Production Planning and Detailed Scheduling PPDS in SCM
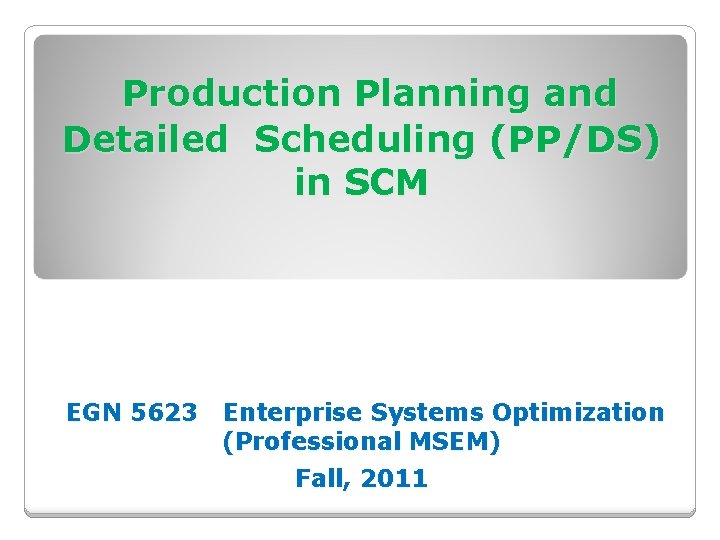
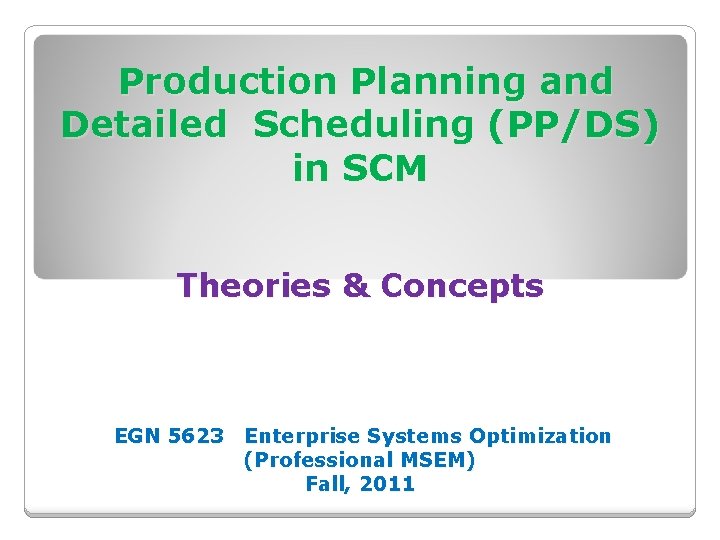
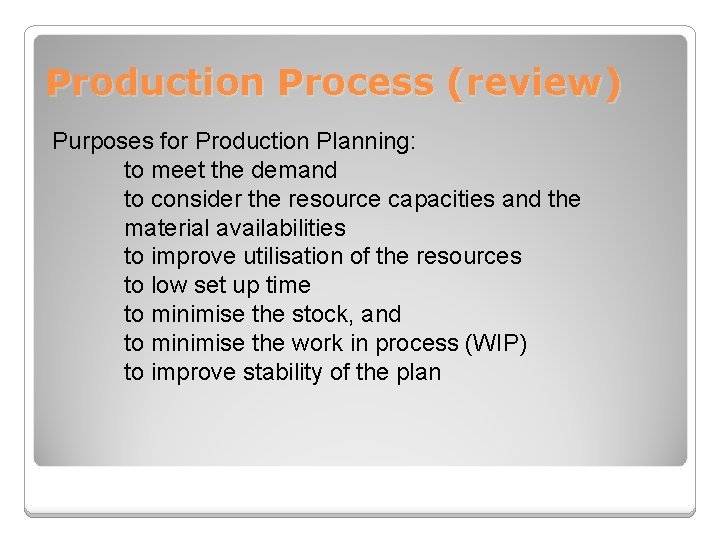
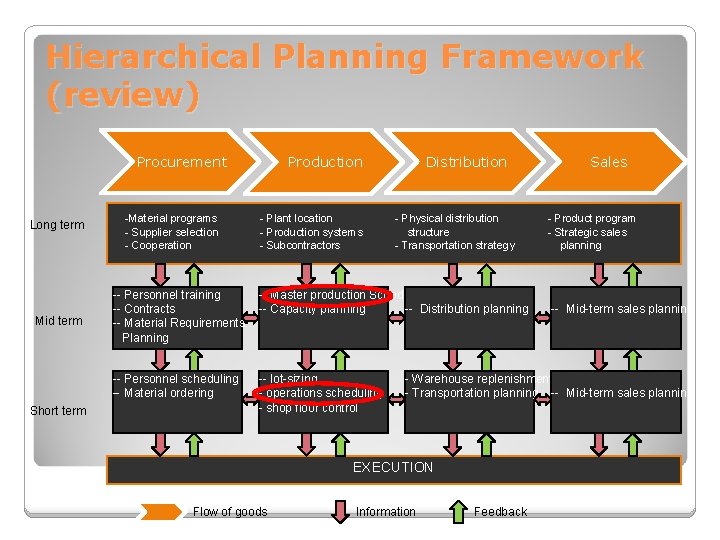
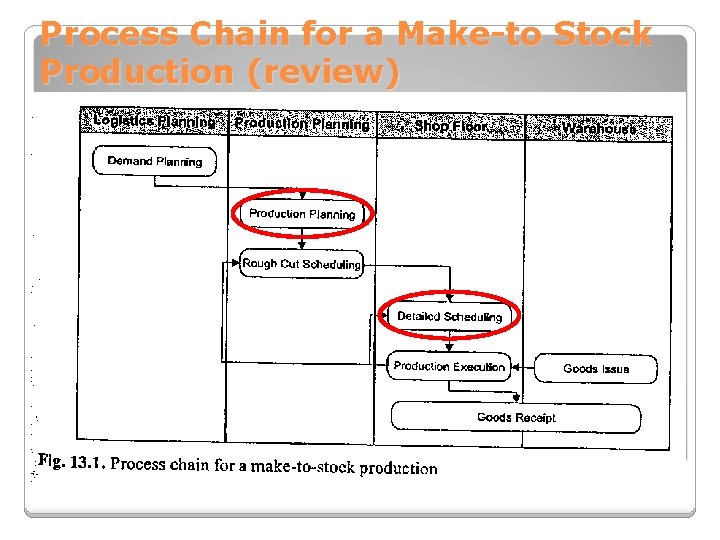
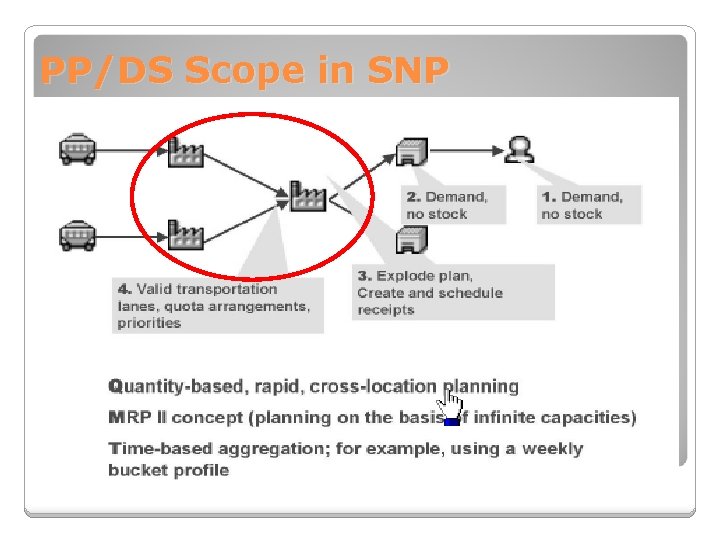
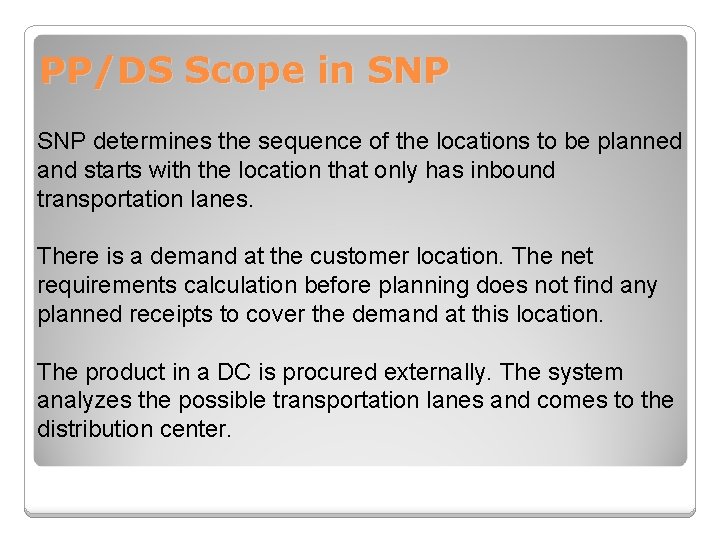
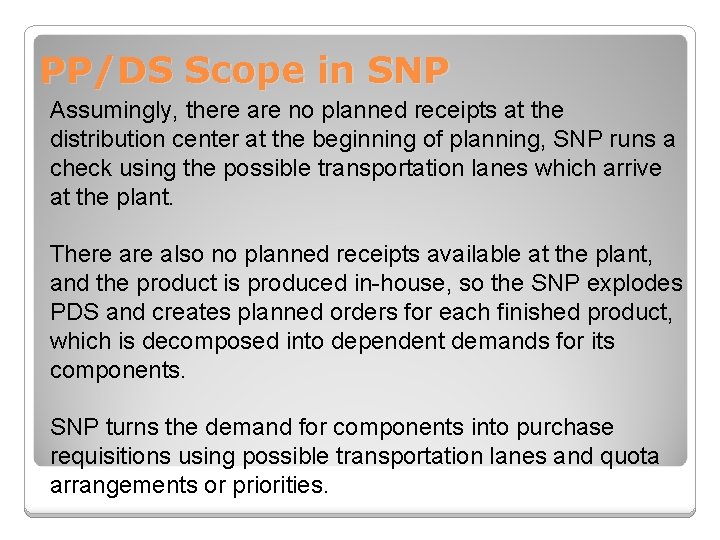
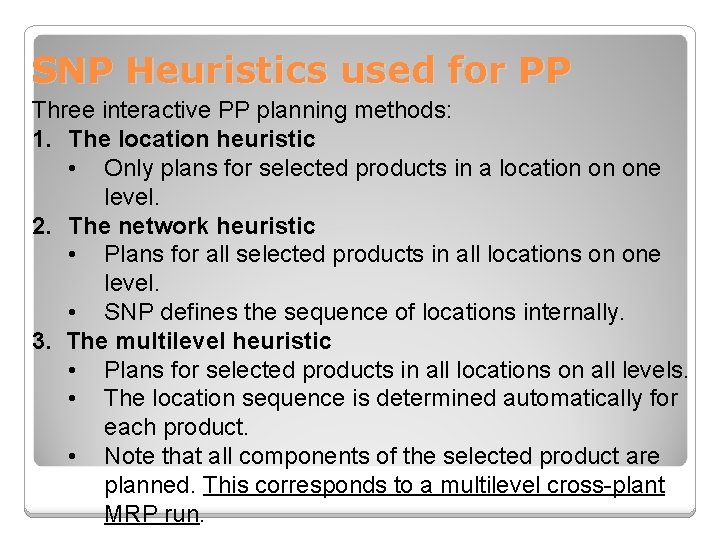
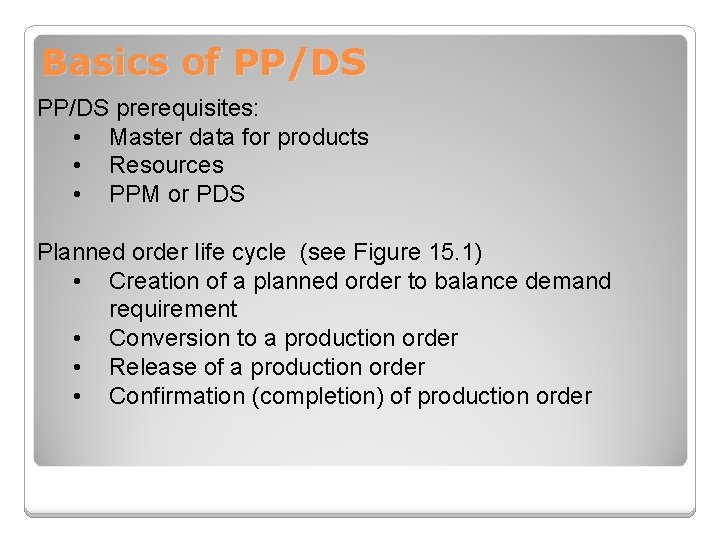
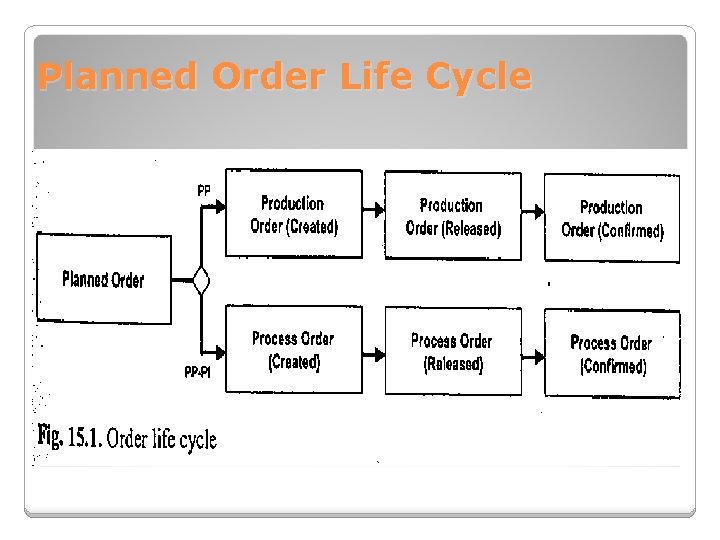
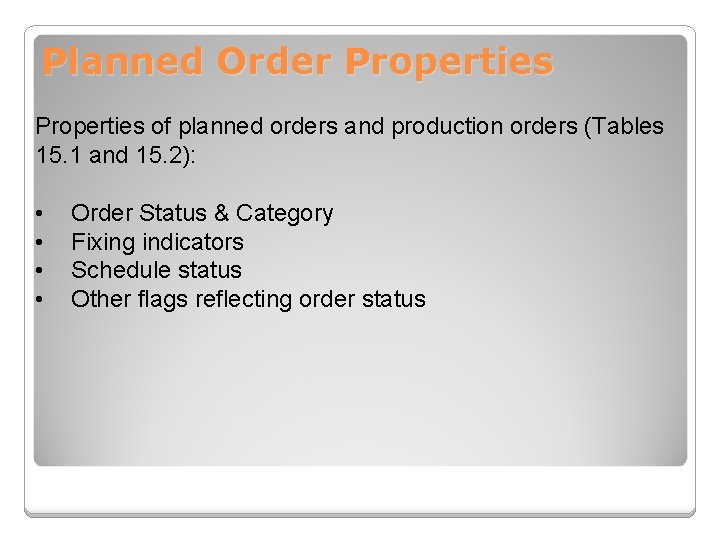
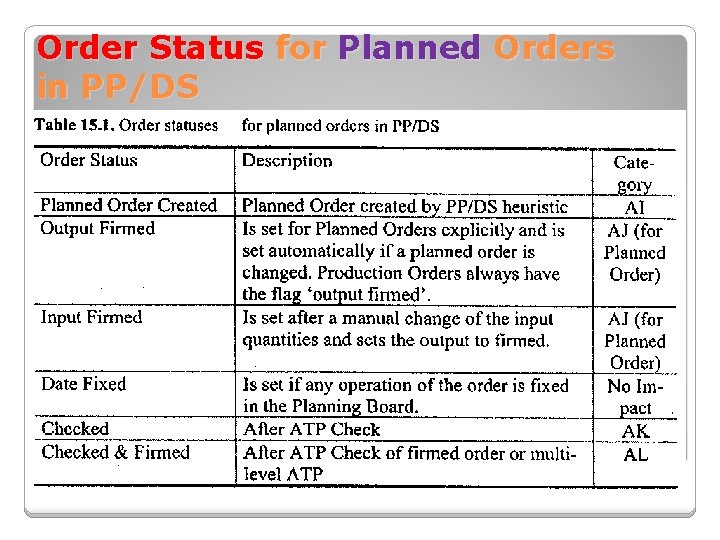
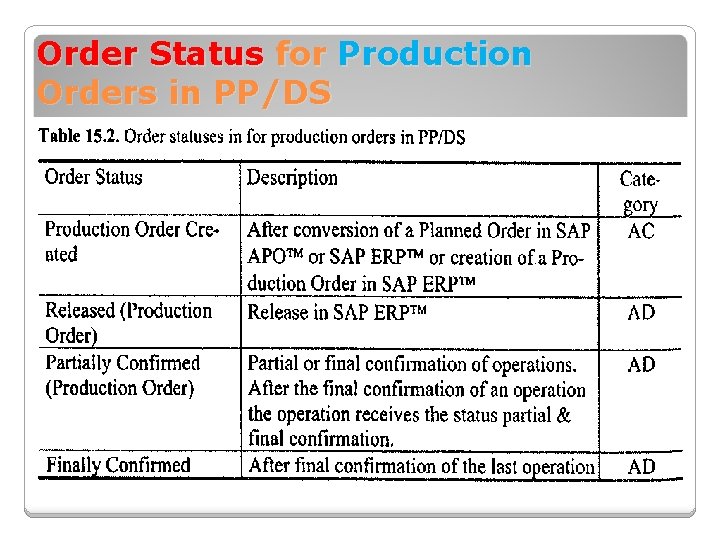
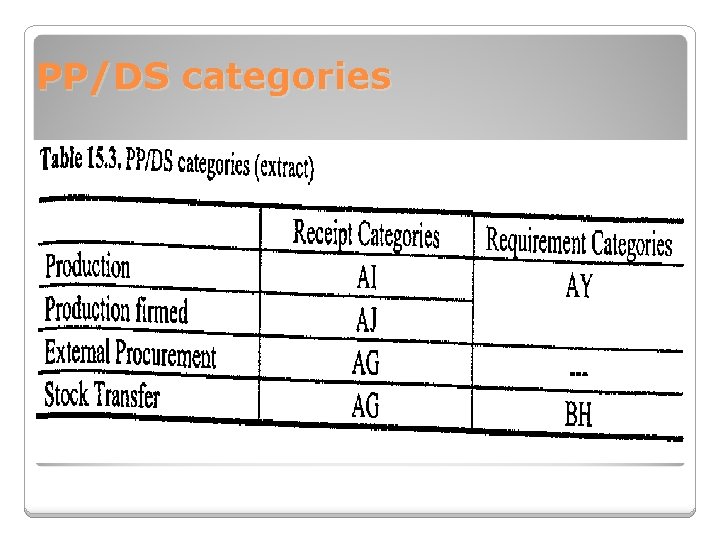
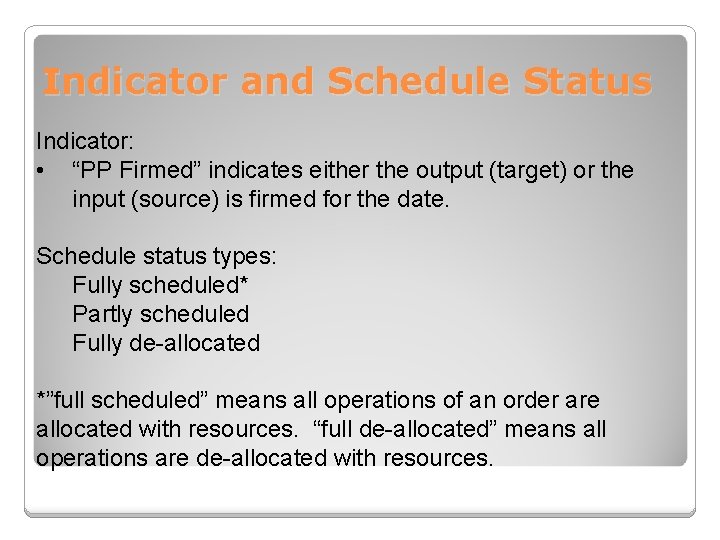
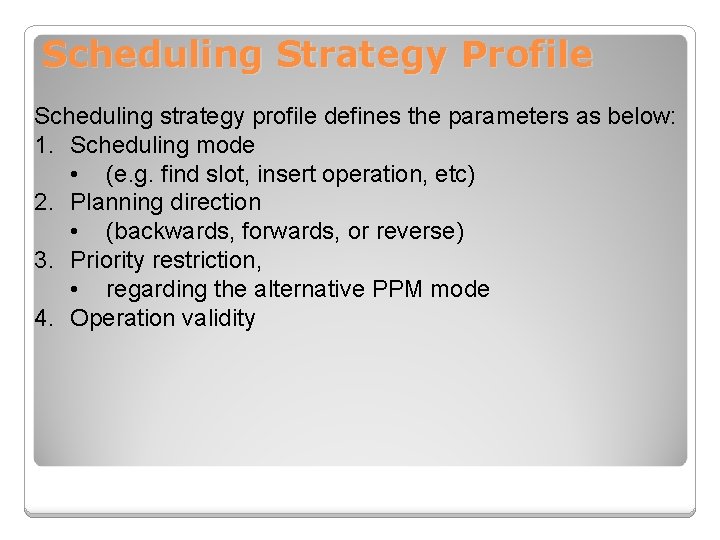
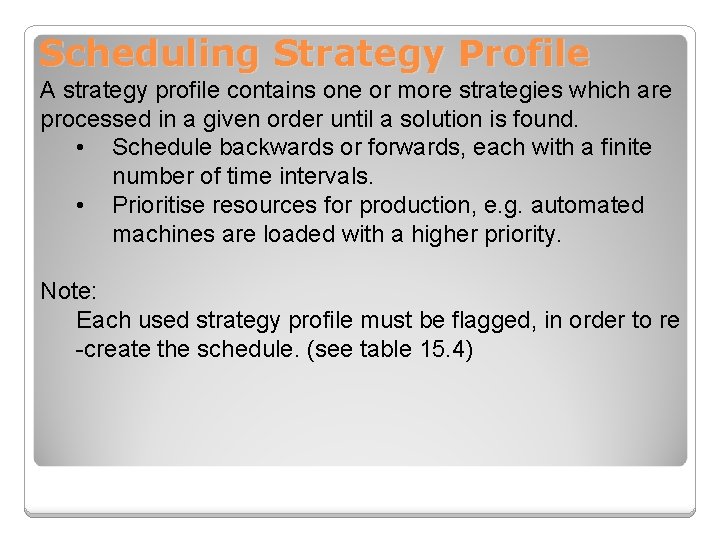
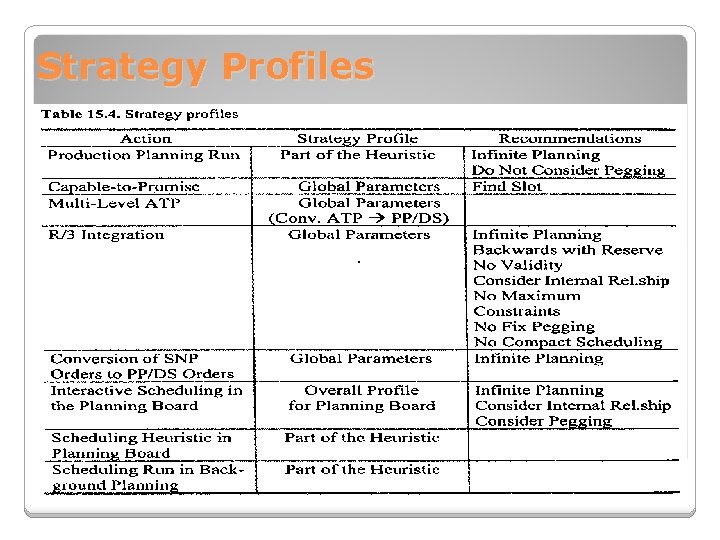
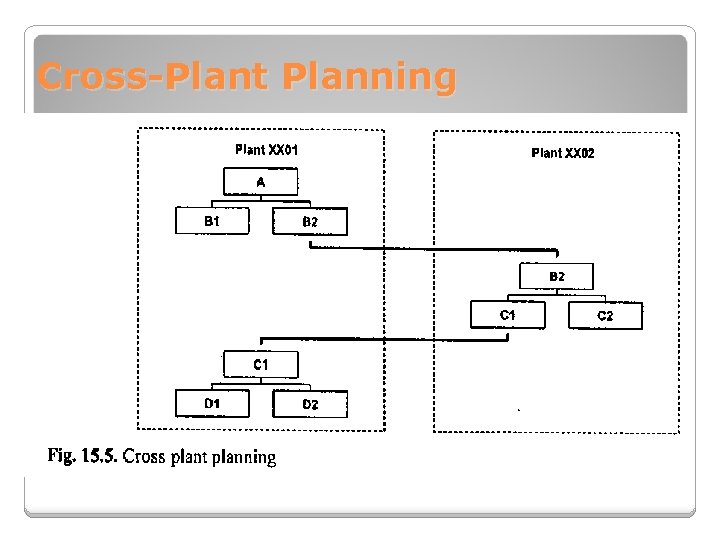
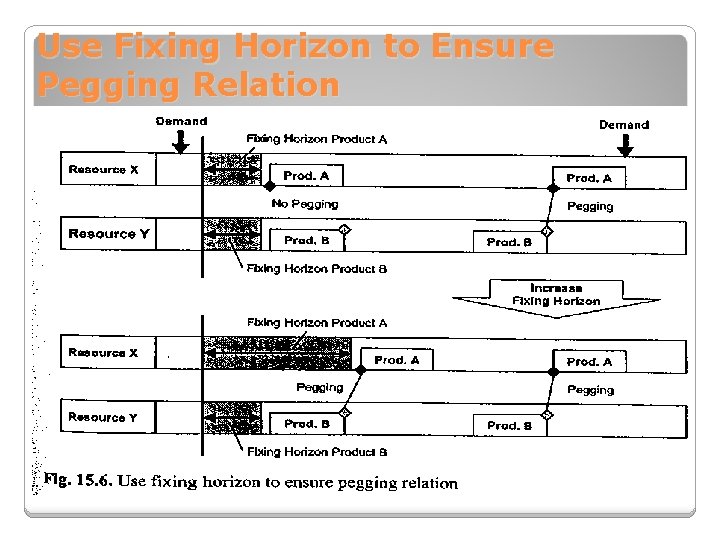
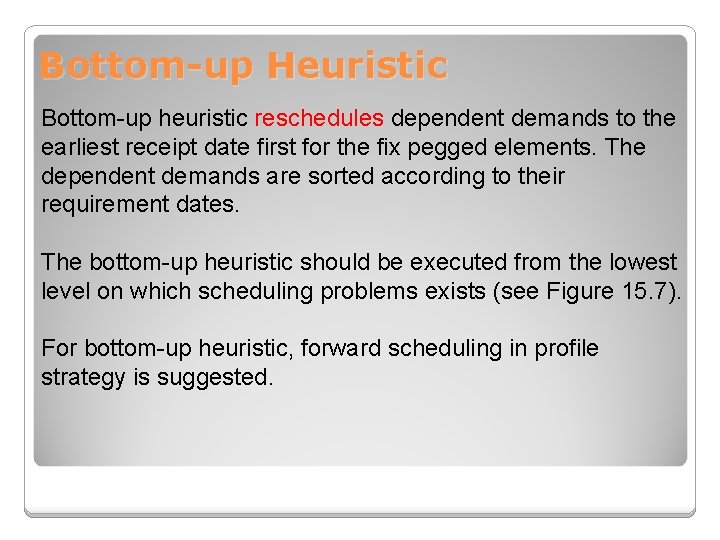
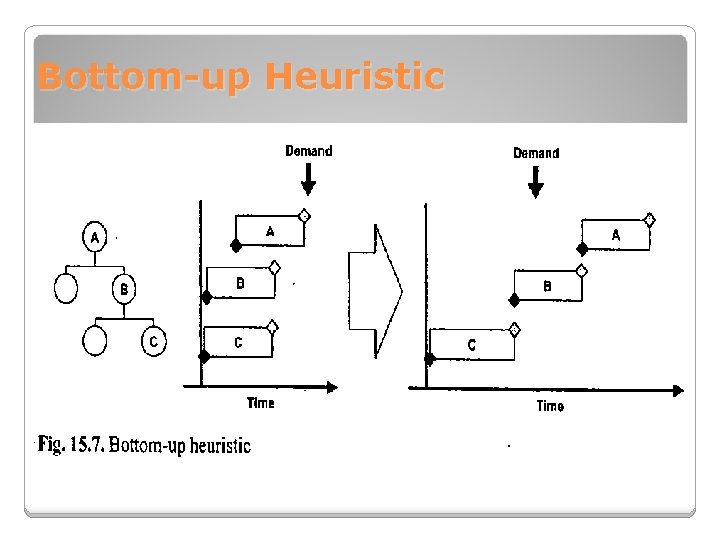
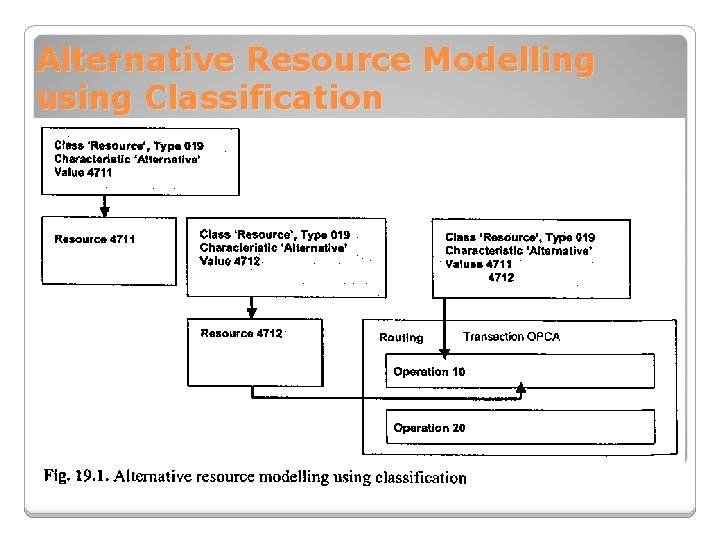
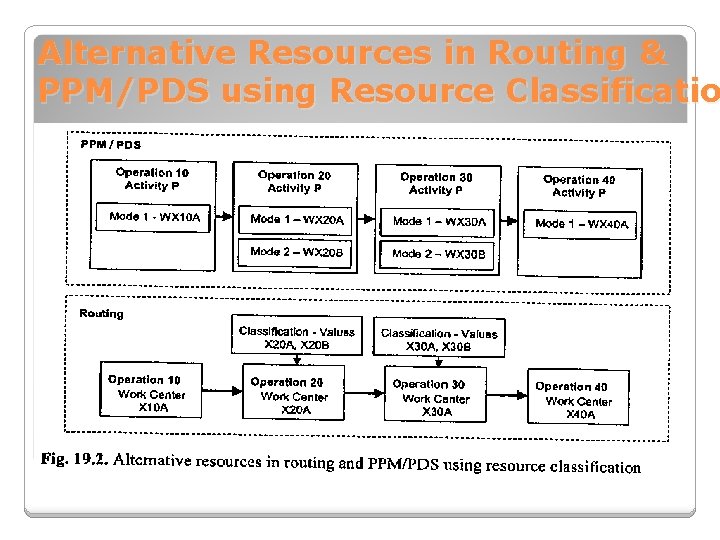
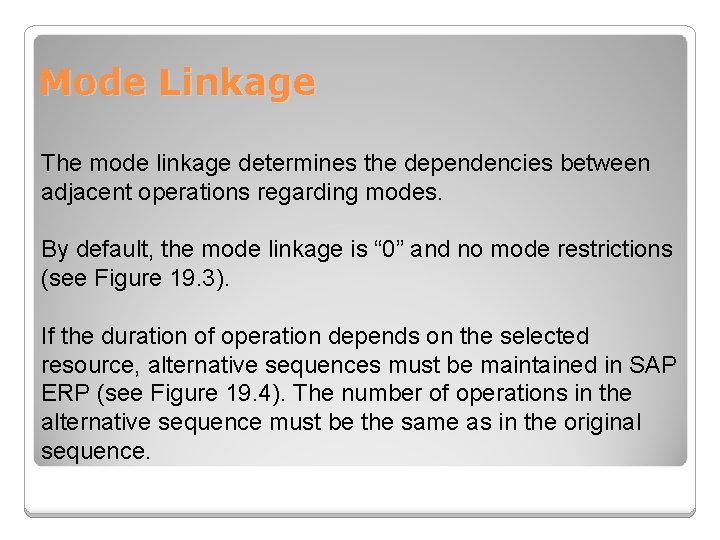
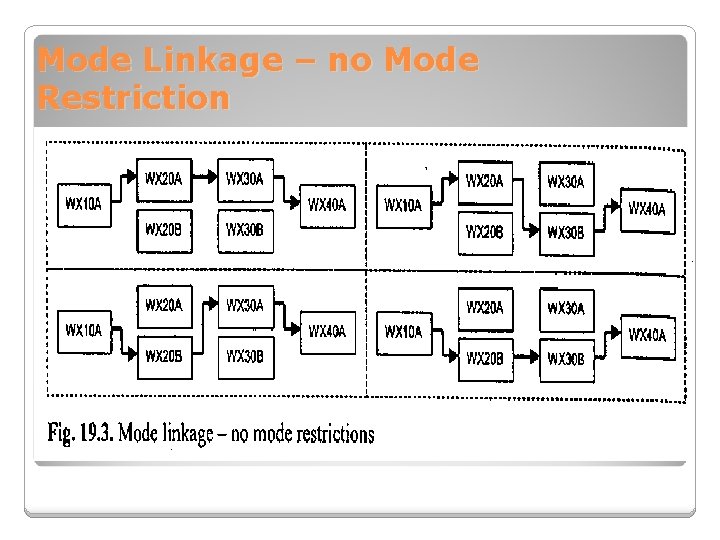
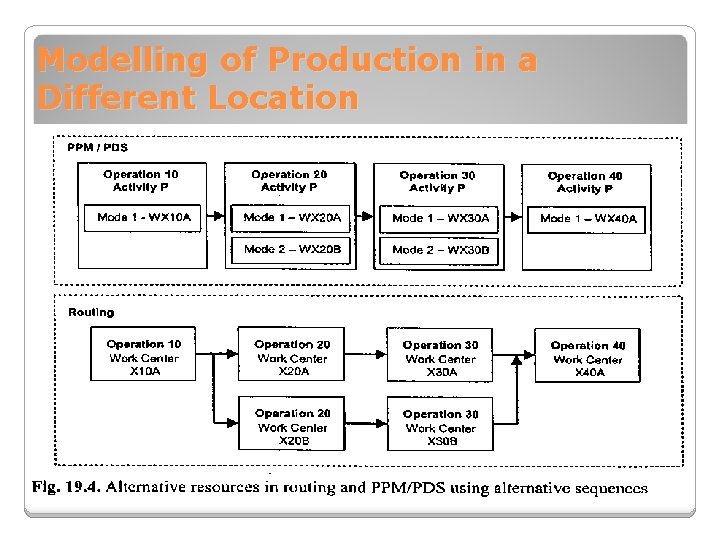
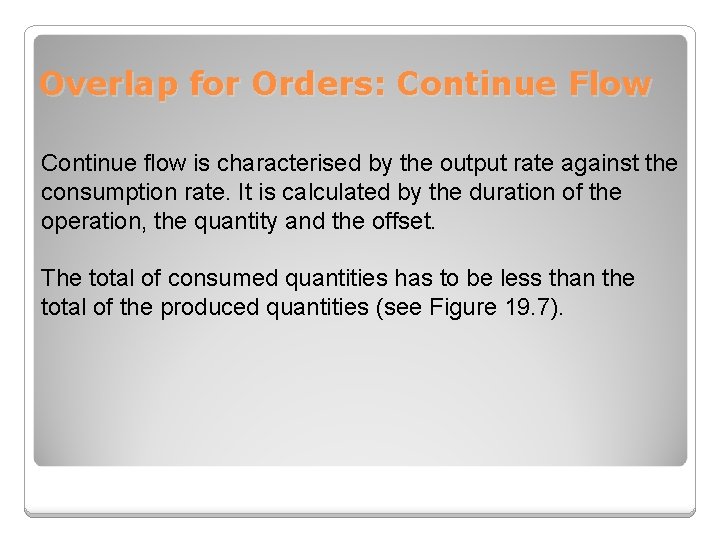
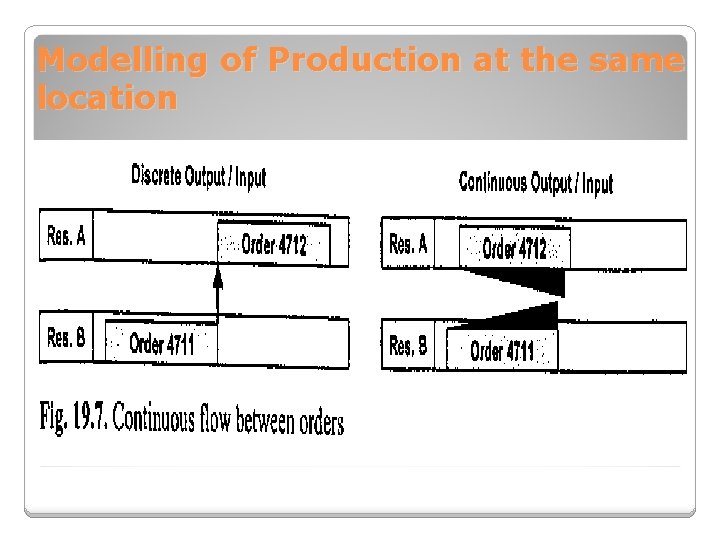
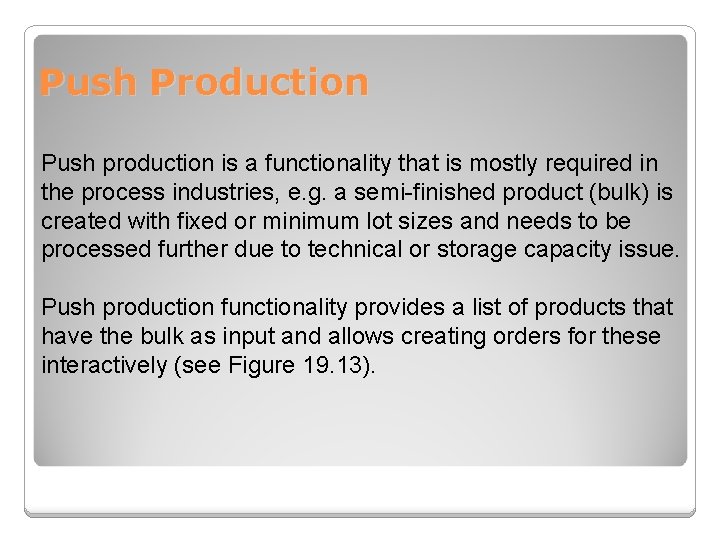
