Joint Heavy LiftJHL JSF Lift Fan Derivative Ryan
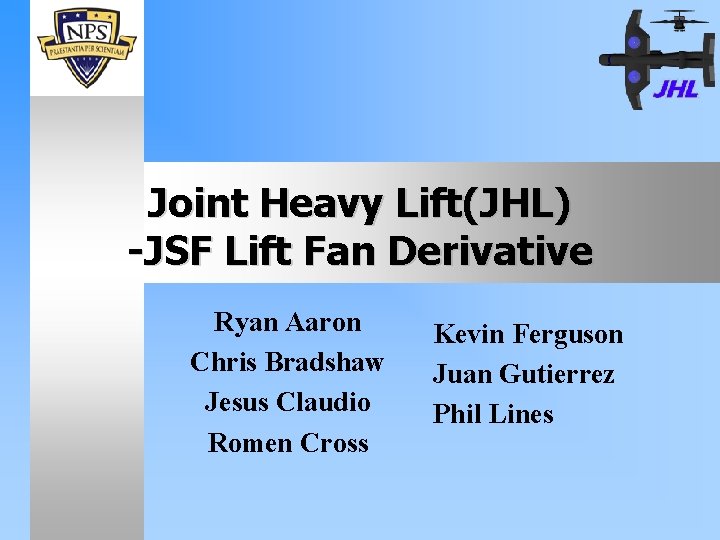
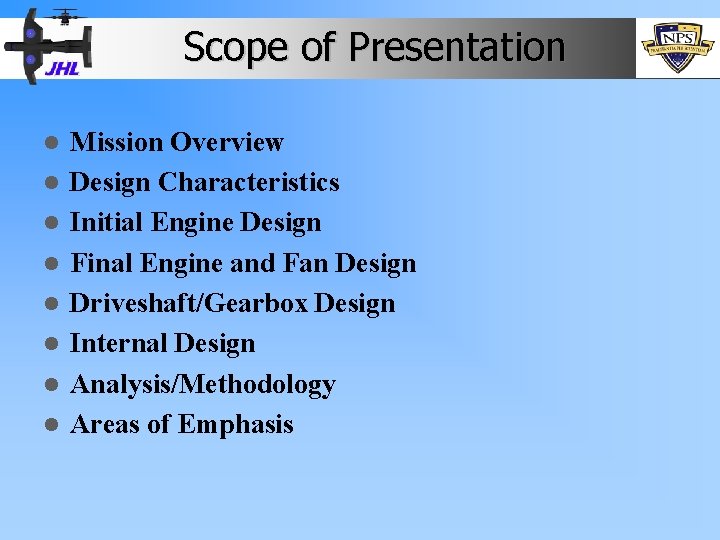

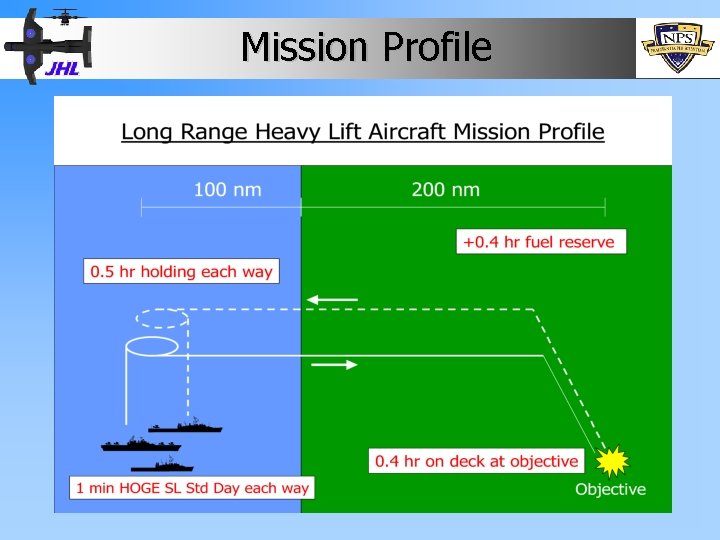
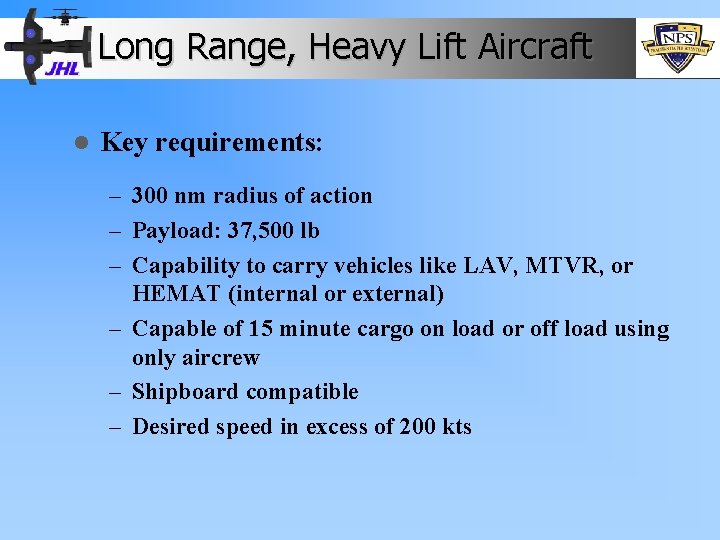
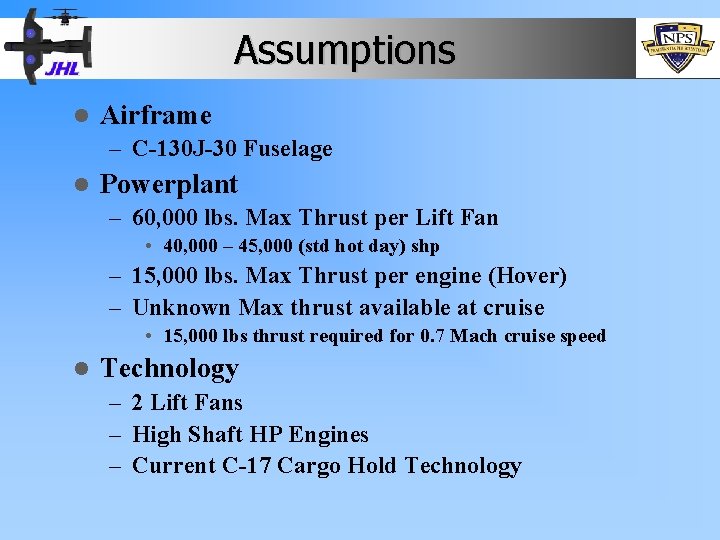
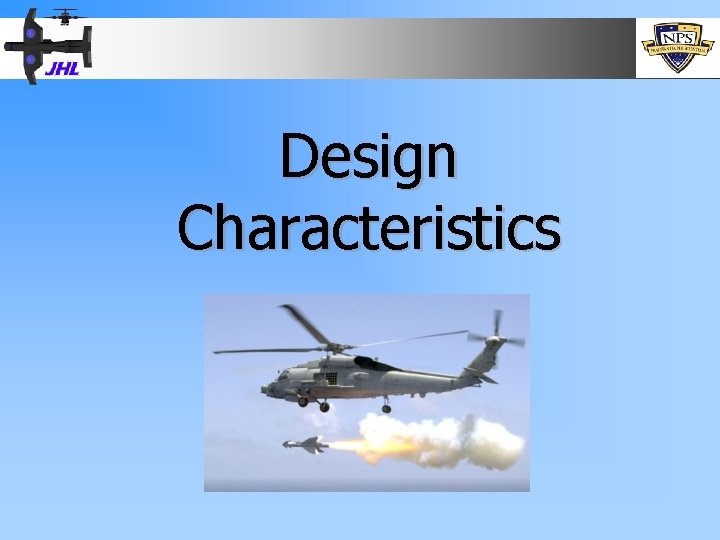
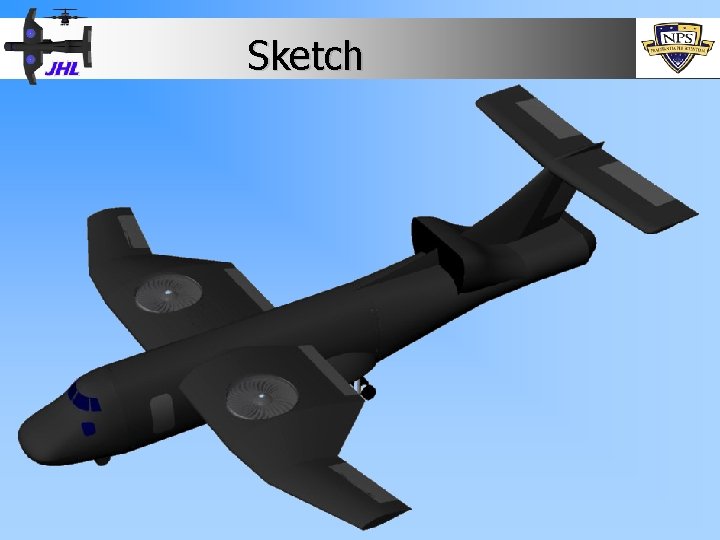
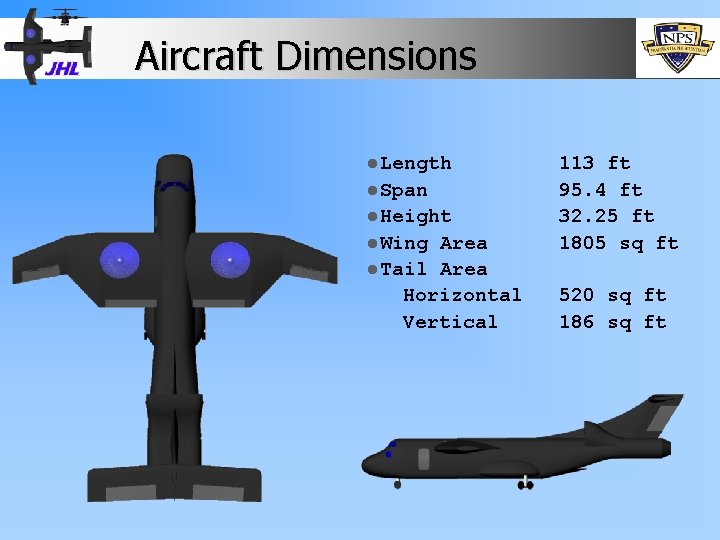
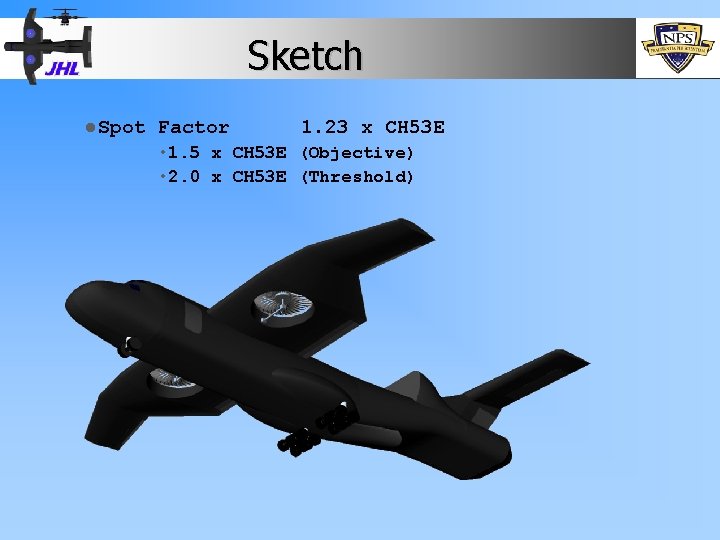
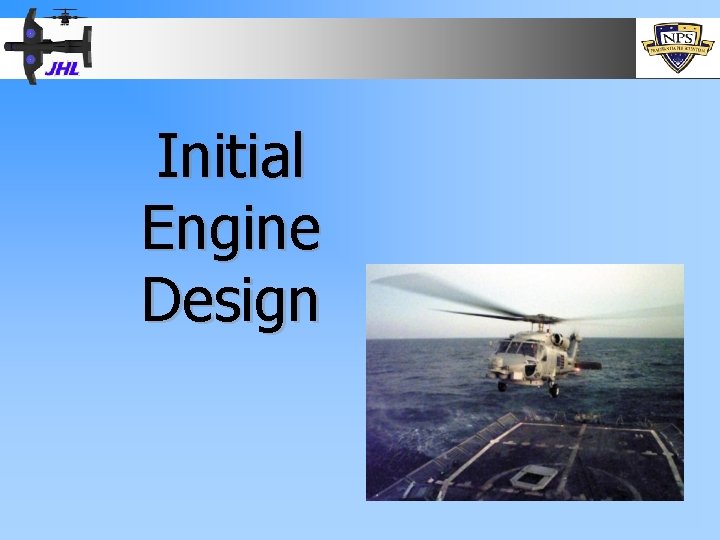
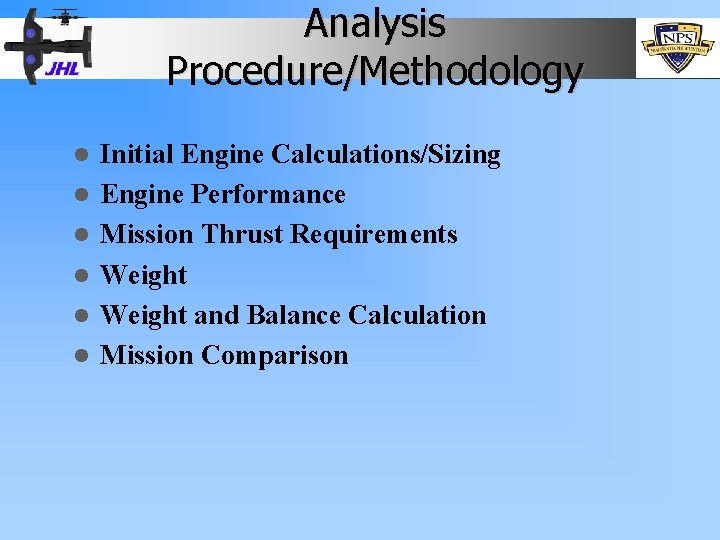
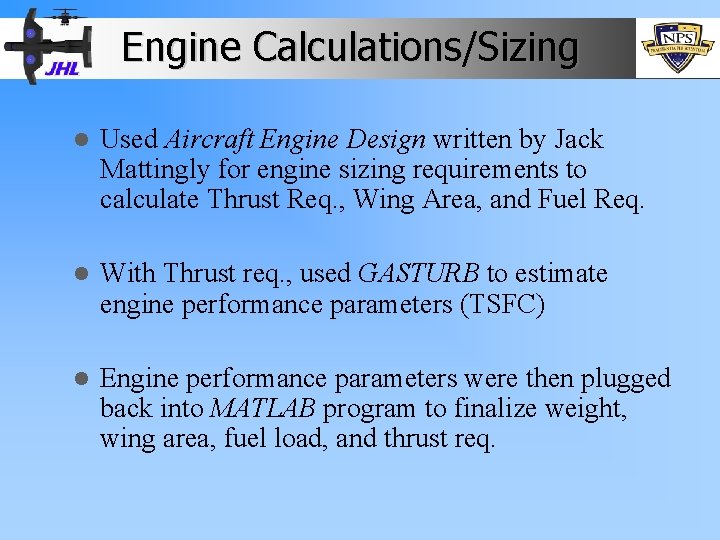
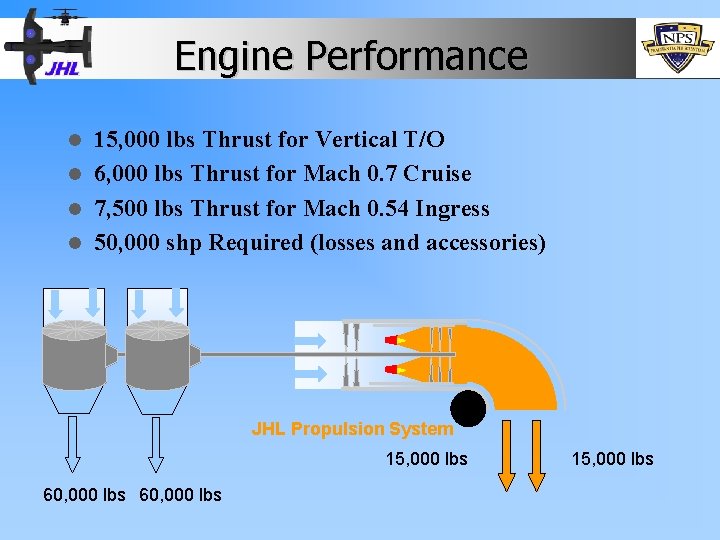
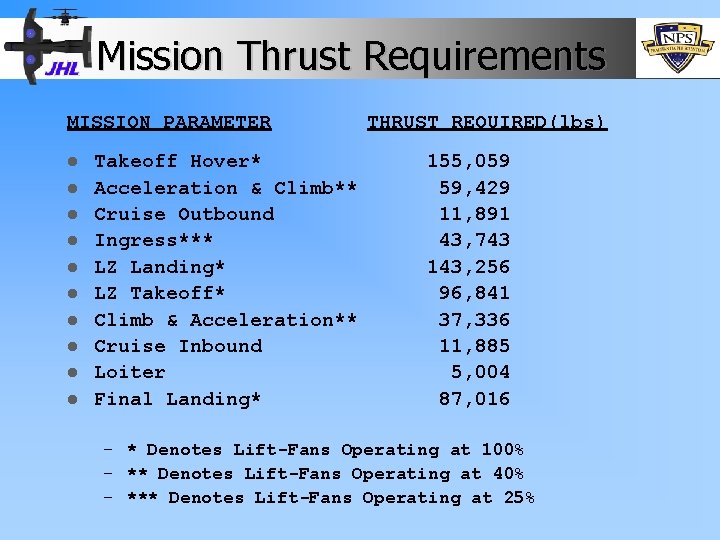
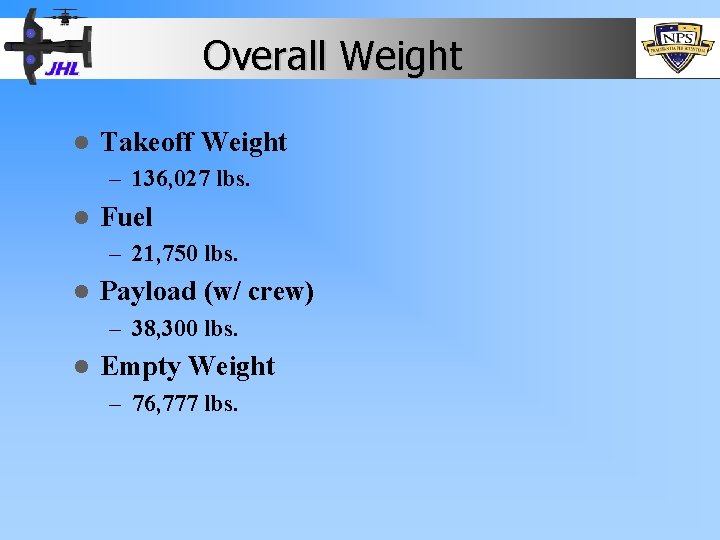
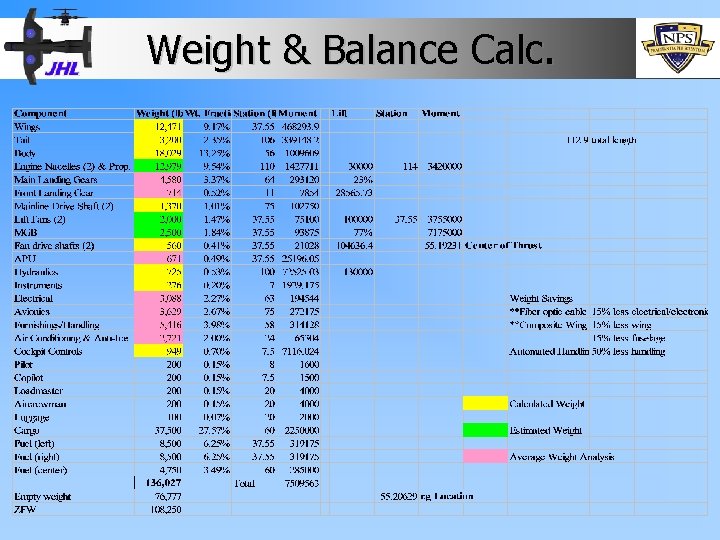
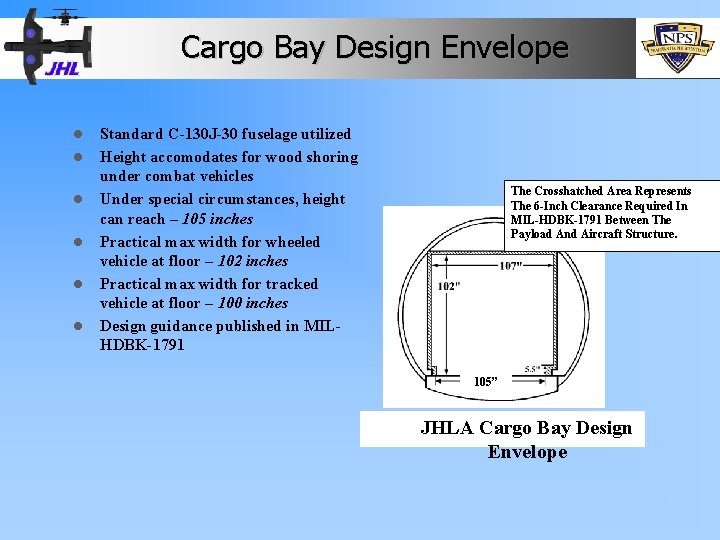
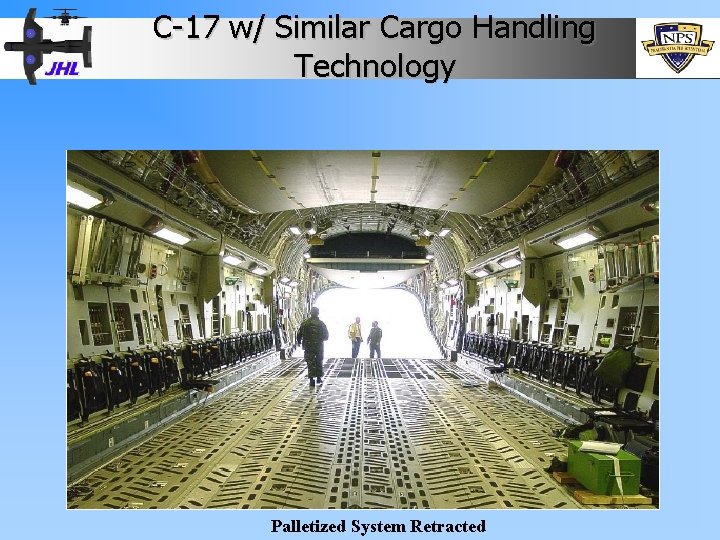
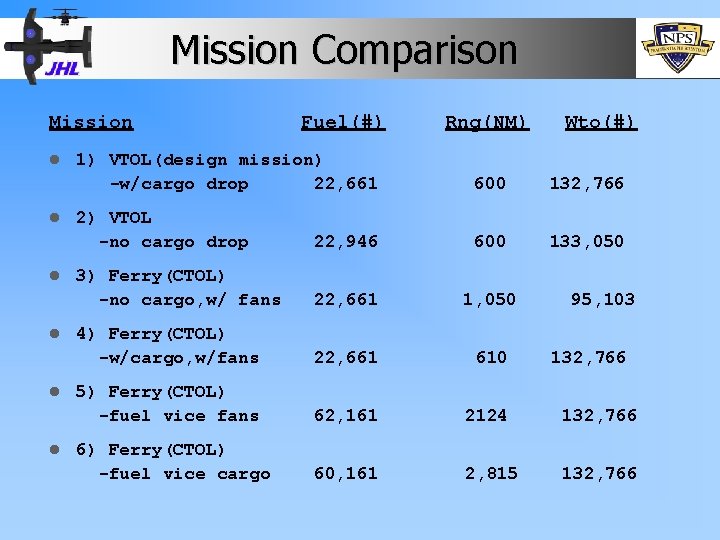
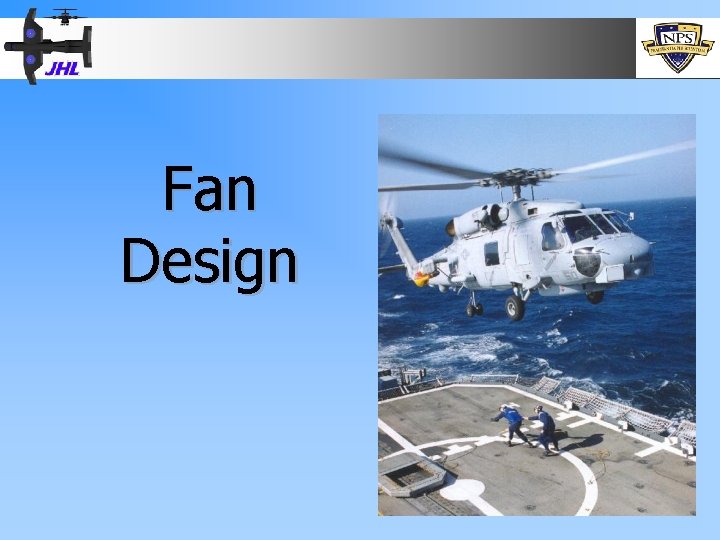
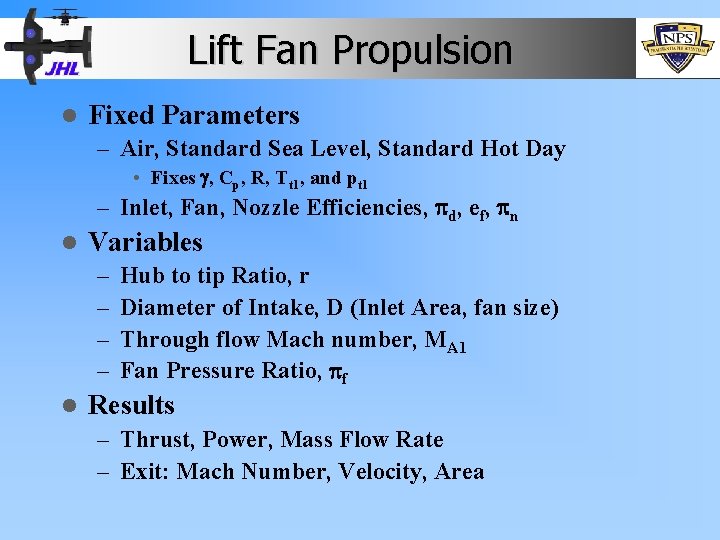
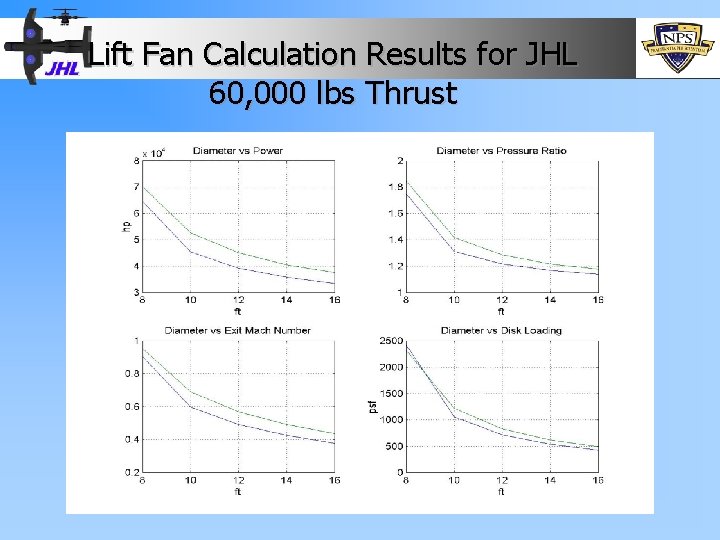
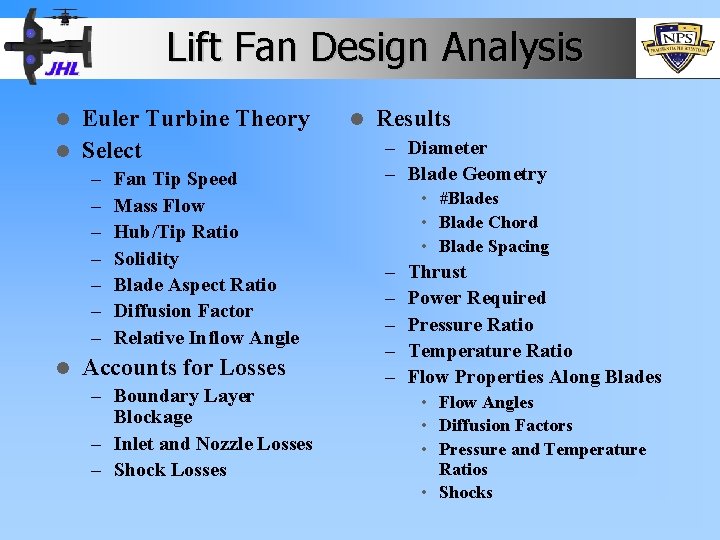
