DPT 321 INJECTION MOLD DESIGN School of Manufacturing
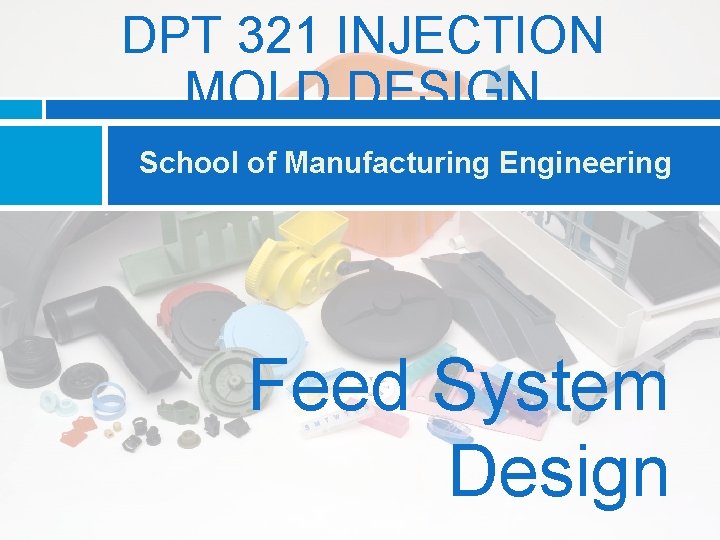
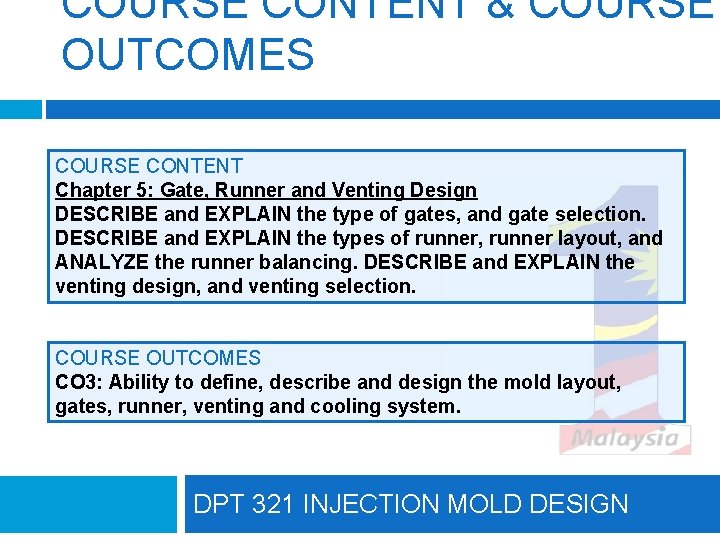
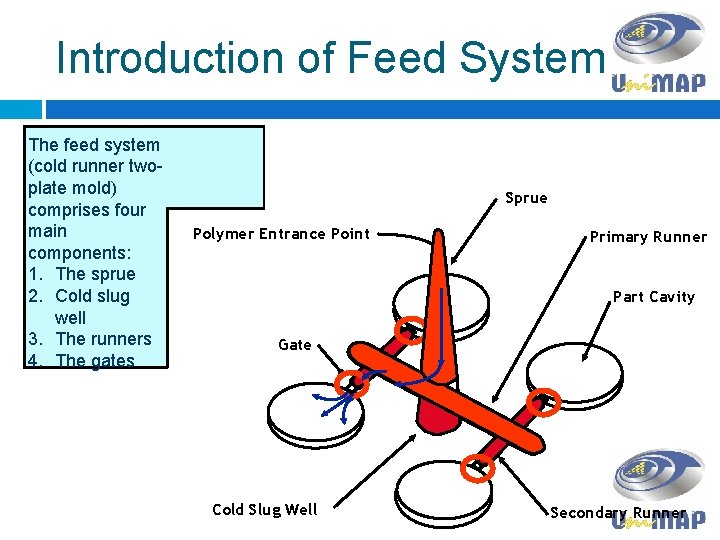

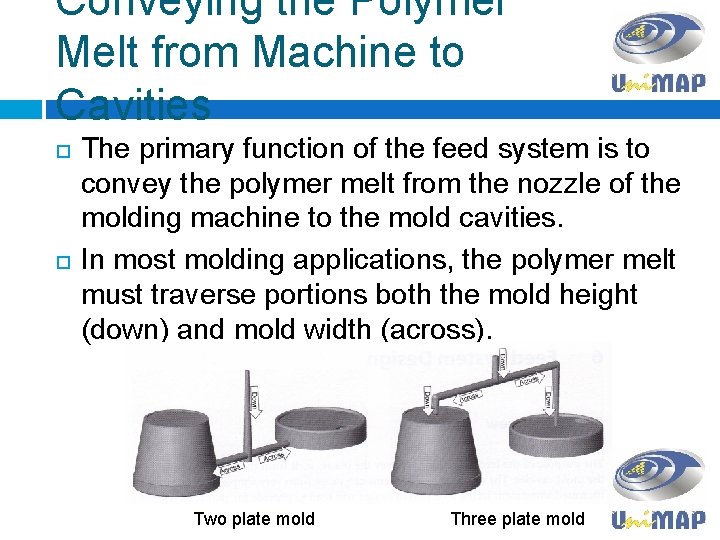
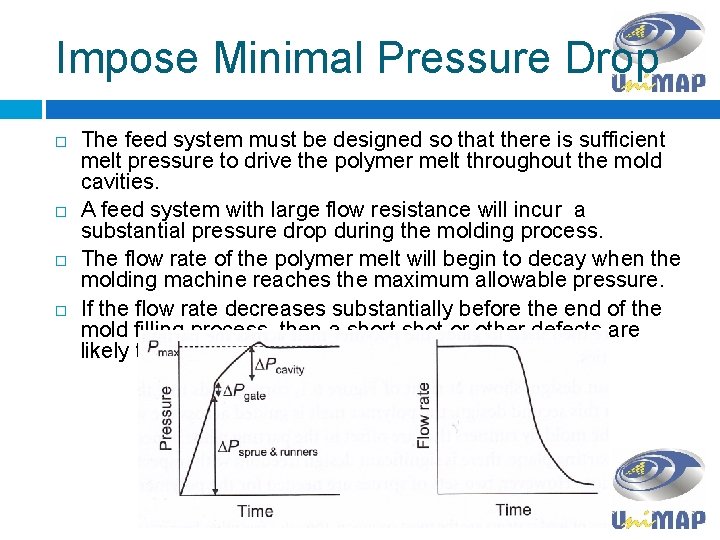
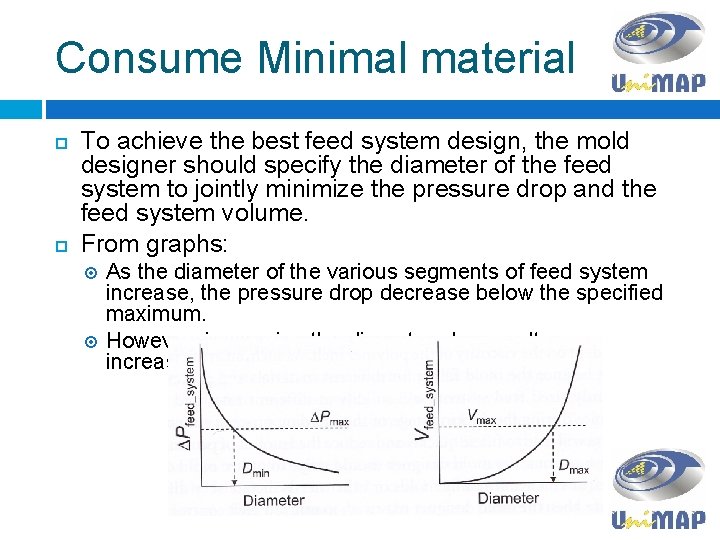

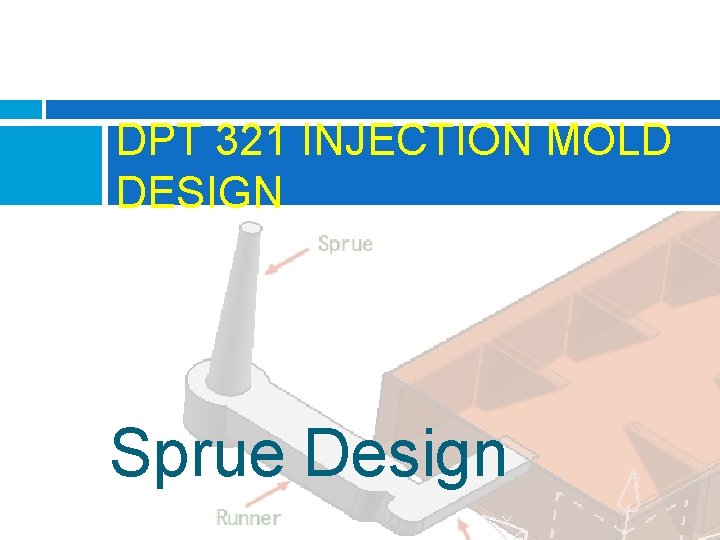
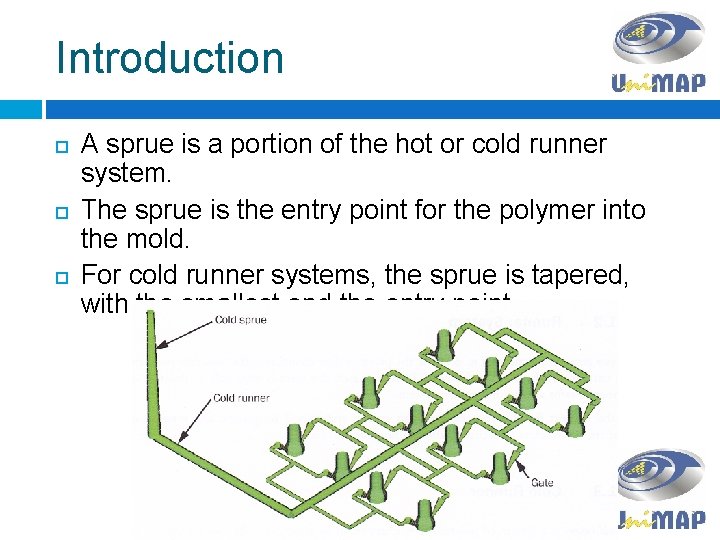
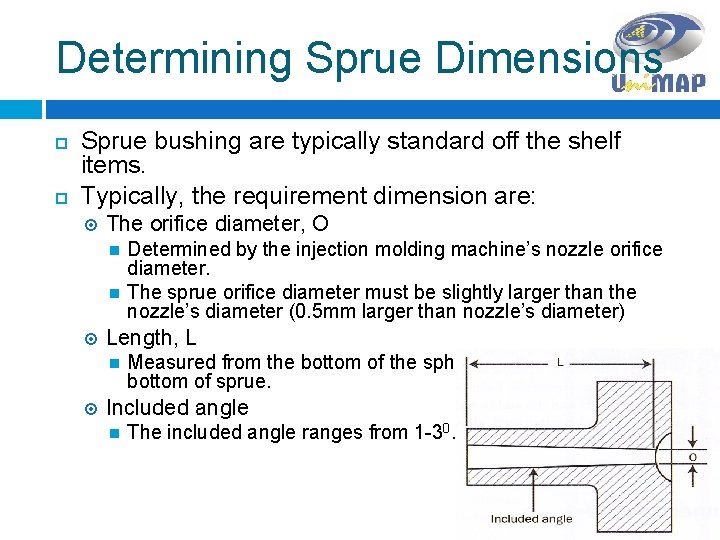
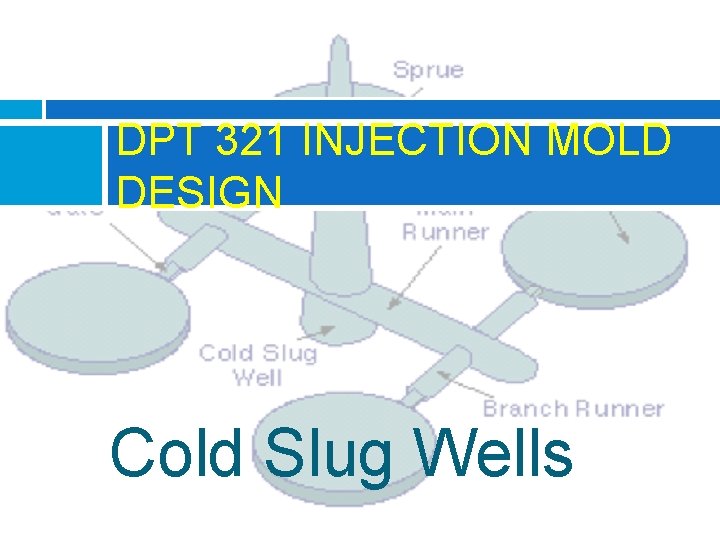
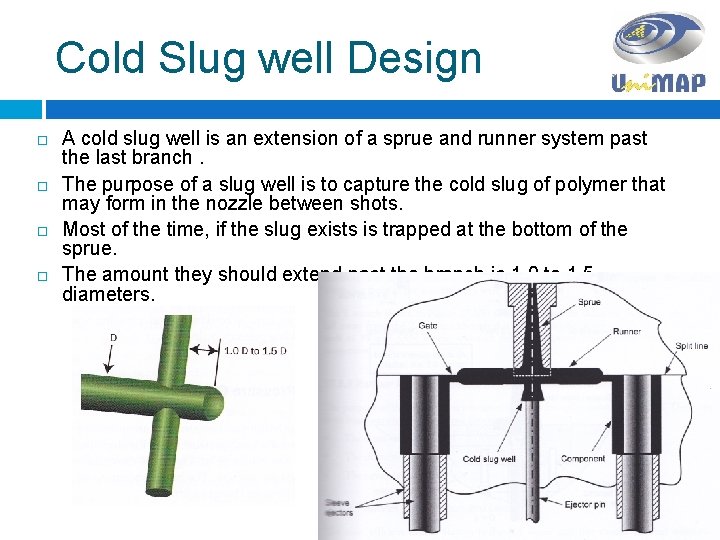
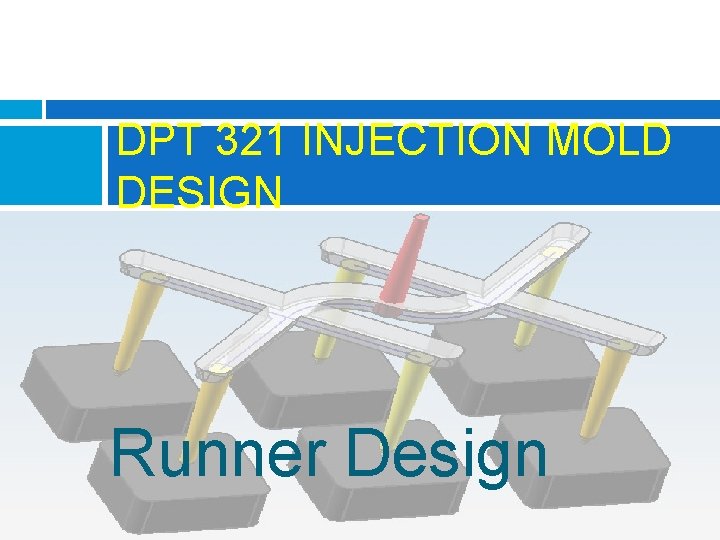
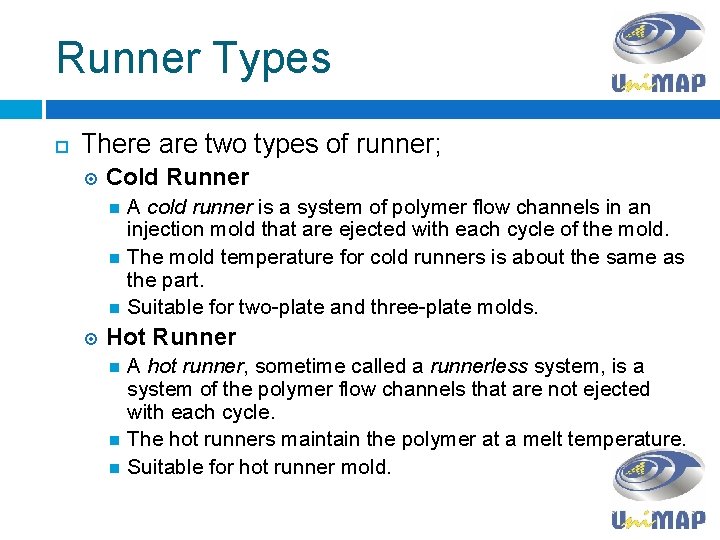
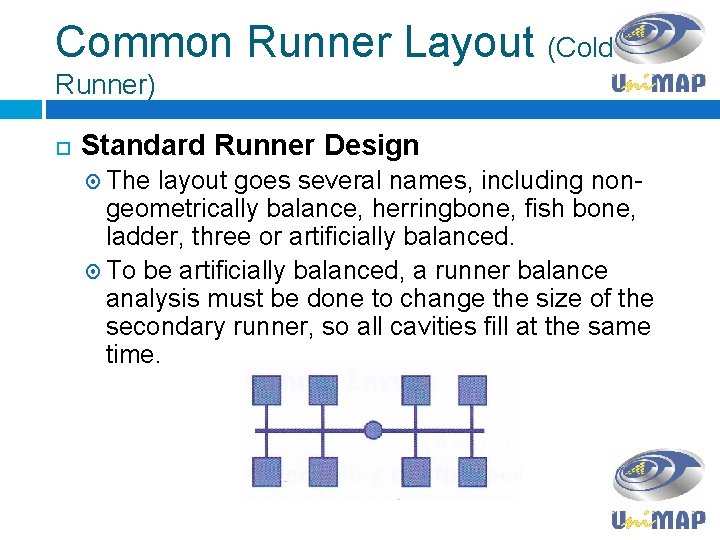
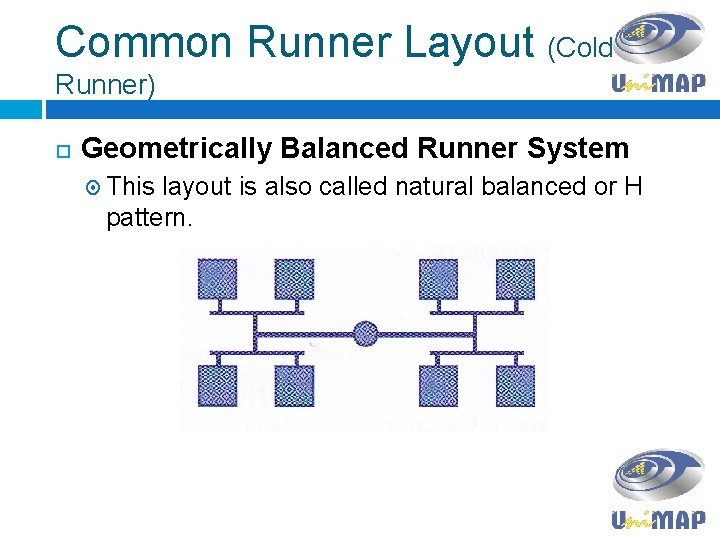
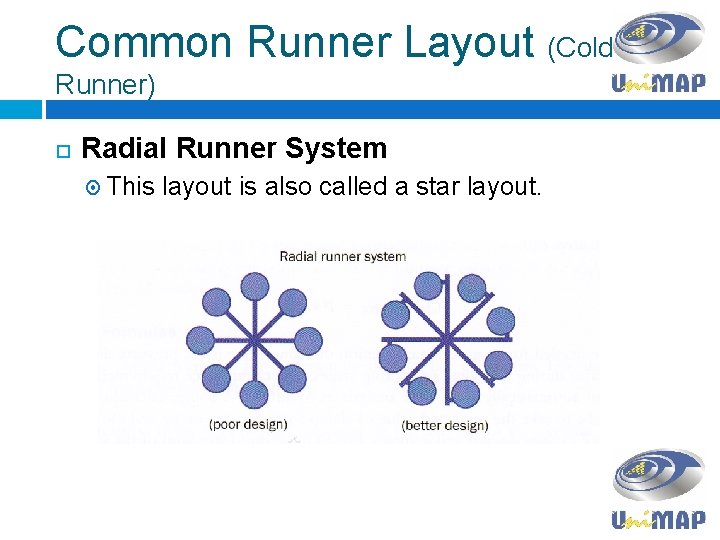
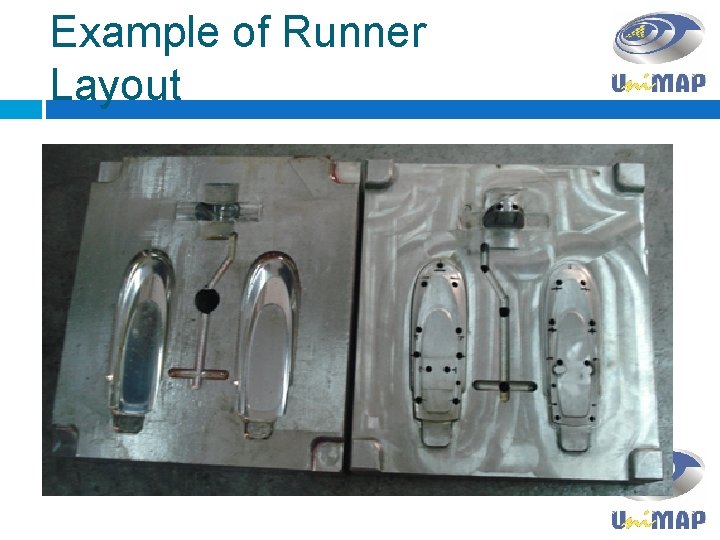
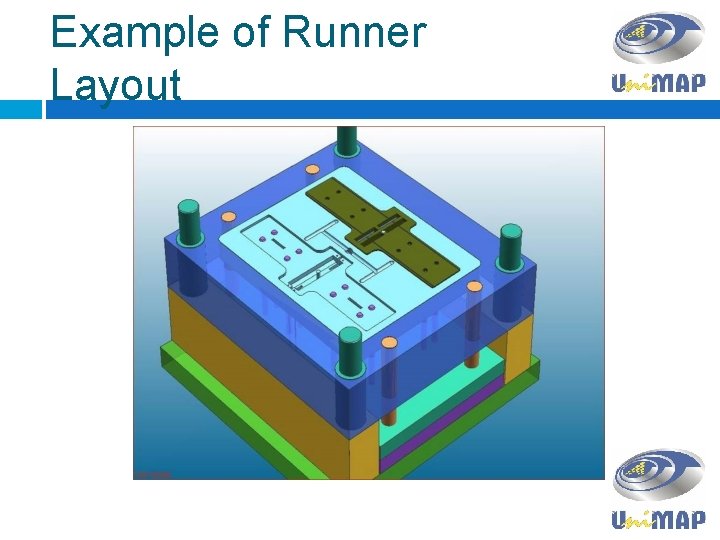
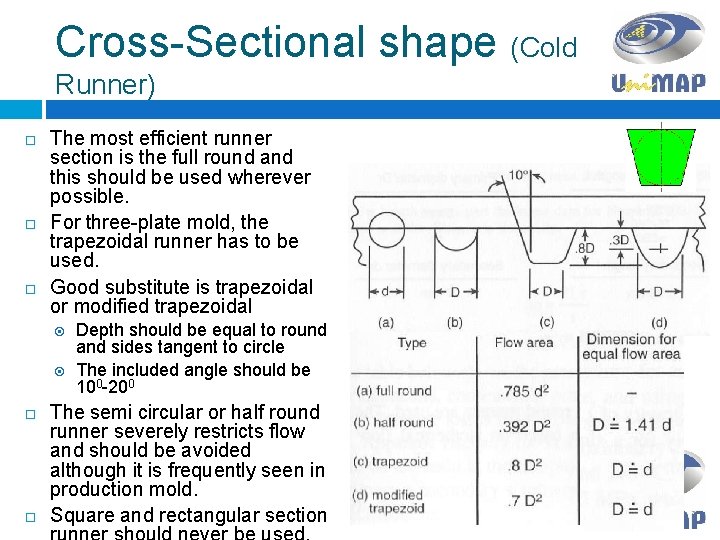
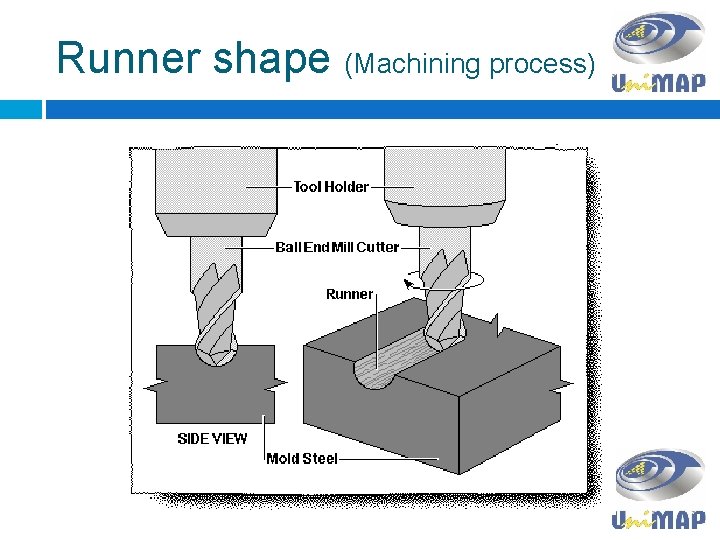
