What is Cost and Project Cost Management Cost
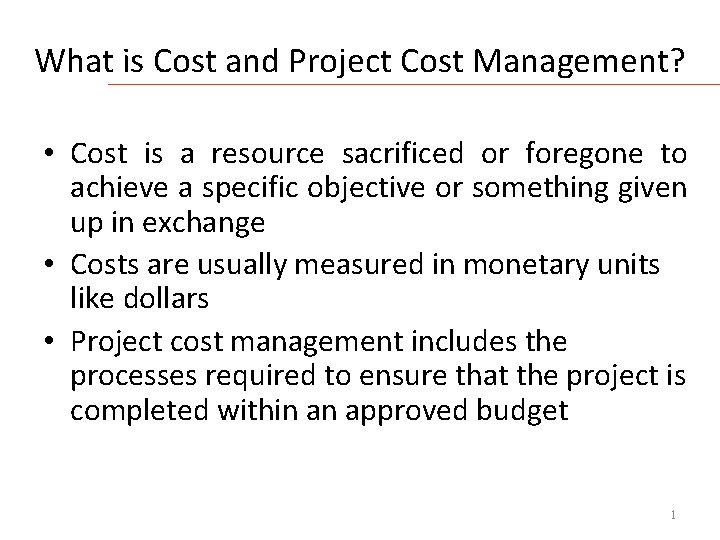
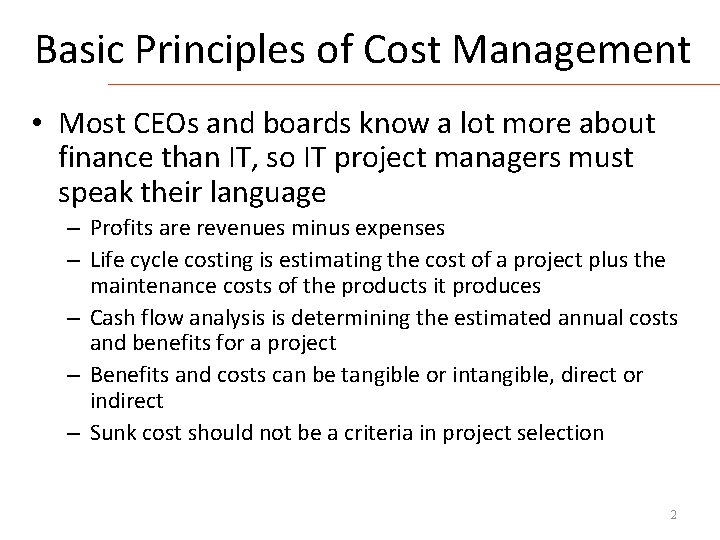
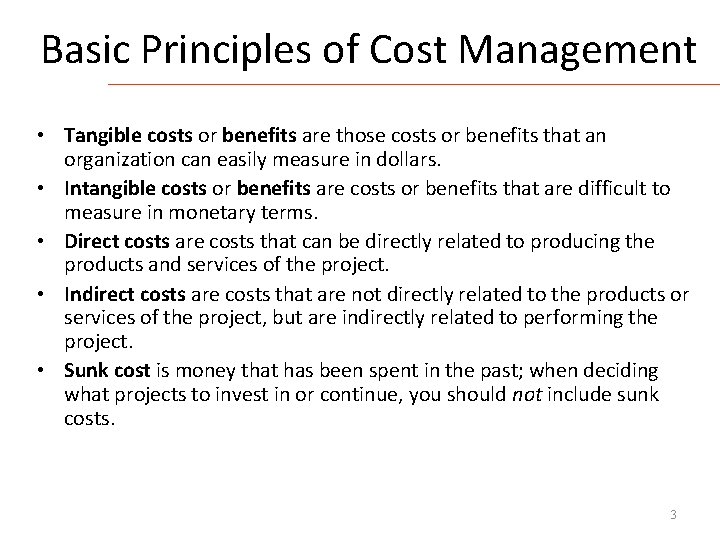
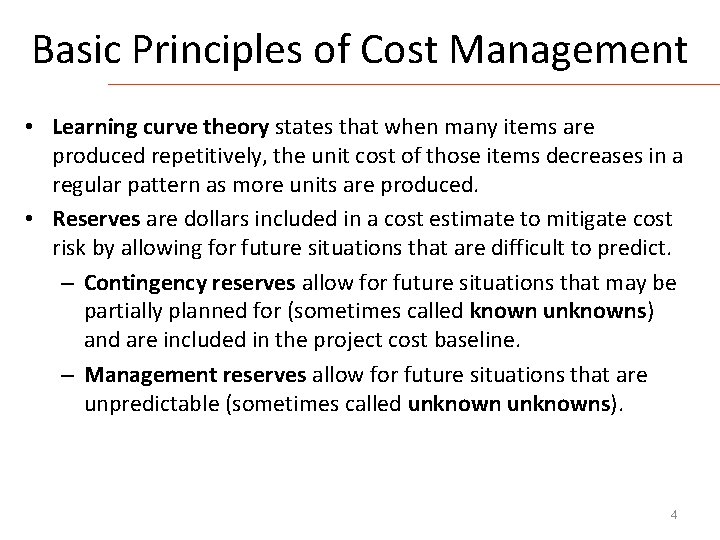
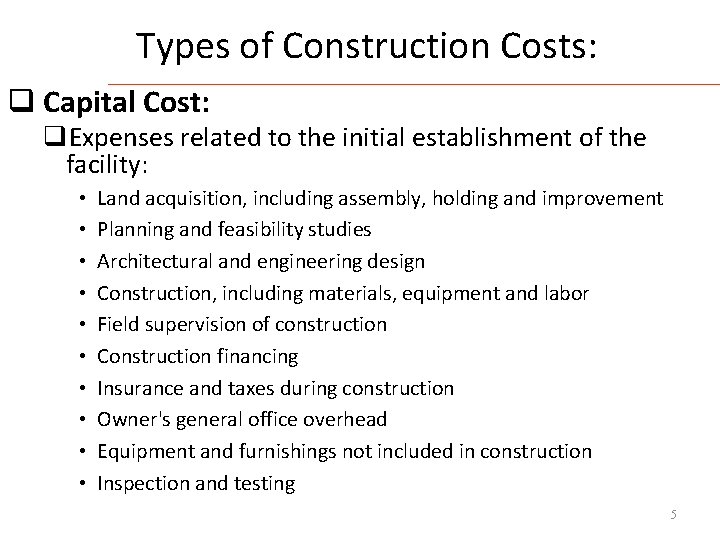
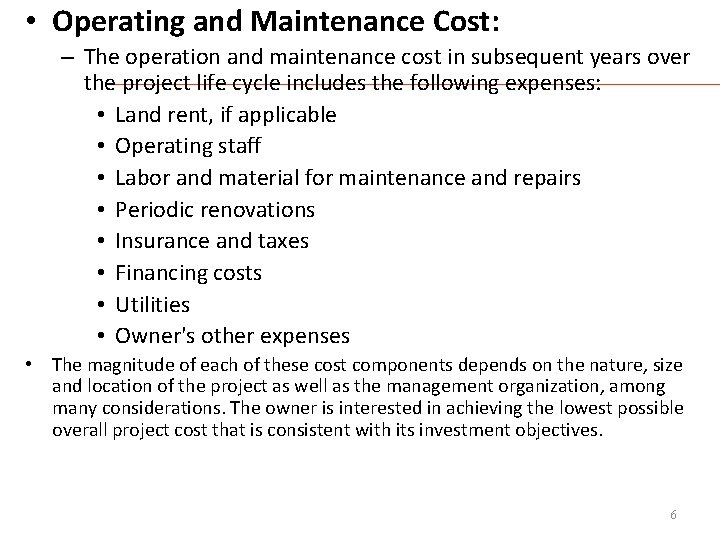
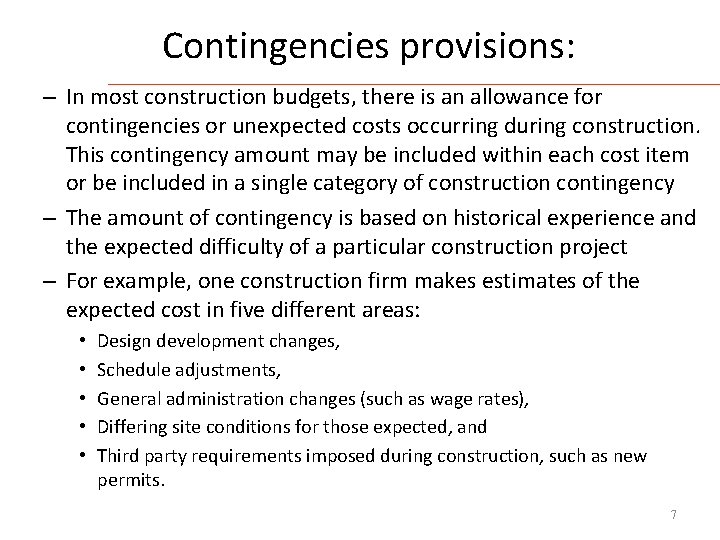
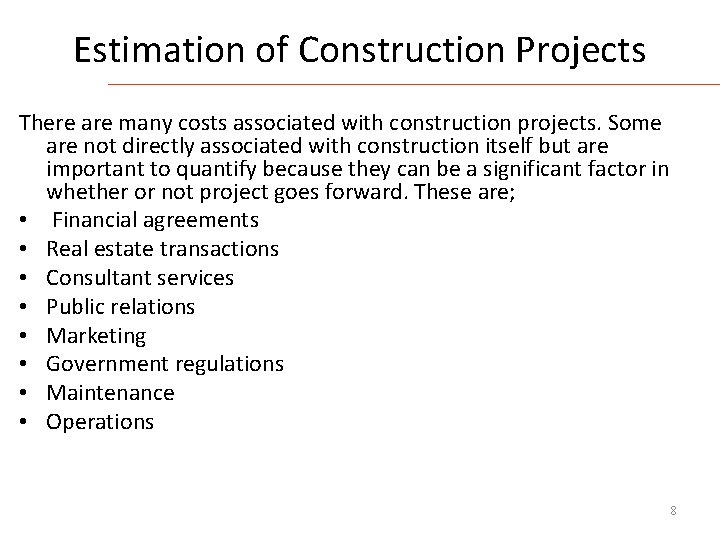
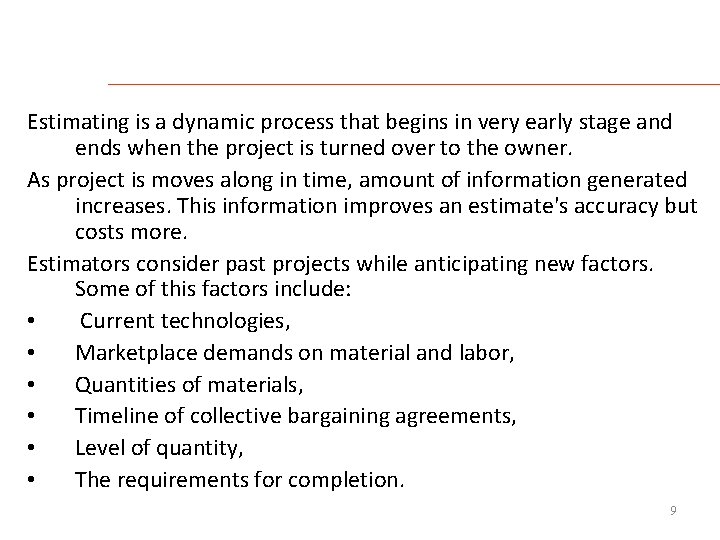
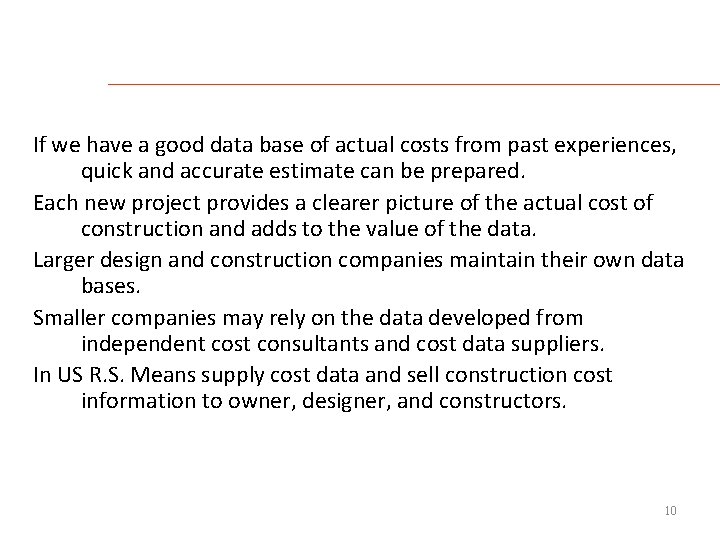
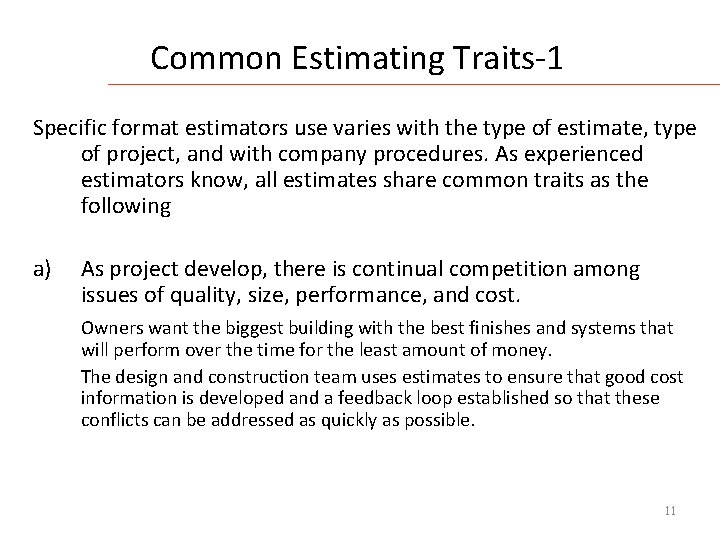
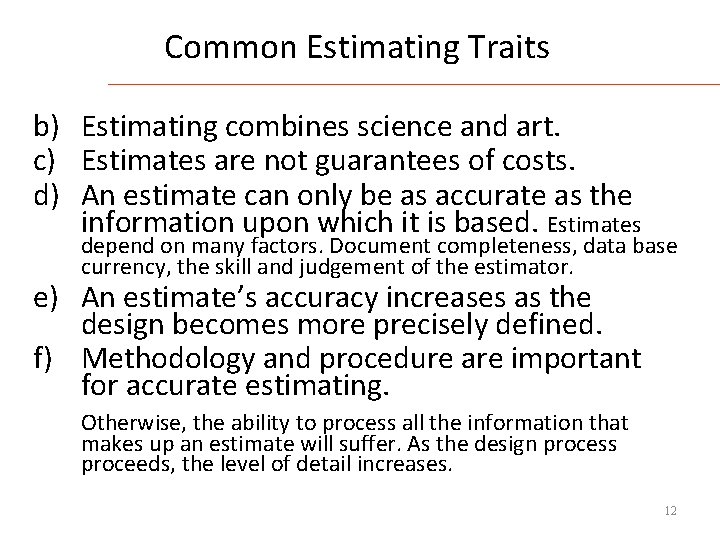
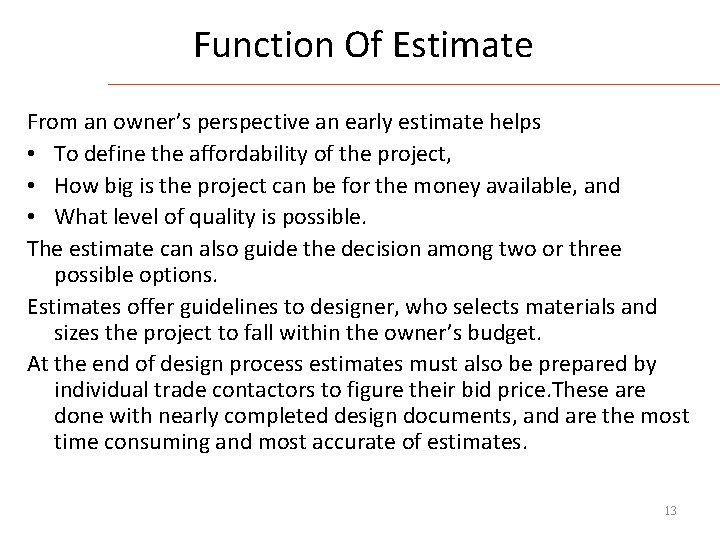
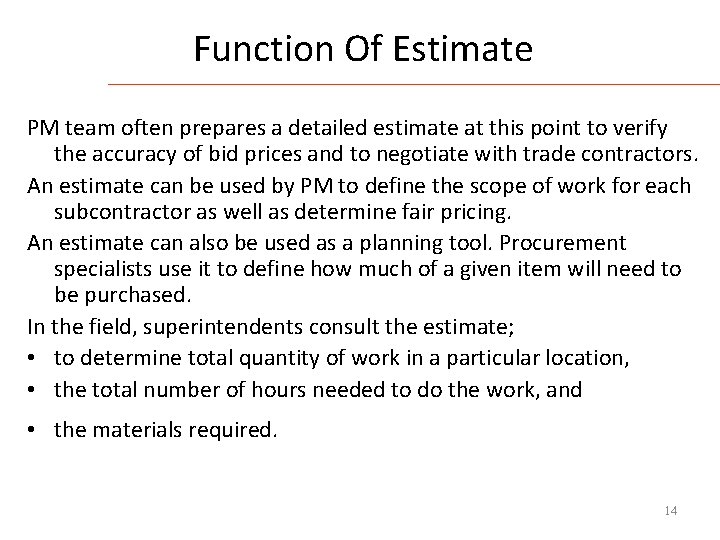
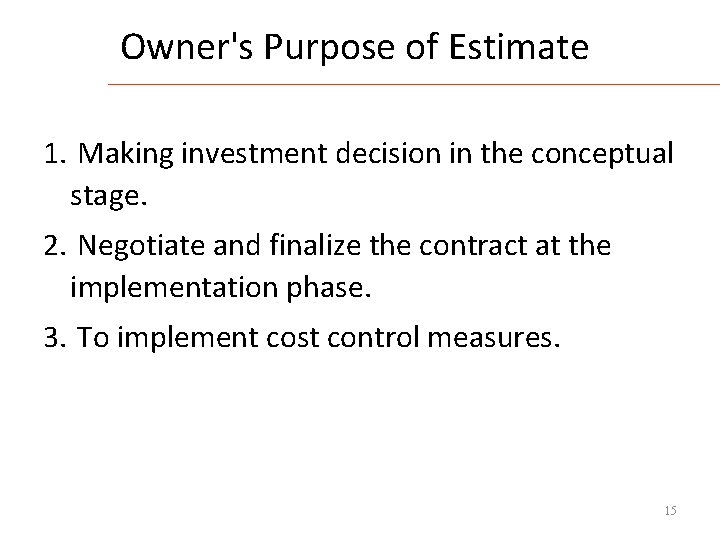
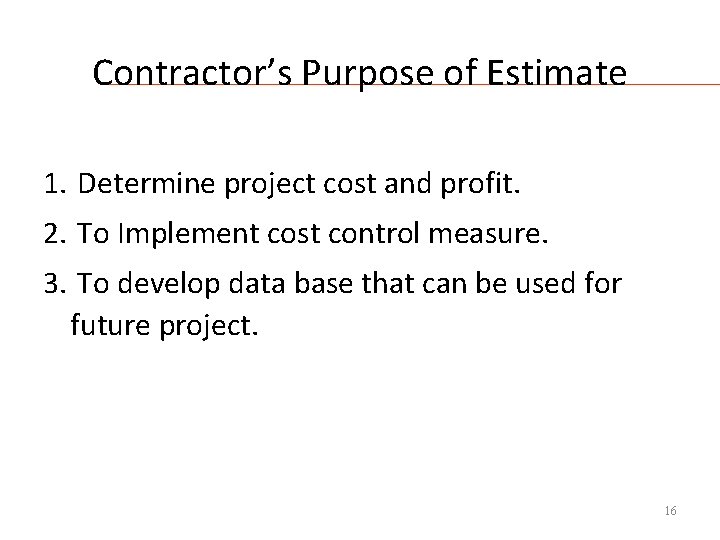
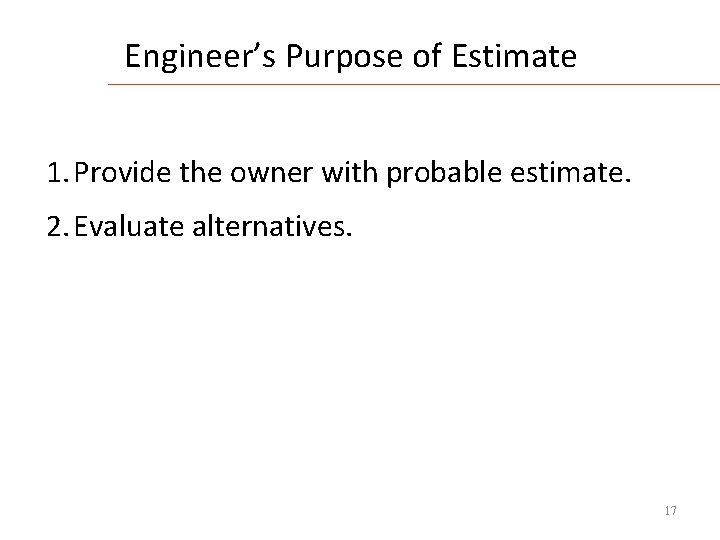
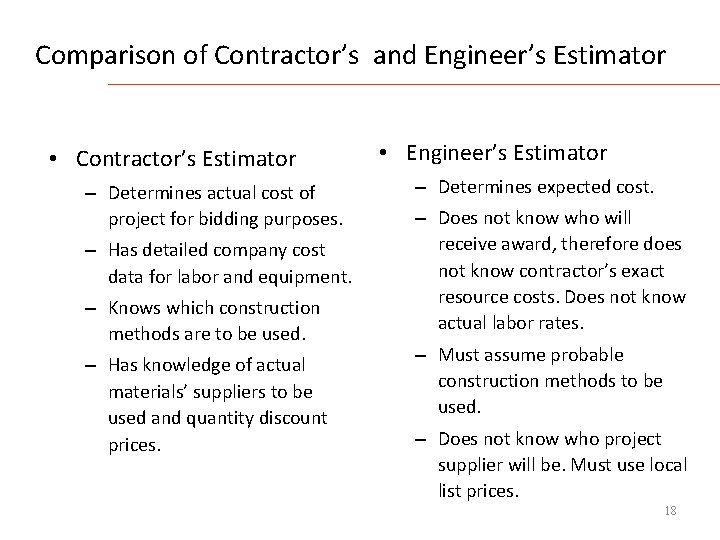
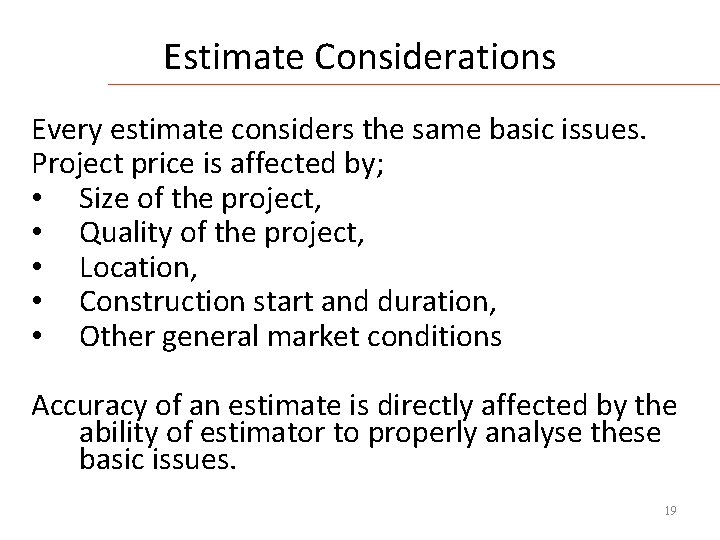
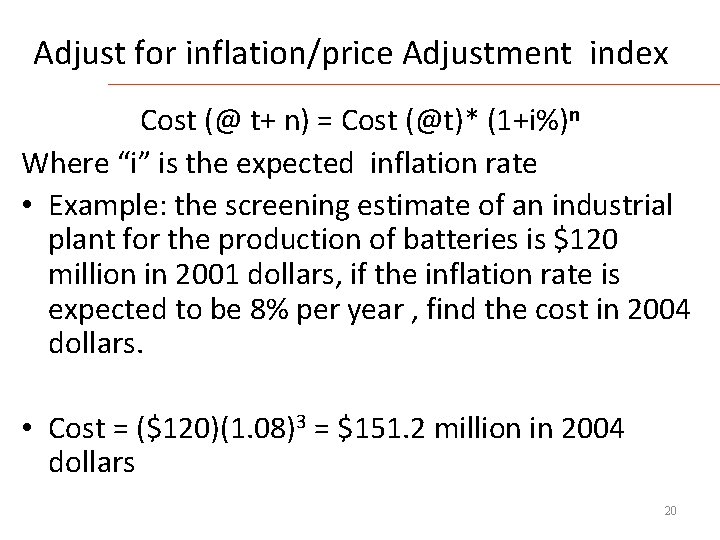
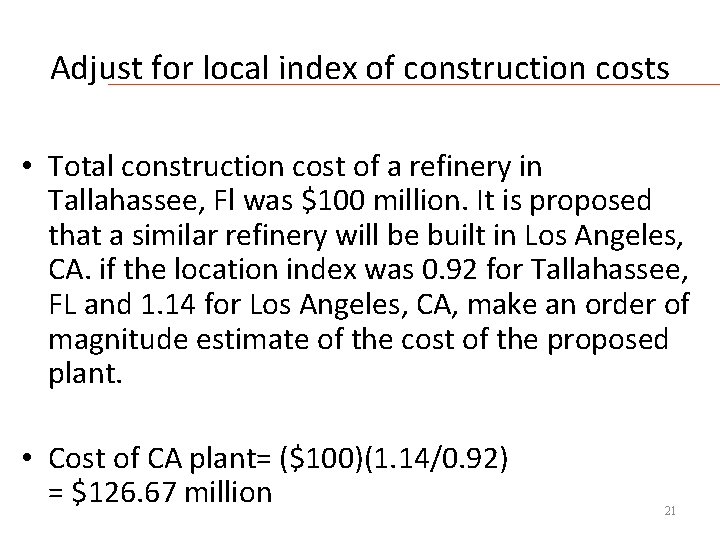
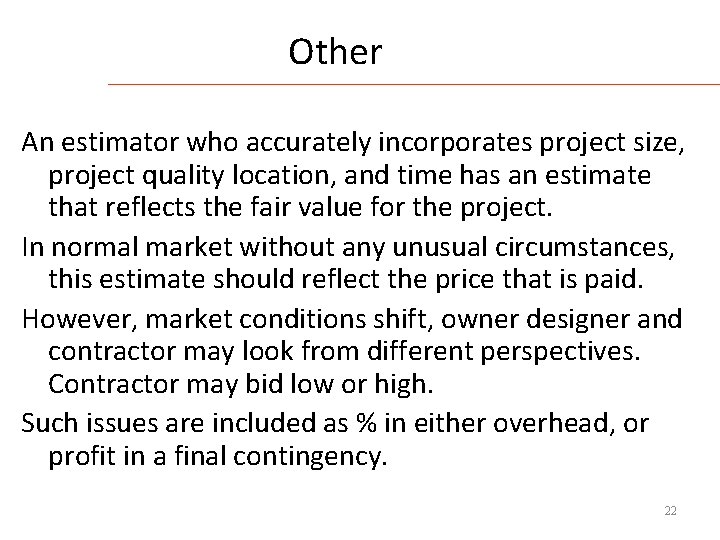
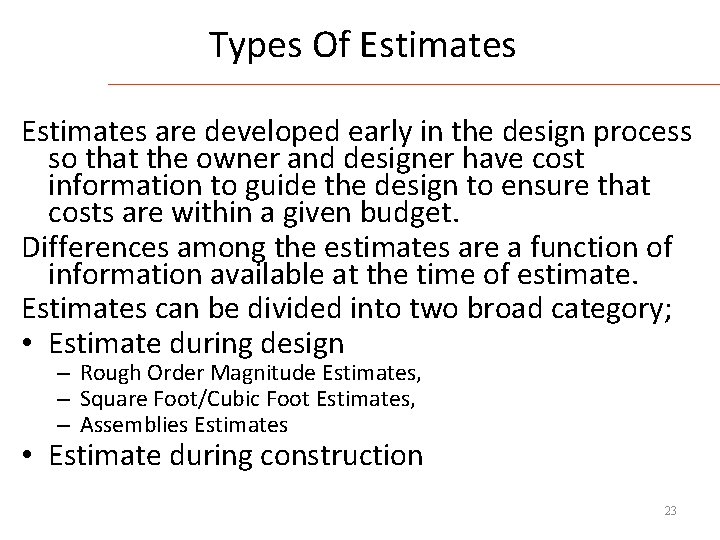

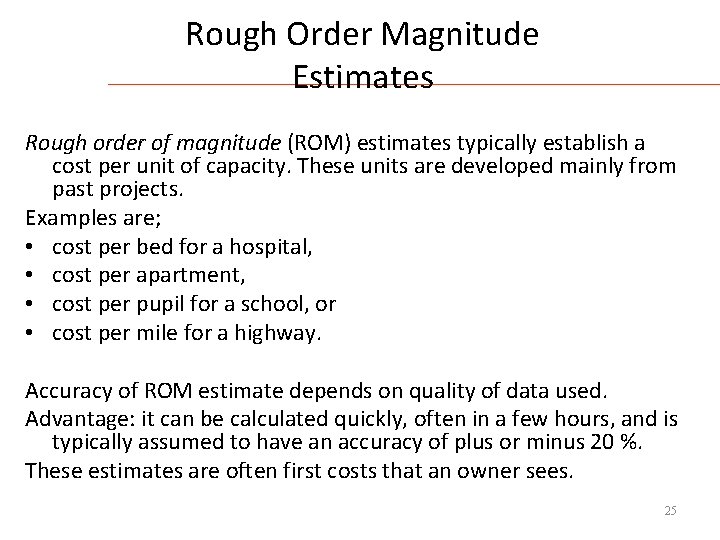
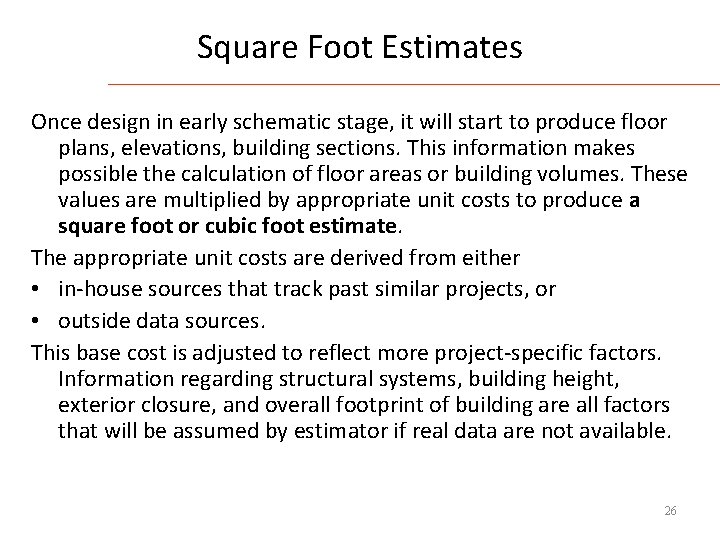
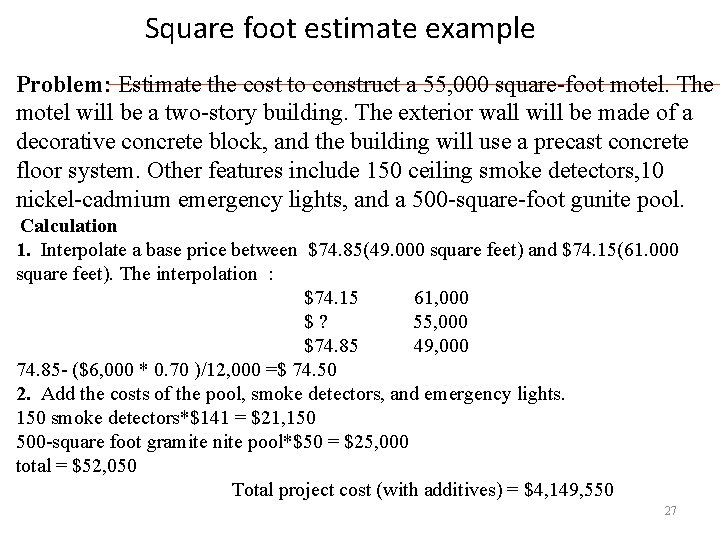
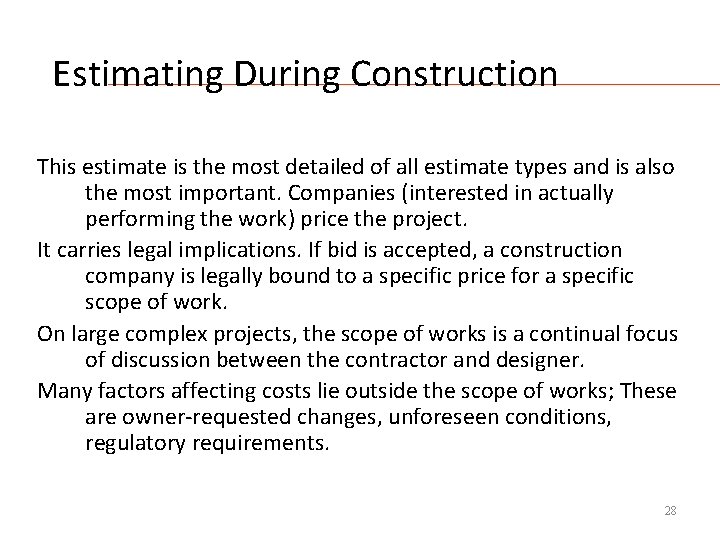

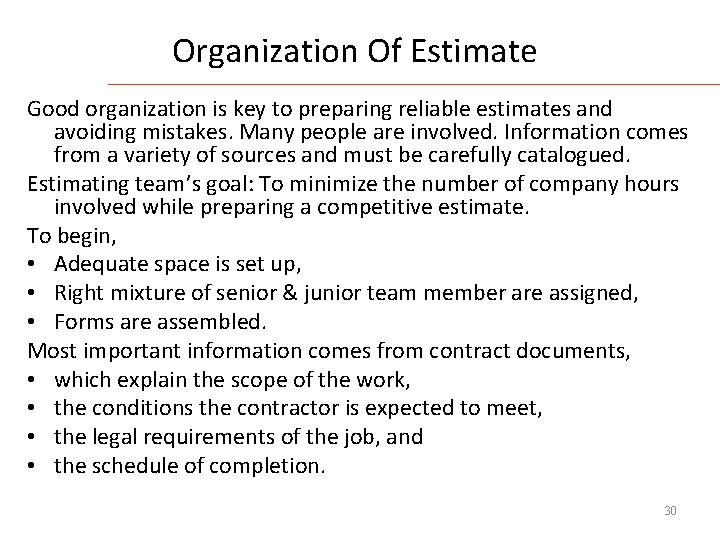
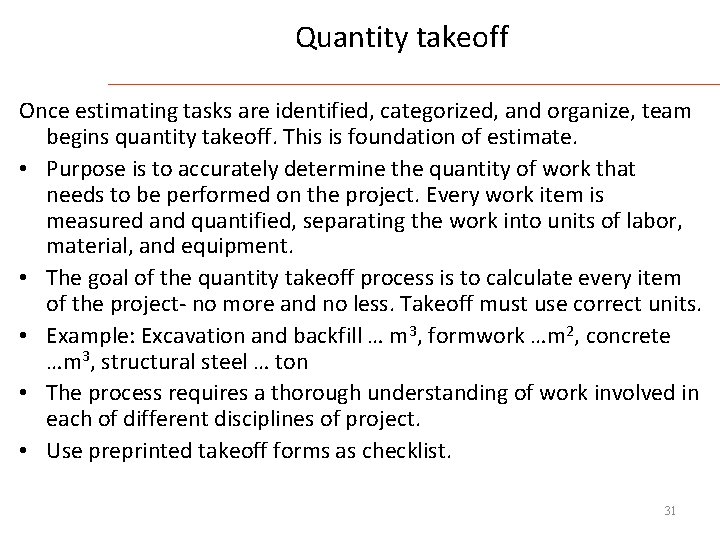
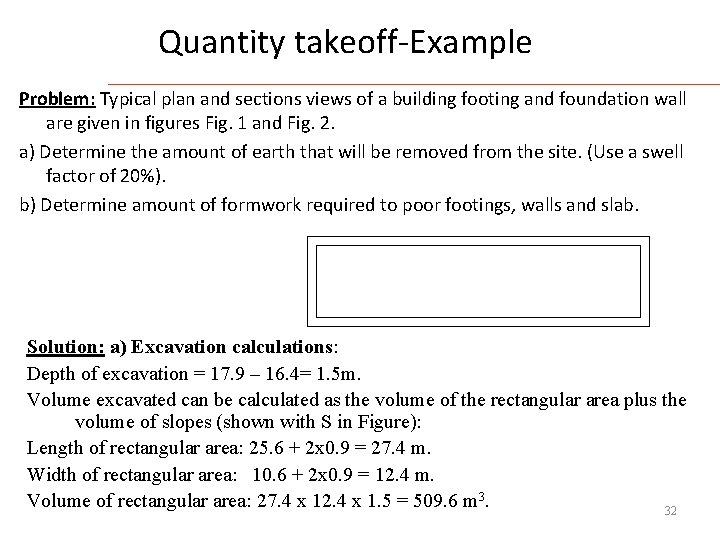
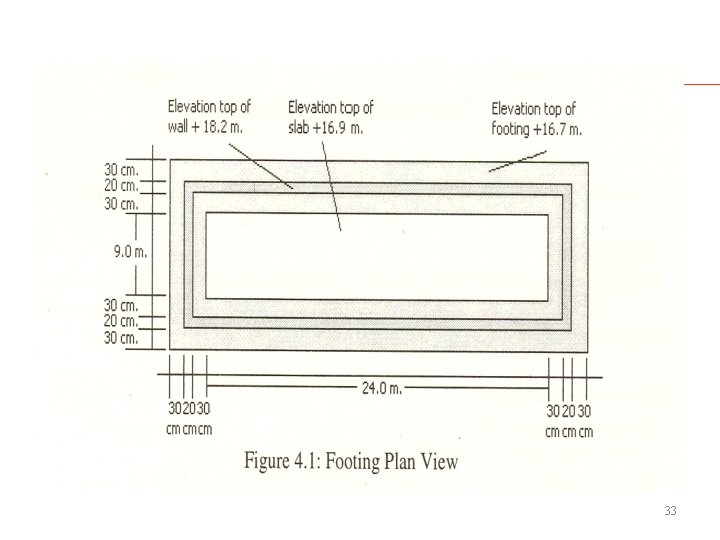
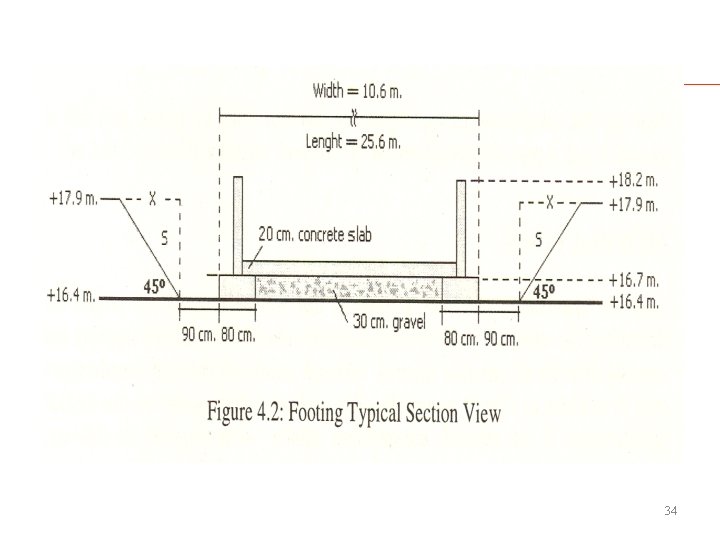
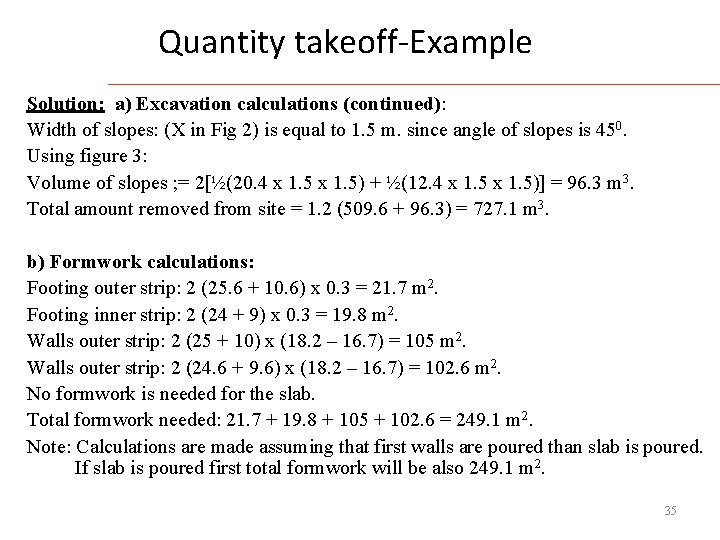
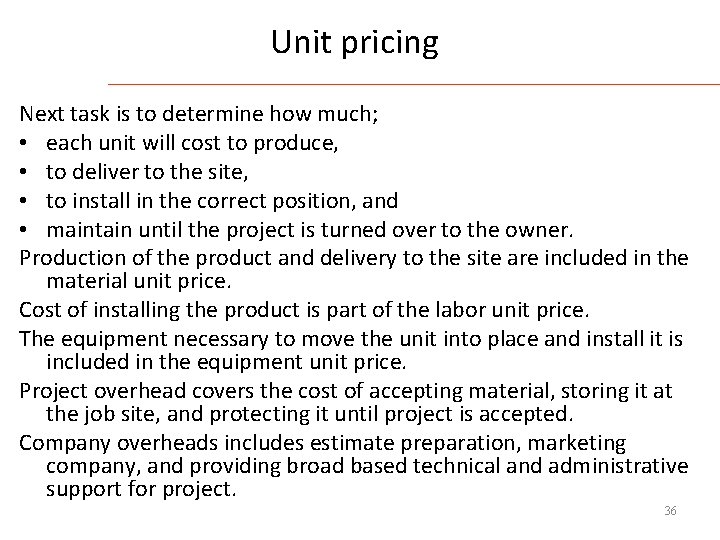
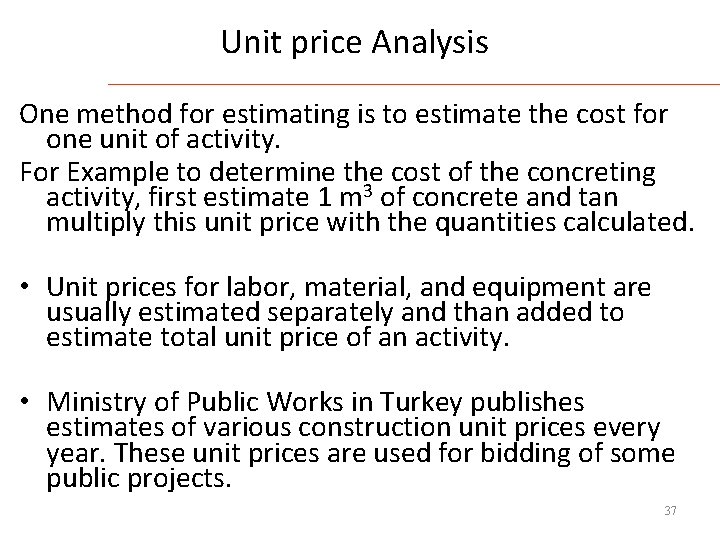
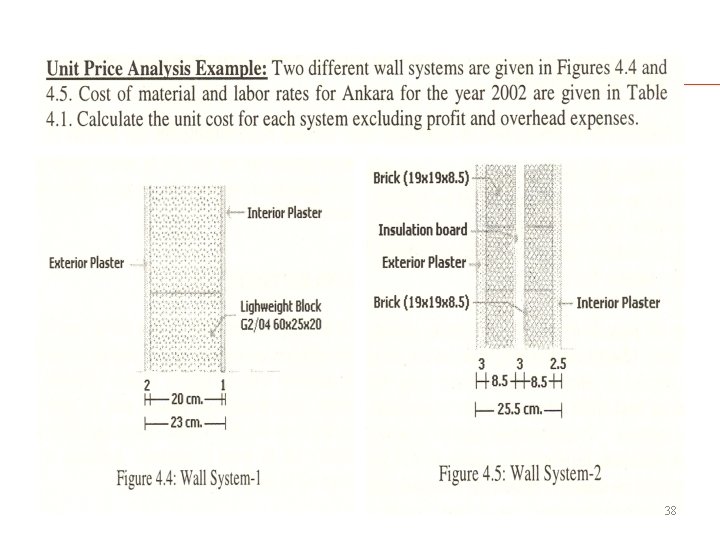
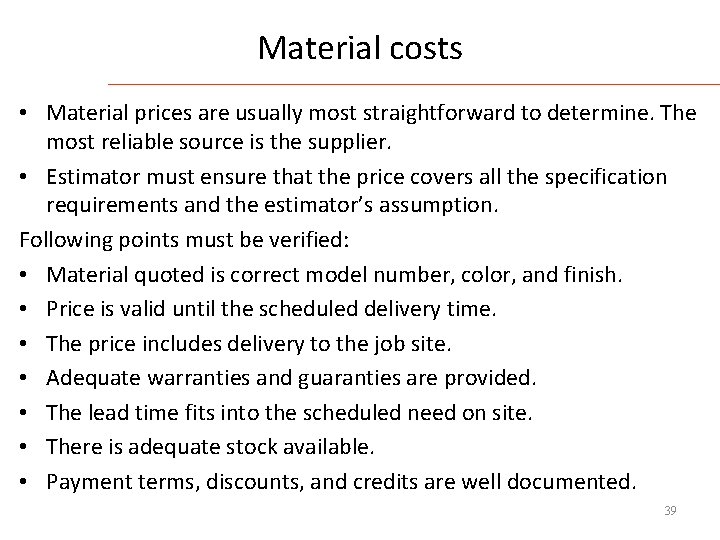
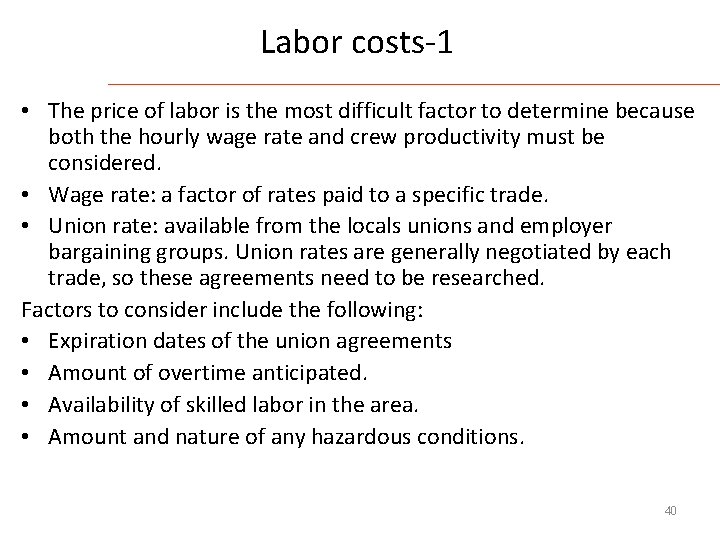
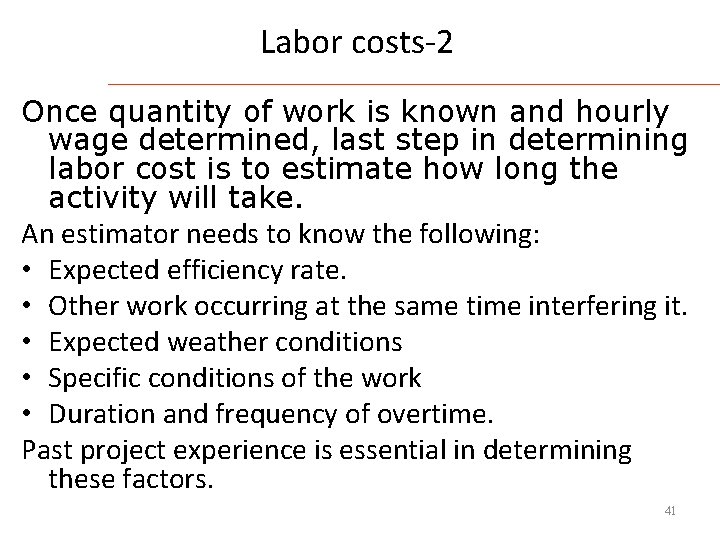
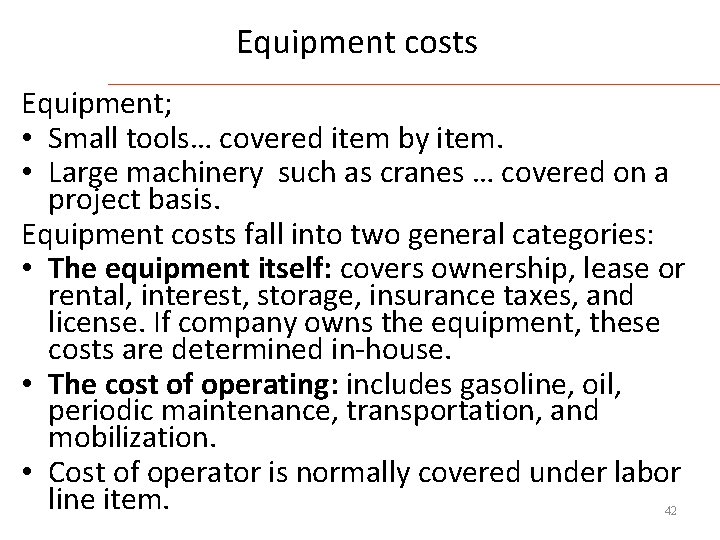
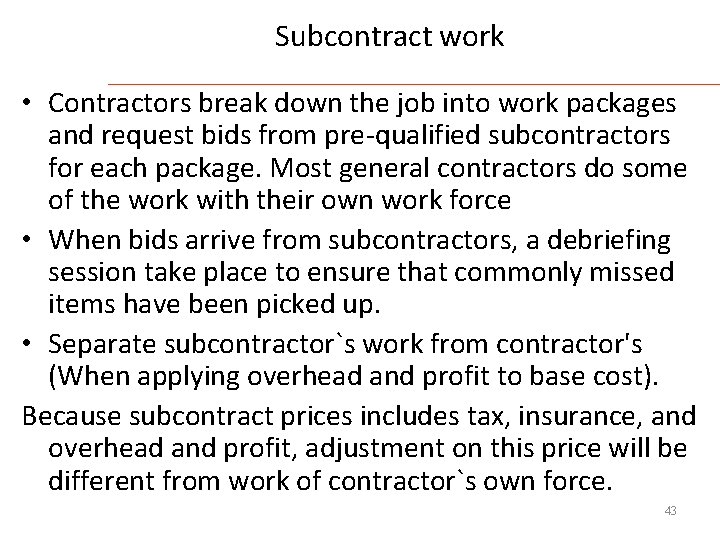
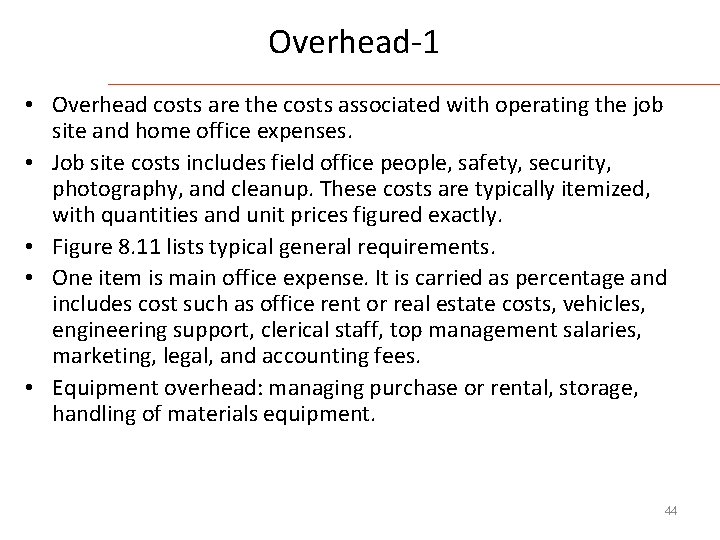
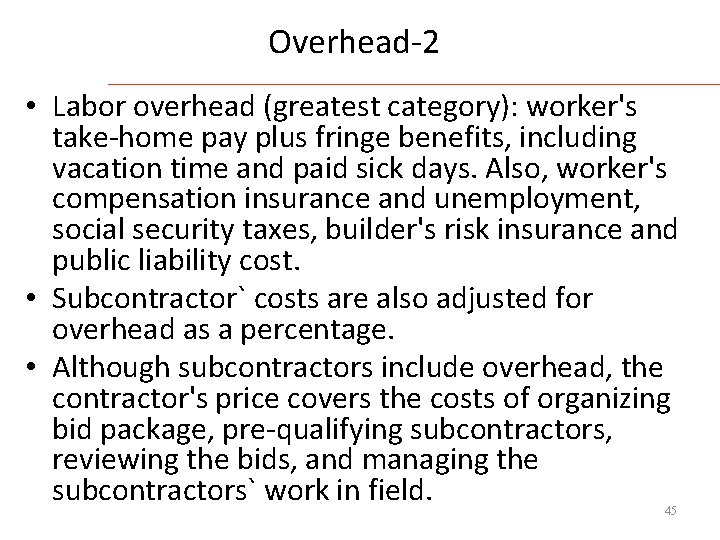
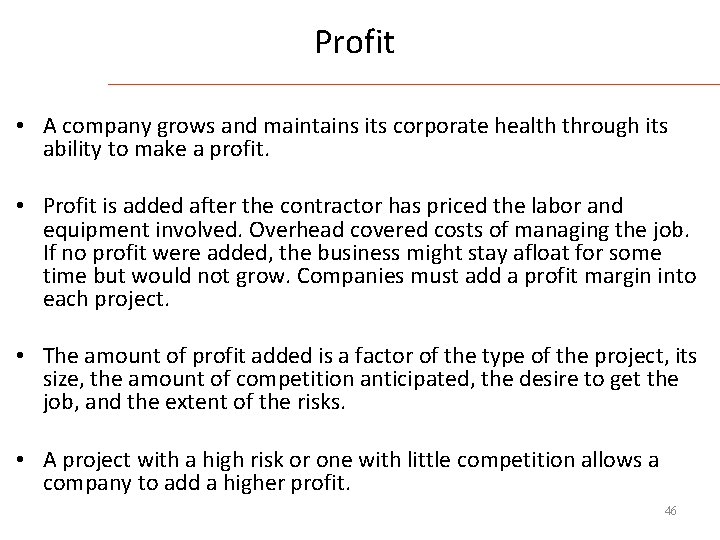
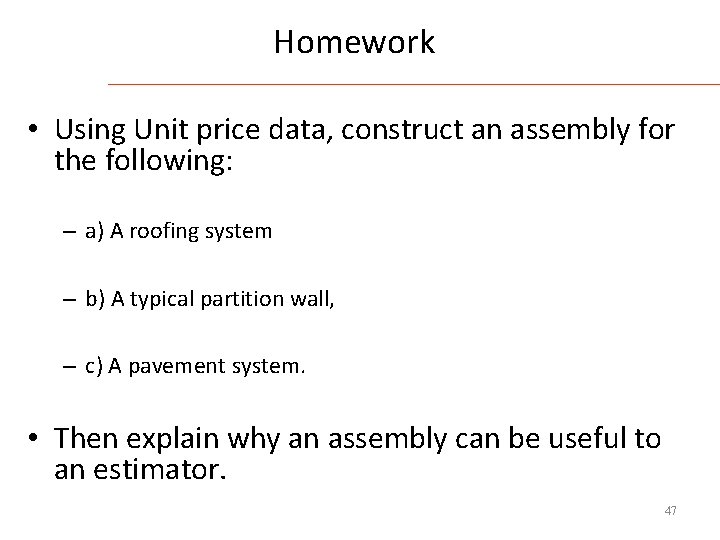
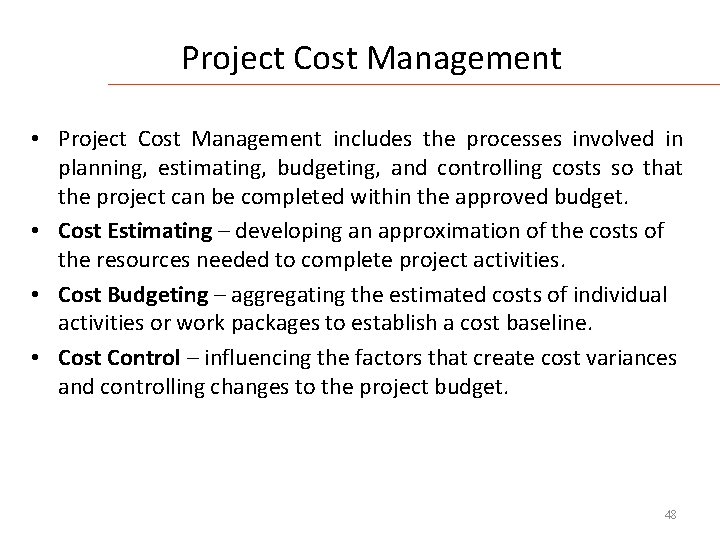
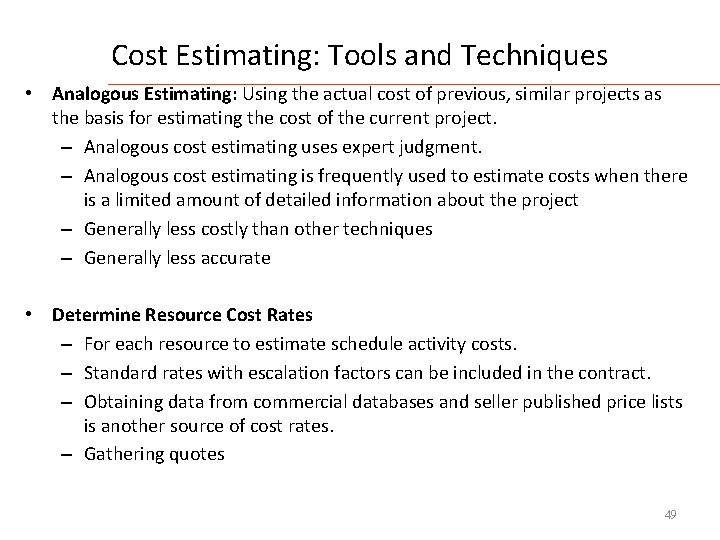
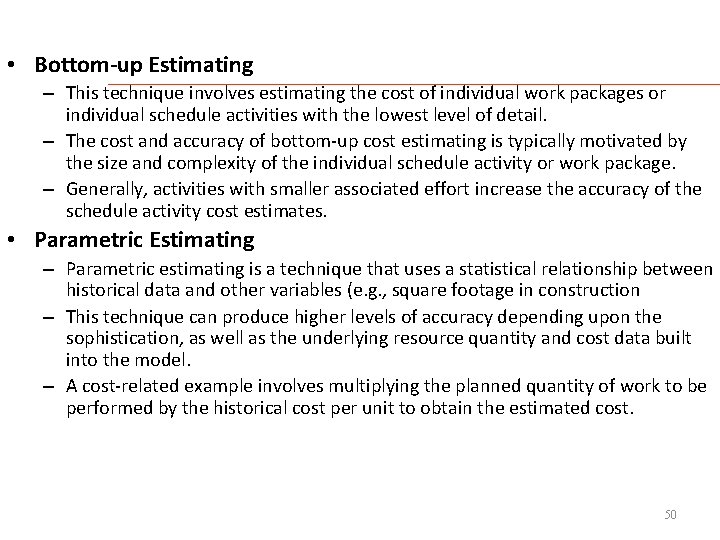
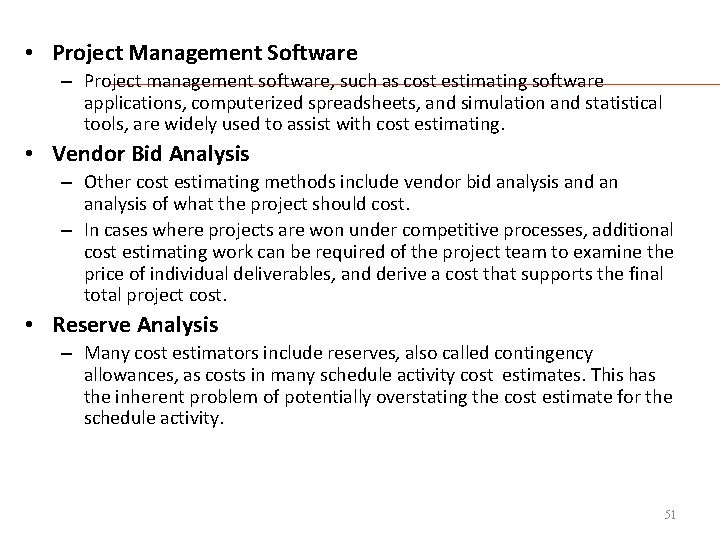
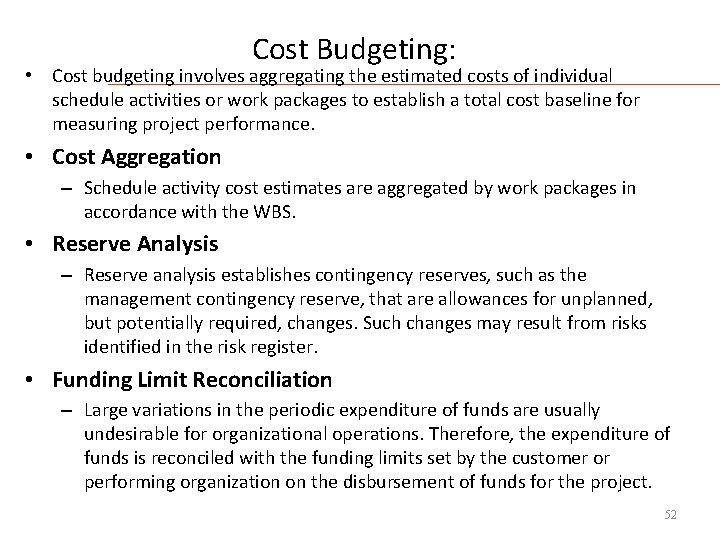
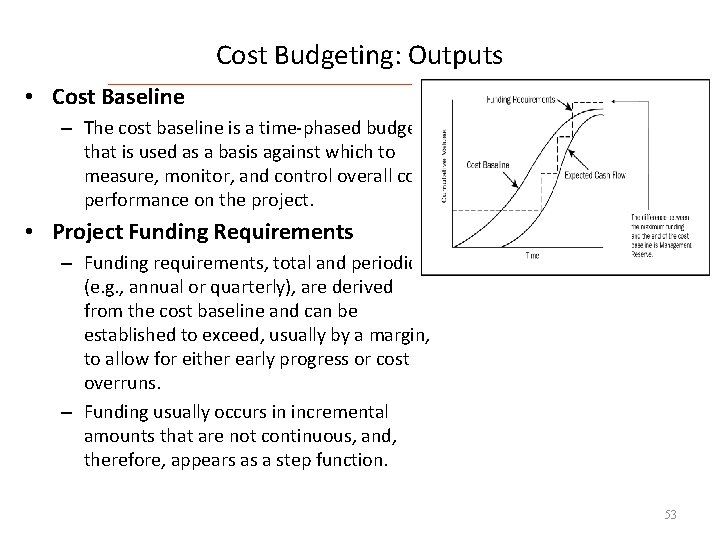
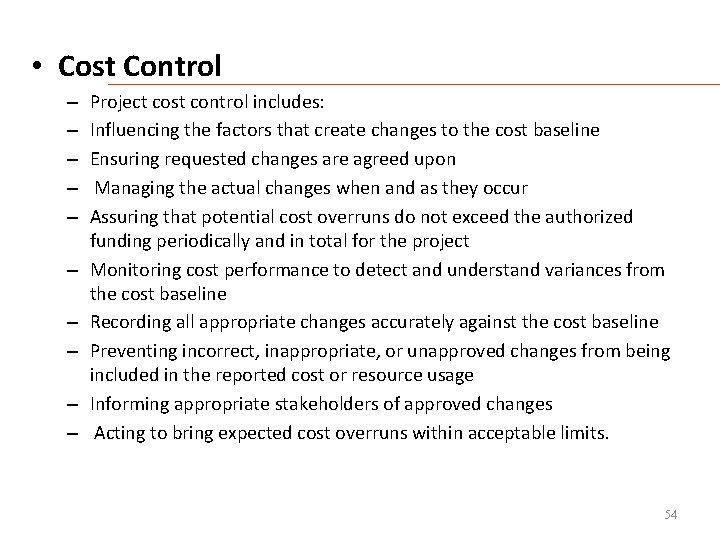
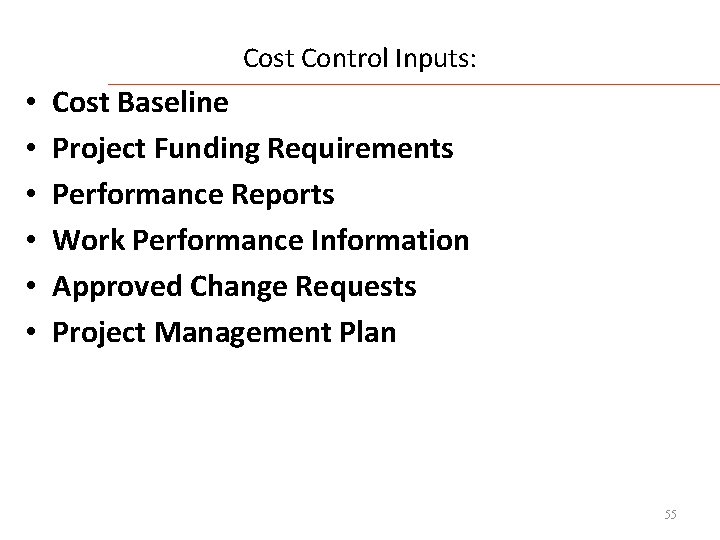
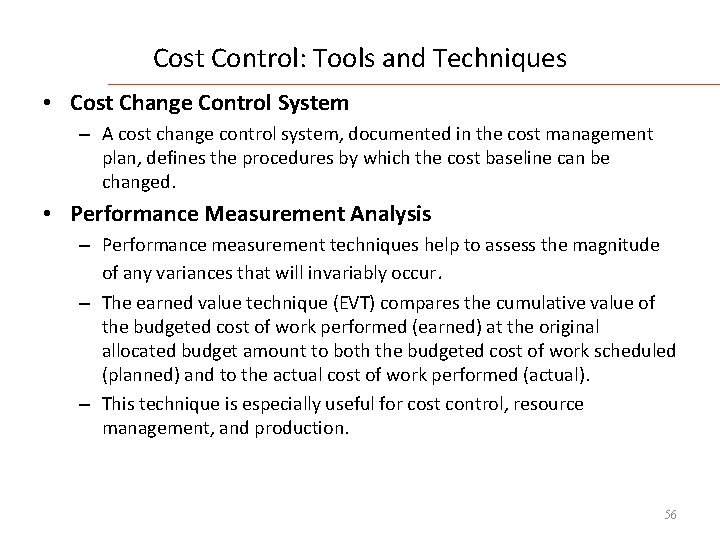
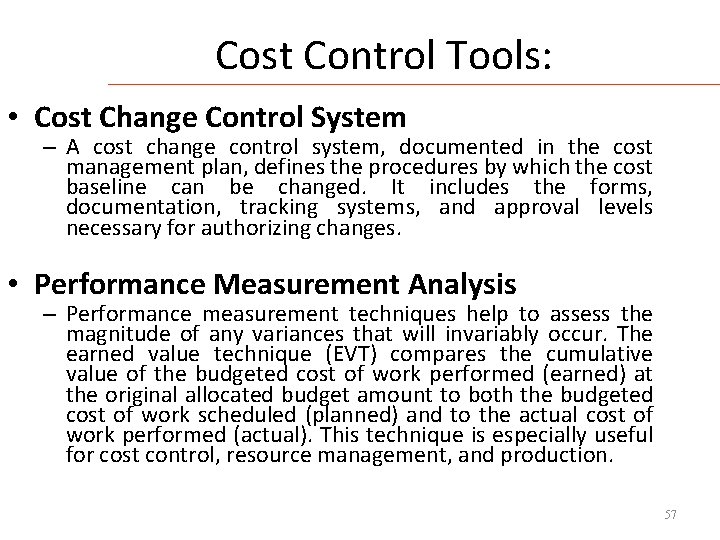
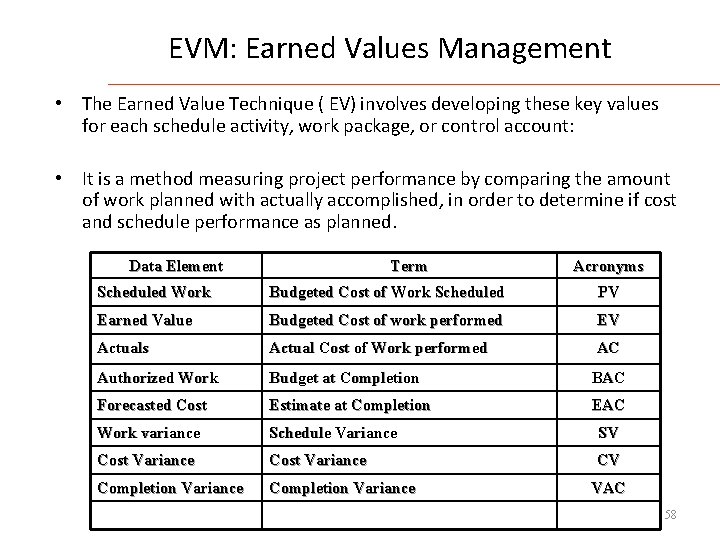
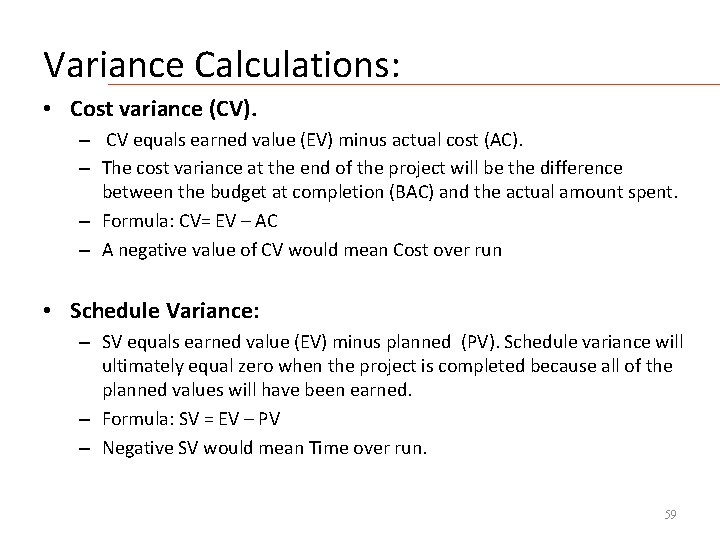
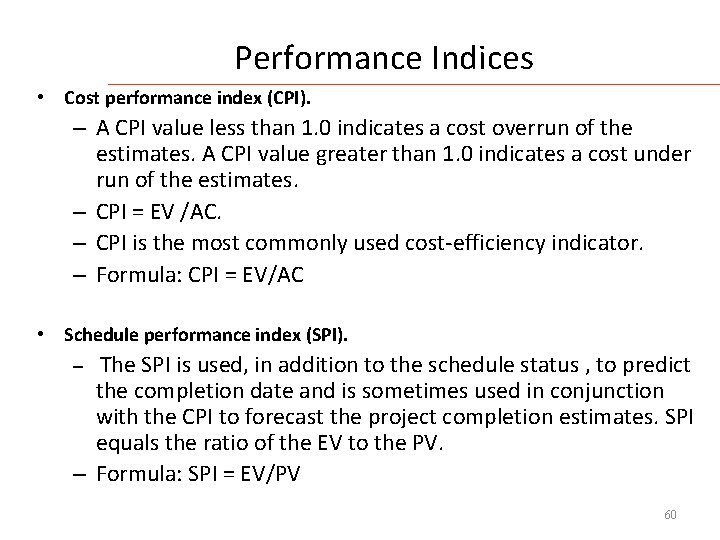
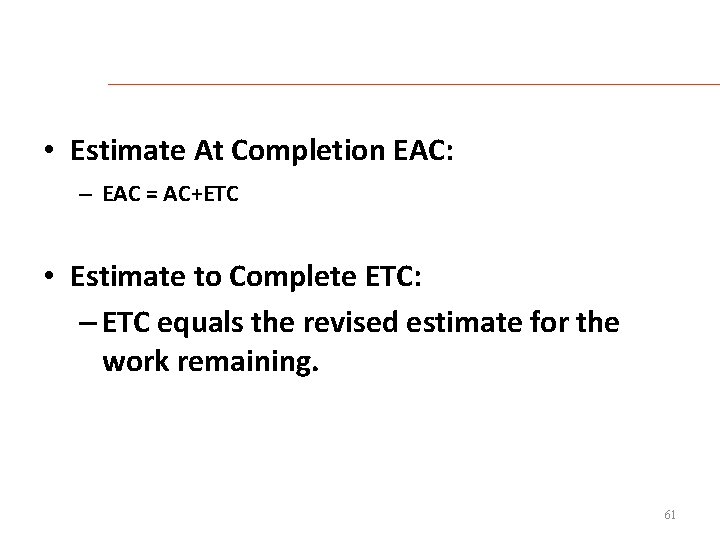
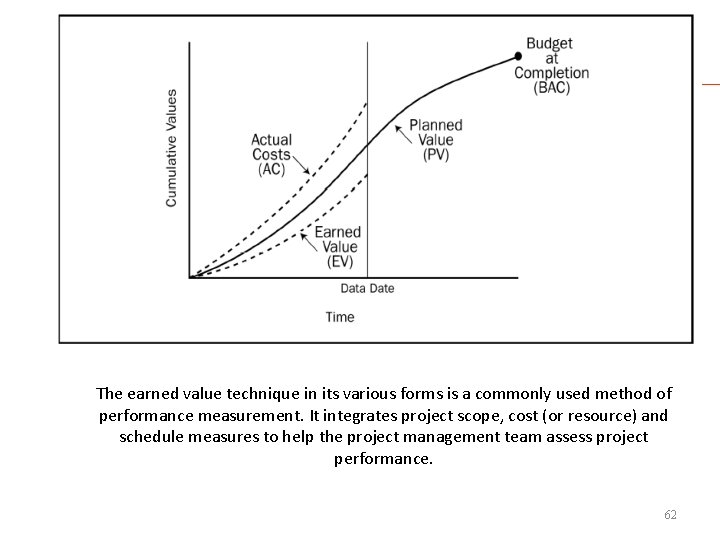
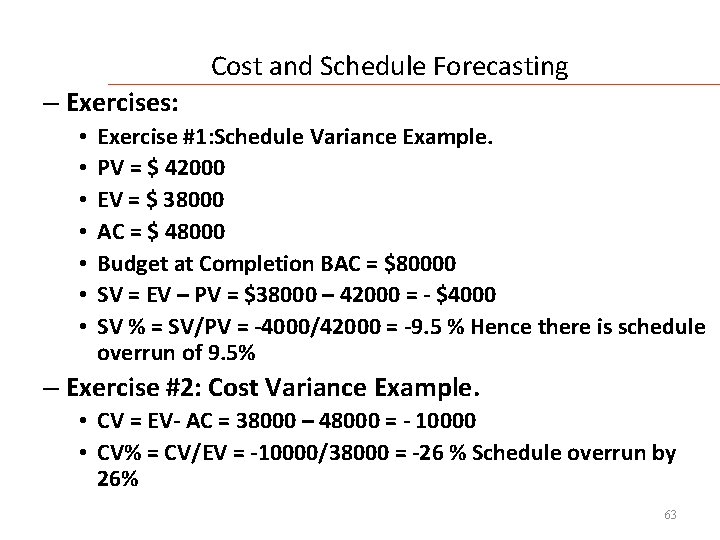
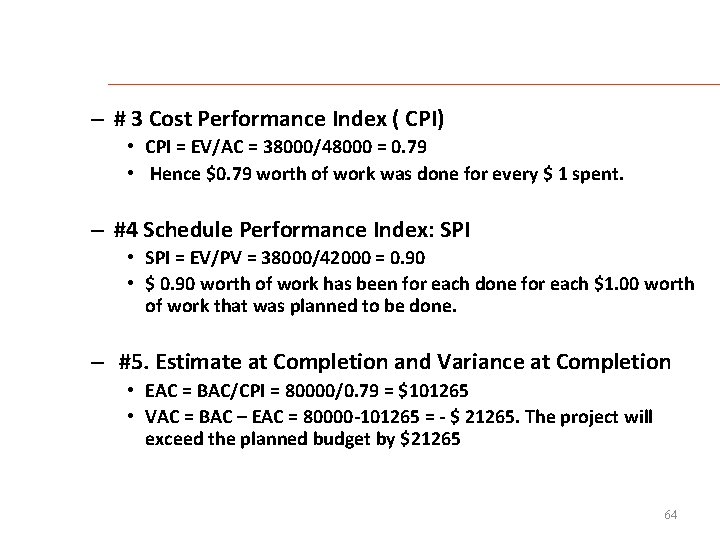
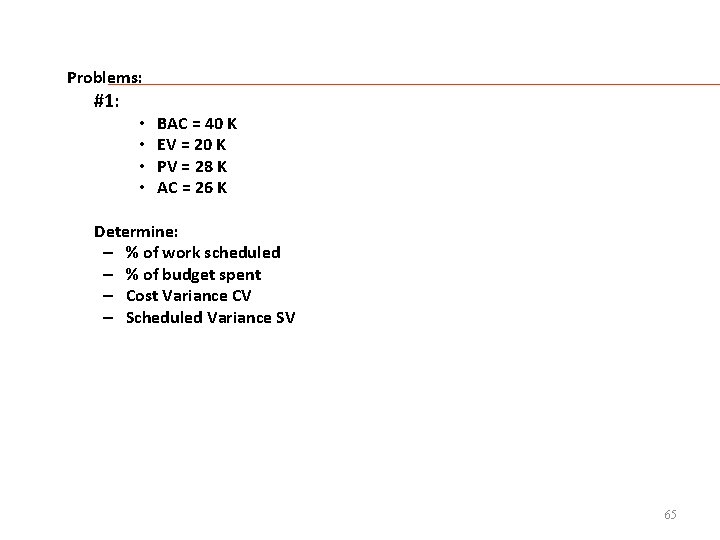
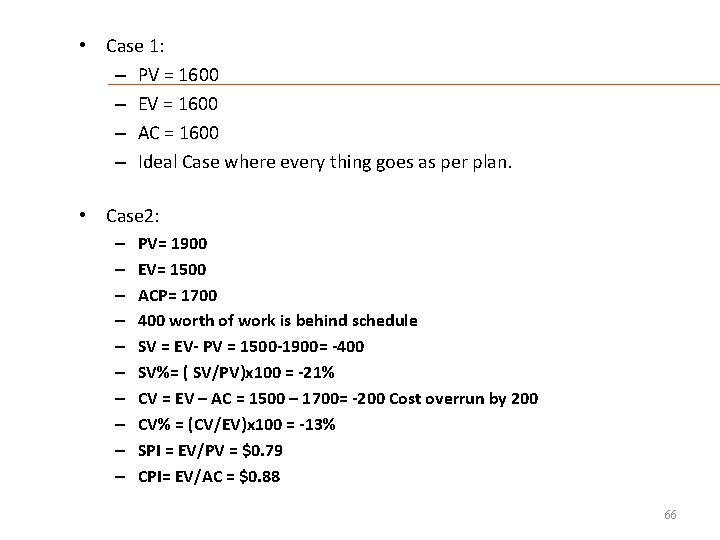
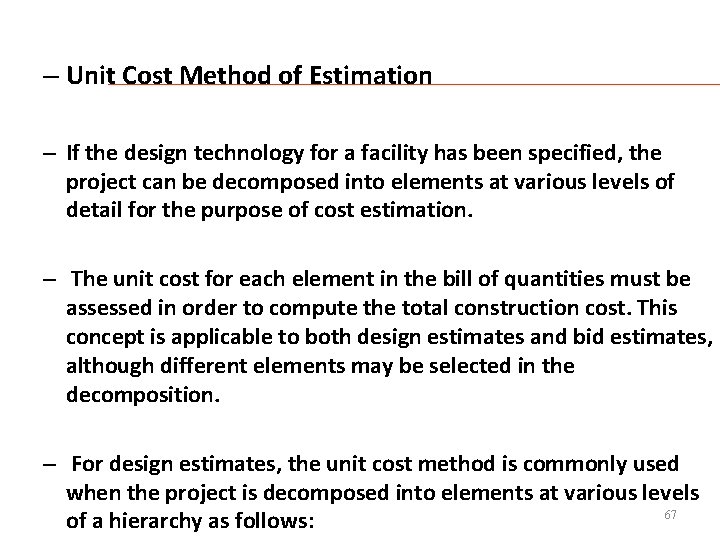
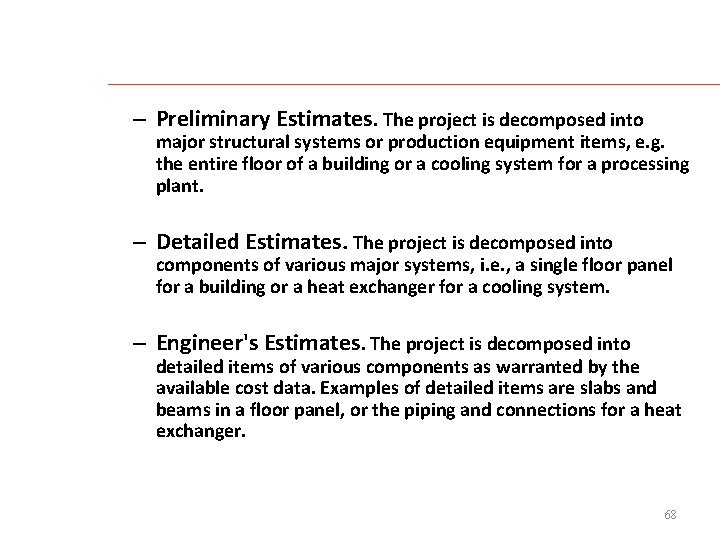
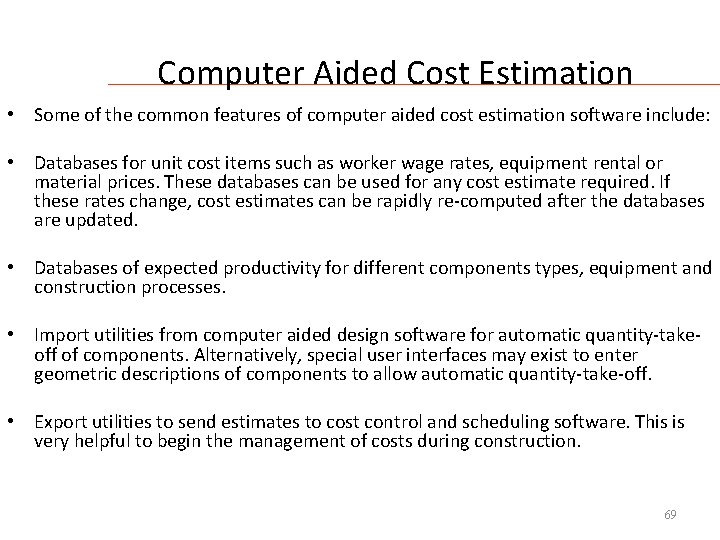
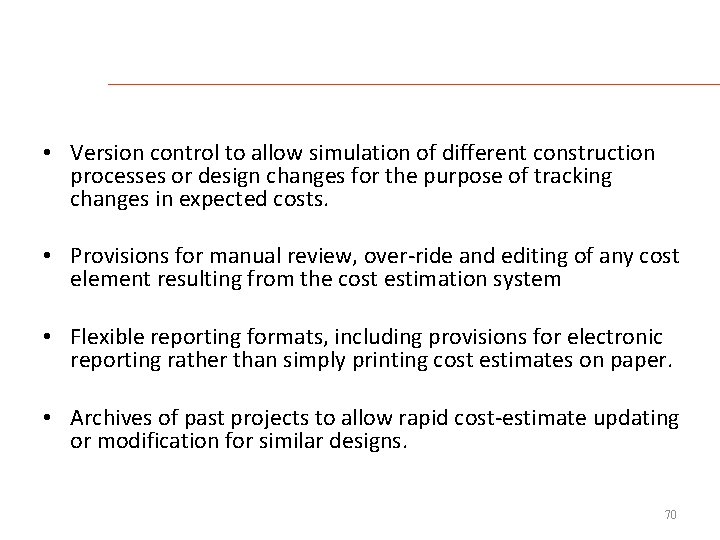
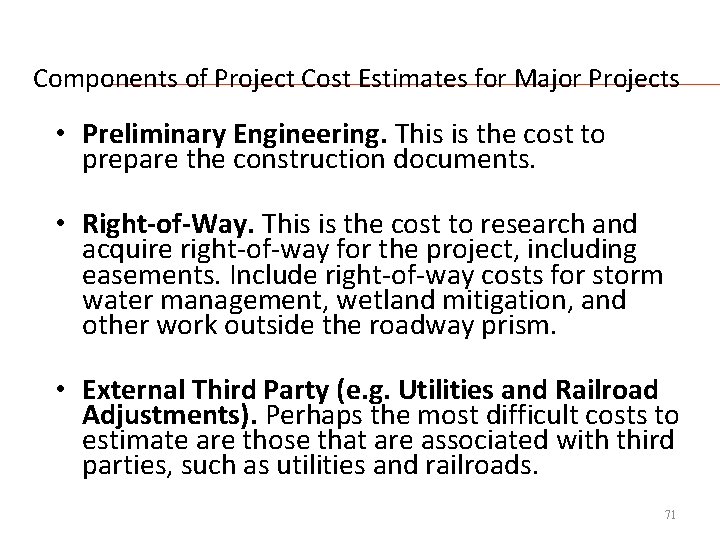
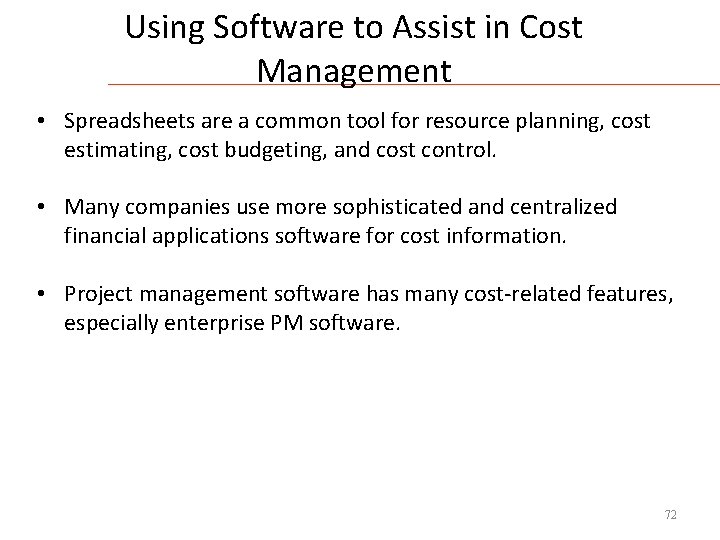
- Slides: 72
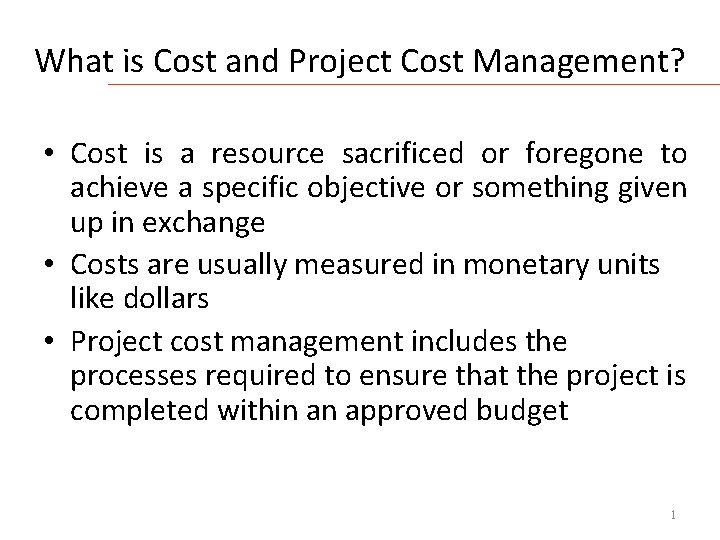
What is Cost and Project Cost Management? • Cost is a resource sacrificed or foregone to achieve a specific objective or something given up in exchange • Costs are usually measured in monetary units like dollars • Project cost management includes the processes required to ensure that the project is completed within an approved budget 1
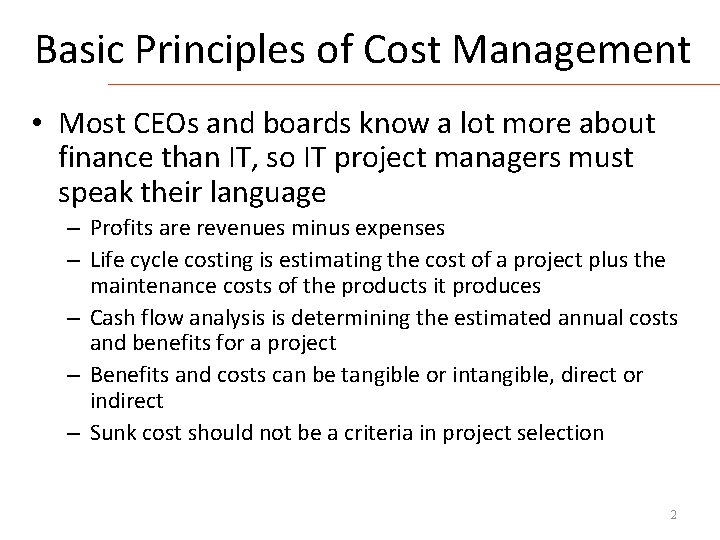
Basic Principles of Cost Management • Most CEOs and boards know a lot more about finance than IT, so IT project managers must speak their language – Profits are revenues minus expenses – Life cycle costing is estimating the cost of a project plus the maintenance costs of the products it produces – Cash flow analysis is determining the estimated annual costs and benefits for a project – Benefits and costs can be tangible or intangible, direct or indirect – Sunk cost should not be a criteria in project selection 2
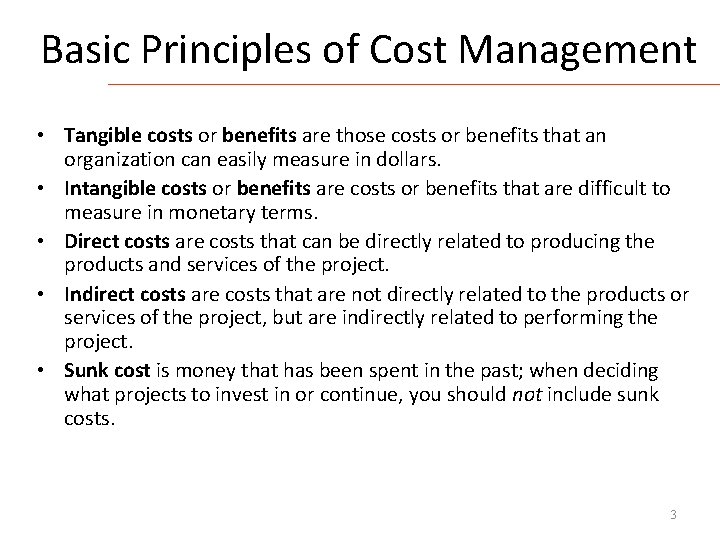
Basic Principles of Cost Management • Tangible costs or benefits are those costs or benefits that an organization can easily measure in dollars. • Intangible costs or benefits are costs or benefits that are difficult to measure in monetary terms. • Direct costs are costs that can be directly related to producing the products and services of the project. • Indirect costs are costs that are not directly related to the products or services of the project, but are indirectly related to performing the project. • Sunk cost is money that has been spent in the past; when deciding what projects to invest in or continue, you should not include sunk costs. 3
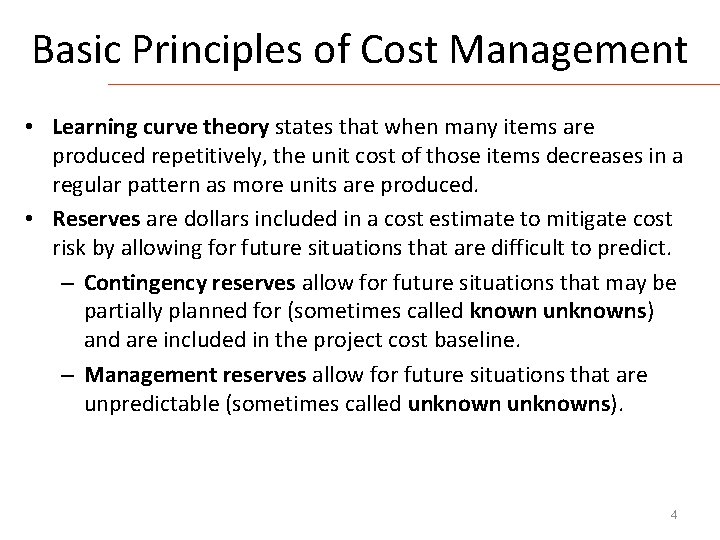
Basic Principles of Cost Management • Learning curve theory states that when many items are produced repetitively, the unit cost of those items decreases in a regular pattern as more units are produced. • Reserves are dollars included in a cost estimate to mitigate cost risk by allowing for future situations that are difficult to predict. – Contingency reserves allow for future situations that may be partially planned for (sometimes called known unknowns) and are included in the project cost baseline. – Management reserves allow for future situations that are unpredictable (sometimes called unknowns). 4
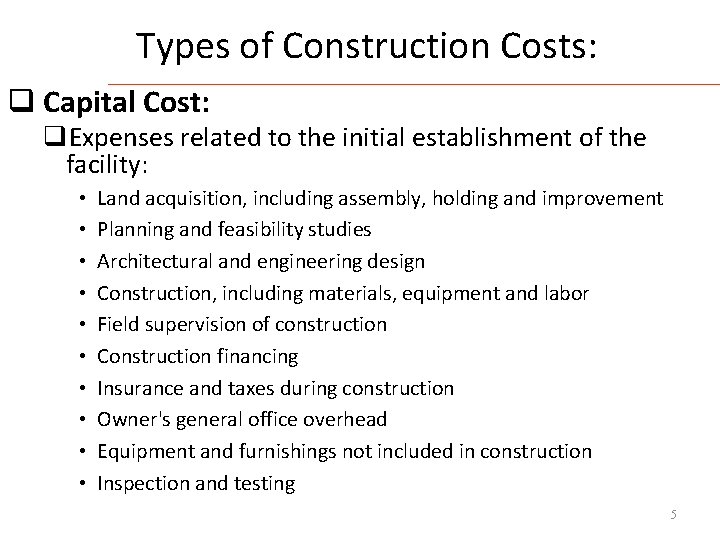
Types of Construction Costs: q Capital Cost: q. Expenses related to the initial establishment of the facility: • • • Land acquisition, including assembly, holding and improvement Planning and feasibility studies Architectural and engineering design Construction, including materials, equipment and labor Field supervision of construction Construction financing Insurance and taxes during construction Owner's general office overhead Equipment and furnishings not included in construction Inspection and testing 5
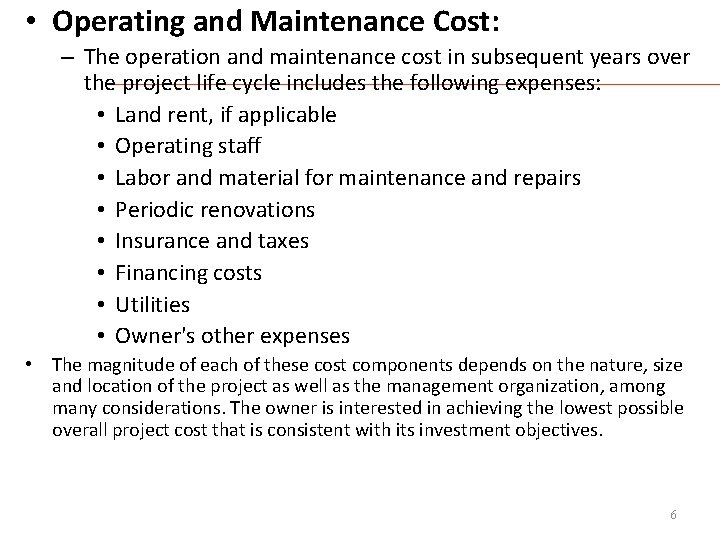
