Manual Handling Training ADEs 1 Key Principles Manual
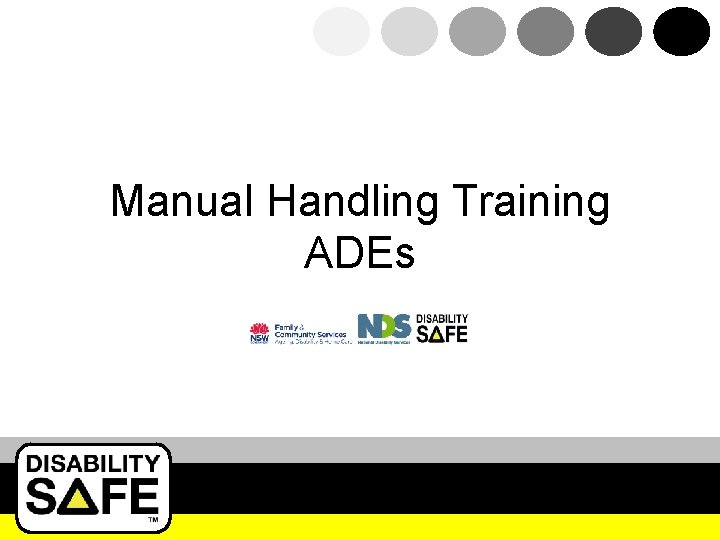
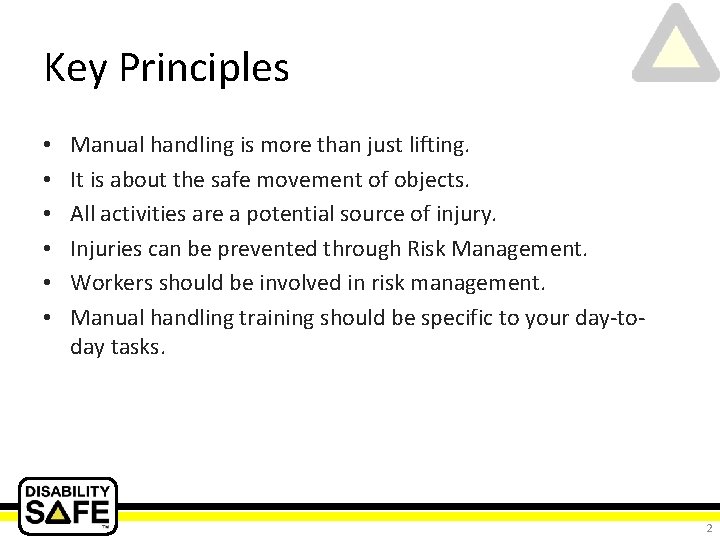
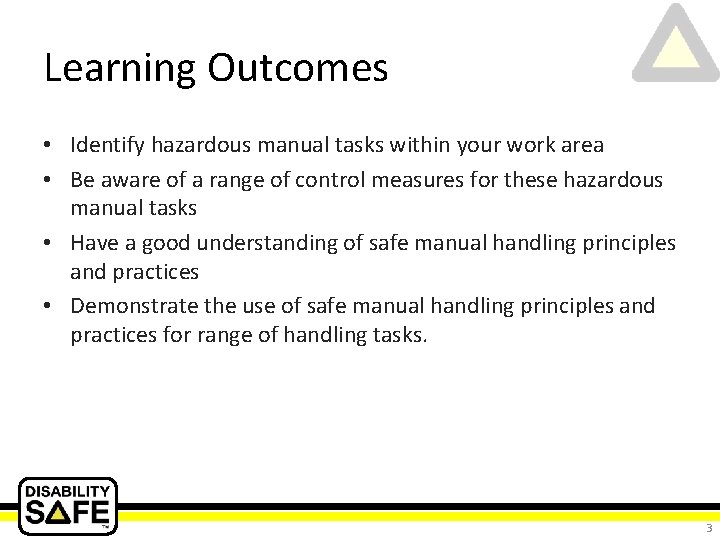
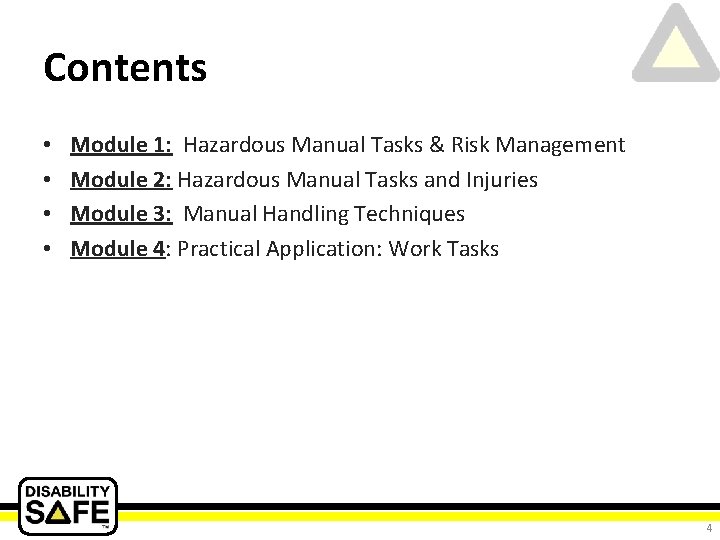
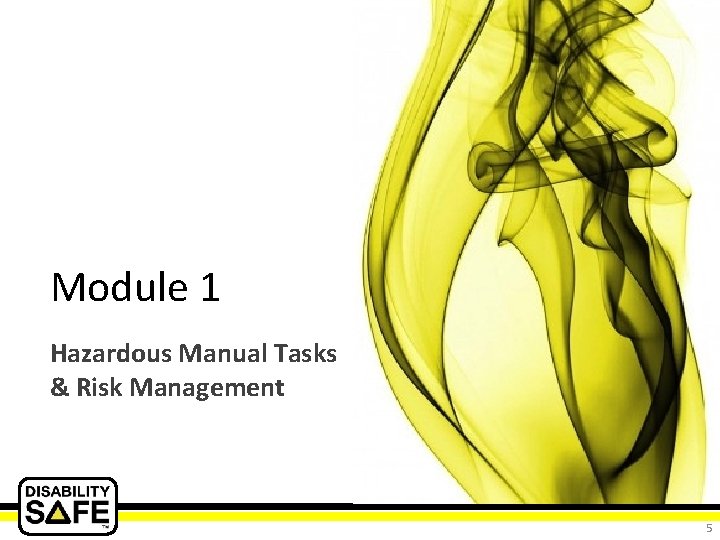
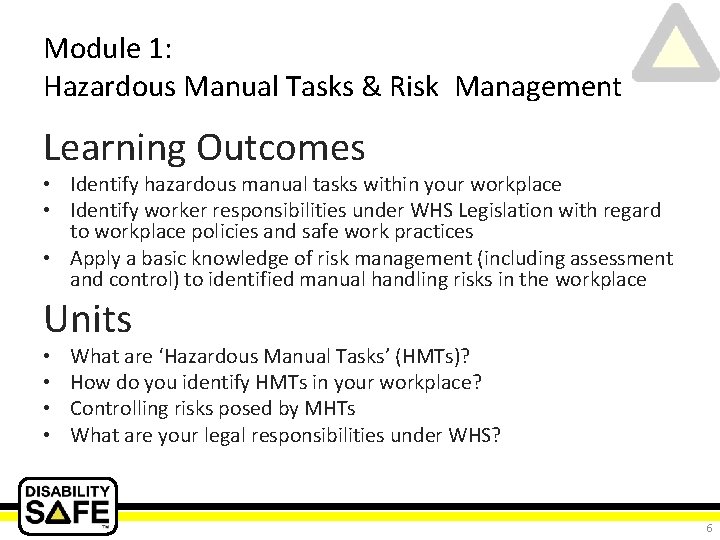
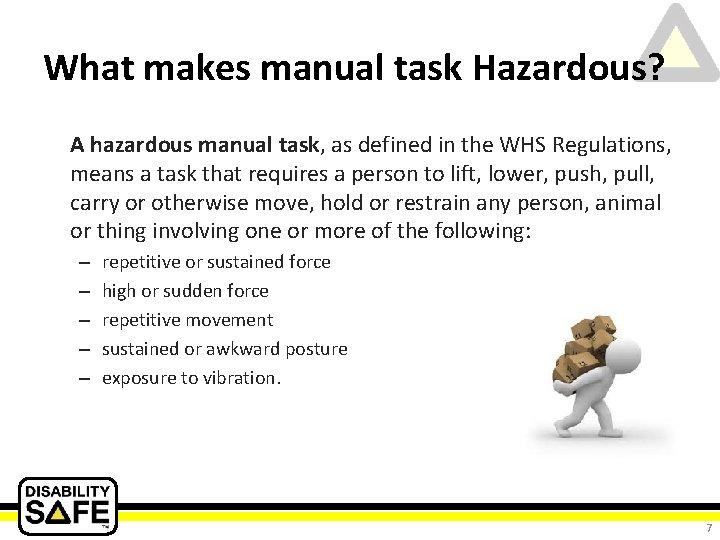
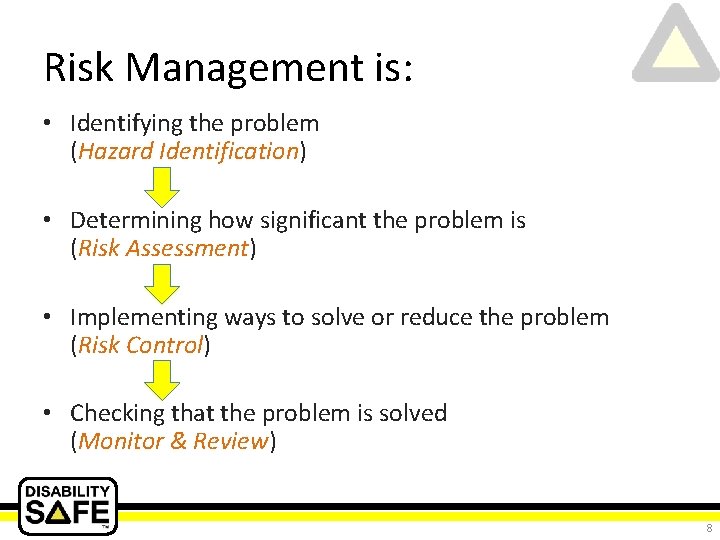
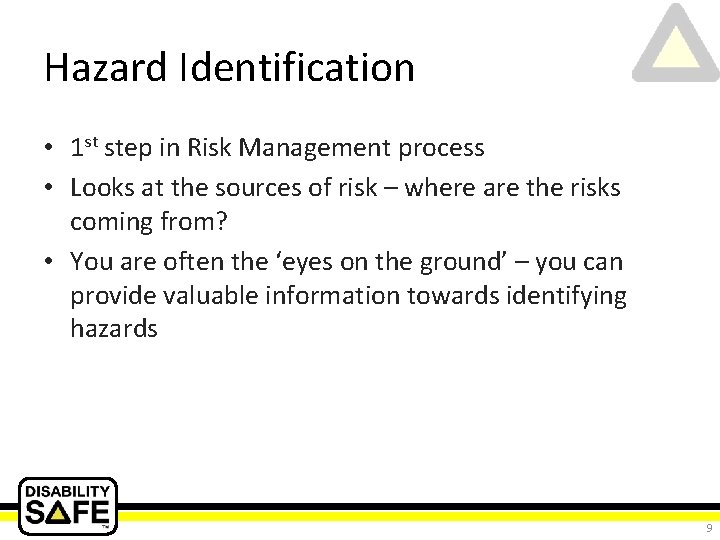
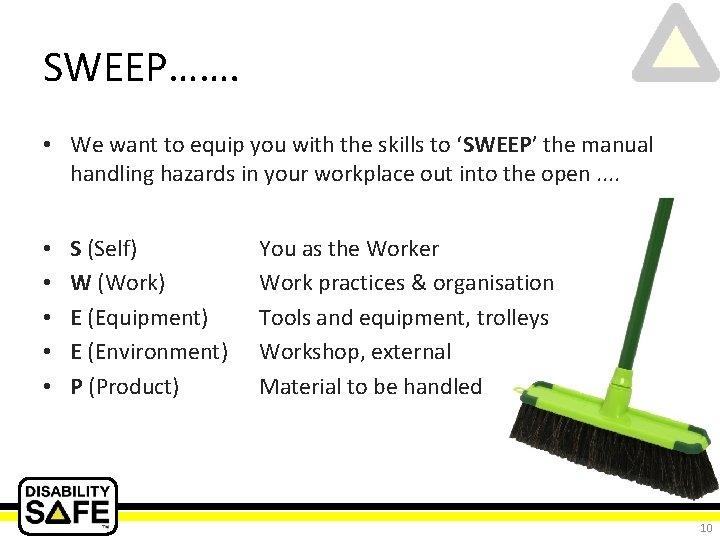
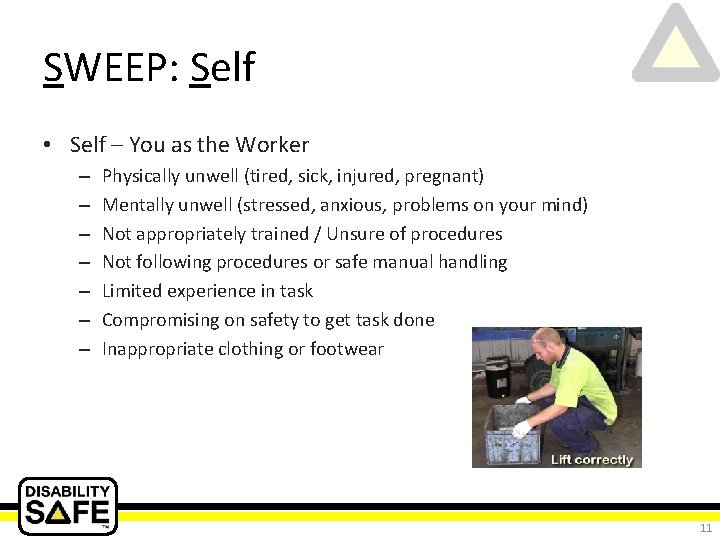
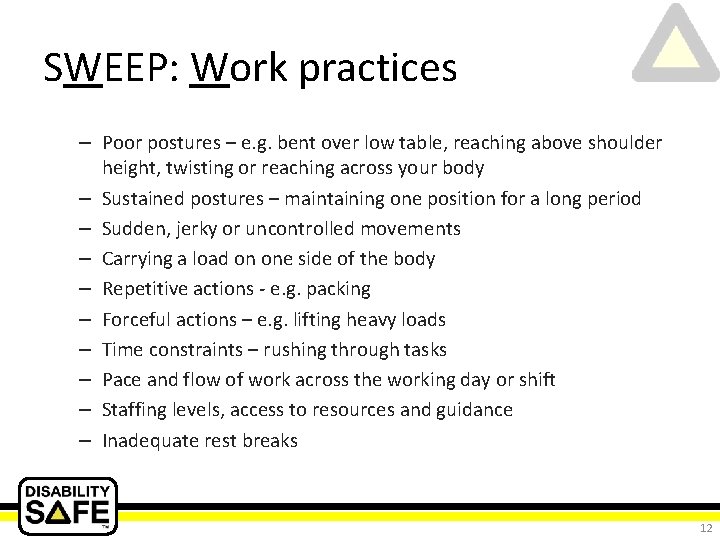
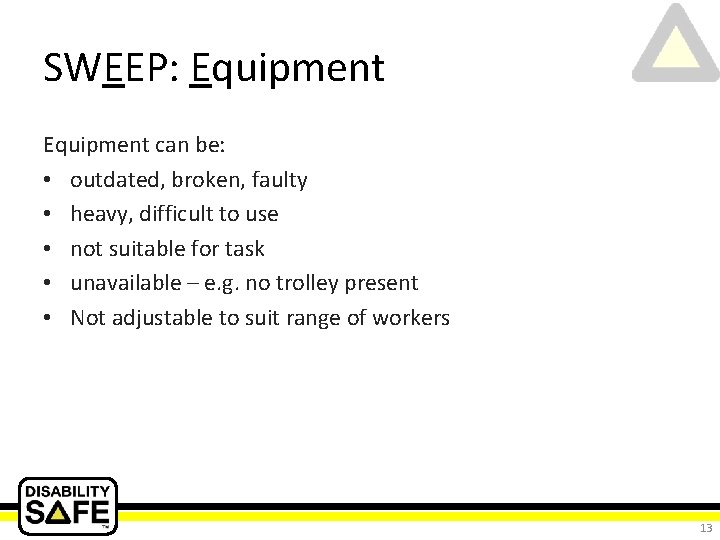
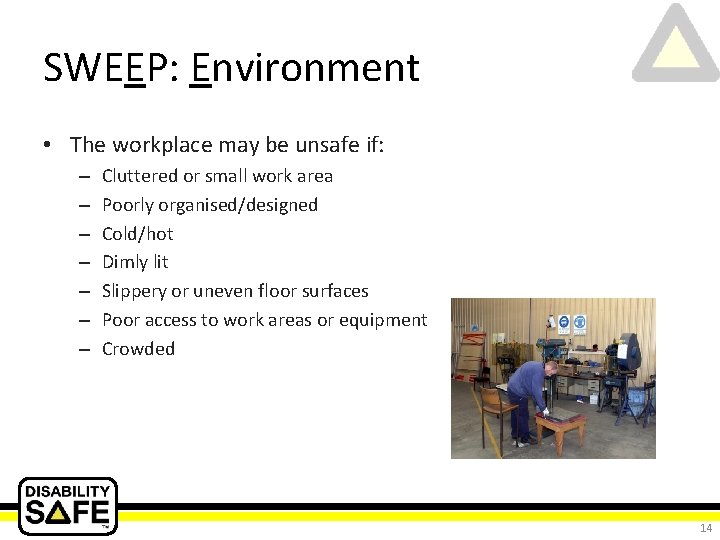
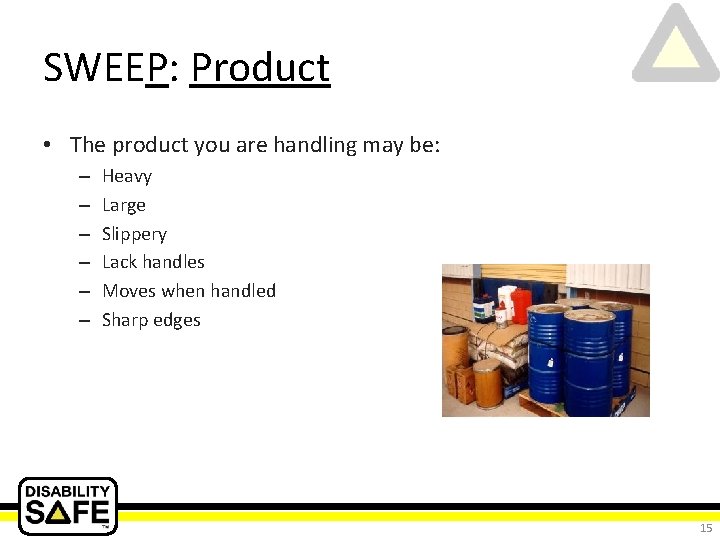
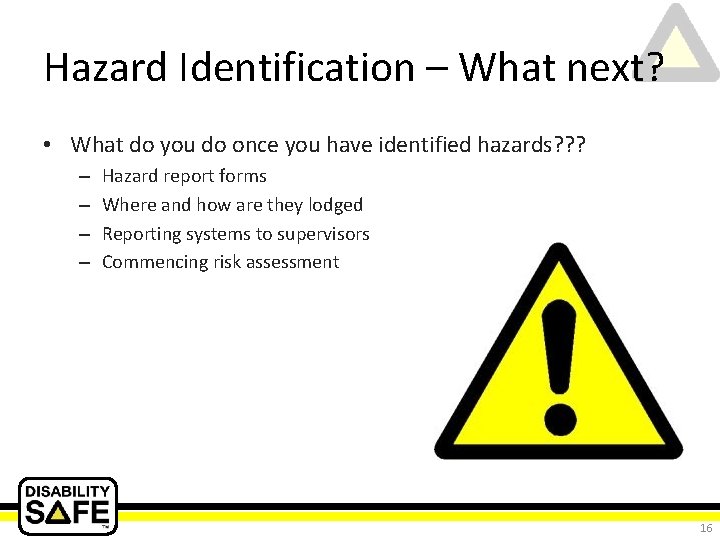
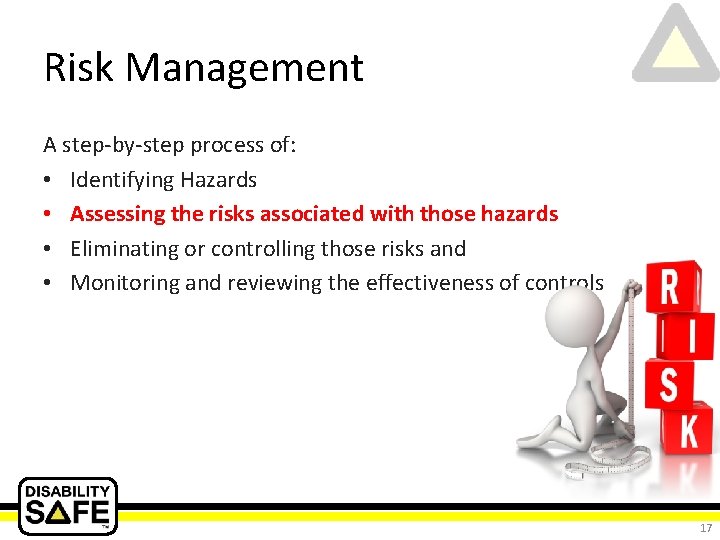
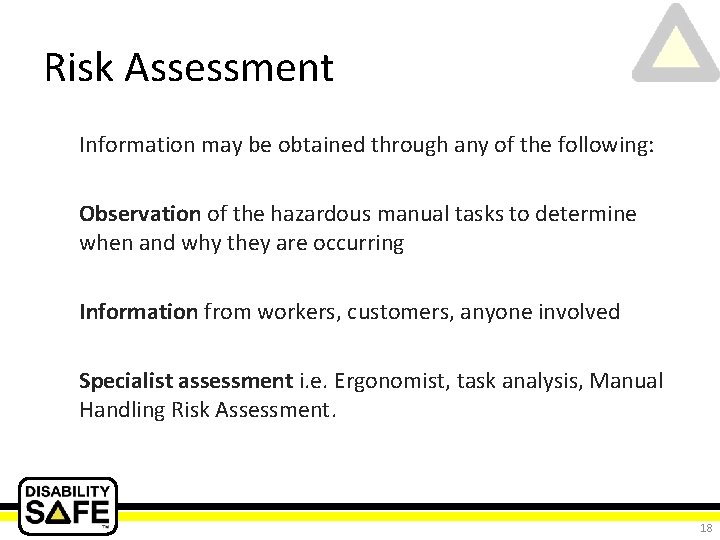
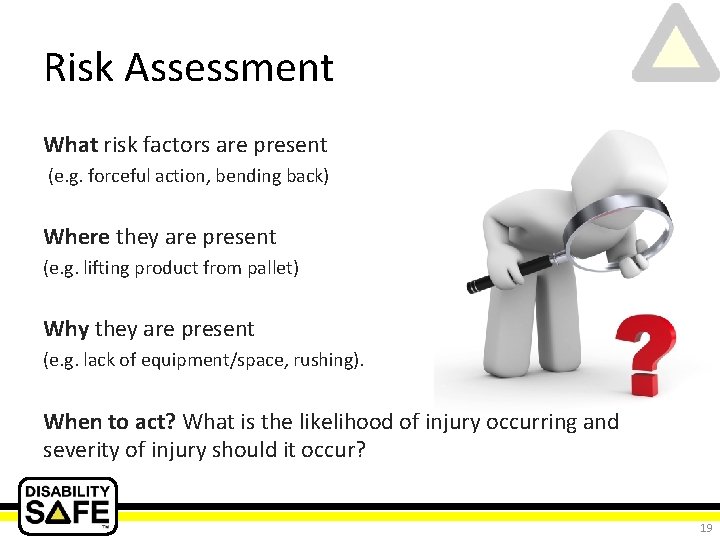
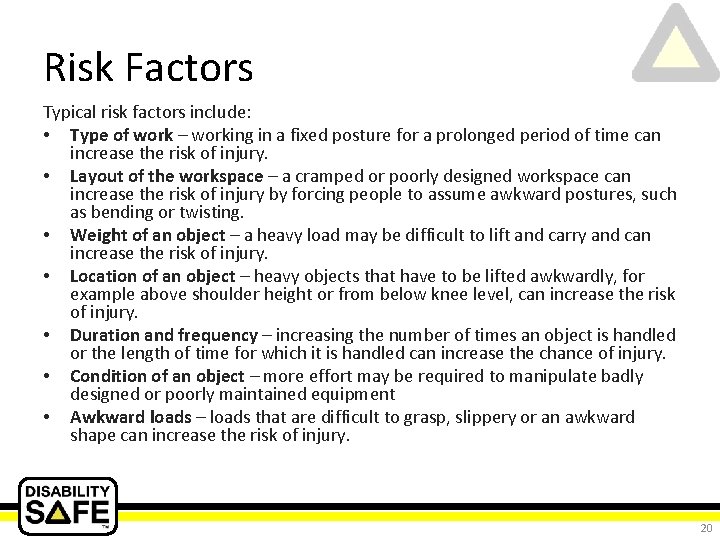
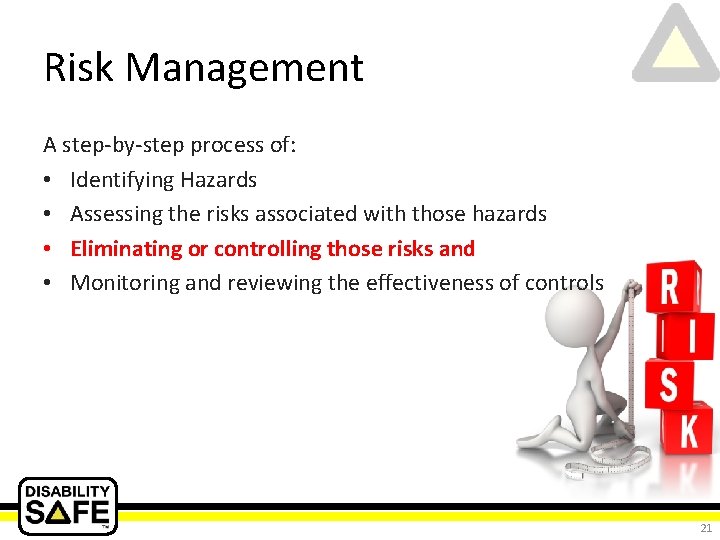
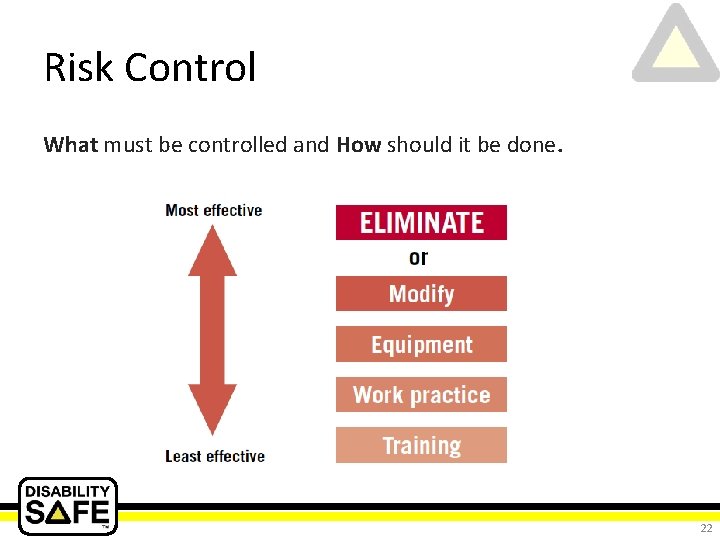
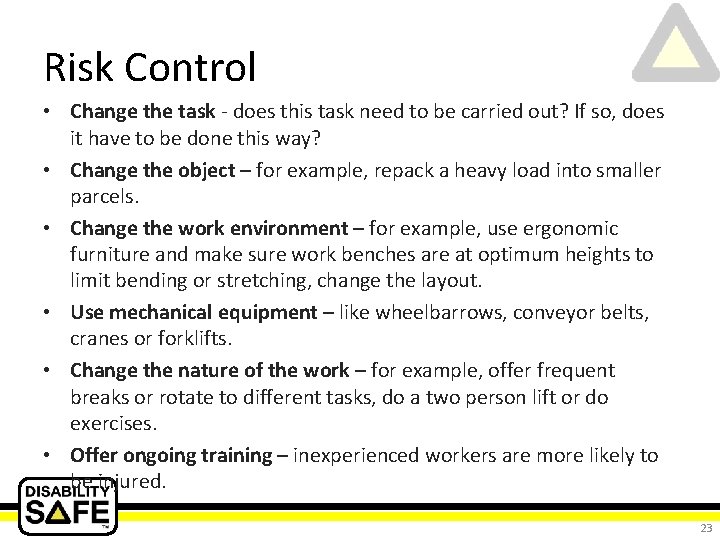
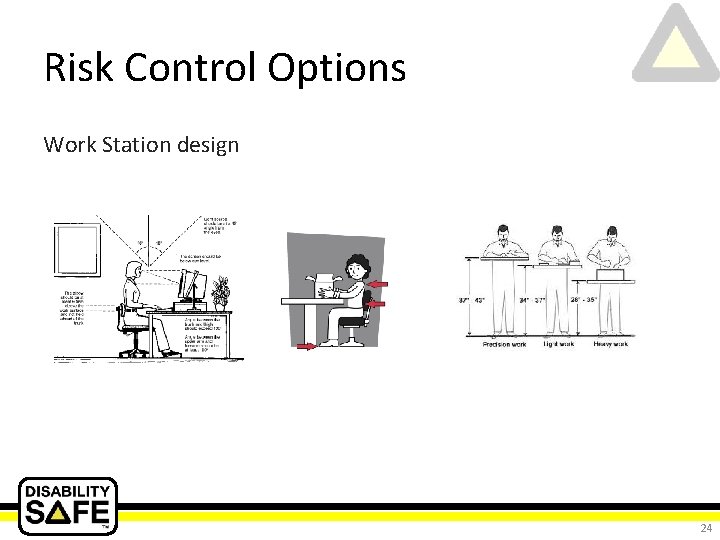
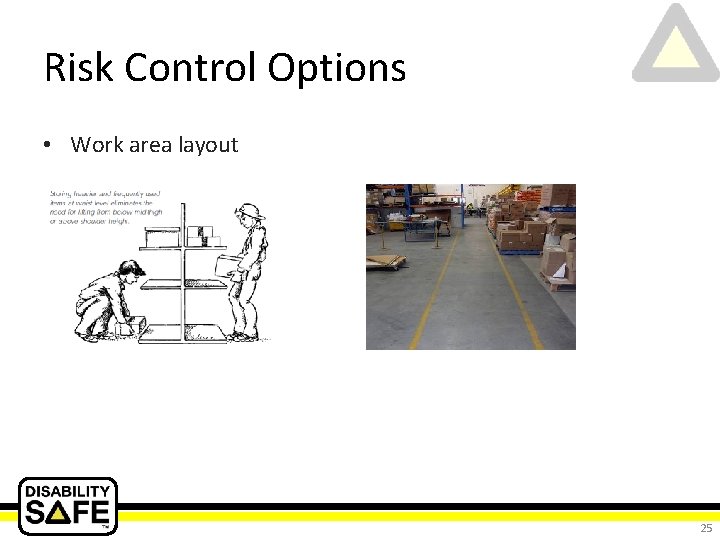
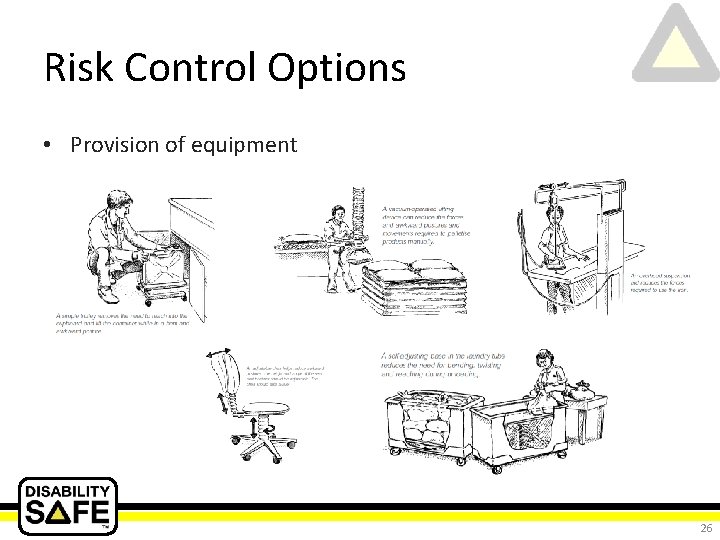
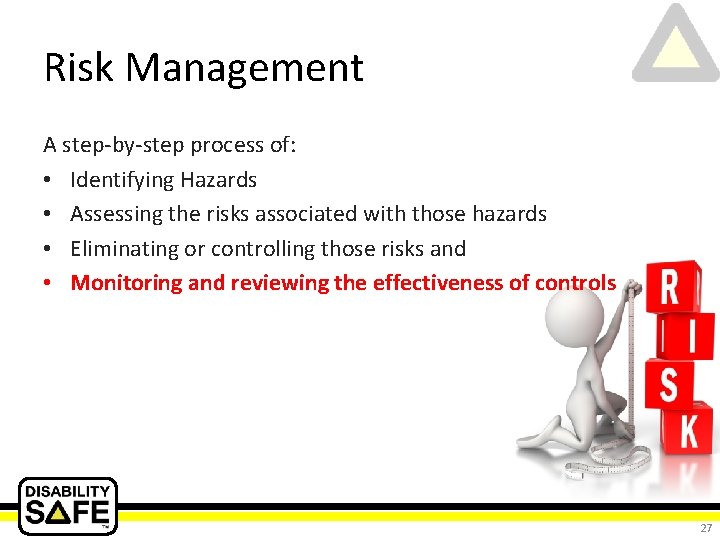
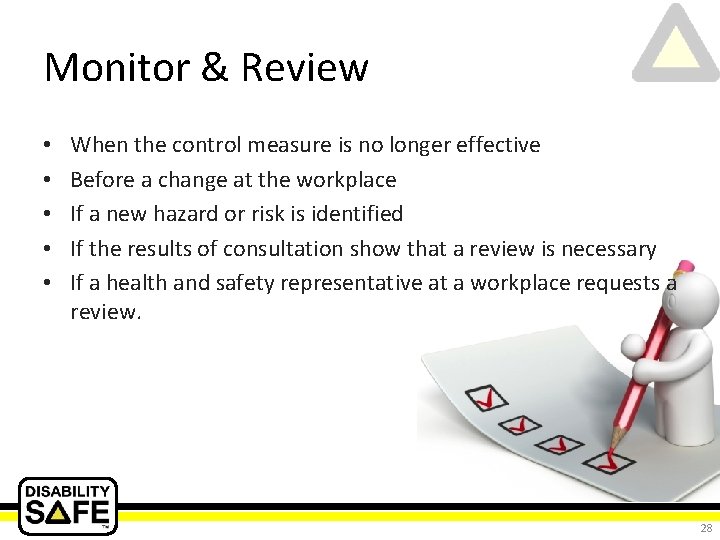
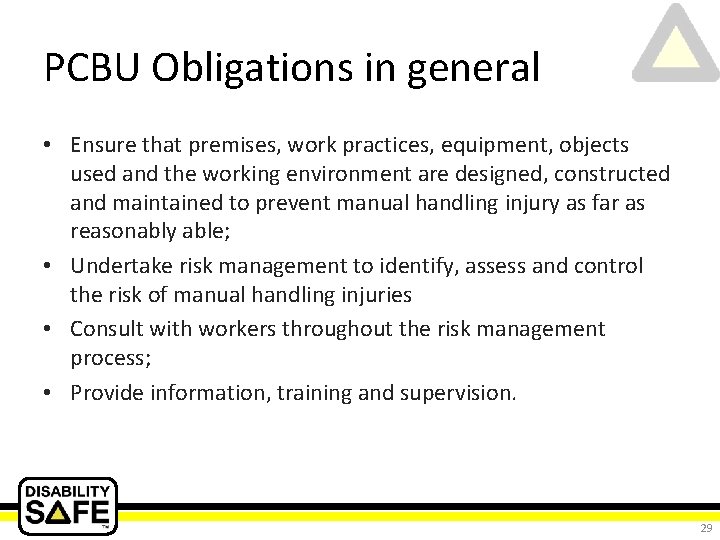
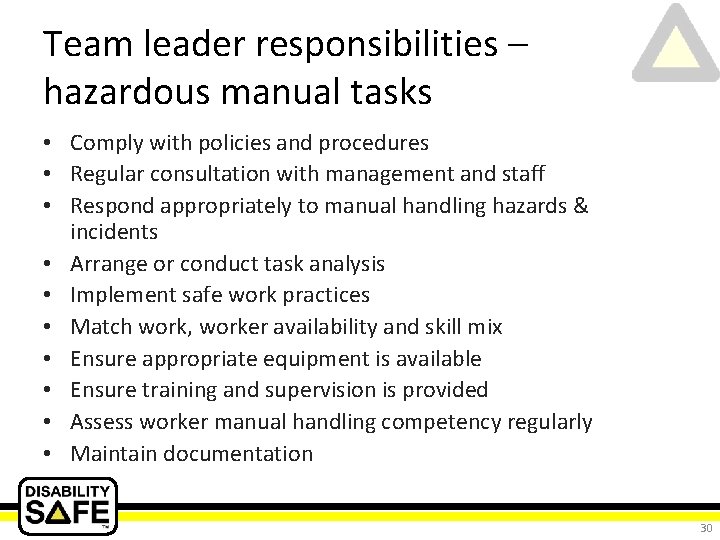
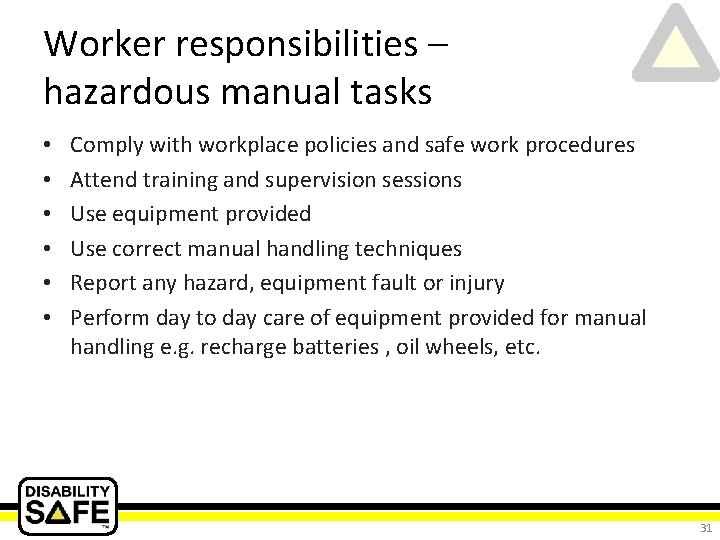
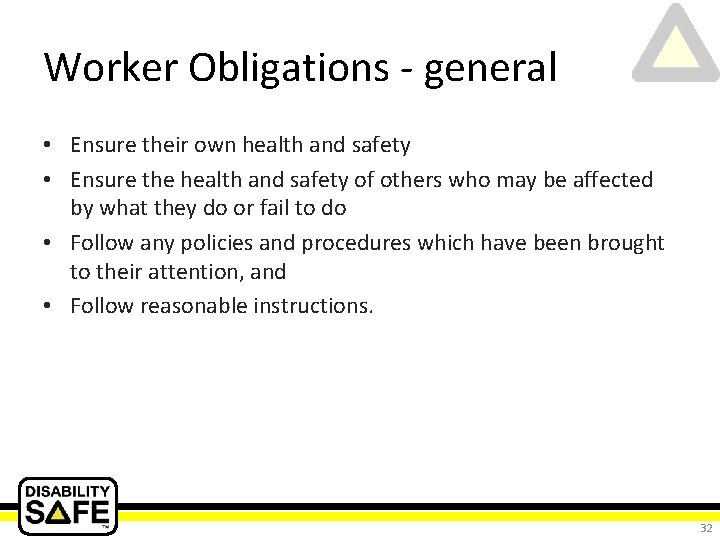
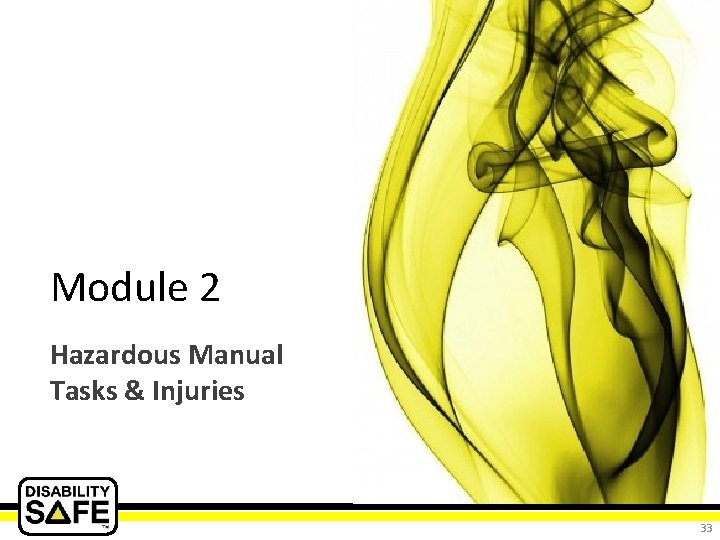
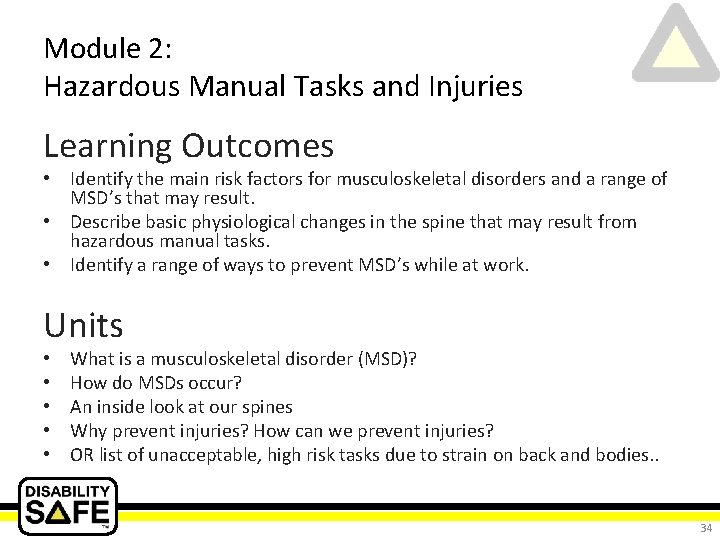
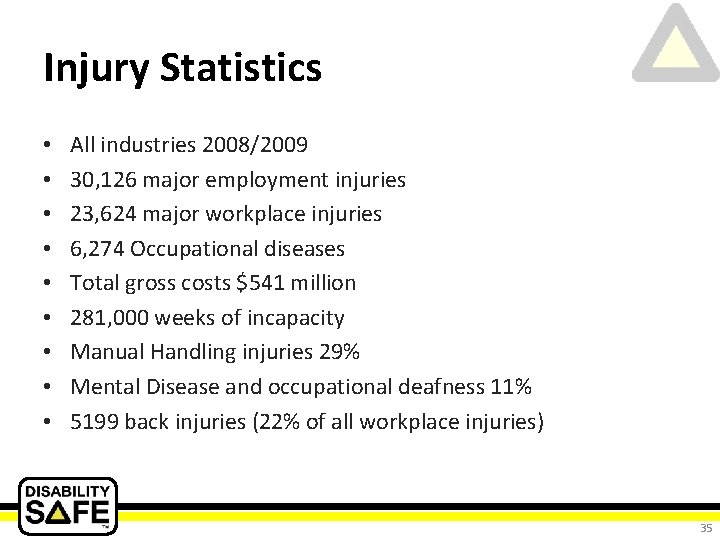
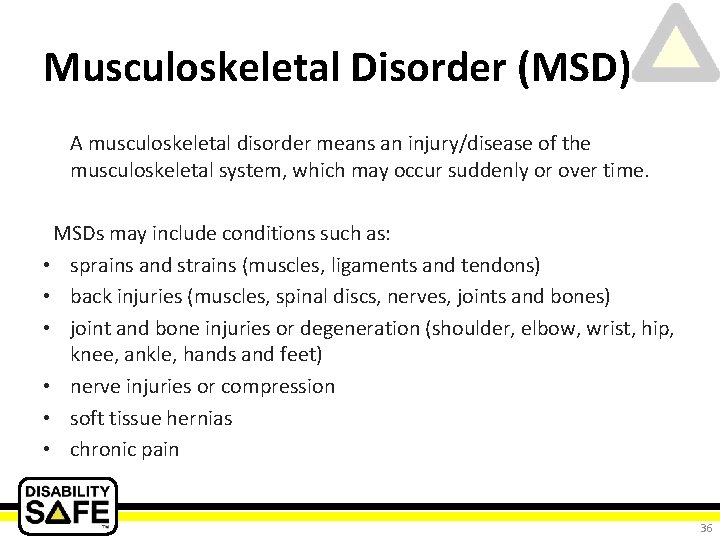
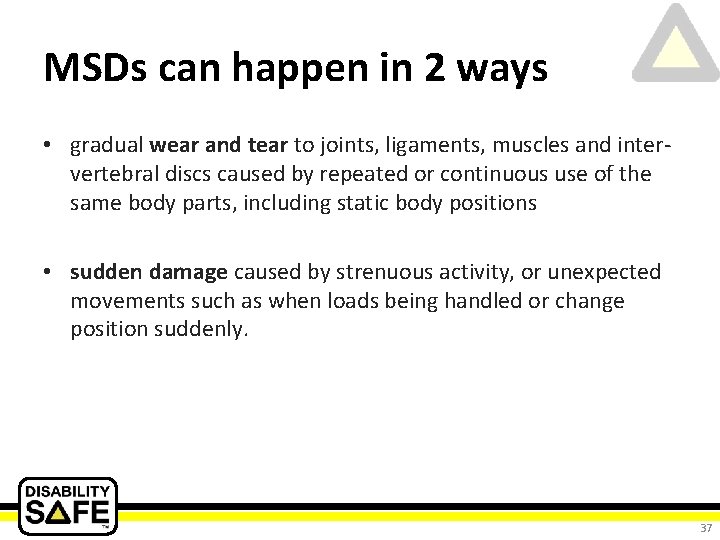
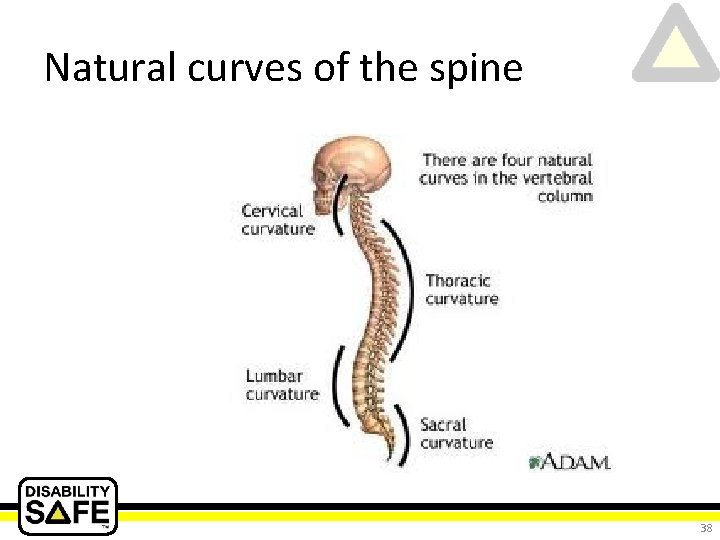
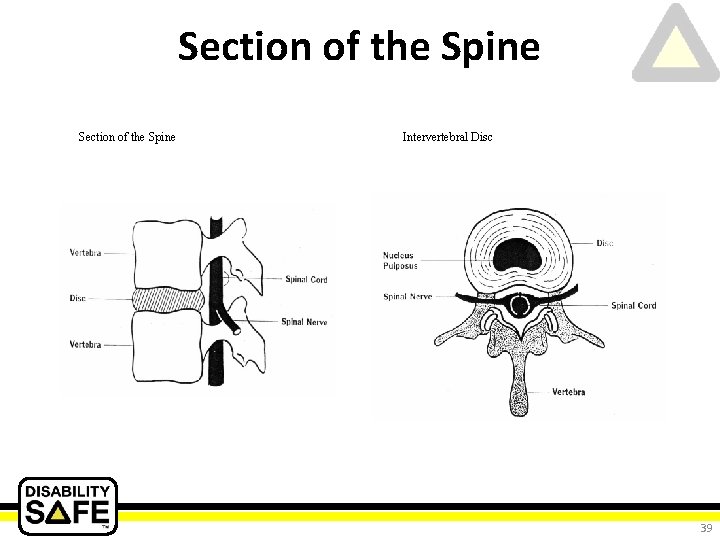
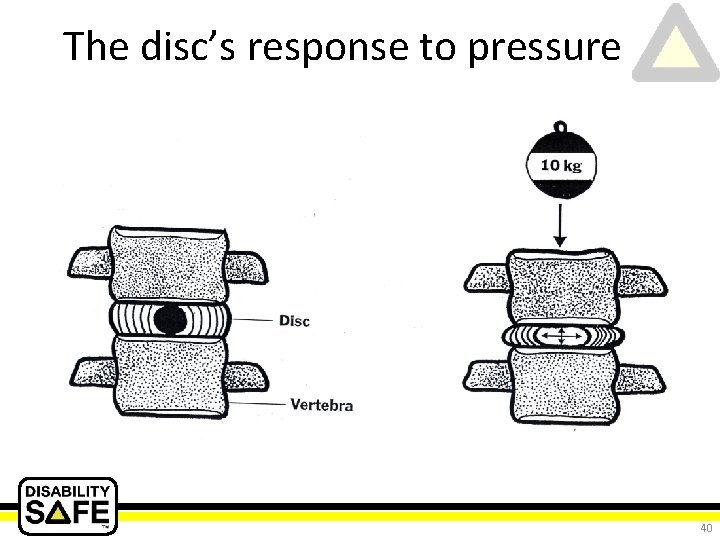
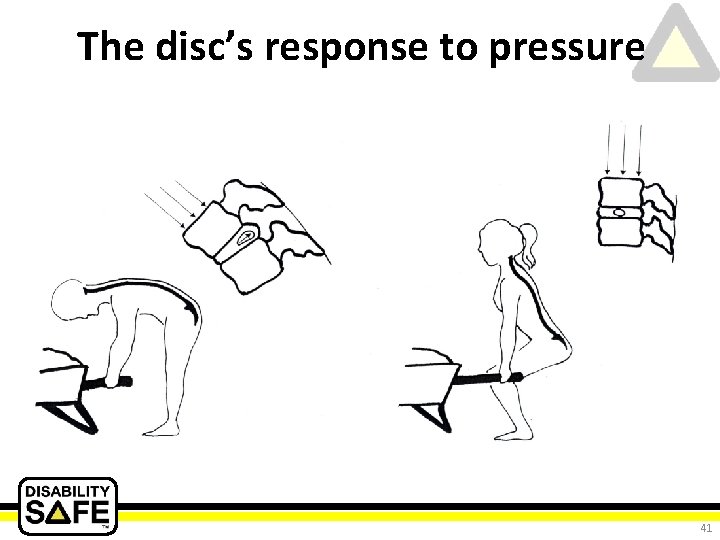
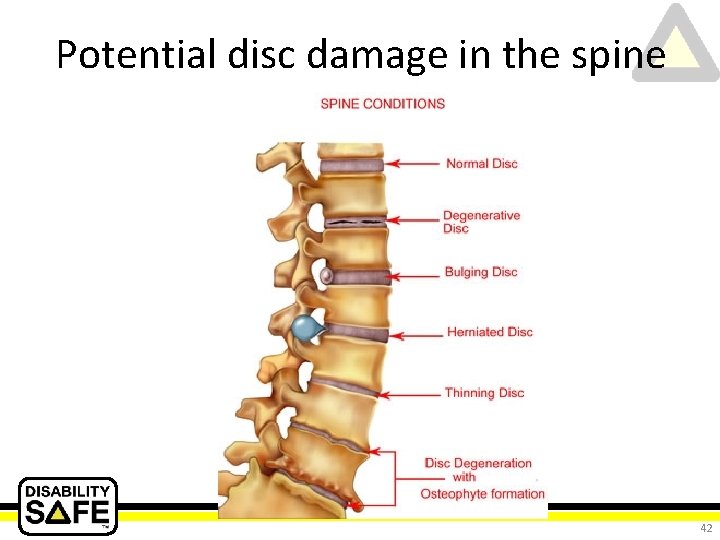
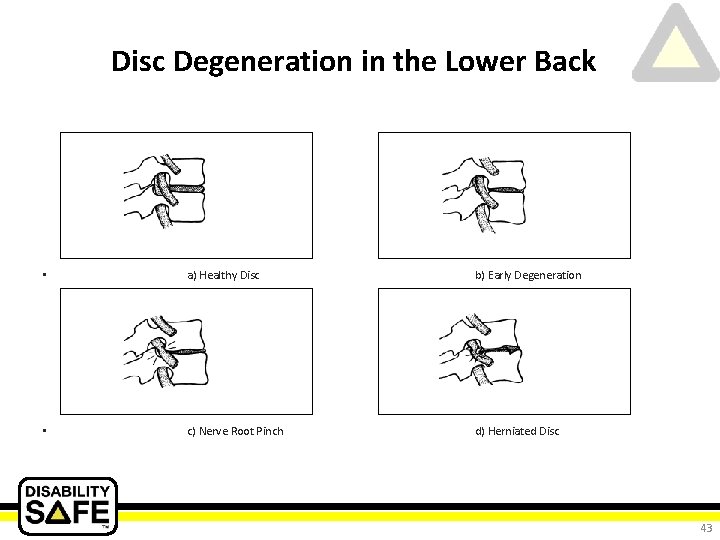
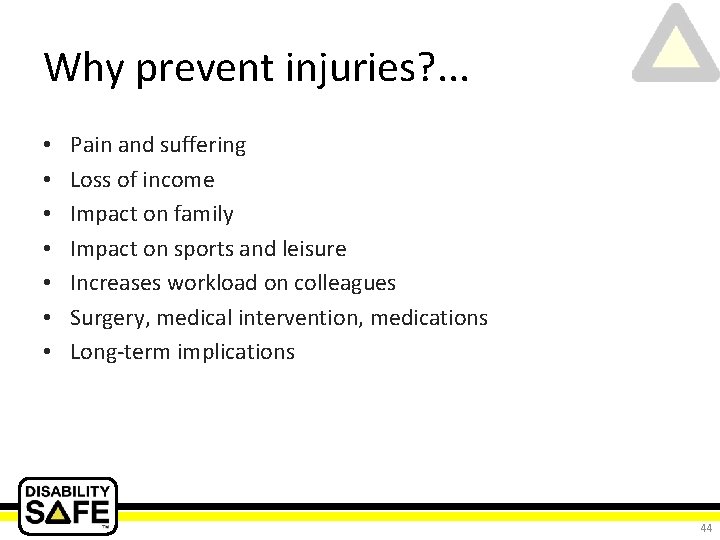

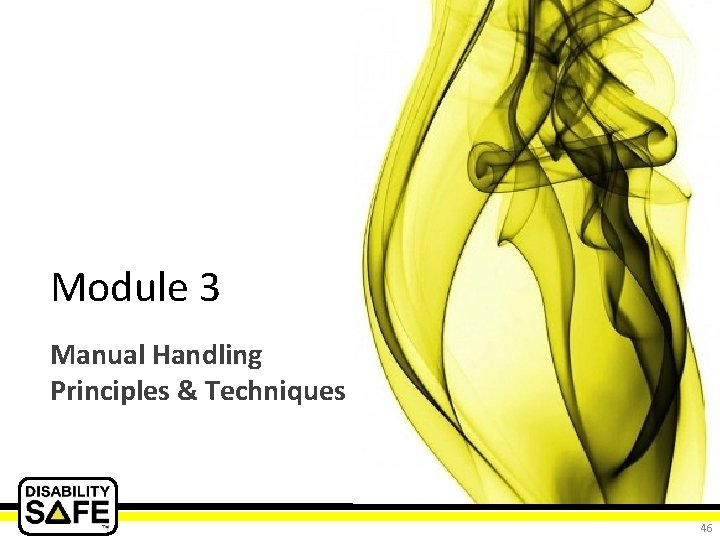
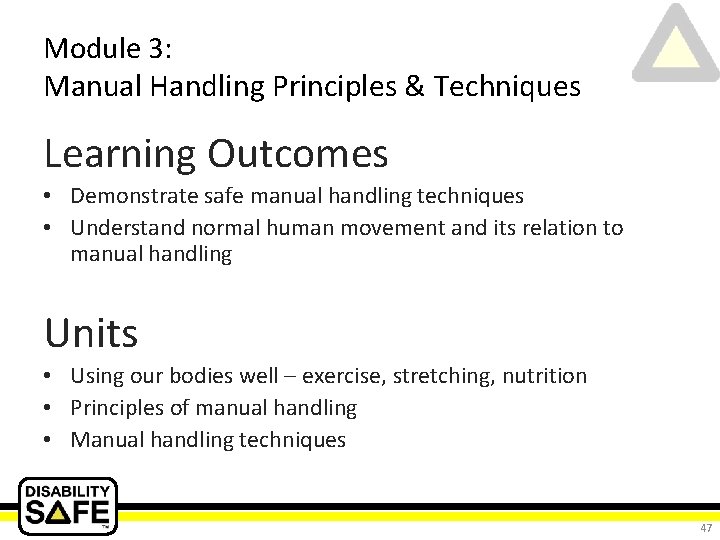
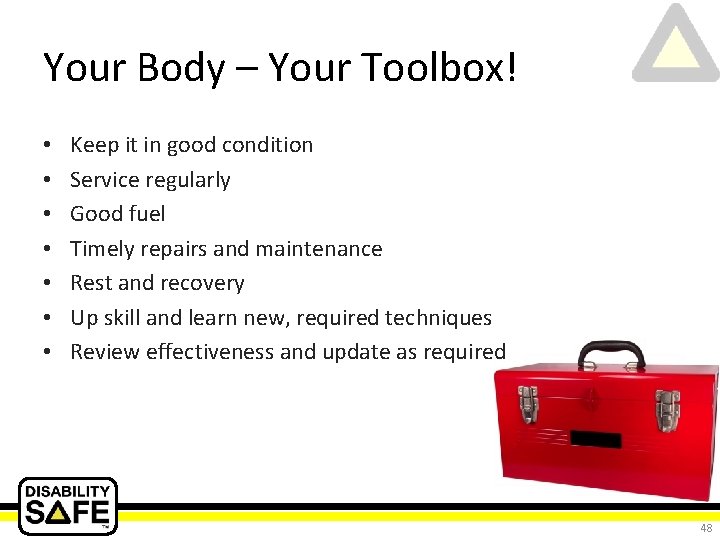
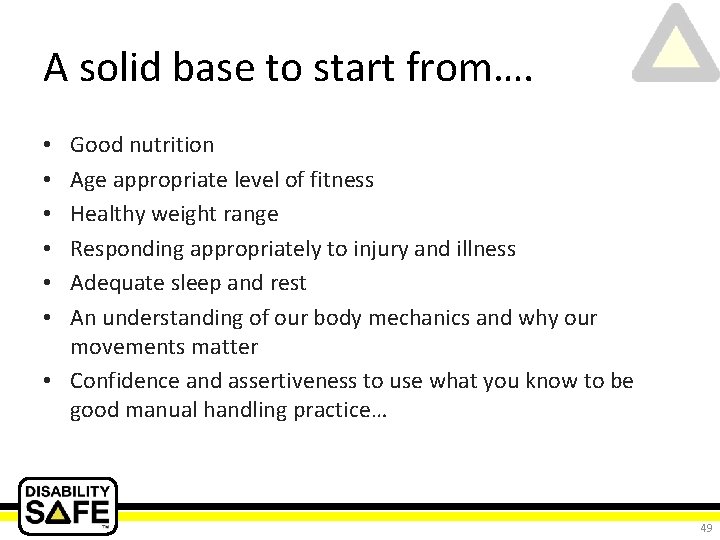
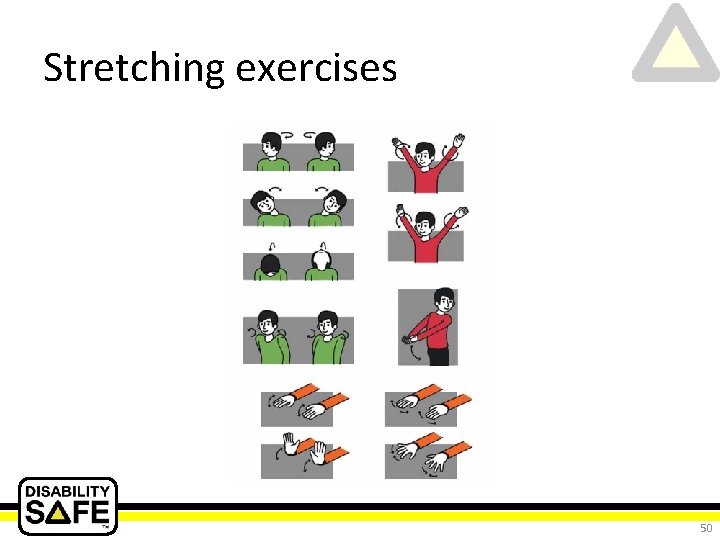
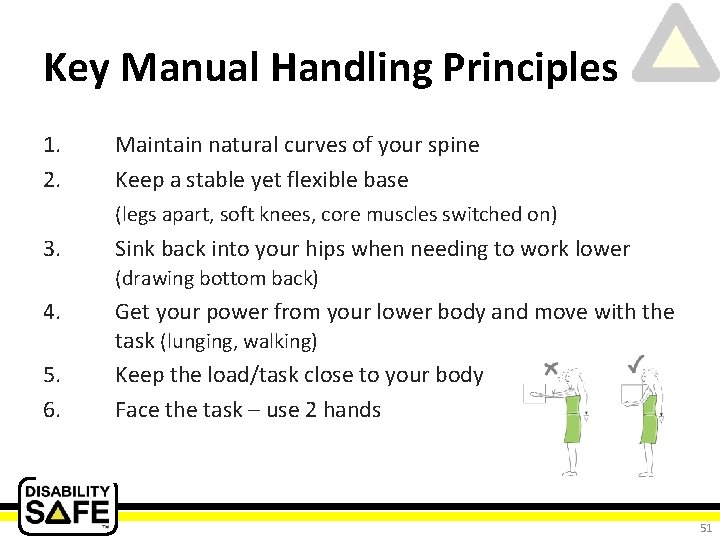
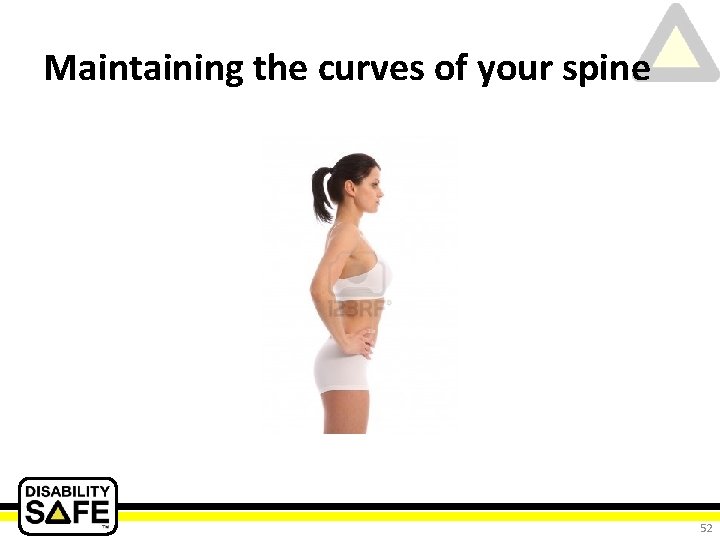
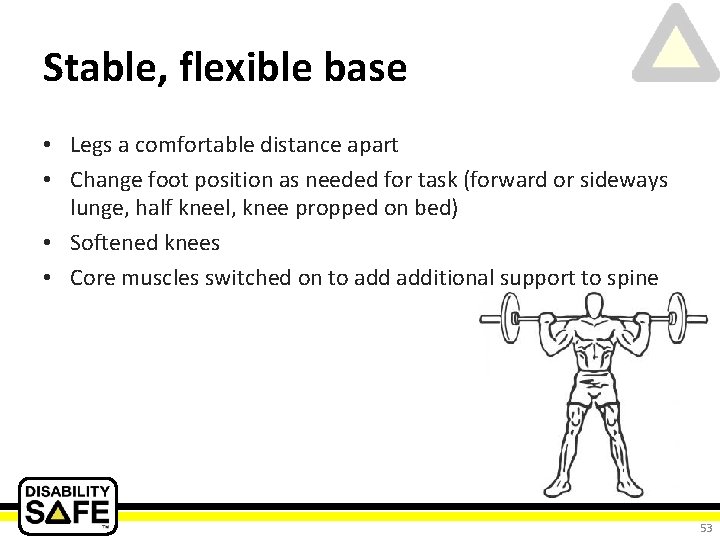
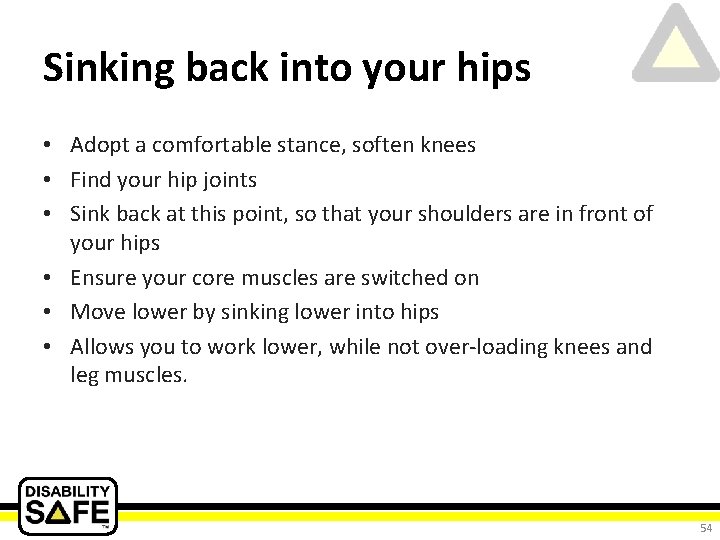
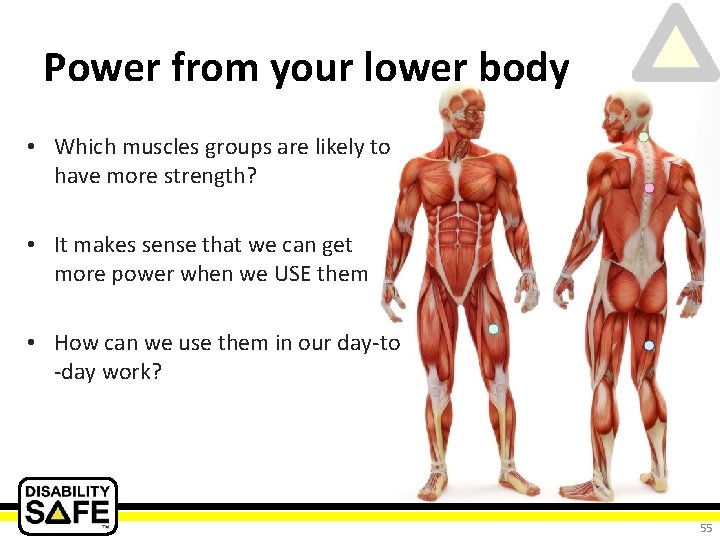
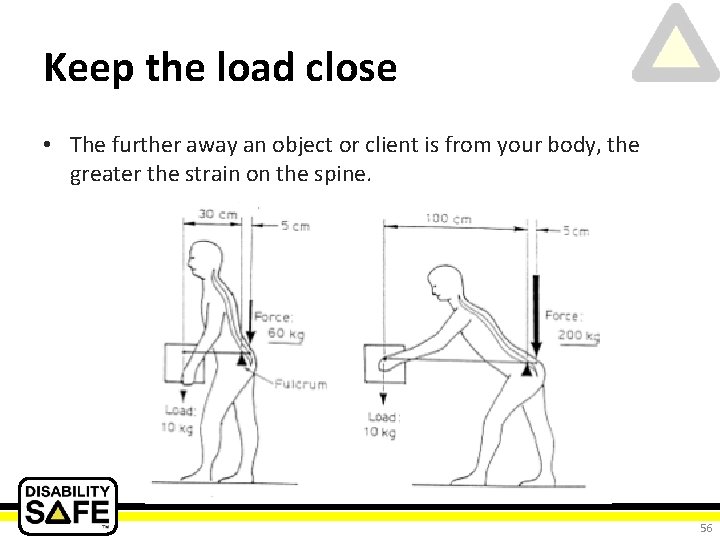
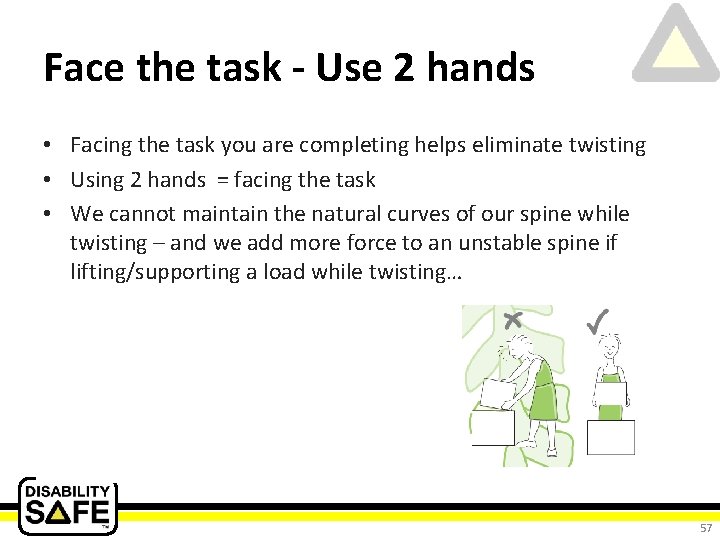
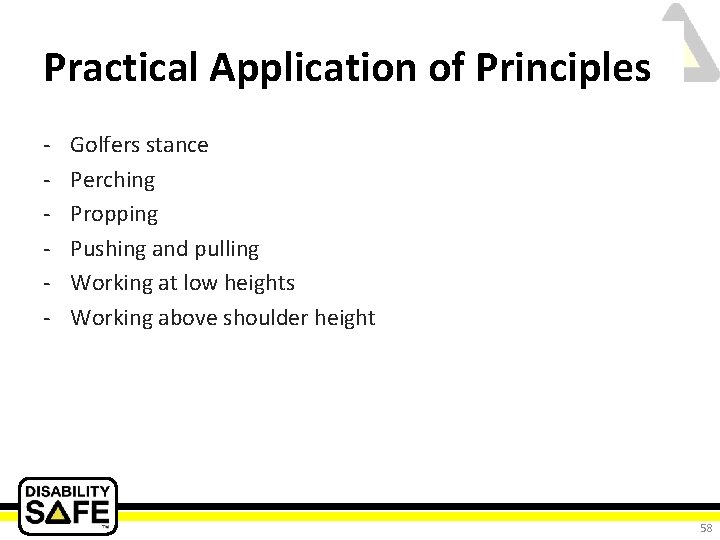
- Slides: 58
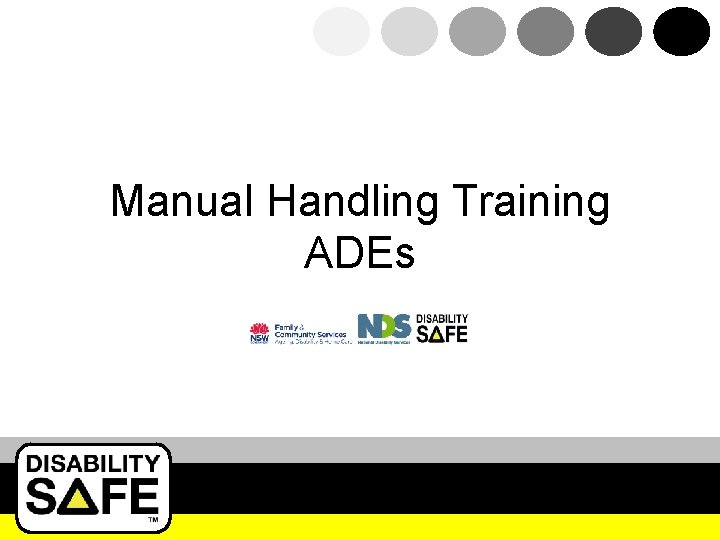
Manual Handling Training ADEs 1
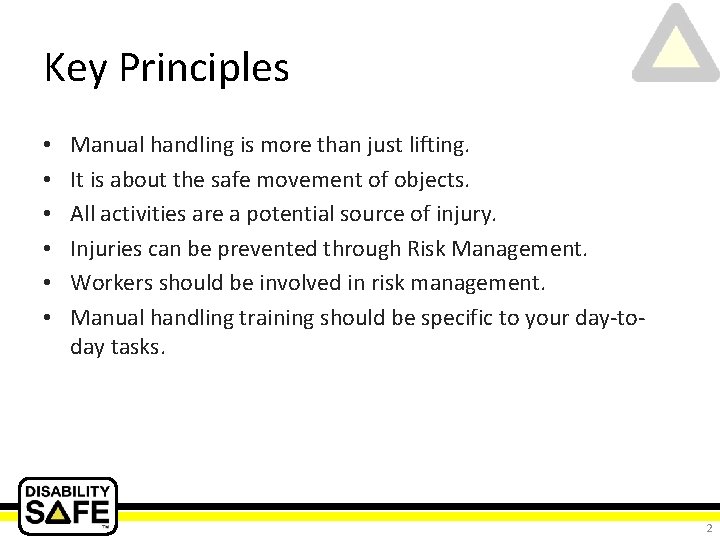
