Heat transfer simulation using COMSOL Multiphysics 4 1
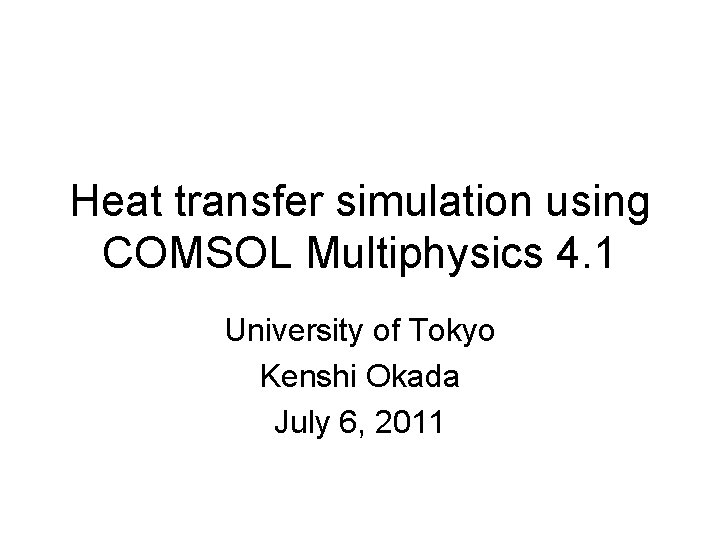
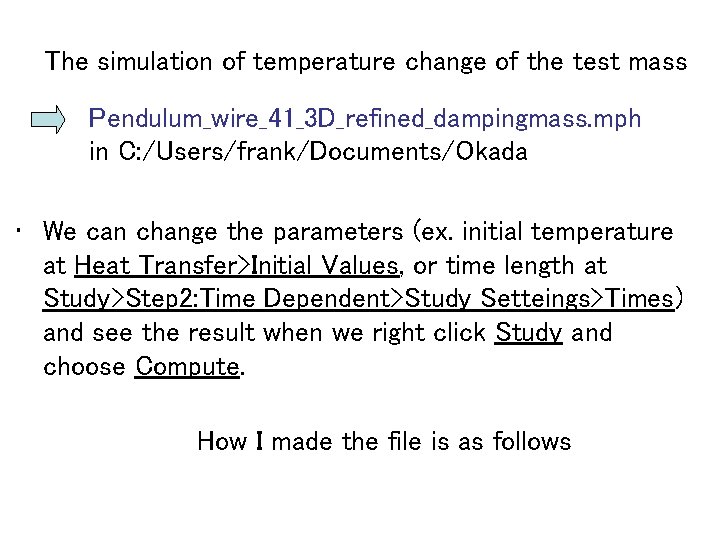
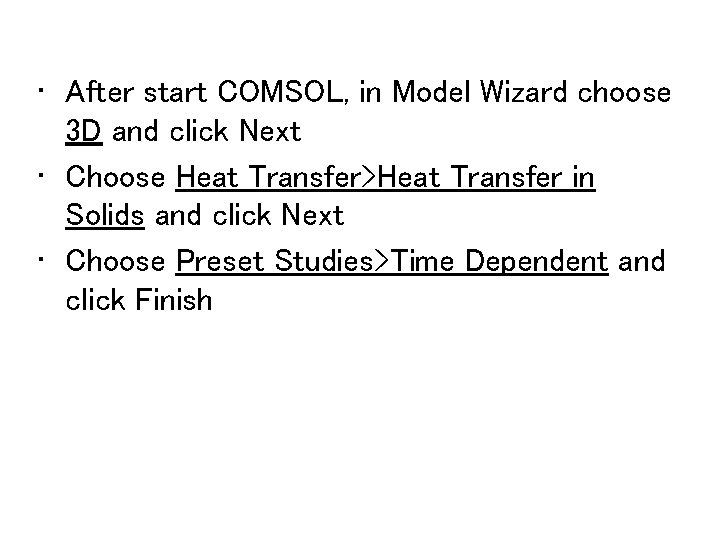
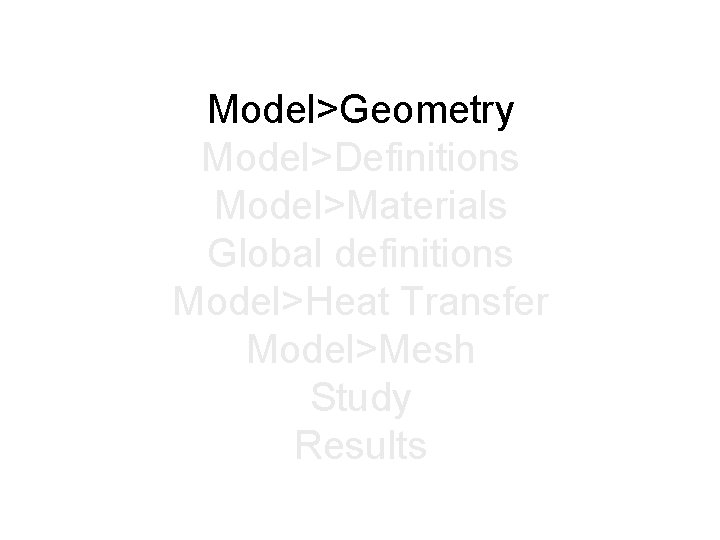
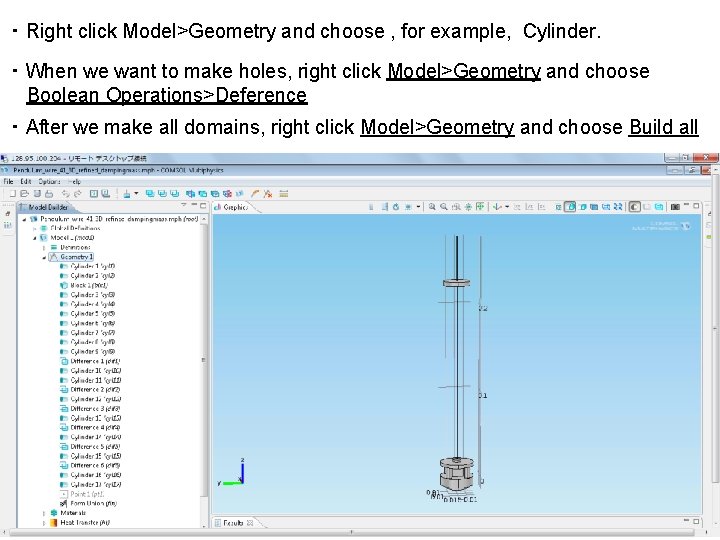
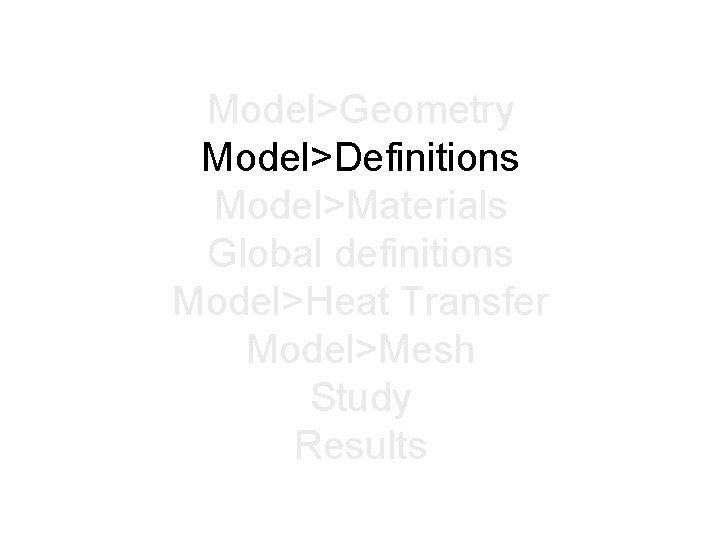
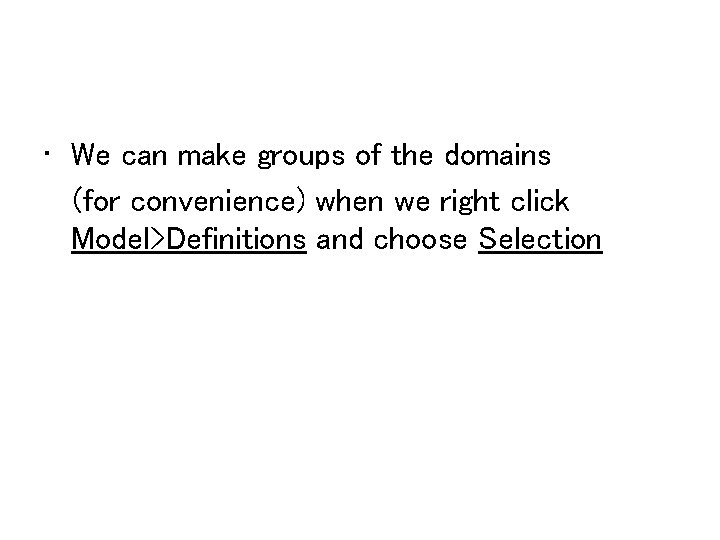
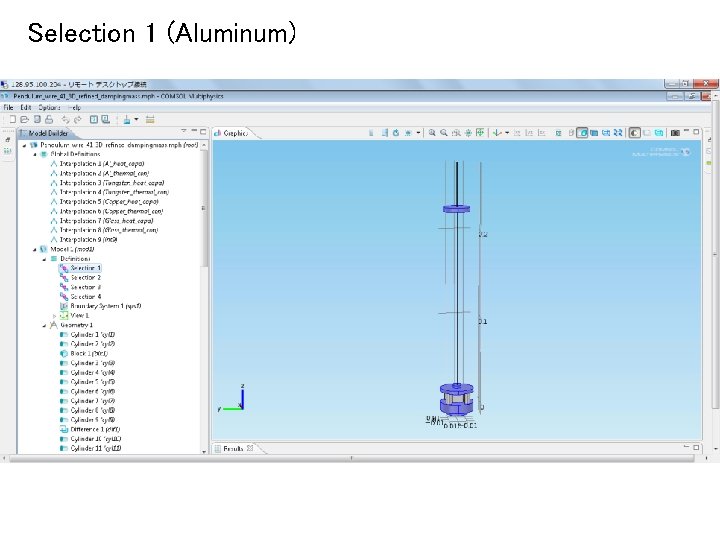

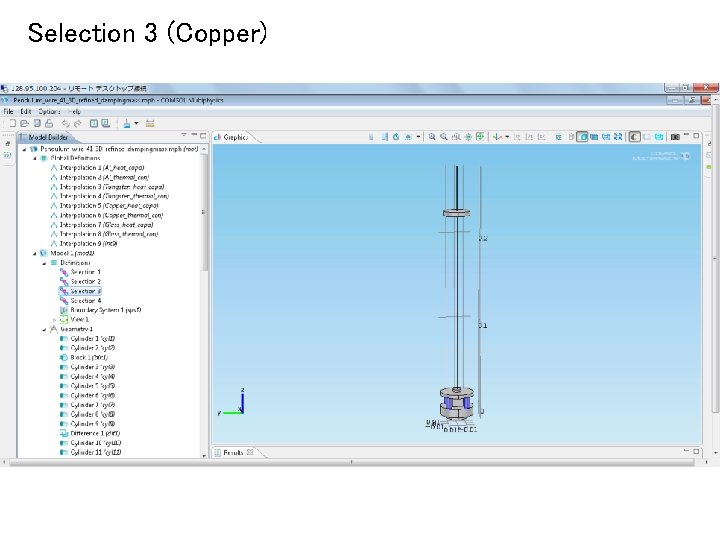
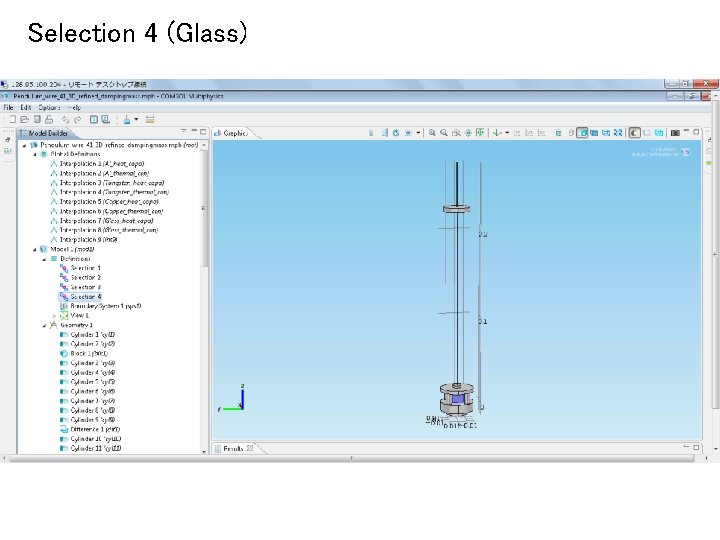
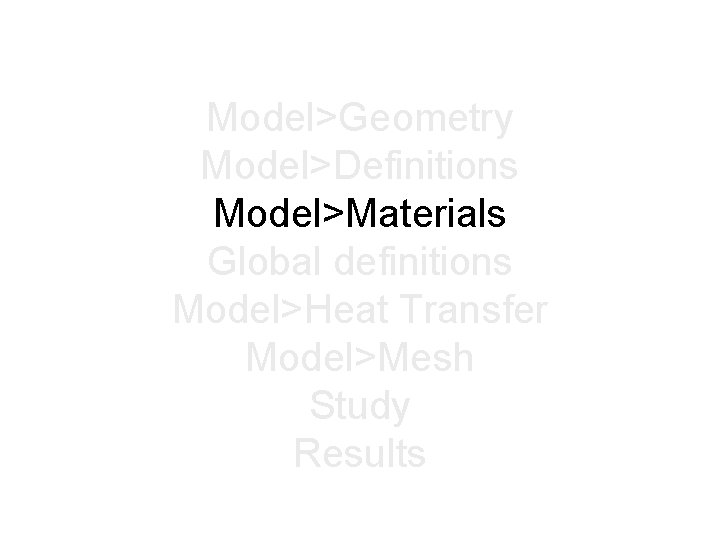
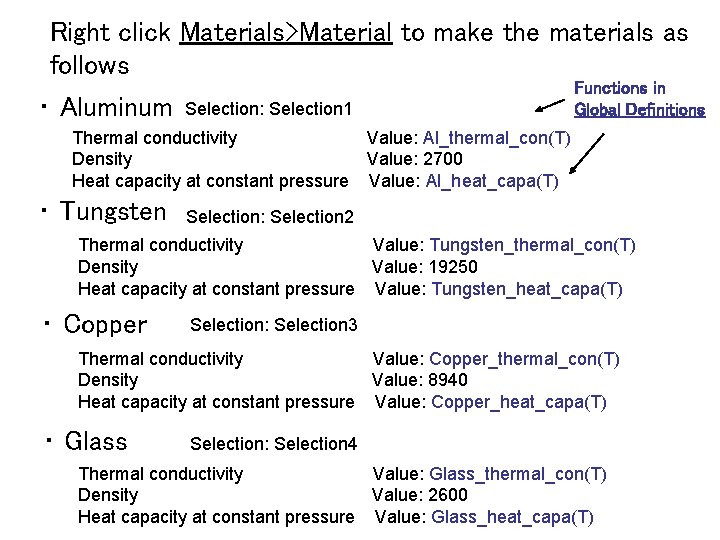
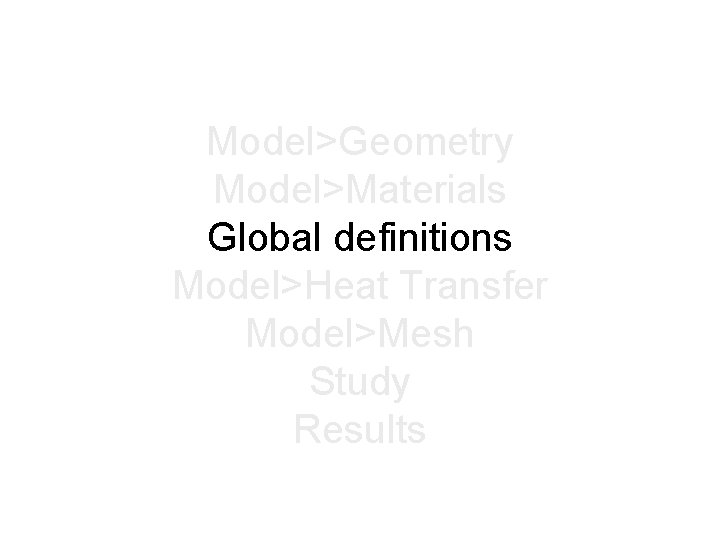
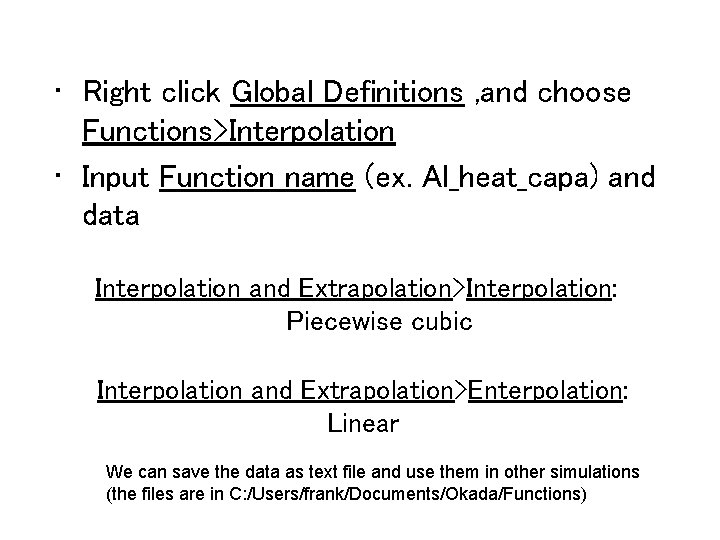
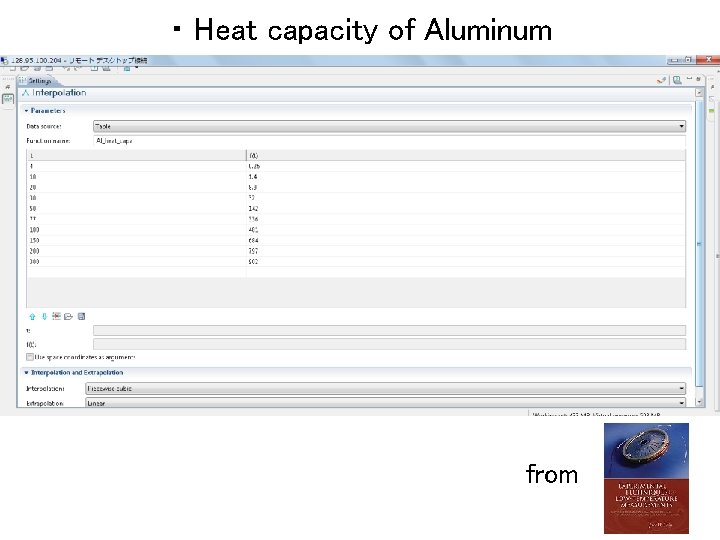
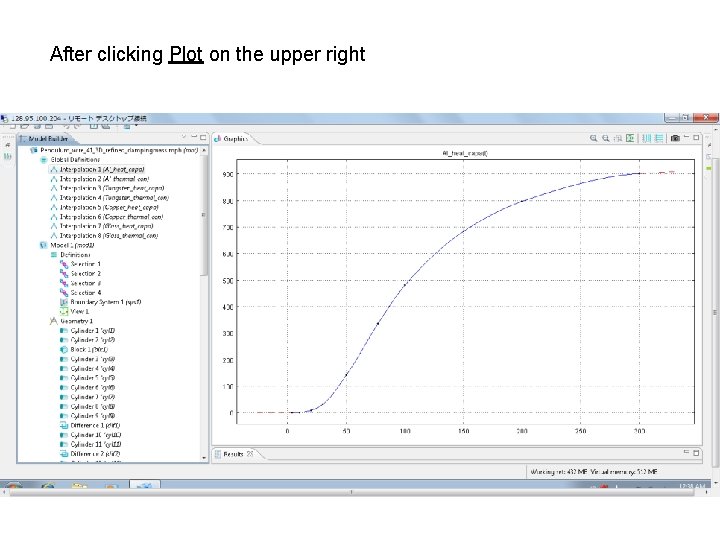
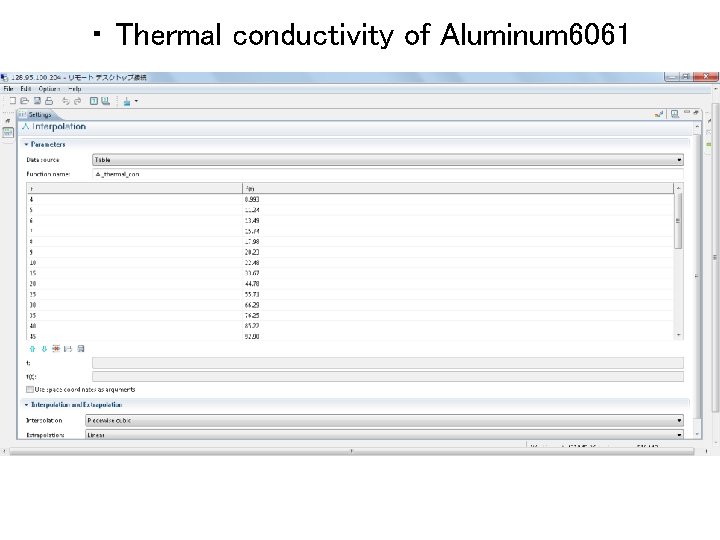
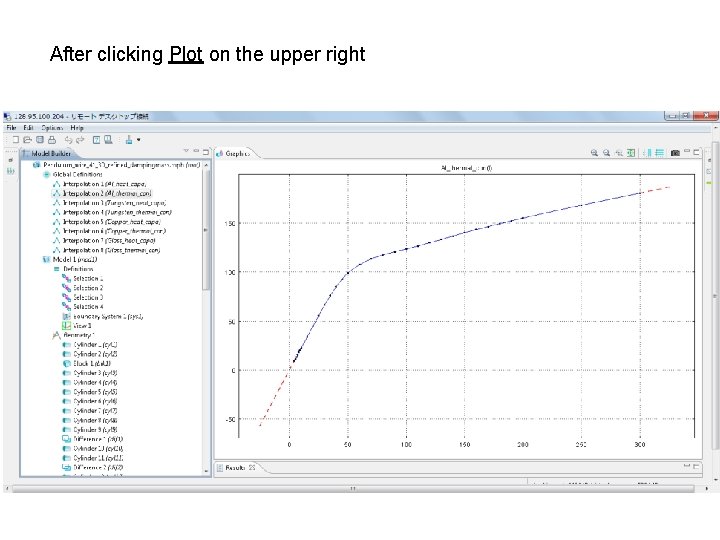
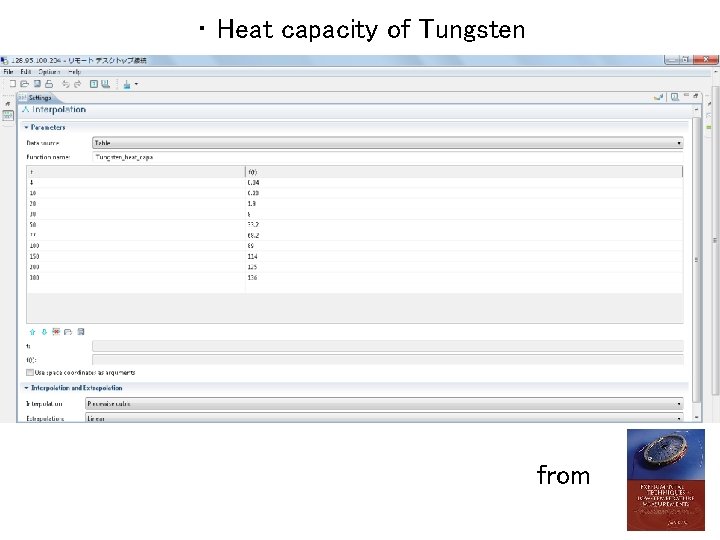
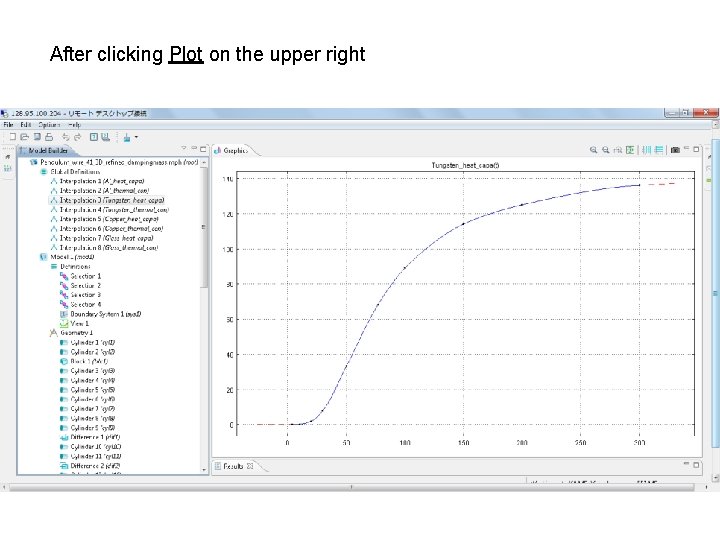
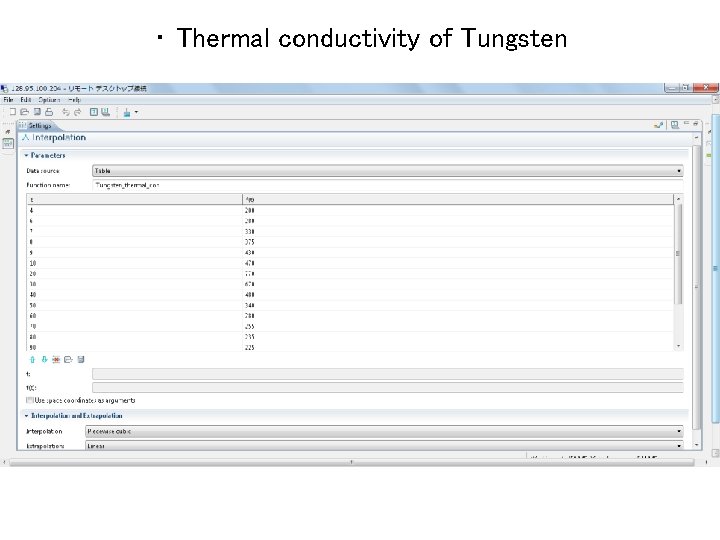
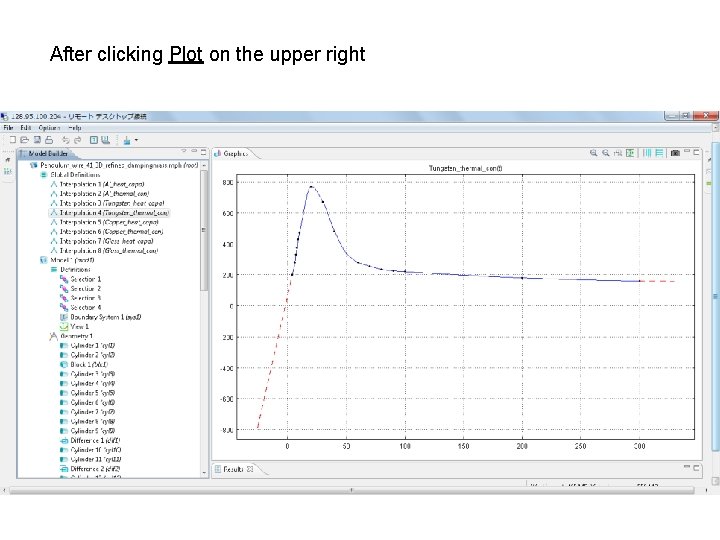
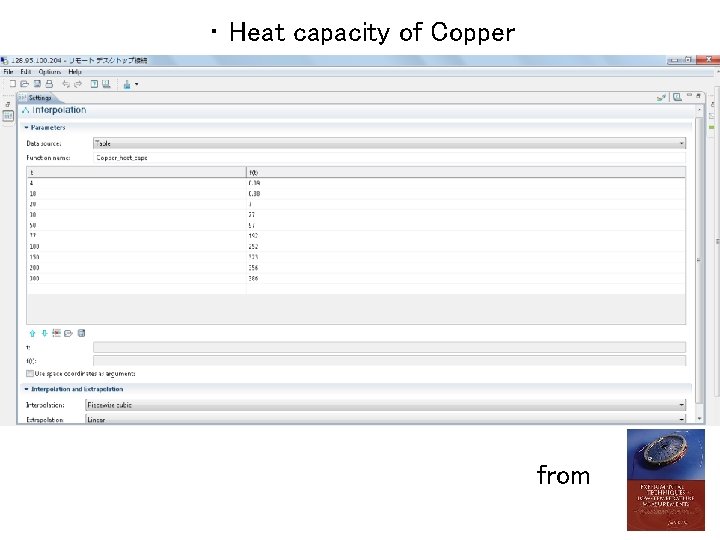
