Digital Microfluidics Control System II Detailed Design P
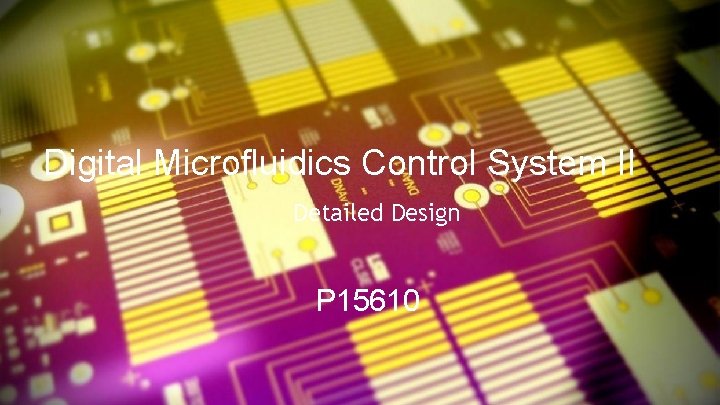
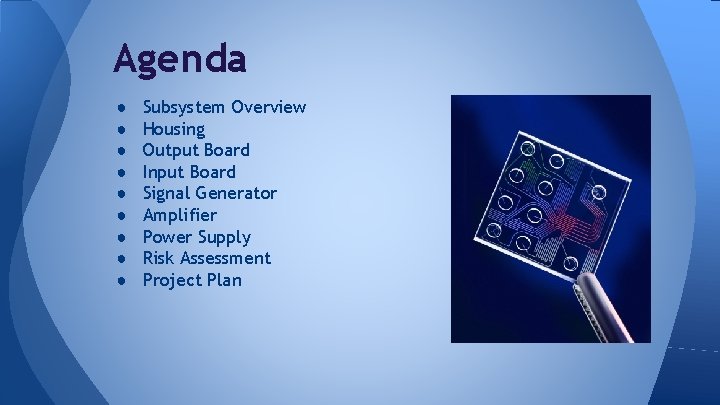
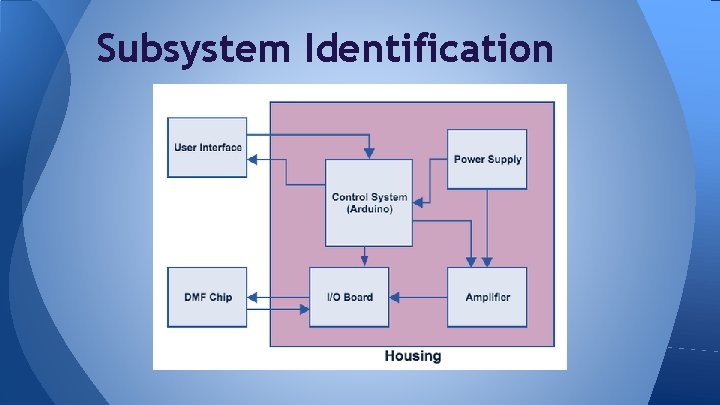
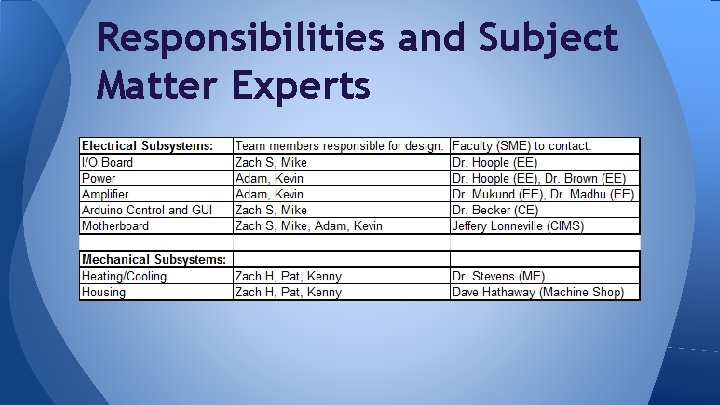

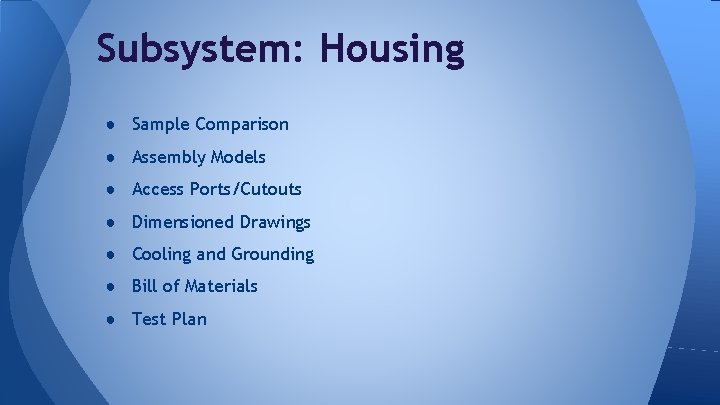
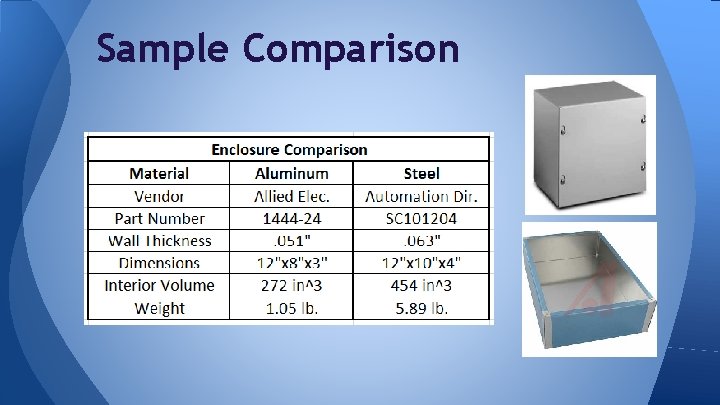
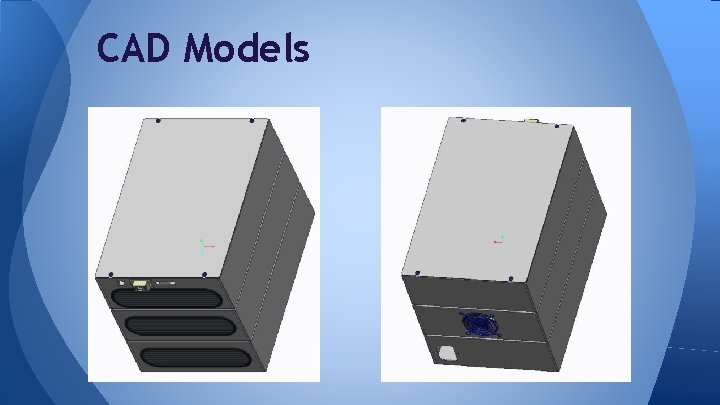
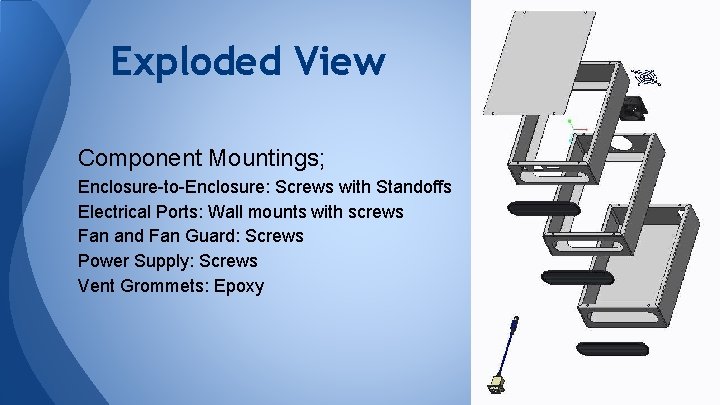
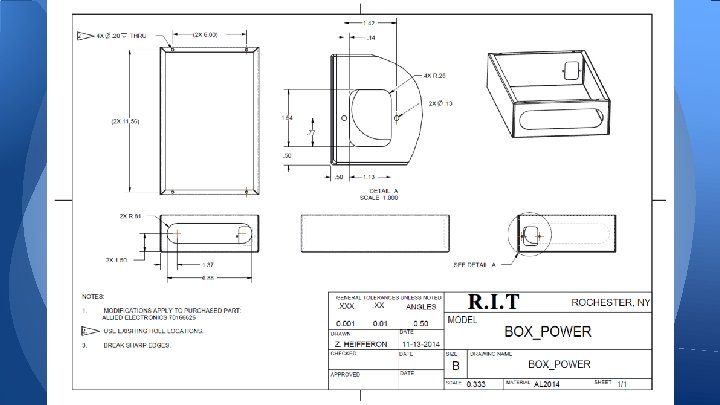
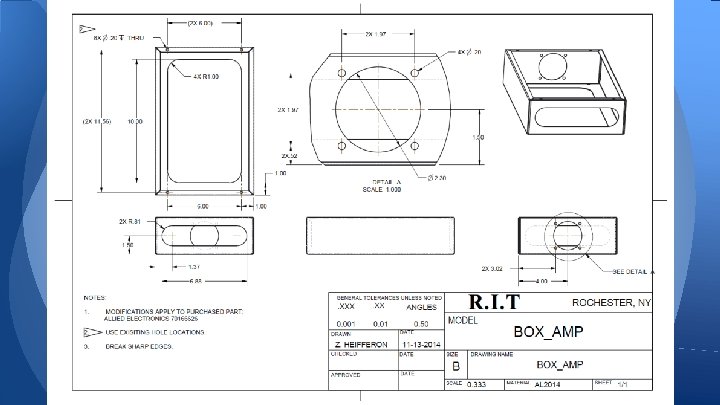
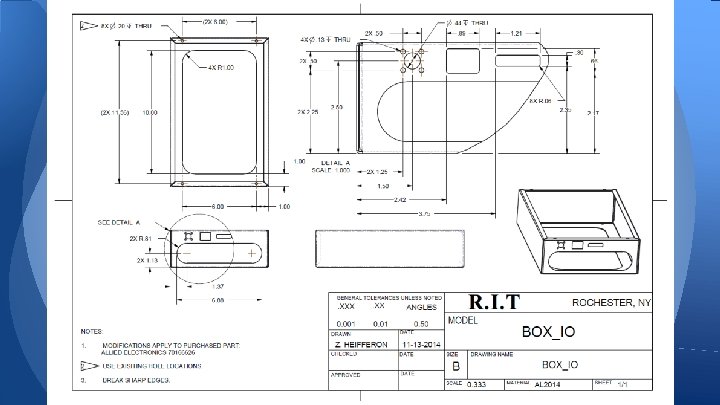
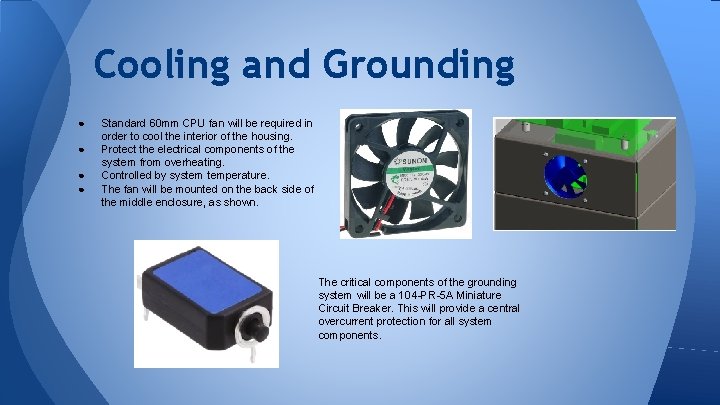
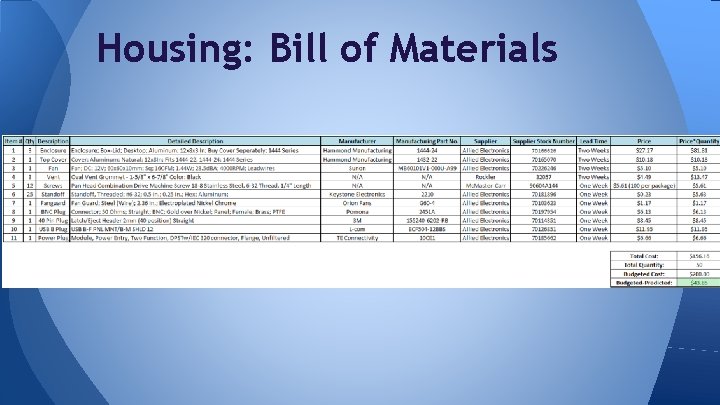

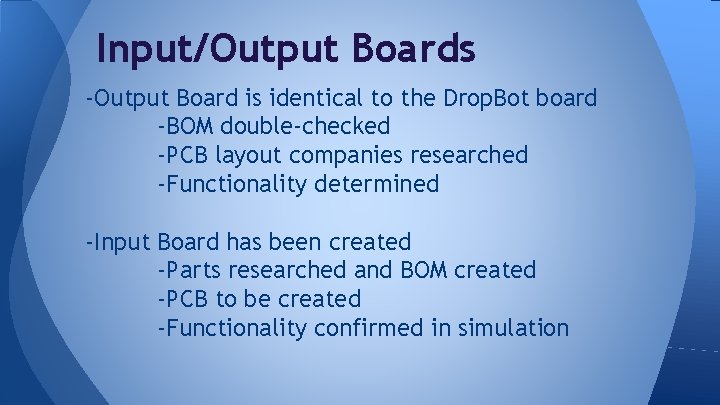
