ETA Environmental Health and Safety Monthly Metrics July
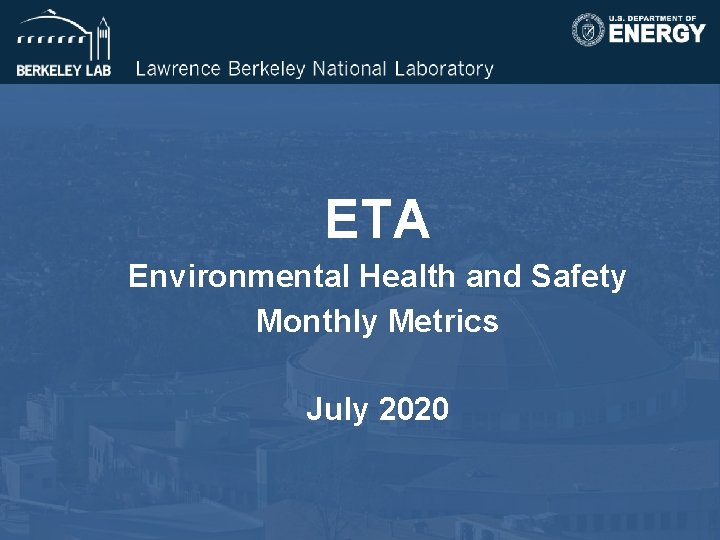
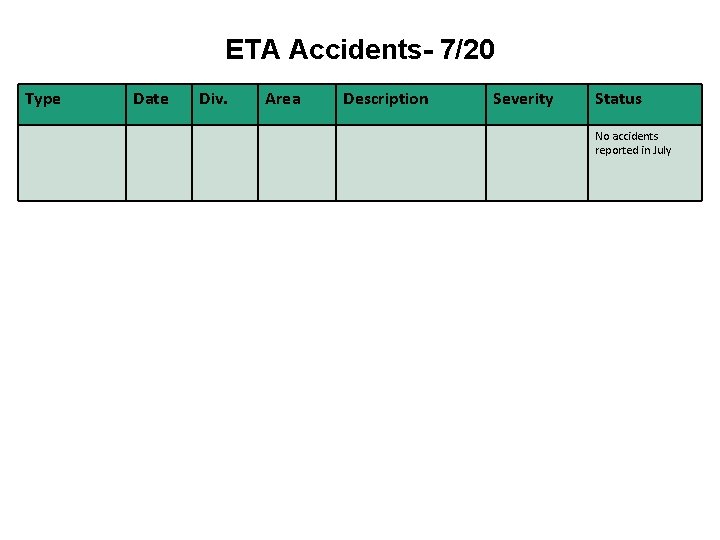
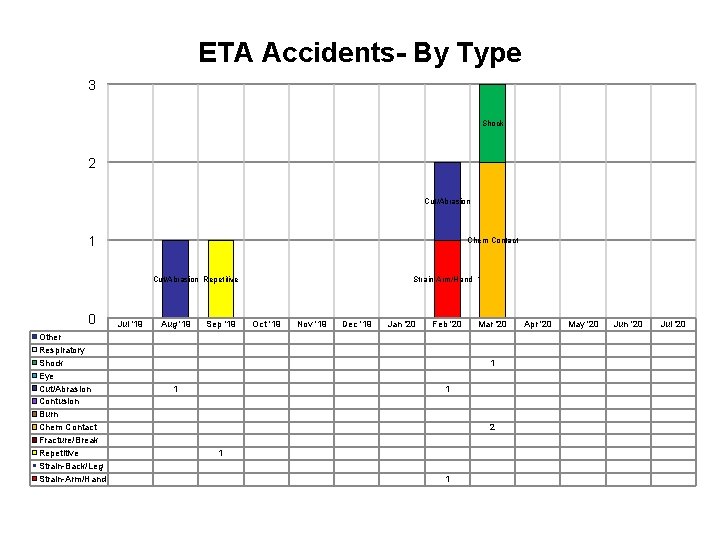
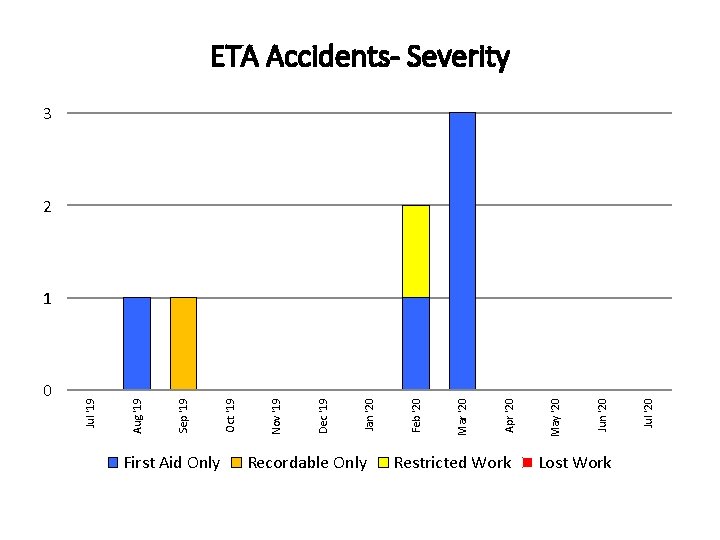
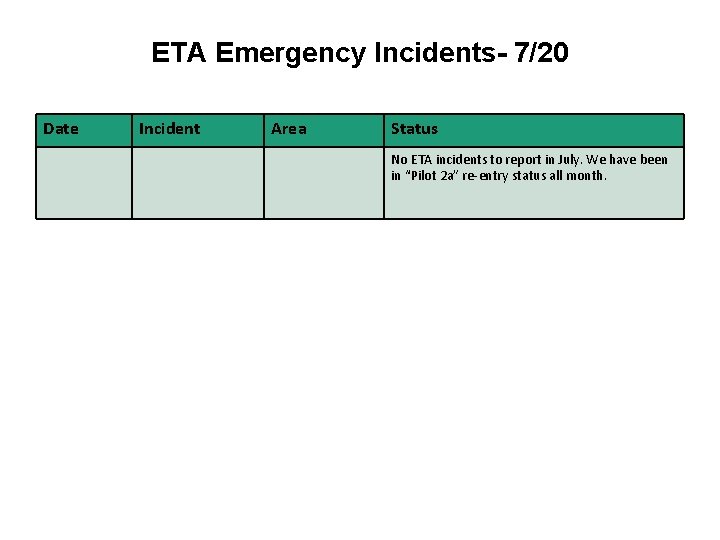
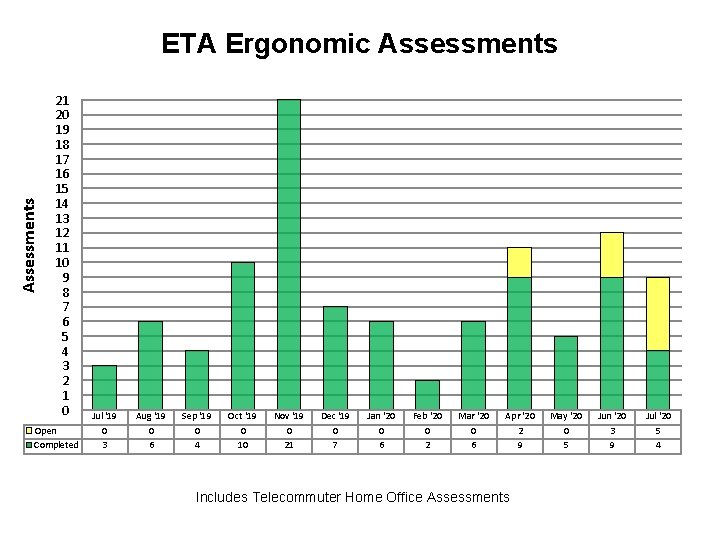
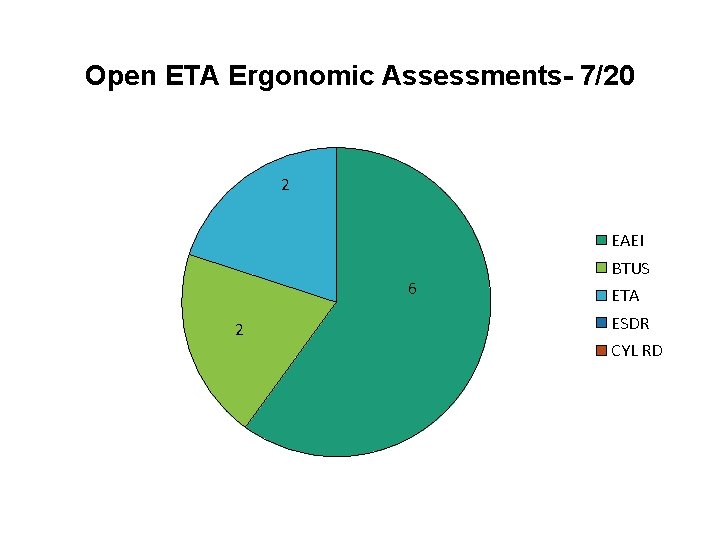
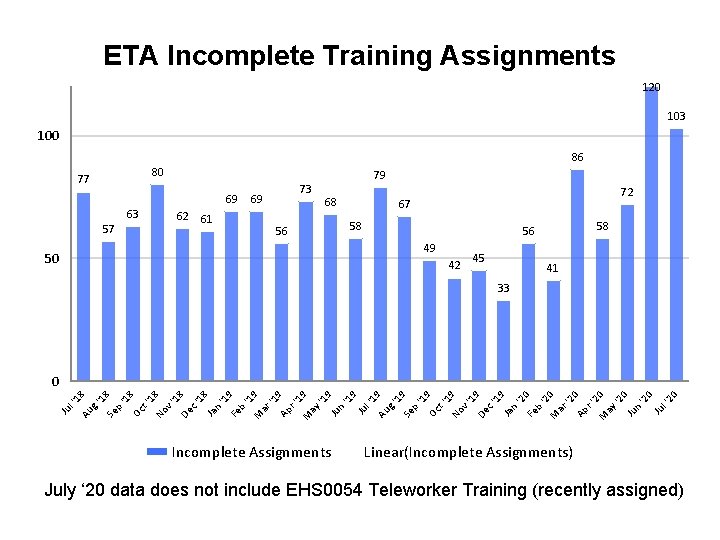
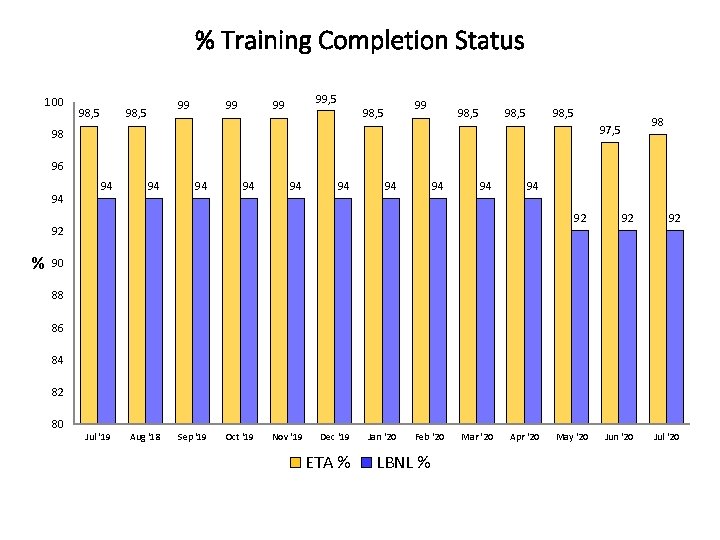
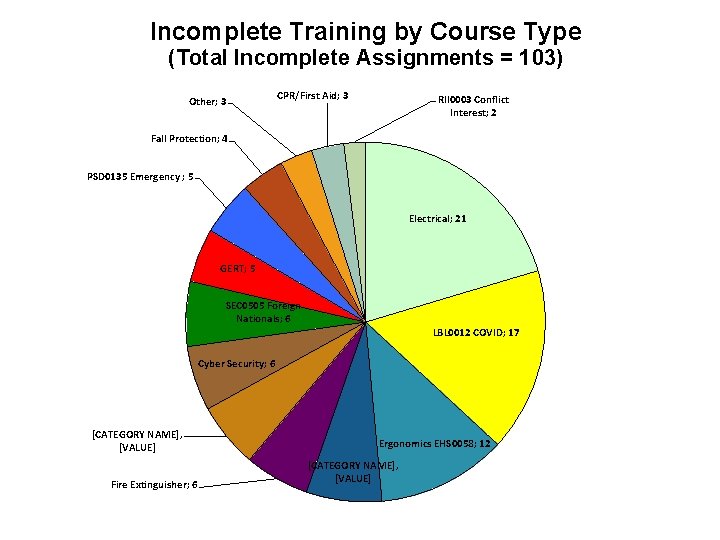
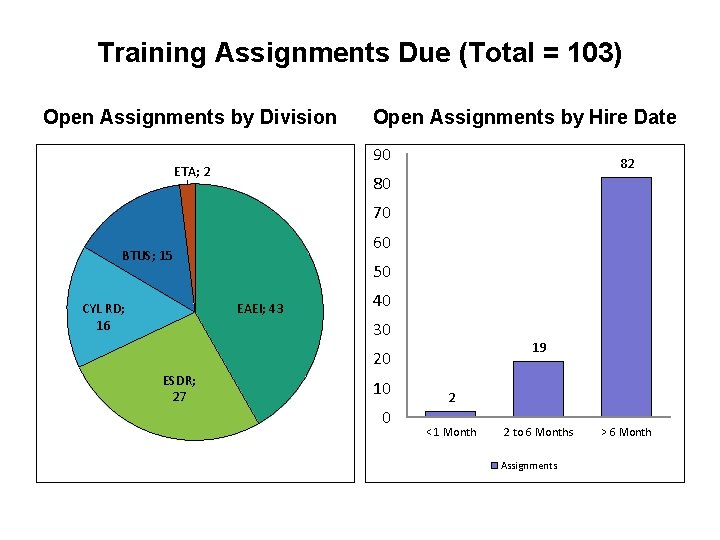
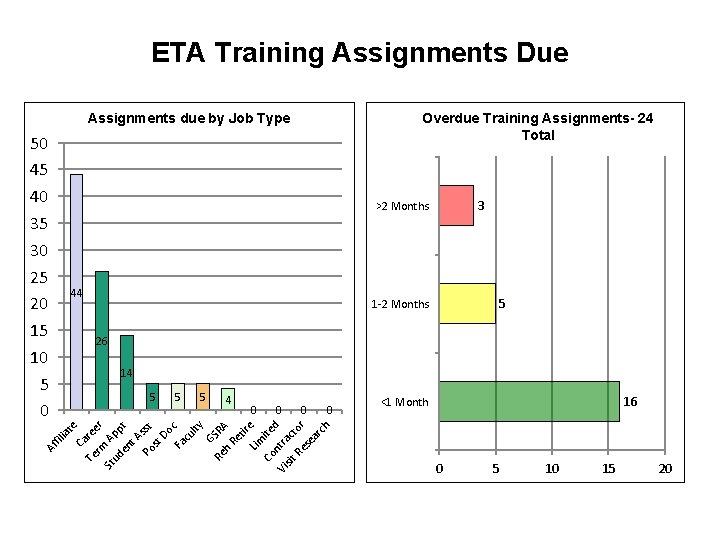
