MGT 563 OPERATIONS STRATEGIES Dr Aneel SALMAN Department
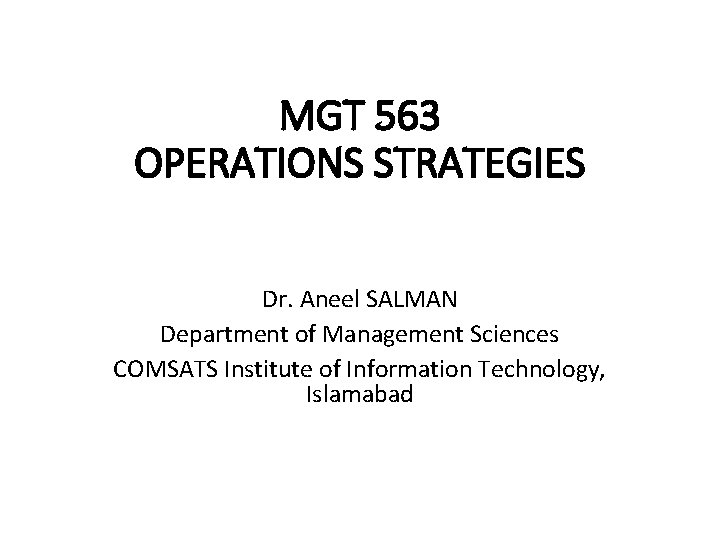
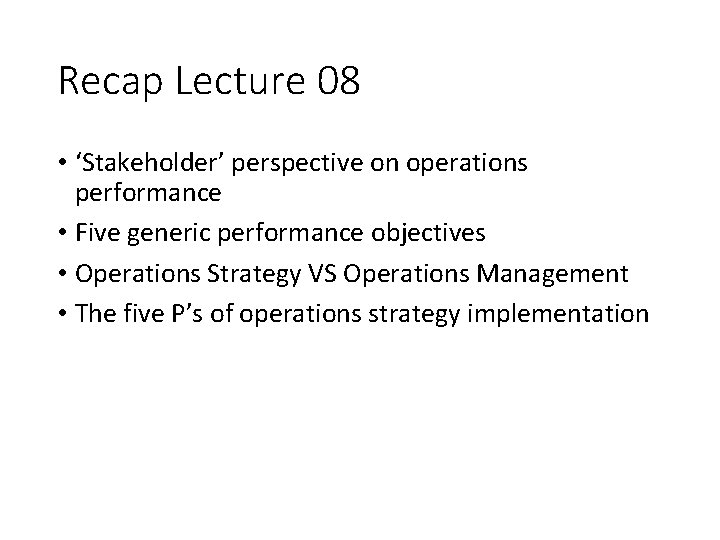
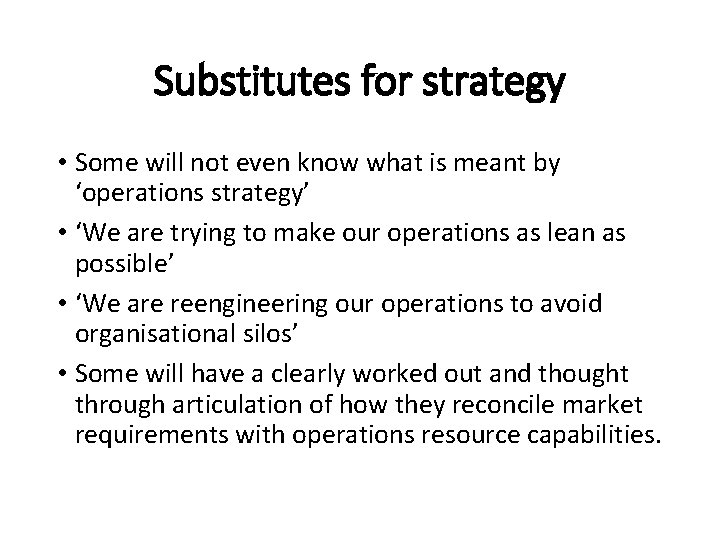
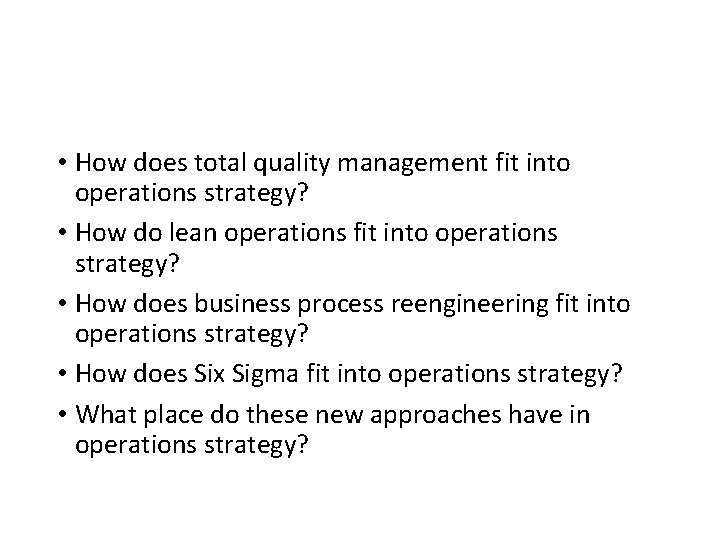
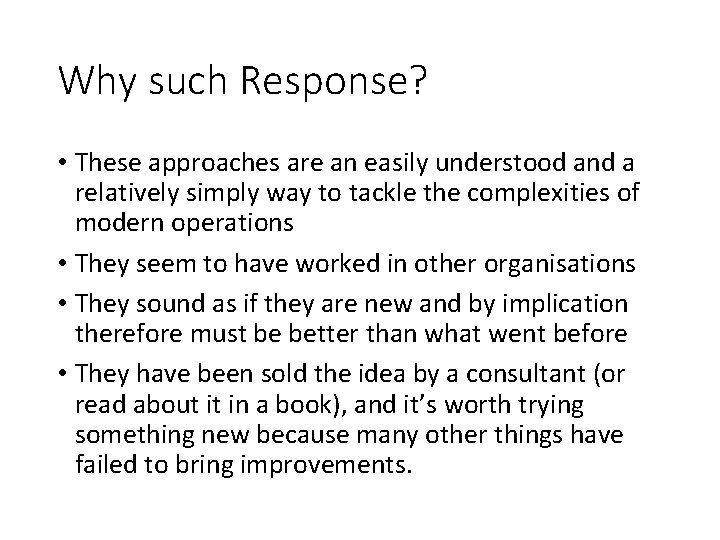
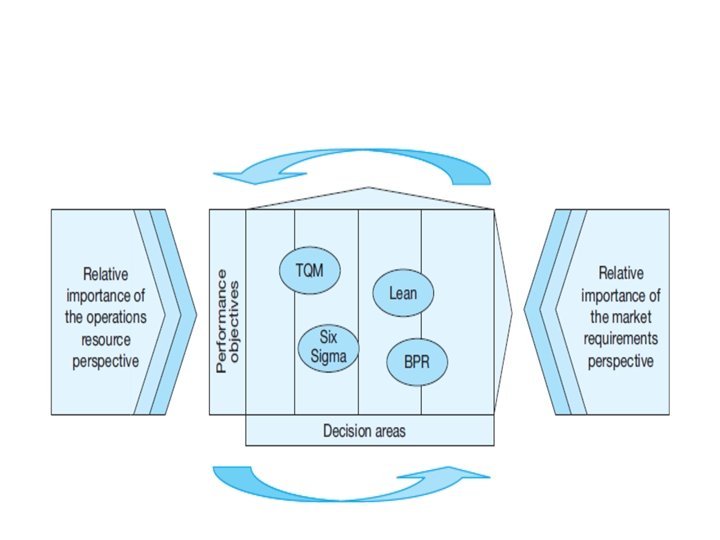
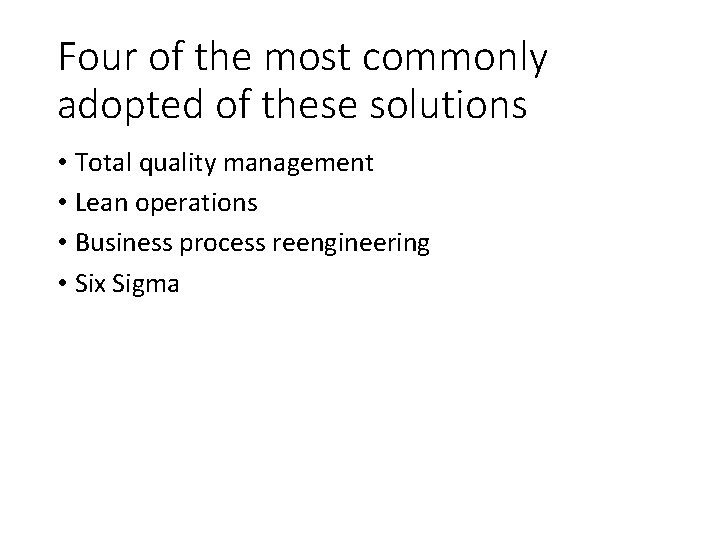
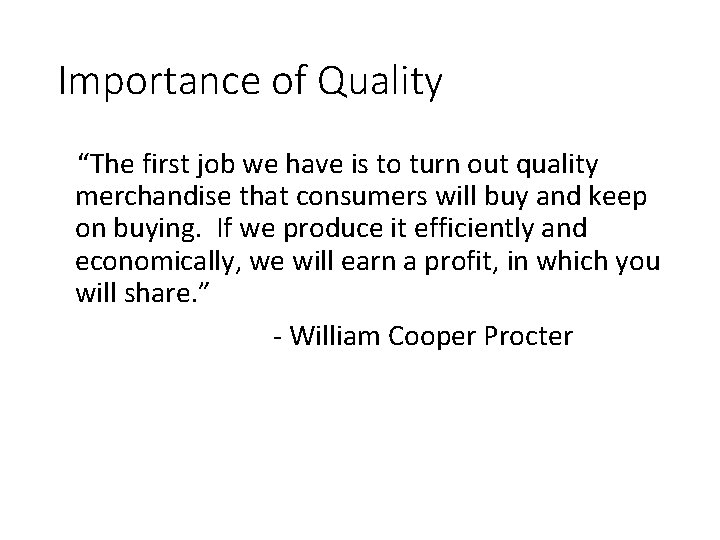
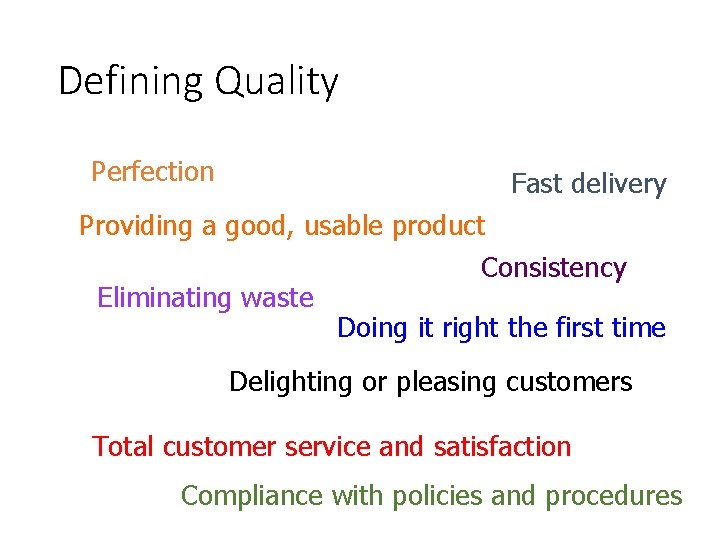
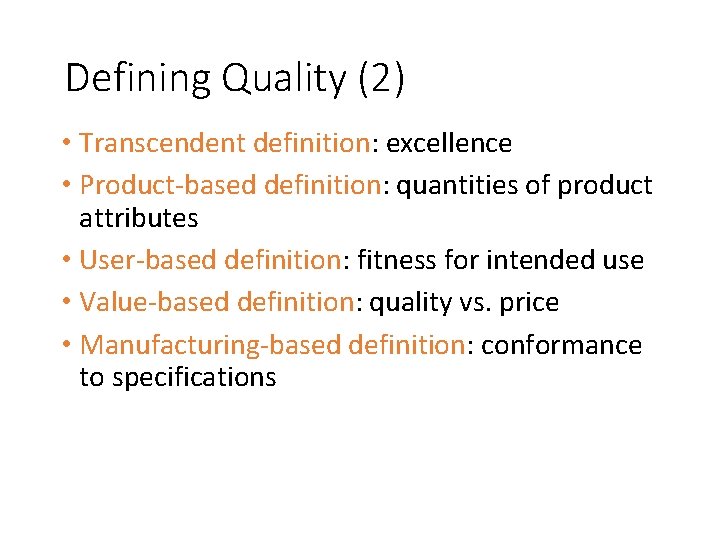

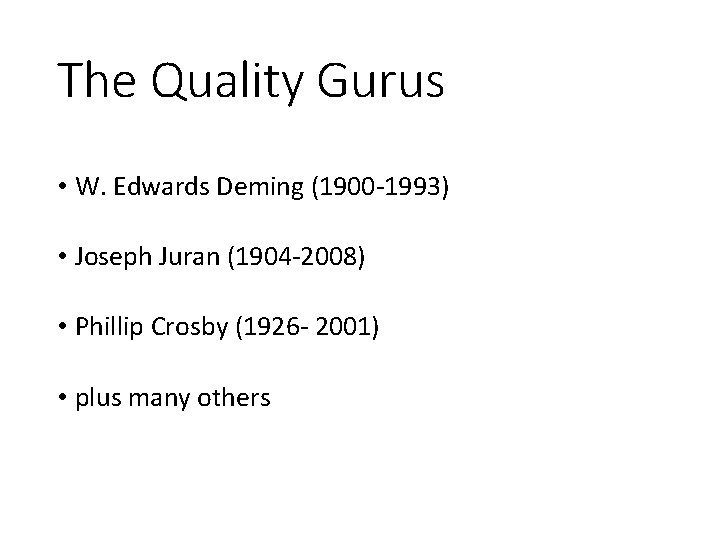
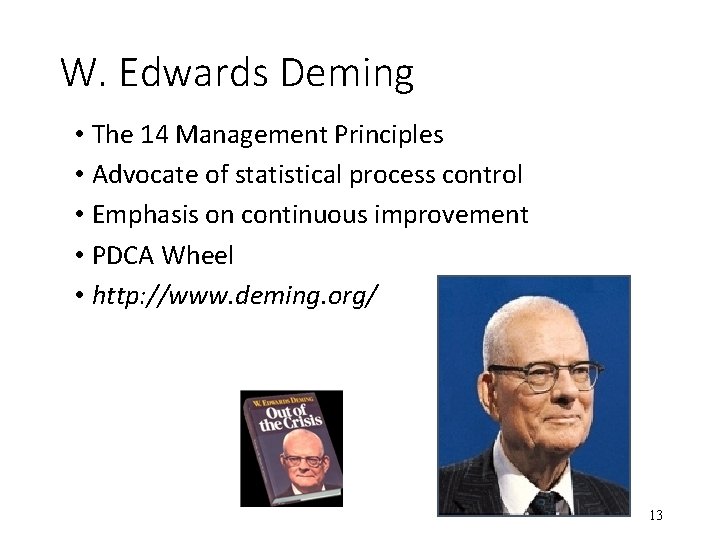
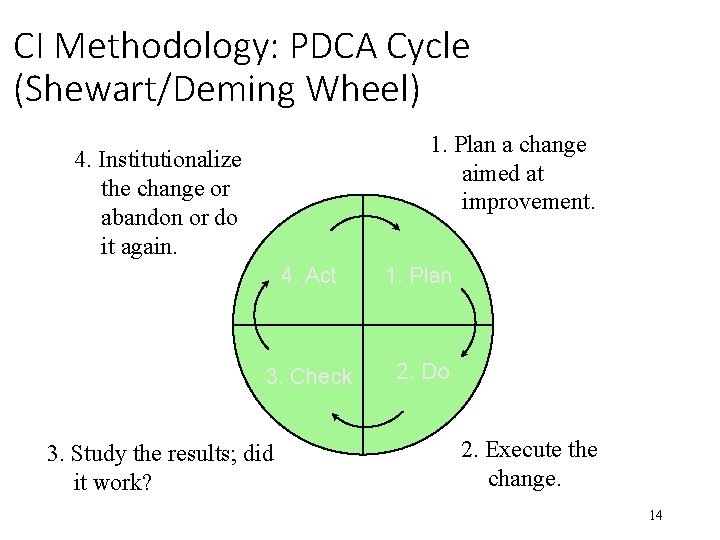