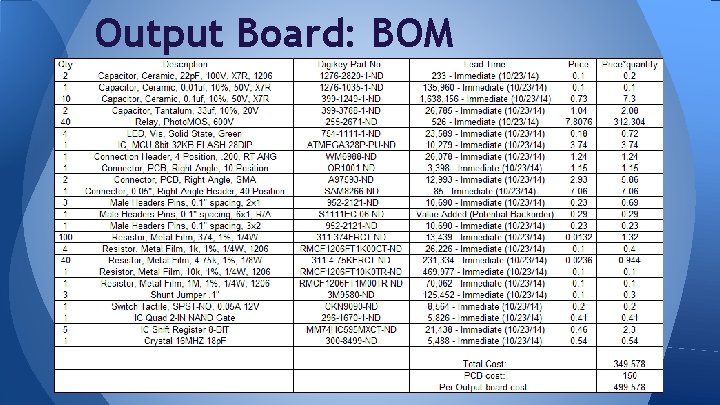
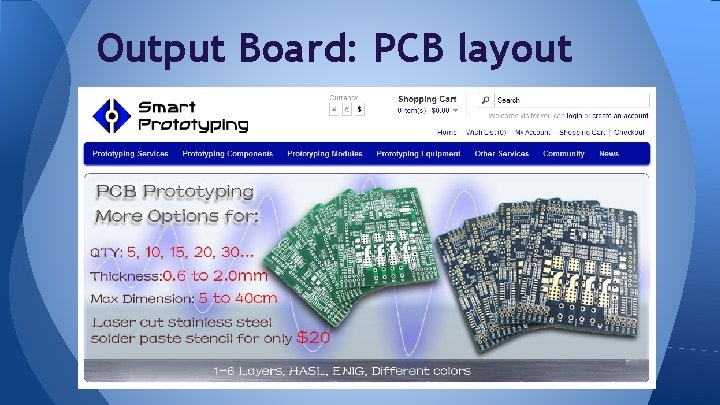
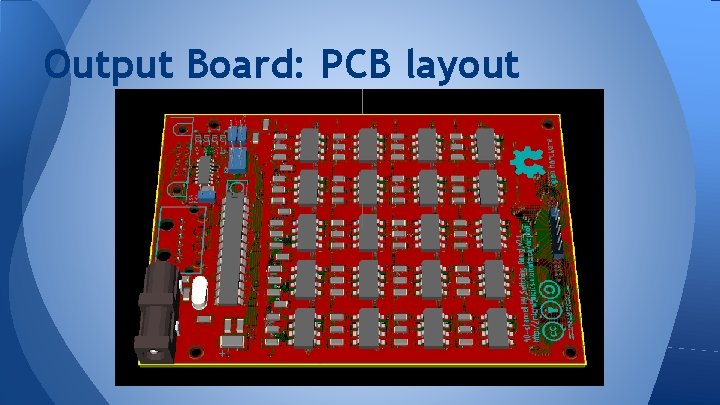
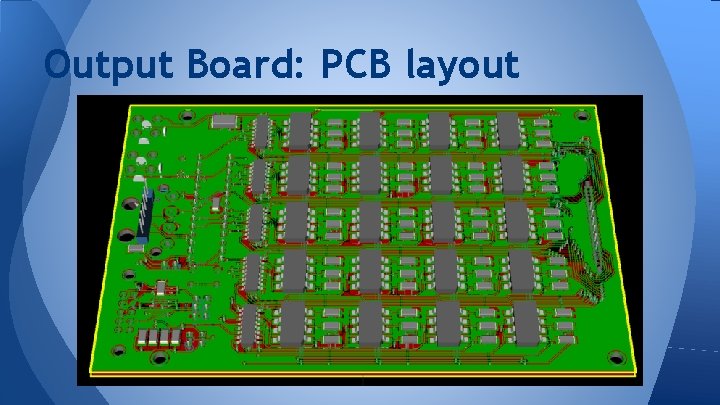
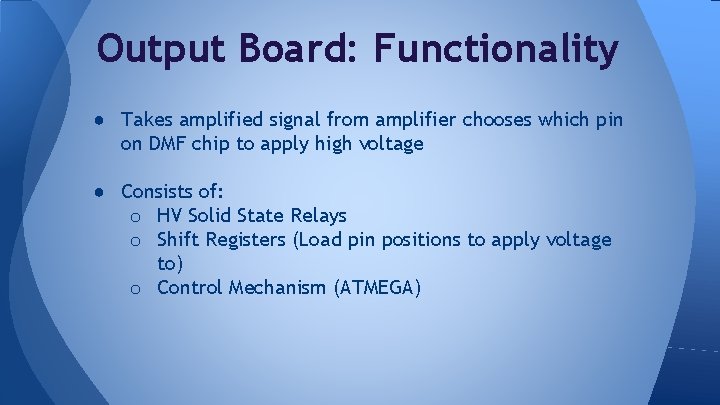
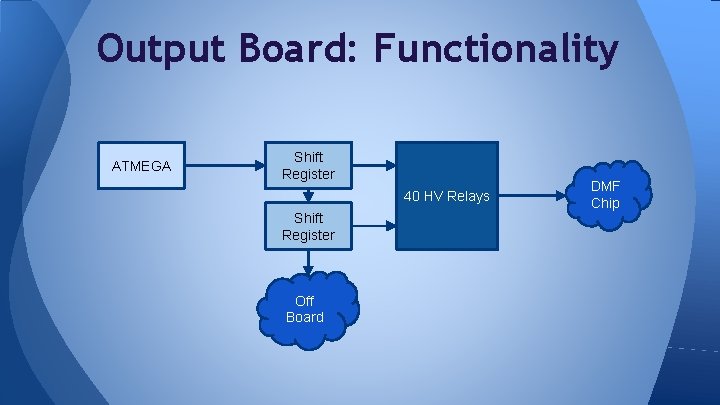
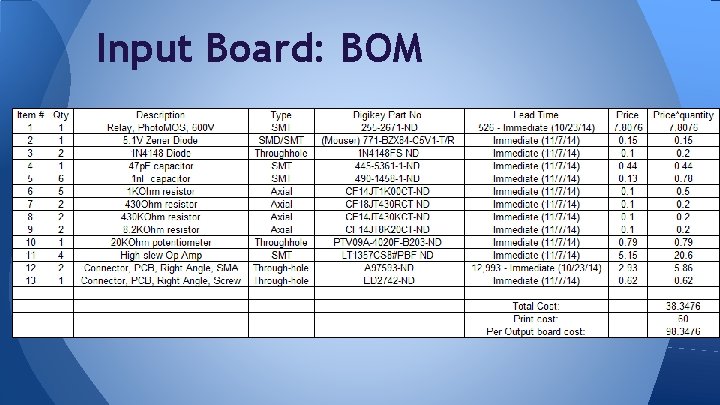
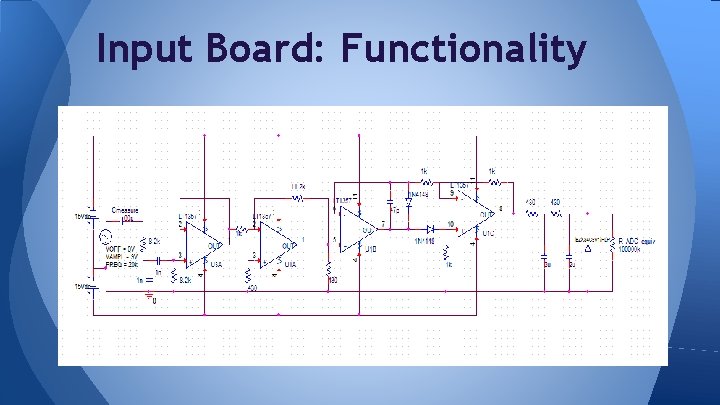

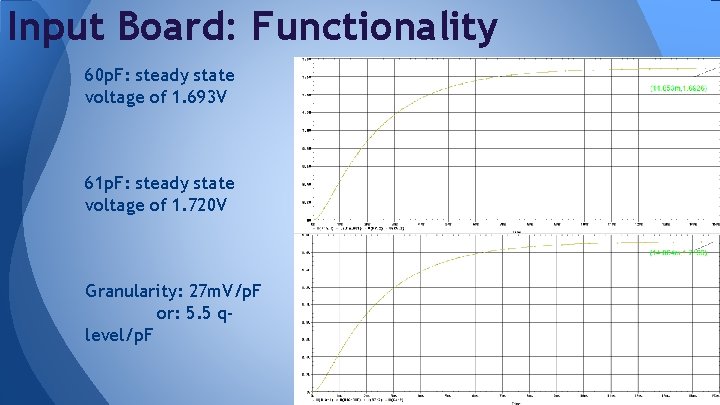
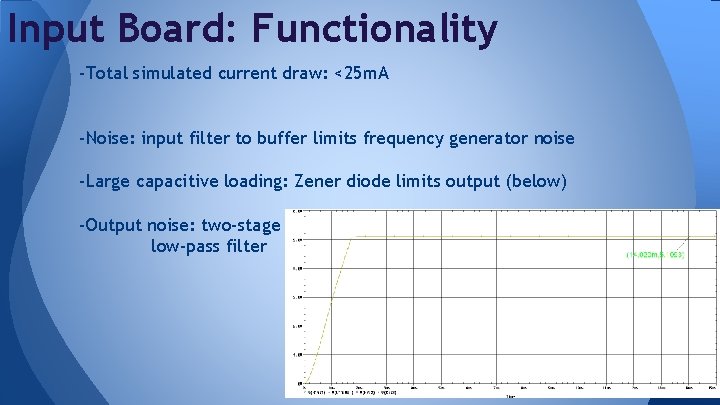
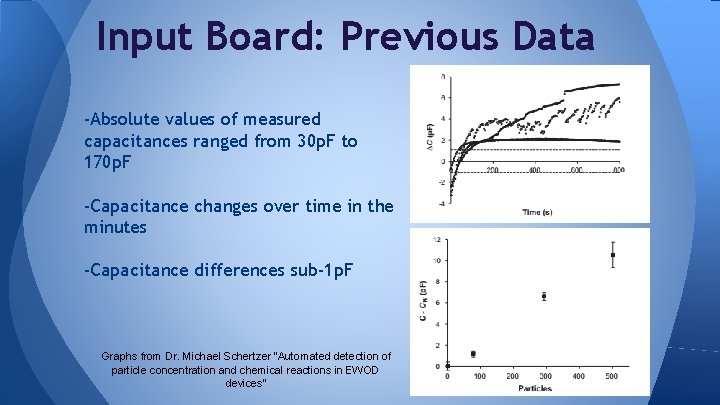
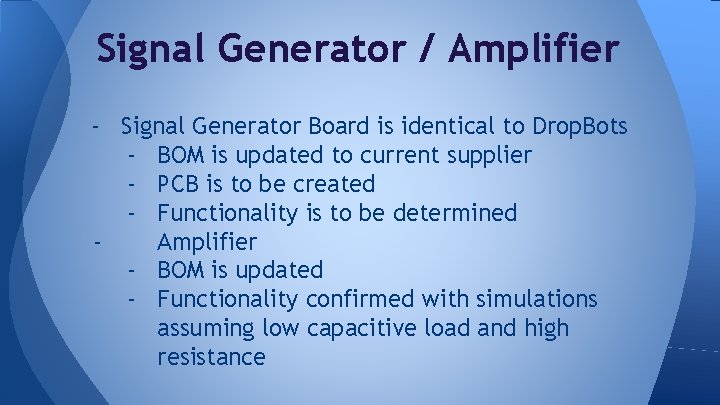
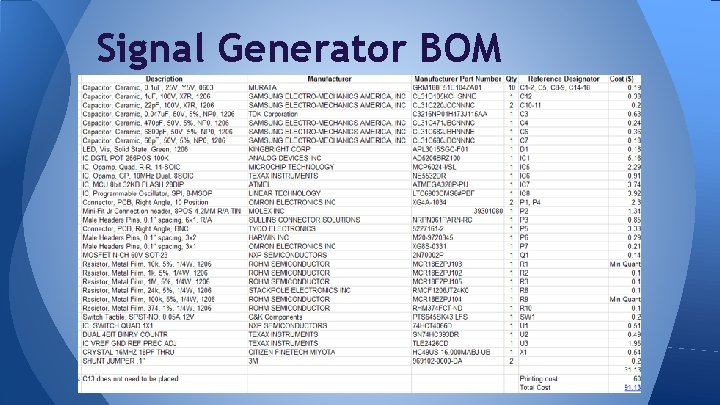
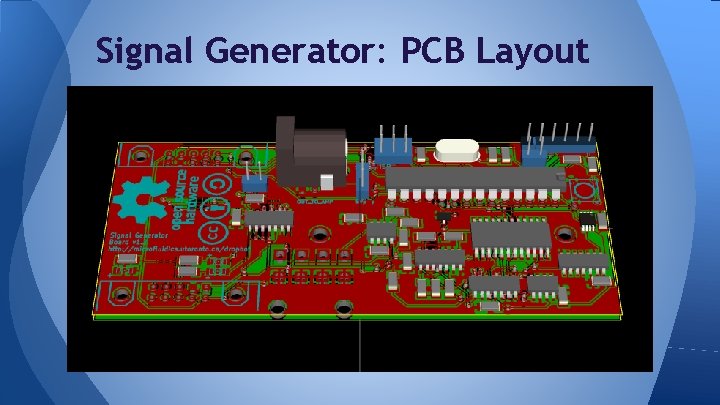
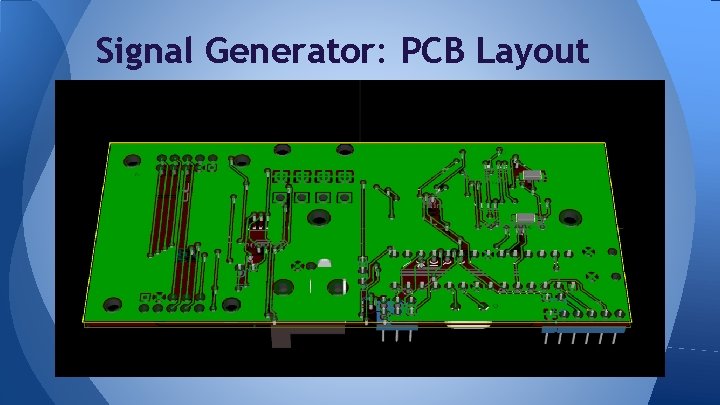
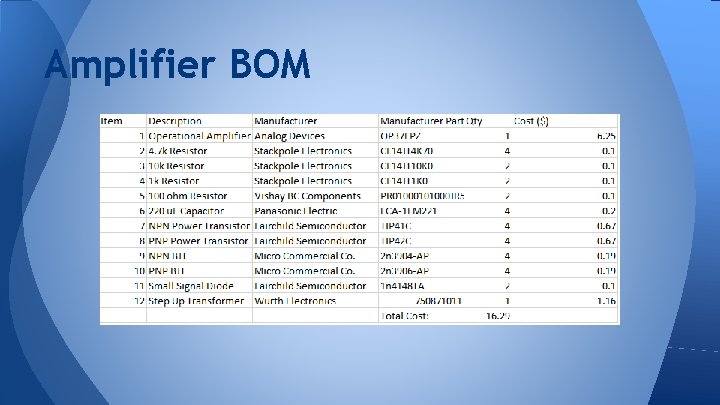
