PRT 101 Introduction to Process Technology Test 1
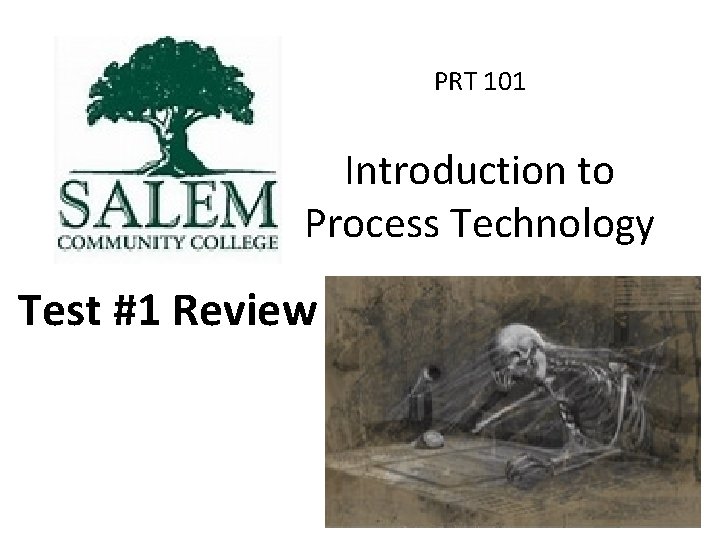
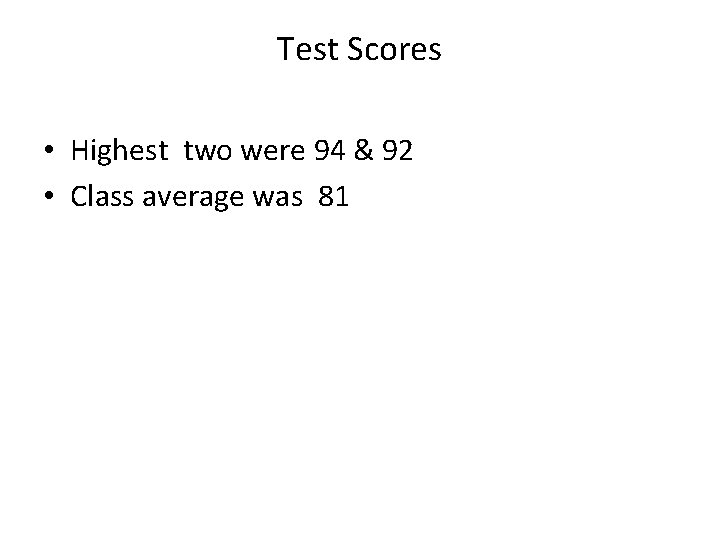
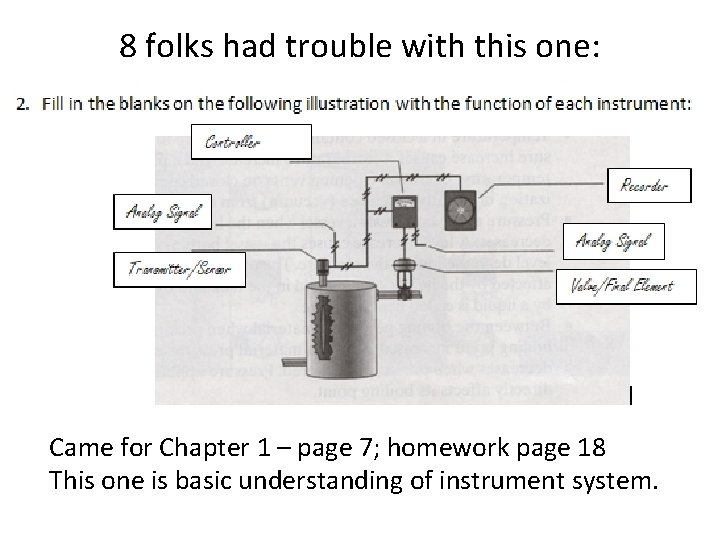
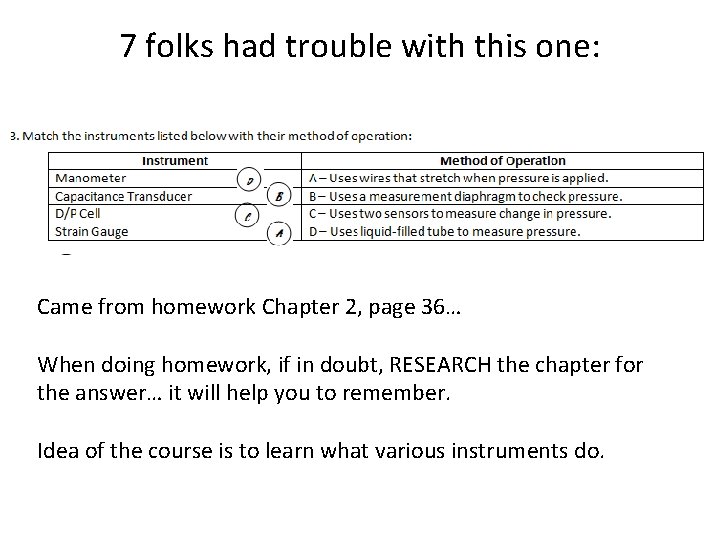

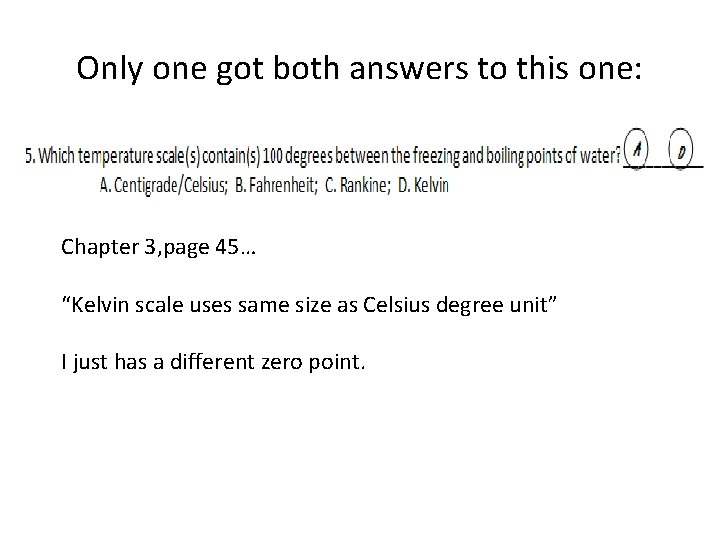
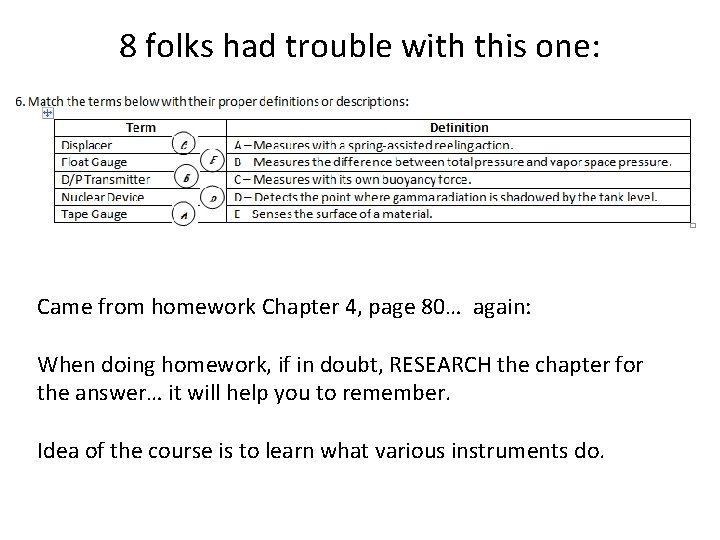
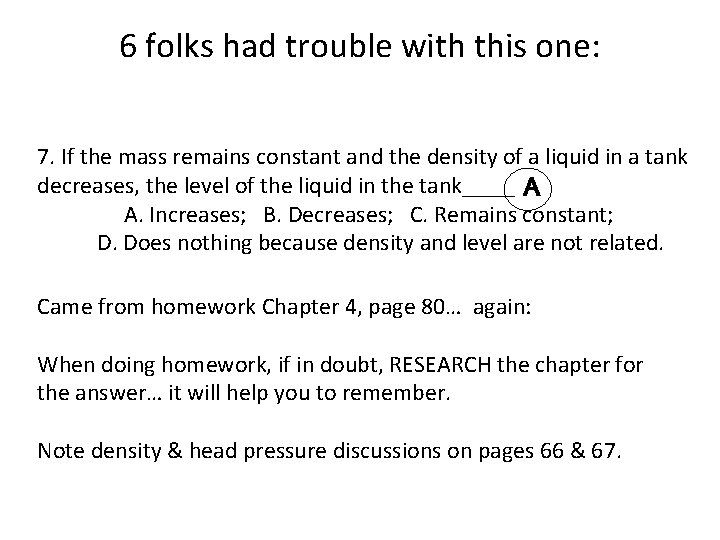
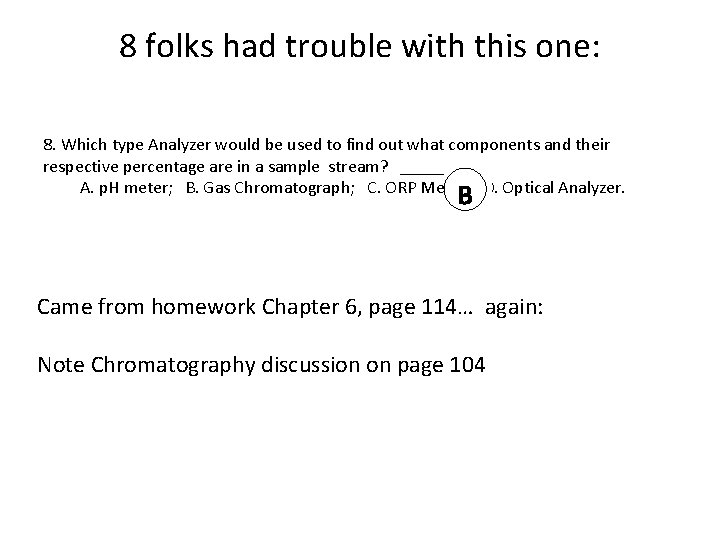
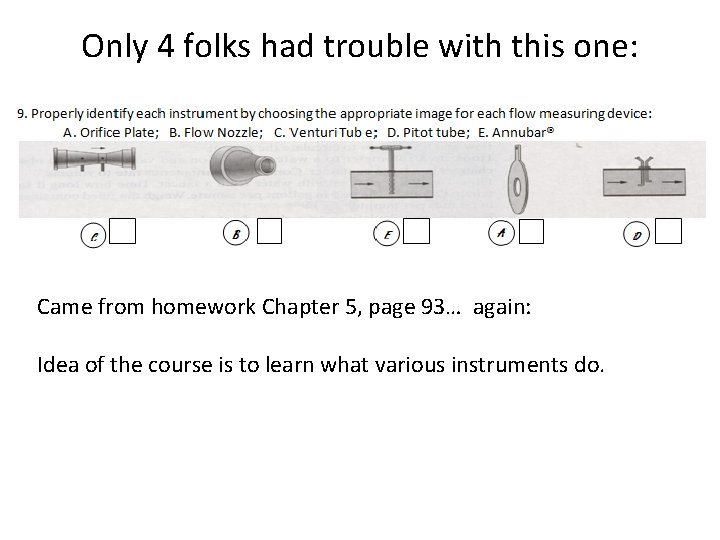
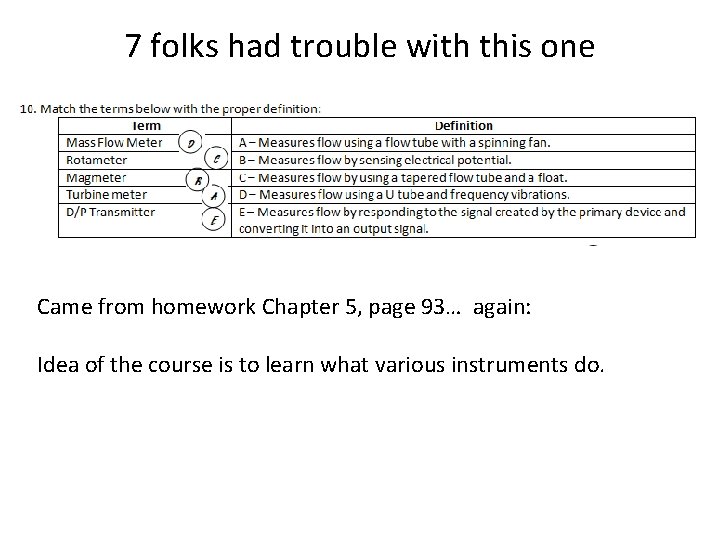
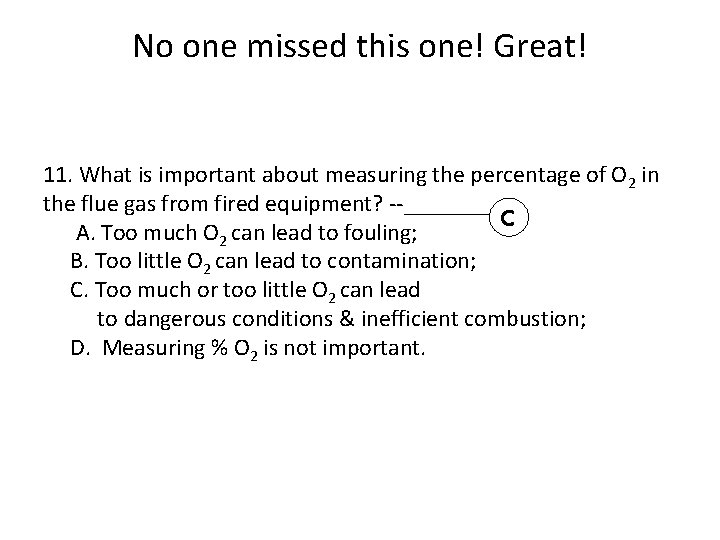
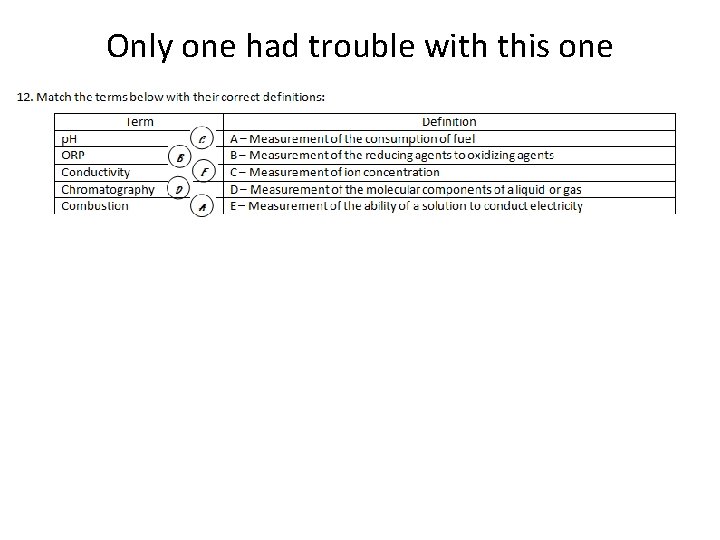
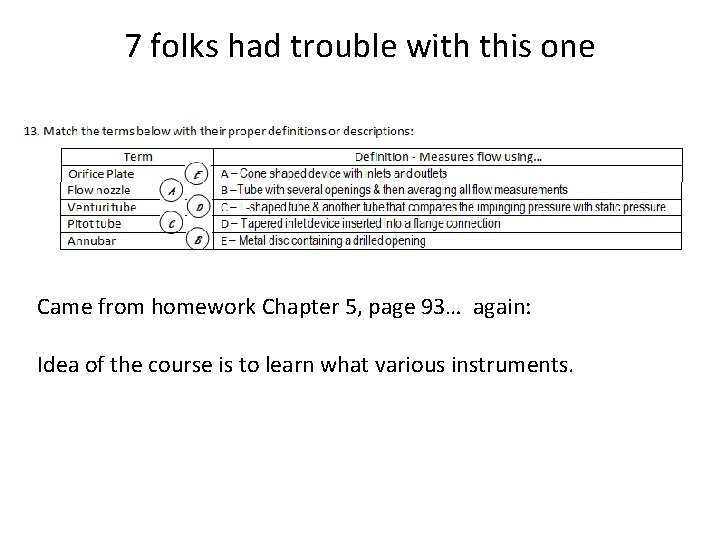
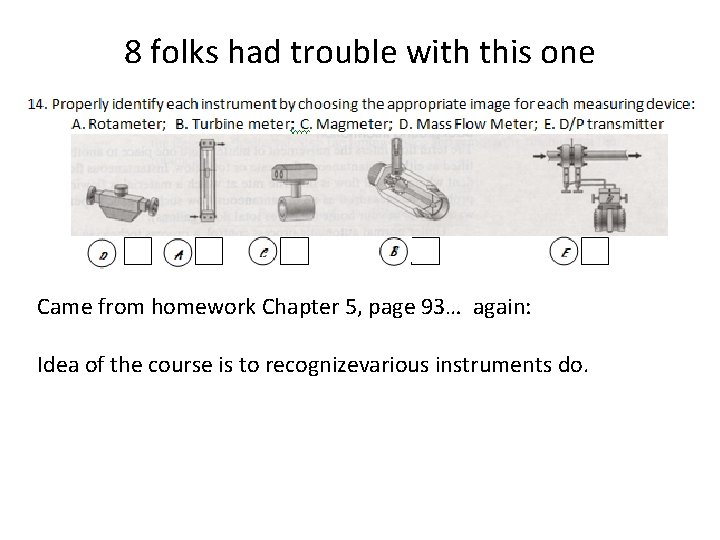

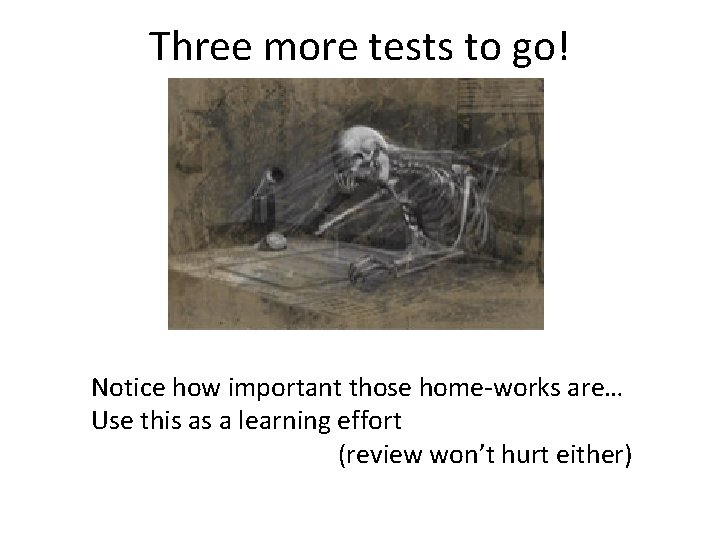
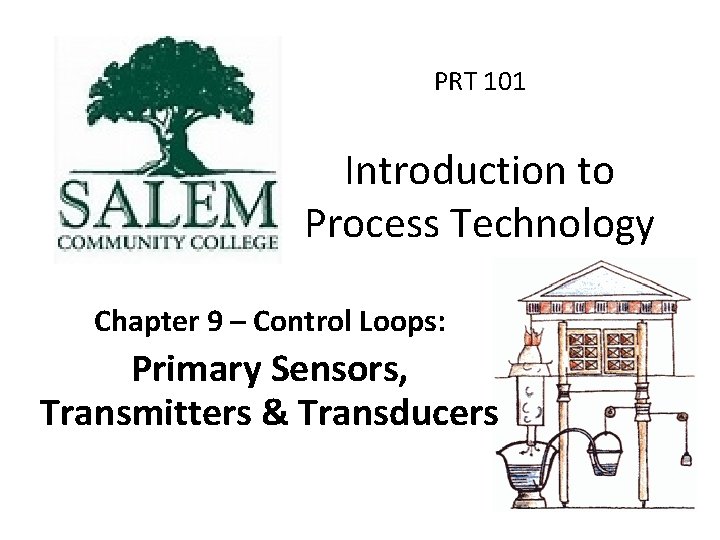
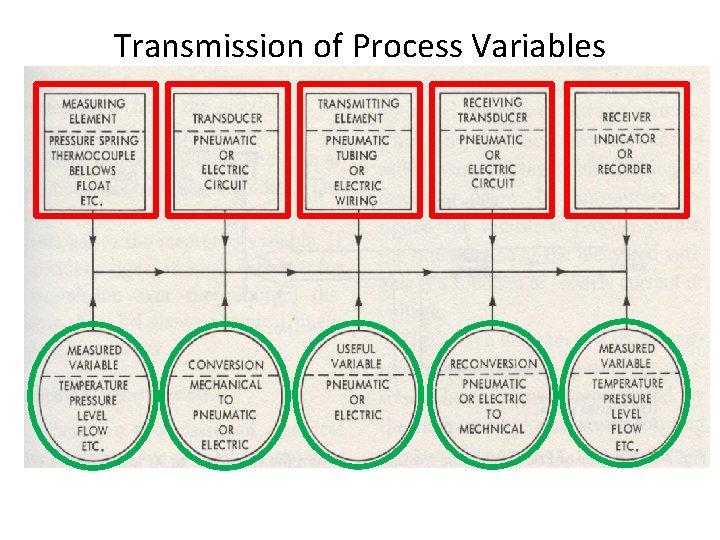
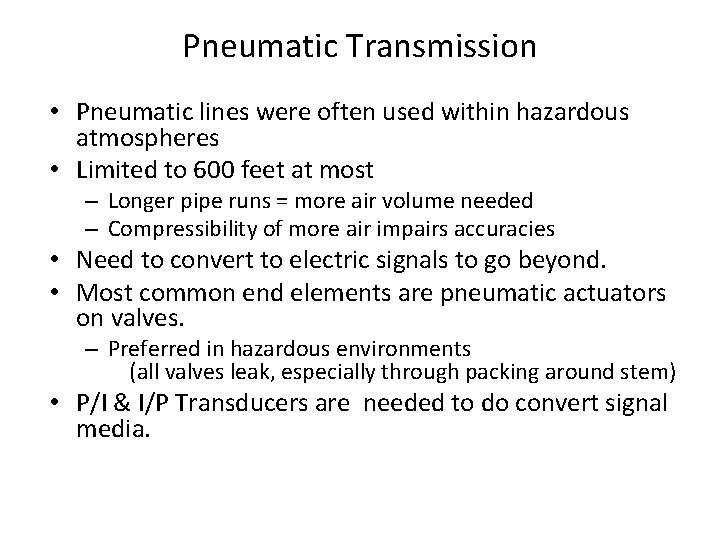
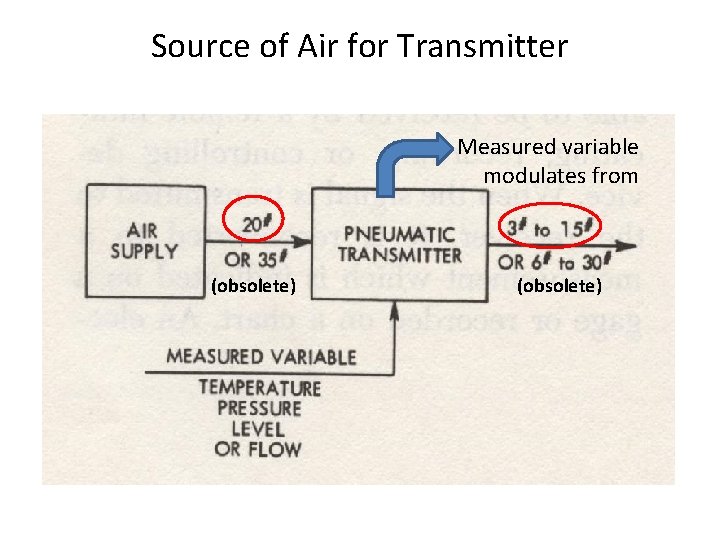
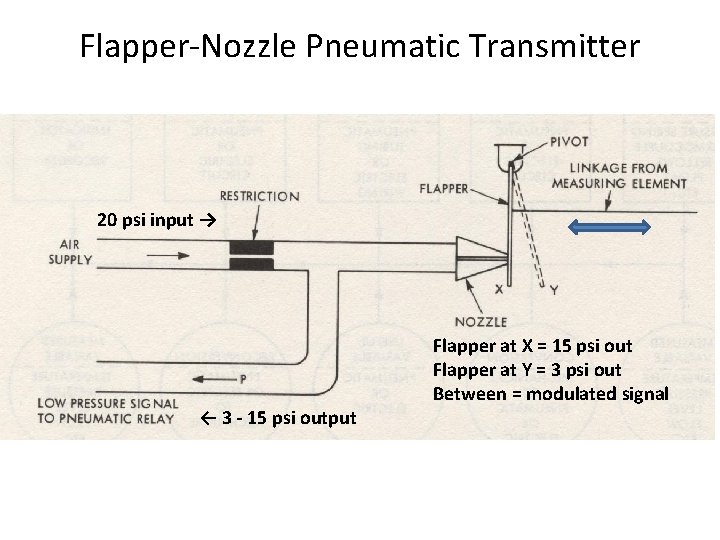
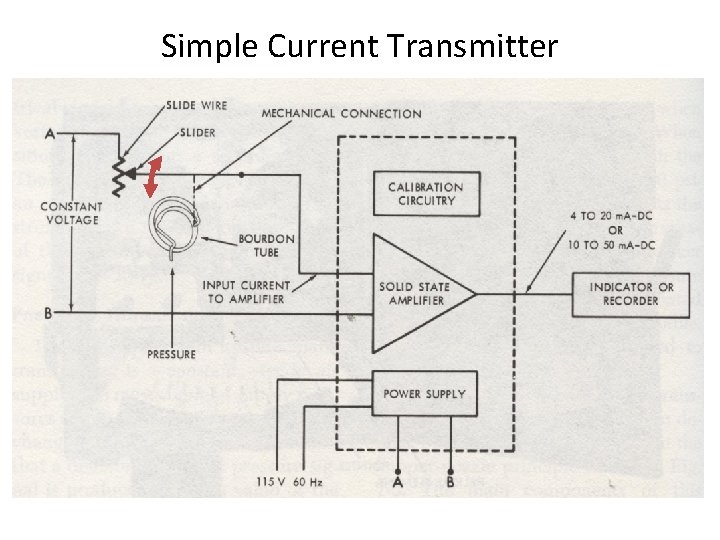