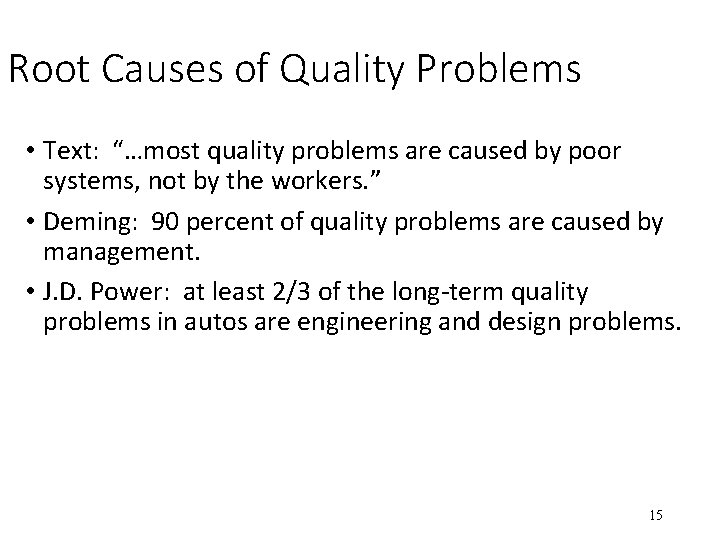
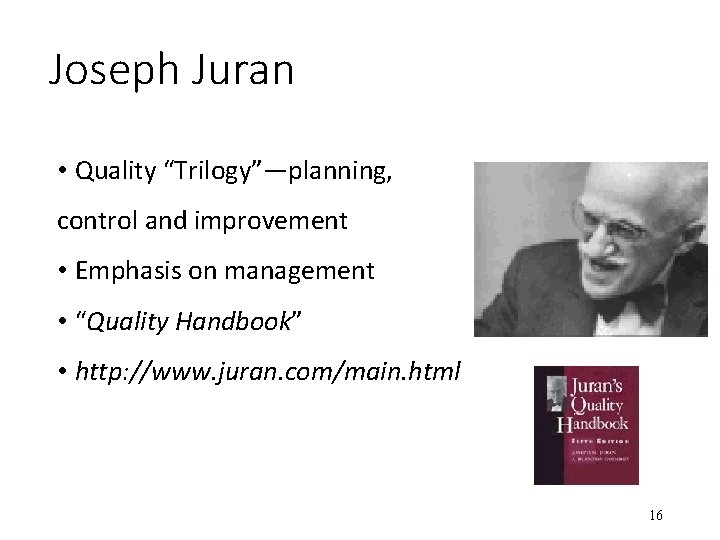
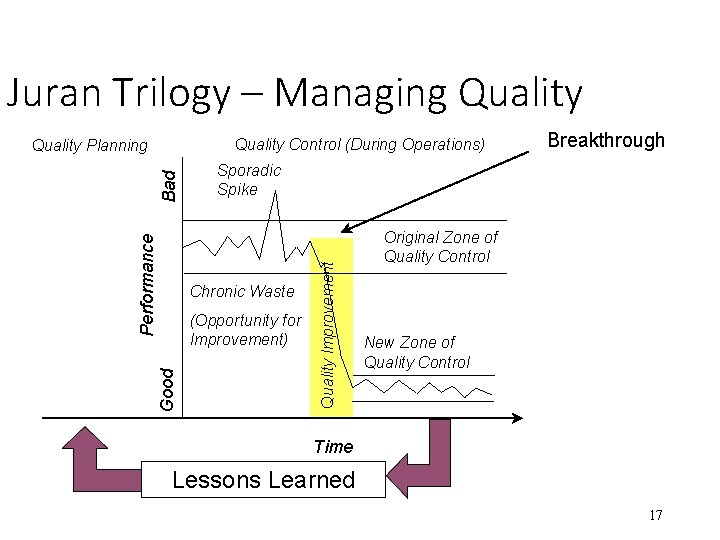
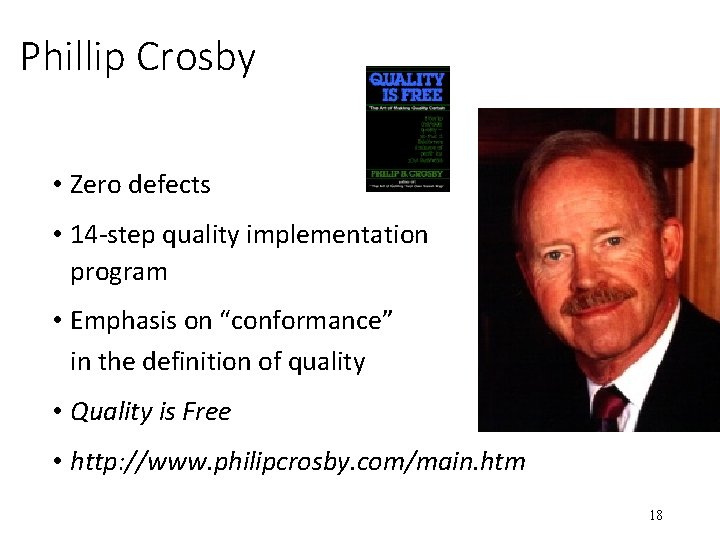
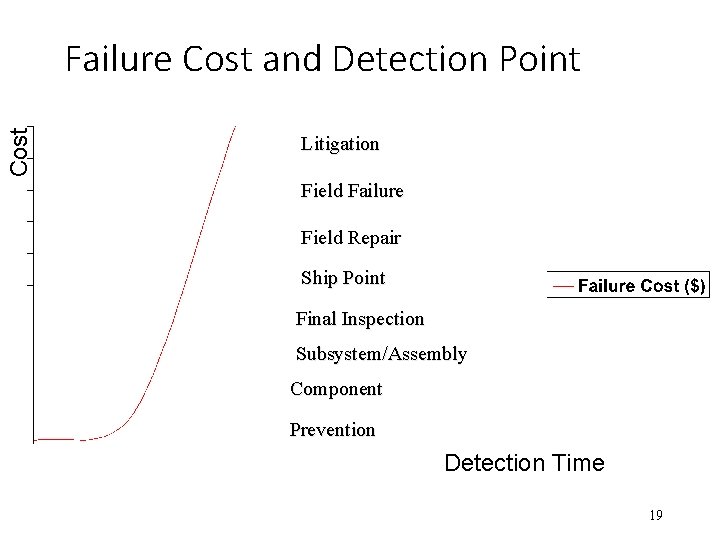
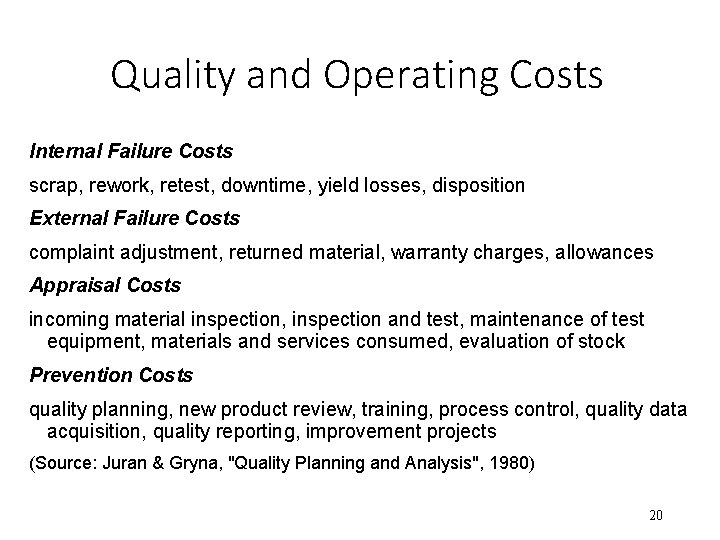
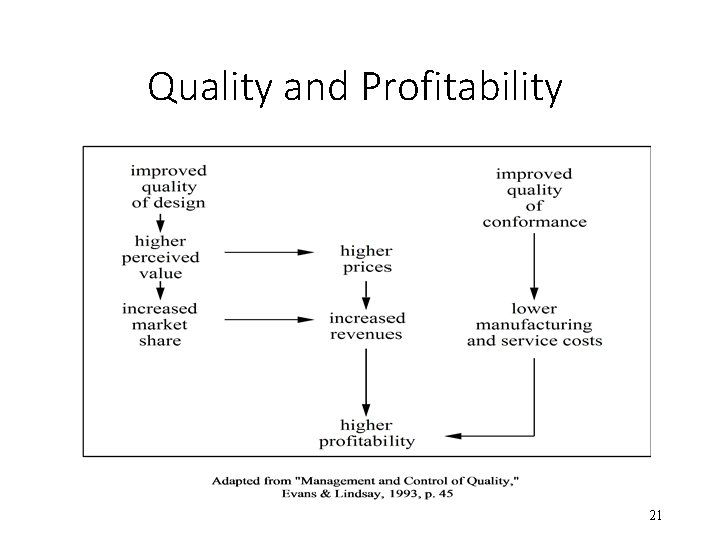
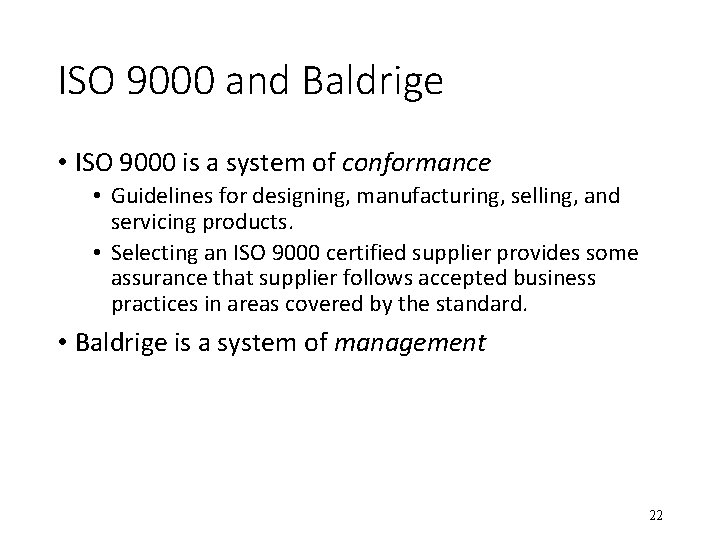
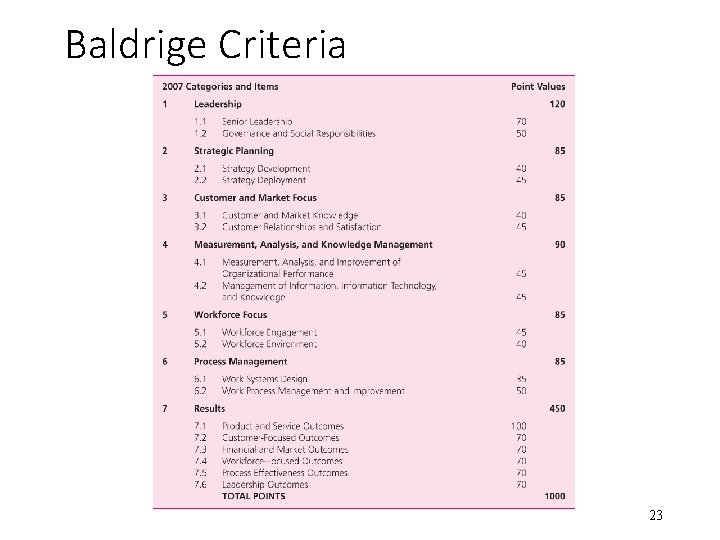
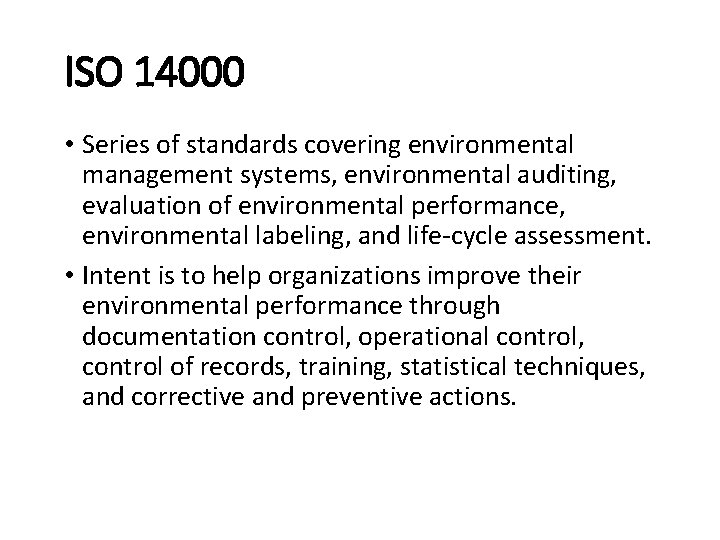
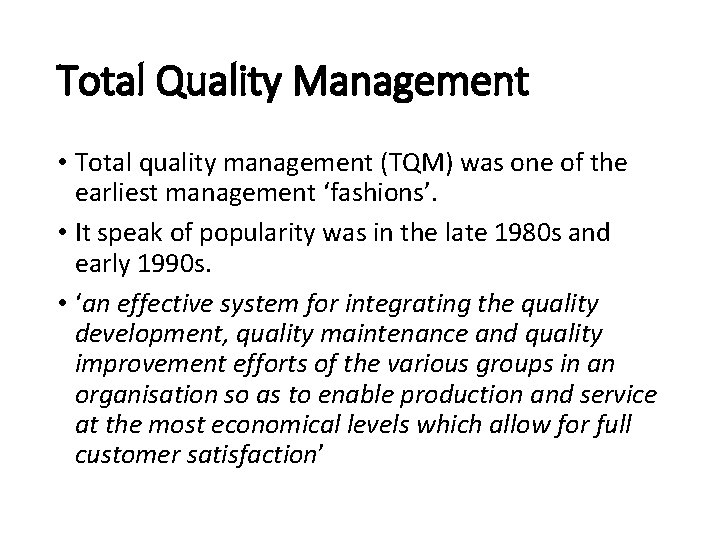
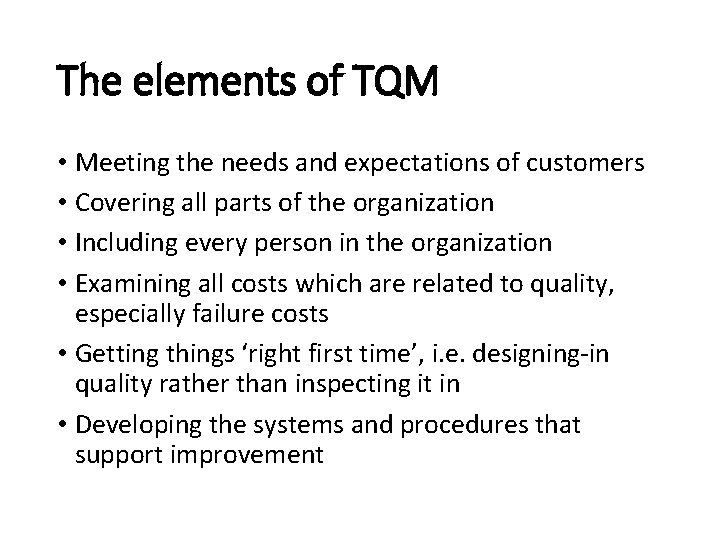
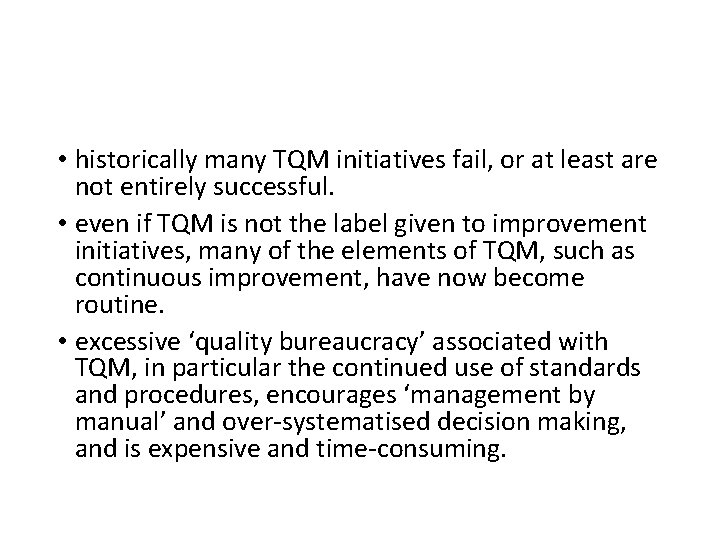
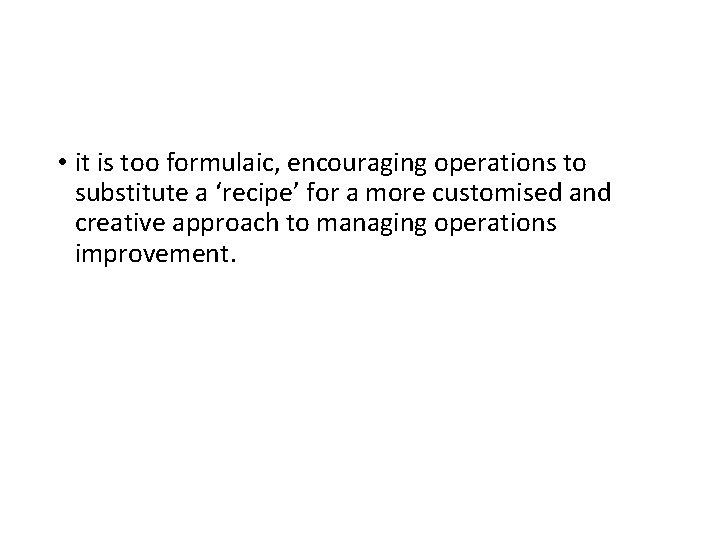
