Operations Management Your Garden Gloves Team Papaya Nick
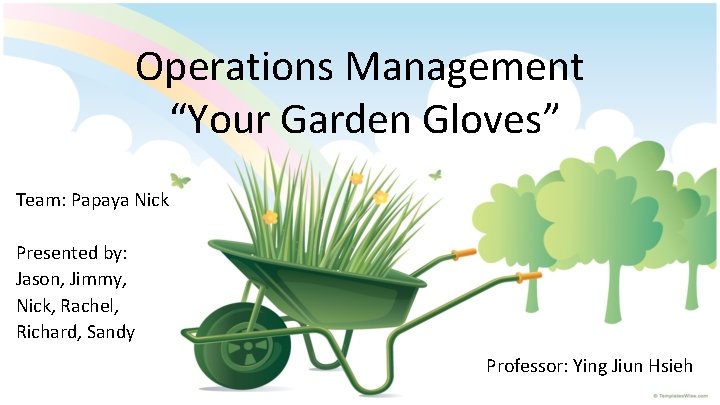
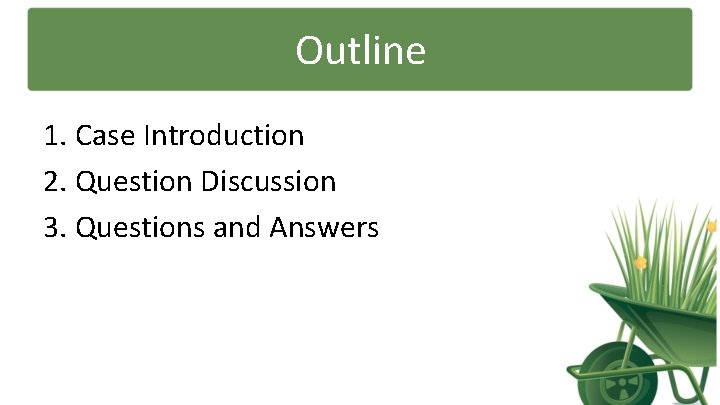
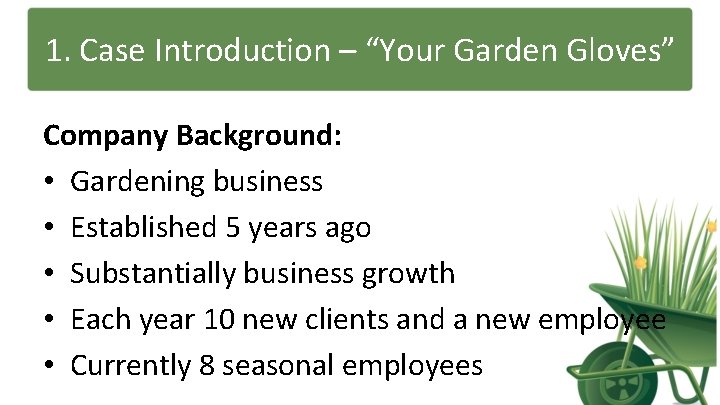
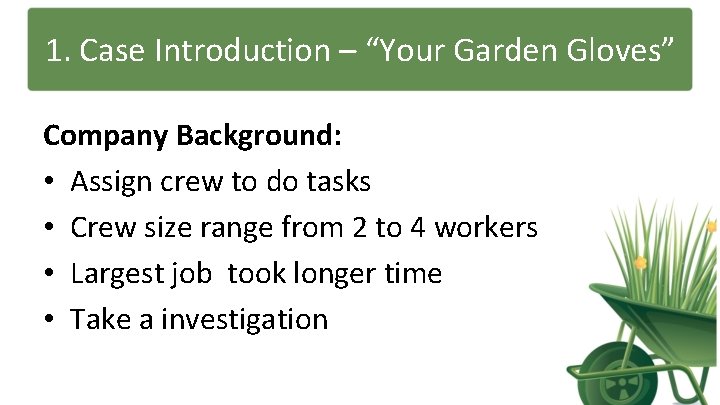
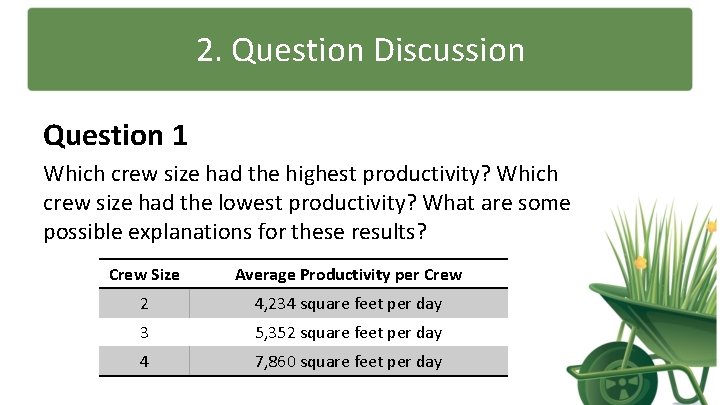
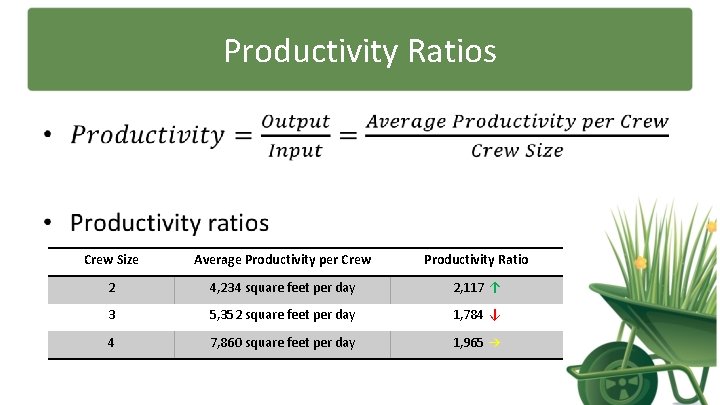
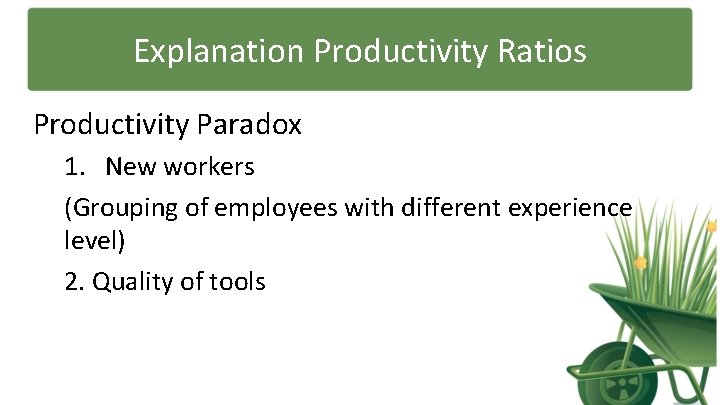
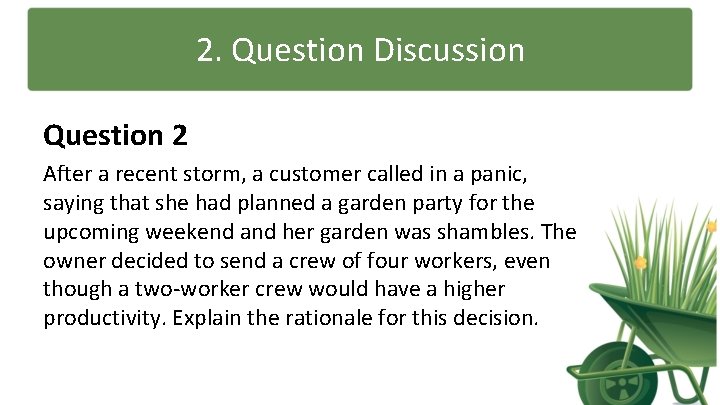
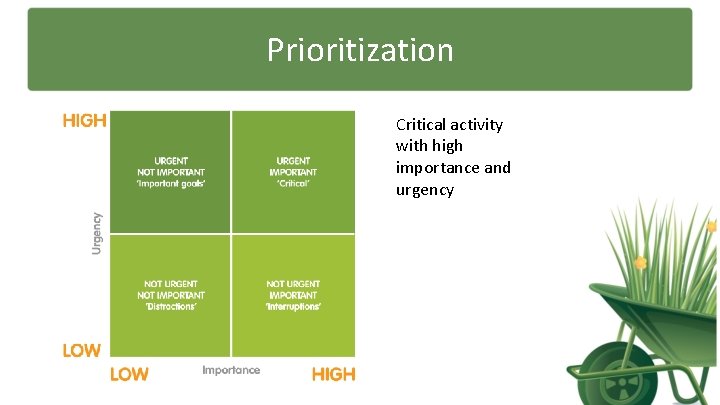
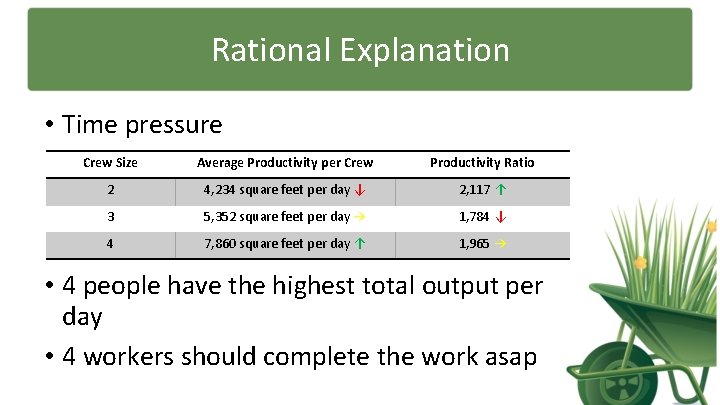
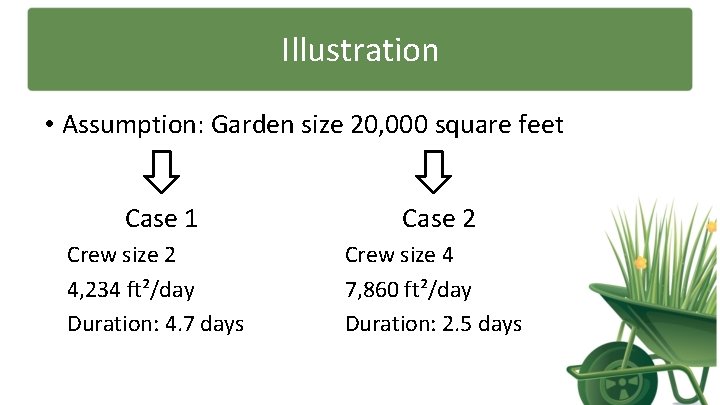
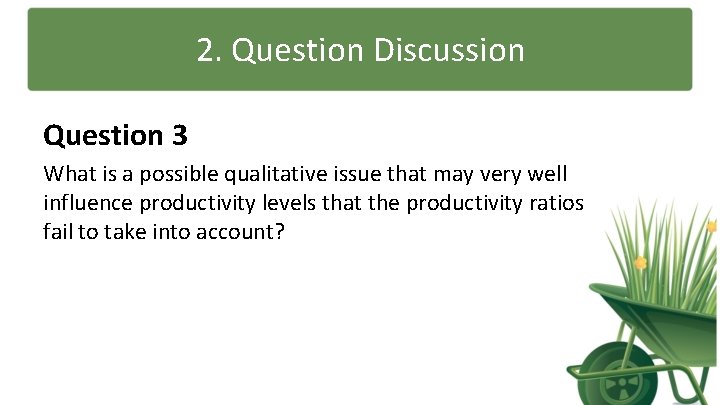
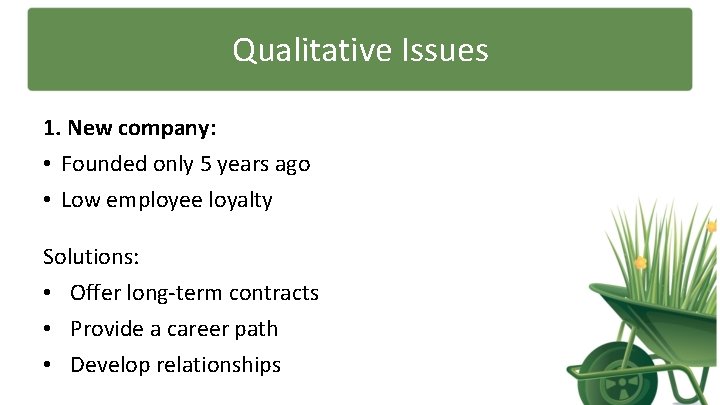
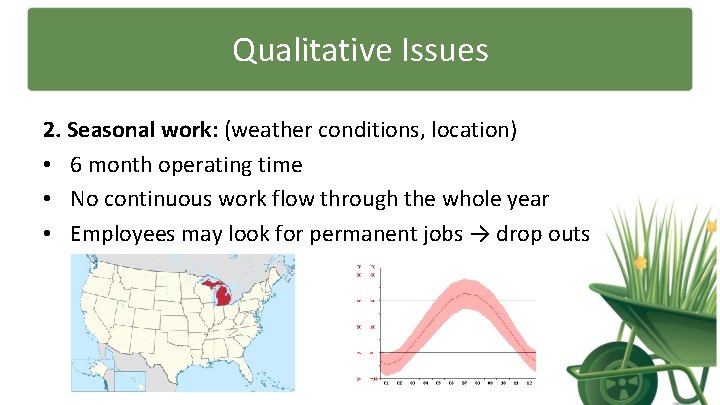
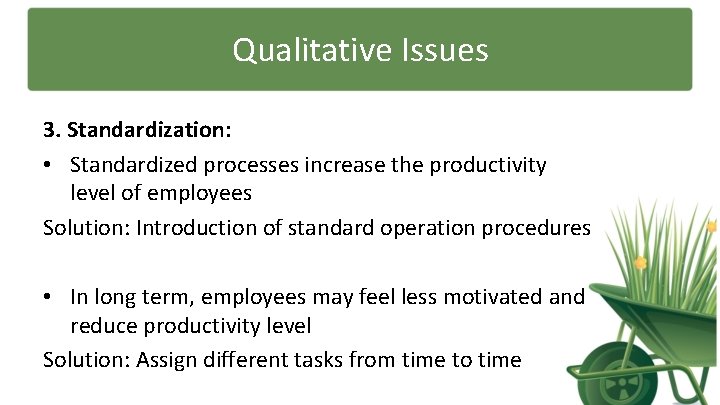
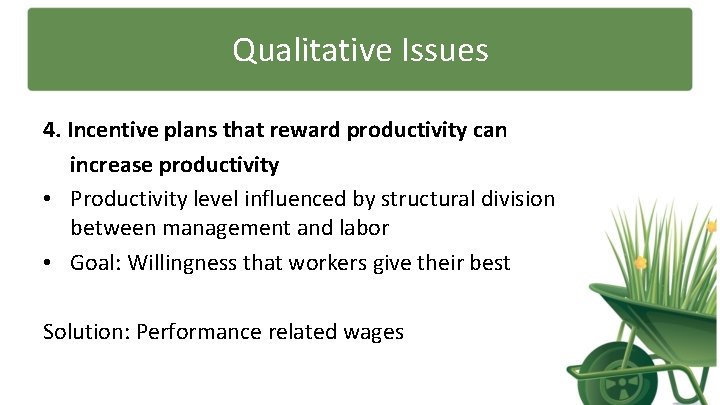
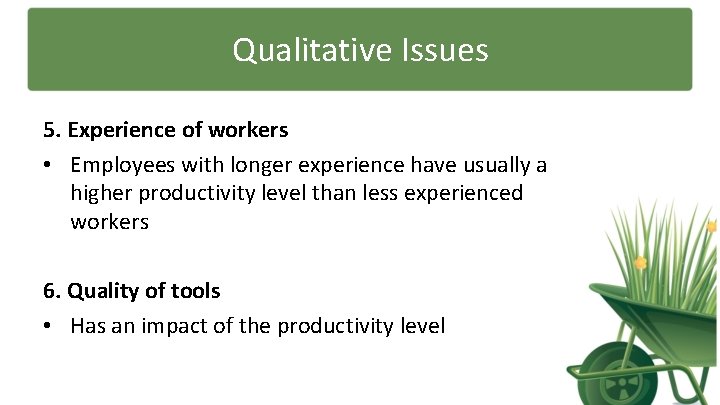