• Operating and Maintenance Cost: – The operation and maintenance cost in subsequent years over the project life cycle includes the following expenses: • Land rent, if applicable • Operating staff • Labor and material for maintenance and repairs • Periodic renovations • Insurance and taxes • Financing costs • Utilities • Owner's other expenses • The magnitude of each of these cost components depends on the nature, size and location of the project as well as the management organization, among many considerations. The owner is interested in achieving the lowest possible overall project cost that is consistent with its investment objectives. 6
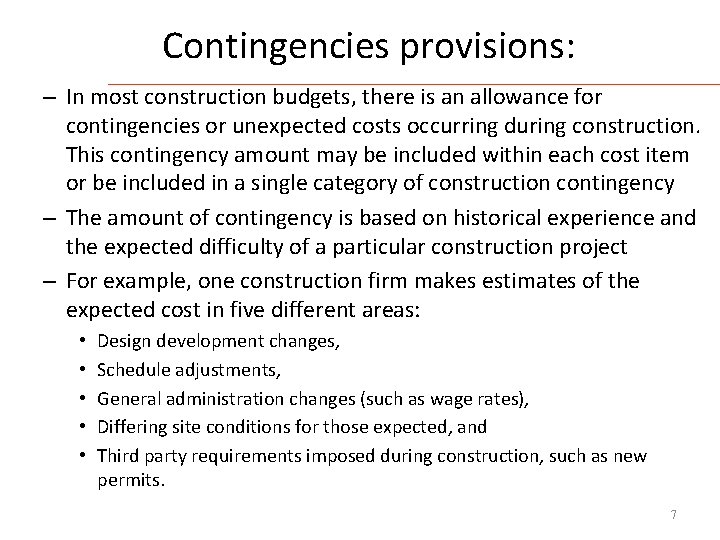
Contingencies provisions: – In most construction budgets, there is an allowance for contingencies or unexpected costs occurring during construction. This contingency amount may be included within each cost item or be included in a single category of construction contingency – The amount of contingency is based on historical experience and the expected difficulty of a particular construction project – For example, one construction firm makes estimates of the expected cost in five different areas: • • • Design development changes, Schedule adjustments, General administration changes (such as wage rates), Differing site conditions for those expected, and Third party requirements imposed during construction, such as new permits. 7
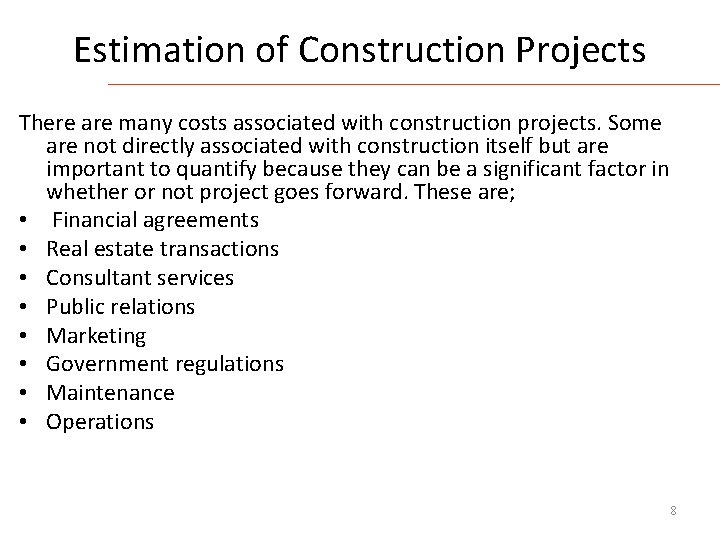
Estimation of Construction Projects There are many costs associated with construction projects. Some are not directly associated with construction itself but are important to quantify because they can be a significant factor in whether or not project goes forward. These are; • Financial agreements • Real estate transactions • Consultant services • Public relations • Marketing • Government regulations • Maintenance • Operations 8
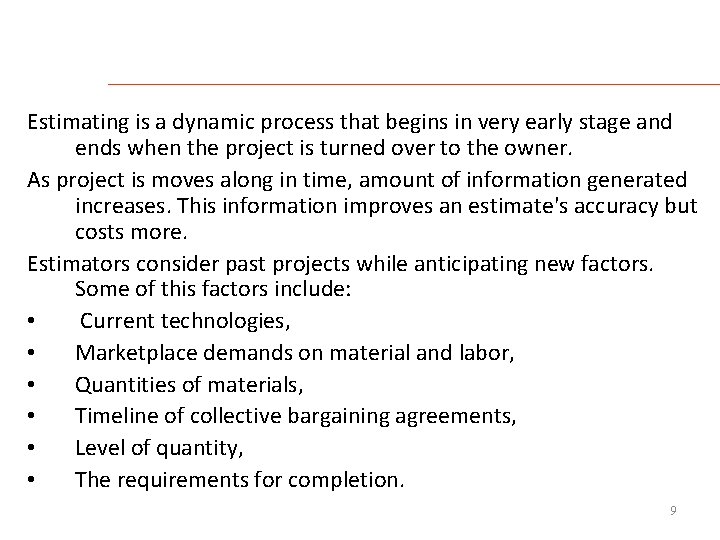
Estimating is a dynamic process that begins in very early stage and ends when the project is turned over to the owner. As project is moves along in time, amount of information generated increases. This information improves an estimate's accuracy but costs more. Estimators consider past projects while anticipating new factors. Some of this factors include: • Current technologies, • Marketplace demands on material and labor, • Quantities of materials, • Timeline of collective bargaining agreements, • Level of quantity, • The requirements for completion. 9
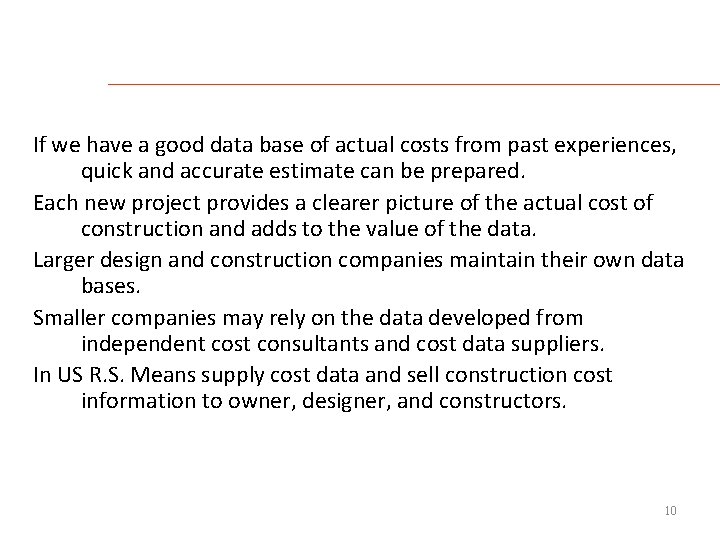
If we have a good data base of actual costs from past experiences, quick and accurate estimate can be prepared. Each new project provides a clearer picture of the actual cost of construction and adds to the value of the data. Larger design and construction companies maintain their own data bases. Smaller companies may rely on the data developed from independent cost consultants and cost data suppliers. In US R. S. Means supply cost data and sell construction cost information to owner, designer, and constructors. 10
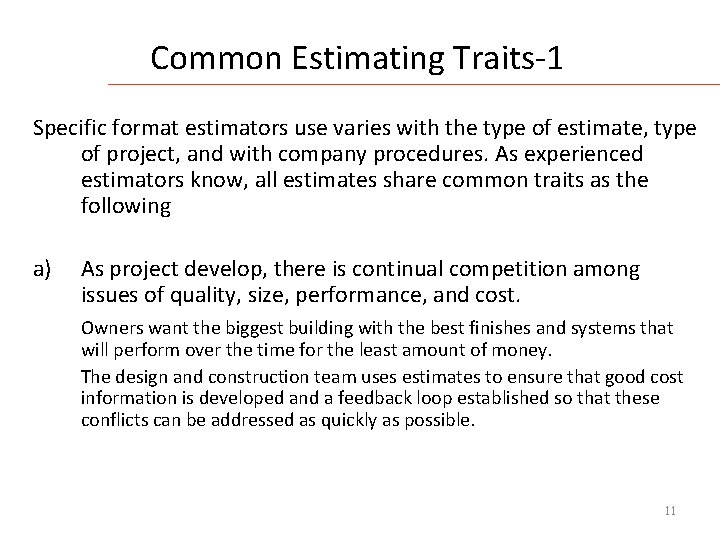
Common Estimating Traits-1 Specific format estimators use varies with the type of estimate, type of project, and with company procedures. As experienced estimators know, all estimates share common traits as the following a) As project develop, there is continual competition among issues of quality, size, performance, and cost. Owners want the biggest building with the best finishes and systems that will perform over the time for the least amount of money. The design and construction team uses estimates to ensure that good cost information is developed and a feedback loop established so that these conflicts can be addressed as quickly as possible. 11
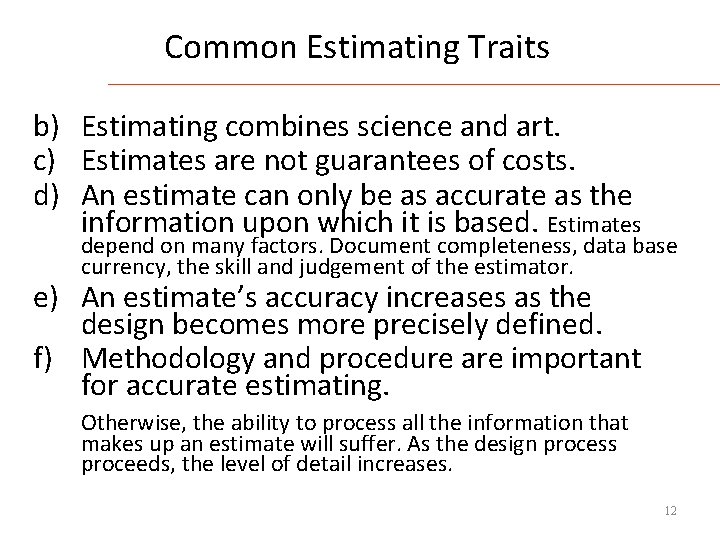
Common Estimating Traits b) Estimating combines science and art. c) Estimates are not guarantees of costs. d) An estimate can only be as accurate as the information upon which it is based. Estimates depend on many factors. Document completeness, data base currency, the skill and judgement of the estimator. e) An estimate’s accuracy increases as the design becomes more precisely defined. f) Methodology and procedure are important for accurate estimating. Otherwise, the ability to process all the information that makes up an estimate will suffer. As the design process proceeds, the level of detail increases. 12
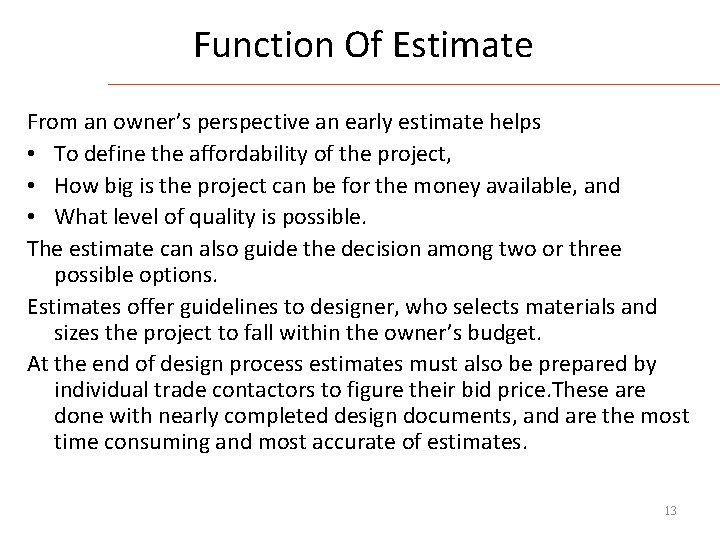
Function Of Estimate From an owner’s perspective an early estimate helps • To define the affordability of the project, • How big is the project can be for the money available, and • What level of quality is possible. The estimate can also guide the decision among two or three possible options. Estimates offer guidelines to designer, who selects materials and sizes the project to fall within the owner’s budget. At the end of design process estimates must also be prepared by individual trade contactors to figure their bid price. These are done with nearly completed design documents, and are the most time consuming and most accurate of estimates. 13
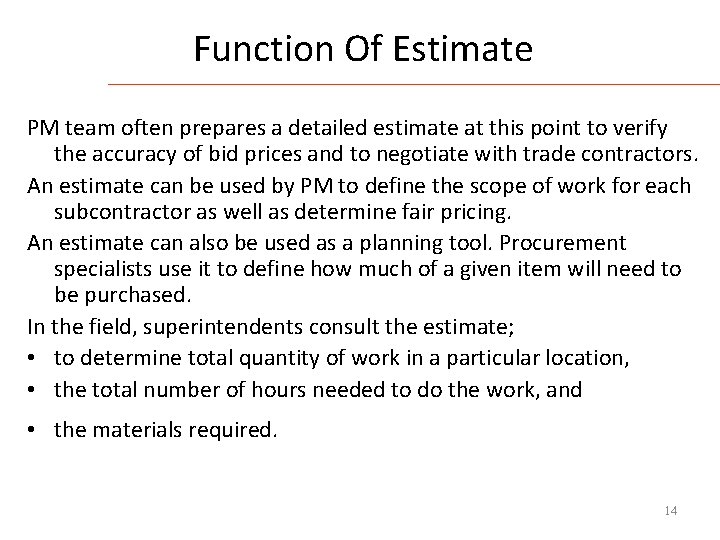
Function Of Estimate PM team often prepares a detailed estimate at this point to verify the accuracy of bid prices and to negotiate with trade contractors. An estimate can be used by PM to define the scope of work for each subcontractor as well as determine fair pricing. An estimate can also be used as a planning tool. Procurement specialists use it to define how much of a given item will need to be purchased. In the field, superintendents consult the estimate; • to determine total quantity of work in a particular location, • the total number of hours needed to do the work, and • the materials required. 14
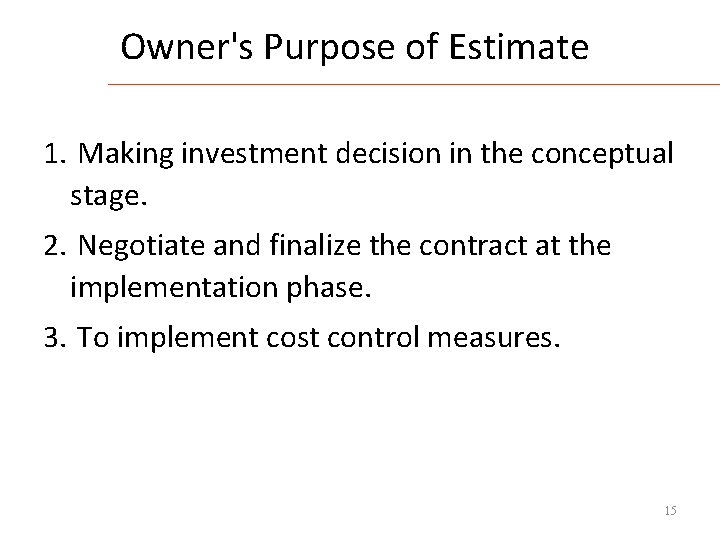
Owner's Purpose of Estimate 1. Making investment decision in the conceptual stage. 2. Negotiate and finalize the contract at the implementation phase. 3. To implement cost control measures. 15
