VIGILANCE ASPECTS CASE STUDIES God has gifted us
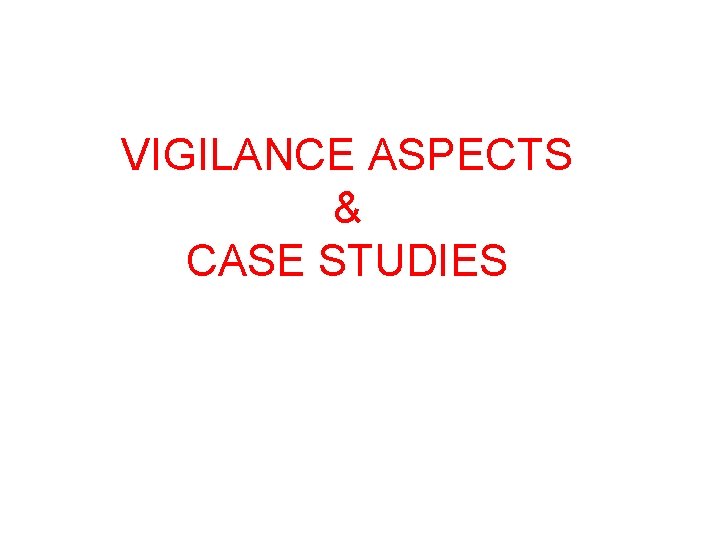
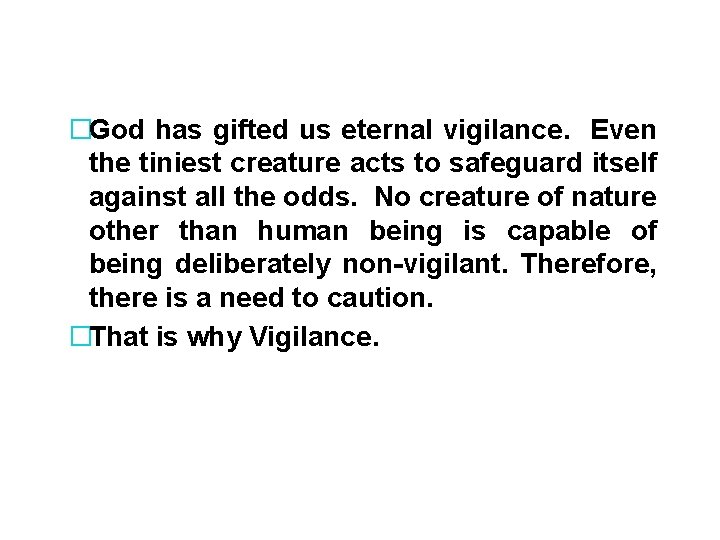
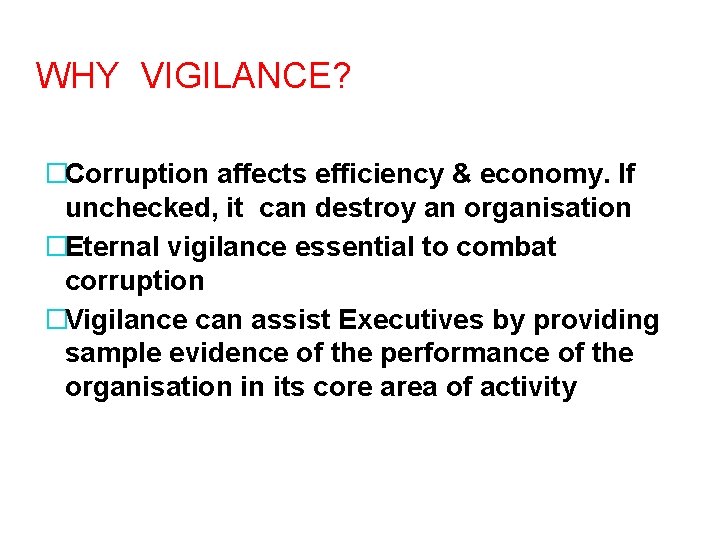
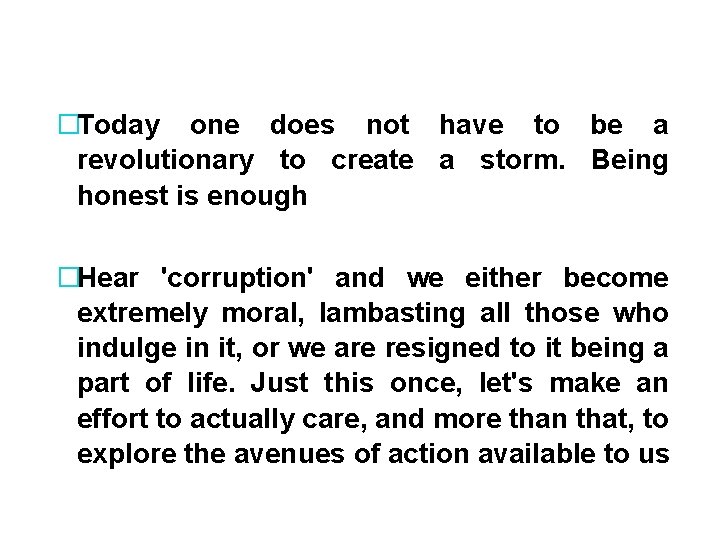
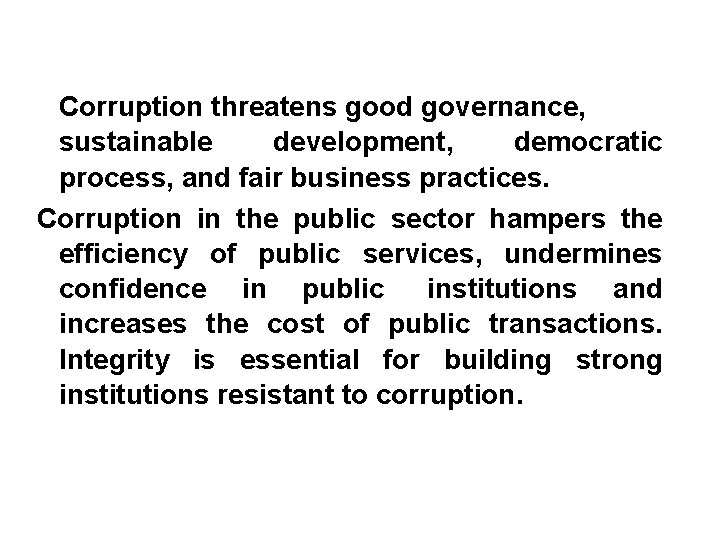
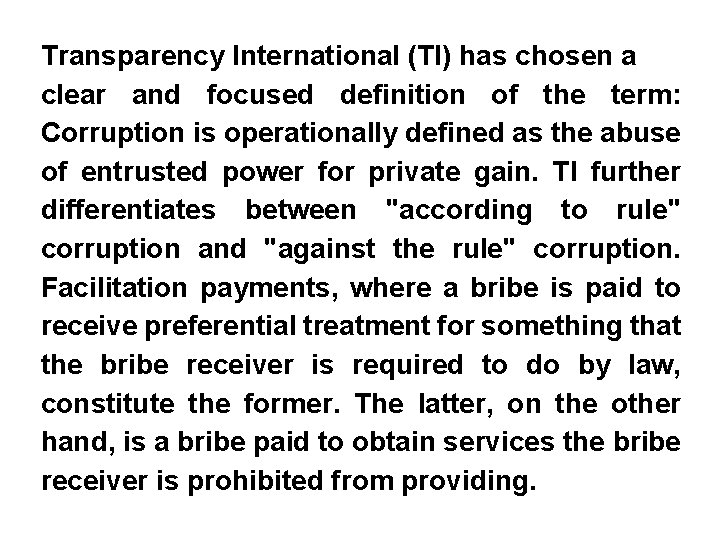
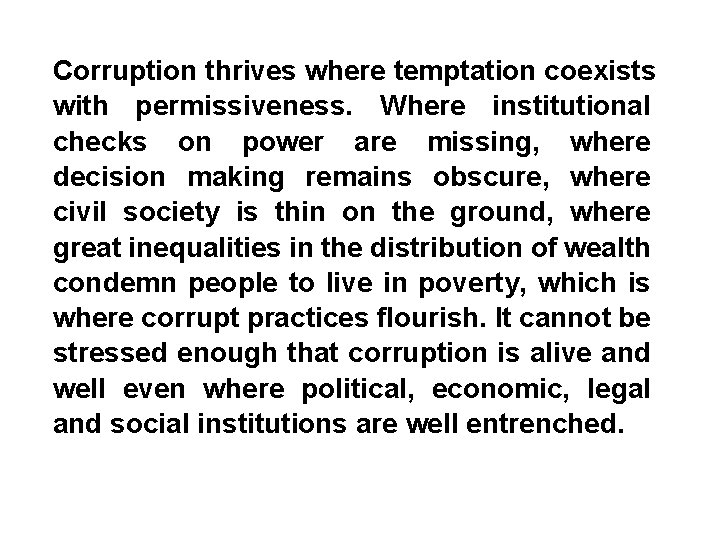
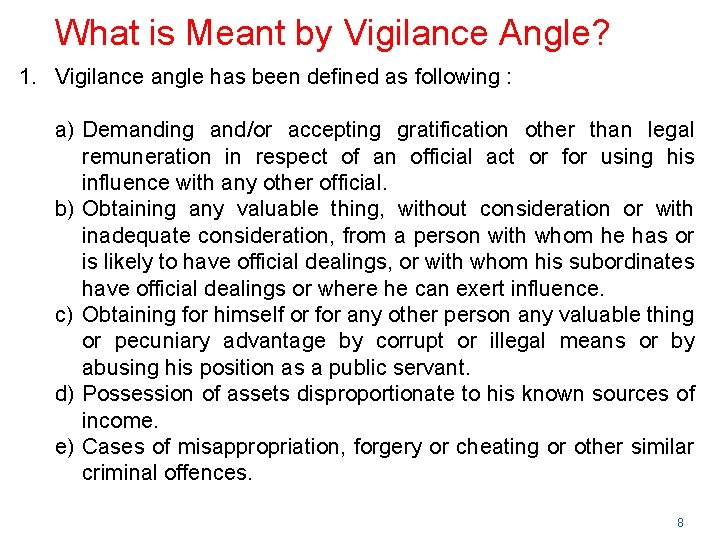
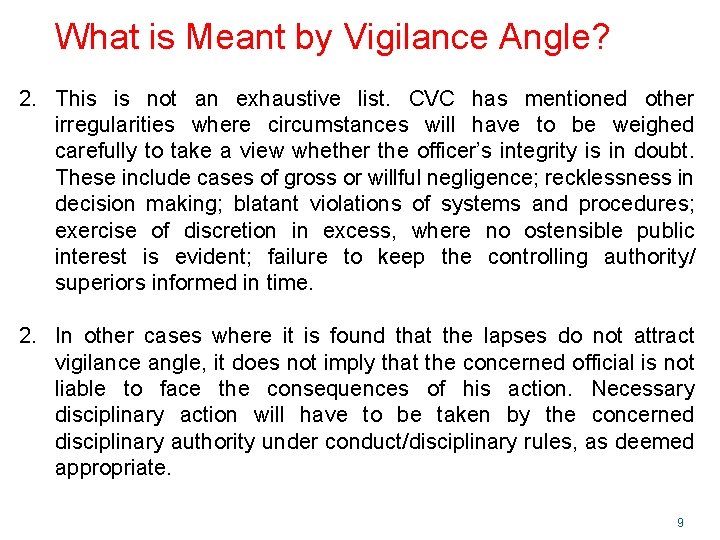
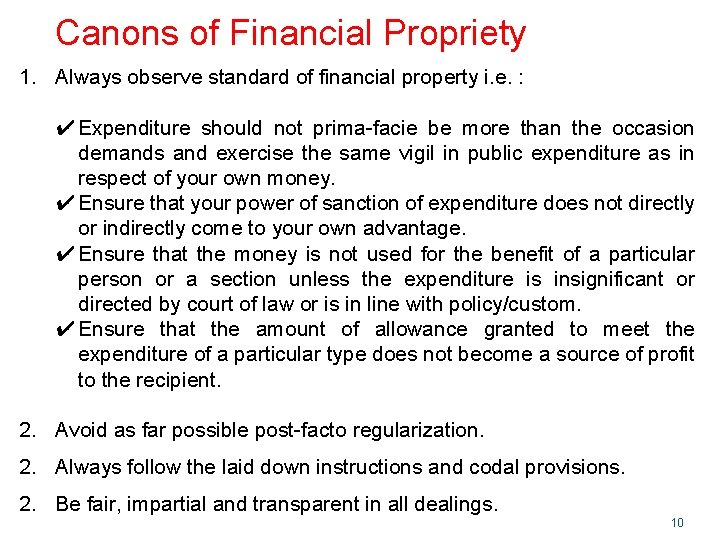
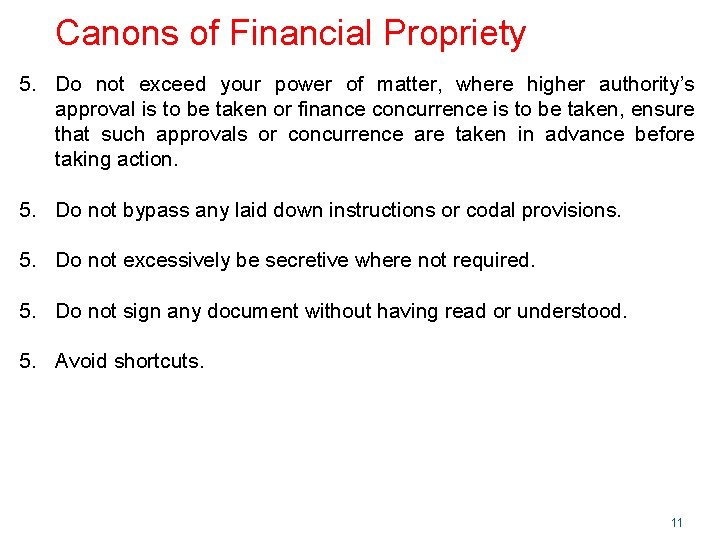
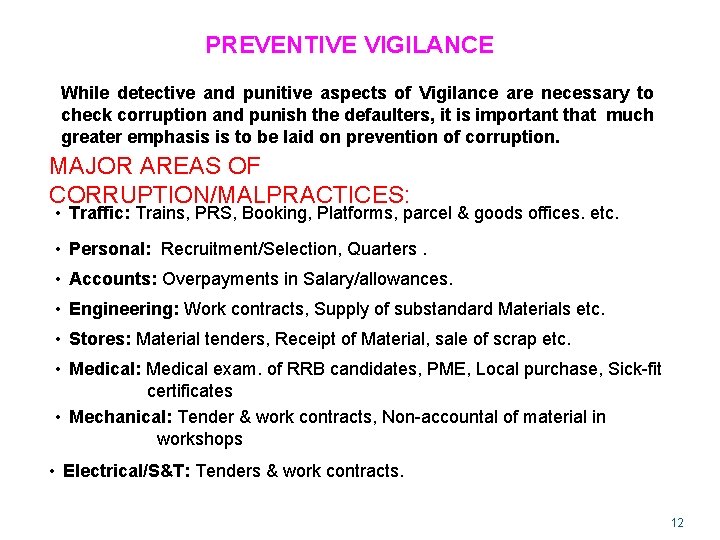

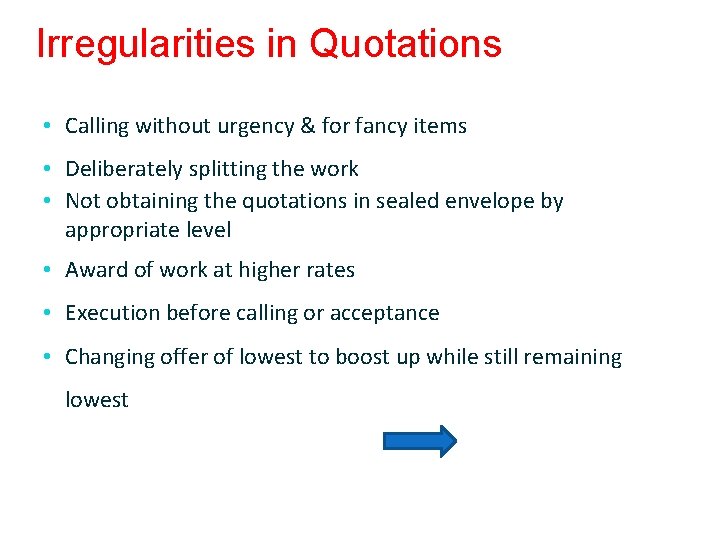
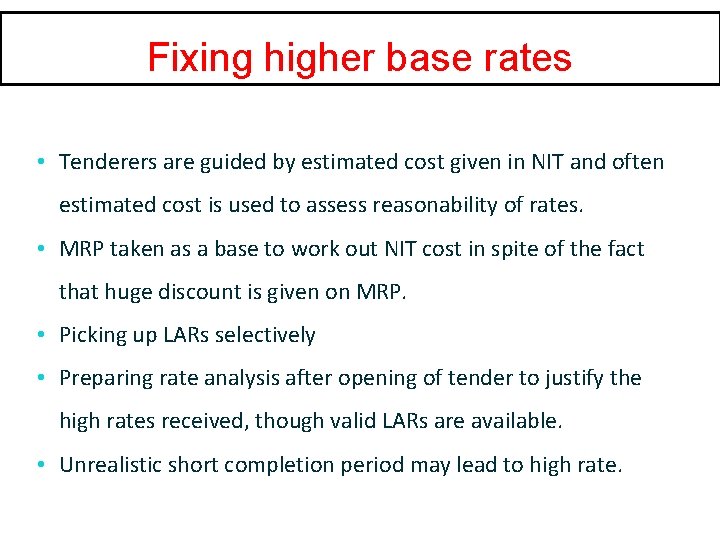
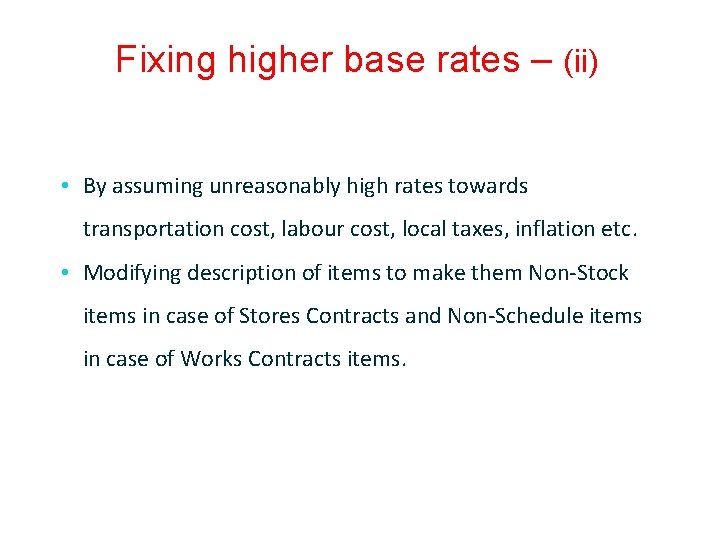

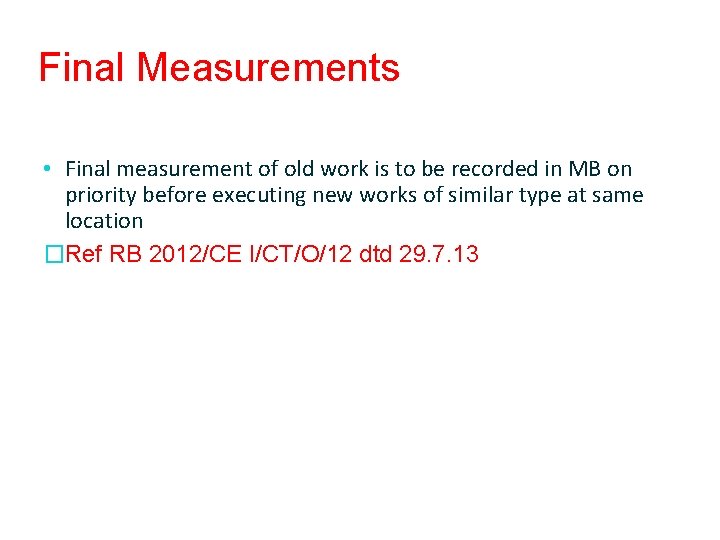
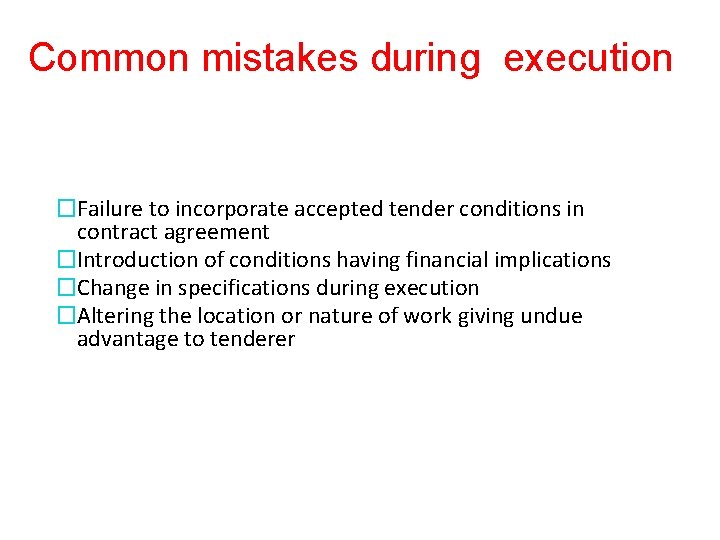
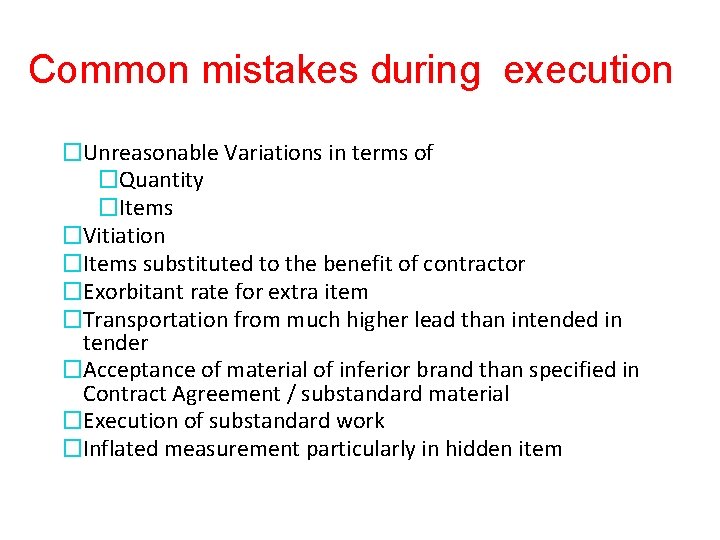
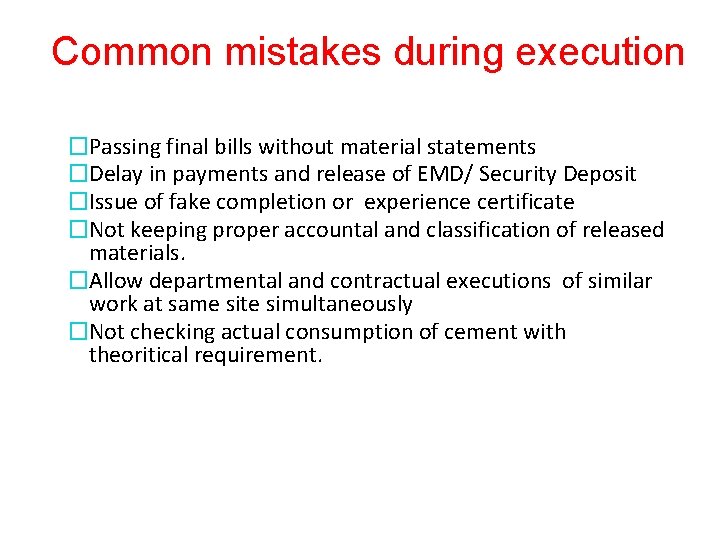
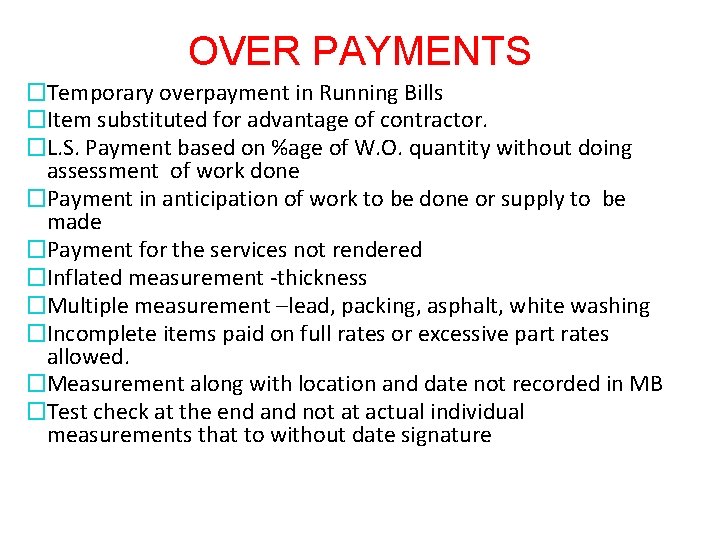
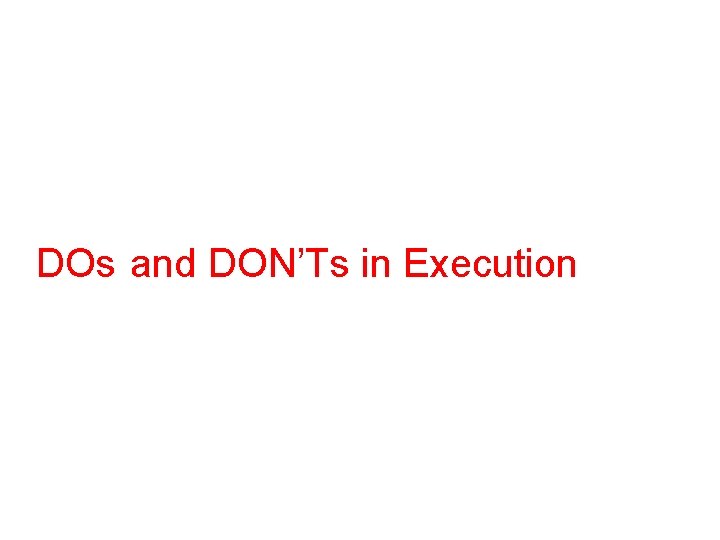
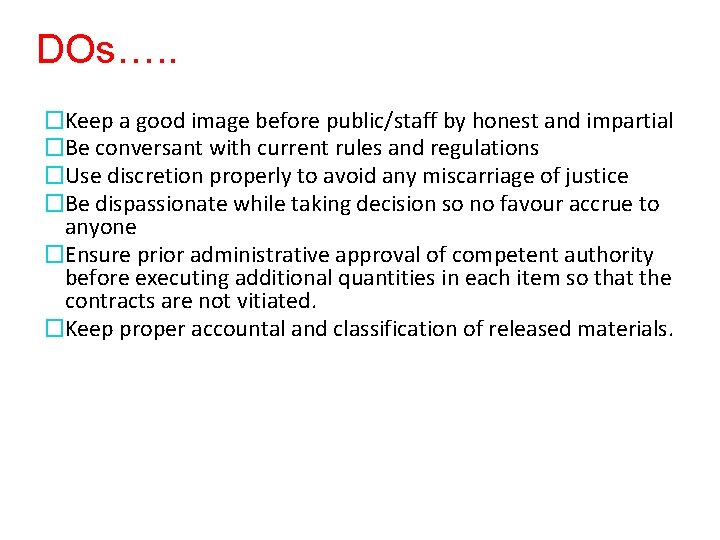
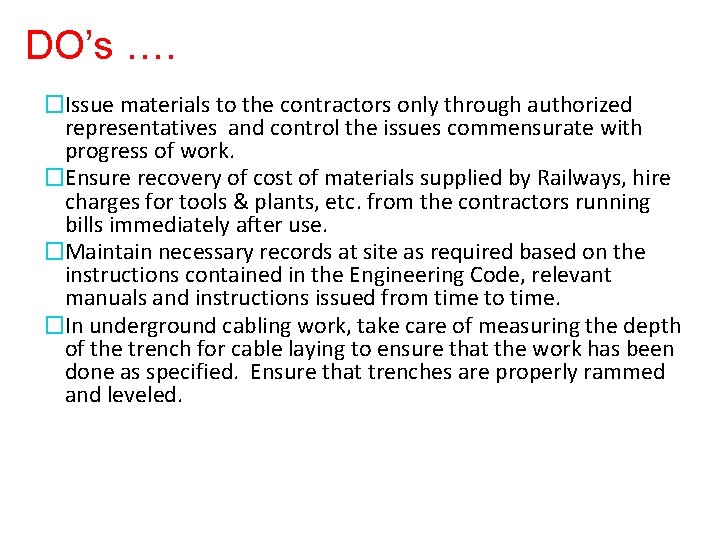
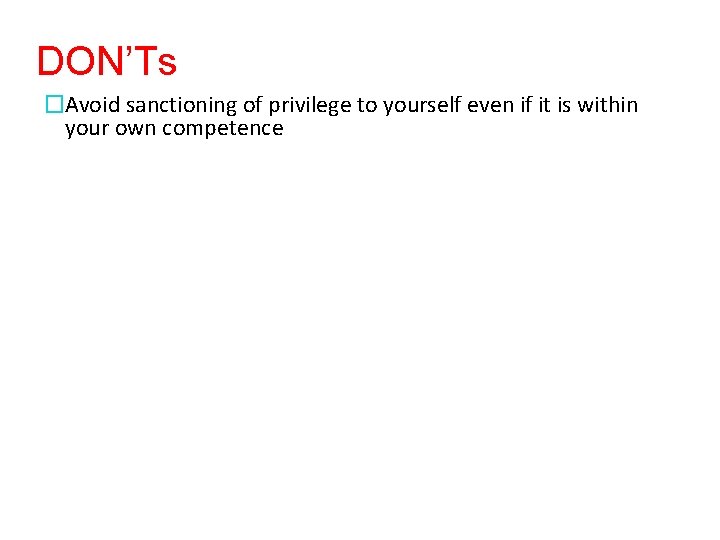
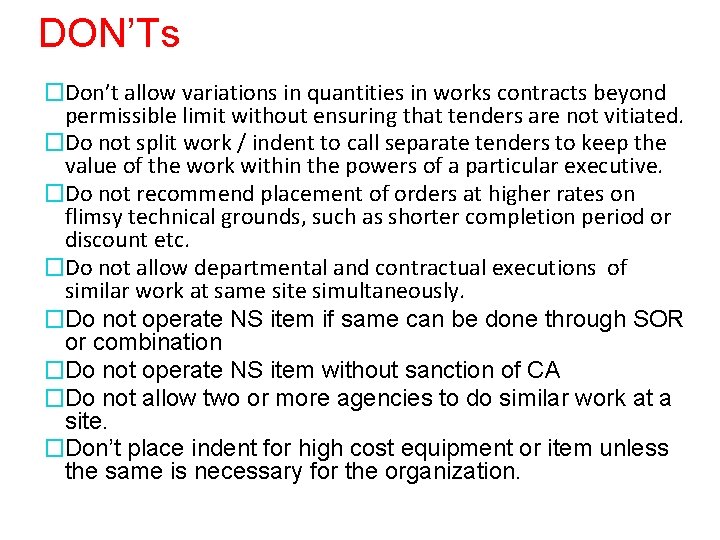
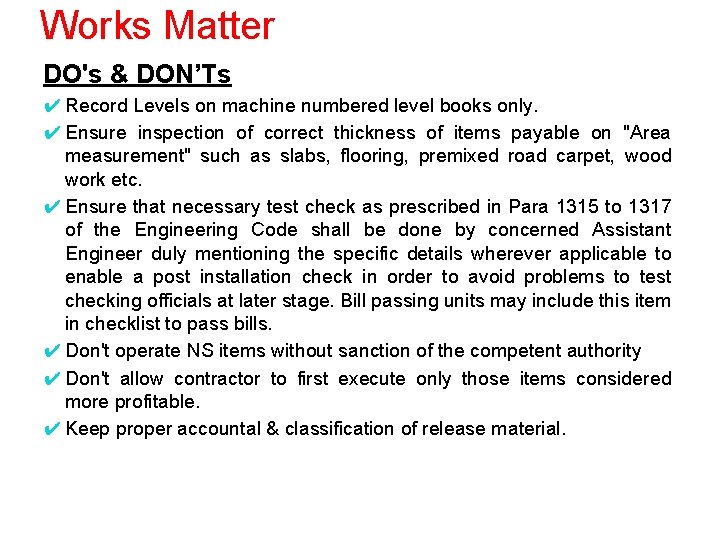
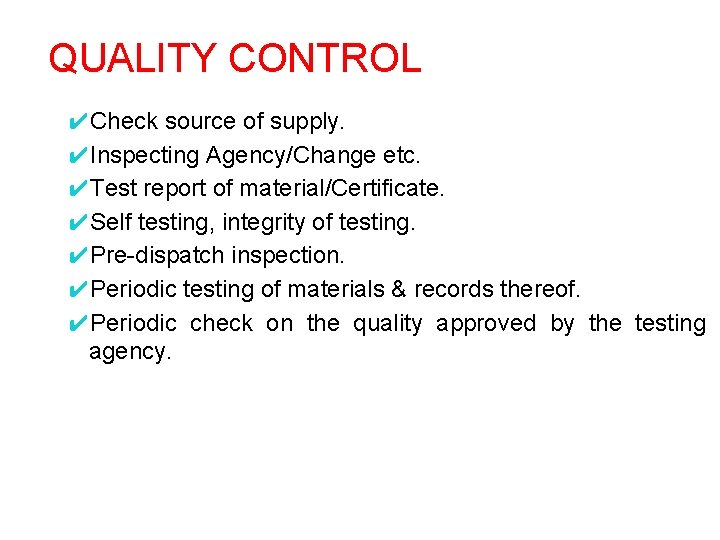
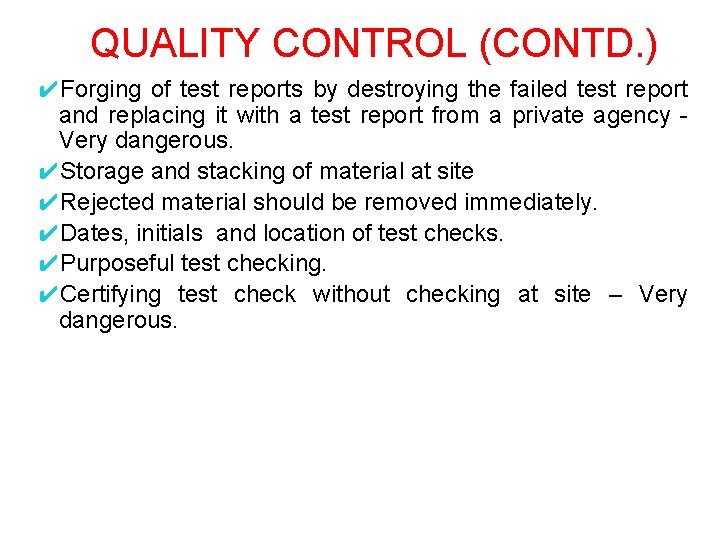
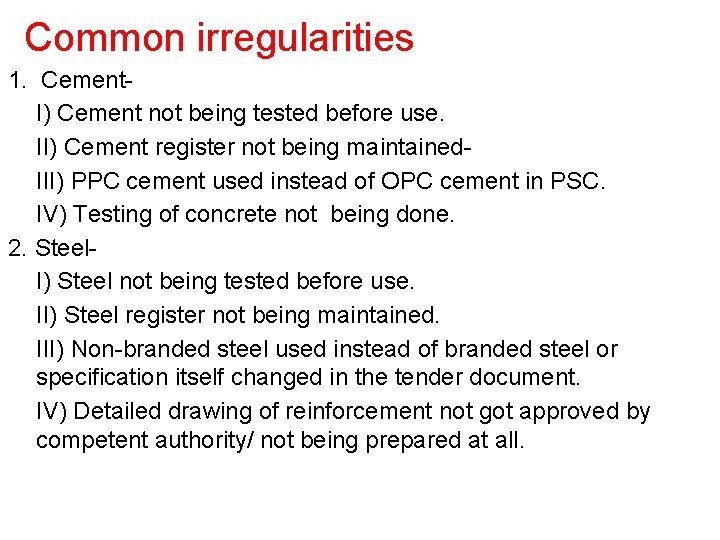
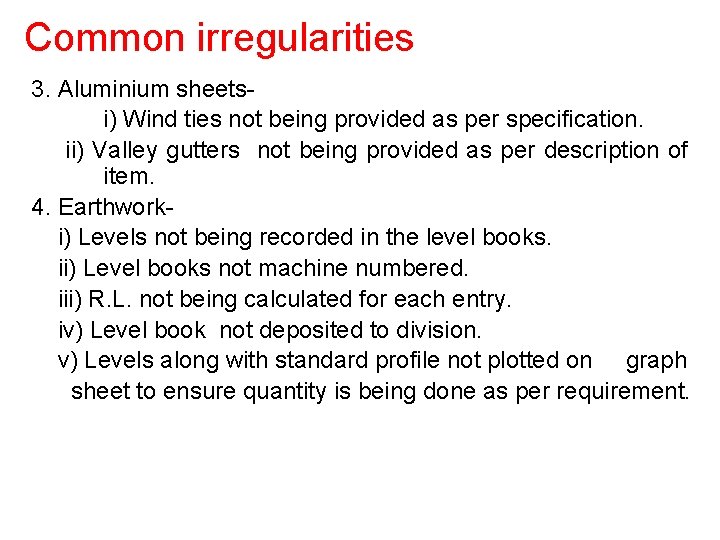