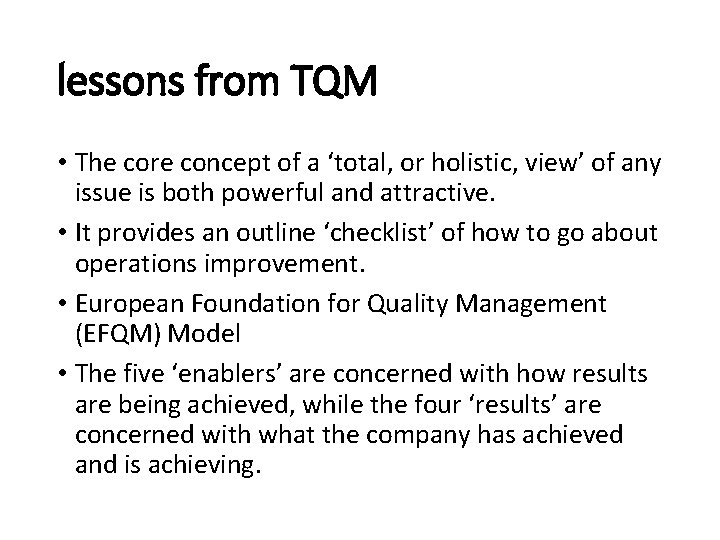
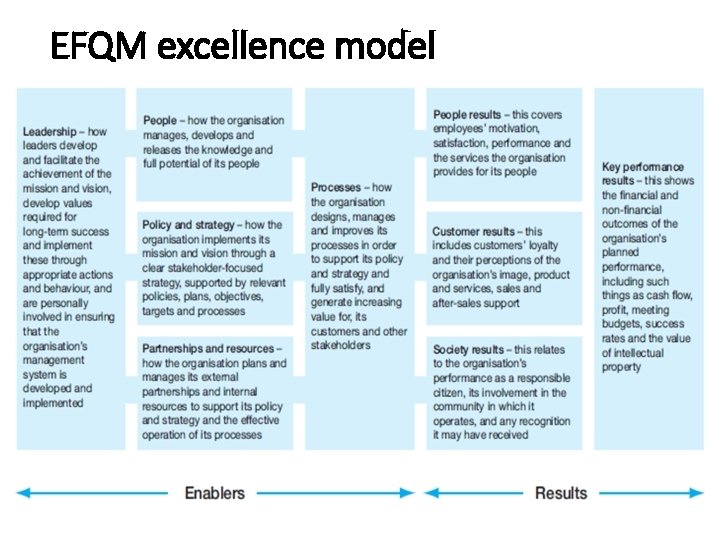
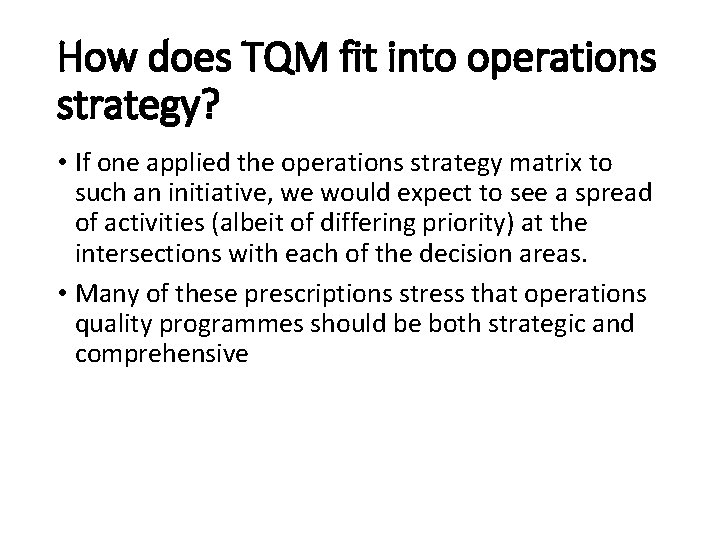
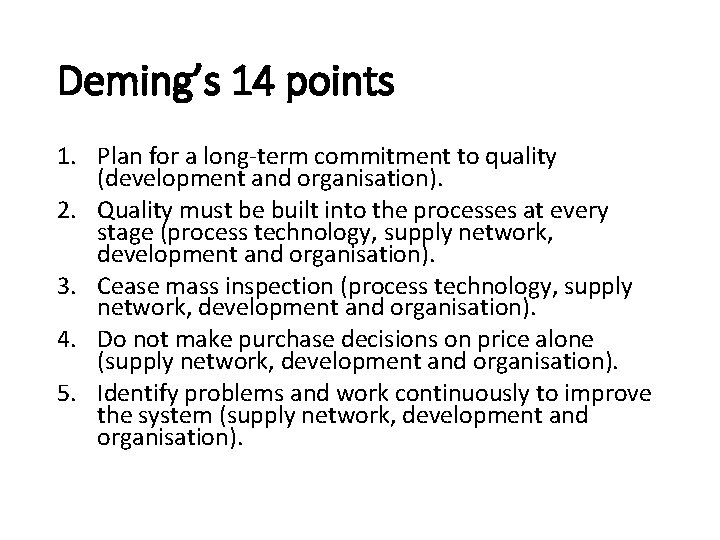
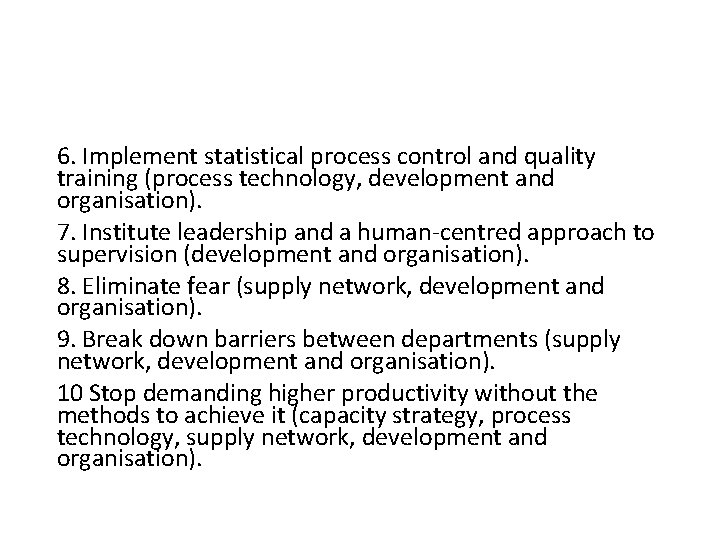
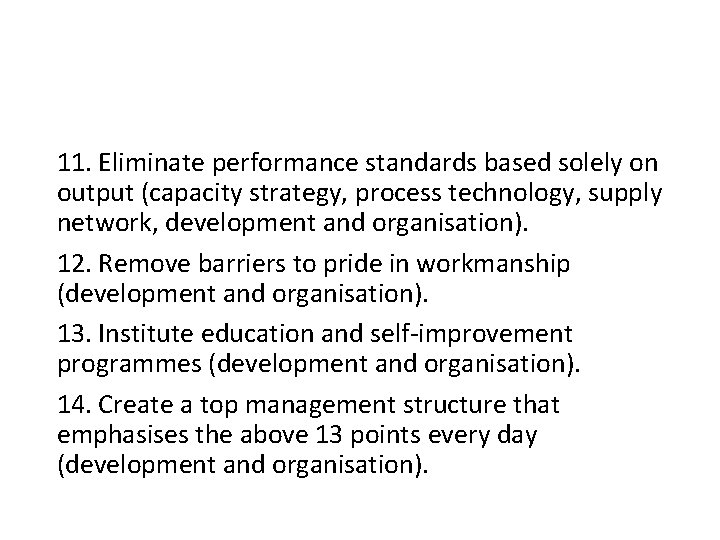
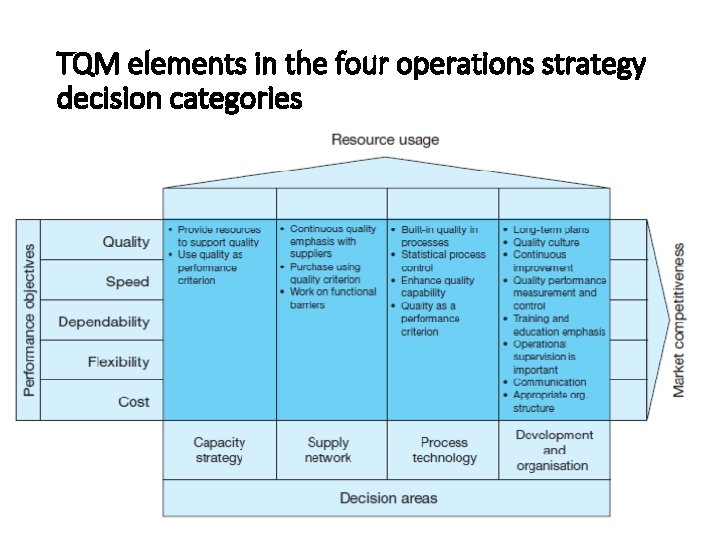
- Slides: 35
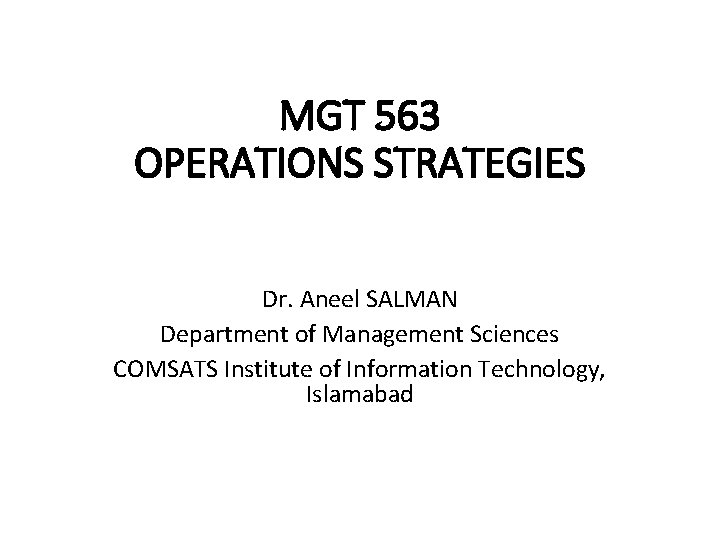
MGT 563 OPERATIONS STRATEGIES Dr. Aneel SALMAN Department of Management Sciences COMSATS Institute of Information Technology, Islamabad
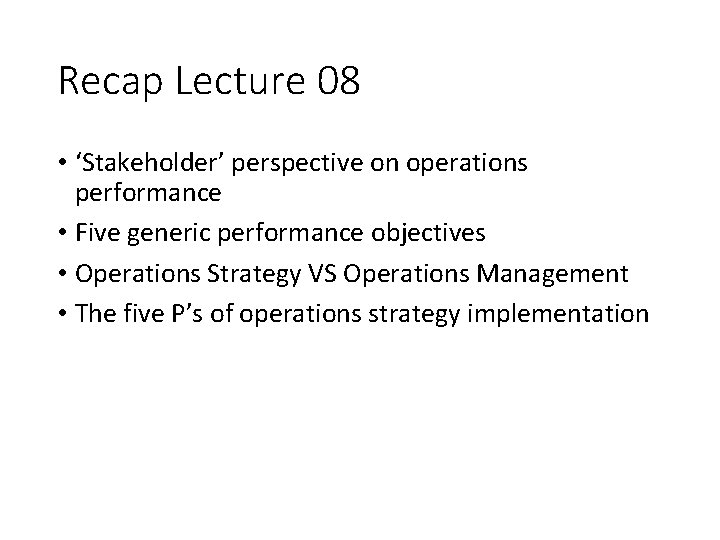
