Constant Extension Rate Testing of Additively Manufactured 17
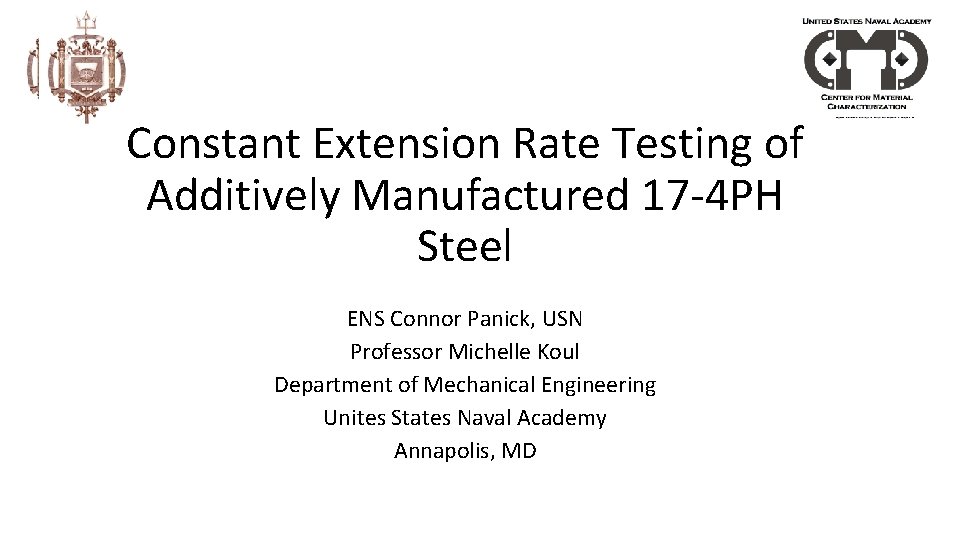
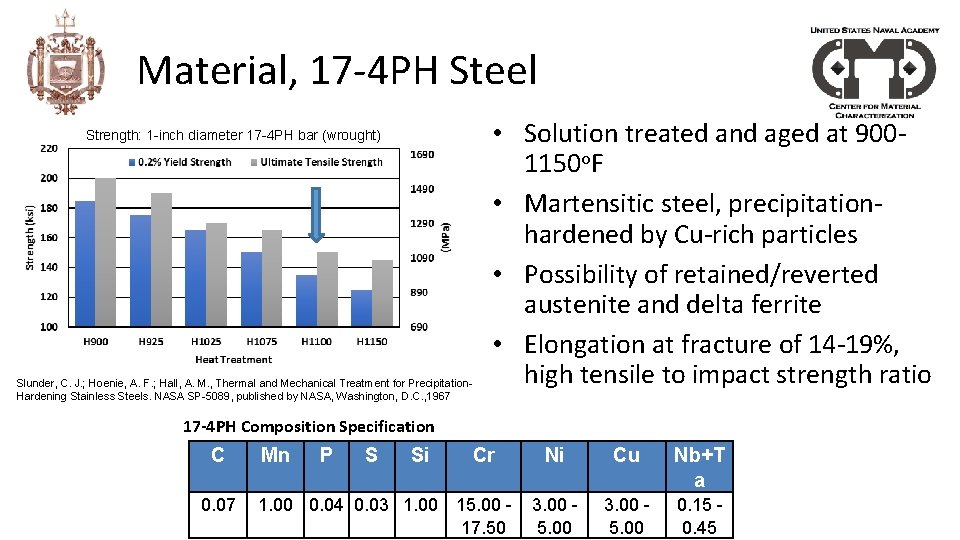
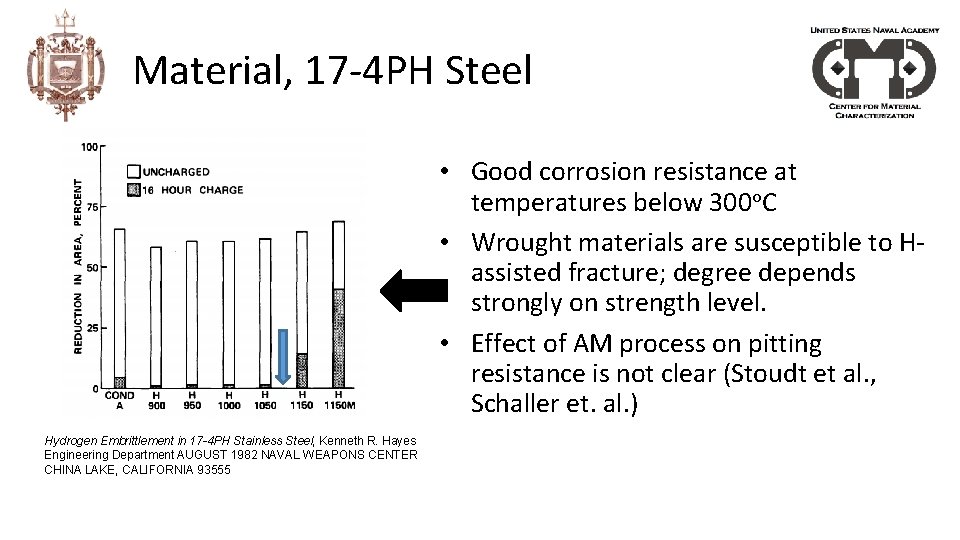
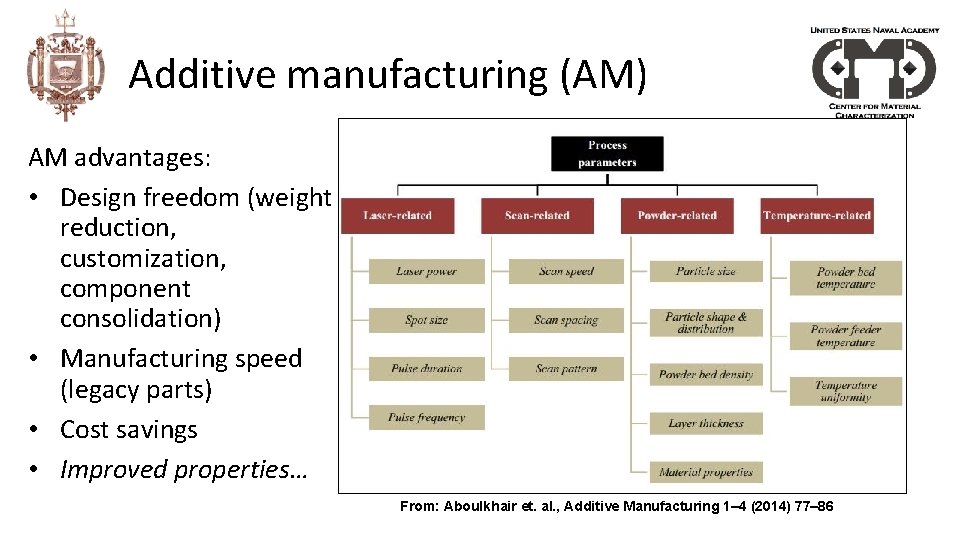
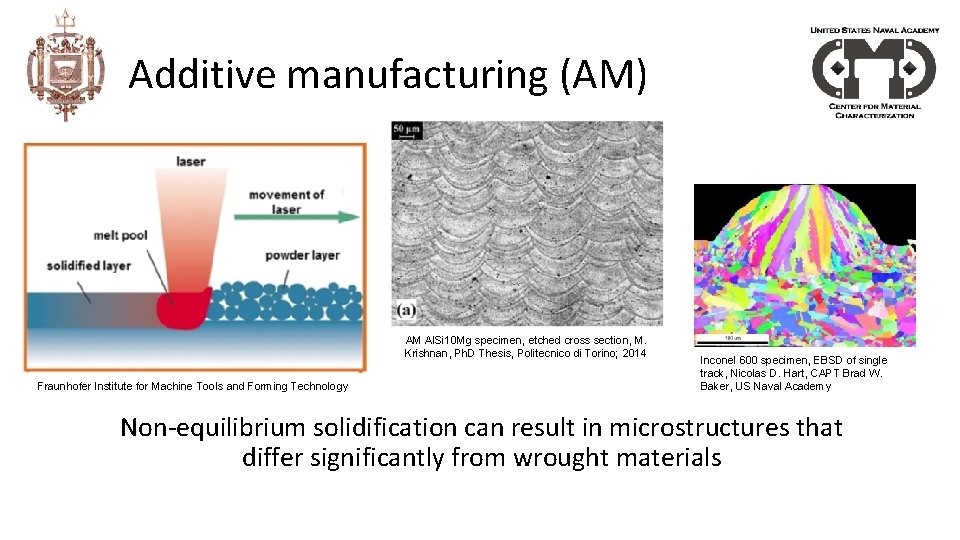
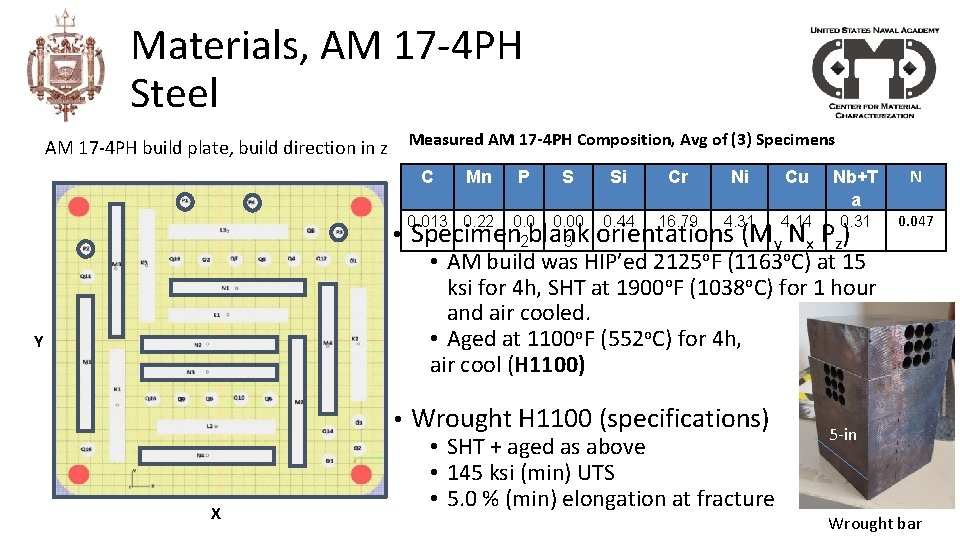
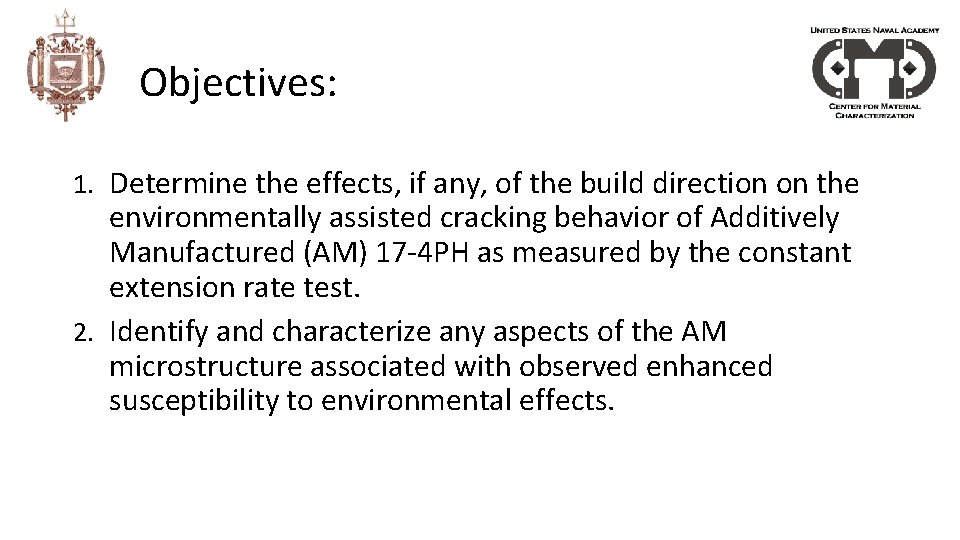
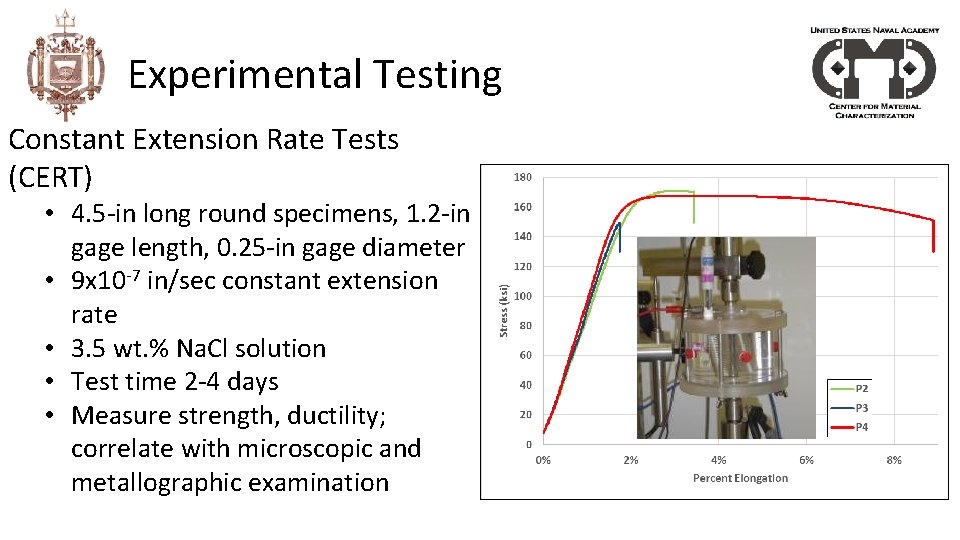
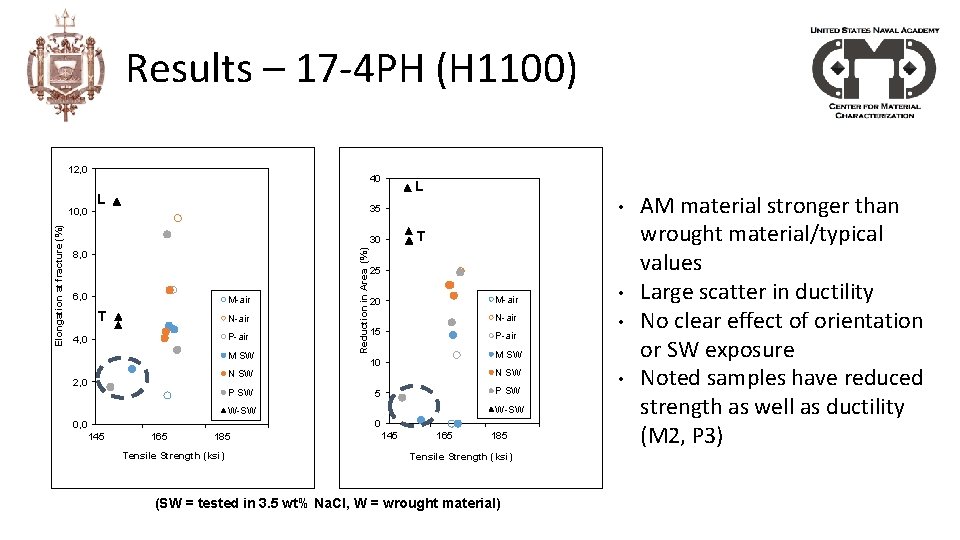
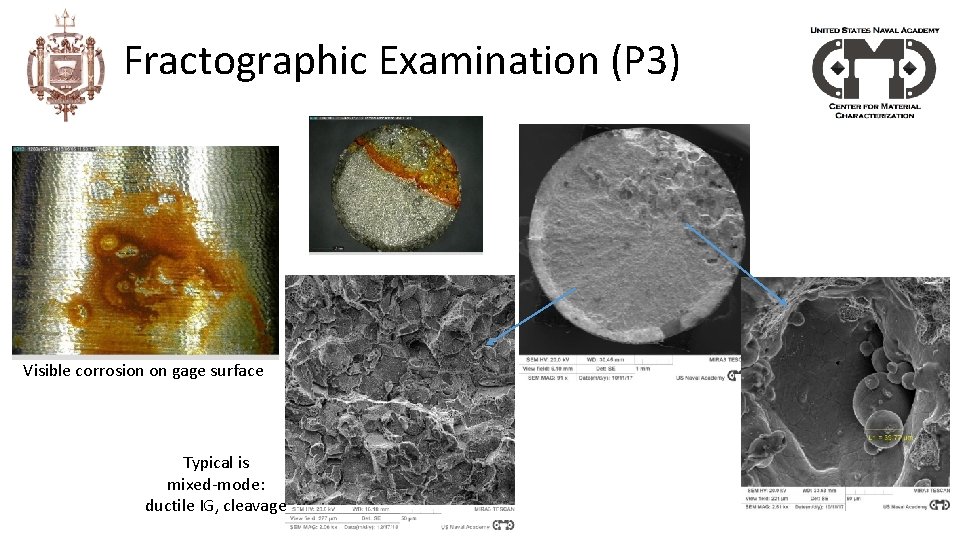
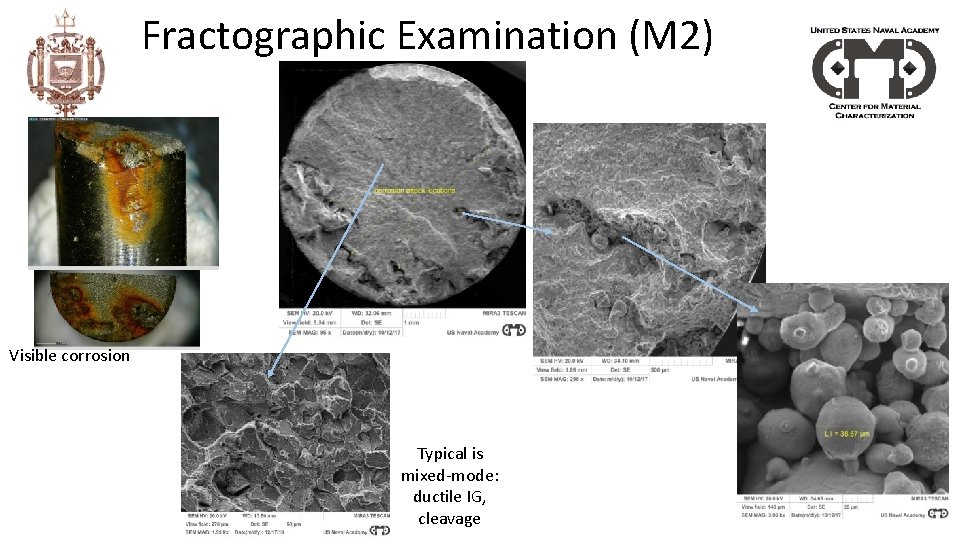
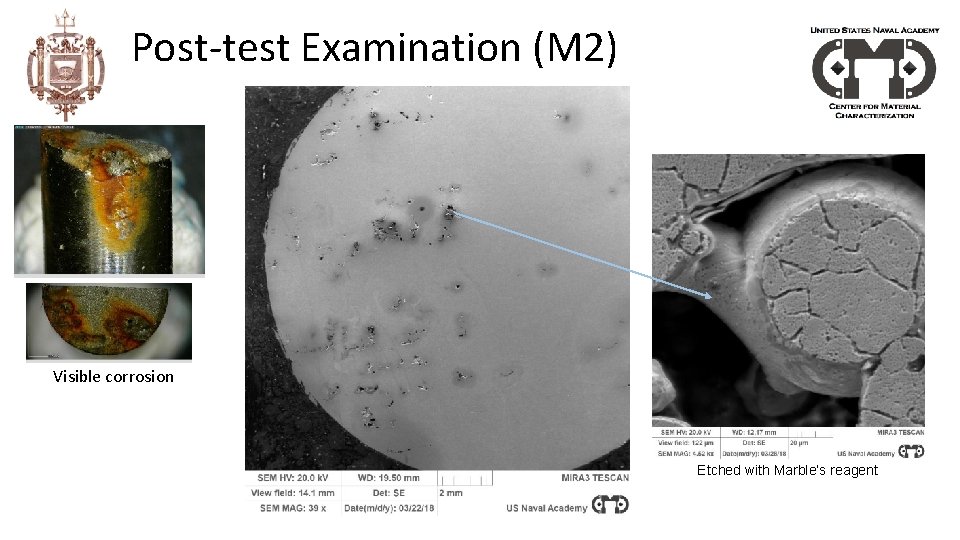
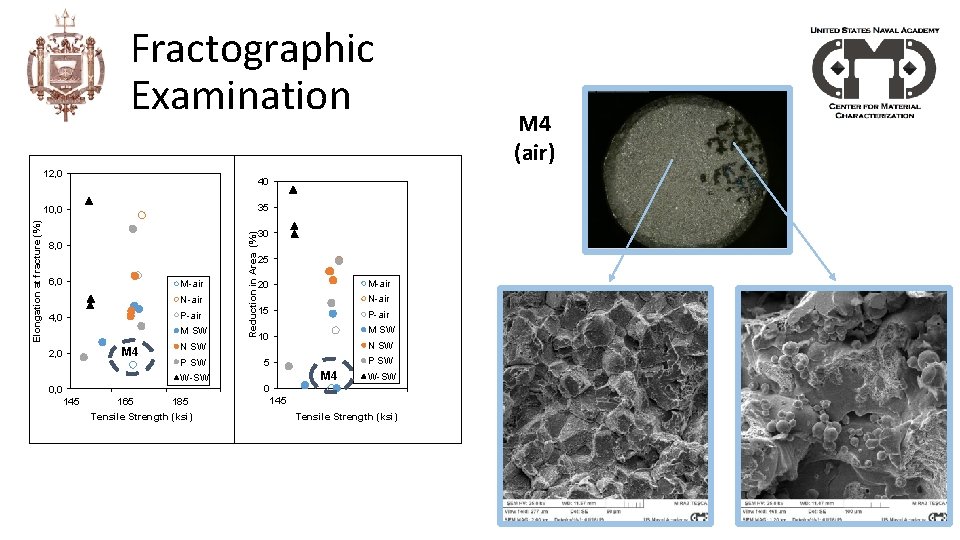
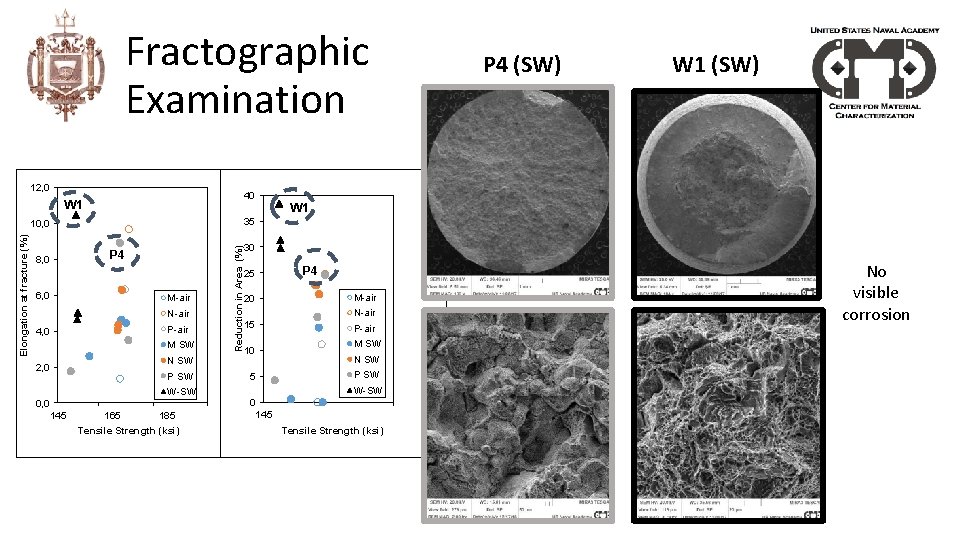
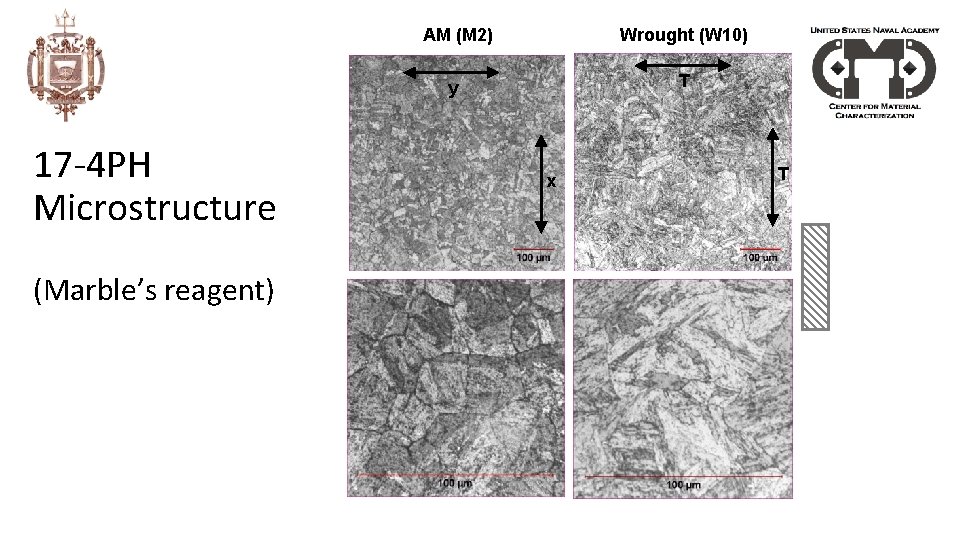
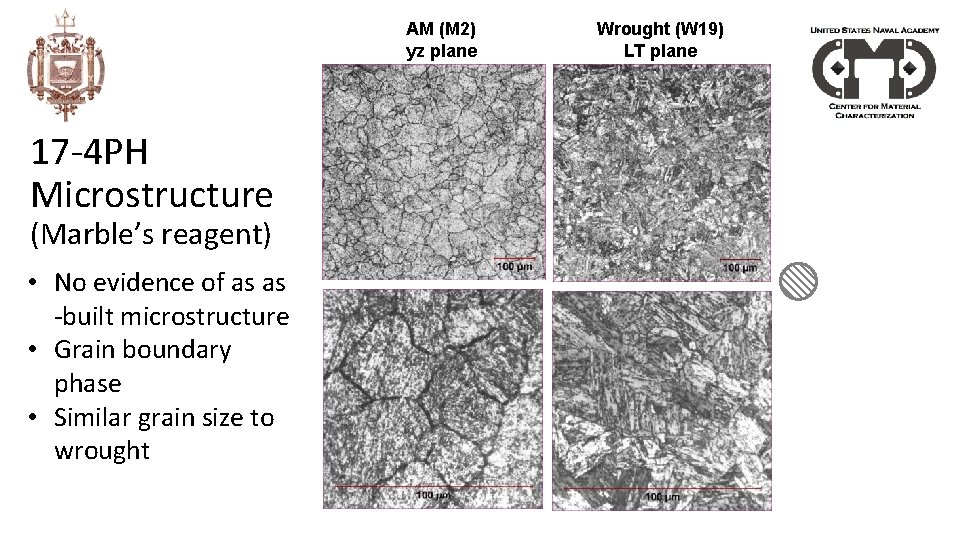
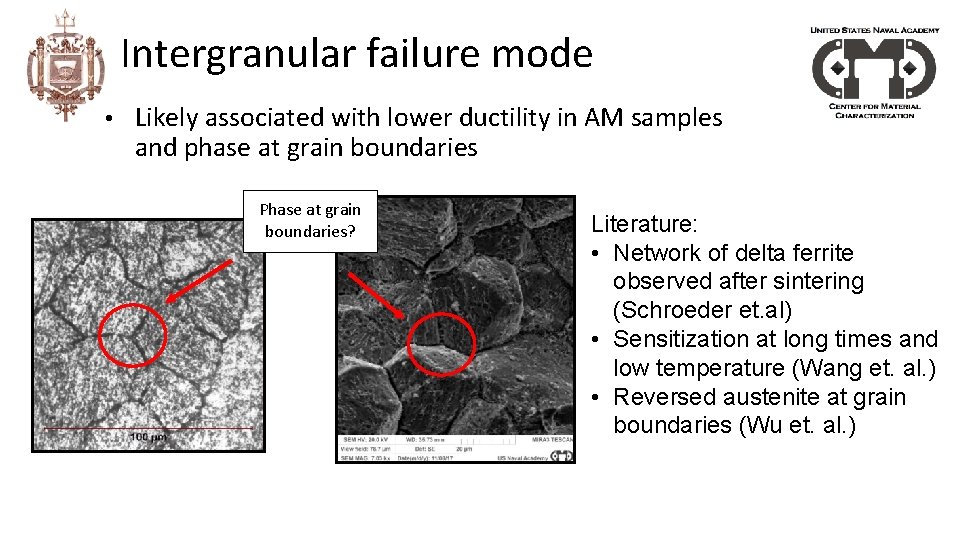
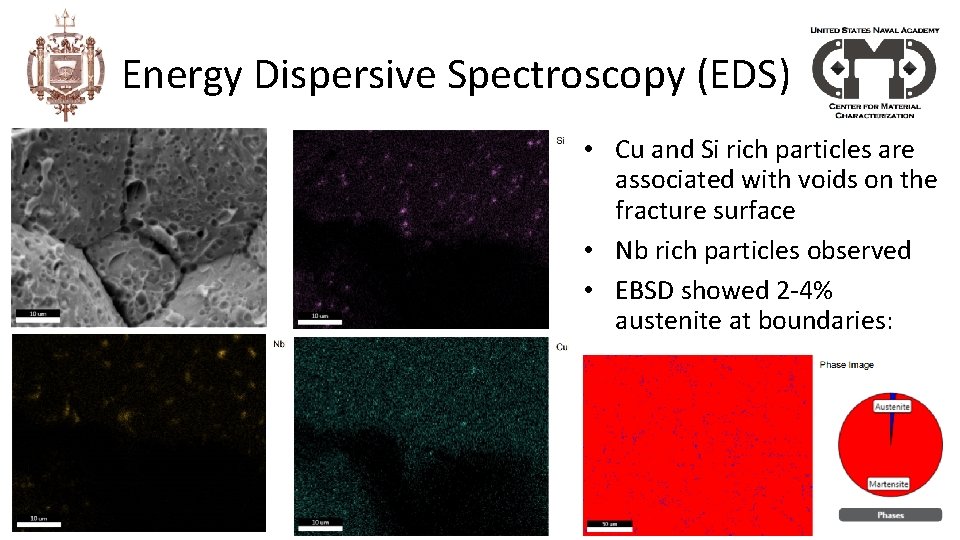
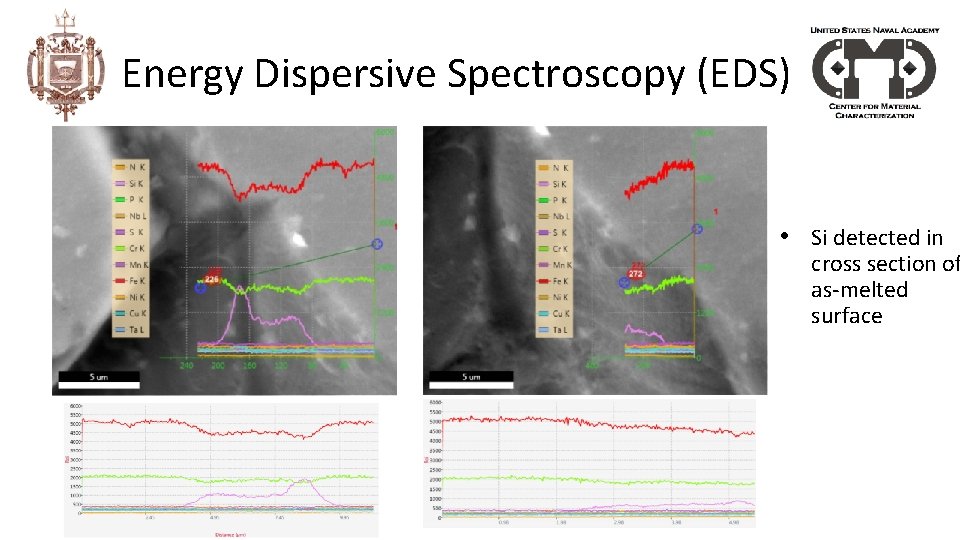
