UNIT 047 ADVANCED TURNING FACTORS THAT AFFECTING THE
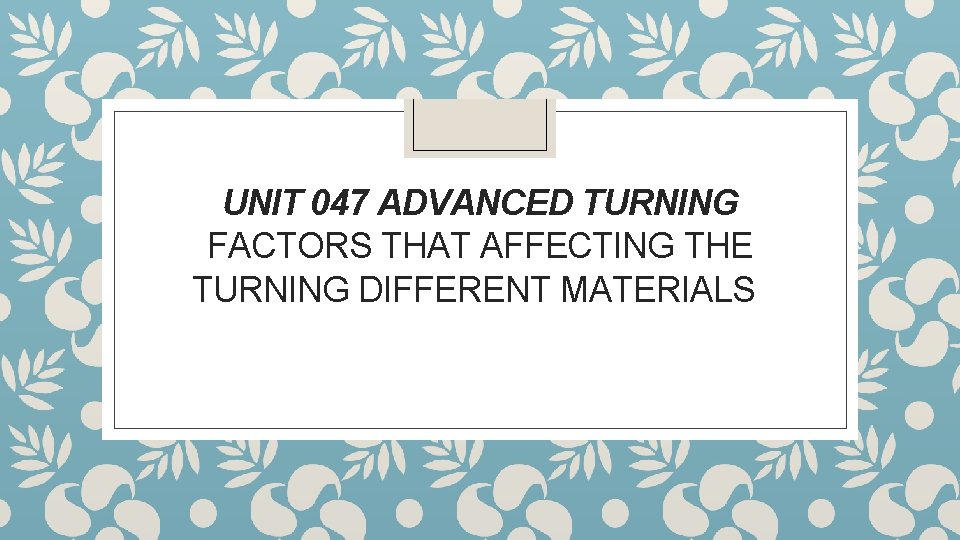
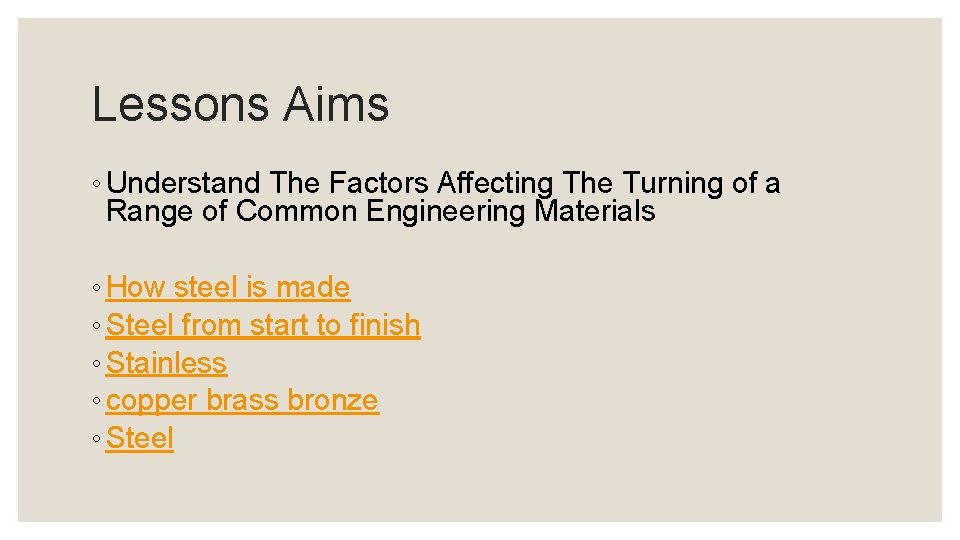
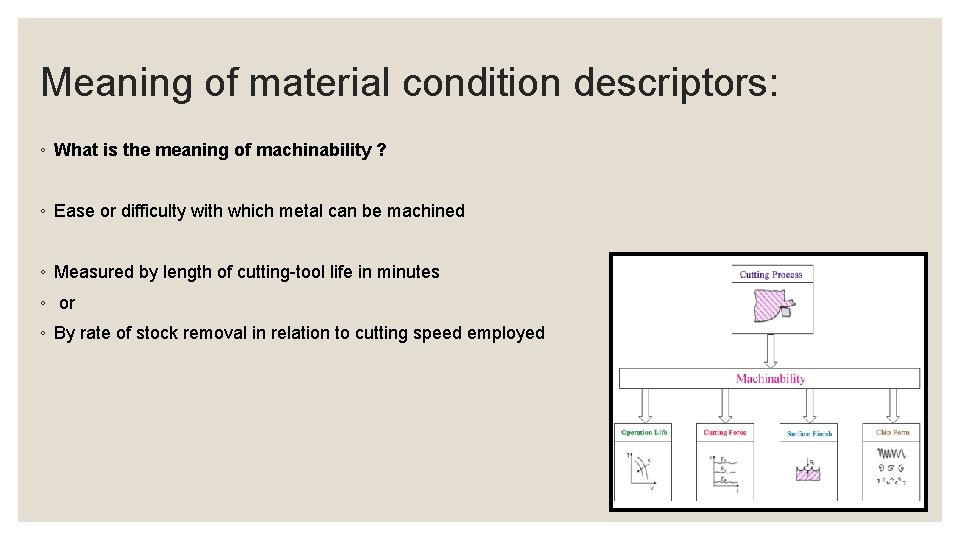
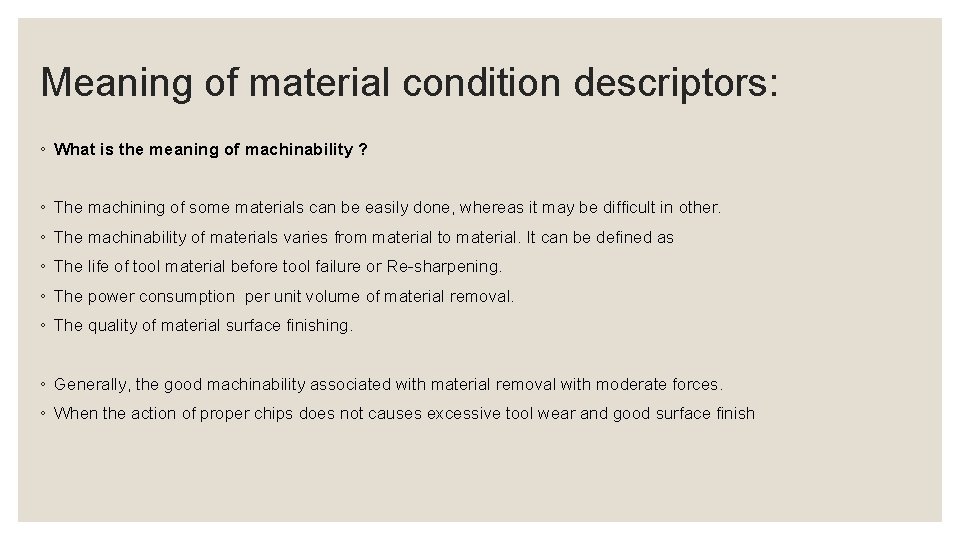
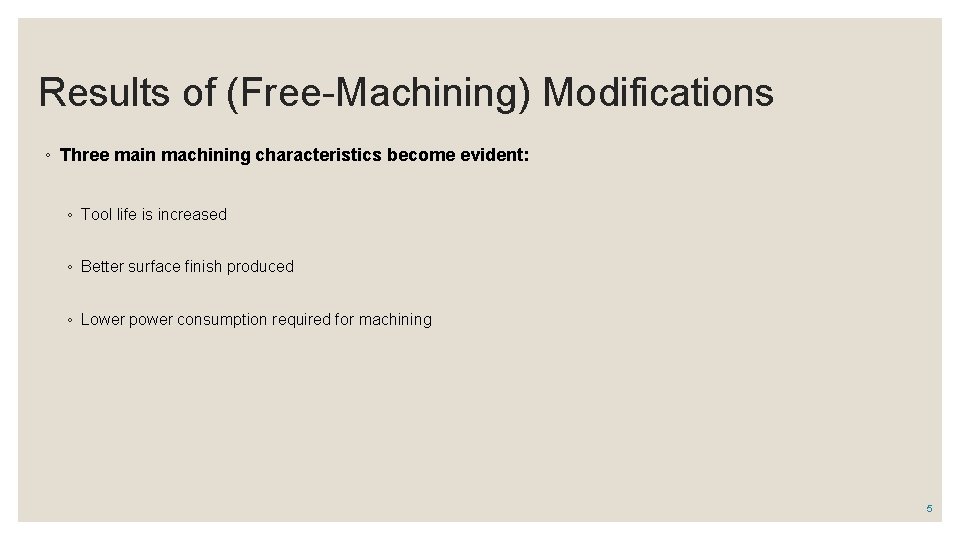
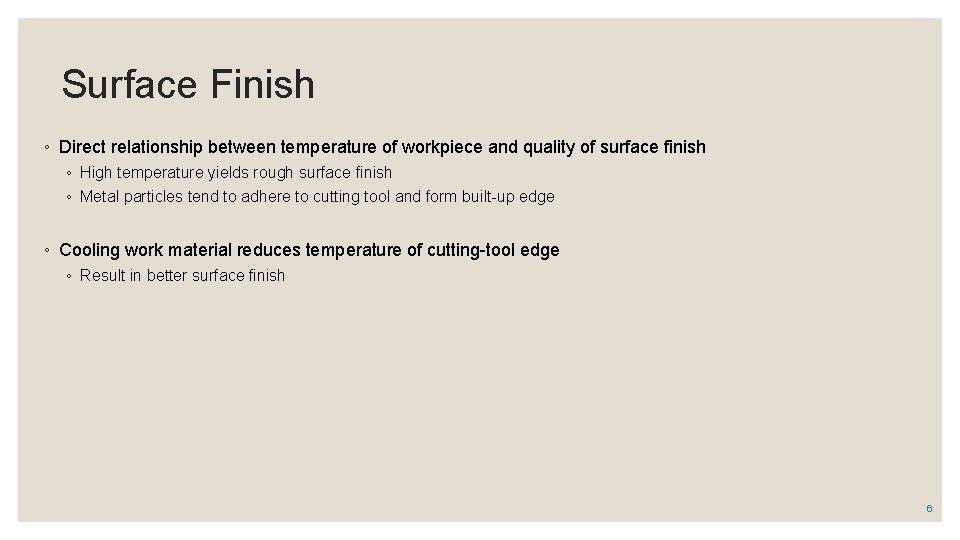
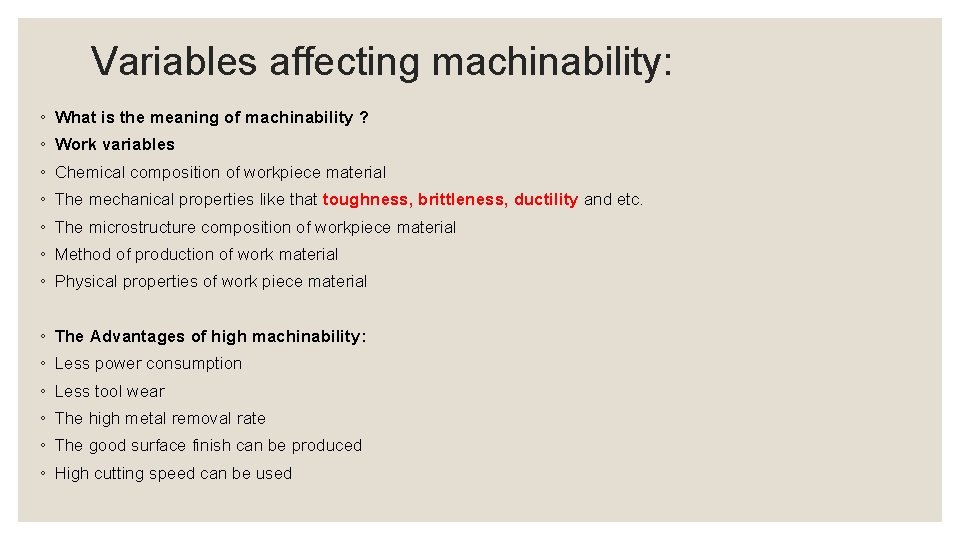
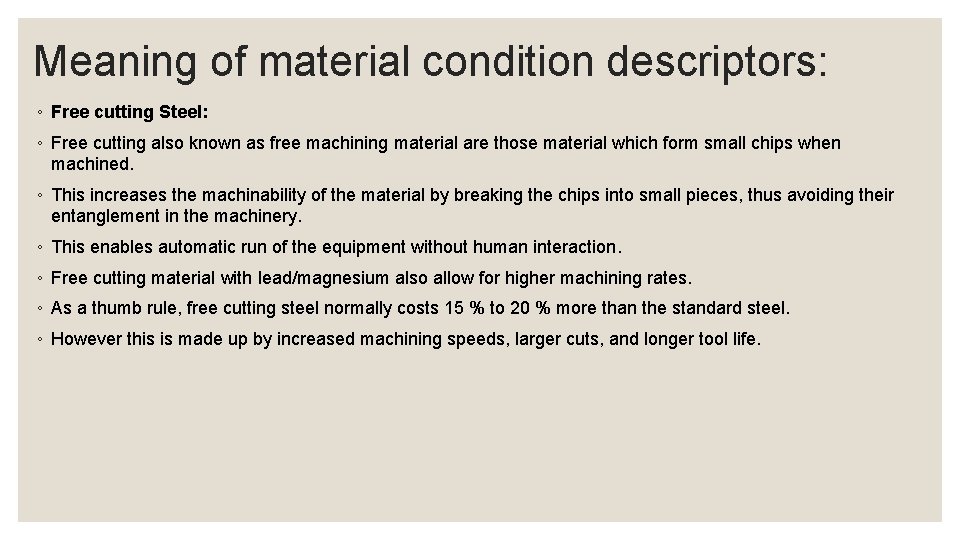
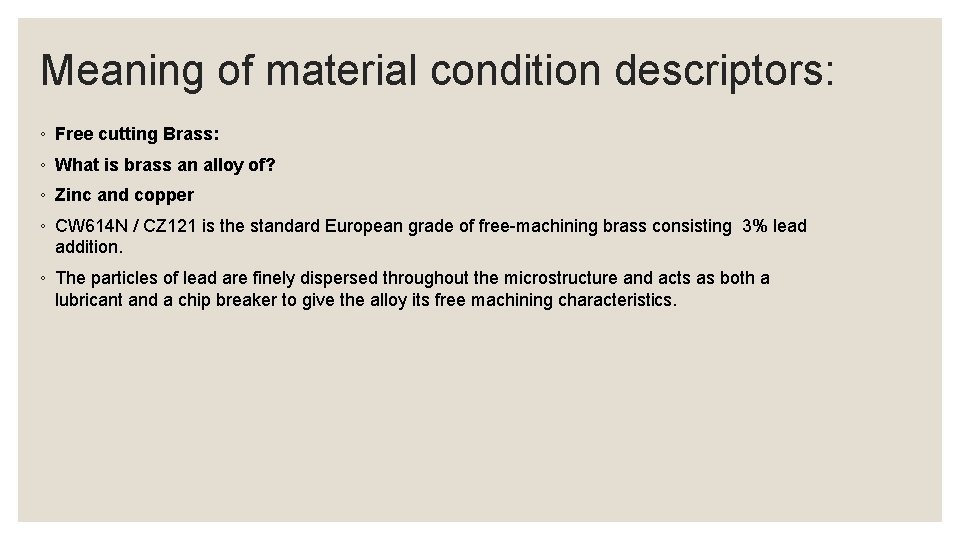
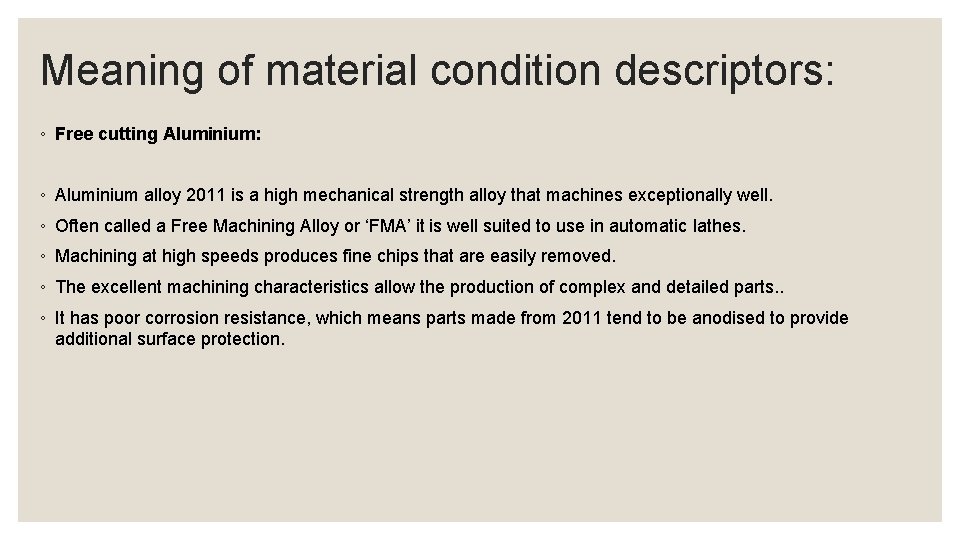
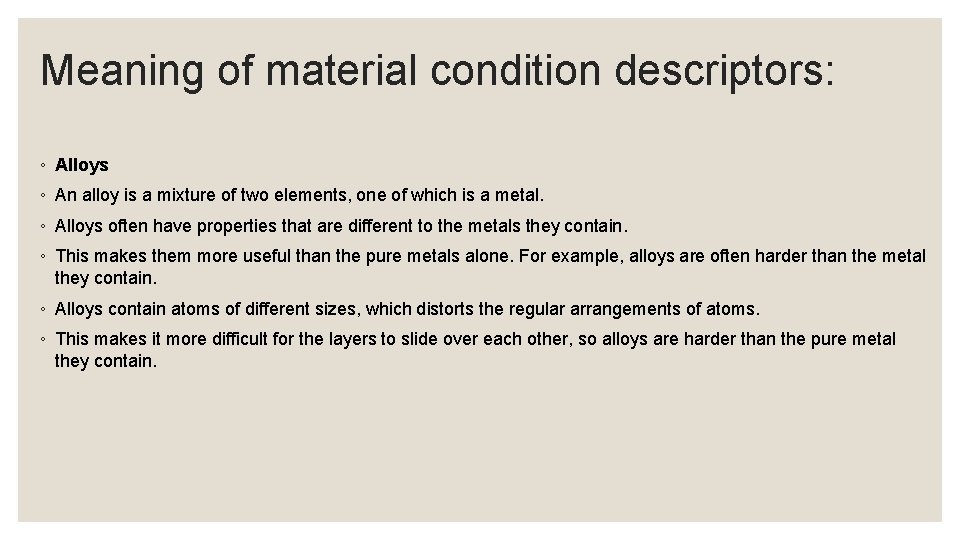

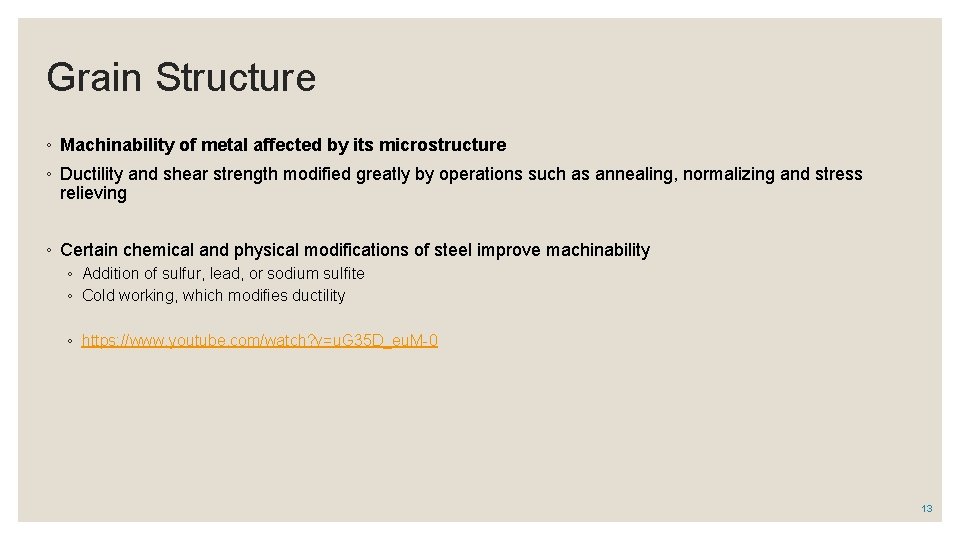
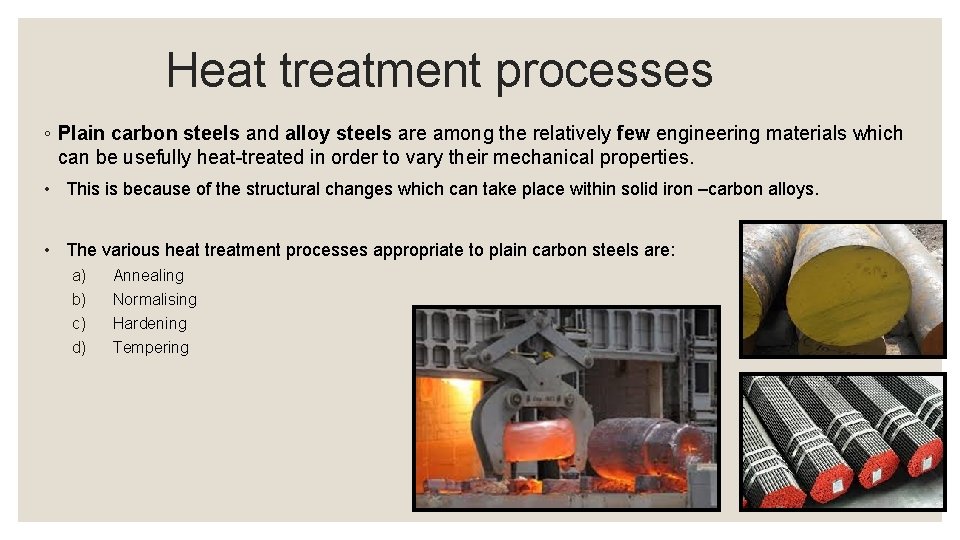

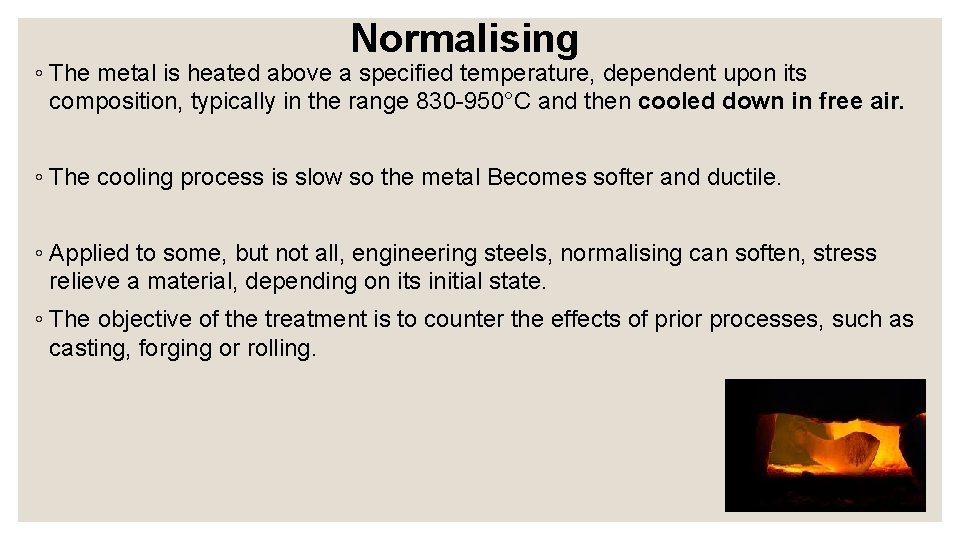
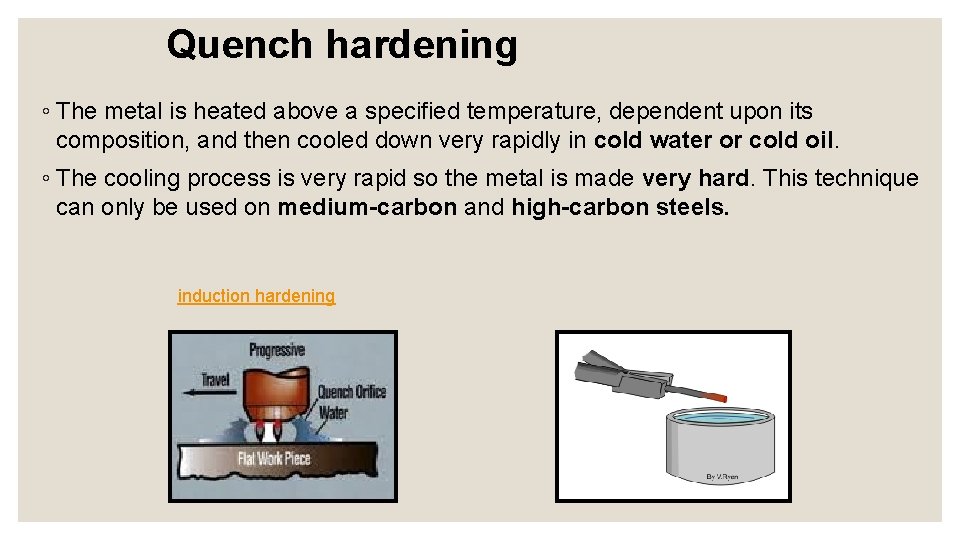
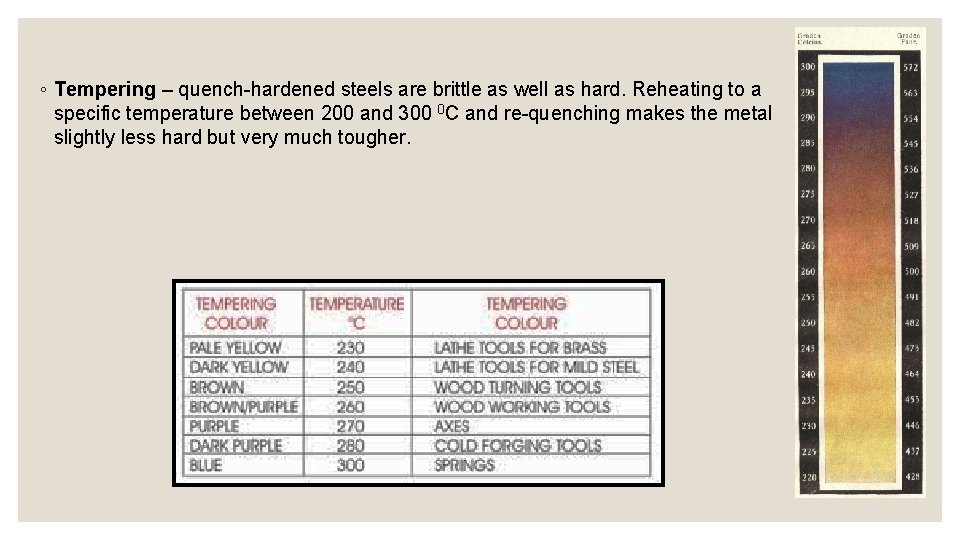
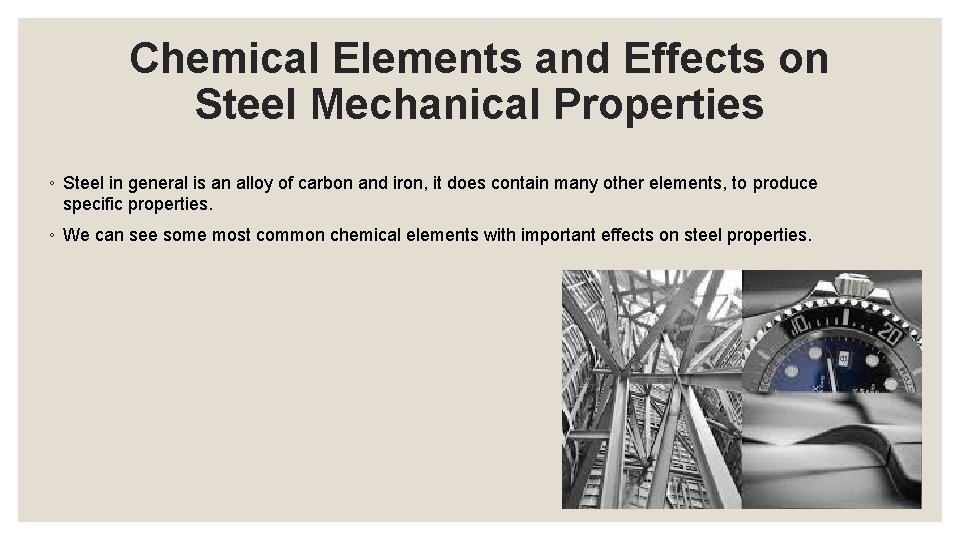
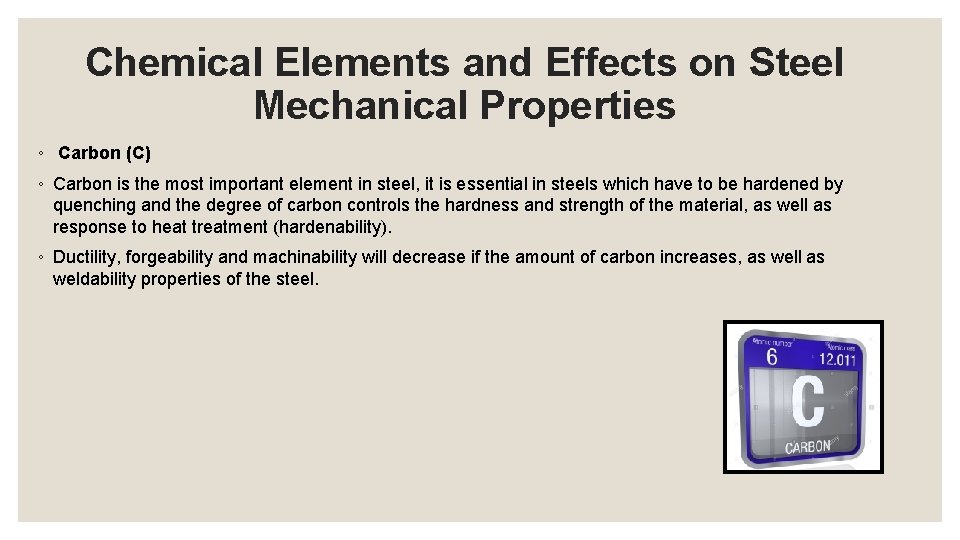
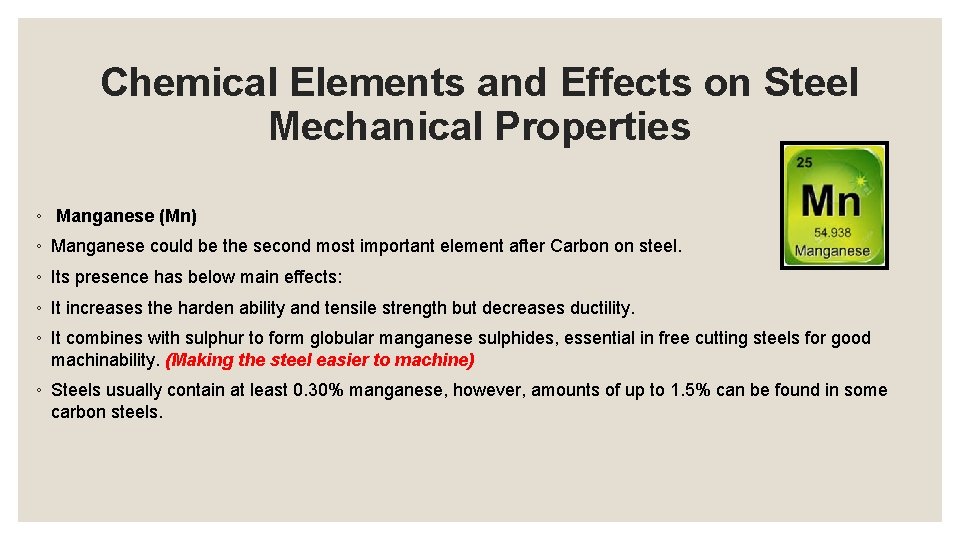
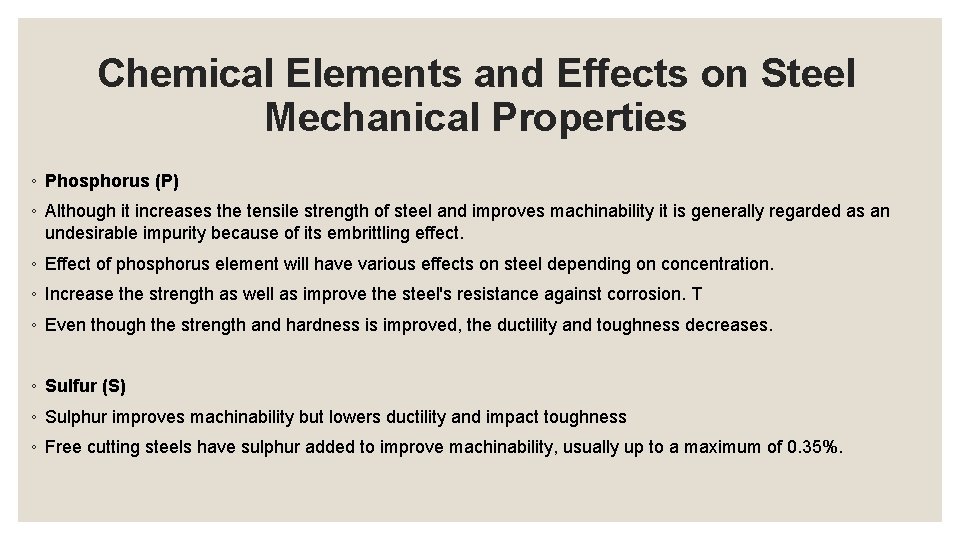
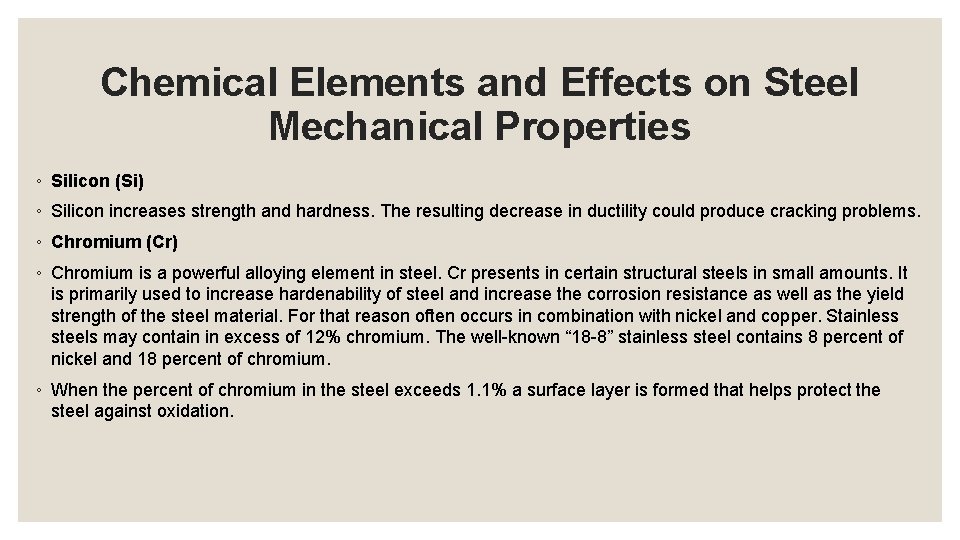
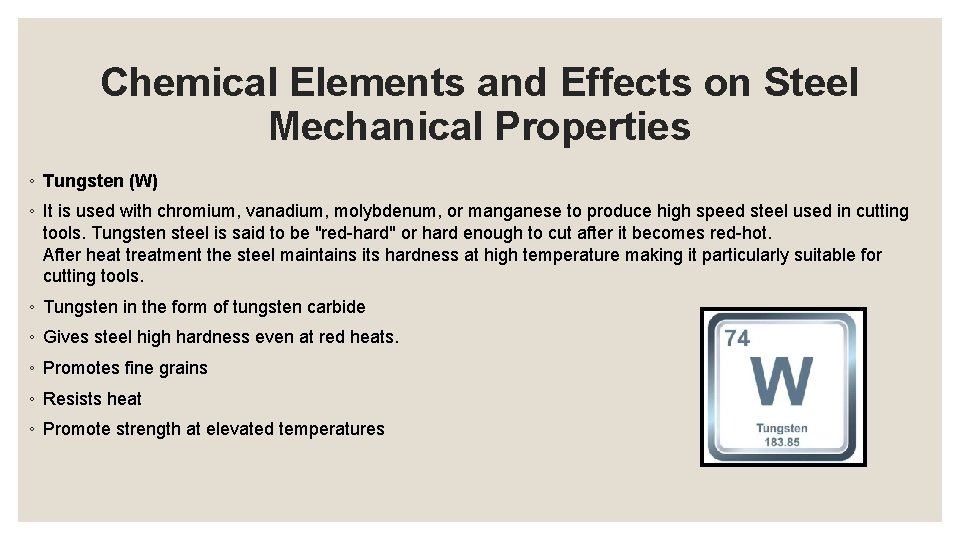
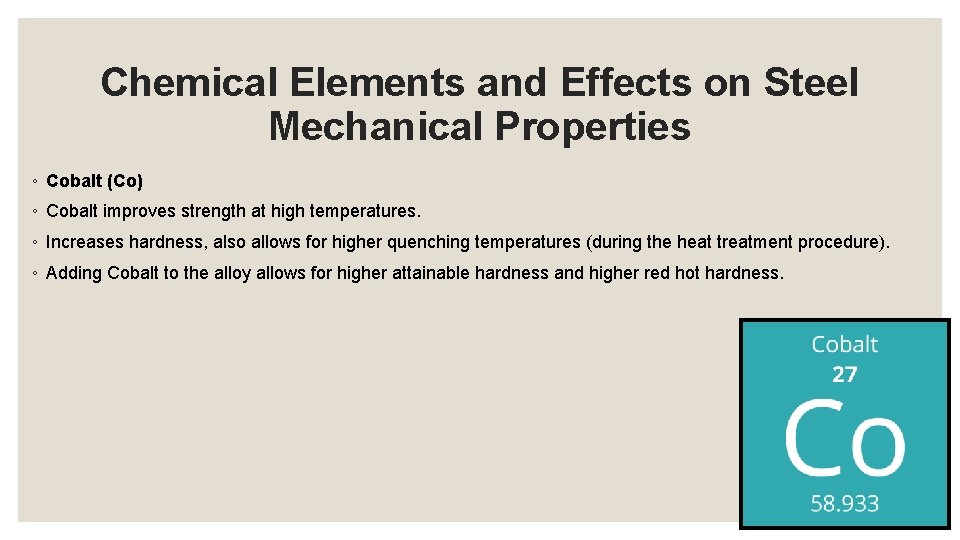
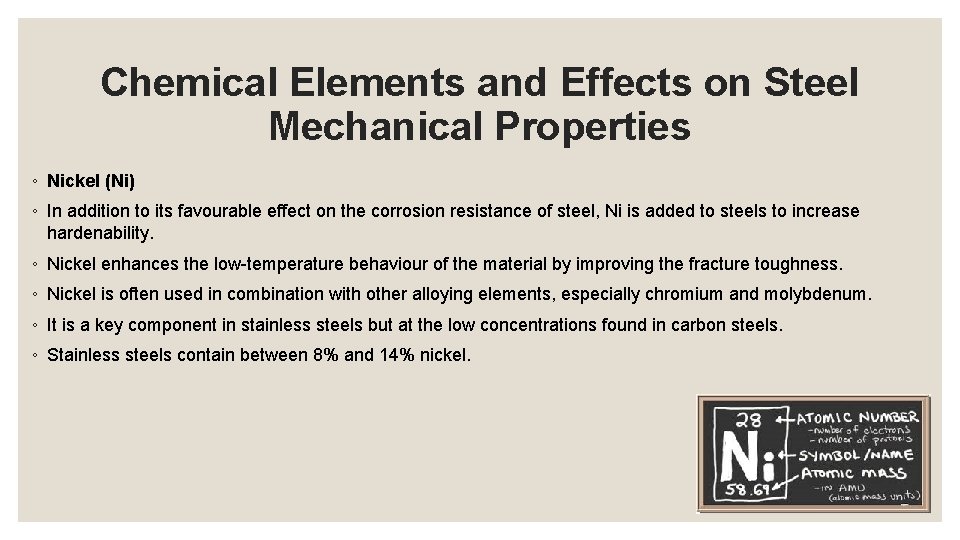
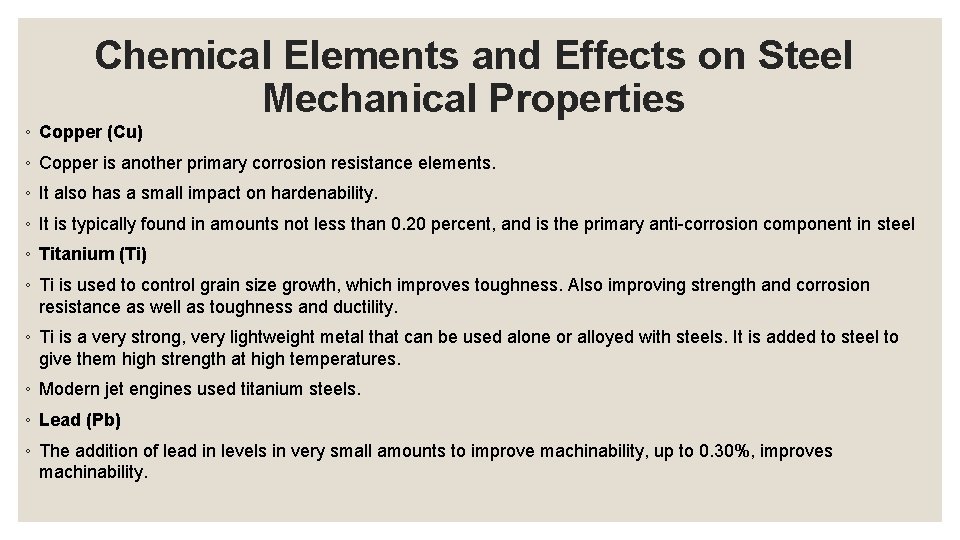
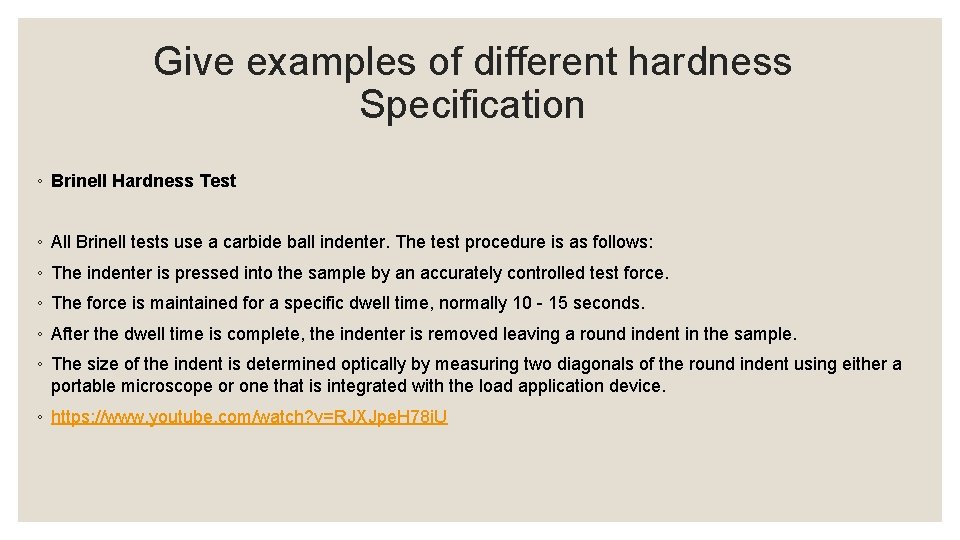
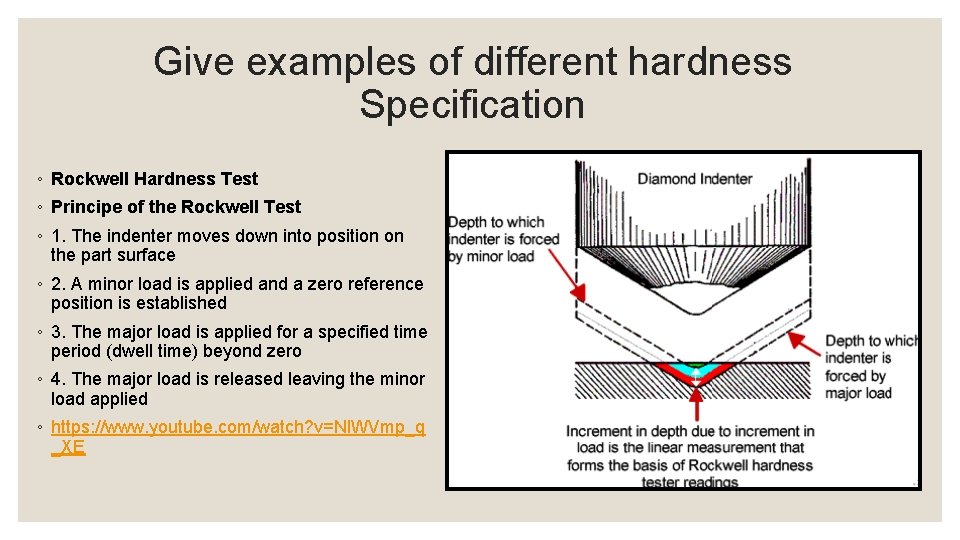
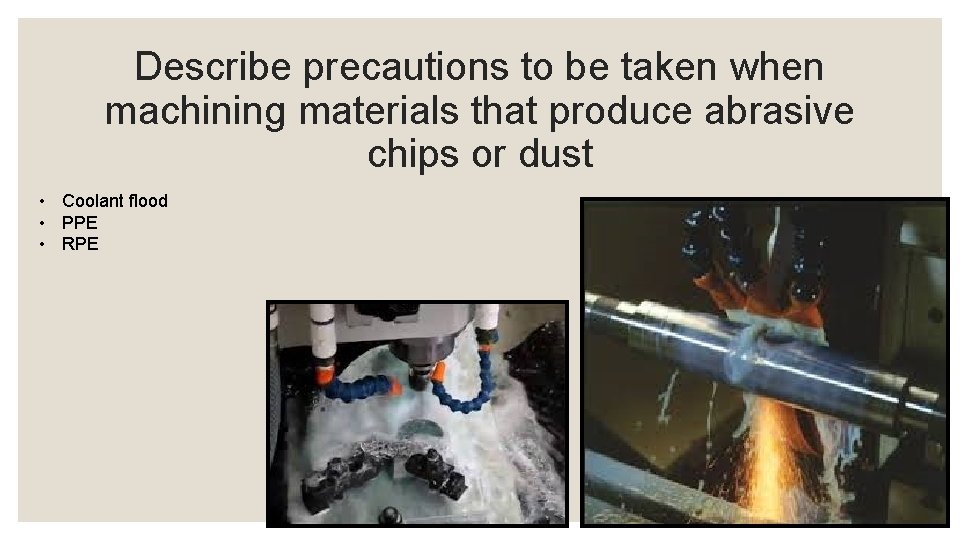
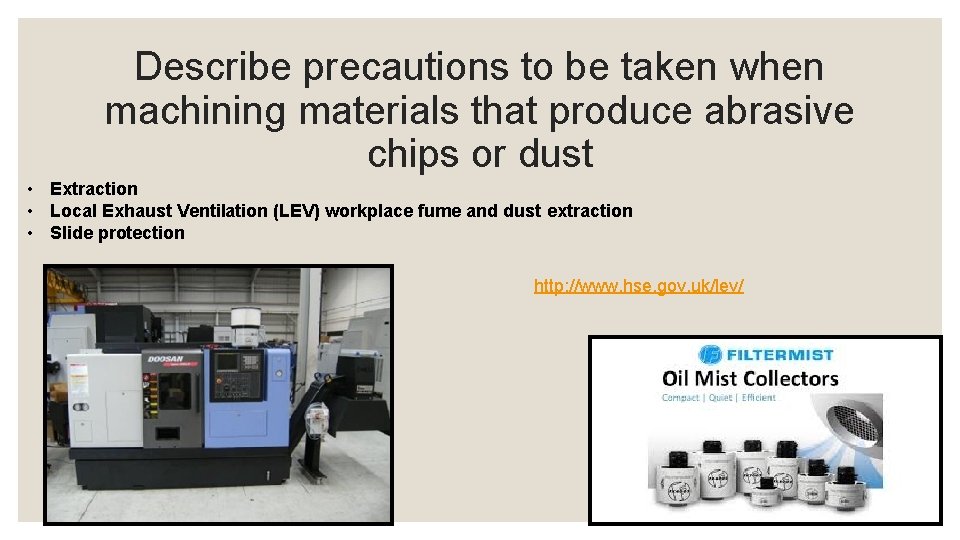
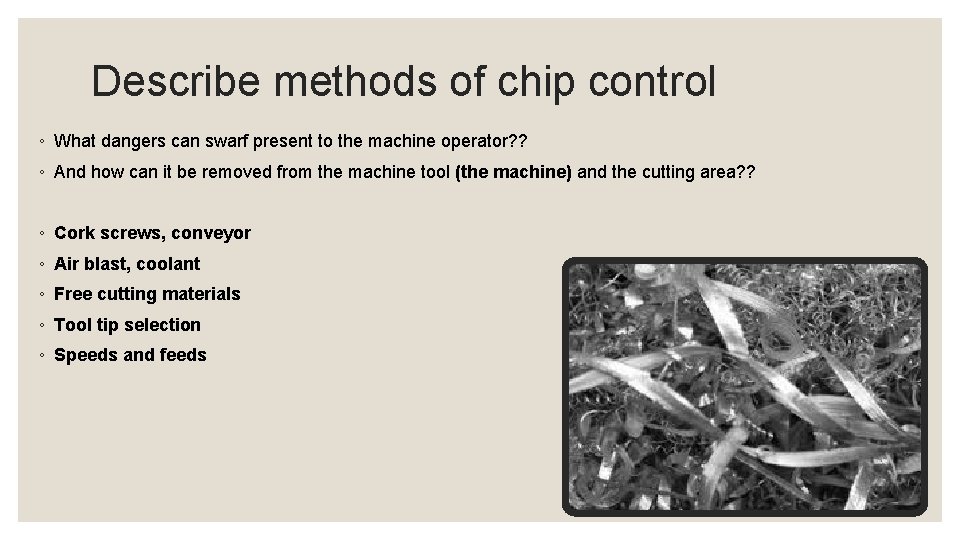
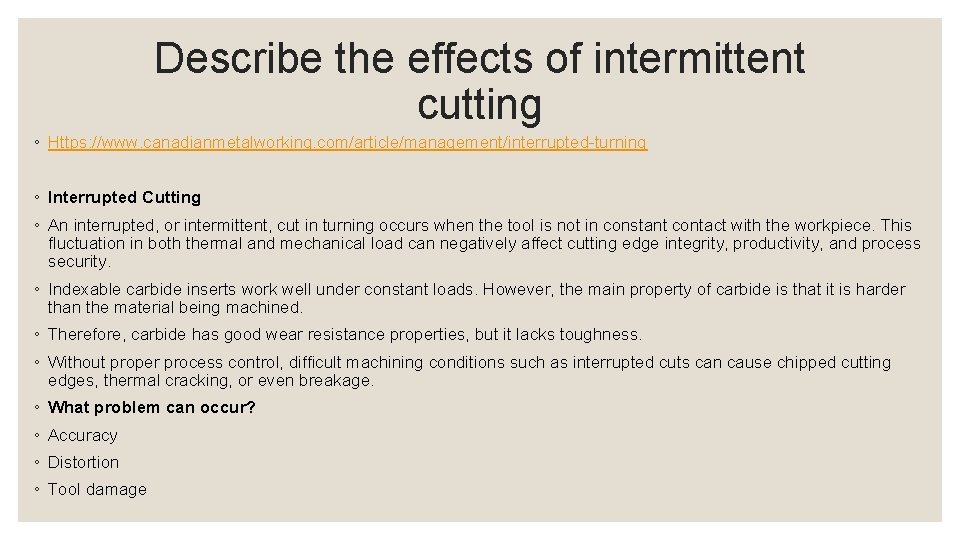
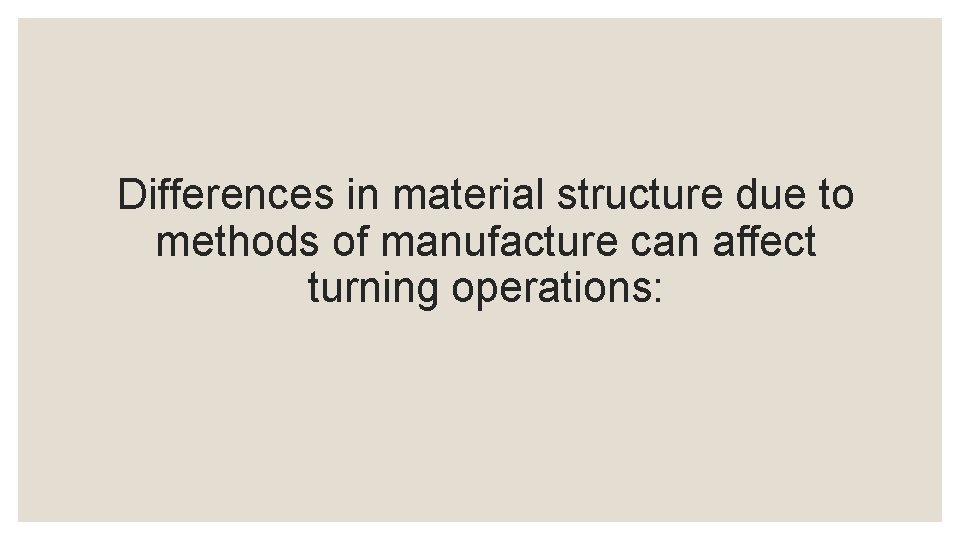
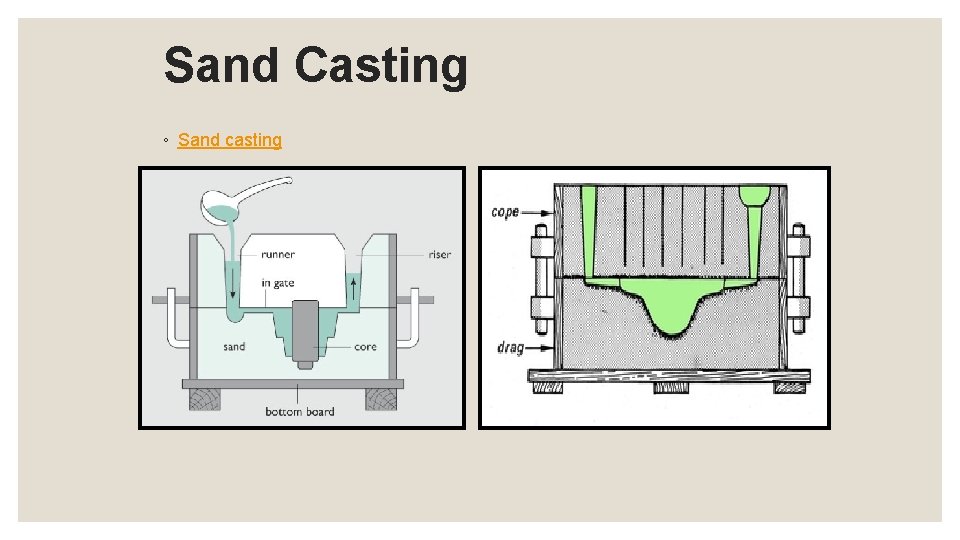
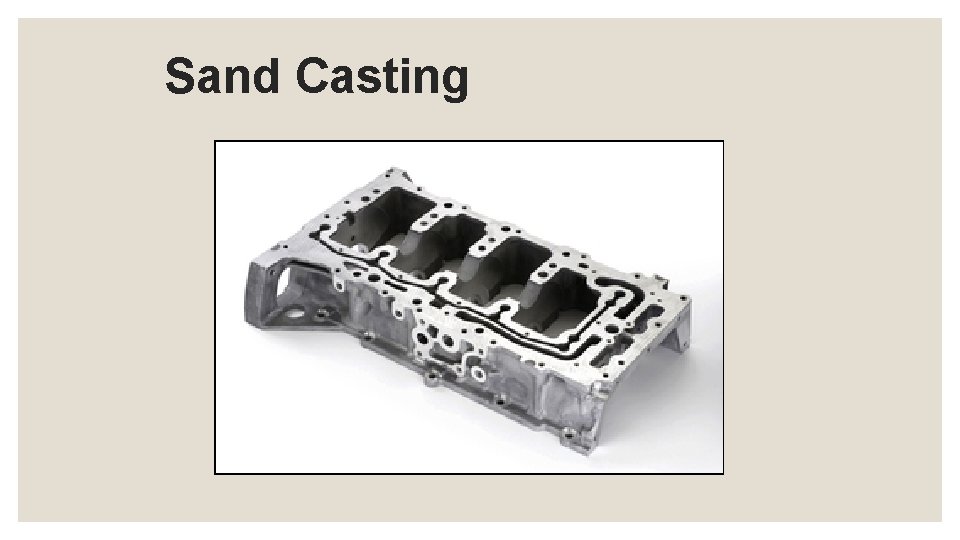
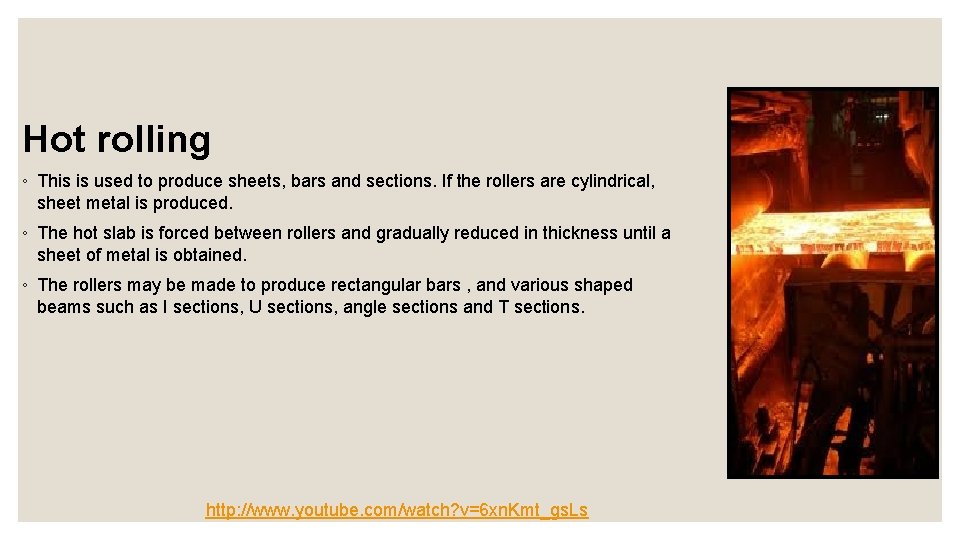
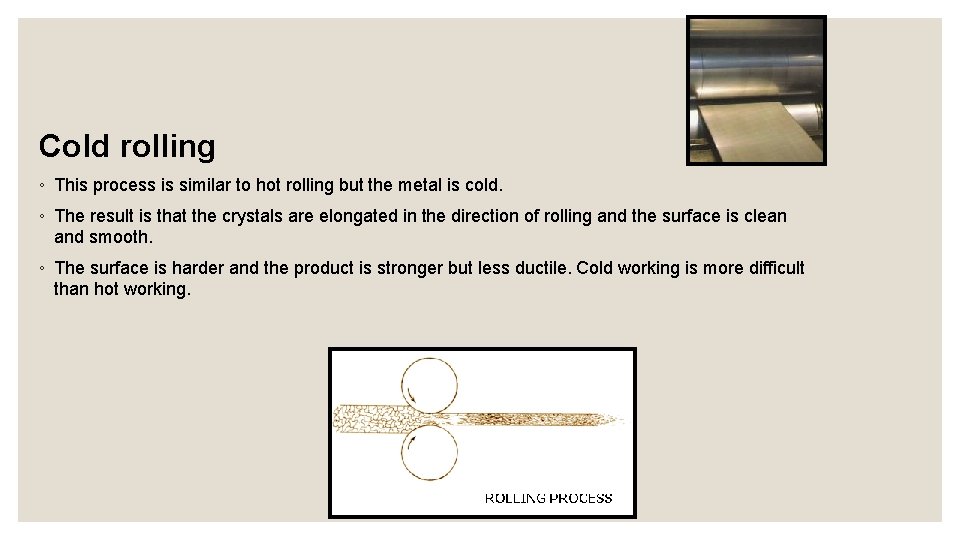
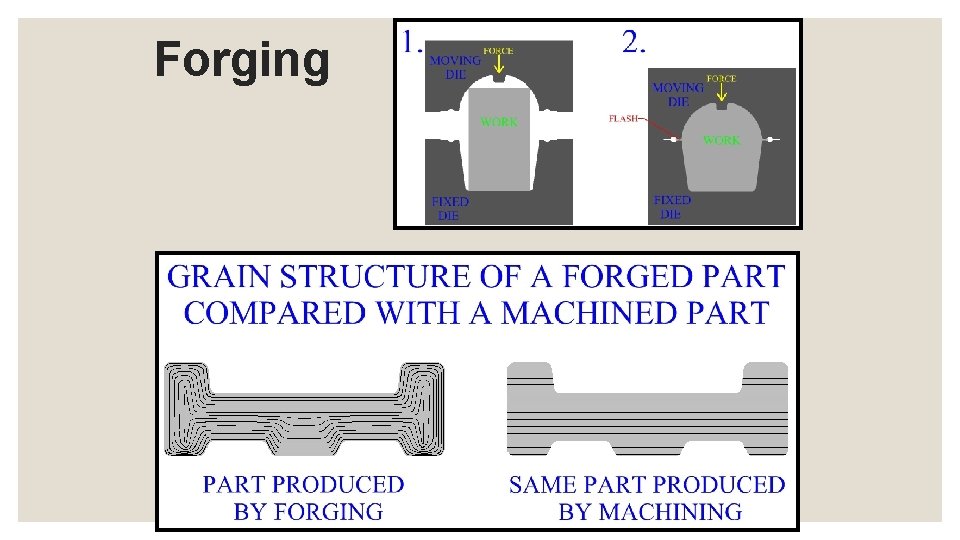
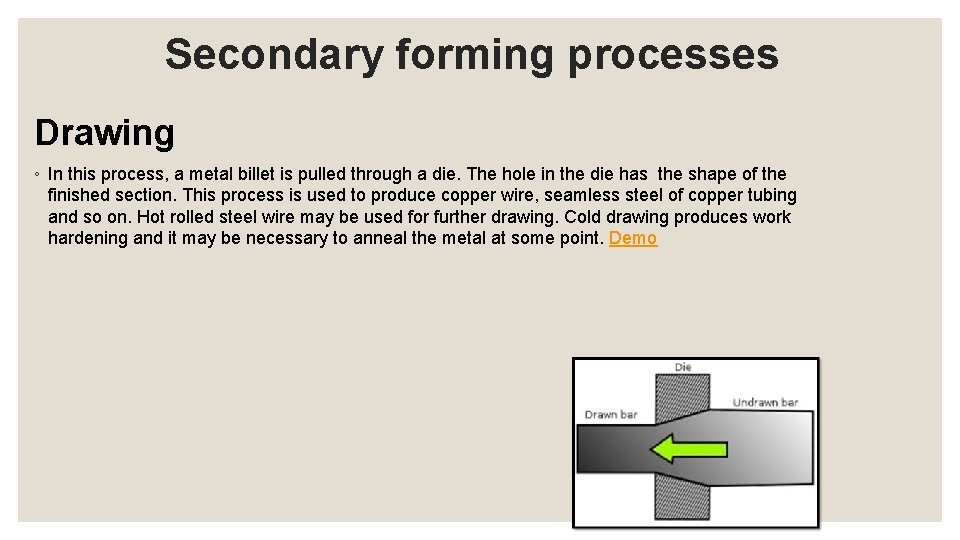
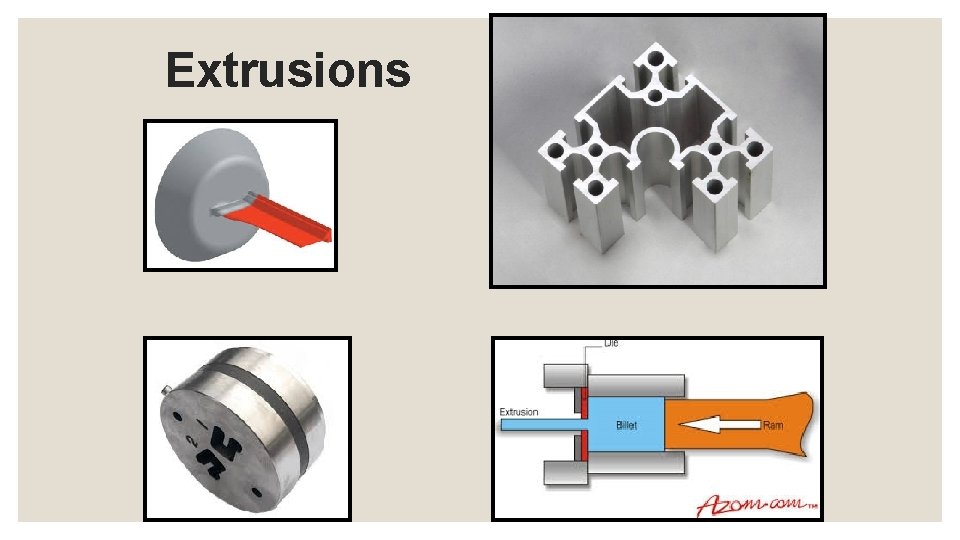

