Hydrochar Catalysts for Efficient WastetoFuel Conversion Marcus Wright
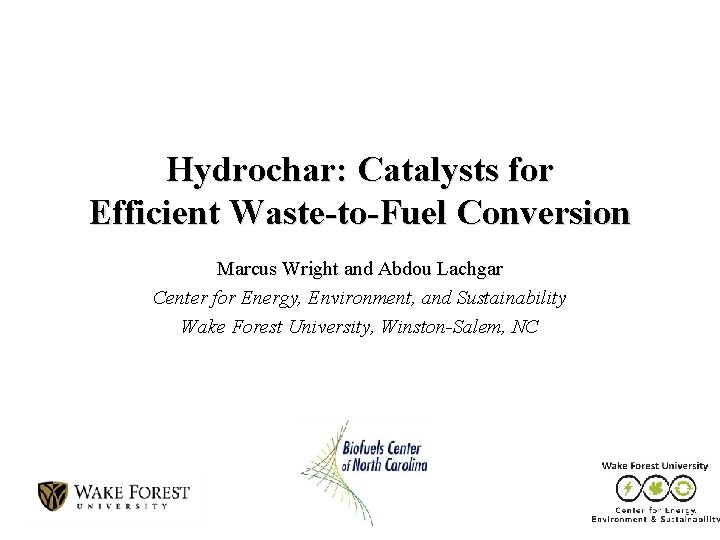
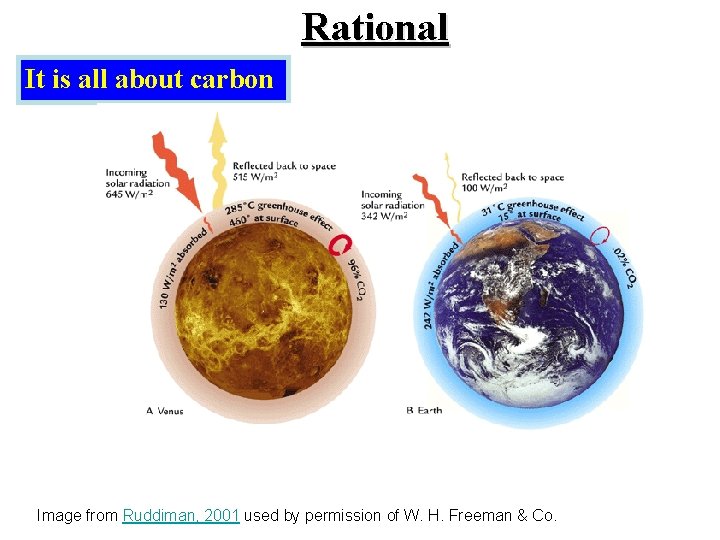
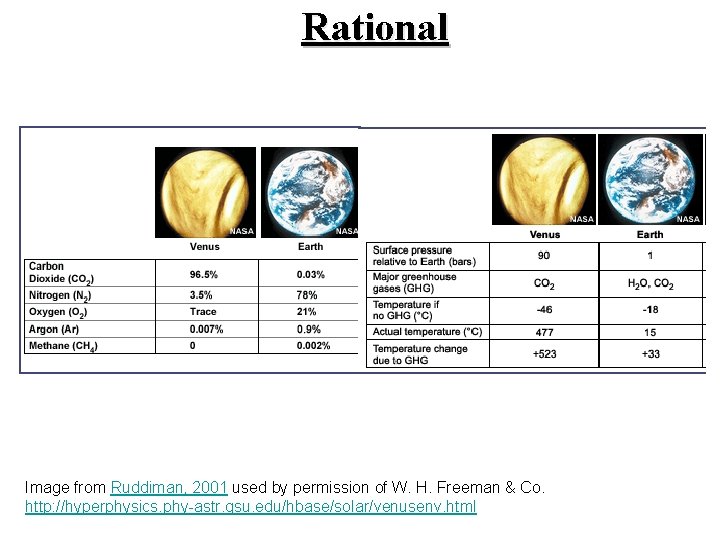
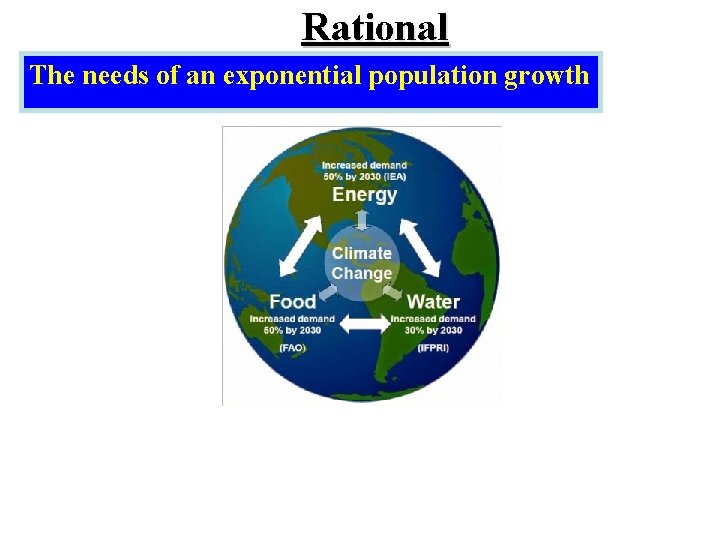
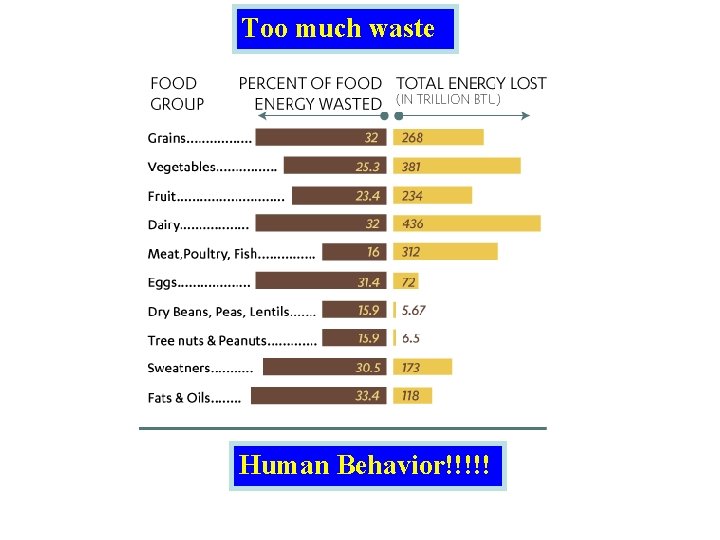
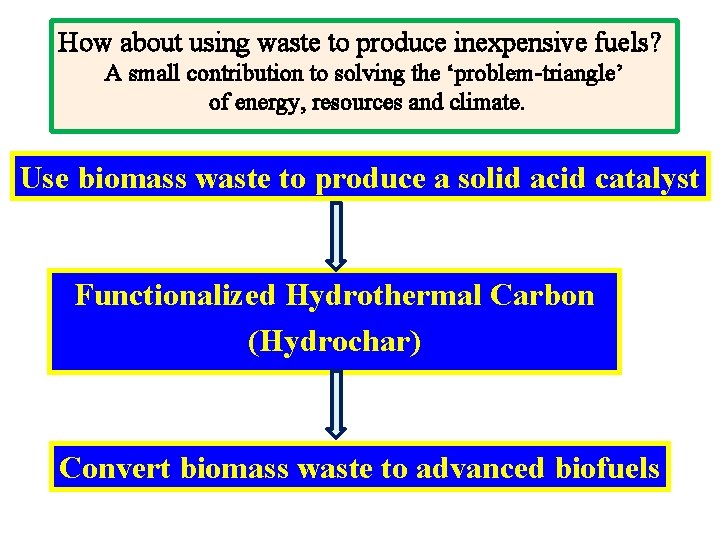
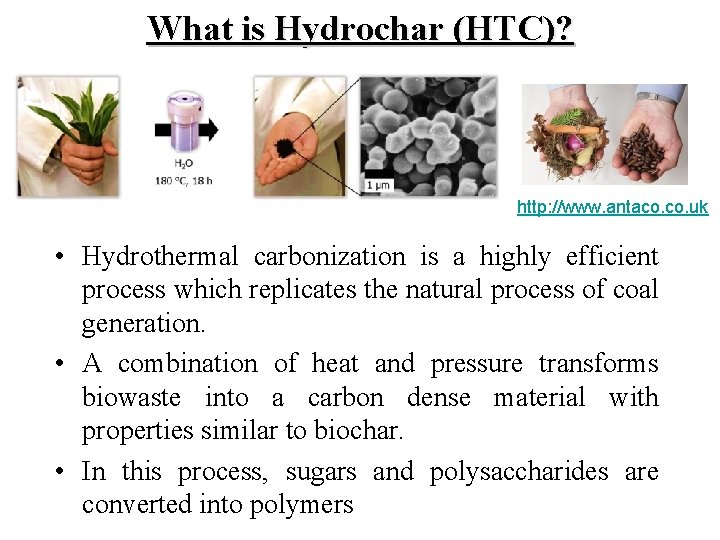
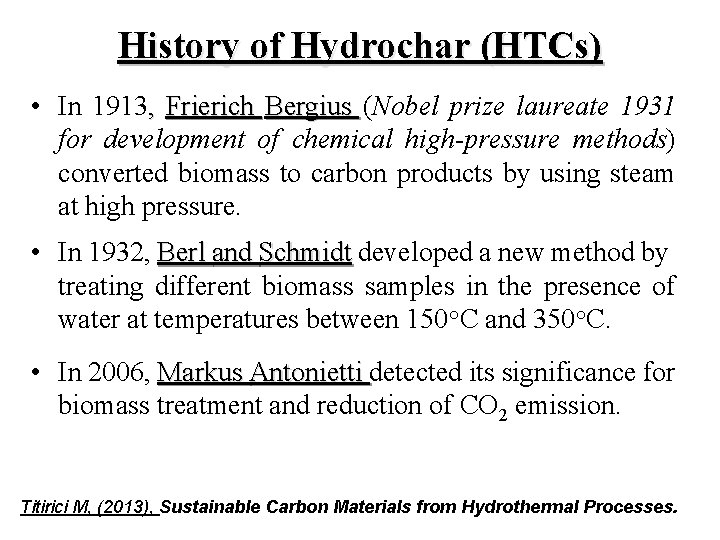
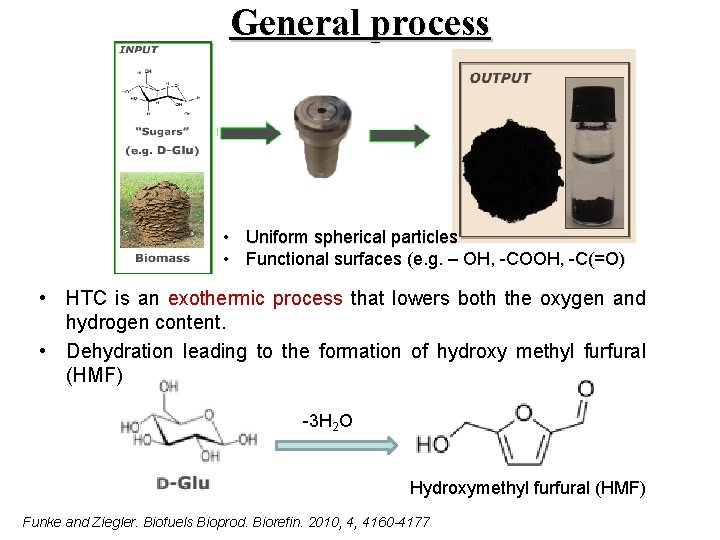
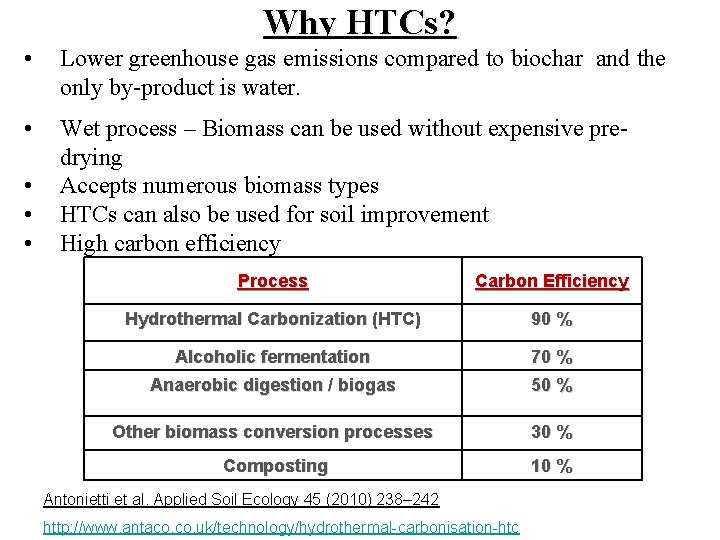
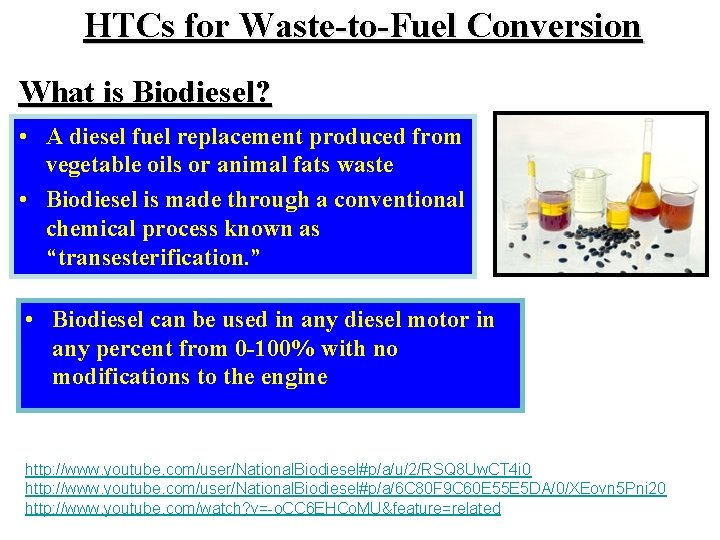