Key Principles • • • Manual handling is more than just lifting. It is about the safe movement of objects. All activities are a potential source of injury. Injuries can be prevented through Risk Management. Workers should be involved in risk management. Manual handling training should be specific to your day-today tasks. 2
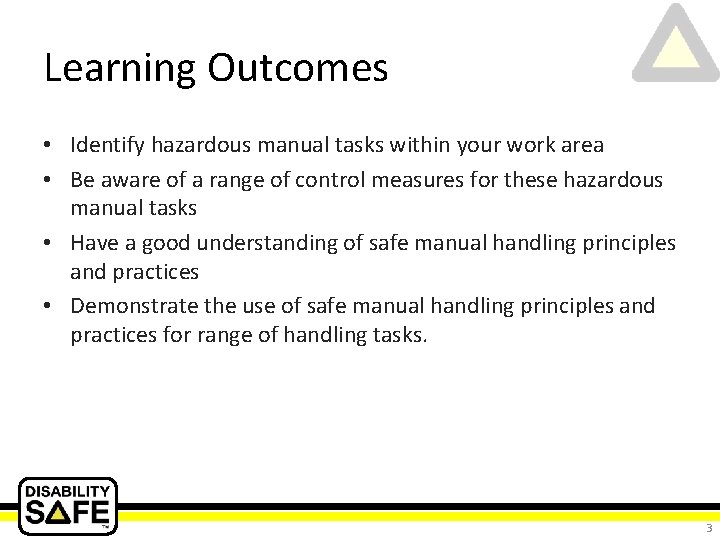
Learning Outcomes • Identify hazardous manual tasks within your work area • Be aware of a range of control measures for these hazardous manual tasks • Have a good understanding of safe manual handling principles and practices • Demonstrate the use of safe manual handling principles and practices for range of handling tasks. 3
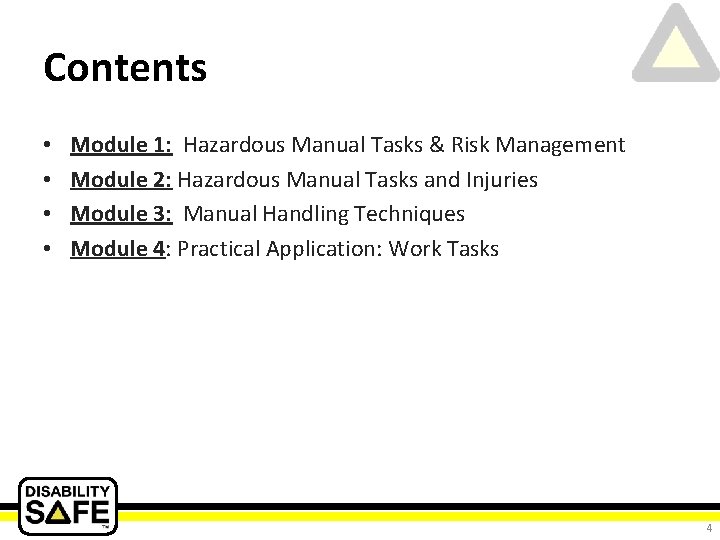
Contents • • Module 1: Hazardous Manual Tasks & Risk Management Module 2: Hazardous Manual Tasks and Injuries Module 3: Manual Handling Techniques Module 4: Practical Application: Work Tasks 4
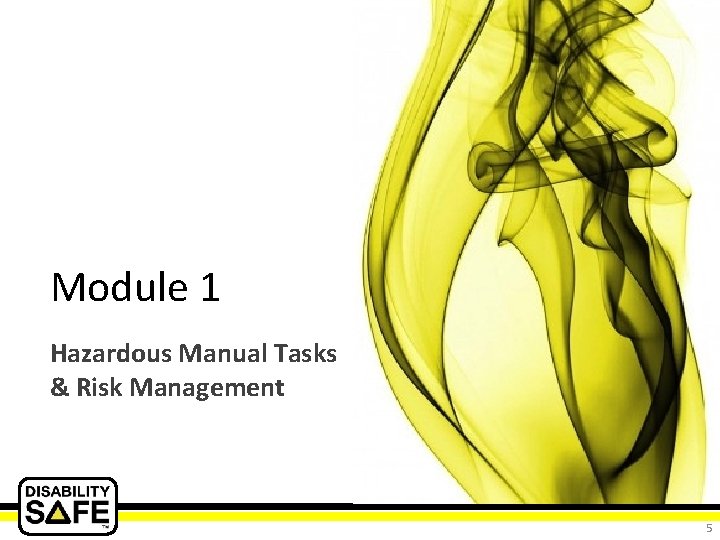
Module 1 Hazardous Manual Tasks & Risk Management 5
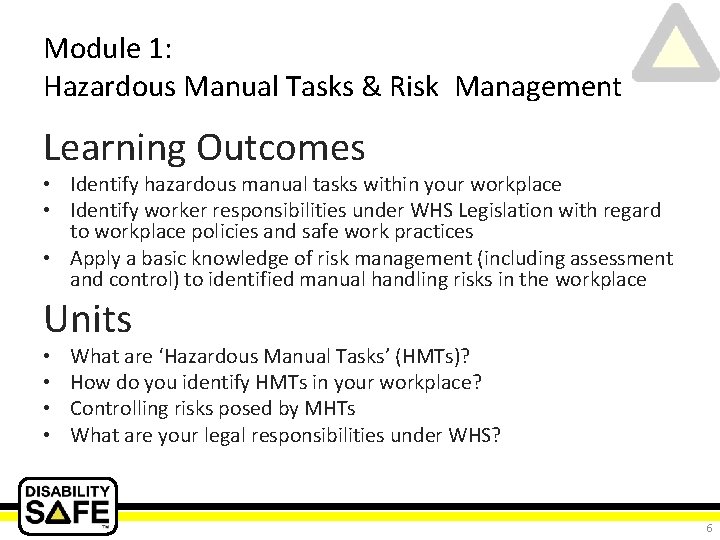
Module 1: Hazardous Manual Tasks & Risk Management Learning Outcomes • Identify hazardous manual tasks within your workplace • Identify worker responsibilities under WHS Legislation with regard to workplace policies and safe work practices • Apply a basic knowledge of risk management (including assessment and control) to identified manual handling risks in the workplace Units • • What are ‘Hazardous Manual Tasks’ (HMTs)? How do you identify HMTs in your workplace? Controlling risks posed by MHTs What are your legal responsibilities under WHS? 6
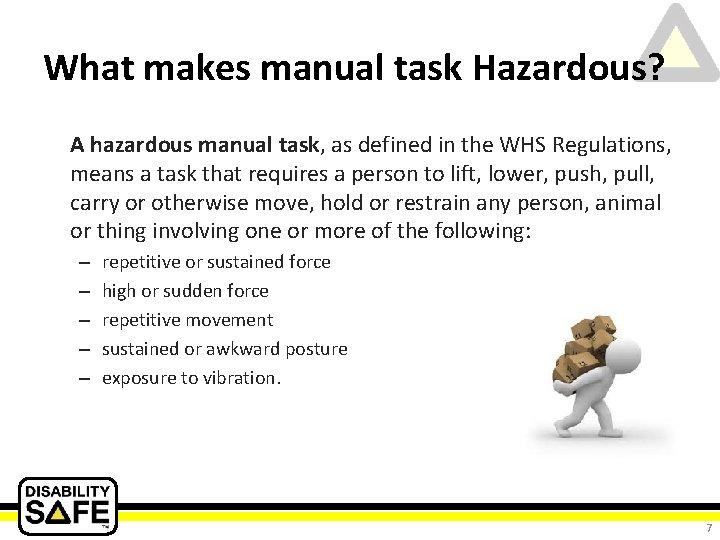
What makes manual task Hazardous? A hazardous manual task, as defined in the WHS Regulations, means a task that requires a person to lift, lower, push, pull, carry or otherwise move, hold or restrain any person, animal or thing involving one or more of the following: – – – repetitive or sustained force high or sudden force repetitive movement sustained or awkward posture exposure to vibration. 7
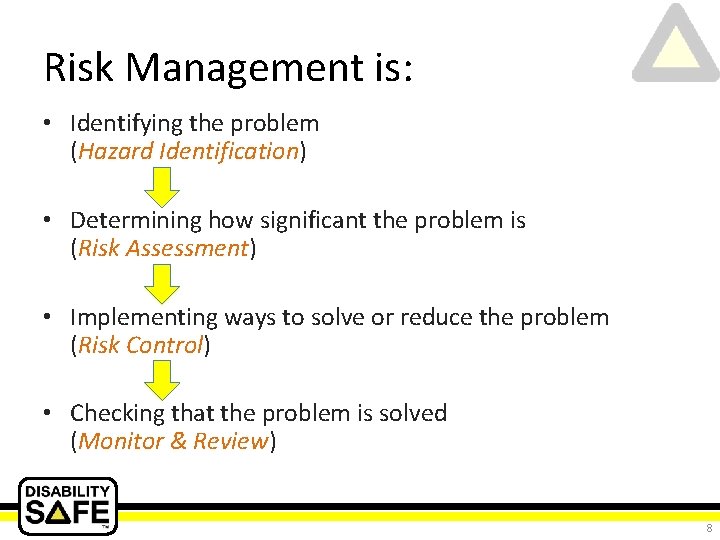
Risk Management is: • Identifying the problem (Hazard Identification) • Determining how significant the problem is (Risk Assessment) • Implementing ways to solve or reduce the problem (Risk Control) • Checking that the problem is solved (Monitor & Review) 8
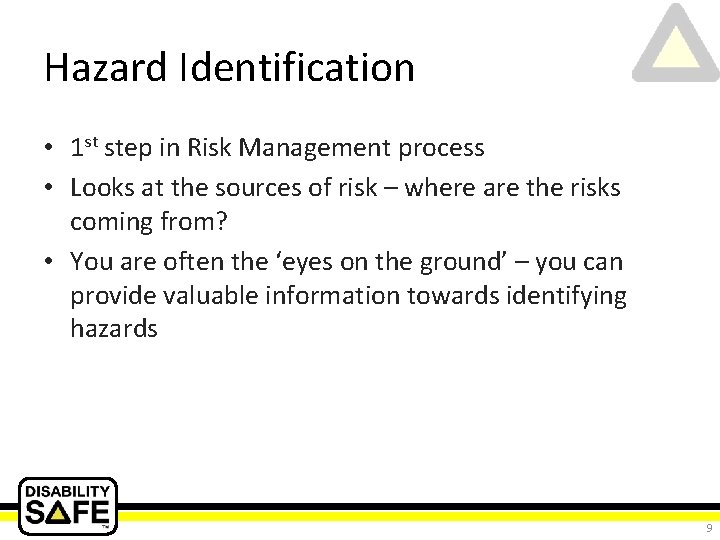
Hazard Identification • 1 st step in Risk Management process • Looks at the sources of risk – where are the risks coming from? • You are often the ‘eyes on the ground’ – you can provide valuable information towards identifying hazards 9