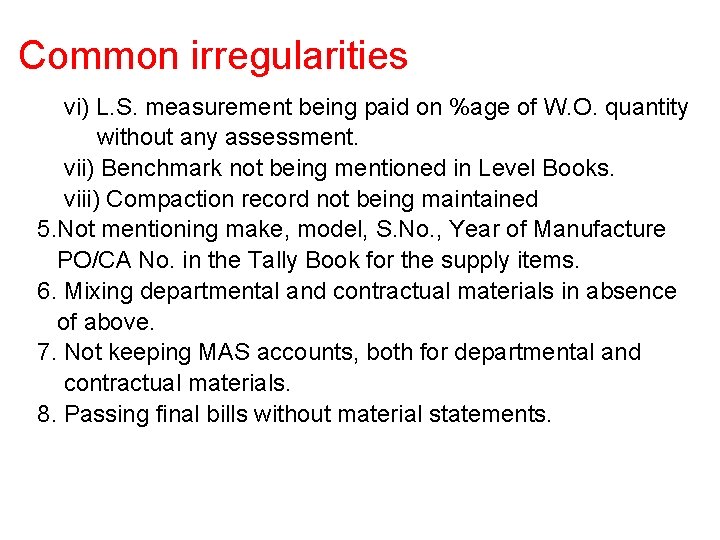

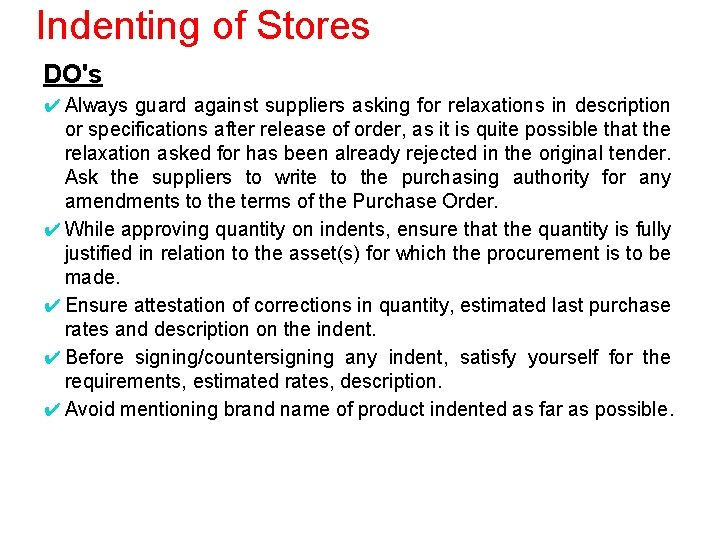
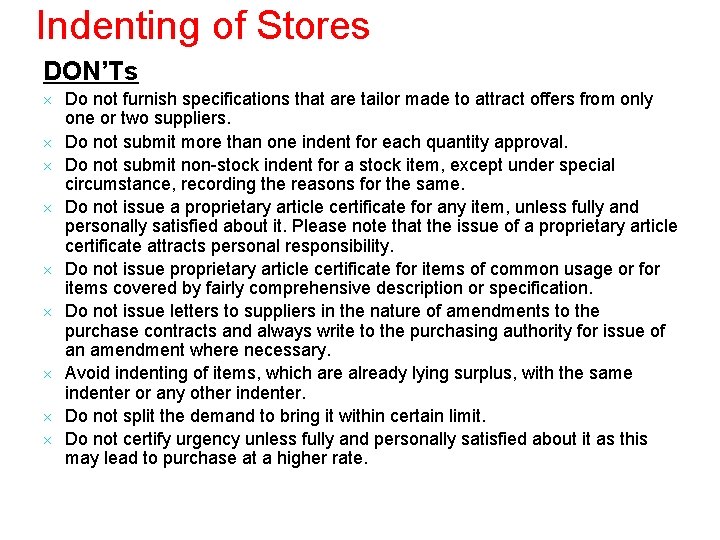
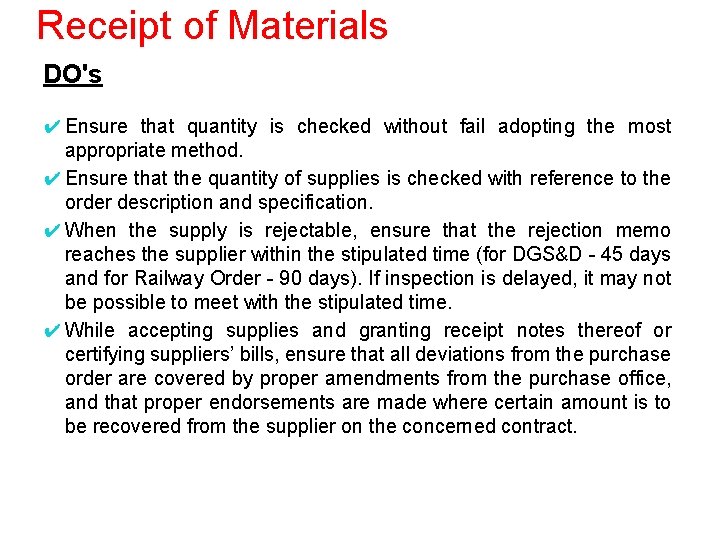
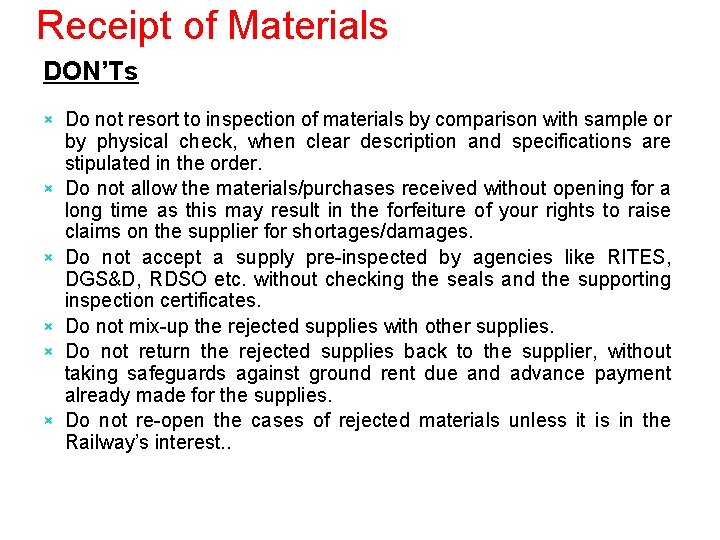
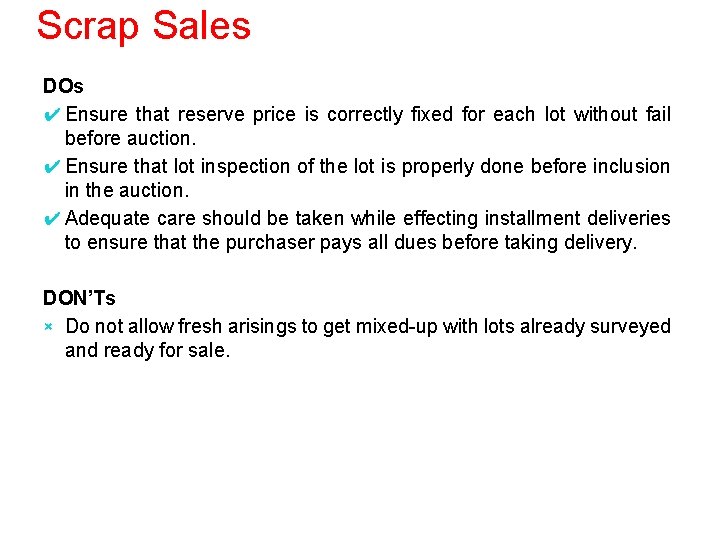
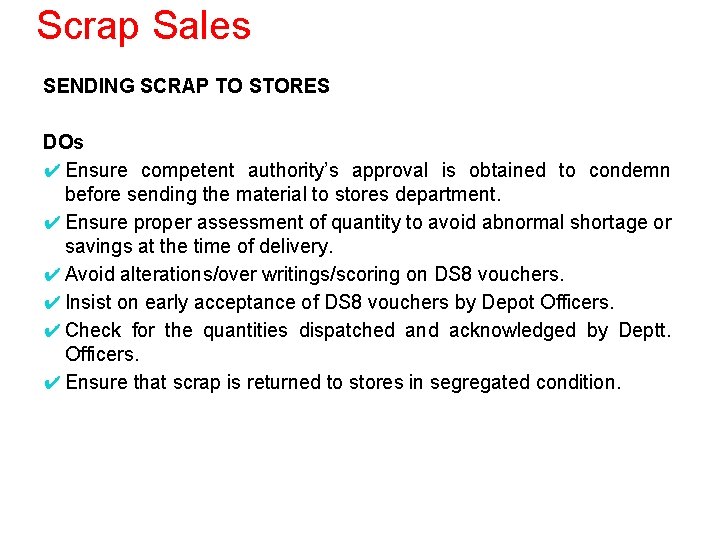
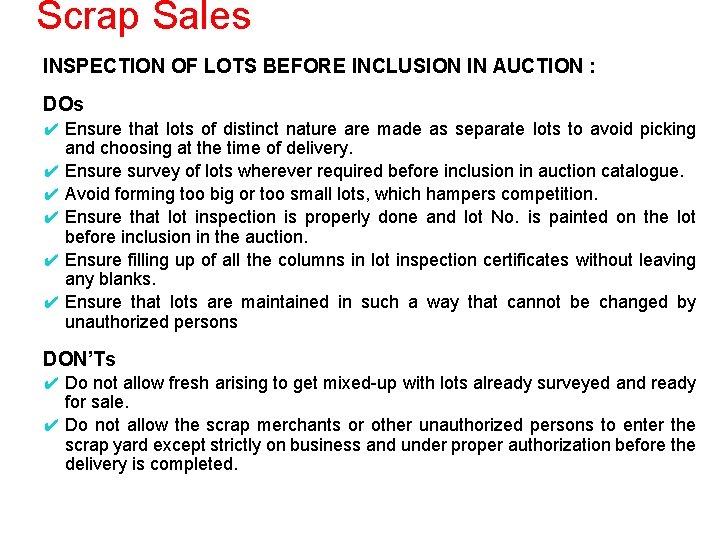
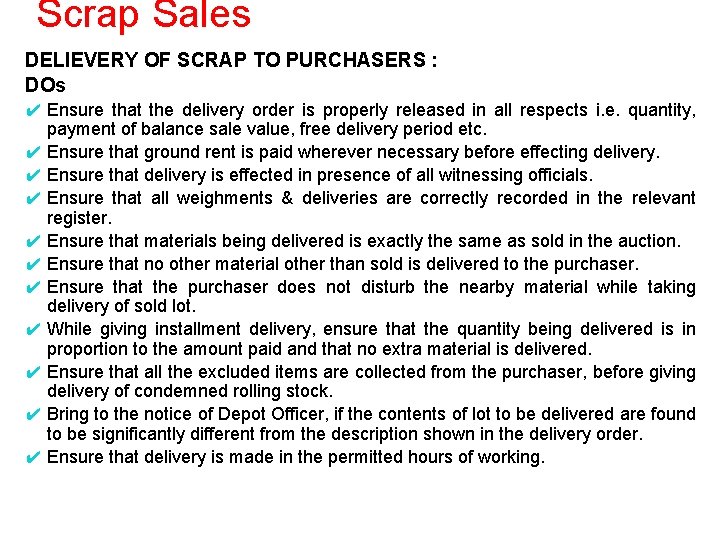
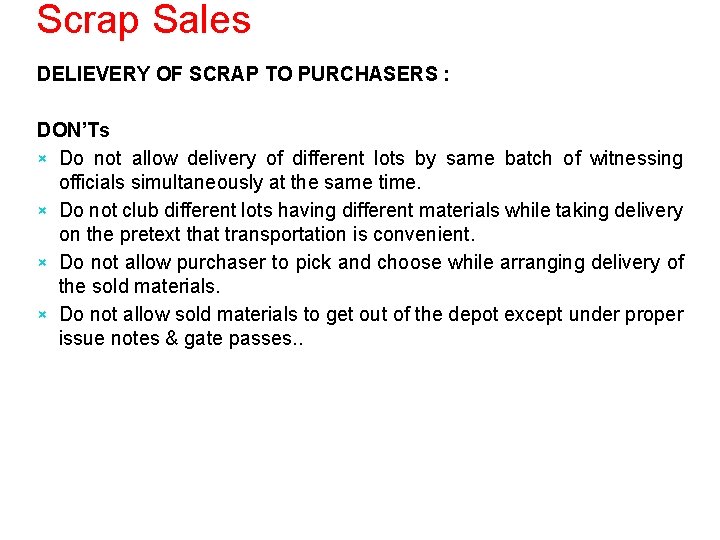
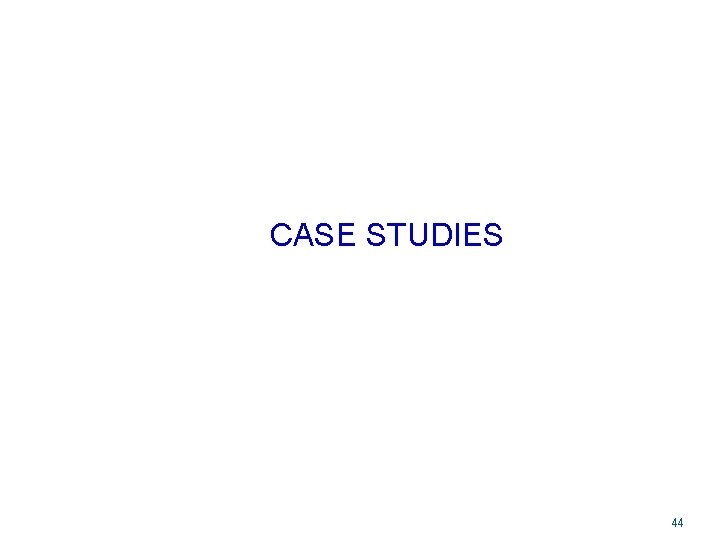
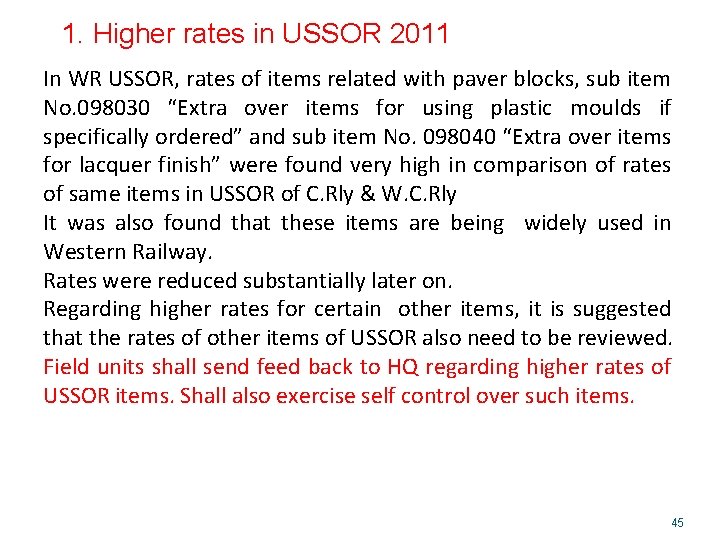
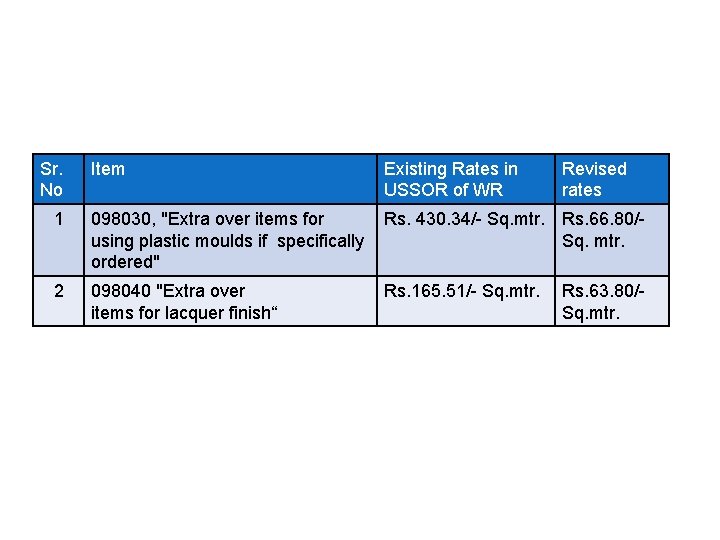
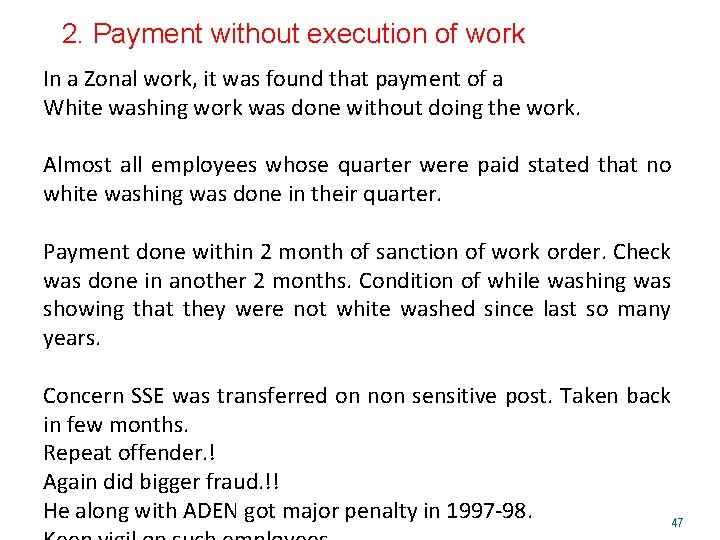
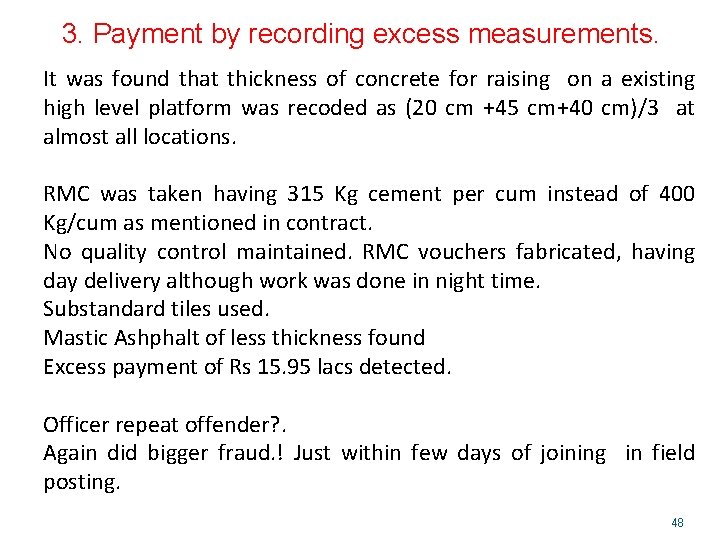
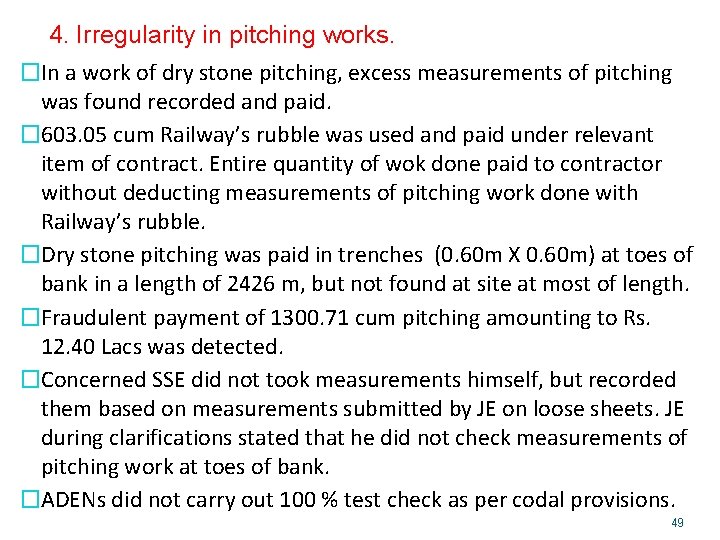
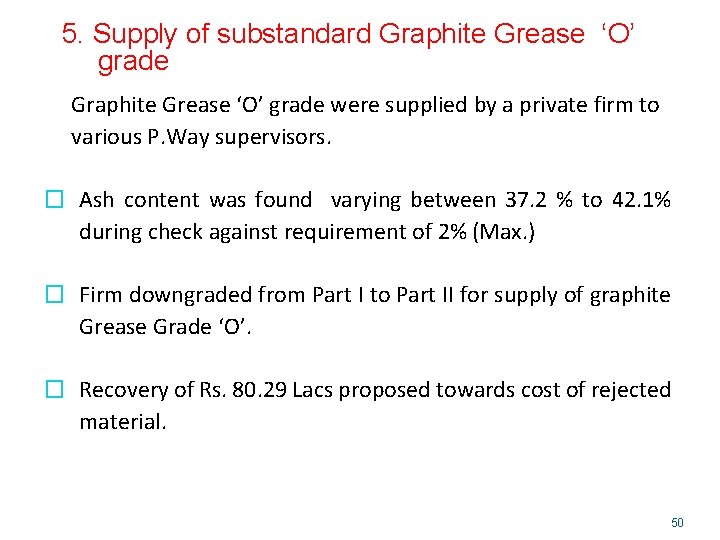
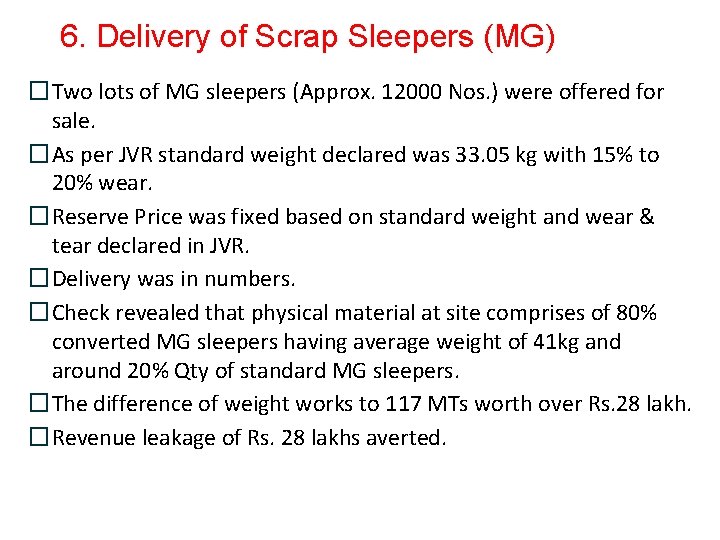
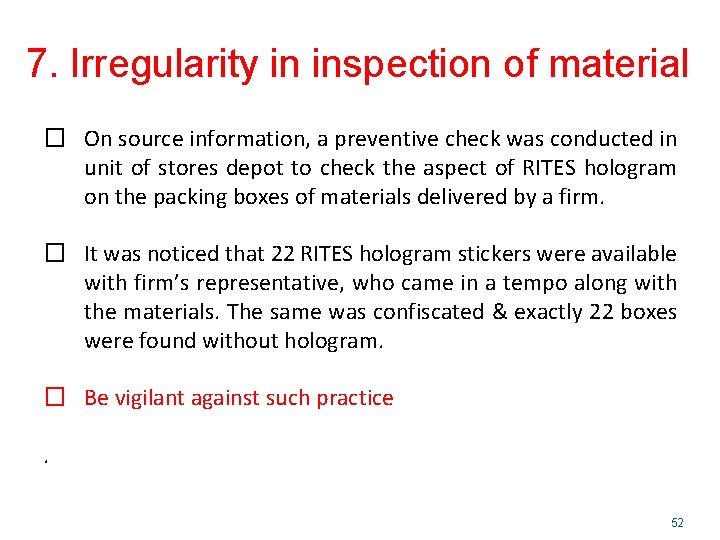
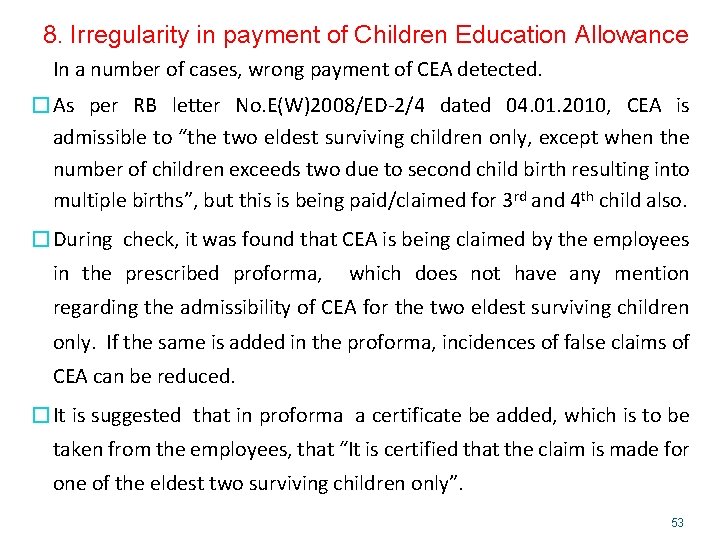
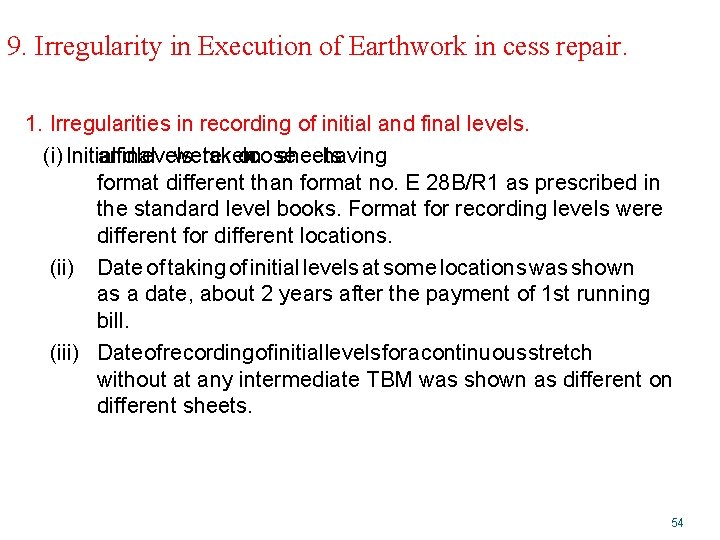
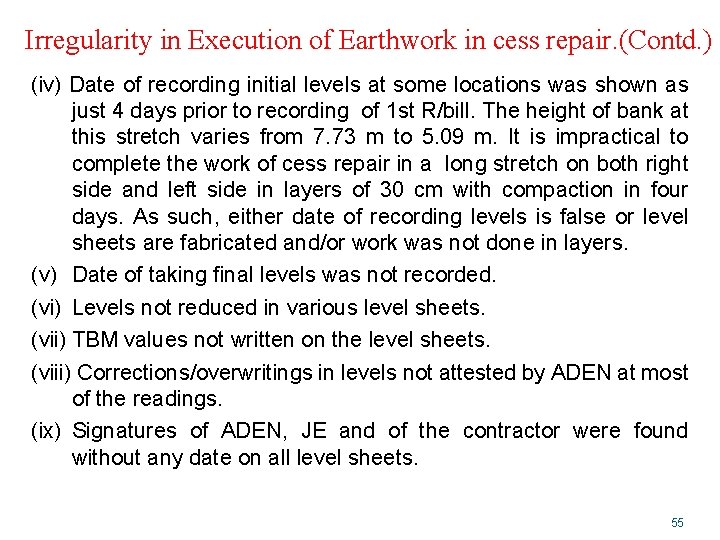
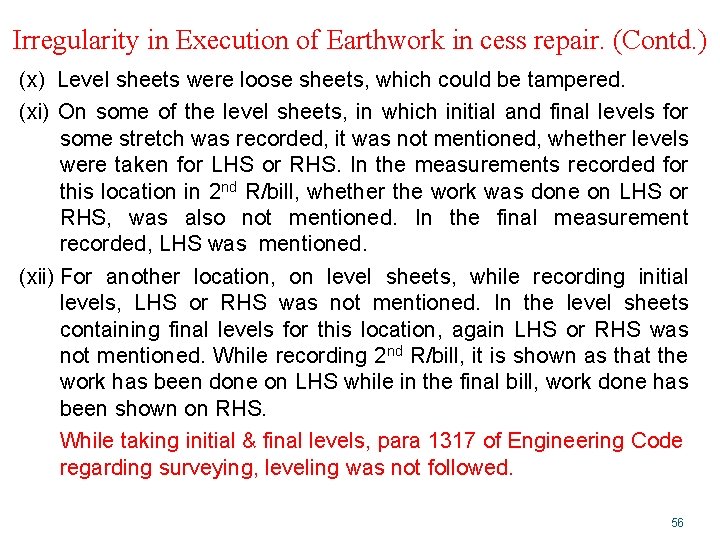
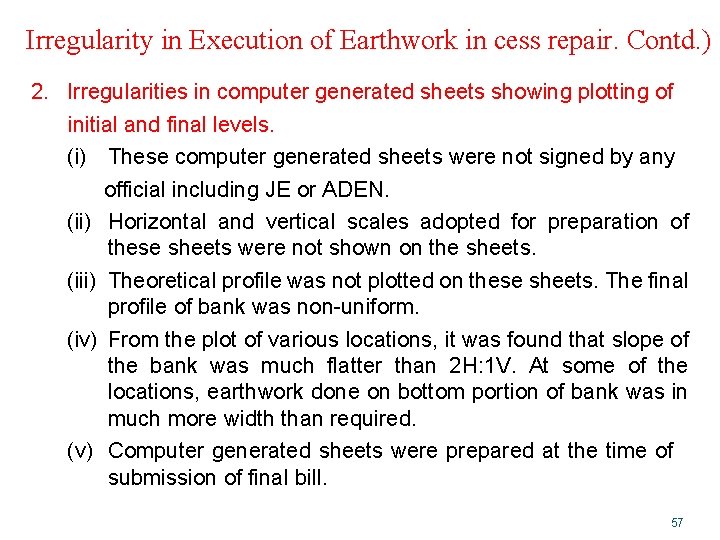
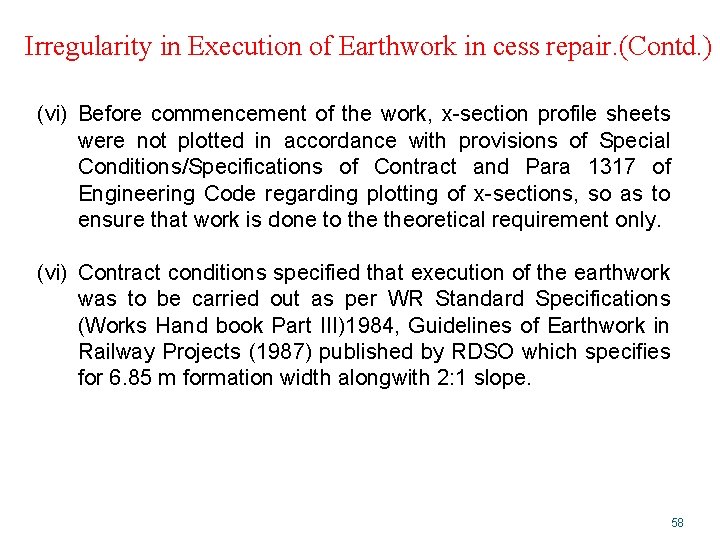

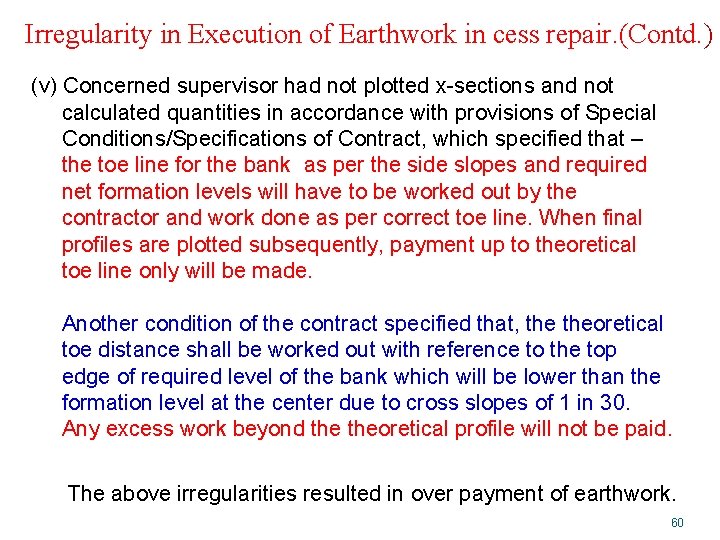
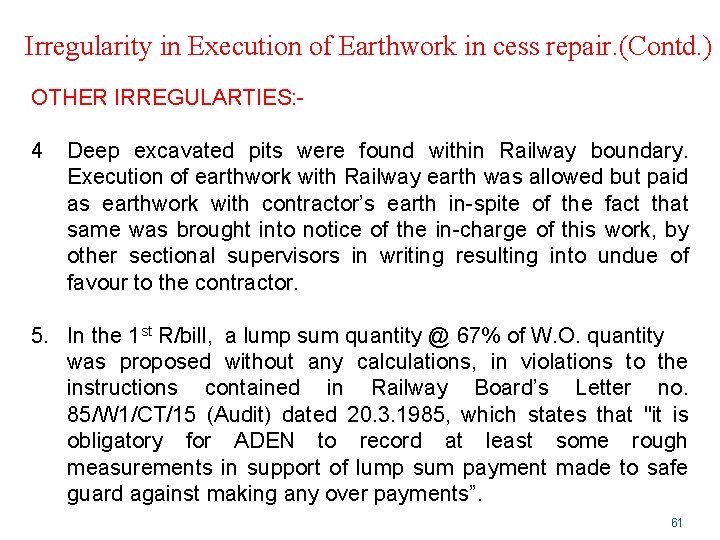
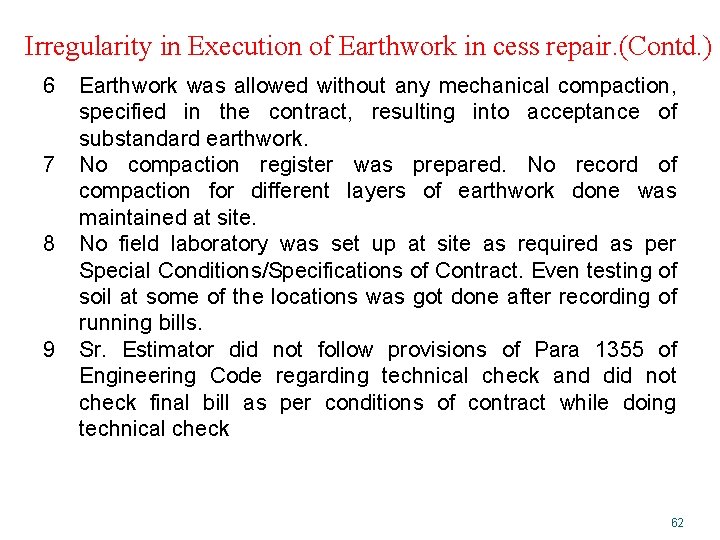
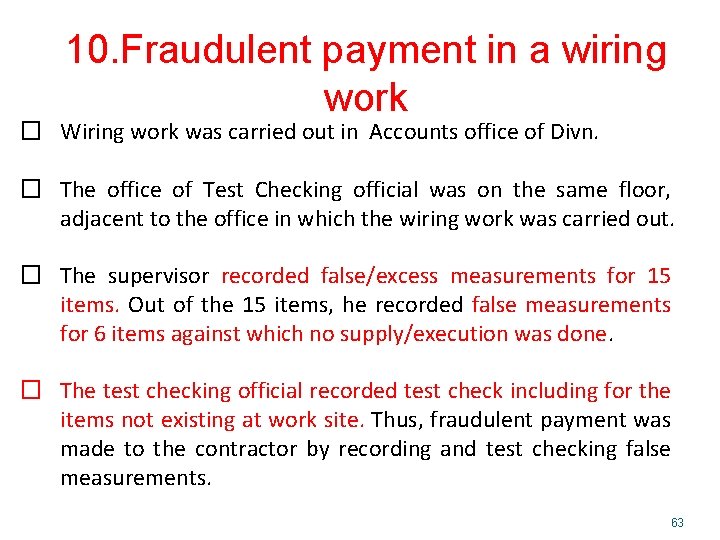
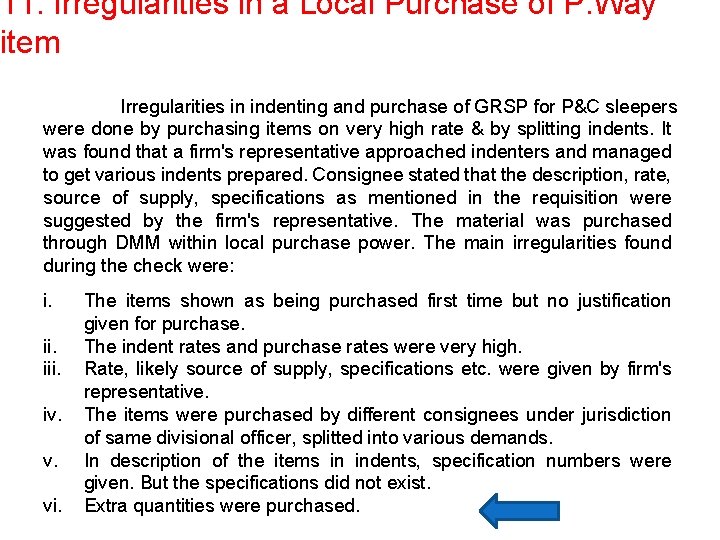

- Slides: 65
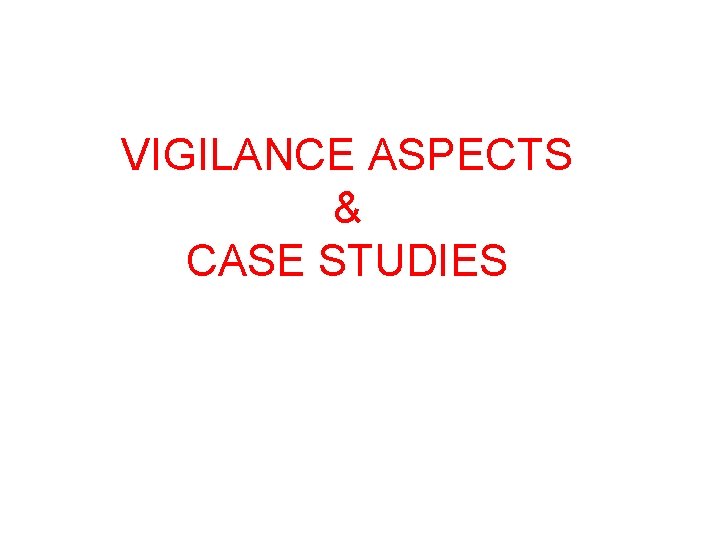