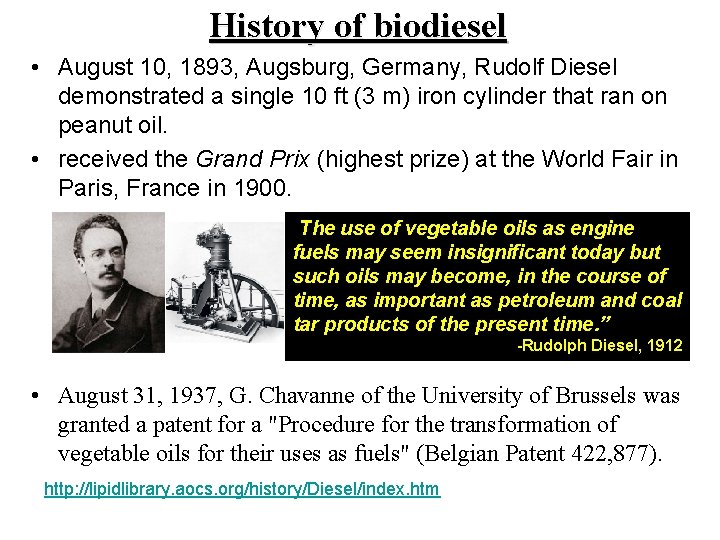
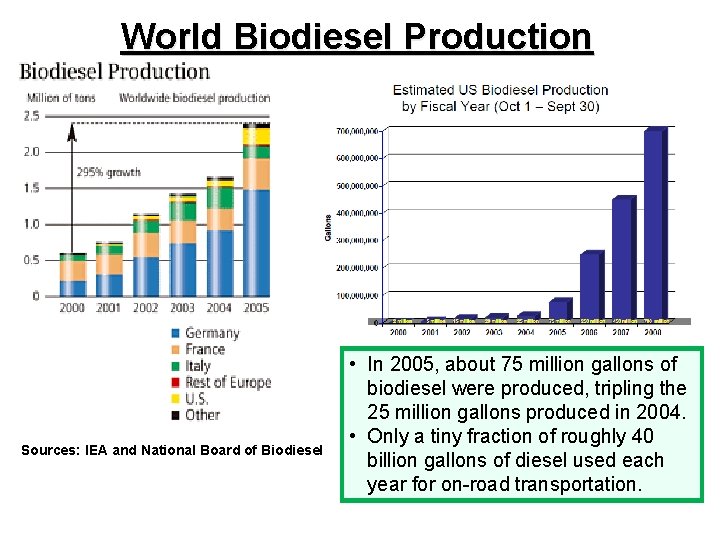
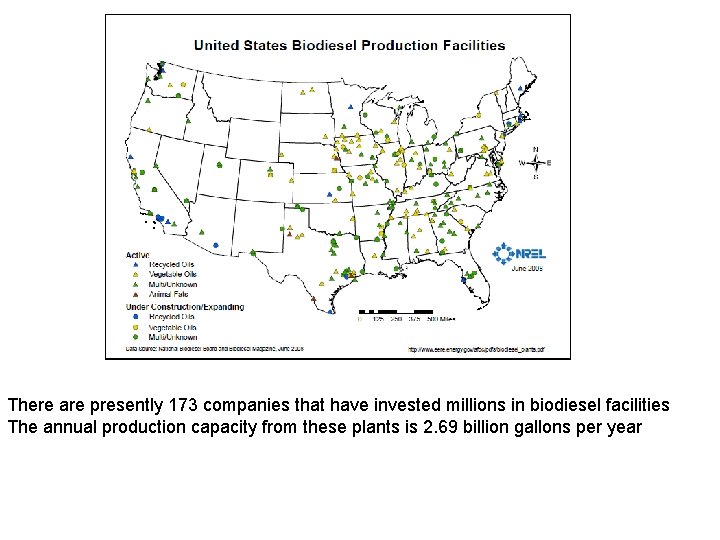
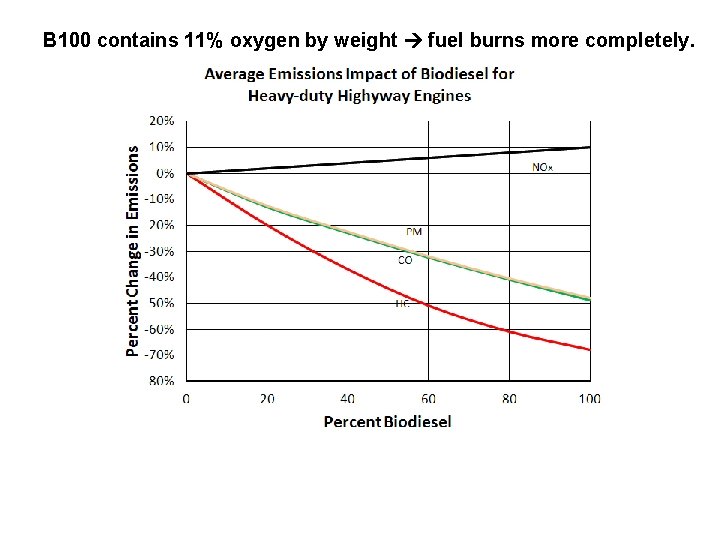
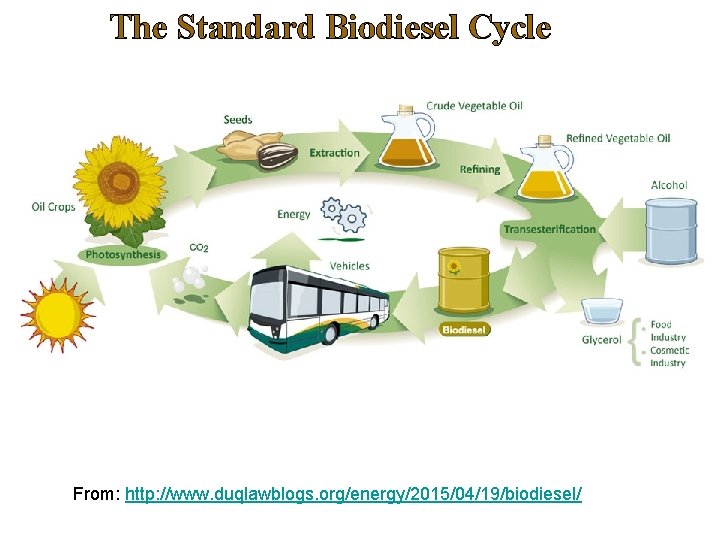
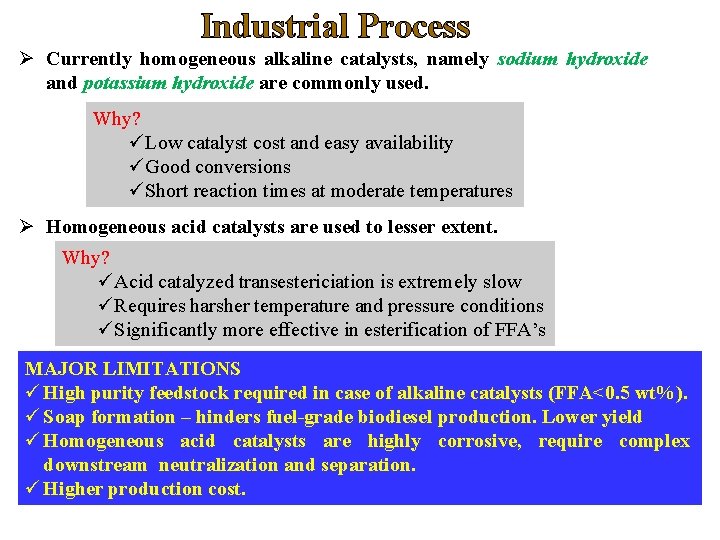
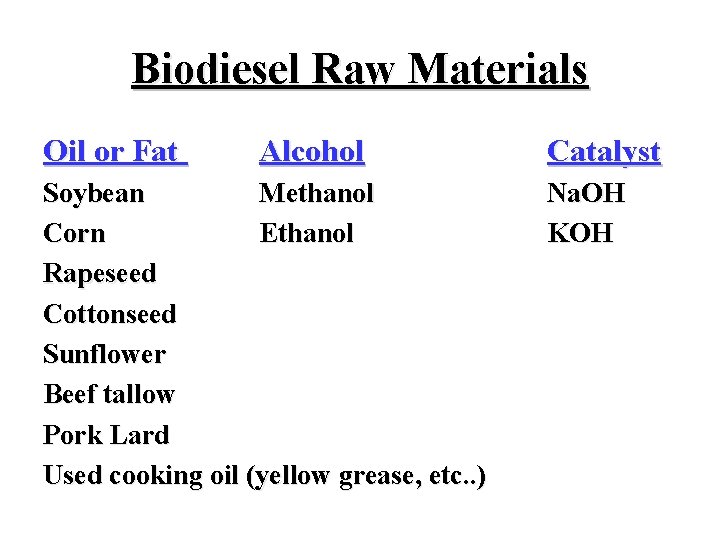
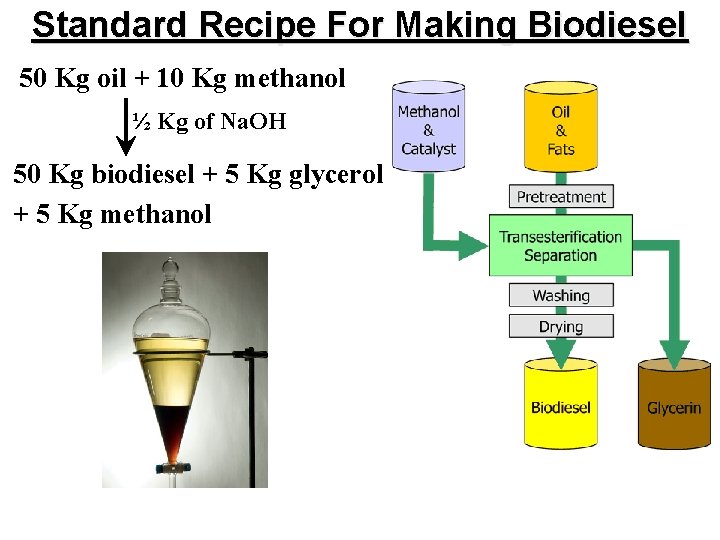
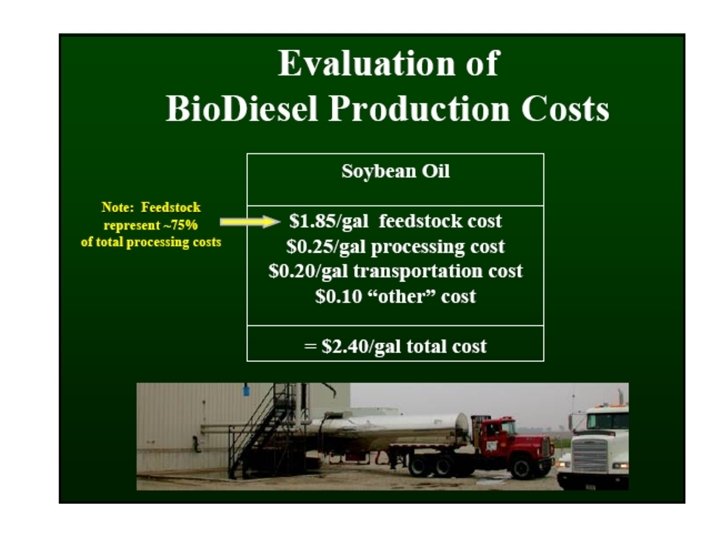
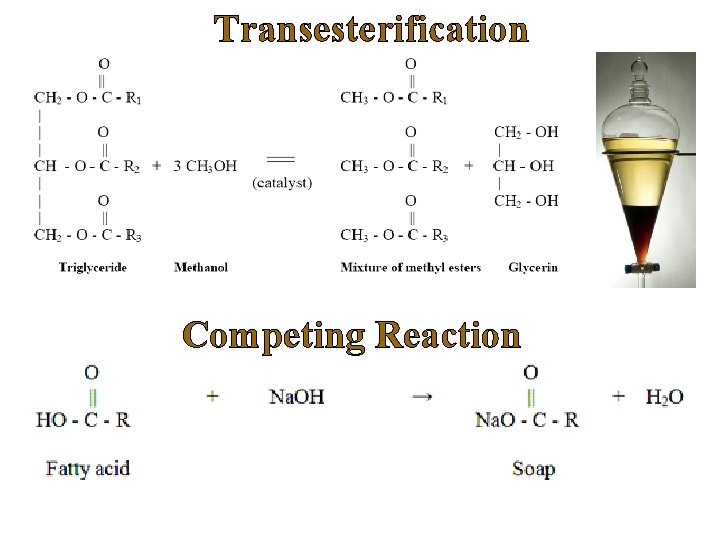
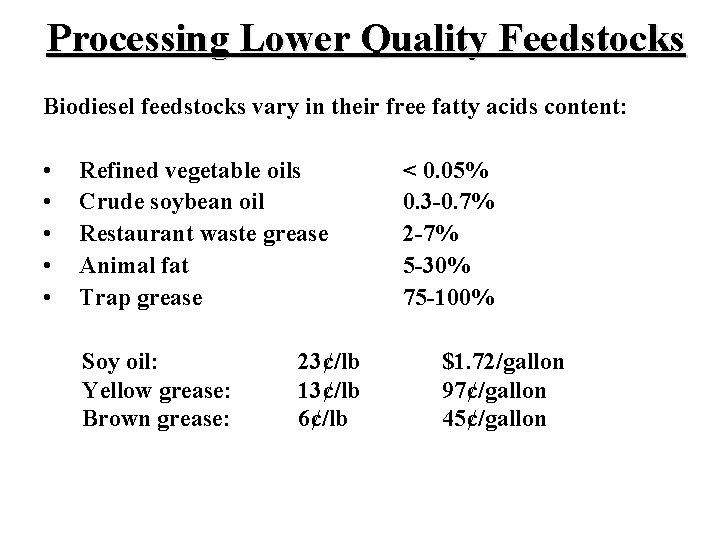
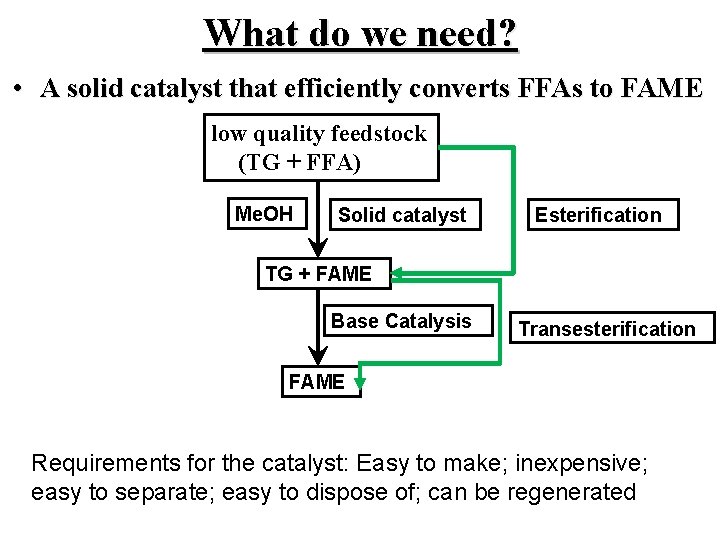
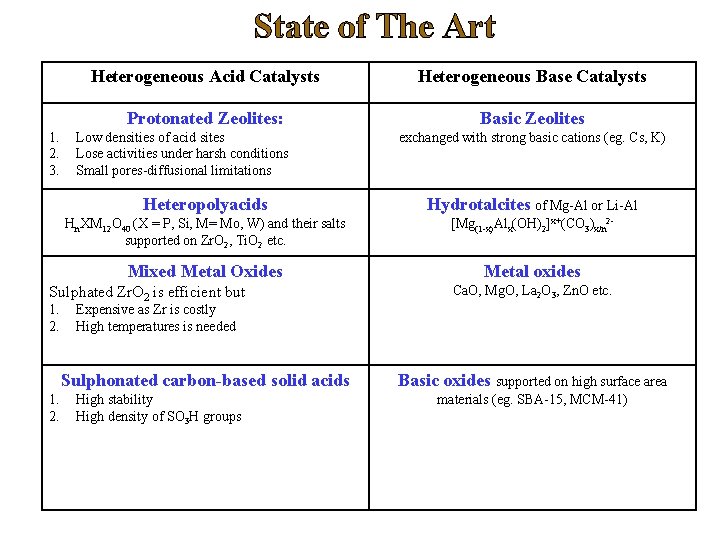
