CASE STUDY PETRON POLYPROPYLENE PLANT 5 Che C
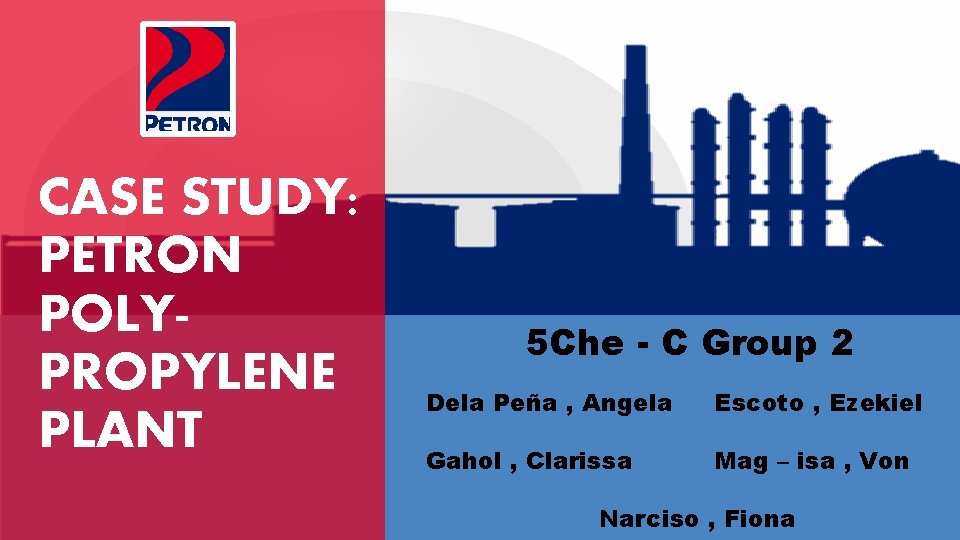
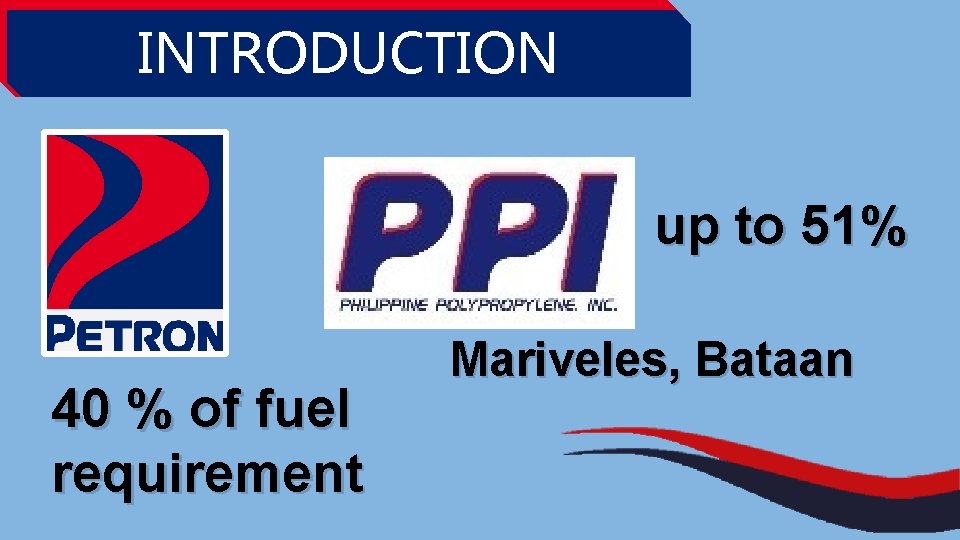
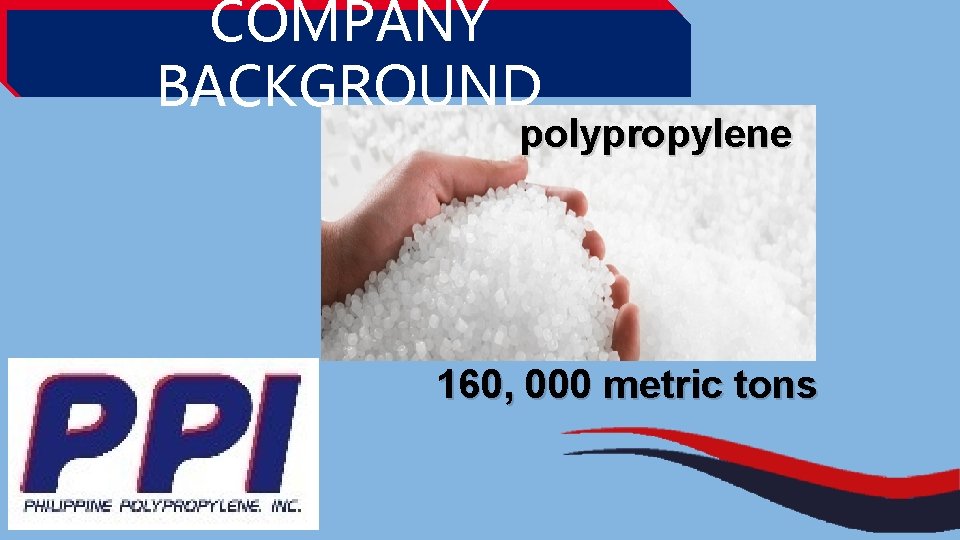
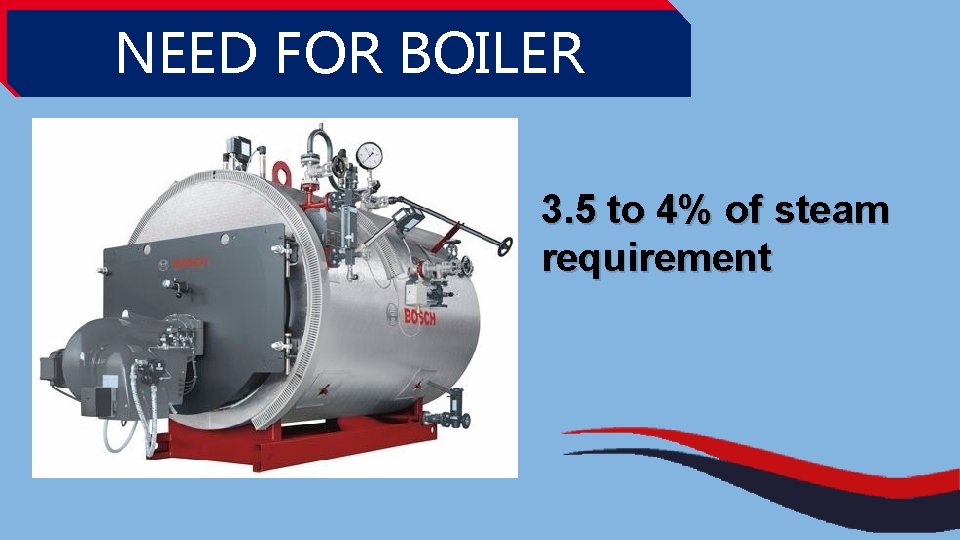
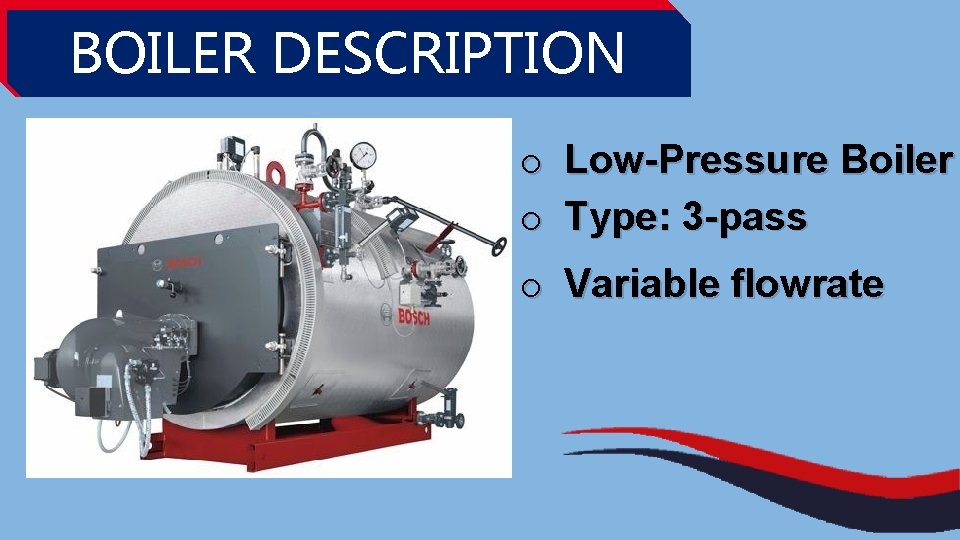
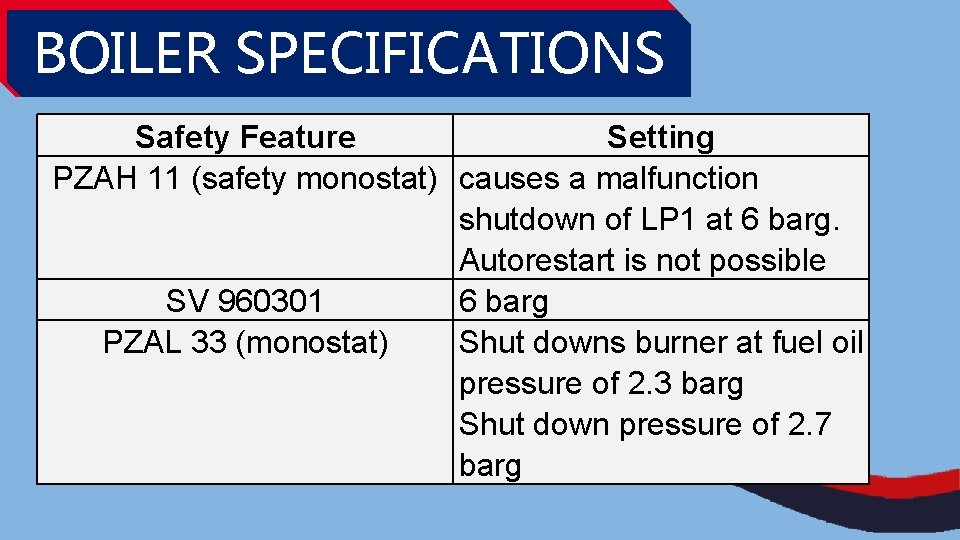
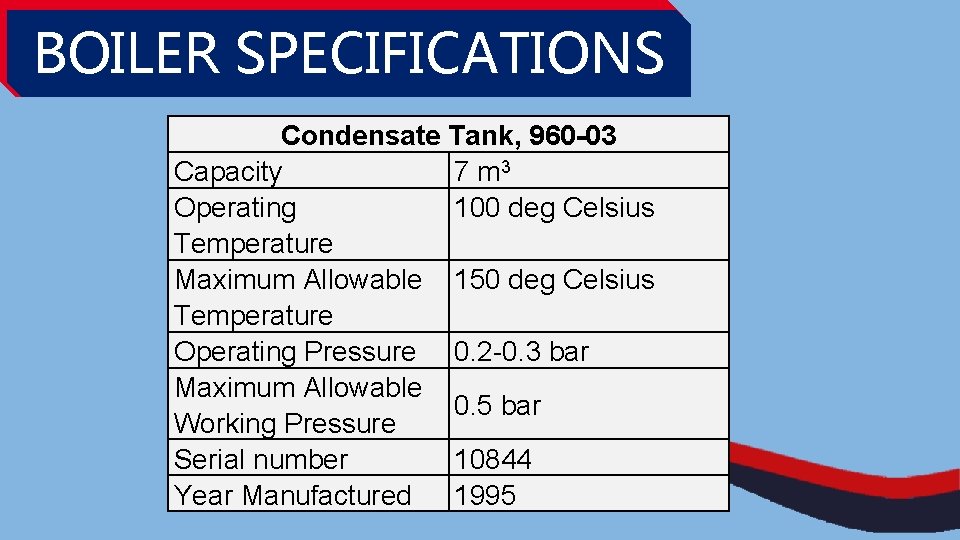
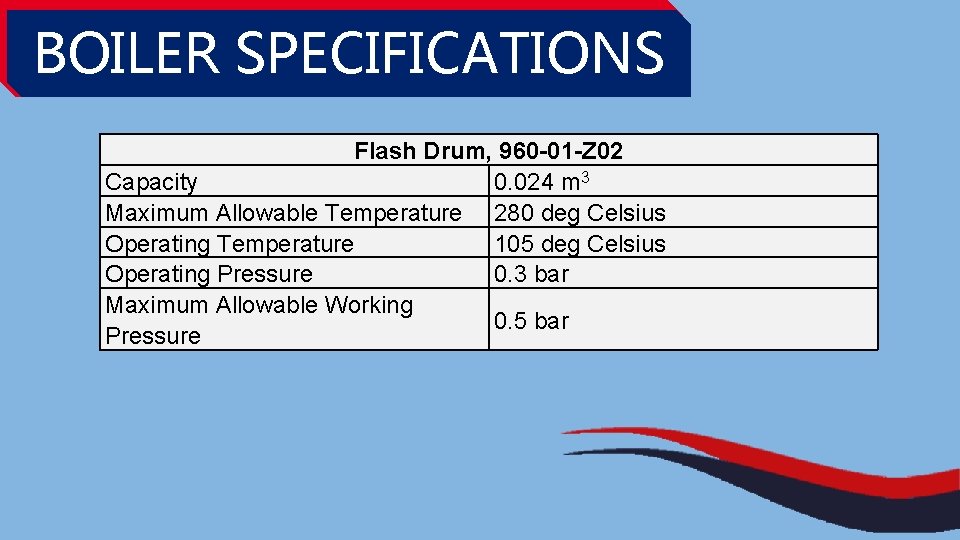
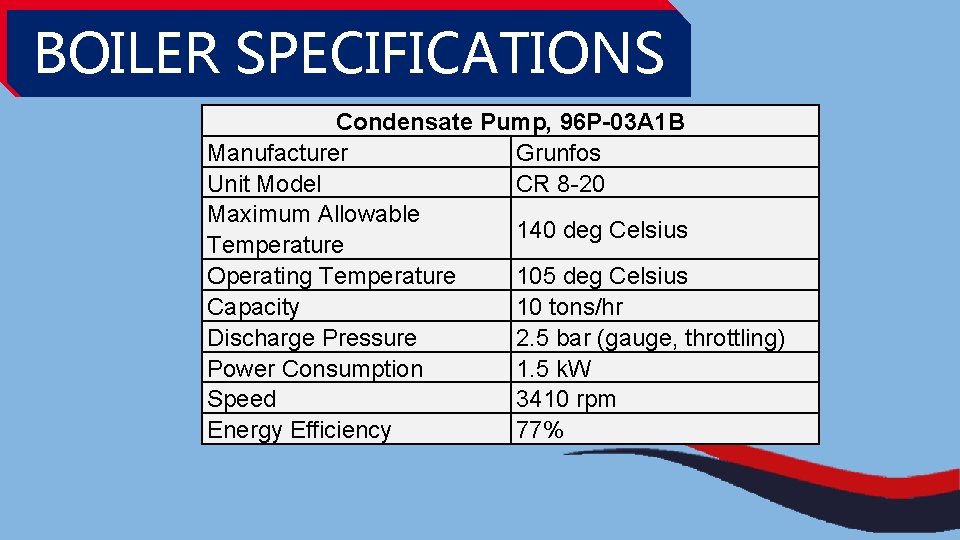
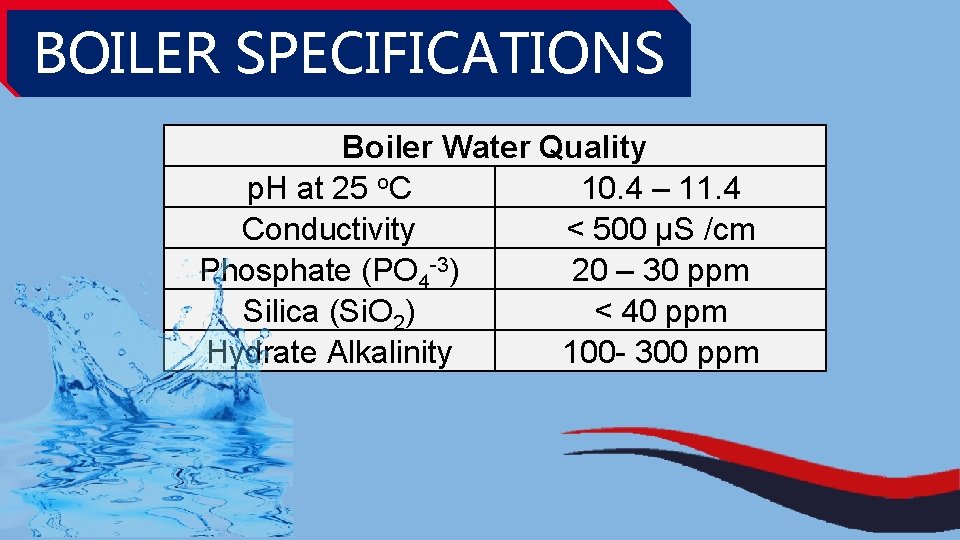
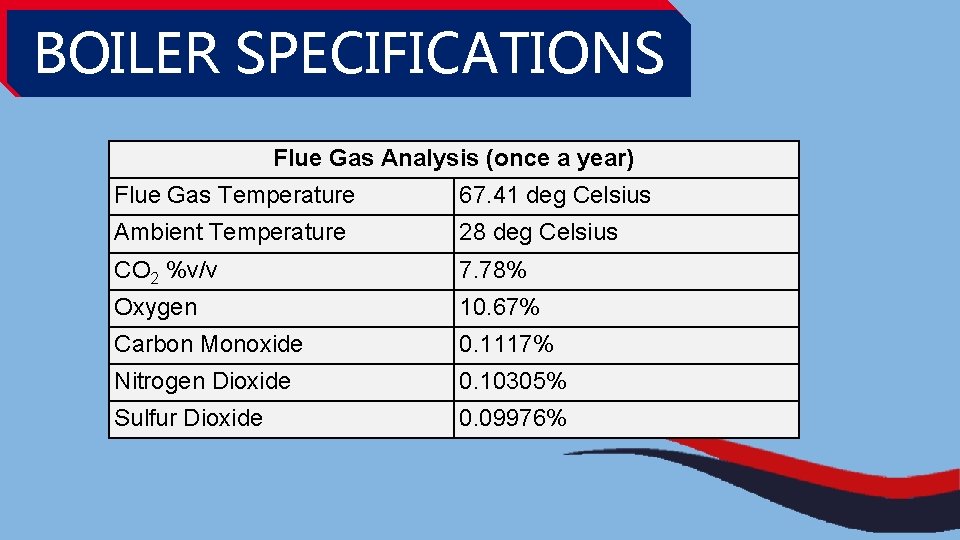
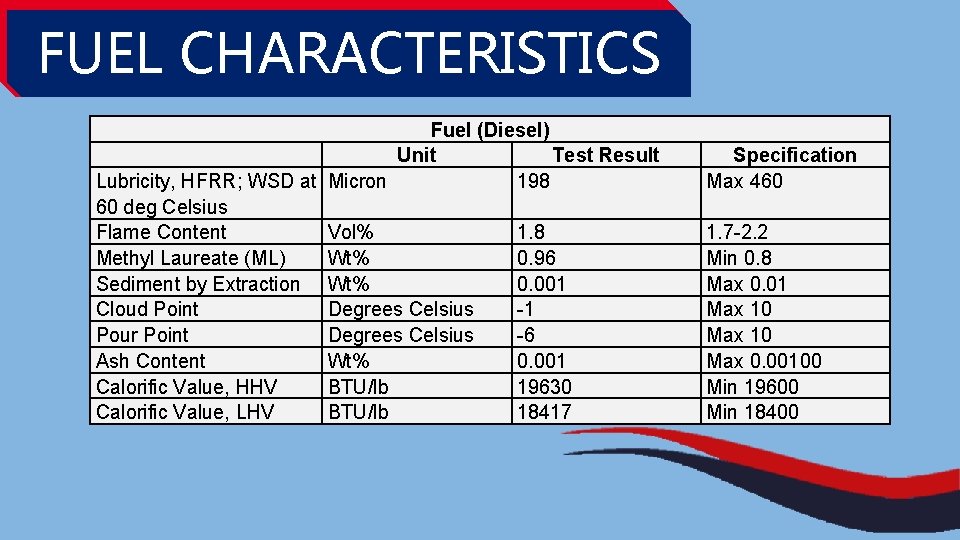
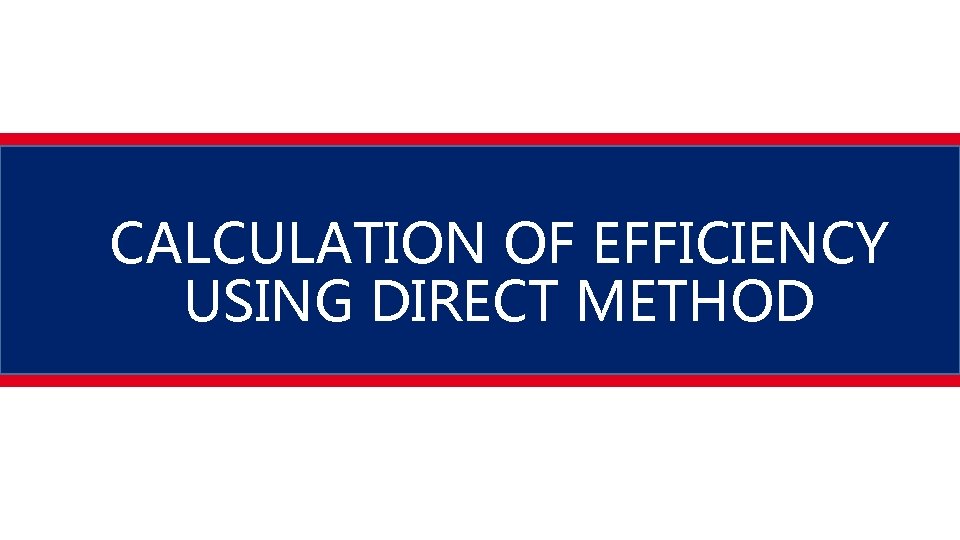
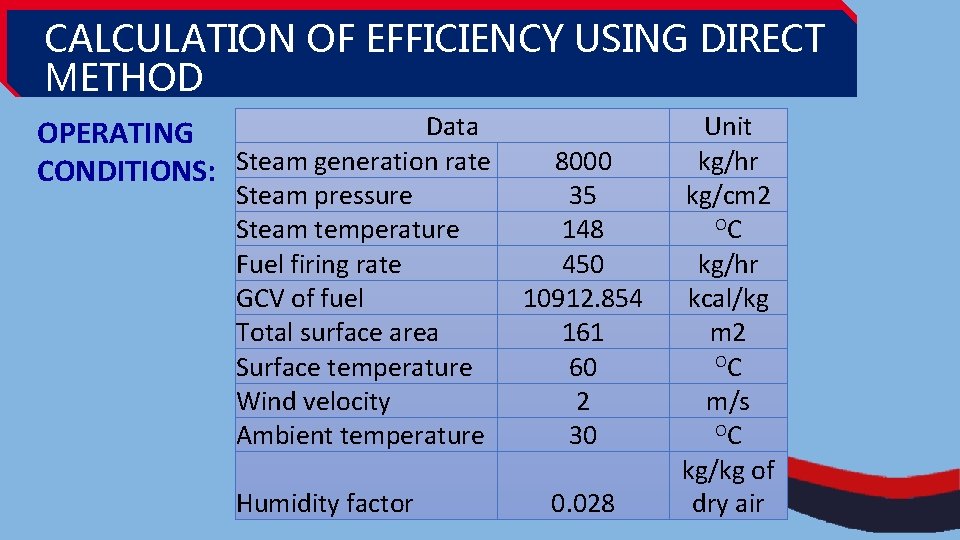
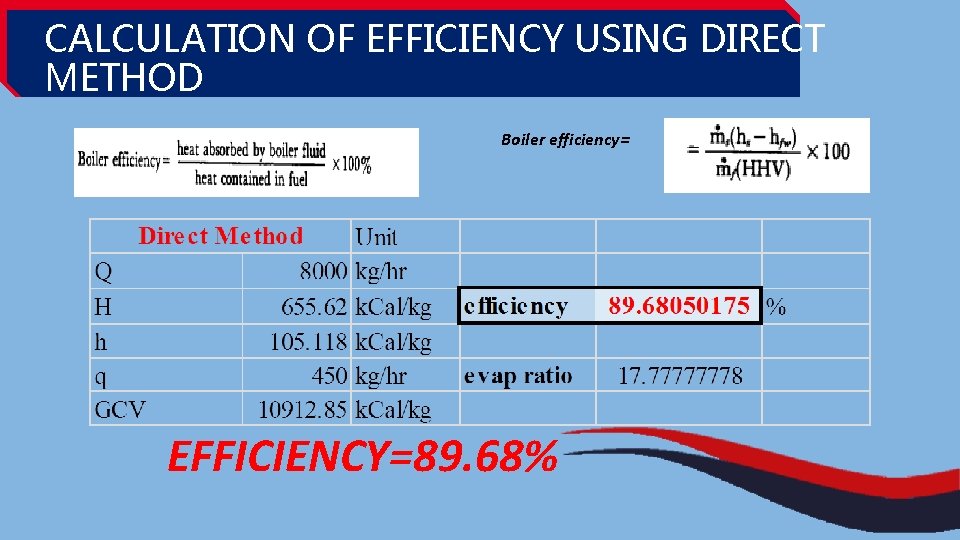
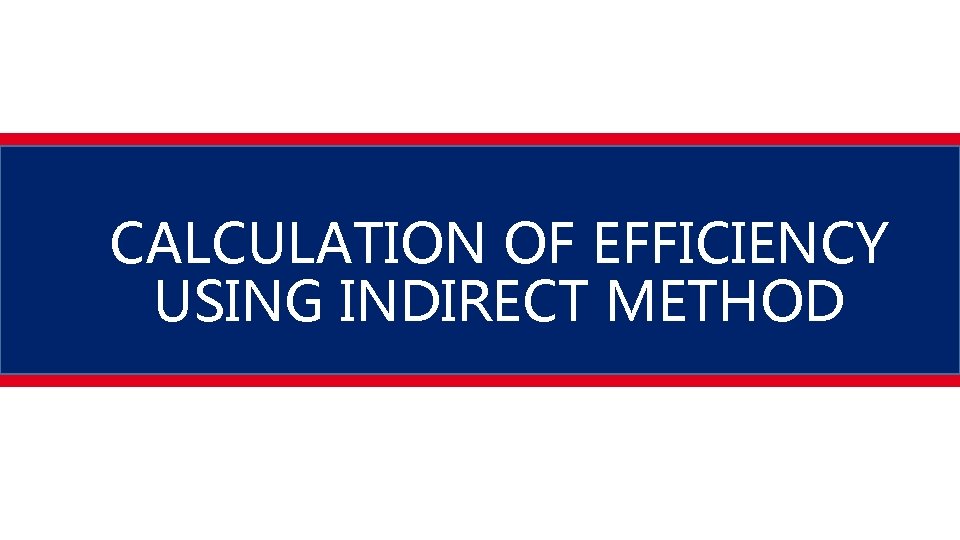
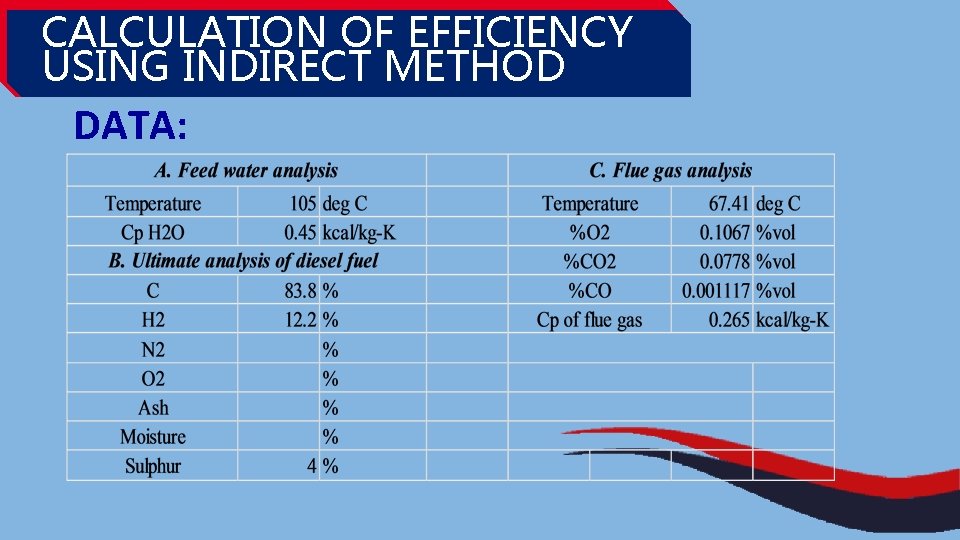
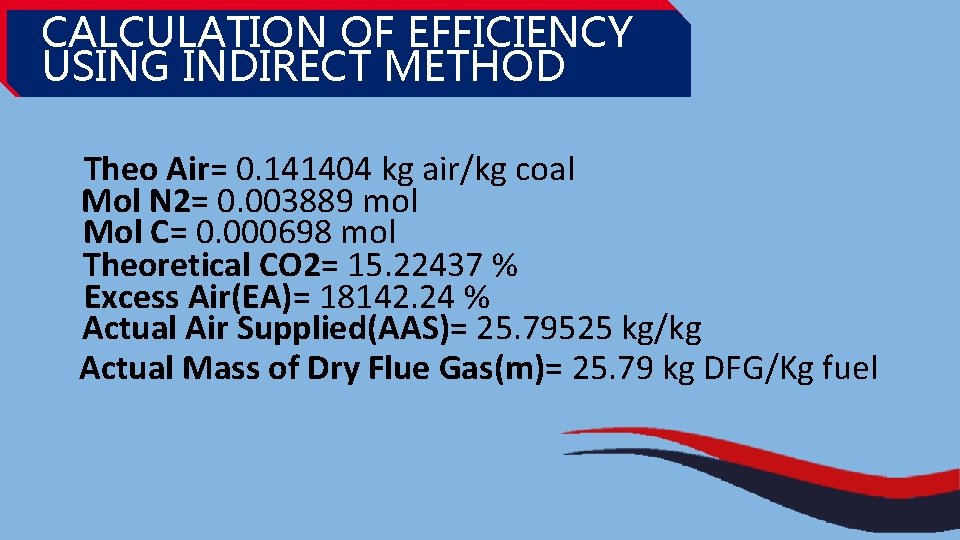
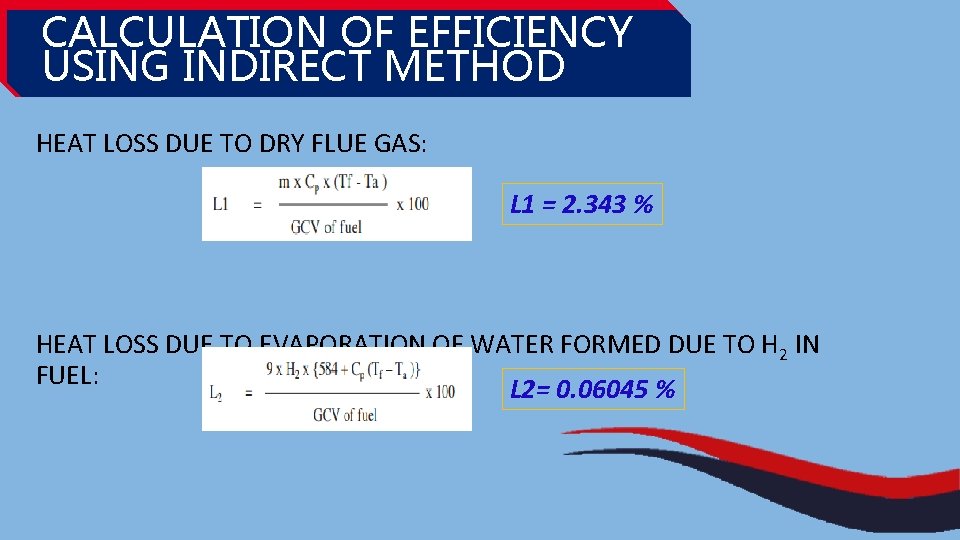
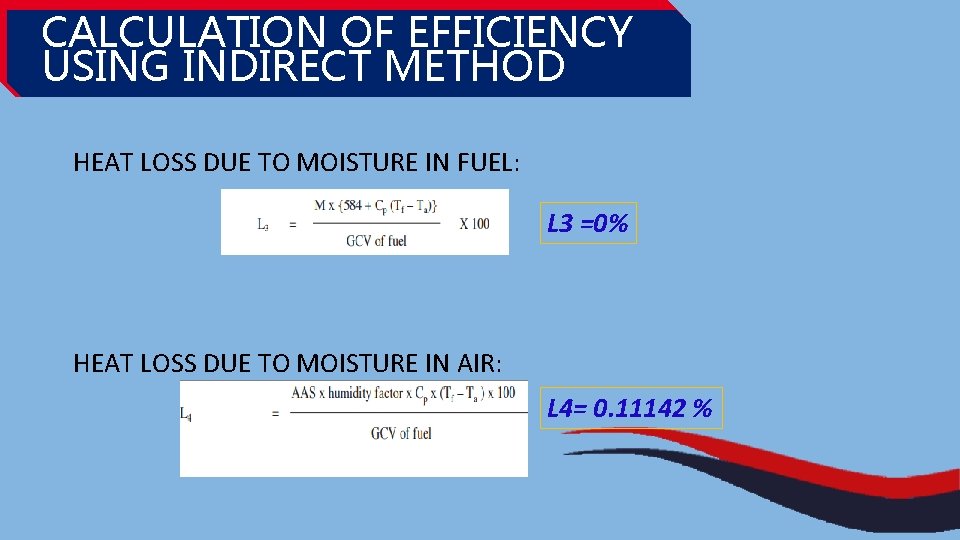
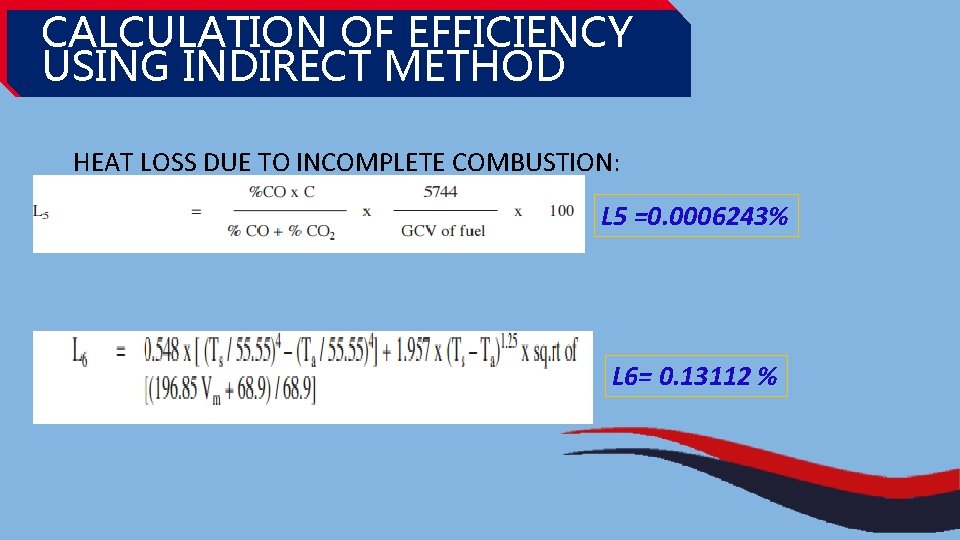
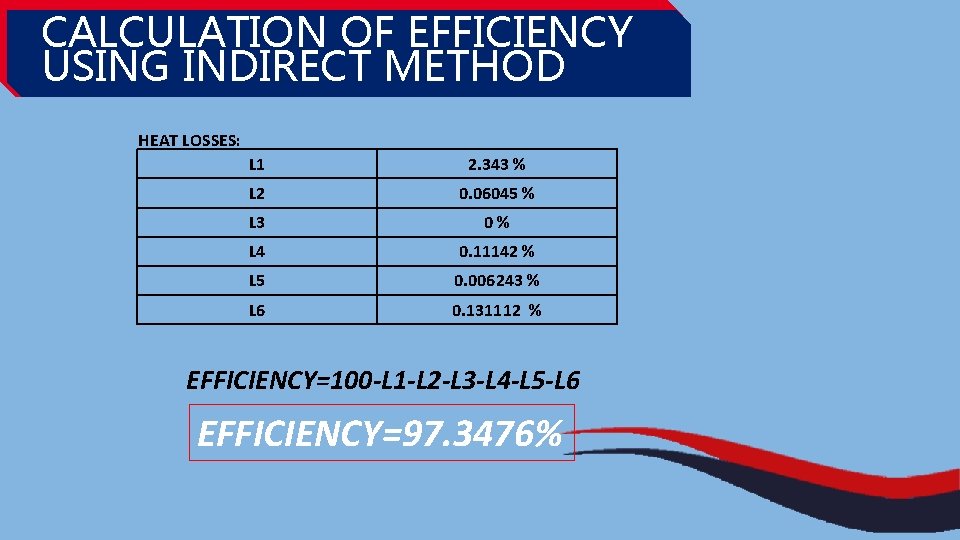
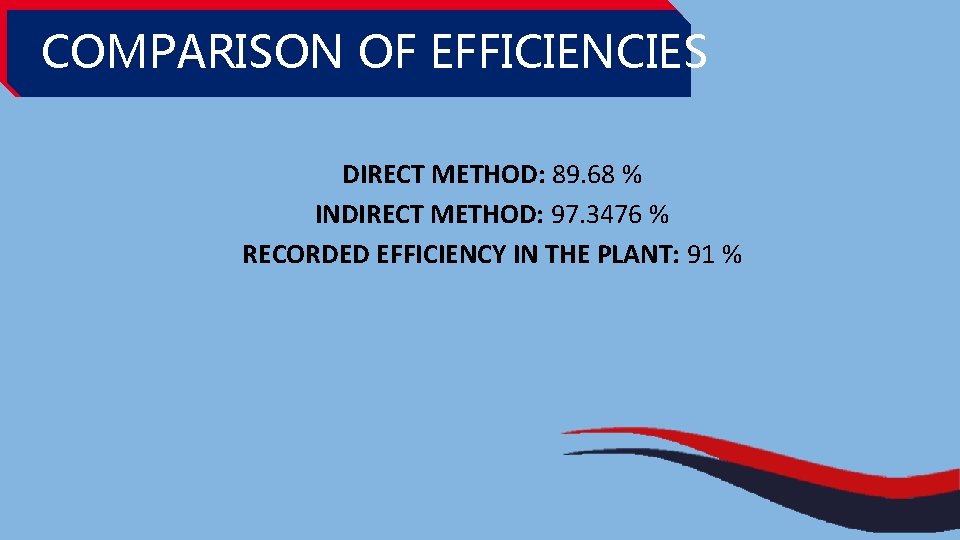
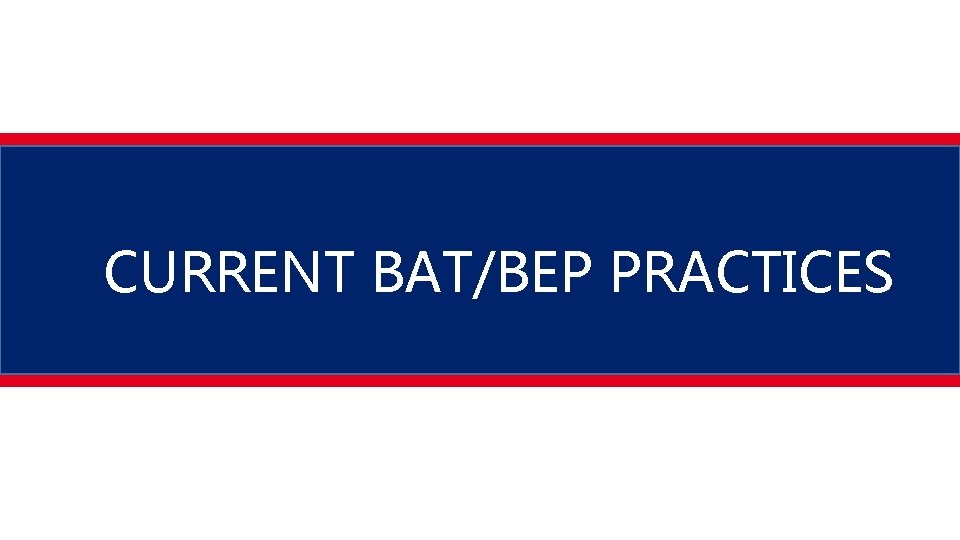
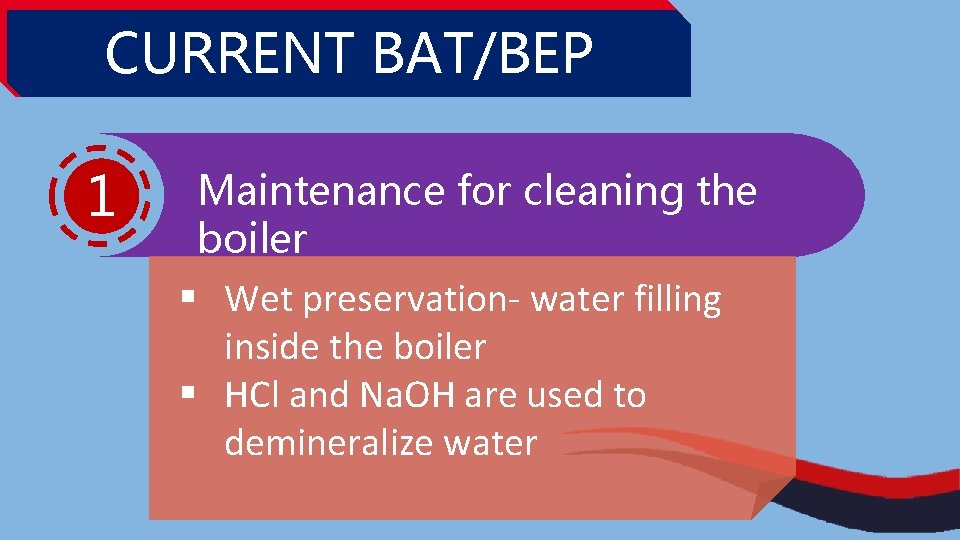
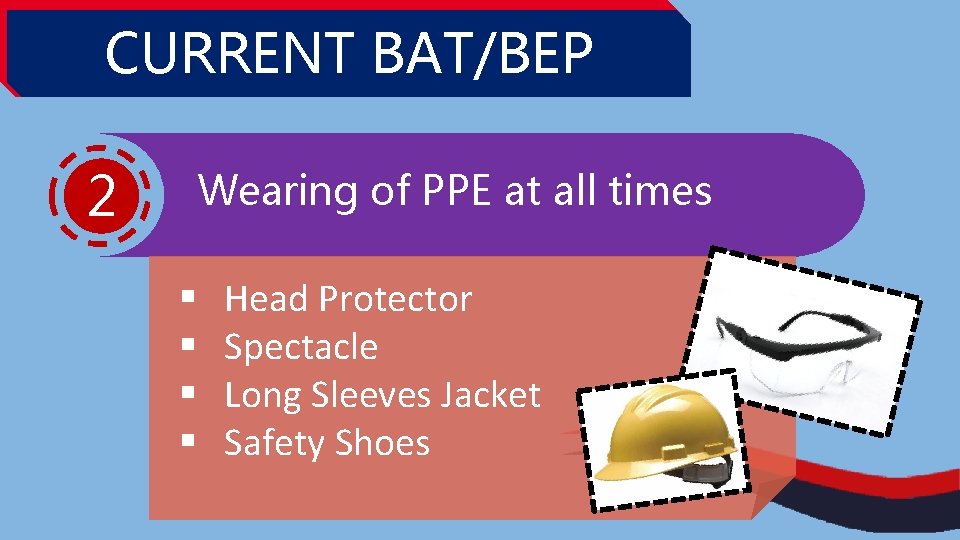
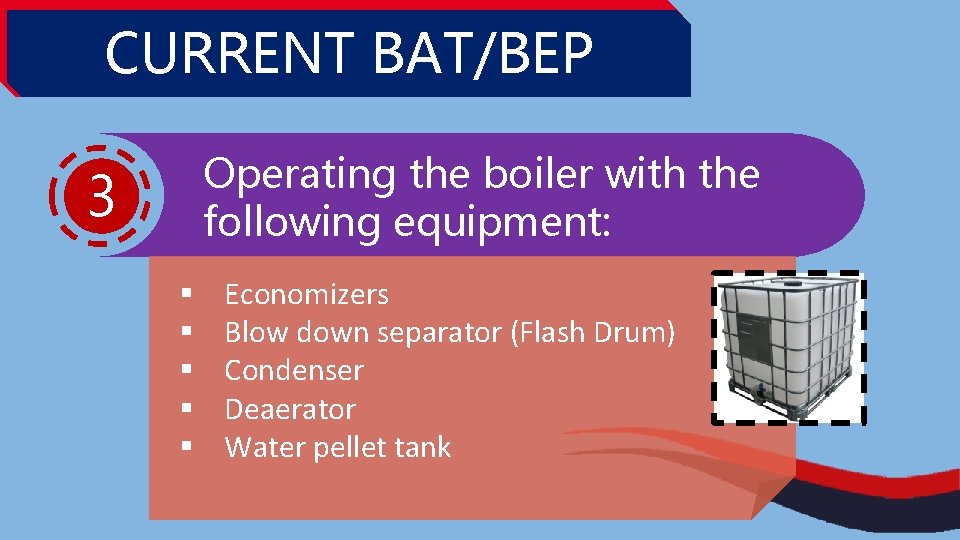
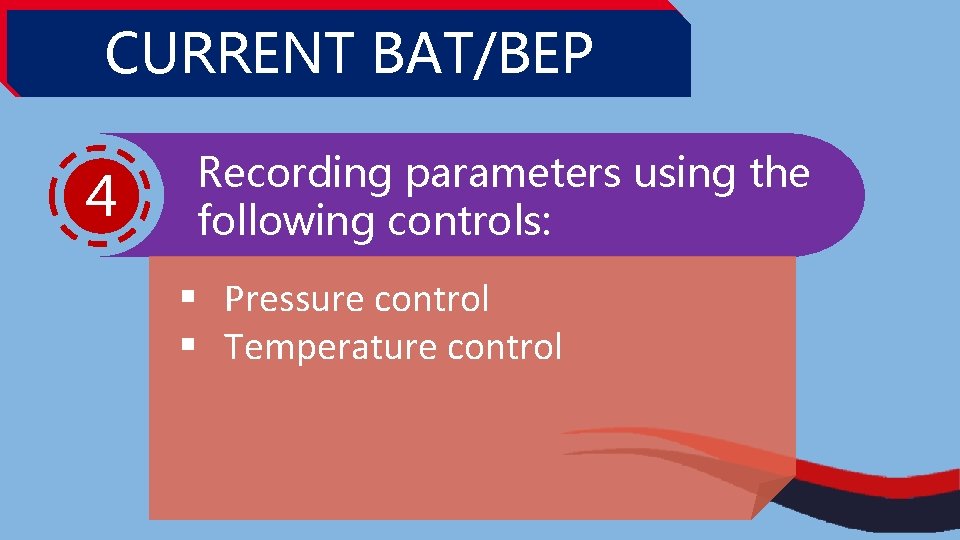
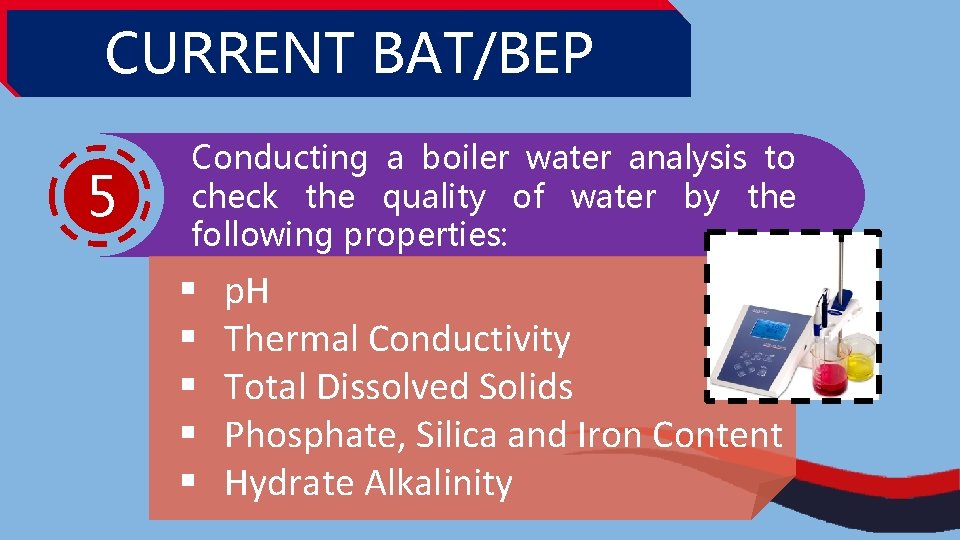
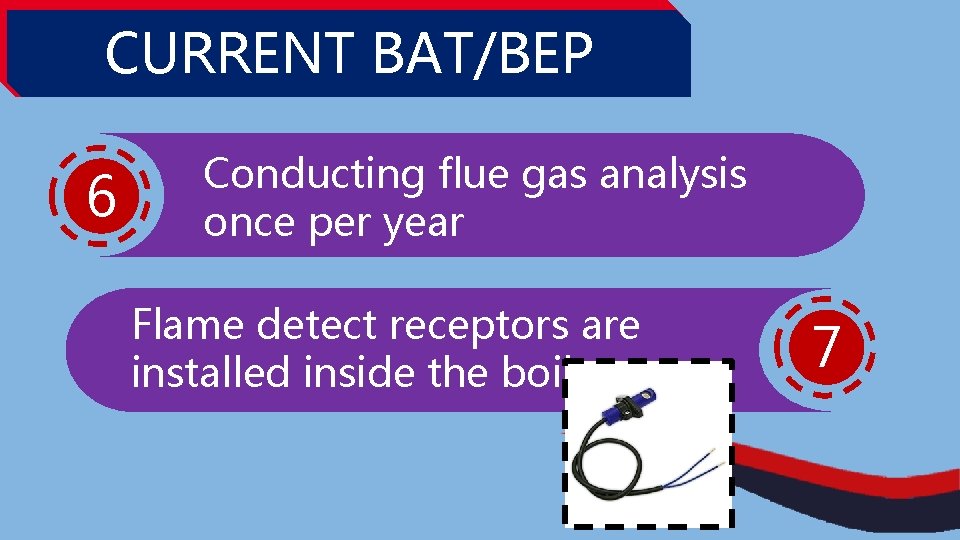
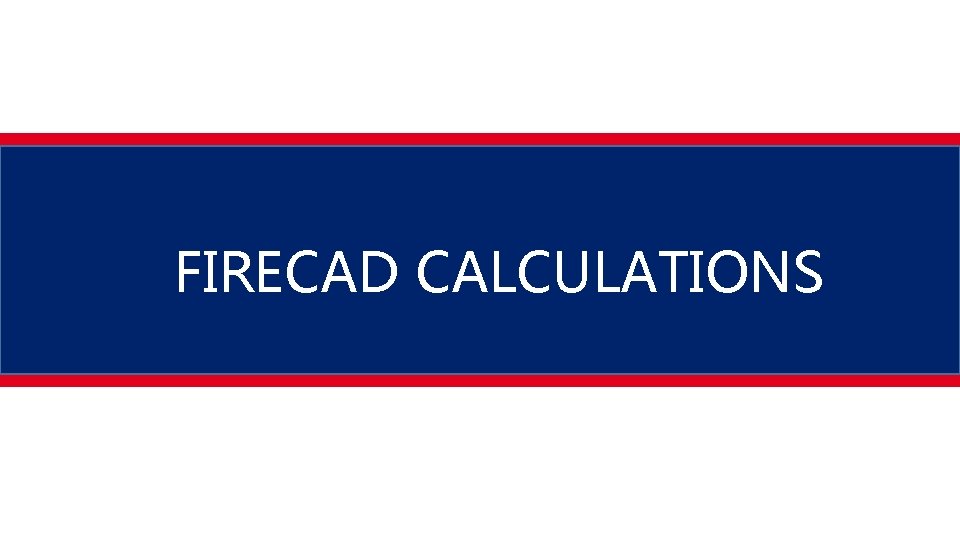
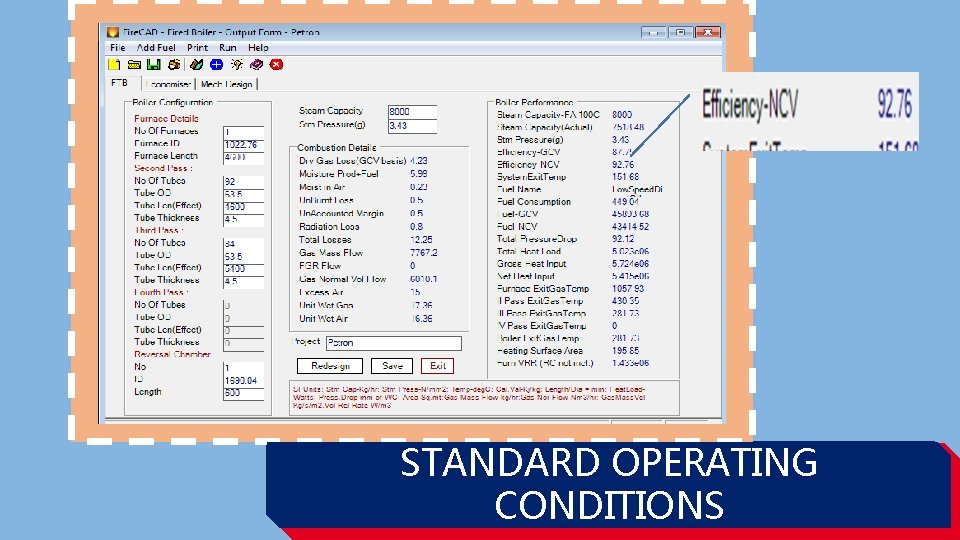
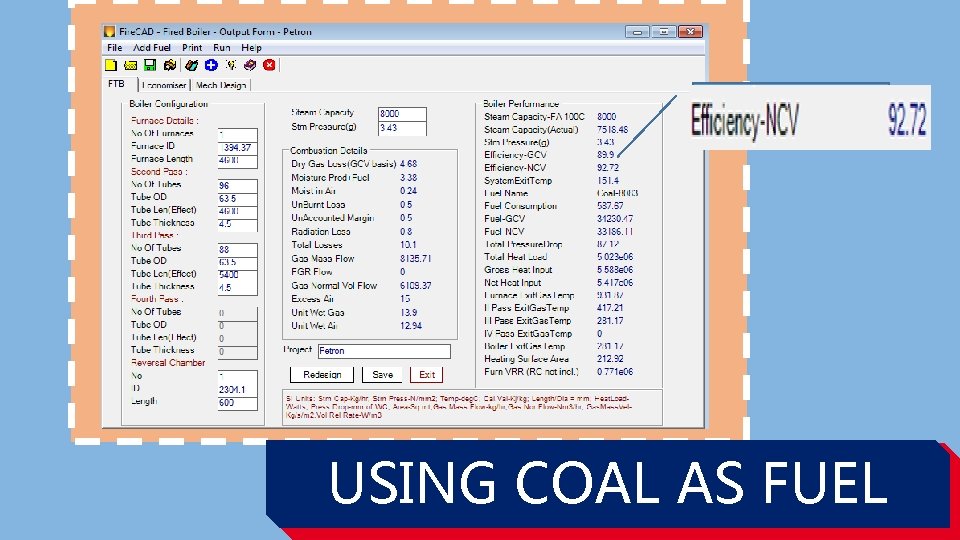
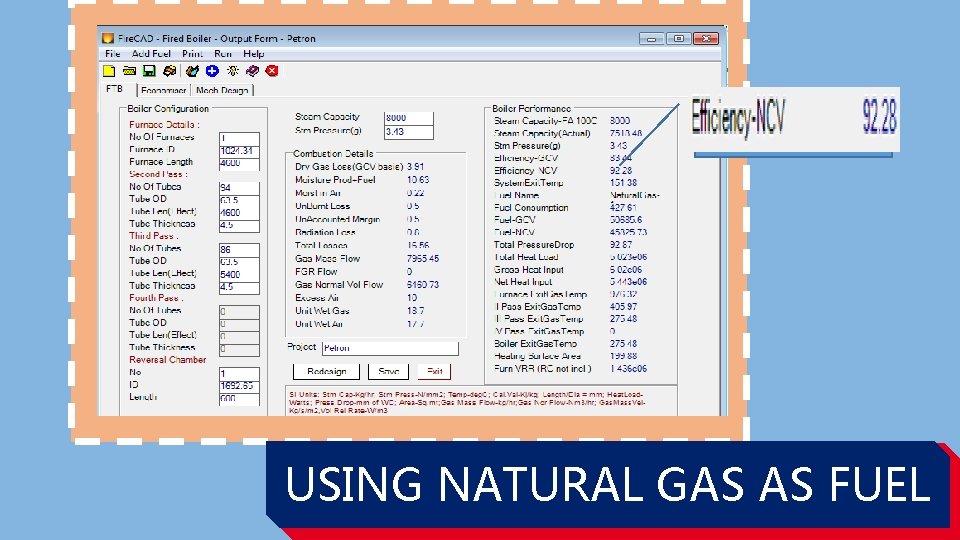
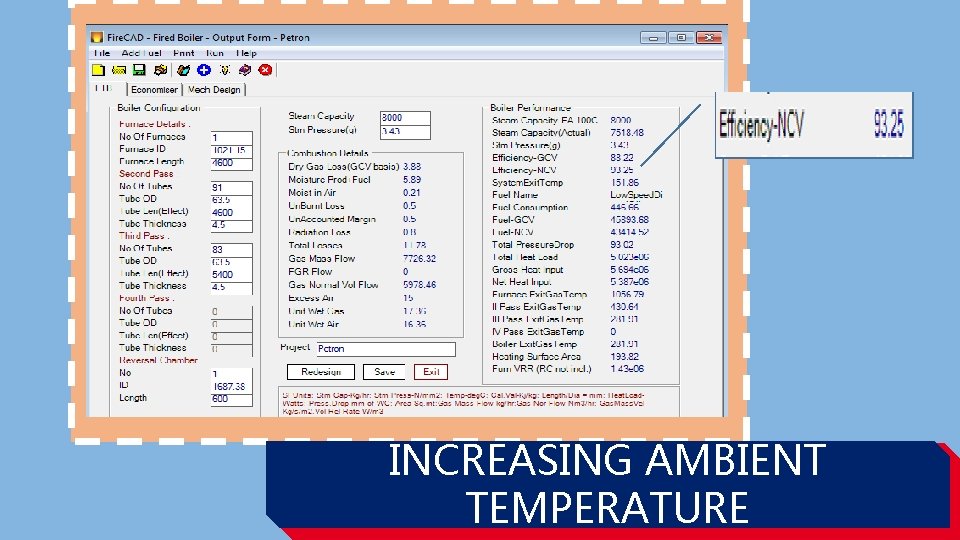
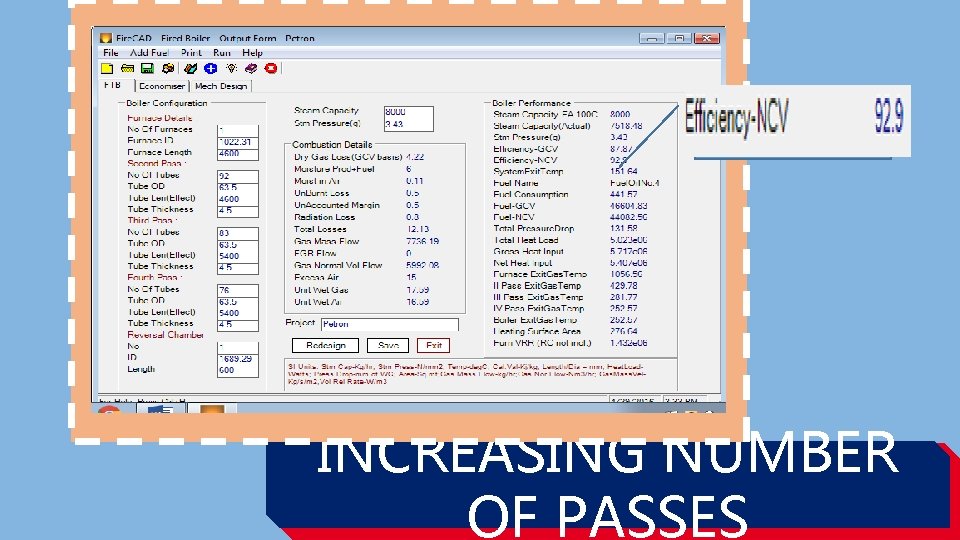
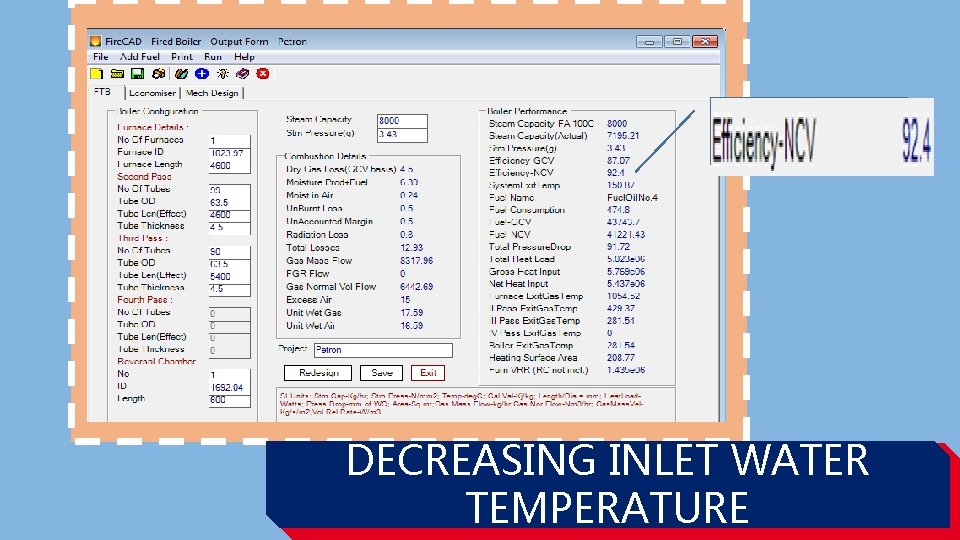
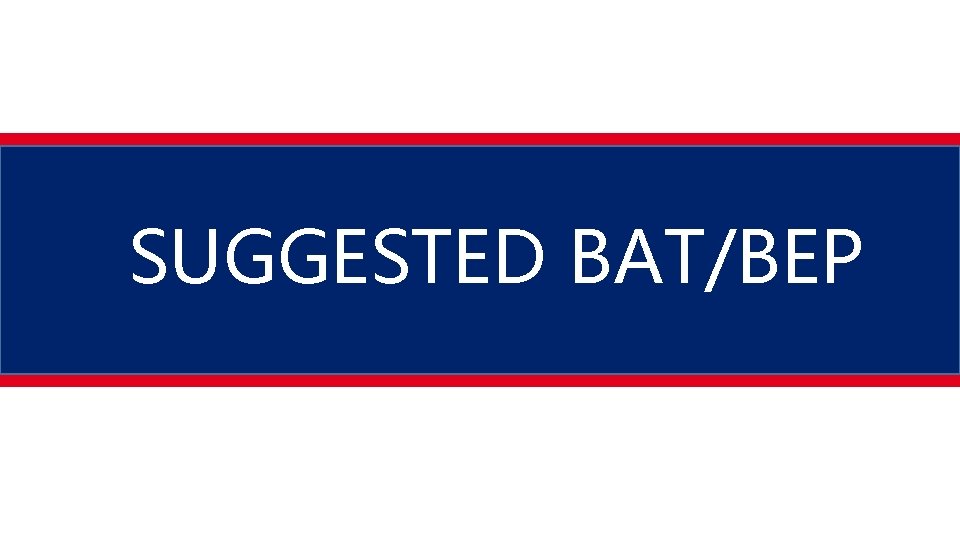
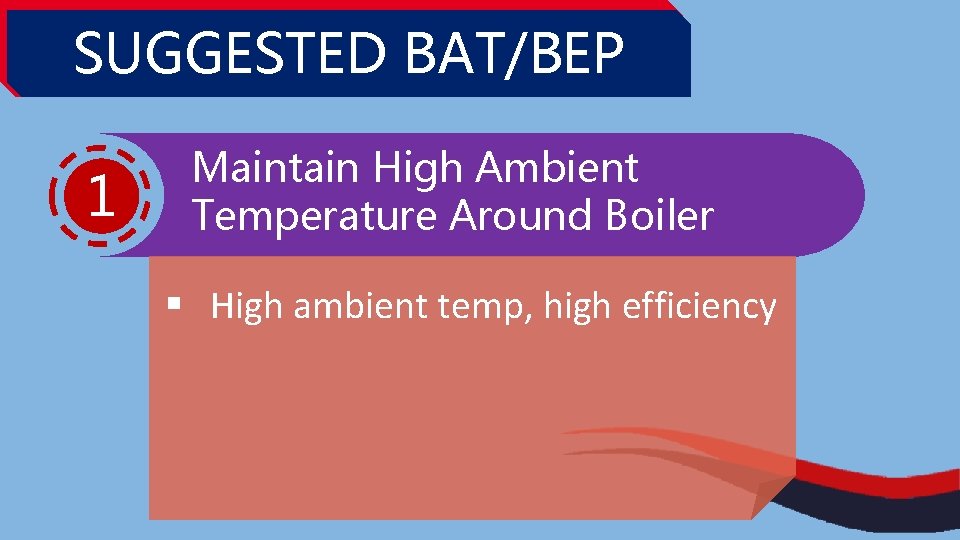
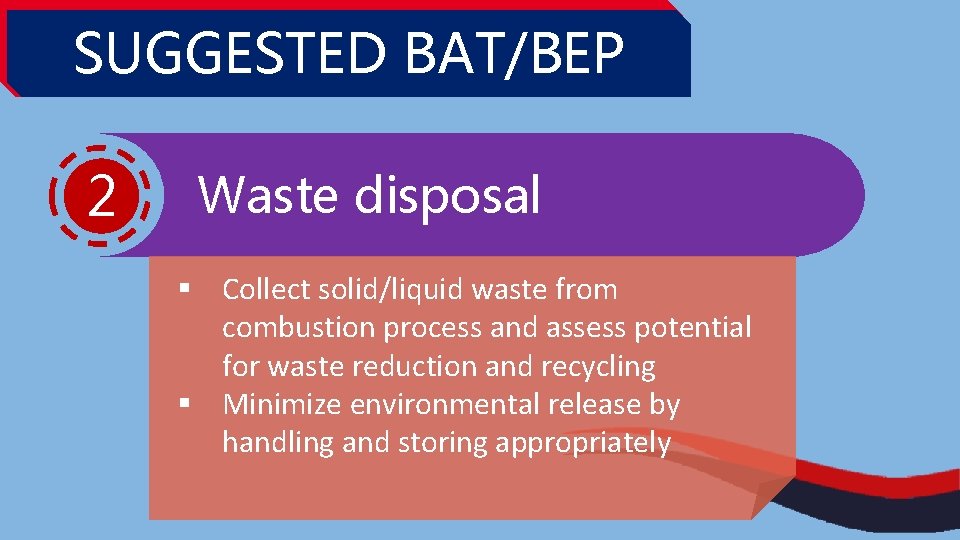
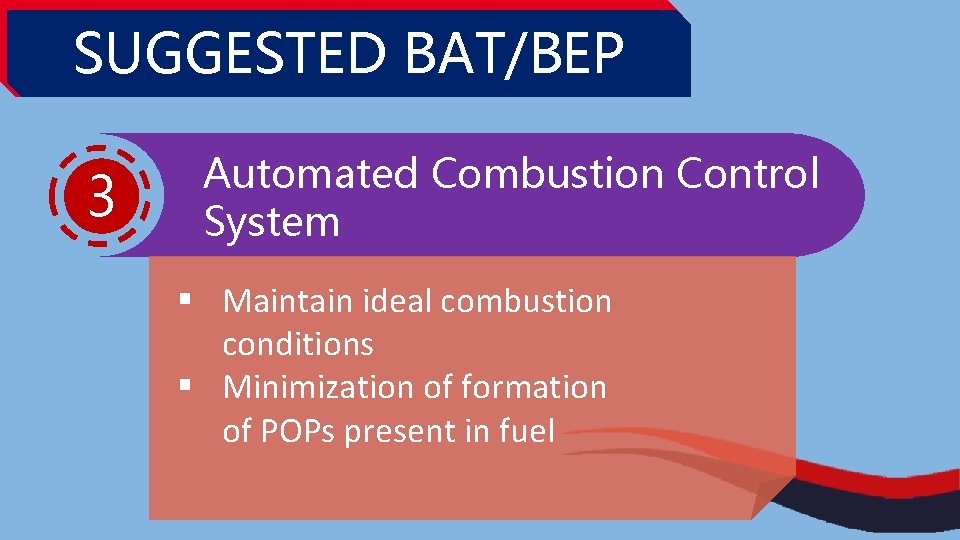
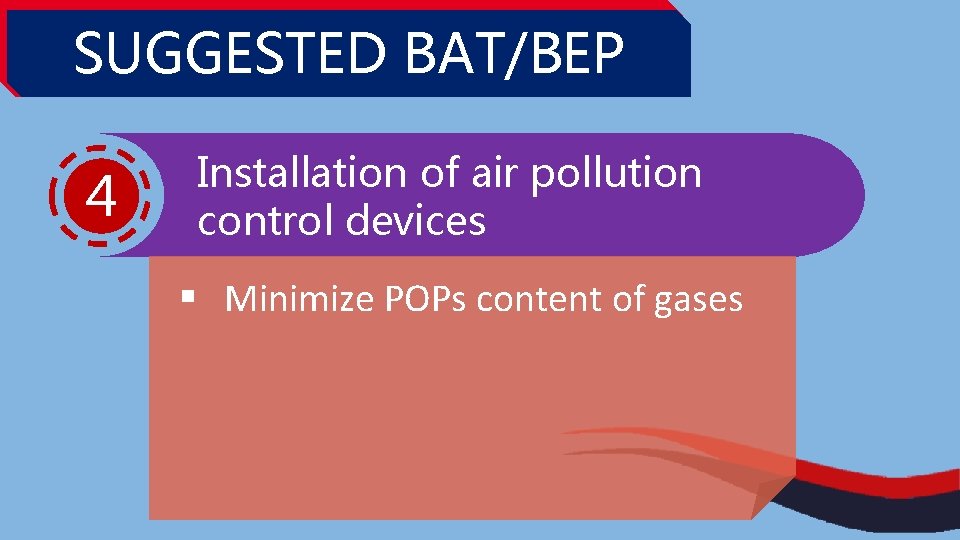
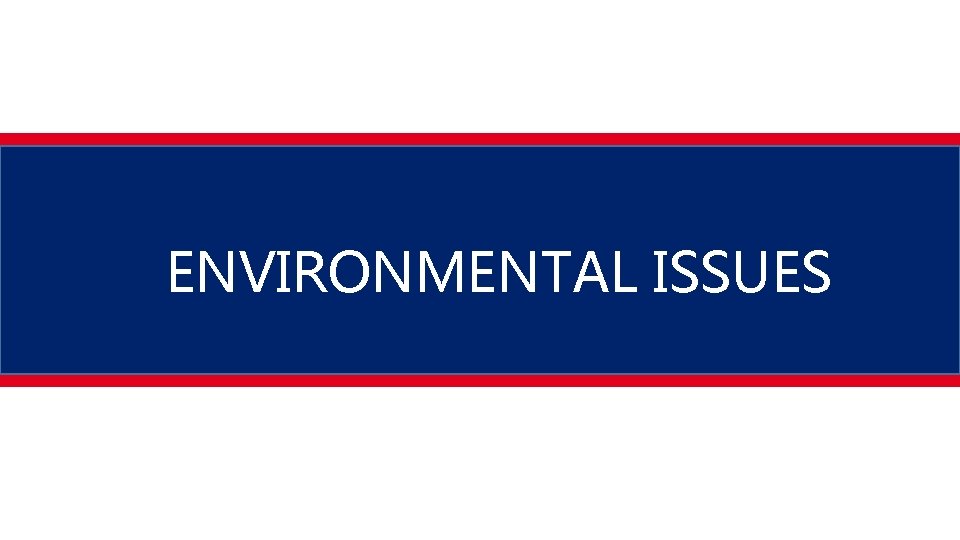
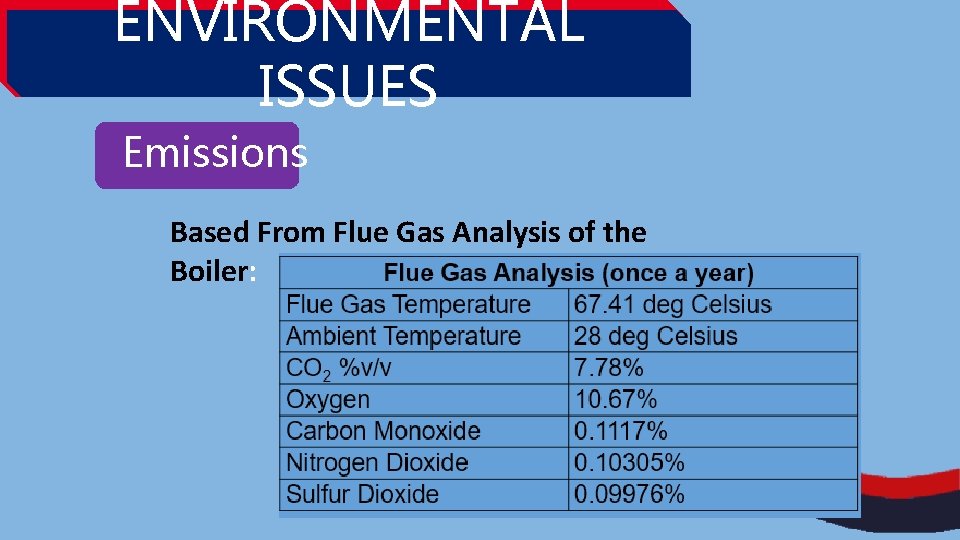
