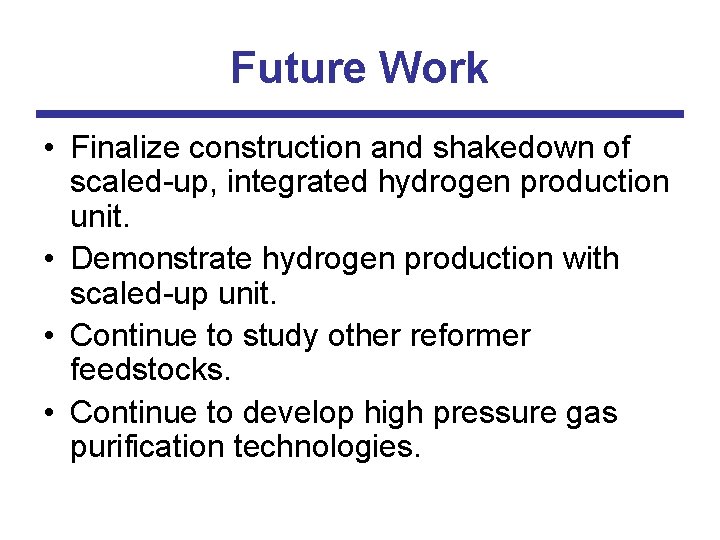
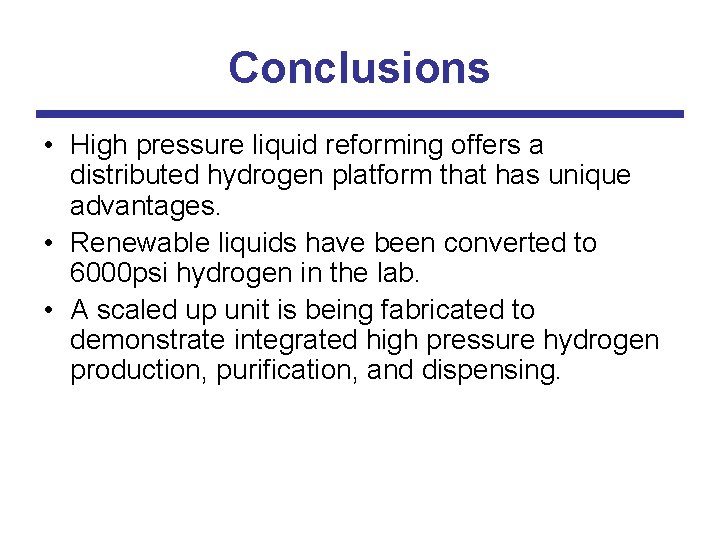

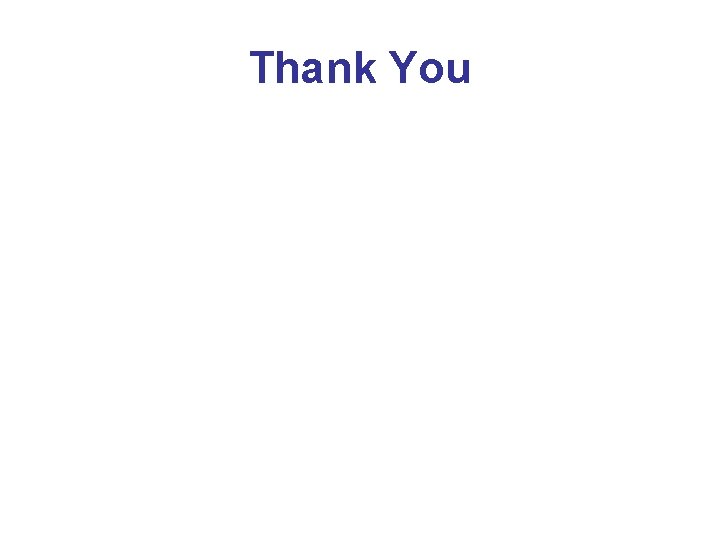
![Cited Sources • • [1] DOE Hydrogen Program. Hydrogen distribution and delivery infrastructure. Fact Cited Sources • • [1] DOE Hydrogen Program. Hydrogen distribution and delivery infrastructure. Fact](https://slidetodoc.com/presentation_image_h2/881d591719b9309cd6b7039a7cf5c801/image-32.jpg)
- Slides: 32
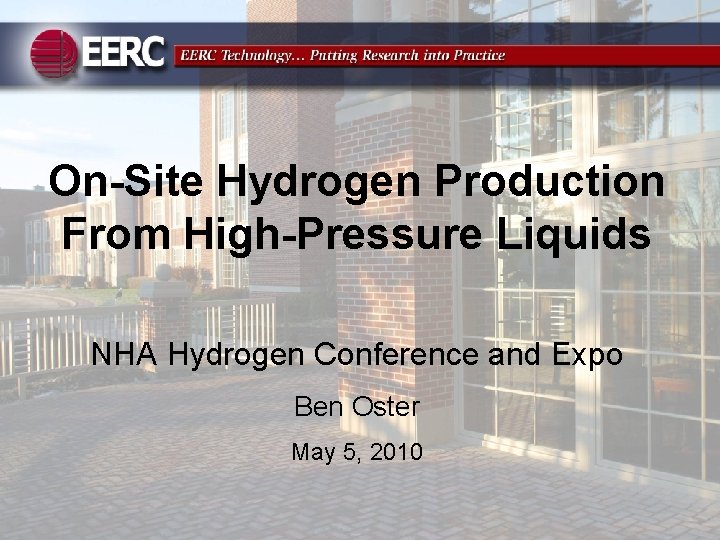
On-Site Hydrogen Production From High-Pressure Liquids NHA Hydrogen Conference and Expo Ben Oster May 5, 2010
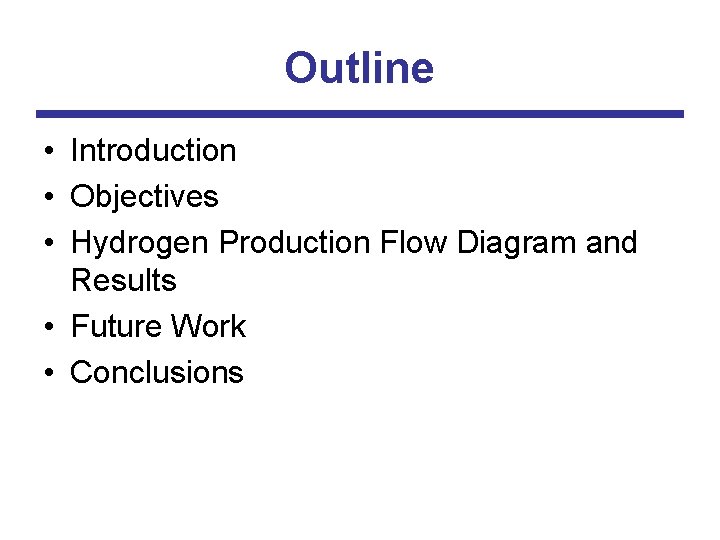
Outline • Introduction • Objectives • Hydrogen Production Flow Diagram and Results • Future Work • Conclusions
