MAINTAIN MECHANICAL SERVICES EQUIPMENT CPCPMS 3009 A INTRODUCTION
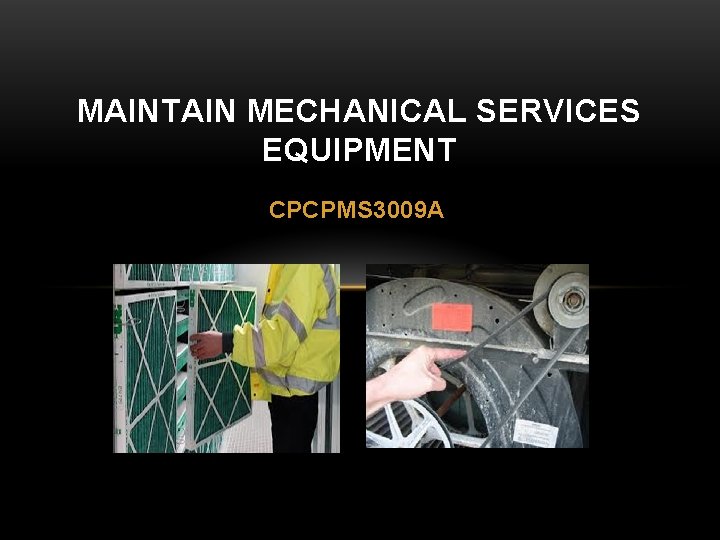
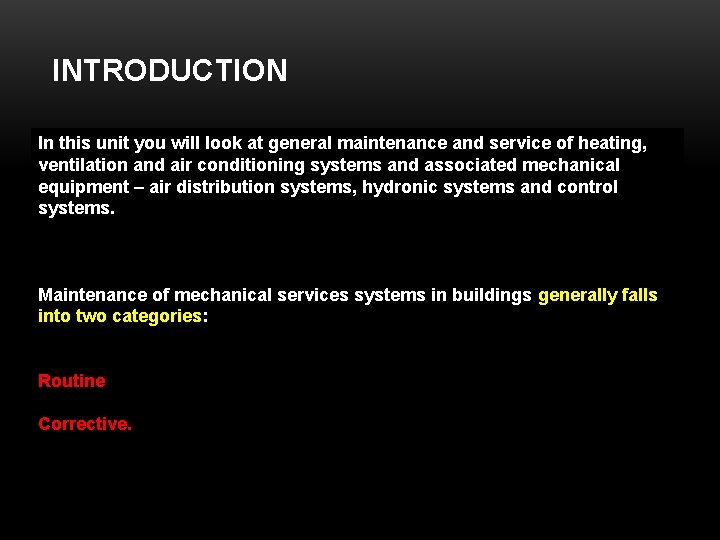
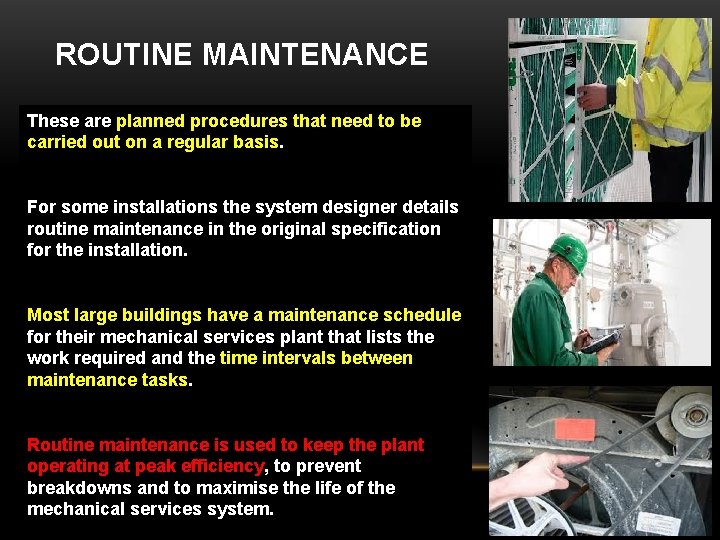
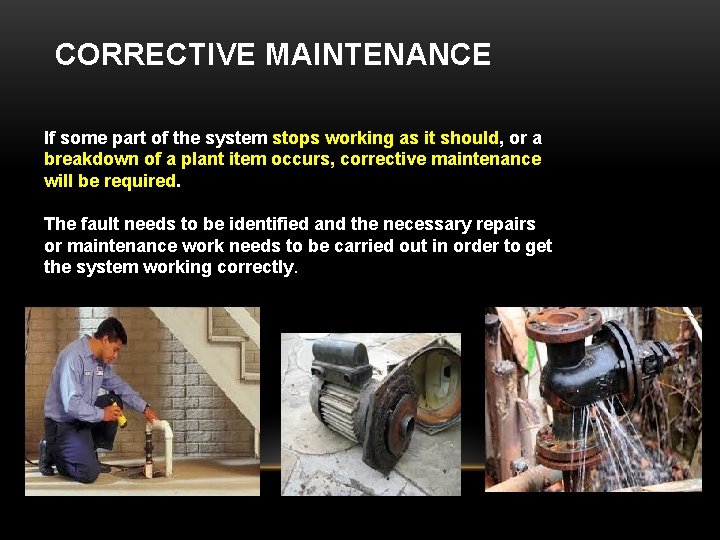
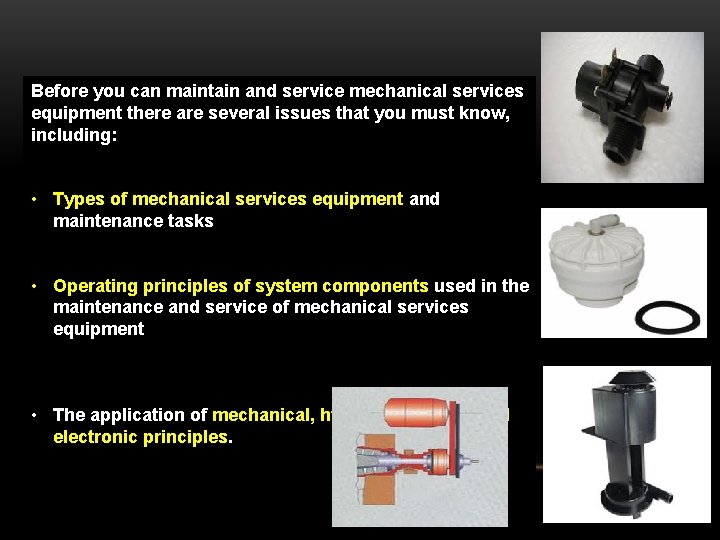
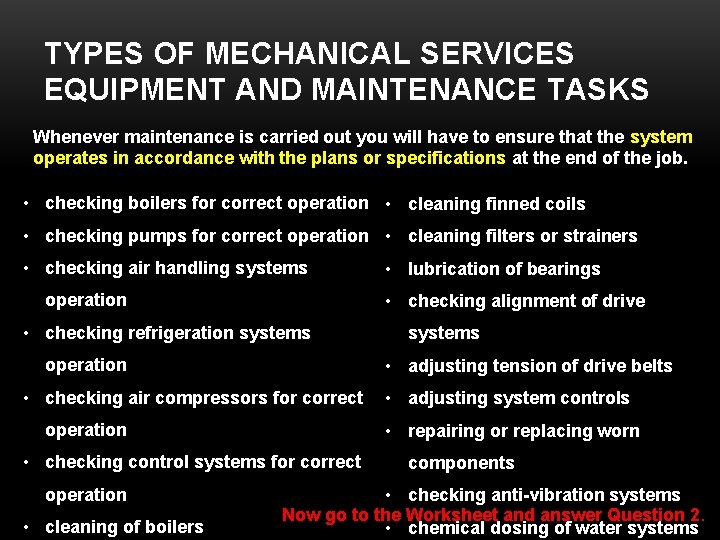
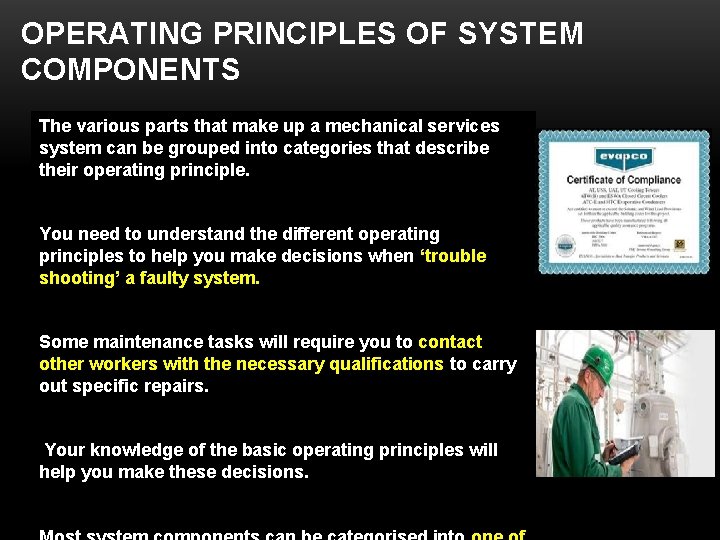
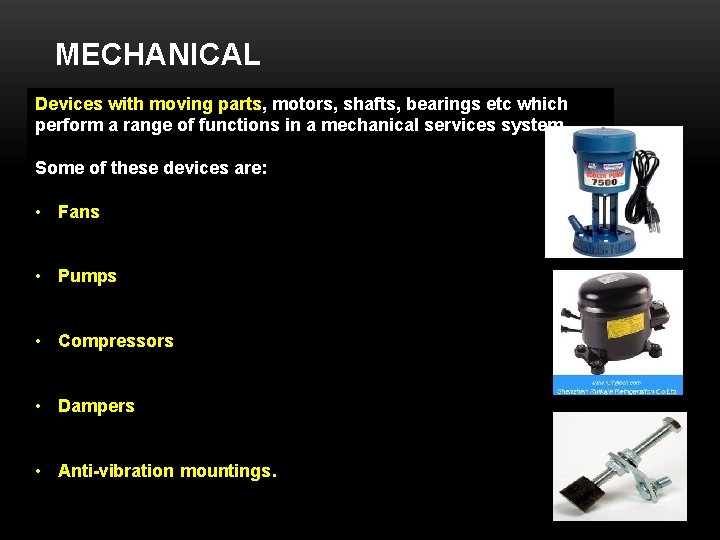
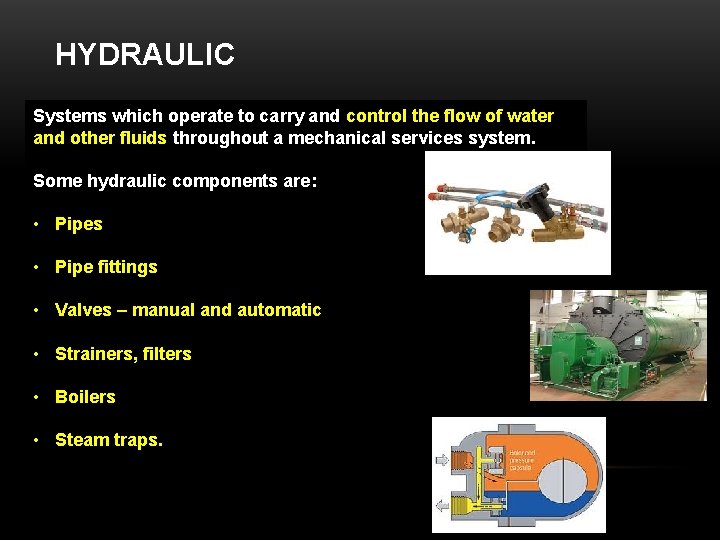
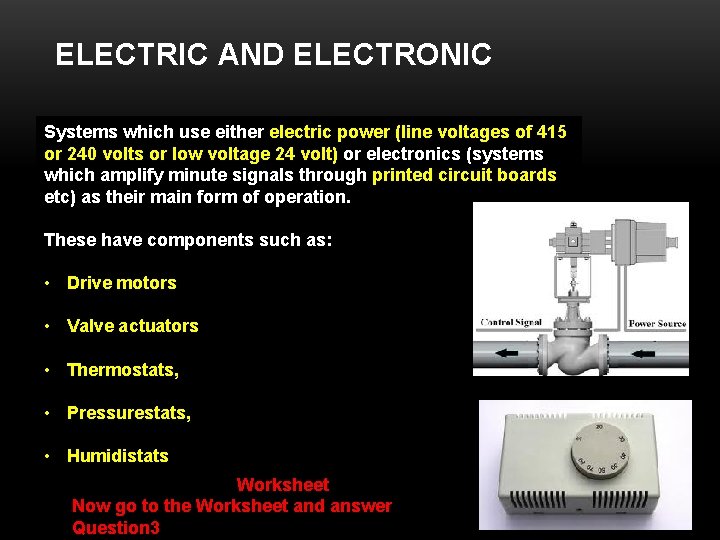
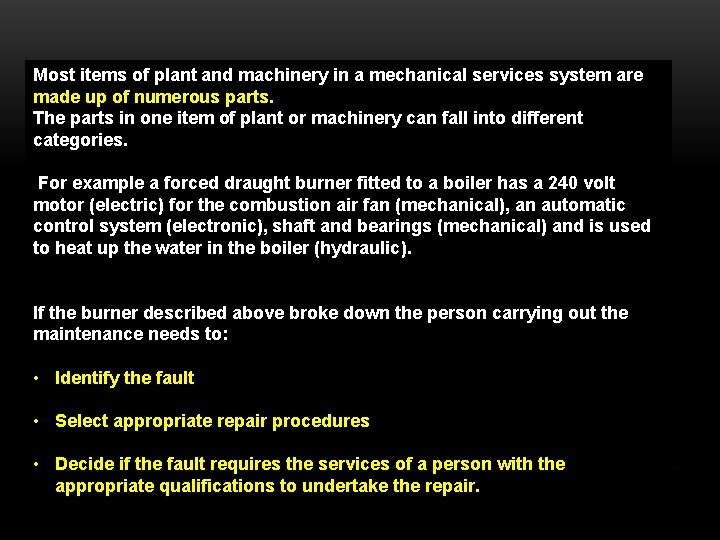
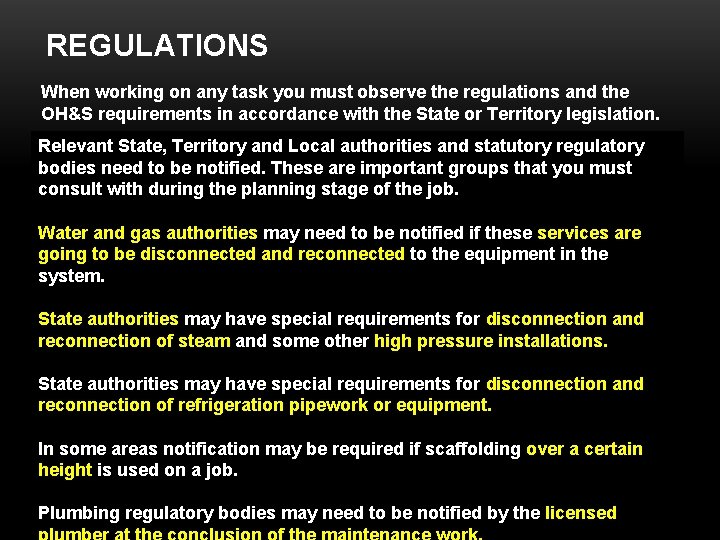
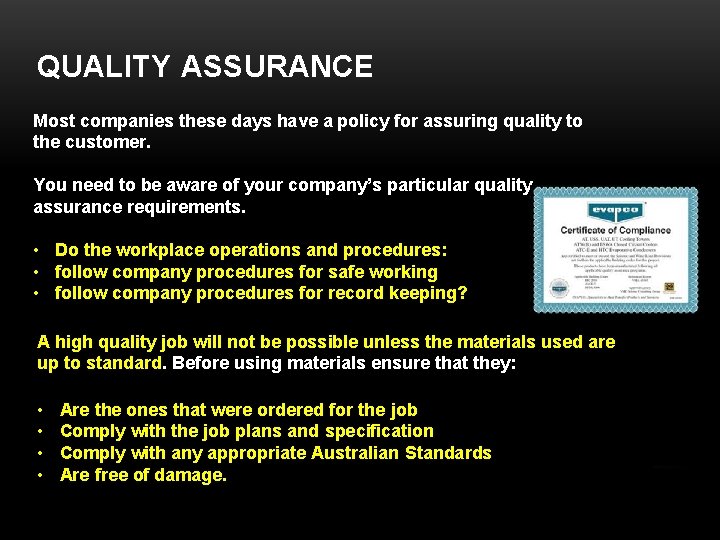
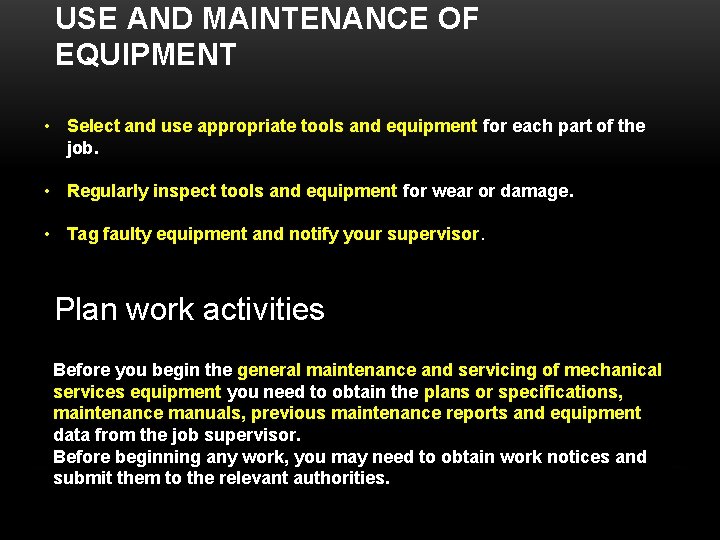
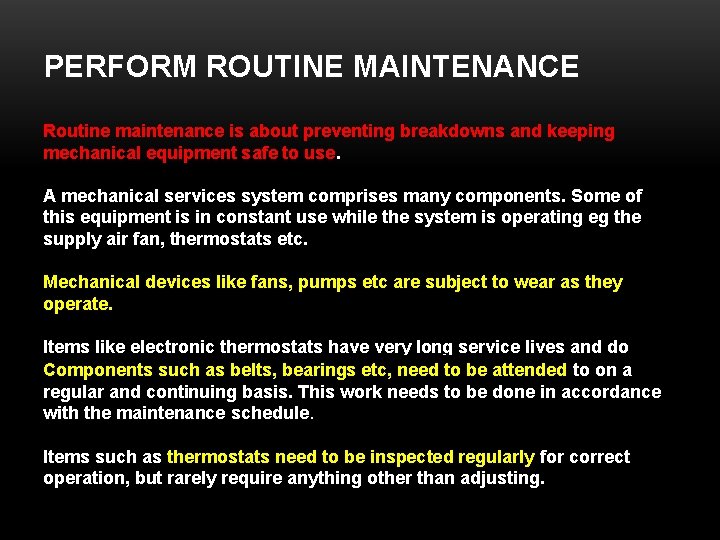
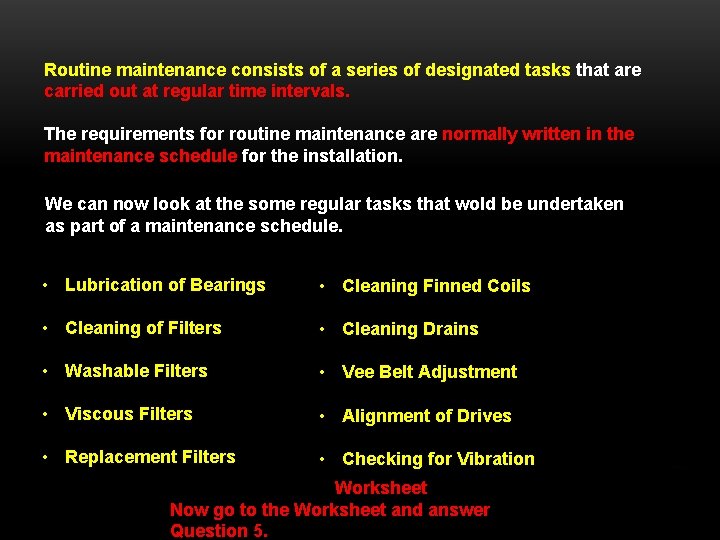
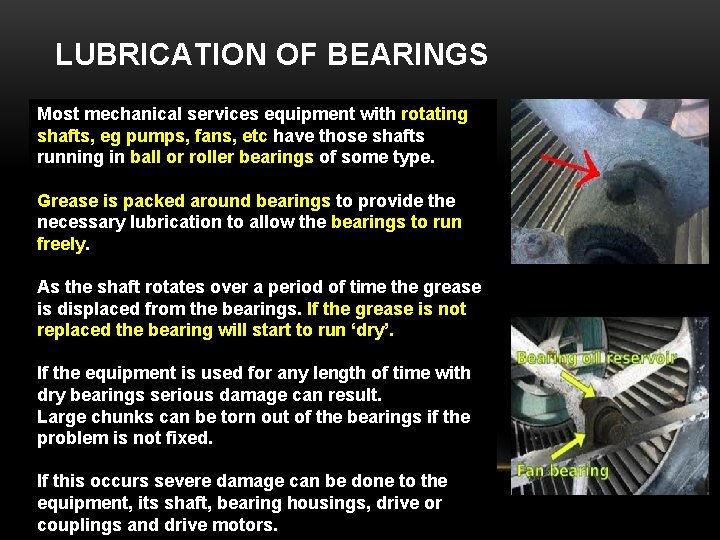
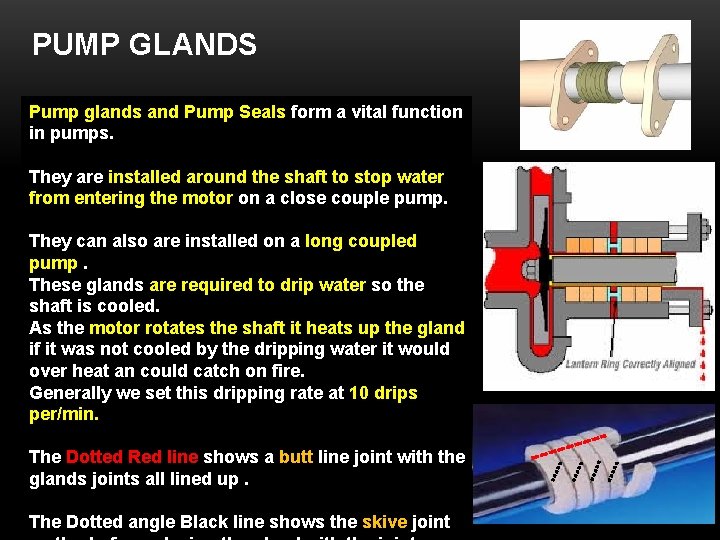
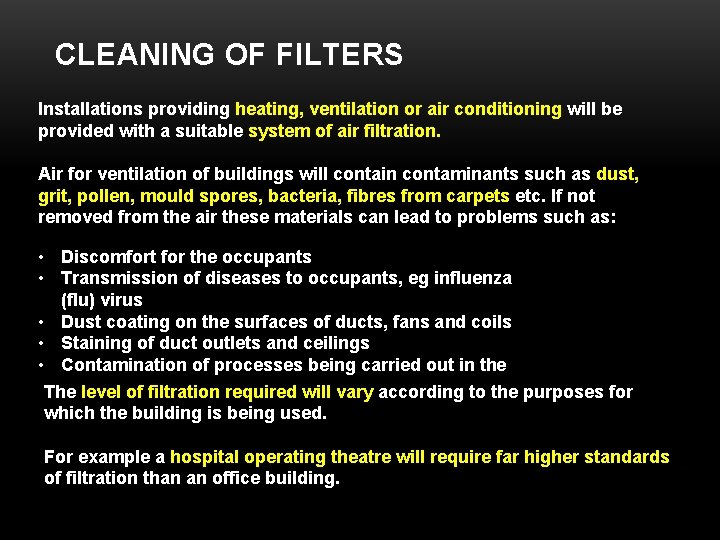
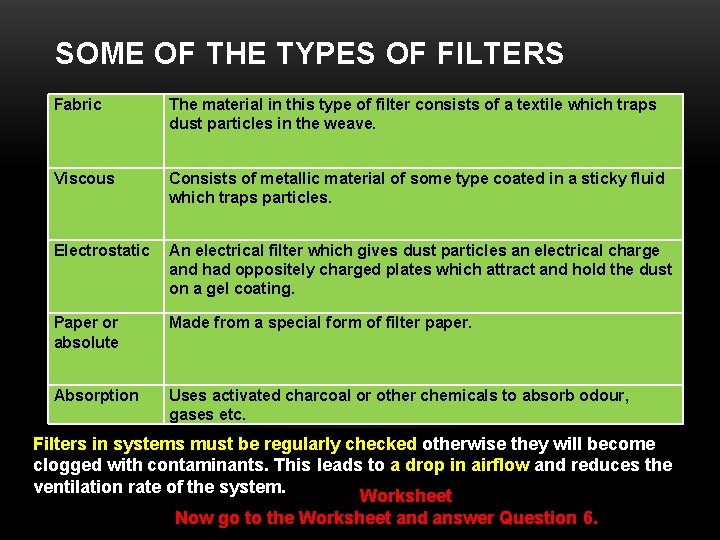
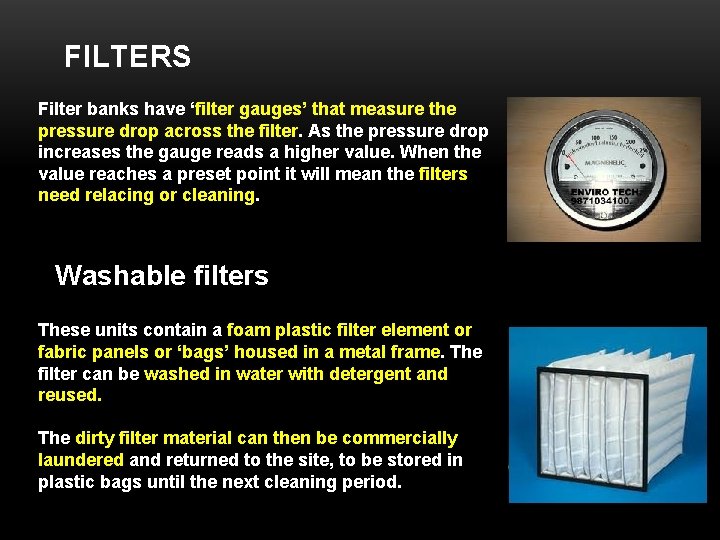
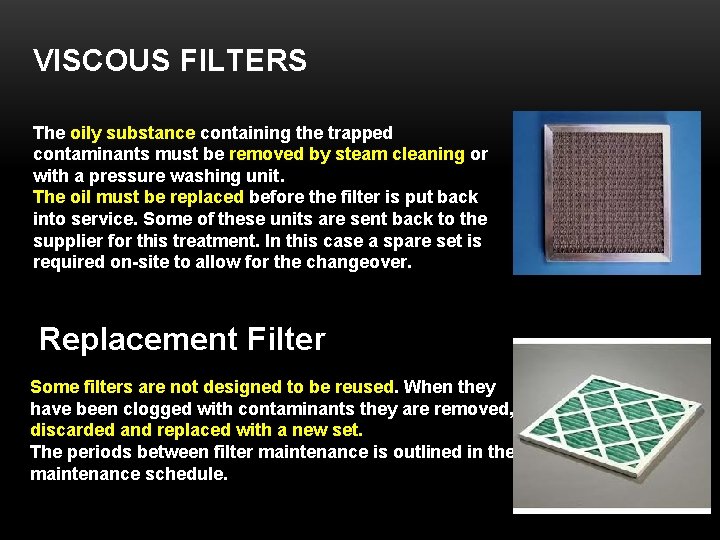
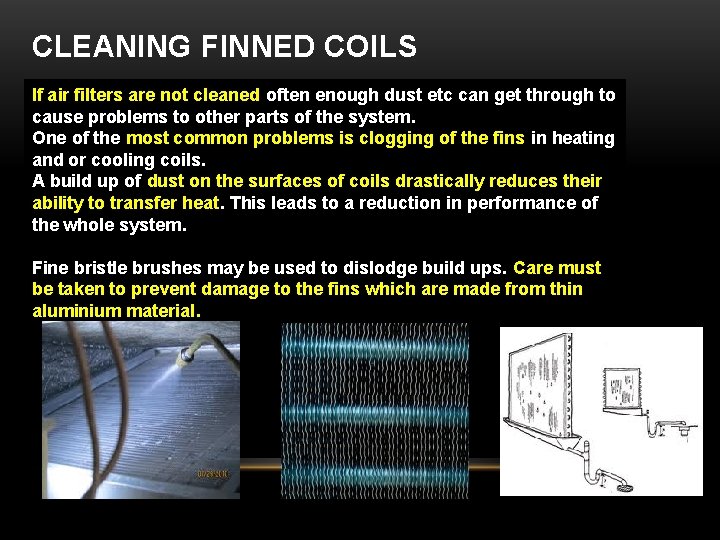
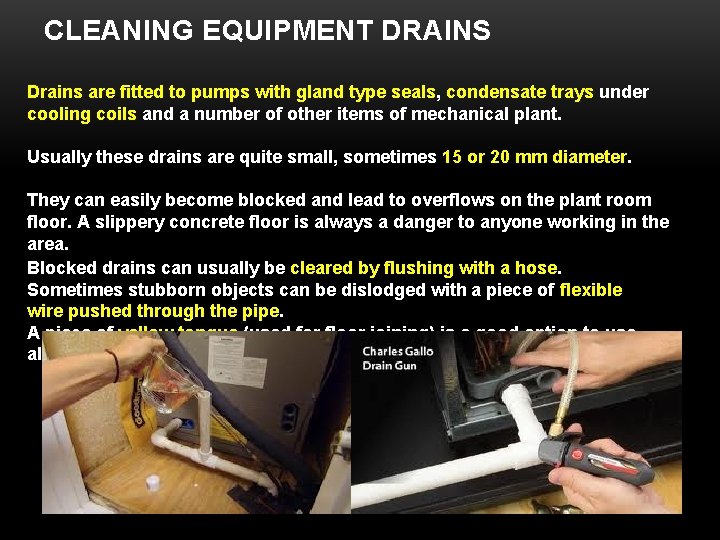
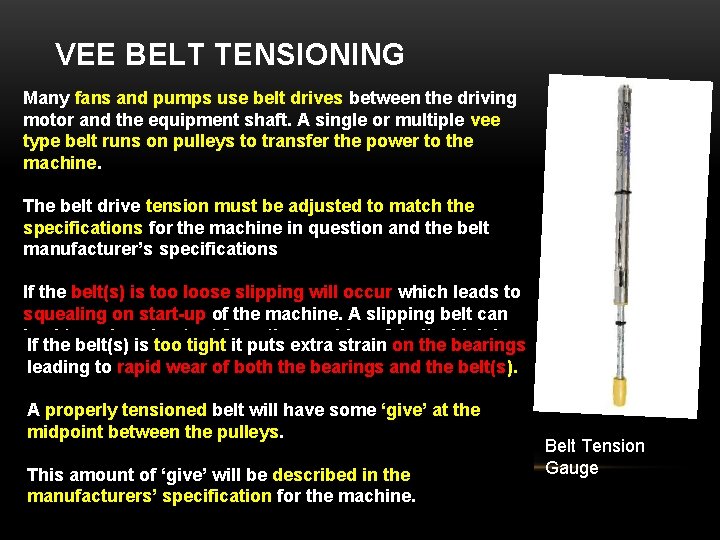
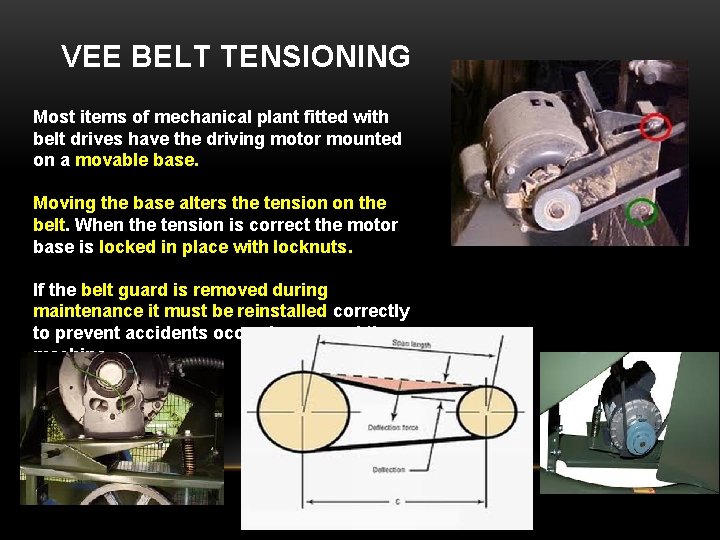
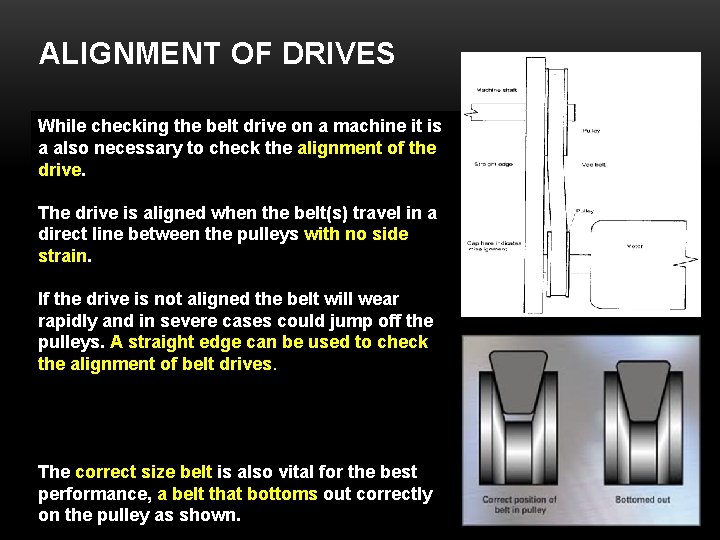
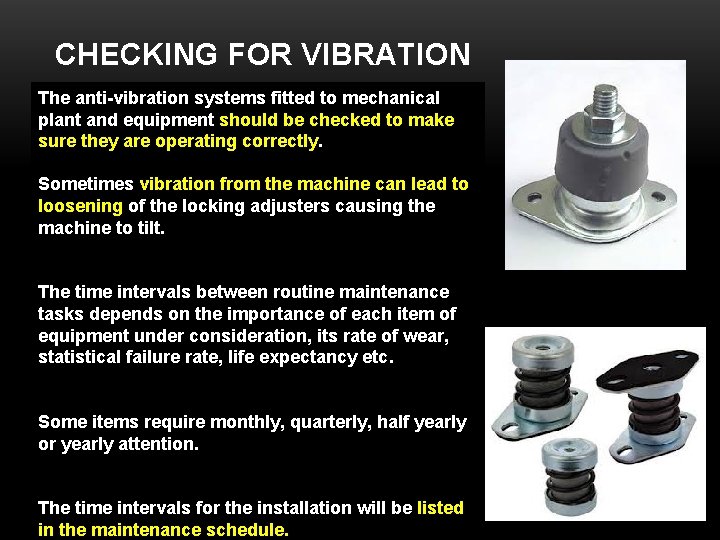
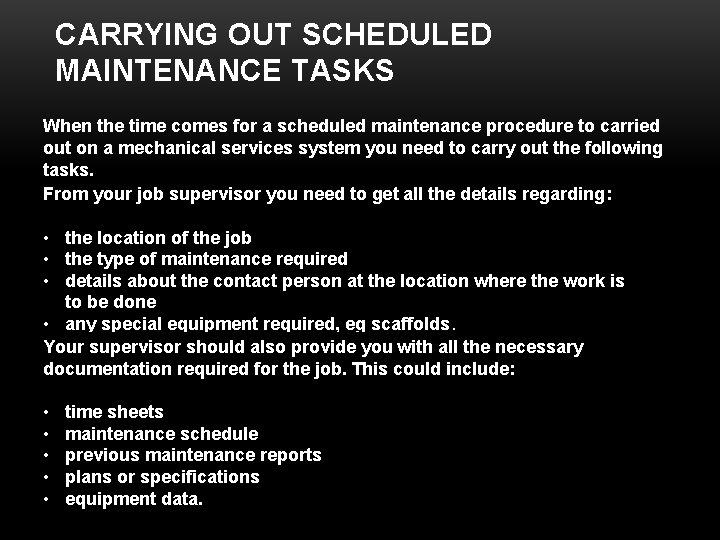
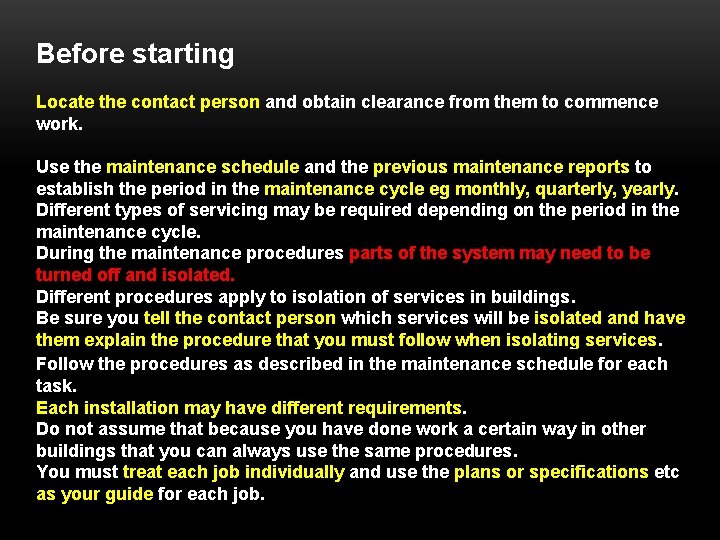
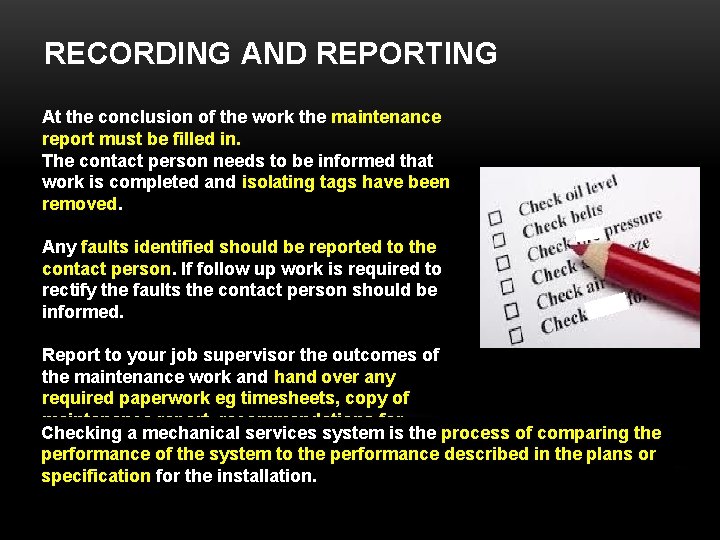
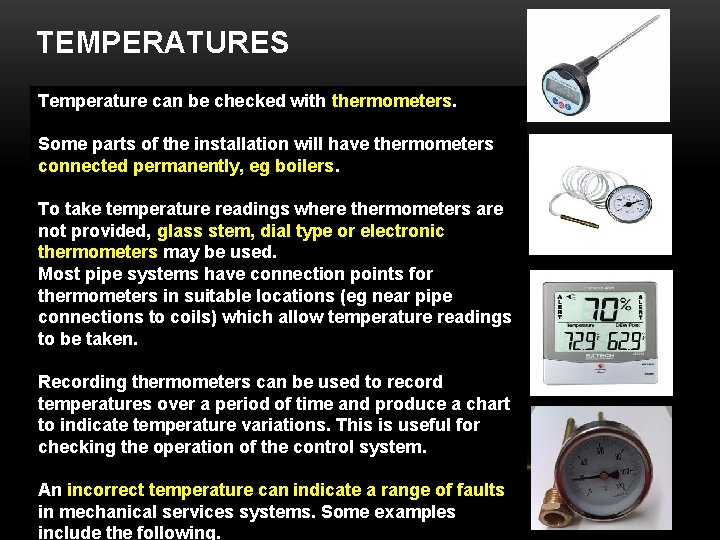
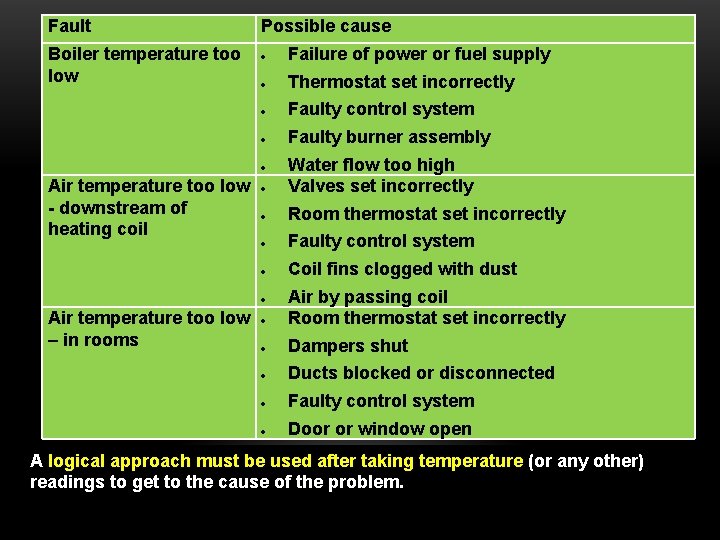
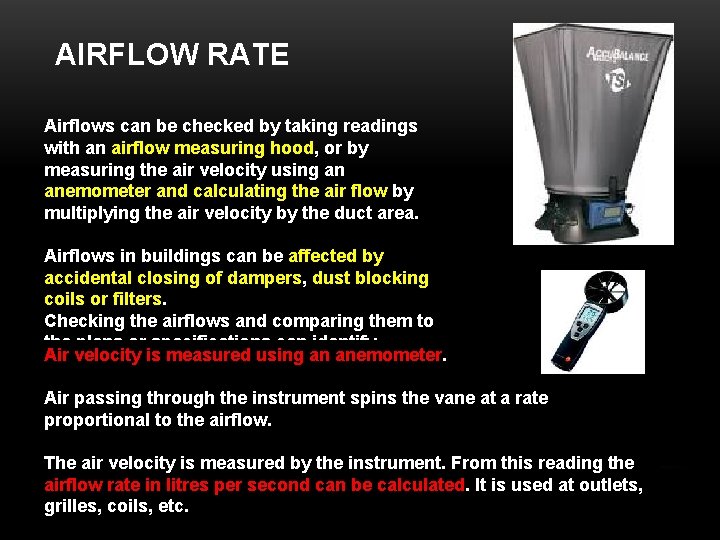
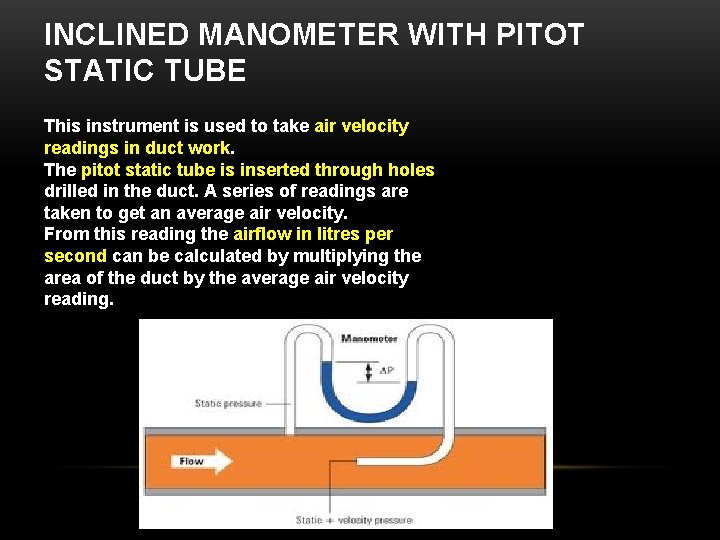
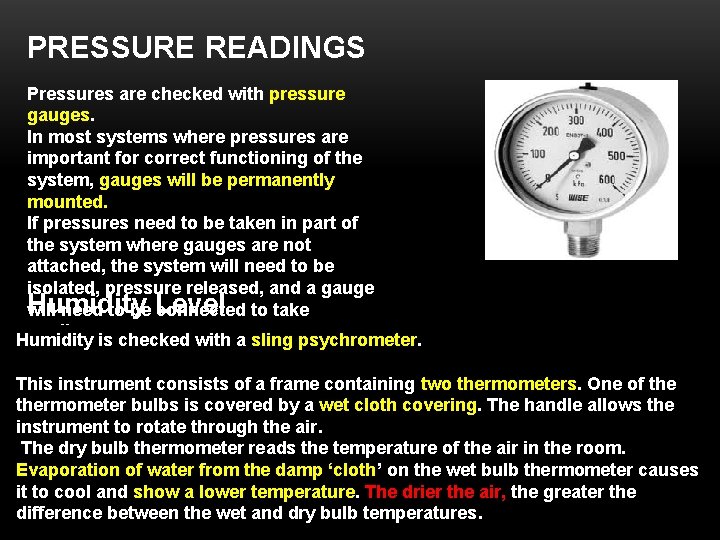
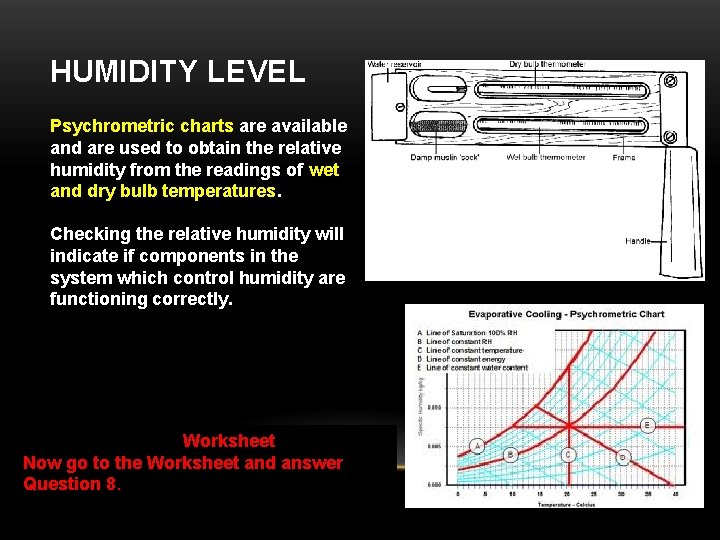