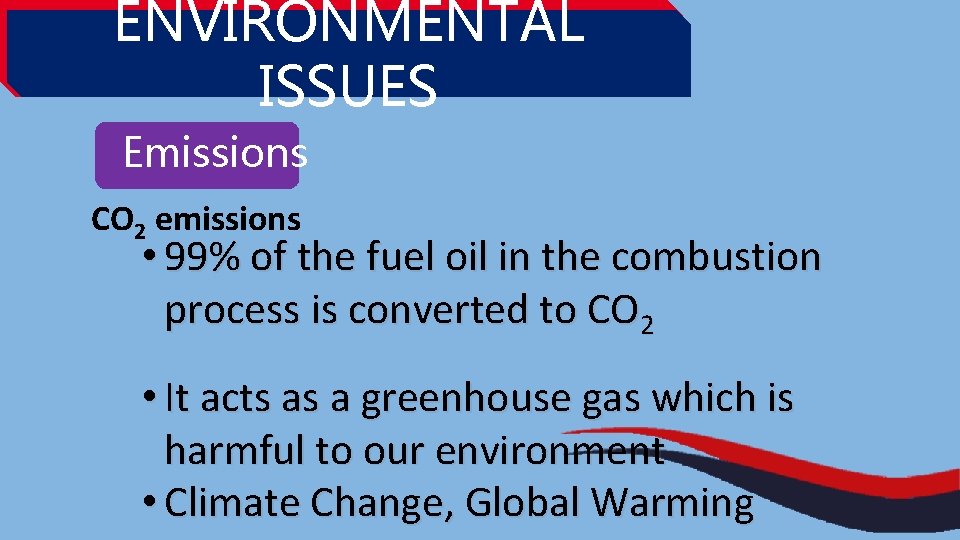
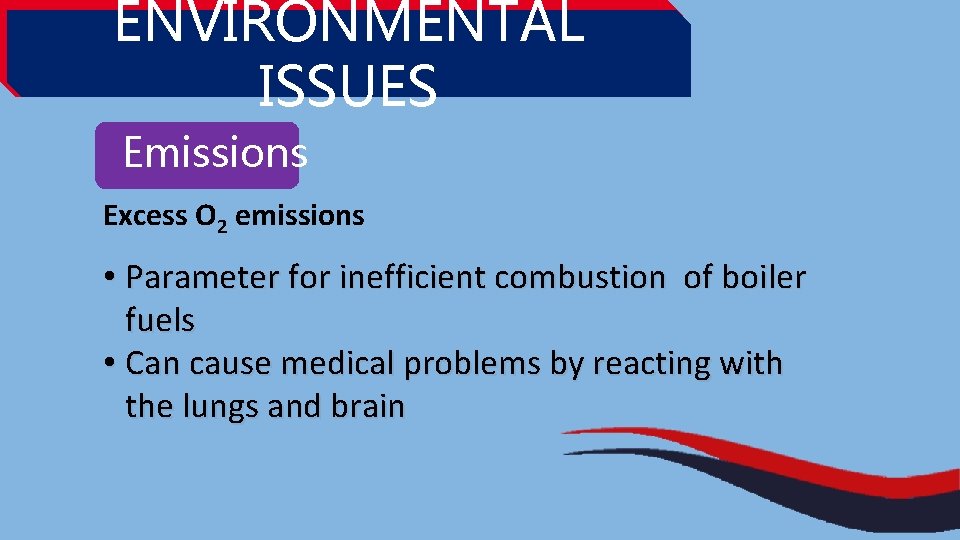
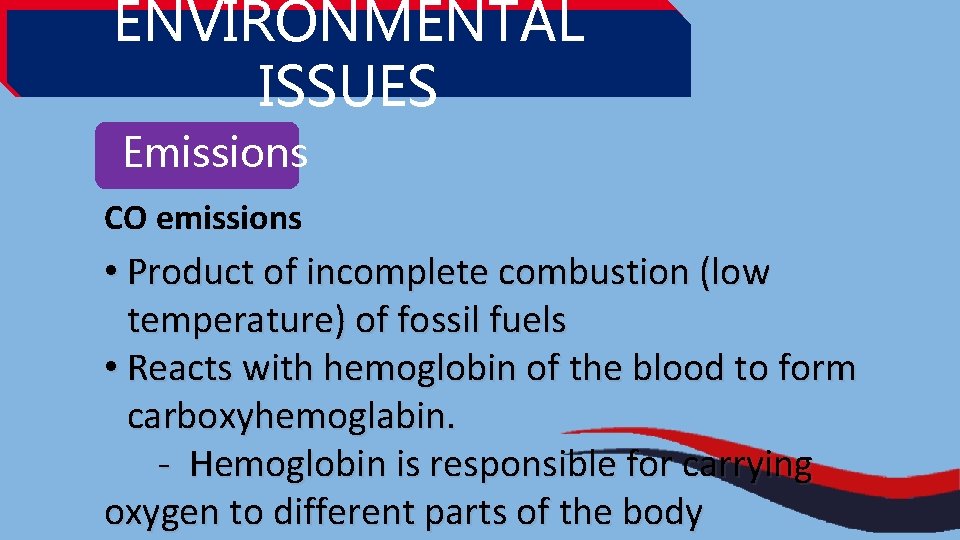
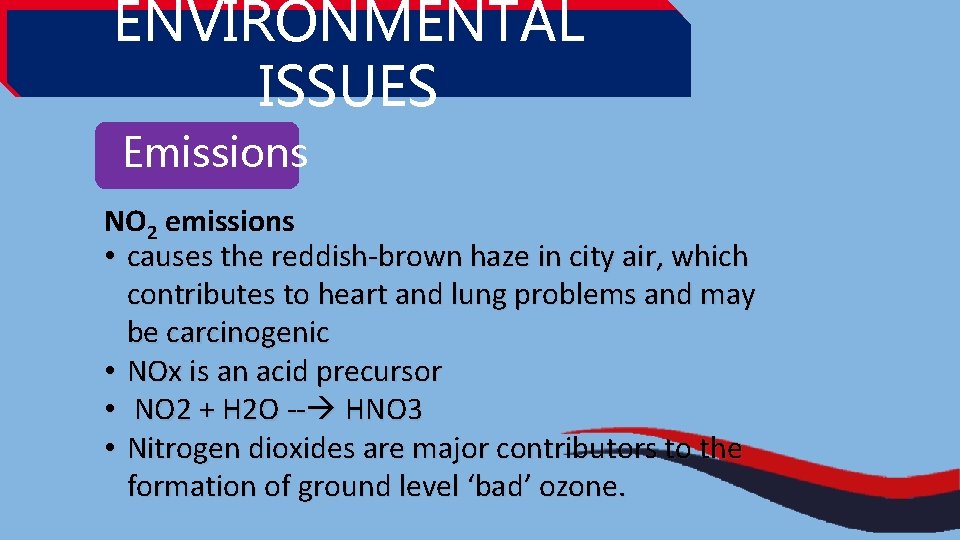
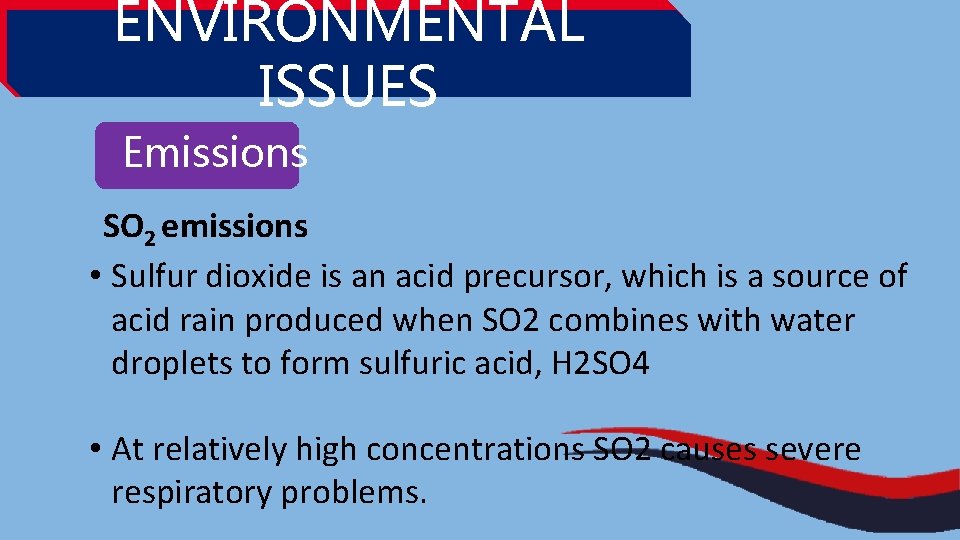
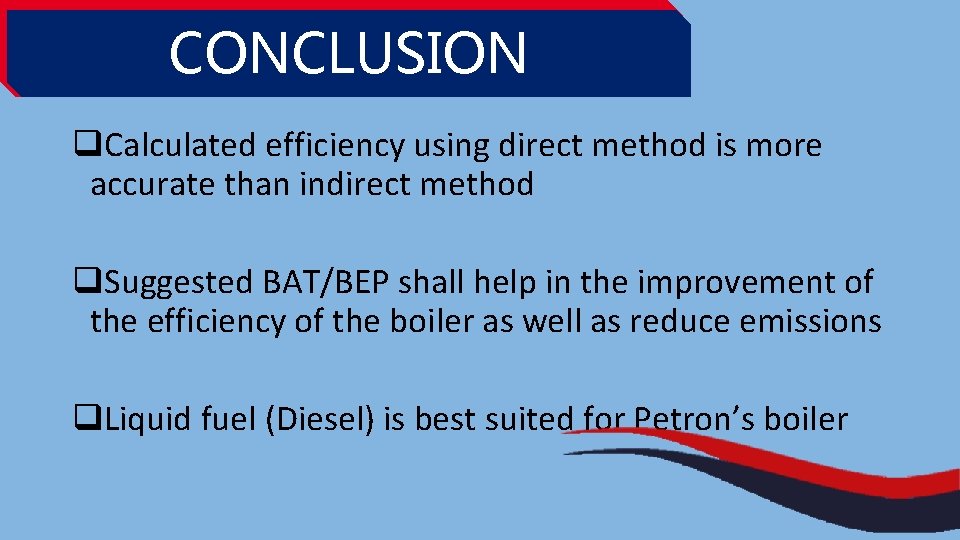
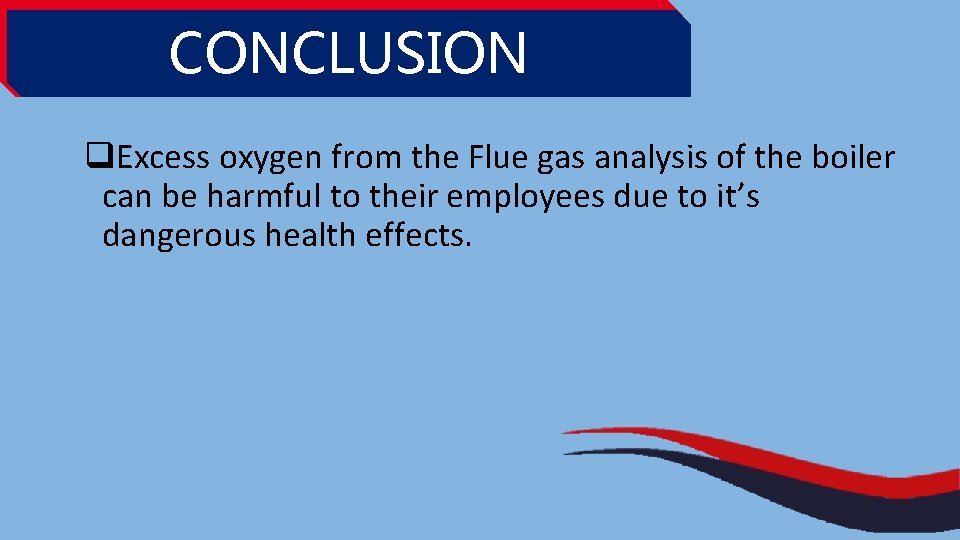
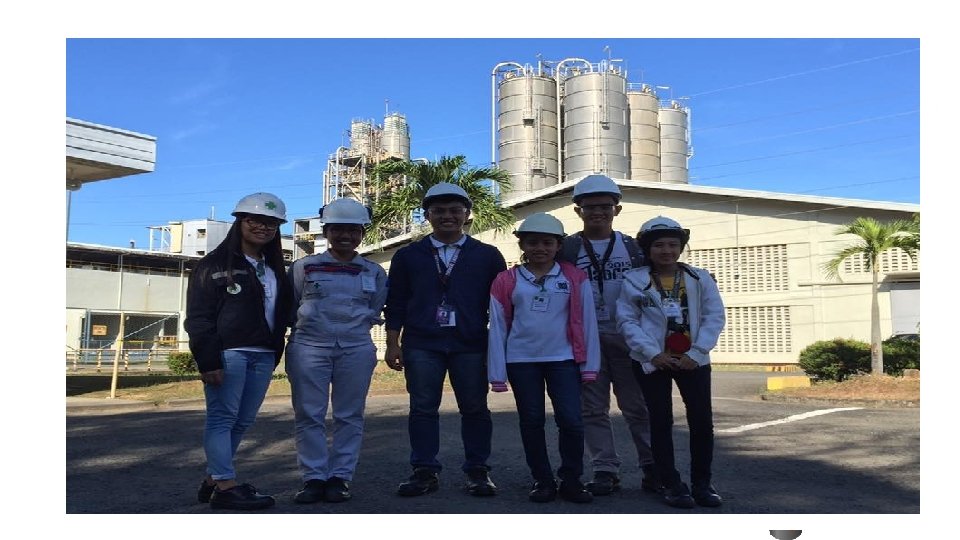
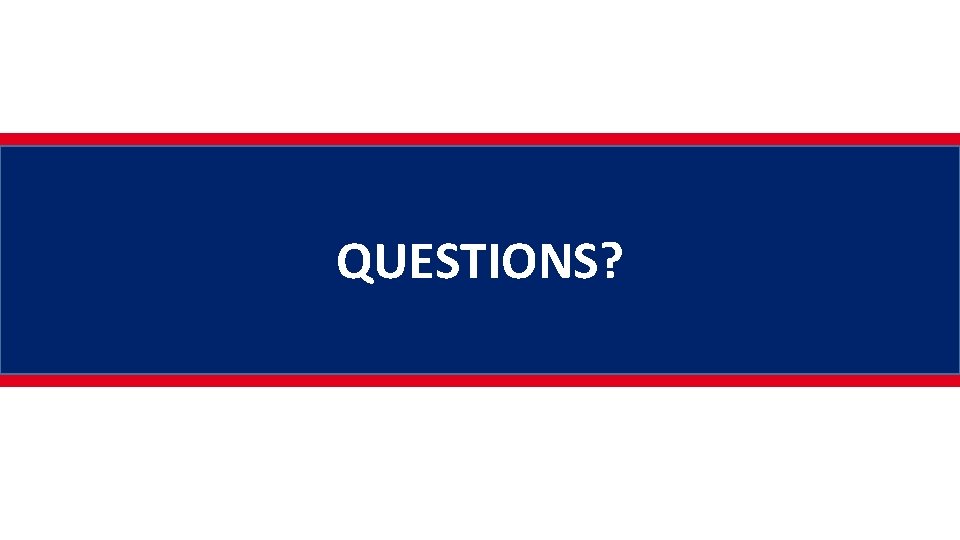
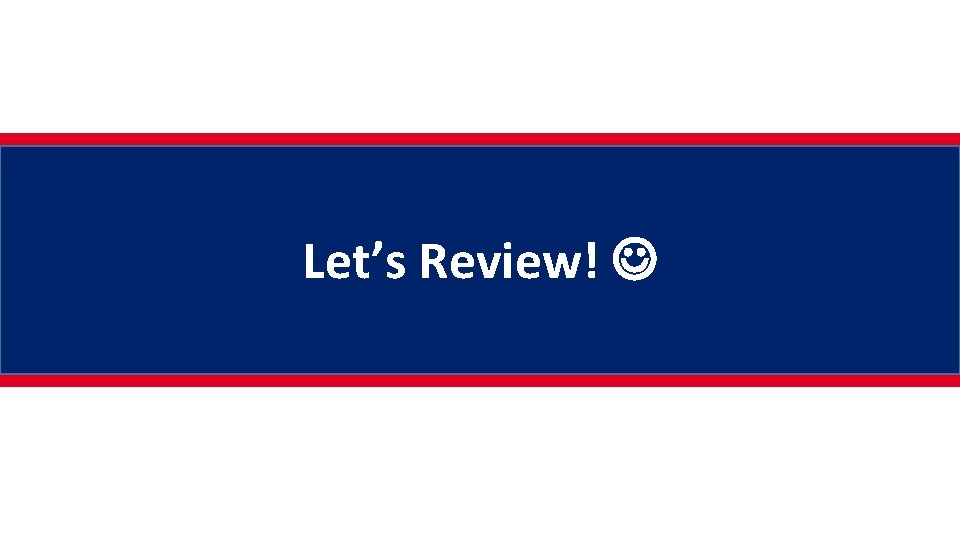

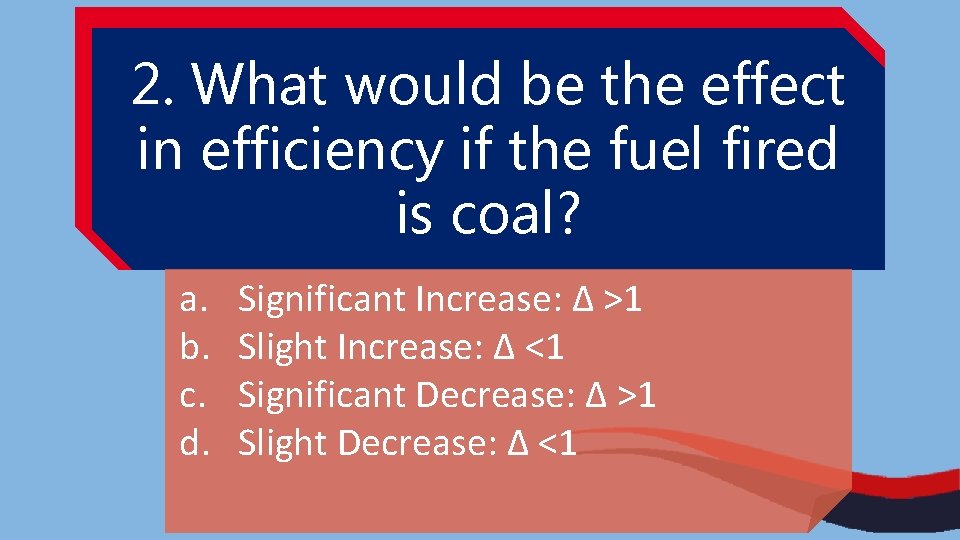
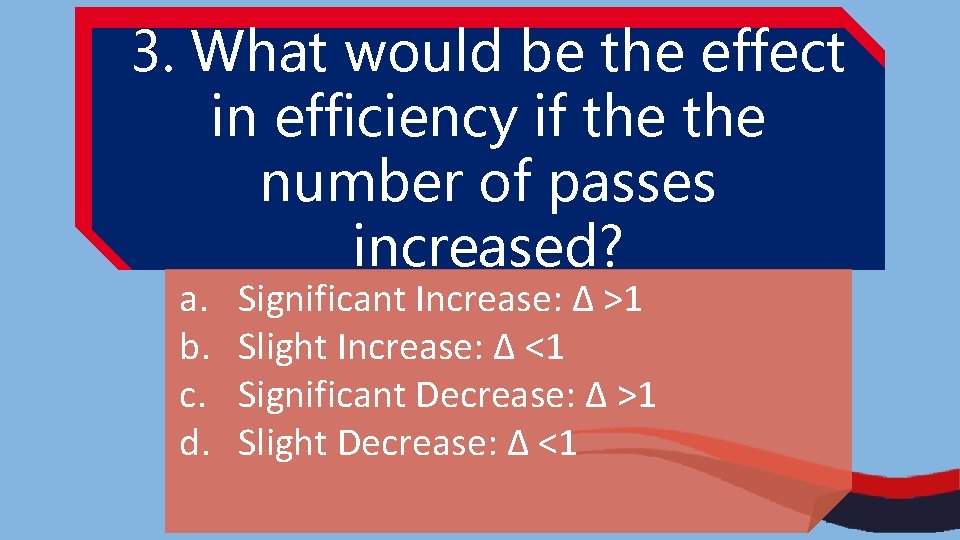
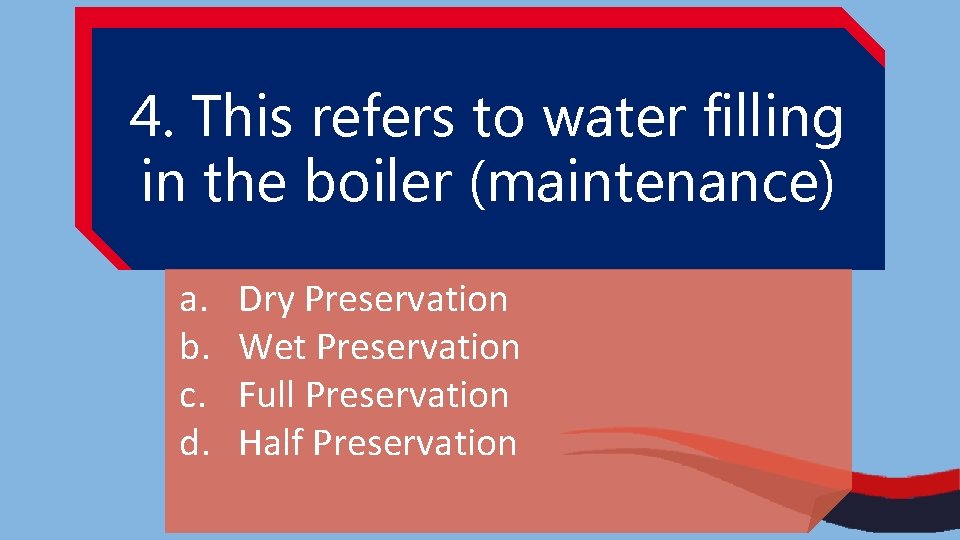
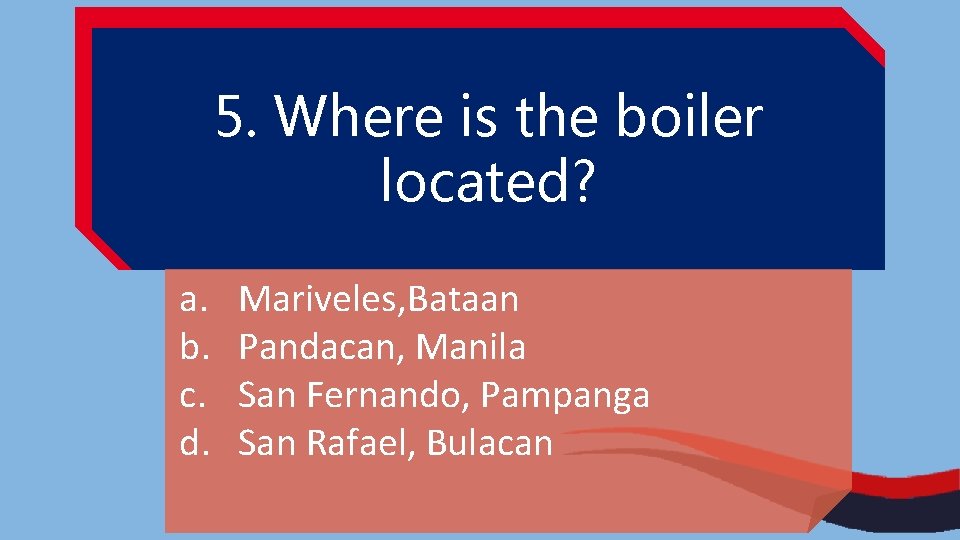
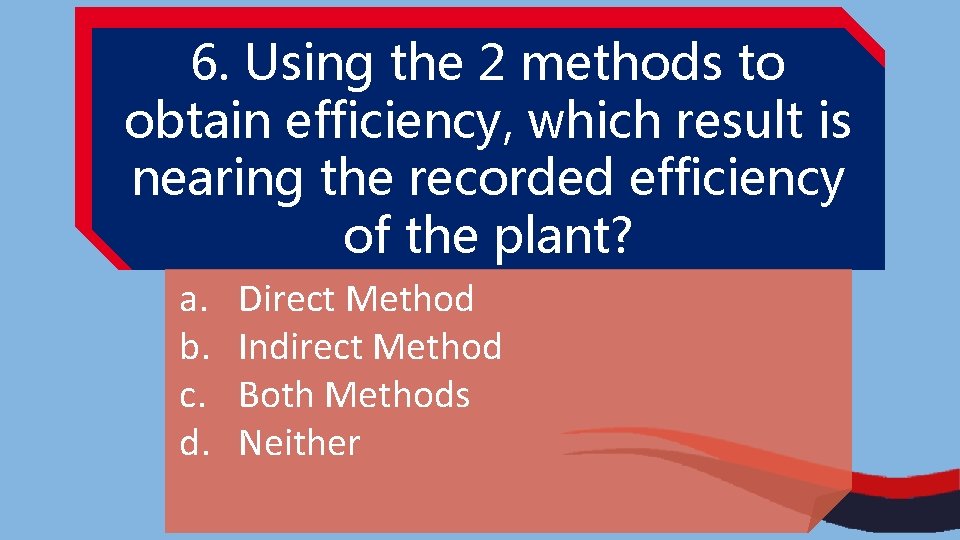
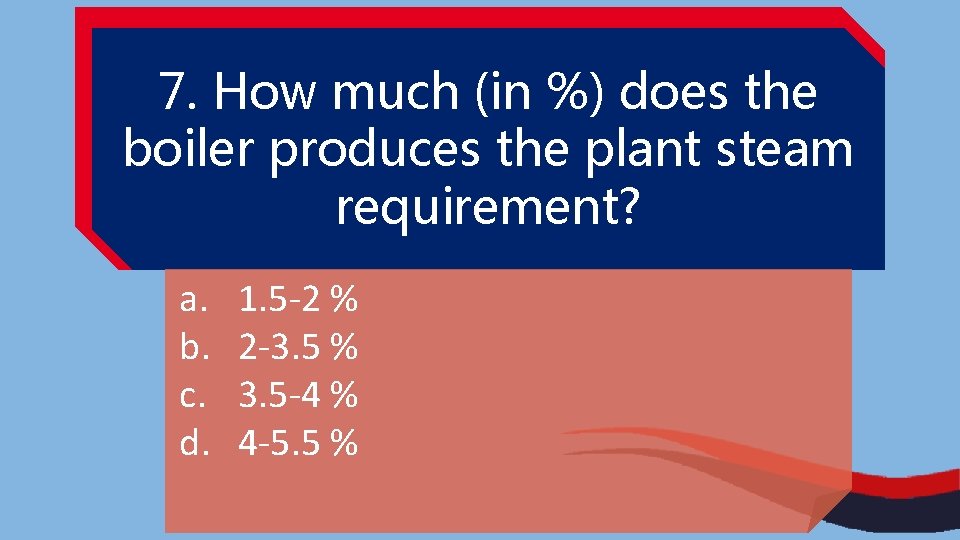
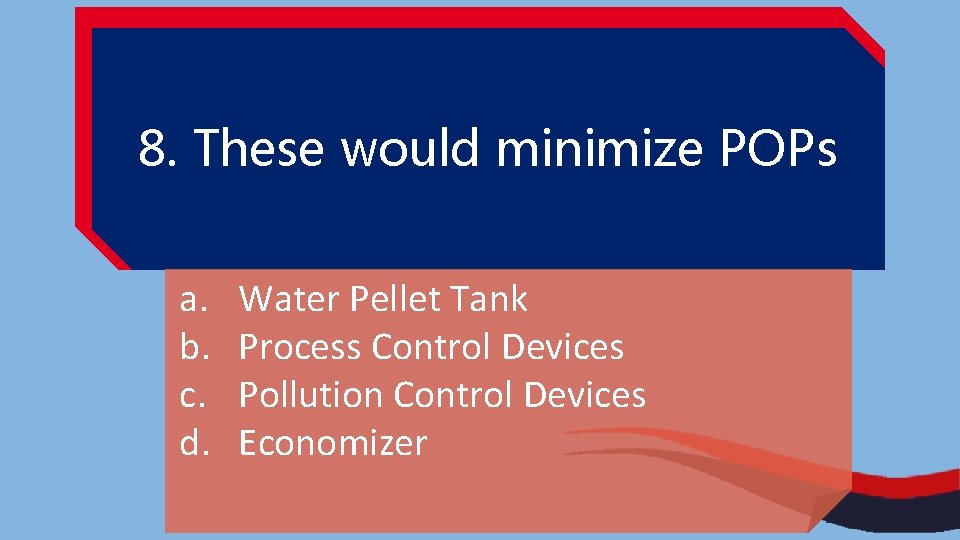
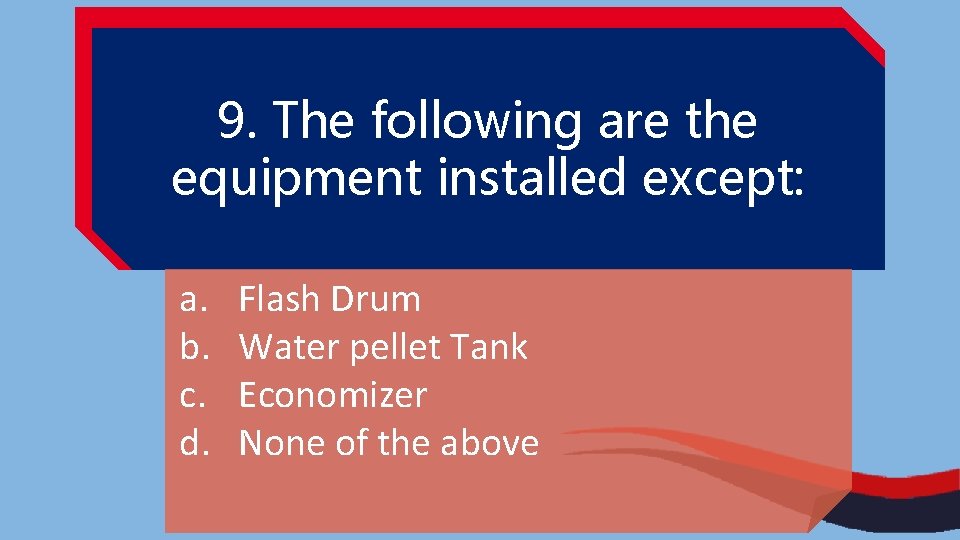
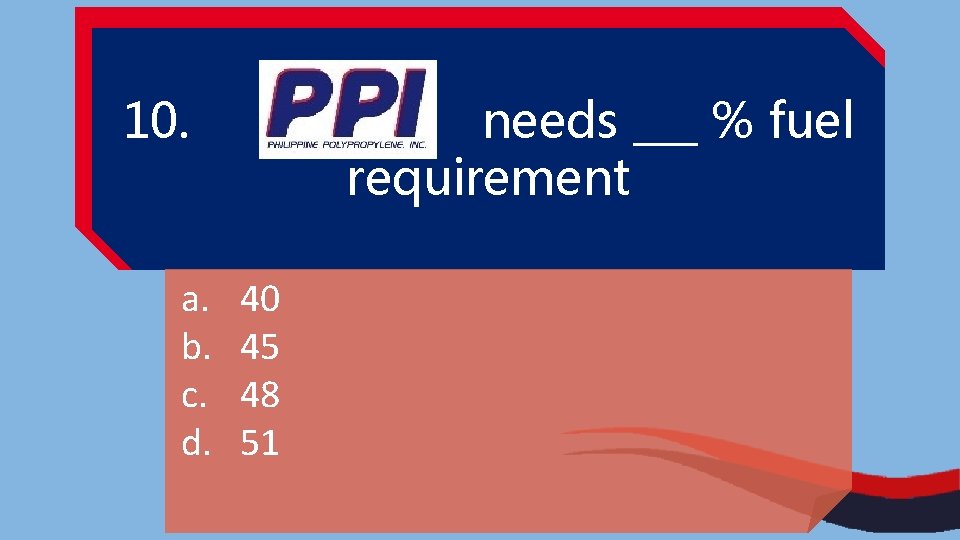
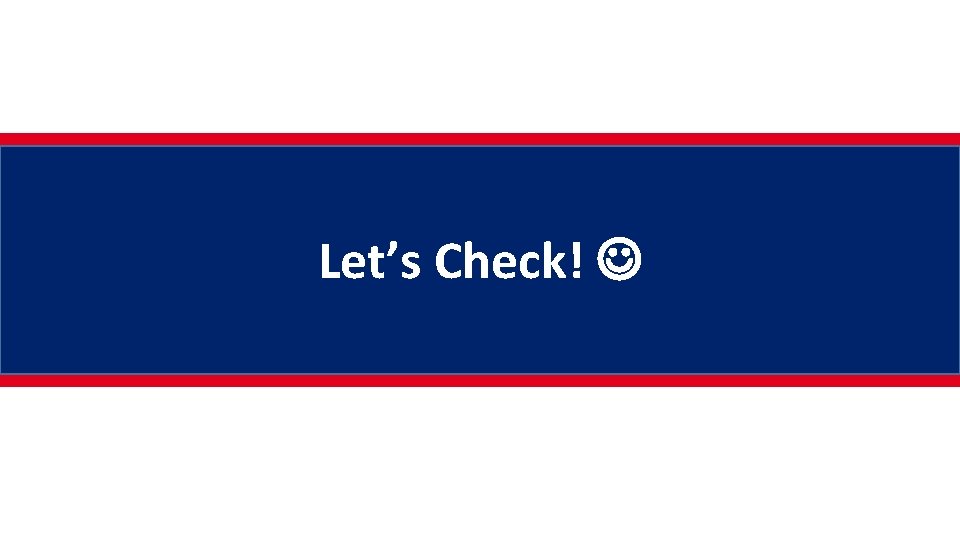
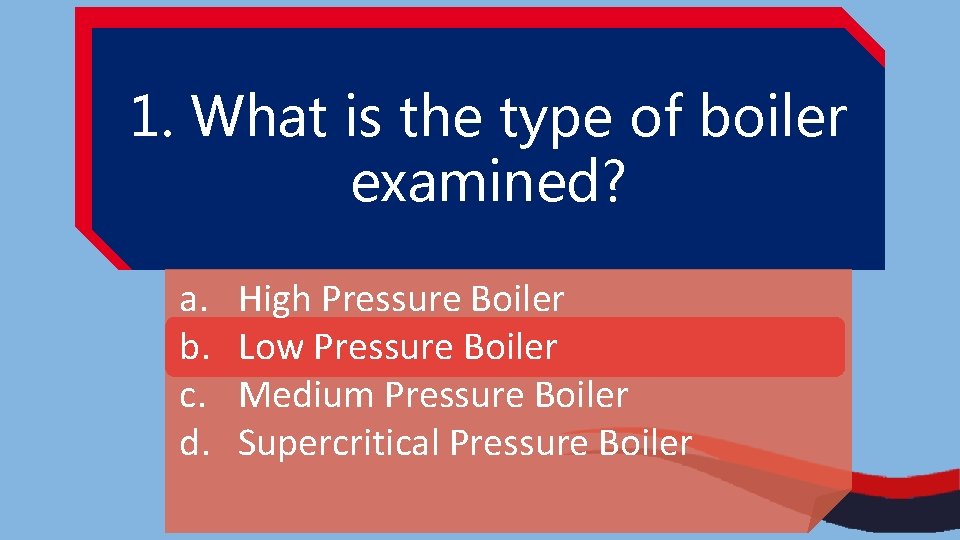
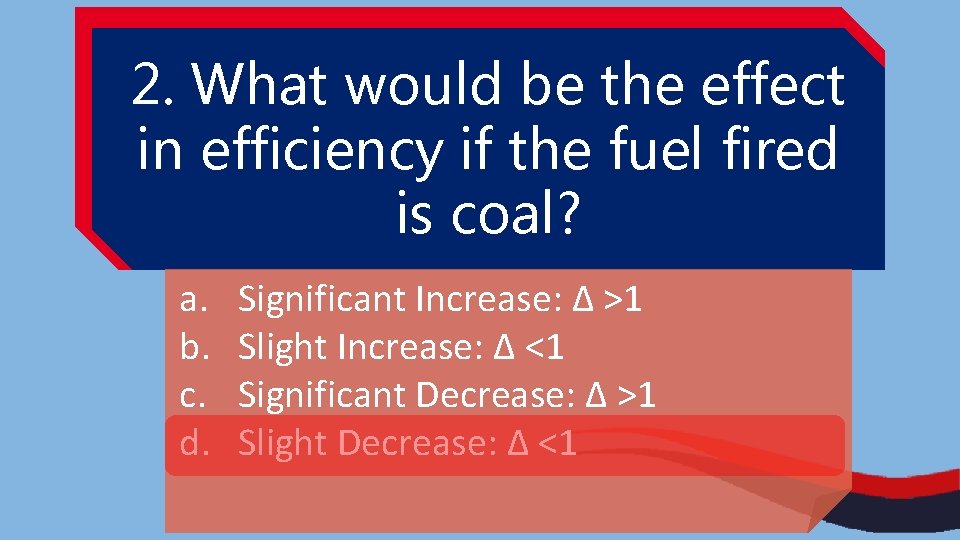
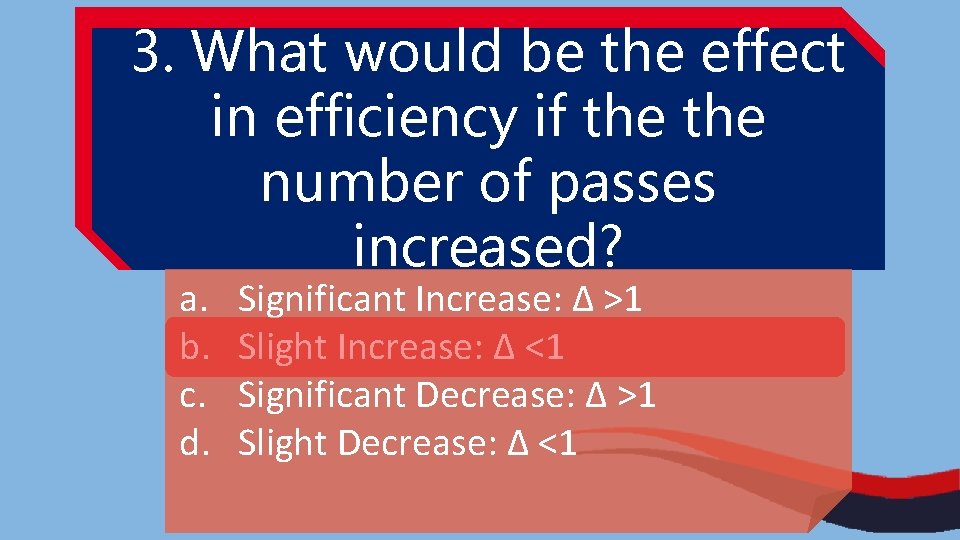
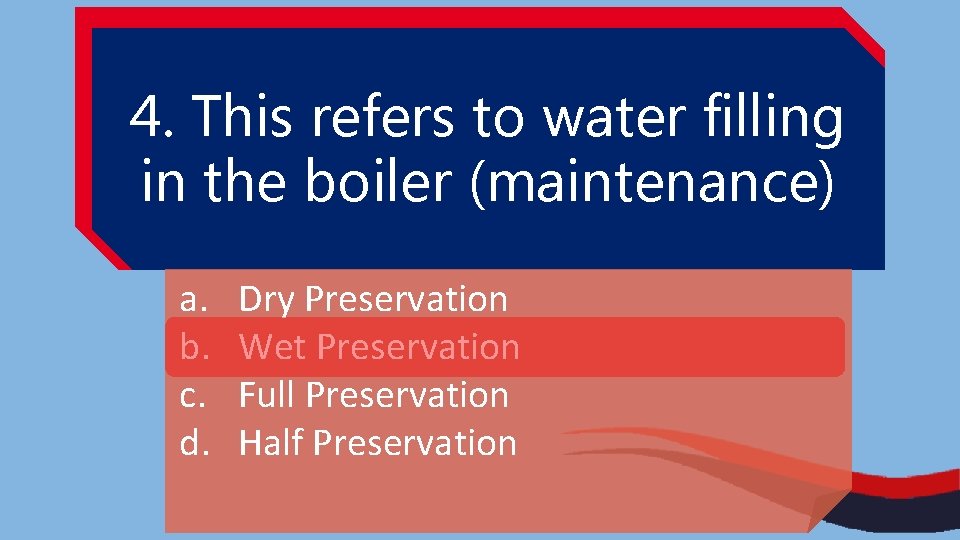
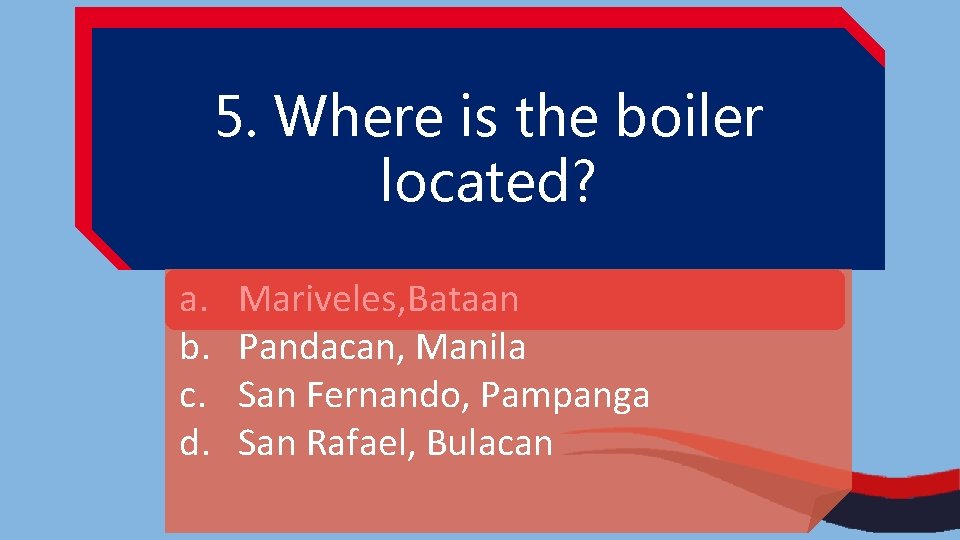
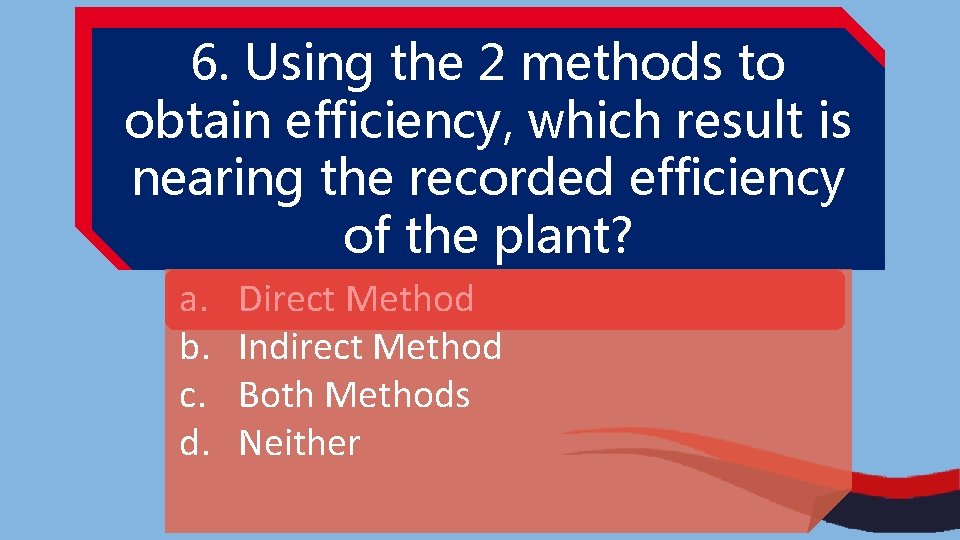
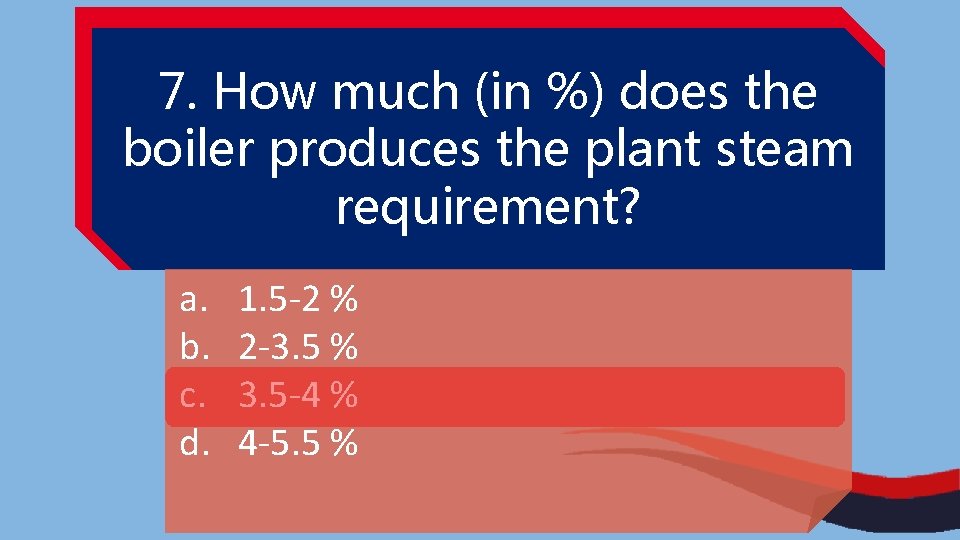
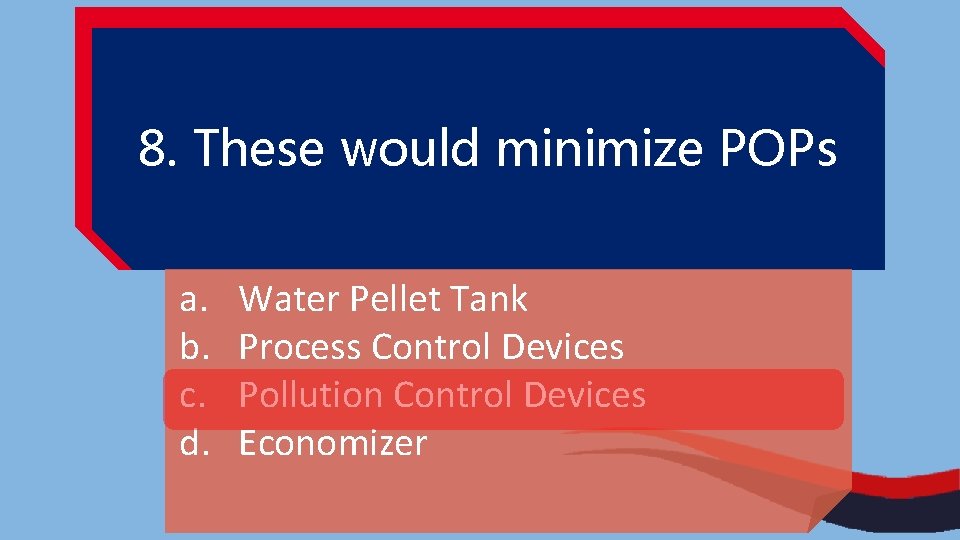
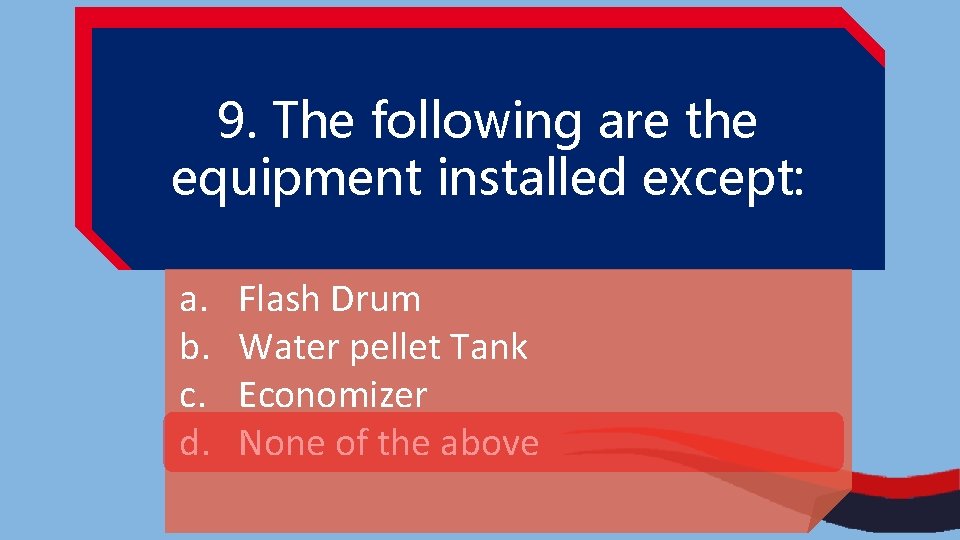
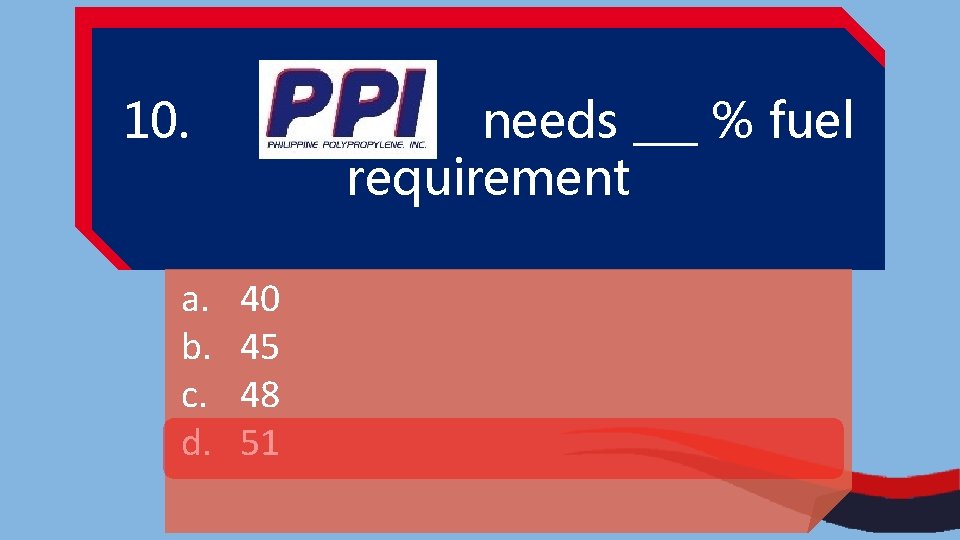
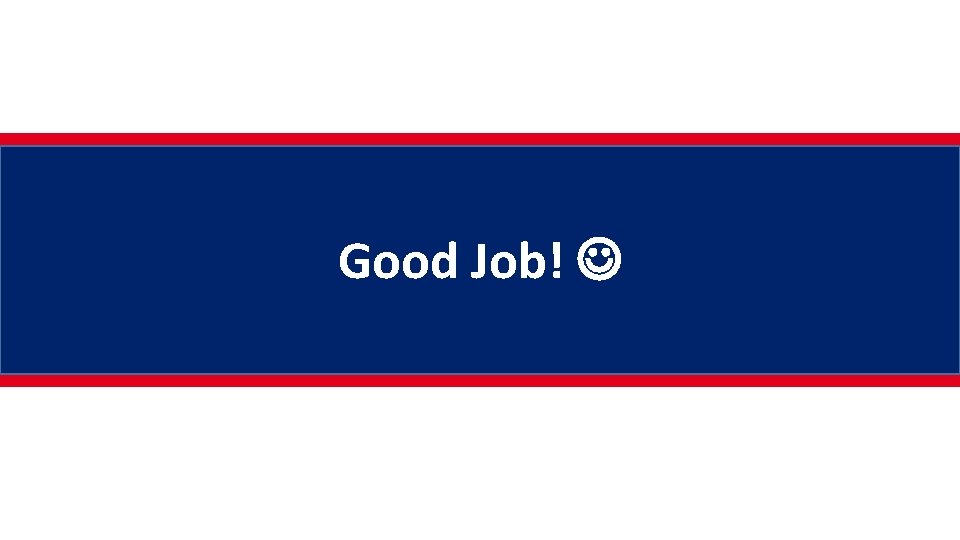
- Slides: 76
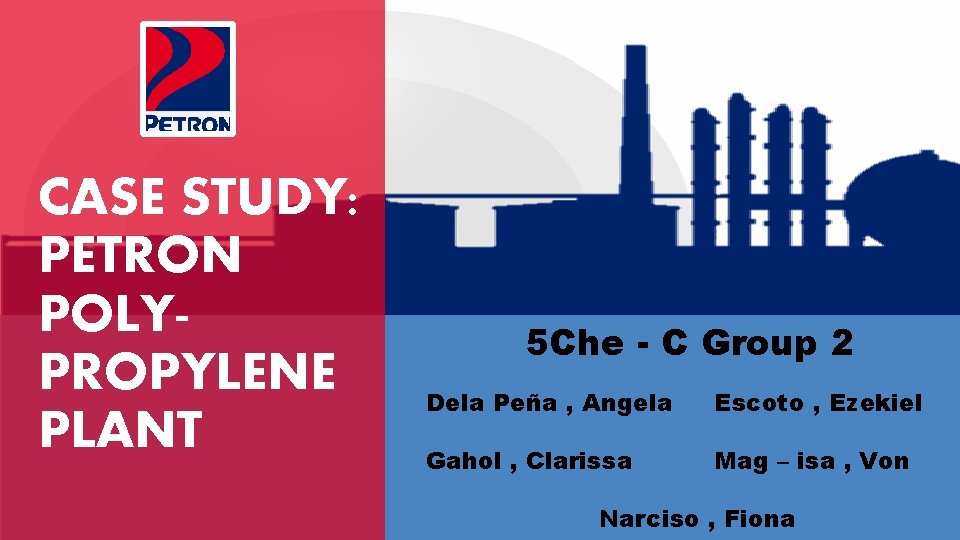
CASE STUDY: PETRON POLYPROPYLENE PLANT 5 Che - C Group 2 Dela Peña , Angela Escoto , Ezekiel Gahol , Clarissa Mag – isa , Von Narciso , Fiona
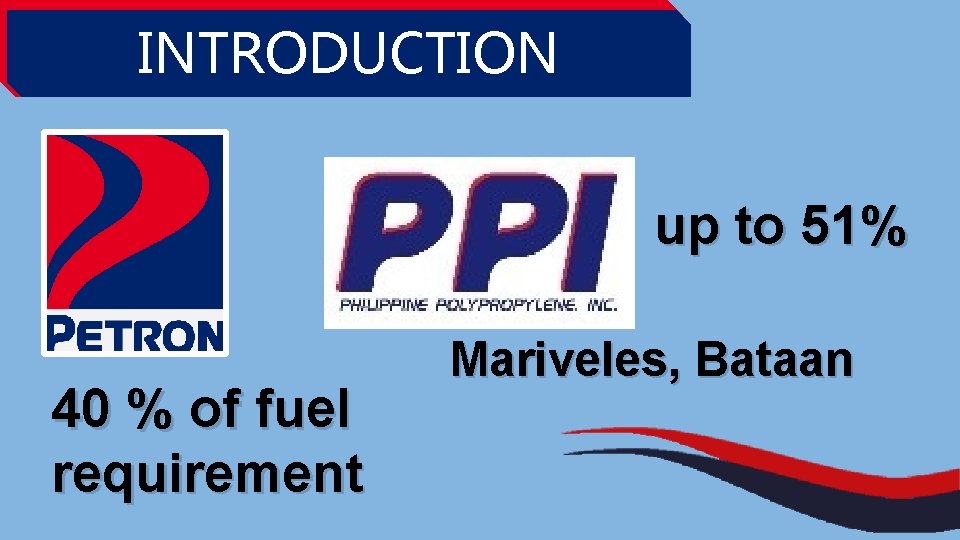
INTRODUCTION up to 51% 40 % of fuel requirement Mariveles, Bataan
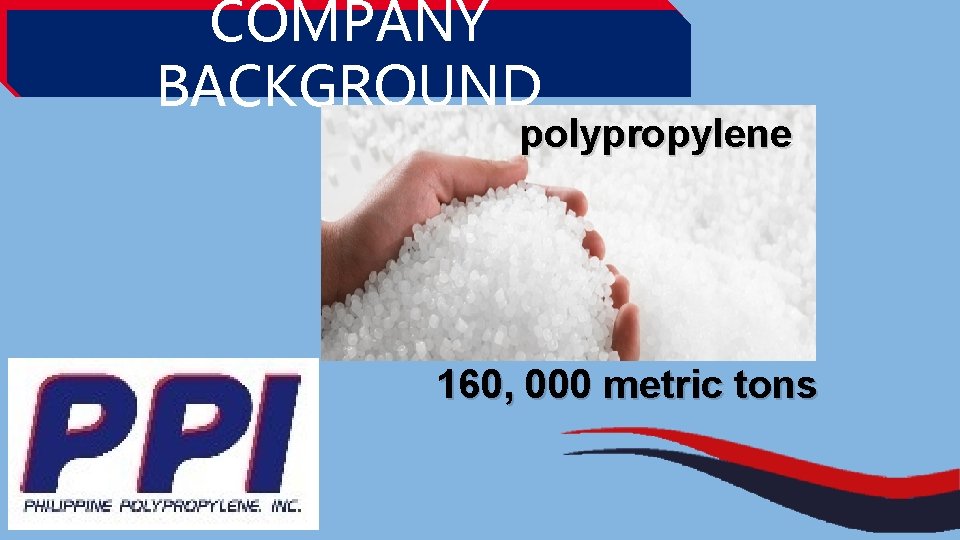
COMPANY BACKGROUND polypropylene 160, 000 metric tons
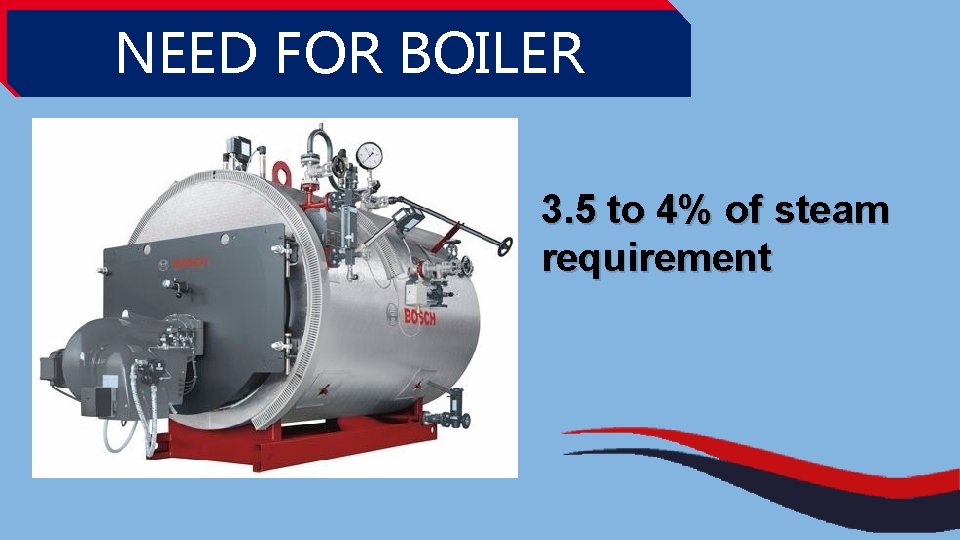
NEED FOR BOILER 3. 5 to 4% of steam requirement
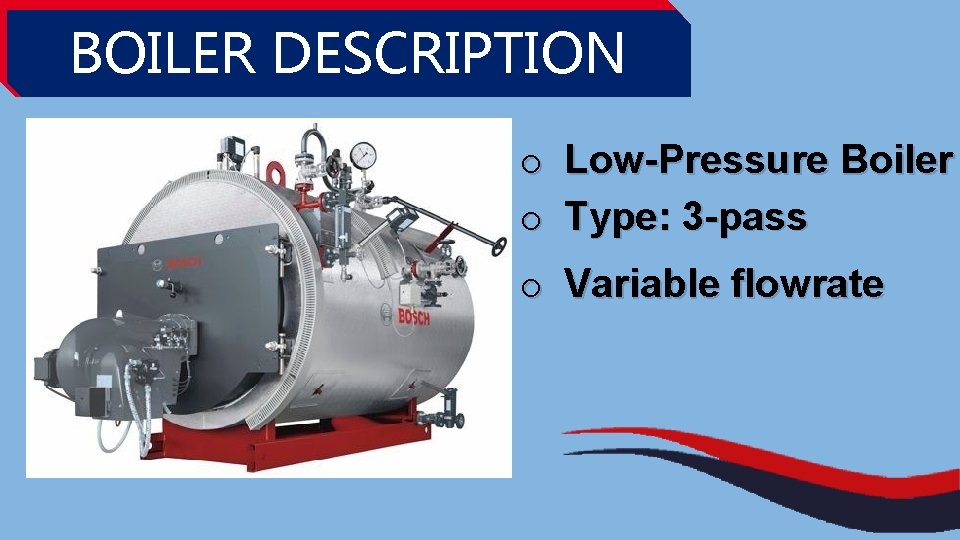
BOILER DESCRIPTION o Low-Pressure Boiler o Type: 3 -pass o Variable flowrate