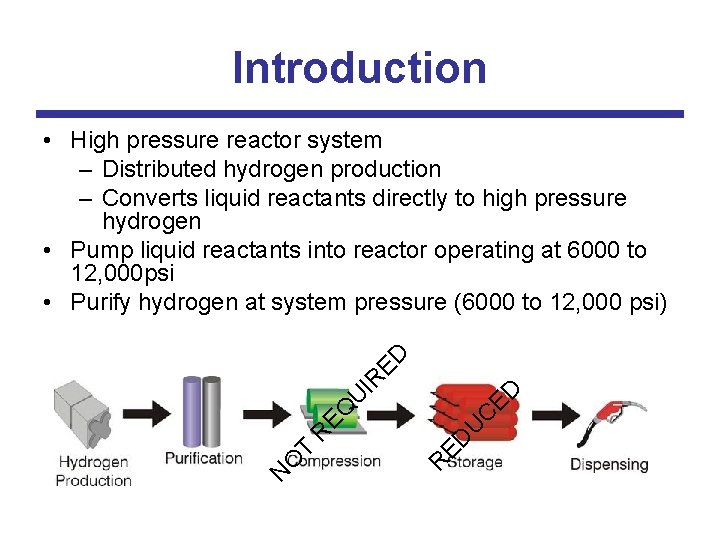
Introduction C U ED R N O T R EQ U ED IR ED • High pressure reactor system – Distributed hydrogen production – Converts liquid reactants directly to high pressure hydrogen • Pump liquid reactants into reactor operating at 6000 to 12, 000 psi • Purify hydrogen at system pressure (6000 to 12, 000 psi)
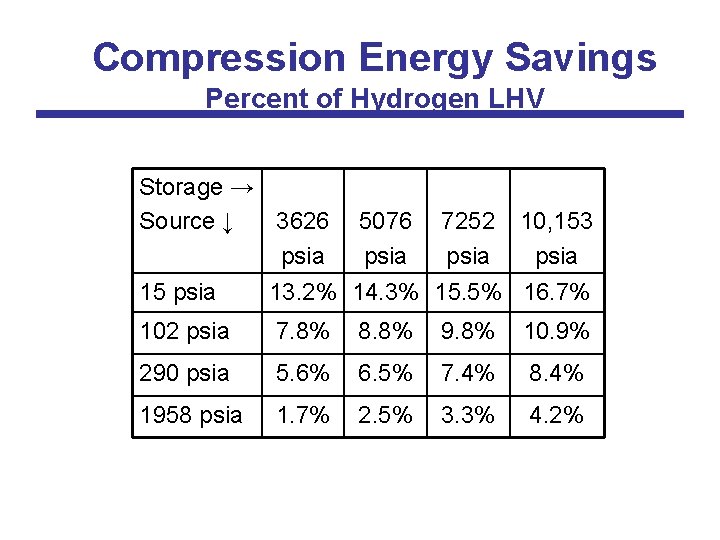
Compression Energy Savings Percent of Hydrogen LHV Storage → Source ↓ 3626 psia 5076 psia 7252 psia 10, 153 psia 15 psia 13. 2% 14. 3% 15. 5% 16. 7% 102 psia 7. 8% 8. 8% 9. 8% 10. 9% 290 psia 5. 6% 6. 5% 7. 4% 8. 4% 1958 psia 1. 7% 2. 5% 3. 3% 4. 2% Source: Air Products and Chemicals, Inc.