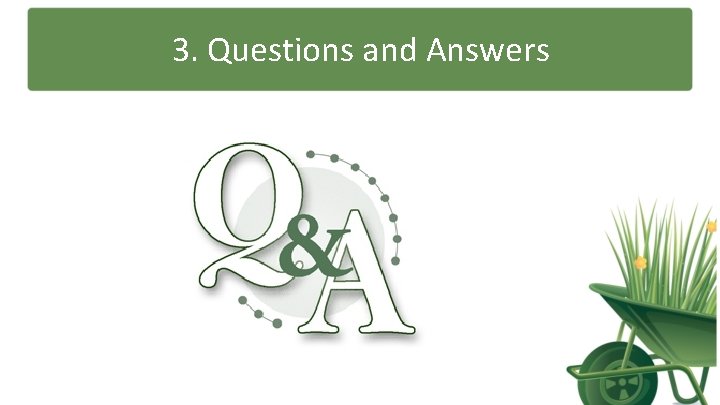
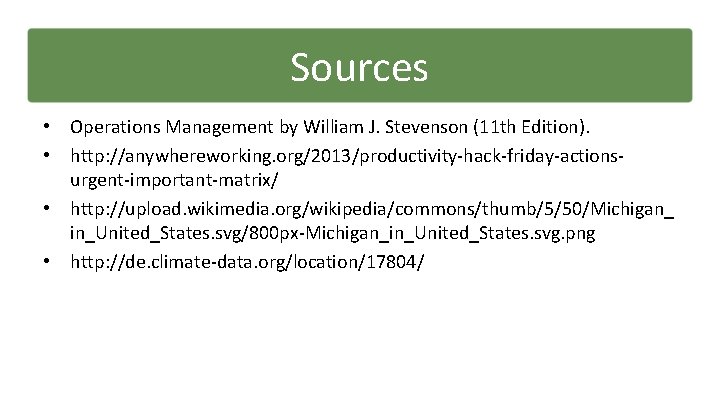
- Slides: 19
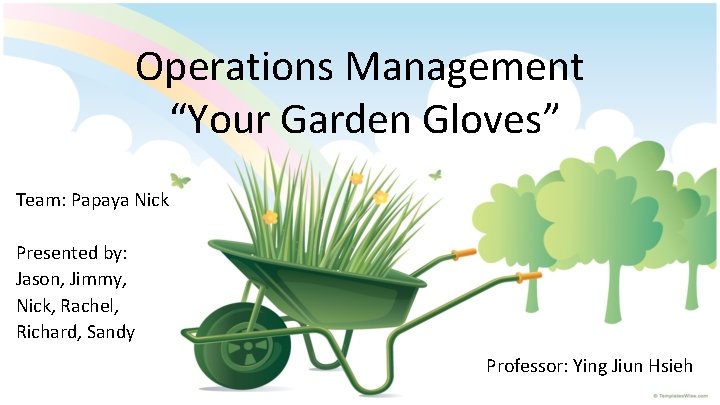
Operations Management “Your Garden Gloves” Team: Papaya Nick Presented by: Jason, Jimmy, Nick, Rachel, Richard, Sandy Professor: Ying Jiun Hsieh
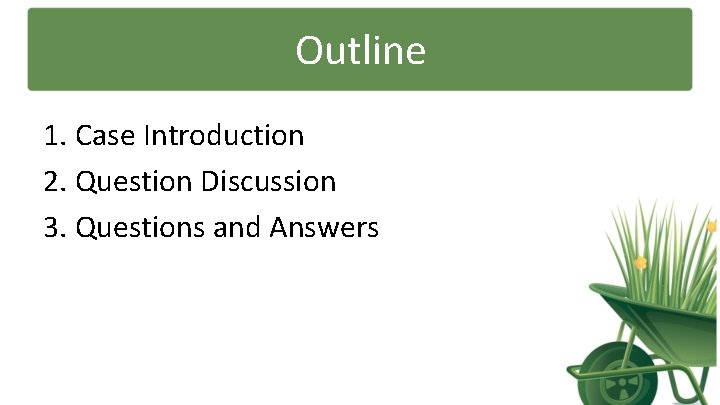
Outline 1. Case Introduction 2. Question Discussion 3. Questions and Answers
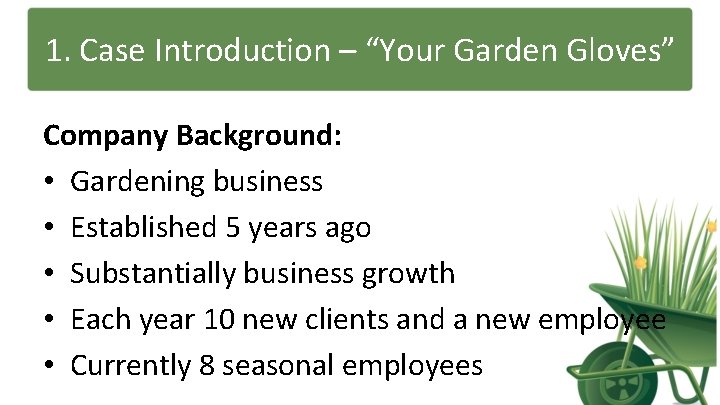
1. Case Introduction – “Your Garden Gloves” Company Background: • Gardening business • Established 5 years ago • Substantially business growth • Each year 10 new clients and a new employee • Currently 8 seasonal employees
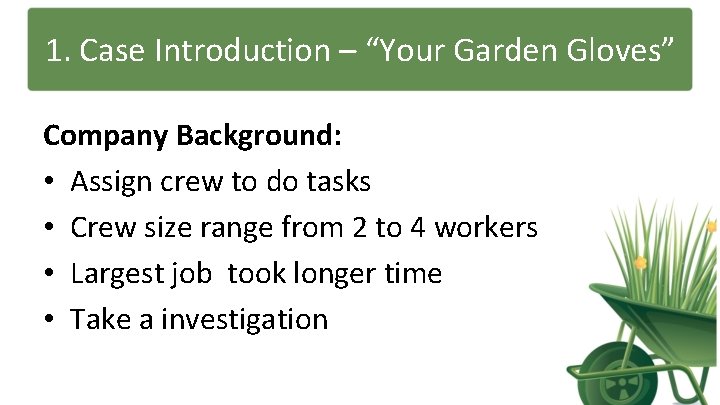
