CHAPTER 7 MECHANICAL PROPERTIES CHAPTER 7 MECHANICAL PROPERTIES
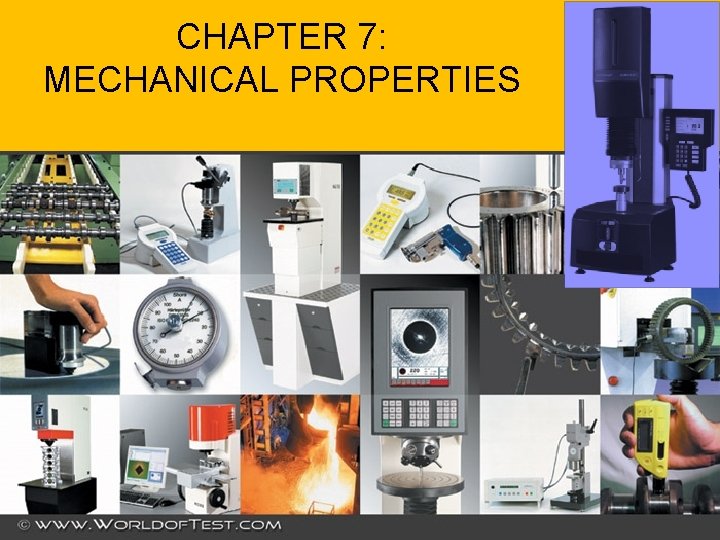
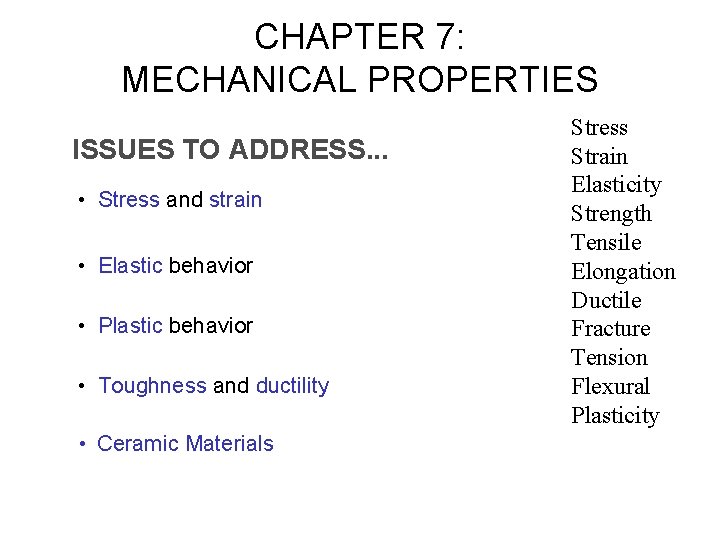
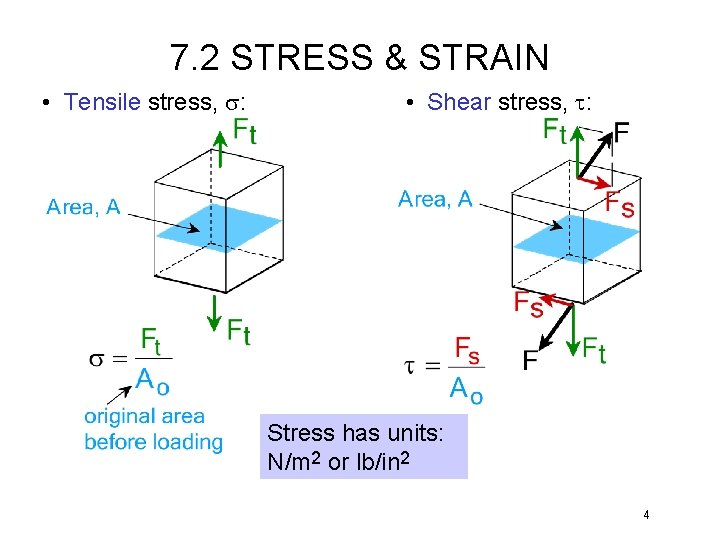
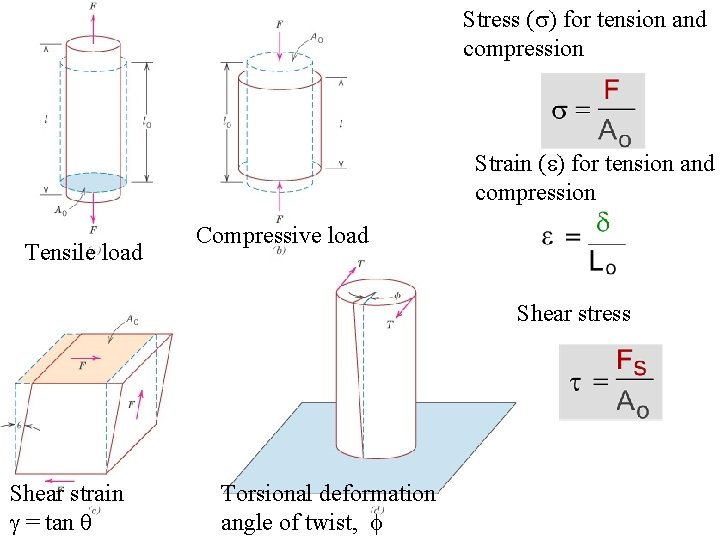
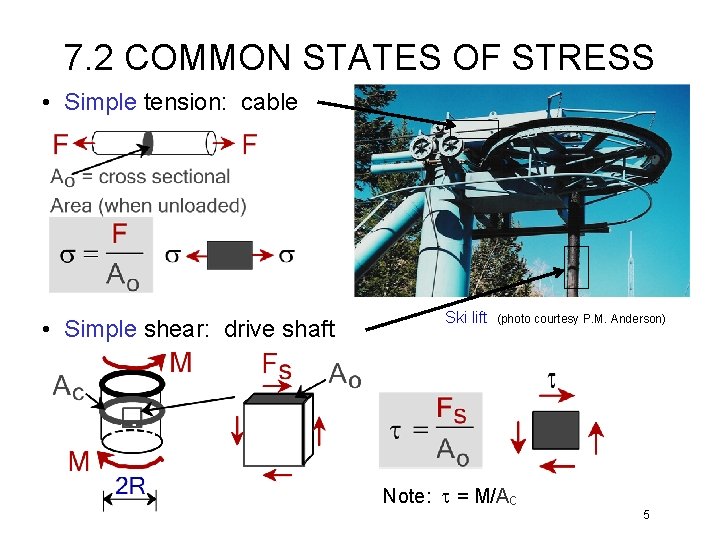
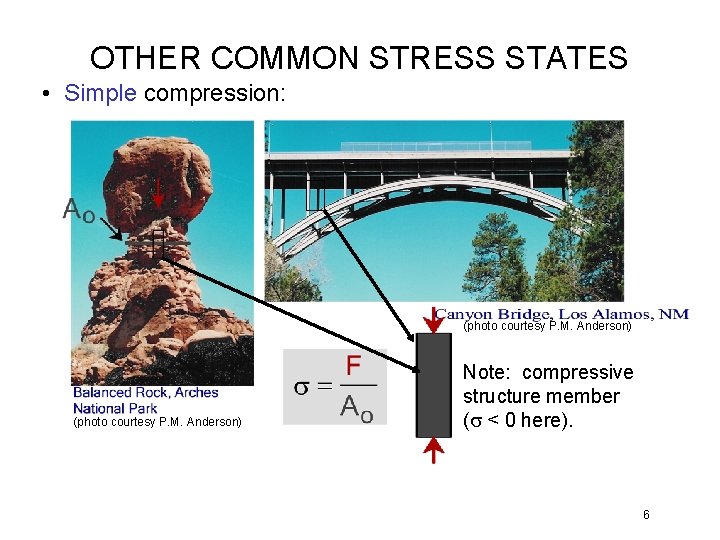
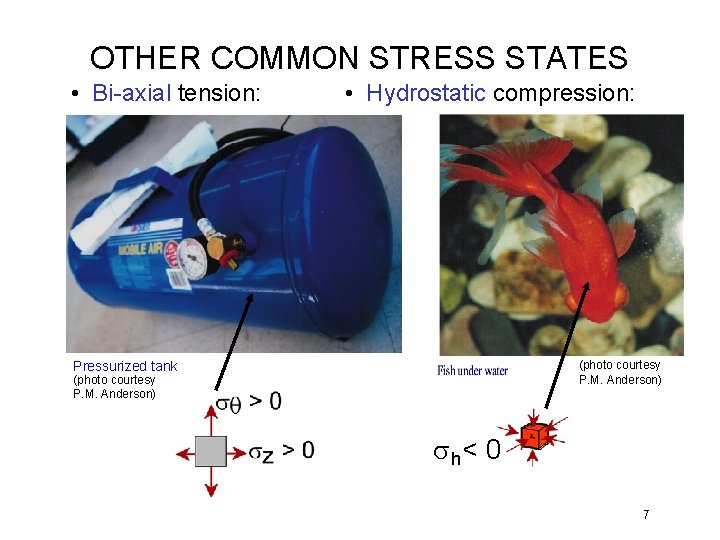
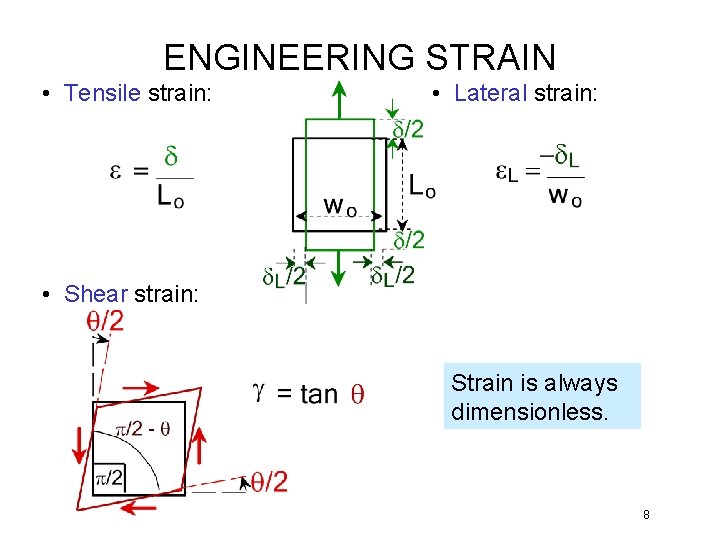
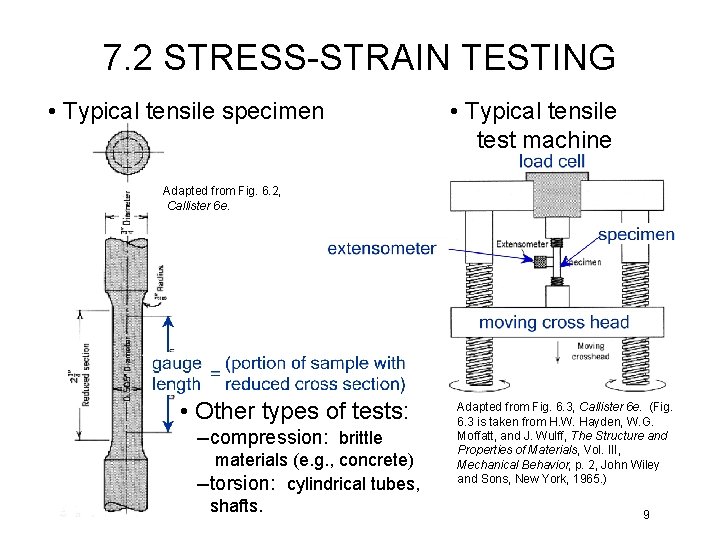
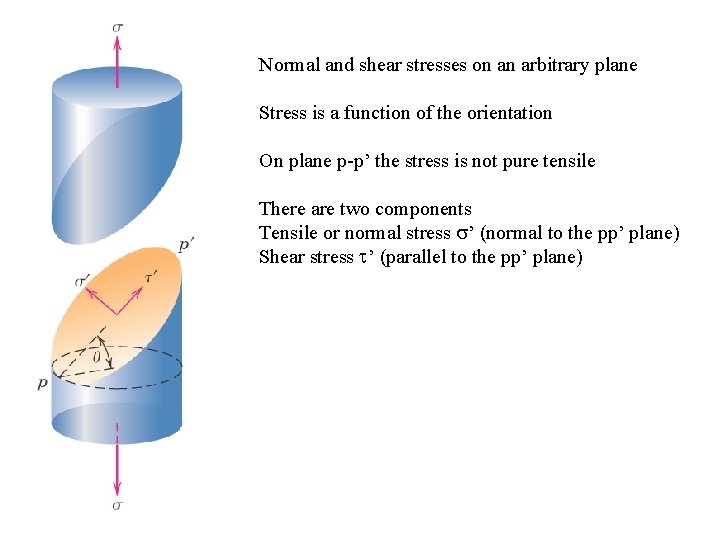
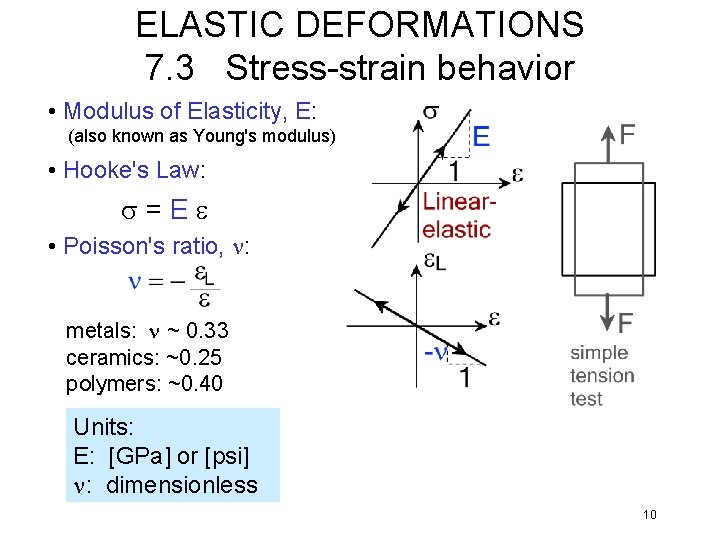
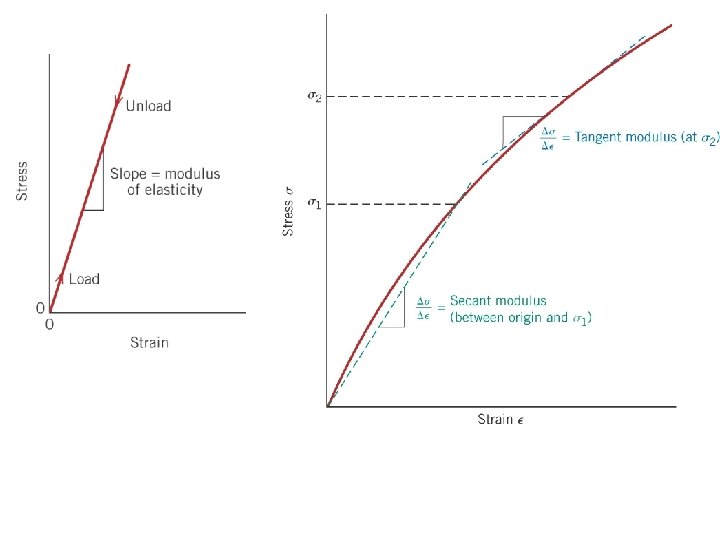
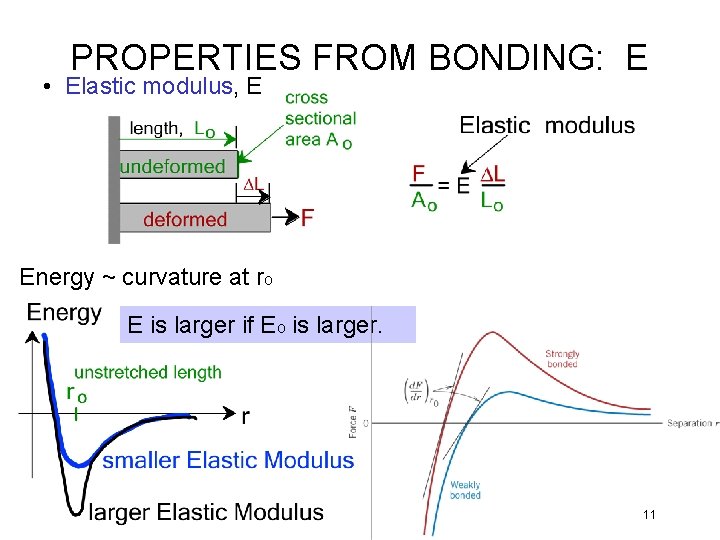
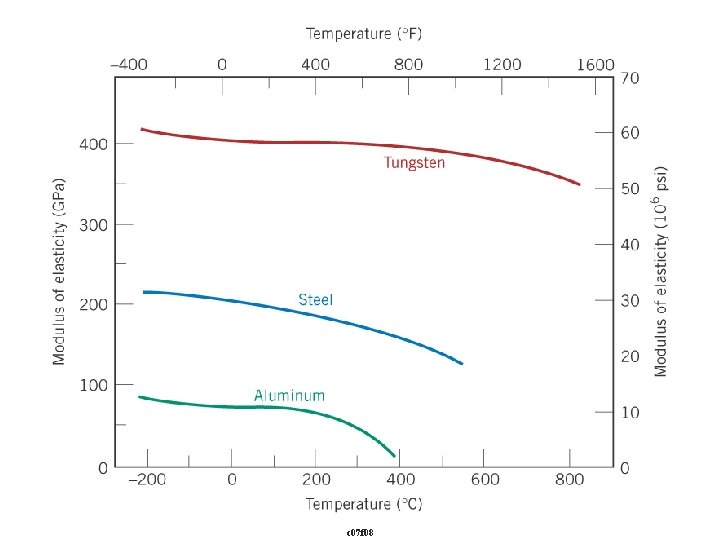
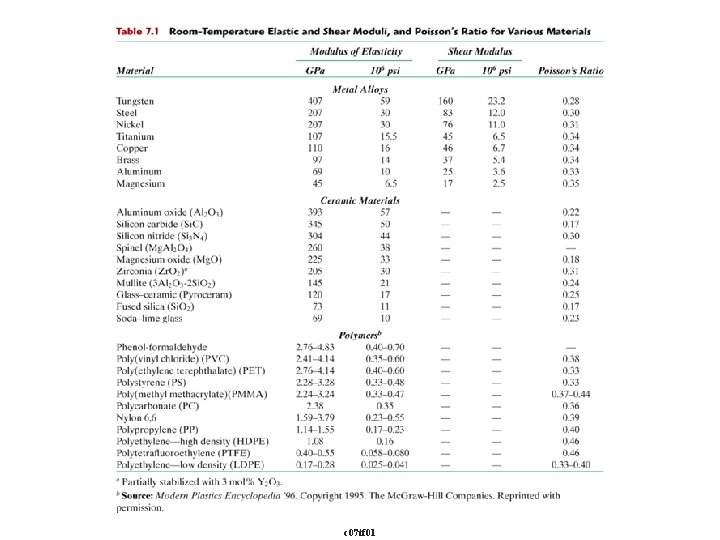
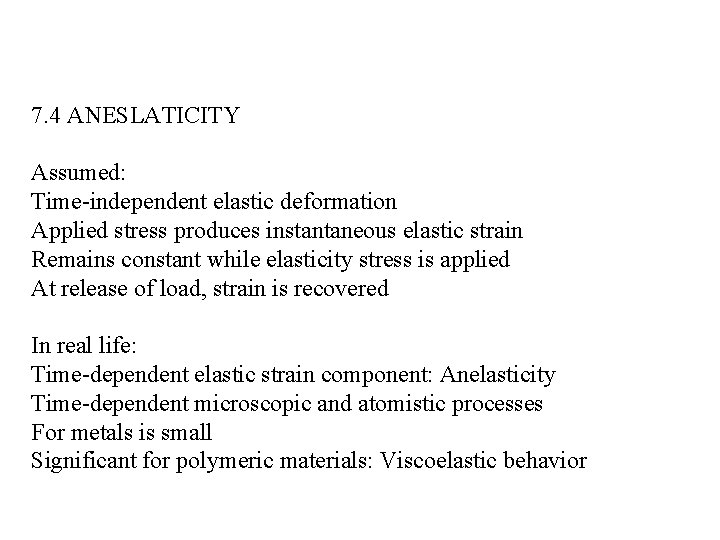
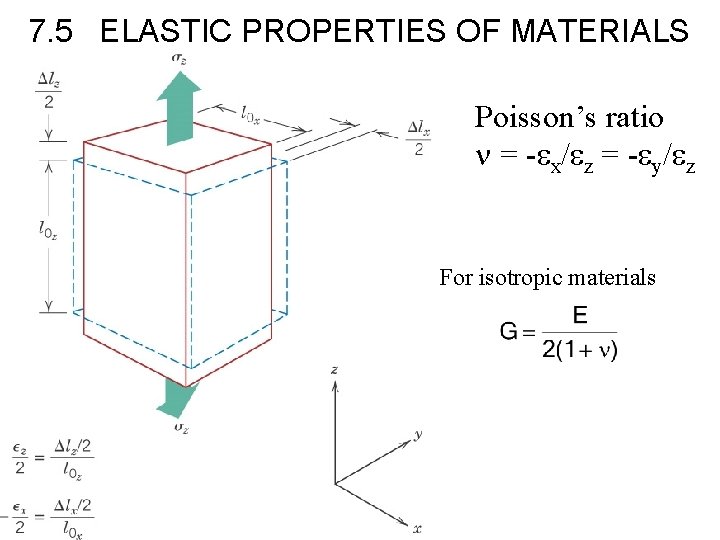
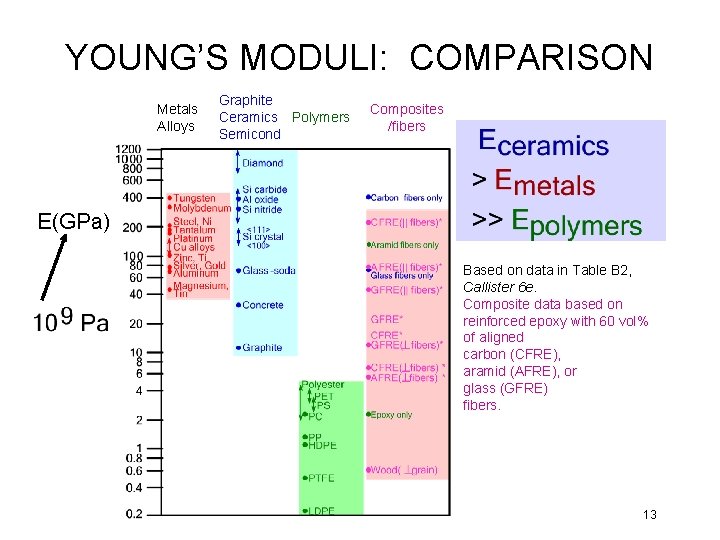
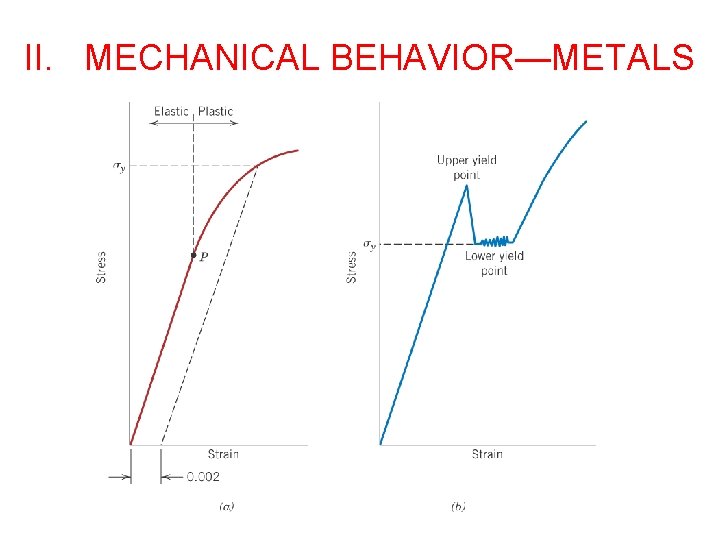
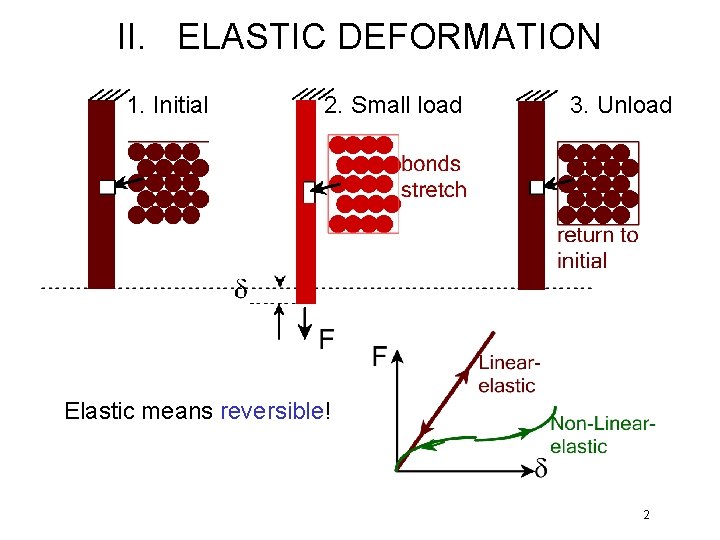
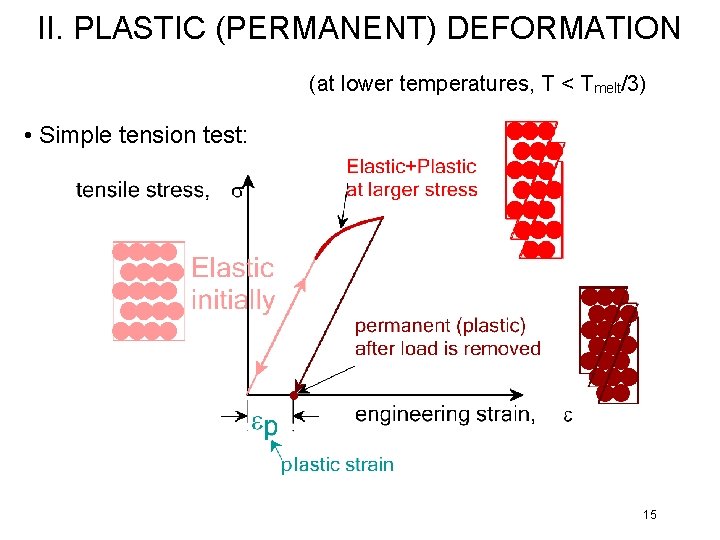
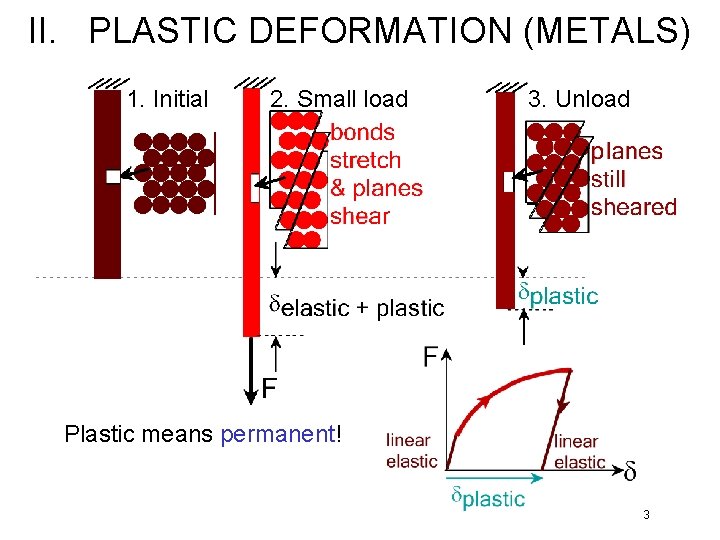
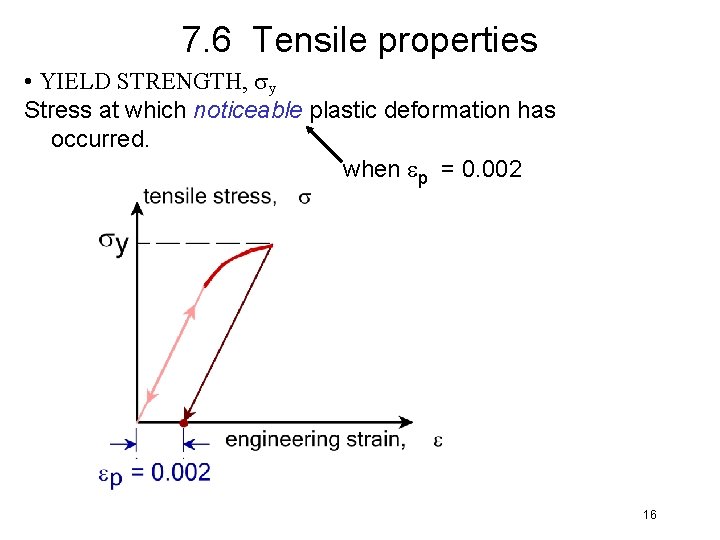
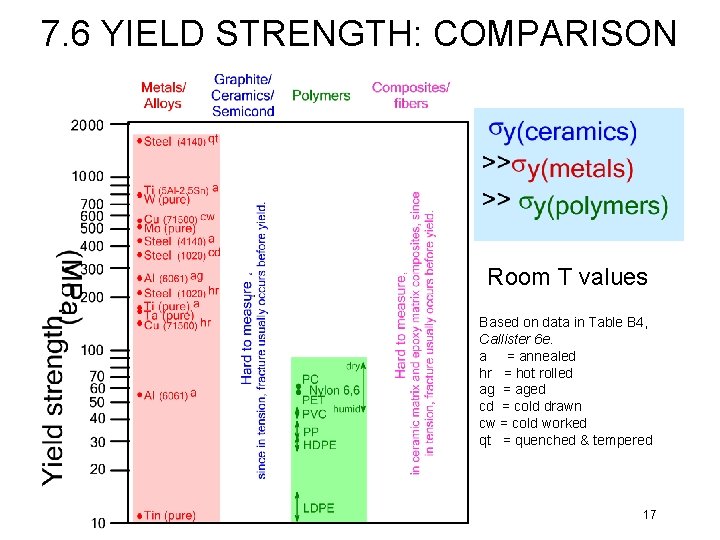
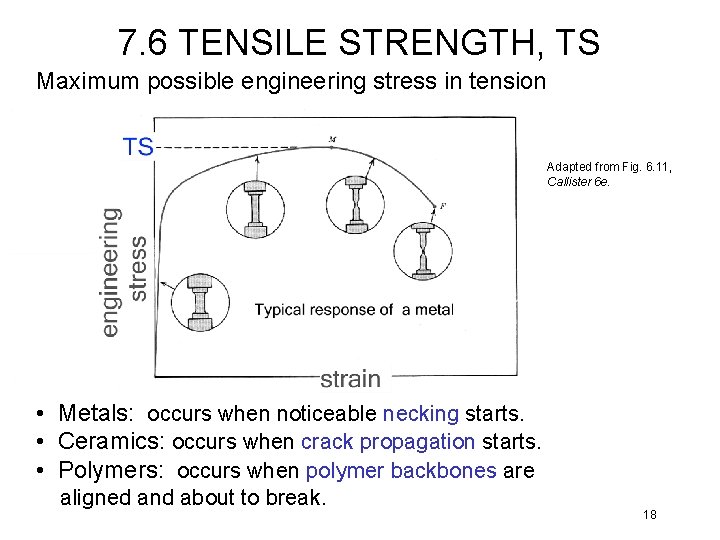
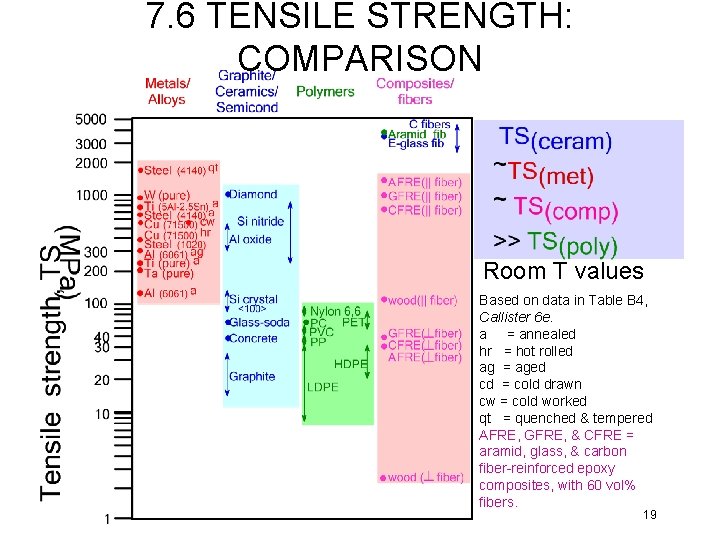
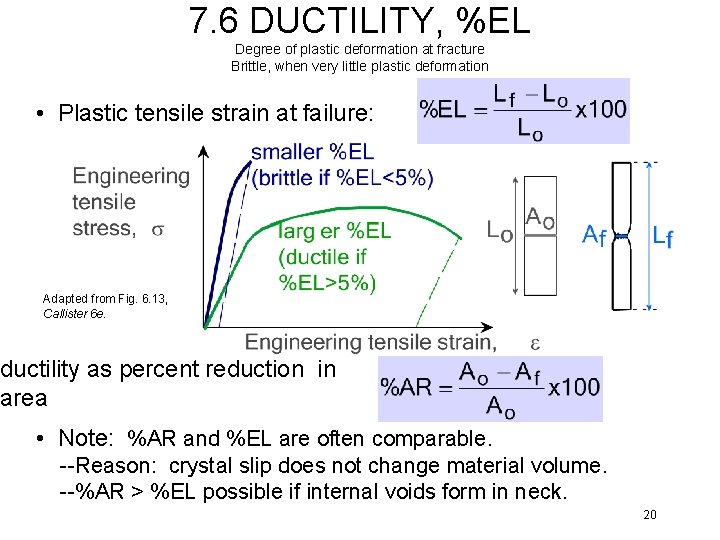
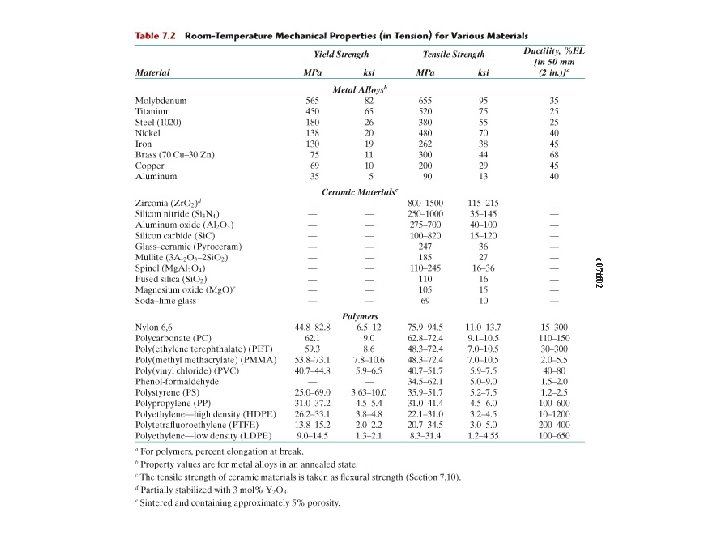
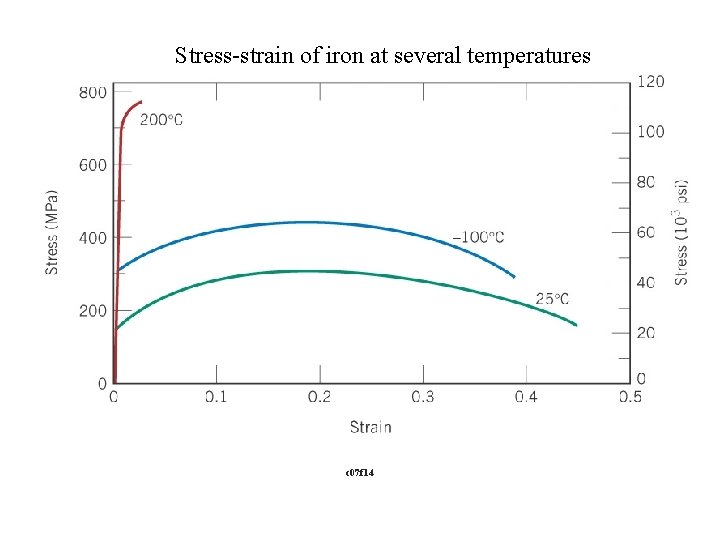
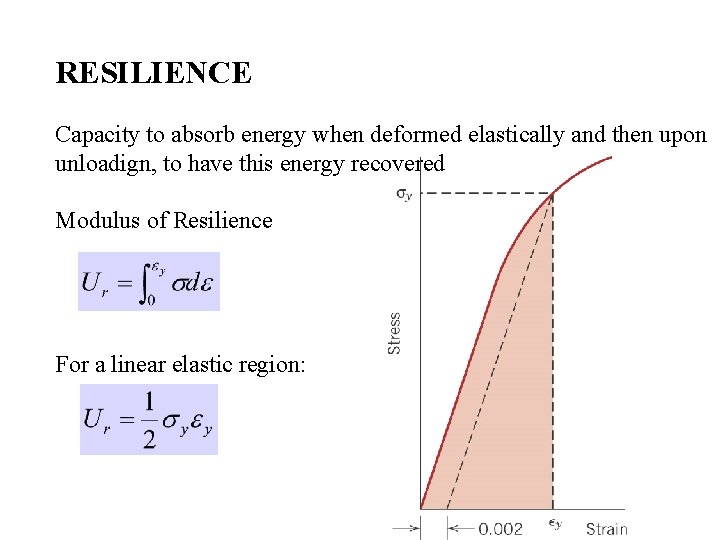
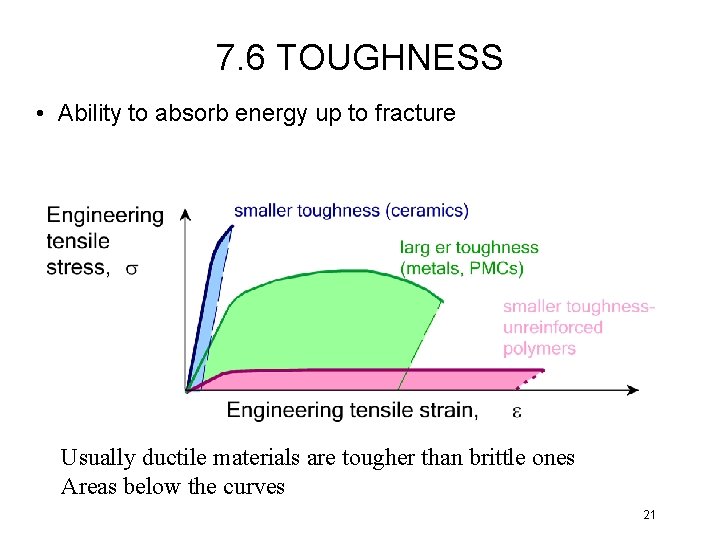
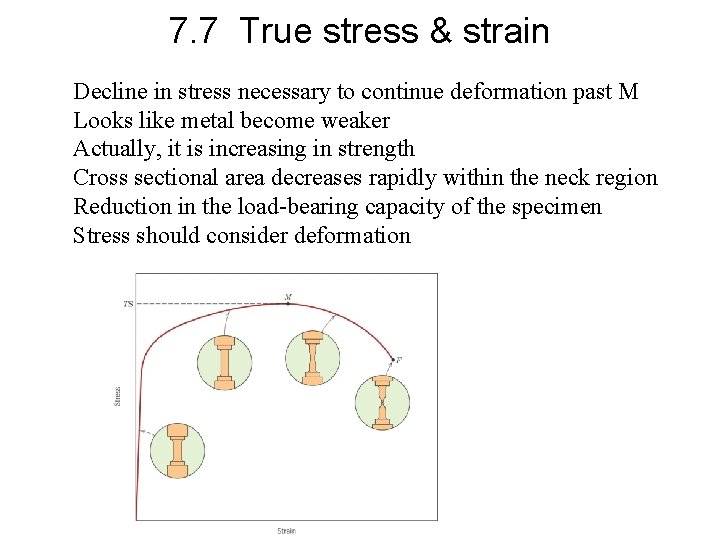
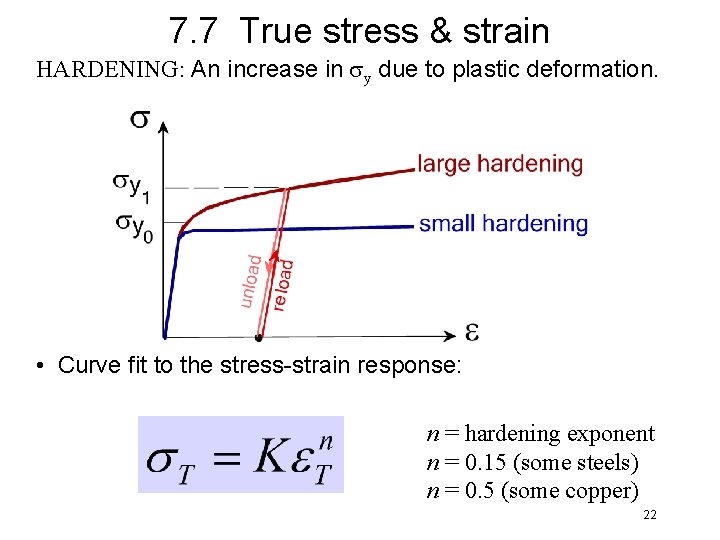
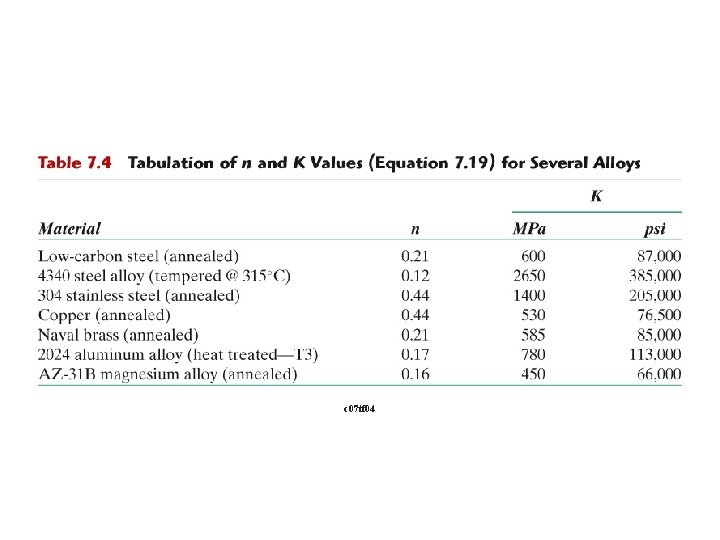
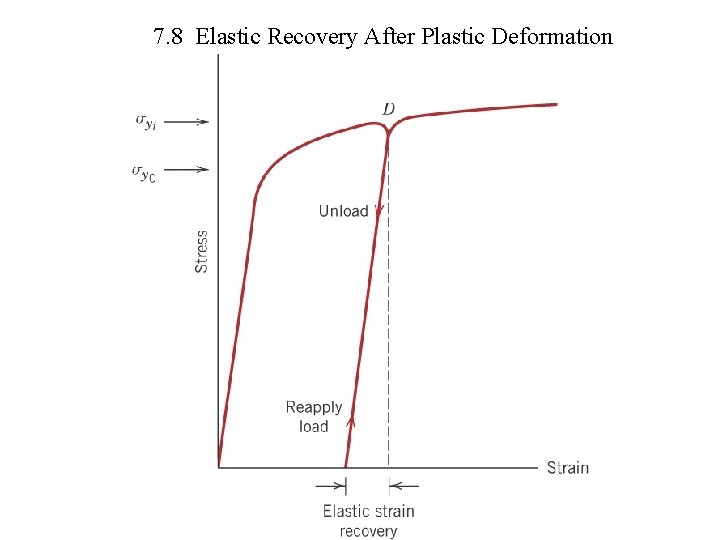
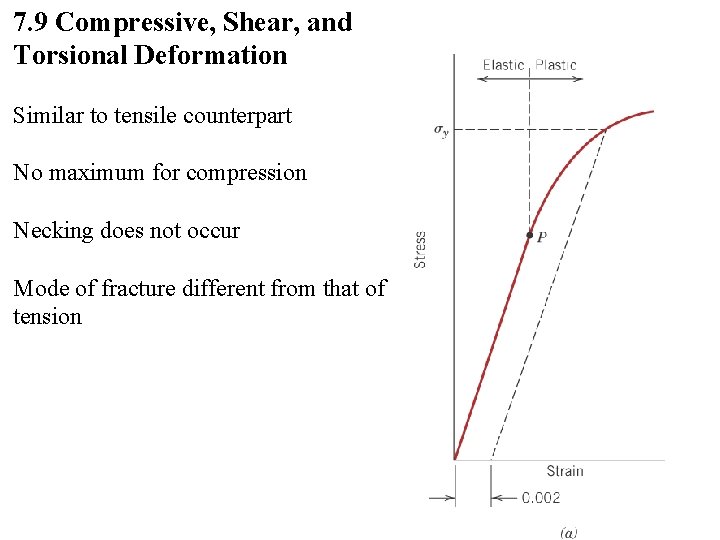
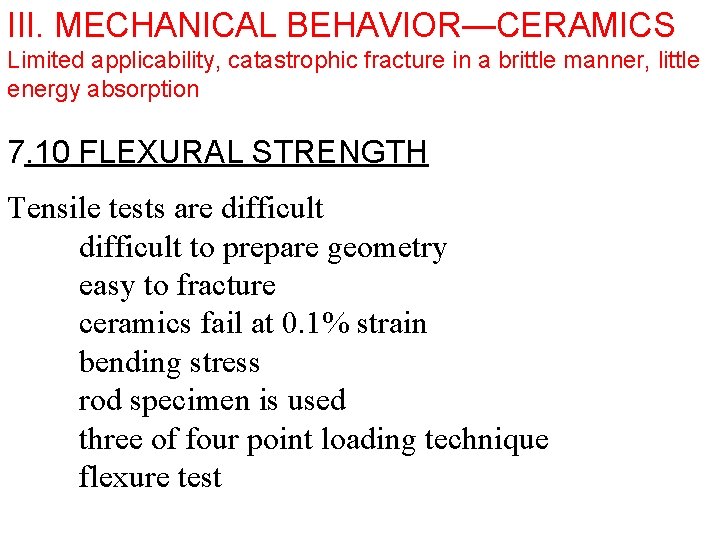

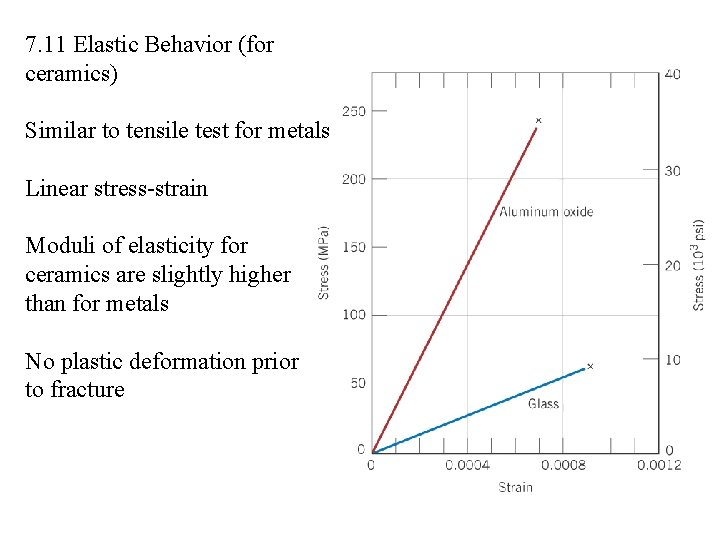
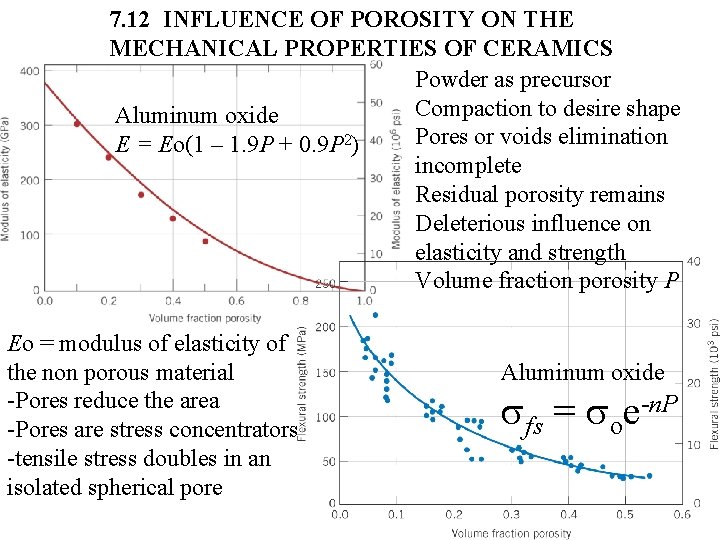
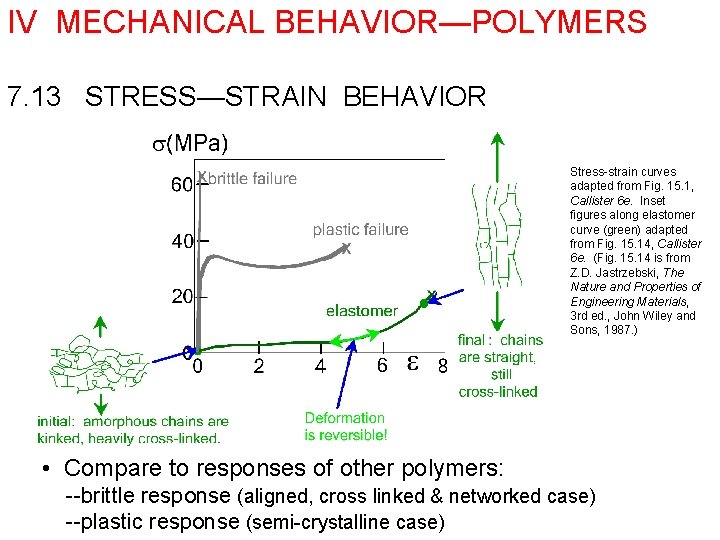
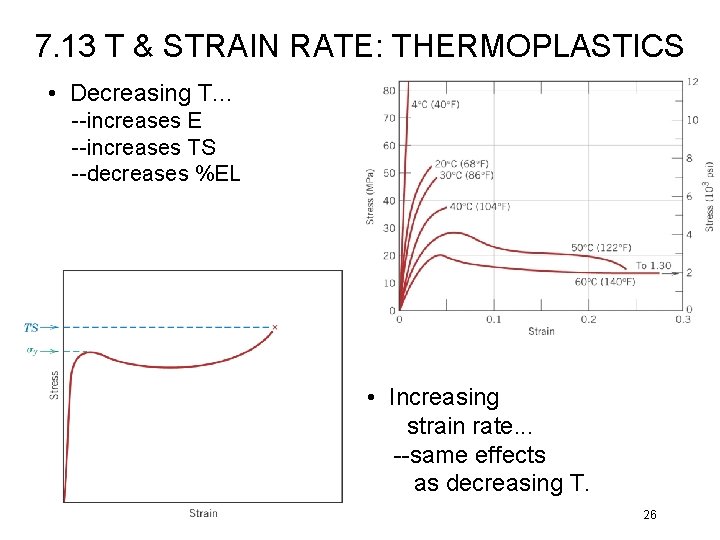
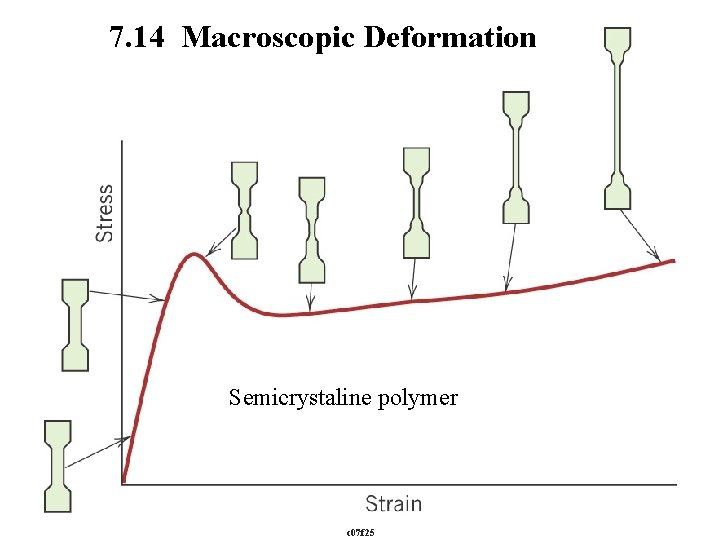
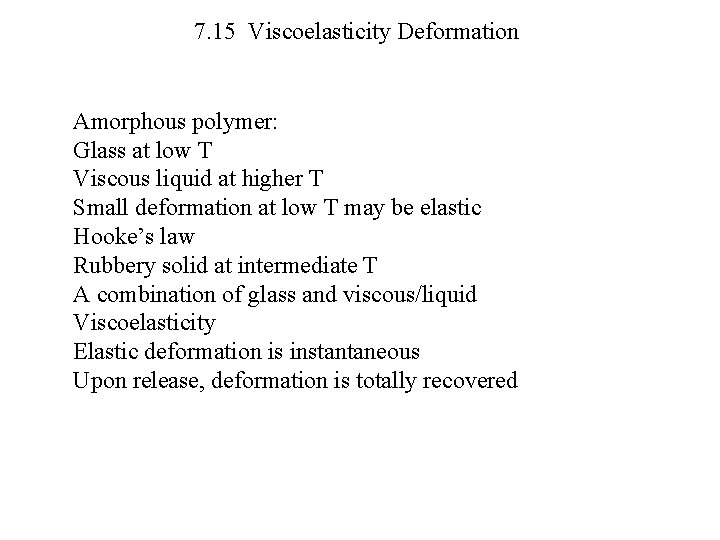
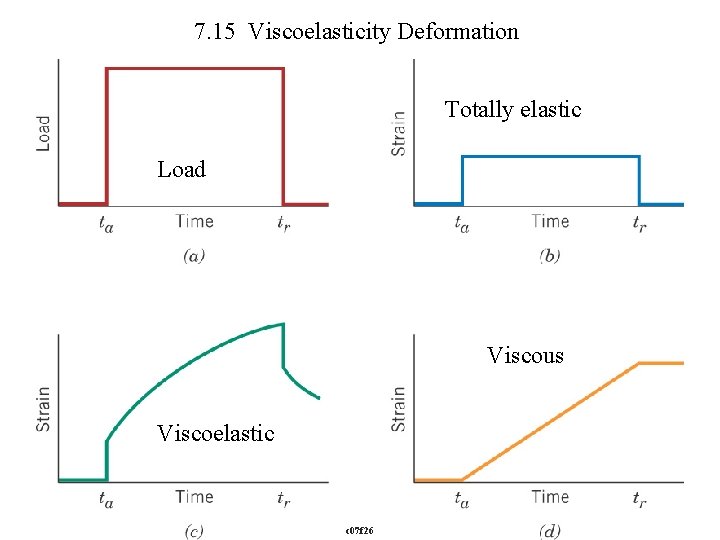
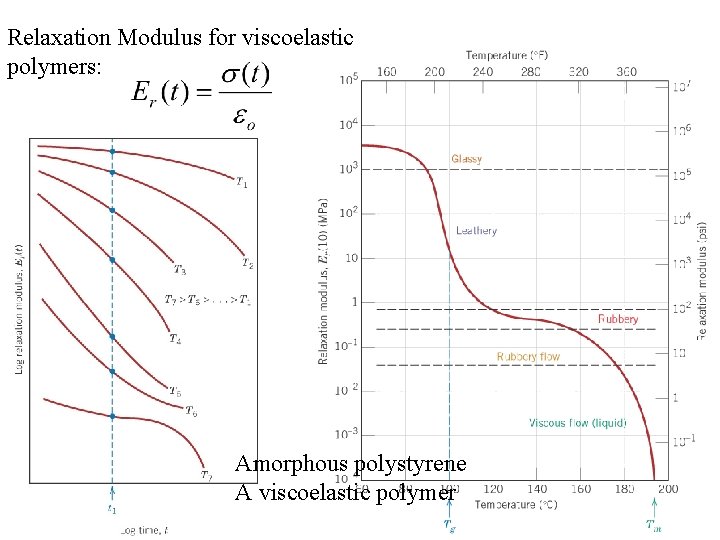
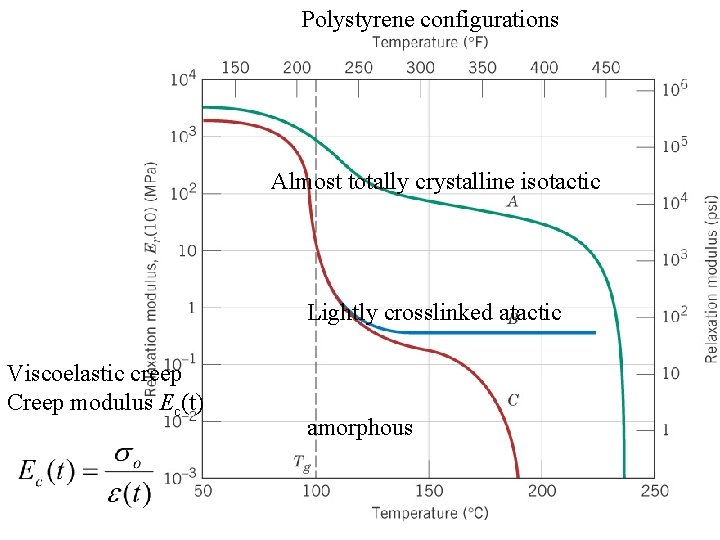
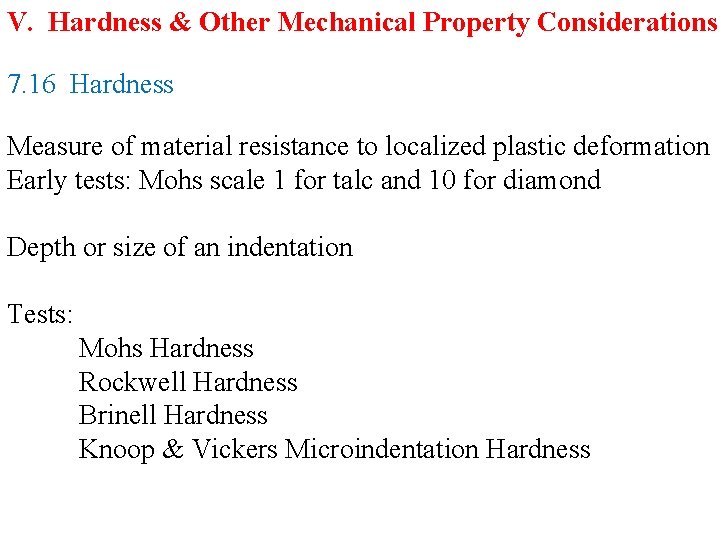
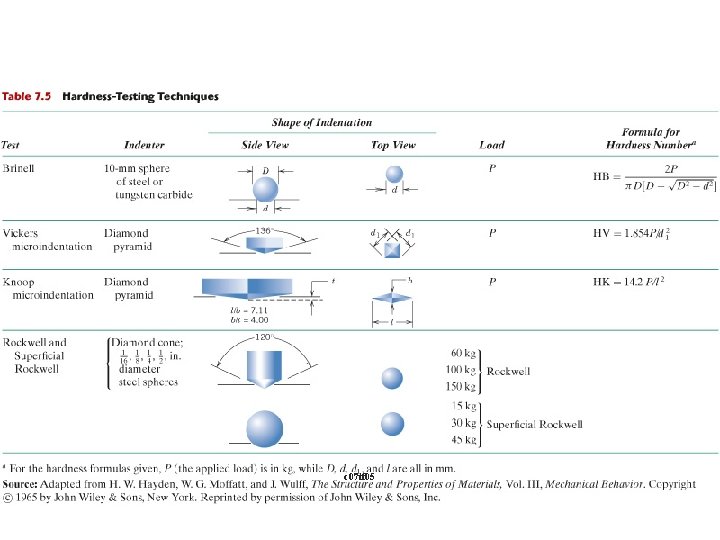
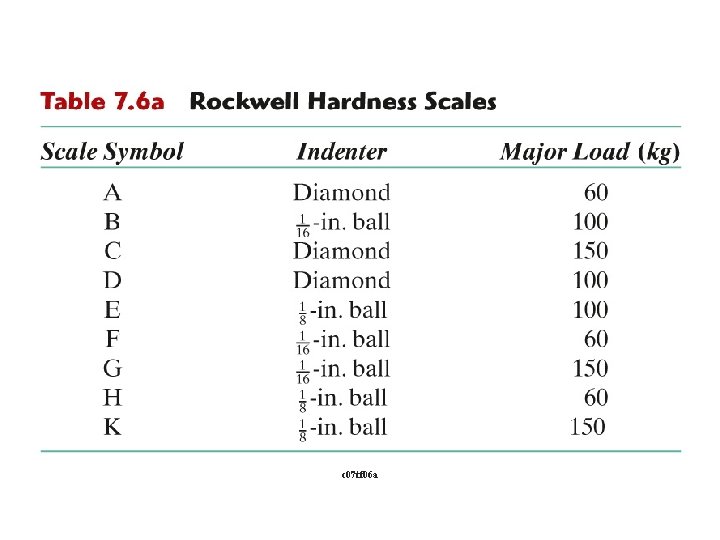
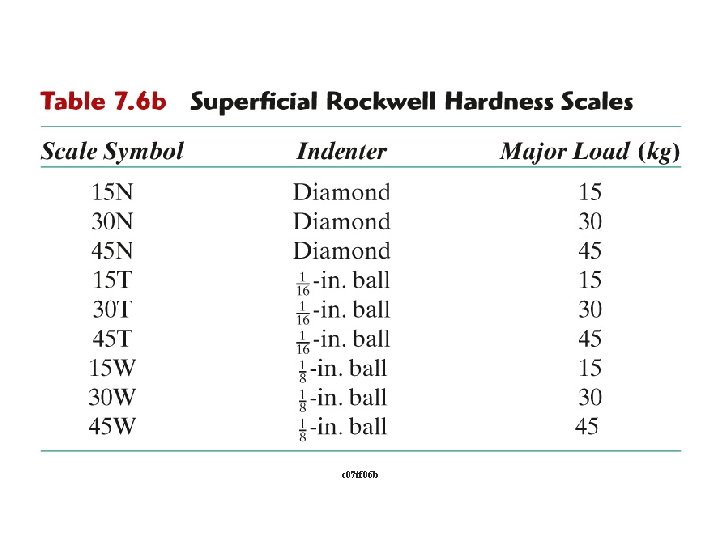