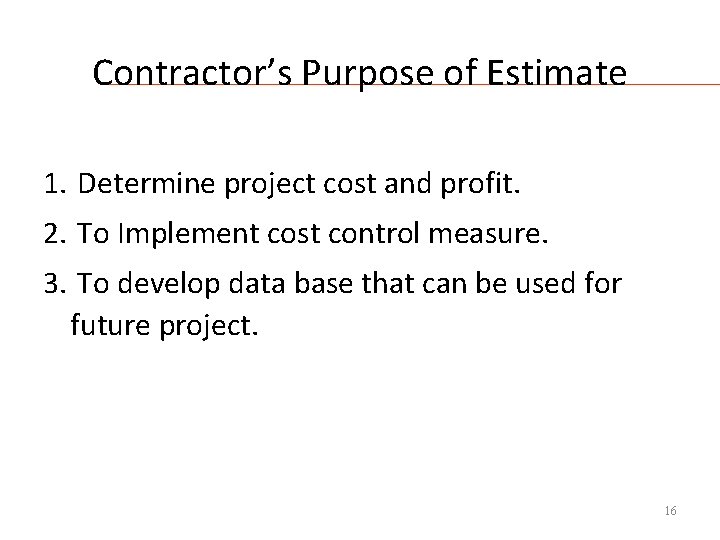
Contractor’s Purpose of Estimate 1. Determine project cost and profit. 2. To Implement cost control measure. 3. To develop data base that can be used for future project. 16
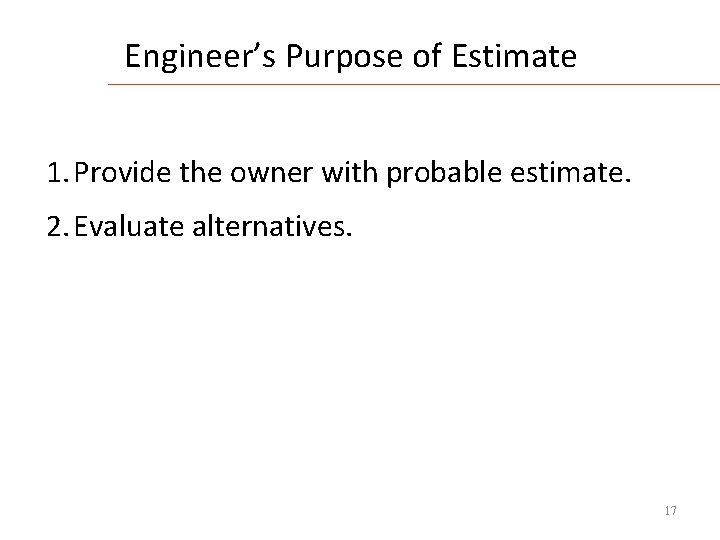
Engineer’s Purpose of Estimate 1. Provide the owner with probable estimate. 2. Evaluate alternatives. 17
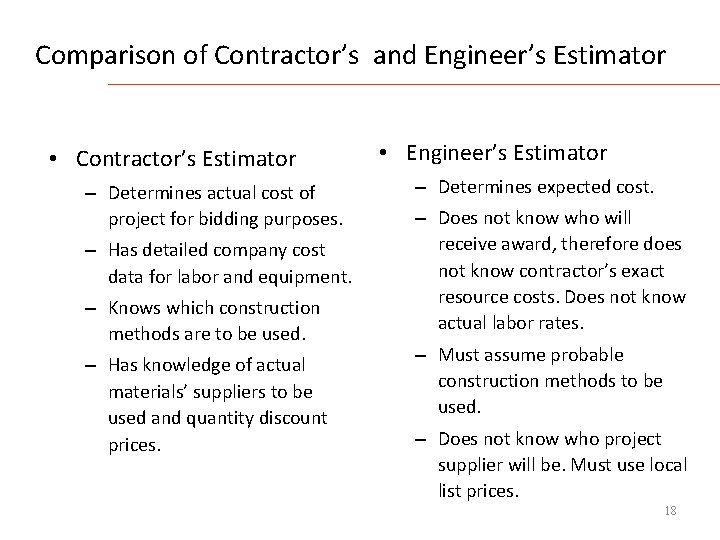
Comparison of Contractor’s and Engineer’s Estimator • Contractor’s Estimator – Determines actual cost of project for bidding purposes. – Has detailed company cost data for labor and equipment. – Knows which construction methods are to be used. – Has knowledge of actual materials’ suppliers to be used and quantity discount prices. • Engineer’s Estimator – Determines expected cost. – Does not know who will receive award, therefore does not know contractor’s exact resource costs. Does not know actual labor rates. – Must assume probable construction methods to be used. – Does not know who project supplier will be. Must use local list prices. 18
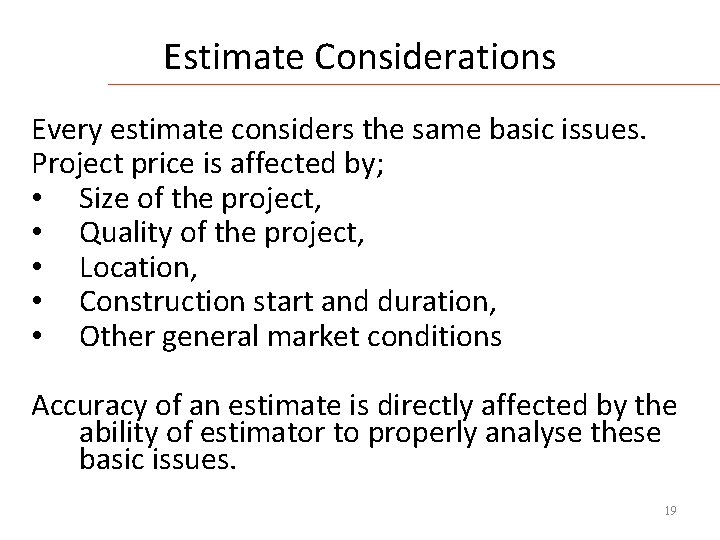
Estimate Considerations Every estimate considers the same basic issues. Project price is affected by; • Size of the project, • Quality of the project, • Location, • Construction start and duration, • Other general market conditions Accuracy of an estimate is directly affected by the ability of estimator to properly analyse these basic issues. 19
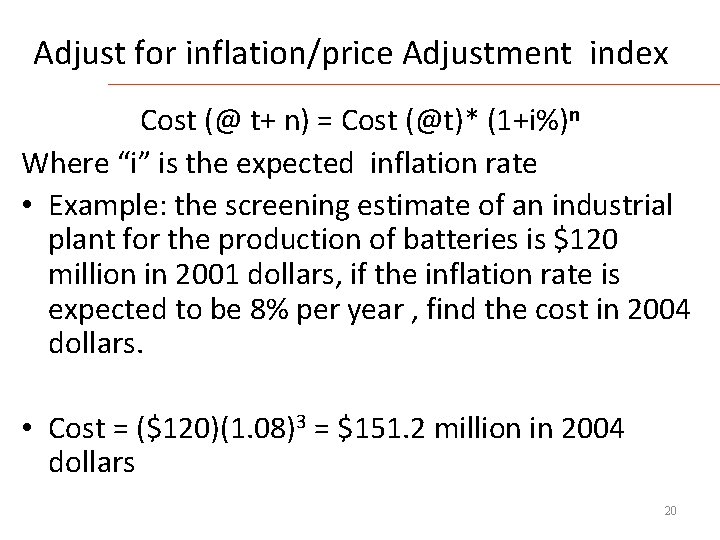
Adjust for inflation/price Adjustment index Cost (@ t+ n) = Cost (@t)* (1+i%)n Where “i” is the expected inflation rate • Example: the screening estimate of an industrial plant for the production of batteries is $120 million in 2001 dollars, if the inflation rate is expected to be 8% per year , find the cost in 2004 dollars. • Cost = ($120)(1. 08)3 = $151. 2 million in 2004 dollars 20
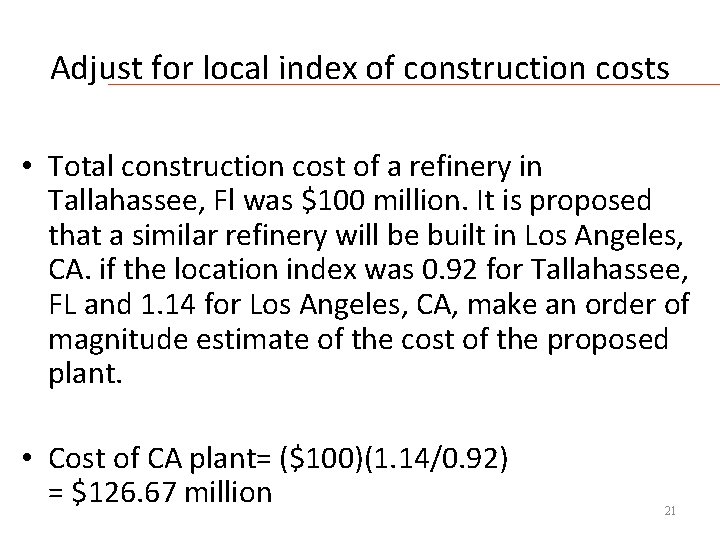
Adjust for local index of construction costs • Total construction cost of a refinery in Tallahassee, Fl was $100 million. It is proposed that a similar refinery will be built in Los Angeles, CA. if the location index was 0. 92 for Tallahassee, FL and 1. 14 for Los Angeles, CA, make an order of magnitude estimate of the cost of the proposed plant. • Cost of CA plant= ($100)(1. 14/0. 92) = $126. 67 million 21
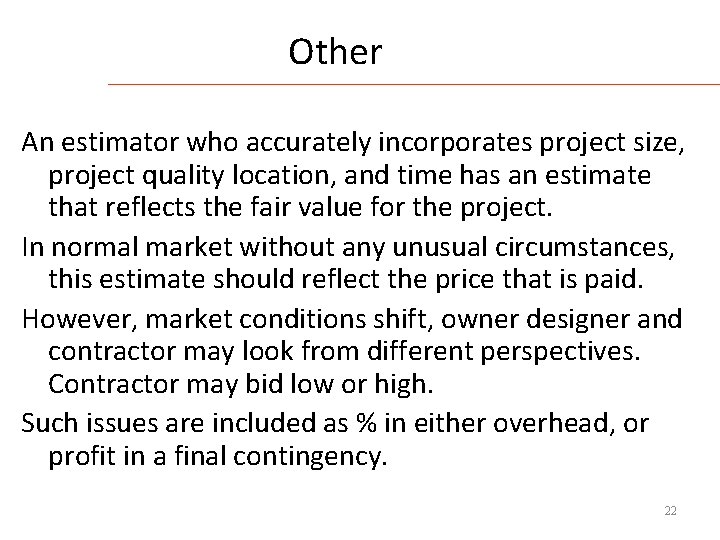
Other An estimator who accurately incorporates project size, project quality location, and time has an estimate that reflects the fair value for the project. In normal market without any unusual circumstances, this estimate should reflect the price that is paid. However, market conditions shift, owner designer and contractor may look from different perspectives. Contractor may bid low or high. Such issues are included as % in either overhead, or profit in a final contingency. 22
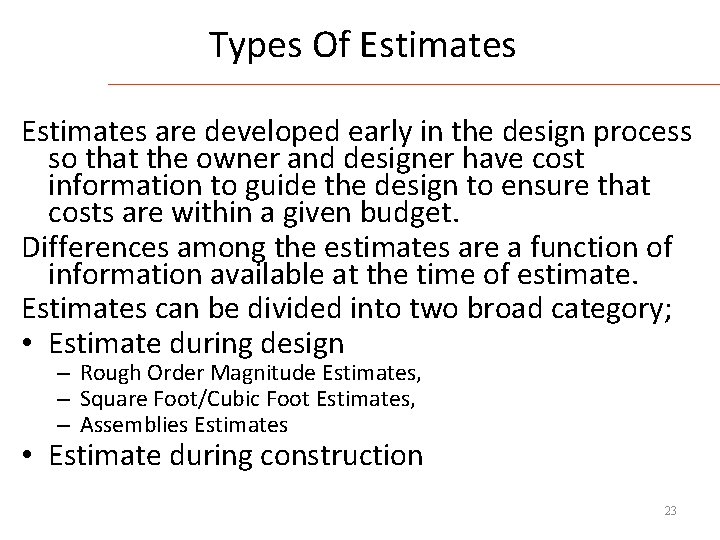
Types Of Estimates are developed early in the design process so that the owner and designer have cost information to guide the design to ensure that costs are within a given budget. Differences among the estimates are a function of information available at the time of estimate. Estimates can be divided into two broad category; • Estimate during design – Rough Order Magnitude Estimates, – Square Foot/Cubic Foot Estimates, – Assemblies Estimates • Estimate during construction 23

Types Of Estimates ESTIMATING DURING DESIGN: Design estimates are important tools for the owner and the project management team as they develop the project’s scope of work. The discipline of providing cost information throughout the design phase makes cost a significant driver for project team. By providing cost information early and updating it, project team is kept in the realities of cost. • Rough Order Magnitude Estimates • Square Foot/Cubic Foot Estimates • Assemblies Estimates 24
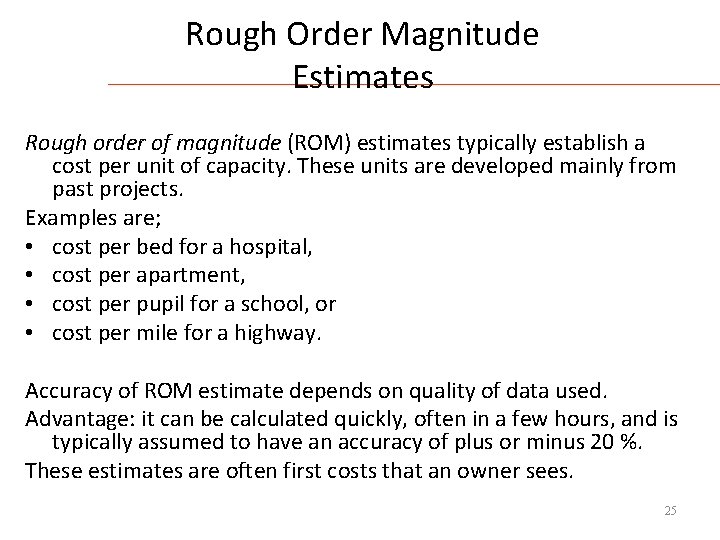
Rough Order Magnitude Estimates Rough order of magnitude (ROM) estimates typically establish a cost per unit of capacity. These units are developed mainly from past projects. Examples are; • cost per bed for a hospital, • cost per apartment, • cost per pupil for a school, or • cost per mile for a highway. Accuracy of ROM estimate depends on quality of data used. Advantage: it can be calculated quickly, often in a few hours, and is typically assumed to have an accuracy of plus or minus 20 %. These estimates are often first costs that an owner sees. 25
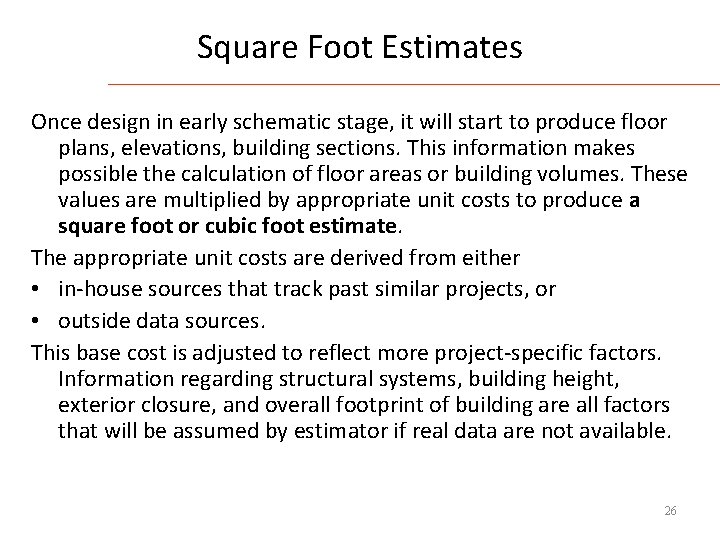
Square Foot Estimates Once design in early schematic stage, it will start to produce floor plans, elevations, building sections. This information makes possible the calculation of floor areas or building volumes. These values are multiplied by appropriate unit costs to produce a square foot or cubic foot estimate. The appropriate unit costs are derived from either • in-house sources that track past similar projects, or • outside data sources. This base cost is adjusted to reflect more project-specific factors. Information regarding structural systems, building height, exterior closure, and overall footprint of building are all factors that will be assumed by estimator if real data are not available. 26
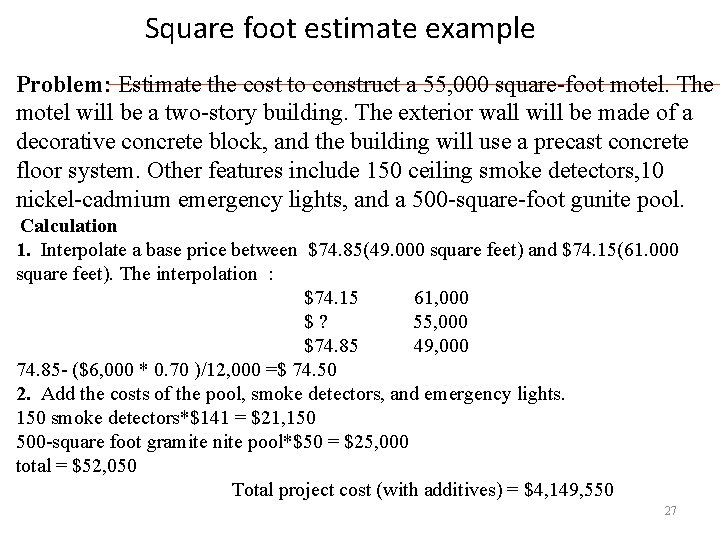
Square foot estimate example Problem: Estimate the cost to construct a 55, 000 square-foot motel. The motel will be a two-story building. The exterior wall will be made of a decorative concrete block, and the building will use a precast concrete floor system. Other features include 150 ceiling smoke detectors, 10 nickel-cadmium emergency lights, and a 500 -square-foot gunite pool. Calculation 1. Interpolate a base price between $74. 85(49. 000 square feet) and $74. 15(61. 000 square feet). The interpolation : $74. 15 61, 000 $? 55, 000 $74. 85 49, 000 74. 85 - ($6, 000 * 0. 70 )/12, 000 =$ 74. 50 2. Add the costs of the pool, smoke detectors, and emergency lights. 150 smoke detectors*$141 = $21, 150 500 -square foot gramite nite pool*$50 = $25, 000 total = $52, 050 Total project cost (with additives) = $4, 149, 550 27