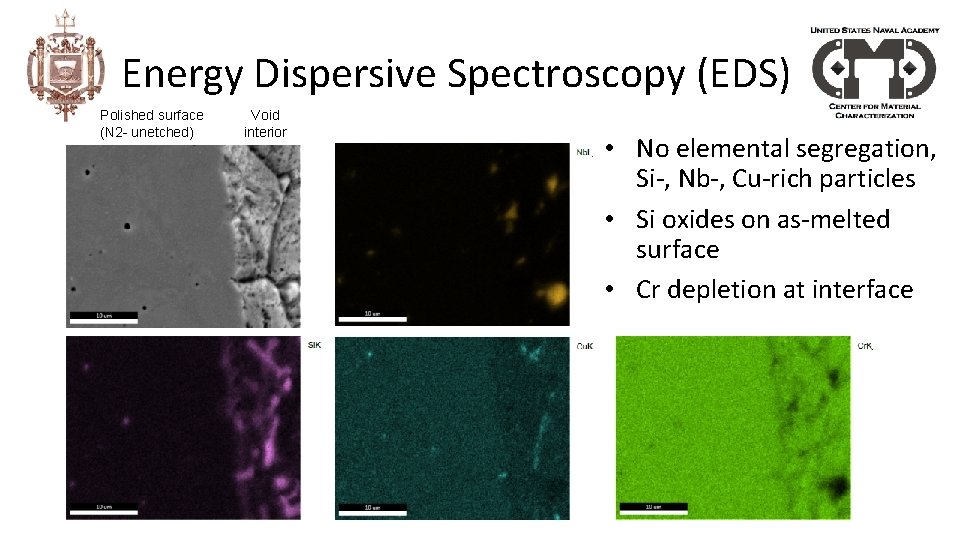
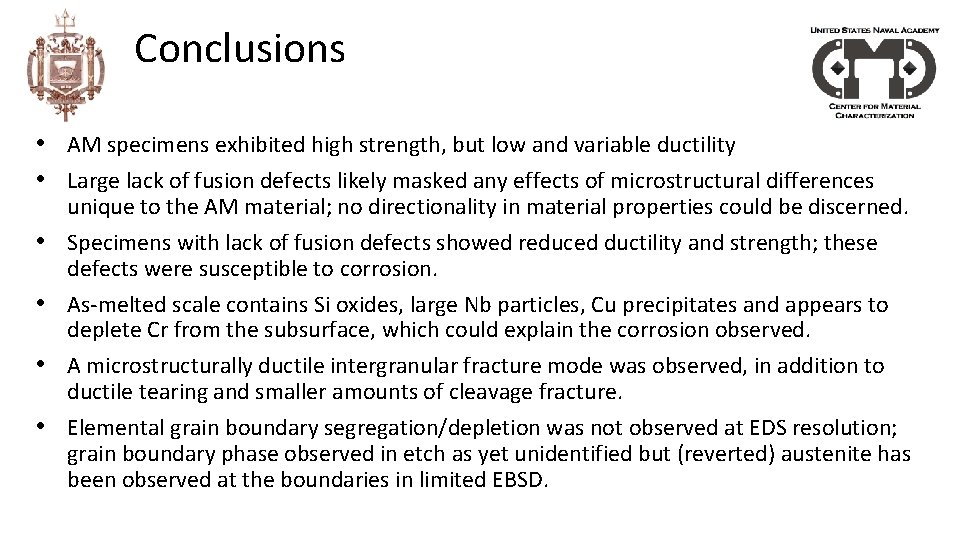
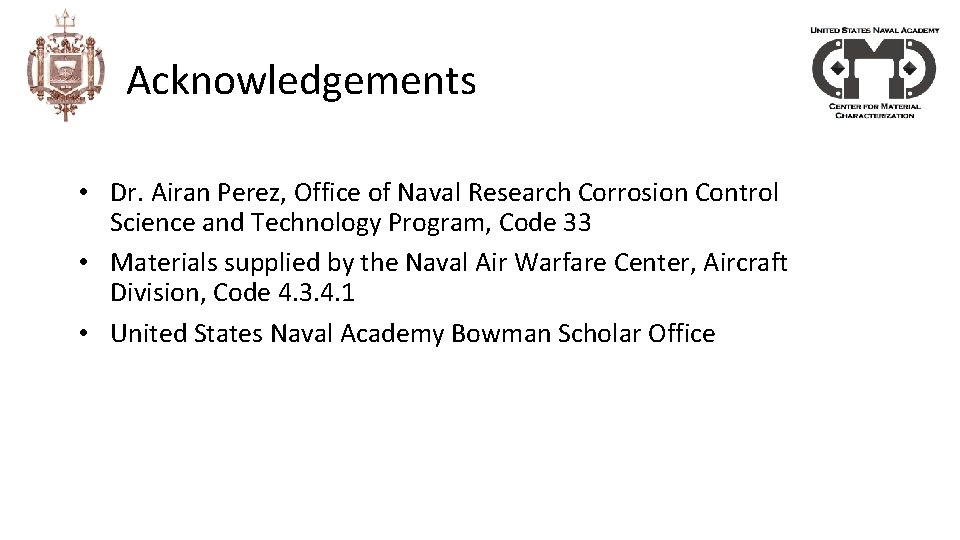
- Slides: 22
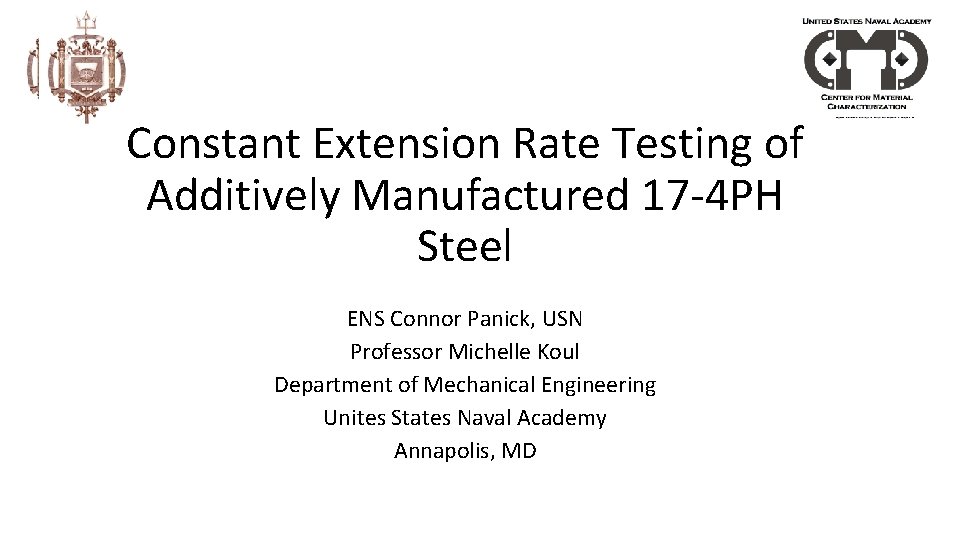
Constant Extension Rate Testing of Additively Manufactured 17 -4 PH Steel ENS Connor Panick, USN Professor Michelle Koul Department of Mechanical Engineering Unites States Naval Academy Annapolis, MD
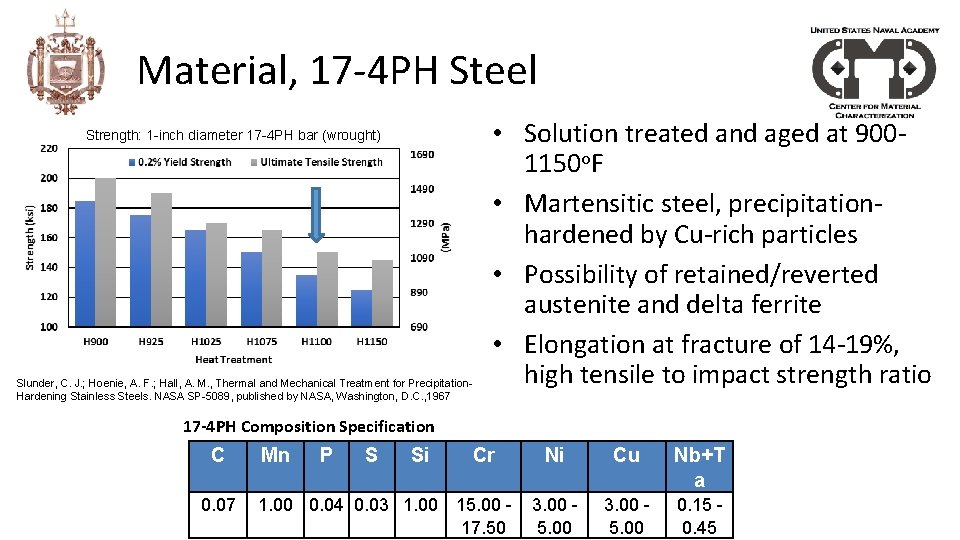
Material, 17 -4 PH Steel Strength: 1 -inch diameter 17 -4 PH bar (wrought) Slunder, C. J. ; Hoenie, A. F. ; Hall, A. M. , Thermal and Mechanical Treatment for Precipitation. Hardening Stainless Steels. NASA SP-5089, published by NASA, Washington, D. C. , 1967 • Solution treated and aged at 9001150 o. F • Martensitic steel, precipitationhardened by Cu-rich particles • Possibility of