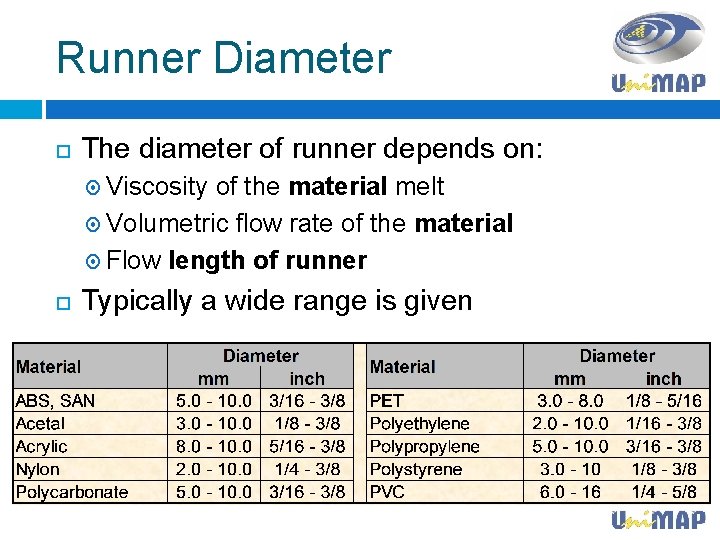
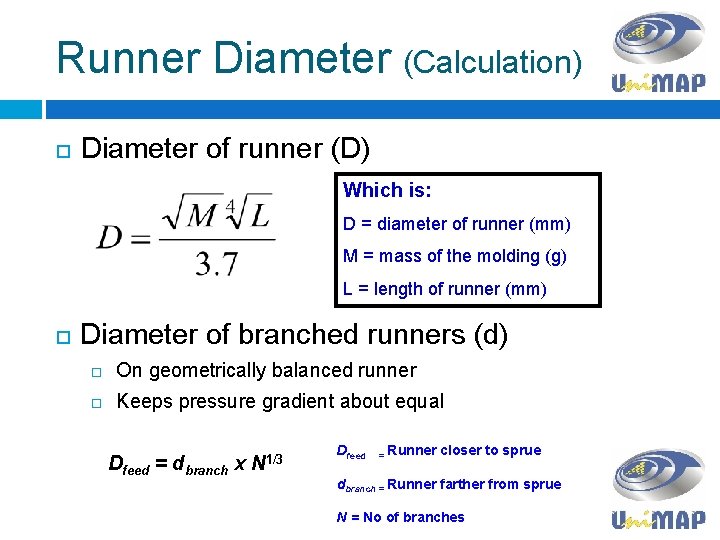
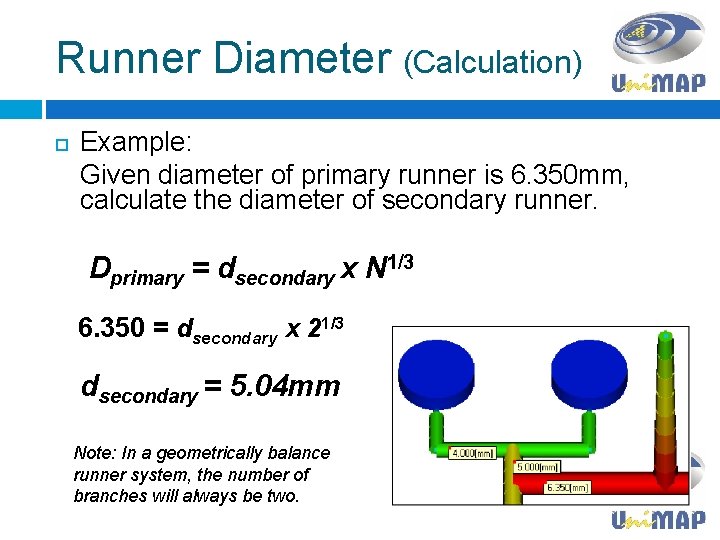
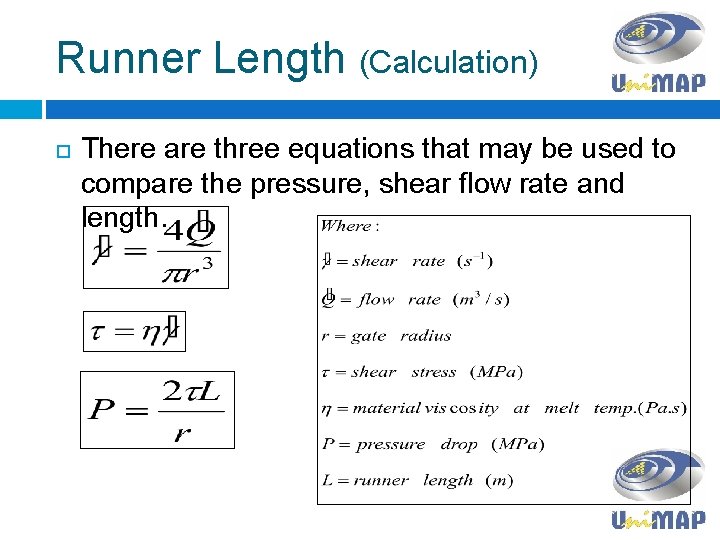
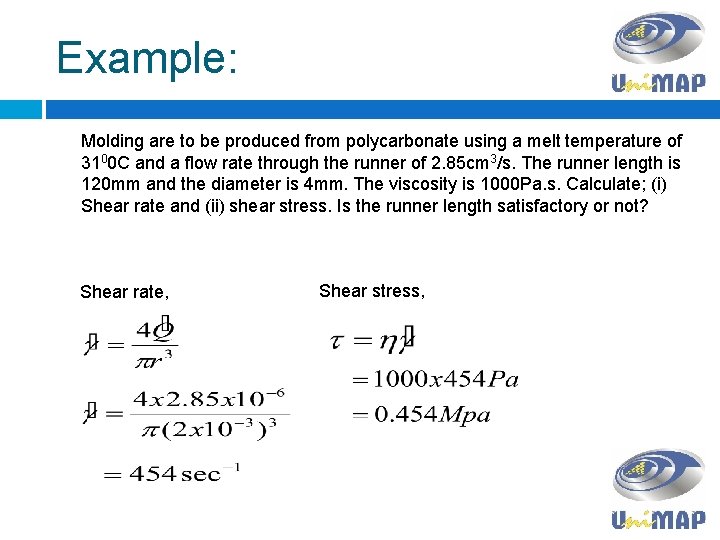
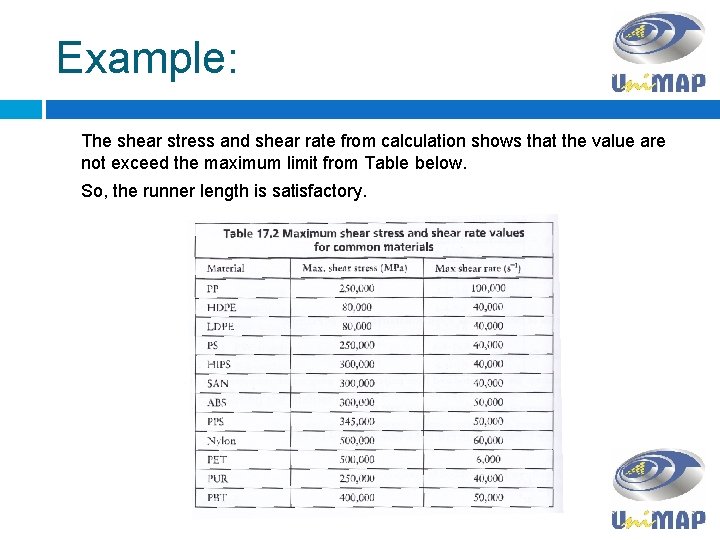
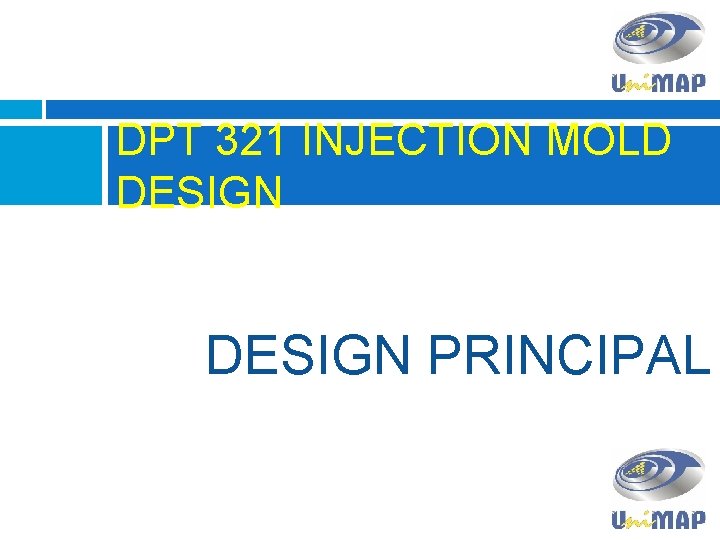
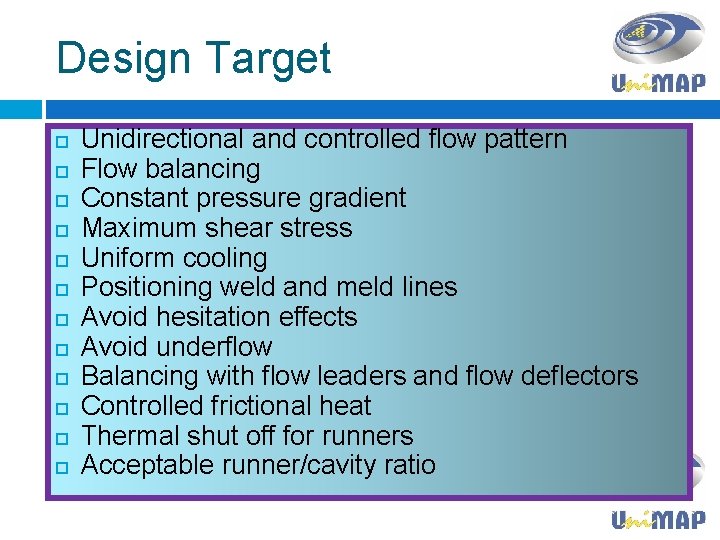
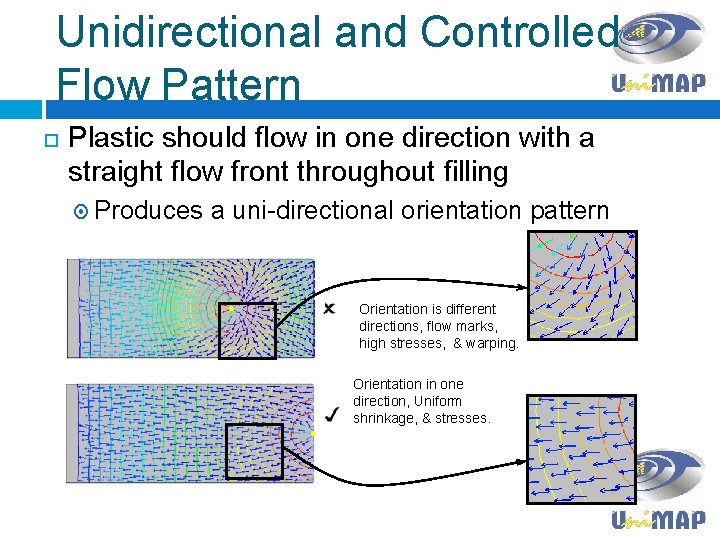
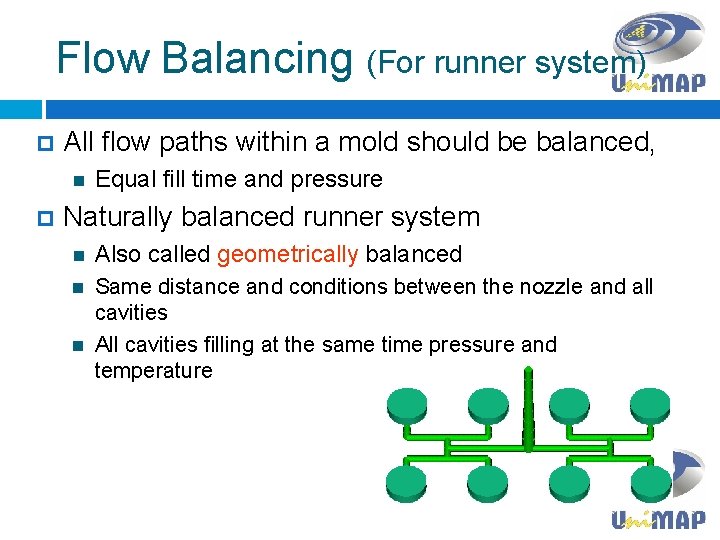
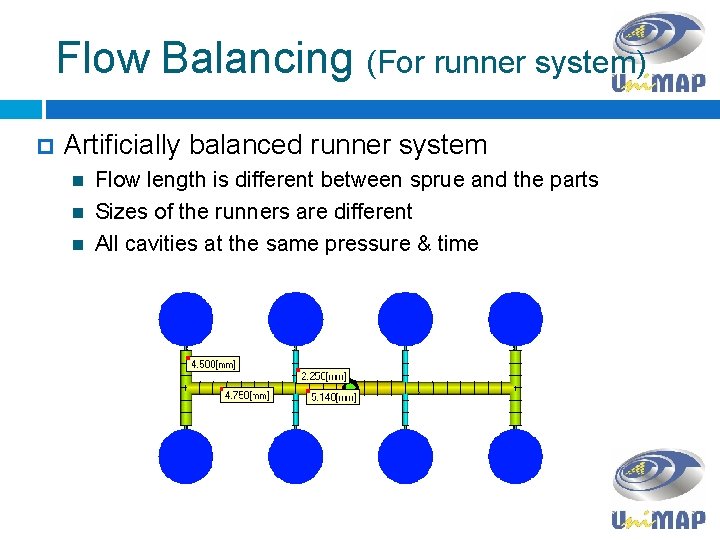
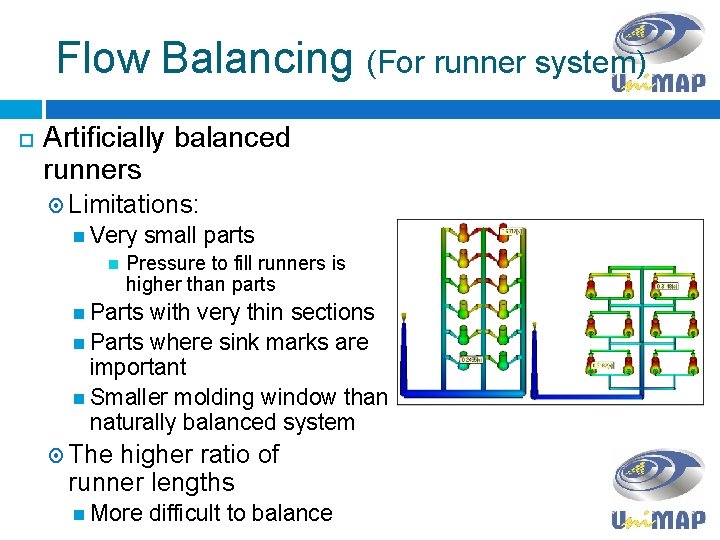
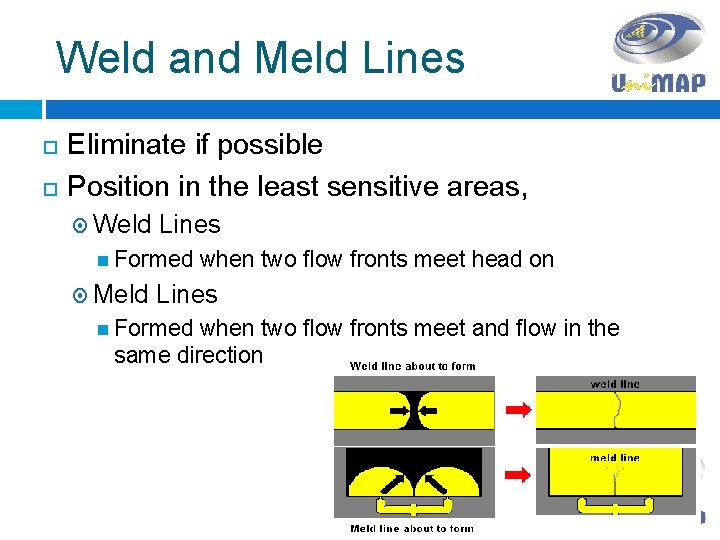
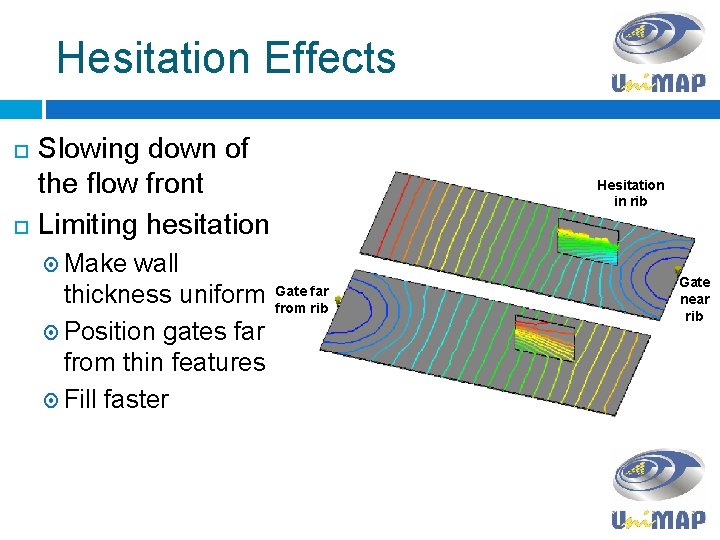
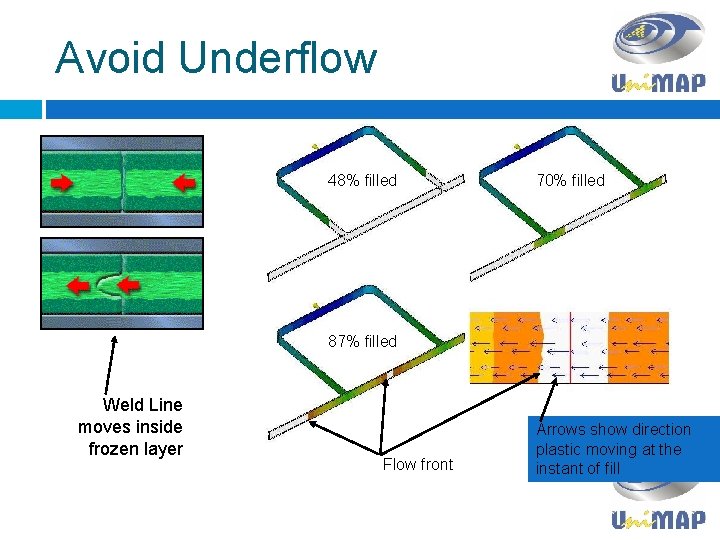
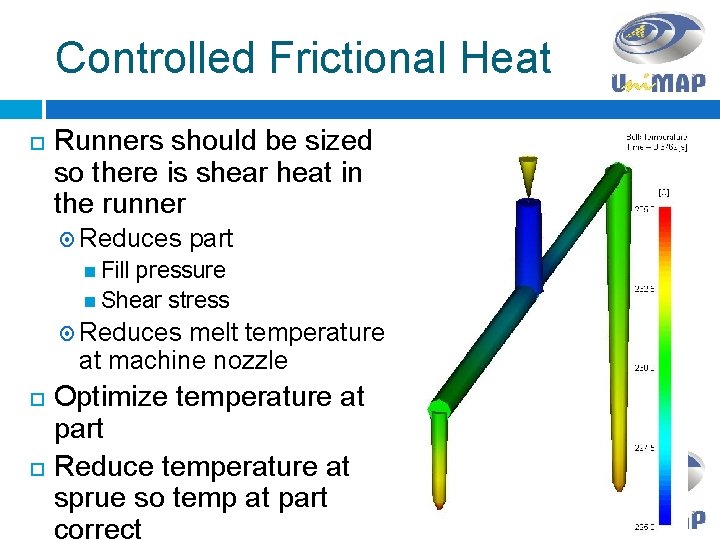
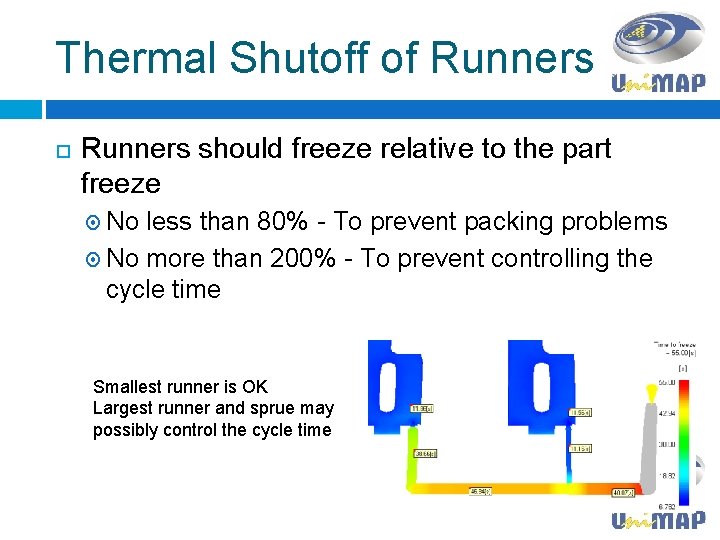
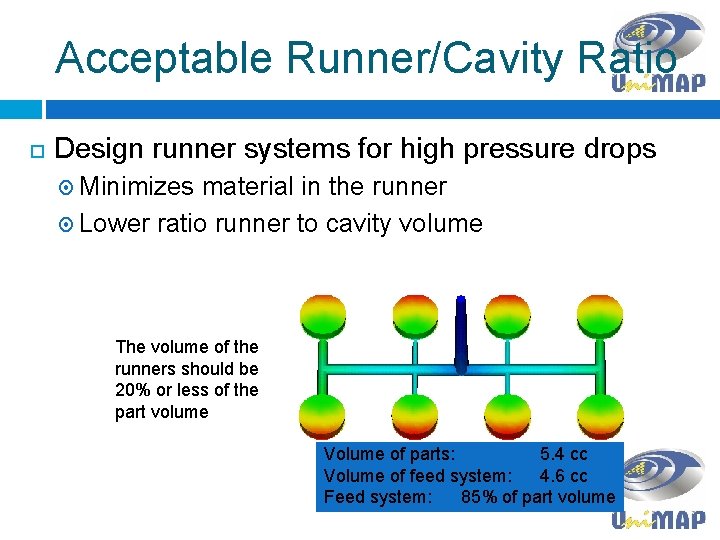
- Slides: 40
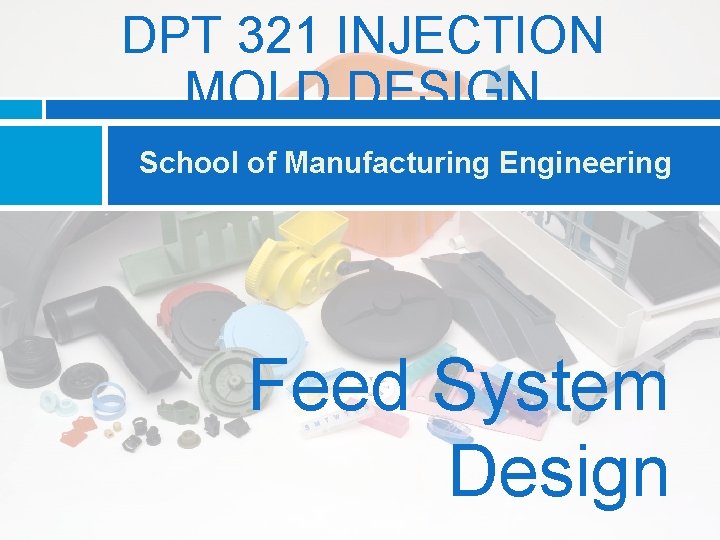
DPT 321 INJECTION MOLD DESIGN School of Manufacturing Engineering Feed System Design
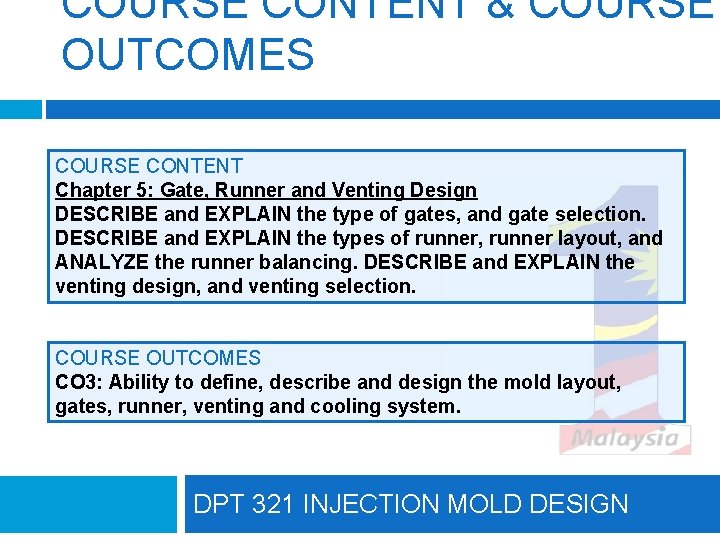
