d SPACE DS 1103 Control Workstation Tutorial and
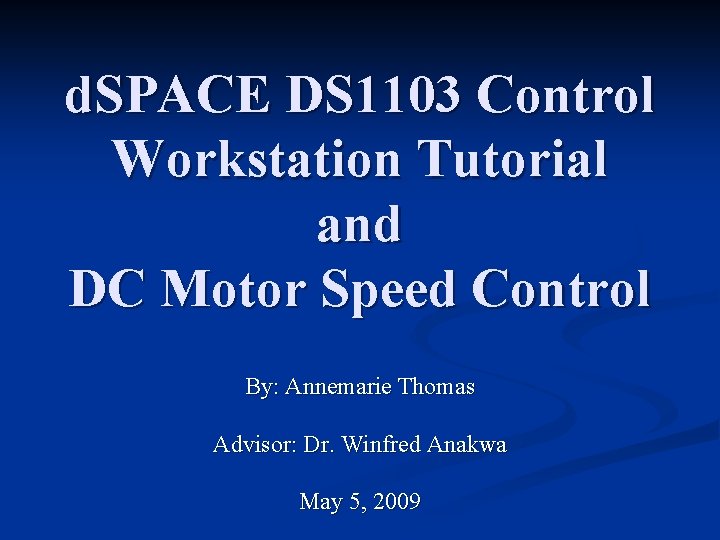
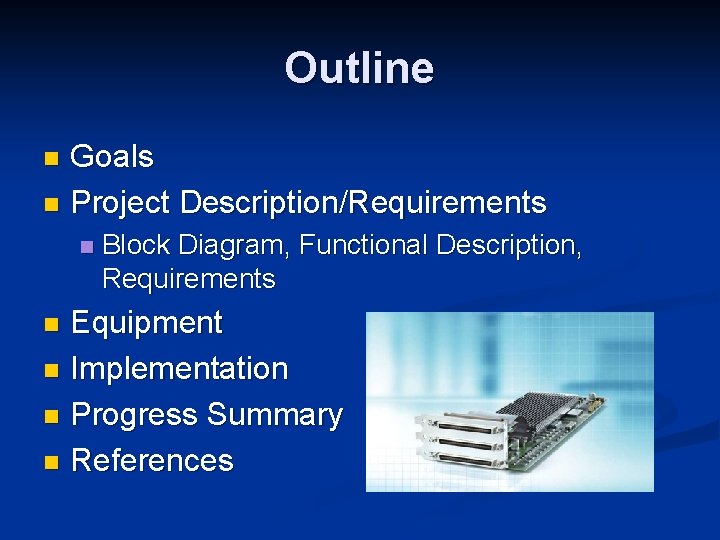
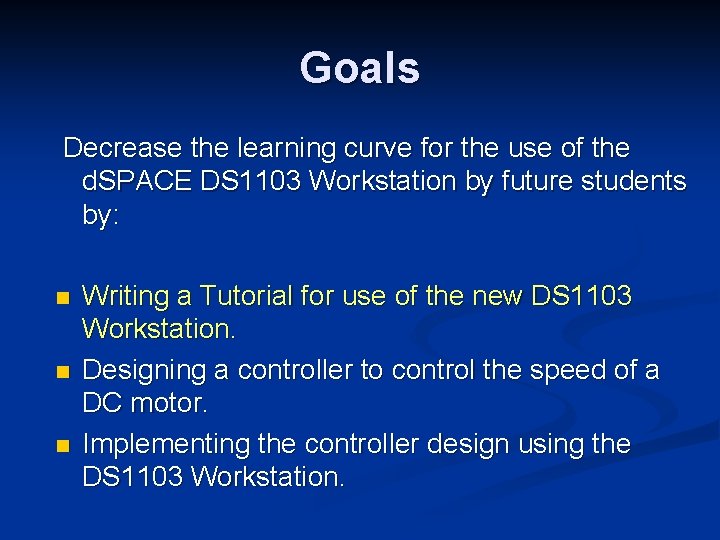
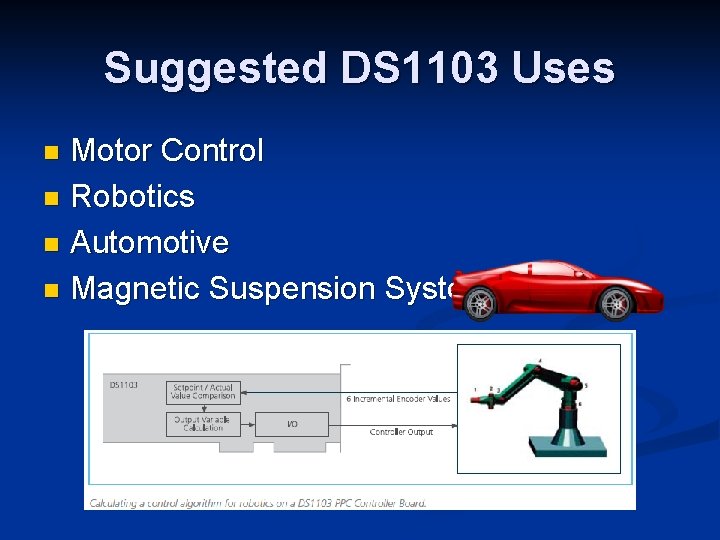
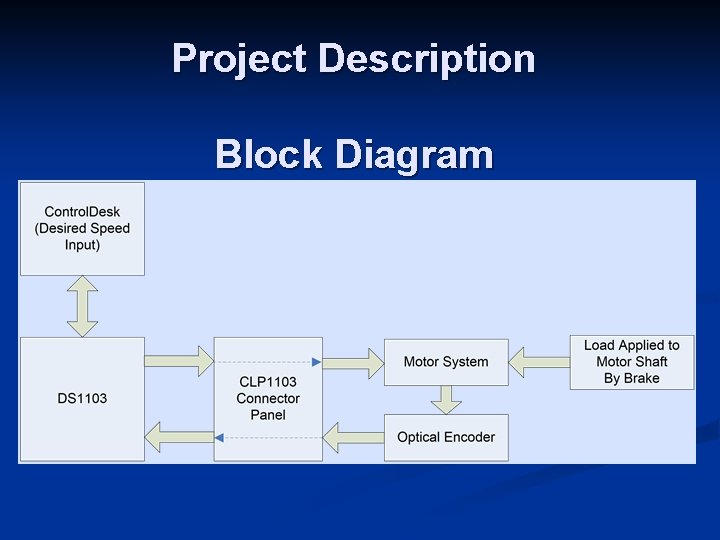
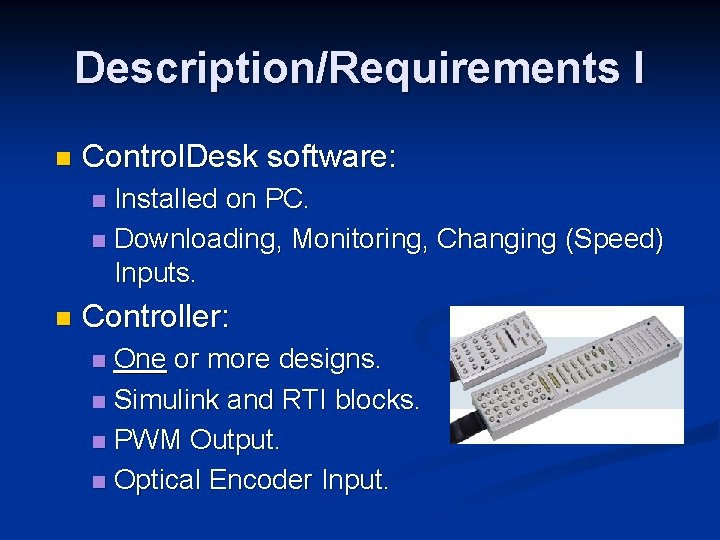
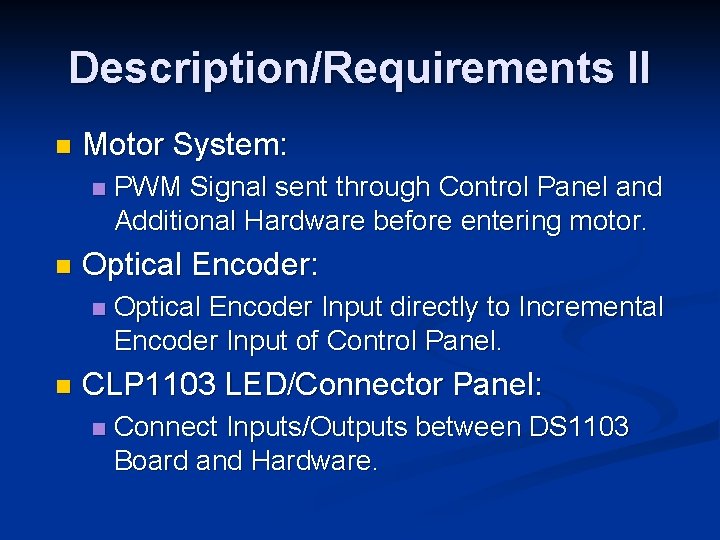
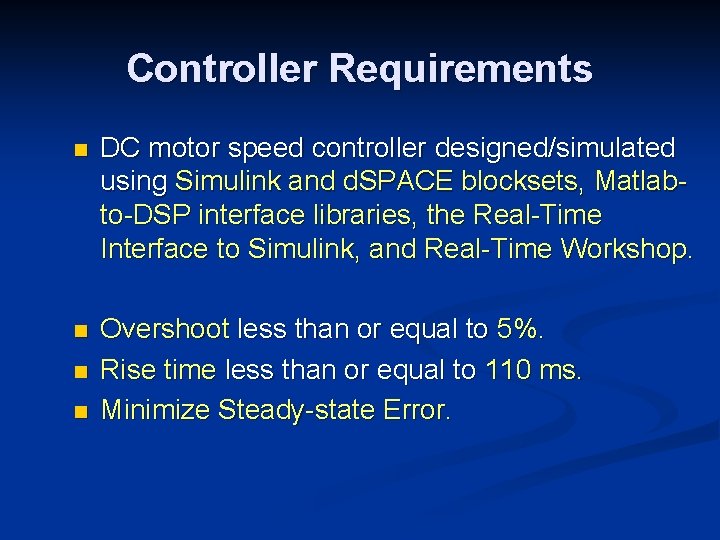
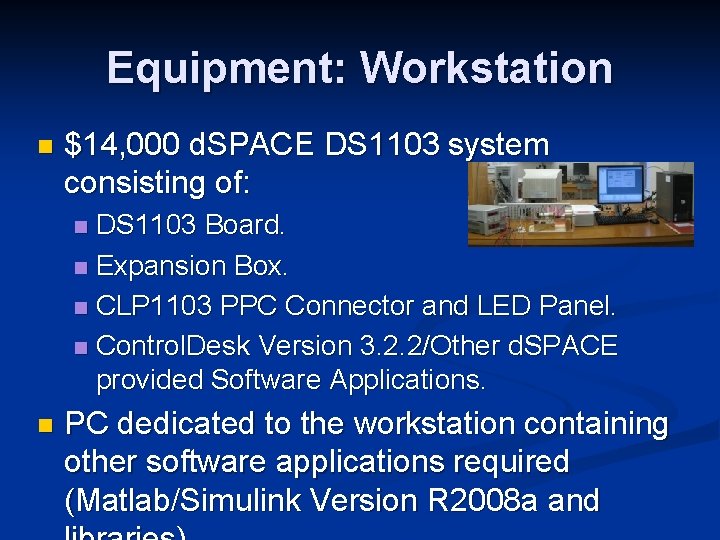
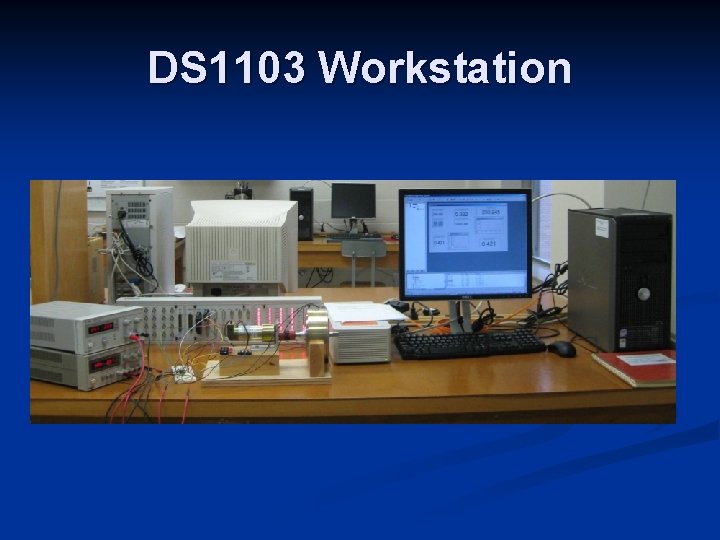
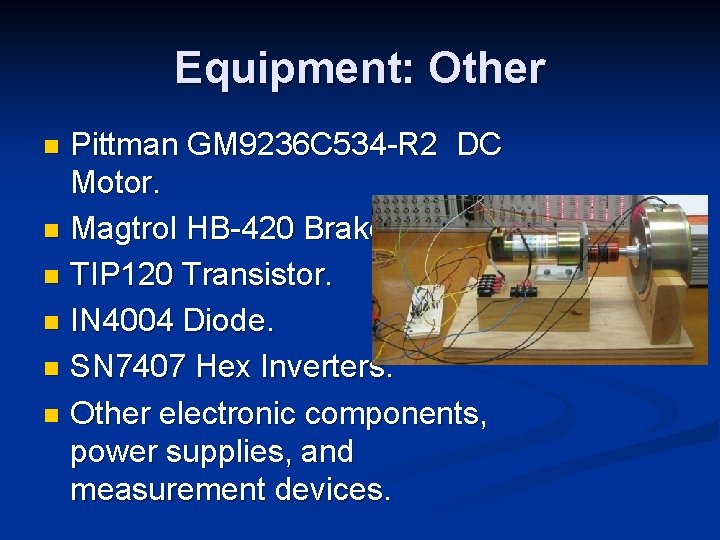
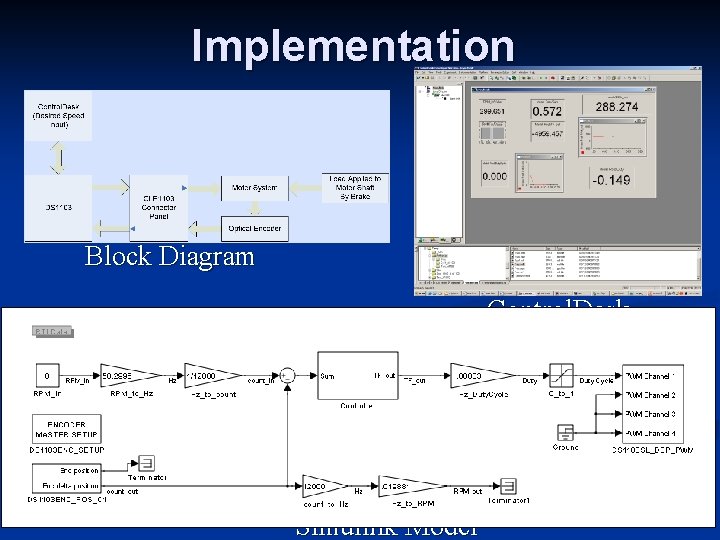
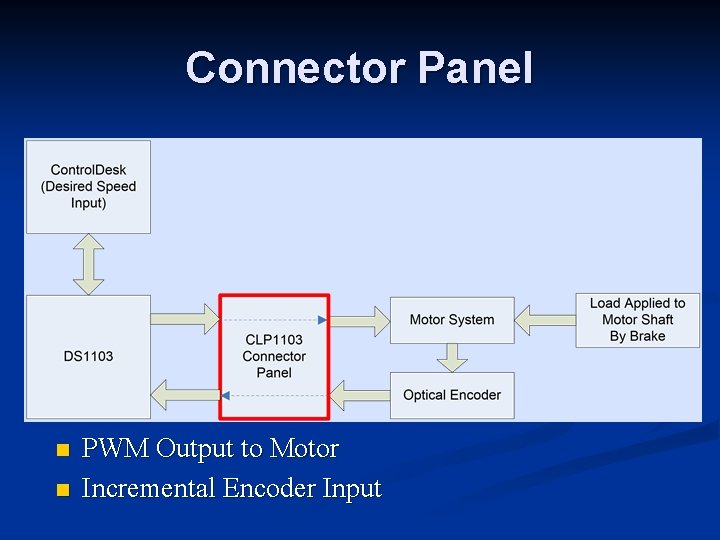
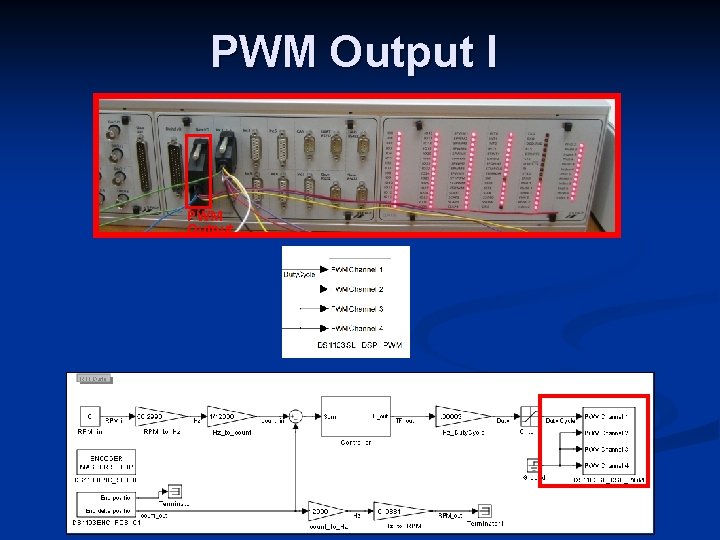