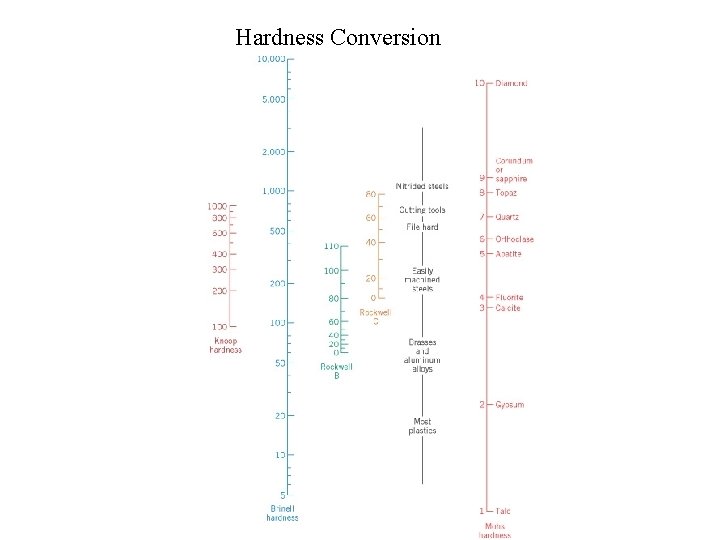
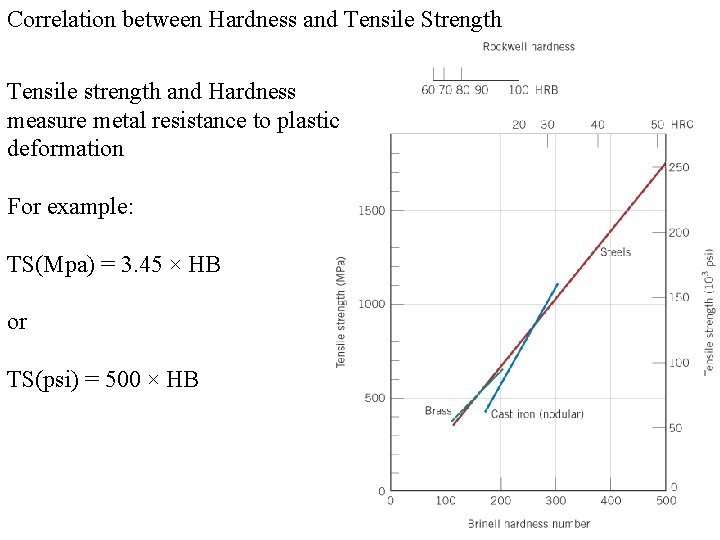
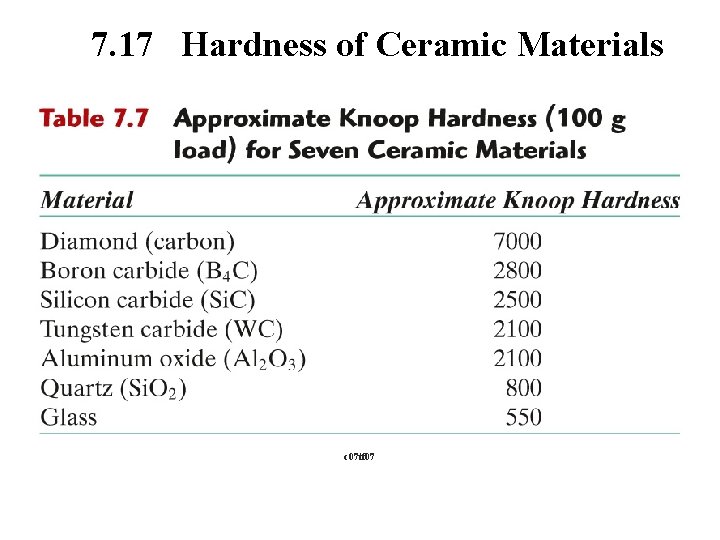
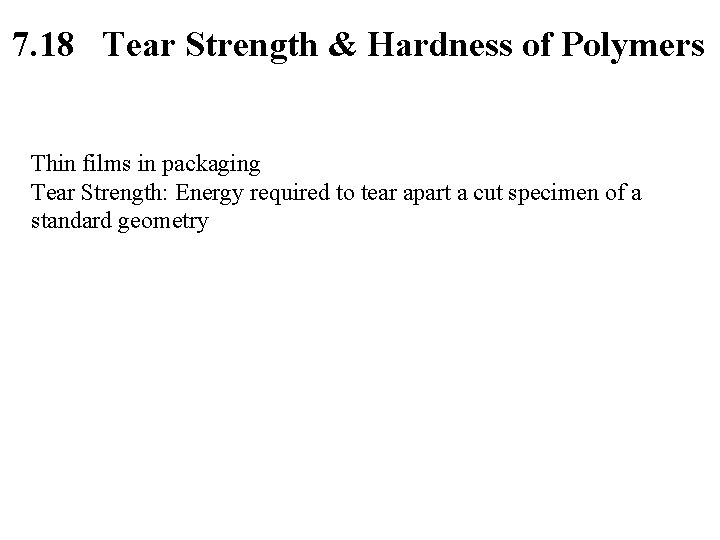
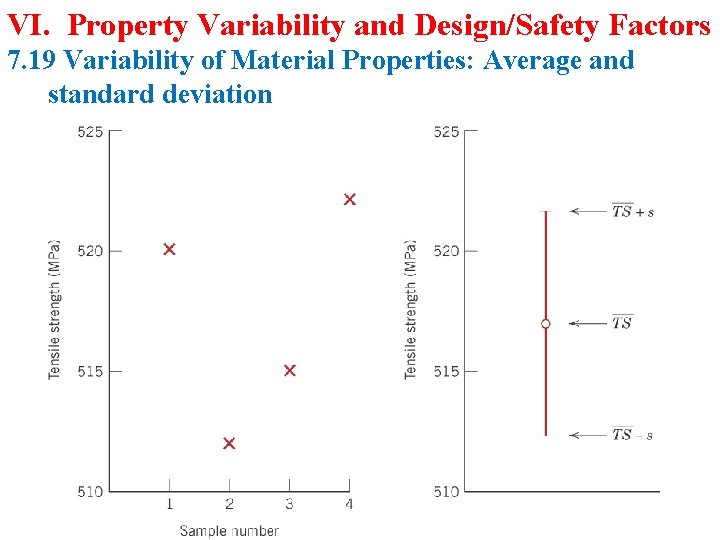
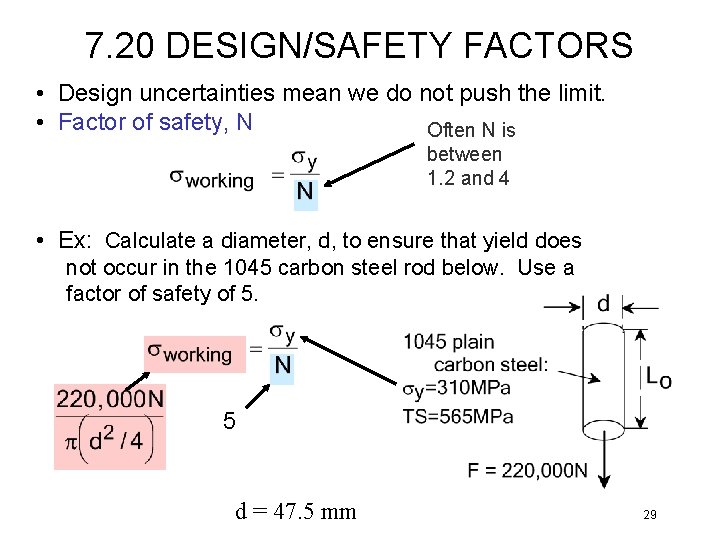
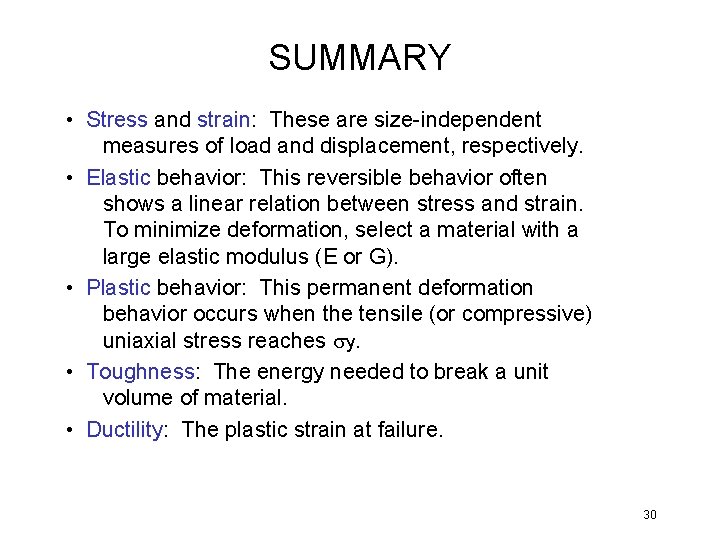
- Slides: 58
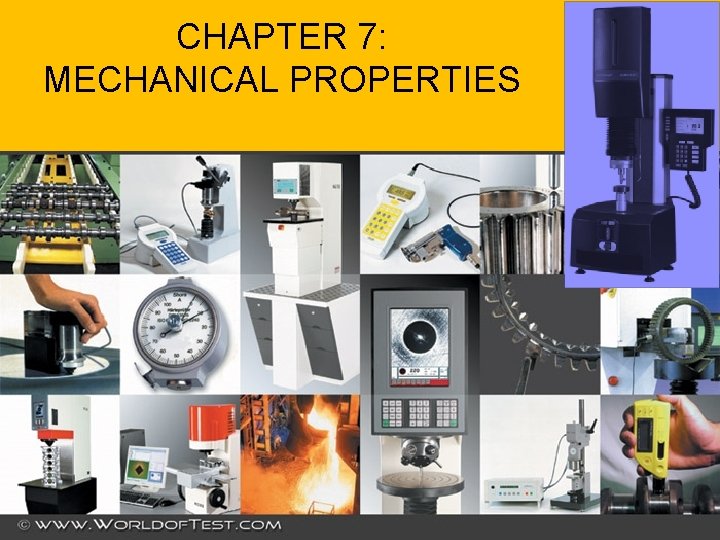
CHAPTER 7: MECHANICAL PROPERTIES
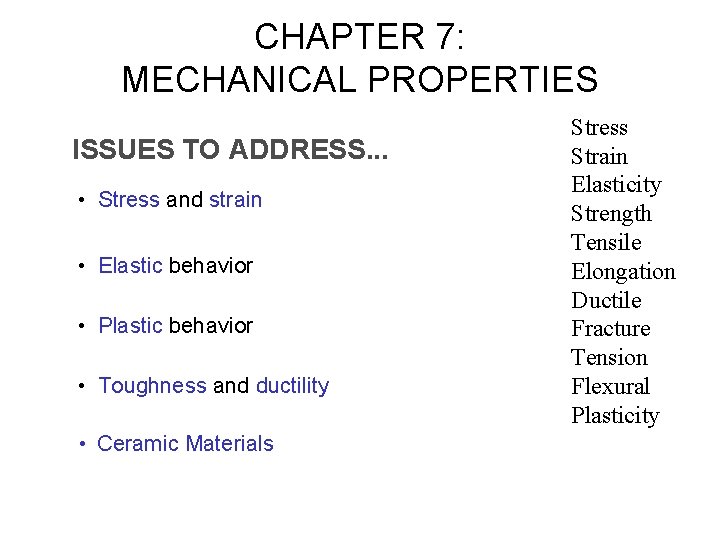
CHAPTER 7: MECHANICAL PROPERTIES ISSUES TO ADDRESS. . . • Stress and strain • Elastic behavior • Plastic behavior • Toughness and ductility • Ceramic Materials Stress Strain Elasticity Strength Tensile Elongation Ductile Fracture Tension Flexural Plasticity
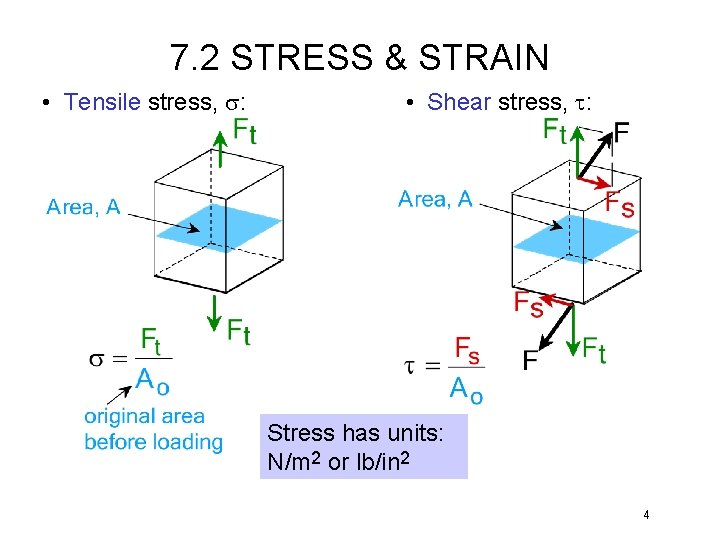
7. 2 STRESS & STRAIN • Tensile stress, s: • Shear stress, t: Stress has units: N/m 2 or lb/in 2 4
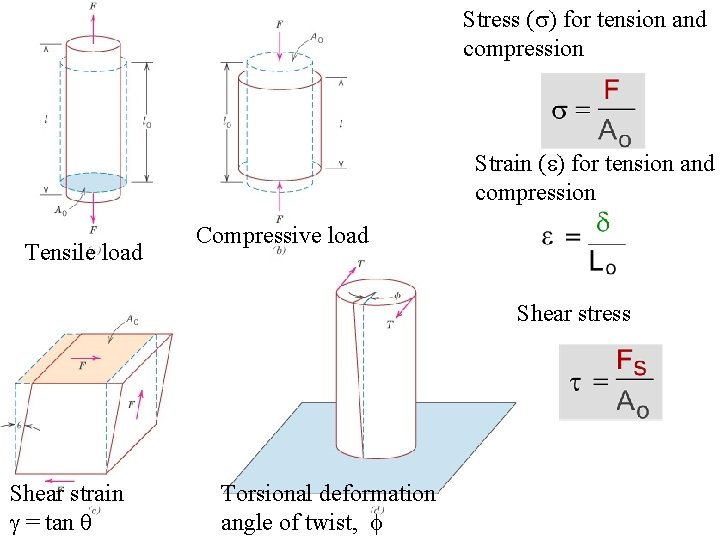
Stress (s) for tension and compression Strain (e) for tension and compression Tensile load Compressive load Shear stress Shear strain g = tan q Torsional deformation angle of twist, f
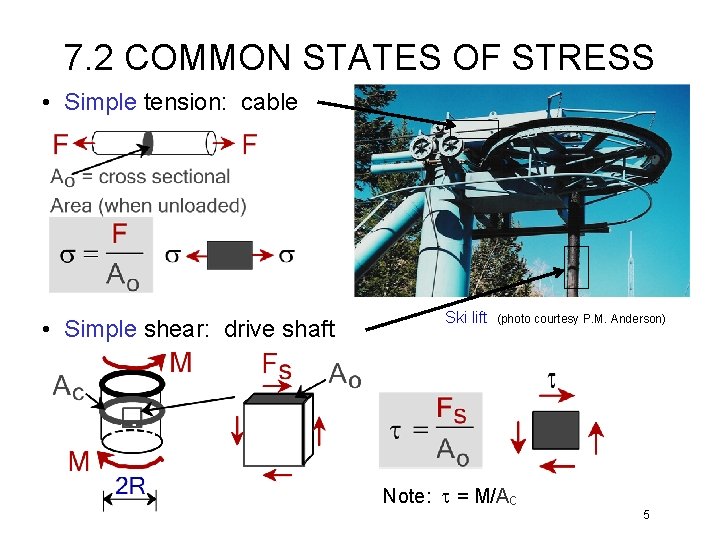
7. 2 COMMON STATES OF STRESS • Simple tension: cable • Simple shear: drive shaft Ski lift (photo courtesy P. M. Anderson) Note: t = M/Ac 5
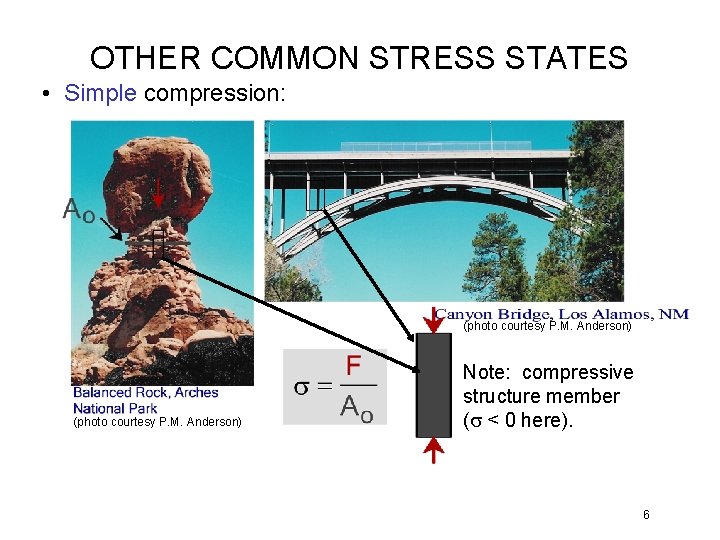
OTHER COMMON STRESS STATES • Simple compression: (photo courtesy P. M. Anderson) Note: compressive structure member (s < 0 here). 6
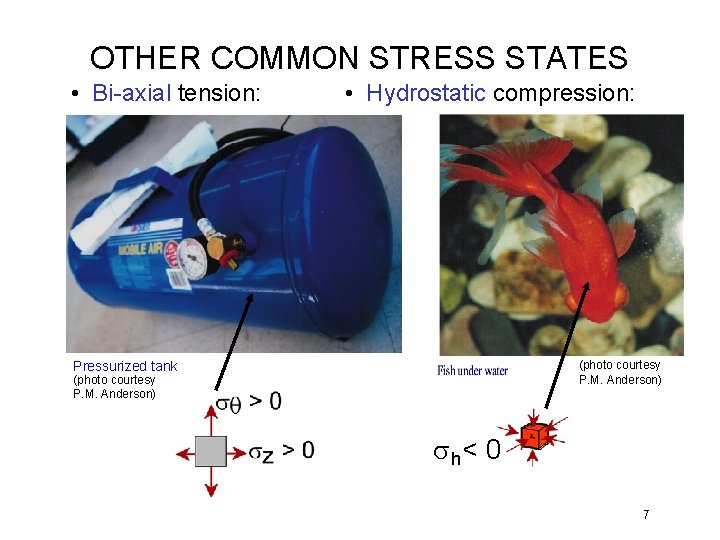
OTHER COMMON STRESS STATES • Bi-axial tension: • Hydrostatic compression: (photo courtesy P. M. Anderson) Pressurized tank (photo courtesy P. M. Anderson) sh< 0 7
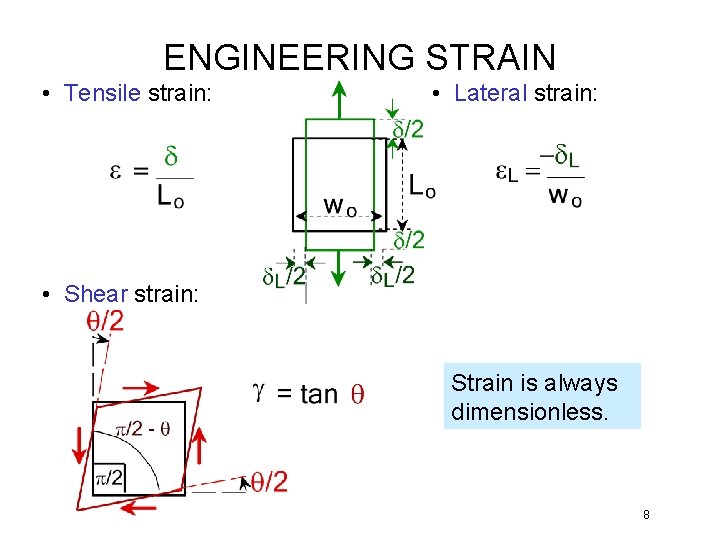
ENGINEERING STRAIN • Tensile strain: • Lateral strain: • Shear strain: Strain is always dimensionless. 8
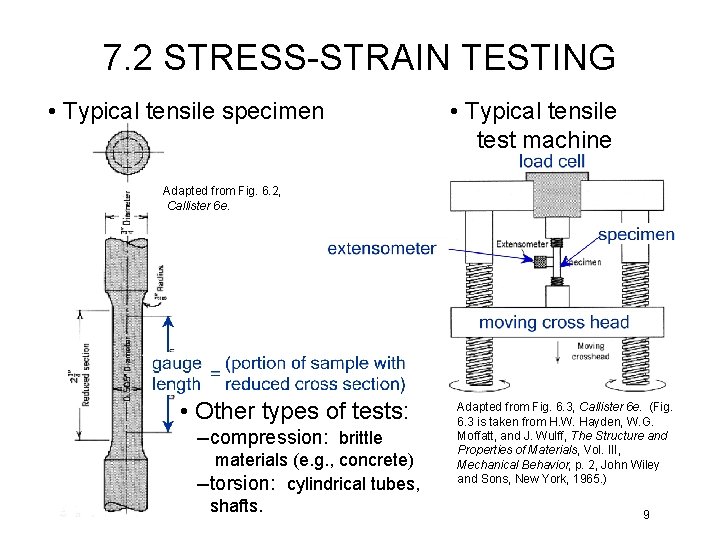
7. 2 STRESS-STRAIN TESTING • Typical tensile specimen • Typical tensile test machine Adapted from Fig. 6. 2, Callister 6 e. • Other types of tests: --compression: brittle materials (e. g. , concrete) --torsion: cylindrical tubes, shafts. Adapted from Fig. 6. 3, Callister 6 e. (Fig. 6. 3 is taken from H. W. Hayden, W. G. Moffatt, and J. Wulff, The Structure and Properties of Materials, Vol. III, Mechanical Behavior, p. 2, John Wiley and Sons, New York, 1965. ) 9
