Course Metallic Materials Engineering Module II The martensitic
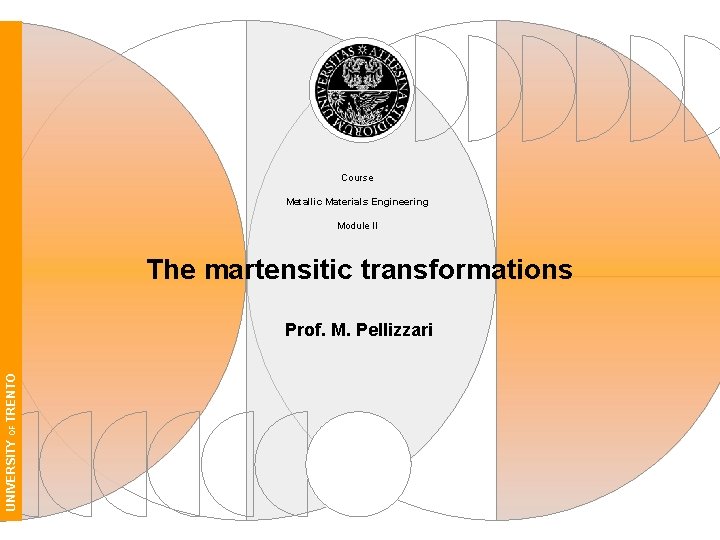
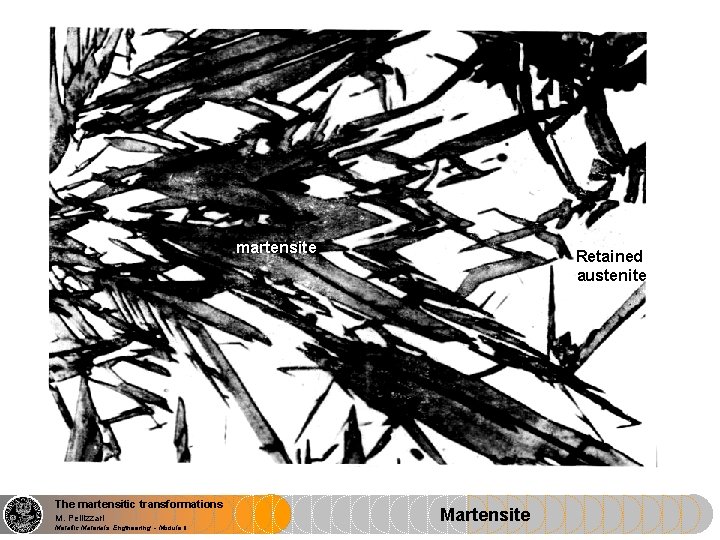
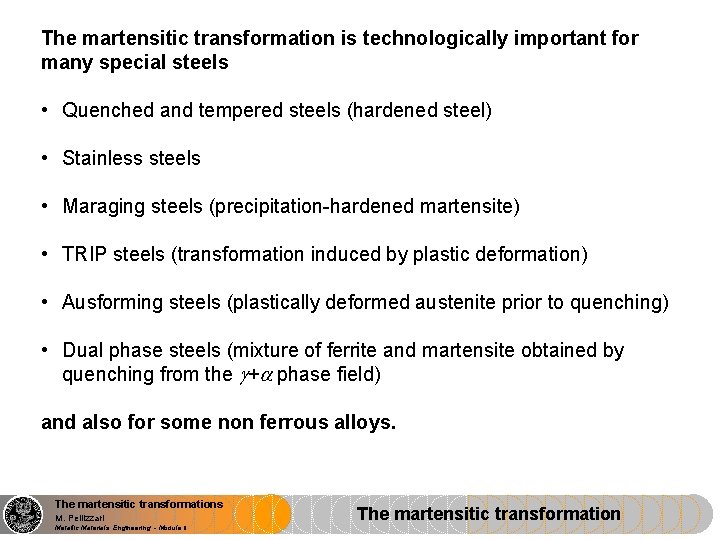
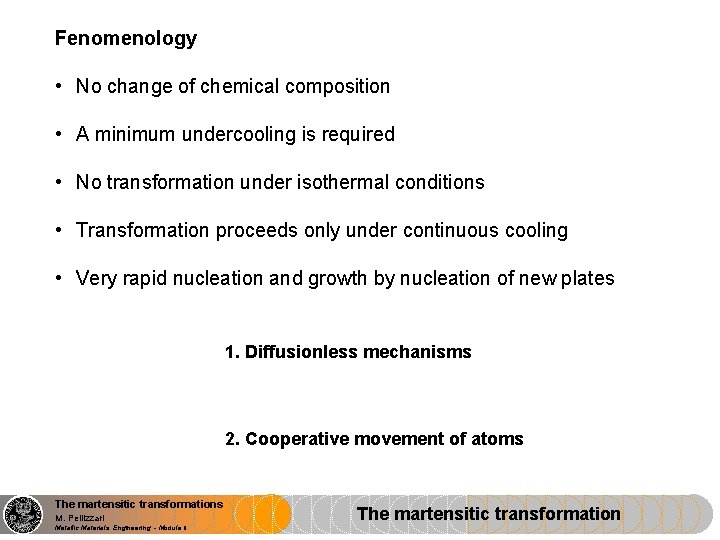
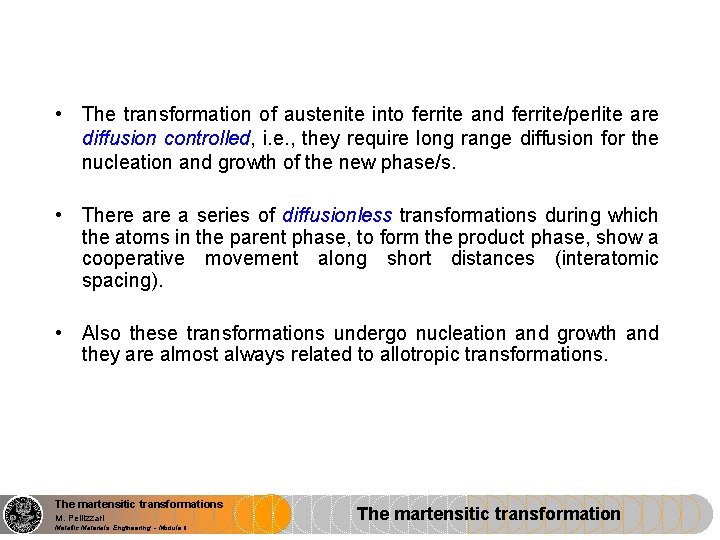
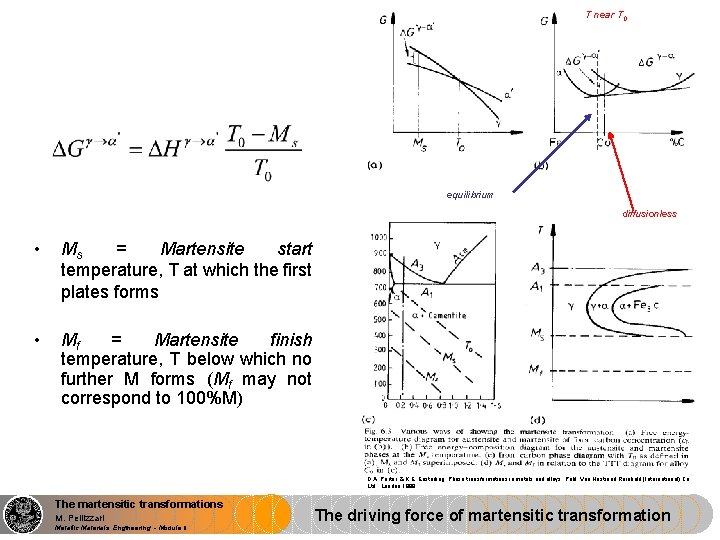
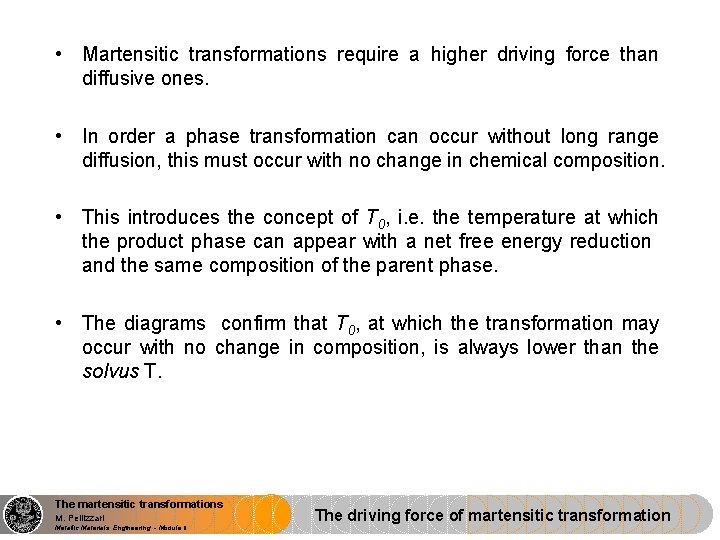
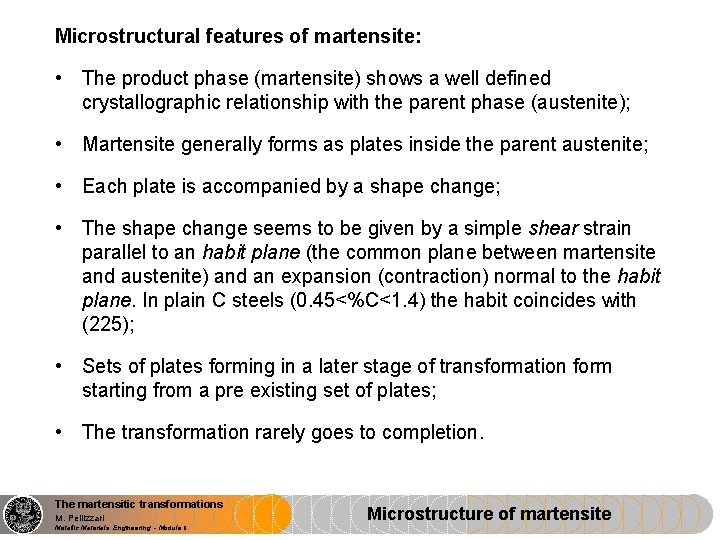
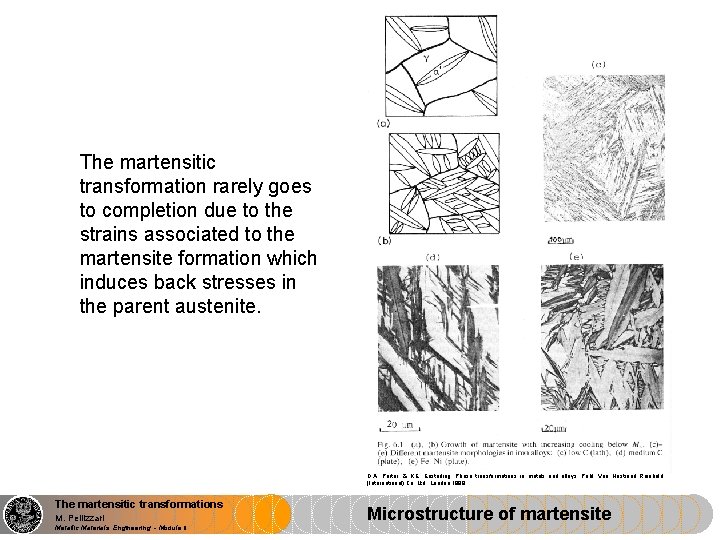
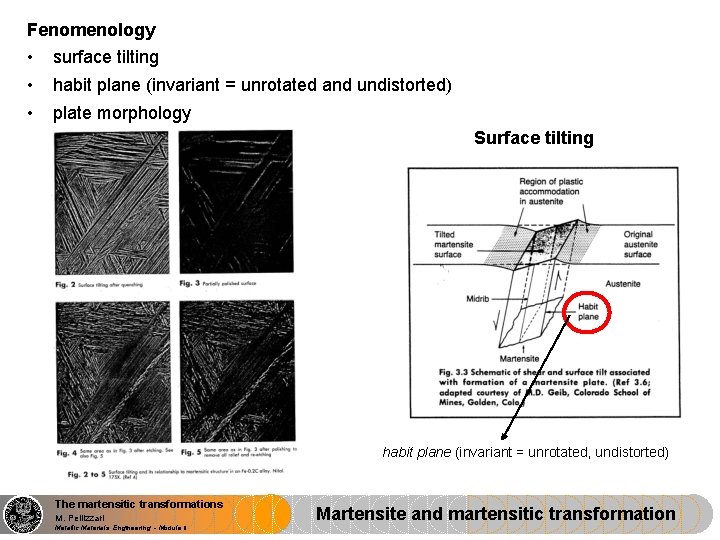
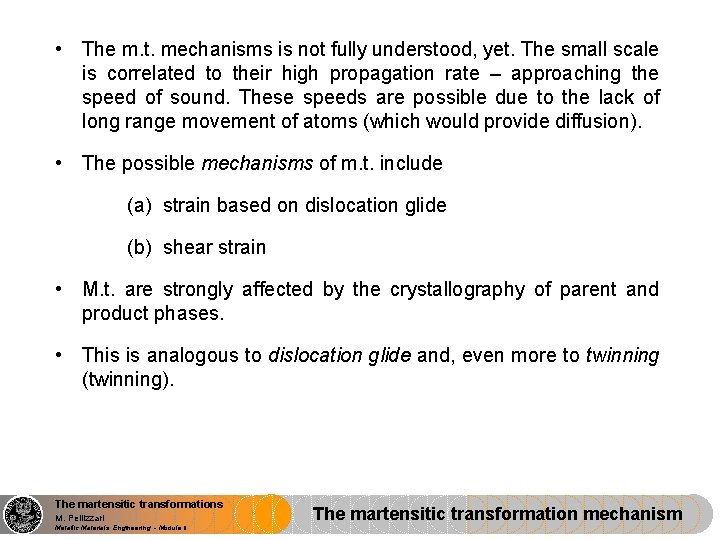
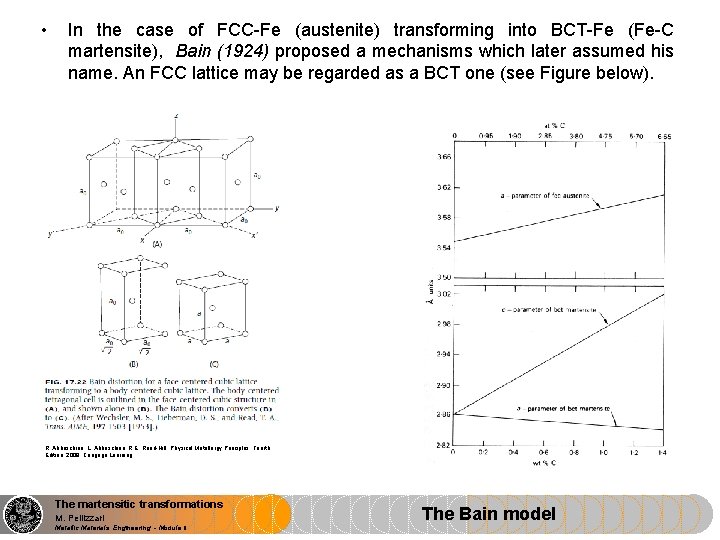

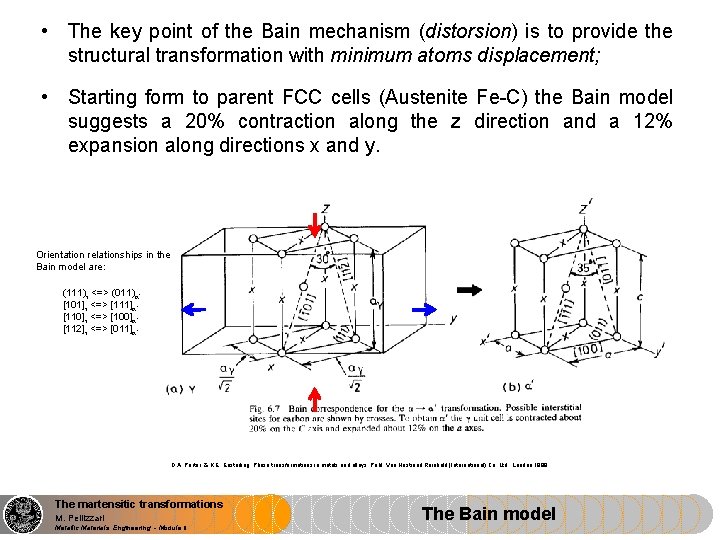
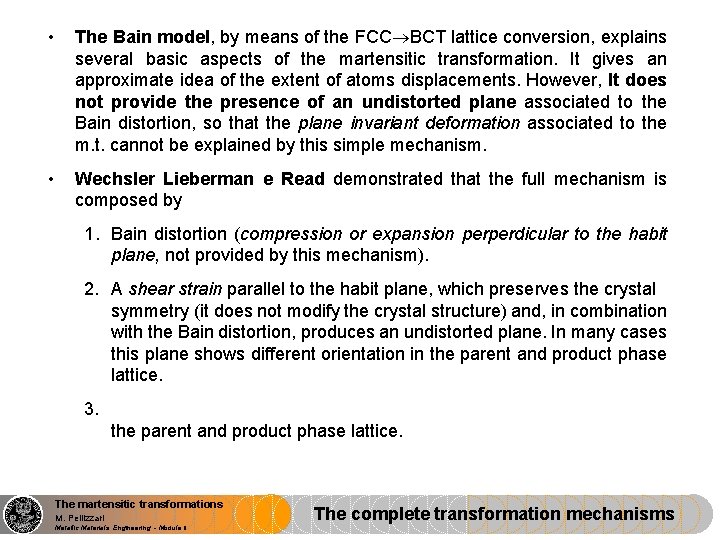
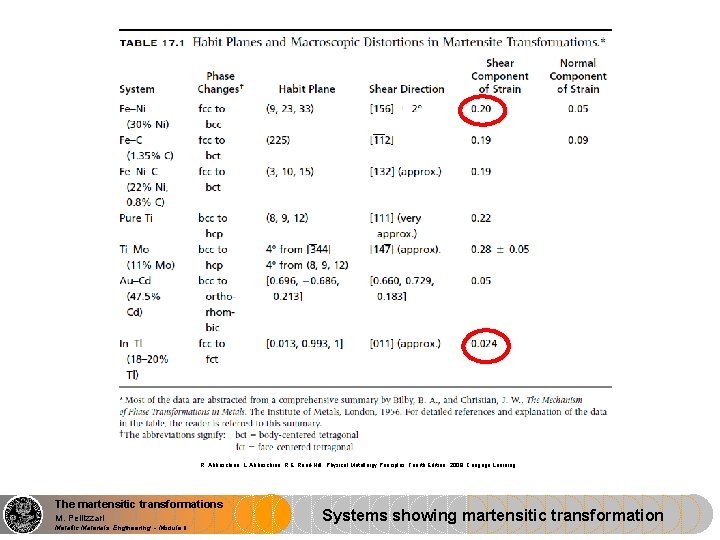
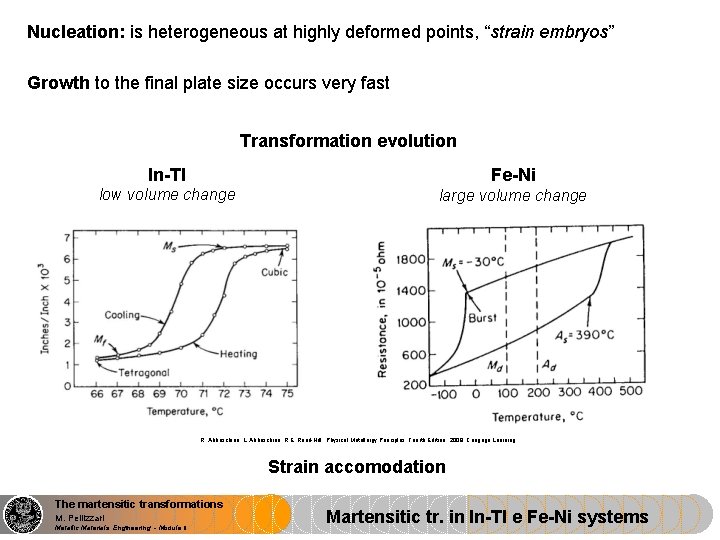
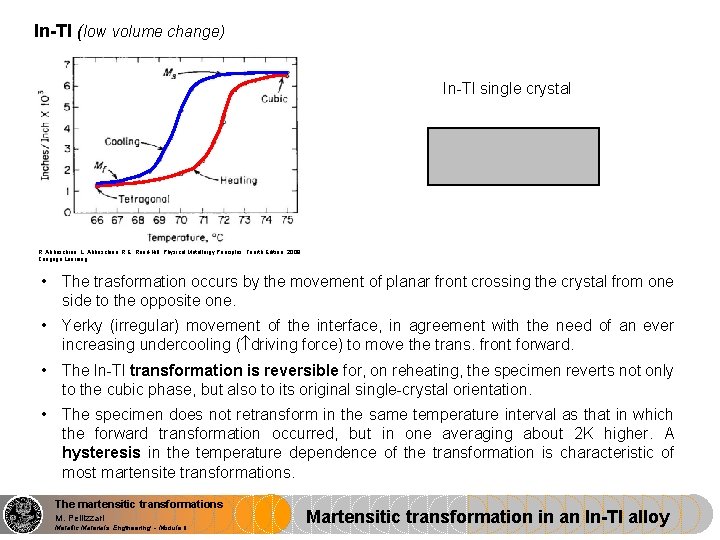
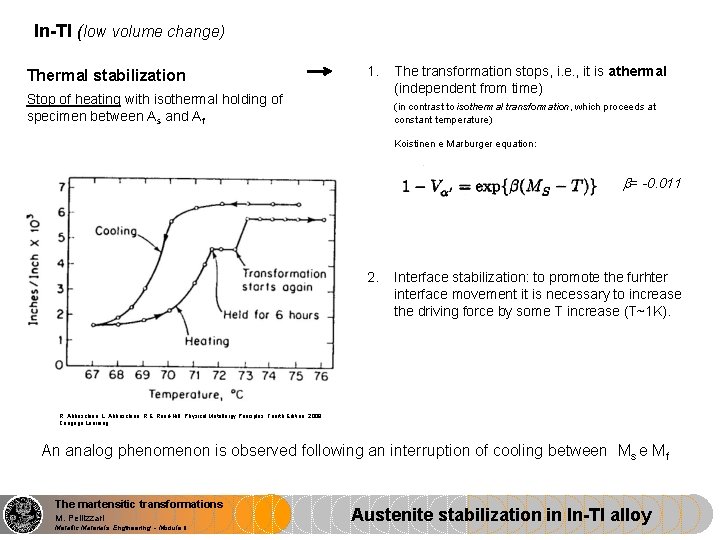
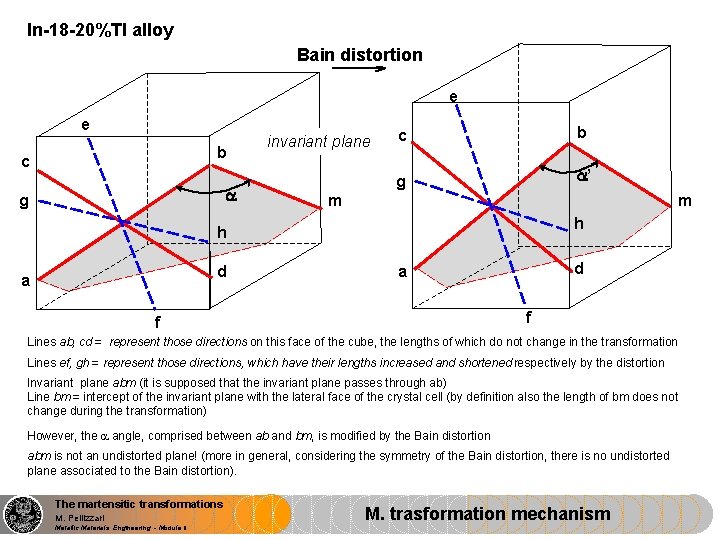
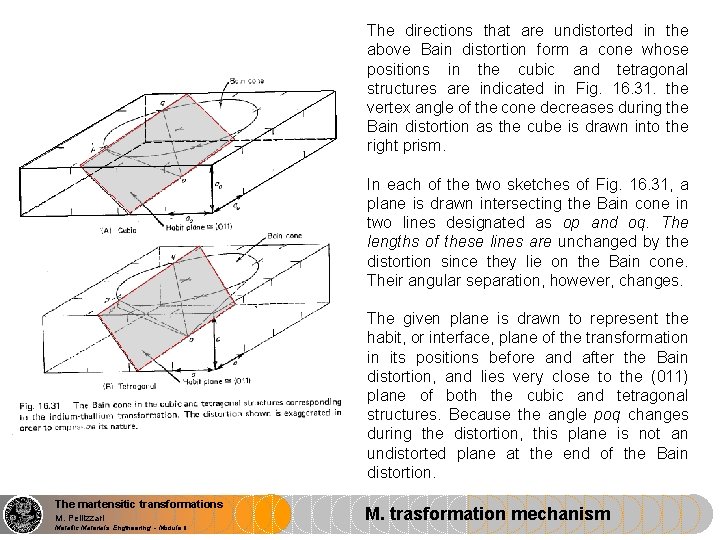
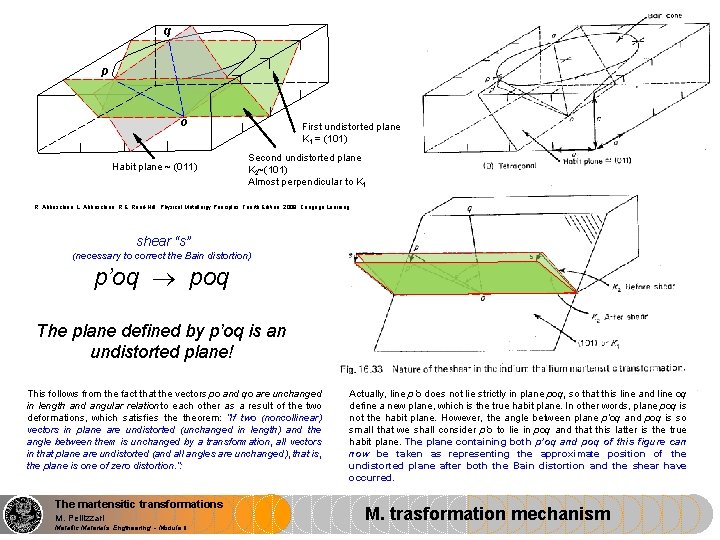
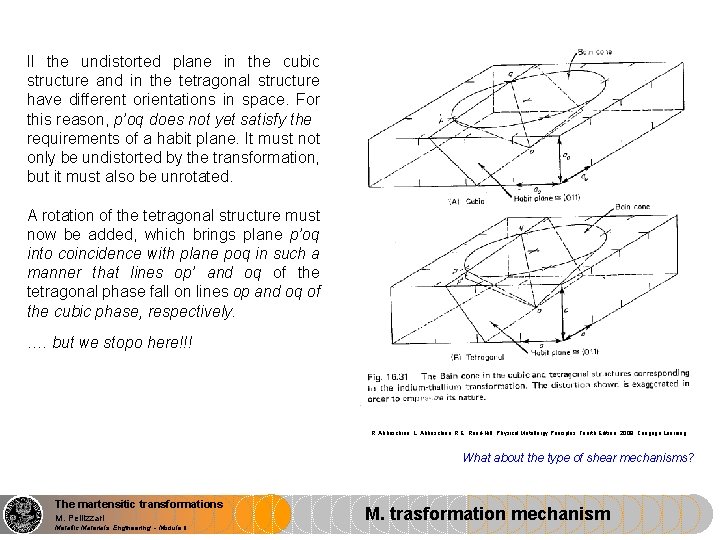
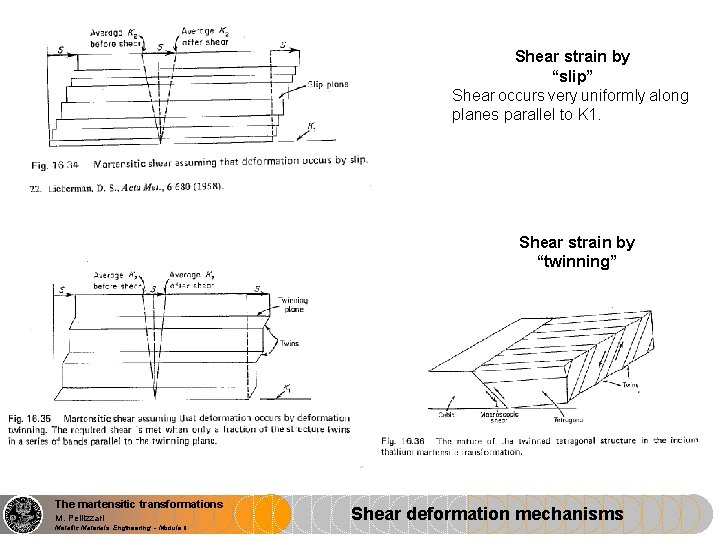
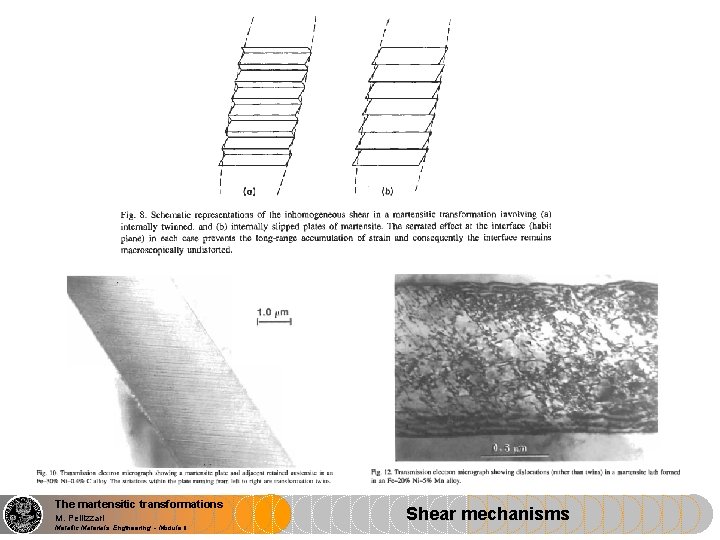
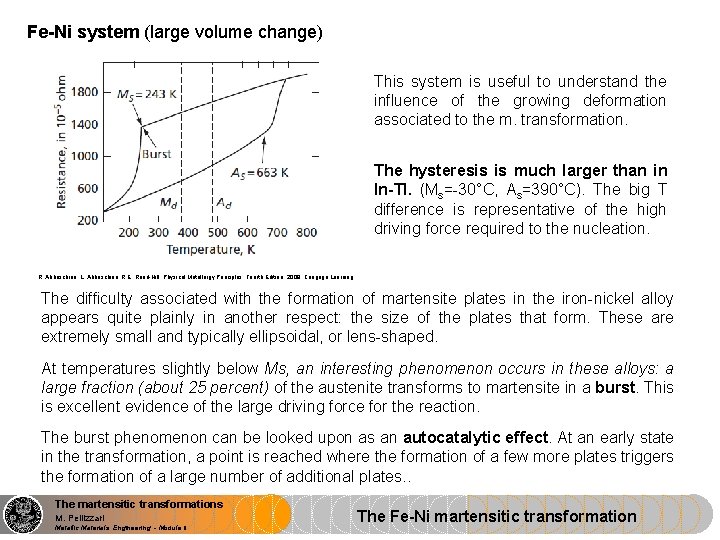
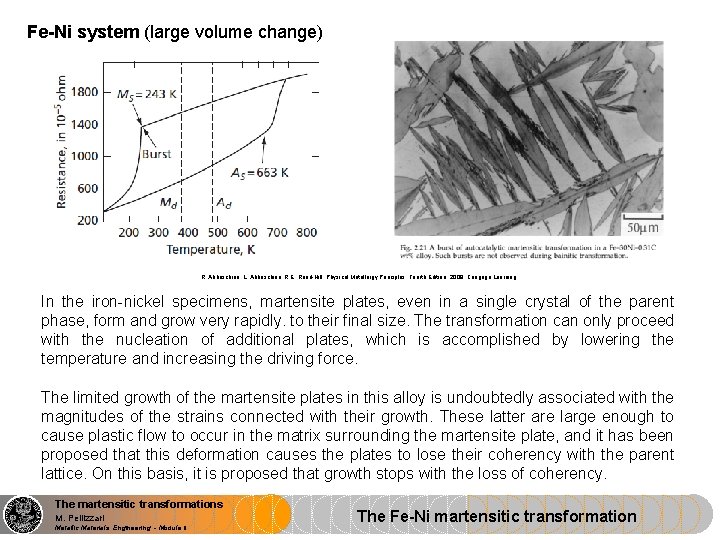
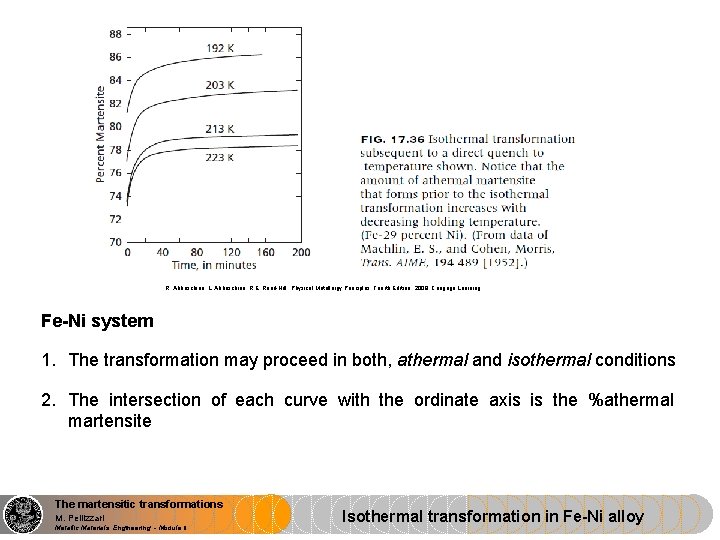
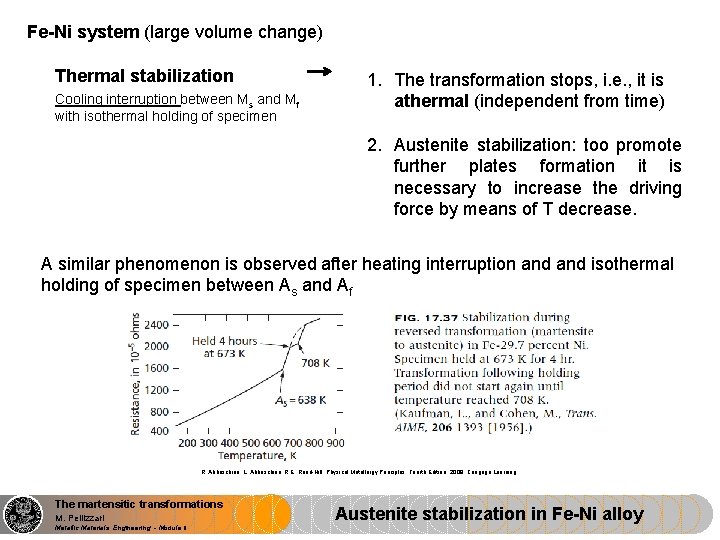
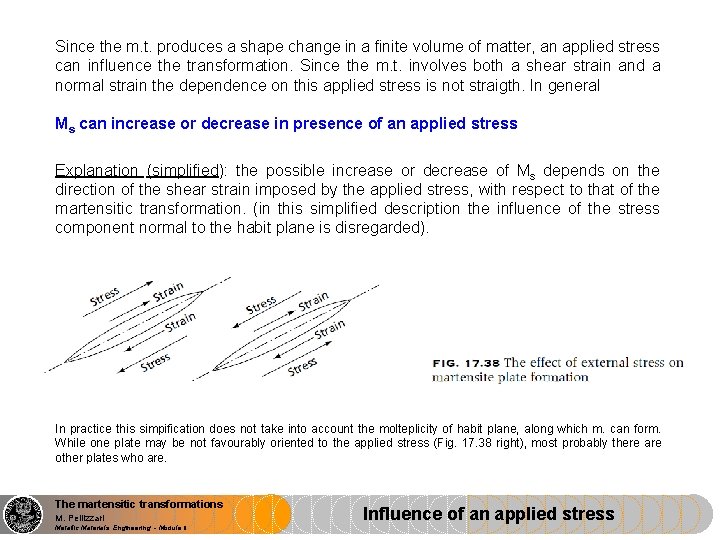
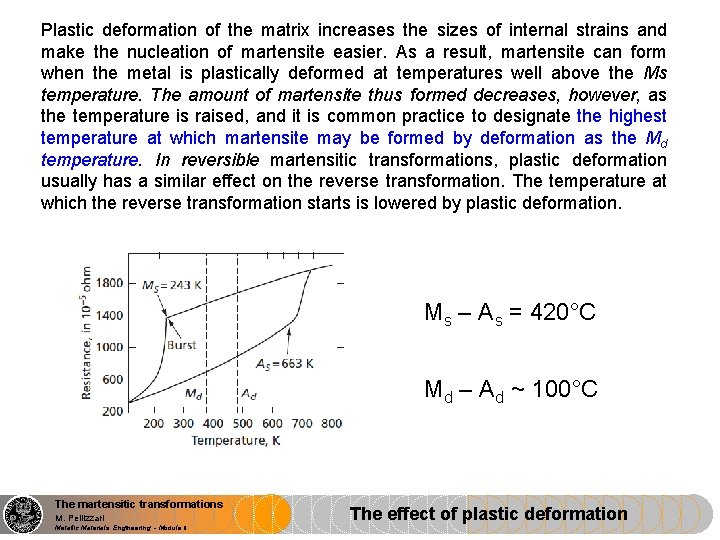
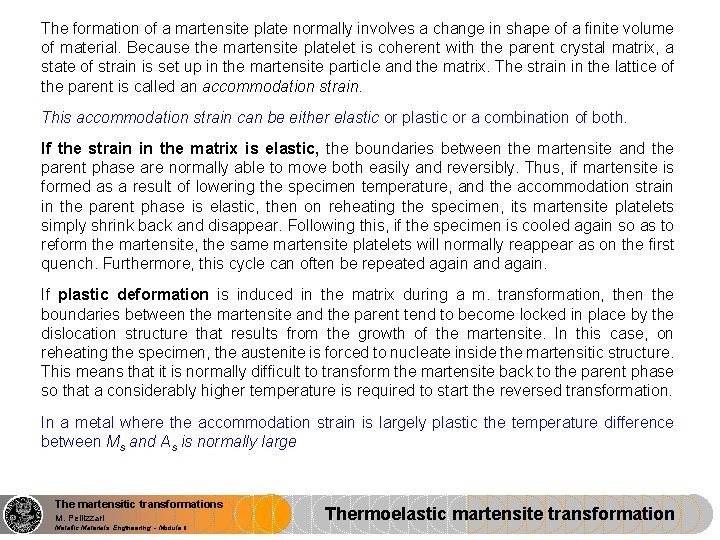
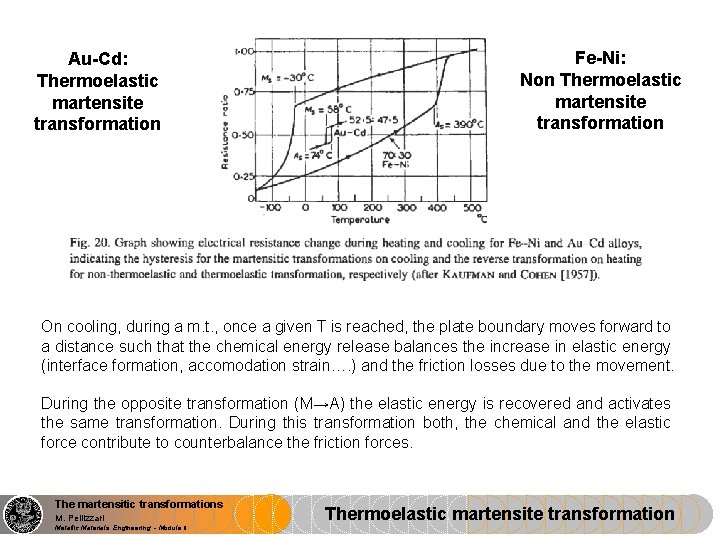
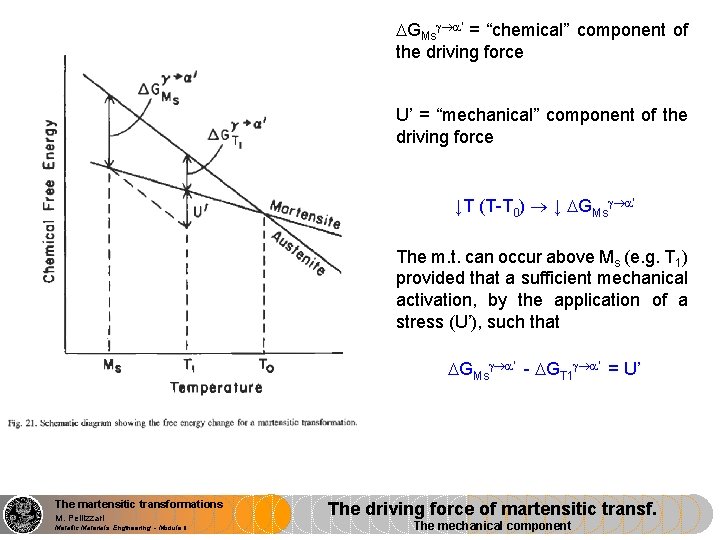
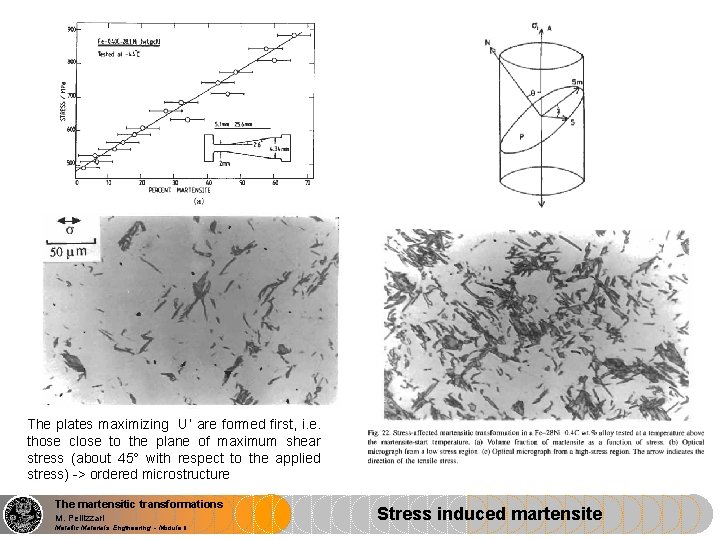
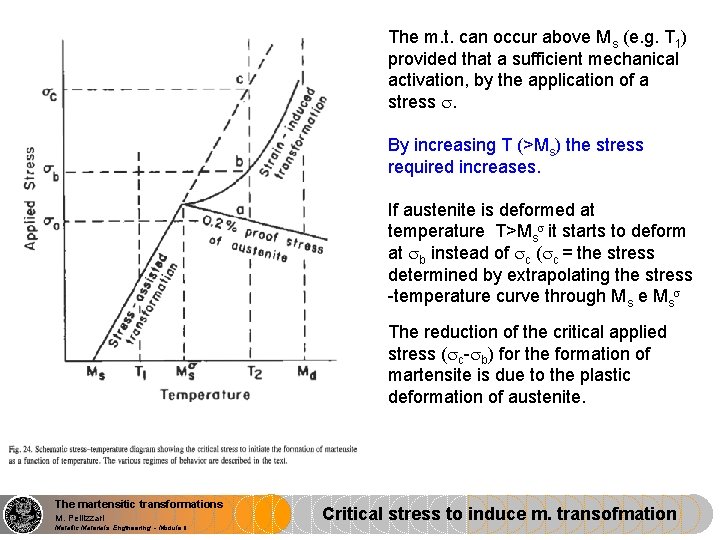
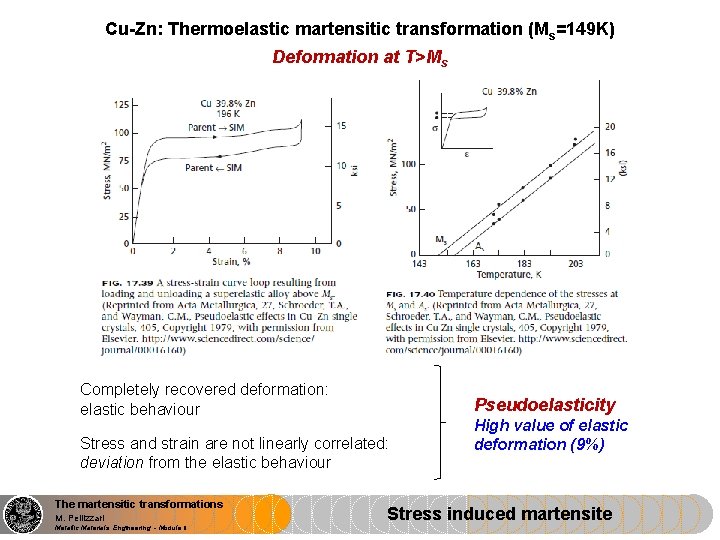
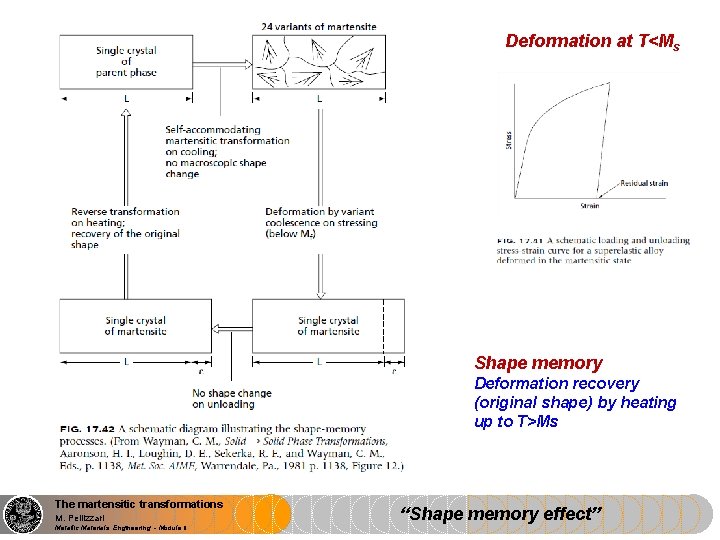
- Slides: 38
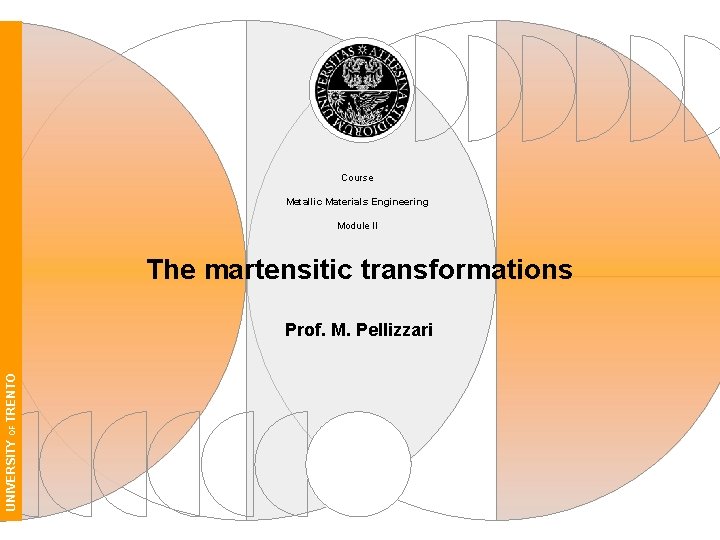
Course Metallic Materials Engineering Module II The martensitic transformations UNIVERSITY OF TRENTO Prof. M. Pellizzari
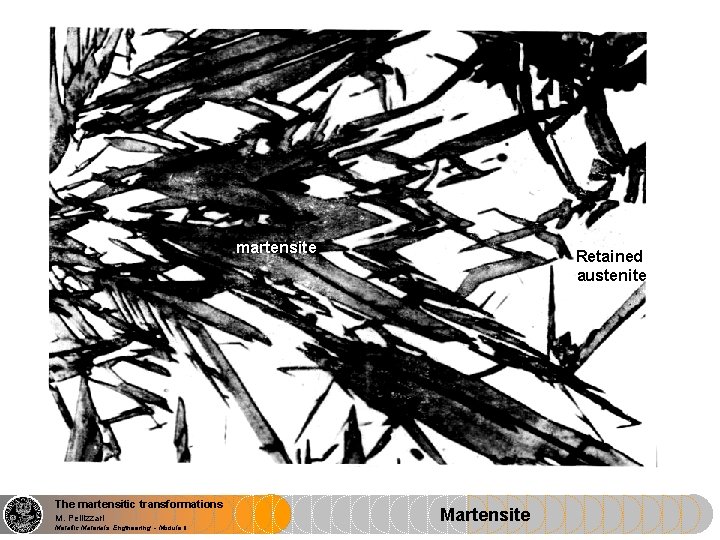
martensite The martensitic transformations M. Pellizzari Metallic Materials Engineering - Module II Retained austenite Martensite
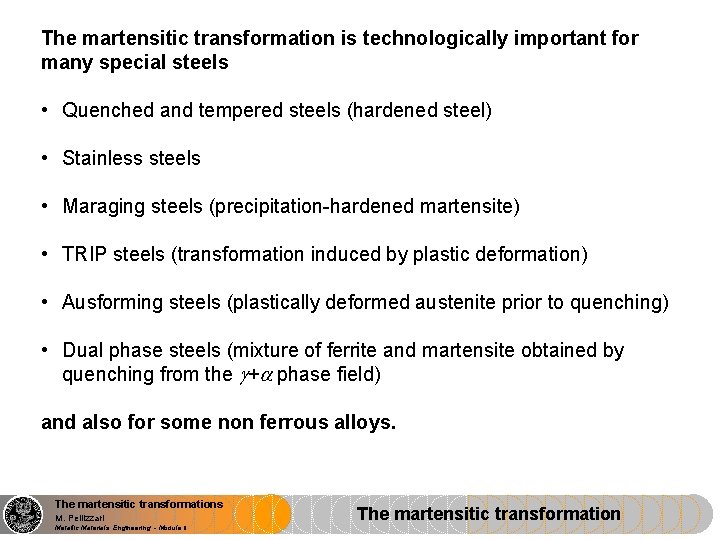
The martensitic transformation is technologically important for many special steels • Quenched and tempered steels (hardened steel) • Stainless steels • Maraging steels (precipitation-hardened martensite) • TRIP steels (transformation induced by plastic deformation) • Ausforming steels (plastically deformed austenite prior to quenching) • Dual phase steels (mixture of ferrite and martensite obtained by quenching from the + phase field) and also for some non ferrous alloys. The martensitic transformations M. Pellizzari Metallic Materials Engineering - Module II The martensitic transformation
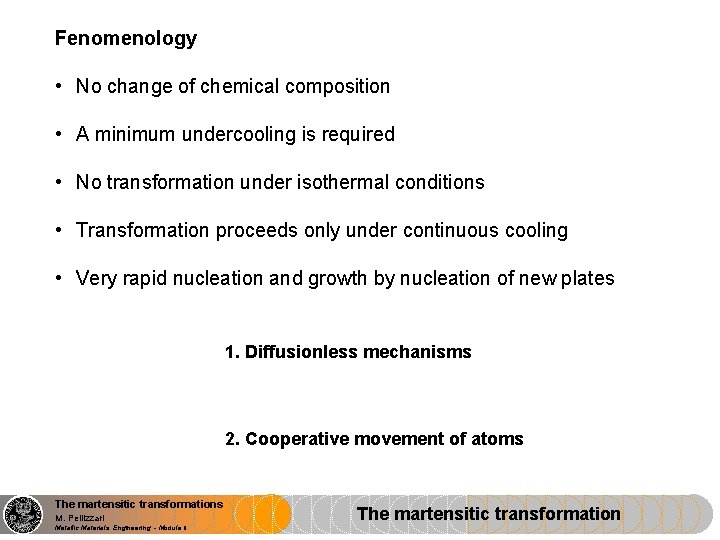
Fenomenology • No change of chemical composition • A minimum undercooling is required • No transformation under isothermal conditions • Transformation proceeds only under continuous cooling • Very rapid nucleation and growth by nucleation of new plates 1. Diffusionless mechanisms 2. Cooperative movement of atoms The martensitic transformations M. Pellizzari Metallic Materials Engineering - Module II The martensitic transformation
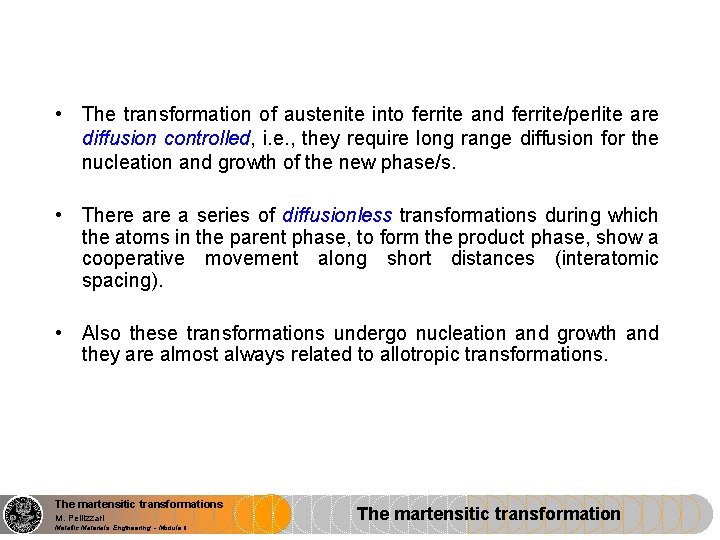
• The transformation of austenite into ferrite and ferrite/perlite are diffusion controlled, i. e. , they require long range diffusion for the nucleation and growth of the new phase/s. • There a series of diffusionless transformations during which the atoms in the parent phase, to form the product phase, show a cooperative movement along short distances (interatomic spacing). • Also these transformations undergo nucleation and growth and they are almost always related to allotropic transformations. The martensitic transformations M. Pellizzari Metallic Materials Engineering - Module II The martensitic transformation