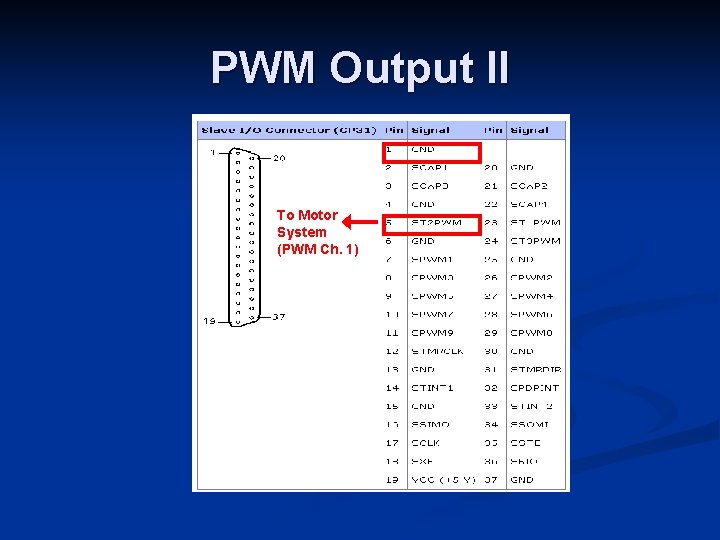
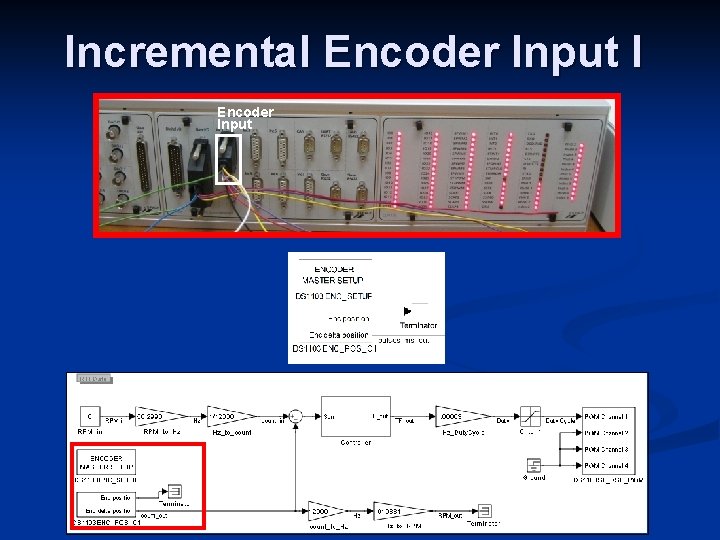
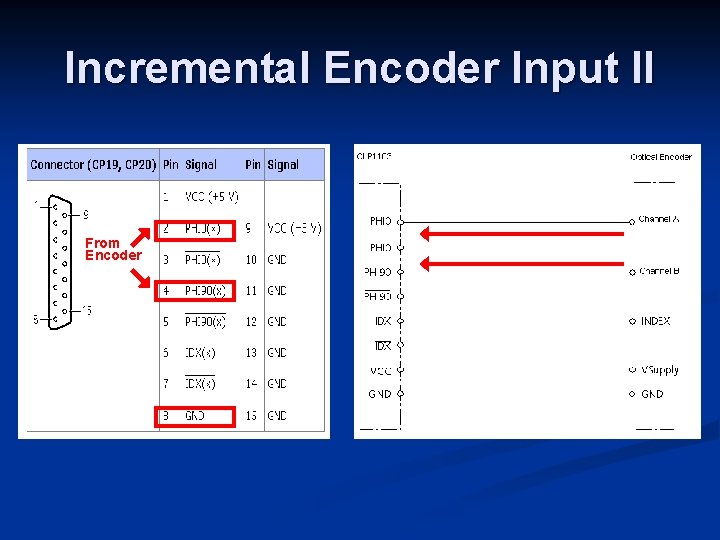
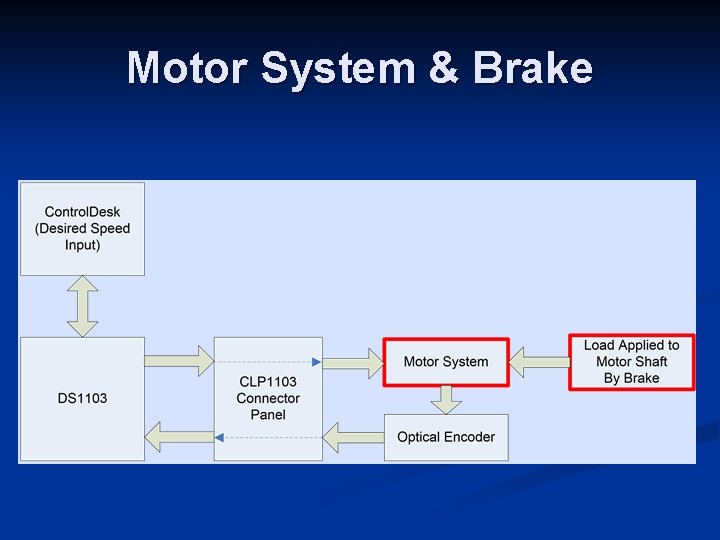
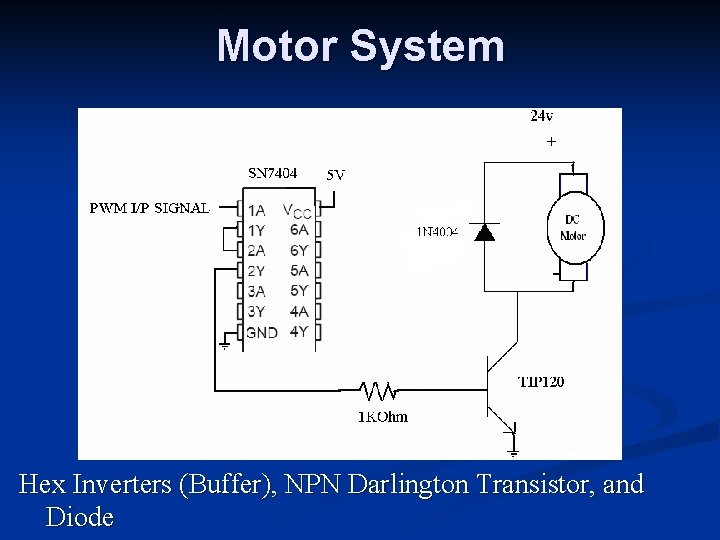
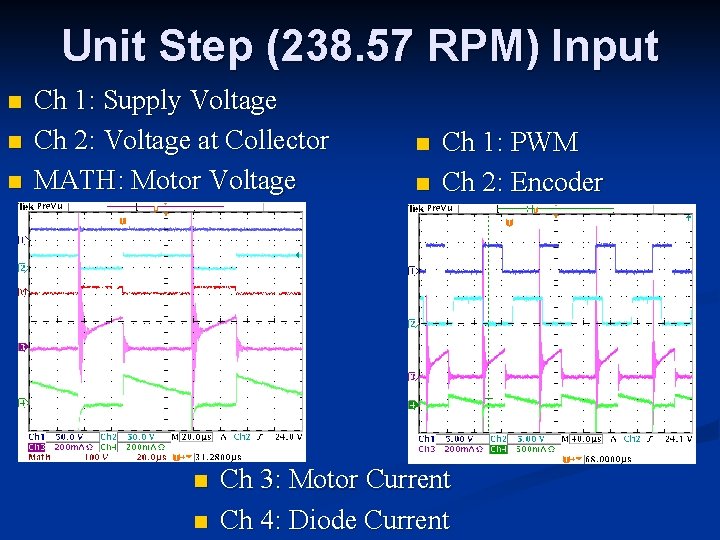
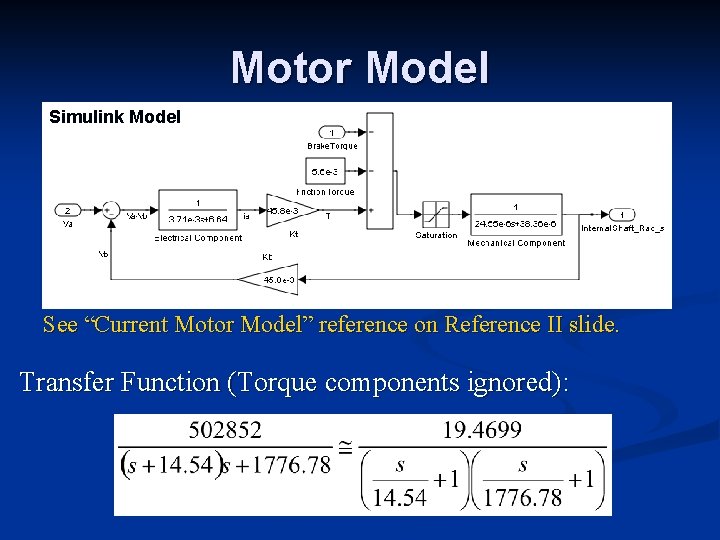
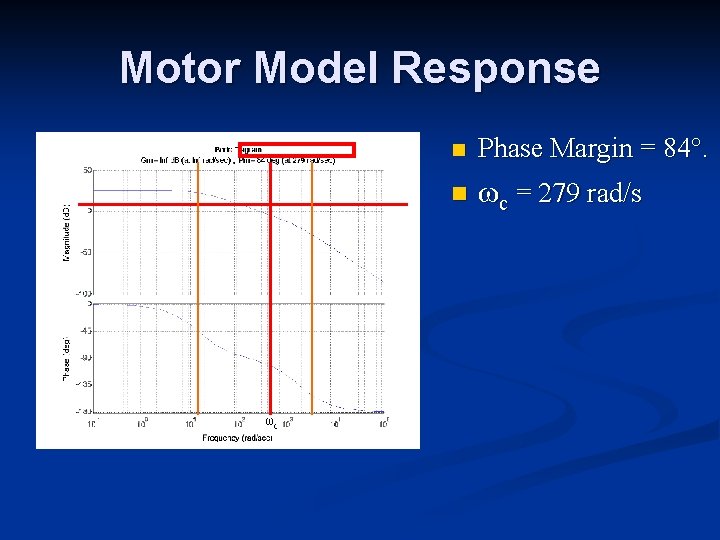

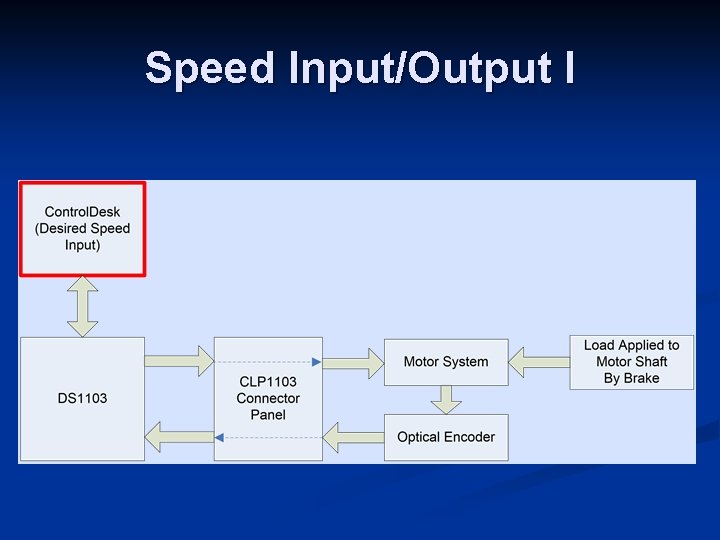
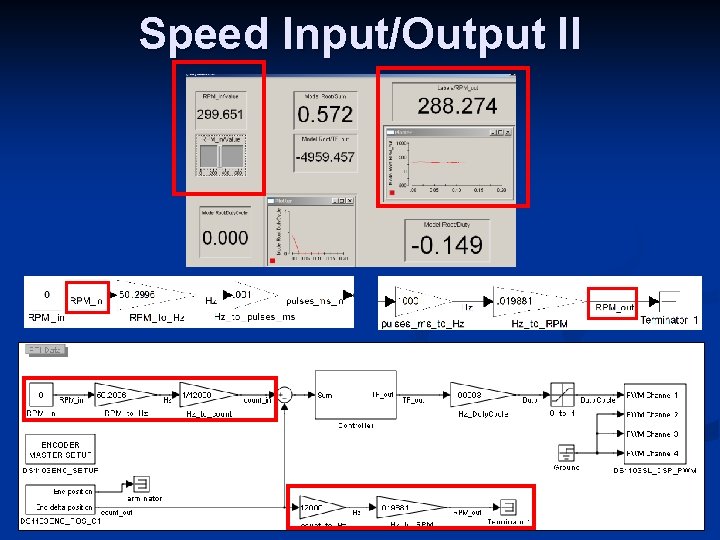
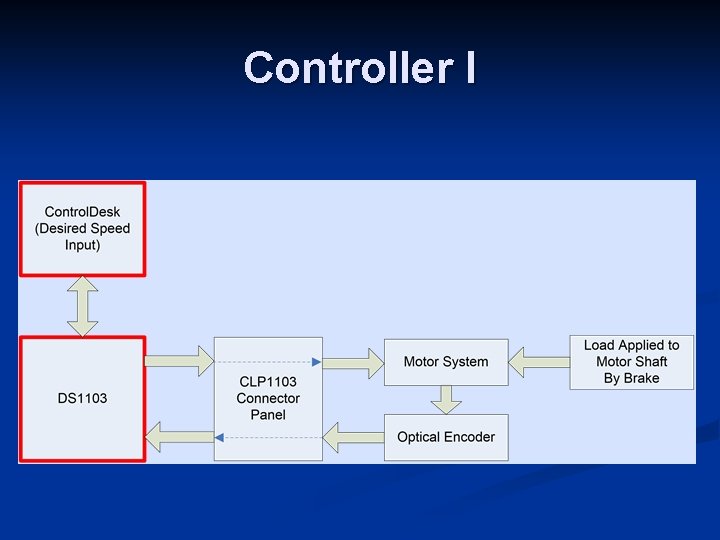
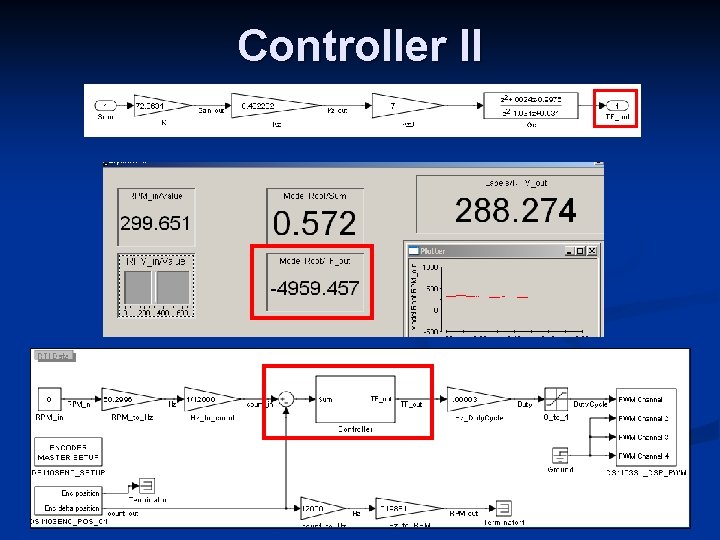
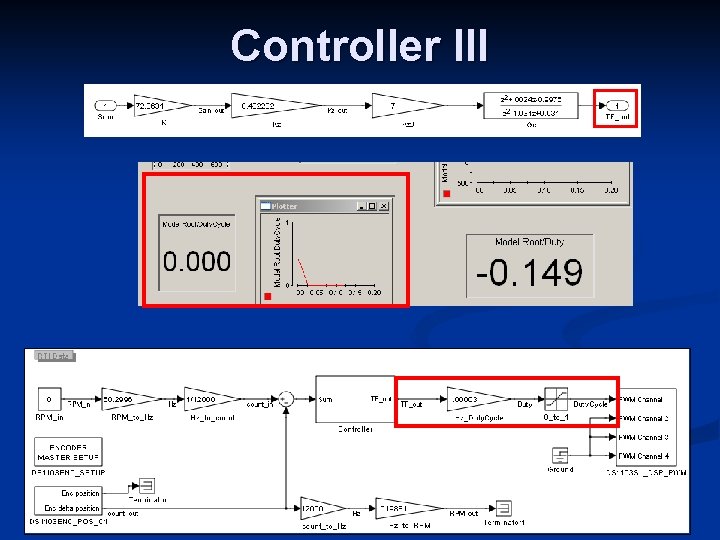
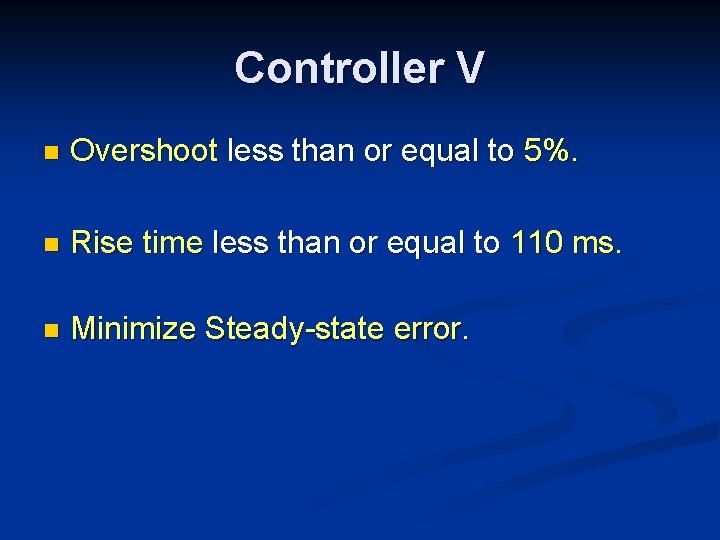
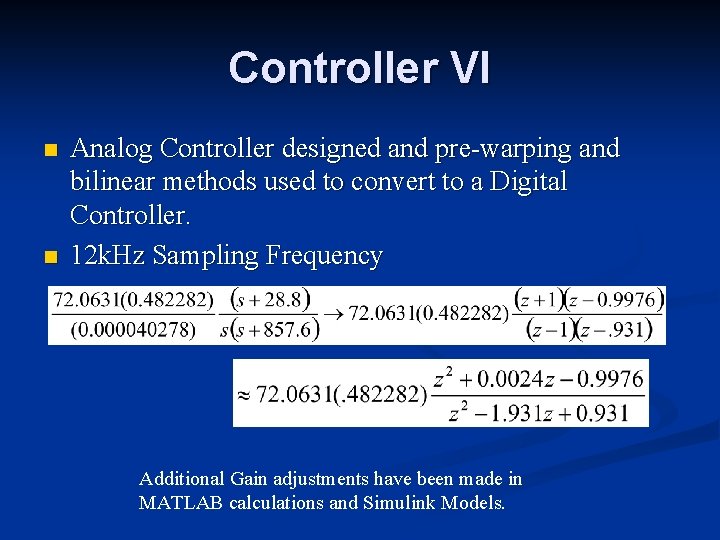
