GSO1100 Operations and logistics Facility Layout Leandro C
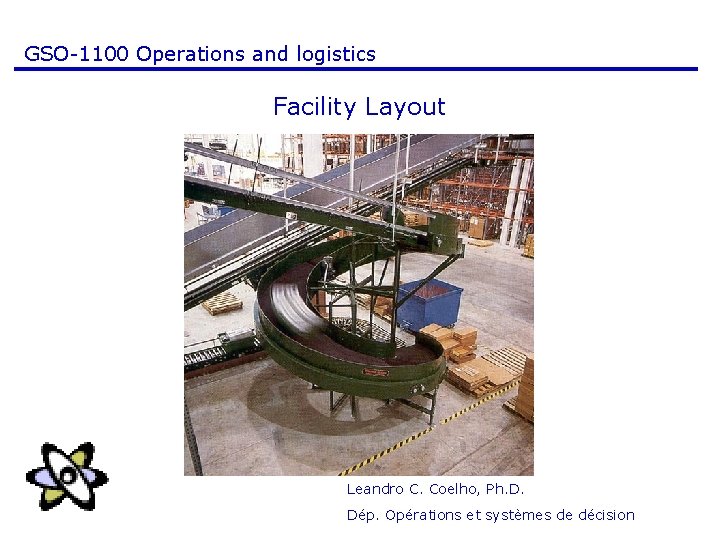

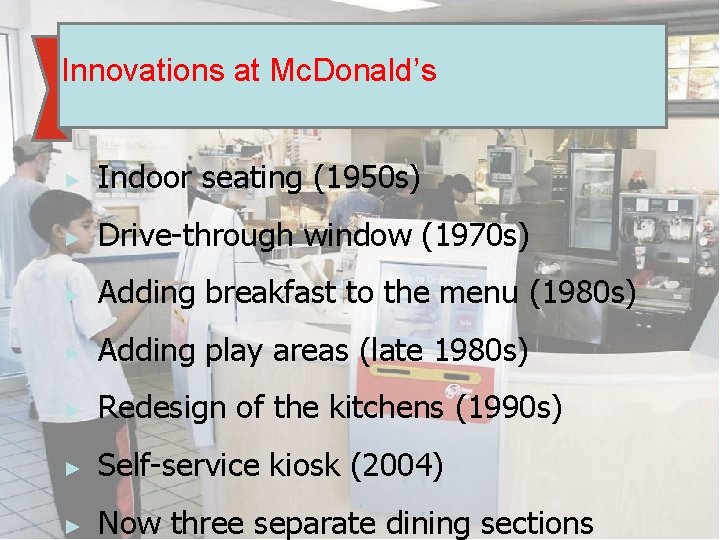

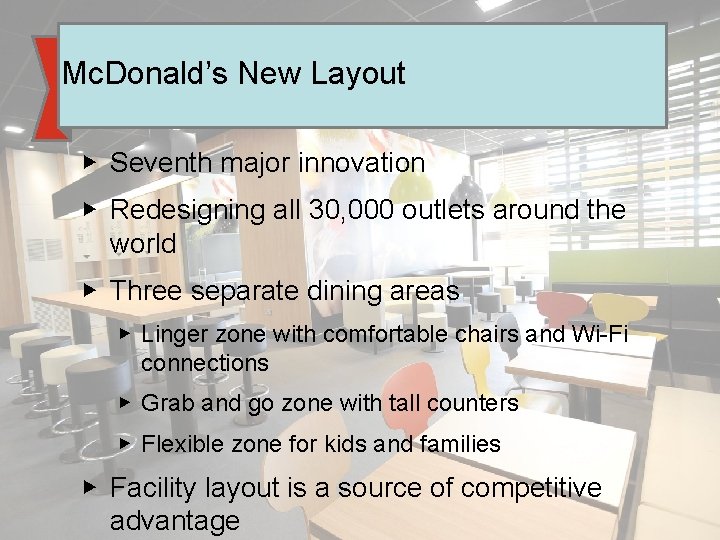
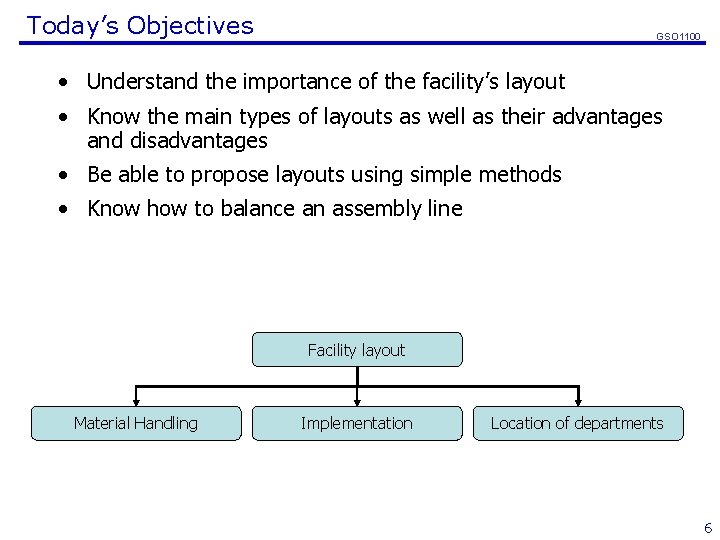
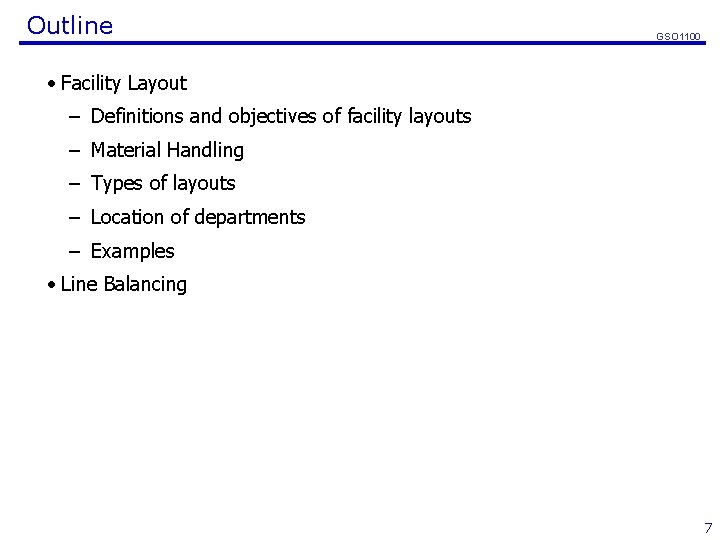
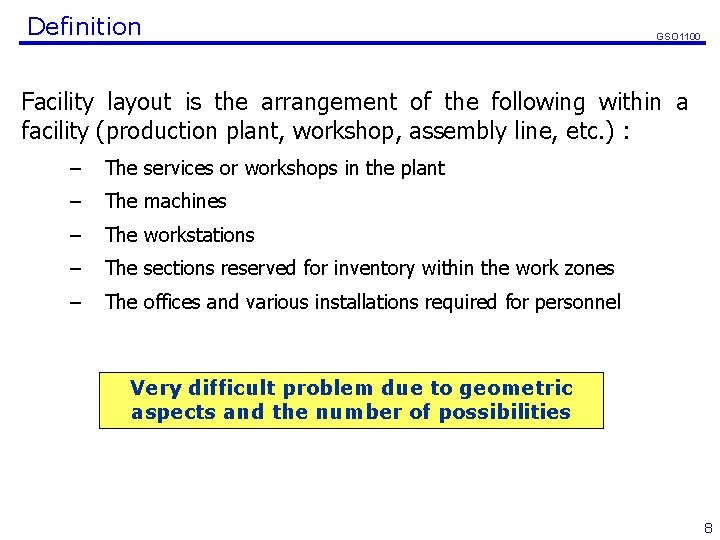
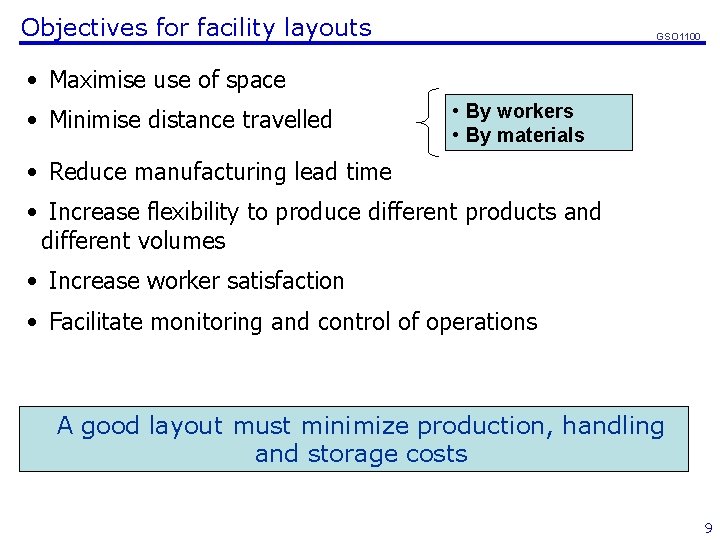
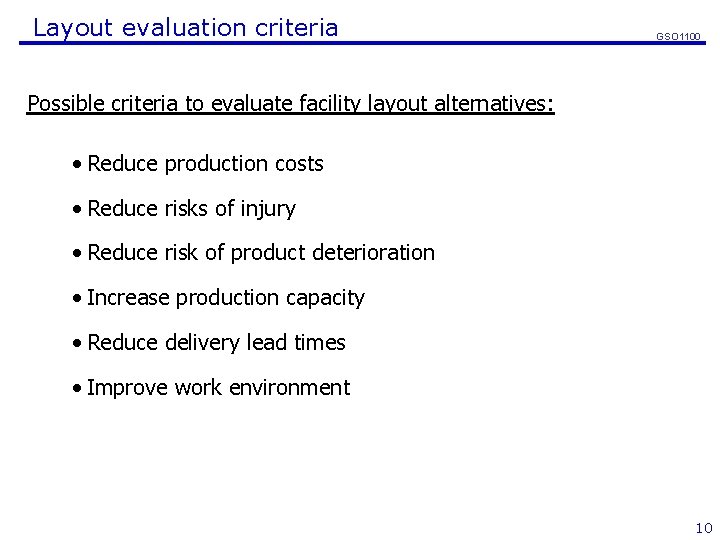
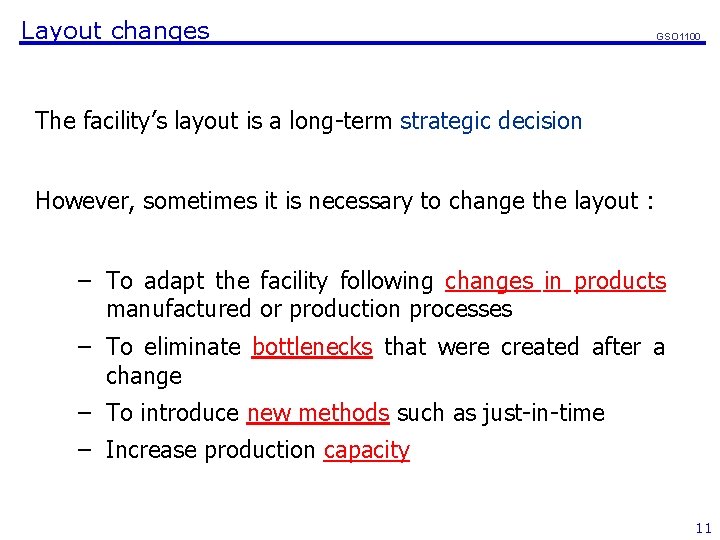
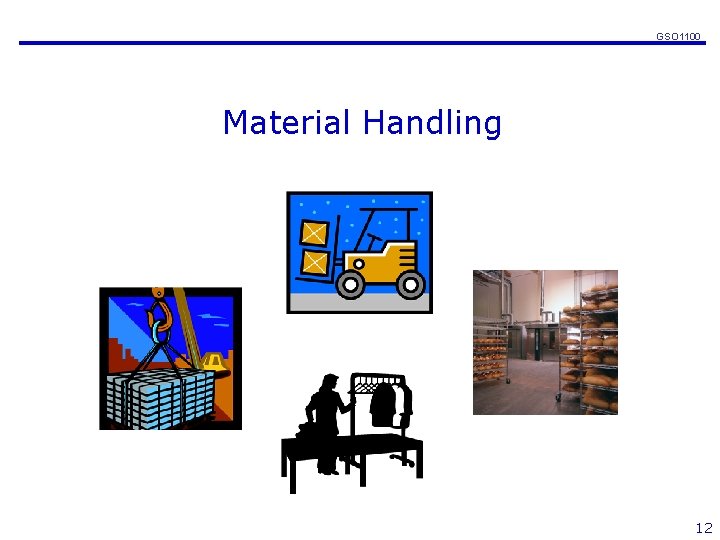
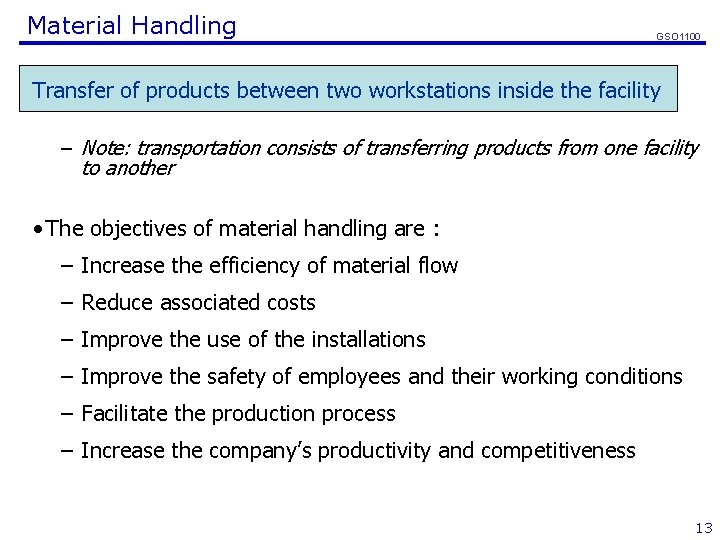
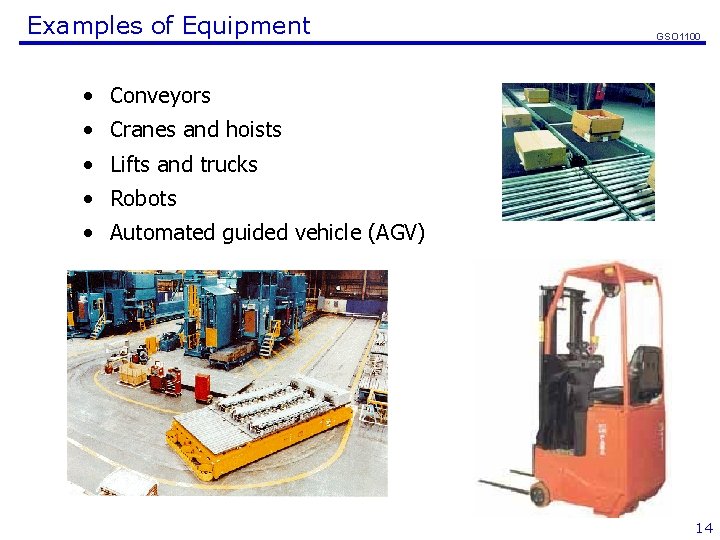
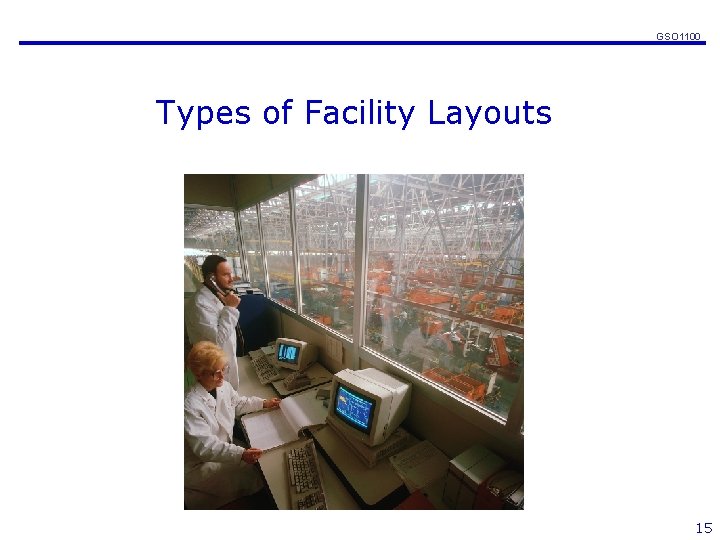
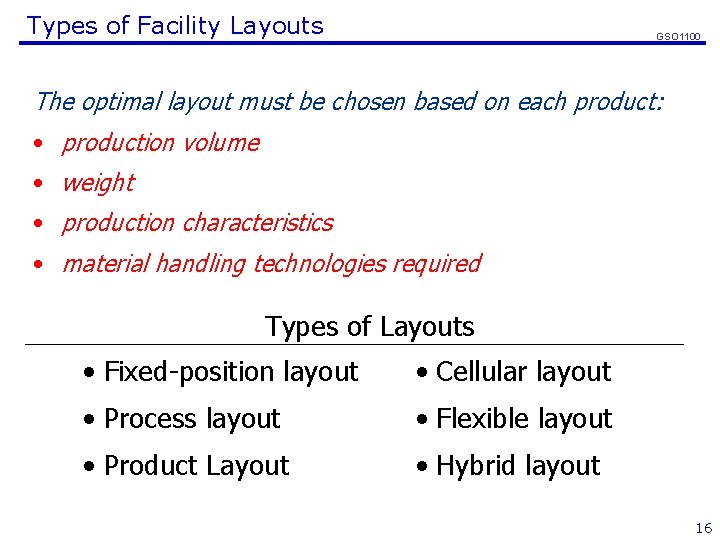
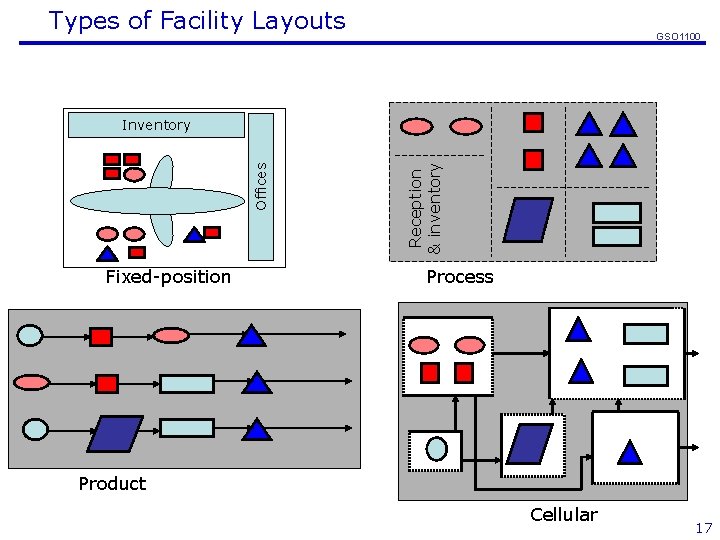
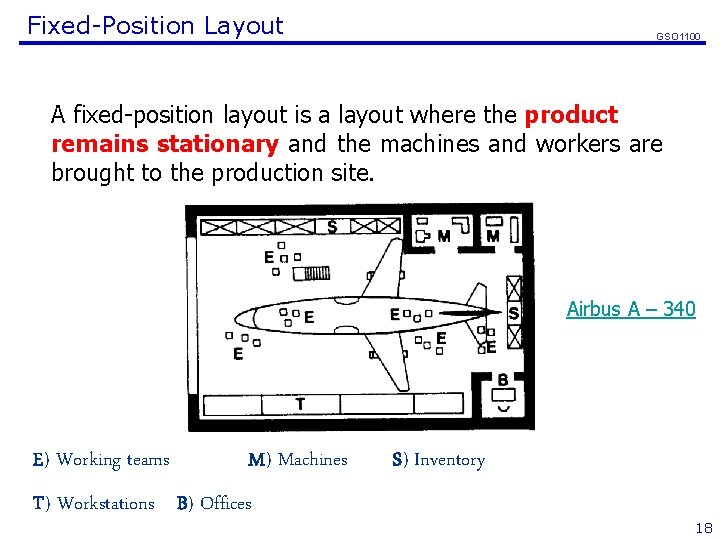
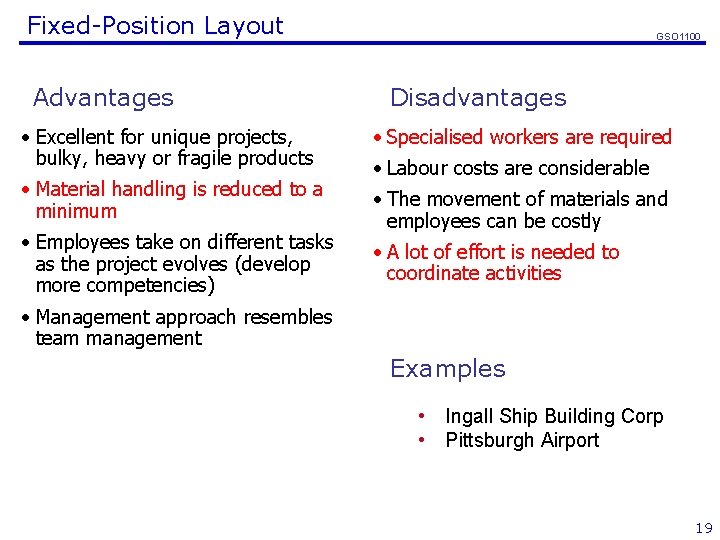
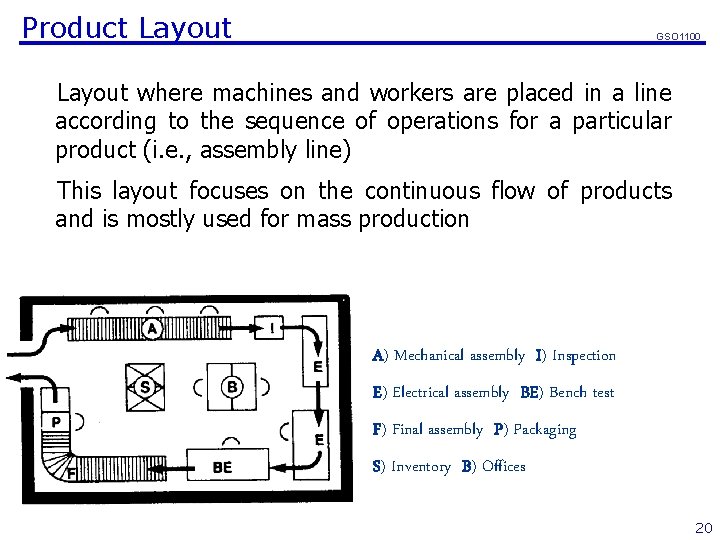
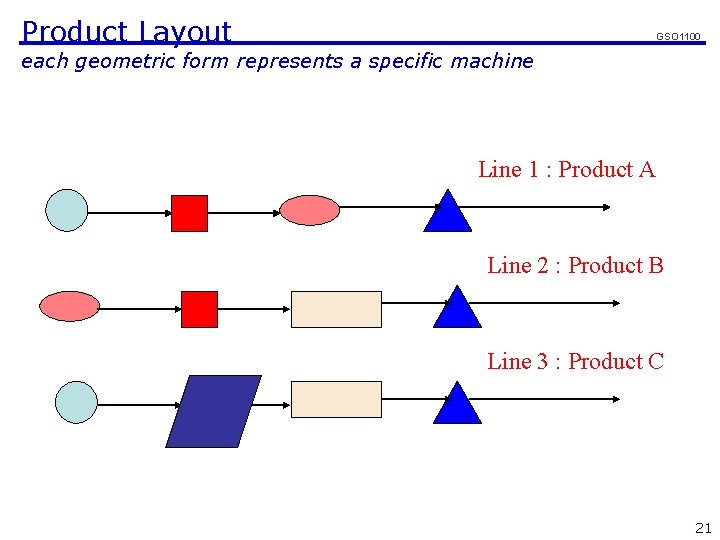
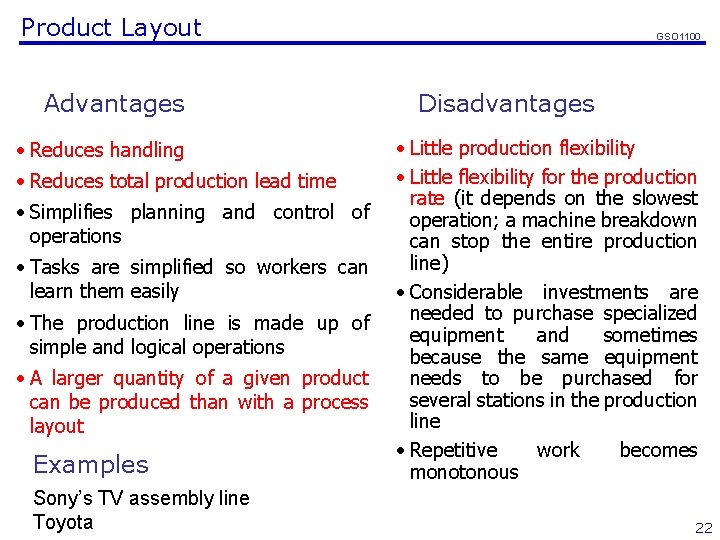
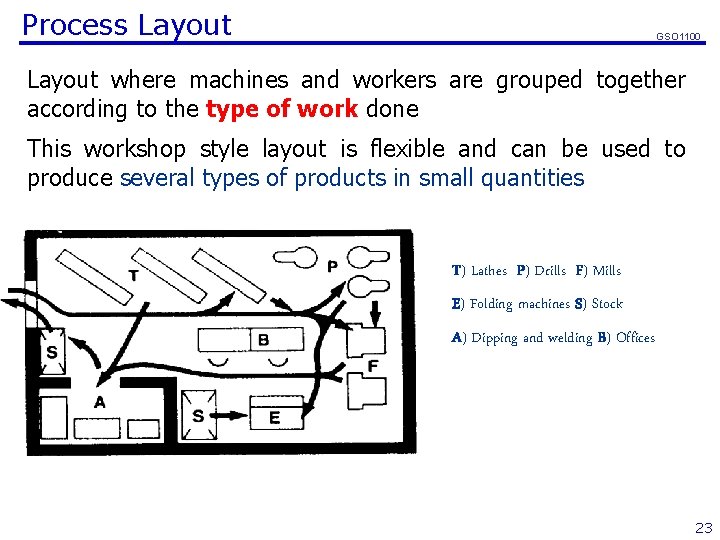
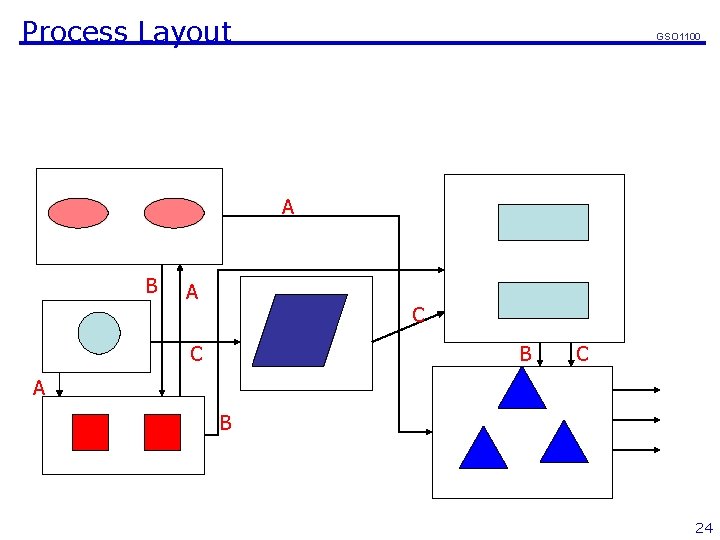
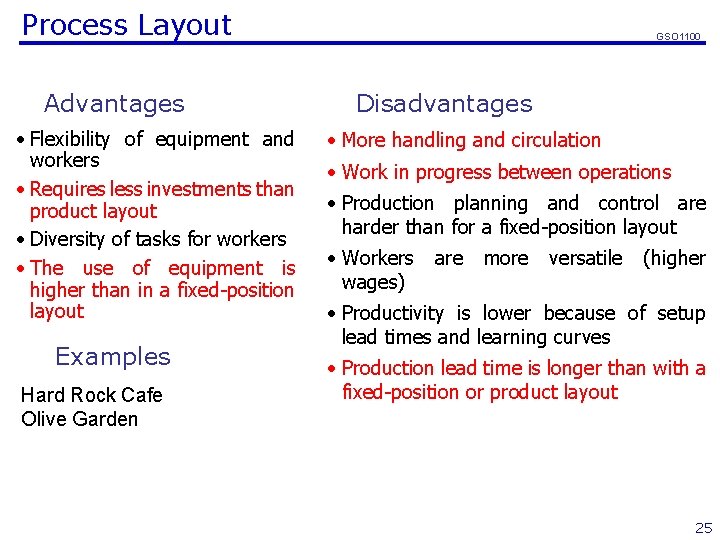
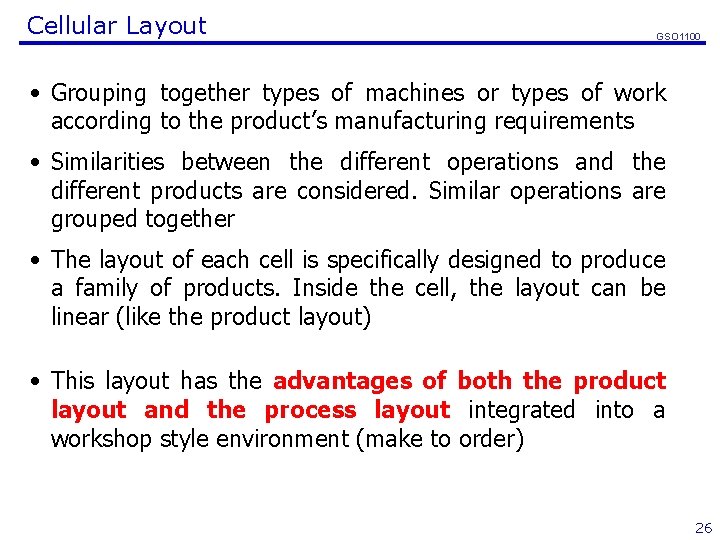
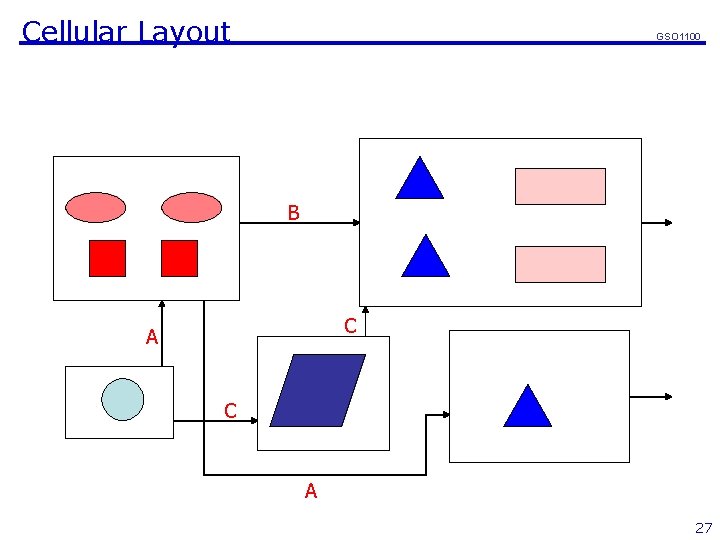
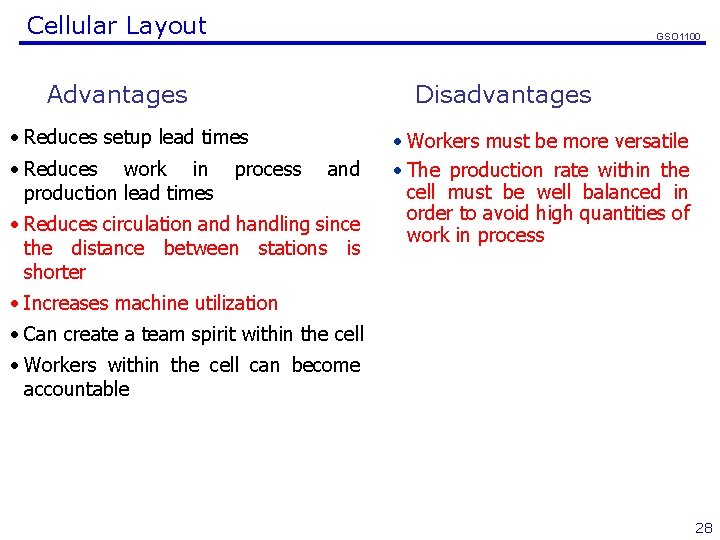
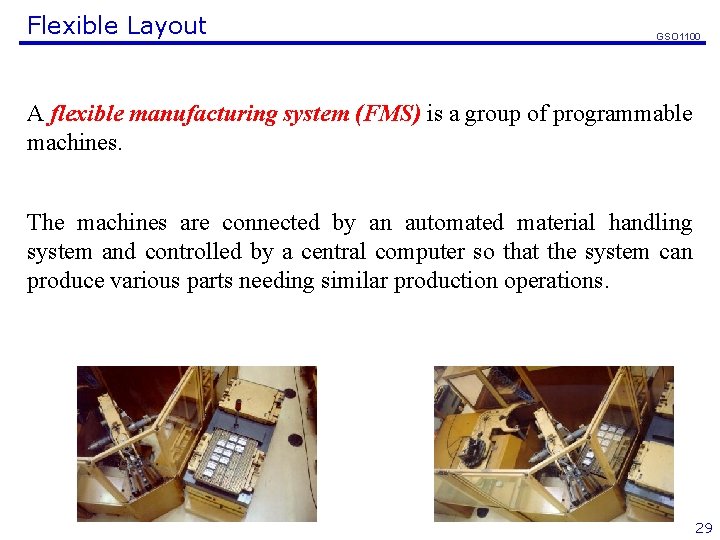
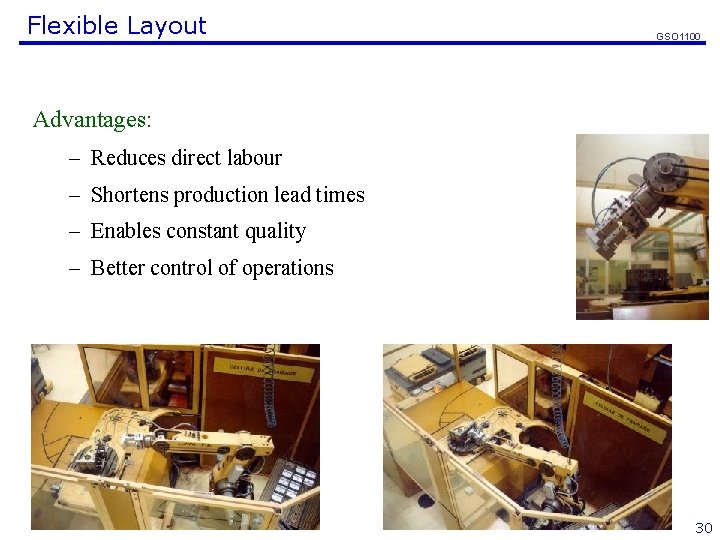
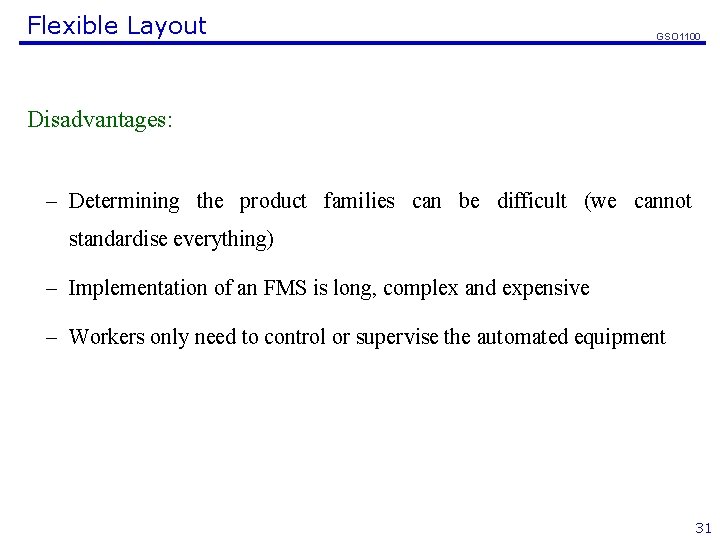
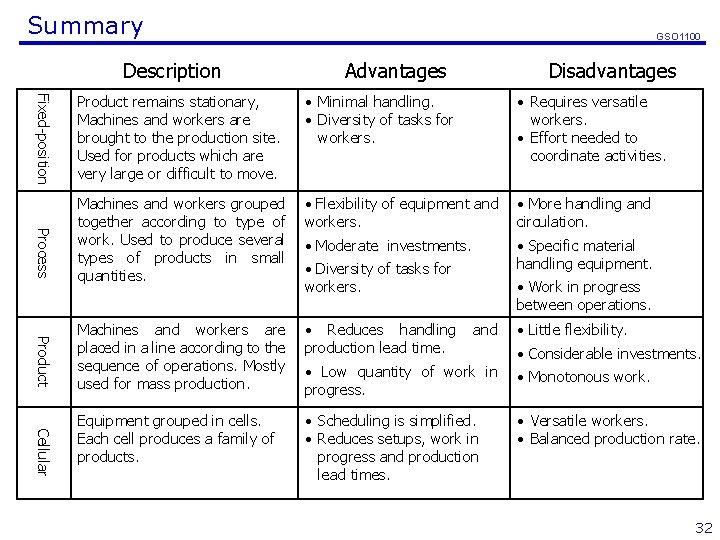
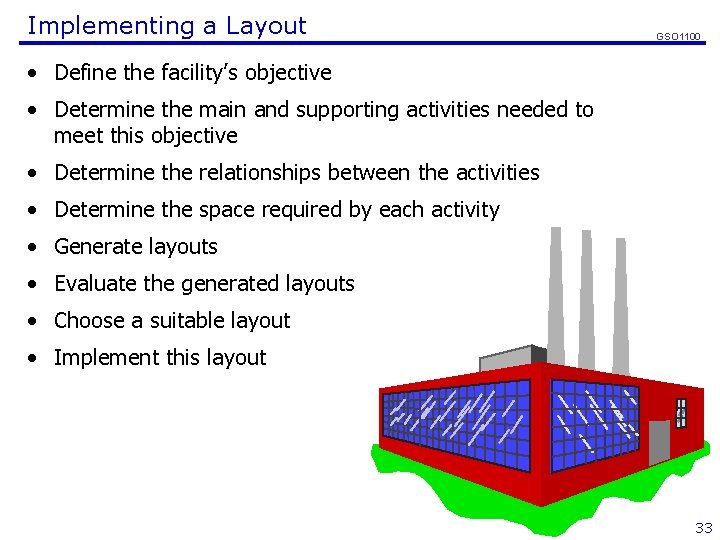
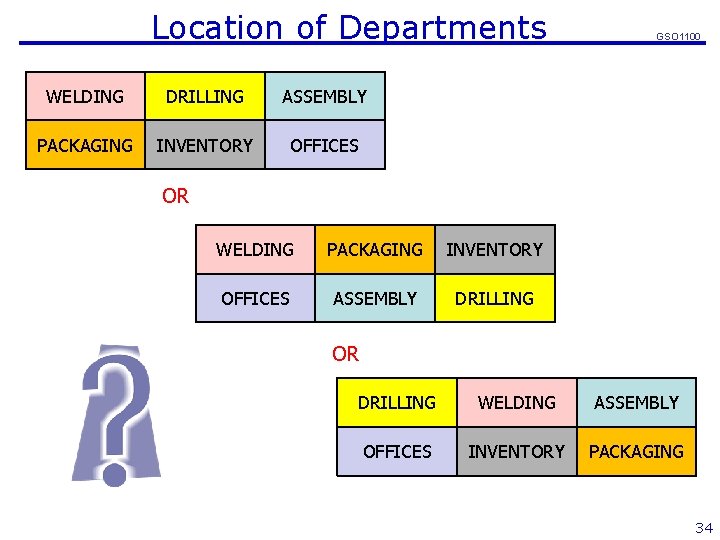
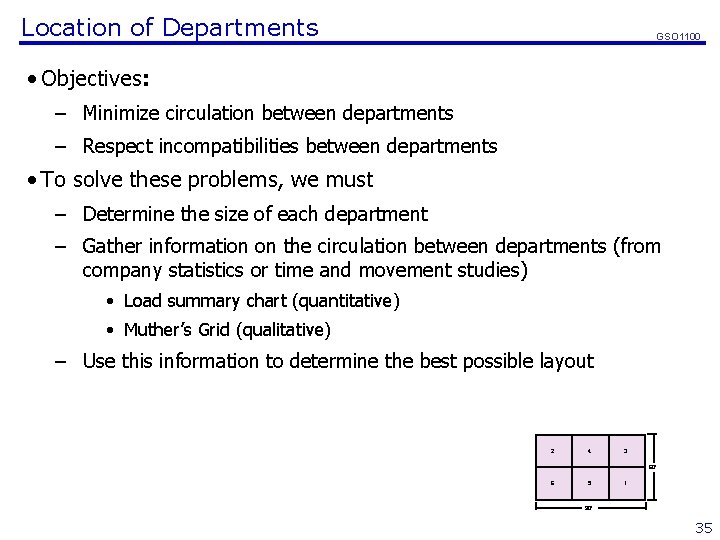
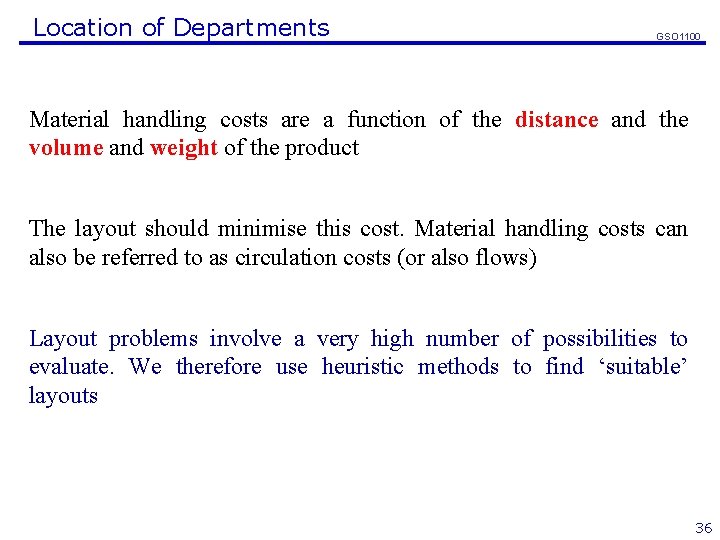
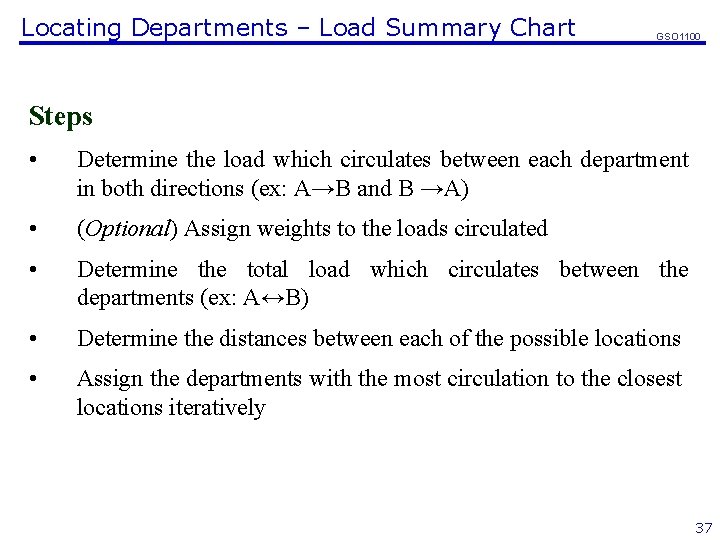
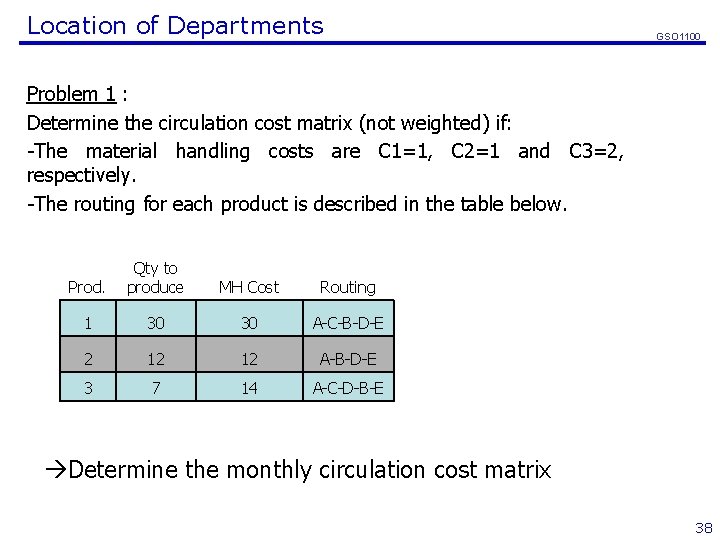
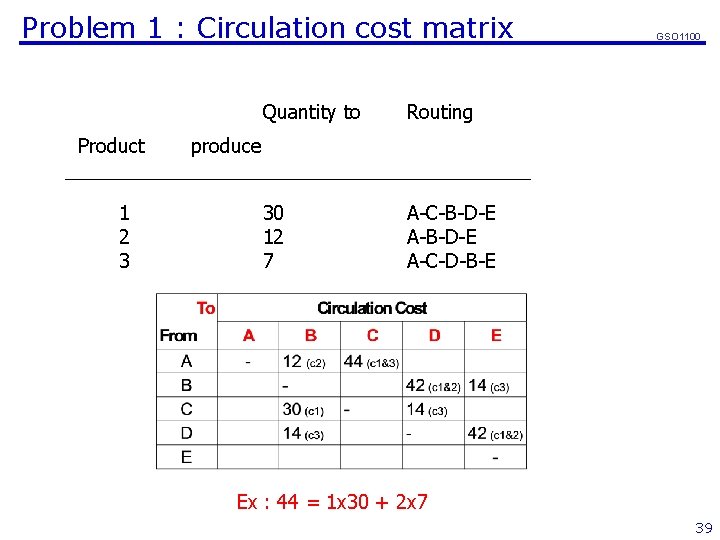
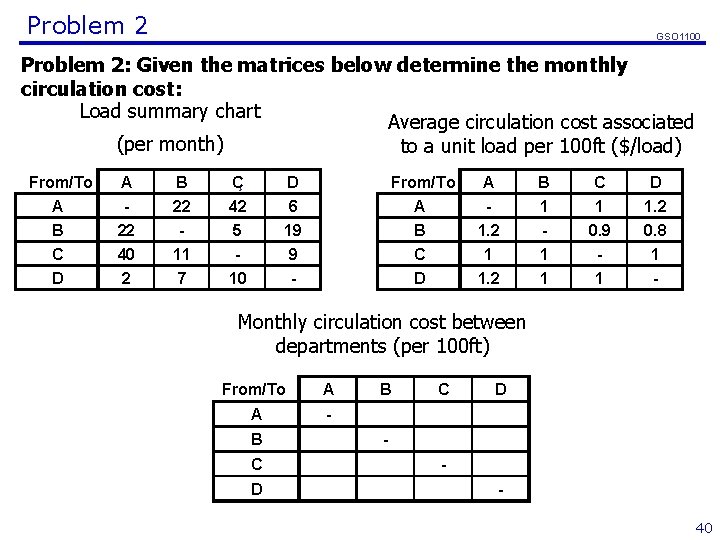
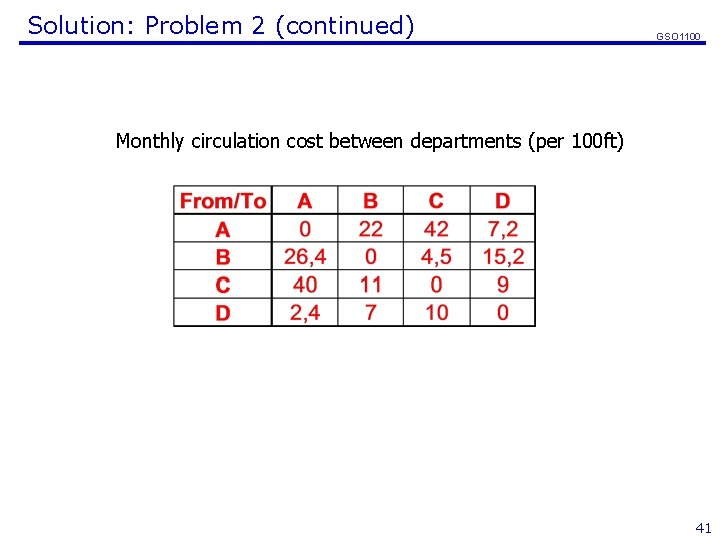
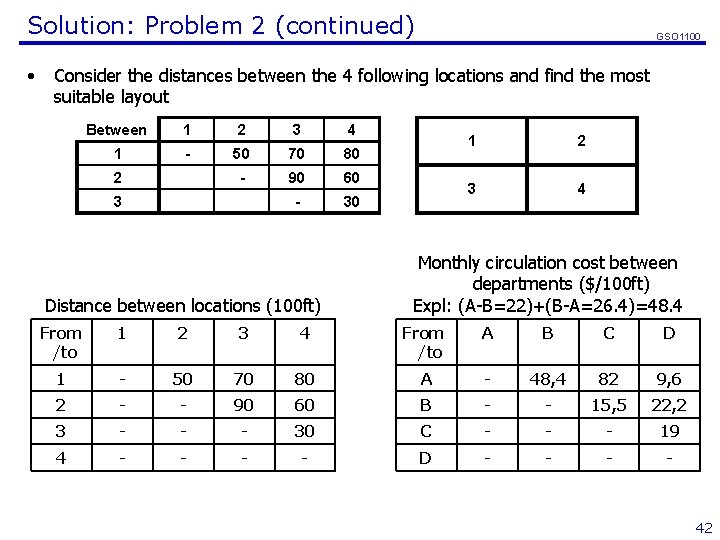
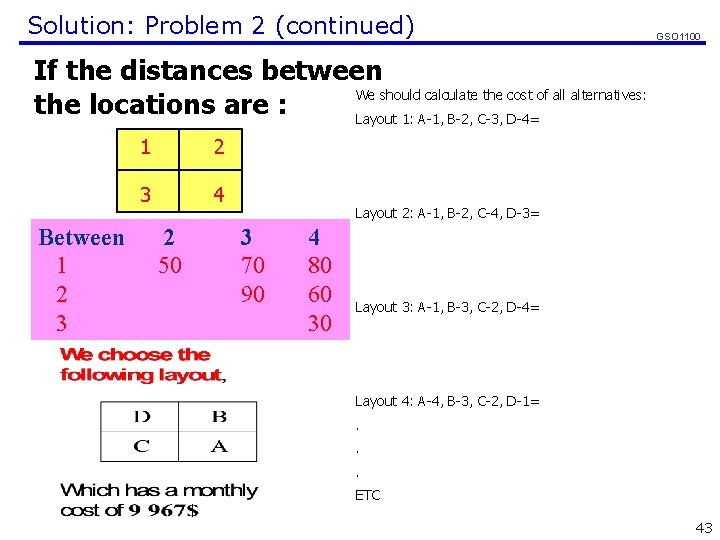
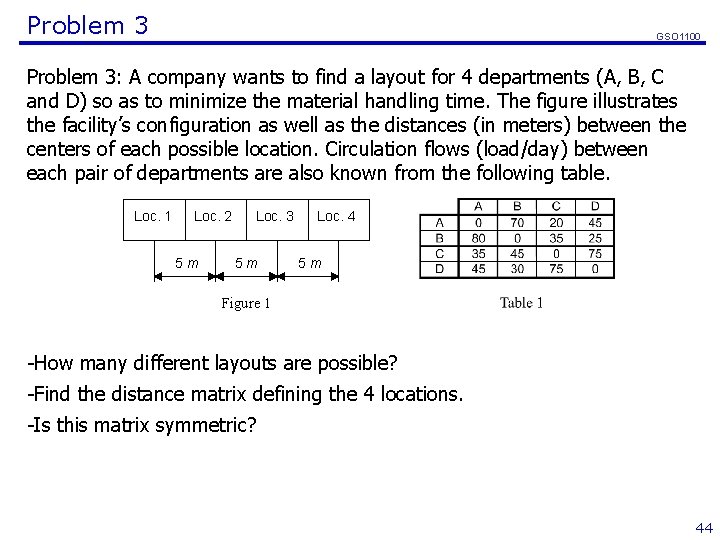
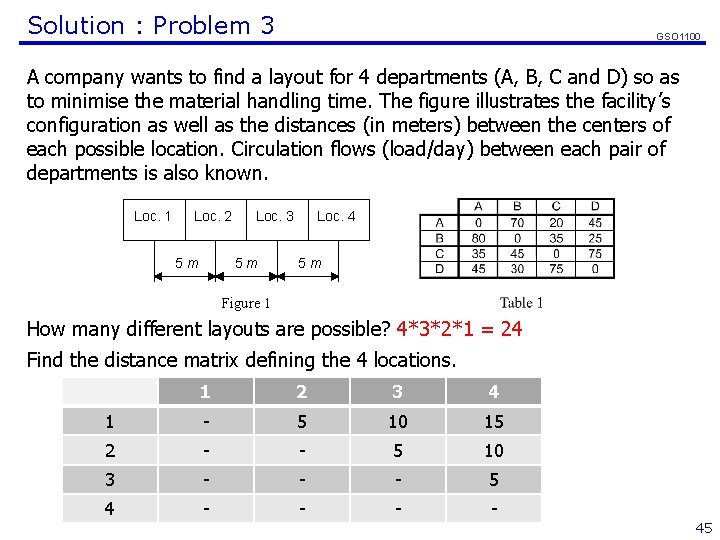
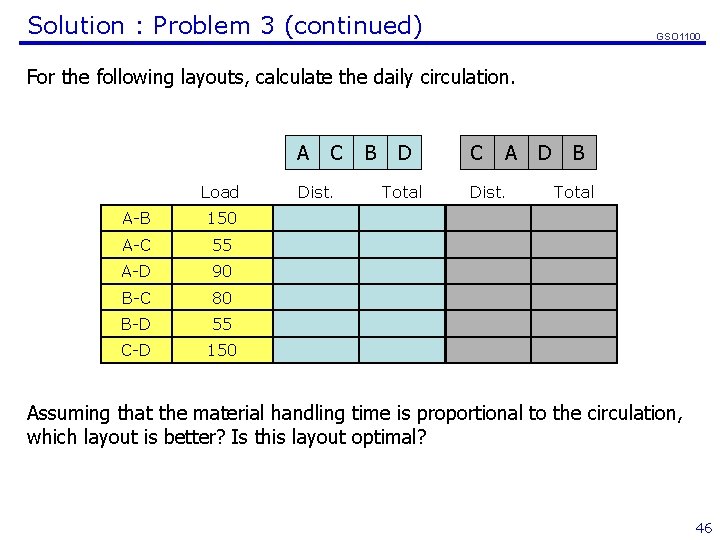
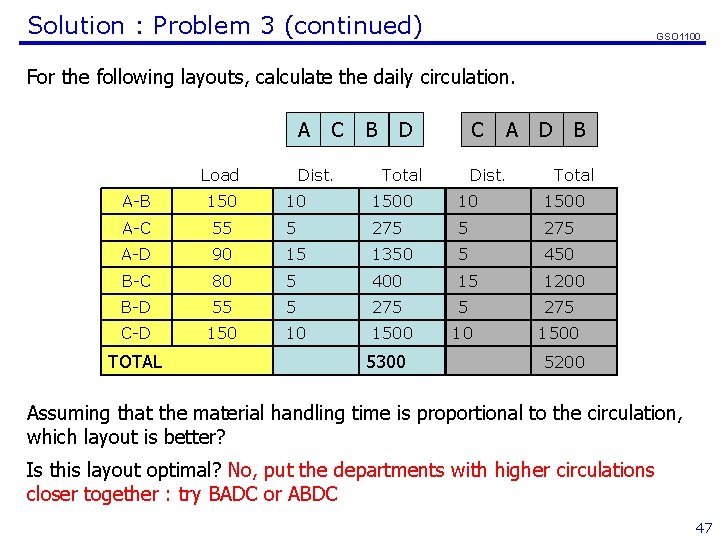
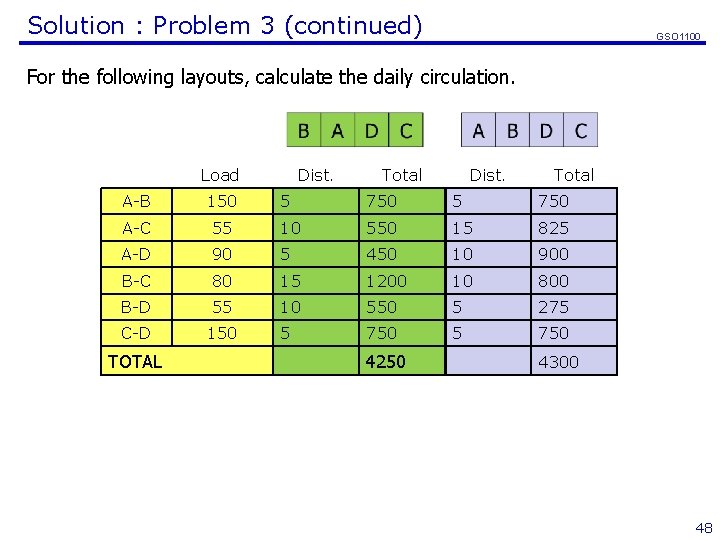
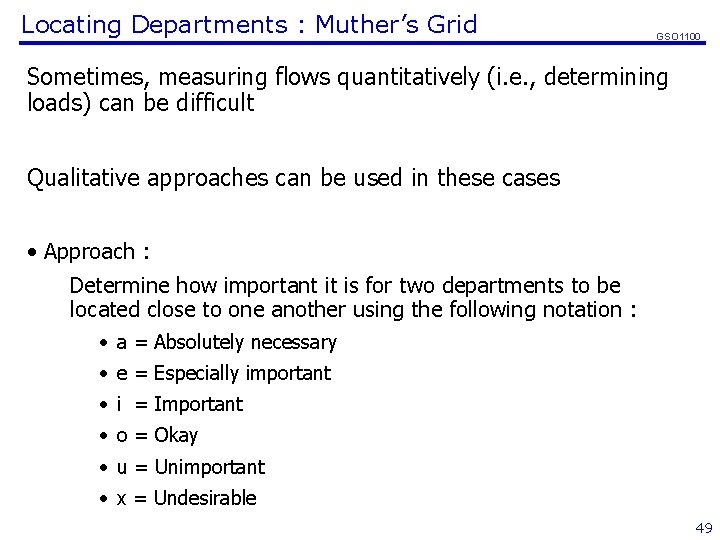
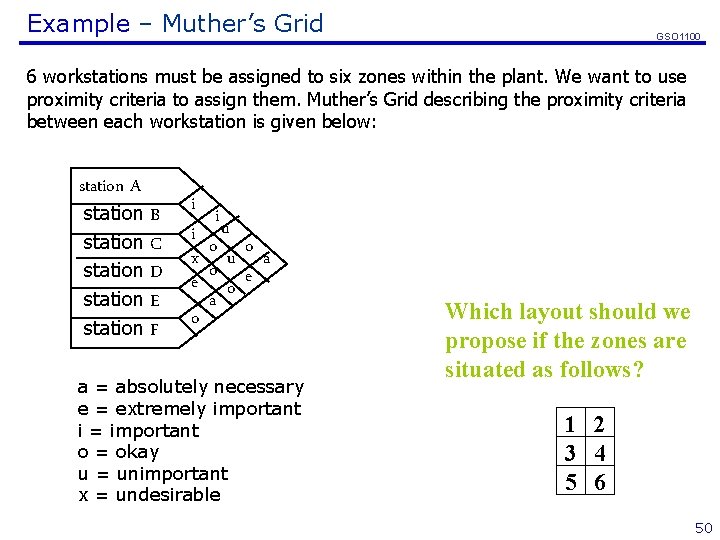
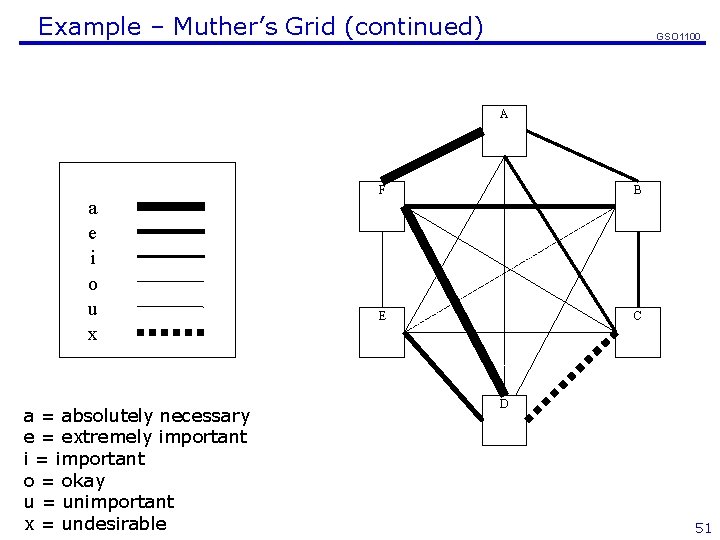
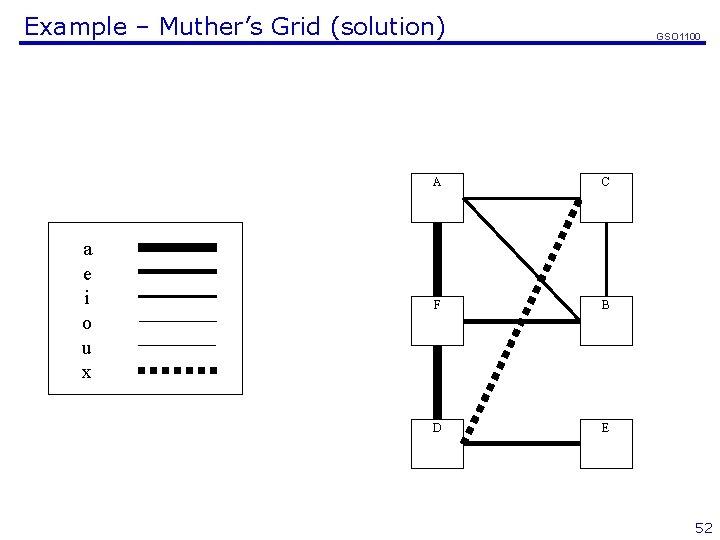
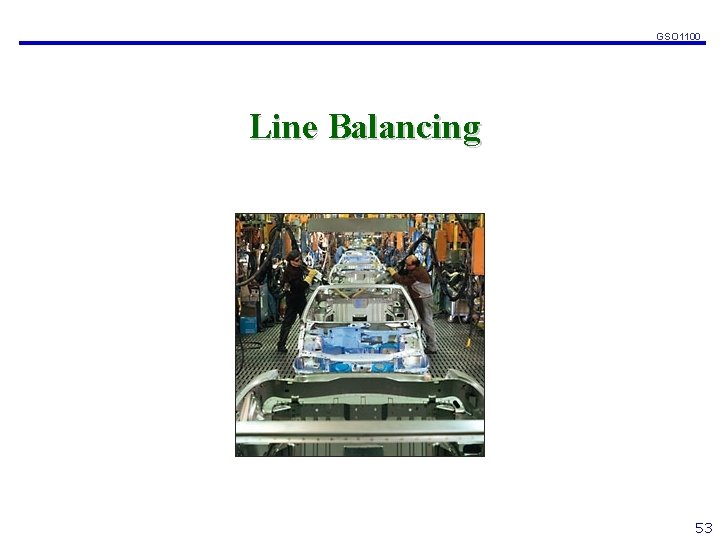
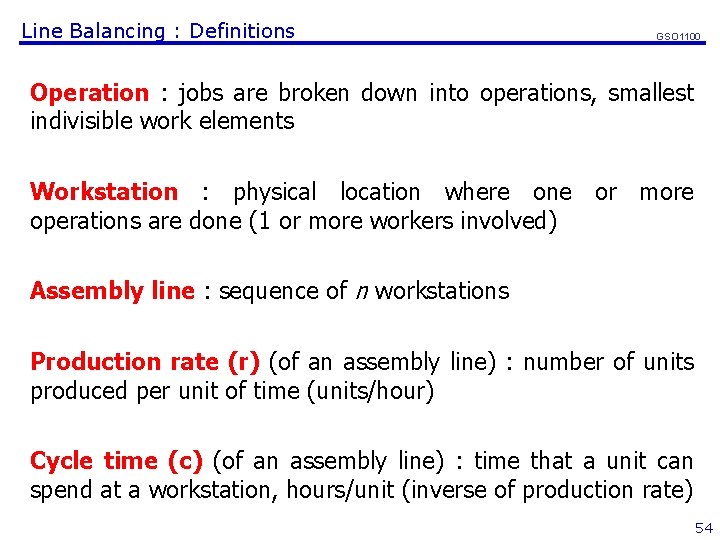
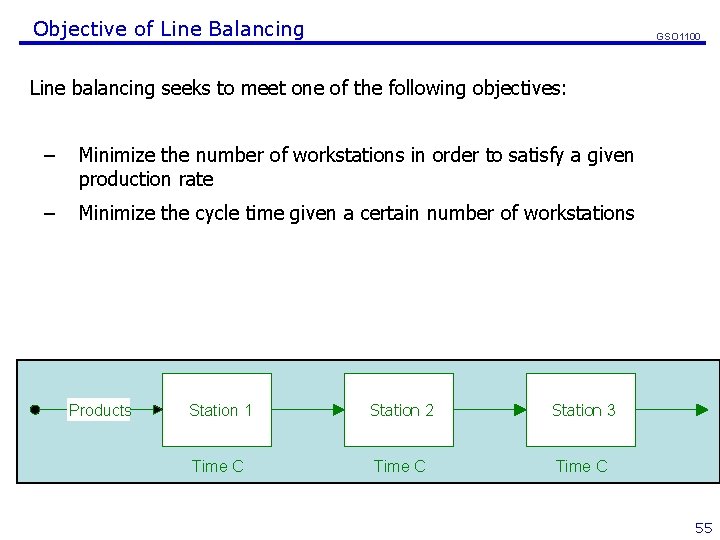
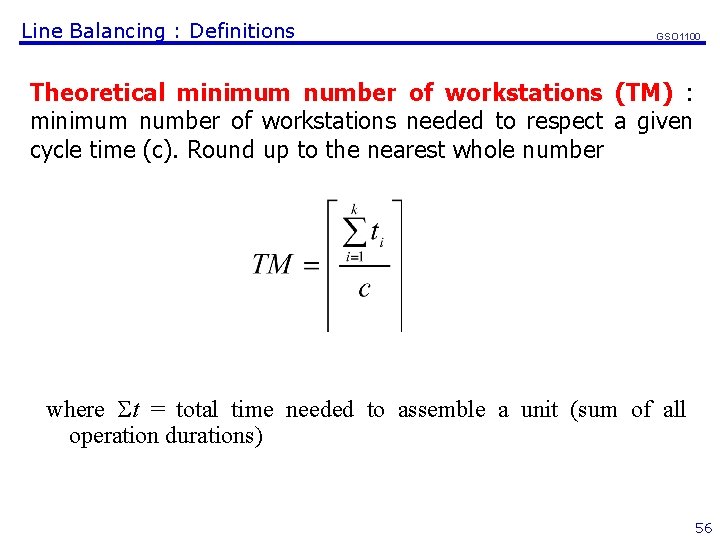
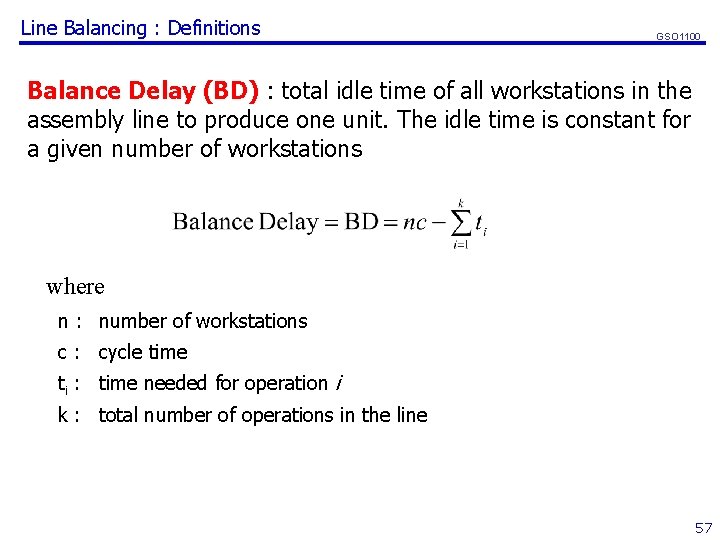
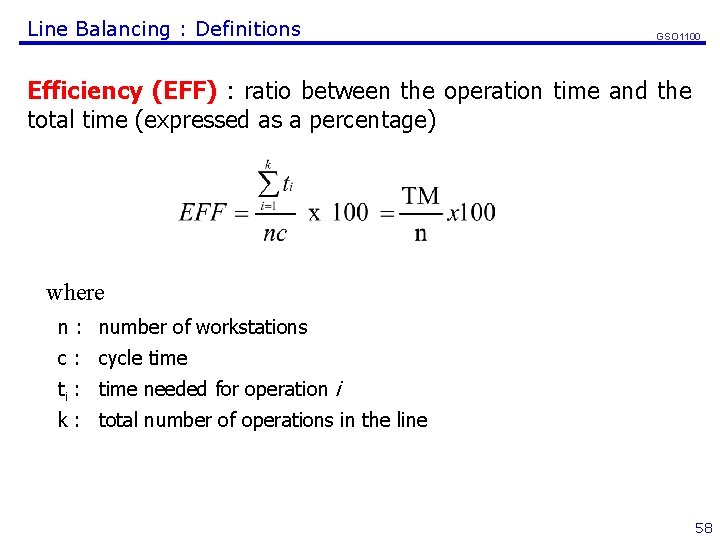
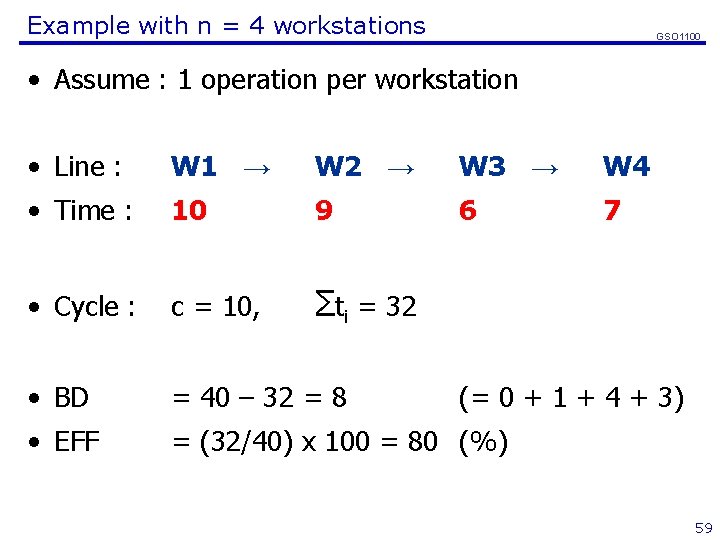
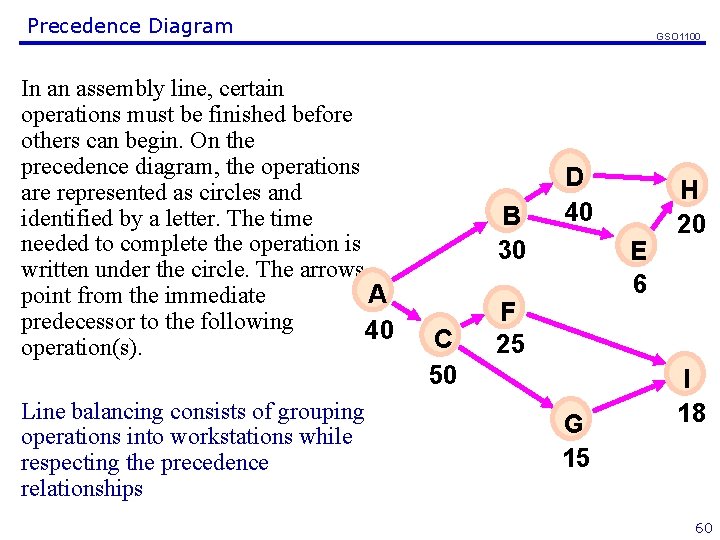
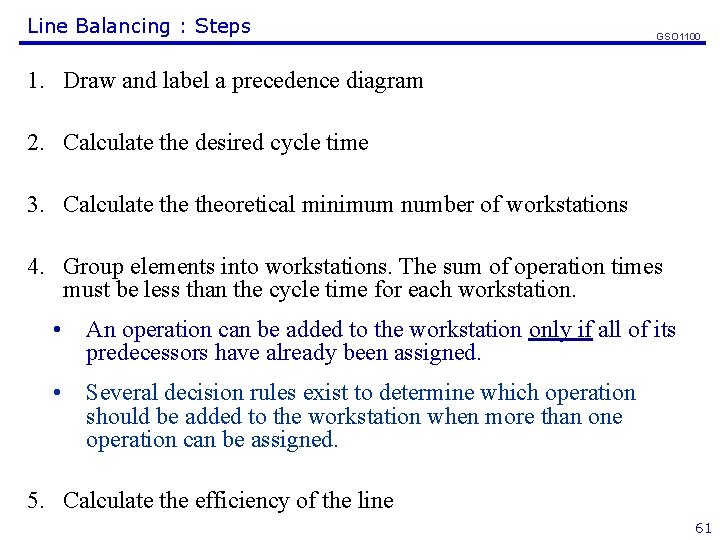
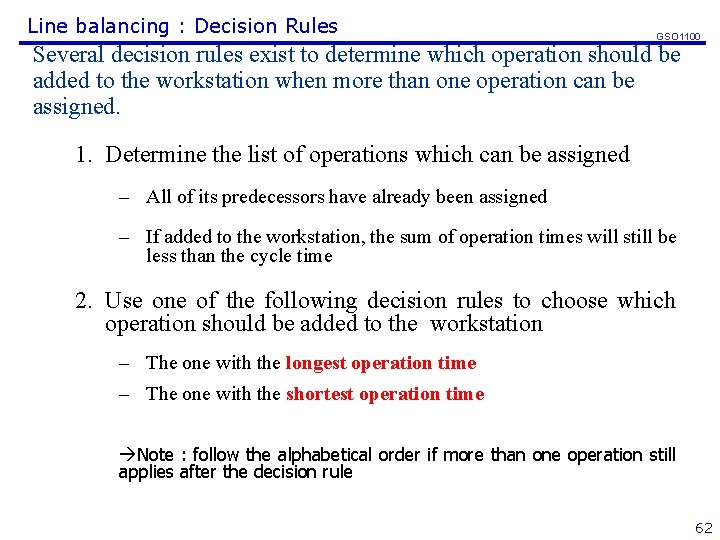

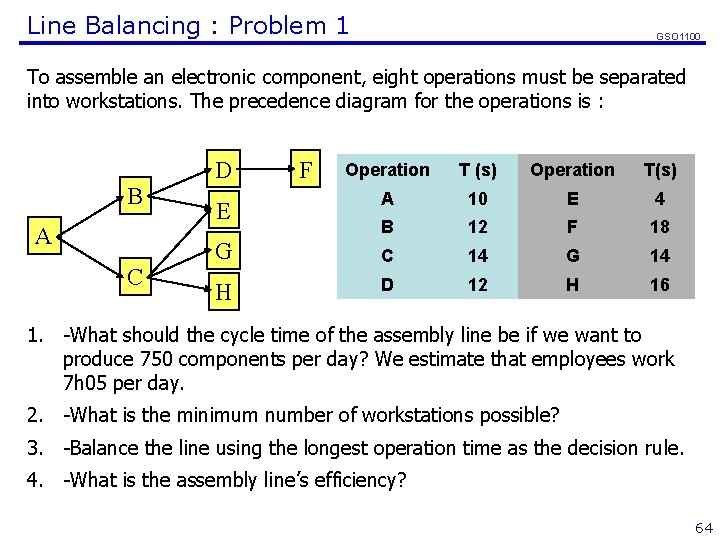
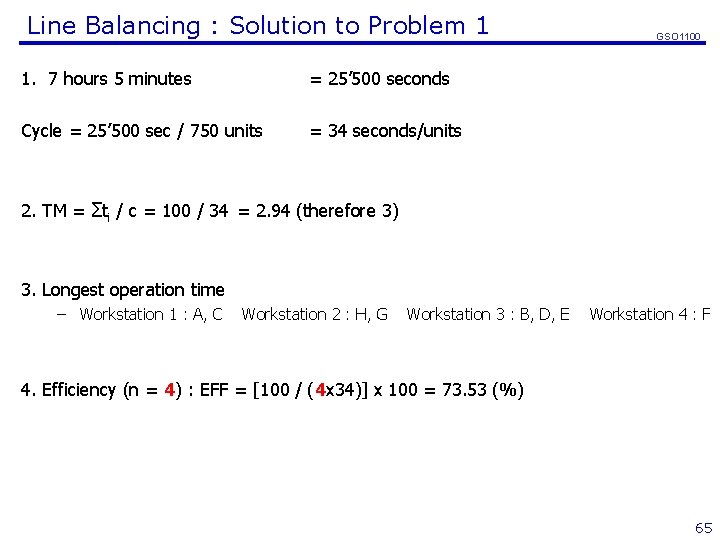
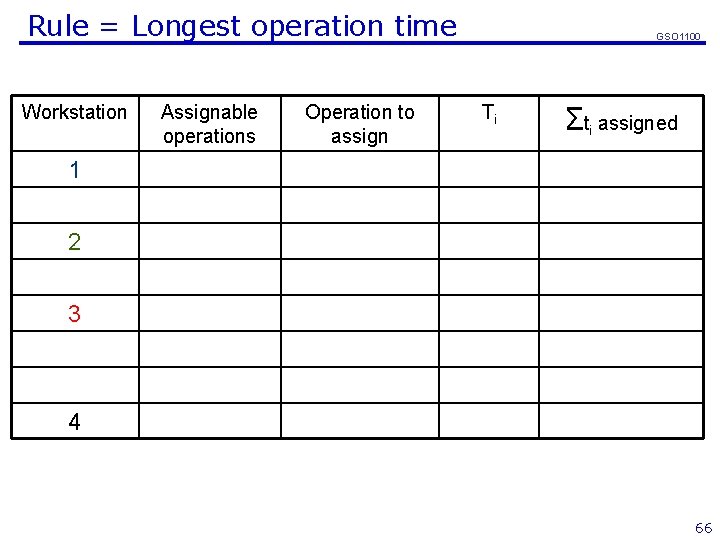
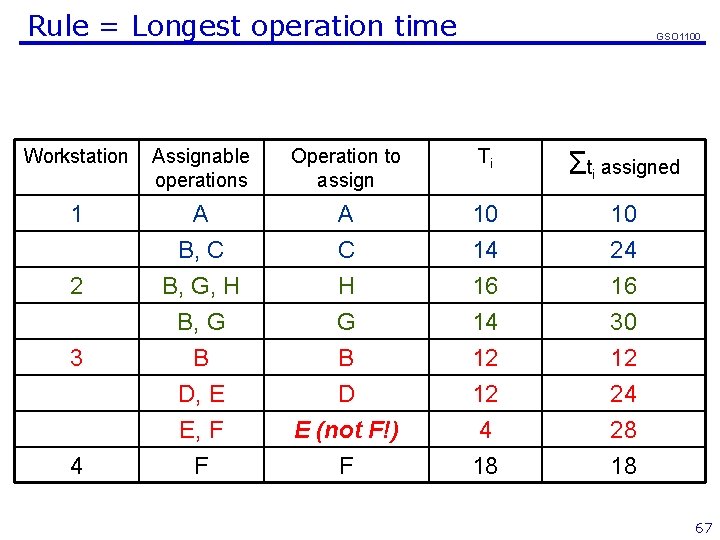
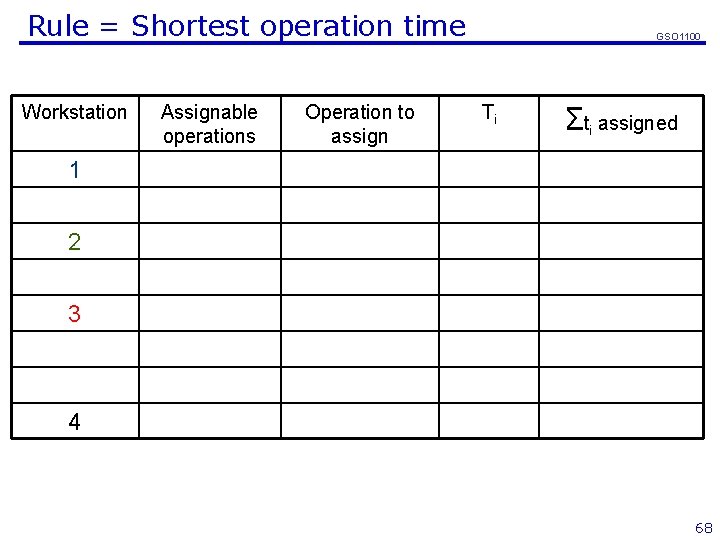
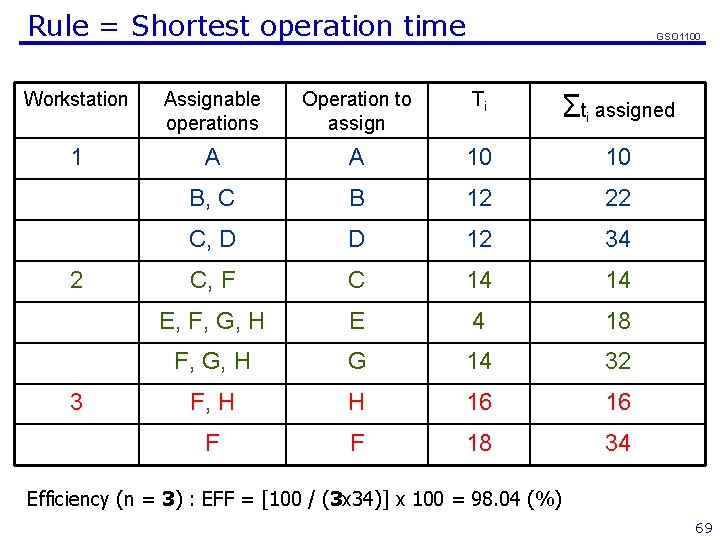
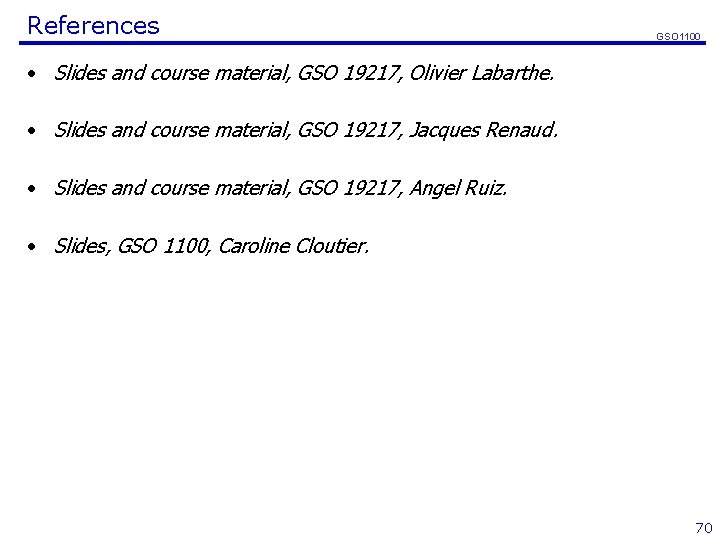
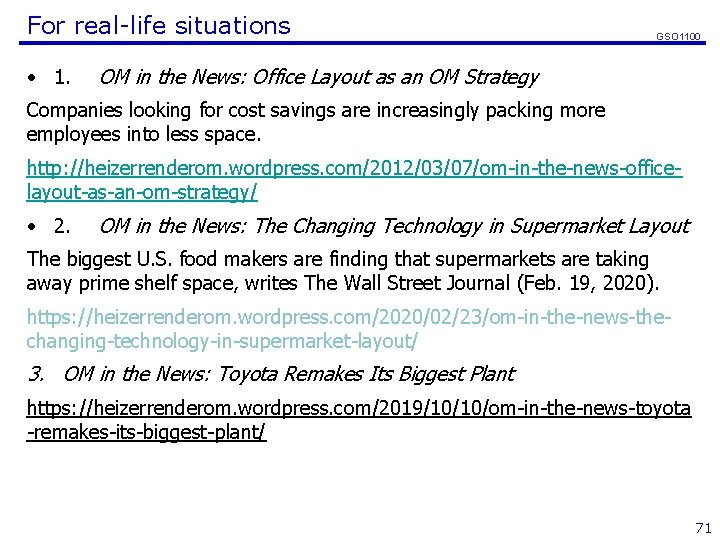
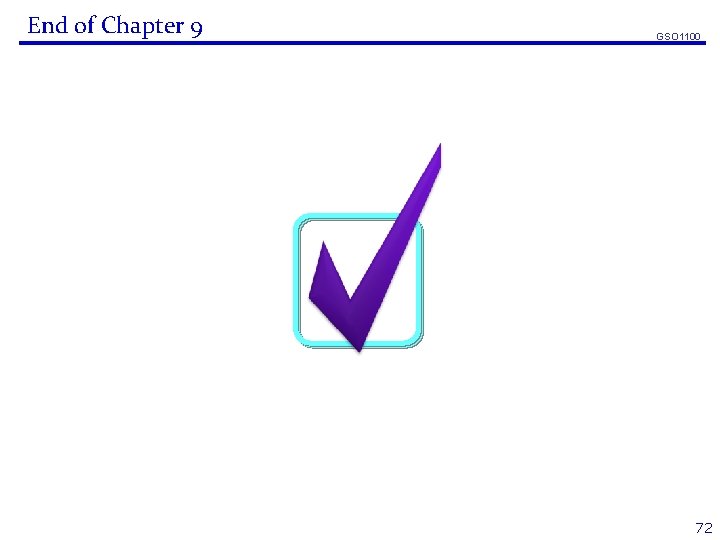
- Slides: 72
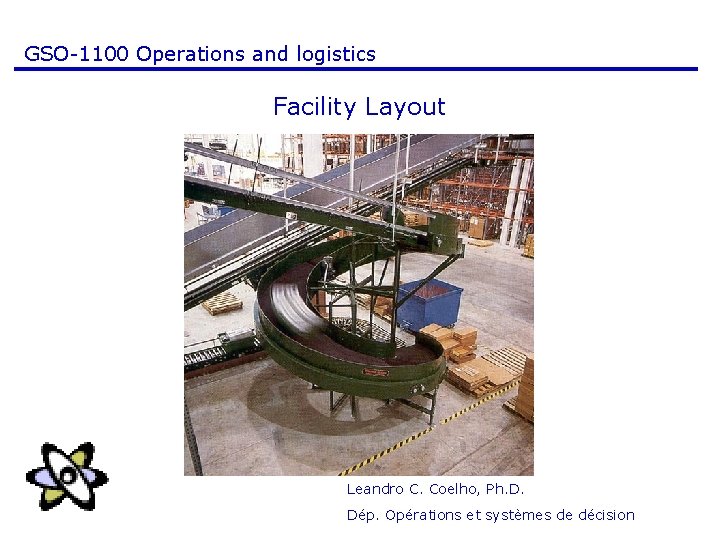
GSO-1100 Operations and logistics Facility Layout Leandro C. Coelho, Ph. D. Dép. Opérations et systèmes de décision

GSO 1100 College of Business Operations Management Dr. Rahma Lahyani Layout strategies (chapter 9) 2
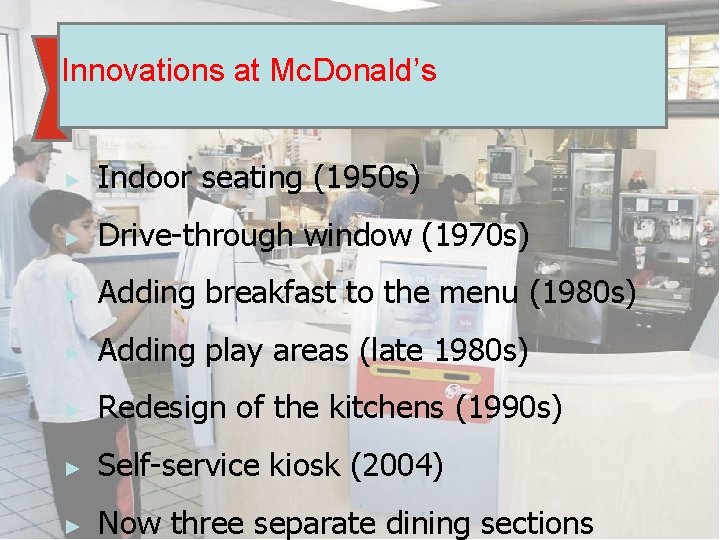
GSO 1100 Innovations at Mc. Donald’s ► Indoor seating (1950 s) ► Drive-through window (1970 s) ► Adding breakfast to the menu (1980 s) ► Adding play areas (late 1980 s) ► Redesign of the kitchens (1990 s) ► Self-service kiosk (2004) ► Now three separate dining sections 3

GSO 1100 Innovations at Mc. Donald’s ► Indoor seating (1950 s) ► Drive-through window (1970 s) Six out of the seven are Adding breakfast to the menu (1980 s) layout decisions! Adding play areas (late 1980 s) ► Redesign of the kitchens (1990 s) ► Self-service kiosk (2004) ► Now three separate dining sections ► ► 4
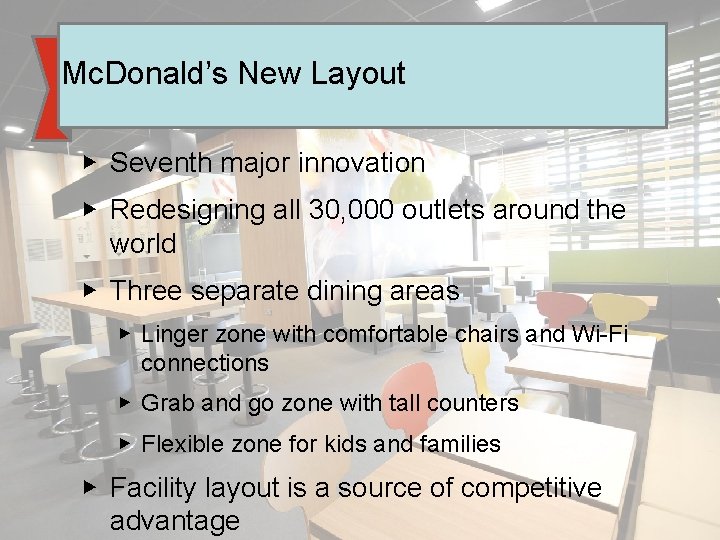