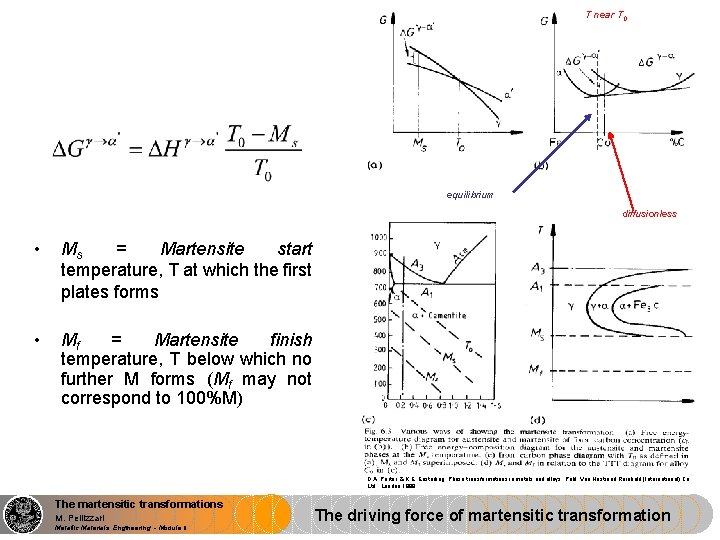
T near T 0 equilibrium diffusionless • Ms = Martensite start temperature, T at which the first plates forms • Mf = Martensite finish temperature, T below which no further M forms (Mf may not correspond to 100%M) D. A. Porter, & K. E. Easterling, Phase transformations in metals and alloys, Publ. Van Nostrand Reinhold (International) Co. Ltd. , London 1989 The martensitic transformations M. Pellizzari Metallic Materials Engineering - Module II The driving force of martensitic transformation
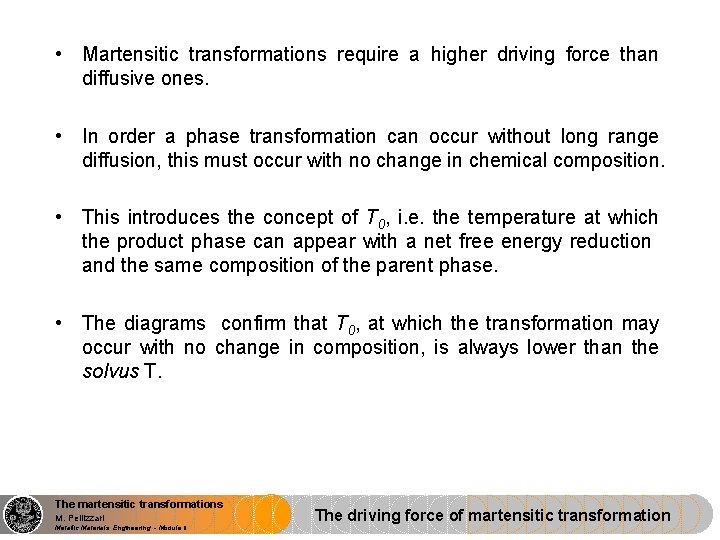
• Martensitic transformations require a higher driving force than diffusive ones. • In order a phase transformation can occur without long range diffusion, this must occur with no change in chemical composition. • This introduces the concept of T 0, i. e. the temperature at which the product phase can appear with a net free energy reduction and the same composition of the parent phase. • The diagrams confirm that T 0, at which the transformation may occur with no change in composition, is always lower than the solvus T. The martensitic transformations M. Pellizzari Metallic Materials Engineering - Module II The driving force of martensitic transformation
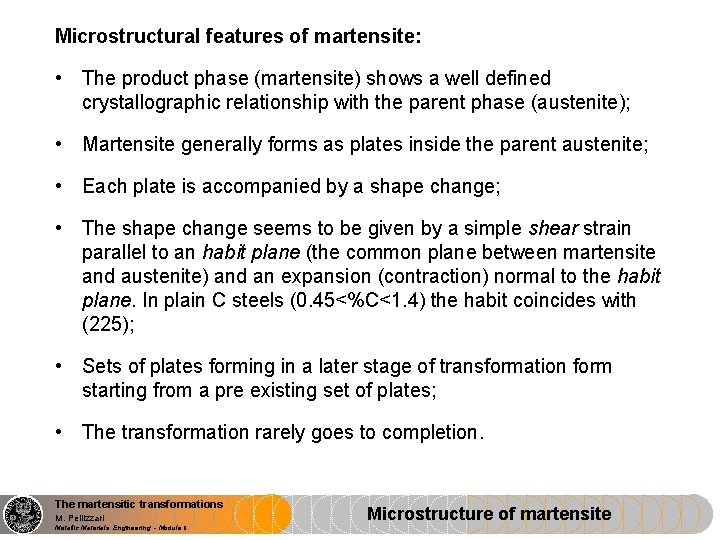
Microstructural features of martensite: • The product phase (martensite) shows a well defined crystallographic relationship with the parent phase (austenite); • Martensite generally forms as plates inside the parent austenite; • Each plate is accompanied by a shape change; • The shape change seems to be given by a simple shear strain parallel to an habit plane (the common plane between martensite and austenite) and an expansion (contraction) normal to the habit plane. In plain C steels (0. 45<%C<1. 4) the habit coincides with (225); • Sets of plates forming in a later stage of transformation form starting from a pre existing set of plates; • The transformation rarely goes to completion. The martensitic transformations M. Pellizzari Metallic Materials Engineering - Module II Microstructure of martensite
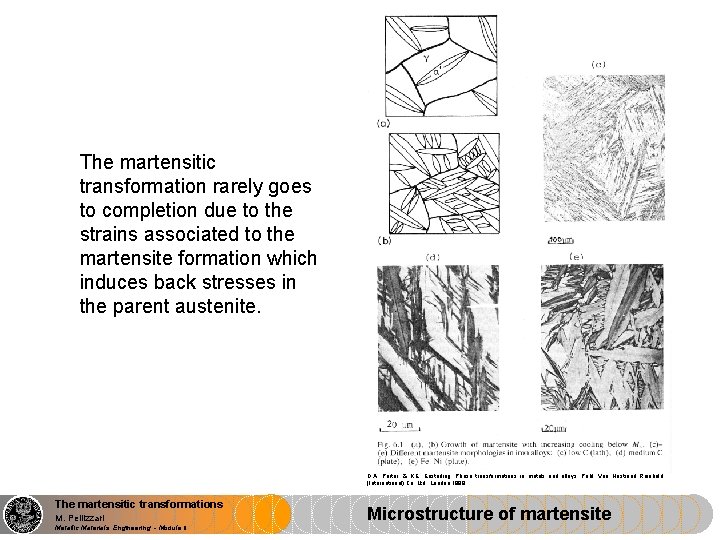
The martensitic transformation rarely goes to completion due to the strains associated to the martensite formation which induces back stresses in the parent austenite. D. A. Porter, & K. E. Easterling, Phase transformations in metals and alloys, Publ. Van Nostrand Reinhold (International) Co. Ltd. , London 1989 The martensitic transformations M. Pellizzari Metallic Materials Engineering - Module II Microstructure of martensite
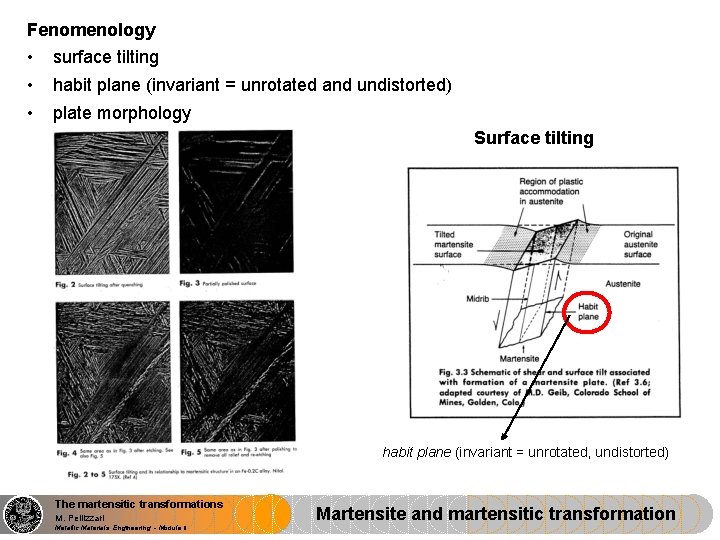
Fenomenology • • • surface tilting habit plane (invariant = unrotated and undistorted) plate morphology Surface tilting habit plane (invariant = unrotated, undistorted) The martensitic transformations M. Pellizzari Metallic Materials Engineering - Module II Martensite and martensitic transformation
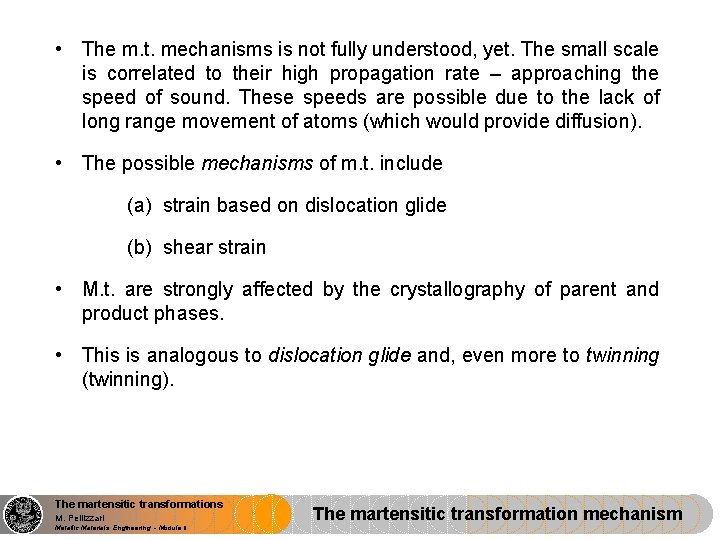
• The m. t. mechanisms is not fully understood, yet. The small scale is correlated to their high propagation rate – approaching the speed of sound. These speeds are possible due to the lack of long range movement of atoms (which would provide diffusion). • The possible mechanisms of m. t. include (a) strain based on dislocation glide (b) shear strain • M. t. are strongly affected by the crystallography of parent and product phases. • This is analogous to dislocation glide and, even more to twinning (twinning). The martensitic transformations M. Pellizzari Metallic Materials Engineering - Module II The martensitic transformation mechanism