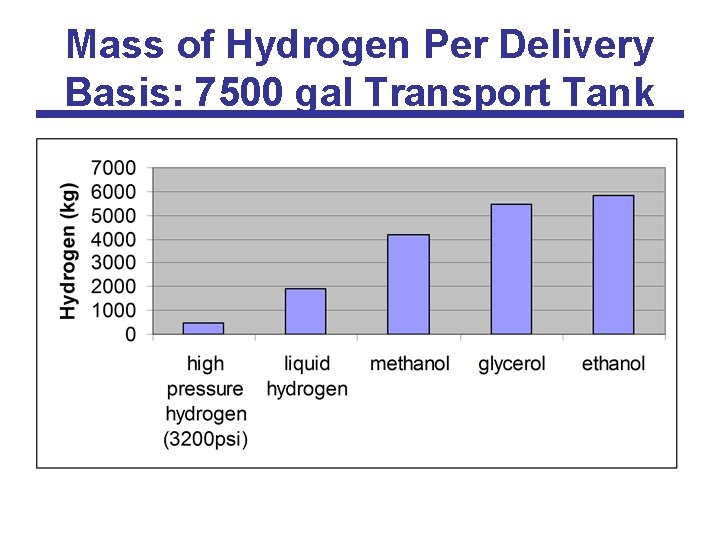
Mass of Hydrogen Per Delivery Basis: 7500 gal Transport Tank
![Hydrogen Pipeline Challenges Least expensive way to transport large amounts of hydrogen 1 Hydrogen Pipeline Challenges • Least expensive way to transport large amounts of hydrogen [1]](https://slidetodoc.com/presentation_image_h2/881d591719b9309cd6b7039a7cf5c801/image-6.jpg)
Hydrogen Pipeline Challenges • Least expensive way to transport large amounts of hydrogen [1] • Existing hydrogen pipeline is 0. 33% of natural gas pipeline in length with only 200 delivery points [2] • $1. 2 million/mile (transmission) and $0. 3 million/mile (distribution) [3] • Advancements could decrease costs >50% [4] • Distributed hydrogen generation provides a near term solution
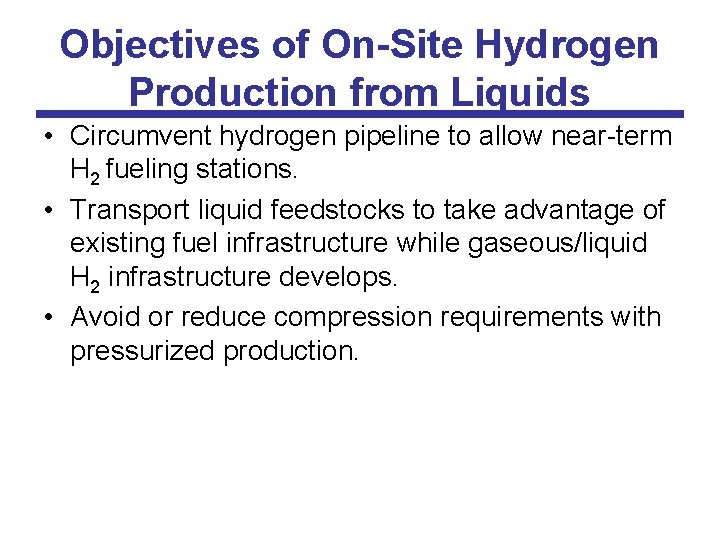
Objectives of On-Site Hydrogen Production from Liquids • Circumvent hydrogen pipeline to allow near-term H 2 fueling stations. • Transport liquid feedstocks to take advantage of existing fuel infrastructure while gaseous/liquid H 2 infrastructure develops. • Avoid or reduce compression requirements with pressurized production.
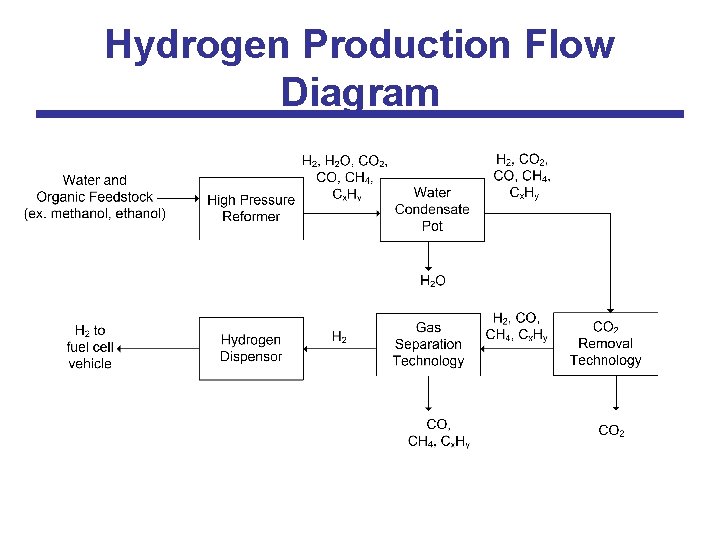
Hydrogen Production Flow Diagram
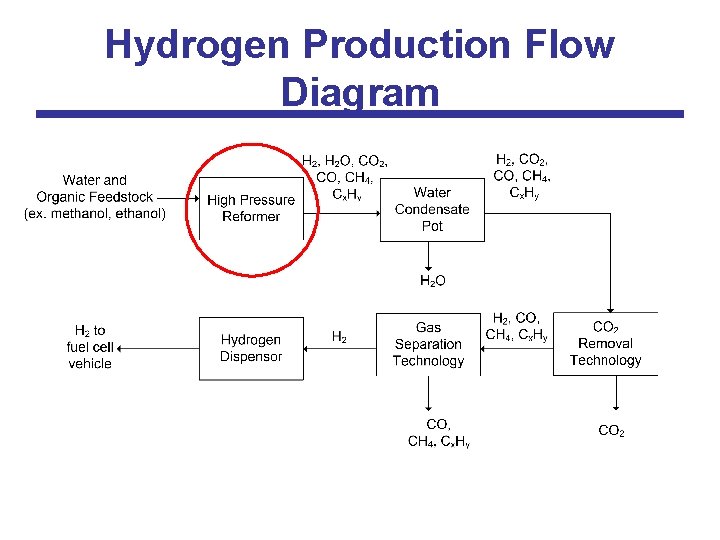
Hydrogen Production Flow Diagram
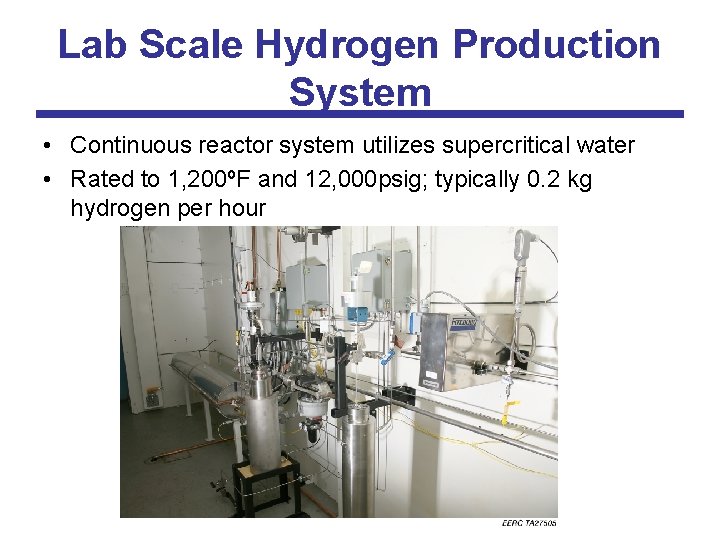
Lab Scale Hydrogen Production System • Continuous reactor system utilizes supercritical water • Rated to 1, 200ºF and 12, 000 psig; typically 0. 2 kg hydrogen per hour

