FACILITY LAYOUT Facility Layout Defined Facility layout can
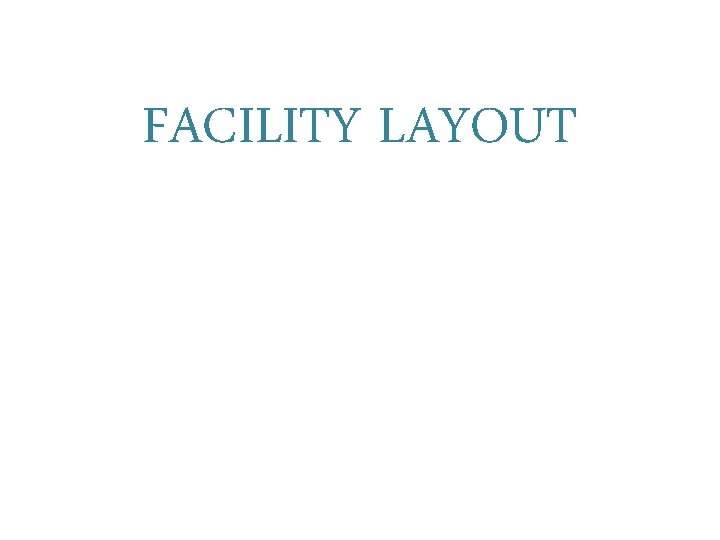
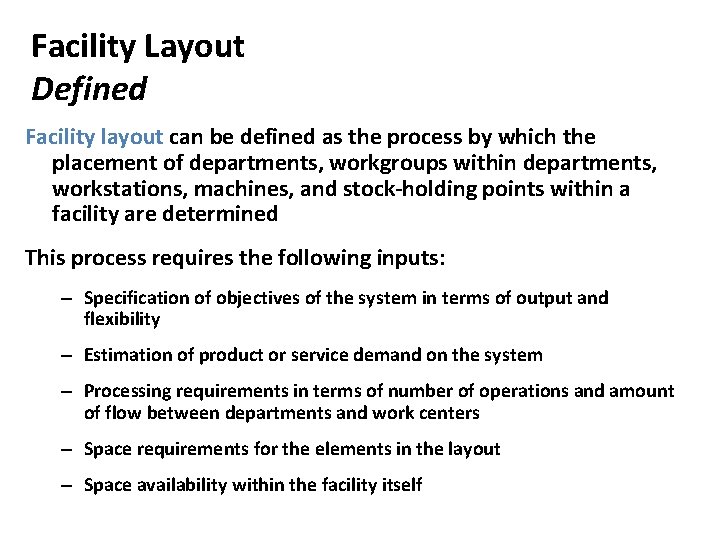
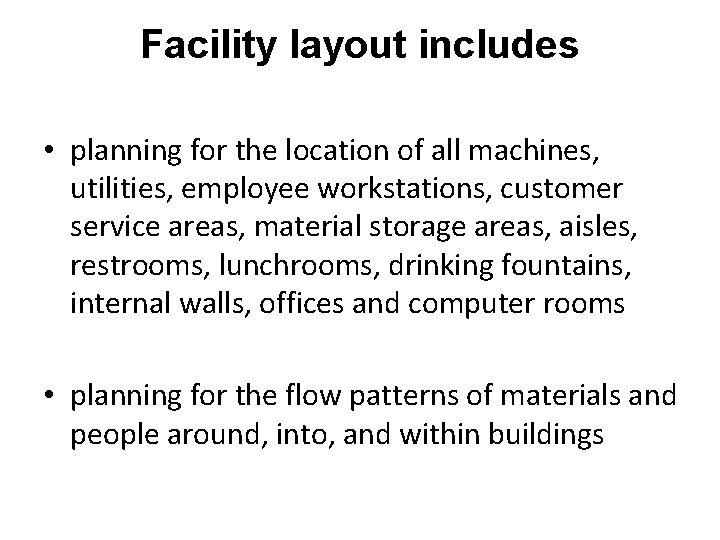
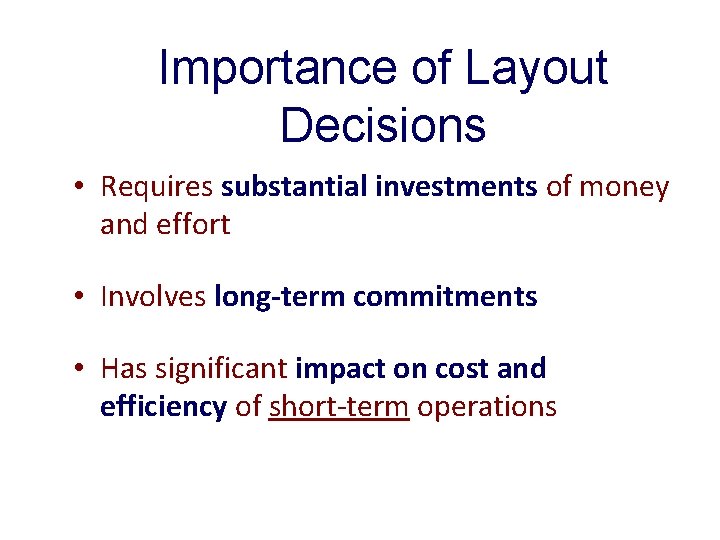
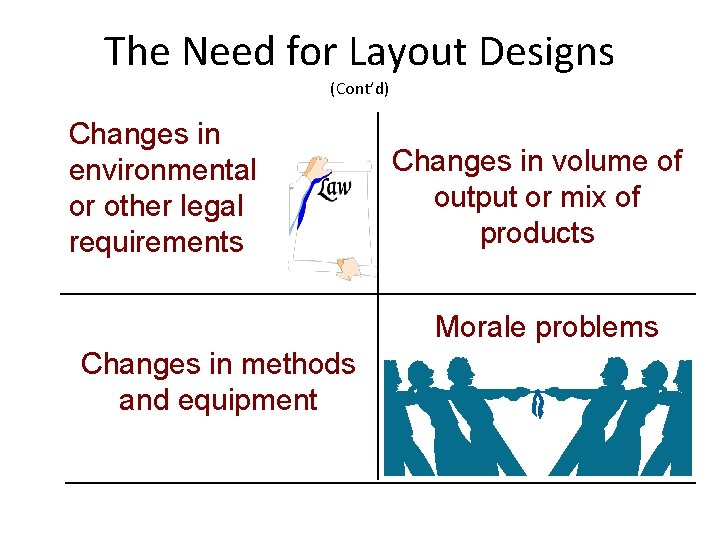
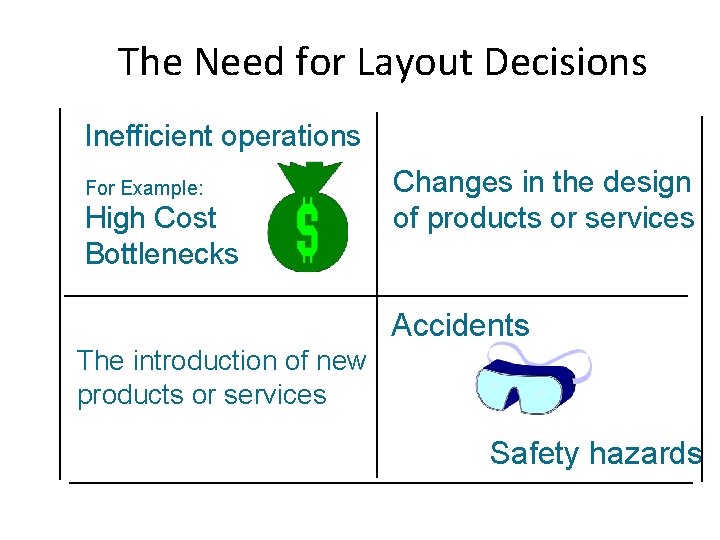
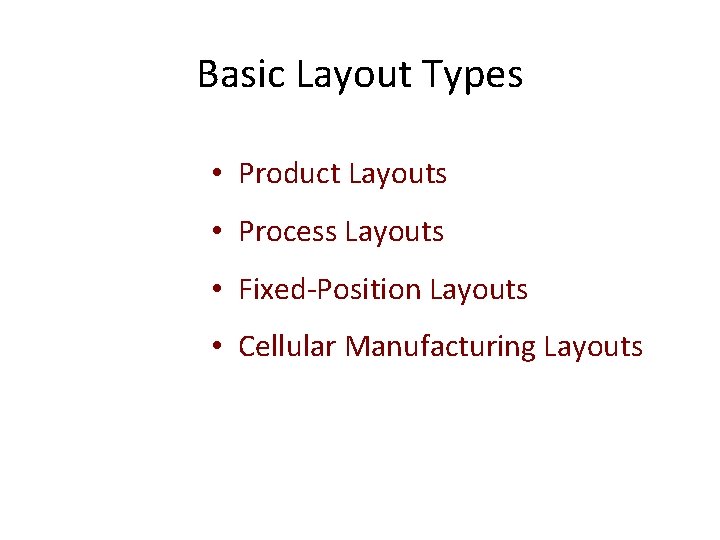
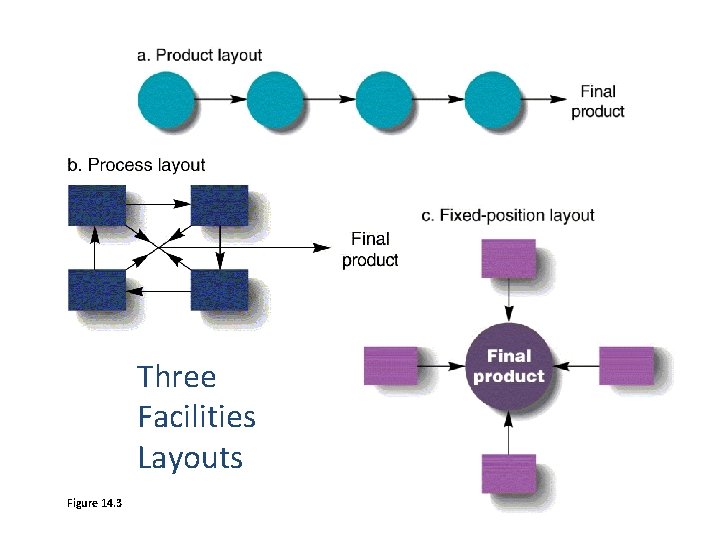
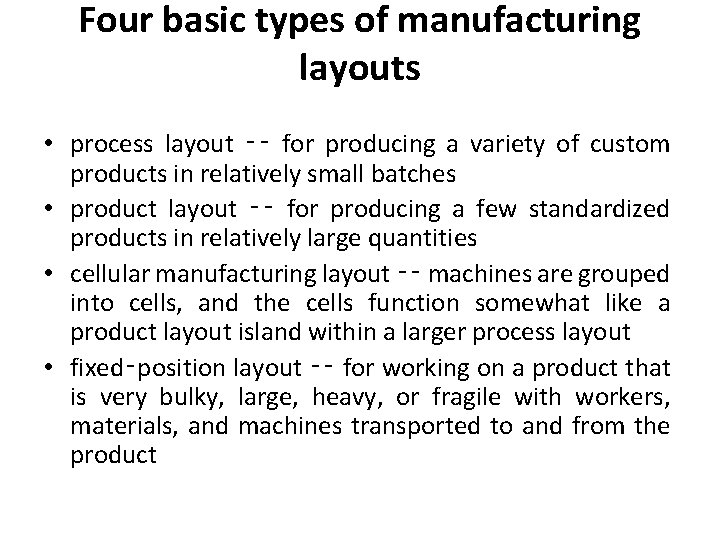
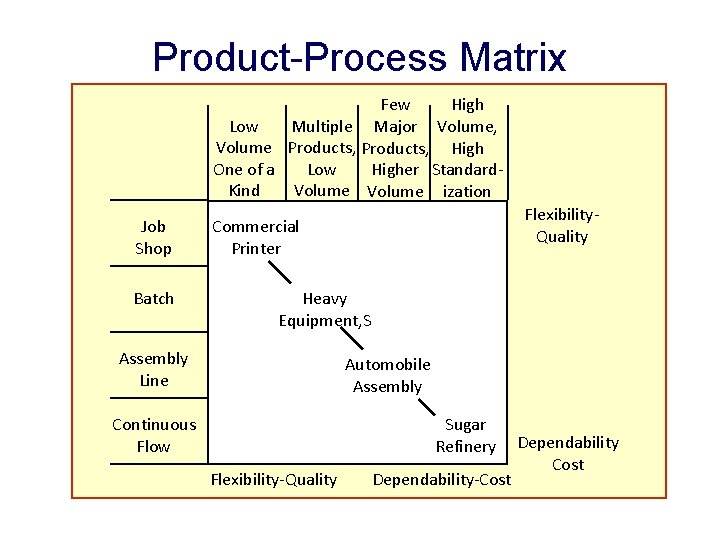
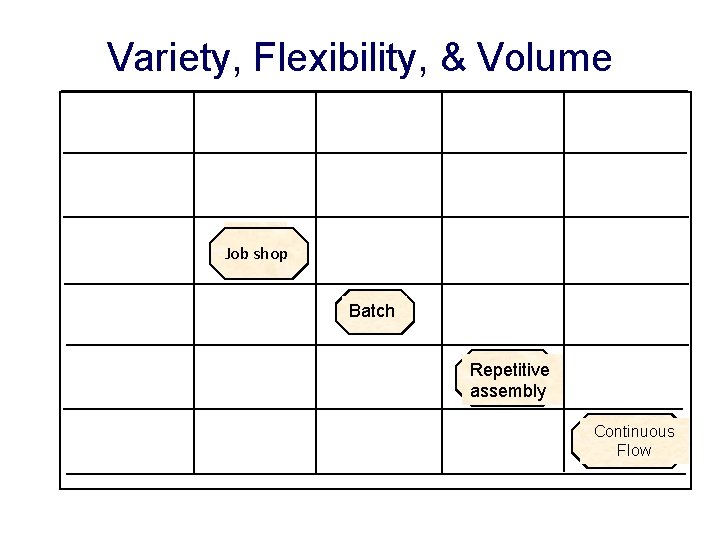
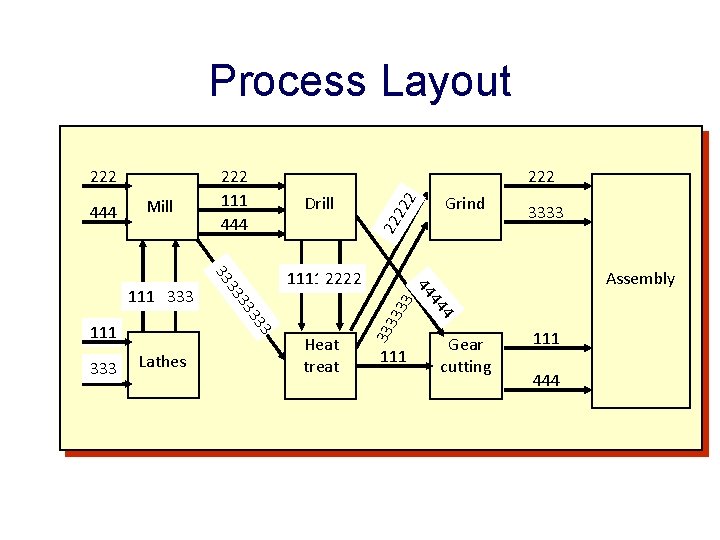
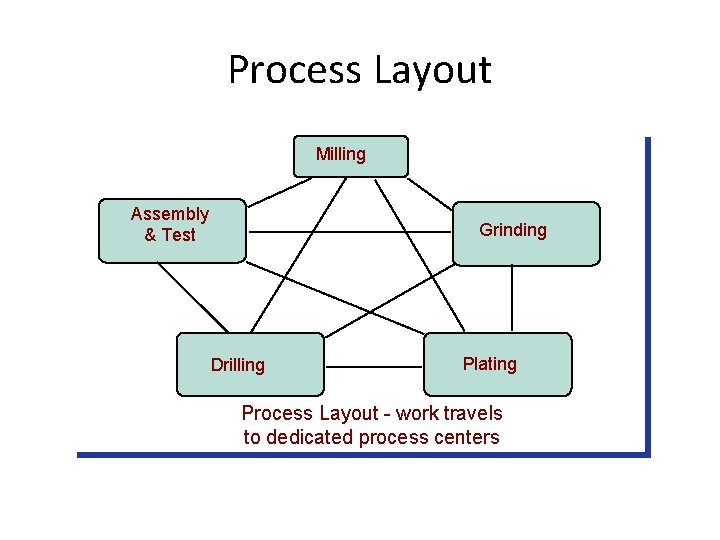
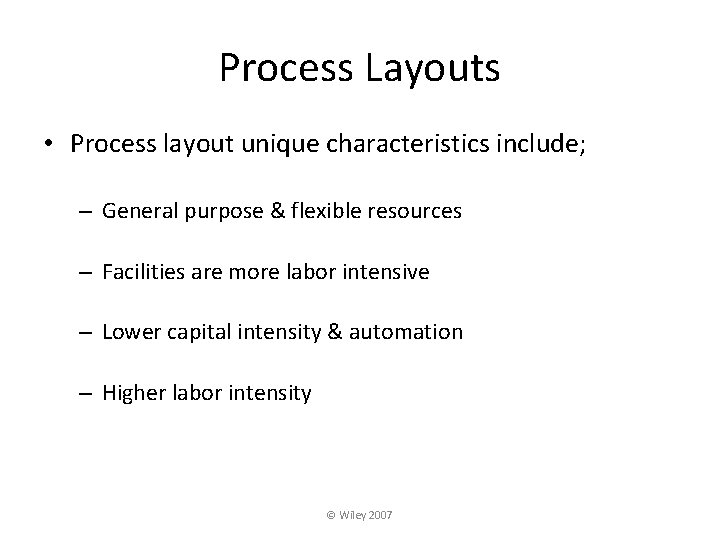
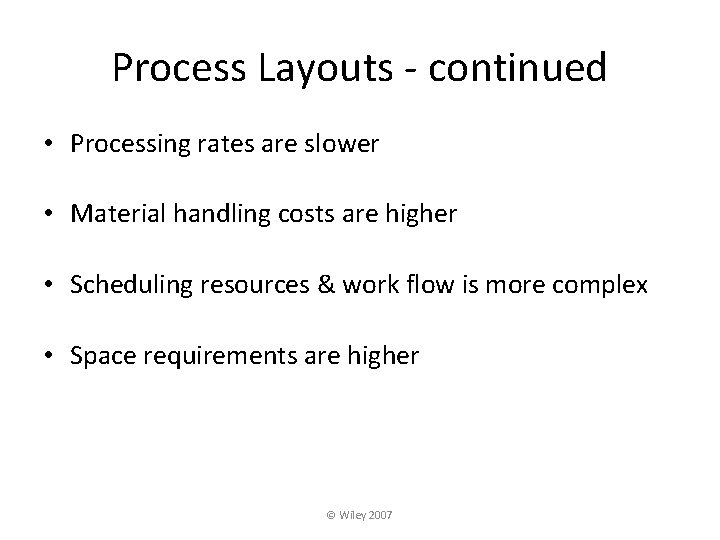
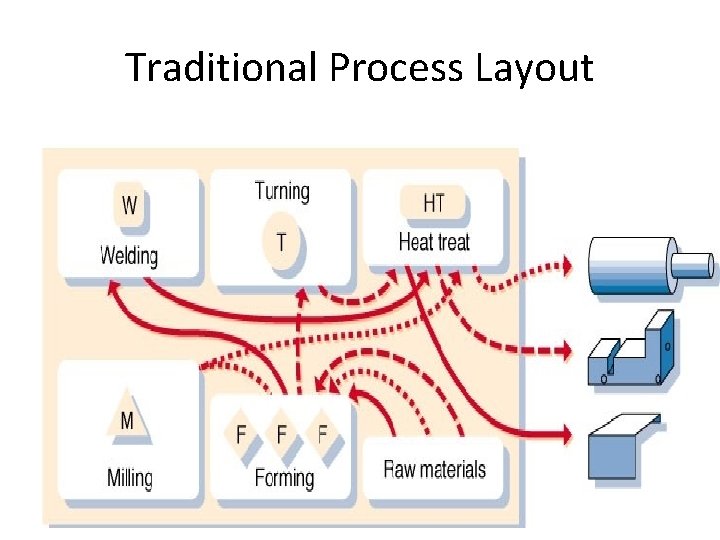
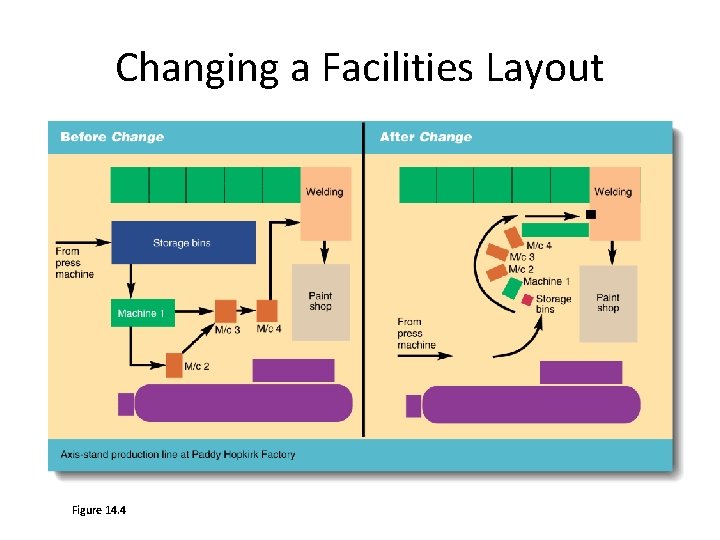
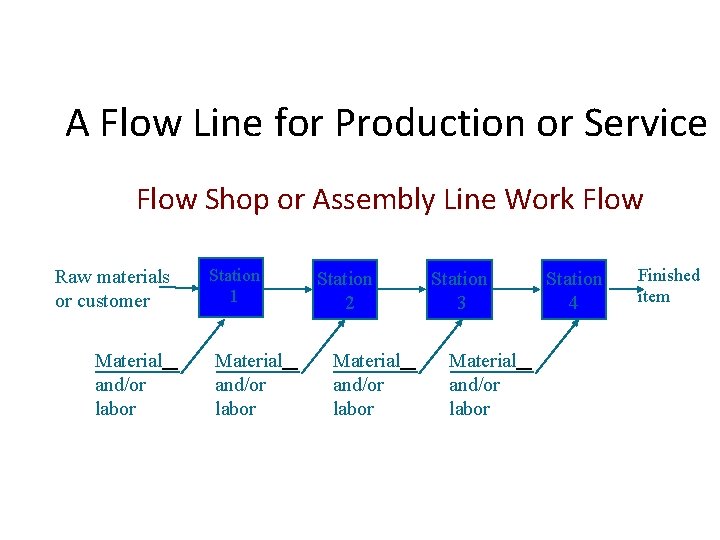
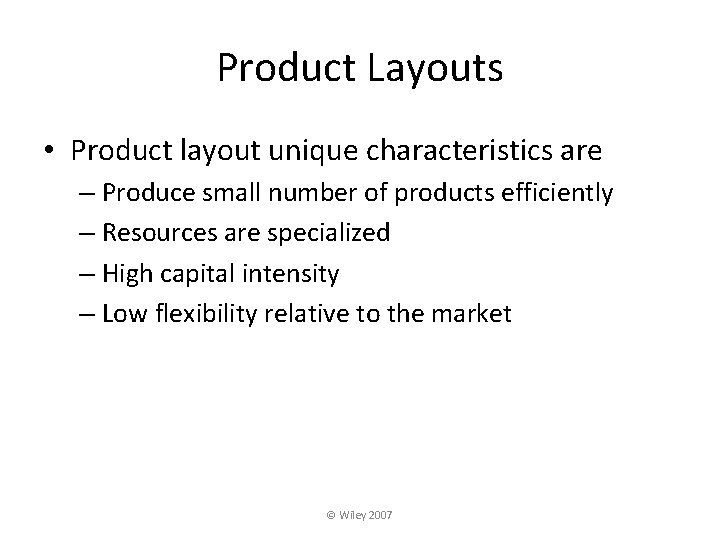
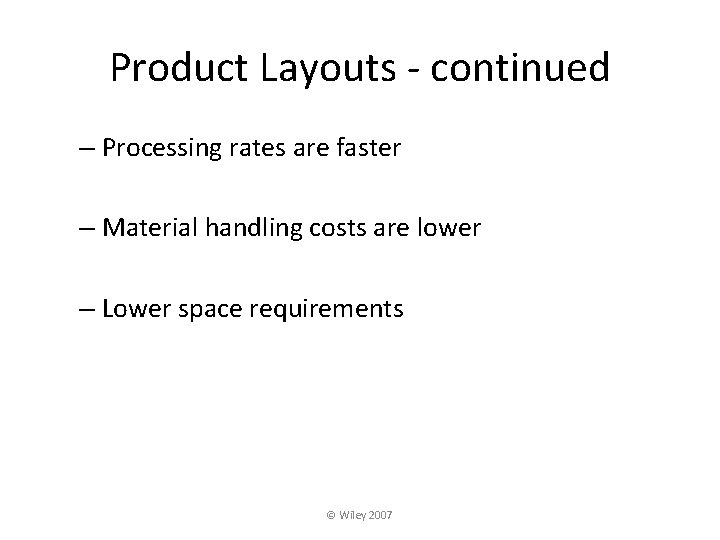
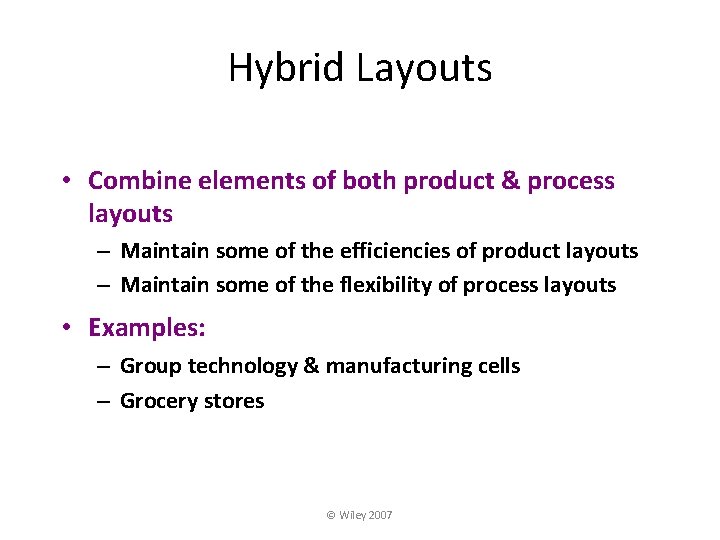
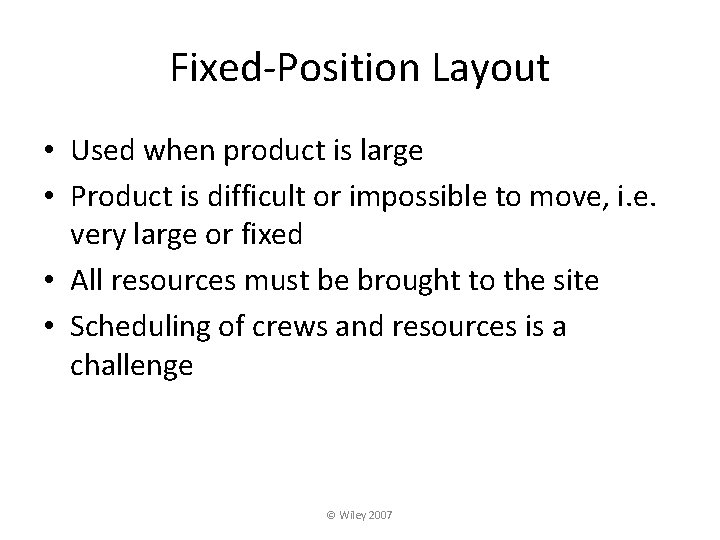
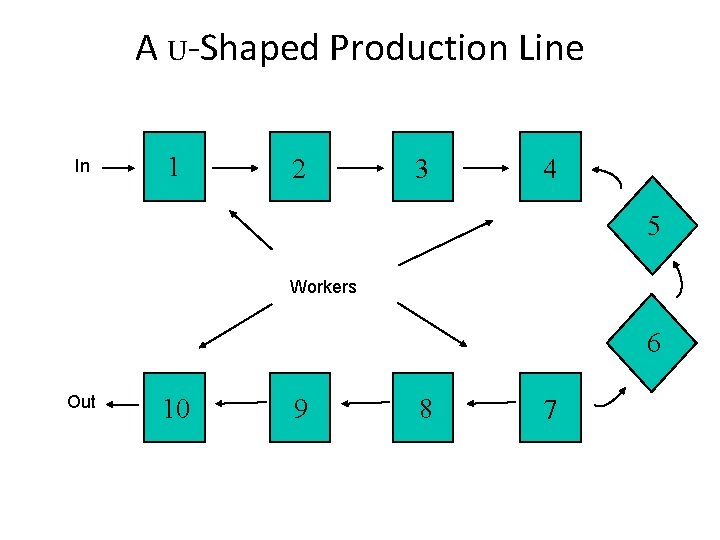
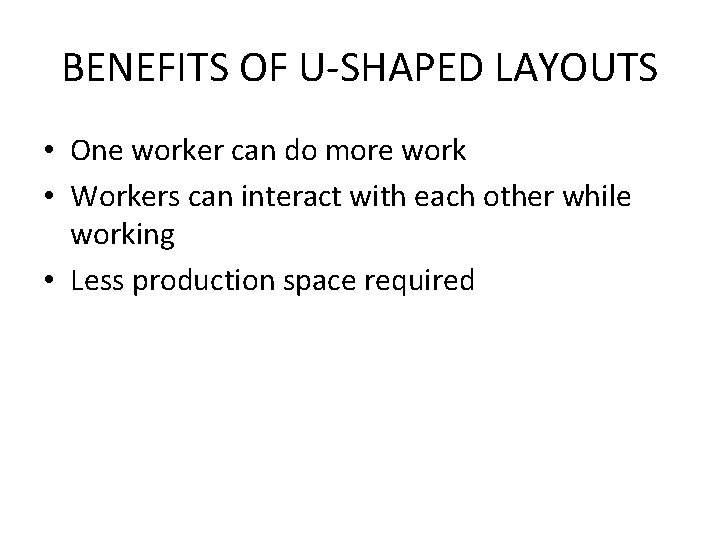
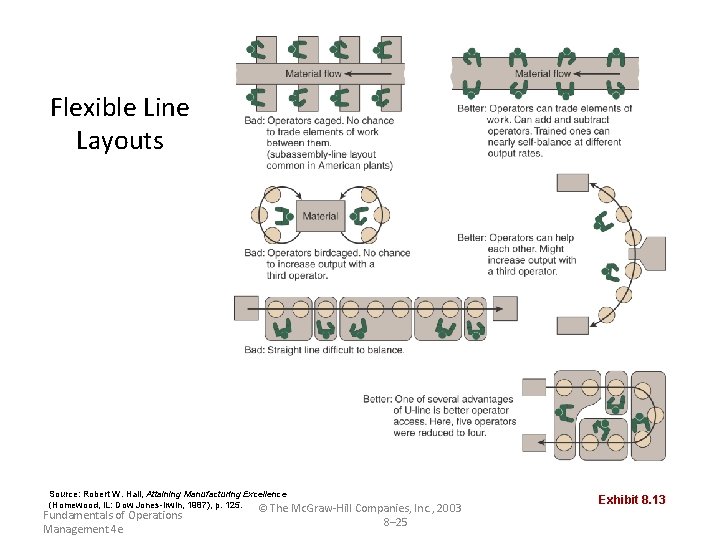
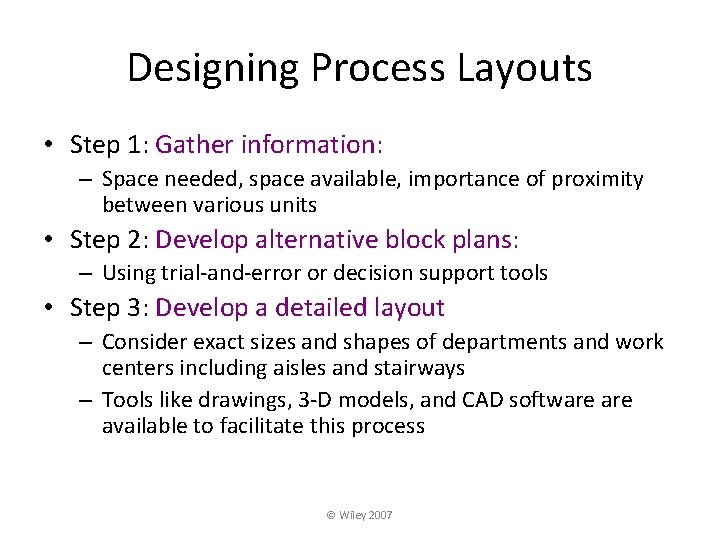
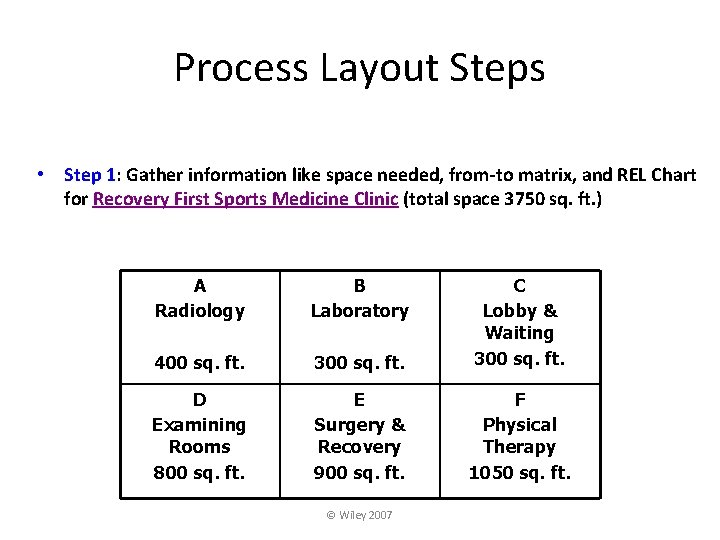
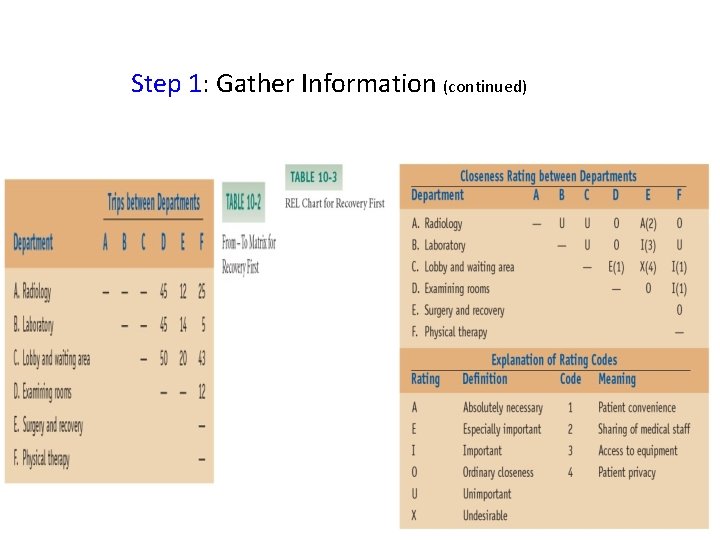
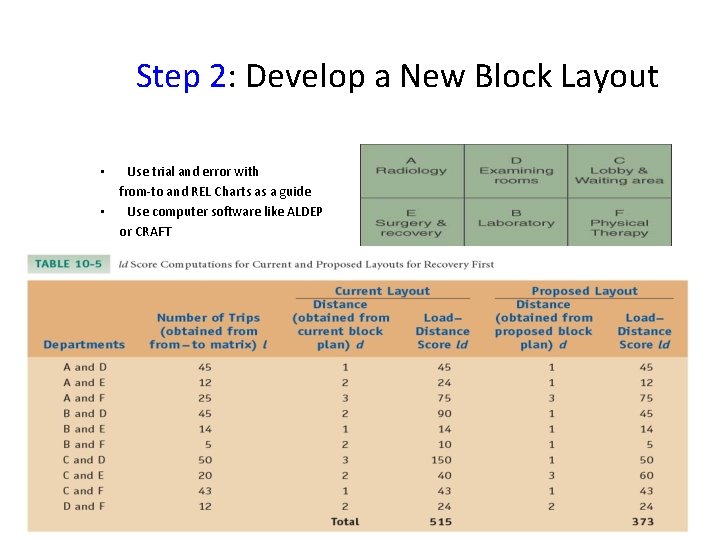
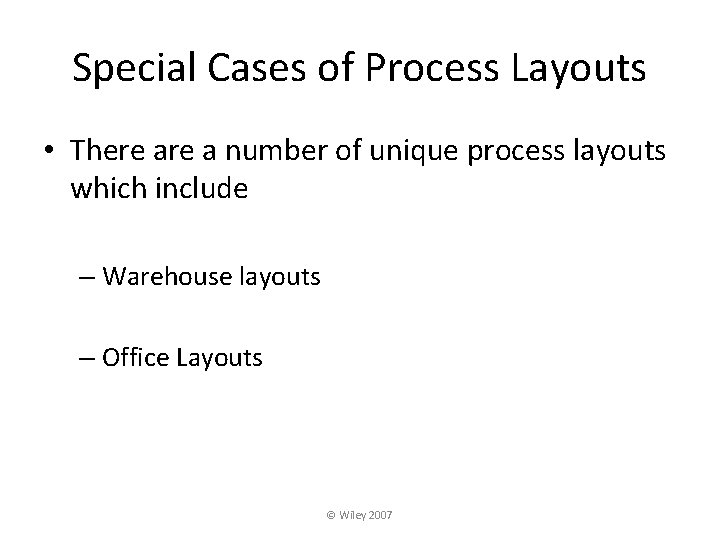
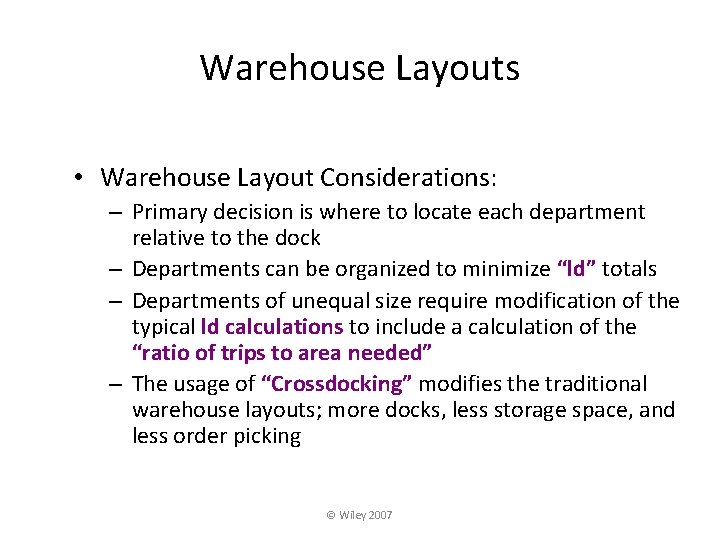
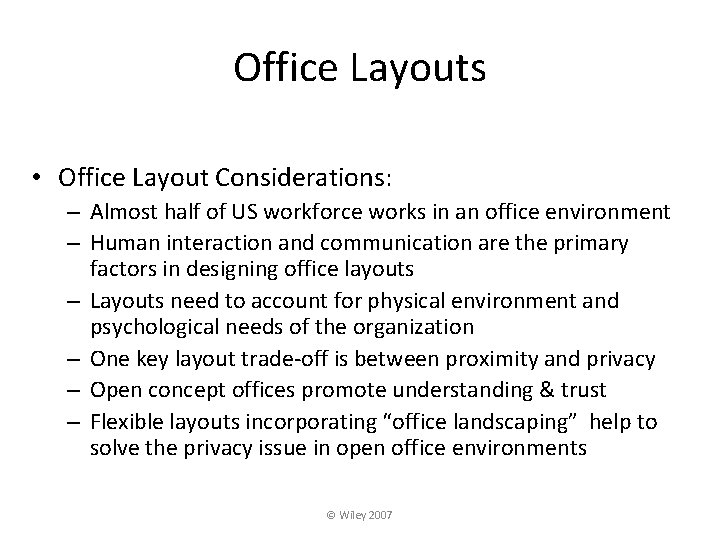
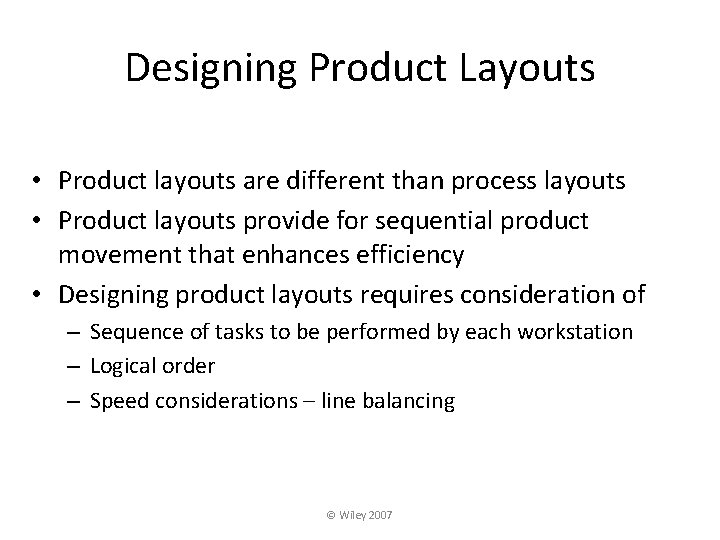
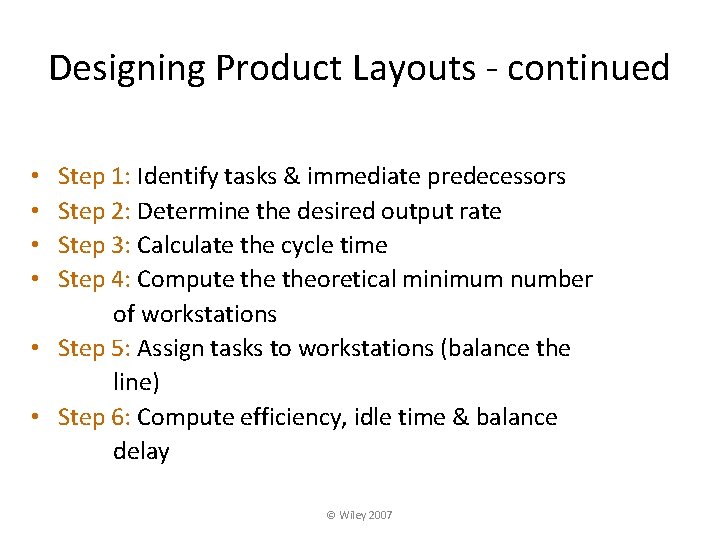
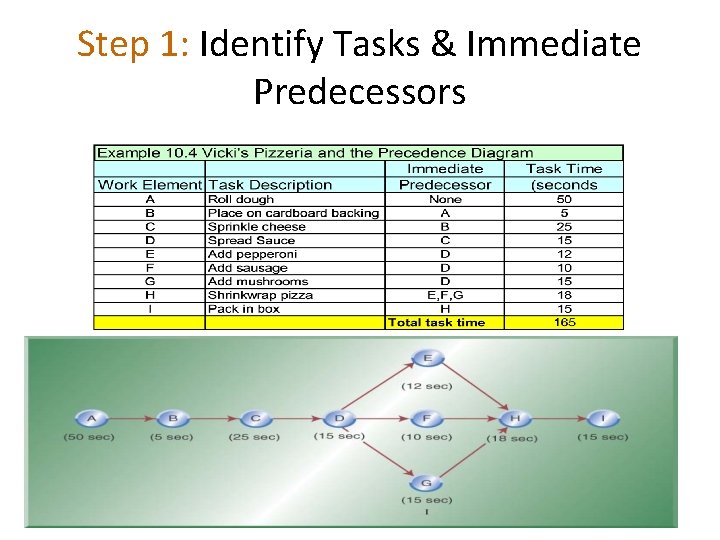
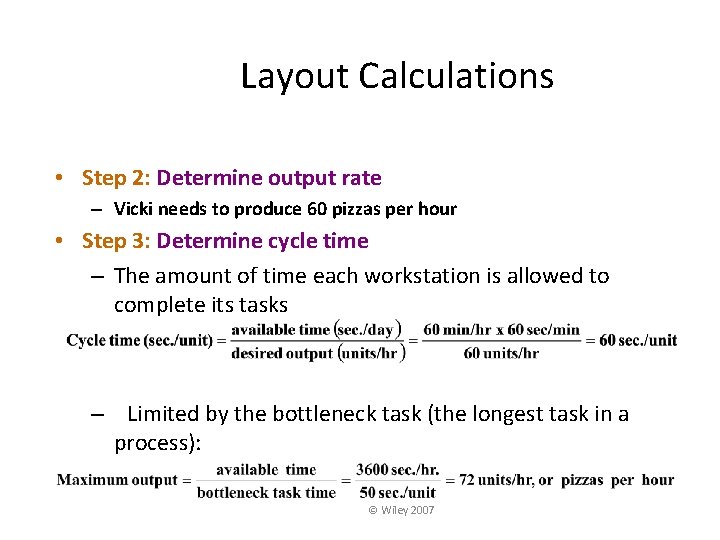
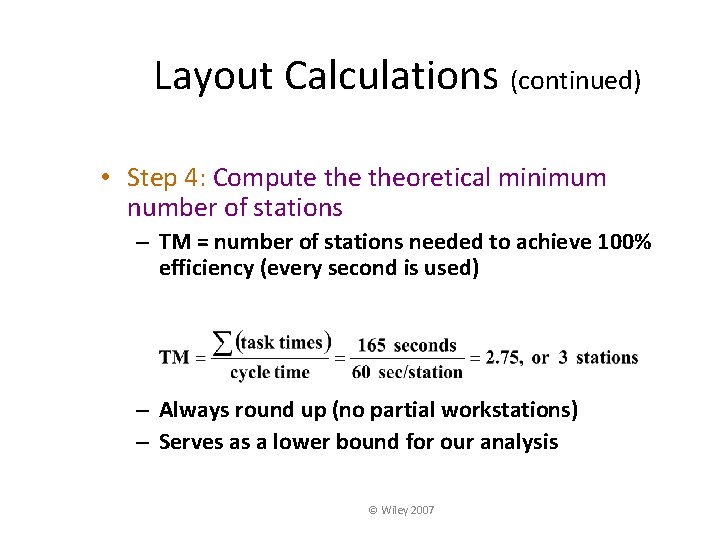
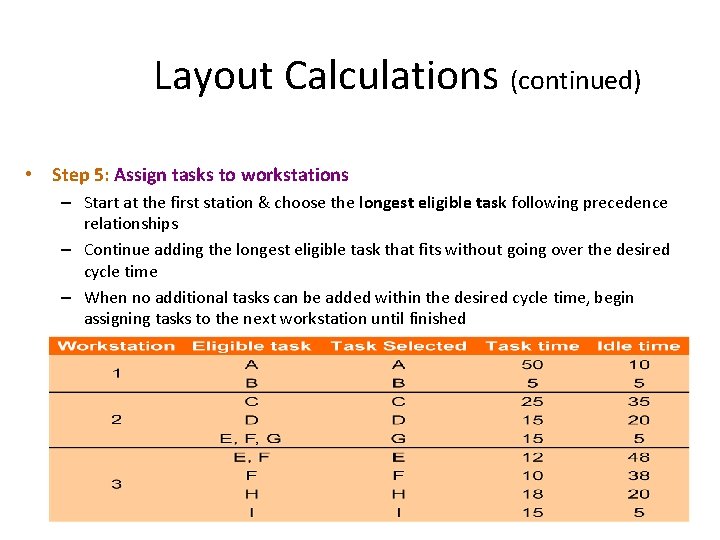
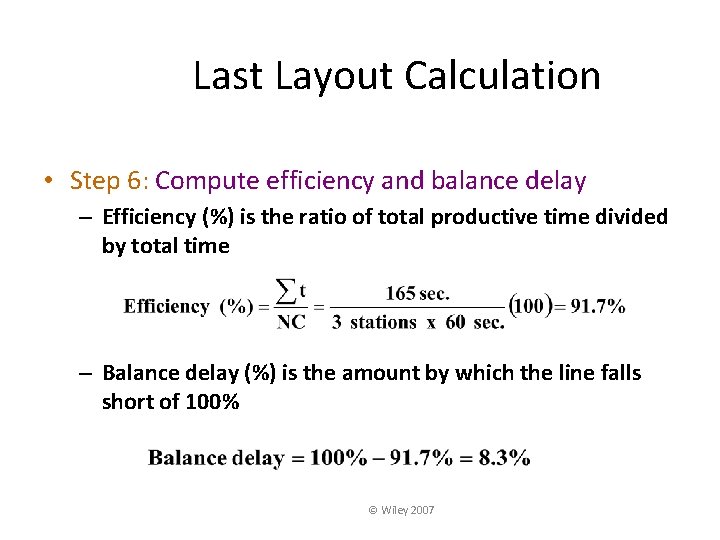
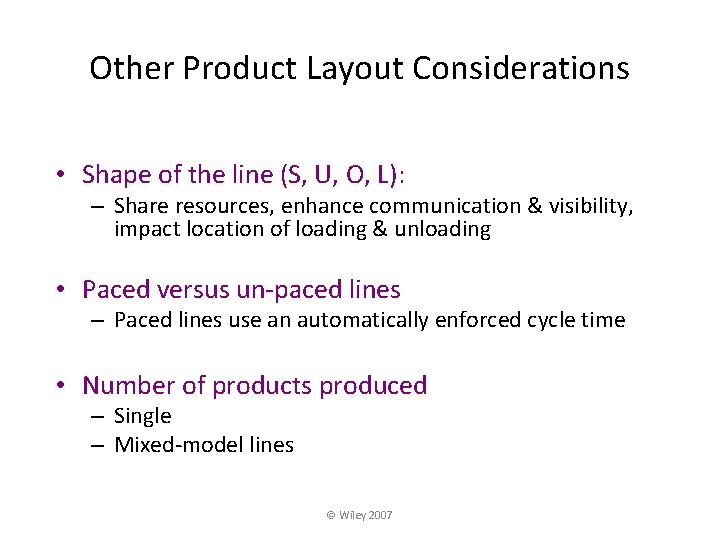
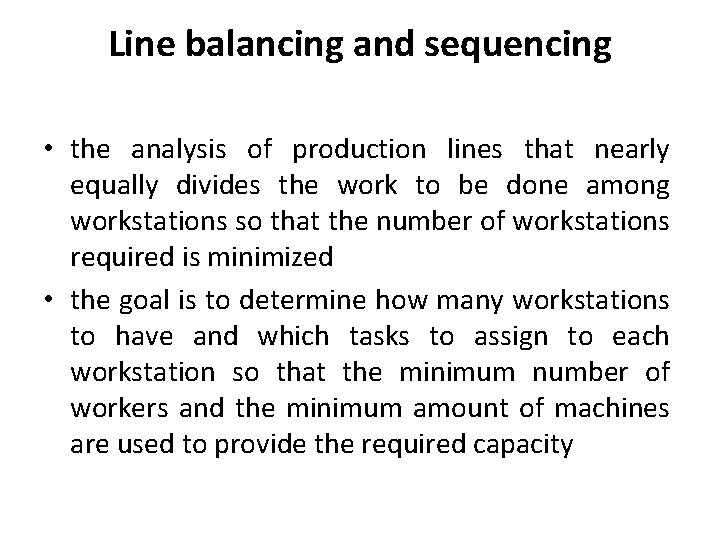
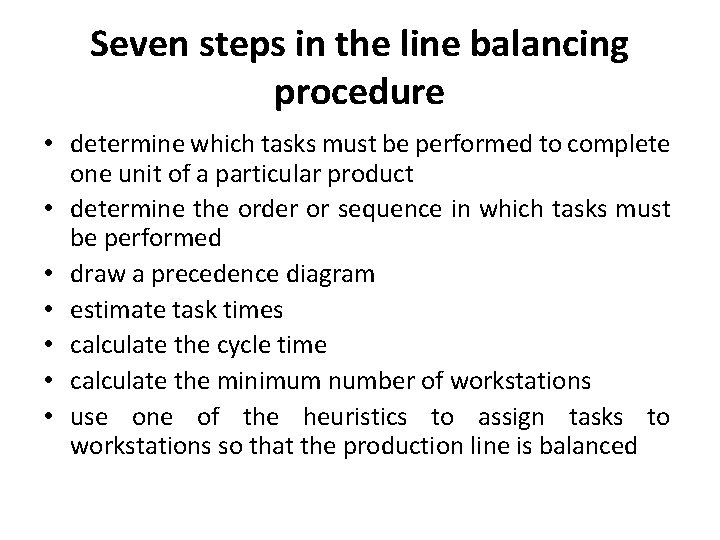
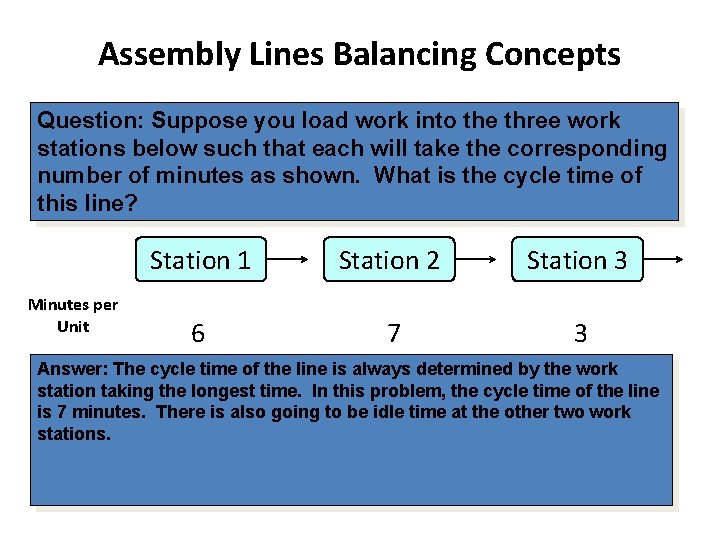
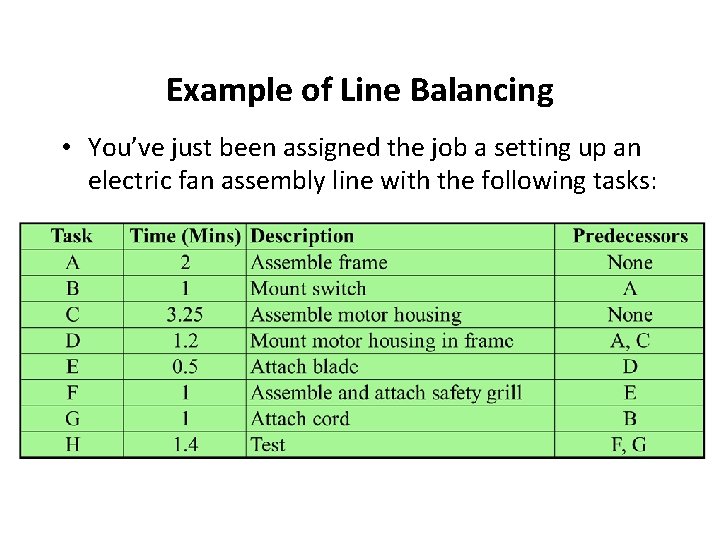
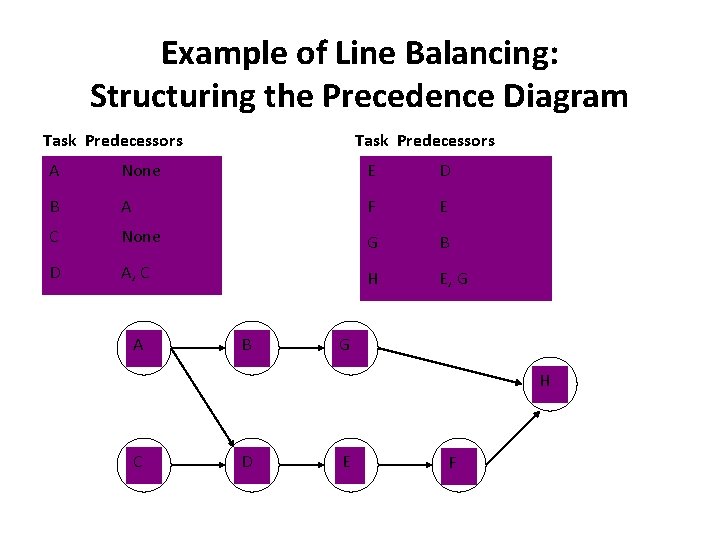
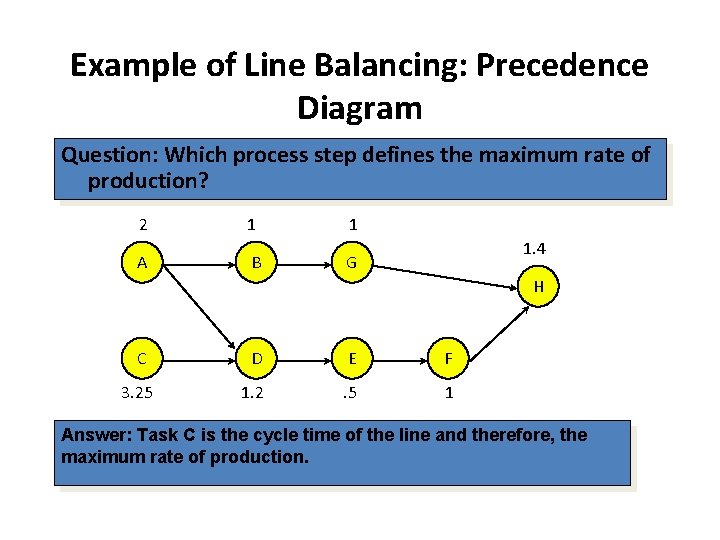
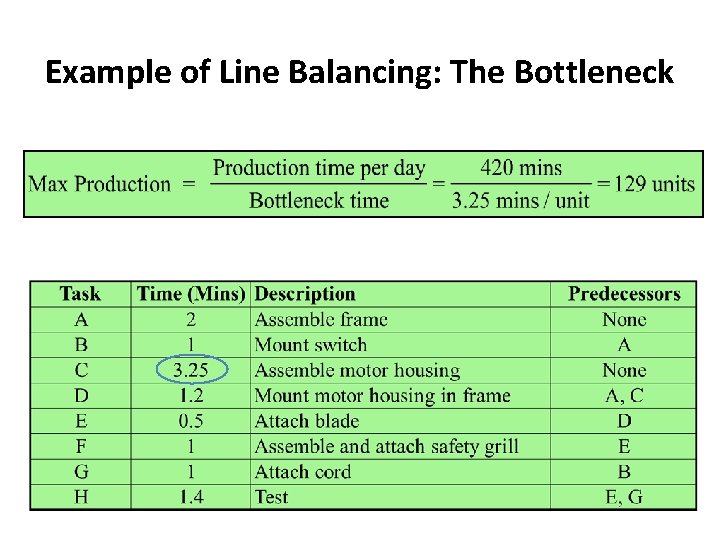
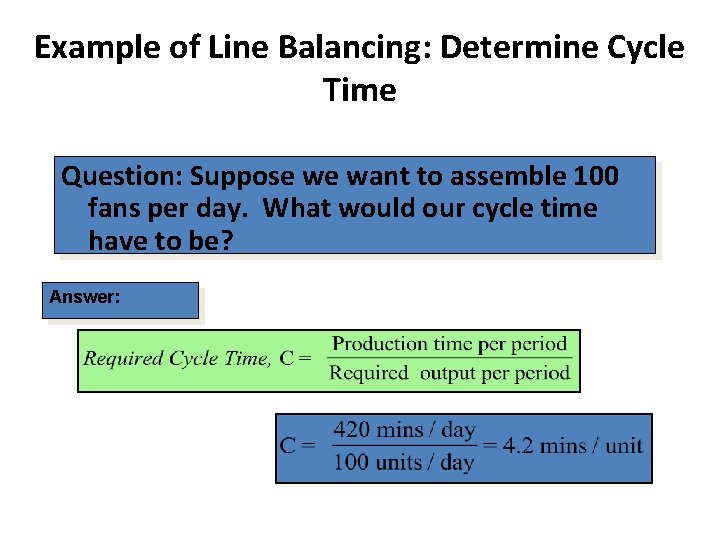
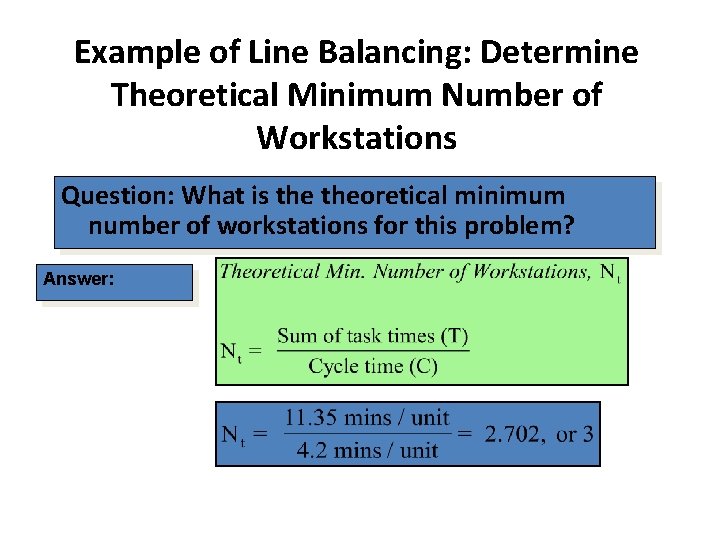
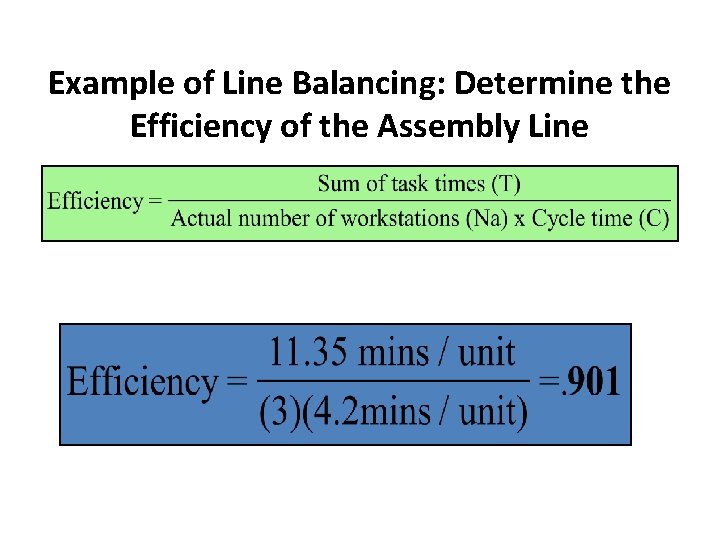
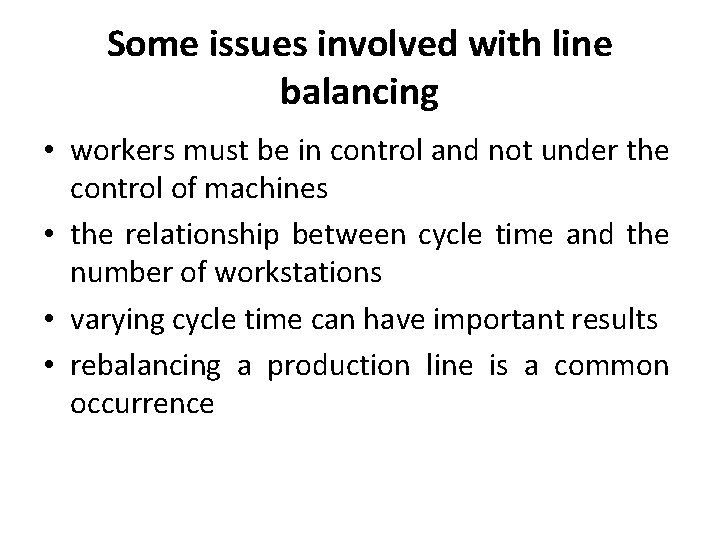
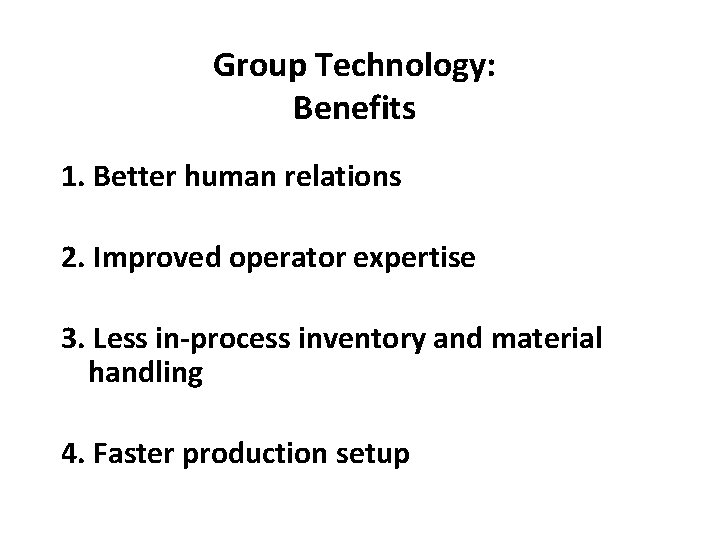
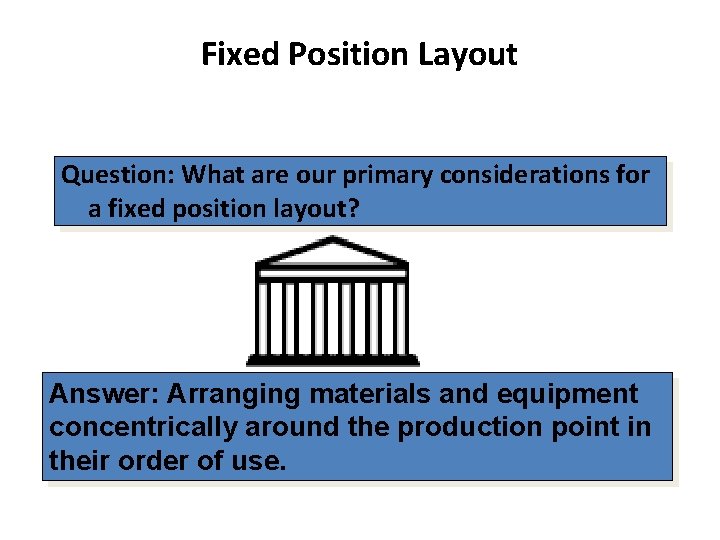
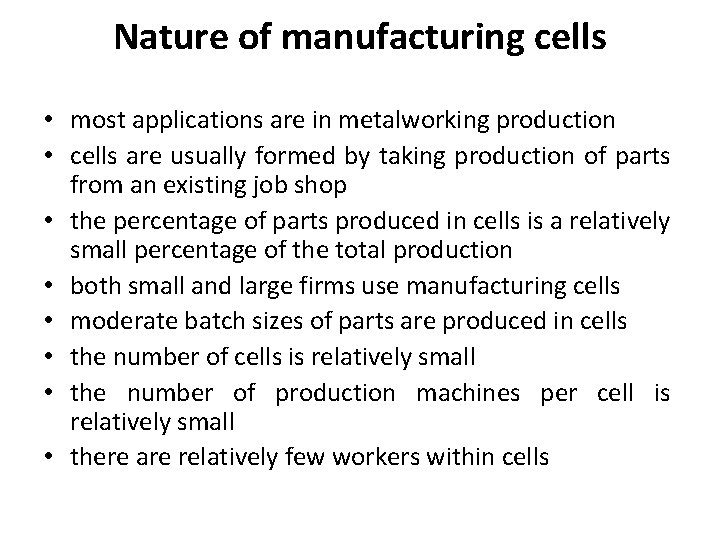
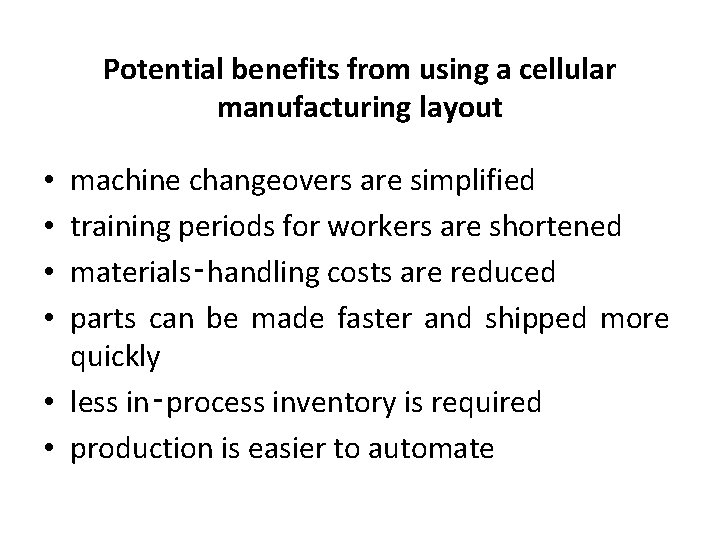
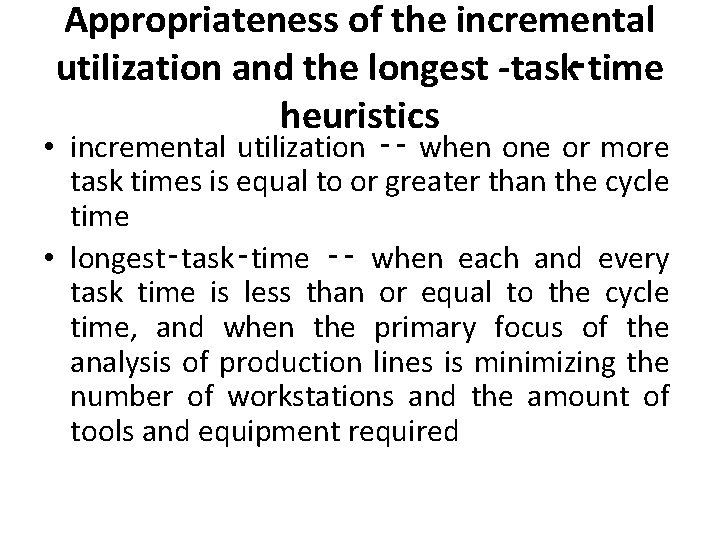
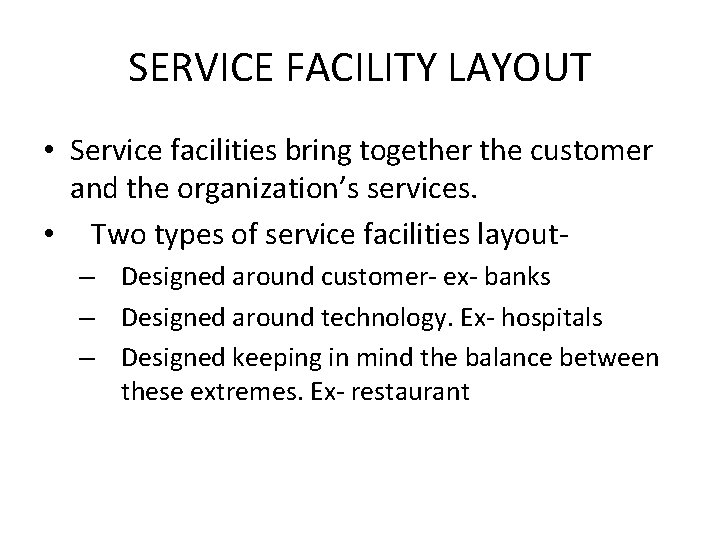
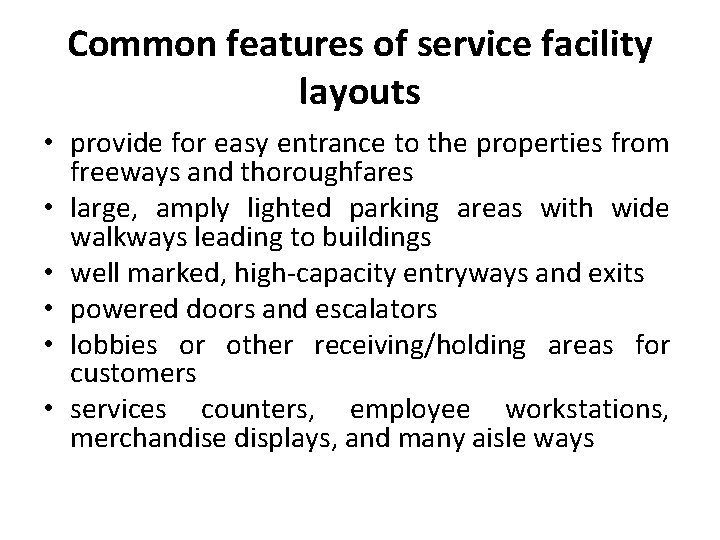
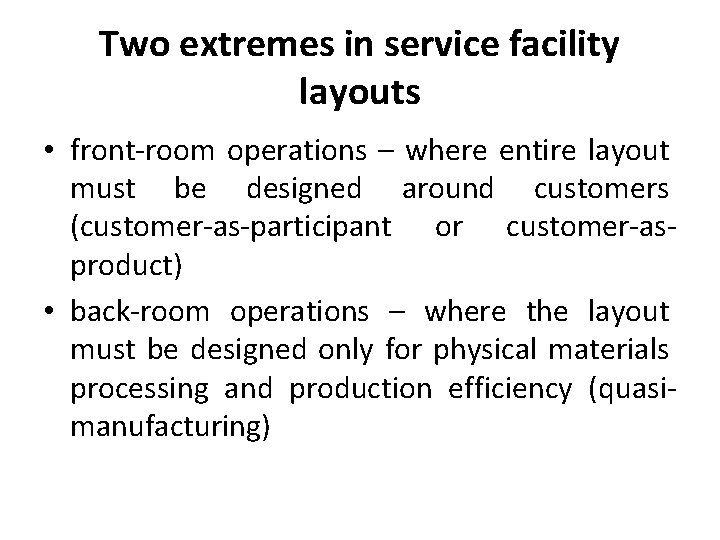
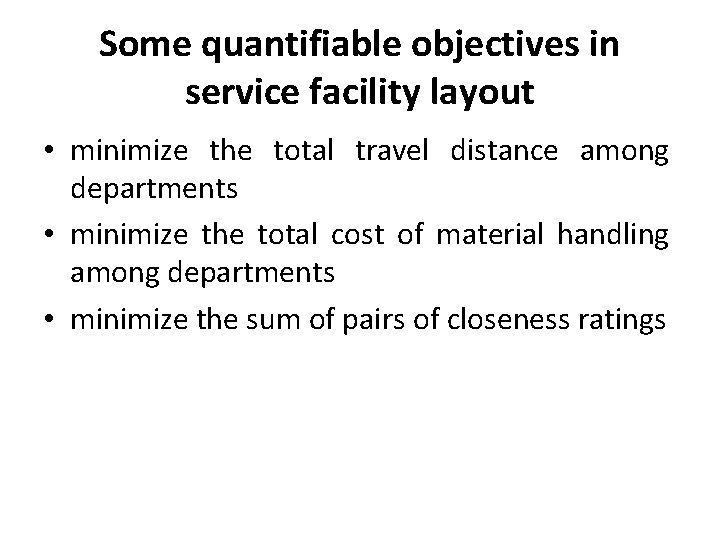
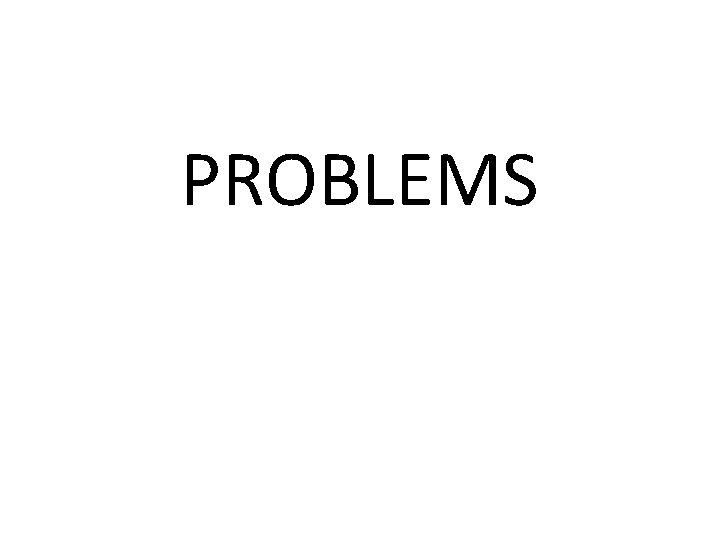
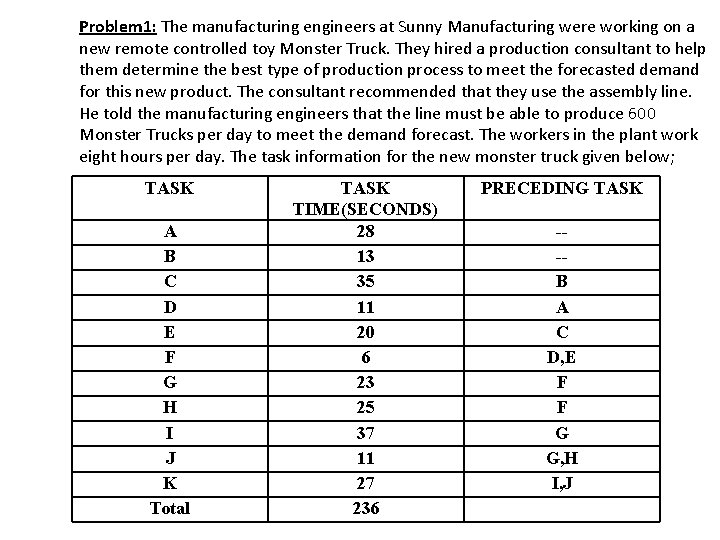

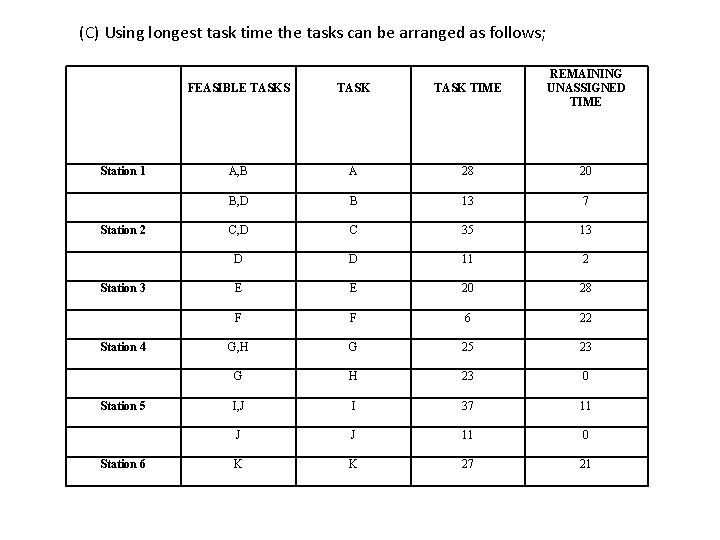
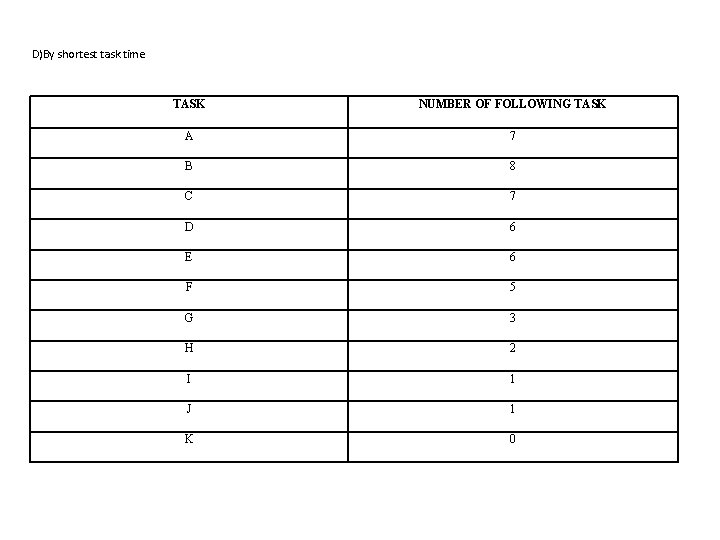
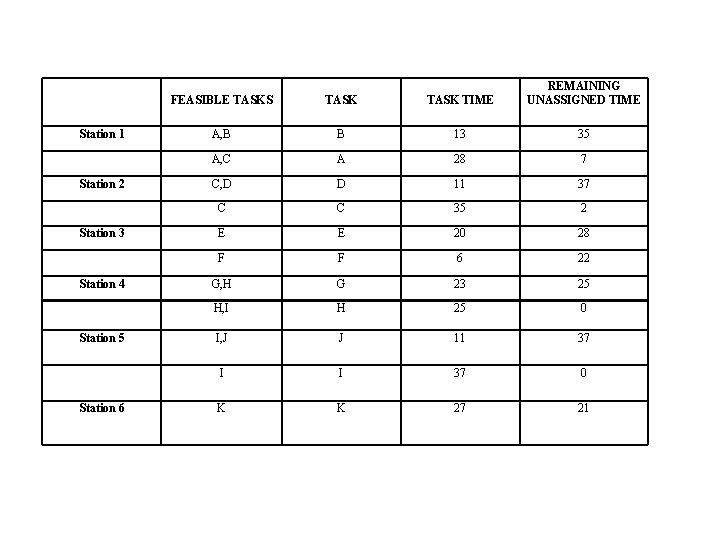
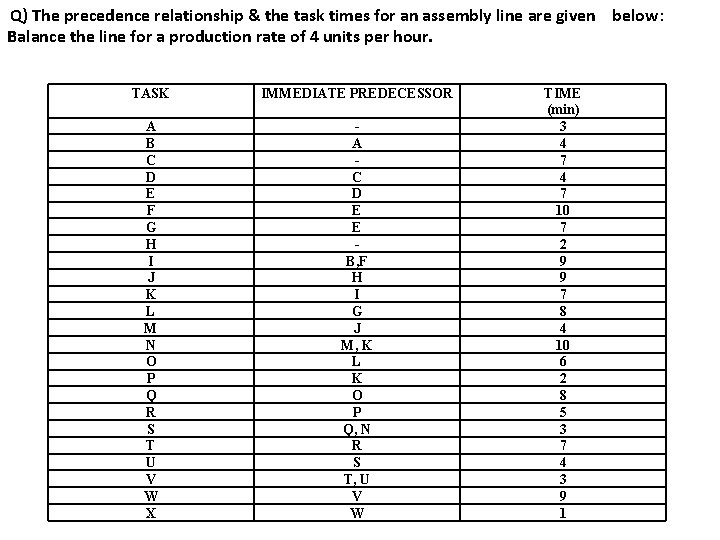
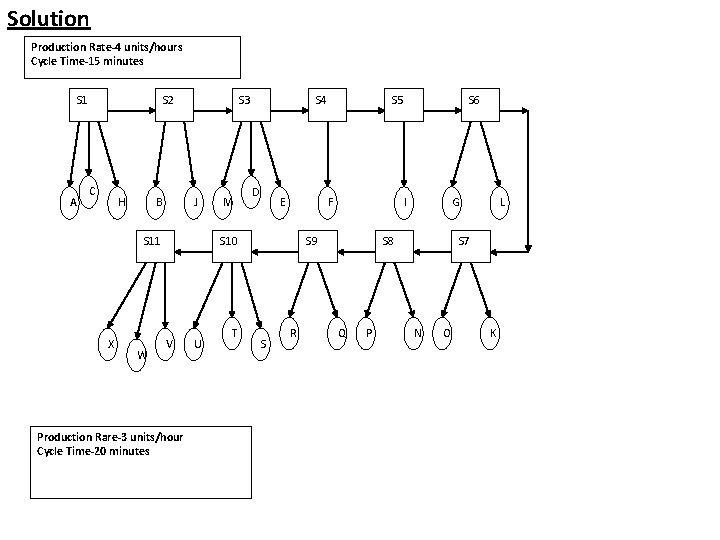
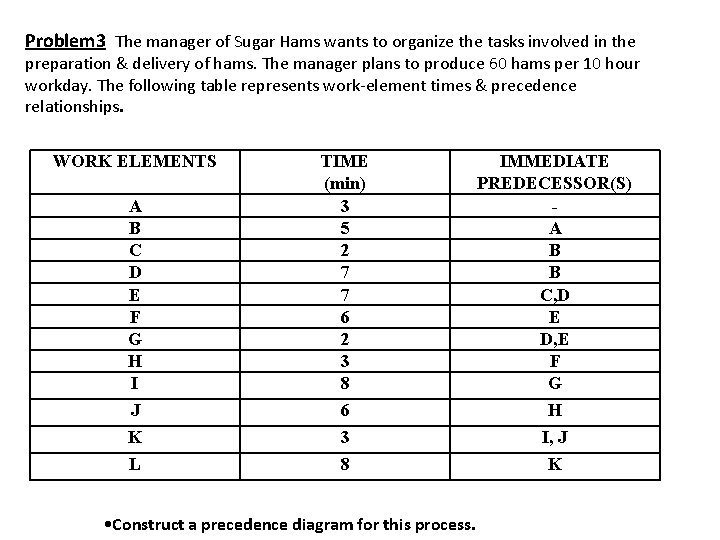
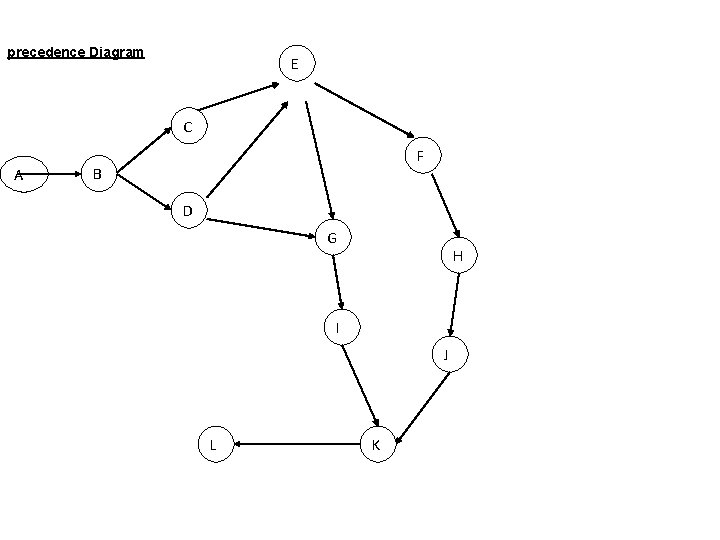
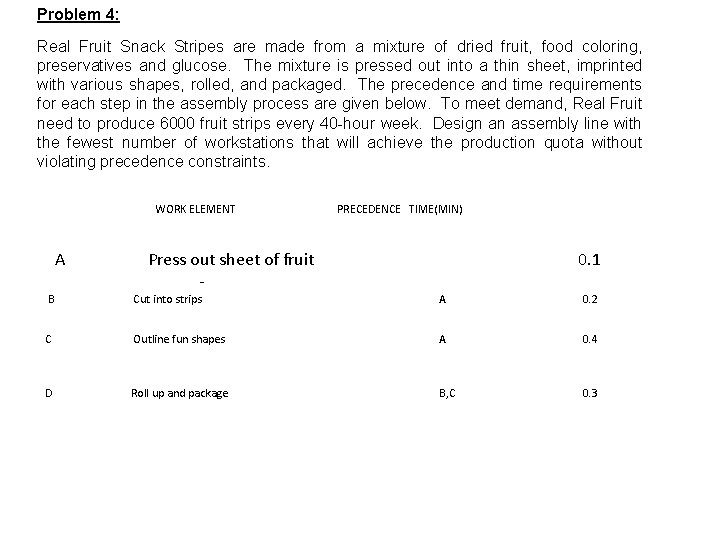
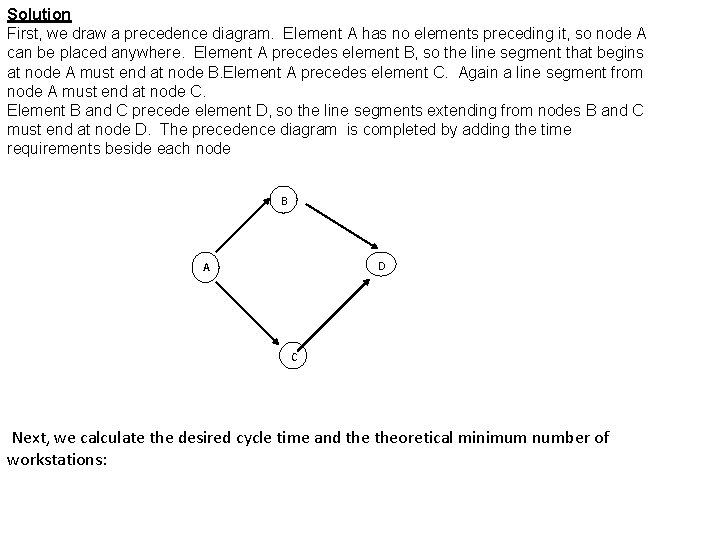
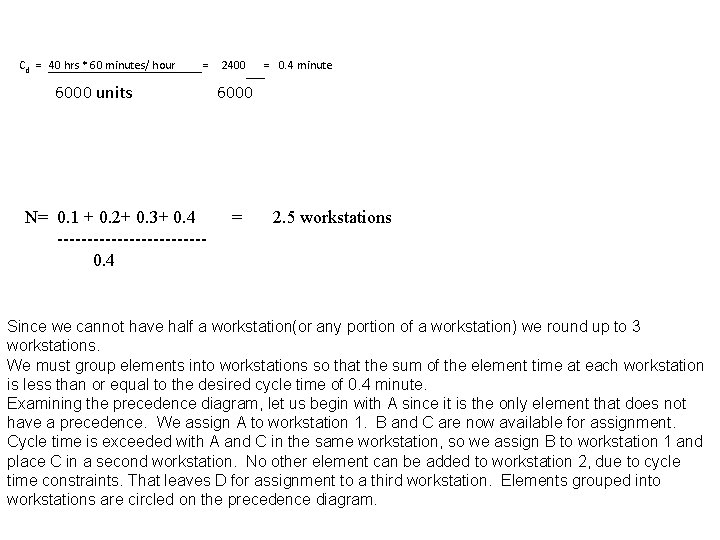
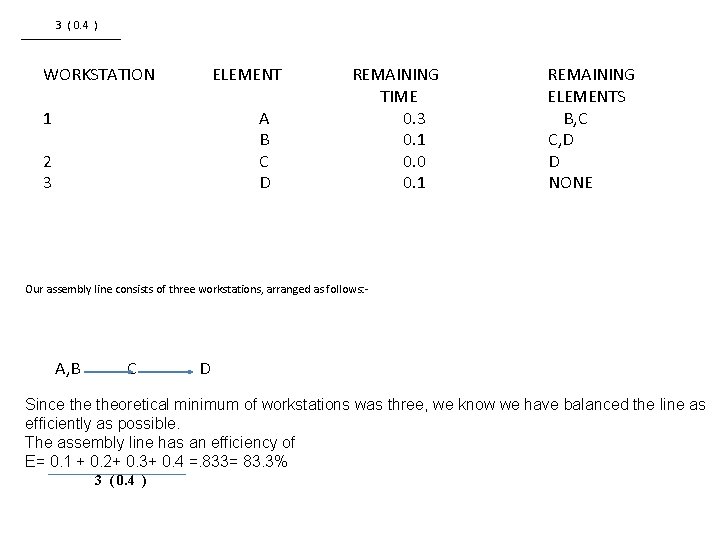