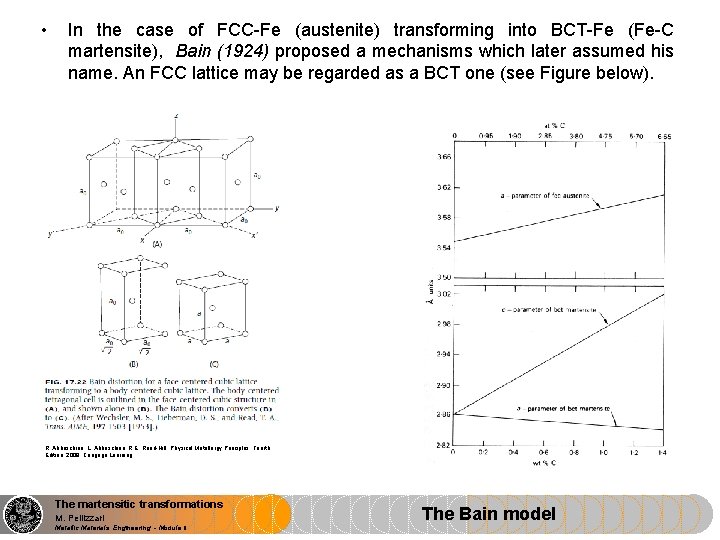
• In the case of FCC-Fe (austenite) transforming into BCT-Fe (Fe-C martensite), Bain (1924) proposed a mechanisms which later assumed his name. An FCC lattice may be regarded as a BCT one (see Figure below). R. Abbaschian, L. Abbaschian, R. E. Reed-Hill: Physical Metallurgy Principles, Fourth Edition, 2009, Cengage Learning The martensitic transformations M. Pellizzari Metallic Materials Engineering - Module II The Bain model

b 3 a 2 b 1 b 2 a 1 (a) Austenite - FCC (b) Austenite – BCT (in red) STRAIN Bain distorsion (c) Austenite - BCT The martensitic transformations M. Pellizzari Metallic Materials Engineering - Module II (d) Martensite - BCC The shape change due to M transf.
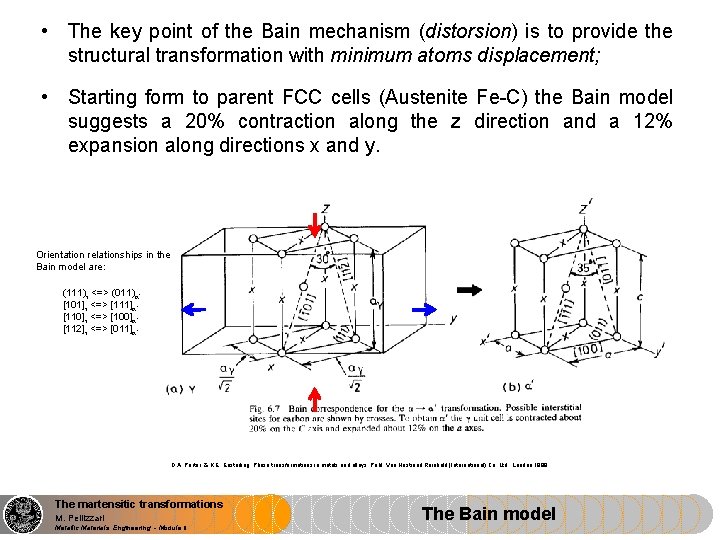
• The key point of the Bain mechanism (distorsion) is to provide the structural transformation with minimum atoms displacement; • Starting form to parent FCC cells (Austenite Fe-C) the Bain model suggests a 20% contraction along the z direction and a 12% expansion along directions x and y. Orientation relationships in the Bain model are: (111) <=> (011) ’ [101] <=> [111] ’ [110] <=> [100] ’ [112] <=> [011] ’ D. A. Porter, & K. E. Easterling, Phase transformations in metals and alloys, Publ. Van Nostrand Reinhold (International) Co. Ltd. , London 1989 The martensitic transformations M. Pellizzari Metallic Materials Engineering - Module II The Bain model
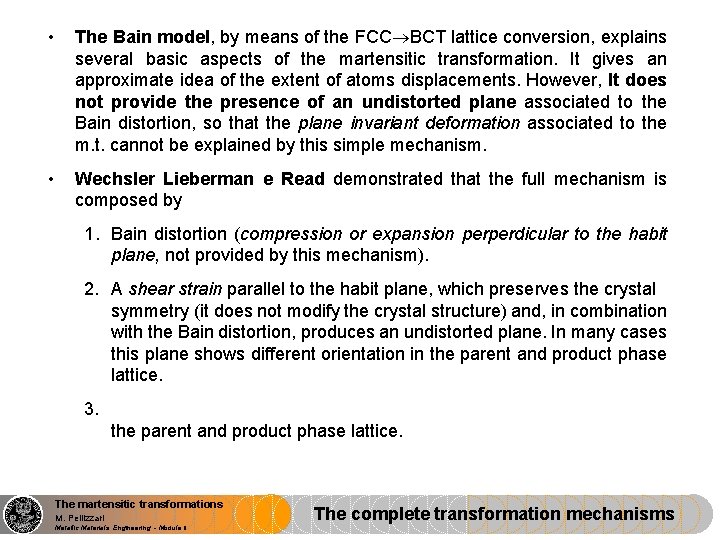
• The Bain model, by means of the FCC BCT lattice conversion, explains several basic aspects of the martensitic transformation. It gives an approximate idea of the extent of atoms displacements. However, It does not provide the presence of an undistorted plane associated to the Bain distortion, so that the plane invariant deformation associated to the m. t. cannot be explained by this simple mechanism. • Wechsler Lieberman e Read demonstrated that the full mechanism is composed by 1. Bain distortion (compression or expansion perperdicular to the habit plane, not provided by this mechanism). 2. A shear strain parallel to the habit plane, which preserves the crystal symmetry (it does not modify the crystal structure) and, in combination with the Bain distortion, produces an undistorted plane. In many cases this plane shows different orientation in the parent and product phase lattice. 3. the parent and product phase lattice. The martensitic transformations M. Pellizzari Metallic Materials Engineering - Module II The complete transformation mechanisms
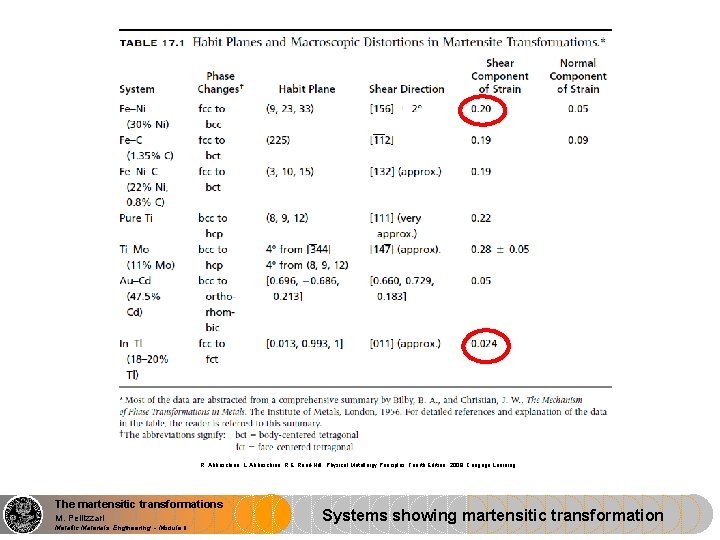
R. Abbaschian, L. Abbaschian, R. E. Reed-Hill: Physical Metallurgy Principles, Fourth Edition, 2009, Cengage Learning The martensitic transformations M. Pellizzari Metallic Materials Engineering - Module II Systems showing martensitic transformation
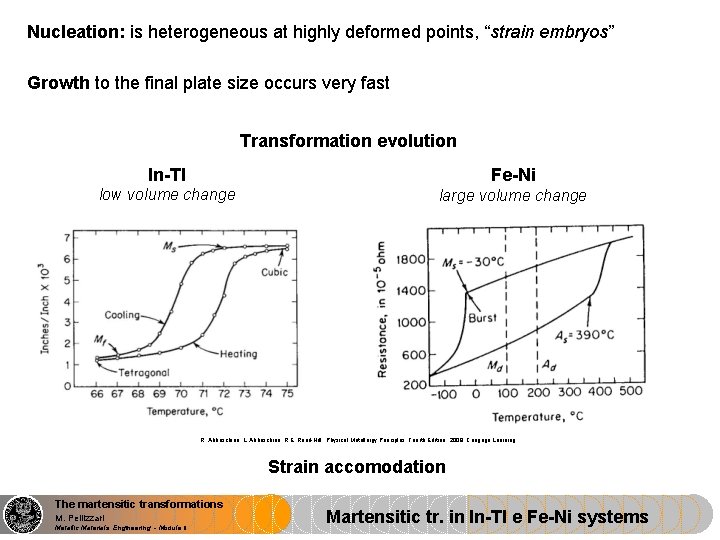
Nucleation: is heterogeneous at highly deformed points, “strain embryos” Growth to the final plate size occurs very fast Transformation evolution In-Tl Fe-Ni low volume change large volume change R. Abbaschian, L. Abbaschian, R. E. Reed-Hill: Physical Metallurgy Principles, Fourth Edition, 2009, Cengage Learning Strain accomodation The martensitic transformations M. Pellizzari Metallic Materials Engineering - Module II Martensitic tr. in In-Tl e Fe-Ni systems
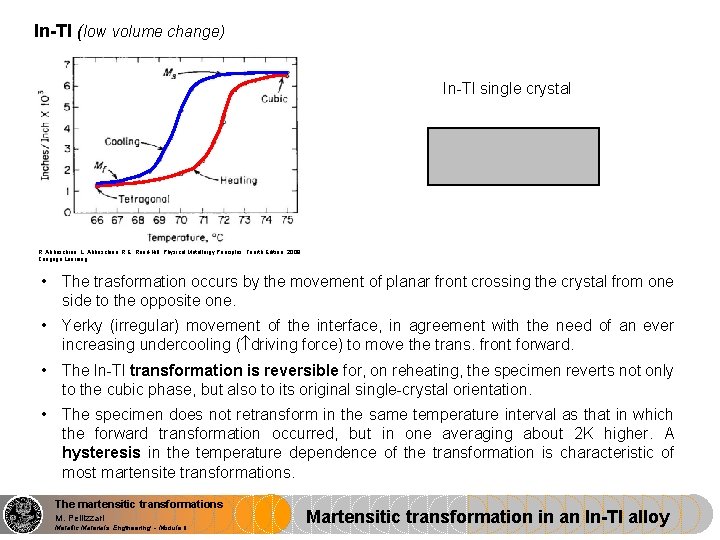