VIGILANCE ASPECTS & CASE STUDIES
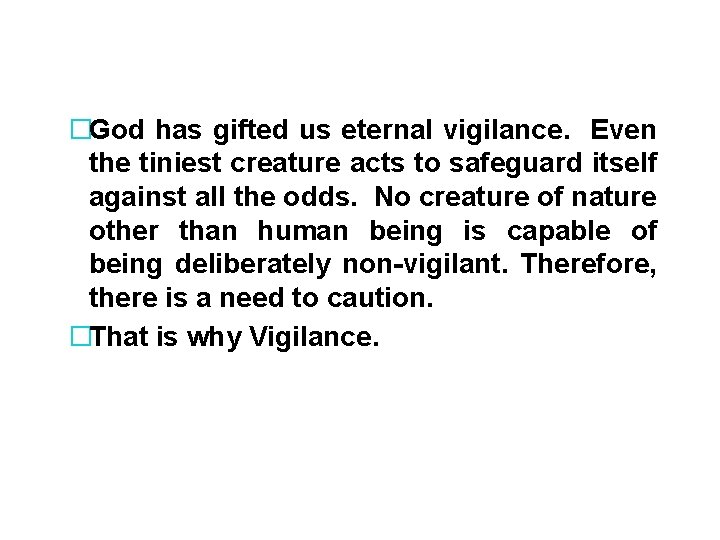
�God has gifted us eternal vigilance. Even the tiniest creature acts to safeguard itself against all the odds. No creature of nature other than human being is capable of being deliberately non-vigilant. Therefore, there is a need to caution. �That is why Vigilance.
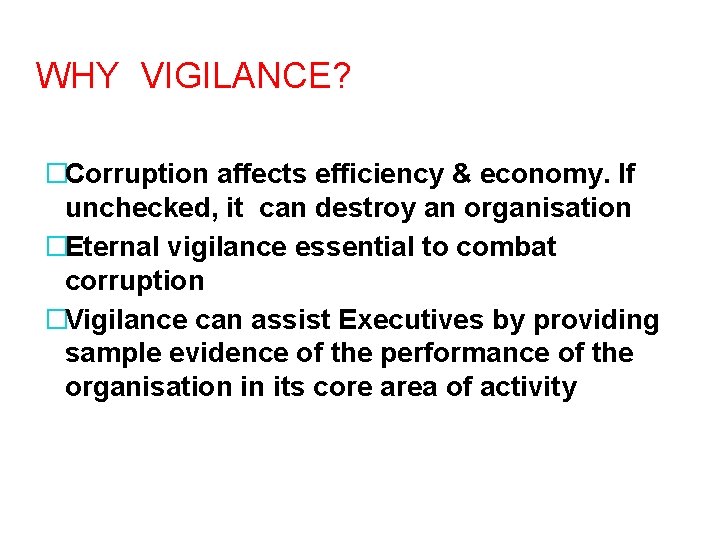
WHY VIGILANCE? �Corruption affects efficiency & economy. If unchecked, it can destroy an organisation �Eternal vigilance essential to combat corruption �Vigilance can assist Executives by providing sample evidence of the performance of the organisation in its core area of activity
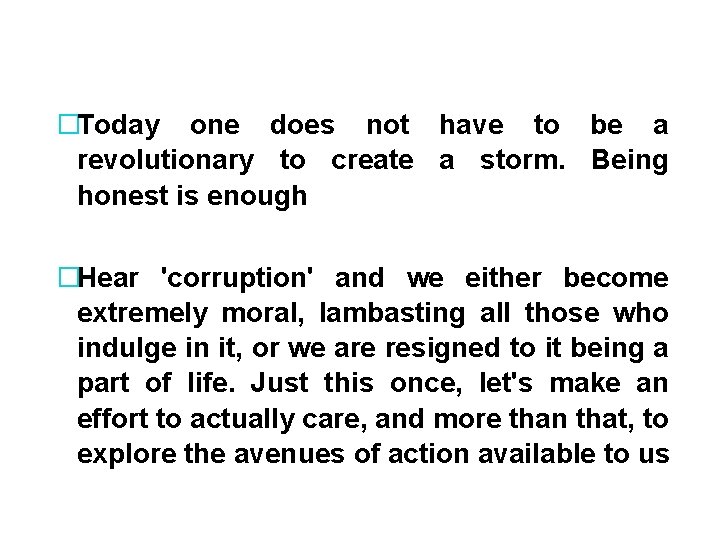
�Today one does not have to be a revolutionary to create a storm. Being honest is enough �Hear 'corruption' and we either become extremely moral, lambasting all those who indulge in it, or we are resigned to it being a part of life. Just this once, let's make an effort to actually care, and more than that, to explore the avenues of action available to us
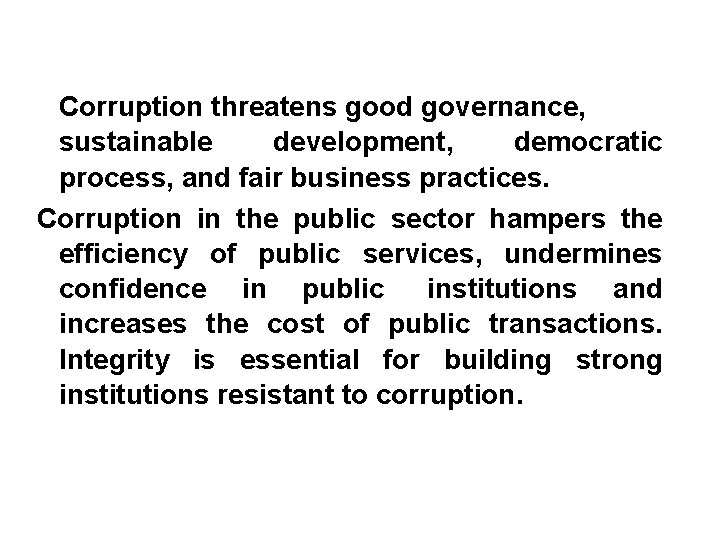
Corruption threatens good governance, sustainable development, democratic process, and fair business practices. Corruption in the public sector hampers the efficiency of public services, undermines confidence in public institutions and increases the cost of public transactions. Integrity is essential for building strong institutions resistant to corruption.