COURSE CONTENT & COURSE OUTCOMES COURSE CONTENT Chapter 5: Gate, Runner and Venting Design DESCRIBE and EXPLAIN the type of gates, and gate selection. DESCRIBE and EXPLAIN the types of runner, runner layout, and ANALYZE the runner balancing. DESCRIBE and EXPLAIN the venting design, and venting selection. COURSE OUTCOMES CO 3: Ability to define, describe and design the mold layout, gates, runner, venting and cooling system. DPT 321 INJECTION MOLD DESIGN
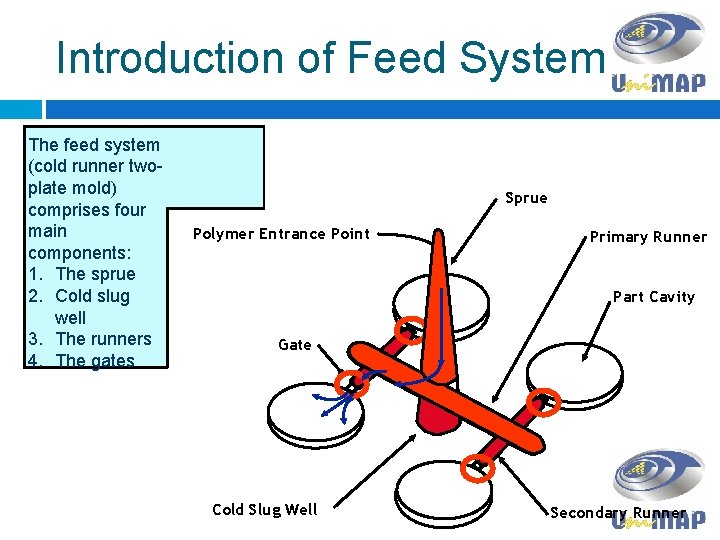
Introduction of Feed System The feed system (cold runner twoplate mold) comprises four main components: 1. The sprue 2. Cold slug well 3. The runners 4. The gates Sprue Polymer Entrance Point Primary Runner Part Cavity Gate Cold Slug Well Secondary Runner

DPT 321 INJECTION MOLD DESIGN OBJECTIVES IN FEED SYSTEM DESIGN
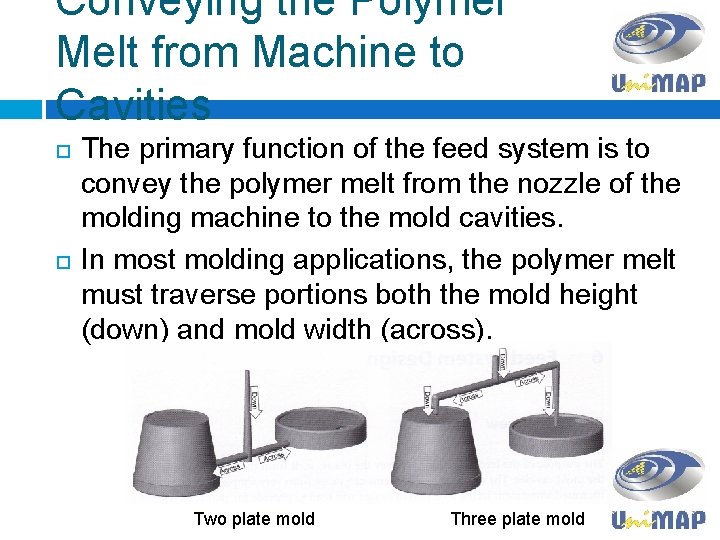