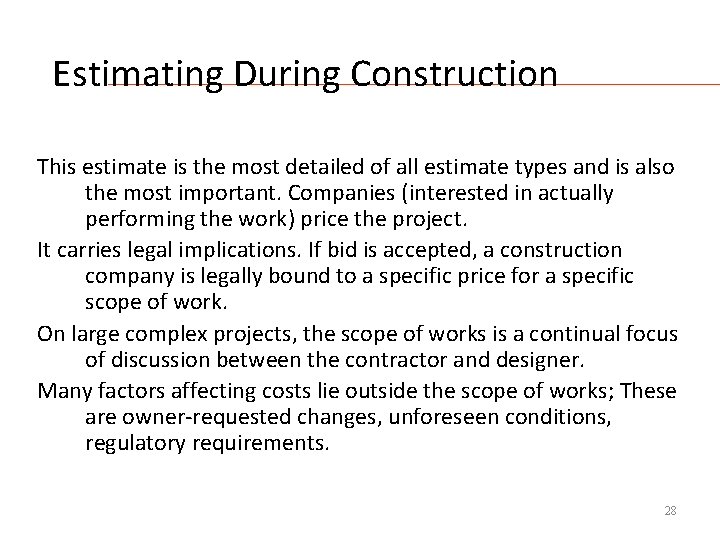
Estimating During Construction This estimate is the most detailed of all estimate types and is also the most important. Companies (interested in actually performing the work) price the project. It carries legal implications. If bid is accepted, a construction company is legally bound to a specific price for a specific scope of work. On large complex projects, the scope of works is a continual focus of discussion between the contractor and designer. Many factors affecting costs lie outside the scope of works; These are owner-requested changes, unforeseen conditions, regulatory requirements. 28

Bid estimates The contractor's bid estimates often reflect the desire of the contractor to secure the job as well as the estimating tools at its disposal. Some contractors have well established cost estimating procedures while others do not. If all or part of the construction is to be undertaken by the general contractor, a bid estimate may be prepared on the basis of quantity takeoffs from the plans provided by the owner or on the basis of the construction procedures devised by the contractor for implementing the project. Example: The cost of a footing of a certain type and size may be found in commercial publications on cost data which can be used to facilitate cost estimates from quantity takeoffs. Items such as labor, material and equipment needed to perform various tasks may be used as parameters for the cost estimates. 29
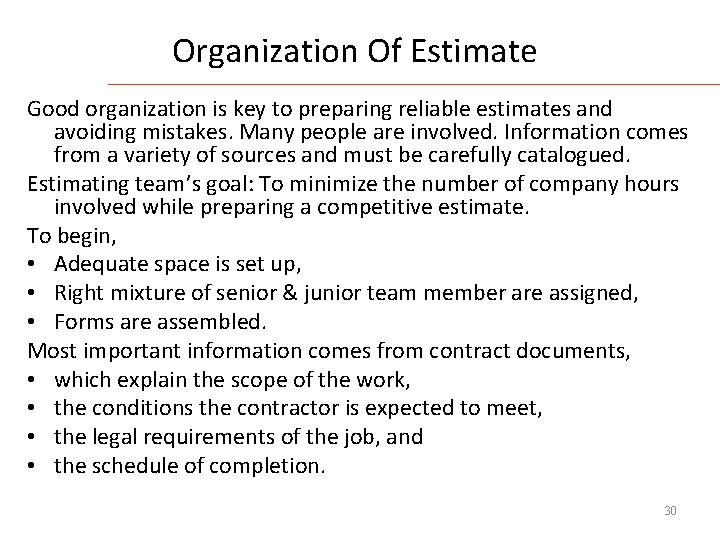
Organization Of Estimate Good organization is key to preparing reliable estimates and avoiding mistakes. Many people are involved. Information comes from a variety of sources and must be carefully catalogued. Estimating team’s goal: To minimize the number of company hours involved while preparing a competitive estimate. To begin, • Adequate space is set up, • Right mixture of senior & junior team member are assigned, • Forms are assembled. Most important information comes from contract documents, • which explain the scope of the work, • the conditions the contractor is expected to meet, • the legal requirements of the job, and • the schedule of completion. 30
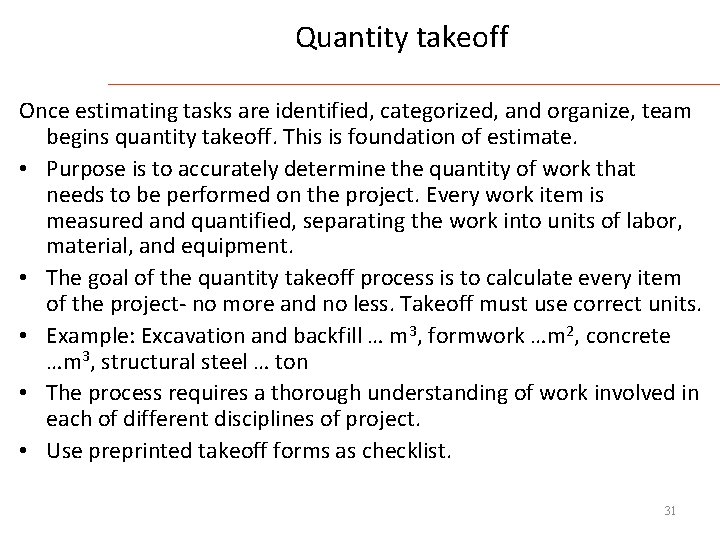
Quantity takeoff Once estimating tasks are identified, categorized, and organize, team begins quantity takeoff. This is foundation of estimate. • Purpose is to accurately determine the quantity of work that needs to be performed on the project. Every work item is measured and quantified, separating the work into units of labor, material, and equipment. • The goal of the quantity takeoff process is to calculate every item of the project- no more and no less. Takeoff must use correct units. • Example: Excavation and backfill … m 3, formwork …m 2, concrete …m 3, structural steel … ton • The process requires a thorough understanding of work involved in each of different disciplines of project. • Use preprinted takeoff forms as checklist. 31
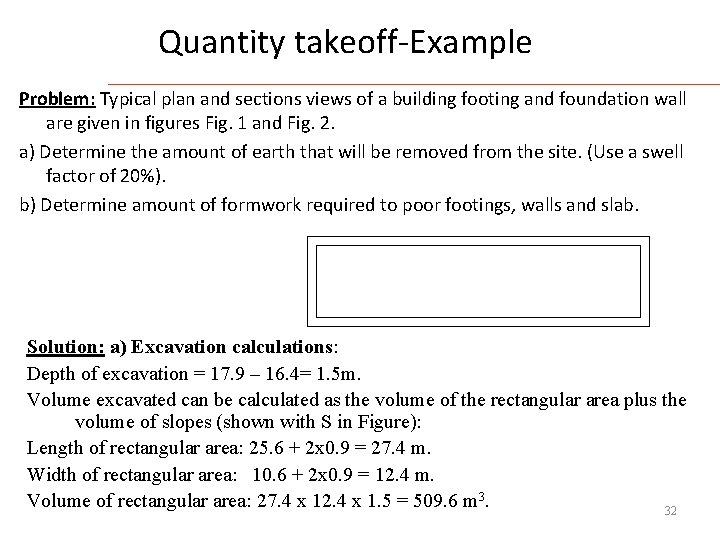
Quantity takeoff-Example Problem: Typical plan and sections views of a building footing and foundation wall are given in figures Fig. 1 and Fig. 2. a) Determine the amount of earth that will be removed from the site. (Use a swell factor of 20%). b) Determine amount of formwork required to poor footings, walls and slab. Solution: a) Excavation calculations: Depth of excavation = 17. 9 – 16. 4= 1. 5 m. Volume excavated can be calculated as the volume of the rectangular area plus the volume of slopes (shown with S in Figure): Length of rectangular area: 25. 6 + 2 x 0. 9 = 27. 4 m. Width of rectangular area: 10. 6 + 2 x 0. 9 = 12. 4 m. Volume of rectangular area: 27. 4 x 12. 4 x 1. 5 = 509. 6 m 3. 32
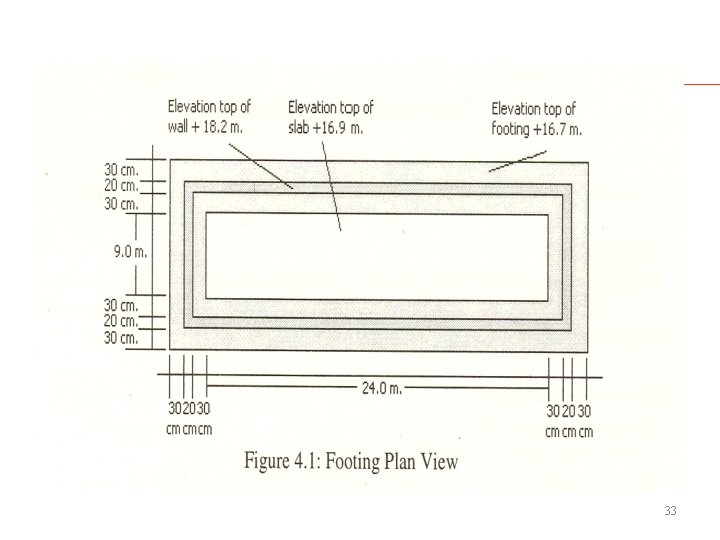
33
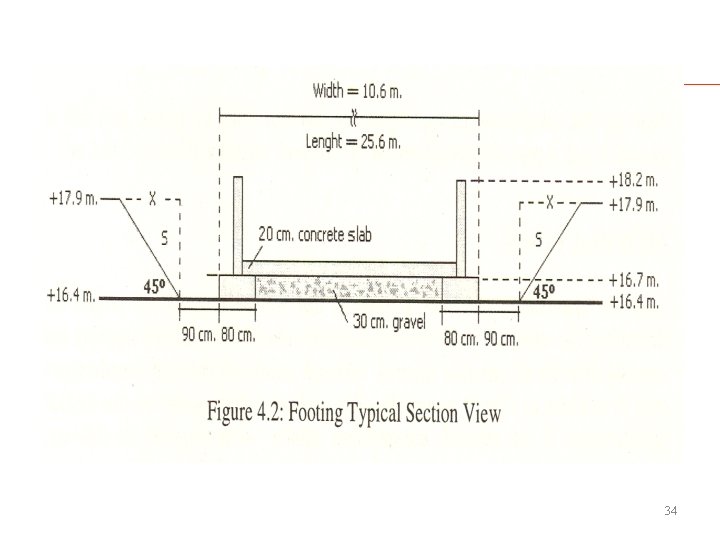
34
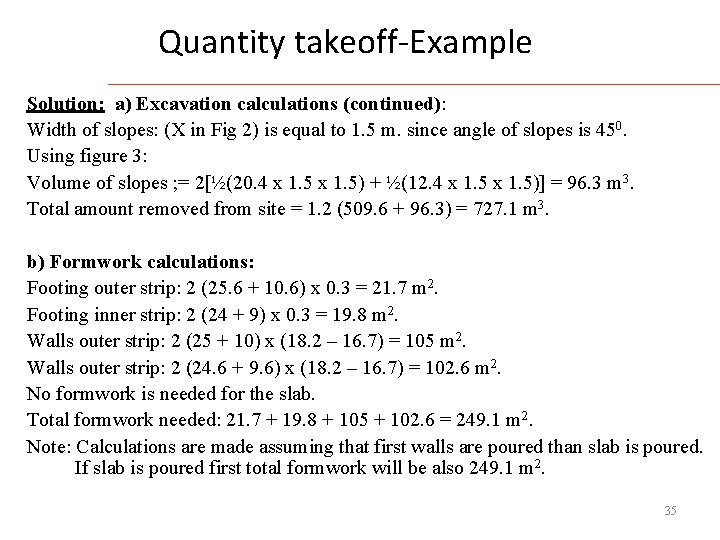
Quantity takeoff-Example Solution: a) Excavation calculations (continued): Width of slopes: (X in Fig 2) is equal to 1. 5 m. since angle of slopes is 450. Using figure 3: Volume of slopes ; = 2[½(20. 4 x 1. 5) + ½(12. 4 x 1. 5)] = 96. 3 m 3. Total amount removed from site = 1. 2 (509. 6 + 96. 3) = 727. 1 m 3. b) Formwork calculations: Footing outer strip: 2 (25. 6 + 10. 6) x 0. 3 = 21. 7 m 2. Footing inner strip: 2 (24 + 9) x 0. 3 = 19. 8 m 2. Walls outer strip: 2 (25 + 10) x (18. 2 – 16. 7) = 105 m 2. Walls outer strip: 2 (24. 6 + 9. 6) x (18. 2 – 16. 7) = 102. 6 m 2. No formwork is needed for the slab. Total formwork needed: 21. 7 + 19. 8 + 105 + 102. 6 = 249. 1 m 2. Note: Calculations are made assuming that first walls are poured than slab is poured. If slab is poured first total formwork will be also 249. 1 m 2. 35
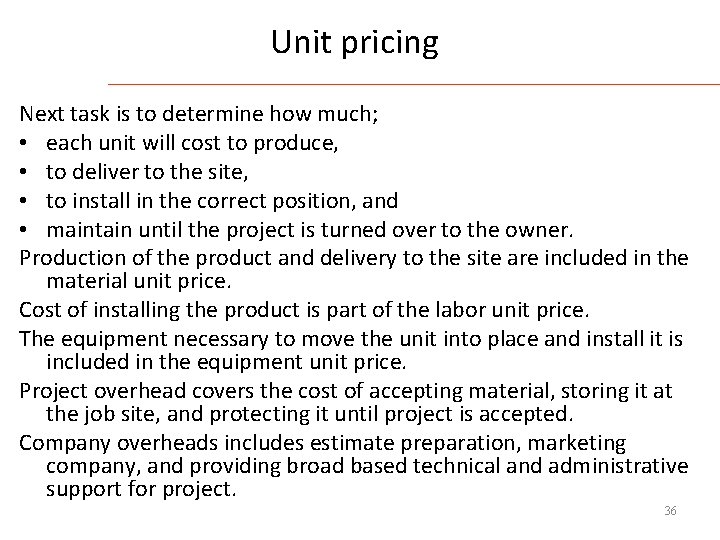
Unit pricing Next task is to determine how much; • each unit will cost to produce, • to deliver to the site, • to install in the correct position, and • maintain until the project is turned over to the owner. Production of the product and delivery to the site are included in the material unit price. Cost of installing the product is part of the labor unit price. The equipment necessary to move the unit into place and install it is included in the equipment unit price. Project overhead covers the cost of accepting material, storing it at the job site, and protecting it until project is accepted. Company overheads includes estimate preparation, marketing company, and providing broad based technical and administrative support for project. 36
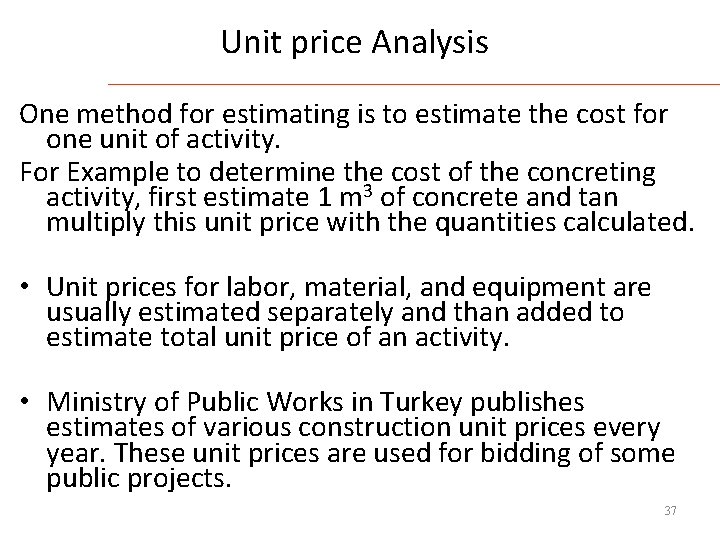