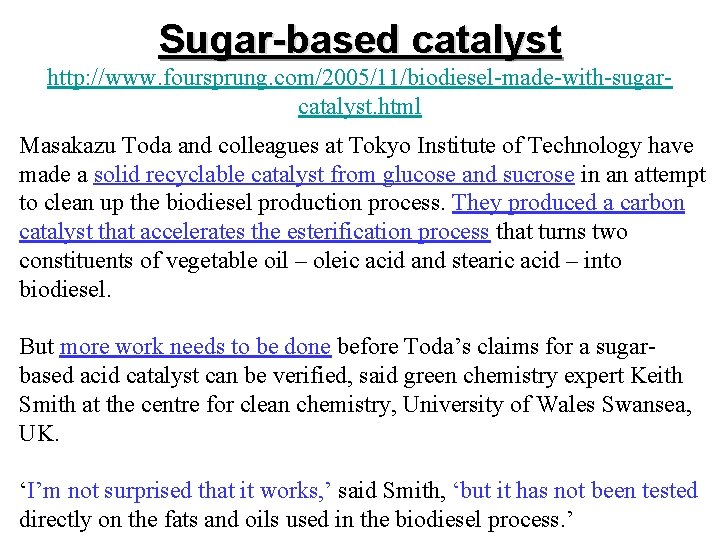
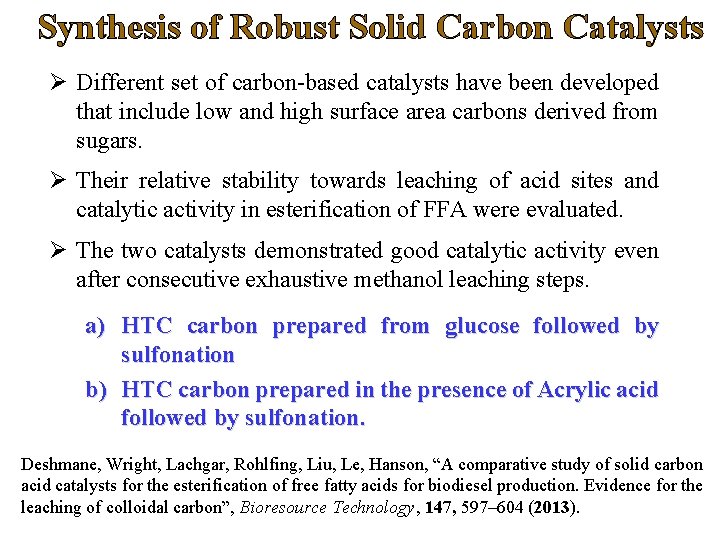
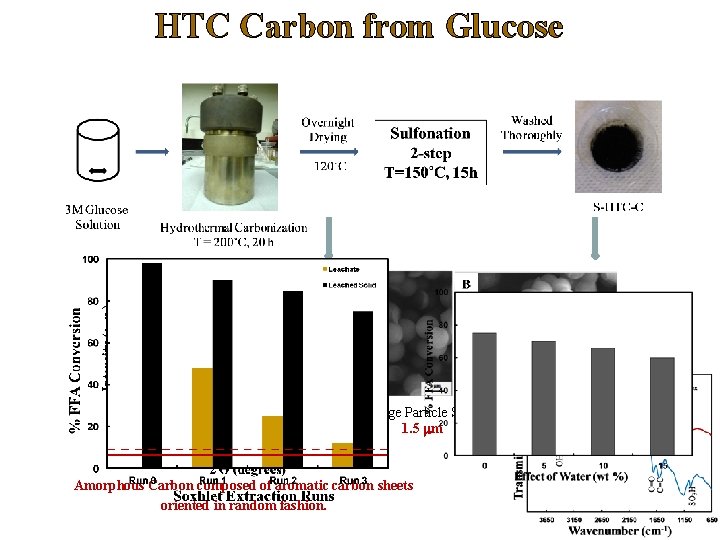
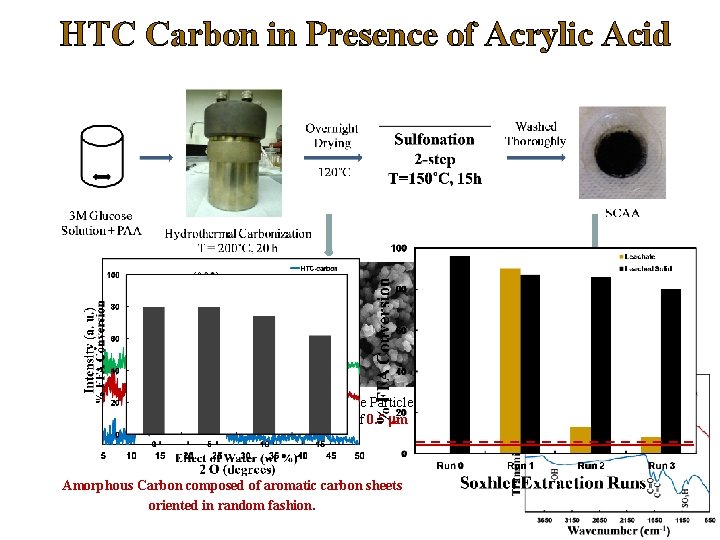
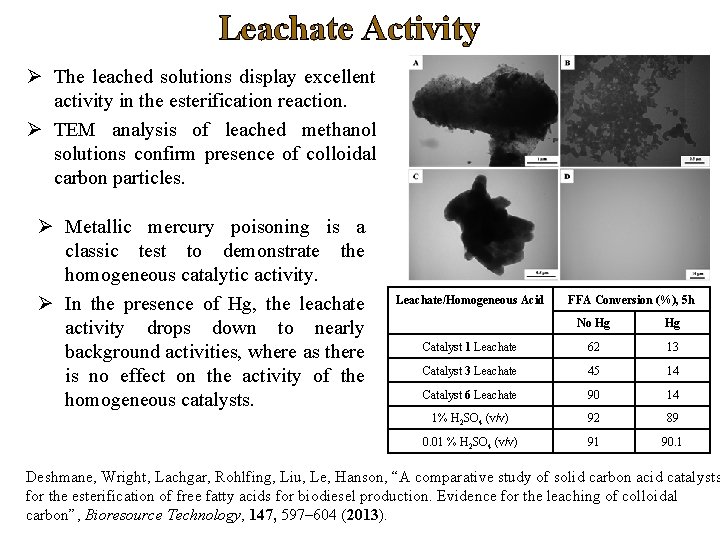
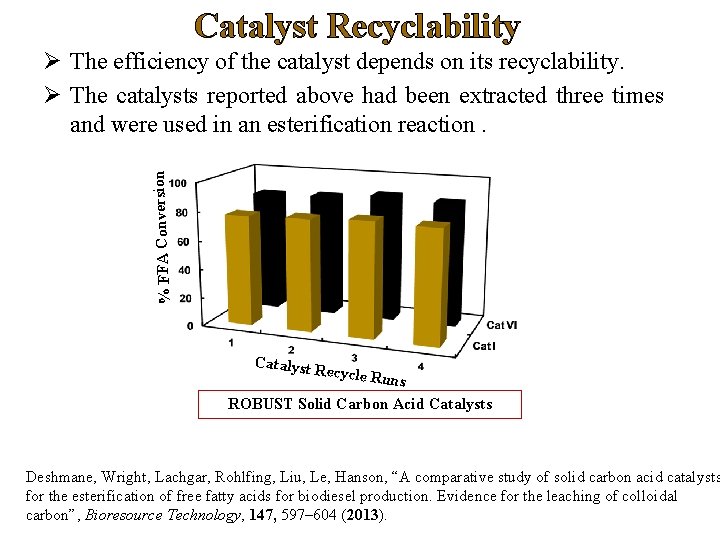
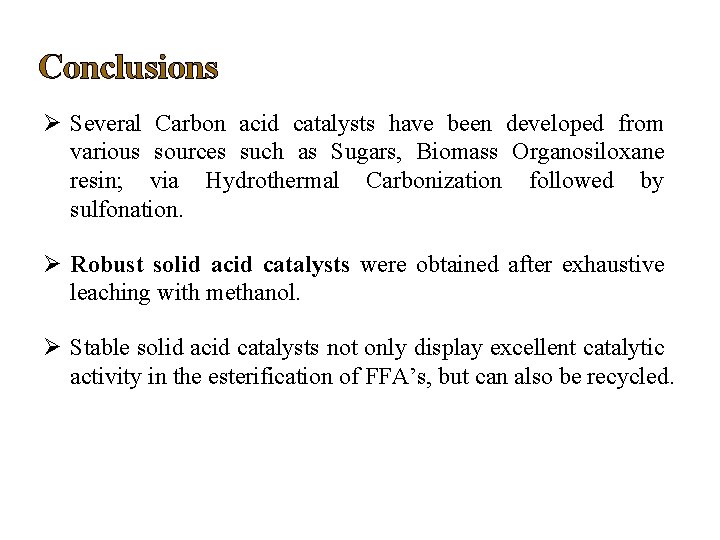
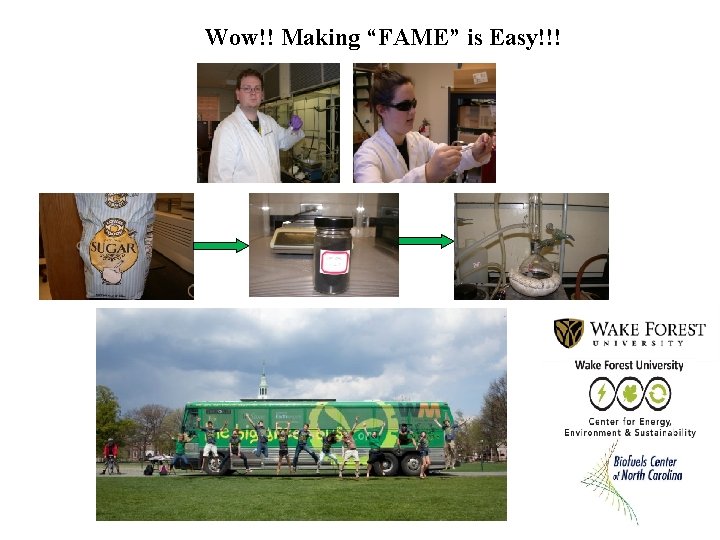
- Slides: 32
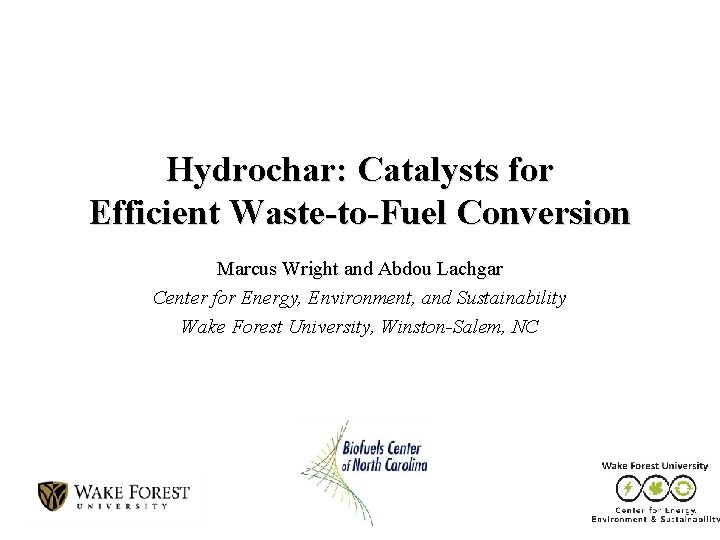
Hydrochar: Catalysts for Efficient Waste-to-Fuel Conversion Marcus Wright and Abdou Lachgar Center for Energy, Environment, and Sustainability Wake Forest University, Winston-Salem, NC