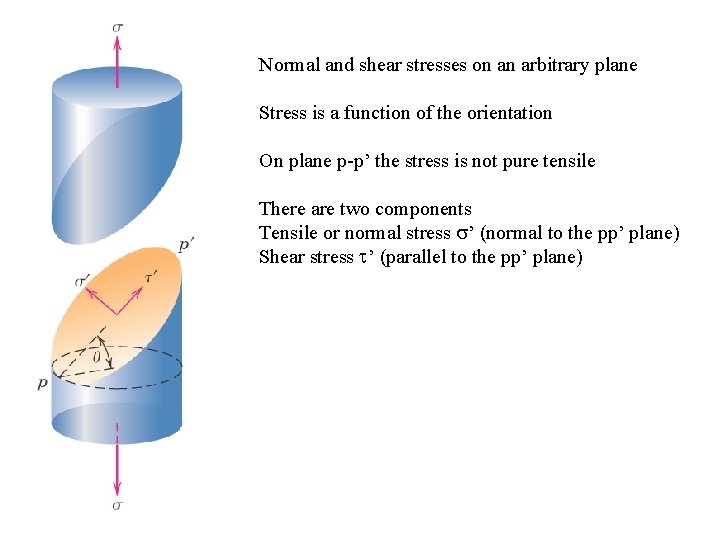
Normal and shear stresses on an arbitrary plane Stress is a function of the orientation On plane p-p’ the stress is not pure tensile There are two components Tensile or normal stress s’ (normal to the pp’ plane) Shear stress t’ (parallel to the pp’ plane)
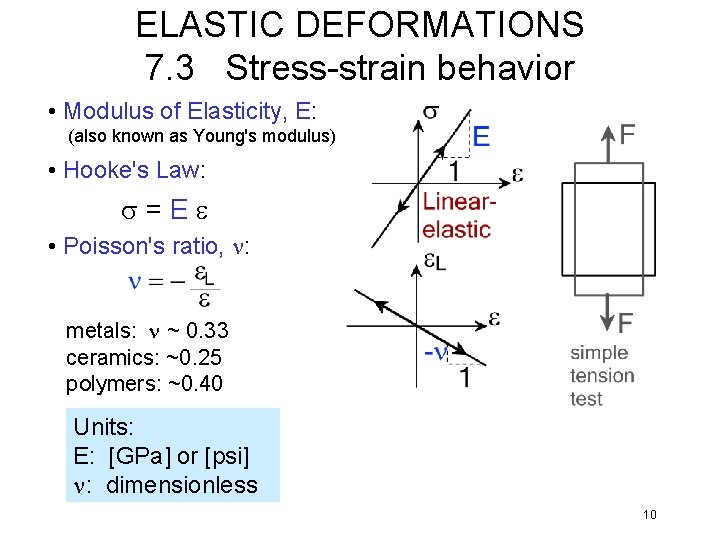
ELASTIC DEFORMATIONS 7. 3 Stress-strain behavior • Modulus of Elasticity, E: (also known as Young's modulus) • Hooke's Law: s=Ee • Poisson's ratio, n: metals: n ~ 0. 33 ceramics: ~0. 25 polymers: ~0. 40 Units: E: [GPa] or [psi] n: dimensionless 10
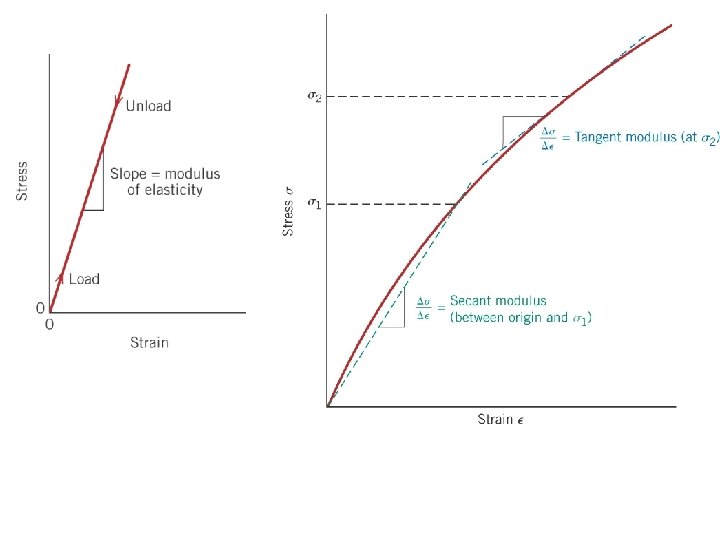
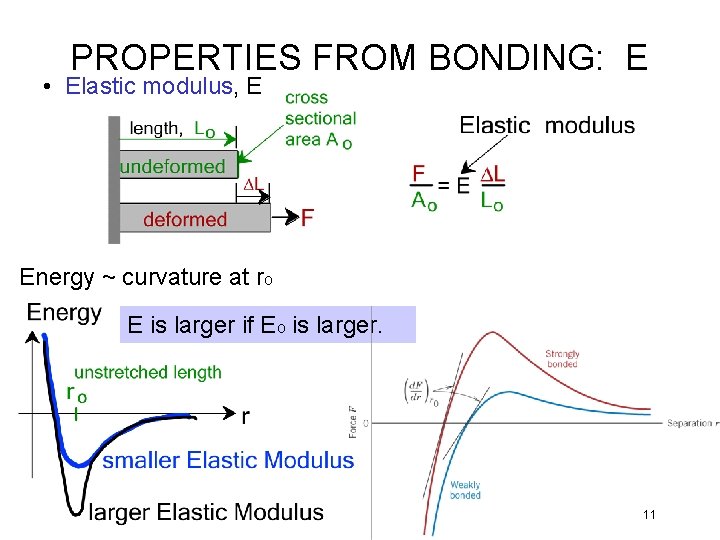
PROPERTIES FROM BONDING: E • Elastic modulus, E Energy ~ curvature at ro E is larger if Eo is larger. 11
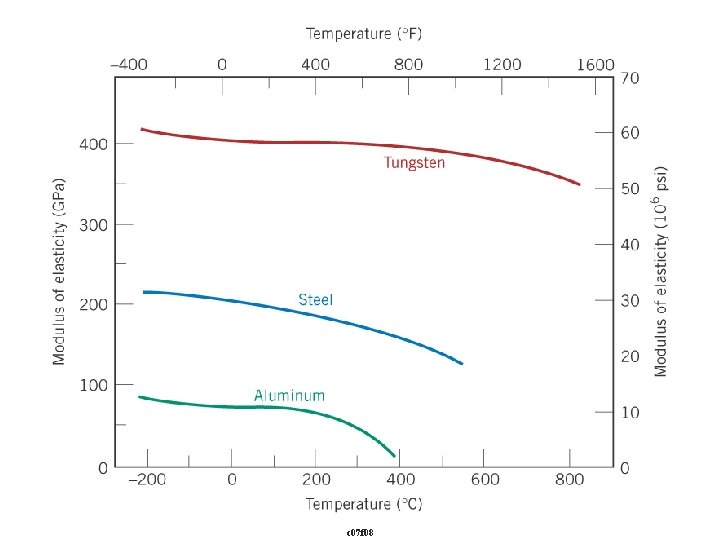
c 07 f 08
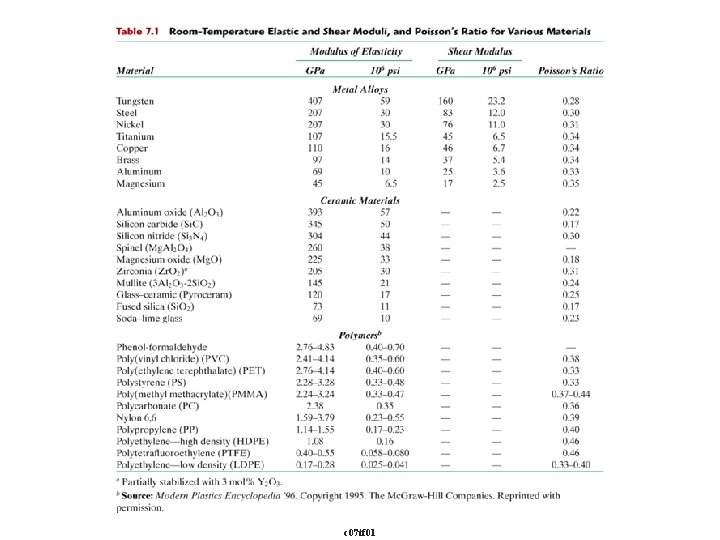
c 07 tf 01
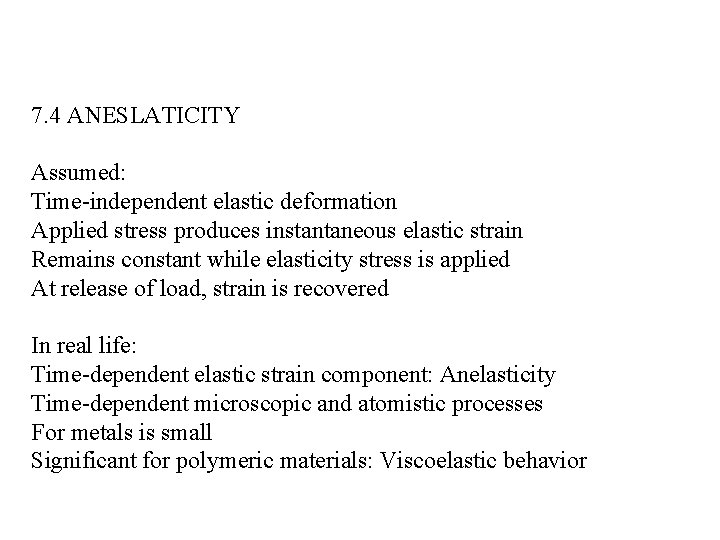
7. 4 ANESLATICITY Assumed: Time-independent elastic deformation Applied stress produces instantaneous elastic strain Remains constant while elasticity stress is applied At release of load, strain is recovered In real life: Time-dependent elastic strain component: Anelasticity Time-dependent microscopic and atomistic processes For metals is small Significant for polymeric materials: Viscoelastic behavior
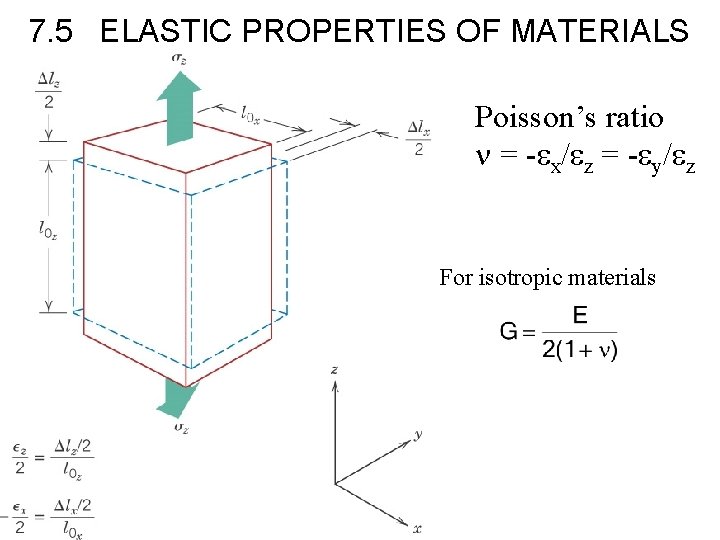
7. 5 ELASTIC PROPERTIES OF MATERIALS Poisson’s ratio n = -ex/ez = -ey/ez For isotropic materials
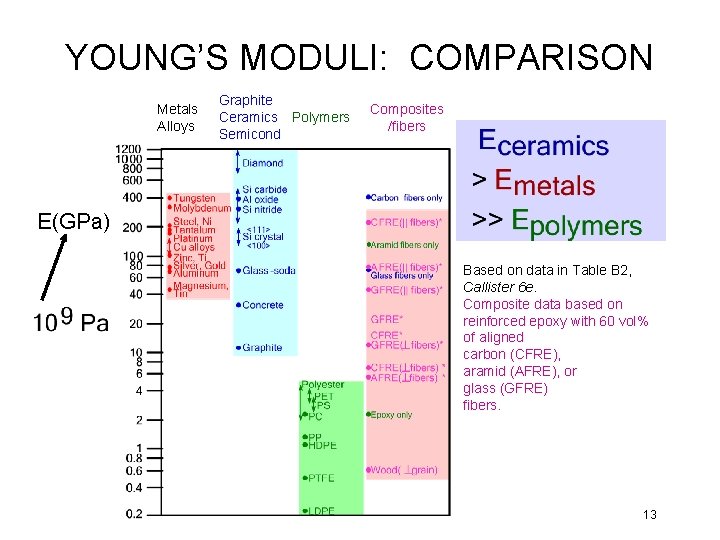
YOUNG’S MODULI: COMPARISON Metals Alloys Graphite Ceramics Polymers Semicond Composites /fibers E(GPa) Based on data in Table B 2, Callister 6 e. Composite data based on reinforced epoxy with 60 vol% of aligned carbon (CFRE), aramid (AFRE), or glass (GFRE) fibers. 13
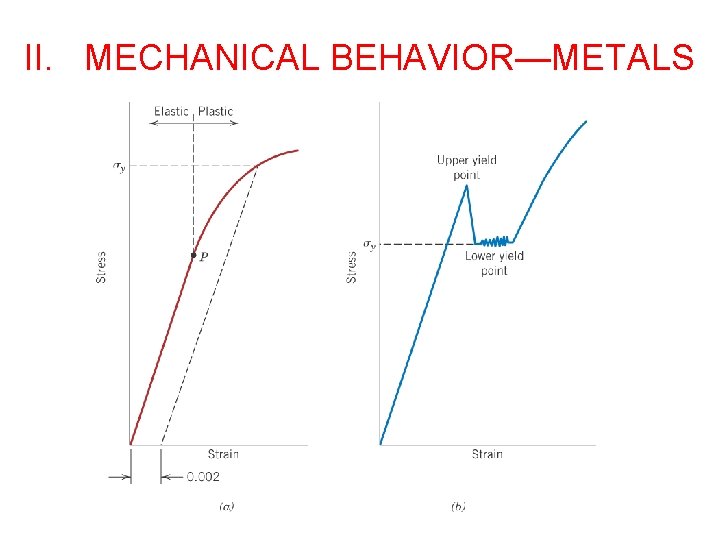
II. MECHANICAL BEHAVIOR—METALS
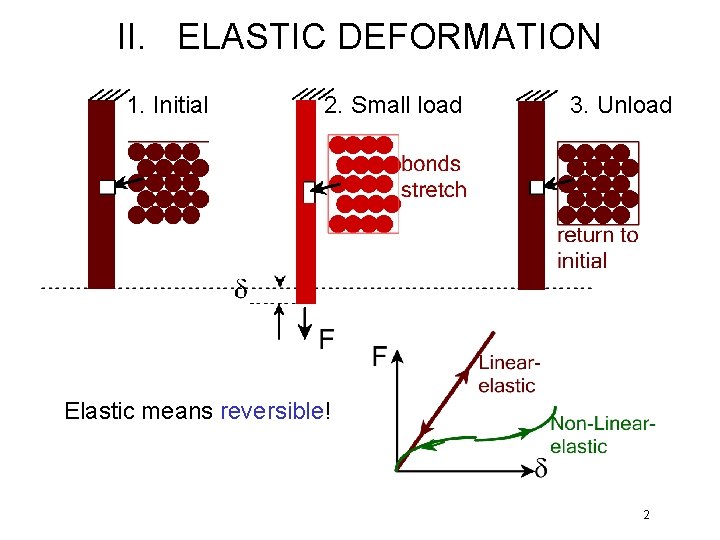
II. ELASTIC DEFORMATION 1. Initial 2. Small load 3. Unload Elastic means reversible! 2
