CHAPTER5 FACILITY LAYOUT INTRODUCTION Facility layout refers to
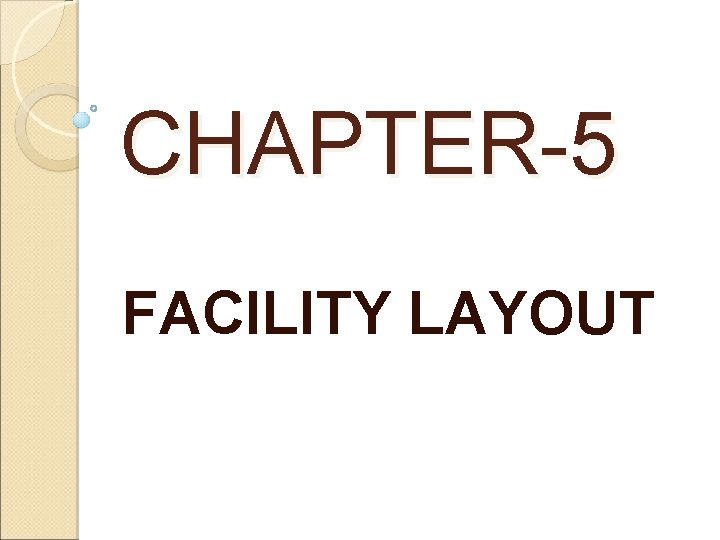
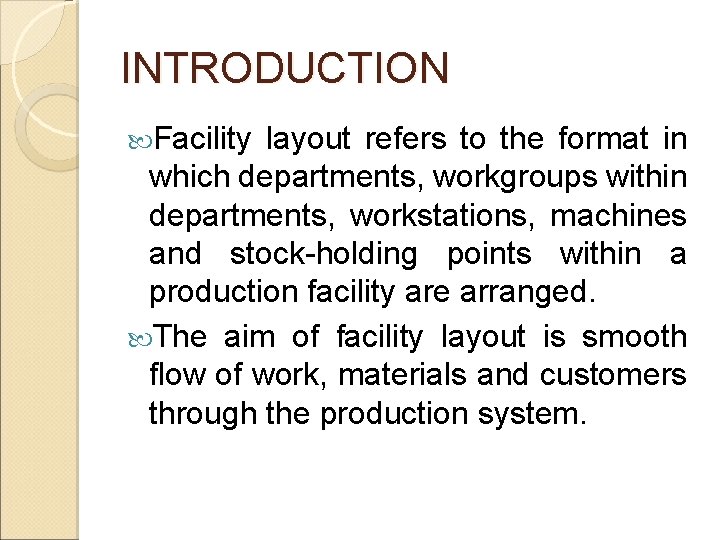
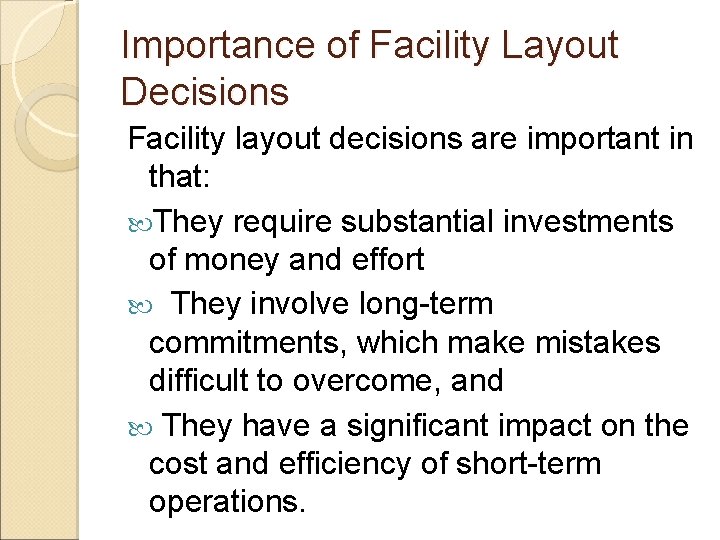
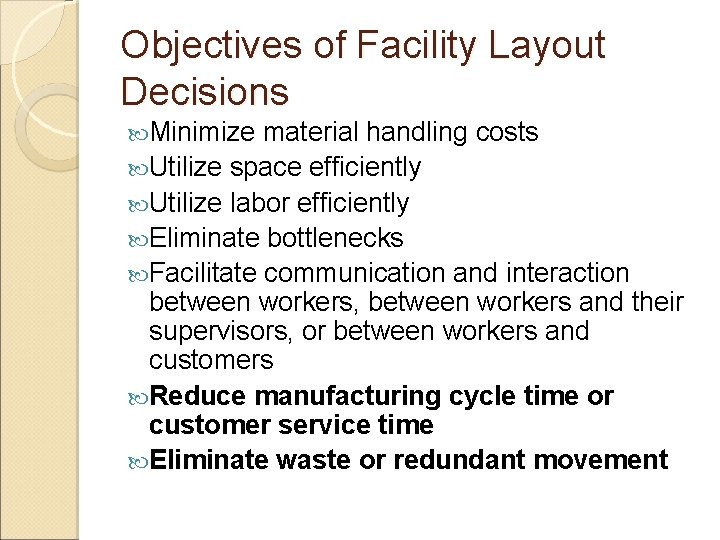
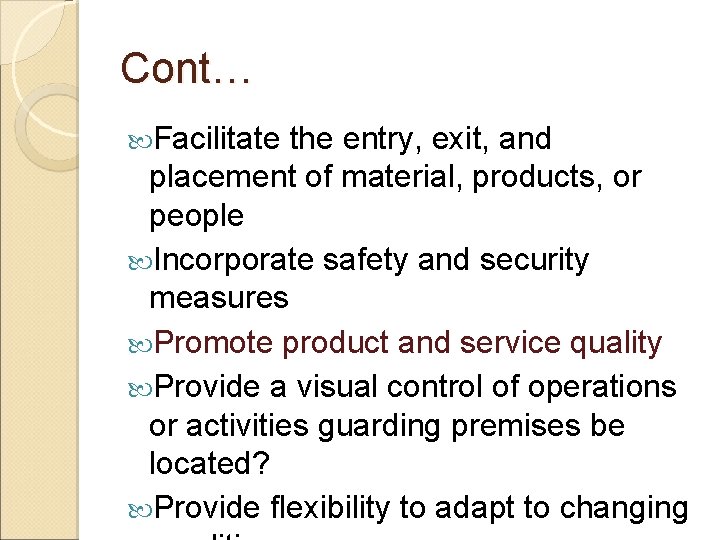
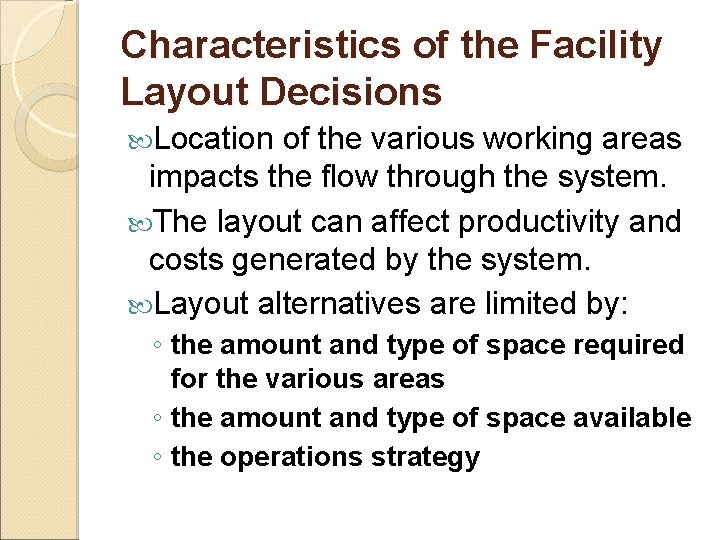
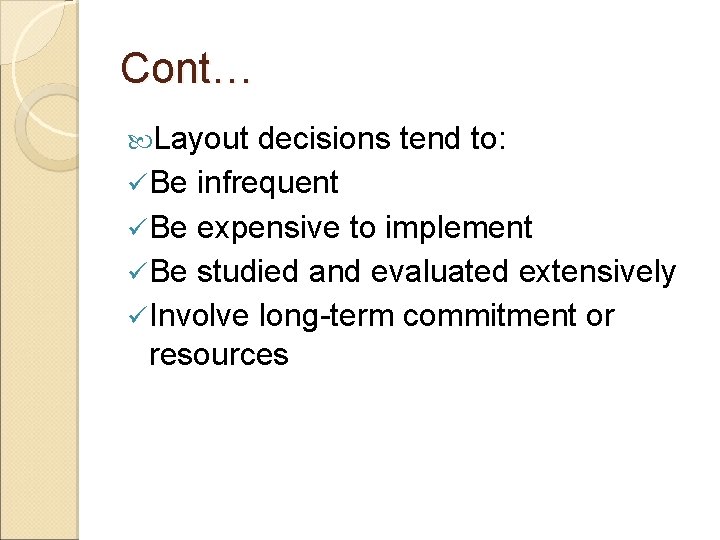
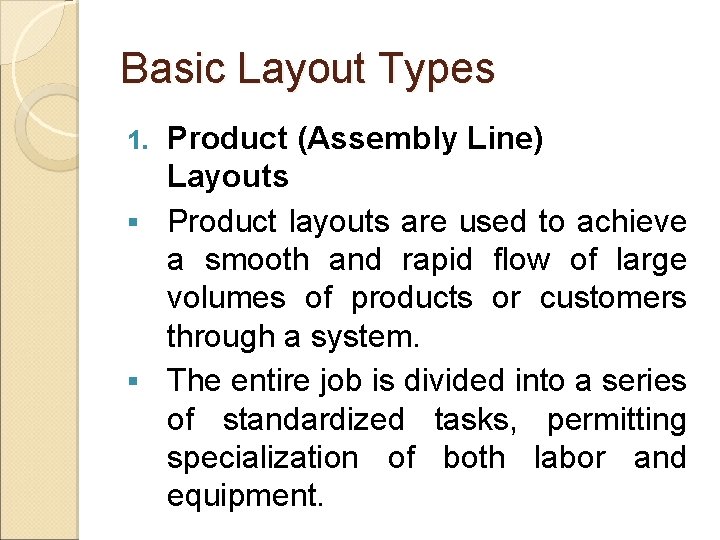