retained/reverted austenite and delta ferrite • Elongation at fracture of 14 -19%, high tensile to impact strength ratio 17 -4 PH Composition Specification C 0. 07 Mn P S Si Cr 1. 00 0. 04 0. 03 1. 00 15. 00 17. 50 Ni Cu Nb+T a 3. 00 5. 00 0. 15 0. 45
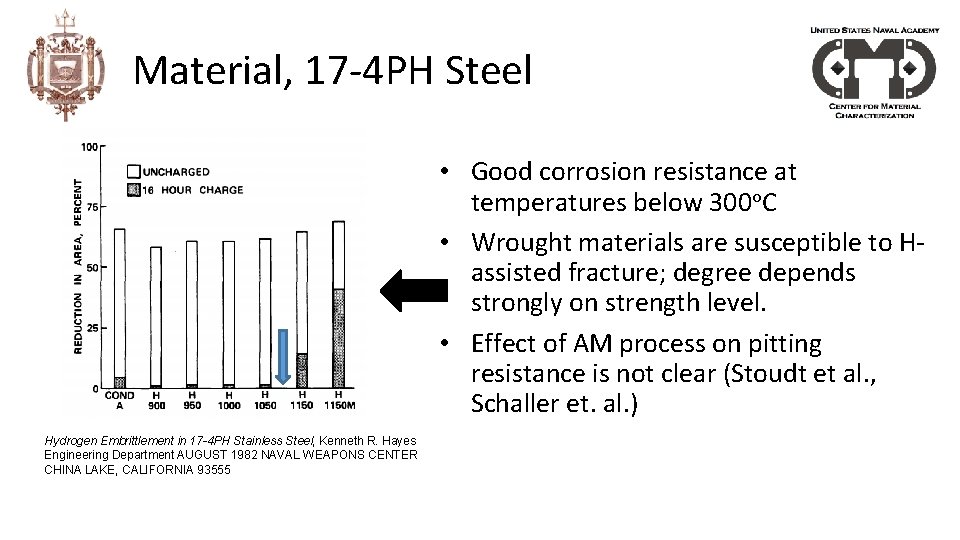
Material, 17 -4 PH Steel • Good corrosion resistance at temperatures below 300 o. C • Wrought materials are susceptible to Hassisted fracture; degree depends strongly on strength level. • Effect of AM process on pitting resistance is not clear (Stoudt et al. , Schaller et. al. ) Hydrogen Embrittlement in 17 -4 PH Stainless Steel, Kenneth R. Hayes Engineering Department AUGUST 1982 NAVAL WEAPONS CENTER CHINA LAKE, CALIFORNIA 93555
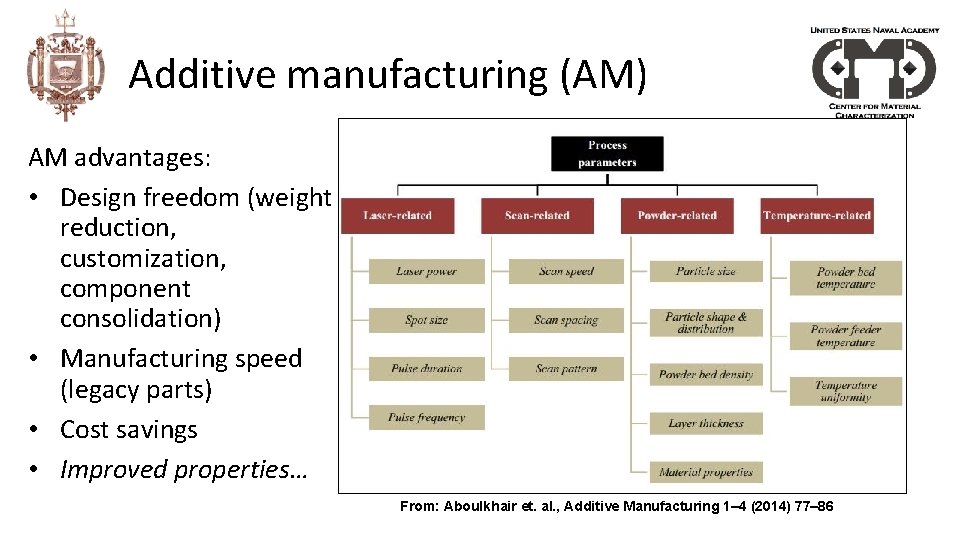