1. Case Introduction – “Your Garden Gloves” Company Background: • Assign crew to do tasks • Crew size range from 2 to 4 workers • Largest job took longer time • Take a investigation
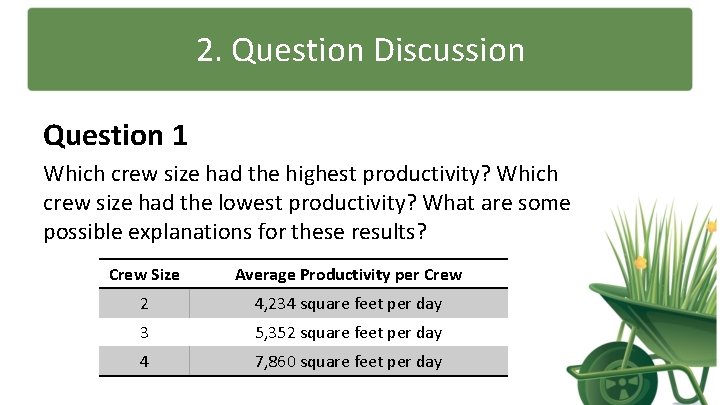
2. Question Discussion Question 1 Which crew size had the highest productivity? Which crew size had the lowest productivity? What are some possible explanations for these results? Crew Size Average Productivity per Crew 2 4, 234 square feet per day 3 5, 352 square feet per day 4 7, 860 square feet per day
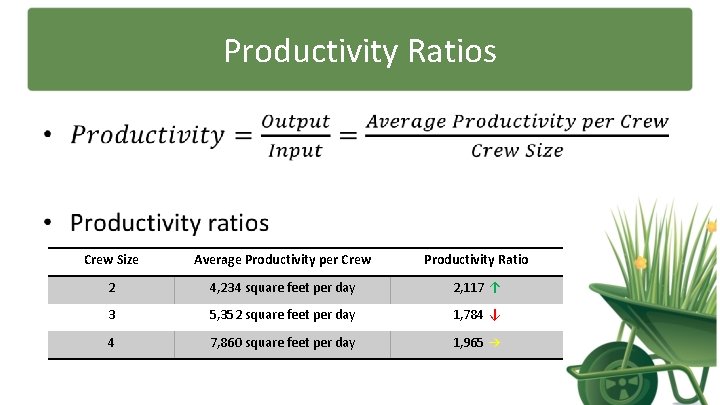
Productivity Ratios • Crew Size Average Productivity per Crew Productivity Ratio 2 4, 234 square feet per day 2, 117 ↑ 3 5, 352 square feet per day 1, 784 ↓ 4 7, 860 square feet per day 1, 965 →