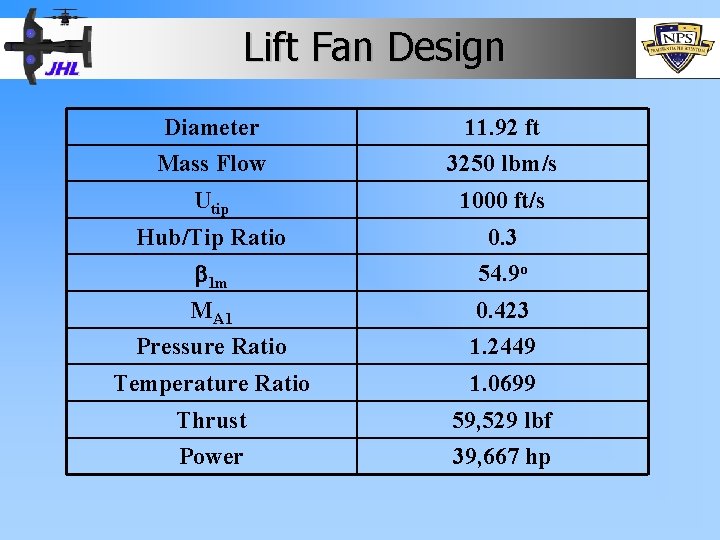

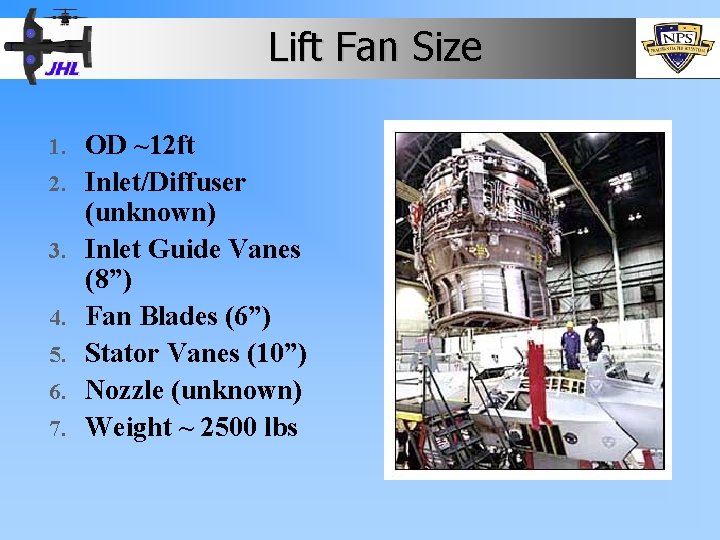
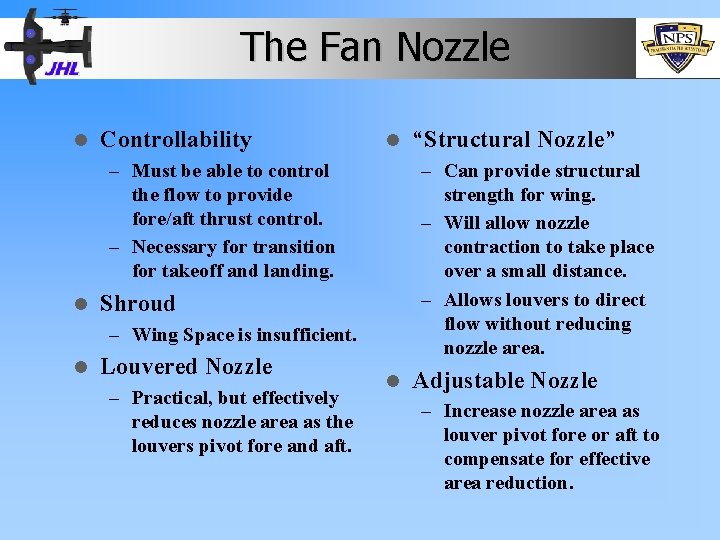
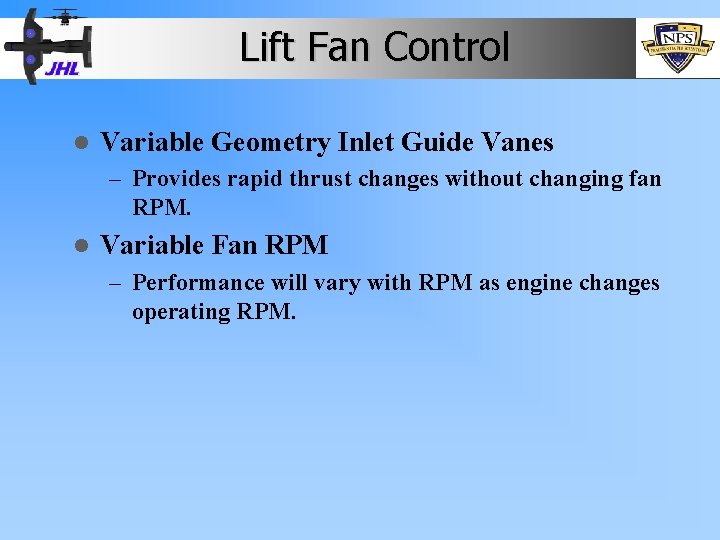
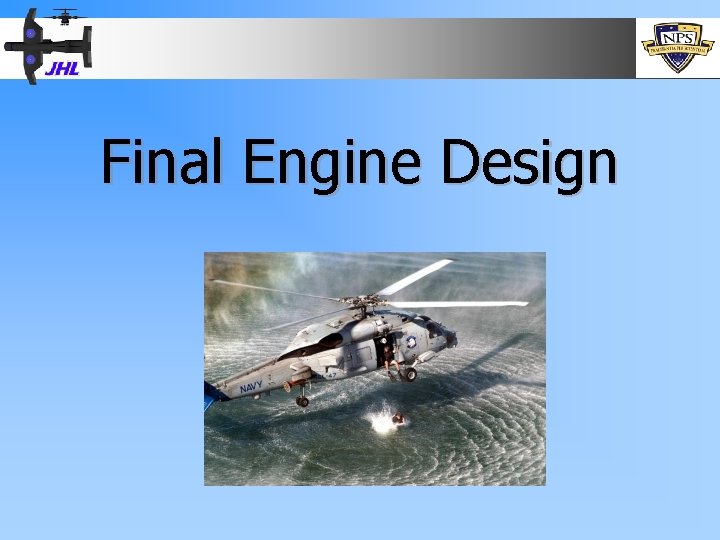
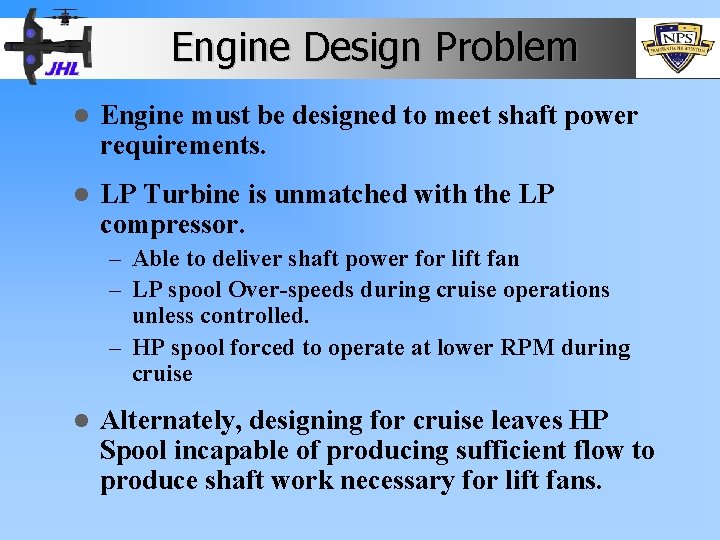
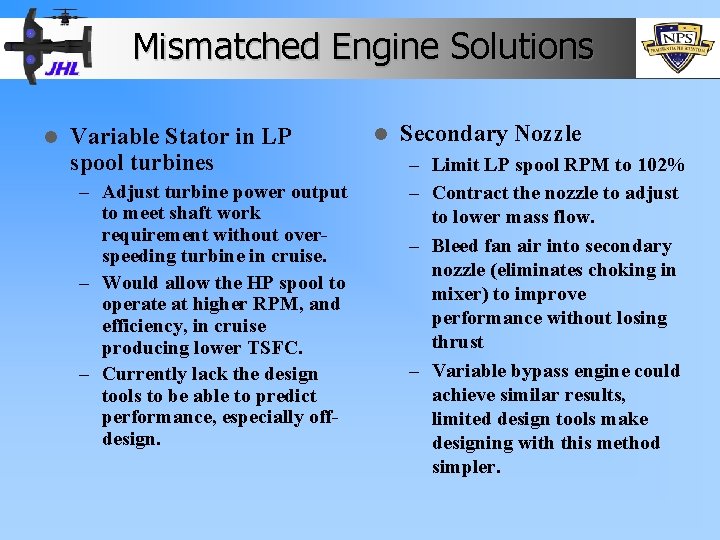
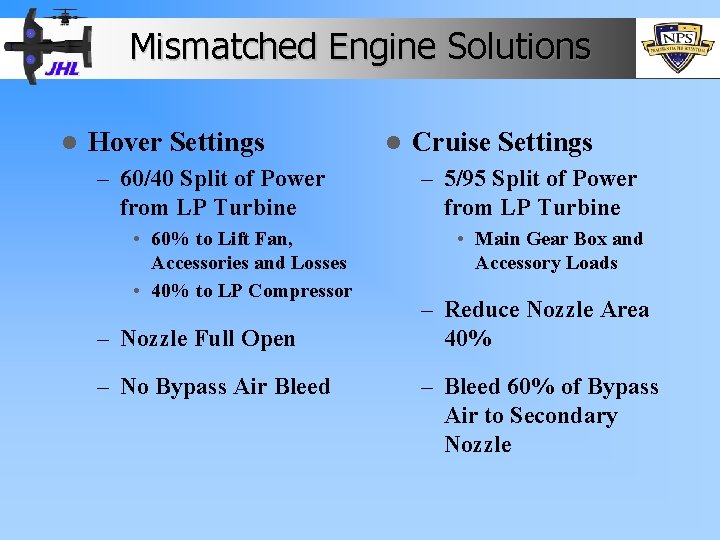
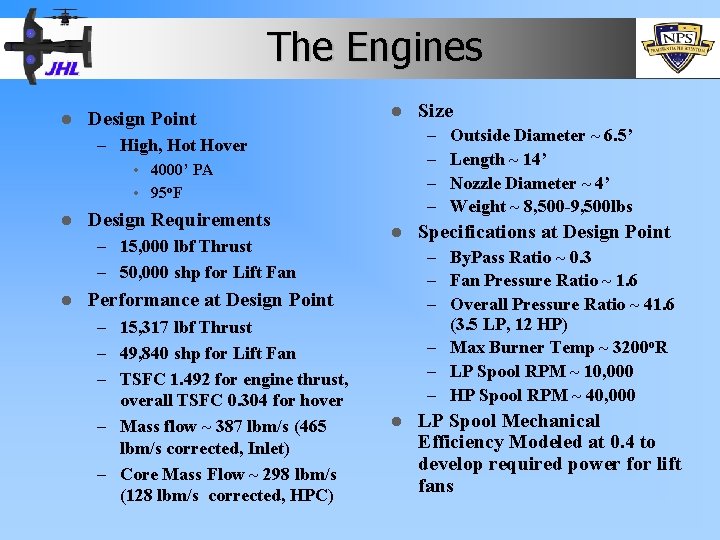
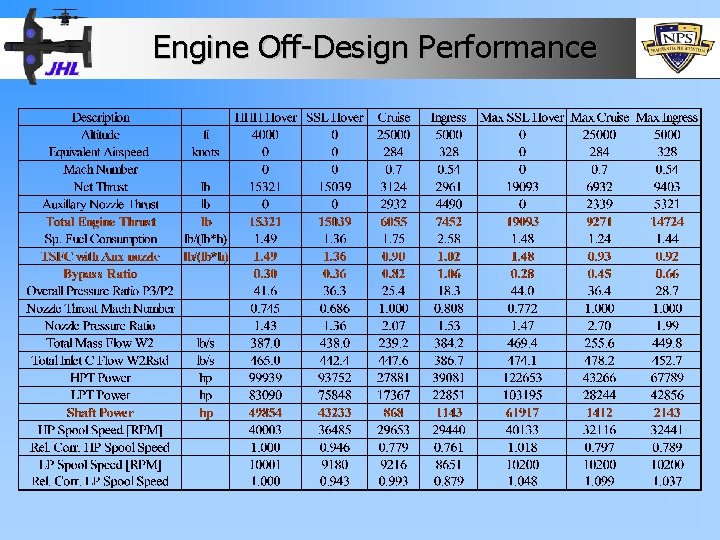
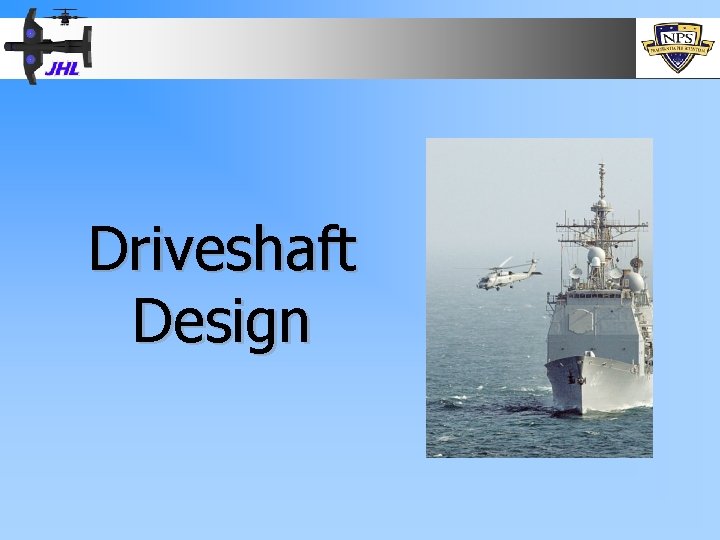
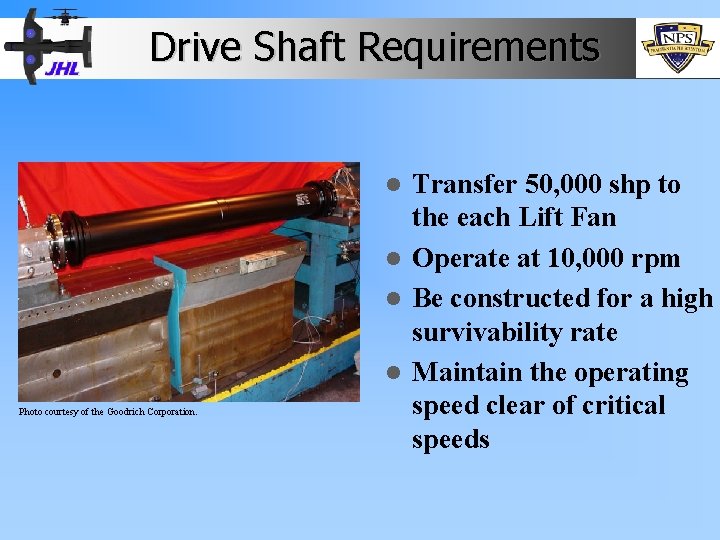
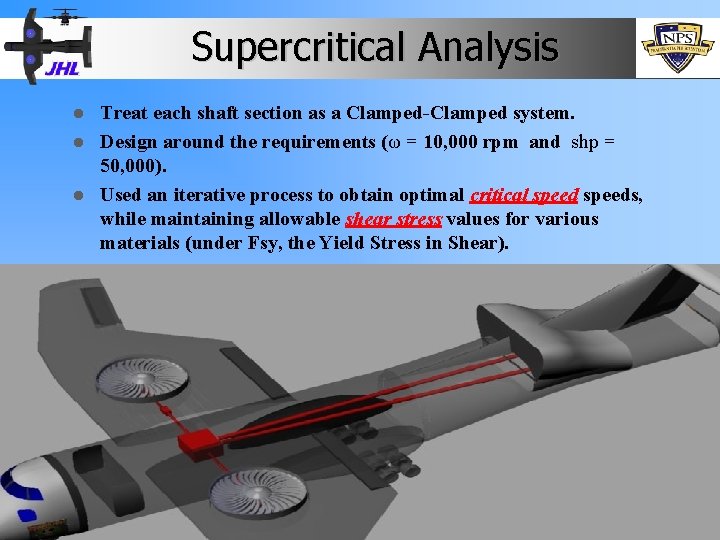
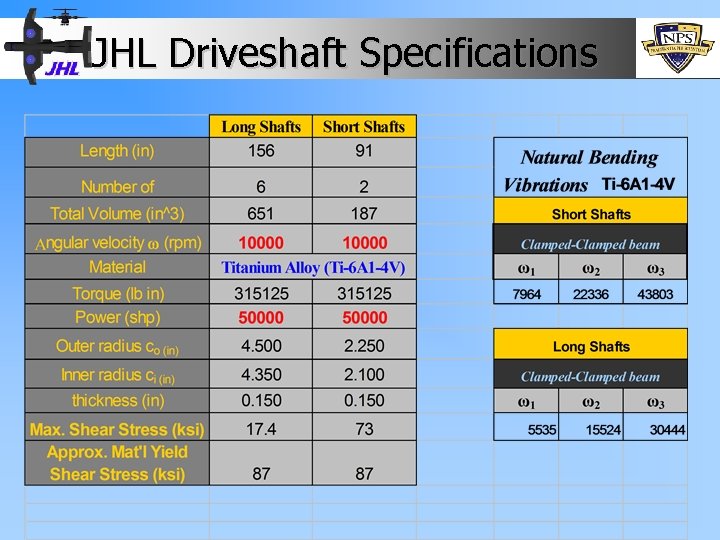
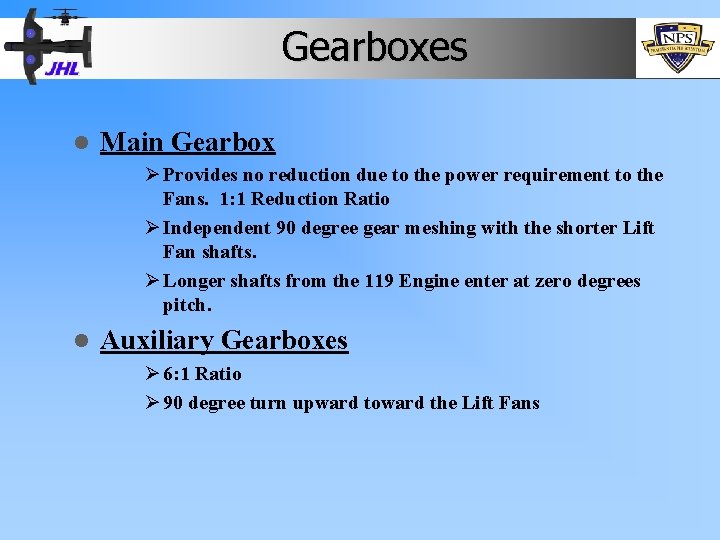
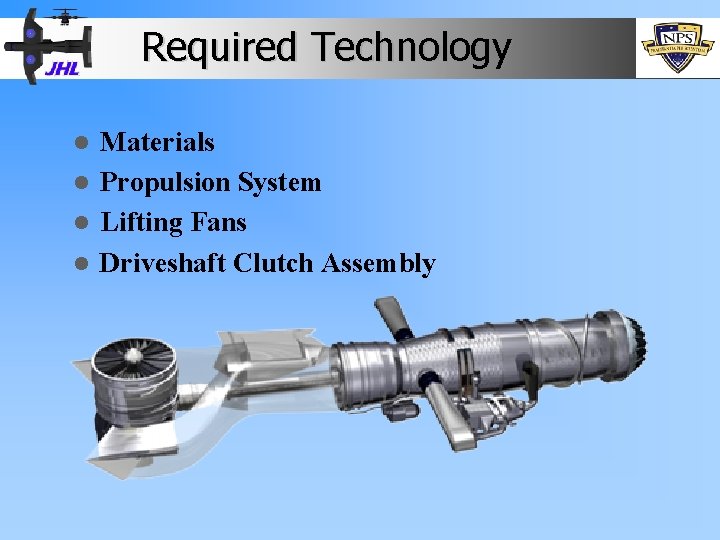
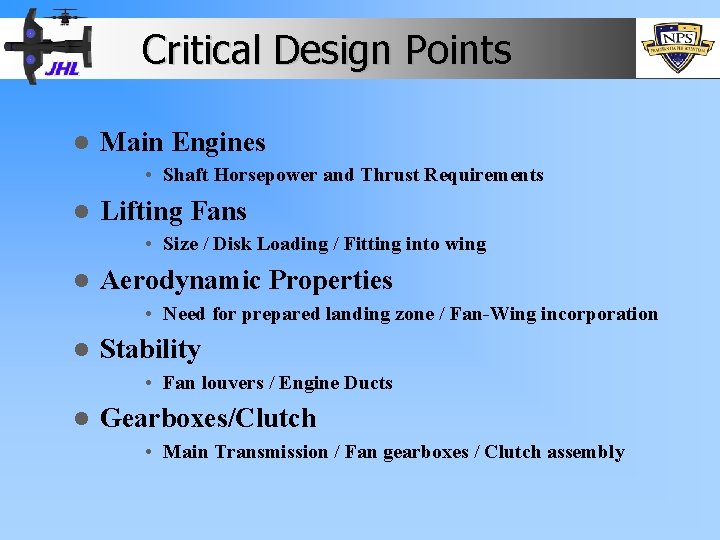
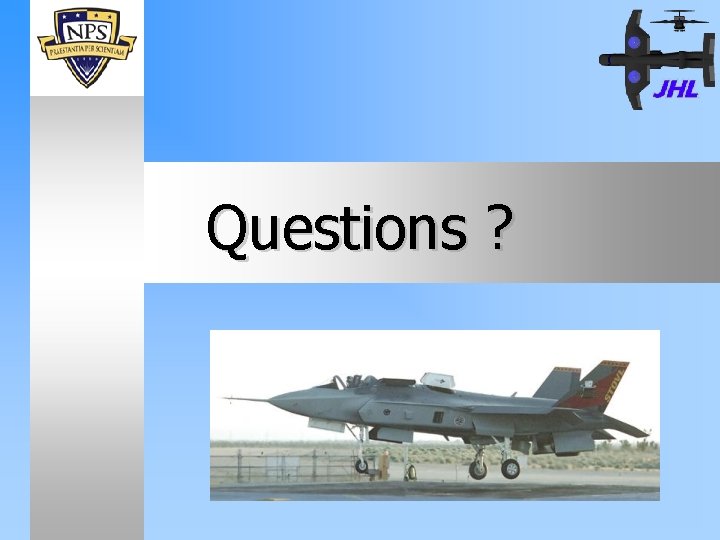
- Slides: 43
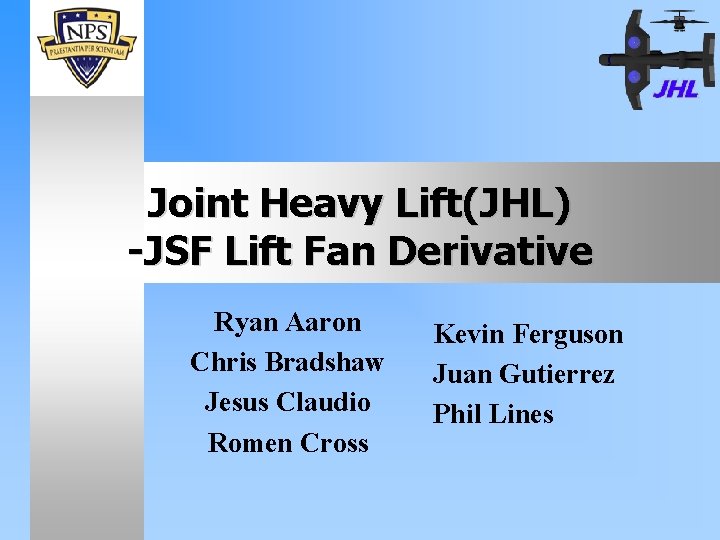
Joint Heavy Lift(JHL) -JSF Lift Fan Derivative Ryan Aaron Chris Bradshaw Jesus Claudio Romen Cross Kevin Ferguson Juan Gutierrez Phil Lines
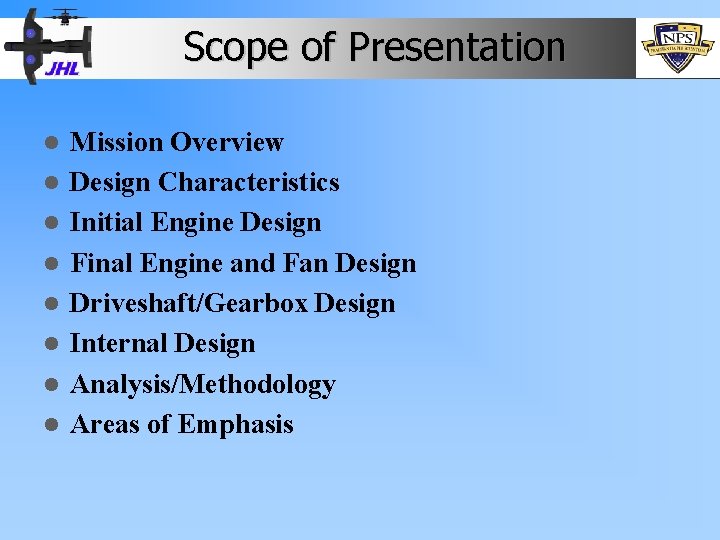
