Catalysis L V Catalytic reactors and physical forms
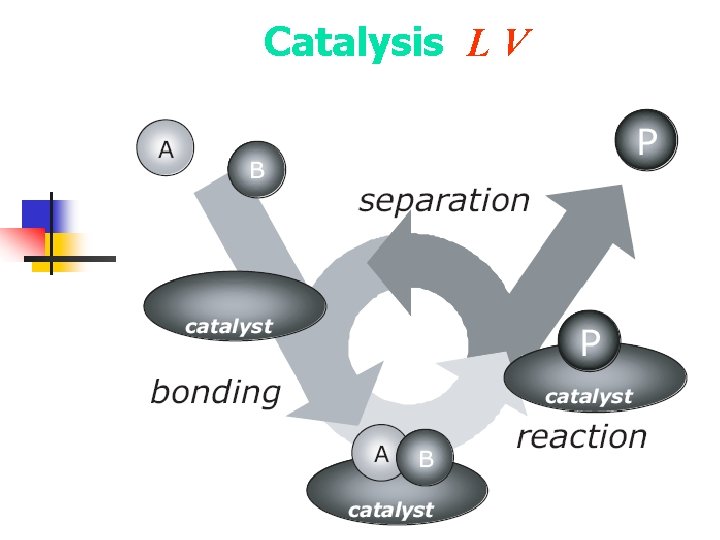
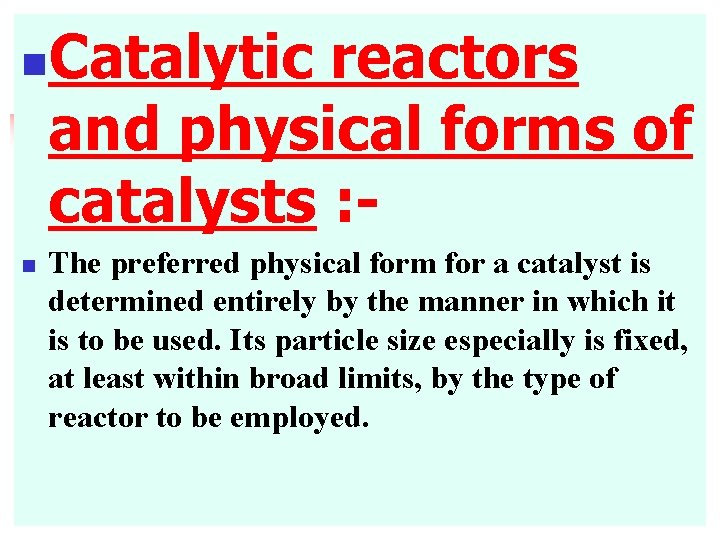
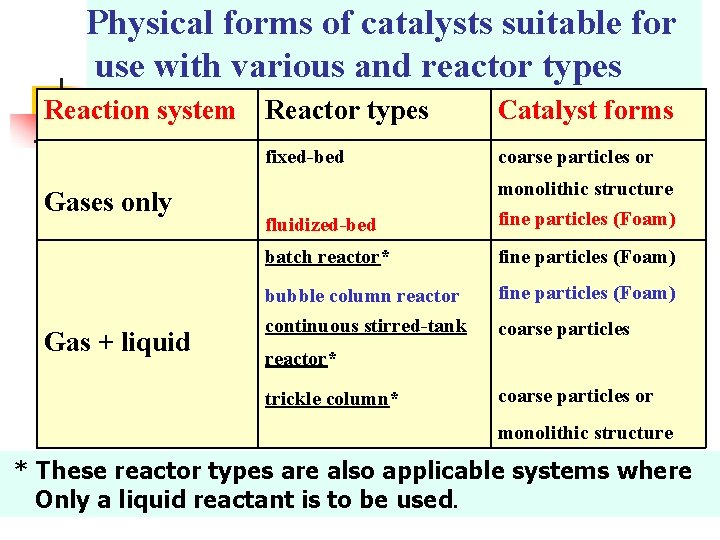
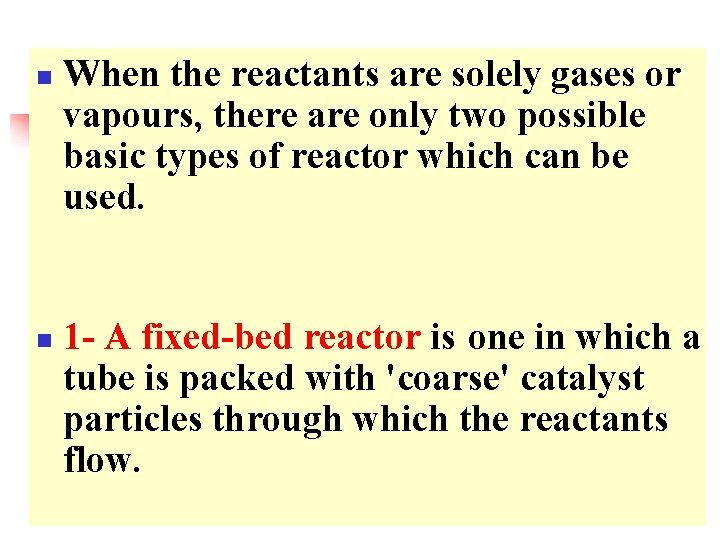
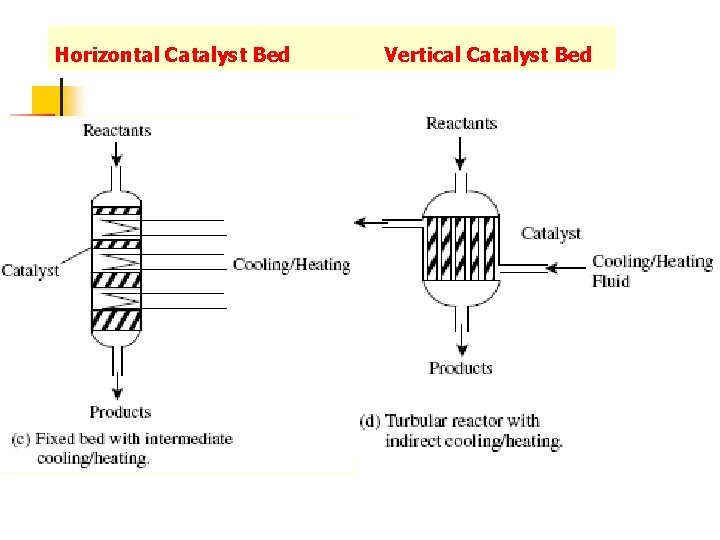
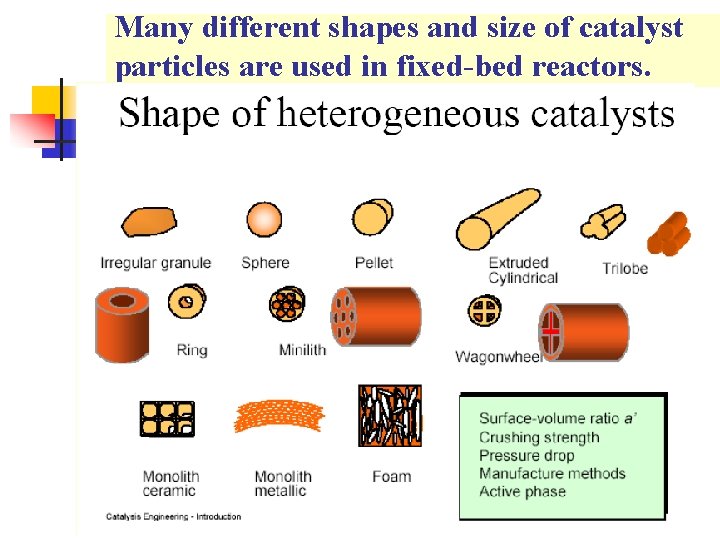
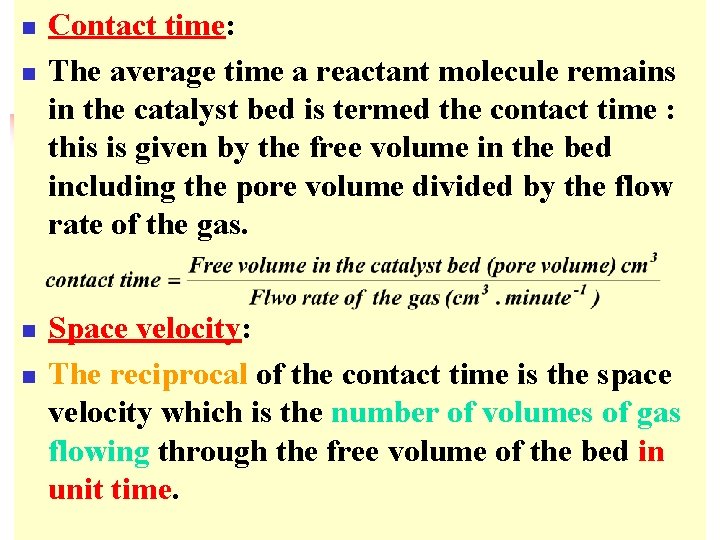
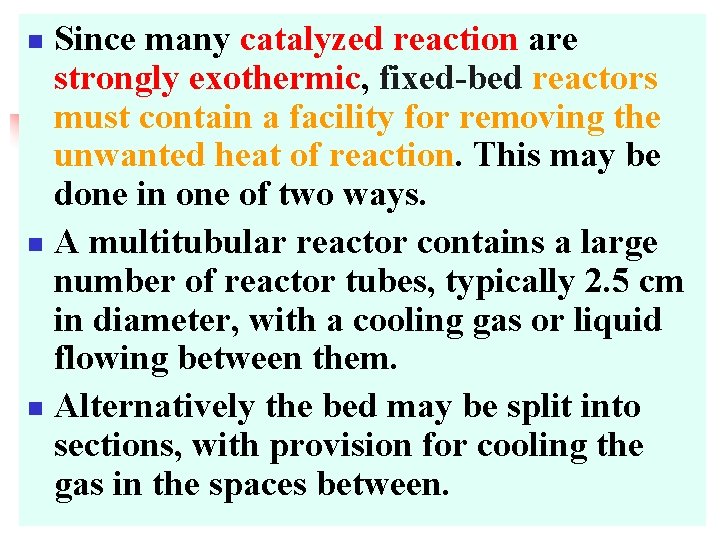
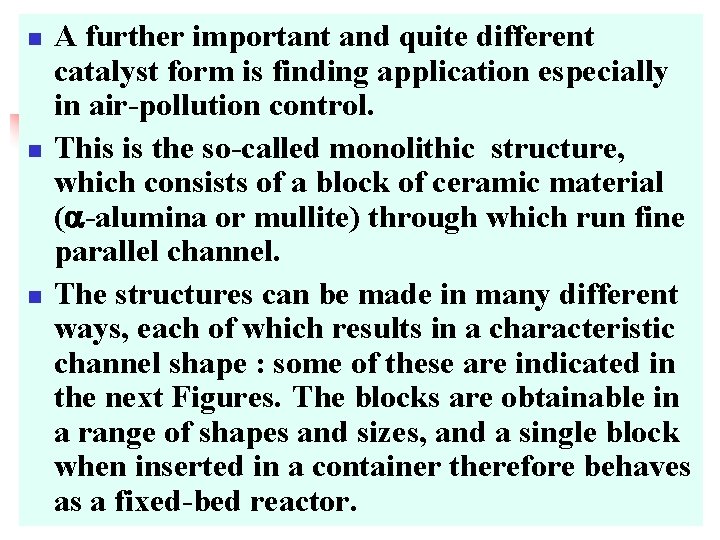