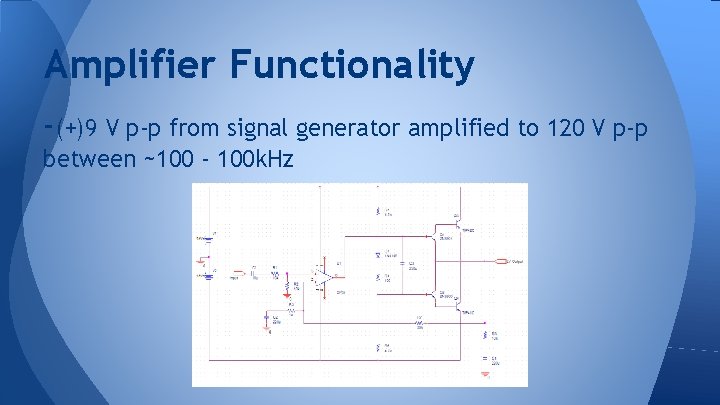
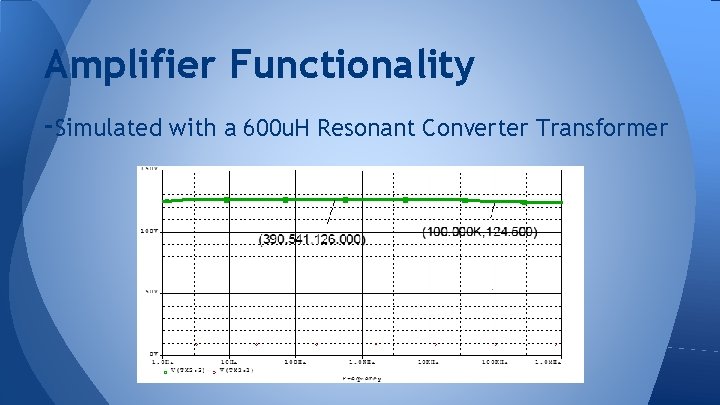
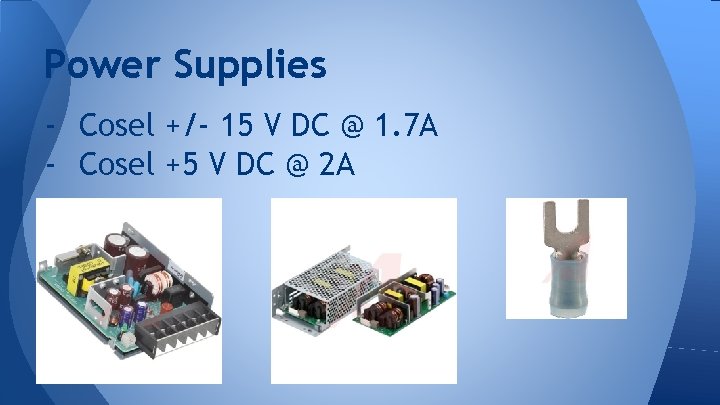
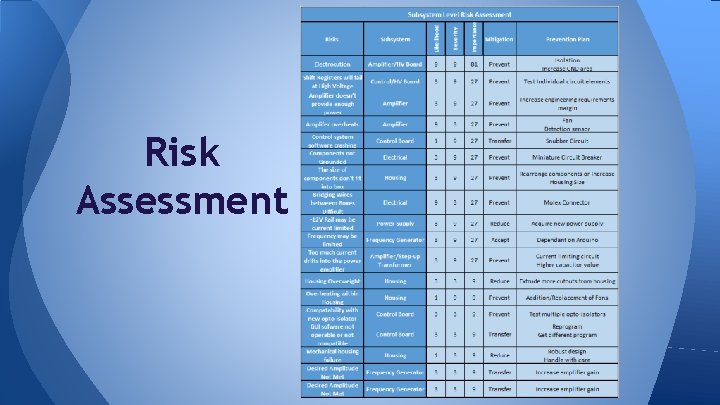
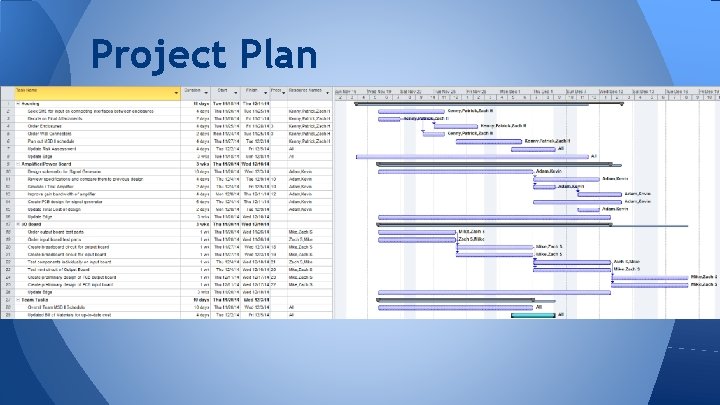
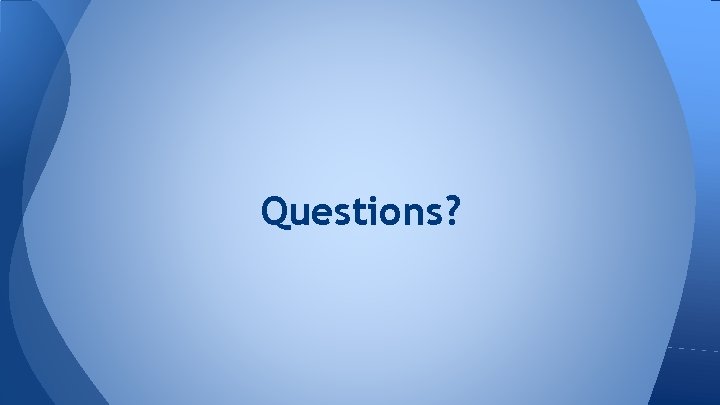
- Slides: 39
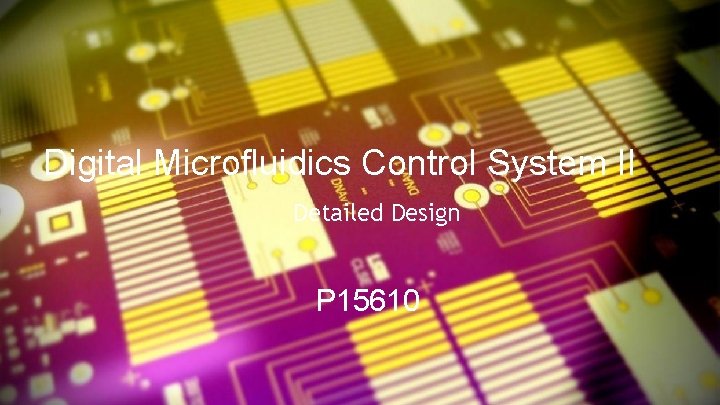
Digital Microfluidics Control System II Detailed Design P 15610
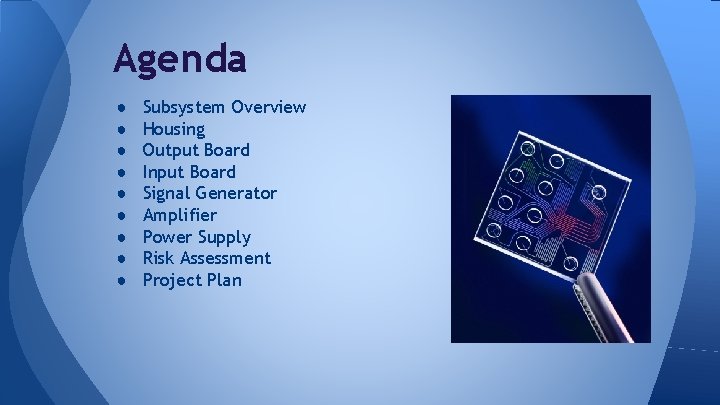
Agenda ● ● ● ● ● Subsystem Overview Housing Output Board Input Board Signal Generator Amplifier Power Supply Risk Assessment Project Plan
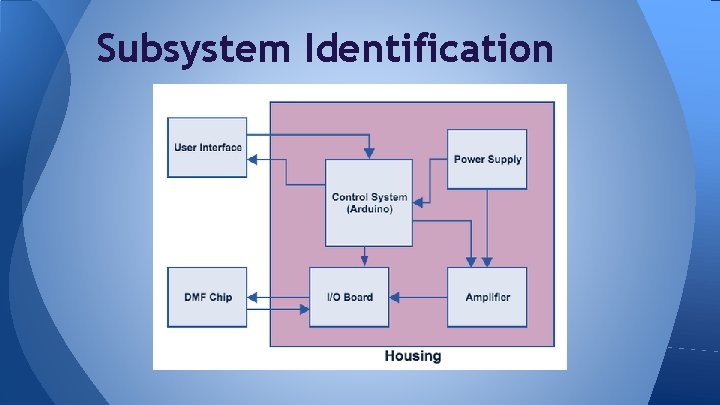
Subsystem Identification