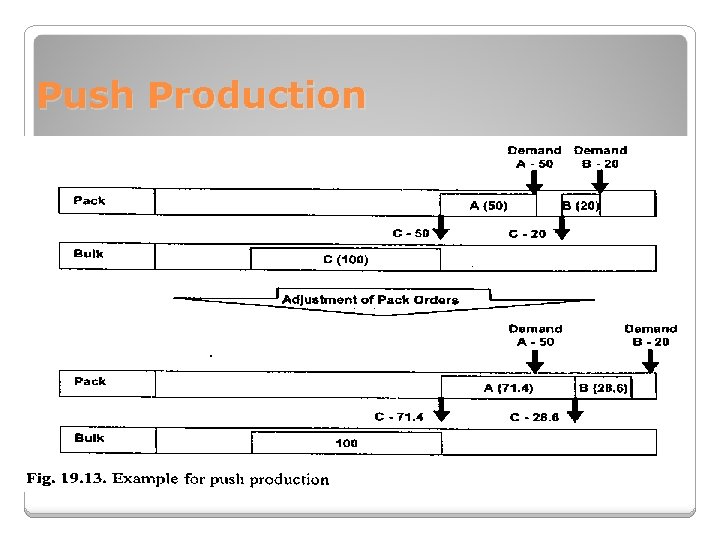
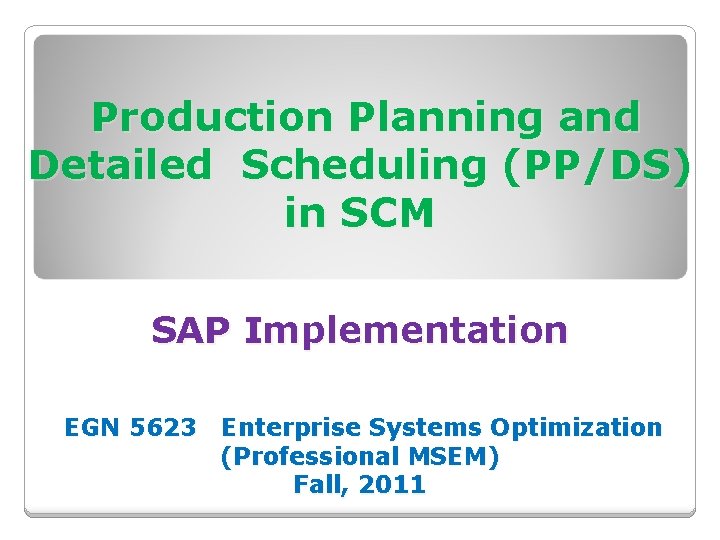
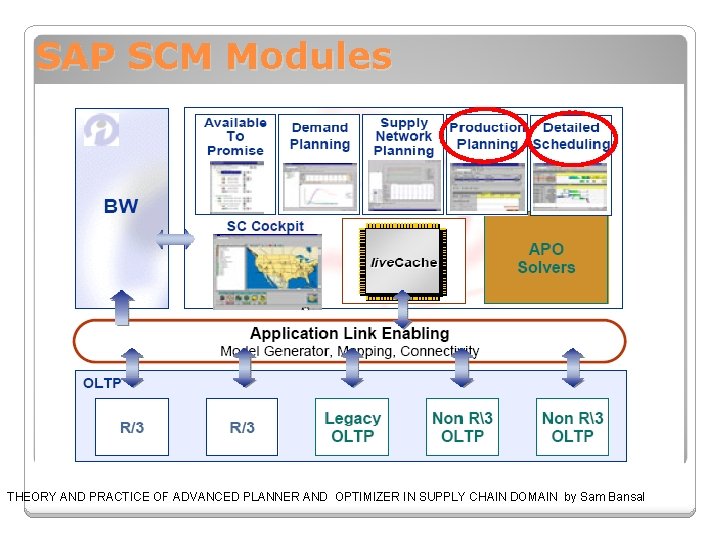
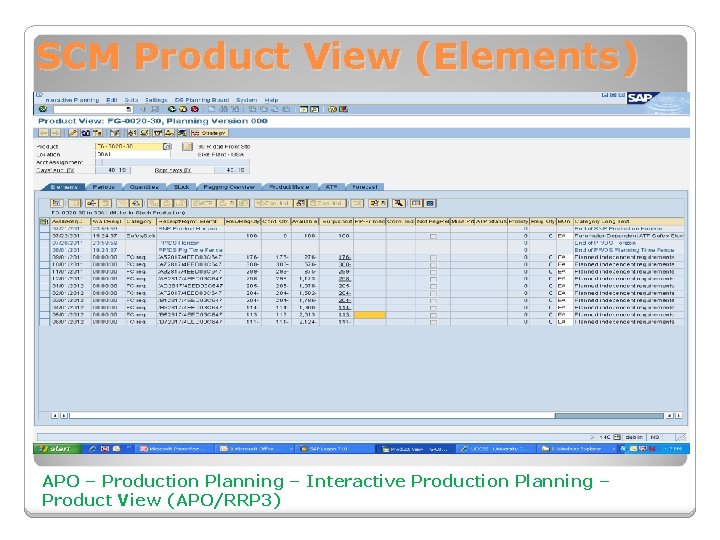
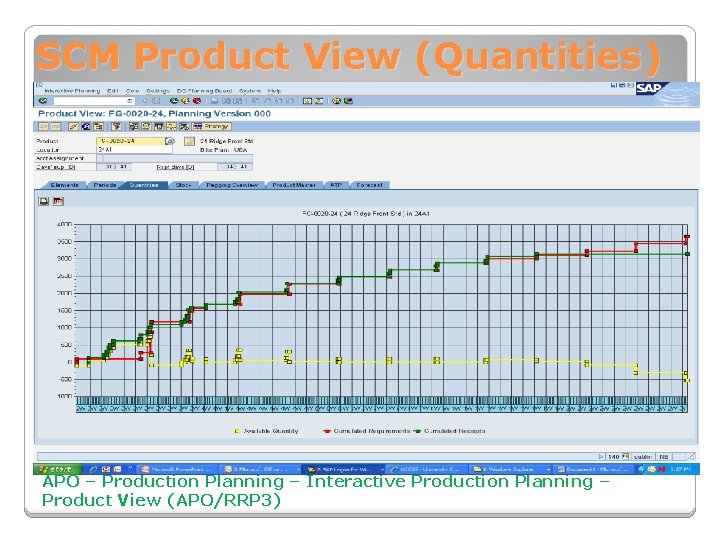
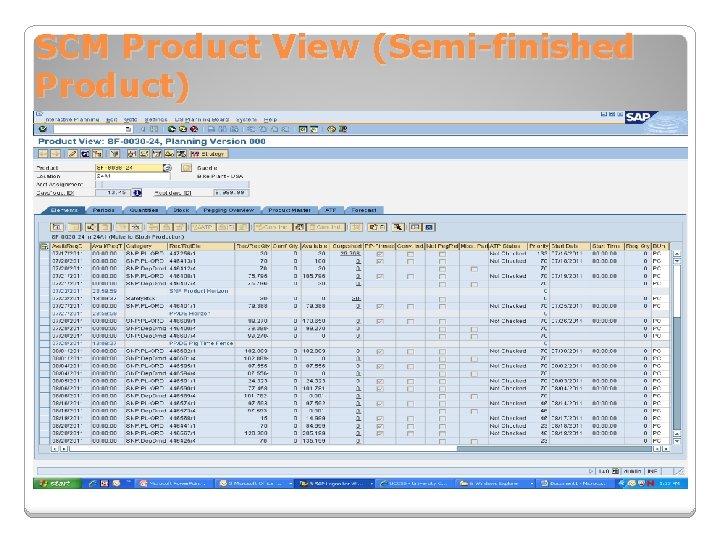

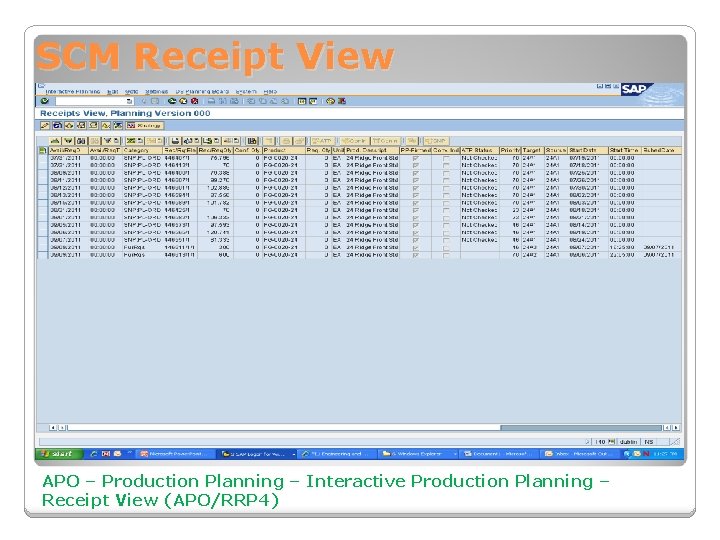
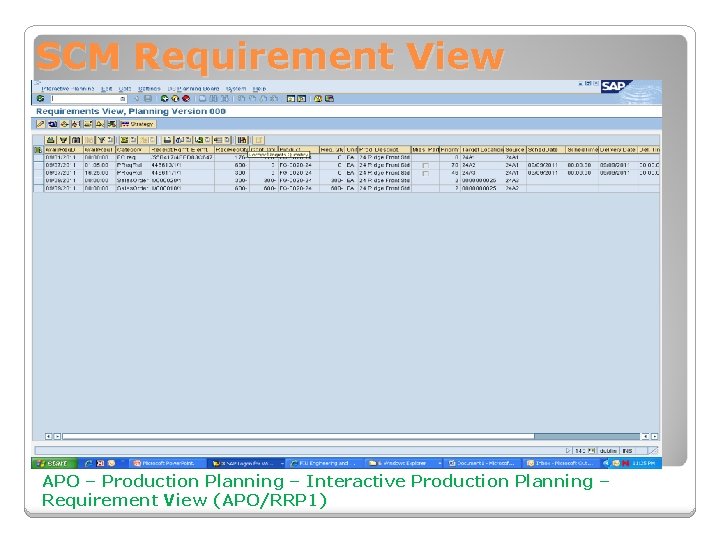
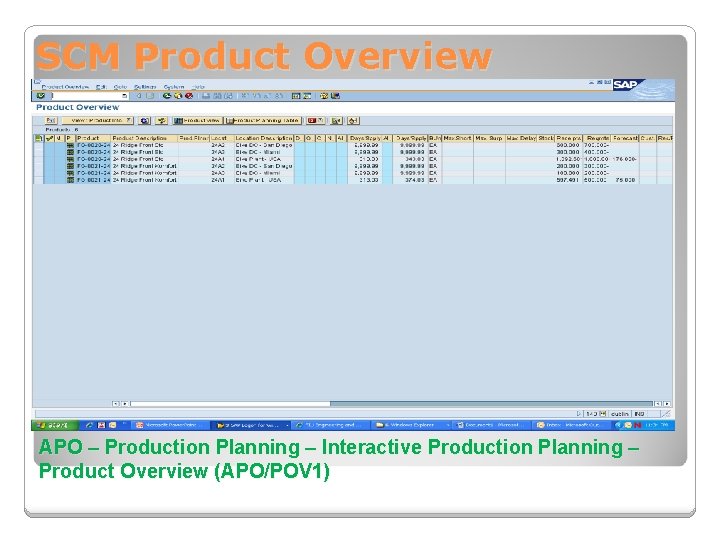
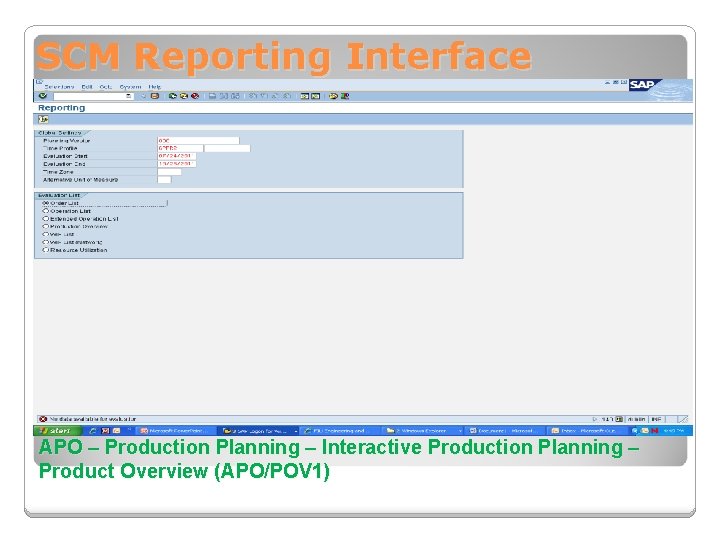
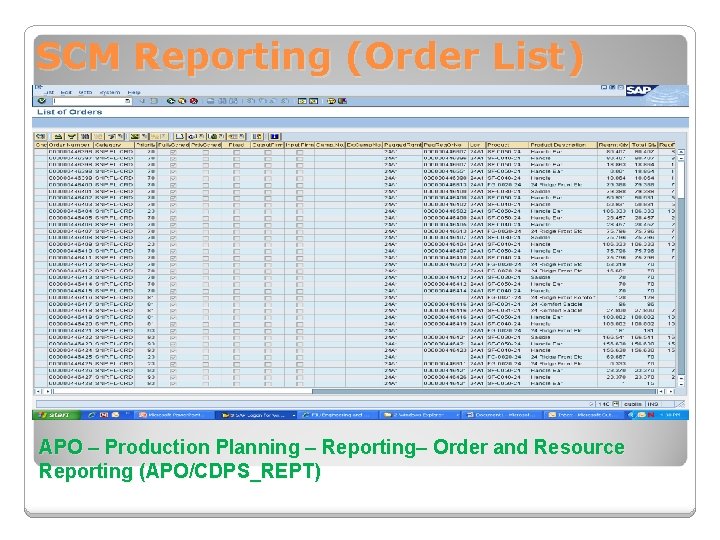
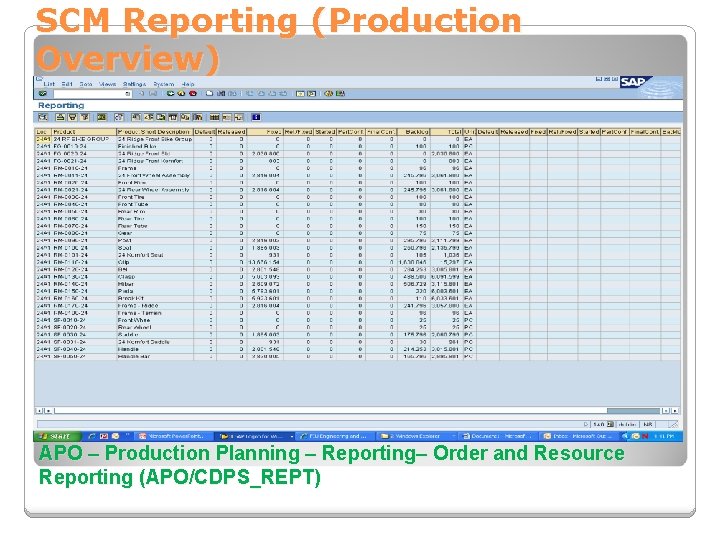
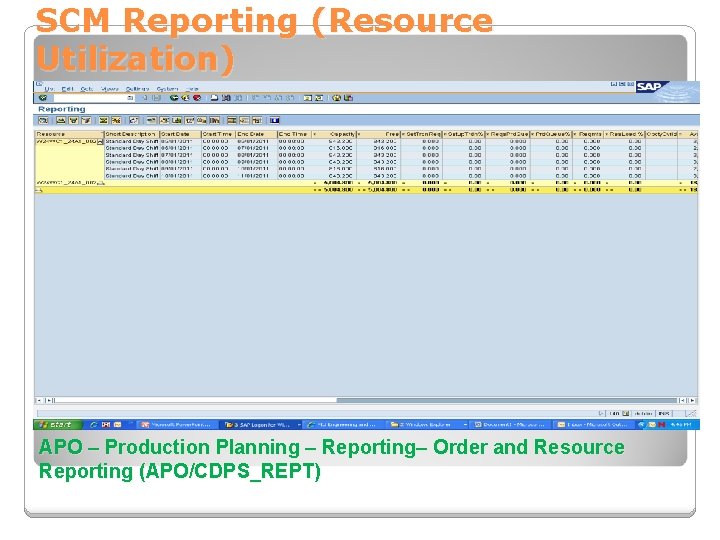
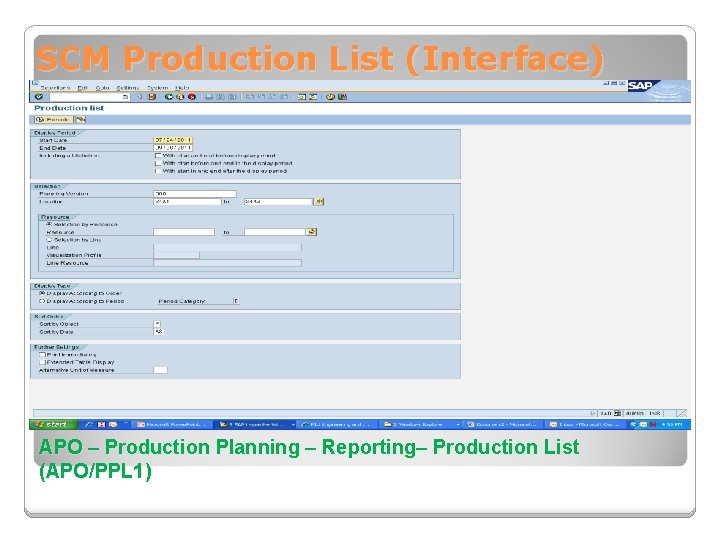

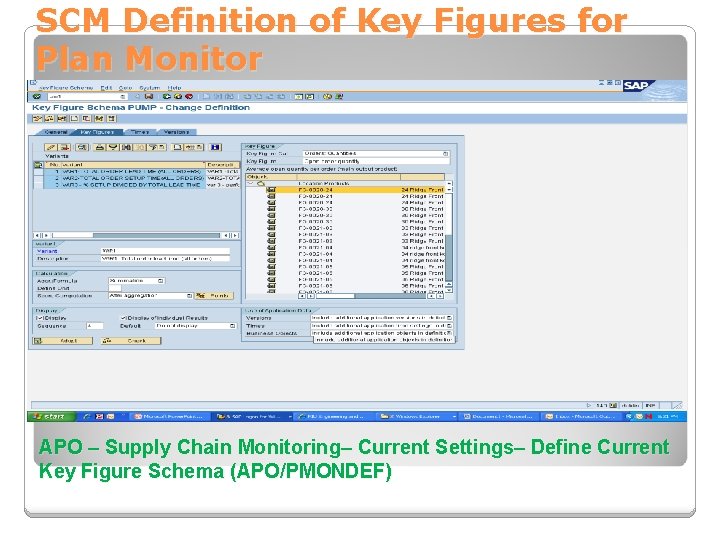
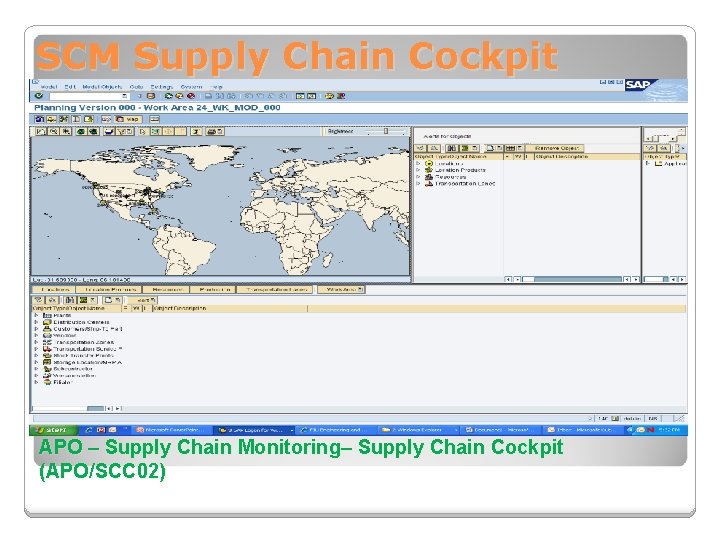
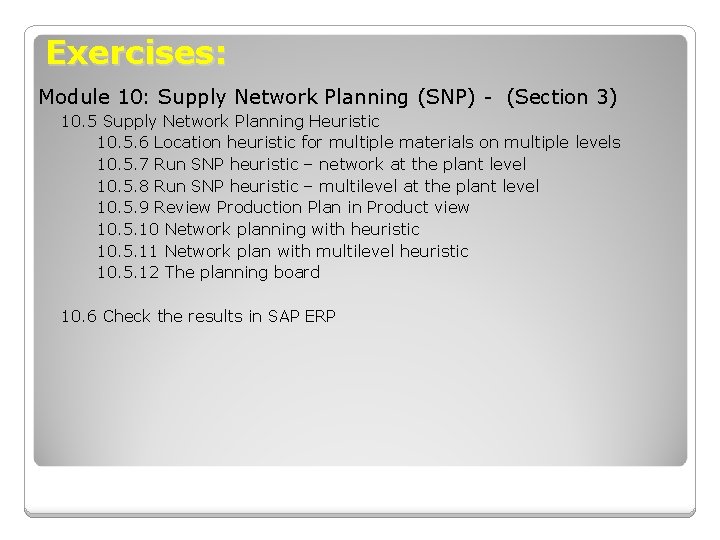
- Slides: 50
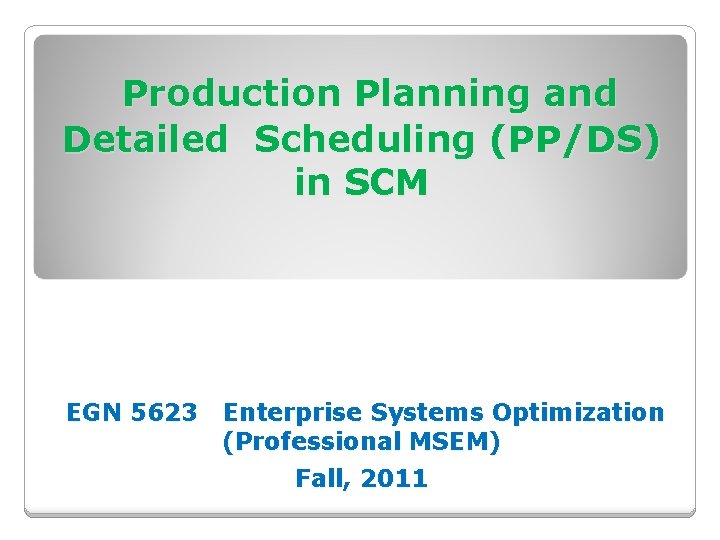
Production Planning and Detailed Scheduling (PP/DS) in SCM EGN 5623 Enterprise Systems Optimization (Professional MSEM) Fall, 2011
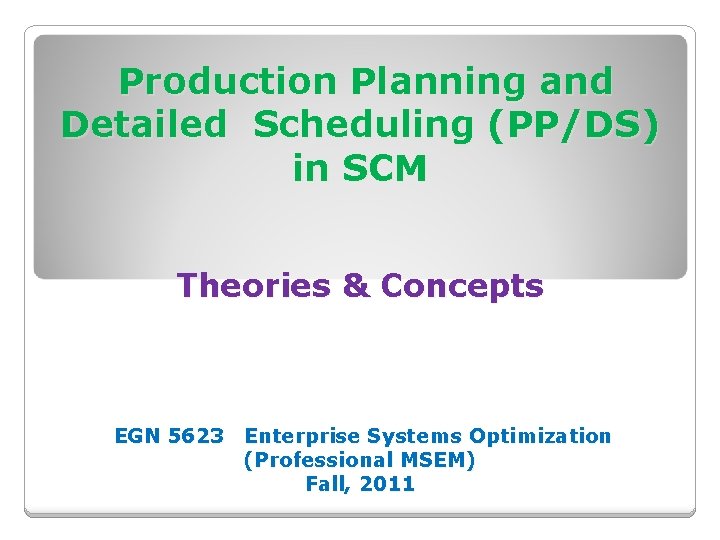
Production Planning and Detailed Scheduling (PP/DS) in SCM Theories & Concepts EGN 5623 Enterprise Systems Optimization (Professional MSEM) Fall, 2011
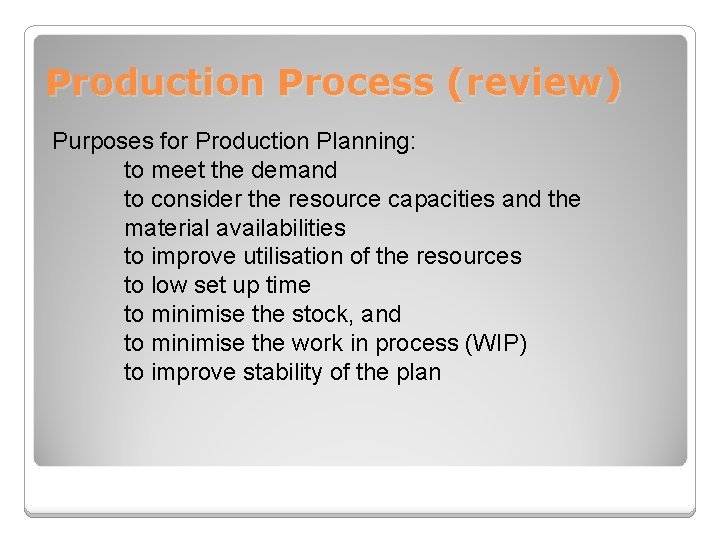
Production Process (review) Purposes for Production Planning: to meet the demand to consider the resource capacities and the material availabilities to improve utilisation of the resources to low set up time to minimise the stock, and to minimise the work in process (WIP) to improve stability of the plan
