Ceramics Mechanical Properties and Processing of Ceramic Mechanical
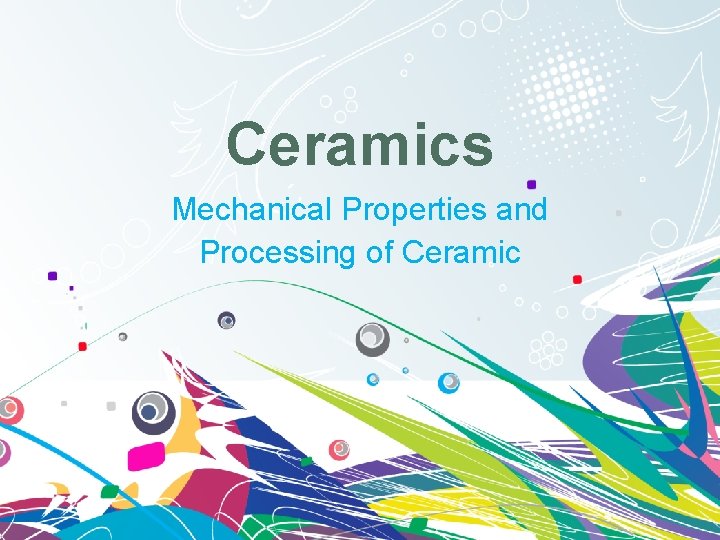
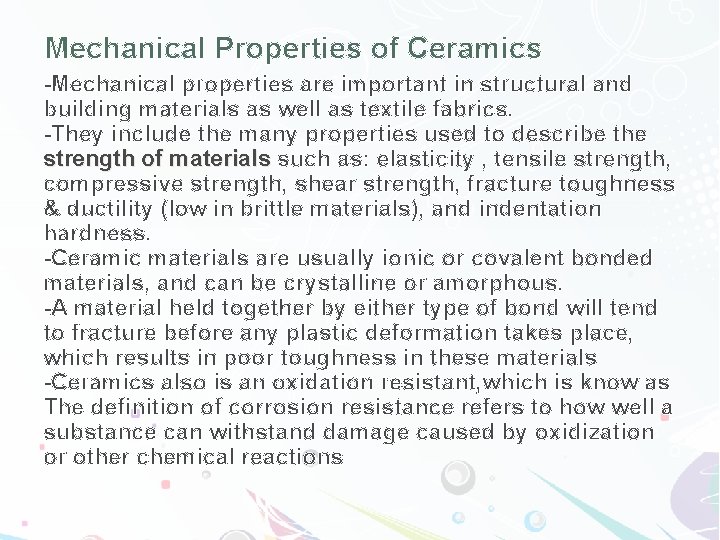
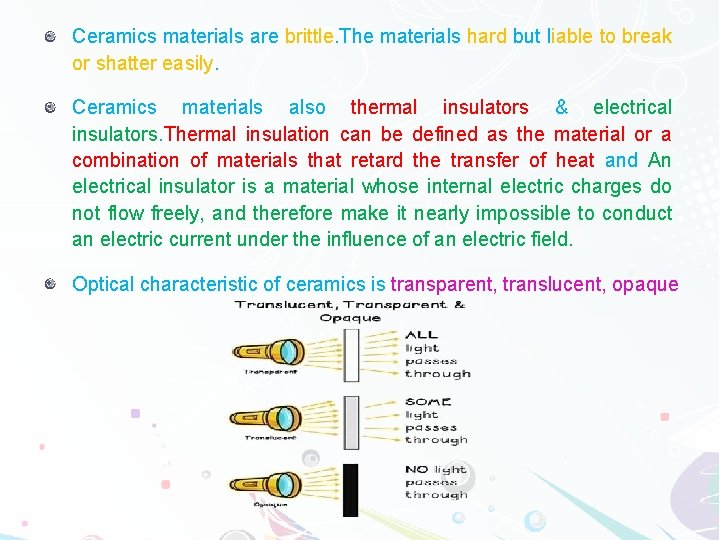
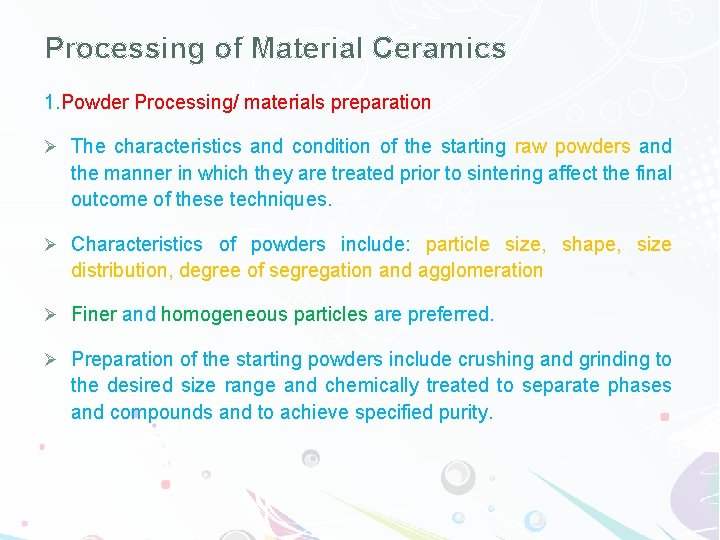
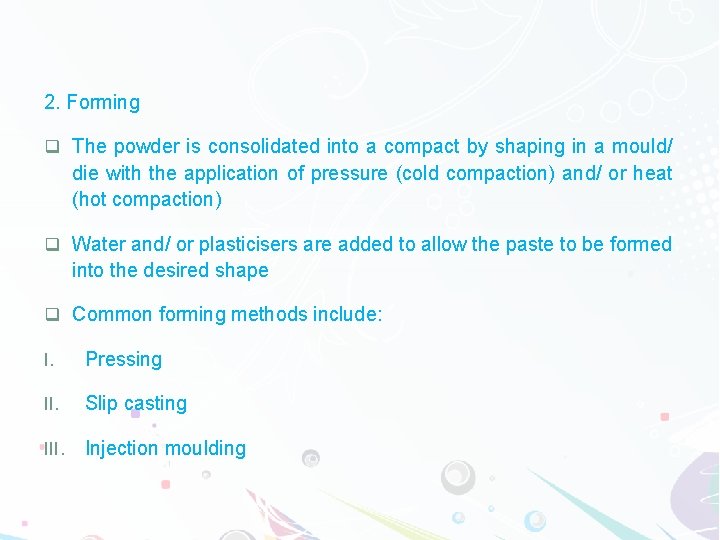
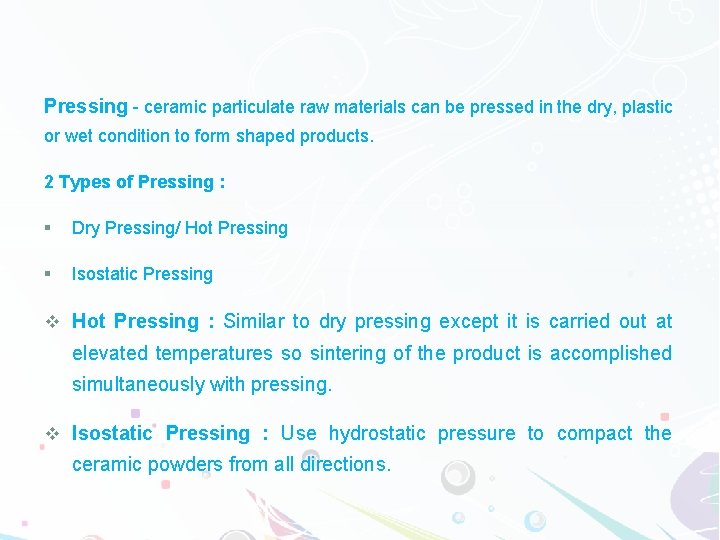
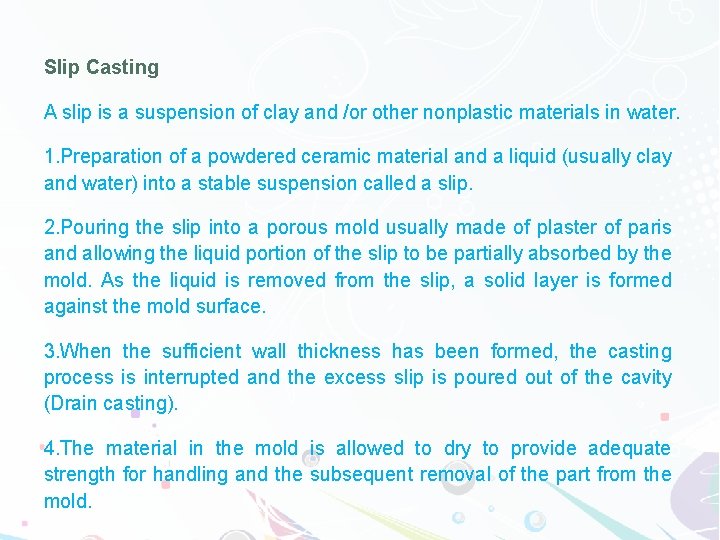
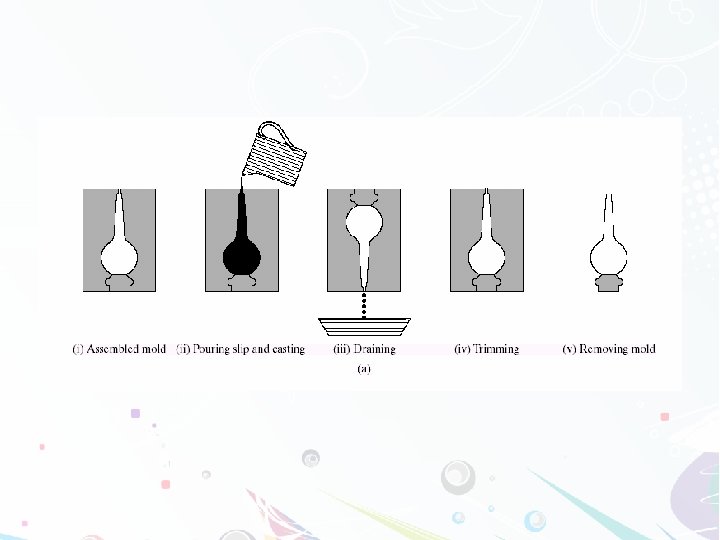
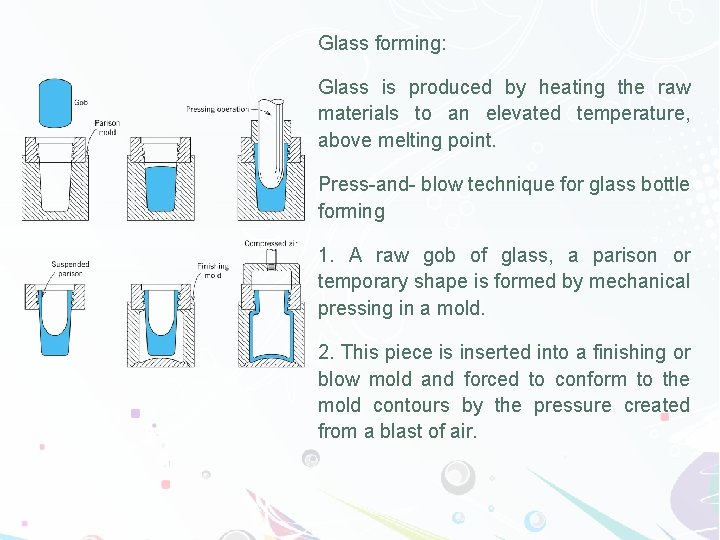

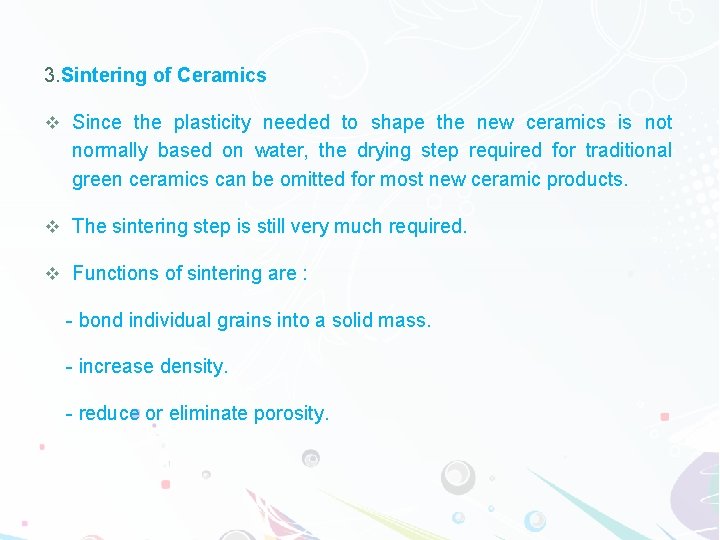
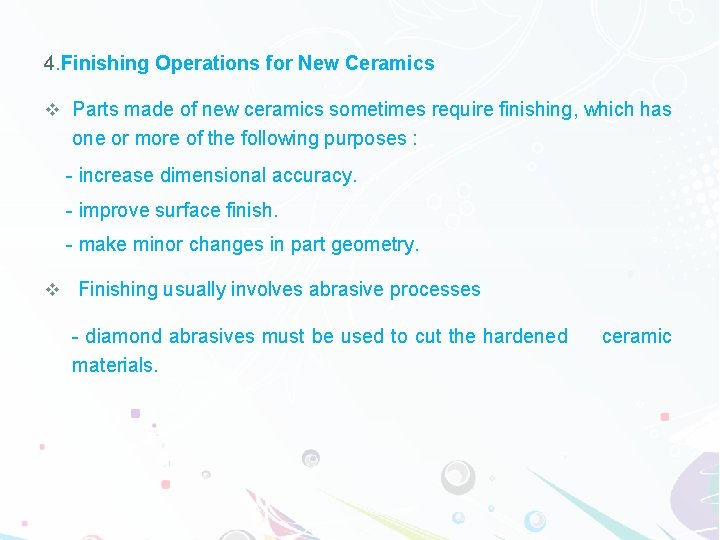
- Slides: 12