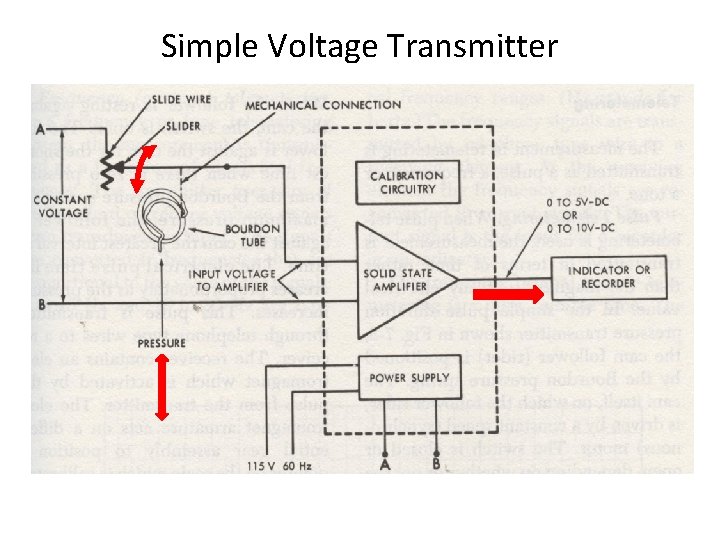
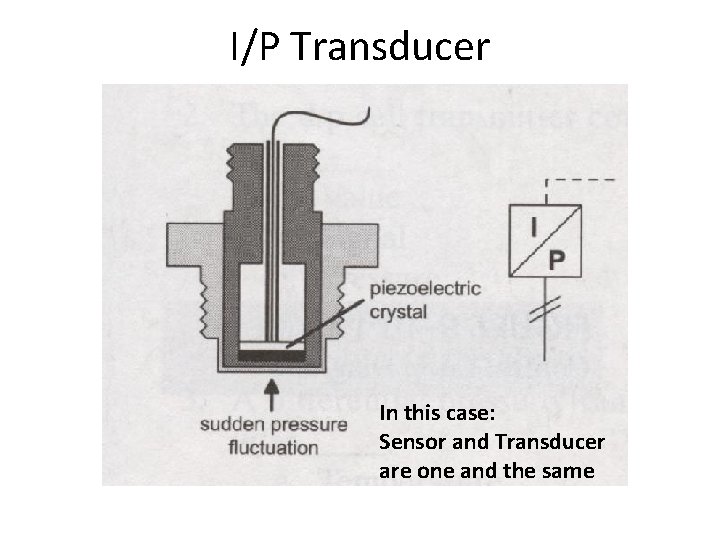
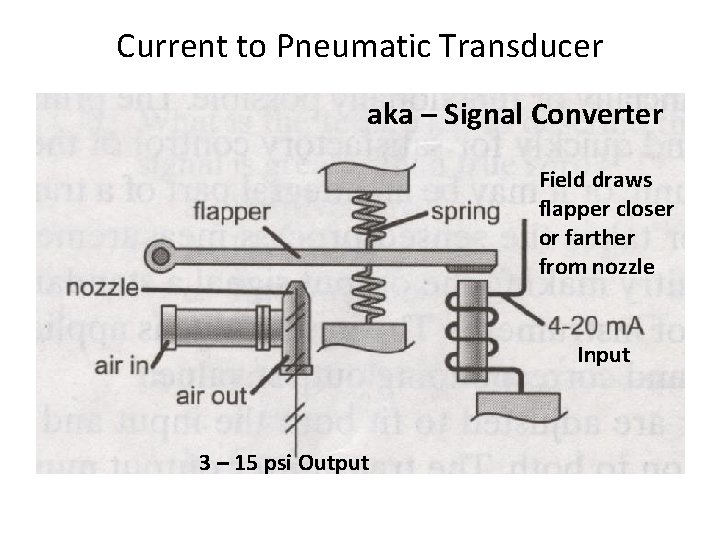
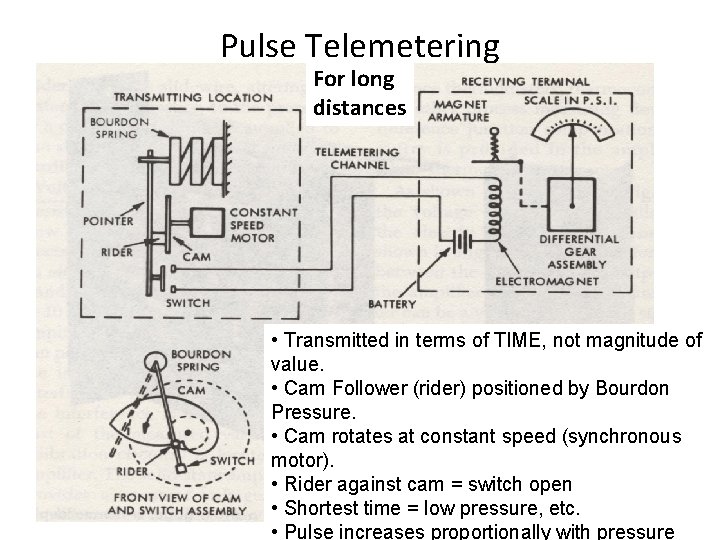
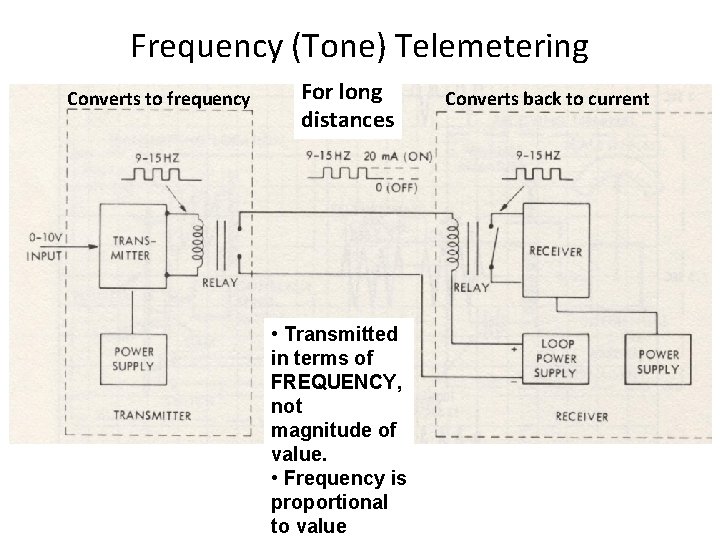
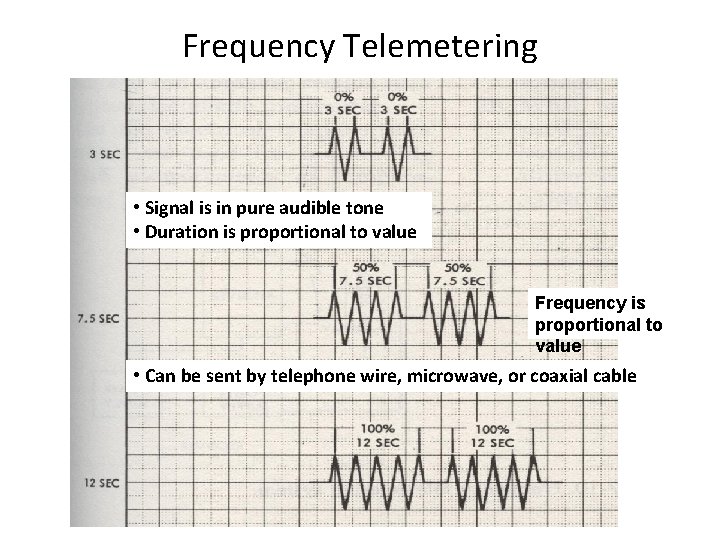
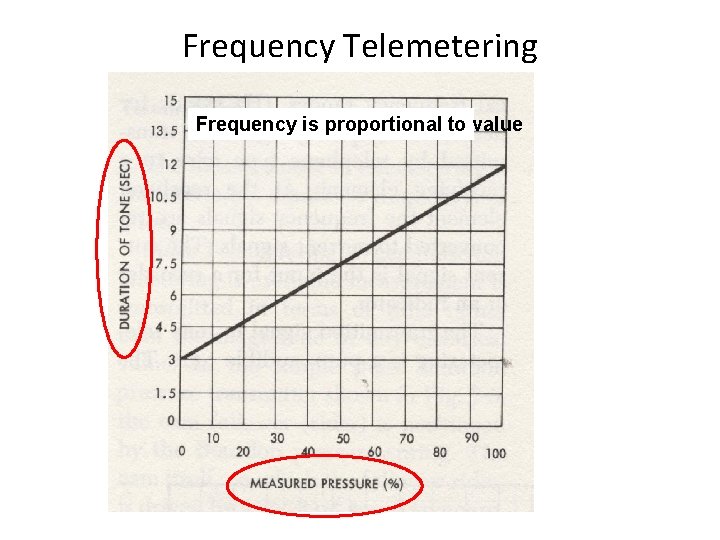
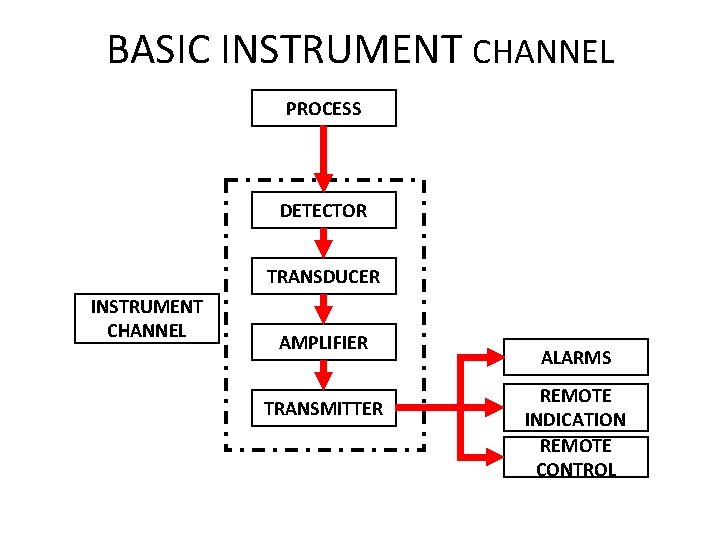
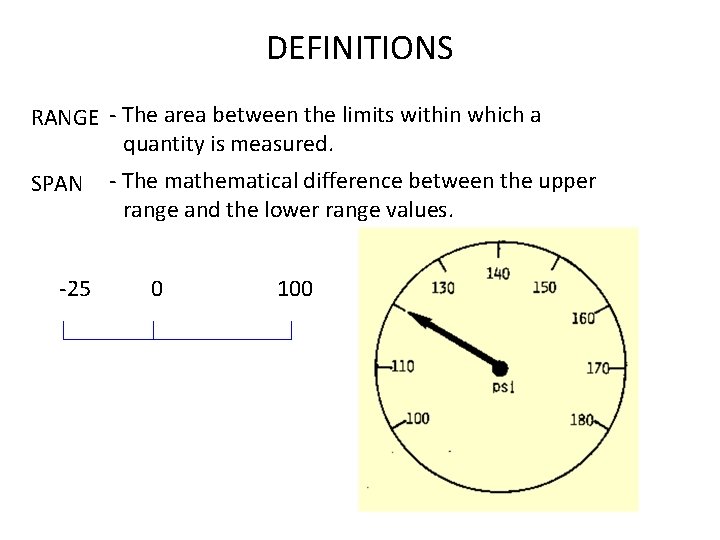
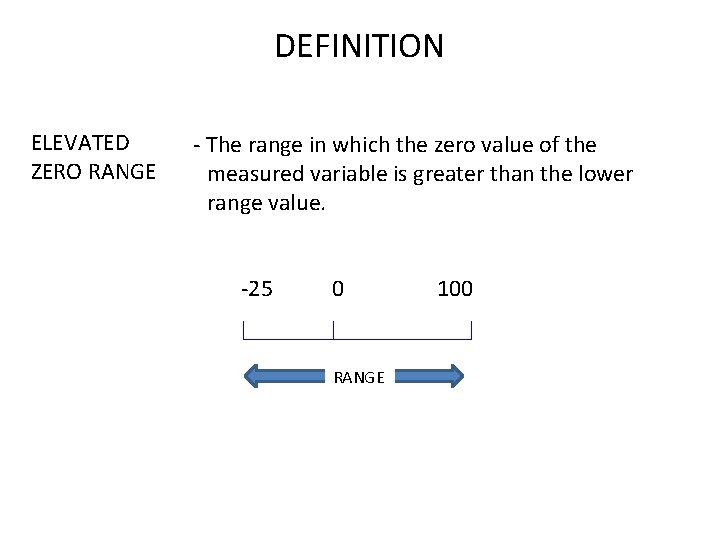

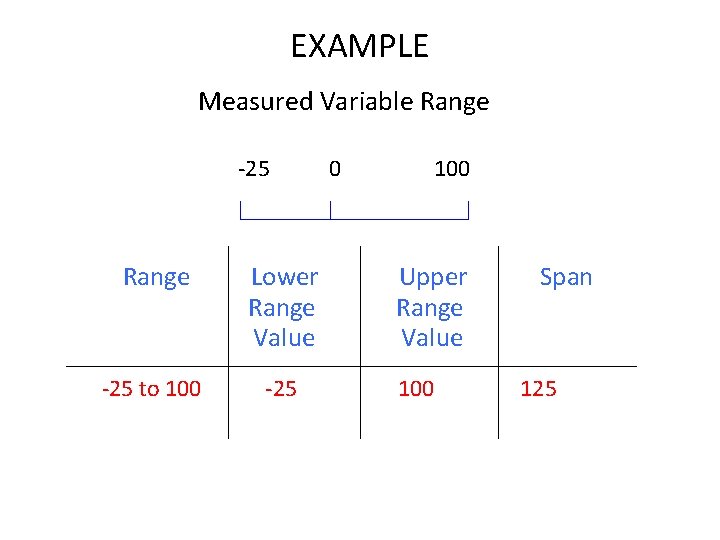
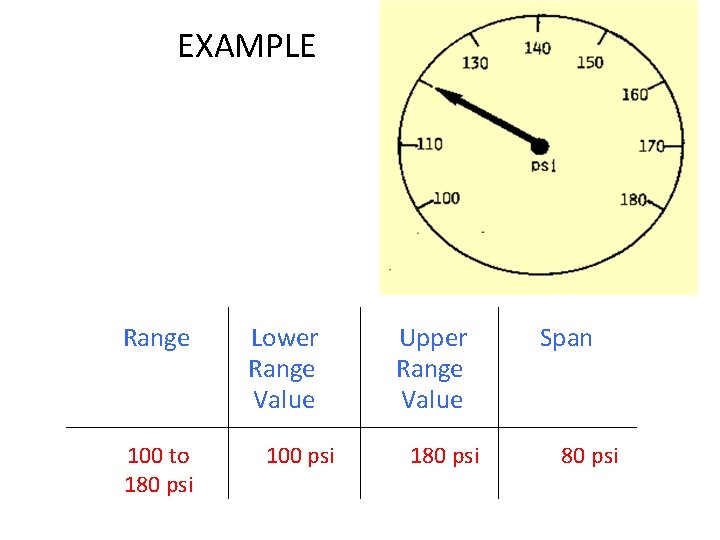
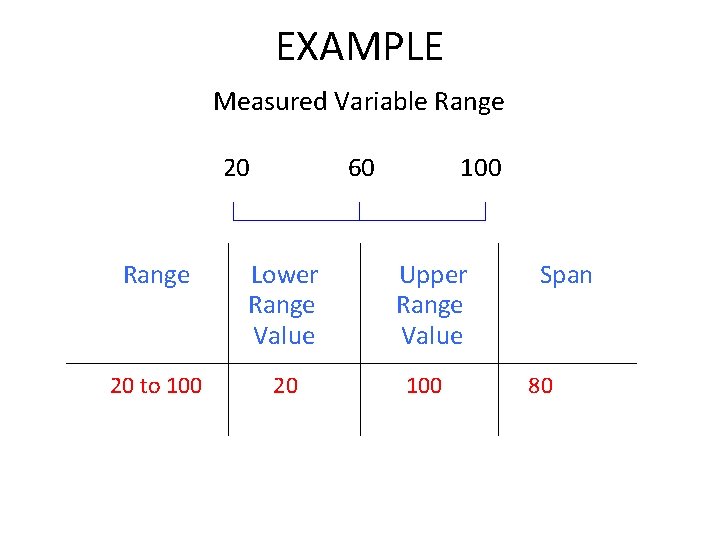
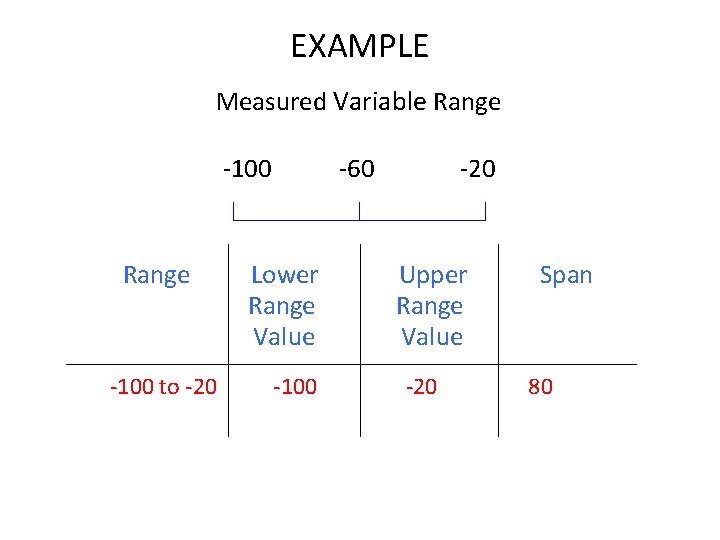
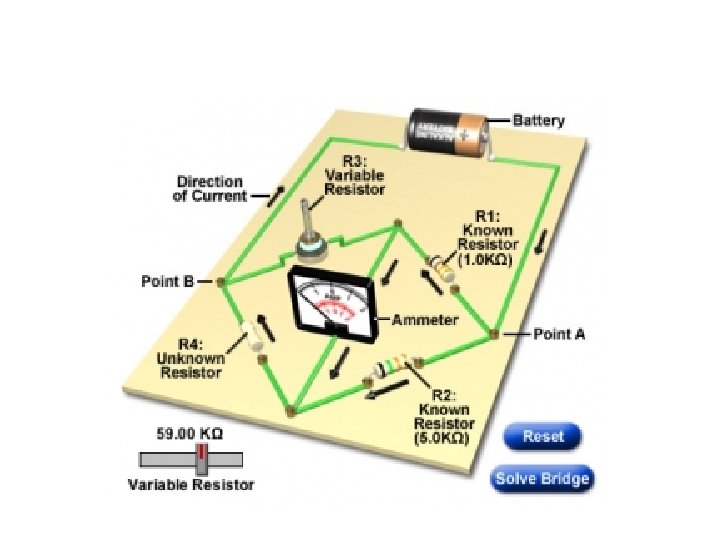
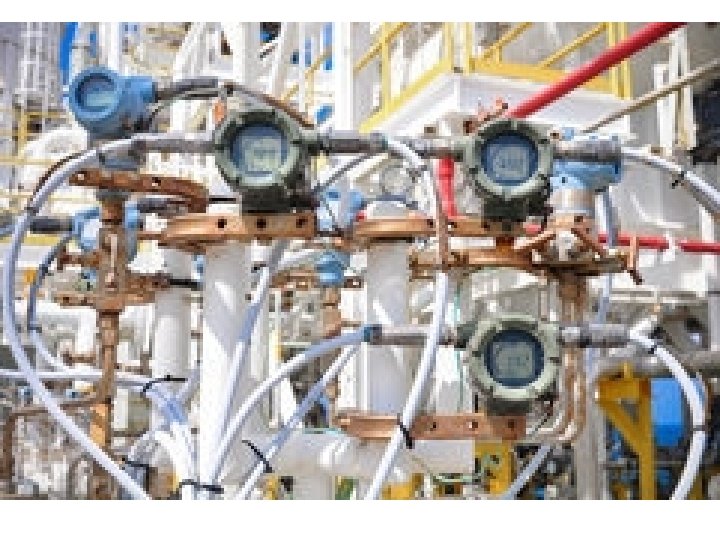
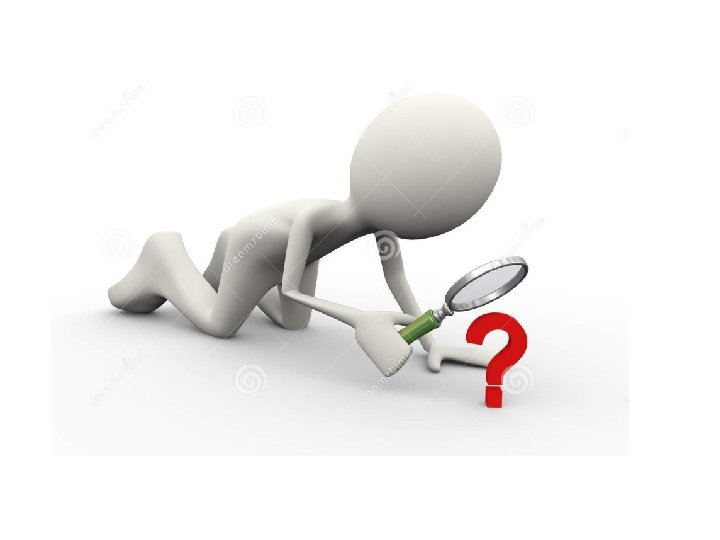
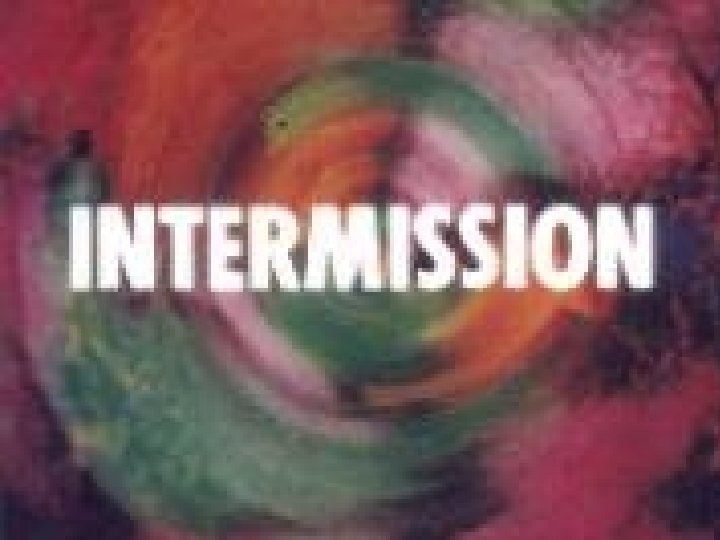
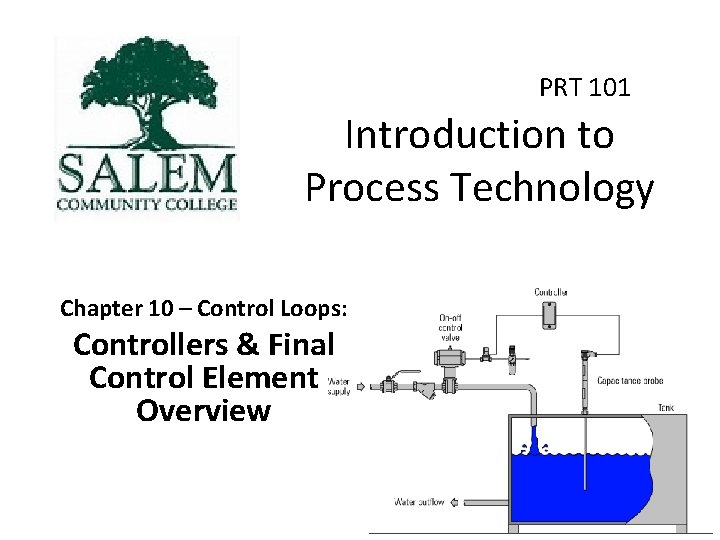
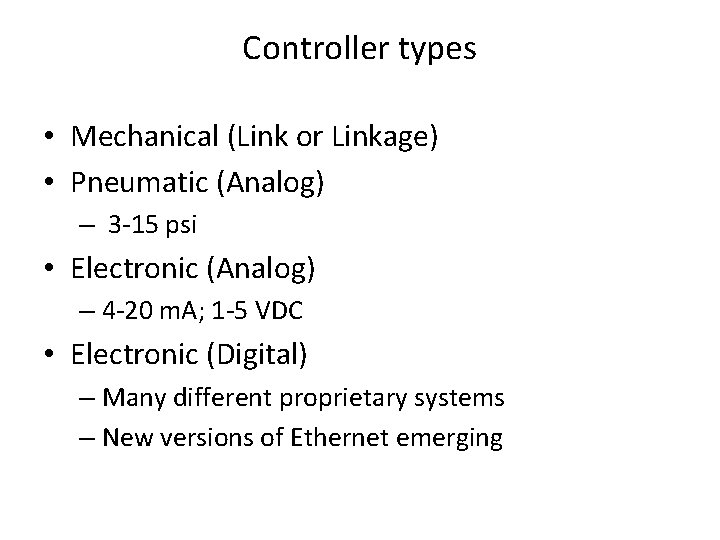
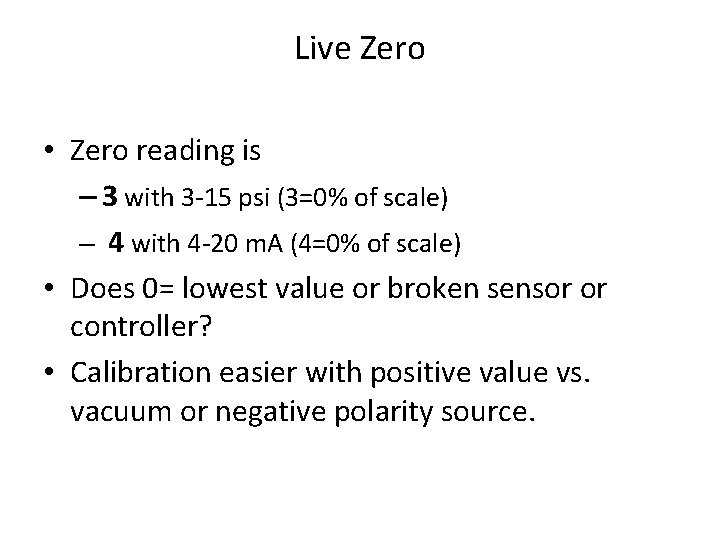
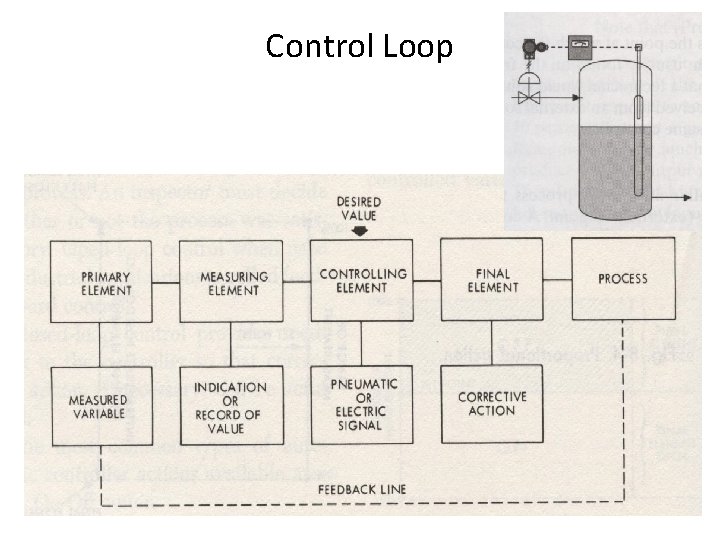
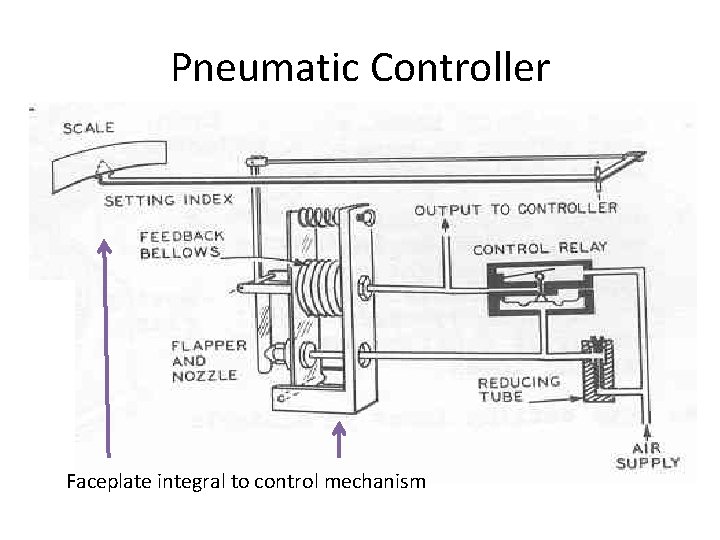