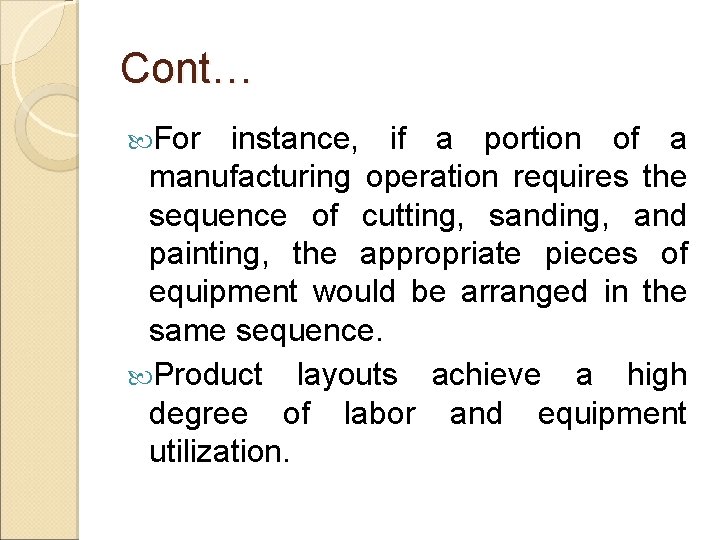
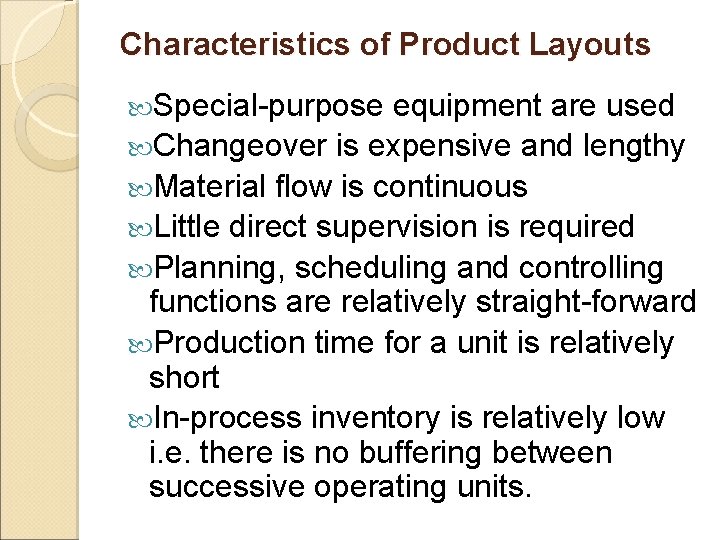
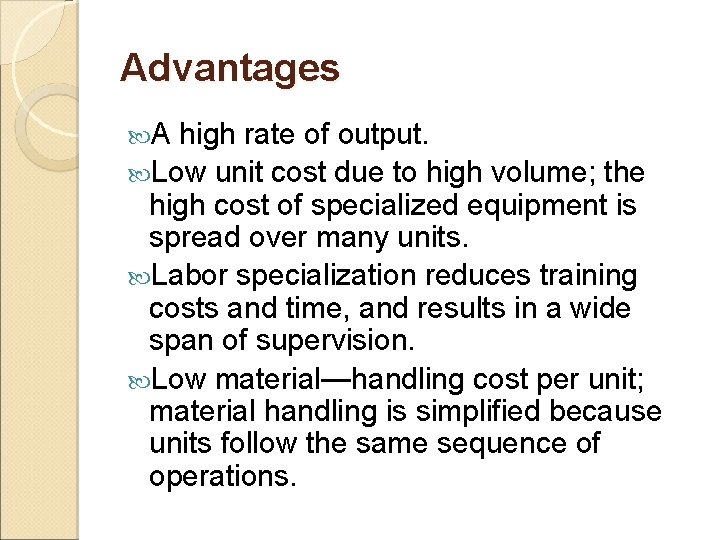
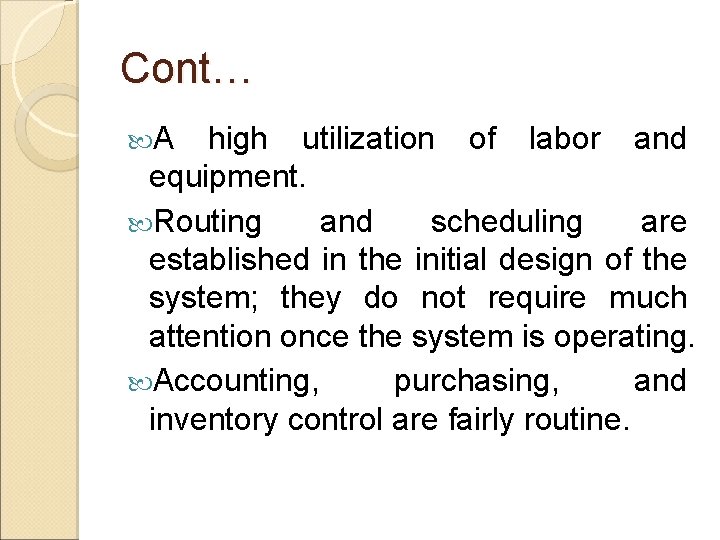
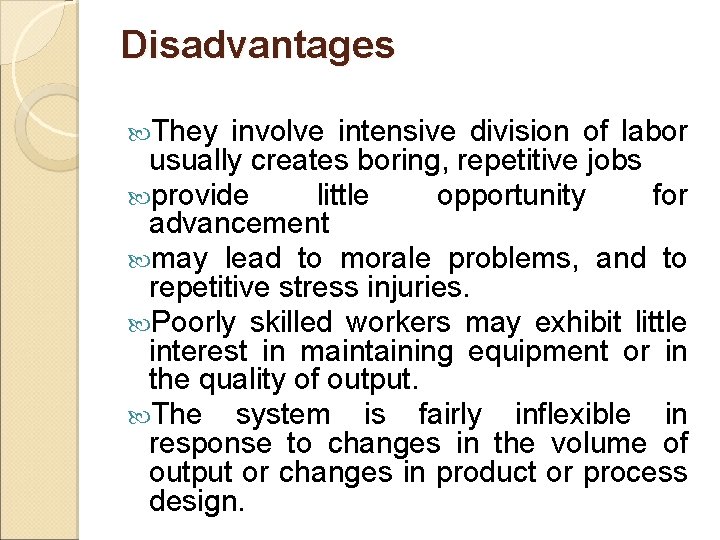
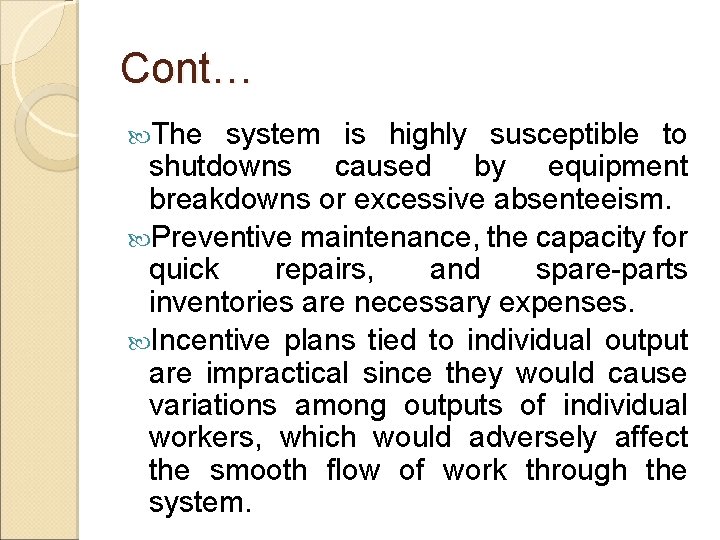
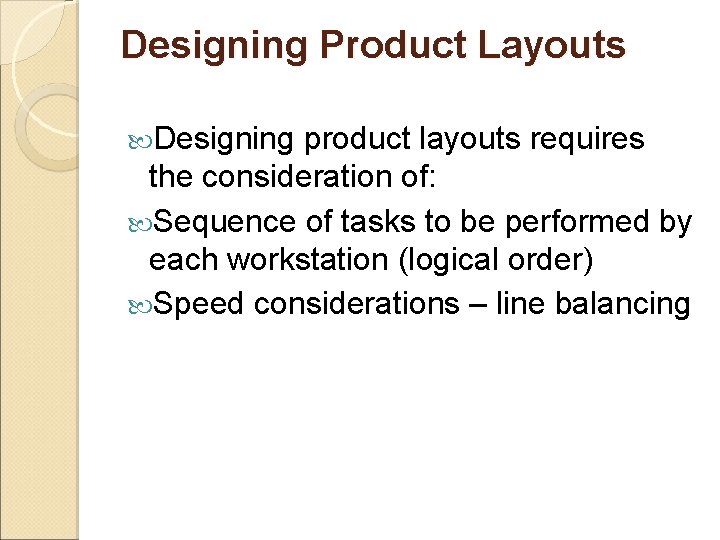
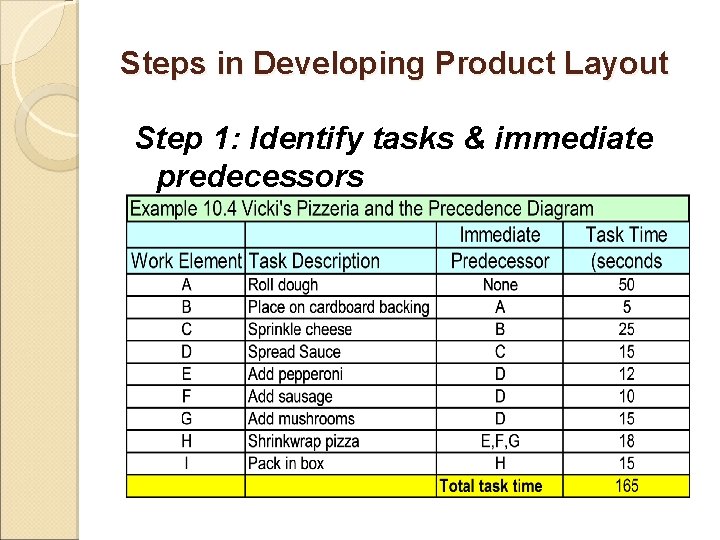
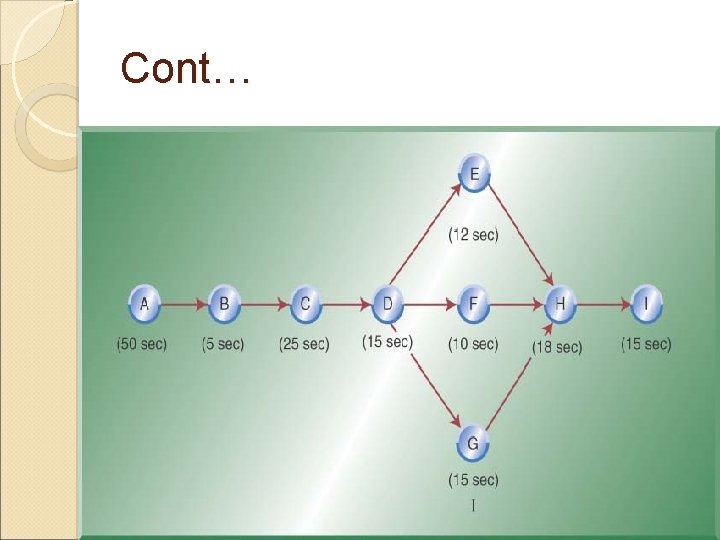