Conveying the Polymer Melt from Machine to Cavities The primary function of the feed system is to convey the polymer melt from the nozzle of the molding machine to the mold cavities. In most molding applications, the polymer melt must traverse portions both the mold height (down) and mold width (across). Two plate mold Three plate mold
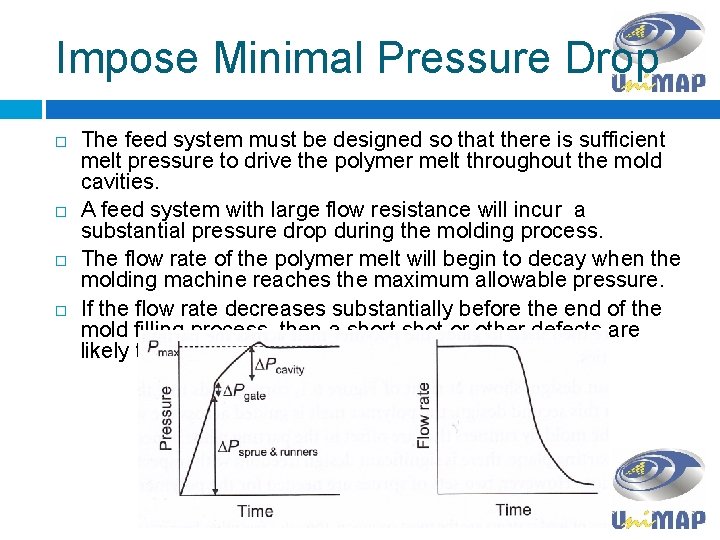
Impose Minimal Pressure Drop The feed system must be designed so that there is sufficient melt pressure to drive the polymer melt throughout the mold cavities. A feed system with large flow resistance will incur a substantial pressure drop during the molding process. The flow rate of the polymer melt will begin to decay when the molding machine reaches the maximum allowable pressure. If the flow rate decreases substantially before the end of the mold filling process, then a short shot or other defects are likely to occur.