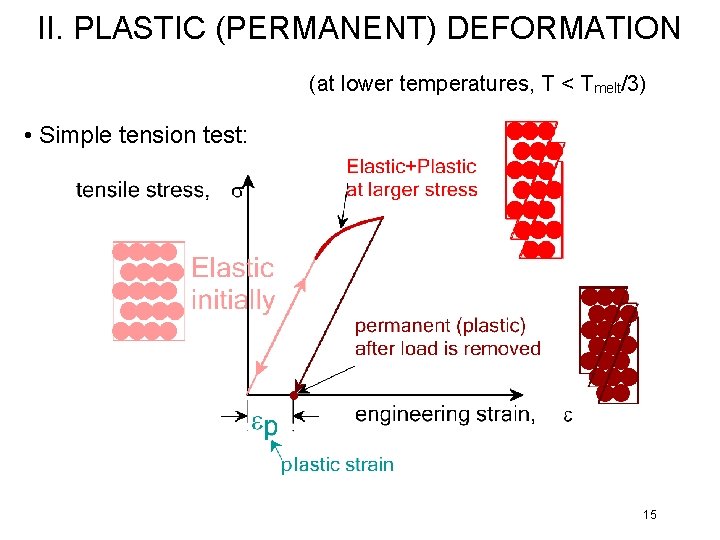
II. PLASTIC (PERMANENT) DEFORMATION (at lower temperatures, T < Tmelt/3) • Simple tension test: 15
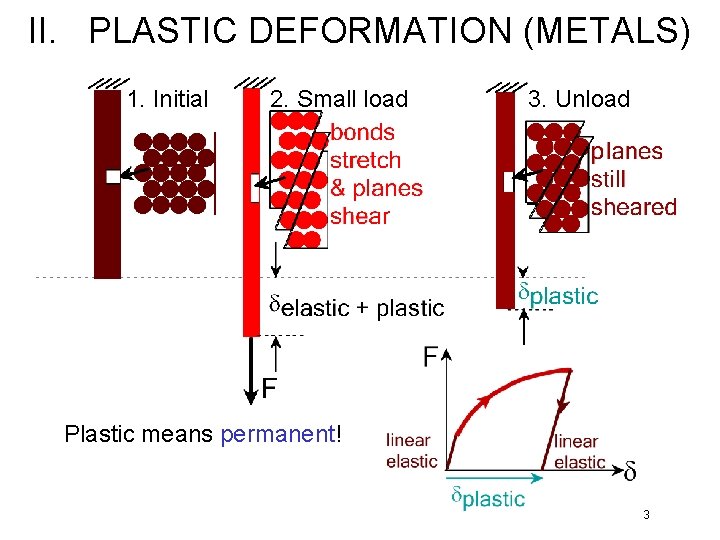
II. PLASTIC DEFORMATION (METALS) 1. Initial 2. Small load 3. Unload Plastic means permanent! 3
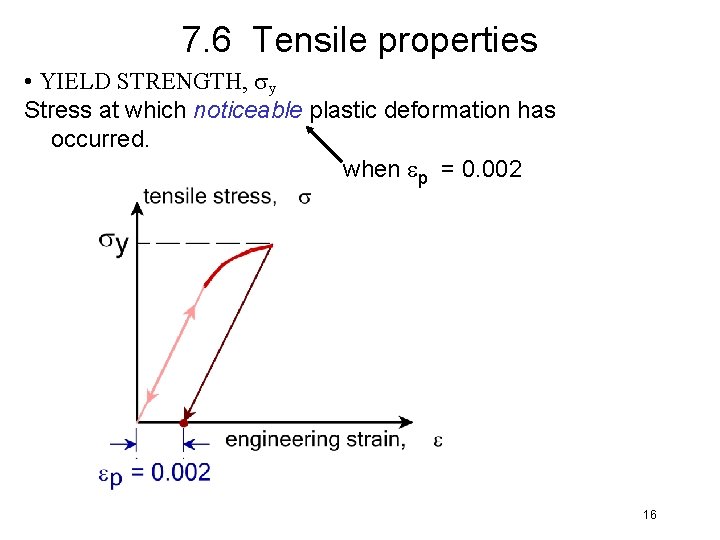
7. 6 Tensile properties • YIELD STRENGTH, sy Stress at which noticeable plastic deformation has occurred. when ep = 0. 002 16
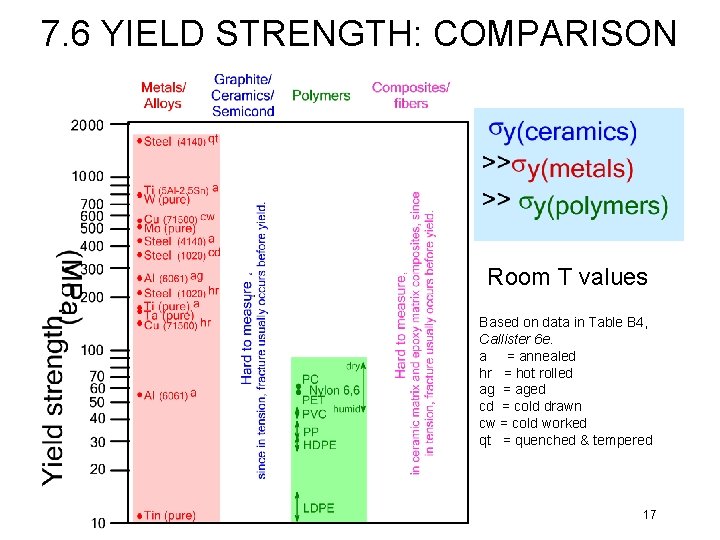
7. 6 YIELD STRENGTH: COMPARISON Room T values Based on data in Table B 4, Callister 6 e. a = annealed hr = hot rolled ag = aged cd = cold drawn cw = cold worked qt = quenched & tempered 17
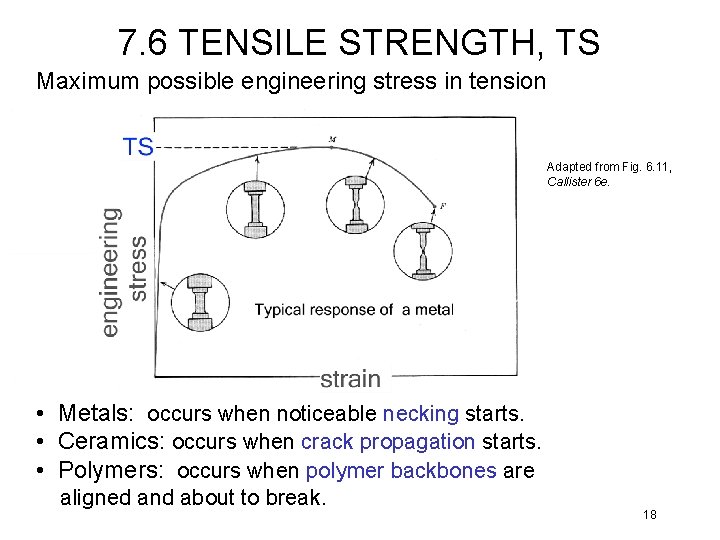
7. 6 TENSILE STRENGTH, TS Maximum possible engineering stress in tension Adapted from Fig. 6. 11, Callister 6 e. • Metals: occurs when noticeable necking starts. • Ceramics: occurs when crack propagation starts. • Polymers: occurs when polymer backbones are aligned and about to break. 18
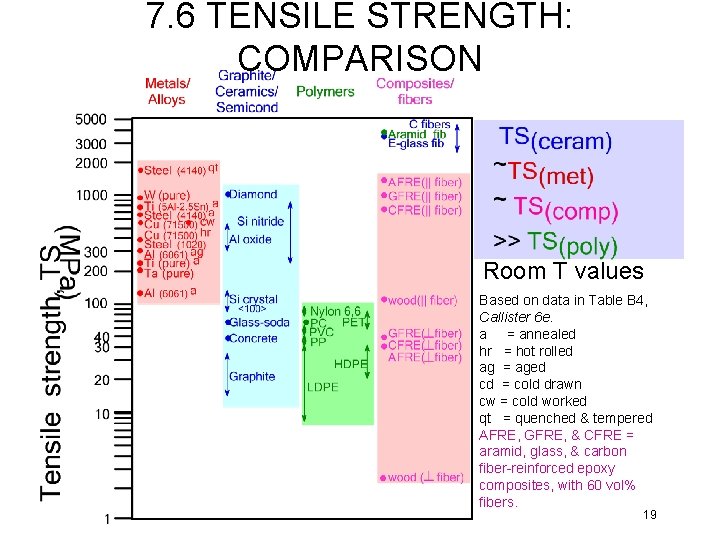
7. 6 TENSILE STRENGTH: COMPARISON Room T values Based on data in Table B 4, Callister 6 e. a = annealed hr = hot rolled ag = aged cd = cold drawn cw = cold worked qt = quenched & tempered AFRE, GFRE, & CFRE = aramid, glass, & carbon fiber-reinforced epoxy composites, with 60 vol% fibers. 19
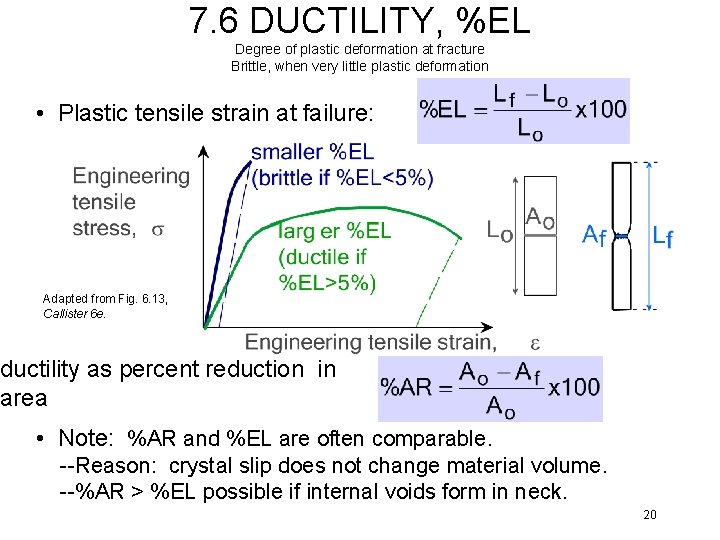
7. 6 DUCTILITY, %EL Degree of plastic deformation at fracture Brittle, when very little plastic deformation • Plastic tensile strain at failure: Adapted from Fig. 6. 13, Callister 6 e. ductility as percent reduction in area • Note: %AR and %EL are often comparable. --Reason: crystal slip does not change material volume. --%AR > %EL possible if internal voids form in neck. 20
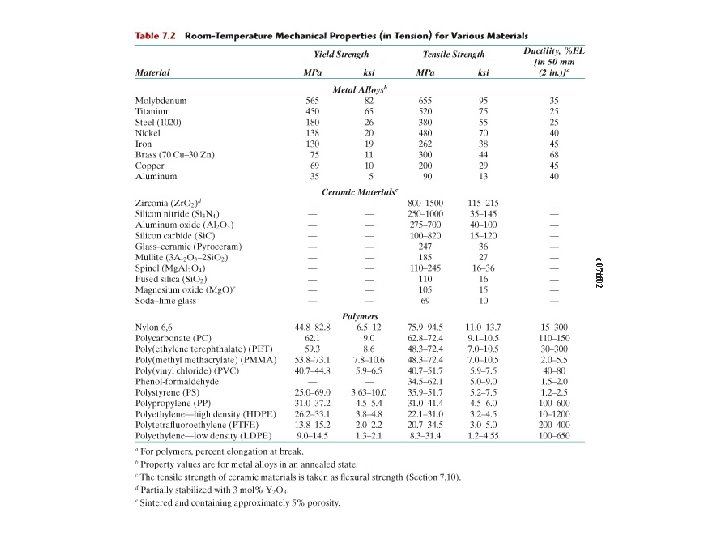
c 07 tf 02
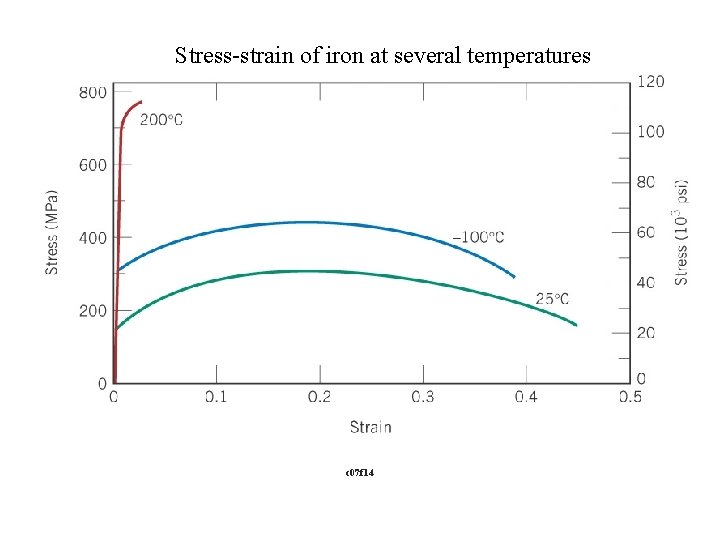
Stress-strain of iron at several temperatures c 07 f 14
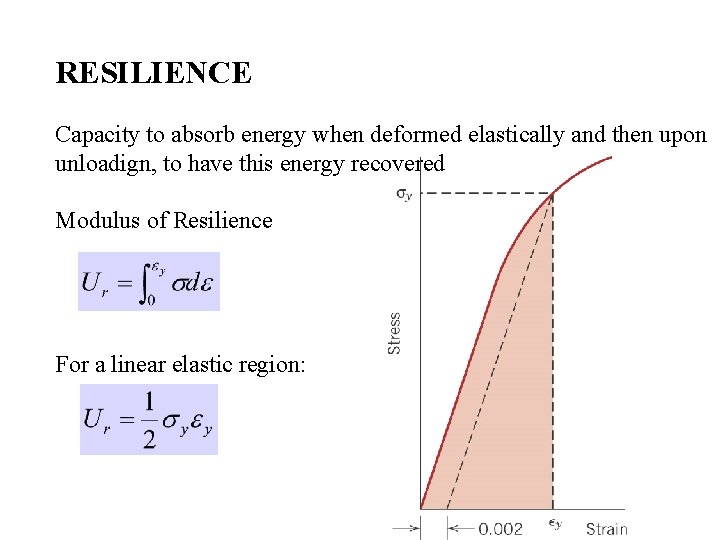
RESILIENCE Capacity to absorb energy when deformed elastically and then upon unloadign, to have this energy recovered Modulus of Resilience For a linear elastic region:
