SERAMK MALZEMELERN RETM SRELER NDEKLER TOZLARIN HAZIRLANMASI VE
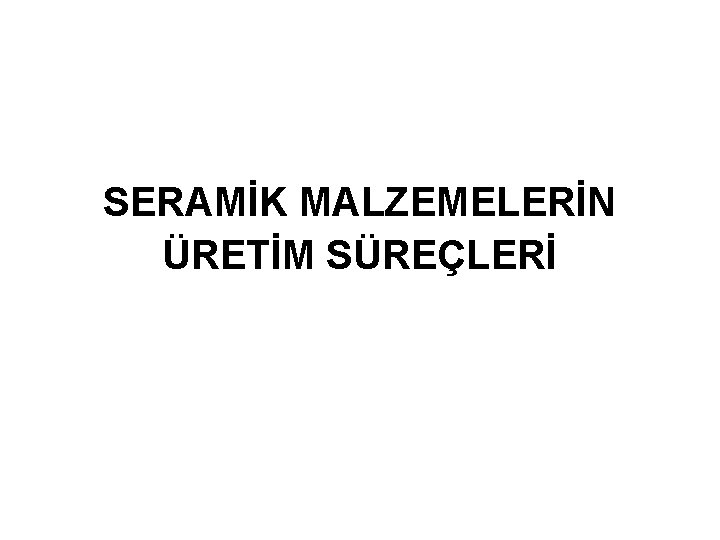
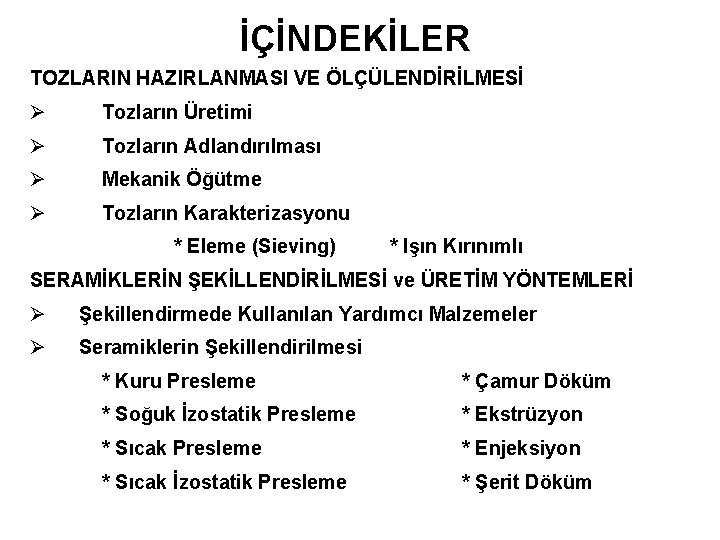
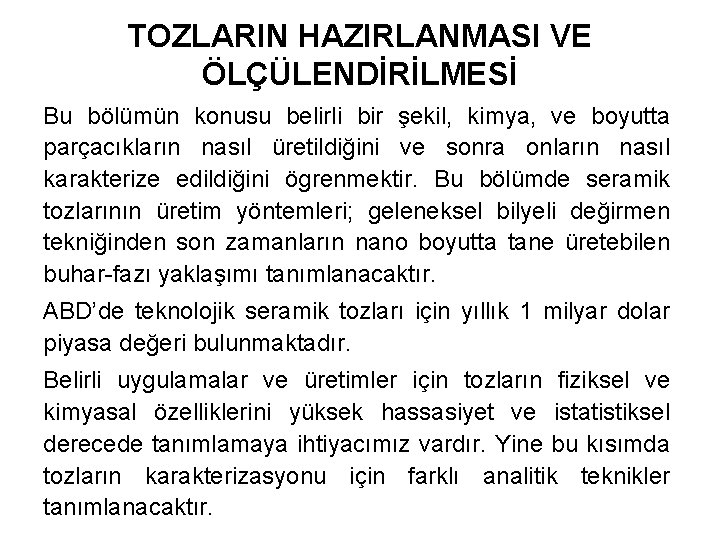
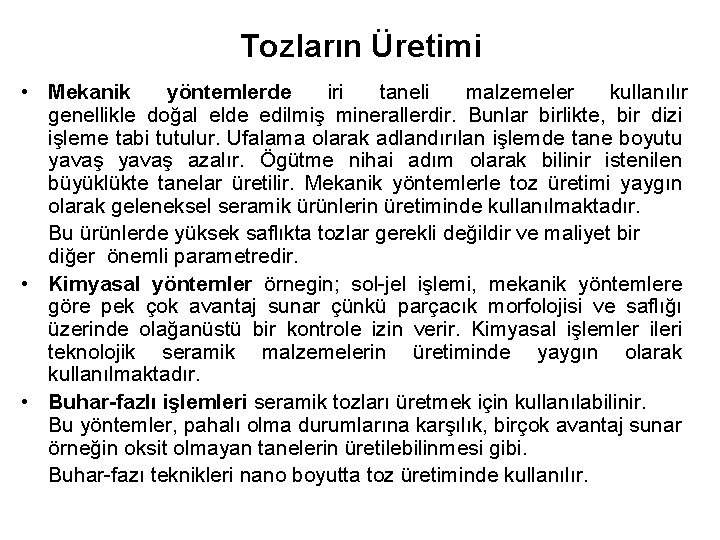
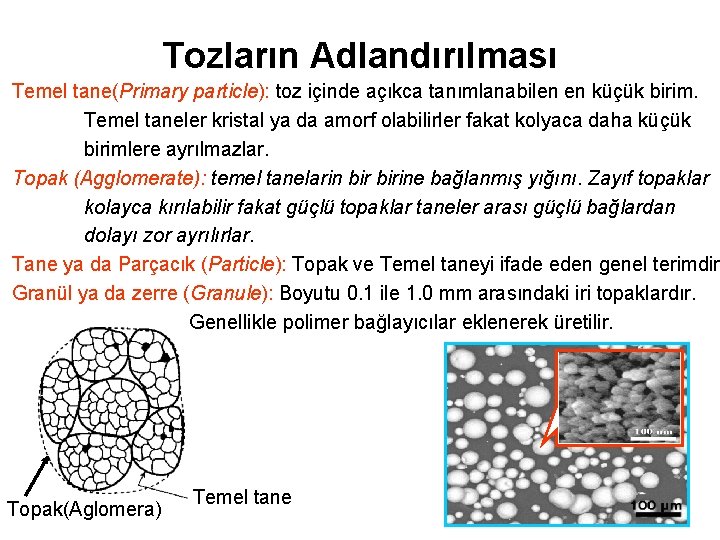
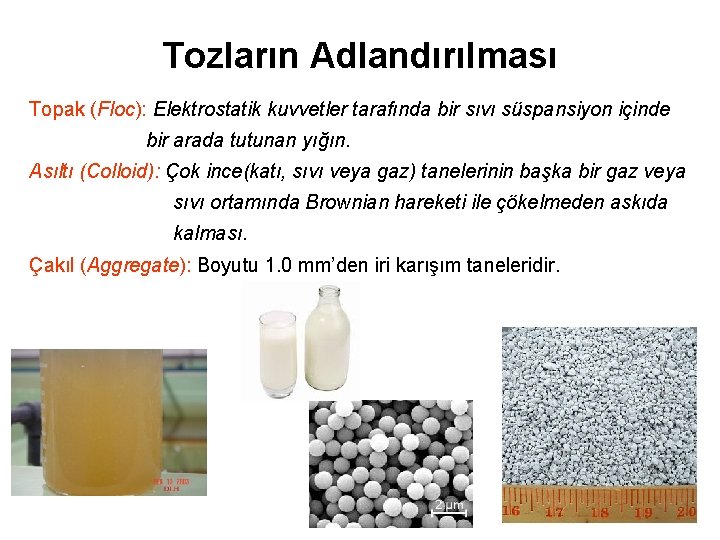
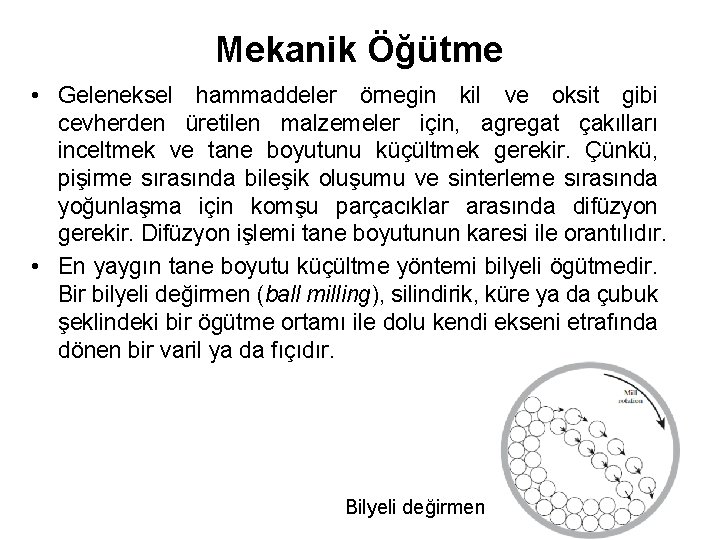
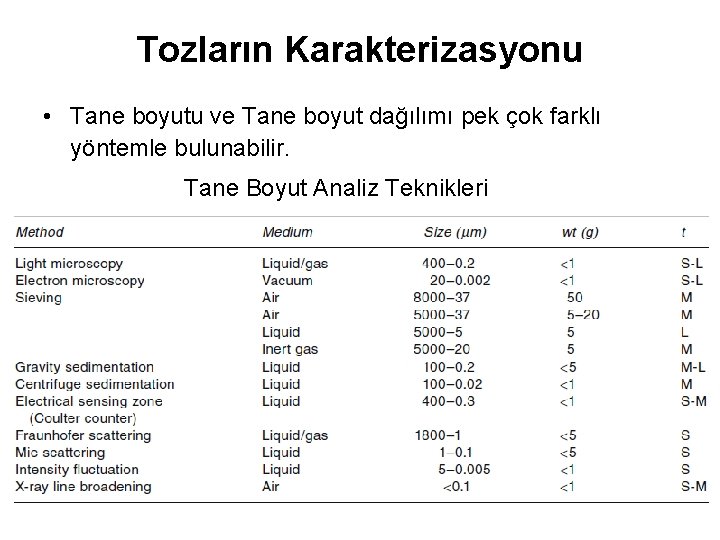
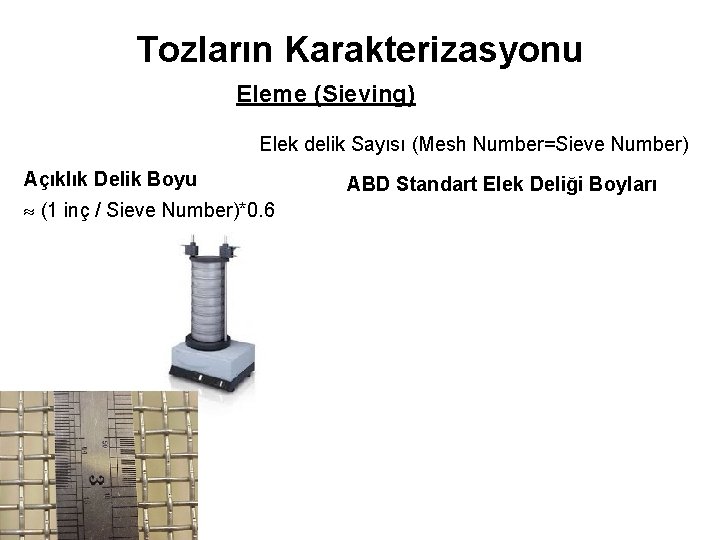
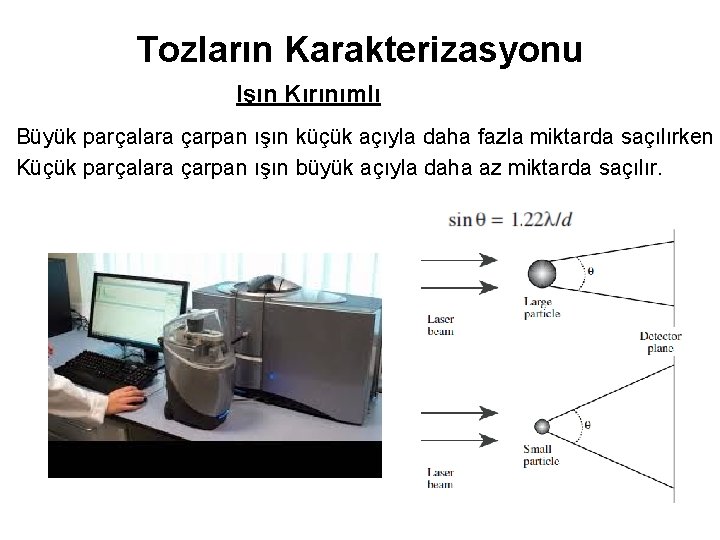
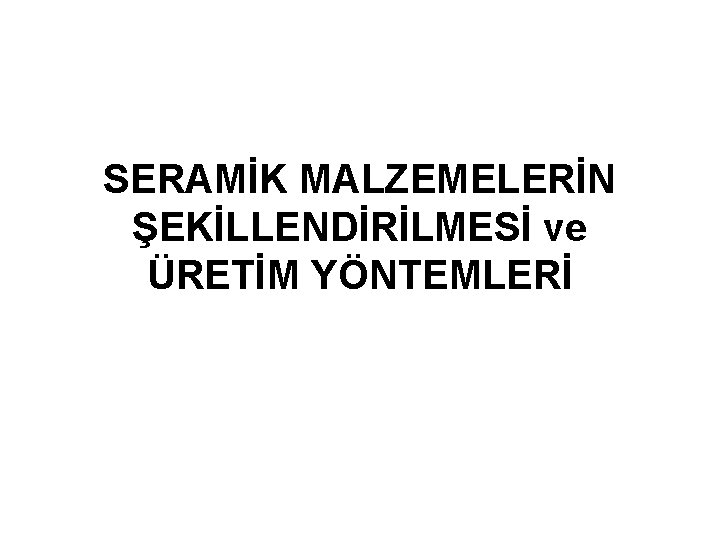
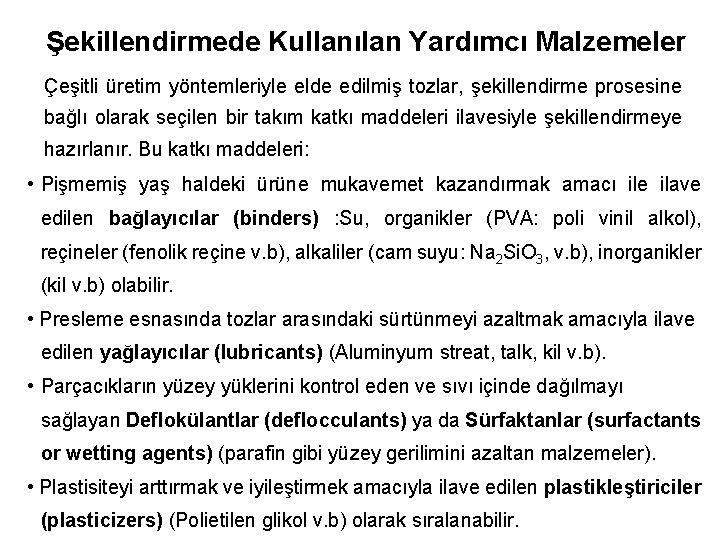
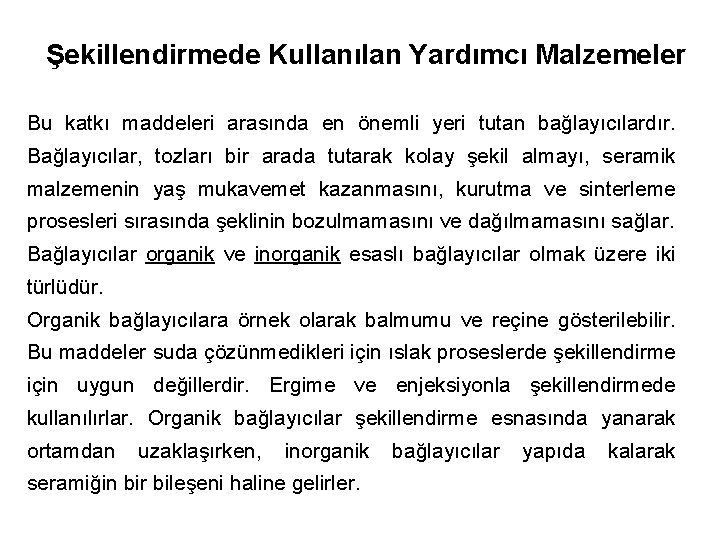
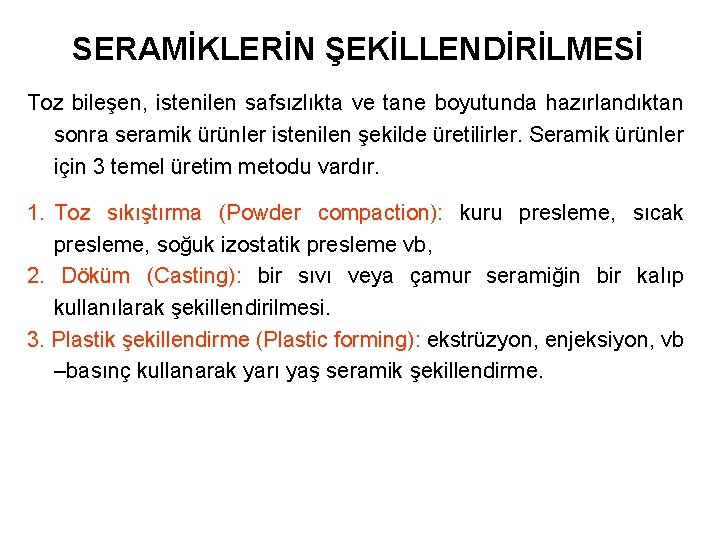
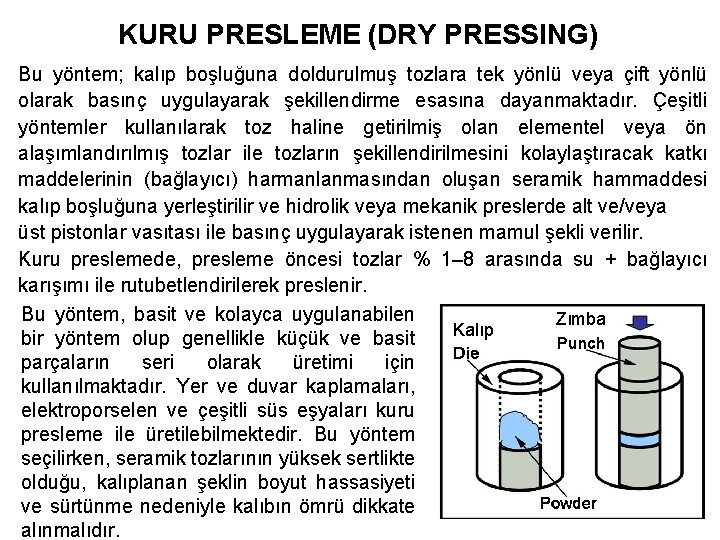
![Soğuk İzostatik Presleme [COLD ISOSTATIC PRESSING(CIP)] CIP, kuru presle şekillendirme imkânı olmayan kompleks şekil Soğuk İzostatik Presleme [COLD ISOSTATIC PRESSING(CIP)] CIP, kuru presle şekillendirme imkânı olmayan kompleks şekil](https://slidetodoc.com/presentation_image/10391fae18951bc6ca5deecd28f434d3/image-16.jpg)
![Soğuk İzostatik Presleme [COLD ISOSTATIC PRESSING(CIP)] Uyluk kemiği Sinterlenmiş Zirkonya Seramik Soğuk İzostatik Presleme [COLD ISOSTATIC PRESSING(CIP)] Uyluk kemiği Sinterlenmiş Zirkonya Seramik](https://slidetodoc.com/presentation_image/10391fae18951bc6ca5deecd28f434d3/image-17.jpg)
