Tessellations and granular materials Niels P Kruyt Department
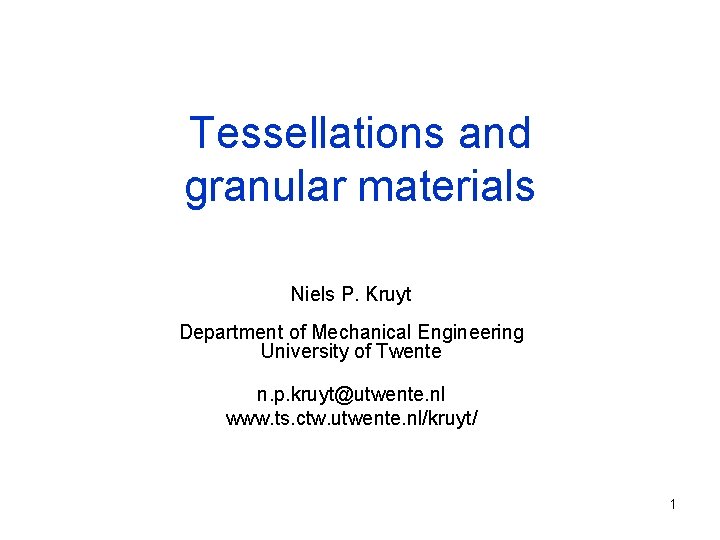
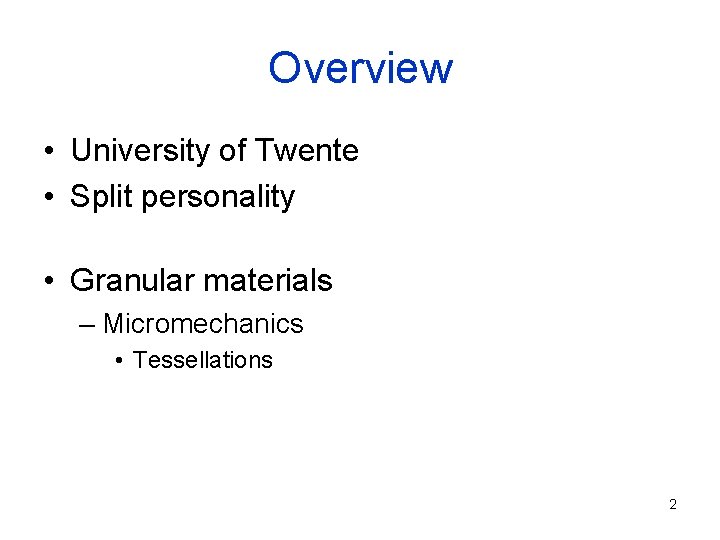
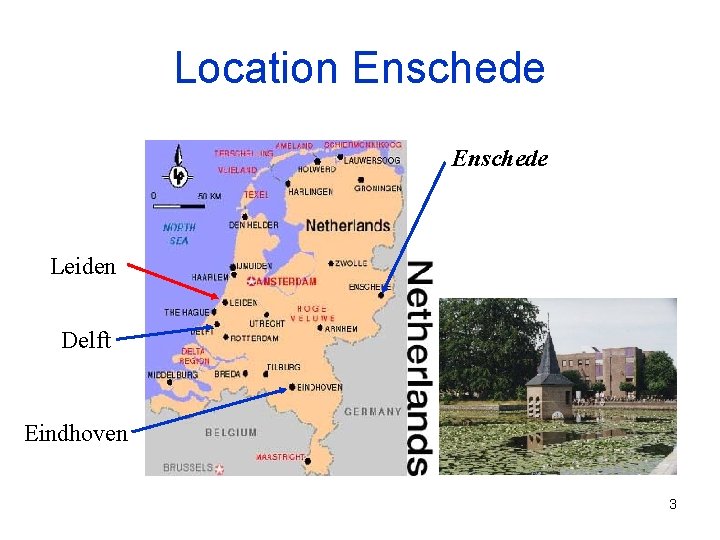
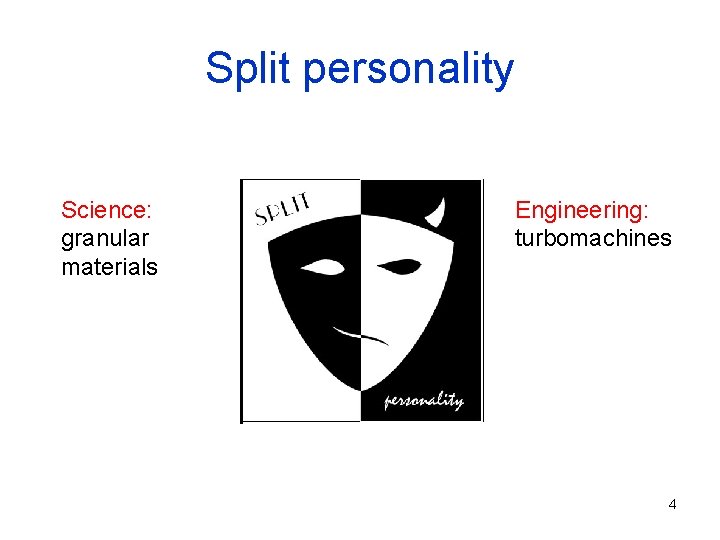
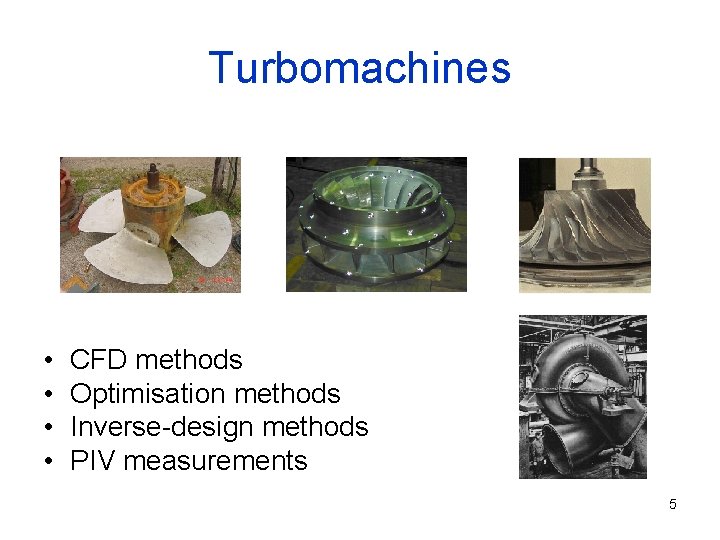
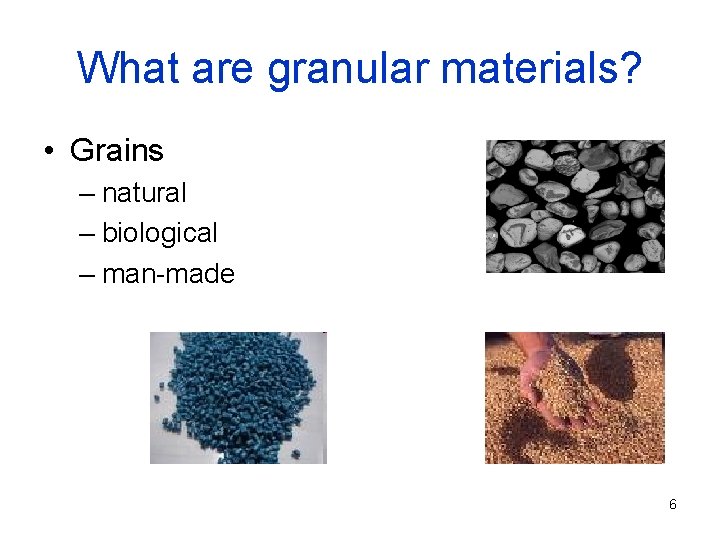
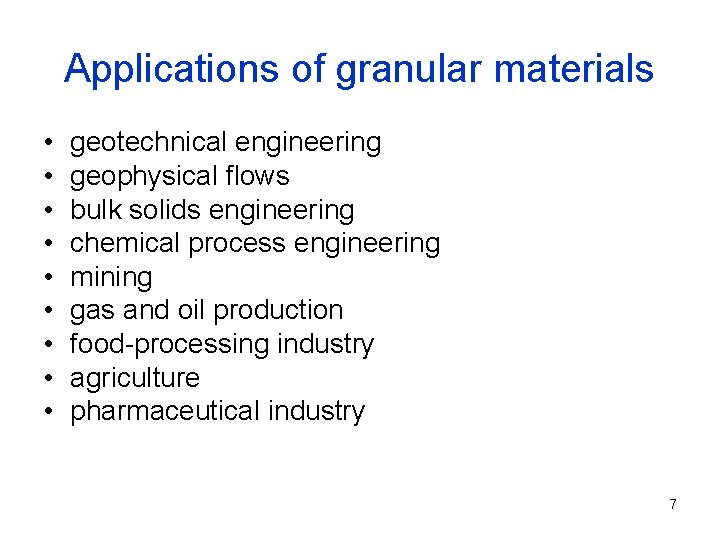
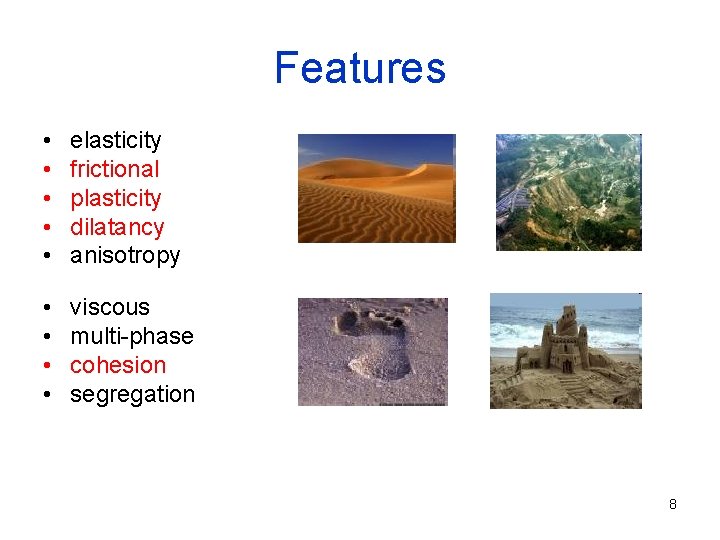
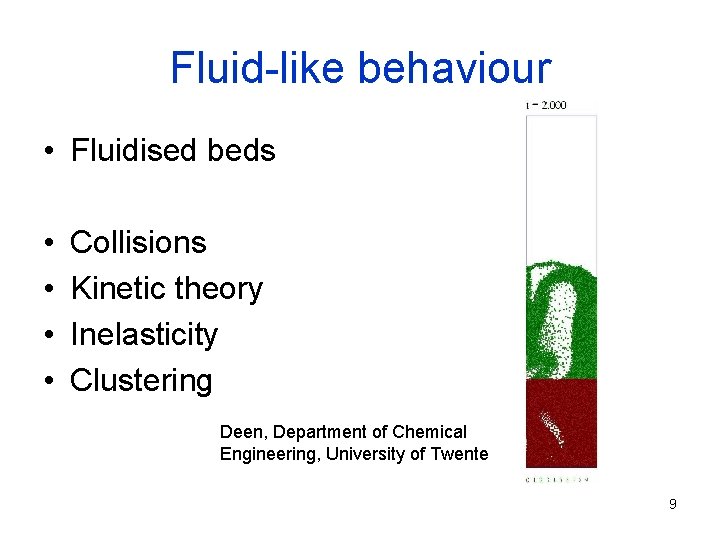
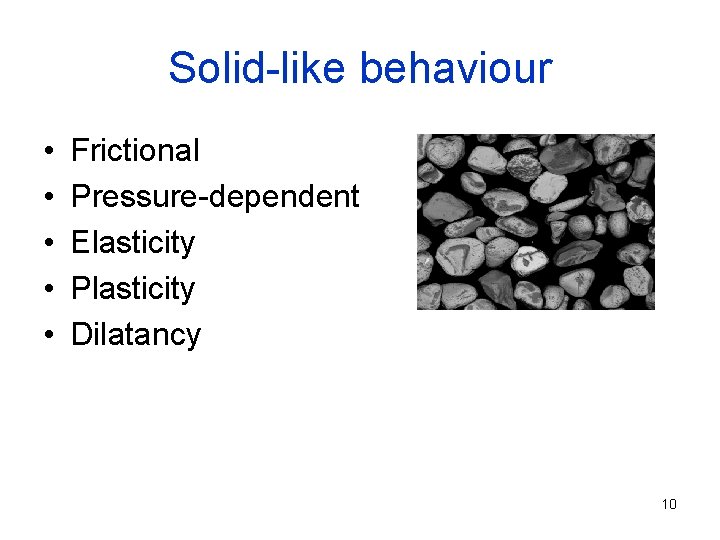
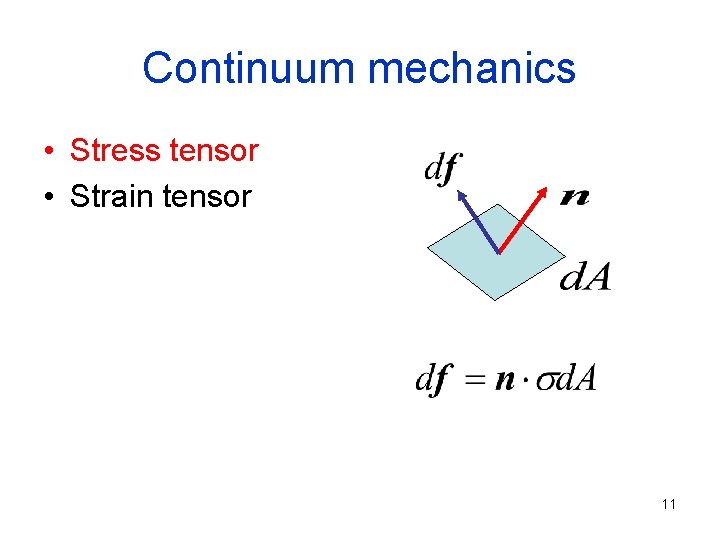
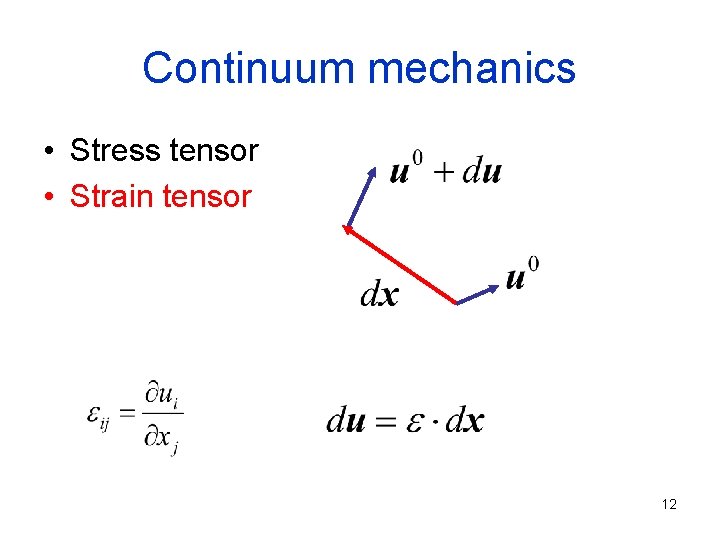
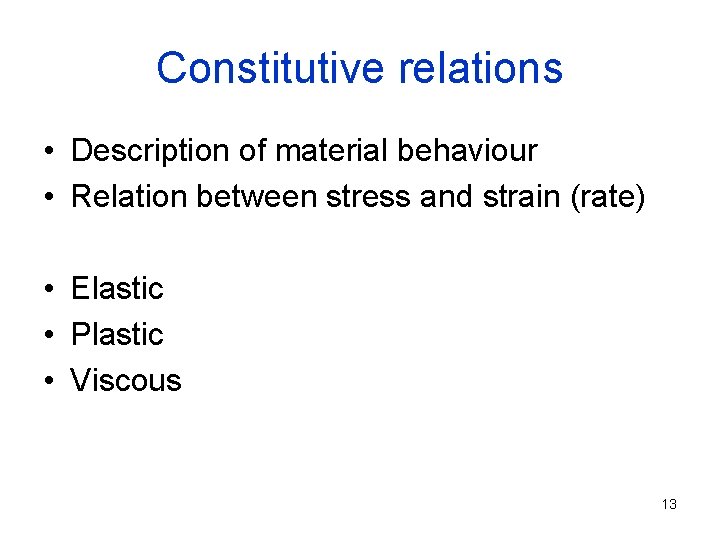
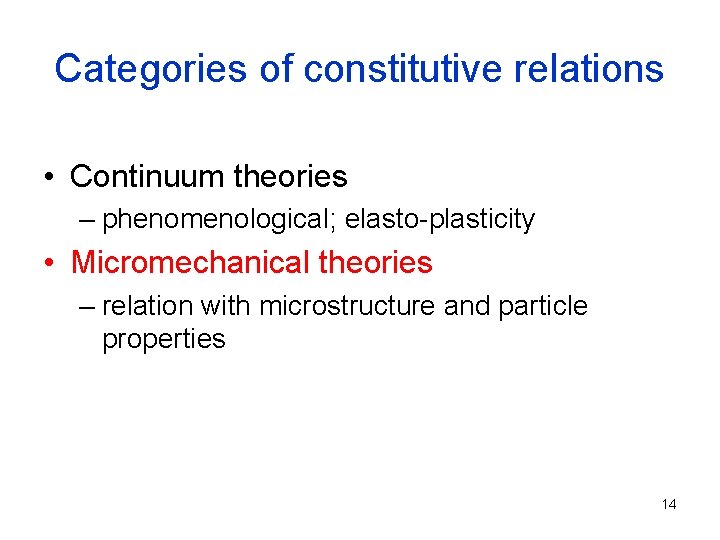
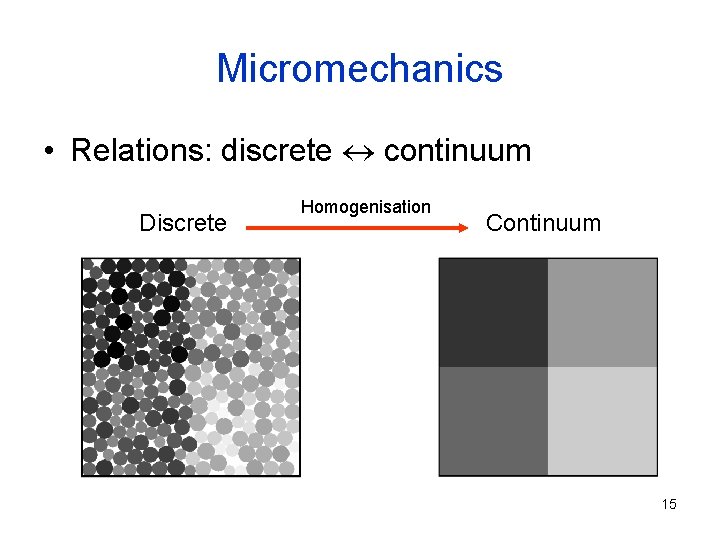
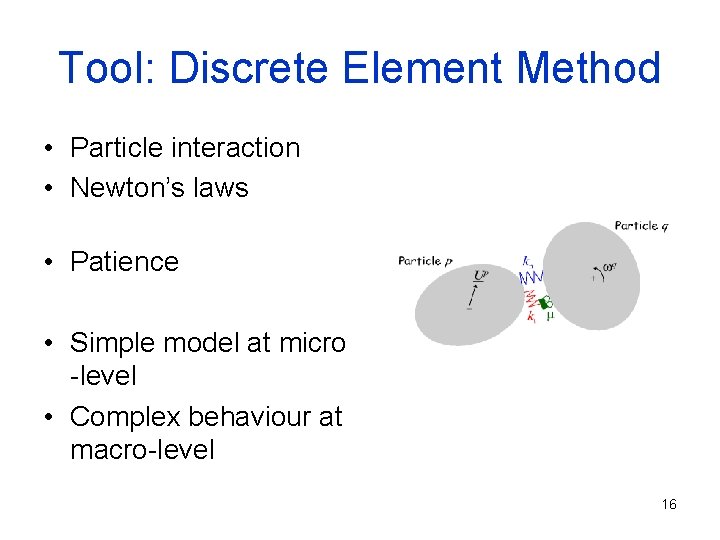
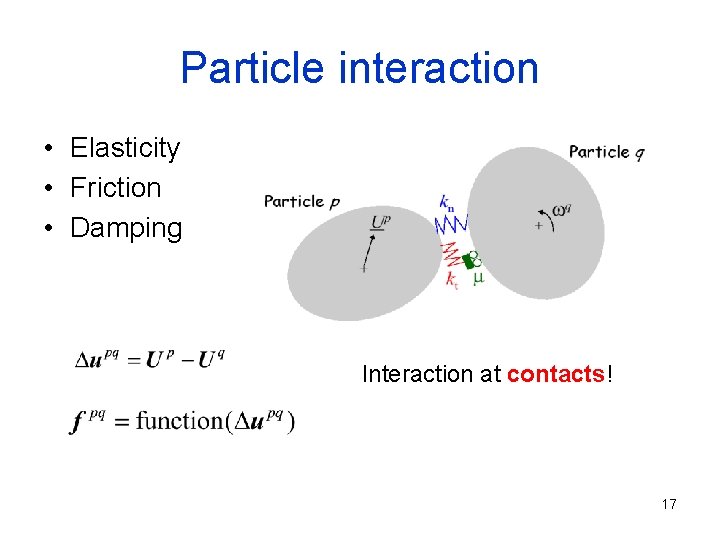
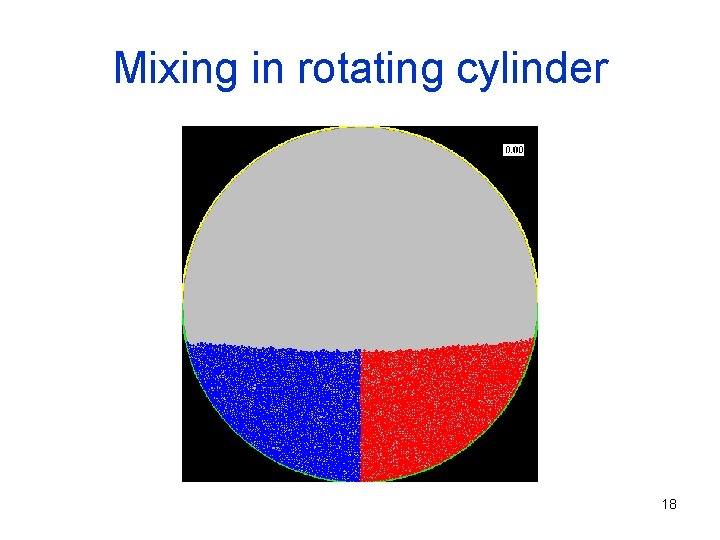
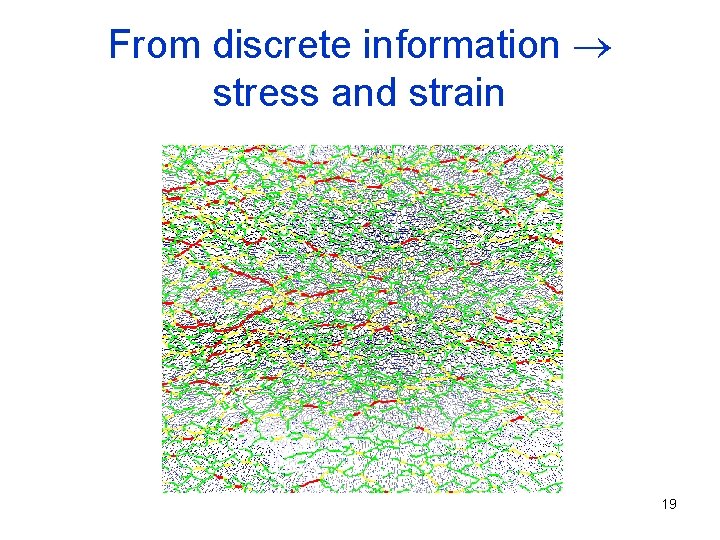
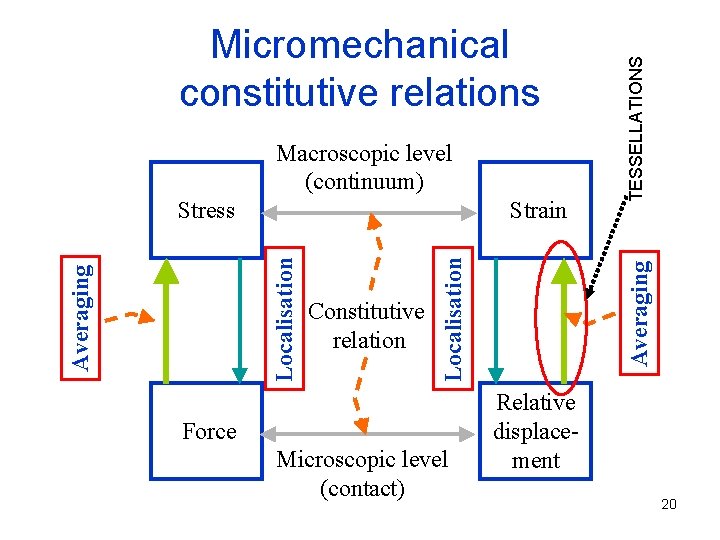