Unit price Analysis One method for estimating is to estimate the cost for one unit of activity. For Example to determine the cost of the concreting activity, first estimate 1 m 3 of concrete and tan multiply this unit price with the quantities calculated. • Unit prices for labor, material, and equipment are usually estimated separately and than added to estimate total unit price of an activity. • Ministry of Public Works in Turkey publishes estimates of various construction unit prices every year. These unit prices are used for bidding of some public projects. 37
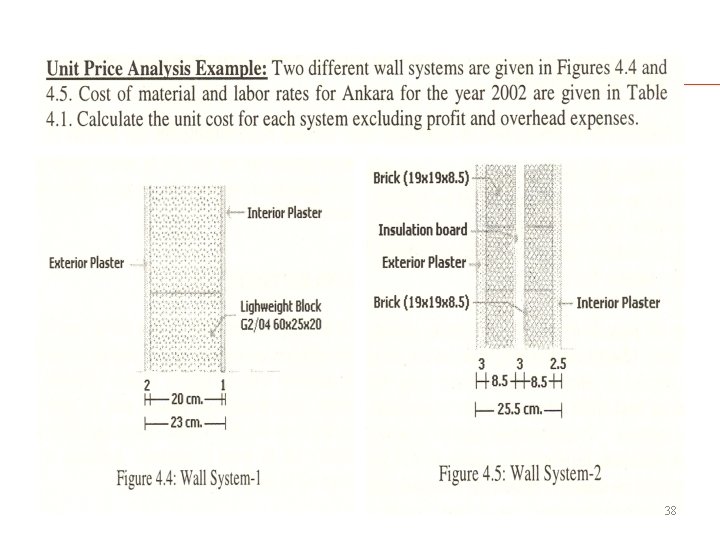
38
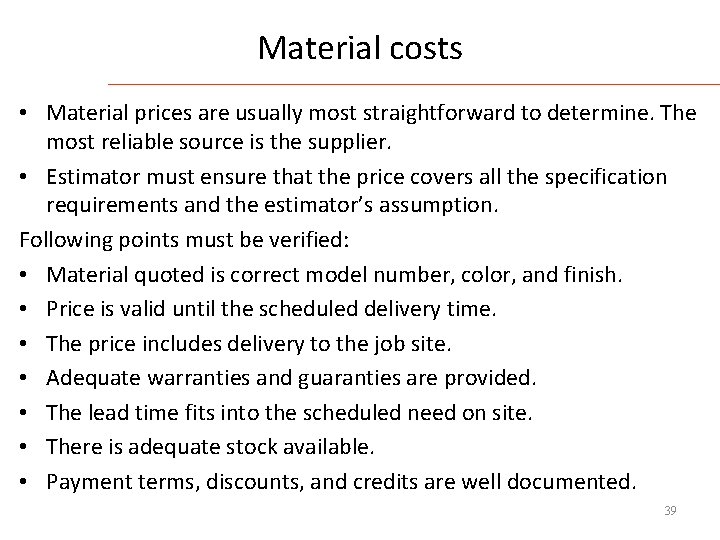
Material costs • Material prices are usually most straightforward to determine. The most reliable source is the supplier. • Estimator must ensure that the price covers all the specification requirements and the estimator’s assumption. Following points must be verified: • Material quoted is correct model number, color, and finish. • Price is valid until the scheduled delivery time. • The price includes delivery to the job site. • Adequate warranties and guaranties are provided. • The lead time fits into the scheduled need on site. • There is adequate stock available. • Payment terms, discounts, and credits are well documented. 39
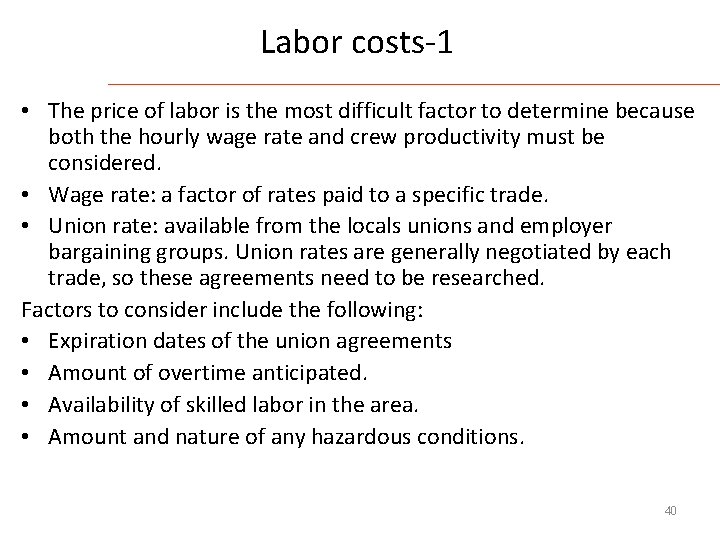
Labor costs-1 • The price of labor is the most difficult factor to determine because both the hourly wage rate and crew productivity must be considered. • Wage rate: a factor of rates paid to a specific trade. • Union rate: available from the locals unions and employer bargaining groups. Union rates are generally negotiated by each trade, so these agreements need to be researched. Factors to consider include the following: • Expiration dates of the union agreements • Amount of overtime anticipated. • Availability of skilled labor in the area. • Amount and nature of any hazardous conditions. 40
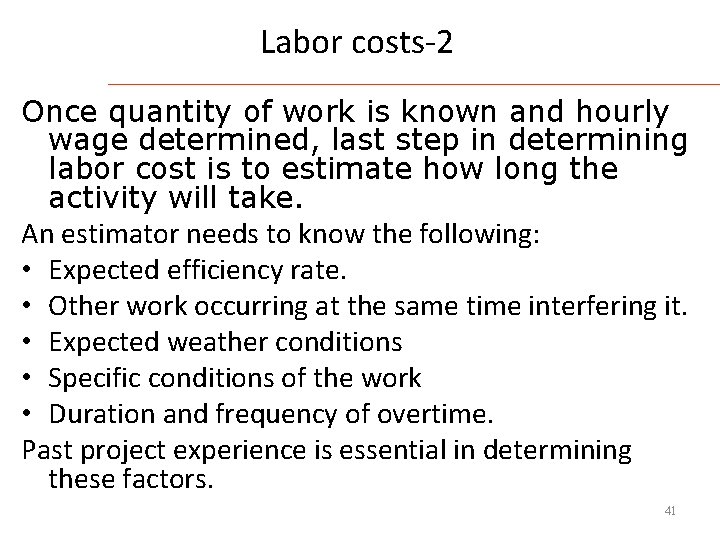
Labor costs-2 Once quantity of work is known and hourly wage determined, last step in determining labor cost is to estimate how long the activity will take. An estimator needs to know the following: • Expected efficiency rate. • Other work occurring at the same time interfering it. • Expected weather conditions • Specific conditions of the work • Duration and frequency of overtime. Past project experience is essential in determining these factors. 41
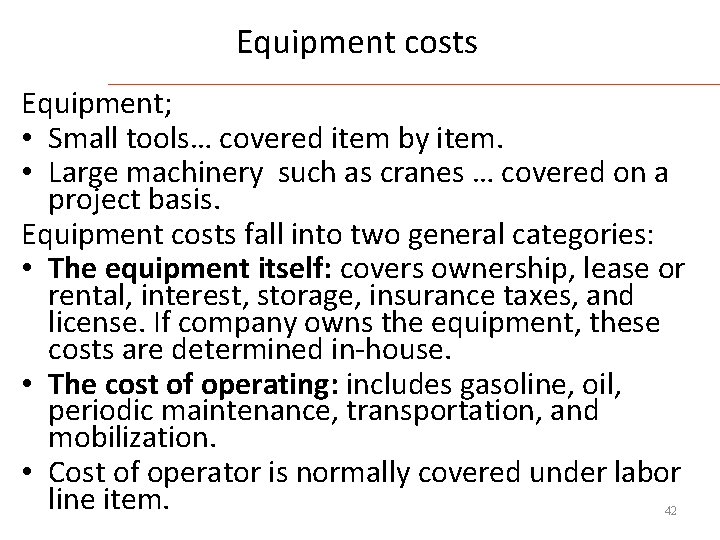
Equipment costs Equipment; • Small tools… covered item by item. • Large machinery such as cranes … covered on a project basis. Equipment costs fall into two general categories: • The equipment itself: covers ownership, lease or rental, interest, storage, insurance taxes, and license. If company owns the equipment, these costs are determined in-house. • The cost of operating: includes gasoline, oil, periodic maintenance, transportation, and mobilization. • Cost of operator is normally covered under labor line item. 42
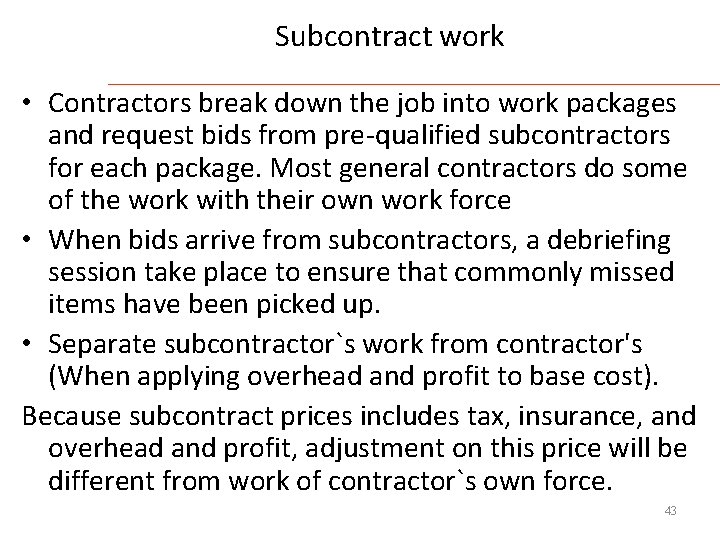
Subcontract work • Contractors break down the job into work packages and request bids from pre-qualified subcontractors for each package. Most general contractors do some of the work with their own work force • When bids arrive from subcontractors, a debriefing session take place to ensure that commonly missed items have been picked up. • Separate subcontractor`s work from contractor's (When applying overhead and profit to base cost). Because subcontract prices includes tax, insurance, and overhead and profit, adjustment on this price will be different from work of contractor`s own force. 43
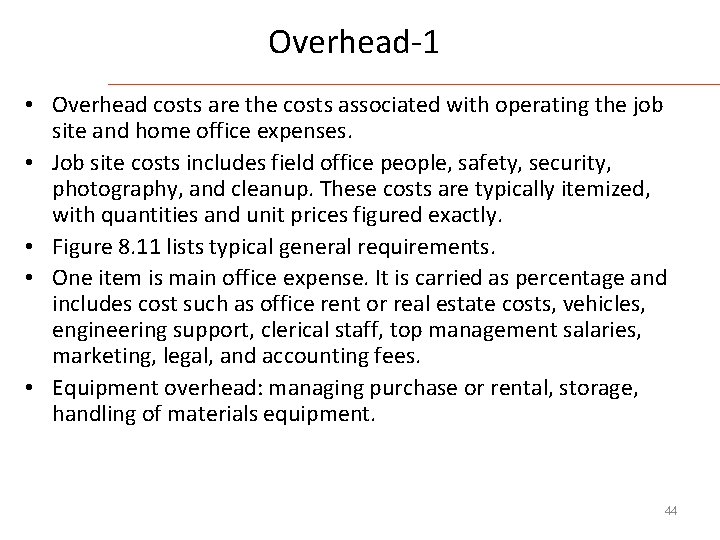
Overhead-1 • Overhead costs are the costs associated with operating the job site and home office expenses. • Job site costs includes field office people, safety, security, photography, and cleanup. These costs are typically itemized, with quantities and unit prices figured exactly. • Figure 8. 11 lists typical general requirements. • One item is main office expense. It is carried as percentage and includes cost such as office rent or real estate costs, vehicles, engineering support, clerical staff, top management salaries, marketing, legal, and accounting fees. • Equipment overhead: managing purchase or rental, storage, handling of materials equipment. 44
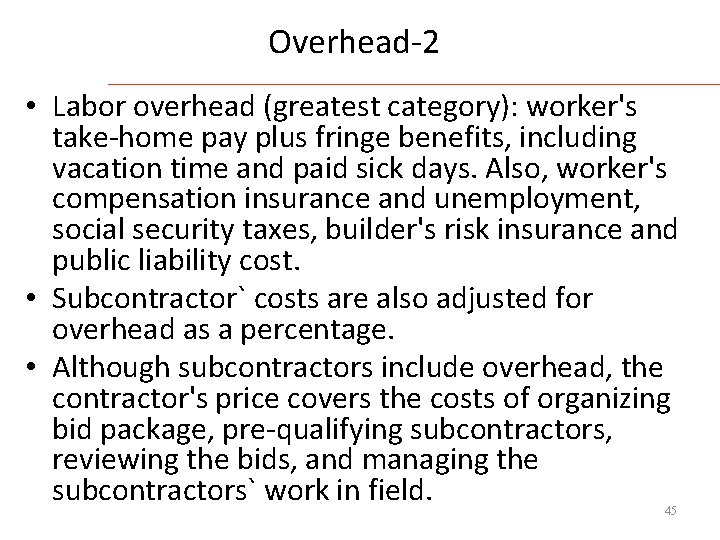
Overhead-2 • Labor overhead (greatest category): worker's take-home pay plus fringe benefits, including vacation time and paid sick days. Also, worker's compensation insurance and unemployment, social security taxes, builder's risk insurance and public liability cost. • Subcontractor` costs are also adjusted for overhead as a percentage. • Although subcontractors include overhead, the contractor's price covers the costs of organizing bid package, pre-qualifying subcontractors, reviewing the bids, and managing the subcontractors` work in field. 45
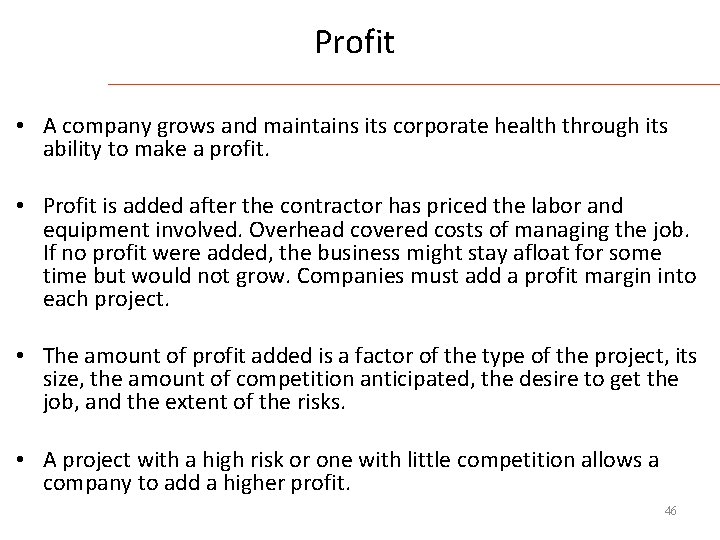
Profit • A company grows and maintains its corporate health through its ability to make a profit. • Profit is added after the contractor has priced the labor and equipment involved. Overhead covered costs of managing the job. If no profit were added, the business might stay afloat for some time but would not grow. Companies must add a profit margin into each project. • The amount of profit added is a factor of the type of the project, its size, the amount of competition anticipated, the desire to get the job, and the extent of the risks. • A project with a high risk or one with little competition allows a company to add a higher profit. 46
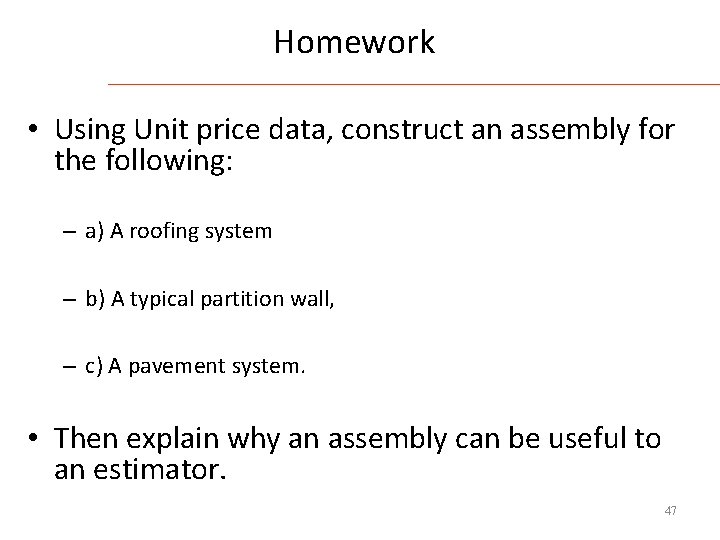
Homework • Using Unit price data, construct an assembly for the following: – a) A roofing system – b) A typical partition wall, – c) A pavement system. • Then explain why an assembly can be useful to an estimator. 47
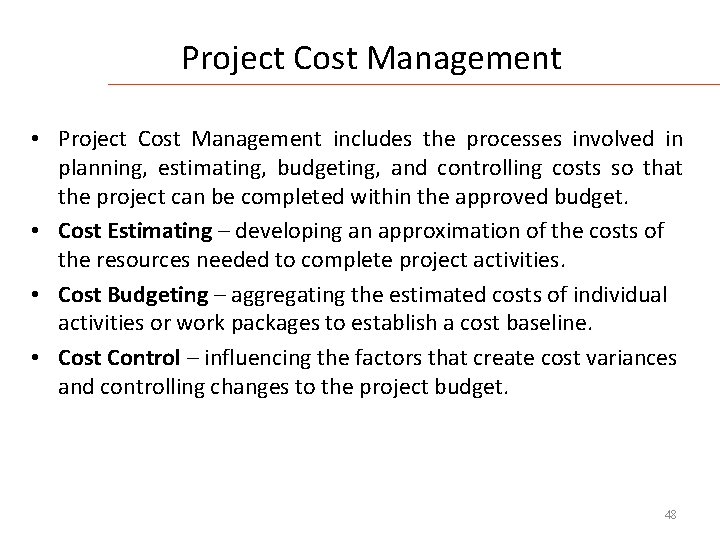