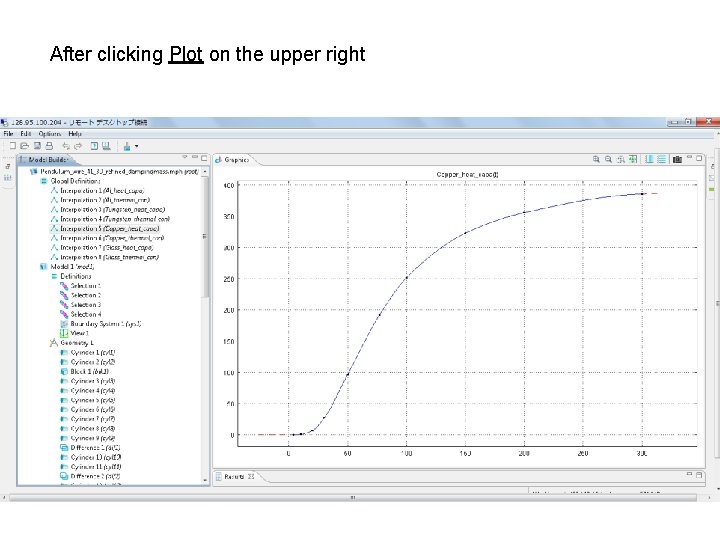
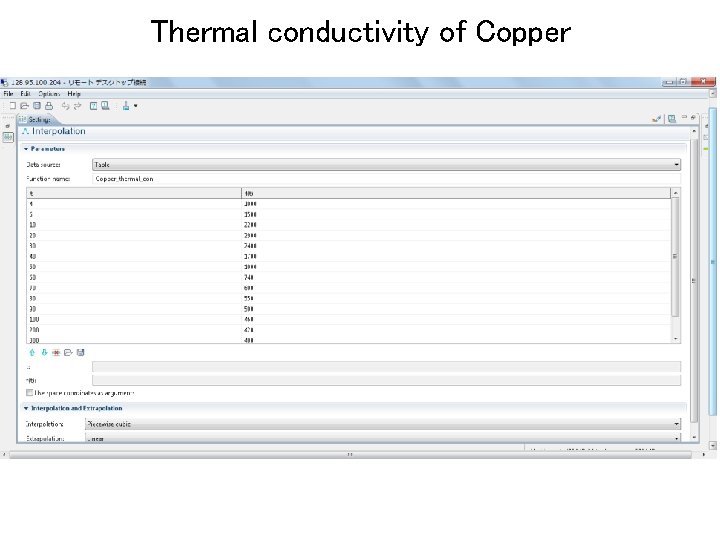
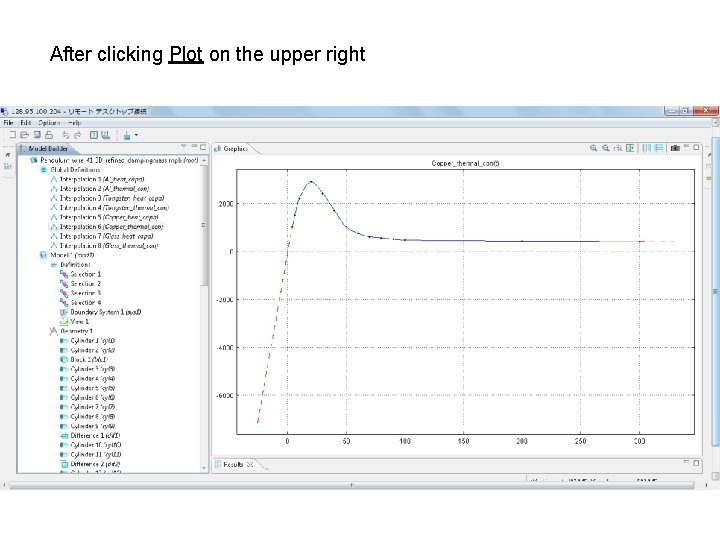
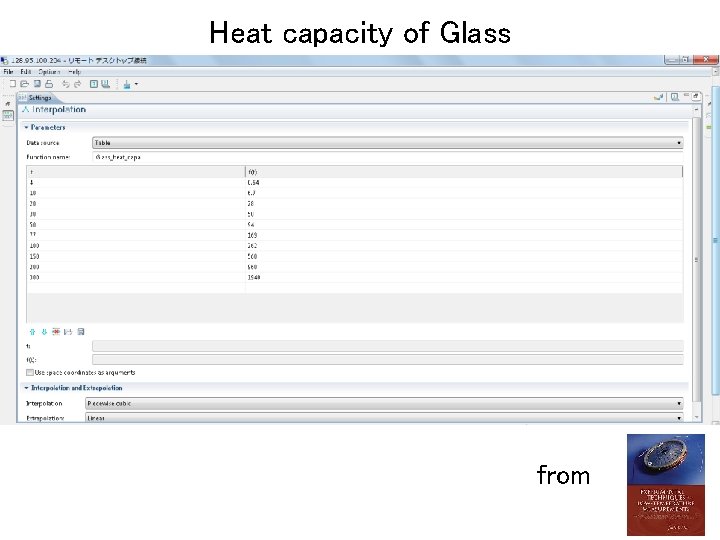
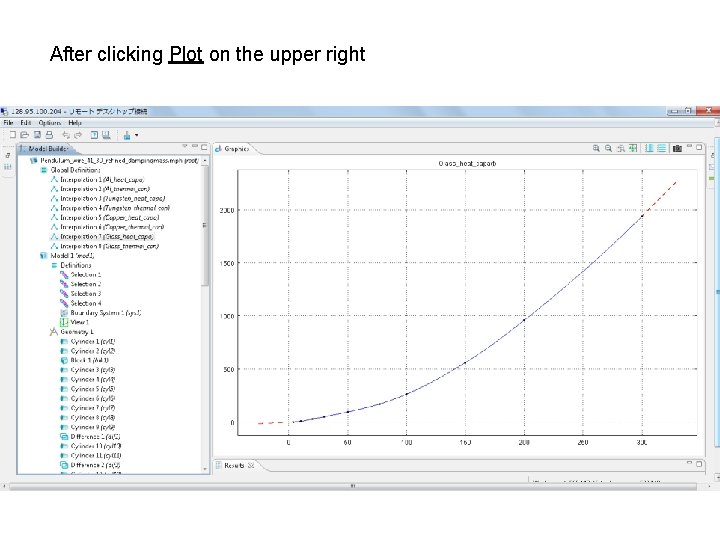
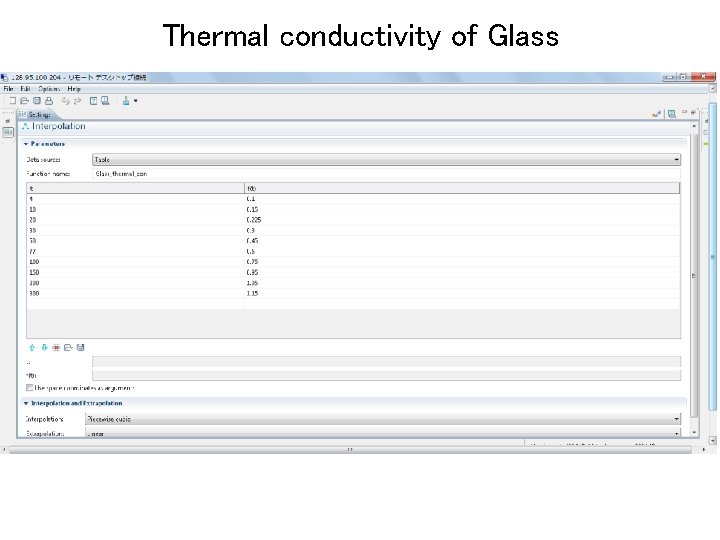

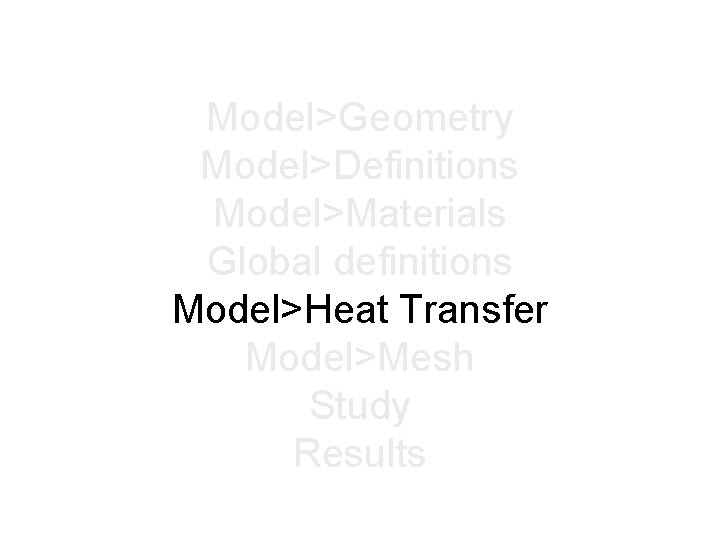
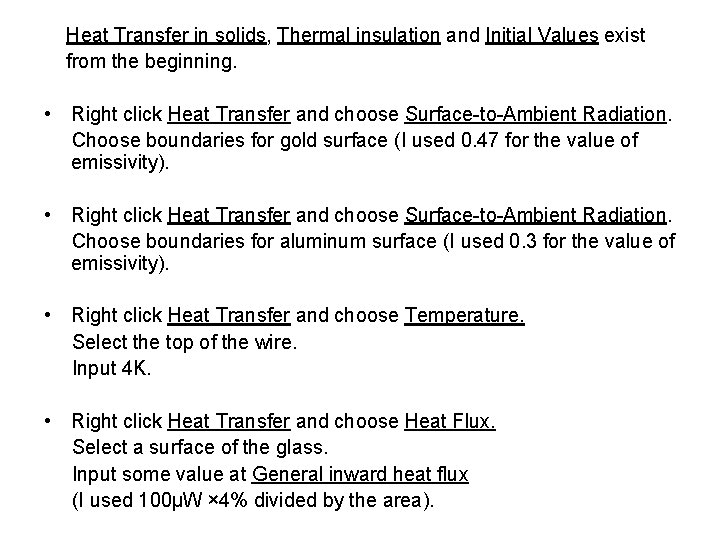
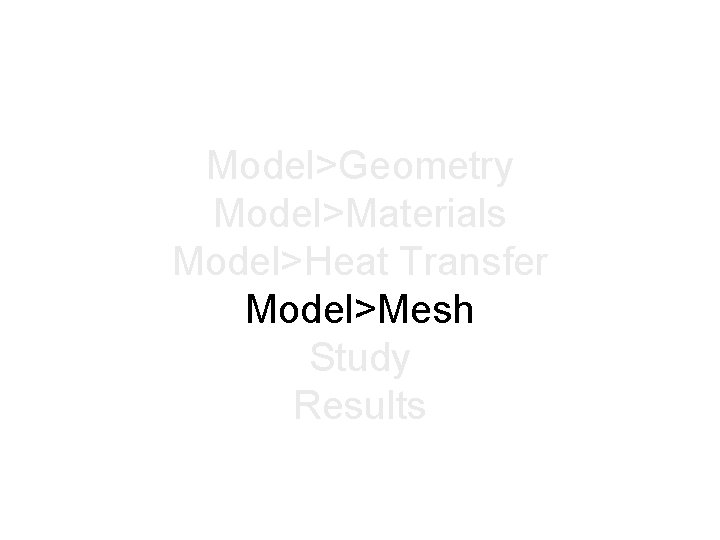
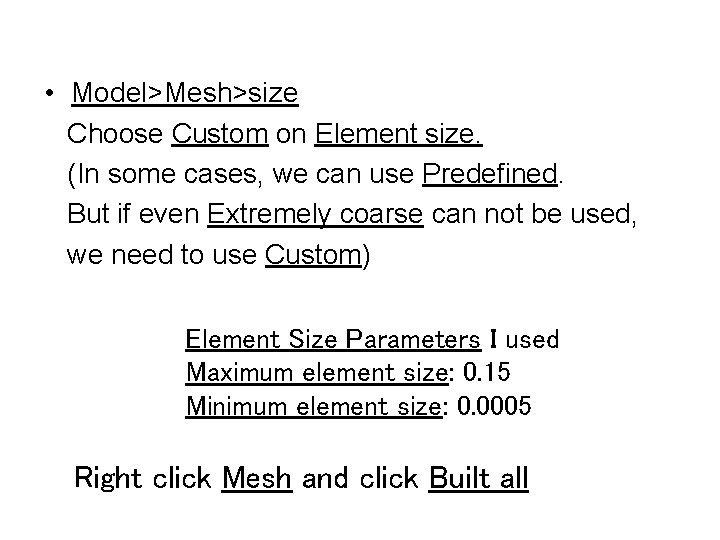
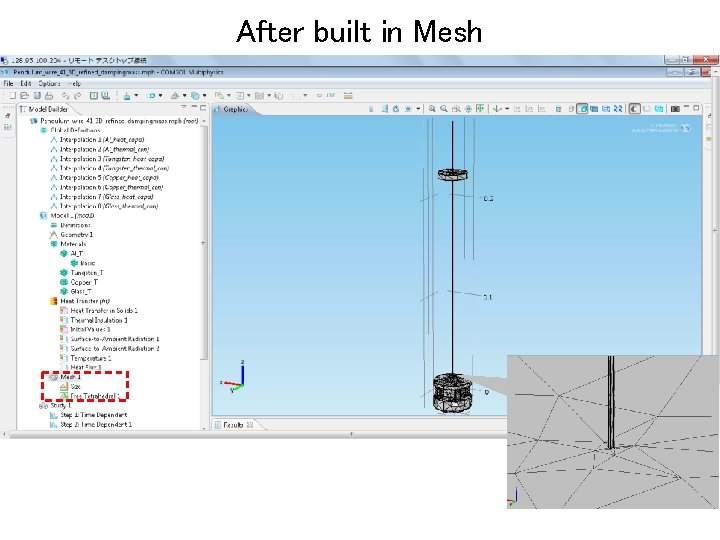
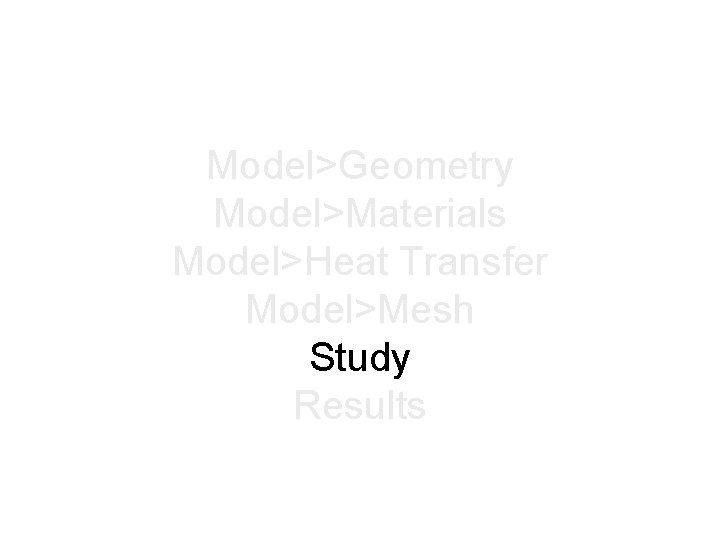
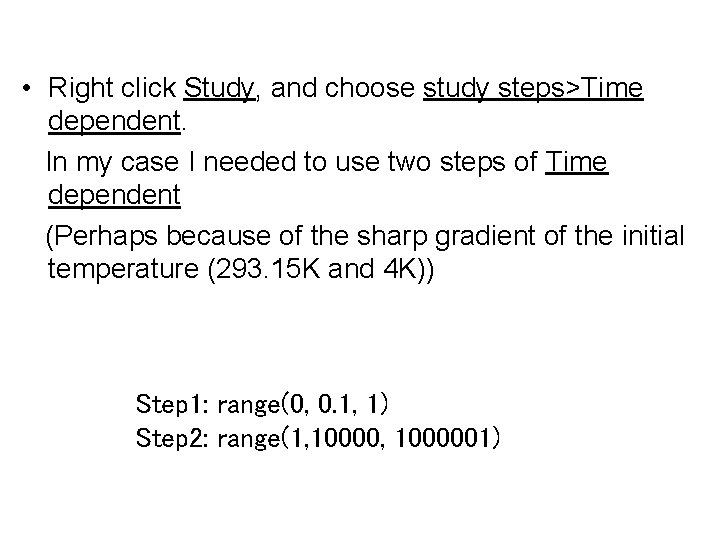
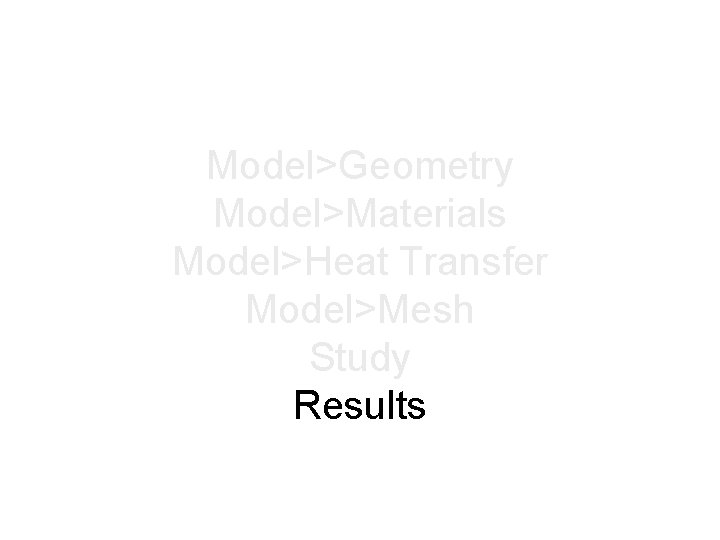
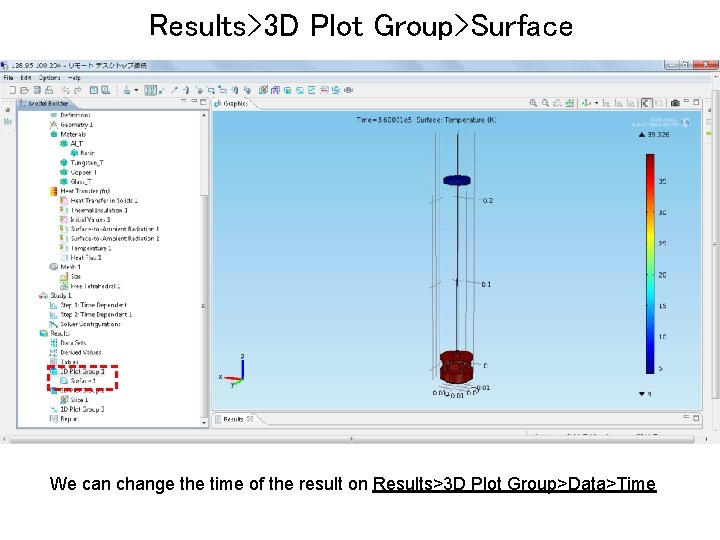
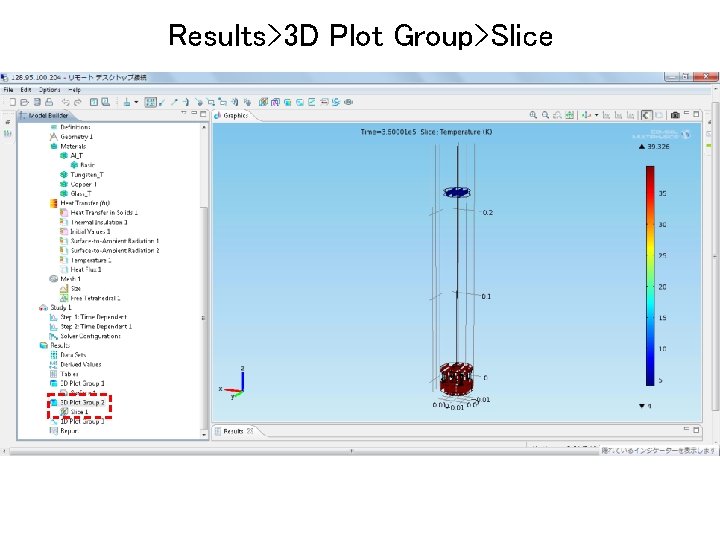
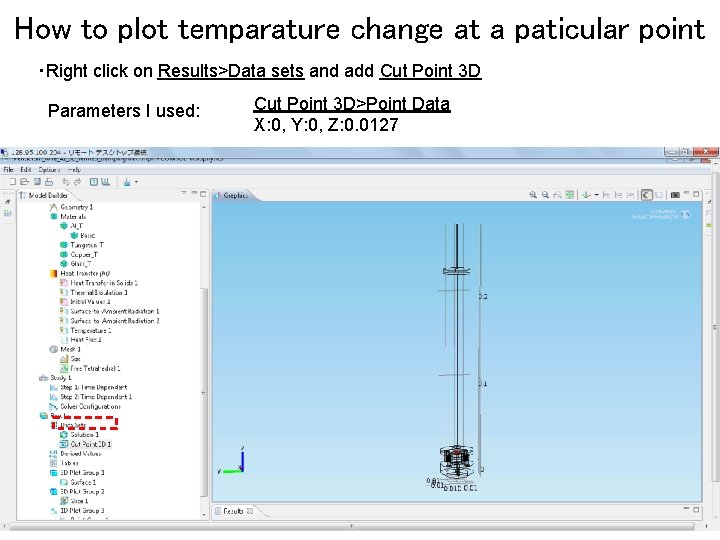

- Slides: 43
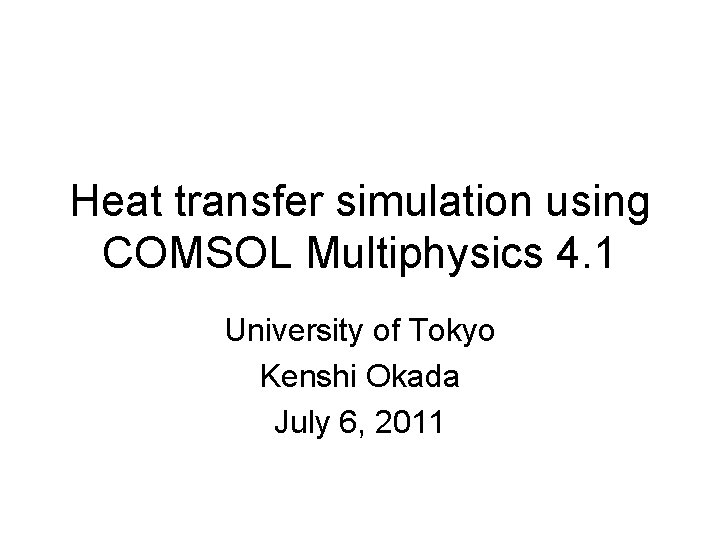
Heat transfer simulation using COMSOL Multiphysics 4. 1 University of Tokyo Kenshi Okada July 6, 2011
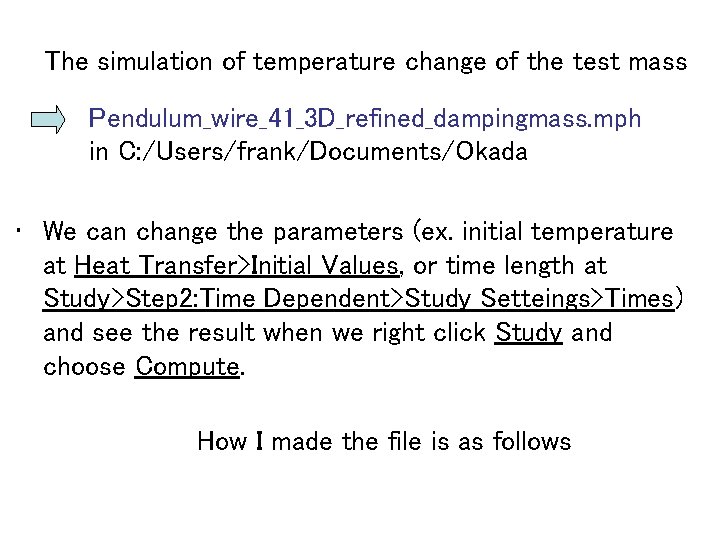