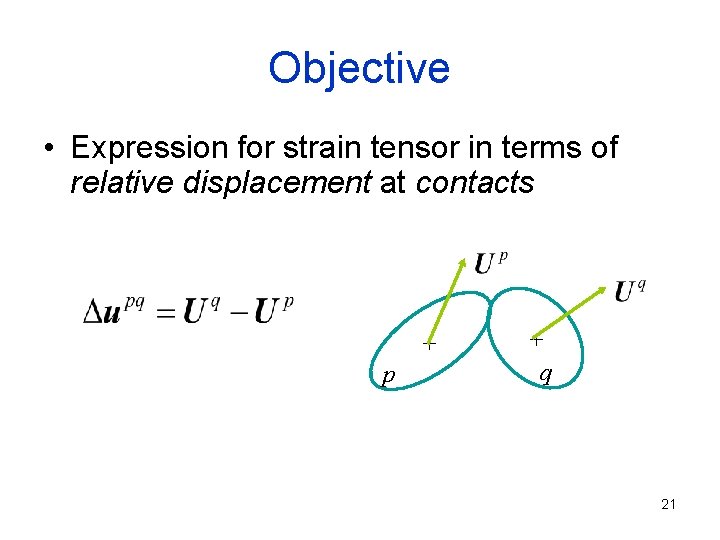
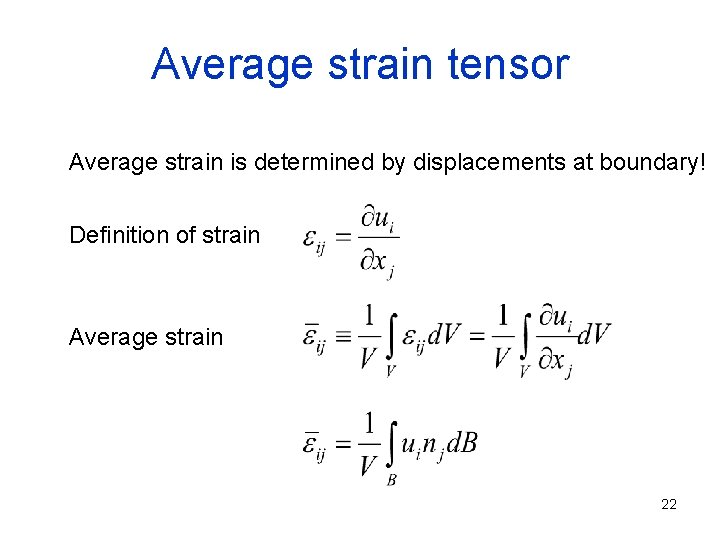
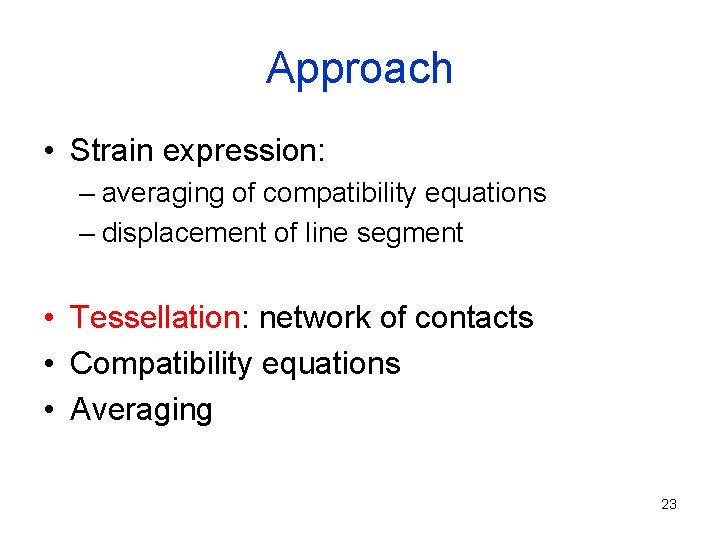
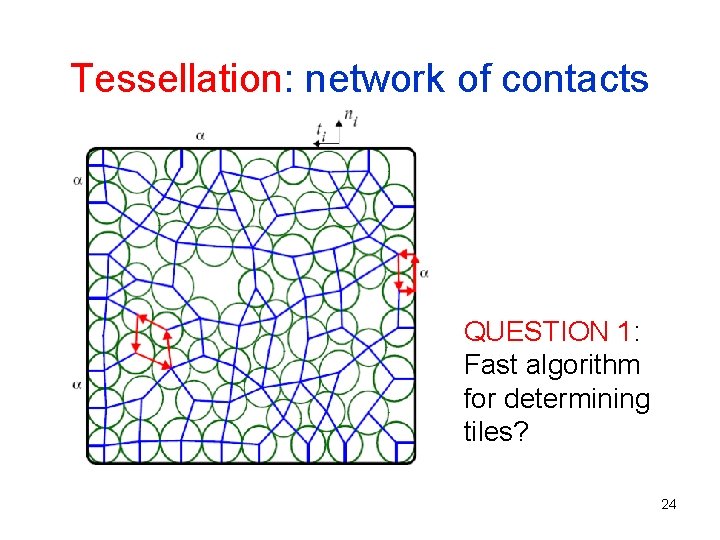
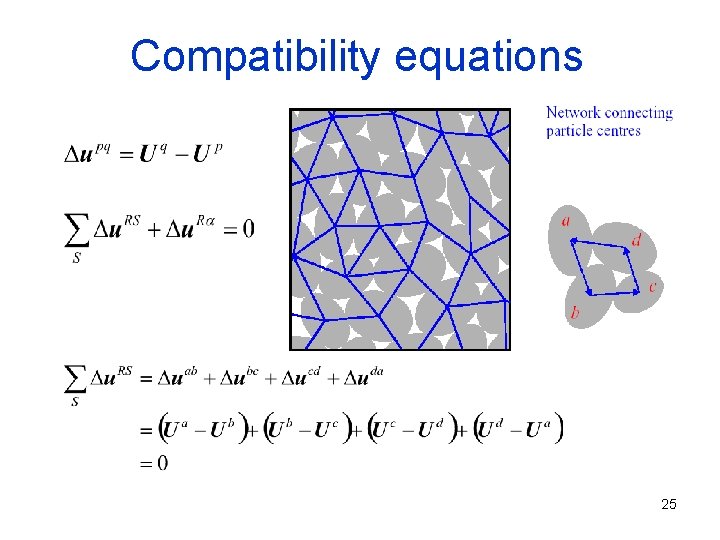
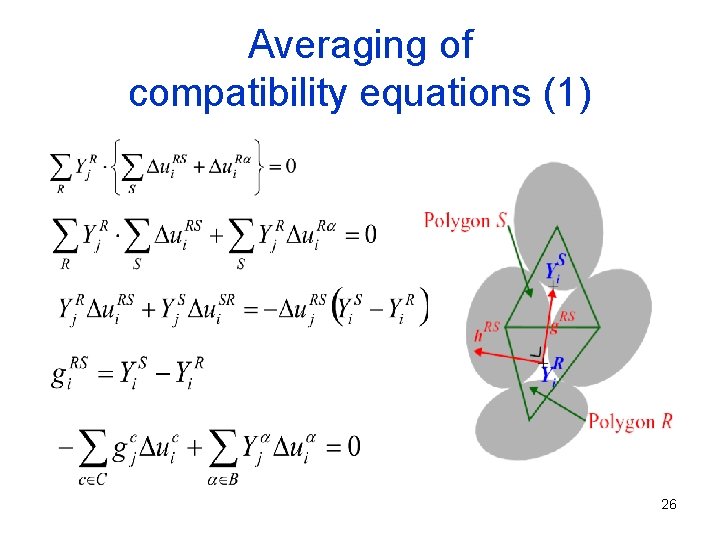
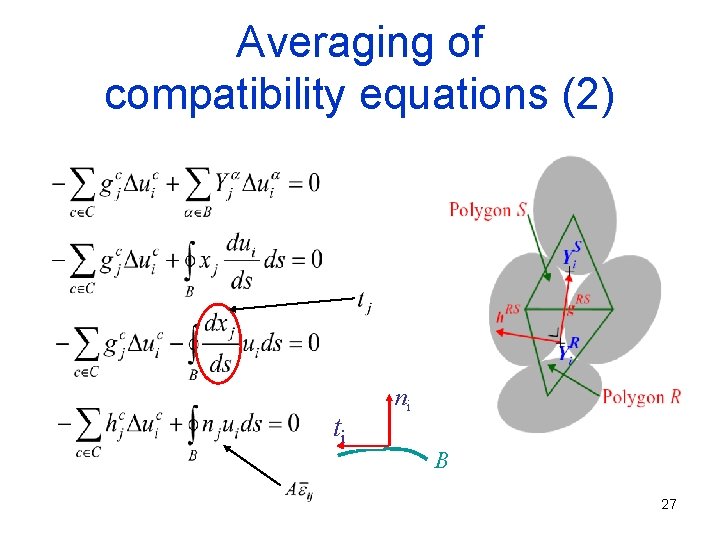
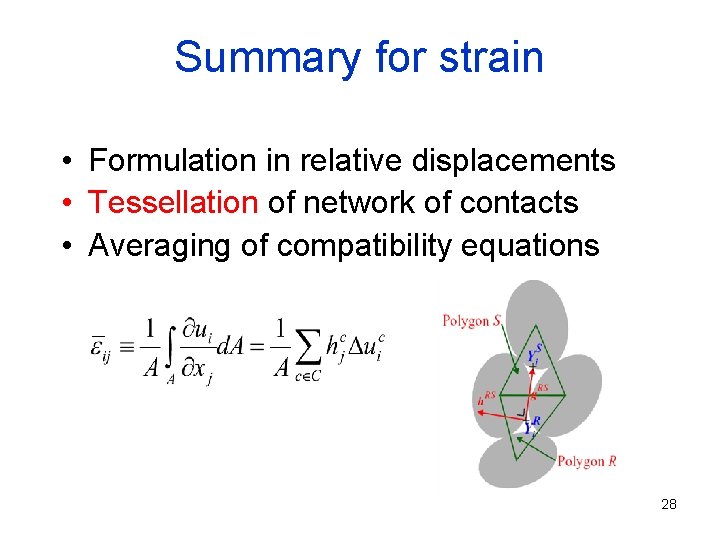
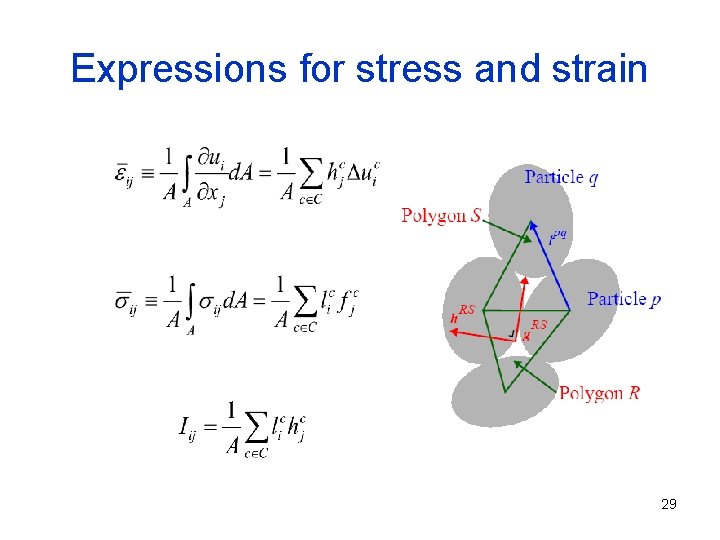
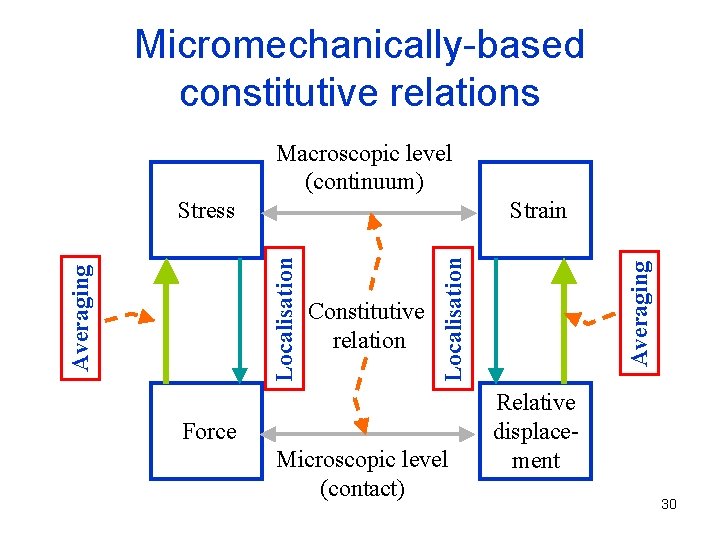
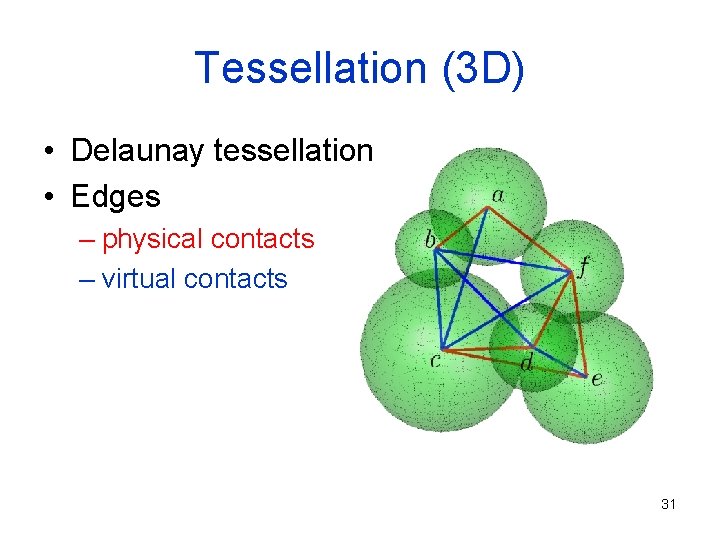
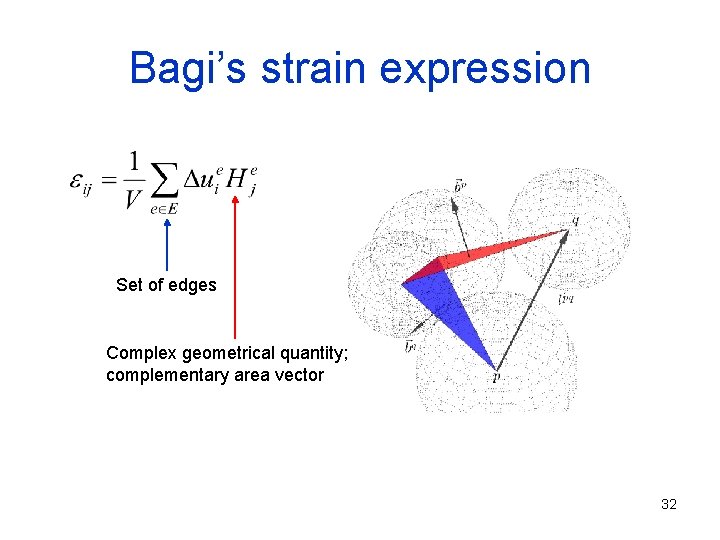
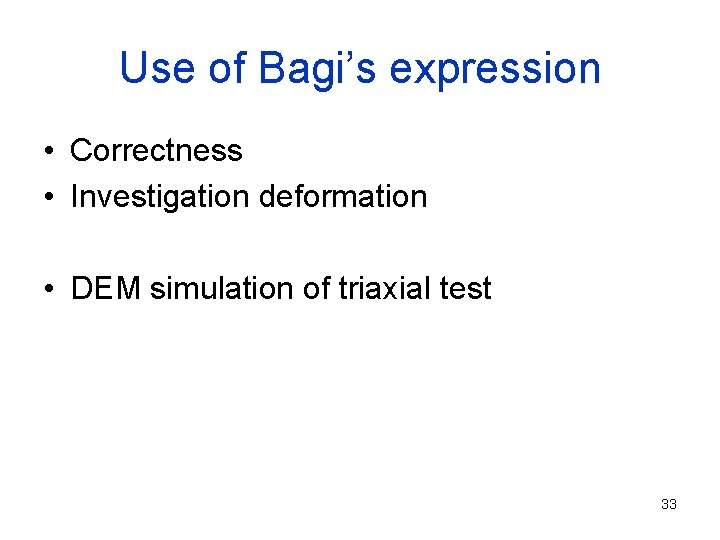
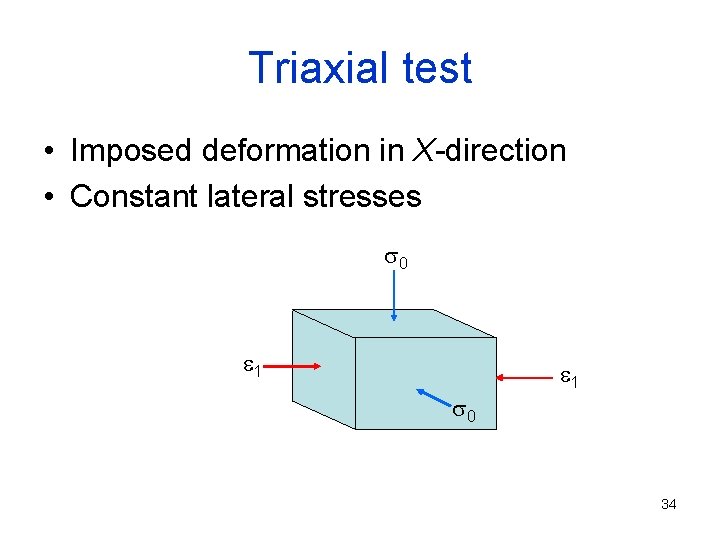
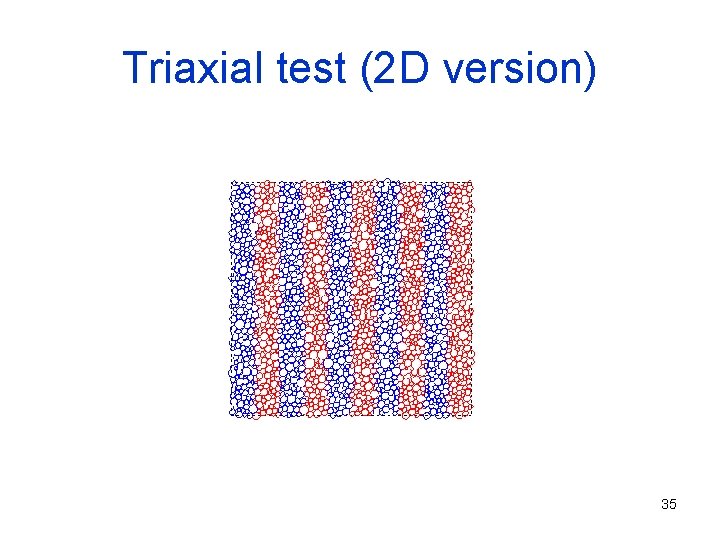
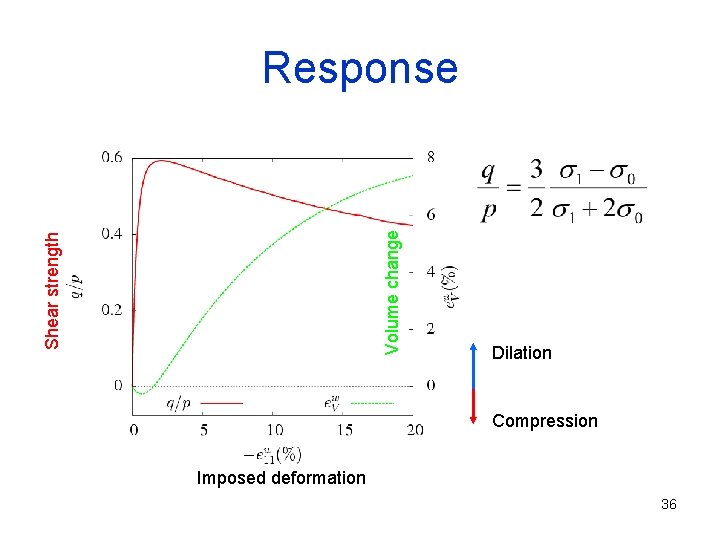
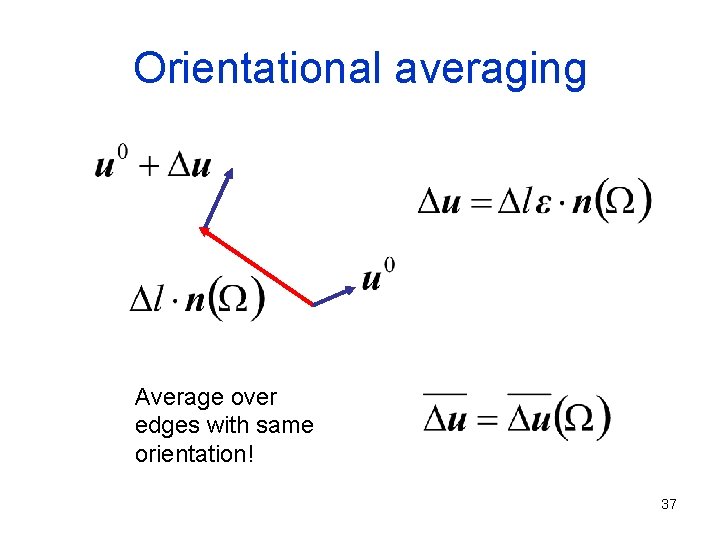
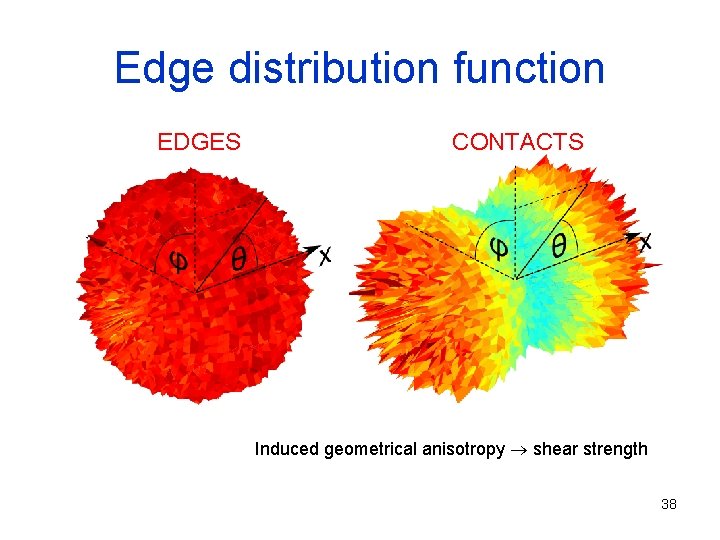
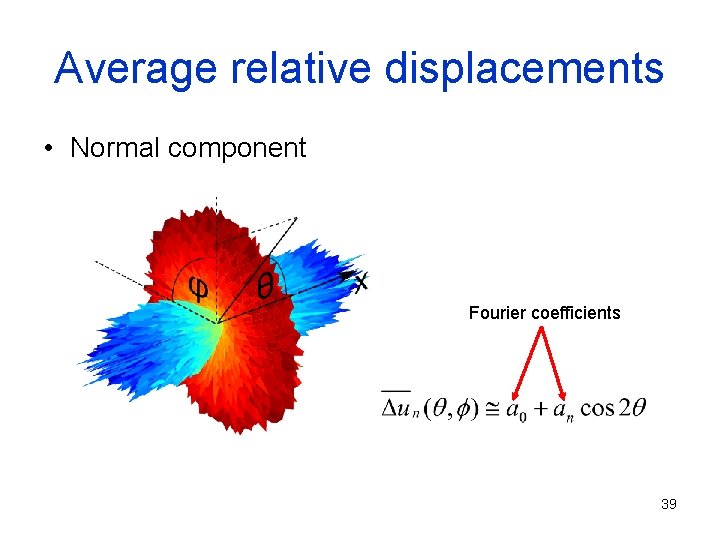
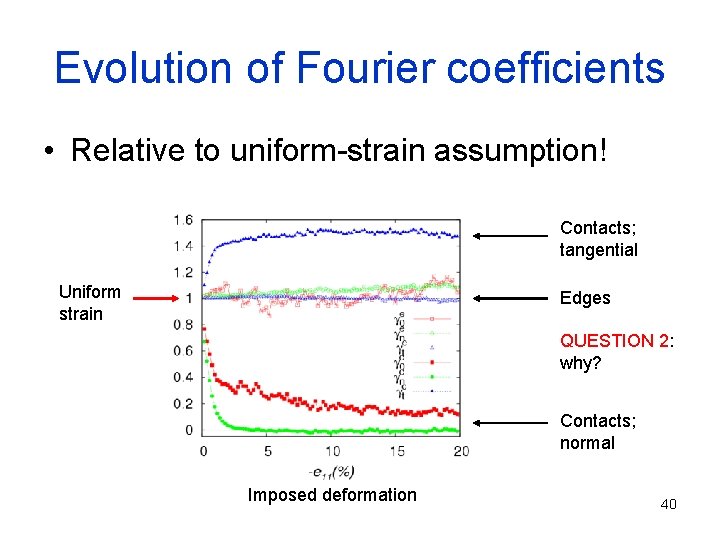
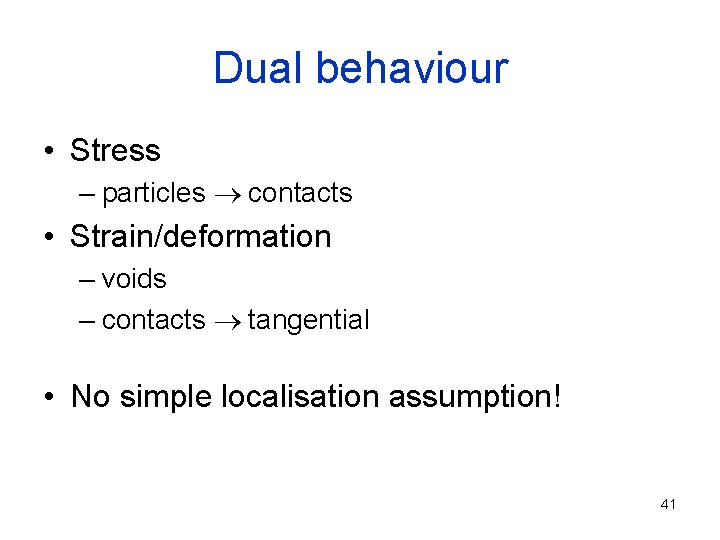