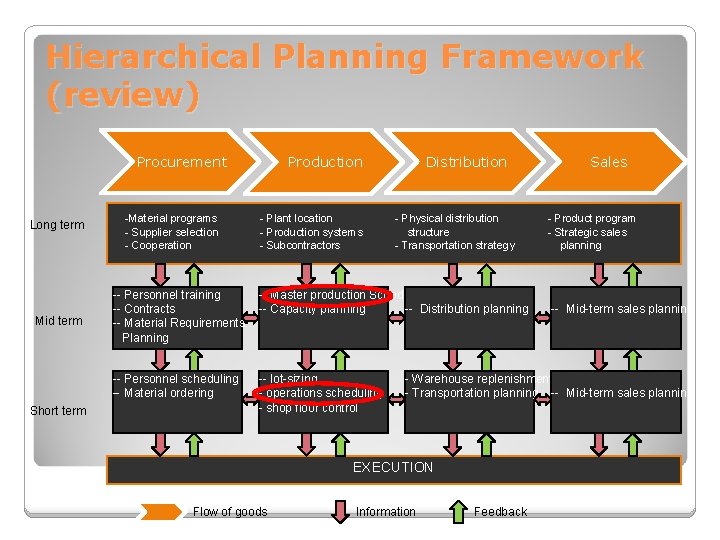
Hierarchical Planning Framework (review) Procurement Long term Mid term Short term -Material programs - Supplier selection - Cooperation Distribution Production - Plant location - Production systems - Subcontractors - Physical distribution structure - Transportation strategy -- Personnel training -- Contracts -- Material Requirements Planning -- Master production Scheduling -- Capacity planning -- Distribution planning -- Personnel scheduling -- Material ordering -- lot-sizing - operations scheduling - shop floor control - Product program - Strategic sales planning -- Mid-term sales planning - Warehouse replenishment - Transportation planning -- Mid-term sales planning EXECUTION Flow of goods Sales Information Feedback
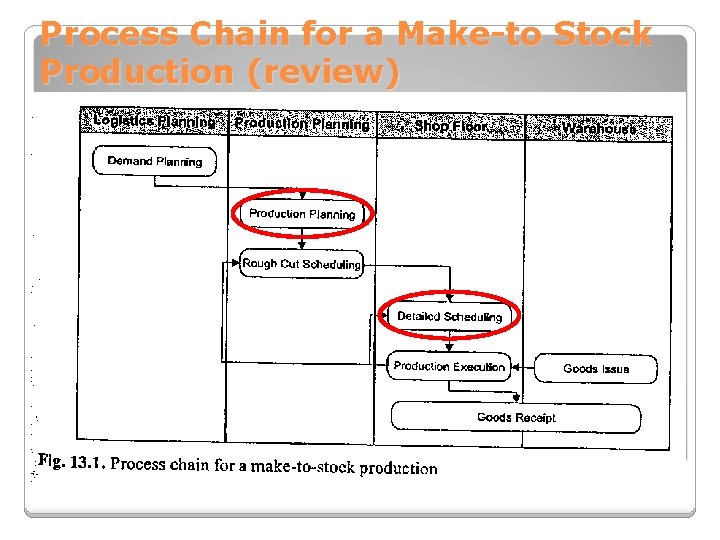
Process Chain for a Make-to Stock Production (review)
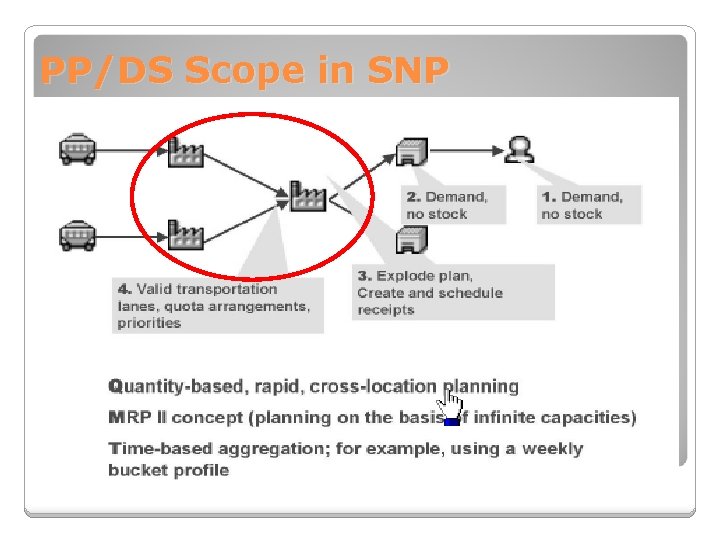
PP/DS Scope in SNP
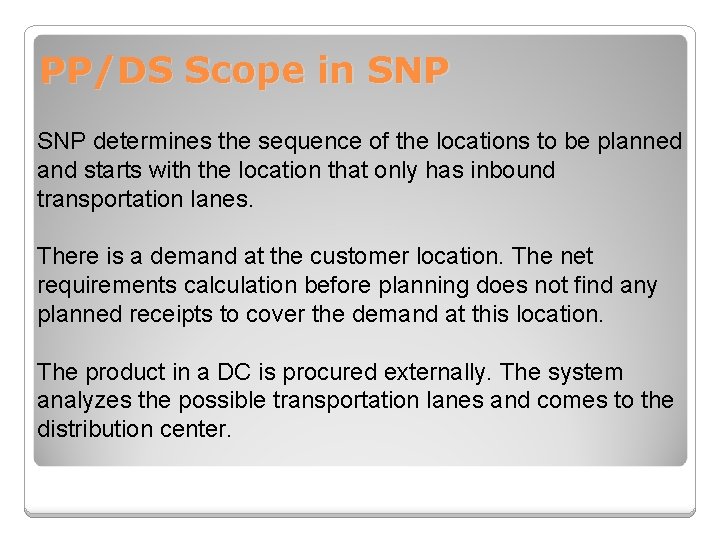
PP/DS Scope in SNP determines the sequence of the locations to be planned and starts with the location that only has inbound transportation lanes. There is a demand at the customer location. The net requirements calculation before planning does not find any planned receipts to cover the demand at this location. The product in a DC is procured externally. The system analyzes the possible transportation lanes and comes to the distribution center.