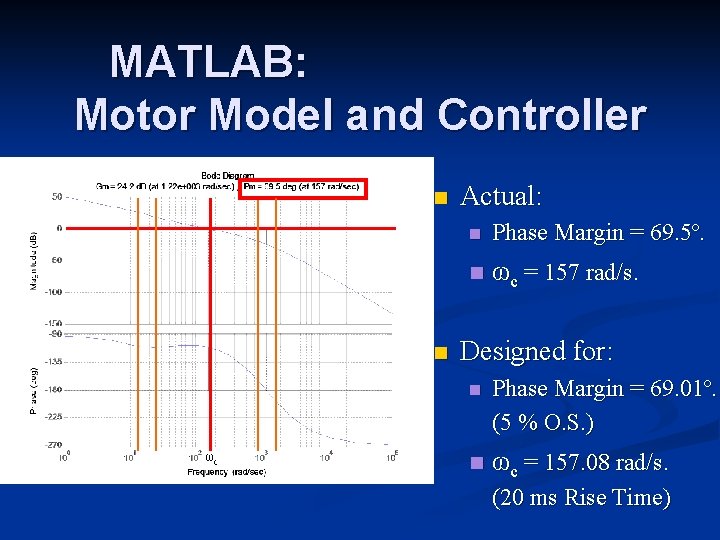
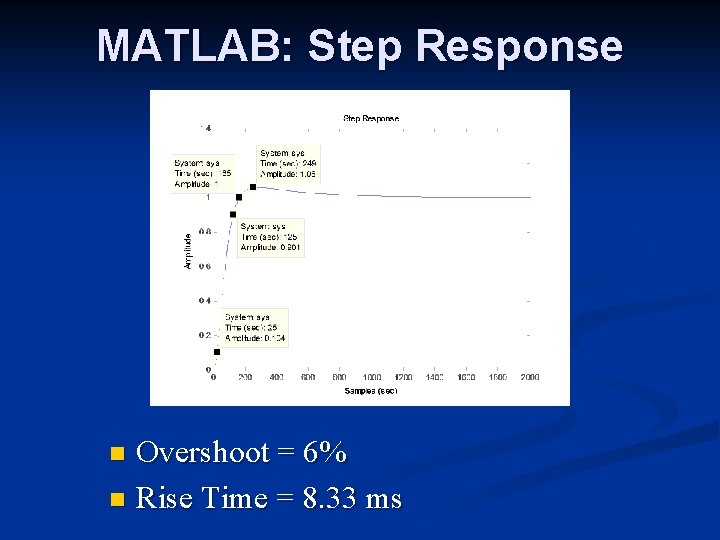
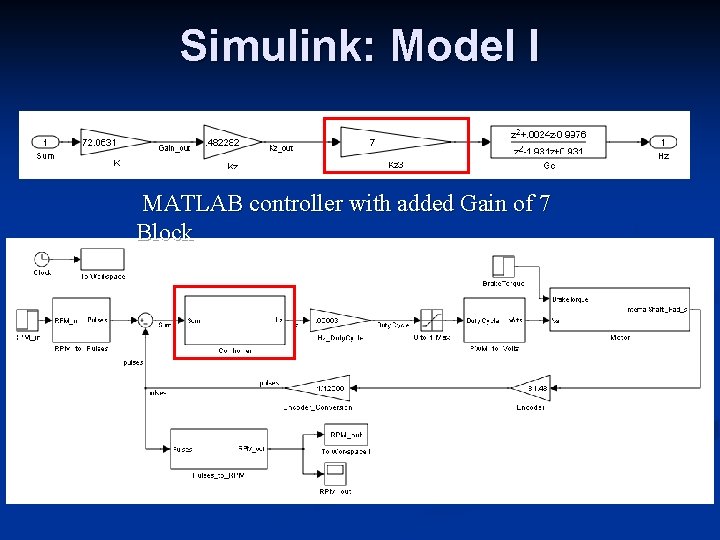
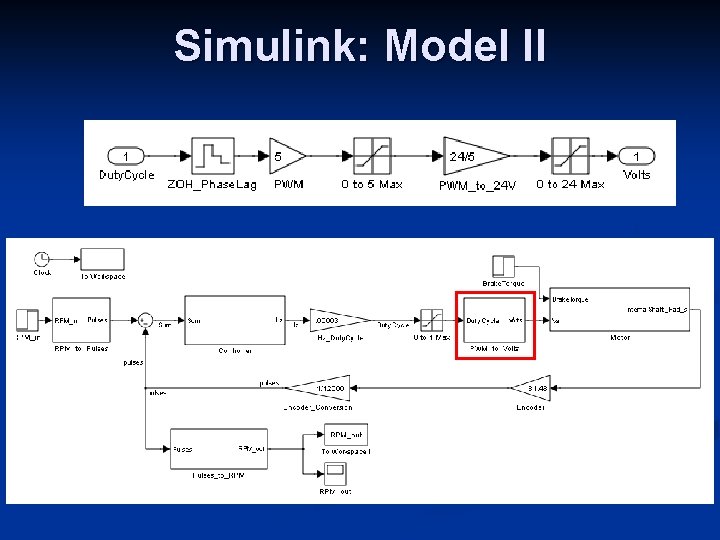
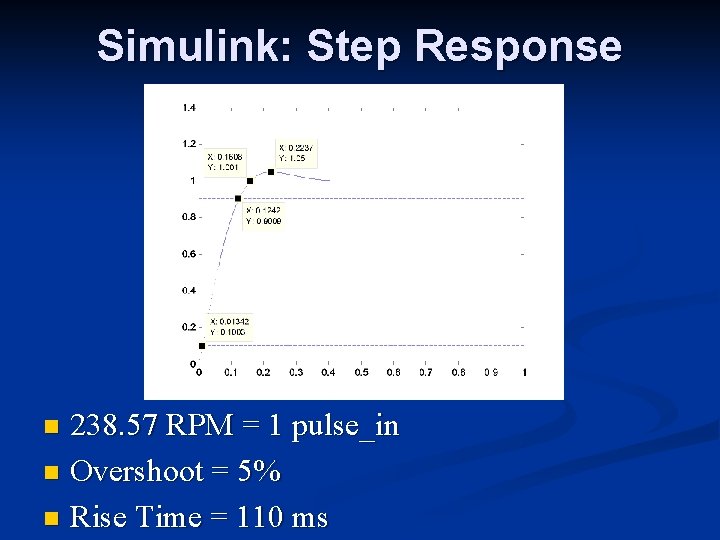
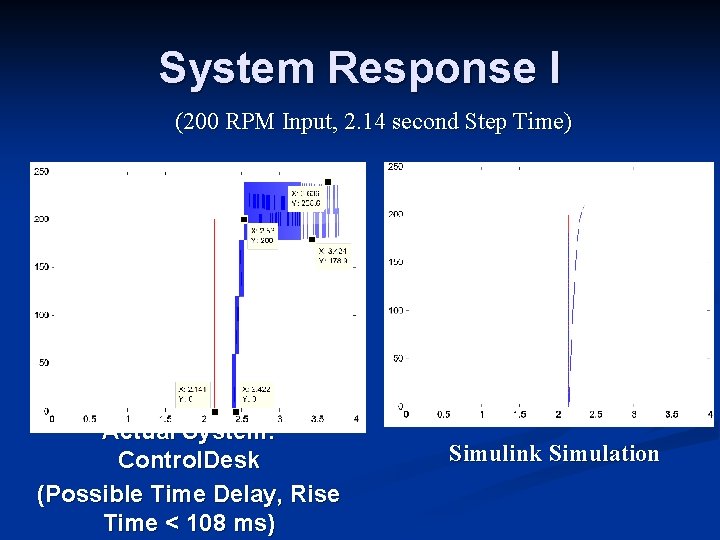
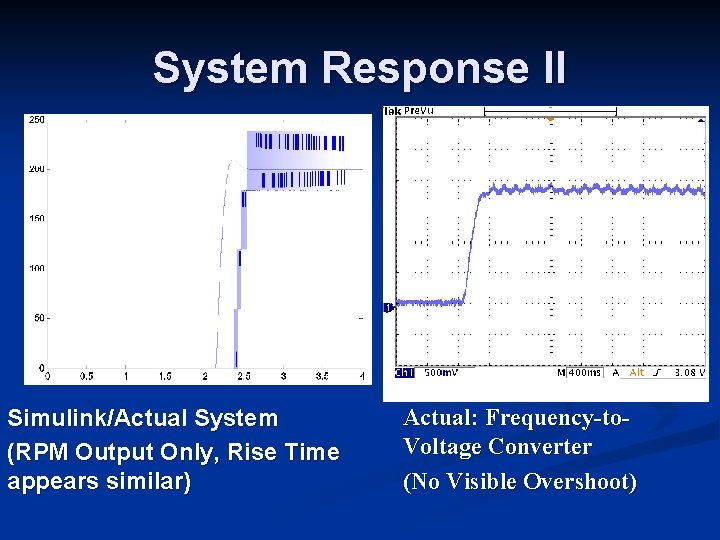
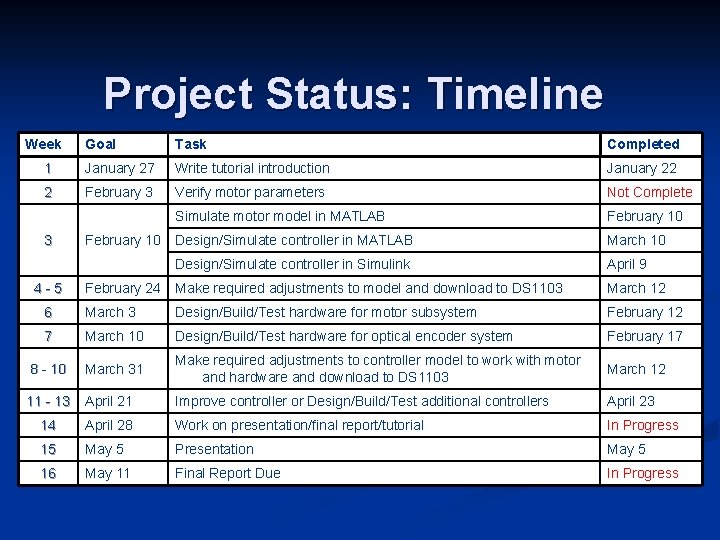
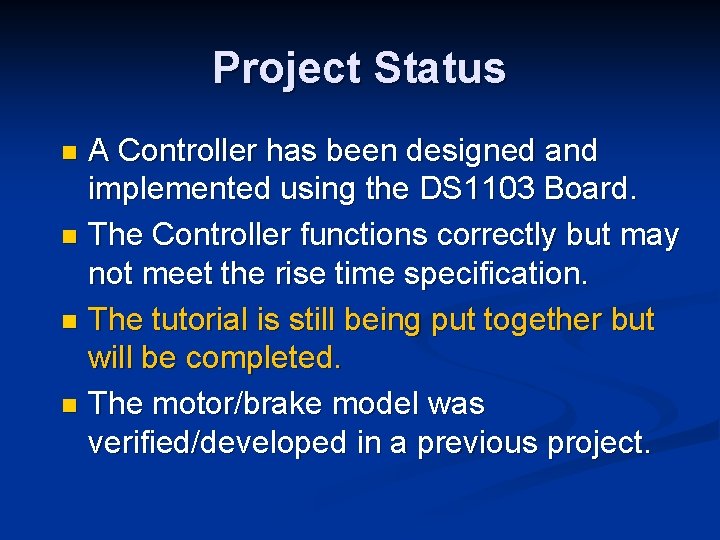
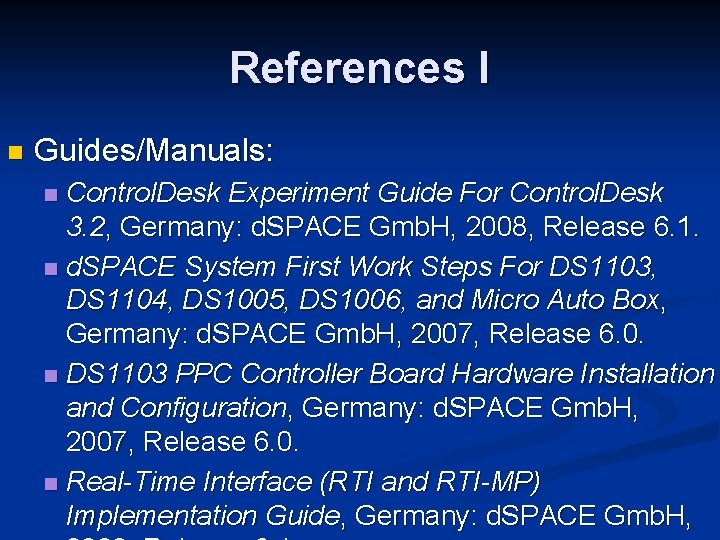
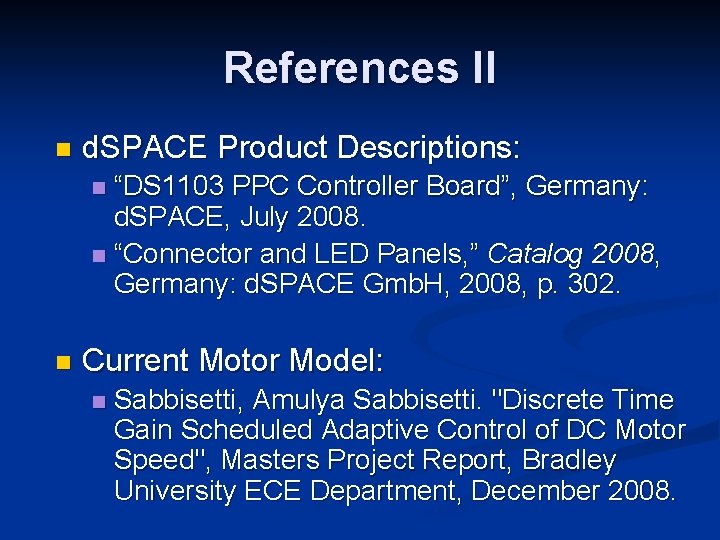
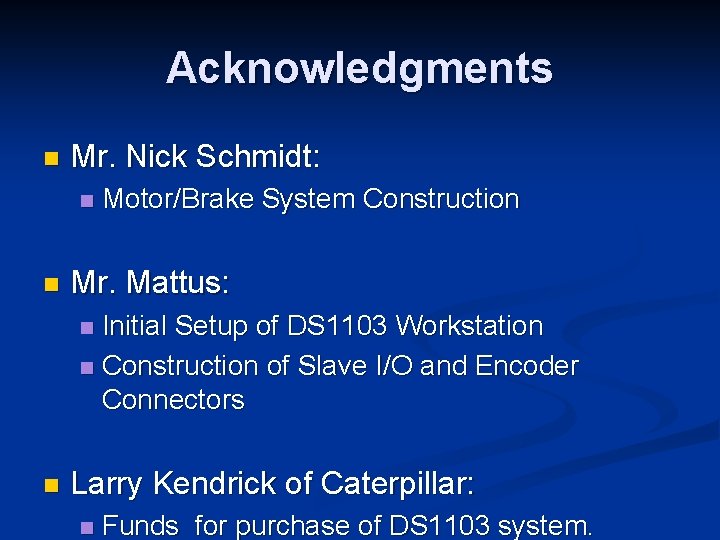
- Slides: 42
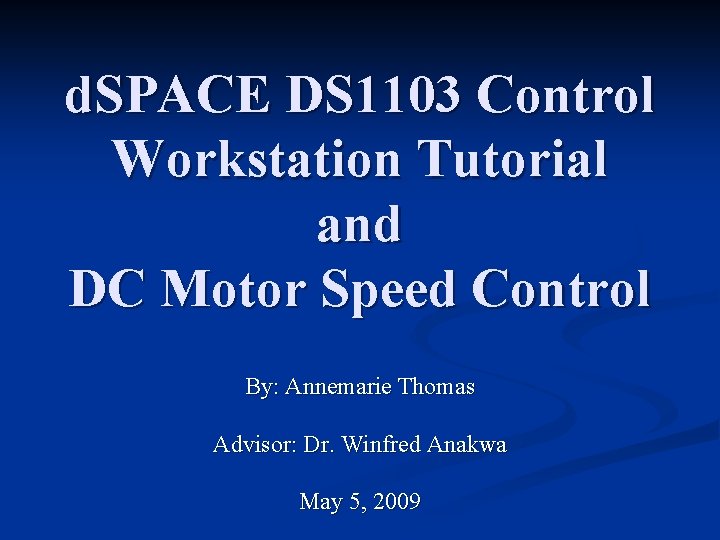