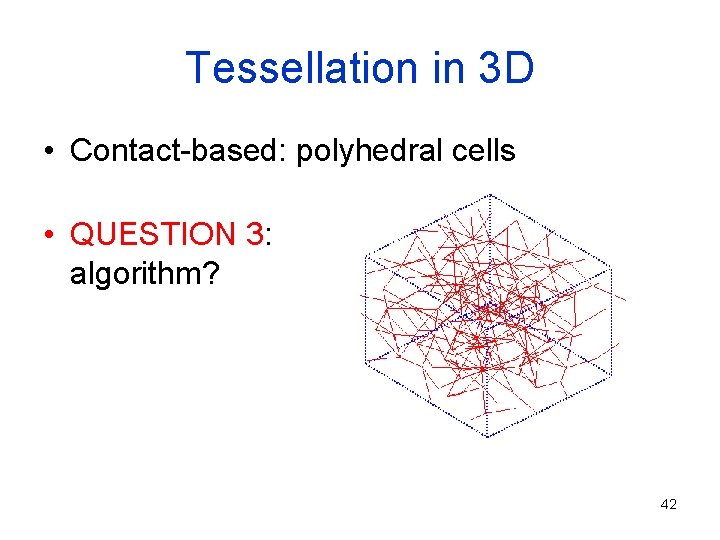
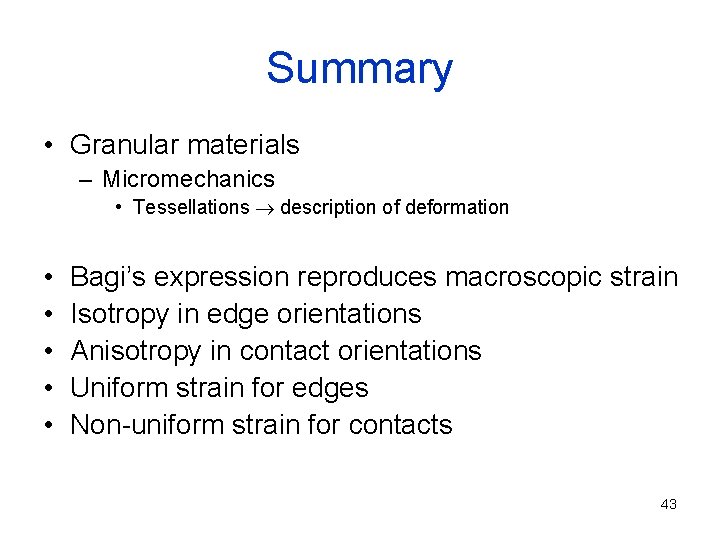
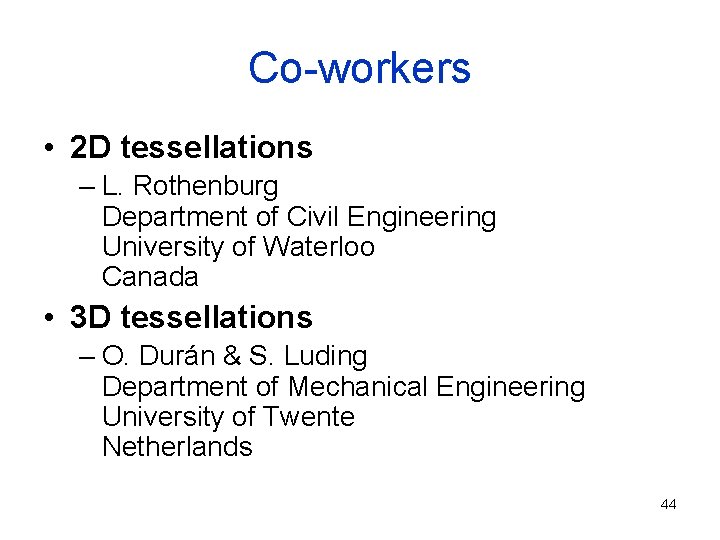
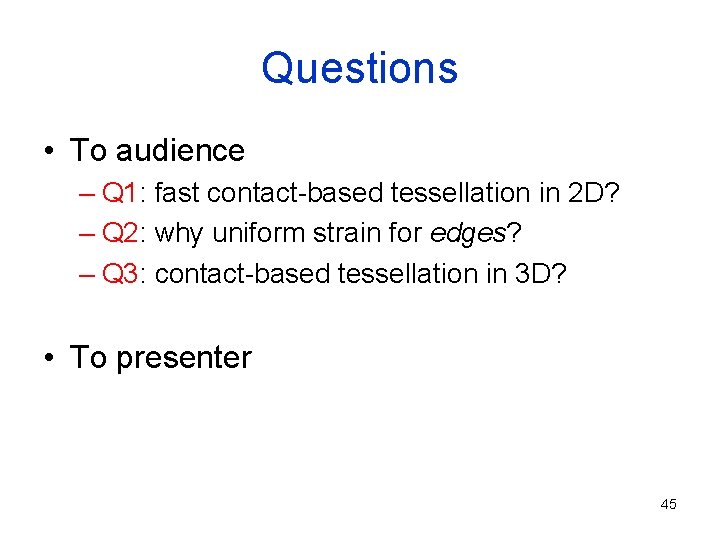
- Slides: 45
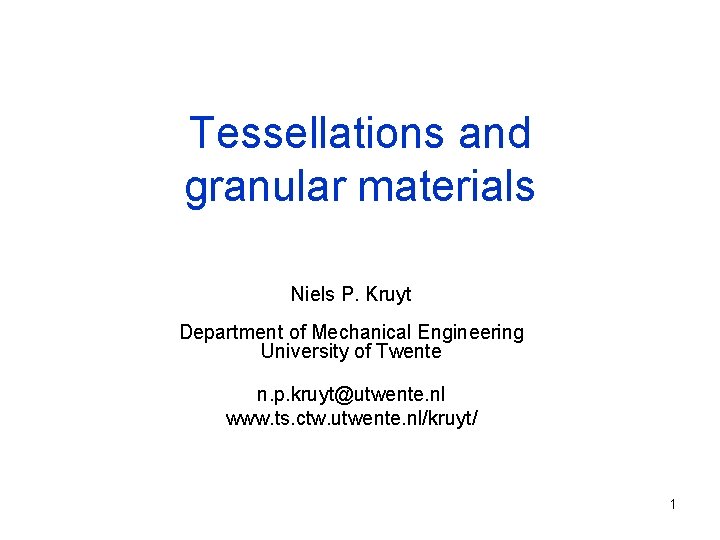
Tessellations and granular materials Niels P. Kruyt Department of Mechanical Engineering University of Twente n. p. kruyt@utwente. nl www. ts. ctw. utwente. nl/kruyt/ 1
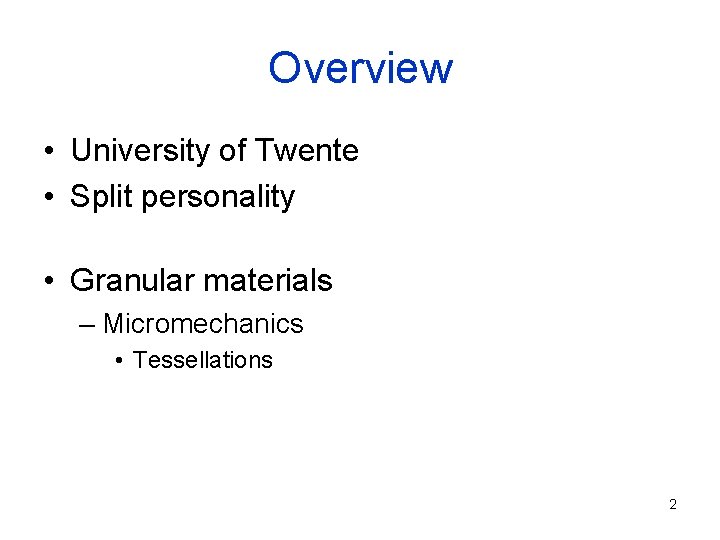
Overview • University of Twente • Split personality • Granular materials – Micromechanics • Tessellations 2
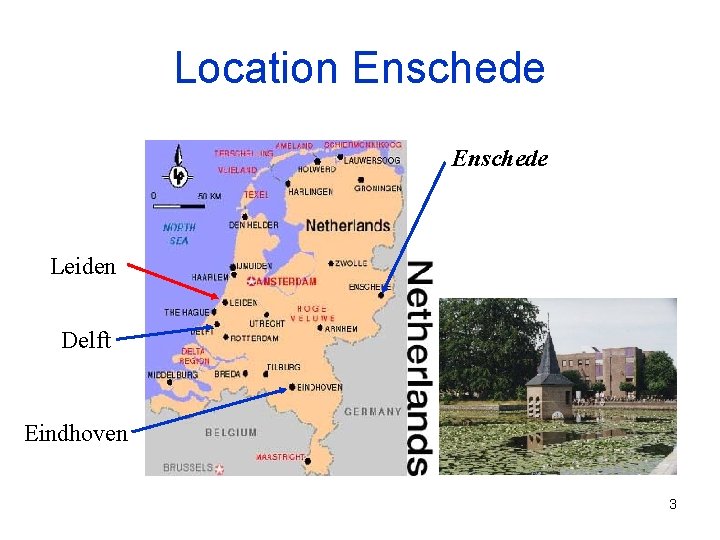
Location Enschede Leiden Delft Eindhoven 3
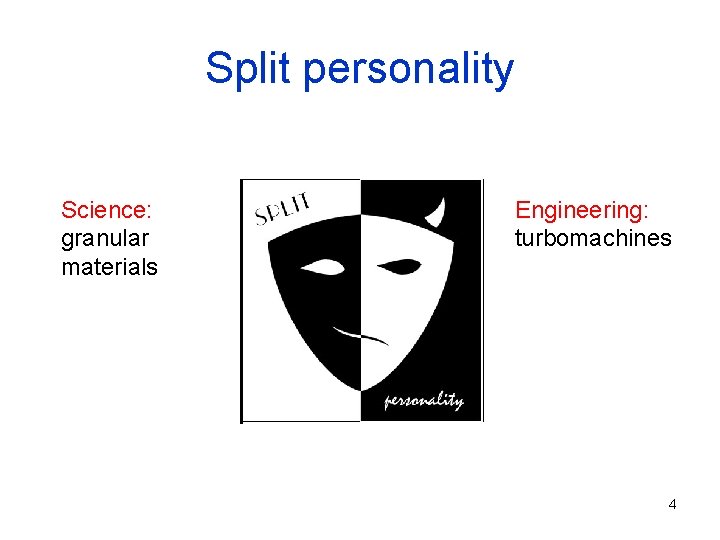
Split personality Science: granular materials Engineering: turbomachines 4
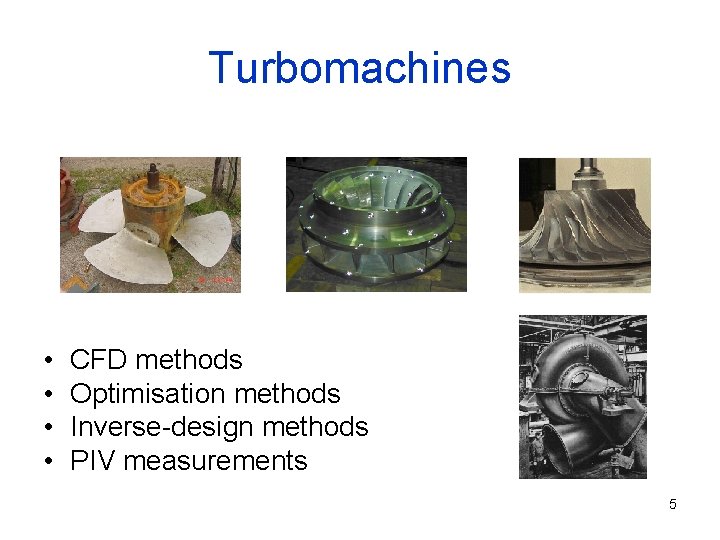
Turbomachines • • CFD methods Optimisation methods Inverse-design methods PIV measurements 5