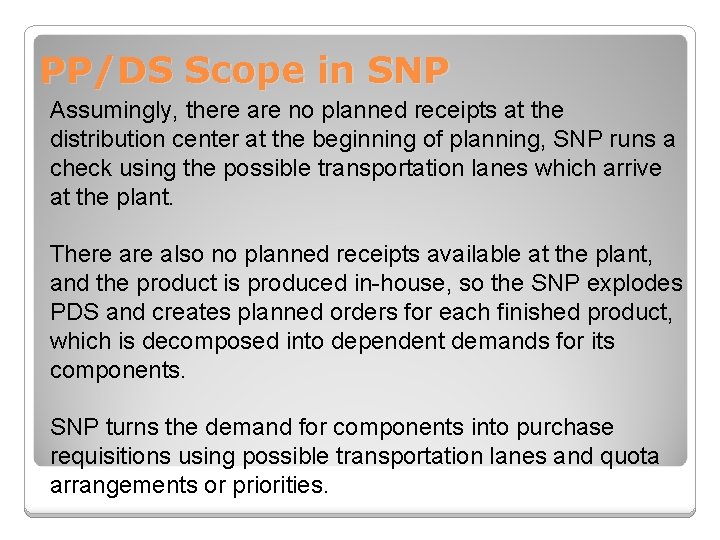
PP/DS Scope in SNP Assumingly, there are no planned receipts at the distribution center at the beginning of planning, SNP runs a check using the possible transportation lanes which arrive at the plant. There also no planned receipts available at the plant, and the product is produced in-house, so the SNP explodes PDS and creates planned orders for each finished product, which is decomposed into dependent demands for its components. SNP turns the demand for components into purchase requisitions using possible transportation lanes and quota arrangements or priorities.
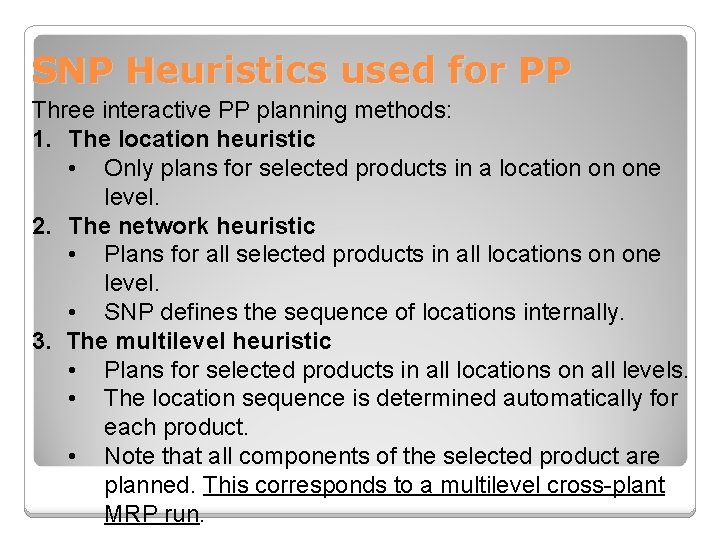
SNP Heuristics used for PP Three interactive PP planning methods: 1. The location heuristic • Only plans for selected products in a location on one level. 2. The network heuristic • Plans for all selected products in all locations on one level. • SNP defines the sequence of locations internally. 3. The multilevel heuristic • Plans for selected products in all locations on all levels. • The location sequence is determined automatically for each product. • Note that all components of the selected product are planned. This corresponds to a multilevel cross-plant MRP run.