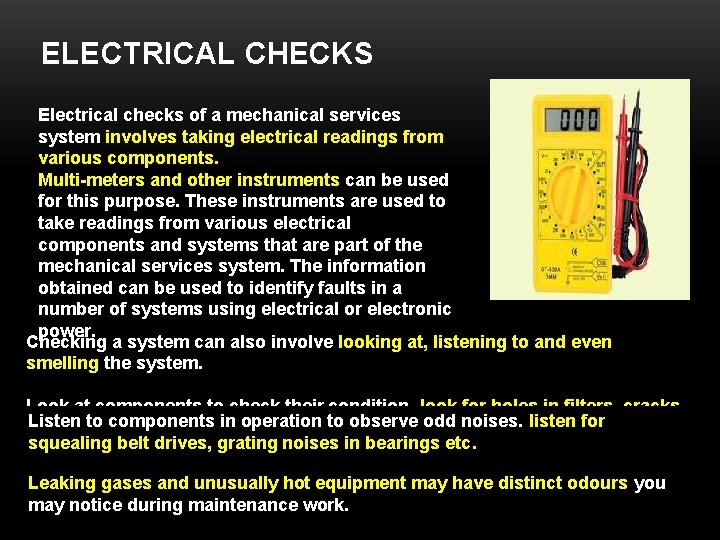
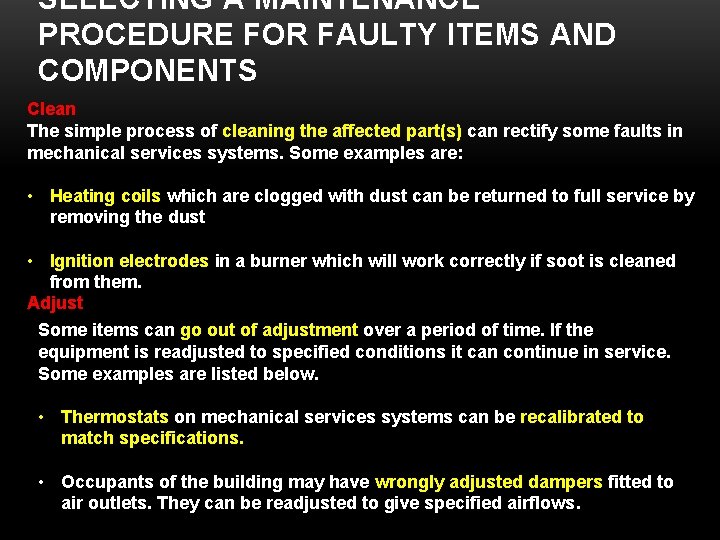
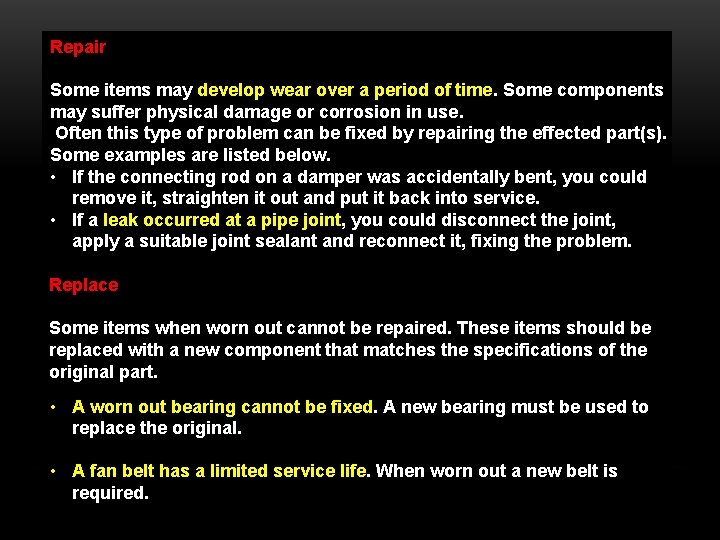
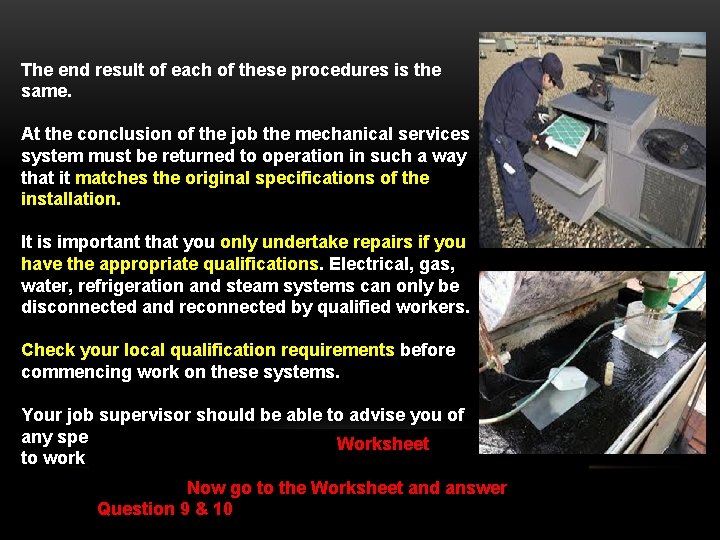
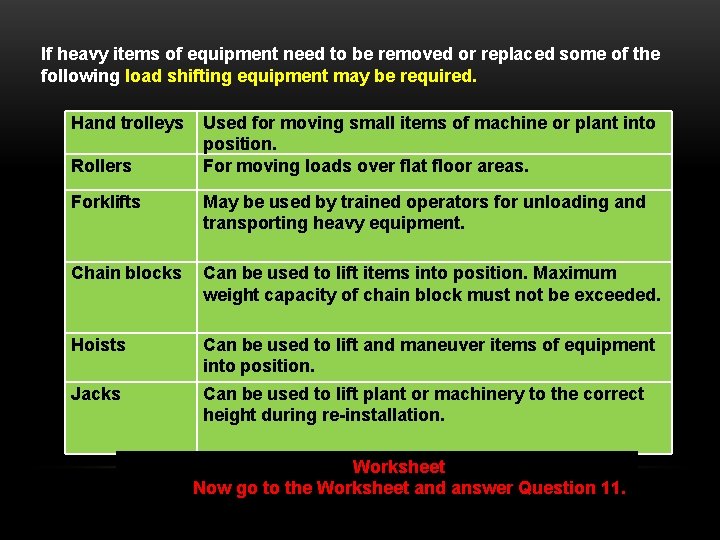
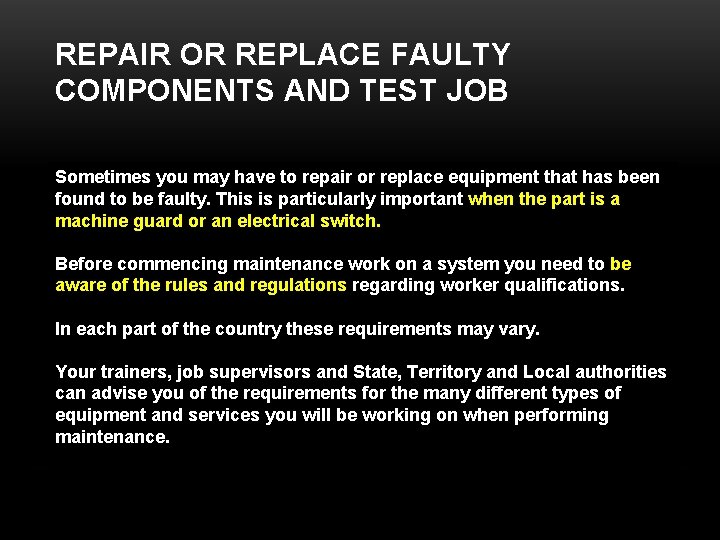
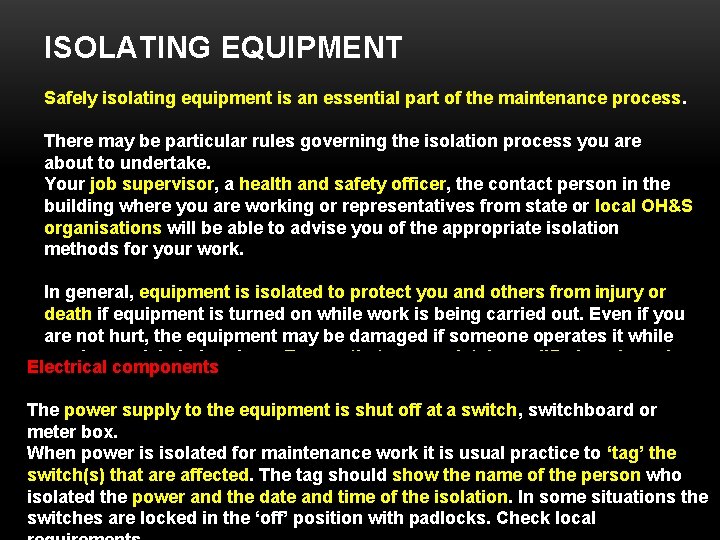
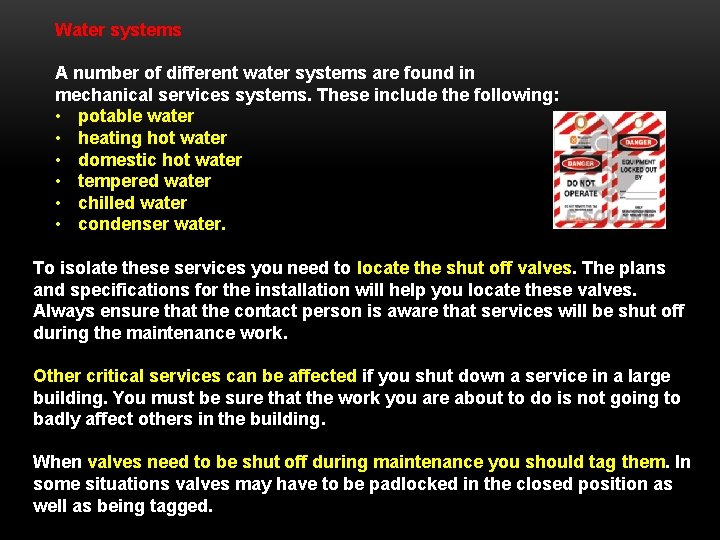
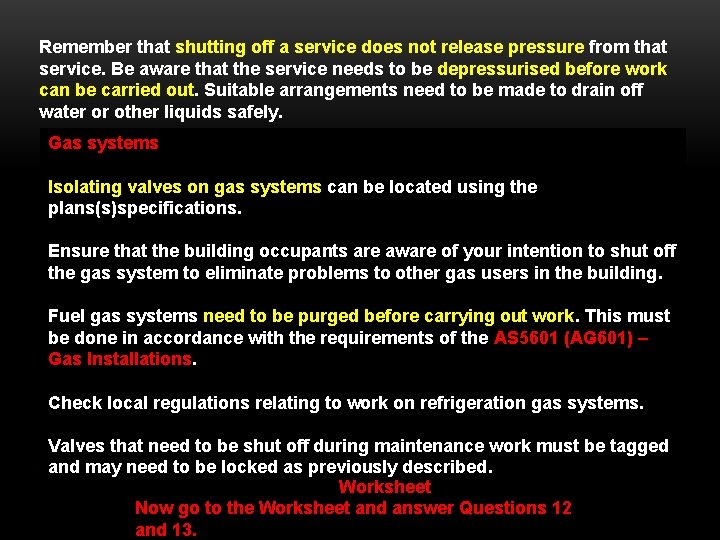
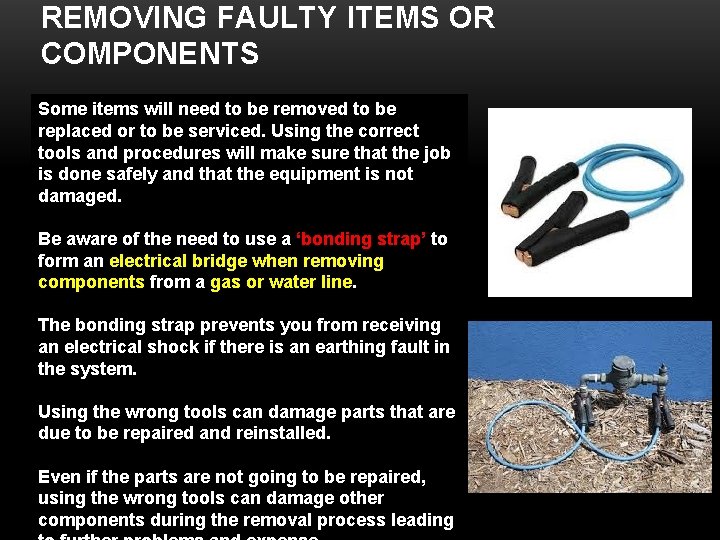
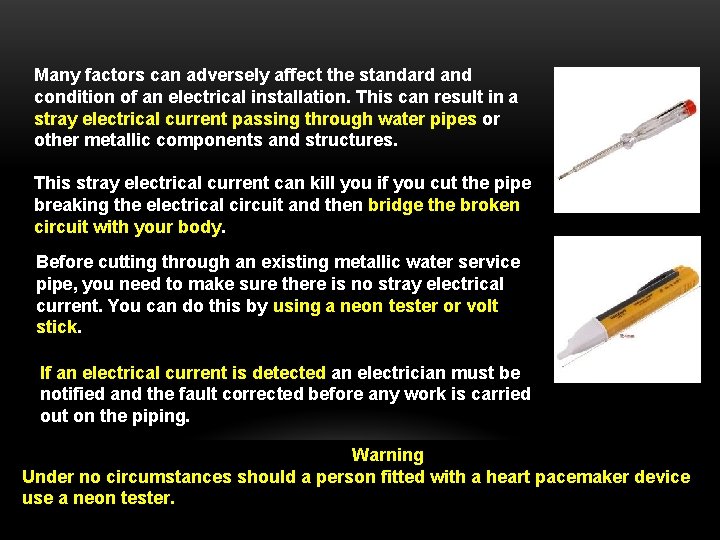
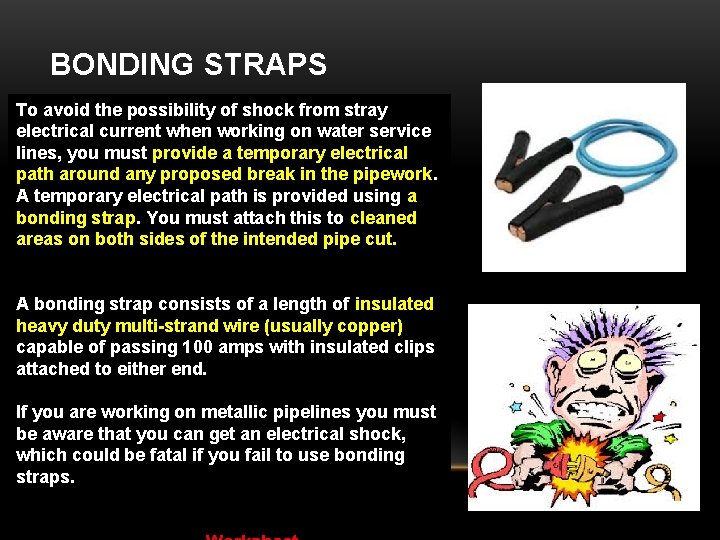
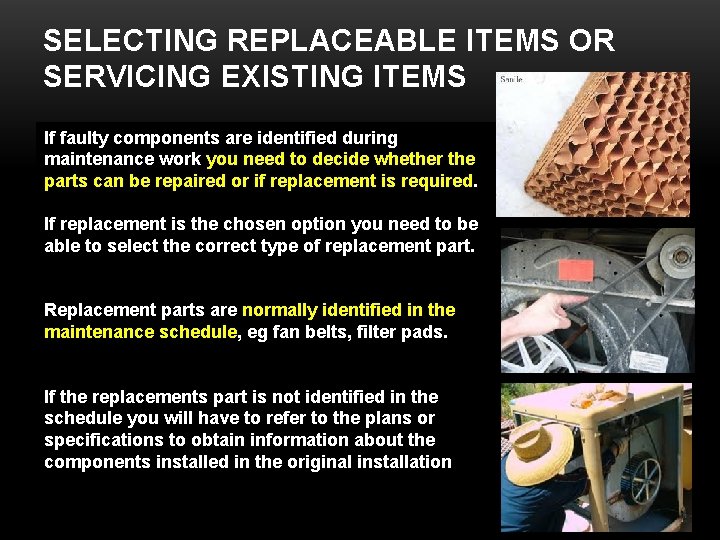
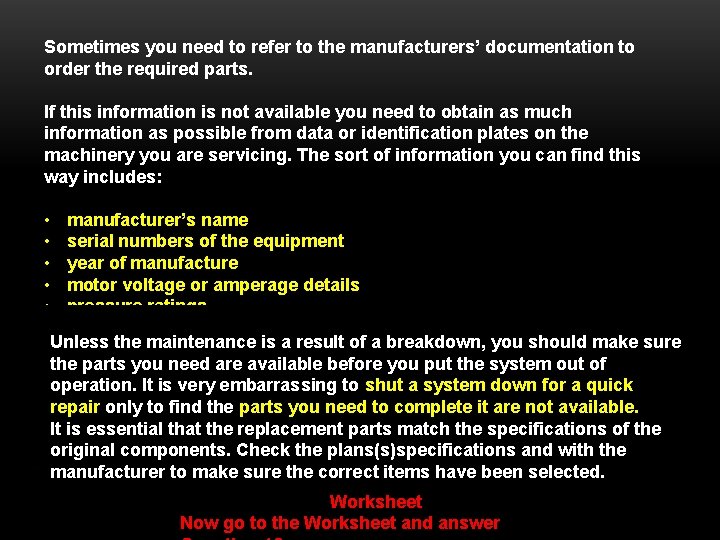
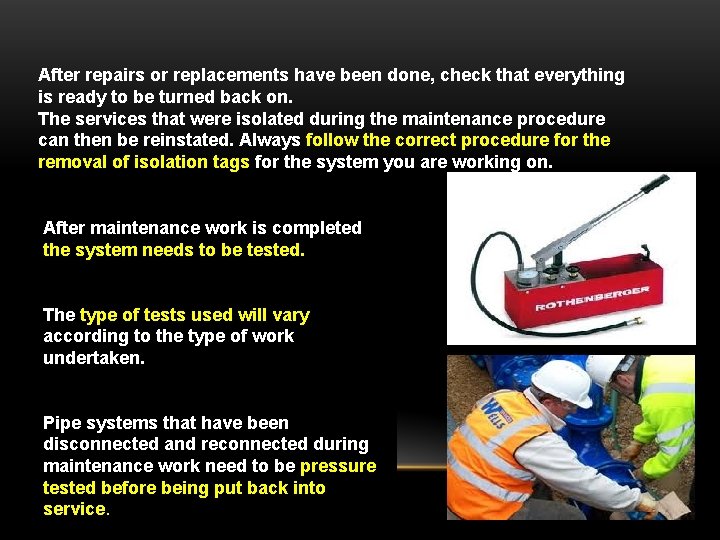
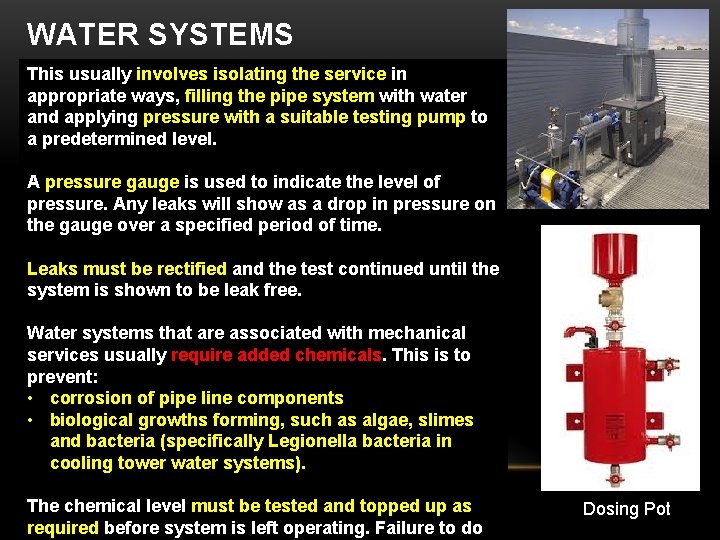
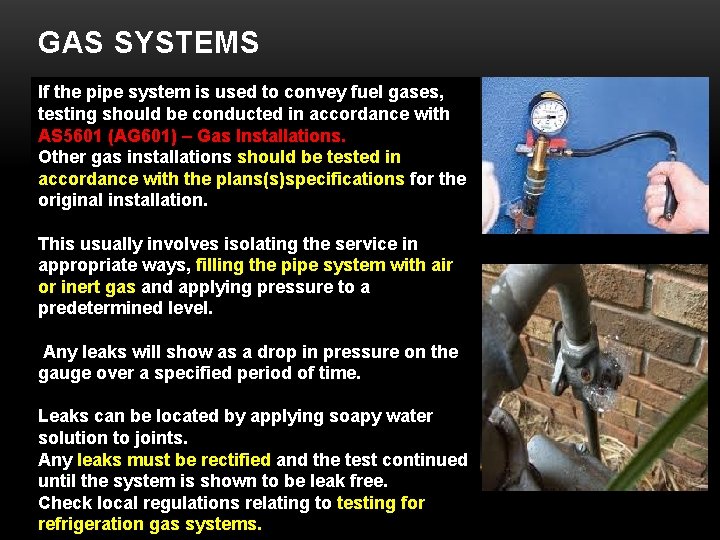
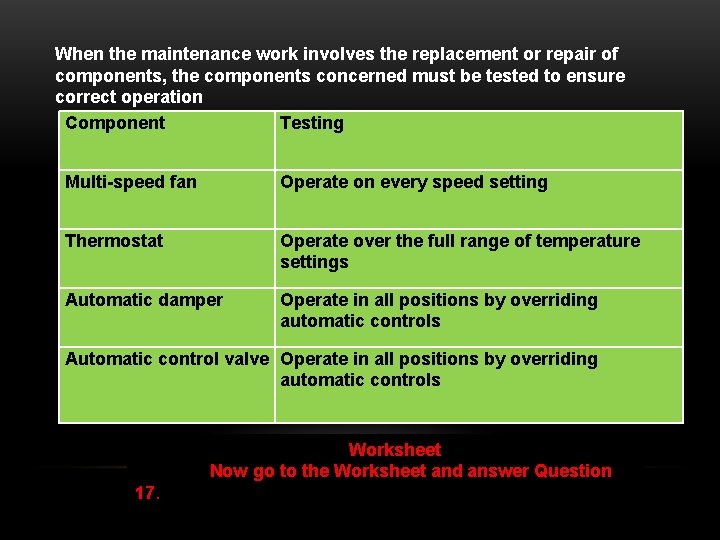
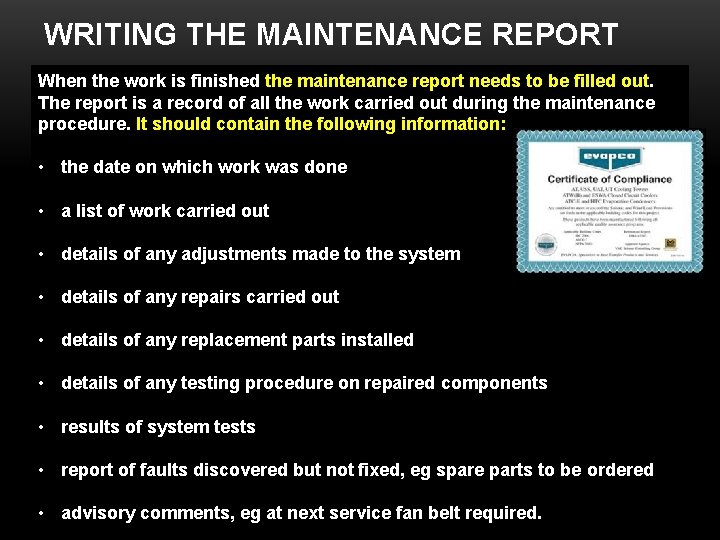
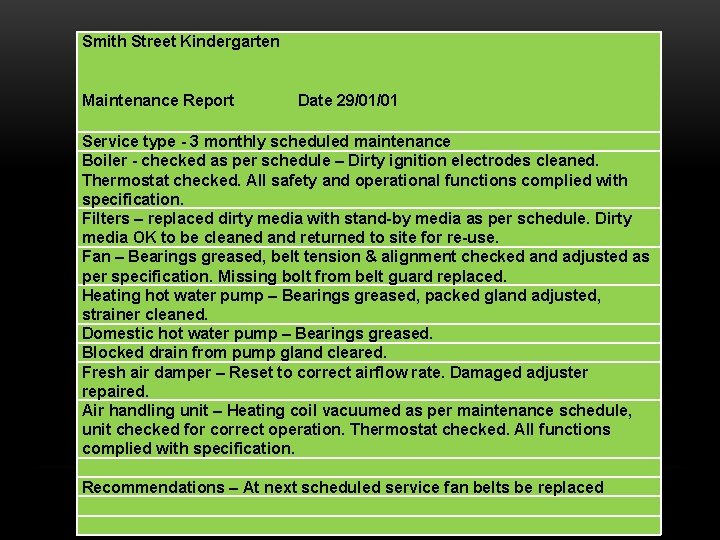
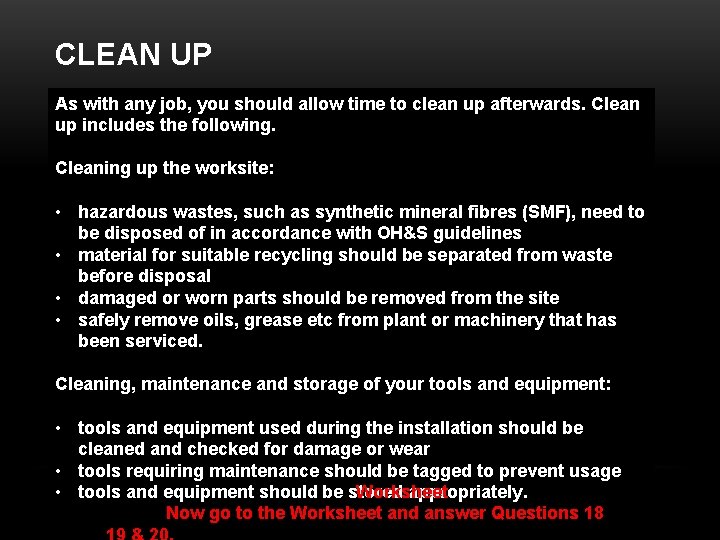
- Slides: 58
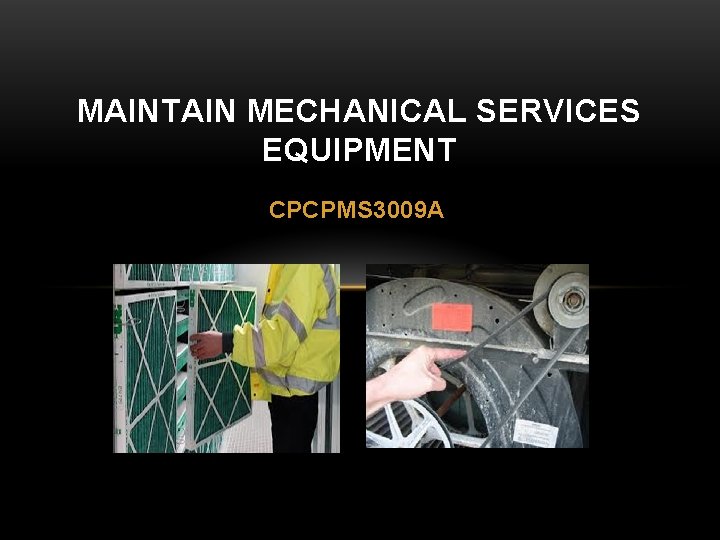
MAINTAIN MECHANICAL SERVICES EQUIPMENT CPCPMS 3009 A
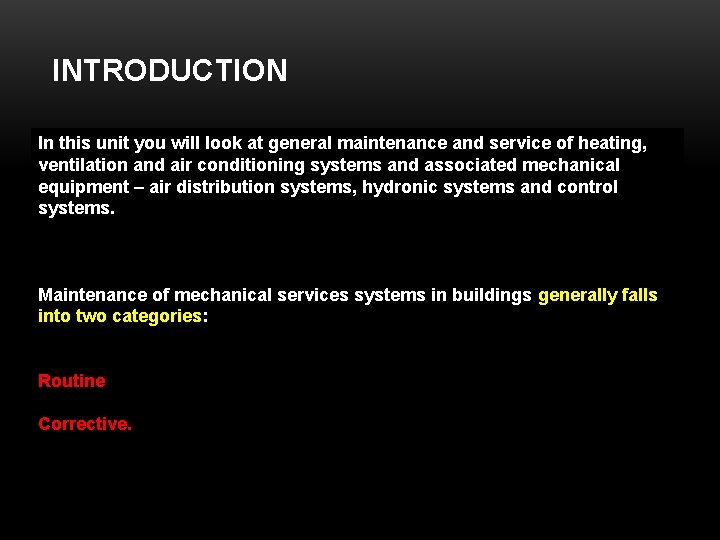
INTRODUCTION In this unit you will look at general maintenance and service of heating, ventilation and air conditioning systems and associated mechanical equipment – air distribution systems, hydronic systems and control systems. Maintenance of mechanical services systems in buildings generally falls into two categories: Routine Corrective.
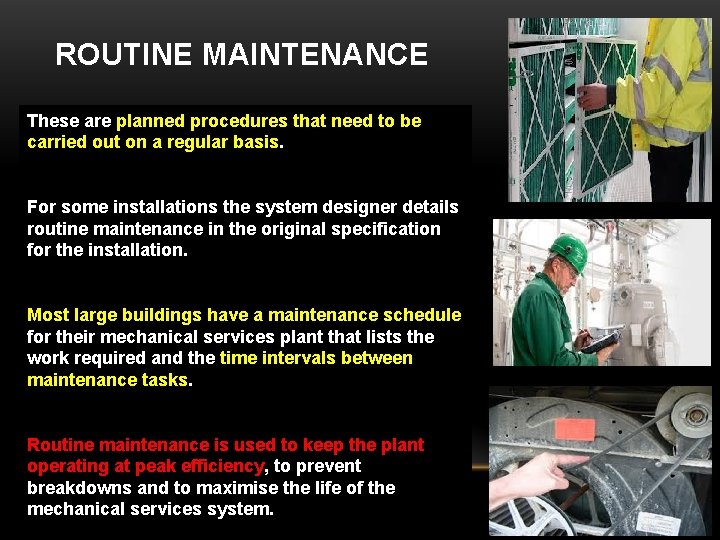