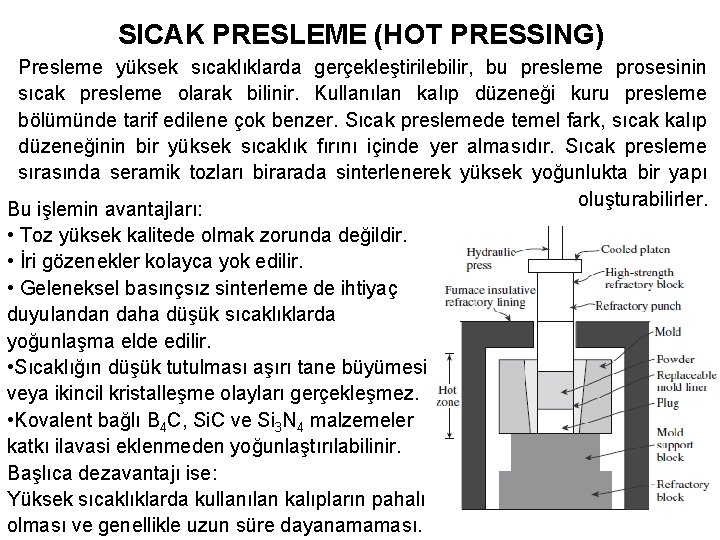
![Sıcak İzostatik Presleme [HOT ISOSTATIC PRESSING (HIP)] Sıcak izostatik preslemede (HIP) ısı ve basınç Sıcak İzostatik Presleme [HOT ISOSTATIC PRESSING (HIP)] Sıcak izostatik preslemede (HIP) ısı ve basınç](https://slidetodoc.com/presentation_image/10391fae18951bc6ca5deecd28f434d3/image-19.jpg)
![Sıcak İzostatik Presleme [HOT ISOSTATIC PRESSING (HIP)] Sıcak İzostatik Presleme [HOT ISOSTATIC PRESSING (HIP)]](https://slidetodoc.com/presentation_image/10391fae18951bc6ca5deecd28f434d3/image-20.jpg)
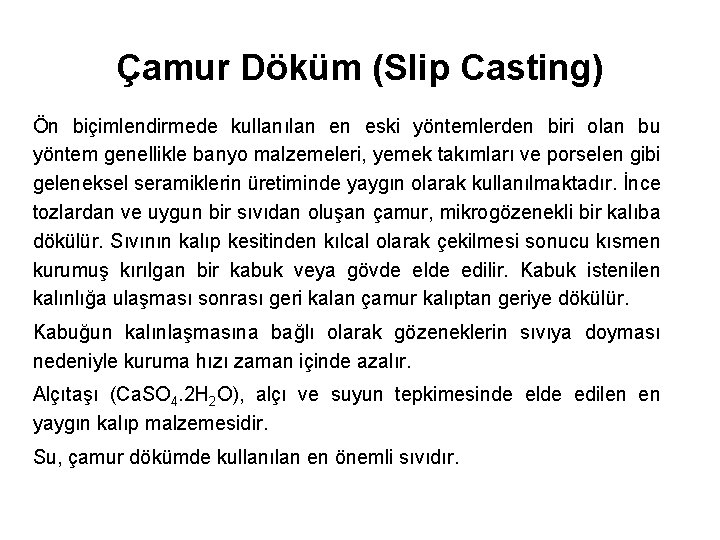
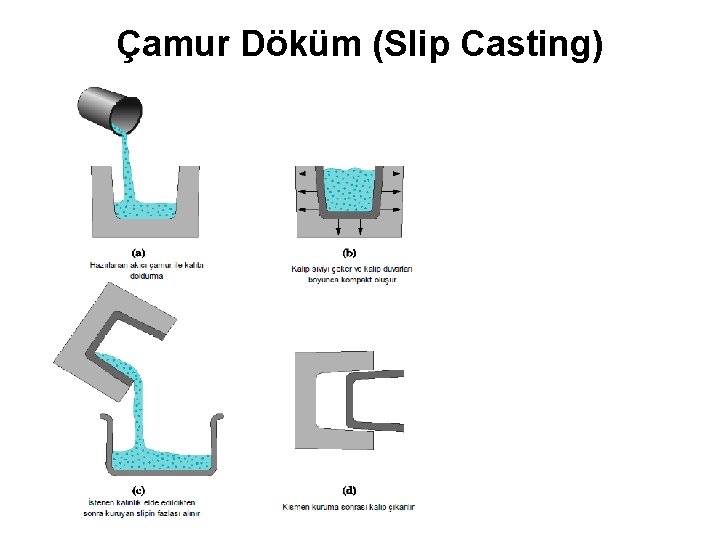
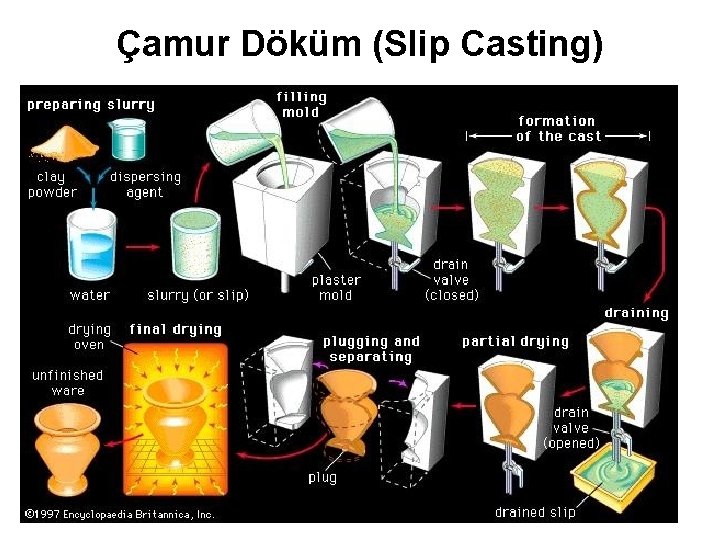
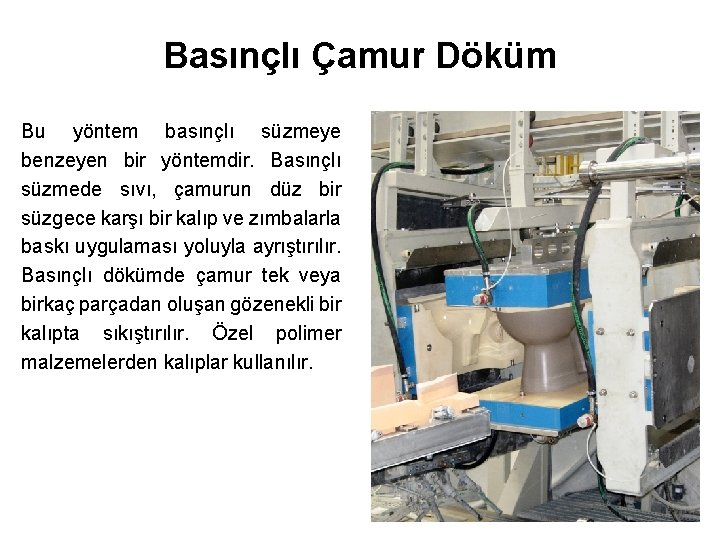
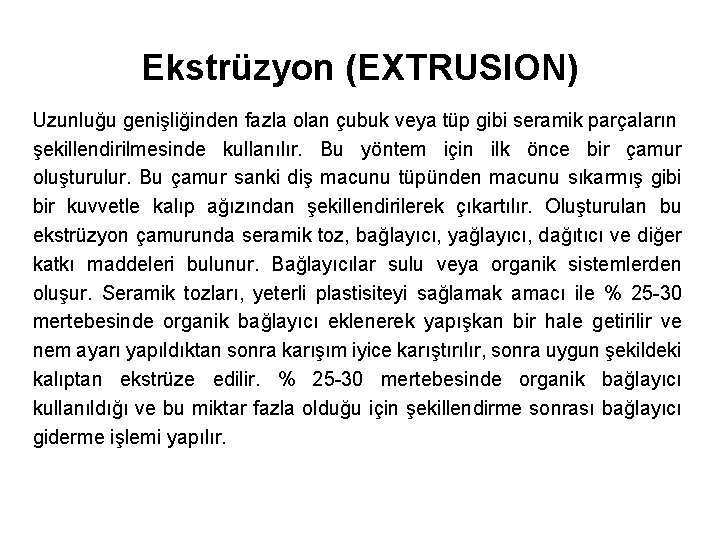
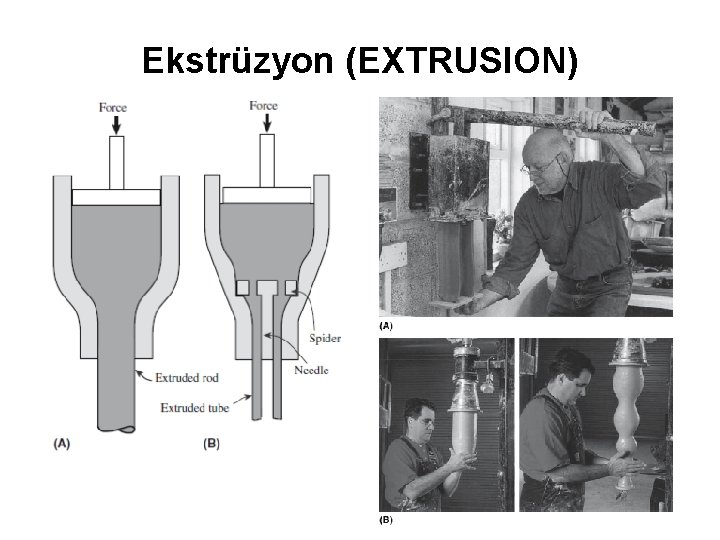

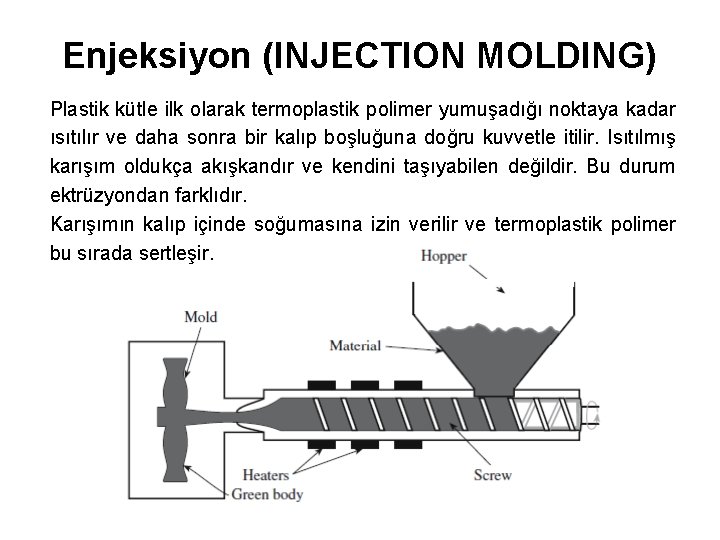
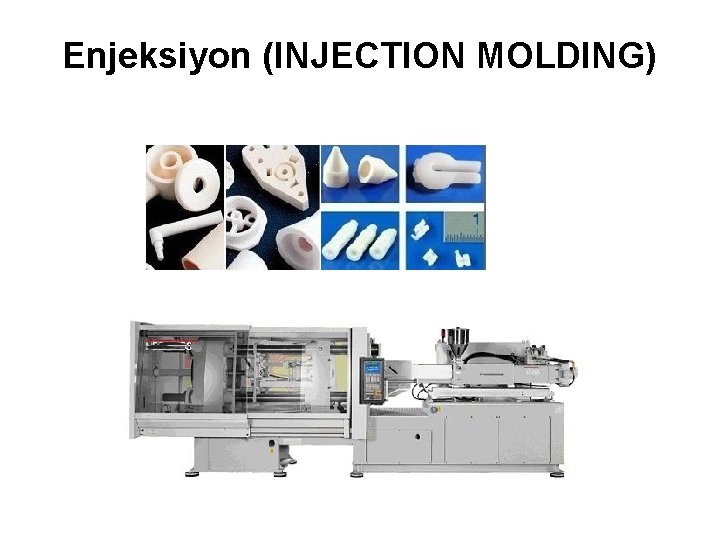
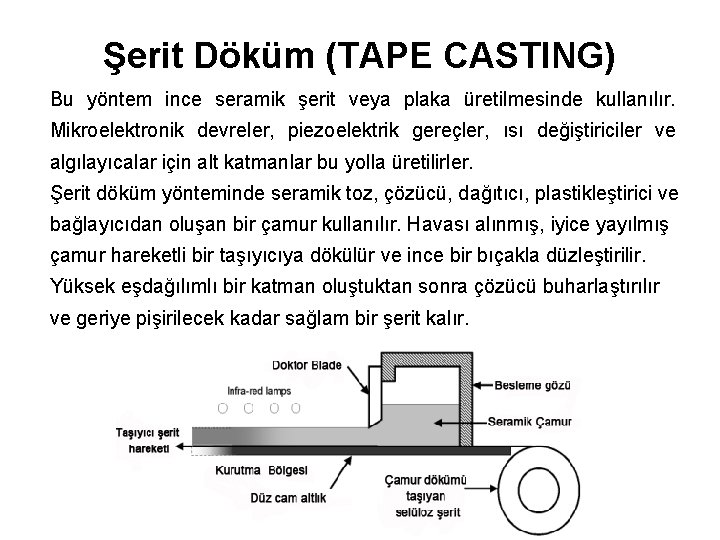
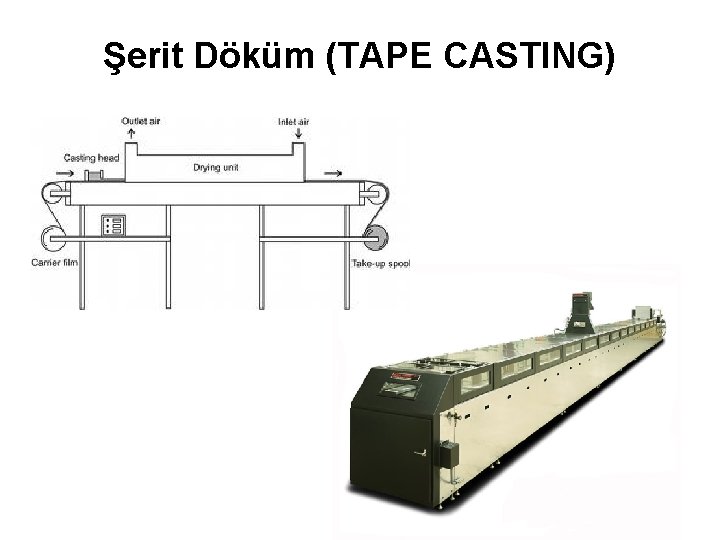
- Slides: 31
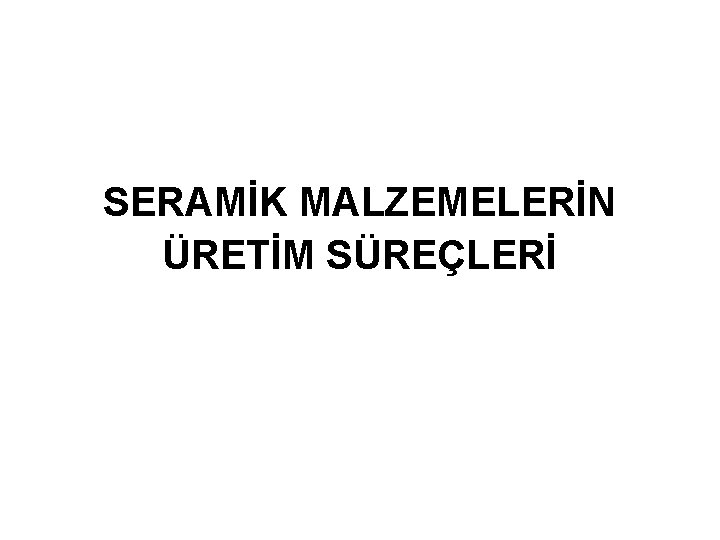