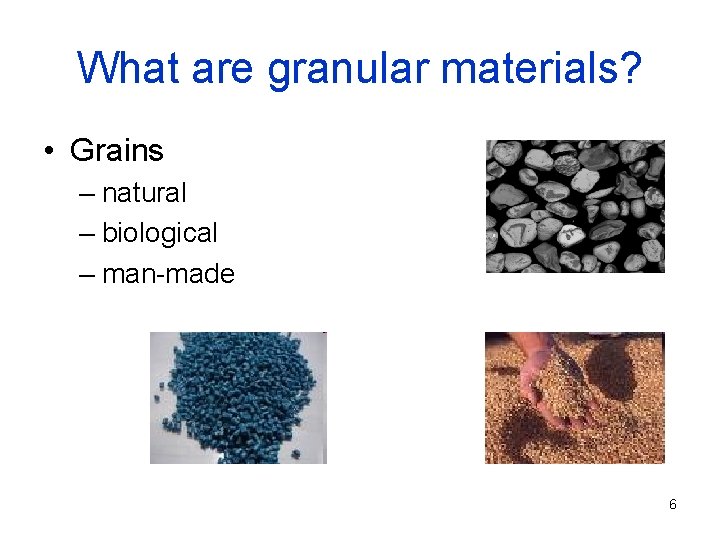
What are granular materials? • Grains – natural – biological – man-made 6
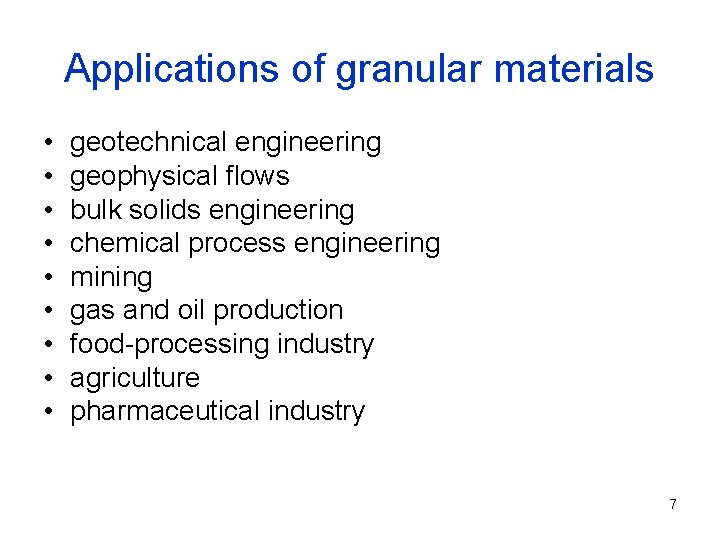
Applications of granular materials • • • geotechnical engineering geophysical flows bulk solids engineering chemical process engineering mining gas and oil production food-processing industry agriculture pharmaceutical industry 7
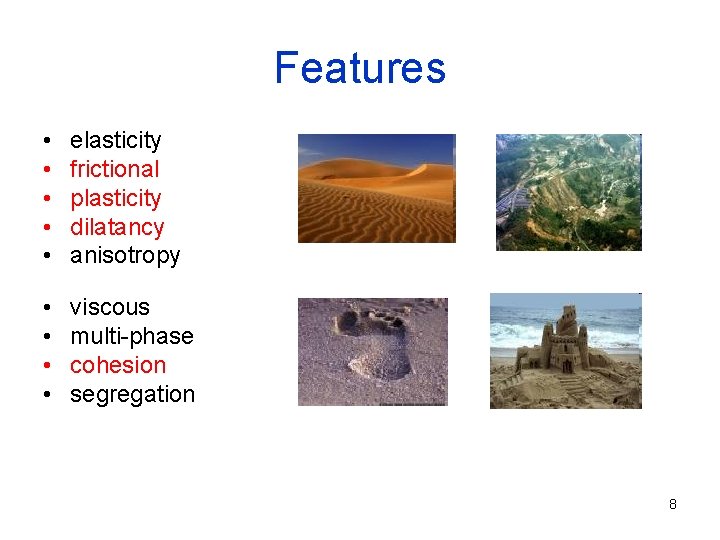
Features • • • elasticity frictional plasticity dilatancy anisotropy • • viscous multi-phase cohesion segregation 8
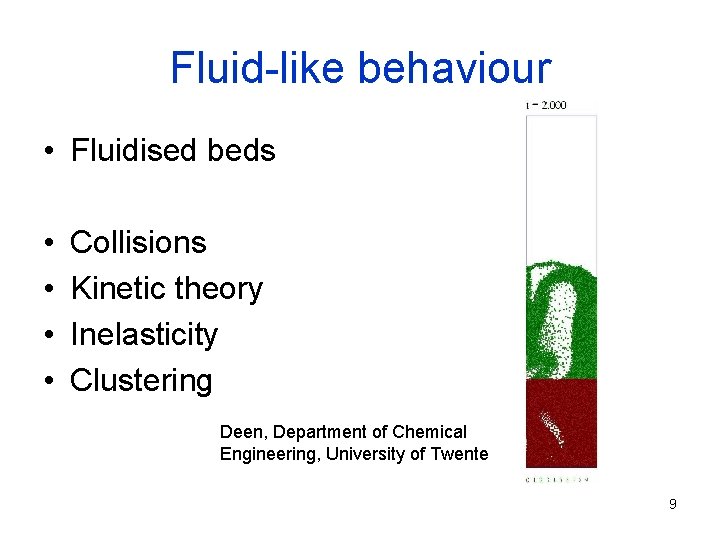
Fluid-like behaviour • Fluidised beds • • Collisions Kinetic theory Inelasticity Clustering Deen, Department of Chemical Engineering, University of Twente 9
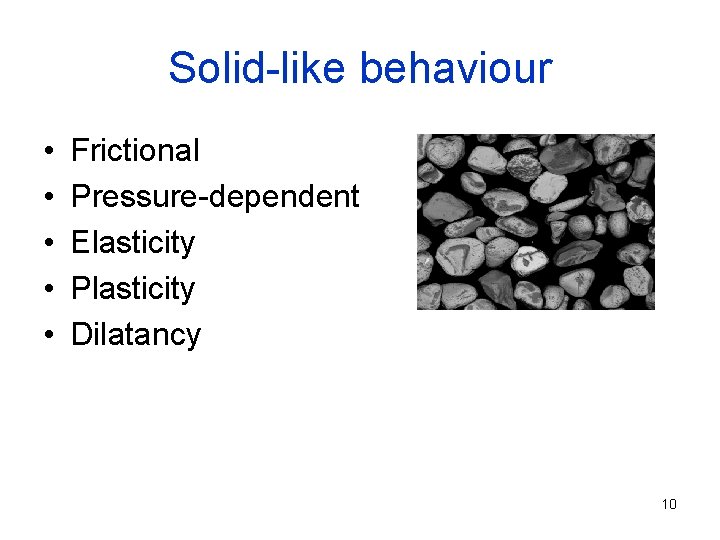
Solid-like behaviour • • • Frictional Pressure-dependent Elasticity Plasticity Dilatancy 10