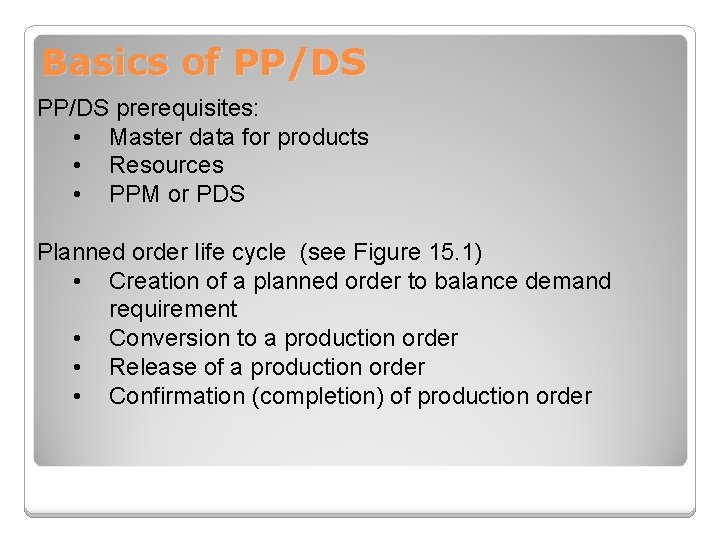
Basics of PP/DS prerequisites: • Master data for products • Resources • PPM or PDS Planned order life cycle (see Figure 15. 1) • Creation of a planned order to balance demand requirement • Conversion to a production order • Release of a production order • Confirmation (completion) of production order
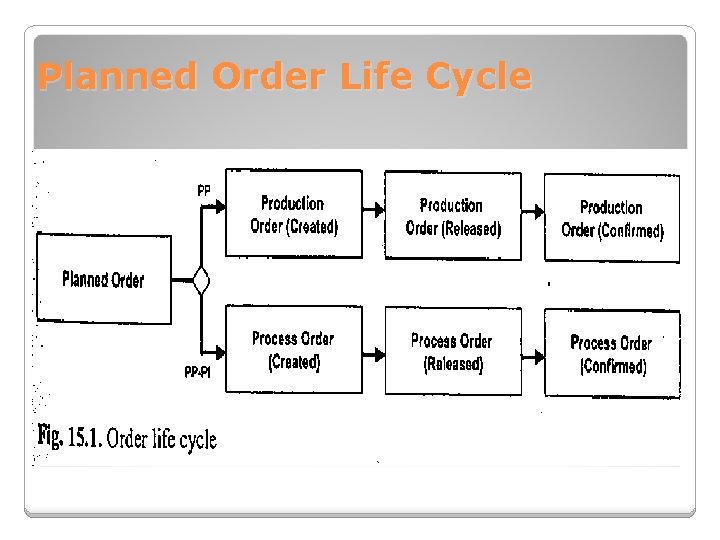
Planned Order Life Cycle
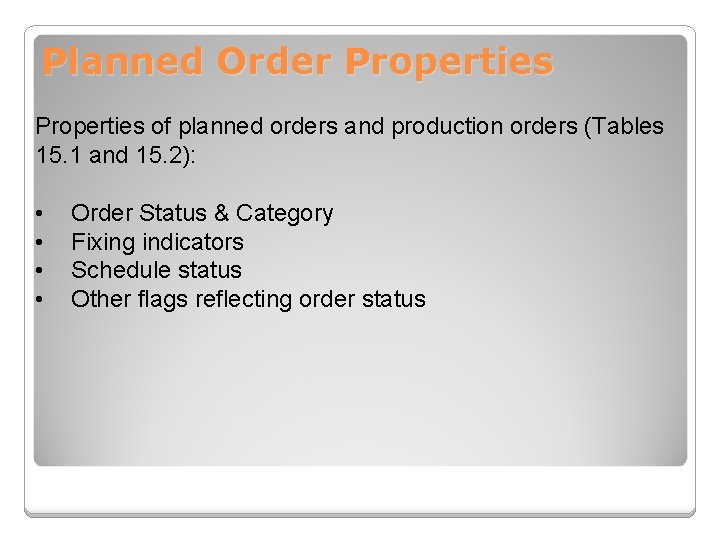
Planned Order Properties of planned orders and production orders (Tables 15. 1 and 15. 2): • • Order Status & Category Fixing indicators Schedule status Other flags reflecting order status
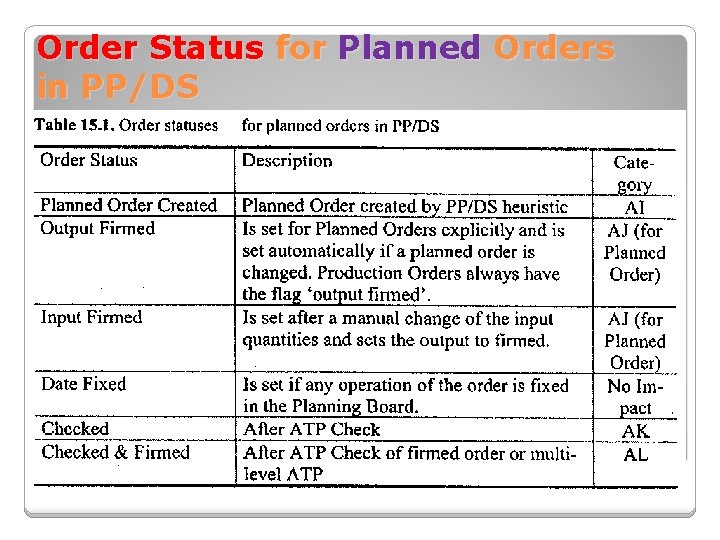
Order Status for Planned Orders in PP/DS
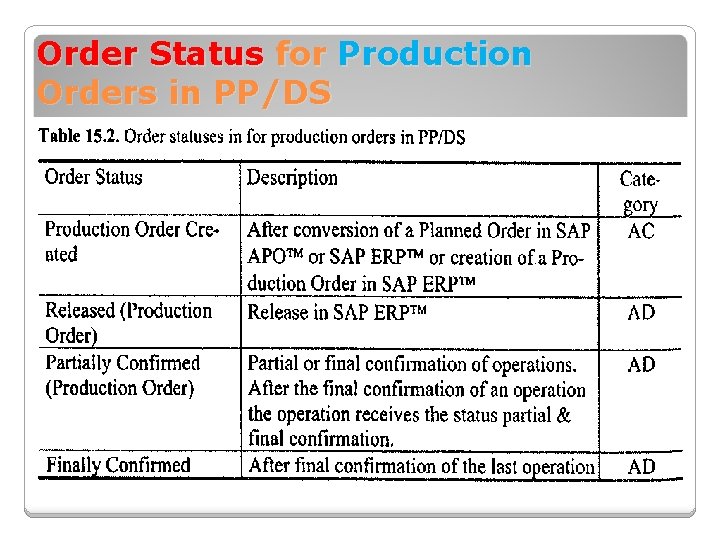
Order Status for Production Orders in PP/DS
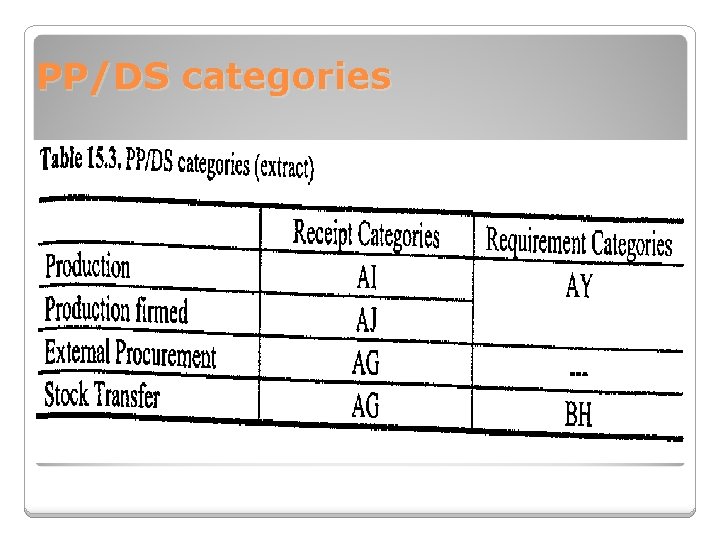
PP/DS categories
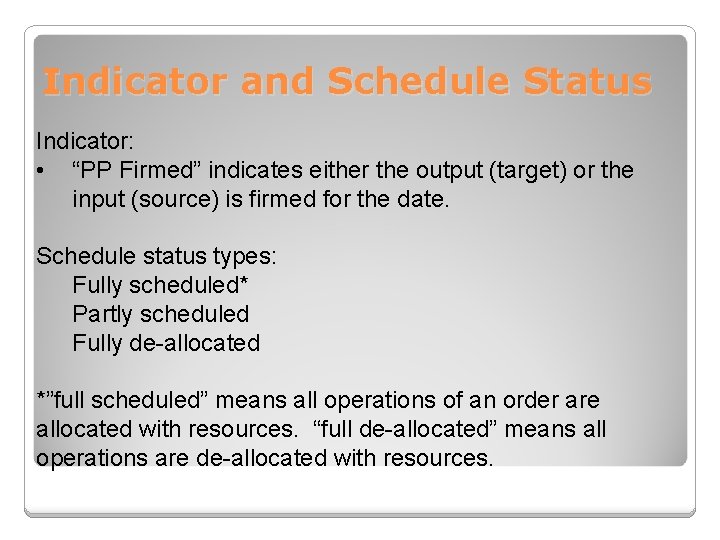
Indicator and Schedule Status Indicator: • “PP Firmed” indicates either the output (target) or the input (source) is firmed for the date. Schedule status types: Fully scheduled* Partly scheduled Fully de-allocated *”full scheduled” means all operations of an order are allocated with resources. “full de-allocated” means all operations are de-allocated with resources.