SERAMİK MALZEMELERİN ÜRETİM SÜREÇLERİ
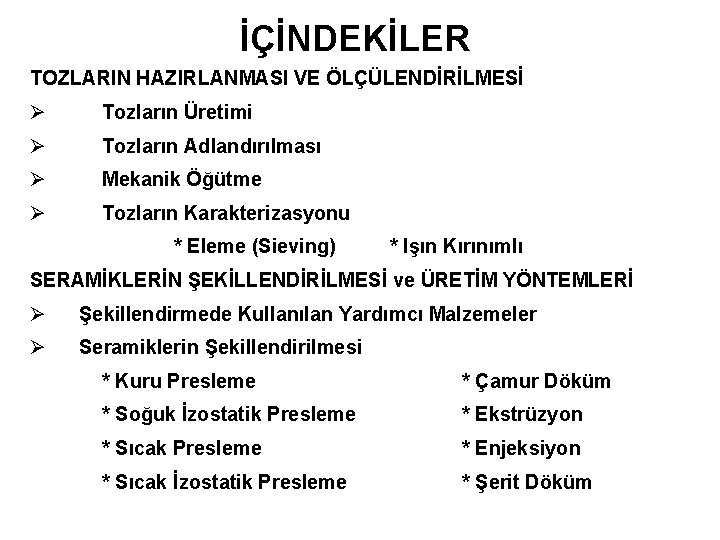
İÇİNDEKİLER TOZLARIN HAZIRLANMASI VE ÖLÇÜLENDİRİLMESİ Ø Tozların Üretimi Ø Tozların Adlandırılması Ø Mekanik Öğütme Ø Tozların Karakterizasyonu * Eleme (Sieving) * Işın Kırınımlı SERAMİKLERİN ŞEKİLLENDİRİLMESİ ve ÜRETİM YÖNTEMLERİ Ø Şekillendirmede Kullanılan Yardımcı Malzemeler Ø Seramiklerin Şekillendirilmesi * Kuru Presleme * Çamur Döküm * Soğuk İzostatik Presleme * Ekstrüzyon * Sıcak Presleme * Enjeksiyon * Sıcak İzostatik Presleme * Şerit Döküm
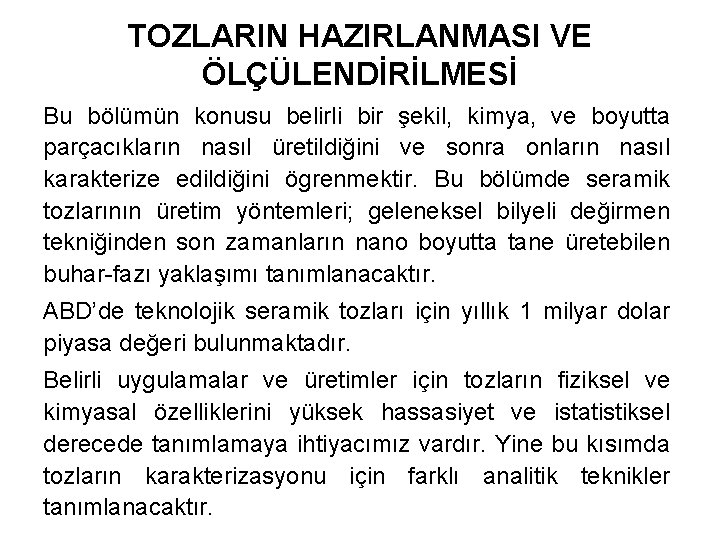
TOZLARIN HAZIRLANMASI VE ÖLÇÜLENDİRİLMESİ Bu bölümün konusu belirli bir şekil, kimya, ve boyutta parçacıkların nasıl üretildiğini ve sonra onların nasıl karakterize edildiğini ögrenmektir. Bu bölümde seramik tozlarının üretim yöntemleri; geleneksel bilyeli değirmen tekniğinden son zamanların nano boyutta tane üretebilen buhar-fazı yaklaşımı tanımlanacaktır. ABD’de teknolojik seramik tozları için yıllık 1 milyar dolar piyasa değeri bulunmaktadır. Belirli uygulamalar ve üretimler için tozların fiziksel ve kimyasal özelliklerini yüksek hassasiyet ve istatistiksel derecede tanımlamaya ihtiyacımız vardır. Yine bu kısımda tozların karakterizasyonu için farklı analitik teknikler tanımlanacaktır.