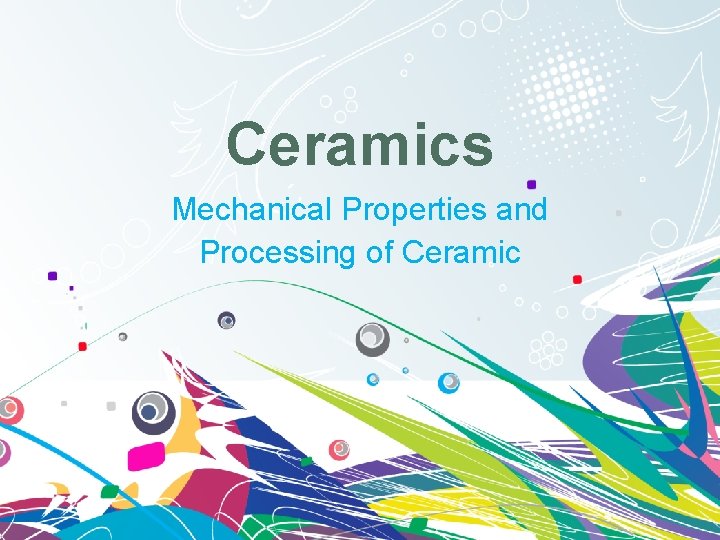
Ceramics Mechanical Properties and Processing of Ceramic
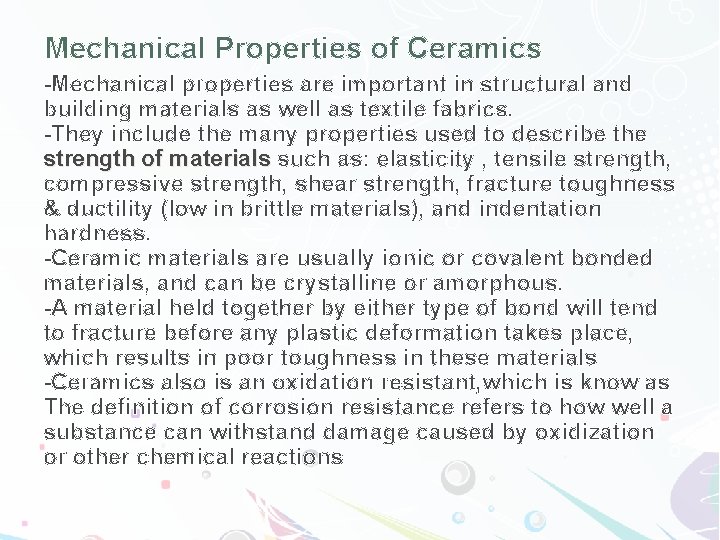
Mechanical Properties of Ceramics -Mechanical properties are important in structural and building materials as well as textile fabrics. -They include the many properties used to describe the strength of materials such as: elasticity , tensile strength, compressive strength, shear strength, fracture toughness & ductility (low in brittle materials), and indentation hardness. -Ceramic materials are usually ionic or covalent