d. SPACE DS 1103 Control Workstation Tutorial and DC Motor Speed Control By: Annemarie Thomas Advisor: Dr. Winfred Anakwa May 5, 2009
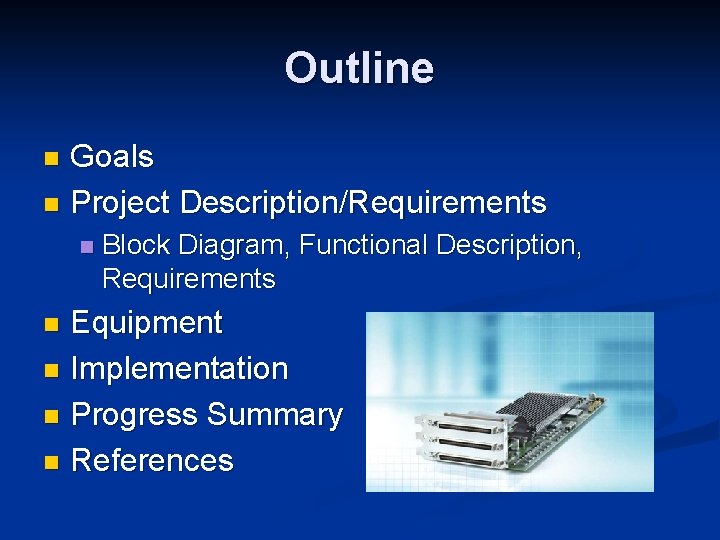
Outline Goals n Project Description/Requirements n n Block Diagram, Functional Description, Requirements Equipment n Implementation n Progress Summary n References n
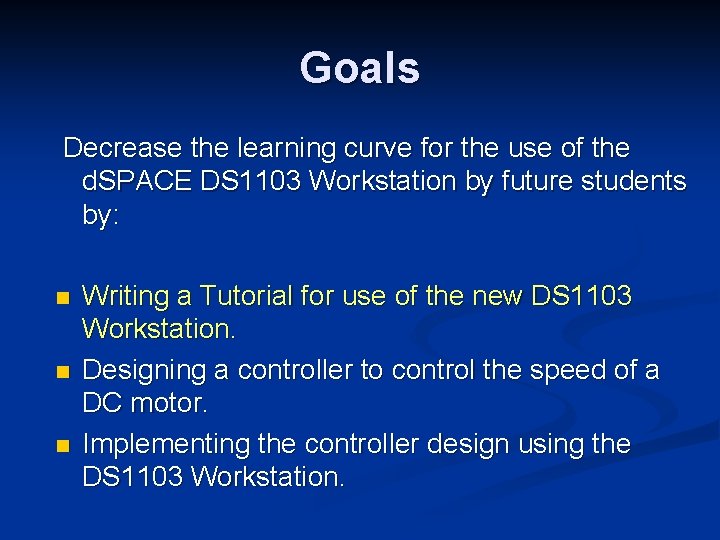
Goals Decrease the learning curve for the use of the d. SPACE DS 1103 Workstation by future students by: n n n Writing a Tutorial for use of the new DS 1103 Workstation. Designing a controller to control the speed of a DC motor. Implementing the controller design using the DS 1103 Workstation.