ROUTINE MAINTENANCE These are planned procedures that need to be carried out on a regular basis. For some installations the system designer details routine maintenance in the original specification for the installation. Most large buildings have a maintenance schedule for their mechanical services plant that lists the work required and the time intervals between maintenance tasks. Routine maintenance is used to keep the plant operating at peak efficiency, to prevent breakdowns and to maximise the life of the mechanical services system.
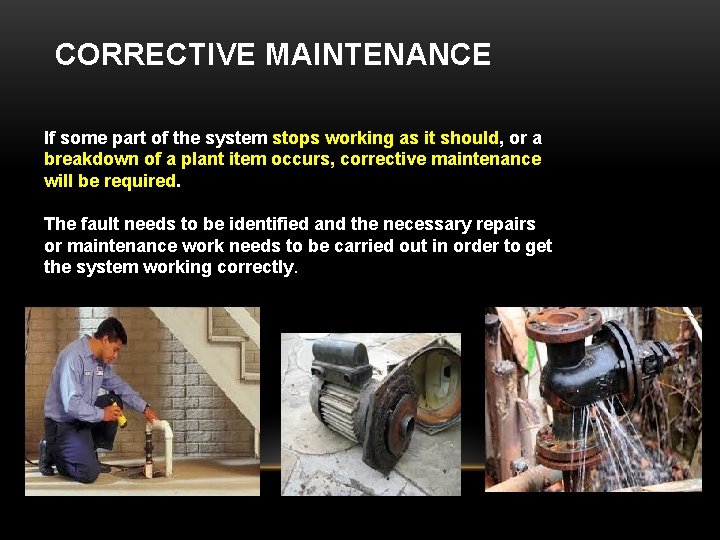
CORRECTIVE MAINTENANCE If some part of the system stops working as it should, or a breakdown of a plant item occurs, corrective maintenance will be required. The fault needs to be identified and the necessary repairs or maintenance work needs to be carried out in order to get the system working correctly.
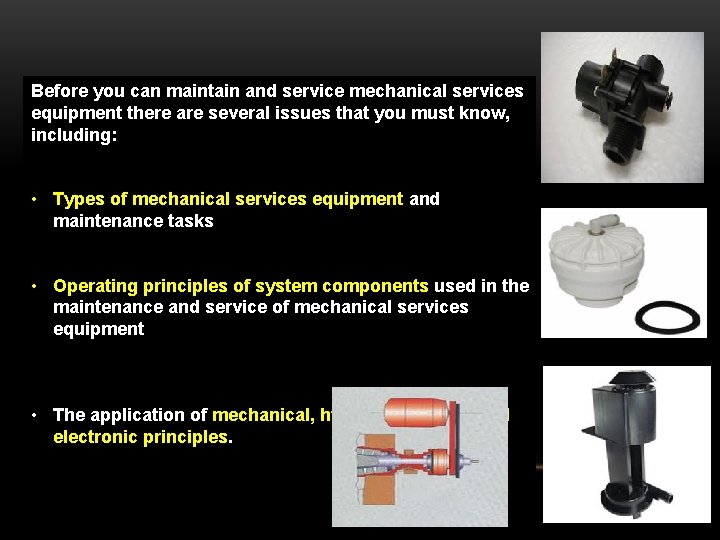
Before you can maintain and service mechanical services equipment there are several issues that you must know, including: • Types of mechanical services equipment and maintenance tasks • Operating principles of system components used in the maintenance and service of mechanical services equipment • The application of mechanical, hydraulic, electric and electronic principles.
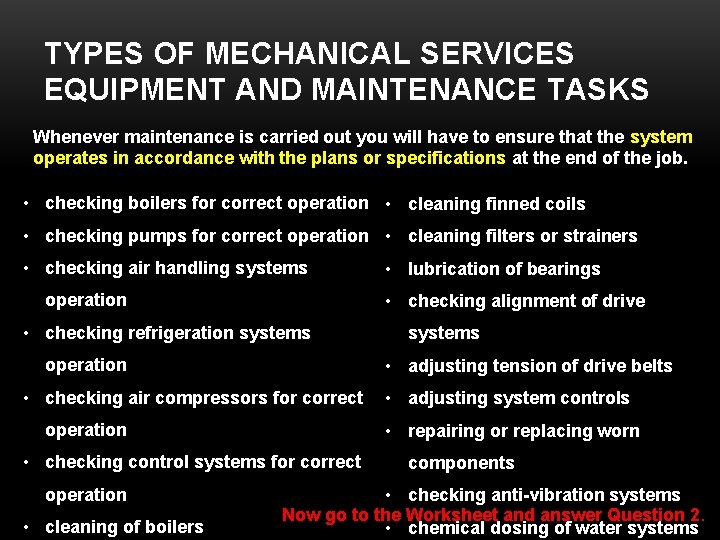
TYPES OF MECHANICAL SERVICES EQUIPMENT AND MAINTENANCE TASKS Whenever maintenance is carried out you will have to ensure that the system operates in accordance with the plans or specifications at the end of the job. • checking boilers for correct operation • cleaning finned coils • checking pumps for correct operation • cleaning filters or strainers • checking air handling systems operation • lubrication of bearings • checking alignment of drive • checking refrigeration systems operation systems • adjusting tension of drive belts • checking air compressors for correct • adjusting system controls operation • repairing or replacing worn • checking control systems for correct operation • cleaning of boilers components • checking anti-vibration systems Now go to the Worksheet and answer Question 2. • chemical dosing of water systems
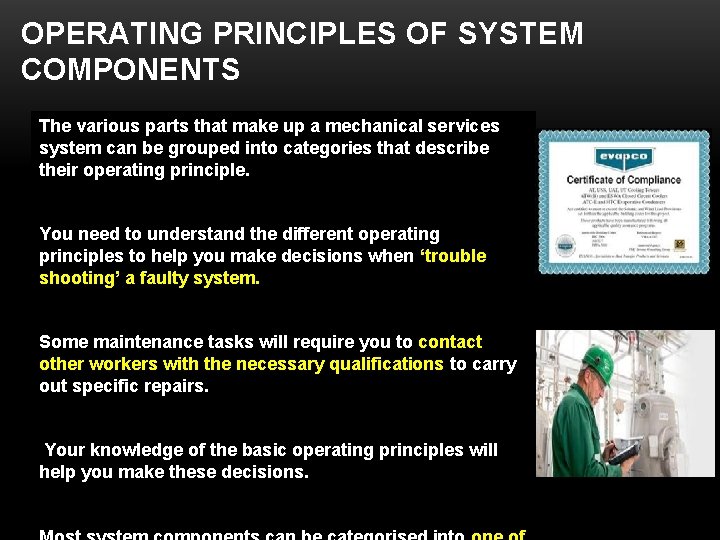
OPERATING PRINCIPLES OF SYSTEM COMPONENTS The various parts that make up a mechanical services system can be grouped into categories that describe their operating principle. You need to understand the different operating principles to help you make decisions when ‘trouble shooting’ a faulty system. Some maintenance tasks will require you to contact other workers with the necessary qualifications to carry out specific repairs. Your knowledge of the basic operating principles will help you make these decisions.
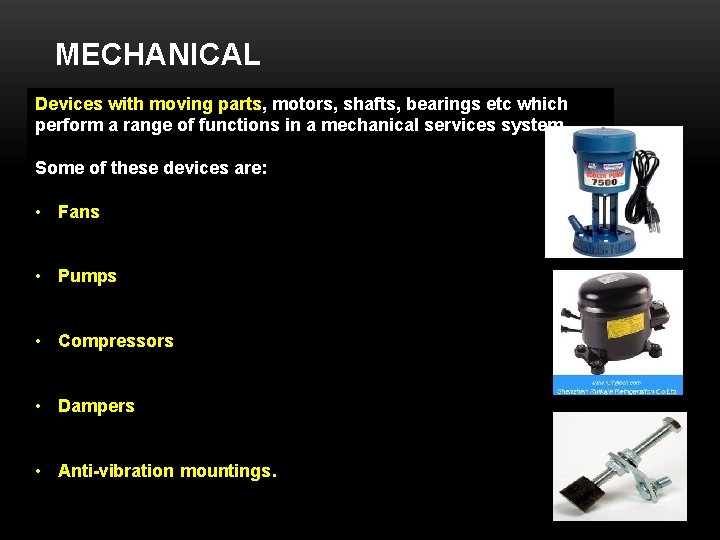
MECHANICAL Devices with moving parts, motors, shafts, bearings etc which perform a range of functions in a mechanical services system. Some of these devices are: • Fans • Pumps • Compressors • Dampers • Anti-vibration mountings.
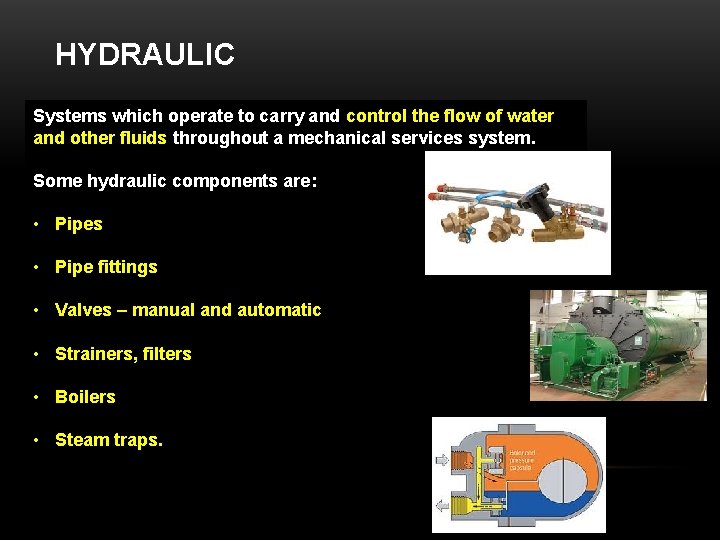
HYDRAULIC Systems which operate to carry and control the flow of water and other fluids throughout a mechanical services system. Some hydraulic components are: • Pipes • Pipe fittings • Valves – manual and automatic • Strainers, filters • Boilers • Steam traps.