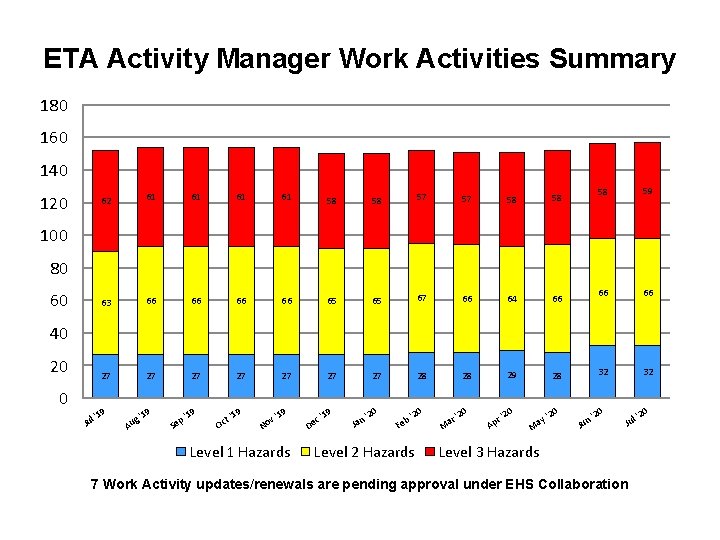
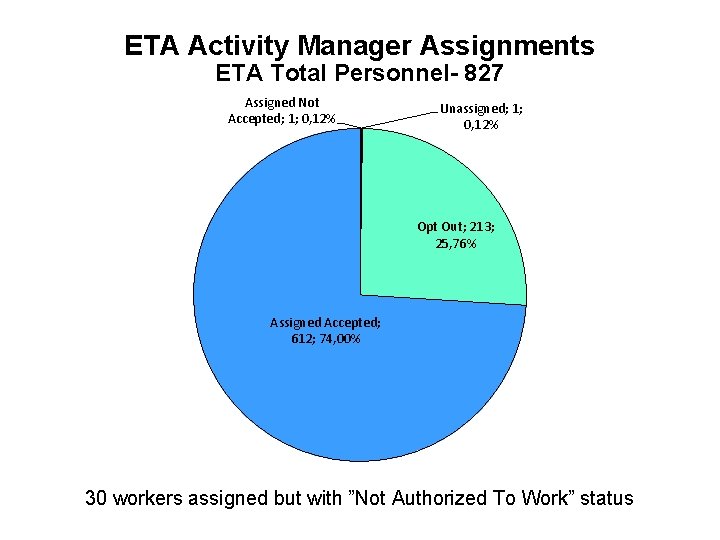
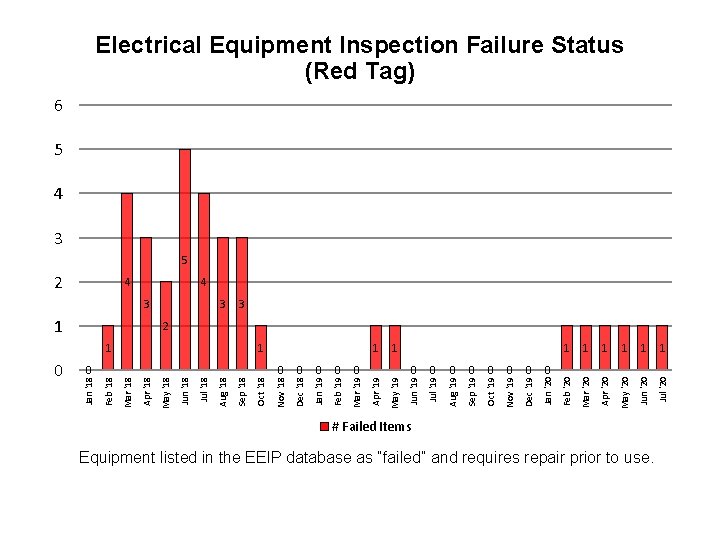
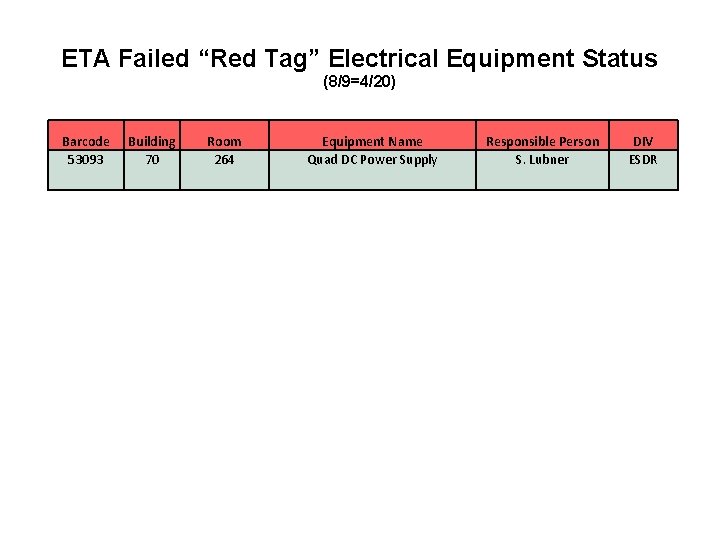
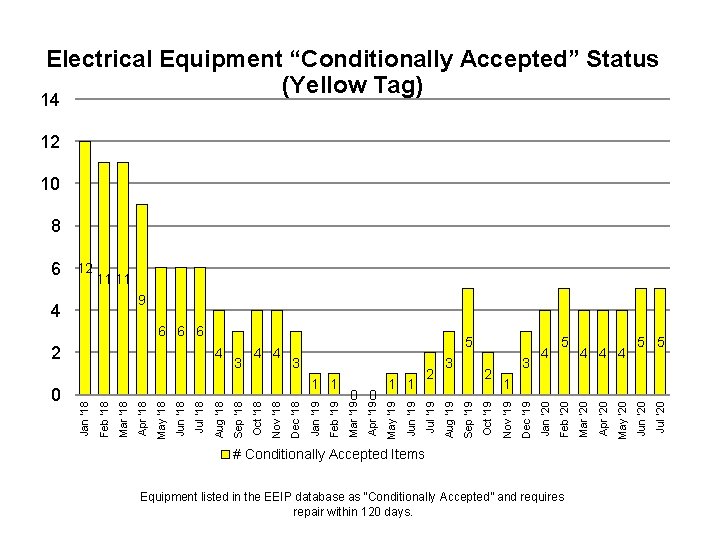
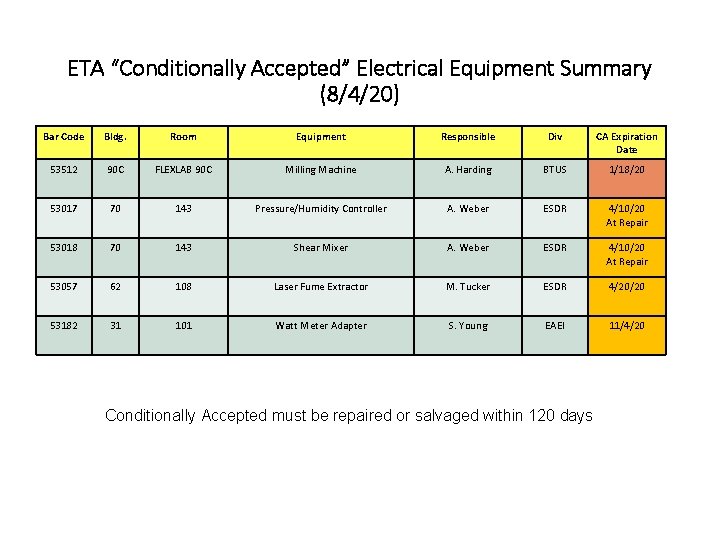
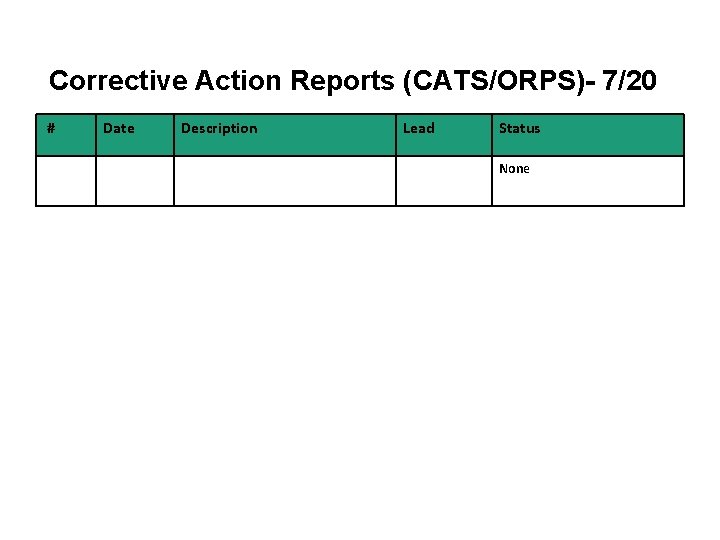
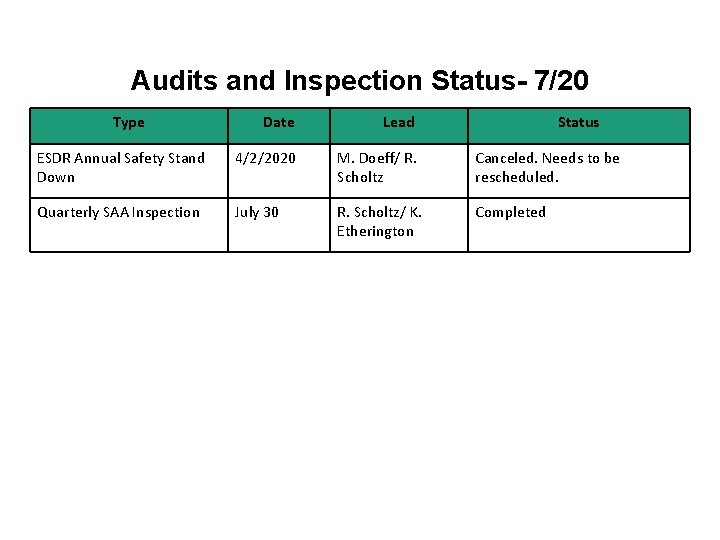
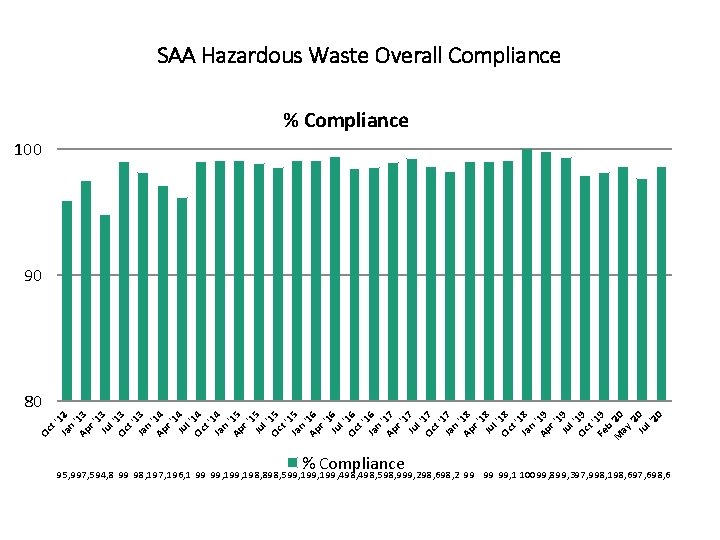
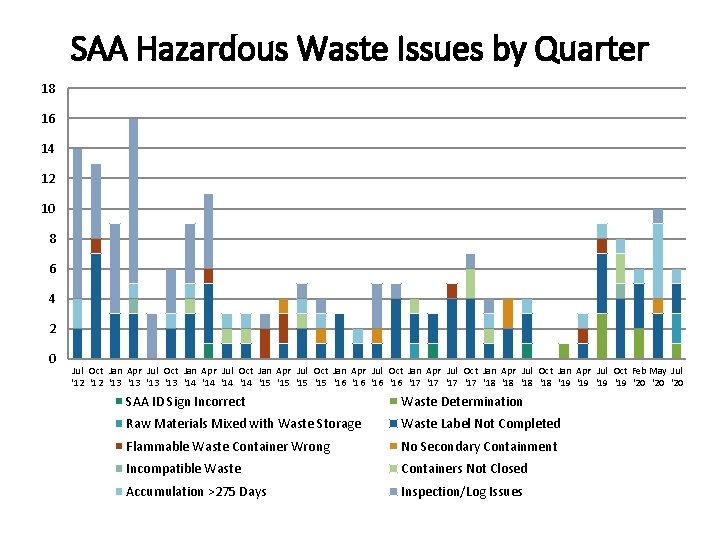
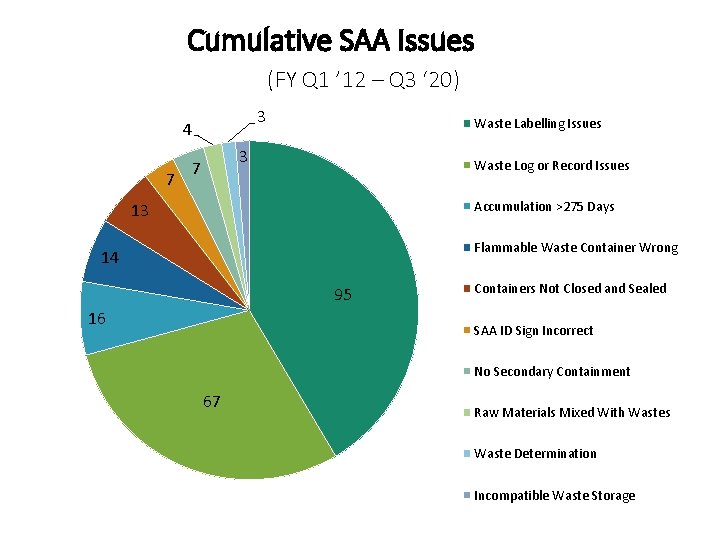
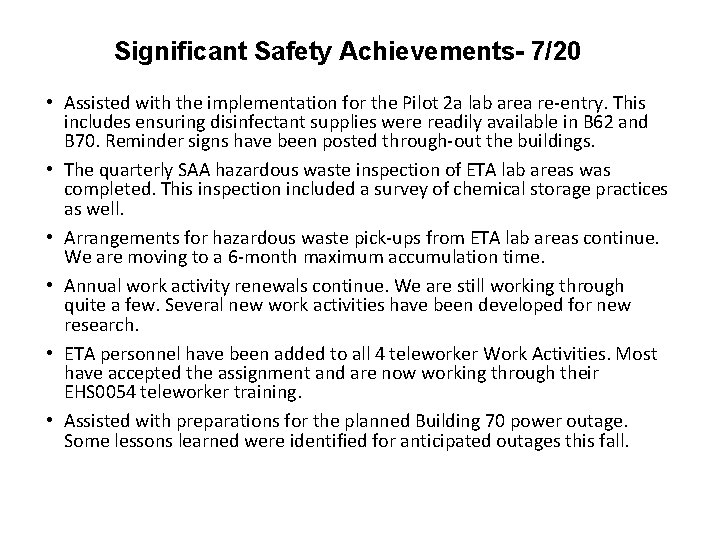
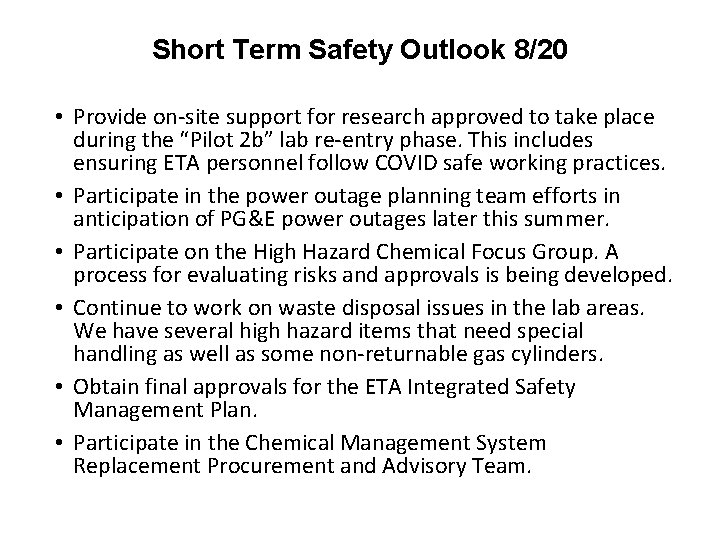