Recap Lecture 08 • ‘Stakeholder’ perspective on operations performance • Five generic performance objectives • Operations Strategy VS Operations Management • The five P’s of operations strategy implementation
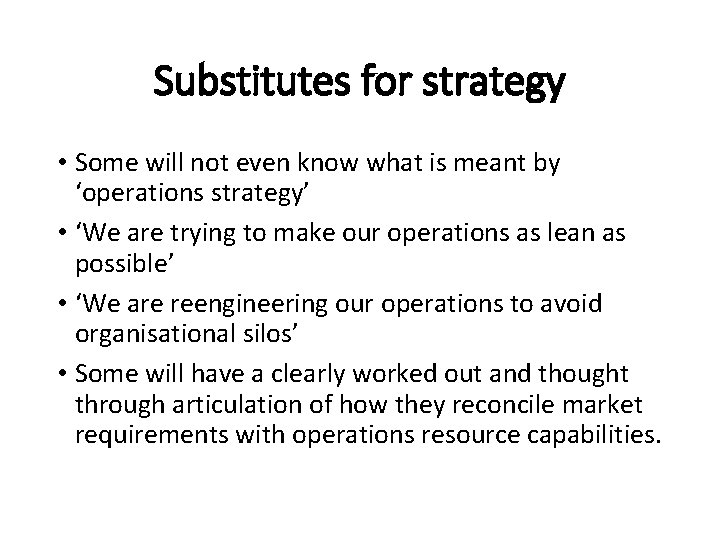
Substitutes for strategy • Some will not even know what is meant by ‘operations strategy’ • ‘We are trying to make our operations as lean as possible’ • ‘We are reengineering our operations to avoid organisational silos’ • Some will have a clearly worked out and thought through articulation of how they reconcile market requirements with operations resource capabilities.