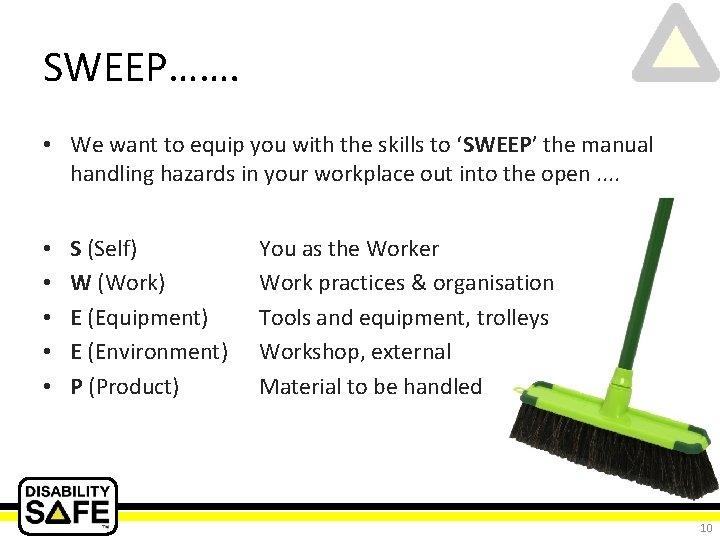
SWEEP……. • We want to equip you with the skills to ‘SWEEP’ the manual handling hazards in your workplace out into the open. . • • • S (Self) W (Work) E (Equipment) E (Environment) P (Product) You as the Worker Work practices & organisation Tools and equipment, trolleys Workshop, external Material to be handled 10
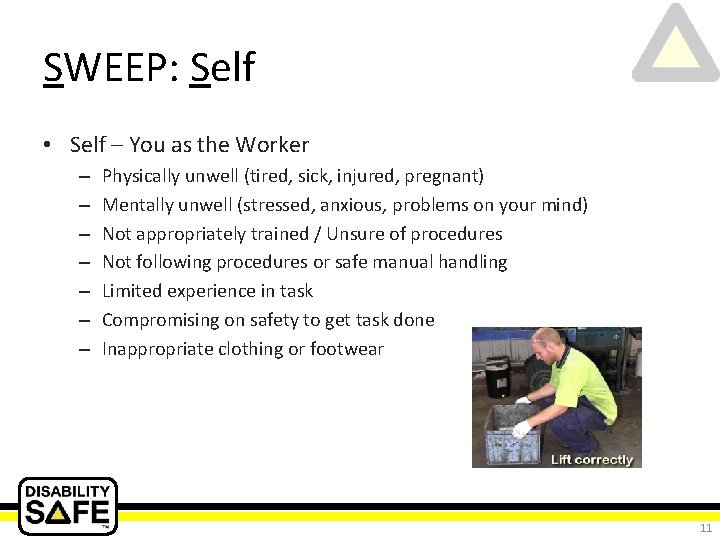
SWEEP: Self • Self – You as the Worker – – – – Physically unwell (tired, sick, injured, pregnant) Mentally unwell (stressed, anxious, problems on your mind) Not appropriately trained / Unsure of procedures Not following procedures or safe manual handling Limited experience in task Compromising on safety to get task done Inappropriate clothing or footwear 11
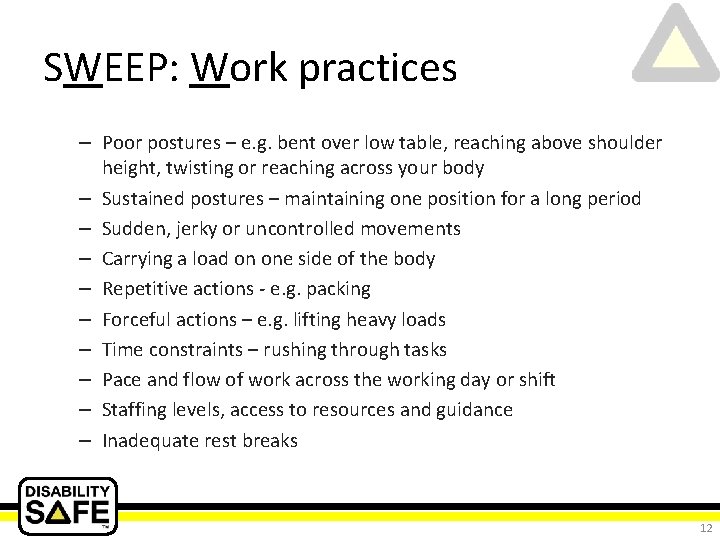
SWEEP: Work practices – Poor postures – e. g. bent over low table, reaching above shoulder height, twisting or reaching across your body – Sustained postures – maintaining one position for a long period – Sudden, jerky or uncontrolled movements – Carrying a load on one side of the body – Repetitive actions - e. g. packing – Forceful actions – e. g. lifting heavy loads – Time constraints – rushing through tasks – Pace and flow of work across the working day or shift – Staffing levels, access to resources and guidance – Inadequate rest breaks 12
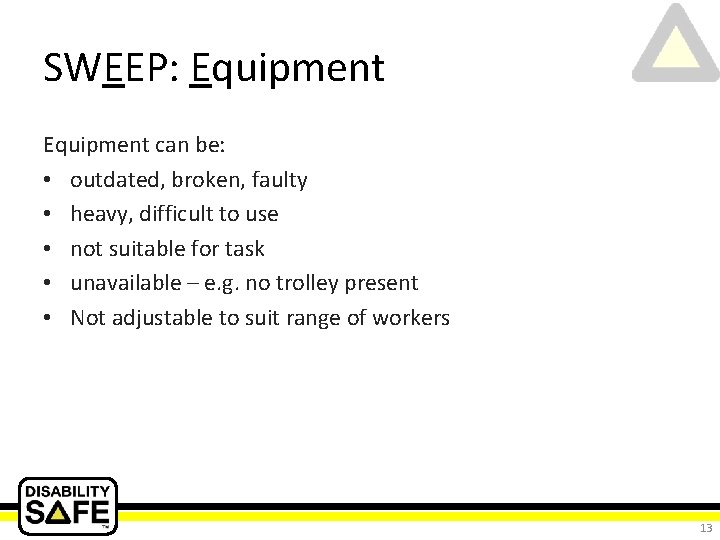
SWEEP: Equipment can be: • outdated, broken, faulty • heavy, difficult to use • not suitable for task • unavailable – e. g. no trolley present • Not adjustable to suit range of workers 13
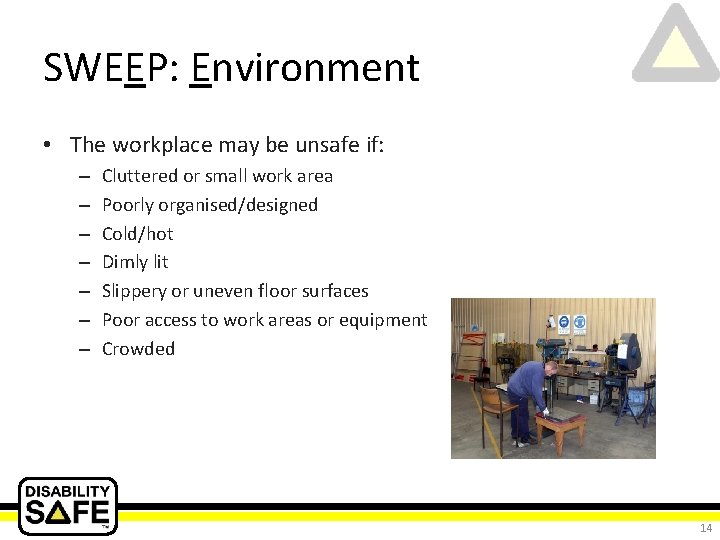
SWEEP: Environment • The workplace may be unsafe if: – – – – Cluttered or small work area Poorly organised/designed Cold/hot Dimly lit Slippery or uneven floor surfaces Poor access to work areas or equipment Crowded 14
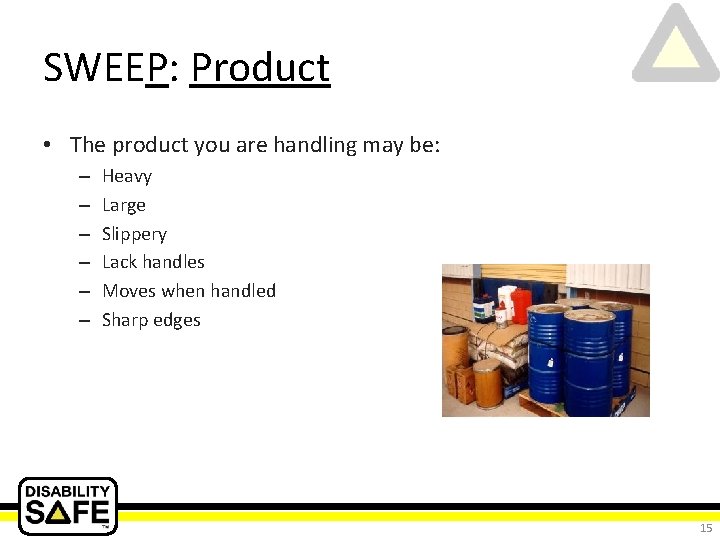
SWEEP: Product • The product you are handling may be: – – – Heavy Large Slippery Lack handles Moves when handled Sharp edges 15
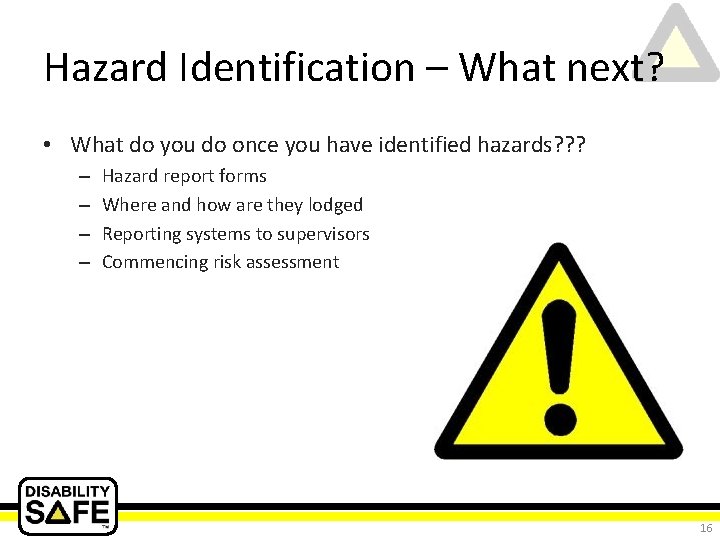
Hazard Identification – What next? • What do you do once you have identified hazards? ? ? – – Hazard report forms Where and how are they lodged Reporting systems to supervisors Commencing risk assessment 16
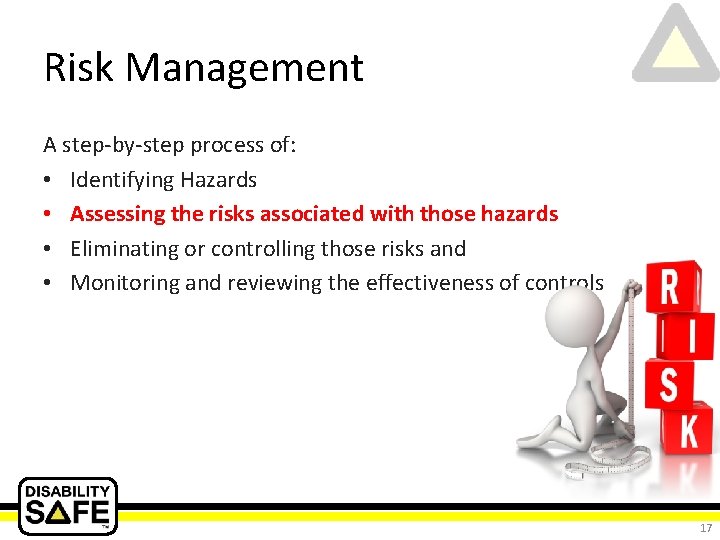
Risk Management A step-by-step process of: • Identifying Hazards • Assessing the risks associated with those hazards • Eliminating or controlling those risks and • Monitoring and reviewing the effectiveness of controls 17
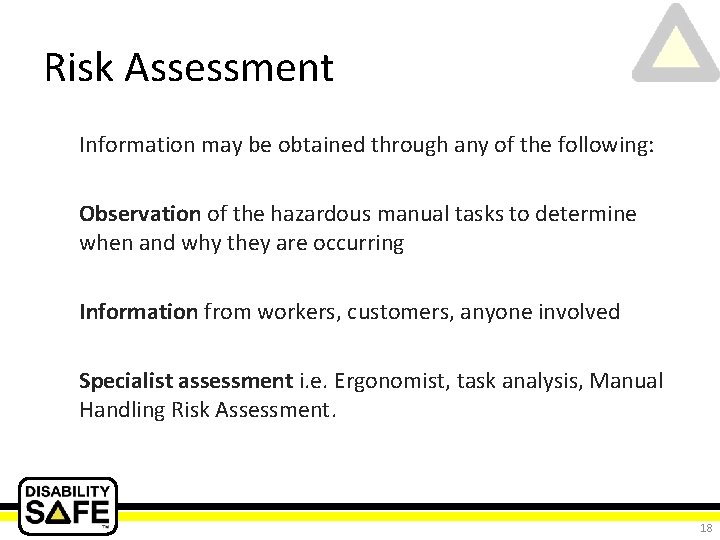