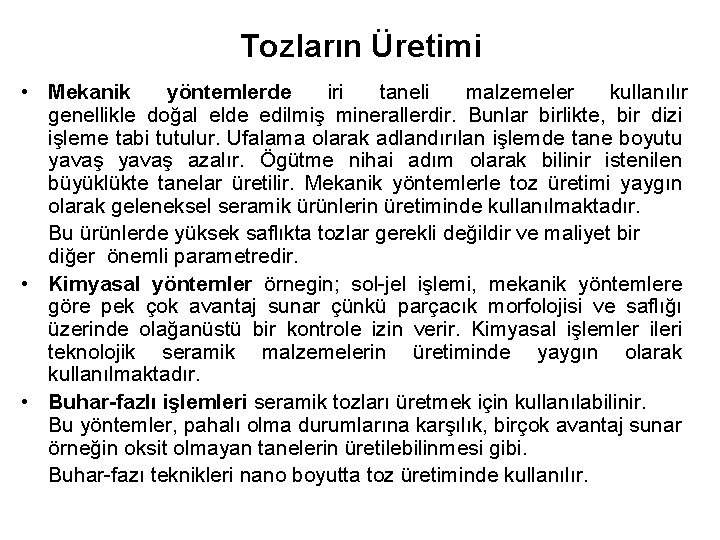
Tozların Üretimi • Mekanik yöntemlerde iri taneli malzemeler kullanılır genellikle doğal elde edilmiş minerallerdir. Bunlar birlikte, bir dizi işleme tabi tutulur. Ufalama olarak adlandırılan işlemde tane boyutu yavaş azalır. Ögütme nihai adım olarak bilinir istenilen büyüklükte tanelar üretilir. Mekanik yöntemlerle toz üretimi yaygın olarak geleneksel seramik ürünlerin üretiminde kullanılmaktadır. Bu ürünlerde yüksek saflıkta tozlar gerekli değildir ve maliyet bir diğer önemli parametredir. • Kimyasal yöntemler örnegin; sol-jel işlemi, mekanik yöntemlere göre pek çok avantaj sunar çünkü parçacık morfolojisi ve saflığı üzerinde olağanüstü bir kontrole izin verir. Kimyasal işlemler ileri teknolojik seramik malzemelerin üretiminde yaygın olarak kullanılmaktadır. • Buhar-fazlı işlemleri seramik tozları üretmek için kullanılabilinir. Bu yöntemler, pahalı olma durumlarına karşılık, birçok avantaj sunar örneğin oksit olmayan tanelerin üretilebilinmesi gibi. Buhar-fazı teknikleri nano boyutta toz üretiminde kullanılır.