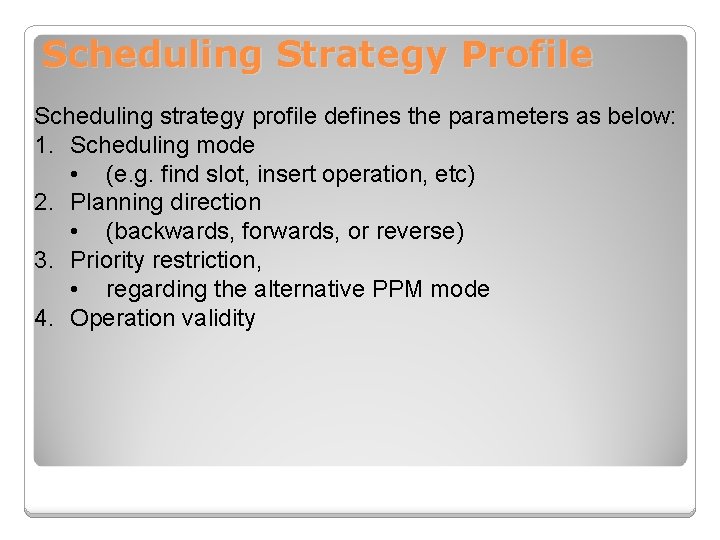
Scheduling Strategy Profile Scheduling strategy profile defines the parameters as below: 1. Scheduling mode • (e. g. find slot, insert operation, etc) 2. Planning direction • (backwards, forwards, or reverse) 3. Priority restriction, • regarding the alternative PPM mode 4. Operation validity
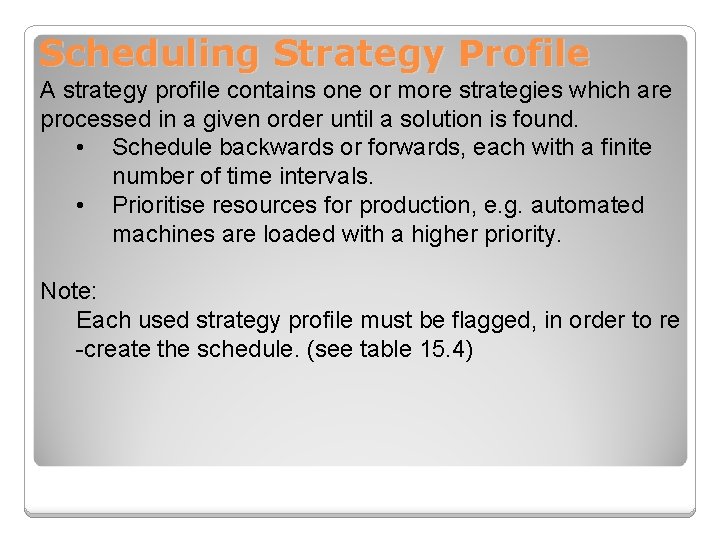
Scheduling Strategy Profile A strategy profile contains one or more strategies which are processed in a given order until a solution is found. • Schedule backwards or forwards, each with a finite number of time intervals. • Prioritise resources for production, e. g. automated machines are loaded with a higher priority. Note: Each used strategy profile must be flagged, in order to re -create the schedule. (see table 15. 4)
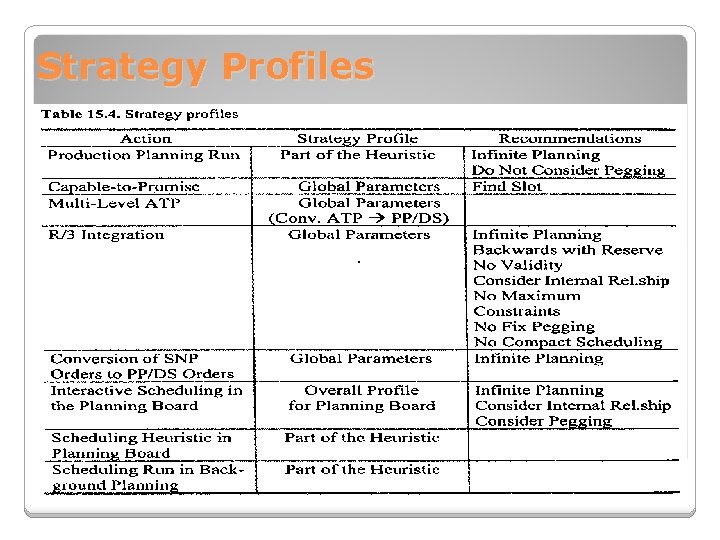
Strategy Profiles
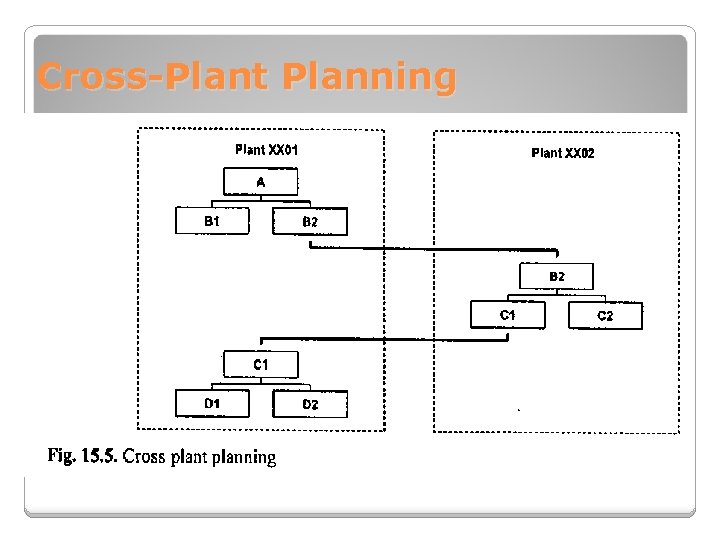
Cross-Plant Planning
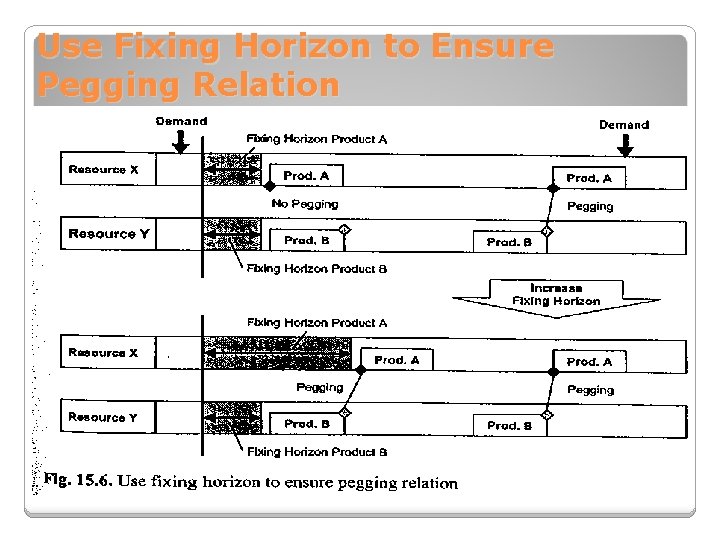
Use Fixing Horizon to Ensure Pegging Relation
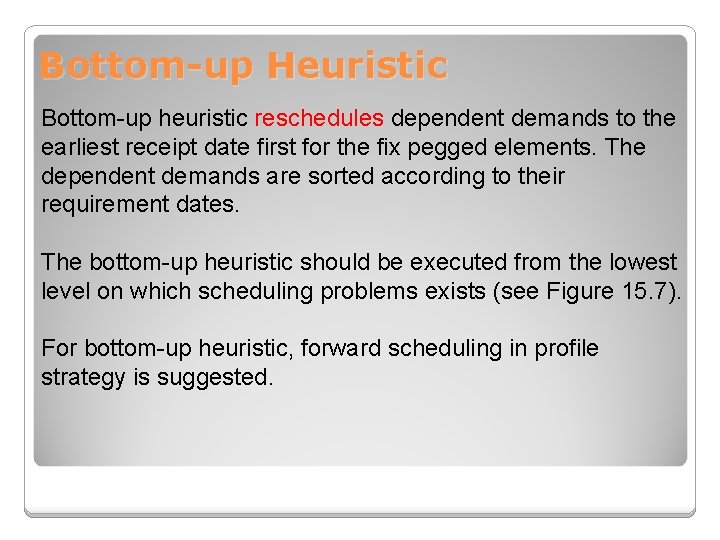
Bottom-up Heuristic Bottom-up heuristic reschedules dependent demands to the earliest receipt date first for the fix pegged elements. The dependent demands are sorted according to their requirement dates. The bottom-up heuristic should be executed from the lowest level on which scheduling problems exists (see Figure 15. 7). For bottom-up heuristic, forward scheduling in profile strategy is suggested.
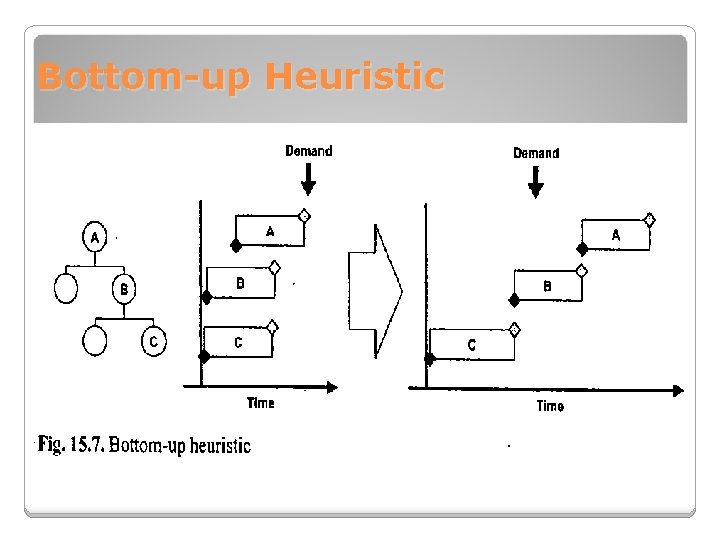
Bottom-up Heuristic
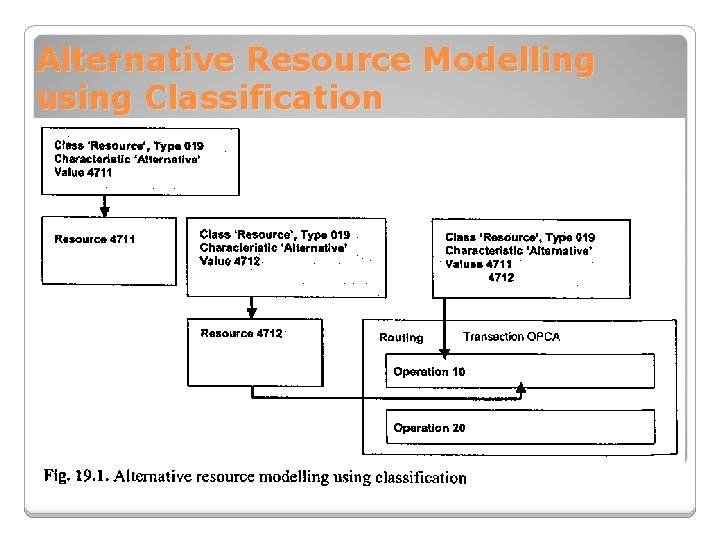
Alternative Resource Modelling using Classification
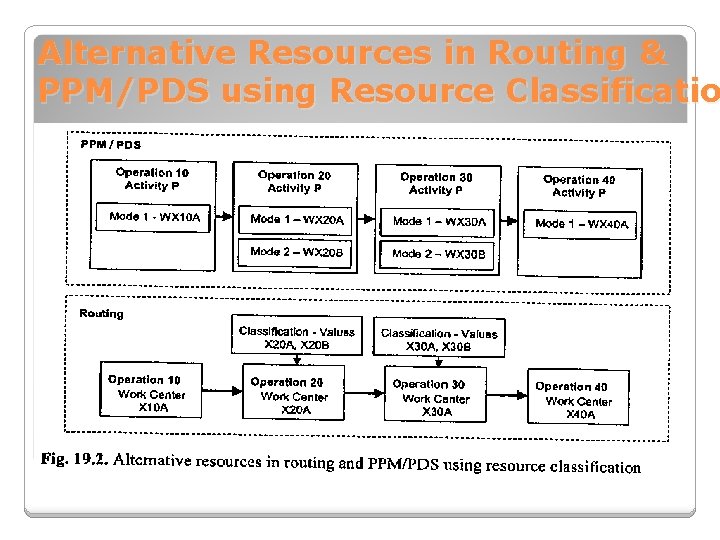
Alternative Resources in Routing & PPM/PDS using Resource Classificatio
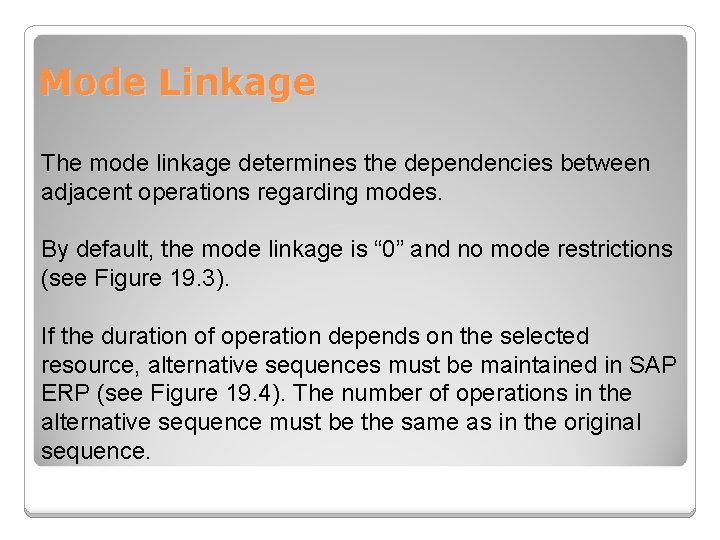
Mode Linkage The mode linkage determines the dependencies between adjacent operations regarding modes. By default, the mode linkage is “ 0” and no mode restrictions (see Figure 19. 3). If the duration of operation depends on the selected resource, alternative sequences must be maintained in SAP ERP (see Figure 19. 4). The number of operations in the alternative sequence must be the same as in the original sequence.