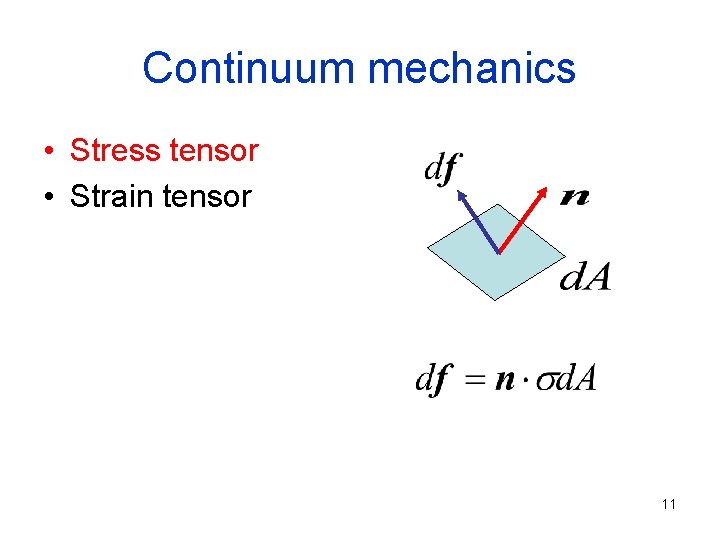
Continuum mechanics • Stress tensor • Strain tensor 11
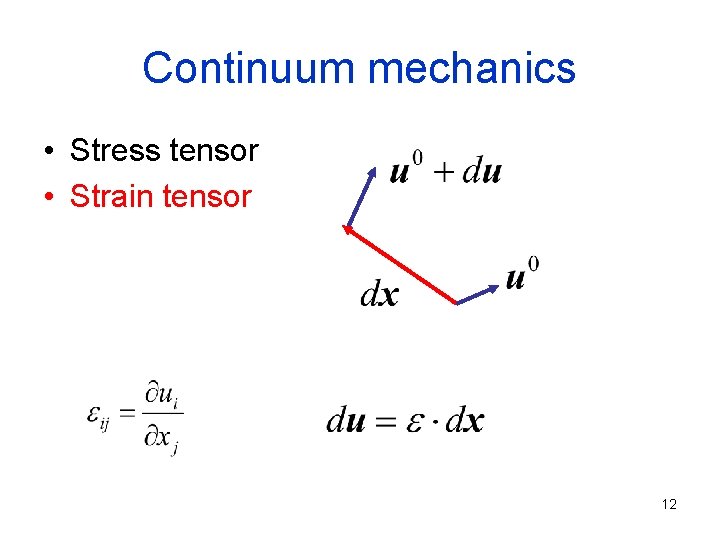
Continuum mechanics • Stress tensor • Strain tensor 12
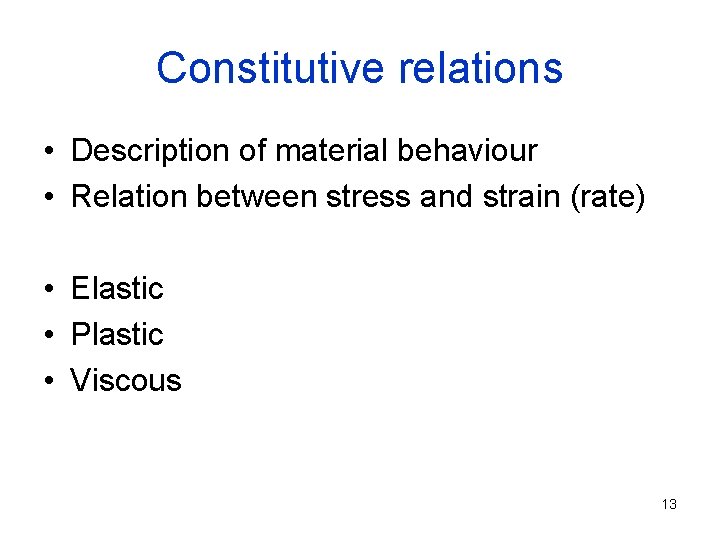
Constitutive relations • Description of material behaviour • Relation between stress and strain (rate) • Elastic • Plastic • Viscous 13
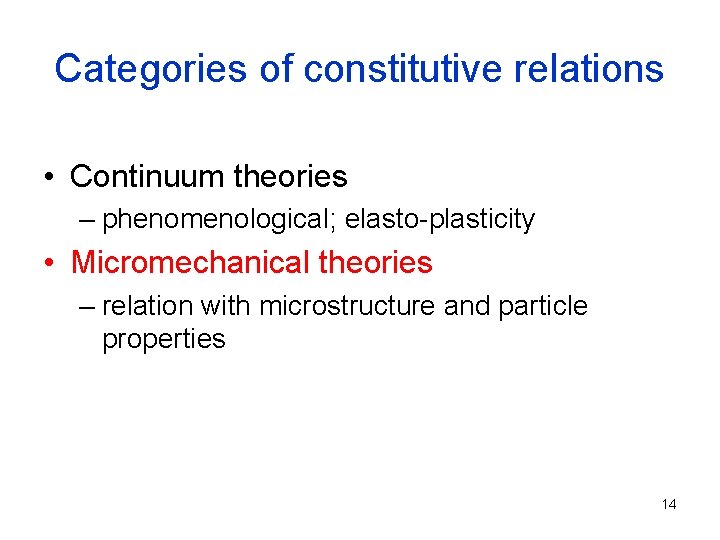
Categories of constitutive relations • Continuum theories – phenomenological; elasto-plasticity • Micromechanical theories – relation with microstructure and particle properties 14
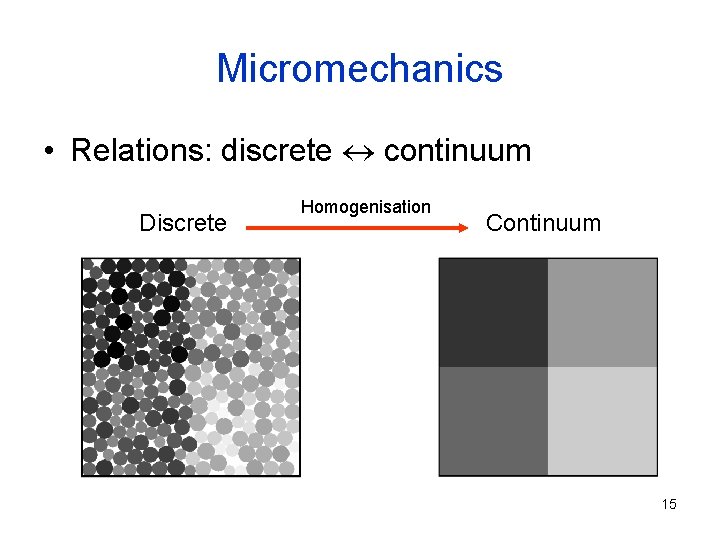
Micromechanics • Relations: discrete « continuum Discrete Homogenisation Continuum 15
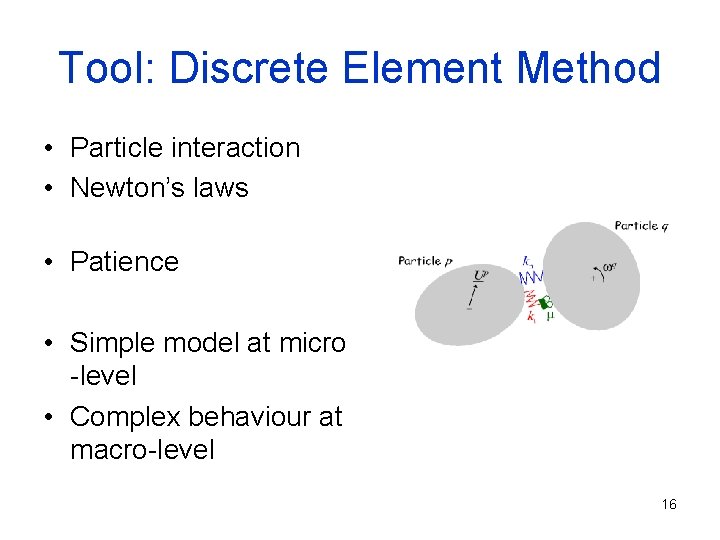
Tool: Discrete Element Method • Particle interaction • Newton’s laws • Patience • Simple model at micro -level • Complex behaviour at macro-level 16