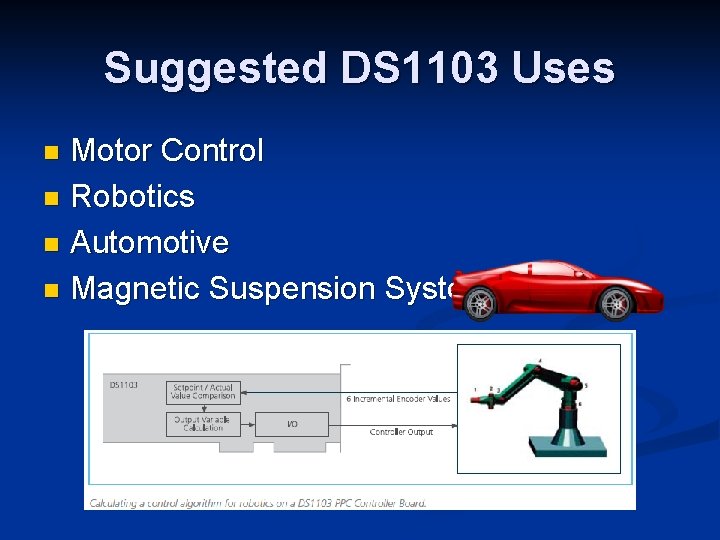
Suggested DS 1103 Uses Motor Control n Robotics n Automotive n Magnetic Suspension Systems n
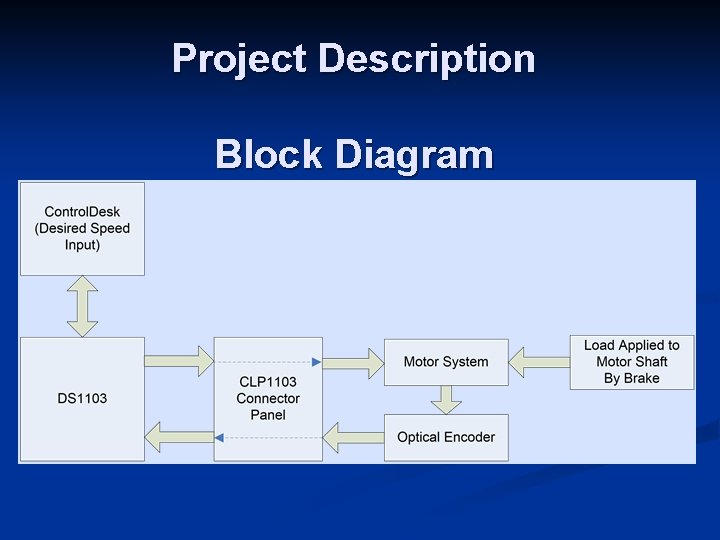
Project Description Block Diagram
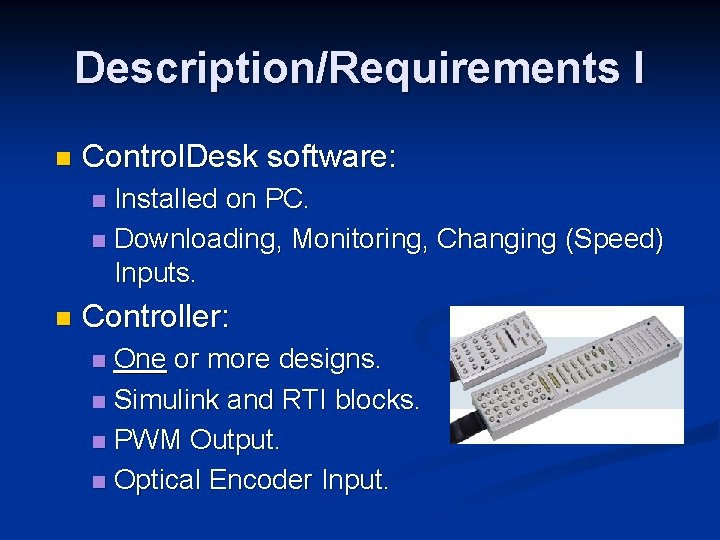
Description/Requirements I n Control. Desk software: Installed on PC. n Downloading, Monitoring, Changing (Speed) Inputs. n n Controller: One or more designs. n Simulink and RTI blocks. n PWM Output. n Optical Encoder Input. n
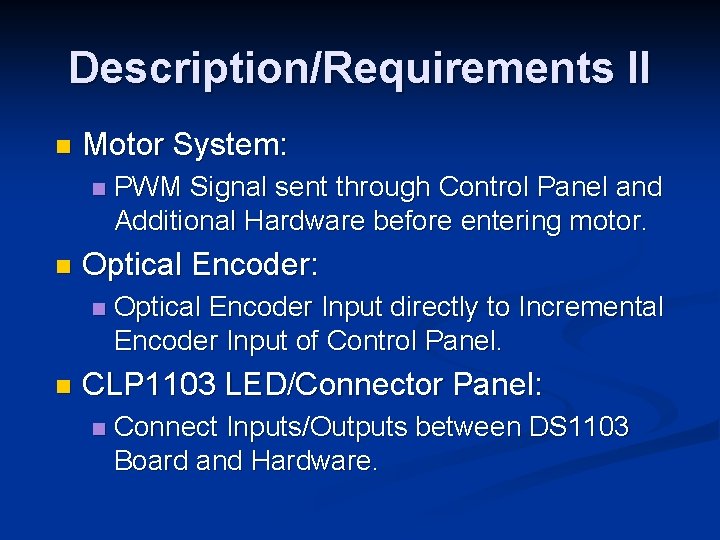
Description/Requirements II n Motor System: n n Optical Encoder: n n PWM Signal sent through Control Panel and Additional Hardware before entering motor. Optical Encoder Input directly to Incremental Encoder Input of Control Panel. CLP 1103 LED/Connector Panel: n Connect Inputs/Outputs between DS 1103 Board and Hardware.
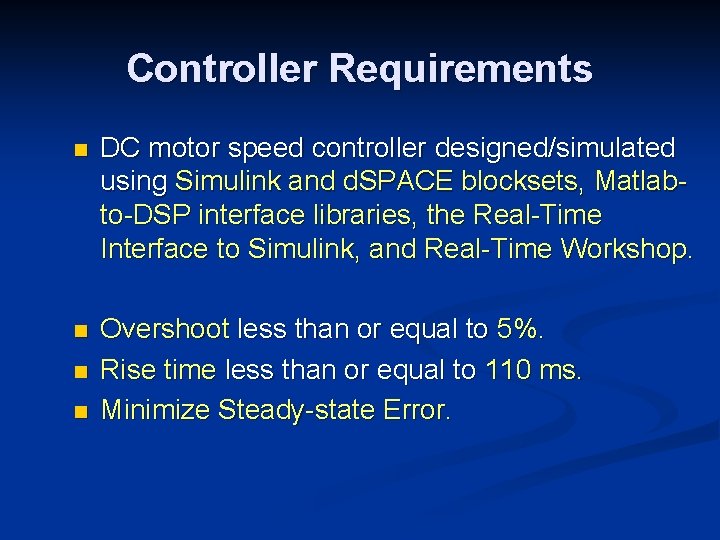
Controller Requirements n DC motor speed controller designed/simulated using Simulink and d. SPACE blocksets, Matlabto-DSP interface libraries, the Real-Time Interface to Simulink, and Real-Time Workshop. n Overshoot less than or equal to 5%. Rise time less than or equal to 110 ms. Minimize Steady-state Error. n n
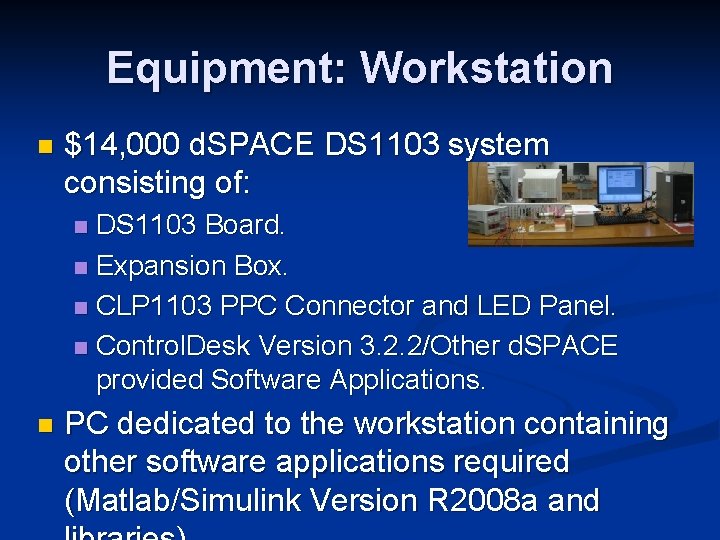
Equipment: Workstation n $14, 000 d. SPACE DS 1103 system consisting of: DS 1103 Board. n Expansion Box. n CLP 1103 PPC Connector and LED Panel. n Control. Desk Version 3. 2. 2/Other d. SPACE provided Software Applications. n n PC dedicated to the workstation containing other software applications required (Matlab/Simulink Version R 2008 a and
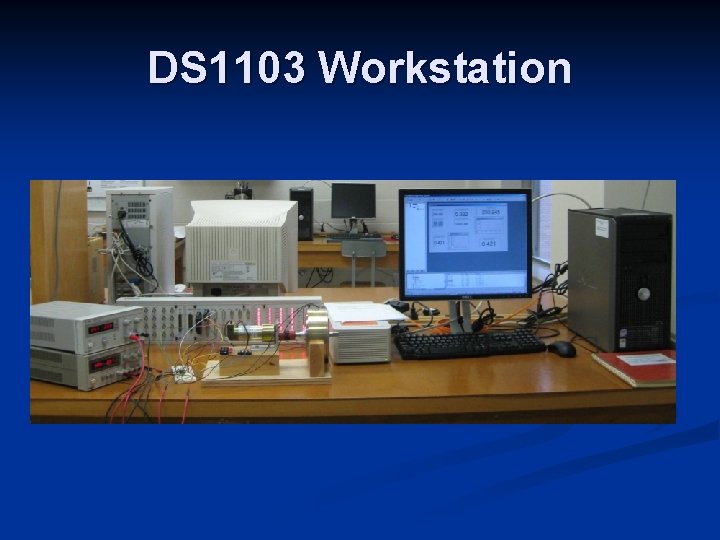
DS 1103 Workstation
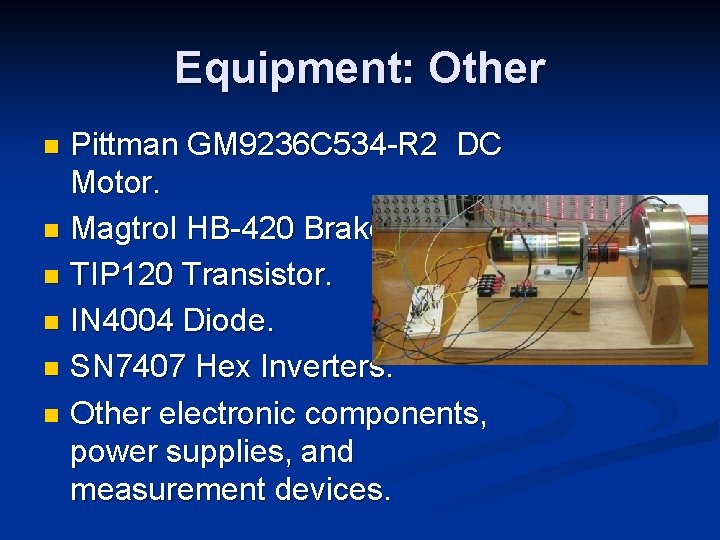
Equipment: Other Pittman GM 9236 C 534 -R 2 DC Motor. n Magtrol HB-420 Brake. n TIP 120 Transistor. n IN 4004 Diode. n SN 7407 Hex Inverters. n Other electronic components, power supplies, and measurement devices. n
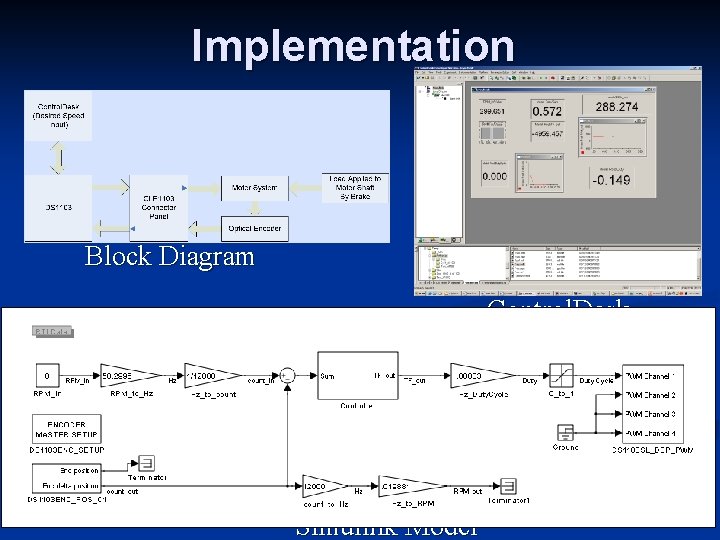
Implementation Block Diagram Control. Desk Simulink Model
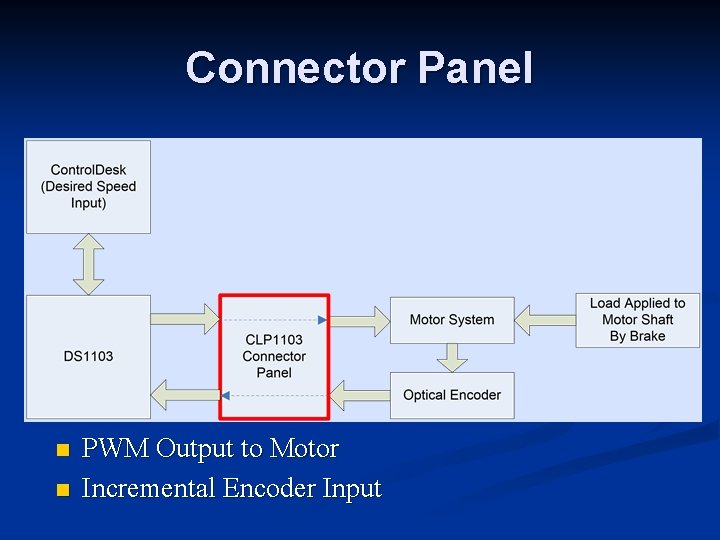
Connector Panel n n PWM Output to Motor Incremental Encoder Input