Scope of Presentation l l l l Mission Overview Design Characteristics Initial Engine Design Final Engine and Fan Design Driveshaft/Gearbox Design Internal Design Analysis/Methodology Areas of Emphasis

Mission Profile
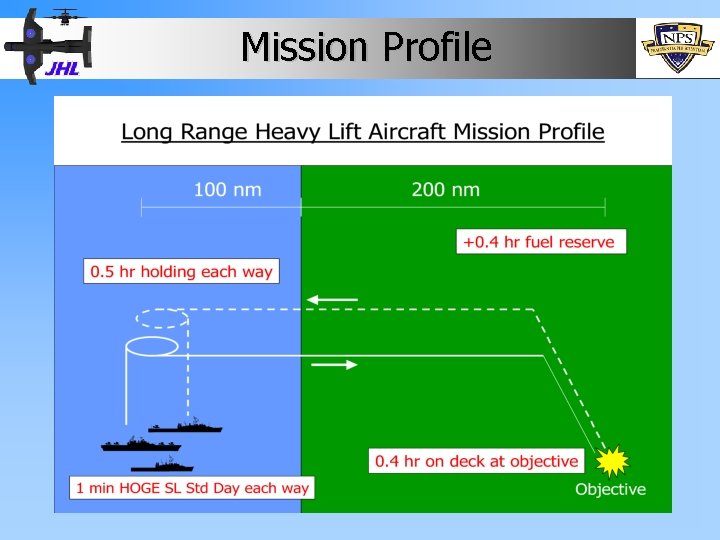
Mission Profile
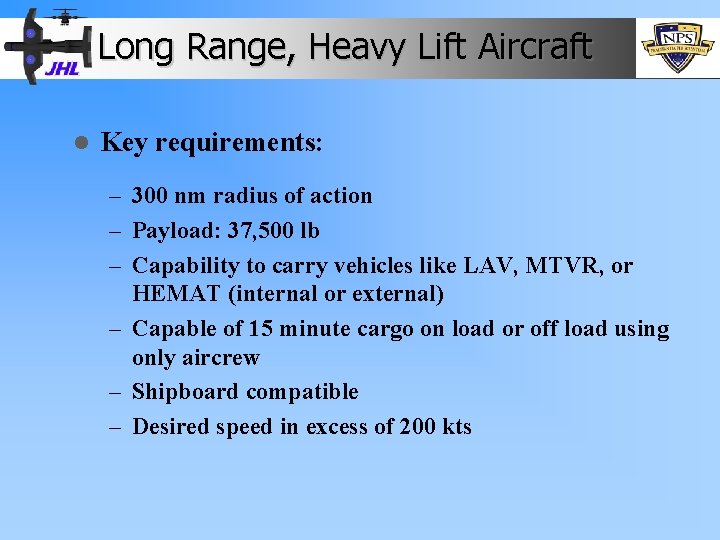
Long Range, Heavy Lift Aircraft l Key requirements: – 300 nm radius of action – Payload: 37, 500 lb – Capability to carry vehicles like LAV, MTVR, or HEMAT (internal or external) – Capable of 15 minute cargo on load or off load using only aircrew – Shipboard compatible – Desired speed in excess of 200 kts
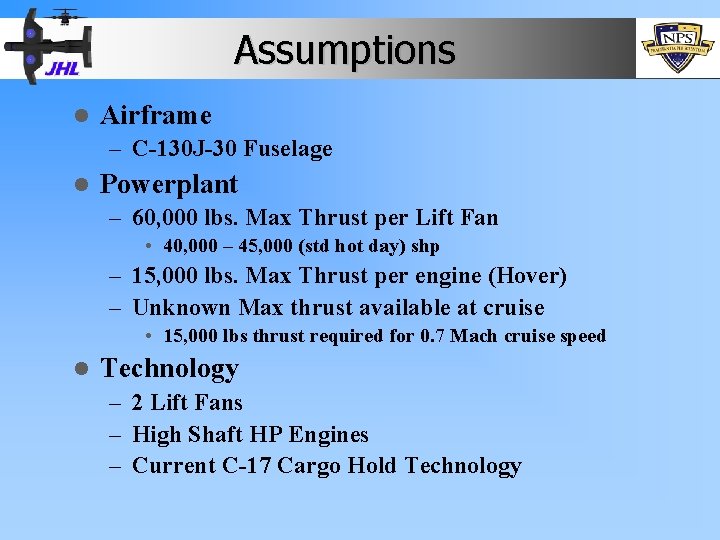
Assumptions l Airframe – C-130 J-30 Fuselage l Powerplant – 60, 000 lbs. Max Thrust per Lift Fan • 40, 000 – 45, 000 (std hot day) shp – 15, 000 lbs. Max Thrust per engine (Hover) – Unknown Max thrust available at cruise • 15, 000 lbs thrust required for 0. 7 Mach cruise speed l Technology – 2 Lift Fans – High Shaft HP Engines – Current C-17 Cargo Hold Technology
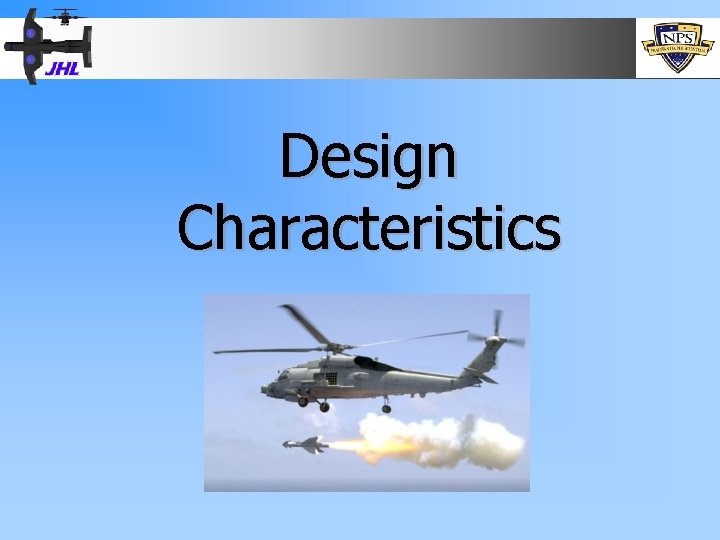