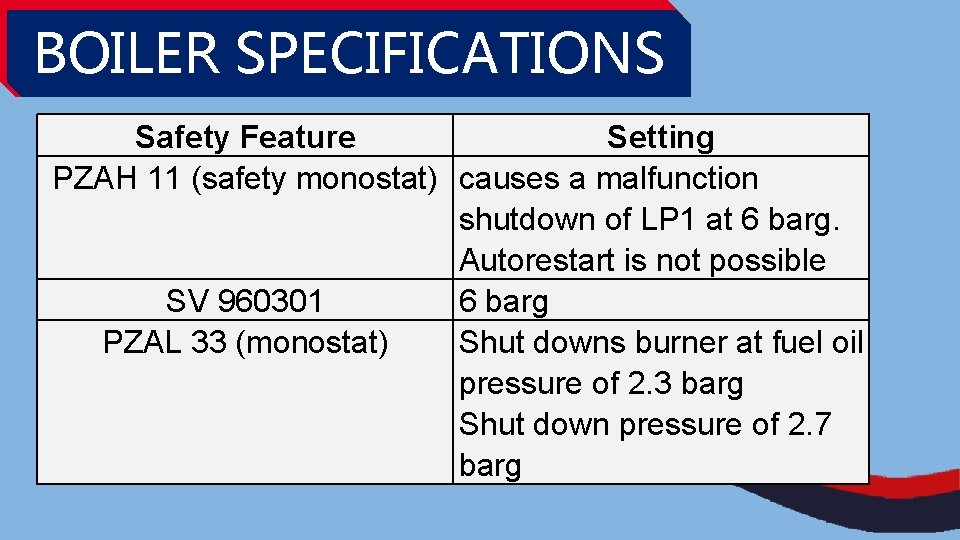
BOILER SPECIFICATIONS Safety Feature Setting PZAH 11 (safety monostat) causes a malfunction shutdown of LP 1 at 6 barg. Autorestart is not possible SV 960301 6 barg PZAL 33 (monostat) Shut downs burner at fuel oil pressure of 2. 3 barg Shut down pressure of 2. 7 barg
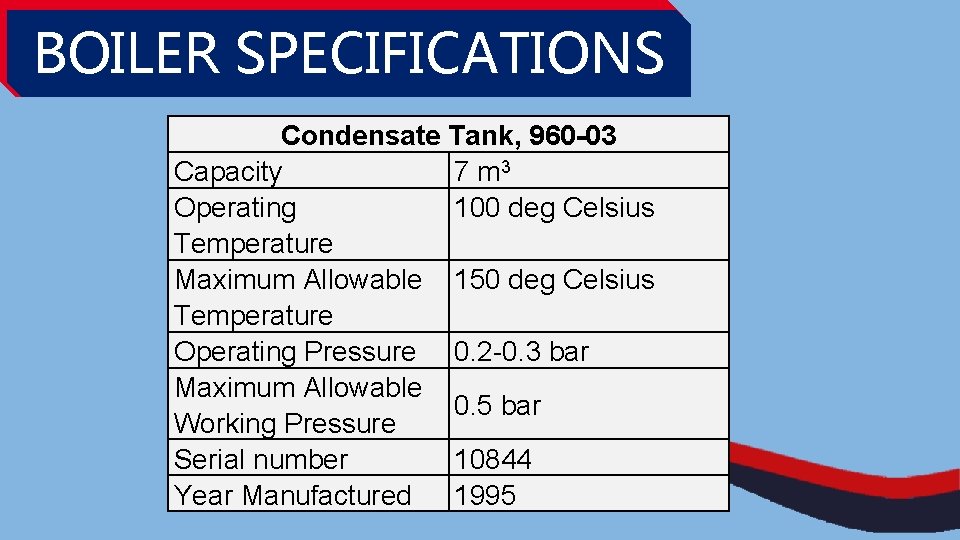
BOILER SPECIFICATIONS Condensate Tank, 960 -03 Capacity 7 m 3 Operating 100 deg Celsius Temperature Maximum Allowable 150 deg Celsius Temperature Operating Pressure 0. 2 -0. 3 bar Maximum Allowable 0. 5 bar Working Pressure Serial number 10844 Year Manufactured 1995
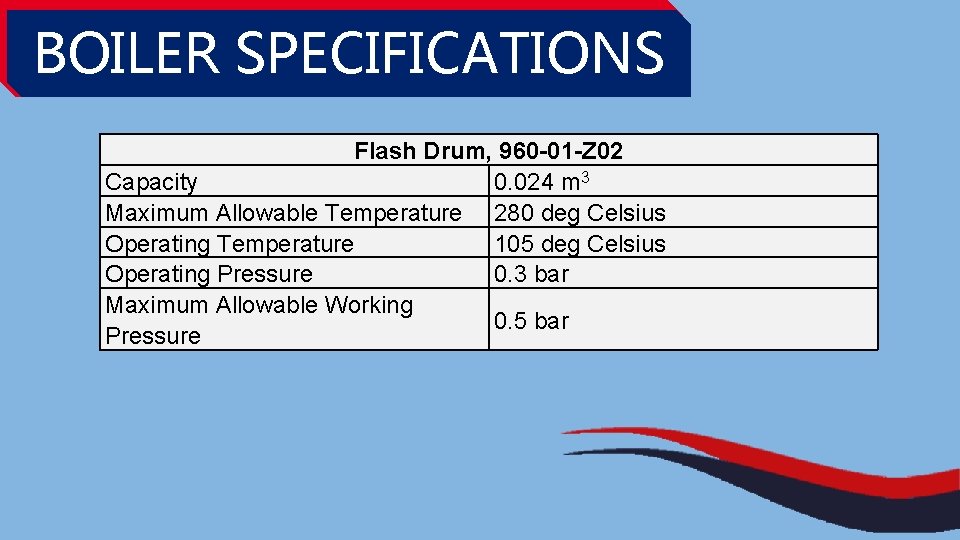
BOILER SPECIFICATIONS Flash Drum, 960 -01 -Z 02 Capacity 0. 024 m 3 Maximum Allowable Temperature 280 deg Celsius Operating Temperature 105 deg Celsius Operating Pressure 0. 3 bar Maximum Allowable Working 0. 5 bar Pressure
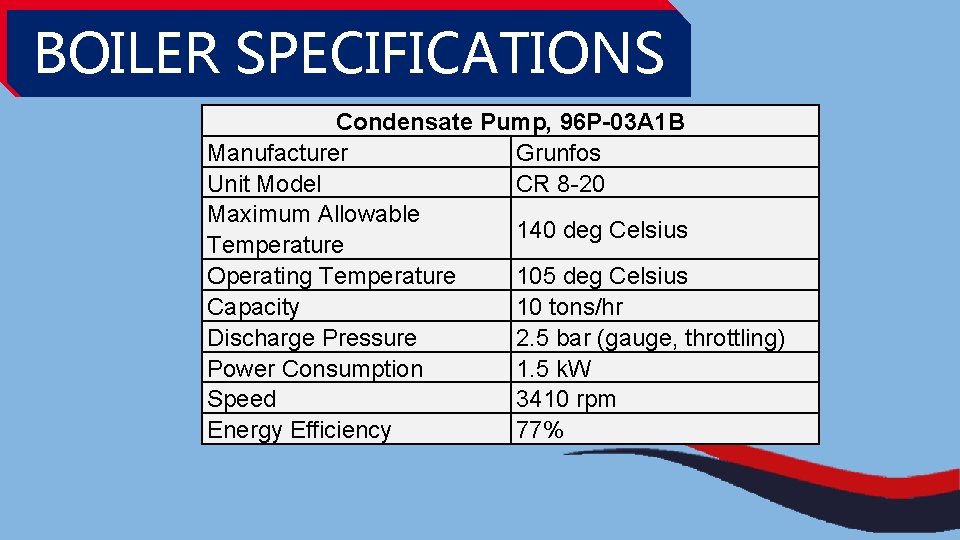
BOILER SPECIFICATIONS Condensate Pump, 96 P-03 A 1 B Manufacturer Grunfos Unit Model CR 8 -20 Maximum Allowable 140 deg Celsius Temperature Operating Temperature 105 deg Celsius Capacity 10 tons/hr Discharge Pressure 2. 5 bar (gauge, throttling) Power Consumption 1. 5 k. W Speed 3410 rpm Energy Efficiency 77%
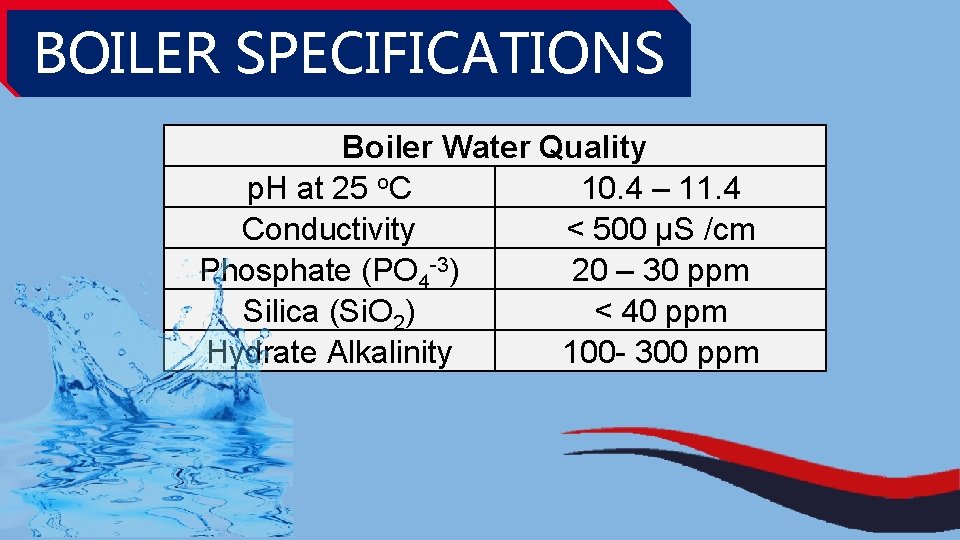
BOILER SPECIFICATIONS Boiler Water Quality p. H at 25 o. C 10. 4 – 11. 4 Conductivity < 500 µS /cm Phosphate (PO 4 -3) 20 – 30 ppm Silica (Si. O 2) < 40 ppm Hydrate Alkalinity 100 - 300 ppm
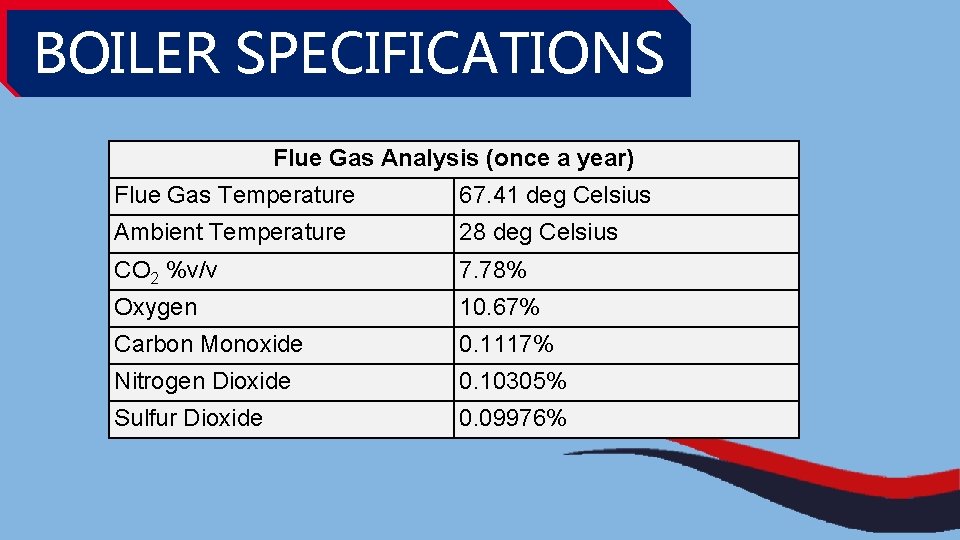
BOILER SPECIFICATIONS Flue Gas Analysis (once a year) Flue Gas Temperature 67. 41 deg Celsius Ambient Temperature 28 deg Celsius CO 2 %v/v 7. 78% Oxygen 10. 67% Carbon Monoxide 0. 1117% Nitrogen Dioxide 0. 10305% Sulfur Dioxide 0. 09976%
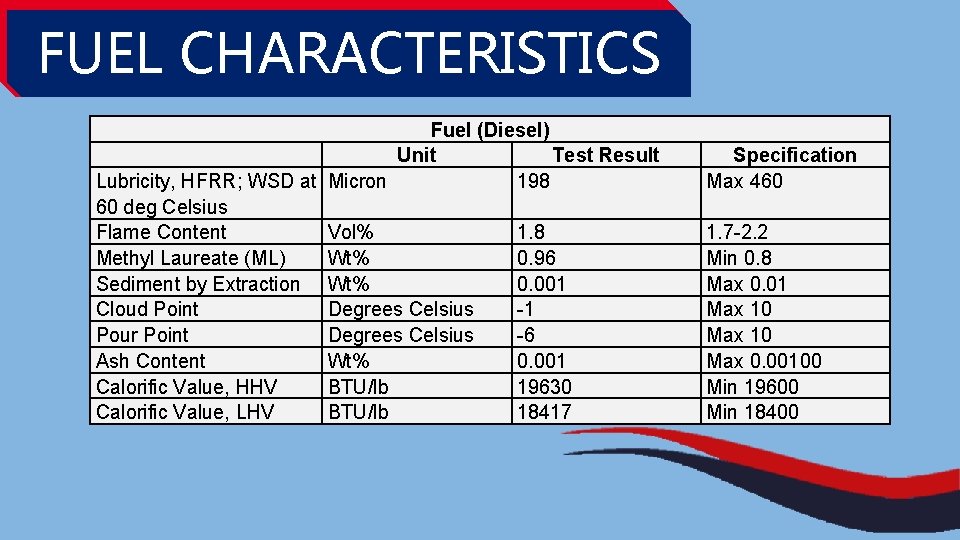