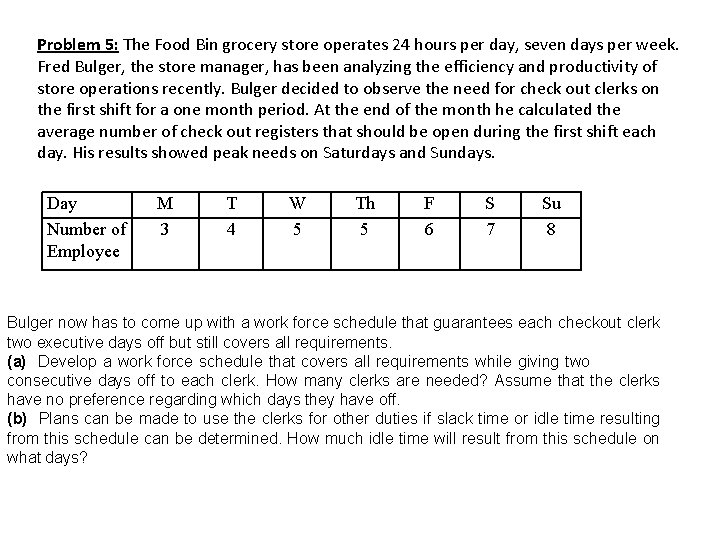
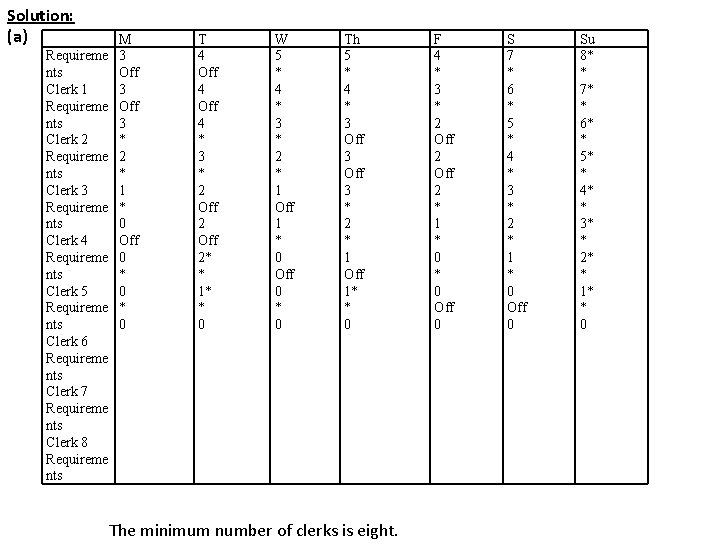
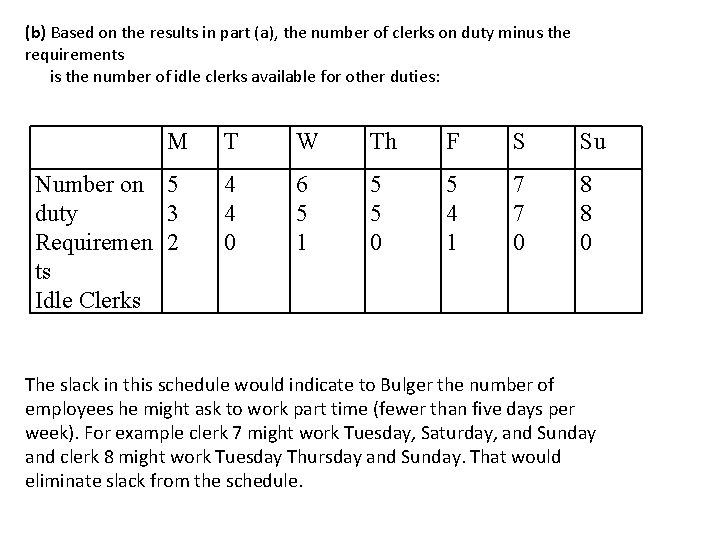
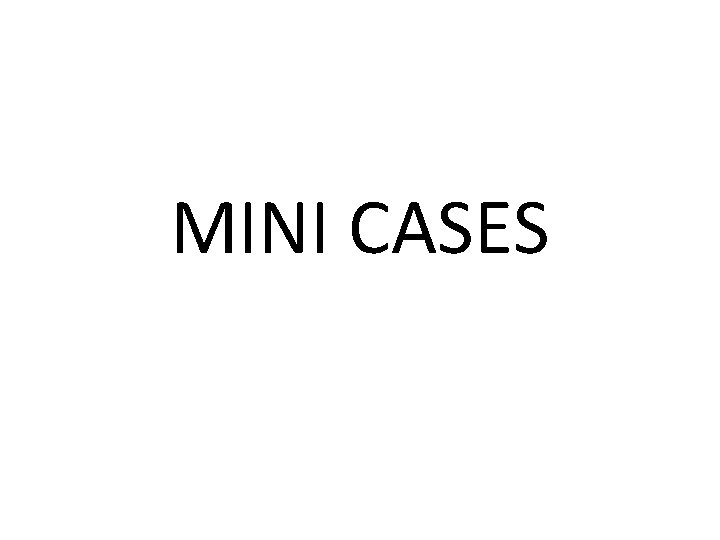
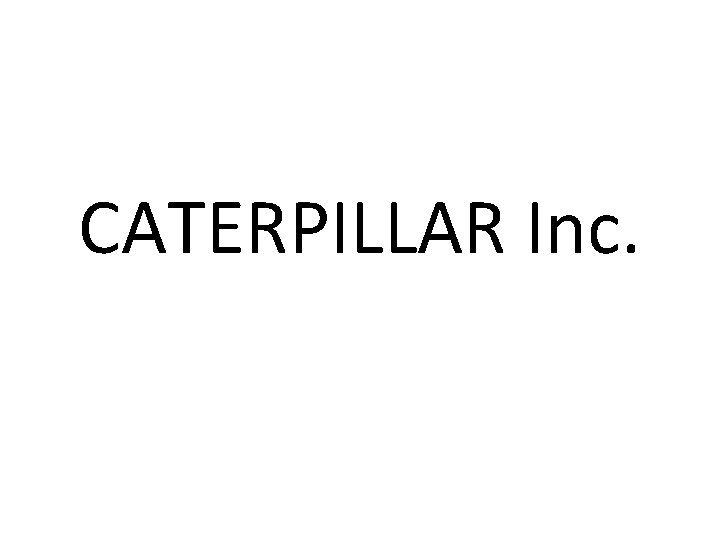
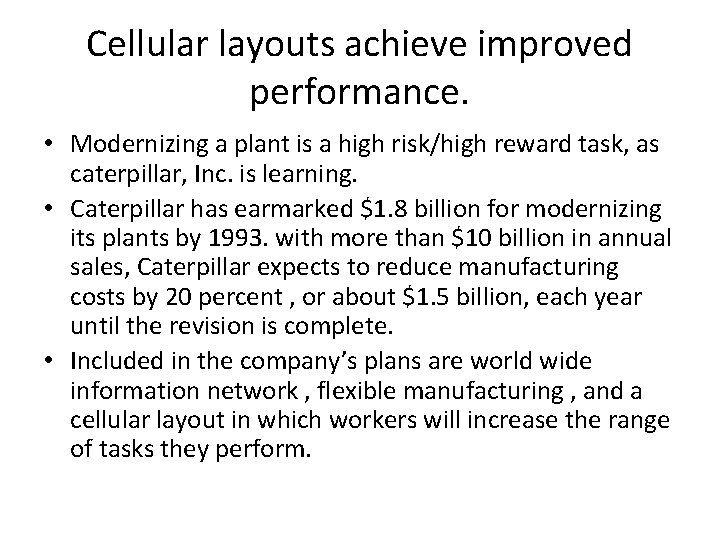
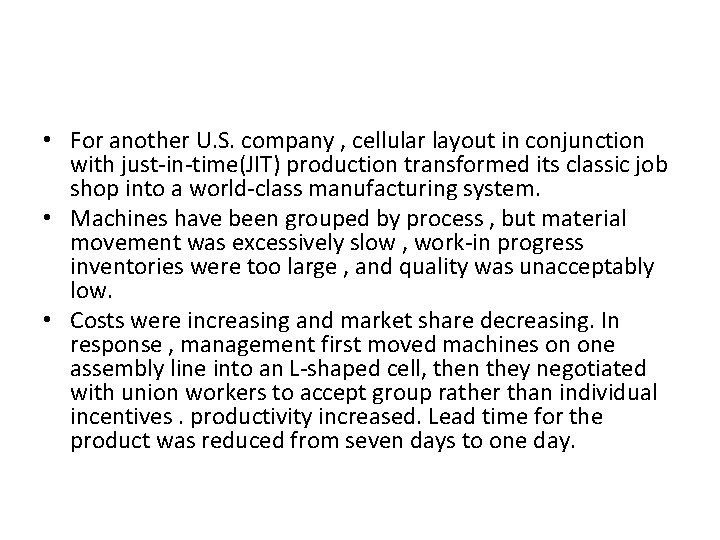
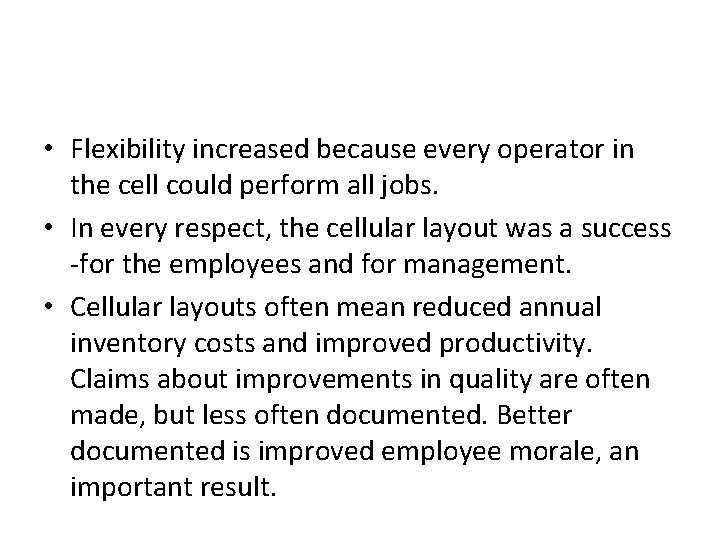
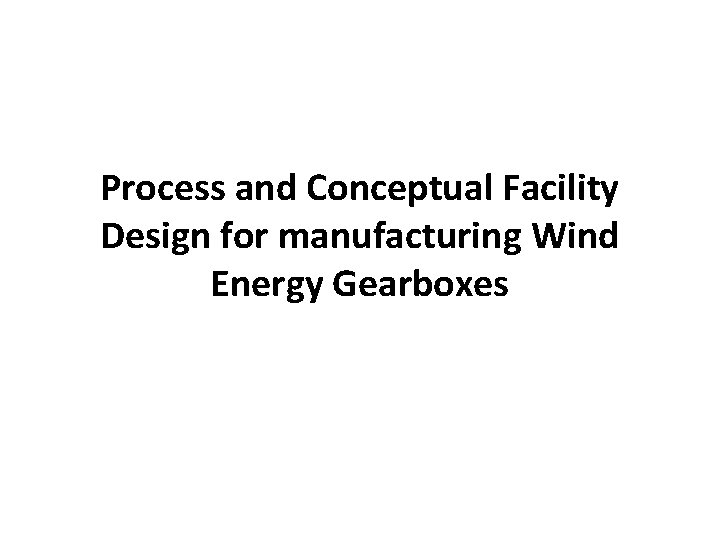
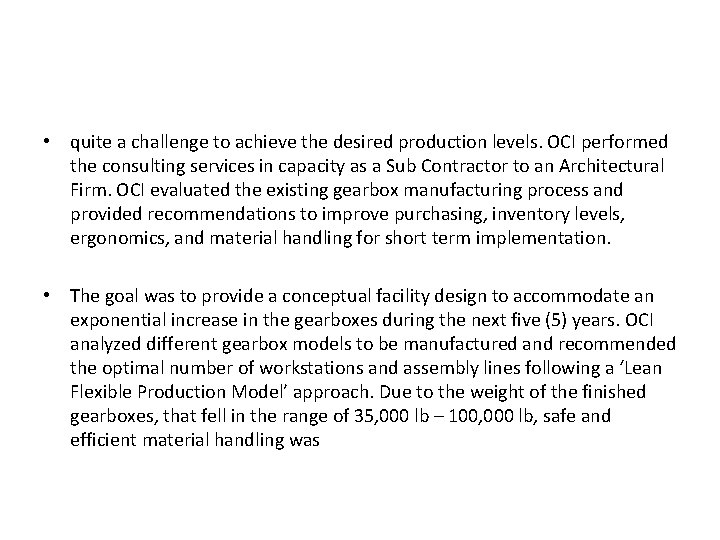
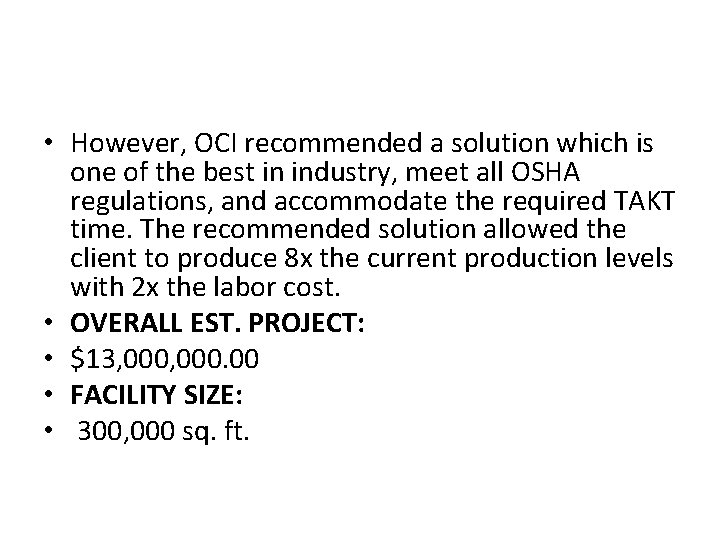
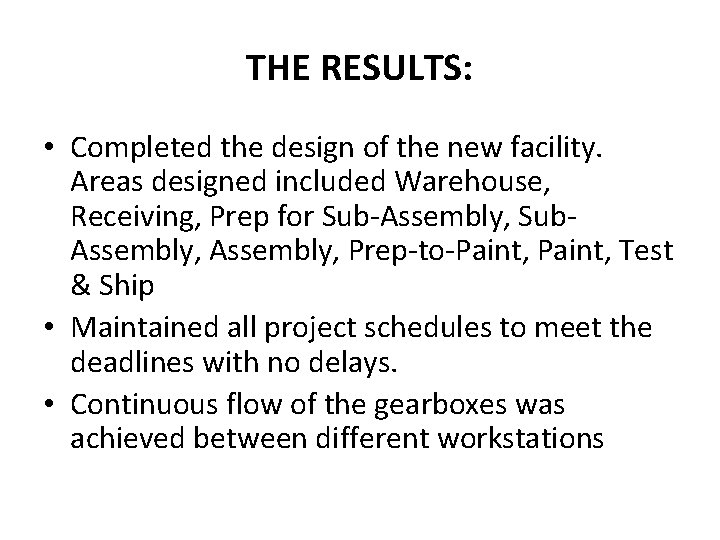
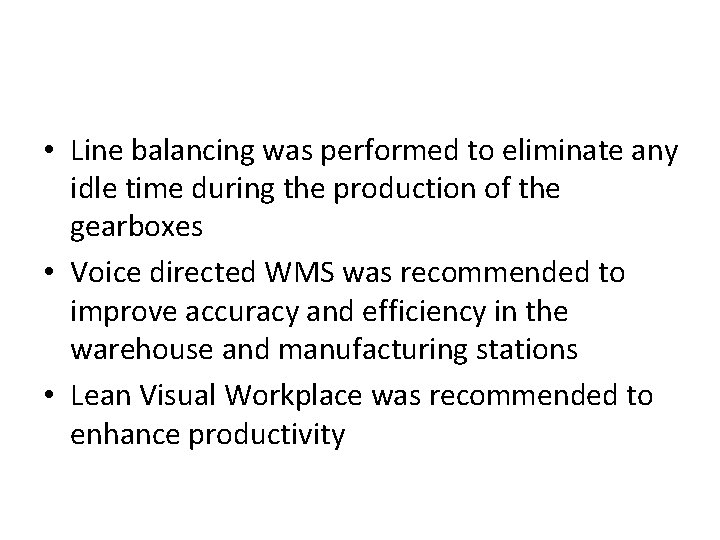
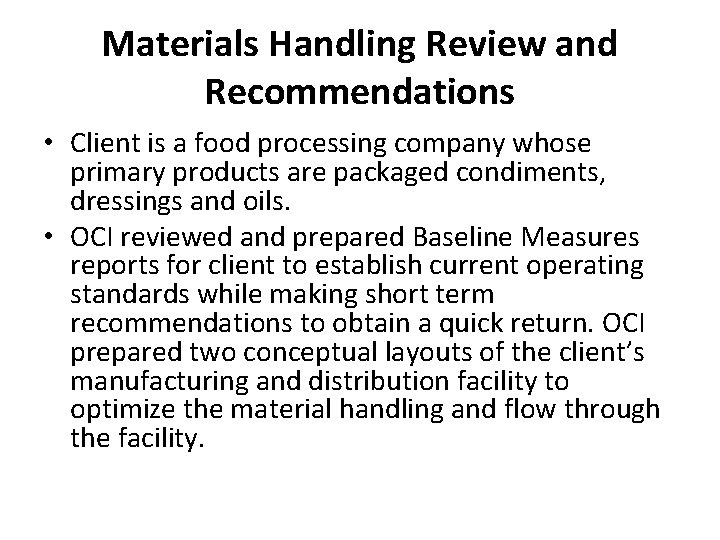
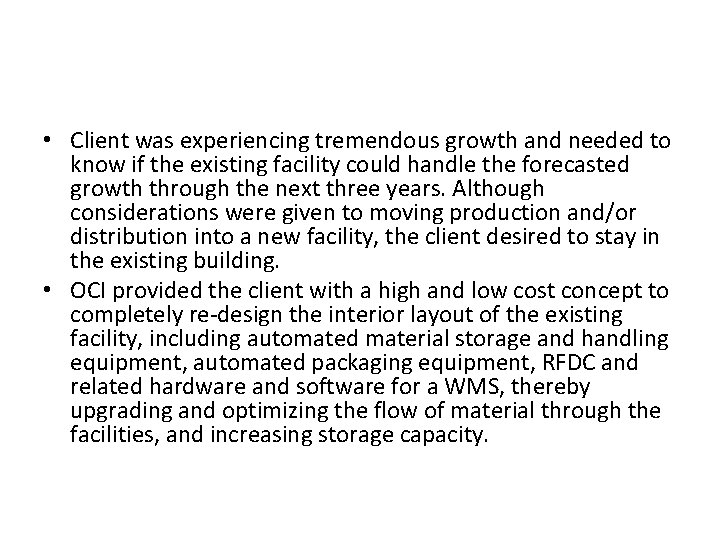
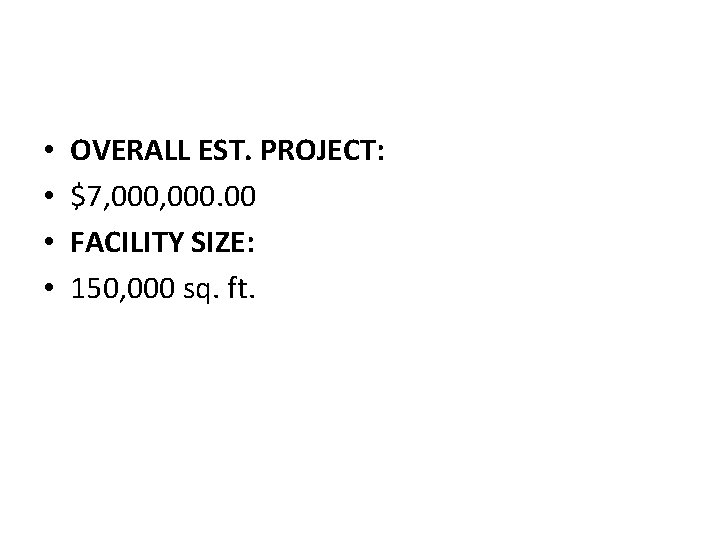
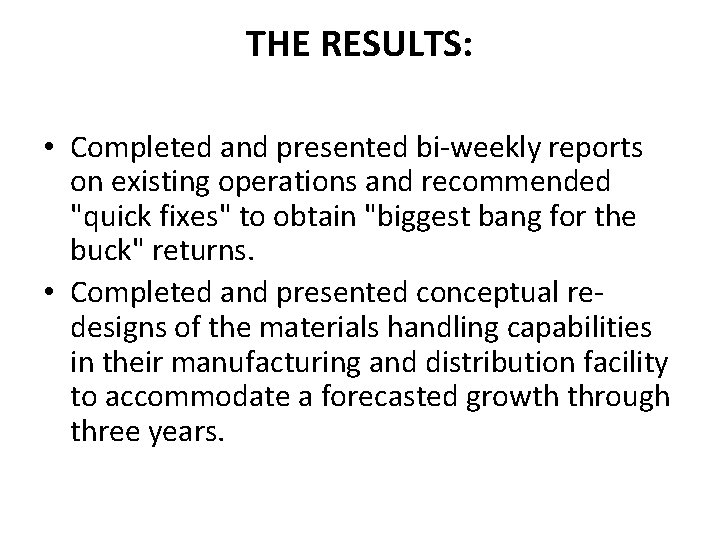
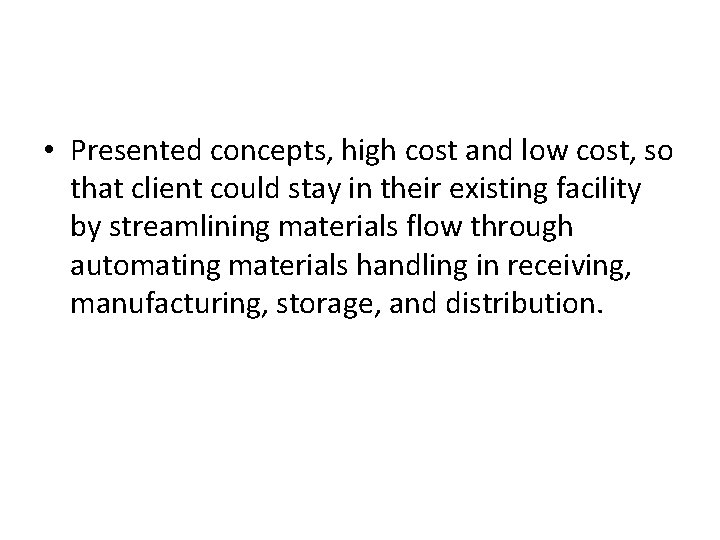
- Slides: 92
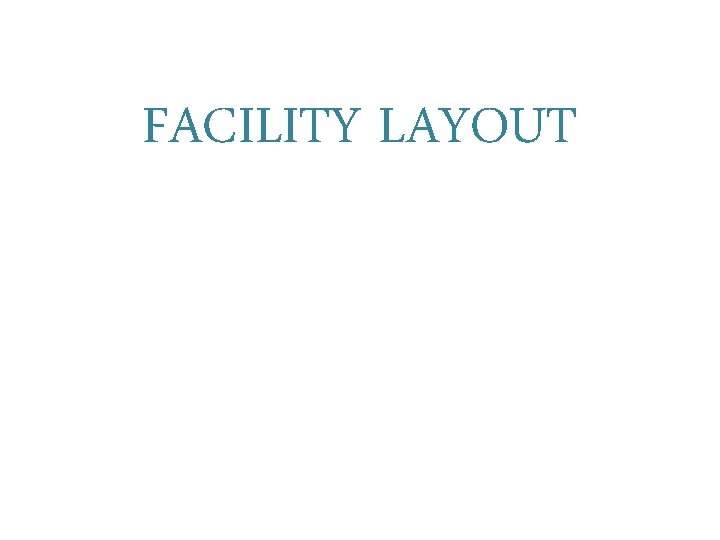
FACILITY LAYOUT
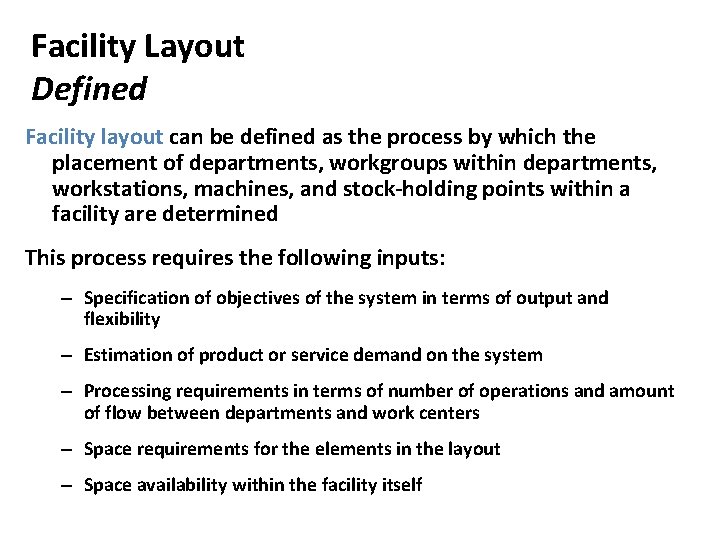
Facility Layout Defined Facility layout can be defined as the process by which the placement of departments, workgroups within departments, workstations, machines, and stock holding points within a facility are determined This process requires the following inputs: – Specification of objectives of the system in terms of output and flexibility – Estimation of product or service demand on the system – Processing requirements in terms of number of operations and amount of flow between departments and work centers – Space requirements for the elements in the layout – Space availability within the facility itself
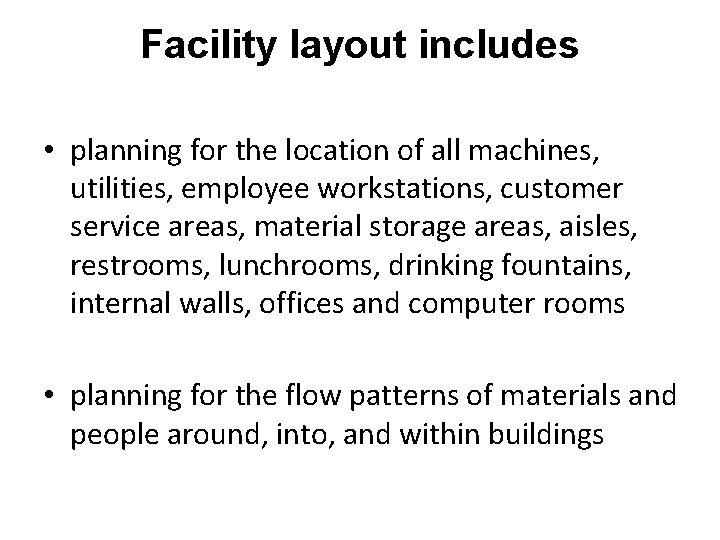
Facility layout includes • planning for the location of all machines, utilities, employee workstations, customer service areas, material storage areas, aisles, restrooms, lunchrooms, drinking fountains, internal walls, offices and computer rooms • planning for the flow patterns of materials and people around, into, and within buildings
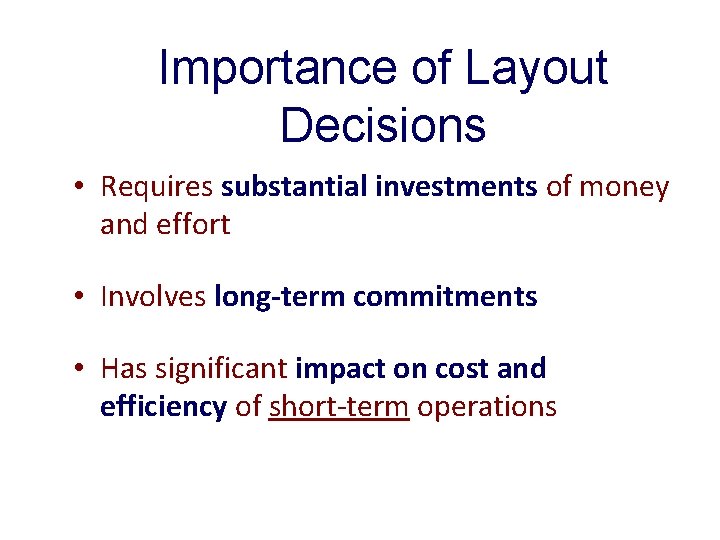
Importance of Layout Decisions • Requires substantial investments of money and effort • Involves long term commitments • Has significant impact on cost and efficiency of short-term operations
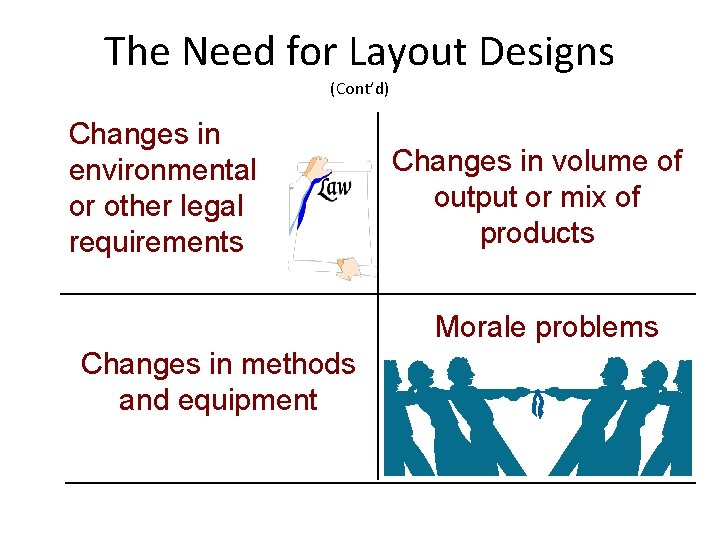
The Need for Layout Designs (Cont’d) Changes in environmental or other legal requirements Changes in volume of output or mix of products Morale problems Changes in methods and equipment
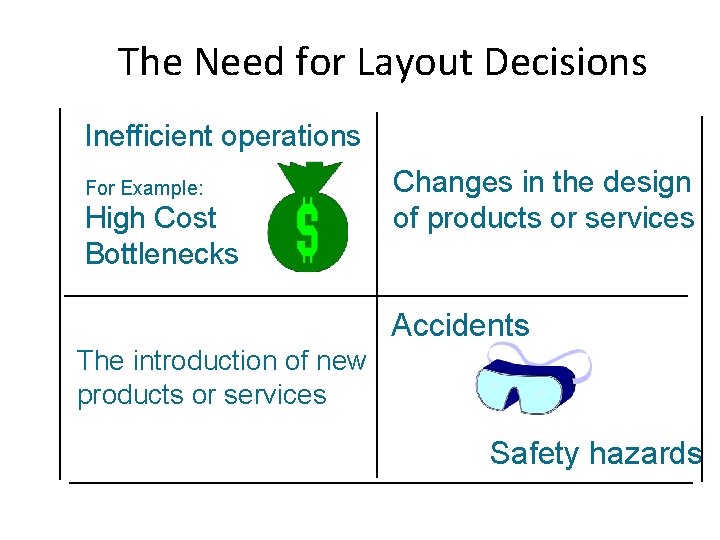
The Need for Layout Decisions Inefficient operations For Example: High Cost Bottlenecks Changes in the design of products or services Accidents The introduction of new products or services Safety hazards
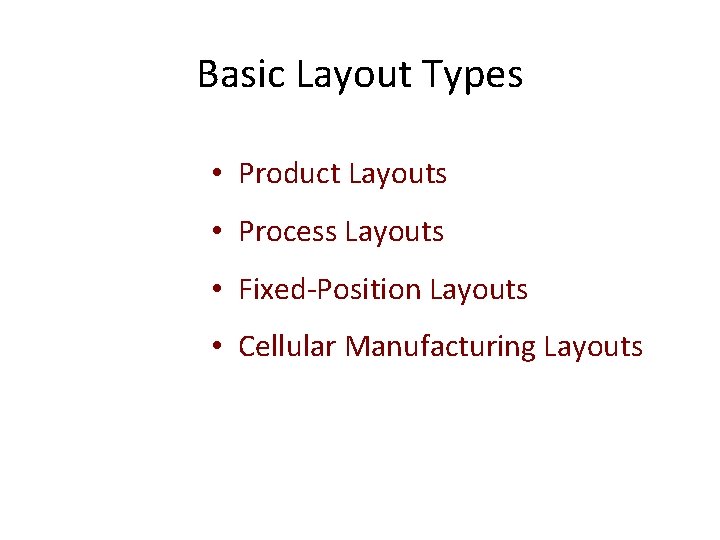
Basic Layout Types • Product Layouts • Process Layouts • Fixed-Position Layouts • Cellular Manufacturing Layouts
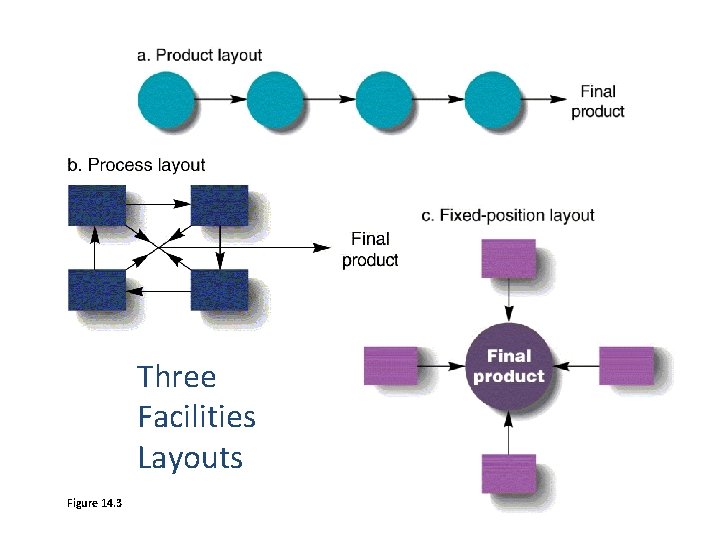
Three Facilities Layouts Figure 14. 3
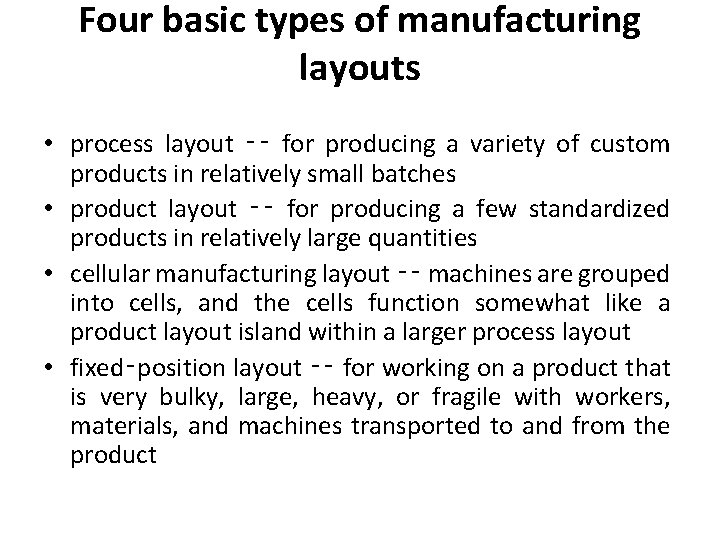