- Slides: 25
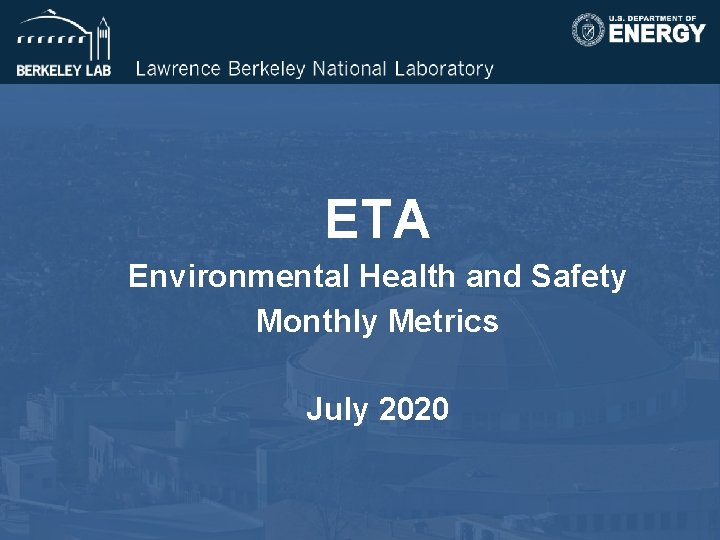
ETA Environmental Health and Safety Monthly Metrics July 2020
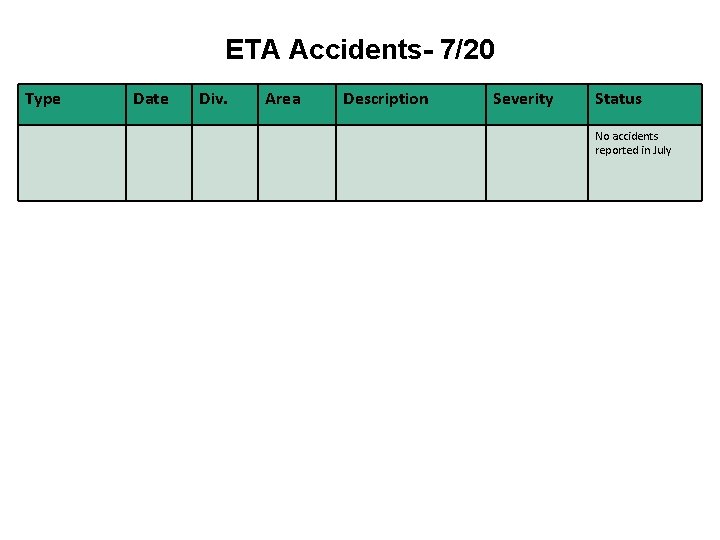
ETA Accidents- 7/20 Type Date Div. Area Description Severity Status No accidents reported in July
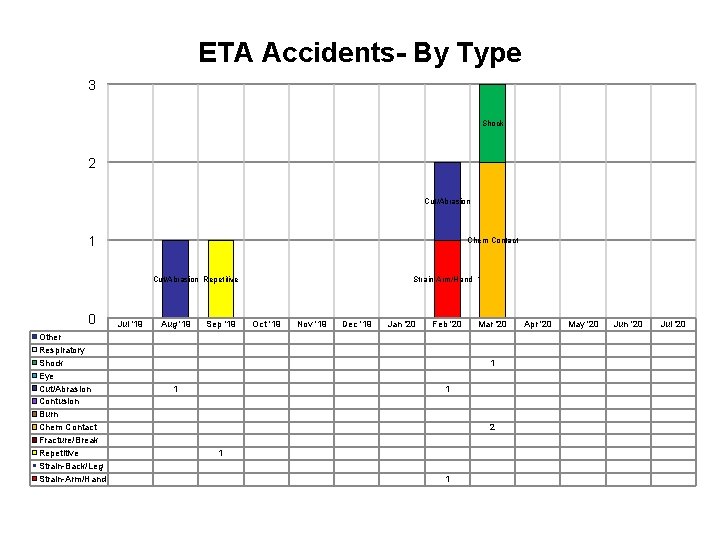
ETA Accidents- By Type 3 Shock 2 Cut/Abrasion 1 Chem Contact Cut/Abrasion Repetitive 0 Other Respiratory Shock Eye Cut/Abrasion Contusion Burn Chem Contact Fracture/Break Repetitive Strain-Back/Leg Strain-Arm/Hand Jul '19 Aug '19 Sep '19 Strain-Arm/Hand 1 Oct '19 Nov '19 Dec '19 Jan '20 Feb '20 Mar '20 1 1 1 2 1 1 Apr '20 May '20 Jun '20 Jul '20
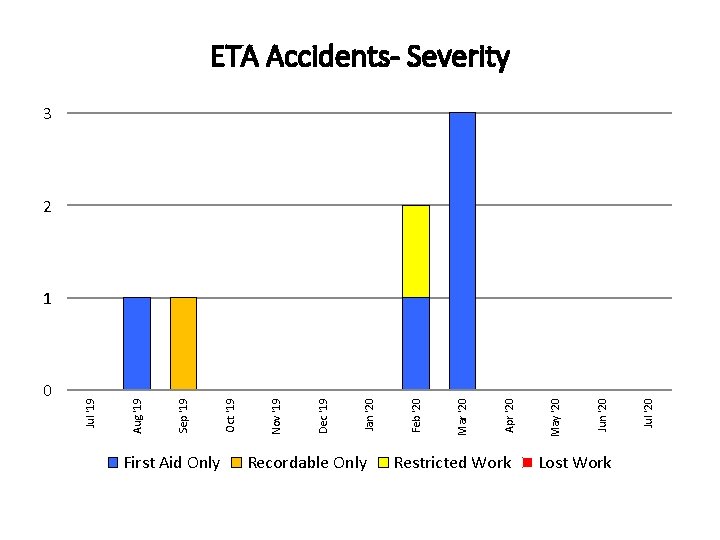
0 First Aid Only Recordable Only Restricted Work Lost Work Jul '20 Jun '20 May '20 Apr '20 Mar '20 Feb '20 Jan '20 Dec '19 Nov '19 Oct '19 Sep '19 Aug '19 Jul '19 ETA Accidents- Severity 3 2 1
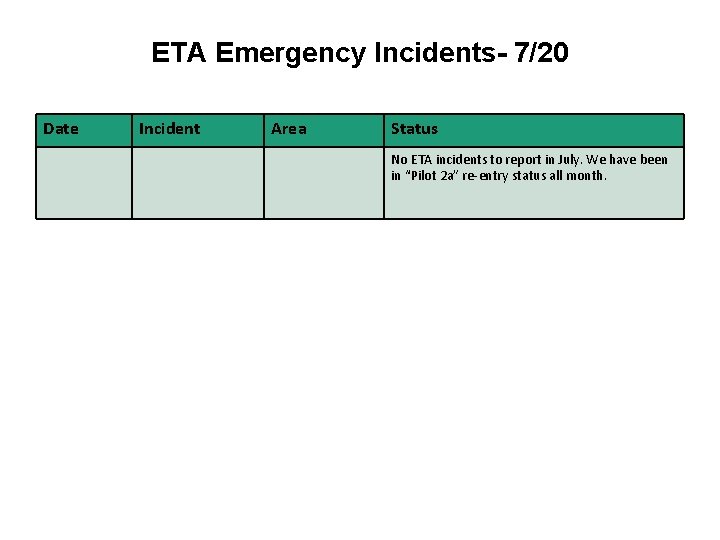
ETA Emergency Incidents- 7/20 Date Incident Area Status No ETA incidents to report in July. We have been in “Pilot 2 a” re-entry status all month.