- Slides: 42
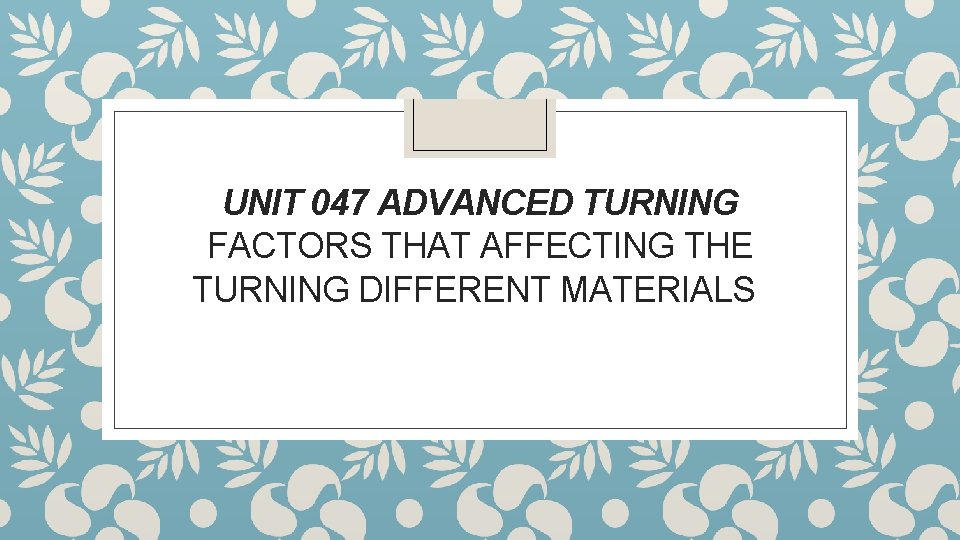
UNIT 047 ADVANCED TURNING FACTORS THAT AFFECTING THE TURNING DIFFERENT MATERIALS
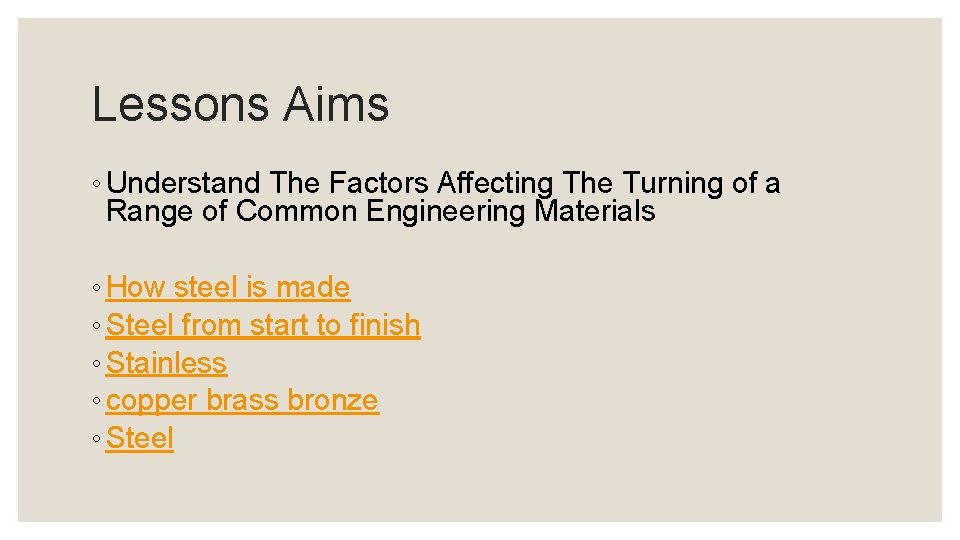
Lessons Aims ◦ Understand The Factors Affecting The Turning of a Range of Common Engineering Materials ◦ How steel is made ◦ Steel from start to finish ◦ Stainless ◦ copper brass bronze ◦ Steel
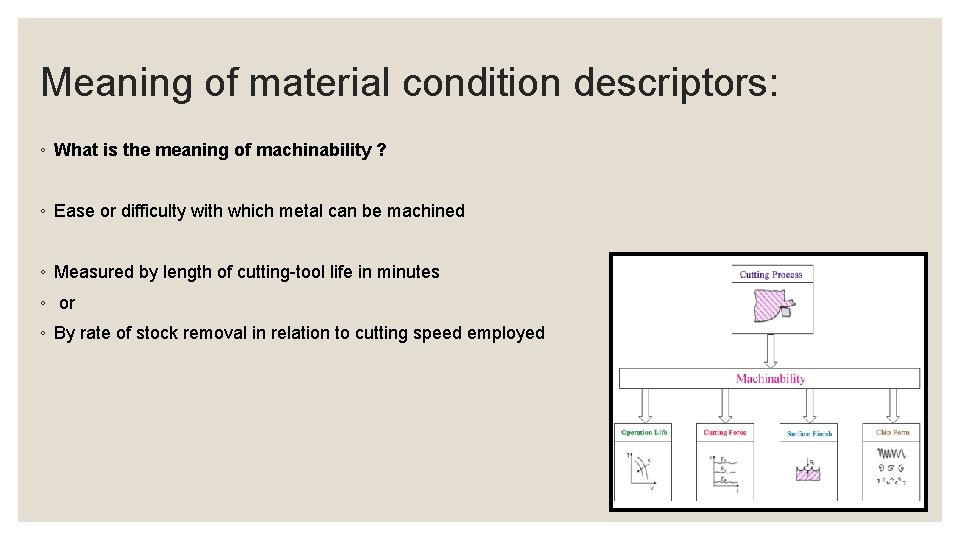
Meaning of material condition descriptors: ◦ What is the meaning of machinability ? ◦ Ease or difficulty with which metal can be machined ◦ Measured by length of cutting-tool life in minutes ◦ or ◦ By rate of stock removal in relation to cutting speed employed
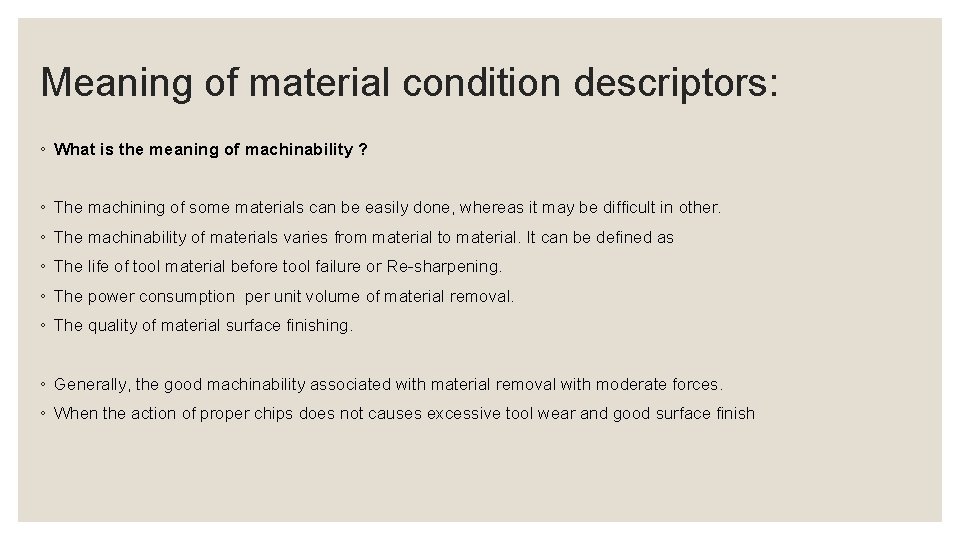
Meaning of material condition descriptors: ◦ What is the meaning of machinability ? ◦ The machining of some materials can be easily done, whereas it may be difficult in other. ◦ The machinability of materials varies from material to material. It can be defined as ◦ The life of tool material before tool failure or Re-sharpening. ◦ The power consumption per unit volume of material removal. ◦ The quality of material surface finishing. ◦ Generally, the good machinability associated with material removal with moderate forces. ◦ When the action of proper chips does not causes excessive tool wear and good surface finish
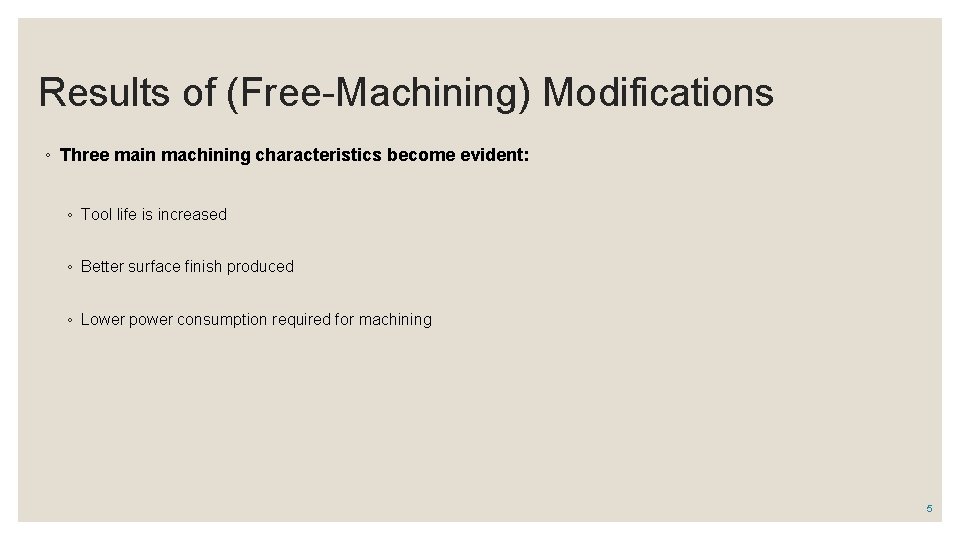
Results of (Free-Machining) Modifications ◦ Three main machining characteristics become evident: ◦ Tool life is increased ◦ Better surface finish produced ◦ Lower power consumption required for machining 5
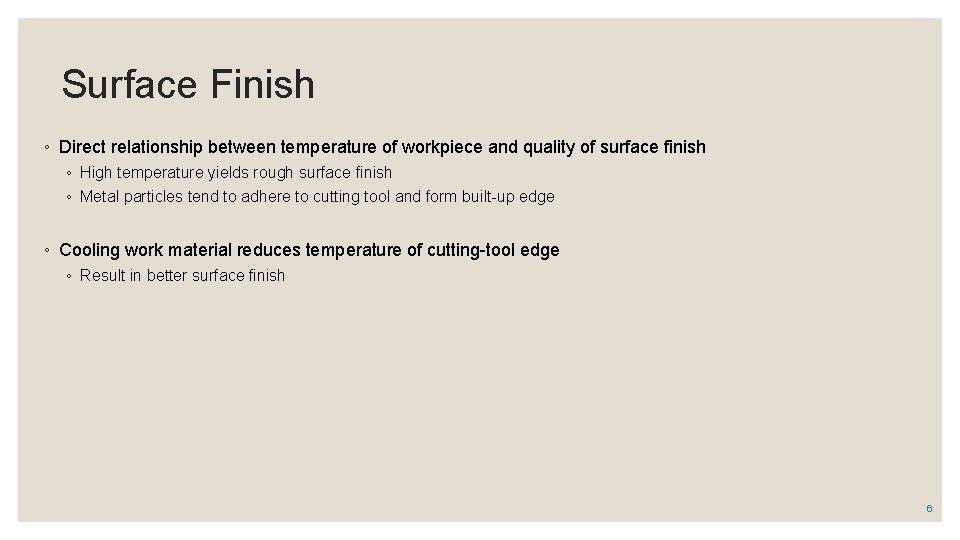