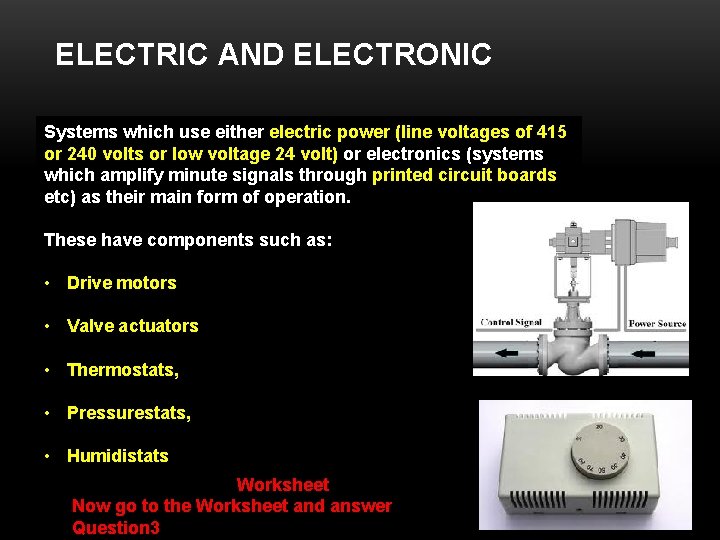
ELECTRIC AND ELECTRONIC Systems which use either electric power (line voltages of 415 or 240 volts or low voltage 24 volt) or electronics (systems which amplify minute signals through printed circuit boards etc) as their main form of operation. These have components such as: • Drive motors • Valve actuators • Thermostats, • Pressurestats, • Humidistats Worksheet Now go to the Worksheet and answer Question 3
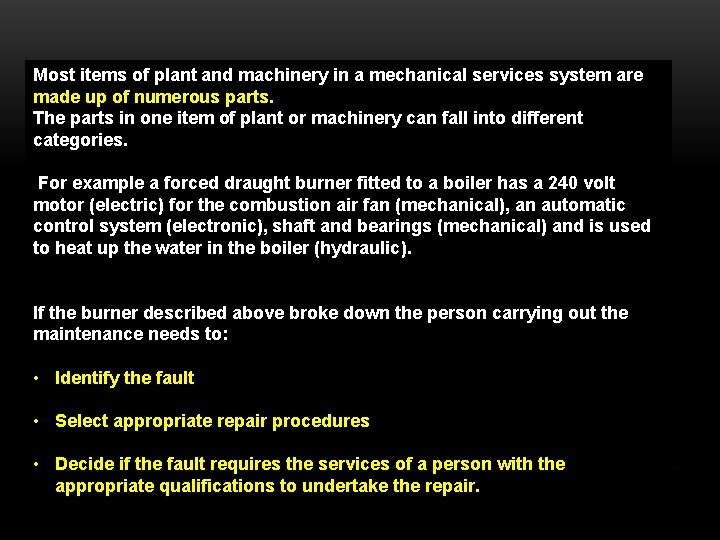
Most items of plant and machinery in a mechanical services system are made up of numerous parts. The parts in one item of plant or machinery can fall into different categories. For example a forced draught burner fitted to a boiler has a 240 volt motor (electric) for the combustion air fan (mechanical), an automatic control system (electronic), shaft and bearings (mechanical) and is used to heat up the water in the boiler (hydraulic). If the burner described above broke down the person carrying out the maintenance needs to: • Identify the fault • Select appropriate repair procedures • Decide if the fault requires the services of a person with the appropriate qualifications to undertake the repair.
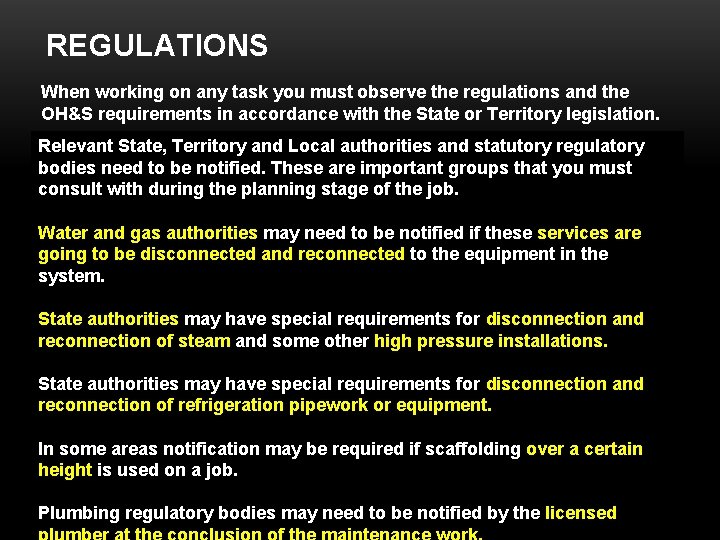
REGULATIONS When working on any task you must observe the regulations and the OH&S requirements in accordance with the State or Territory legislation. Relevant State, Territory and Local authorities and statutory regulatory bodies need to be notified. These are important groups that you must consult with during the planning stage of the job. Water and gas authorities may need to be notified if these services are going to be disconnected and reconnected to the equipment in the system. State authorities may have special requirements for disconnection and reconnection of steam and some other high pressure installations. State authorities may have special requirements for disconnection and reconnection of refrigeration pipework or equipment. In some areas notification may be required if scaffolding over a certain height is used on a job. Plumbing regulatory bodies may need to be notified by the licensed
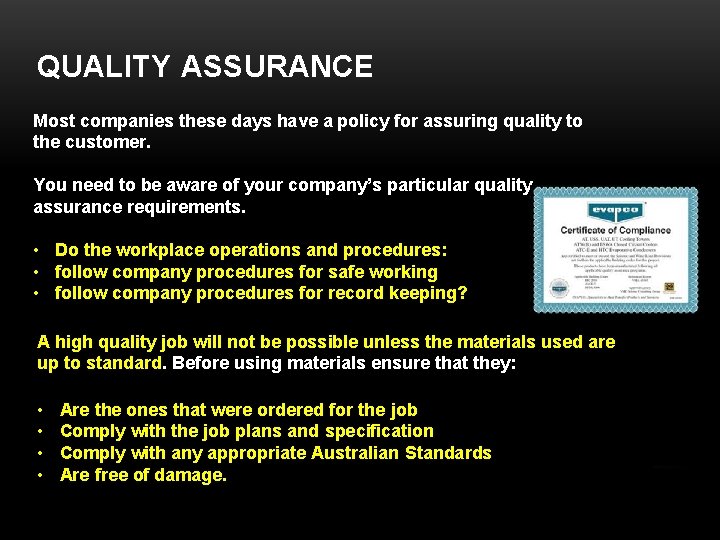
QUALITY ASSURANCE Most companies these days have a policy for assuring quality to the customer. You need to be aware of your company’s particular quality assurance requirements. • Do the workplace operations and procedures: • follow company procedures for safe working • follow company procedures for record keeping? A high quality job will not be possible unless the materials used are up to standard. Before using materials ensure that they: • • Are the ones that were ordered for the job Comply with the job plans and specification Comply with any appropriate Australian Standards Are free of damage.
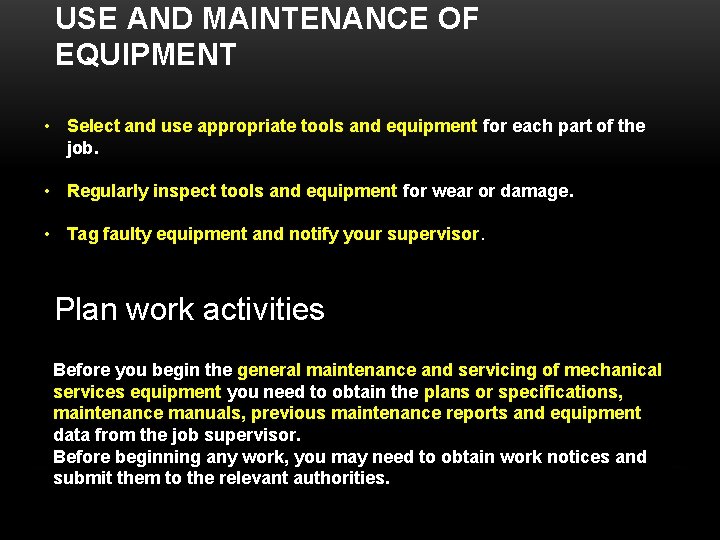
USE AND MAINTENANCE OF EQUIPMENT • Select and use appropriate tools and equipment for each part of the job. • Regularly inspect tools and equipment for wear or damage. • Tag faulty equipment and notify your supervisor. Plan work activities Before you begin the general maintenance and servicing of mechanical services equipment you need to obtain the plans or specifications, maintenance manuals, previous maintenance reports and equipment data from the job supervisor. Before beginning any work, you may need to obtain work notices and submit them to the relevant authorities.
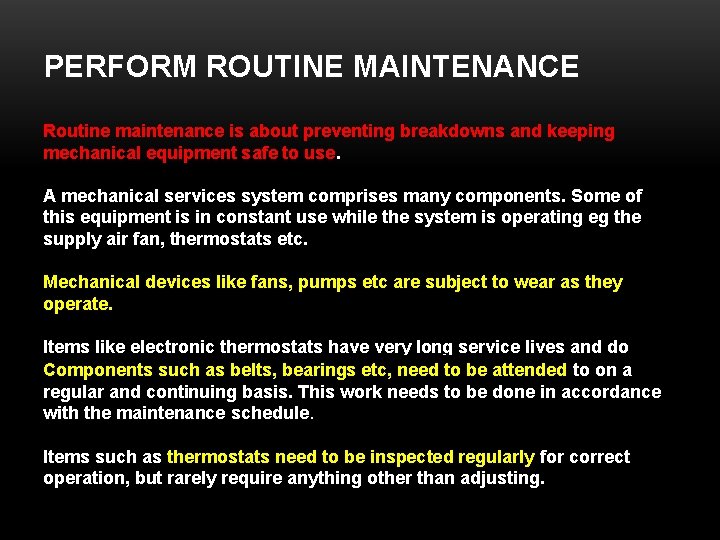
PERFORM ROUTINE MAINTENANCE Routine maintenance is about preventing breakdowns and keeping mechanical equipment safe to use. A mechanical services system comprises many components. Some of this equipment is in constant use while the system is operating eg the supply air fan, thermostats etc. Mechanical devices like fans, pumps etc are subject to wear as they operate. Items like electronic thermostats have very long service lives and do not often wear out. Components such as belts, bearings etc, need to be attended to on a regular and continuing basis. This work needs to be done in accordance with the maintenance schedule. Items such as thermostats need to be inspected regularly for correct operation, but rarely require anything other than adjusting.
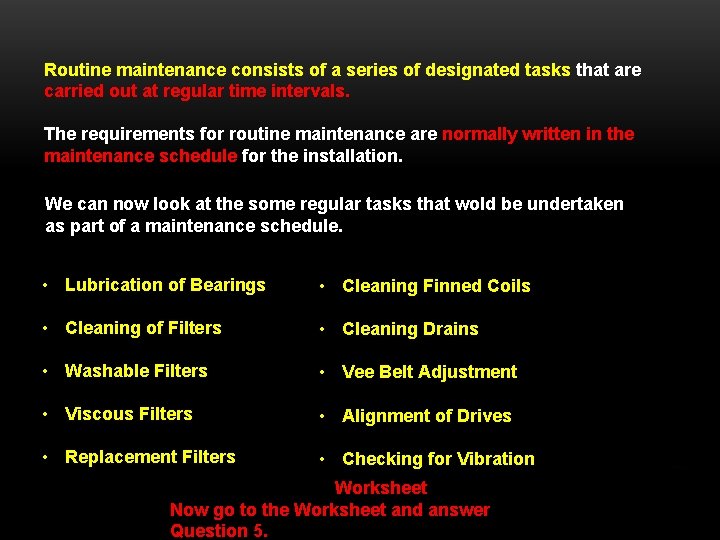
Routine maintenance consists of a series of designated tasks that are carried out at regular time intervals. The requirements for routine maintenance are normally written in the maintenance schedule for the installation. We can now look at the some regular tasks that wold be undertaken as part of a maintenance schedule. • Lubrication of Bearings • Cleaning Finned Coils • Cleaning of Filters • Cleaning Drains • Washable Filters • Vee Belt Adjustment • Viscous Filters • Alignment of Drives • Replacement Filters • Checking for Vibration Worksheet Now go to the Worksheet and answer Question 5.
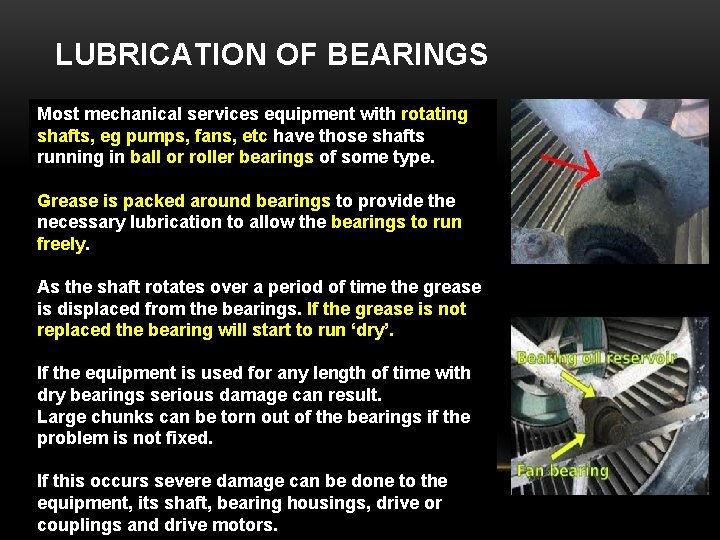
LUBRICATION OF BEARINGS Most mechanical services equipment with rotating shafts, eg pumps, fans, etc have those shafts running in ball or roller bearings of some type. Grease is packed around bearings to provide the necessary lubrication to allow the bearings to run freely. As the shaft rotates over a period of time the grease is displaced from the bearings. If the grease is not replaced the bearing will start to run ‘dry’. If the equipment is used for any length of time with dry bearings serious damage can result. Large chunks can be torn out of the bearings if the problem is not fixed. If this occurs severe damage can be done to the equipment, its shaft, bearing housings, drive or couplings and drive motors.
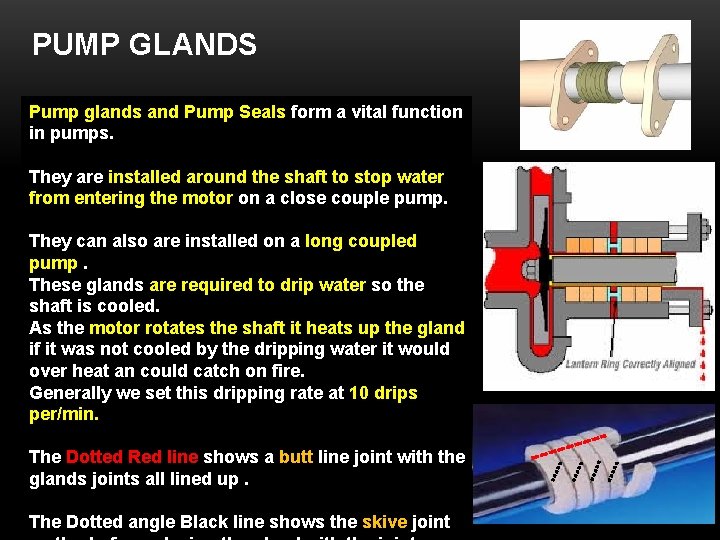
PUMP GLANDS Pump glands and Pump Seals form a vital function in pumps. They are installed around the shaft to stop water from entering the motor on a close couple pump. They can also are installed on a long coupled pump. These glands are required to drip water so the shaft is cooled. As the motor rotates the shaft it heats up the gland if it was not cooled by the dripping water it would over heat an could catch on fire. Generally we set this dripping rate at 10 drips per/min. The Dotted Red line shows a butt line joint with the glands joints all lined up. The Dotted angle Black line shows the skive joint
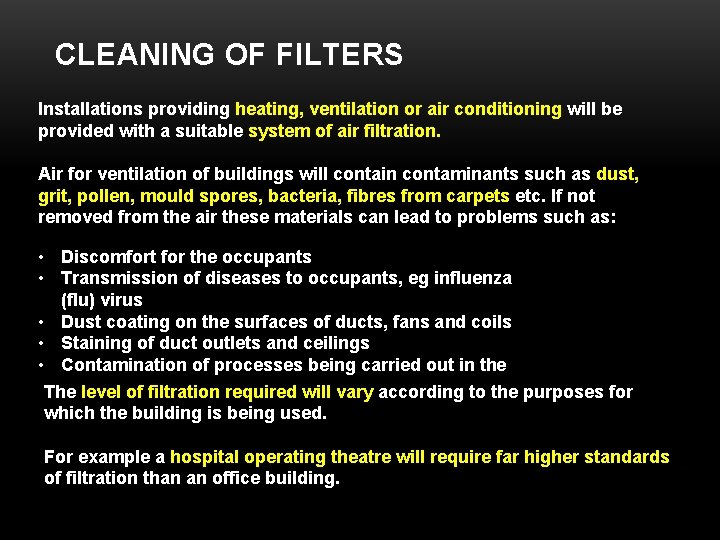
CLEANING OF FILTERS Installations providing heating, ventilation or air conditioning will be provided with a suitable system of air filtration. Air for ventilation of buildings will contain contaminants such as dust, grit, pollen, mould spores, bacteria, fibres from carpets etc. If not removed from the air these materials can lead to problems such as: • Discomfort for the occupants • Transmission of diseases to occupants, eg influenza (flu) virus • Dust coating on the surfaces of ducts, fans and coils • Staining of duct outlets and ceilings • Contamination of processes being carried out in the building. The level of filtration required will vary according to the purposes for which the building is being used. For example a hospital operating theatre will require far higher standards of filtration than an office building.
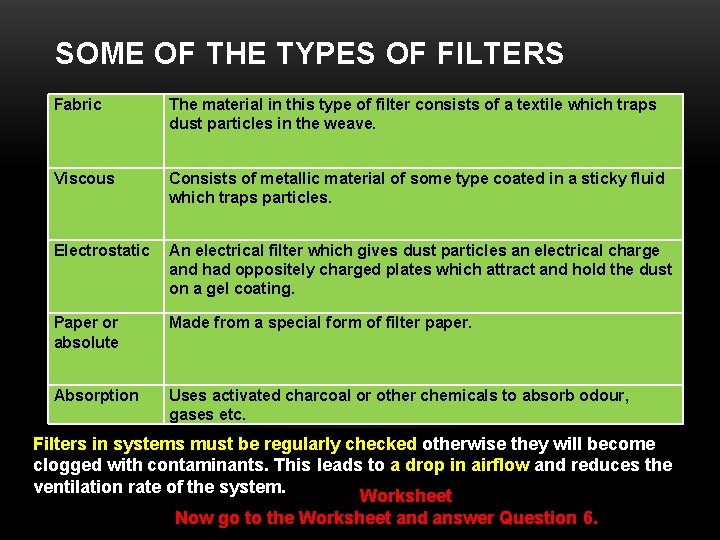
SOME OF THE TYPES OF FILTERS Fabric The material in this type of filter consists of a textile which traps dust particles in the weave. Viscous Consists of metallic material of some type coated in a sticky fluid which traps particles. Electrostatic An electrical filter which gives dust particles an electrical charge and had oppositely charged plates which attract and hold the dust on a gel coating. Paper or absolute Made from a special form of filter paper. Absorption Uses activated charcoal or other chemicals to absorb odour, gases etc. Filters in systems must be regularly checked otherwise they will become clogged with contaminants. This leads to a drop in airflow and reduces the ventilation rate of the system. Worksheet Now go to the Worksheet and answer Question 6.
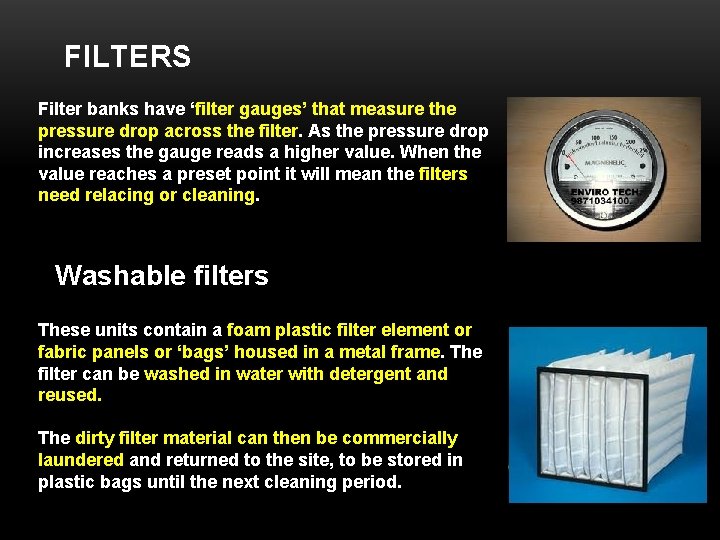
FILTERS Filter banks have ‘filter gauges’ that measure the pressure drop across the filter. As the pressure drop increases the gauge reads a higher value. When the value reaches a preset point it will mean the filters need relacing or cleaning. Washable filters These units contain a foam plastic filter element or fabric panels or ‘bags’ housed in a metal frame. The filter can be washed in water with detergent and reused. The dirty filter material can then be commercially laundered and returned to the site, to be stored in plastic bags until the next cleaning period.
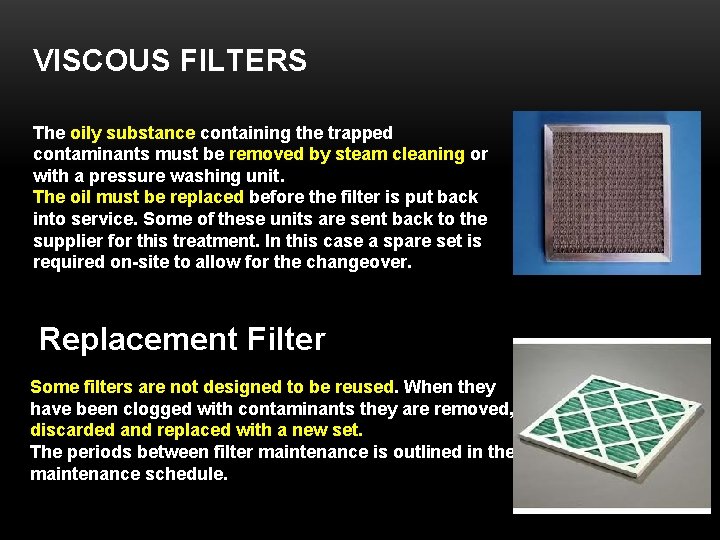
VISCOUS FILTERS The oily substance containing the trapped contaminants must be removed by steam cleaning or with a pressure washing unit. The oil must be replaced before the filter is put back into service. Some of these units are sent back to the supplier for this treatment. In this case a spare set is required on-site to allow for the changeover. Replacement Filter Some filters are not designed to be reused. When they have been clogged with contaminants they are removed, discarded and replaced with a new set. The periods between filter maintenance is outlined in the maintenance schedule.