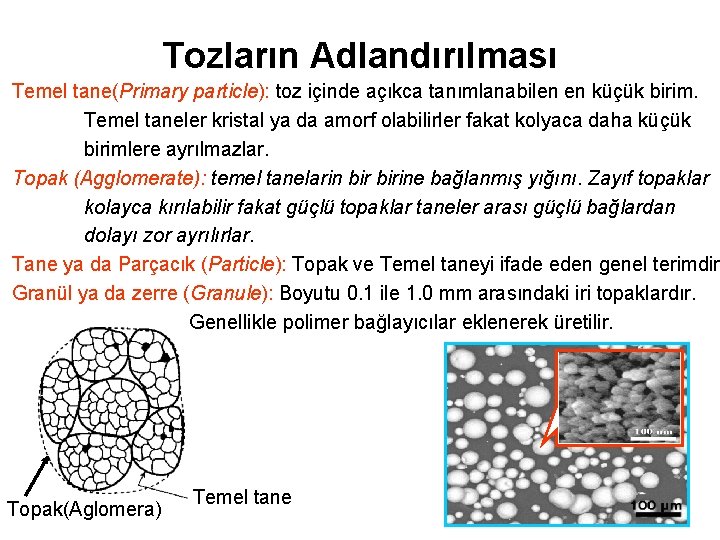
Tozların Adlandırılması Temel tane(Primary particle): toz içinde açıkca tanımlanabilen en küçük birim. Temel taneler kristal ya da amorf olabilirler fakat kolyaca daha küçük birimlere ayrılmazlar. Topak (Agglomerate): temel tanelarin birine bağlanmış yığını. Zayıf topaklar kolayca kırılabilir fakat güçlü topaklar taneler arası güçlü bağlardan dolayı zor ayrılırlar. Tane ya da Parçacık (Particle): Topak ve Temel taneyi ifade eden genel terimdir Granül ya da zerre (Granule): Boyutu 0. 1 ile 1. 0 mm arasındaki iri topaklardır. Genellikle polimer bağlayıcılar eklenerek üretilir. Topak(Aglomera) Temel tane
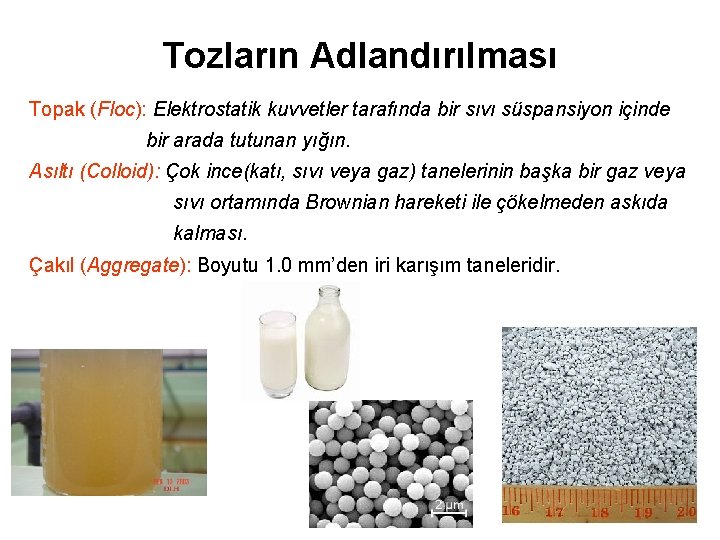
Tozların Adlandırılması Topak (Floc): Elektrostatik kuvvetler tarafında bir sıvı süspansiyon içinde bir arada tutunan yığın. Asıltı (Colloid): Çok ince(katı, sıvı veya gaz) tanelerinin başka bir gaz veya sıvı ortamında Brownian hareketi ile çökelmeden askıda kalması. Çakıl (Aggregate): Boyutu 1. 0 mm’den iri karışım taneleridir.
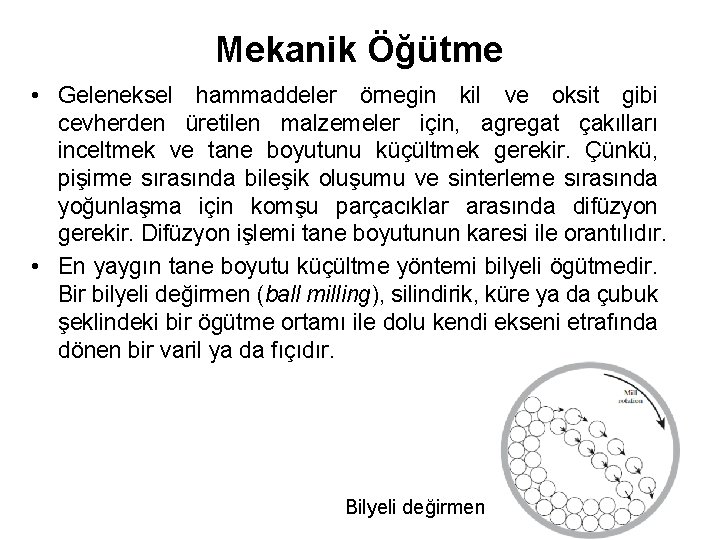
Mekanik Öğütme • Geleneksel hammaddeler örnegin kil ve oksit gibi cevherden üretilen malzemeler için, agregat çakılları inceltmek ve tane boyutunu küçültmek gerekir. Çünkü, pişirme sırasında bileşik oluşumu ve sinterleme sırasında yoğunlaşma için komşu parçacıklar arasında difüzyon gerekir. Difüzyon işlemi tane boyutunun karesi ile orantılıdır. • En yaygın tane boyutu küçültme yöntemi bilyeli ögütmedir. Bir bilyeli değirmen (ball milling), silindirik, küre ya da çubuk şeklindeki bir ögütme ortamı ile dolu kendi ekseni etrafında dönen bir varil ya da fıçıdır. Bilyeli değirmen
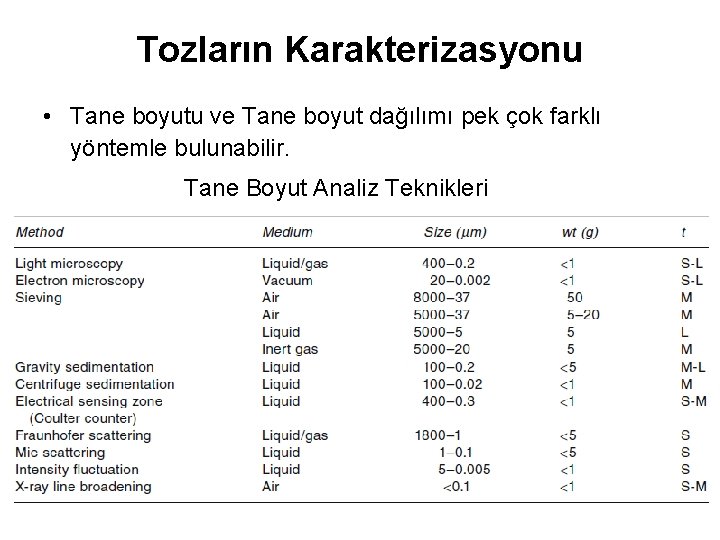
Tozların Karakterizasyonu • Tane boyutu ve Tane boyut dağılımı pek çok farklı yöntemle bulunabilir. Tane Boyut Analiz Teknikleri
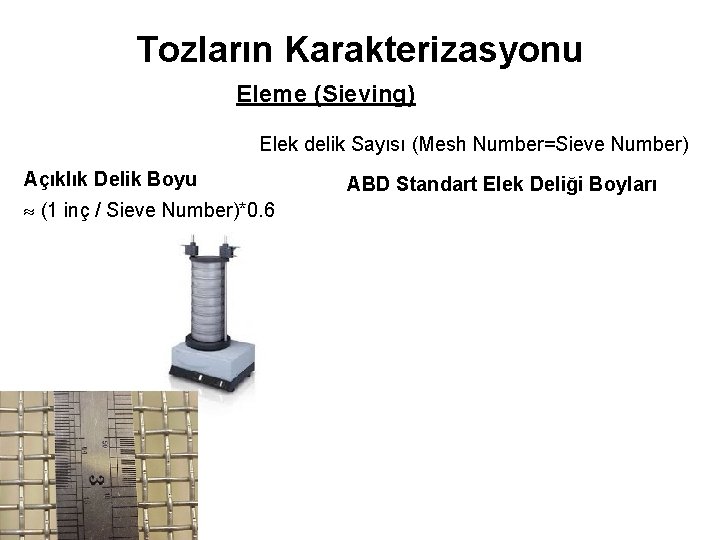
Tozların Karakterizasyonu Eleme (Sieving) Elek delik Sayısı (Mesh Number=Sieve Number) Açıklık Delik Boyu (1 inç / Sieve Number)*0. 6 ABD Standart Elek Deliği Boyları
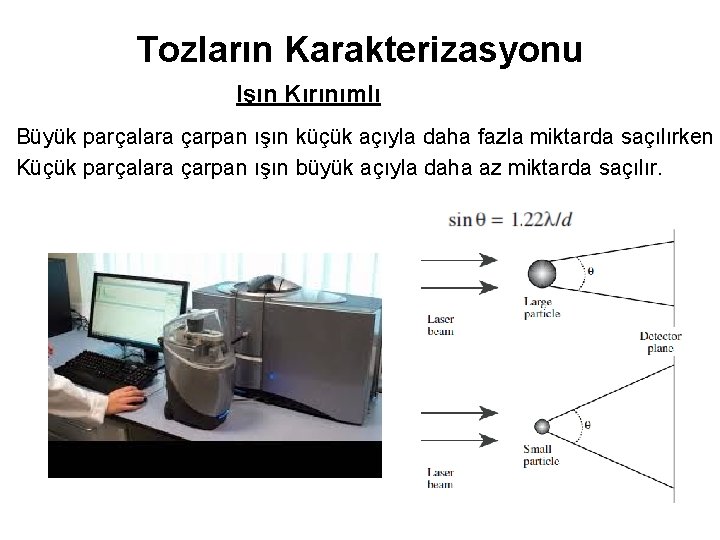
Tozların Karakterizasyonu Işın Kırınımlı Büyük parçalara çarpan ışın küçük açıyla daha fazla miktarda saçılırken Küçük parçalara çarpan ışın büyük açıyla daha az miktarda saçılır.
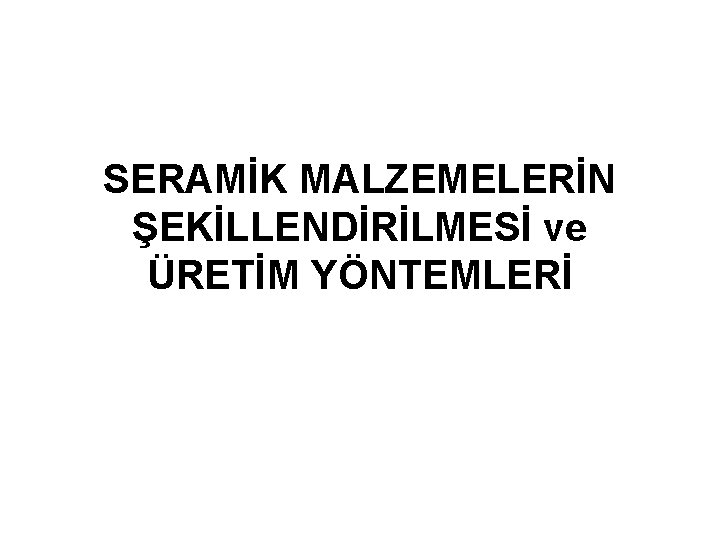
SERAMİK MALZEMELERİN ŞEKİLLENDİRİLMESİ ve ÜRETİM YÖNTEMLERİ
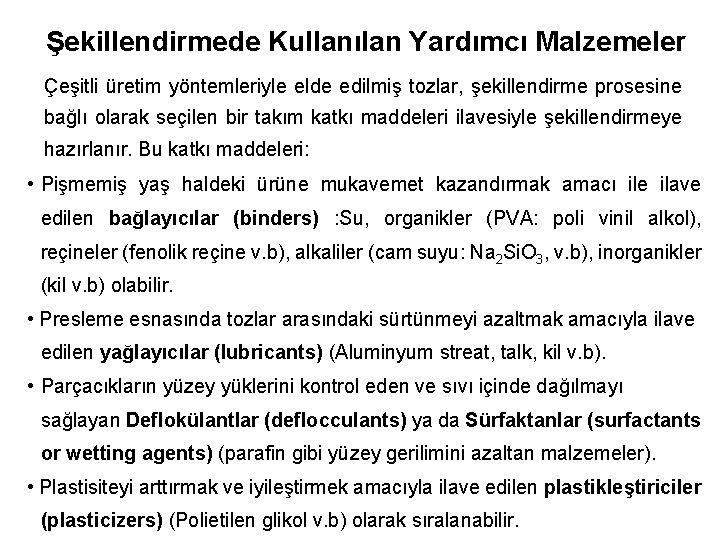
Şekillendirmede Kullanılan Yardımcı Malzemeler Çeşitli üretim yöntemleriyle elde edilmiş tozlar, şekillendirme prosesine bağlı olarak seçilen bir takım katkı maddeleri ilavesiyle şekillendirmeye hazırlanır. Bu katkı maddeleri: • Pişmemiş yaş haldeki ürüne mukavemet kazandırmak amacı ile ilave edilen bağlayıcılar (binders) : Su, organikler (PVA: poli vinil alkol), reçineler (fenolik reçine v. b), alkaliler (cam suyu: Na 2 Si. O 3, v. b), inorganikler (kil v. b) olabilir. • Presleme esnasında tozlar arasındaki sürtünmeyi azaltmak amacıyla ilave edilen yağlayıcılar (lubricants) (Aluminyum streat, talk, kil v. b). • Parçacıkların yüzey yüklerini kontrol eden ve sıvı içinde dağılmayı sağlayan Deflokülantlar (deflocculants) ya da Sürfaktanlar (surfactants or wetting agents) (parafin gibi yüzey gerilimini azaltan malzemeler). • Plastisiteyi arttırmak ve iyileştirmek amacıyla ilave edilen plastikleştiriciler (plasticizers) (Polietilen glikol v. b) olarak sıralanabilir.