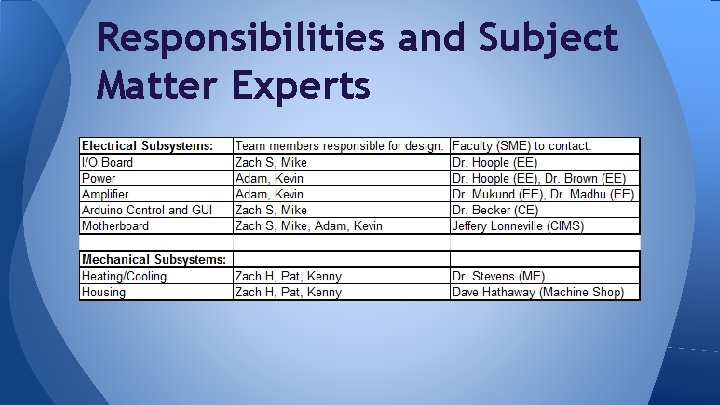
Responsibilities and Subject Matter Experts

Subsystem Specifications
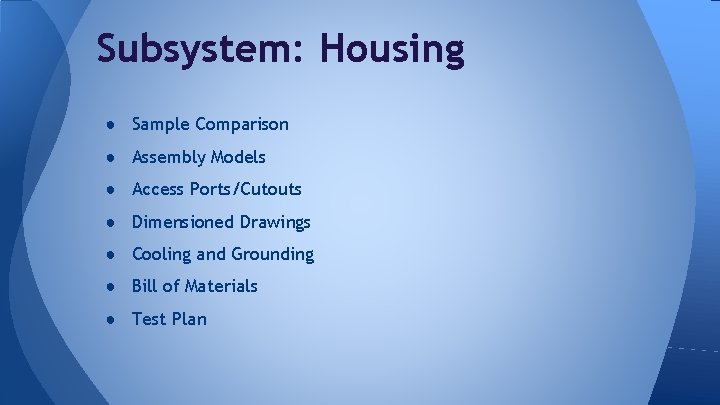
Subsystem: Housing ● Sample Comparison ● Assembly Models ● Access Ports/Cutouts ● Dimensioned Drawings ● Cooling and Grounding ● Bill of Materials ● Test Plan
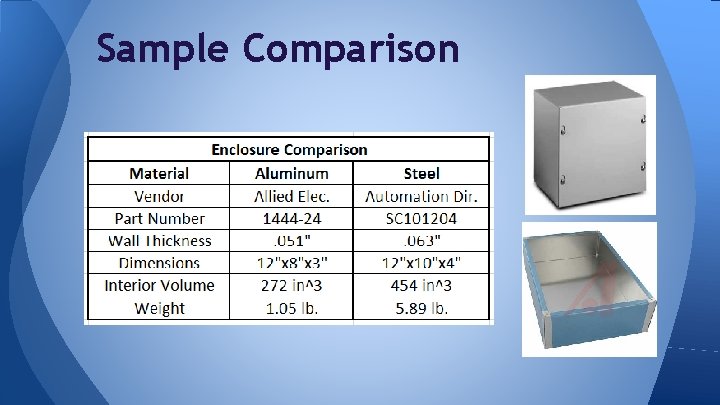
Sample Comparison
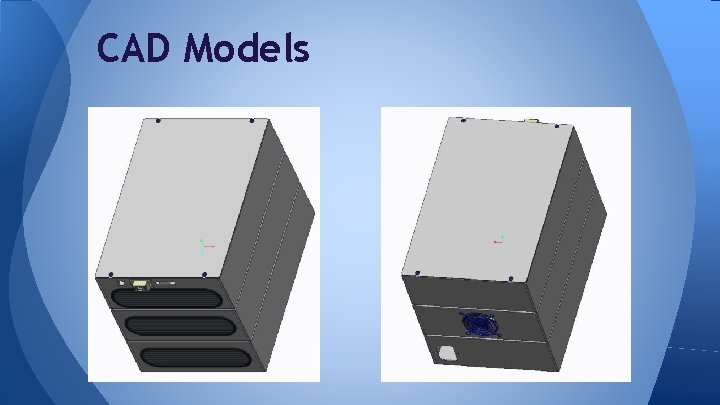
CAD Models
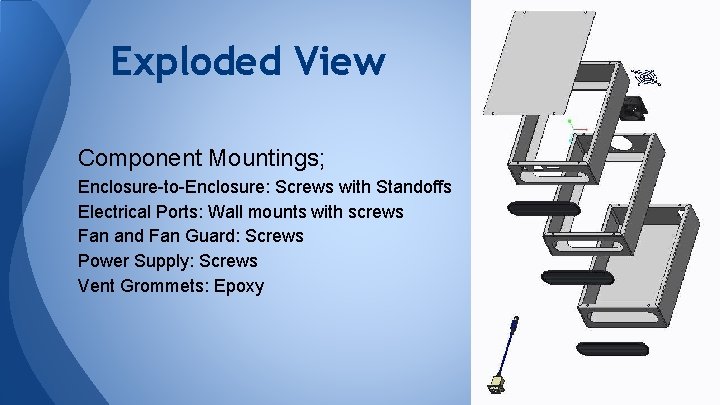
Exploded View Component Mountings; Enclosure-to-Enclosure: Screws with Standoffs Electrical Ports: Wall mounts with screws Fan and Fan Guard: Screws Power Supply: Screws Vent Grommets: Epoxy