Surface Finish ◦ Direct relationship between temperature of workpiece and quality of surface finish ◦ High temperature yields rough surface finish ◦ Metal particles tend to adhere to cutting tool and form built-up edge ◦ Cooling work material reduces temperature of cutting-tool edge ◦ Result in better surface finish 6
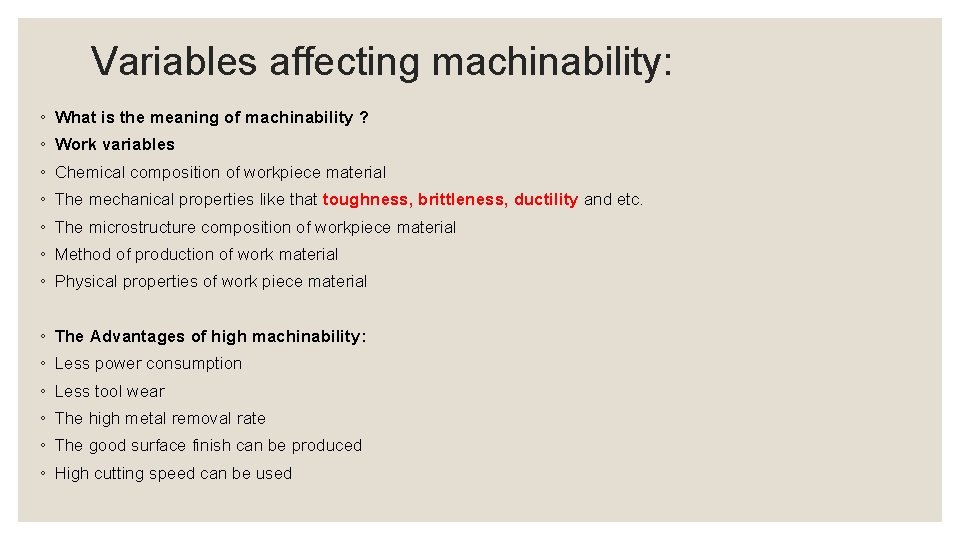
Variables affecting machinability: ◦ What is the meaning of machinability ? ◦ Work variables ◦ Chemical composition of workpiece material ◦ The mechanical properties like that toughness, brittleness, ductility and etc. ◦ The microstructure composition of workpiece material ◦ Method of production of work material ◦ Physical properties of work piece material ◦ The Advantages of high machinability: ◦ Less power consumption ◦ Less tool wear ◦ The high metal removal rate ◦ The good surface finish can be produced ◦ High cutting speed can be used
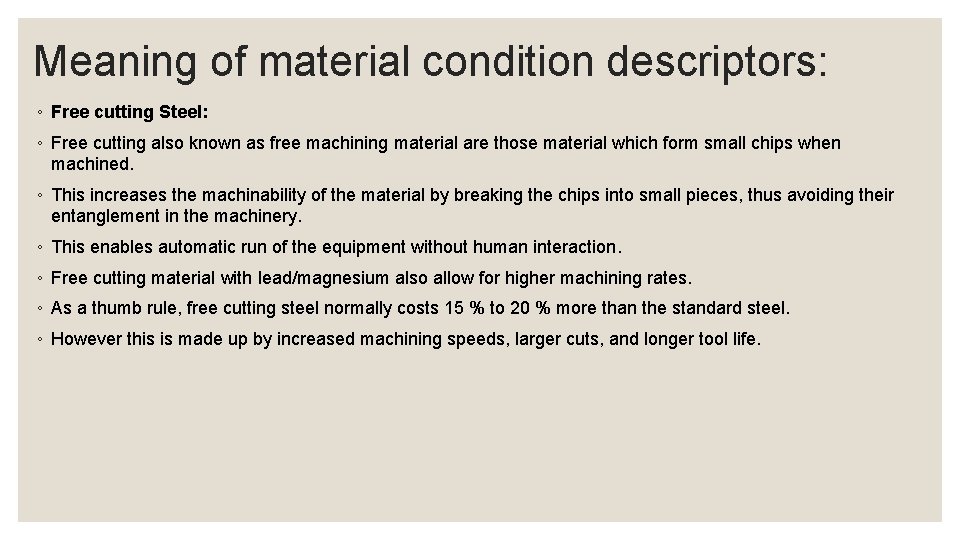
Meaning of material condition descriptors: ◦ Free cutting Steel: ◦ Free cutting also known as free machining material are those material which form small chips when machined. ◦ This increases the machinability of the material by breaking the chips into small pieces, thus avoiding their entanglement in the machinery. ◦ This enables automatic run of the equipment without human interaction. ◦ Free cutting material with lead/magnesium also allow for higher machining rates. ◦ As a thumb rule, free cutting steel normally costs 15 % to 20 % more than the standard steel. ◦ However this is made up by increased machining speeds, larger cuts, and longer tool life.
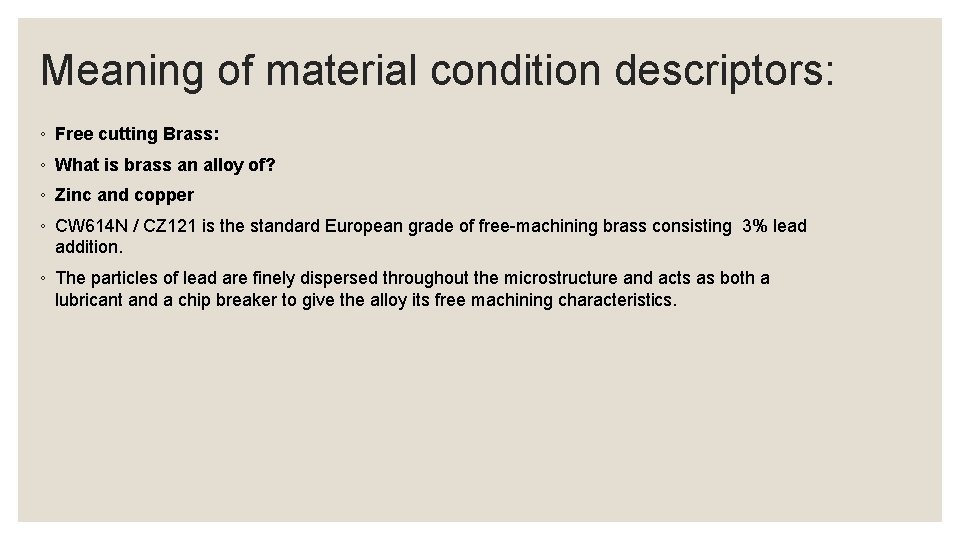