GSO 1100 Mc. Donald’s New Layout ▶ Seventh major innovation ▶ Redesigning all 30, 000 outlets around the world ▶ Three separate dining areas ▶ Linger zone with comfortable chairs and Wi-Fi connections ▶ Grab and go zone with tall counters ▶ Flexible zone for kids and families ▶ Facility layout is a source of competitive advantage 5
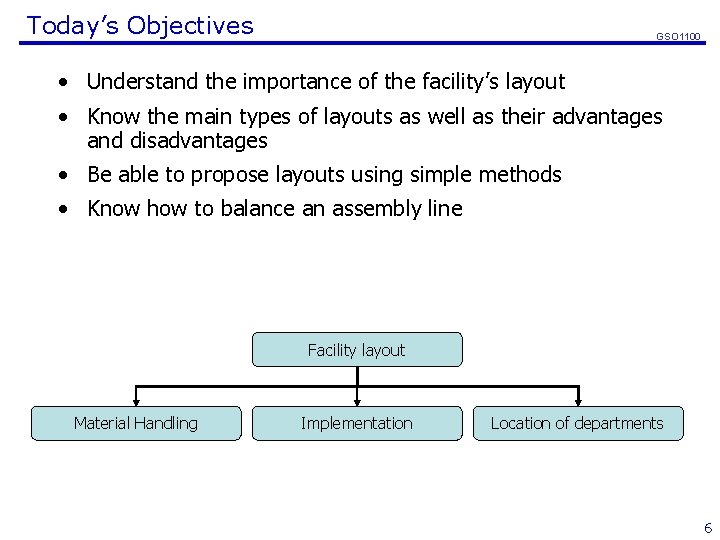
Today’s Objectives GSO 1100 • Understand the importance of the facility’s layout • Know the main types of layouts as well as their advantages and disadvantages • Be able to propose layouts using simple methods • Know how to balance an assembly line Facility layout Material Handling Implementation Location of departments 6
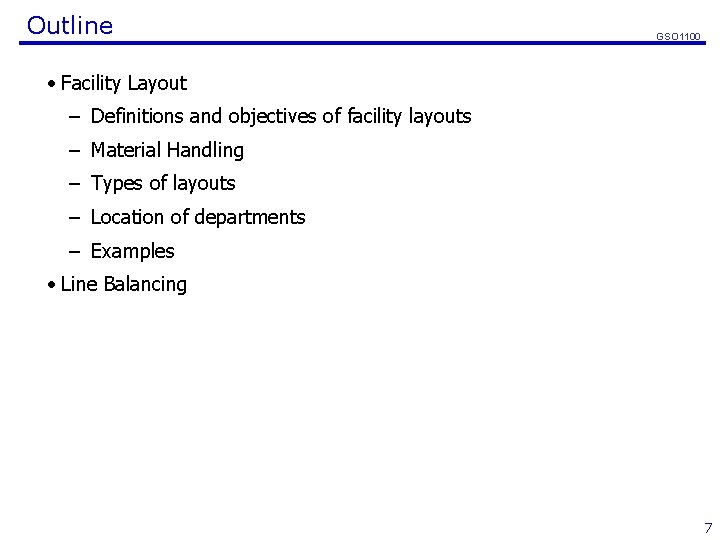
Outline GSO 1100 • Facility Layout – Definitions and objectives of facility layouts – Material Handling – Types of layouts – Location of departments – Examples • Line Balancing 7
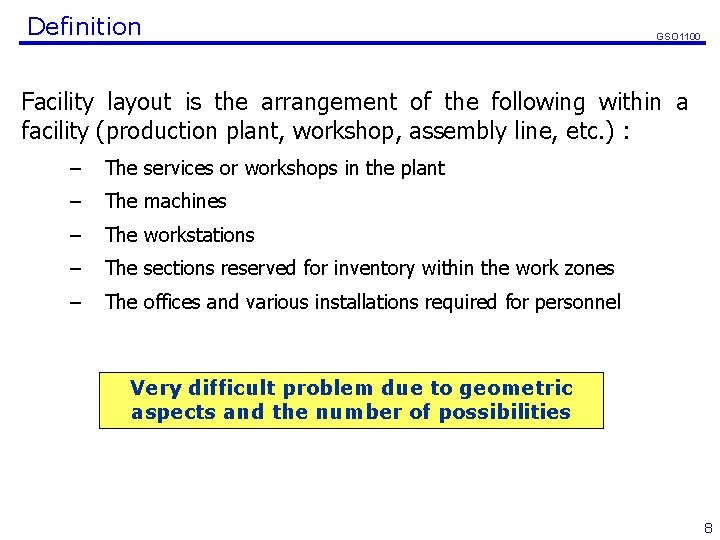
Definition GSO 1100 Facility layout is the arrangement of the following within a facility (production plant, workshop, assembly line, etc. ) : – The services or workshops in the plant – The machines – The workstations – The sections reserved for inventory within the work zones – The offices and various installations required for personnel Very difficult problem due to geometric aspects and the number of possibilities 8
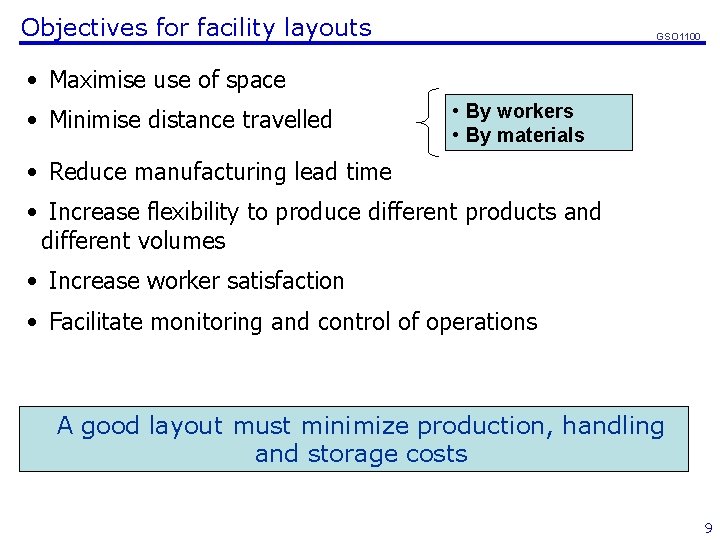
Objectives for facility layouts GSO 1100 • Maximise use of space • Minimise distance travelled • By workers • By materials • Reduce manufacturing lead time • Increase flexibility to produce different products and different volumes • Increase worker satisfaction • Facilitate monitoring and control of operations A good layout must minimize production, handling and storage costs 9
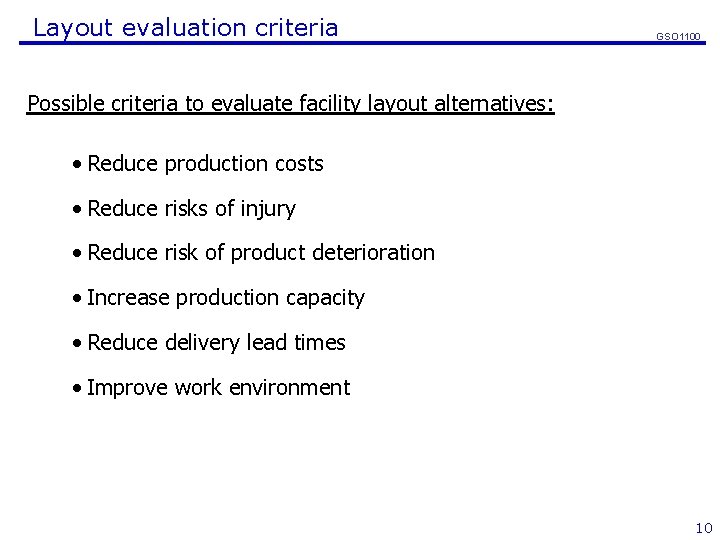
Layout evaluation criteria GSO 1100 Possible criteria to evaluate facility layout alternatives: • Reduce production costs • Reduce risks of injury • Reduce risk of product deterioration • Increase production capacity • Reduce delivery lead times • Improve work environment 10
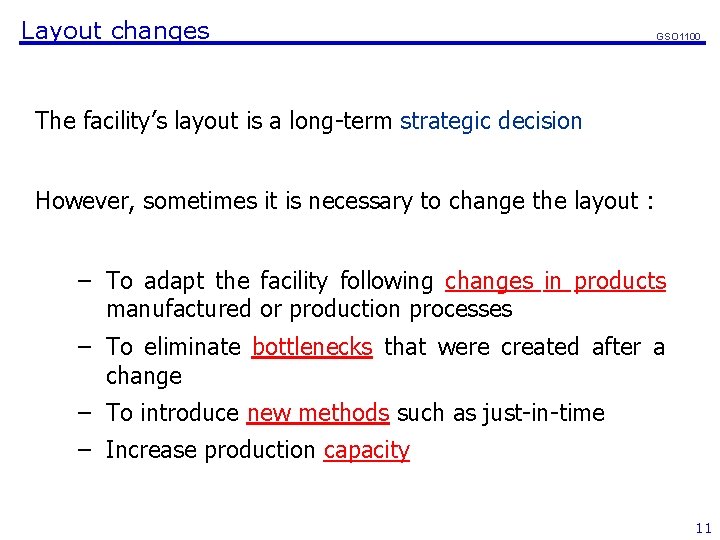
Layout changes GSO 1100 The facility’s layout is a long-term strategic decision However, sometimes it is necessary to change the layout : – To adapt the facility following changes in products manufactured or production processes – To eliminate bottlenecks that were created after a change – To introduce new methods such as just-in-time – Increase production capacity 11
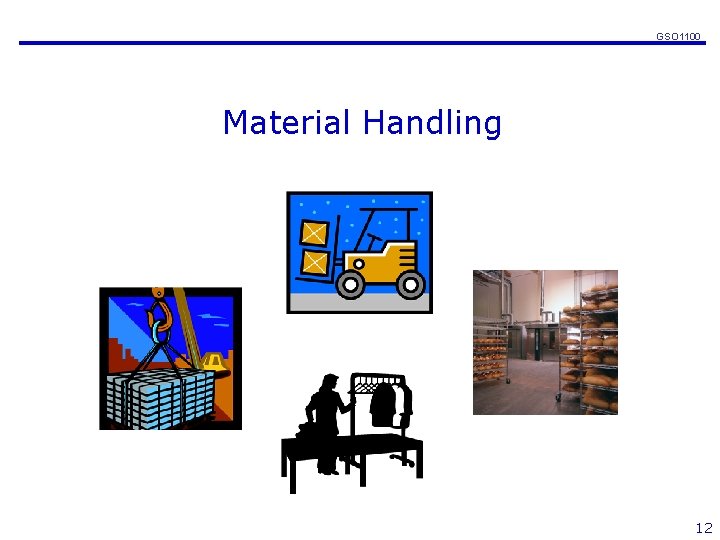
GSO 1100 Material Handling 12
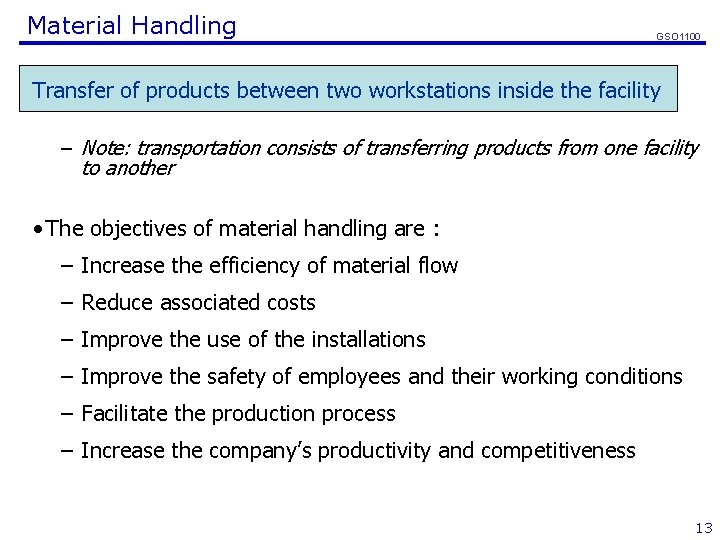
Material Handling GSO 1100 Transfer of products between two workstations inside the facility – Note: transportation consists of transferring products from one facility to another • The objectives of material handling are : – Increase the efficiency of material flow – Reduce associated costs – Improve the use of the installations – Improve the safety of employees and their working conditions – Facilitate the production process – Increase the company’s productivity and competitiveness 13
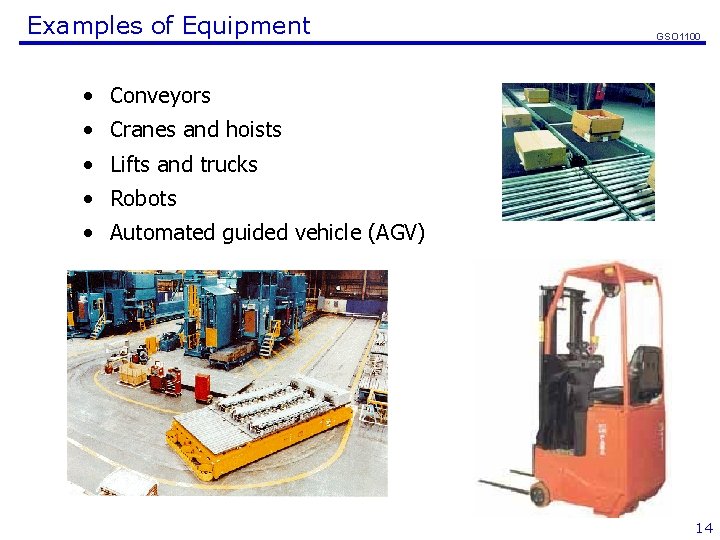
Examples of Equipment GSO 1100 • Conveyors • Cranes and hoists • Lifts and trucks • Robots • Automated guided vehicle (AGV) 14
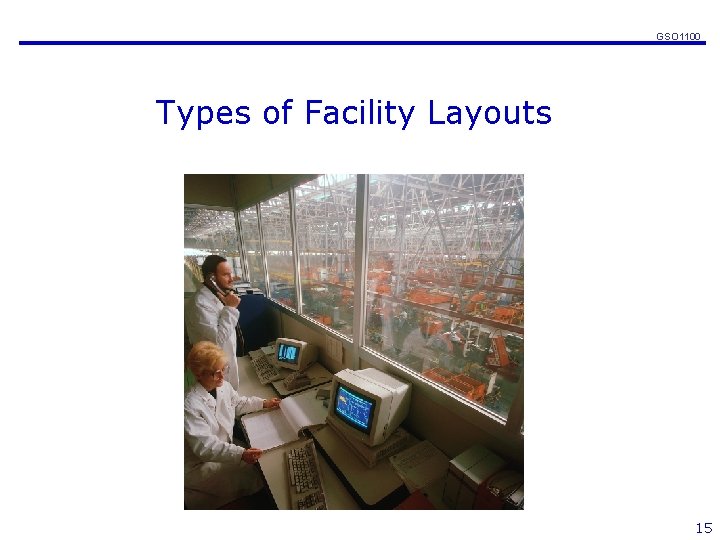
GSO 1100 Types of Facility Layouts 15
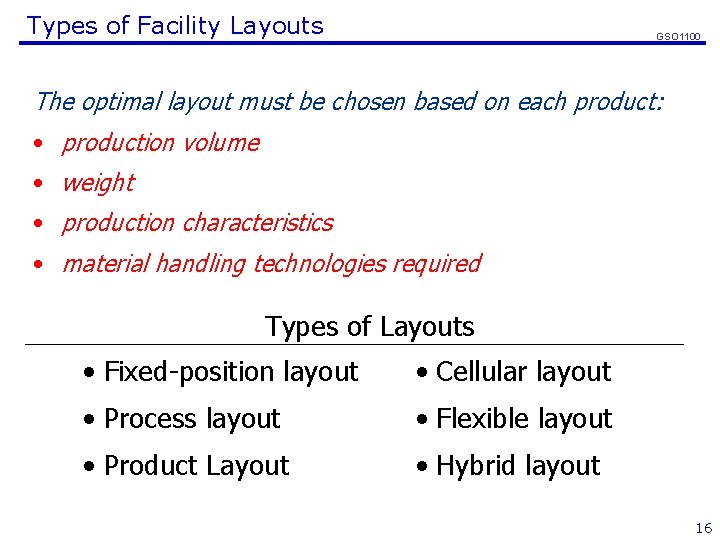
Types of Facility Layouts GSO 1100 The optimal layout must be chosen based on each product: • production volume • weight • production characteristics • material handling technologies required Types of Layouts • Fixed-position layout • Cellular layout • Process layout • Flexible layout • Product Layout • Hybrid layout 16
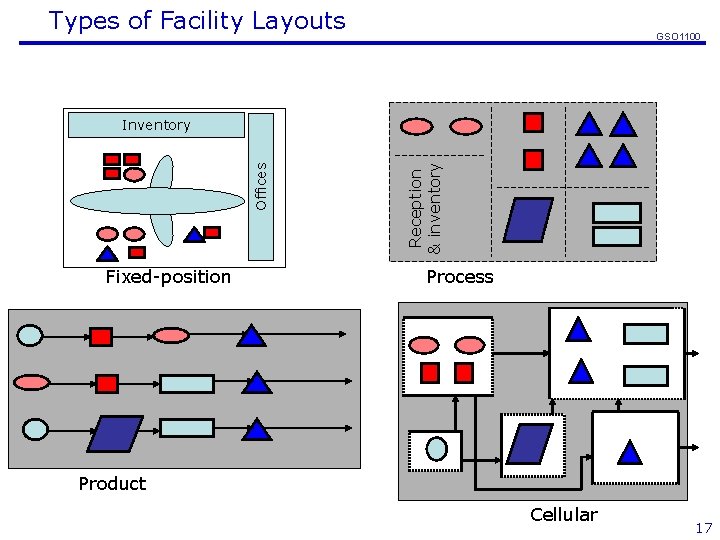
Types of Facility Layouts GSO 1100 Fixed-position Reception & inventory Offices Inventory Process Product Cellular 17
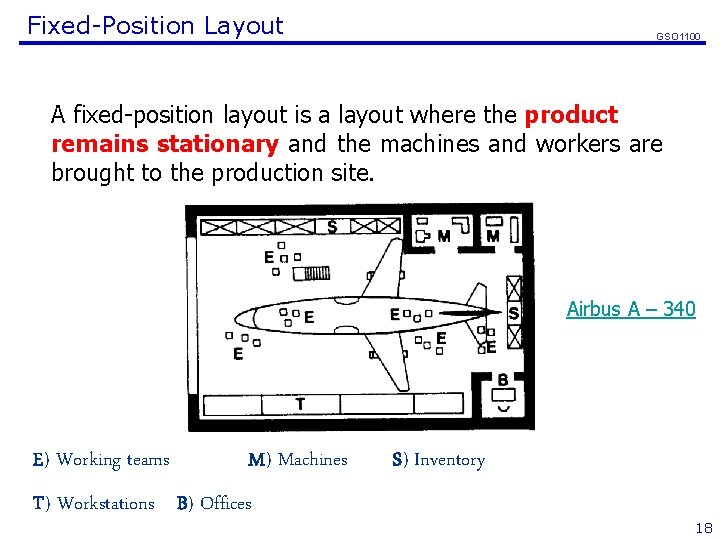
Fixed-Position Layout GSO 1100 A fixed-position layout is a layout where the product remains stationary and the machines and workers are brought to the production site. Airbus A – 340 E) Working teams M) Machines T) Workstations B) Offices S) Inventory 18