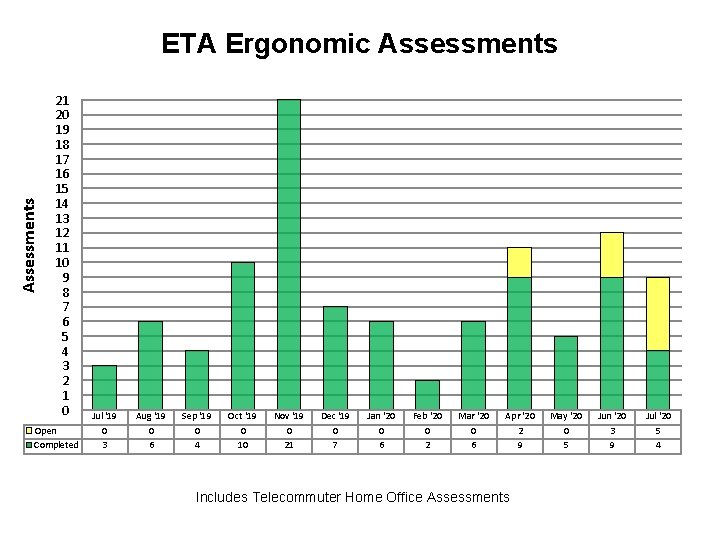
Assessments ETA Ergonomic Assessments 21 20 19 18 17 16 15 14 13 12 11 10 9 8 7 6 5 4 3 2 1 0 Open Completed Jul '19 0 3 Aug '19 0 6 Sep '19 0 4 Oct '19 0 10 Nov '19 0 21 Dec '19 0 7 Jan '20 0 6 Feb '20 0 2 Mar '20 0 6 Apr '20 2 9 Includes Telecommuter Home Office Assessments May '20 0 5 Jun '20 3 9 Jul '20 5 4
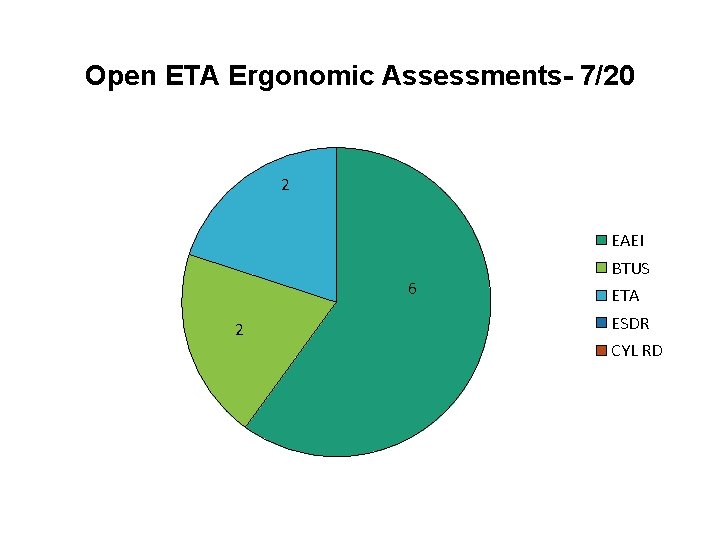
Open ETA Ergonomic Assessments- 7/20 2 EAEI 6 2 BTUS ETA ESDR CYL RD
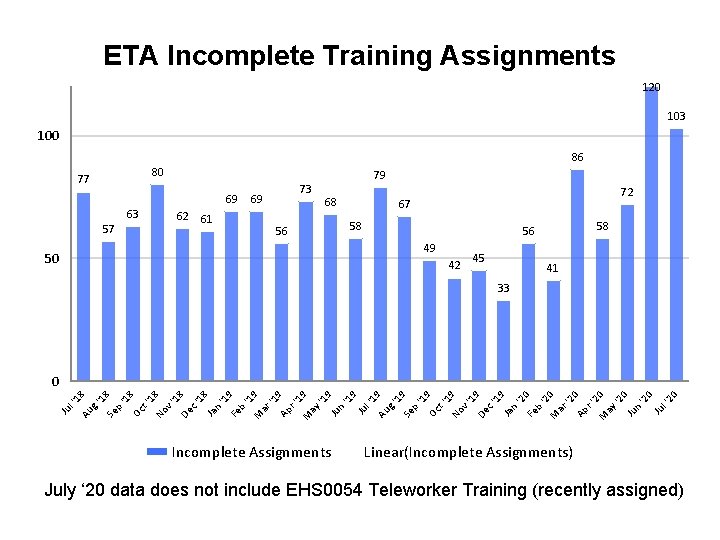
ETA Incomplete Training Assignments 120 103 100 86 80 77 79 69 63 57 62 61 73 69 68 56 72 67 58 49 50 58 56 42 45 41 33 t' 1 No 8 v' 1 De 8 c' 18 Ja n '1 9 Fe b '1 M 9 ar '1 9 Ap r' 1 M 9 ay '1 9 Ju n '1 9 Ju l '1 Au 9 g' 19 Se p '1 9 Oc t' 1 No 9 v' 1 De 9 c' 19 Ja n '2 0 Fe b '2 M 0 ar '2 0 Ap r' 2 M 0 ay '2 0 Ju n '2 0 Ju l '2 0 8 '1 Oc 18 Se p g' Au Ju l '1 8 0 Incomplete Assignments Linear(Incomplete Assignments) July ‘ 20 data does not include EHS 0054 Teleworker Training (recently assigned)
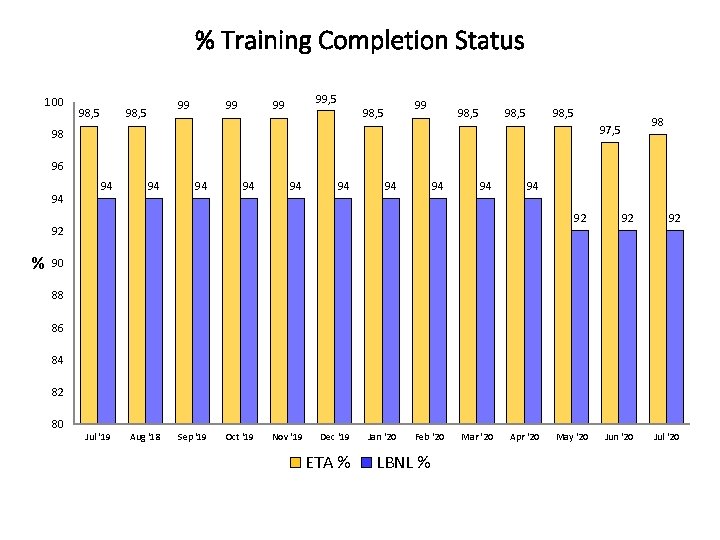
% Training Completion Status 100 98, 5 99 99, 5 99 99 98, 5 98 97, 5 98 96 94 94 94 92 % 92 92 92 May '20 Jun '20 Jul '20 90 88 86 84 82 80 Jul '19 Aug '18 Sep '19 Oct '19 Nov '19 Dec '19 ETA % Jan '20 Feb '20 LBNL % Mar '20 Apr '20
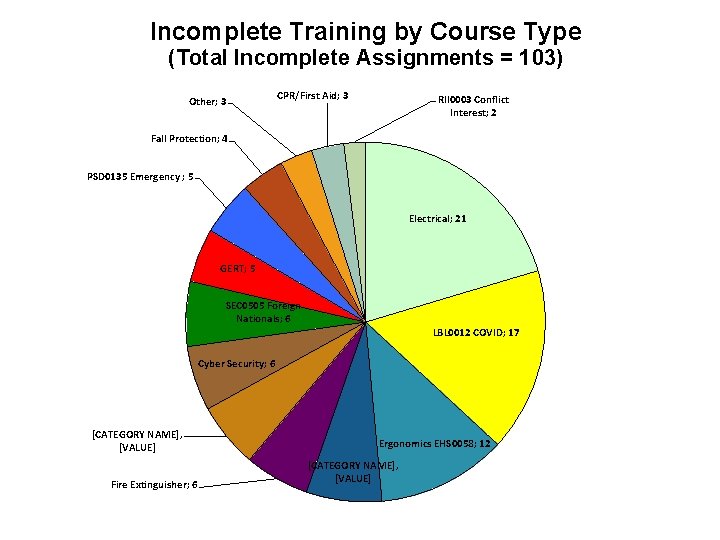
Incomplete Training by Course Type (Total Incomplete Assignments = 103) Other; 3 CPR/First Aid; 3 RII 0003 Conflict Interest; 2 Fall Protection; 4 PSD 0135 Emergency ; 5 Electrical; 21 GERT; 5 SEC 0505 Foreign Nationals; 6 LBL 0012 COVID; 17 Cyber Security; 6 [CATEGORY NAME], [VALUE] Fire Extinguisher; 6 Ergonomics EHS 0058; 12 [CATEGORY NAME], [VALUE]
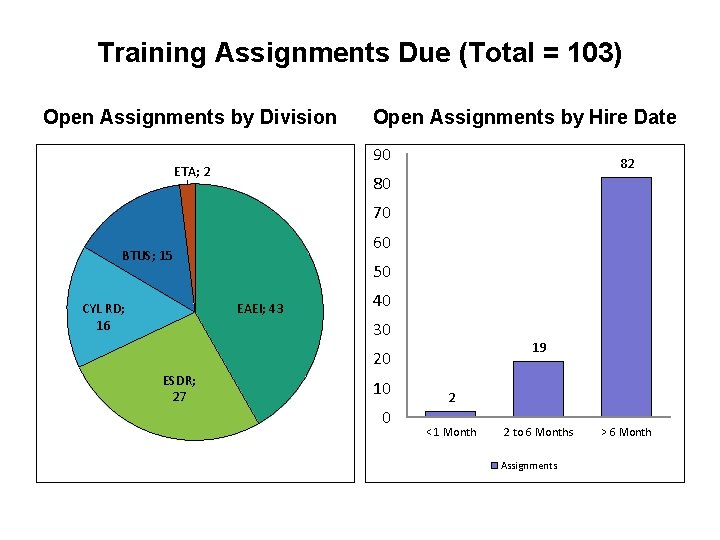