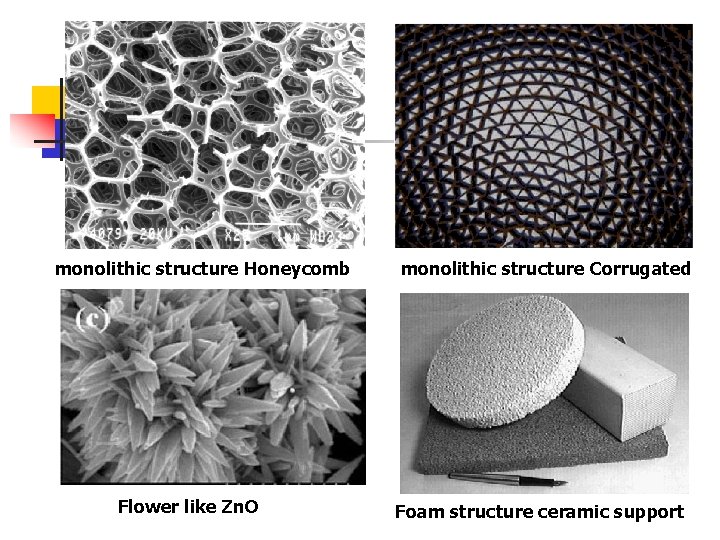
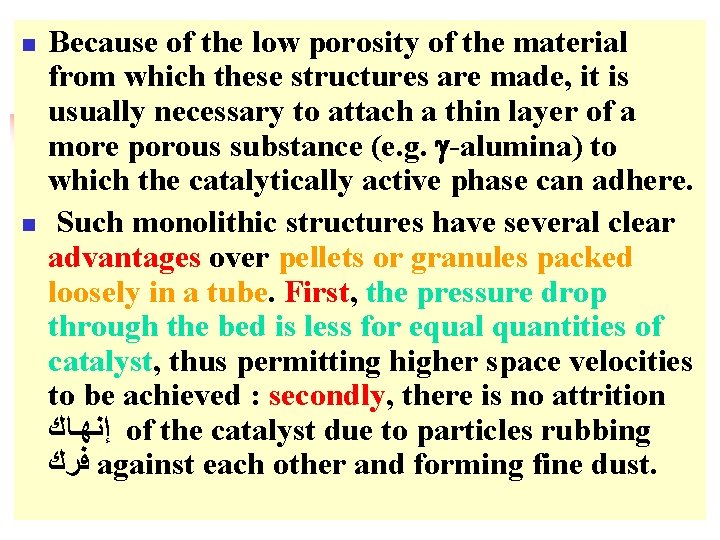
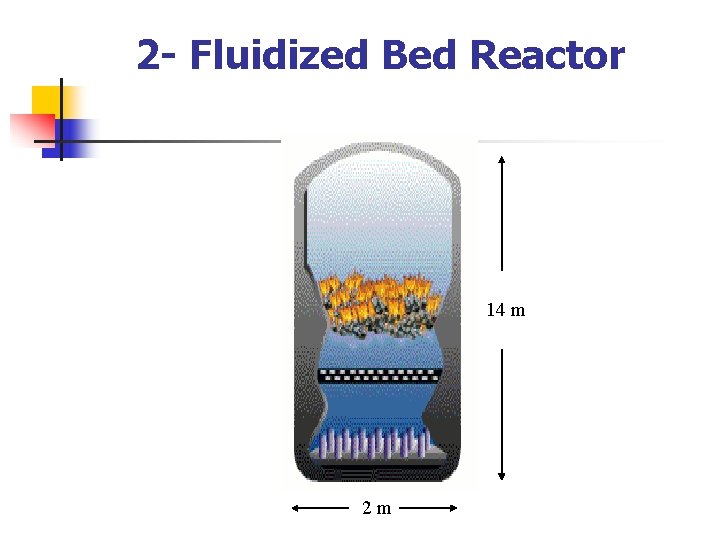
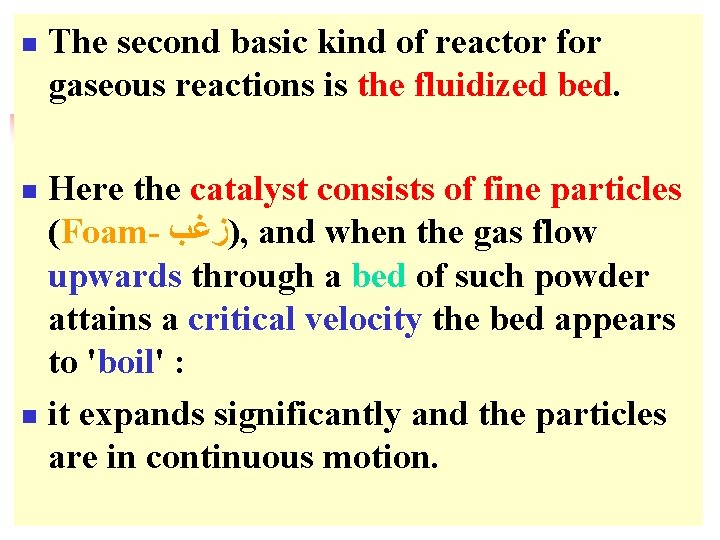
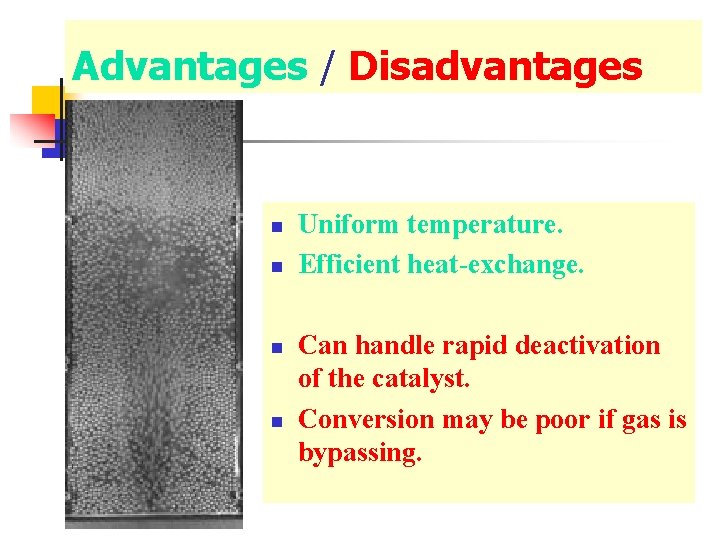
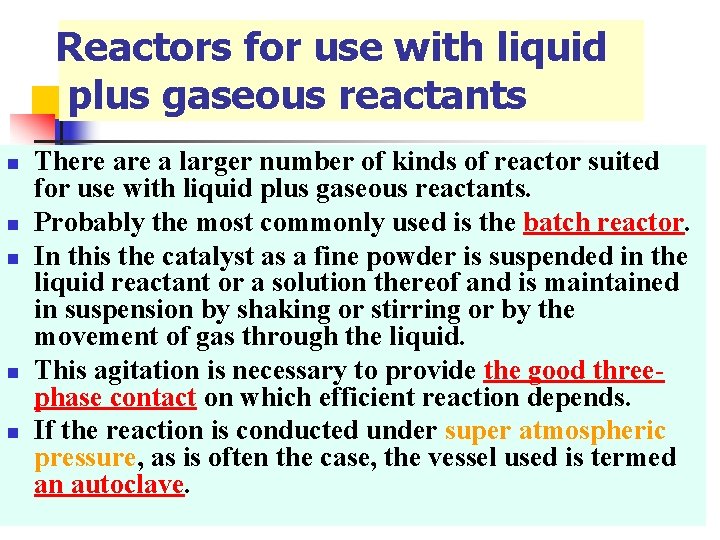
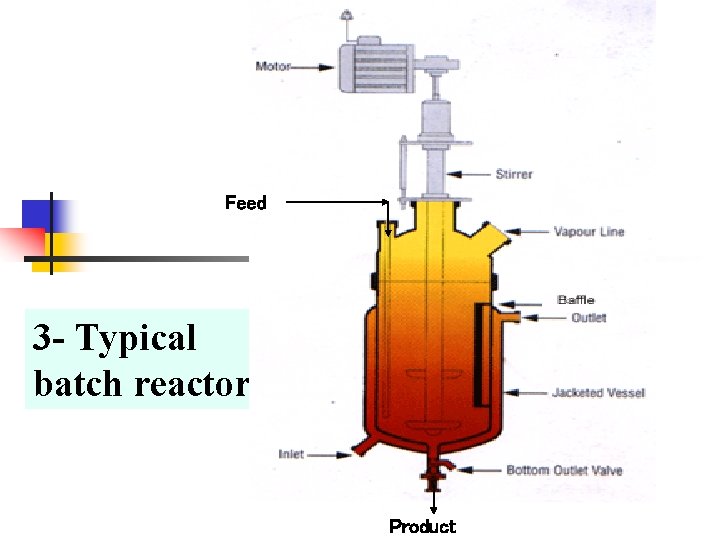
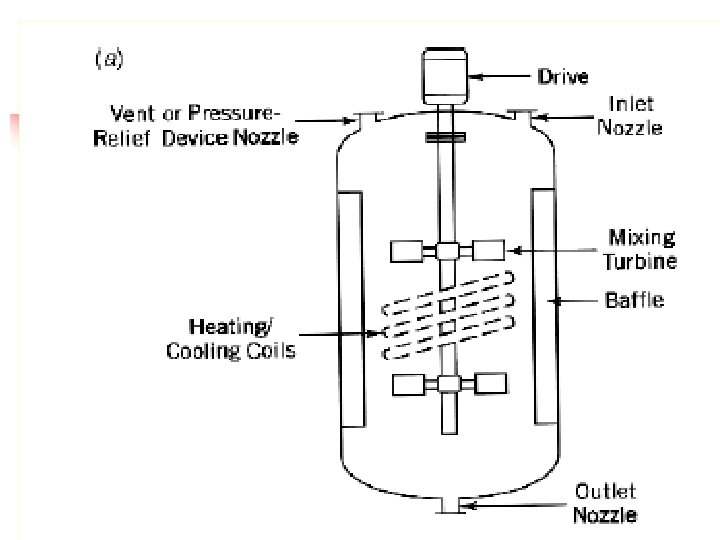
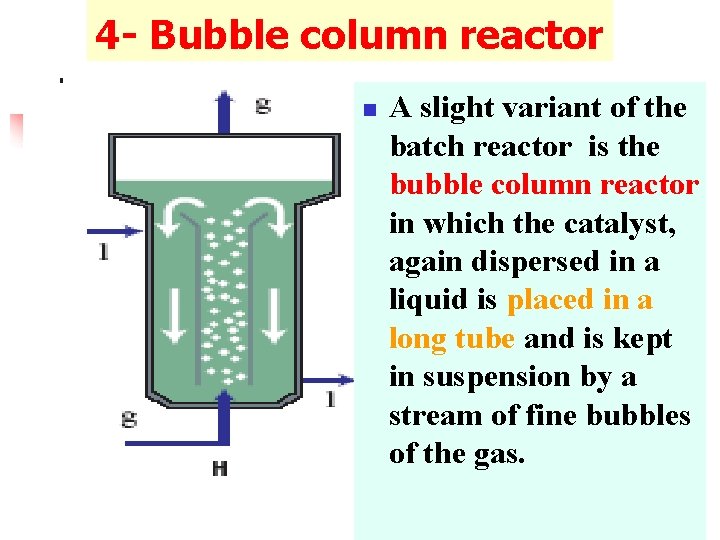
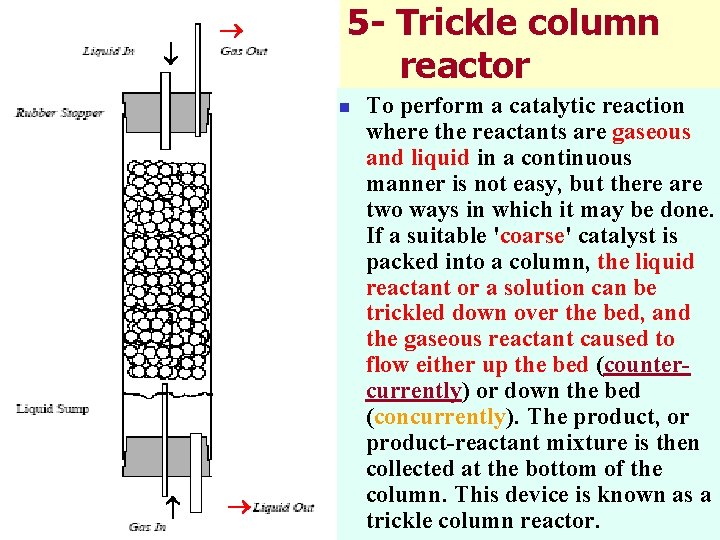
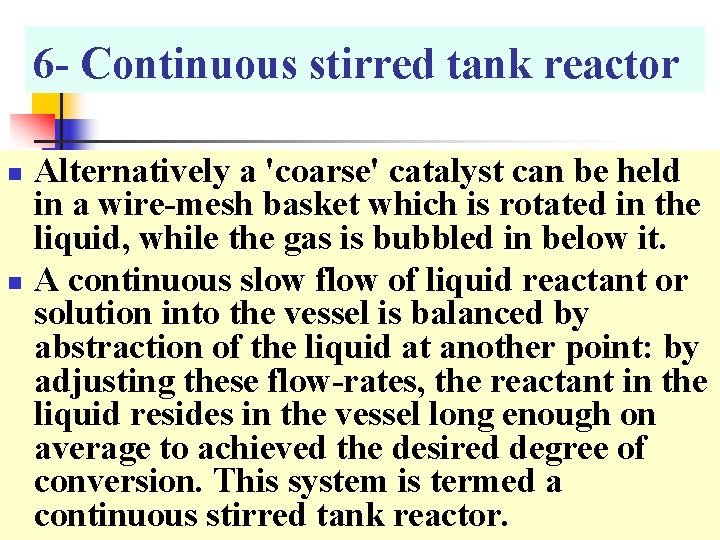