The simulation of temperature change of the test mass Pendulum_wire_41_3 D_refined_dampingmass. mph in C: /Users/frank/Documents/Okada • We can change the parameters (ex. initial temperature at Heat Transfer>Initial Values, or time length at Study>Step 2: Time Dependent>Study Setteings>Times) and see the result when we right click Study and choose Compute. How I made the file is as follows
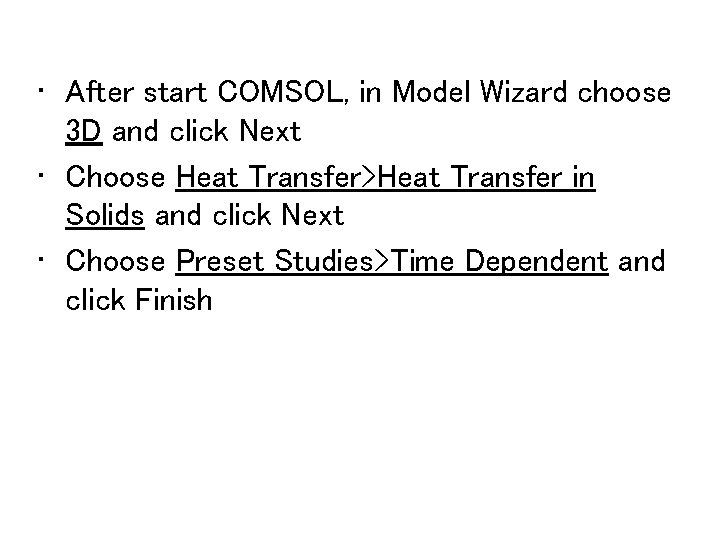
• After start COMSOL, in Model Wizard choose 3 D and click Next • Choose Heat Transfer>Heat Transfer in Solids and click Next • Choose Preset Studies>Time Dependent and click Finish
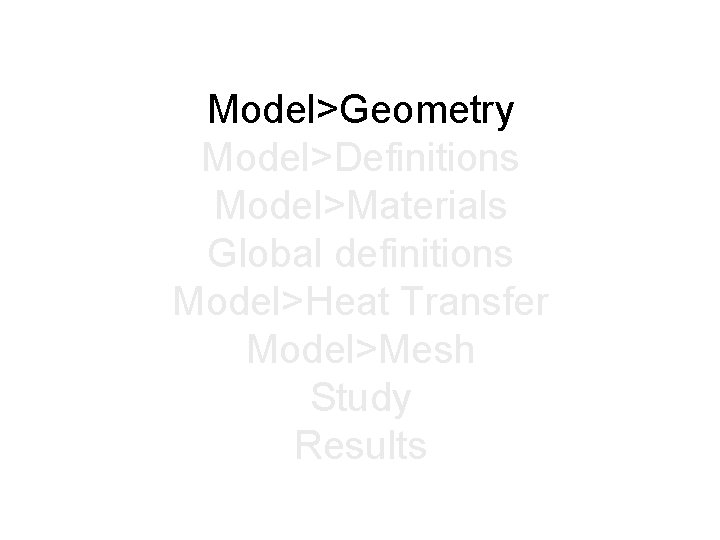
Model>Geometry Model>Definitions Model>Materials Global definitions Model>Heat Transfer Model>Mesh Study Results
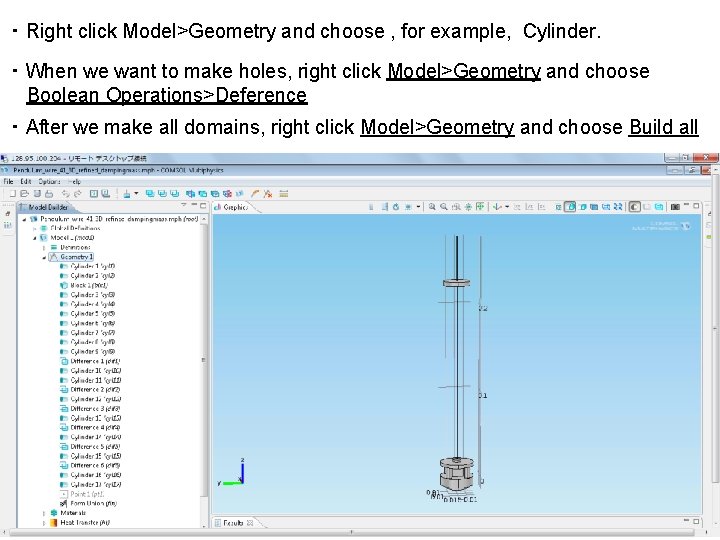
・ Right click Model>Geometry and choose , for example, Cylinder. ・ When we want to make holes, right click Model>Geometry and choose Boolean Operations>Deference ・ After we make all domains, right click Model>Geometry and choose Build all
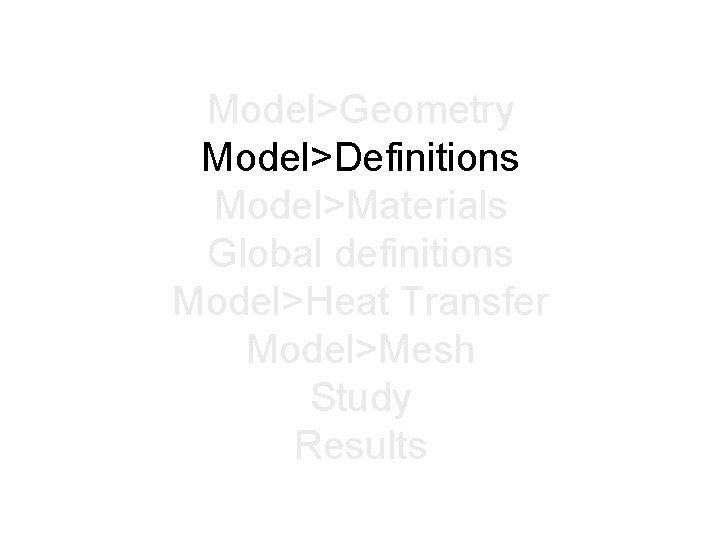