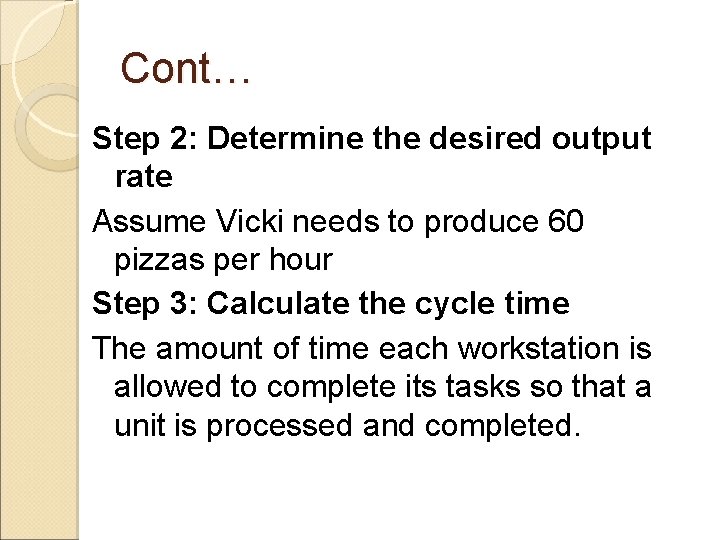
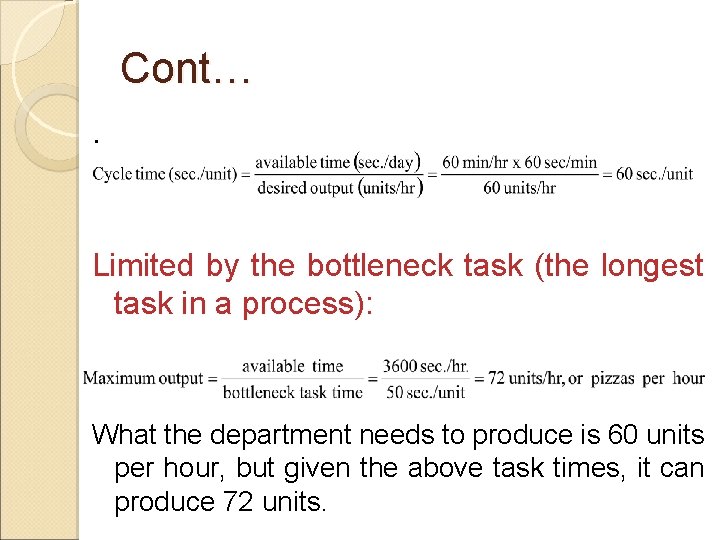
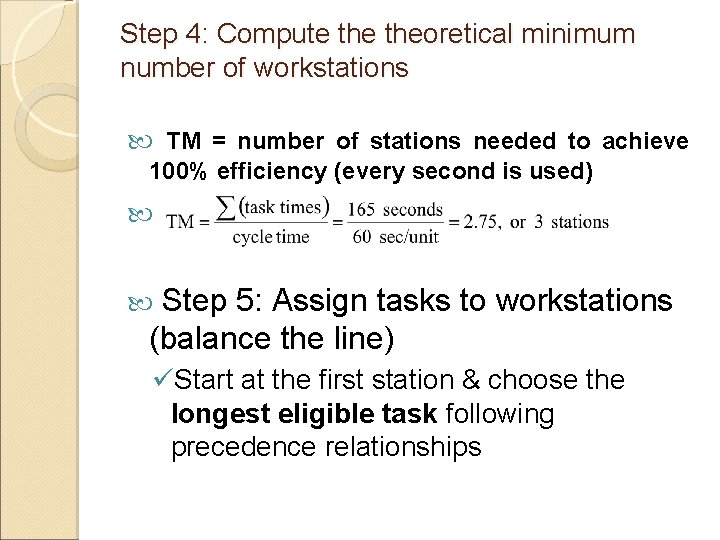
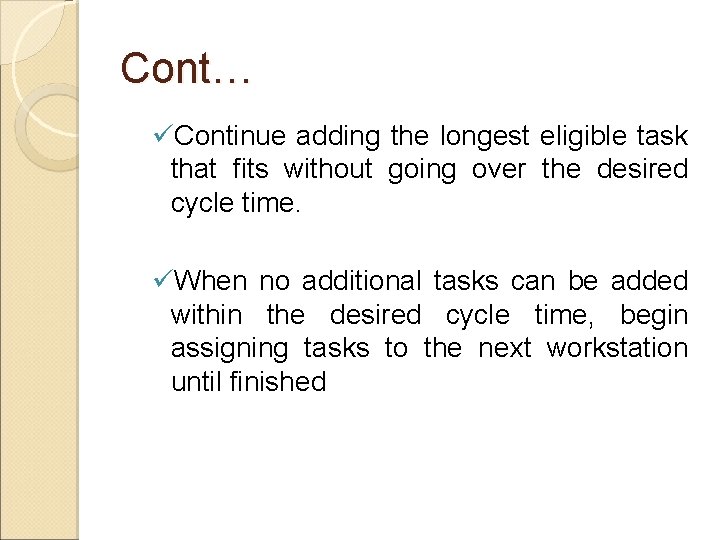
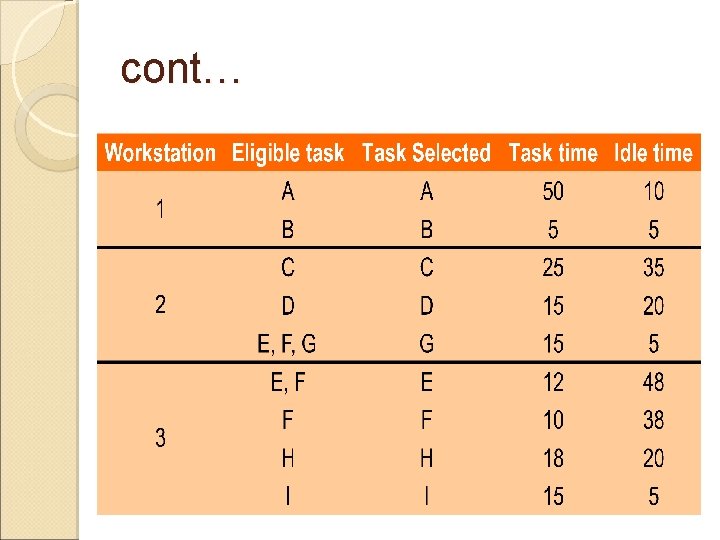
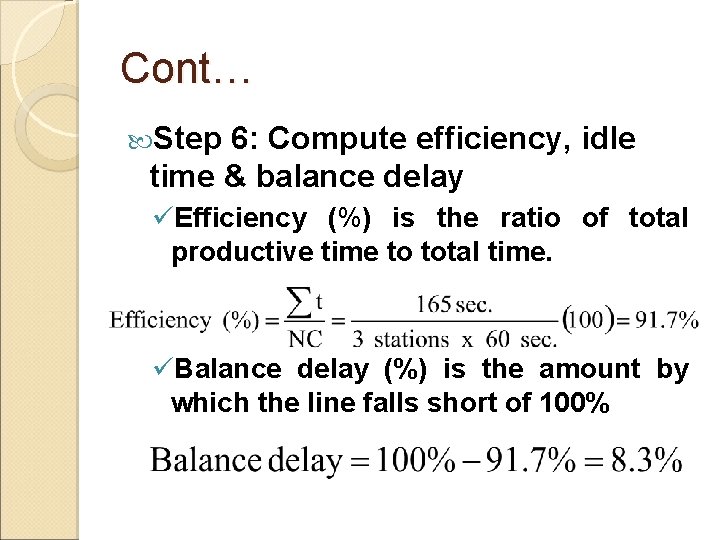
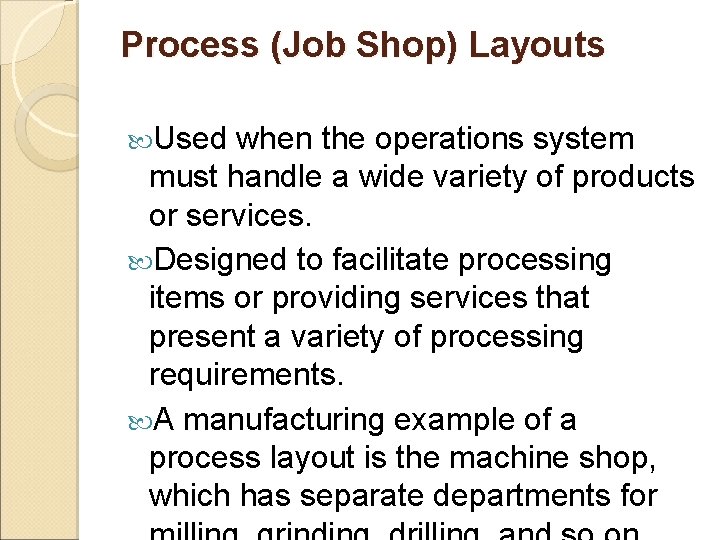
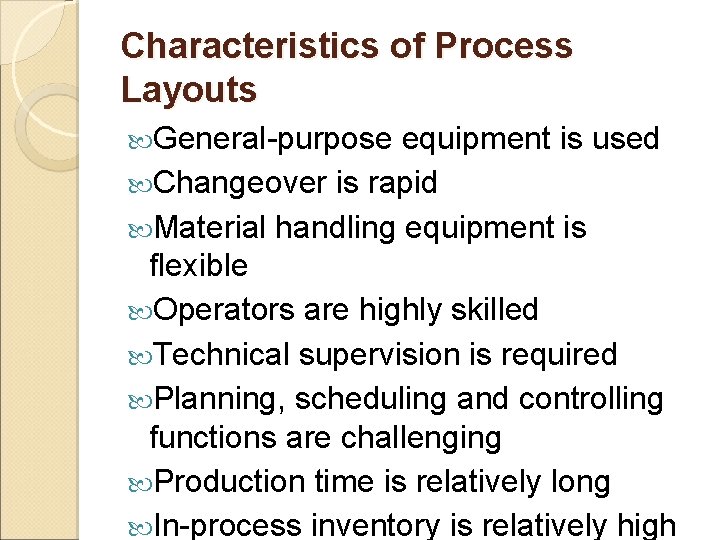
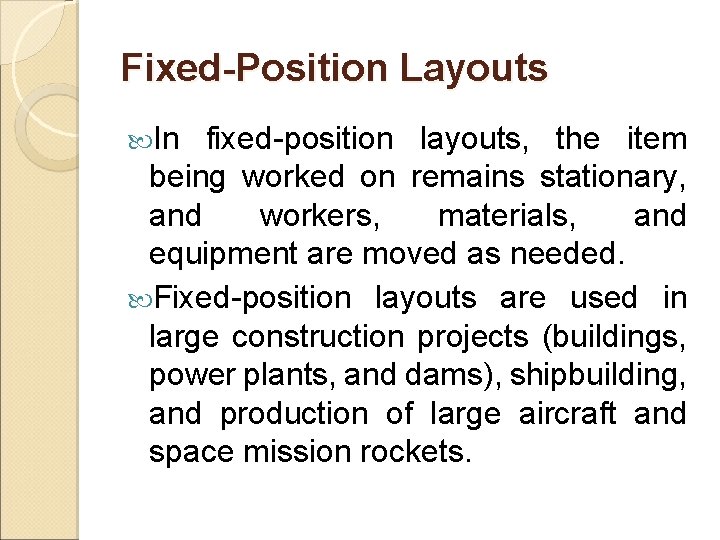
- Slides: 26