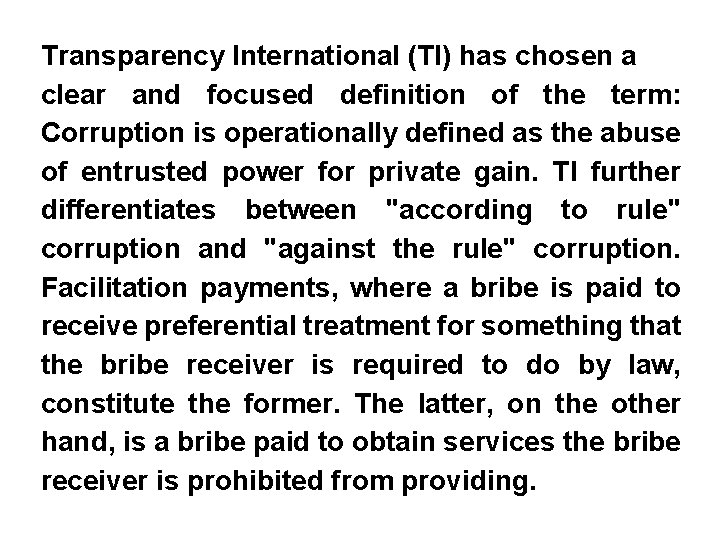
Transparency International (TI) has chosen a clear and focused definition of the term: Corruption is operationally defined as the abuse of entrusted power for private gain. TI further differentiates between "according to rule" corruption and "against the rule" corruption. Facilitation payments, where a bribe is paid to receive preferential treatment for something that the bribe receiver is required to do by law, constitute the former. The latter, on the other hand, is a bribe paid to obtain services the bribe receiver is prohibited from providing.
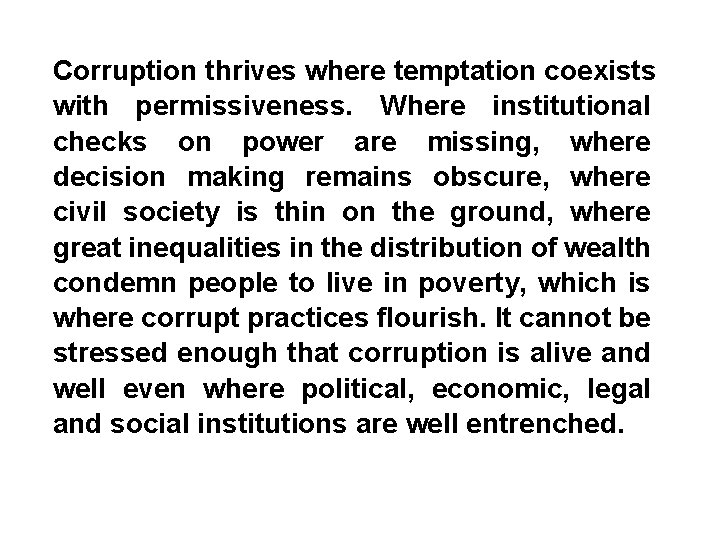
Corruption thrives where temptation coexists with permissiveness. Where institutional checks on power are missing, where decision making remains obscure, where civil society is thin on the ground, where great inequalities in the distribution of wealth condemn people to live in poverty, which is where corrupt practices flourish. It cannot be stressed enough that corruption is alive and well even where political, economic, legal and social institutions are well entrenched.