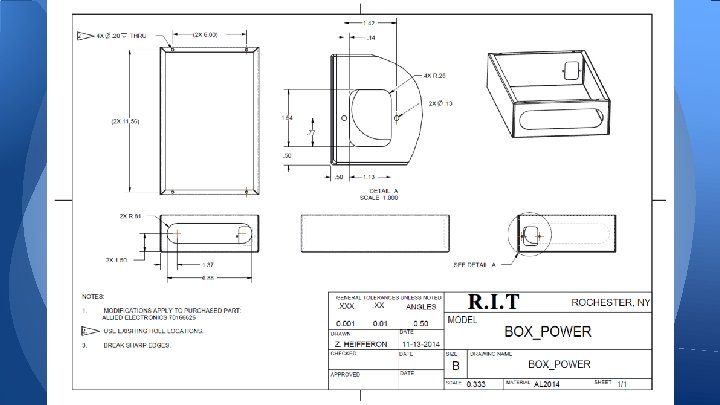
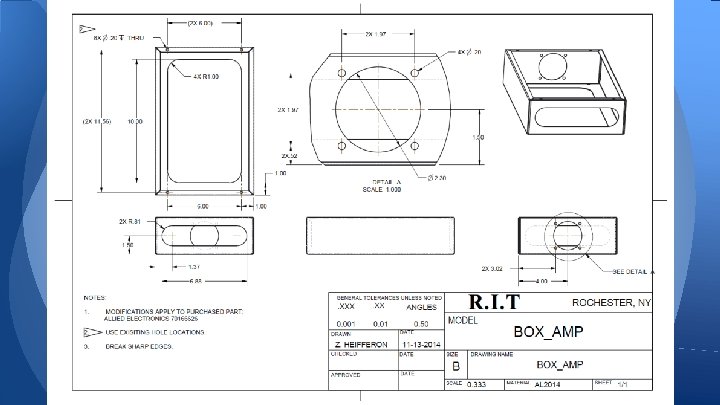
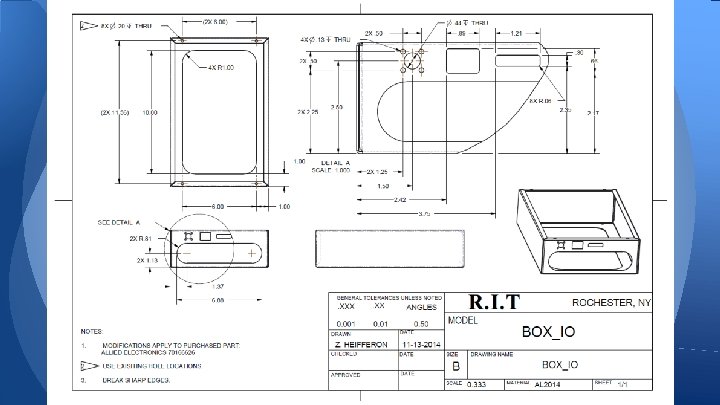
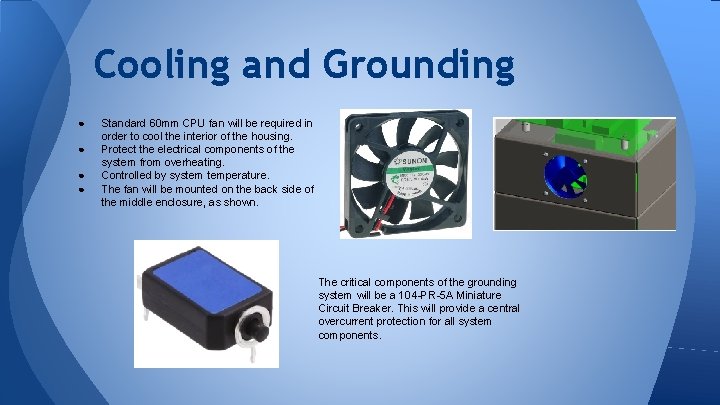
Cooling and Grounding ● ● Standard 60 mm CPU fan will be required in order to cool the interior of the housing. Protect the electrical components of the system from overheating. Controlled by system temperature. The fan will be mounted on the back side of the middle enclosure, as shown. The critical components of the grounding system will be a 104 -PR-5 A Miniature Circuit Breaker. This will provide a central overcurrent protection for all system components.