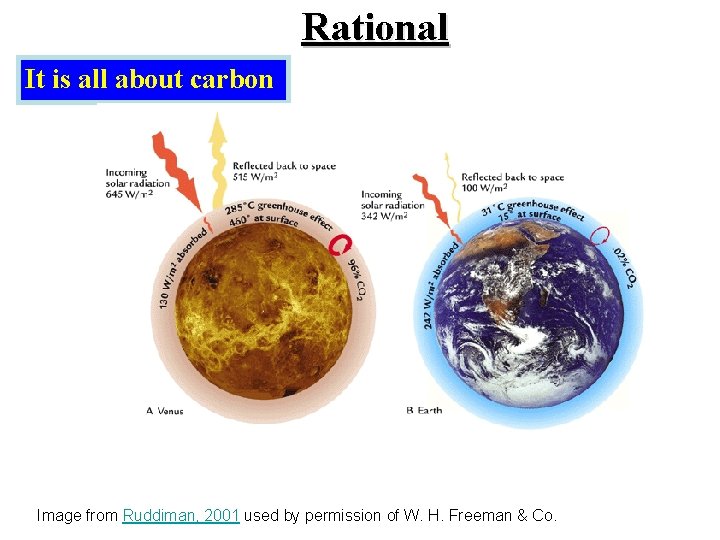
Rational It is all about carbon Image from Ruddiman, 2001 used by permission of W. H. Freeman & Co.
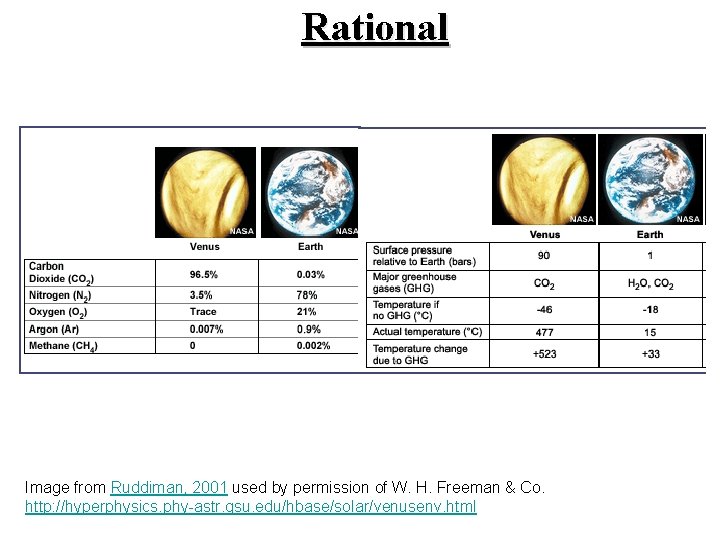
Rational Image from Ruddiman, 2001 used by permission of W. H. Freeman & Co. http: //hyperphysics. phy-astr. gsu. edu/hbase/solar/venusenv. html
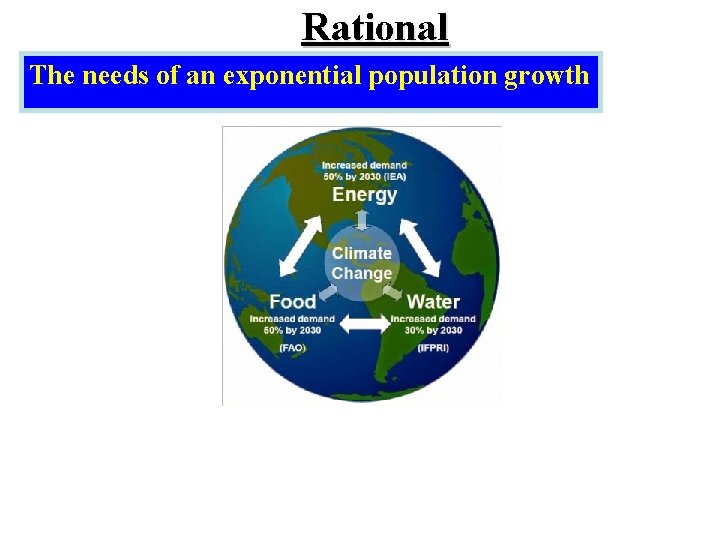
Rational The needs of an exponential population growth
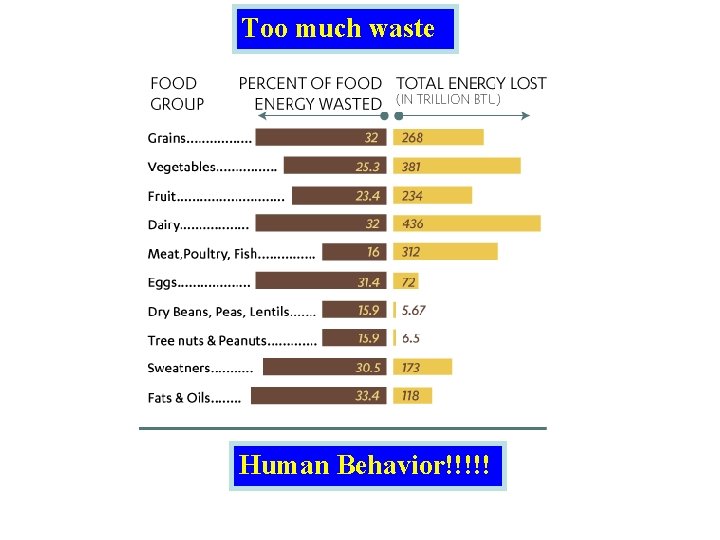
Too much waste Human Behavior!!!!!