Training Assignments Due (Total = 103) Open Assignments by Division Open Assignments by Hire Date 90 ETA; 2 82 80 70 60 BTUS; 15 CYL RD; 16 50 EAEI; 43 40 30 19 20 ESDR; 27 10 0 2 < 1 Month 2 to 6 Months Assignments > 6 Month
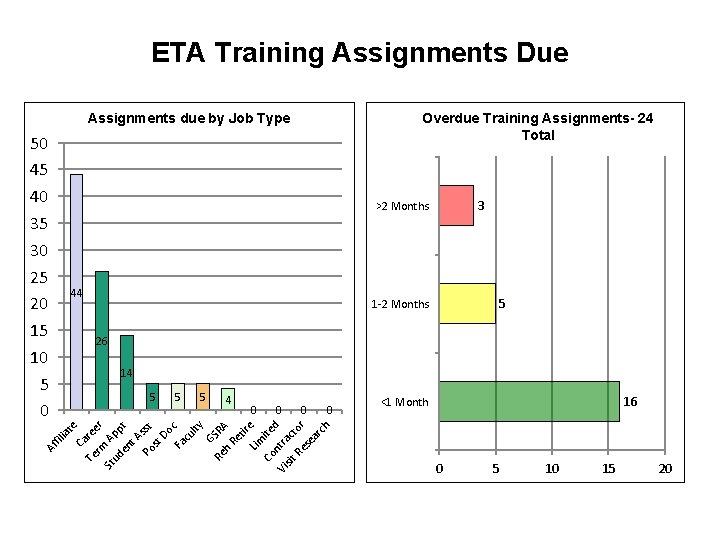
ETA Training Assignments Due Overdue Training Assignments- 24 Total Assignments due by Job Type 50 45 40 35 30 25 20 15 10 5 0 3 >2 Months 44 5 1 -2 Months 26 14 5 4 0 0 Te ree rm r St ud App en t. t. A Po sst. st Do Fa c. cu lty G Re SRA h Re tir Lim e Co ite d Vi ntra sit c Re tor se ar ch 5 16 <1 Month Ca Af fi lia te 5 0 5 10 15 20
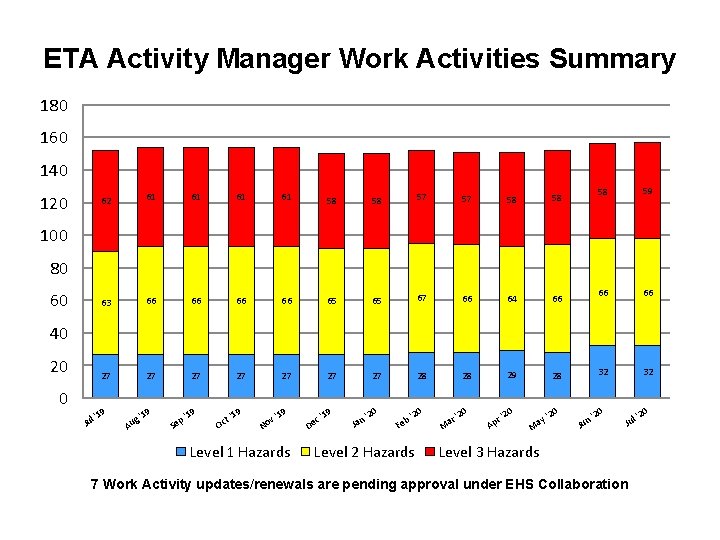
ETA Activity Manager Work Activities Summary 180 160 140 120 62 61 61 58 58 57 57 58 58 63 66 66 65 65 67 66 64 66 27 27 28 28 29 28 58 59 66 66 32 32 100 80 60 40 20 0 Jul '19 g Au '19 p Se '19 t Oc '19 v No '19 Level 1 Hazards c De '19 Jan '20 b Fe '20 Level 2 Hazards r Ma '20 0 r '2 Ap y Ma '20 Jun '20 Jul Level 3 Hazards 7 Work Activity updates/renewals are pending approval under EHS Collaboration '20
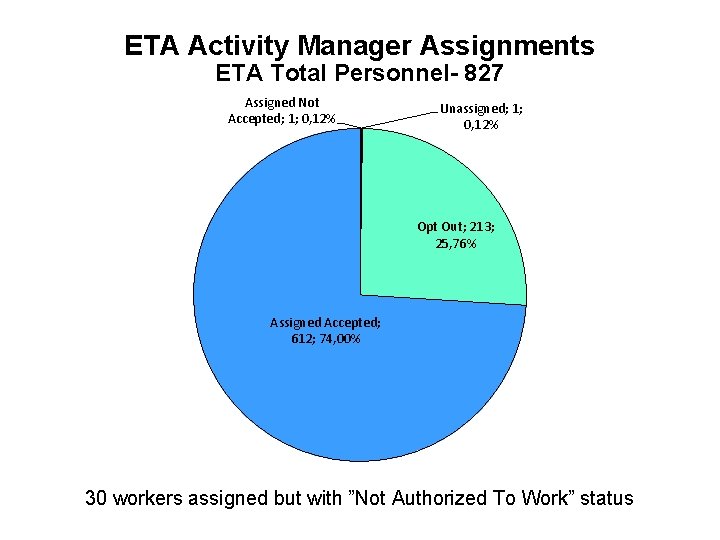
ETA Activity Manager Assignments ETA Total Personnel- 827 Assigned Not Accepted; 1; 0, 12% Unassigned; 1; 0, 12% Opt Out; 213; 25, 76% Assigned Accepted; 612; 74, 00% 30 workers assigned but with ”Not Authorized To Work” status
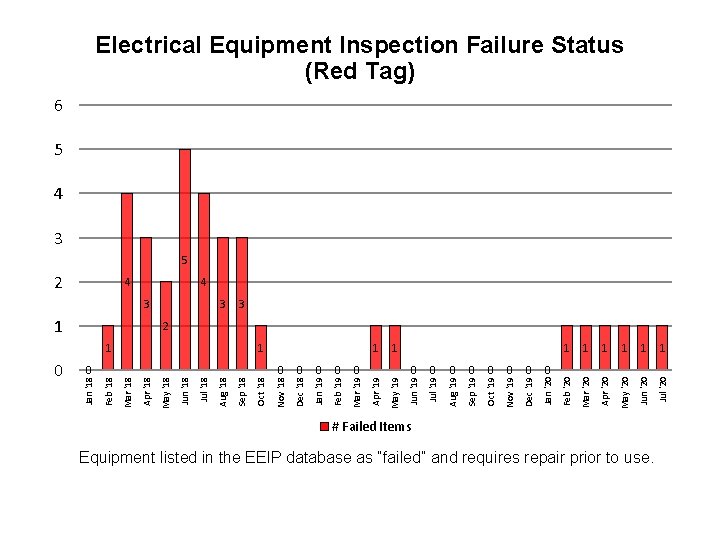
0 0 Nov '18 0 Dec '18 0 Jan '19 0 Feb '19 0 Mar '19 0 Jun '19 0 Jul '19 0 Aug '19 0 Sep '19 0 Oct '19 0 Nov '19 0 Dec '19 0 Jan '20 1 May '19 1 Apr '19 1 Oct '18 1 1 1 Apr '20 May '20 Jun '20 Jul '20 0 1 Mar '20 1 Feb '20 3 Sep '18 3 Aug '18 4 Jul '18 Jun '18 1 May '18 Apr '18 2 Mar '18 Feb '18 Jan '18 Electrical Equipment Inspection Failure Status (Red Tag) 6 5 4 3 2 # Failed Items Equipment listed in the EEIP database as “failed” and requires repair prior to use.