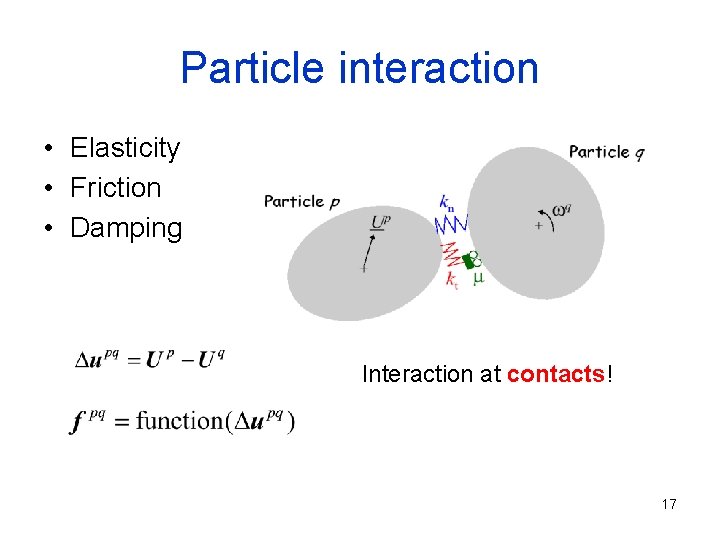
Particle interaction • Elasticity • Friction • Damping Interaction at contacts! 17
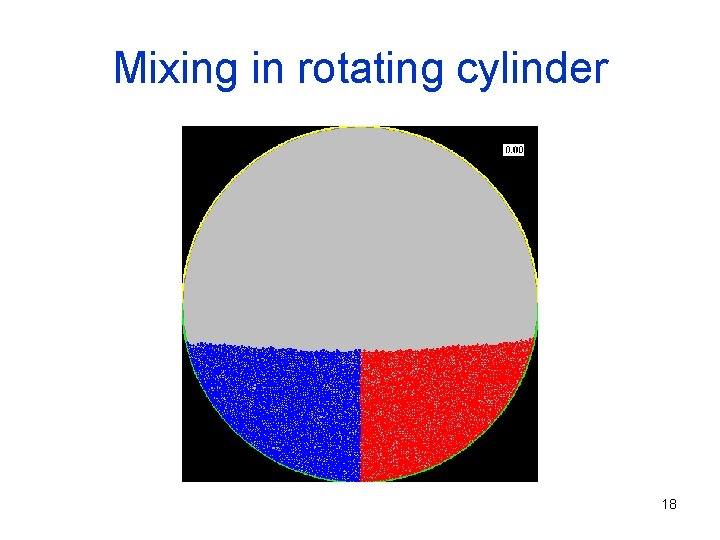
Mixing in rotating cylinder 18
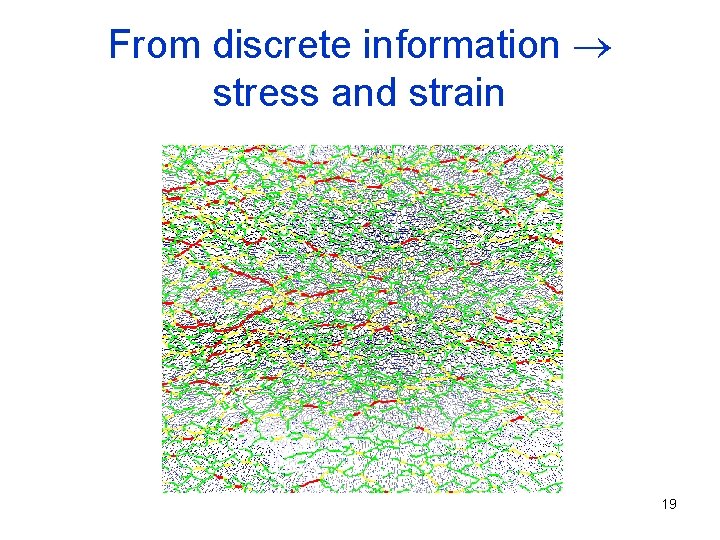
From discrete information ® stress and strain 19
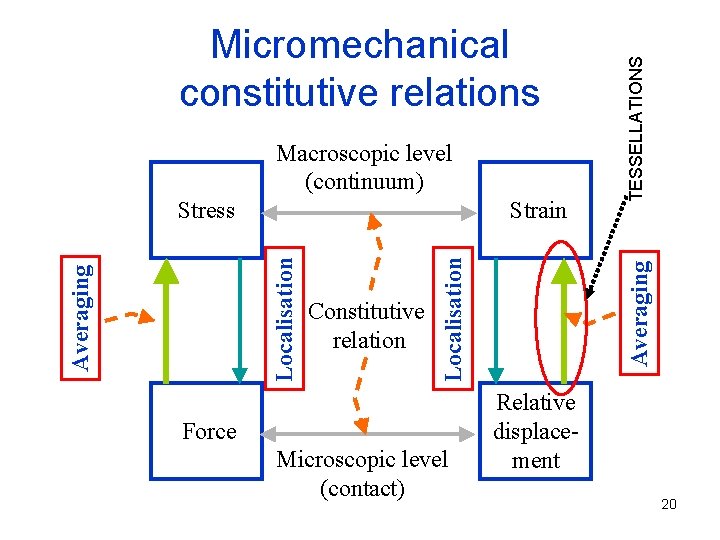
Macroscopic level (continuum) Force Microscopic level (contact) Averaging Constitutive relation Localisation Strain Localisation Stress TESSELLATIONS Micromechanical constitutive relations Relative displacement 20
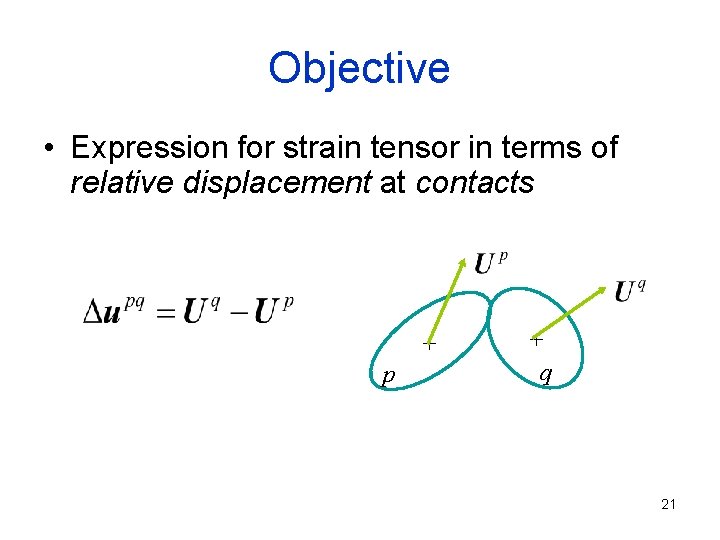
Objective • Expression for strain tensor in terms of relative displacement at contacts + p + q 21
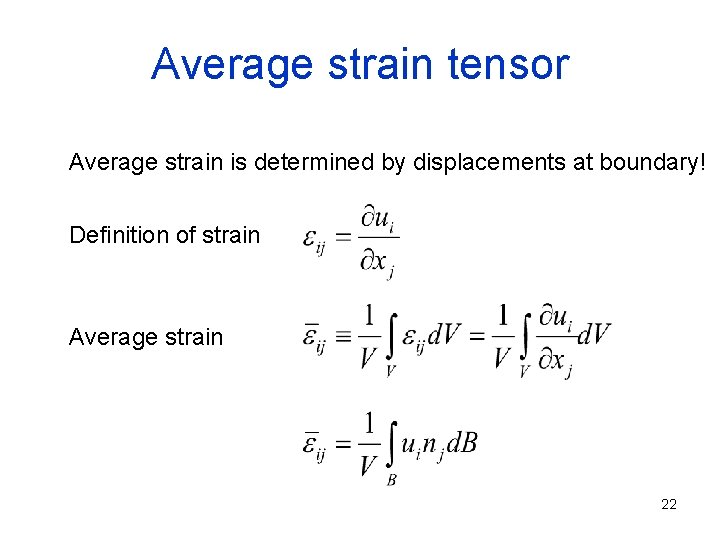
Average strain tensor Average strain is determined by displacements at boundary! Definition of strain Average strain 22