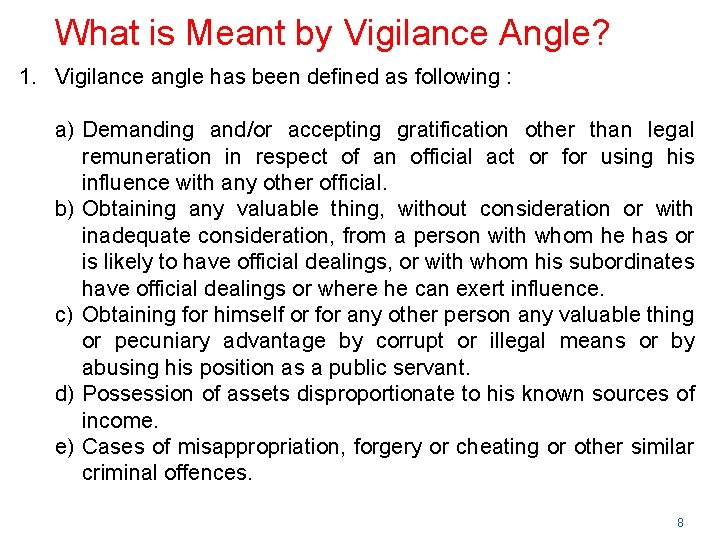
What is Meant by Vigilance Angle? 1. Vigilance angle has been defined as following : a) Demanding and/or accepting gratification other than legal remuneration in respect of an official act or for using his influence with any other official. b) Obtaining any valuable thing, without consideration or with inadequate consideration, from a person with whom he has or is likely to have official dealings, or with whom his subordinates have official dealings or where he can exert influence. c) Obtaining for himself or for any other person any valuable thing or pecuniary advantage by corrupt or illegal means or by abusing his position as a public servant. d) Possession of assets disproportionate to his known sources of income. e) Cases of misappropriation, forgery or cheating or other similar criminal offences. 8
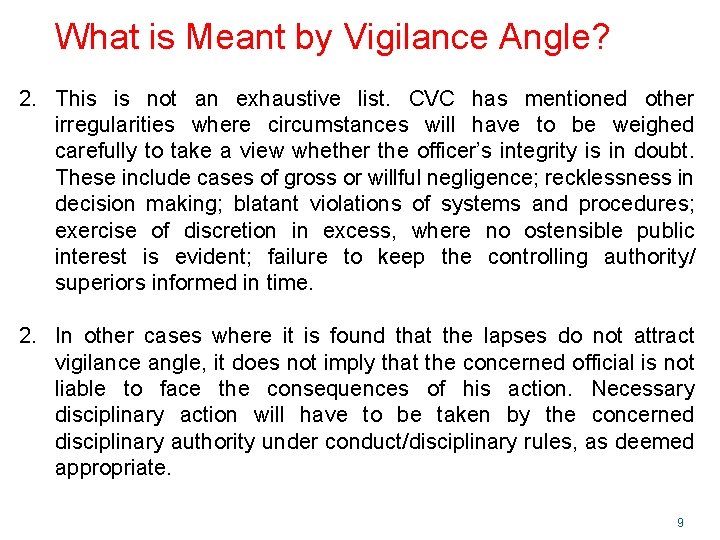
What is Meant by Vigilance Angle? 2. This is not an exhaustive list. CVC has mentioned other irregularities where circumstances will have to be weighed carefully to take a view whether the officer’s integrity is in doubt. These include cases of gross or willful negligence; recklessness in decision making; blatant violations of systems and procedures; exercise of discretion in excess, where no ostensible public interest is evident; failure to keep the controlling authority/ superiors informed in time. 2. In other cases where it is found that the lapses do not attract vigilance angle, it does not imply that the concerned official is not liable to face the consequences of his action. Necessary disciplinary action will have to be taken by the concerned disciplinary authority under conduct/disciplinary rules, as deemed appropriate. 9
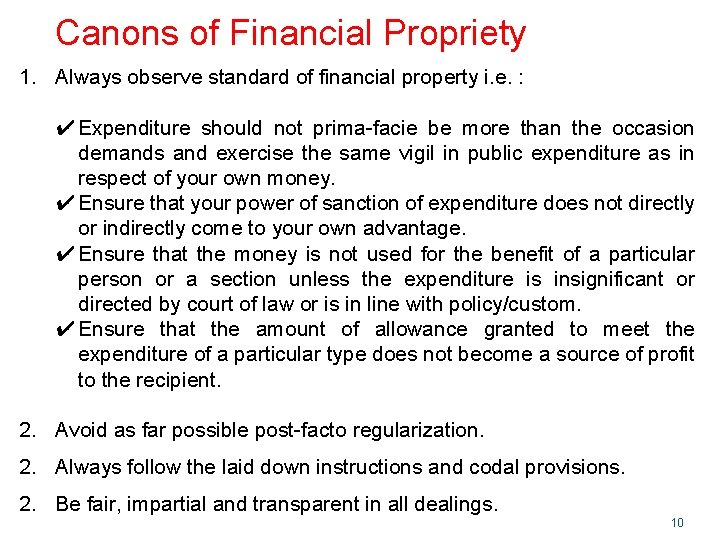
Canons of Financial Propriety 1. Always observe standard of financial property i. e. : ✔Expenditure should not prima-facie be more than the occasion demands and exercise the same vigil in public expenditure as in respect of your own money. ✔Ensure that your power of sanction of expenditure does not directly or indirectly come to your own advantage. ✔Ensure that the money is not used for the benefit of a particular person or a section unless the expenditure is insignificant or directed by court of law or is in line with policy/custom. ✔Ensure that the amount of allowance granted to meet the expenditure of a particular type does not become a source of profit to the recipient. 2. Avoid as far possible post-facto regularization. 2. Always follow the laid down instructions and codal provisions. 2. Be fair, impartial and transparent in all dealings. 10
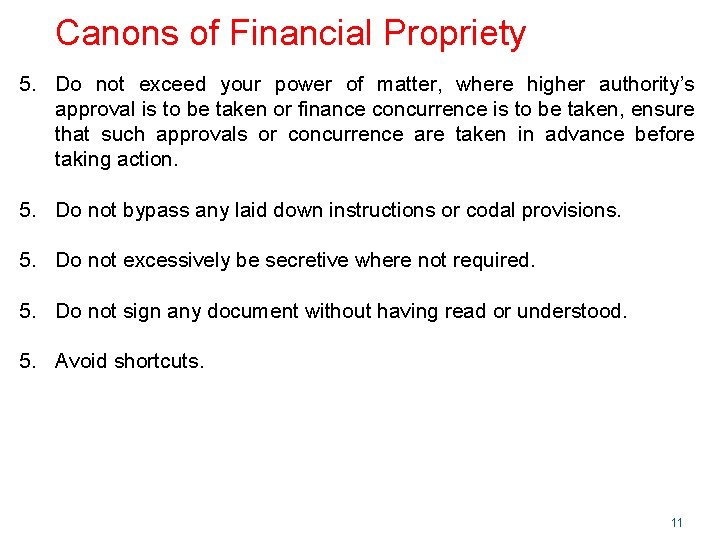
Canons of Financial Propriety 5. Do not exceed your power of matter, where higher authority’s approval is to be taken or finance concurrence is to be taken, ensure that such approvals or concurrence are taken in advance before taking action. 5. Do not bypass any laid down instructions or codal provisions. 5. Do not excessively be secretive where not required. 5. Do not sign any document without having read or understood. 5. Avoid shortcuts. 11
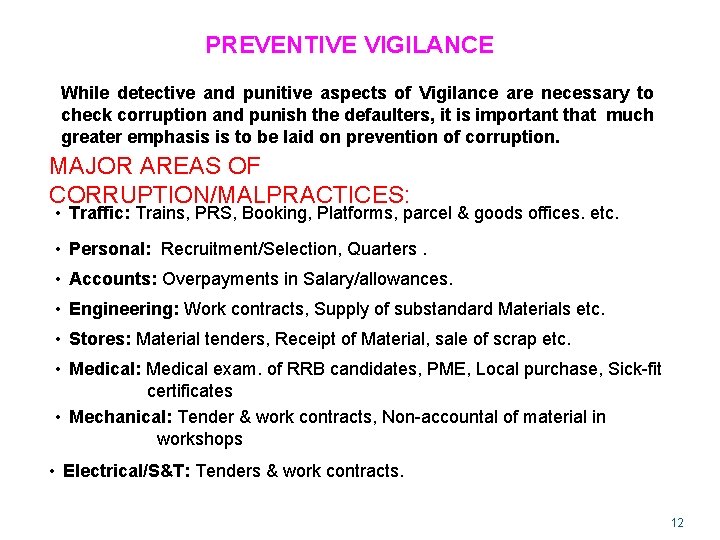
PREVENTIVE VIGILANCE While detective and punitive aspects of Vigilance are necessary to check corruption and punish the defaulters, it is important that much greater emphasis is to be laid on prevention of corruption. MAJOR AREAS OF CORRUPTION/MALPRACTICES: • Traffic: Trains, PRS, Booking, Platforms, parcel & goods offices. etc. • Personal: Recruitment/Selection, Quarters. • Accounts: Overpayments in Salary/allowances. • Engineering: Work contracts, Supply of substandard Materials etc. • Stores: Material tenders, Receipt of Material, sale of scrap etc. • Medical: Medical exam. of RRB candidates, PME, Local purchase, Sick-fit certificates • Mechanical: Tender & work contracts, Non-accountal of material in workshops • Electrical/S&T: Tenders & work contracts. 12

Common Irregularities
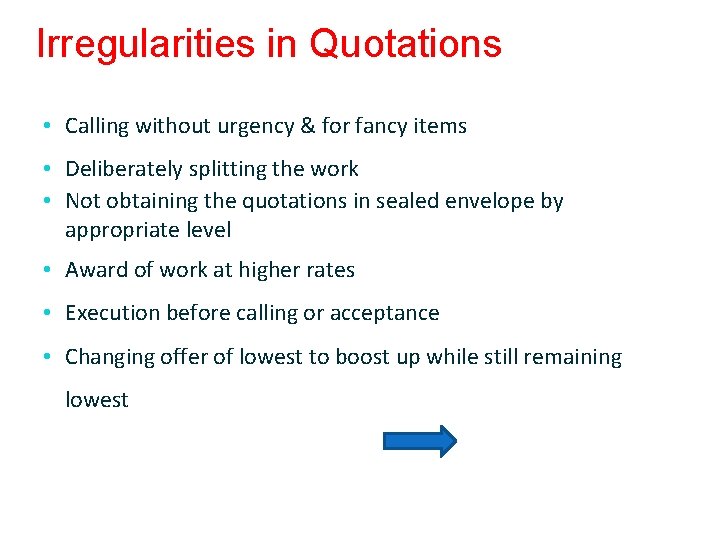
Irregularities in Quotations • Calling without urgency & for fancy items • Deliberately splitting the work • Not obtaining the quotations in sealed envelope by appropriate level • Award of work at higher rates • Execution before calling or acceptance • Changing offer of lowest to boost up while still remaining lowest
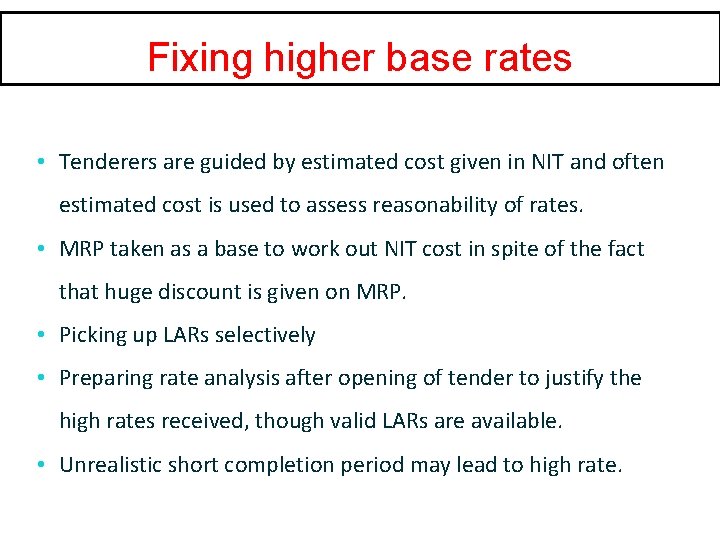
Fixing higher base rates • Tenderers are guided by estimated cost given in NIT and often estimated cost is used to assess reasonability of rates. • MRP taken as a base to work out NIT cost in spite of the fact that huge discount is given on MRP. • Picking up LARs selectively • Preparing rate analysis after opening of tender to justify the high rates received, though valid LARs are available. • Unrealistic short completion period may lead to high rate.
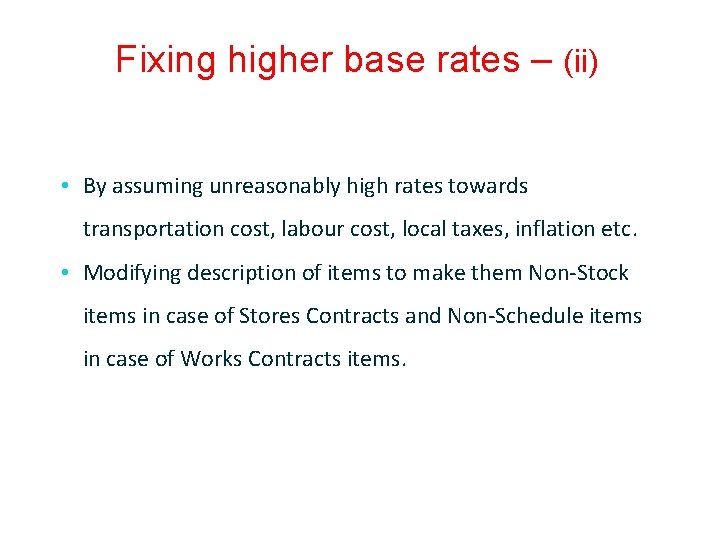
Fixing higher base rates – (ii) • By assuming unreasonably high rates towards transportation cost, labour cost, local taxes, inflation etc. • Modifying description of items to make them Non-Stock items in case of Stores Contracts and Non-Schedule items in case of Works Contracts items.

Rate restriction in LOA (Ref: 2012/CE-I/CT/0/10 dated 26. 08. 13) • If any accepted rate has been restricted for future references by the tender committee and the accepting authority, it should invariably be mentioned so in the letter of acceptance such mention shall be in the contract agreement, if the accepting authority issues specific direction in this regard.
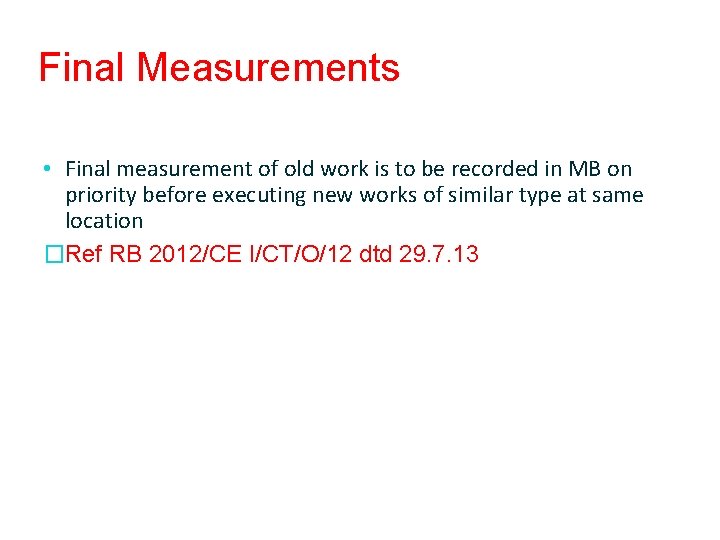
Final Measurements • Final measurement of old work is to be recorded in MB on priority before executing new works of similar type at same location �Ref RB 2012/CE I/CT/O/12 dtd 29. 7. 13
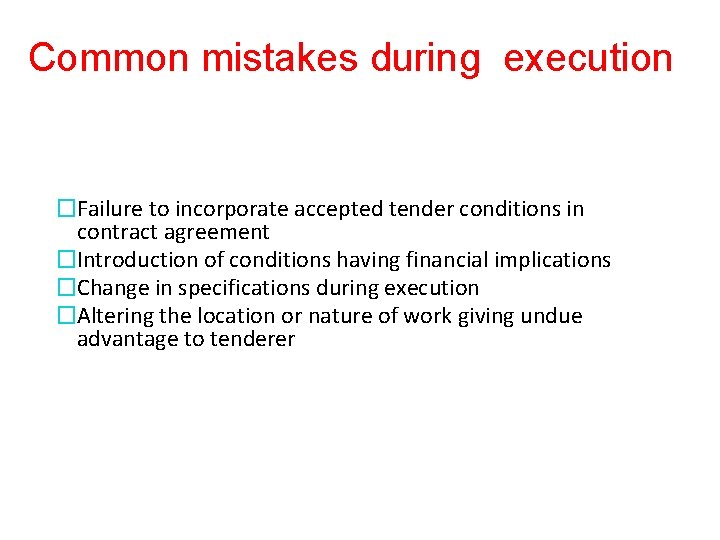
Common mistakes during execution �Failure to incorporate accepted tender conditions in contract agreement �Introduction of conditions having financial implications �Change in specifications during execution �Altering the location or nature of work giving undue advantage to tenderer
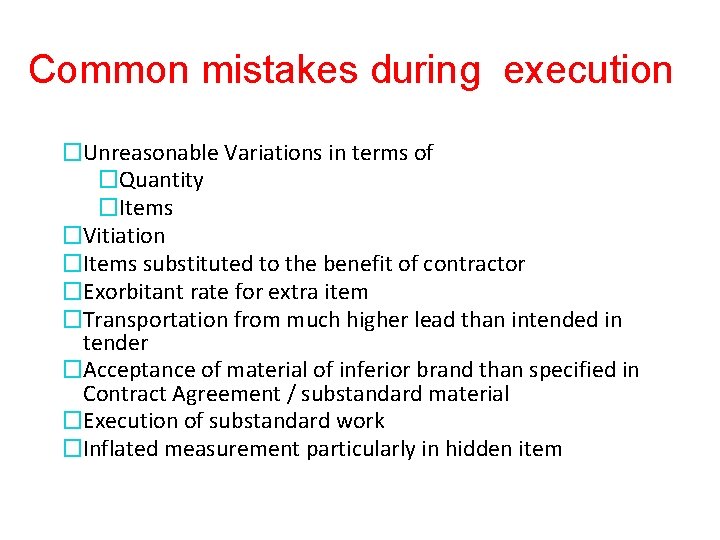
Common mistakes during execution �Unreasonable Variations in terms of �Quantity �Items �Vitiation �Items substituted to the benefit of contractor �Exorbitant rate for extra item �Transportation from much higher lead than intended in tender �Acceptance of material of inferior brand than specified in Contract Agreement / substandard material �Execution of substandard work �Inflated measurement particularly in hidden item
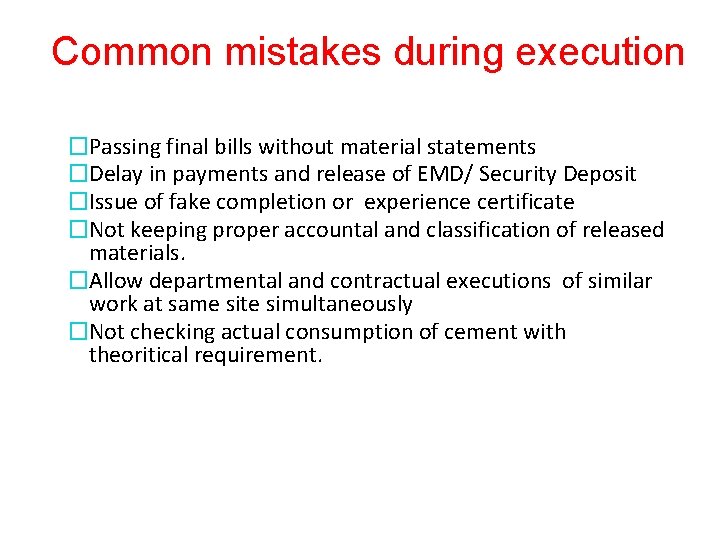
Common mistakes during execution �Passing final bills without material statements �Delay in payments and release of EMD/ Security Deposit �Issue of fake completion or experience certificate �Not keeping proper accountal and classification of released materials. �Allow departmental and contractual executions of similar work at same site simultaneously �Not checking actual consumption of cement with theoritical requirement.
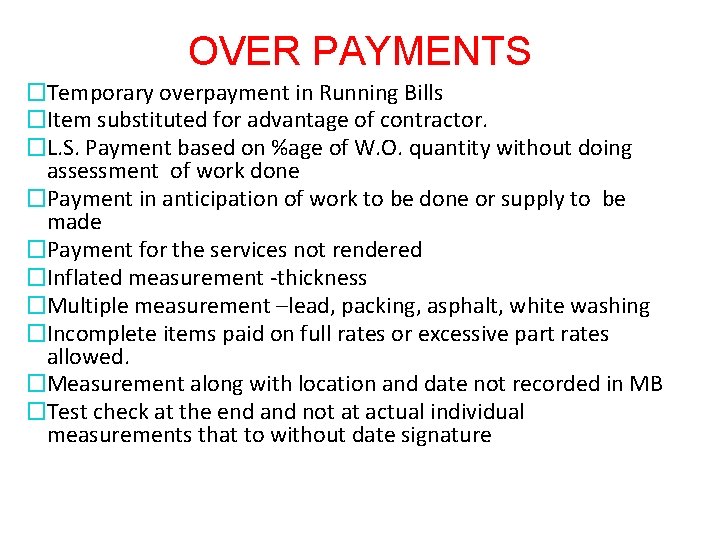
OVER PAYMENTS �Temporary overpayment in Running Bills �Item substituted for advantage of contractor. �L. S. Payment based on %age of W. O. quantity without doing assessment of work done �Payment in anticipation of work to be done or supply to be made �Payment for the services not rendered �Inflated measurement -thickness �Multiple measurement –lead, packing, asphalt, white washing �Incomplete items paid on full rates or excessive part rates allowed. �Measurement along with location and date not recorded in MB �Test check at the end and not at actual individual measurements that to without date signature
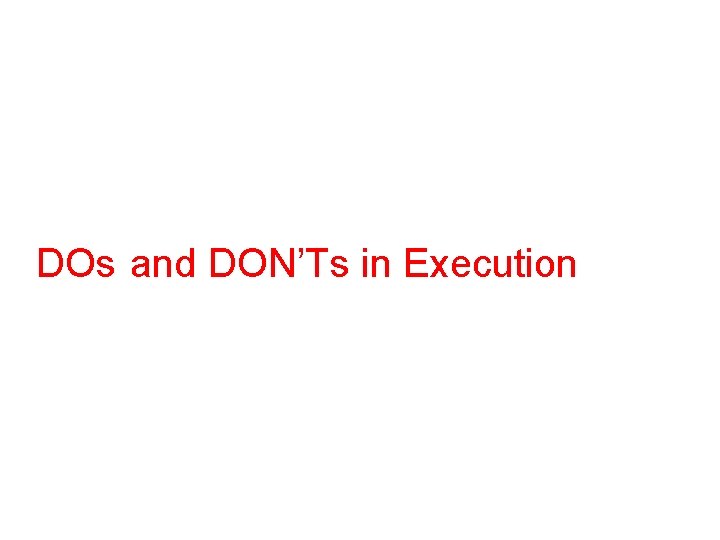
DOs and DON’Ts in Execution
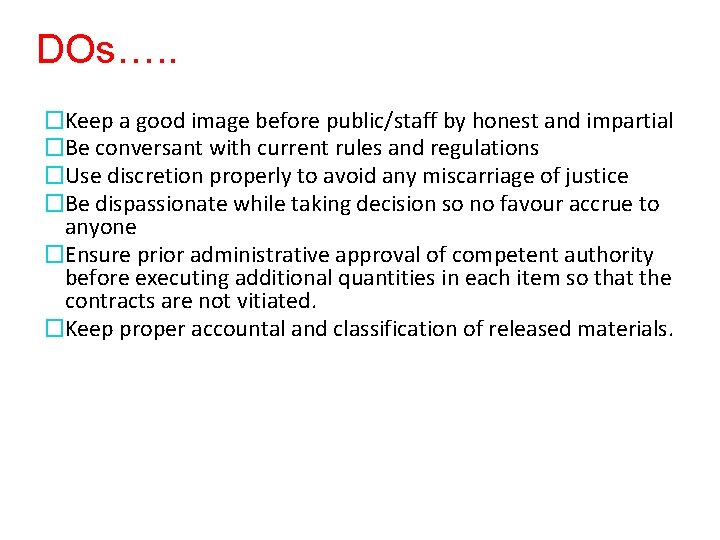
DOs…. . �Keep a good image before public/staff by honest and impartial �Be conversant with current rules and regulations �Use discretion properly to avoid any miscarriage of justice �Be dispassionate while taking decision so no favour accrue to anyone �Ensure prior administrative approval of competent authority before executing additional quantities in each item so that the contracts are not vitiated. �Keep proper accountal and classification of released materials.
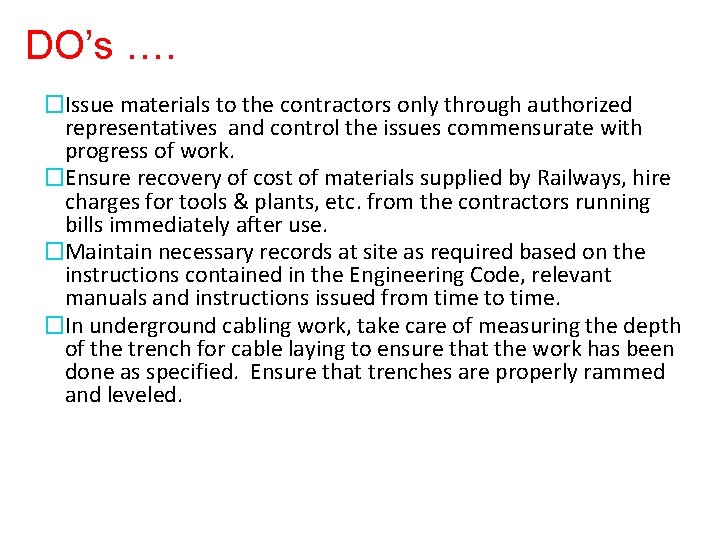
DO’s …. �Issue materials to the contractors only through authorized representatives and control the issues commensurate with progress of work. �Ensure recovery of cost of materials supplied by Railways, hire charges for tools & plants, etc. from the contractors running bills immediately after use. �Maintain necessary records at site as required based on the instructions contained in the Engineering Code, relevant manuals and instructions issued from time to time. �In underground cabling work, take care of measuring the depth of the trench for cable laying to ensure that the work has been done as specified. Ensure that trenches are properly rammed and leveled.