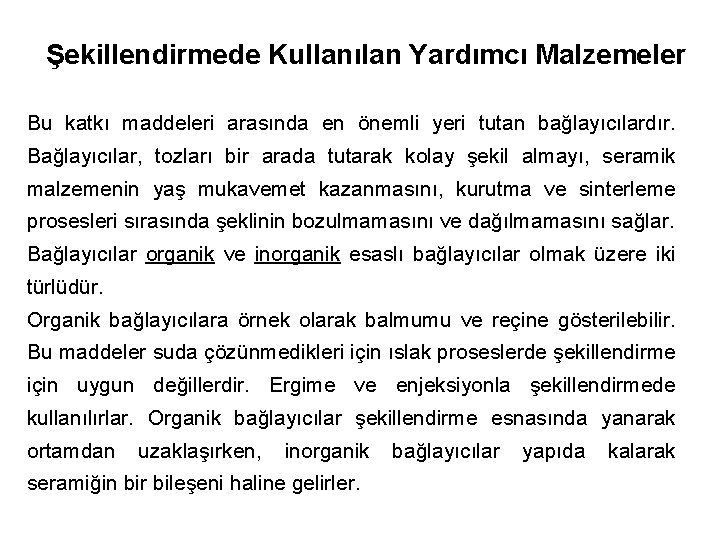
Şekillendirmede Kullanılan Yardımcı Malzemeler Bu katkı maddeleri arasında en önemli yeri tutan bağlayıcılardır. Bağlayıcılar, tozları bir arada tutarak kolay şekil almayı, seramik malzemenin yaş mukavemet kazanmasını, kurutma ve sinterleme prosesleri sırasında şeklinin bozulmamasını ve dağılmamasını sağlar. Bağlayıcılar organik ve inorganik esaslı bağlayıcılar olmak üzere iki türlüdür. Organik bağlayıcılara örnek olarak balmumu ve reçine gösterilebilir. Bu maddeler suda çözünmedikleri için ıslak proseslerde şekillendirme için uygun değillerdir. Ergime ve enjeksiyonla şekillendirmede kullanılırlar. Organik bağlayıcılar şekillendirme esnasında yanarak ortamdan uzaklaşırken, inorganik seramiğin bir bileşeni haline gelirler. bağlayıcılar yapıda kalarak
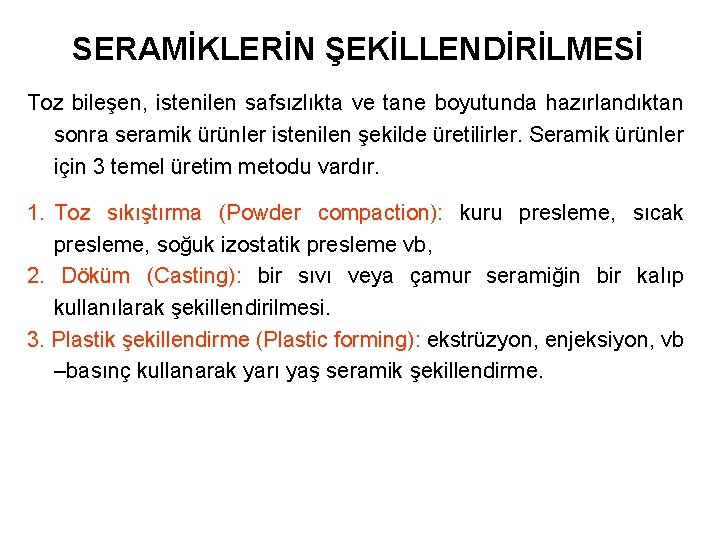
SERAMİKLERİN ŞEKİLLENDİRİLMESİ Toz bileşen, istenilen safsızlıkta ve tane boyutunda hazırlandıktan sonra seramik ürünler istenilen şekilde üretilirler. Seramik ürünler için 3 temel üretim metodu vardır. 1. Toz sıkıştırma (Powder compaction): kuru presleme, sıcak presleme, soğuk izostatik presleme vb, 2. Döküm (Casting): bir sıvı veya çamur seramiğin bir kalıp kullanılarak şekillendirilmesi. 3. Plastik şekillendirme (Plastic forming): ekstrüzyon, enjeksiyon, vb –basınç kullanarak yarı yaş seramik şekillendirme.
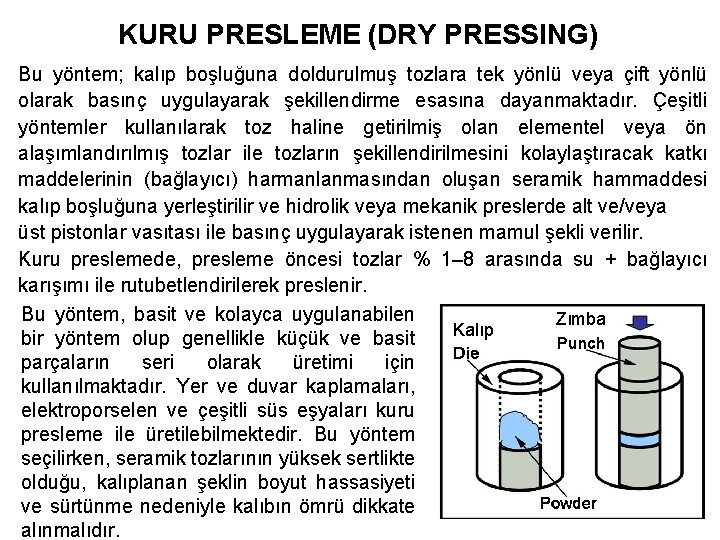
KURU PRESLEME (DRY PRESSING) Bu yöntem; kalıp boşluğuna doldurulmuş tozlara tek yönlü veya çift yönlü olarak basınç uygulayarak şekillendirme esasına dayanmaktadır. Çeşitli yöntemler kullanılarak toz haline getirilmiş olan elementel veya ön alaşımlandırılmış tozlar ile tozların şekillendirilmesini kolaylaştıracak katkı maddelerinin (bağlayıcı) harmanlanmasından oluşan seramik hammaddesi kalıp boşluğuna yerleştirilir ve hidrolik veya mekanik preslerde alt ve/veya üst pistonlar vasıtası ile basınç uygulayarak istenen mamul şekli verilir. Kuru preslemede, presleme öncesi tozlar % 1– 8 arasında su + bağlayıcı karışımı ile rutubetlendirilerek preslenir. Bu yöntem, basit ve kolayca uygulanabilen Zımba Kalıp bir yöntem olup genellikle küçük ve basit parçaların seri olarak üretimi için kullanılmaktadır. Yer ve duvar kaplamaları, elektroporselen ve çeşitli süs eşyaları kuru presleme ile üretilebilmektedir. Bu yöntem seçilirken, seramik tozlarının yüksek sertlikte olduğu, kalıplanan şeklin boyut hassasiyeti ve sürtünme nedeniyle kalıbın ömrü dikkate alınmalıdır.
![Soğuk İzostatik Presleme COLD ISOSTATIC PRESSINGCIP CIP kuru presle şekillendirme imkânı olmayan kompleks şekil Soğuk İzostatik Presleme [COLD ISOSTATIC PRESSING(CIP)] CIP, kuru presle şekillendirme imkânı olmayan kompleks şekil](https://slidetodoc.com/presentation_image/10391fae18951bc6ca5deecd28f434d3/image-16.jpg)
Soğuk İzostatik Presleme [COLD ISOSTATIC PRESSING(CIP)] CIP, kuru presle şekillendirme imkânı olmayan kompleks şekil ve kalitedeki ürünlerin şekillendirmesinde kullanılan bir yöntemdir. Bu yöntem, dayanıklı esnek kauçuk veya sentetik bir malzemeden yapılan kalıp içerisine seramik hammaddesinin doldurulması ve hidrolik basıncın ürünü meydana getirecek toz üzerine homojen bir şekilde tatbik edilmesi sağlanarak malzemenin şekillendirilmesi esasına dayanır. Bu yöntemle üretim yapılmadan önce istenilen şekle bağlı olarak 30 MPa’dan daha düşük bir basınçta ön şekillendirmenin yapılması gerekebilir. CIP’de kompakt hale getirilmiş olan parçaya, yüksek sıcaklık sinterlemesi uygulanarak daha yüksek yoğunluğa sahip ürünler elde edilmektedir.