Design Characteristics
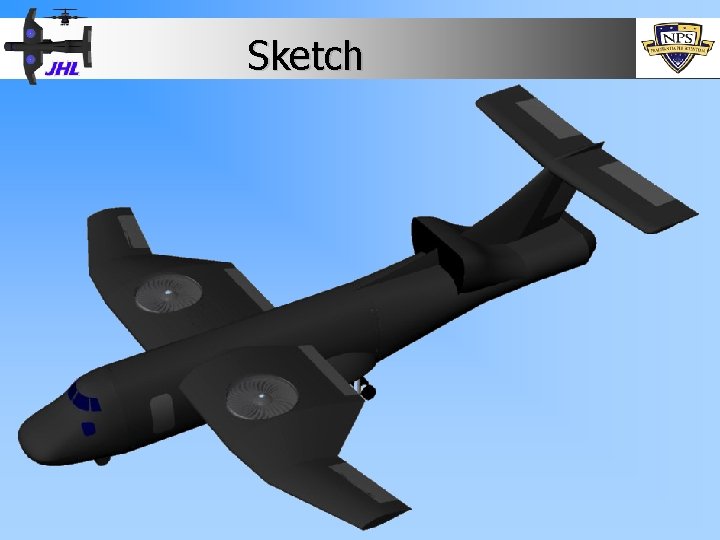
Sketch
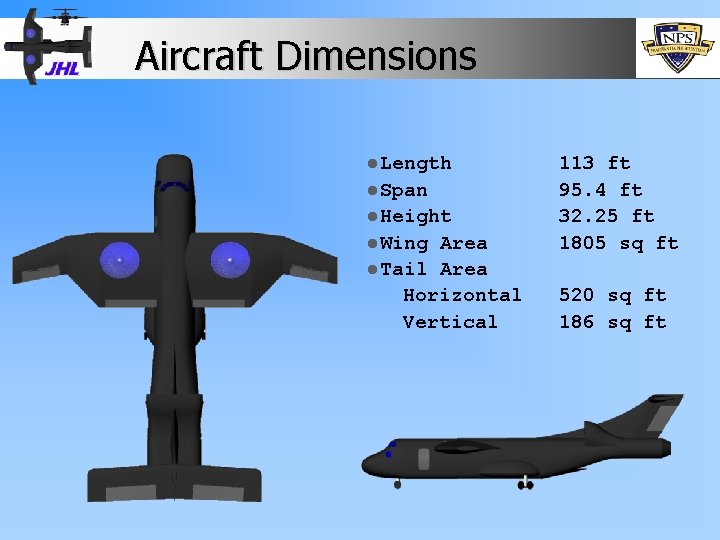
Aircraft Dimensions l. Length l. Span l. Height l. Wing Area l. Tail Area Horizontal Vertical 113 ft 95. 4 ft 32. 25 ft 1805 sq ft 520 sq ft 186 sq ft
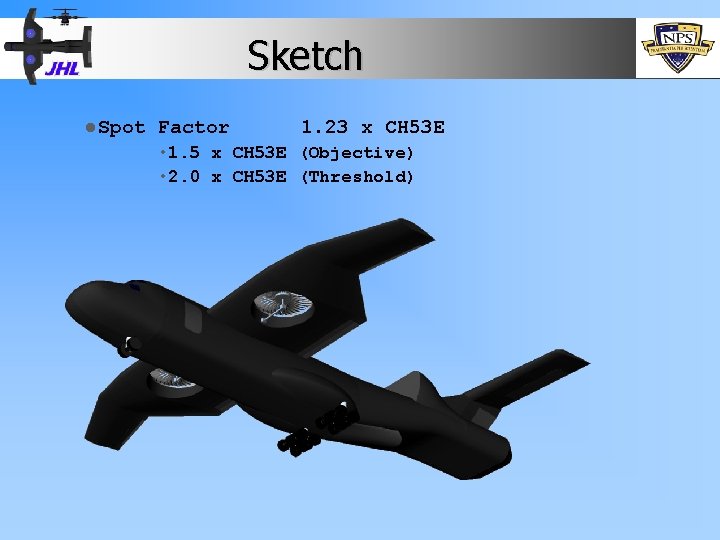
Sketch l. Spot Factor 1. 23 x CH 53 E • 1. 5 x CH 53 E (Objective) • 2. 0 x CH 53 E (Threshold)
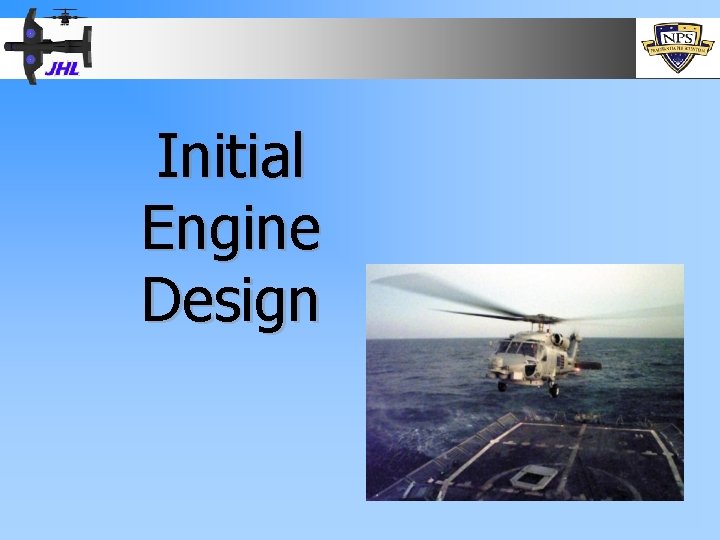
Initial Engine Design
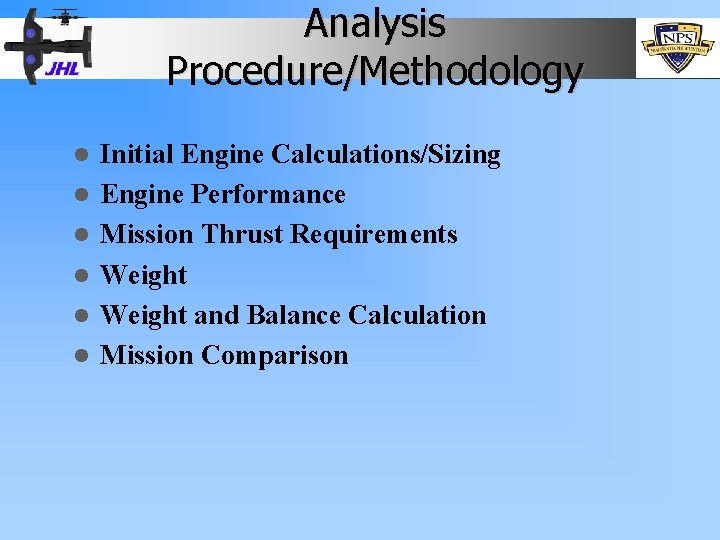
Analysis Procedure/Methodology l l l Initial Engine Calculations/Sizing Engine Performance Mission Thrust Requirements Weight and Balance Calculation Mission Comparison
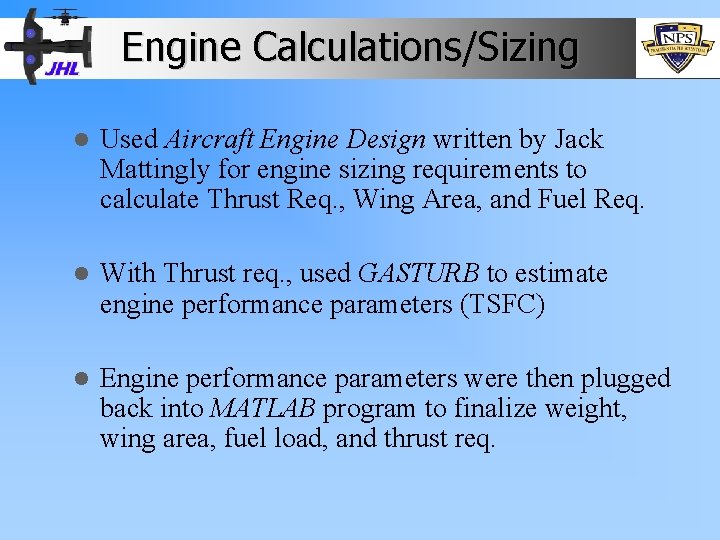
Engine Calculations/Sizing l Used Aircraft Engine Design written by Jack Mattingly for engine sizing requirements to calculate Thrust Req. , Wing Area, and Fuel Req. l With Thrust req. , used GASTURB to estimate engine performance parameters (TSFC) l Engine performance parameters were then plugged back into MATLAB program to finalize weight, wing area, fuel load, and thrust req.