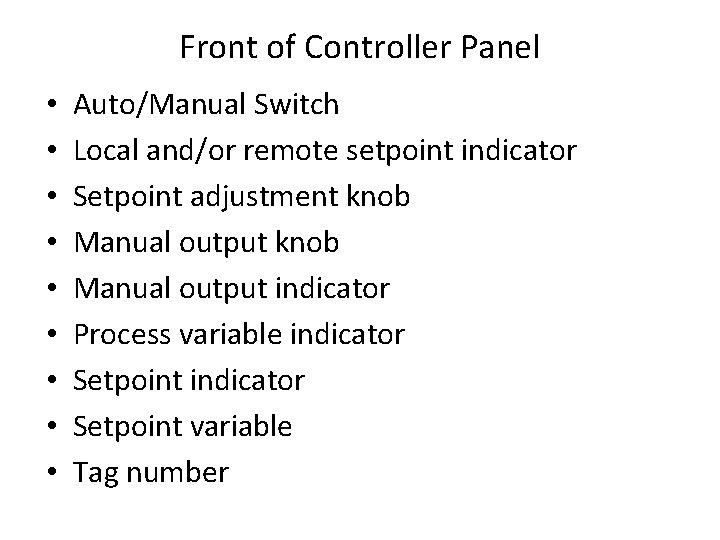
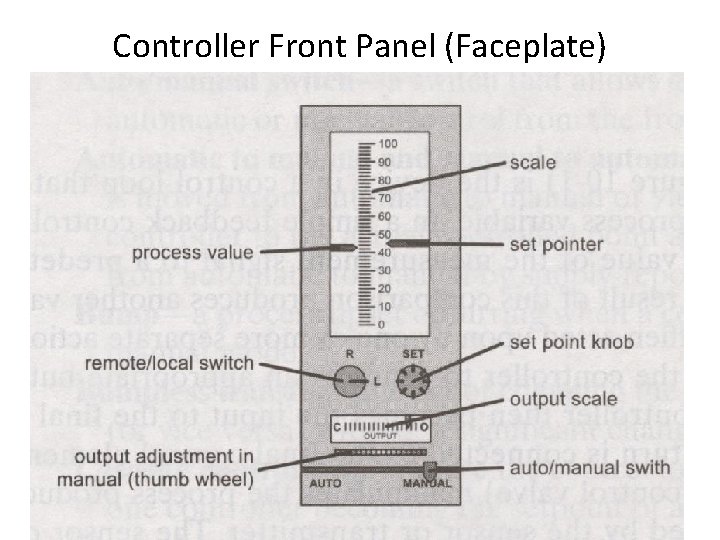
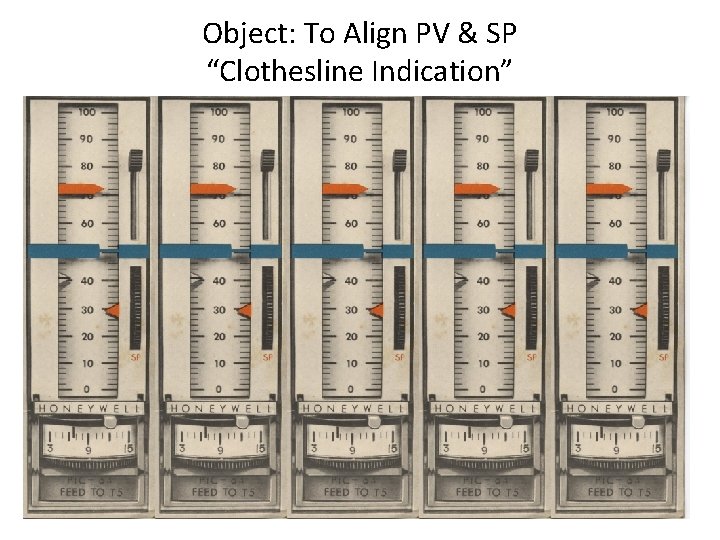
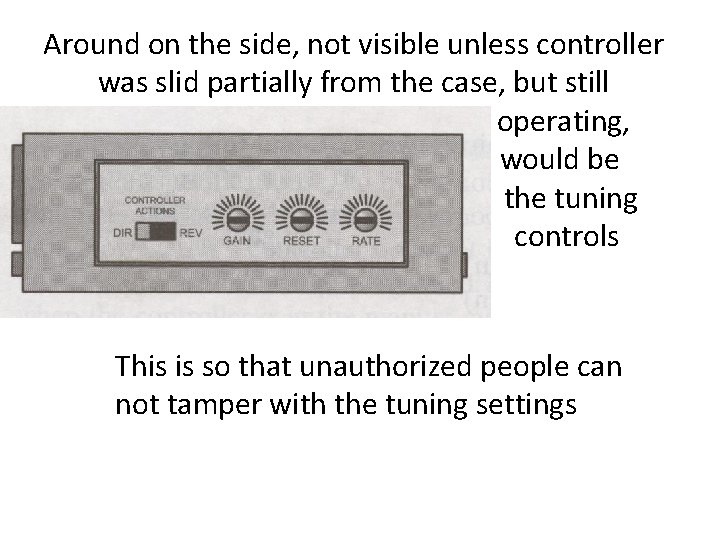
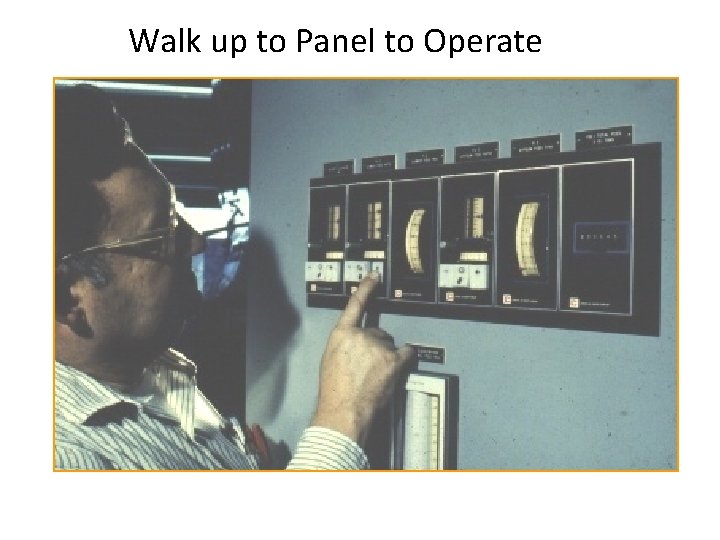
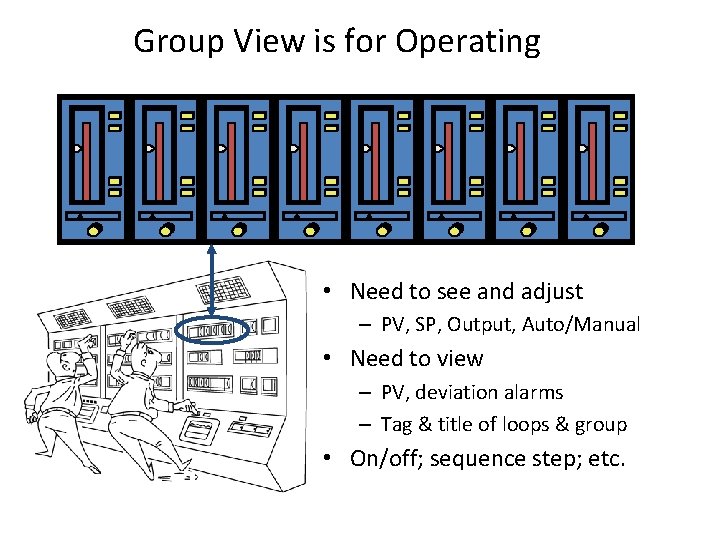


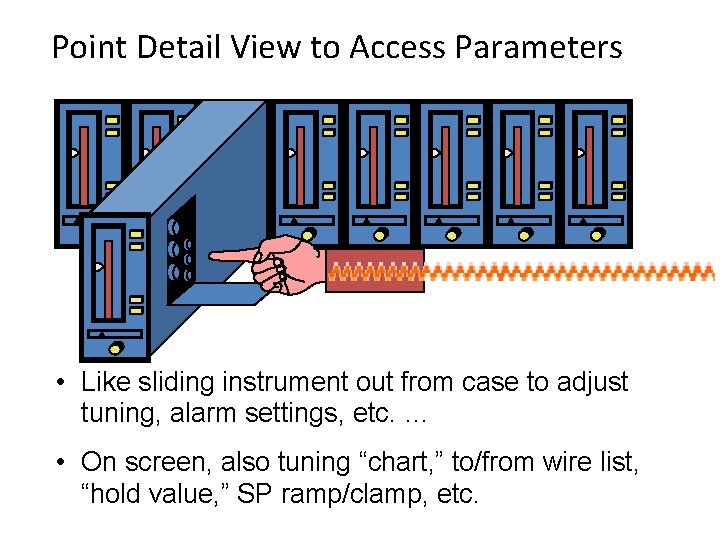
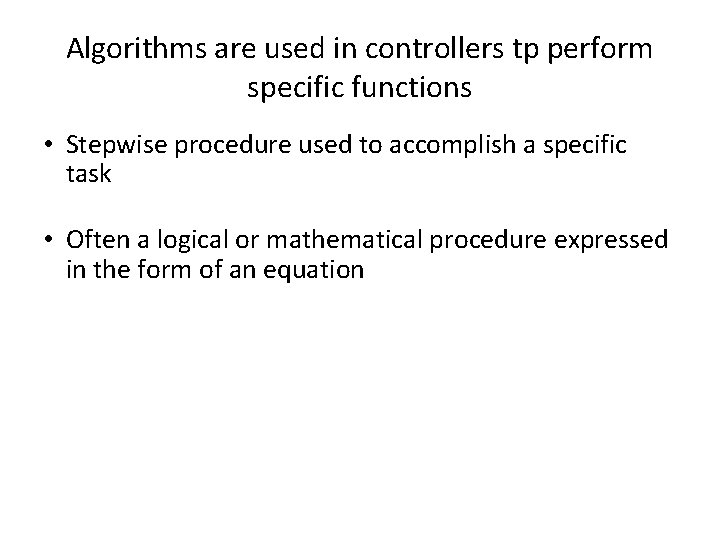
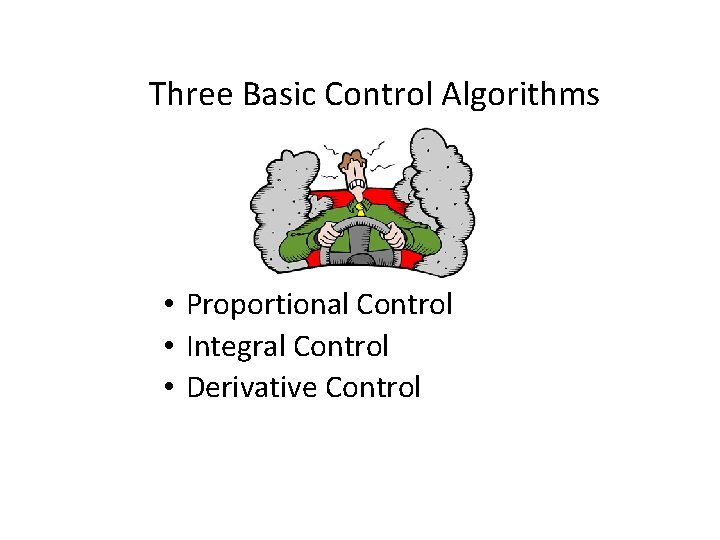
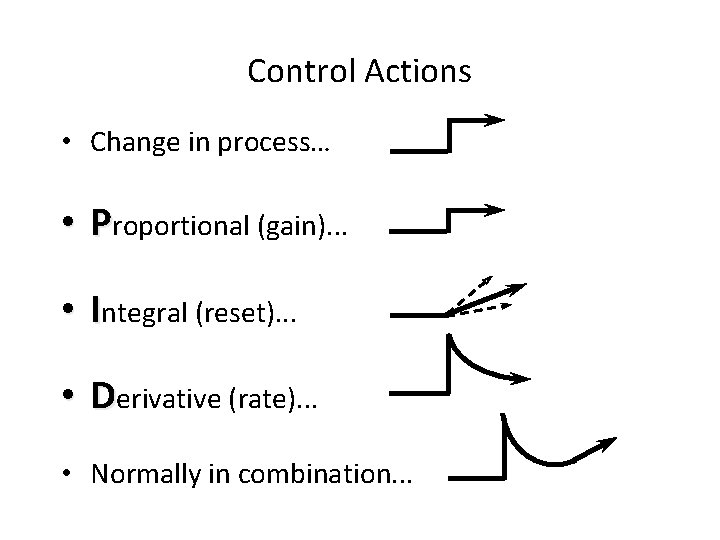
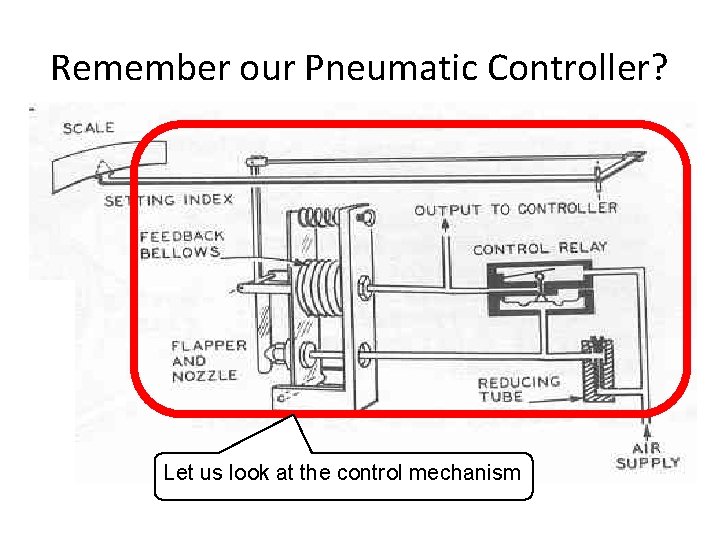
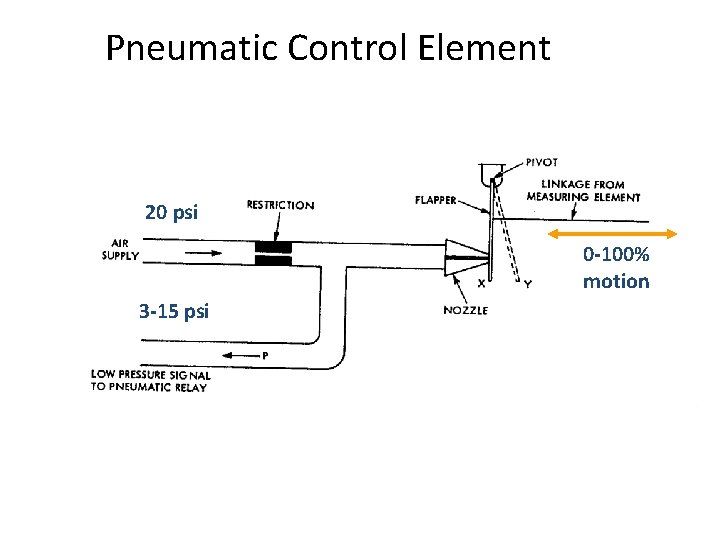
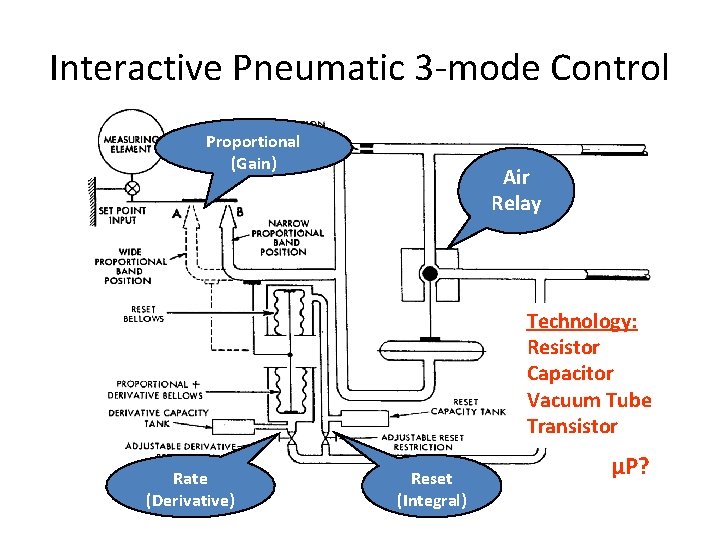
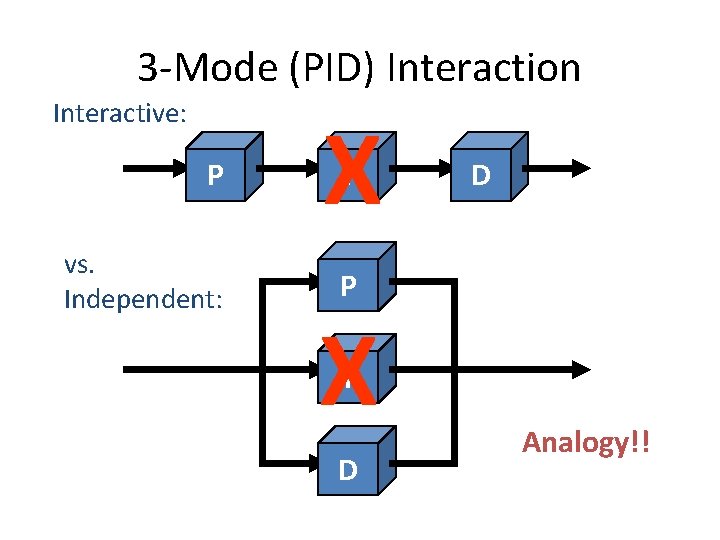
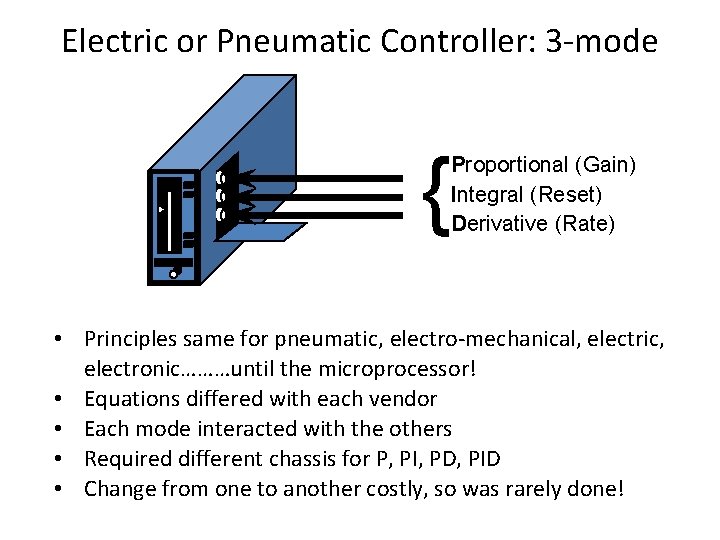
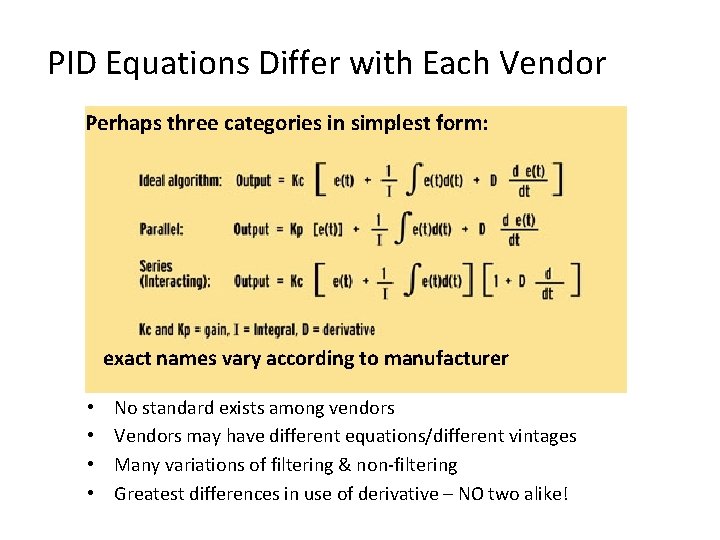
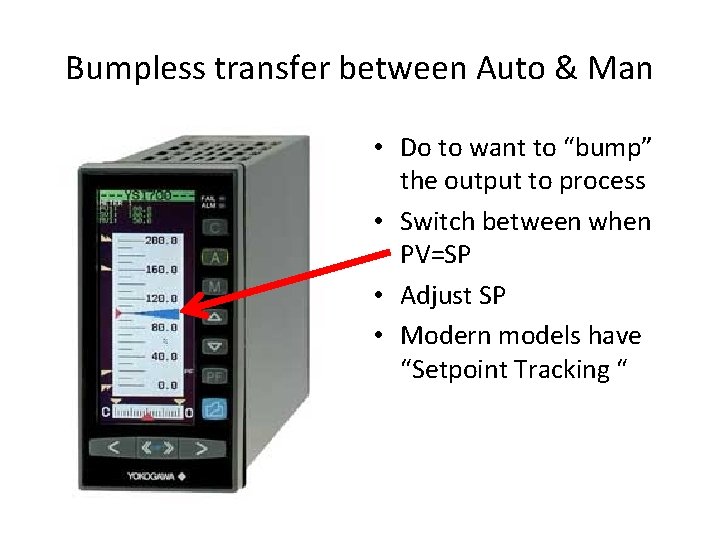
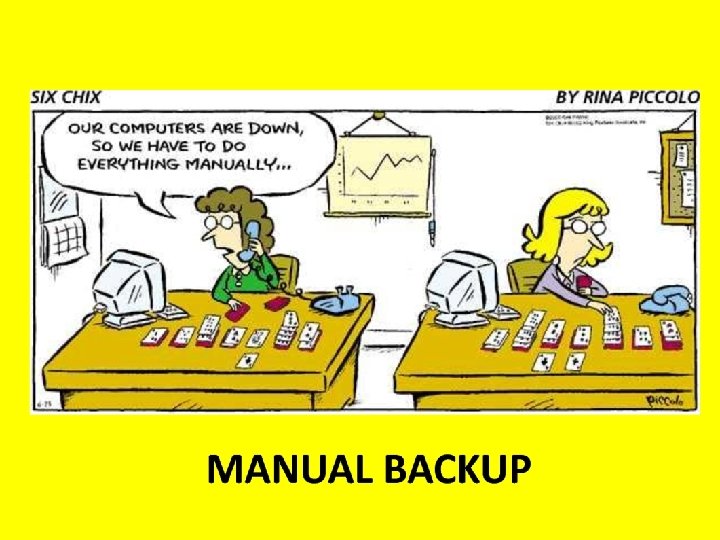
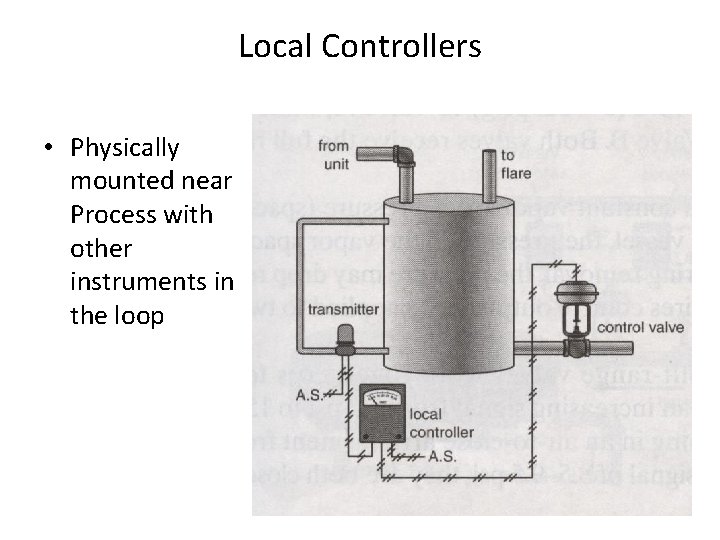
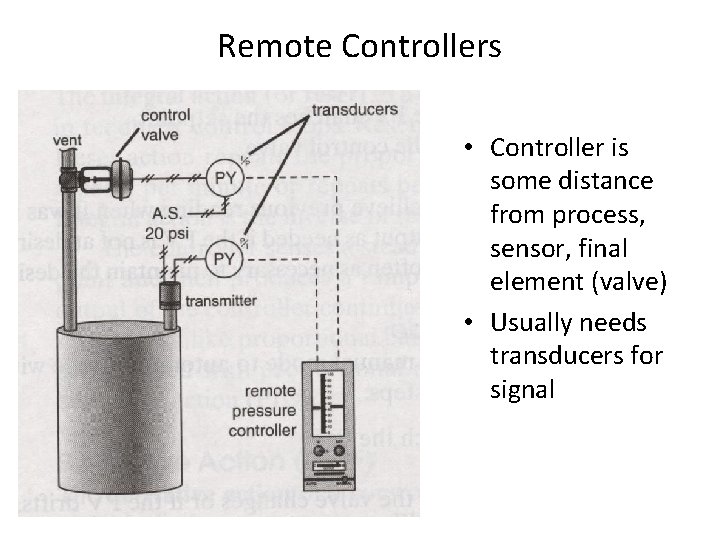
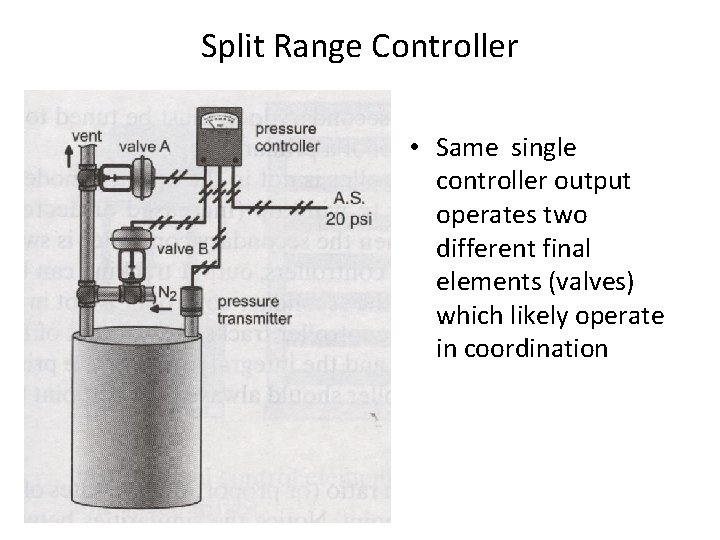
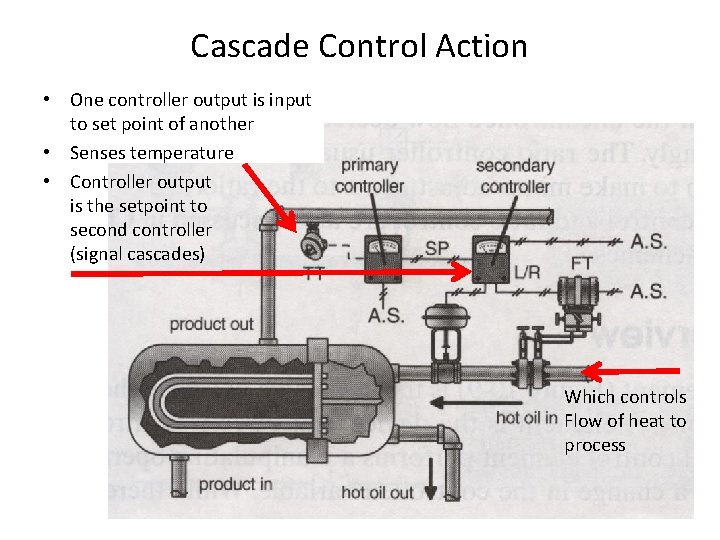
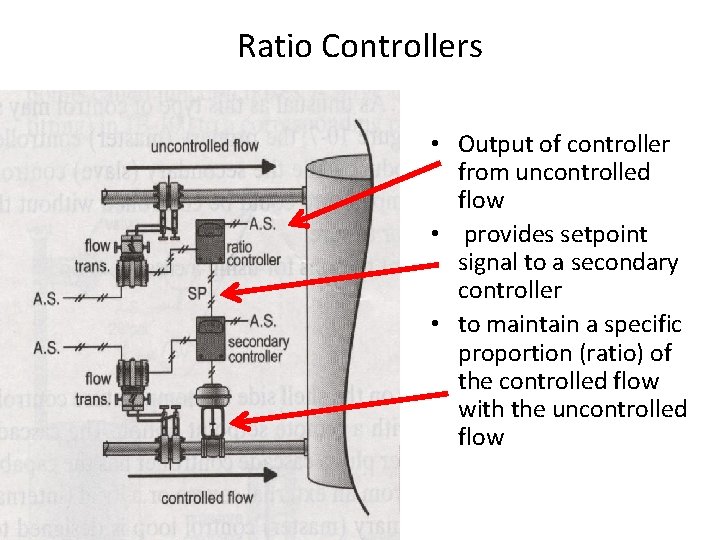