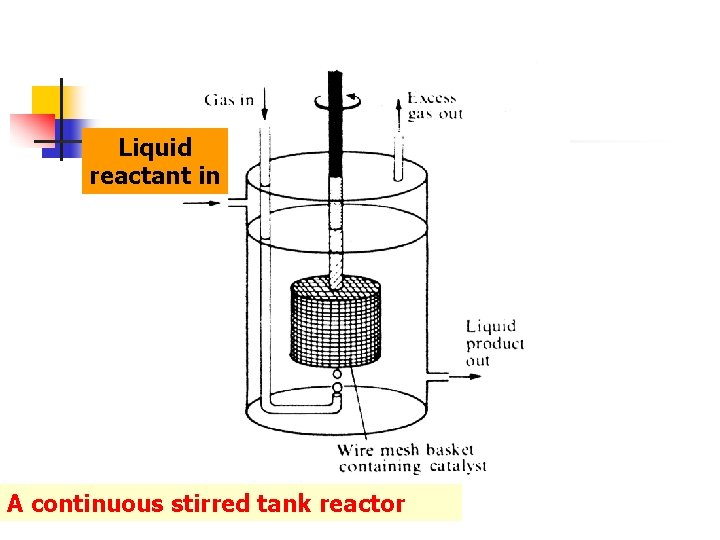
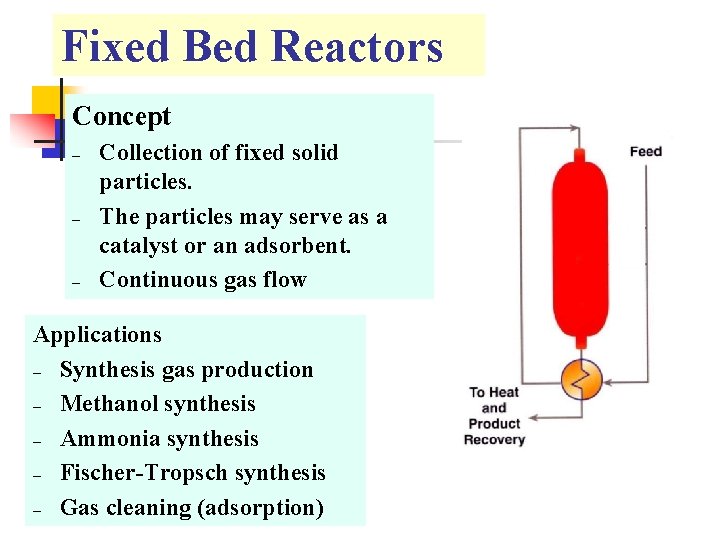
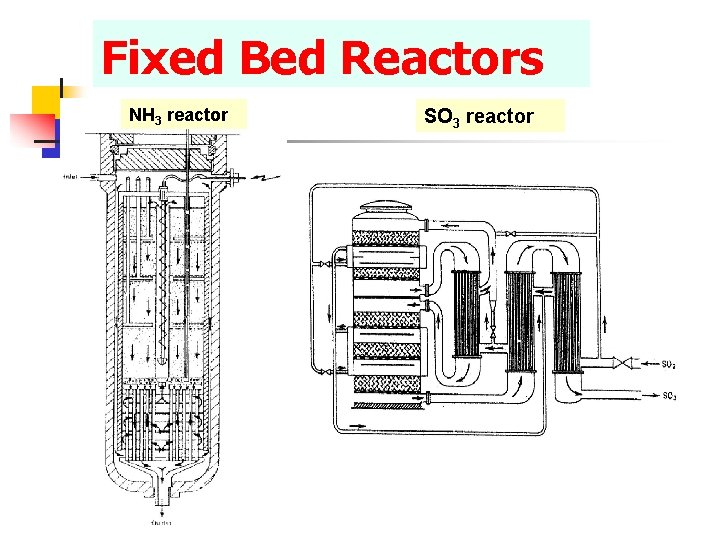
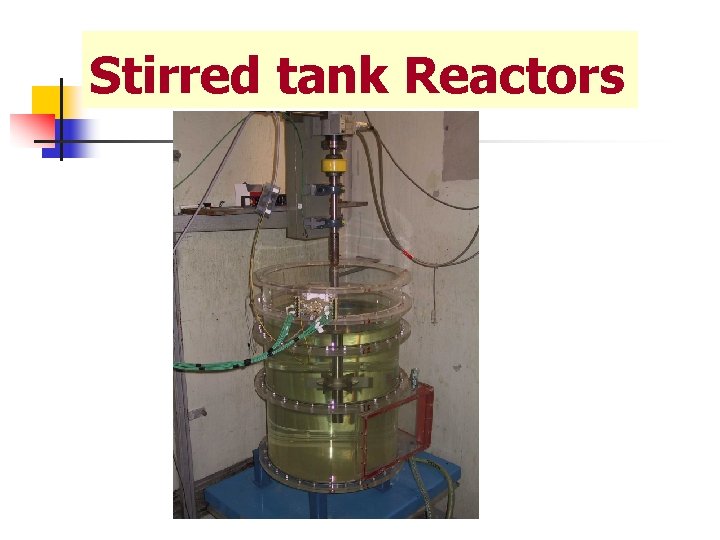
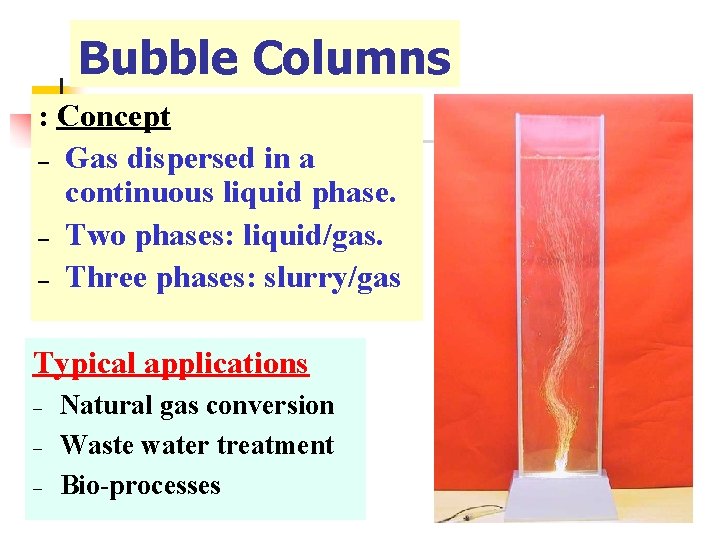
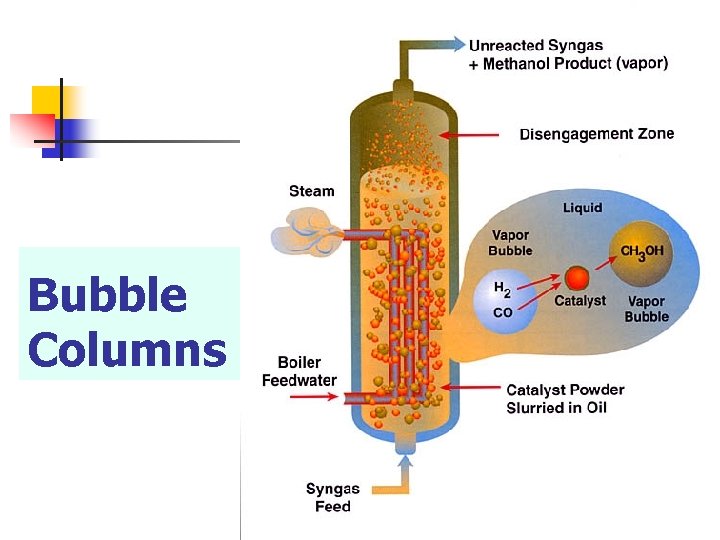
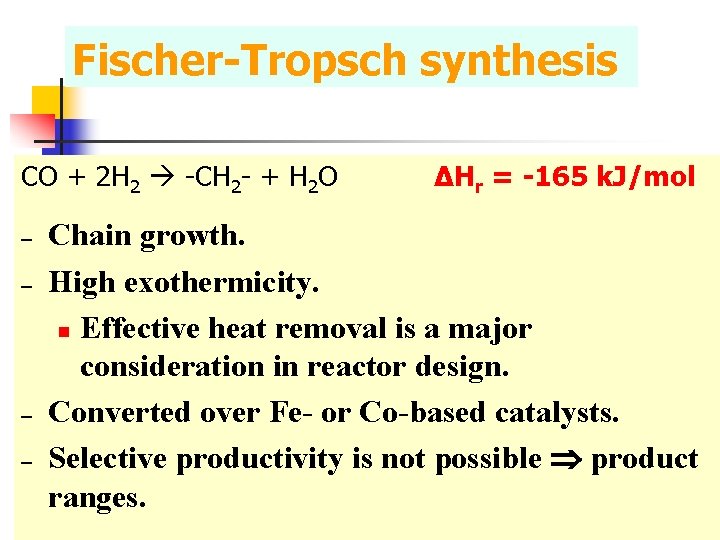
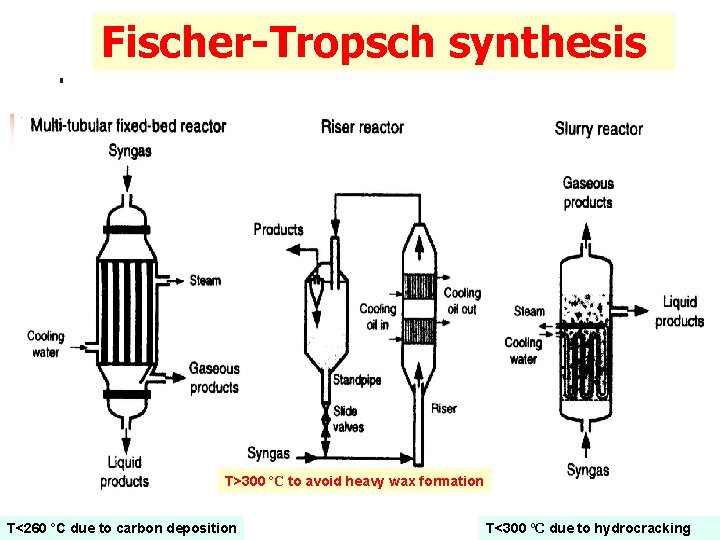
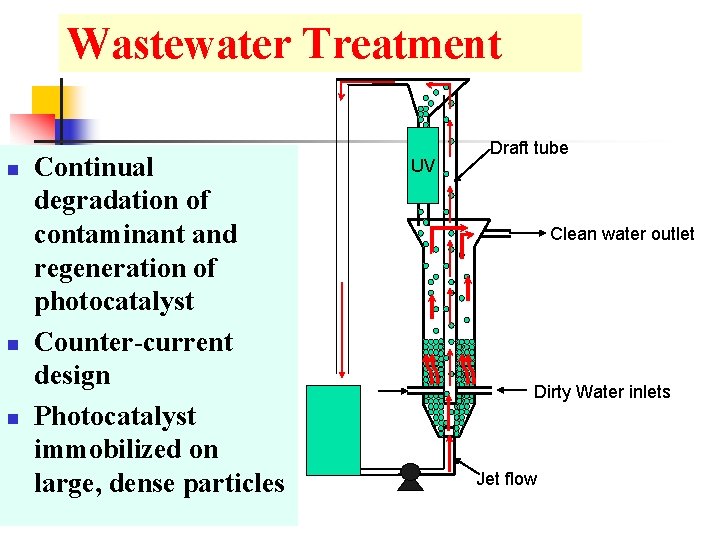
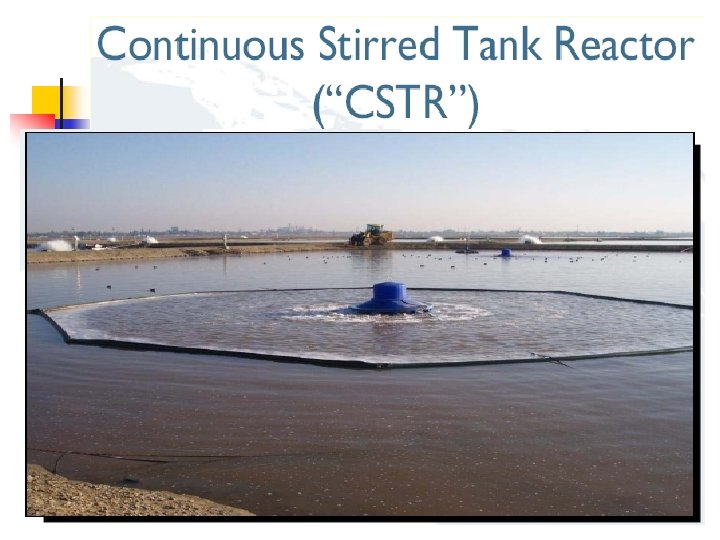
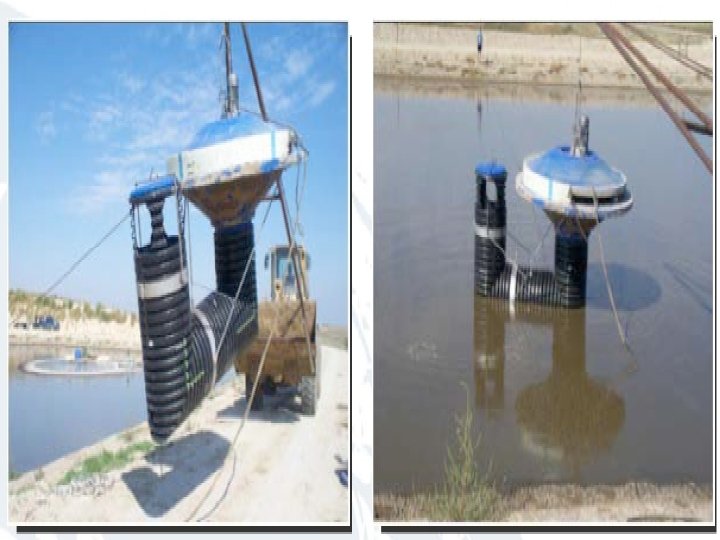