Project Cost Management • Project Cost Management includes the processes involved in planning, estimating, budgeting, and controlling costs so that the project can be completed within the approved budget. • Cost Estimating – developing an approximation of the costs of the resources needed to complete project activities. • Cost Budgeting – aggregating the estimated costs of individual activities or work packages to establish a cost baseline. • Cost Control – influencing the factors that create cost variances and controlling changes to the project budget. 48
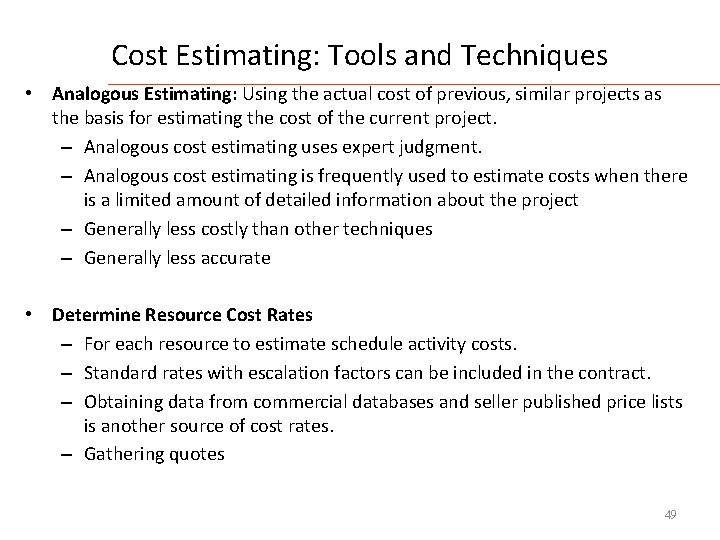
Cost Estimating: Tools and Techniques • Analogous Estimating: Using the actual cost of previous, similar projects as the basis for estimating the cost of the current project. – Analogous cost estimating uses expert judgment. – Analogous cost estimating is frequently used to estimate costs when there is a limited amount of detailed information about the project – Generally less costly than other techniques – Generally less accurate • Determine Resource Cost Rates – For each resource to estimate schedule activity costs. – Standard rates with escalation factors can be included in the contract. – Obtaining data from commercial databases and seller published price lists is another source of cost rates. – Gathering quotes 49
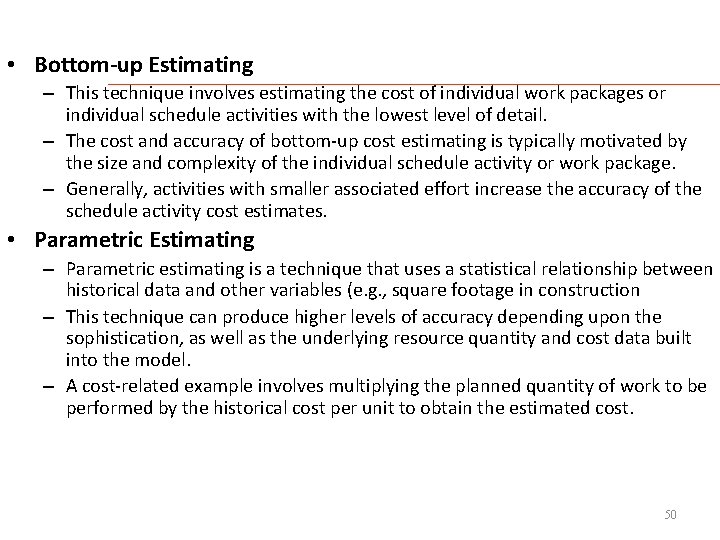
• Bottom-up Estimating – This technique involves estimating the cost of individual work packages or individual schedule activities with the lowest level of detail. – The cost and accuracy of bottom-up cost estimating is typically motivated by the size and complexity of the individual schedule activity or work package. – Generally, activities with smaller associated effort increase the accuracy of the schedule activity cost estimates. • Parametric Estimating – Parametric estimating is a technique that uses a statistical relationship between historical data and other variables (e. g. , square footage in construction – This technique can produce higher levels of accuracy depending upon the sophistication, as well as the underlying resource quantity and cost data built into the model. – A cost-related example involves multiplying the planned quantity of work to be performed by the historical cost per unit to obtain the estimated cost. 50
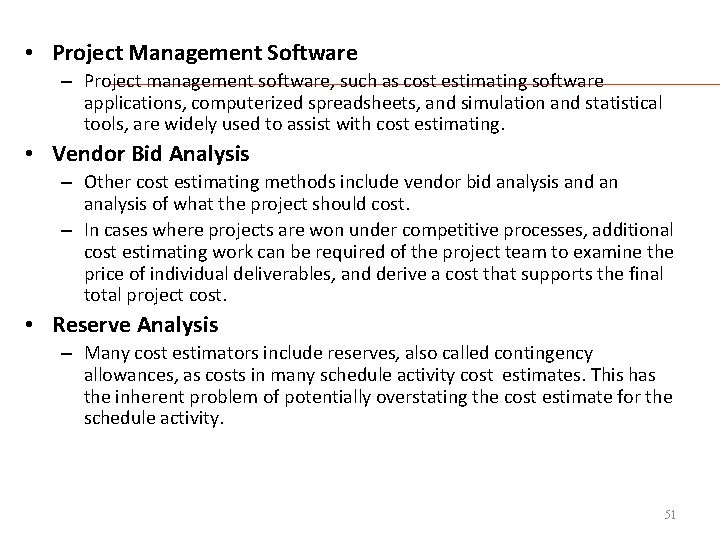
• Project Management Software – Project management software, such as cost estimating software applications, computerized spreadsheets, and simulation and statistical tools, are widely used to assist with cost estimating. • Vendor Bid Analysis – Other cost estimating methods include vendor bid analysis and an analysis of what the project should cost. – In cases where projects are won under competitive processes, additional cost estimating work can be required of the project team to examine the price of individual deliverables, and derive a cost that supports the final total project cost. • Reserve Analysis – Many cost estimators include reserves, also called contingency allowances, as costs in many schedule activity cost estimates. This has the inherent problem of potentially overstating the cost estimate for the schedule activity. 51
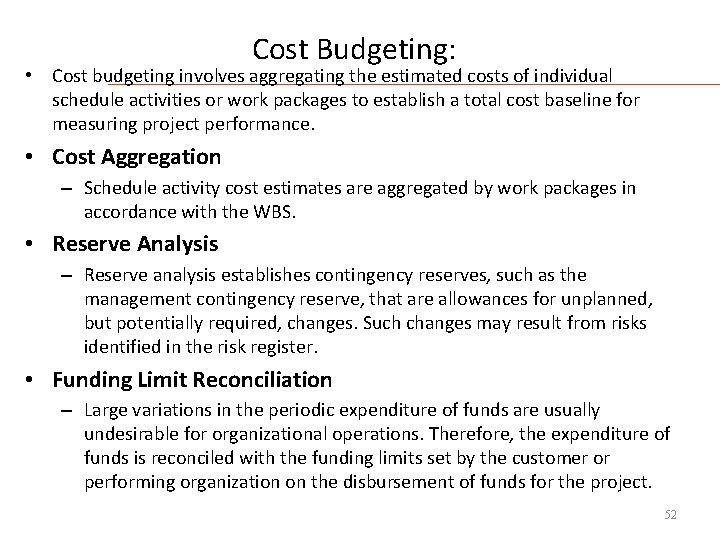
Cost Budgeting: • Cost budgeting involves aggregating the estimated costs of individual schedule activities or work packages to establish a total cost baseline for measuring project performance. • Cost Aggregation – Schedule activity cost estimates are aggregated by work packages in accordance with the WBS. • Reserve Analysis – Reserve analysis establishes contingency reserves, such as the management contingency reserve, that are allowances for unplanned, but potentially required, changes. Such changes may result from risks identified in the risk register. • Funding Limit Reconciliation – Large variations in the periodic expenditure of funds are usually undesirable for organizational operations. Therefore, the expenditure of funds is reconciled with the funding limits set by the customer or performing organization on the disbursement of funds for the project. 52
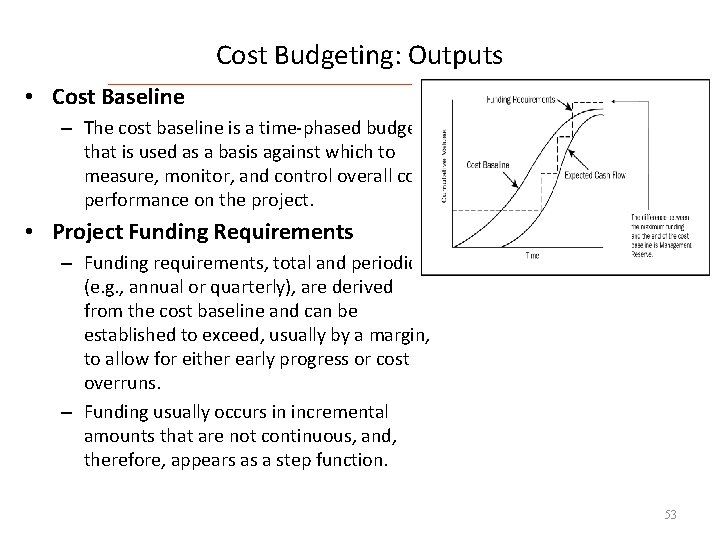
Cost Budgeting: Outputs • Cost Baseline – The cost baseline is a time-phased budget that is used as a basis against which to measure, monitor, and control overall cost performance on the project. • Project Funding Requirements – Funding requirements, total and periodic (e. g. , annual or quarterly), are derived from the cost baseline and can be established to exceed, usually by a margin, to allow for either early progress or cost overruns. – Funding usually occurs in incremental amounts that are not continuous, and, therefore, appears as a step function. 53
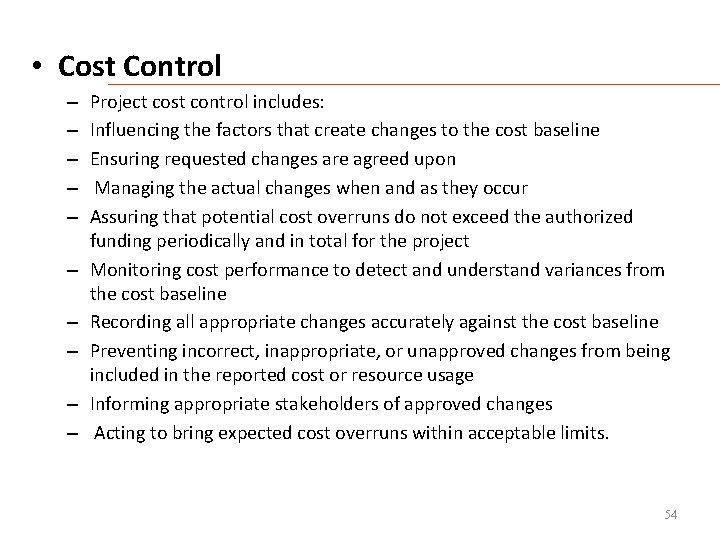
• Cost Control – – – – – Project cost control includes: Influencing the factors that create changes to the cost baseline Ensuring requested changes are agreed upon Managing the actual changes when and as they occur Assuring that potential cost overruns do not exceed the authorized funding periodically and in total for the project Monitoring cost performance to detect and understand variances from the cost baseline Recording all appropriate changes accurately against the cost baseline Preventing incorrect, inappropriate, or unapproved changes from being included in the reported cost or resource usage Informing appropriate stakeholders of approved changes Acting to bring expected cost overruns within acceptable limits. 54
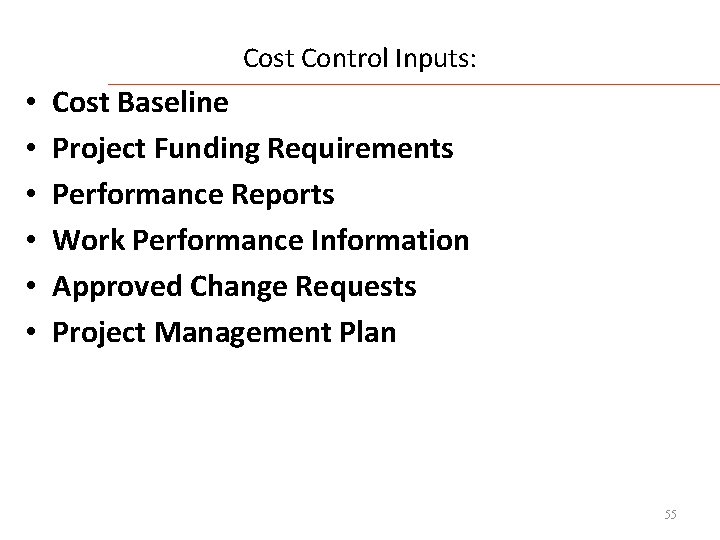
Cost Control Inputs: • • • Cost Baseline Project Funding Requirements Performance Reports Work Performance Information Approved Change Requests Project Management Plan 55
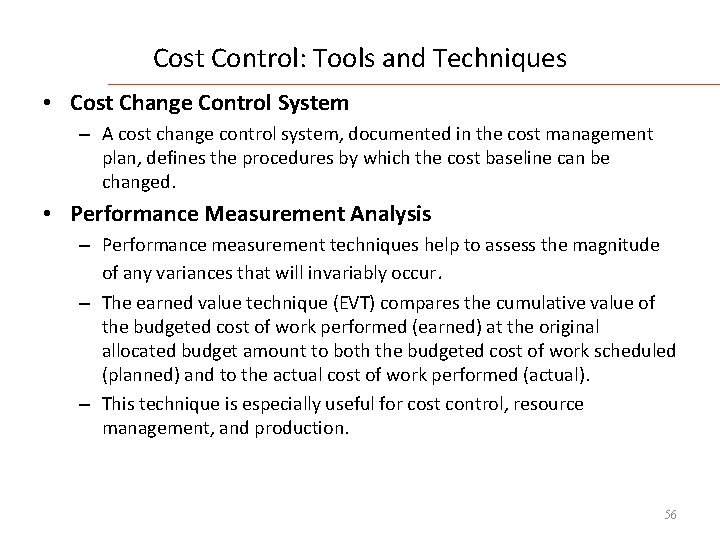