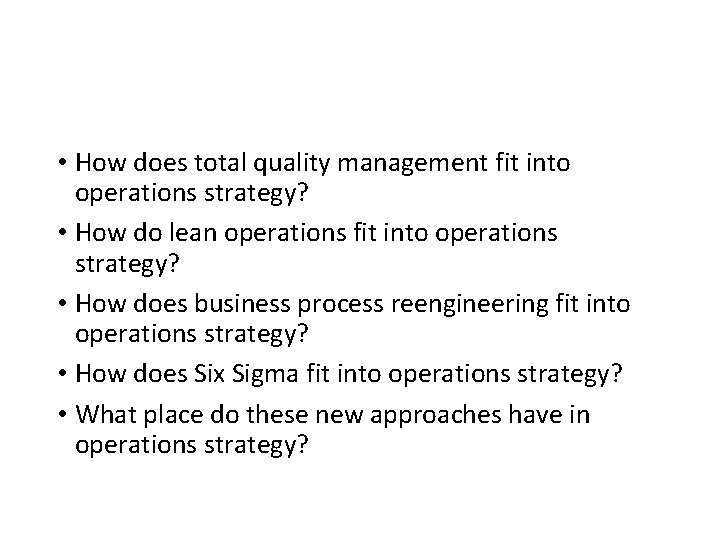
• How does total quality management fit into operations strategy? • How do lean operations fit into operations strategy? • How does business process reengineering fit into operations strategy? • How does Six Sigma fit into operations strategy? • What place do these new approaches have in operations strategy?
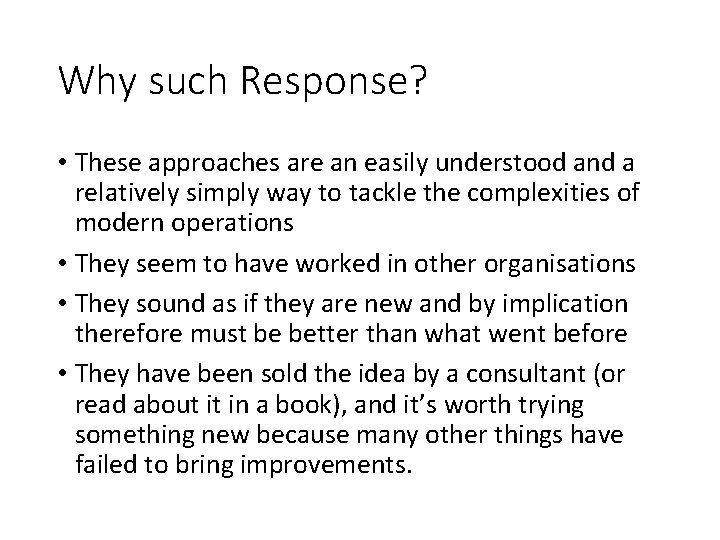
Why such Response? • These approaches are an easily understood and a relatively simply way to tackle the complexities of modern operations • They seem to have worked in other organisations • They sound as if they are new and by implication therefore must be better than what went before • They have been sold the idea by a consultant (or read about it in a book), and it’s worth trying something new because many other things have failed to bring improvements.
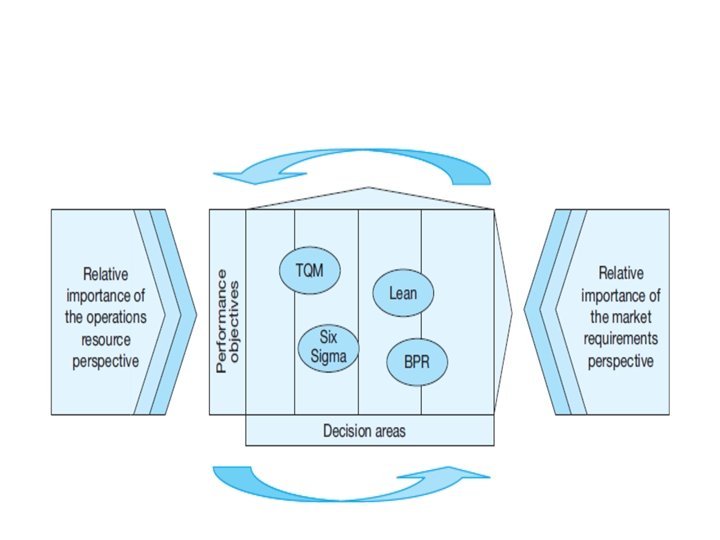
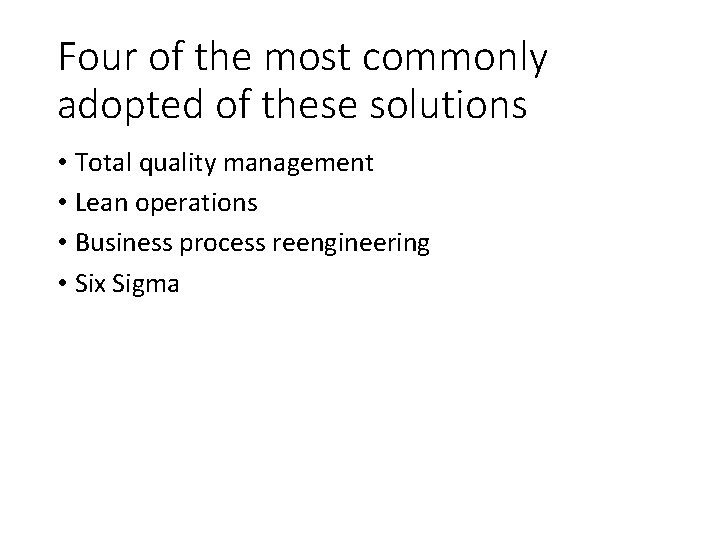
Four of the most commonly adopted of these solutions • Total quality management • Lean operations • Business process reengineering • Six Sigma
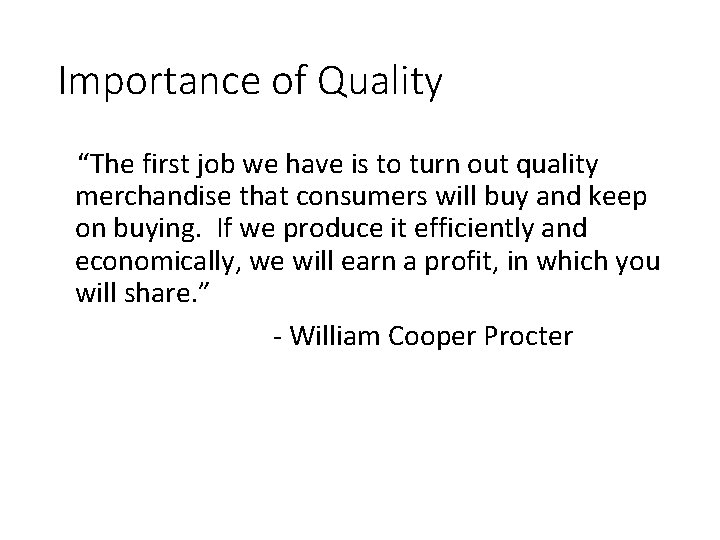
Importance of Quality “The first job we have is to turn out quality merchandise that consumers will buy and keep on buying. If we produce it efficiently and economically, we will earn a profit, in which you will share. ” - William Cooper Procter
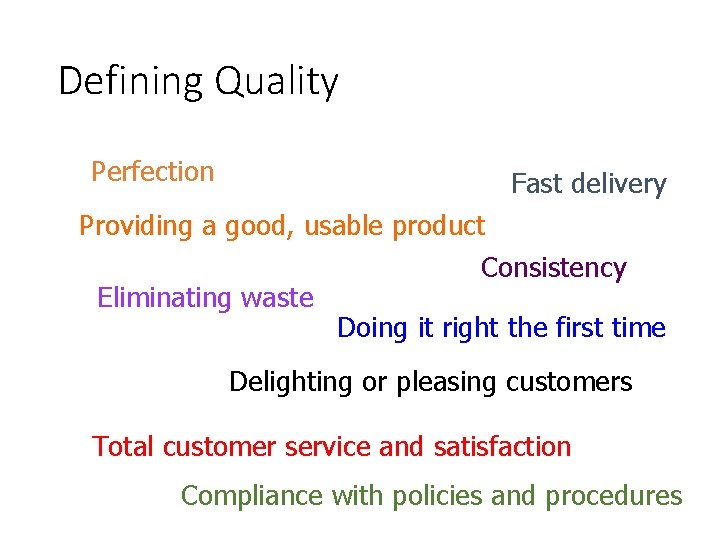
Defining Quality Perfection Fast delivery Providing a good, usable product Eliminating waste Consistency Doing it right the first time Delighting or pleasing customers Total customer service and satisfaction Compliance with policies and procedures
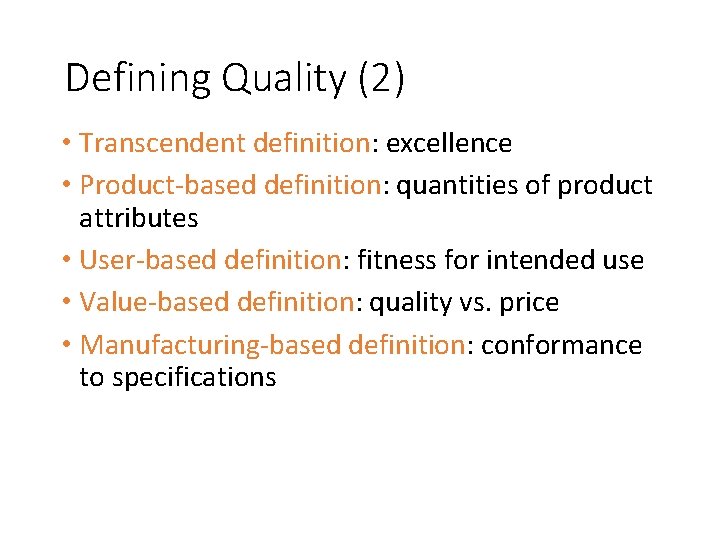
Defining Quality (2) • Transcendent definition: excellence • Product-based definition: quantities of product attributes • User-based definition: fitness for intended use • Value-based definition: quality vs. price • Manufacturing-based definition: conformance to specifications

Quality Definition • Broadly: Meeting or exceeding customer expectations now and in the future • Specifically: Dimensions of Quality • Design • Determined before the product is produced • Conformance • Producing a product to meet the specifications • “Abilities” • Availability, reliability, maintainability • Field Service • Promptness, competence, integrity
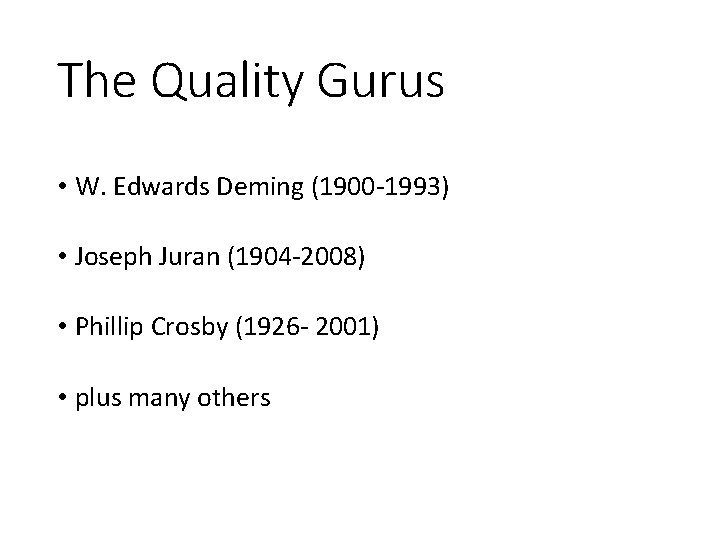
The Quality Gurus • W. Edwards Deming (1900 -1993) • Joseph Juran (1904 -2008) • Phillip Crosby (1926 - 2001) • plus many others