In-Tl (low volume change) In-Tl single crystal R. Abbaschian, L. Abbaschian, R. E. Reed-Hill: Physical Metallurgy Principles, Fourth Edition, 2009, Cengage Learning • The trasformation occurs by the movement of planar front crossing the crystal from one side to the opposite one. • Yerky (irregular) movement of the interface, in agreement with the need of an ever increasing undercooling ( driving force) to move the trans. front forward. • The In-Tl transformation is reversible for, on reheating, the specimen reverts not only to the cubic phase, but also to its original single-crystal orientation. • The specimen does not retransform in the same temperature interval as that in which the forward transformation occurred, but in one averaging about 2 K higher. A hysteresis in the temperature dependence of the transformation is characteristic of most martensite transformations. The martensitic transformations M. Pellizzari Metallic Materials Engineering - Module II Martensitic transformation in an In-Tl alloy
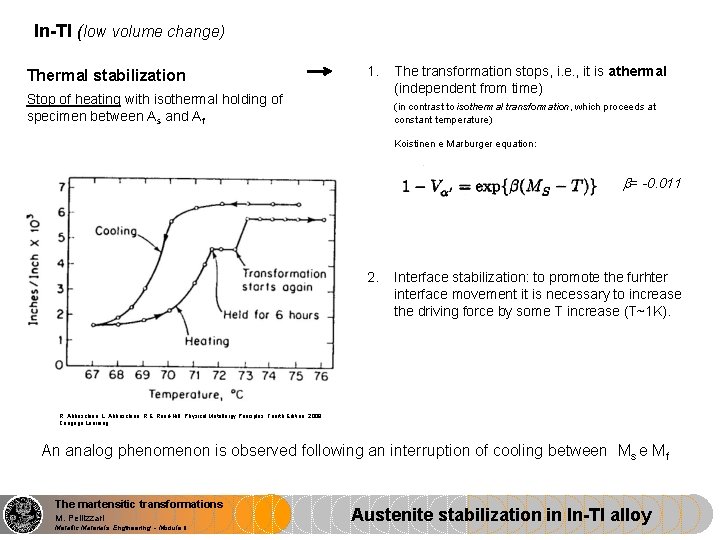
In-Tl (low volume change) Thermal stabilization 1. Stop of heating with isothermal holding of specimen between As and Af The transformation stops, i. e. , it is athermal (independent from time) (in contrast to isothermal transformation, which proceeds at constant temperature) Koistinen e Marburger equation: = -0. 011 2. Interface stabilization: to promote the furhter interface movement it is necessary to increase the driving force by some T increase (T~1 K). R. Abbaschian, L. Abbaschian, R. E. Reed-Hill: Physical Metallurgy Principles, Fourth Edition, 2009, Cengage Learning An analog phenomenon is observed following an interruption of cooling between Ms e Mf The martensitic transformations M. Pellizzari Metallic Materials Engineering - Module II Austenite stabilization in In-Tl alloy
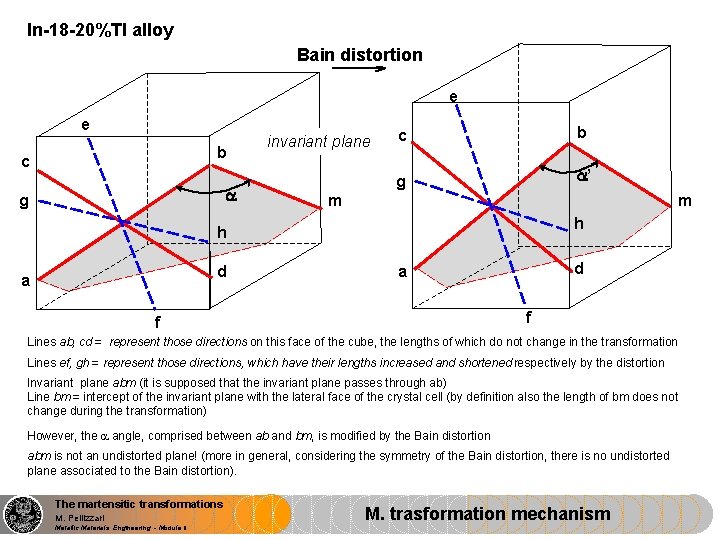
In-18 -20%Tl alloy Bain distortion e e b c g invariant plane c b g ’ m m h h d a f f Lines ab, cd = represent those directions on this face of the cube, the lengths of which do not change in the transformation Lines ef, gh = represent those directions, which have their lengths increased and shortened respectively by the distortion Invariant plane abm (it is supposed that the invariant plane passes through ab) Line bm = intercept of the invariant plane with the lateral face of the crystal cell (by definition also the length of bm does not change during the transformation) However, the angle, comprised between ab and bm, is modified by the Bain distortion abm is not an undistorted plane! (more in general, considering the symmetry of the Bain distortion, there is no undistorted plane associated to the Bain distortion). The martensitic transformations M. Pellizzari Metallic Materials Engineering - Module II M. trasformation mechanism
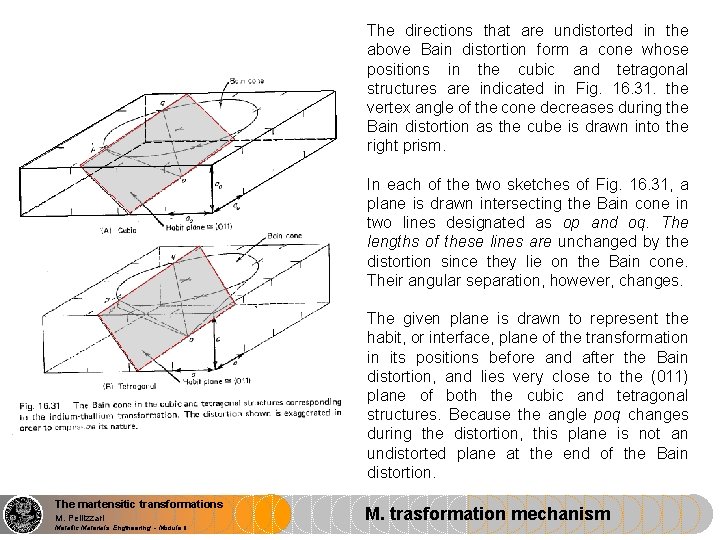
The directions that are undistorted in the above Bain distortion form a cone whose positions in the cubic and tetragonal structures are indicated in Fig. 16. 31. the vertex angle of the cone decreases during the Bain distortion as the cube is drawn into the right prism. In each of the two sketches of Fig. 16. 31, a plane is drawn intersecting the Bain cone in two lines designated as op and oq. The lengths of these lines are unchanged by the distortion since they lie on the Bain cone. Their angular separation, however, changes. The given plane is drawn to represent the habit, or interface, plane of the transformation in its positions before and after the Bain distortion, and lies very close to the (011) plane of both the cubic and tetragonal structures. Because the angle poq changes during the distortion, this plane is not an undistorted plane at the end of the Bain distortion. The martensitic transformations M. Pellizzari Metallic Materials Engineering - Module II M. trasformation mechanism