Cost Control: Tools and Techniques • Cost Change Control System – A cost change control system, documented in the cost management plan, defines the procedures by which the cost baseline can be changed. • Performance Measurement Analysis – Performance measurement techniques help to assess the magnitude of any variances that will invariably occur. – The earned value technique (EVT) compares the cumulative value of the budgeted cost of work performed (earned) at the original allocated budget amount to both the budgeted cost of work scheduled (planned) and to the actual cost of work performed (actual). – This technique is especially useful for cost control, resource management, and production. 56
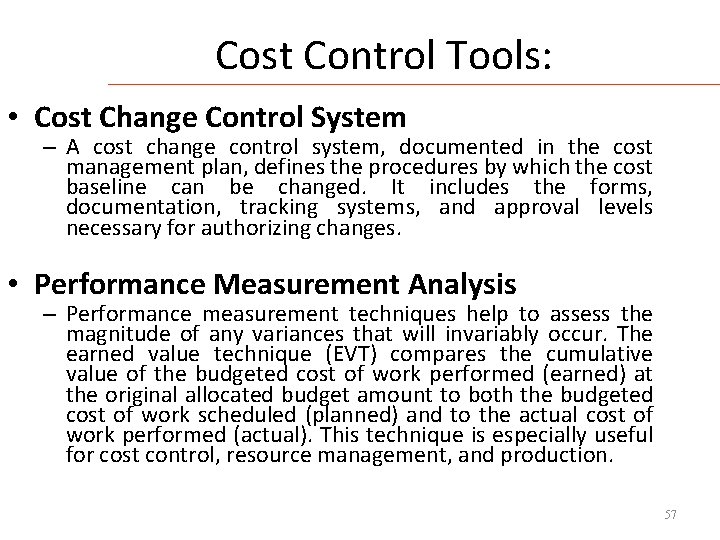
Cost Control Tools: • Cost Change Control System – A cost change control system, documented in the cost management plan, defines the procedures by which the cost baseline can be changed. It includes the forms, documentation, tracking systems, and approval levels necessary for authorizing changes. • Performance Measurement Analysis – Performance measurement techniques help to assess the magnitude of any variances that will invariably occur. The earned value technique (EVT) compares the cumulative value of the budgeted cost of work performed (earned) at the original allocated budget amount to both the budgeted cost of work scheduled (planned) and to the actual cost of work performed (actual). This technique is especially useful for cost control, resource management, and production. 57
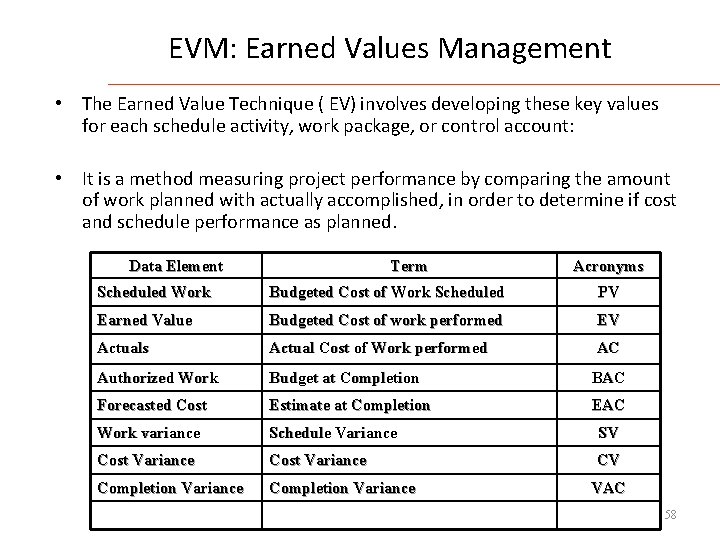
EVM: Earned Values Management • The Earned Value Technique ( EV) involves developing these key values for each schedule activity, work package, or control account: • It is a method measuring project performance by comparing the amount of work planned with actually accomplished, in order to determine if cost and schedule performance as planned. Data Element Term Acronyms Scheduled Work Budgeted Cost of Work Scheduled PV Earned Value Budgeted Cost of work performed EV Actuals Actual Cost of Work performed AC Authorized Work Budget at Completion BAC Forecasted Cost Estimate at Completion EAC Work variance Schedule Variance SV Cost Variance CV Completion Variance VAC 58
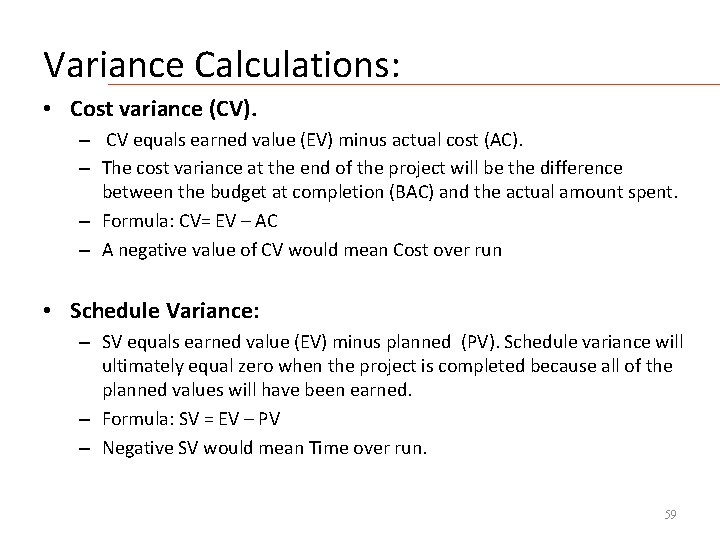
Variance Calculations: • Cost variance (CV). – CV equals earned value (EV) minus actual cost (AC). – The cost variance at the end of the project will be the difference between the budget at completion (BAC) and the actual amount spent. – Formula: CV= EV – AC – A negative value of CV would mean Cost over run • Schedule Variance: – SV equals earned value (EV) minus planned (PV). Schedule variance will ultimately equal zero when the project is completed because all of the planned values will have been earned. – Formula: SV = EV – PV – Negative SV would mean Time over run. 59
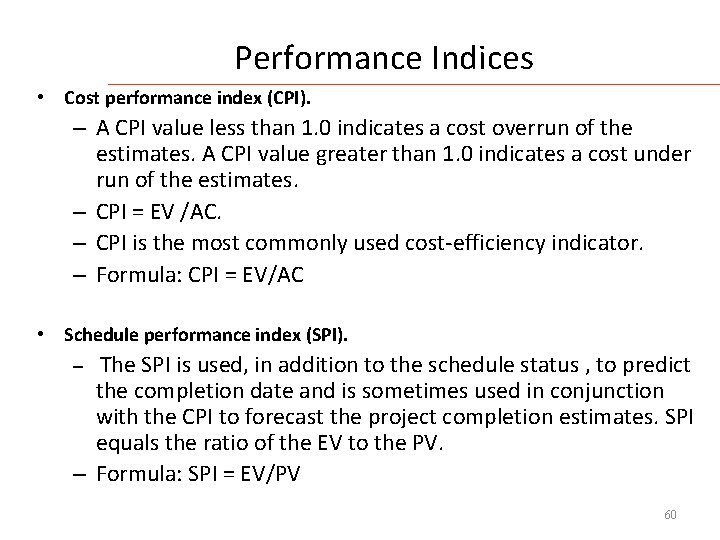
Performance Indices • Cost performance index (CPI). – A CPI value less than 1. 0 indicates a cost overrun of the estimates. A CPI value greater than 1. 0 indicates a cost under run of the estimates. – CPI = EV /AC. – CPI is the most commonly used cost-efficiency indicator. – Formula: CPI = EV/AC • Schedule performance index (SPI). The SPI is used, in addition to the schedule status , to predict the completion date and is sometimes used in conjunction with the CPI to forecast the project completion estimates. SPI equals the ratio of the EV to the PV. – Formula: SPI = EV/PV – 60
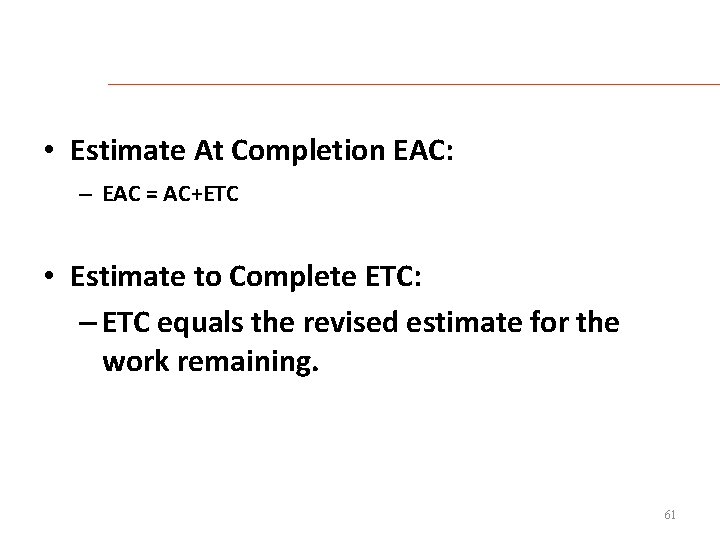
• Estimate At Completion EAC: – EAC = AC+ETC • Estimate to Complete ETC: – ETC equals the revised estimate for the work remaining. 61
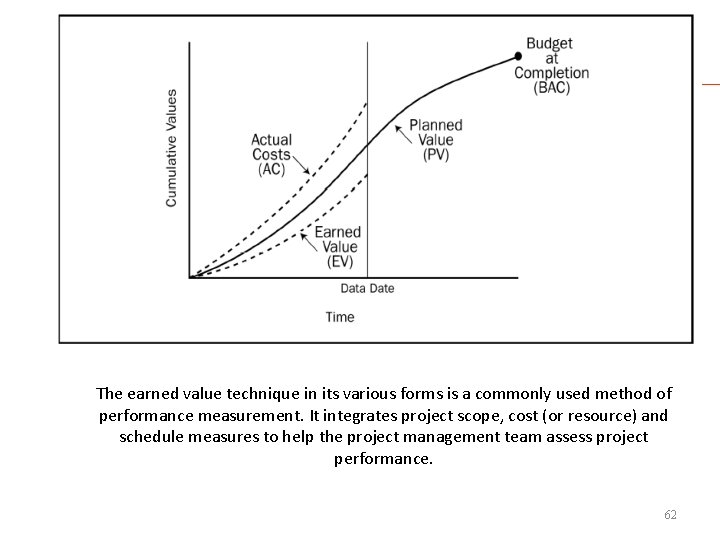
The earned value technique in its various forms is a commonly used method of performance measurement. It integrates project scope, cost (or resource) and schedule measures to help the project management team assess project performance. 62
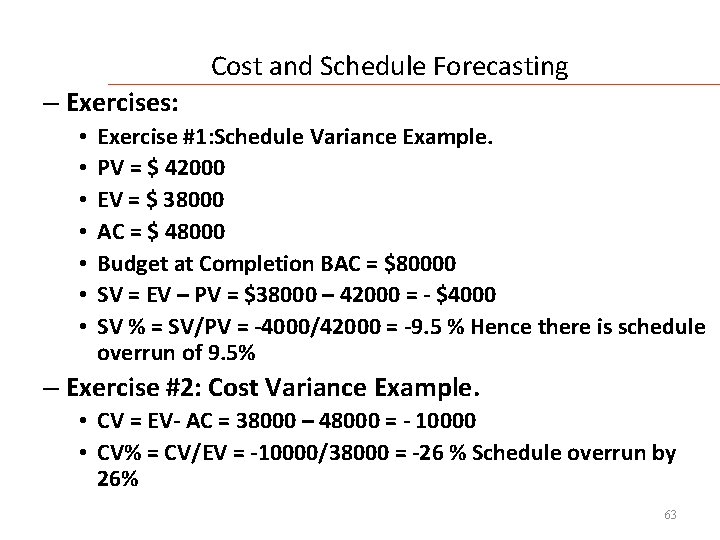
Cost and Schedule Forecasting – Exercises: • • Exercise #1: Schedule Variance Example. PV = $ 42000 EV = $ 38000 AC = $ 48000 Budget at Completion BAC = $80000 SV = EV – PV = $38000 – 42000 = - $4000 SV % = SV/PV = -4000/42000 = -9. 5 % Hence there is schedule overrun of 9. 5% – Exercise #2: Cost Variance Example. • CV = EV- AC = 38000 – 48000 = - 10000 • CV% = CV/EV = -10000/38000 = -26 % Schedule overrun by 26% 63
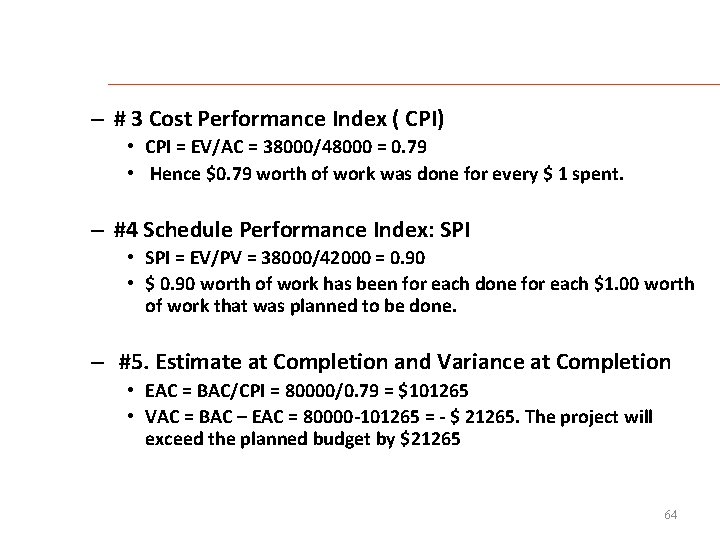
– # 3 Cost Performance Index ( CPI) • CPI = EV/AC = 38000/48000 = 0. 79 • Hence $0. 79 worth of work was done for every $ 1 spent. – #4 Schedule Performance Index: SPI • SPI = EV/PV = 38000/42000 = 0. 90 • $ 0. 90 worth of work has been for each done for each $1. 00 worth of work that was planned to be done. – #5. Estimate at Completion and Variance at Completion • EAC = BAC/CPI = 80000/0. 79 = $101265 • VAC = BAC – EAC = 80000 -101265 = - $ 21265. The project will exceed the planned budget by $21265 64
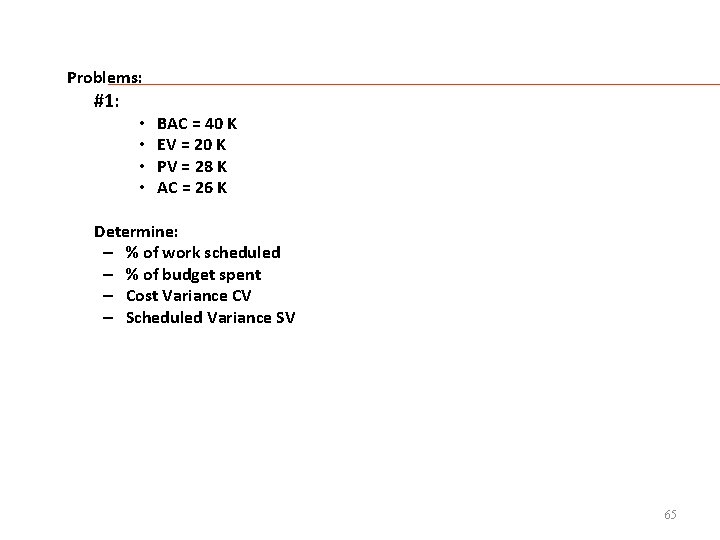
Problems: #1: • • BAC = 40 K EV = 20 K PV = 28 K AC = 26 K Determine: – % of work scheduled – % of budget spent – Cost Variance CV – Scheduled Variance SV 65
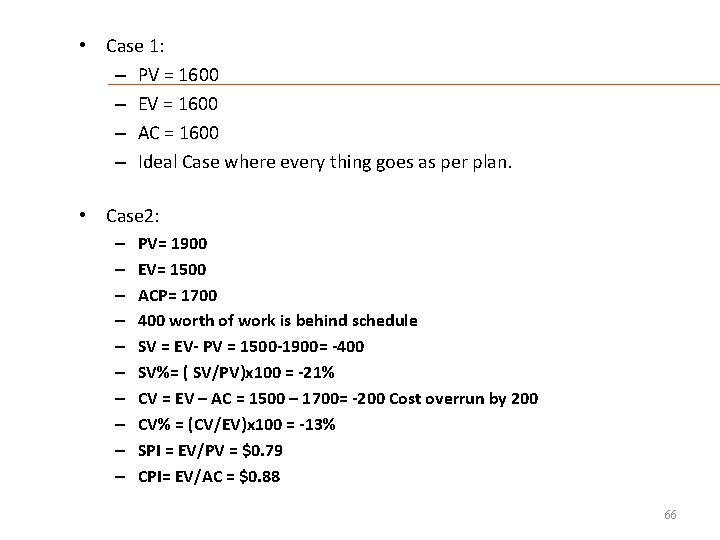
• Case 1: – PV = 1600 – EV = 1600 – AC = 1600 – Ideal Case where every thing goes as per plan. • Case 2: – – – – – PV= 1900 EV= 1500 ACP= 1700 400 worth of work is behind schedule SV = EV- PV = 1500 -1900= -400 SV%= ( SV/PV)x 100 = -21% CV = EV – AC = 1500 – 1700= -200 Cost overrun by 200 CV% = (CV/EV)x 100 = -13% SPI = EV/PV = $0. 79 CPI= EV/AC = $0. 88 66
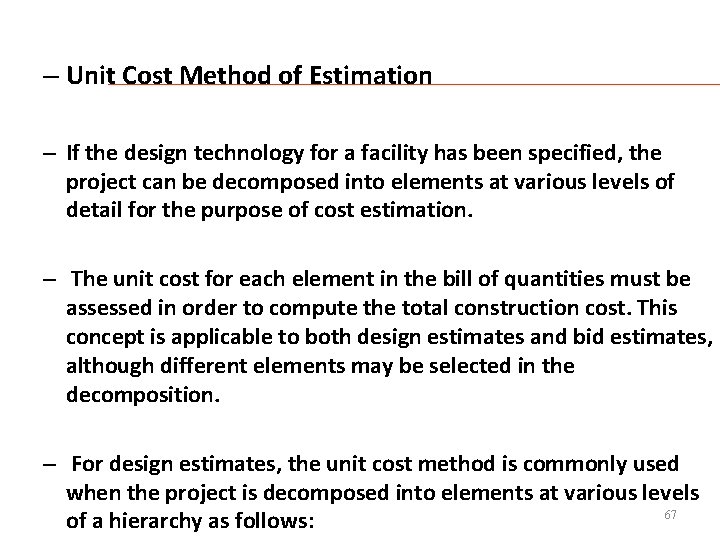
– Unit Cost Method of Estimation – If the design technology for a facility has been specified, the project can be decomposed into elements at various levels of detail for the purpose of cost estimation. – The unit cost for each element in the bill of quantities must be assessed in order to compute the total construction cost. This concept is applicable to both design estimates and bid estimates, although different elements may be selected in the decomposition. – For design estimates, the unit cost method is commonly used when the project is decomposed into elements at various levels 67 of a hierarchy as follows:
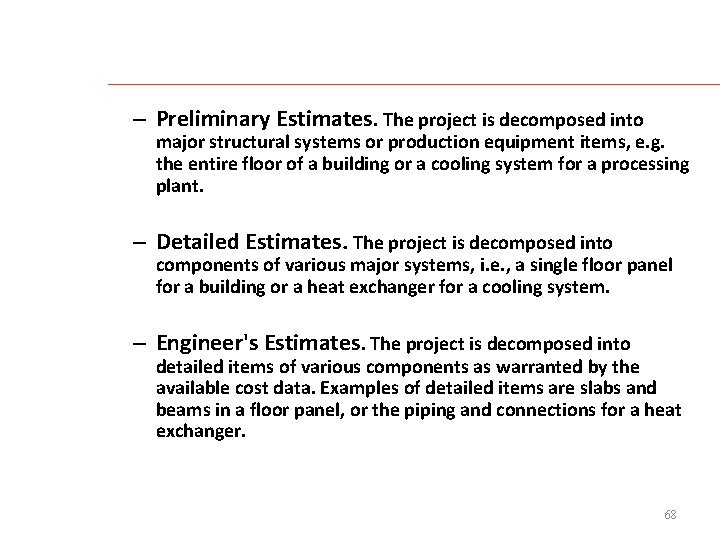
– Preliminary Estimates. The project is decomposed into major structural systems or production equipment items, e. g. the entire floor of a building or a cooling system for a processing plant. – Detailed Estimates. The project is decomposed into components of various major systems, i. e. , a single floor panel for a building or a heat exchanger for a cooling system. – Engineer's Estimates. The project is decomposed into detailed items of various components as warranted by the available cost data. Examples of detailed items are slabs and beams in a floor panel, or the piping and connections for a heat exchanger. 68
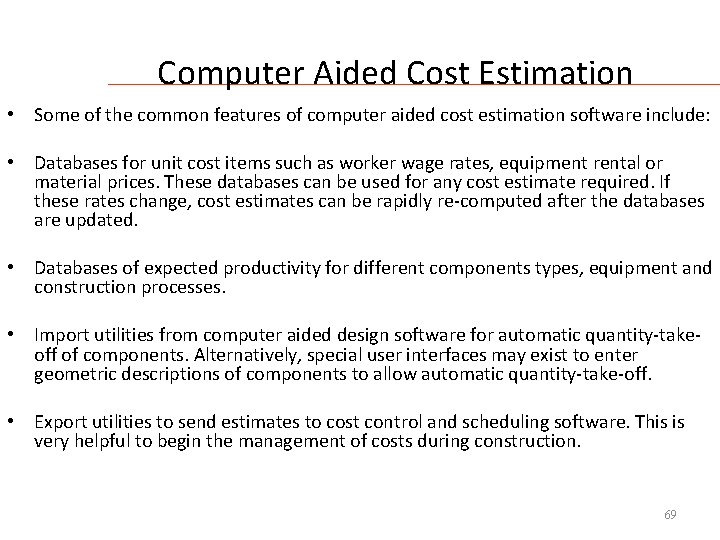
Computer Aided Cost Estimation • Some of the common features of computer aided cost estimation software include: • Databases for unit cost items such as worker wage rates, equipment rental or material prices. These databases can be used for any cost estimate required. If these rates change, cost estimates can be rapidly re-computed after the databases are updated. • Databases of expected productivity for different components types, equipment and construction processes. • Import utilities from computer aided design software for automatic quantity-takeoff of components. Alternatively, special user interfaces may exist to enter geometric descriptions of components to allow automatic quantity-take-off. • Export utilities to send estimates to cost control and scheduling software. This is very helpful to begin the management of costs during construction. 69
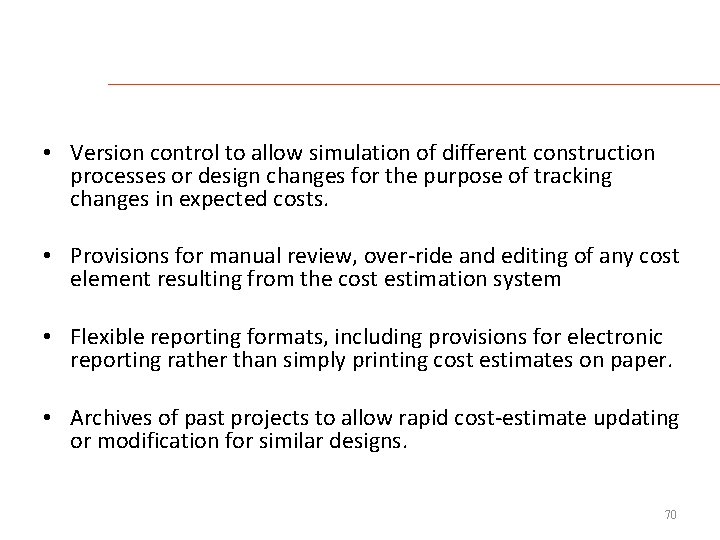
• Version control to allow simulation of different construction processes or design changes for the purpose of tracking changes in expected costs. • Provisions for manual review, over-ride and editing of any cost element resulting from the cost estimation system • Flexible reporting formats, including provisions for electronic reporting rather than simply printing cost estimates on paper. • Archives of past projects to allow rapid cost-estimate updating or modification for similar designs. 70
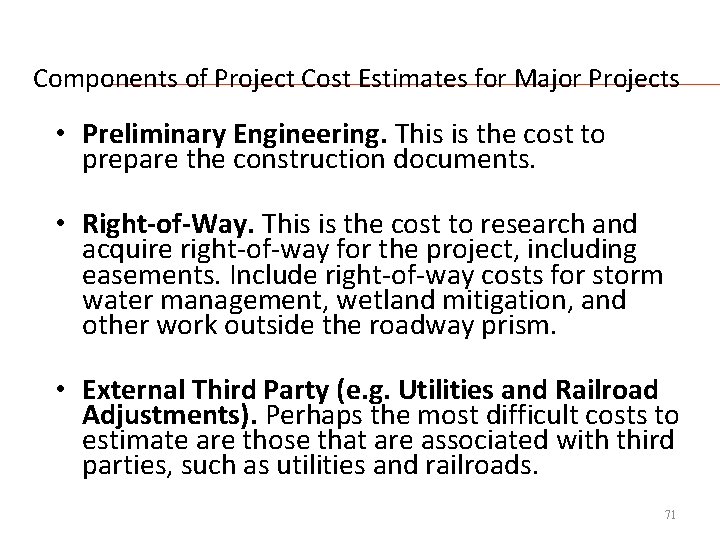
Components of Project Cost Estimates for Major Projects • Preliminary Engineering. This is the cost to prepare the construction documents. • Right-of-Way. This is the cost to research and acquire right-of-way for the project, including easements. Include right-of-way costs for storm water management, wetland mitigation, and other work outside the roadway prism. • External Third Party (e. g. Utilities and Railroad Adjustments). Perhaps the most difficult costs to estimate are those that are associated with third parties, such as utilities and railroads. 71
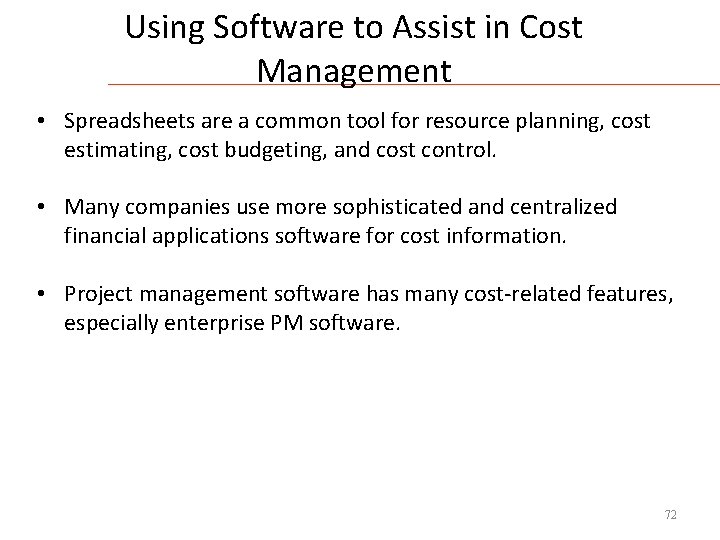
Using Software to Assist in Cost Management • Spreadsheets are a common tool for resource planning, cost estimating, cost budgeting, and cost control. • Many companies use more sophisticated and centralized financial applications software for cost information. • Project management software has many cost-related features, especially enterprise PM software. 72
Traditional vs modern project management
Principles of project cost management
Cost control and cost reduction project report
Cost control and cost reduction project report
The role of project management in achieving project success
Iteration workflows in software project management
Cost duration graph
Introduction to project management kathy schwalbe
Project evaluation in software project management
Perpetual project closure
Ms project agile template
Project termination
Cost management presentation
Project cost adalah
Objectives of cost management
Importance of project cost management
Contoh project cost management
Pmi intranet
Project cost management lecture notes
Cost management pmp
Asset management vs project management
Configuration management in project management
Project configuration management
Focusing on broad organizational needs
Estimating project time and cost
Top down budgeting vs bottom up budgeting
Estimating project time and cost
Cost analysis and estimating for engineering and management
Cost analysis and estimating for engineering and management
Cost analysis and estimating for engineering and management
Cost analysis and estimating for engineering and management
Cost analysis and estimating for engineering and management
Top management middle management first line management
Management pyramid
Basic concepts of management
Cost accumulation and cost assignment
Cost accumulation and cost assignment
Cost pools
Cost accumulation and cost assignment
Dennis geyer
Site:slidetodoc.com
Distinguish between average cost and marginal cost
Cost control and cost reduction difference
The flow of costs in job order costing
Ordering cost and carrying cost
Trade offs and opportunity cost
Cost behavior patterns
Background project proposal
Integrating metrics within the software process
Theoretical background
Security analysis and portfolio management project
Security analysis and portfolio management project
Project management pert
Project management principles and practices
Project selection matrix
Hp project management
Ppm tools gartner magic quadrant
Project management in itil
Forward and backward pass in project management
Network diagram aoa
Risk ranking in project management
Project appraisal and management
Dummy activity in network diagram
Project management tools for ediscovery and litigation
Project management in system analysis and design
Meredith and mantel three stage model
Probability and impact matrix in project management
It analysis design and project management
Project management principles and practices
Project management past and present
Maven is a project management and comprehension tool
Project management process group and knowledge area mapping
Digitization workflow