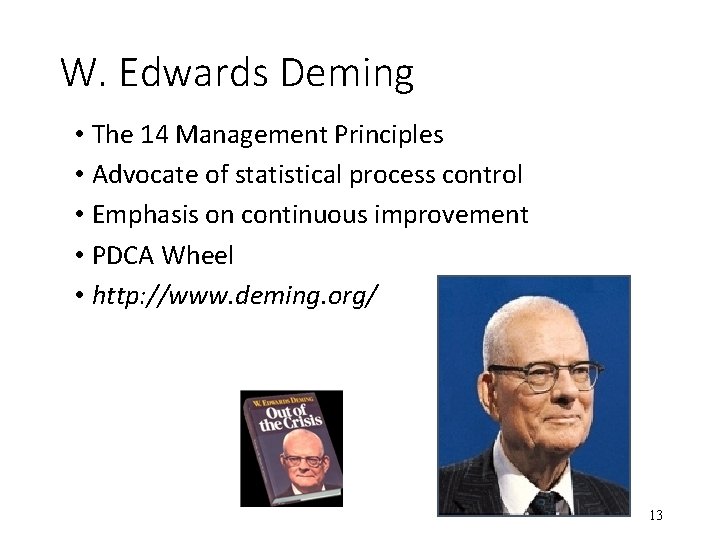
W. Edwards Deming • The 14 Management Principles • Advocate of statistical process control • Emphasis on continuous improvement • PDCA Wheel • http: //www. deming. org/ 13
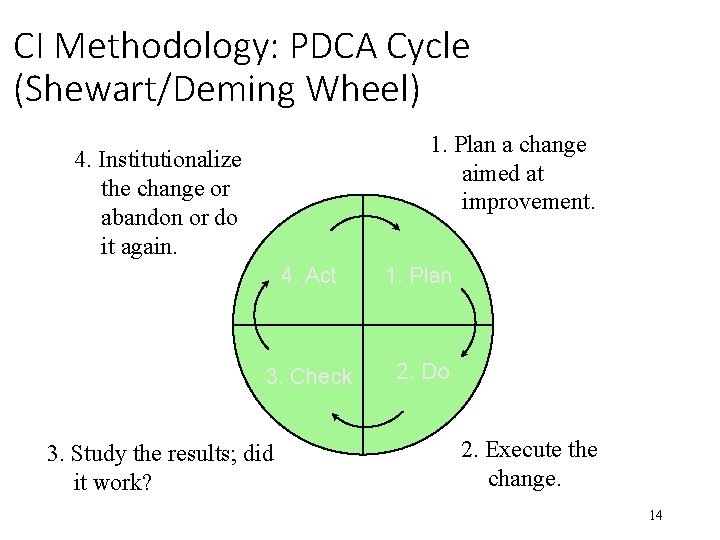
CI Methodology: PDCA Cycle (Shewart/Deming Wheel) 1. Plan a change aimed at improvement. 4. Institutionalize the change or abandon or do it again. 4. Act 1. Plan 3. Check 2. Do 3. Study the results; did it work? 2. Execute the change. 14
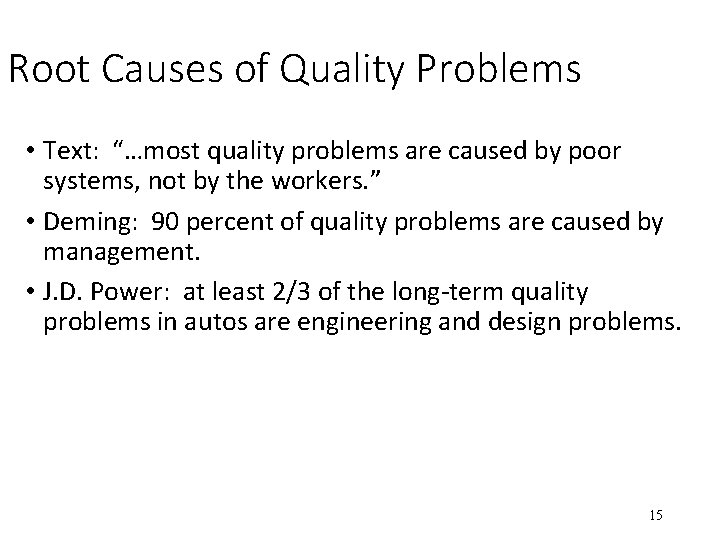
Root Causes of Quality Problems • Text: “…most quality problems are caused by poor systems, not by the workers. ” • Deming: 90 percent of quality problems are caused by management. • J. D. Power: at least 2/3 of the long-term quality problems in autos are engineering and design problems. 15
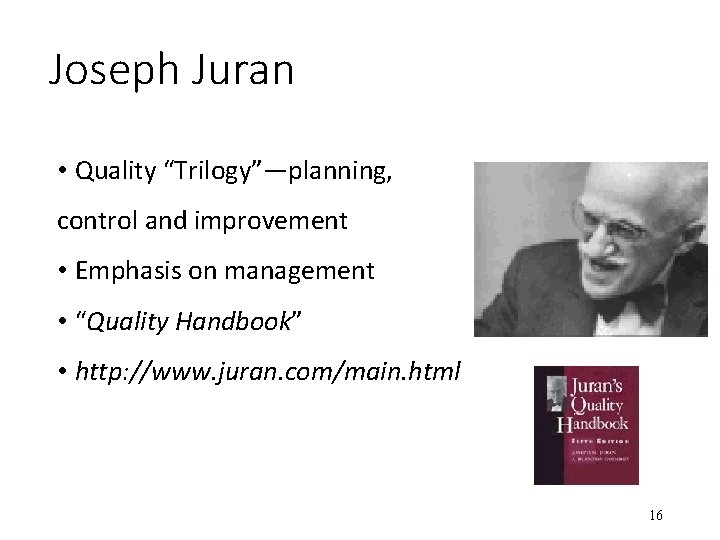
Joseph Juran • Quality “Trilogy”—planning, control and improvement • Emphasis on management • “Quality Handbook” • http: //www. juran. com/main. html 16
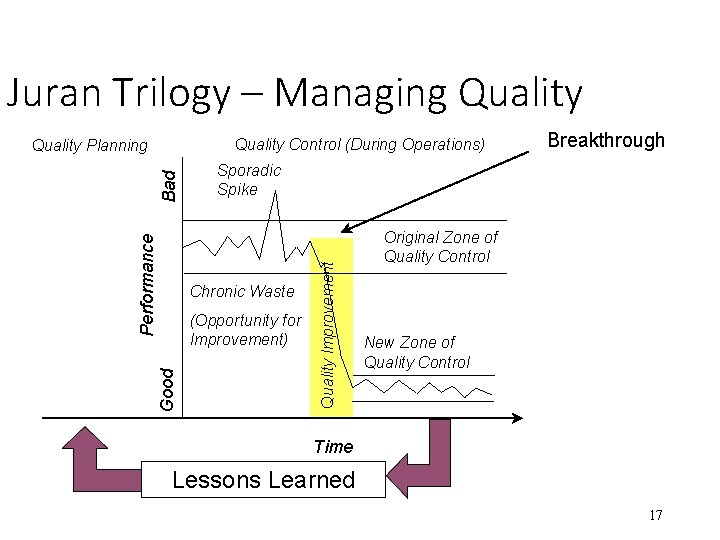
Juran Trilogy – Managing Quality Control (During Operations) Chronic Waste (Opportunity for Improvement) Good Breakthrough Sporadic Spike Quality Improvement Performance Bad Quality Planning Original Zone of Quality Control New Zone of Quality Control Time Lessons Learned 17
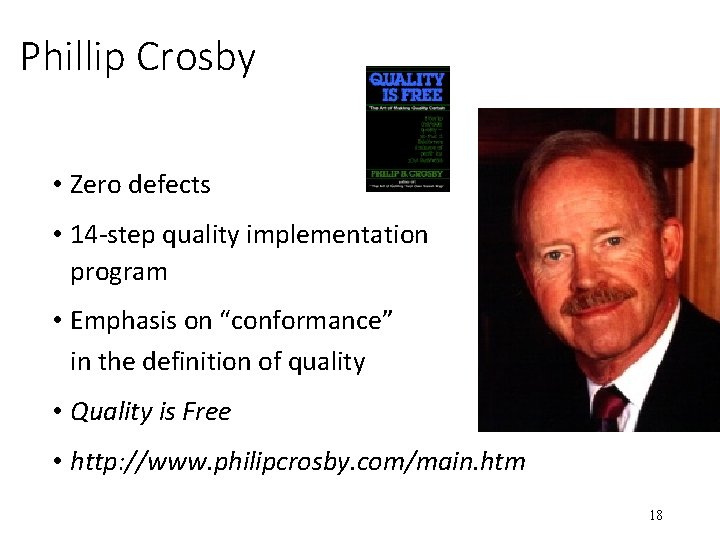
Phillip Crosby • Zero defects • 14 -step quality implementation program • Emphasis on “conformance” in the definition of quality • Quality is Free • http: //www. philipcrosby. com/main. htm 18
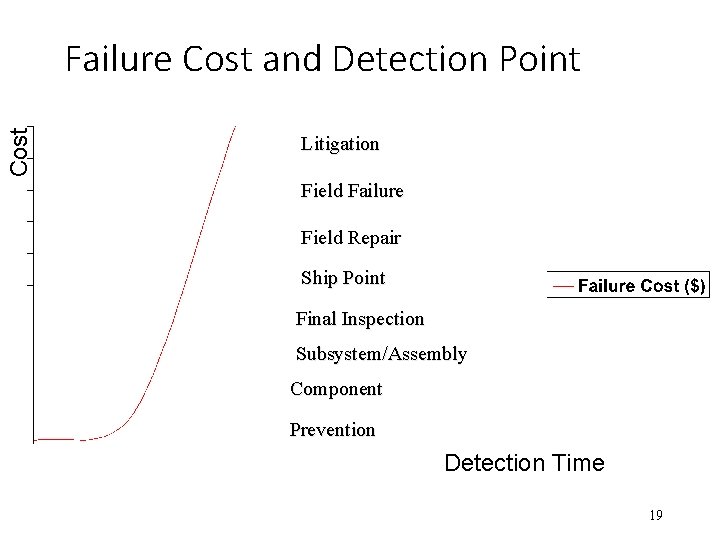
Cost Failure Cost and Detection Point Litigation Field Failure Field Repair Ship Point Final Inspection Subsystem/Assembly Component Prevention Detection Time 19
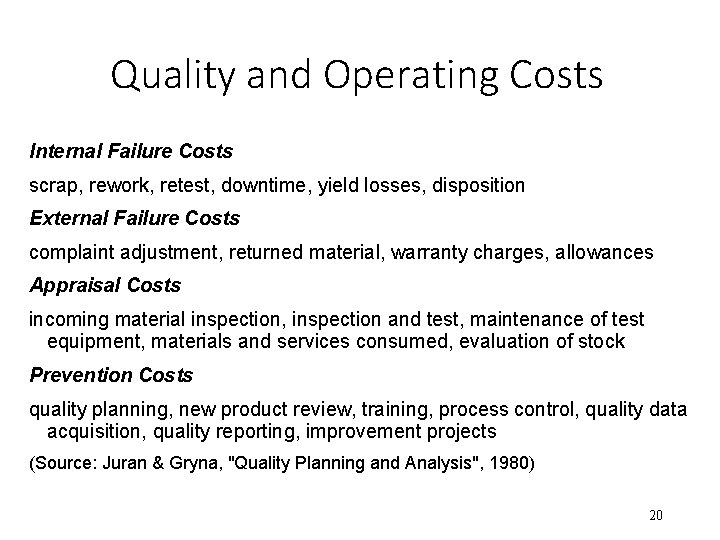
Quality and Operating Costs Internal Failure Costs scrap, rework, retest, downtime, yield losses, disposition External Failure Costs complaint adjustment, returned material, warranty charges, allowances Appraisal Costs incoming material inspection, inspection and test, maintenance of test equipment, materials and services consumed, evaluation of stock Prevention Costs quality planning, new product review, training, process control, quality data acquisition, quality reporting, improvement projects (Source: Juran & Gryna, "Quality Planning and Analysis", 1980) 20
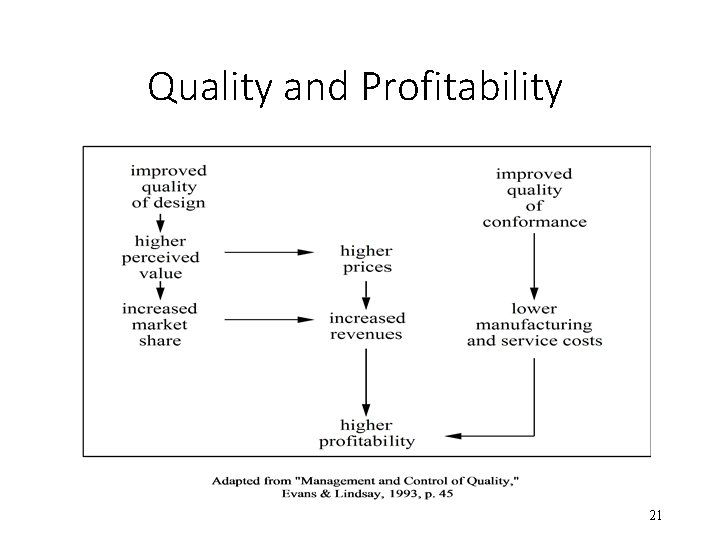
Quality and Profitability 21