Risk Assessment Information may be obtained through any of the following: Observation of the hazardous manual tasks to determine when and why they are occurring Information from workers, customers, anyone involved Specialist assessment i. e. Ergonomist, task analysis, Manual Handling Risk Assessment. 18
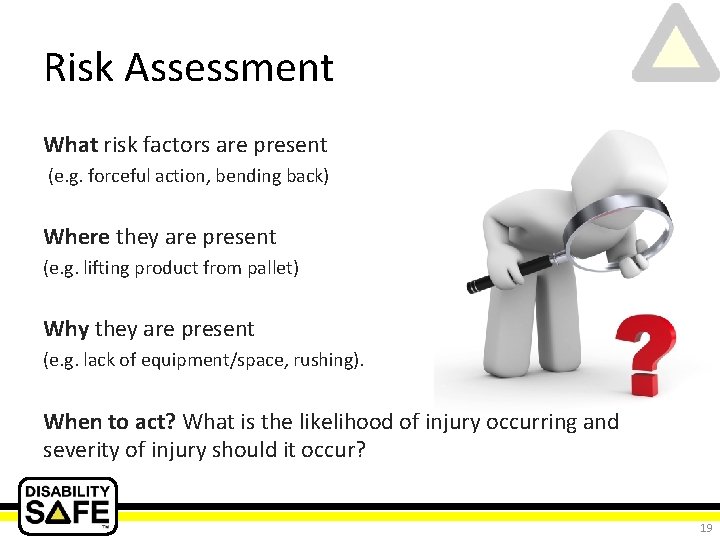
Risk Assessment What risk factors are present (e. g. forceful action, bending back) Where they are present (e. g. lifting product from pallet) Why they are present (e. g. lack of equipment/space, rushing). When to act? What is the likelihood of injury occurring and severity of injury should it occur? 19
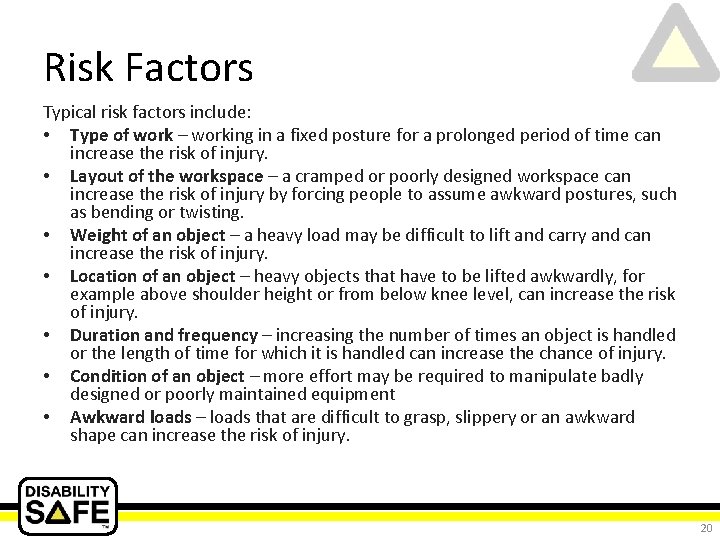
Risk Factors Typical risk factors include: • Type of work – working in a fixed posture for a prolonged period of time can increase the risk of injury. • Layout of the workspace – a cramped or poorly designed workspace can increase the risk of injury by forcing people to assume awkward postures, such as bending or twisting. • Weight of an object – a heavy load may be difficult to lift and carry and can increase the risk of injury. • Location of an object – heavy objects that have to be lifted awkwardly, for example above shoulder height or from below knee level, can increase the risk of injury. • Duration and frequency – increasing the number of times an object is handled or the length of time for which it is handled can increase the chance of injury. • Condition of an object – more effort may be required to manipulate badly designed or poorly maintained equipment • Awkward loads – loads that are difficult to grasp, slippery or an awkward shape can increase the risk of injury. 20
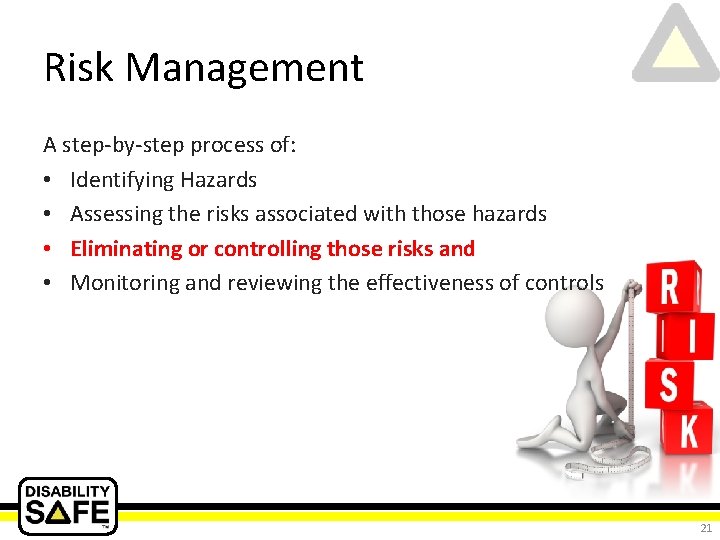
Risk Management A step-by-step process of: • Identifying Hazards • Assessing the risks associated with those hazards • Eliminating or controlling those risks and • Monitoring and reviewing the effectiveness of controls 21
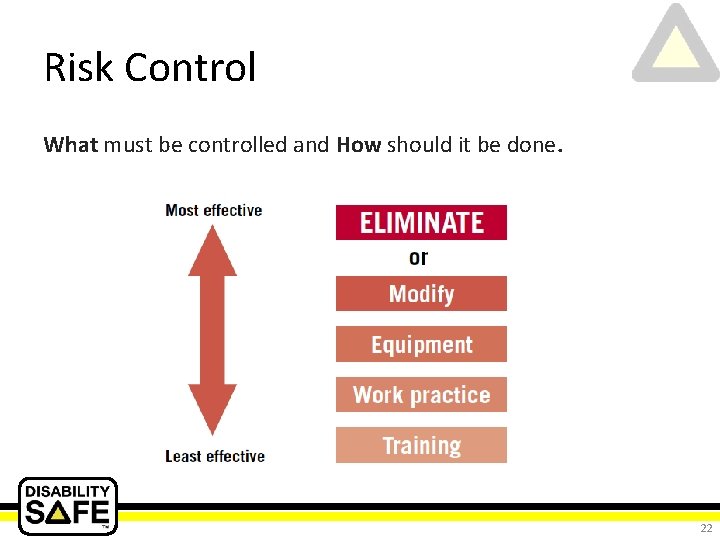
Risk Control What must be controlled and How should it be done. 22
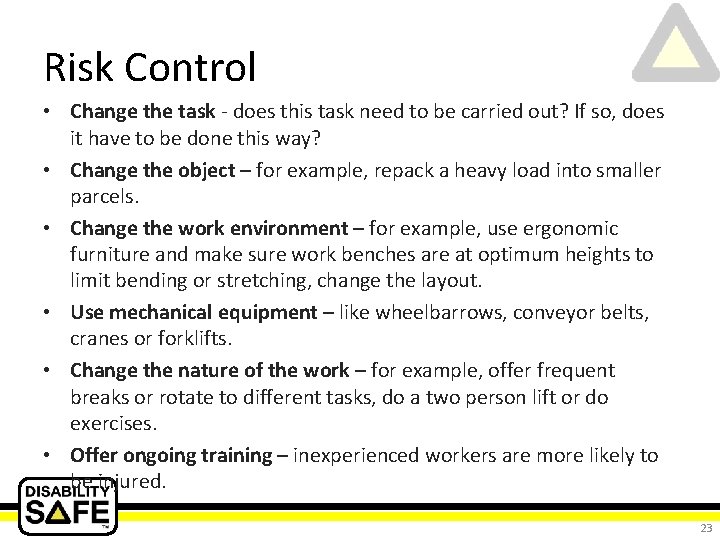
Risk Control • Change the task - does this task need to be carried out? If so, does it have to be done this way? • Change the object – for example, repack a heavy load into smaller parcels. • Change the work environment – for example, use ergonomic furniture and make sure work benches are at optimum heights to limit bending or stretching, change the layout. • Use mechanical equipment – like wheelbarrows, conveyor belts, cranes or forklifts. • Change the nature of the work – for example, offer frequent breaks or rotate to different tasks, do a two person lift or do exercises. • Offer ongoing training – inexperienced workers are more likely to be injured. 23