Model>Geometry Model>Definitions Model>Materials Global definitions Model>Heat Transfer Model>Mesh Study Results
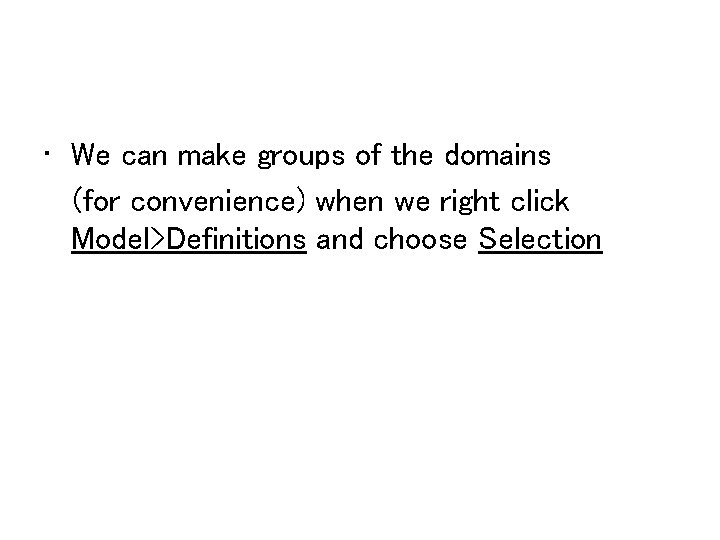
• We can make groups of the domains (for convenience) when we right click Model>Definitions and choose Selection
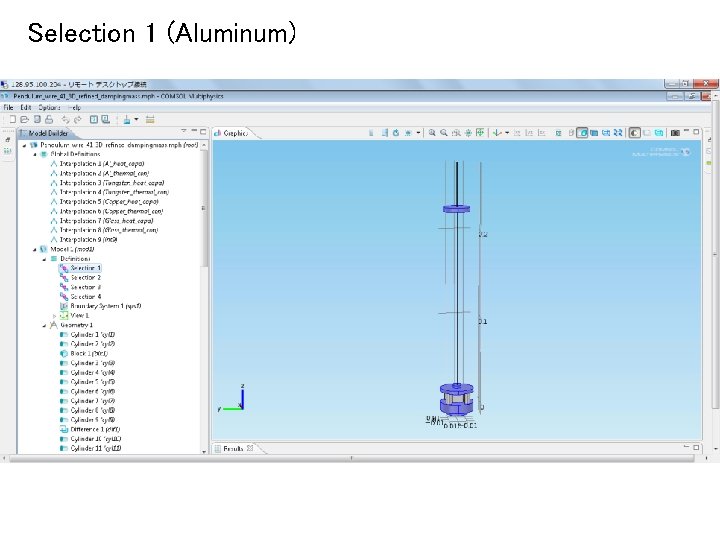
Selection 1 (Aluminum)

Selection 2 (Tungsten)
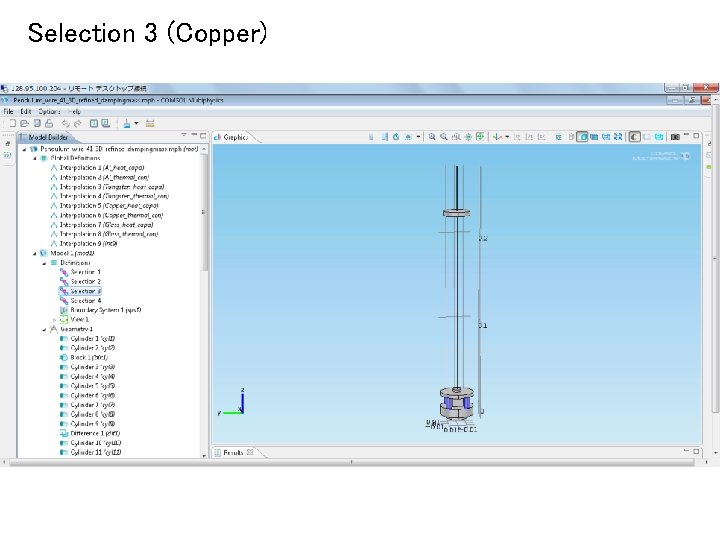
Selection 3 (Copper)
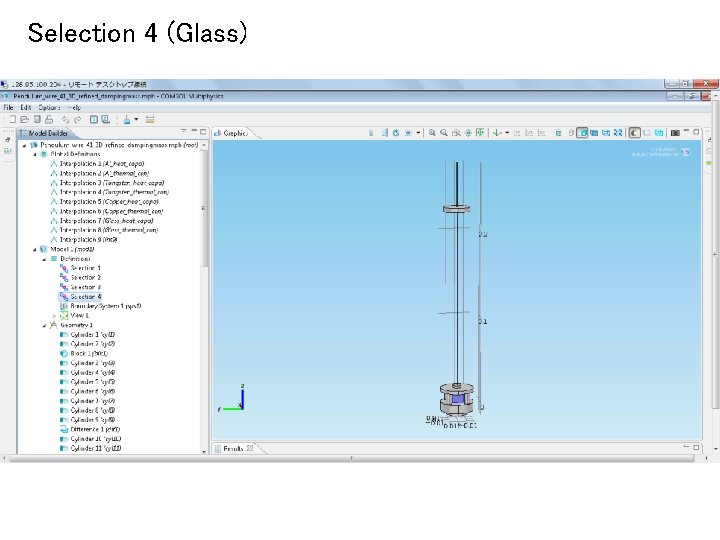
Selection 4 (Glass)
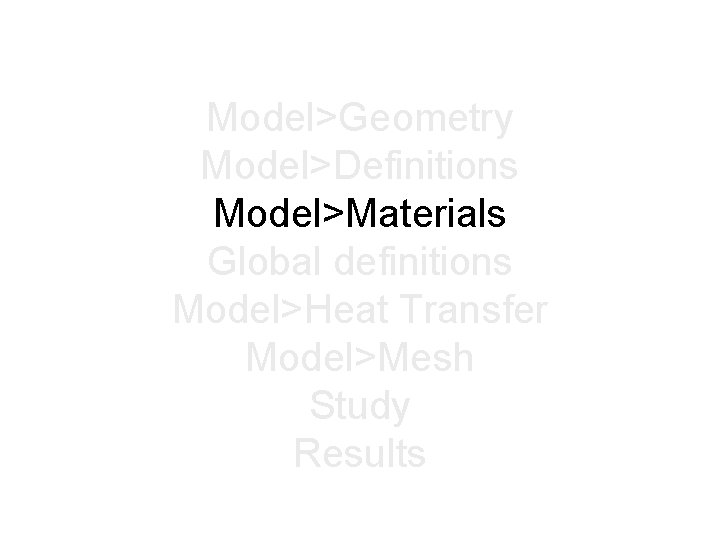
Model>Geometry Model>Definitions Model>Materials Global definitions Model>Heat Transfer Model>Mesh Study Results
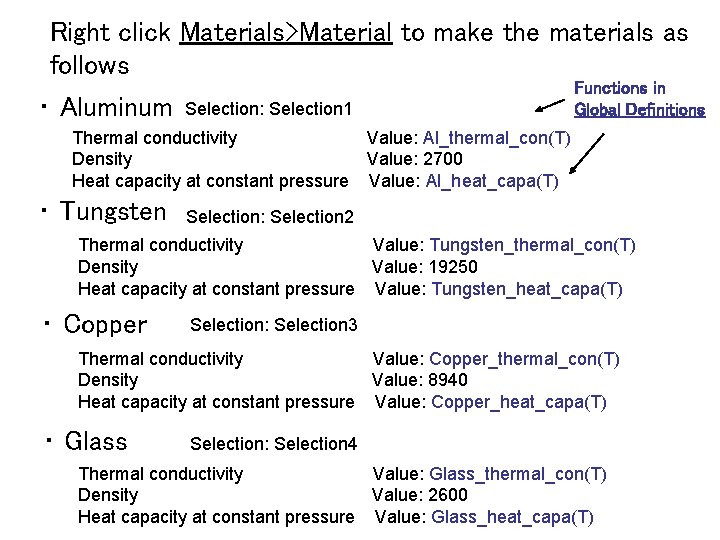
Right click Materials>Material to make the materials as follows Functions in Global Definitions ・ Aluminum Selection: Selection 1 Thermal conductivity Value: Al_thermal_con(T) Density Value: 2700 Heat capacity at constant pressure Value: Al_heat_capa(T) ・ Tungsten Selection: Selection 2 Thermal conductivity Value: Tungsten_thermal_con(T) Density Value: 19250 Heat capacity at constant pressure Value: Tungsten_heat_capa(T) ・ Copper Selection: Selection 3 Thermal conductivity Value: Copper_thermal_con(T) Density Value: 8940 Heat capacity at constant pressure Value: Copper_heat_capa(T) ・ Glass Selection: Selection 4 Thermal conductivity Value: Glass_thermal_con(T) Density Value: 2600 Heat capacity at constant pressure Value: Glass_heat_capa(T)
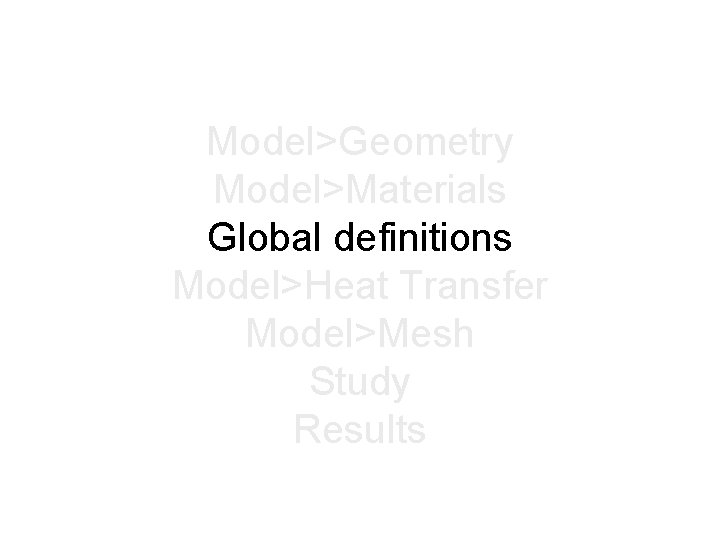
Model>Geometry Model>Materials Global definitions Model>Heat Transfer Model>Mesh Study Results
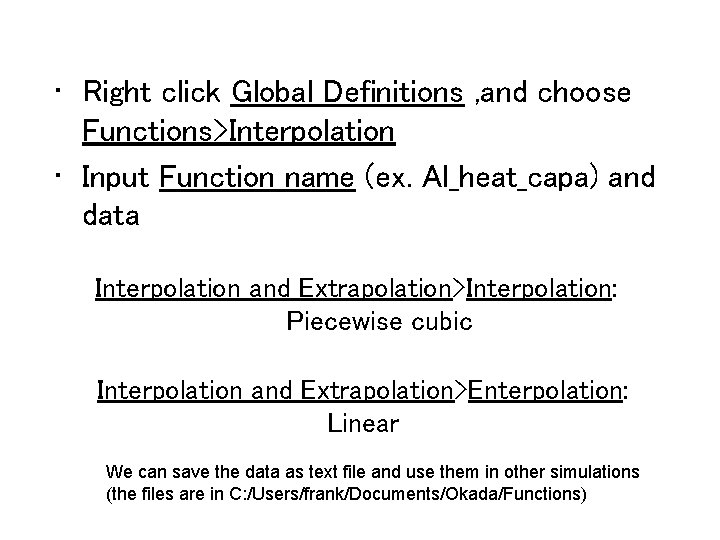
• Right click Global Definitions , and choose Functions>Interpolation • Input Function name (ex. Al_heat_capa) and data Interpolation and Extrapolation>Interpolation: Piecewise cubic Interpolation and Extrapolation>Enterpolation: Linear We can save the data as text file and use them in other simulations (the files are in C: /Users/frank/Documents/Okada/Functions)
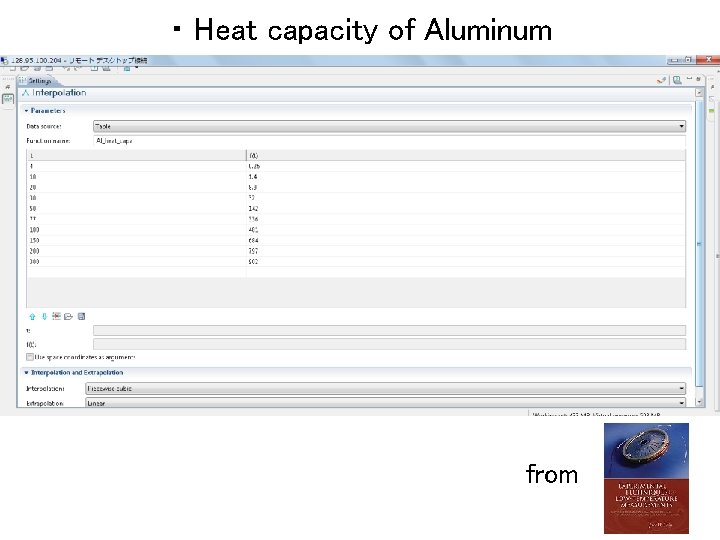