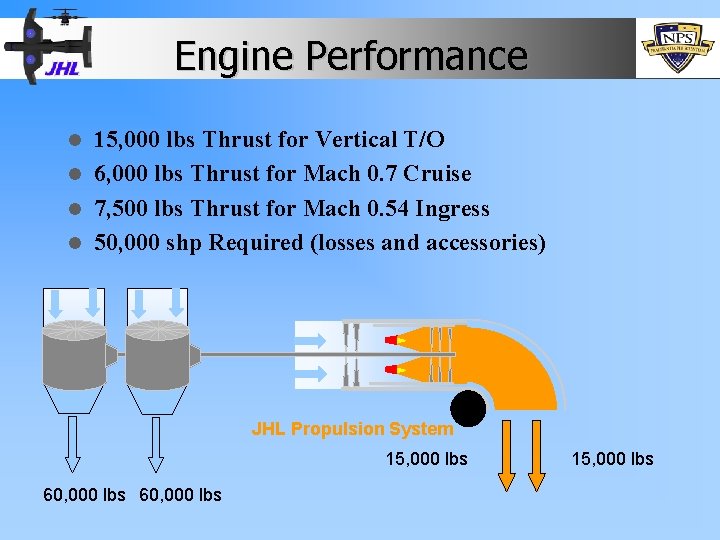
Engine Performance 15, 000 lbs Thrust for Vertical T/O l 6, 000 lbs Thrust for Mach 0. 7 Cruise l 7, 500 lbs Thrust for Mach 0. 54 Ingress l 50, 000 shp Required (losses and accessories) l JHL Propulsion System 15, 000 lbs 60, 000 lbs 15, 000 lbs
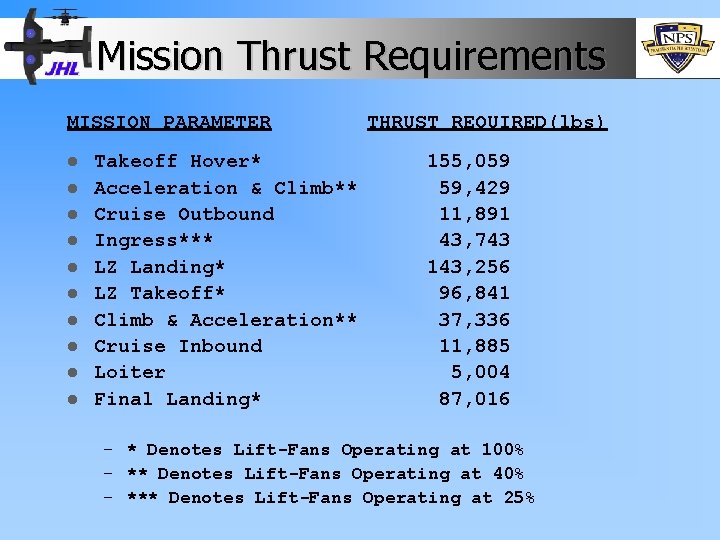
Mission Thrust Requirements MISSION PARAMETER l l l l l Takeoff Hover* Acceleration & Climb** Cruise Outbound Ingress*** LZ Landing* LZ Takeoff* Climb & Acceleration** Cruise Inbound Loiter Final Landing* THRUST REQUIRED(lbs) 155, 059 59, 429 11, 891 43, 743 143, 256 96, 841 37, 336 11, 885 5, 004 87, 016 – * Denotes Lift-Fans Operating at 100% – ** Denotes Lift-Fans Operating at 40% – *** Denotes Lift-Fans Operating at 25%
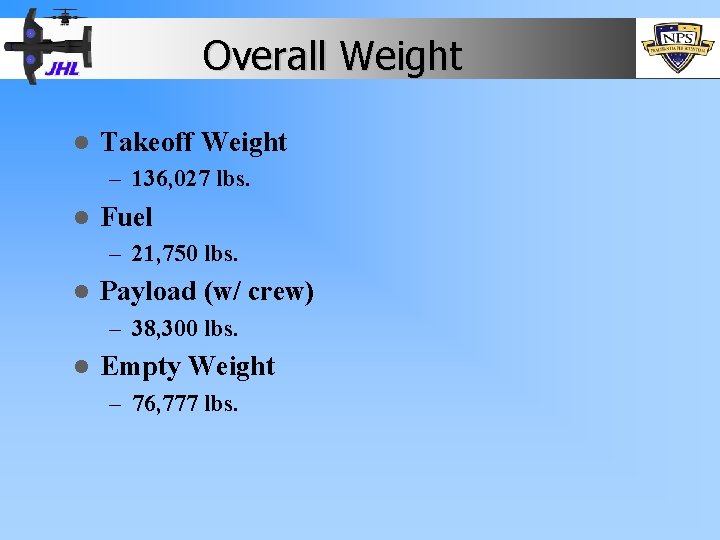
Overall Weight l Takeoff Weight – 136, 027 lbs. l Fuel – 21, 750 lbs. l Payload (w/ crew) – 38, 300 lbs. l Empty Weight – 76, 777 lbs.