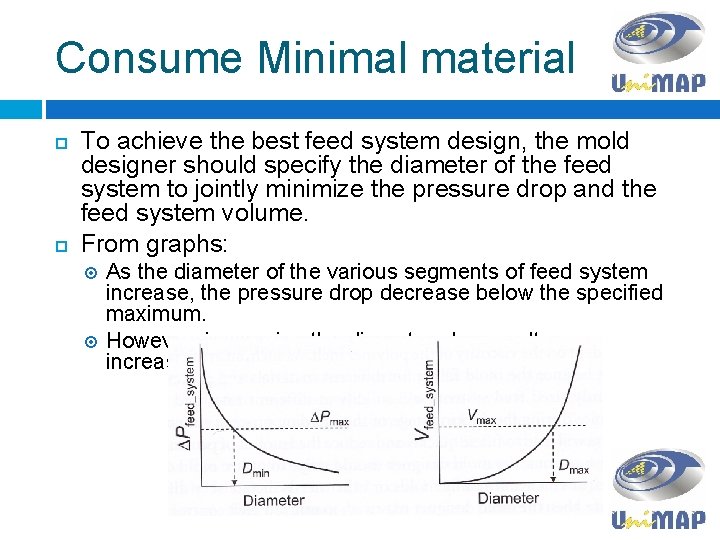
Consume Minimal material To achieve the best feed system design, the mold designer should specify the diameter of the feed system to jointly minimize the pressure drop and the feed system volume. From graphs: As the diameter of the various segments of feed system increase, the pressure drop decrease below the specified maximum. However, increasing the diameter also results an increasing the volume of the feed system.

Control Flow Rates Application: In Multi-cavity (family) mold, the molding application may require different pressure drops in each leg of feed system to cause the different mold cavities to fill at same time. In multi-gated mold, a common objective in the feed system design is to control the polymer melt flowing through the feed system to alter the melt front advancement in a multi-gated mold.
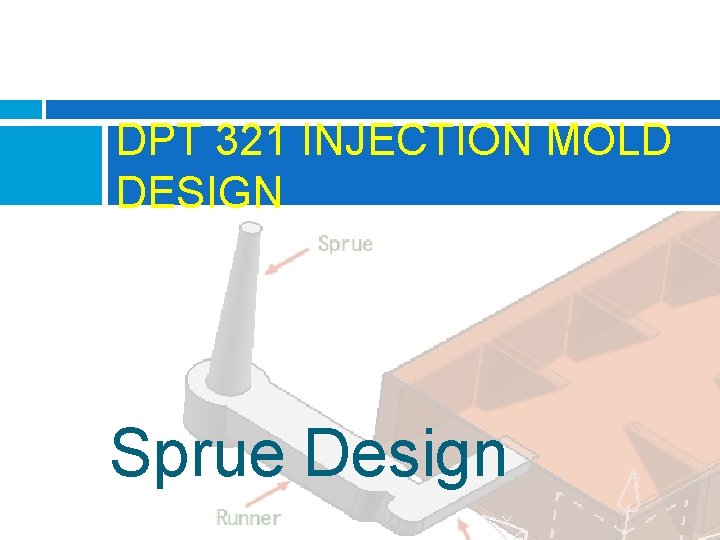
DPT 321 INJECTION MOLD DESIGN Sprue Design
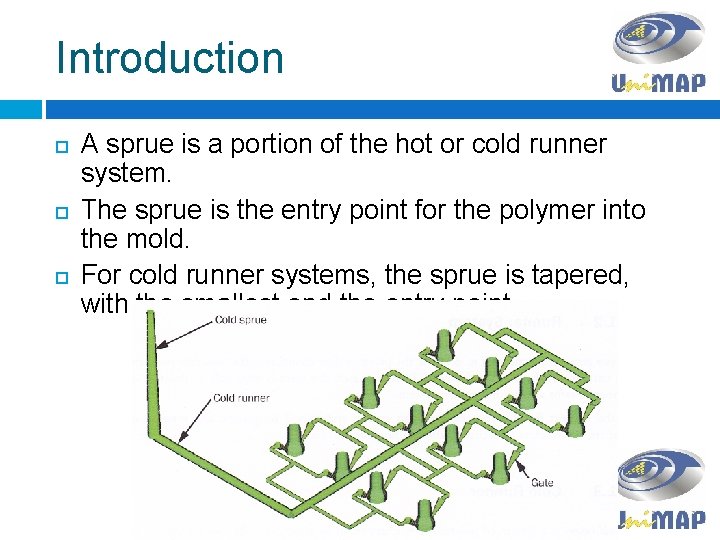
Introduction A sprue is a portion of the hot or cold runner system. The sprue is the entry point for the polymer into the mold. For cold runner systems, the sprue is tapered, with the smallest end the entry point.
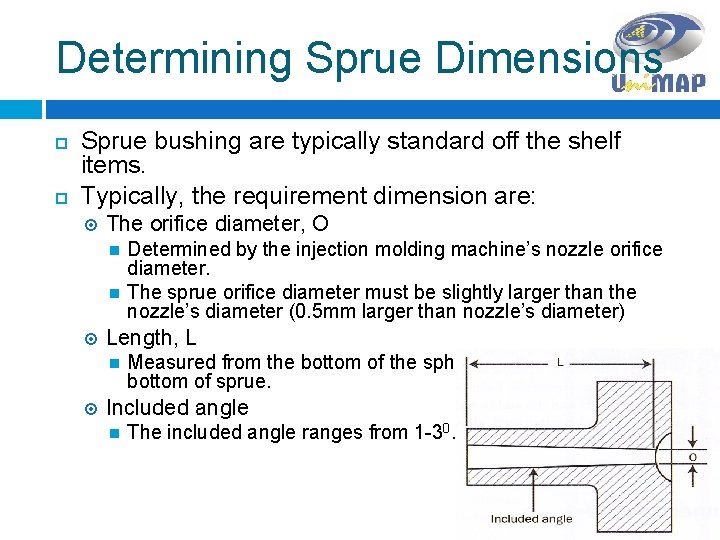
Determining Sprue Dimensions Sprue bushing are typically standard off the shelf items. Typically, the requirement dimension are: The orifice diameter, O Length, L Determined by the injection molding machine’s nozzle orifice diameter. The sprue orifice diameter must be slightly larger than the nozzle’s diameter (0. 5 mm larger than nozzle’s diameter) Measured from the bottom of the spherical radius to the bottom of sprue. Included angle The included angle ranges from 1 -30.
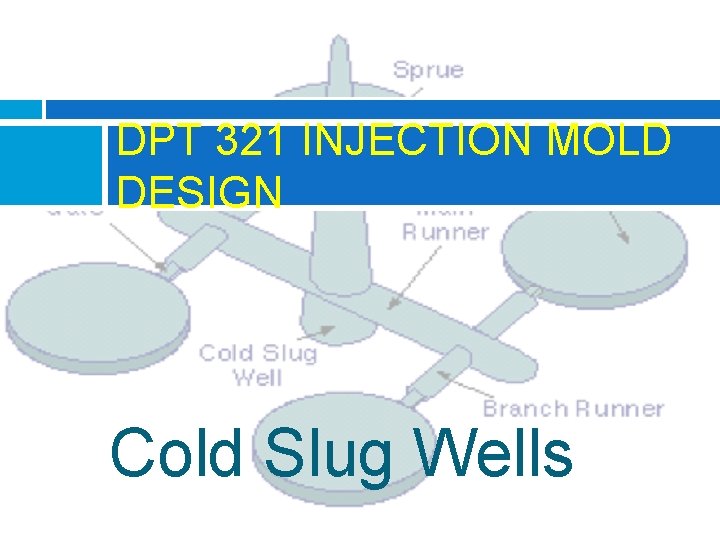
DPT 321 INJECTION MOLD DESIGN Cold Slug Wells
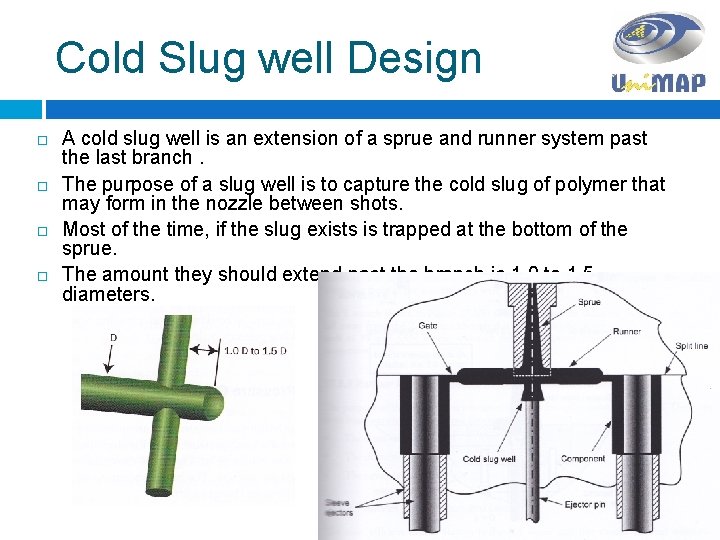
Cold Slug well Design A cold slug well is an extension of a sprue and runner system past the last branch. The purpose of a slug well is to capture the cold slug of polymer that may form in the nozzle between shots. Most of the time, if the slug exists is trapped at the bottom of the sprue. The amount they should extend past the branch is 1. 0 to 1. 5 diameters.