FUEL CHARACTERISTICS Fuel (Diesel) Unit Test Result Lubricity, HFRR; WSD at Micron 198 60 deg Celsius Flame Content Vol% 1. 8 Methyl Laureate (ML) Wt% 0. 96 Sediment by Extraction Wt% 0. 001 Cloud Point Degrees Celsius -1 Pour Point Degrees Celsius -6 Ash Content Wt% 0. 001 Calorific Value, HHV BTU/lb 19630 Calorific Value, LHV BTU/lb 18417 Specification Max 460 1. 7 -2. 2 Min 0. 8 Max 0. 01 Max 10 Max 0. 00100 Min 19600 Min 18400
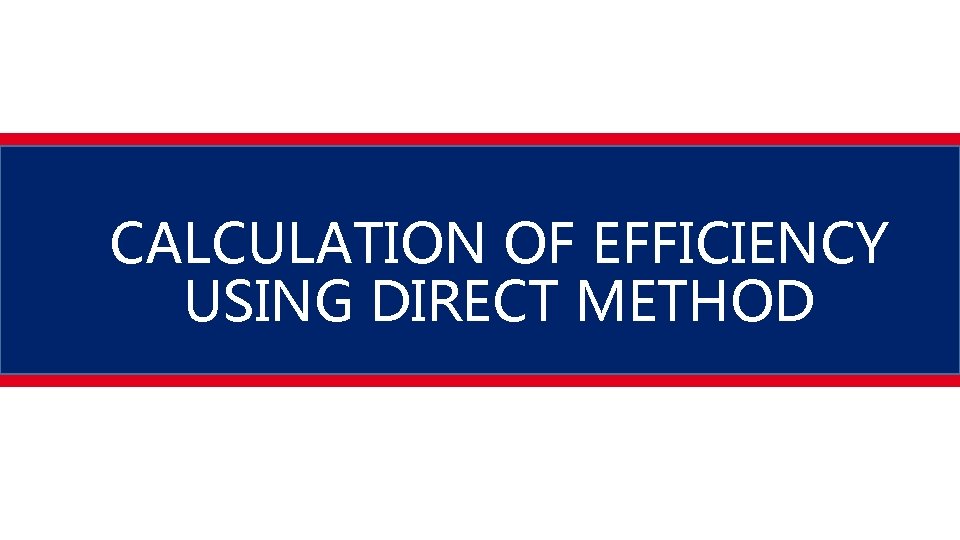
CALCULATION OF EFFICIENCY USING DIRECT METHOD
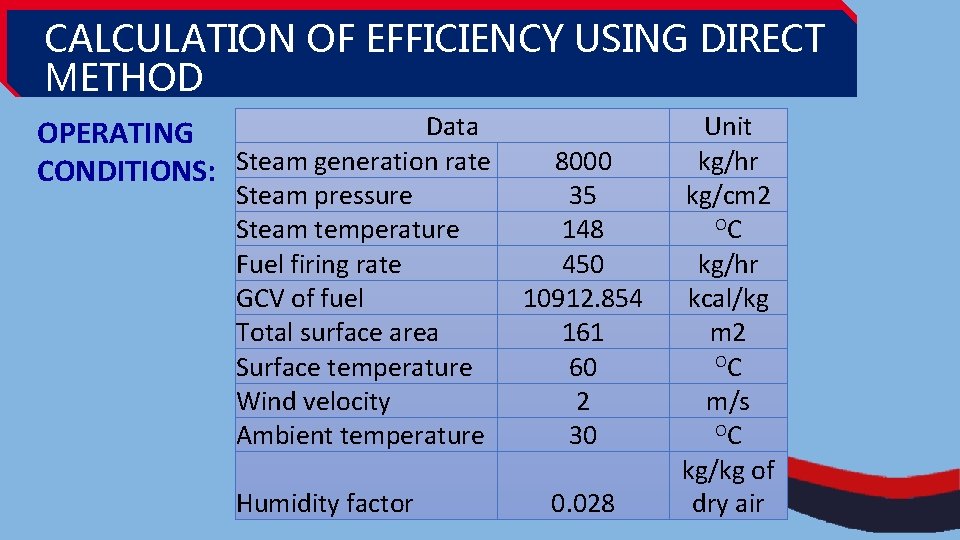
CALCULATION OF EFFICIENCY USING DIRECT METHOD Data OPERATING CONDITIONS: Steam generation rate Steam pressure Steam temperature Fuel firing rate GCV of fuel Total surface area Surface temperature Wind velocity Ambient temperature Humidity factor 8000 35 148 450 10912. 854 161 60 2 30 0. 028 Unit kg/hr kg/cm 2 OC kg/hr kcal/kg m 2 OC m/s OC kg/kg of dry air
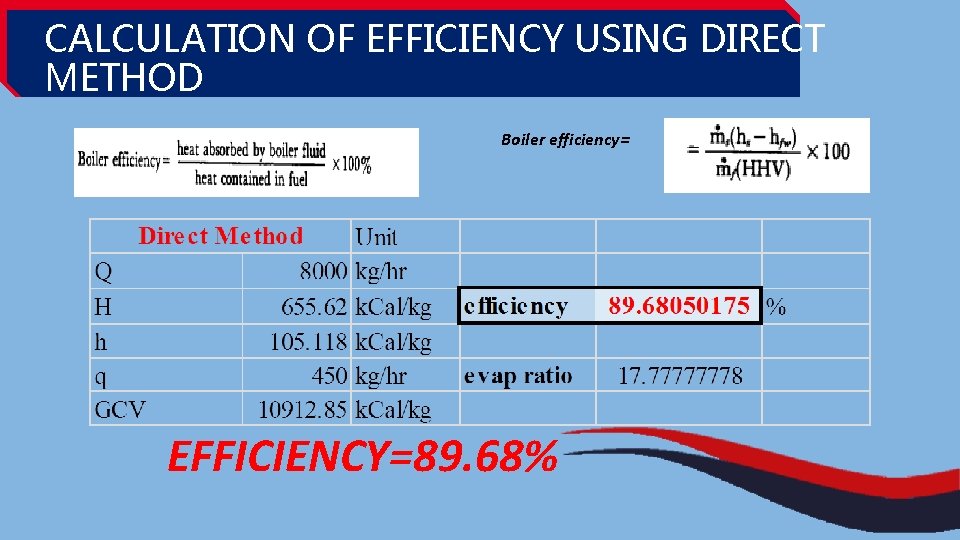
CALCULATION OF EFFICIENCY USING DIRECT METHOD Boiler efficiency= EFFICIENCY=89. 68%
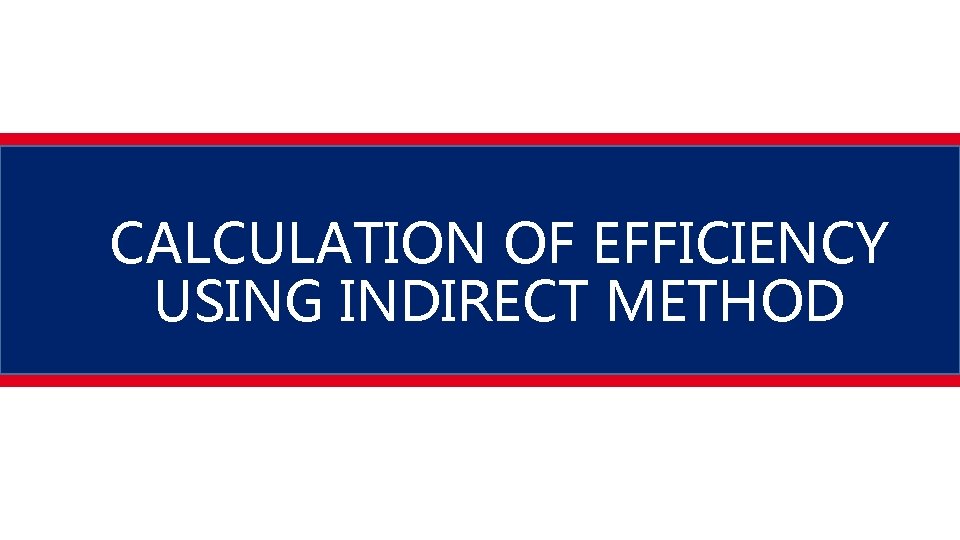
CALCULATION OF EFFICIENCY USING INDIRECT METHOD
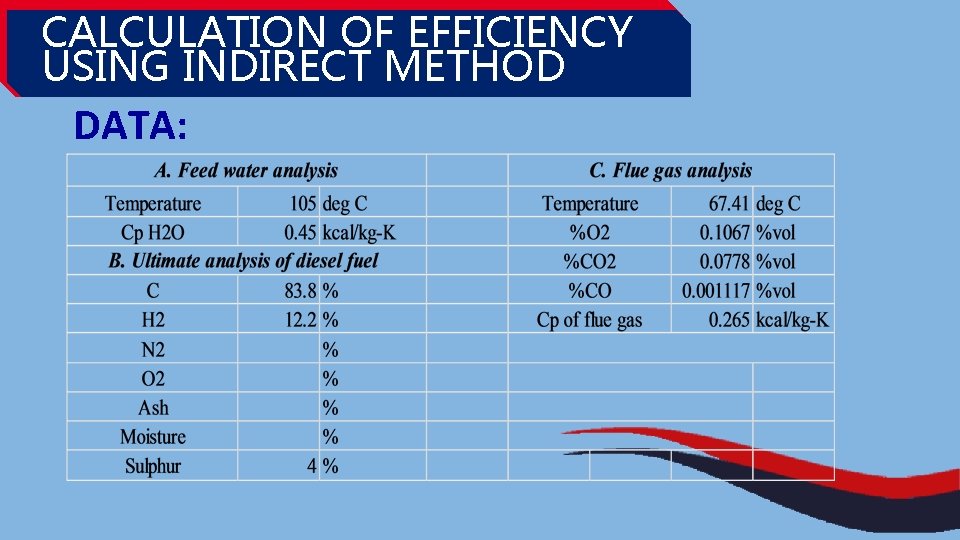
CALCULATION OF EFFICIENCY USING INDIRECT METHOD DATA:
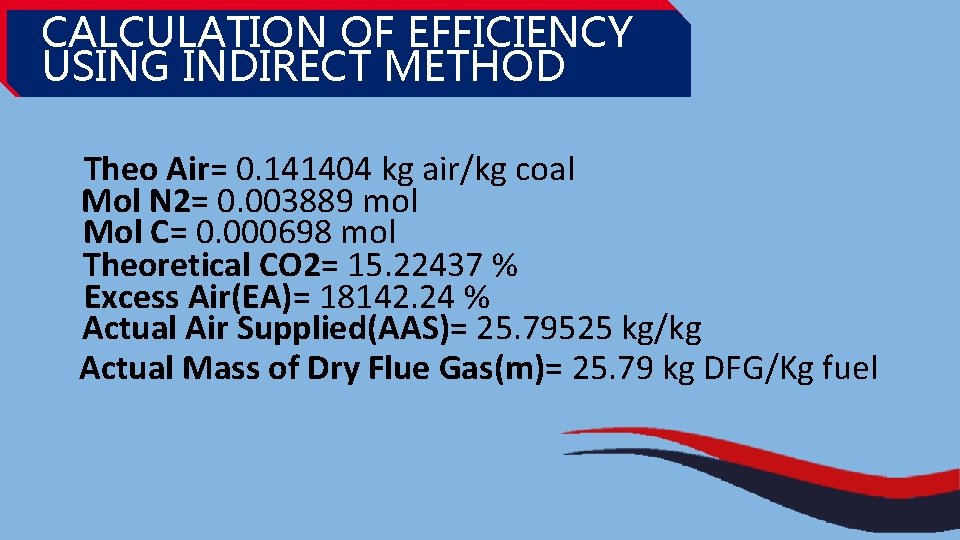
CALCULATION OF EFFICIENCY USING INDIRECT METHOD Theo Air= 0. 141404 kg air/kg coal Mol N 2= 0. 003889 mol Mol C= 0. 000698 mol Theoretical CO 2= 15. 22437 % Excess Air(EA)= 18142. 24 % Actual Air Supplied(AAS)= 25. 79525 kg/kg Actual Mass of Dry Flue Gas(m)= 25. 79 kg DFG/Kg fuel
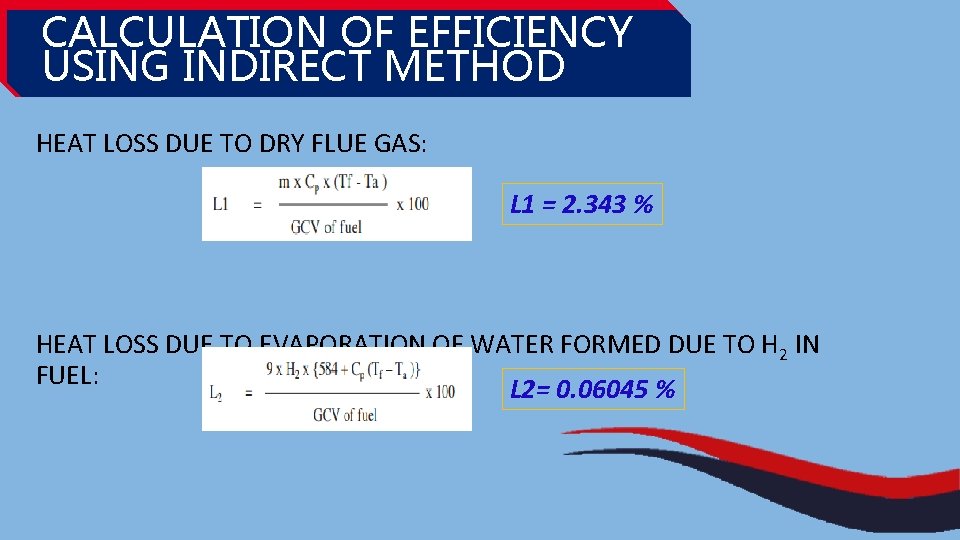
CALCULATION OF EFFICIENCY USING INDIRECT METHOD HEAT LOSS DUE TO DRY FLUE GAS: L 1 = 2. 343 % HEAT LOSS DUE TO EVAPORATION OF WATER FORMED DUE TO H 2 IN FUEL: L 2= 0. 06045 %
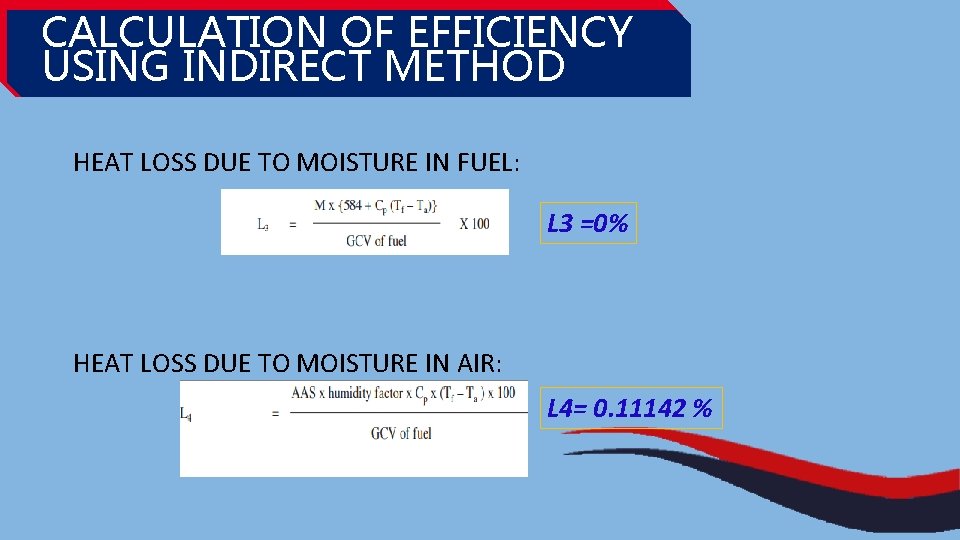
CALCULATION OF EFFICIENCY USING INDIRECT METHOD HEAT LOSS DUE TO MOISTURE IN FUEL: L 3 =0% HEAT LOSS DUE TO MOISTURE IN AIR: L 4= 0. 11142 %