bonded materials, and can be crystalline or amorphous. -A material held together by either type of bond will tend to fracture before any plastic deformation takes place, which results in poor toughness in these materials -Ceramics also is an oxidation resistant, which is know as The definition of corrosion resistance refers to how well a substance can withstand damage caused by oxidization or other chemical reactions
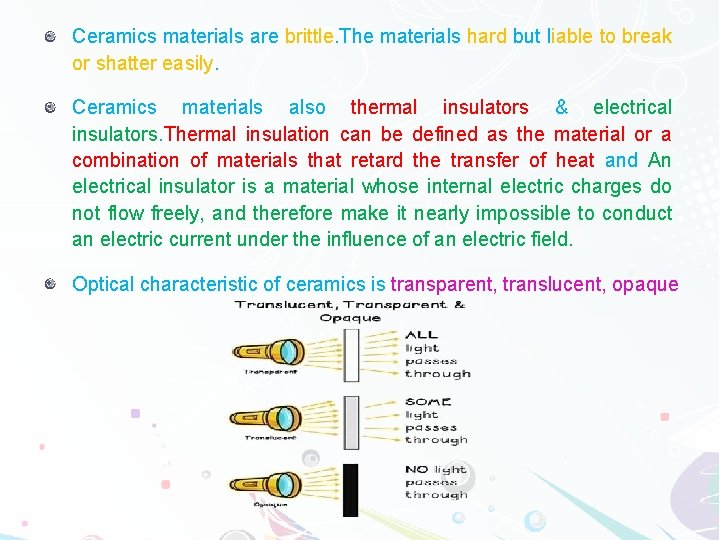
Ceramics materials are brittle. The materials hard but liable to break or shatter