![Soğuk İzostatik Presleme COLD ISOSTATIC PRESSINGCIP Uyluk kemiği Sinterlenmiş Zirkonya Seramik Soğuk İzostatik Presleme [COLD ISOSTATIC PRESSING(CIP)] Uyluk kemiği Sinterlenmiş Zirkonya Seramik](https://slidetodoc.com/presentation_image/10391fae18951bc6ca5deecd28f434d3/image-17.jpg)
Soğuk İzostatik Presleme [COLD ISOSTATIC PRESSING(CIP)] Uyluk kemiği Sinterlenmiş Zirkonya Seramik
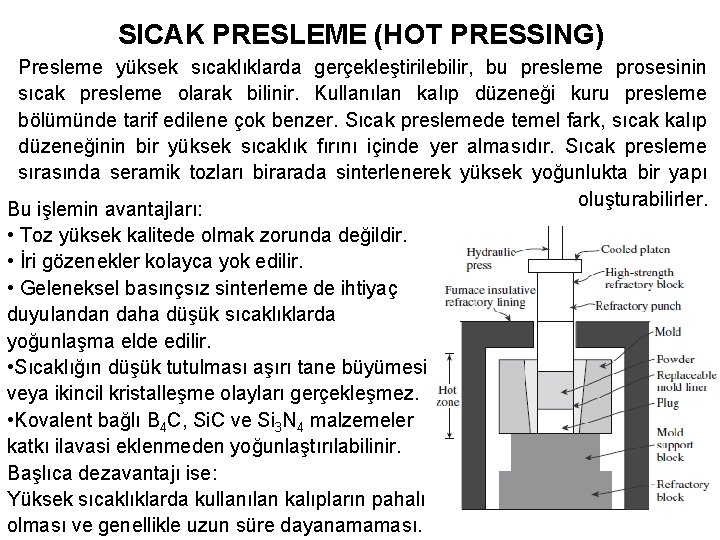
SICAK PRESLEME (HOT PRESSING) Presleme yüksek sıcaklıklarda gerçekleştirilebilir, bu presleme prosesinin sıcak presleme olarak bilinir. Kullanılan kalıp düzeneği kuru presleme bölümünde tarif edilene çok benzer. Sıcak preslemede temel fark, sıcak kalıp düzeneğinin bir yüksek sıcaklık fırını içinde yer almasıdır. Sıcak presleme sırasında seramik tozları birarada sinterlenerek yüksek yoğunlukta bir yapı oluşturabilirler. Bu işlemin avantajları: • Toz yüksek kalitede olmak zorunda değildir. • İri gözenekler kolayca yok edilir. • Geleneksel basınçsız sinterleme de ihtiyaç duyulandan daha düşük sıcaklıklarda yoğunlaşma elde edilir. • Sıcaklığın düşük tutulması aşırı tane büyümesi veya ikincil kristalleşme olayları gerçekleşmez. • Kovalent bağlı B 4 C, Si. C ve Si 3 N 4 malzemeler katkı ilavasi eklenmeden yoğunlaştırılabilinir. Başlıca dezavantajı ise: Yüksek sıcaklıklarda kullanılan kalıpların pahalı olması ve genellikle uzun süre dayanamaması.
![Sıcak İzostatik Presleme HOT ISOSTATIC PRESSING HIP Sıcak izostatik preslemede HIP ısı ve basınç Sıcak İzostatik Presleme [HOT ISOSTATIC PRESSING (HIP)] Sıcak izostatik preslemede (HIP) ısı ve basınç](https://slidetodoc.com/presentation_image/10391fae18951bc6ca5deecd28f434d3/image-19.jpg)
Sıcak İzostatik Presleme [HOT ISOSTATIC PRESSING (HIP)] Sıcak izostatik preslemede (HIP) ısı ve basınç eşzamanlı olarak uygulanır. Fırın, yüksek basınca dayanan bir tank içine inşa edilir ve preslenecek nesneler içine yerleştirilir. Sıcaklıklar 2000°C‘ye kadar olabilir ve basınç 30300 MPa aralığındadır. CIP işlemi aksine, bir gaz basınç ortamı olarak kullanılır. CIP işleminde bir sıvı genellikle kullanılır. Argon basınç için en çok kullanılan gazdır fakat oksitleyici ya da reaktif gazlar da kullanılabilir. Günümüzde HIP geniş bir seramik (ve metalik) yelpazede örneğin alümina esaslı alet uçları ve baca gazı kükürt giderme kullanılan silisyum nitrür nozullar gibi. HIP işlemi yapısal seramikler konusunda örneğin Si 3 N 4 gibi seramiklerin büyütülmesi avantajları nedeniyle önem kazanmaktadır. Oksit olmayan seramiklerin tam yoğunluğa tane boyutları büyümeden ulaşması sağlanır. Çünkü yüksek yoğunluk, düşük tane boyutu ile malzemeye özel mekanik özellikler kazandırır. Dezavantajı : maliyet
![Sıcak İzostatik Presleme HOT ISOSTATIC PRESSING HIP Sıcak İzostatik Presleme [HOT ISOSTATIC PRESSING (HIP)]](https://slidetodoc.com/presentation_image/10391fae18951bc6ca5deecd28f434d3/image-20.jpg)
Sıcak İzostatik Presleme [HOT ISOSTATIC PRESSING (HIP)]
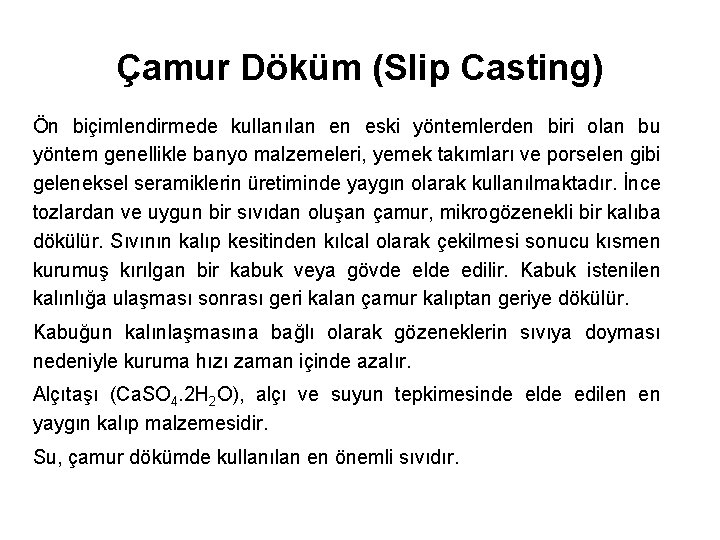
Çamur Döküm (Slip Casting) Ön biçimlendirmede kullanılan en eski yöntemlerden biri olan bu yöntem genellikle banyo malzemeleri, yemek takımları ve porselen gibi geleneksel seramiklerin üretiminde yaygın olarak kullanılmaktadır. İnce tozlardan ve uygun bir sıvıdan oluşan çamur, mikrogözenekli bir kalıba dökülür. Sıvının kalıp kesitinden kılcal olarak çekilmesi sonucu kısmen kurumuş kırılgan bir kabuk veya gövde elde edilir. Kabuk istenilen kalınlığa ulaşması sonrası geri kalan çamur kalıptan geriye dökülür. Kabuğun kalınlaşmasına bağlı olarak gözeneklerin sıvıya doyması nedeniyle kuruma hızı zaman içinde azalır. Alçıtaşı (Ca. SO 4. 2 H 2 O), alçı ve suyun tepkimesinde elde edilen en yaygın kalıp malzemesidir. Su, çamur dökümde kullanılan en önemli sıvıdır.
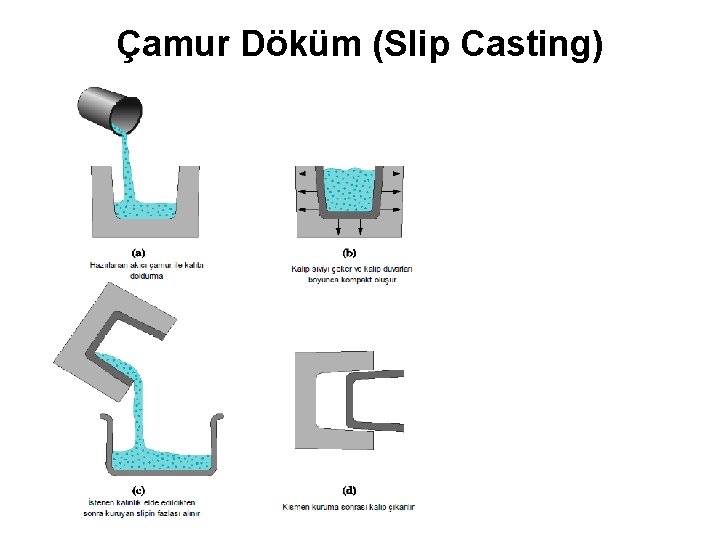
Çamur Döküm (Slip Casting)
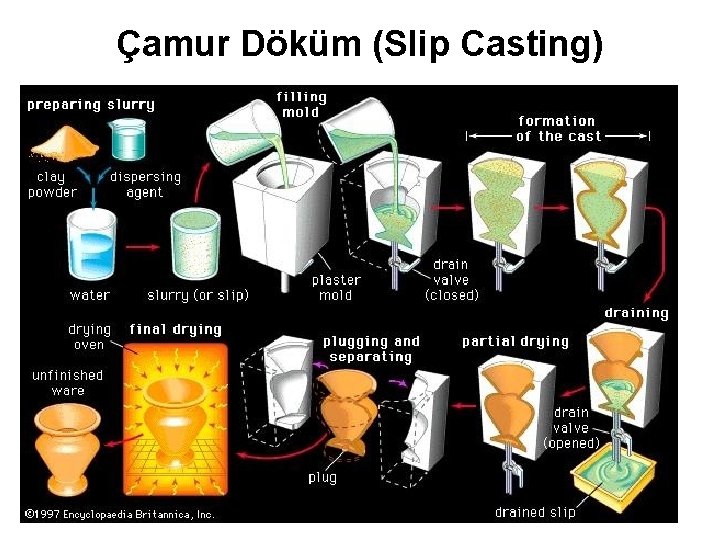
Çamur Döküm (Slip Casting)
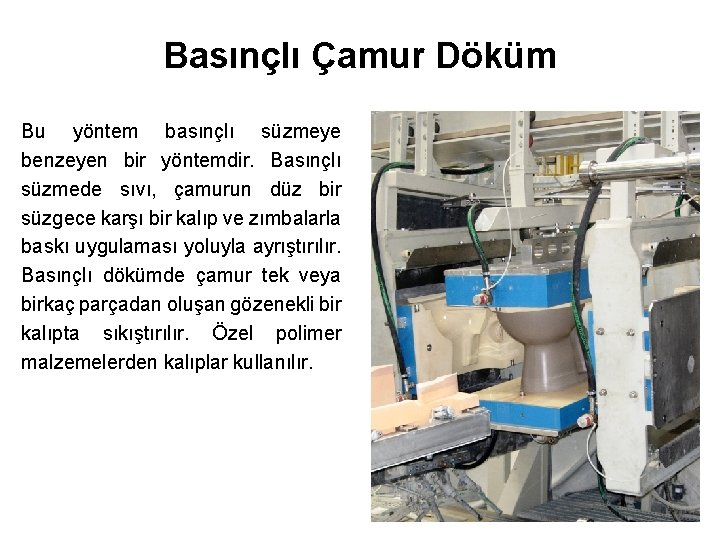
Basınçlı Çamur Döküm Bu yöntem basınçlı süzmeye benzeyen bir yöntemdir. Basınçlı süzmede sıvı, çamurun düz bir süzgece karşı bir kalıp ve zımbalarla baskı uygulaması yoluyla ayrıştırılır. Basınçlı dökümde çamur tek veya birkaç parçadan oluşan gözenekli bir kalıpta sıkıştırılır. Özel polimer malzemelerden kalıplar kullanılır.