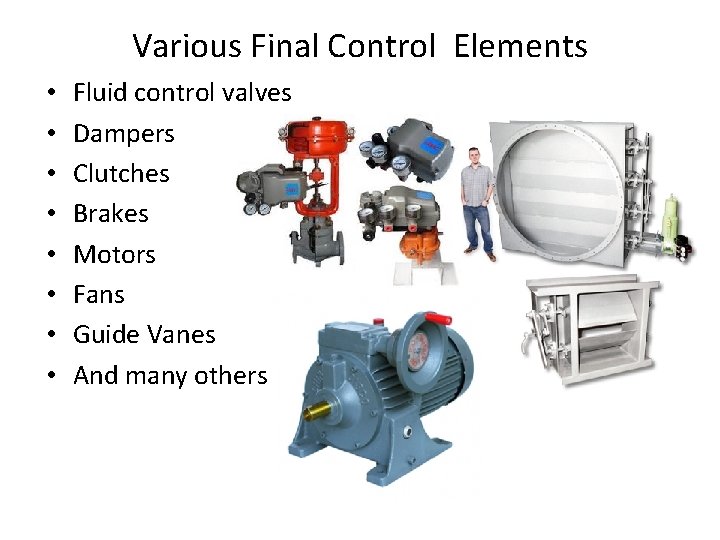
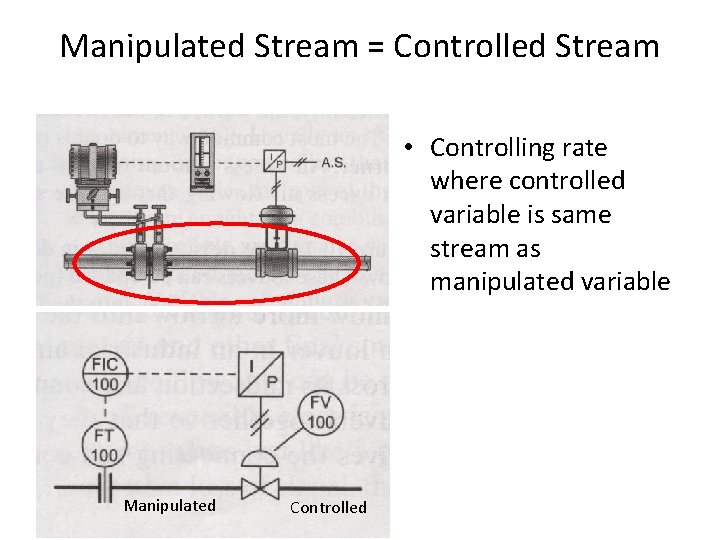
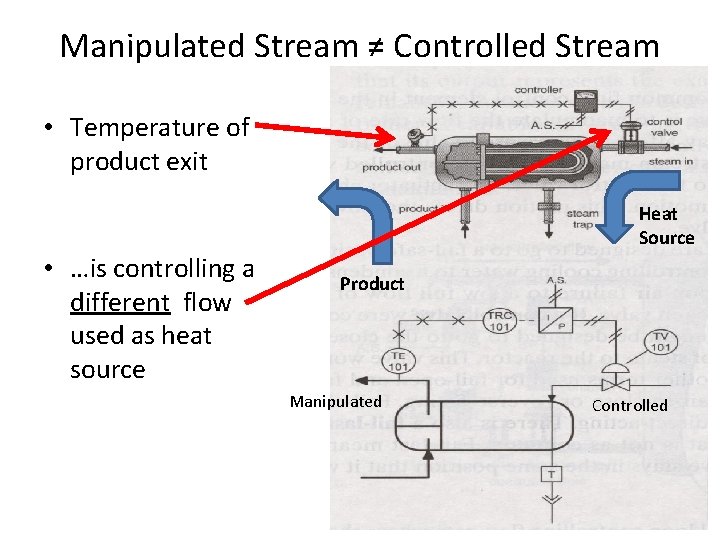
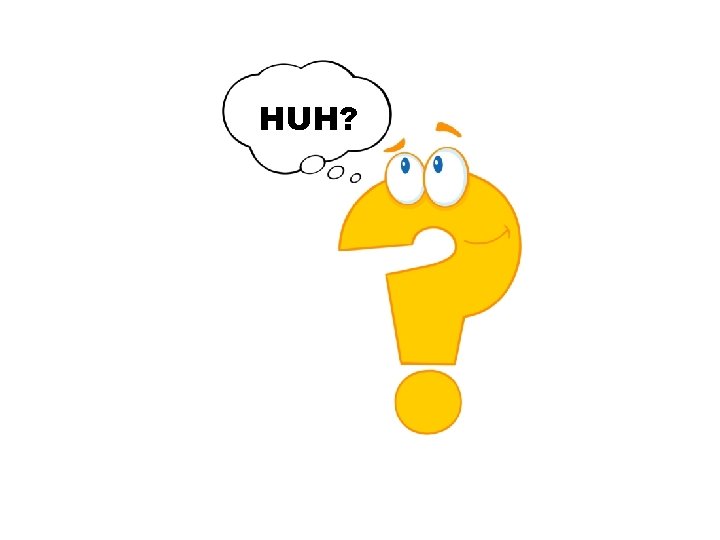
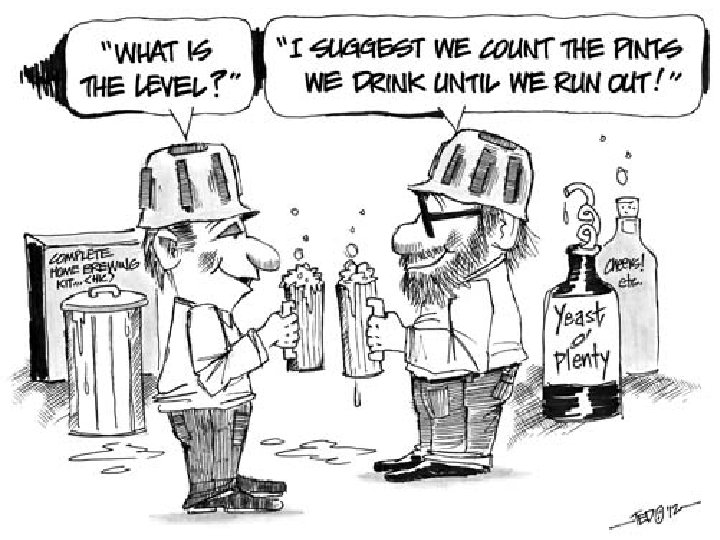
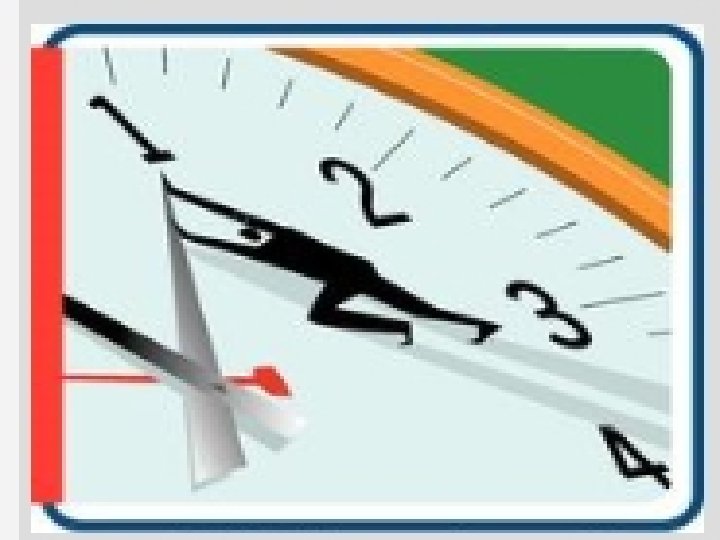
- Slides: 78
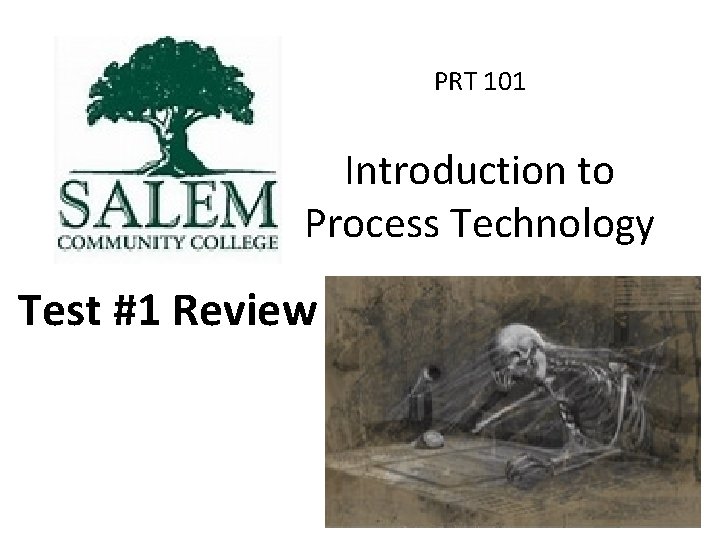
PRT 101 Introduction to Process Technology Test #1 Review
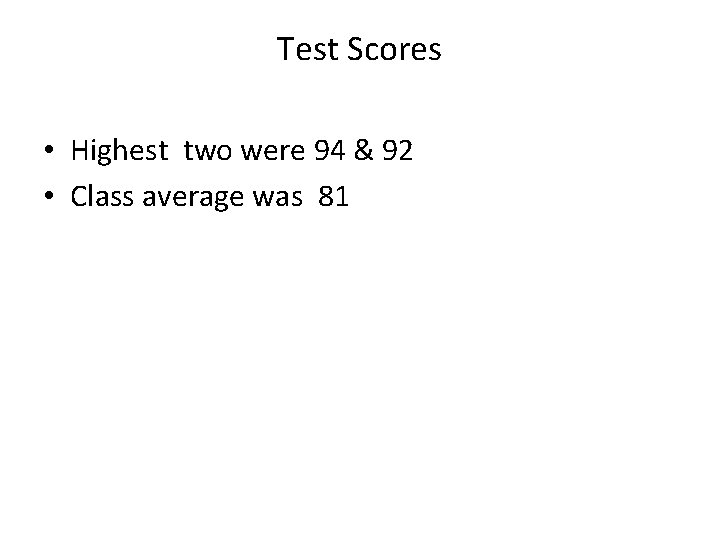
Test Scores • Highest two were 94 & 92 • Class average was 81
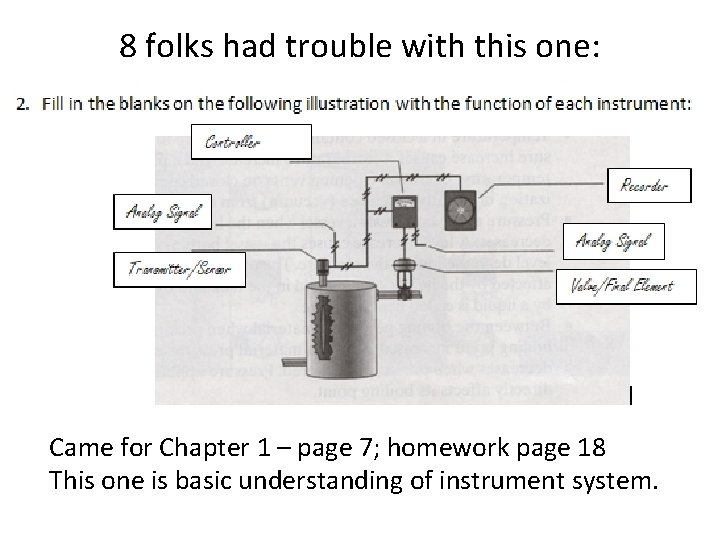
8 folks had trouble with this one: Came for Chapter 1 – page 7; homework page 18 This one is basic understanding of instrument system.
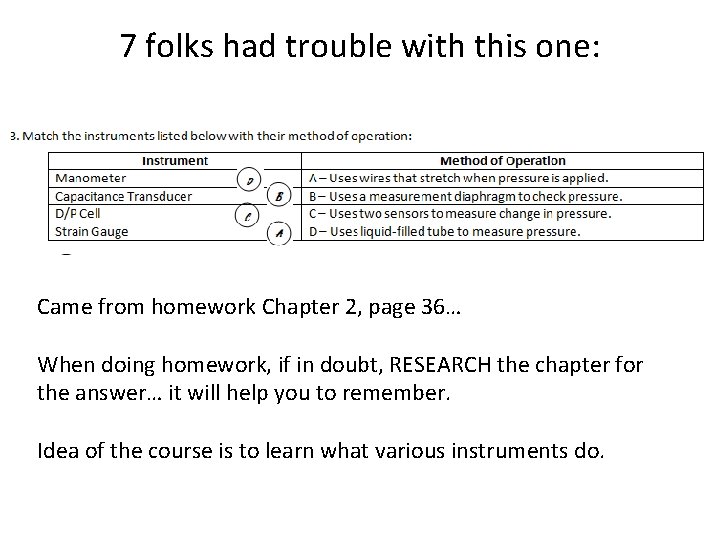
7 folks had trouble with this one: Came from homework Chapter 2, page 36… When doing homework, if in doubt, RESEARCH the chapter for the answer… it will help you to remember. Idea of the course is to learn what various instruments do.