easily. Ceramics materials also thermal insulators & electrical insulators. Thermal insulation can be defined as the material or a combination of materials that retard the transfer of heat and An electrical insulator is a material whose internal electric charges do not flow freely, and therefore make it nearly impossible to conduct an electric current under the influence of an electric field. Optical characteristic of ceramics is transparent, translucent, opaque
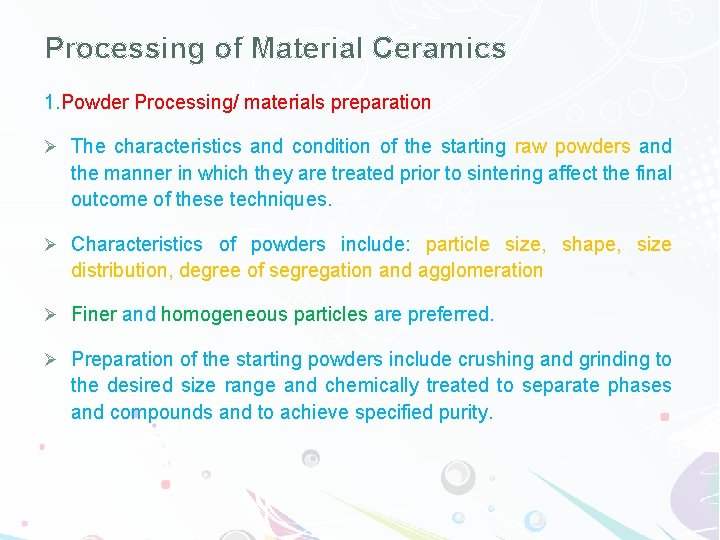
Processing of Material Ceramics 1. Powder Processing/ materials preparation Ø The characteristics and condition of the starting raw powders and the manner in which they are treated prior to sintering affect the final outcome of these techniques. Ø Characteristics of powders include: particle size, shape, size distribution, degree of segregation and agglomeration Ø Finer and homogeneous particles are preferred. Ø Preparation of the starting powders include crushing and grinding to the desired size range and chemically treated to separate phases and compounds and to achieve specified purity.