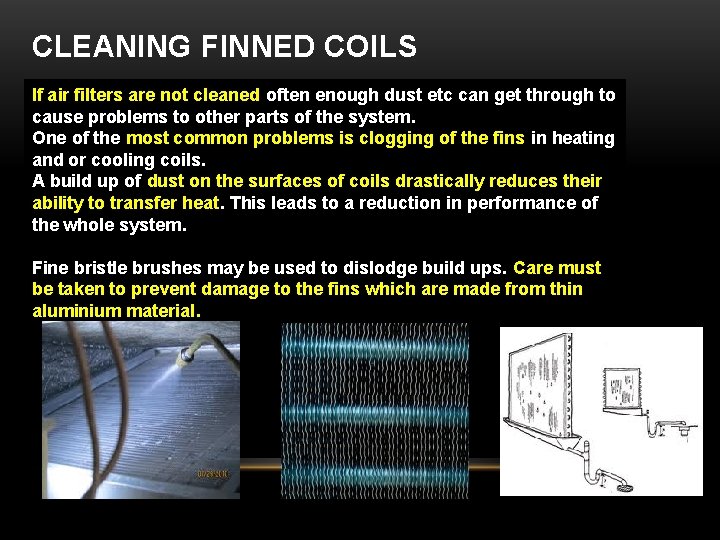
CLEANING FINNED COILS If air filters are not cleaned often enough dust etc can get through to cause problems to other parts of the system. One of the most common problems is clogging of the fins in heating and or cooling coils. A build up of dust on the surfaces of coils drastically reduces their ability to transfer heat. This leads to a reduction in performance of the whole system. Fine bristle brushes may be used to dislodge build ups. Care must be taken to prevent damage to the fins which are made from thin aluminium material.
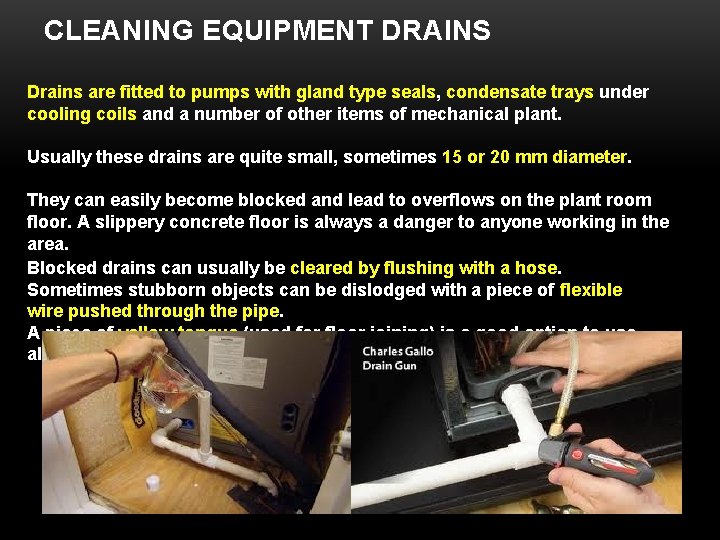
CLEANING EQUIPMENT DRAINS Drains are fitted to pumps with gland type seals, condensate trays under cooling coils and a number of other items of mechanical plant. Usually these drains are quite small, sometimes 15 or 20 mm diameter. They can easily become blocked and lead to overflows on the plant room floor. A slippery concrete floor is always a danger to anyone working in the area. Blocked drains can usually be cleared by flushing with a hose. Sometimes stubborn objects can be dislodged with a piece of flexible wire pushed through the pipe. A piece of yellow tongue (used for floor joining) is a good option to use also.
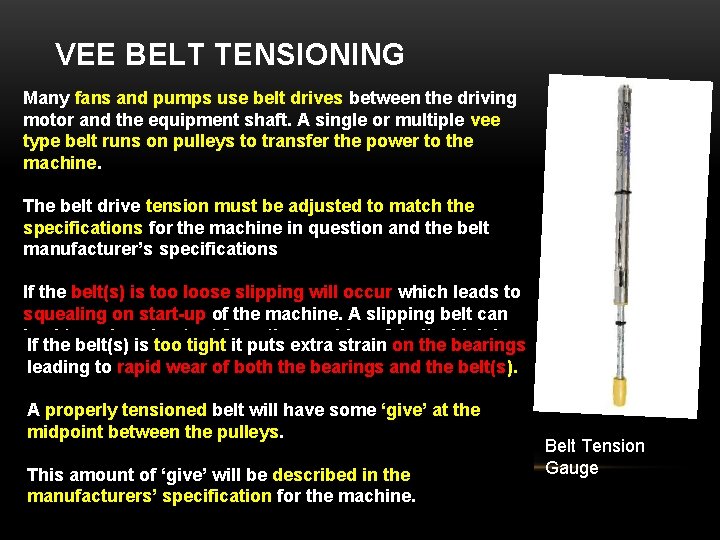
VEE BELT TENSIONING Many fans and pumps use belt drives between the driving motor and the equipment shaft. A single or multiple vee type belt runs on pulleys to transfer the power to the machine. The belt drive tension must be adjusted to match the specifications for the machine in question and the belt manufacturer’s specifications If the belt(s) is too loose slipping will occur which leads to squealing on start-up of the machine. A slipping belt can lead to reduced output from the machine. A belt which is If the belt(s) is too tight it puts extra strain on the bearings slipping also wears very quickly and will require premature leading to rapid wear of both the bearings and the belt(s). replacement. A properly tensioned belt will have some ‘give’ at the midpoint between the pulleys. This amount of ‘give’ will be described in the manufacturers’ specification for the machine. Belt Tension Gauge
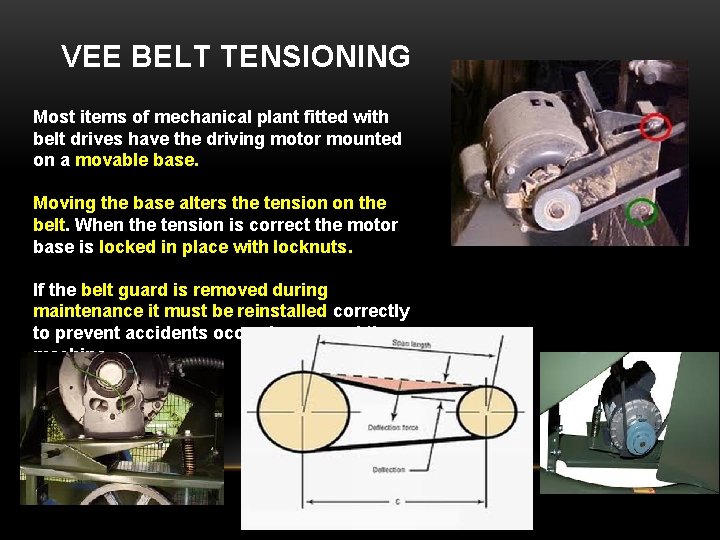
VEE BELT TENSIONING Most items of mechanical plant fitted with belt drives have the driving motor mounted on a movable base. Moving the base alters the tension on the belt. When the tension is correct the motor base is locked in place with locknuts. If the belt guard is removed during maintenance it must be reinstalled correctly to prevent accidents occurring around the machine.
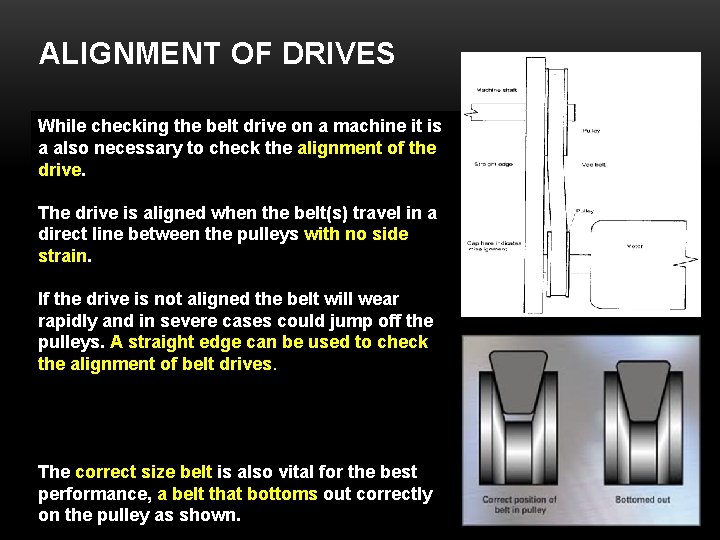
ALIGNMENT OF DRIVES While checking the belt drive on a machine it is a also necessary to check the alignment of the drive. The drive is aligned when the belt(s) travel in a direct line between the pulleys with no side strain. If the drive is not aligned the belt will wear rapidly and in severe cases could jump off the pulleys. A straight edge can be used to check the alignment of belt drives. The correct size belt is also vital for the best performance, a belt that bottoms out correctly on the pulley as shown.
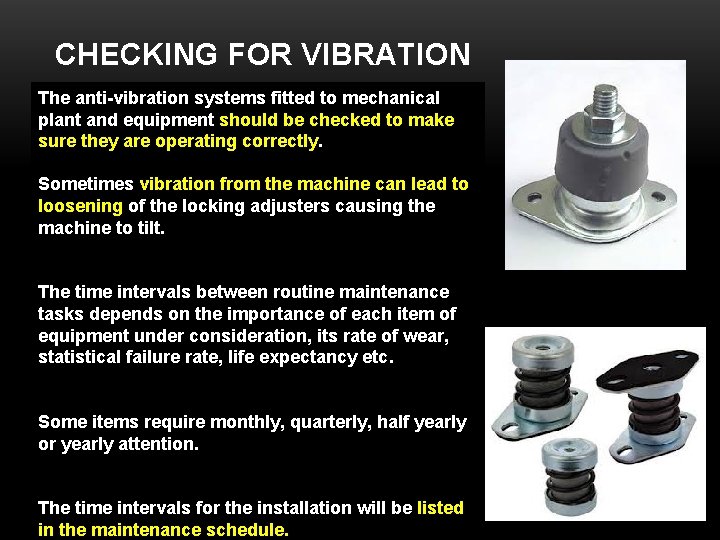
CHECKING FOR VIBRATION The anti-vibration systems fitted to mechanical plant and equipment should be checked to make sure they are operating correctly. Sometimes vibration from the machine can lead to loosening of the locking adjusters causing the machine to tilt. The time intervals between routine maintenance tasks depends on the importance of each item of equipment under consideration, its rate of wear, statistical failure rate, life expectancy etc. Some items require monthly, quarterly, half yearly or yearly attention. The time intervals for the installation will be listed in the maintenance schedule.
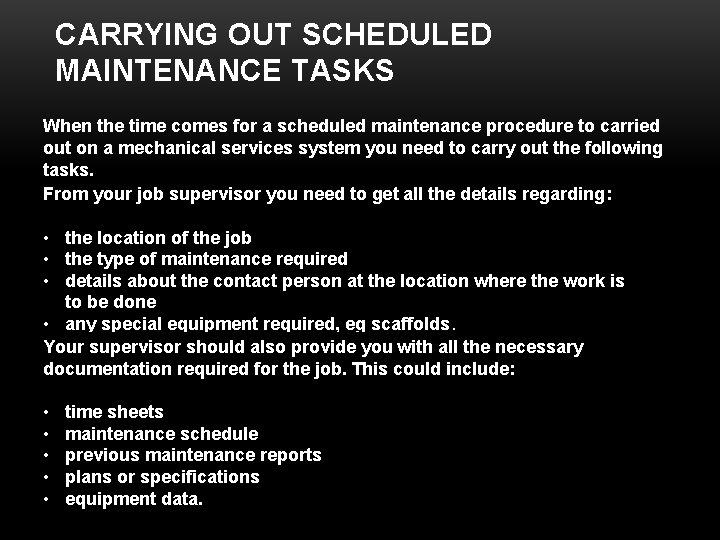
CARRYING OUT SCHEDULED MAINTENANCE TASKS When the time comes for a scheduled maintenance procedure to carried out on a mechanical services system you need to carry out the following tasks. From your job supervisor you need to get all the details regarding: • the location of the job • the type of maintenance required • details about the contact person at the location where the work is to be done • any special equipment required, eg scaffolds. Your supervisor should also provide you with all the necessary documentation required for the job. This could include: • • • time sheets maintenance schedule previous maintenance reports plans or specifications equipment data.
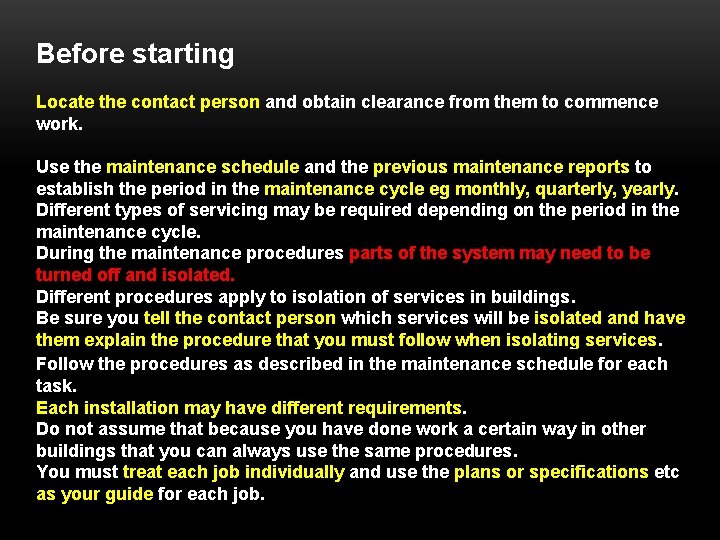
Before starting Locate the contact person and obtain clearance from them to commence work. Use the maintenance schedule and the previous maintenance reports to establish the period in the maintenance cycle eg monthly, quarterly, yearly. Different types of servicing may be required depending on the period in the maintenance cycle. During the maintenance procedures parts of the system may need to be turned off and isolated. Different procedures apply to isolation of services in buildings. Be sure you tell the contact person which services will be isolated and have them explain the procedure that you must follow when isolating services. Follow the procedures as described in the maintenance schedule for each task. Each installation may have different requirements. Do not assume that because you have done work a certain way in other buildings that you can always use the same procedures. You must treat each job individually and use the plans or specifications etc as your guide for each job.
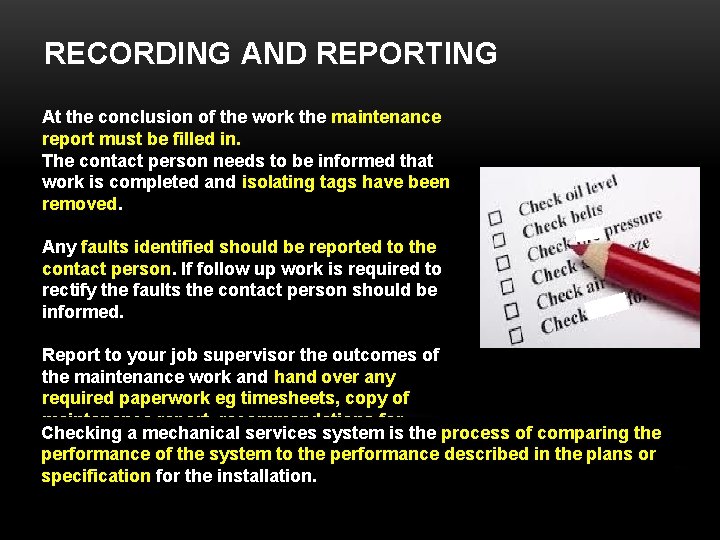
RECORDING AND REPORTING At the conclusion of the work the maintenance report must be filled in. The contact person needs to be informed that work is completed and isolating tags have been removed. Any faults identified should be reported to the contact person. If follow up work is required to rectify the faults the contact person should be informed. Report to your job supervisor the outcomes of the maintenance work and hand over any required paperwork eg timesheets, copy of maintenance report, recommendations for Checking a mechanical services system is the process of comparing the follow up work etc. performance of the system to the performance described in the plans or specification for the installation.
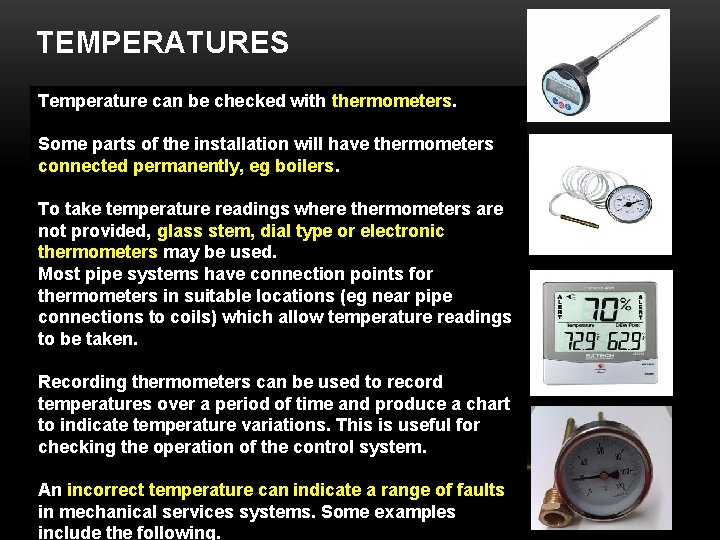
TEMPERATURES Temperature can be checked with thermometers. Some parts of the installation will have thermometers connected permanently, eg boilers. To take temperature readings where thermometers are not provided, glass stem, dial type or electronic thermometers may be used. Most pipe systems have connection points for thermometers in suitable locations (eg near pipe connections to coils) which allow temperature readings to be taken. Recording thermometers can be used to record temperatures over a period of time and produce a chart to indicate temperature variations. This is useful for checking the operation of the control system. An incorrect temperature can indicate a range of faults in mechanical services systems. Some examples include the following.
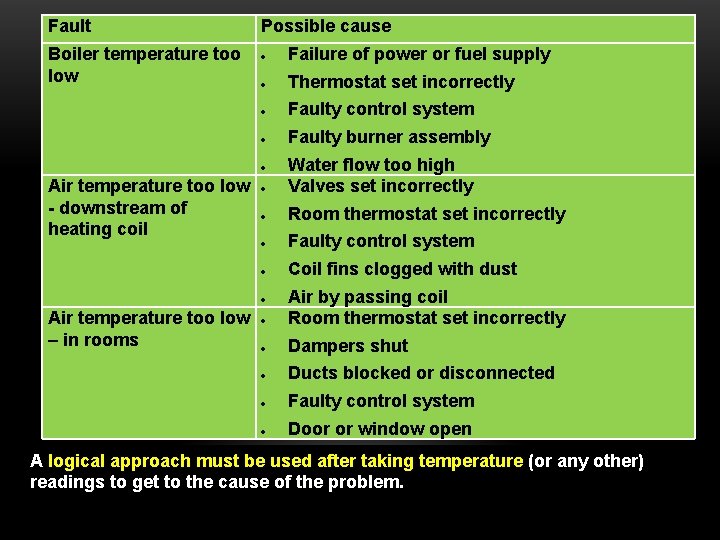
Fault Boiler temperature too low Possible cause Failure of power or fuel supply Thermostat set incorrectly Faulty control system Faulty burner assembly Water flow too high Valves set incorrectly Room thermostat set incorrectly Faulty control system Coil fins clogged with dust Air temperature too low - downstream of heating coil Air by passing coil Room thermostat set incorrectly Dampers shut Ducts blocked or disconnected Faulty control system Door or window open Air temperature too low – in rooms A logical approach must be used after taking temperature (or any other) readings to get to the cause of the problem.
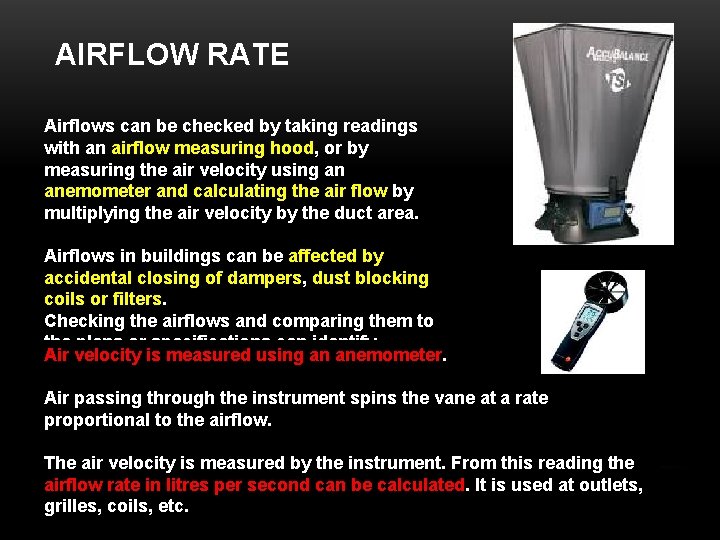
AIRFLOW RATE Airflows can be checked by taking readings with an airflow measuring hood, or by measuring the air velocity using an anemometer and calculating the air flow by multiplying the air velocity by the duct area. Airflows in buildings can be affected by accidental closing of dampers, dust blocking coils or filters. Checking the airflows and comparing them to the plans or specifications can identify Air velocity is measured using an anemometer. problems. Air passing through the instrument spins the vane at a rate proportional to the airflow. The air velocity is measured by the instrument. From this reading the airflow rate in litres per second can be calculated. It is used at outlets, grilles, coils, etc.
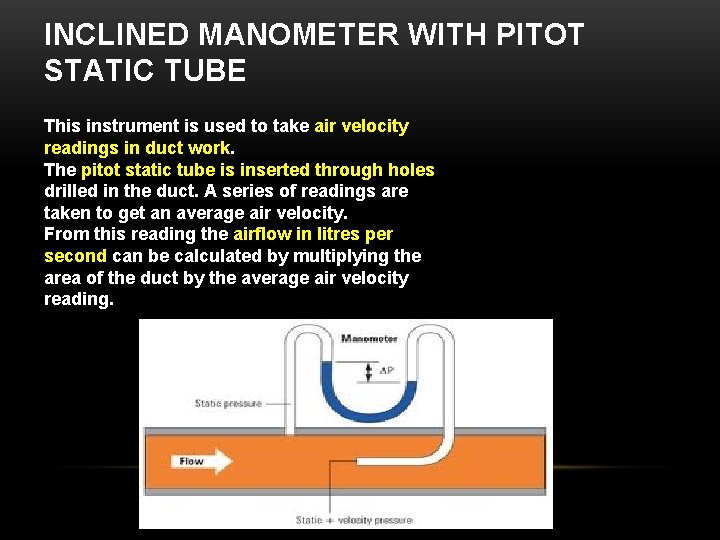
INCLINED MANOMETER WITH PITOT STATIC TUBE This instrument is used to take air velocity readings in duct work. The pitot static tube is inserted through holes drilled in the duct. A series of readings are taken to get an average air velocity. From this reading the airflow in litres per second can be calculated by multiplying the area of the duct by the average air velocity reading.