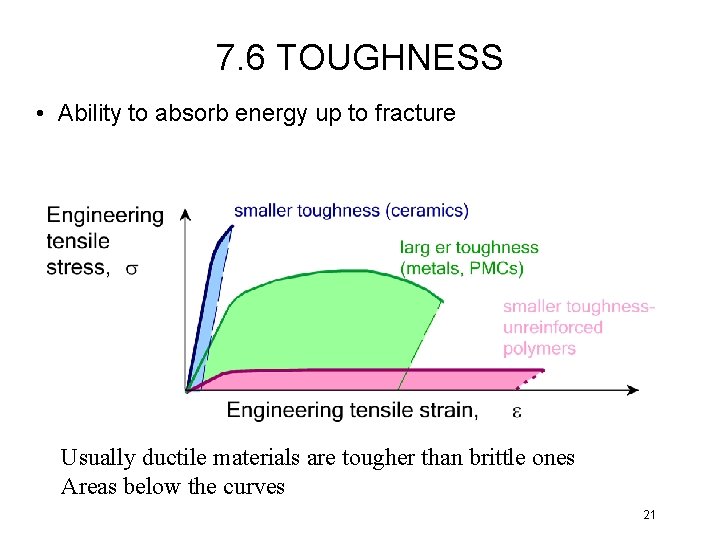
7. 6 TOUGHNESS • Ability to absorb energy up to fracture Usually ductile materials are tougher than brittle ones Areas below the curves 21
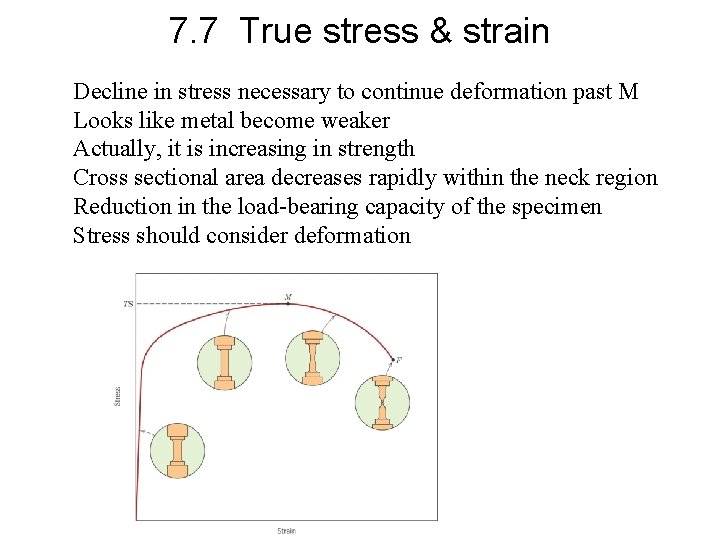
7. 7 True stress & strain Decline in stress necessary to continue deformation past M Looks like metal become weaker Actually, it is increasing in strength Cross sectional area decreases rapidly within the neck region Reduction in the load-bearing capacity of the specimen Stress should consider deformation
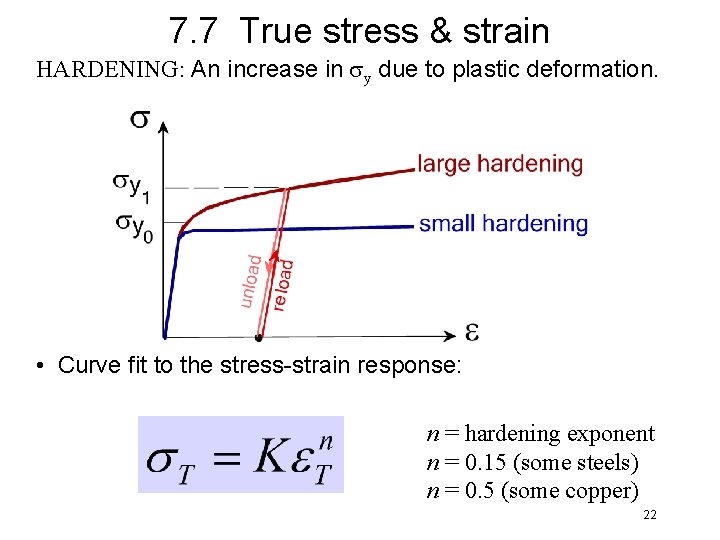
7. 7 True stress & strain HARDENING: An increase in sy due to plastic deformation. • Curve fit to the stress-strain response: n = hardening exponent n = 0. 15 (some steels) n = 0. 5 (some copper) 22
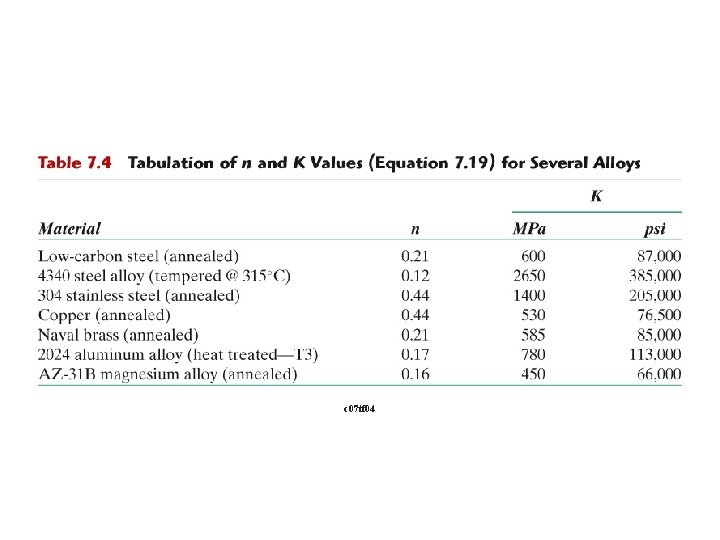
c 07 tf 04
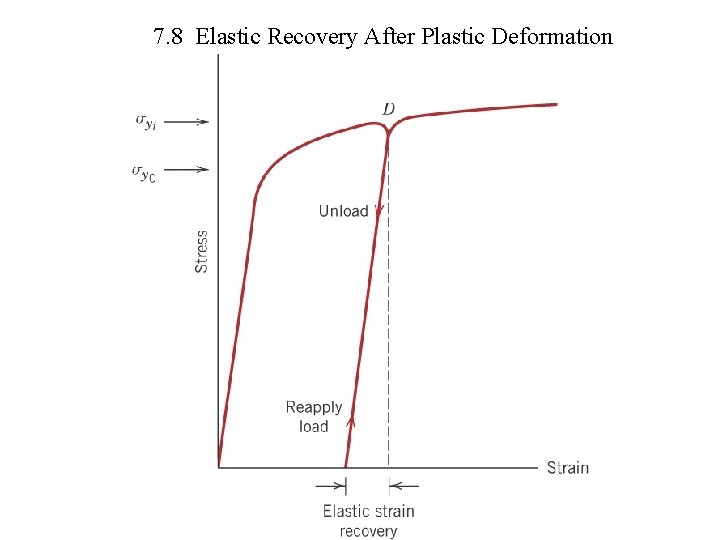
7. 8 Elastic Recovery After Plastic Deformation
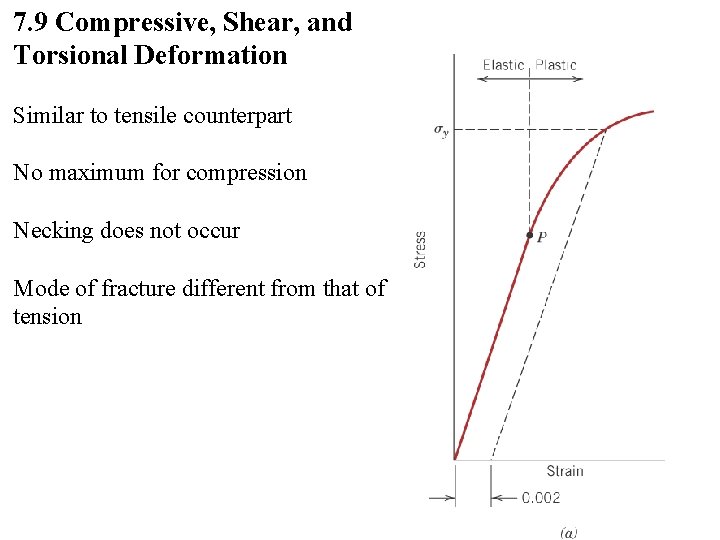
7. 9 Compressive, Shear, and Torsional Deformation Similar to tensile counterpart No maximum for compression Necking does not occur Mode of fracture different from that of tension
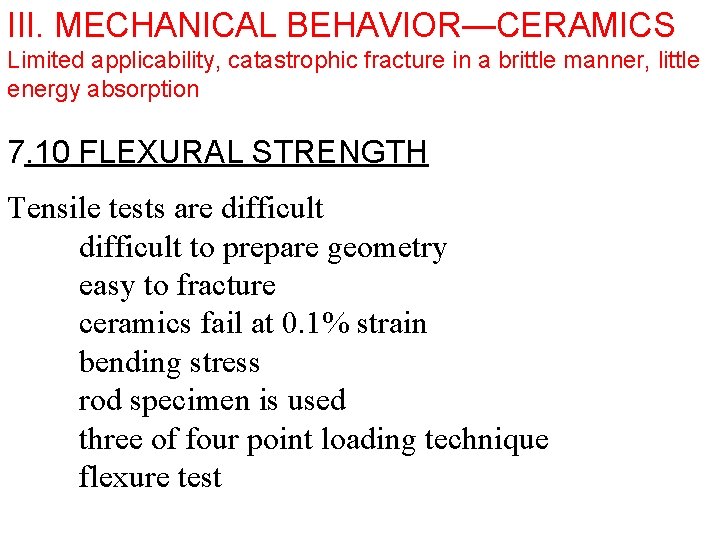
III. MECHANICAL BEHAVIOR—CERAMICS Limited applicability, catastrophic fracture in a brittle manner, little energy absorption 7. 10 FLEXURAL STRENGTH Tensile tests are difficult to prepare geometry easy to fracture ceramics fail at 0. 1% strain bending stress rod specimen is used three of four point loading technique flexure test

7. 10 MEASURING STRENGTH • Flexural strength= modulus of rupture = fracture strength = bend strength • Type values: Si nitride 700 -1000 300 Si carbide 550 -860 430 Al oxide 275 -550 390 glass (soda) 69 69 Data from Table 12. 5, Callister 6 e.
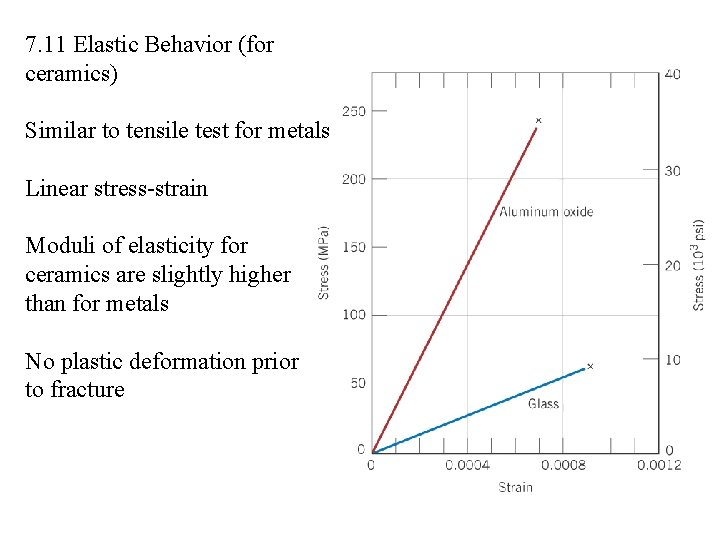
7. 11 Elastic Behavior (for ceramics) Similar to tensile test for metals Linear stress-strain Moduli of elasticity for ceramics are slightly higher than for metals No plastic deformation prior to fracture
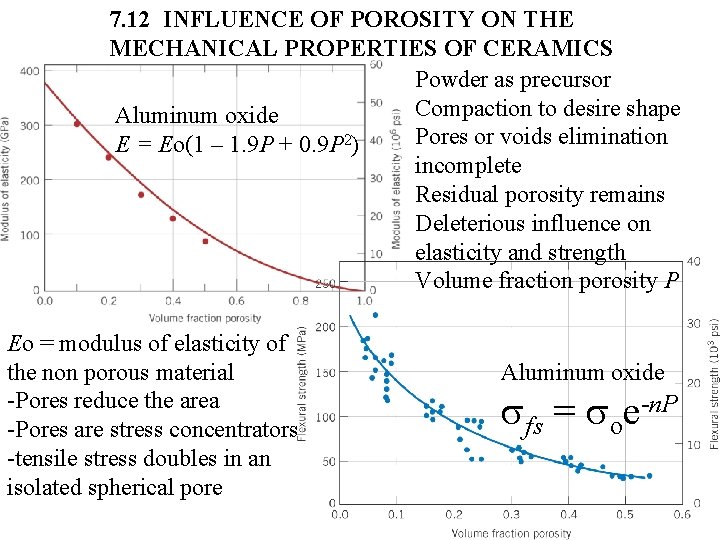