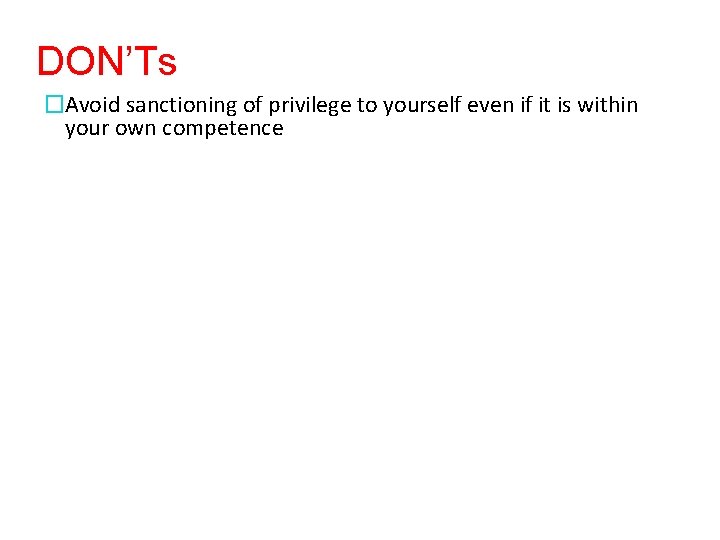
DON’Ts �Avoid sanctioning of privilege to yourself even if it is within your own competence
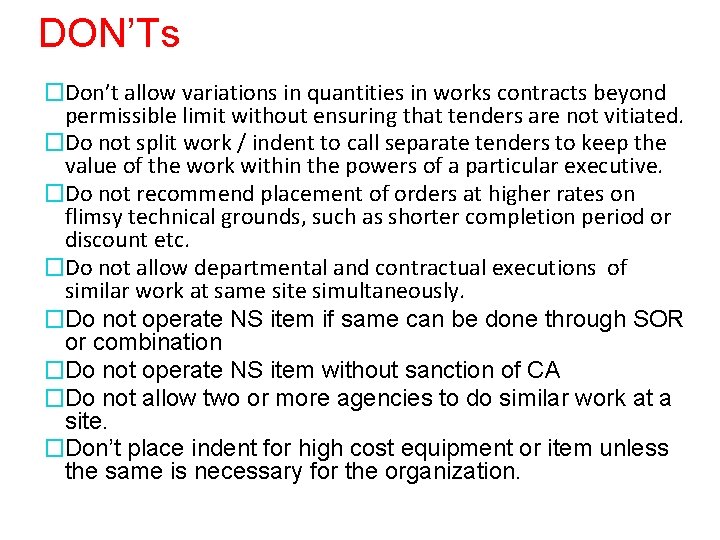
DON’Ts �Don’t allow variations in quantities in works contracts beyond permissible limit without ensuring that tenders are not vitiated. �Do not split work / indent to call separate tenders to keep the value of the work within the powers of a particular executive. �Do not recommend placement of orders at higher rates on flimsy technical grounds, such as shorter completion period or discount etc. �Do not allow departmental and contractual executions of similar work at same site simultaneously. �Do not operate NS item if same can be done through SOR or combination �Do not operate NS item without sanction of CA �Do not allow two or more agencies to do similar work at a site. �Don’t place indent for high cost equipment or item unless the same is necessary for the organization.
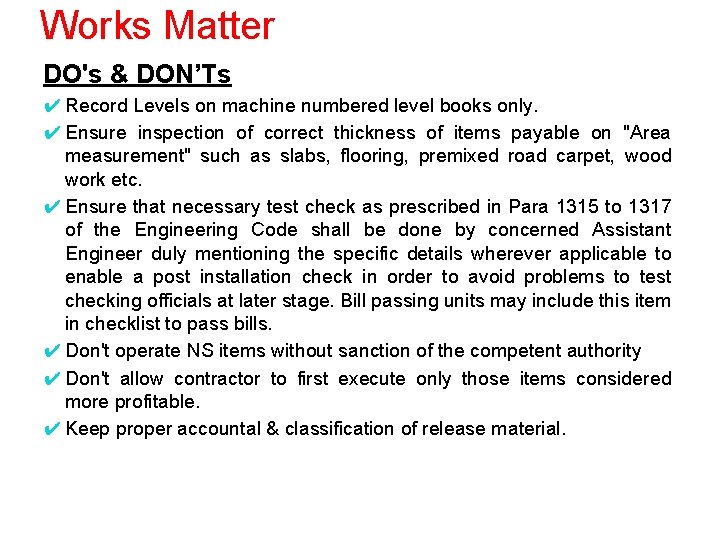
Works Matter DO's & DON’Ts ✔ Record Levels on machine numbered level books only. ✔ Ensure inspection of correct thickness of items payable on "Area measurement" such as slabs, flooring, premixed road carpet, wood work etc. ✔ Ensure that necessary test check as prescribed in Para 1315 to 1317 of the Engineering Code shall be done by concerned Assistant Engineer duly mentioning the specific details wherever applicable to enable a post installation check in order to avoid problems to test checking officials at later stage. Bill passing units may include this item in checklist to pass bills. ✔ Don't operate NS items without sanction of the competent authority ✔ Don't allow contractor to first execute only those items considered more profitable. ✔ Keep proper accountal & classification of release material.
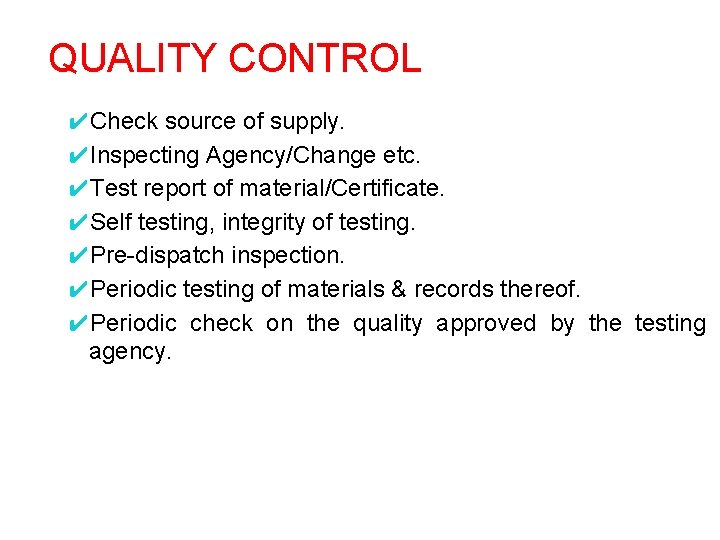
QUALITY CONTROL ✔Check source of supply. ✔Inspecting Agency/Change etc. ✔Test report of material/Certificate. ✔Self testing, integrity of testing. ✔Pre-dispatch inspection. ✔Periodic testing of materials & records thereof. ✔Periodic check on the quality approved by the testing agency.
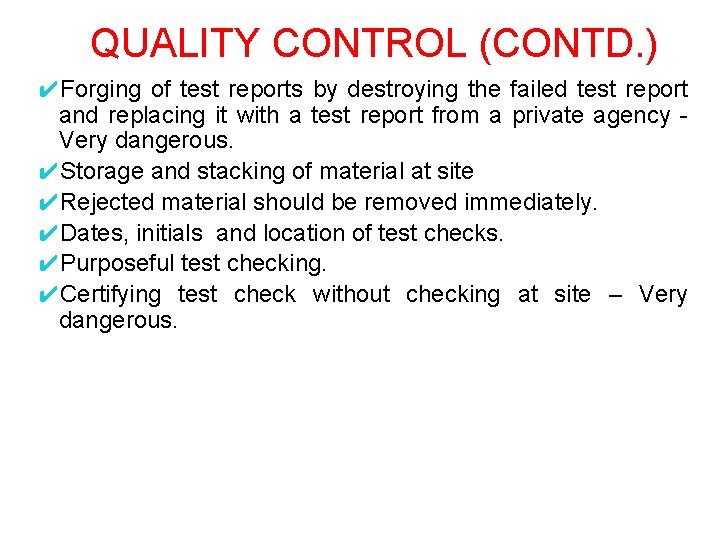
QUALITY CONTROL (CONTD. ) ✔Forging of test reports by destroying the failed test report and replacing it with a test report from a private agency Very dangerous. ✔Storage and stacking of material at site ✔Rejected material should be removed immediately. ✔Dates, initials and location of test checks. ✔Purposeful test checking. ✔Certifying test check without checking at site – Very dangerous.
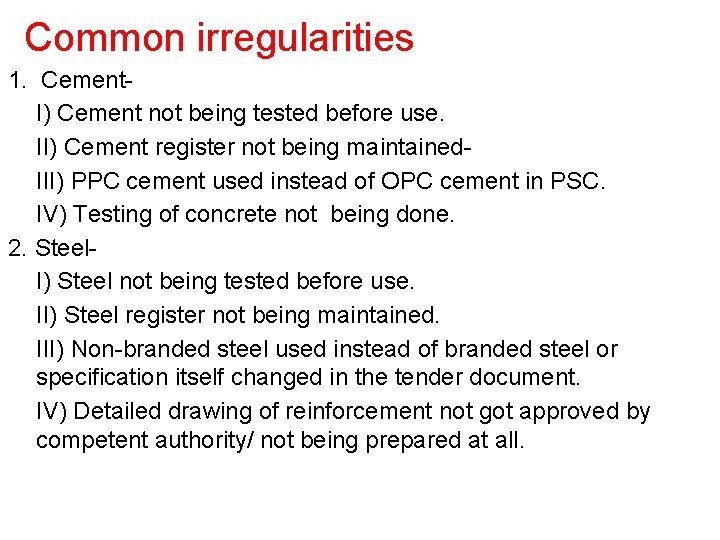
Common irregularities 1. Cement. I) Cement not being tested before use. II) Cement register not being maintained. III) PPC cement used instead of OPC cement in PSC. IV) Testing of concrete not being done. 2. Steel. I) Steel not being tested before use. II) Steel register not being maintained. III) Non-branded steel used instead of branded steel or specification itself changed in the tender document. IV) Detailed drawing of reinforcement not got approved by competent authority/ not being prepared at all.
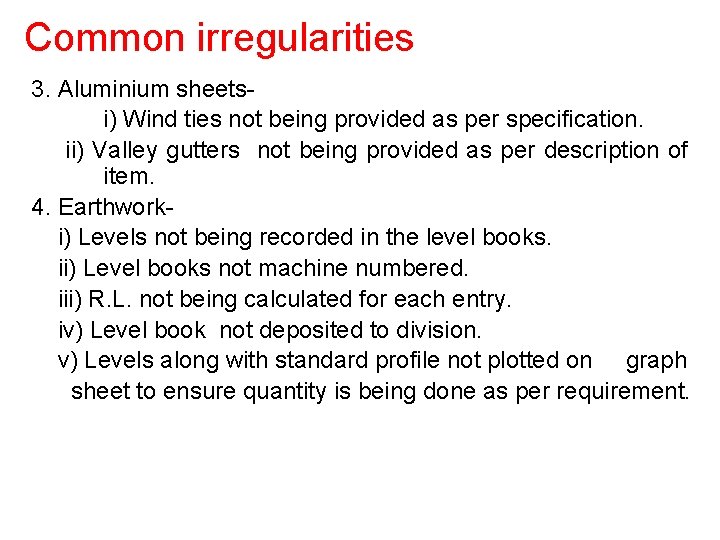
Common irregularities 3. Aluminium sheetsi) Wind ties not being provided as per specification. ii) Valley gutters not being provided as per description of item. 4. Earthworki) Levels not being recorded in the level books. ii) Level books not machine numbered. iii) R. L. not being calculated for each entry. iv) Level book not deposited to division. v) Levels along with standard profile not plotted on graph sheet to ensure quantity is being done as per requirement.
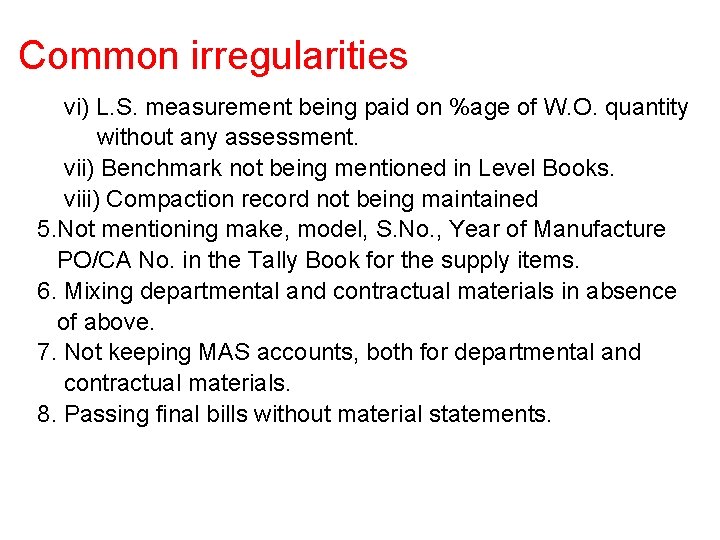
Common irregularities vi) L. S. measurement being paid on %age of W. O. quantity without any assessment. vii) Benchmark not being mentioned in Level Books. viii) Compaction record not being maintained 5. Not mentioning make, model, S. No. , Year of Manufacture PO/CA No. in the Tally Book for the supply items. 6. Mixing departmental and contractual materials in absence of above. 7. Not keeping MAS accounts, both for departmental and contractual materials. 8. Passing final bills without material statements.

Indenting of Stores DO's ✔ Furnish detailed and unambiguous description with specification and drawing number. ✔ Indicate quantity, both in figures and words. ✔ Ensure that the quantity indented is as per approval of the approving authority. ✔ Specify a reasonable delivery period. Avoid terms like “Urgent” and “Immediate” and be specific about the date by which the material is required. ✔ Double check the rates indicated as the estimated rate or last purchase rate before signing the indent. Furnish the basis of this rate, such as the last purchase order no. , date, quantity and source or/and any other detail on which it has been estimated. ✔ Indicate the estimated or last purchase rate in figures as well as words. ✔ Avoid calling for supplies of samples as far as possible.
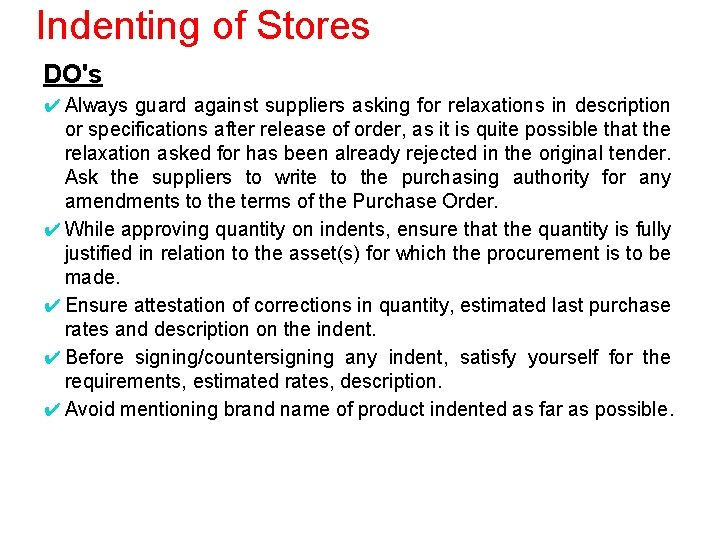
Indenting of Stores DO's ✔ Always guard against suppliers asking for relaxations in description or specifications after release of order, as it is quite possible that the relaxation asked for has been already rejected in the original tender. Ask the suppliers to write to the purchasing authority for any amendments to the terms of the Purchase Order. ✔ While approving quantity on indents, ensure that the quantity is fully justified in relation to the asset(s) for which the procurement is to be made. ✔ Ensure attestation of corrections in quantity, estimated last purchase rates and description on the indent. ✔ Before signing/countersigning any indent, satisfy yourself for the requirements, estimated rates, description. ✔ Avoid mentioning brand name of product indented as far as possible.
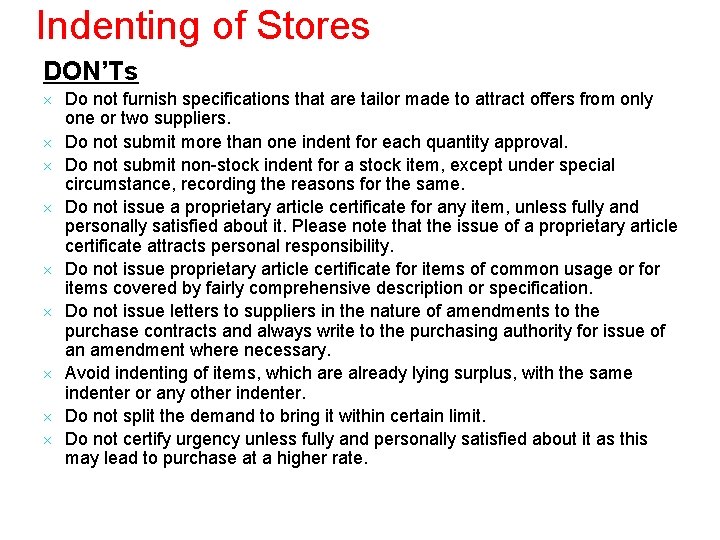
Indenting of Stores DON’Ts × Do not furnish specifications that are tailor made to attract offers from only × × × × one or two suppliers. Do not submit more than one indent for each quantity approval. Do not submit non-stock indent for a stock item, except under special circumstance, recording the reasons for the same. Do not issue a proprietary article certificate for any item, unless fully and personally satisfied about it. Please note that the issue of a proprietary article certificate attracts personal responsibility. Do not issue proprietary article certificate for items of common usage or for items covered by fairly comprehensive description or specification. Do not issue letters to suppliers in the nature of amendments to the purchase contracts and always write to the purchasing authority for issue of an amendment where necessary. Avoid indenting of items, which are already lying surplus, with the same indenter or any other indenter. Do not split the demand to bring it within certain limit. Do not certify urgency unless fully and personally satisfied about it as this may lead to purchase at a higher rate.
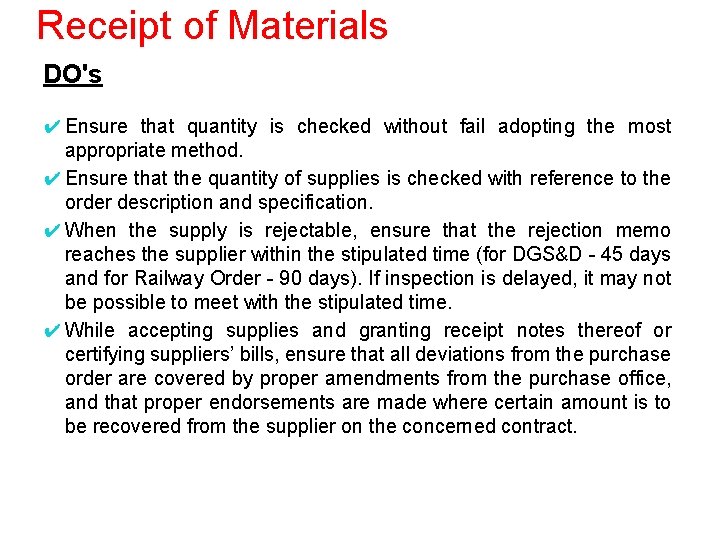
Receipt of Materials DO's ✔ Ensure that quantity is checked without fail adopting the most appropriate method. ✔ Ensure that the quantity of supplies is checked with reference to the order description and specification. ✔ When the supply is rejectable, ensure that the rejection memo reaches the supplier within the stipulated time (for DGS&D - 45 days and for Railway Order - 90 days). If inspection is delayed, it may not be possible to meet with the stipulated time. ✔ While accepting supplies and granting receipt notes thereof or certifying suppliers’ bills, ensure that all deviations from the purchase order are covered by proper amendments from the purchase office, and that proper endorsements are made where certain amount is to be recovered from the supplier on the concerned contract.
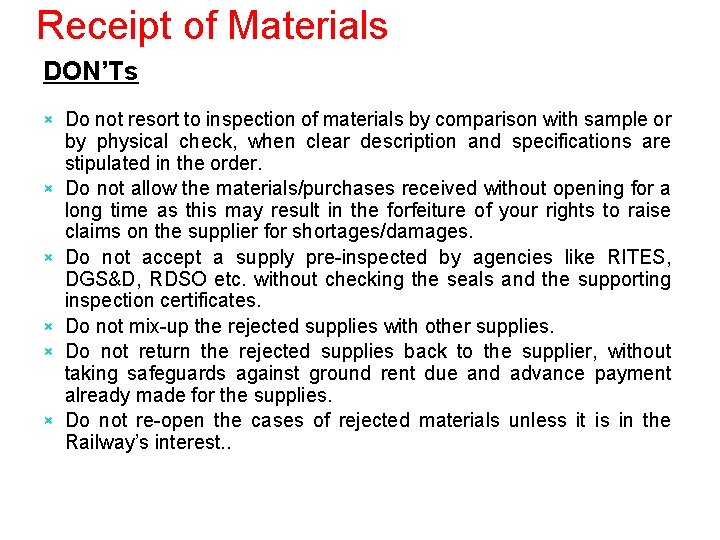
Receipt of Materials DON’Ts × Do not resort to inspection of materials by comparison with sample or × × × by physical check, when clear description and specifications are stipulated in the order. Do not allow the materials/purchases received without opening for a long time as this may result in the forfeiture of your rights to raise claims on the supplier for shortages/damages. Do not accept a supply pre-inspected by agencies like RITES, DGS&D, RDSO etc. without checking the seals and the supporting inspection certificates. Do not mix-up the rejected supplies with other supplies. Do not return the rejected supplies back to the supplier, without taking safeguards against ground rent due and advance payment already made for the supplies. Do not re-open the cases of rejected materials unless it is in the Railway’s interest. .
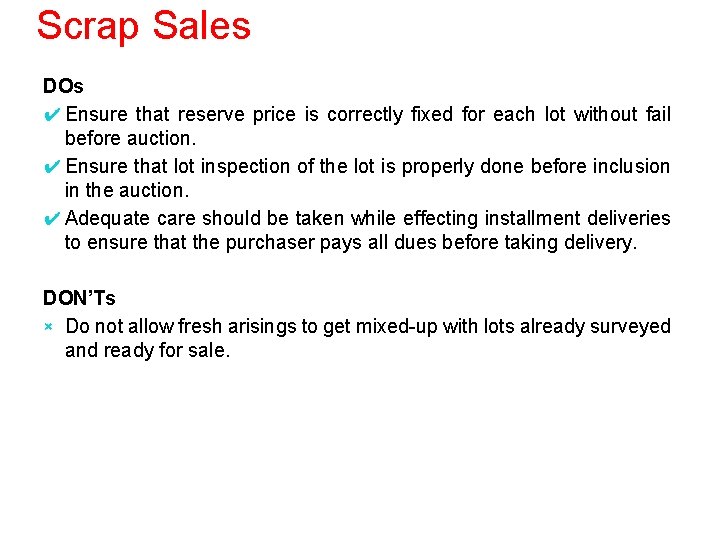
Scrap Sales DOs ✔ Ensure that reserve price is correctly fixed for each lot without fail before auction. ✔ Ensure that lot inspection of the lot is properly done before inclusion in the auction. ✔ Adequate care should be taken while effecting installment deliveries to ensure that the purchaser pays all dues before taking delivery. DON’Ts × Do not allow fresh arisings to get mixed-up with lots already surveyed and ready for sale.