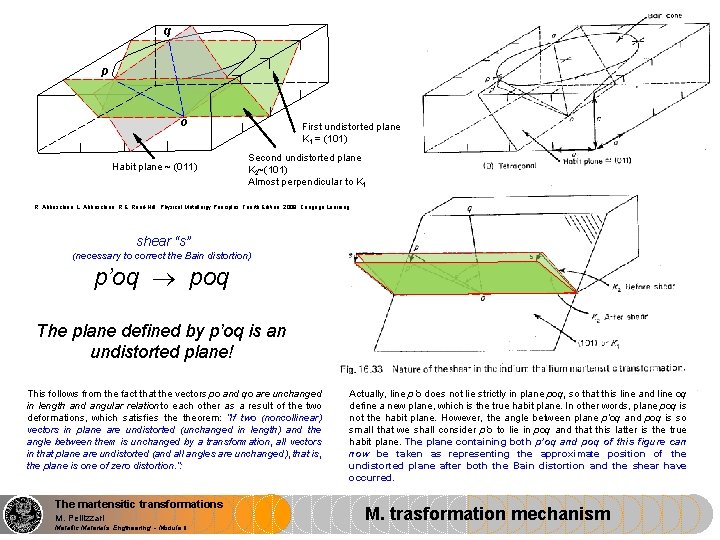
q p o Habit plane ~ (011) First undistorted plane K 1 = (101) Second undistorted plane K 2~(101) Almost perpendicular to K 1 R. Abbaschian, L. Abbaschian, R. E. Reed-Hill: Physical Metallurgy Principles, Fourth Edition, 2009, Cengage Learning shear “s” (necessary to correct the Bain distortion) p’oq poq The plane defined by p’oq is an undistorted plane! This follows from the fact that the vectors po and qo are unchanged in length and angular relationto each other as a result of the two deformations, which satisfies theorem: “If two (noncollinear) vectors in plane are undistorted (unchanged in length) and the angle between them is unchanged by a transformation, all vectors in that plane are undistorted (and all angles are unchanged), that is, the plane is one of zero distortion. ”: The martensitic transformations M. Pellizzari Metallic Materials Engineering - Module II Actually, line p’o does not lie strictly in plane poq, so that this line and line oq define a new plane, which is the true habit plane. In other words, plane poq is not the habit plane. However, the angle between plane p’oq and poq is so small that we shall consider p’o to lie in poq and that this latter is the true habit plane. The plane containing both p’oq and poq of this figure can now be taken as representing the approximate position of the undistorted plane after both the Bain distortion and the shear have occurred. M. trasformation mechanism
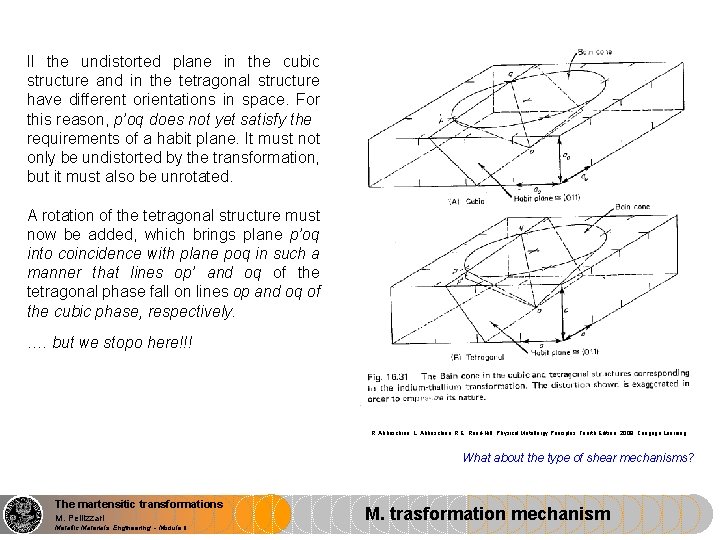
Il the undistorted plane in the cubic structure and in the tetragonal structure have different orientations in space. For this reason, p’oq does not yet satisfy the requirements of a habit plane. It must not only be undistorted by the transformation, but it must also be unrotated. A rotation of the tetragonal structure must now be added, which brings plane p’oq into coincidence with plane poq in such a manner that lines op’ and oq of the tetragonal phase fall on lines op and oq of the cubic phase, respectively. …. but we stopo here!!! R. Abbaschian, L. Abbaschian, R. E. Reed-Hill: Physical Metallurgy Principles, Fourth Edition, 2009, Cengage Learning What about the type of shear mechanisms? The martensitic transformations M. Pellizzari Metallic Materials Engineering - Module II M. trasformation mechanism
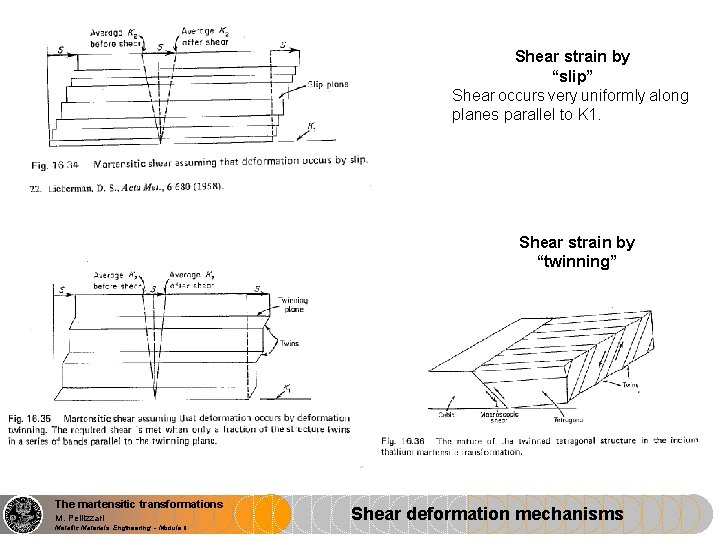
Shear strain by “slip” Shear occurs very uniformly along planes parallel to K 1. Shear strain by “twinning” The martensitic transformations M. Pellizzari Metallic Materials Engineering - Module II Shear deformation mechanisms
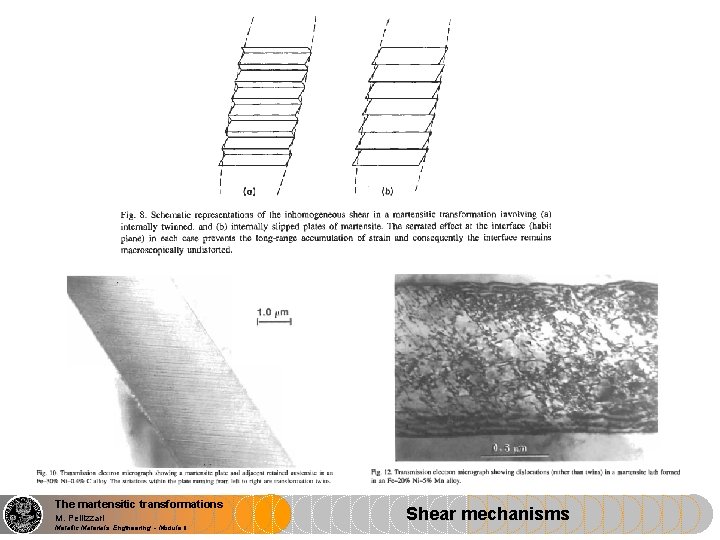
The martensitic transformations M. Pellizzari Metallic Materials Engineering - Module II Shear mechanisms
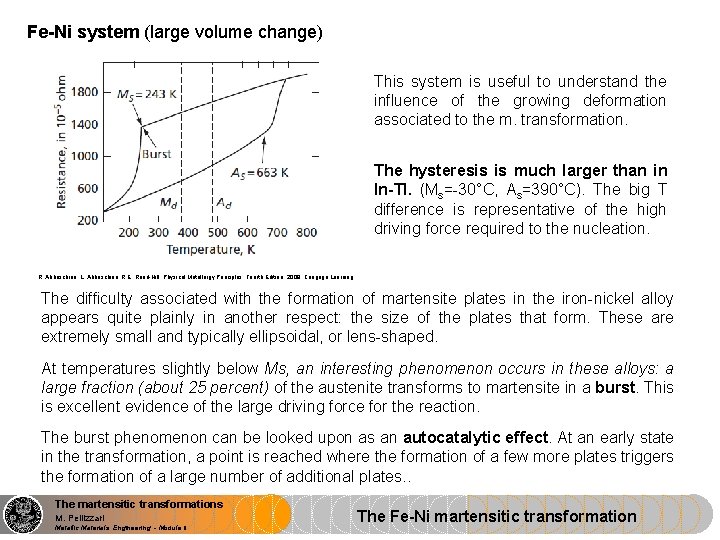
Fe-Ni system (large volume change) This system is useful to understand the influence of the growing deformation associated to the m. transformation. The hysteresis is much larger than in In-Tl. (Ms=-30°C, As=390°C). The big T difference is representative of the high driving force required to the nucleation. R. Abbaschian, L. Abbaschian, R. E. Reed-Hill: Physical Metallurgy Principles, Fourth Edition, 2009, Cengage Learning The difficulty associated with the formation of martensite plates in the iron-nickel alloy appears quite plainly in another respect: the size of the plates that form. These are extremely small and typically ellipsoidal, or lens-shaped. At temperatures slightly below