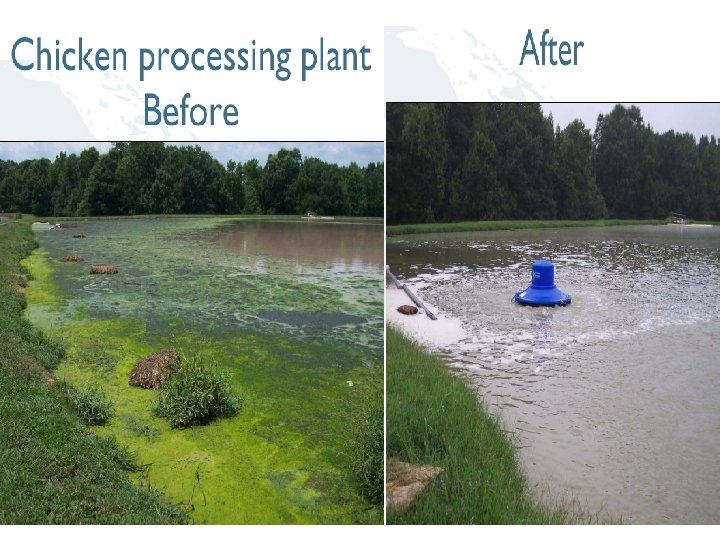
- Slides: 32
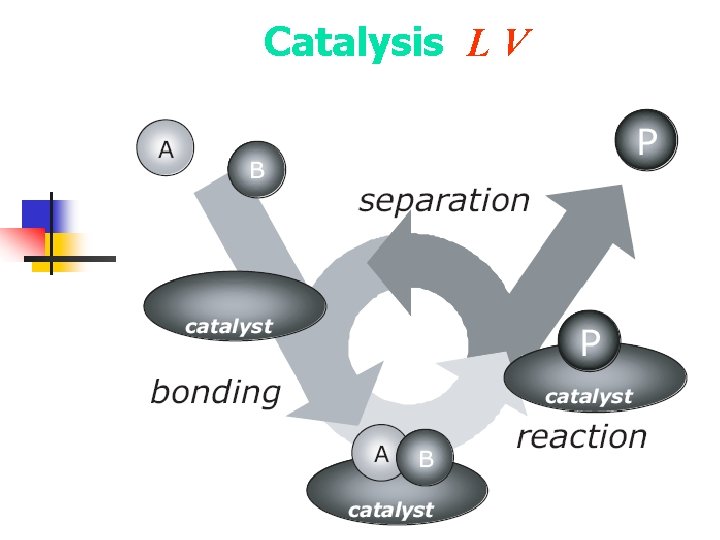
Catalysis L V
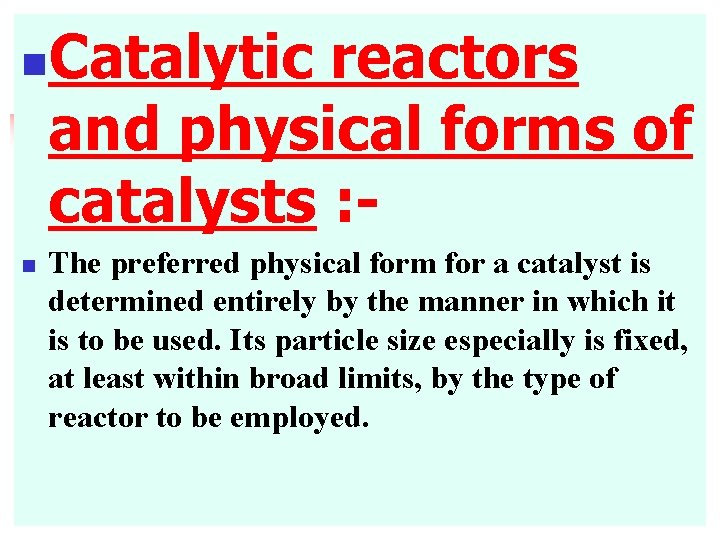
Catalytic reactors and physical forms of catalysts : - n n The preferred physical form for a catalyst is determined entirely by the manner in which it is to be used. Its particle size especially is fixed, at least within broad limits, by the type of reactor to be employed.