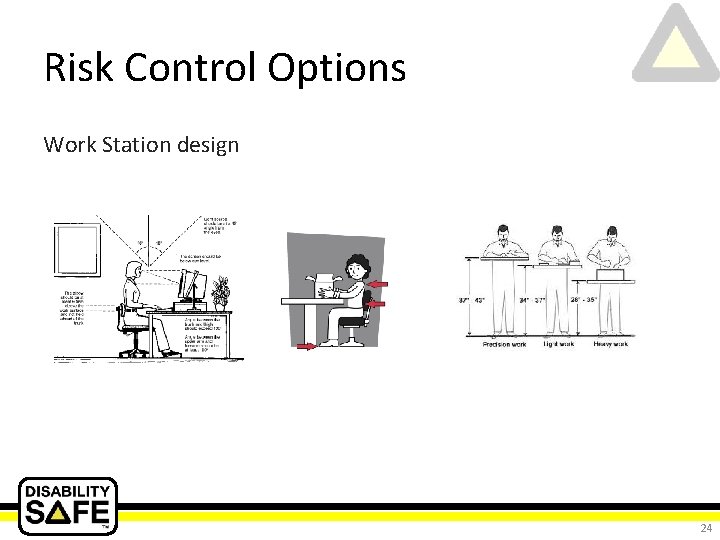
Risk Control Options Work Station design 24
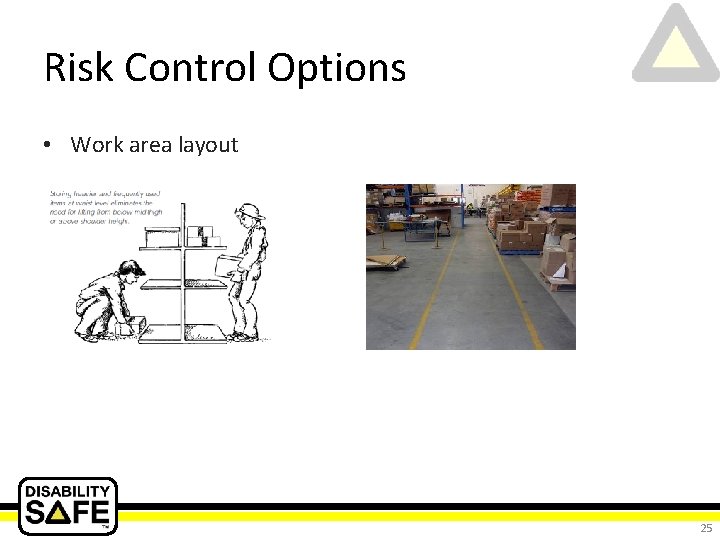
Risk Control Options • Work area layout 25
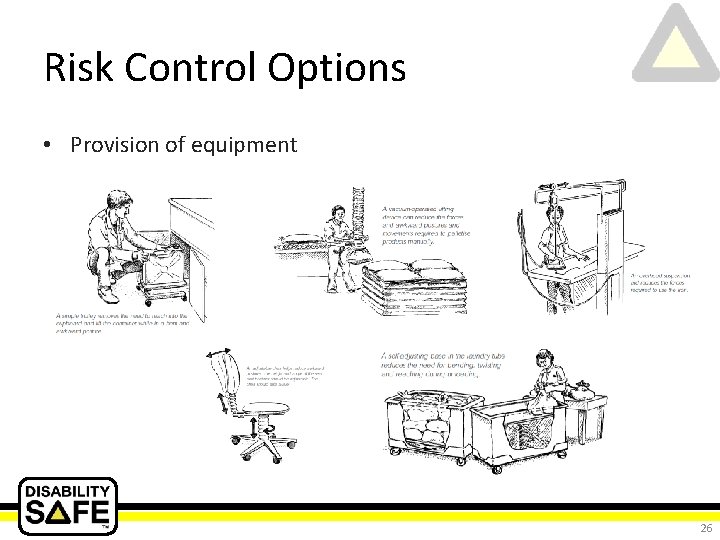
Risk Control Options • Provision of equipment 26
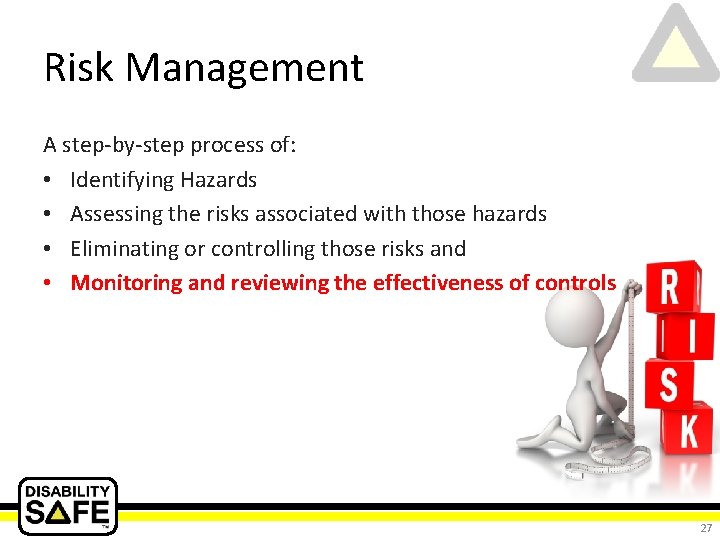
Risk Management A step-by-step process of: • Identifying Hazards • Assessing the risks associated with those hazards • Eliminating or controlling those risks and • Monitoring and reviewing the effectiveness of controls 27
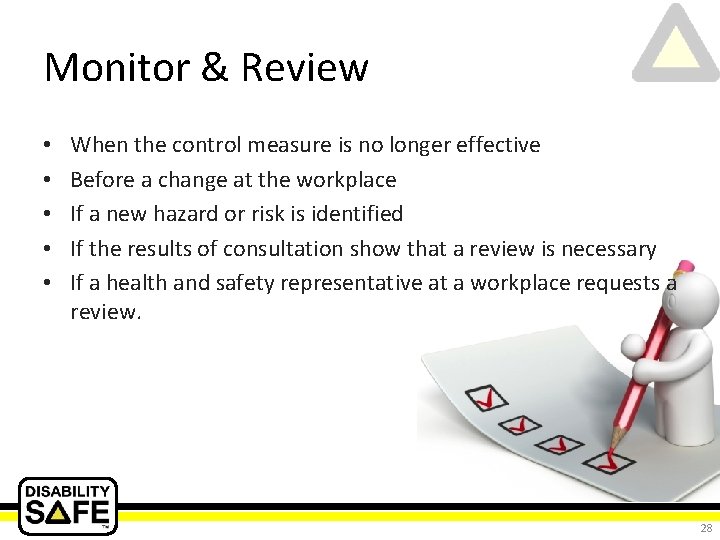
Monitor & Review • • • When the control measure is no longer effective Before a change at the workplace If a new hazard or risk is identified If the results of consultation show that a review is necessary If a health and safety representative at a workplace requests a review. 28
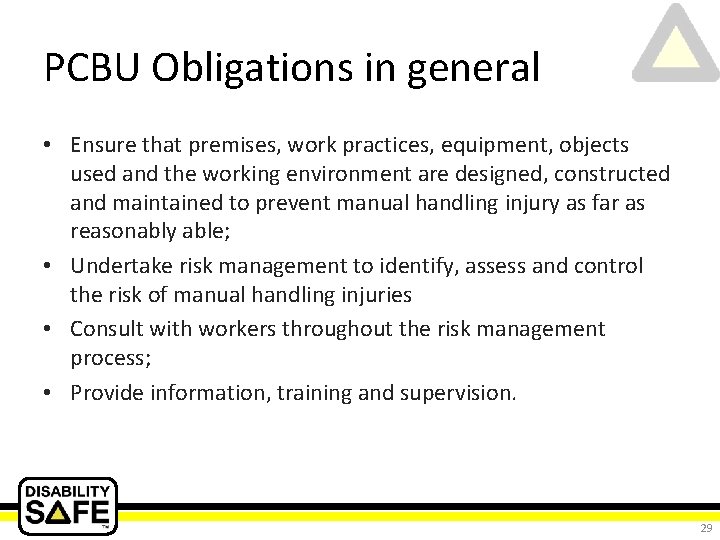
PCBU Obligations in general • Ensure that premises, work practices, equipment, objects used and the working environment are designed, constructed and maintained to prevent manual handling injury as far as reasonably able; • Undertake risk management to identify, assess and control the risk of manual handling injuries • Consult with workers throughout the risk management process; • Provide information, training and supervision. 29
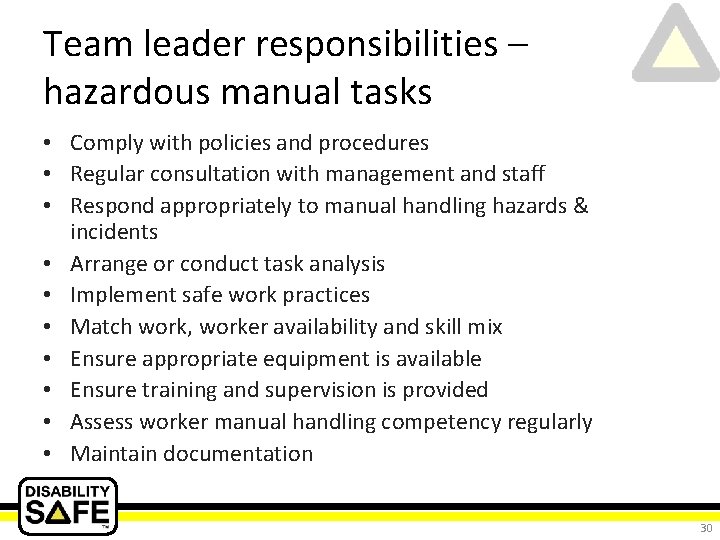
Team leader responsibilities – hazardous manual tasks • Comply with policies and procedures • Regular consultation with management and staff • Respond appropriately to manual handling hazards & incidents • Arrange or conduct task analysis • Implement safe work practices • Match work, worker availability and skill mix • Ensure appropriate equipment is available • Ensure training and supervision is provided • Assess worker manual handling competency regularly • Maintain documentation 30
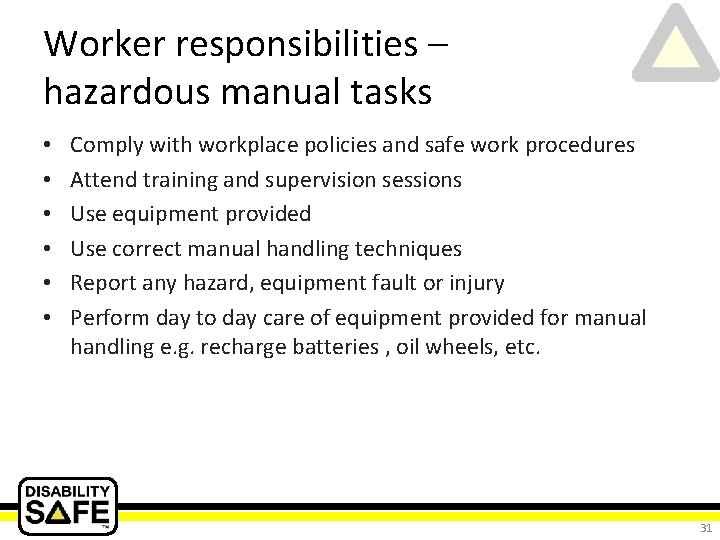
Worker responsibilities – hazardous manual tasks • • • Comply with workplace policies and safe work procedures Attend training and supervision sessions Use equipment provided Use correct manual handling techniques Report any hazard, equipment fault or injury Perform day to day care of equipment provided for manual handling e. g. recharge batteries , oil wheels, etc. 31
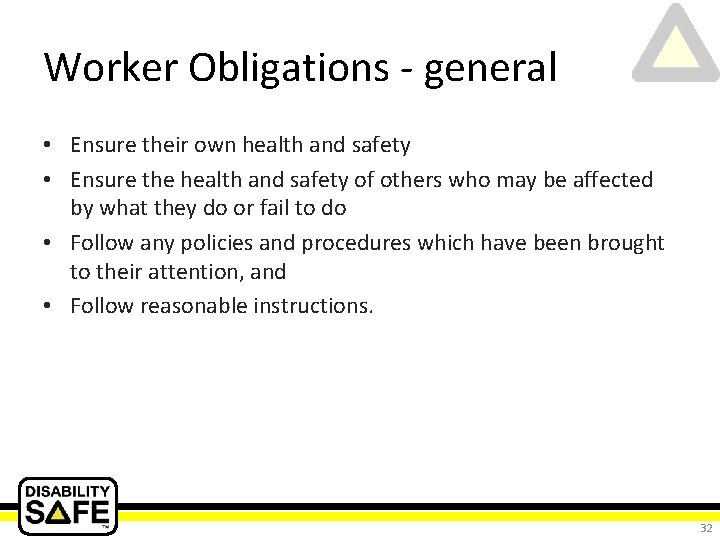