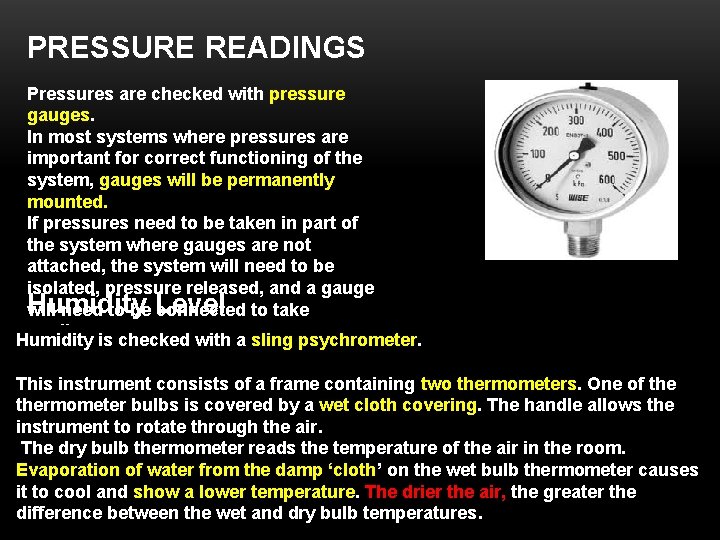
PRESSURE READINGS Pressures are checked with pressure gauges. In most systems where pressures are important for correct functioning of the system, gauges will be permanently mounted. If pressures need to be taken in part of the system where gauges are not attached, the system will need to be isolated, pressure released, and a gauge Humidity Level will need to be connected to take readings. Humidity is checked with a sling psychrometer. This instrument consists of a frame containing two thermometers. One of thermometer bulbs is covered by a wet cloth covering. The handle allows the instrument to rotate through the air. The dry bulb thermometer reads the temperature of the air in the room. Evaporation of water from the damp ‘cloth’ on the wet bulb thermometer causes it to cool and show a lower temperature. The drier the air, the greater the difference between the wet and dry bulb temperatures.
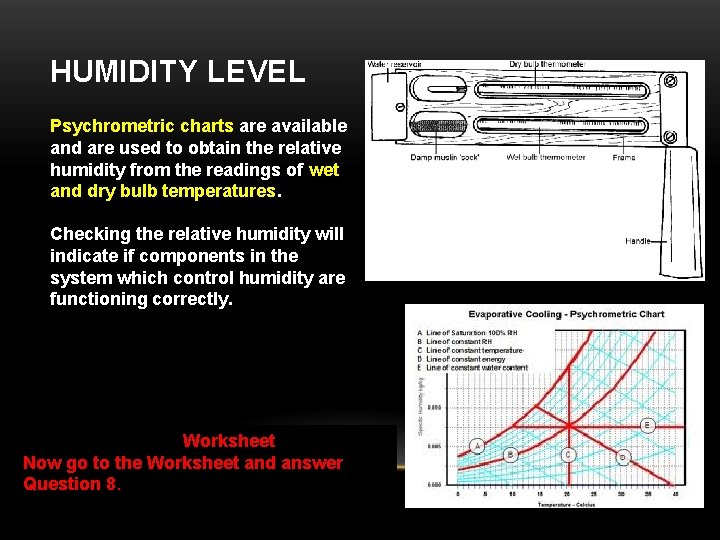
HUMIDITY LEVEL Psychrometric charts are available and are used to obtain the relative humidity from the readings of wet and dry bulb temperatures. Checking the relative humidity will indicate if components in the system which control humidity are functioning correctly. Worksheet Now go to the Worksheet and answer Question 8.
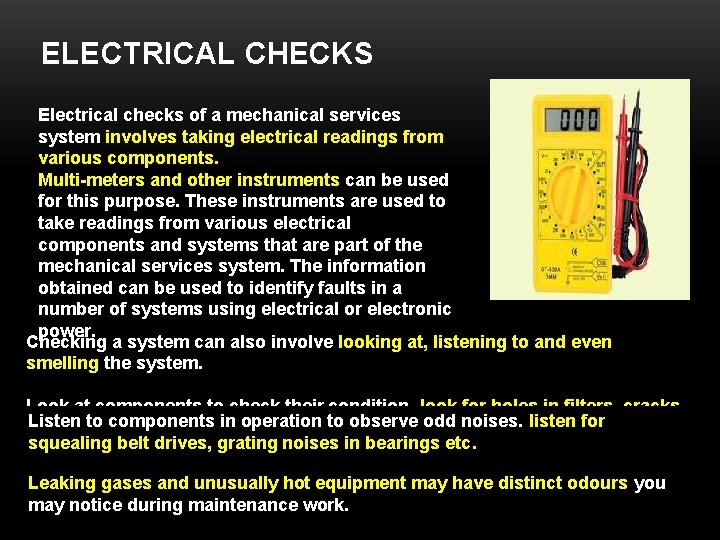
ELECTRICAL CHECKS Electrical checks of a mechanical services system involves taking electrical readings from various components. Multi-meters and other instruments can be used for this purpose. These instruments are used to take readings from various electrical components and systems that are part of the mechanical services system. The information obtained can be used to identify faults in a number of systems using electrical or electronic power. Checking a system can also involve looking at, listening to and even smelling the system. Look at components to check their condition. look for holes in filters, cracks Listen to components in operation to observe odd noises. listen for in vee belts etc. squealing belt drives, grating noises in bearings etc. Leaking gases and unusually hot equipment may have distinct odours you may notice during maintenance work.
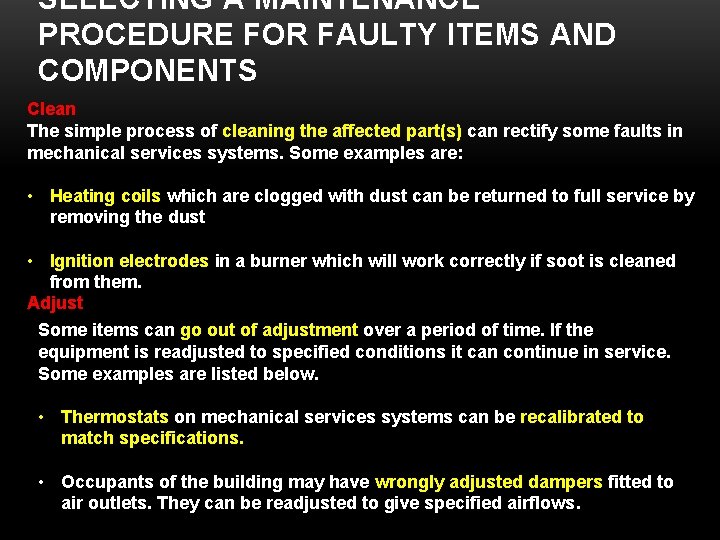
SELECTING A MAINTENANCE PROCEDURE FOR FAULTY ITEMS AND COMPONENTS Clean The simple process of cleaning the affected part(s) can rectify some faults in mechanical services systems. Some examples are: • Heating coils which are clogged with dust can be returned to full service by removing the dust • Ignition electrodes in a burner which will work correctly if soot is cleaned from them. Adjust Some items can go out of adjustment over a period of time. If the equipment is readjusted to specified conditions it can continue in service. Some examples are listed below. • Thermostats on mechanical services systems can be recalibrated to match specifications. • Occupants of the building may have wrongly adjusted dampers fitted to air outlets. They can be readjusted to give specified airflows.
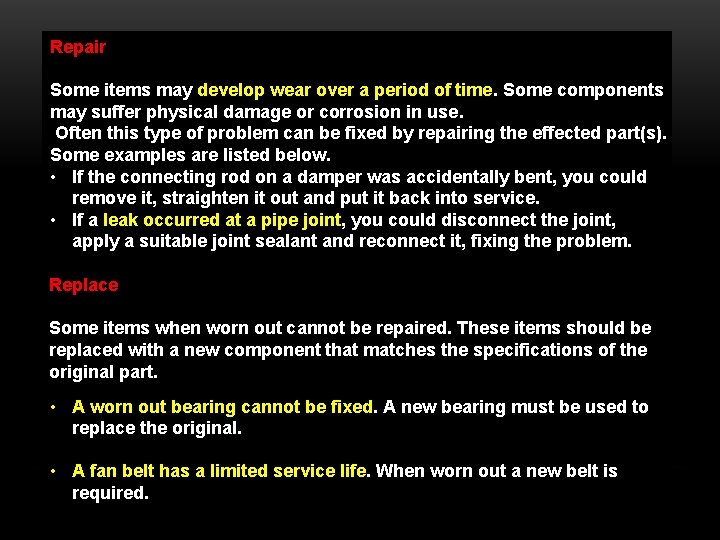
Repair Some items may develop wear over a period of time. Some components may suffer physical damage or corrosion in use. Often this type of problem can be fixed by repairing the effected part(s). Some examples are listed below. • If the connecting rod on a damper was accidentally bent, you could remove it, straighten it out and put it back into service. • If a leak occurred at a pipe joint, you could disconnect the joint, apply a suitable joint sealant and reconnect it, fixing the problem. Replace Some items when worn out cannot be repaired. These items should be replaced with a new component that matches the specifications of the original part. • A worn out bearing cannot be fixed. A new bearing must be used to replace the original. • A fan belt has a limited service life. When worn out a new belt is required.
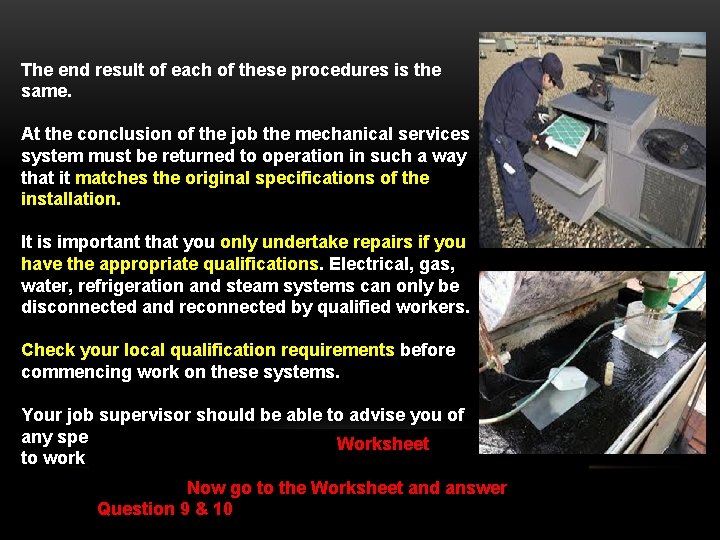
The end result of each of these procedures is the same. At the conclusion of the job the mechanical services system must be returned to operation in such a way that it matches the original specifications of the installation. It is important that you only undertake repairs if you have the appropriate qualifications. Electrical, gas, water, refrigeration and steam systems can only be disconnected and reconnected by qualified workers. Check your local qualification requirements before commencing work on these systems. Your job supervisor should be able to advise you of any special requirements for the jobs you are going Worksheet to work on. Now go to the Worksheet and answer Question 9 & 10
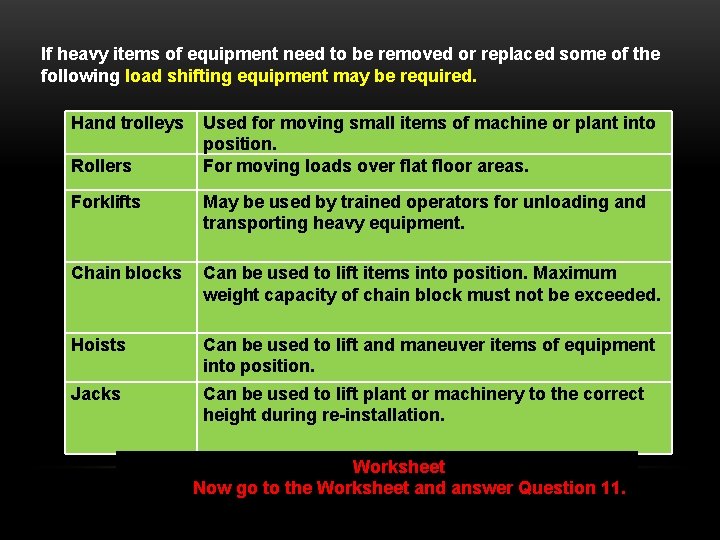
If heavy items of equipment need to be removed or replaced some of the following load shifting equipment may be required. Hand trolleys Rollers Used for moving small items of machine or plant into position. For moving loads over flat floor areas. Forklifts May be used by trained operators for unloading and transporting heavy equipment. Chain blocks Can be used to lift items into position. Maximum weight capacity of chain block must not be exceeded. Hoists Can be used to lift and maneuver items of equipment into position. Jacks Can be used to lift plant or machinery to the correct height during re-installation. Worksheet Now go to the Worksheet and answer Question 11.
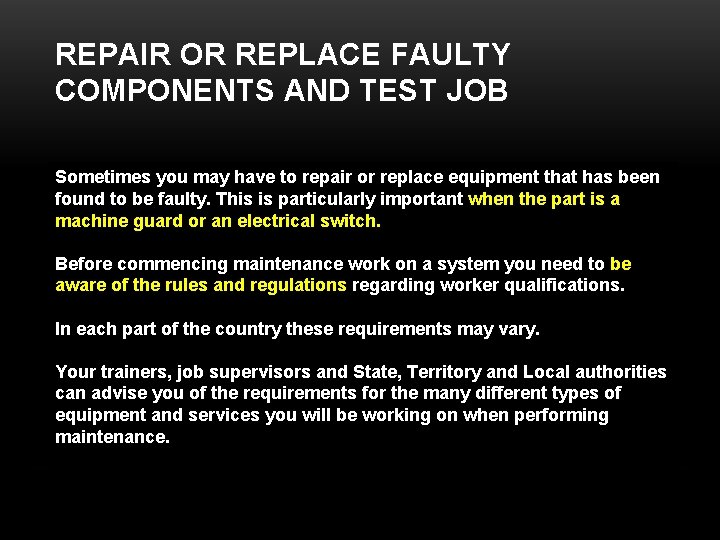
REPAIR OR REPLACE FAULTY COMPONENTS AND TEST JOB Sometimes you may have to repair or replace equipment that has been found to be faulty. This is particularly important when the part is a machine guard or an electrical switch. Before commencing maintenance work on a system you need to be aware of the rules and regulations regarding worker qualifications. In each part of the country these requirements may vary. Your trainers, job supervisors and State, Territory and Local authorities can advise you of the requirements for the many different types of equipment and services you will be working on when performing maintenance.
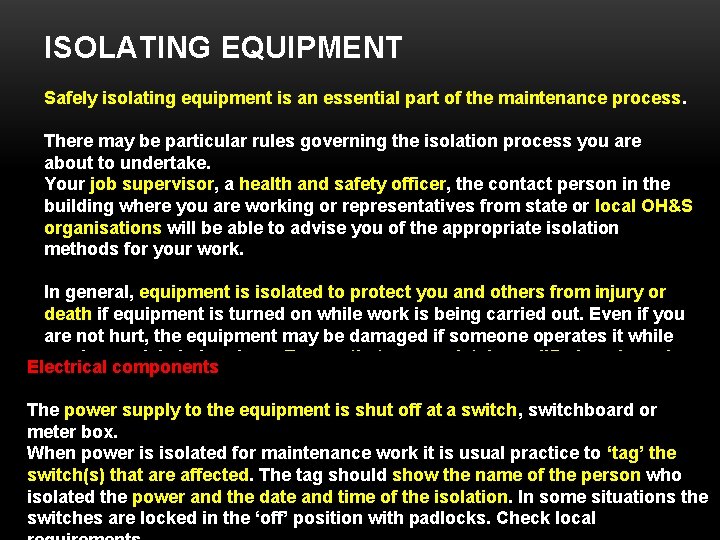
ISOLATING EQUIPMENT Safely isolating equipment is an essential part of the maintenance process. There may be particular rules governing the isolation process you are about to undertake. Your job supervisor, a health and safety officer, the contact person in the building where you are working or representatives from state or local OH&S organisations will be able to advise you of the appropriate isolation methods for your work. In general, equipment is isolated to protect you and others from injury or death if equipment is turned on while work is being carried out. Even if you are not hurt, the equipment may be damaged if someone operates it while service work is being done. Ensure that appropriately qualified workers do Electrical components isolation work. The power supply to the equipment is shut off at a switch, switchboard or meter box. When power is isolated for maintenance work it is usual practice to ‘tag’ the switch(s) that are affected. The tag should show the name of the person who isolated the power and the date and time of the isolation. In some situations the switches are locked in the ‘off’ position with padlocks. Check local
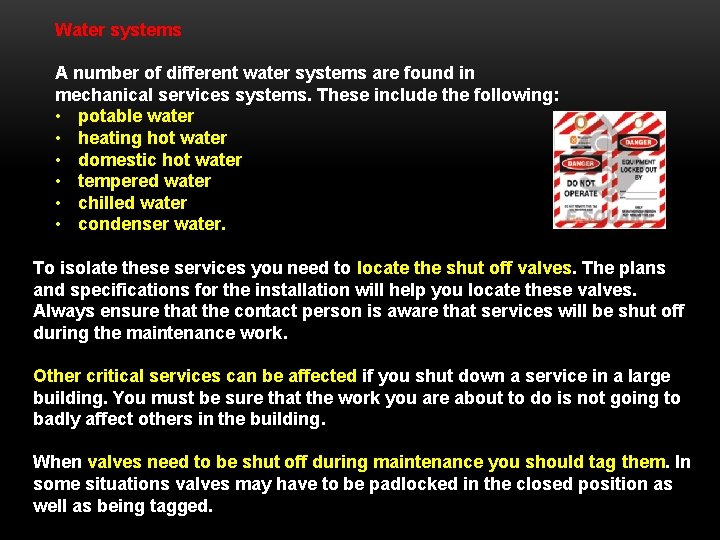
Water systems A number of different water systems are found in mechanical services systems. These include the following: • potable water • heating hot water • domestic hot water • tempered water • chilled water • condenser water. To isolate these services you need to locate the shut off valves. The plans and specifications for the installation will help you locate these valves. Always ensure that the contact person is aware that services will be shut off during the maintenance work. Other critical services can be affected if you shut down a service in a large building. You must be sure that the work you are about to do is not going to badly affect others in the building. When valves need to be shut off during maintenance you should tag them. In some situations valves may have to be padlocked in the closed position as well as being tagged.
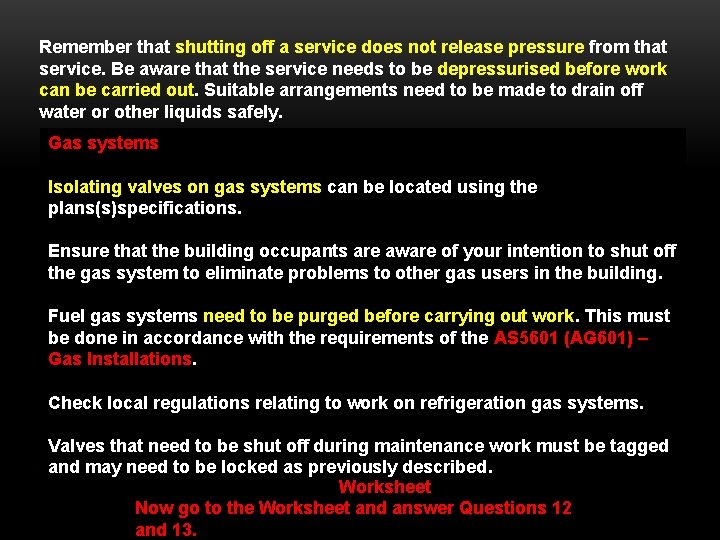
Remember that shutting off a service does not release pressure from that service. Be aware that the service needs to be depressurised before work can be carried out. Suitable arrangements need to be made to drain off water or other liquids safely. Gas systems Isolating valves on gas systems can be located using the plans(s)specifications. Ensure that the building occupants are aware of your intention to shut off the gas system to eliminate problems to other gas users in the building. Fuel gas systems need to be purged before carrying out work. This must be done in accordance with the requirements of the AS 5601 (AG 601) – Gas Installations. Check local regulations relating to work on refrigeration gas systems. Valves that need to be shut off during maintenance work must be tagged and may need to be locked as previously described. Worksheet Now go to the Worksheet and answer Questions 12 and 13.