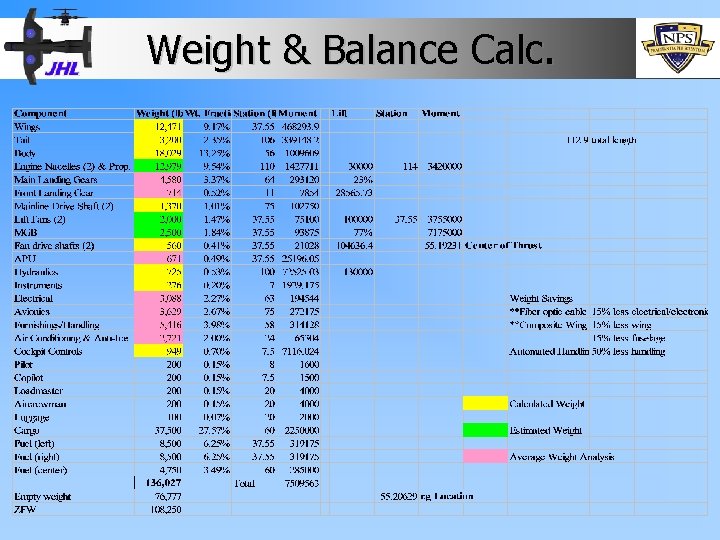
Weight & Balance Calc.
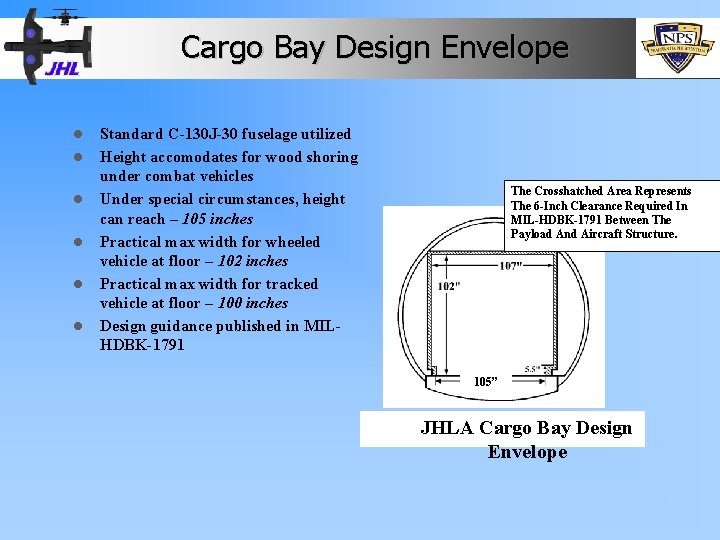
Cargo Bay Design Envelope l l l Standard C-130 J-30 fuselage utilized Height accomodates for wood shoring under combat vehicles Under special circumstances, height can reach – 105 inches Practical max width for wheeled vehicle at floor – 102 inches Practical max width for tracked vehicle at floor – 100 inches Design guidance published in MILHDBK-1791 The Crosshatched Area Represents Required The 6 -Inch Clearance Required In MIL-HDBK-1791 Between The Payload And Aircraft Structure. 105” JHLA Cargo Bay Design Envelope
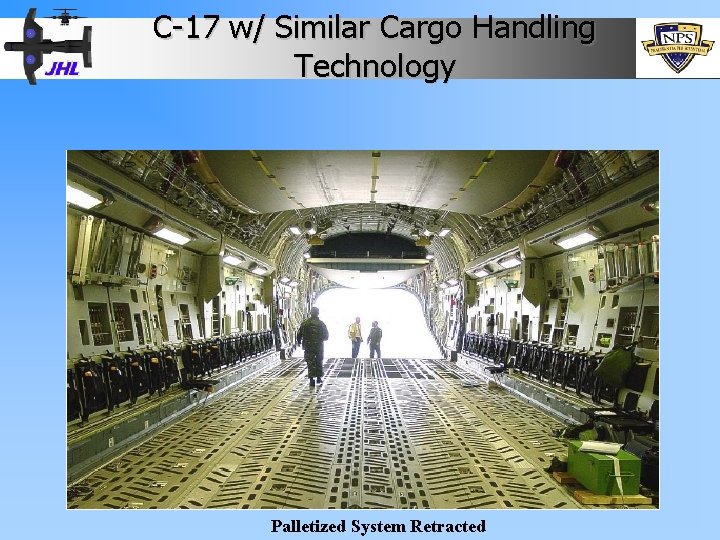
C-17 w/ Similar Cargo Handling Technology Palletized System Retracted
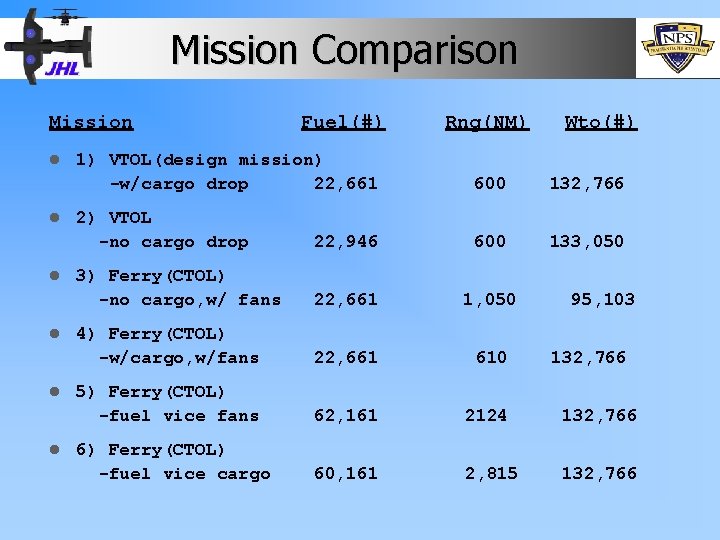
Mission Comparison Mission l l l Fuel(#) Rng(NM) Wto(#) 1) VTOL(design mission) -w/cargo drop 22, 661 600 132, 766 2) VTOL -no cargo drop 22, 946 600 133, 050 3) Ferry(CTOL) -no cargo, w/ fans 22, 661 1, 050 4) Ferry(CTOL) -w/cargo, w/fans 22, 661 610 5) Ferry(CTOL) -fuel vice fans 62, 161 2124 132, 766 6) Ferry(CTOL) -fuel vice cargo 60, 161 2, 815 132, 766 95, 103 132, 766
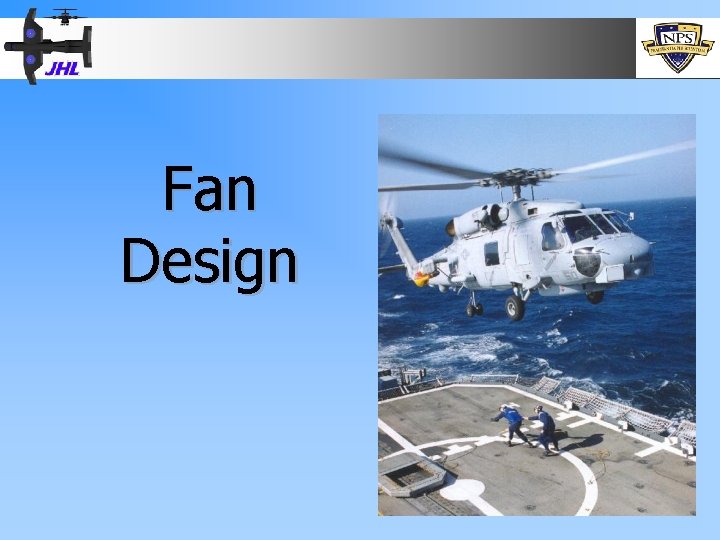
Fan Design
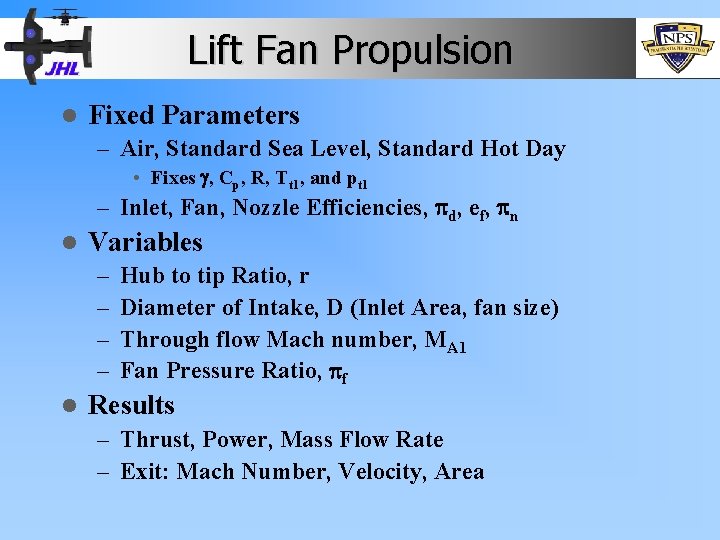
Lift Fan Propulsion l Fixed Parameters – Air, Standard Sea Level, Standard Hot Day • Fixes g, Cp, R, Tt 1, and pt 1 – Inlet, Fan, Nozzle Efficiencies, pd, ef, pn l Variables – – l Hub to tip Ratio, r Diameter of Intake, D (Inlet Area, fan size) Through flow Mach number, MA 1 Fan Pressure Ratio, pf Results – Thrust, Power, Mass Flow Rate – Exit: Mach Number, Velocity, Area
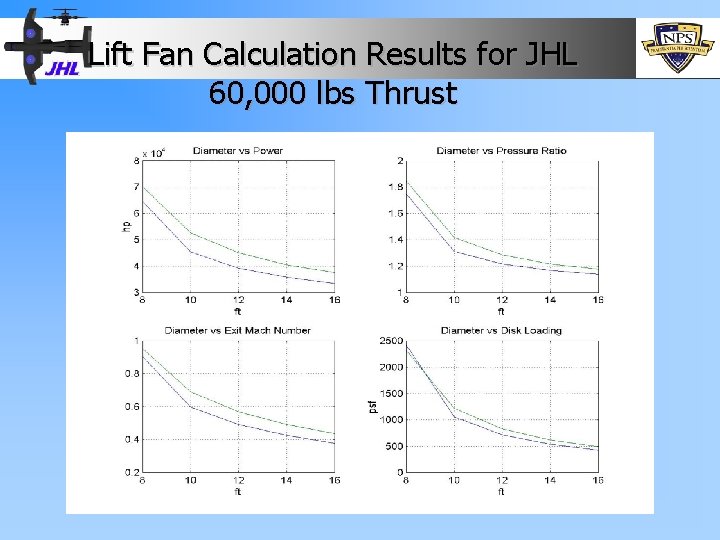
Lift Fan Calculation Results for JHL 60, 000 lbs Thrust
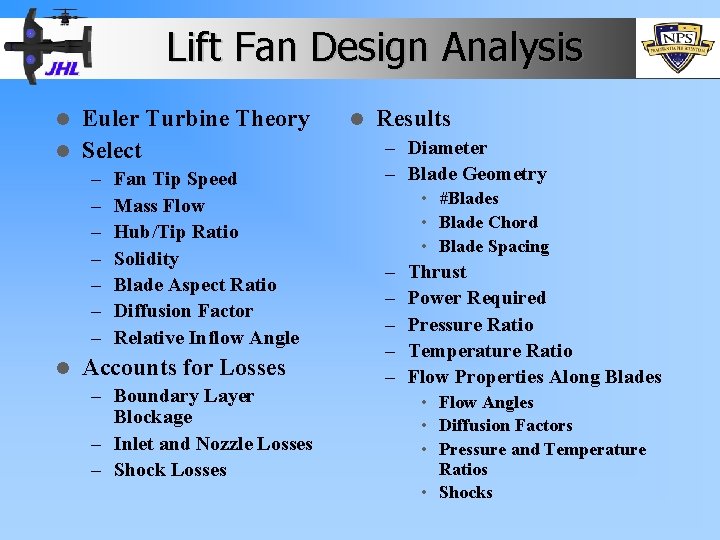
Lift Fan Design Analysis Euler Turbine Theory l Select l – – – – l Fan Tip Speed Mass Flow Hub/Tip Ratio Solidity Blade Aspect Ratio Diffusion Factor Relative Inflow Angle Accounts for Losses – Boundary Layer Blockage – Inlet and Nozzle Losses – Shock Losses l Results – Diameter – Blade Geometry • #Blades • Blade Chord • Blade Spacing – – – Thrust Power Required Pressure Ratio Temperature Ratio Flow Properties Along Blades • Flow Angles • Diffusion Factors • Pressure and Temperature Ratios • Shocks
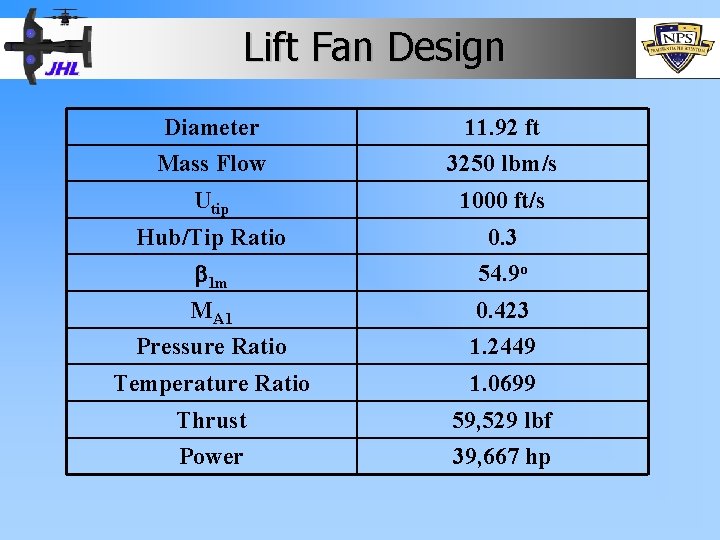
Lift Fan Design Diameter 11. 92 ft Mass Flow 3250 lbm/s Utip 1000 ft/s Hub/Tip Ratio 0. 3 b 1 m 54. 9 o MA 1 0. 423 Pressure Ratio 1. 2449 Temperature Ratio 1. 0699 Thrust 59, 529 lbf Power 39, 667 hp