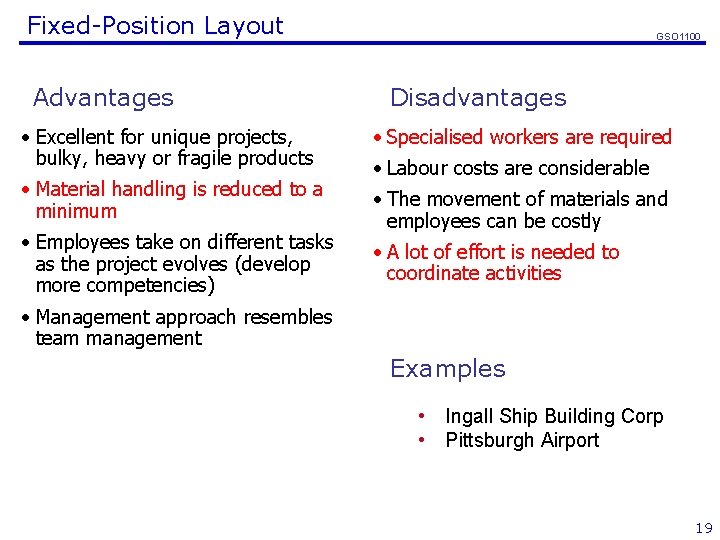
Fixed-Position Layout Advantages GSO 1100 Disadvantages • Excellent for unique projects, bulky, heavy or fragile products • Specialised workers are required • Material handling is reduced to a minimum • The movement of materials and employees can be costly • Employees take on different tasks as the project evolves (develop more competencies) • Labour costs are considerable • A lot of effort is needed to coordinate activities • Management approach resembles team management Examples • Ingall Ship Building Corp • Pittsburgh Airport 19
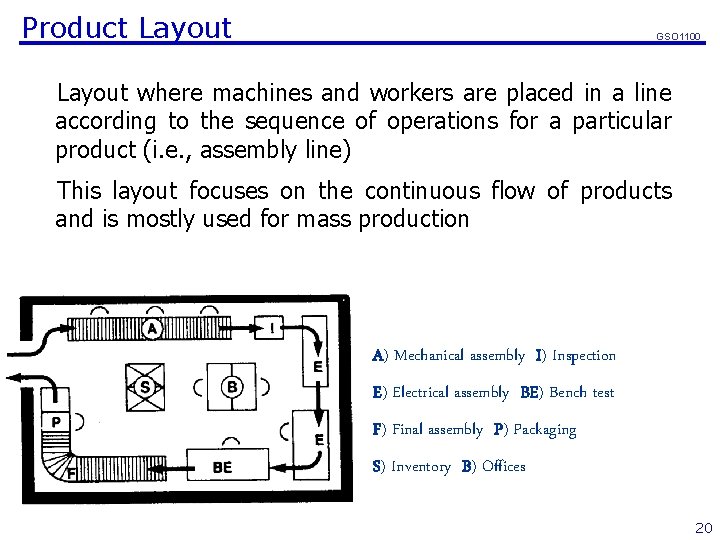
Product Layout GSO 1100 Layout where machines and workers are placed in a line according to the sequence of operations for a particular product (i. e. , assembly line) This layout focuses on the continuous flow of products and is mostly used for mass production A) Mechanical assembly I) Inspection E) Electrical assembly BE) Bench test F) Final assembly P) Packaging S) Inventory B) Offices 20
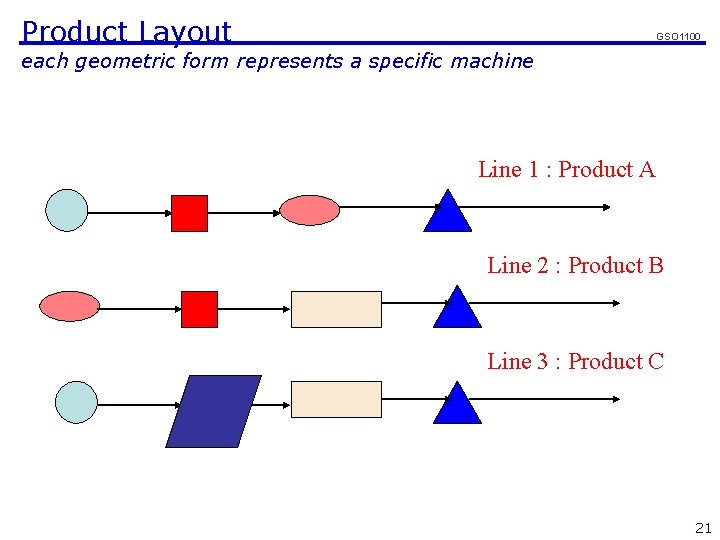
Product Layout GSO 1100 each geometric form represents a specific machine Line 1 : Product A Line 2 : Product B Line 3 : Product C 21
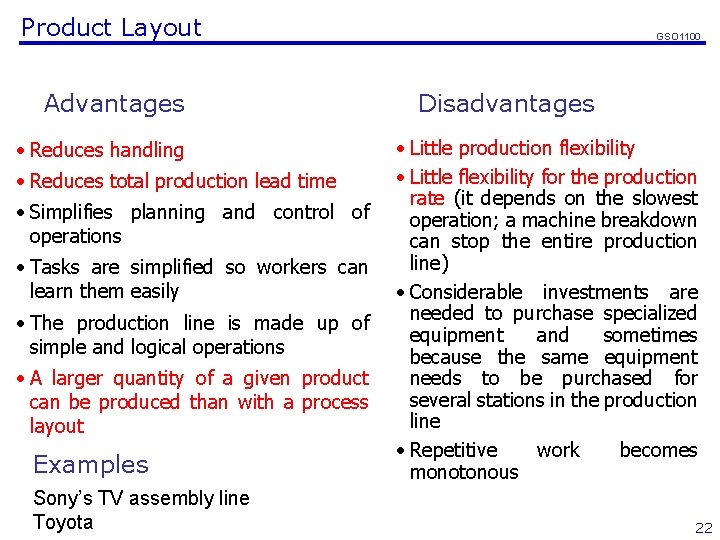
Product Layout Advantages • Reduces handling • Reduces total production lead time • Simplifies planning and control of operations • Tasks are simplified so workers can learn them easily • The production line is made up of simple and logical operations • A larger quantity of a given product can be produced than with a process layout Examples Sony’s TV assembly line Toyota GSO 1100 Disadvantages • Little production flexibility • Little flexibility for the production rate (it depends on the slowest operation; a machine breakdown can stop the entire production line) • Considerable investments are needed to purchase specialized equipment and sometimes because the same equipment needs to be purchased for several stations in the production line • Repetitive work becomes monotonous 22
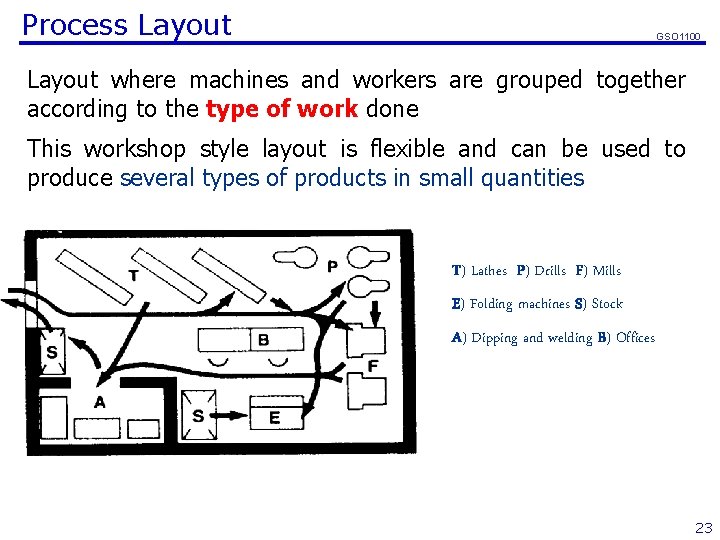
Process Layout GSO 1100 Layout where machines and workers are grouped together according to the type of work done This workshop style layout is flexible and can be used to produce several types of products in small quantities T) Lathes P) Drills F) Mills E) Folding machines S) Stock A) Dipping and welding B) Offices 23
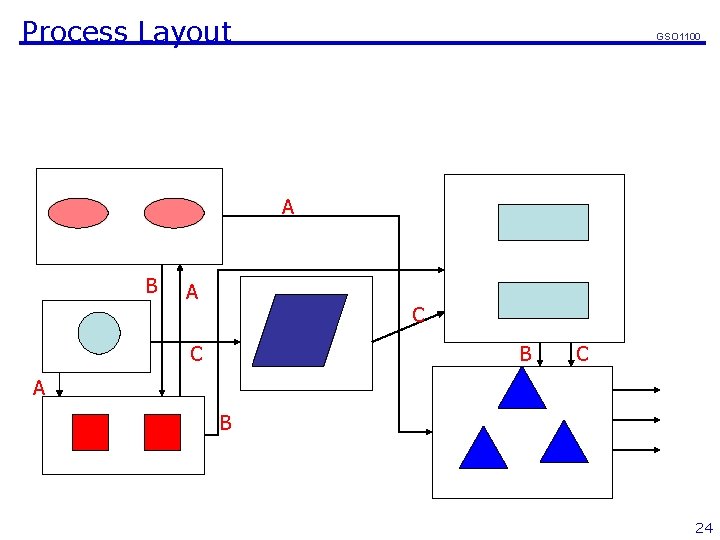
Process Layout GSO 1100 A B A C C B C A B 24
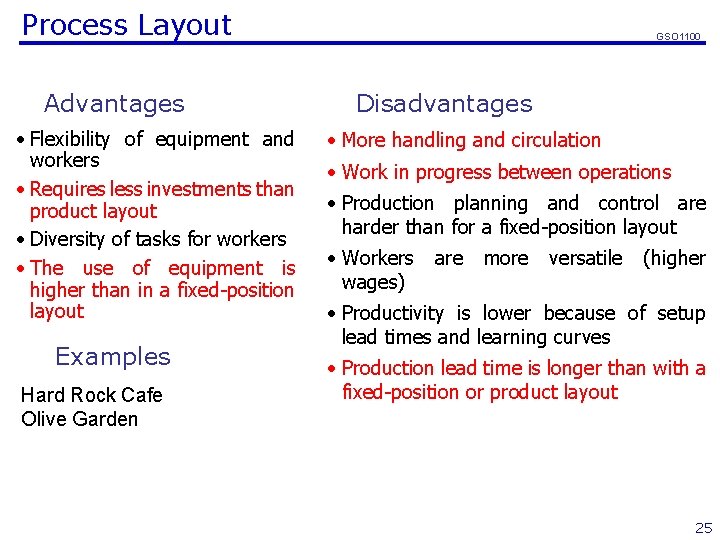
Process Layout Advantages • Flexibility of equipment and workers • Requires less investments than product layout • Diversity of tasks for workers • The use of equipment is higher than in a fixed-position layout Examples Hard Rock Cafe Olive Garden GSO 1100 Disadvantages • More handling and circulation • Work in progress between operations • Production planning and control are harder than for a fixed-position layout • Workers are more versatile (higher wages) • Productivity is lower because of setup lead times and learning curves • Production lead time is longer than with a fixed-position or product layout 25
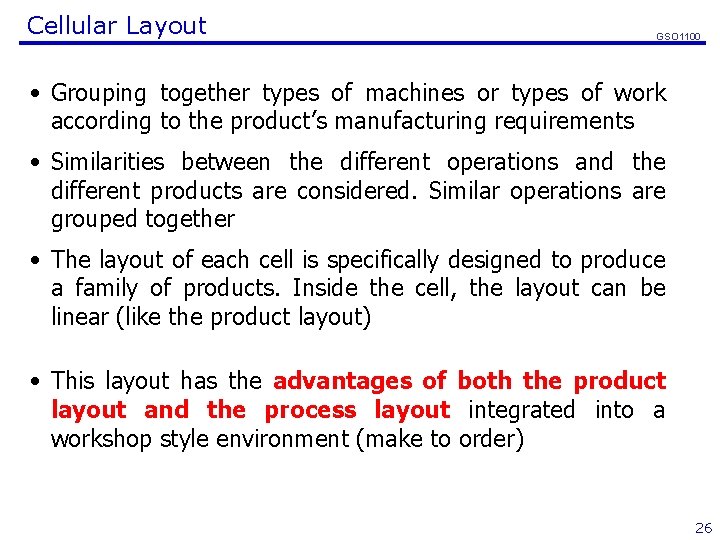
Cellular Layout GSO 1100 • Grouping together types of machines or types of work according to the product’s manufacturing requirements • Similarities between the different operations and the different products are considered. Similar operations are grouped together • The layout of each cell is specifically designed to produce a family of products. Inside the cell, the layout can be linear (like the product layout) • This layout has the advantages of both the product layout and the process layout integrated into a workshop style environment (make to order) 26
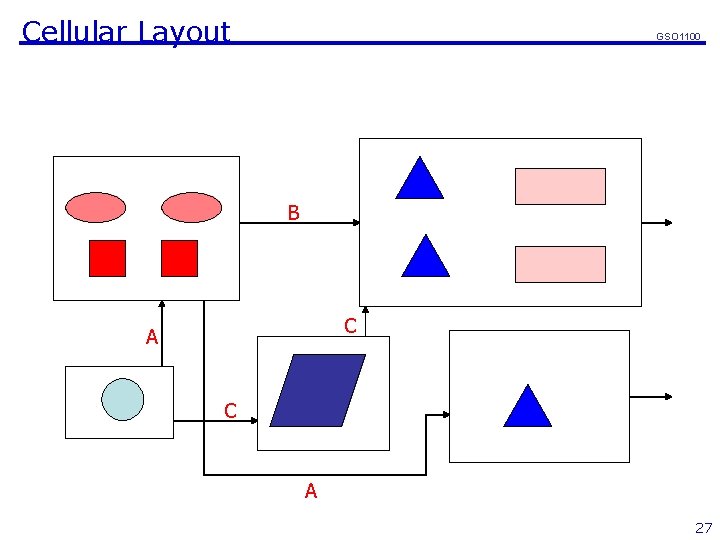
Cellular Layout GSO 1100 B C A 27
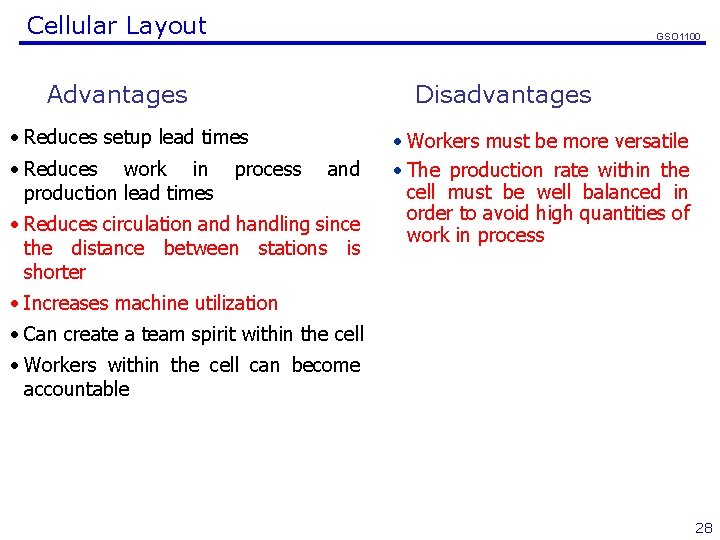