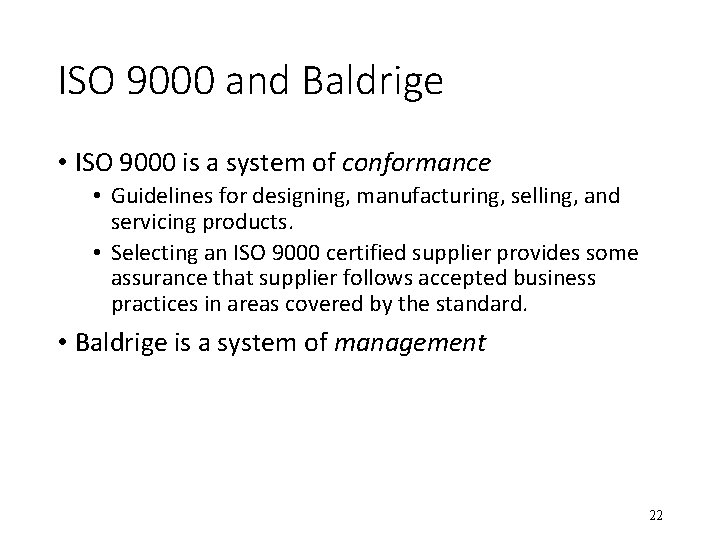
ISO 9000 and Baldrige • ISO 9000 is a system of conformance • Guidelines for designing, manufacturing, selling, and servicing products. • Selecting an ISO 9000 certified supplier provides some assurance that supplier follows accepted business practices in areas covered by the standard. • Baldrige is a system of management 22
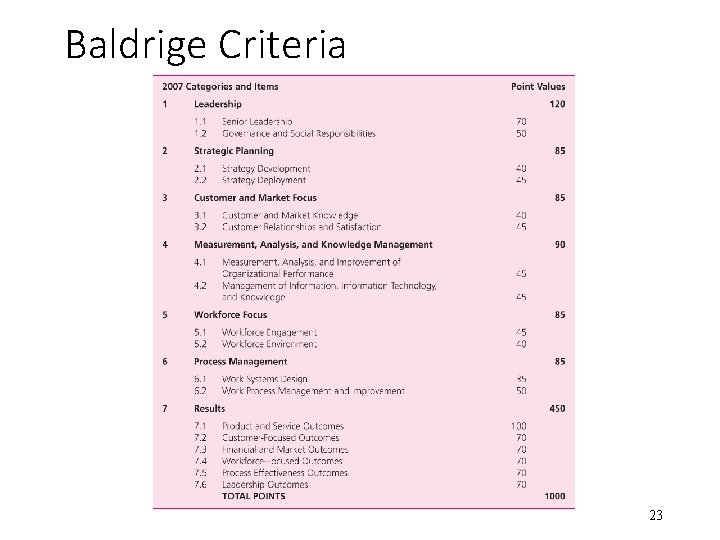
Baldrige Criteria 23
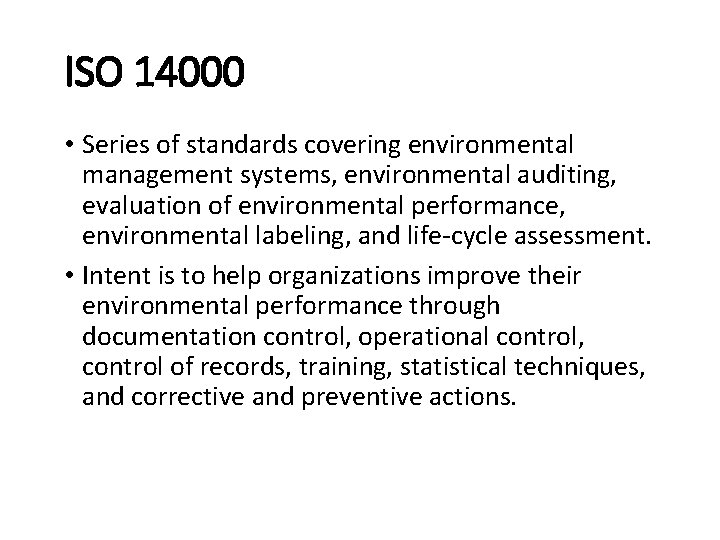
ISO 14000 • Series of standards covering environmental management systems, environmental auditing, evaluation of environmental performance, environmental labeling, and life-cycle assessment. • Intent is to help organizations improve their environmental performance through documentation control, operational control, control of records, training, statistical techniques, and corrective and preventive actions.
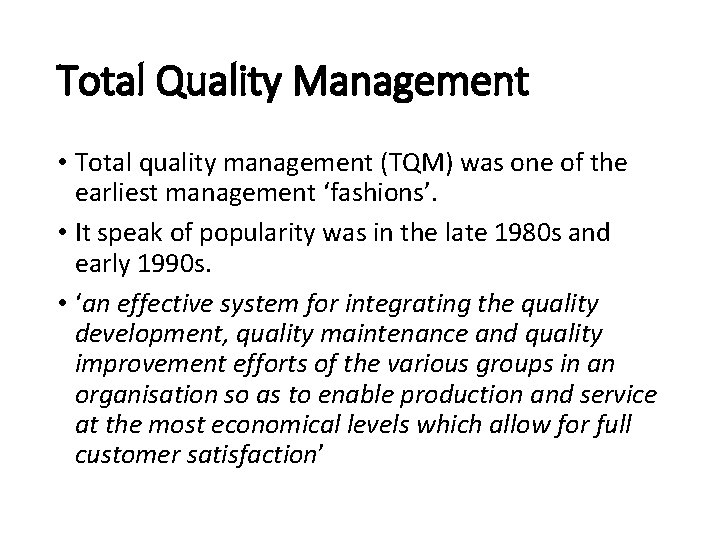
Total Quality Management • Total quality management (TQM) was one of the earliest management ‘fashions’. • It speak of popularity was in the late 1980 s and early 1990 s. • ‘an effective system for integrating the quality development, quality maintenance and quality improvement efforts of the various groups in an organisation so as to enable production and service at the most economical levels which allow for full customer satisfaction’
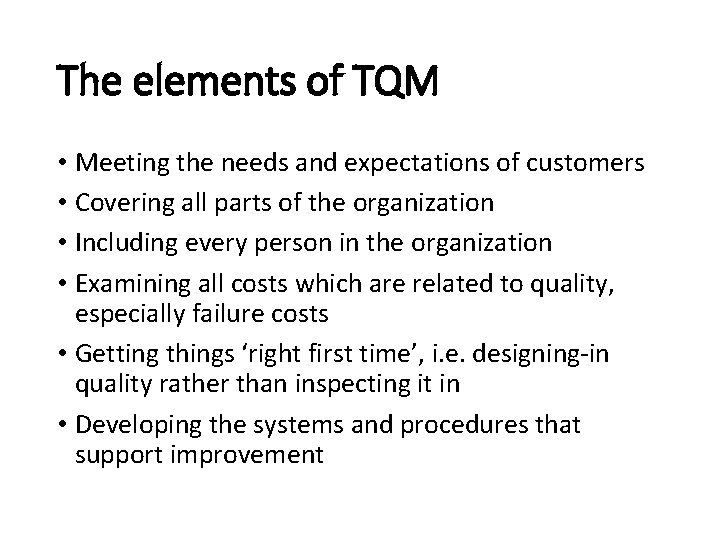
The elements of TQM • Meeting the needs and expectations of customers • Covering all parts of the organization • Including every person in the organization • Examining all costs which are related to quality, especially failure costs • Getting things ‘right first time’, i. e. designing-in quality rather than inspecting it in • Developing the systems and procedures that support improvement
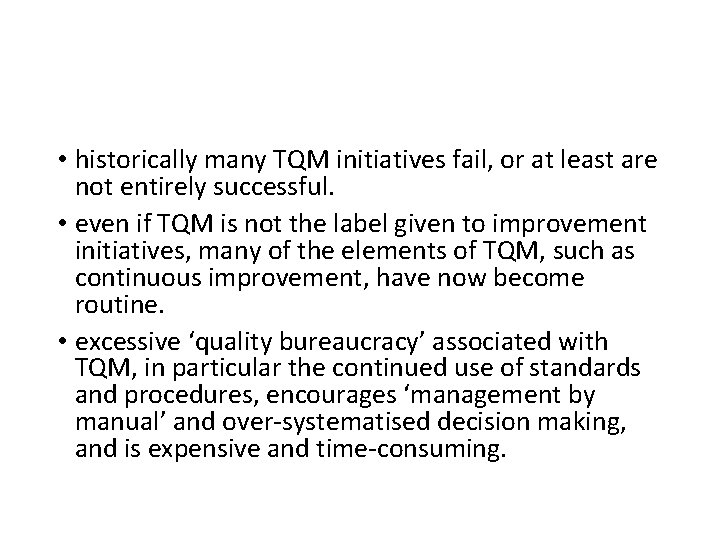
• historically many TQM initiatives fail, or at least are not entirely successful. • even if TQM is not the label given to improvement initiatives, many of the elements of TQM, such as continuous improvement, have now become routine. • excessive ‘quality bureaucracy’ associated with TQM, in particular the continued use of standards and procedures, encourages ‘management by manual’ and over-systematised decision making, and is expensive and time-consuming.
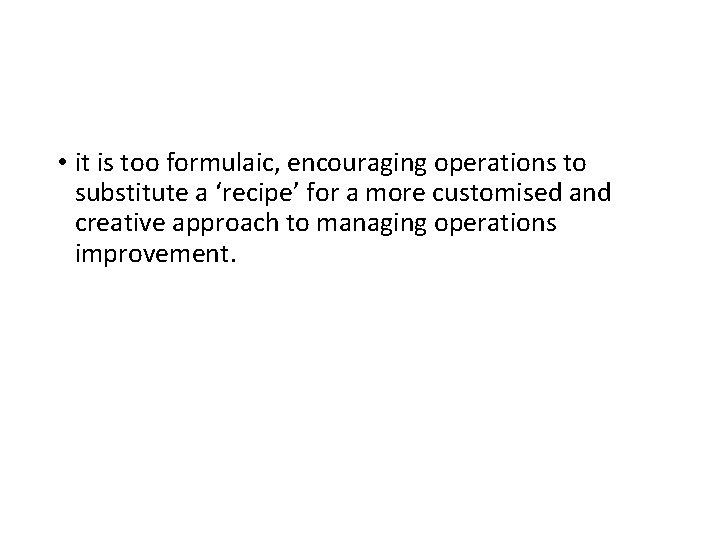
• it is too formulaic, encouraging operations to substitute a ‘recipe’ for a more customised and creative approach to managing operations improvement.