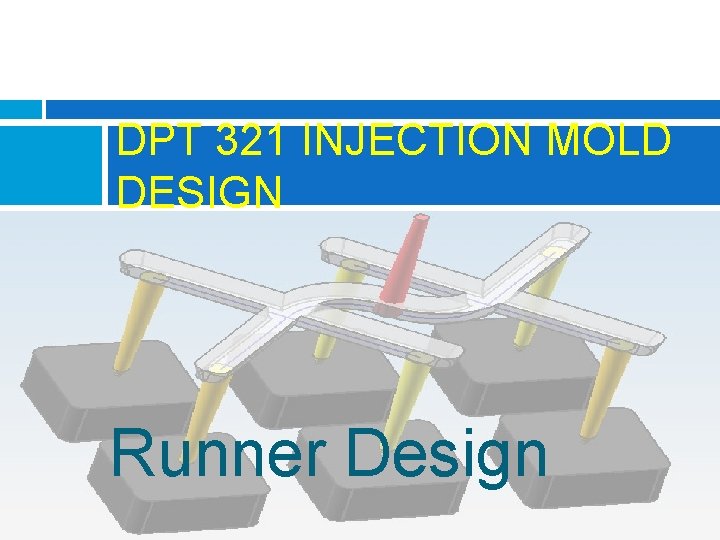
DPT 321 INJECTION MOLD DESIGN Runner Design
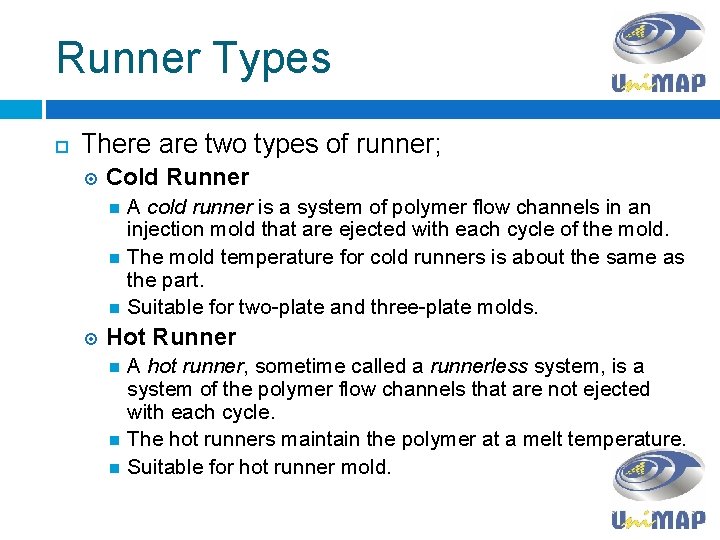
Runner Types There are two types of runner; Cold Runner A cold runner is a system of polymer flow channels in an injection mold that are ejected with each cycle of the mold. The mold temperature for cold runners is about the same as the part. Suitable for two-plate and three-plate molds. Hot Runner A hot runner, sometime called a runnerless system, is a system of the polymer flow channels that are not ejected with each cycle. The hot runners maintain the polymer at a melt temperature. Suitable for hot runner mold.
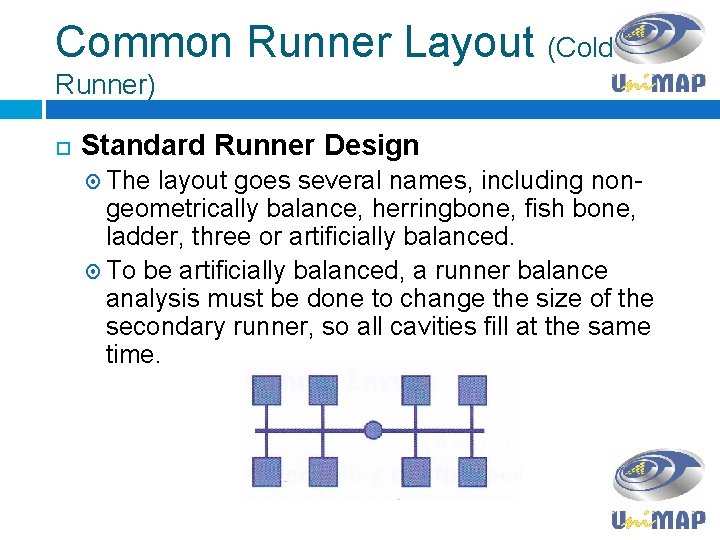
Common Runner Layout (Cold Runner) Standard Runner Design The layout goes several names, including nongeometrically balance, herringbone, fish bone, ladder, three or artificially balanced. To be artificially balanced, a runner balance analysis must be done to change the size of the secondary runner, so all cavities fill at the same time.
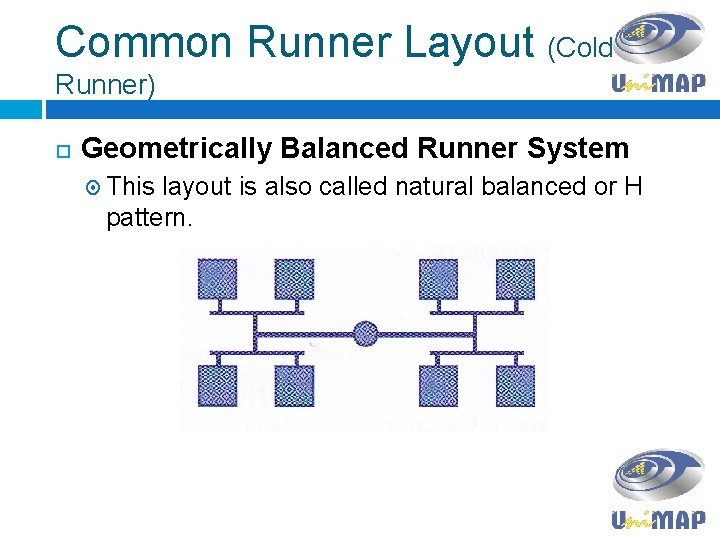
Common Runner Layout (Cold Runner) Geometrically Balanced Runner System This layout is also called natural balanced or H pattern.
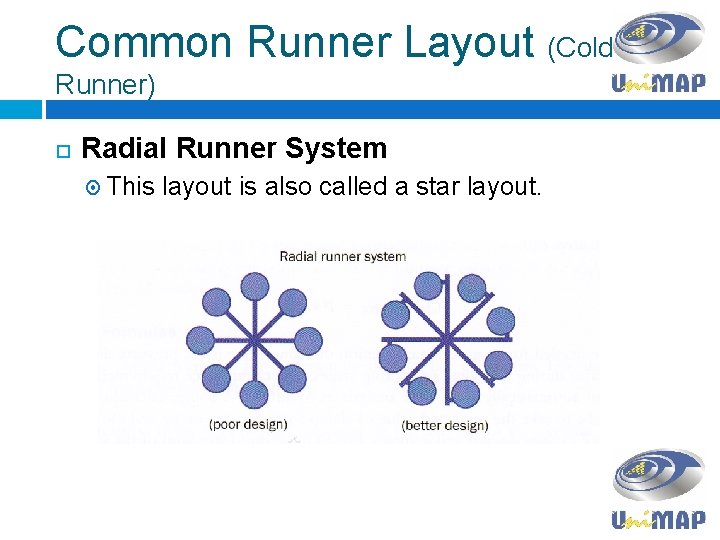
Common Runner Layout (Cold Runner) Radial Runner System This layout is also called a star layout.
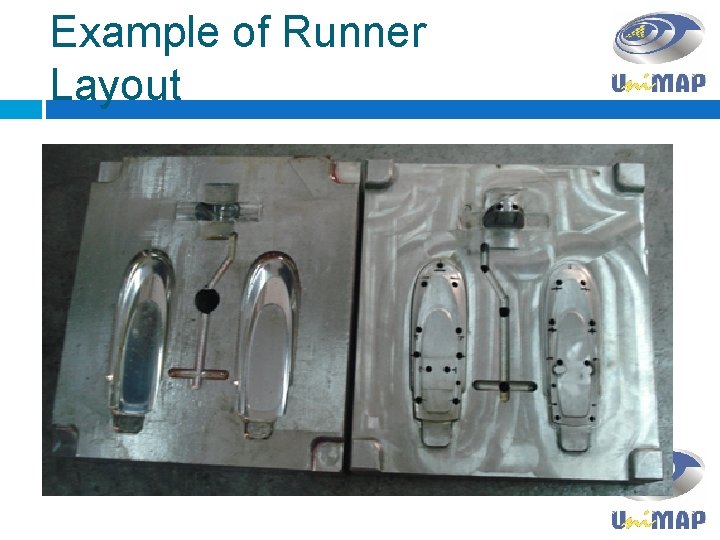
Example of Runner Layout
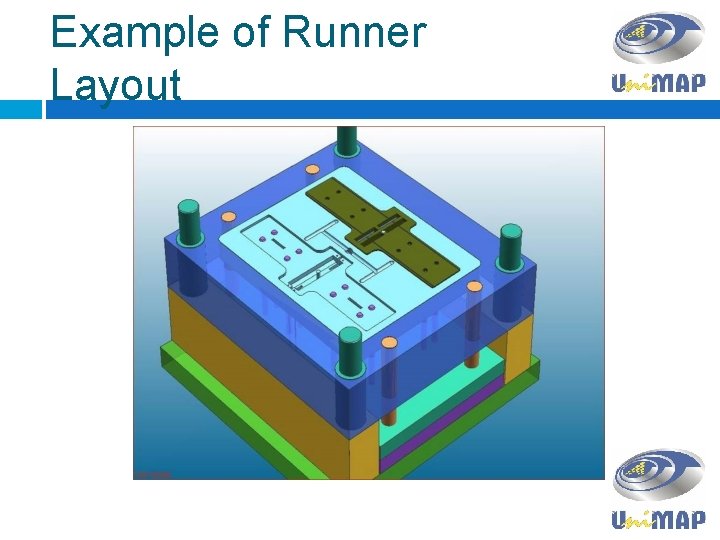
Example of Runner Layout
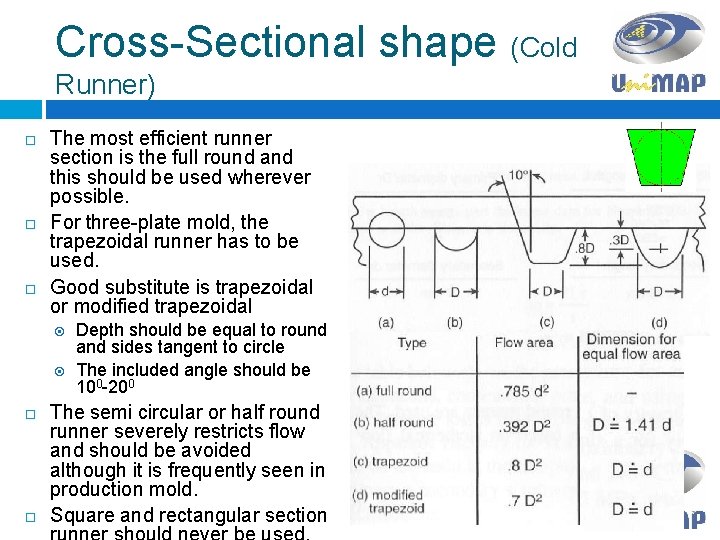
Cross-Sectional shape (Cold Runner) The most efficient runner section is the full round and this should be used wherever possible. For three-plate mold, the trapezoidal runner has to be used. Good substitute is trapezoidal or modified trapezoidal Depth should be equal to round and sides tangent to circle The included angle should be 100 -200 The semi circular or half round runner severely restricts flow and should be avoided although it is frequently seen in production mold. Square and rectangular section
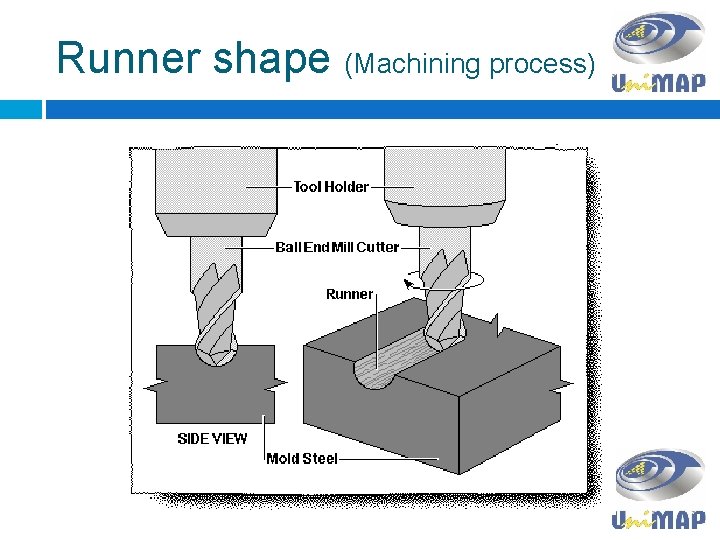
Runner shape (Machining process)
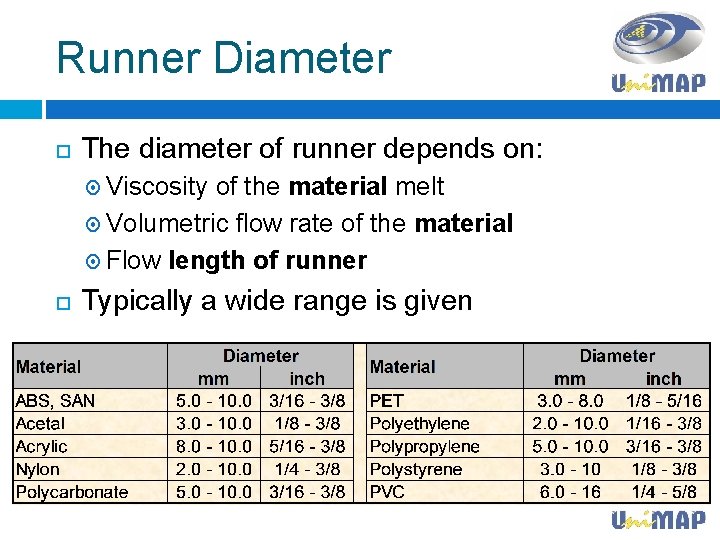
Runner Diameter The diameter of runner depends on: Viscosity of the material melt Volumetric flow rate of the material Flow length of runner Typically a wide range is given
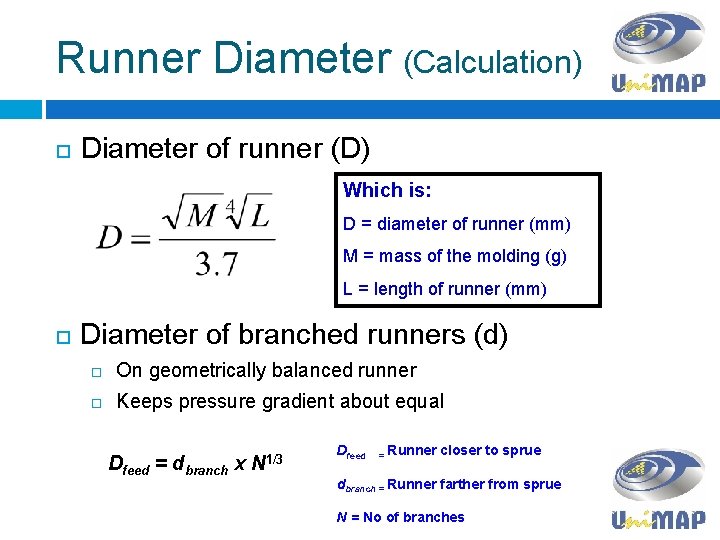
Runner Diameter (Calculation) Diameter of runner (D) Which is: D = diameter of runner (mm) M = mass of the molding (g) L = length of runner (mm) Diameter of branched runners (d) On geometrically balanced runner Keeps pressure gradient about equal Dfeed = dbranch x N 1/3 Dfeed = Runner closer to sprue dbranch = Runner farther from sprue N = No of branches
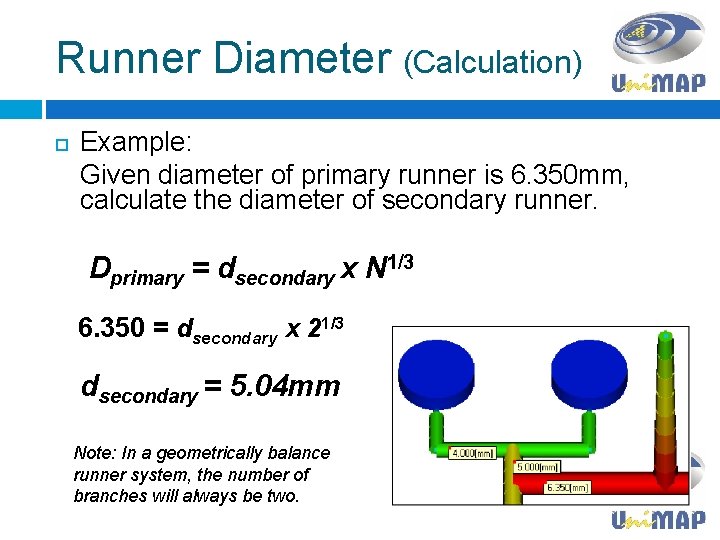
Runner Diameter (Calculation) Example: Given diameter of primary runner is 6. 350 mm, calculate the diameter of secondary runner. Dprimary = dsecondary x N 1/3 6. 350 = dsecondary x 21/3 dsecondary = 5. 04 mm Note: In a geometrically balance runner system, the number of branches will always be two.