Cellular Layout Advantages • Reduces setup lead times • Reduces work in process and production lead times • Reduces circulation and handling since the distance between stations is shorter GSO 1100 Disadvantages • Workers must be more versatile • The production rate within the cell must be well balanced in order to avoid high quantities of work in process • Increases machine utilization • Can create a team spirit within the cell • Workers within the cell can become accountable 28
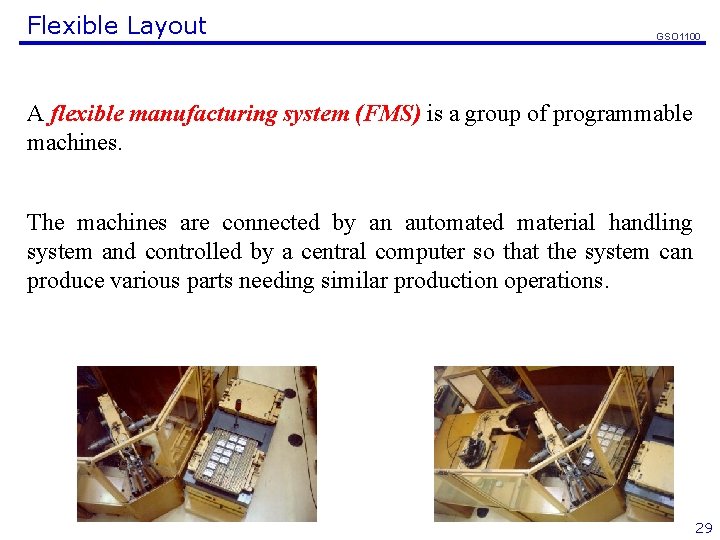
Flexible Layout GSO 1100 A flexible manufacturing system (FMS) is a group of programmable machines. The machines are connected by an automated material handling system and controlled by a central computer so that the system can produce various parts needing similar production operations. 29
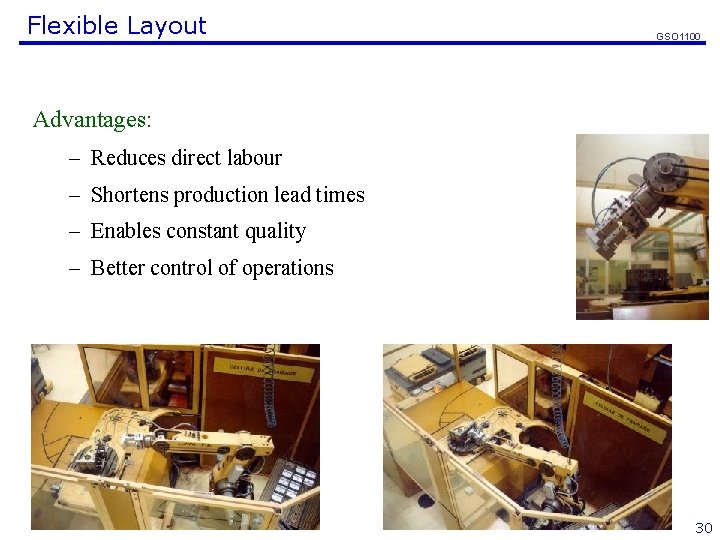
Flexible Layout GSO 1100 Advantages: – Reduces direct labour – Shortens production lead times – Enables constant quality – Better control of operations 30
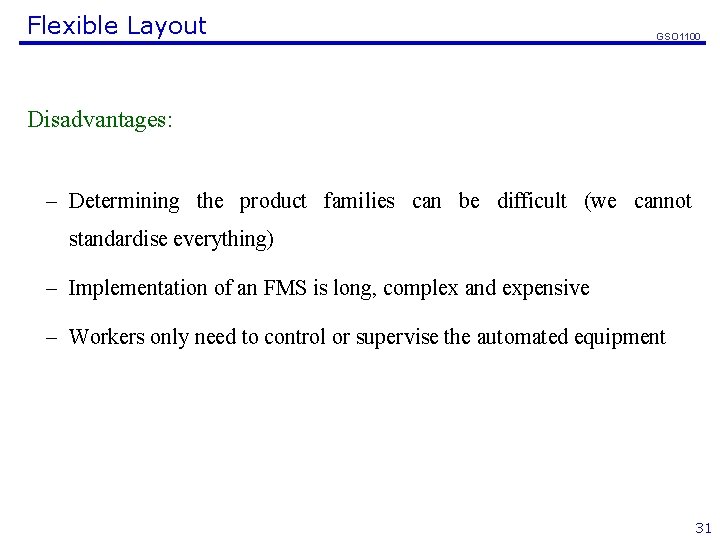
Flexible Layout GSO 1100 Disadvantages: – Determining the product families can be difficult (we cannot standardise everything) – Implementation of an FMS is long, complex and expensive – Workers only need to control or supervise the automated equipment 31
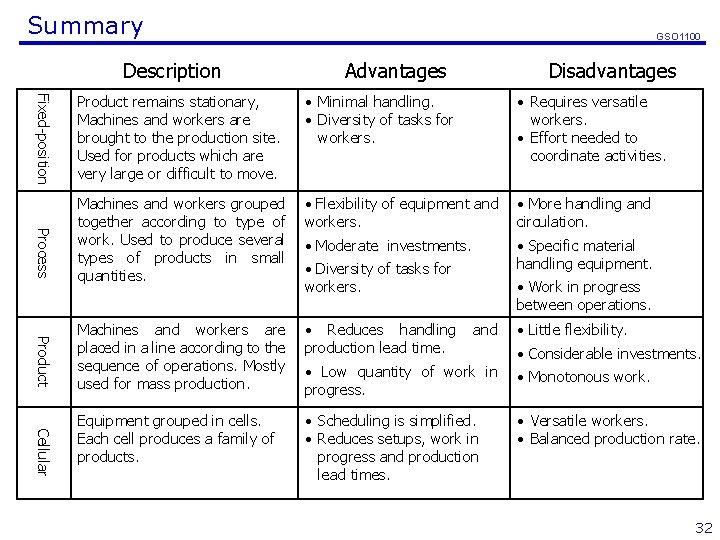
Summary Description GSO 1100 Advantages Disadvantages • Minimal handling. • Diversity of tasks for workers. Process Machines and workers grouped together according to type of work. Used to produce several types of products in small quantities. • Flexibility of equipment and • More handling and workers. circulation. Product Machines and workers are placed in a line according to the sequence of operations. Mostly used for mass production. • Reduces handling and • Little flexibility. production lead time. • Considerable investments. • Low quantity of work in • Monotonous work. progress. Equipment grouped in cells. Each cell produces a family of products. • Scheduling is simplified. • Reduces setups, work in progress and production lead times. Cellular Fixed-position Product remains stationary, Machines and workers are brought to the production site. Used for products which are very large or difficult to move. • Moderate investments. • Diversity of tasks for workers. • Requires versatile workers. • Effort needed to coordinate activities. • Specific material handling equipment. • Work in progress between operations. • Versatile workers. • Balanced production rate. 32
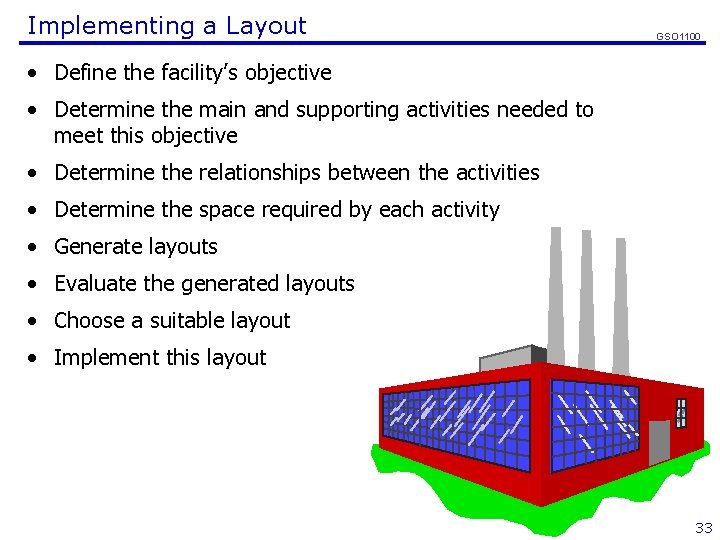
Implementing a Layout GSO 1100 • Define the facility’s objective • Determine the main and supporting activities needed to meet this objective • Determine the relationships between the activities • Determine the space required by each activity • Generate layouts • Evaluate the generated layouts • Choose a suitable layout • Implement this layout 33
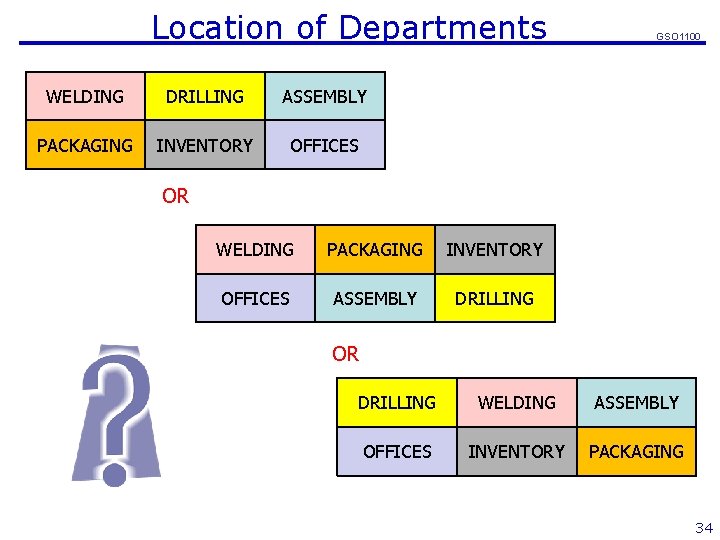
Location of Departments WELDING DRILLING ASSEMBLY PACKAGING INVENTORY OFFICES GSO 1100 OR WELDING PACKAGING INVENTORY OFFICES ASSEMBLY DRILLING OR DRILLING WELDING ASSEMBLY OFFICES INVENTORY PACKAGING 34
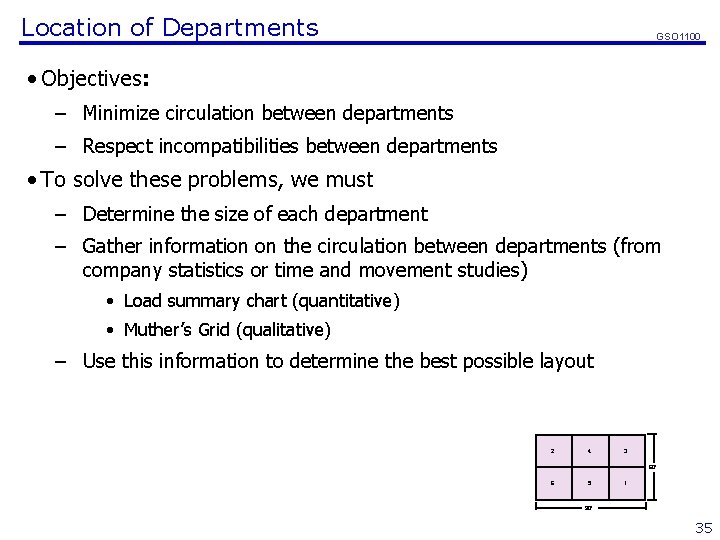
Location of Departments GSO 1100 • Objectives: – Minimize circulation between departments – Respect incompatibilities between departments • To solve these problems, we must – Determine the size of each department – Gather information on the circulation between departments (from company statistics or time and movement studies) • Load summary chart (quantitative) • Muther’s Grid (qualitative) – Use this information to determine the best possible layout 2 4 3 60' 6 5 1 90' 35
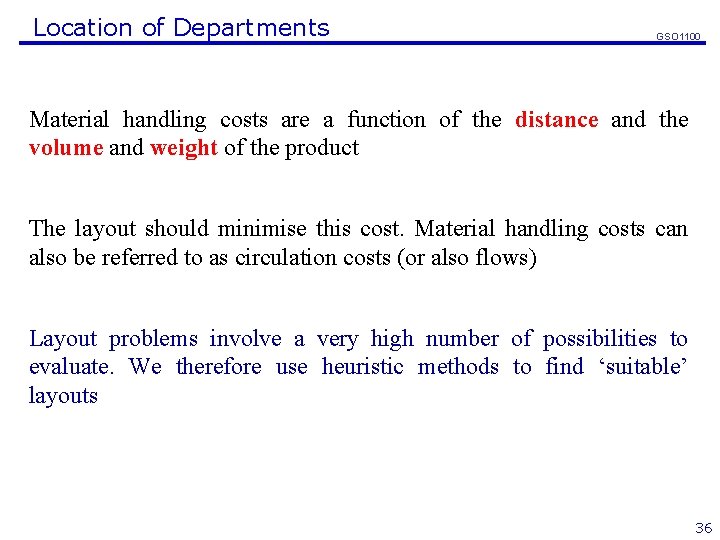
Location of Departments GSO 1100 Material handling costs are a function of the distance and the volume and weight of the product The layout should minimise this cost. Material handling costs can also be referred to as circulation costs (or also flows) Layout problems involve a very high number of possibilities to evaluate. We therefore use heuristic methods to find ‘suitable’ layouts 36