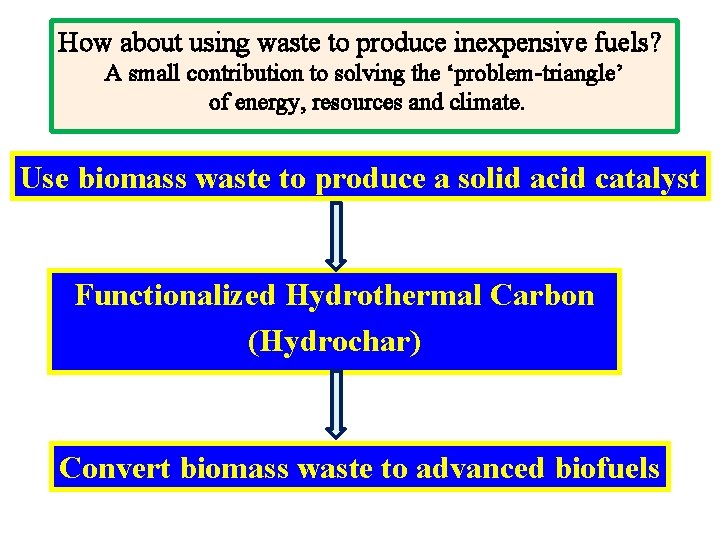
How about using waste to produce inexpensive fuels? A small contribution to solving the ‘problem-triangle’ of energy, resources and climate. Use biomass waste to produce a solid acid catalyst Functionalized Hydrothermal Carbon (Hydrochar) Convert biomass waste to advanced biofuels
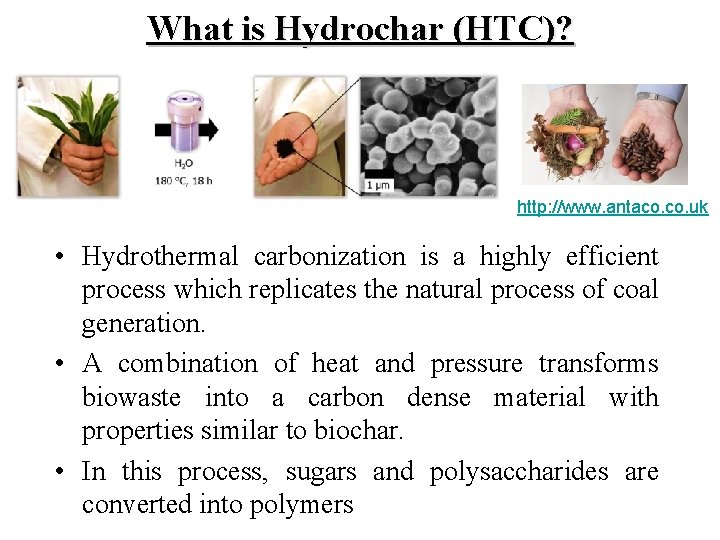
What is Hydrochar (HTC)? http: //www. antaco. uk • Hydrothermal carbonization is a highly efficient process which replicates the natural process of coal generation. • A combination of heat and pressure transforms biowaste into a carbon dense material with properties similar to biochar. • In this process, sugars and polysaccharides are converted into polymers
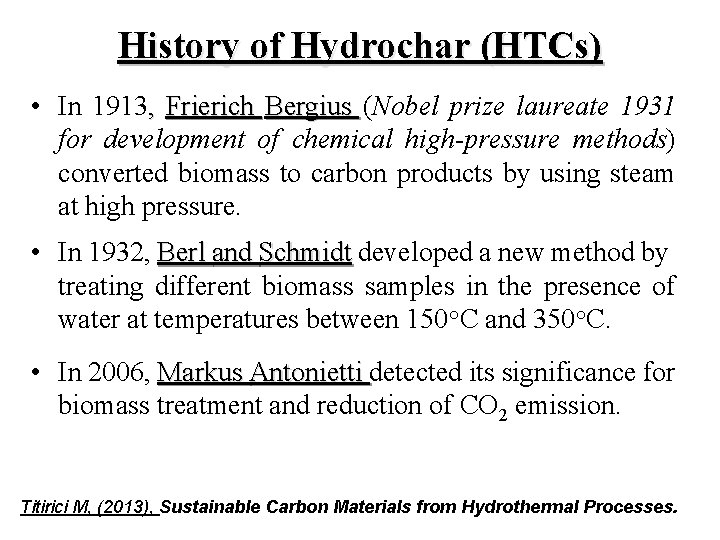
History of Hydrochar (HTCs) • In 1913, Frierich Bergius (Nobel prize laureate 1931 for development of chemical high-pressure methods) converted biomass to carbon products by using steam at high pressure. • In 1932, Berl and Schmidt developed a new method by treating different biomass samples in the presence of water at temperatures between 150○C and 350○C. • In 2006, Markus Antonietti detected its significance for biomass treatment and reduction of CO 2 emission. Titirici M, (2013), Sustainable Carbon Materials from Hydrothermal Processes.
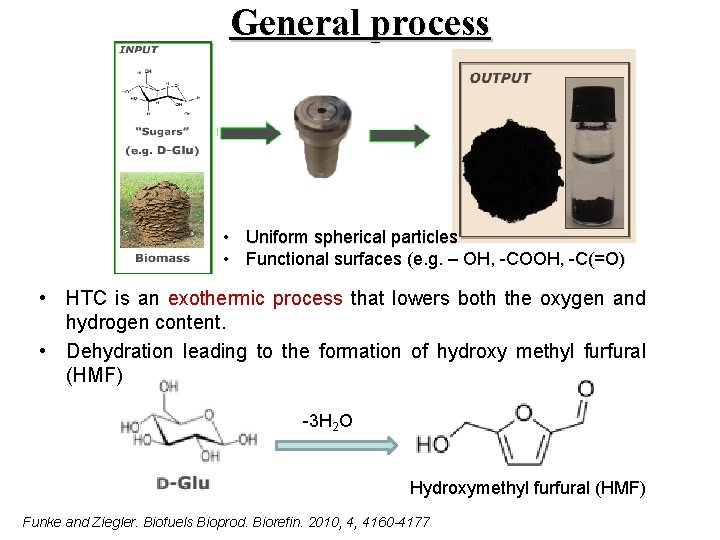
General process • Uniform spherical particles • Functional surfaces (e. g. – OH, -COOH, -C(=O) • HTC is an exothermic process that lowers both the oxygen and hydrogen content. • Dehydration leading to the formation of hydroxy methyl furfural (HMF) -3 H 2 O Hydroxymethyl furfural (HMF) Funke and Ziegler. Biofuels Bioprod. Biorefin. 2010, 4, 4160 -4177
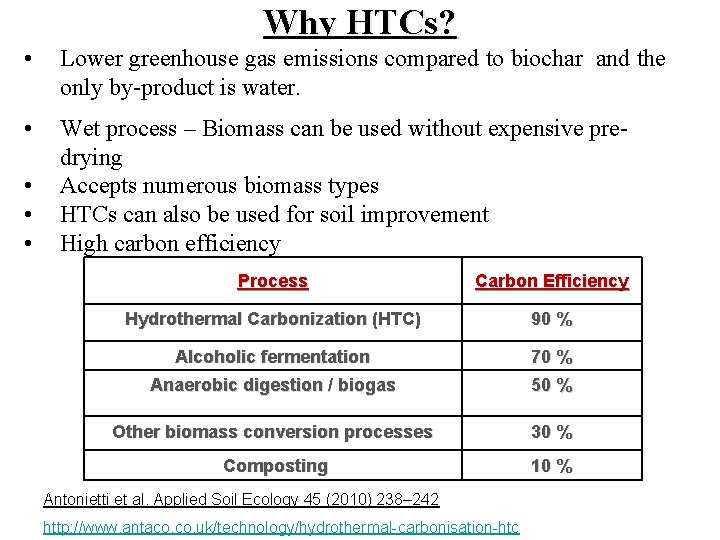
Why HTCs? • Lower greenhouse gas emissions compared to biochar and the only by-product is water. • Wet process – Biomass can be used without expensive predrying Accepts numerous biomass types HTCs can also be used for soil improvement High carbon efficiency • • • Process Carbon Efficiency Hydrothermal Carbonization (HTC) 90 % Alcoholic fermentation 70 % Anaerobic digestion / biogas 50 % Other biomass conversion processes 30 % Composting 10 % Antonietti et al. Applied Soil Ecology 45 (2010) 238– 242 http: //www. antaco. uk/technology/hydrothermal-carbonisation-htc
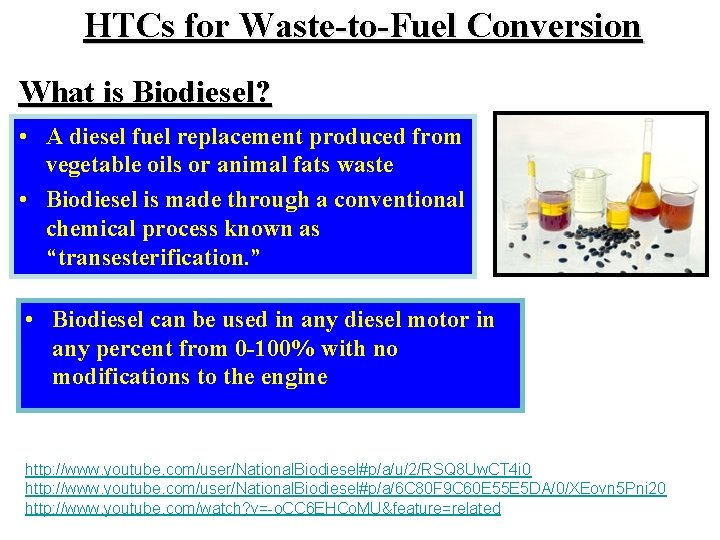
HTCs for Waste-to-Fuel Conversion What is Biodiesel? • A diesel fuel replacement produced from vegetable oils or animal fats waste • Biodiesel is made through a conventional chemical process known as “transesterification. ” • Biodiesel can be used in any diesel motor in any percent from 0 -100% with no modifications to the engine http: //www. youtube. com/user/National. Biodiesel#p/a/u/2/RSQ 8 Uw. CT 4 i 0 http: //www. youtube. com/user/National. Biodiesel#p/a/6 C 80 F 9 C 60 E 55 E 5 DA/0/XEovn 5 Pni 20 http: //www. youtube. com/watch? v=-o. CC 6 EHCo. MU&feature=related
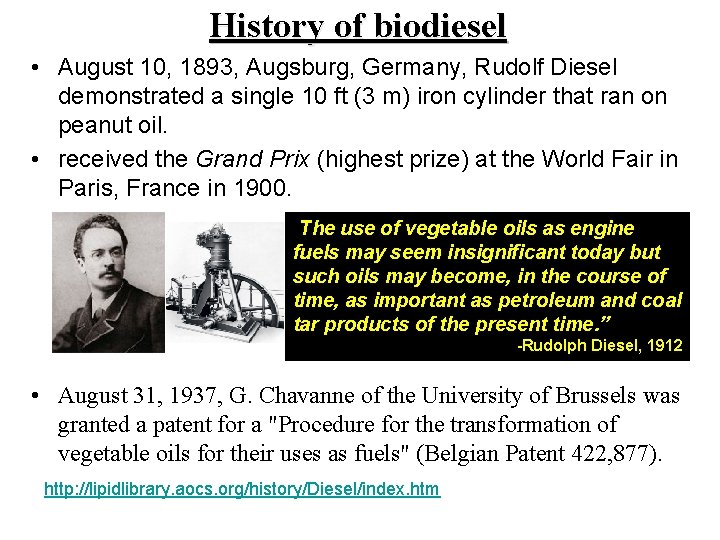
History of biodiesel • August 10, 1893, Augsburg, Germany, Rudolf Diesel demonstrated a single 10 ft (3 m) iron cylinder that ran on peanut oil. • received the Grand Prix (highest prize) at the World Fair in Paris, France in 1900. “The use of vegetable oils as engine fuels may seem insignificant today but such oils may become, in the course of time, as important as petroleum and coal tar products of the present time. ” -Rudolph Diesel, 1912 • August 31, 1937, G. Chavanne of the University of Brussels was granted a patent for a "Procedure for the transformation of vegetable oils for their uses as fuels" (Belgian Patent 422, 877). http: //lipidlibrary. aocs. org/history/Diesel/index. htm
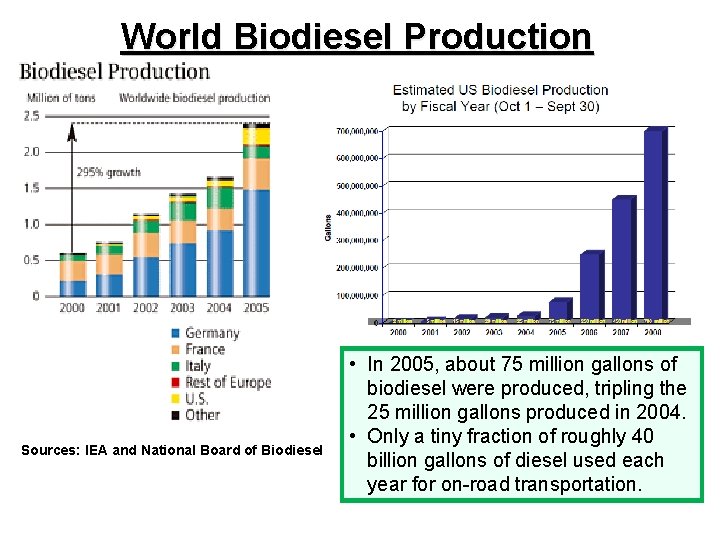
World Biodiesel Production Sources: IEA and National Board of Biodiesel • In 2005, about 75 million gallons of biodiesel were produced, tripling the 25 million gallons produced in 2004. • Only a tiny fraction of roughly 40 billion gallons of diesel used each year for on-road transportation.