・ Heat capacity of Aluminum from
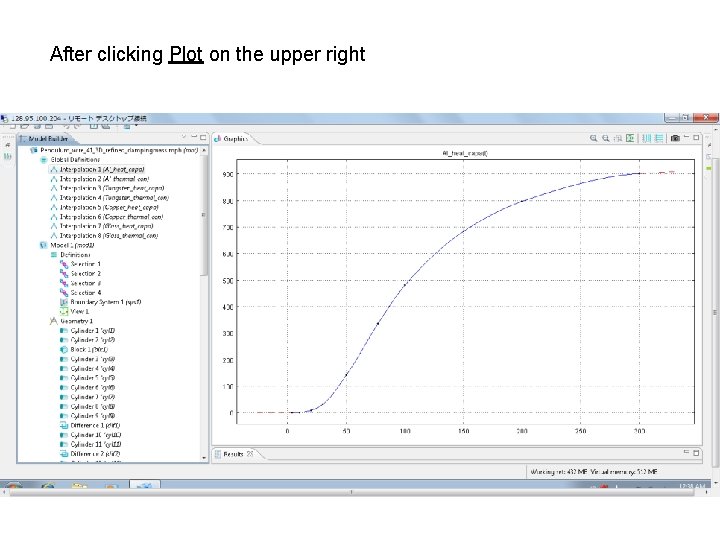
After clicking Plot on the upper right
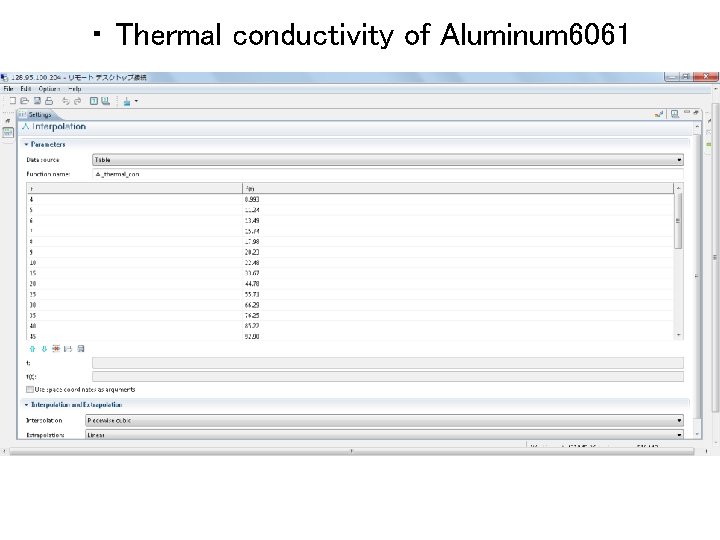
・ Thermal conductivity of Aluminum 6061
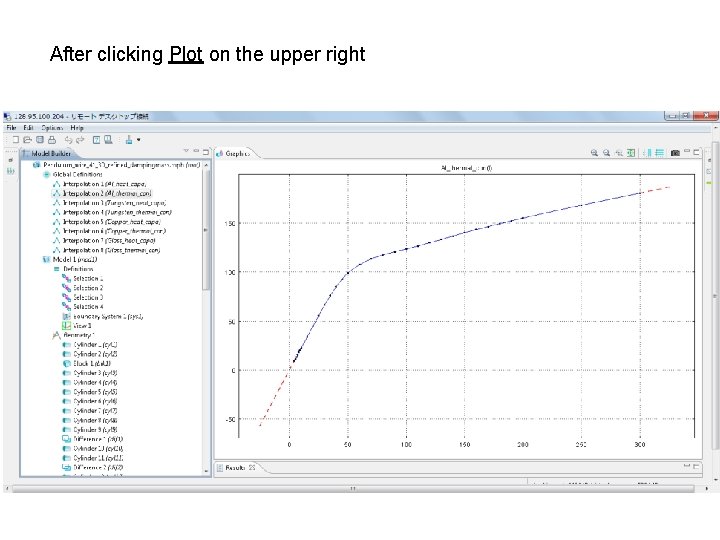
After clicking Plot on the upper right
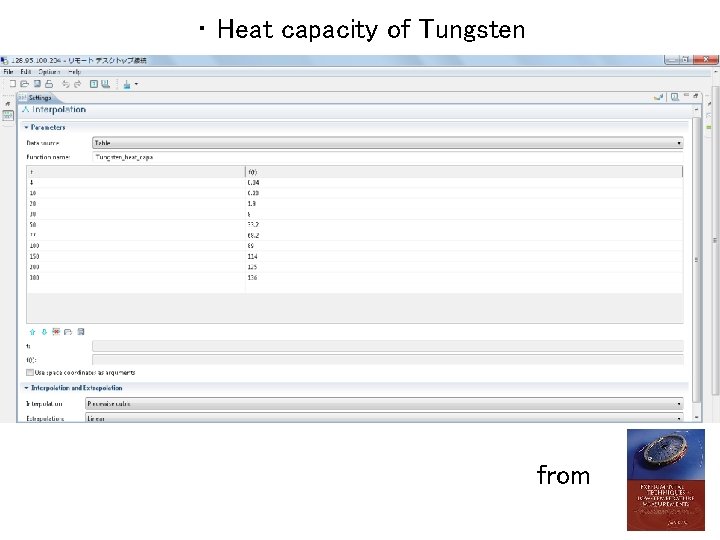
・ Heat capacity of Tungsten from
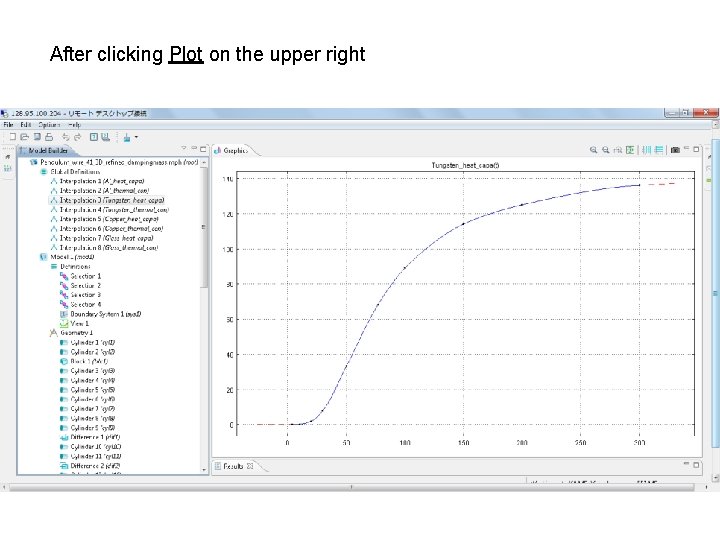
After clicking Plot on the upper right
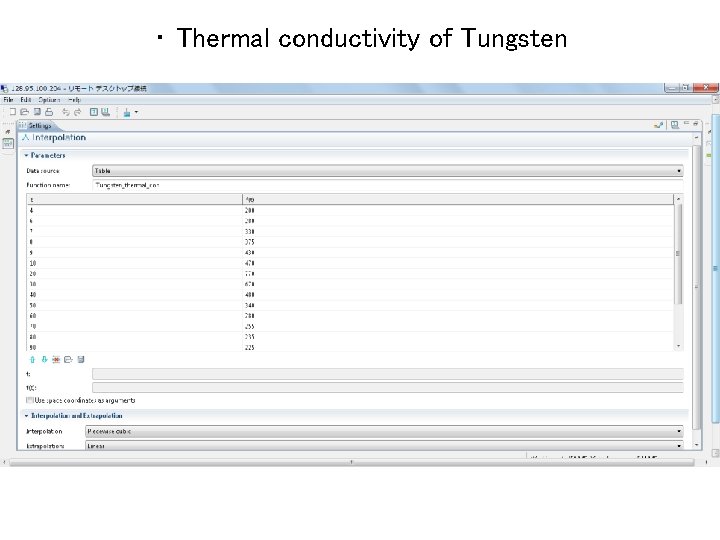
・ Thermal conductivity of Tungsten
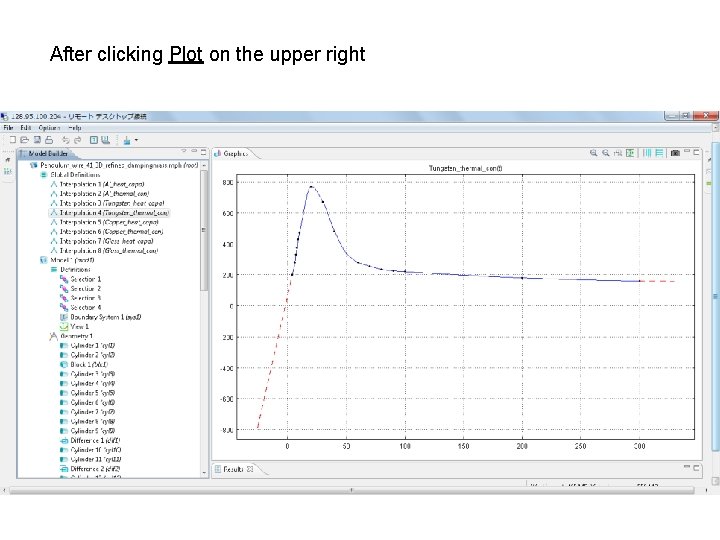
After clicking Plot on the upper right
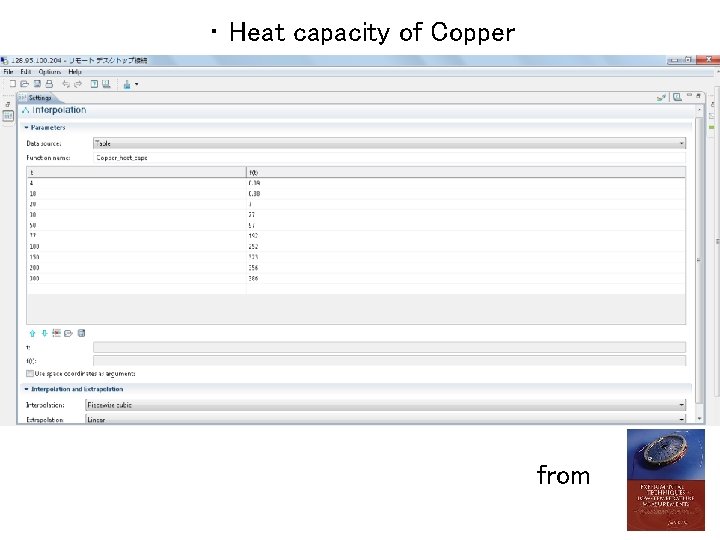
・ Heat capacity of Copper from
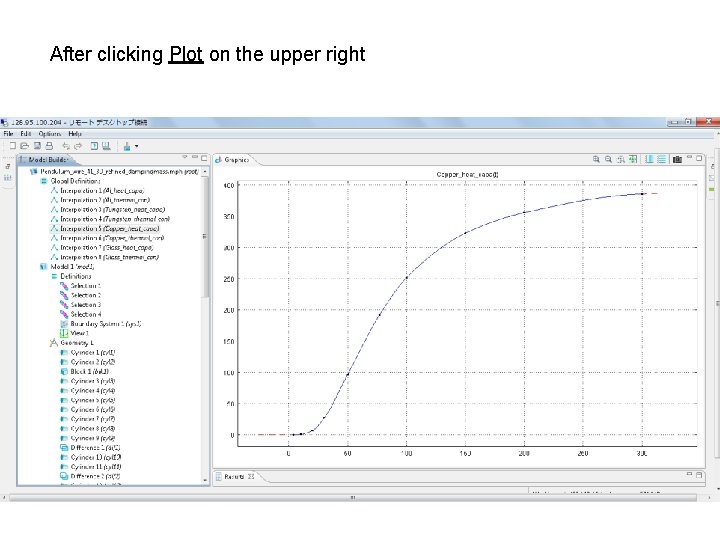
After clicking Plot on the upper right
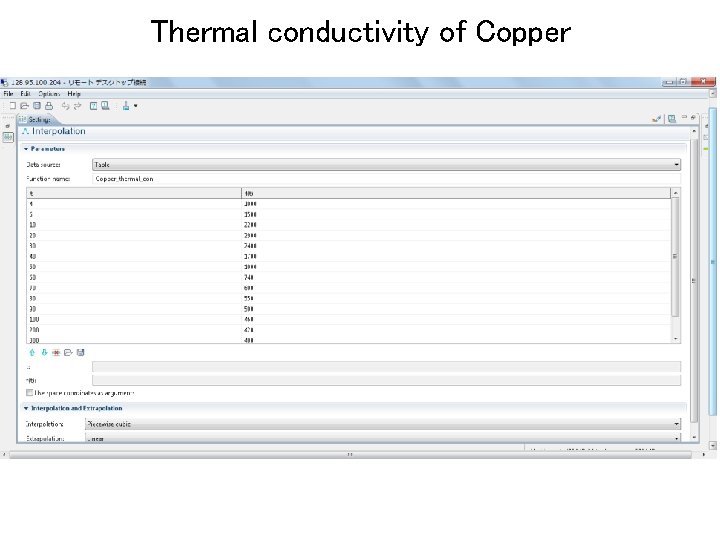
Thermal conductivity of Copper
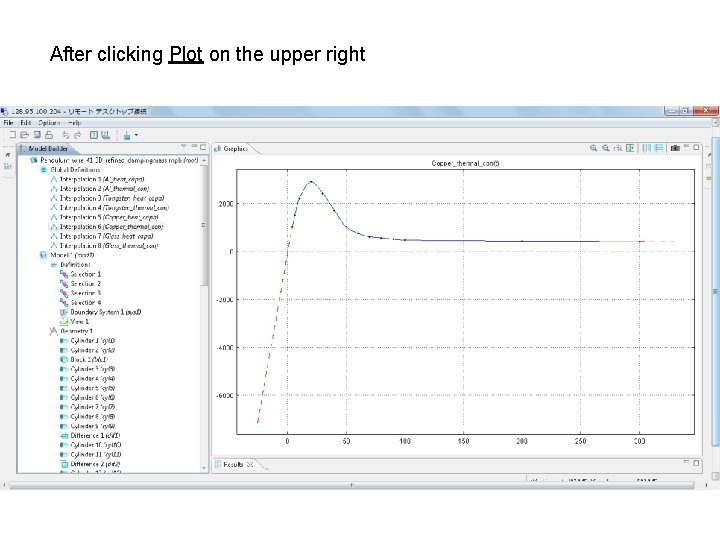
After clicking Plot on the upper right
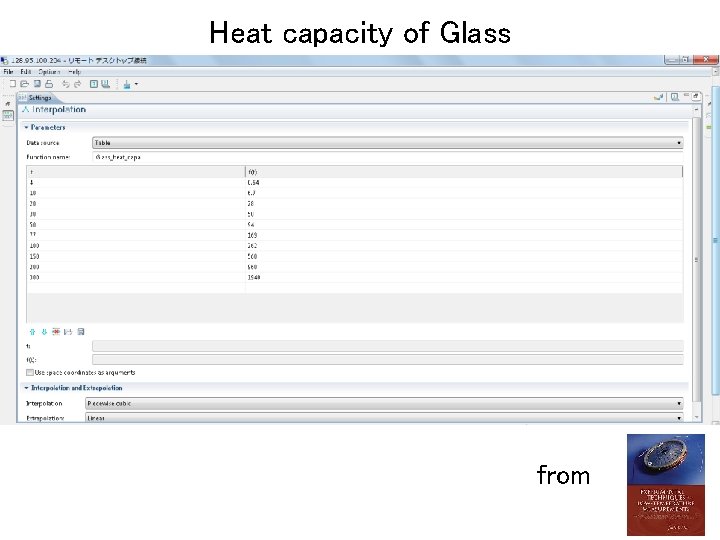
Heat capacity of Glass from
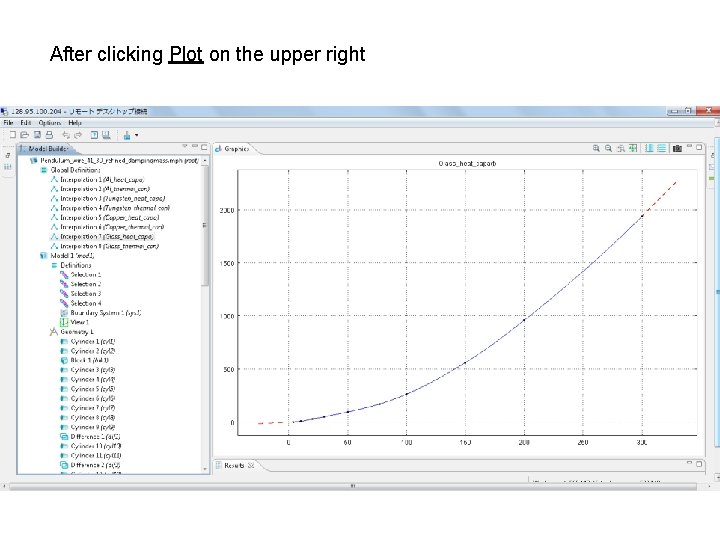