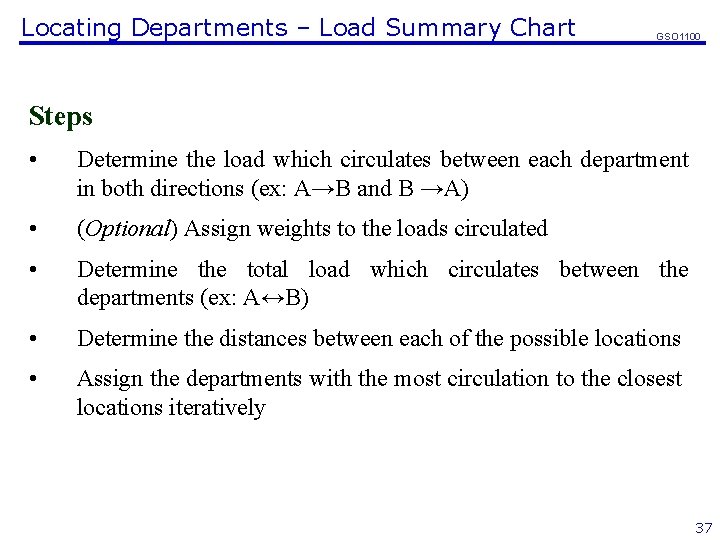
Locating Departments – Load Summary Chart GSO 1100 Steps • Determine the load which circulates between each department in both directions (ex: A→B and B →A) • (Optional) Assign weights to the loads circulated • Determine the total load which circulates between the departments (ex: A↔B) • Determine the distances between each of the possible locations • Assign the departments with the most circulation to the closest locations iteratively 37
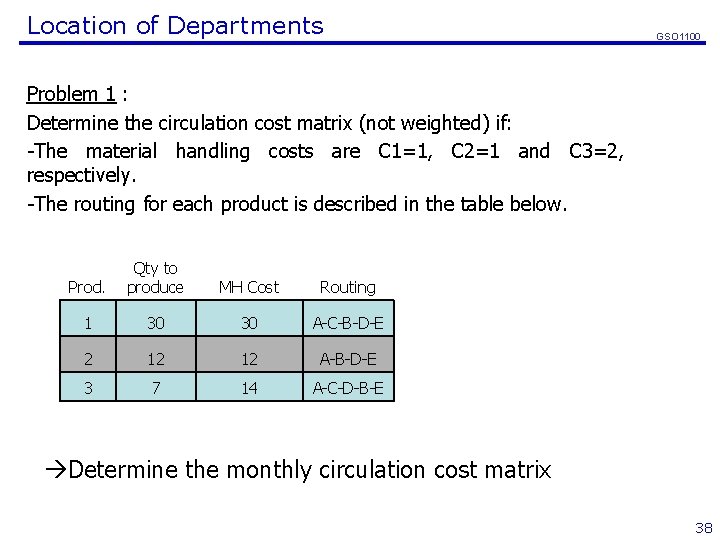
Location of Departments GSO 1100 Problem 1 : Determine the circulation cost matrix (not weighted) if: -The material handling costs are C 1=1, C 2=1 and C 3=2, respectively. -The routing for each product is described in the table below. Prod. Qty to produce MH Cost Routing 1 30 30 A-C-B-D-E 2 12 12 A-B-D-E 3 7 14 A-C-D-B-E Determine the monthly circulation cost matrix 38
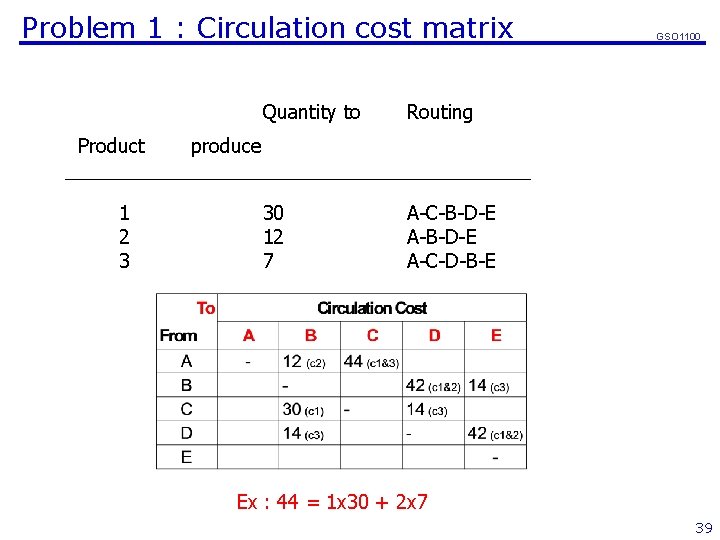
Problem 1 : Circulation cost matrix Quantity to Product 1 2 3 GSO 1100 Routing produce 30 12 7 A-C-B-D-E A-C-D-B-E Ex : 44 = 1 x 30 + 2 x 7 39
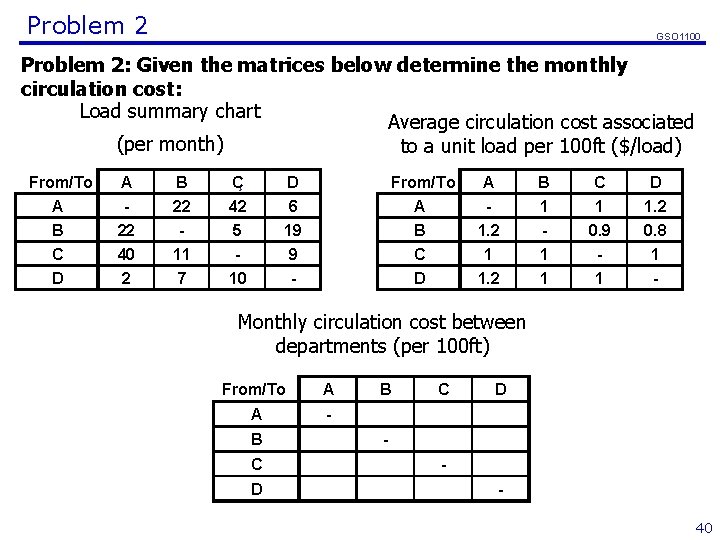
Problem 2 GSO 1100 Problem 2: Given the matrices below determine the monthly circulation cost: Load summary chart Average circulation cost associated (per month) to a unit load per 100 ft ($/load) From/To A A - B 22 C 42 D 6 From/To A A - B 1 C 1 D 1. 2 B 22 - 5 19 B 1. 2 - 0. 9 0. 8 C 40 11 - 9 C 1 1 - 1 D 2 7 10 - D 1. 2 1 1 - Monthly circulation cost between departments (per 100 ft) From/To A A - B C D 40
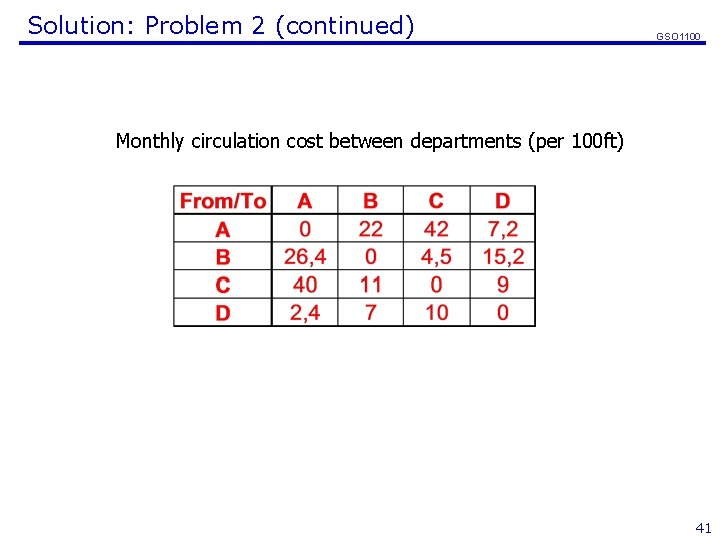
Solution: Problem 2 (continued) GSO 1100 Monthly circulation cost between departments (per 100 ft) 41
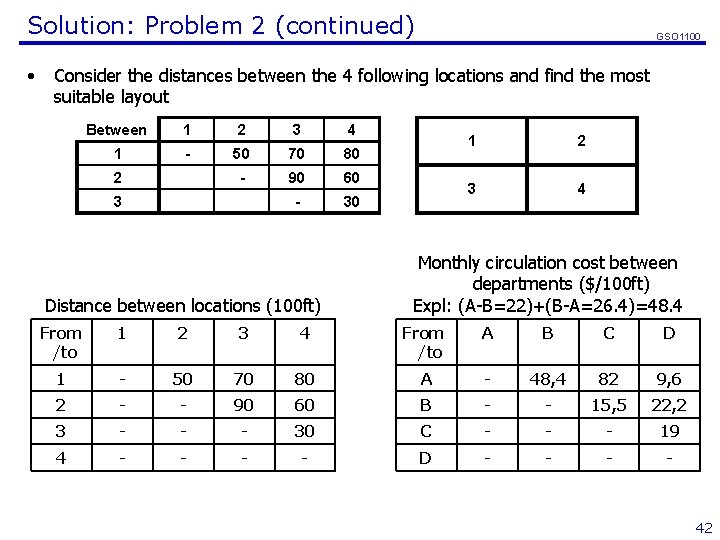
Solution: Problem 2 (continued) • GSO 1100 Consider the distances between the 4 following locations and find the most suitable layout Between 1 2 3 4 1 - 50 70 80 - 90 60 - 30 2 3 Distance between locations (100 ft) 1 2 3 4 Monthly circulation cost between departments ($/100 ft) Expl: (A-B=22)+(B-A=26. 4)=48. 4 From /to 1 2 3 4 From /to A B C D 1 - 50 70 80 A - 48, 4 82 9, 6 2 - - 90 60 B - - 15, 5 22, 2 3 - - - 30 C - - - 19 4 - - D - - 42
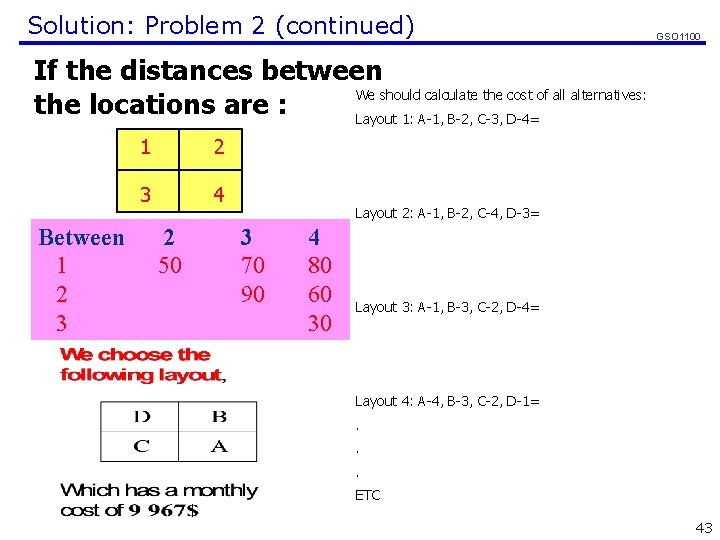
Solution: Problem 2 (continued) GSO 1100 If the distances between We should calculate the cost of all alternatives: the locations are : Layout 1: A-1, B-2, C-3, D-4= 1 2 3 4 Between 1 2 3 2 50 Layout 2: A-1, B-2, C-4, D-3= 3 70 90 4 80 60 30 Layout 3: A-1, B-3, C-2, D-4= Layout 4: A-4, B-3, C-2, D-1=. . . ETC 43
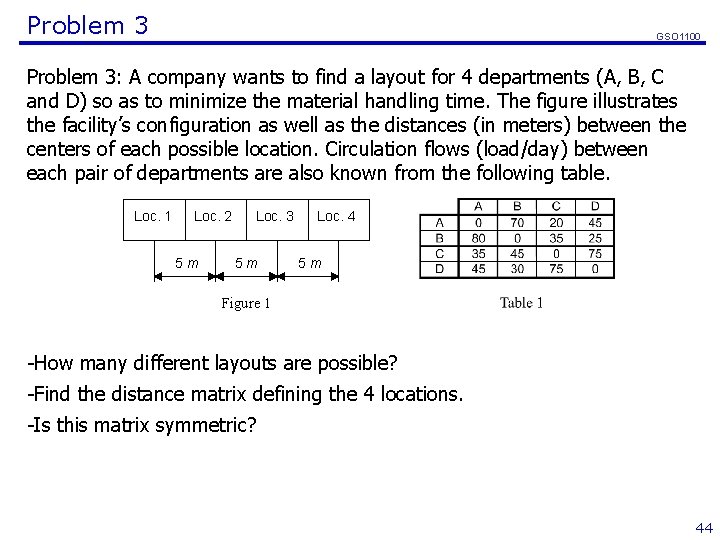
Problem 3 GSO 1100 Problem 3: A company wants to find a layout for 4 departments (A, B, C and D) so as to minimize the material handling time. The figure illustrates the facility’s configuration as well as the distances (in meters) between the centers of each possible location. Circulation flows (load/day) between each pair of departments are also known from the following table. Loc. 1 Loc. 2 5 m Loc. 3 5 m Loc. 4 5 m Figure 1 -How many different layouts are possible? -Find the distance matrix defining the 4 locations. -Is this matrix symmetric? 44
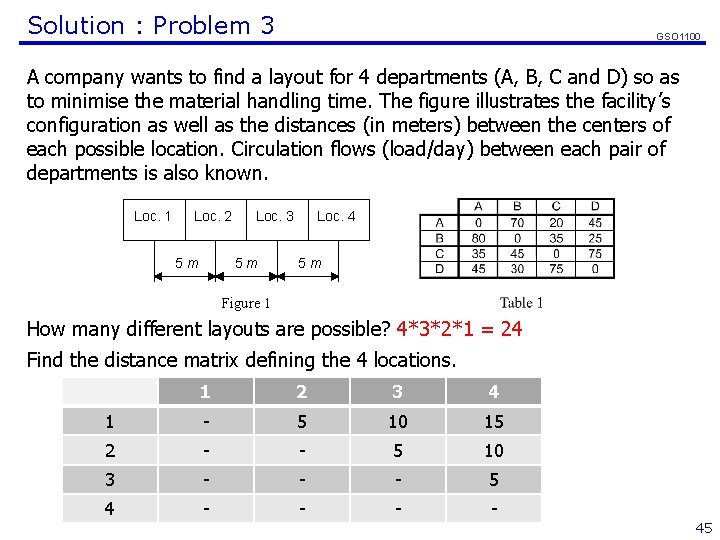
Solution : Problem 3 GSO 1100 A company wants to find a layout for 4 departments (A, B, C and D) so as to minimise the material handling time. The figure illustrates the facility’s configuration as well as the distances (in meters) between the centers of each possible location. Circulation flows (load/day) between each pair of departments is also known. Loc. 1 Loc. 2 5 m Loc. 3 5 m Loc. 4 5 m Figure 1 How many different layouts are possible? 4*3*2*1 = 24 Find the distance matrix defining the 4 locations. 1 2 3 4 1 - 5 10 15 2 - - 5 10 3 - - - 5 4 - - - 45
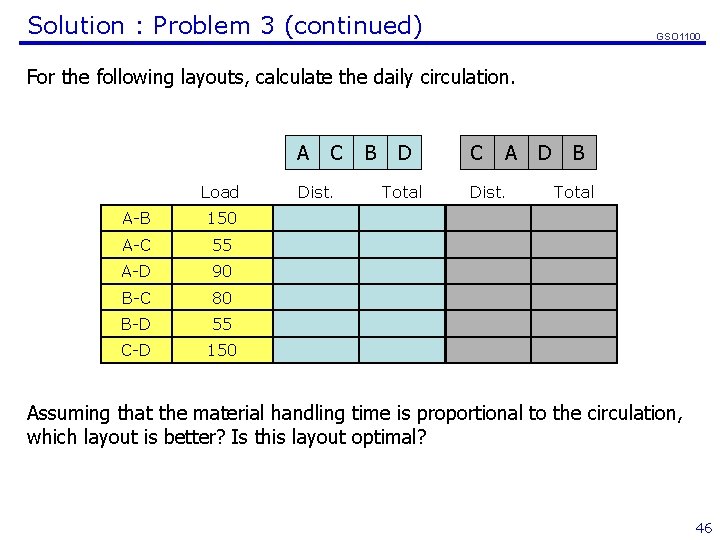