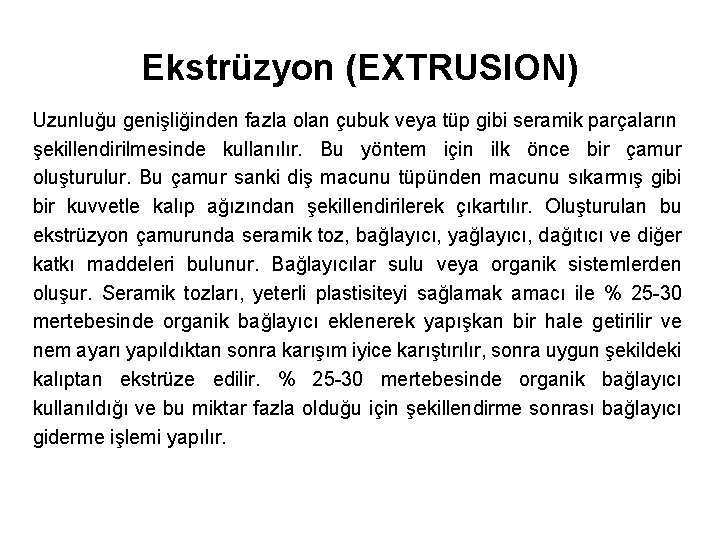
Ekstrüzyon (EXTRUSION) Uzunluğu genişliğinden fazla olan çubuk veya tüp gibi seramik parçaların şekillendirilmesinde kullanılır. Bu yöntem için ilk önce bir çamur oluşturulur. Bu çamur sanki diş macunu tüpünden macunu sıkarmış gibi bir kuvvetle kalıp ağızından şekillendirilerek çıkartılır. Oluşturulan bu ekstrüzyon çamurunda seramik toz, bağlayıcı, yağlayıcı, dağıtıcı ve diğer katkı maddeleri bulunur. Bağlayıcılar sulu veya organik sistemlerden oluşur. Seramik tozları, yeterli plastisiteyi sağlamak amacı ile % 25 -30 mertebesinde organik bağlayıcı eklenerek yapışkan bir hale getirilir ve nem ayarı yapıldıktan sonra karışım iyice karıştırılır, sonra uygun şekildeki kalıptan ekstrüze edilir. % 25 -30 mertebesinde organik bağlayıcı kullanıldığı ve bu miktar fazla olduğu için şekillendirme sonrası bağlayıcı giderme işlemi yapılır.
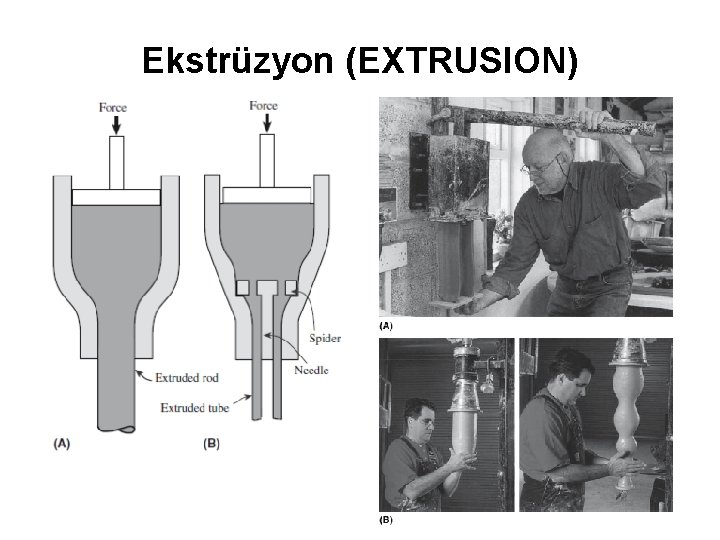
Ekstrüzyon (EXTRUSION)

Enjeksiyon (INJECTION MOLDING) Enjeksiyon kalıplama termoplastik polimerlerin şekillendirilmesinde kullanılan bir tekniktir. Bir termoplastik polimer ısıtıldığı zaman yumuşayan ve soğutulduğu zaman sertleşen bir malzemedir. Bu işlemler tamamen geri çevrimli ve belkide tekrarlanabilirdir. Şayet seramik toz bir termoplastik polimere eklenirse, enjeksiyon kalıplama seramiklerin şekillendirilmesinde ve biçimlendirilmesinde uygulanabilinir. Seramikleri enjeksiyon kalıplamayla biçimlendirdiğimizde, polimer genelde bağlayıcı olarak tanımlanır (fakat bunun yerine malzemeye seramik yüklü polimer diyebiliriz. ) Seramik toz bağlayıcıya eklenir ve istenilen reolojik özelliklere sahip bir kütle sağlamak için çeşitli organik malzemeler ile beraber karıştırılırlar. Karışımın hacimce yaklaşık %40’ını organik kısım oluşturur. Karışımda yüksek miktarda organik malzeme kullanıldığı için, enjeksiyon kalıplanmış parçalarda sinterleme sırasında yüksek oranda büzülme olur. Büzülme genelde %15 -20 arasındadır ve dolayısıyla parçaların boyutlarını kesin ve tam olarak kontrol etmek zordur. Fakat, sinterleme sırasında kompleks şekillerde çok az bozulmalar kalır çünkü yoğunluklar düşük olsada oldukça homojendir.
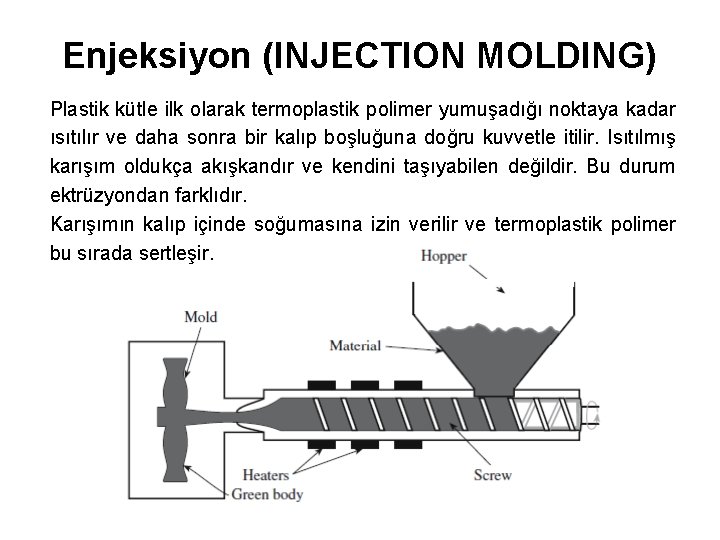
Enjeksiyon (INJECTION MOLDING) Plastik kütle ilk olarak termoplastik polimer yumuşadığı noktaya kadar ısıtılır ve daha sonra bir kalıp boşluğuna doğru kuvvetle itilir. Isıtılmış karışım oldukça akışkandır ve kendini taşıyabilen değildir. Bu durum ektrüzyondan farklıdır. Karışımın kalıp içinde soğumasına izin verilir ve termoplastik polimer bu sırada sertleşir.
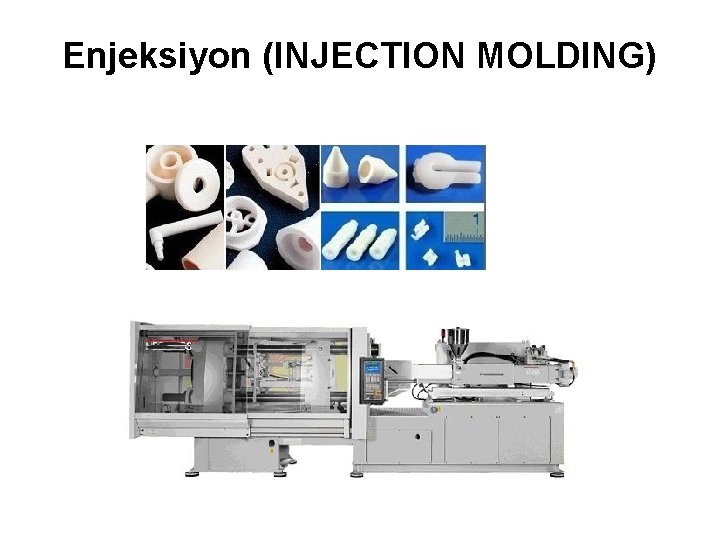
Enjeksiyon (INJECTION MOLDING)
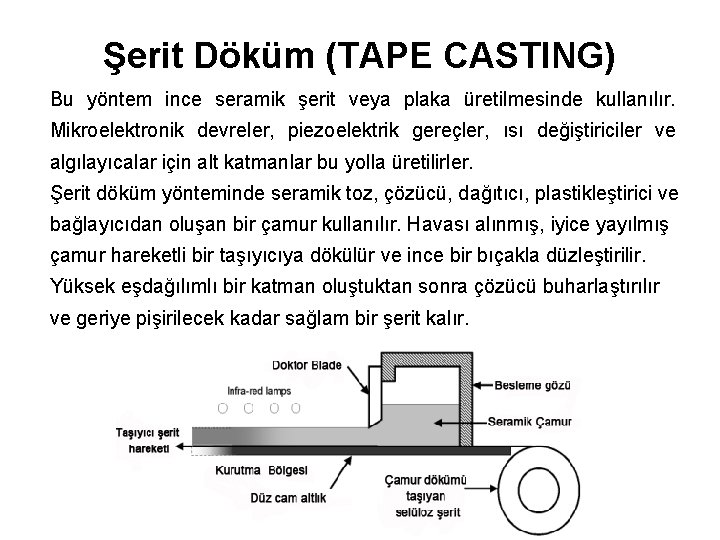
Şerit Döküm (TAPE CASTING) Bu yöntem ince seramik şerit veya plaka üretilmesinde kullanılır. Mikroelektronik devreler, piezoelektrik gereçler, ısı değiştiriciler ve algılayıcalar için alt katmanlar bu yolla üretilirler. Şerit döküm yönteminde seramik toz, çözücü, dağıtıcı, plastikleştirici ve bağlayıcıdan oluşan bir çamur kullanılır. Havası alınmış, iyice yayılmış çamur hareketli bir taşıyıcıya dökülür ve ince bir bıçakla düzleştirilir. Yüksek eşdağılımlı bir katman oluştuktan sonra çözücü buharlaştırılır ve geriye pişirilecek kadar sağlam bir şerit kalır.
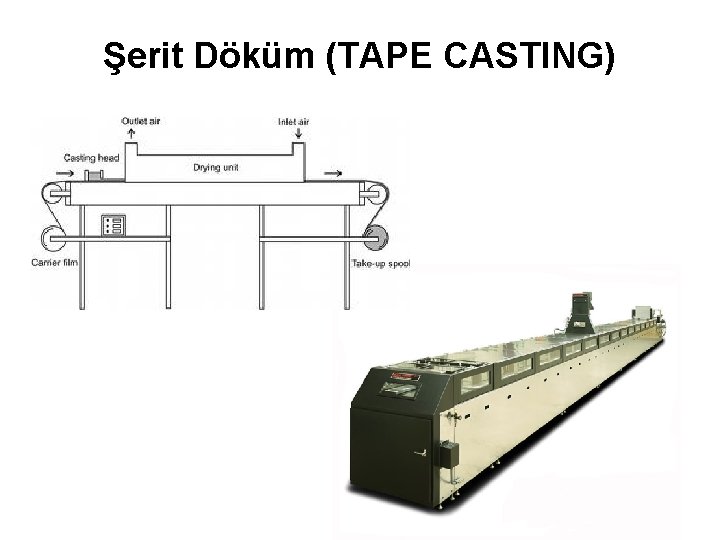
Şerit Döküm (TAPE CASTING)