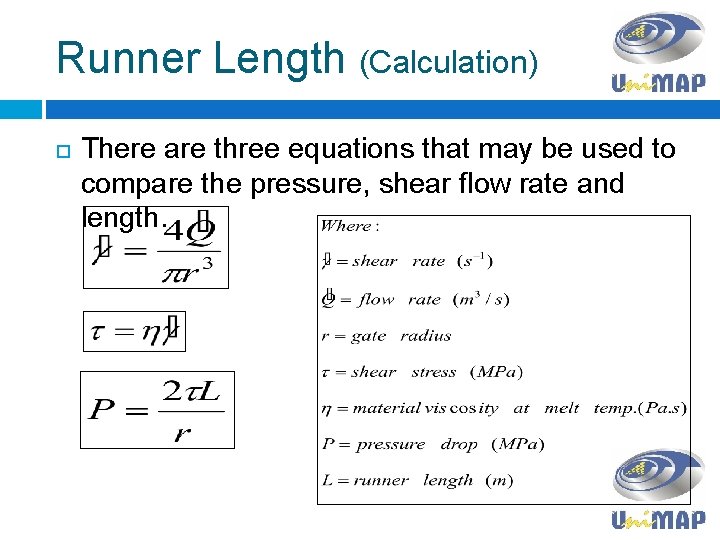
Runner Length (Calculation) There are three equations that may be used to compare the pressure, shear flow rate and length.
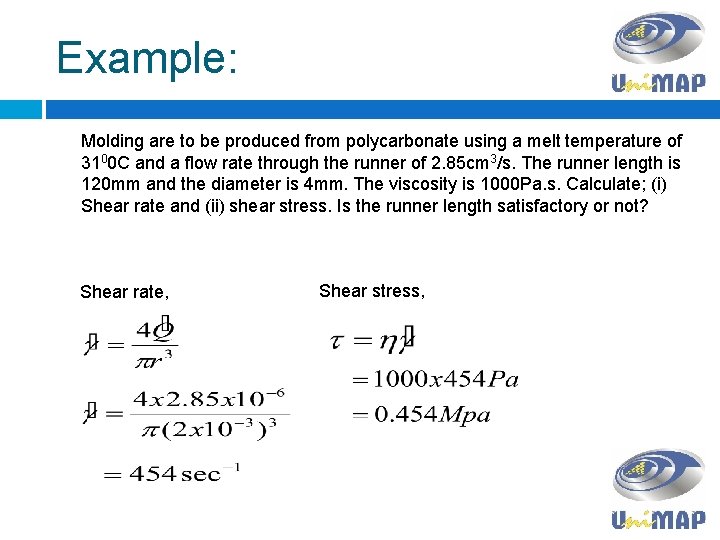
Example: Molding are to be produced from polycarbonate using a melt temperature of 3100 C and a flow rate through the runner of 2. 85 cm 3/s. The runner length is 120 mm and the diameter is 4 mm. The viscosity is 1000 Pa. s. Calculate; (i) Shear rate and (ii) shear stress. Is the runner length satisfactory or not? Shear rate, Shear stress,
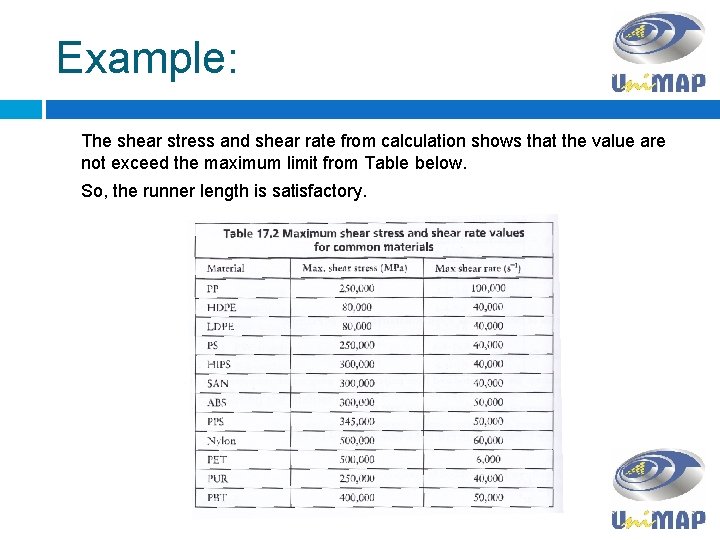
Example: The shear stress and shear rate from calculation shows that the value are not exceed the maximum limit from Table below. So, the runner length is satisfactory.
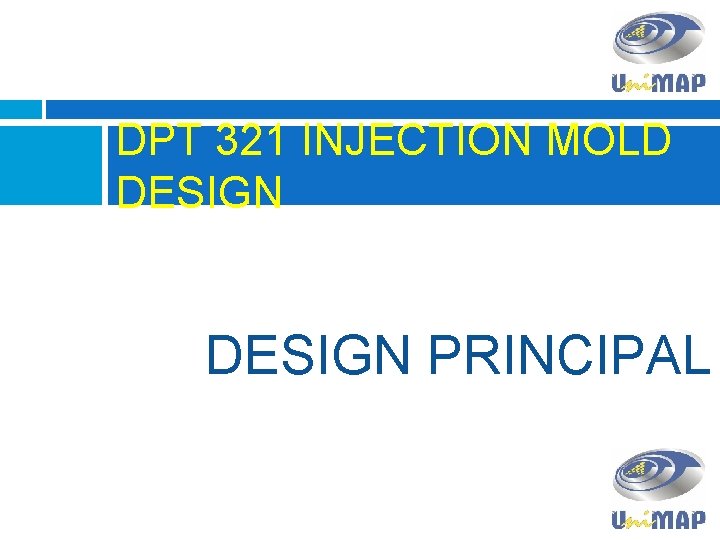
DPT 321 INJECTION MOLD DESIGN PRINCIPAL
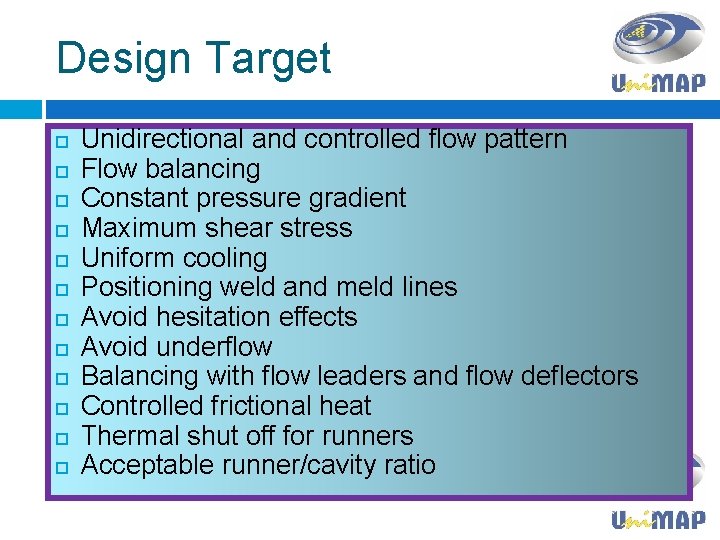
Design Target Unidirectional and controlled flow pattern Flow balancing Constant pressure gradient Maximum shear stress Uniform cooling Positioning weld and meld lines Avoid hesitation effects Avoid underflow Balancing with flow leaders and flow deflectors Controlled frictional heat Thermal shut off for runners Acceptable runner/cavity ratio
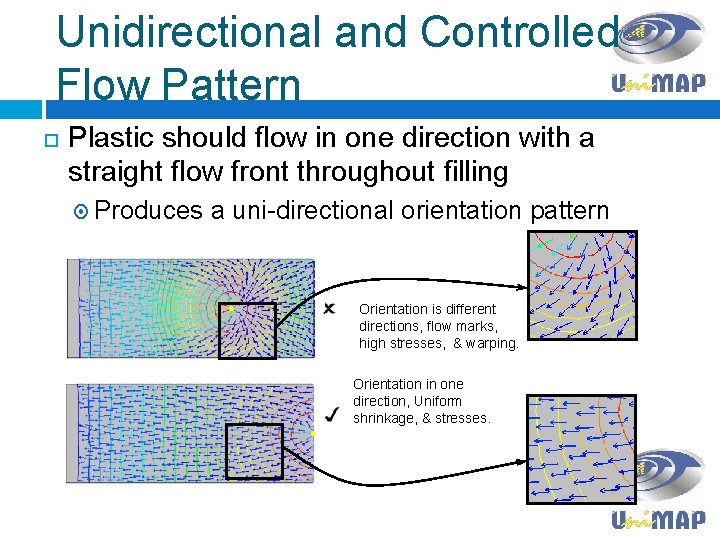
Unidirectional and Controlled Flow Pattern Plastic should flow in one direction with a straight flow front throughout filling Produces a uni-directional orientation pattern Orientation is different directions, flow marks, high stresses, & warping. Orientation in one direction, Uniform shrinkage, & stresses.