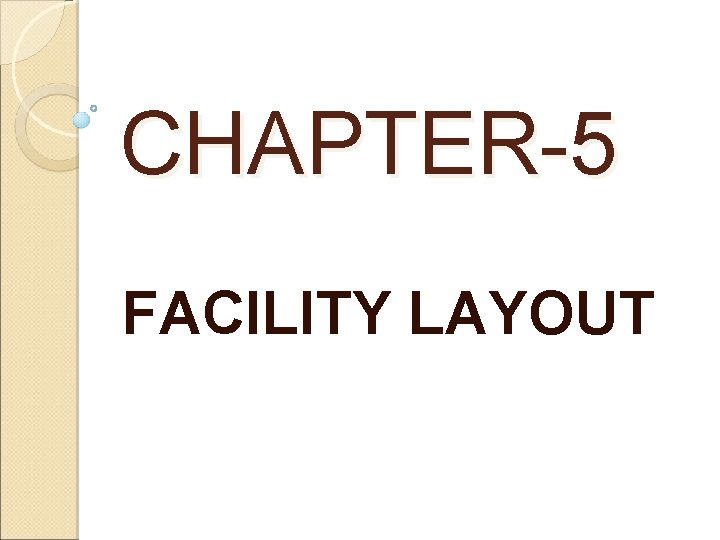
CHAPTER-5 FACILITY LAYOUT
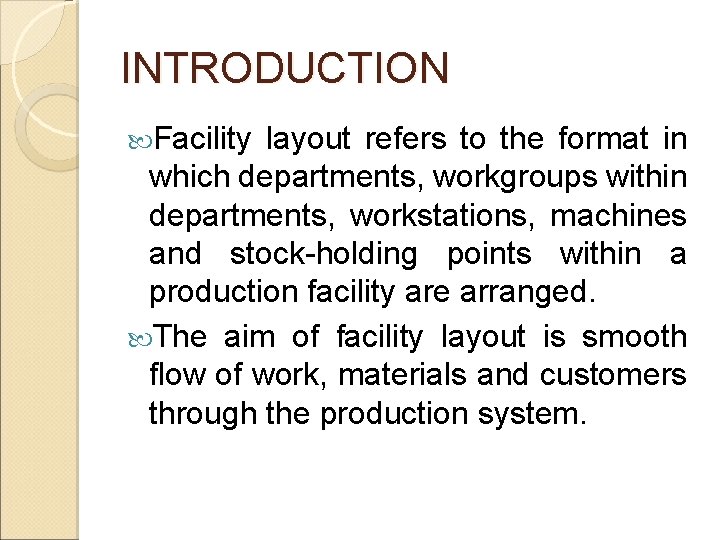
INTRODUCTION Facility layout refers to the format in which departments, workgroups within departments, workstations, machines and stock-holding points within a production facility are arranged. The aim of facility layout is smooth flow of work, materials and customers through the production system.