Additive manufacturing (AM) AM advantages: • Design freedom (weight reduction, customization, component consolidation) • Manufacturing speed (legacy parts) • Cost savings • Improved properties… From: Aboulkhair et. al. , Additive Manufacturing 1– 4 (2014) 77– 86
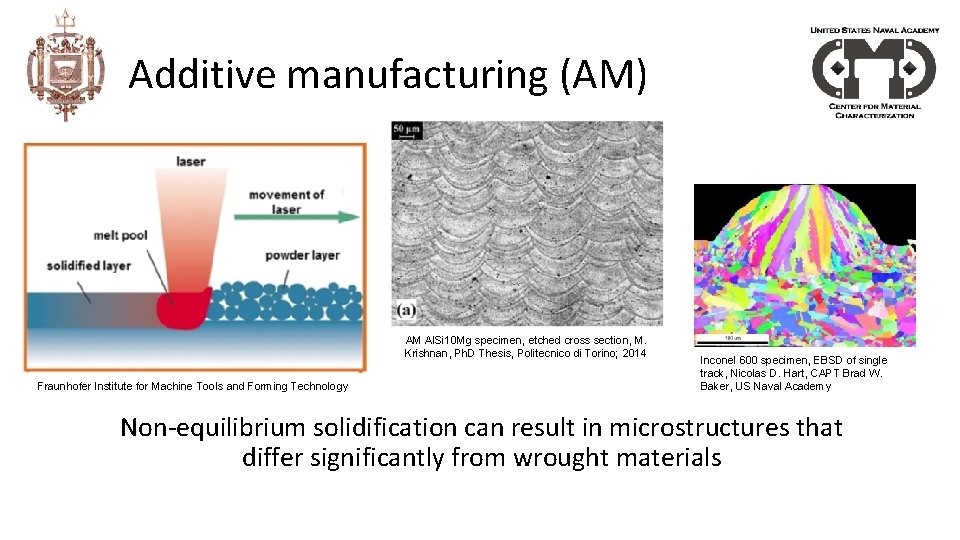
Additive manufacturing (AM) AM Al. Si 10 Mg specimen, etched cross section, M. Krishnan, Ph. D Thesis, Politecnico di Torino; 2014 Fraunhofer Institute for Machine Tools and Forming Technology Inconel 600 specimen, EBSD of single track, Nicolas D. Hart, CAPT Brad W. Baker, US Naval Academy Non-equilibrium solidification can result in microstructures that differ significantly from wrought materials
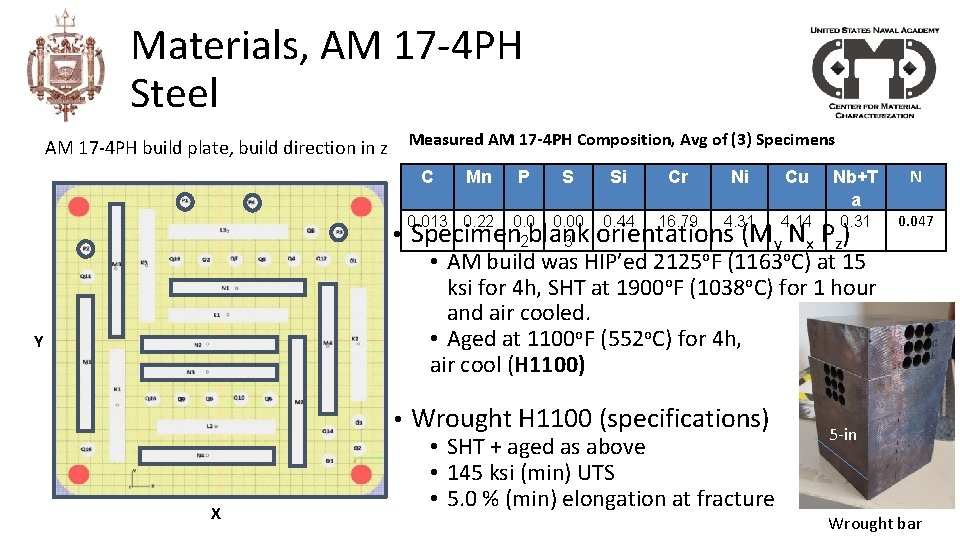
Materials, AM 17 -4 PH Steel AM 17 -4 PH build plate, build direction in z Measured AM 17 -4 PH Composition, Avg of (3) Specimens C Mn 0. 013 0. 