Four basic types of manufacturing layouts • process layout ‑‑ for producing a variety of custom products in relatively small batches • product layout ‑‑ for producing a few standardized products in relatively large quantities • cellular manufacturing layout ‑‑ machines are grouped into cells, and the cells function somewhat like a product layout island within a larger process layout • fixed‑position layout ‑‑ for working on a product that is very bulky, large, heavy, or fragile with workers, materials, and machines transported to and from the product
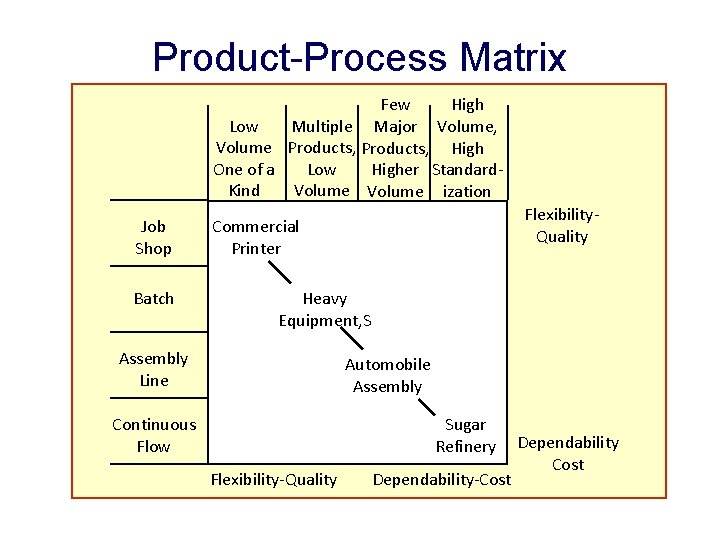
Product-Process Matrix Few High Low Multiple Major Volume, Volume Products, High One of a Low Higher Standard. Kind Volume ization Job Shop Batch Flexibility. Quality Commercial Printer Heavy Equipment, S Assembly Line Automobile Assembly Continuous Flow Sugar Refinery Flexibility-Quality Dependability-Cost Dependability Cost
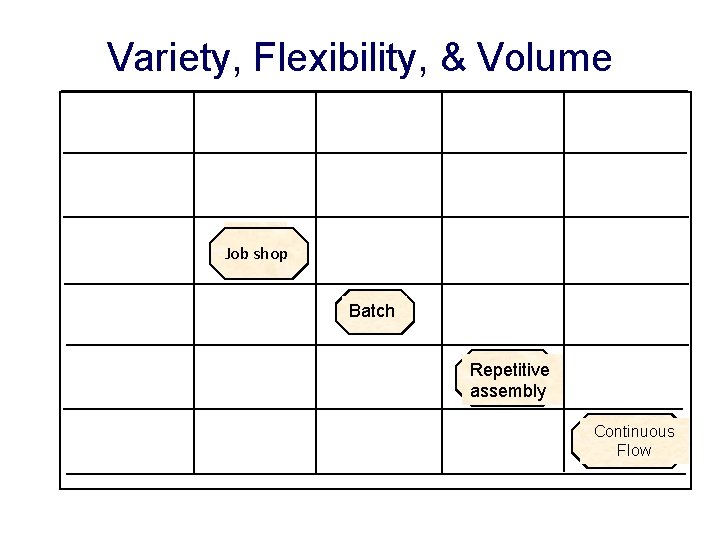
Variety, Flexibility, & Volume Job shop Shop Batch Repetitive assembly Continuous Flow
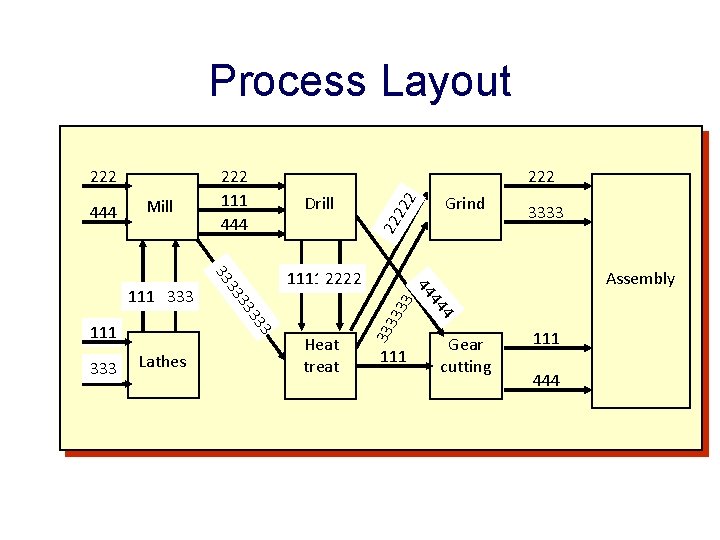
Process Layout Assembly 2 111 4 Heat treat 3333 44 3 Lathes Grind 44 1111 2222 33 33 33 111 333 Drill 22 Mill 222 22 444 222 111 444 33 33 33 222 Gear cutting 111 444
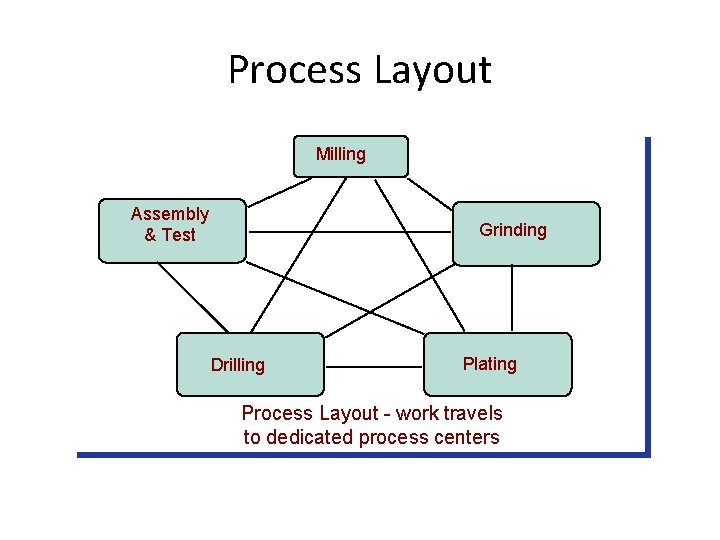
Process Layout Milling Assembly & Test Grinding Drilling Plating Process Layout - work travels to dedicated process centers
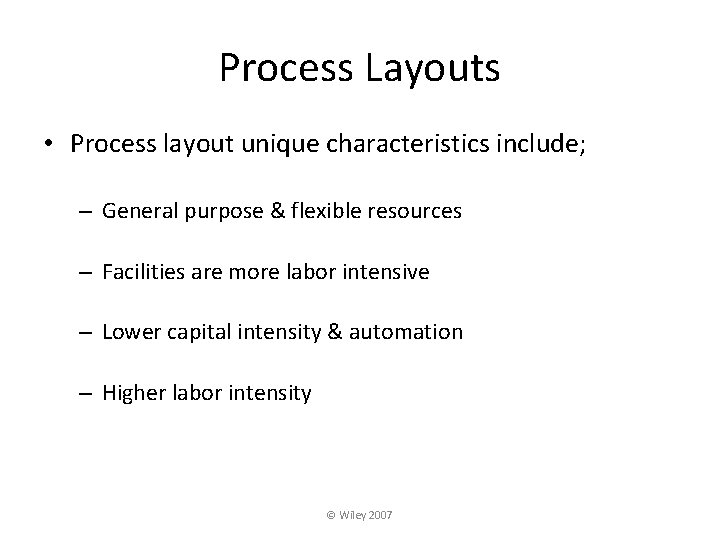
Process Layouts • Process layout unique characteristics include; – General purpose & flexible resources – Facilities are more labor intensive – Lower capital intensity & automation – Higher labor intensity © Wiley 2007
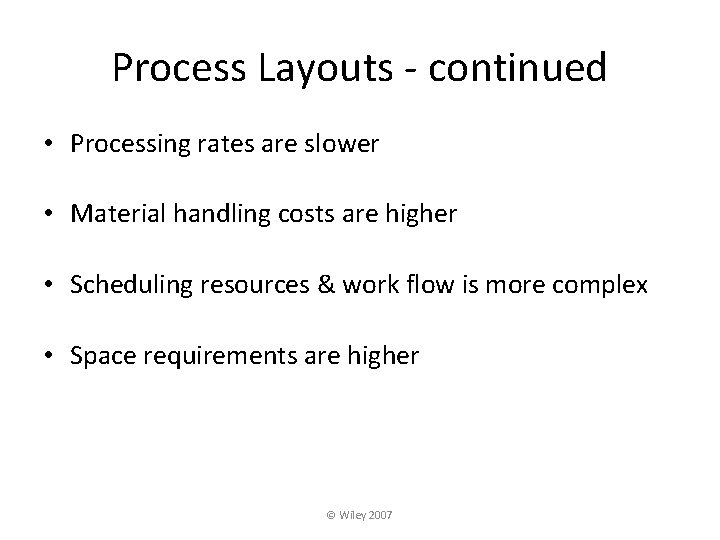
Process Layouts - continued • Processing rates are slower • Material handling costs are higher • Scheduling resources & work flow is more complex • Space requirements are higher © Wiley 2007
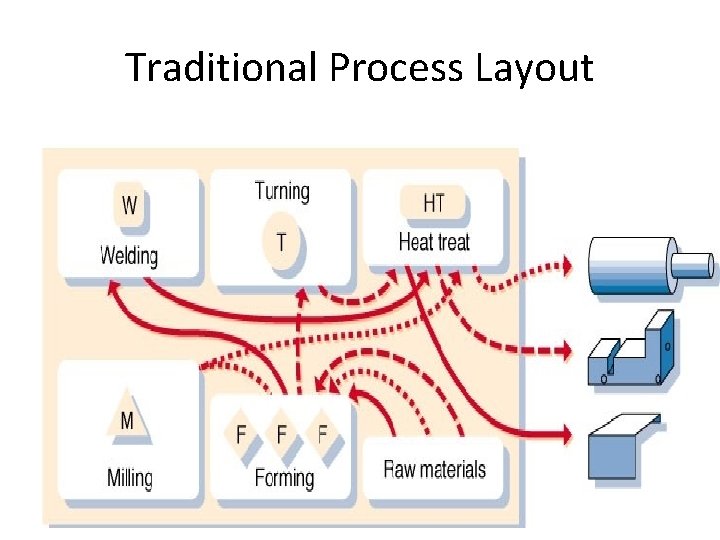
Traditional Process Layout
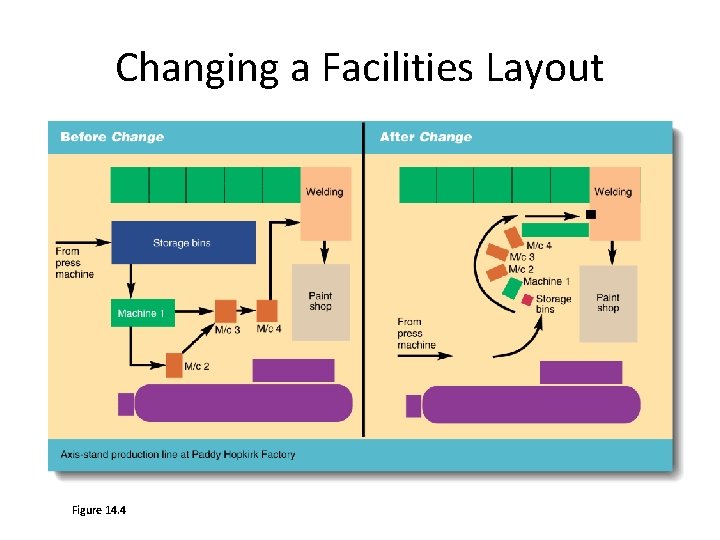
Changing a Facilities Layout Figure 14. 4
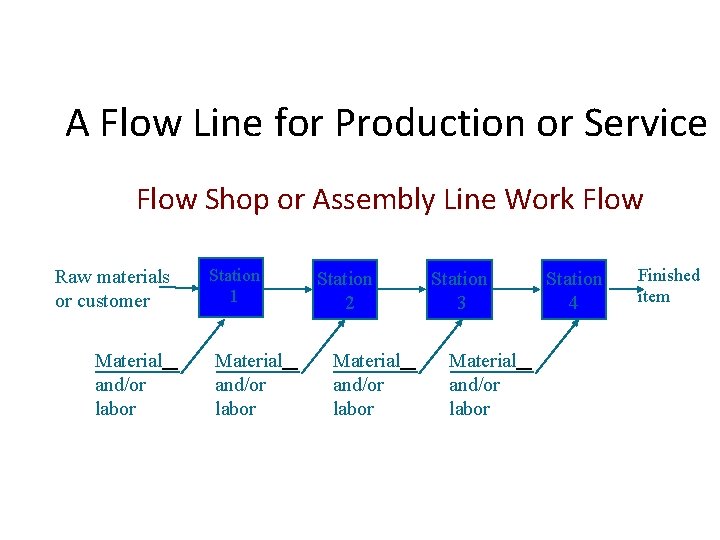
A Flow Line for Production or Service Flow Shop or Assembly Line Work Flow Raw materials or customer Material and/or labor Station 1 Material and/or labor Station 2 Material and/or labor Station 3 Material and/or labor Station 4 Finished item
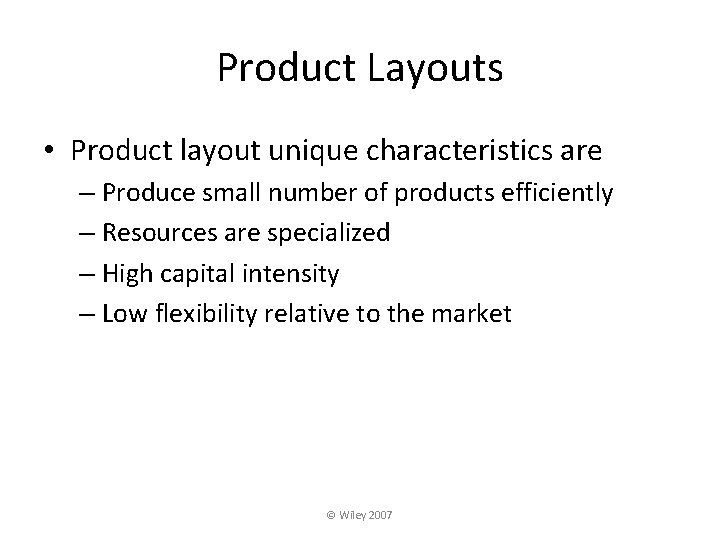
Product Layouts • Product layout unique characteristics are – Produce small number of products efficiently – Resources are specialized – High capital intensity – Low flexibility relative to the market © Wiley 2007
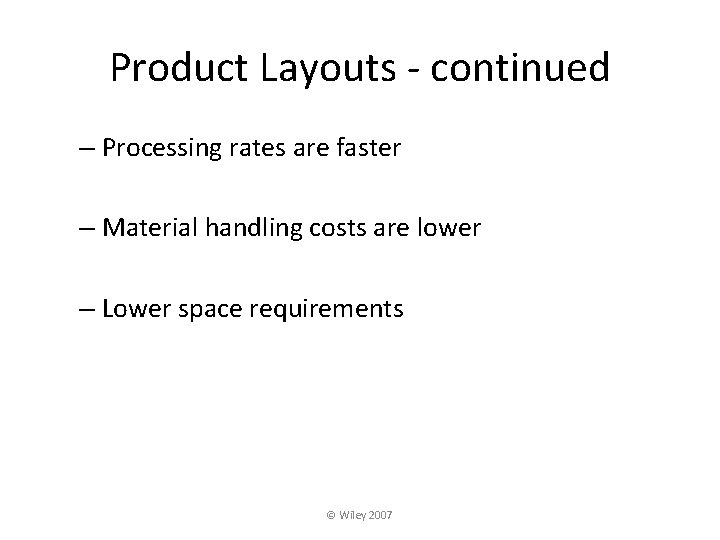
Product Layouts - continued – Processing rates are faster – Material handling costs are lower – Lower space requirements © Wiley 2007
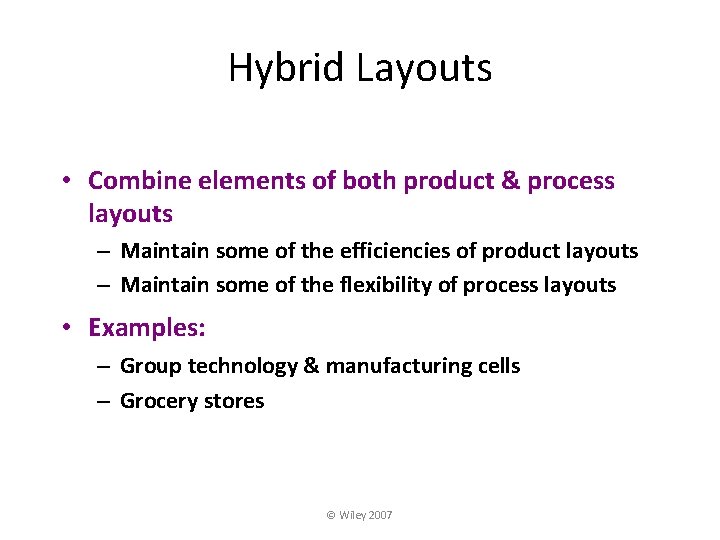
Hybrid Layouts • Combine elements of both product & process layouts – Maintain some of the efficiencies of product layouts – Maintain some of the flexibility of process layouts • Examples: – Group technology & manufacturing cells – Grocery stores © Wiley 2007
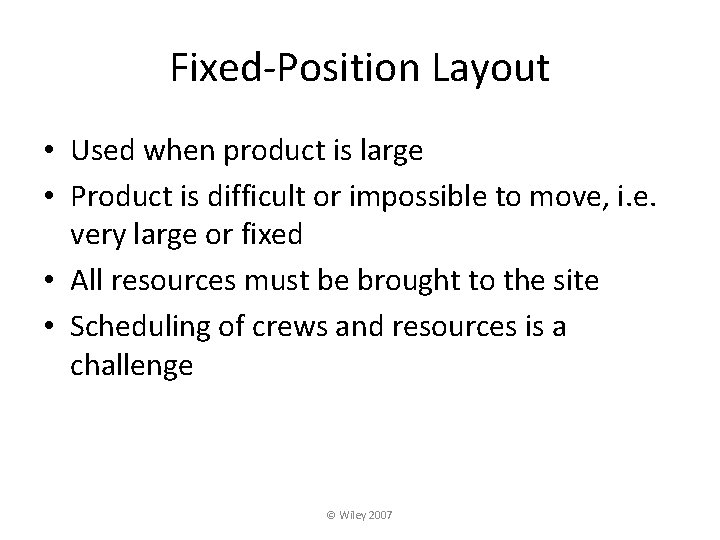
Fixed-Position Layout • Used when product is large • Product is difficult or impossible to move, i. e. very large or fixed • All resources must be brought to the site • Scheduling of crews and resources is a challenge © Wiley 2007