Meaning of material condition descriptors: ◦ Free cutting Brass: ◦ What is brass an alloy of? ◦ Zinc and copper ◦ CW 614 N / CZ 121 is the standard European grade of free-machining brass consisting 3% lead addition. ◦ The particles of lead are finely dispersed throughout the microstructure and acts as both a lubricant and a chip breaker to give the alloy its free machining characteristics.
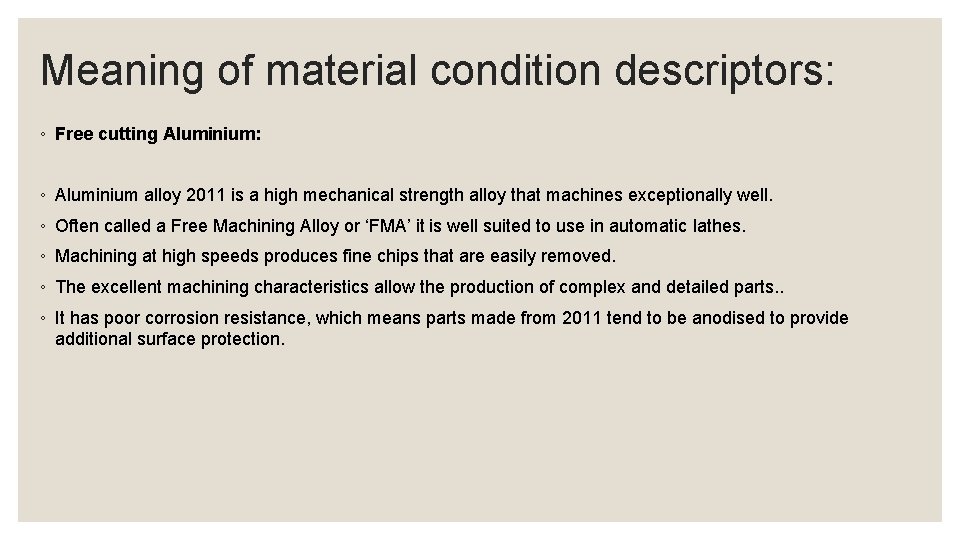
Meaning of material condition descriptors: ◦ Free cutting Aluminium: ◦ Aluminium alloy 2011 is a high mechanical strength alloy that machines exceptionally well. ◦ Often called a Free Machining Alloy or ‘FMA’ it is well suited to use in automatic lathes. ◦ Machining at high speeds produces fine chips that are easily removed. ◦ The excellent machining characteristics allow the production of complex and detailed parts. . ◦ It has poor corrosion resistance, which means parts made from 2011 tend to be anodised to provide additional surface protection.
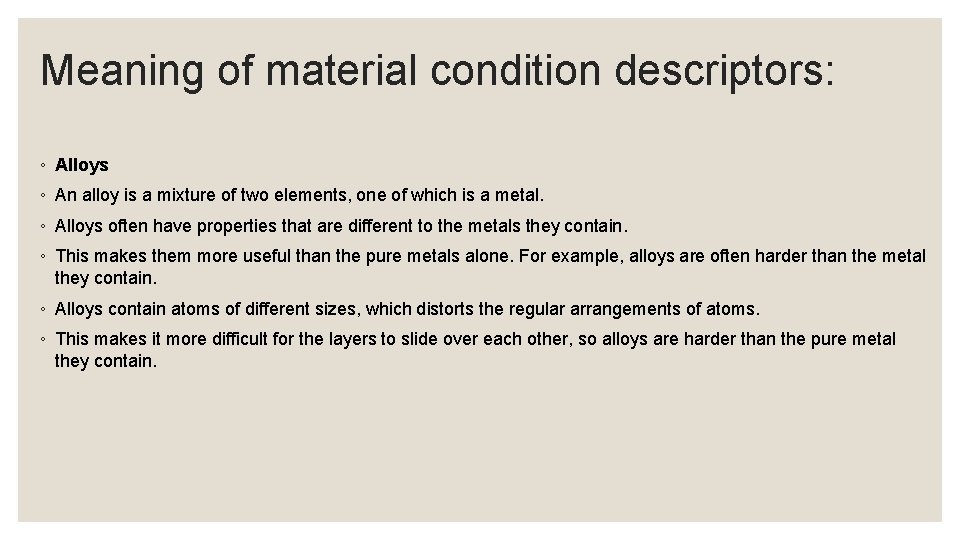
Meaning of material condition descriptors: ◦ Alloys ◦ An alloy is a mixture of two elements, one of which is a metal. ◦ Alloys often have properties that are different to the metals they contain. ◦ This makes them more useful than the pure metals alone. For example, alloys are often harder than the metal they contain. ◦ Alloys contain atoms of different sizes, which distorts the regular arrangements of atoms. ◦ This makes it more difficult for the layers to slide over each other, so alloys are harder than the pure metal they contain.