Ms, an interesting phenomenon occurs in these alloys: a large fraction (about 25 percent) of the austenite transforms to martensite in a burst. This is excellent evidence of the large driving force for the reaction. The burst phenomenon can be looked upon as an autocatalytic effect. At an early state in the transformation, a point is reached where the formation of a few more plates triggers the formation of a large number of additional plates. . The martensitic transformations M. Pellizzari Metallic Materials Engineering - Module II The Fe-Ni martensitic transformation
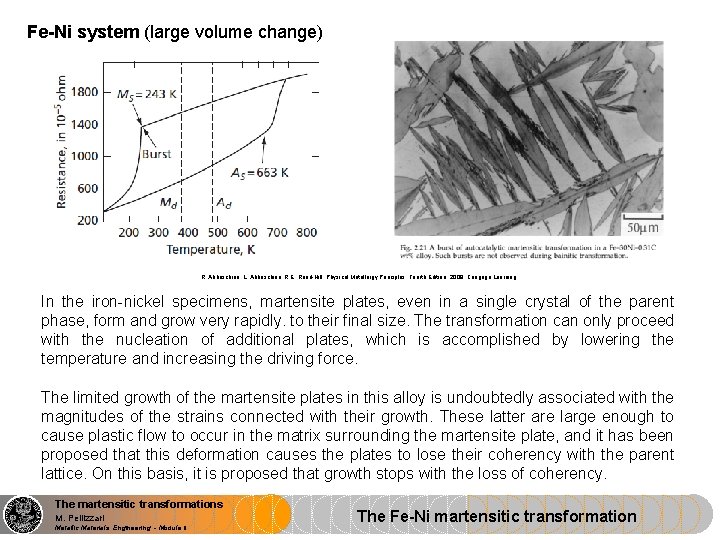
Fe-Ni system (large volume change) R. Abbaschian, L. Abbaschian, R. E. Reed-Hill: Physical Metallurgy Principles, Fourth Edition, 2009, Cengage Learning In the iron-nickel specimens, martensite plates, even in a single crystal of the parent phase, form and grow very rapidly. to their final size. The transformation can only proceed with the nucleation of additional plates, which is accomplished by lowering the temperature and increasing the driving force. The limited growth of the martensite plates in this alloy is undoubtedly associated with the magnitudes of the strains connected with their growth. These latter are large enough to cause plastic flow to occur in the matrix surrounding the martensite plate, and it has been proposed that this deformation causes the plates to lose their coherency with the parent lattice. On this basis, it is proposed that growth stops with the loss of coherency. The martensitic transformations M. Pellizzari Metallic Materials Engineering - Module II The Fe-Ni martensitic transformation
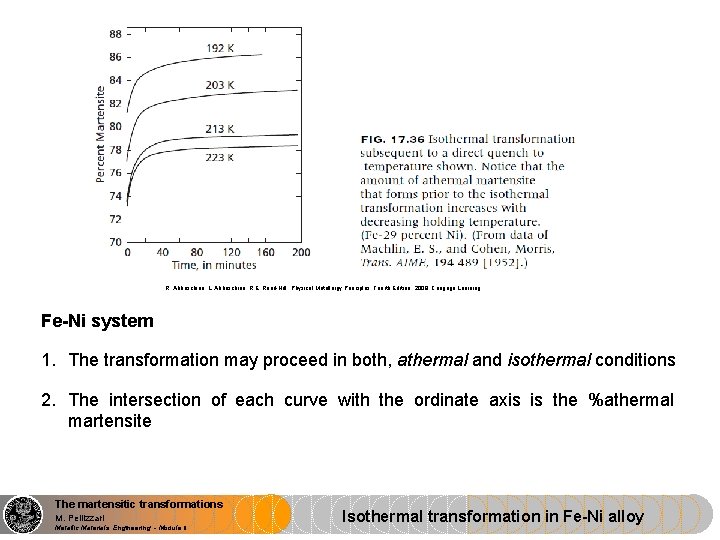
R. Abbaschian, L. Abbaschian, R. E. Reed-Hill: Physical Metallurgy Principles, Fourth Edition, 2009, Cengage Learning Fe-Ni system 1. The transformation may proceed in both, athermal and isothermal conditions 2. The intersection of each curve with the ordinate axis is the %athermal martensite The martensitic transformations M. Pellizzari Metallic Materials Engineering - Module II Isothermal transformation in Fe-Ni alloy
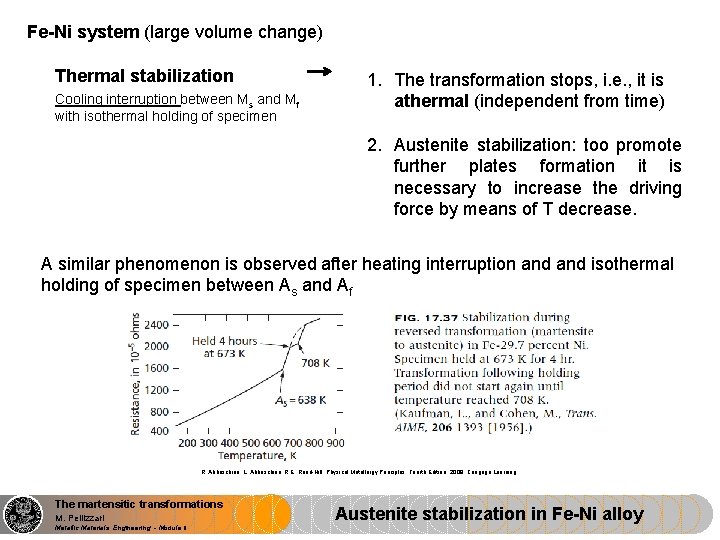
Fe-Ni system (large volume change) Thermal stabilization Cooling interruption between Ms and Mf with isothermal holding of specimen 1. The transformation stops, i. e. , it is athermal (independent from time) 2. Austenite stabilization: too promote further plates formation it is necessary to increase the driving force by means of T decrease. A similar phenomenon is observed after heating interruption and isothermal holding of specimen between As and Af R. Abbaschian, L. Abbaschian, R. E. Reed-Hill: Physical Metallurgy Principles, Fourth Edition, 2009, Cengage Learning The martensitic transformations M. Pellizzari Metallic Materials Engineering - Module II Austenite stabilization in Fe-Ni alloy
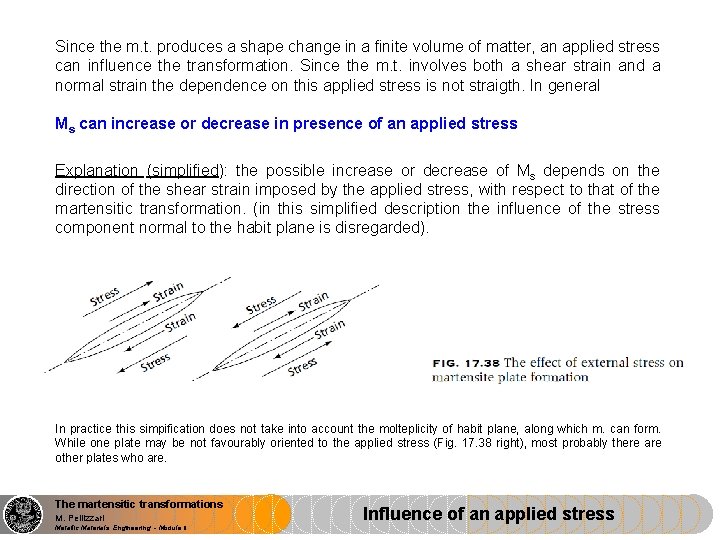
Since the m. t. produces a shape change in a finite volume of matter, an applied stress can influence the transformation. Since the m. t. involves both a shear strain and a normal strain the dependence on this applied stress is not straigth. In general Ms can increase or decrease in presence of an applied stress Explanation (simplified): the possible increase or decrease of Ms depends on the direction of the shear strain imposed by the applied stress, with respect to that of the martensitic transformation. (in this simplified description the influence of the stress component normal to the habit plane is disregarded). In practice this simpification does not take into account the molteplicity of habit plane, along which m. can form. While one plate may be not favourably oriented to the applied stress (Fig. 17. 38 right), most probably there are other plates who are. The martensitic transformations M. Pellizzari Metallic Materials Engineering - Module II Influence of an applied stress