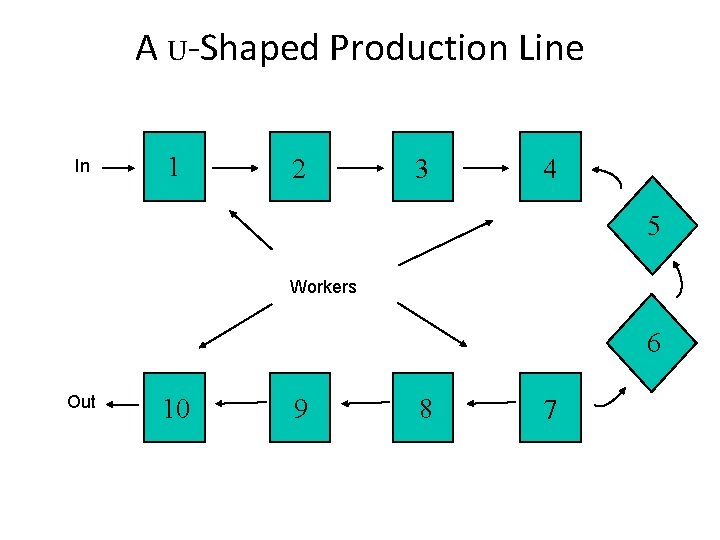
A U-Shaped Production Line In 1 2 3 4 5 Workers 6 Out 10 9 8 7
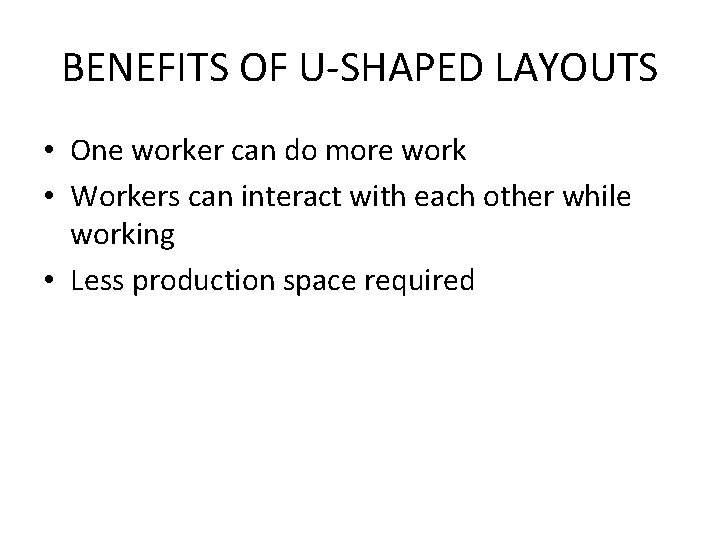
BENEFITS OF U-SHAPED LAYOUTS • One worker can do more work • Workers can interact with each other while working • Less production space required
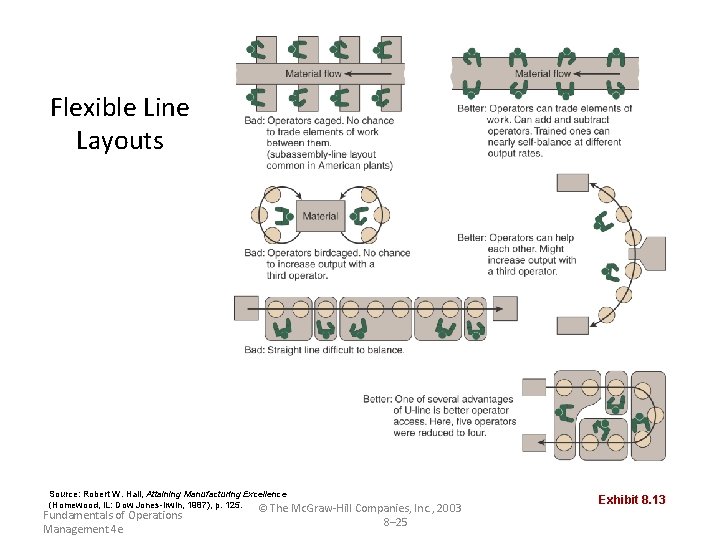
Flexible Line Layouts Source: Robert W. Hall, Attaining Manufacturing Excellence (Homewood, IL: Dow Jones-Irwin, 1987), p. 125. © The Fundamentals of Operations Management 4 e Mc. Graw-Hill Companies, Inc. , 2003 8– 25 Exhibit 8. 13
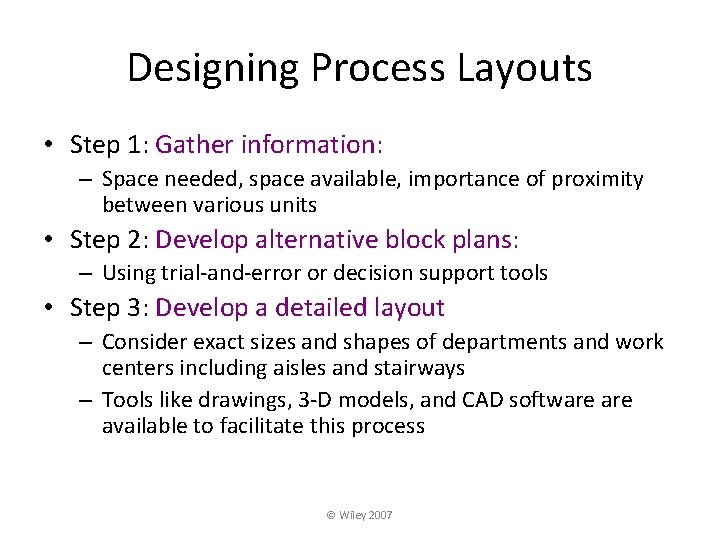
Designing Process Layouts • Step 1: Gather information: – Space needed, space available, importance of proximity between various units • Step 2: Develop alternative block plans: – Using trial-and-error or decision support tools • Step 3: Develop a detailed layout – Consider exact sizes and shapes of departments and work centers including aisles and stairways – Tools like drawings, 3 -D models, and CAD software available to facilitate this process © Wiley 2007
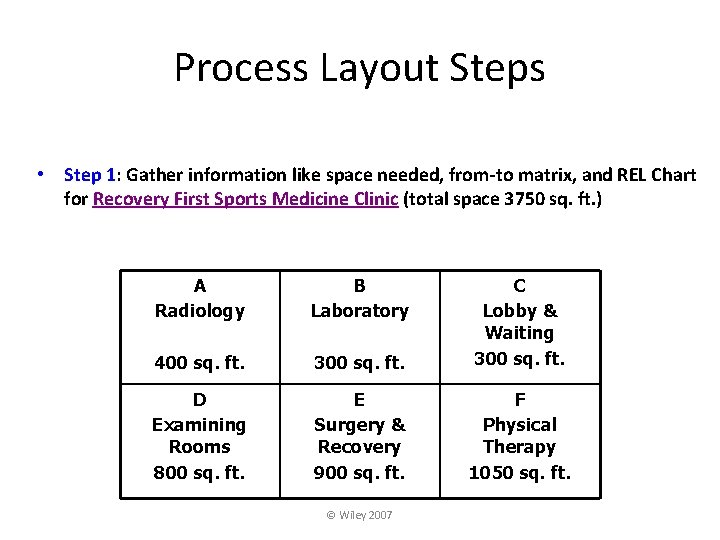
Process Layout Steps • Step 1: Gather information like space needed, from to matrix, and REL Chart for Recovery First Sports Medicine Clinic (total space 3750 sq. ft. ) A Radiology B Laboratory 400 sq. ft. 300 sq. ft. C Lobby & Waiting 300 sq. ft. D Examining Rooms 800 sq. ft. E Surgery & Recovery 900 sq. ft. F Physical Therapy 1050 sq. ft. © Wiley 2007
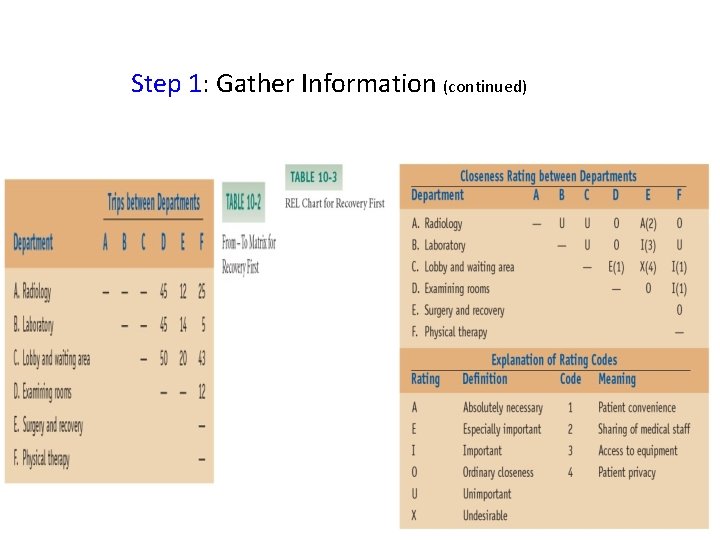
Step 1: Gather Information (continued) © Wiley 2007
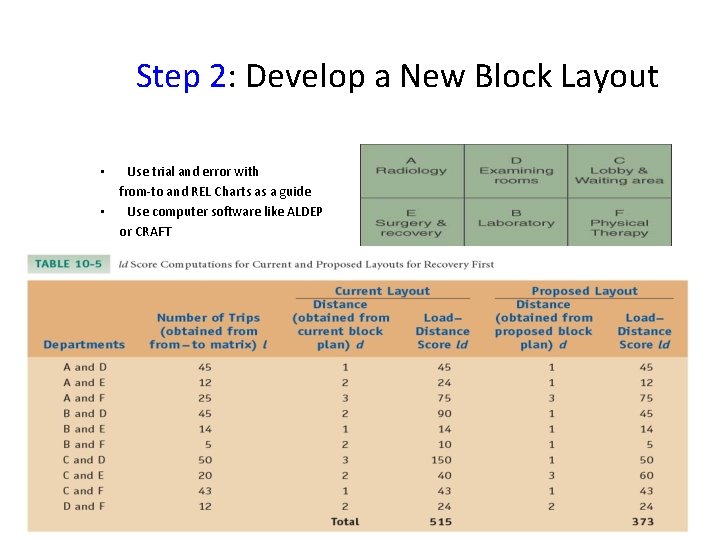
Step 2: Develop a New Block Layout Use trial and error with from-to and REL Charts as a guide • Use computer software like ALDEP or CRAFT • © Wiley 2007
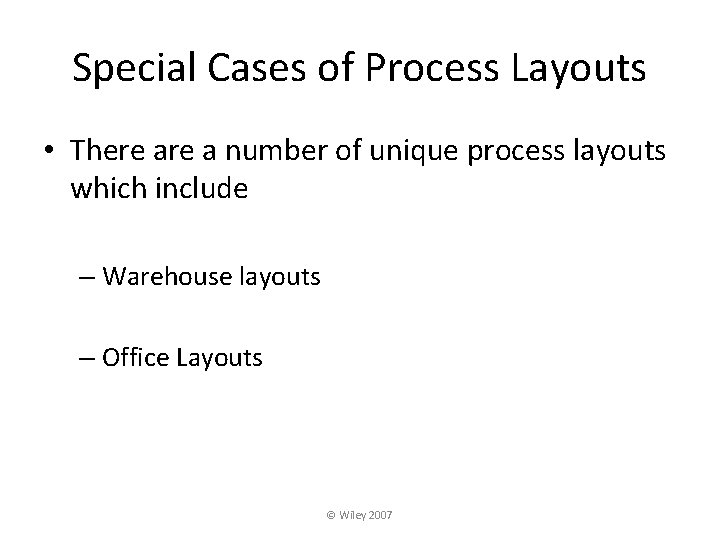
Special Cases of Process Layouts • There a number of unique process layouts which include – Warehouse layouts – Office Layouts © Wiley 2007
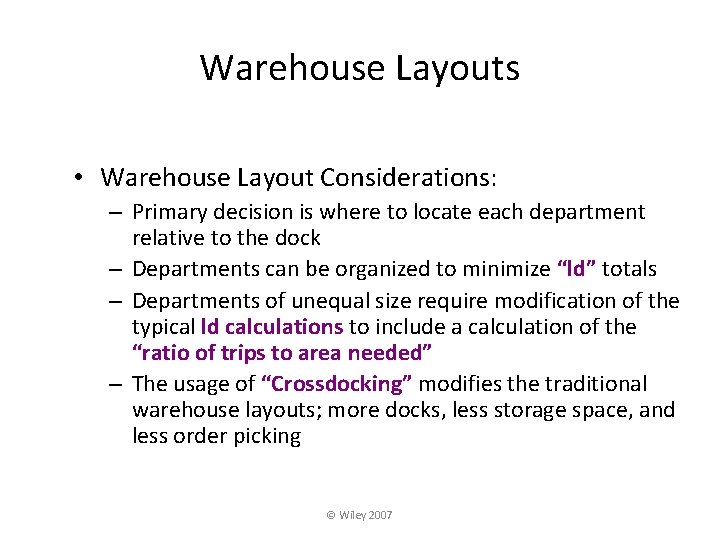
Warehouse Layouts • Warehouse Layout Considerations: – Primary decision is where to locate each department relative to the dock – Departments can be organized to minimize “ld” totals – Departments of unequal size require modification of the typical ld calculations to include a calculation of the “ratio of trips to area needed” – The usage of “Crossdocking” modifies the traditional warehouse layouts; more docks, less storage space, and less order picking © Wiley 2007
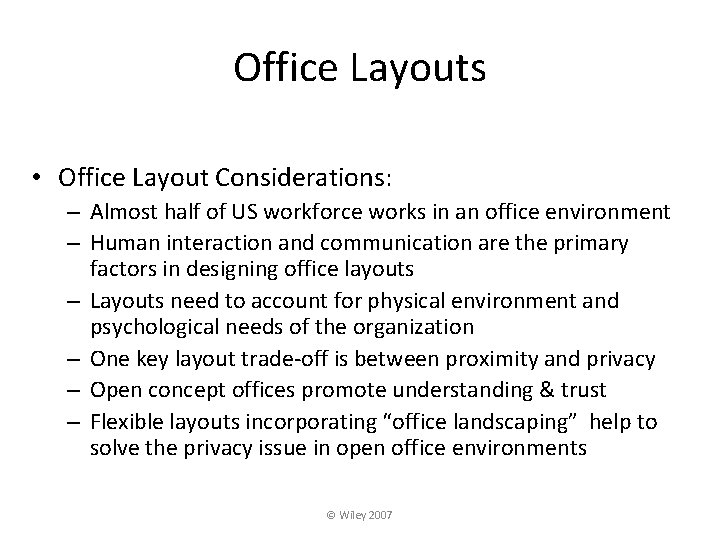
Office Layouts • Office Layout Considerations: – Almost half of US workforce works in an office environment – Human interaction and communication are the primary factors in designing office layouts – Layouts need to account for physical environment and psychological needs of the organization – One key layout trade-off is between proximity and privacy – Open concept offices promote understanding & trust – Flexible layouts incorporating “office landscaping” help to solve the privacy issue in open office environments © Wiley 2007