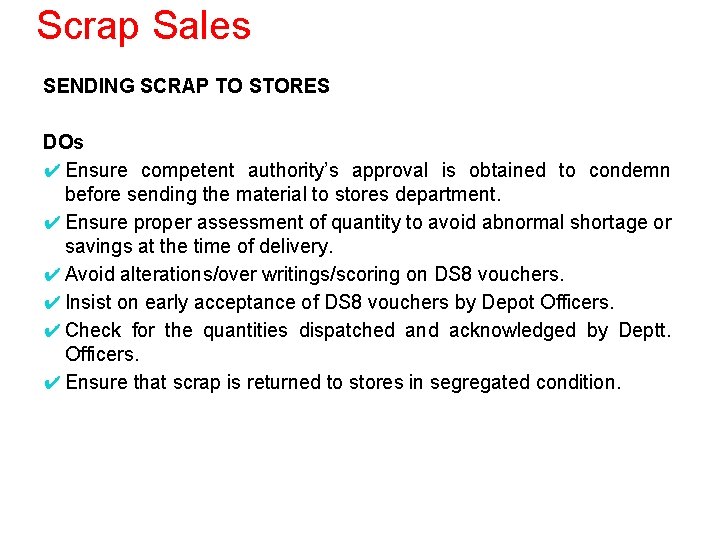
Scrap Sales SENDING SCRAP TO STORES DOs ✔ Ensure competent authority’s approval is obtained to condemn before sending the material to stores department. ✔ Ensure proper assessment of quantity to avoid abnormal shortage or savings at the time of delivery. ✔ Avoid alterations/over writings/scoring on DS 8 vouchers. ✔ Insist on early acceptance of DS 8 vouchers by Depot Officers. ✔ Check for the quantities dispatched and acknowledged by Deptt. Officers. ✔ Ensure that scrap is returned to stores in segregated condition.
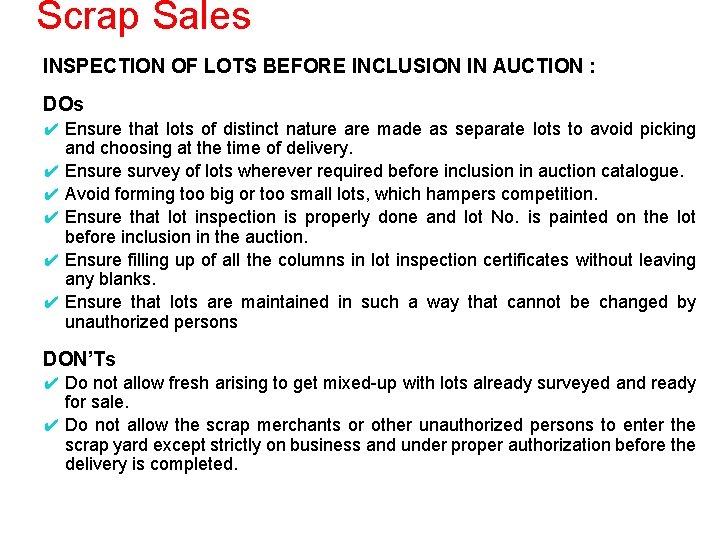
Scrap Sales INSPECTION OF LOTS BEFORE INCLUSION IN AUCTION : DOs ✔ Ensure that lots of distinct nature are made as separate lots to avoid picking and choosing at the time of delivery. ✔ Ensure survey of lots wherever required before inclusion in auction catalogue. ✔ Avoid forming too big or too small lots, which hampers competition. ✔ Ensure that lot inspection is properly done and lot No. is painted on the lot before inclusion in the auction. ✔ Ensure filling up of all the columns in lot inspection certificates without leaving any blanks. ✔ Ensure that lots are maintained in such a way that cannot be changed by unauthorized persons DON’Ts ✔ Do not allow fresh arising to get mixed-up with lots already surveyed and ready for sale. ✔ Do not allow the scrap merchants or other unauthorized persons to enter the scrap yard except strictly on business and under proper authorization before the delivery is completed.
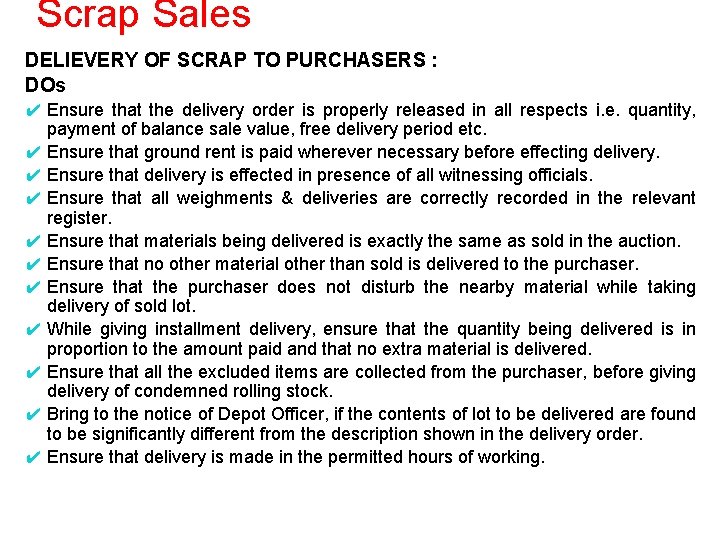
Scrap Sales DELIEVERY OF SCRAP TO PURCHASERS : DOs ✔ Ensure that the delivery order is properly released in all respects i. e. quantity, payment of balance sale value, free delivery period etc. ✔ Ensure that ground rent is paid wherever necessary before effecting delivery. ✔ Ensure that delivery is effected in presence of all witnessing officials. ✔ Ensure that all weighments & deliveries are correctly recorded in the relevant register. ✔ Ensure that materials being delivered is exactly the same as sold in the auction. ✔ Ensure that no other material other than sold is delivered to the purchaser. ✔ Ensure that the purchaser does not disturb the nearby material while taking delivery of sold lot. ✔ While giving installment delivery, ensure that the quantity being delivered is in proportion to the amount paid and that no extra material is delivered. ✔ Ensure that all the excluded items are collected from the purchaser, before giving delivery of condemned rolling stock. ✔ Bring to the notice of Depot Officer, if the contents of lot to be delivered are found to be significantly different from the description shown in the delivery order. ✔ Ensure that delivery is made in the permitted hours of working.
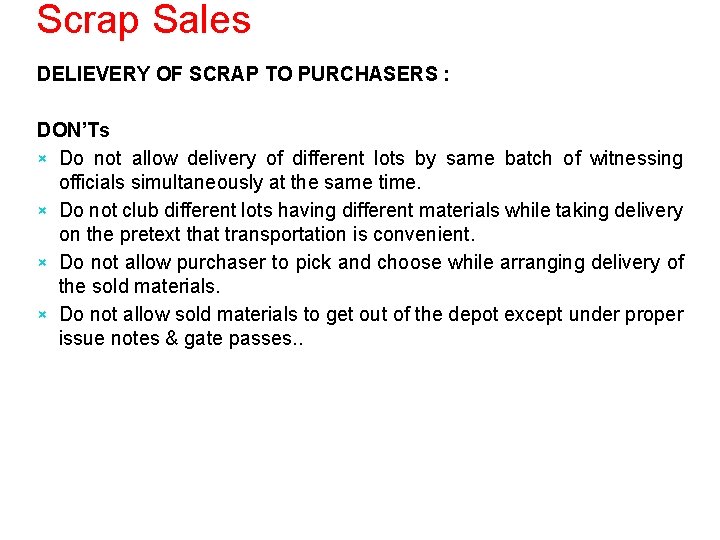
Scrap Sales DELIEVERY OF SCRAP TO PURCHASERS : DON’Ts × Do not allow delivery of different lots by same batch of witnessing officials simultaneously at the same time. × Do not club different lots having different materials while taking delivery on the pretext that transportation is convenient. × Do not allow purchaser to pick and choose while arranging delivery of the sold materials. × Do not allow sold materials to get out of the depot except under proper issue notes & gate passes. .
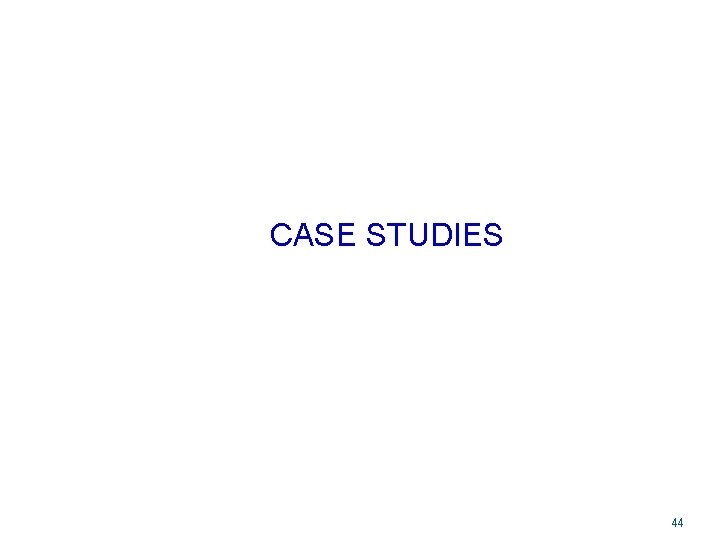
CASE STUDIES 44
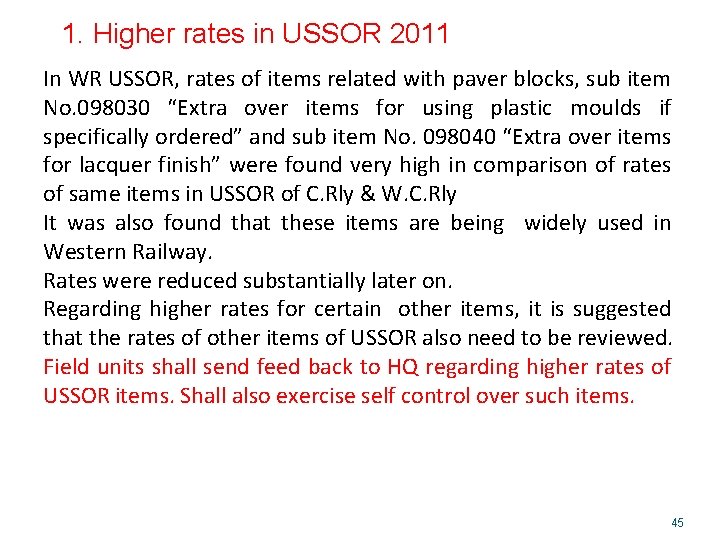
1. Higher rates in USSOR 2011 In WR USSOR, rates of items related with paver blocks, sub item No. 098030 “Extra over items for using plastic moulds if specifically ordered” and sub item No. 098040 “Extra over items for lacquer finish” were found very high in comparison of rates of same items in USSOR of C. Rly & W. C. Rly It was also found that these items are being widely used in Western Railway. Rates were reduced substantially later on. Regarding higher rates for certain other items, it is suggested that the rates of other items of USSOR also need to be reviewed. Field units shall send feed back to HQ regarding higher rates of USSOR items. Shall also exercise self control over such items. 45
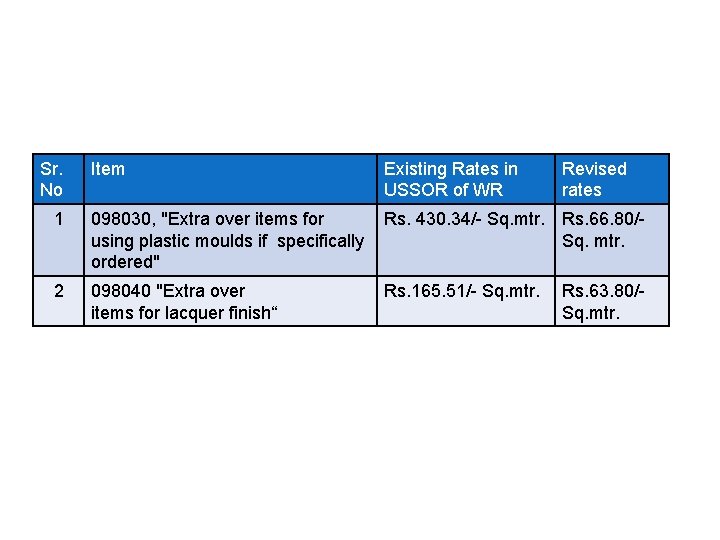
Sr. No Item Existing Rates in USSOR of WR Revised rates 1 098030, "Extra over items for using plastic moulds if specifically ordered" Rs. 430. 34/- Sq. mtr. Rs. 66. 80/Sq. mtr. 2 098040 "Extra over items for lacquer finish“ Rs. 165. 51/- Sq. mtr. Rs. 63. 80/Sq. mtr.
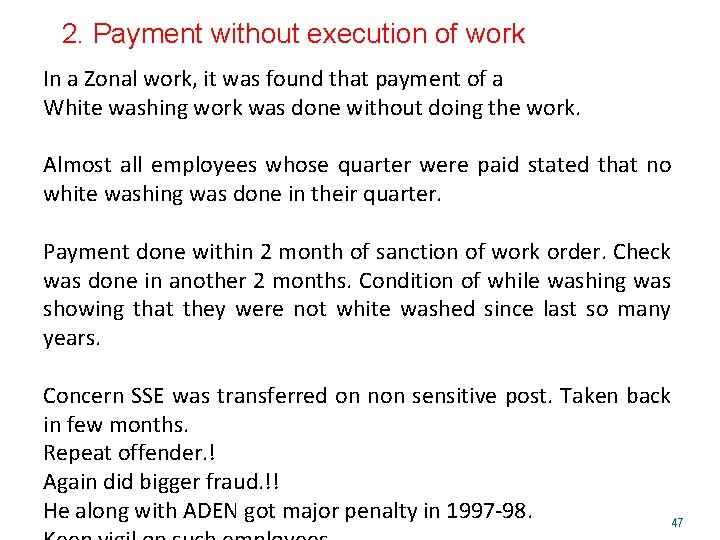
2. Payment without execution of work In a Zonal work, it was found that payment of a White washing work was done without doing the work. Almost all employees whose quarter were paid stated that no white washing was done in their quarter. Payment done within 2 month of sanction of work order. Check was done in another 2 months. Condition of while washing was showing that they were not white washed since last so many years. Concern SSE was transferred on non sensitive post. Taken back in few months. Repeat offender. ! Again did bigger fraud. !! He along with ADEN got major penalty in 1997 -98. 47
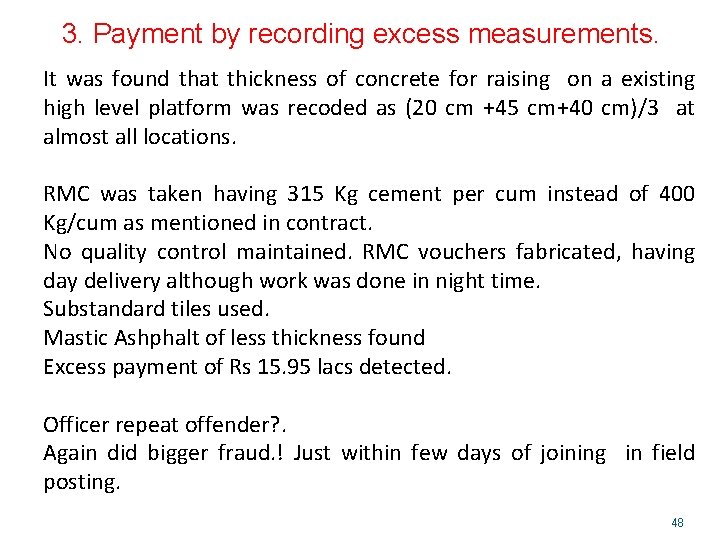
3. Payment by recording excess measurements. It was found that thickness of concrete for raising on a existing high level platform was recoded as (20 cm +45 cm+40 cm)/3 at almost all locations. RMC was taken having 315 Kg cement per cum instead of 400 Kg/cum as mentioned in contract. No quality control maintained. RMC vouchers fabricated, having day delivery although work was done in night time. Substandard tiles used. Mastic Ashphalt of less thickness found Excess payment of Rs 15. 95 lacs detected. Officer repeat offender? . Again did bigger fraud. ! Just within few days of joining in field posting. 48
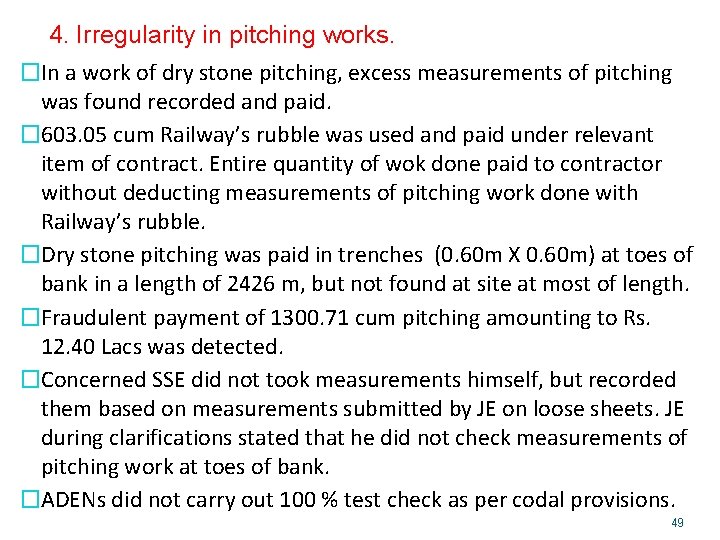
4. Irregularity in pitching works. �In a work of dry stone pitching, excess measurements of pitching was found recorded and paid. � 603. 05 cum Railway’s rubble was used and paid under relevant item of contract. Entire quantity of wok done paid to contractor without deducting measurements of pitching work done with Railway’s rubble. �Dry stone pitching was paid in trenches (0. 60 m X 0. 60 m) at toes of bank in a length of 2426 m, but not found at site at most of length. �Fraudulent payment of 1300. 71 cum pitching amounting to Rs. 12. 40 Lacs was detected. �Concerned SSE did not took measurements himself, but recorded them based on measurements submitted by JE on loose sheets. JE during clarifications stated that he did not check measurements of pitching work at toes of bank. �ADENs did not carry out 100 % test check as per codal provisions. 49
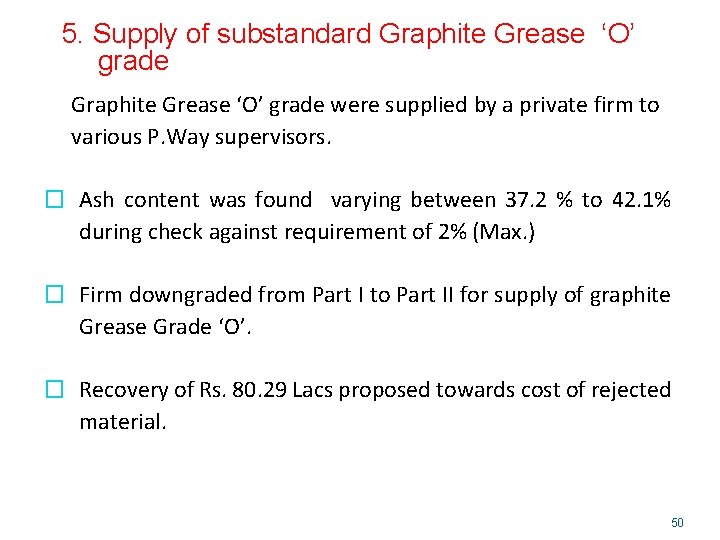
5. Supply of substandard Graphite Grease ‘O’ grade were supplied by a private firm to various P. Way supervisors. � Ash content was found varying between 37. 2 % to 42. 1% during check against requirement of 2% (Max. ) � Firm downgraded from Part I to Part II for supply of graphite Grease Grade ‘O’. � Recovery of Rs. 80. 29 Lacs proposed towards cost of rejected material. 50
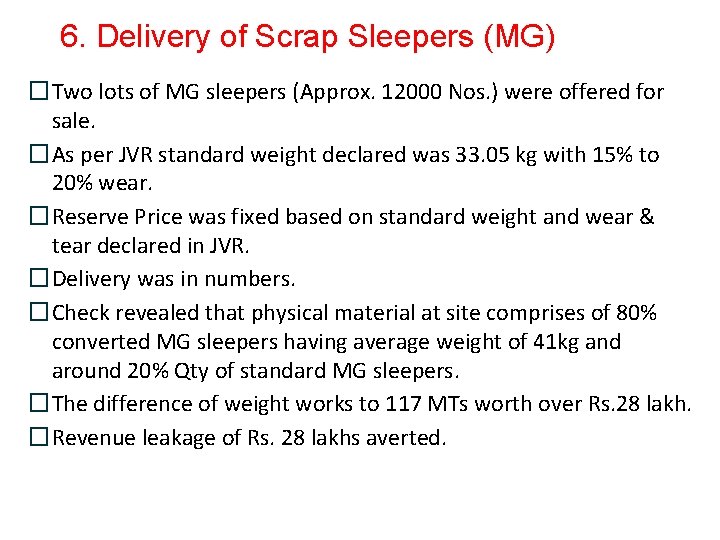
6. Delivery of Scrap Sleepers (MG) �Two lots of MG sleepers (Approx. 12000 Nos. ) were offered for sale. �As per JVR standard weight declared was 33. 05 kg with 15% to 20% wear. �Reserve Price was fixed based on standard weight and wear & tear declared in JVR. �Delivery was in numbers. �Check revealed that physical material at site comprises of 80% converted MG sleepers having average weight of 41 kg and around 20% Qty of standard MG sleepers. �The difference of weight works to 117 MTs worth over Rs. 28 lakh. �Revenue leakage of Rs. 28 lakhs averted.