Ethanol • On-site hydrogen generation from ethanol – Ethanol is an available and renewable feedstock – Crude ethanol/water mixture could be a less expensive feedstock • Long term data needed to study catalyst activity over time • Potentially cheaper due to less processing at the ethanol production facility • Water is a non-issue as it is a required reactant • Other contaminants need to be examined more closely with respect to potential plugging & coking issues
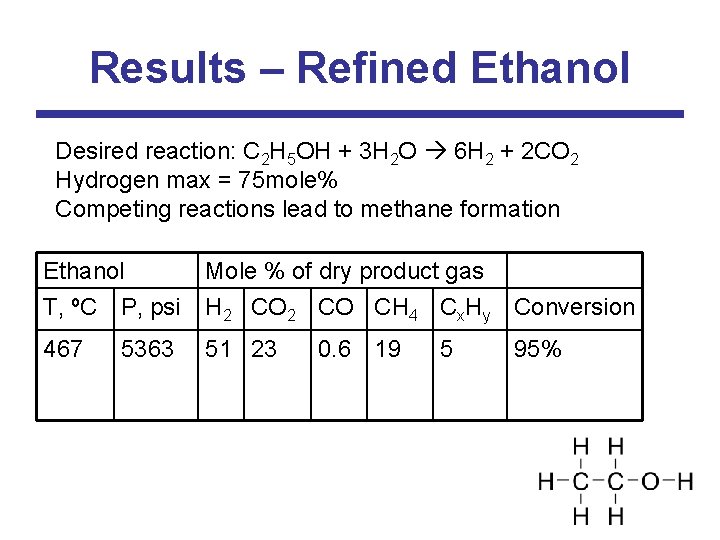
Results – Refined Ethanol Desired reaction: C 2 H 5 OH + 3 H 2 O 6 H 2 + 2 CO 2 Hydrogen max = 75 mole% Competing reactions lead to methane formation Ethanol T, ºC P, psi Mole % of dry product gas H 2 CO CH 4 Cx. Hy Conversion 467 51 23 5363 0. 6 19 5 95%
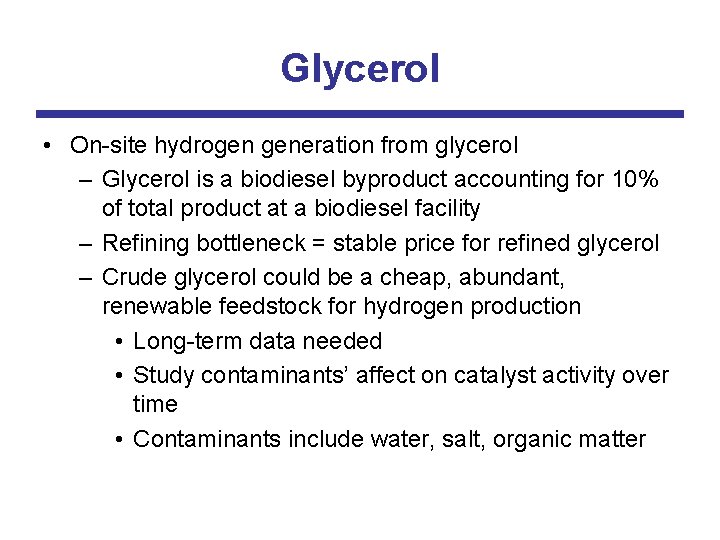
Glycerol • On-site hydrogen generation from glycerol – Glycerol is a biodiesel byproduct accounting for 10% of total product at a biodiesel facility – Refining bottleneck = stable price for refined glycerol – Crude glycerol could be a cheap, abundant, renewable feedstock for hydrogen production • Long-term data needed • Study contaminants’ affect on catalyst activity over time • Contaminants include water, salt, organic matter
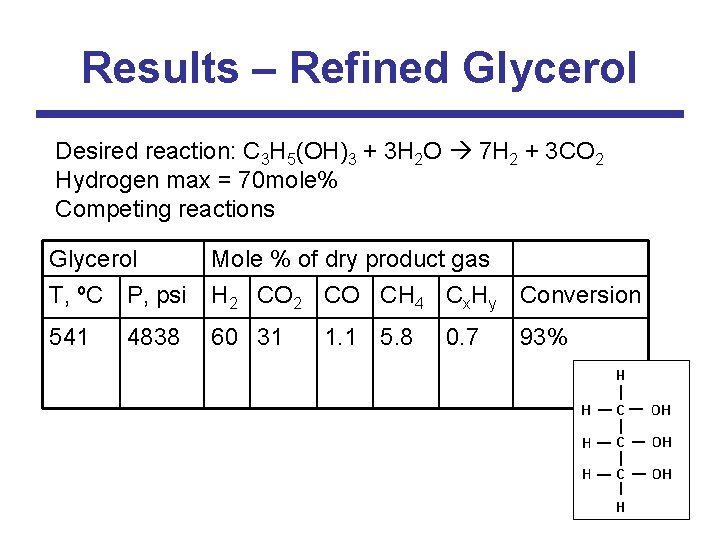
Results – Refined Glycerol Desired reaction: C 3 H 5(OH)3 + 3 H 2 O 7 H 2 + 3 CO 2 Hydrogen max = 70 mole% Competing reactions Glycerol T, ºC P, psi Mole % of dry product gas H 2 CO CH 4 Cx. Hy Conversion 541 60 31 4838 1. 1 5. 8 0. 7 93%