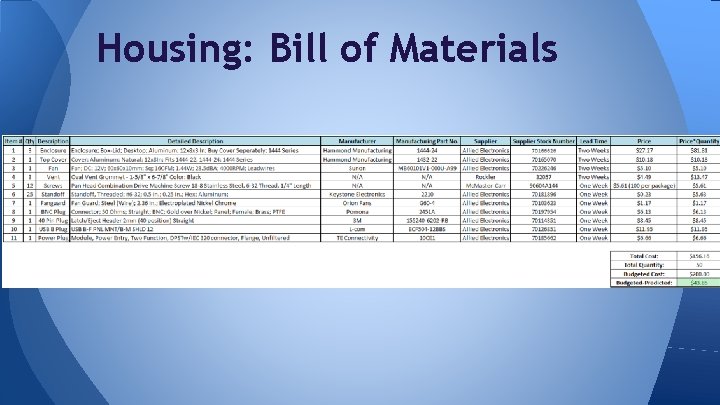
Housing: Bill of Materials

Housing: Test Plan ● Continuity testing will be performed throughout the components of the housing to ensure components are fully grounded. ● The fully assembled system will be run while the fan is operating at its available speed. The internal temperature of the system will be monitored until it reaches steady state, along with the power draw of the fan. a. Ideal Temperature < 60 degrees C b. Ideal Power Draw < 10 Watts ● Housing will be emptied of electrical components, placed on a scale, and weighed. Overall dimensions of the housing will be measured and the total volume will be calculated. a. Ideal Weight < 15 lbs b. Ideal Volume < 2000 in^3 ● Emptied housing will be fully disassembled and reassembled by single person while being timed. a. Ideal Time < 5 minutes Parts necessary ● Digital Multimeter ● Tape measure ● Scale ● Thermocouples
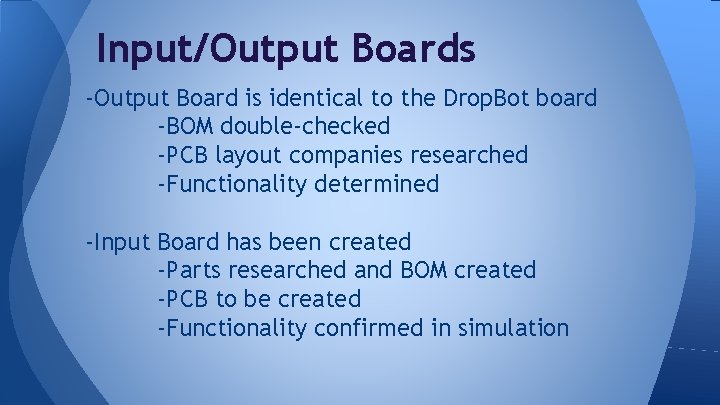
Input/Output Boards -Output Board is identical to the Drop. Bot board -BOM double-checked -PCB layout companies researched -Functionality determined -Input Board has been created -Parts researched and BOM created -PCB to be created -Functionality confirmed in simulation
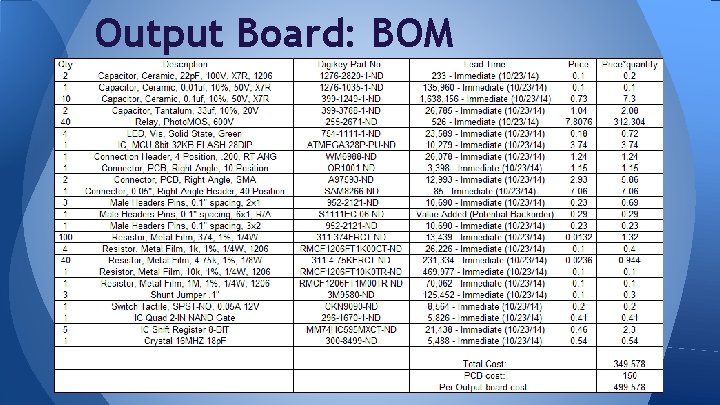
Output Board: BOM
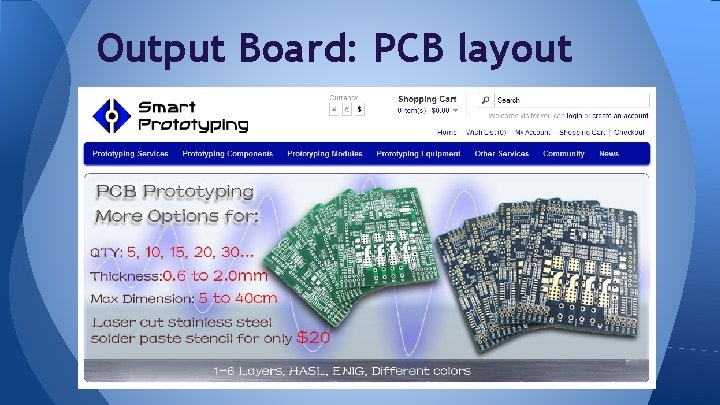
Output Board: PCB layout
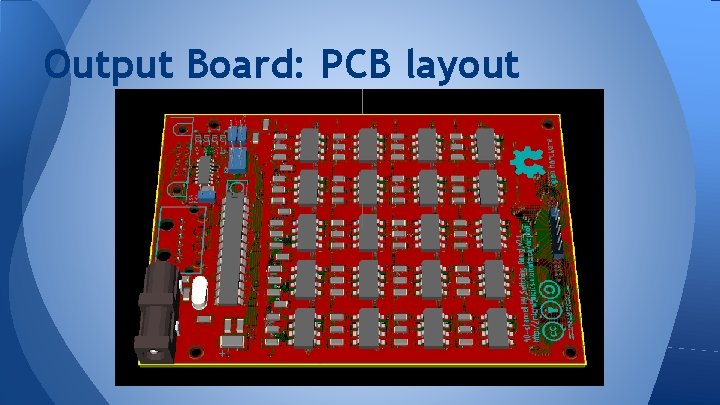
Output Board: PCB layout
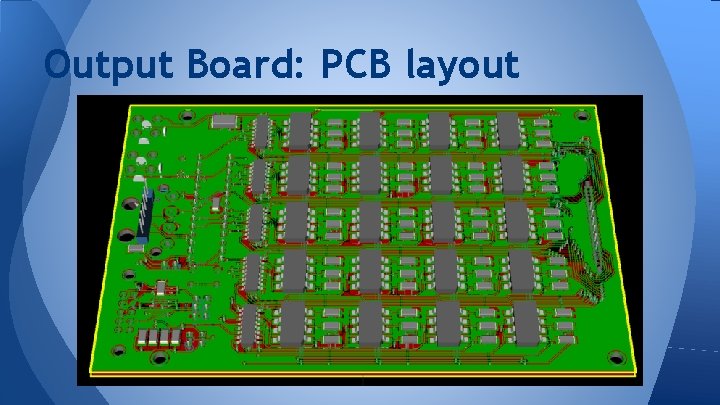
Output Board: PCB layout
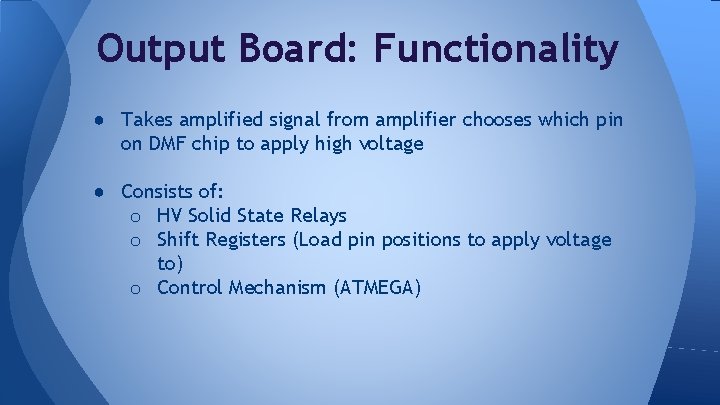
Output Board: Functionality ● Takes amplified signal from amplifier chooses which pin on DMF chip to apply high voltage ● Consists of: o HV Solid State Relays o Shift Registers (Load pin positions to apply voltage to) o Control Mechanism (ATMEGA)