After clicking Plot on the upper right
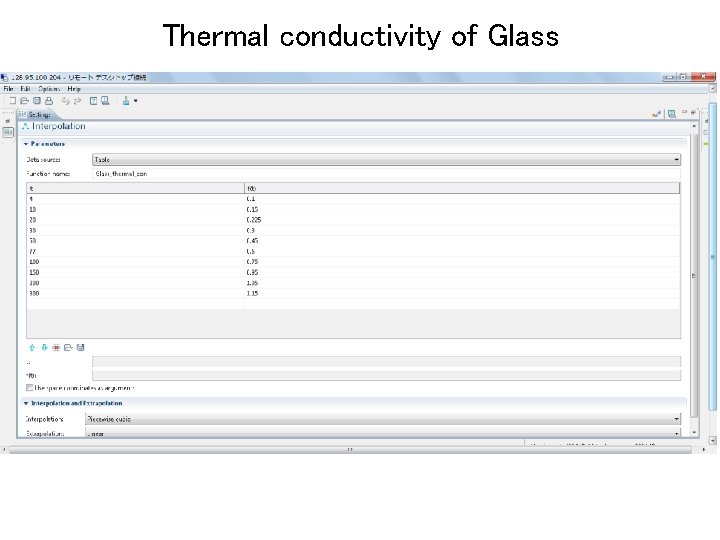
Thermal conductivity of Glass

After clicking Plot on the upper right
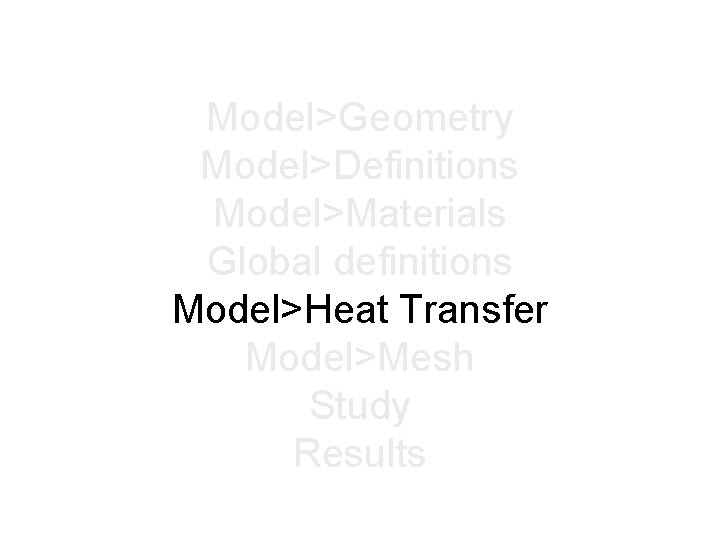
Model>Geometry Model>Definitions Model>Materials Global definitions Model>Heat Transfer Model>Mesh Study Results
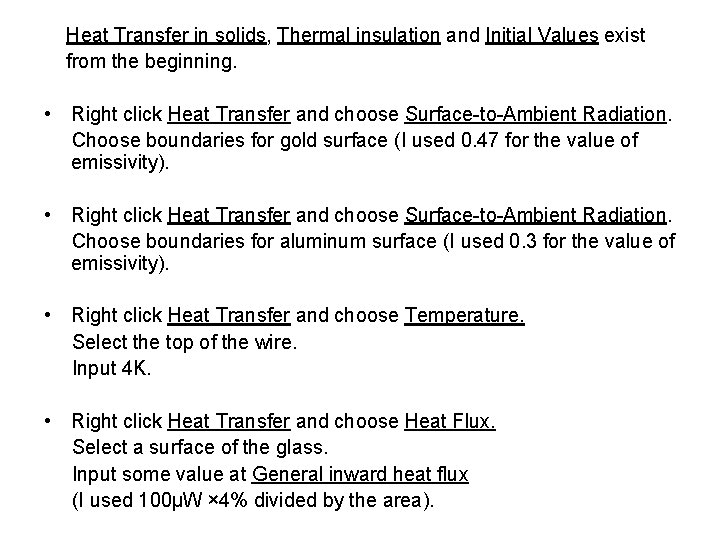
Heat Transfer in solids, Thermal insulation and Initial Values exist from the beginning. • Right click Heat Transfer and choose Surface-to-Ambient Radiation. Choose boundaries for gold surface (I used 0. 47 for the value of emissivity). • Right click Heat Transfer and choose Surface-to-Ambient Radiation. Choose boundaries for aluminum surface (I used 0. 3 for the value of emissivity). • Right click Heat Transfer and choose Temperature. Select the top of the wire. Input 4 K. • Right click Heat Transfer and choose Heat Flux. Select a surface of the glass. Input some value at General inward heat flux (I used 100μW × 4% divided by the area).