Methanol • Methanol is currently synthesized from natural gas • Methanol can be synthesized from renewable biomass • Methanol is a simple molecule and reforms completely at high pressures and relatively low temperatures
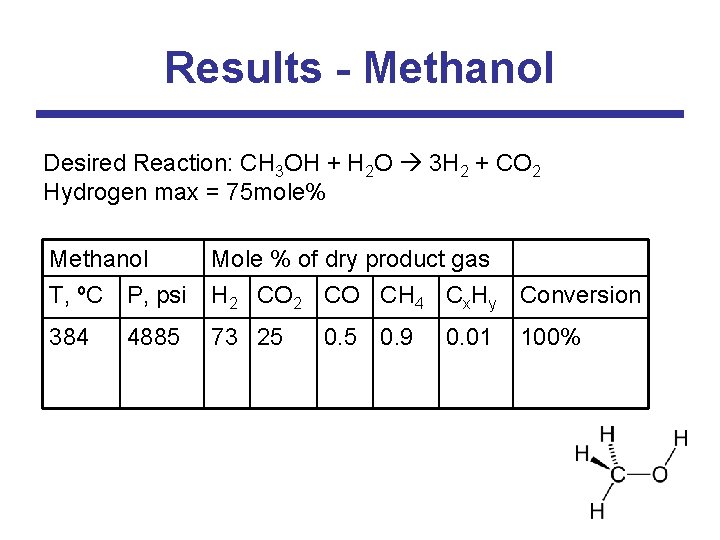
Results - Methanol Desired Reaction: CH 3 OH + H 2 O 3 H 2 + CO 2 Hydrogen max = 75 mole% Methanol T, ºC P, psi Mole % of dry product gas H 2 CO CH 4 Cx. Hy Conversion 384 73 25 4885 0. 9 0. 01 100%
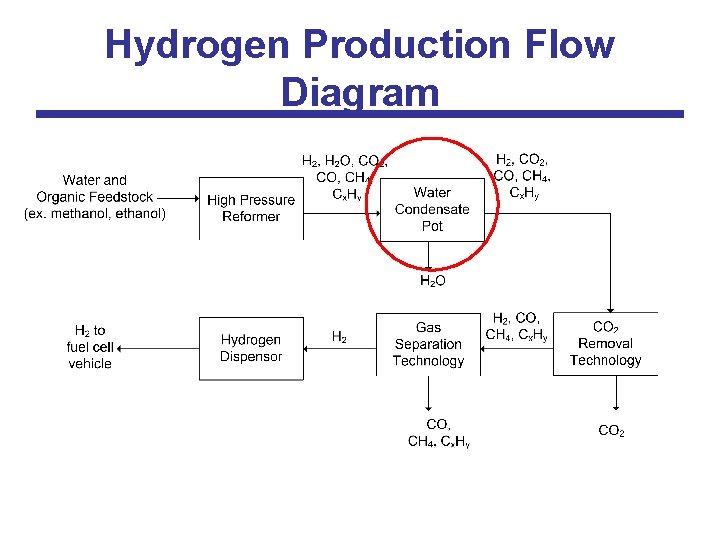
Hydrogen Production Flow Diagram
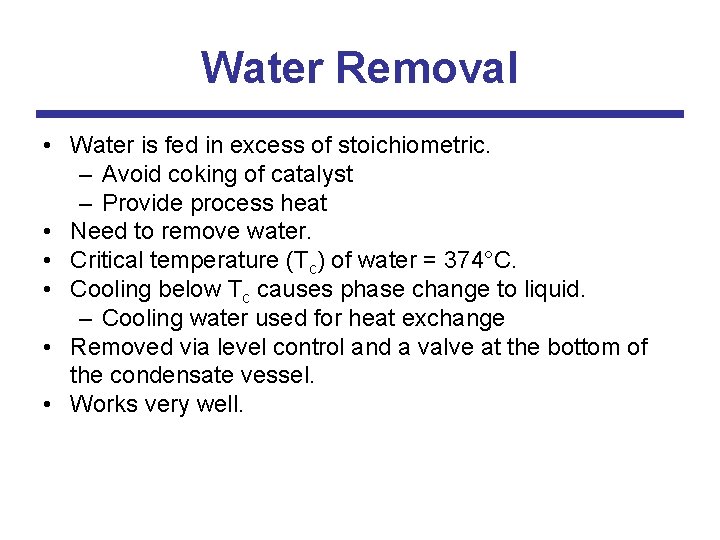
Water Removal • Water is fed in excess of stoichiometric. – Avoid coking of catalyst – Provide process heat • Need to remove water. • Critical temperature (Tc) of water = 374°C. • Cooling below Tc causes phase change to liquid. – Cooling water used for heat exchange • Removed via level control and a valve at the bottom of the condensate vessel. • Works very well.
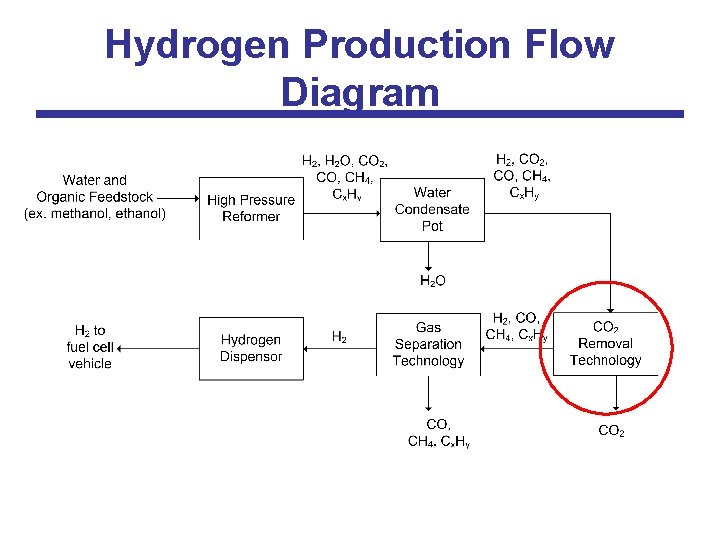
Hydrogen Production Flow Diagram
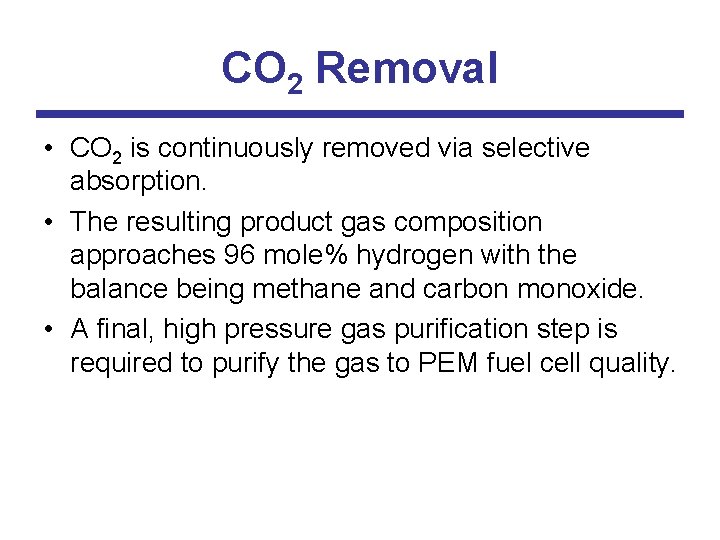
CO 2 Removal • CO 2 is continuously removed via selective absorption. • The resulting product gas composition approaches 96 mole% hydrogen with the balance being methane and carbon monoxide. • A final, high pressure gas purification step is required to purify the gas to PEM fuel cell quality.