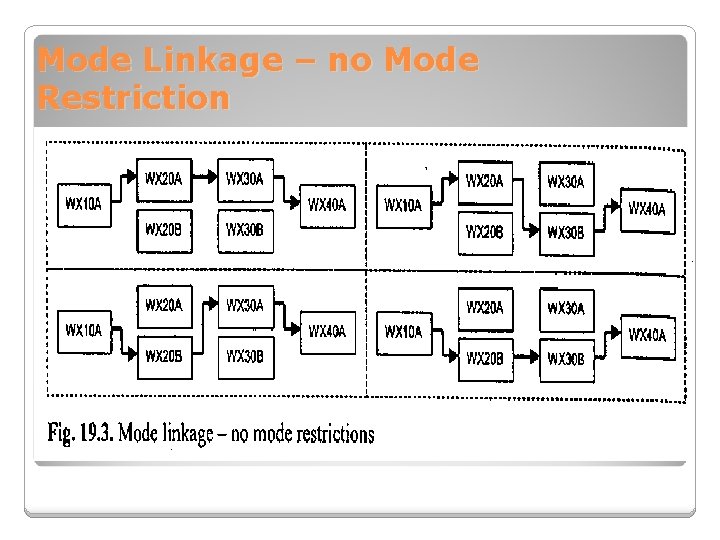
Mode Linkage – no Mode Restriction
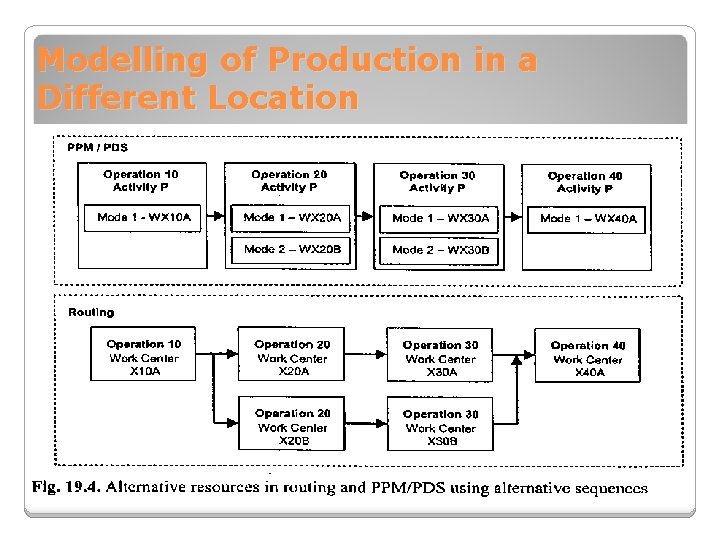
Modelling of Production in a Different Location
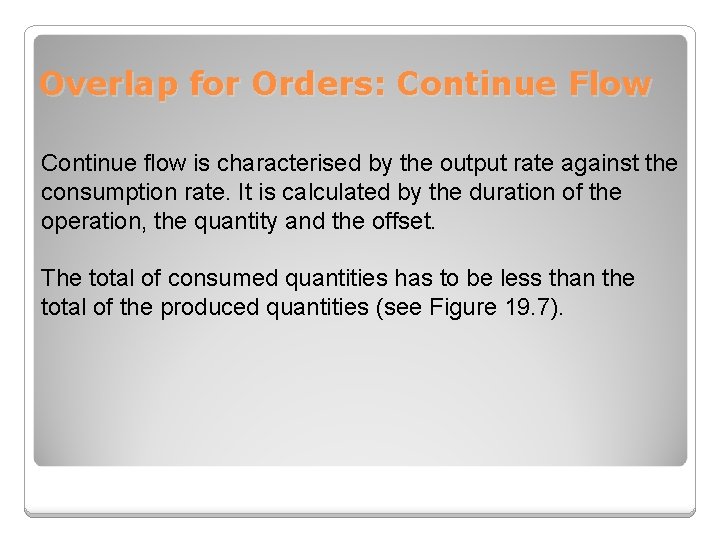
Overlap for Orders: Continue Flow Continue flow is characterised by the output rate against the consumption rate. It is calculated by the duration of the operation, the quantity and the offset. The total of consumed quantities has to be less than the total of the produced quantities (see Figure 19. 7).
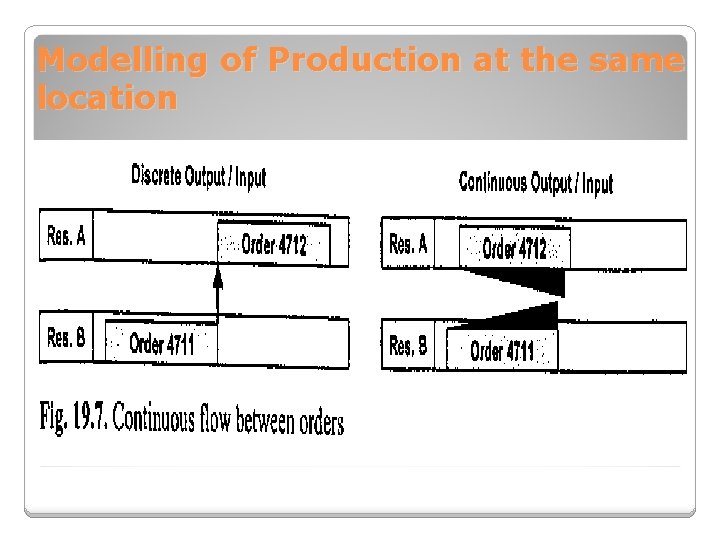
Modelling of Production at the same location
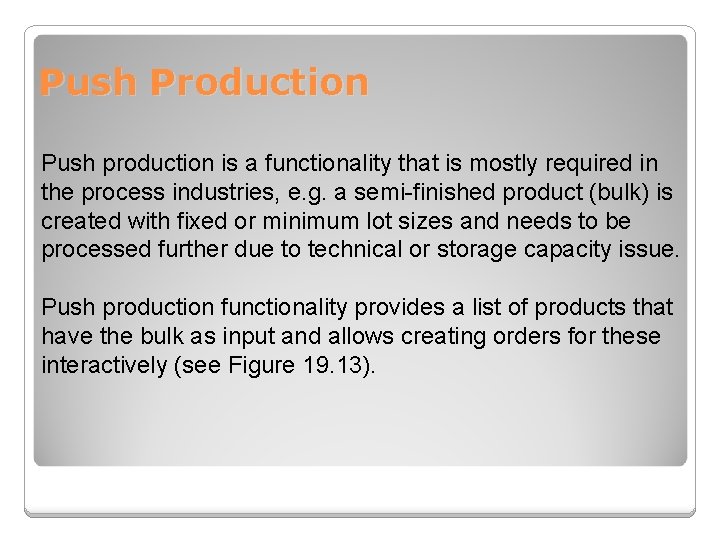
Push Production Push production is a functionality that is mostly required in the process industries, e. g. a semi-finished product (bulk) is created with fixed or minimum lot sizes and needs to be processed further due to technical or storage capacity issue. Push production functionality provides a list of products that have the bulk as input and allows creating orders for these interactively (see Figure 19. 13).
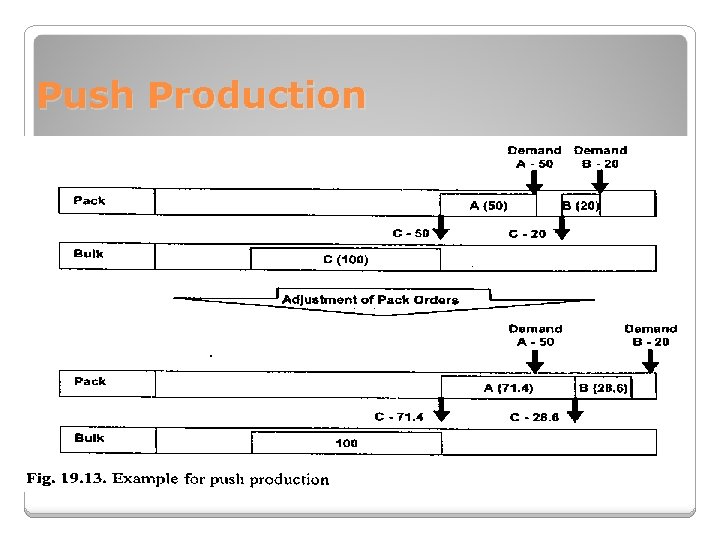
Push Production
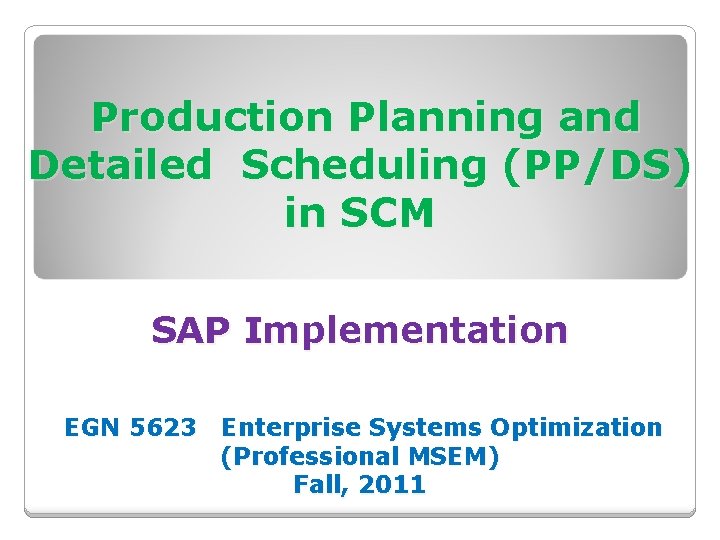
Production Planning and Detailed Scheduling (PP/DS) in SCM SAP Implementation EGN 5623 Enterprise Systems Optimization (Professional MSEM) Fall, 2011
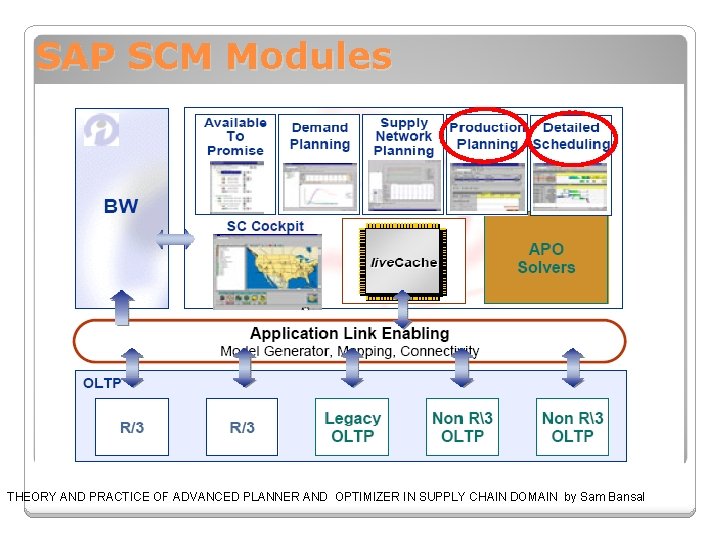
SAP SCM Modules THEORY AND PRACTICE OF ADVANCED PLANNER AND OPTIMIZER IN SUPPLY CHAIN DOMAIN by Sam Bansal
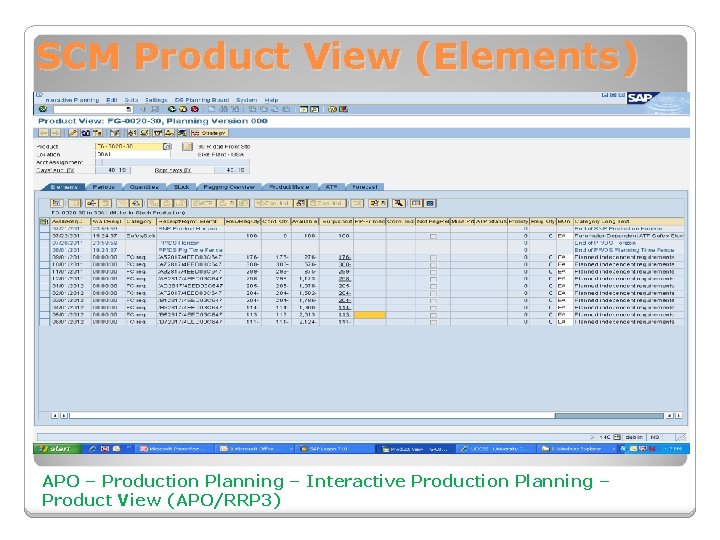
SCM Product View (Elements) APO – Production Planning – Interactive Production Planning – Product View (APO/RRP 3)
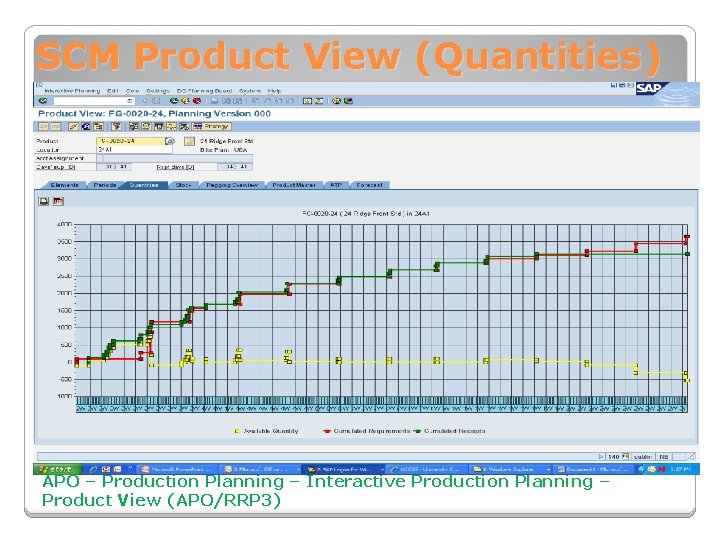
SCM Product View (Quantities) APO – Production Planning – Interactive Production Planning – Product View (APO/RRP 3)
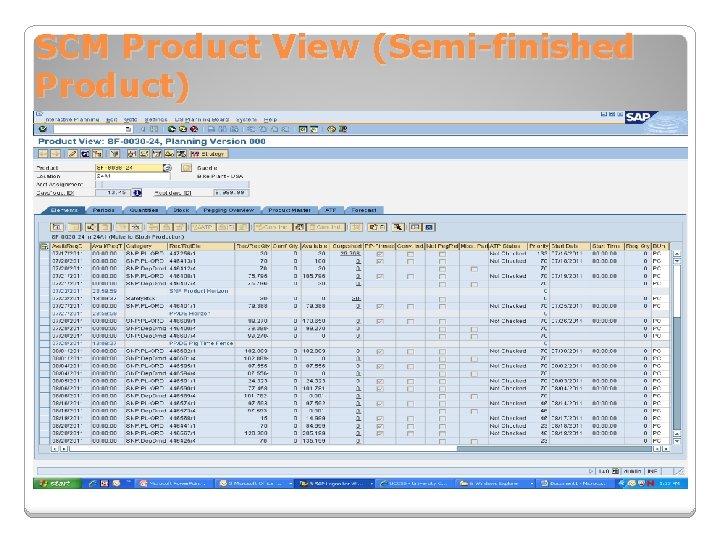
SCM Product View (Semi-finished Product)

SCM Product View (Raw Materials)
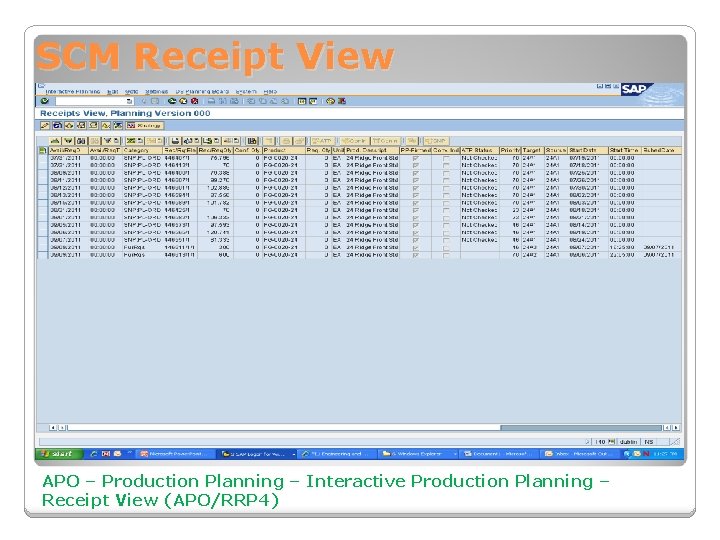
SCM Receipt View APO – Production Planning – Interactive Production Planning – Receipt View (APO/RRP 4)
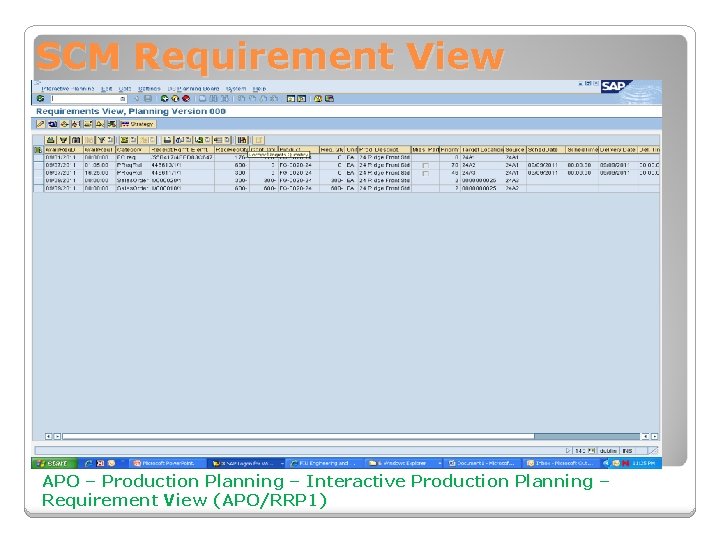
SCM Requirement View APO – Production Planning – Interactive Production Planning – Requirement View (APO/RRP 1)
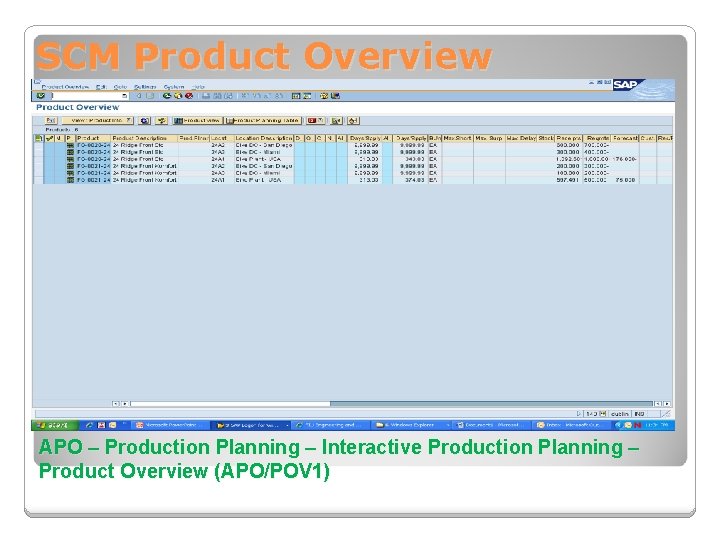
SCM Product Overview APO – Production Planning – Interactive Production Planning – Product Overview (APO/POV 1)
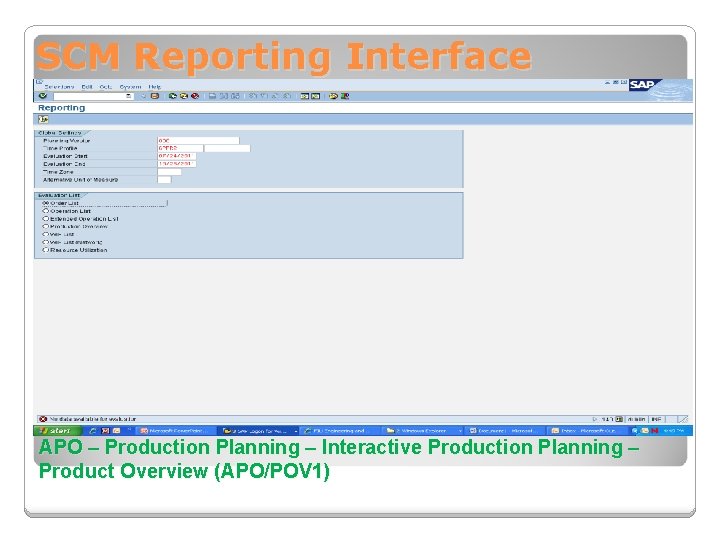
SCM Reporting Interface APO – Production Planning – Interactive Production Planning – Product Overview (APO/POV 1)
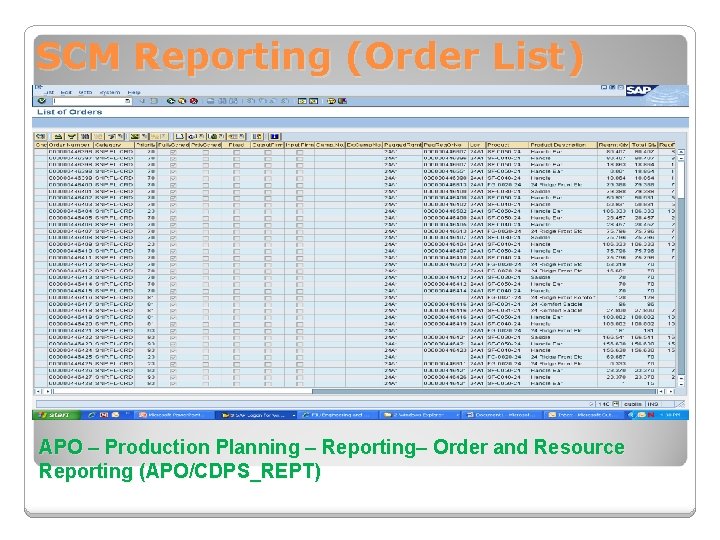
SCM Reporting (Order List) APO – Production Planning – Reporting– Order and Resource Reporting (APO/CDPS_REPT)
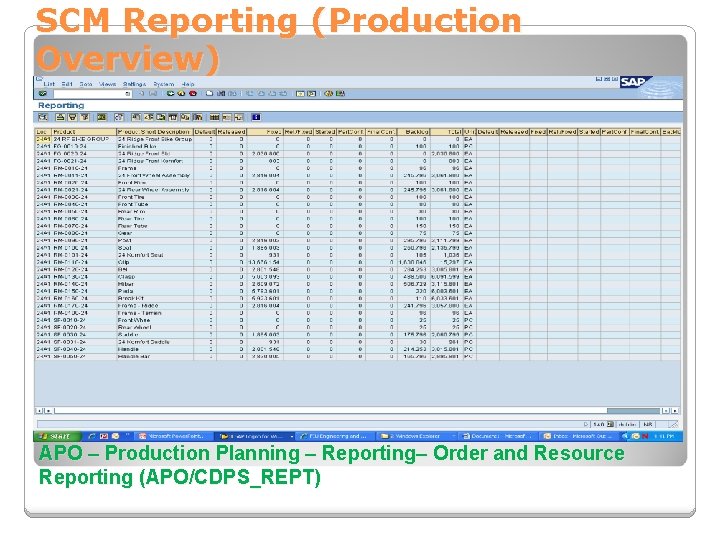
SCM Reporting (Production Overview) APO – Production Planning – Reporting– Order and Resource Reporting (APO/CDPS_REPT)