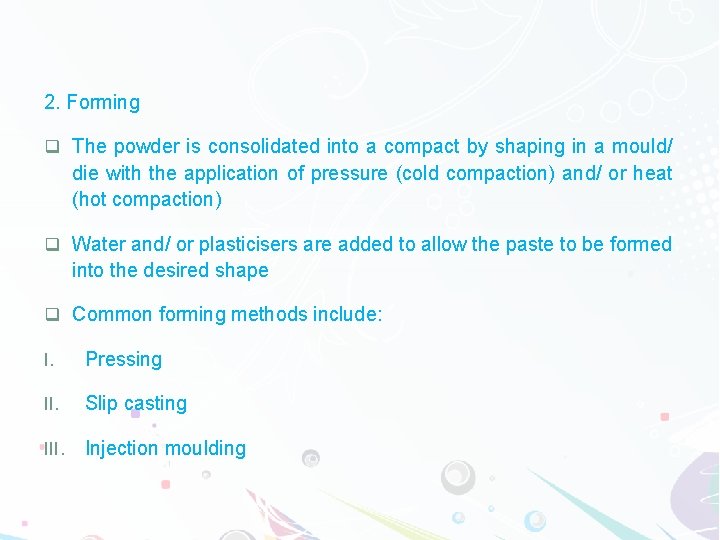
2. Forming q The powder is consolidated into a compact by shaping in a mould/ die with the application of pressure (cold compaction) and/ or heat (hot compaction) q Water and/ or plasticisers are added to allow the paste to be formed into the desired shape q Common forming methods include: I. Pressing II. Slip casting III. Injection moulding
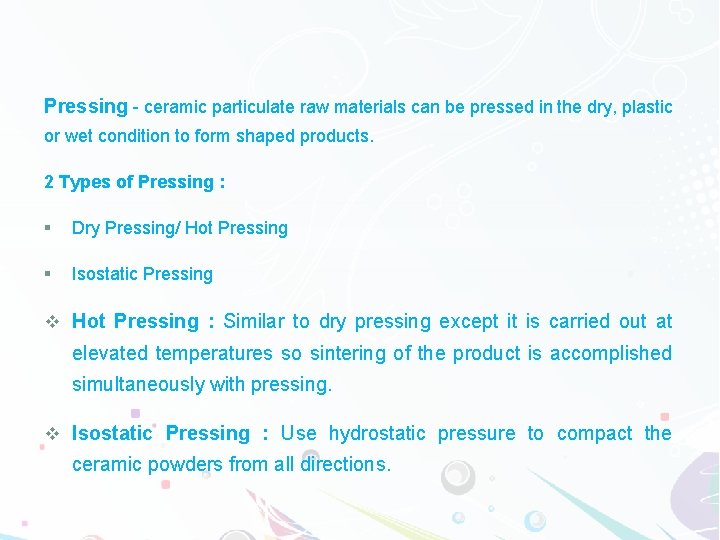
Pressing - ceramic particulate raw materials can be pressed in the dry, plastic or wet condition to form shaped products. 2 Types of Pressing : § Dry Pressing/ Hot Pressing § Isostatic Pressing v Hot Pressing : Similar to dry pressing except it is carried out at elevated temperatures so sintering of the product is accomplished simultaneously with pressing. v Isostatic Pressing : Use hydrostatic pressure to compact the ceramic powders from all directions.