Solution : Problem 3 (continued) GSO 1100 For the following layouts, calculate the daily circulation. A Load C B Dist. D C Total A D Dist. B Total A-B 150 A-C 55 A-D 90 B-C 80 B-D 55 C-D 150 Assuming that the material handling time is proportional to the circulation, which layout is better? Is this layout optimal? 46
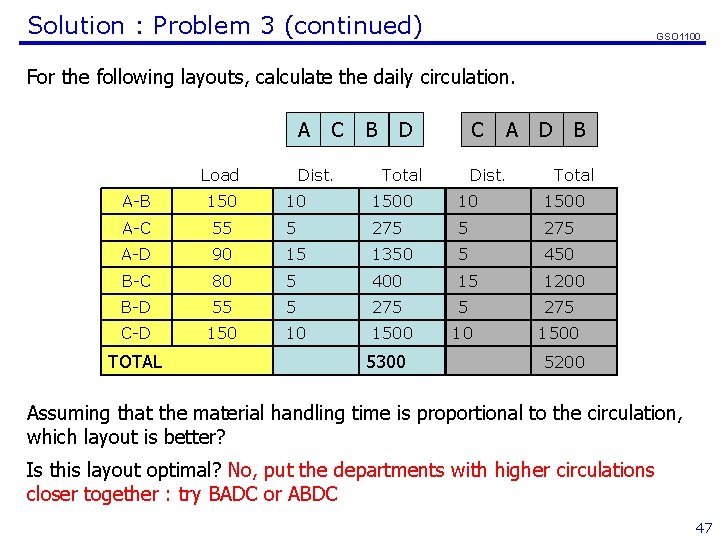
Solution : Problem 3 (continued) GSO 1100 For the following layouts, calculate the daily circulation. A Load A-B 150 A-C C Dist. B D C Total A Dist. D B Total 10 1500 55 5 275 A-D 90 15 1350 5 450 B-C 80 5 400 15 1200 B-D 55 5 275 C-D 1500 10 1500 5300 5200 TOTAL Assuming that the material handling time is proportional to the circulation, which layout is better? Is this layout optimal? No, put the departments with higher circulations closer together : try BADC or ABDC 47
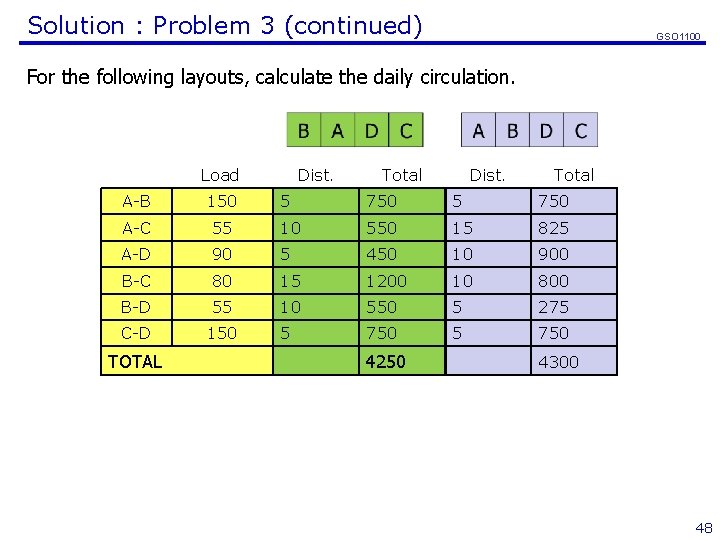
Solution : Problem 3 (continued) GSO 1100 For the following layouts, calculate the daily circulation. Load A-B 150 A-C Dist. Total 5 750 55 10 550 15 825 A-D 90 5 450 10 900 B-C 80 15 1200 10 800 B-D 55 10 550 5 275 C-D 150 5 750 TOTAL 4250 4300 48
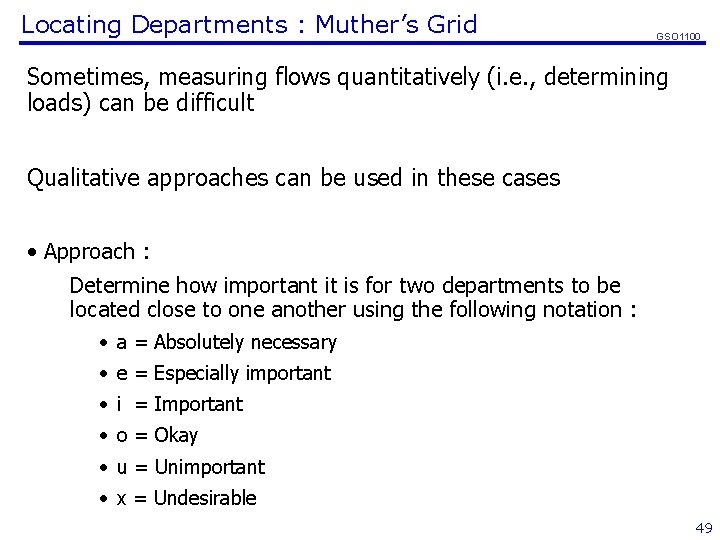
Locating Departments : Muther’s Grid GSO 1100 Sometimes, measuring flows quantitatively (i. e. , determining loads) can be difficult Qualitative approaches can be used in these cases • Approach : Determine how important it is for two departments to be located close to one another using the following notation : • a = Absolutely necessary • e = Especially important • i = Important • o = Okay • u = Unimportant • x = Undesirable 49
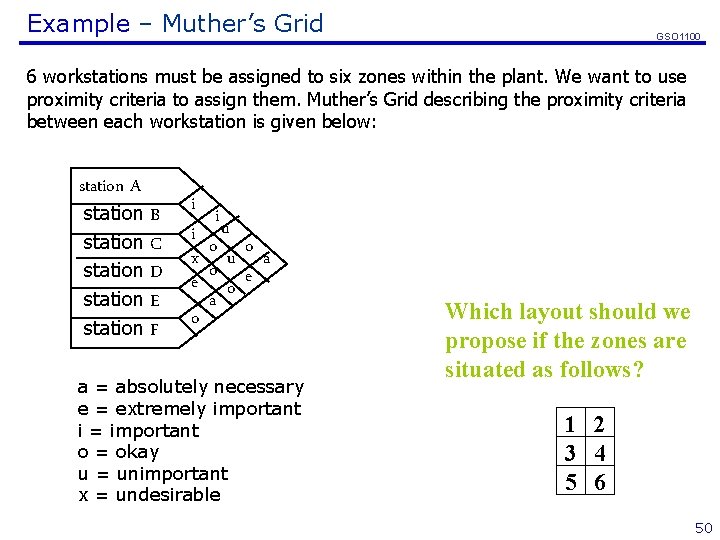
Example – Muther’s Grid GSO 1100 6 workstations must be assigned to six zones within the plant. We want to use proximity criteria to assign them. Muther’s Grid describing the proximity criteria between each workstation is given below: station A station B station C station D station E station F i i x e o iu o uo a o e a o a = absolutely necessary e = extremely important i = important o = okay u = unimportant x = undesirable Which layout should we propose if the zones are situated as follows? 1 2 3 4 5 6 50
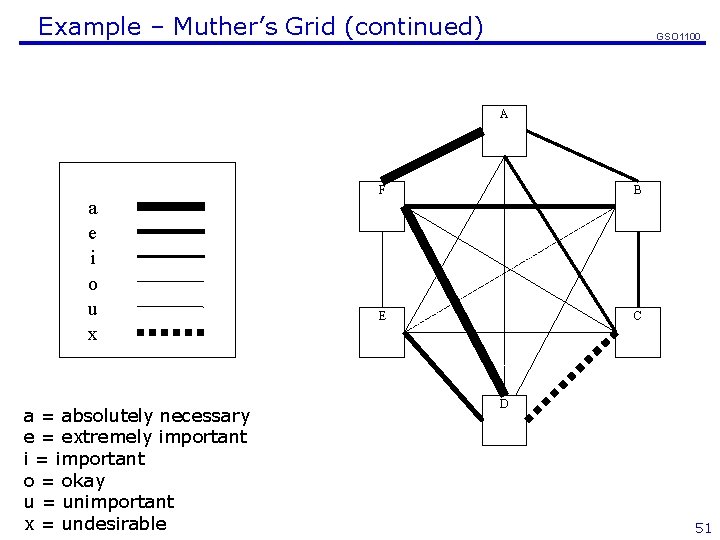
Example – Muther’s Grid (continued) GSO 1100 A a e i o u x a = absolutely necessary e = extremely important i = important o = okay u = unimportant x = undesirable F B E C D 51
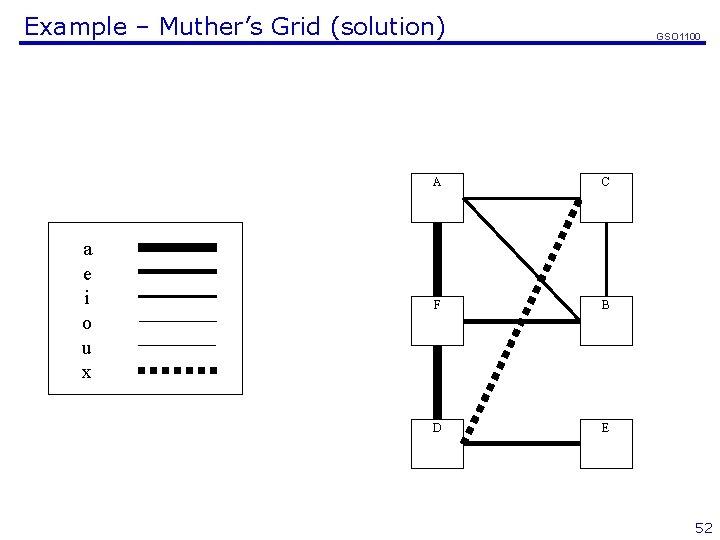
Example – Muther’s Grid (solution) a e i o u x GSO 1100 A C F B D E 52
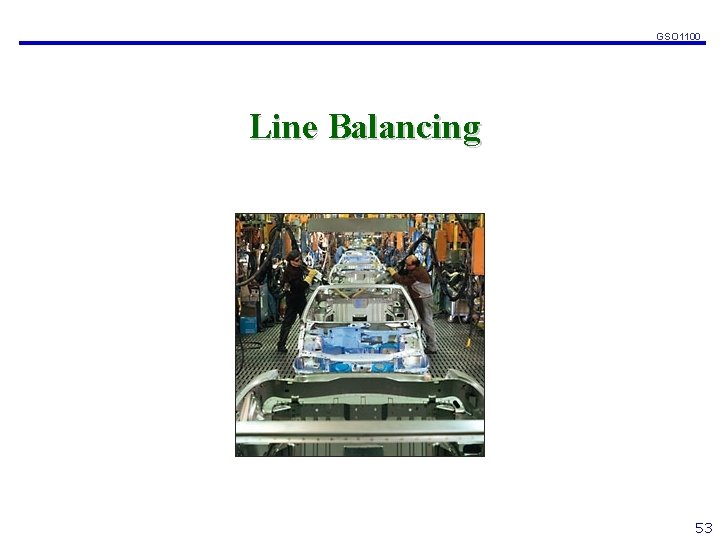
GSO 1100 Line Balancing 53
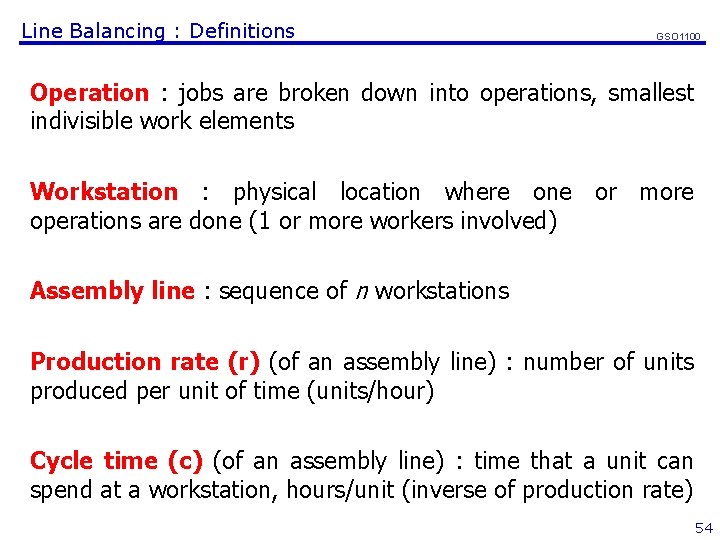
Line Balancing : Definitions GSO 1100 Operation : jobs are broken down into operations, smallest indivisible work elements Workstation : physical location where one or more operations are done (1 or more workers involved) Assembly line : sequence of n workstations Production rate (r) (of an assembly line) : number of units produced per unit of time (units/hour) Cycle time (c) (of an assembly line) : time that a unit can spend at a workstation, hours/unit (inverse of production rate) 54
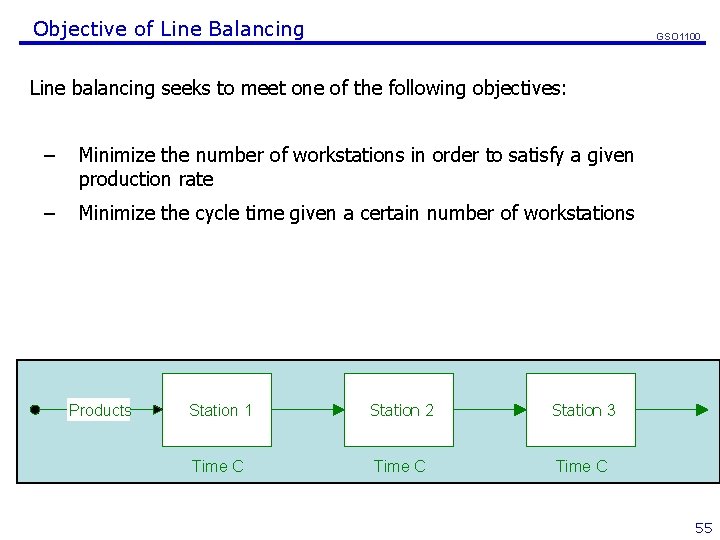
Objective of Line Balancing GSO 1100 Line balancing seeks to meet one of the following objectives: – Minimize the number of workstations in order to satisfy a given production rate – Minimize the cycle time given a certain number of workstations Products Station 1 Station 2 Station 3 Time C 55
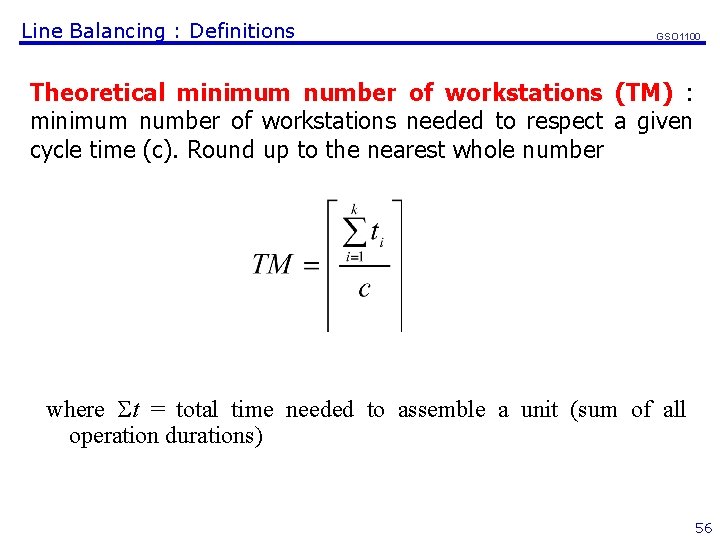
Line Balancing : Definitions GSO 1100 Theoretical minimum number of workstations (TM) : minimum number of workstations needed to respect a given cycle time (c). Round up to the nearest whole number where t = total time needed to assemble a unit (sum of all operation durations) 56
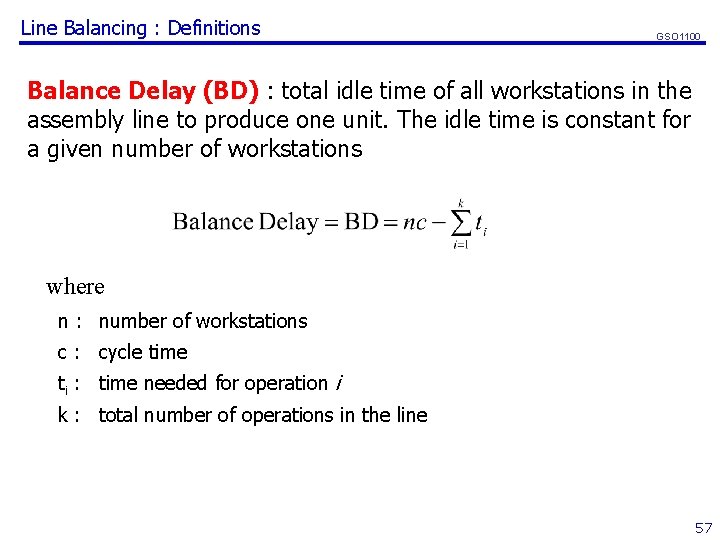
Line Balancing : Definitions GSO 1100 Balance Delay (BD) : total idle time of all workstations in the assembly line to produce one unit. The idle time is constant for a given number of workstations where n : number of workstations c : cycle time ti : time needed for operation i k : total number of operations in the line 57