7. 12 INFLUENCE OF POROSITY ON THE MECHANICAL PROPERTIES OF CERAMICS Powder as precursor Compaction to desire shape Aluminum oxide Pores or voids elimination E = Eo(1 – 1. 9 P + 0. 9 P 2) incomplete Residual porosity remains Deleterious influence on elasticity and strength Volume fraction porosity P Eo = modulus of elasticity of the non porous material -Pores reduce the area -Pores are stress concentrators -tensile stress doubles in an isolated spherical pore Aluminum oxide sfs = soe-n. P
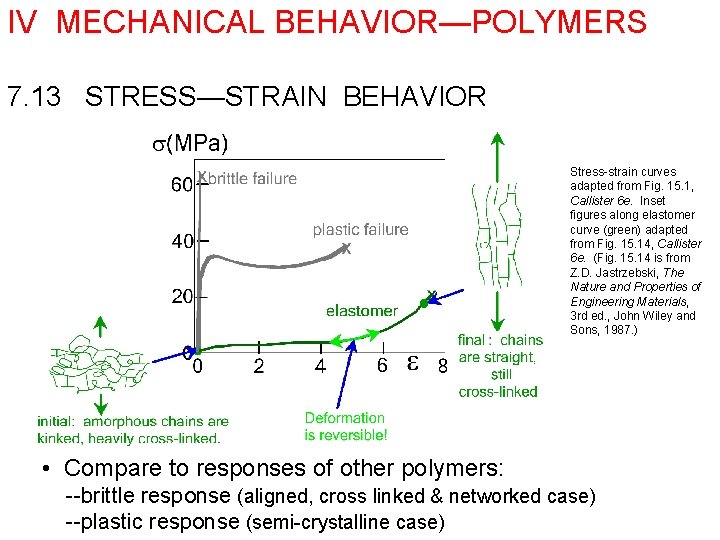
IV MECHANICAL BEHAVIOR—POLYMERS 7. 13 STRESS—STRAIN BEHAVIOR Stress-strain curves adapted from Fig. 15. 1, Callister 6 e. Inset figures along elastomer curve (green) adapted from Fig. 15. 14, Callister 6 e. (Fig. 15. 14 is from Z. D. Jastrzebski, The Nature and Properties of Engineering Materials, 3 rd ed. , John Wiley and Sons, 1987. ) • Compare to responses of other polymers: --brittle response (aligned, cross linked & networked case) --plastic response (semi-crystalline case)
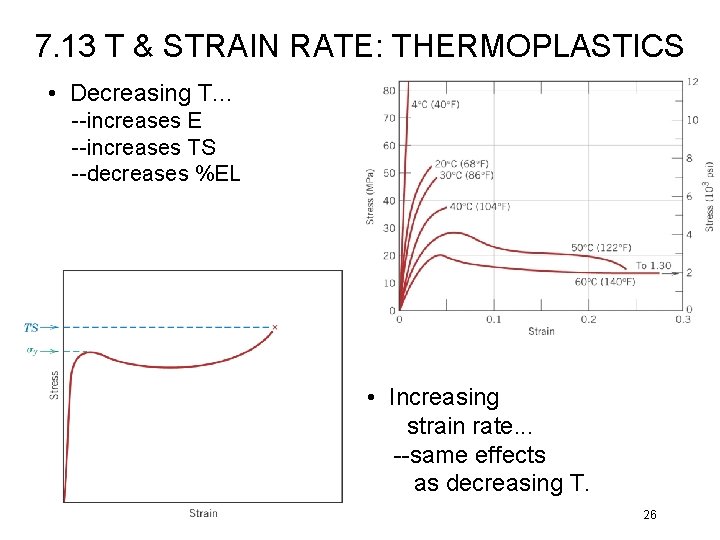
7. 13 T & STRAIN RATE: THERMOPLASTICS • Decreasing T. . . --increases E --increases TS --decreases %EL • Increasing strain rate. . . --same effects as decreasing T. 26
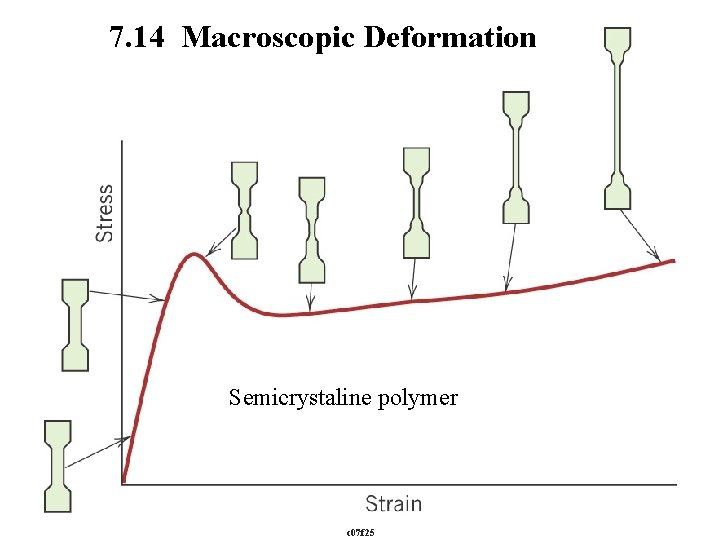
7. 14 Macroscopic Deformation Semicrystaline polymer c 07 f 25
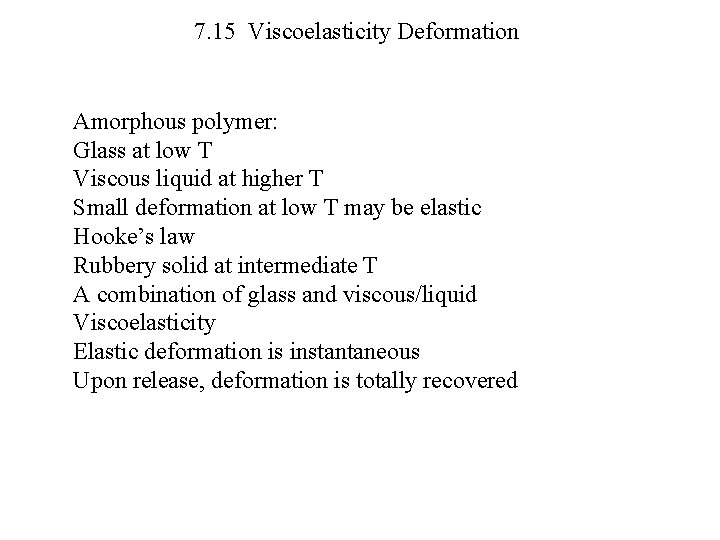
7. 15 Viscoelasticity Deformation Amorphous polymer: Glass at low T Viscous liquid at higher T Small deformation at low T may be elastic Hooke’s law Rubbery solid at intermediate T A combination of glass and viscous/liquid Viscoelasticity Elastic deformation is instantaneous Upon release, deformation is totally recovered
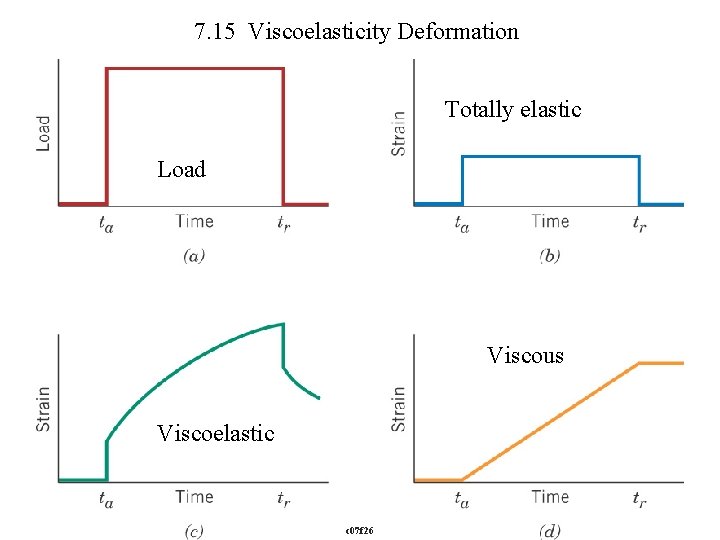
7. 15 Viscoelasticity Deformation Totally elastic Load Viscous Viscoelastic c 07 f 26
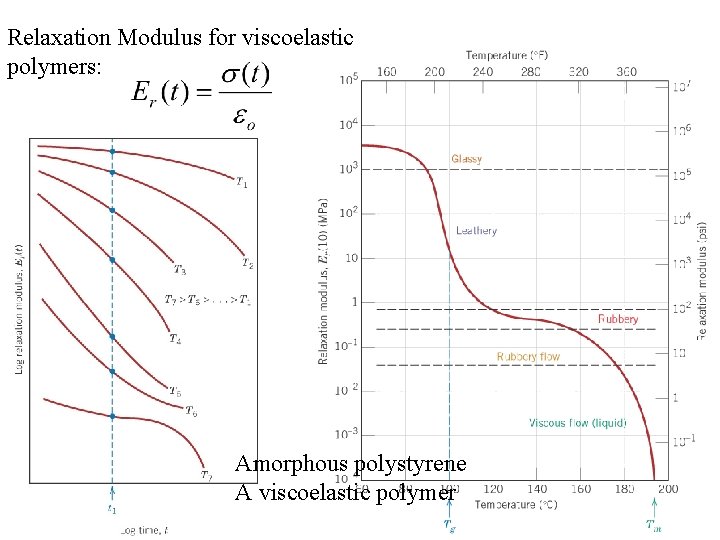
Relaxation Modulus for viscoelastic polymers: Amorphous polystyrene A viscoelastic polymer
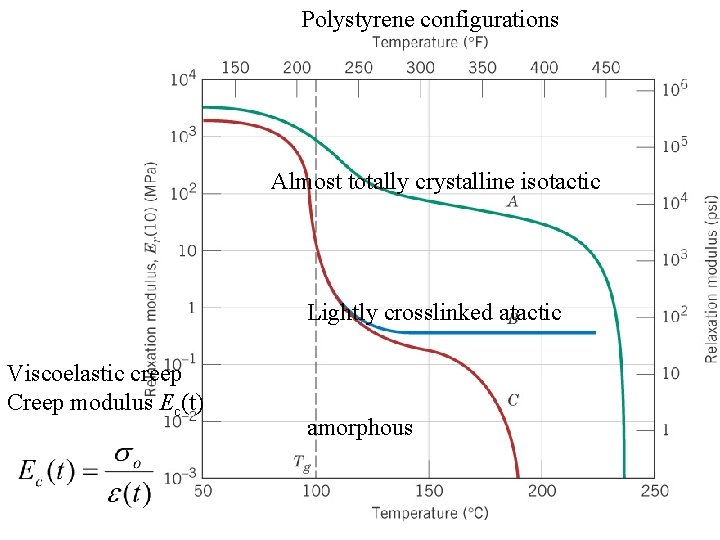
Polystyrene configurations Almost totally crystalline isotactic Lightly crosslinked atactic Viscoelastic creep Creep modulus Ec(t) amorphous