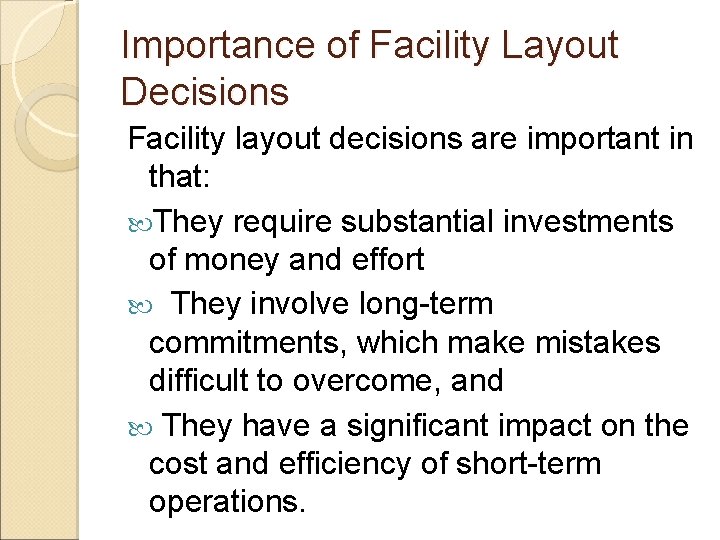
Importance of Facility Layout Decisions Facility layout decisions are important in that: They require substantial investments of money and effort They involve long-term commitments, which make mistakes difficult to overcome, and They have a significant impact on the cost and efficiency of short-term operations.
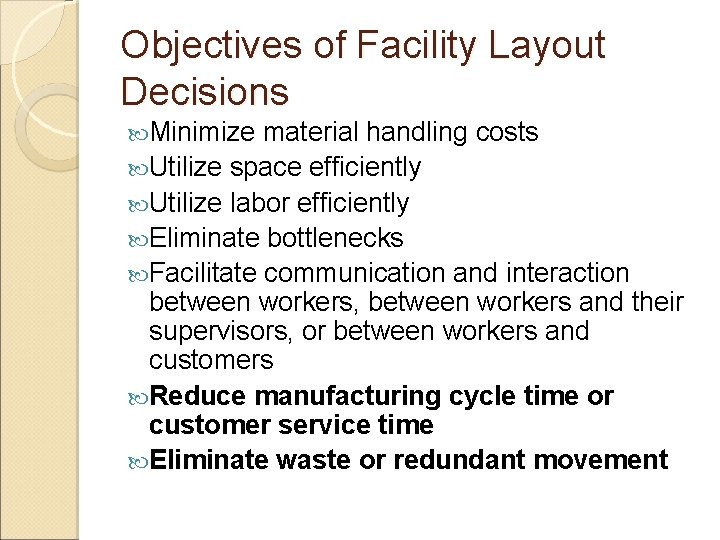
Objectives of Facility Layout Decisions Minimize material handling costs Utilize space efficiently Utilize labor efficiently Eliminate bottlenecks Facilitate communication and interaction between workers, between workers and their supervisors, or between workers and customers Reduce manufacturing cycle time or customer service time Eliminate waste or redundant movement
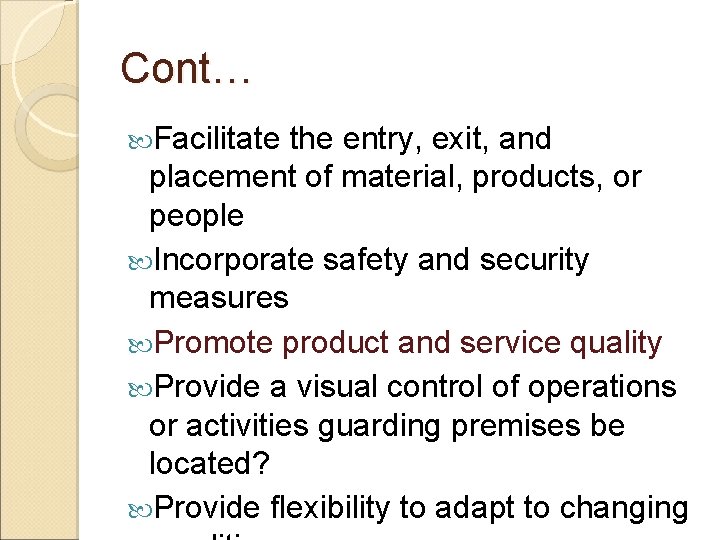
Cont… Facilitate the entry, exit, and placement of material, products, or people Incorporate safety and security measures Promote product and service quality Provide a visual control of operations or activities guarding premises be located? Provide flexibility to adapt to changing
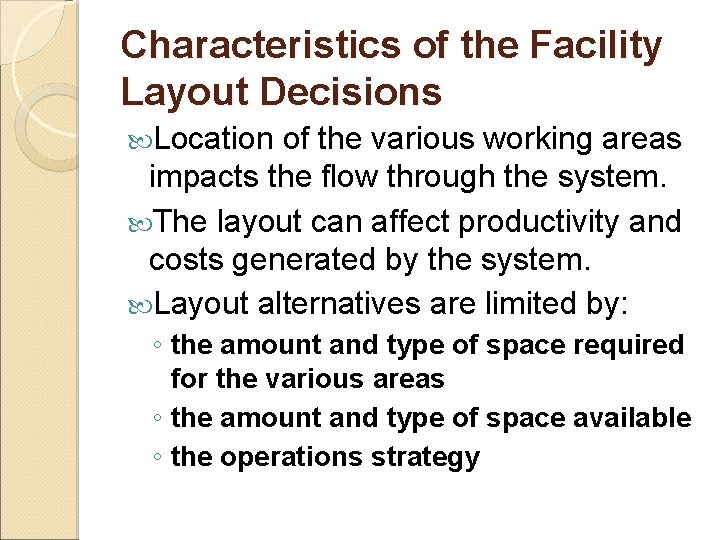
Characteristics of the Facility Layout Decisions Location of the various working areas impacts the flow through the system. The layout can affect productivity and costs generated by the system. Layout alternatives are limited by: ◦ the amount and type of space required for the various areas ◦ the amount and type of space available ◦ the operations strategy
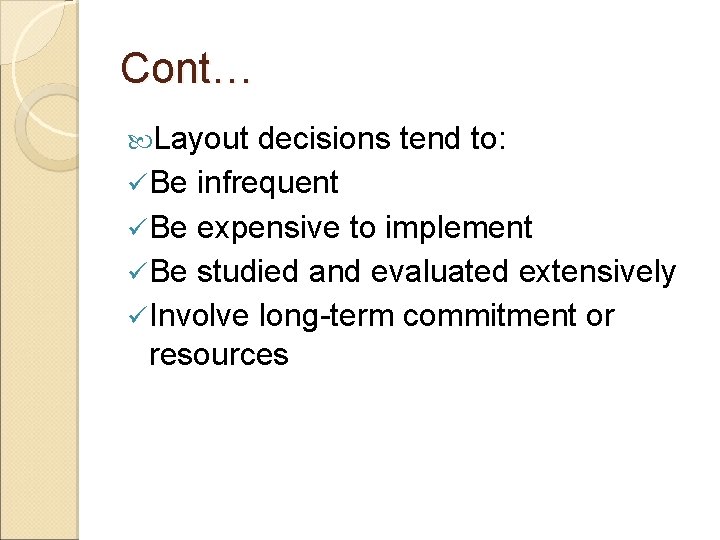
Cont… Layout decisions tend to: ü Be infrequent ü Be expensive to implement ü Be studied and evaluated extensively ü Involve long-term commitment or resources
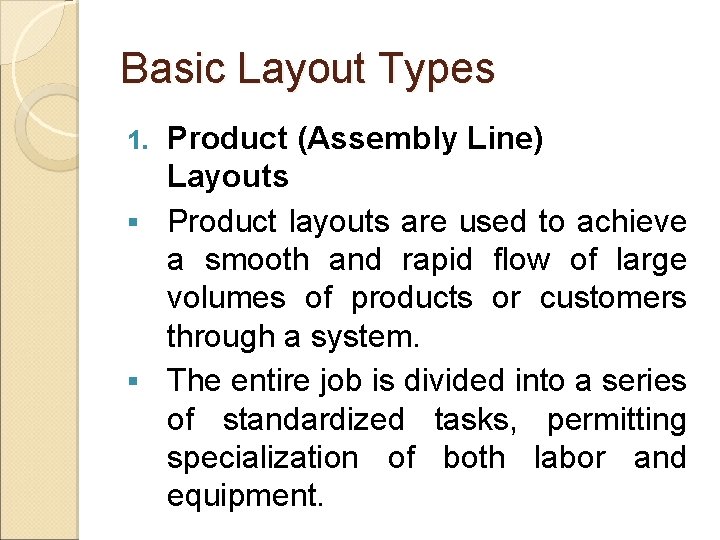
Basic Layout Types Product (Assembly Line) Layouts § Product layouts are used to achieve a smooth and rapid flow of large volumes of products or customers through a system. § The entire job is divided into a series of standardized tasks, permitting specialization of both labor and equipment. 1.