6 folks had trouble with this one: From Chapter 3, page 43… Consider that “ through Matter” is a solid by definitions (see first sentence under “Conduction”)
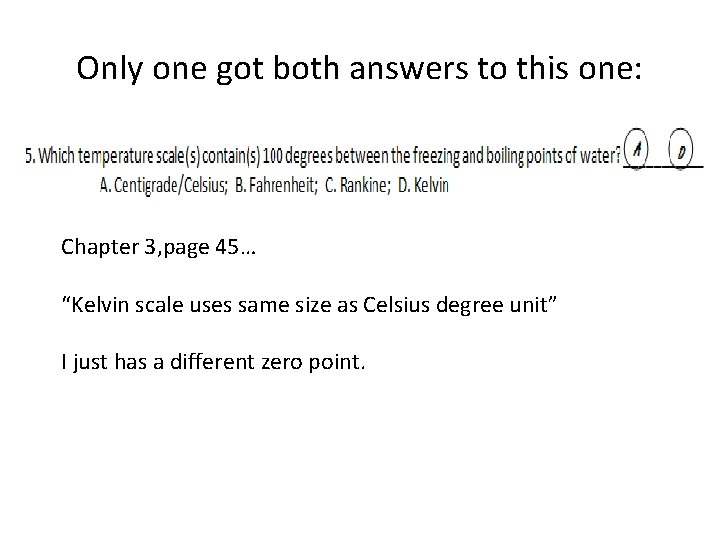
Only one got both answers to this one: Chapter 3, page 45… “Kelvin scale uses same size as Celsius degree unit” I just has a different zero point.
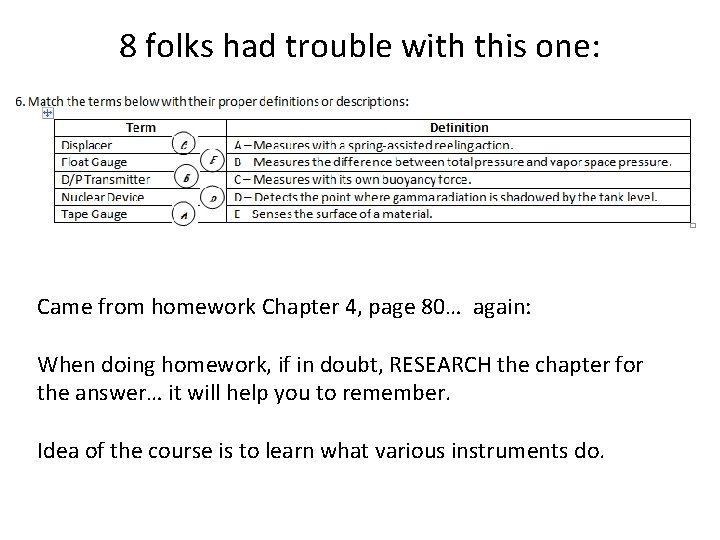
8 folks had trouble with this one: Came from homework Chapter 4, page 80… again: When doing homework, if in doubt, RESEARCH the chapter for the answer… it will help you to remember. Idea of the course is to learn what various instruments do.
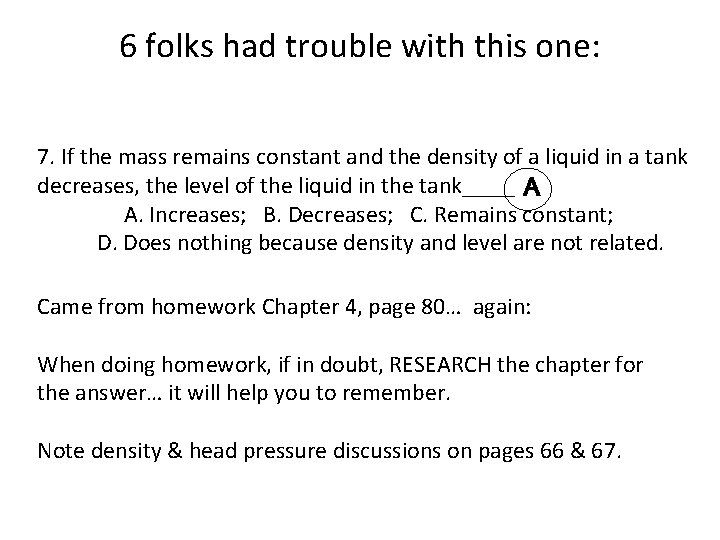
6 folks had trouble with this one: 7. If the mass remains constant and the density of a liquid in a tank decreases, the level of the liquid in the tank_______ A A. Increases; B. Decreases; C. Remains constant; D. Does nothing because density and level are not related. Came from homework Chapter 4, page 80… again: When doing homework, if in doubt, RESEARCH the chapter for the answer… it will help you to remember. Note density & head pressure discussions on pages 66 & 67.
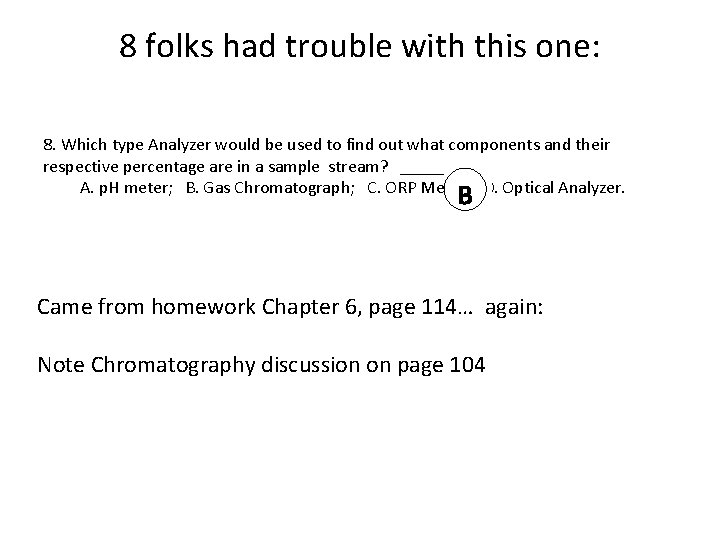
8 folks had trouble with this one: 8. Which type Analyzer would be used to find out what components and their respective percentage are in a sample stream? _______ A. p. H meter; B. Gas Chromatograph; C. ORP Meter; D. Optical Analyzer. B Came from homework Chapter 6, page 114… again: Note Chromatography discussion on page 104
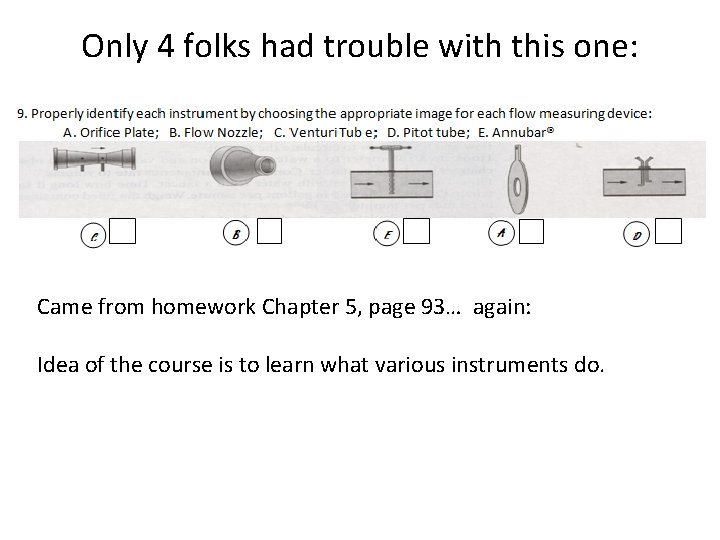
Only 4 folks had trouble with this one: Came from homework Chapter 5, page 93… again: Idea of the course is to learn what various instruments do.
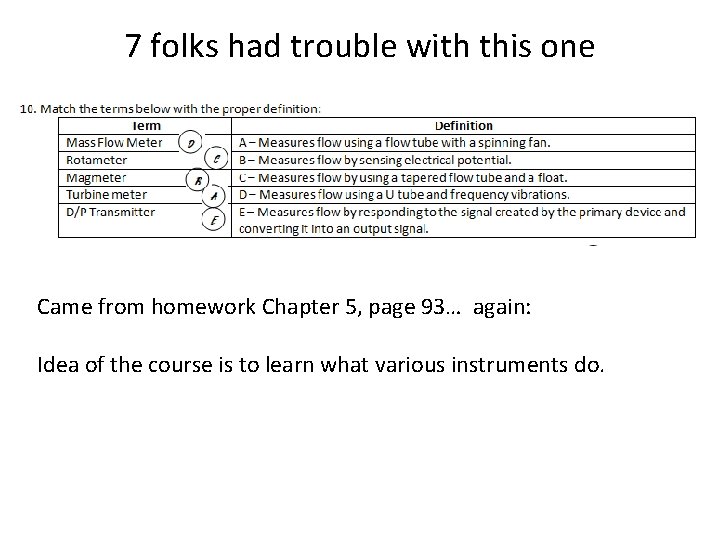
7 folks had trouble with this one Came from homework Chapter 5, page 93… again: Idea of the course is to learn what various instruments do.
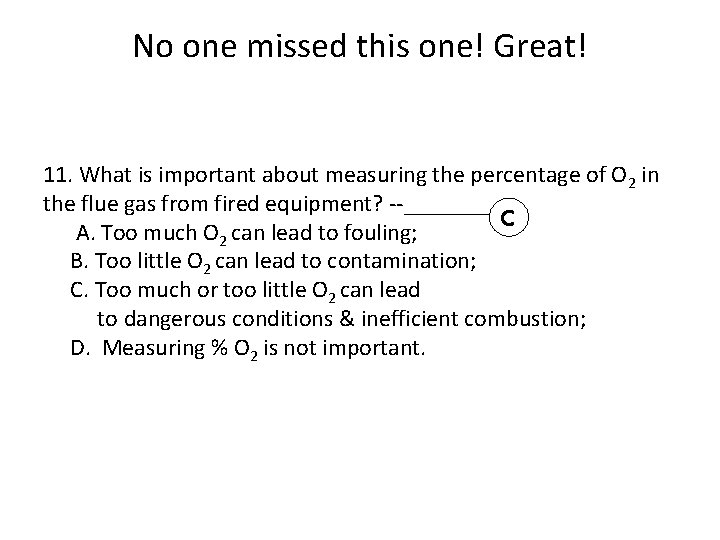
No one missed this one! Great! 11. What is important about measuring the percentage of O 2 in the flue gas from fired equipment? ____ C A. Too much O 2 can lead to fouling; B. Too little O 2 can lead to contamination; C. Too much or too little O 2 can lead to dangerous conditions & inefficient combustion; D. Measuring % O 2 is not important.
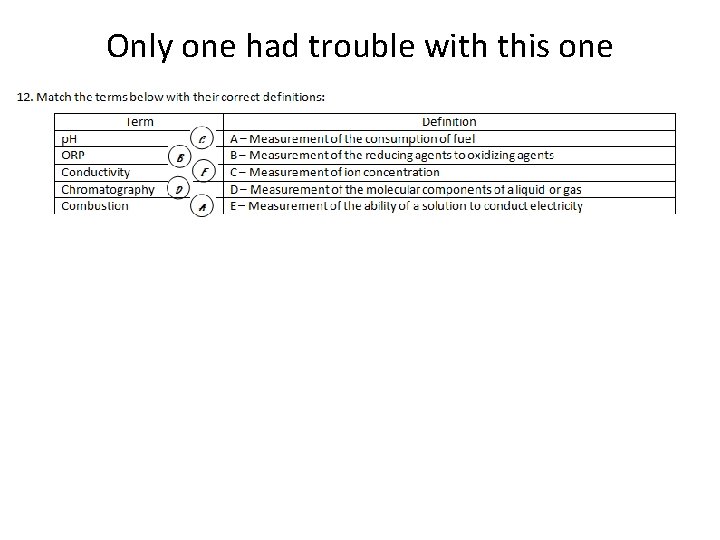
Only one had trouble with this one
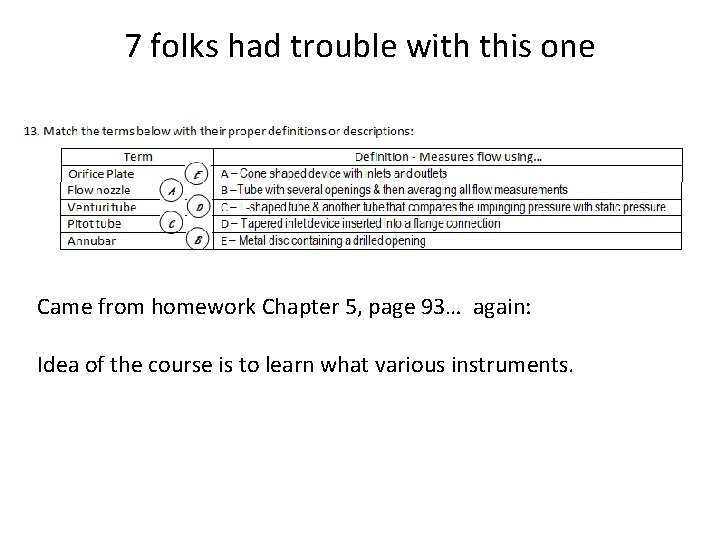
7 folks had trouble with this one Came from homework Chapter 5, page 93… again: Idea of the course is to learn what various instruments.
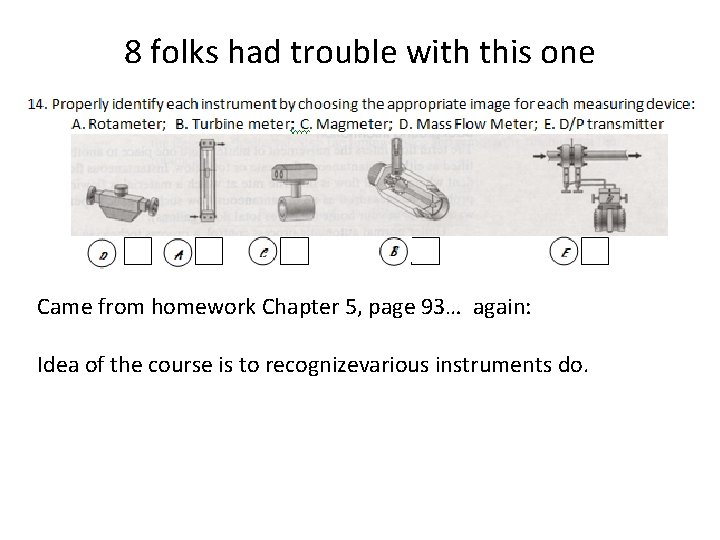
8 folks had trouble with this one Came from homework Chapter 5, page 93… again: Idea of the course is to recognizevarious instruments do.

All but one got this! 15. True or False: Process technicians are often responsible for monitoring process analyzers and sampling systems.
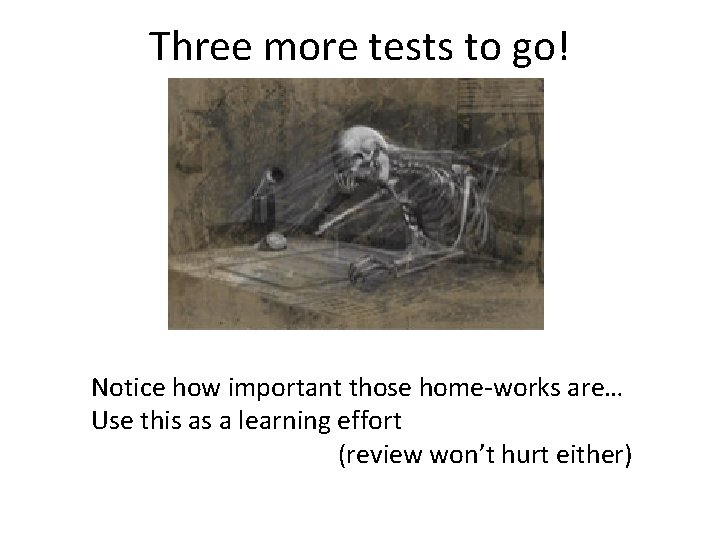
Three more tests to go! Notice how important those home works are… Use this as a learning effort (review won’t hurt either)
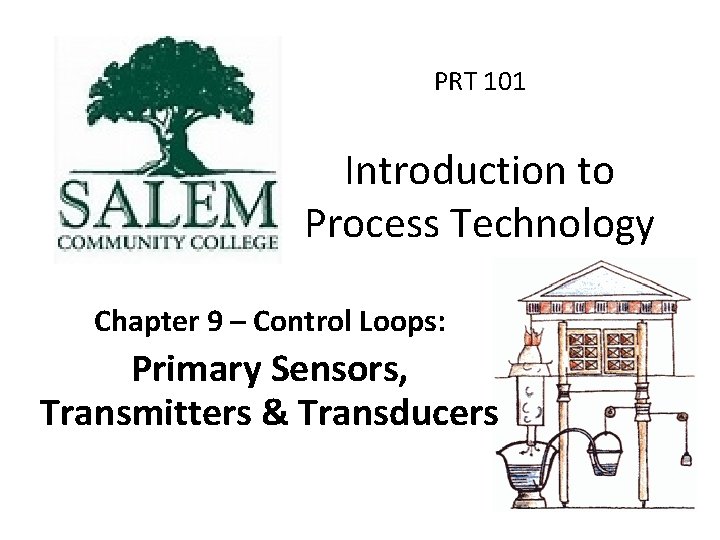
PRT 101 Introduction to Process Technology Chapter 9 – Control Loops: Primary Sensors, Transmitters & Transducers
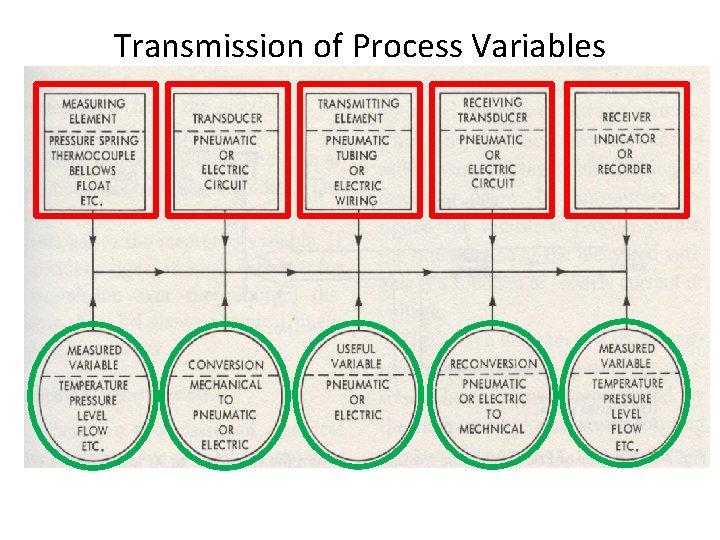
Transmission of Process Variables
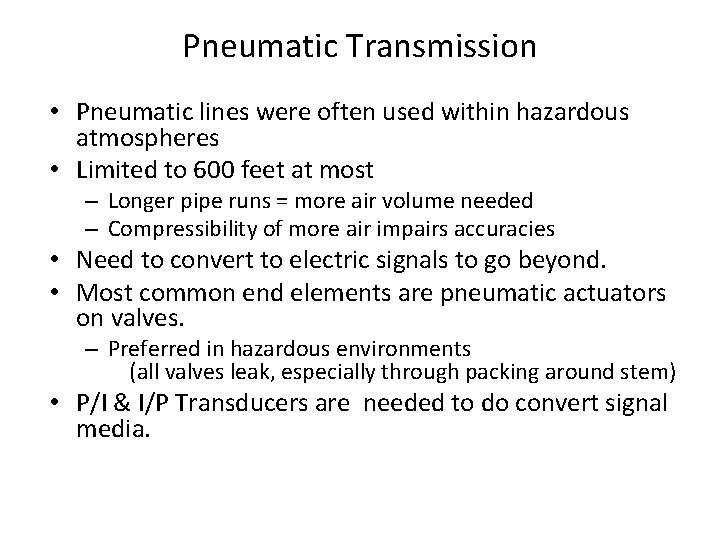
Pneumatic Transmission • Pneumatic lines were often used within hazardous atmospheres • Limited to 600 feet at most – Longer pipe runs = more air volume needed – Compressibility of more air impairs accuracies • Need to convert to electric signals to go beyond. • Most common end elements are pneumatic actuators on valves. – Preferred in hazardous environments (all valves leak, especially through packing around stem) • P/I & I/P Transducers are needed to do convert signal media.