Structure of materials ◦ Pure and Alloys ◦ The atoms in pure iron are arranged in densely-packed layers. These layers can slide over each other. This makes pure iron a very soft material. ◦ The atoms of other elements are different sizes. When other elements are added to iron, their atoms distort the regular structure of the iron atoms. ◦ It is more difficult for the layers of iron atoms in steel to slide over each other and so this alloy is stronger than pure iron.
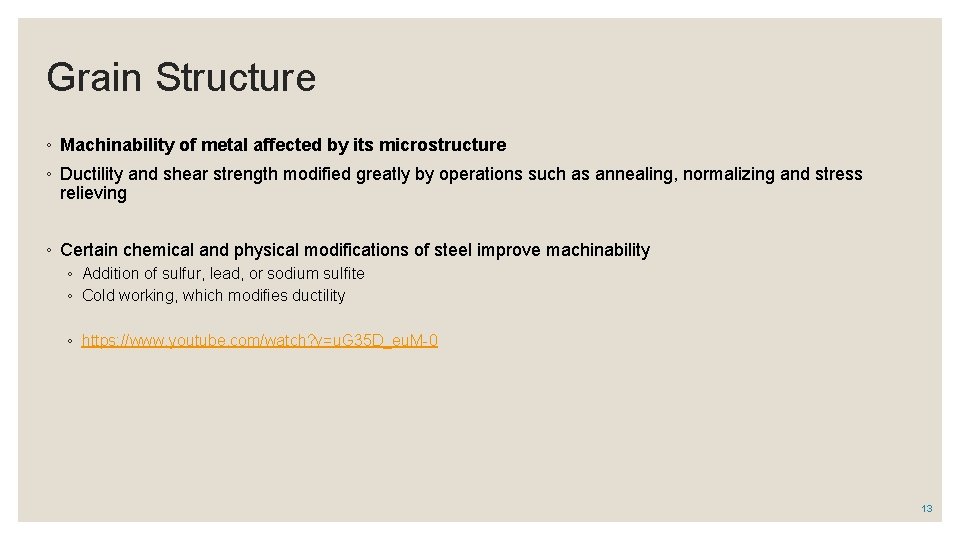
Grain Structure ◦ Machinability of metal affected by its microstructure ◦ Ductility and shear strength modified greatly by operations such as annealing, normalizing and stress relieving ◦ Certain chemical and physical modifications of steel improve machinability ◦ Addition of sulfur, lead, or sodium sulfite ◦ Cold working, which modifies ductility ◦ https: //www. youtube. com/watch? v=u. G 35 D_eu. M-0 13
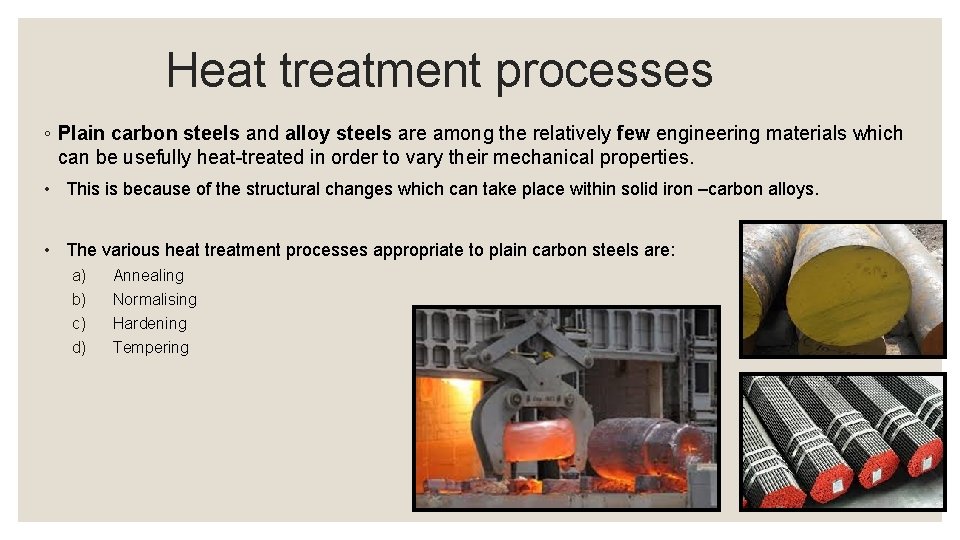
Heat treatment processes ◦ Plain carbon steels and alloy steels are among the relatively few engineering materials which can be usefully heat-treated in order to vary their mechanical properties. • This is because of the structural changes which can take place within solid iron –carbon alloys. • The various heat treatment processes appropriate to plain carbon steels are: a) b) c) d) Annealing Normalising Hardening Tempering

Annealing ◦ This is the process used to soften steels that have already been hardened. The metal is heated above a specified temperature, dependent upon its composition, and then cooled down. ◦ Ferrous metals must be cooled very slowly normally in the oven to anneal. ◦ Copper, brass and other non-ferrous metals can be cooled slowly in air or quickly by quenching in water.