Worker Obligations - general • Ensure their own health and safety • Ensure the health and safety of others who may be affected by what they do or fail to do • Follow any policies and procedures which have been brought to their attention, and • Follow reasonable instructions. 32
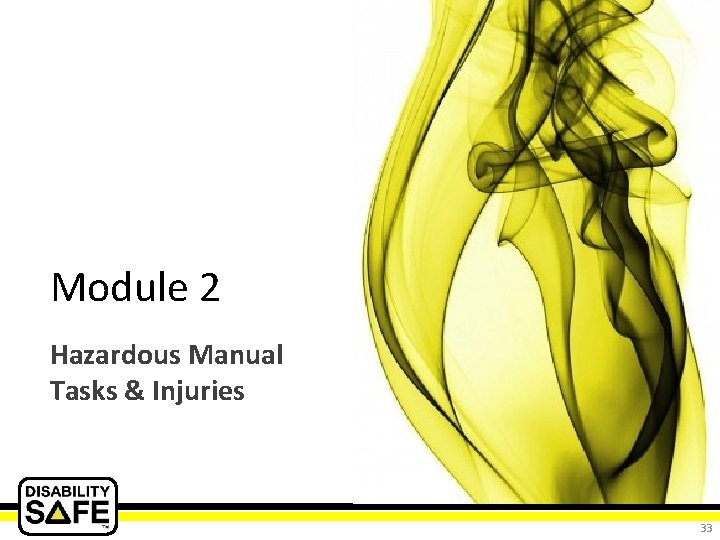
Module 2 Hazardous Manual Tasks & Injuries 33
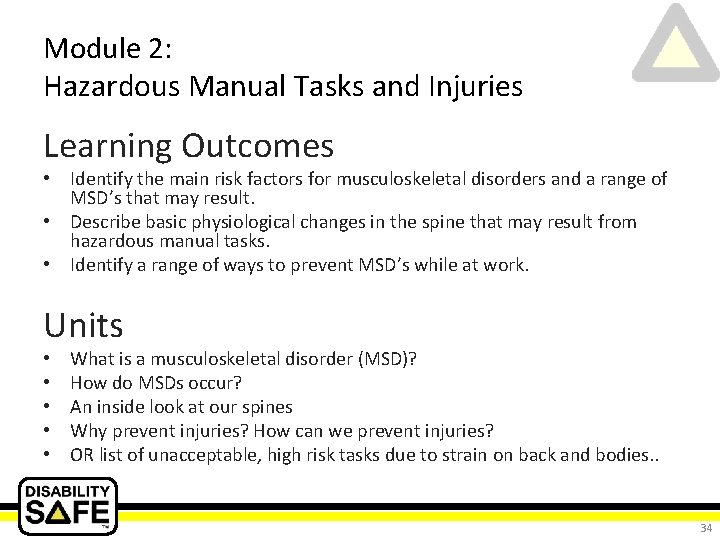
Module 2: Hazardous Manual Tasks and Injuries Learning Outcomes • Identify the main risk factors for musculoskeletal disorders and a range of MSD’s that may result. • Describe basic physiological changes in the spine that may result from hazardous manual tasks. • Identify a range of ways to prevent MSD’s while at work. Units • • • What is a musculoskeletal disorder (MSD)? How do MSDs occur? An inside look at our spines Why prevent injuries? How can we prevent injuries? OR list of unacceptable, high risk tasks due to strain on back and bodies. . 34
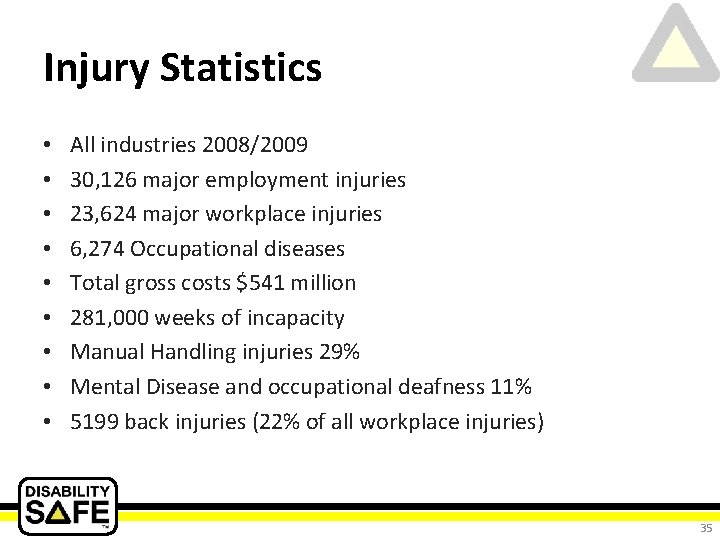
Injury Statistics • • • All industries 2008/2009 30, 126 major employment injuries 23, 624 major workplace injuries 6, 274 Occupational diseases Total gross costs $541 million 281, 000 weeks of incapacity Manual Handling injuries 29% Mental Disease and occupational deafness 11% 5199 back injuries (22% of all workplace injuries) 35
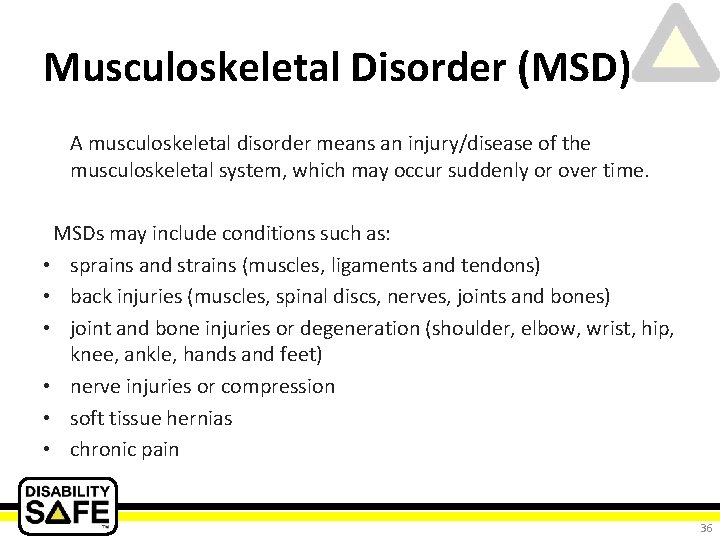
Musculoskeletal Disorder (MSD) A musculoskeletal disorder means an injury/disease of the musculoskeletal system, which may occur suddenly or over time. MSDs may include conditions such as: • sprains and strains (muscles, ligaments and tendons) • back injuries (muscles, spinal discs, nerves, joints and bones) • joint and bone injuries or degeneration (shoulder, elbow, wrist, hip, knee, ankle, hands and feet) • nerve injuries or compression • soft tissue hernias • chronic pain 36
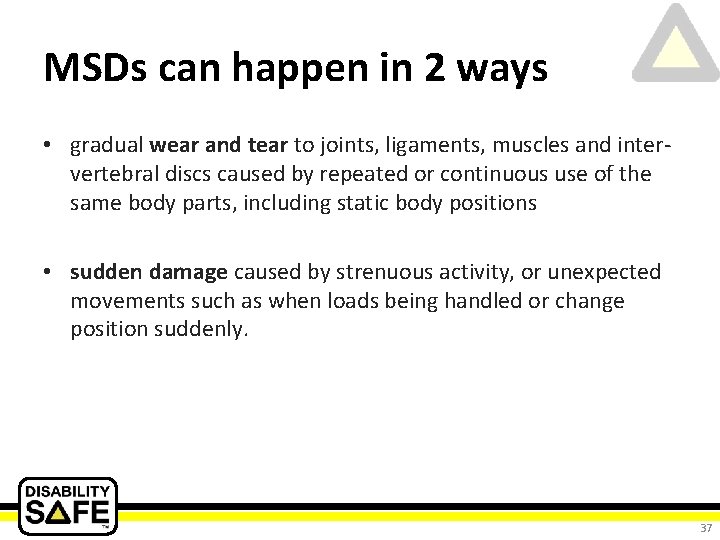
MSDs can happen in 2 ways • gradual wear and tear to joints, ligaments, muscles and intervertebral discs caused by repeated or continuous use of the same body parts, including static body positions • sudden damage caused by strenuous activity, or unexpected movements such as when loads being handled or change position suddenly. 37
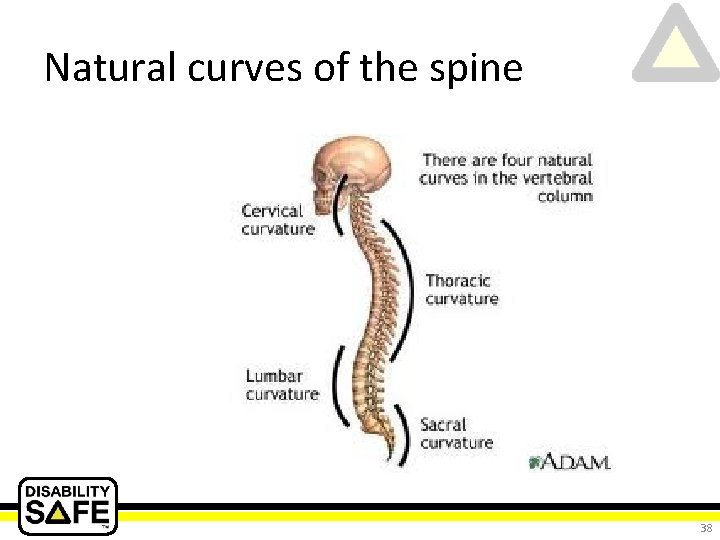
Natural curves of the spine 38
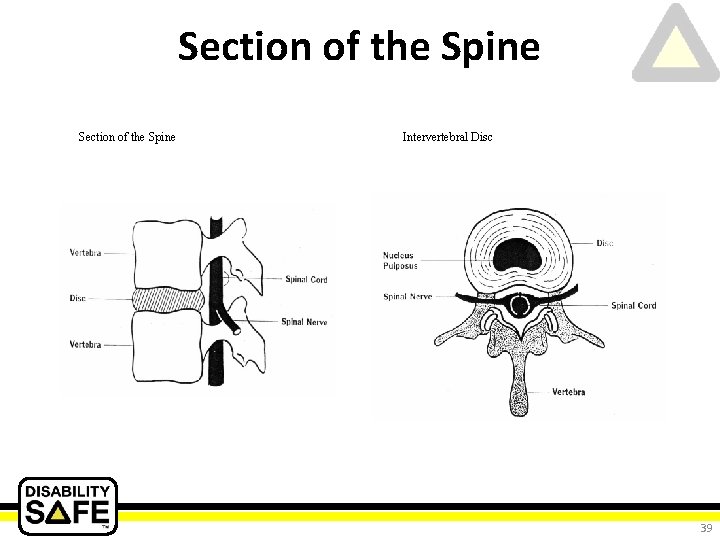
Section of the Spine Intervertebral Disc 39
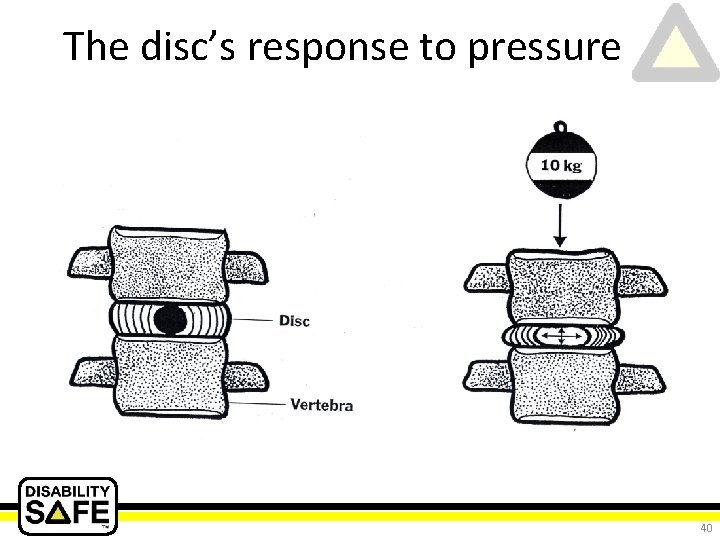
The disc’s response to pressure 40
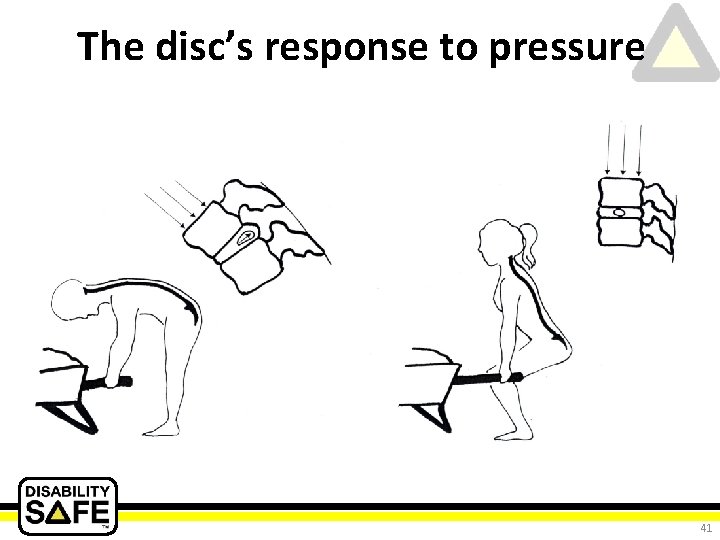
The disc’s response to pressure 41
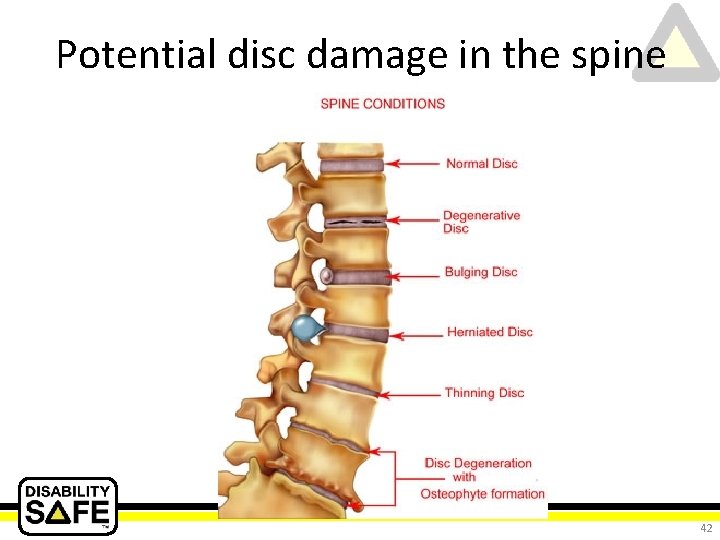
Potential disc damage in the spine 42
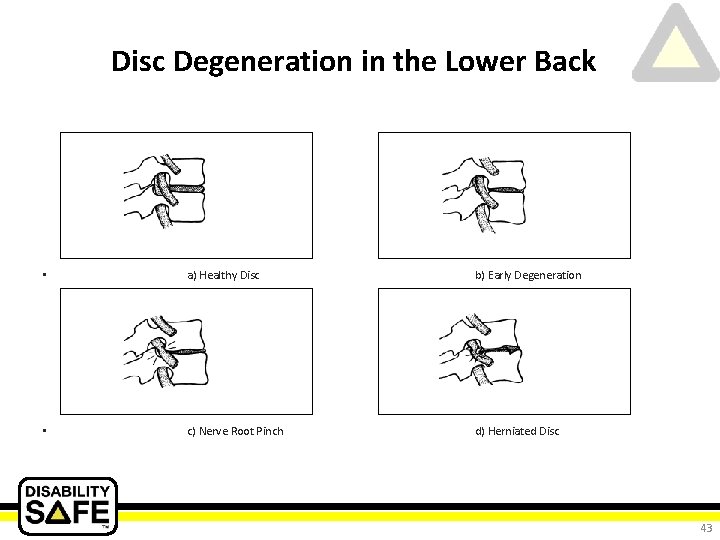