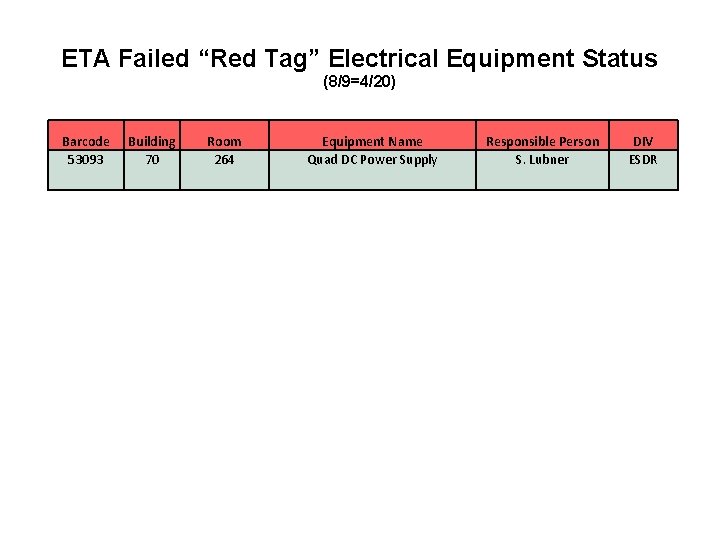
ETA Failed “Red Tag” Electrical Equipment Status (8/9=4/20) Barcode 53093 Building 70 Room 264 Equipment Name Quad DC Power Supply Responsible Person S. Lubner DIV ESDR
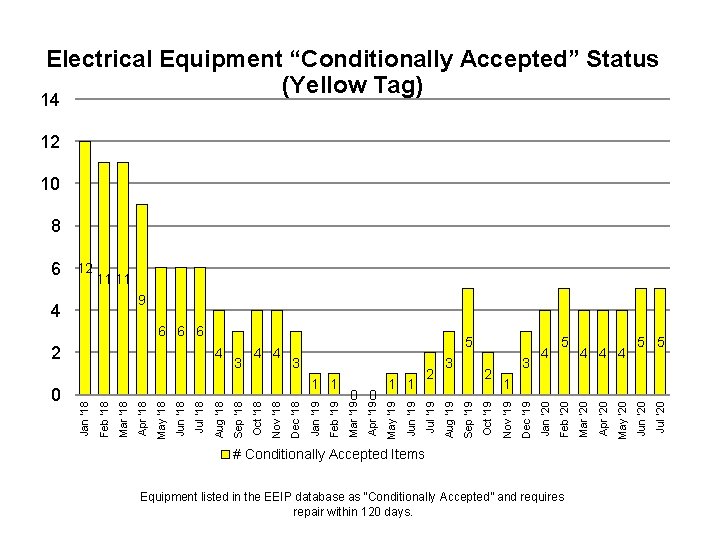
Electrical Equipment “Conditionally Accepted” Status (Yellow Tag) 14 12 10 8 12 11 11 9 5 3 4 5 4 4 4 5 5 # Conditionally Accepted Items Equipment listed in the EEIP database as “Conditionally Accepted” and requires repair within 120 days. Jul '20 Jun '20 May '20 Apr '20 Mar '20 1 Feb '20 2 Dec '19 3 Nov '19 Jul '19 Jun '19 1 1 May '19 Feb '19 Jan '19 Dec '18 Nov '18 Oct '18 Sep '18 Aug '18 Jul '18 Jun '18 May '18 Apr '18 Mar '18 Feb '18 0 0 2 Aug '19 3 Apr '19 3 4 4 1 1 Jan '18 0 4 Mar '19 2 Jan '20 6 6 6 Oct '19 4 Sep '19 6
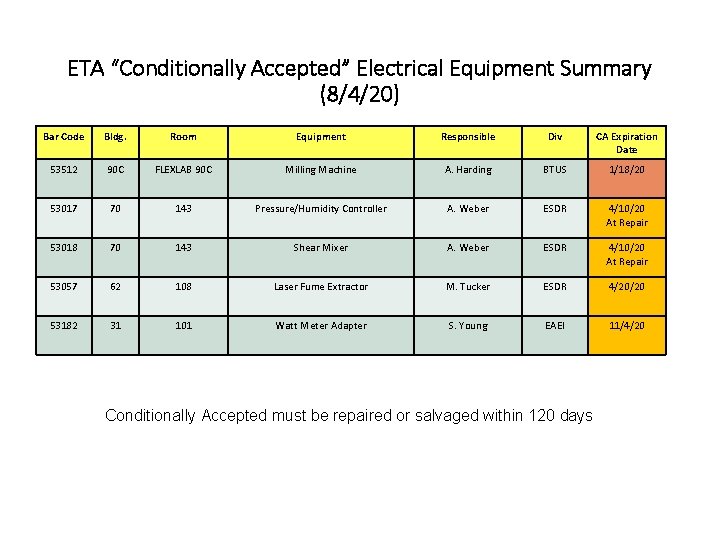
ETA “Conditionally Accepted” Electrical Equipment Summary (8/4/20) Bar Code Bldg. Room Equipment Responsible Div CA Expiration Date 53512 90 C FLEXLAB 90 C Milling Machine A. Harding BTUS 1/18/20 53017 70 143 Pressure/Humidity Controller A. Weber ESDR 4/10/20 At Repair 53018 70 143 Shear Mixer A. Weber ESDR 4/10/20 At Repair 53057 62 108 Laser Fume Extractor M. Tucker ESDR 4/20/20 53182 31 101 Watt Meter Adapter S. Young EAEI 11/4/20 Conditionally Accepted must be repaired or salvaged within 120 days
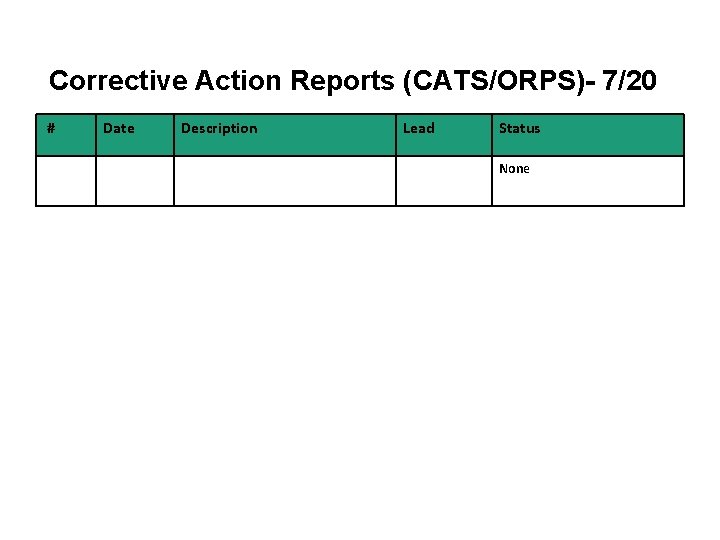
Corrective Action Reports (CATS/ORPS)- 7/20 # Date Description Lead Status None
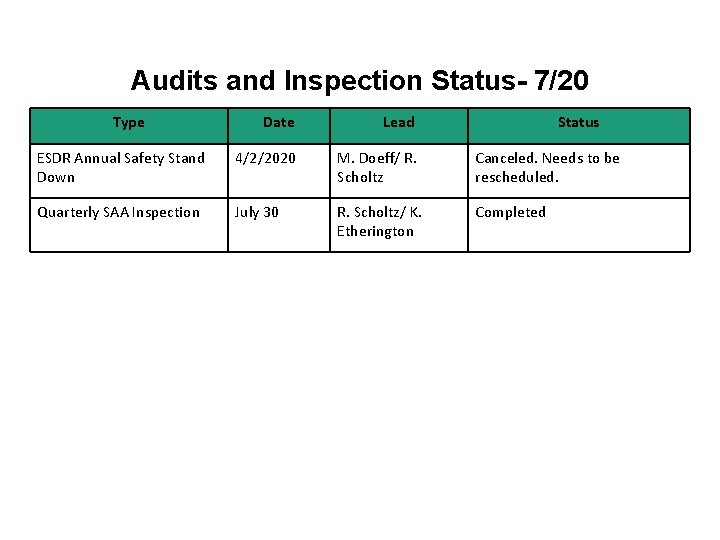
Audits and Inspection Status- 7/20 Type Date Lead Status ESDR Annual Safety Stand Down 4/2/2020 M. Doeff/ R. Scholtz Canceled. Needs to be rescheduled. Quarterly SAA Inspection July 30 R. Scholtz/ K. Etherington Completed
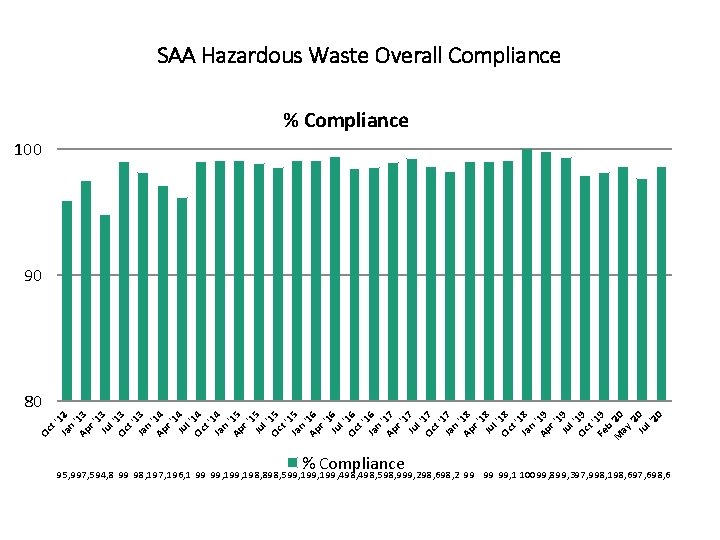
Oc t' Ja 12 n ' Ap 13 r' 1 Ju 3 l '1 Oc 3 t' Ja 13 n ' Ap 14 r' 1 Ju 4 l' Oc 14 t' Ja 14 n ' Ap 15 r' 1 Ju 5 l' Oc 15 t' Ja 15 n ' Ap 16 r' 1 Ju 6 l '1 Oc 6 t' Ja 16 n ' Ap 17 r' 1 Ju 7 l '1 Oc 7 t' Ja 17 n ' Ap 18 r' 1 Ju 8 l '1 Oc 8 t' Ja 18 n ' Ap 19 r' 1 Ju 9 l' Oc 19 t' Fe 19 b M '20 ay '2 Ju 0 l '2 0 SAA Hazardous Waste Overall Compliance % Compliance 100 90 80 95, 997, 594, 8 99 98, 197, 196, 1 99 99, 198, 898, 599, 199, 498, 598, 999, 298, 698, 2 99 99 99, 1 100 99, 899, 397, 998, 198, 697, 698, 6 % Compliance
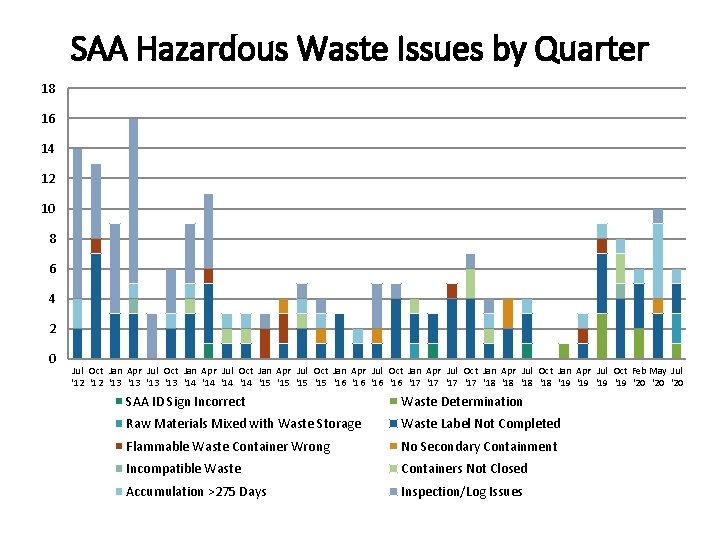
SAA Hazardous Waste Issues by Quarter 18 16 14 12 10 8 6 4 2 0 Jul Oct Jan Apr Jul Oct Jan Apr Jul Oct Feb May Jul '12 '13 '13 '14 '14 '15 '15 '16 '16 '17 '17 '18 '18 '19 '19 '20 '20 SAA ID Sign Incorrect Waste Determination Raw Materials Mixed with Waste Storage Waste Label Not Completed Flammable Waste Container Wrong No Secondary Containment Incompatible Waste Containers Not Closed Accumulation >275 Days Inspection/Log Issues
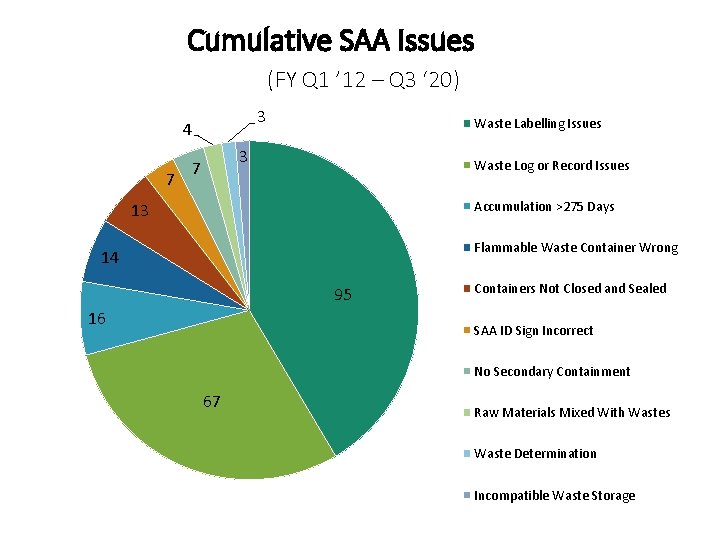