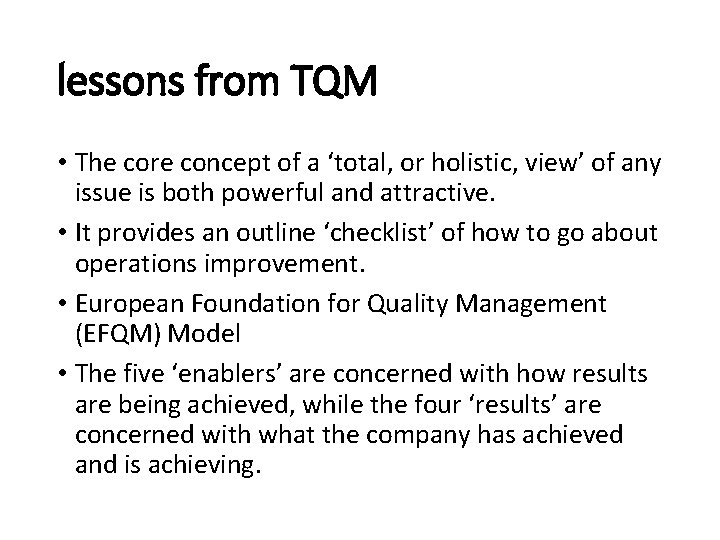
lessons from TQM • The core concept of a ‘total, or holistic, view’ of any issue is both powerful and attractive. • It provides an outline ‘checklist’ of how to go about operations improvement. • European Foundation for Quality Management (EFQM) Model • The five ‘enablers’ are concerned with how results are being achieved, while the four ‘results’ are concerned with what the company has achieved and is achieving.
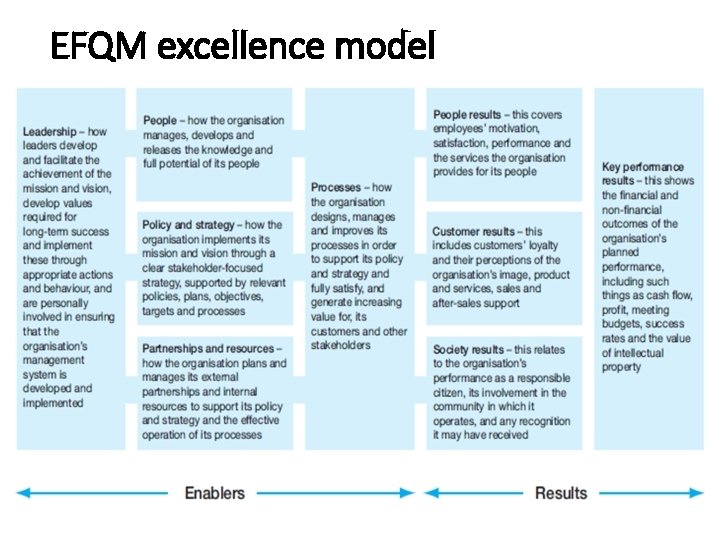
EFQM excellence model
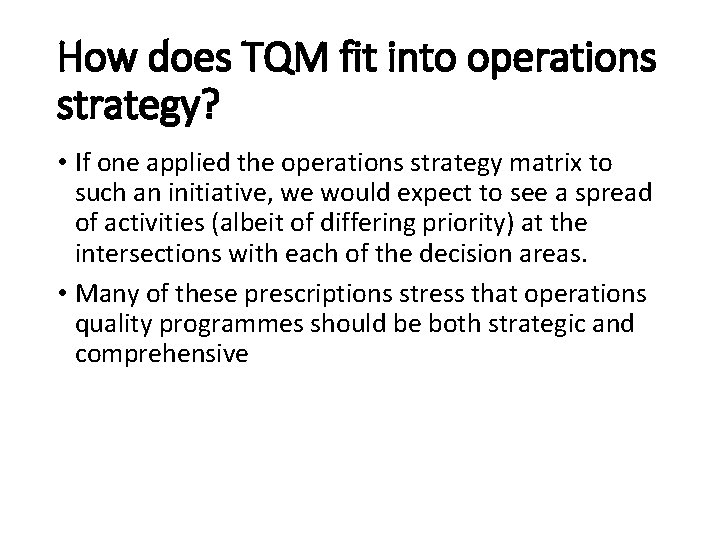
How does TQM fit into operations strategy? • If one applied the operations strategy matrix to such an initiative, we would expect to see a spread of activities (albeit of differing priority) at the intersections with each of the decision areas. • Many of these prescriptions stress that operations quality programmes should be both strategic and comprehensive
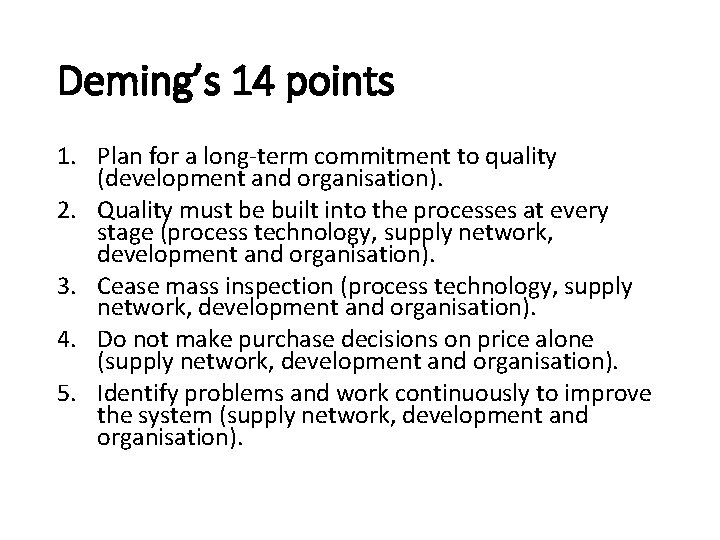
Deming’s 14 points 1. Plan for a long-term commitment to quality (development and organisation). 2. Quality must be built into the processes at every stage (process technology, supply network, development and organisation). 3. Cease mass inspection (process technology, supply network, development and organisation). 4. Do not make purchase decisions on price alone (supply network, development and organisation). 5. Identify problems and work continuously to improve the system (supply network, development and organisation).
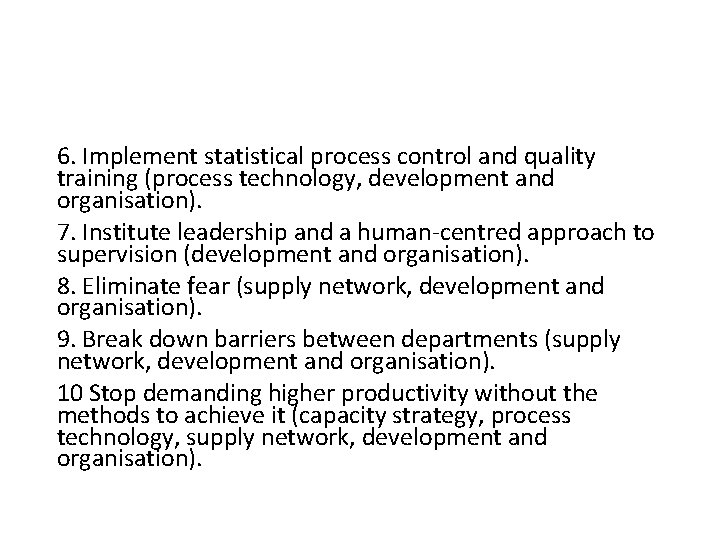
6. Implement statistical process control and quality training (process technology, development and organisation). 7. Institute leadership and a human-centred approach to supervision (development and organisation). 8. Eliminate fear (supply network, development and organisation). 9. Break down barriers between departments (supply network, development and organisation). 10 Stop demanding higher productivity without the methods to achieve it (capacity strategy, process technology, supply network, development and organisation).
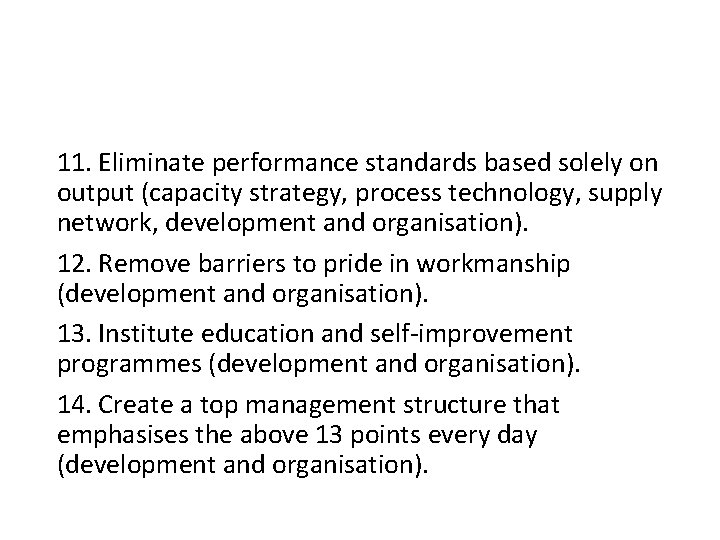
11. Eliminate performance standards based solely on output (capacity strategy, process technology, supply network, development and organisation). 12. Remove barriers to pride in workmanship (development and organisation). 13. Institute education and self-improvement programmes (development and organisation). 14. Create a top management structure that emphasises the above 13 points every day (development and organisation).
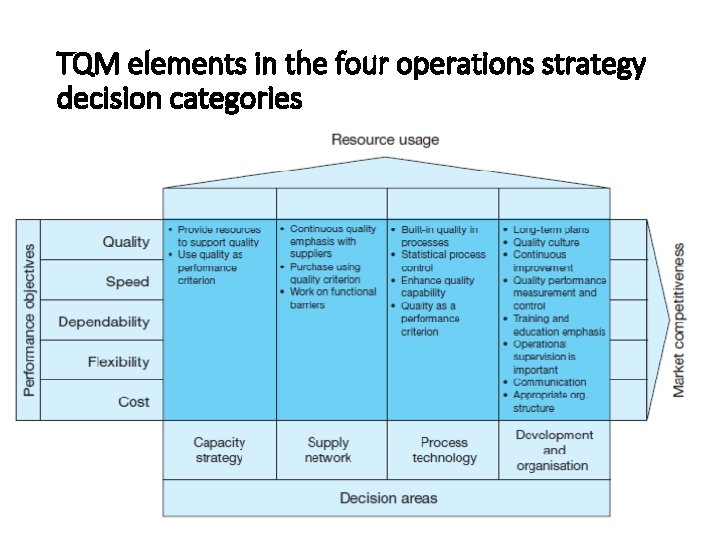
TQM elements in the four operations strategy decision categories
Aneel salman
Aneel salman
Aneel salman
Natural gender
Cs 563 uiuc
563 b.c
563 bc
Vajarayana
Aneel
Maralfalfa seed
Iasc aneel
Citenel
Aneel
Qrt aneel
Audincia
Aneel karnani
S3a aneel
Aneel
Saad azhar saeed ucp
Deque salman
Salman arain md
Nuran salman
Dr muhammad salman
Salman ahmad awan
Deque salman
Idrees farooq fiverr
Entrepre meaning
Ahmed salman rushdie
Salman rudhdie
Sinan salman
Dr mahmoud salman
Salman azhar
Salman avestimehr
Mirza salman baig
Salman hukuk
Example of process strategy