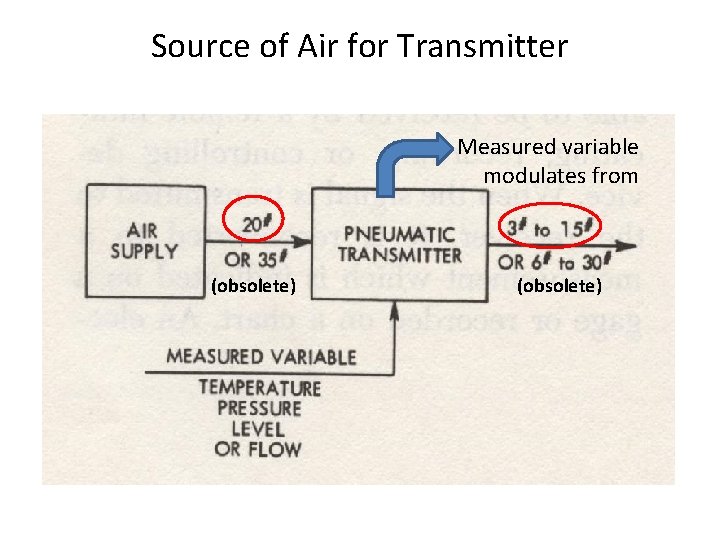
Source of Air for Transmitter Measured variable modulates from (obsolete)
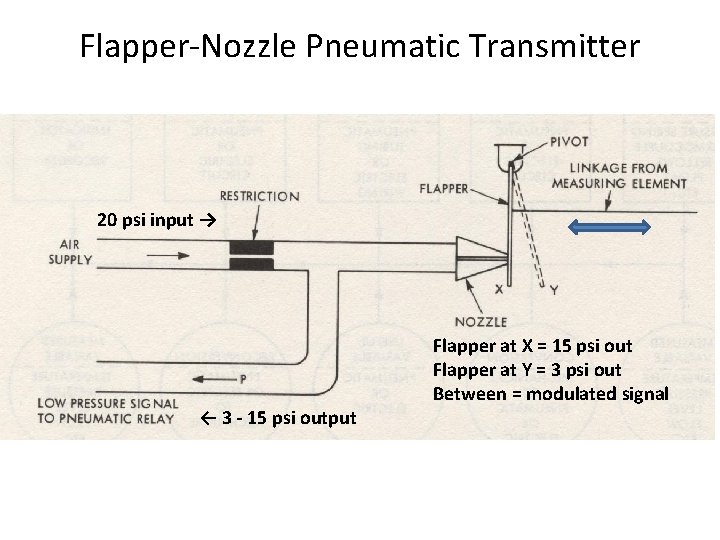
Flapper Nozzle Pneumatic Transmitter 20 psi input → ← 3 - 15 psi output Flapper at X = 15 psi out Flapper at Y = 3 psi out Between = modulated signal
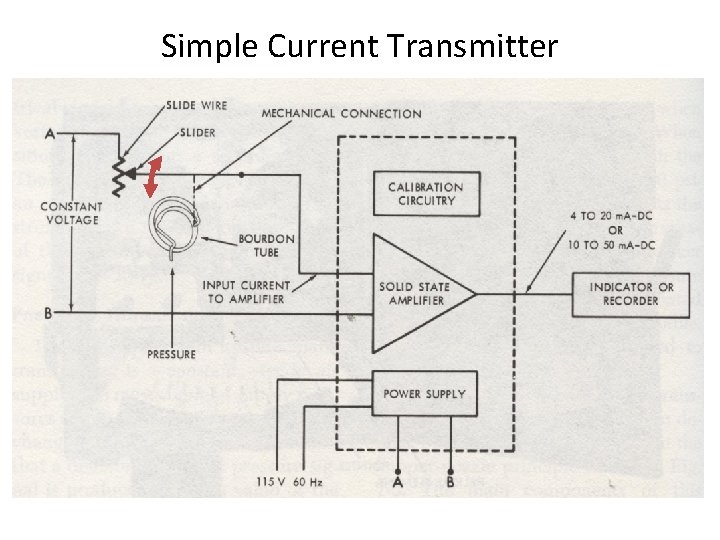
Simple Current Transmitter
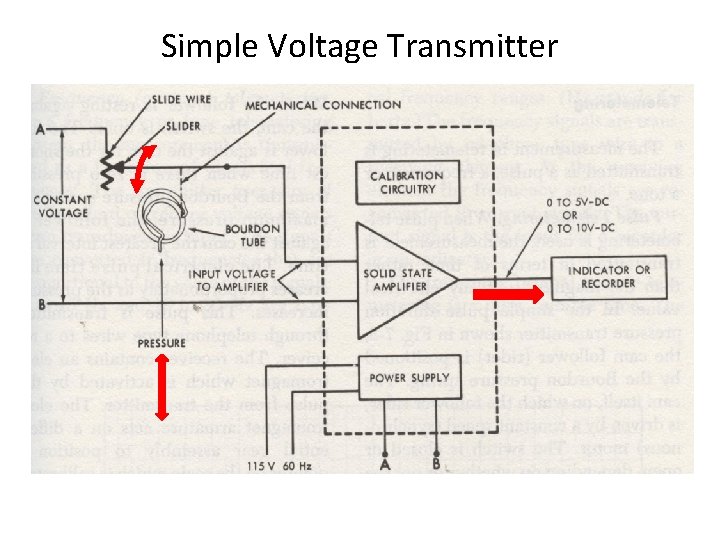
Simple Voltage Transmitter
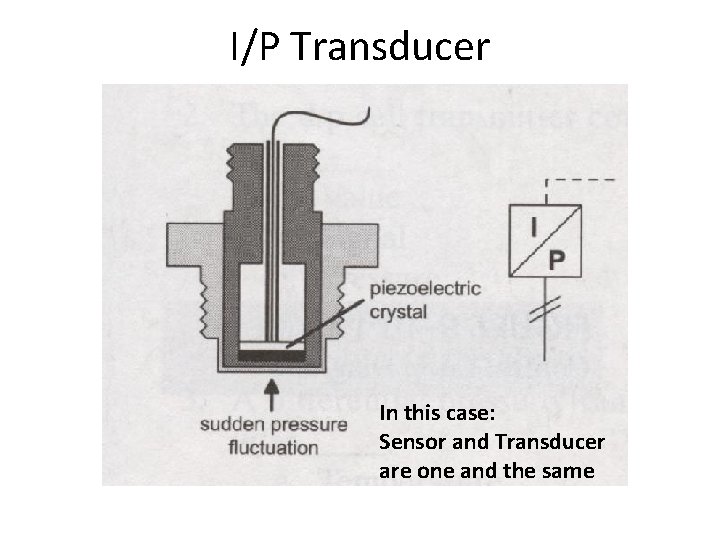
I/P Transducer In this case: Sensor and Transducer are one and the same
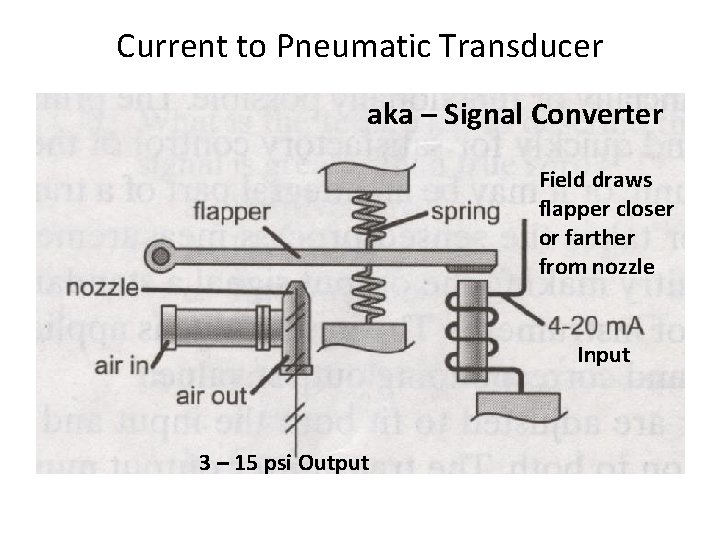
Current to Pneumatic Transducer aka – Signal Converter Field draws flapper closer or farther from nozzle Input 3 – 15 psi Output
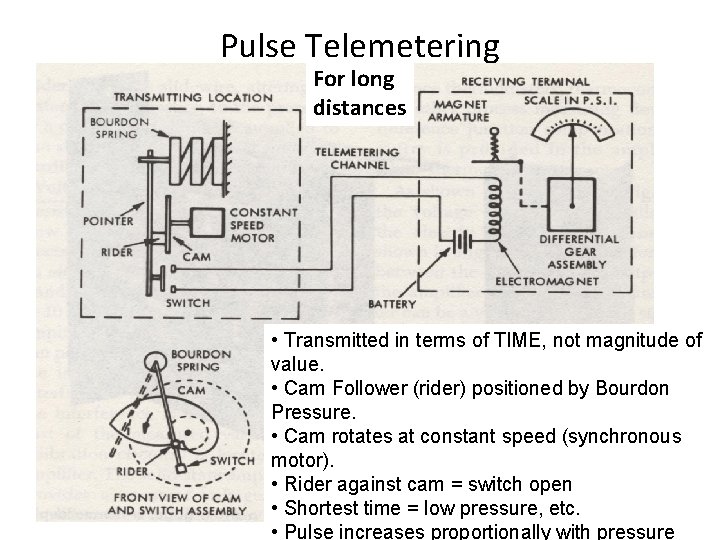
Pulse Telemetering For long distances • Transmitted in terms of TIME, not magnitude of value. • Cam Follower (rider) positioned by Bourdon Pressure. • Cam rotates at constant speed (synchronous motor). • Rider against cam = switch open • Shortest time = low pressure, etc. • Pulse increases proportionally with pressure
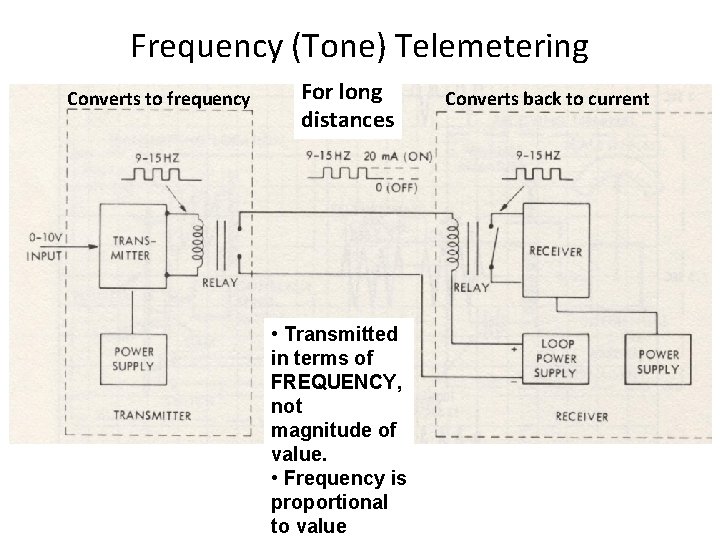
Frequency (Tone) Telemetering Converts to frequency For long distances • Transmitted in terms of FREQUENCY, not magnitude of value. • Frequency is proportional to value Converts back to current
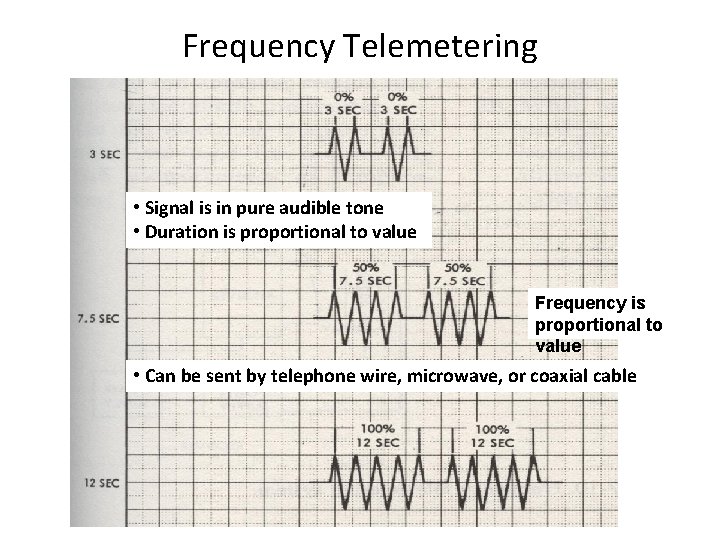
Frequency Telemetering • Signal is in pure audible tone • Duration is proportional to value Frequency is proportional to value • Can be sent by telephone wire, microwave, or coaxial cable
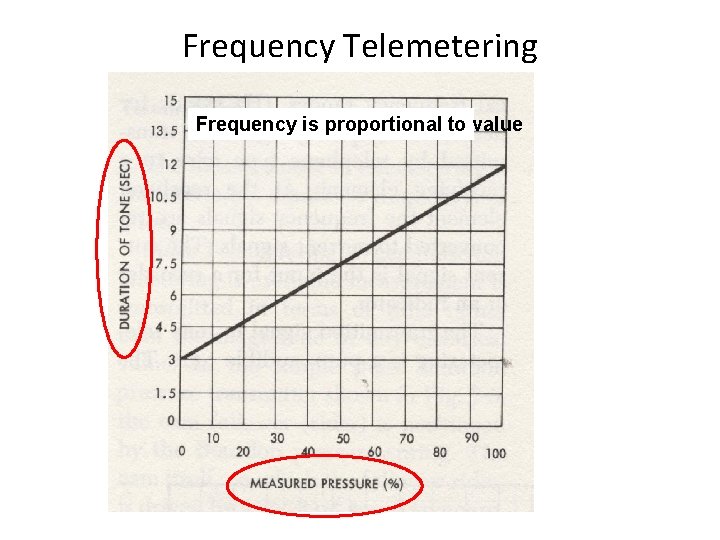
Frequency Telemetering Frequency is proportional to value
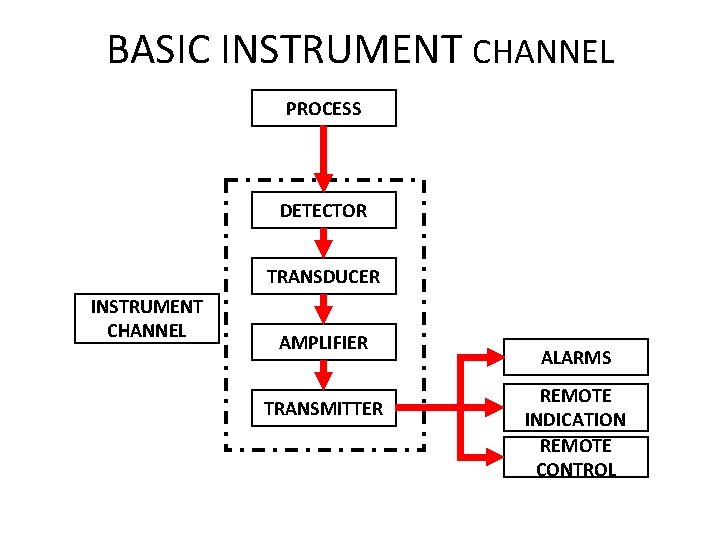
BASIC INSTRUMENT CHANNEL PROCESS DETECTOR TRANSDUCER INSTRUMENT CHANNEL AMPLIFIER TRANSMITTER ALARMS REMOTE INDICATION REMOTE CONTROL
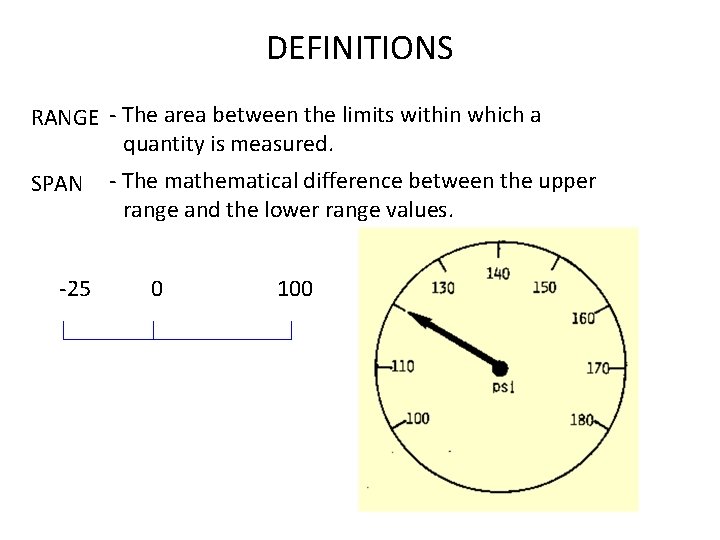
DEFINITIONS RANGE The area between the limits within which a quantity is measured. SPAN 25 The mathematical difference between the upper range and the lower range values. 0 100
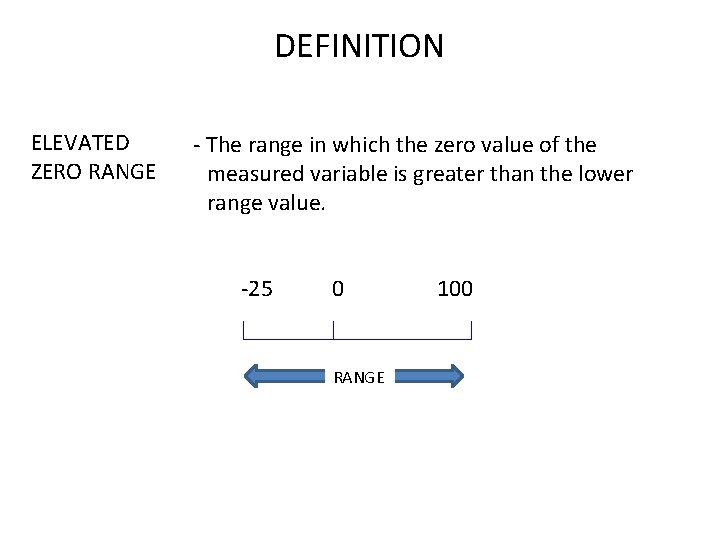
DEFINITION ELEVATED ZERO RANGE The range in which the zero value of the measured variable is greater than the lower range value. 25 0 RANGE 100

DEFINITION SUPPRESSED ZERO RANGE The range in which the zero value of the measured variable is less than the lower range value. 0 25 100 RANGE
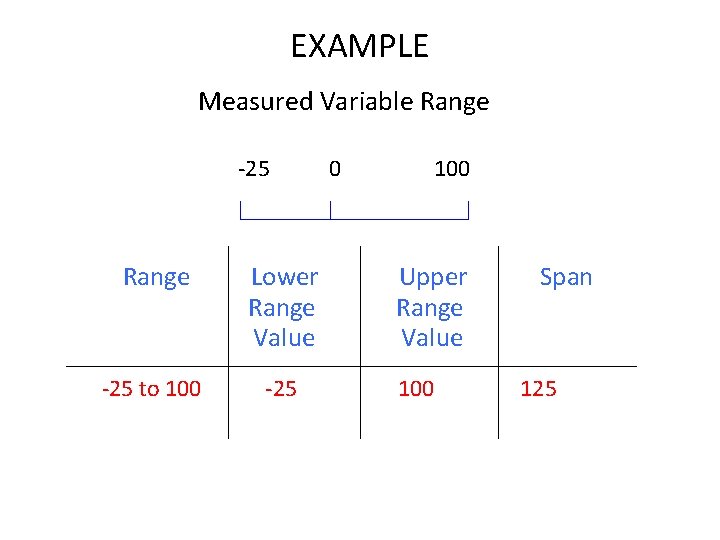
EXAMPLE Measured Variable Range 25 Range Lower Range Value 25 to 100 25 0 100 Upper Range Value 100 Span 125
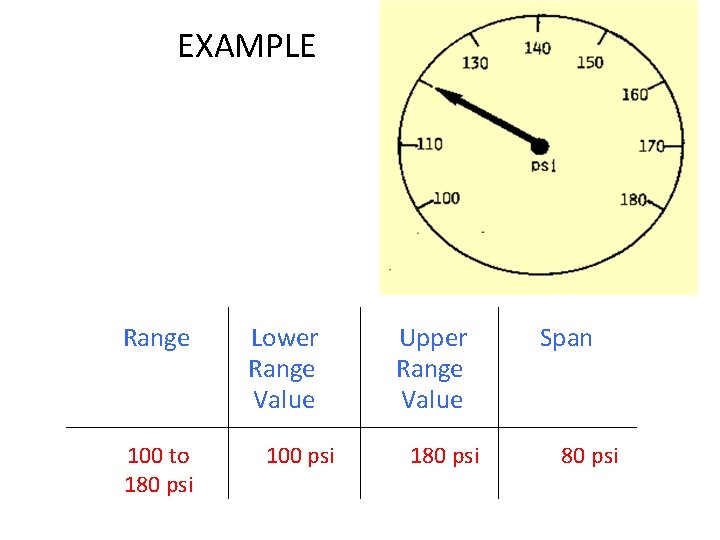
EXAMPLE Range 100 to 180 psi Lower Range Value 100 psi Upper Range Value 180 psi Span 80 psi
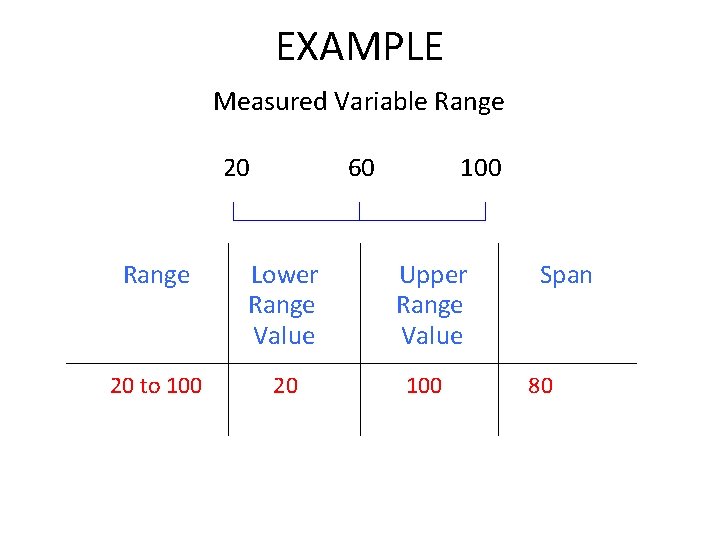
EXAMPLE Measured Variable Range 20 60 Range Lower Range Value 20 to 100 20 100 Upper Range Value 100 Span 80
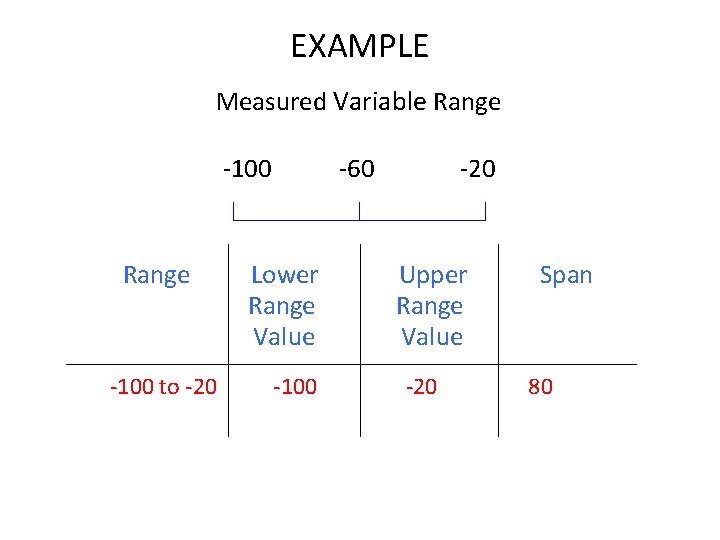
EXAMPLE Measured Variable Range 100 Range 100 to 20 60 Lower Range Value 100 20 Upper Range Value 20 Span 80
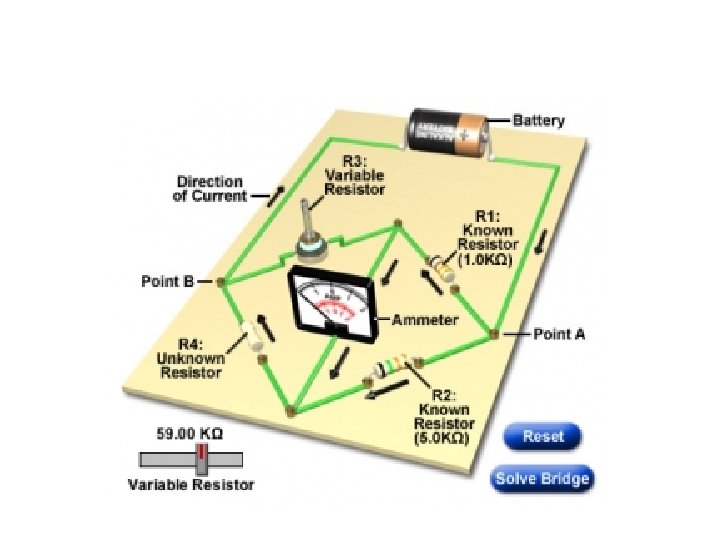
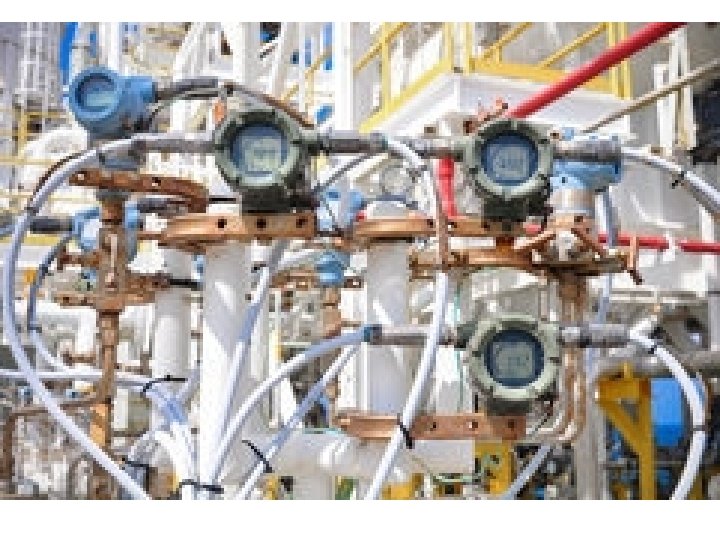
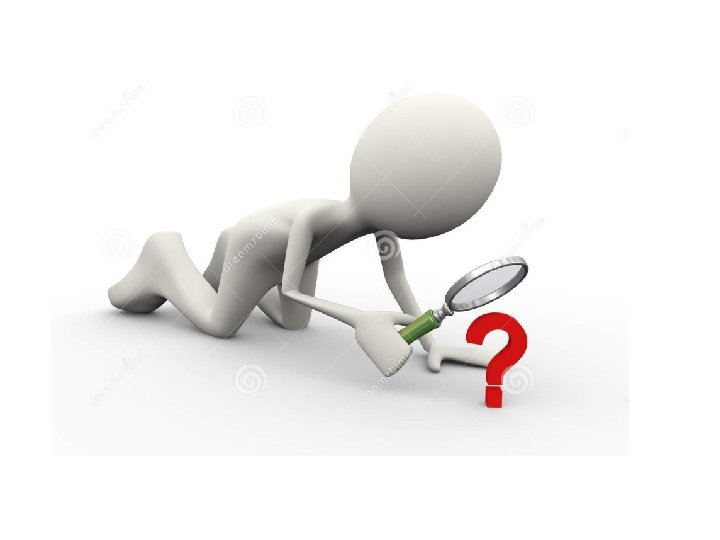
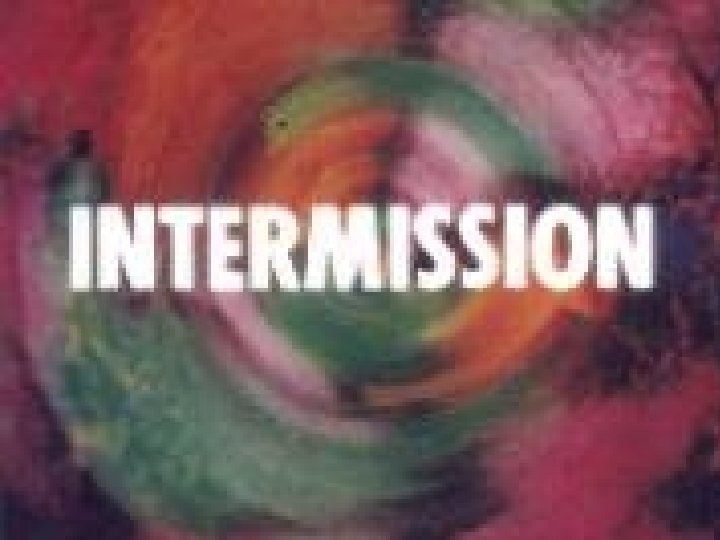
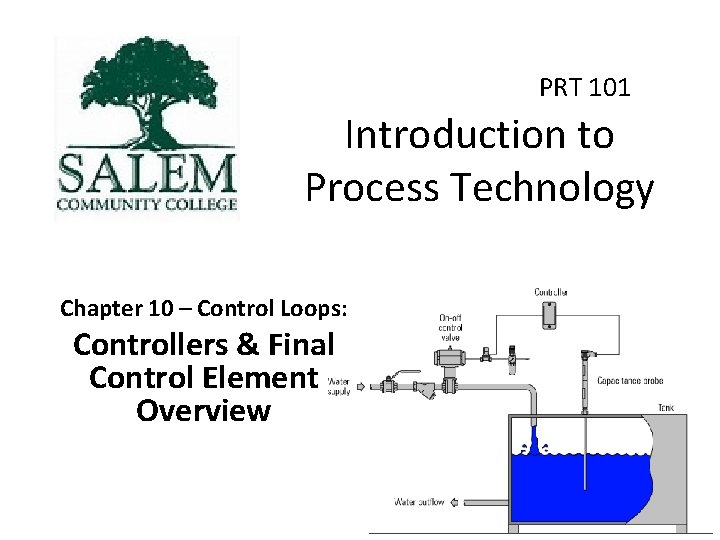
PRT 101 Introduction to Process Technology Chapter 10 – Control Loops: Controllers & Final Control Element Overview
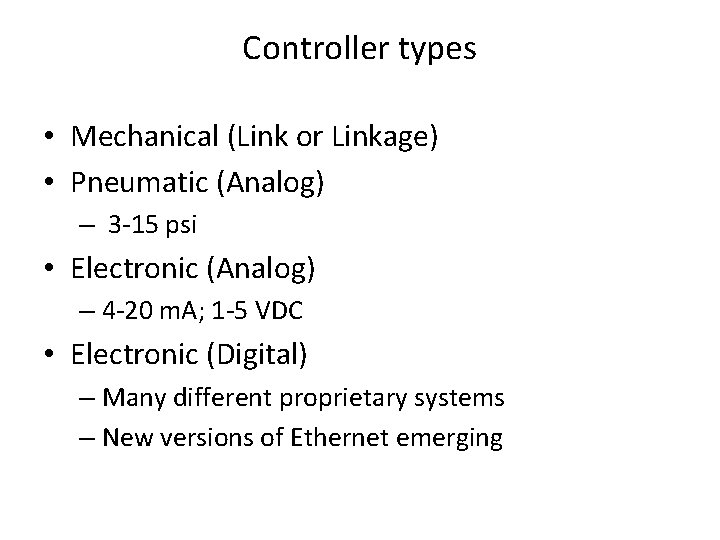
Controller types • Mechanical (Link or Linkage) • Pneumatic (Analog) – 3 15 psi • Electronic (Analog) – 4 20 m. A; 1 5 VDC • Electronic (Digital) – Many different proprietary systems – New versions of Ethernet emerging
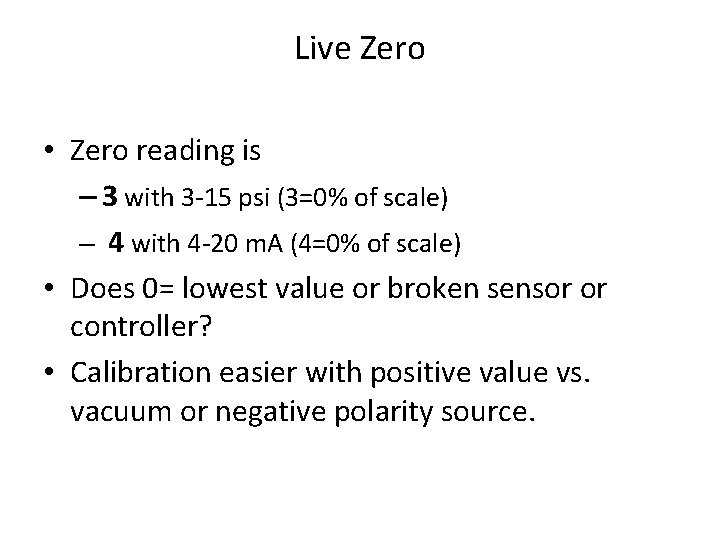
Live Zero • Zero reading is – 3 with 3 15 psi (3=0% of scale) – 4 with 4 20 m. A (4=0% of scale) • Does 0= lowest value or broken sensor or controller? • Calibration easier with positive value vs. vacuum or negative polarity source.