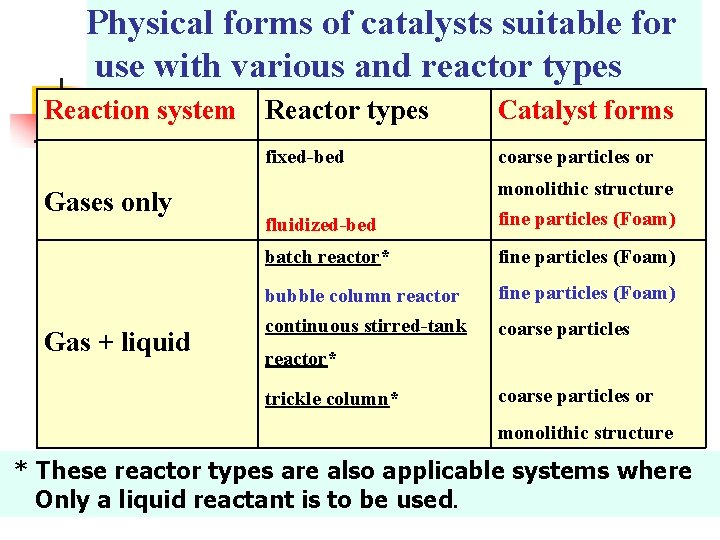
Physical forms of catalysts suitable for use with various and reactor types Reaction system Reactor types Gases only Gas + liquid Catalyst forms fixed-bed coarse particles or fluidized-bed monolithic structure fine particles (Foam) batch reactor* fine particles (Foam) bubble column reactor continuous stirred-tank fine particles (Foam) coarse particles reactor* trickle column* coarse particles or monolithic structure * These reactor types are also applicable systems where Only a liquid reactant is to be used.
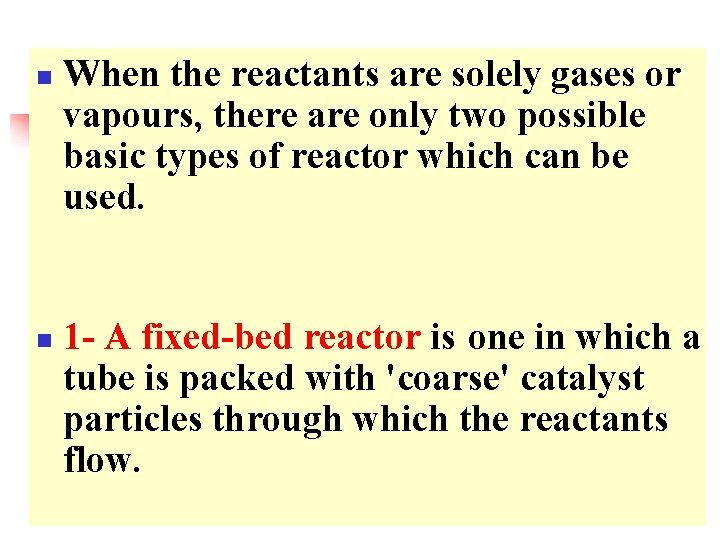
n n When the reactants are solely gases or vapours, there are only two possible basic types of reactor which can be used. 1 - A fixed-bed reactor is one in which a tube is packed with 'coarse' catalyst particles through which the reactants flow.
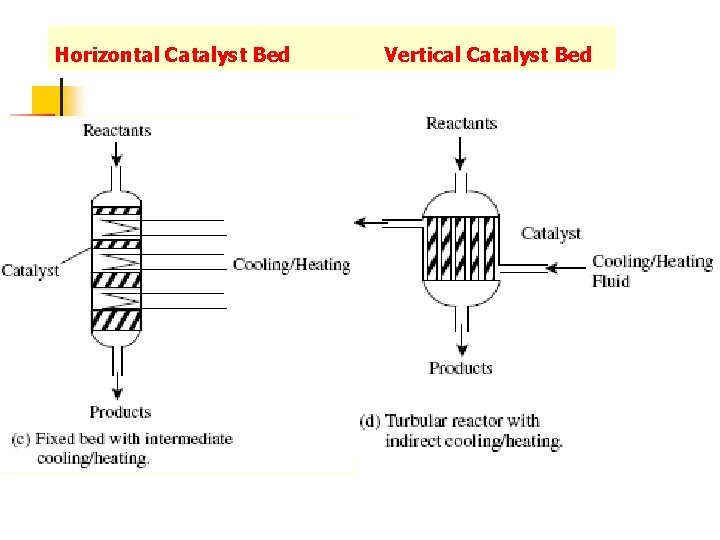
Horizontal Catalyst Bed Vertical Catalyst Bed
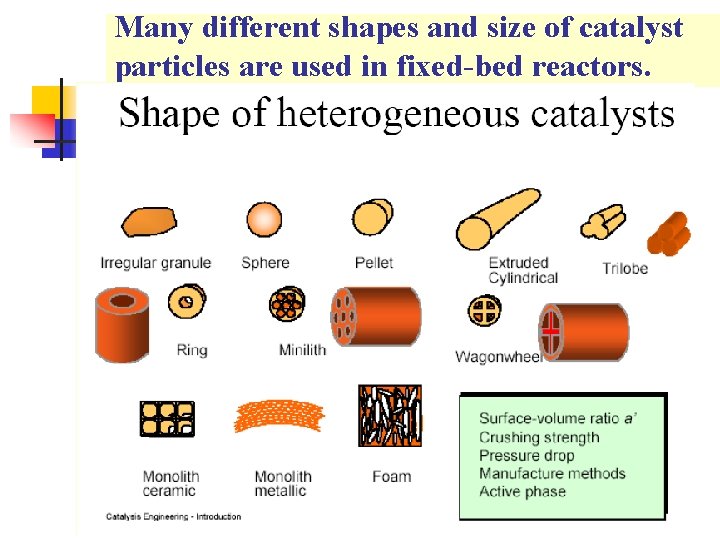
Many different shapes and size of catalyst particles are used in fixed-bed reactors.
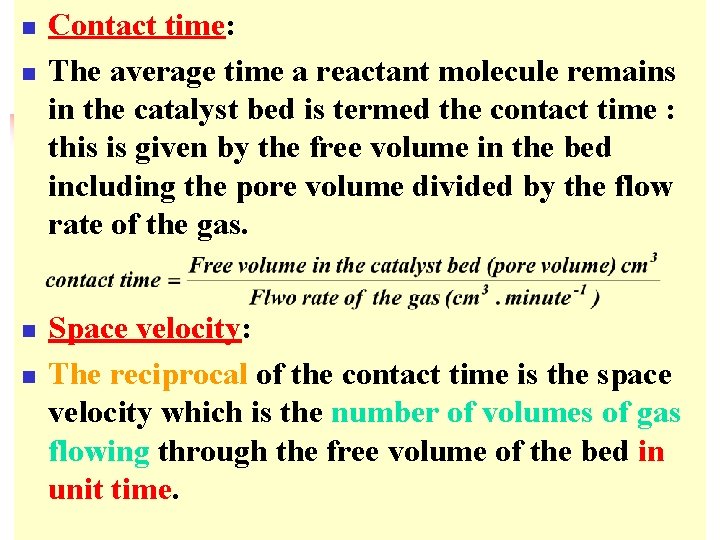
n n Contact time: The average time a reactant molecule remains in the catalyst bed is termed the contact time : this is given by the free volume in the bed including the pore volume divided by the flow rate of the gas. Space velocity: The reciprocal of the contact time is the space velocity which is the number of volumes of gas flowing through the free volume of the bed in unit time.
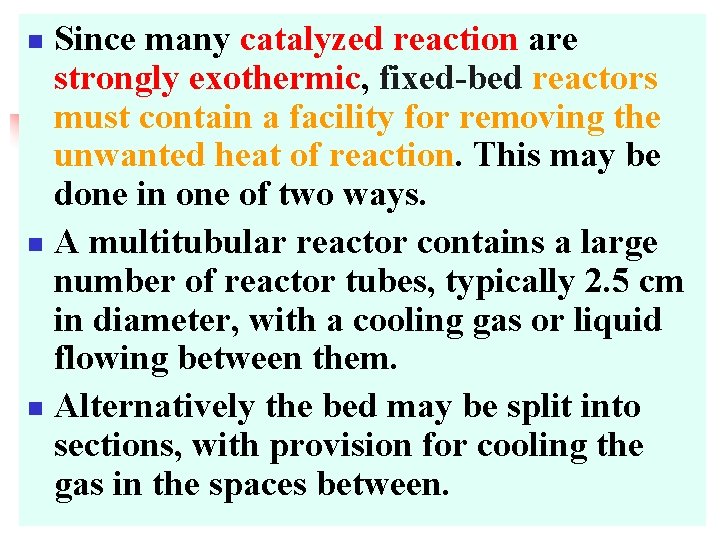
Since many catalyzed reaction are strongly exothermic, fixed-bed reactors must contain a facility for removing the unwanted heat of reaction. This may be done in one of two ways. n A multitubular reactor contains a large number of reactor tubes, typically 2. 5 cm in diameter, with a cooling gas or liquid flowing between them. n Alternatively the bed may be split into sections, with provision for cooling the gas in the spaces between. n
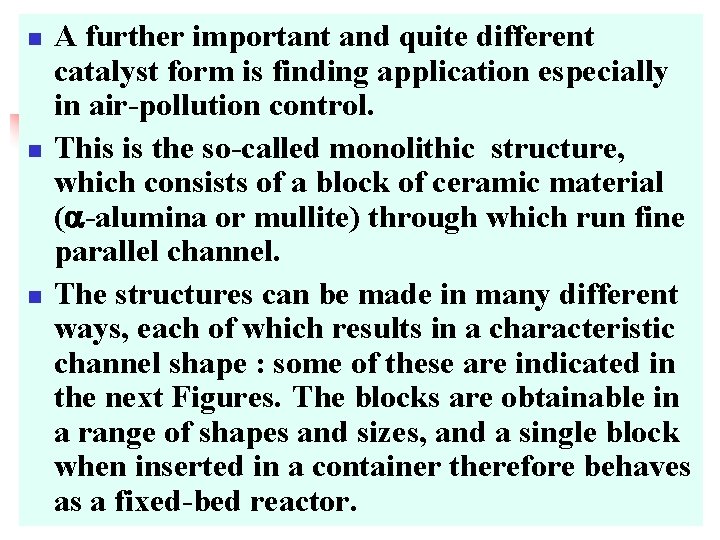
n n n A further important and quite different catalyst form is finding application especially in air-pollution control. This is the so-called monolithic structure, which consists of a block of ceramic material ( -alumina or mullite) through which run fine parallel channel. The structures can be made in many different ways, each of which results in a characteristic channel shape : some of these are indicated in the next Figures. The blocks are obtainable in a range of shapes and sizes, and a single block when inserted in a container therefore behaves as a fixed-bed reactor.