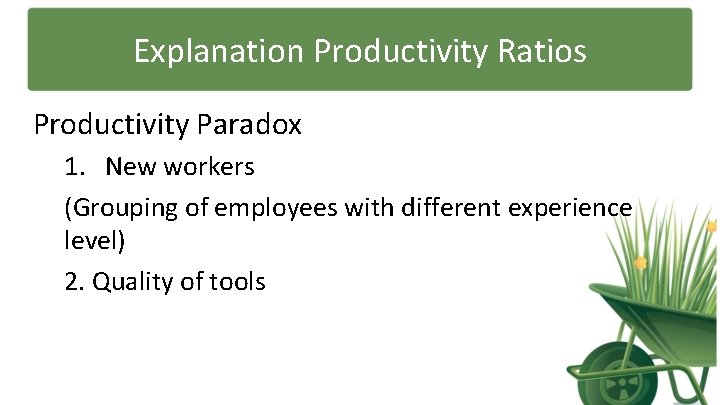
Explanation Productivity Ratios Productivity Paradox 1. New workers (Grouping of employees with different experience level) 2. Quality of tools
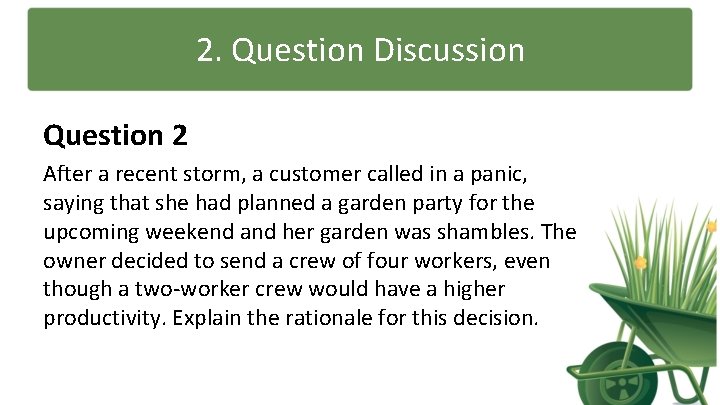
2. Question Discussion Question 2 After a recent storm, a customer called in a panic, saying that she had planned a garden party for the upcoming weekend and her garden was shambles. The owner decided to send a crew of four workers, even though a two-worker crew would have a higher productivity. Explain the rationale for this decision.
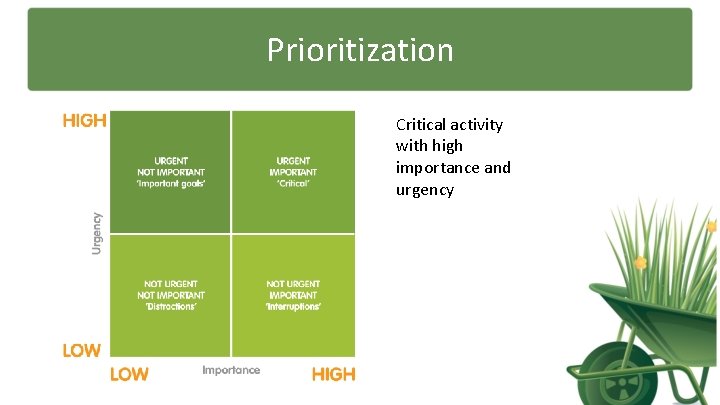
Prioritization Critical activity with high importance and urgency
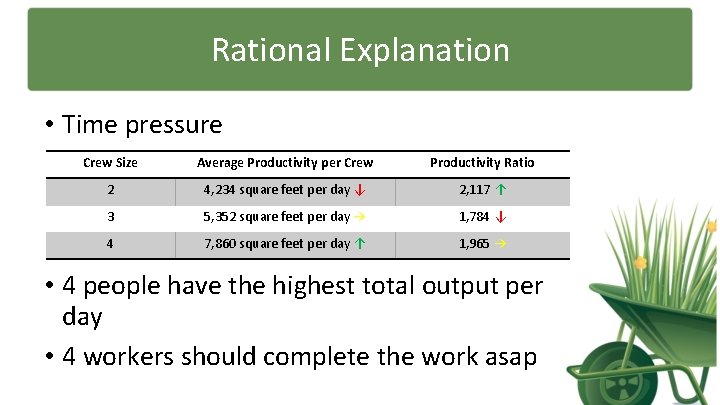