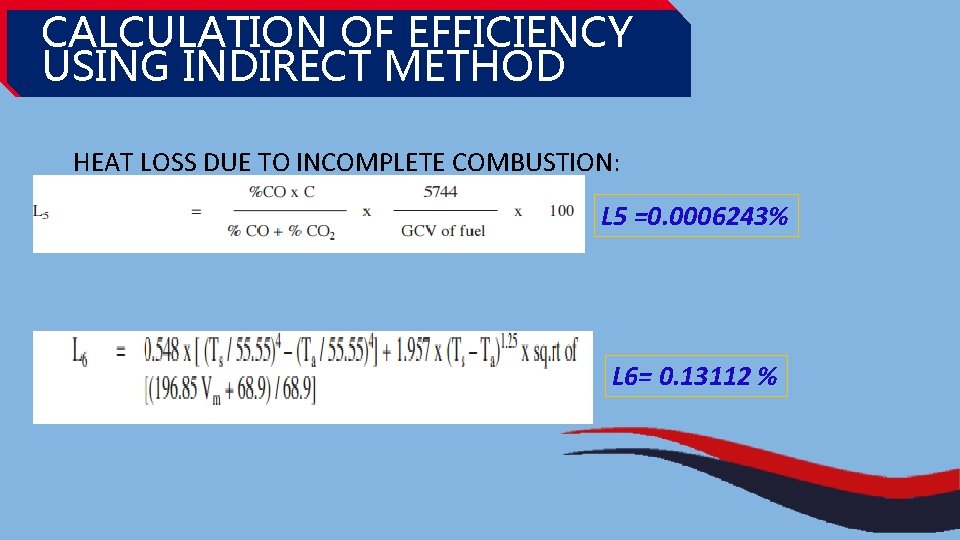
CALCULATION OF EFFICIENCY USING INDIRECT METHOD HEAT LOSS DUE TO INCOMPLETE COMBUSTION: L 5 =0. 0006243% HEAT DUE TO MOISTURE IN AIR: L 6= 0. 13112 %
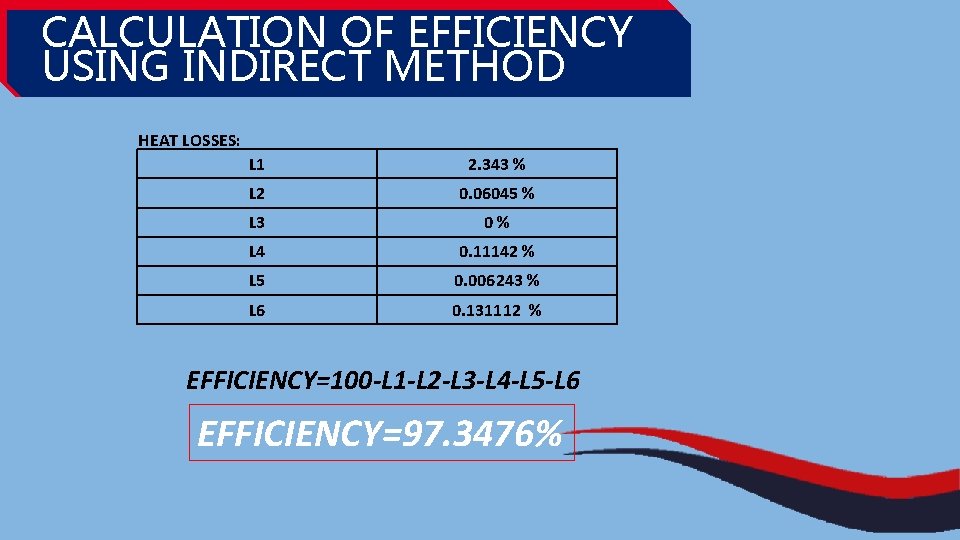
CALCULATION OF EFFICIENCY USING INDIRECT METHOD HEAT LOSSES: L 1 2. 343 % L 2 0. 06045 % L 3 0% L 4 0. 11142 % L 5 0. 006243 % L 6 0. 131112 % EFFICIENCY=100 -L 1 -L 2 -L 3 -L 4 -L 5 -L 6 EFFICIENCY=97. 3476%
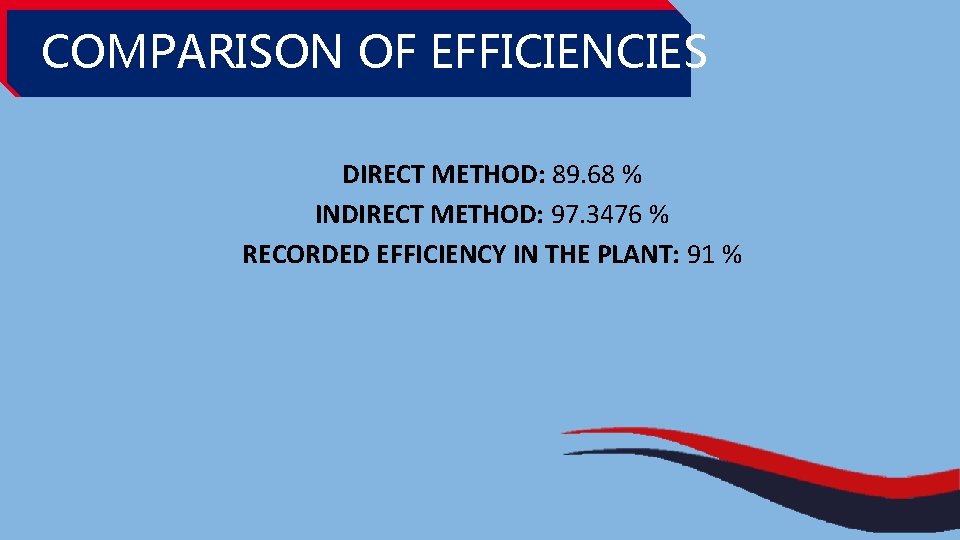
COMPARISON OF EFFICIENCIES DIRECT METHOD: 89. 68 % INDIRECT METHOD: 97. 3476 % RECORDED EFFICIENCY IN THE PLANT: 91 %
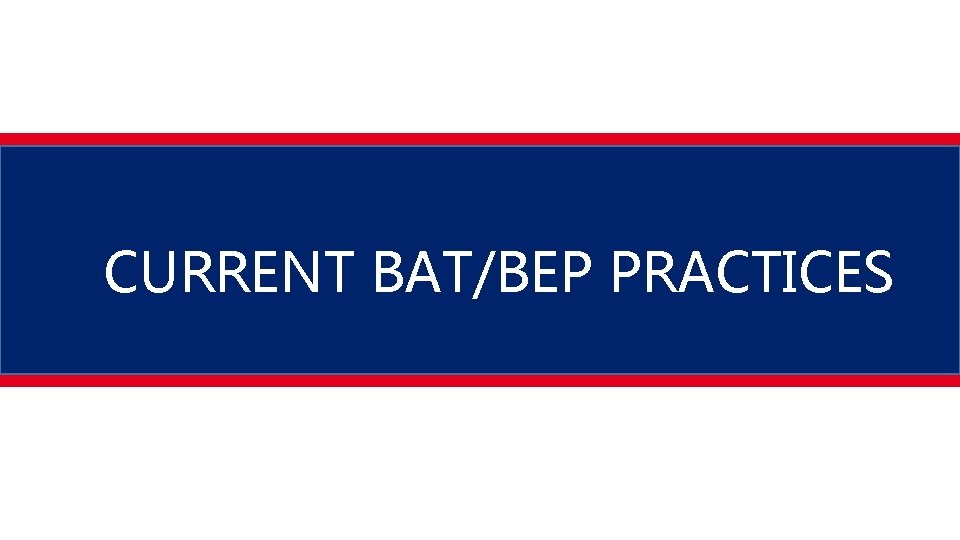
CURRENT BAT/BEP PRACTICES
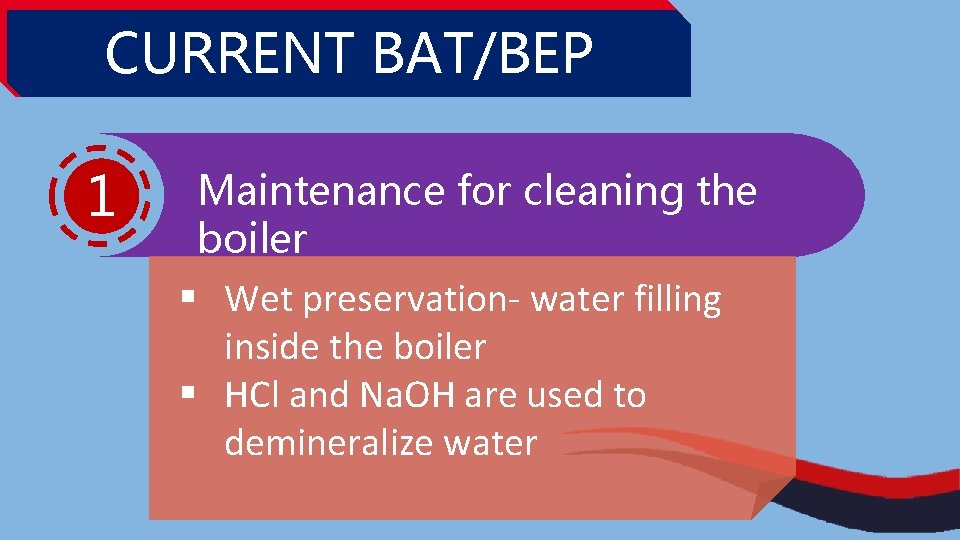
CURRENT BAT/BEP 1 Maintenance for cleaning the boiler § Wet preservation- water filling inside the boiler § HCl and Na. OH are used to demineralize water
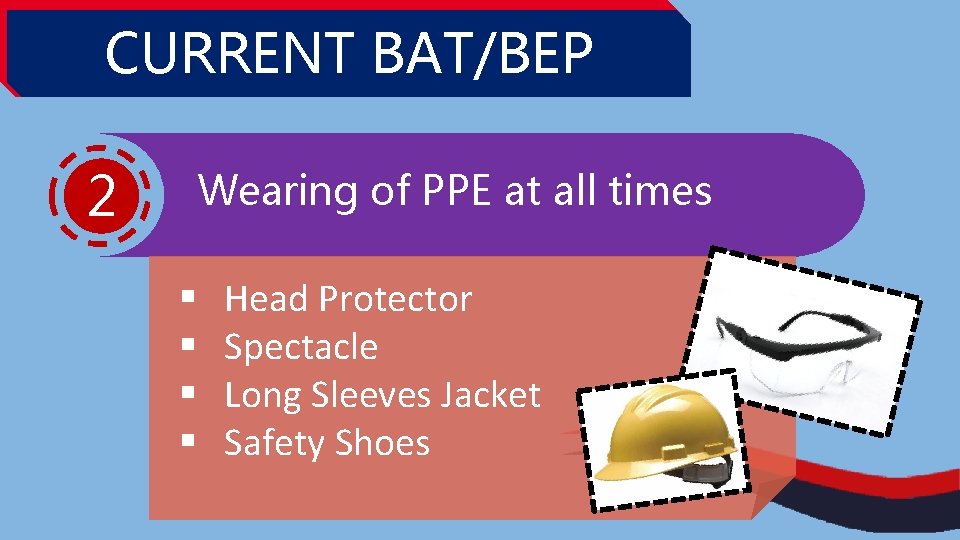
CURRENT BAT/BEP 2 Wearing of PPE at all times § § Head Protector Spectacle Long Sleeves Jacket Safety Shoes
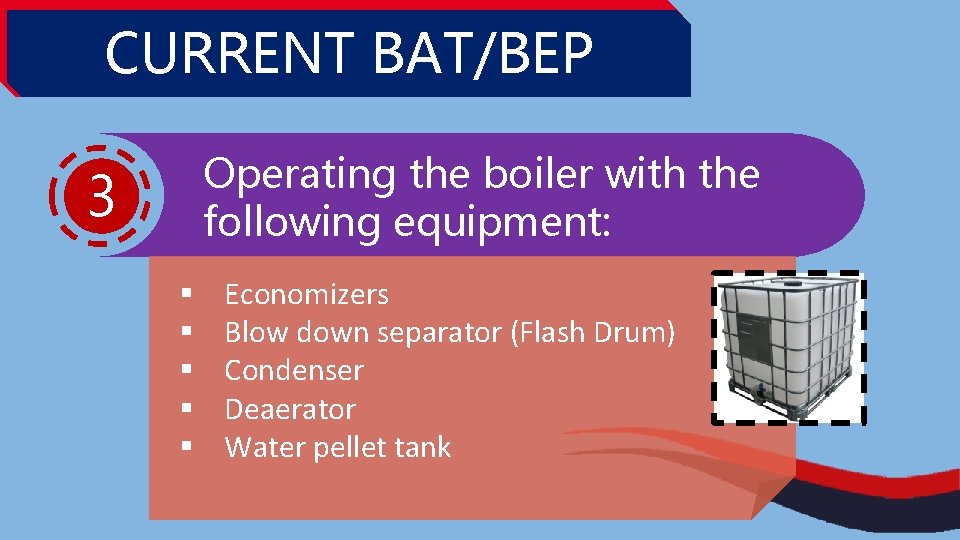
CURRENT BAT/BEP Operating the boiler with the following equipment: 3 § § § Economizers Blow down separator (Flash Drum) Condenser Deaerator Water pellet tank
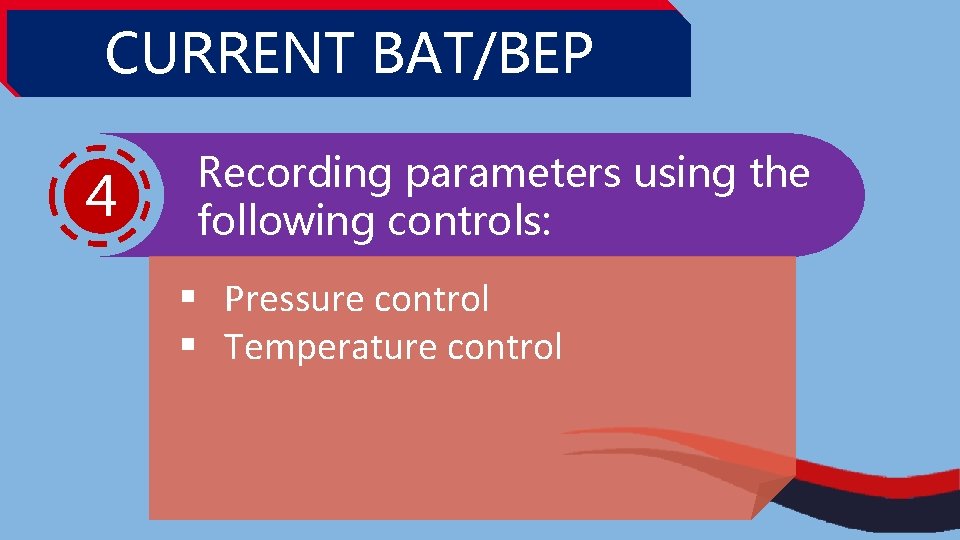
CURRENT BAT/BEP 4 Recording parameters using the following controls: § Pressure control § Temperature control
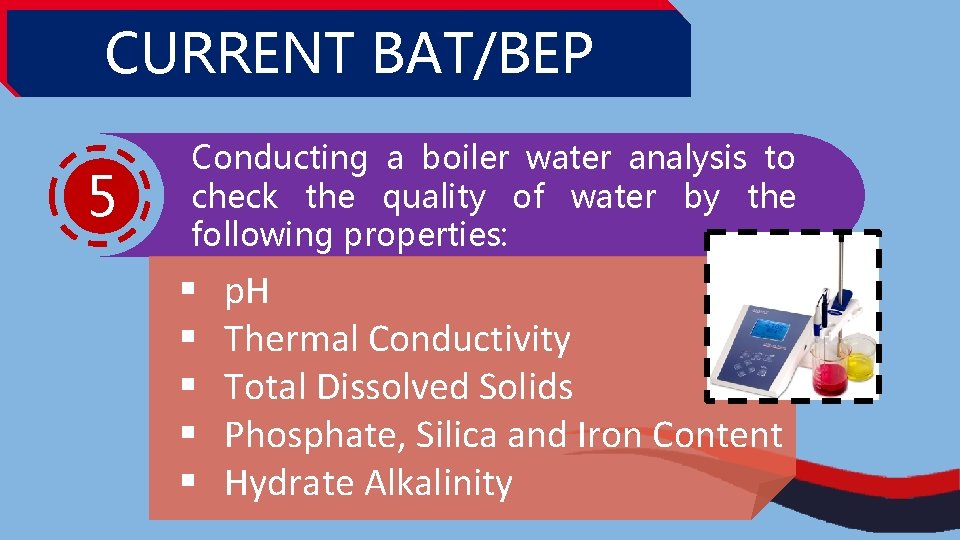
CURRENT BAT/BEP 5 Conducting a boiler water analysis to check the quality of water by the following properties: § § § p. H Thermal Conductivity Total Dissolved Solids Phosphate, Silica and Iron Content Hydrate Alkalinity
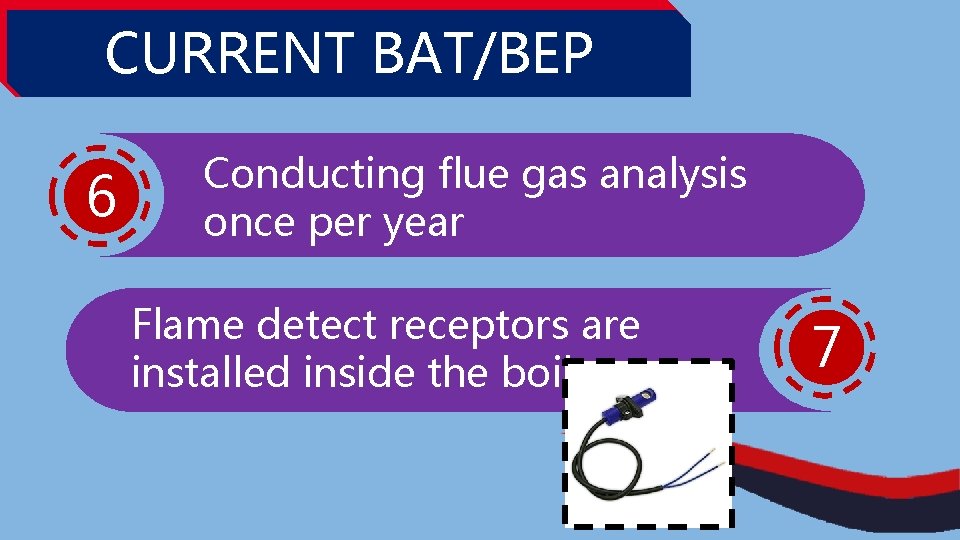
CURRENT BAT/BEP 6 Conducting flue gas analysis once per year Flame detect receptors are installed inside the boiler 7