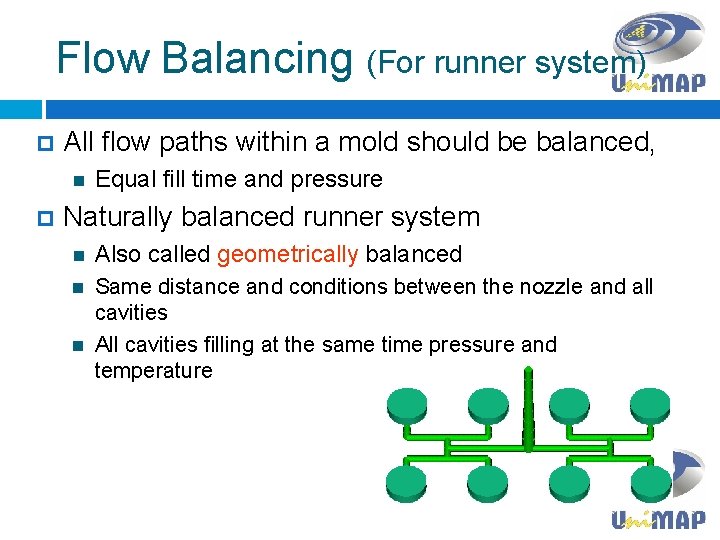
Flow Balancing (For runner system) p All flow paths within a mold should be balanced, p Equal fill time and pressure Naturally balanced runner system Also called geometrically balanced Same distance and conditions between the nozzle and all cavities All cavities filling at the same time pressure and temperature
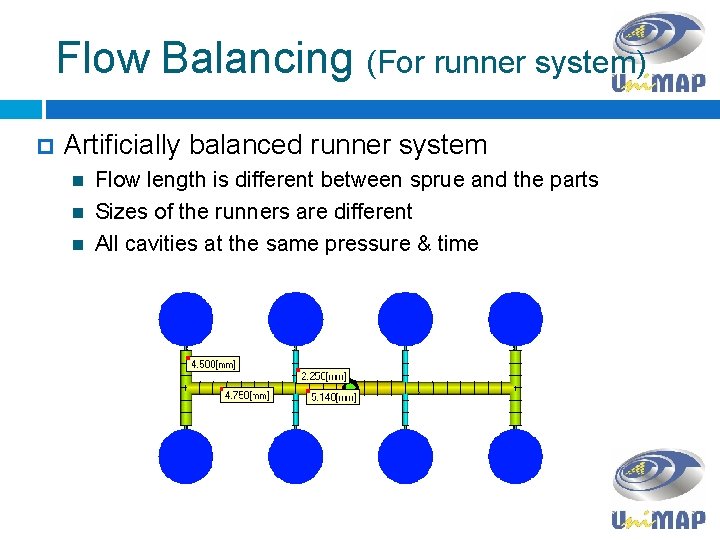
Flow Balancing (For runner system) p Artificially balanced runner system Flow length is different between sprue and the parts Sizes of the runners are different All cavities at the same pressure & time
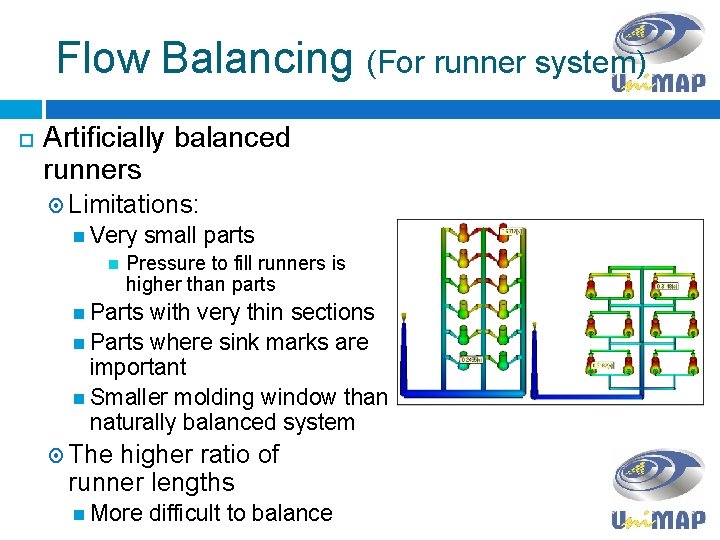
Flow Balancing (For runner system) Artificially balanced runners Limitations: Very small parts Pressure to fill runners is higher than parts Parts with very thin sections Parts where sink marks are important Smaller molding window than naturally balanced system The higher ratio of runner lengths More difficult to balance
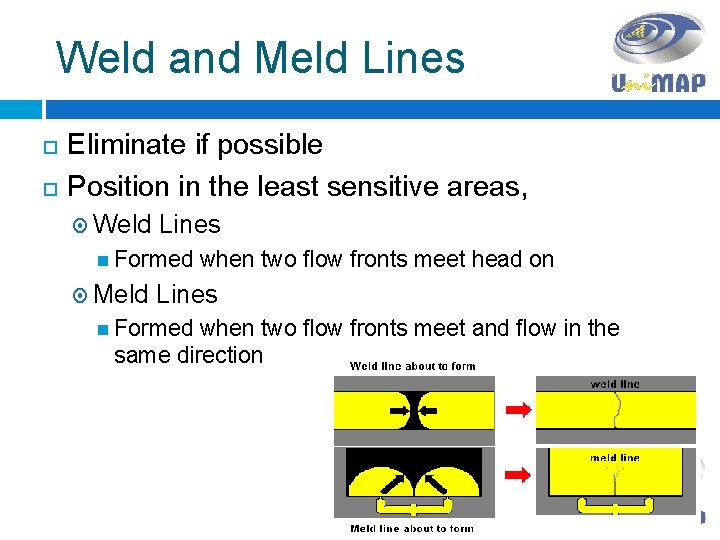
Weld and Meld Lines Eliminate if possible Position in the least sensitive areas, Weld Lines Formed Meld when two flow fronts meet head on Lines Formed when two flow fronts meet and flow in the same direction
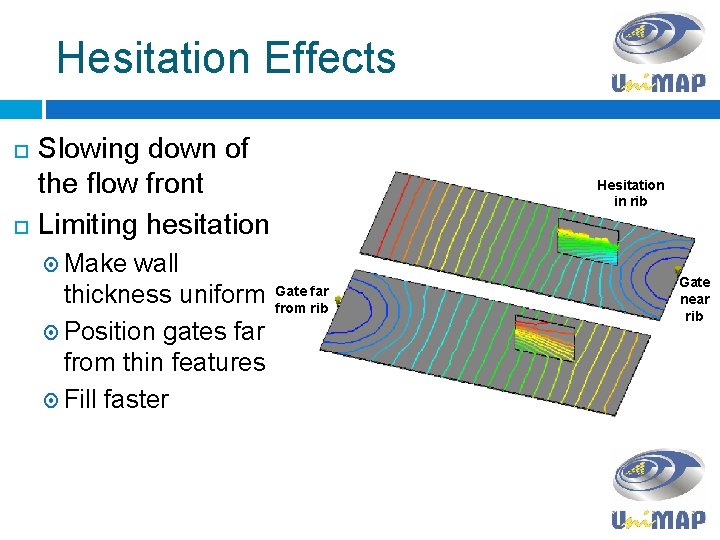
Hesitation Effects Slowing down of the flow front Limiting hesitation wall thickness uniform Position gates far from thin features Fill faster Hesitation in rib Make Gate far from rib Gate near rib
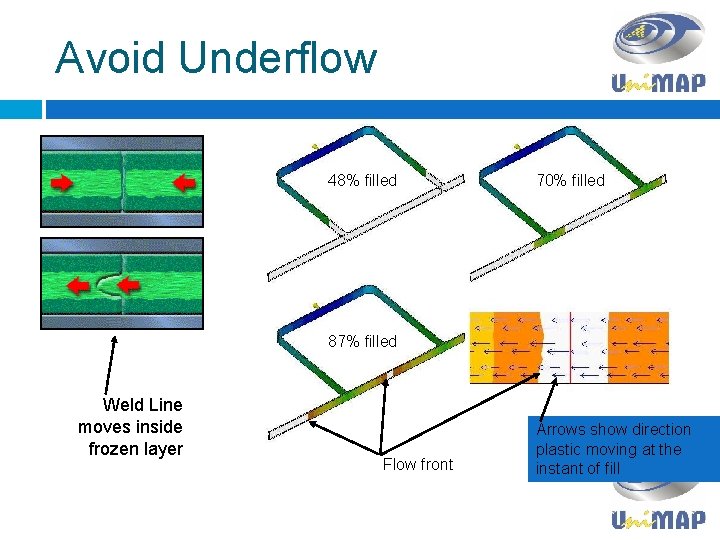
Avoid Underflow 48% filled 70% filled 87% filled Weld Line moves inside frozen layer Flow front Arrows show direction plastic moving at the instant of fill
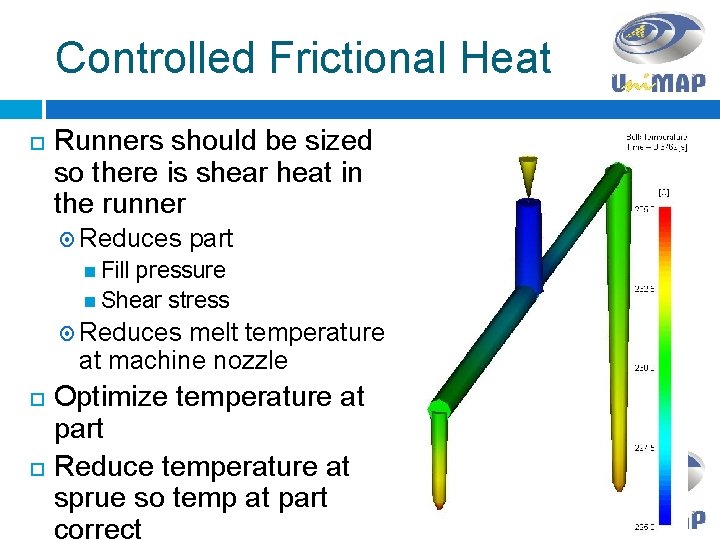
Controlled Frictional Heat Runners should be sized so there is shear heat in the runner Reduces part Fill pressure Shear stress Reduces melt temperature at machine nozzle Optimize temperature at part Reduce temperature at sprue so temp at part correct
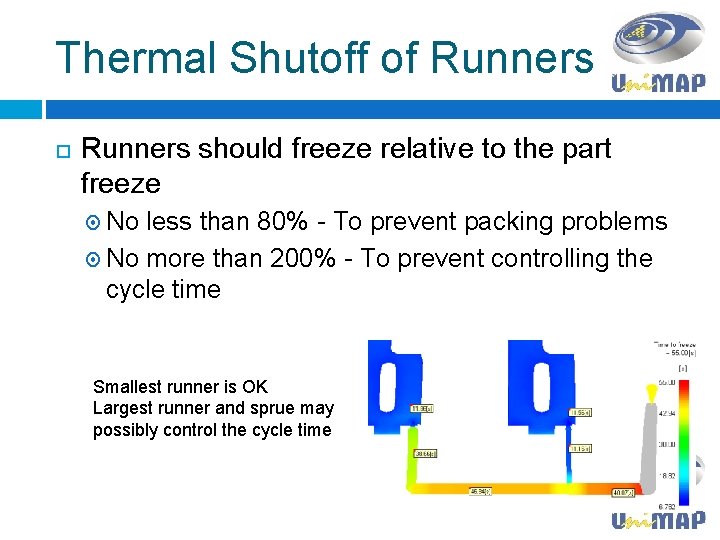
Thermal Shutoff of Runners should freeze relative to the part freeze No less than 80% - To prevent packing problems No more than 200% - To prevent controlling the cycle time Smallest runner is OK Largest runner and sprue may possibly control the cycle time
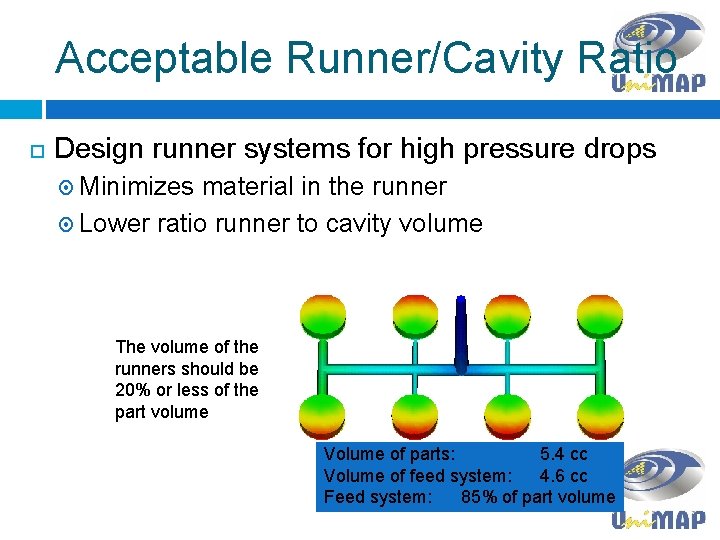
Acceptable Runner/Cavity Ratio Design runner systems for high pressure drops Minimizes material in the runner Lower ratio runner to cavity volume The volume of the runners should be 20% or less of the part volume Volume of parts: 5. 4 cc Volume of feed system: 4. 6 cc Feed system: 85% of part volume
Mostly unicellular
Compression molded
Pot type mold & plunger type mold are the classification of
Cold slug well design
Dpt test procedure
Dpt psychology
Dpt 110
Dpt 110
Dpt psychology
For unsaturated air the value of dpt is
Vcu dpt
Manufacturing cost vs non manufacturing cost
Job costing vs process costing
Commited cost
Manufacturing cost vs non manufacturing cost
Additively
Injection molding school
Edel 321
321 vs 338 fiduciary
Csi 321
123 132 213 231 312 321
Apokalypsis 321
Oam 321
Andreas klappenecker
Mgt 321 chapter 1
Ics 321
Ics 321
Entry type 86
Eccentric leveling lugs
321 feedback
Acuerdo 0321 de 2011 cali
What is project scheduling in software engineering
3 2 1 dough
+add callholdrecord
Bio spiritual ecology
Proximal processes
The royal gorge bridge in colorado rises 321
Law of probability
Evard life cycle
How to get voicemail on airtel
Ics-321