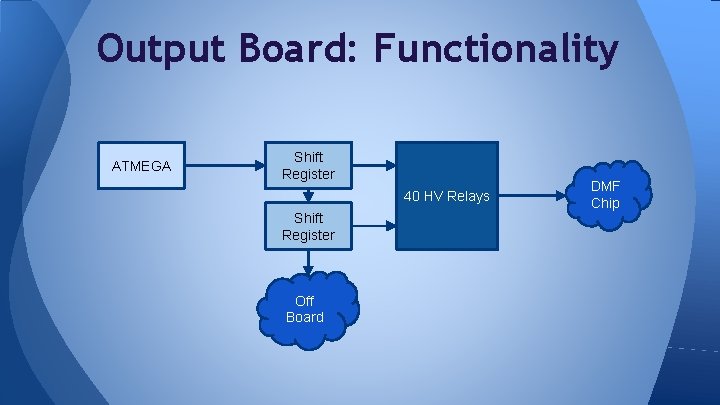
Output Board: Functionality ATMEGA Shift Register 40 HV Relays Shift Register Off Board DMF Chip
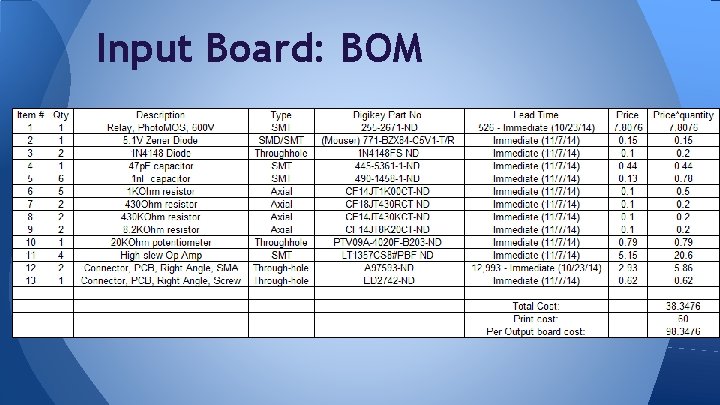
Input Board: BOM
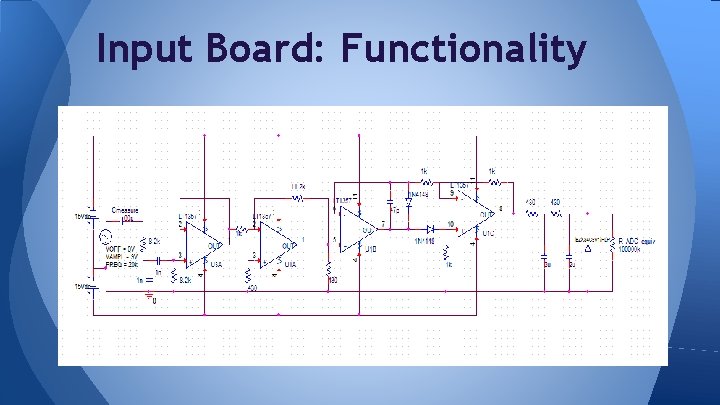
Input Board: Functionality

Input Board: Functionality 1 p. F: steady state voltage of 29 m. V 200 p. F: steady state voltage of 5. 00 V Rise time: <10 ms
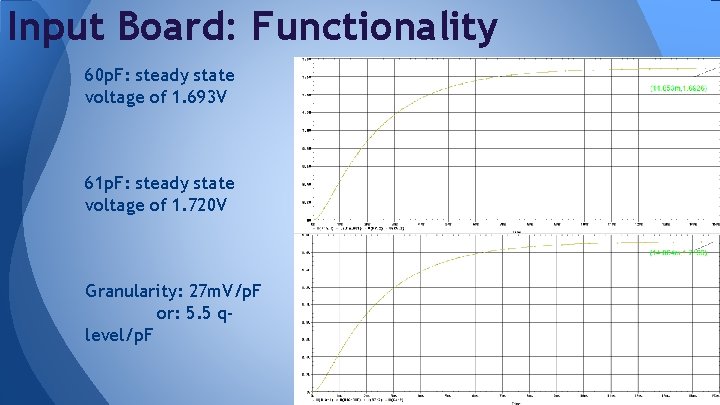
Input Board: Functionality 60 p. F: steady state voltage of 1. 693 V 61 p. F: steady state voltage of 1. 720 V Granularity: 27 m. V/p. F or: 5. 5 qlevel/p. F
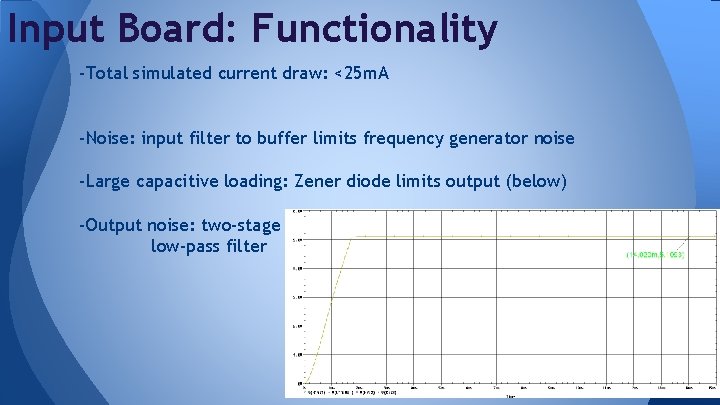
Input Board: Functionality -Total simulated current draw: <25 m. A -Noise: input filter to buffer limits frequency generator noise -Large capacitive loading: Zener diode limits output (below) -Output noise: two-stage low-pass filter
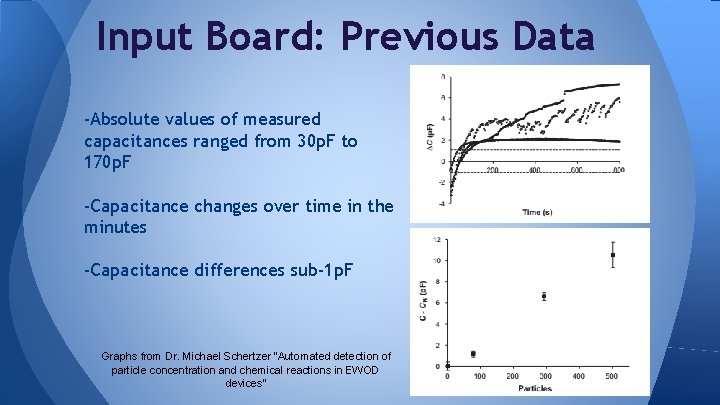
Input Board: Previous Data -Absolute values of measured capacitances ranged from 30 p. F to 170 p. F -Capacitance changes over time in the minutes -Capacitance differences sub-1 p. F Graphs from Dr. Michael Schertzer “Automated detection of particle concentration and chemical reactions in EWOD devices”
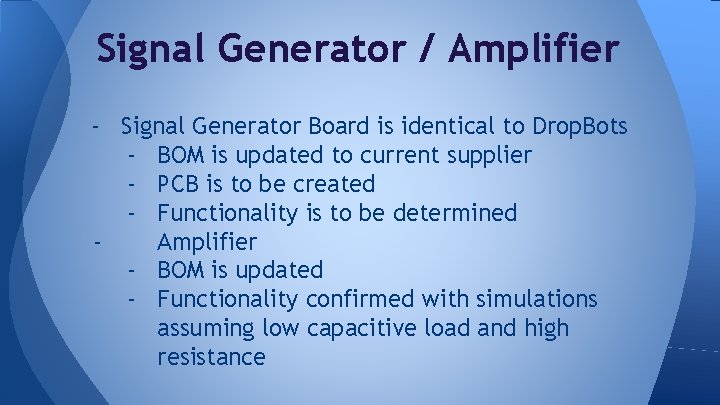
Signal Generator / Amplifier - Signal Generator Board is identical to Drop. Bots - BOM is updated to current supplier - PCB is to be created - Functionality is to be determined Amplifier - BOM is updated - Functionality confirmed with simulations assuming low capacitive load and high resistance
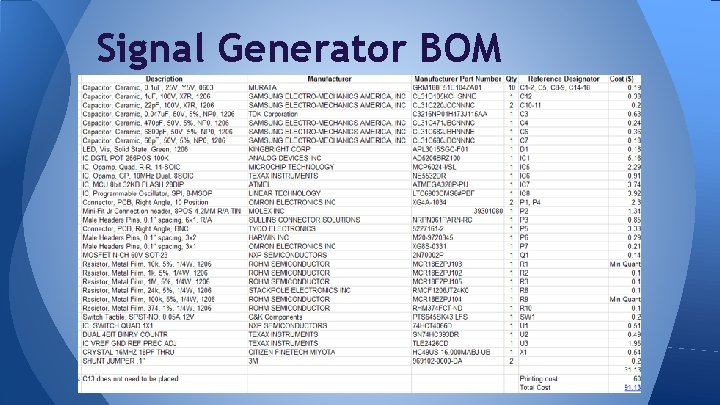
Signal Generator BOM
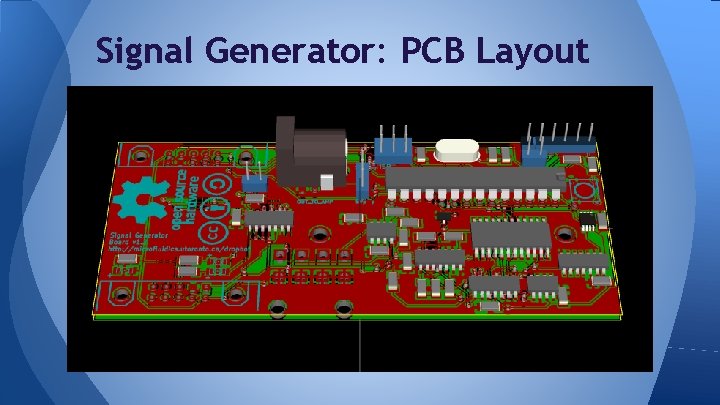
Signal Generator: PCB Layout
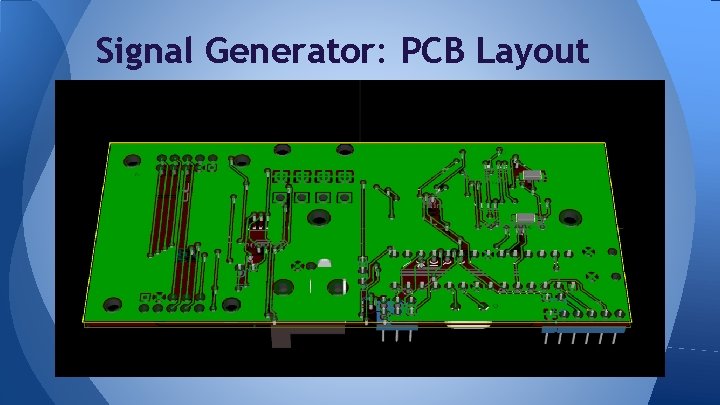