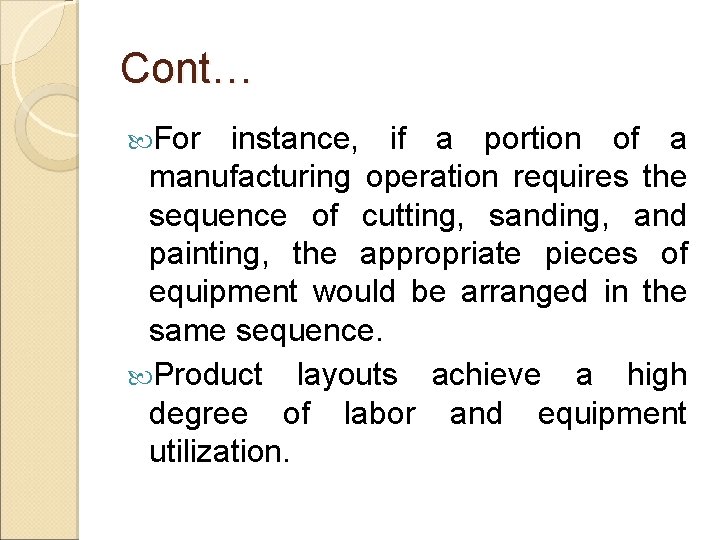
Cont… For instance, if a portion of a manufacturing operation requires the sequence of cutting, sanding, and painting, the appropriate pieces of equipment would be arranged in the same sequence. Product layouts achieve a high degree of labor and equipment utilization.
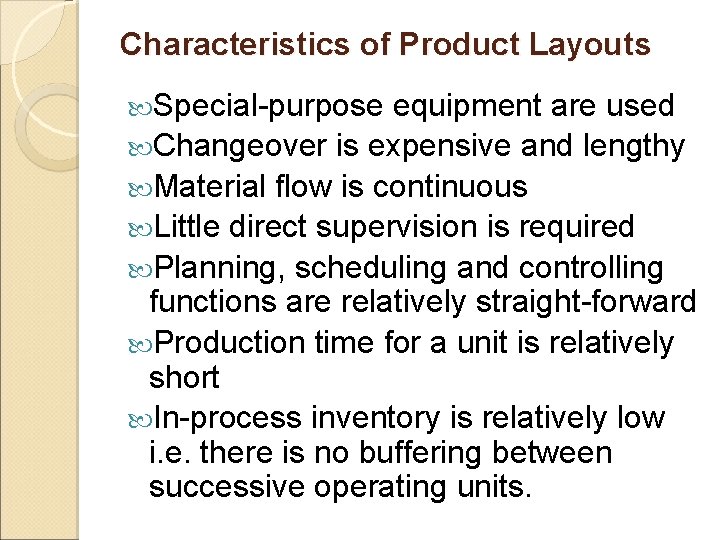
Characteristics of Product Layouts Special-purpose equipment are used Changeover is expensive and lengthy Material flow is continuous Little direct supervision is required Planning, scheduling and controlling functions are relatively straight-forward Production time for a unit is relatively short In-process inventory is relatively low i. e. there is no buffering between successive operating units.
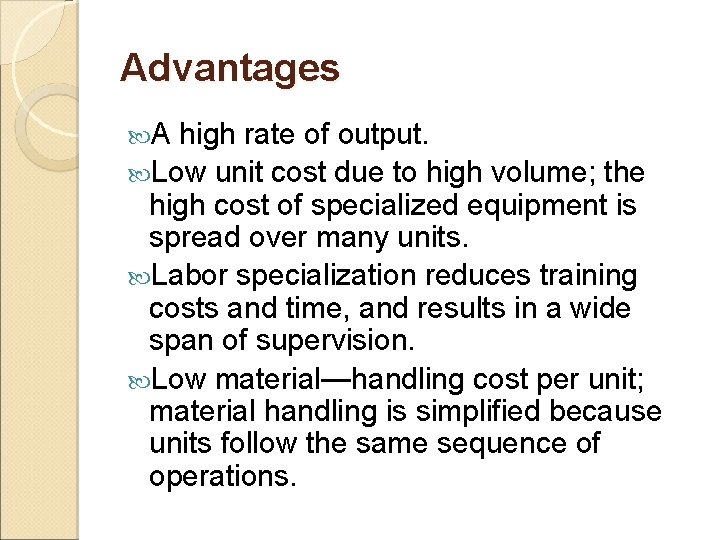
Advantages A high rate of output. Low unit cost due to high volume; the high cost of specialized equipment is spread over many units. Labor specialization reduces training costs and time, and results in a wide span of supervision. Low material—handling cost per unit; material handling is simplified because units follow the same sequence of operations.
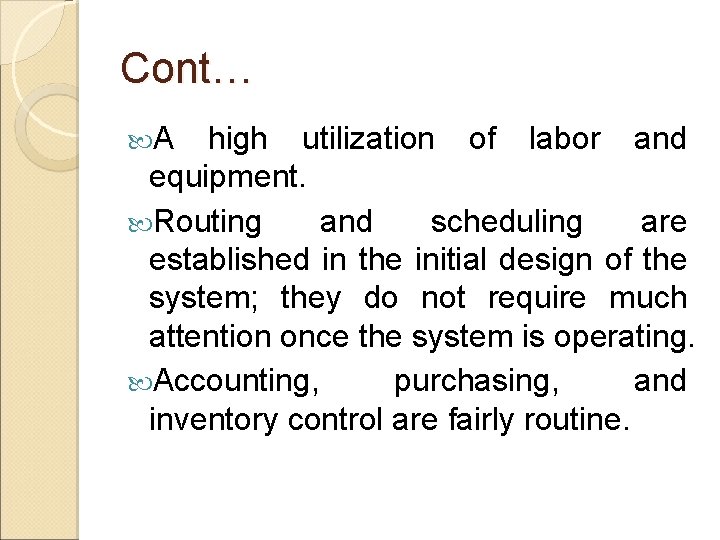
Cont… A high utilization of labor and equipment. Routing and scheduling are established in the initial design of the system; they do not require much attention once the system is operating. Accounting, purchasing, and inventory control are fairly routine.
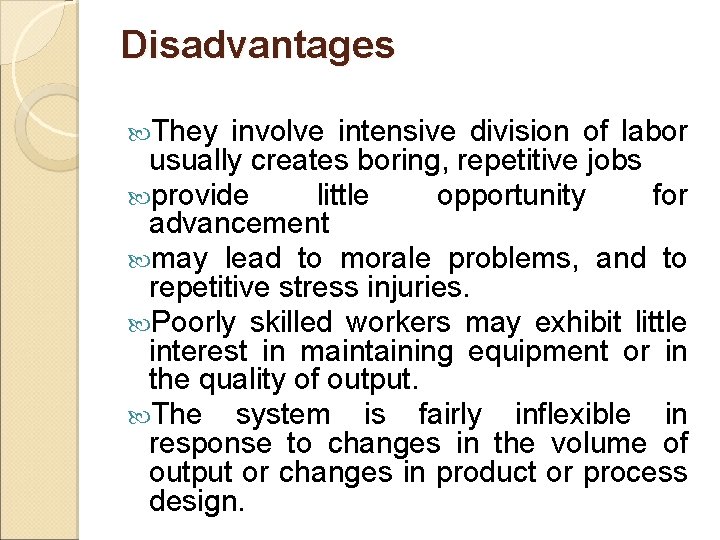
Disadvantages They involve intensive division of labor usually creates boring, repetitive jobs provide little opportunity for advancement may lead to morale problems, and to repetitive stress injuries. Poorly skilled workers may exhibit little interest in maintaining equipment or in the quality of output. The system is fairly inflexible in response to changes in the volume of output or changes in product or process design.
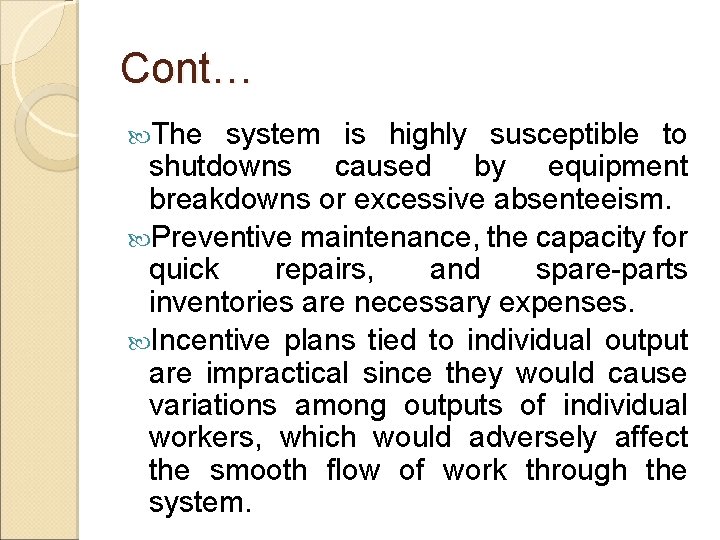
Cont… The system is highly susceptible to shutdowns caused by equipment breakdowns or excessive absenteeism. Preventive maintenance, the capacity for quick repairs, and spare-parts inventories are necessary expenses. Incentive plans tied to individual output are impractical since they would cause variations among outputs of individual workers, which would adversely affect the smooth flow of work through the system.