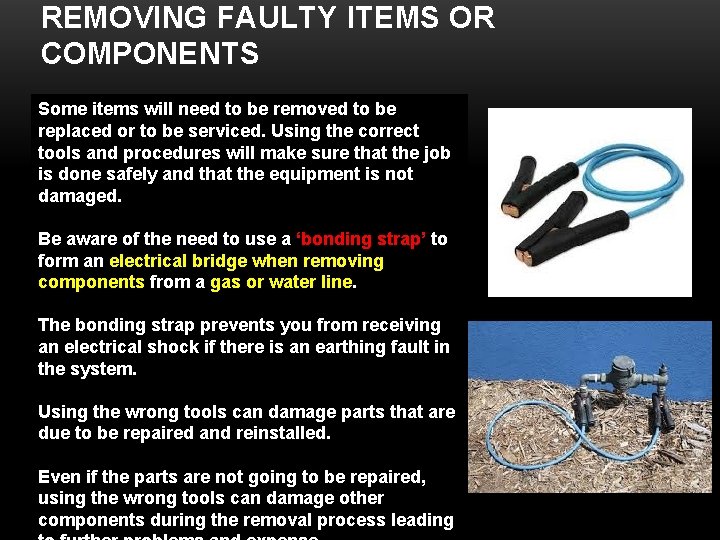
REMOVING FAULTY ITEMS OR COMPONENTS Some items will need to be removed to be replaced or to be serviced. Using the correct tools and procedures will make sure that the job is done safely and that the equipment is not damaged. Be aware of the need to use a ‘bonding strap’ to form an electrical bridge when removing components from a gas or water line. The bonding strap prevents you from receiving an electrical shock if there is an earthing fault in the system. Using the wrong tools can damage parts that are due to be repaired and reinstalled. Even if the parts are not going to be repaired, using the wrong tools can damage other components during the removal process leading
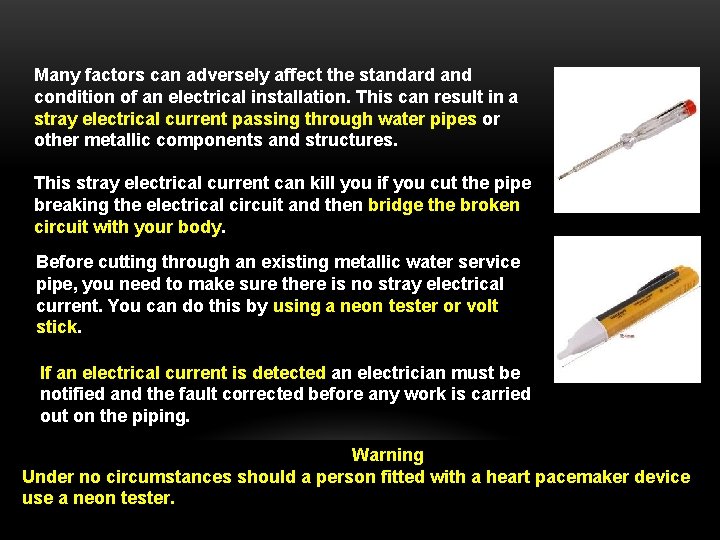
Many factors can adversely affect the standard and condition of an electrical installation. This can result in a stray electrical current passing through water pipes or other metallic components and structures. This stray electrical current can kill you if you cut the pipe breaking the electrical circuit and then bridge the broken circuit with your body. Before cutting through an existing metallic water service pipe, you need to make sure there is no stray electrical current. You can do this by using a neon tester or volt stick. If an electrical current is detected an electrician must be notified and the fault corrected before any work is carried out on the piping. Warning Under no circumstances should a person fitted with a heart pacemaker device use a neon tester.
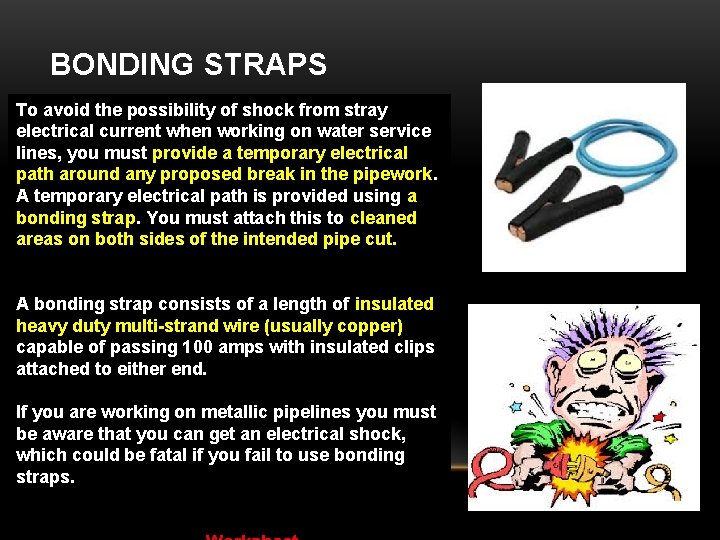
BONDING STRAPS To avoid the possibility of shock from stray electrical current when working on water service lines, you must provide a temporary electrical path around any proposed break in the pipework. A temporary electrical path is provided using a bonding strap. You must attach this to cleaned areas on both sides of the intended pipe cut. A bonding strap consists of a length of insulated heavy duty multi-strand wire (usually copper) capable of passing 100 amps with insulated clips attached to either end. If you are working on metallic pipelines you must be aware that you can get an electrical shock, which could be fatal if you fail to use bonding straps.
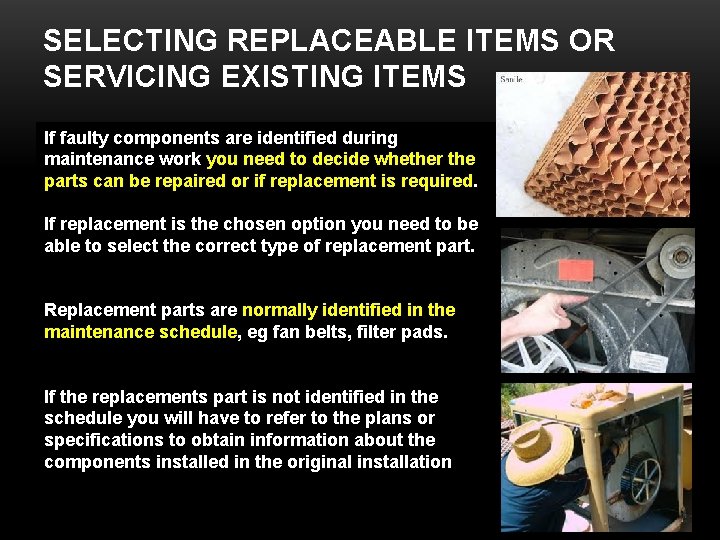
SELECTING REPLACEABLE ITEMS OR SERVICING EXISTING ITEMS If faulty components are identified during maintenance work you need to decide whether the parts can be repaired or if replacement is required. If replacement is the chosen option you need to be able to select the correct type of replacement part. Replacement parts are normally identified in the maintenance schedule, eg fan belts, filter pads. If the replacements part is not identified in the schedule you will have to refer to the plans or specifications to obtain information about the components installed in the original installation
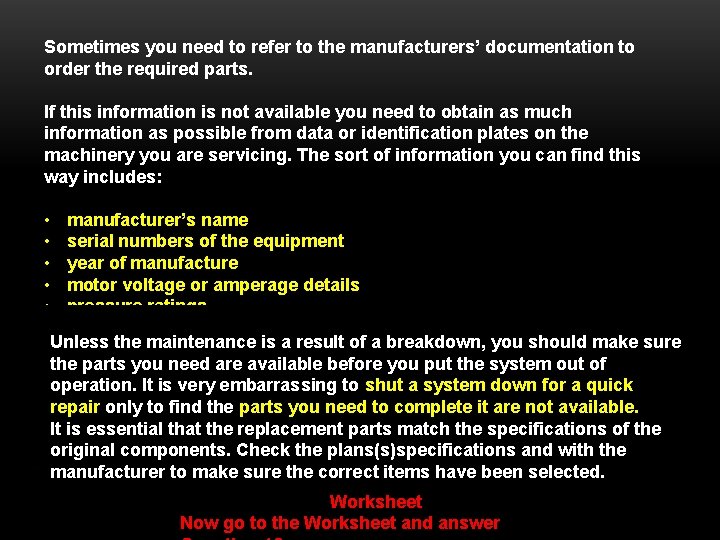
Sometimes you need to refer to the manufacturers’ documentation to order the required parts. If this information is not available you need to obtain as much information as possible from data or identification plates on the machinery you are servicing. The sort of information you can find this way includes: • manufacturer’s name • serial numbers of the equipment • year of manufacture • motor voltage or amperage details • pressure ratings. Unless the maintenance is a result of a breakdown, you should make sure the parts you need are available before you put the system out of operation. It is very embarrassing to shut a system down for a quick repair only to find the parts you need to complete it are not available. It is essential that the replacement parts match the specifications of the original components. Check the plans(s)specifications and with the manufacturer to make sure the correct items have been selected. Worksheet Now go to the Worksheet and answer
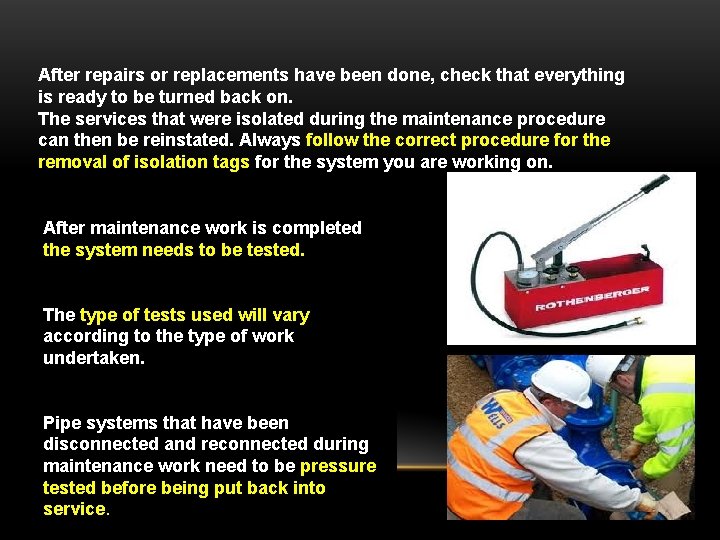
After repairs or replacements have been done, check that everything is ready to be turned back on. The services that were isolated during the maintenance procedure can then be reinstated. Always follow the correct procedure for the removal of isolation tags for the system you are working on. After maintenance work is completed the system needs to be tested. The type of tests used will vary according to the type of work undertaken. Pipe systems that have been disconnected and reconnected during maintenance work need to be pressure tested before being put back into service.
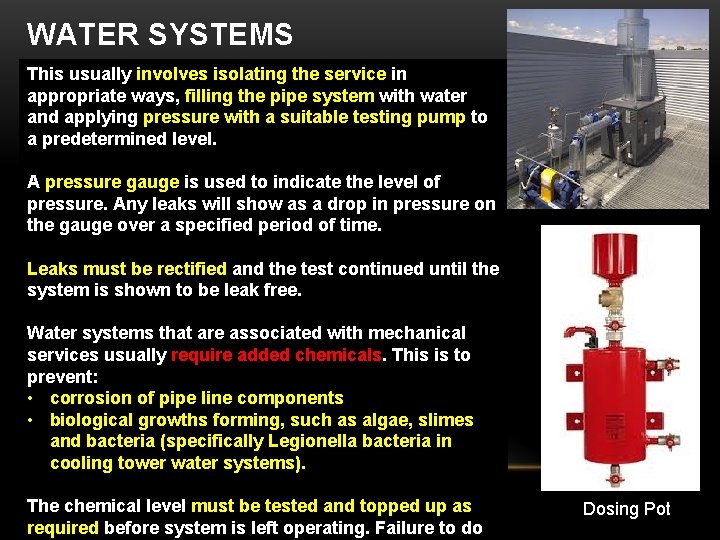
WATER SYSTEMS This usually involves isolating the service in appropriate ways, filling the pipe system with water and applying pressure with a suitable testing pump to a predetermined level. A pressure gauge is used to indicate the level of pressure. Any leaks will show as a drop in pressure on the gauge over a specified period of time. Leaks must be rectified and the test continued until the system is shown to be leak free. Water systems that are associated with mechanical services usually require added chemicals. This is to prevent: • corrosion of pipe line components • biological growths forming, such as algae, slimes and bacteria (specifically Legionella bacteria in cooling tower water systems). The chemical level must be tested and topped up as required before system is left operating. Failure to do Dosing Pot
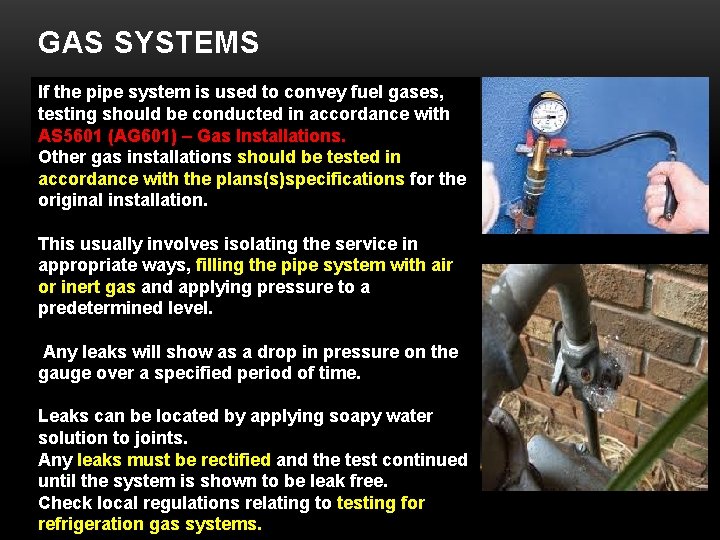
GAS SYSTEMS If the pipe system is used to convey fuel gases, testing should be conducted in accordance with AS 5601 (AG 601) – Gas Installations. Other gas installations should be tested in accordance with the plans(s)specifications for the original installation. This usually involves isolating the service in appropriate ways, filling the pipe system with air or inert gas and applying pressure to a predetermined level. Any leaks will show as a drop in pressure on the gauge over a specified period of time. Leaks can be located by applying soapy water solution to joints. Any leaks must be rectified and the test continued until the system is shown to be leak free. Check local regulations relating to testing for refrigeration gas systems.
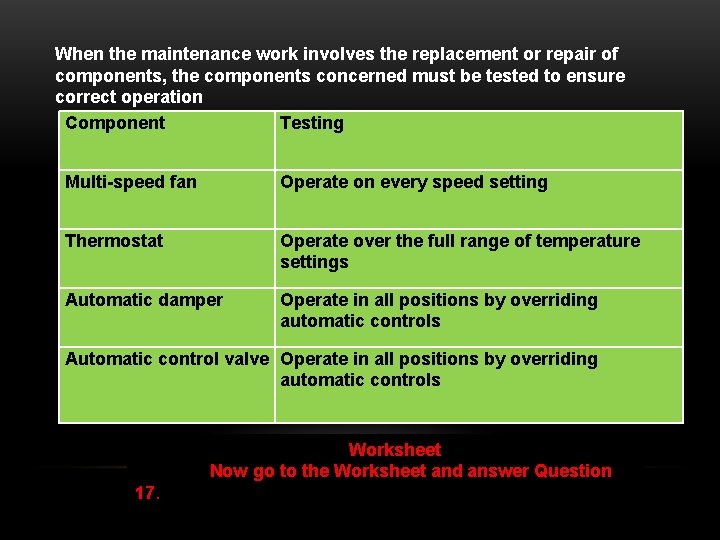
When the maintenance work involves the replacement or repair of components, the components concerned must be tested to ensure correct operation Component Testing Multi-speed fan Operate on every speed setting Thermostat Operate over the full range of temperature settings Automatic damper Operate in all positions by overriding automatic controls Automatic control valve Operate in all positions by overriding automatic controls Worksheet Now go to the Worksheet and answer Question 17.
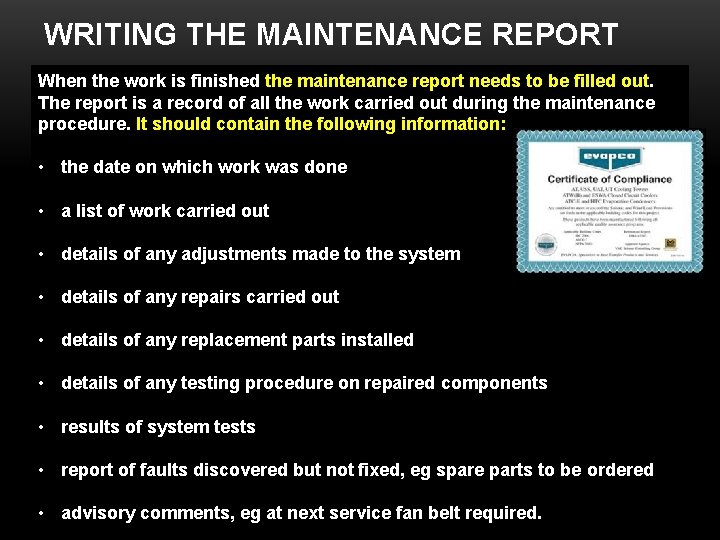
WRITING THE MAINTENANCE REPORT When the work is finished the maintenance report needs to be filled out. The report is a record of all the work carried out during the maintenance procedure. It should contain the following information: • the date on which work was done • a list of work carried out • details of any adjustments made to the system • details of any repairs carried out • details of any replacement parts installed • details of any testing procedure on repaired components • results of system tests • report of faults discovered but not fixed, eg spare parts to be ordered • advisory comments, eg at next service fan belt required.
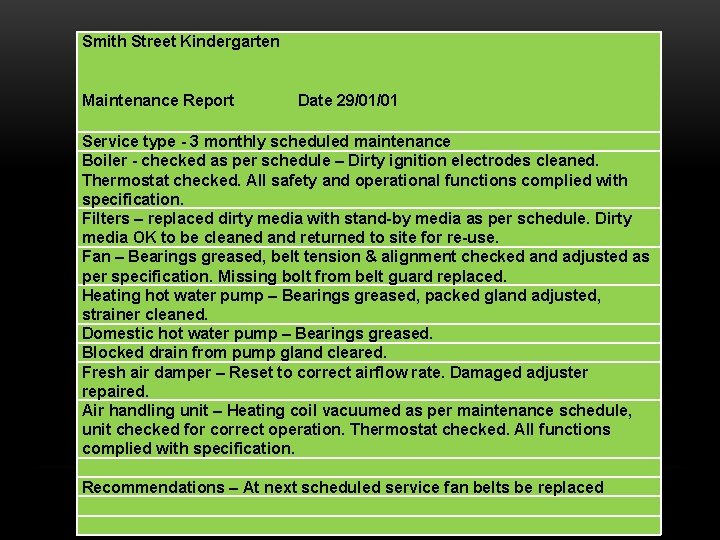
Smith Street Kindergarten Maintenance Report Date 29/01/01 Service type - 3 monthly scheduled maintenance Boiler - checked as per schedule – Dirty ignition electrodes cleaned. Thermostat checked. All safety and operational functions complied with specification. Filters – replaced dirty media with stand-by media as per schedule. Dirty media OK to be cleaned and returned to site for re-use. Fan – Bearings greased, belt tension & alignment checked and adjusted as per specification. Missing bolt from belt guard replaced. Heating hot water pump – Bearings greased, packed gland adjusted, strainer cleaned. Domestic hot water pump – Bearings greased. Blocked drain from pump gland cleared. Fresh air damper – Reset to correct airflow rate. Damaged adjuster repaired. Air handling unit – Heating coil vacuumed as per maintenance schedule, unit checked for correct operation. Thermostat checked. All functions complied with specification. Recommendations – At next scheduled service fan belts be replaced
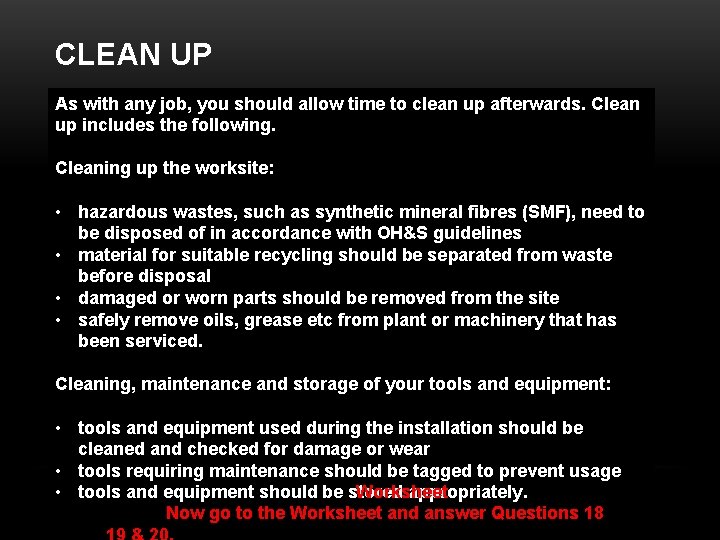
CLEAN UP As with any job, you should allow time to clean up afterwards. Clean up includes the following. Cleaning up the worksite: • hazardous wastes, such as synthetic mineral fibres (SMF), need to be disposed of in accordance with OH&S guidelines • material for suitable recycling should be separated from waste before disposal • damaged or worn parts should be removed from the site • safely remove oils, grease etc from plant or machinery that has been serviced. Cleaning, maintenance and storage of your tools and equipment: • tools and equipment used during the installation should be cleaned and checked for damage or wear • tools requiring maintenance should be tagged to prevent usage Worksheet • tools and equipment should be stored appropriately. Now go to the Worksheet and answer Questions 18
What are ways to install and maintain equipment
Kitchen premises
Maintain mechanical
Mechanical measuring devices
Mechanical design of process equipment
Actual mechanical advantage vs ideal mechanical advantage
Dod taxonomy
How to maintain spiritual stability
How to maintain friendships
Struggle to maintain faith
How to maintain your deliverance
Section 5-2 review active transport
How do cells maintain homeostasis
What is homeostasis
What helps maintain the eyeball's spherical shape
Forensic duplication tools
An internet is a collection of utility programs designed
Records and reports in nursing
The health triangle
One way cells maintain homeostasis is by controlling
Apics certification maintenance
Monitor and manage small business operations
Respiratory system maintain homeostasis
My health triangle
What are multimedia presentations
How does mitosis maintain genetic continuity
Maintain formal style definition
Past tense of maintain
Formal negative sanctions examples
Dynamic strategic activity systems help a firm to maintain
The energy needed to maintain life-sustaining activities
Stick lengthwise balance
Nutrition body
How do we achieve servlet collaboration mcq
Maintaining ecological balance
Foster and maintain business relationships
What do unicellular organisms do to maintain homeostasis
What is the average speed of an unladen swallow
Maintain your assigned protective mask
How did stalin gain and maintain power in the u.s.s.r.?
Nutrient substance
Whats a health triangle
According to interventionists how would aiding
Objectives of tally
Aeroplane flight training manual
Fitness components for golf
How to maintain housing society accounts in tally
How to maintain housing society accounts in tally
Global stratification definition
Explain how to correctly remove hard light cured gels
How do elites maintain stratification
Bsbebu401 review and maintain a website
How did louis xiv gain consolidate and maintain power
Crr in accounting
Integrated services vs differentiated services
Wake county human services community services center
Introduction of school health services
Family welfare services introduction
An introduction to human services policy and practice