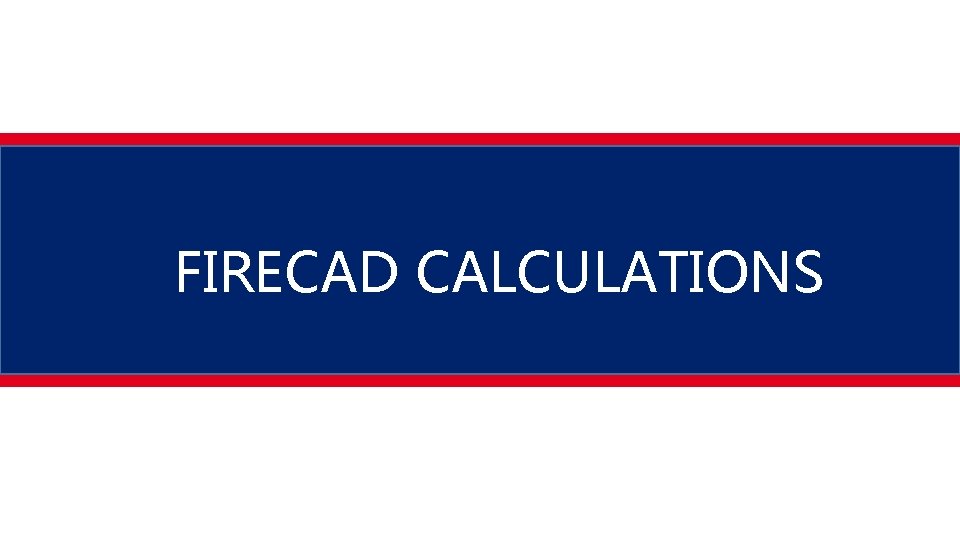
FIRECAD CALCULATIONS
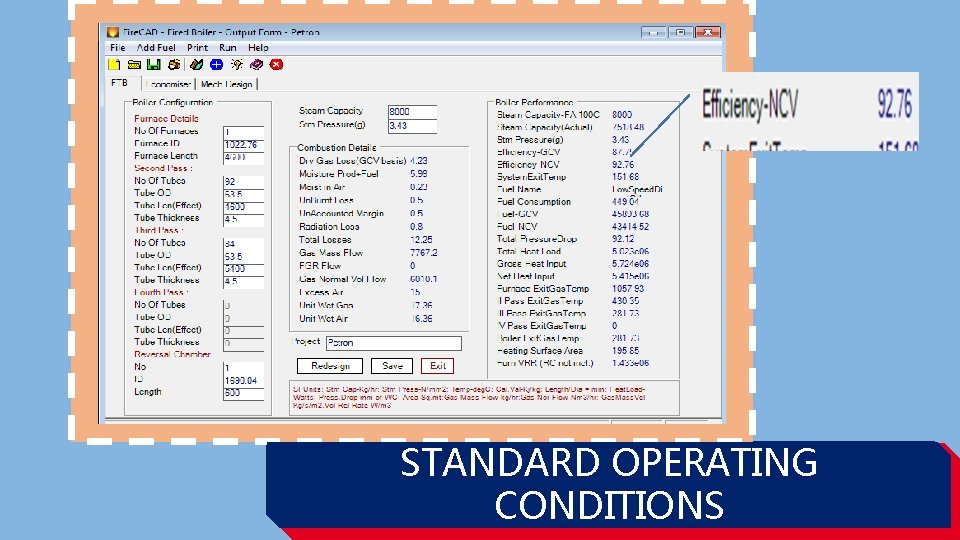
Put your calculations Here STANDARD OPERATING CONDITIONS
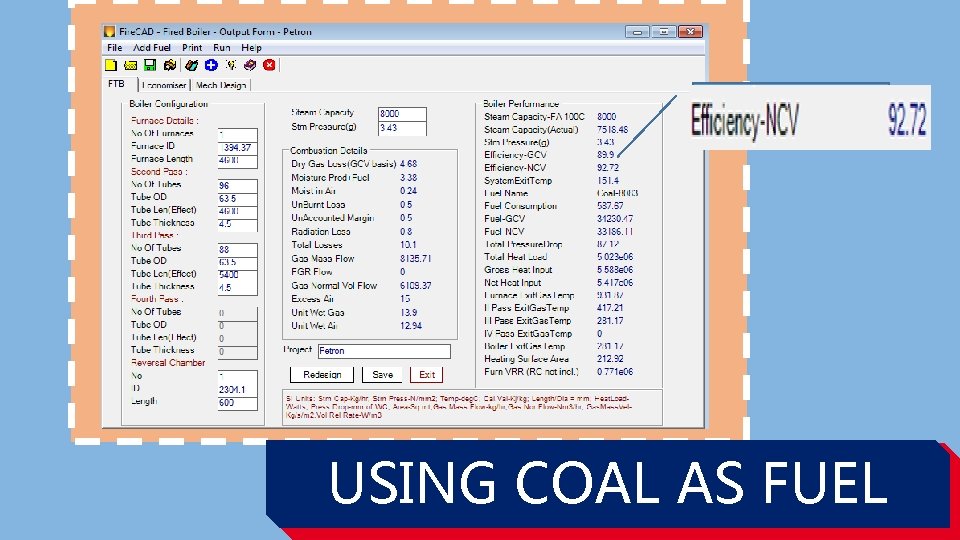
Put your calculations Here USING COAL AS FUEL
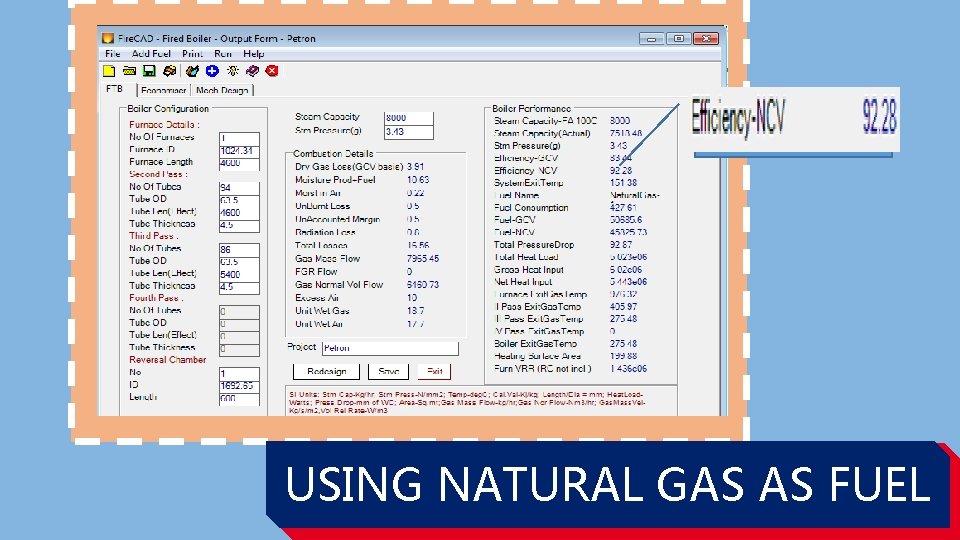
Put your calculations Here USING NATURAL GAS AS FUEL
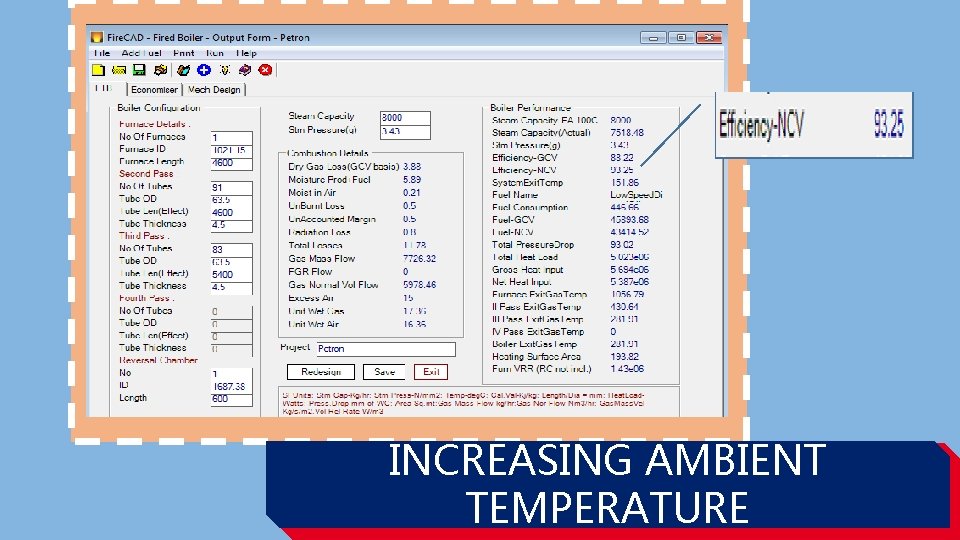
Put your calculations Here INCREASING AMBIENT TEMPERATURE
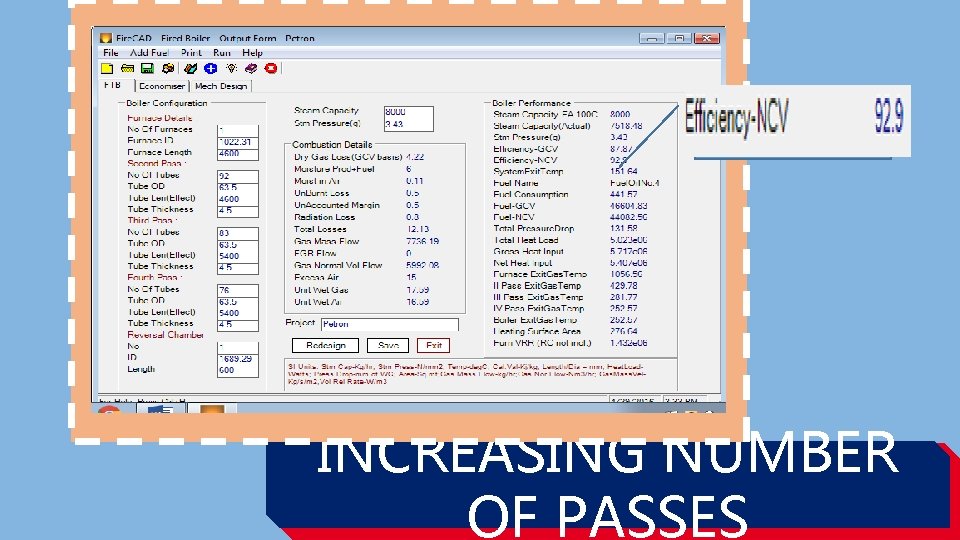
Put your calculations Here INCREASING NUMBER OF PASSES
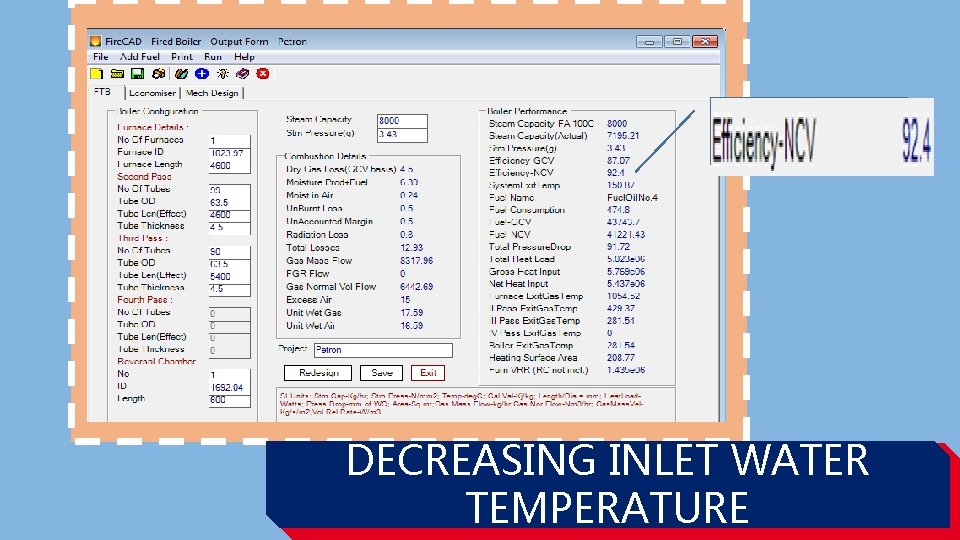
Put your calculations Here DECREASING INLET WATER TEMPERATURE
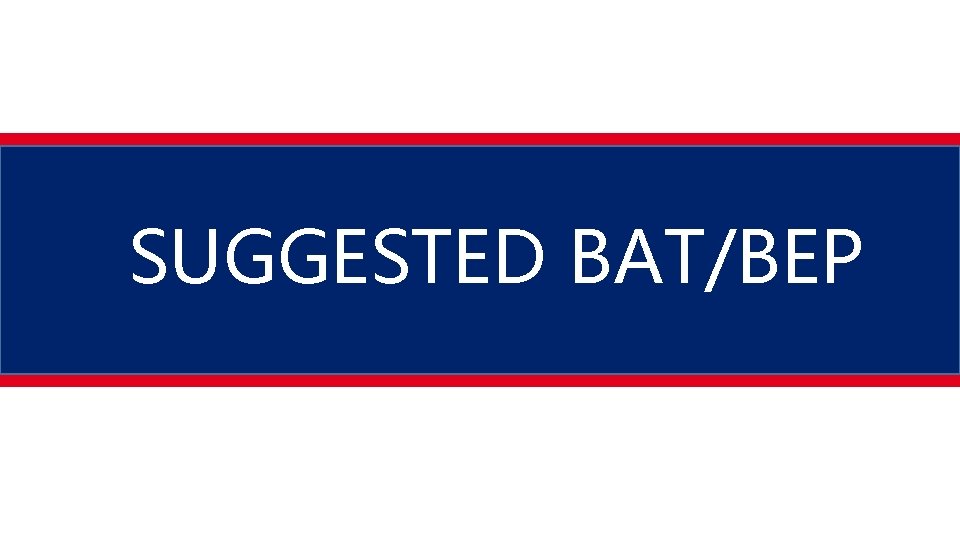
SUGGESTED BAT/BEP
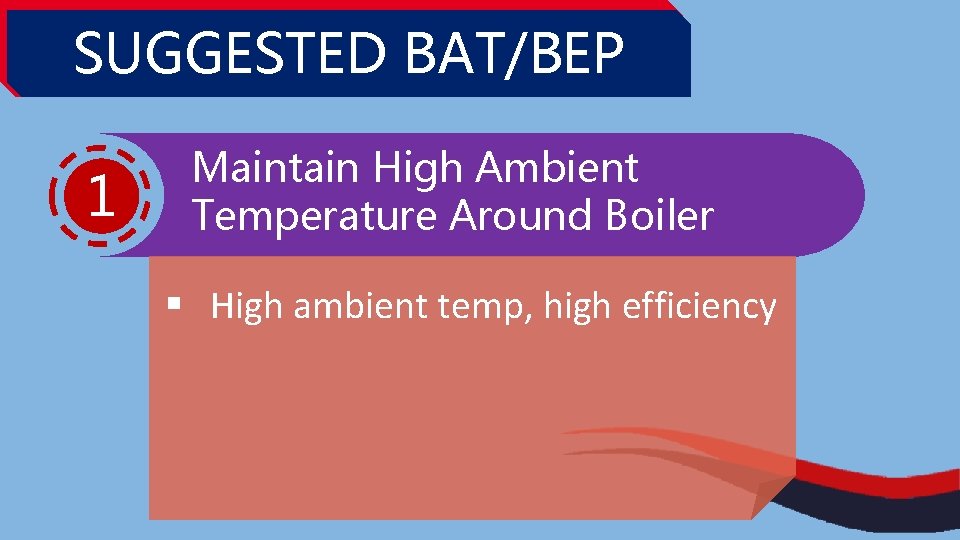
SUGGESTED BAT/BEP 1 Maintain High Ambient Temperature Around Boiler § High ambient temp, high efficiency
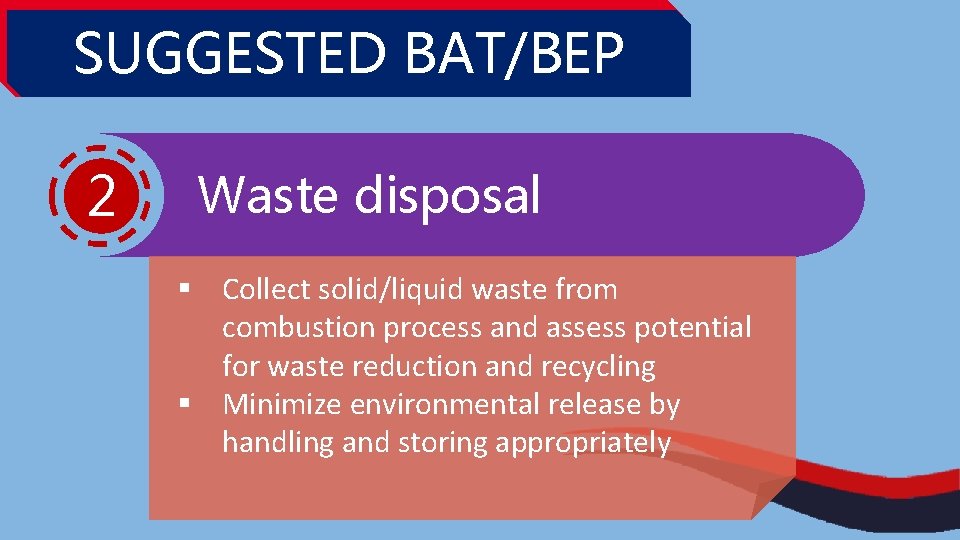
SUGGESTED BAT/BEP 2 Waste disposal § Collect solid/liquid waste from combustion process and assess potential for waste reduction and recycling § Minimize environmental release by handling and storing appropriately
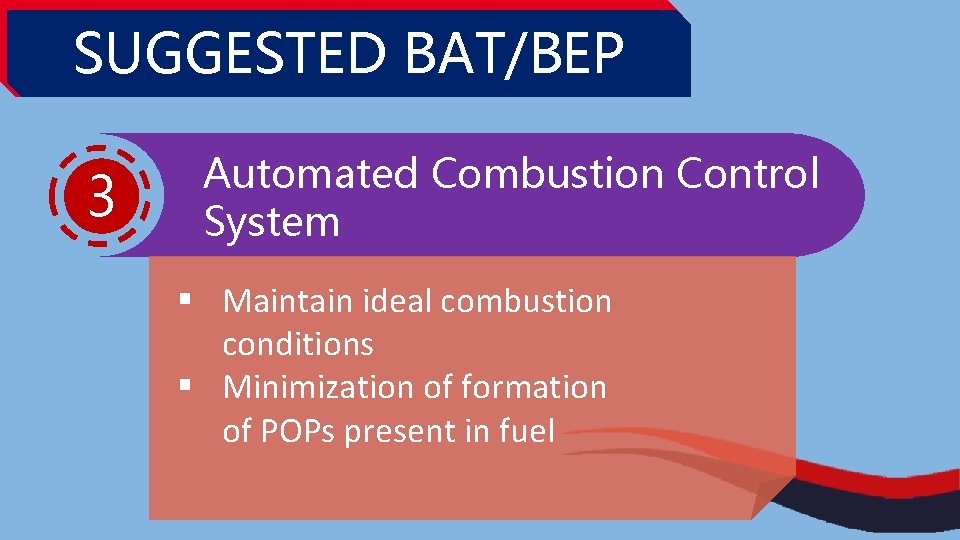
SUGGESTED BAT/BEP 3 Automated Combustion Control System § Maintain ideal combustion conditions § Minimization of formation of POPs present in fuel
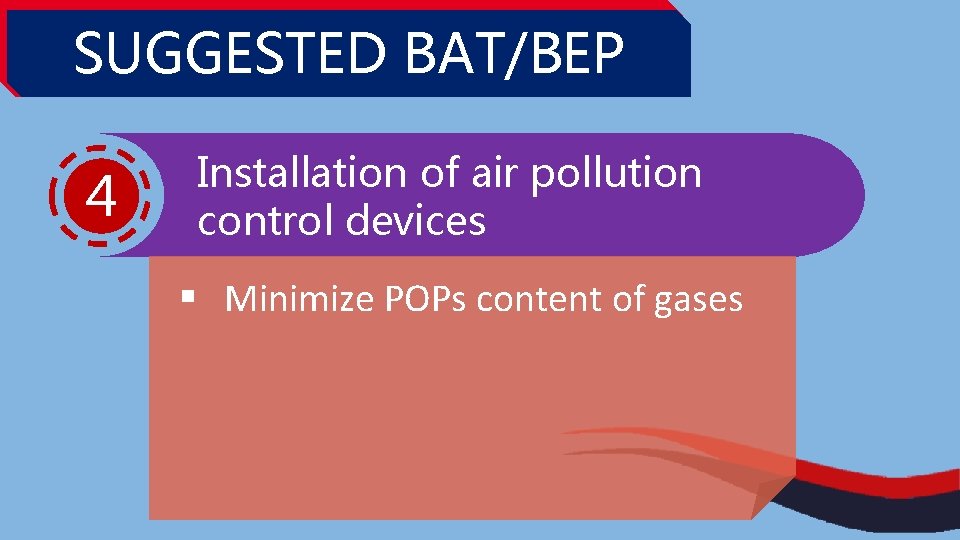
SUGGESTED BAT/BEP 4 Installation of air pollution control devices § Minimize POPs content of gases
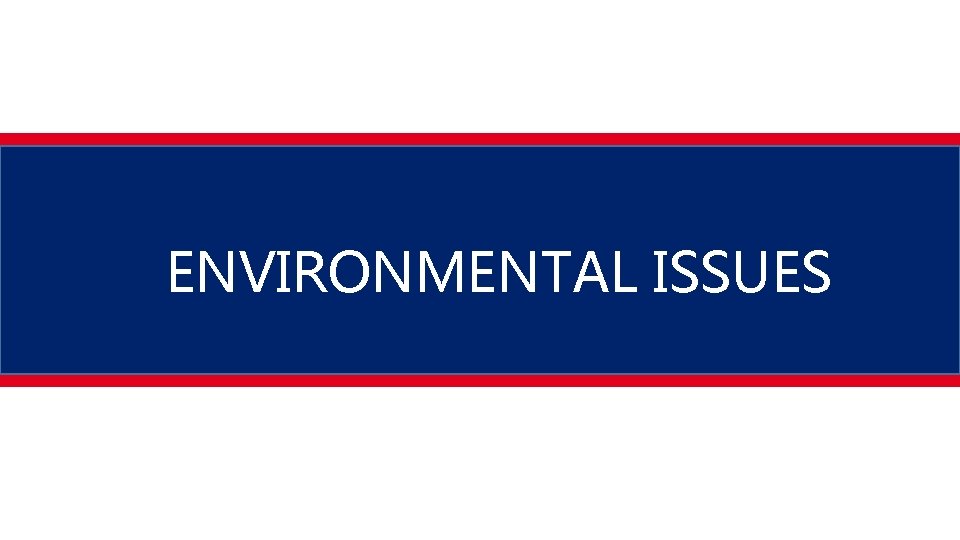
ENVIRONMENTAL ISSUES
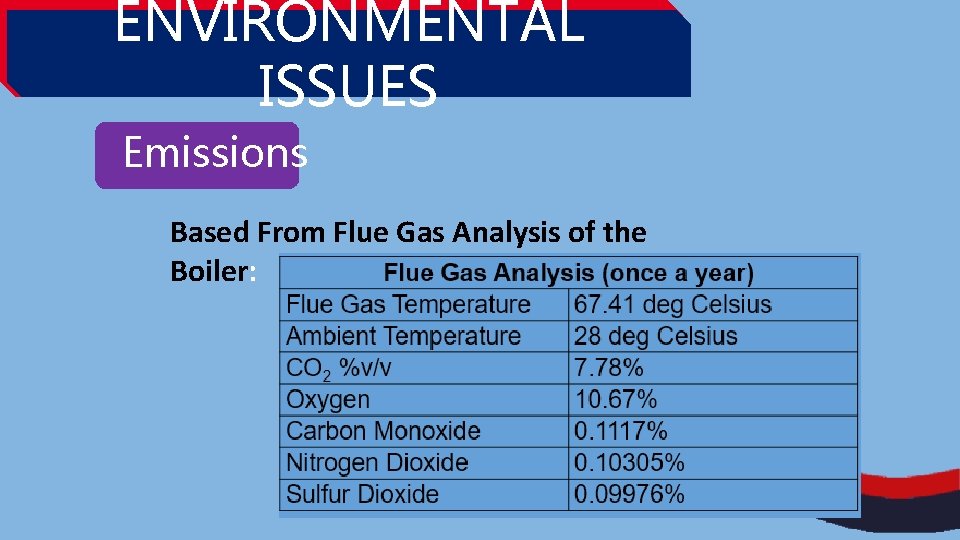
ENVIRONMENTAL ISSUES Emissions Based From Flue Gas Analysis of the Boiler:
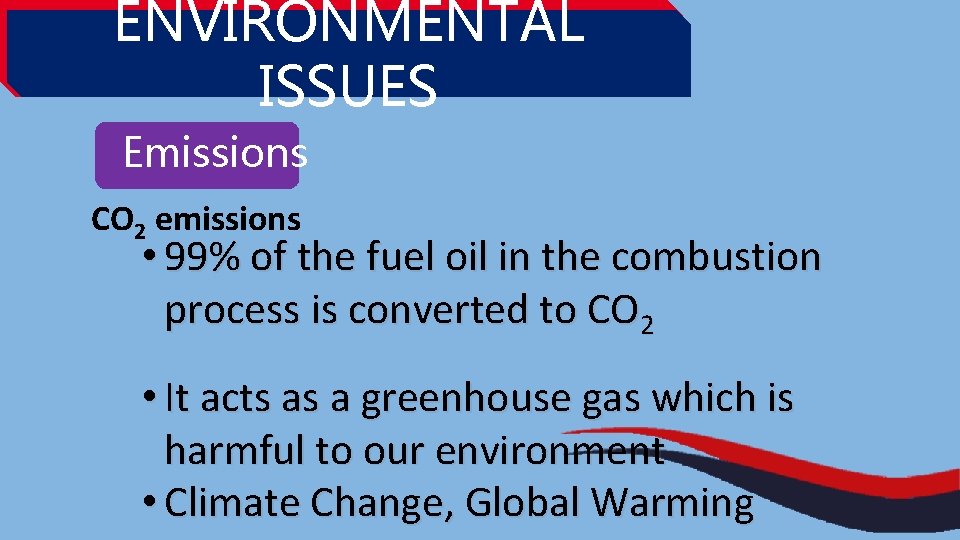
ENVIRONMENTAL ISSUES Emissions CO 2 emissions • 99% of the fuel oil in the combustion process is converted to CO 2 • It acts as a greenhouse gas which is harmful to our environment • Climate Change, Global Warming