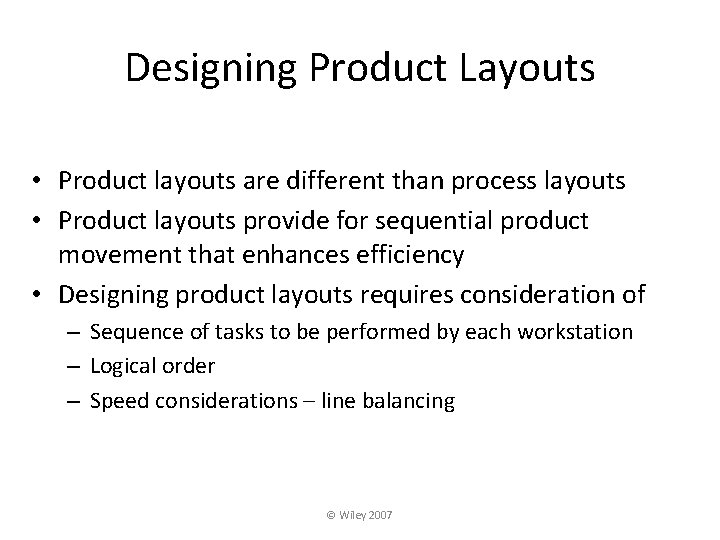
Designing Product Layouts • Product layouts are different than process layouts • Product layouts provide for sequential product movement that enhances efficiency • Designing product layouts requires consideration of – Sequence of tasks to be performed by each workstation – Logical order – Speed considerations – line balancing © Wiley 2007
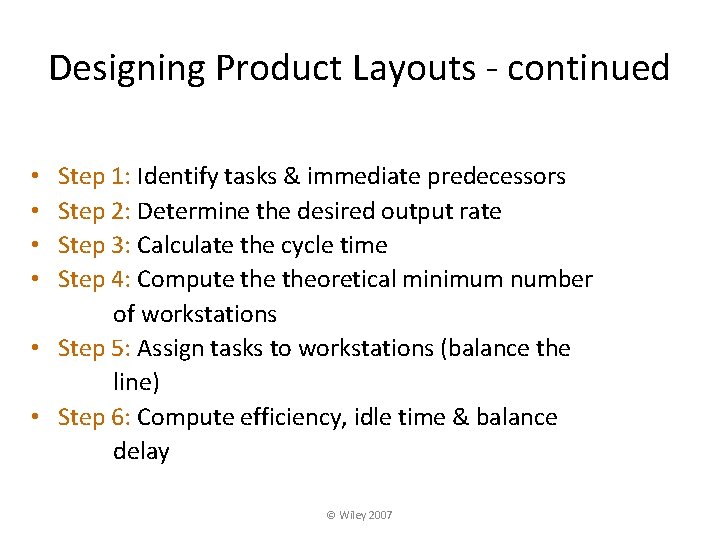
Designing Product Layouts - continued Step 1: Identify tasks & immediate predecessors Step 2: Determine the desired output rate Step 3: Calculate the cycle time Step 4: Compute theoretical minimum number of workstations • Step 5: Assign tasks to workstations (balance the line) • Step 6: Compute efficiency, idle time & balance delay • • © Wiley 2007
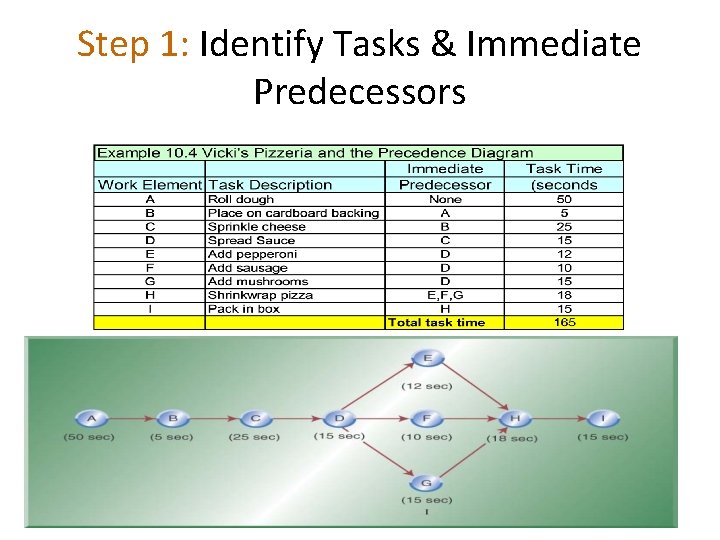
Step 1: Identify Tasks & Immediate Predecessors © Wiley 2007
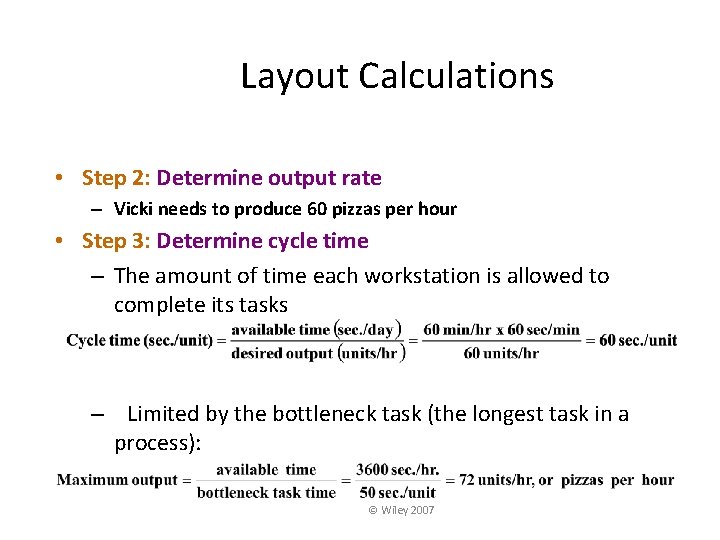
Layout Calculations • Step 2: Determine output rate – Vicki needs to produce 60 pizzas per hour • Step 3: Determine cycle time – The amount of time each workstation is allowed to complete its tasks – Limited by the bottleneck task (the longest task in a process): © Wiley 2007
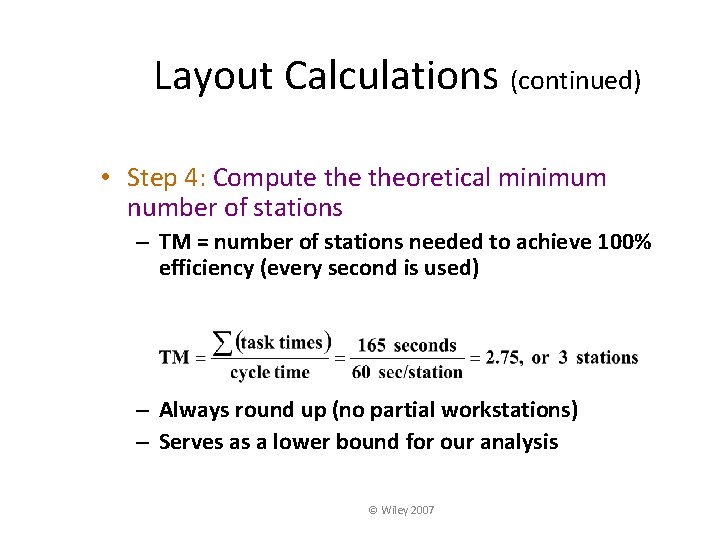
Layout Calculations (continued) • Step 4: Compute theoretical minimum number of stations – TM = number of stations needed to achieve 100% efficiency (every second is used) – Always round up (no partial workstations) – Serves as a lower bound for our analysis © Wiley 2007
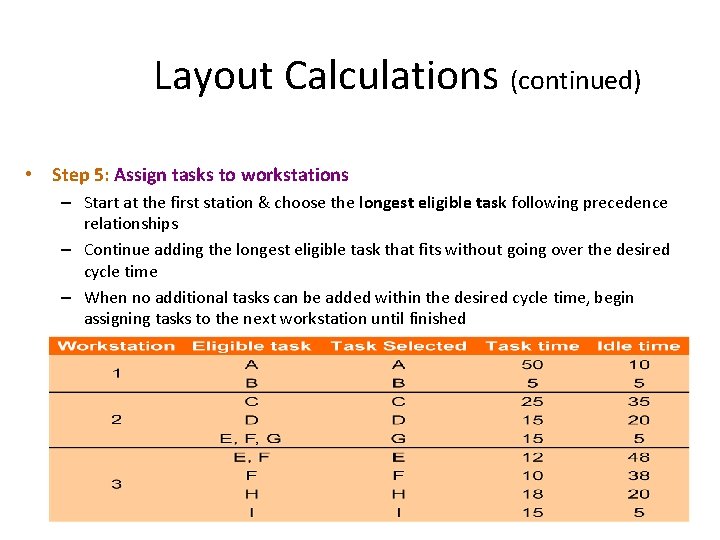
Layout Calculations (continued) • Step 5: Assign tasks to workstations – Start at the first station & choose the longest eligible task following precedence relationships – Continue adding the longest eligible task that fits without going over the desired cycle time – When no additional tasks can be added within the desired cycle time, begin assigning tasks to the next workstation until finished © Wiley 2007
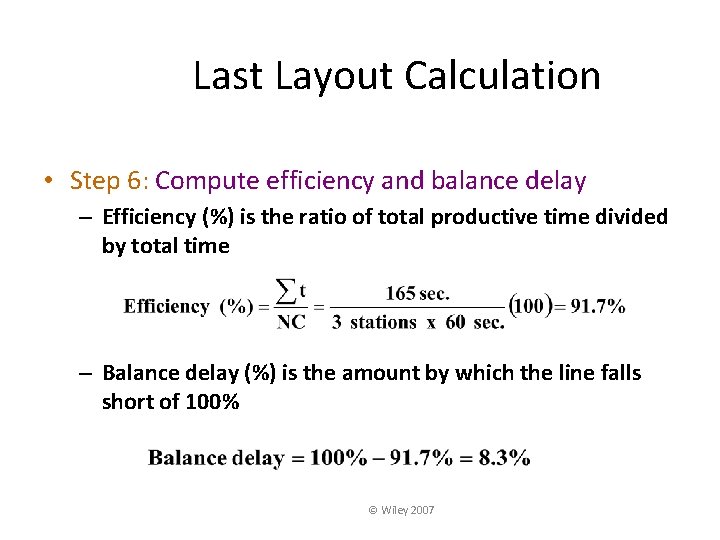
Last Layout Calculation • Step 6: Compute efficiency and balance delay – Efficiency (%) is the ratio of total productive time divided by total time – Balance delay (%) is the amount by which the line falls short of 100% © Wiley 2007
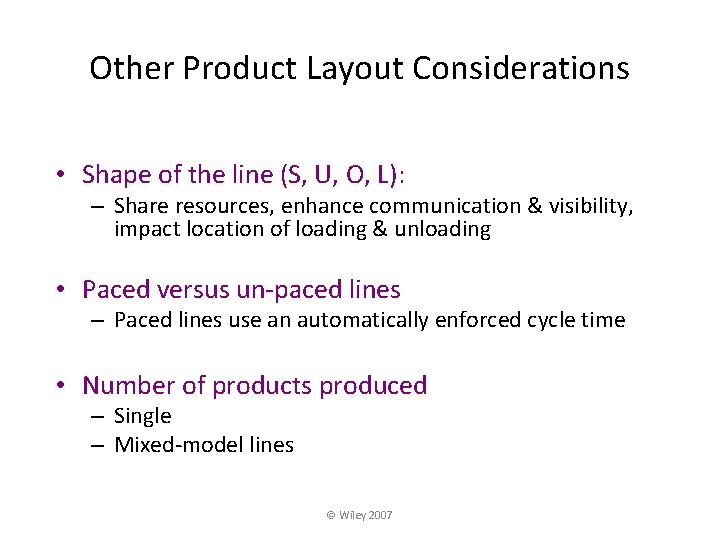
Other Product Layout Considerations • Shape of the line (S, U, O, L): – Share resources, enhance communication & visibility, impact location of loading & unloading • Paced versus un-paced lines – Paced lines use an automatically enforced cycle time • Number of products produced – Single – Mixed-model lines © Wiley 2007
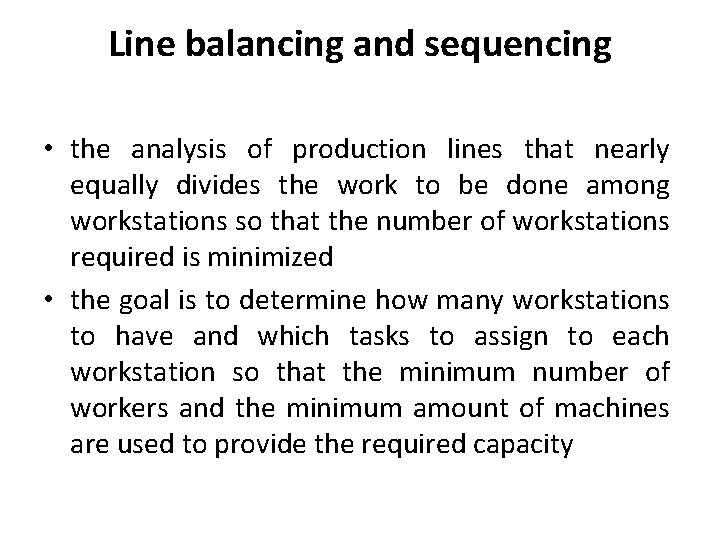
Line balancing and sequencing • the analysis of production lines that nearly equally divides the work to be done among workstations so that the number of workstations required is minimized • the goal is to determine how many workstations to have and which tasks to assign to each workstation so that the minimum number of workers and the minimum amount of machines are used to provide the required capacity