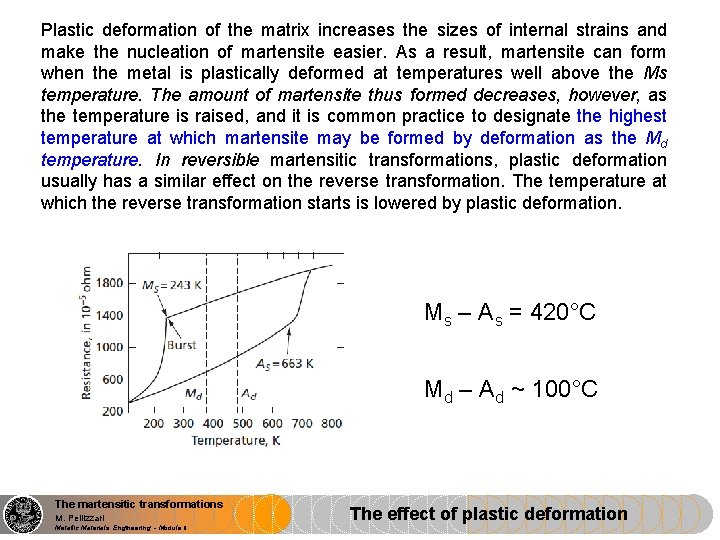
Plastic deformation of the matrix increases the sizes of internal strains and make the nucleation of martensite easier. As a result, martensite can form when the metal is plastically deformed at temperatures well above the Ms temperature. The amount of martensite thus formed decreases, however, as the temperature is raised, and it is common practice to designate the highest temperature at which martensite may be formed by deformation as the Md temperature. In reversible martensitic transformations, plastic deformation usually has a similar effect on the reverse transformation. The temperature at which the reverse transformation starts is lowered by plastic deformation. Ms – As = 420°C Md – Ad ~ 100°C The martensitic transformations M. Pellizzari Metallic Materials Engineering - Module II The effect of plastic deformation
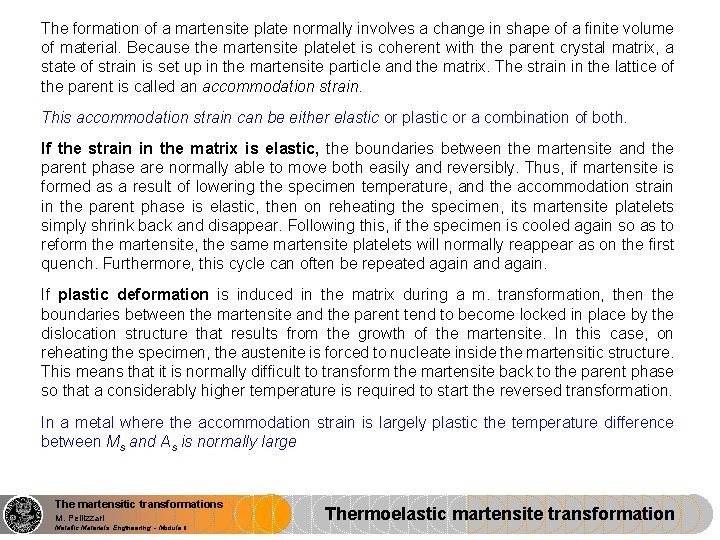
The formation of a martensite plate normally involves a change in shape of a finite volume of material. Because the martensite platelet is coherent with the parent crystal matrix, a state of strain is set up in the martensite particle and the matrix. The strain in the lattice of the parent is called an accommodation strain. This accommodation strain can be either elastic or plastic or a combination of both. If the strain in the matrix is elastic, the boundaries between the martensite and the parent phase are normally able to move both easily and reversibly. Thus, if martensite is formed as a result of lowering the specimen temperature, and the accommodation strain in the parent phase is elastic, then on reheating the specimen, its martensite platelets simply shrink back and disappear. Following this, if the specimen is cooled again so as to reform the martensite, the same martensite platelets will normally reappear as on the first quench. Furthermore, this cycle can often be repeated again and again. If plastic deformation is induced in the matrix during a m. transformation, then the boundaries between the martensite and the parent tend to become locked in place by the dislocation structure that results from the growth of the martensite. In this case, on reheating the specimen, the austenite is forced to nucleate inside the martensitic structure. This means that it is normally difficult to transform the martensite back to the parent phase so that a considerably higher temperature is required to start the reversed transformation. In a metal where the accommodation strain is largely plastic the temperature difference between Ms and As is normally large The martensitic transformations M. Pellizzari Metallic Materials Engineering - Module II Thermoelastic martensite transformation
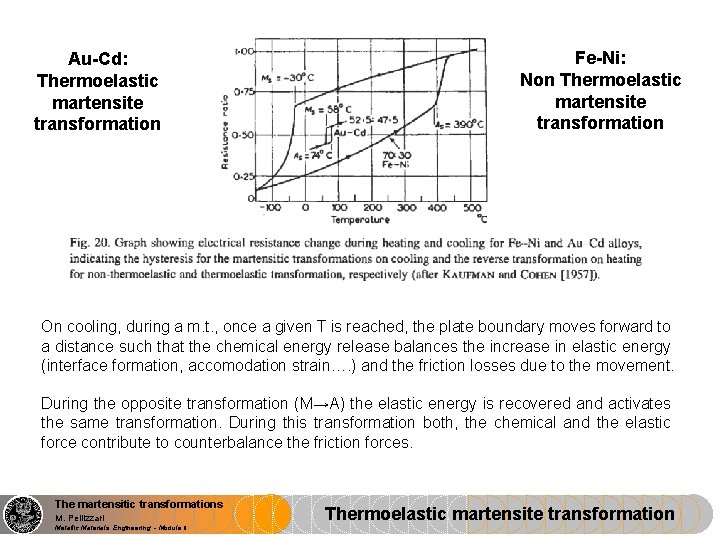
Au-Cd: Thermoelastic martensite transformation Fe-Ni: Non Thermoelastic martensite transformation On cooling, during a m. t. , once a given T is reached, the plate boundary moves forward to a distance such that the chemical energy release balances the increase in elastic energy (interface formation, accomodation strain…. ) and the friction losses due to the movement. During the opposite transformation (M→A) the elastic energy is recovered and activates the same transformation. During this transformation both, the chemical and the elastic force contribute to counterbalance the friction forces. The martensitic transformations M. Pellizzari Metallic Materials Engineering - Module II Thermoelastic martensite transformation