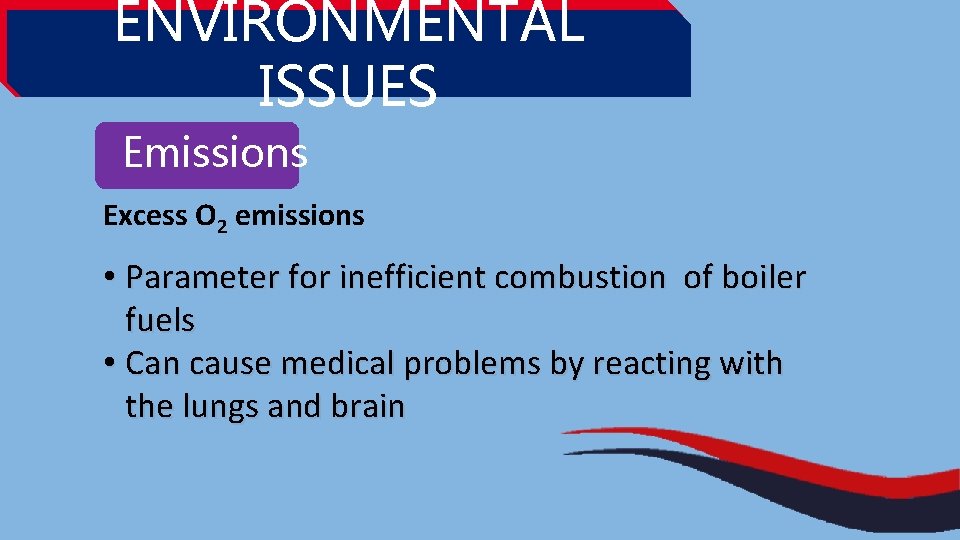
ENVIRONMENTAL ISSUES Emissions Excess O 2 emissions • Parameter for inefficient combustion of boiler fuels • Can cause medical problems by reacting with the lungs and brain
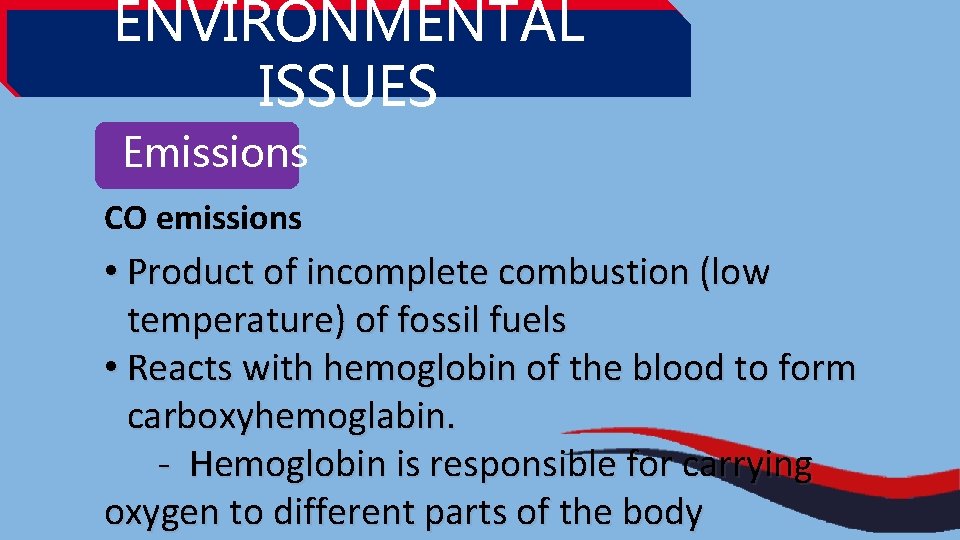
ENVIRONMENTAL ISSUES Emissions CO emissions • Product of incomplete combustion (low temperature) of fossil fuels • Reacts with hemoglobin of the blood to form carboxyhemoglabin. - Hemoglobin is responsible for carrying oxygen to different parts of the body
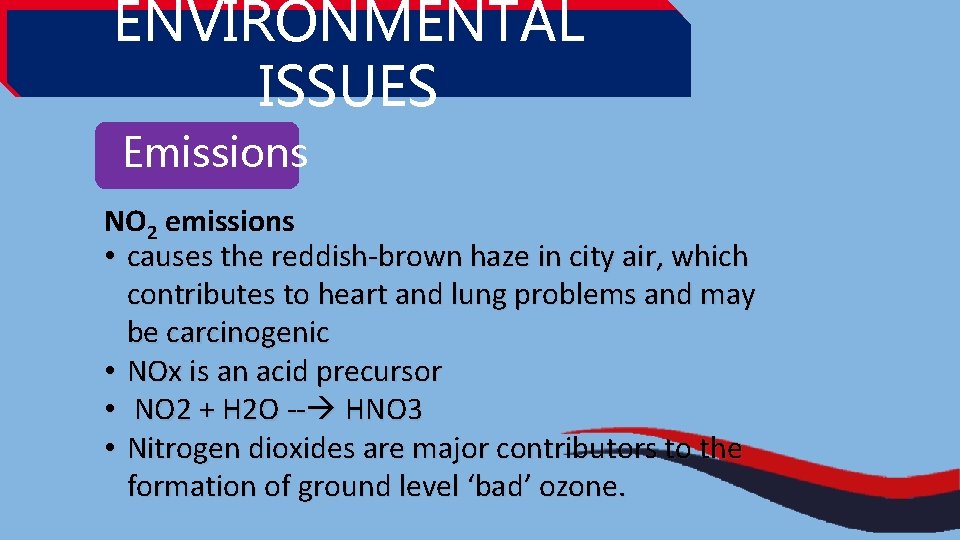
ENVIRONMENTAL ISSUES Emissions NO 2 emissions • causes the reddish-brown haze in city air, which contributes to heart and lung problems and may be carcinogenic • NOx is an acid precursor • NO 2 + H 2 O -- HNO 3 • Nitrogen dioxides are major contributors to the formation of ground level ‘bad’ ozone.
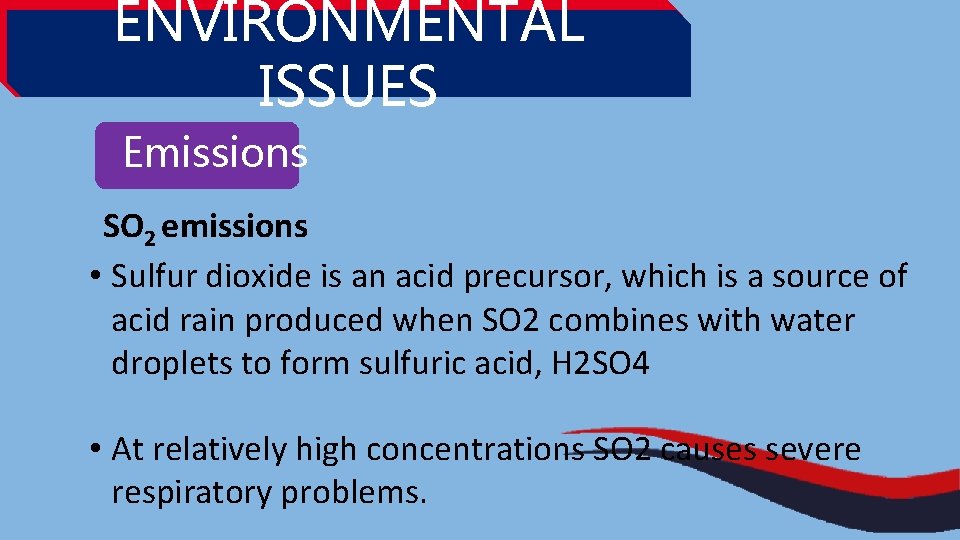
ENVIRONMENTAL ISSUES Emissions SO 2 emissions • Sulfur dioxide is an acid precursor, which is a source of acid rain produced when SO 2 combines with water droplets to form sulfuric acid, H 2 SO 4 • At relatively high concentrations SO 2 causes severe respiratory problems.
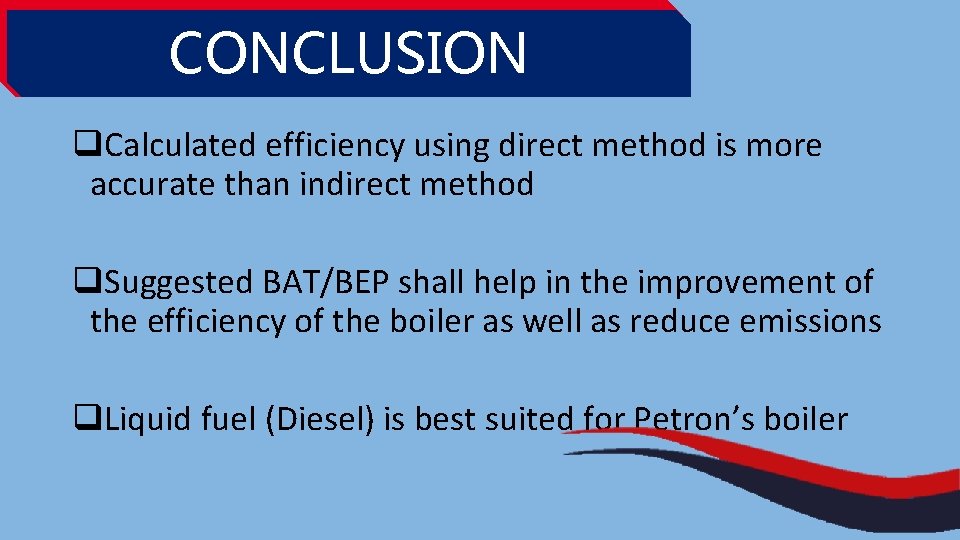
CONCLUSION q. Calculated efficiency using direct method is more accurate than indirect method q. Suggested BAT/BEP shall help in the improvement of the efficiency of the boiler as well as reduce emissions q. Liquid fuel (Diesel) is best suited for Petron’s boiler
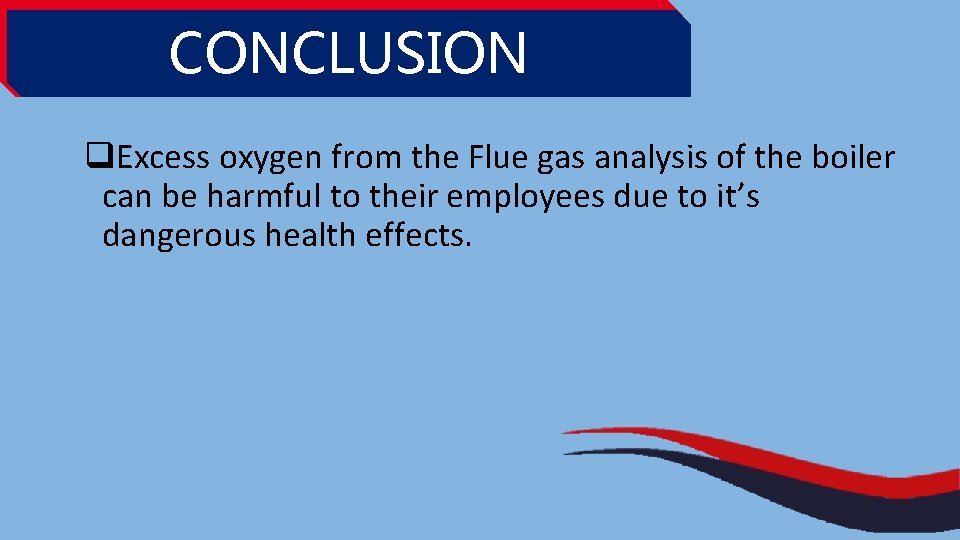
CONCLUSION q. Excess oxygen from the Flue gas analysis of the boiler can be harmful to their employees due to it’s dangerous health effects.
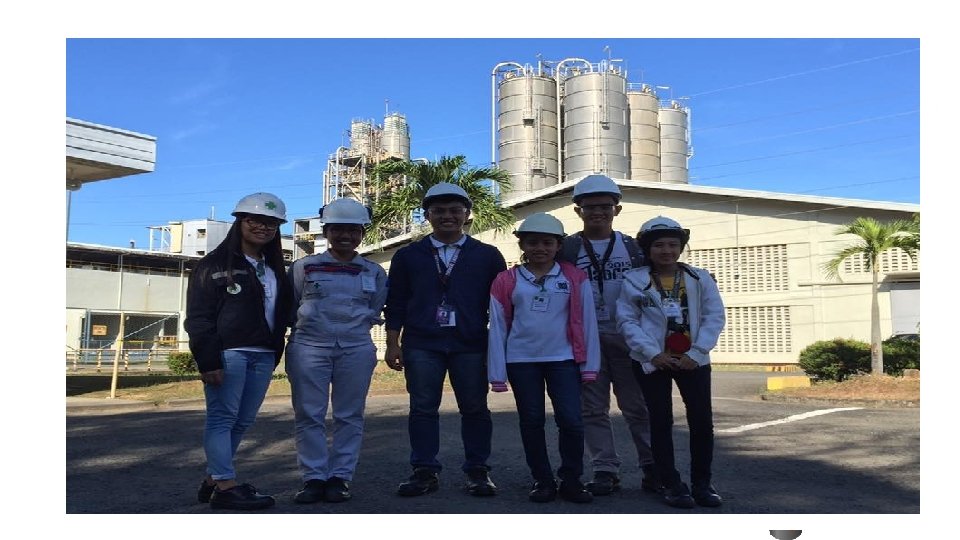
THANK YOU FOR YOUR ATTENTION! Inse rt Gr o up p ic here
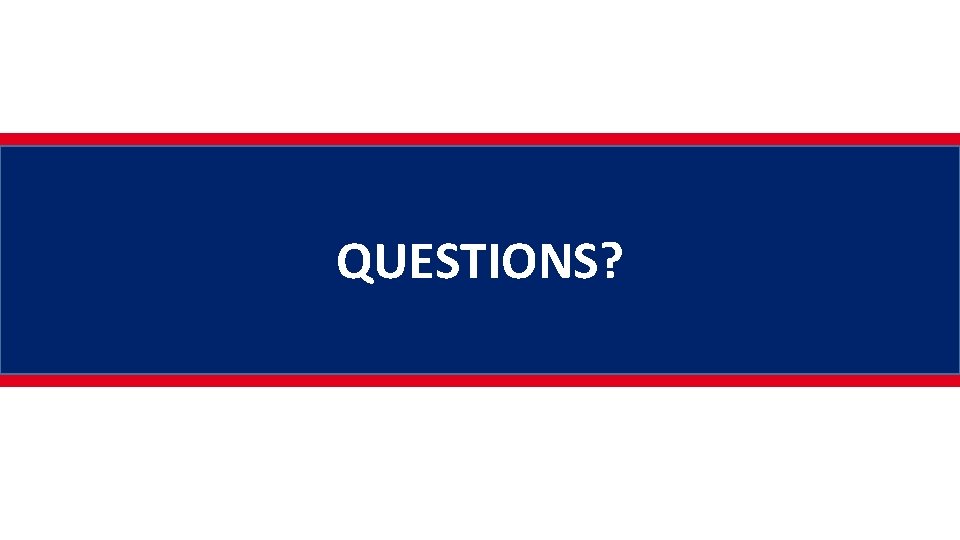
QUESTIONS?
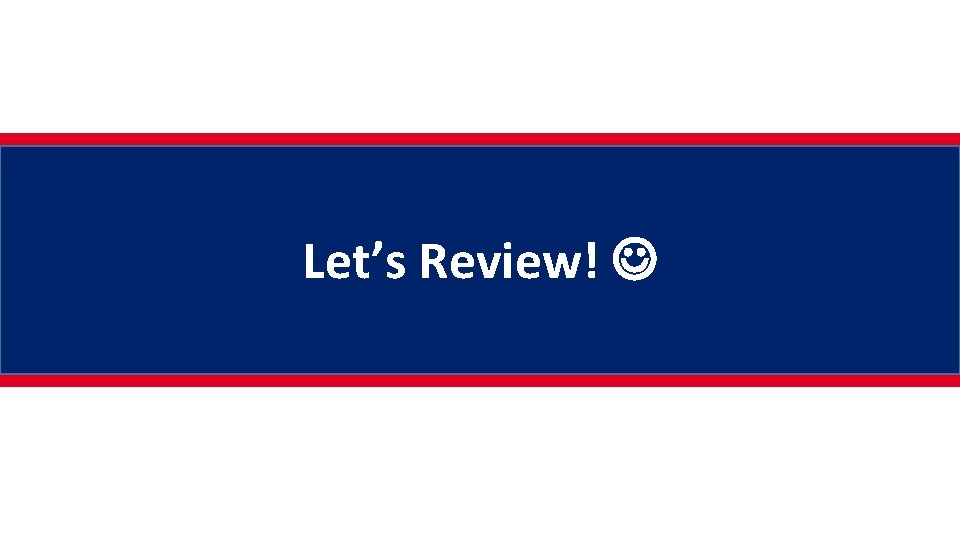
Let’s Review!