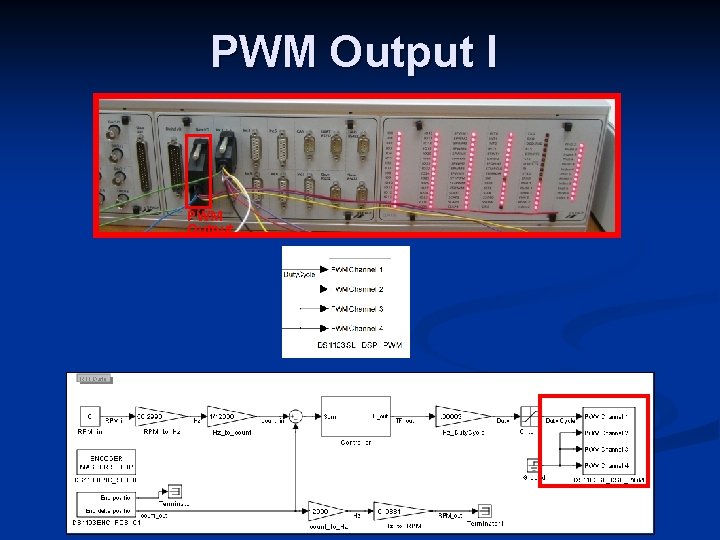
PWM Output I PWM Output
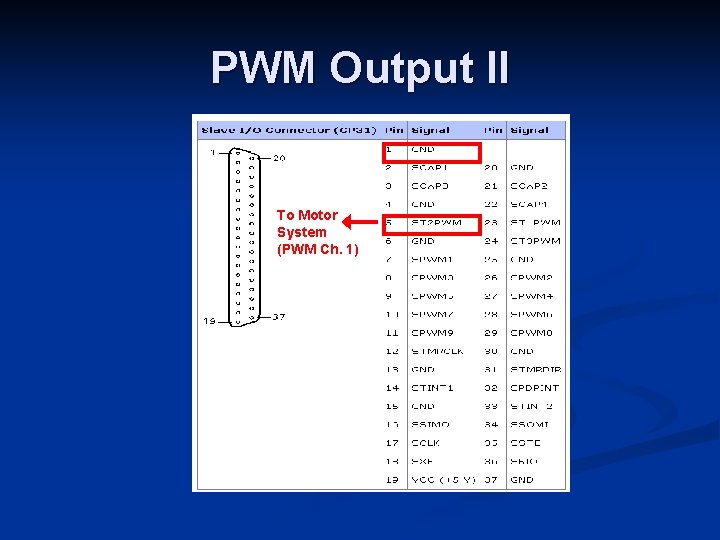
PWM Output II To Motor System (PWM Ch. 1)
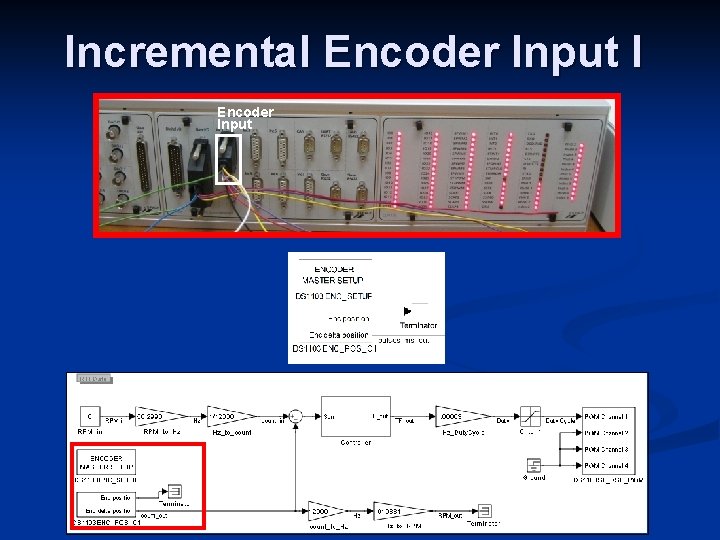
Incremental Encoder Input I Encoder Input
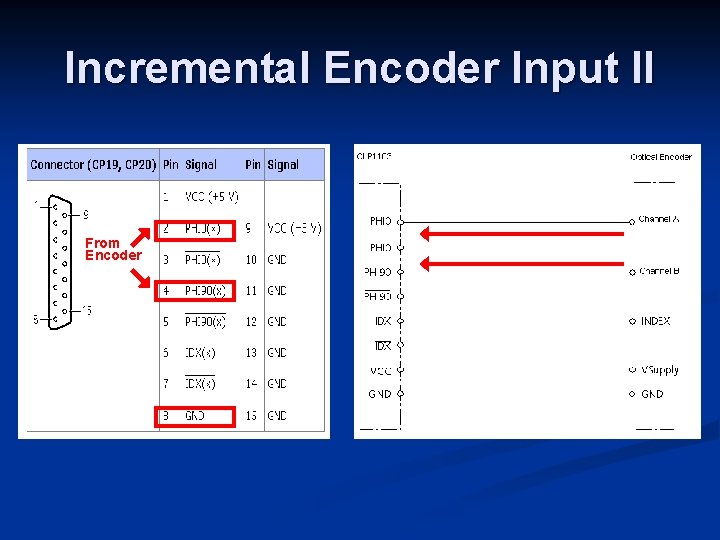
Incremental Encoder Input II From Encoder
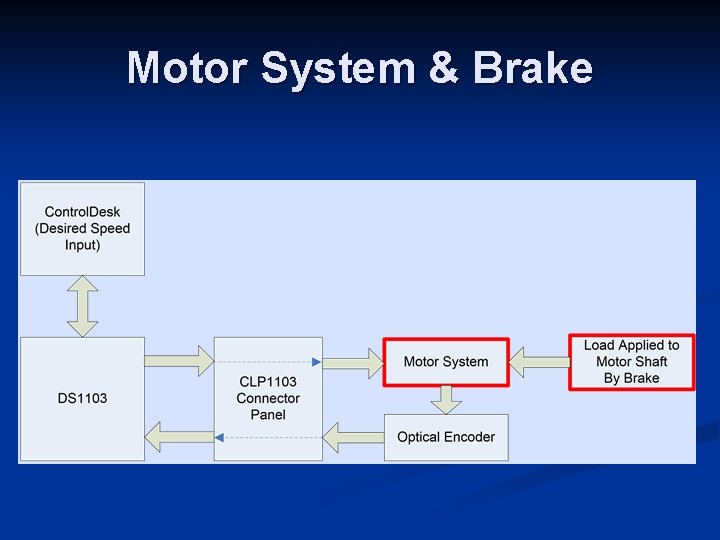
Motor System & Brake
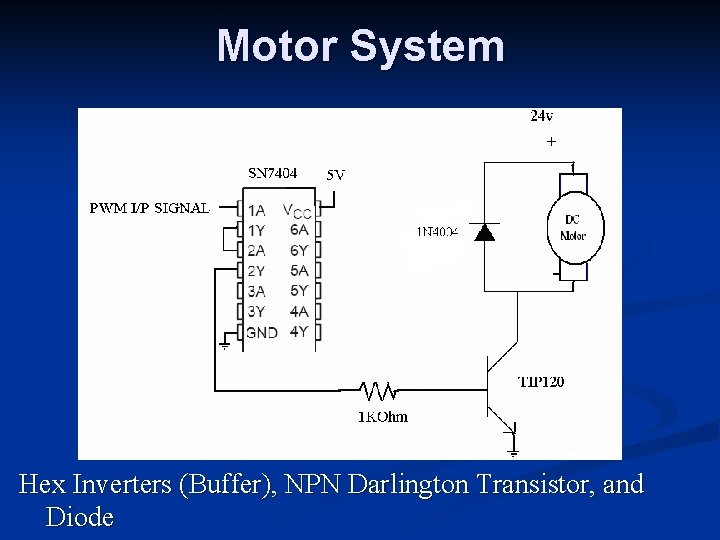
Motor System + - Hex Inverters (Buffer), NPN Darlington Transistor, and Diode
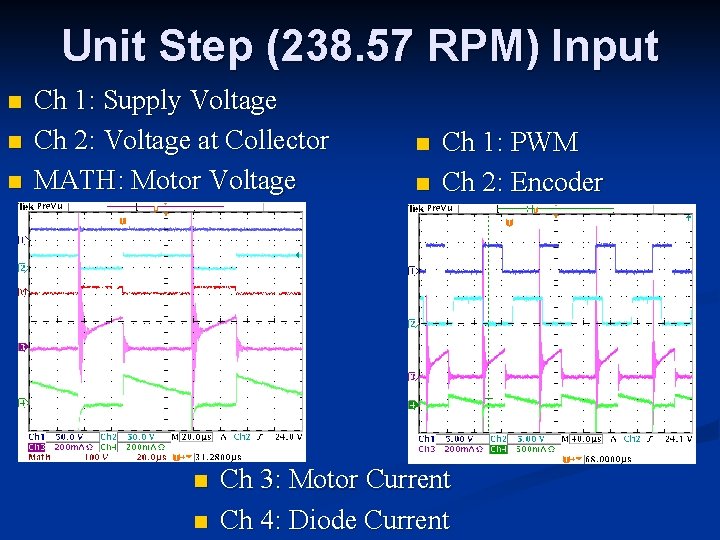
Unit Step (238. 57 RPM) Input n n n Ch 1: Supply Voltage Ch 2: Voltage at Collector MATH: Motor Voltage n n Ch 1: PWM Ch 2: Encoder Ch 3: Motor Current Ch 4: Diode Current
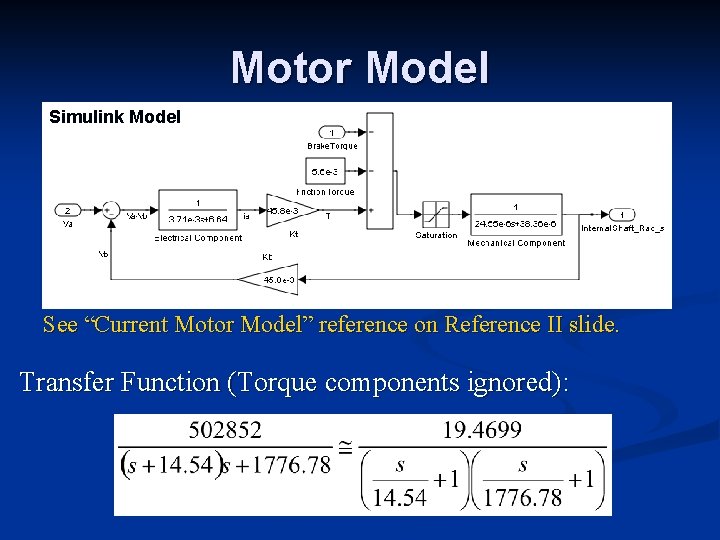
Motor Model Simulink Model See “Current Motor Model” reference on Reference II slide. Transfer Function (Torque components ignored):
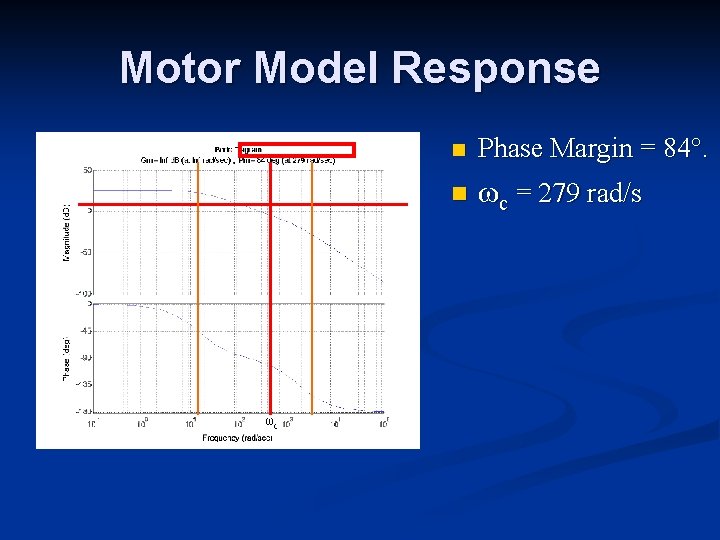
Motor Model Response ωc n Phase Margin = 84°. n ωc = 279 rad/s

Brake n Systems Stops at approximately: n 0. 375 Nm -OR- 50 Oz. In
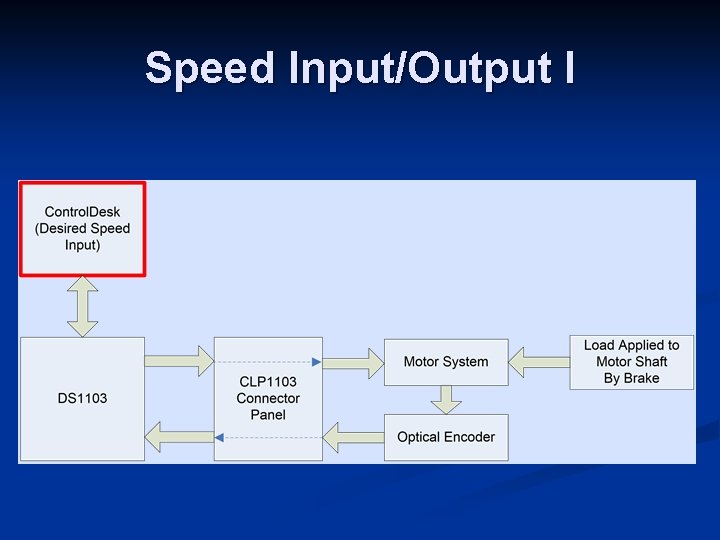
Speed Input/Output I
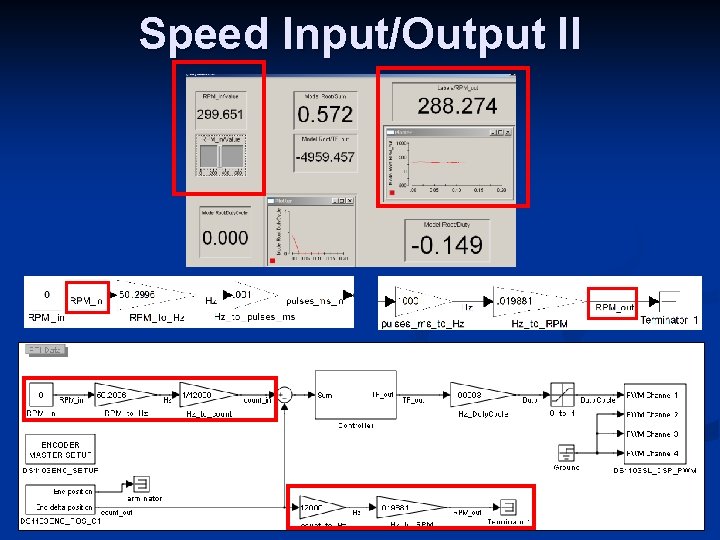
Speed Input/Output II
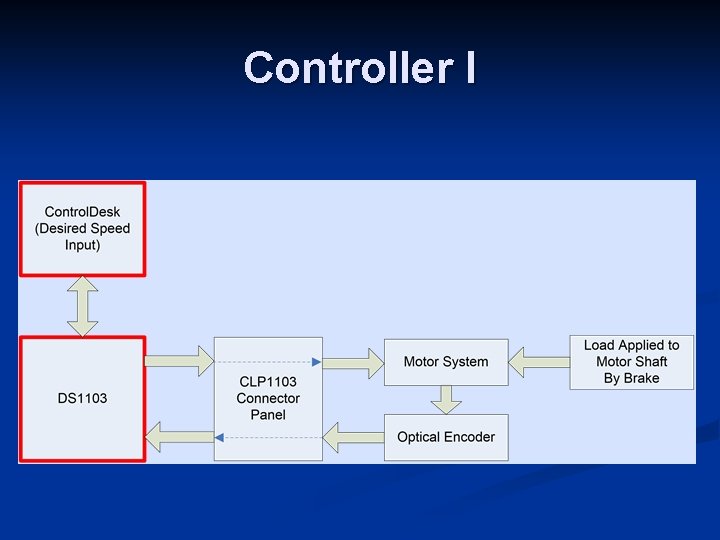
Controller I
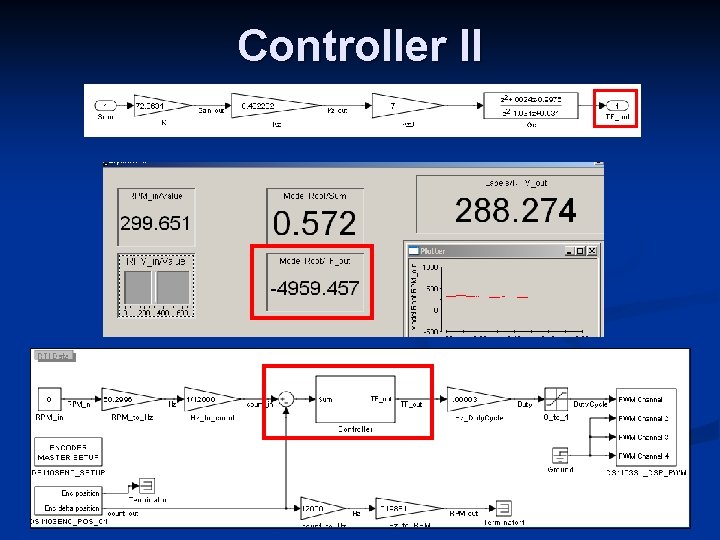
Controller II
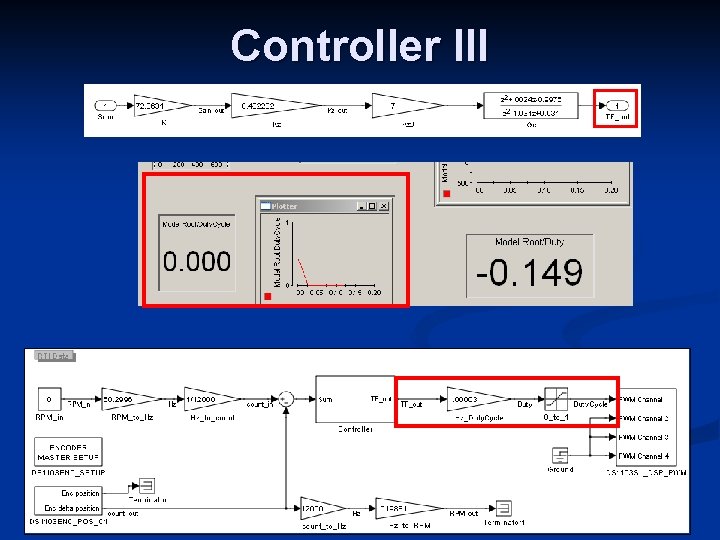
Controller III
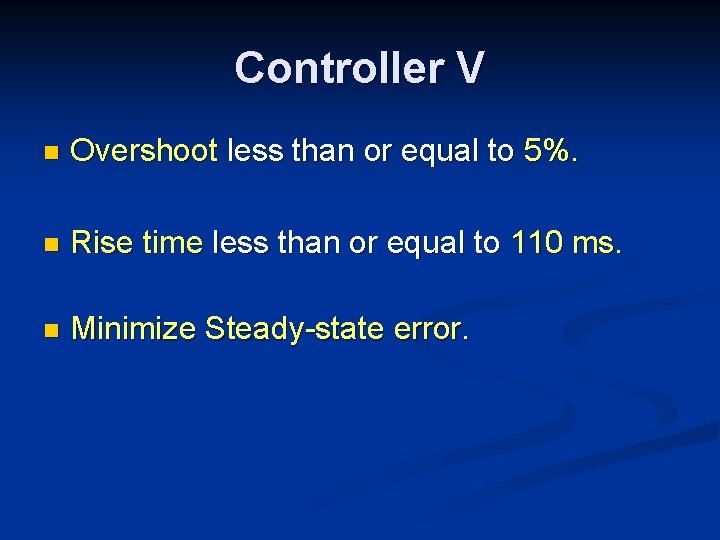
Controller V n Overshoot less than or equal to 5%. n Rise time less than or equal to 110 ms. n Minimize Steady-state error.
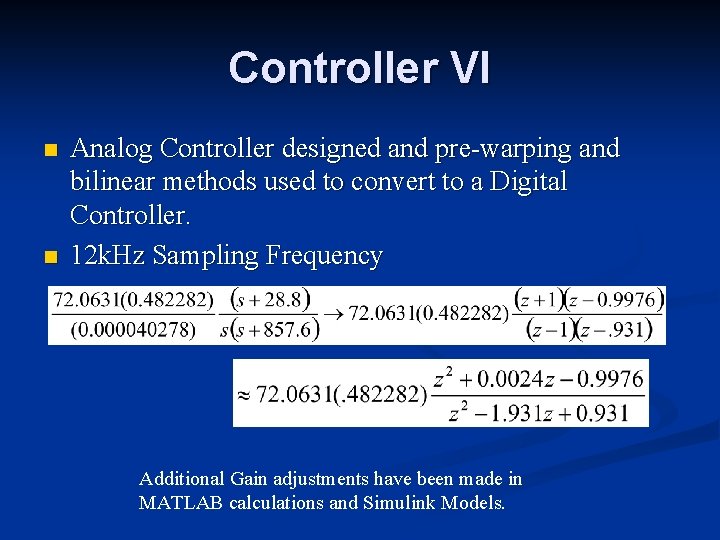
Controller VI n n Analog Controller designed and pre-warping and bilinear methods used to convert to a Digital Controller. 12 k. Hz Sampling Frequency Additional Gain adjustments have been made in MATLAB calculations and Simulink Models.
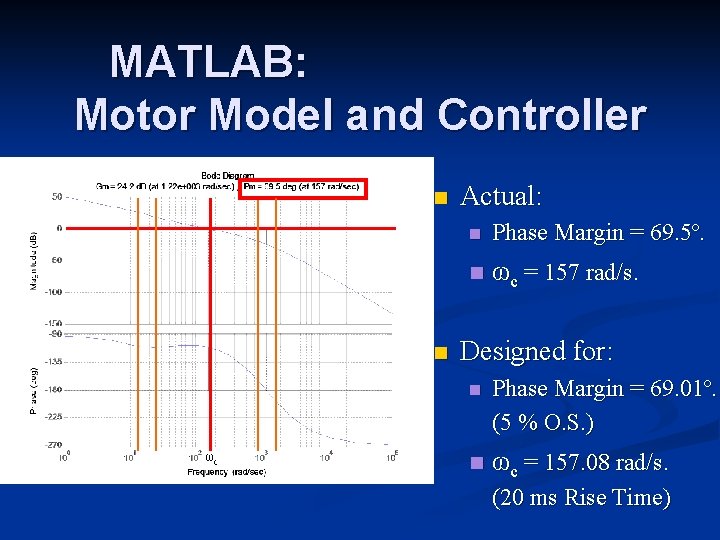
MATLAB: Motor Model and Controller n n ωc Actual: n Phase Margin = 69. 5º. n ωc = 157 rad/s. Designed for: n Phase Margin = 69. 01º. (5 % O. S. ) n ωc = 157. 08 rad/s. (20 ms Rise Time)
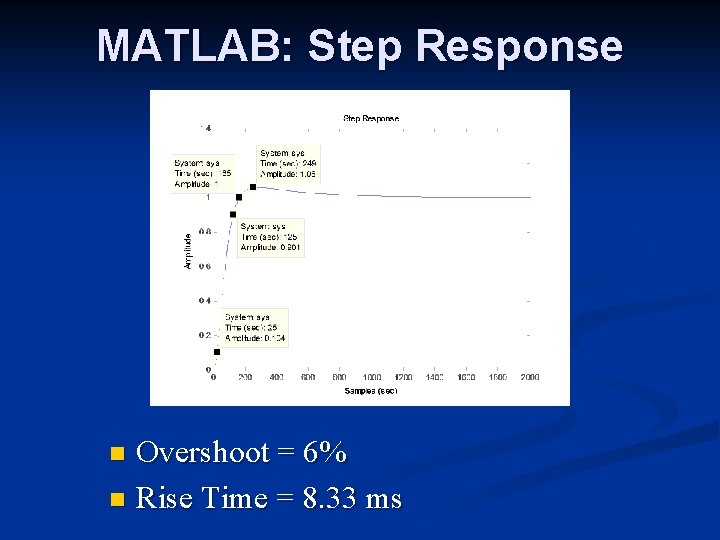
MATLAB: Step Response Overshoot = 6% n Rise Time = 8. 33 ms n