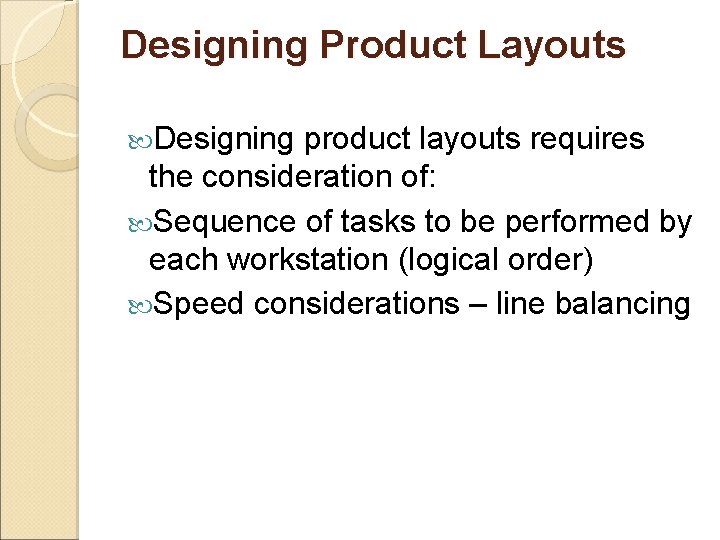
Designing Product Layouts Designing product layouts requires the consideration of: Sequence of tasks to be performed by each workstation (logical order) Speed considerations – line balancing
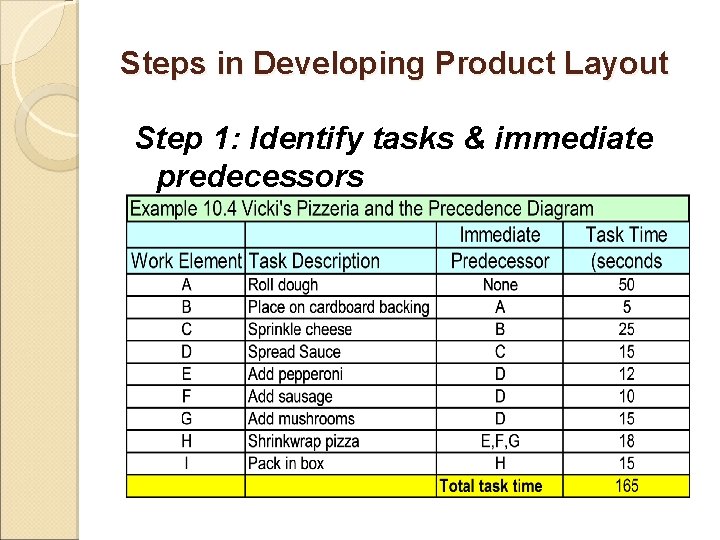
Steps in Developing Product Layout Step 1: Identify tasks & immediate predecessors
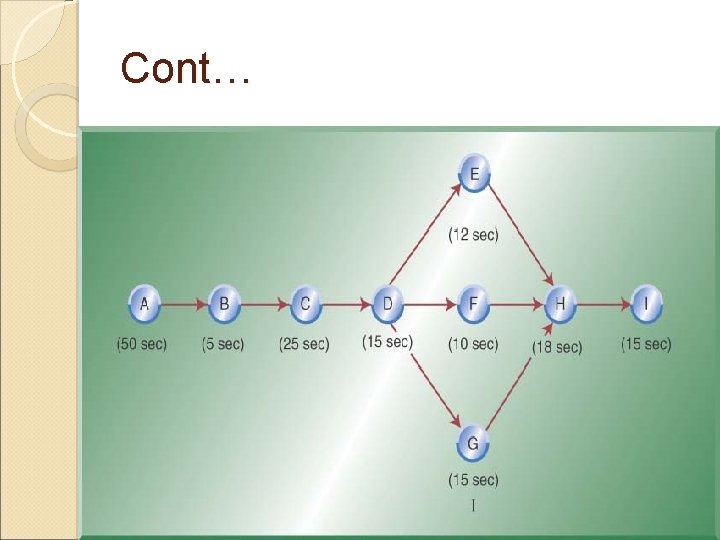
Cont…
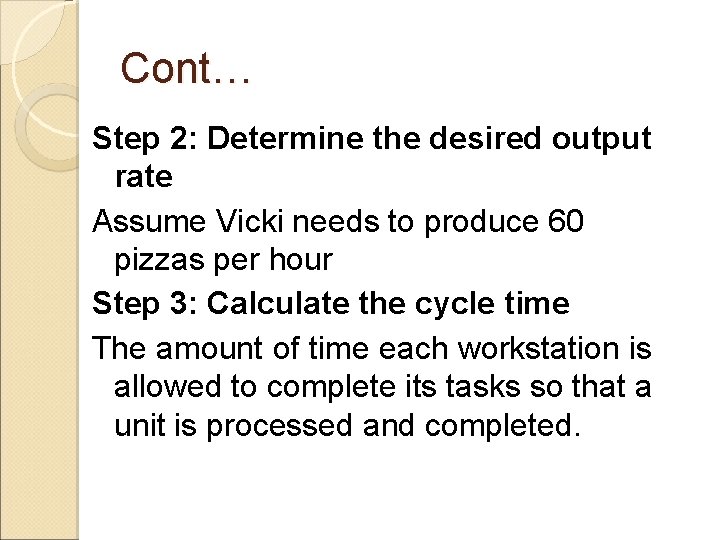
Cont… Step 2: Determine the desired output rate Assume Vicki needs to produce 60 pizzas per hour Step 3: Calculate the cycle time The amount of time each workstation is allowed to complete its tasks so that a unit is processed and completed.
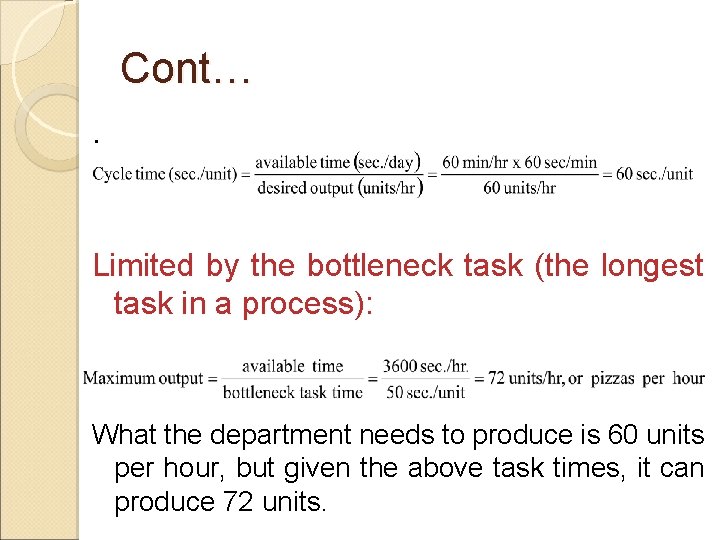
Cont…. Limited by the bottleneck task (the longest task in a process): What the department needs to produce is 60 units per hour, but given the above task times, it can produce 72 units.