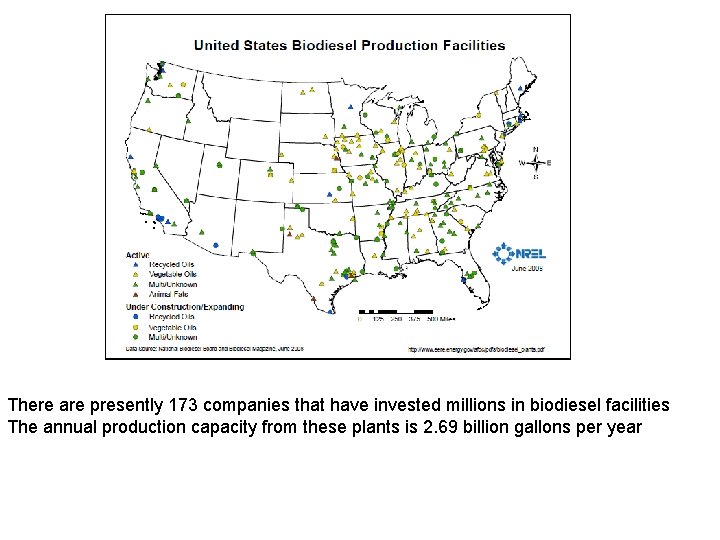
There are presently 173 companies that have invested millions in biodiesel facilities The annual production capacity from these plants is 2. 69 billion gallons per year
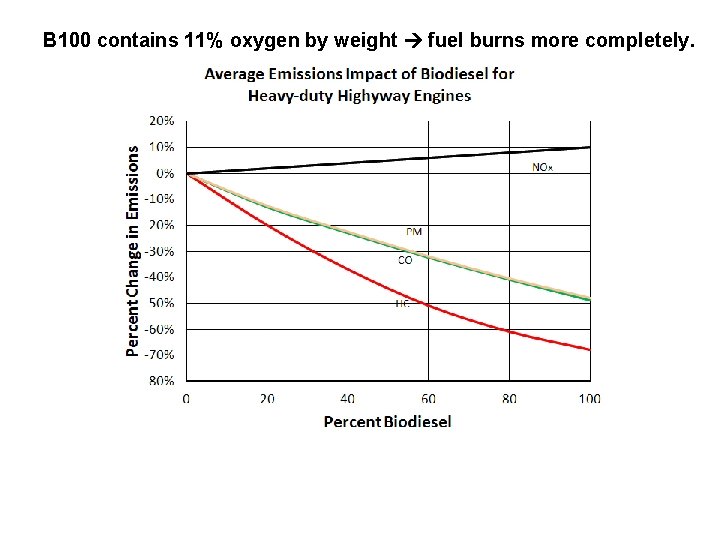
B 100 contains 11% oxygen by weight fuel burns more completely.
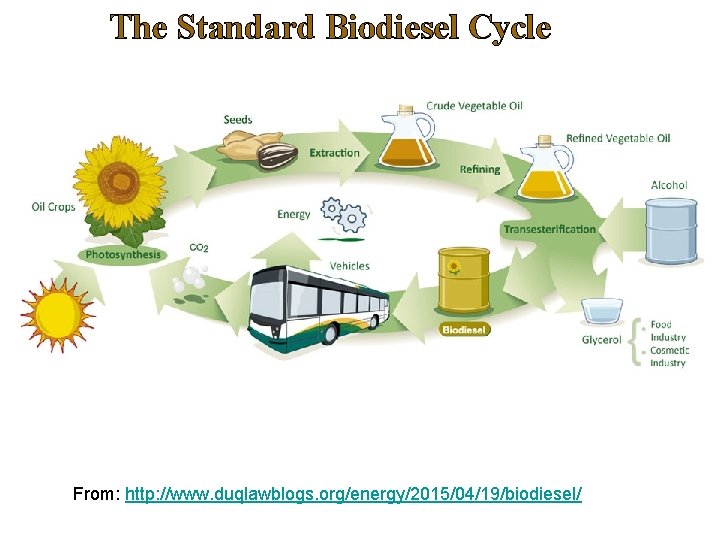
The Standard Biodiesel Cycle From: http: //www. duqlawblogs. org/energy/2015/04/19/biodiesel/
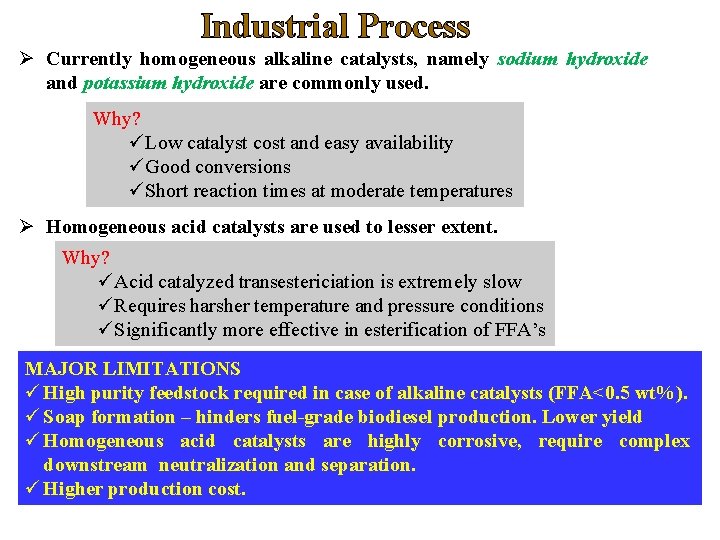
Industrial Process Ø Currently homogeneous alkaline catalysts, namely sodium hydroxide and potassium hydroxide are commonly used. Why? üLow catalyst cost and easy availability üGood conversions üShort reaction times at moderate temperatures Ø Homogeneous acid catalysts are used to lesser extent. Why? üAcid catalyzed transestericiation is extremely slow üRequires harsher temperature and pressure conditions üSignificantly more effective in esterification of FFA’s MAJOR LIMITATIONS ü High purity feedstock required in case of alkaline catalysts (FFA<0. 5 wt%). ü Soap formation – hinders fuel-grade biodiesel production. Lower yield ü Homogeneous acid catalysts are highly corrosive, require complex downstream neutralization and separation. ü Higher production cost.