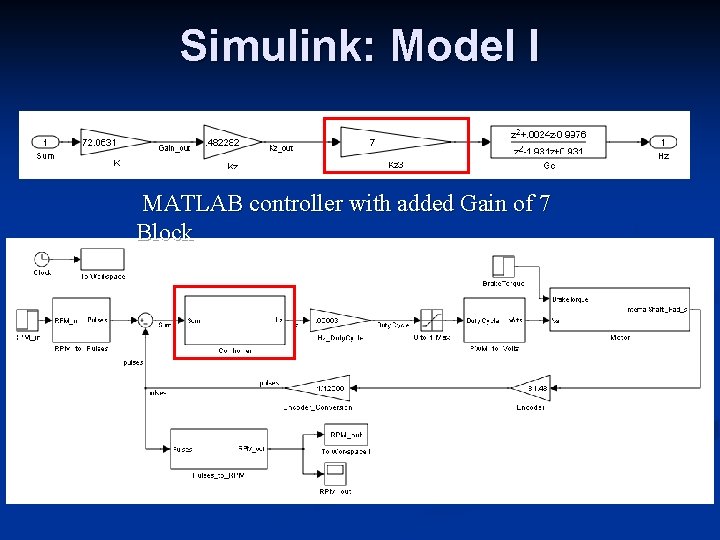
Simulink: Model I MATLAB controller with added Gain of 7 Block
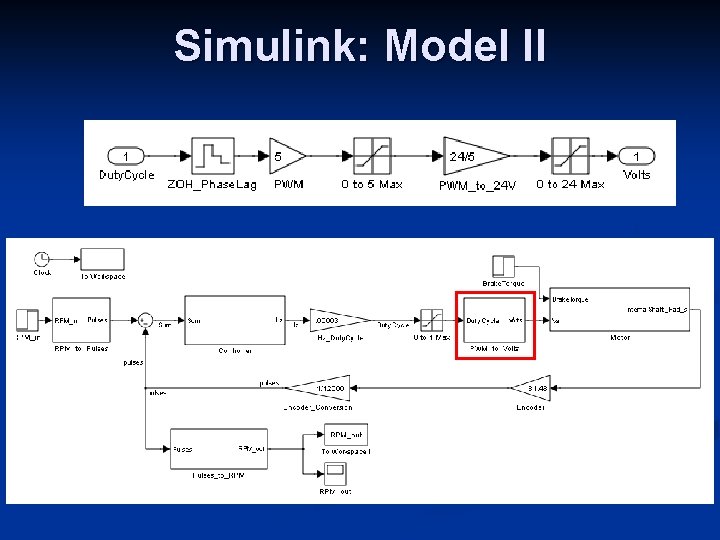
Simulink: Model II
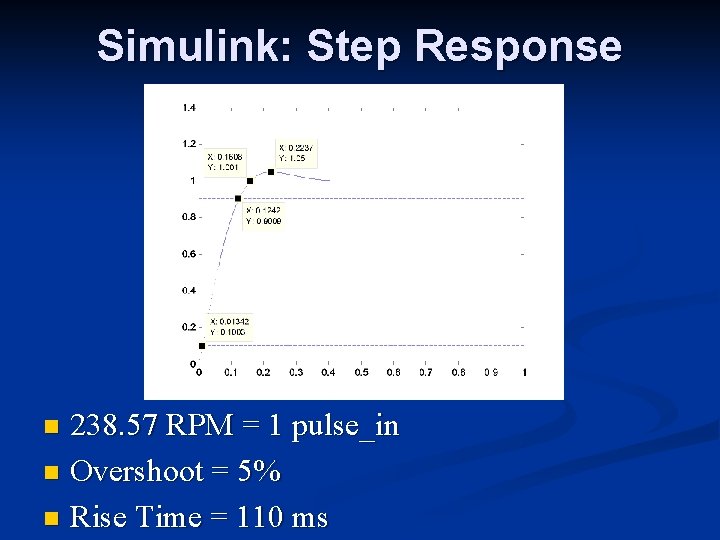
Simulink: Step Response 238. 57 RPM = 1 pulse_in n Overshoot = 5% n Rise Time = 110 ms n
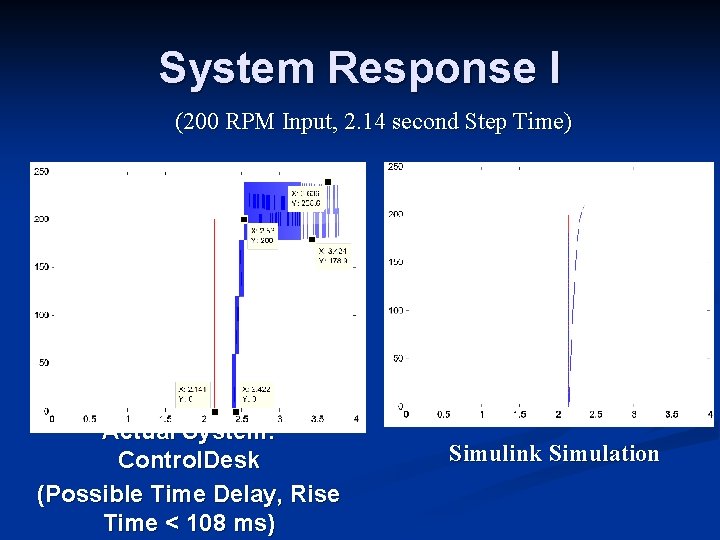
System Response I (200 RPM Input, 2. 14 second Step Time) Actual System: Control. Desk (Possible Time Delay, Rise Time < 108 ms) Simulink Simulation
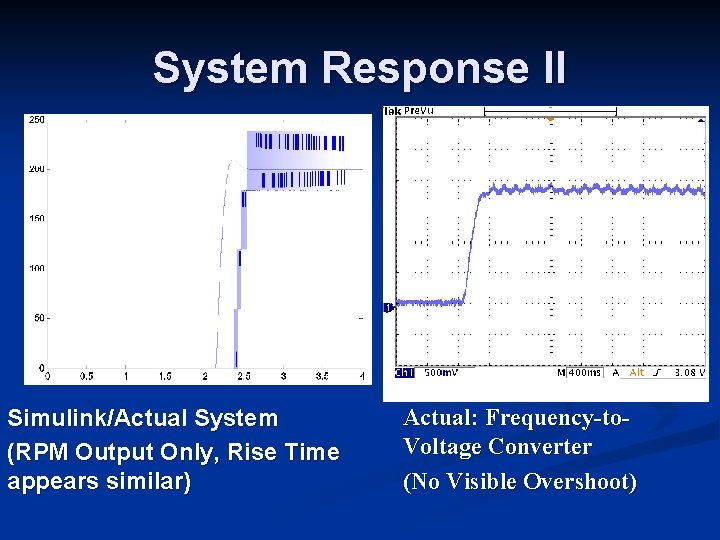
System Response II Simulink/Actual System (RPM Output Only, Rise Time appears similar) Actual: Frequency-to. Voltage Converter (No Visible Overshoot)
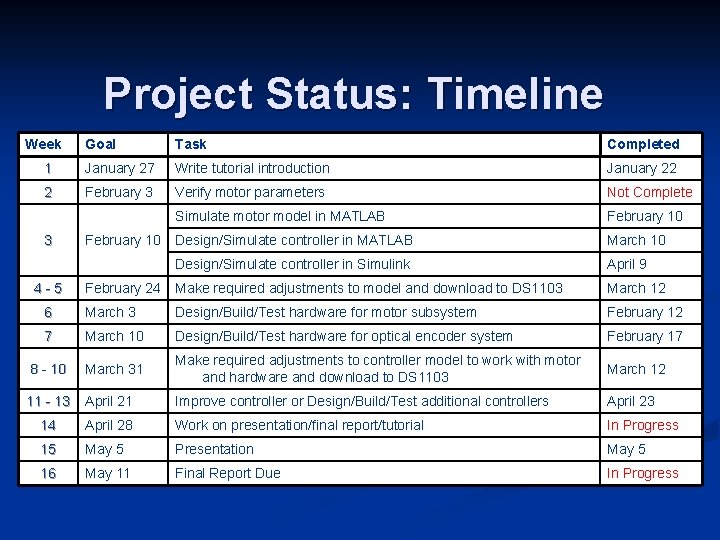
Project Status: Timeline Week Goal Task Completed 1 January 27 Write tutorial introduction January 22 2 February 3 Verify motor parameters Not Complete Simulate motor model in MATLAB February 10 Design/Simulate controller in MATLAB March 10 Design/Simulate controller in Simulink April 9 February 24 Make required adjustments to model and download to DS 1103 March 12 6 March 3 Design/Build/Test hardware for motor subsystem February 12 7 March 10 Design/Build/Test hardware for optical encoder system February 17 8 - 10 March 31 Make required adjustments to controller model to work with motor and hardware and download to DS 1103 March 12 11 - 13 April 21 Improve controller or Design/Build/Test additional controllers April 23 14 April 28 Work on presentation/final report/tutorial In Progress 15 May 5 Presentation May 5 16 May 11 Final Report Due In Progress 3 4 -5 February 10
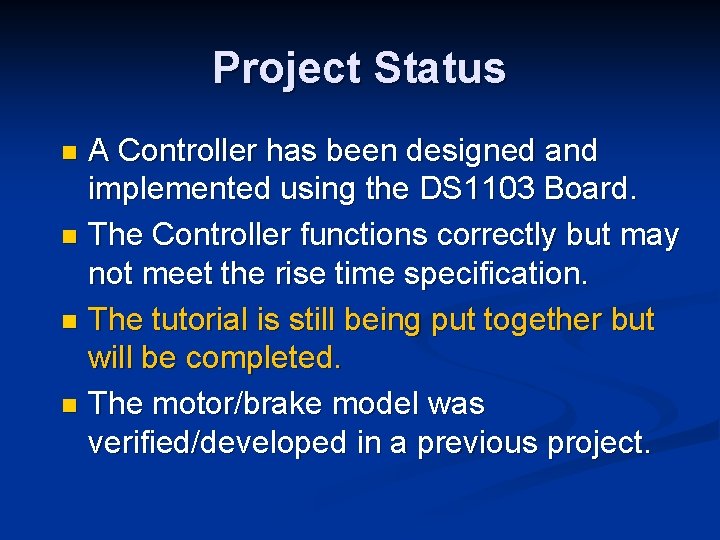
Project Status A Controller has been designed and implemented using the DS 1103 Board. n The Controller functions correctly but may not meet the rise time specification. n The tutorial is still being put together but will be completed. n The motor/brake model was verified/developed in a previous project. n
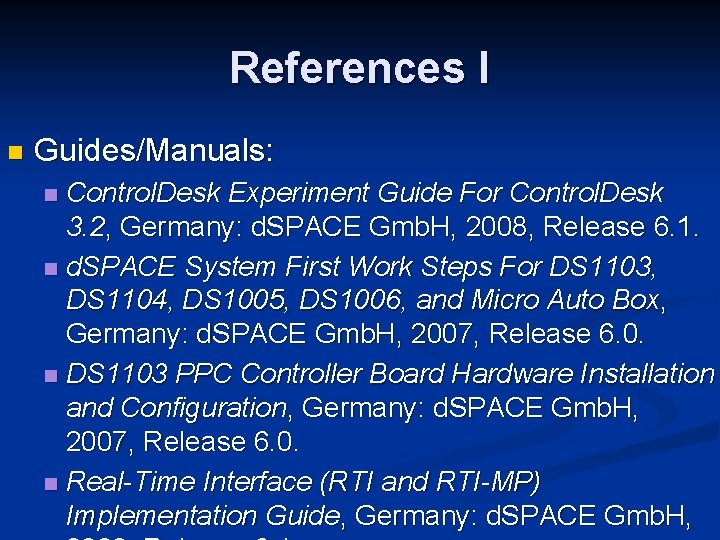