22 P S Si Cr Ni Cu Nb+T a N 0. 0 2 0. 00 3 0. 44 16. 79 4. 31 4. 14 0. 31 0. 047 • Specimen blank orientations (My Nx Pz) • AM build was HIP’ed 2125 o. F (1163 o. C) at 15 ksi for 4 h, SHT at 1900 o. F (1038 o. C) for 1 hour and air cooled. • Aged at 1100 o. F (552 o. C) for 4 h, air cool (H 1100) Y X • Wrought H 1100 (specifications) • SHT + aged as above • 145 ksi (min) UTS • 5. 0 % (min) elongation at fracture 5 -in Wrought bar
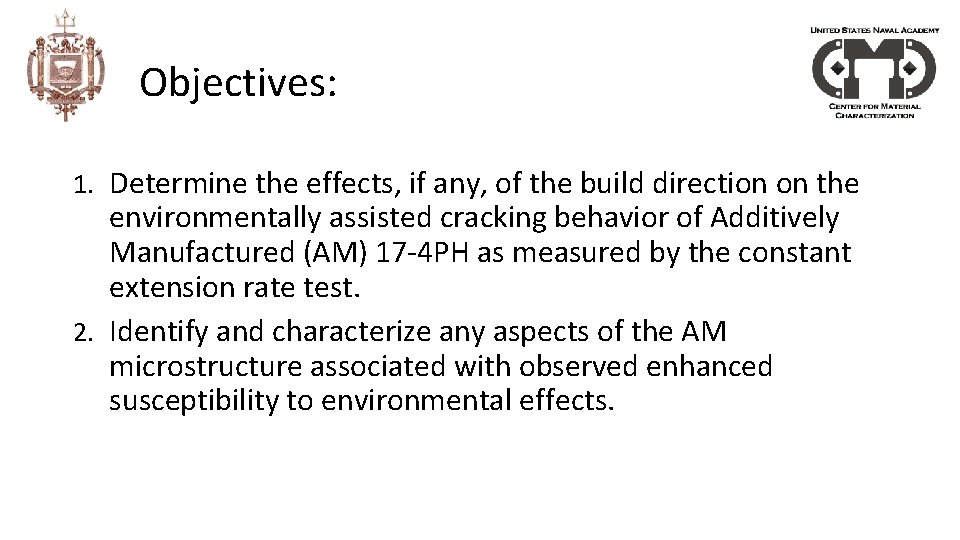
Objectives: 1. Determine the effects, if any, of the build direction on the environmentally assisted cracking behavior of Additively Manufactured (AM) 17 -4 PH as measured by the constant extension rate test. 2. Identify and characterize any aspects of the AM microstructure associated with observed enhanced susceptibility to environmental effects.