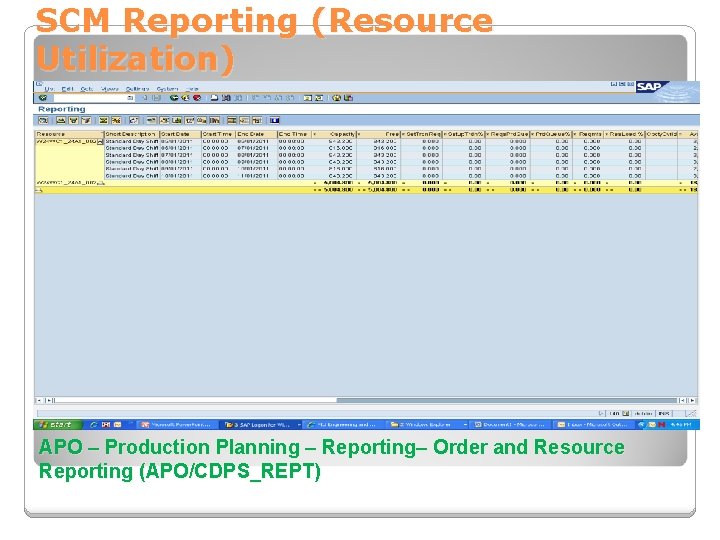
SCM Reporting (Resource Utilization) APO – Production Planning – Reporting– Order and Resource Reporting (APO/CDPS_REPT)
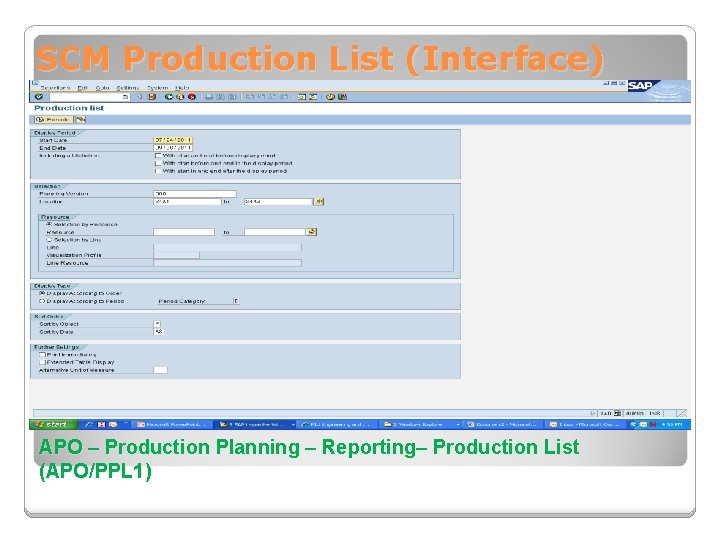
SCM Production List (Interface) APO – Production Planning – Reporting– Production List (APO/PPL 1)

SCM Production List APO – Production Planning – Reporting– Production List (APO/PPL 1)
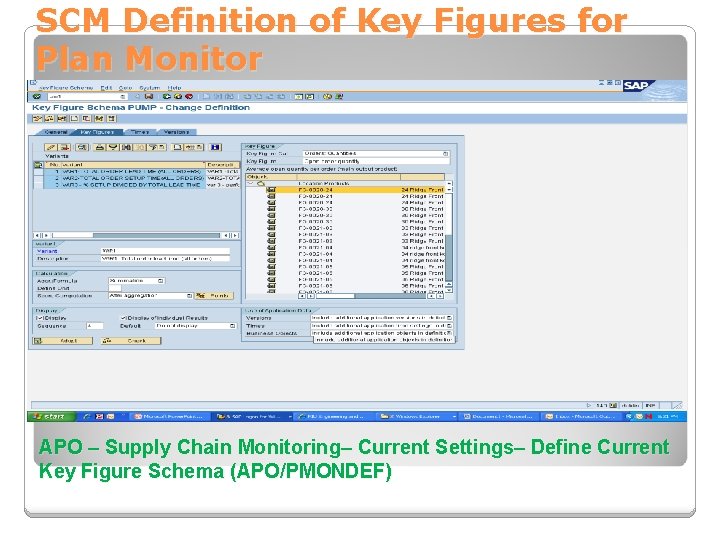
SCM Definition of Key Figures for Plan Monitor APO – Supply Chain Monitoring– Current Settings– Define Current Key Figure Schema (APO/PMONDEF)
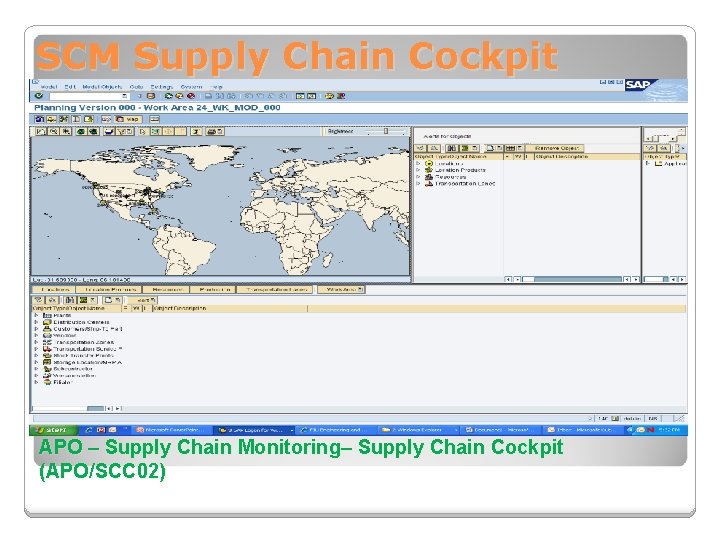
SCM Supply Chain Cockpit APO – Supply Chain Monitoring– Supply Chain Cockpit (APO/SCC 02)
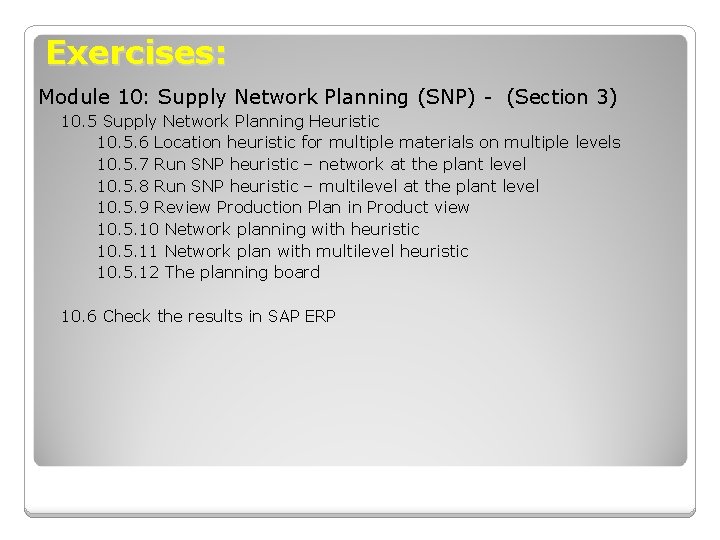
Exercises: Module 10: Supply Network Planning (SNP) - (Section 3) 10. 5 Supply Network Planning Heuristic 10. 5. 6 Location heuristic for multiple materials on multiple levels 10. 5. 7 Run SNP heuristic – network at the plant level 10. 5. 8 Run SNP heuristic – multilevel at the plant level 10. 5. 9 Review Production Plan in Product view 10. 5. 10 Network planning with heuristic 10. 5. 11 Network plan with multilevel heuristic 10. 5. 12 The planning board 10. 6 Check the results in SAP ERP
Production planning and detailed scheduling services
Ppds planning
Production planning inventory control
Pgds dokter spesialis
Dokter gizi semarang
Sebutkan 3 proses produksi multimedia
Sjn scheduling
Script breakdown software
Master production schedule problems
Master production schedule example
Inputs of aggregate planning
Media scheduling strategies
Scheduling and planning
Pulsing media schedule example
Disaggregating the aggregate plan
Solid in engineering drawing
Skim scan and detailed reading
Functional components of ecrm
Crm and scm
Scm, crm, and erp are all extended erp components.
Production plans meaning
Production planning and quality control
Ppc planning sheet
Pre production planning for video film and multimedia
Detailed use case description example
Detailed analysis sometimes is called
Hairdressing lesson plans
Feasibility analysis matrix
Elizabeth bishop uses highly detailed observation
Detailed routing
Detailed cocomo model
Joint drawing
Detailed lesson plan about problem solving
Detailed design in software engineering
Detailed drawing example
Heart of darkness summary by joseph conrad
Function oriented design
Detailed business case
Cocomo equation
Write a detailed note on unicast routing protocols
Definition of detail drawing
Standard drawing scale
Southern spain map
Complete the riddle
First cut detailed sequence diagram
Detailed comprehension
Need of energy audit ppt
Provide increasingly detailed data about a situation
Cima practical experience time limit
Uml book
Detailed range card