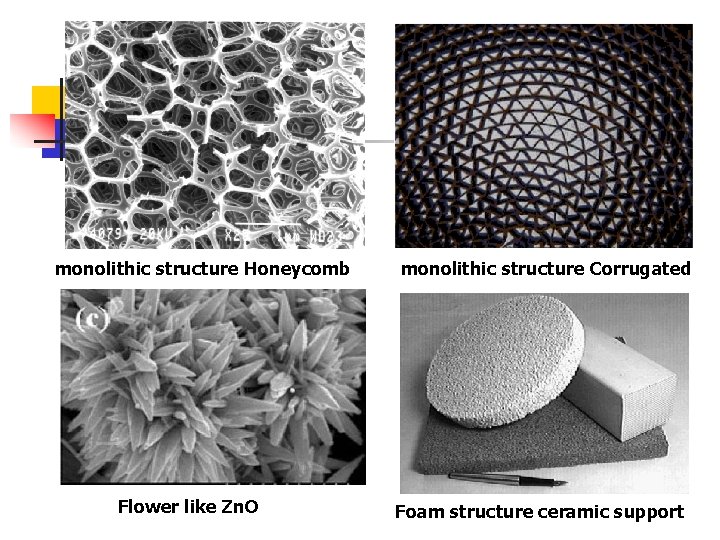
monolithic structure Honeycomb Flower like Zn. O monolithic structure Corrugated Foam structure ceramic support
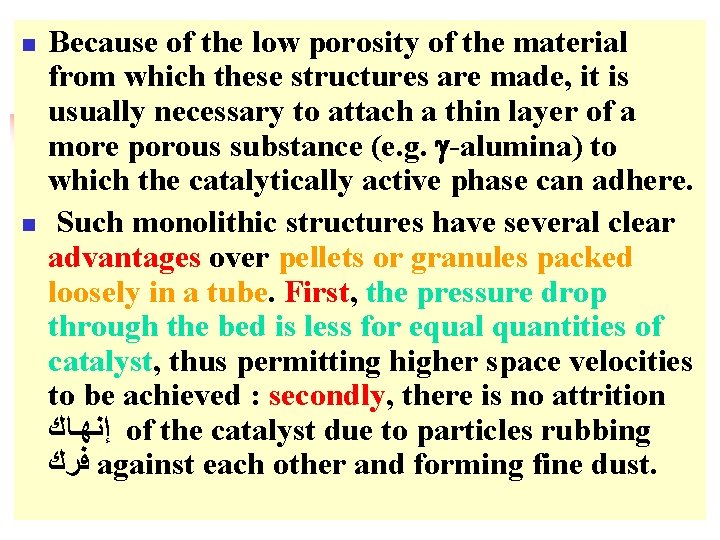
n n Because of the low porosity of the material from which these structures are made, it is usually necessary to attach a thin layer of a more porous substance (e. g. -alumina) to which the catalytically active phase can adhere. Such monolithic structures have several clear advantages over pellets or granules packed loosely in a tube. First, the pressure drop through the bed is less for equal quantities of catalyst, thus permitting higher space velocities to be achieved : secondly, there is no attrition ﺇﻧﻬـﺎﻙ of the catalyst due to particles rubbing ﻓﺮﻙ against each other and forming fine dust.
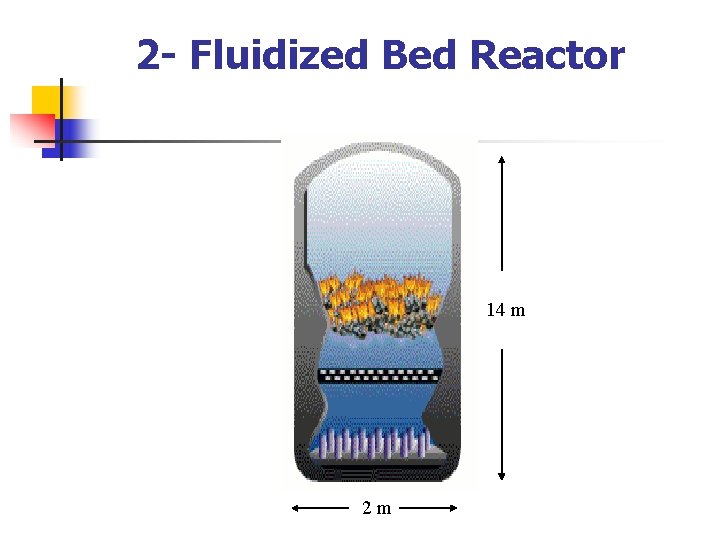
2 - Fluidized Bed Reactor 14 m 2 m
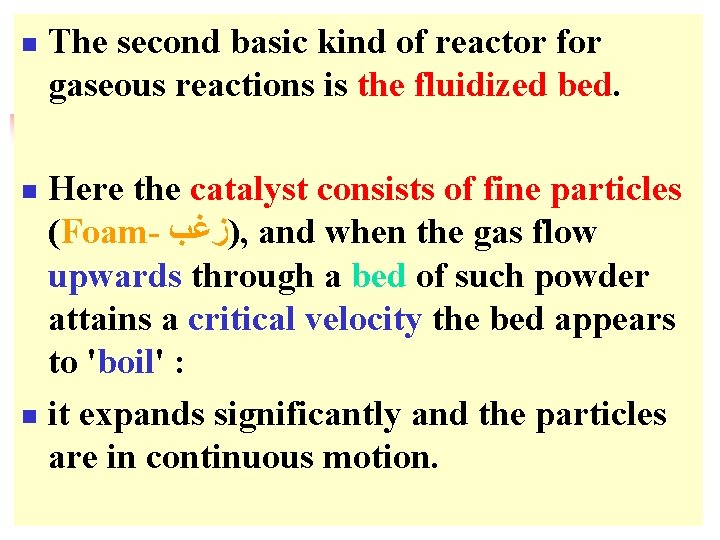
n The second basic kind of reactor for gaseous reactions is the fluidized bed. Here the catalyst consists of fine particles (Foam- )ﺯﻏﺐ , and when the gas flow upwards through a bed of such powder attains a critical velocity the bed appears to 'boil' : n it expands significantly and the particles are in continuous motion. n
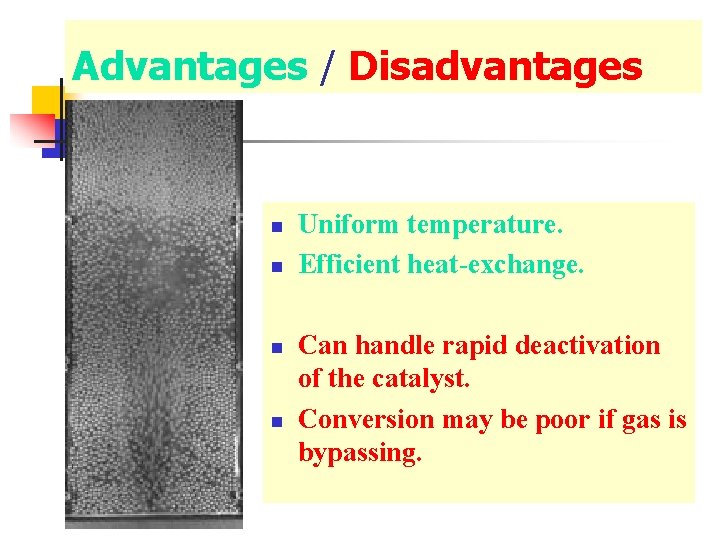
Advantages / Disadvantages n n Uniform temperature. Efficient heat-exchange. Can handle rapid deactivation of the catalyst. Conversion may be poor if gas is bypassing.
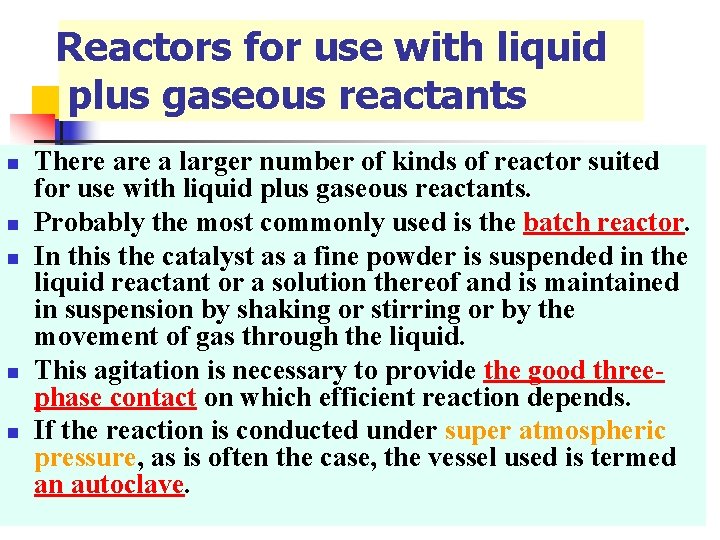
Reactors for use with liquid plus gaseous reactants n n n There a larger number of kinds of reactor suited for use with liquid plus gaseous reactants. Probably the most commonly used is the batch reactor. In this the catalyst as a fine powder is suspended in the liquid reactant or a solution thereof and is maintained in suspension by shaking or stirring or by the movement of gas through the liquid. This agitation is necessary to provide the good threephase contact on which efficient reaction depends. If the reaction is conducted under super atmospheric pressure, as is often the case, the vessel used is termed an autoclave.
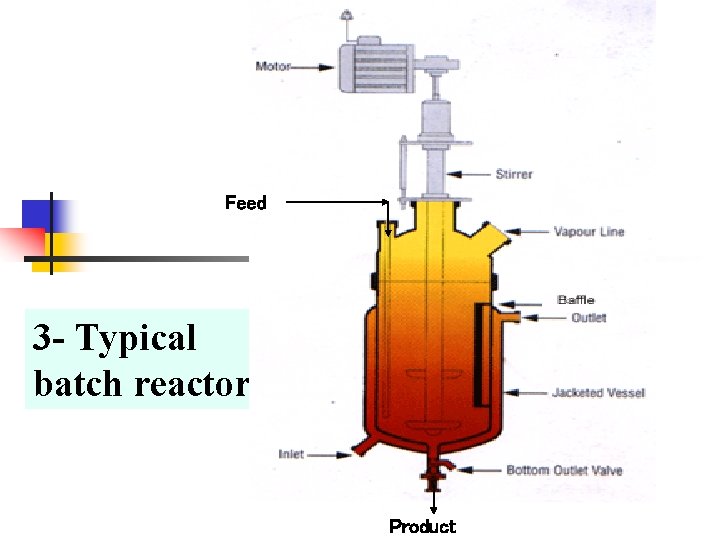
Feed 3 - Typical batch reactor Product
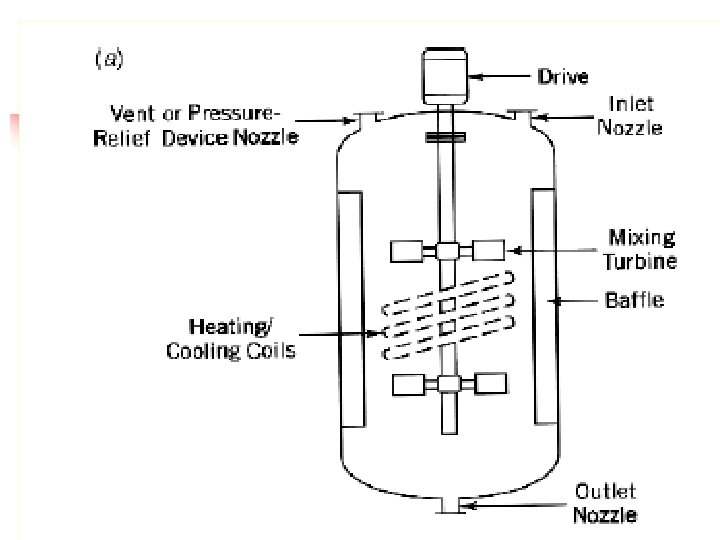
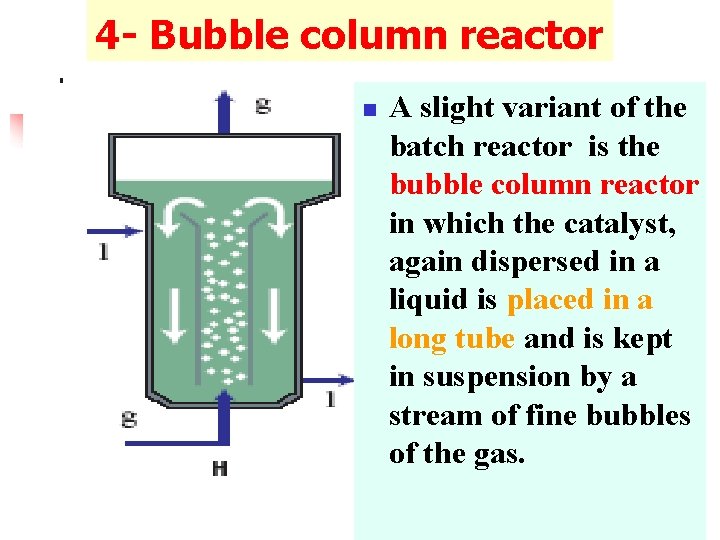
4 - Bubble column reactor n A slight variant of the batch reactor is the bubble column reactor in which the catalyst, again dispersed in a liquid is placed in a long tube and is kept in suspension by a stream of fine bubbles of the gas.