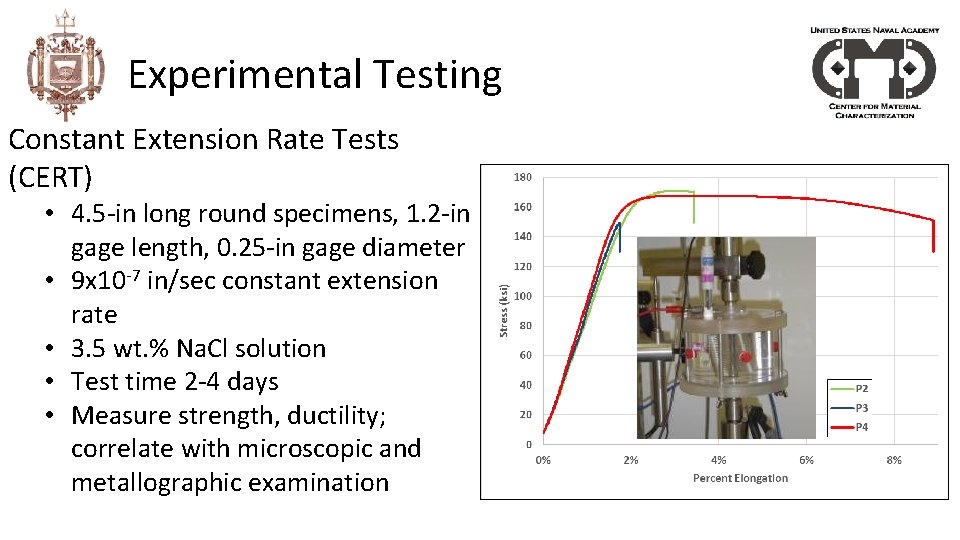
Experimental Testing Constant Extension Rate Tests (CERT) • 4. 5 -in long round specimens, 1. 2 -in gage length, 0. 25 -in gage diameter • 9 x 10 -7 in/sec constant extension rate • 3. 5 wt. % Na. Cl solution • Test time 2 -4 days • Measure strength, ductility; correlate with microscopic and metallographic examination
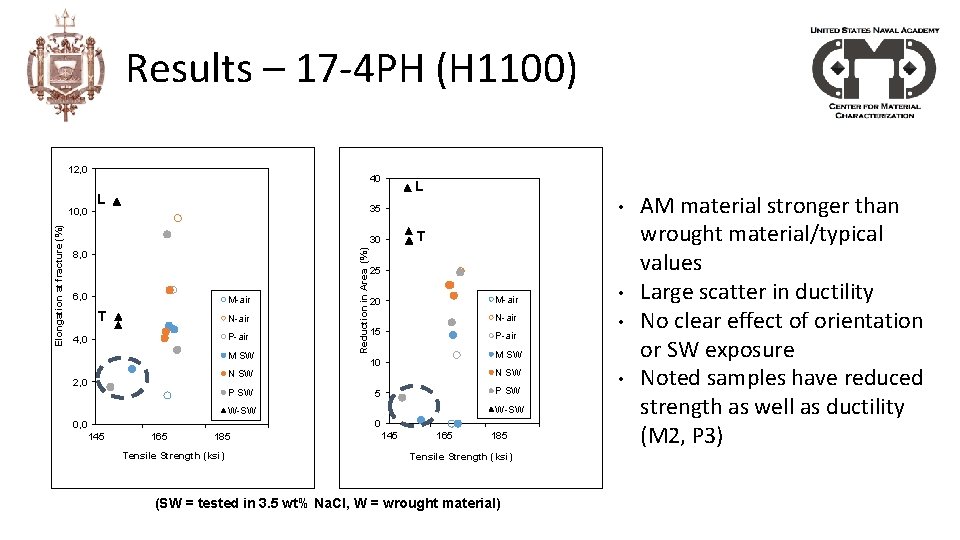
Results – 17 -4 PH (H 1100) 12, 0 L L • 35 T 30 8, 0 6, 0 M-air T N-air P-air 4, 0 M SW Reduction in Area (%) Elongation at fracture (%) 10, 0 40 25 M-air 20 N-air 15 P-air P SW N SW P SW 5 W-SW 0 0, 0 145 165 185 Tensile Strength (ksi) • M SW 10 N SW 2, 0 • 145 165 185 Tensile Strength (ksi) (SW = tested in 3. 5 wt% Na. Cl, W = wrought material) • AM material stronger than wrought material/typical values Large scatter in ductility No clear effect of orientation or SW exposure Noted samples have reduced strength as well as ductility (M 2, P 3)
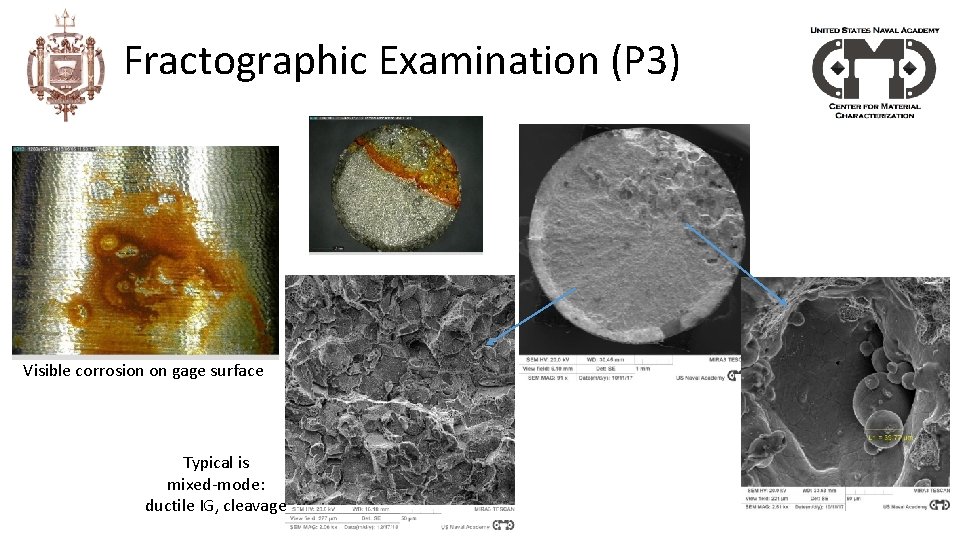
Fractographic Examination (P 3) Visible corrosion on gage surface Typical is mixed-mode: ductile IG, cleavage
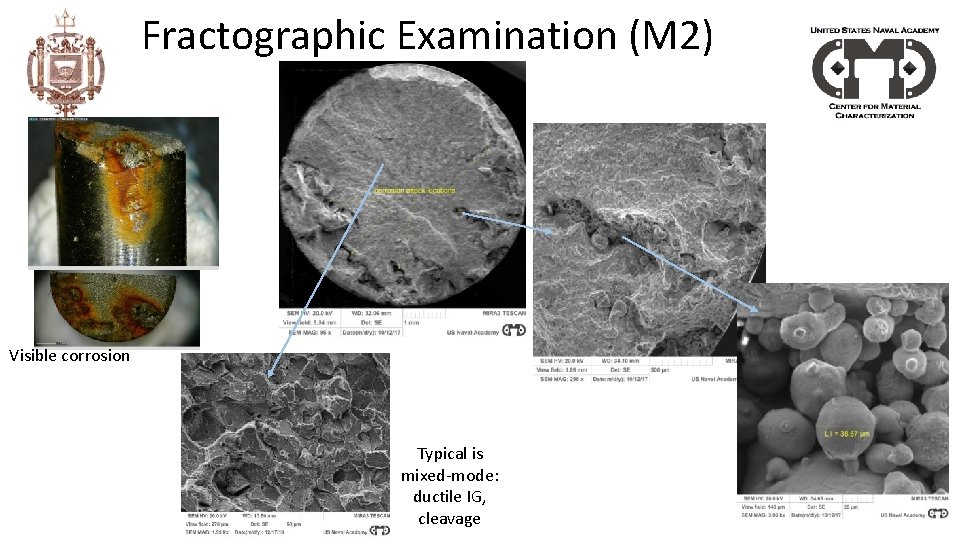
Fractographic Examination (M 2) Visible corrosion Typical is mixed-mode: ductile IG, cleavage
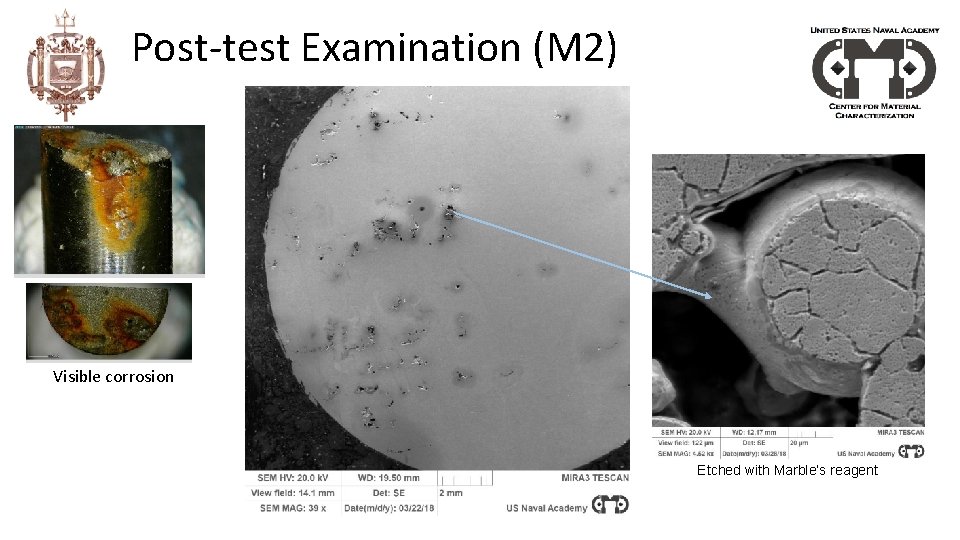
Post-test Examination (M 2) Visible corrosion Etched with Marble’s reagent
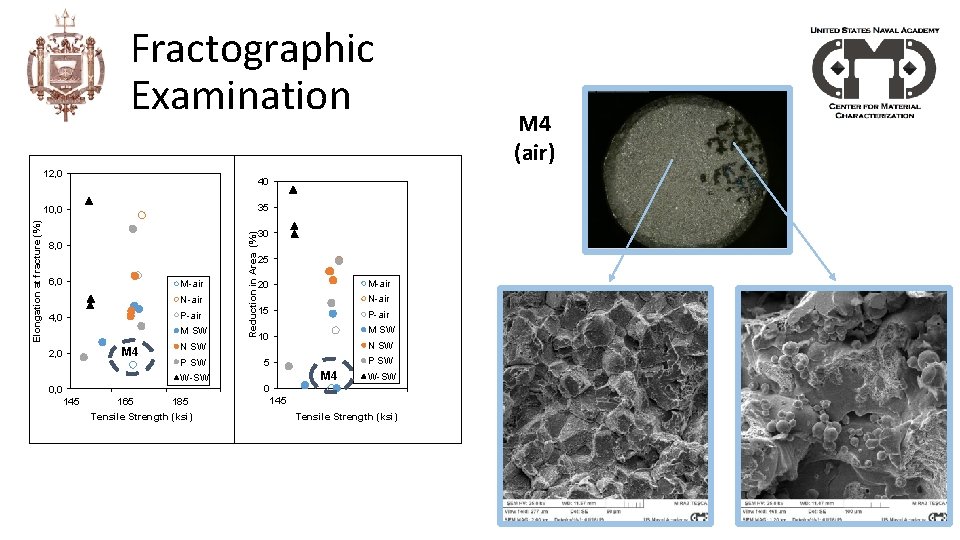
Fractographic Examination 12, 0 40 35 8, 0 6, 0 M-air N-air P-air 4, 0 M SW M 4 2, 0 N SW P SW W-SW 0, 0 145 165 185 Tensile Strength (ksi) Reduction in Area (%) Elongation at fracture (%) 10, 0 30 25 M-air 20 N-air 15 P-air M SW 10 N SW P SW 5 M 4 W-SW 0 145 Tensile Strength (ksi) M 4 (air)
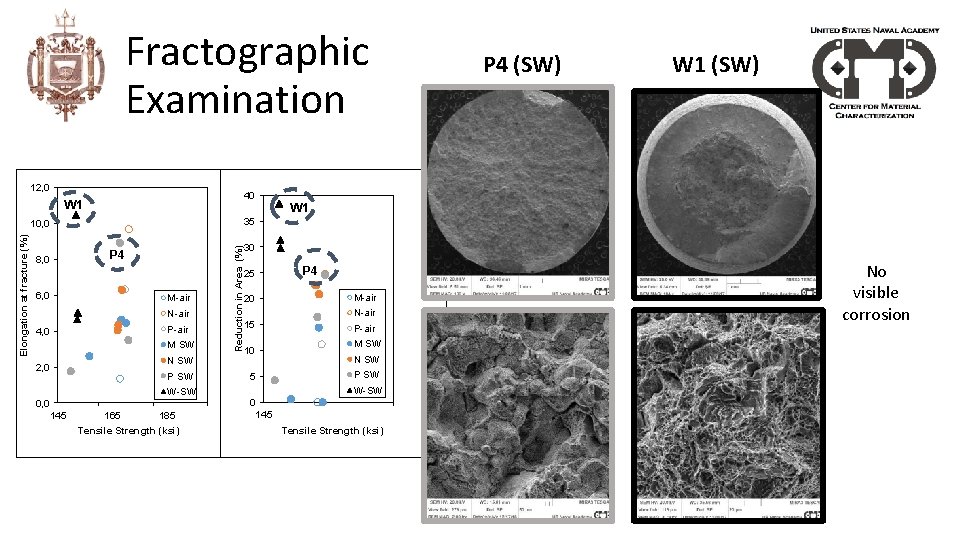