Lift Fan Geometry Blade Geometry R/Rbar Chord/ Spacing Setting Diffusion Angle Factor Aspect Ratio: 6 0. 4615 3. 83”/3. 06” Rotor Solidity: 1. 25 1 8. 30”/6. 64” # Blades: 44 1. 5385 12. 77”/10. 22” -4. 6 o 44. 6 o 62. 4 o 0. 3894 0. 4636 0. 2523 Aspect Ratio: 8 0. 4615 Stator Solidity: 1. 25 1 # Blades: 58 1. 5385 28. 7 o 17. 9 o 12. 5 o 0. 7966 0. 4218 0. 2635 2. 91”/2. 33” 6. 30”/5. 04” 9. 69”/7. 75”
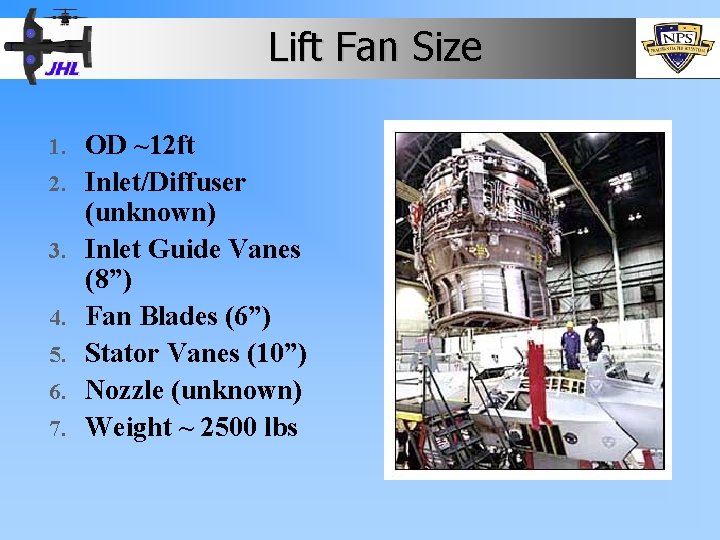
Lift Fan Size 1. 2. 3. 4. 5. 6. 7. OD ~12 ft Inlet/Diffuser (unknown) Inlet Guide Vanes (8”) Fan Blades (6”) Stator Vanes (10”) Nozzle (unknown) Weight ~ 2500 lbs
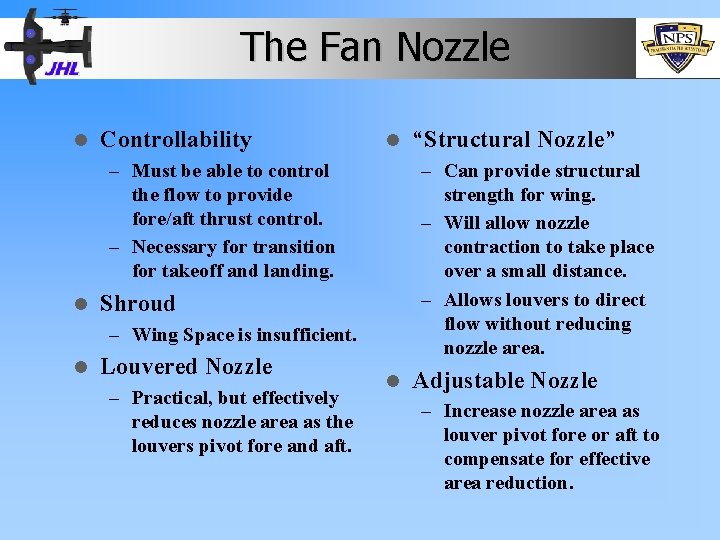
The Fan Nozzle l Controllability l – Must be able to control the flow to provide fore/aft thrust control. – Necessary for transition for takeoff and landing. l – Can provide structural strength for wing. – Will allow nozzle contraction to take place over a small distance. – Allows louvers to direct flow without reducing nozzle area. Shroud – Wing Space is insufficient. l Louvered Nozzle – Practical, but effectively reduces nozzle area as the louvers pivot fore and aft. “Structural Nozzle” l Adjustable Nozzle – Increase nozzle area as louver pivot fore or aft to compensate for effective area reduction.
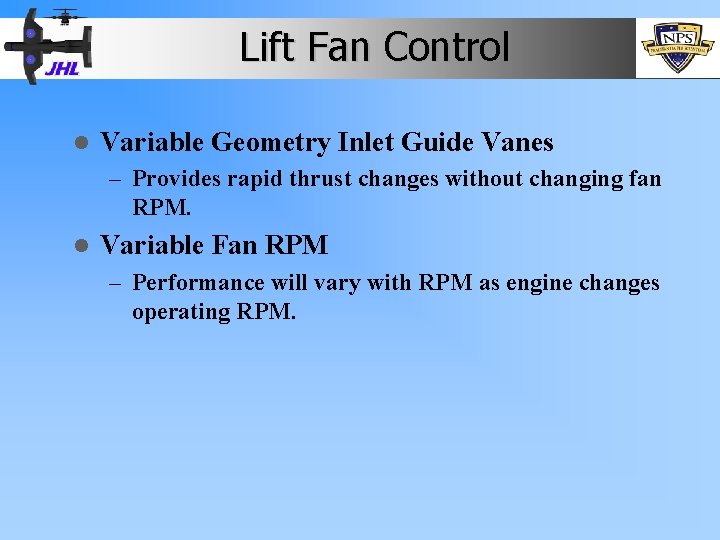
Lift Fan Control l Variable Geometry Inlet Guide Vanes – Provides rapid thrust changes without changing fan RPM. l Variable Fan RPM – Performance will vary with RPM as engine changes operating RPM.
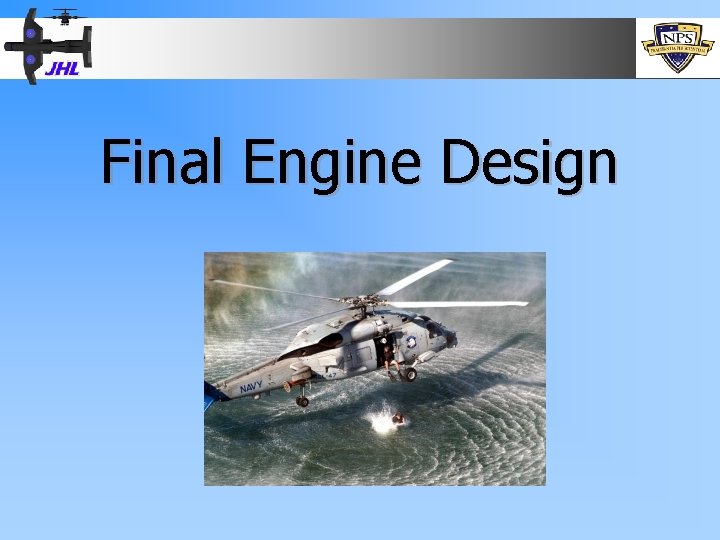
Final Engine Design
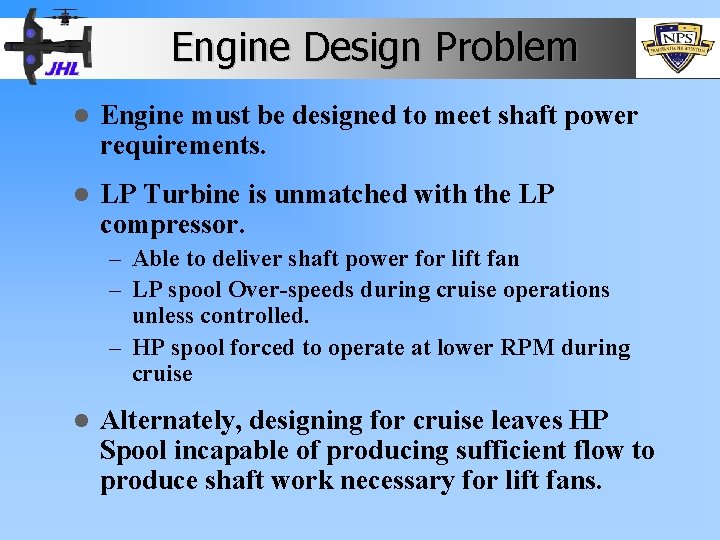
Engine Design Problem l Engine must be designed to meet shaft power requirements. l LP Turbine is unmatched with the LP compressor. – Able to deliver shaft power for lift fan – LP spool Over-speeds during cruise operations unless controlled. – HP spool forced to operate at lower RPM during cruise l Alternately, designing for cruise leaves HP Spool incapable of producing sufficient flow to produce shaft work necessary for lift fans.
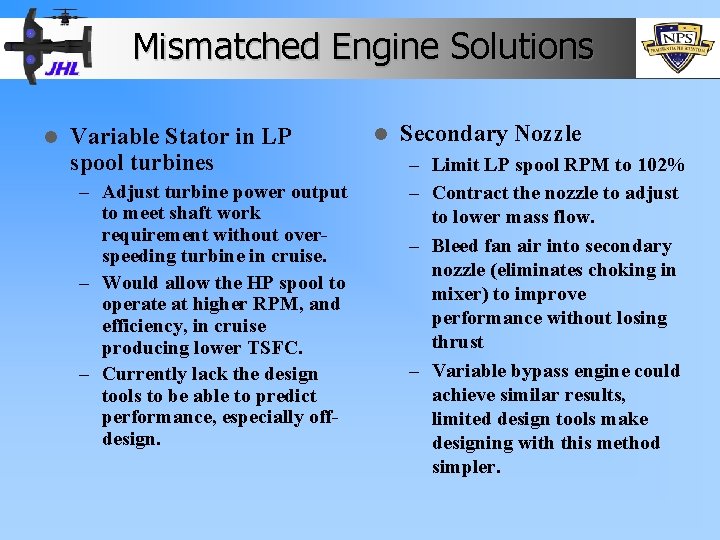
Mismatched Engine Solutions l Variable Stator in LP spool turbines – Adjust turbine power output to meet shaft work requirement without overspeeding turbine in cruise. – Would allow the HP spool to operate at higher RPM, and efficiency, in cruise producing lower TSFC. – Currently lack the design tools to be able to predict performance, especially offdesign. l Secondary Nozzle – Limit LP spool RPM to 102% – Contract the nozzle to adjust to lower mass flow. – Bleed fan air into secondary nozzle (eliminates choking in mixer) to improve performance without losing thrust – Variable bypass engine could achieve similar results, limited design tools make designing with this method simpler.