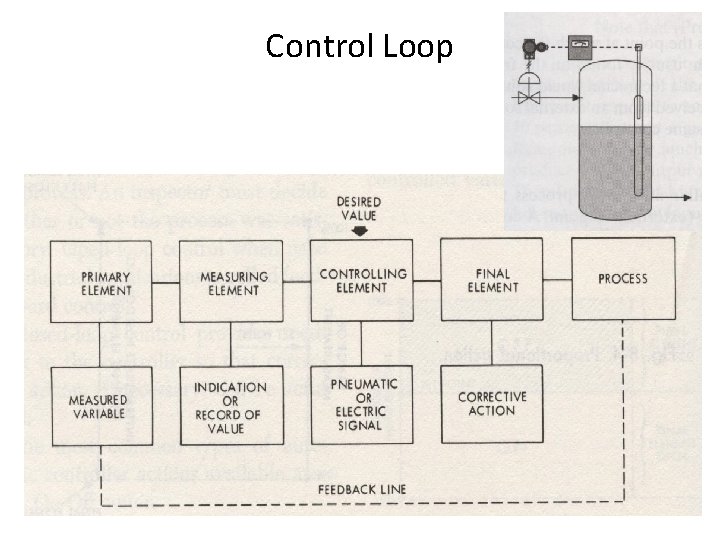
Control Loop
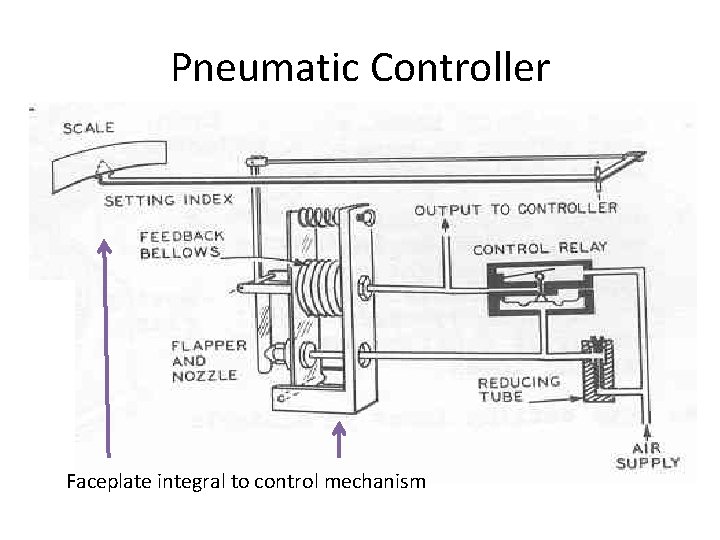
Pneumatic Controller Faceplate integral to control mechanism
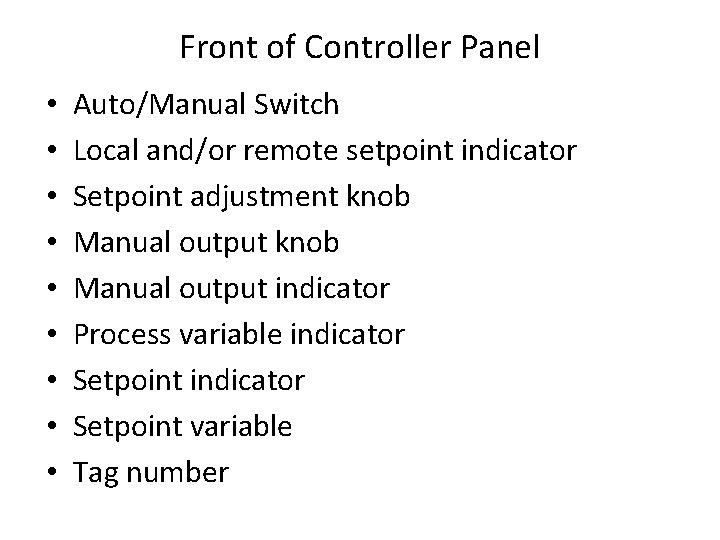
Front of Controller Panel • • • Auto/Manual Switch Local and/or remote setpoint indicator Setpoint adjustment knob Manual output indicator Process variable indicator Setpoint variable Tag number
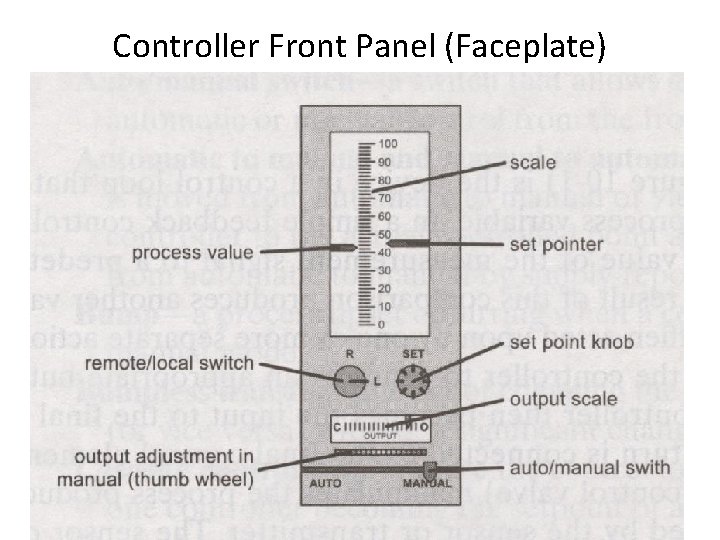
Controller Front Panel (Faceplate)
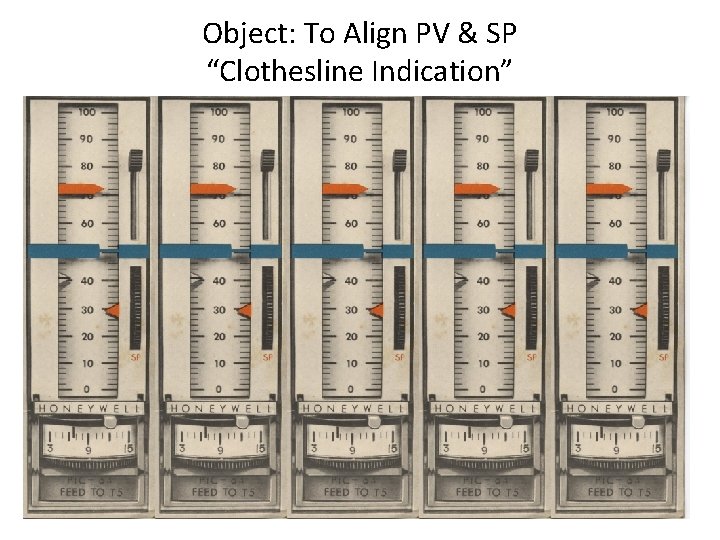
Object: To Align PV & SP “Clothesline Indication”
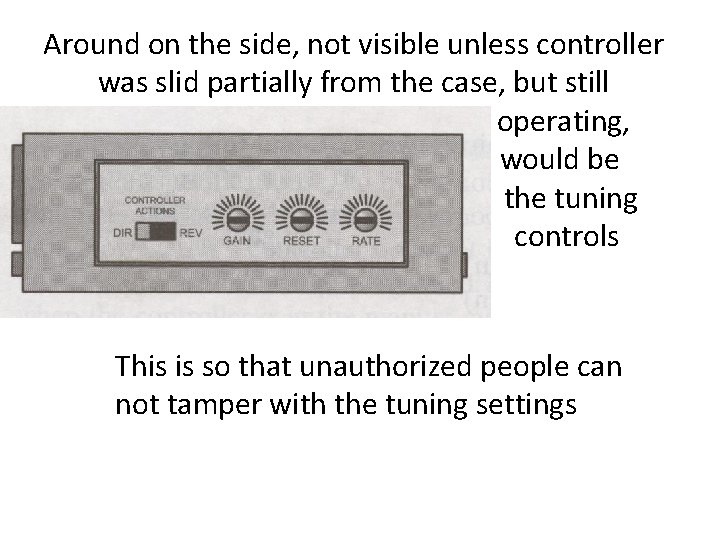
Around on the side, not visible unless controller was slid partially from the case, but still operating, would be the tuning controls This is so that unauthorized people can not tamper with the tuning settings
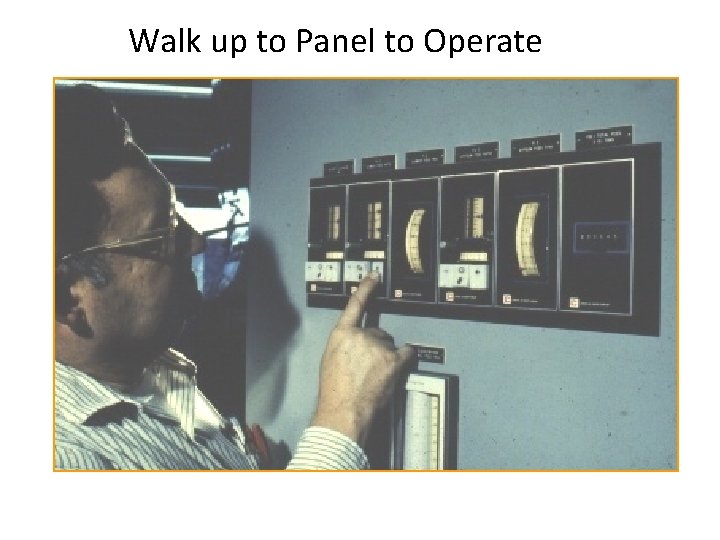
Walk up to Panel to Operate
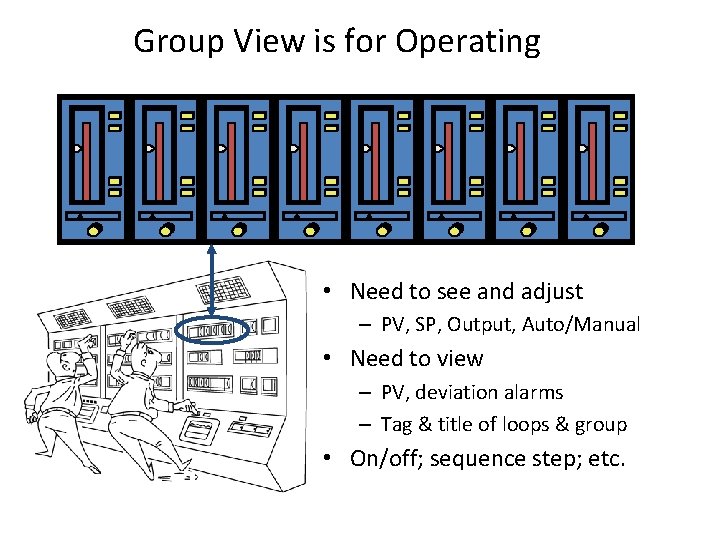
Group View is for Operating • Need to see and adjust – PV, SP, Output, Auto/Manual • Need to view – PV, deviation alarms – Tag & title of loops & group • On/off; sequence step; etc.

Group View of Controllers – Alarm List Above Video view of new DCS systems often mimics traditional faceplates

Faceplates may be “adjustable’ in content when using video screens in newer DCS systems of some brands Minimal – Normal – Expanded
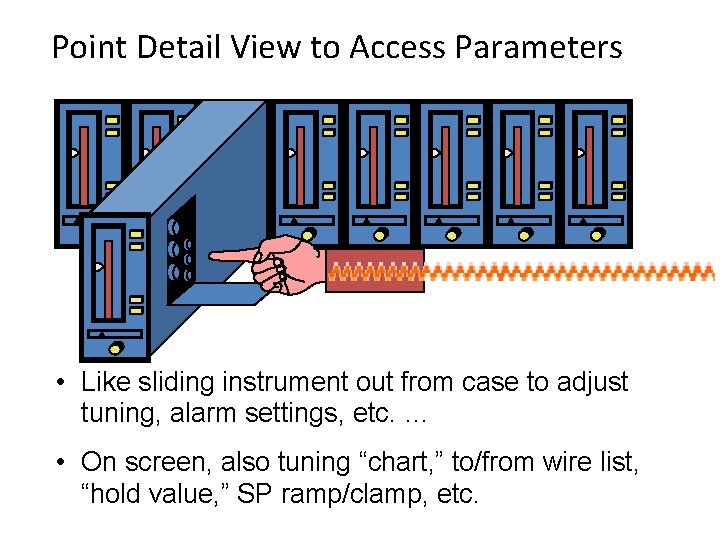
Point Detail View to Access Parameters • Like sliding instrument out from case to adjust tuning, alarm settings, etc. … • On screen, also tuning “chart, ” to/from wire list, “hold value, ” SP ramp/clamp, etc.
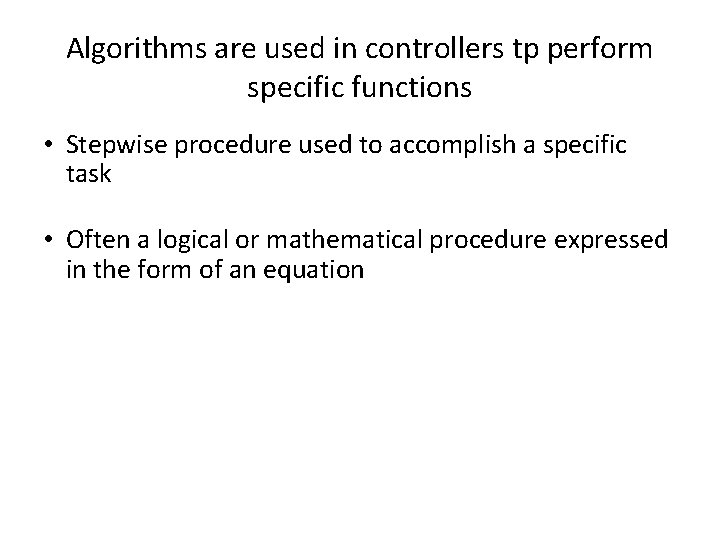
Algorithms are used in controllers tp perform specific functions • Stepwise procedure used to accomplish a specific task • Often a logical or mathematical procedure expressed in the form of an equation
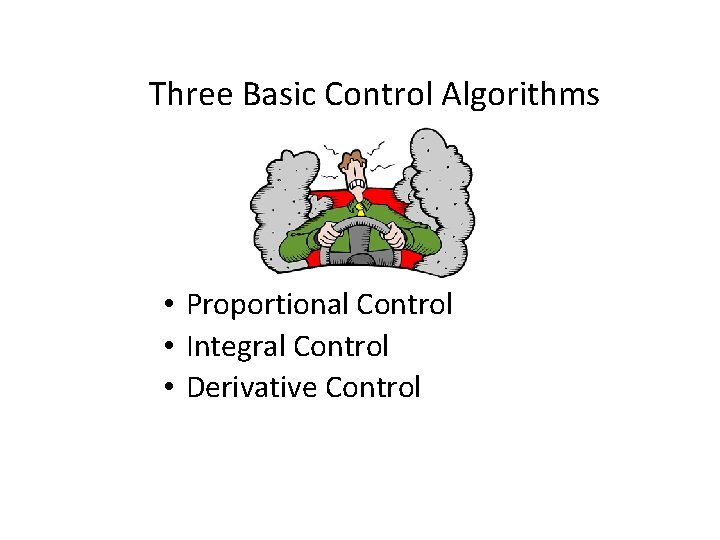
Three Basic Control Algorithms • Proportional Control • Integral Control • Derivative Control
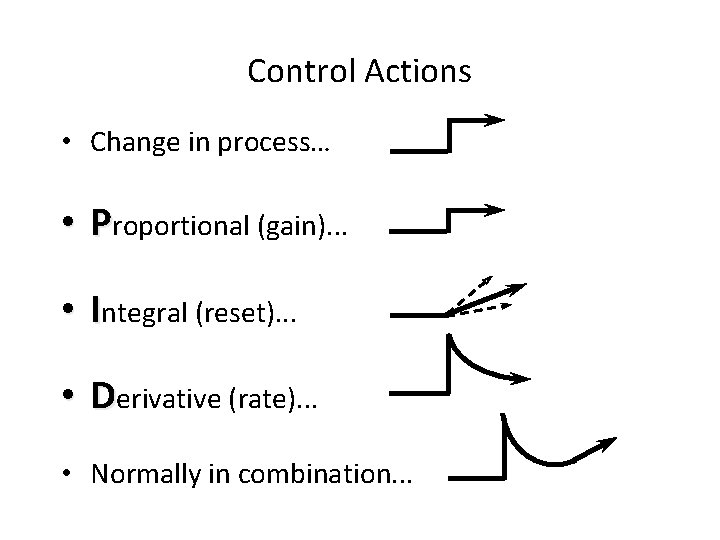
Control Actions • Change in process… • Proportional (gain). . . • Integral (reset). . . • Derivative (rate). . . • Normally in combination. . .
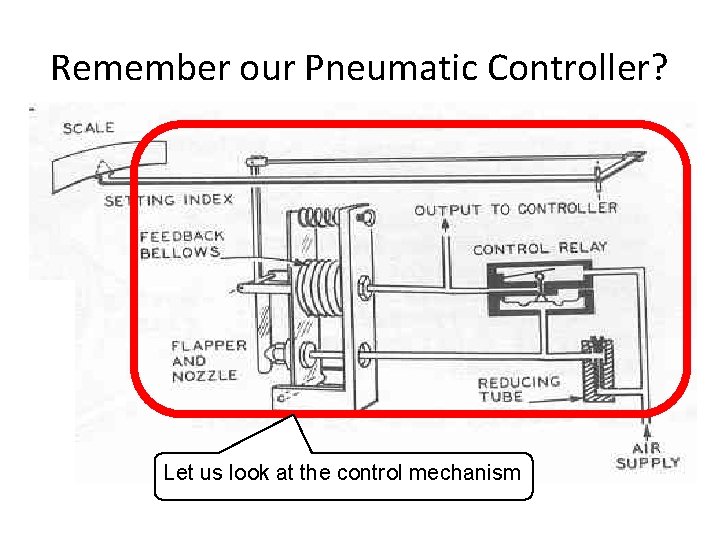
Remember our Pneumatic Controller? Let us look at the control mechanism
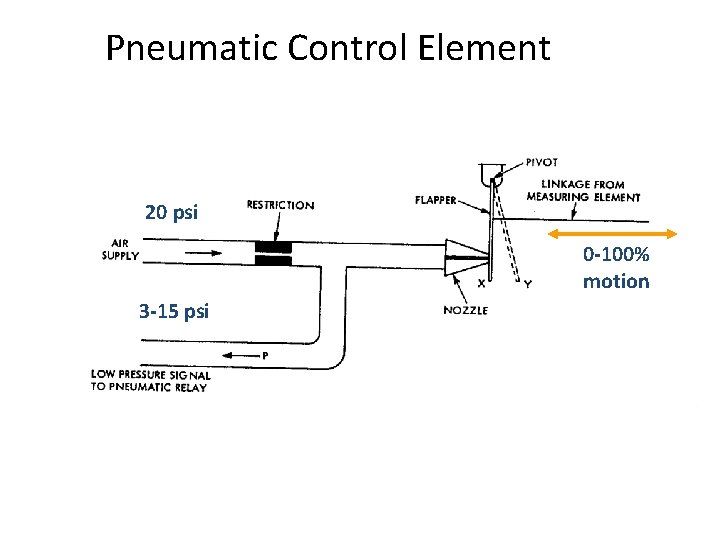
Pneumatic Control Element 20 psi 0 -100% motion 3 -15 psi
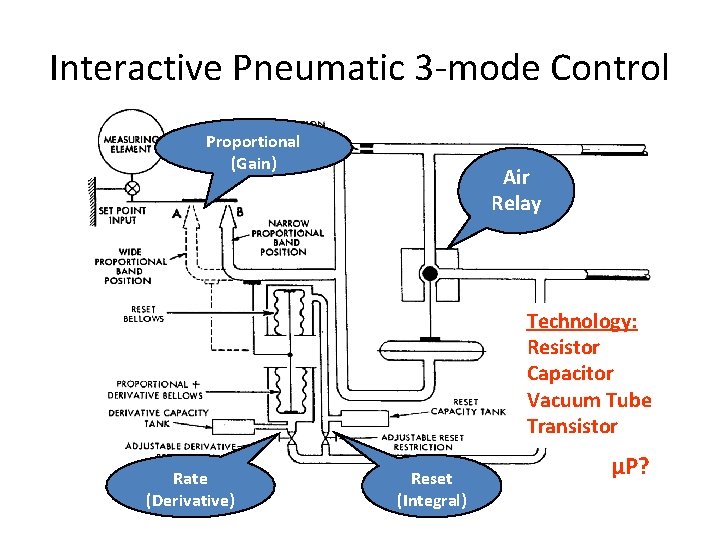
Interactive Pneumatic 3 mode Control Proportional (Gain) Air Relay Technology: Resistor Capacitor Vacuum Tube Transistor Rate (Derivative) Reset (Integral) μP?