Disc Degeneration in the Lower Back • a) Healthy Disc b) Early Degeneration • c) Nerve Root Pinch d) Herniated Disc 43
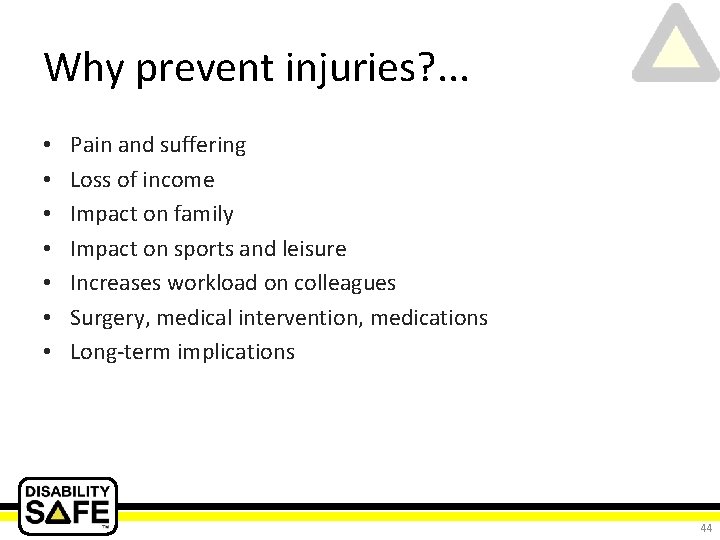
Why prevent injuries? . . . • • Pain and suffering Loss of income Impact on family Impact on sports and leisure Increases workload on colleagues Surgery, medical intervention, medications Long-term implications 44

Work Postures to Avoid 45
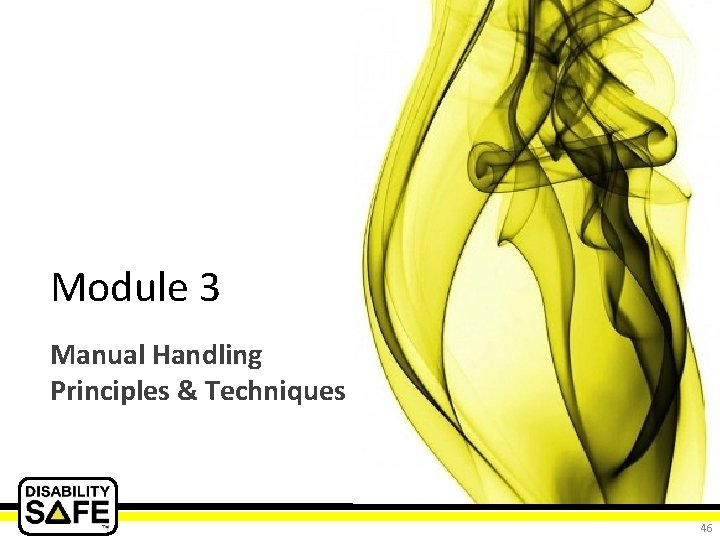
Module 3 Manual Handling Principles & Techniques 46
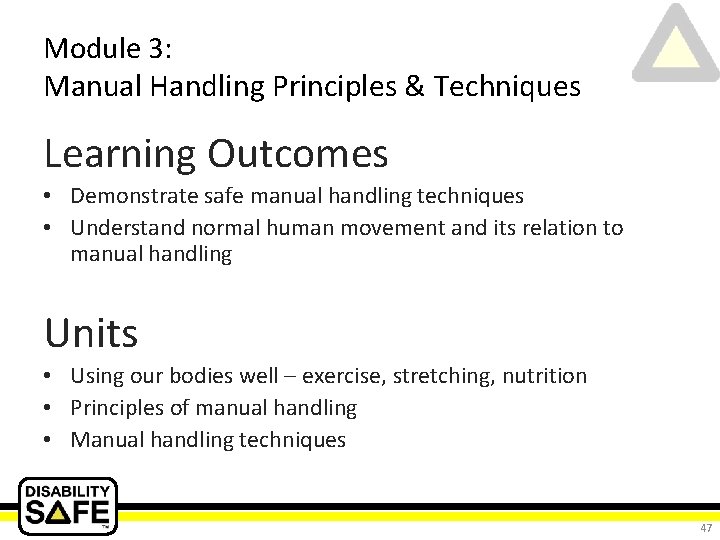
Module 3: Manual Handling Principles & Techniques Learning Outcomes • Demonstrate safe manual handling techniques • Understand normal human movement and its relation to manual handling Units • Using our bodies well – exercise, stretching, nutrition • Principles of manual handling • Manual handling techniques 47
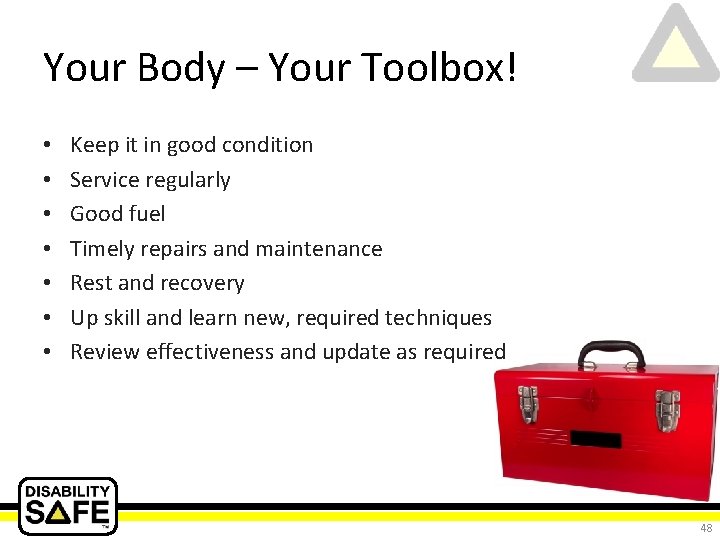
Your Body – Your Toolbox! • • Keep it in good condition Service regularly Good fuel Timely repairs and maintenance Rest and recovery Up skill and learn new, required techniques Review effectiveness and update as required 48
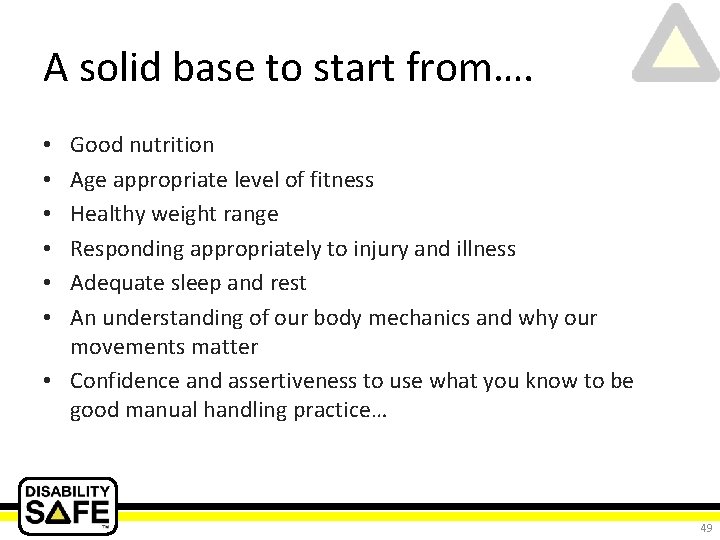
A solid base to start from…. Good nutrition Age appropriate level of fitness Healthy weight range Responding appropriately to injury and illness Adequate sleep and rest An understanding of our body mechanics and why our movements matter • Confidence and assertiveness to use what you know to be good manual handling practice… • • • 49
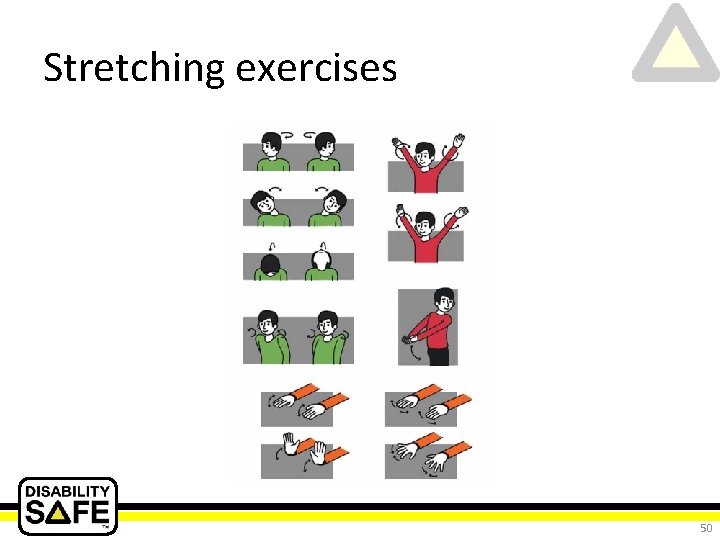
Stretching exercises 50
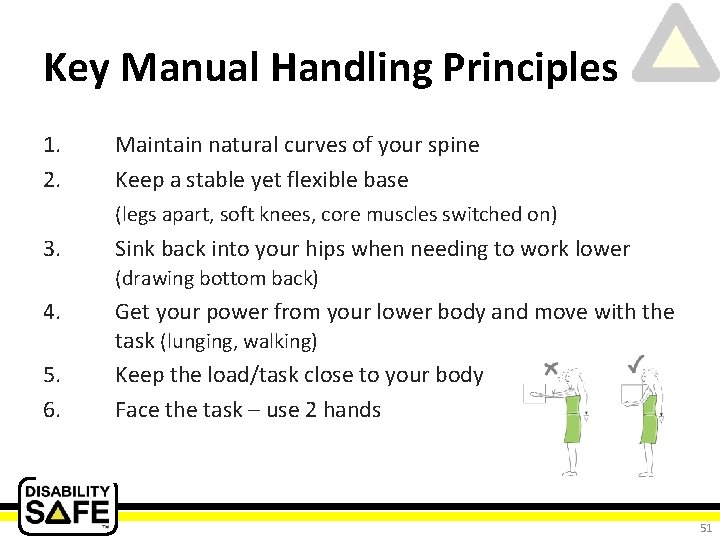
Key Manual Handling Principles 1. 2. Maintain natural curves of your spine Keep a stable yet flexible base (legs apart, soft knees, core muscles switched on) 3. Sink back into your hips when needing to work lower (drawing bottom back) 4. 5. 6. Get your power from your lower body and move with the task (lunging, walking) Keep the load/task close to your body Face the task – use 2 hands 51
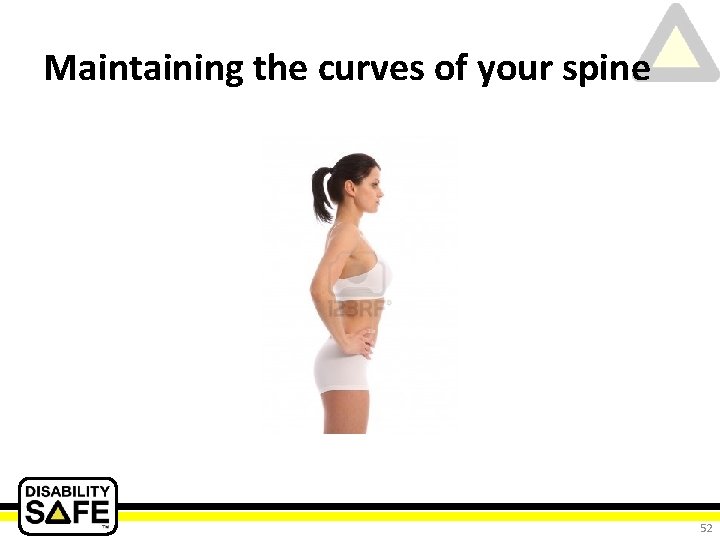
Maintaining the curves of your spine 52
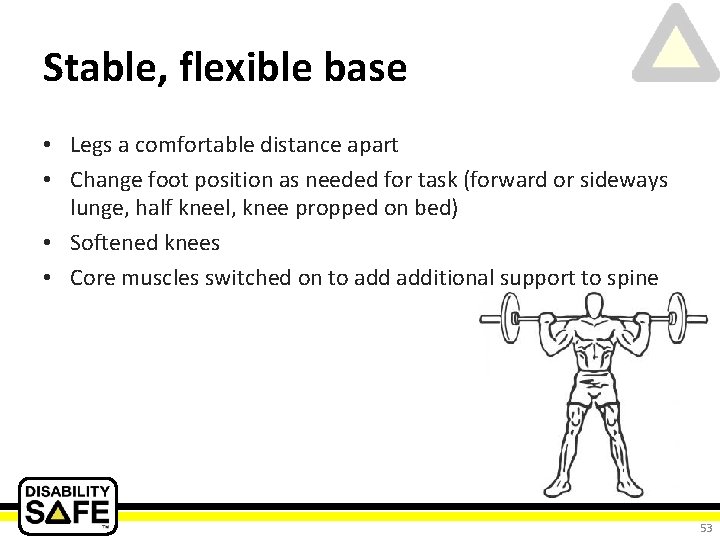
Stable, flexible base • Legs a comfortable distance apart • Change foot position as needed for task (forward or sideways lunge, half kneel, knee propped on bed) • Softened knees • Core muscles switched on to additional support to spine 53
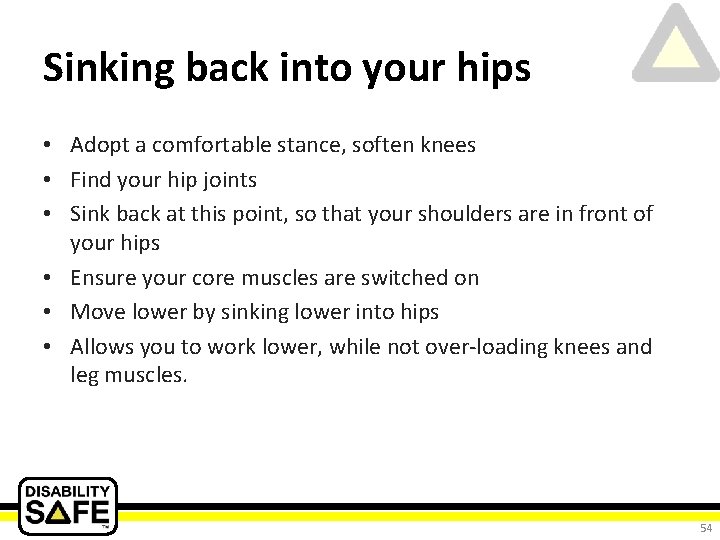
Sinking back into your hips • Adopt a comfortable stance, soften knees • Find your hip joints • Sink back at this point, so that your shoulders are in front of your hips • Ensure your core muscles are switched on • Move lower by sinking lower into hips • Allows you to work lower, while not over-loading knees and leg muscles. 54