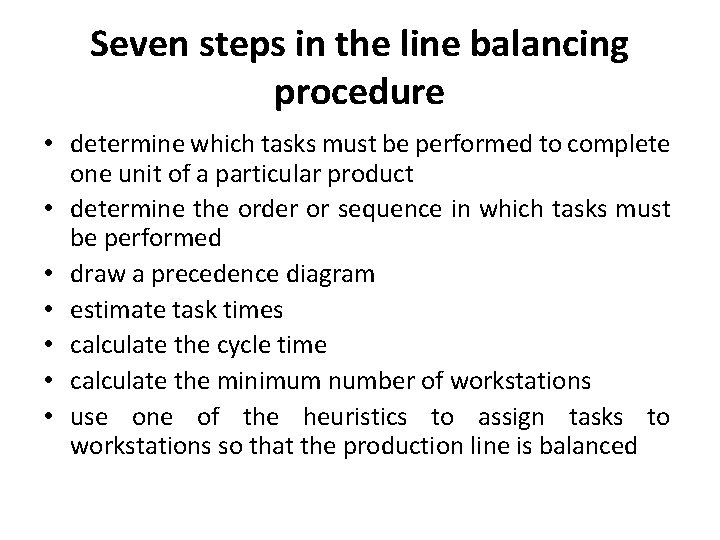
Seven steps in the line balancing procedure • determine which tasks must be performed to complete one unit of a particular product • determine the order or sequence in which tasks must be performed • draw a precedence diagram • estimate task times • calculate the cycle time • calculate the minimum number of workstations • use one of the heuristics to assign tasks to workstations so that the production line is balanced
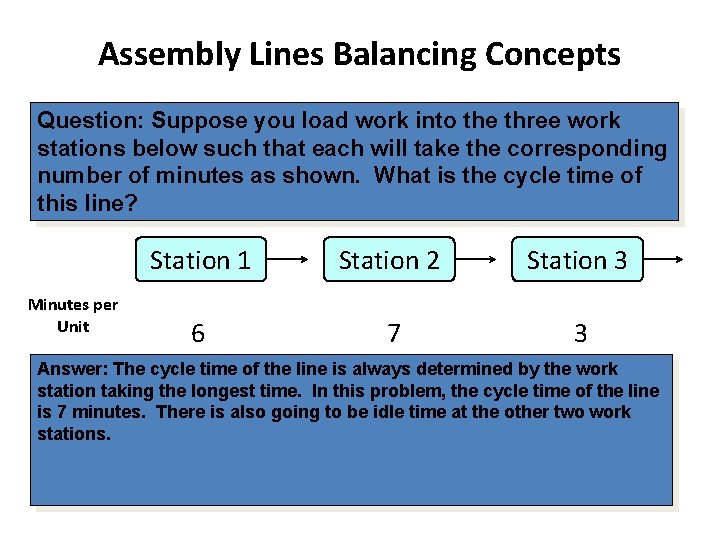
Assembly Lines Balancing Concepts Question: Suppose you load work into the three work stations below such that each will take the corresponding number of minutes as shown. What is the cycle time of this line? Minutes per Unit Station 1 Station 2 Station 3 6 7 3 Answer: The cycle time of the line is always determined by the work station taking the longest time. In this problem, the cycle time of the line is 7 minutes. There is also going to be idle time at the other two work stations.
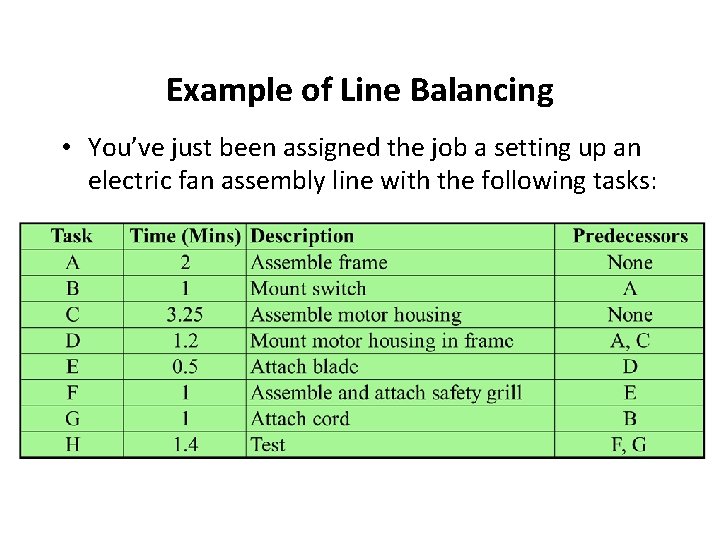
Example of Line Balancing • You’ve just been assigned the job a setting up an electric fan assembly line with the following tasks:
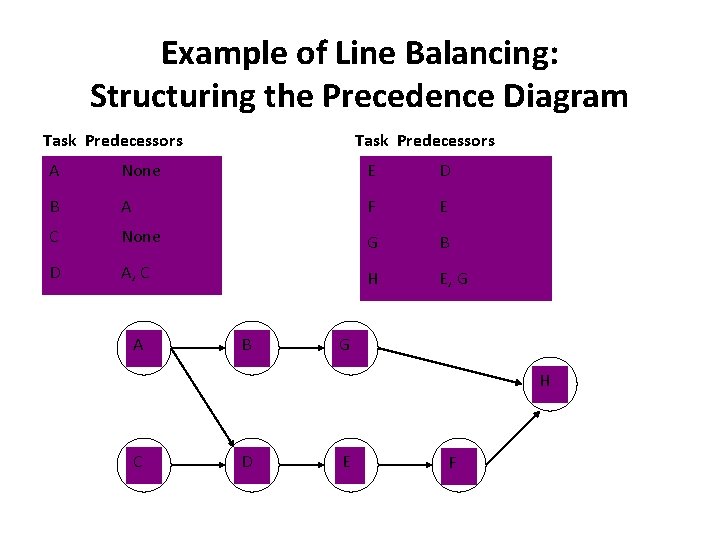
Example of Line Balancing: Structuring the Precedence Diagram Task Predecessors A None E D B A F E C None G B D A, C H E, G A B G H C D E F
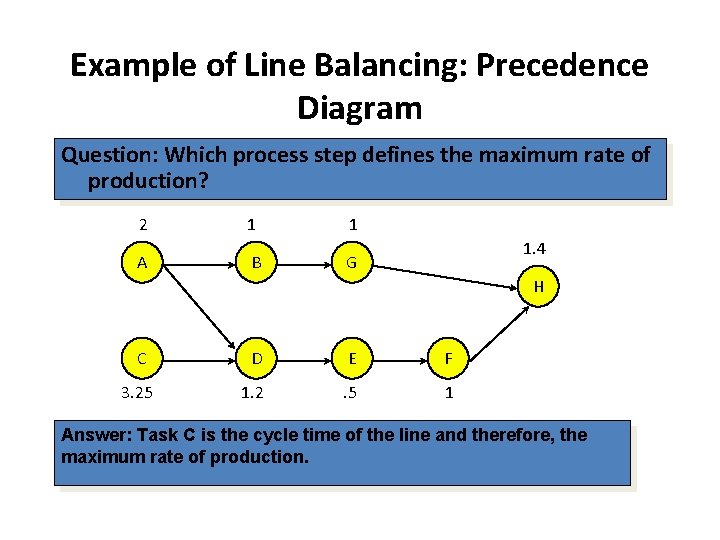
Example of Line Balancing: Precedence Diagram Question: Which process step defines the maximum rate of production? 2 A 1 B 1 1. 4 G H C D E F 3. 25 1. 2 . 5 1 Answer: Task C is the cycle time of the line and therefore, the maximum rate of production.
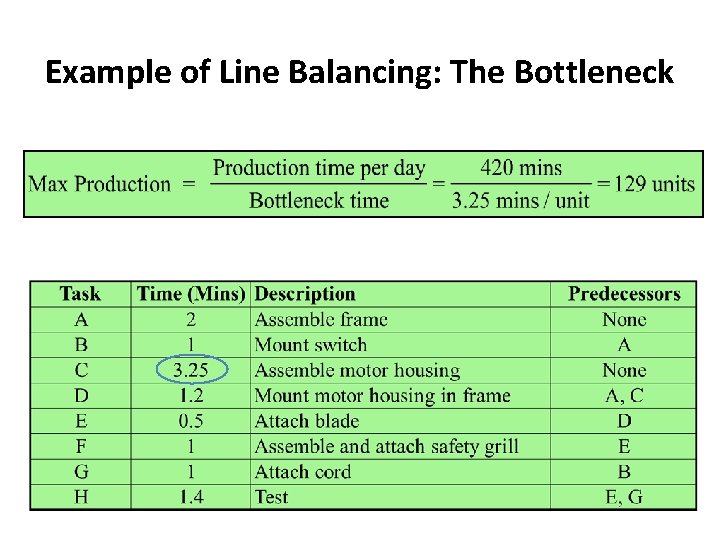
Example of Line Balancing: The Bottleneck
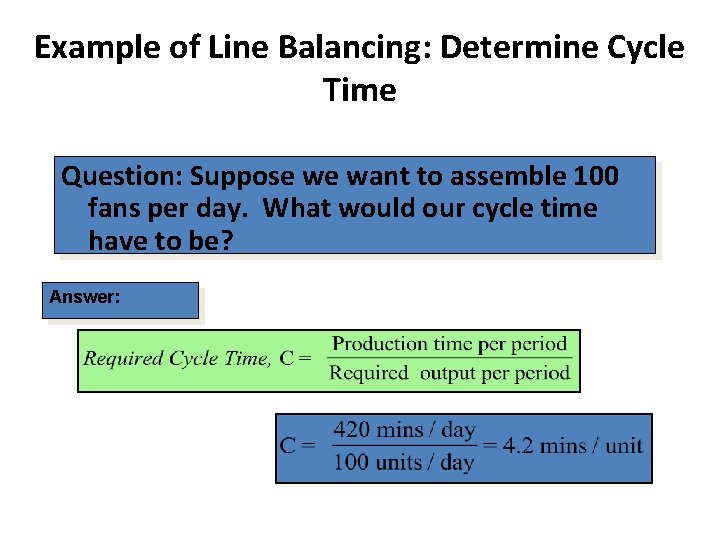
Example of Line Balancing: Determine Cycle Time Question: Suppose we want to assemble 100 fans per day. What would our cycle time have to be? Answer:
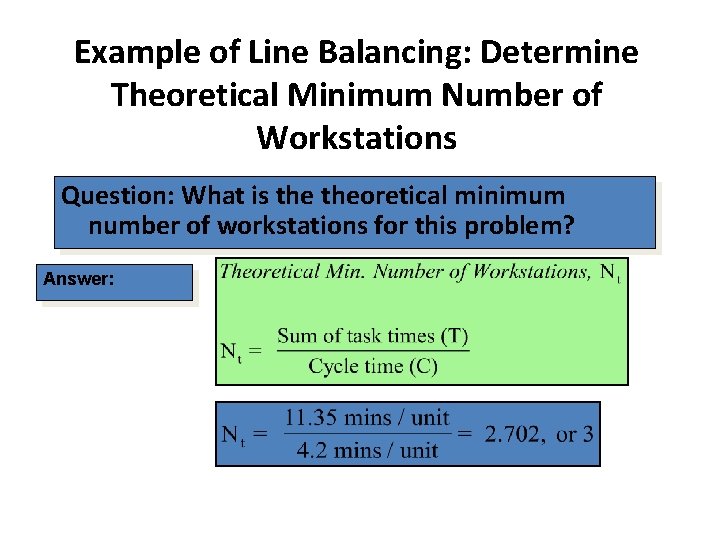
Example of Line Balancing: Determine Theoretical Minimum Number of Workstations Question: What is theoretical minimum number of workstations for this problem? Answer:
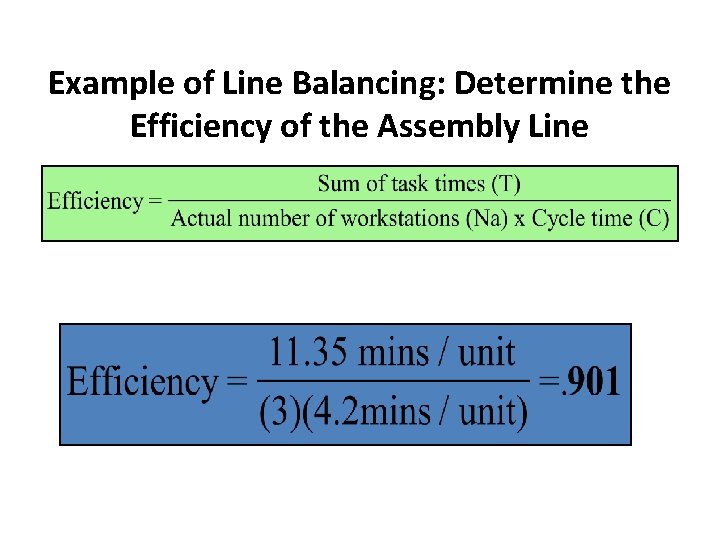
Example of Line Balancing: Determine the Efficiency of the Assembly Line
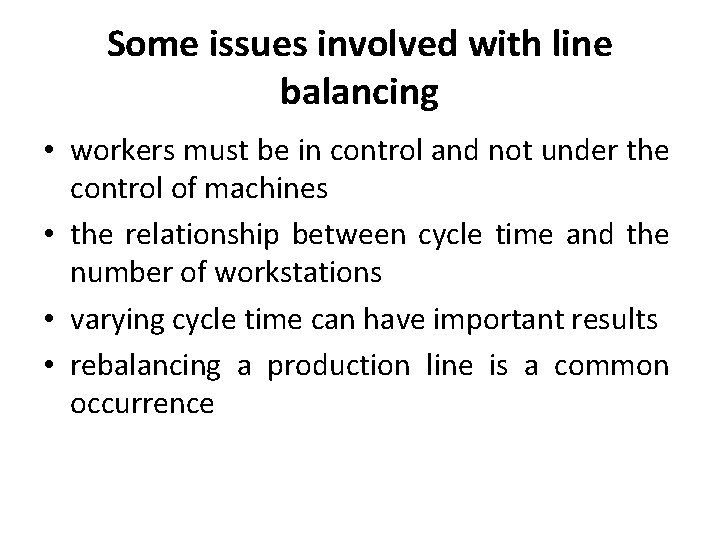
Some issues involved with line balancing • workers must be in control and not under the control of machines • the relationship between cycle time and the number of workstations • varying cycle time can have important results • rebalancing a production line is a common occurrence
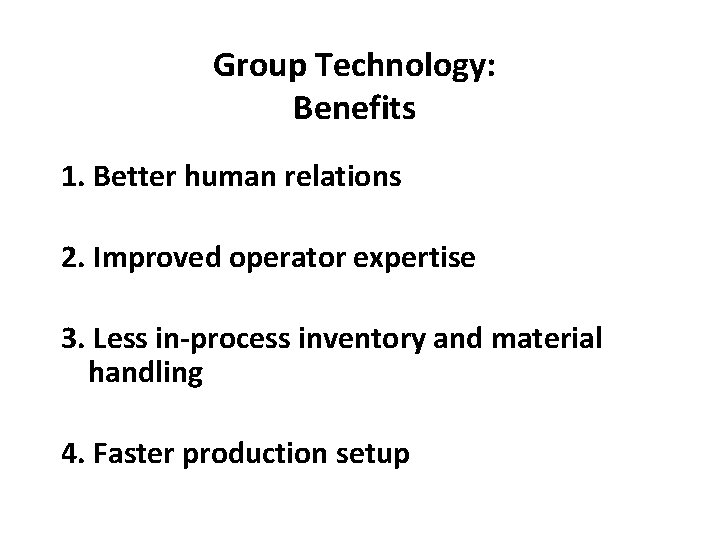
Group Technology: Benefits 1. Better human relations 2. Improved operator expertise 3. Less in process inventory and material handling 4. Faster production setup
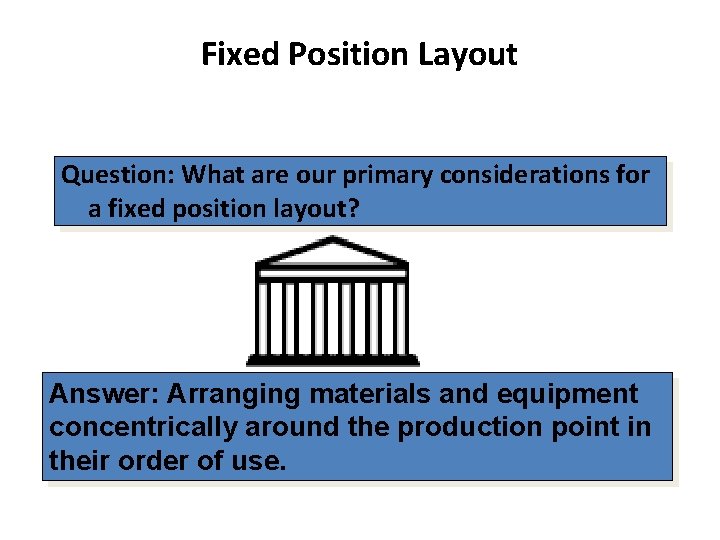
Fixed Position Layout Question: What are our primary considerations for a fixed position layout? Answer: Arranging materials and equipment concentrically around the production point in their order of use.