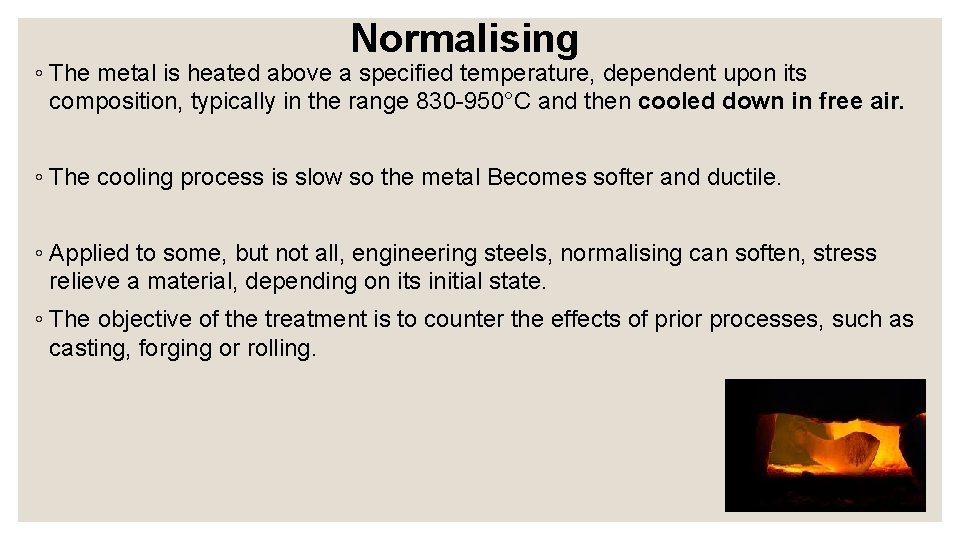
Normalising ◦ The metal is heated above a specified temperature, dependent upon its composition, typically in the range 830 -950°C and then cooled down in free air. ◦ The cooling process is slow so the metal Becomes softer and ductile. ◦ Applied to some, but not all, engineering steels, normalising can soften, stress relieve a material, depending on its initial state. ◦ The objective of the treatment is to counter the effects of prior processes, such as casting, forging or rolling.
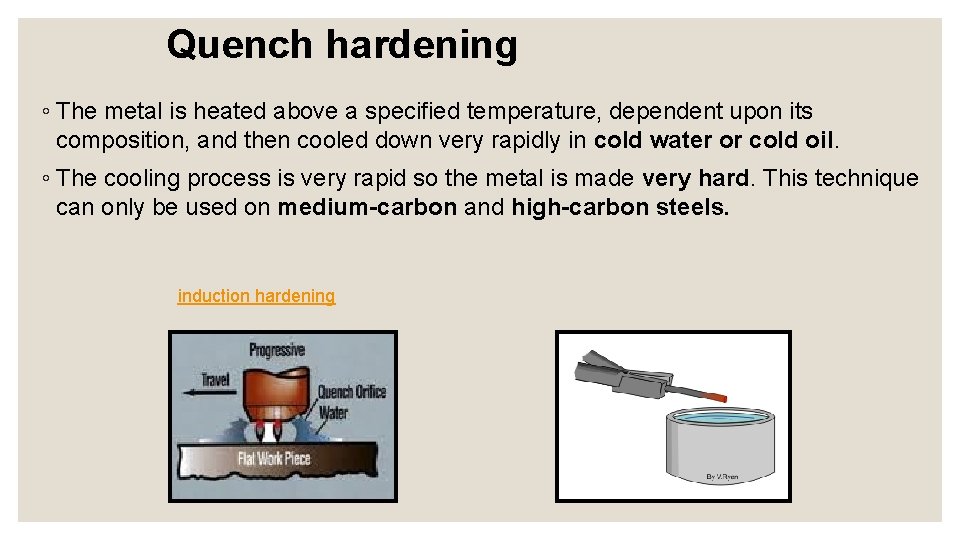
Quench hardening ◦ The metal is heated above a specified temperature, dependent upon its composition, and then cooled down very rapidly in cold water or cold oil. ◦ The cooling process is very rapid so the metal is made very hard. This technique can only be used on medium-carbon and high-carbon steels. induction hardening
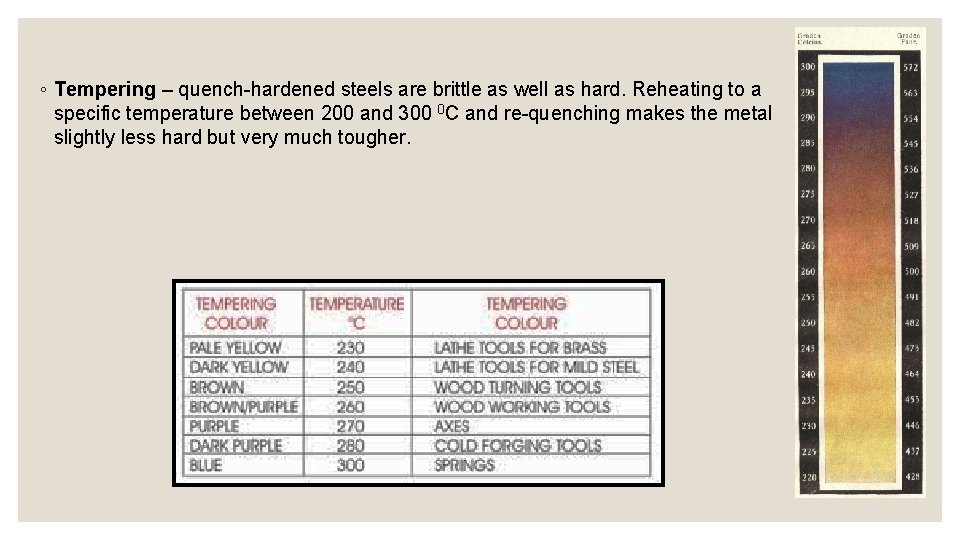
◦ Tempering – quench-hardened steels are brittle as well as hard. Reheating to a specific temperature between 200 and 300 0 C and re-quenching makes the metal slightly less hard but very much tougher.
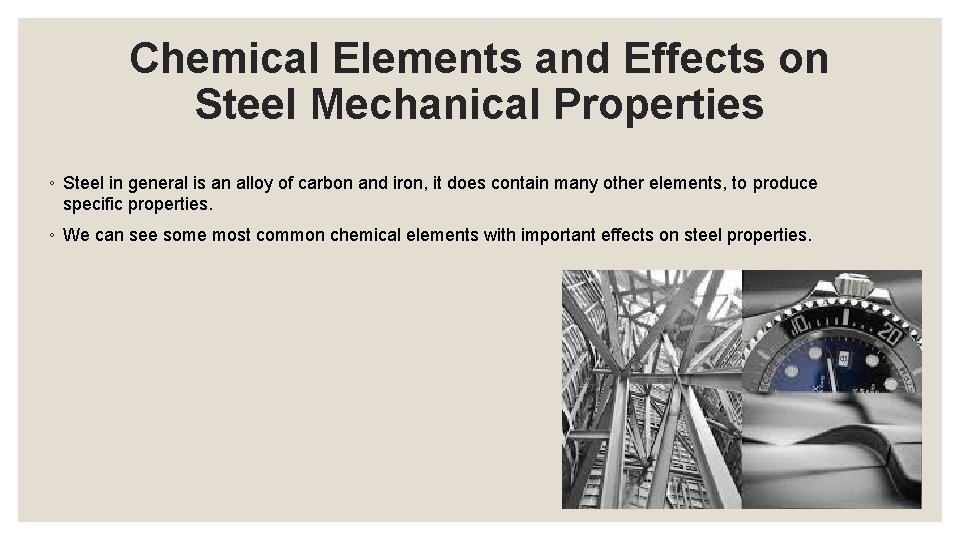
Chemical Elements and Effects on Steel Mechanical Properties ◦ Steel in general is an alloy of carbon and iron, it does contain many other elements, to produce specific properties. ◦ We can see some most common chemical elements with important effects on steel properties.
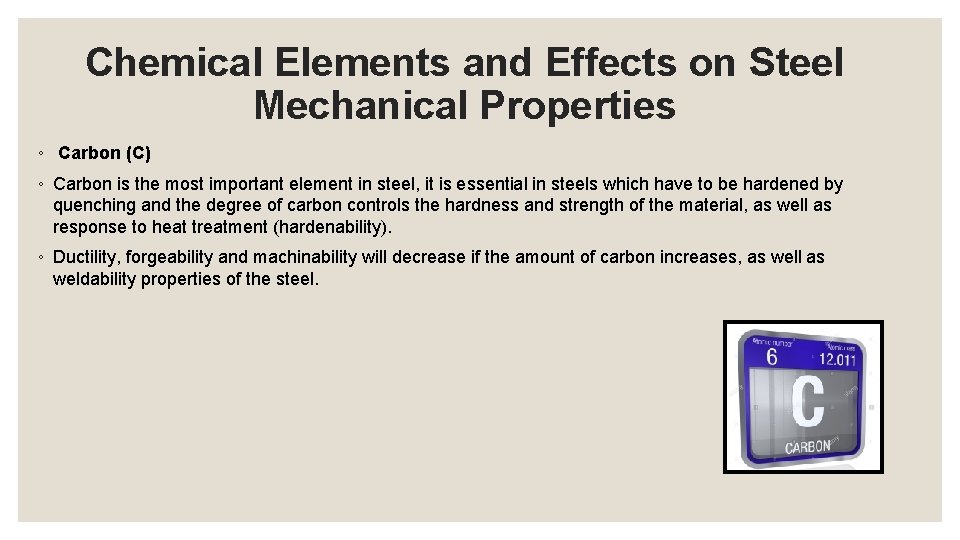
Chemical Elements and Effects on Steel Mechanical Properties ◦ Carbon (C) ◦ Carbon is the most important element in steel, it is essential in steels which have to be hardened by quenching and the degree of carbon controls the hardness and strength of the material, as well as response to heat treatment (hardenability). ◦ Ductility, forgeability and machinability will decrease if the amount of carbon increases, as well as weldability properties of the steel.
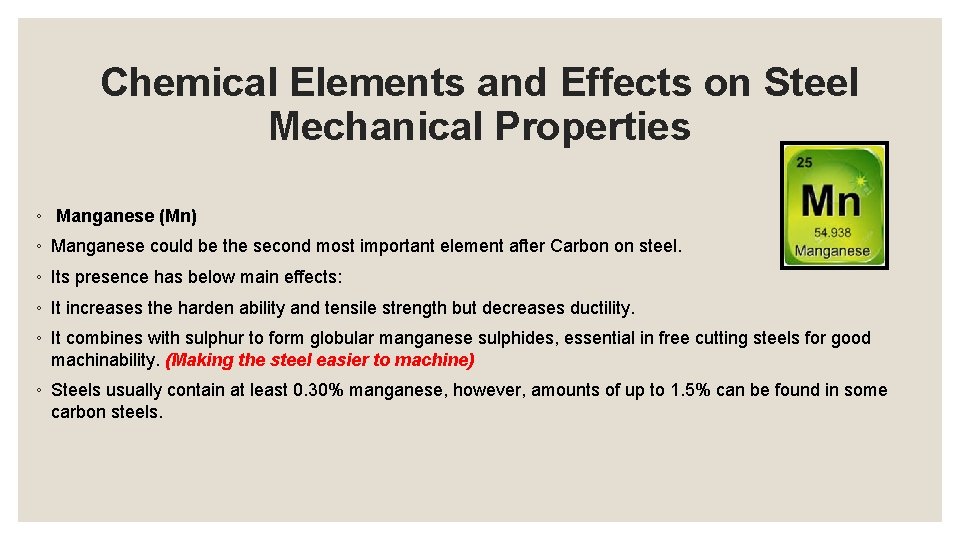
Chemical Elements and Effects on Steel Mechanical Properties ◦ Manganese (Mn) ◦ Manganese could be the second most important element after Carbon on steel. ◦ Its presence has below main effects: ◦ It increases the harden ability and tensile strength but decreases ductility. ◦ It combines with sulphur to form globular manganese sulphides, essential in free cutting steels for good machinability. (Making the steel easier to machine) ◦ Steels usually contain at least 0. 30% manganese, however, amounts of up to 1. 5% can be found in some carbon steels.
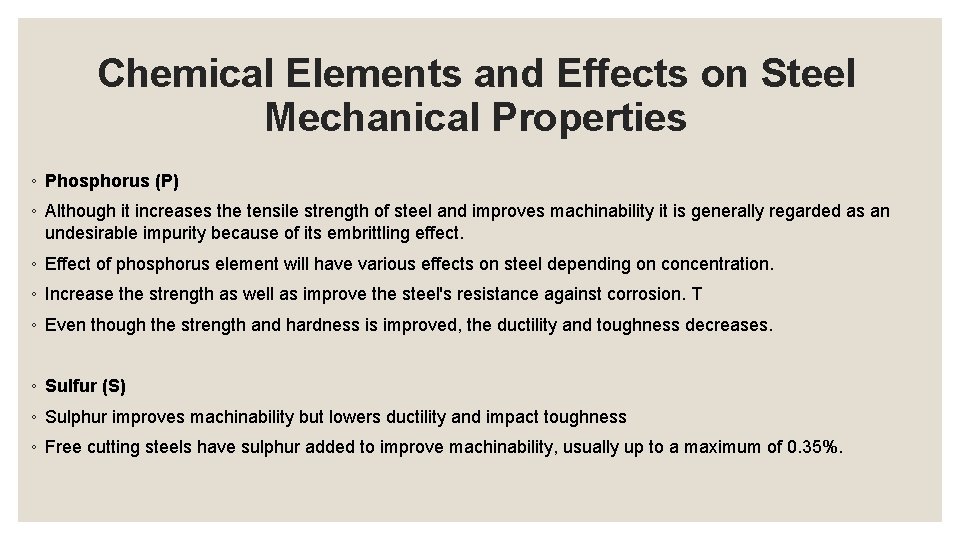
Chemical Elements and Effects on Steel Mechanical Properties ◦ Phosphorus (P) ◦ Although it increases the tensile strength of steel and improves machinability it is generally regarded as an undesirable impurity because of its embrittling effect. ◦ Effect of phosphorus element will have various effects on steel depending on concentration. ◦ Increase the strength as well as improve the steel's resistance against corrosion. T ◦ Even though the strength and hardness is improved, the ductility and toughness decreases. ◦ Sulfur (S) ◦ Sulphur improves machinability but lowers ductility and impact toughness ◦ Free cutting steels have sulphur added to improve machinability, usually up to a maximum of 0. 35%.
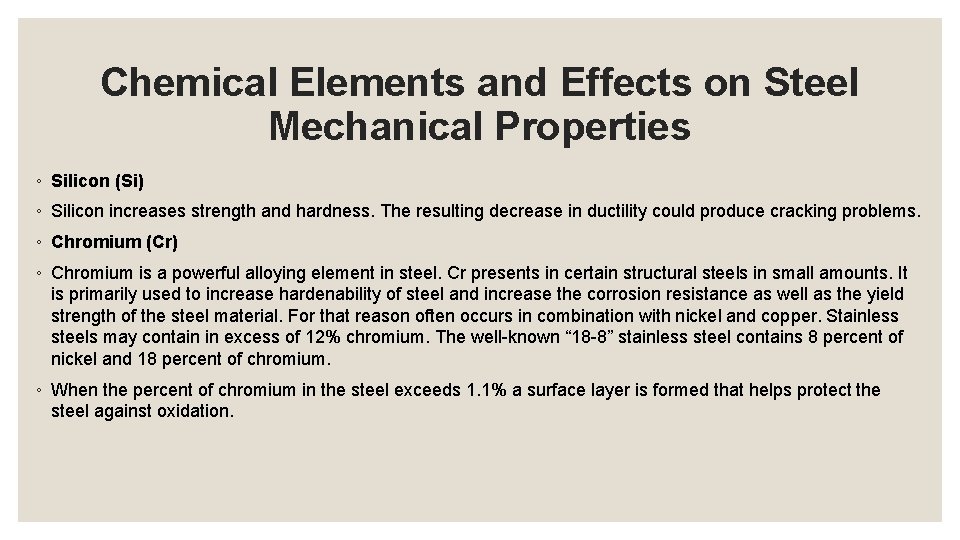
Chemical Elements and Effects on Steel Mechanical Properties ◦ Silicon (Si) ◦ Silicon increases strength and hardness. The resulting decrease in ductility could produce cracking problems. ◦ Chromium (Cr) ◦ Chromium is a powerful alloying element in steel. Cr presents in certain structural steels in small amounts. It is primarily used to increase hardenability of steel and increase the corrosion resistance as well as the yield strength of the steel material. For that reason often occurs in combination with nickel and copper. Stainless steels may contain in excess of 12% chromium. The well-known “ 18 -8” stainless steel contains 8 percent of nickel and 18 percent of chromium. ◦ When the percent of chromium in the steel exceeds 1. 1% a surface layer is formed that helps protect the steel against oxidation.