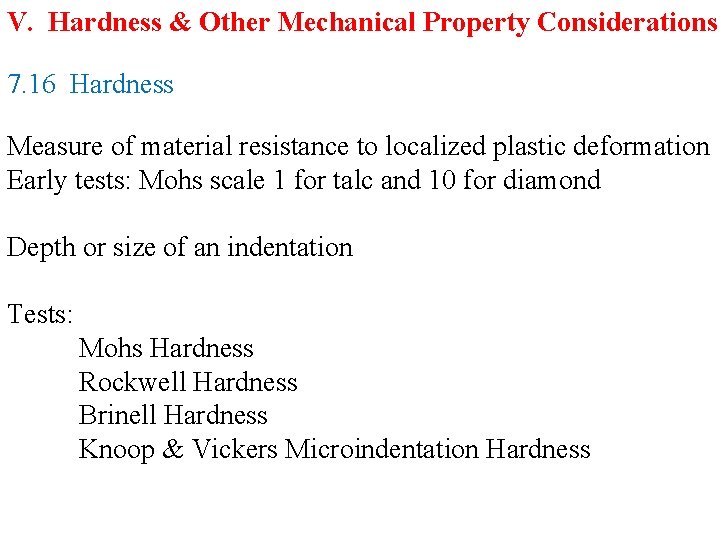
V. Hardness & Other Mechanical Property Considerations 7. 16 Hardness Measure of material resistance to localized plastic deformation Early tests: Mohs scale 1 for talc and 10 for diamond Depth or size of an indentation Tests: Mohs Hardness Rockwell Hardness Brinell Hardness Knoop & Vickers Microindentation Hardness
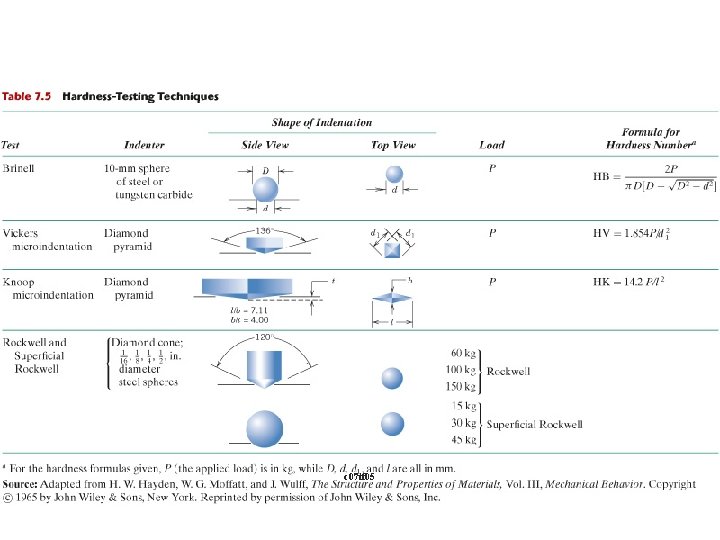
c 07 tf 05
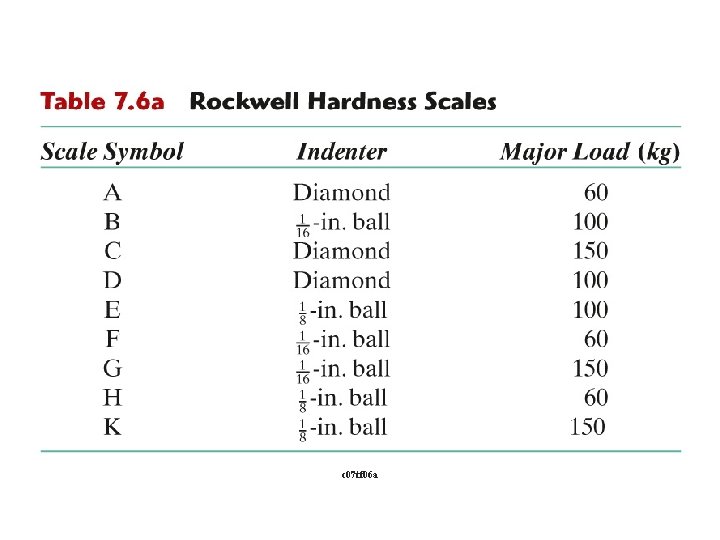
c 07 tf 06 a
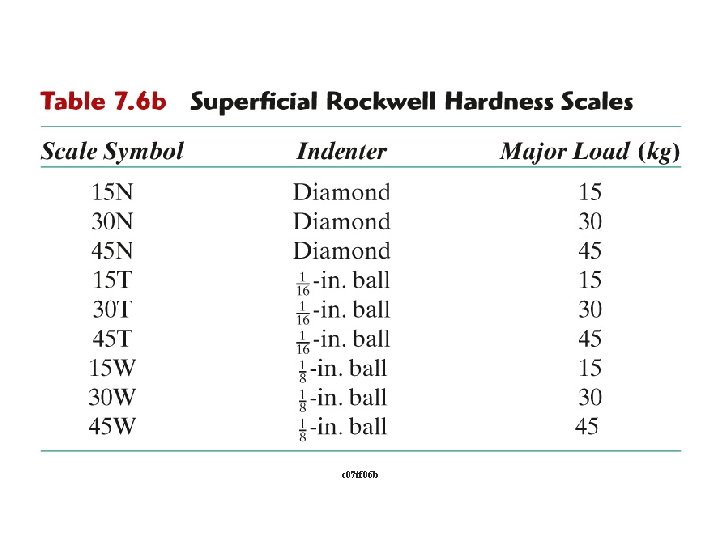
c 07 tf 06 b
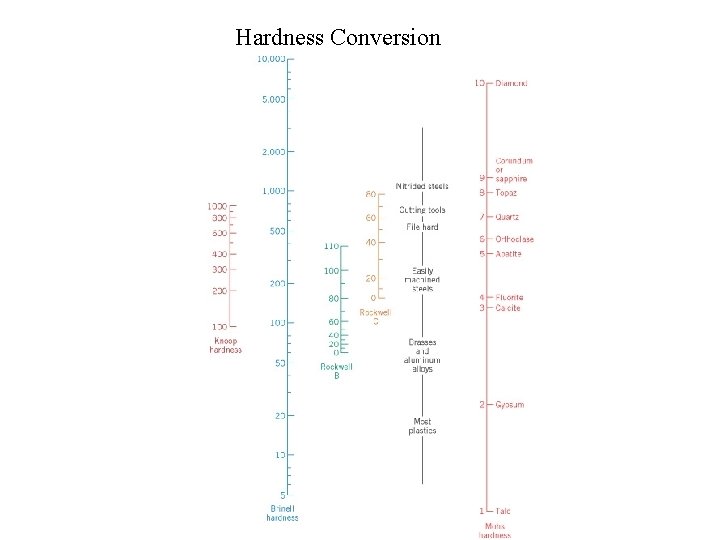
Hardness Conversion
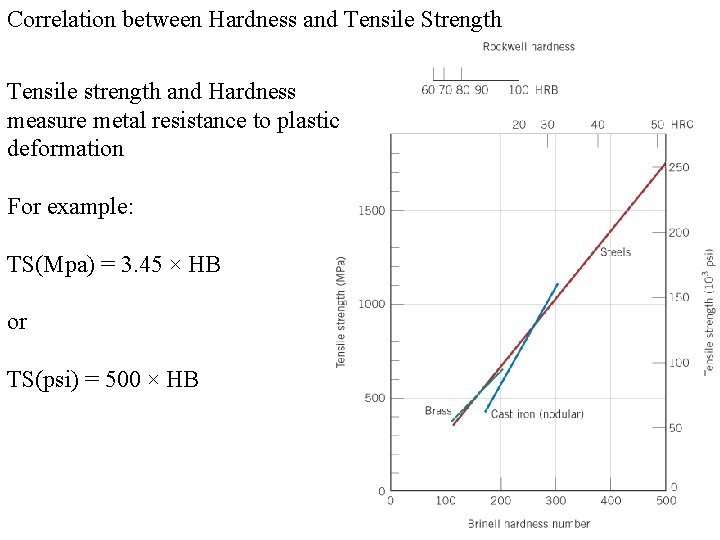
Correlation between Hardness and Tensile Strength Tensile strength and Hardness measure metal resistance to plastic deformation For example: TS(Mpa) = 3. 45 × HB or TS(psi) = 500 × HB
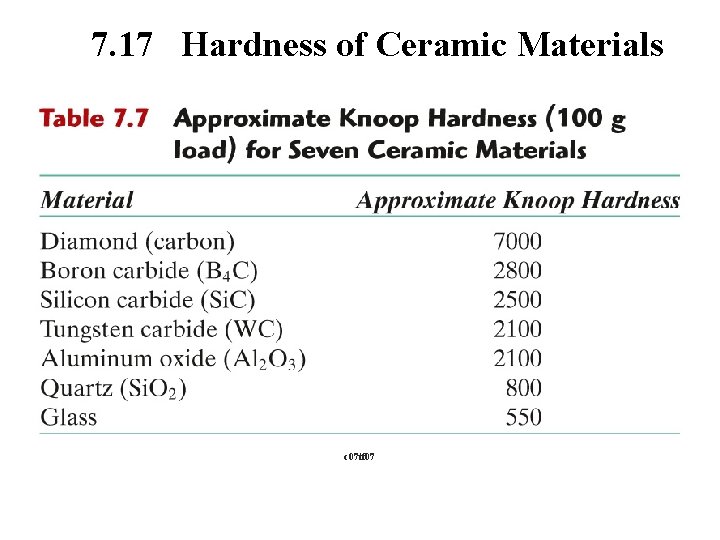
7. 17 Hardness of Ceramic Materials c 07 tf 07
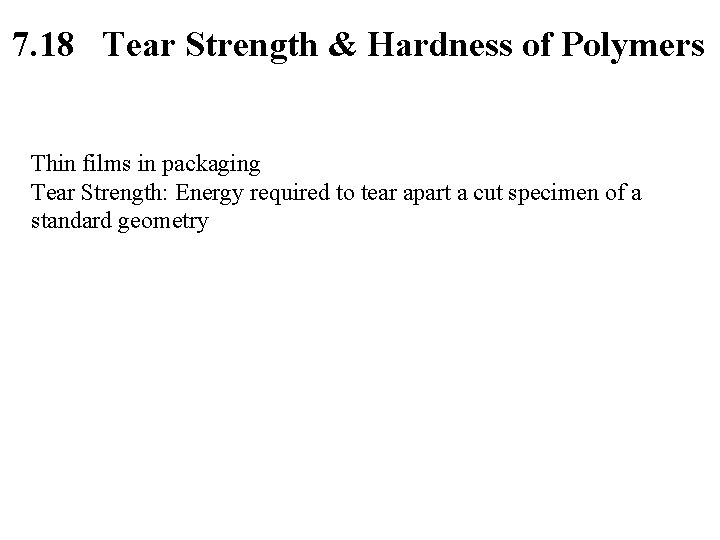
7. 18 Tear Strength & Hardness of Polymers Thin films in packaging Tear Strength: Energy required to tear apart a cut specimen of a standard geometry
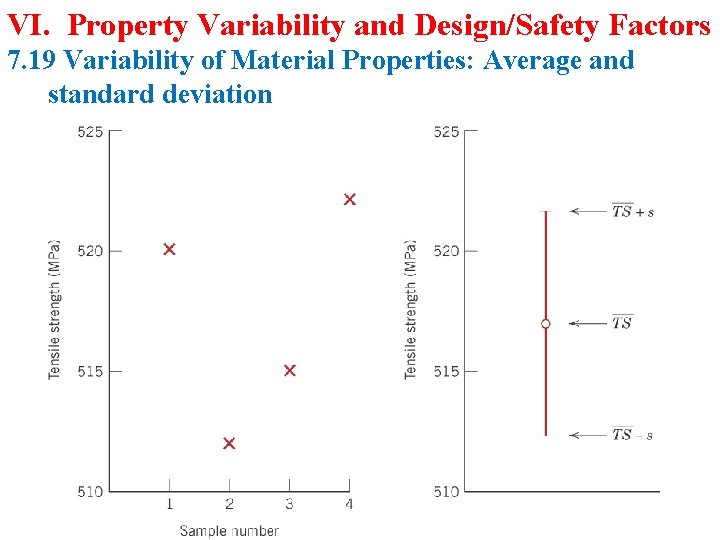
VI. Property Variability and Design/Safety Factors 7. 19 Variability of Material Properties: Average and standard deviation
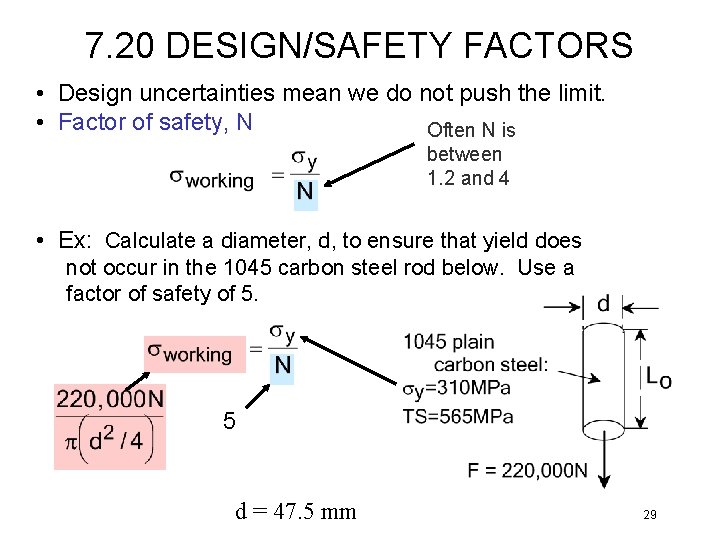
7. 20 DESIGN/SAFETY FACTORS • Design uncertainties mean we do not push the limit. • Factor of safety, N Often N is between 1. 2 and 4 • Ex: Calculate a diameter, d, to ensure that yield does not occur in the 1045 carbon steel rod below. Use a factor of safety of 5. 5 d = 47. 5 mm 29
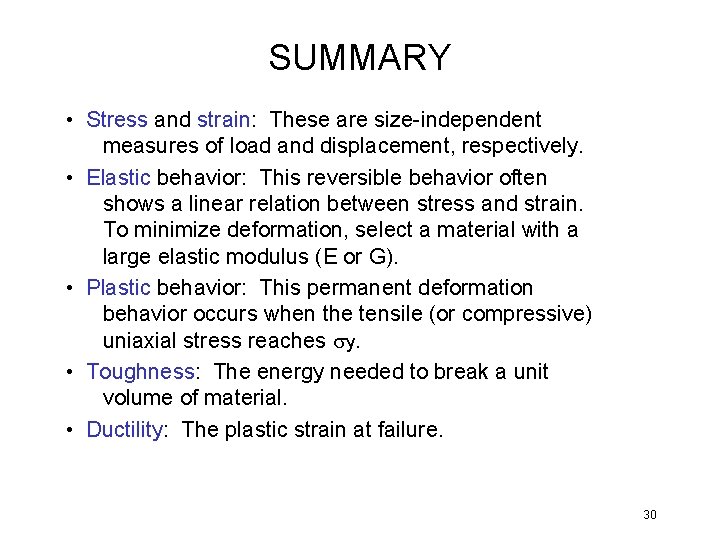
SUMMARY • Stress and strain: These are size-independent measures of load and displacement, respectively. • Elastic behavior: This reversible behavior often shows a linear relation between stress and strain. To minimize deformation, select a material with a large elastic modulus (E or G). • Plastic behavior: This permanent deformation behavior occurs when the tensile (or compressive) uniaxial stress reaches sy. • Toughness: The energy needed to break a unit volume of material. • Ductility: The plastic strain at failure. 30