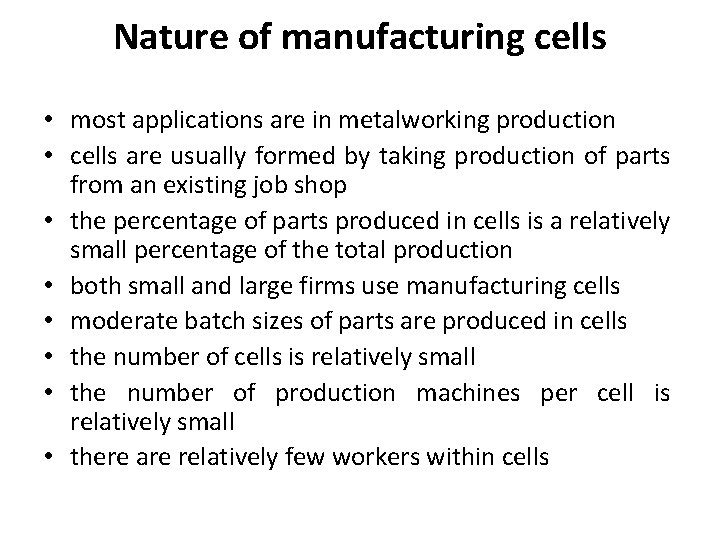
Nature of manufacturing cells • most applications are in metalworking production • cells are usually formed by taking production of parts from an existing job shop • the percentage of parts produced in cells is a relatively small percentage of the total production • both small and large firms use manufacturing cells • moderate batch sizes of parts are produced in cells • the number of cells is relatively small • the number of production machines per cell is relatively small • there are relatively few workers within cells
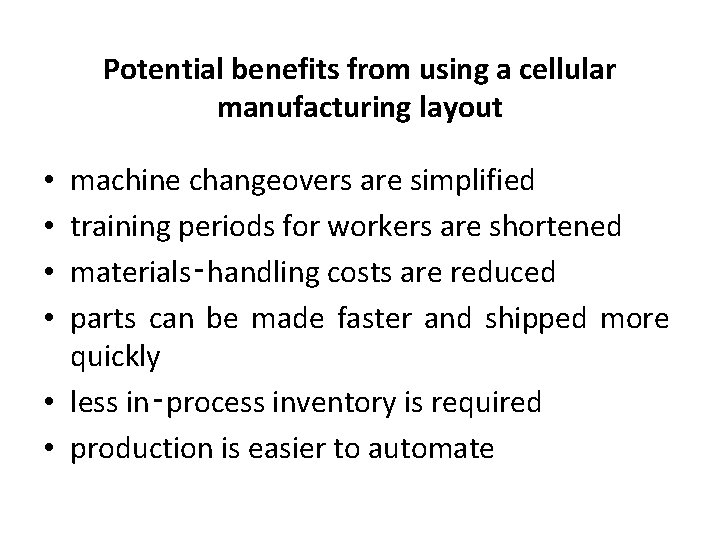
Potential benefits from using a cellular manufacturing layout machine changeovers are simplified training periods for workers are shortened materials‑handling costs are reduced parts can be made faster and shipped more quickly • less in‑process inventory is required • production is easier to automate • •
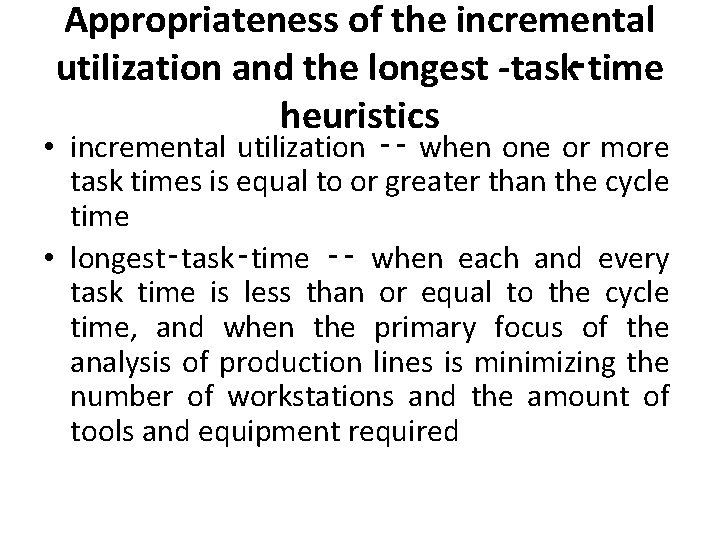
Appropriateness of the incremental utilization and the longest task‑time heuristics • incremental utilization ‑‑ when one or more task times is equal to or greater than the cycle time • longest‑task‑time ‑‑ when each and every task time is less than or equal to the cycle time, and when the primary focus of the analysis of production lines is minimizing the number of workstations and the amount of tools and equipment required
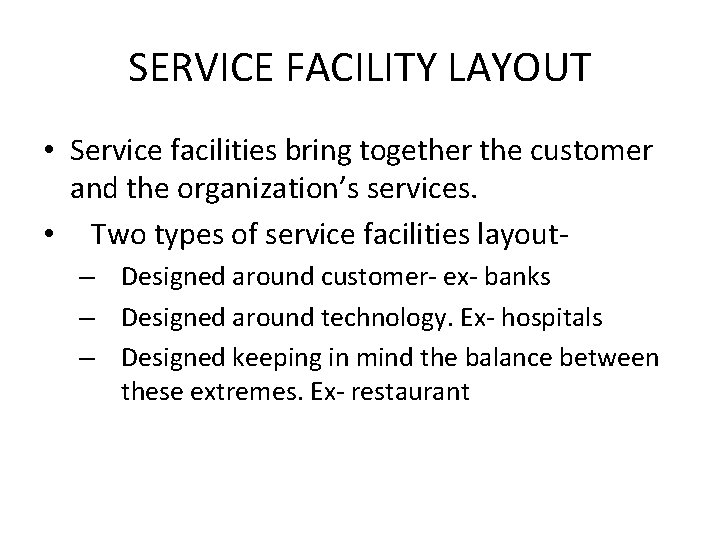
SERVICE FACILITY LAYOUT • Service facilities bring together the customer and the organization’s services. • Two types of service facilities layout– Designed around customer- ex- banks – Designed around technology. Ex- hospitals – Designed keeping in mind the balance between these extremes. Ex- restaurant
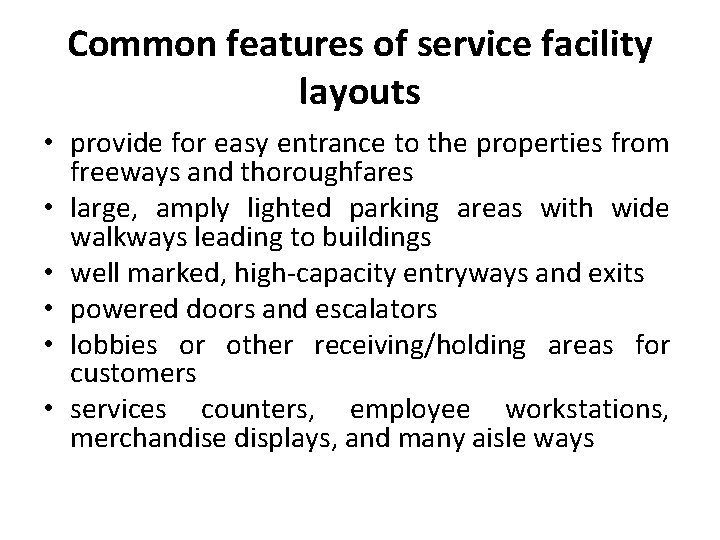
Common features of service facility layouts • provide for easy entrance to the properties from freeways and thoroughfares • large, amply lighted parking areas with wide walkways leading to buildings • well marked, high-capacity entryways and exits • powered doors and escalators • lobbies or other receiving/holding areas for customers • services counters, employee workstations, merchandise displays, and many aisle ways
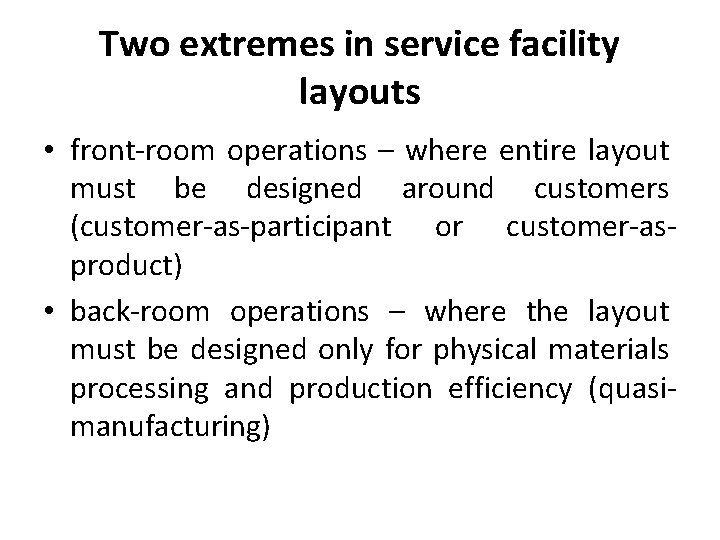
Two extremes in service facility layouts • front-room operations – where entire layout must be designed around customers (customer-as-participant or customer-asproduct) • back-room operations – where the layout must be designed only for physical materials processing and production efficiency (quasimanufacturing)
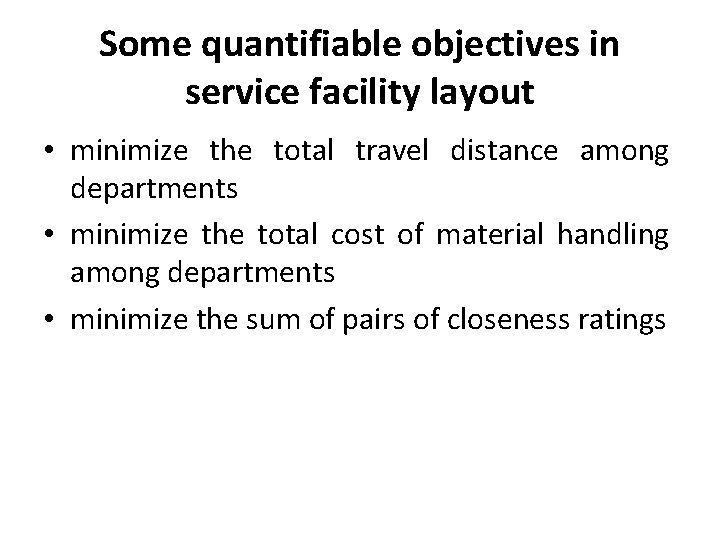
Some quantifiable objectives in service facility layout • minimize the total travel distance among departments • minimize the total cost of material handling among departments • minimize the sum of pairs of closeness ratings
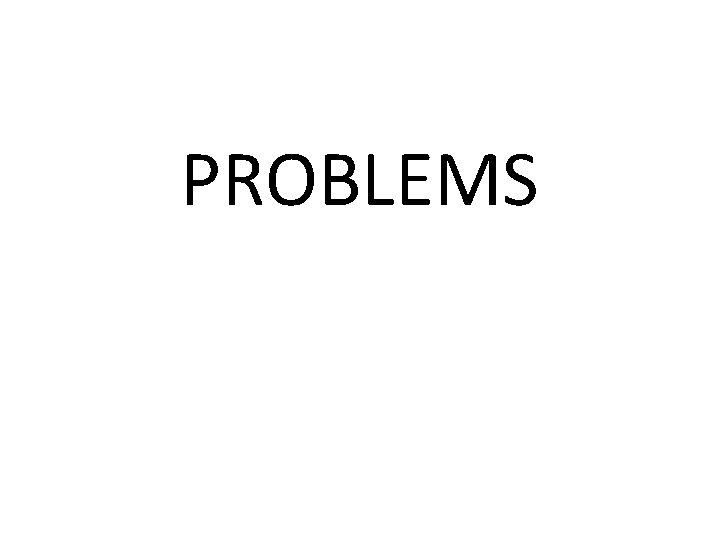
PROBLEMS
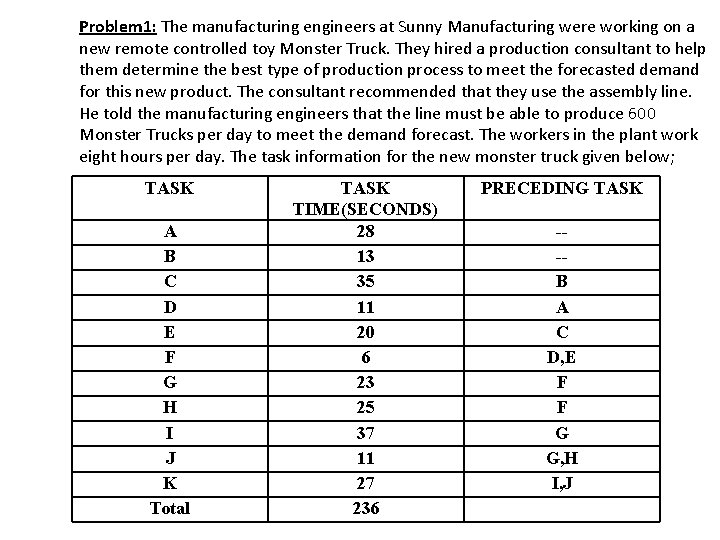
Problem 1: The manufacturing engineers at Sunny Manufacturing were working on a new remote controlled toy Monster Truck. They hired a production consultant to help them determine the best type of production process to meet the forecasted demand for this new product. The consultant recommended that they use the assembly line. He told the manufacturing engineers that the line must be able to produce 600 Monster Trucks per day to meet the demand forecast. The workers in the plant work eight hours per day. The task information for the new monster truck given below; TASK A B C D E F G H I J K Total TASK TIME(SECONDS) 28 13 35 11 20 6 23 25 37 11 27 236 PRECEDING TASK --B A C D, E F F G G, H I, J

Questions A)What is the required cycle time to meet the forecasted demand of 600 trucks per day based on an eight hour work day? B)What is theoretical minimum number of workstations given the answer in part b? C)Use longest task time with alphabetical order as the tie breaker and balance the line in the minimum number of workstations to produce 600 trucks per day. D)Use shortest task time with largest number of following task as the tie breaker and balance the line in the minimum number of stations to produce 600 trucks per day. Solution: (A) The required cycle time will be equal to = Production time per day / Output per day = 60 * 480 / 600 = 48 seconds (B) The minimum number of theoretical workstations are = Total time / Cycle time = 236 / 48 = 4. 92 = 5 (rounded up)
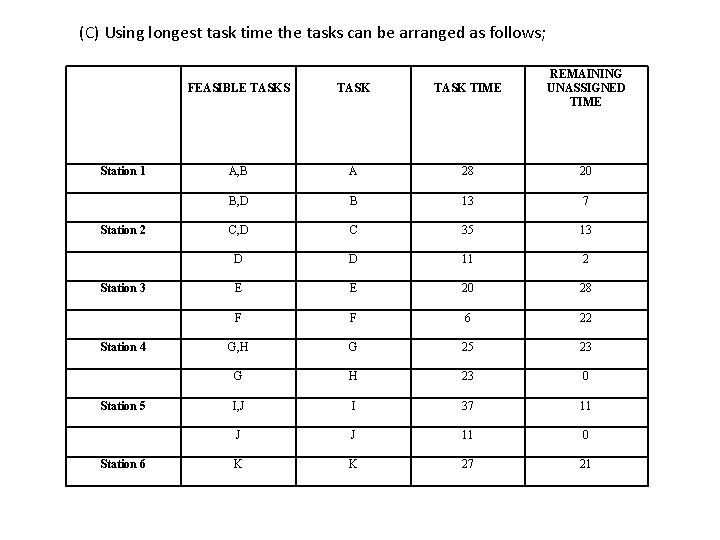
(C) Using longest task time the tasks can be arranged as follows; Station 1 Station 2 Station 3 Station 4 Station 5 Station 6 FEASIBLE TASKS TASK TIME REMAINING UNASSIGNED TIME A, B A 28 20 B, D B 13 7 C, D C 35 13 D D 11 2 E E 20 28 F F 6 22 G, H G 25 23 G H 23 0 I, J I 37 11 J J 11 0 K K 27 21
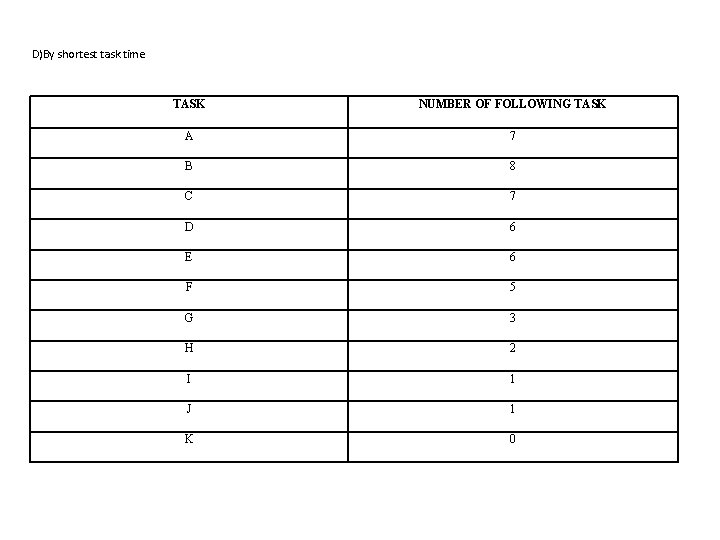
D)By shortest task time TASK NUMBER OF FOLLOWING TASK A 7 B 8 C 7 D 6 E 6 F 5 G 3 H 2 I 1 J 1 K 0
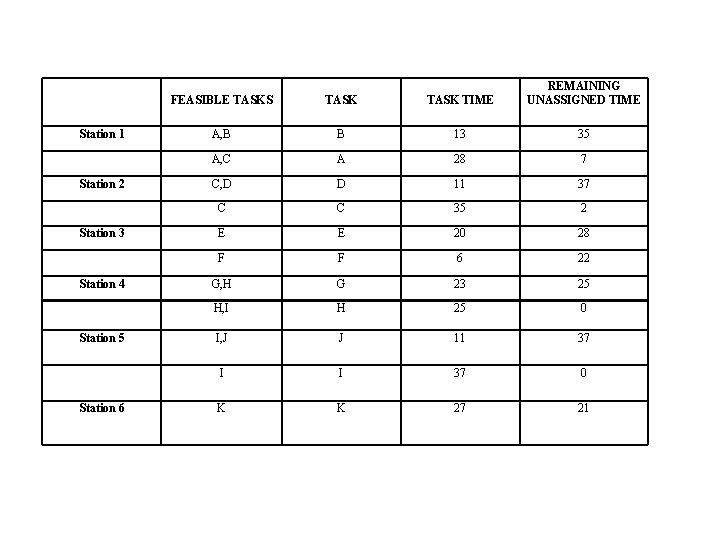
Station 1 Station 2 Station 3 Station 4 Station 5 Station 6 FEASIBLE TASKS TASK TIME REMAINING UNASSIGNED TIME A, B B 13 35 A, C A 28 7 C, D D 11 37 C C 35 2 E E 20 28 F F 6 22 G, H G 23 25 H, I H 25 0 I, J J 11 37 I I 37 0 K K 27 21
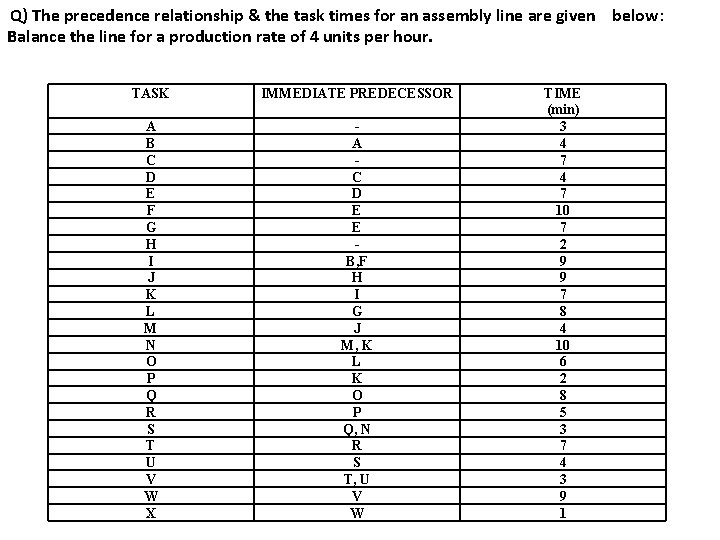
Q) The precedence relationship & the task times for an assembly line are given below: Balance the line for a production rate of 4 units per hour. TASK IMMEDIATE PREDECESSOR A B C D E F G H I J K L M N O P Q R S T U V W X A C D E E B, F H I G J M, K L K O P Q, N R S T, U V W TIME (min) 3 4 7 10 7 2 9 9 7 8 4 10 6 2 8 5 3 7 4 3 9 1
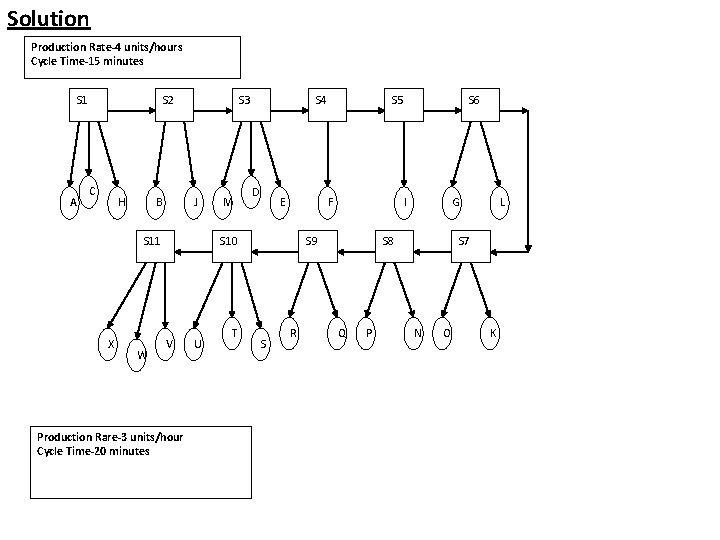
Solution Production Rate 4 units/hours Cycle Time 15 minutes S 1 A S 2 C B H S 3 J S 11 X W M S 4 D E F S 10 V Production Rare 3 units/hour Cycle Time 20 minutes U T S 5 I S 9 S R S 6 G S 8 Q P L S 7 N O K
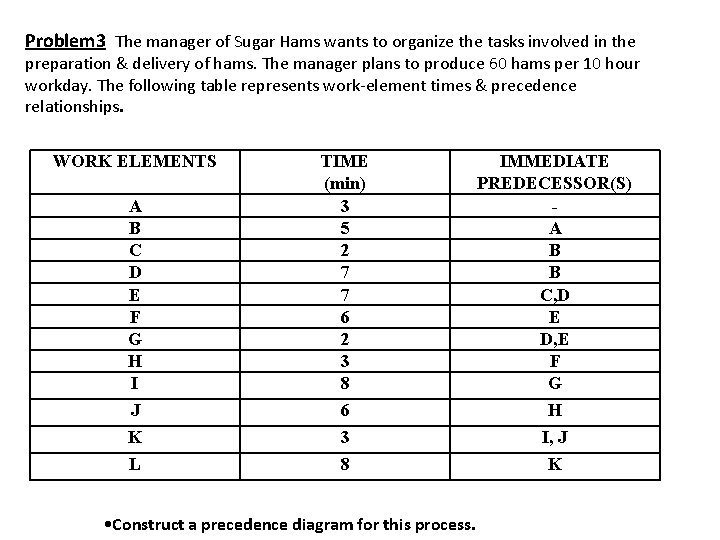
Problem 3 The manager of Sugar Hams wants to organize the tasks involved in the preparation & delivery of hams. The manager plans to produce 60 hams per 10 hour workday. The following table represents work-element times & precedence relationships. WORK ELEMENTS A B C D E F G H I J K L TIME (min) 3 5 2 7 7 6 2 3 8 6 3 8 • Construct a precedence diagram for this process. IMMEDIATE PREDECESSOR(S) A B B C, D E D, E F G H I, J K
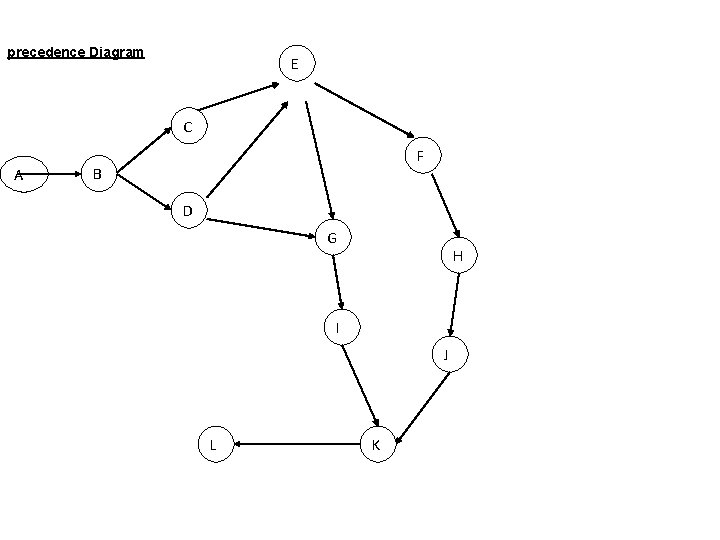
precedence Diagram E C A F B D G H I J L K
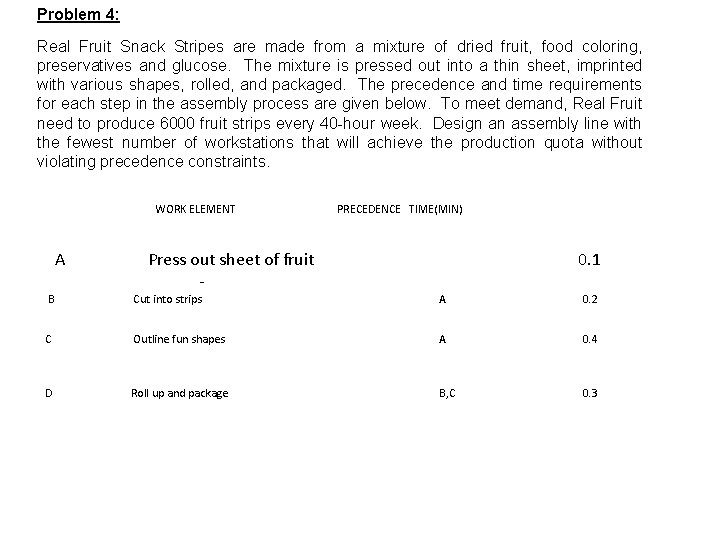
Problem 4: Real Fruit Snack Stripes are made from a mixture of dried fruit, food coloring, preservatives and glucose. The mixture is pressed out into a thin sheet, imprinted with various shapes, rolled, and packaged. The precedence and time requirements for each step in the assembly process are given below. To meet demand, Real Fruit need to produce 6000 fruit strips every 40 -hour week. Design an assembly line with the fewest number of workstations that will achieve the production quota without violating precedence constraints. WORK ELEMENT A PRECEDENCE TIME(MIN) Press out sheet of fruit - 0. 1 B Cut into strips A 0. 2 C Outline fun shapes A 0. 4 D Roll up and package B, C 0. 3
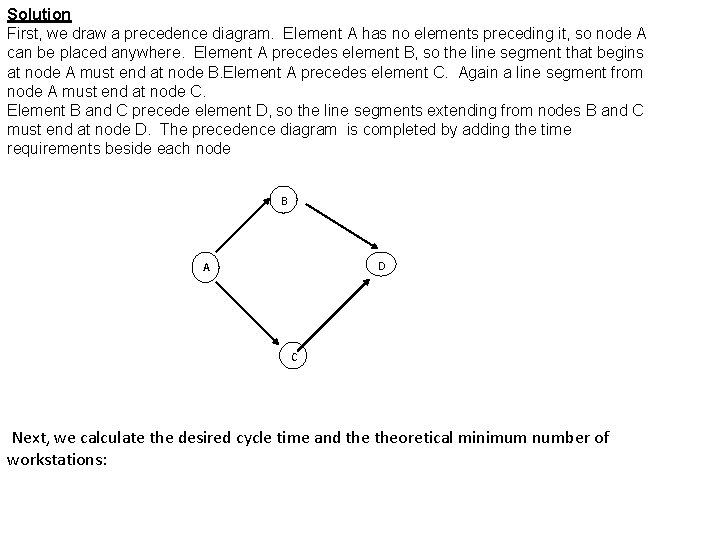
Solution First, we draw a precedence diagram. Element A has no elements preceding it, so node A can be placed anywhere. Element A precedes element B, so the line segment that begins at node A must end at node B. Element A precedes element C. Again a line segment from node A must end at node C. Element B and C precede element D, so the line segments extending from nodes B and C must end at node D. The precedence diagram is completed by adding the time requirements beside each node B D A C Next, we calculate the desired cycle time and theoretical minimum number of workstations:
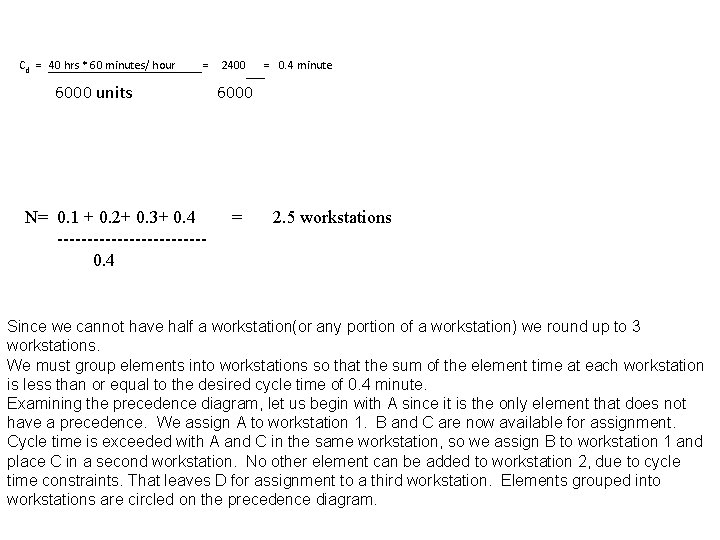
Cd = 40 hrs * 60 minutes/ hour = 6000 units N= 0. 1 + 0. 2+ 0. 3+ 0. 4 ------------0. 4 2400 = 0. 4 minute 6000 = 2. 5 workstations Since we cannot have half a workstation(or any portion of a workstation) we round up to 3 workstations. We must group elements into workstations so that the sum of the element time at each workstation is less than or equal to the desired cycle time of 0. 4 minute. Examining the precedence diagram, let us begin with A since it is the only element that does not have a precedence. We assign A to workstation 1. B and C are now available for assignment. Cycle time is exceeded with A and C in the same workstation, so we assign B to workstation 1 and place C in a second workstation. No other element can be added to workstation 2, due to cycle time constraints. That leaves D for assignment to a third workstation. Elements grouped into workstations are circled on the precedence diagram.