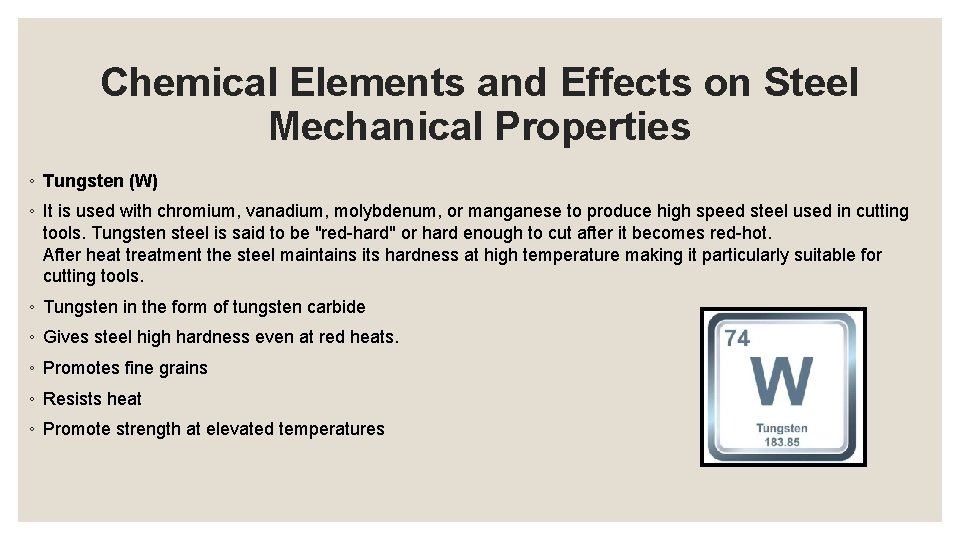
Chemical Elements and Effects on Steel Mechanical Properties ◦ Tungsten (W) ◦ It is used with chromium, vanadium, molybdenum, or manganese to produce high speed steel used in cutting tools. Tungsten steel is said to be "red-hard" or hard enough to cut after it becomes red-hot. After heat treatment the steel maintains its hardness at high temperature making it particularly suitable for cutting tools. ◦ Tungsten in the form of tungsten carbide ◦ Gives steel high hardness even at red heats. ◦ Promotes fine grains ◦ Resists heat ◦ Promote strength at elevated temperatures
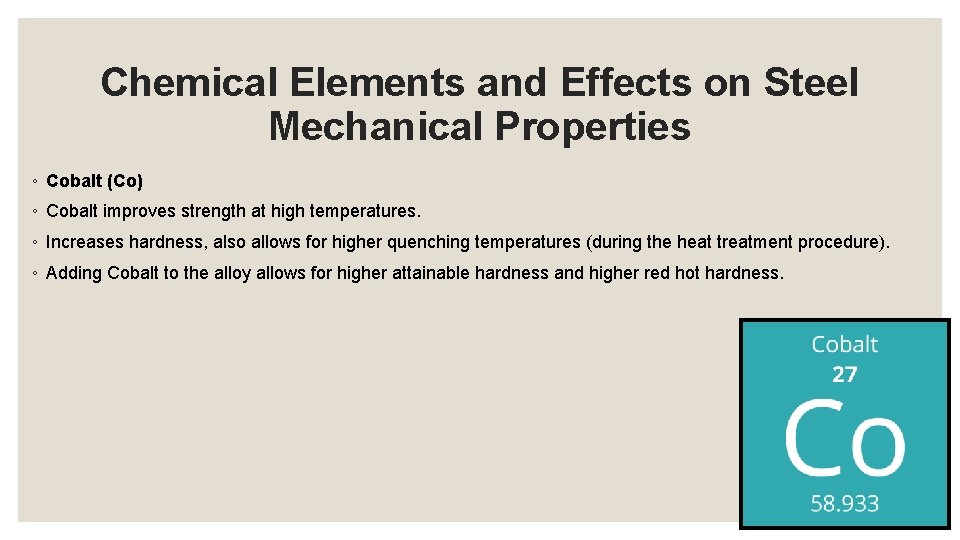
Chemical Elements and Effects on Steel Mechanical Properties ◦ Cobalt (Co) ◦ Cobalt improves strength at high temperatures. ◦ Increases hardness, also allows for higher quenching temperatures (during the heat treatment procedure). ◦ Adding Cobalt to the alloy allows for higher attainable hardness and higher red hot hardness.
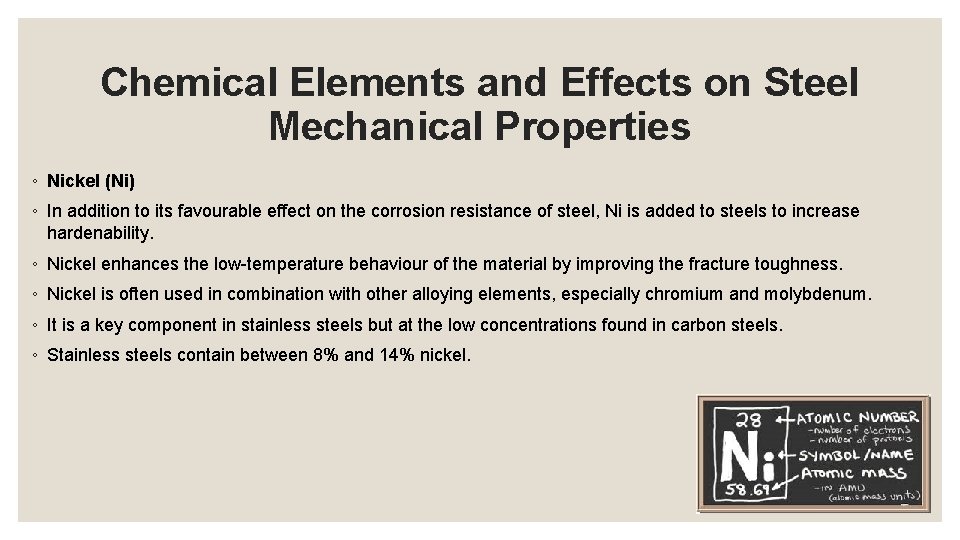
Chemical Elements and Effects on Steel Mechanical Properties ◦ Nickel (Ni) ◦ In addition to its favourable effect on the corrosion resistance of steel, Ni is added to steels to increase hardenability. ◦ Nickel enhances the low-temperature behaviour of the material by improving the fracture toughness. ◦ Nickel is often used in combination with other alloying elements, especially chromium and molybdenum. ◦ It is a key component in stainless steels but at the low concentrations found in carbon steels. ◦ Stainless steels contain between 8% and 14% nickel.
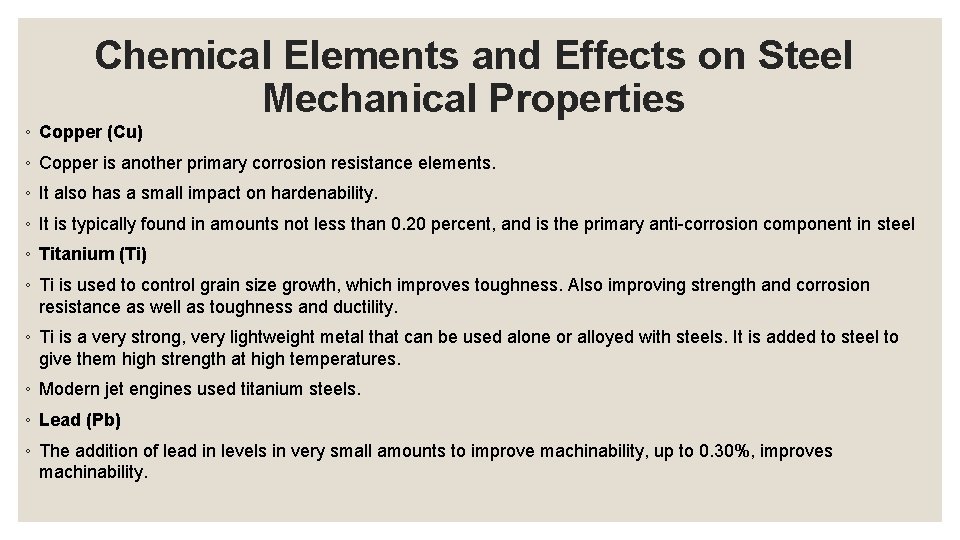
Chemical Elements and Effects on Steel Mechanical Properties ◦ Copper (Cu) ◦ Copper is another primary corrosion resistance elements. ◦ It also has a small impact on hardenability. ◦ It is typically found in amounts not less than 0. 20 percent, and is the primary anti-corrosion component in steel ◦ Titanium (Ti) ◦ Ti is used to control grain size growth, which improves toughness. Also improving strength and corrosion resistance as well as toughness and ductility. ◦ Ti is a very strong, very lightweight metal that can be used alone or alloyed with steels. It is added to steel to give them high strength at high temperatures. ◦ Modern jet engines used titanium steels. ◦ Lead (Pb) ◦ The addition of lead in levels in very small amounts to improve machinability, up to 0. 30%, improves machinability.
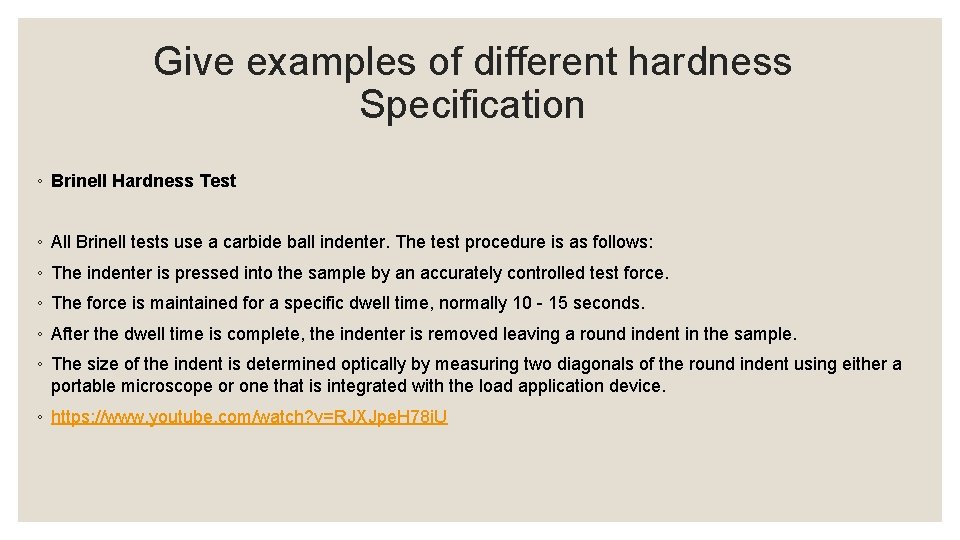
Give examples of different hardness Specification ◦ Brinell Hardness Test ◦ All Brinell tests use a carbide ball indenter. The test procedure is as follows: ◦ The indenter is pressed into the sample by an accurately controlled test force. ◦ The force is maintained for a specific dwell time, normally 10 - 15 seconds. ◦ After the dwell time is complete, the indenter is removed leaving a round indent in the sample. ◦ The size of the indent is determined optically by measuring two diagonals of the round indent using either a portable microscope or one that is integrated with the load application device. ◦ https: //www. youtube. com/watch? v=RJXJpe. H 78 i. U
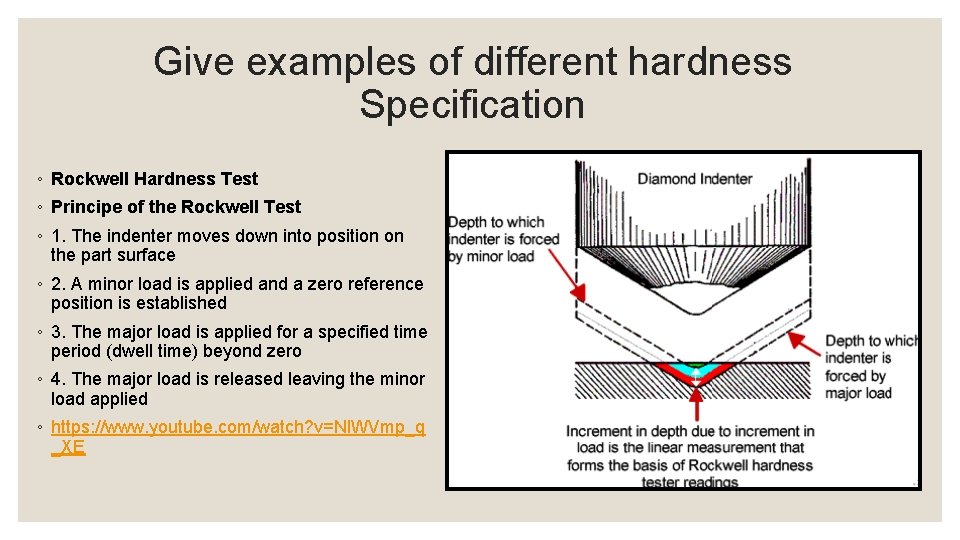
Give examples of different hardness Specification ◦ Rockwell Hardness Test ◦ Principe of the Rockwell Test ◦ 1. The indenter moves down into position on the part surface ◦ 2. A minor load is applied and a zero reference position is established ◦ 3. The major load is applied for a specified time period (dwell time) beyond zero ◦ 4. The major load is released leaving the minor load applied ◦ https: //www. youtube. com/watch? v=Nl. WVmp_q _XE
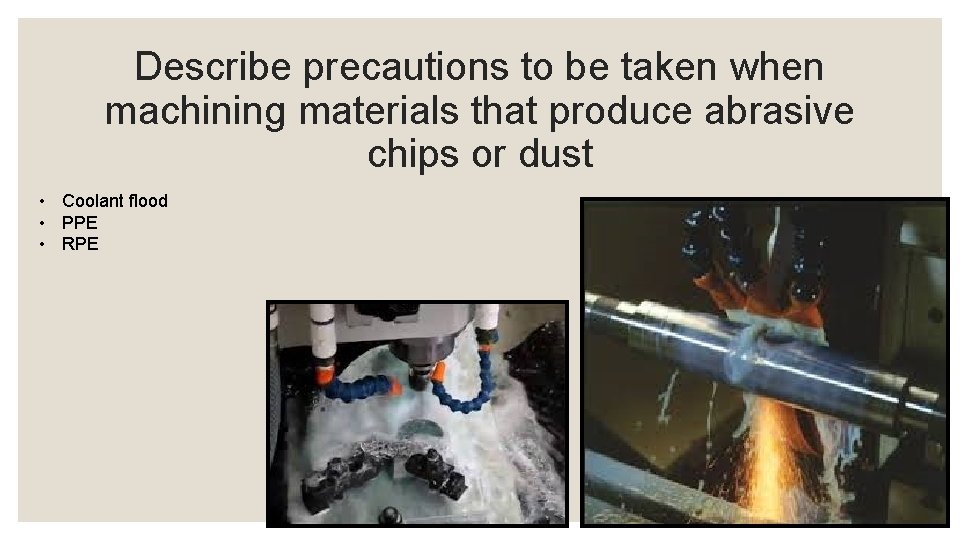
Describe precautions to be taken when machining materials that produce abrasive chips or dust • Coolant flood • PPE • RPE
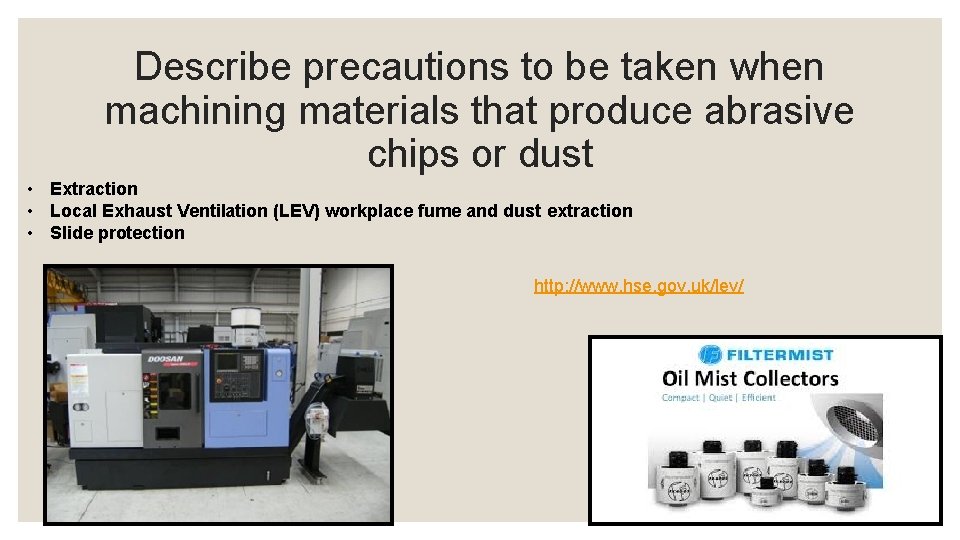
Describe precautions to be taken when machining materials that produce abrasive chips or dust • Extraction • Local Exhaust Ventilation (LEV) workplace fume and dust extraction • Slide protection http: //www. hse. gov. uk/lev/
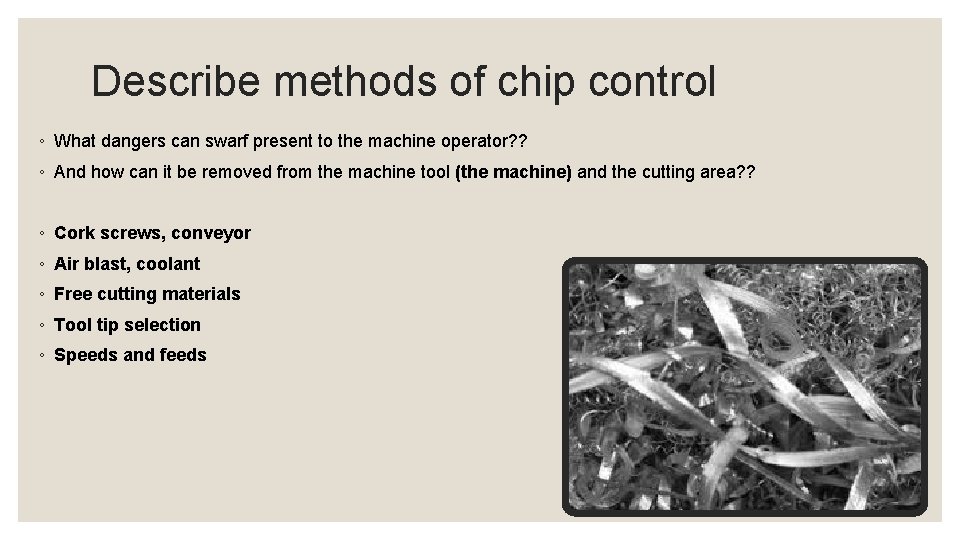
Describe methods of chip control ◦ What dangers can swarf present to the machine operator? ? ◦ And how can it be removed from the machine tool (the machine) and the cutting area? ? ◦ Cork screws, conveyor ◦ Air blast, coolant ◦ Free cutting materials ◦ Tool tip selection ◦ Speeds and feeds