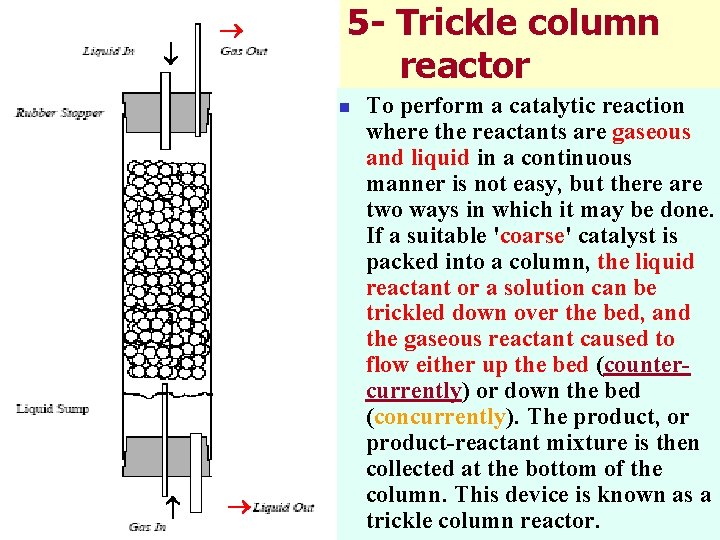
5 - Trickle column reactor n To perform a catalytic reaction where the reactants are gaseous and liquid in a continuous manner is not easy, but there are two ways in which it may be done. If a suitable 'coarse' catalyst is packed into a column, the liquid reactant or a solution can be trickled down over the bed, and the gaseous reactant caused to flow either up the bed (countercurrently) or down the bed (concurrently). The product, or product-reactant mixture is then collected at the bottom of the column. This device is known as a trickle column reactor.
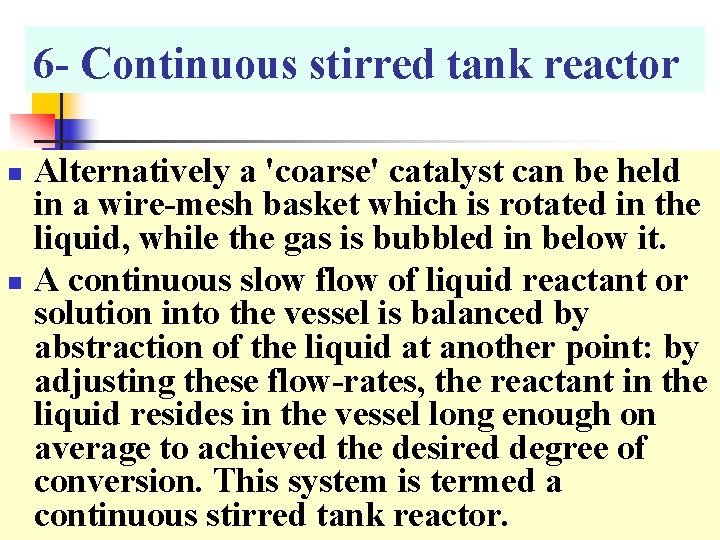
6 - Continuous stirred tank reactor n n Alternatively a 'coarse' catalyst can be held in a wire-mesh basket which is rotated in the liquid, while the gas is bubbled in below it. A continuous slow flow of liquid reactant or solution into the vessel is balanced by abstraction of the liquid at another point: by adjusting these flow-rates, the reactant in the liquid resides in the vessel long enough on average to achieved the desired degree of conversion. This system is termed a continuous stirred tank reactor.
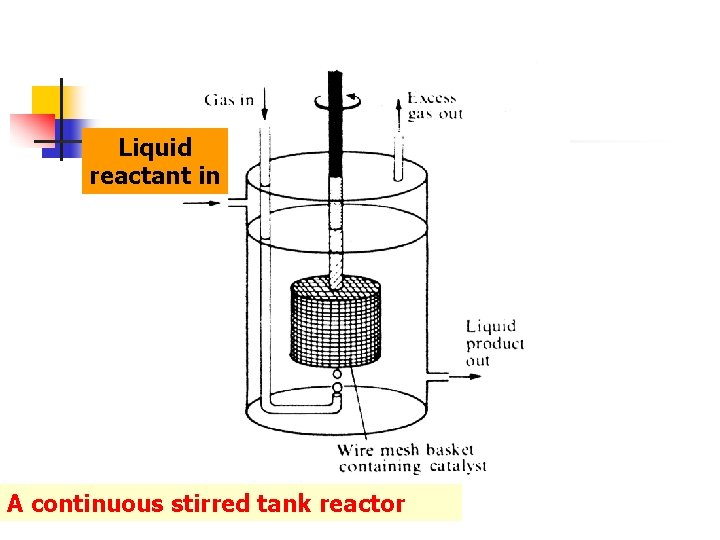
Liquid reactant in A continuous stirred tank reactor
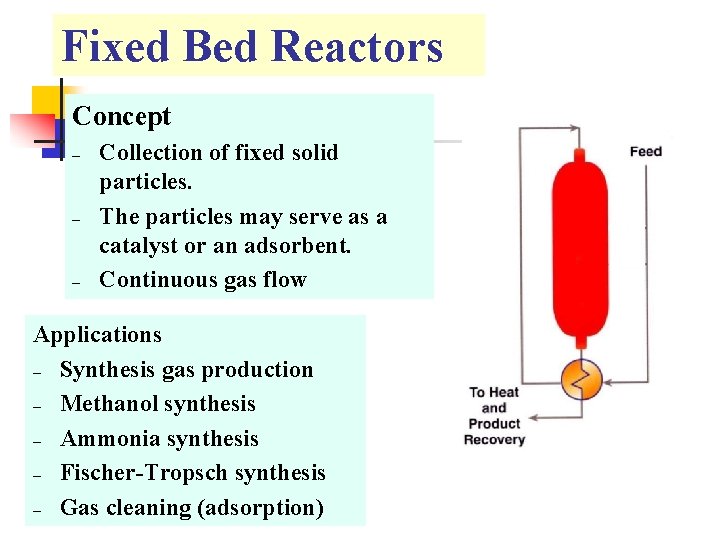
Fixed Bed Reactors Concept – – – Collection of fixed solid particles. The particles may serve as a catalyst or an adsorbent. Continuous gas flow Applications – Synthesis gas production – Methanol synthesis – Ammonia synthesis – Fischer-Tropsch synthesis – Gas cleaning (adsorption)
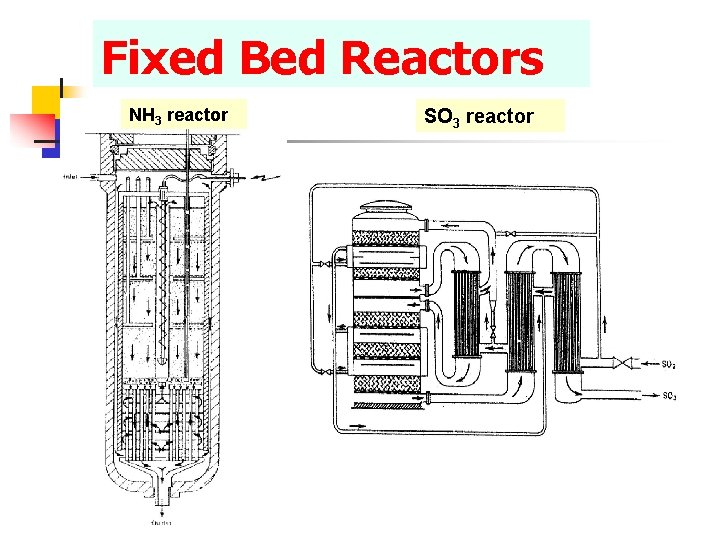
Fixed Bed Reactors NH 3 reactor SO 3 reactor
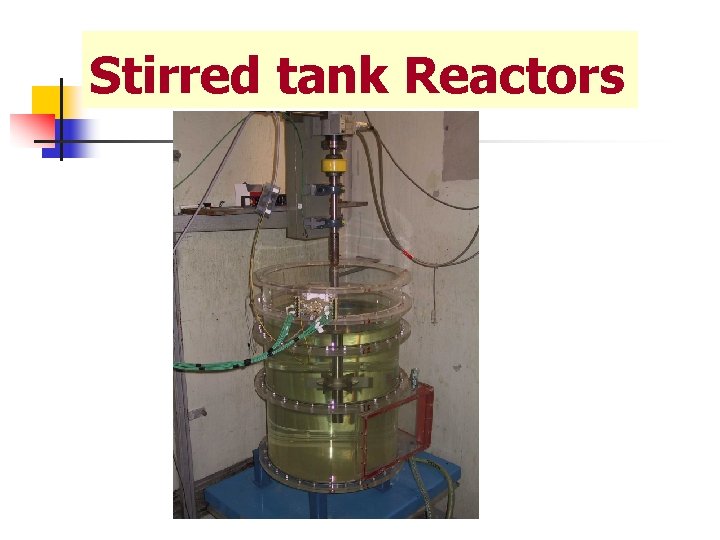
Stirred tank Reactors
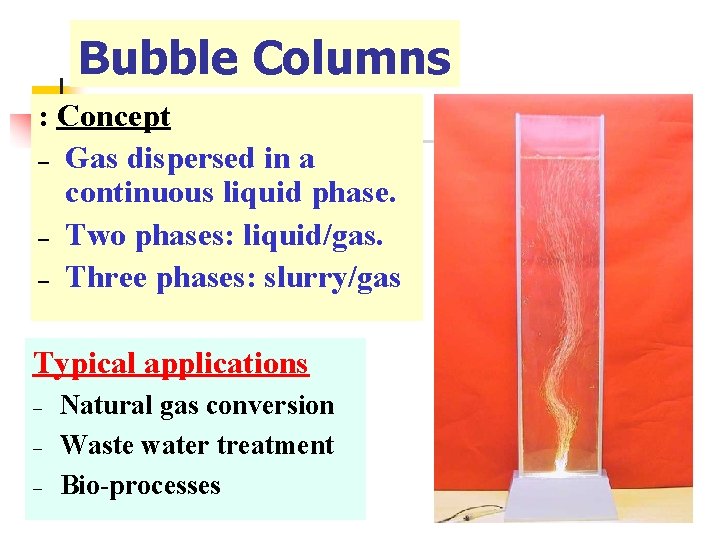
Bubble Columns : Concept – Gas dispersed in a continuous liquid phase. – Two phases: liquid/gas. – Three phases: slurry/gas Typical applications – – – Natural gas conversion Waste water treatment Bio-processes