Cumulative SAA Issues (FY Q 1 ’ 12 – Q 3 ‘ 20) 3 4 7 Waste Labelling Issues 3 7 Waste Log or Record Issues Accumulation >275 Days 13 Flammable Waste Container Wrong 14 95 16 Containers Not Closed and Sealed SAA ID Sign Incorrect No Secondary Containment 67 Raw Materials Mixed With Wastes Waste Determination Incompatible Waste Storage
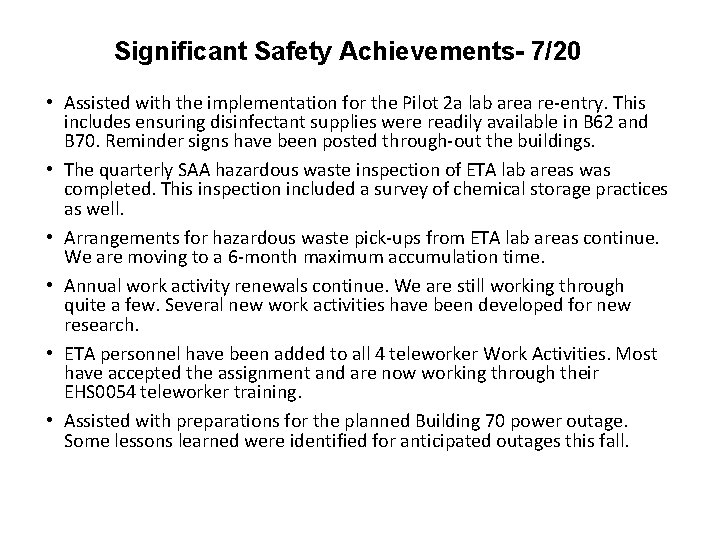
Significant Safety Achievements- 7/20 • Assisted with the implementation for the Pilot 2 a lab area re-entry. This includes ensuring disinfectant supplies were readily available in B 62 and B 70. Reminder signs have been posted through-out the buildings. • The quarterly SAA hazardous waste inspection of ETA lab areas was completed. This inspection included a survey of chemical storage practices as well. • Arrangements for hazardous waste pick-ups from ETA lab areas continue. We are moving to a 6 -month maximum accumulation time. • Annual work activity renewals continue. We are still working through quite a few. Several new work activities have been developed for new research. • ETA personnel have been added to all 4 teleworker Work Activities. Most have accepted the assignment and are now working through their EHS 0054 teleworker training. • Assisted with preparations for the planned Building 70 power outage. Some lessons learned were identified for anticipated outages this fall.
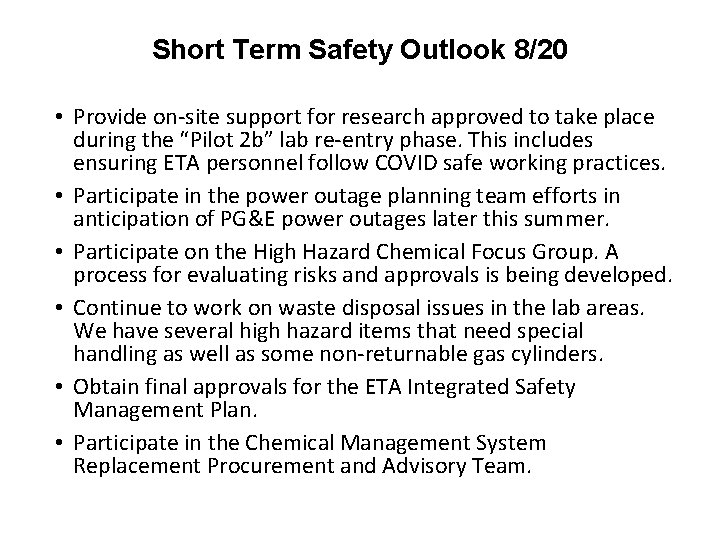
Short Term Safety Outlook 8/20 • Provide on-site support for research approved to take place during the “Pilot 2 b” lab re-entry phase. This includes ensuring ETA personnel follow COVID safe working practices. • Participate in the power outage planning team efforts in anticipation of PG&E power outages later this summer. • Participate on the High Hazard Chemical Focus Group. A process for evaluating risks and approvals is being developed. • Continue to work on waste disposal issues in the lab areas. We have several high hazard items that need special handling as well as some non-returnable gas cylinders. • Obtain final approvals for the ETA Integrated Safety Management Plan. • Participate in the Chemical Management System Replacement Procurement and Advisory Team.
Osu ehs training
Environmental health and safety uf
Oregon state
Wsu environmental health and safety
Penn state environmental health and safety
Esh environmental safety health
Safety margin ratio
Ncq greenwich
Ccps process safety metrics
Health metrics network
Wireless health
Job safety and environmental analysis
February march april may june july august september
Health social and environmental responsibility
Social and environmental responsibility pdf grade 10
Health and environmental sciences institute
Personal community and environmental health
John and marcia monthly spending plan 1 answer key
Portal of entry
Environmental safety signs
No work prior to safety/environmental induction sign
Environmental induction presentation
Missing in venice harris burdick
Captain tory picture
July 1-4 1863
Tender definition