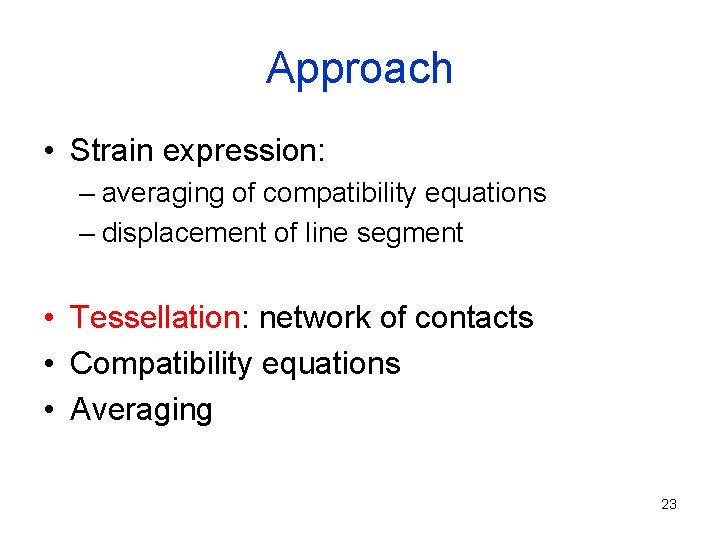
Approach • Strain expression: – averaging of compatibility equations – displacement of line segment • Tessellation: network of contacts • Compatibility equations • Averaging 23
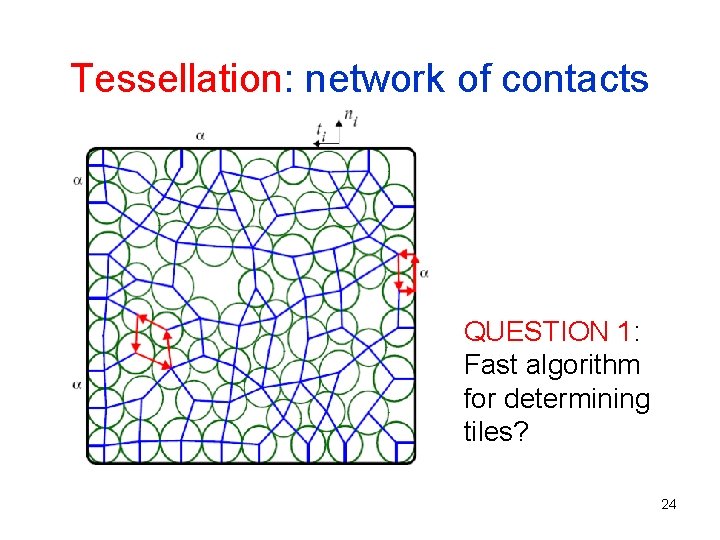
Tessellation: network of contacts QUESTION 1: Fast algorithm for determining tiles? 24
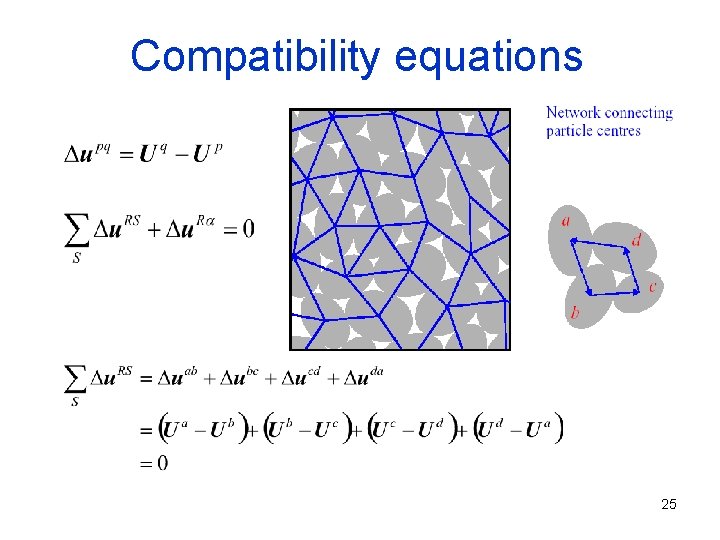
Compatibility equations 25
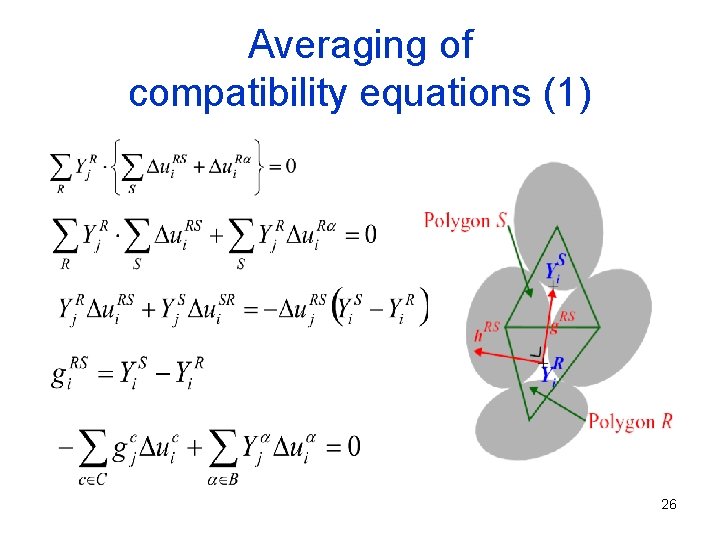
Averaging of compatibility equations (1) 26
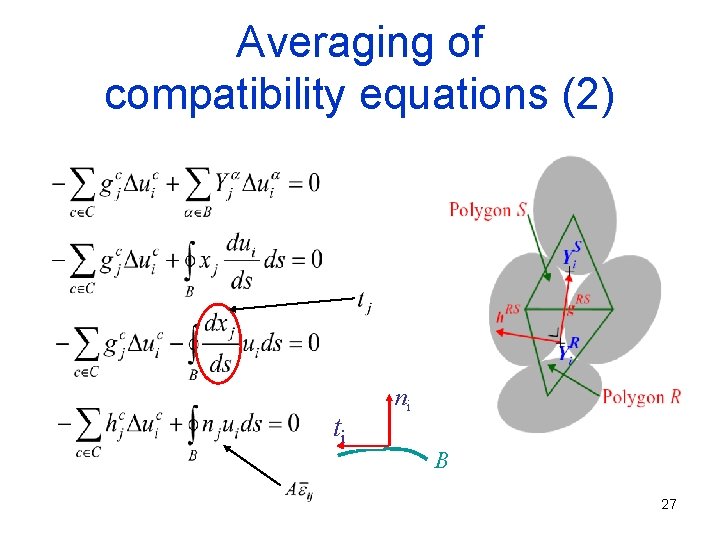
Averaging of compatibility equations (2) ti ni B 27
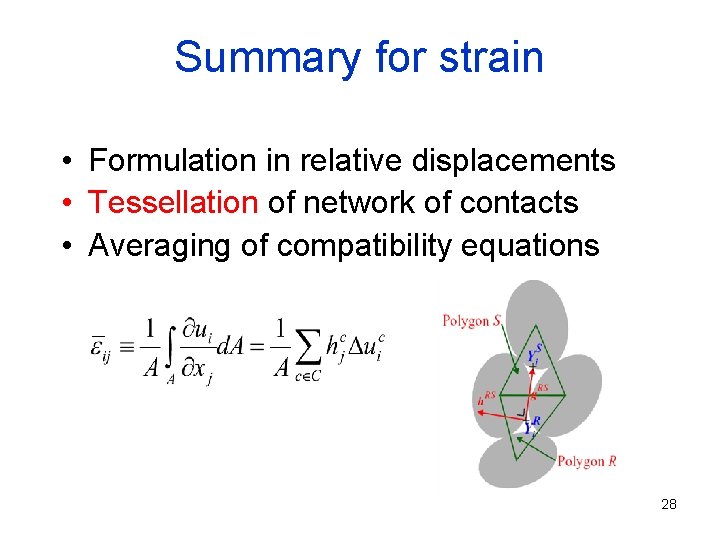
Summary for strain • Formulation in relative displacements • Tessellation of network of contacts • Averaging of compatibility equations 28
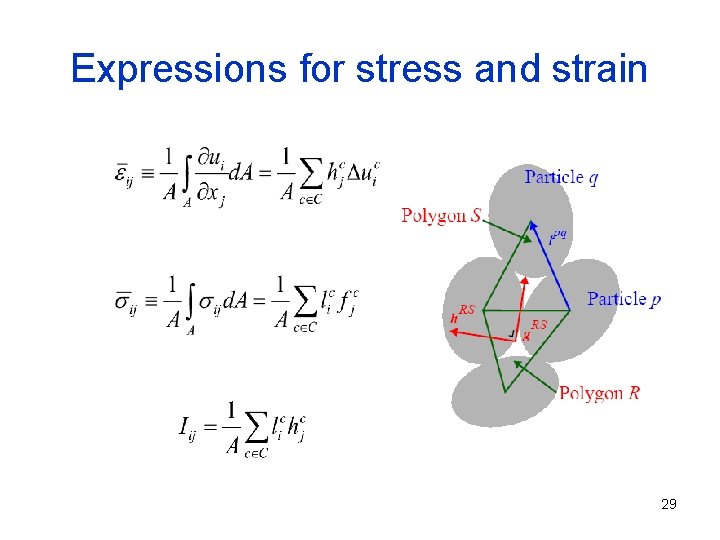
Expressions for stress and strain 29