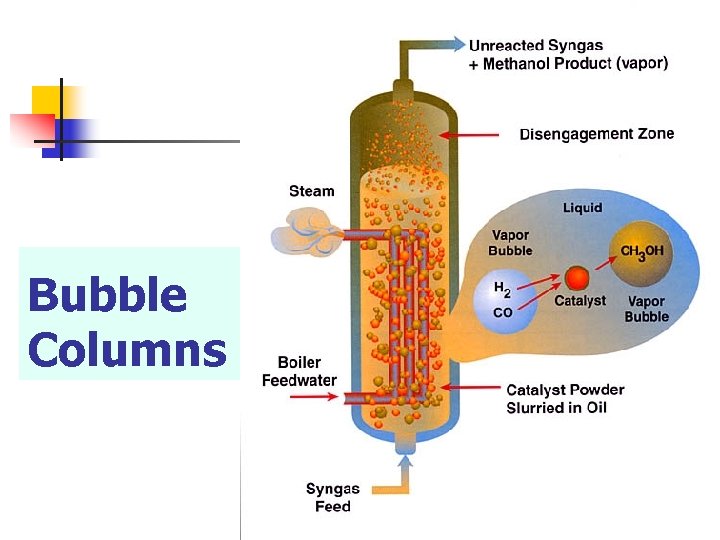
Bubble Columns
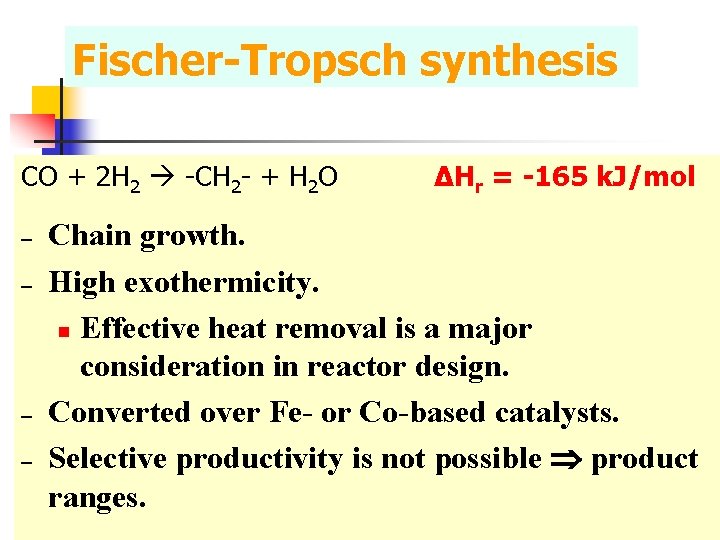
Fischer-Tropsch synthesis CO + 2 H 2 -CH 2 - + H 2 O – – ΔHr = -165 k. J/mol Chain growth. High exothermicity. n Effective heat removal is a major consideration in reactor design. Converted over Fe- or Co-based catalysts. Selective productivity is not possible product ranges.
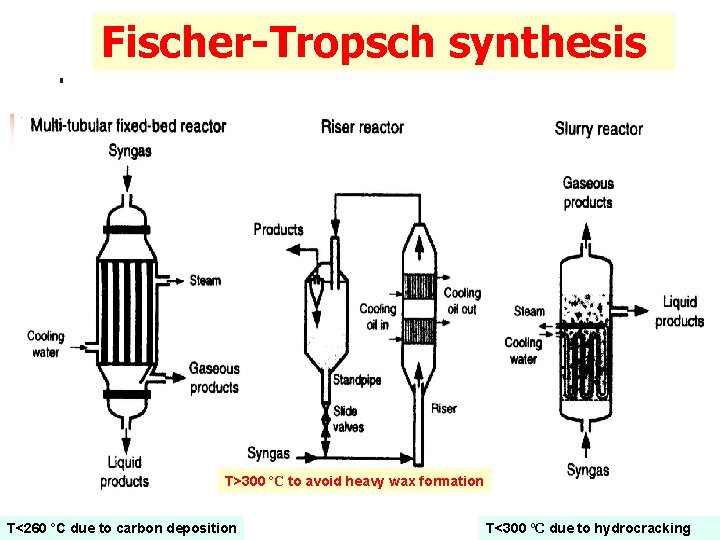
Fischer-Tropsch synthesis T>300 ºC to avoid heavy wax formation T<260 ºC due to carbon deposition T<300 ºC due to hydrocracking
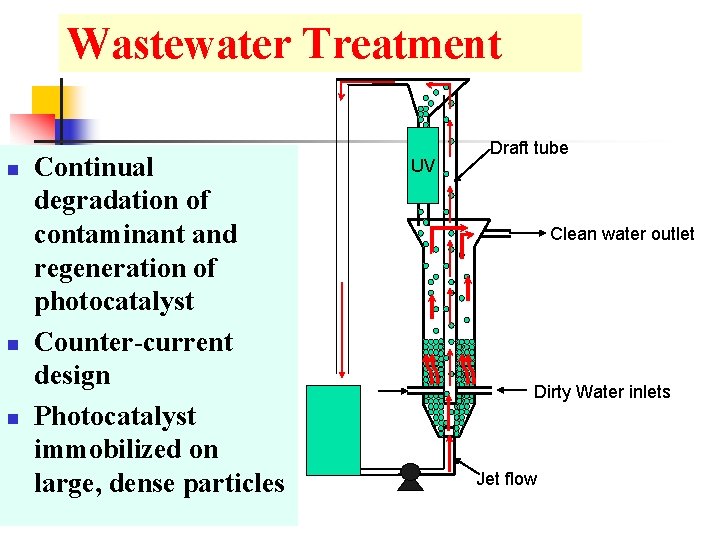
Wastewater Treatment n n n Continual degradation of contaminant and regeneration of photocatalyst Counter-current design Photocatalyst immobilized on large, dense particles UV Draft tube Clean water outlet Dirty Water inlets Jet flow
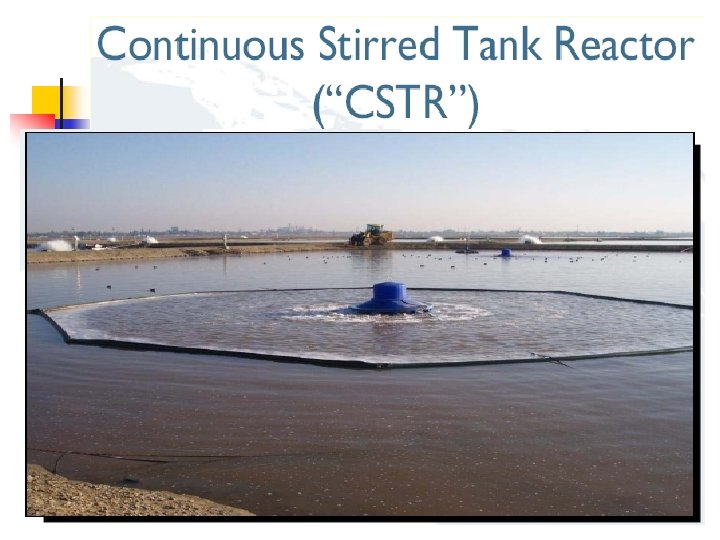
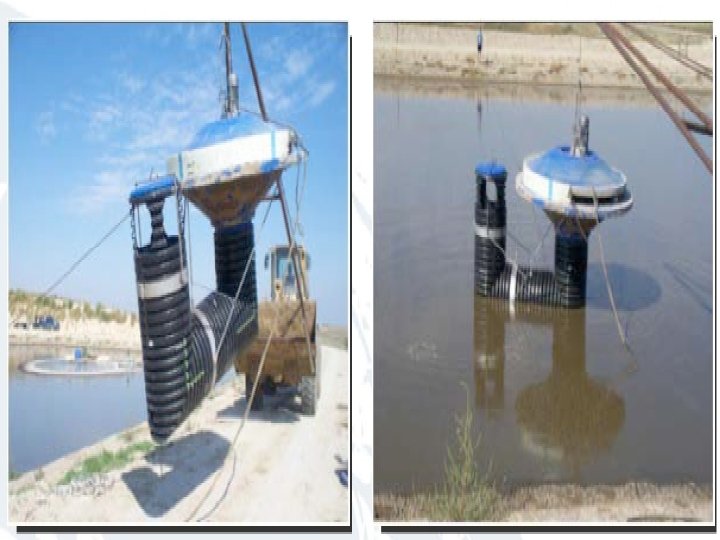
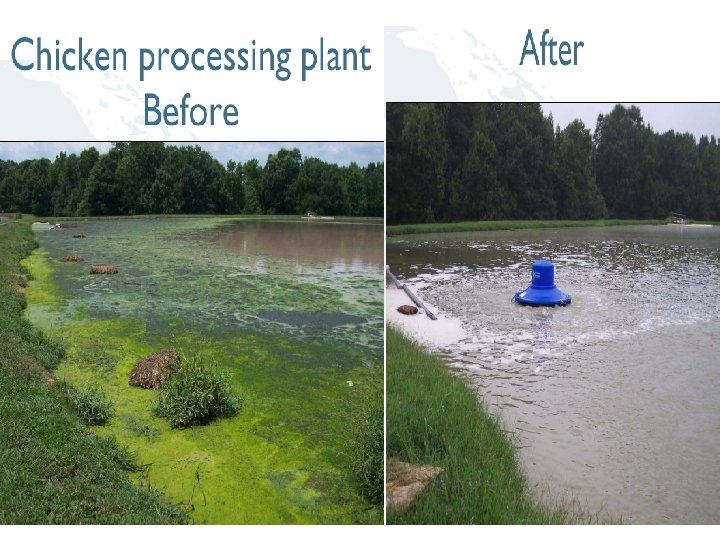
Shunt reactors for power factor correction
Energy catalysis and biosynthesis
Decao
Apoenzyme
What is covalent catalysis
What is covalent catalysis
What is covalent catalysis
Specific acid base catalysis
Specific acid base catalysis
Specific acid base catalysis
Enzyme catalyze
Langmuir-hinshelwood mechanism heterogeneous catalysis
Catalysis lecture notes
Catalytic combustion
Hydroxide catalysis bonding
Catalytic heater oil and gas
Catalytic reforming bottleneck
You can air
Catalytic hydration of ethene
Catalytic converter reaction
Catalytic stripper
Catalytic reforming of hexane
Catalytic converter ingredients
Protein synthesis
Cracking of octane
Catalytic cracking
Naphthenes in crude oil
Proteins with catalytic power are called
Catalytic converter
Chantal stieber
I had contracted form
Weak and strong forms
Why are related forms more agreeable than unrelated forms