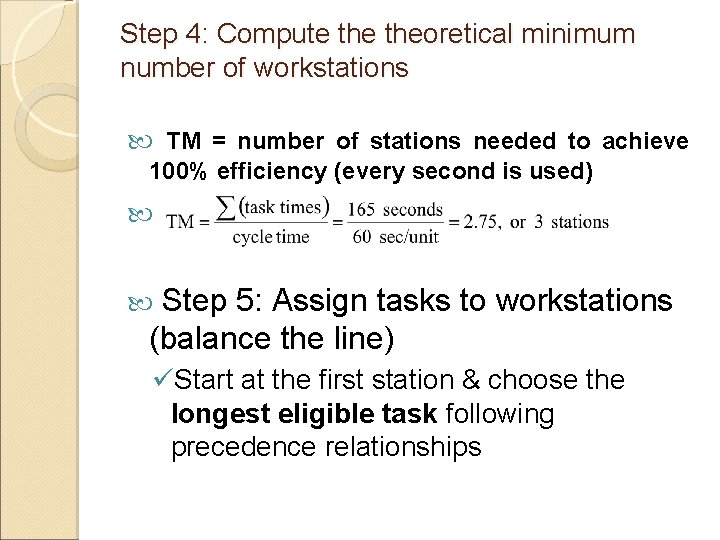
Step 4: Compute theoretical minimum number of workstations TM = number of stations needed to achieve 100% efficiency (every second is used) Step 5: Assign tasks to workstations (balance the line) üStart at the first station & choose the longest eligible task following precedence relationships
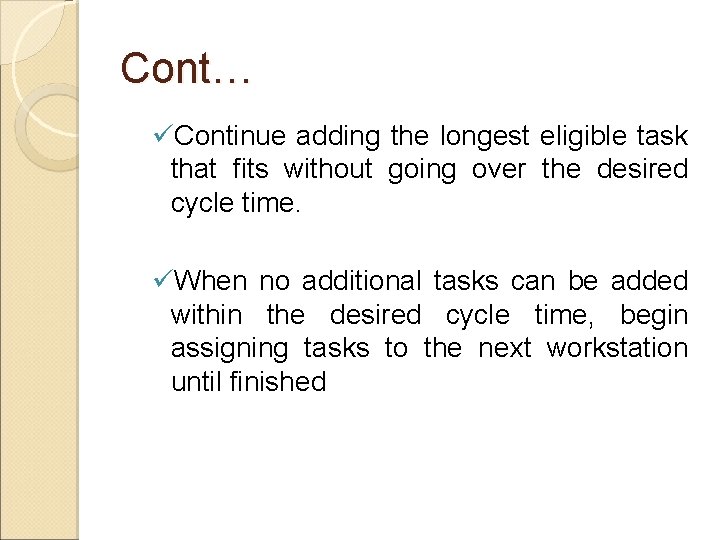
Cont… üContinue adding the longest eligible task that fits without going over the desired cycle time. üWhen no additional tasks can be added within the desired cycle time, begin assigning tasks to the next workstation until finished
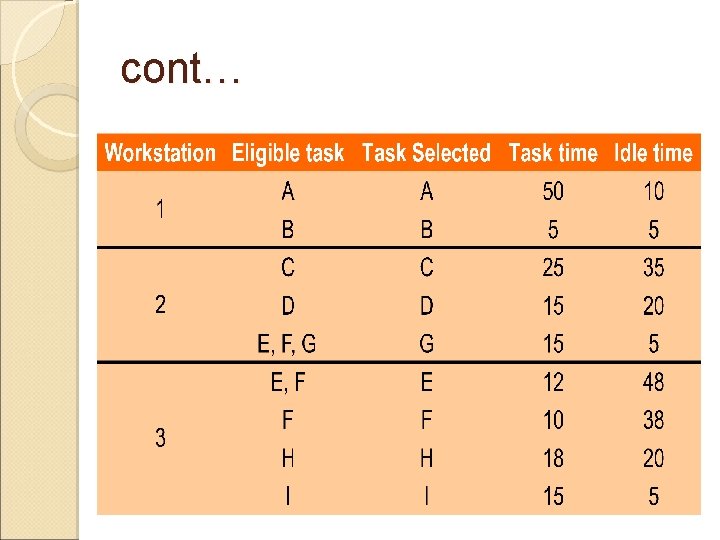
cont….
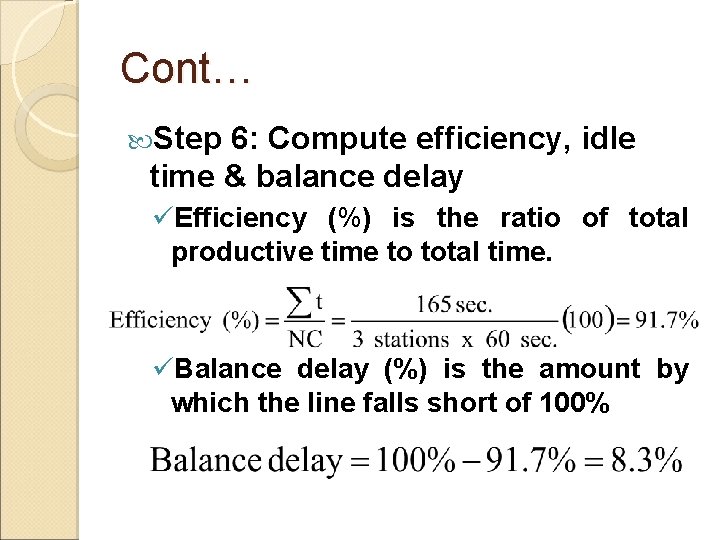
Cont… Step 6: Compute efficiency, idle time & balance delay üEfficiency (%) is the ratio of total productive time to total time. üBalance delay (%) is the amount by which the line falls short of 100%
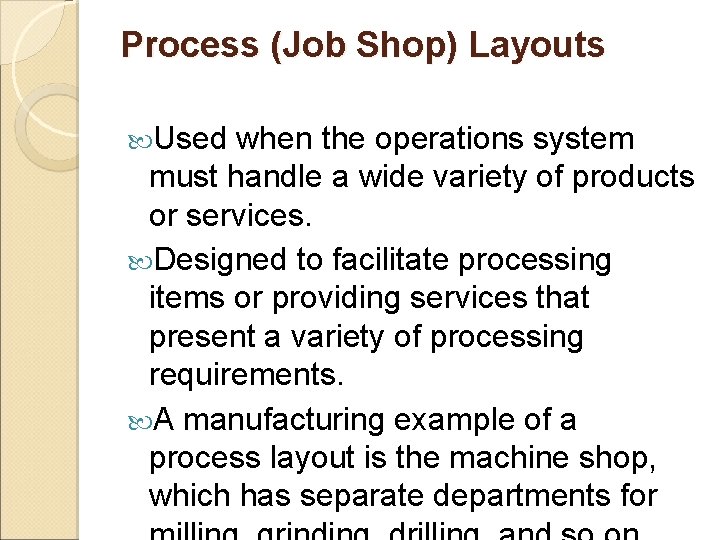
Process (Job Shop) Layouts Used when the operations system must handle a wide variety of products or services. Designed to facilitate processing items or providing services that present a variety of processing requirements. A manufacturing example of a process layout is the machine shop, which has separate departments for
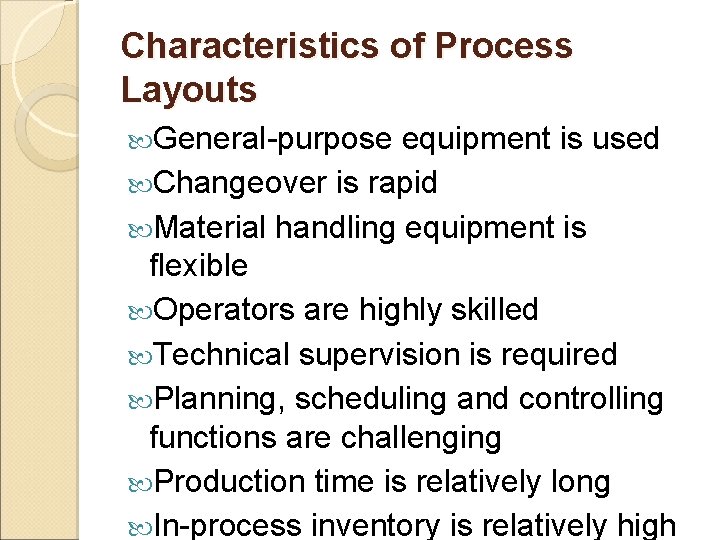
Characteristics of Process Layouts General-purpose equipment is used Changeover is rapid Material handling equipment is flexible Operators are highly skilled Technical supervision is required Planning, scheduling and controlling functions are challenging Production time is relatively long In-process inventory is relatively high
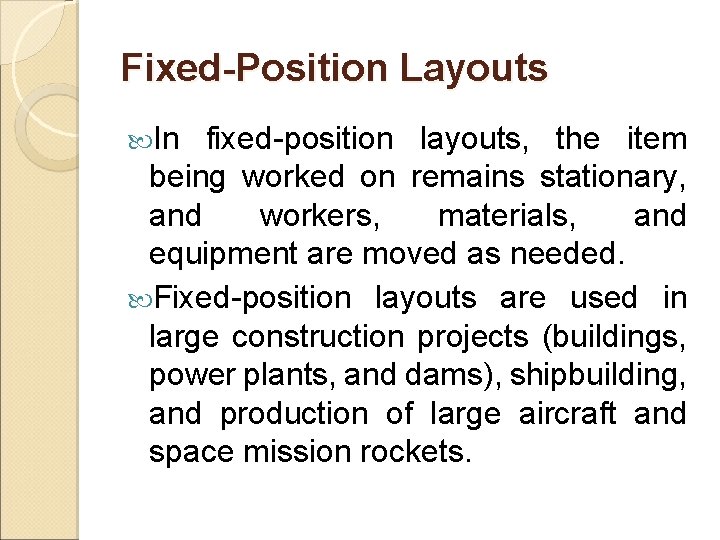
Fixed-Position Layouts In fixed-position layouts, the item being worked on remains stationary, and workers, materials, and equipment are moved as needed. Fixed-position layouts are used in large construction projects (buildings, power plants, and dams), shipbuilding, and production of large aircraft and space mission rockets.