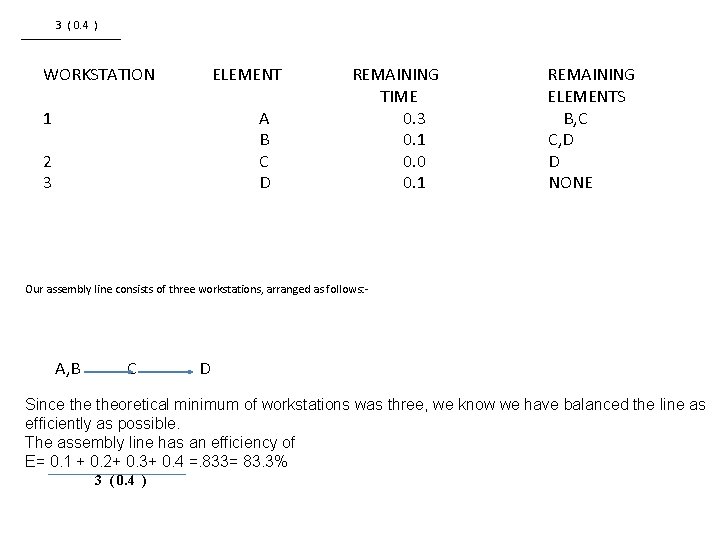
3 ( 0. 4 ) WORKSTATION ELEMENT 1 A B C D 2 3 REMAINING TIME 0. 3 0. 1 0. 0 0. 1 REMAINING ELEMENTS B, C C, D D NONE Our assembly line consists of three workstations, arranged as follows: - A, B C D Since theoretical minimum of workstations was three, we know we have balanced the line as efficiently as possible. The assembly line has an efficiency of E= 0. 1 + 0. 2+ 0. 3+ 0. 4 =. 833= 83. 3% 3 ( 0. 4 )
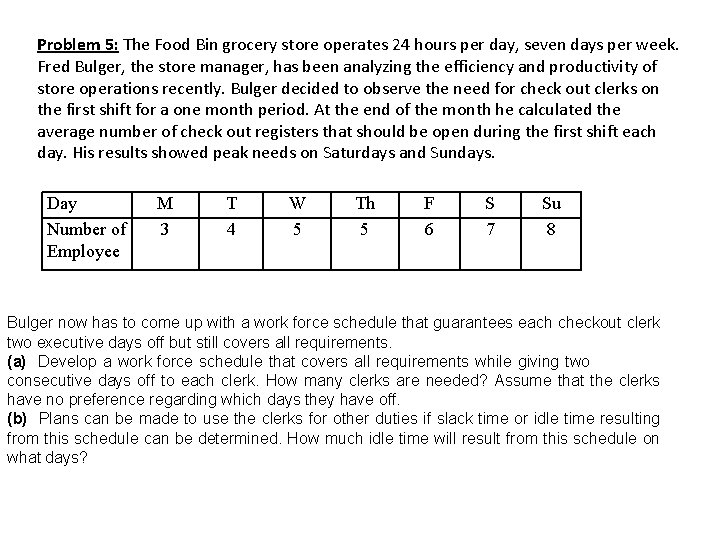
Problem 5: The Food Bin grocery store operates 24 hours per day, seven days per week. Fred Bulger, the store manager, has been analyzing the efficiency and productivity of store operations recently. Bulger decided to observe the need for check out clerks on the first shift for a one month period. At the end of the month he calculated the average number of check out registers that should be open during the first shift each day. His results showed peak needs on Saturdays and Sundays. Day Number of Employee M 3 T 4 W 5 Th 5 F 6 S 7 Su 8 Bulger now has to come up with a work force schedule that guarantees each checkout clerk two executive days off but still covers all requirements. (a) Develop a work force schedule that covers all requirements while giving two consecutive days off to each clerk. How many clerks are needed? Assume that the clerks have no preference regarding which days they have off. (b) Plans can be made to use the clerks for other duties if slack time or idle time resulting from this schedule can be determined. How much idle time will result from this schedule on what days?
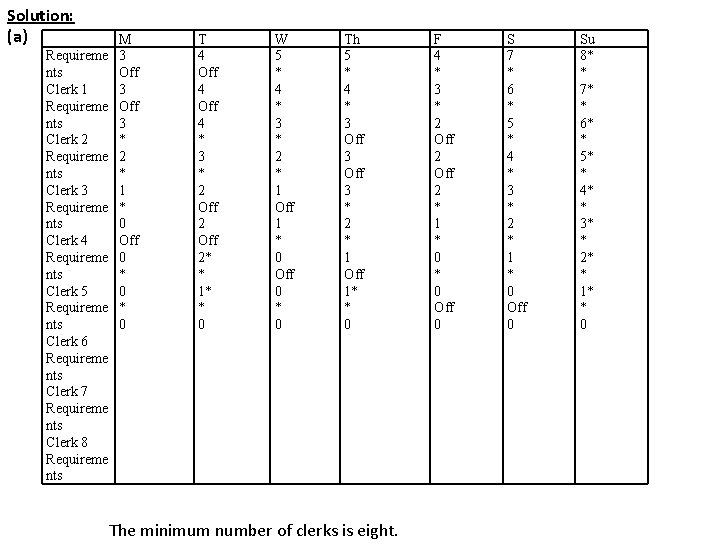
Solution: (a) Requireme nts Clerk 1 Requireme nts Clerk 2 Requireme nts Clerk 3 Requireme nts Clerk 4 Requireme nts Clerk 5 Requireme nts Clerk 6 Requireme nts Clerk 7 Requireme nts Clerk 8 Requireme nts M 3 Off 3 * 2 * 1 * 0 Off 0 * 0 T 4 Off 4 * 3 * 2 Off 2* * 1* * 0 W 5 * 4 * 3 * 2 * 1 Off 1 * 0 Off 0 * 0 Th 5 * 4 * 3 Off 3 * 2 * 1 Off 1* * 0 The minimum number of clerks is eight. F 4 * 3 * 2 Off 2 * 1 * 0 Off 0 S 7 * 6 * 5 * 4 * 3 * 2 * 1 * 0 Off 0 Su 8* * 7* * 6* * 5* * 4* * 3* * 2* * 1* * 0
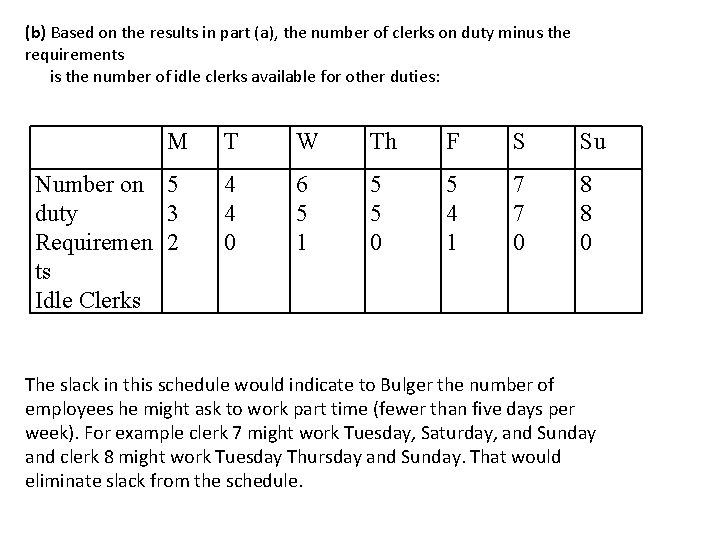
(b) Based on the results in part (a), the number of clerks on duty minus the requirements is the number of idle clerks available for other duties: M Number on 5 duty 3 Requiremen 2 ts Idle Clerks T W Th F S Su 4 4 0 6 5 1 5 5 0 5 4 1 7 7 0 8 8 0 The slack in this schedule would indicate to Bulger the number of employees he might ask to work part time (fewer than five days per week). For example clerk 7 might work Tuesday, Saturday, and Sunday and clerk 8 might work Tuesday Thursday and Sunday. That would eliminate slack from the schedule.
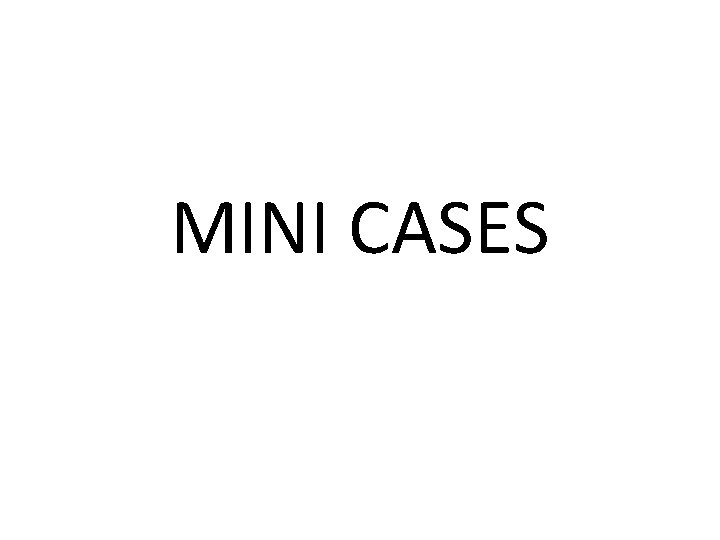
MINI CASES
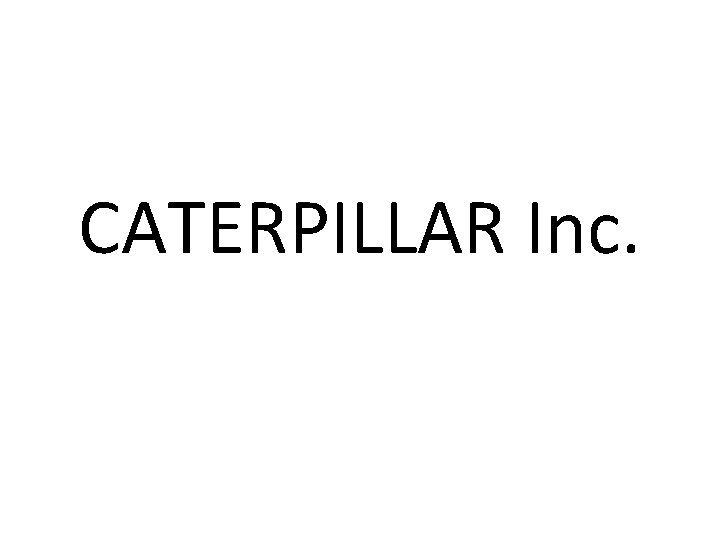
CATERPILLAR Inc.
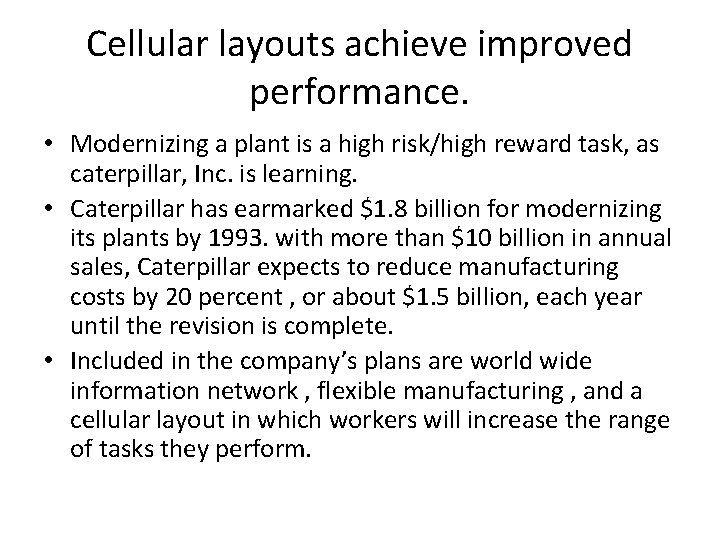
Cellular layouts achieve improved performance. • Modernizing a plant is a high risk/high reward task, as caterpillar, Inc. is learning. • Caterpillar has earmarked $1. 8 billion for modernizing its plants by 1993. with more than $10 billion in annual sales, Caterpillar expects to reduce manufacturing costs by 20 percent , or about $1. 5 billion, each year until the revision is complete. • Included in the company’s plans are world wide information network , flexible manufacturing , and a cellular layout in which workers will increase the range of tasks they perform.
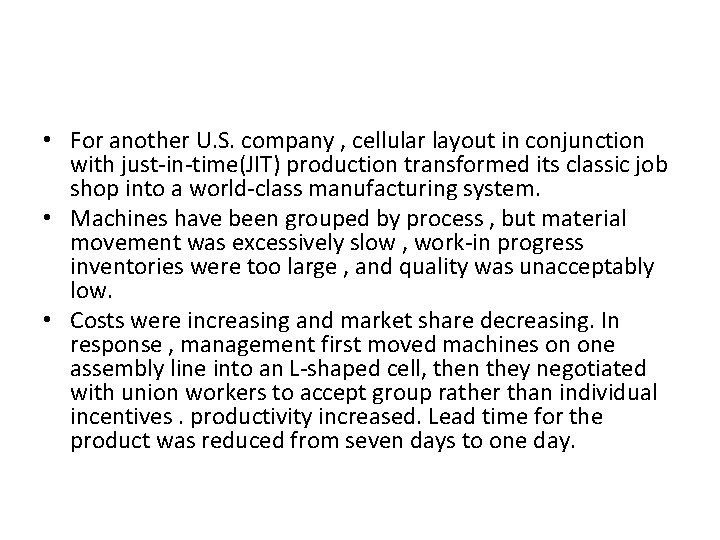
• For another U. S. company , cellular layout in conjunction with just-in-time(JIT) production transformed its classic job shop into a world-class manufacturing system. • Machines have been grouped by process , but material movement was excessively slow , work-in progress inventories were too large , and quality was unacceptably low. • Costs were increasing and market share decreasing. In response , management first moved machines on one assembly line into an L-shaped cell, then they negotiated with union workers to accept group rather than individual incentives. productivity increased. Lead time for the product was reduced from seven days to one day.
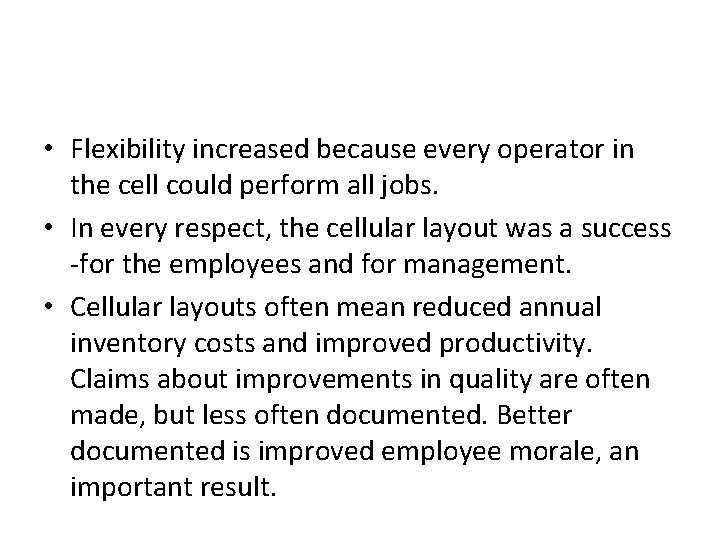
• Flexibility increased because every operator in the cell could perform all jobs. • In every respect, the cellular layout was a success -for the employees and for management. • Cellular layouts often mean reduced annual inventory costs and improved productivity. Claims about improvements in quality are often made, but less often documented. Better documented is improved employee morale, an important result.
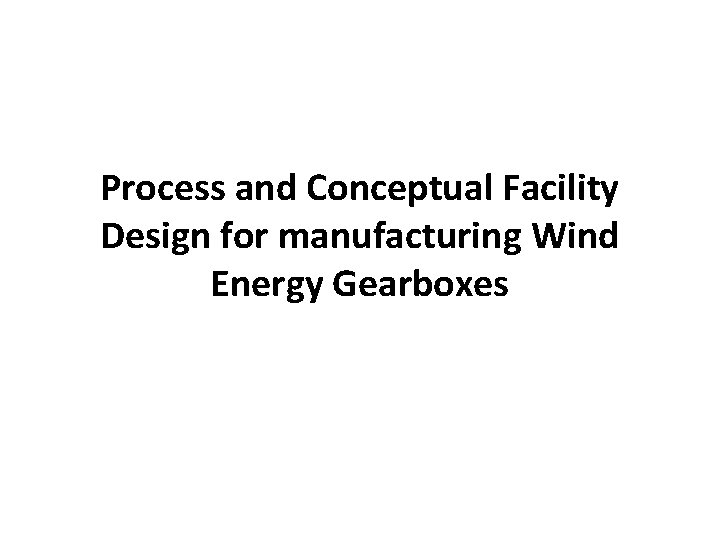
Process and Conceptual Facility Design for manufacturing Wind Energy Gearboxes
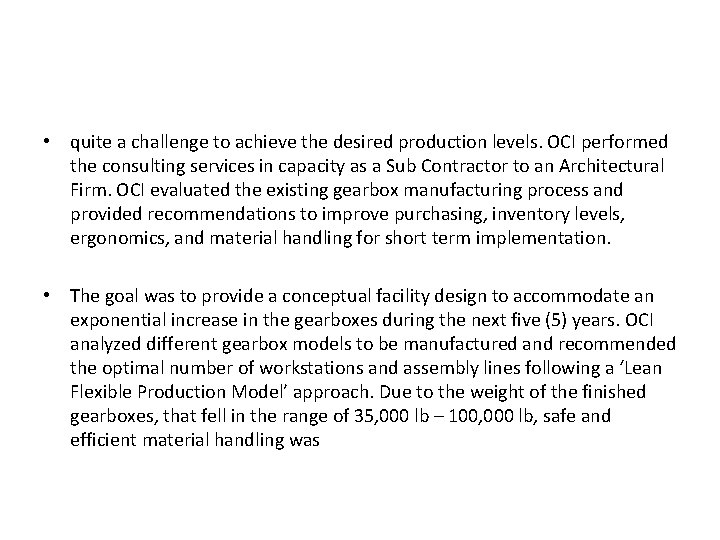
• quite a challenge to achieve the desired production levels. OCI performed the consulting services in capacity as a Sub Contractor to an Architectural Firm. OCI evaluated the existing gearbox manufacturing process and provided recommendations to improve purchasing, inventory levels, ergonomics, and material handling for short term implementation. • The goal was to provide a conceptual facility design to accommodate an exponential increase in the gearboxes during the next five (5) years. OCI analyzed different gearbox models to be manufactured and recommended the optimal number of workstations and assembly lines following a ‘Lean Flexible Production Model’ approach. Due to the weight of the finished gearboxes, that fell in the range of 35, 000 lb – 100, 000 lb, safe and efficient material handling was
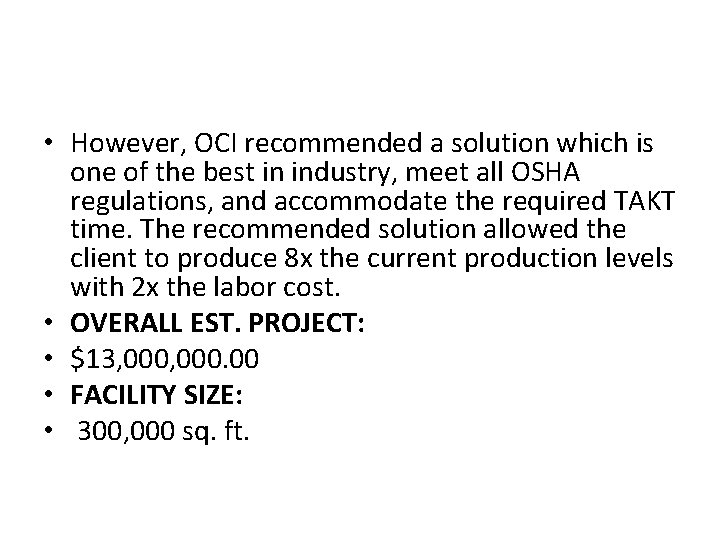
• However, OCI recommended a solution which is one of the best in industry, meet all OSHA regulations, and accommodate the required TAKT time. The recommended solution allowed the client to produce 8 x the current production levels with 2 x the labor cost. • OVERALL EST. PROJECT: • $13, 000. 00 • FACILITY SIZE: • 300, 000 sq. ft.
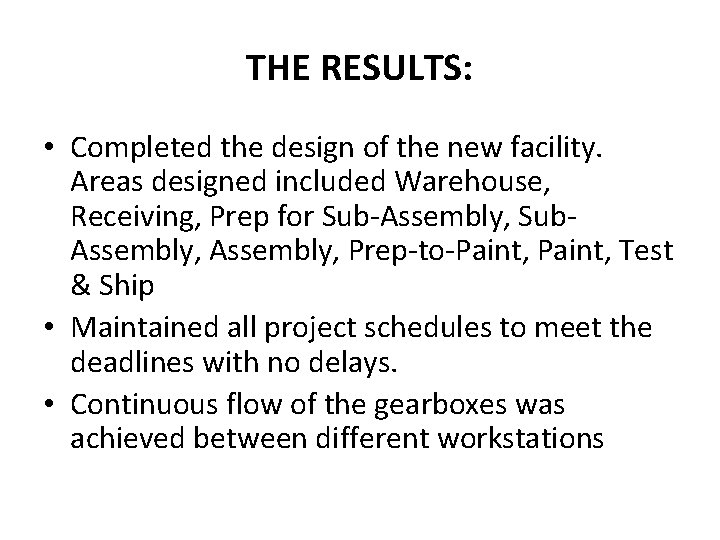
THE RESULTS: • Completed the design of the new facility. Areas designed included Warehouse, Receiving, Prep for Sub-Assembly, Sub. Assembly, Prep-to-Paint, Test & Ship • Maintained all project schedules to meet the deadlines with no delays. • Continuous flow of the gearboxes was achieved between different workstations
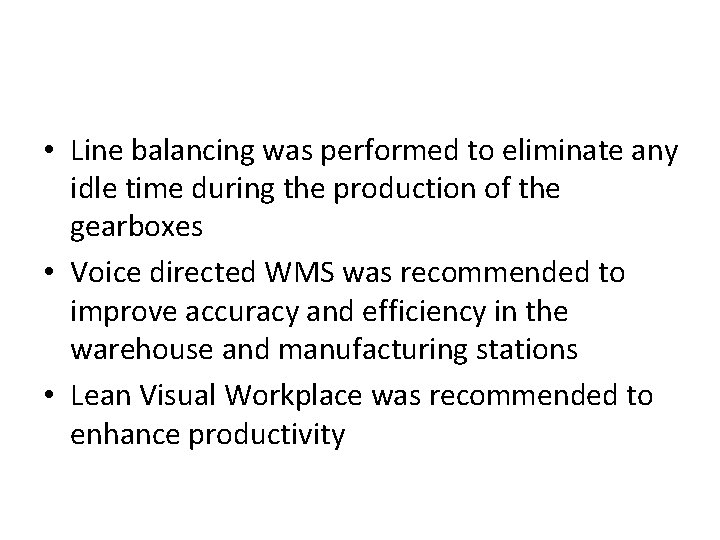
• Line balancing was performed to eliminate any idle time during the production of the gearboxes • Voice directed WMS was recommended to improve accuracy and efficiency in the warehouse and manufacturing stations • Lean Visual Workplace was recommended to enhance productivity
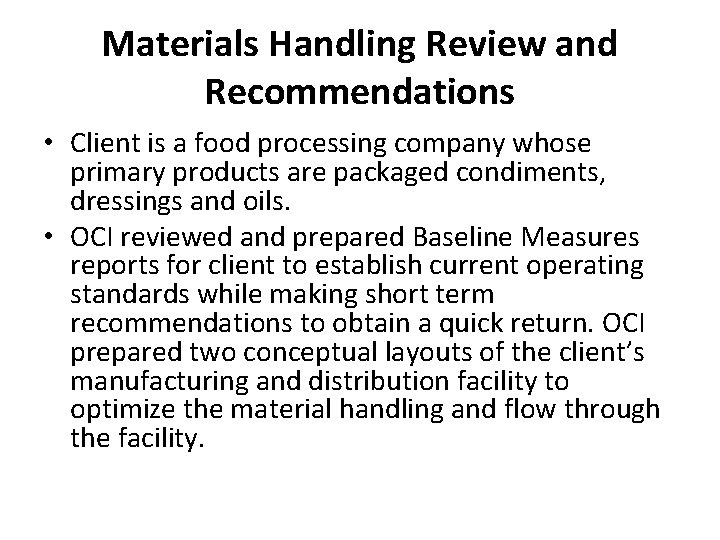
Materials Handling Review and Recommendations • Client is a food processing company whose primary products are packaged condiments, dressings and oils. • OCI reviewed and prepared Baseline Measures reports for client to establish current operating standards while making short term recommendations to obtain a quick return. OCI prepared two conceptual layouts of the client’s manufacturing and distribution facility to optimize the material handling and flow through the facility.
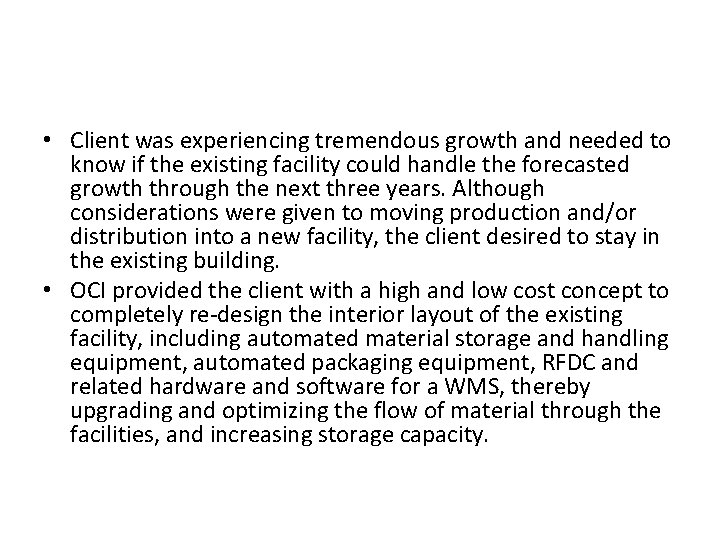
• Client was experiencing tremendous growth and needed to know if the existing facility could handle the forecasted growth through the next three years. Although considerations were given to moving production and/or distribution into a new facility, the client desired to stay in the existing building. • OCI provided the client with a high and low cost concept to completely re-design the interior layout of the existing facility, including automated material storage and handling equipment, automated packaging equipment, RFDC and related hardware and software for a WMS, thereby upgrading and optimizing the flow of material through the facilities, and increasing storage capacity.
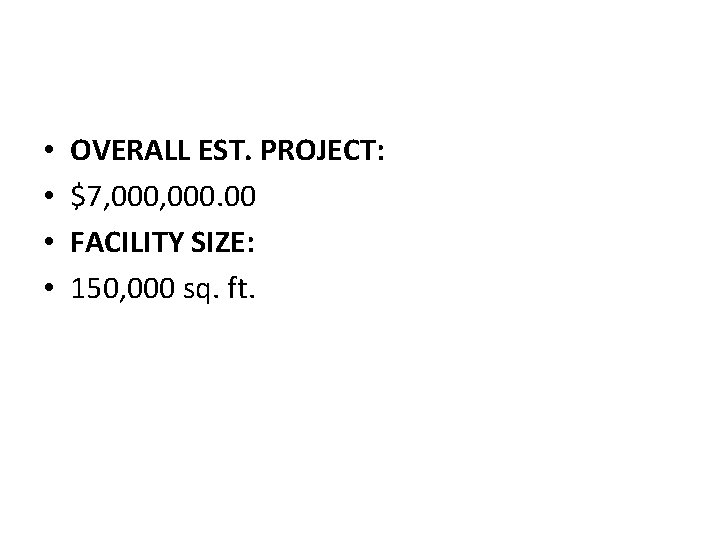
• • OVERALL EST. PROJECT: $7, 000. 00 FACILITY SIZE: 150, 000 sq. ft.
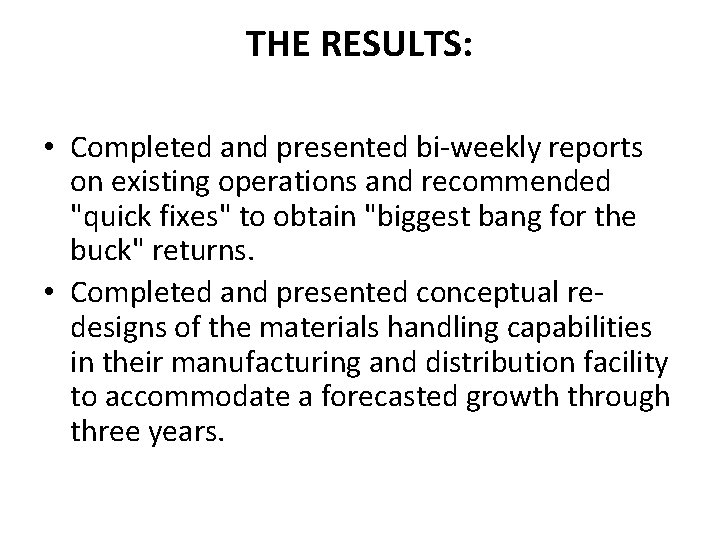
THE RESULTS: • Completed and presented bi-weekly reports on existing operations and recommended "quick fixes" to obtain "biggest bang for the buck" returns. • Completed and presented conceptual redesigns of the materials handling capabilities in their manufacturing and distribution facility to accommodate a forecasted growth through three years.
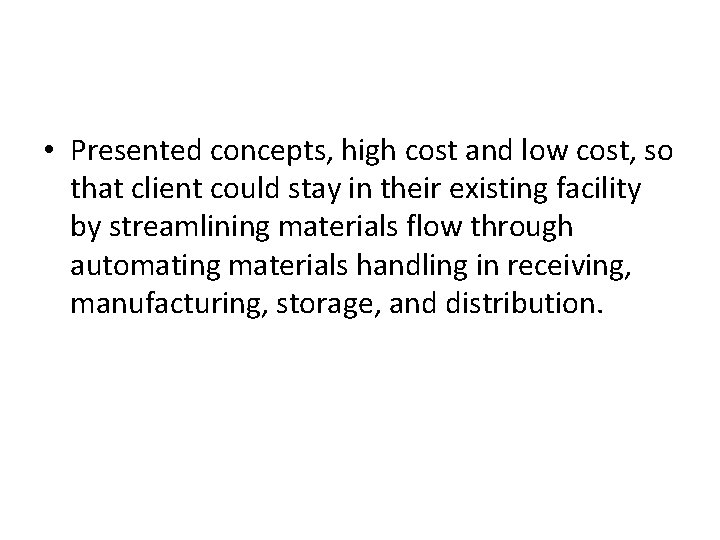
• Presented concepts, high cost and low cost, so that client could stay in their existing facility by streamlining materials flow through automating materials handling in receiving, manufacturing, storage, and distribution.