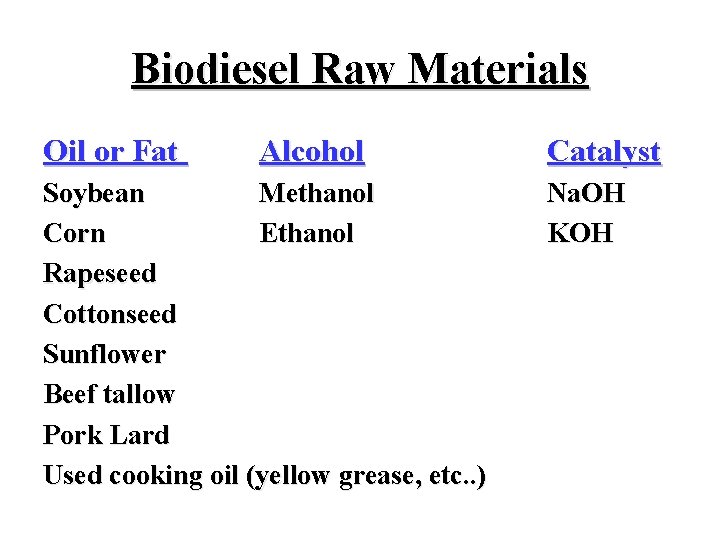
Biodiesel Raw Materials Oil or Fat Alcohol Soybean Methanol Corn Ethanol Rapeseed Cottonseed Sunflower Beef tallow Pork Lard Used cooking oil (yellow grease, etc. . ) Catalyst Na. OH KOH
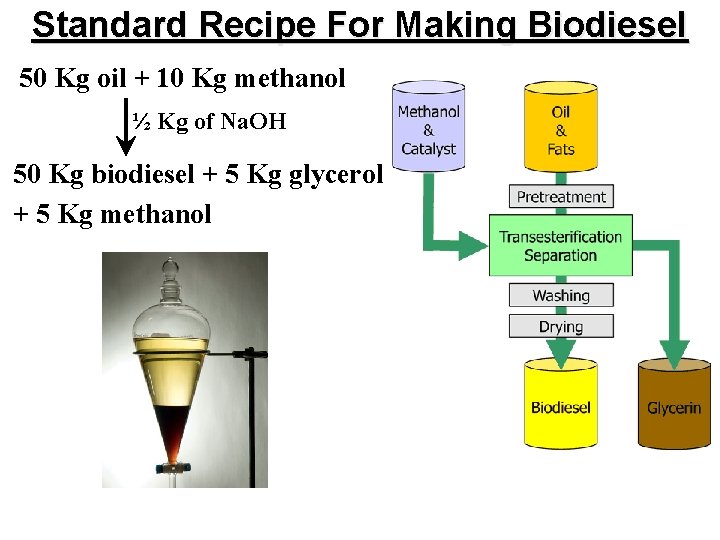
Standard Recipe For Making Biodiesel 50 Kg oil + 10 Kg methanol ½ Kg of Na. OH 50 Kg biodiesel + 5 Kg glycerol + 5 Kg methanol
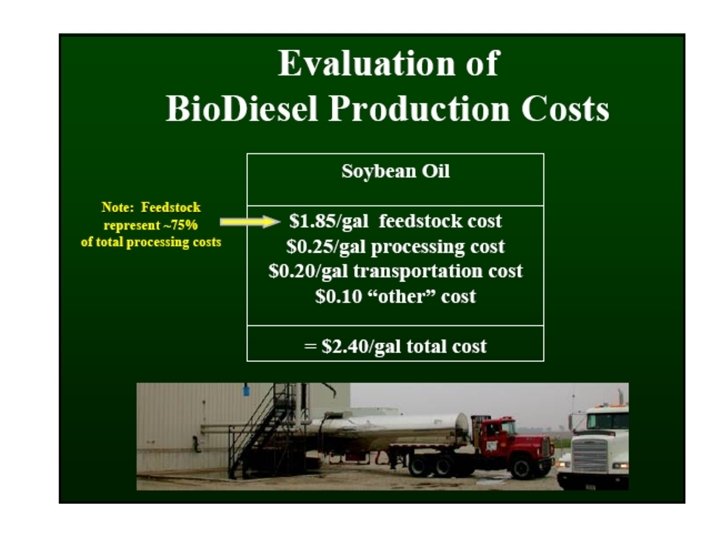
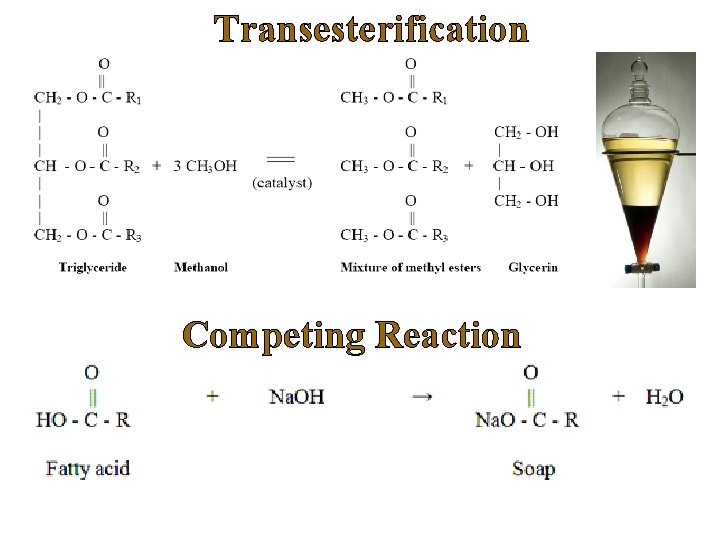
Transesterification Competing Reaction
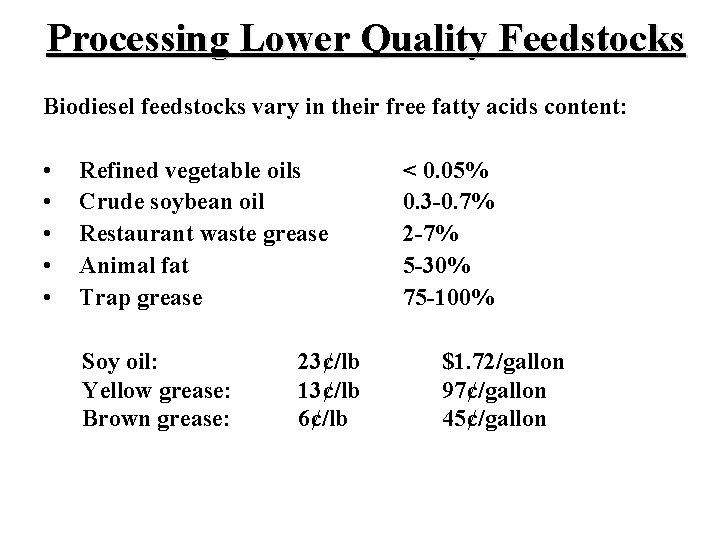
Processing Lower Quality Feedstocks Biodiesel feedstocks vary in their free fatty acids content: • • • Refined vegetable oils Crude soybean oil Restaurant waste grease Animal fat Trap grease Soy oil: Yellow grease: Brown grease: 23¢/lb 13¢/lb 6¢/lb < 0. 05% 0. 3 -0. 7% 2 -7% 5 -30% 75 -100% $1. 72/gallon 97¢/gallon 45¢/gallon
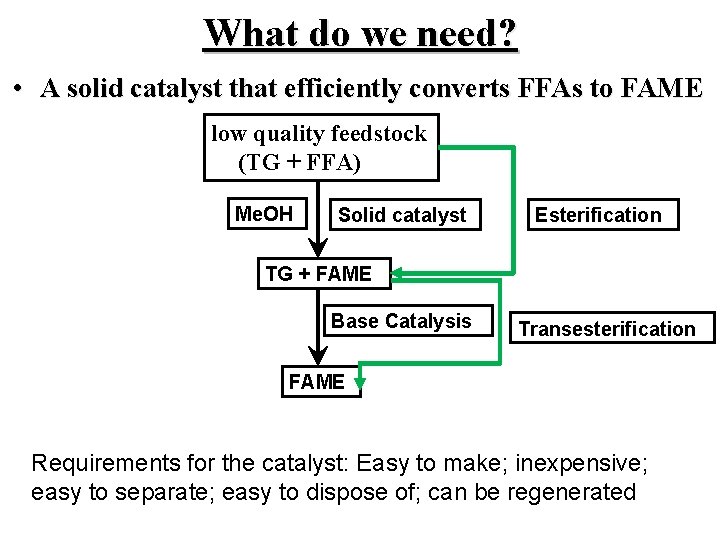
What do we need? • A solid catalyst that efficiently converts FFAs to FAME low quality feedstock (TG + FFA) Me. OH Solid catalyst Esterification TG + FAME Base Catalysis Transesterification FAME Requirements for the catalyst: Easy to make; inexpensive; easy to separate; easy to dispose of; can be regenerated
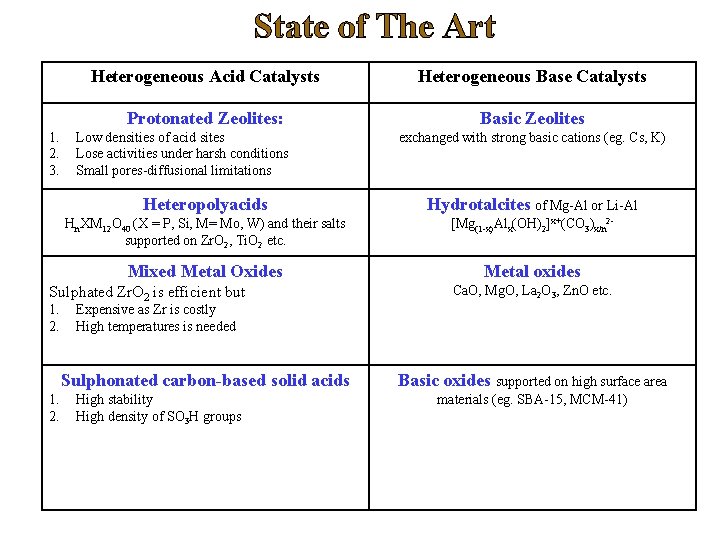
State of The Art 1. 2. 3. Heterogeneous Acid Catalysts Heterogeneous Base Catalysts Protonated Zeolites: Basic Zeolites Low densities of acid sites Lose activities under harsh conditions Small pores-diffusional limitations Heteropolyacids Hydrotalcites of Mg-Al or Li-Al Hn. XM 12 O 40 (X = P, Si, M= Mo, W) and their salts supported on Zr. O 2, Ti. O 2 etc. [Mg(1 -x)Alx(OH)2]x+(CO 3)x/n 2 - Mixed Metal Oxides Metal oxides Sulphated Zr. O 2 is efficient but 1. 2. Ca. O, Mg. O, La 2 O 3, Zn. O etc. Expensive as Zr is costly High temperatures is needed Sulphonated carbon-based solid acids 1. 2. exchanged with strong basic cations (eg. Cs, K) High stability High density of SO 3 H groups Basic oxides supported on high surface area materials (eg. SBA-15, MCM-41)
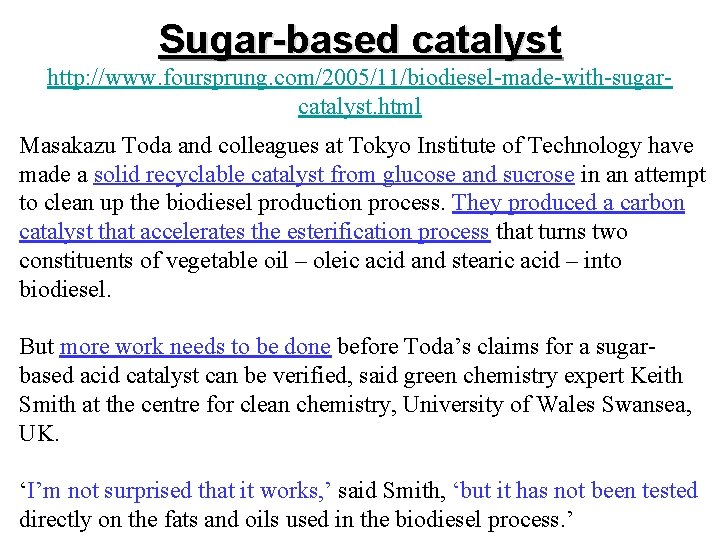
Sugar-based catalyst http: //www. foursprung. com/2005/11/biodiesel-made-with-sugarcatalyst. html Masakazu Toda and colleagues at Tokyo Institute of Technology have made a solid recyclable catalyst from glucose and sucrose in an attempt to clean up the biodiesel production process. They produced a carbon catalyst that accelerates the esterification process that turns two constituents of vegetable oil – oleic acid and stearic acid – into biodiesel. But more work needs to be done before Toda’s claims for a sugarbased acid catalyst can be verified, said green chemistry expert Keith Smith at the centre for clean chemistry, University of Wales Swansea, UK. ‘I’m not surprised that it works, ’ said Smith, ‘but it has not been tested directly on the fats and oils used in the biodiesel process. ’
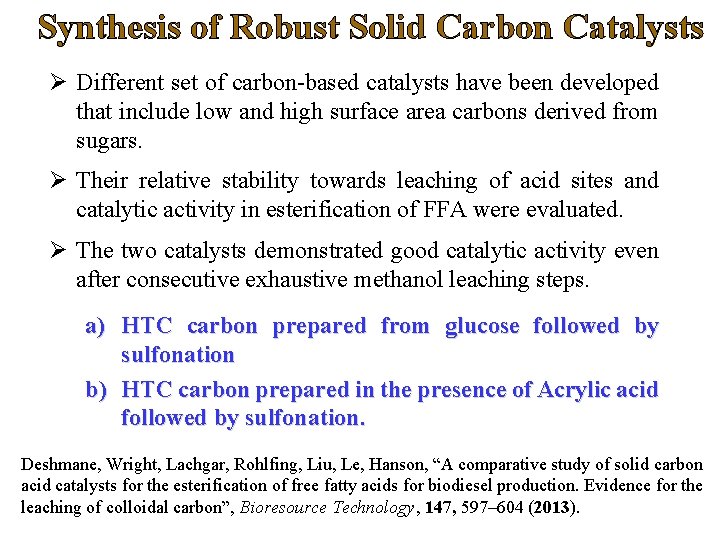
Synthesis of Robust Solid Carbon Catalysts Ø Different set of carbon-based catalysts have been developed that include low and high surface area carbons derived from sugars. Ø Their relative stability towards leaching of acid sites and catalytic activity in esterification of FFA were evaluated. Ø The two catalysts demonstrated good catalytic activity even after consecutive exhaustive methanol leaching steps. a) HTC carbon prepared from glucose followed by sulfonation b) HTC carbon prepared in the presence of Acrylic acid followed by sulfonation. Deshmane, Wright, Lachgar, Rohlfing, Liu, Le, Hanson, “A comparative study of solid carbon acid catalysts for the esterification of free fatty acids for biodiesel production. Evidence for the leaching of colloidal carbon”, Bioresource Technology, 147, 597– 604 (2013).