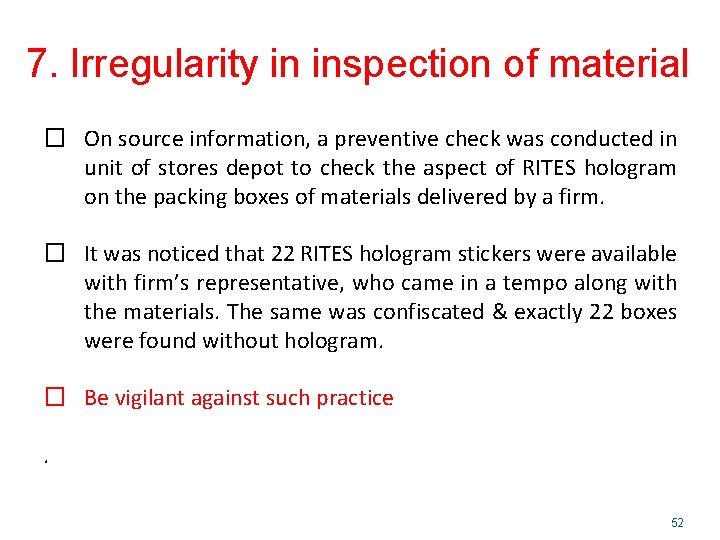
7. Irregularity in inspection of material � On source information, a preventive check was conducted in unit of stores depot to check the aspect of RITES hologram on the packing boxes of materials delivered by a firm. � It was noticed that 22 RITES hologram stickers were available with firm’s representative, who came in a tempo along with the materials. The same was confiscated & exactly 22 boxes were found without hologram. � Be vigilant against such practice. 52
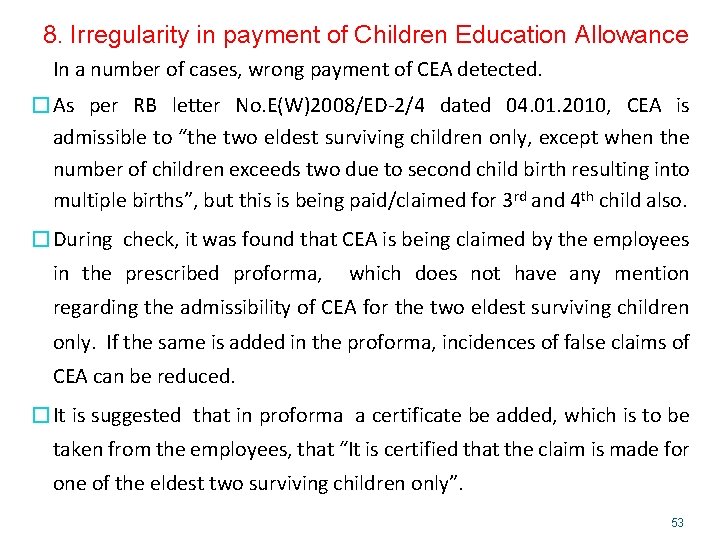
8. Irregularity in payment of Children Education Allowance In a number of cases, wrong payment of CEA detected. � As per RB letter No. E(W)2008/ED-2/4 dated 04. 01. 2010, CEA is admissible to “the two eldest surviving children only, except when the number of children exceeds two due to second child birth resulting into multiple births”, but this is being paid/claimed for 3 rd and 4 th child also. � During check, it was found that CEA is being claimed by the employees in the prescribed proforma, which does not have any mention regarding the admissibility of CEA for the two eldest surviving children only. If the same is added in the proforma, incidences of false claims of CEA can be reduced. � It is suggested that in proforma a certificate be added, which is to be taken from the employees, that “It is certified that the claim is made for one of the eldest two surviving children only”. 53
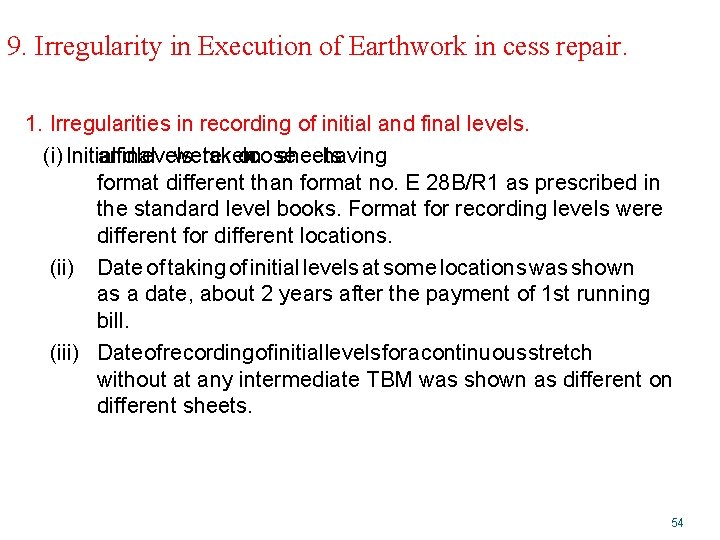
9. Irregularity in Execution of Earthwork in cess repair. 1. Irregularities in recording of initial and final levels. (i) Initial and final levels were taken on loose sheets having format different than format no. E 28 B/R 1 as prescribed in the standard level books. Format for recording levels were different for different locations. (ii) Date of taking of initial levels at some locations was shown as a date, about 2 years after the payment of 1 st running bill. (iii) Dateofrecordingofinitiallevels foracontinuousstretch without at any intermediate TBM was shown as different on different sheets. 54
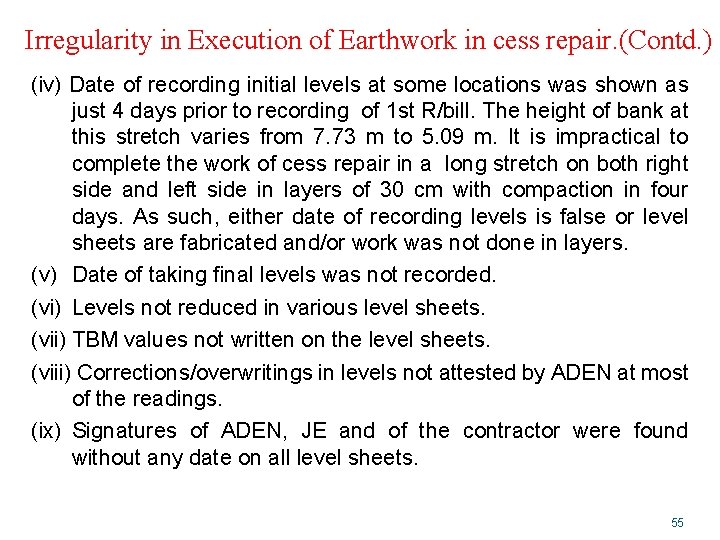
Irregularity in Execution of Earthwork in cess repair. (Contd. ) (iv) Date of recording initial levels at some locations was shown as just 4 days prior to recording of 1 st R/bill. The height of bank at this stretch varies from 7. 73 m to 5. 09 m. It is impractical to complete the work of cess repair in a long stretch on both right side and left side in layers of 30 cm with compaction in four days. As such, either date of recording levels is false or level sheets are fabricated and/or work was not done in layers. (v) Date of taking final levels was not recorded. (vi) Levels not reduced in various level sheets. (vii) TBM values not written on the level sheets. (viii) Corrections/overwritings in levels not attested by ADEN at most of the readings. (ix) Signatures of ADEN, JE and of the contractor were found without any date on all level sheets. 55
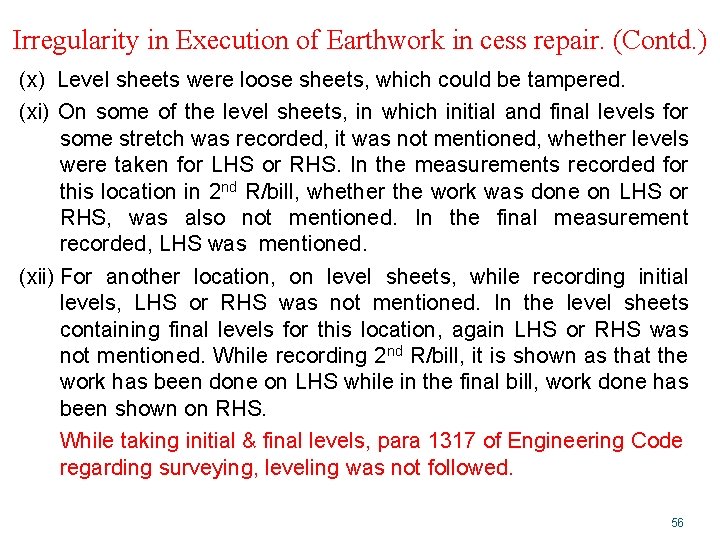
Irregularity in Execution of Earthwork in cess repair. (Contd. ) (x) Level sheets were loose sheets, which could be tampered. (xi) On some of the level sheets, in which initial and final levels for some stretch was recorded, it was not mentioned, whether levels were taken for LHS or RHS. In the measurements recorded for this location in 2 nd R/bill, whether the work was done on LHS or RHS, was also not mentioned. In the final measurement recorded, LHS was mentioned. (xii) For another location, on level sheets, while recording initial levels, LHS or RHS was not mentioned. In the level sheets containing final levels for this location, again LHS or RHS was not mentioned. While recording 2 nd R/bill, it is shown as that the work has been done on LHS while in the final bill, work done has been shown on RHS. While taking initial & final levels, para 1317 of Engineering Code regarding surveying, leveling was not followed. 56
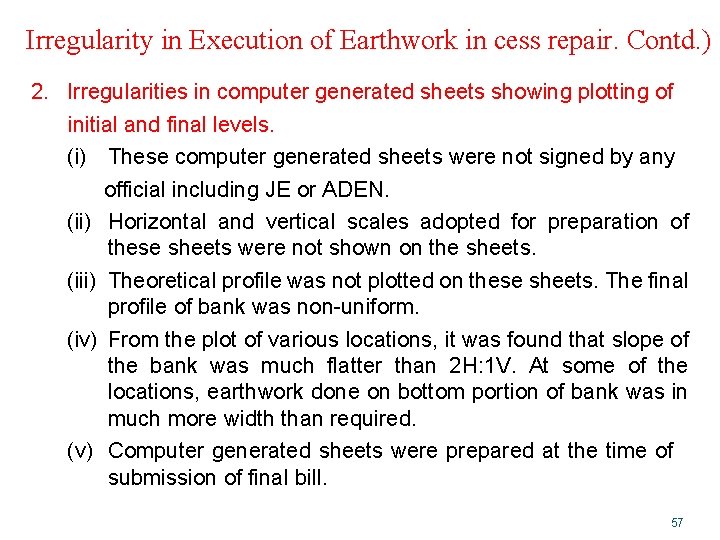
Irregularity in Execution of Earthwork in cess repair. Contd. ) 2. Irregularities in computer generated sheets showing plotting of initial and final levels. (i) These computer generated sheets were not signed by any official including JE or ADEN. (ii) Horizontal and vertical scales adopted for preparation of these sheets were not shown on the sheets. (iii) Theoretical profile was not plotted on these sheets. The final profile of bank was non-uniform. (iv) From the plot of various locations, it was found that slope of the bank was much flatter than 2 H: 1 V. At some of the locations, earthwork done on bottom portion of bank was in much more width than required. (v) Computer generated sheets were prepared at the time of submission of final bill. 57
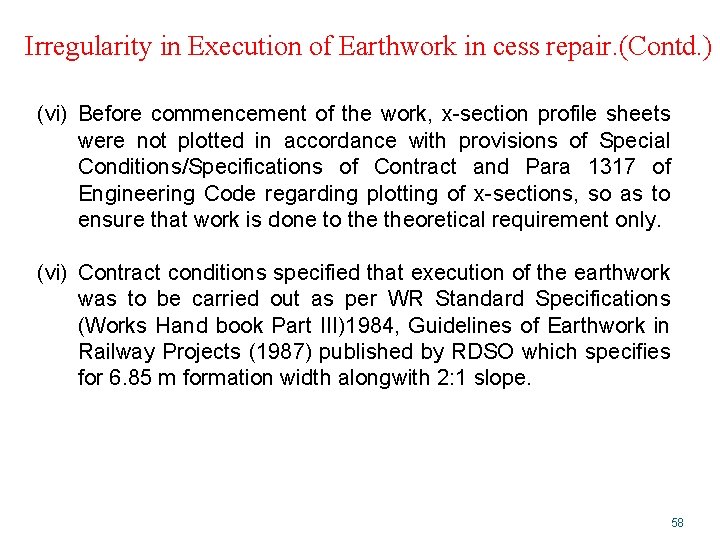
Irregularity in Execution of Earthwork in cess repair. (Contd. ) (vi) Before commencement of the work, x-section profile sheets were not plotted in accordance with provisions of Special Conditions/Specifications of Contract and Para 1317 of Engineering Code regarding plotting of x-sections, so as to ensure that work is done to theoretical requirement only. (vi) Contract conditions specified that execution of the earthwork was to be carried out as per WR Standard Specifications (Works Hand book Part III)1984, Guidelines of Earthwork in Railway Projects (1987) published by RDSO which specifies for 6. 85 m formation width alongwith 2: 1 slope. 58

Irregularity in Execution of Earthwork in cess repair. (Contd. ) 3. Irregularities in computer generated sheets showing calculation of earthwork paid. (i) Only top sheet showing summary of earthwork done at various locations was signed by JE and countersigned by ADEN. No other sheet was signed by these officials or by any official. (ii) For various chainages, final RL required as per 2: 1 slope at any cross distance was not worked out, theoretical toe distance was also not worked out. Area of earthwork done was calculated for final levels recorded without considering requirement of RL at various cross distances and toe as per theoretical profile. (iii) At a number of chainages, in calculations, top width of formation was taken as 3. 75 m , 4 m etc. instead of 3. 43 m. (iv)Concerned supervisor calculated the quantity of earthwork considering whatever level was there at any cross distance, whether it was within theoretical profile or beyond it. 59
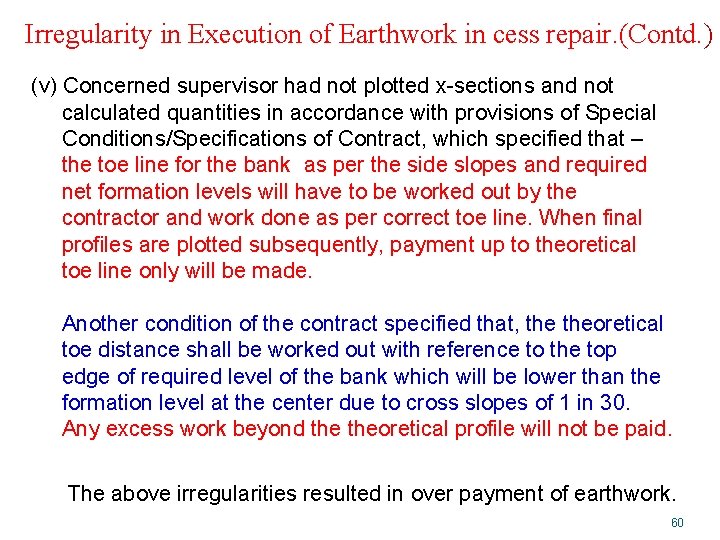
Irregularity in Execution of Earthwork in cess repair. (Contd. ) (v) Concerned supervisor had not plotted x-sections and not calculated quantities in accordance with provisions of Special Conditions/Specifications of Contract, which specified that – the toe line for the bank as per the side slopes and required net formation levels will have to be worked out by the contractor and work done as per correct toe line. When final profiles are plotted subsequently, payment up to theoretical toe line only will be made. Another condition of the contract specified that, theoretical toe distance shall be worked out with reference to the top edge of required level of the bank which will be lower than the formation level at the center due to cross slopes of 1 in 30. Any excess work beyond theoretical profile will not be paid. The above irregularities resulted in over payment of earthwork. 60
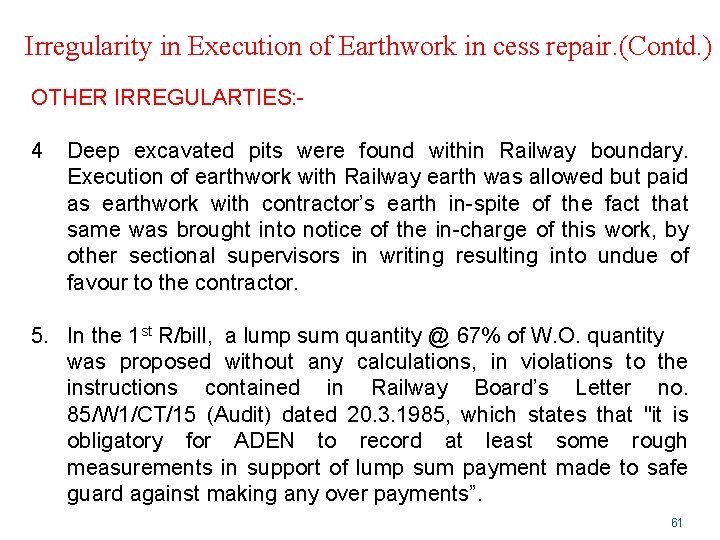
Irregularity in Execution of Earthwork in cess repair. (Contd. ) OTHER IRREGULARTIES: 4 Deep excavated pits were found within Railway boundary. Execution of earthwork with Railway earth was allowed but paid as earthwork with contractor’s earth in-spite of the fact that same was brought into notice of the in-charge of this work, by other sectional supervisors in writing resulting into undue of favour to the contractor. 5. In the 1 st R/bill, a lump sum quantity @ 67% of W. O. quantity was proposed without any calculations, in violations to the instructions contained in Railway Board’s Letter no. 85/W 1/CT/15 (Audit) dated 20. 3. 1985, which states that "it is obligatory for ADEN to record at least some rough measurements in support of lump sum payment made to safe guard against making any over payments”. 61
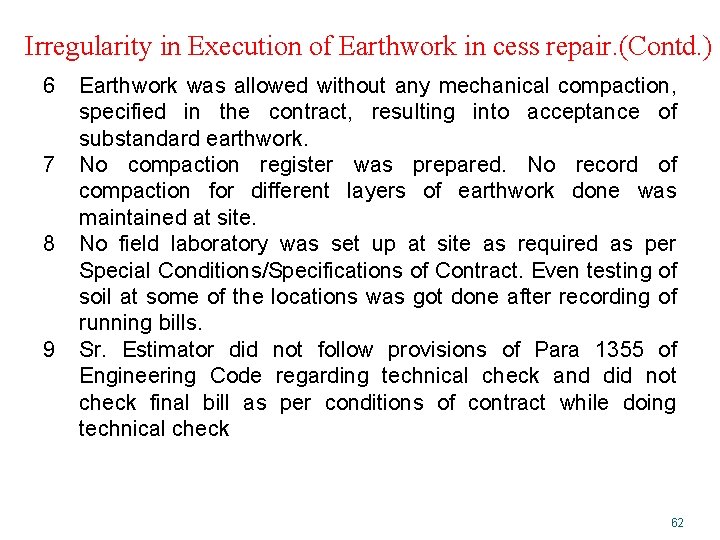
Irregularity in Execution of Earthwork in cess repair. (Contd. ) 6 7 8 9 Earthwork was allowed without any mechanical compaction, specified in the contract, resulting into acceptance of substandard earthwork. No compaction register was prepared. No record of compaction for different layers of earthwork done was maintained at site. No field laboratory was set up at site as required as per Special Conditions/Specifications of Contract. Even testing of soil at some of the locations was got done after recording of running bills. Sr. Estimator did not follow provisions of Para 1355 of Engineering Code regarding technical check and did not check final bill as per conditions of contract while doing technical check 62
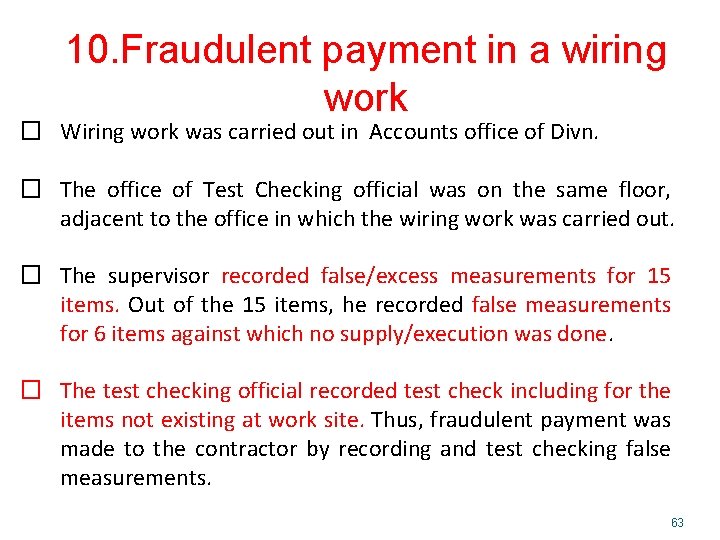
10. Fraudulent payment in a wiring work � Wiring work was carried out in Accounts office of Divn. � The office of Test Checking official was on the same floor, adjacent to the office in which the wiring work was carried out. � The supervisor recorded false/excess measurements for 15 items. Out of the 15 items, he recorded false measurements for 6 items against which no supply/execution was done. � The test checking official recorded test check including for the items not existing at work site. Thus, fraudulent payment was made to the contractor by recording and test checking false measurements. 63
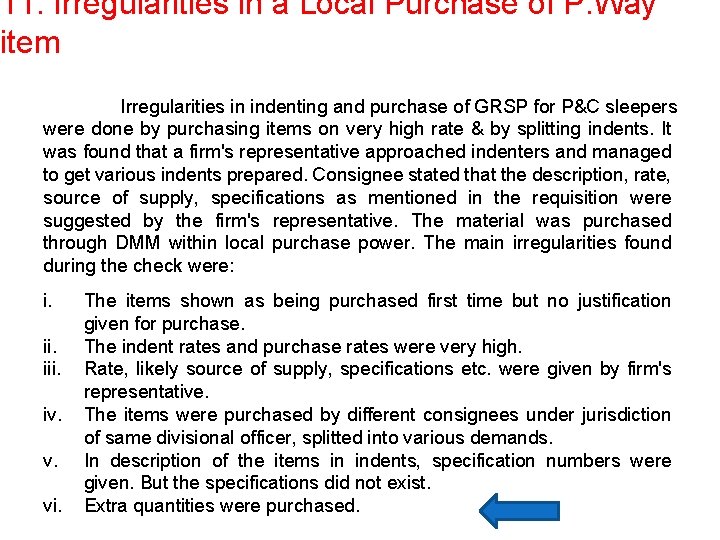
11. Irregularities in a Local Purchase of P. Way item Irregularities in indenting and purchase of GRSP for P&C sleepers were done by purchasing items on very high rate & by splitting indents. It was found that a firm's representative approached indenters and managed to get various indents prepared. Consignee stated that the description, rate, source of supply, specifications as mentioned in the requisition were suggested by the firm's representative. The material was purchased through DMM within local purchase power. The main irregularities found during the check were: i. iii. iv. v. vi. The items shown as being purchased first time but no justification given for purchase. The indent rates and purchase rates were very high. Rate, likely source of supply, specifications etc. were given by firm's representative. The items were purchased by different consignees under jurisdiction of same divisional officer, splitted into various demands. In description of the items in indents, specification numbers were given. But the specifications did not exist. Extra quantities were purchased.

65
God has gifted us
David wechsler
Identito vigilance def
Mad eye moody constant vigilance gif
Vigilance awareness week presentation
Eudra vigilence
Edura vigilance
Eudra vigilance
Constant vigilance
Vigilance partagée mase
Best worst and average case
Paradigm shift from women studies to gender studies
Advantages of descriptive research
Times 100 case studies
Times 100 business case studies
Holistic technology in human values
Advantages and disadvantages of case control studies
Case series
Gdpr case studies
Human geography revision
Tony bland euthanasia
E procurement case studies
Types of case studies
Least likely case
The times 100 business case studies
Nasa case study
Blood group discrepancy
Chemistry-ethics case studies
Nspe code of ethics
Goal2u
Jmp case studies
Case studies of rtos
Ferpa case studies
Social engineering case studies
Plagiarism
Financial management case studies
Digital marketing case studies 2012
Crime solving insects case studies answers
Times 100 case studies
Ref impact case studies
Tanya carmichael
Food safety errors: case studies
Growth hacking case studies
Exercise #1 – evaluate case studies answer key
Dr agnes meyo
Betts neihart profiles of the gifted and talented
Gifted vs talented
Gifted education center
State of the states in gifted education
What is fte
Prince william county specialty programs
The gifted philippines
Gifted iq range
Howard county gifted and talented
Curtis carson sonya carson
Cobb county gifted program
Midvale school for the gifted
Cobb county target program
Bell high school gifted program
Gifted iq
Alvin isd gifted and talented
Hcpss 4th grade math
Interlake course catalog
Counseling strategies for gifted students
History of gifted education
Affective needs of gifted students