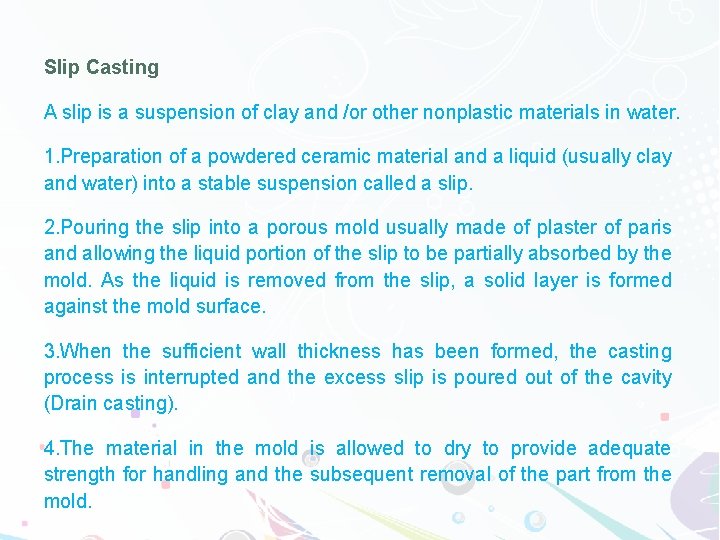
Slip Casting A slip is a suspension of clay and /or other nonplastic materials in water. 1. Preparation of a powdered ceramic material and a liquid (usually clay and water) into a stable suspension called a slip. 2. Pouring the slip into a porous mold usually made of plaster of paris and allowing the liquid portion of the slip to be partially absorbed by the mold. As the liquid is removed from the slip, a solid layer is formed against the mold surface. 3. When the sufficient wall thickness has been formed, the casting process is interrupted and the excess slip is poured out of the cavity (Drain casting). 4. The material in the mold is allowed to dry to provide adequate strength for handling and the subsequent removal of the part from the mold.
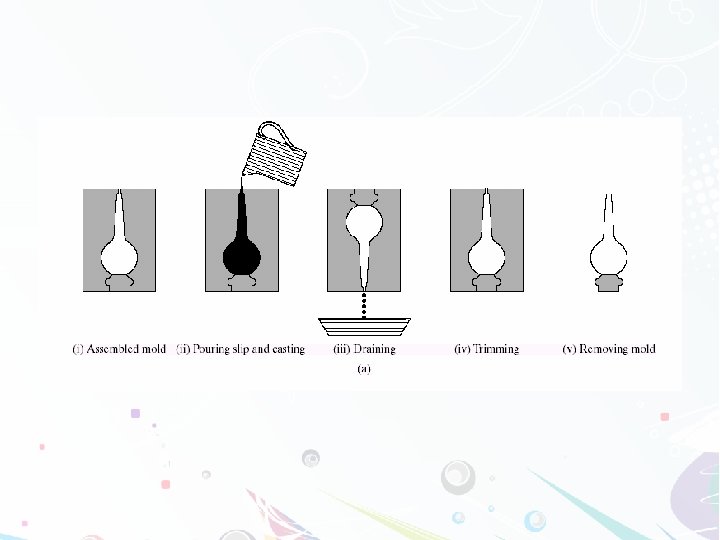
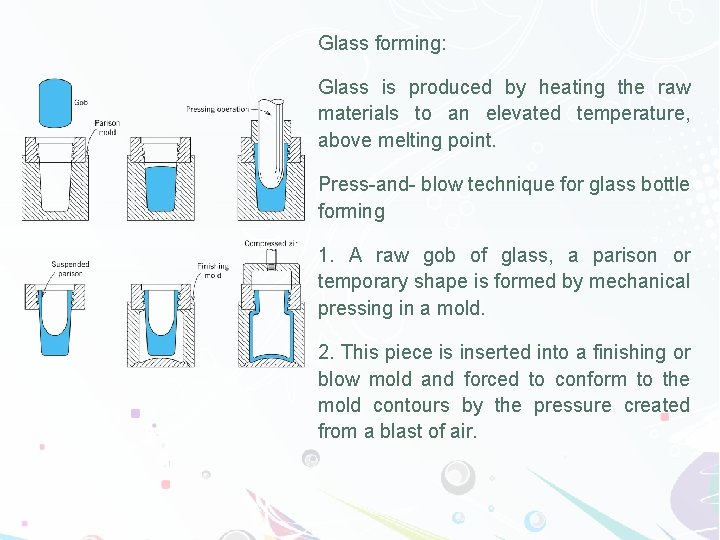
Glass forming: Glass is produced by heating the raw materials to an elevated temperature, above melting point. Press-and- blow technique for glass bottle forming 1. A raw gob of glass, a parison or temporary shape is formed by mechanical pressing in a mold. 2. This piece is inserted into a finishing or blow mold and forced to conform to the mold contours by the pressure created from a blast of air.