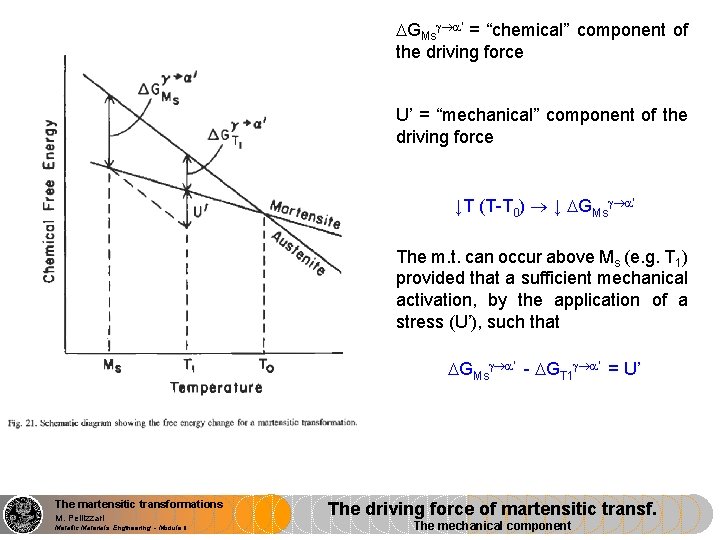
GMs ’ = “chemical” component of the driving force U’ = “mechanical” component of the driving force ↓T (T-T 0) ↓ GMs ’ The m. t. can occur above Ms (e. g. T 1) provided that a sufficient mechanical activation, by the application of a stress (U’), such that GMs ’ - GT 1 ’ = U’ The martensitic transformations M. Pellizzari Metallic Materials Engineering - Module II The driving force of martensitic transf. The mechanical component
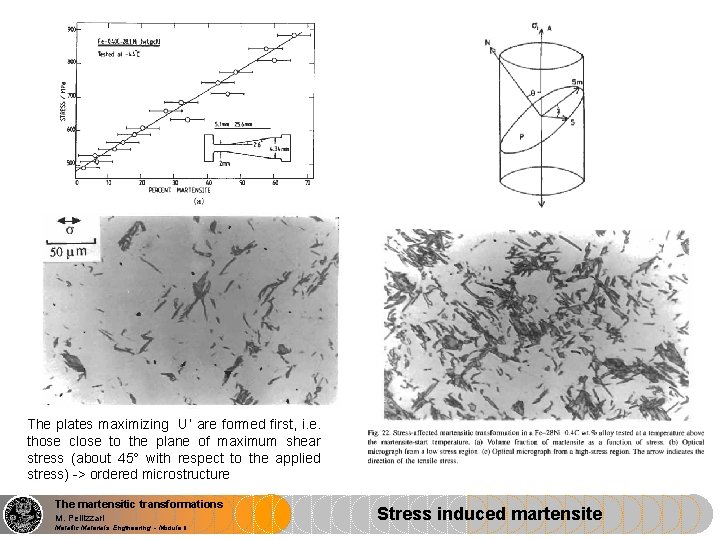
The plates maximizing U’ are formed first, i. e. those close to the plane of maximum shear stress (about 45° with respect to the applied stress) -> ordered microstructure The martensitic transformations M. Pellizzari Metallic Materials Engineering - Module II Stress induced martensite
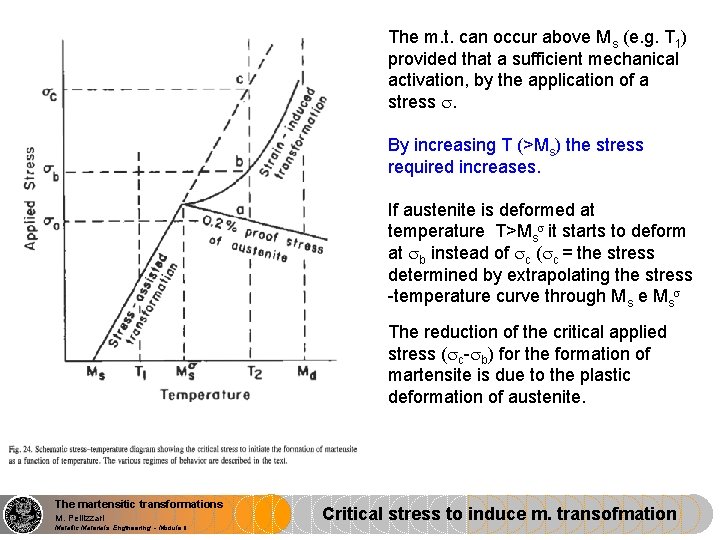
The m. t. can occur above Ms (e. g. T 1) provided that a sufficient mechanical activation, by the application of a stress . By increasing T (>Ms) the stress required increases. If austenite is deformed at temperature T>Ms it starts to deform at b instead of c ( c = the stress determined by extrapolating the stress -temperature curve through Ms e Ms The reduction of the critical applied stress ( c- b) for the formation of martensite is due to the plastic deformation of austenite. The martensitic transformations M. Pellizzari Metallic Materials Engineering - Module II Critical stress to induce m. transofmation
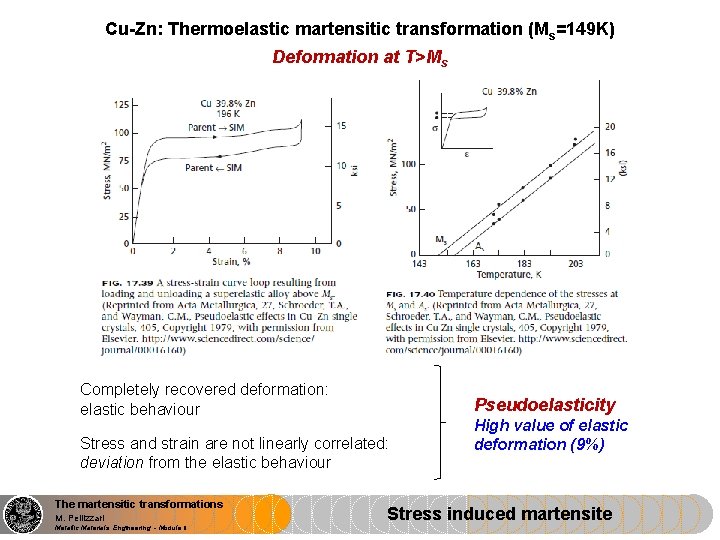
Cu-Zn: Thermoelastic martensitic transformation (Ms=149 K) Deformation at T>Ms Completely recovered deformation: elastic behaviour Pseudoelasticity Stress and strain are not linearly correlated: deviation from the elastic behaviour The martensitic transformations M. Pellizzari Metallic Materials Engineering - Module II High value of elastic deformation (9%) Stress induced martensite
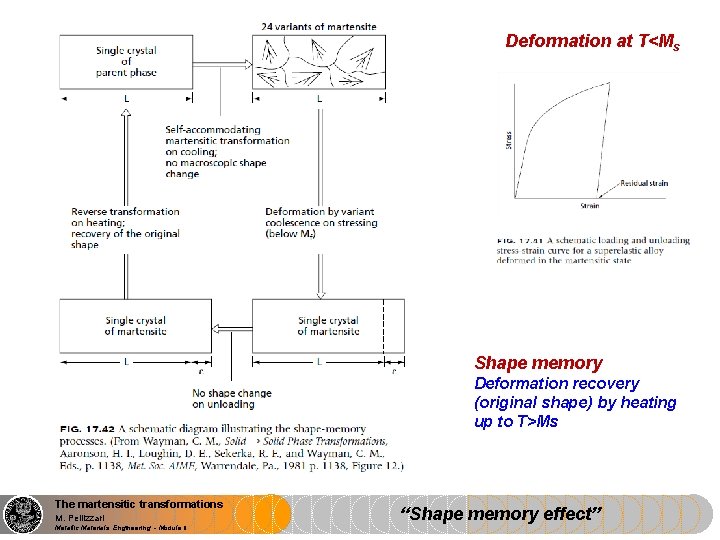
Deformation at T<Ms Shape memory Deformation recovery (original shape) by heating up to T>Ms The martensitic transformations M. Pellizzari Metallic Materials Engineering - Module II “Shape memory effect”
Inorganic non metallic materials examples
C device module module 1
Supervisor development course module 2 answers
Course module sample
What is half brick wall
Course number and title
Chaine parallèle muscle
Ndsu bookstore course materials
Lsu law course materials
Cant stop the feeling trolls go noodle
What are useful materials at home
Natural man made
Differentiate adopting materials and adapting materials
Direct materials budget with multiple materials
What is unit testing in software
Module engineering consultant
Special topics in software engineering
Internet engineering course
Rekayasa sosial pmii
Mechanical engineering course
Mechanical engineering course
Radar systems engineering course
Computer engineering course
Software engineering 1 course outline
Software engineering uottawa course sequence
Manufacturing process for engineering materials
Heat conductivity examples
What is the engineering materials
Optical properties of engineering materials
Materials engineering science processing and design
What is the engineering materials
Engineering materials
Materials for engineering
Integrated computational materials engineering
Eacademics iitd ac in sportal login
Integrated computational materials engineering
Civil engineering source
Hình ảnh bộ gõ cơ thể búng tay
Frameset trong html5