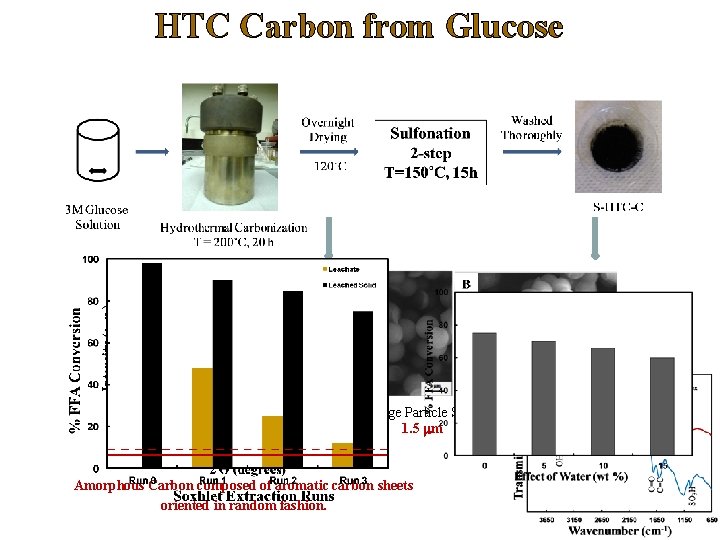
HTC Carbon from Glucose Average Particle Size of 1. 5 mm Amorphous Carbon composed of aromatic carbon sheets oriented in random fashion.
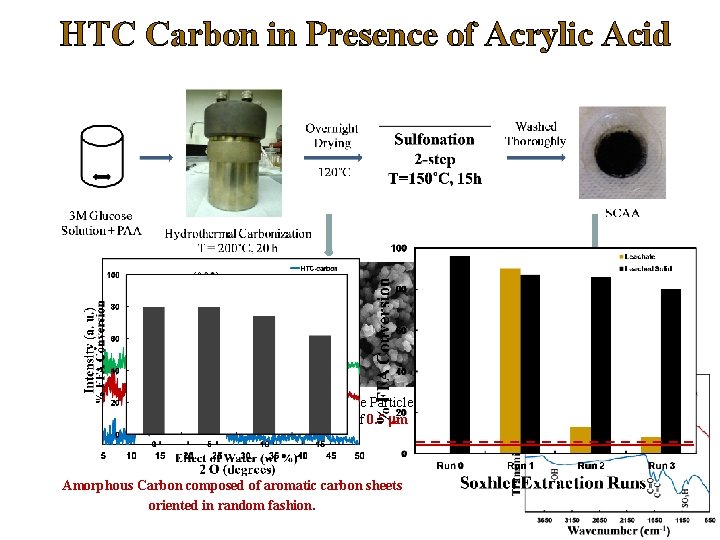
HTC Carbon in Presence of Acrylic Acid Average Particle Size of 0. 5 mm Amorphous Carbon composed of aromatic carbon sheets oriented in random fashion. Average Particle Size of 1. 4 mm
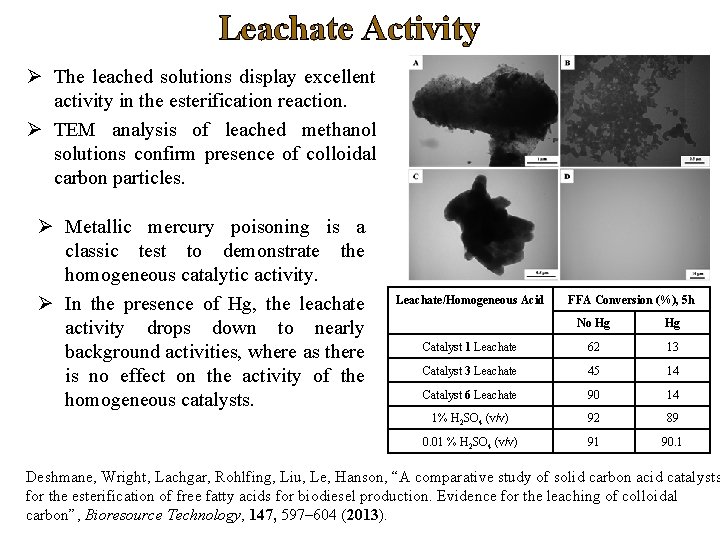
Leachate Activity Ø The leached solutions display excellent activity in the esterification reaction. Ø TEM analysis of leached methanol solutions confirm presence of colloidal carbon particles. Ø Metallic mercury poisoning is a classic test to demonstrate the homogeneous catalytic activity. Ø In the presence of Hg, the leachate activity drops down to nearly background activities, where as there is no effect on the activity of the homogeneous catalysts. Leachate/Homogeneous Acid FFA Conversion (%), 5 h No Hg Hg Catalyst 1 Leachate 62 13 Catalyst 3 Leachate 45 14 Catalyst 6 Leachate 90 14 1% H 2 SO 4 (v/v) 92 89 0. 01 % H 2 SO 4 (v/v) 91 90. 1 Deshmane, Wright, Lachgar, Rohlfing, Liu, Le, Hanson, “A comparative study of solid carbon acid catalysts for the esterification of free fatty acids for biodiesel production. Evidence for the leaching of colloidal carbon”, Bioresource Technology, 147, 597– 604 (2013).
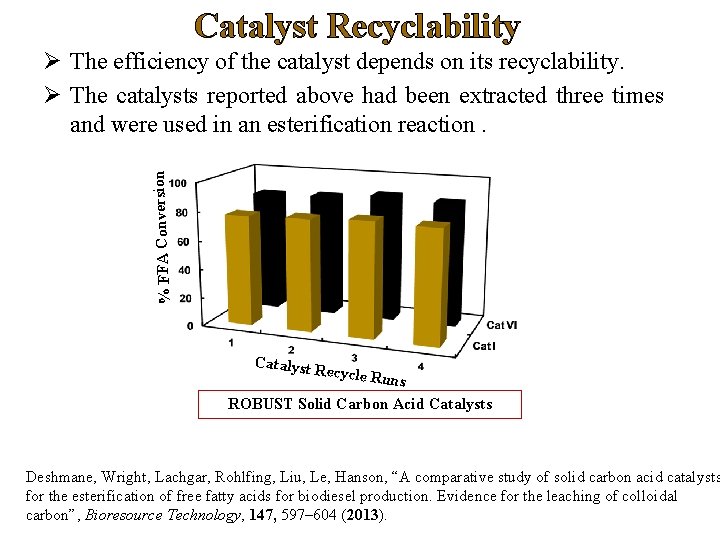
Catalyst Recyclability % FFA Conversion Ø The efficiency of the catalyst depends on its recyclability. Ø The catalysts reported above had been extracted three times and were used in an esterification reaction. Catalyst Recycle R uns ROBUST Solid Carbon Acid Catalysts Deshmane, Wright, Lachgar, Rohlfing, Liu, Le, Hanson, “A comparative study of solid carbon acid catalysts for the esterification of free fatty acids for biodiesel production. Evidence for the leaching of colloidal carbon”, Bioresource Technology, 147, 597– 604 (2013).
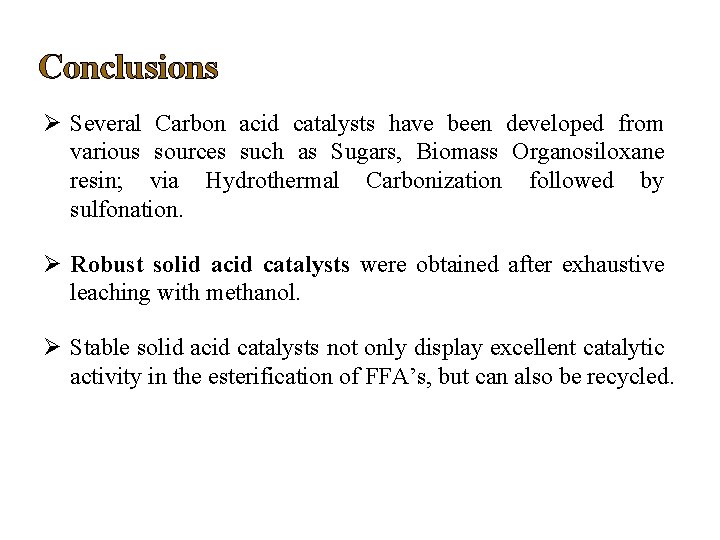
Conclusions Ø Several Carbon acid catalysts have been developed from various sources such as Sugars, Biomass Organosiloxane resin; via Hydrothermal Carbonization followed by sulfonation. Ø Robust solid acid catalysts were obtained after exhaustive leaching with methanol. Ø Stable solid acid catalysts not only display excellent catalytic activity in the esterification of FFA’s, but can also be recycled.
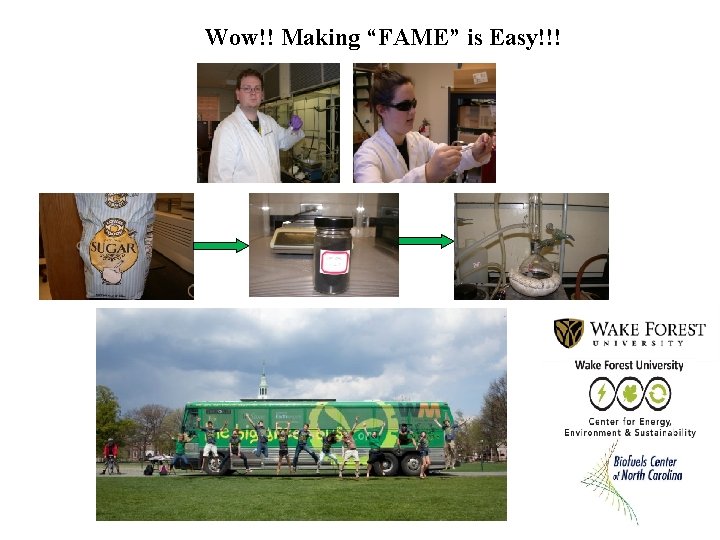
Wow!! Making “FAME” is Easy!!!
Relational escalation catalysts
Productively efficient vs allocatively efficient
Productive inefficiency and allocative inefficiency
Productively efficient vs allocatively efficient
Productively efficient vs allocatively efficient
Productively efficient vs allocatively efficient
Tobinskatten för och nackdelar
Tack för att ni lyssnade bild
Referatmarkeringar
Programskede byggprocessen
Ruin karttecken
Luftstrupen för medicinare
Fuktmätningar i betong enlig rbk
Lufttryck formel
Elektronik för barn
Underlag för särskild löneskatt på pensionskostnader
Densitet vatten
Tack för att ni har lyssnat
Borra hål för knoppar
Smärtskolan kunskap för livet
Bris för vuxna
Teckenspråk minoritetsspråk argument
Frgar
Vilka tal pekar pilarna på
Delegerande ledarskap
Humanitr
Toppslätskivling dos
Vad står k.r.å.k.a.n för
Redogör för vad psykologi är
Mat för unga idrottare
Lek med former i förskolan
Etik och ledarskap etisk kod för chefer
Publik sektor