Injection Moulding - Is a manufacturing process for producting parts by injecting ceramics into a mould.
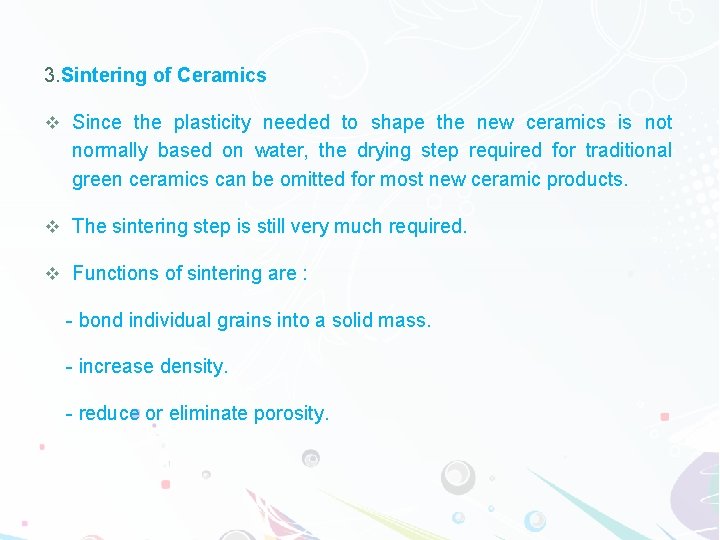
3. Sintering of Ceramics v Since the plasticity needed to shape the new ceramics is not normally based on water, the drying step required for traditional green ceramics can be omitted for most new ceramic products. v The sintering step is still very much required. v Functions of sintering are : - bond individual grains into a solid mass. - increase density. - reduce or eliminate porosity.
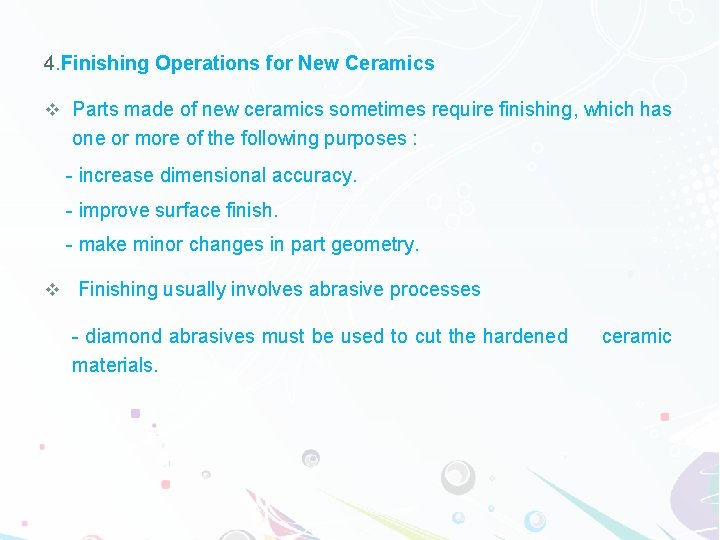
4. Finishing Operations for New Ceramics v Parts made of new ceramics sometimes require finishing, which has one or more of the following purposes : - increase dimensional accuracy. - improve surface finish. - make minor changes in part geometry. v Finishing usually involves abrasive processes - diamond abrasives must be used to cut the hardened materials. ceramic
Ceramic processing upscaling
Ceramic processing upscaling
Structure and properties of ceramics
Rcation/ranion
Plastic forming ceramic
Introduction to clay
Slip casting advantages and disadvantages
Neighborhood averaging in image processing
Primary processing and secondary processing
What is interactive processing
"hot isostatic pressing" and "punches" or "dies" -patent
Die blanks ceramics
Metal rib ceramics definition