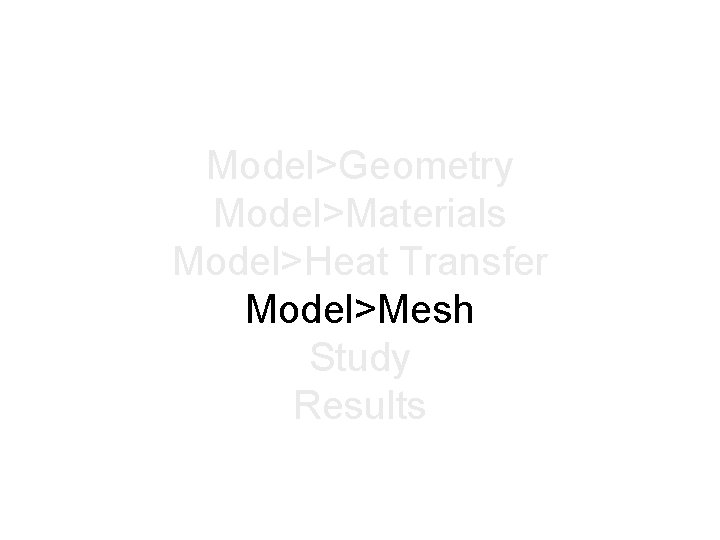
Model>Geometry Model>Materials Model>Heat Transfer Model>Mesh Study Results
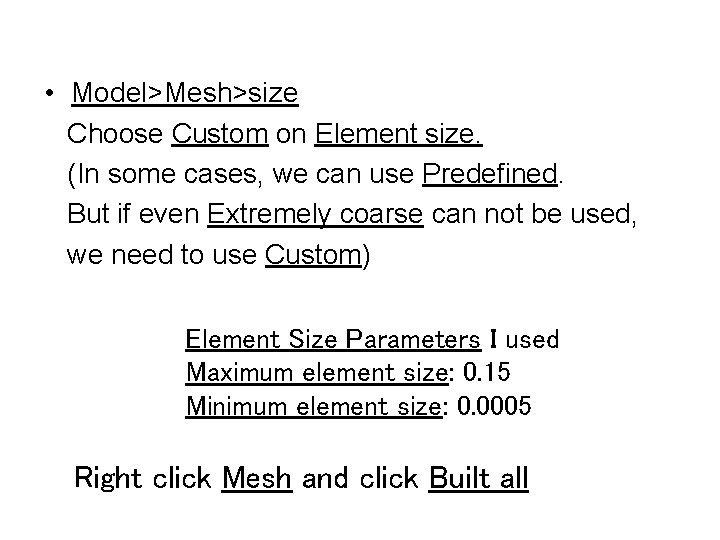
• Model>Mesh>size Choose Custom on Element size. (In some cases, we can use Predefined. But if even Extremely coarse can not be used, we need to use Custom) Element Size Parameters I used Maximum element size: 0. 15 Minimum element size: 0. 0005 Right click Mesh and click Built all
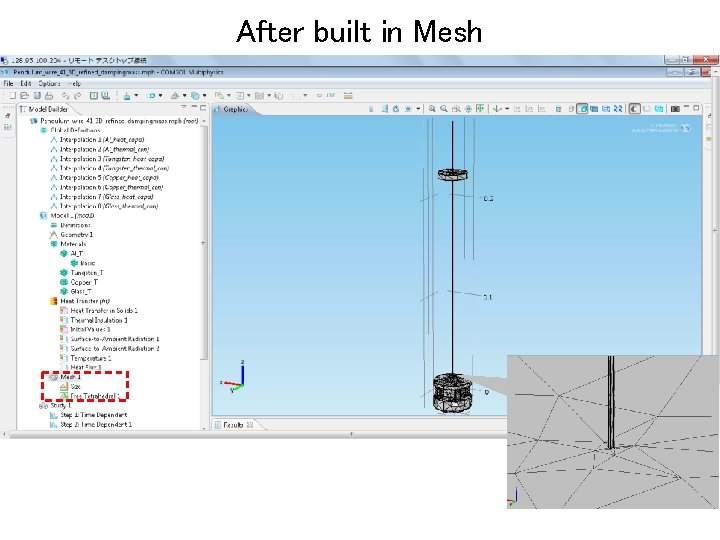
After built in Mesh
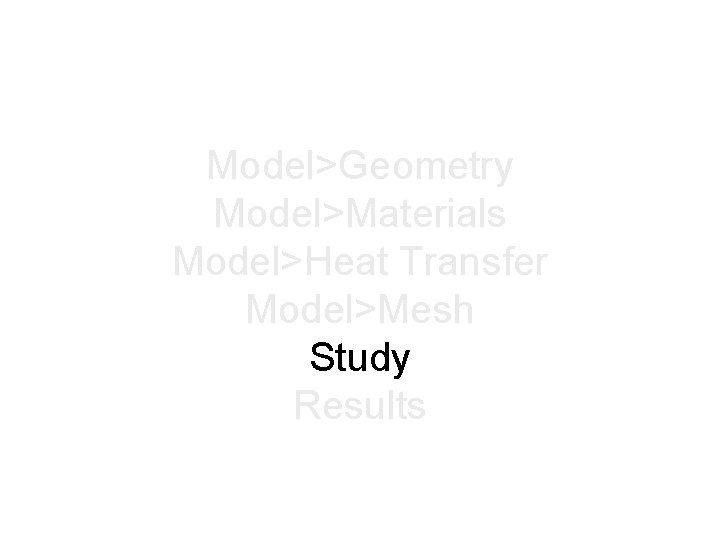
Model>Geometry Model>Materials Model>Heat Transfer Model>Mesh Study Results
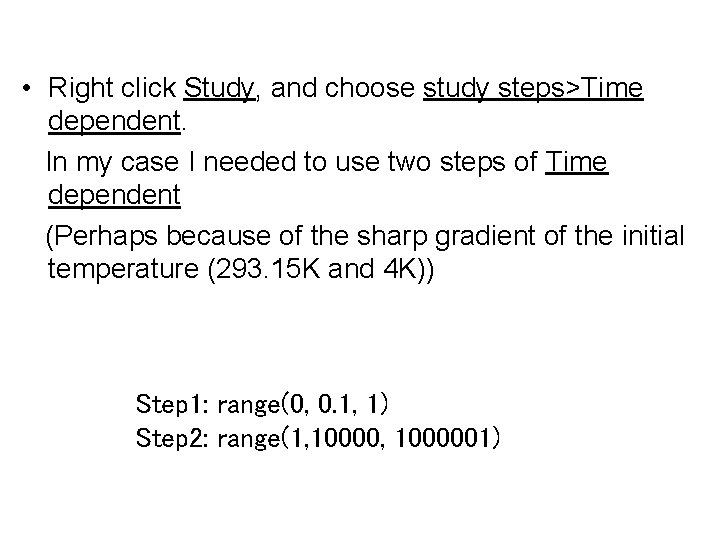
• Right click Study, and choose study steps>Time dependent. In my case I needed to use two steps of Time dependent (Perhaps because of the sharp gradient of the initial temperature (293. 15 K and 4 K)) Step 1: range(0, 0. 1, 1) Step 2: range(1, 1000001)
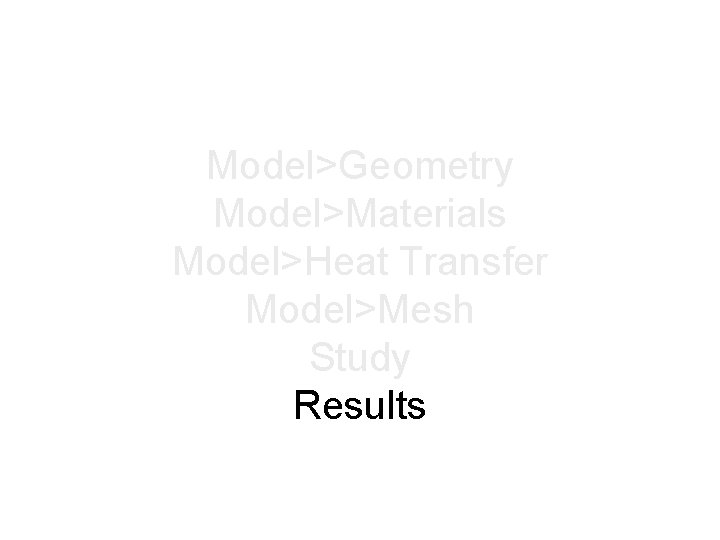
Model>Geometry Model>Materials Model>Heat Transfer Model>Mesh Study Results
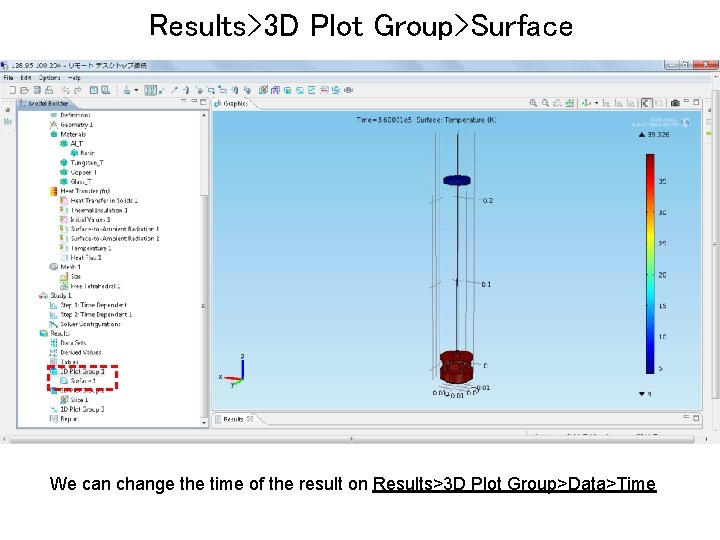
Results>3 D Plot Group>Surface We can change the time of the result on Results>3 D Plot Group>Data>Time
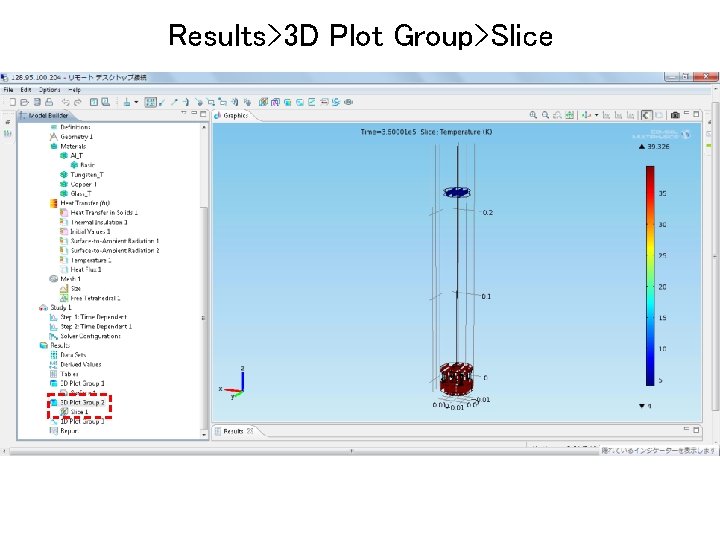
Results>3 D Plot Group>Slice
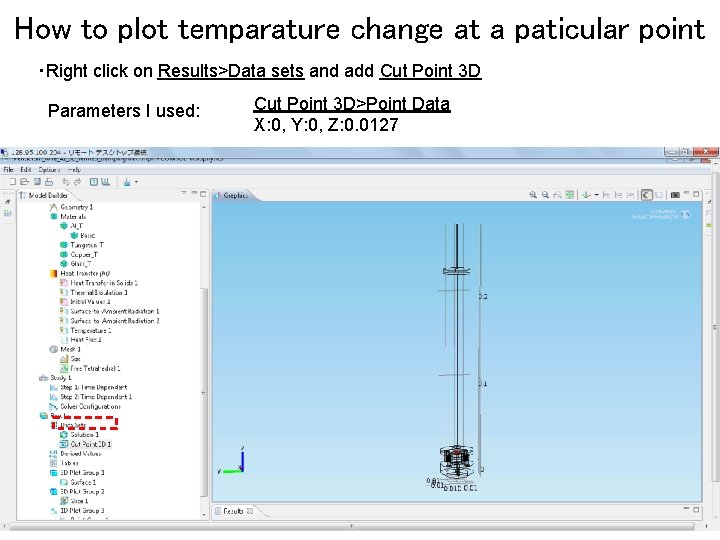
How to plot temparature change at a paticular point ・Right click on Results>Data sets and add Cut Point 3 D Parameters I used: Cut Point 3 D>Point Data X: 0, Y: 0, Z: 0. 0127

・Right click Results, and add 1 D Plot Group ・Choose Cut point 3 D in 1 D Plot Group>Settings>Data set ・Right 1 D Plot Group, and add Point Graph ・Choose Cut point 3 D in 1 D Plot Group>Point Graph>Settings>Data set ・Click Plot on the upper right in Settings
Comsol for students
Free and porous media flow comsol
Process flow simulation software
Convection heat example
Induction heating comsol
Comsol viscoelastic
Comsol fnl
Comsol api
Duplicatice
Defrost using internal heat is accomplished using
Specific heat simulation
Manual simulation using event scheduling
Combinational circuit design and simulation using gates
Combinational circuit design and simulation using gates
Simulation in business analytics
Is a disturbance that transfers energy from place to place
Metal heat transfer
Unit viscosity
Radiated heat always travels downwards
Example of heat energy
Transfer analysis
Heat transfer jeopardy
Example of heat transfer by radiation
Open kettle or pan evaporator
Energy transfer
A double pipe parallel flow heat exchanger
The overall heat transfer coefficient
Shell side reynolds number
Ntu heat transfer
What type of heat transfer is an air popper
Type of heat
Heat transfer on earth
Sunlight melts a wax crayon left outside.
Radiation heat transfer examples
What is heat transfer conduction convection and radiation
Conduction convection radiation examples
Example of heat transfer by radiation
Chapter 22 heat transfer
Q system = -q surroundings
Convection definition
G/4
Radial heat conduction
The overall heat transfer coefficient
Heat and mass transfer cengel 4th edition pdf