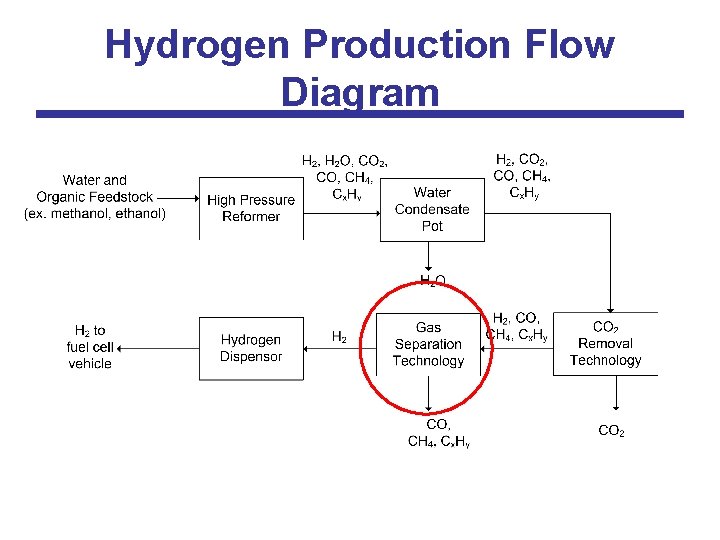
Hydrogen Production Flow Diagram
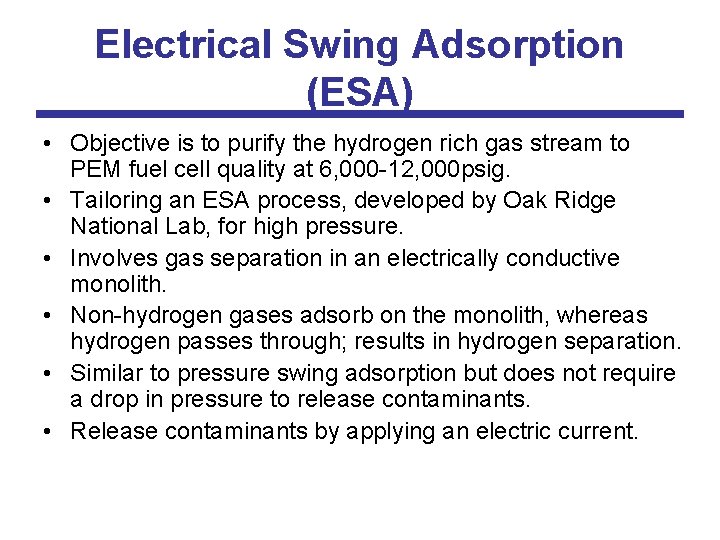
Electrical Swing Adsorption (ESA) • Objective is to purify the hydrogen rich gas stream to PEM fuel cell quality at 6, 000 -12, 000 psig. • Tailoring an ESA process, developed by Oak Ridge National Lab, for high pressure. • Involves gas separation in an electrically conductive monolith. • Non-hydrogen gases adsorb on the monolith, whereas hydrogen passes through; results in hydrogen separation. • Similar to pressure swing adsorption but does not require a drop in pressure to release contaminants. • Release contaminants by applying an electric current.