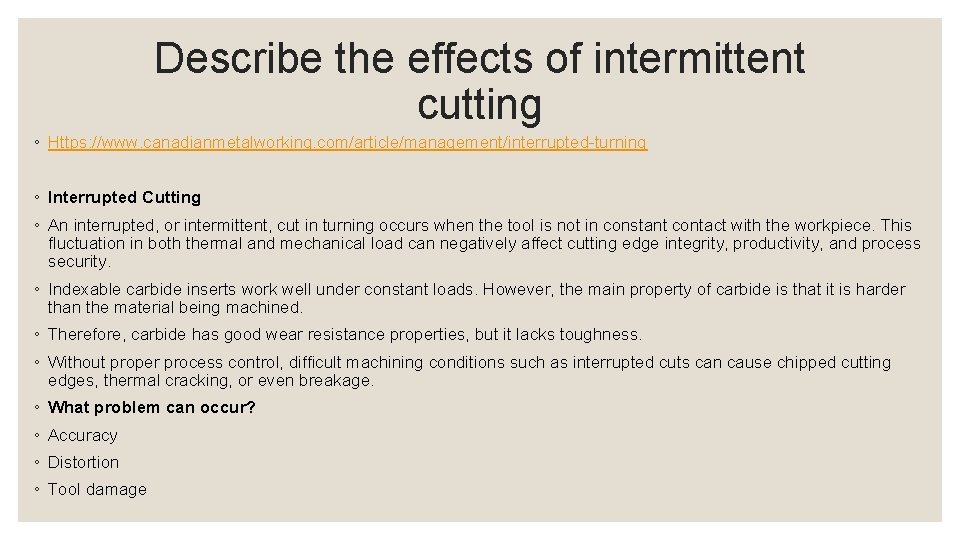
Describe the effects of intermittent cutting ◦ Https: //www. canadianmetalworking. com/article/management/interrupted-turning ◦ Interrupted Cutting ◦ An interrupted, or intermittent, cut in turning occurs when the tool is not in constant contact with the workpiece. This fluctuation in both thermal and mechanical load can negatively affect cutting edge integrity, productivity, and process security. ◦ Indexable carbide inserts work well under constant loads. However, the main property of carbide is that it is harder than the material being machined. ◦ Therefore, carbide has good wear resistance properties, but it lacks toughness. ◦ Without proper process control, difficult machining conditions such as interrupted cuts can cause chipped cutting edges, thermal cracking, or even breakage. ◦ What problem can occur? ◦ Accuracy ◦ Distortion ◦ Tool damage
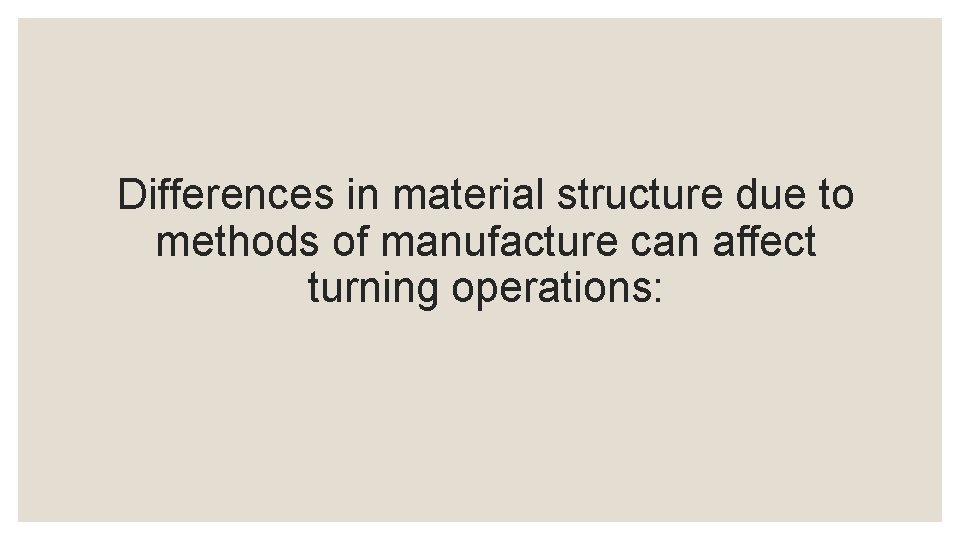
Differences in material structure due to methods of manufacture can affect turning operations:
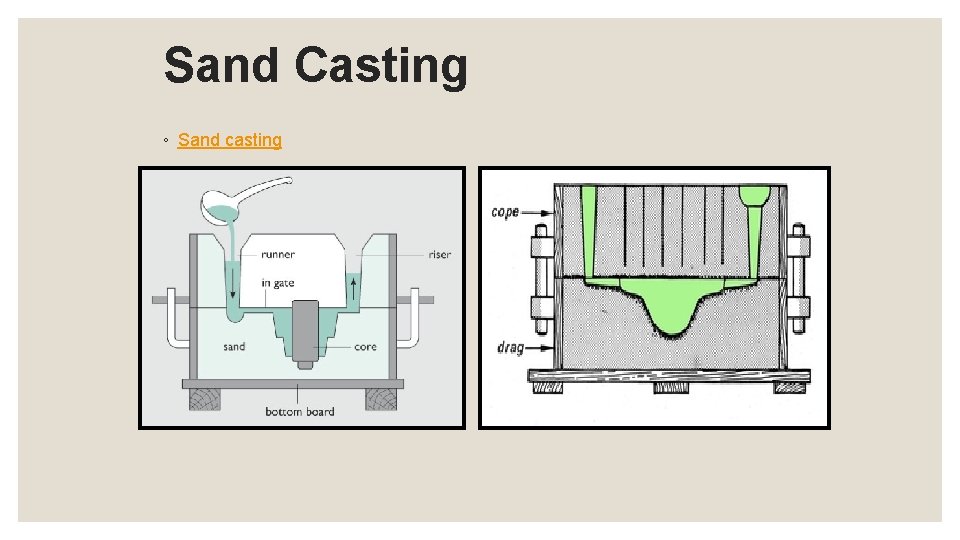
Sand Casting ◦ Sand casting
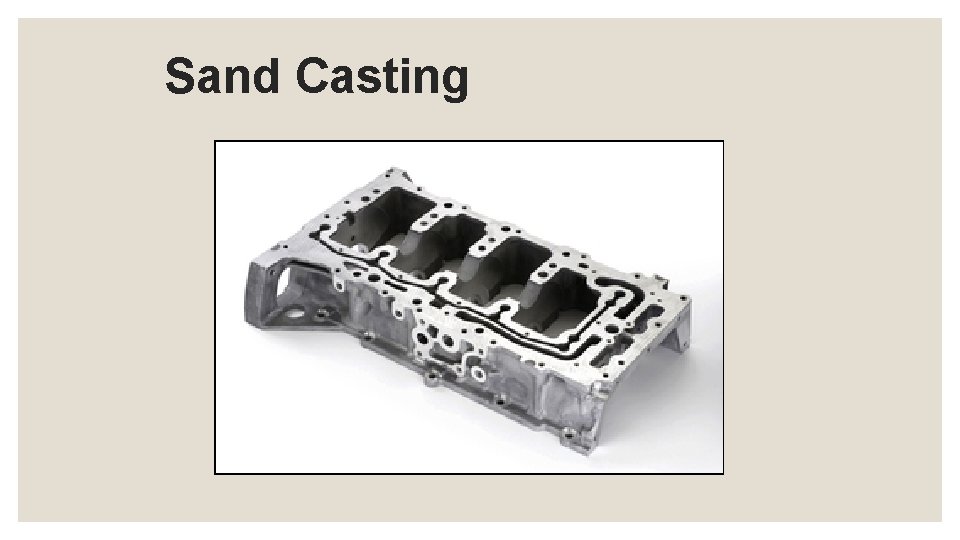
Sand Casting
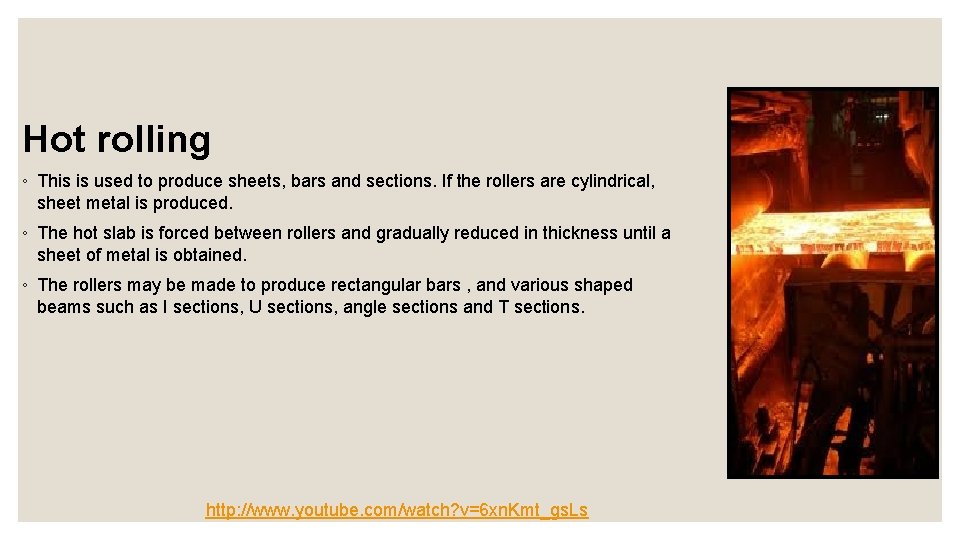
Hot rolling ◦ This is used to produce sheets, bars and sections. If the rollers are cylindrical, sheet metal is produced. ◦ The hot slab is forced between rollers and gradually reduced in thickness until a sheet of metal is obtained. ◦ The rollers may be made to produce rectangular bars , and various shaped beams such as I sections, U sections, angle sections and T sections. http: //www. youtube. com/watch? v=6 xn. Kmt_gs. Ls
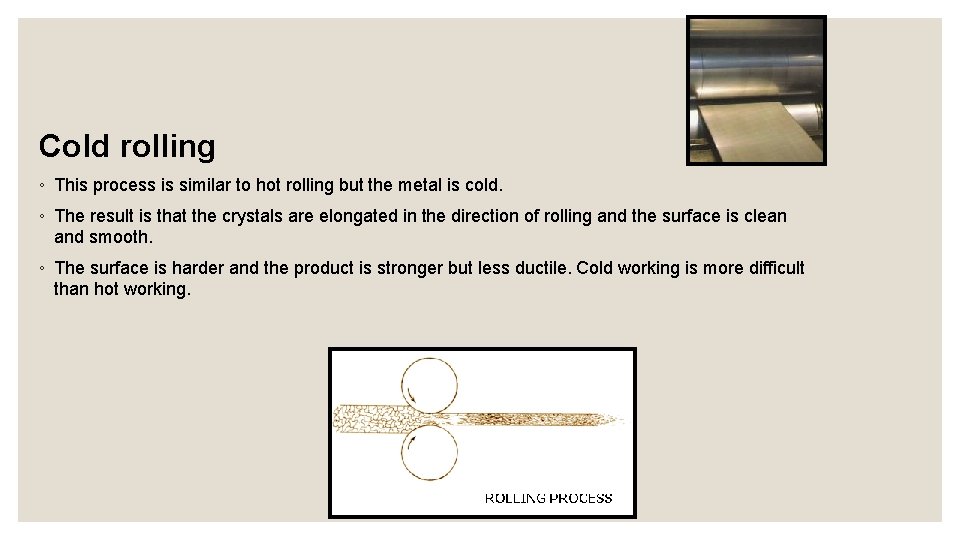
Cold rolling ◦ This process is similar to hot rolling but the metal is cold. ◦ The result is that the crystals are elongated in the direction of rolling and the surface is clean and smooth. ◦ The surface is harder and the product is stronger but less ductile. Cold working is more difficult than hot working.
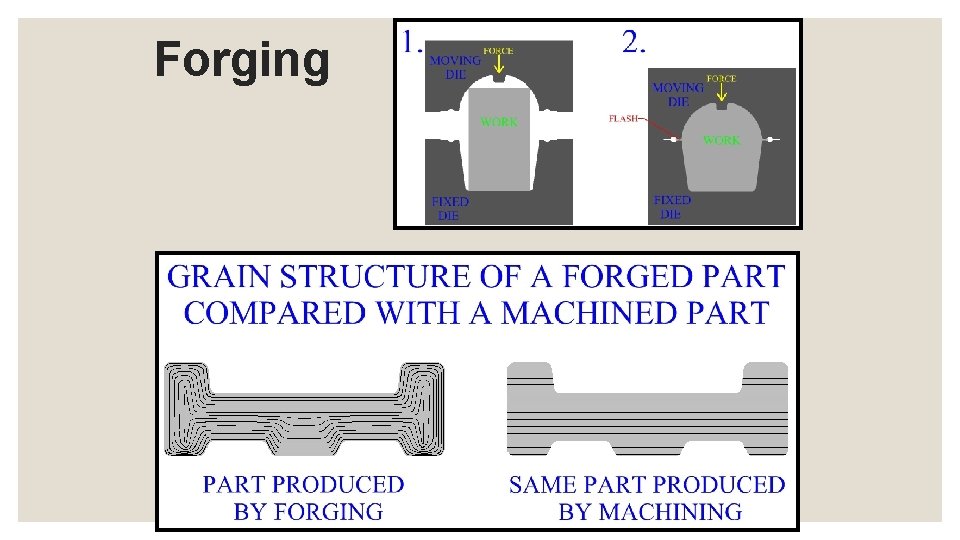
Forging
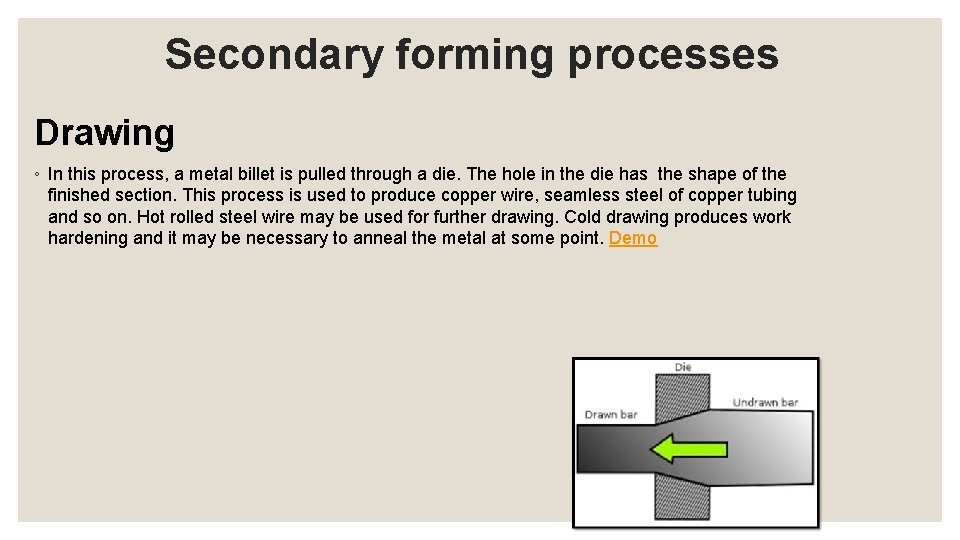
Secondary forming processes Drawing ◦ In this process, a metal billet is pulled through a die. The hole in the die has the shape of the finished section. This process is used to produce copper wire, seamless steel of copper tubing and so on. Hot rolled steel wire may be used for further drawing. Cold drawing produces work hardening and it may be necessary to anneal the metal at some point. Demo
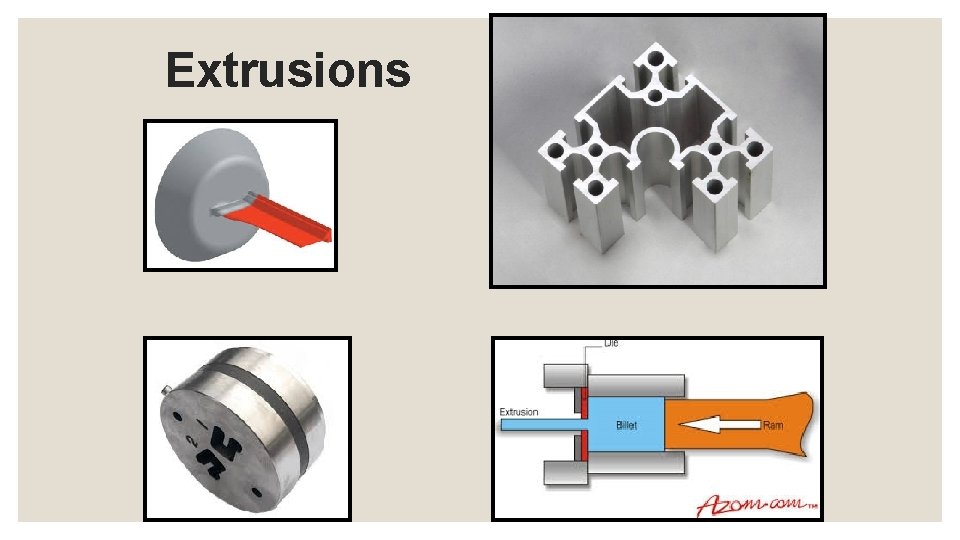
Extrusions

Techniques required to turn different engineering materials ◦ Carbon, alloy and stainless steels correct inserts, speeds, feeds, lubricants ◦ Cast iron correct inserts, speeds, feeds ◦ Non-ferrous metals correct inserts, speeds, feeds, lubricants ◦ Plastics. correct inserts, speeds, feeds, lubricants ◦ Glass-fibre re-enforcement correct inserts, speeds, feeds, lubricants ◦ Certain material must not have coolants ◦ Certain inserts should not have coolants
Calorimetry worksheet answers
H5525 049 04 - local ppo
Turning and turning in the widening gyre chinua achebe
Wb yeats the second coming
Turning and turning in the widening gyre
Phân độ lown
Block av độ 1
Thể thơ truyền thống
Thơ thất ngôn tứ tuyệt đường luật
Walmart thất bại ở nhật
Tìm vết của đường thẳng
Hãy nói thật ít để làm được nhiều
Tôn thất thuyết là ai
Gây tê cơ vuông thắt lưng
Sau thất bại ở hồ điển triệt
What factors shape the climate in canada
Factors affecting microbial growth in food
Types of volcanoes
Factor affecting volcanic eruption
Nozzle lip in carburettor
Factors affecting thermogravimetric curve
Factors that affect housing choices
Factors affecting bilingualism
Five factors affecting human movement
Factors affecting stroke volume
Factors affecting movement in physical education
Baricity of local anesthetics
Factors affecting soil formation
Factors affecting health
Section 17.2 factors affecting chemical equilibrium
Factors affecting sample size
Factors affecting the merchandising function
Factors affecting planning process
Factors affecting evaporation
Factors that affect sports performance
Psychological factors affecting sports performance
What are the different routes of drug administration
Factors affecting cardiac output
Factors affecting transportation decisions
Factors affecting span of control
Steep incisal guidance
Factors affecting bacterial growth ppt
Specialization