Signal Generator: PCB Layout
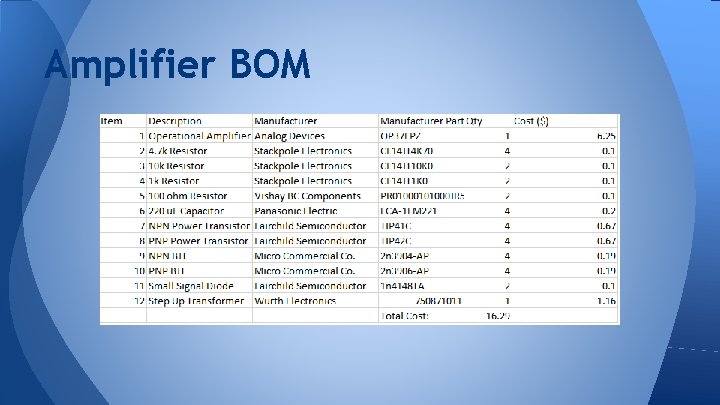
Amplifier BOM
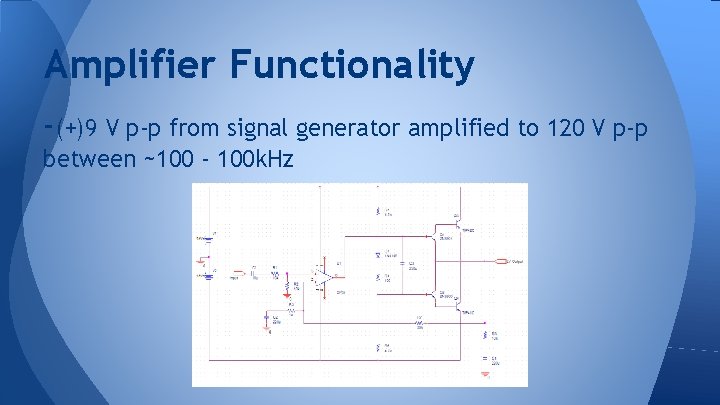
Amplifier Functionality -(+)9 V p-p from signal generator amplified to 120 V p-p between ~100 - 100 k. Hz
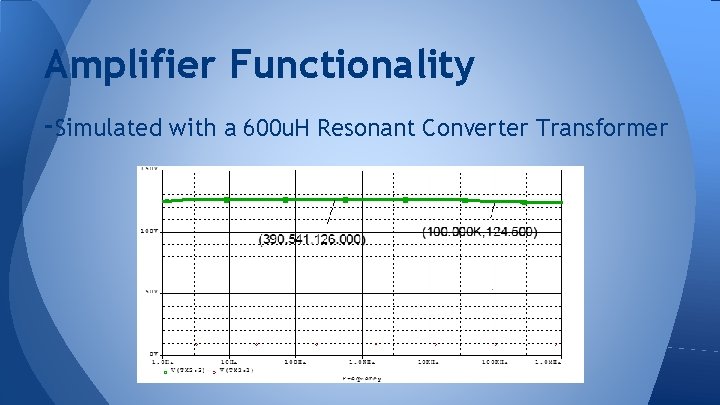
Amplifier Functionality -Simulated with a 600 u. H Resonant Converter Transformer
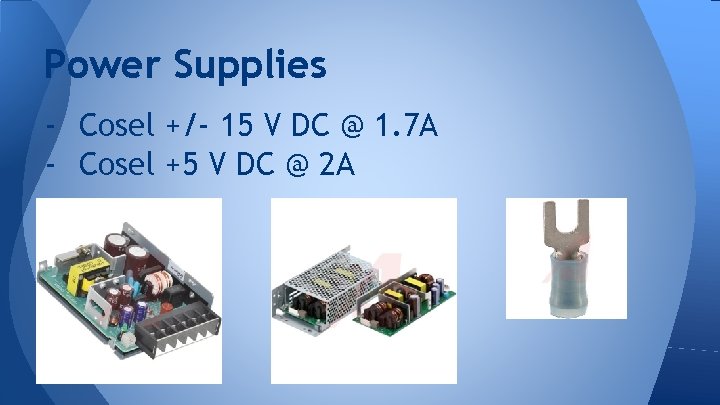
Power Supplies - Cosel +/- 15 V DC @ 1. 7 A - Cosel +5 V DC @ 2 A
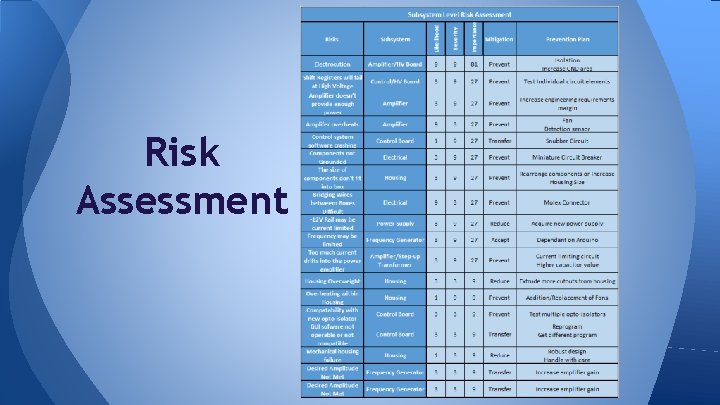
Risk Assessment
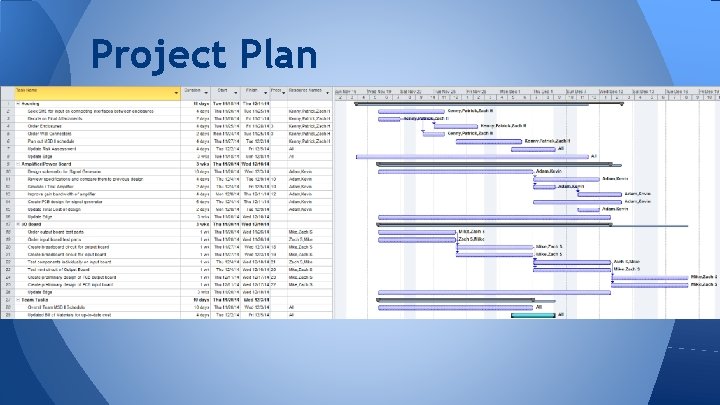
Project Plan
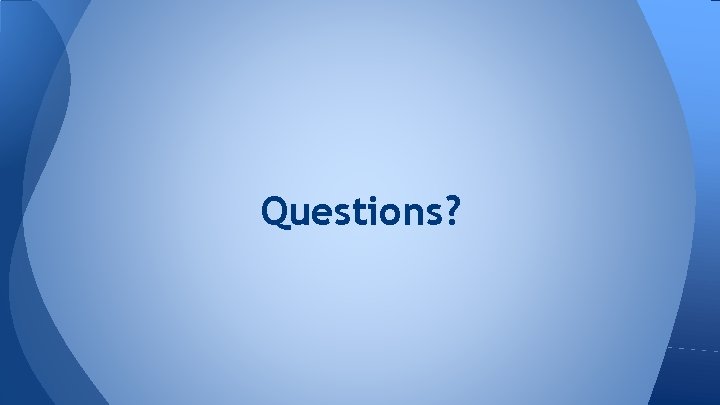
Questions?
Hagen poiseuille law
Dr david kong
Peristaltic pump microfluidics
Digital control
Detailed design in software engineering
Function oriented design in software engineering
Candidate system matrix
Pulse transfer function in digital control system
Feedback matrix examples
Introduction to analog and digital control systems
S domain
Split range
Full use case description
Detailed analysis sometimes is called
Scanning reading images
Detailed scheduling
Detailed lesson plan in hairdressing
Imagery in first death in nova scotia
Antenna effect in vlsi
Cocomo model
Coupling assembly drawing
Detailed lesson plan about quadratic equation
Shaft drawing example
Firewood marlow
Detailed business case
Costructive
Write a detailed note on unicast routing protocols
Purpose of detail drawing
Engineering drawing code
Southern spain map
Solid in engineering drawing
How to write a riddle
First cut detailed sequence diagram
Skim listening
Need of energy audit ppt
Characteristics of dss in mis
Cima detailed record of experience example
Detailed address
Sector sketch vs range card
Detailed lesson plan about coral reefs