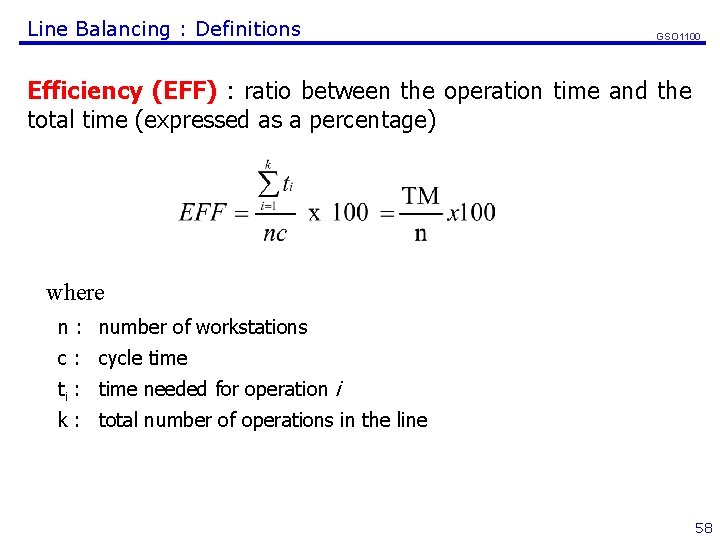
Line Balancing : Definitions GSO 1100 Efficiency (EFF) : ratio between the operation time and the total time (expressed as a percentage) where n : number of workstations c : cycle time ti : time needed for operation i k : total number of operations in the line 58
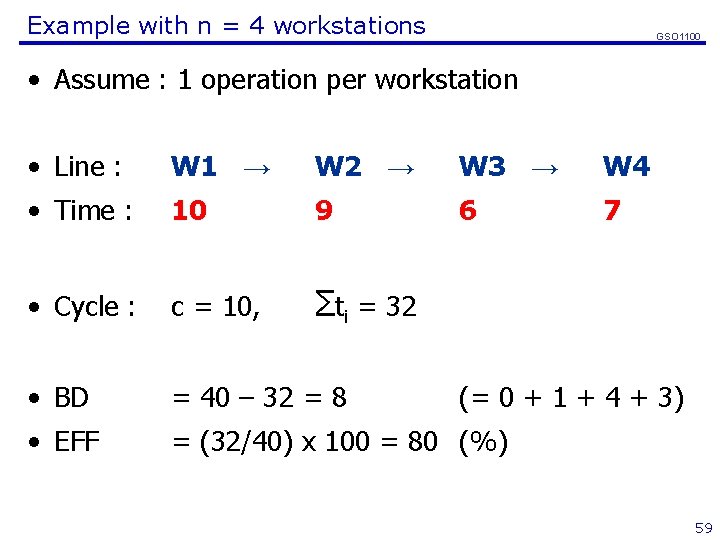
Example with n = 4 workstations GSO 1100 • Assume : 1 operation per workstation • Line : W 1 → W 2 → W 3 → W 4 • Time : 10 9 6 7 • Cycle : c = 10, Σti = 32 • BD = 40 – 32 = 8 • EFF = (32/40) x 100 = 80 (%) (= 0 + 1 + 4 + 3) 59
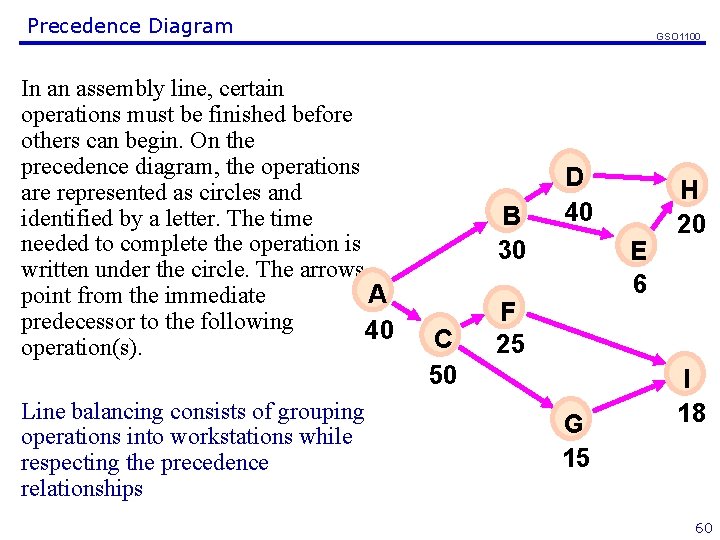
Precedence Diagram In an assembly line, certain operations must be finished before others can begin. On the precedence diagram, the operations are represented as circles and identified by a letter. The time needed to complete the operation is written under the circle. The arrows A point from the immediate predecessor to the following 40 operation(s). Line balancing consists of grouping operations into workstations while respecting the precedence relationships GSO 1100 B 30 C 50 D 40 E 6 F 25 G 15 H 20 I 18 60
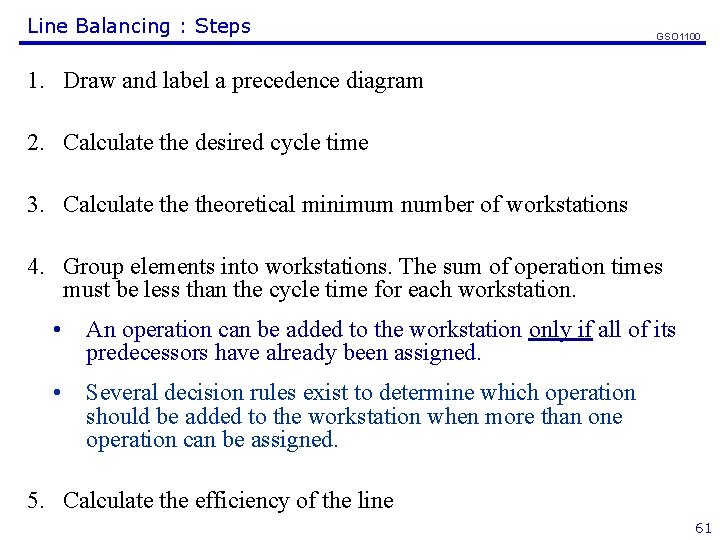
Line Balancing : Steps GSO 1100 1. Draw and label a precedence diagram 2. Calculate the desired cycle time 3. Calculate theoretical minimum number of workstations 4. Group elements into workstations. The sum of operation times must be less than the cycle time for each workstation. • An operation can be added to the workstation only if all of its predecessors have already been assigned. • Several decision rules exist to determine which operation should be added to the workstation when more than one operation can be assigned. 5. Calculate the efficiency of the line 61
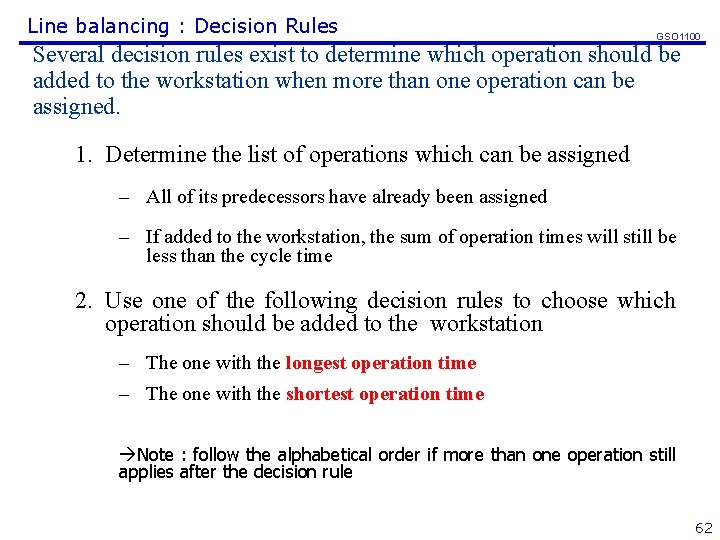
Line balancing : Decision Rules GSO 1100 Several decision rules exist to determine which operation should be added to the workstation when more than one operation can be assigned. 1. Determine the list of operations which can be assigned – All of its predecessors have already been assigned – If added to the workstation, the sum of operation times will still be less than the cycle time 2. Use one of the following decision rules to choose which operation should be added to the workstation – The one with the longest operation time – The one with the shortest operation time Note : follow the alphabetical order if more than one operation still applies after the decision rule 62

Line Balancing : Example GSO 1100 If c = 60, the following assembly line is possible. Its efficiency is 81, 3%. Workstation Σti S 1 40 S 2 50 S 3 55 S 4 55 S 5 44 Total 244 S 1 A 40 B 30 S 3 S 2 C 50 F 25 D 40 S 4 G 15 E 6 H 20 S 5 I 18 Is this the minimum number of workstations? 63
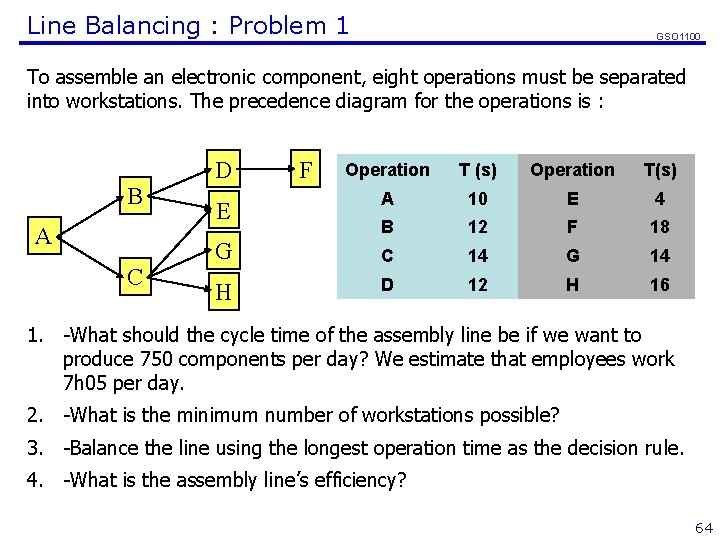
Line Balancing : Problem 1 GSO 1100 To assemble an electronic component, eight operations must be separated into workstations. The precedence diagram for the operations is : B A C D F Operation T (s) Operation T(s) E A 10 E 4 B 12 F 18 G C 14 G 14 H D 12 H 16 1. -What should the cycle time of the assembly line be if we want to produce 750 components per day? We estimate that employees work 7 h 05 per day. 2. -What is the minimum number of workstations possible? 3. -Balance the line using the longest operation time as the decision rule. 4. -What is the assembly line’s efficiency? 64
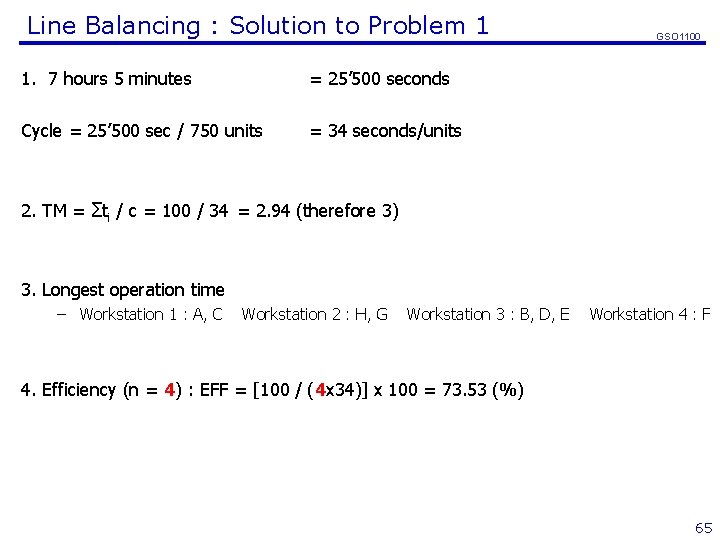
Line Balancing : Solution to Problem 1 1. 7 hours 5 minutes = 25’ 500 seconds Cycle = 25’ 500 sec / 750 units = 34 seconds/units GSO 1100 2. TM = Σti / c = 100 / 34 = 2. 94 (therefore 3) 3. Longest operation time – Workstation 1 : A, C Workstation 2 : H, G Workstation 3 : B, D, E Workstation 4 : F 4. Efficiency (n = 4) : EFF = [100 / (4 x 34)] x 100 = 73. 53 (%) 65
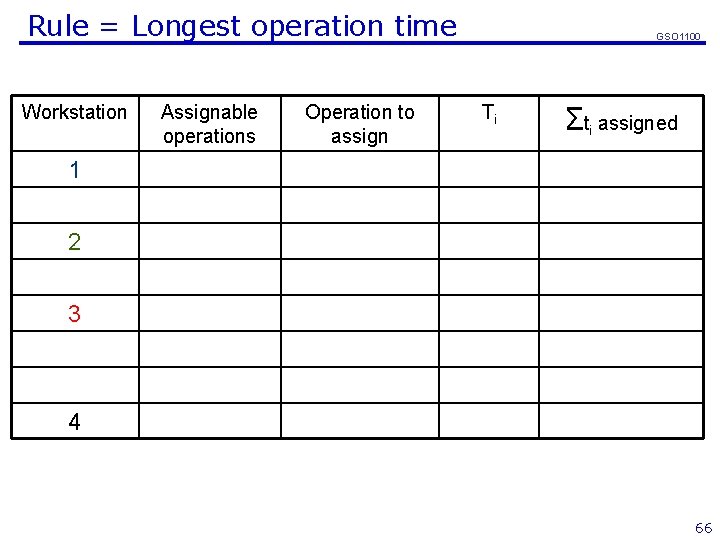
Rule = Longest operation time Workstation Assignable operations Operation to assign GSO 1100 Ti Σti assigned 1 2 3 4 66