Rational Explanation • Time pressure Crew Size Average Productivity per Crew Productivity Ratio 2 4, 234 square feet per day ↓ 2, 117 ↑ 3 5, 352 square feet per day → 1, 784 ↓ 4 7, 860 square feet per day ↑ 1, 965 → • 4 people have the highest total output per day • 4 workers should complete the work asap
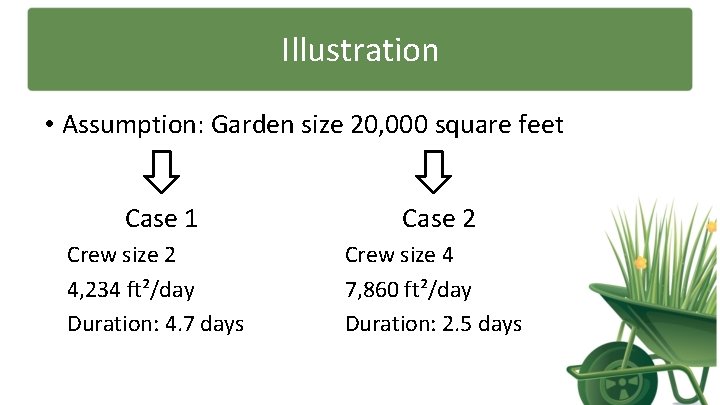
Illustration • Assumption: Garden size 20, 000 square feet Case 1 Case 2 Crew size 2 4, 234 ft²/day Duration: 4. 7 days Crew size 4 7, 860 ft²/day Duration: 2. 5 days
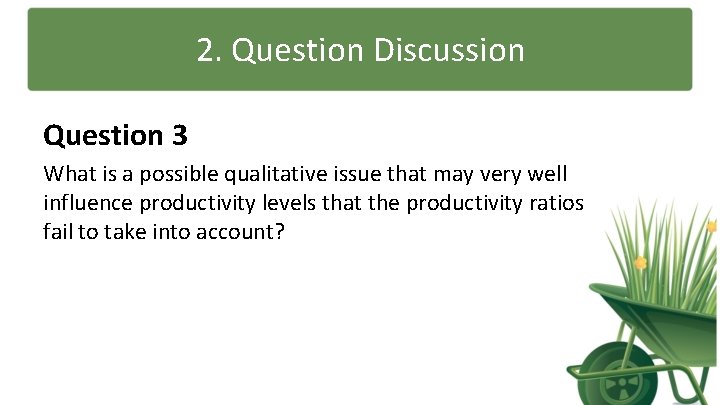
2. Question Discussion Question 3 What is a possible qualitative issue that may very well influence productivity levels that the productivity ratios fail to take into account?
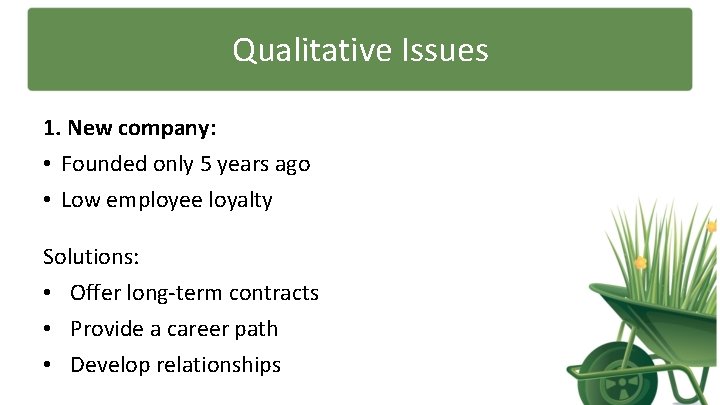