References I n Guides/Manuals: Control. Desk Experiment Guide For Control. Desk 3. 2, Germany: d. SPACE Gmb. H, 2008, Release 6. 1. n d. SPACE System First Work Steps For DS 1103, DS 1104, DS 1005, DS 1006, and Micro Auto Box, Germany: d. SPACE Gmb. H, 2007, Release 6. 0. n DS 1103 PPC Controller Board Hardware Installation and Configuration, Germany: d. SPACE Gmb. H, 2007, Release 6. 0. n Real-Time Interface (RTI and RTI-MP) Implementation Guide, Germany: d. SPACE Gmb. H, n
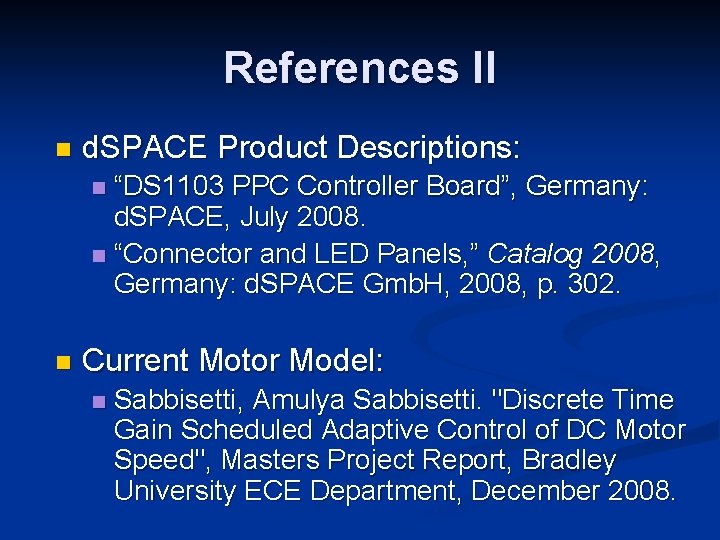
References II n d. SPACE Product Descriptions: “DS 1103 PPC Controller Board”, Germany: d. SPACE, July 2008. n “Connector and LED Panels, ” Catalog 2008, Germany: d. SPACE Gmb. H, 2008, p. 302. n n Current Motor Model: n Sabbisetti, Amulya Sabbisetti. "Discrete Time Gain Scheduled Adaptive Control of DC Motor Speed", Masters Project Report, Bradley University ECE Department, December 2008.
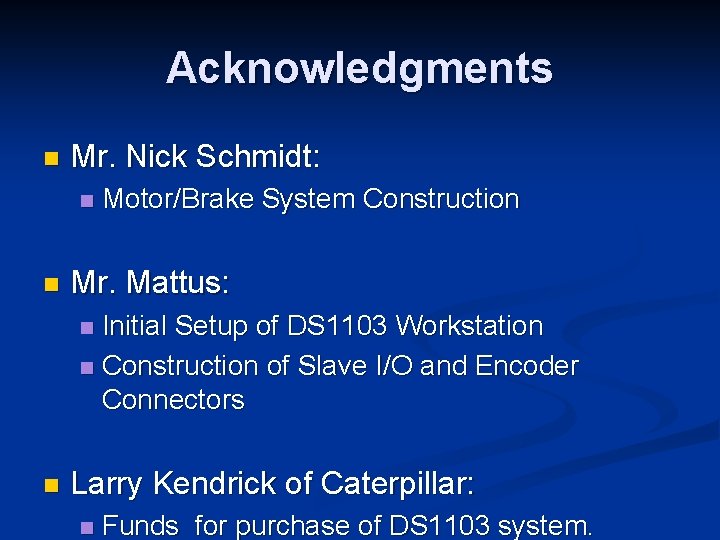
Acknowledgments n Mr. Nick Schmidt: n n Motor/Brake System Construction Mr. Mattus: Initial Setup of DS 1103 Workstation n Construction of Slave I/O and Encoder Connectors n n Larry Kendrick of Caterpillar: n Funds for purchase of DS 1103 system.
Ca workstation esp tutorial
Sls1103
Cs 1103 programming 2
Scp1103
Scp-1103
Scp1103
Scp 1103
Cs 1103
Scp 1103
Scp-1103
Chemsheets as 1047 answers
Graphics monitors and workstations in computer graphics
7 it infrastructure domains
Jubail industrial college
Arm based workstation
Sap treasury workstation
Microsoft privileged access workstations
Port forwarding vmware workstation 16
Pacs modality workstation
What is dicom
Arcinfo workstation
Workstation design definition
Vmware workstation 10
Nbme secure browser
Csie.ntu.edu.tw
Chapter 1 it sim what is a computer
Workstation model in distributed system
How to install nachos on linux in workstation room 217
A workstation in a process is a bottleneck if
Workstation location
Just-in-time philosophy
Digital forensic lab floor plan
Micah dowty
Cluster workstation approach
Workstation fall protection
Csie workstation
Netapp simulator download iso
Xerox 6085 workstation
Building a forensic workstation
Workstation
Connect.cssionline.com
Forensics
Wim coekaerts