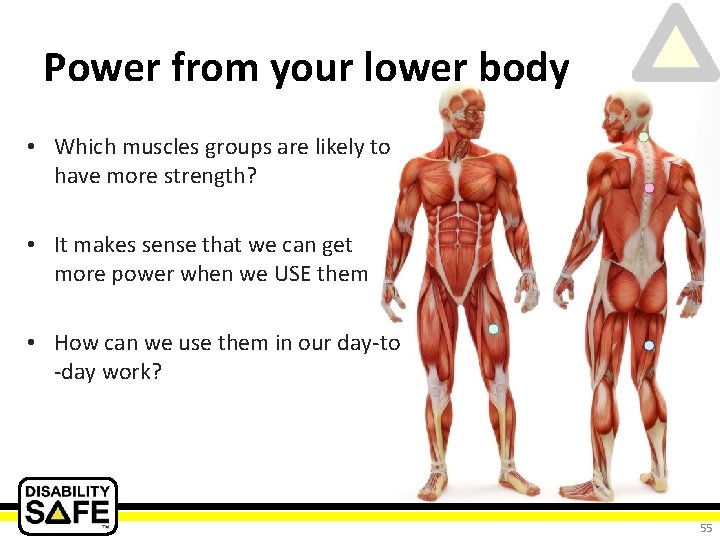
Power from your lower body • Which muscles groups are likely to have more strength? • It makes sense that we can get more power when we USE them • How can we use them in our day-to -day work? 55
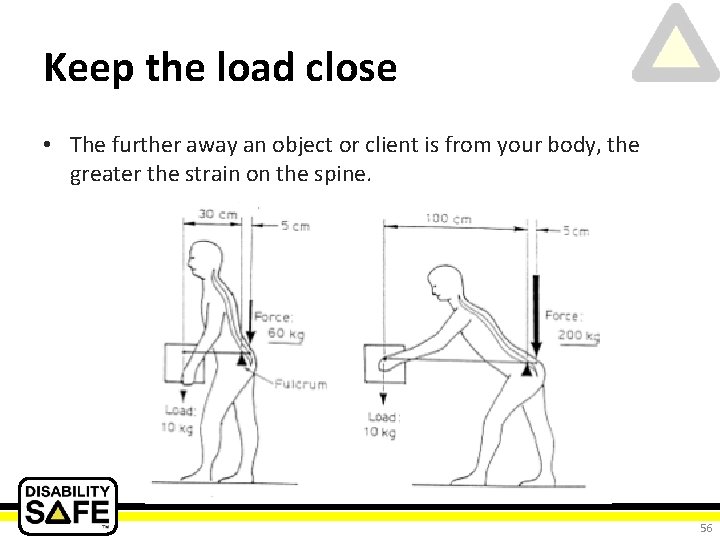
Keep the load close • The further away an object or client is from your body, the greater the strain on the spine. 56
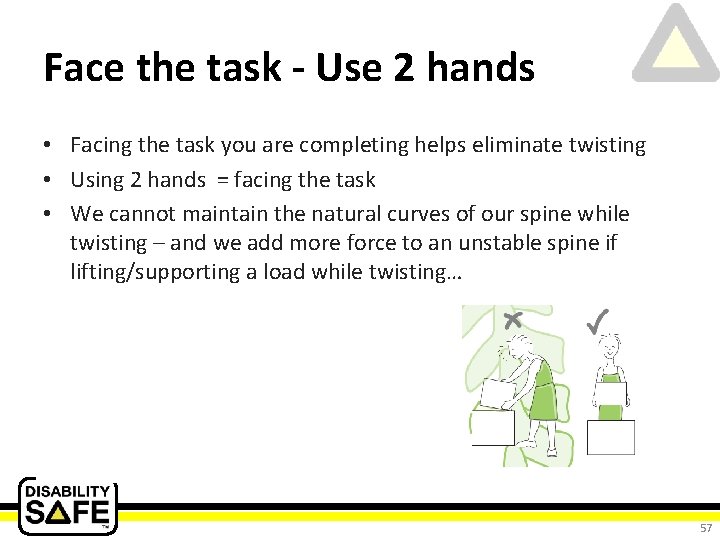
Face the task - Use 2 hands • Facing the task you are completing helps eliminate twisting • Using 2 hands = facing the task • We cannot maintain the natural curves of our spine while twisting – and we add more force to an unstable spine if lifting/supporting a load while twisting… 57
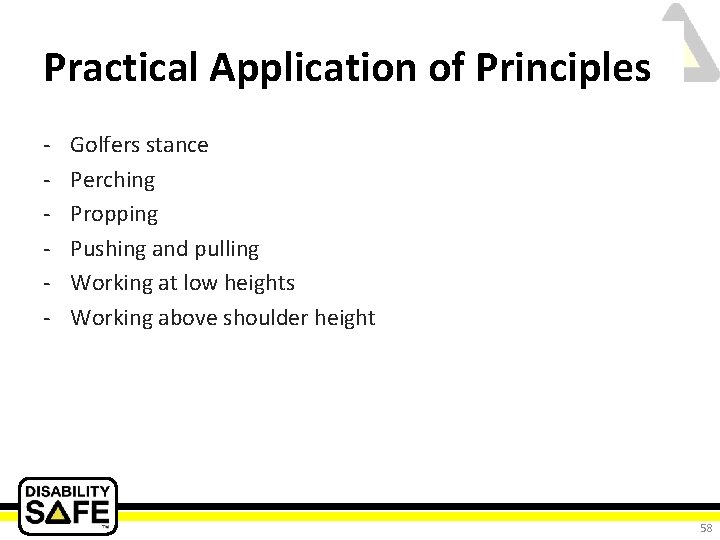
Practical Application of Principles - Golfers stance Perching Propping Pushing and pulling Working at low heights Working above shoulder height 58
Basic principles of manual handling
Sarah ades penn state
Client handling task
Manual handling toolbox talk presentation
Kinetic lifting method
Mhra
Child's play manual handling
The drag lift in manual handling
Manual handling
Ahm iata
Manual handling campaign
Lunge position manual handling
Moving and handling competency assessment template
Material handling means
Aim of manual handling
Wruld examples
Litee manual handling
Manual handling pictures
Material handling principles
Principles of grievance handling
Material handling principle
Liquid nitrogen training
Cash handling training
Stress management vocabulary
Canvas key partners
Key partners
Ansys training manual
Anna bieberdorf
Insurance agent training manual
Altar workers training manual pdf
Ansys workbench manual
Bartender training manual doc
Aeroplane flight training manual
Kde munis guides
Tier.net training manual
Pepperball training manual
Sits training
Social media training manual
Prison ministry training manual download
Training manual design
Tier.net training manual
Eam light cern
Agresso instructions
Sits vision
Examples of critical control points
Financial coaching training manual
Ansys training manual
Principles of training reversibility
Fitness chapter 6
Training principles
5 principles of training
Tedium principle
Tedium exercise examples
The 5 principles of training
9 principles of exercise
Principles of weight training
9 principles of training
Principles of training program
Principles of effective training