Qualitative Issues 1. New company: • Founded only 5 years ago • Low employee loyalty Solutions: • Offer long-term contracts • Provide a career path • Develop relationships
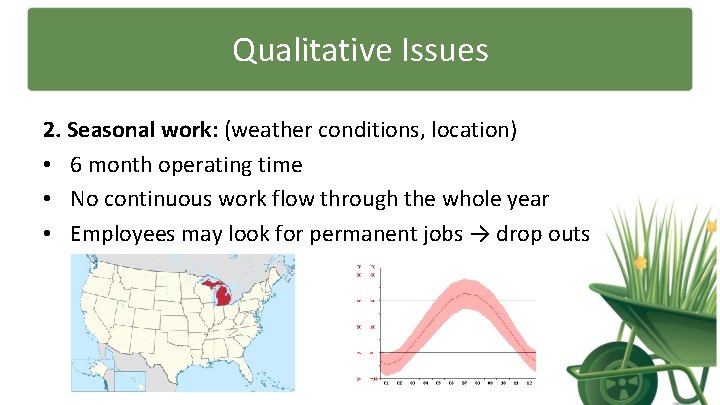
Qualitative Issues 2. Seasonal work: (weather conditions, location) • 6 month operating time • No continuous work flow through the whole year • Employees may look for permanent jobs → drop outs
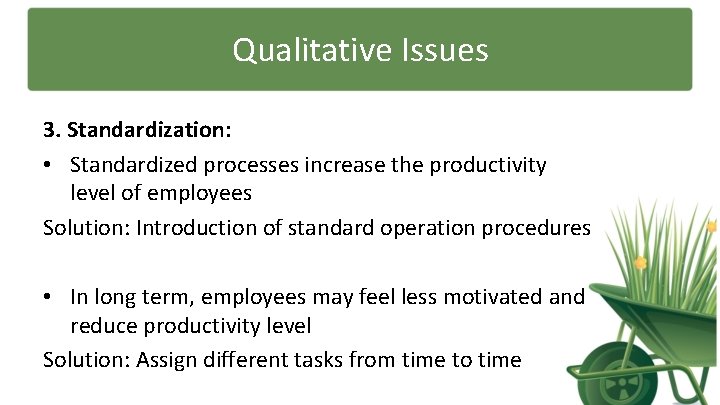
Qualitative Issues 3. Standardization: • Standardized processes increase the productivity level of employees Solution: Introduction of standard operation procedures • In long term, employees may feel less motivated and reduce productivity level Solution: Assign different tasks from time to time