Actual mechanical advantage vs ideal mechanical advantage
Mechanical properties of materials physics
Stress strain curve toughness
Mechanical properties of nano materials
Properties of mechanical wave
Properties of cardboard
Properties of mechanical waves
Properties of mechanical waves
Tensile strength of plastic
Calister
Extensive vs intensive quantity
Is smell a physical property
Mechanical wave
Chapter 17 mechanical waves and sound worksheet answers
Chapter 17 mechanical waves and sound
Chapter 17 mechanical waves and sound
Example of mechanical wave
Chapter 2 mechanical equilibrium
Which travels along a surface separating two media
Segment fg is the angle bisector of ∠efh.
Chapter 11 properties of the hair and scalp answers
Imagep unscramble
The two rows of elements that seem to be disconnected
Chapter 10 properties of circles answers
Limits and their properties
2 properties of matter
Fragilitas crinium
Ap chemistry chapter 7 periodic properties of the elements
List the properties of x radiation chapter 38
Properties of pure substances
Chapter 2 properties of matter answer key
Chapter 1 limits and their properties
Chapter 1 limits and their properties
Geometry unit 10 circles quiz 10-2 answers
Chapter 13 properties of solutions
Elements and their properties section 1 metals
Ytuerasmus
What is cutting tools
Mechanical energy of a system
How does mechanical advantage work
Fixed pulley
Compound machine
How to calculate mechanical advantage
Energy is the ability to
Mechanical isolation
Rit mechanical engineering
Organic solidarity
Physical weathering and chemical weathering venn diagram
Mechanical and chemical weathering venn diagram
Mechanical and chemical weathering venn diagram
Identify three agents of mechanical weathering
Transverse waves move perpendicular
Examples of a mechanical wave
Carries energy through matter
цомчн
Mechanical waves and electromagnetic waves
Pusher vs non pusher mechanical seal
The maximum distance a wave varies from its rest position
Nps mechanical engineering