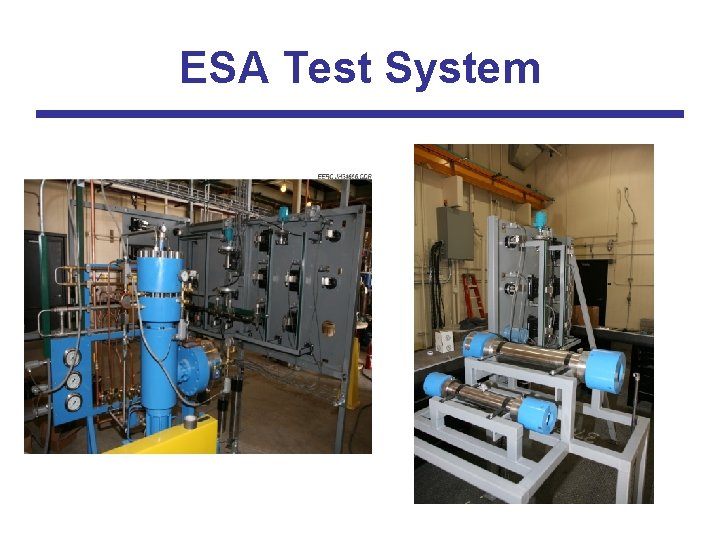
ESA Test System
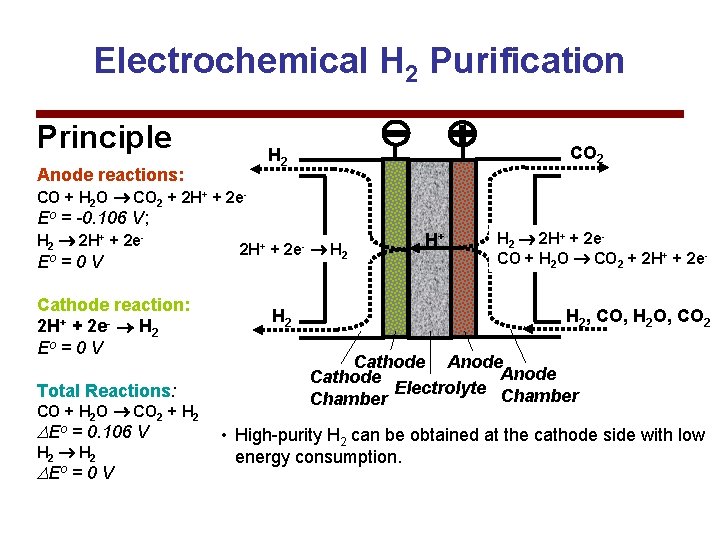
Electrochemical H 2 Purification Principle CO 2 H 2 Anode reactions: CO + H 2 O CO 2 + 2 H+ + 2 e- Eo = -0. 106 V; H 2 2 H+ + 2 e- Eo = 0 V Cathode reaction: 2 H+ + 2 e- H 2 Eo = 0 V Total Reactions: CO + H 2 O CO 2 + H 2 Eo = 0. 106 V H 2 Eo = 0 V 2 H+ + 2 e- H 2 H+ H 2 2 H+ + 2 e. CO + H 2 O CO 2 + 2 H+ + 2 e- H 2, CO, H 2 O, CO 2 Cathode Anode Cathode Electrolyte Chamber • High-purity H 2 can be obtained at the cathode side with low energy consumption.
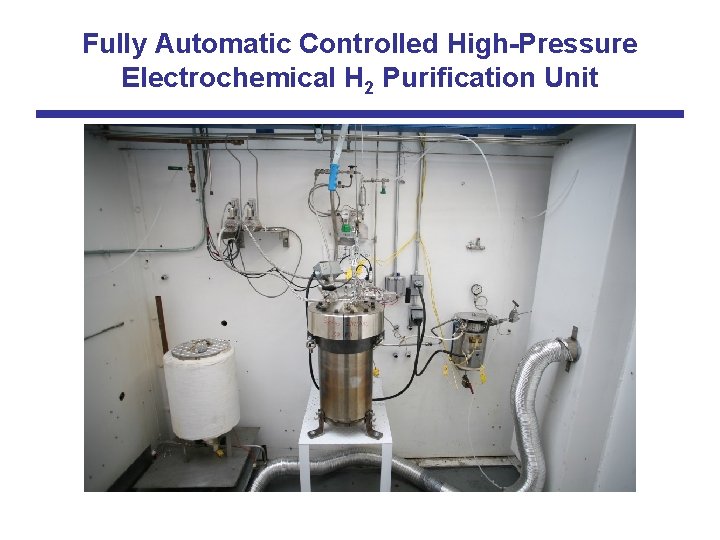
Fully Automatic Controlled High-Pressure Electrochemical H 2 Purification Unit
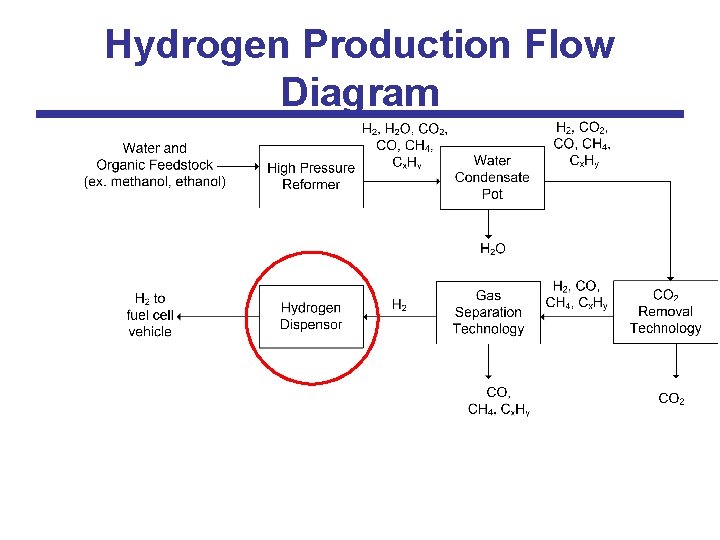
Hydrogen Production Flow Diagram

Scaled-up, Integrated System: Projected H 2 delivery rate of 0. 6 kg/hr CO 2 REMOVAL STORAGE H 2 DISPENSING HYDROGEN PURIFICATION REFORMER REACTOR PREHEATER FEED STORAGE TANKS
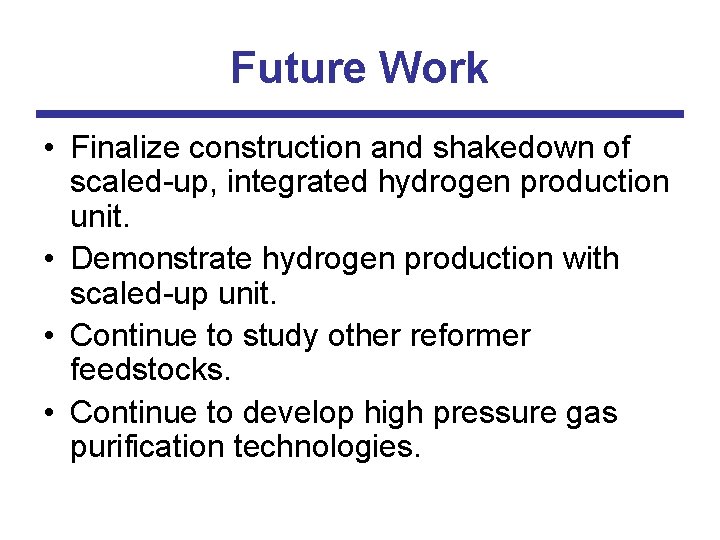
Future Work • Finalize construction and shakedown of scaled-up, integrated hydrogen production unit. • Demonstrate hydrogen production with scaled-up unit. • Continue to study other reformer feedstocks. • Continue to develop high pressure gas purification technologies.