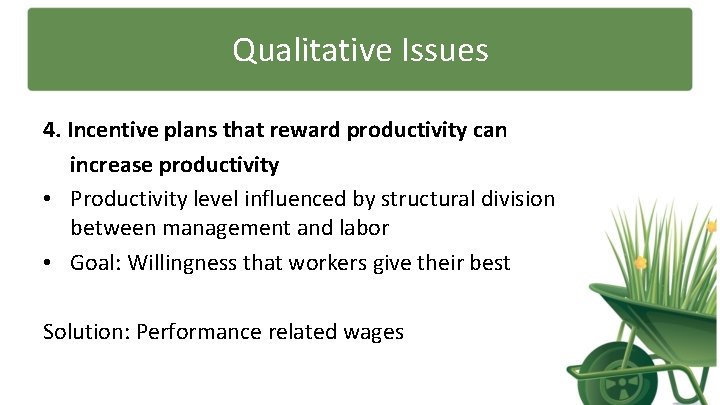
Qualitative Issues 4. Incentive plans that reward productivity can increase productivity • Productivity level influenced by structural division between management and labor • Goal: Willingness that workers give their best Solution: Performance related wages
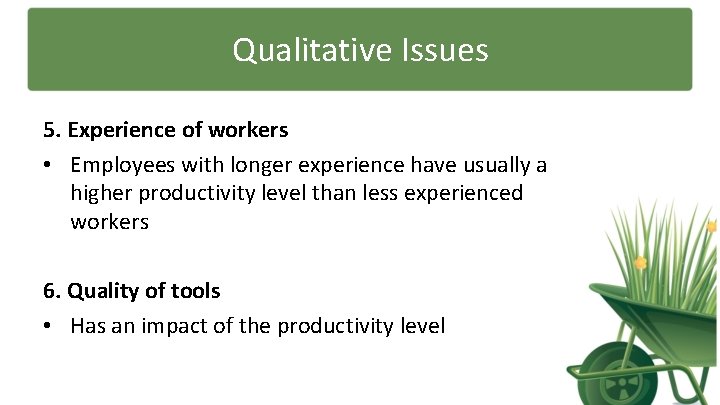
Qualitative Issues 5. Experience of workers • Employees with longer experience have usually a higher productivity level than less experienced workers 6. Quality of tools • Has an impact of the productivity level
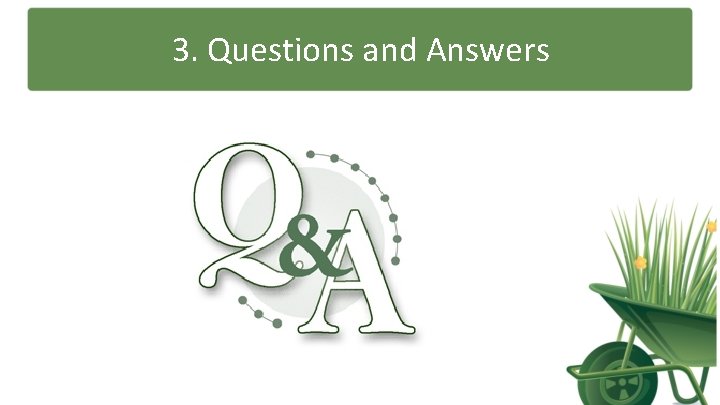
3. Questions and Answers
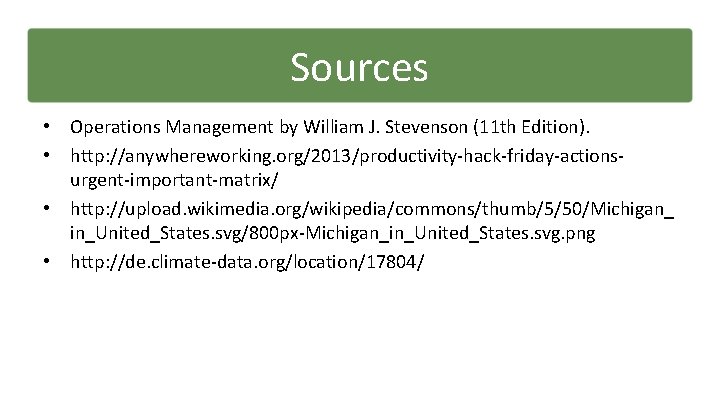
Sources • Operations Management by William J. Stevenson (11 th Edition). • http: //anywhereworking. org/2013/productivity-hack-friday-actionsurgent-important-matrix/ • http: //upload. wikimedia. org/wikipedia/commons/thumb/5/50/Michigan_ in_United_States. svg/800 px-Michigan_in_United_States. svg. png • http: //de. climate-data. org/location/17804/
Wholesale your garden gloves case
The papaya that spoke
Primarenc®
Shake the papaya down lyrics
Kim ha poem
Female flower
Papaya
Why do boxers wear gloves physics
"crimped petals __________ of paper red"
Vital sign normal
Tamara de lempicka young lady with gloves wikipedia
Enable talk gloves
Sparse haptic proxy
Aorn eye prep
What does sterile mean
Clear nitrile gloves
Quincy college portal
Traditional part of speech
Metal gloves worn by knights
Reflexive pronouns