Fractographic Examination 12, 0 W 1 35 P 4 6, 0 M-air N-air P-air 4, 0 M SW N SW 2, 0 P SW W-SW 0, 0 165 185 Tensile Strength (ksi) Reduction in Area (%) Elongation at fracture (%) 10, 0 145 W 1 (SW) 40 W 1 8, 0 P 4 (SW) 30 P 4 25 M-air 20 N-air 15 P-air M SW 10 N SW P SW 5 W-SW 0 145 Tensile Strength (ksi) No visible corrosion
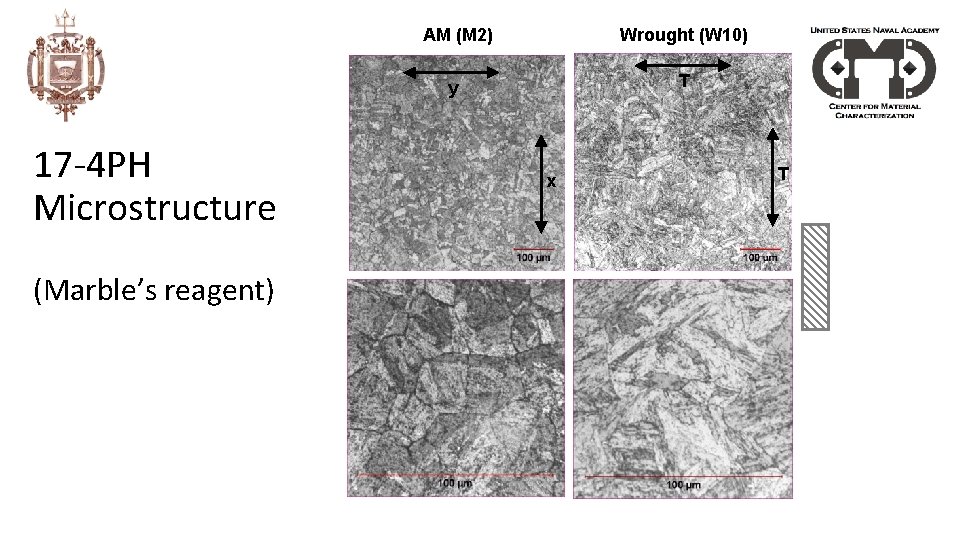
AM (M 2) Wrought (W 10) T y 17 -4 PH Microstructure (Marble’s reagent) x T
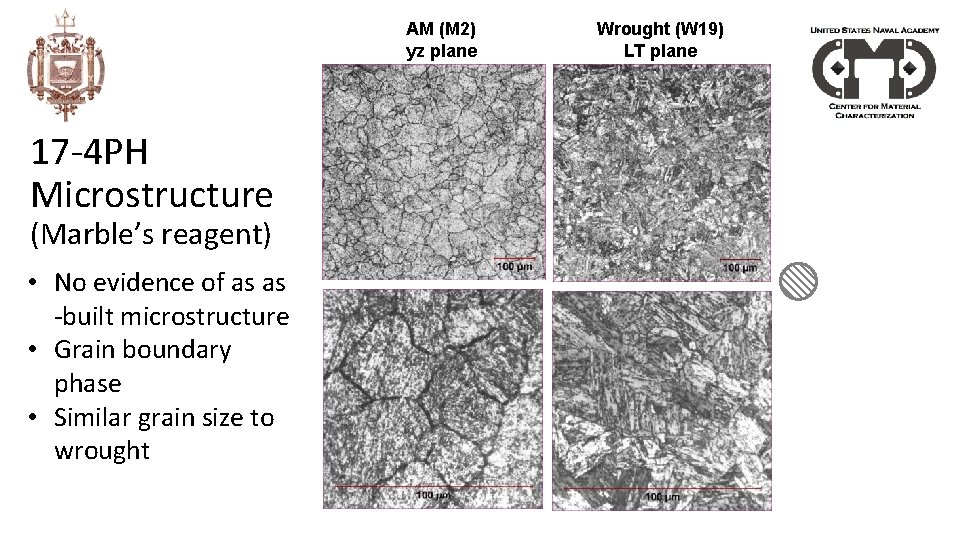
AM (M 2) yz plane 17 -4 PH Microstructure (Marble’s reagent) • No evidence of as as -built microstructure • Grain boundary phase • Similar grain size to wrought Wrought (W 19) LT plane
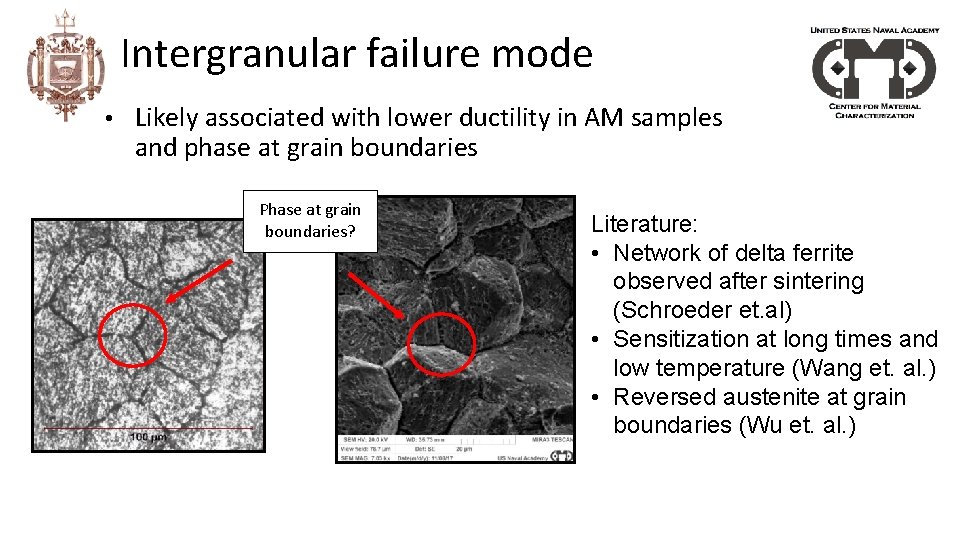
Intergranular failure mode • Likely associated with lower ductility in AM samples and phase at grain boundaries Phase at grain boundaries? Literature: • Network of delta ferrite observed after sintering (Schroeder et. al) • Sensitization at long times and low temperature (Wang et. al. ) • Reversed austenite at grain boundaries (Wu et. al. )
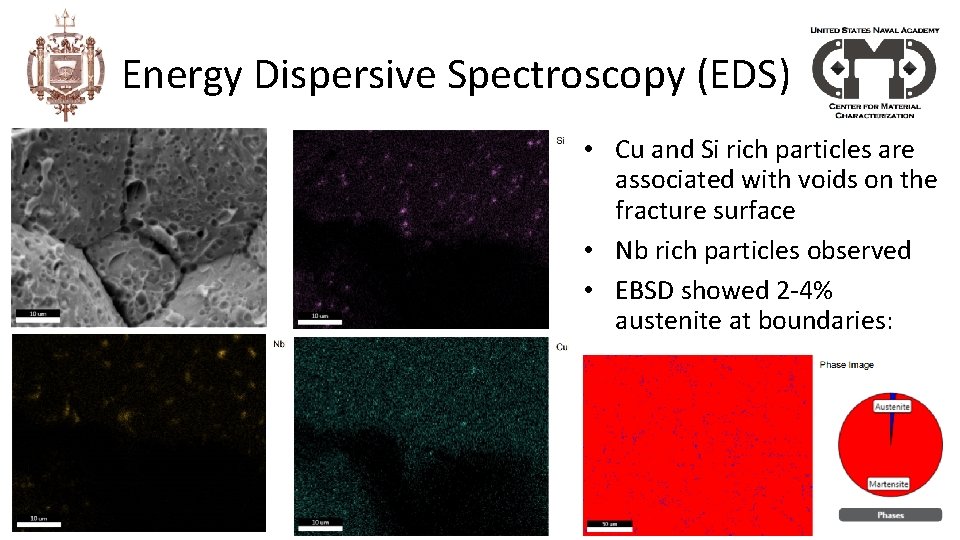
Energy Dispersive Spectroscopy (EDS) • Cu and Si rich particles are associated with voids on the fracture surface • Nb rich particles observed • EBSD showed 2 -4% austenite at boundaries:
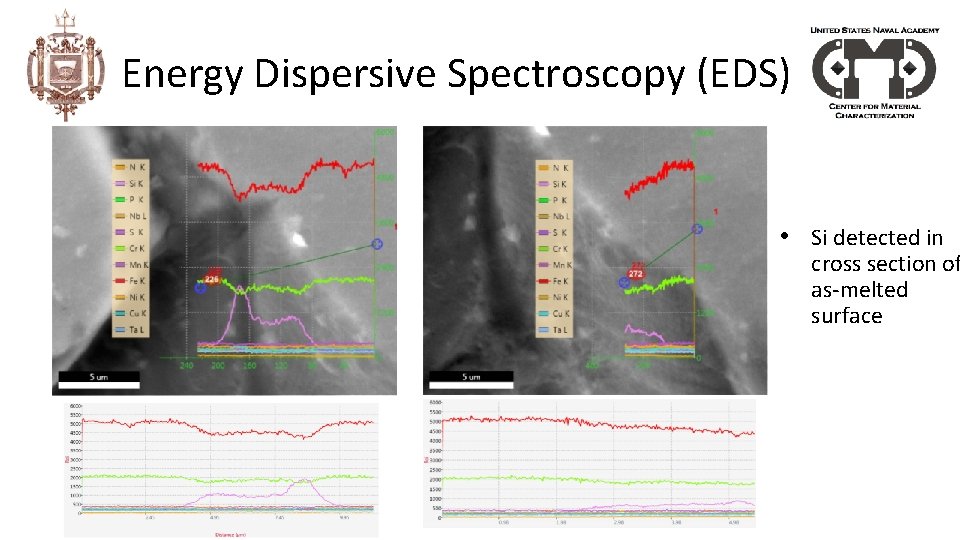
Energy Dispersive Spectroscopy (EDS) • Si detected in cross section of as-melted surface
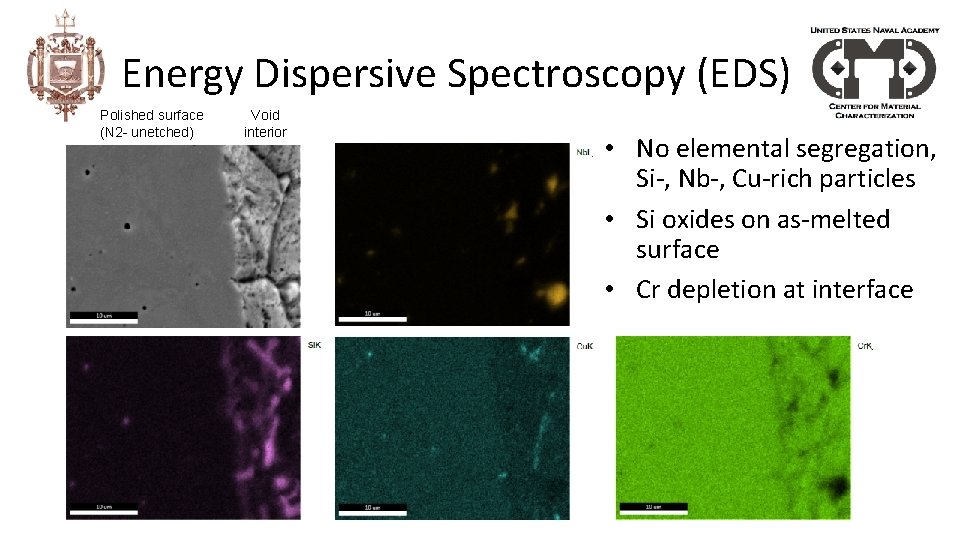
Energy Dispersive Spectroscopy (EDS) Polished surface (N 2 - unetched) Void interior • No elemental segregation, Si-, Nb-, Cu-rich particles • Si oxides on as-melted surface • Cr depletion at interface
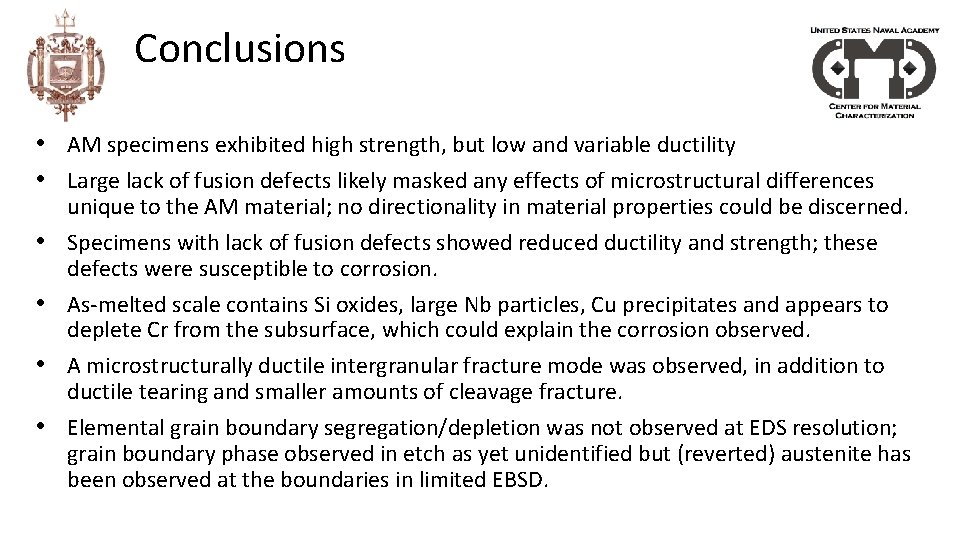