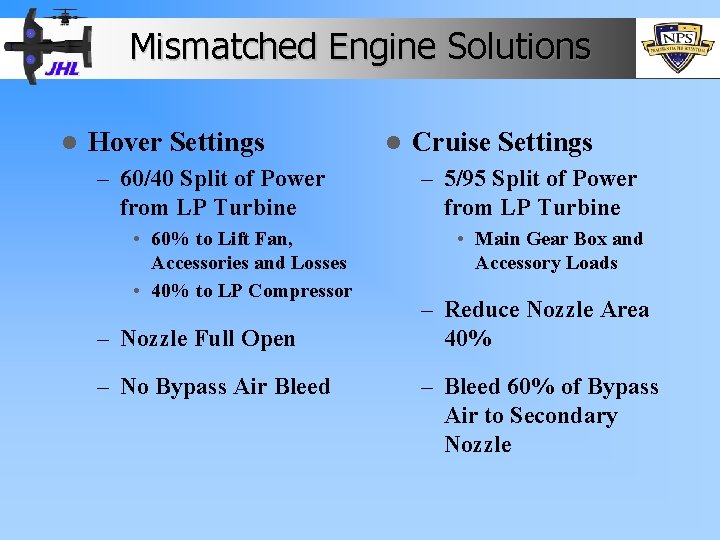
Mismatched Engine Solutions l Hover Settings – 60/40 Split of Power from LP Turbine • 60% to Lift Fan, Accessories and Losses • 40% to LP Compressor – Nozzle Full Open – No Bypass Air Bleed l Cruise Settings – 5/95 Split of Power from LP Turbine • Main Gear Box and Accessory Loads – Reduce Nozzle Area 40% – Bleed 60% of Bypass Air to Secondary Nozzle
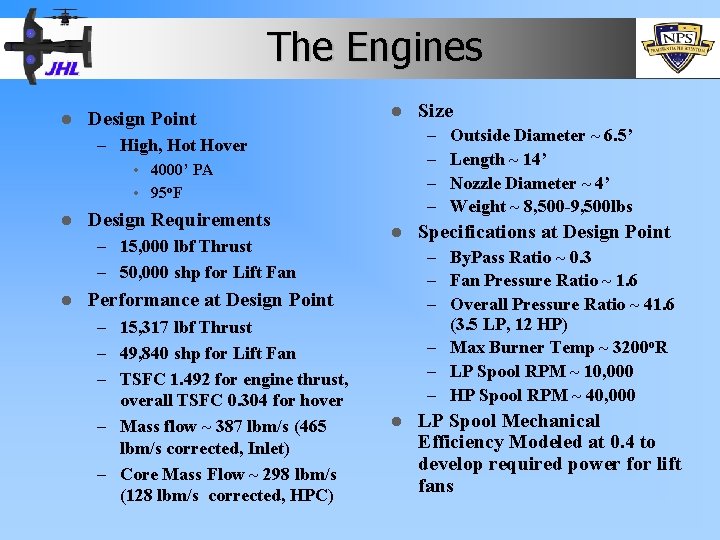
The Engines l Design Point l – – – High, Hot Hover • 4000’ PA • 95 o. F l Design Requirements – 15, 000 lbf Thrust – 50, 000 shp for Lift Fan l l Outside Diameter ~ 6. 5’ Length ~ 14’ Nozzle Diameter ~ 4’ Weight ~ 8, 500 -9, 500 lbs Specifications at Design Point – By. Pass Ratio ~ 0. 3 – Fan Pressure Ratio ~ 1. 6 – Overall Pressure Ratio ~ 41. 6 (3. 5 LP, 12 HP) – Max Burner Temp ~ 3200 o. R – LP Spool RPM ~ 10, 000 – HP Spool RPM ~ 40, 000 Performance at Design Point – 15, 317 lbf Thrust – 49, 840 shp for Lift Fan – TSFC 1. 492 for engine thrust, overall TSFC 0. 304 for hover – Mass flow ~ 387 lbm/s (465 lbm/s corrected, Inlet) – Core Mass Flow ~ 298 lbm/s (128 lbm/s corrected, HPC) Size l LP Spool Mechanical Efficiency Modeled at 0. 4 to develop required power for lift fans
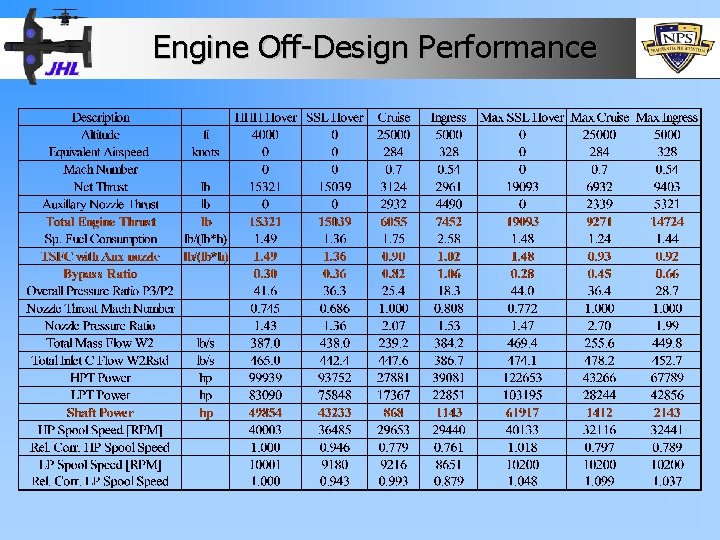
Engine Off-Design Performance
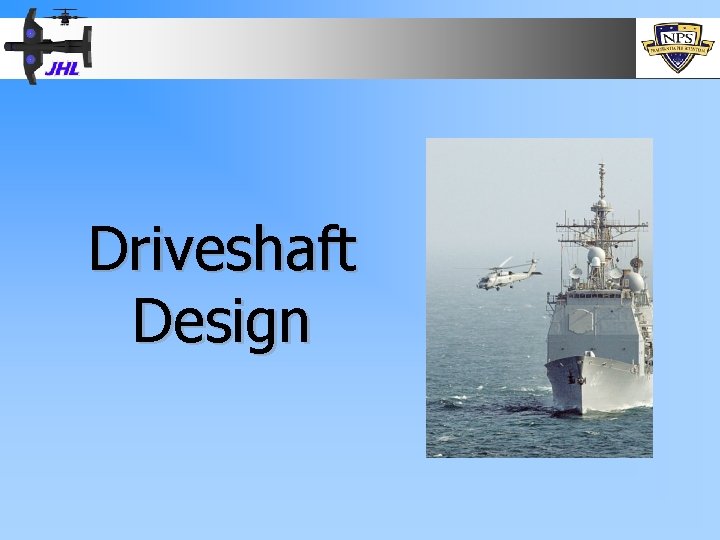
Driveshaft Design
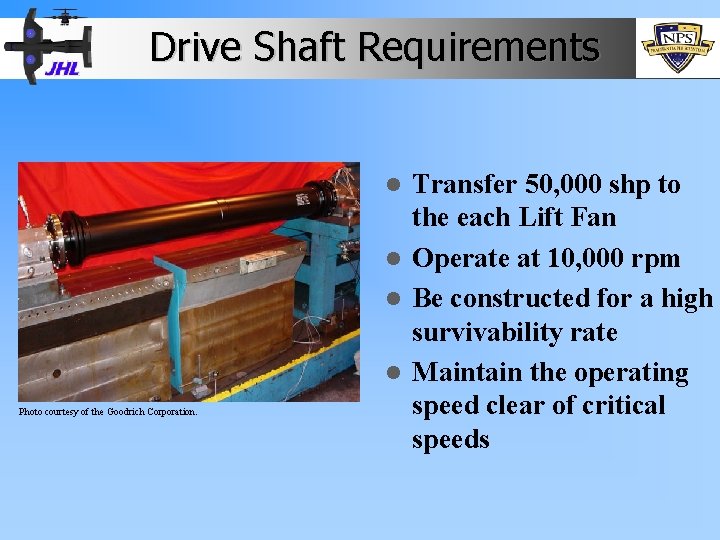
Drive Shaft Requirements Transfer 50, 000 shp to the each Lift Fan l Operate at 10, 000 rpm l Be constructed for a high survivability rate l Maintain the operating speed clear of critical speeds l Photo courtesy of the Goodrich Corporation.
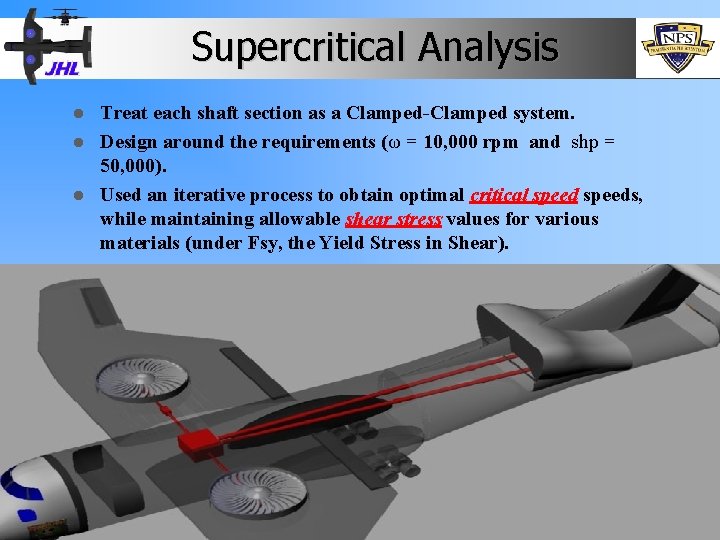
Supercritical Analysis Treat each shaft section as a Clamped-Clamped system. l Design around the requirements (ω = 10, 000 rpm and shp = 50, 000). l Used an iterative process to obtain optimal critical speeds, while maintaining allowable shear stress values for various materials (under Fsy, the Yield Stress in Shear). l
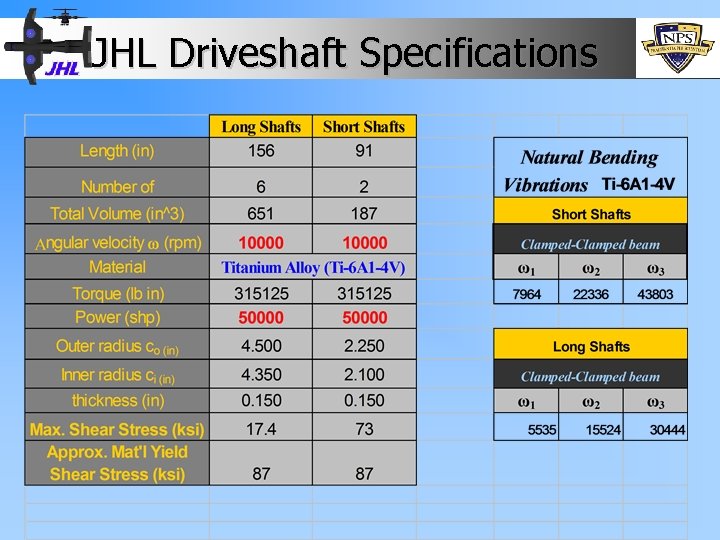
JHL Driveshaft Specifications
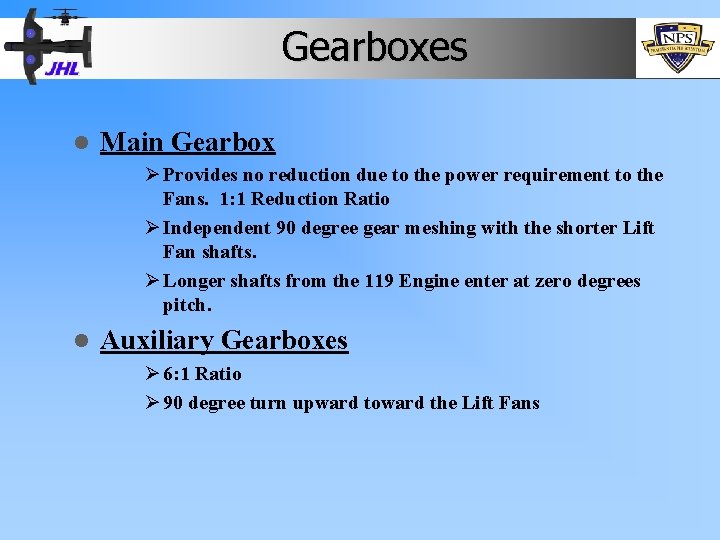
Gearboxes l Main Gearbox Ø Provides no reduction due to the power requirement to the Fans. 1: 1 Reduction Ratio Ø Independent 90 degree gear meshing with the shorter Lift Fan shafts. Ø Longer shafts from the 119 Engine enter at zero degrees pitch. l Auxiliary Gearboxes Ø 6: 1 Ratio Ø 90 degree turn upward toward the Lift Fans
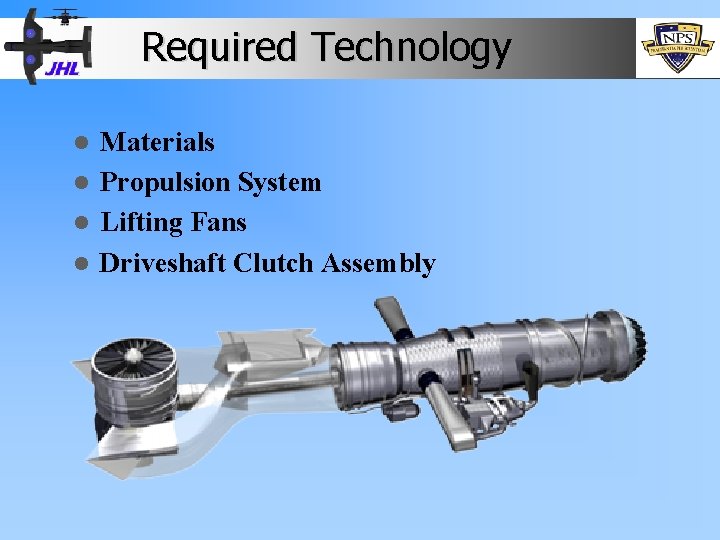
Required Technology Materials l Propulsion System l Lifting Fans l Driveshaft Clutch Assembly l
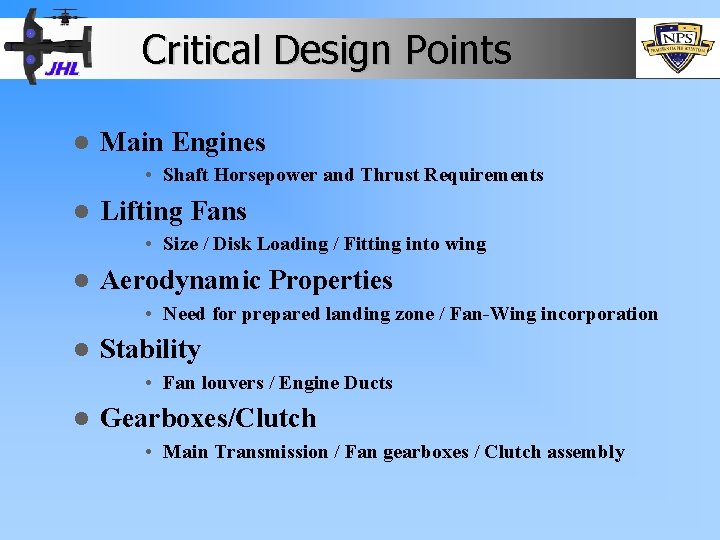
Critical Design Points l Main Engines • Shaft Horsepower and Thrust Requirements l Lifting Fans • Size / Disk Loading / Fitting into wing l Aerodynamic Properties • Need for prepared landing zone / Fan-Wing incorporation l Stability • Fan louvers / Engine Ducts l Gearboxes/Clutch • Main Transmission / Fan gearboxes / Clutch assembly
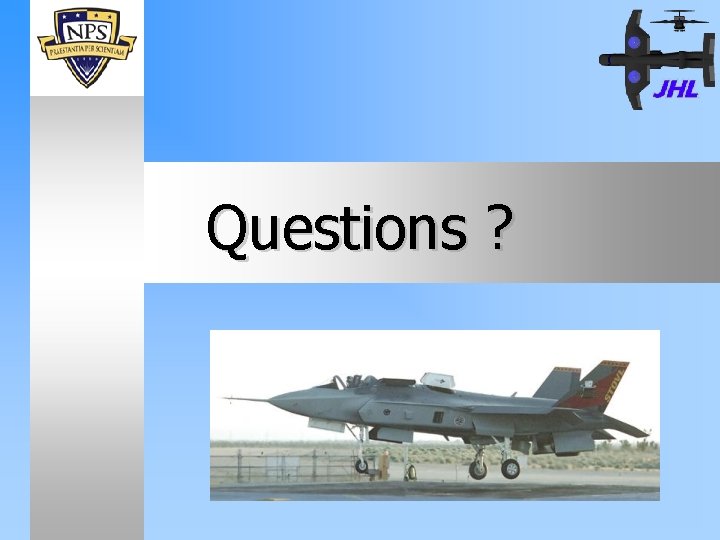
Questions ?
Deu nexia fan sensornexia fan sensor
Fan in cmos
Lift fan drive shaft
Shratey
Heavy lift & transport dequincy
Jsf f:convertnumber
Jsf basics
Server faces
Https://www.prf.gov.br/nada_consta/index.jsf
Jsf life cycle
Jsf bean
Netbeans jsf
Jsf redirect page
Jsf validation
Jsf cours
Que es jsf
Java server pages life cycle
Fastlane concat string
Break joint vs spool joint
Intertransverse ligament
Depression movement
What is permanent joint?
Joint venture accounting journal entries
Spool joint in lambs
Fan culture theory
Suxbat metodi
Nascar fan demographics
Unducted fan engine
Jianping fan
Identify the energy conversion in the illustration below
Fan curve
Hung fan sing
Fan beam
Oracle fan events
What is a stanza poem
Klinik fan 范氏诊所
Fan noli jeta dhe vepra
Lego fan media
Compound howe truss
Dr lin-fan wang
Tarix fanining maqsadi va vazifalari
Nutq o stirish o qish va savodga tayyorgarlik
Energy transformation of microwave oven
Are fan worms decomposers