1. What is the type of boiler examined? a. b. c. d. High Pressure Boiler Low Pressure Boiler Medium Pressure Boiler Supercritical Pressure Boiler
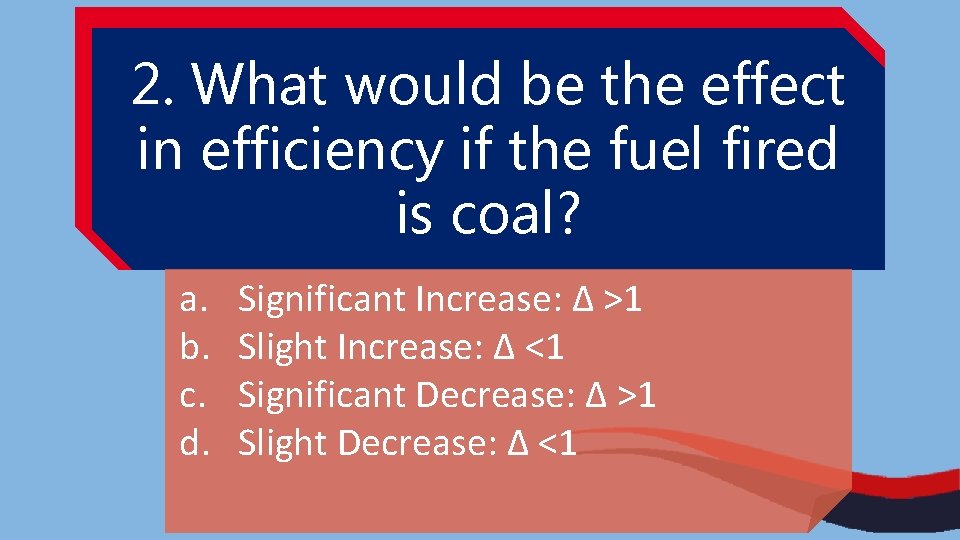
2. What would be the effect in efficiency if the fuel fired is coal? a. b. c. d. Significant Increase: Δ >1 Slight Increase: Δ <1 Significant Decrease: Δ >1 Slight Decrease: Δ <1
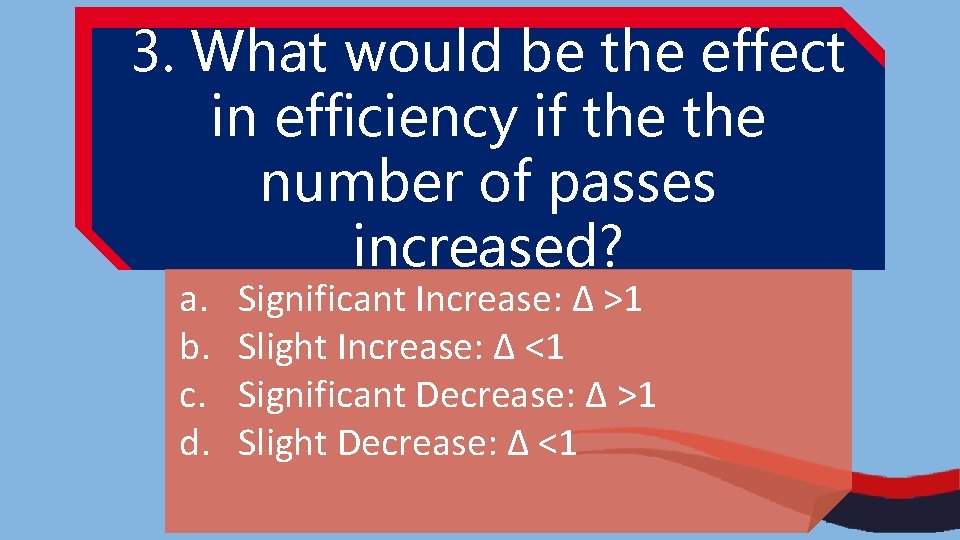
3. What would be the effect in efficiency if the number of passes increased? a. b. c. d. Significant Increase: Δ >1 Slight Increase: Δ <1 Significant Decrease: Δ >1 Slight Decrease: Δ <1
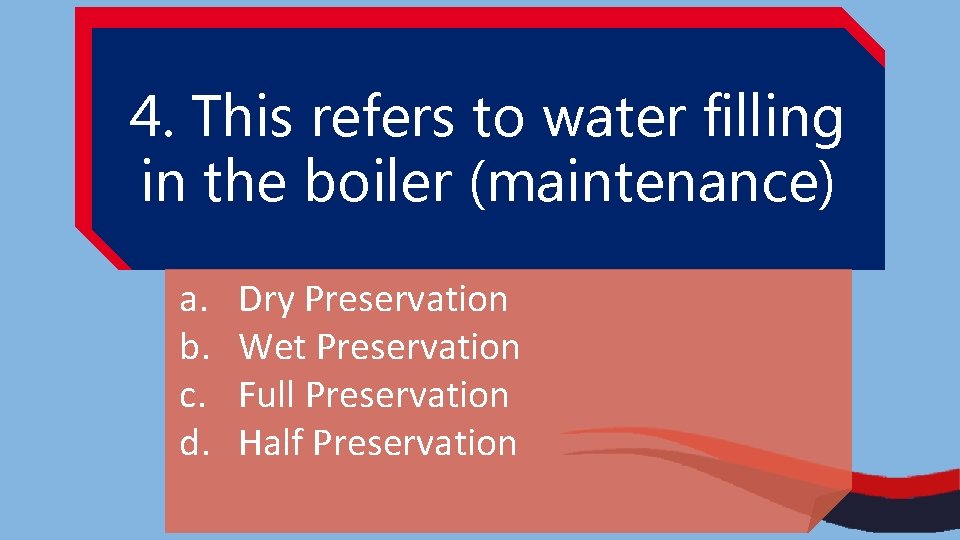
4. This refers to water filling in the boiler (maintenance) a. b. c. d. Dry Preservation Wet Preservation Full Preservation Half Preservation
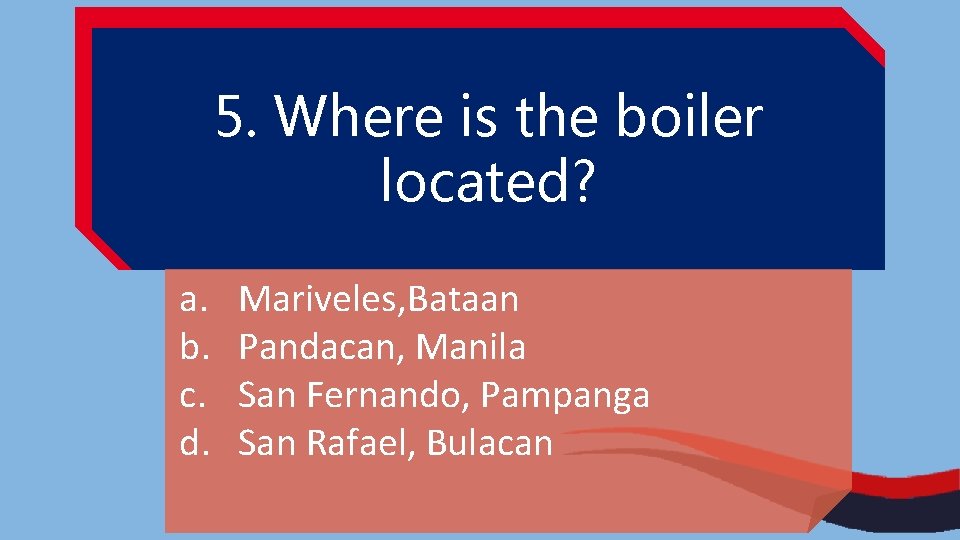
5. Where is the boiler located? a. b. c. d. Mariveles, Bataan Pandacan, Manila San Fernando, Pampanga San Rafael, Bulacan
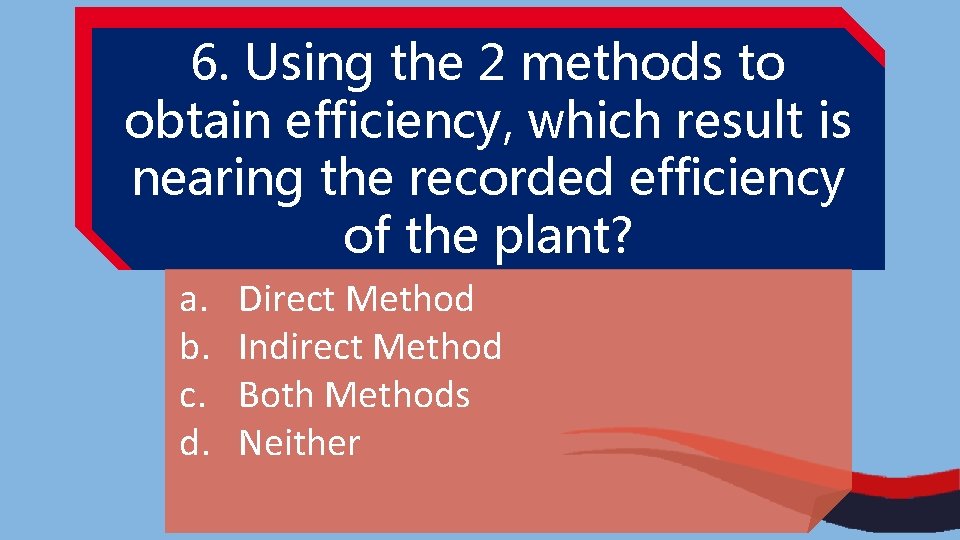
6. Using the 2 methods to obtain efficiency, which result is nearing the recorded efficiency of the plant? a. b. c. d. Direct Method Indirect Method Both Methods Neither
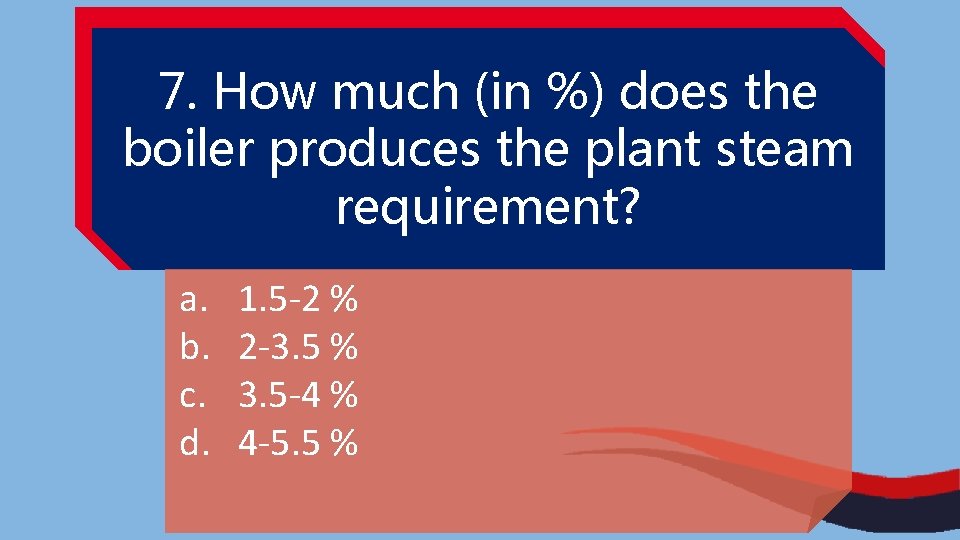
7. How much (in %) does the boiler produces the plant steam requirement? a. b. c. d. 1. 5 -2 % 2 -3. 5 % 3. 5 -4 % 4 -5. 5 %
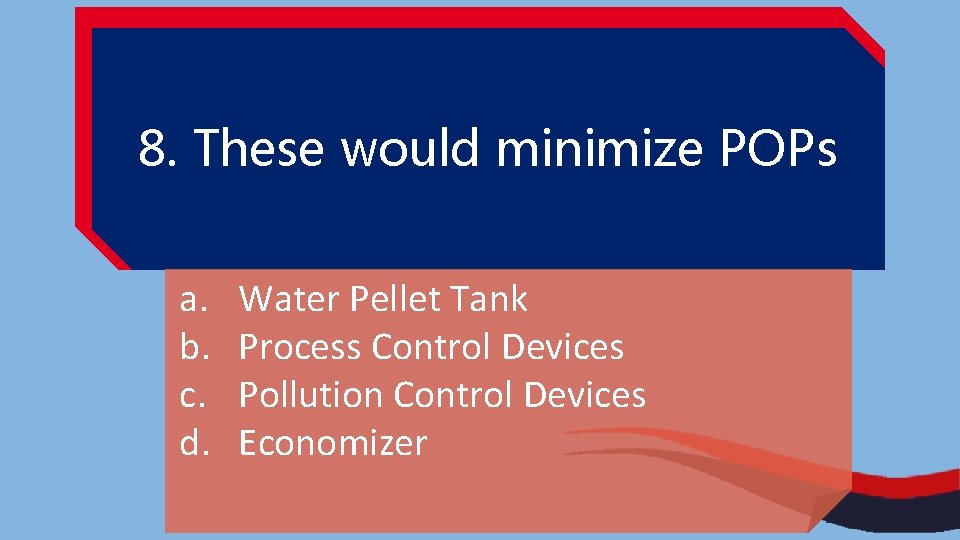
8. These would minimize POPs a. b. c. d. Water Pellet Tank Process Control Devices Pollution Control Devices Economizer
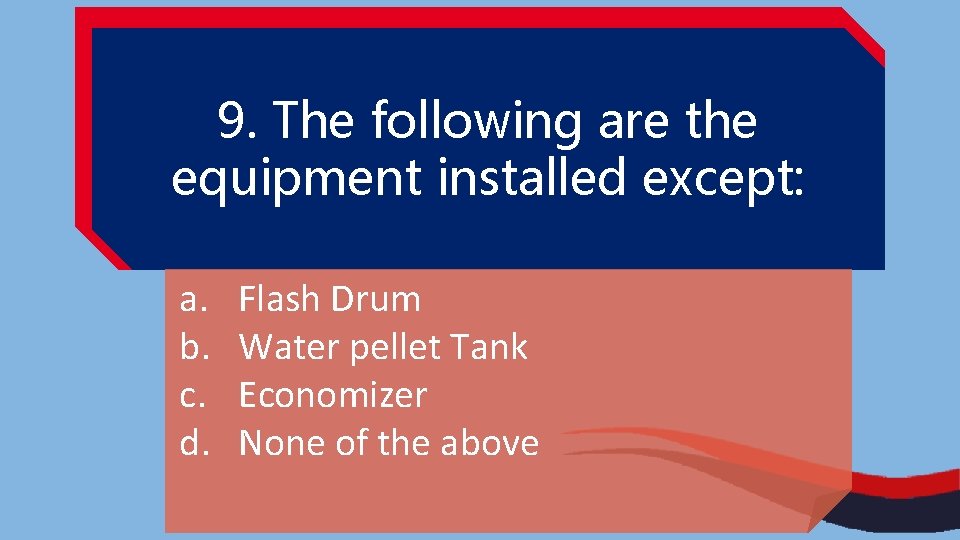
9. The following are the equipment installed except: a. b. c. d. Flash Drum Water pellet Tank Economizer None of the above
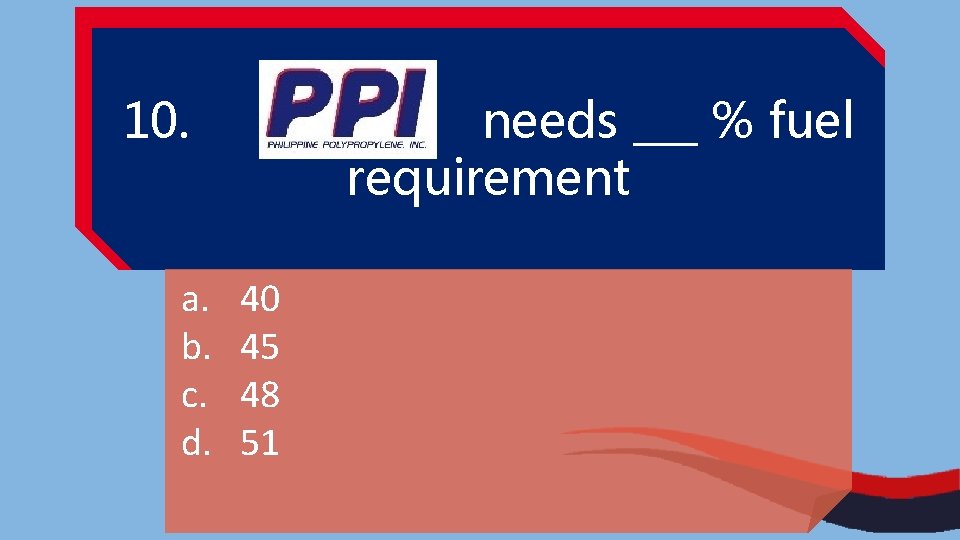
10. a. b. c. d. needs ___ % fuel requirement 40 45 48 51
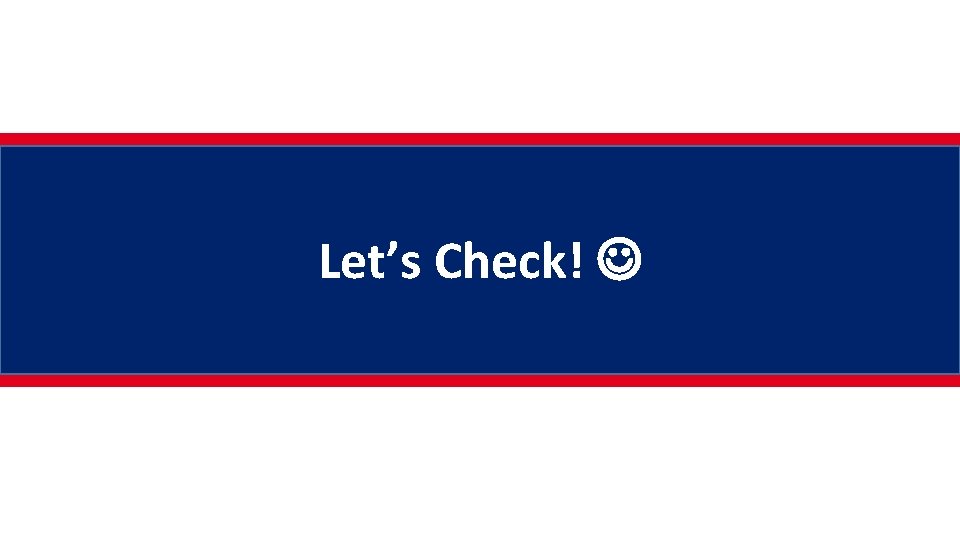
Let’s Check!
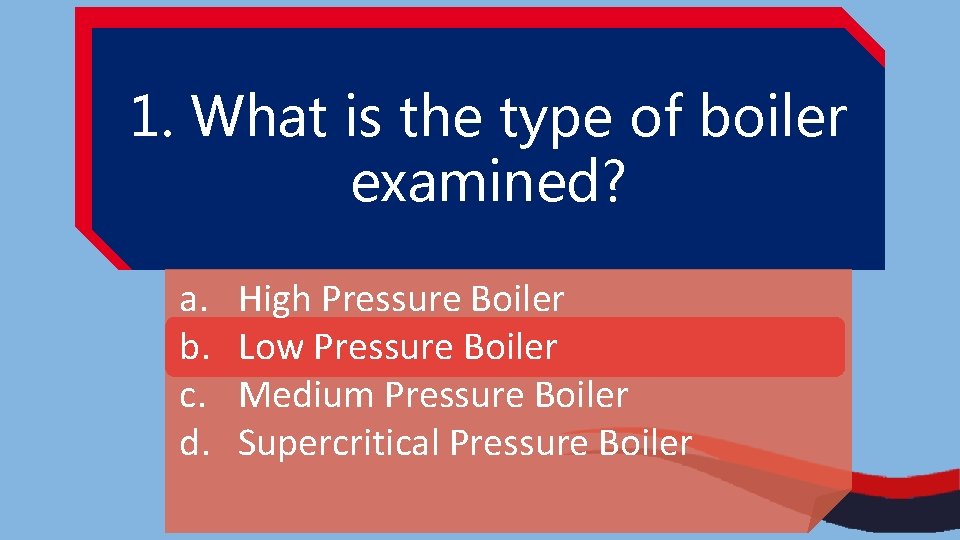
1. What is the type of boiler examined? a. b. c. d. High Pressure Boiler Low Pressure Boiler Medium Pressure Boiler Supercritical Pressure Boiler
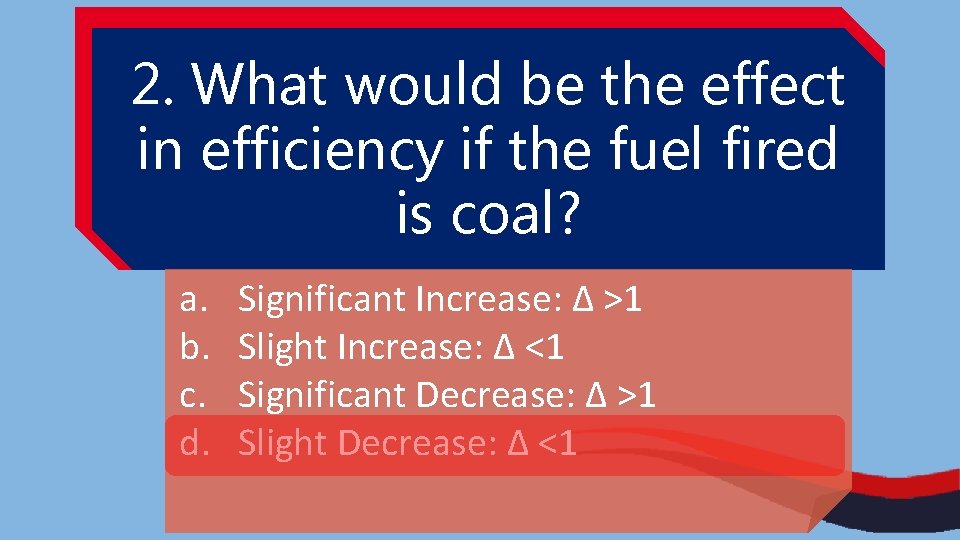
2. What would be the effect in efficiency if the fuel fired is coal? a. b. c. d. Significant Increase: Δ >1 Slight Increase: Δ <1 Significant Decrease: Δ >1 Slight Decrease: Δ <1
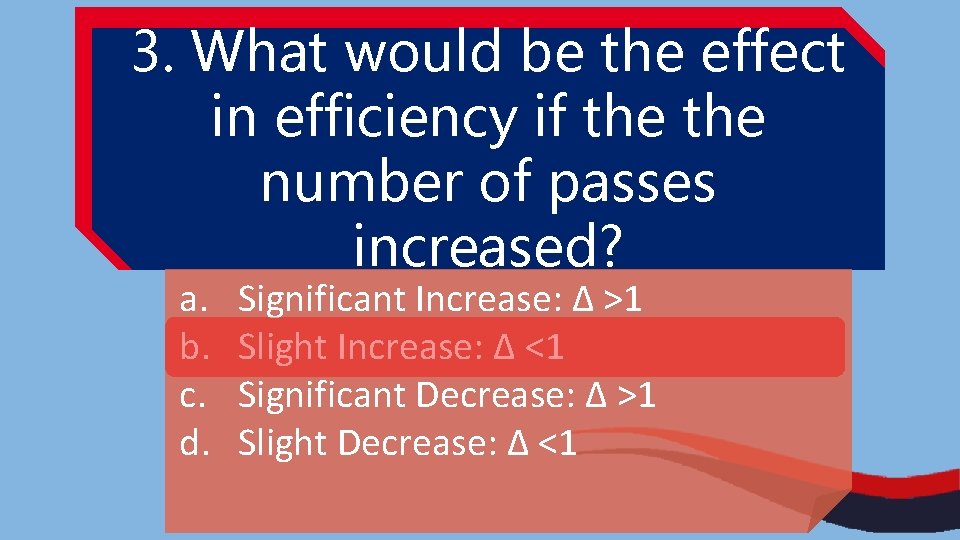
3. What would be the effect in efficiency if the number of passes increased? a. b. c. d. Significant Increase: Δ >1 Slight Increase: Δ <1 Significant Decrease: Δ >1 Slight Decrease: Δ <1
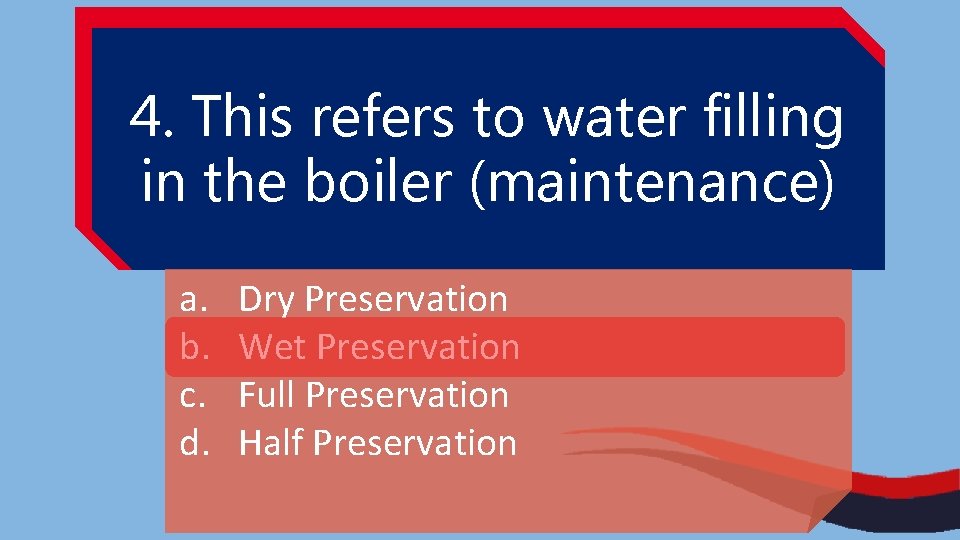
4. This refers to water filling in the boiler (maintenance) a. b. c. d. Dry Preservation Wet Preservation Full Preservation Half Preservation
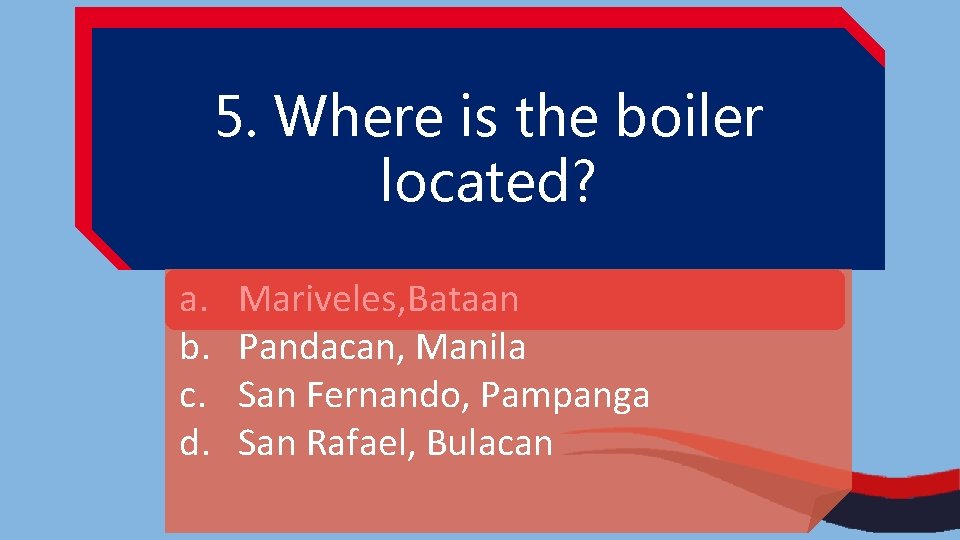
5. Where is the boiler located? a. b. c. d. Mariveles, Bataan Pandacan, Manila San Fernando, Pampanga San Rafael, Bulacan
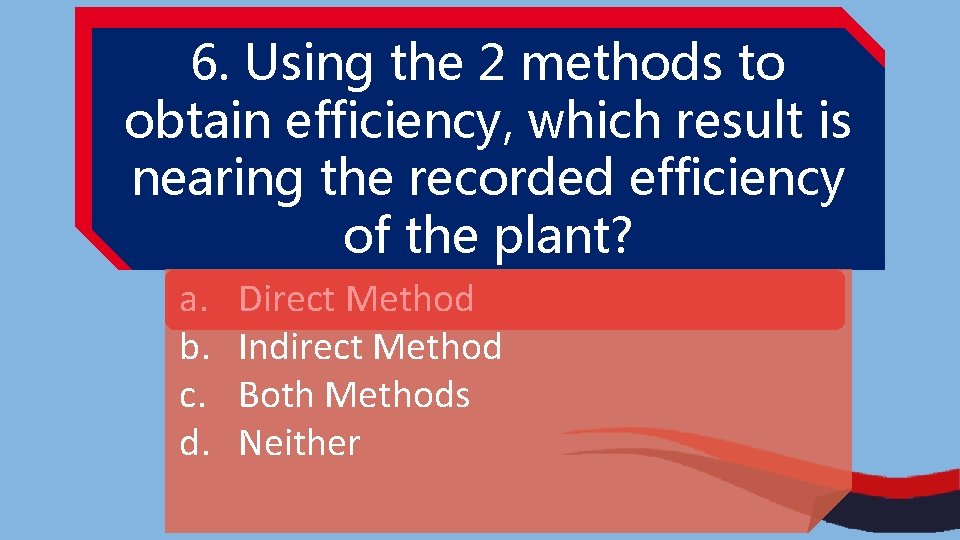
6. Using the 2 methods to obtain efficiency, which result is nearing the recorded efficiency of the plant? a. b. c. d. Direct Method Indirect Method Both Methods Neither
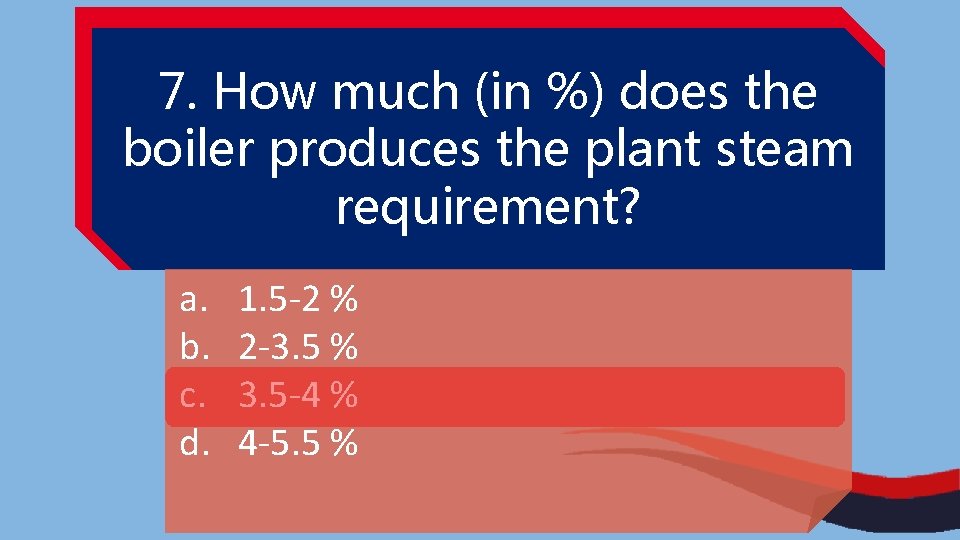
7. How much (in %) does the boiler produces the plant steam requirement? a. b. c. d. 1. 5 -2 % 2 -3. 5 % 3. 5 -4 % 4 -5. 5 %
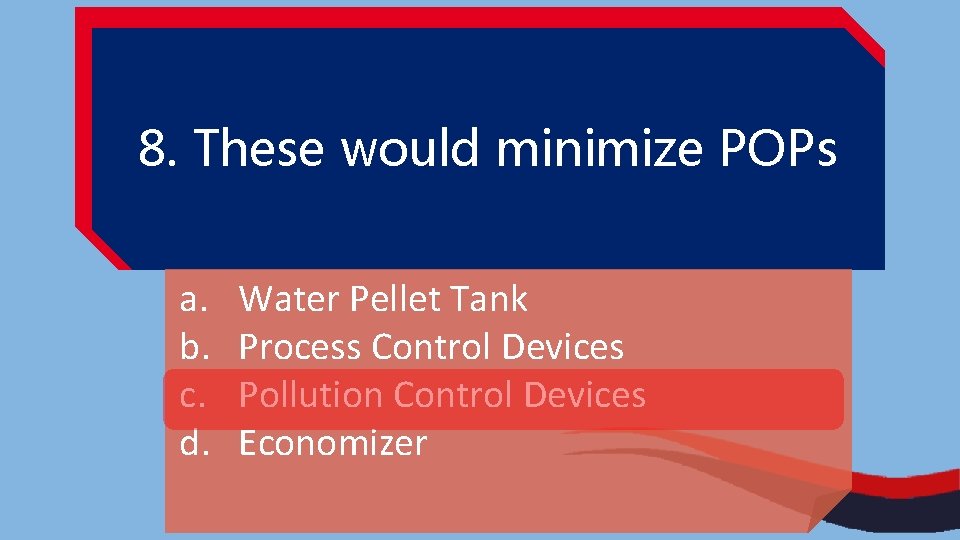
8. These would minimize POPs a. b. c. d. Water Pellet Tank Process Control Devices Pollution Control Devices Economizer
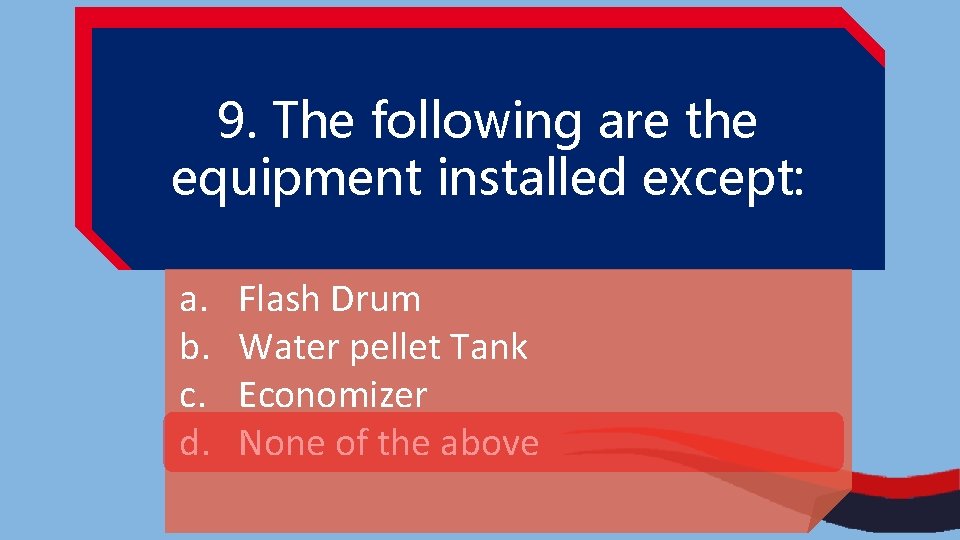
9. The following are the equipment installed except: a. b. c. d. Flash Drum Water pellet Tank Economizer None of the above
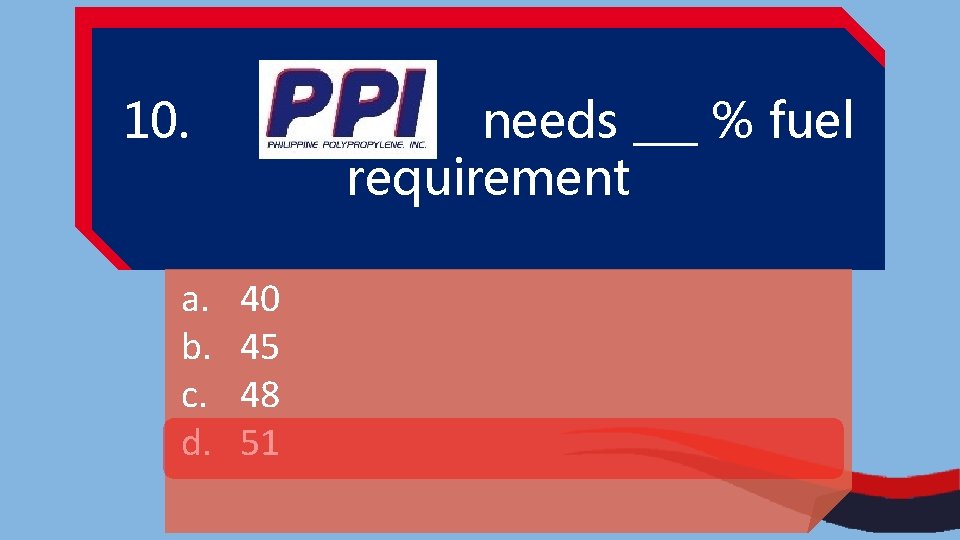
10. a. b. c. d. needs ___ % fuel requirement 40 45 48 51
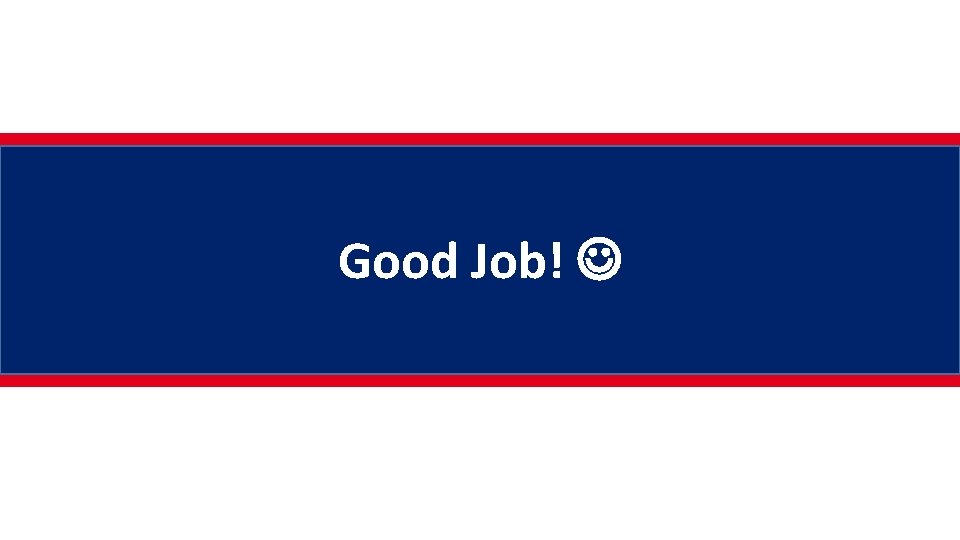
Good Job!
Petron polypropylene plant
Polypropylene functional groups
Advantages of polypropylene
Plant and machinery valuation report sample
Best case worst case average case
Fbi virtual case file case study
Subordinata oggettiva
Ricordo quegli occhi pieni di vita
Che che kooley
Facesti come quei che va di notte che porta il lume
Di queste case non è rimasto che qualche brandello di muro
Introduction in plant breeding
Plant breeding for disease resistance
Plant introduction in plant breeding
Tronsmo plant pathology and plant diseases download
Tronsmo plant pathology and plant diseases download
Tronsmo plant pathology and plant diseases download
Difference between short case and long case
Binary search time complexity worst case
Glennan building cwru
Bubble sort best case and worst case
Bubble sort best case and worst case
Bubble sort best case and worst case
What is a unique triangle
Zara information system
Sheryl kantrowitz
Patient kf case study
Swot analysis of whole foods
Action research vs case study
Volkswagen of america managing it priorities
Mini case study example
Starbucks foreign direct investment case study
Case study 11
Uml case study
Illustrative case study example
Tuna for lunch case study answer key
Tuna for lunch case study answer key
The amazon rainforest case study
Supermarket seo case study
Threats to biodiversity a case study of hawaiian birds
Mount st helens plates involved
Therac-25 case study
Wilderness weather station
Bleve san juanico
Gaslighting case study
Coyote removal case study answers
Semi structured questionaire
Spend analysis case study
Telegram roadmap
Swanage bay case study
Maq corporation case study
Case 7.2 silver fiddle construction
Linear programming case study examples
Rosa parks case study
Advantages and disadvantages of volunteer sampling
Rds case study
Ethnography and case study compare
Phenomenology vs case study
Location strategy in operations management
Climax stage
Pku case study answers
Perioperative case study nursing
Gingival description
Cargill everyday performance management
Patriot missile
Your garden gloves case study answers
Old spice case study
Medical case study presentation
Core competency of nike
National centre for case study teaching in science
National center for case study teaching in science
National center for case study teaching in science
National center for case study teaching in science
Case study on microsoft azure in cloud computing
Mengapa memilih studi kasus
Kelebihan studi kasus
Mgrm case study