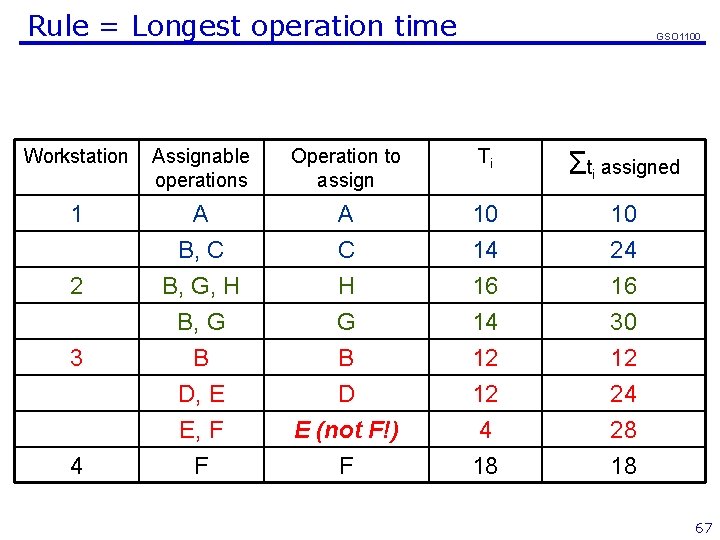
Rule = Longest operation time GSO 1100 Workstation Assignable operations Operation to assign Ti Σti assigned 1 A A 10 10 B, C C 14 24 B, G, H H 16 16 B, G G 14 30 B B 12 12 D, E D 12 24 E, F E (not F!) 4 28 F F 18 18 2 3 4 67
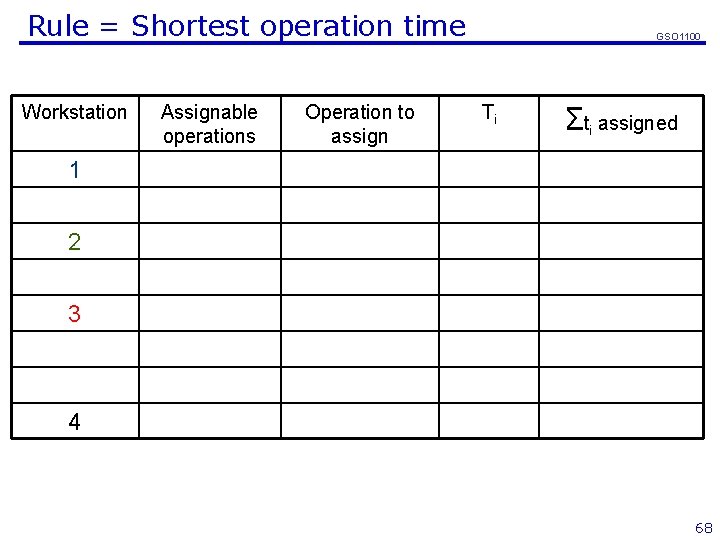
Rule = Shortest operation time Workstation Assignable operations Operation to assign GSO 1100 Ti Σti assigned 1 2 3 4 68
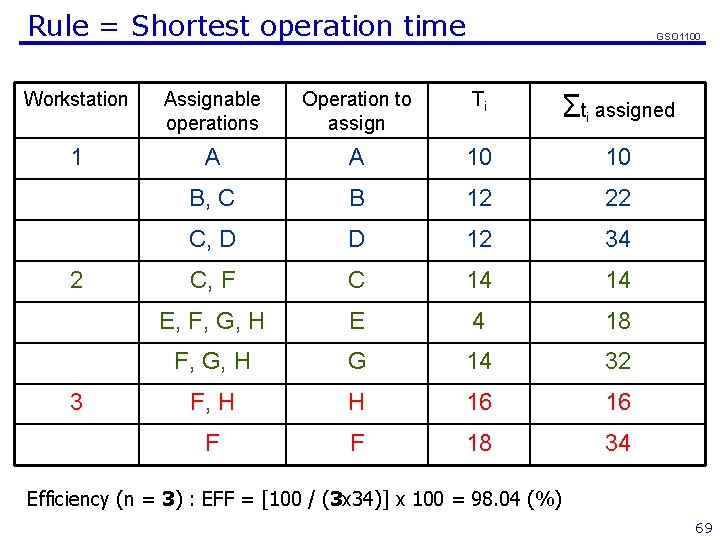
Rule = Shortest operation time GSO 1100 Workstation Assignable operations Operation to assign Ti Σti assigned 1 A A 10 10 B, C B 12 22 C, D D 12 34 C, F C 14 14 E, F, G, H E 4 18 F, G, H G 14 32 F, H H 16 16 F F 18 34 2 3 Efficiency (n = 3) : EFF = [100 / (3 x 34)] x 100 = 98. 04 (%) 69
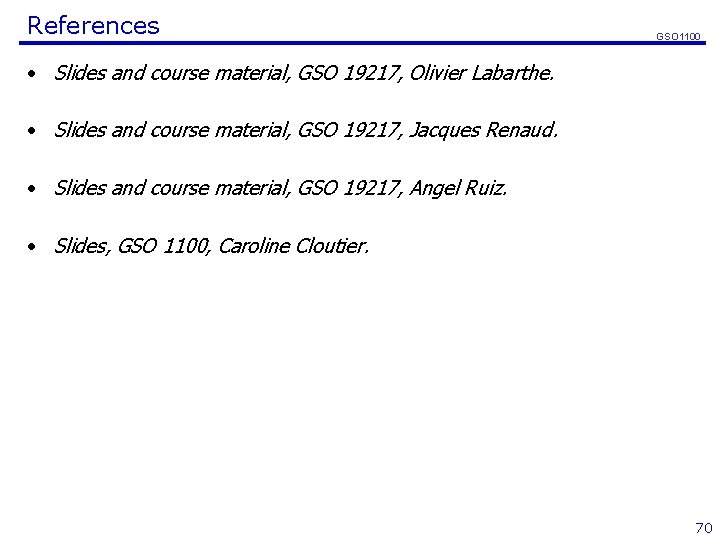
References GSO 1100 • Slides and course material, GSO 19217, Olivier Labarthe. • Slides and course material, GSO 19217, Jacques Renaud. • Slides and course material, GSO 19217, Angel Ruiz. • Slides, GSO 1100, Caroline Cloutier. 70
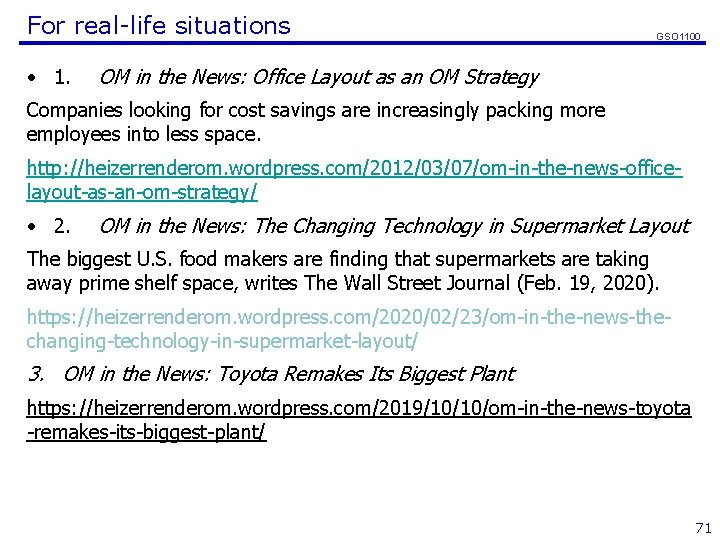
For real-life situations • 1. GSO 1100 OM in the News: Office Layout as an OM Strategy Companies looking for cost savings are increasingly packing more employees into less space. http: //heizerrenderom. wordpress. com/2012/03/07/om-in-the-news-officelayout-as-an-om-strategy/ • 2. OM in the News: The Changing Technology in Supermarket Layout The biggest U. S. food makers are finding that supermarkets are taking away prime shelf space, writes The Wall Street Journal (Feb. 19, 2020). https: //heizerrenderom. wordpress. com/2020/02/23/om-in-the-news-thechanging-technology-in-supermarket-layout/ 3. OM in the News: Toyota Remakes Its Biggest Plant https: //heizerrenderom. wordpress. com/2019/10/10/om-in-the-news-toyota -remakes-its-biggest-plant/ 71
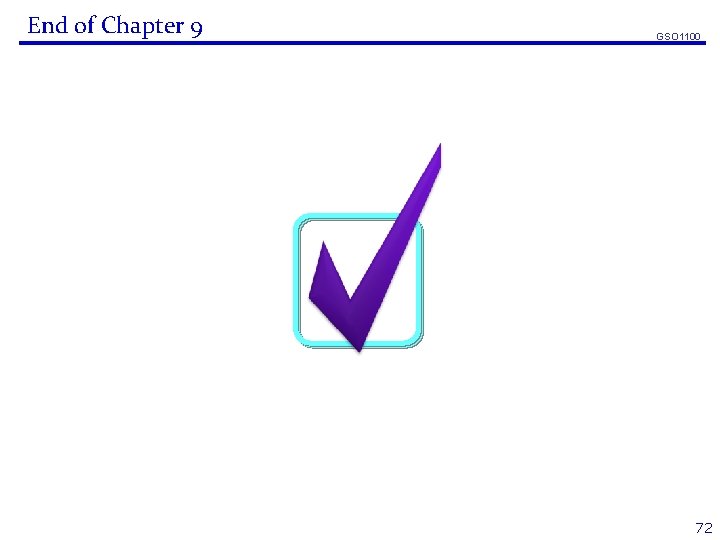
End of Chapter 9 GSO 1100 72
The role of network design in the supply chain
Importance of process selection and facility layout
Process selection and system design
Process selection and facility layout
Product vs process layout
Importance of process selection and facility layout
Process selection and facility layout
Plan location and layout
Facilities layout
Objectives of facility layout
Types of layout
Service facility layout
Aldep refers to
Objectives of facility layout
Program layout design
Facility layout objectives
Satisfactory layout
Fixed position layout
Leandro e stormer
Jean leandro dos santos
Leandro lardone
Leandro consentino
Atriz consuelo leandro
Leandro michelon
"leandro maranghetti"
Leandro pesantes
"leandro maranghetti"
Leandro von werra
Leandro del moral
Leandro huayanay falconi
Leandro ruschel wikipedia
Dr leandro aguiar
Metapatologias
"leandro maranghetti"
Agonista
Leandro pozzo
Dr leandro aguiar
Leandro conte
Rubianos
Leandro consentino
Layout strategy
Layout strategies in operations management
Interdepartmental flow graph
Layout strategy
Group technology layout example
Retail layout operations management
Hybrid layout in operations management
A hybrid layout combines
Layout decisions operations management
Long thin short fat operations management
Tactical operations center layout
Layout strategy in operations management
Denominator layout
Smil head layout root-layout
Smil head layout root-layout
Liquid layout website
Facility management history and evolution
Child care facility rules and regulations
Socio economic trends
Effective methods for software and systems integration
Neal road landfill fees
Electronic payment and collection facility (epcf)
Supporting facilities example
Sport event and facility management
Value chain and supply chain difference
Global production, outsourcing and logistics
Global fashion logistics
Functional components of ecrm
Vha procurement and logistics office
Css homeward bound
International logistics and supply chain outsourcing
Global production, outsourcing, and logistics
Distribution channel and logistics