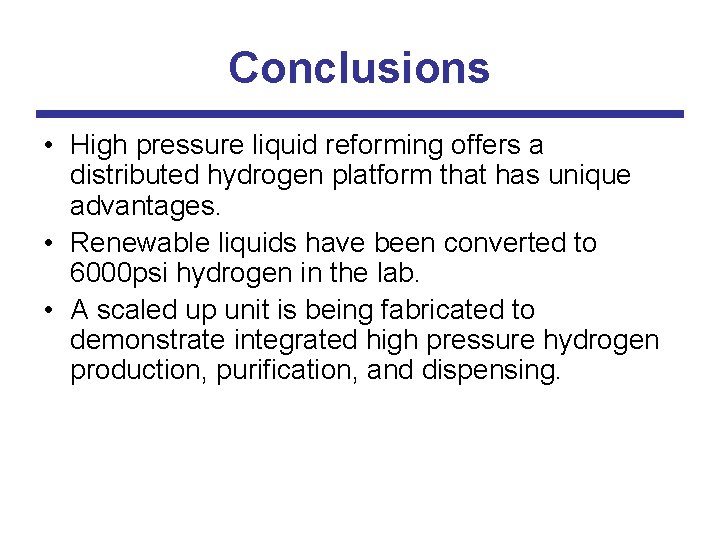
Conclusions • High pressure liquid reforming offers a distributed hydrogen platform that has unique advantages. • Renewable liquids have been converted to 6000 psi hydrogen in the lab. • A scaled up unit is being fabricated to demonstrate integrated high pressure hydrogen production, purification, and dispensing.

Acknowledgements • U. S. Army Corps of Engineers, Engineer Research Development Center, Construction Engineering Research Laboratory (ERDC-CERL) • National Center for Hydrogen Technology (NCHT) sponsored by the U. S. Department of Energy (DOE) National Energy Technology Laboratory (NETL)
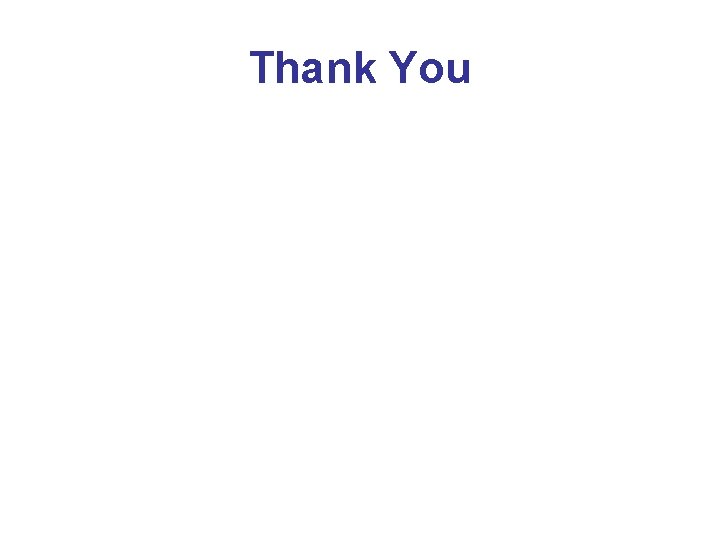
Thank You
![Cited Sources 1 DOE Hydrogen Program Hydrogen distribution and delivery infrastructure Fact Cited Sources • • [1] DOE Hydrogen Program. Hydrogen distribution and delivery infrastructure. Fact](https://slidetodoc.com/presentation_image_h2/881d591719b9309cd6b7039a7cf5c801/image-32.jpg)
Cited Sources • • [1] DOE Hydrogen Program. Hydrogen distribution and delivery infrastructure. Fact Sheet. http: //www. hydrogen. energy. gov/pdfs/doe_h 2_delivery. pdf [2] The Impact of Increased Use of Hydrogen on Petroleum Consumption and carbon Dioxide Emissions. August 2008. Energy Information Administration. Office of Integrated Analysis and Forecasting, Office of Coal, Nuclear, Electric and Alternative Fuels. US Department of Energy. Washington, DC 20585. [3] See U. S. Department of Energy, Energy Efficiency and Renewable Energy, Hydrogen, Fuel Cells & Infrastructure Technologies Program: Multi-Year Research, Development and Demonstration Plan, Table 3. 2. 2 (Washington, DC, October 2007), www 1. eere. energy. gov/hydrogenandfuelcells/mypp. [4] B. Smith, B. Frame, L. Anovitz, and T. Armstrong, “Composite Technology for Hydrogen Pipelines, ” in U. S. Department of Energy, Hydrogen Program, 2008 Annual Merit Review Proceedings, www. hydrogen. energy. gov/annual_review 08_proceedings. html
Onsite hydrogen generation
Carta alir proses pembuatan produk
Onsite supervision
Onsite emergency plan
Cloud.seetest
Onsite design
"onsite energy"
Onsite billing
On site marketing
Production of hydrogen from methane
Steam methane reforming ppt
Vì sao cá sấu mời khỉ đến chơi nhà
Nhà nguyễn ra đời trong hoàn cảnh nào
Dừng chân nghỉ lại nha trang
Trò chơi có nhạc
Anh cút ra khỏi nhà tôi ngay nói giảm nói tránh
Bài tập về nhà
Nhà nguyễn thành lập
Bài tập về nhà
Bác hàng xóm sang chúc tết chỉ có em ở nhà
Bài tập về nhà
Lưỡi cày đồng
Cc t
Thơ em làm thợ xây
Nhà thờ kiếng
Nha organizational chart
Bài tập về nhà
Quản trị chuỗi cung ứng của th true milk
Bài tập về nhà
Bớt đầu thì bé nhất nhà
Bài tập về nhà
Bài tập về nhà
Nhà tôi ở hà nội cách hồ gươm không xa