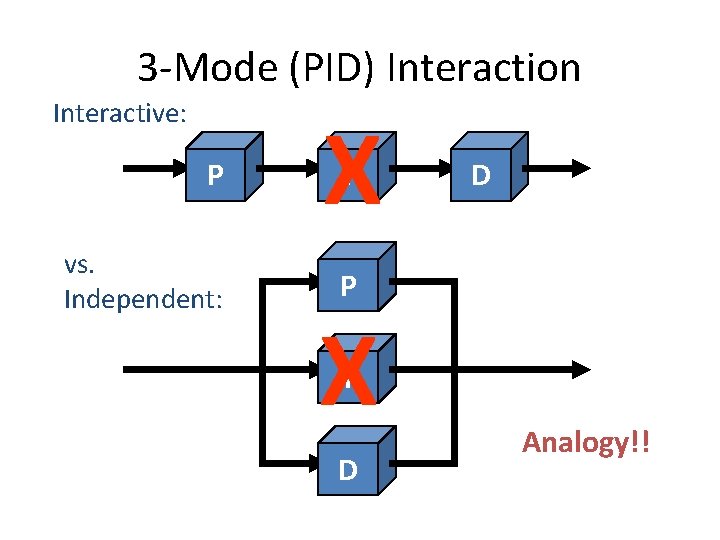
3 Mode (PID) Interaction Interactive: P vs. Independent: X I D P X I D Analogy!!
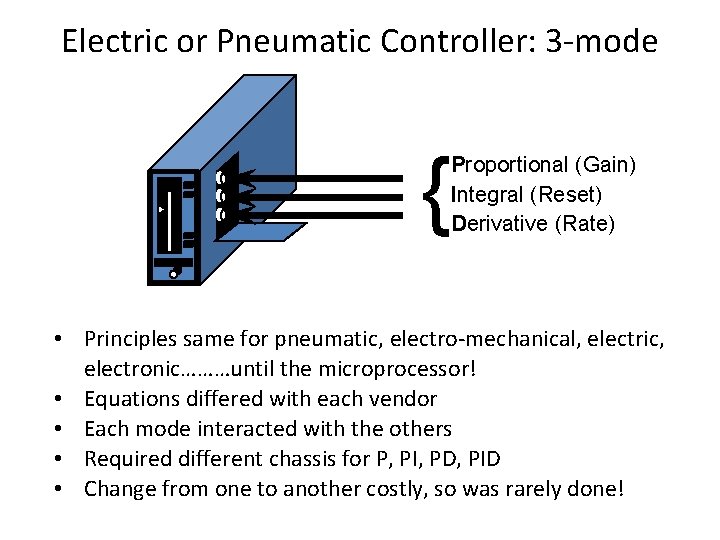
Electric or Pneumatic Controller: 3 mode { Proportional (Gain) Integral (Reset) Derivative (Rate) • Principles same for pneumatic, electro mechanical, electric, electronic………until the microprocessor! • Equations differed with each vendor • Each mode interacted with the others • Required different chassis for P, PI, PD, PID • Change from one to another costly, so was rarely done!
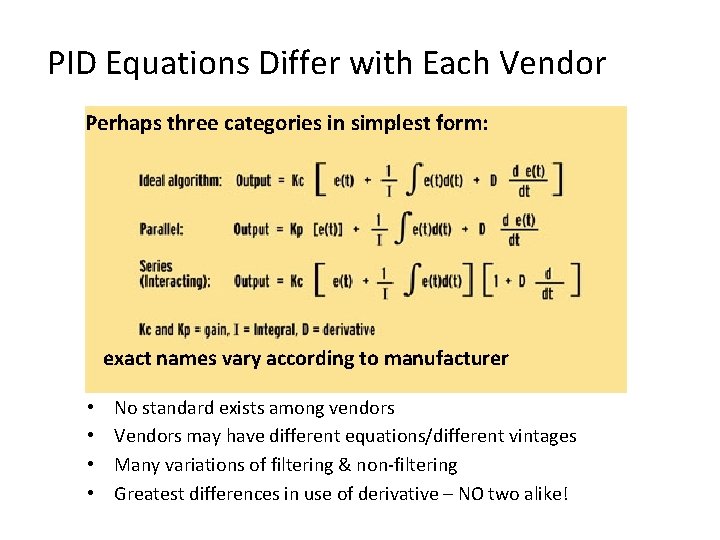
PID Equations Differ with Each Vendor Perhaps three categories in simplest form: exact names vary according to manufacturer • • No standard exists among vendors Vendors may have different equations/different vintages Many variations of filtering & non filtering Greatest differences in use of derivative – NO two alike!
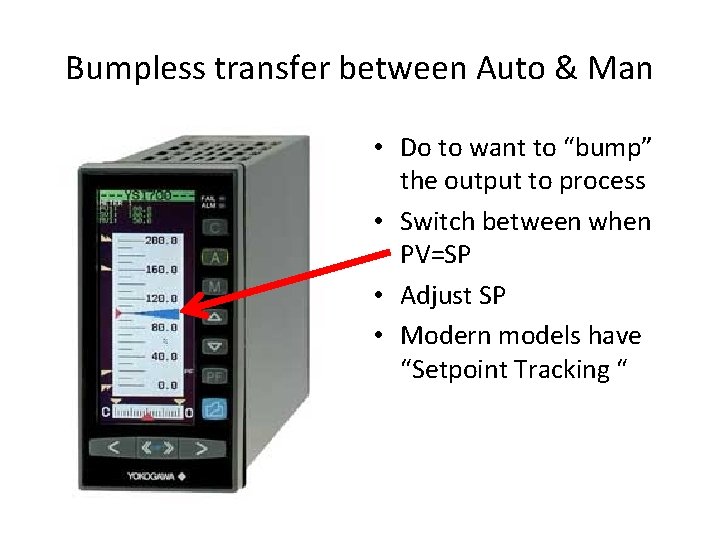
Bumpless transfer between Auto & Man • Do to want to “bump” the output to process • Switch between when PV=SP • Adjust SP • Modern models have “Setpoint Tracking “
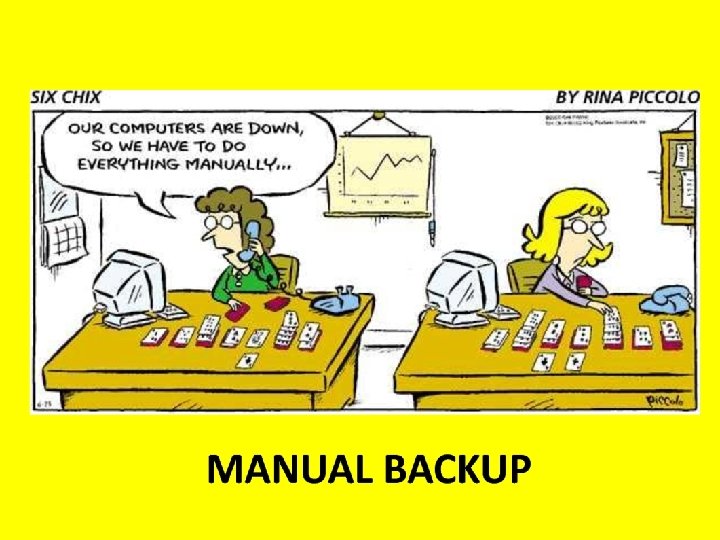
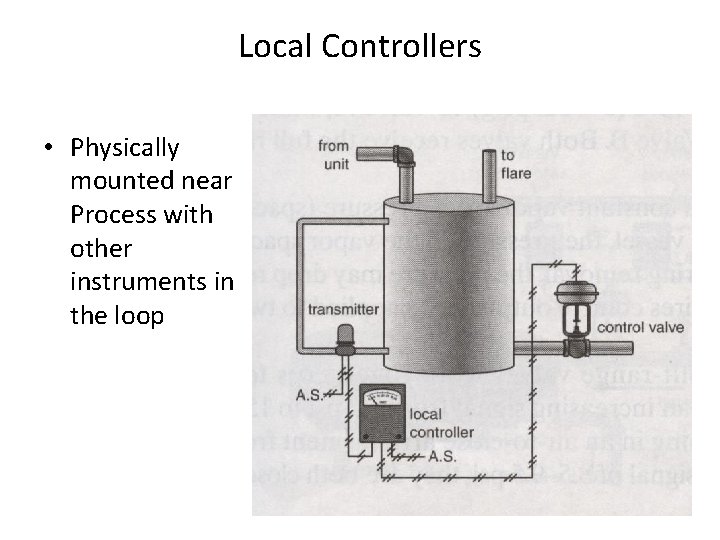
Local Controllers • Physically mounted near Process with other instruments in the loop
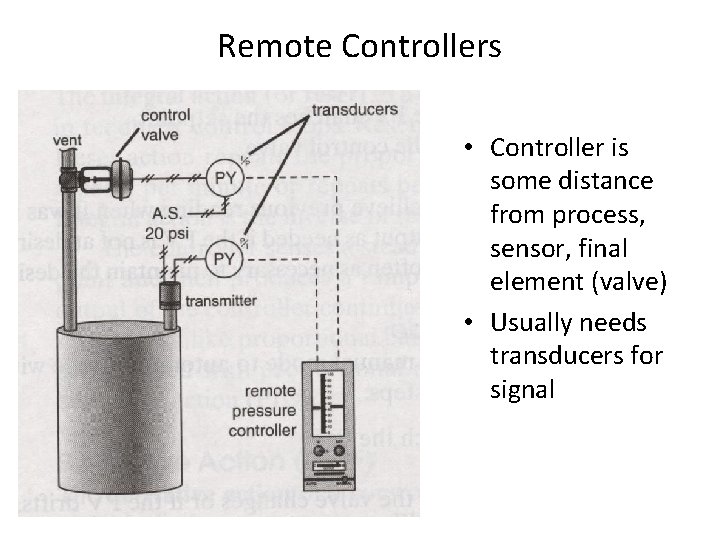
Remote Controllers • Controller is some distance from process, sensor, final element (valve) • Usually needs transducers for signal
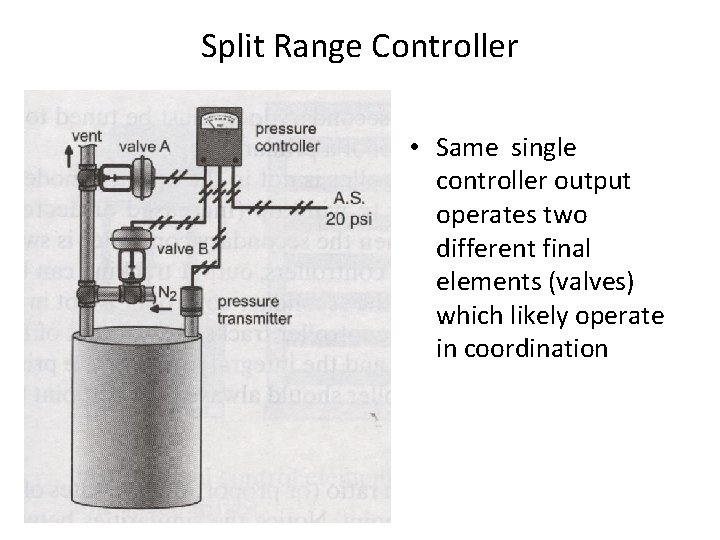
Split Range Controller • Same single controller output operates two different final elements (valves) which likely operate in coordination
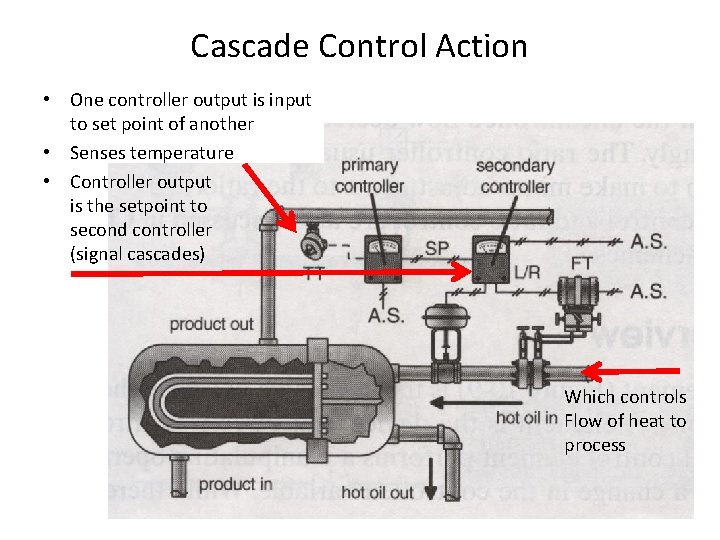
Cascade Control Action • One controller output is input to set point of another • Senses temperature • Controller output is the setpoint to second controller (signal cascades) Which controls Flow of heat to process
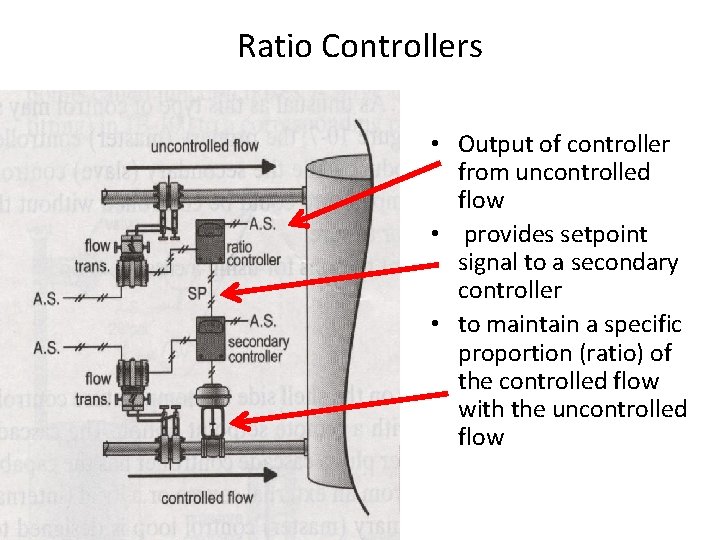
Ratio Controllers • Output of controller from uncontrolled flow • provides setpoint signal to a secondary controller • to maintain a specific proportion (ratio) of the controlled flow with the uncontrolled flow
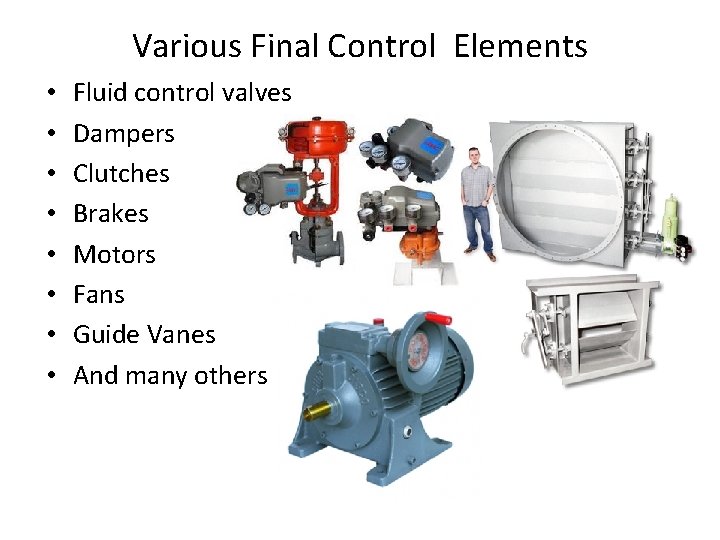
Various Final Control Elements • • Fluid control valves Dampers Clutches Brakes Motors Fans Guide Vanes And many others
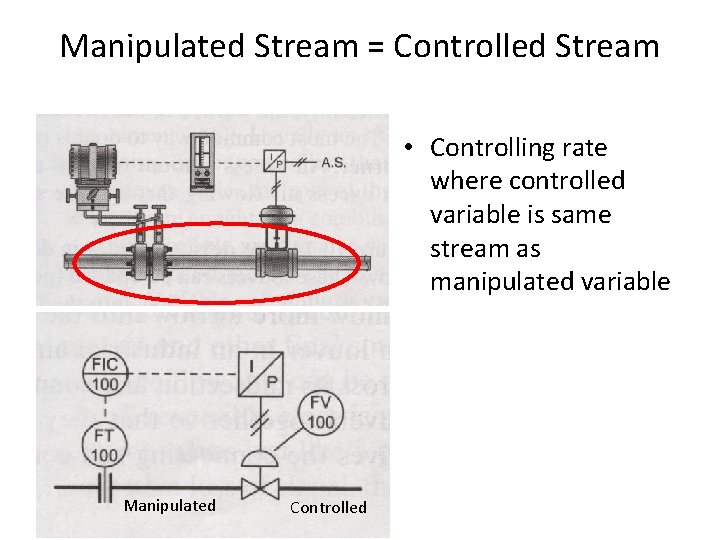
Manipulated Stream = Controlled Stream • Controlling rate where controlled variable is same stream as manipulated variable Manipulated Controlled
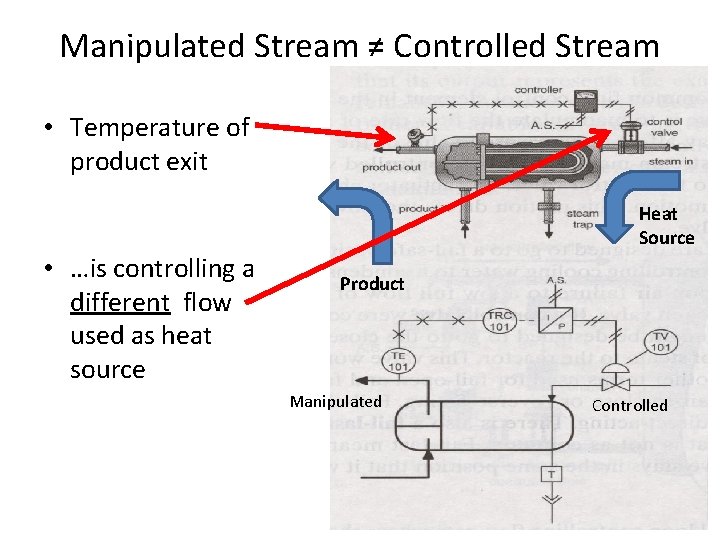
Manipulated Stream ≠ Controlled Stream • Temperature of product exit Heat Source • …is controlling a different flow used as heat source Product Manipulated Controlled
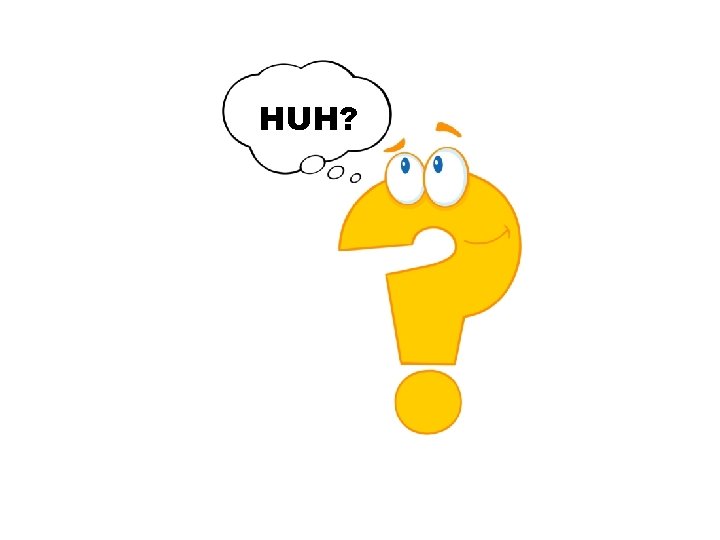
HUH?
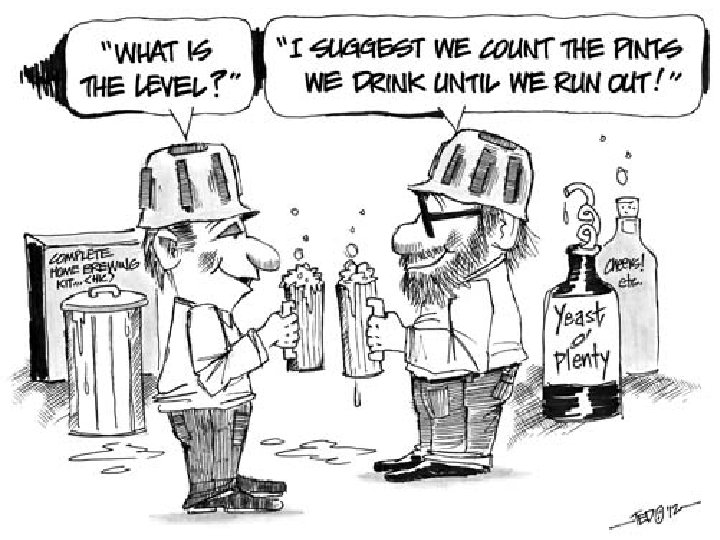
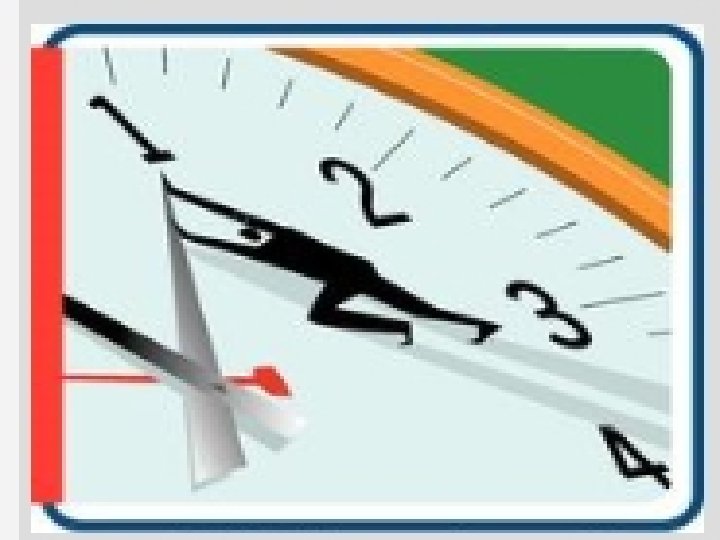
P&id fy
Test permis hauturier
Cern prt tool
Prt formula
I = p r t
Male navy prt standards
Mrt prt
Simple interest definition
Keputusan menteri pupr no 1044/kpts/m/2018 pdf
Handle with care restraint techniques
Carly deposited $800
Prt phases
Le prt
Arvo prt
Ihi leadership alliance
Current state vs future state slide
It 101 - introduction to computing
It 101 - introduction to computing
Cs101 vu edu pk
Qi 101: introduction to health care improvement
Touch screen technology introduction
Low voltage
Introduction to semiconductor manufacturing technology
A collection of unorganized facts
Discuss about information technology and e-business
Strategic hospitality technology investment
An act of transmitting messages
What is tranduser
Science fusion think central
Rover technology introduction
Introduction to information and communication technology
Introduction to veterinary technology
Introduction about technology in general
Nti new technology introduction
Introduction to information technology: your digital world
Introduction to information technology: your digital world
Technology management process
Process control instrumentation technology
Technological forecasting
What is process technology in operations management
Techjm.xyz free
Process technology examples
Design process technology
Project management process technology and practice
Technology commercialization process model
Vacuum process technology
Product process matrix in operations management
Ptec degree salary
Voc vob voe
Chapter 12 computer and technology in health care
Conclusion paragraph format
Integrated business processes with erp systems
Stochastic process introduction
List of manufacturing processes
Introduction to business process management ppt
Process of curriculum development in pakistan
Introduction to process control
Introduction of casting
Introduction of nursing process
Example of community health nursing diagnosis statement
Introduction to the personal software process
New product introduction process
Bones practical exam
Substantive vs procedural due process
Business process levels
Ergodicity
What is process to process delivery
Condylar and coronoid process of mandible
Stable quality
Process-to-process delivery
Process street vs sweet process
Summative and subjective assessment
Introduction to power tools nccer
Introduction of biochemical test
Introduction to computer science midterm exam test
A tool used to hold objects firmly in place is called
Nccer module 3 hand tools
Basic tools and basic hand operations
Test process improvement