Conclusions • AM specimens exhibited high strength, but low and variable ductility • Large lack of fusion defects likely masked any effects of microstructural differences • • unique to the AM material; no directionality in material properties could be discerned. Specimens with lack of fusion defects showed reduced ductility and strength; these defects were susceptible to corrosion. As-melted scale contains Si oxides, large Nb particles, Cu precipitates and appears to deplete Cr from the subsurface, which could explain the corrosion observed. A microstructurally ductile intergranular fracture mode was observed, in addition to ductile tearing and smaller amounts of cleavage fracture. Elemental grain boundary segregation/depletion was not observed at EDS resolution; grain boundary phase observed in etch as yet unidentified but (reverted) austenite has been observed at the boundaries in limited EBSD.
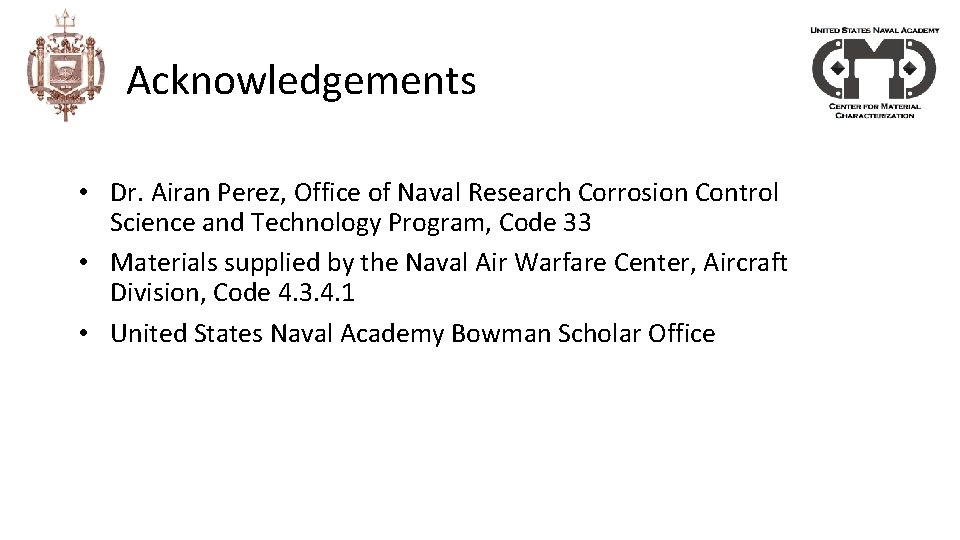
Acknowledgements • Dr. Airan Perez, Office of Naval Research Corrosion Control Science and Technology Program, Code 33 • Materials supplied by the Naval Air Warfare Center, Aircraft Division, Code 4. 3. 4. 1 • United States Naval Academy Bowman Scholar Office
Additive manufacturing vs subtractive manufacturing
Equilibrium occurs when
Big k little k
Cake resistance formula
Flanker brand strategy
Osu extension tulsa soil testing
Constant pointer and pointer to constant
üyou
Constant pointer and pointer to constant
Metals tend to be
Formation constant vs equilibrium constant
Pointer constant in c
Display the address of intval using cout and intptr.
Solubility
Units of universal gas constant
Example of manufactured solution
Financial and managerial accounting weygandt kimmel kieso
Cost of goods manufactured formula
The vegetation and manufactured structures that cover land
Manufactured toponym examples
Different materials have different
Heavy-gauge framing members are manufactured from
Properties of manufactured boards