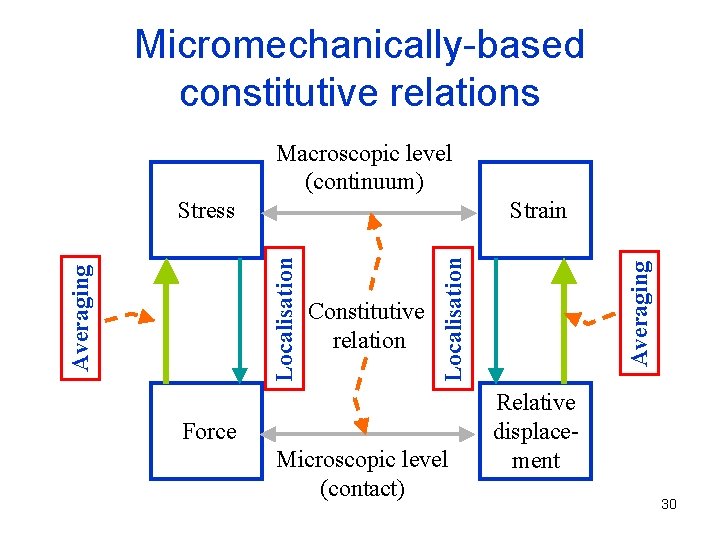
Micromechanically-based constitutive relations Macroscopic level (continuum) Force Microscopic level (contact) Averaging Constitutive relation Localisation Strain Localisation Stress Relative displacement 30
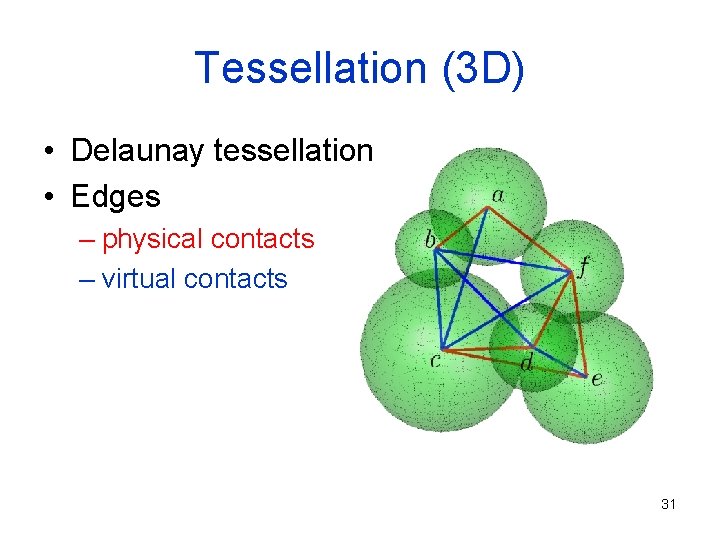
Tessellation (3 D) • Delaunay tessellation • Edges – physical contacts – virtual contacts 31
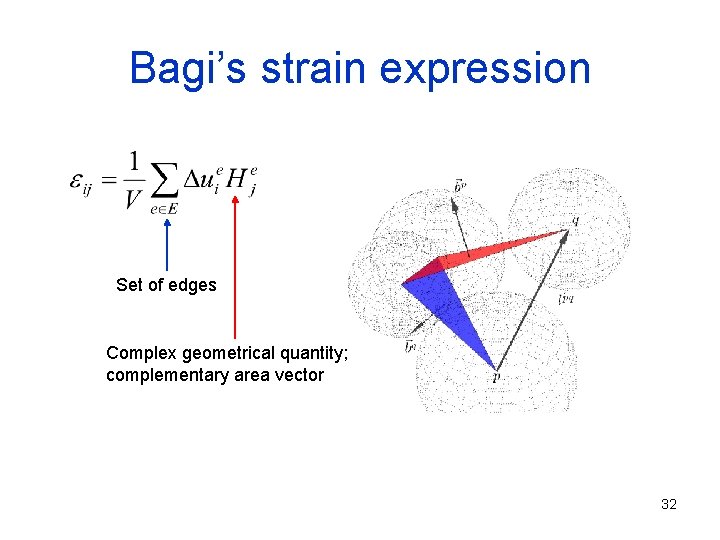
Bagi’s strain expression Set of edges Complex geometrical quantity; complementary area vector 32
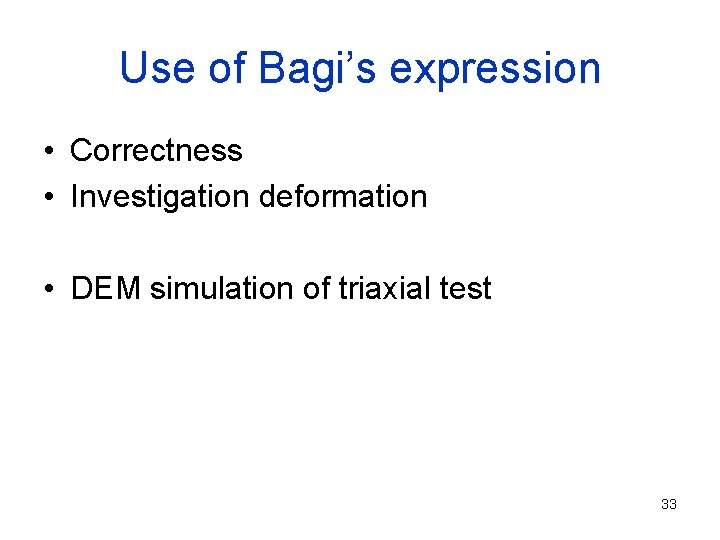
Use of Bagi’s expression • Correctness • Investigation deformation • DEM simulation of triaxial test 33
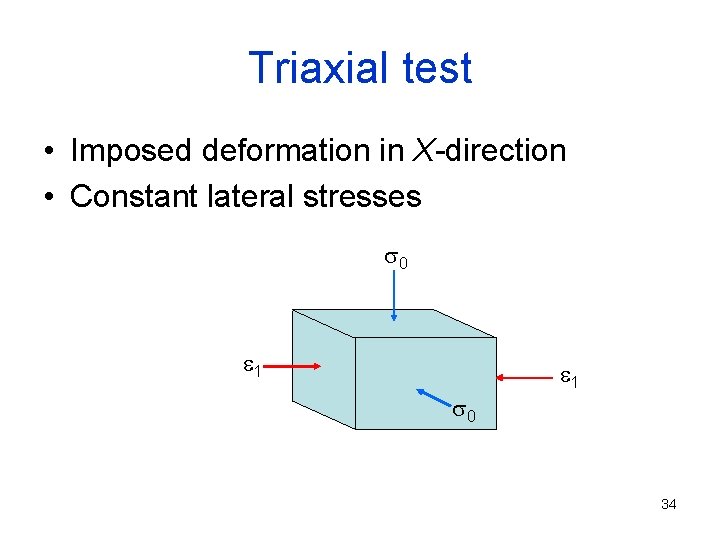
Triaxial test • Imposed deformation in X-direction • Constant lateral stresses s 0 e 1 s 0 34
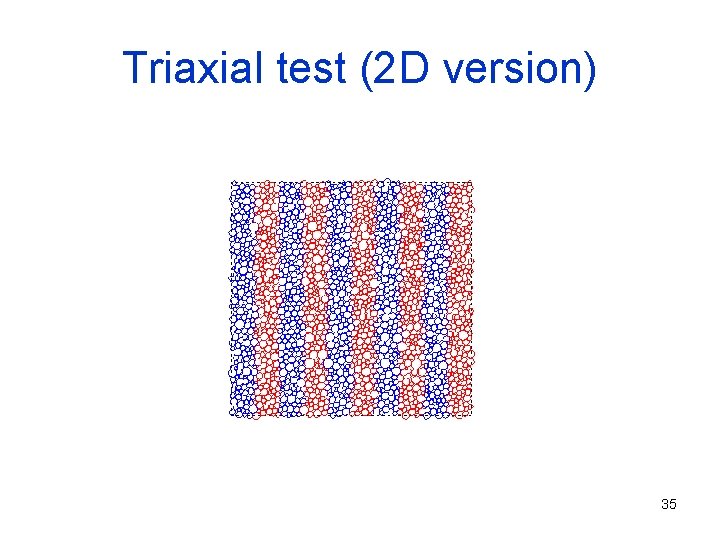
Triaxial test (2 D version) 35
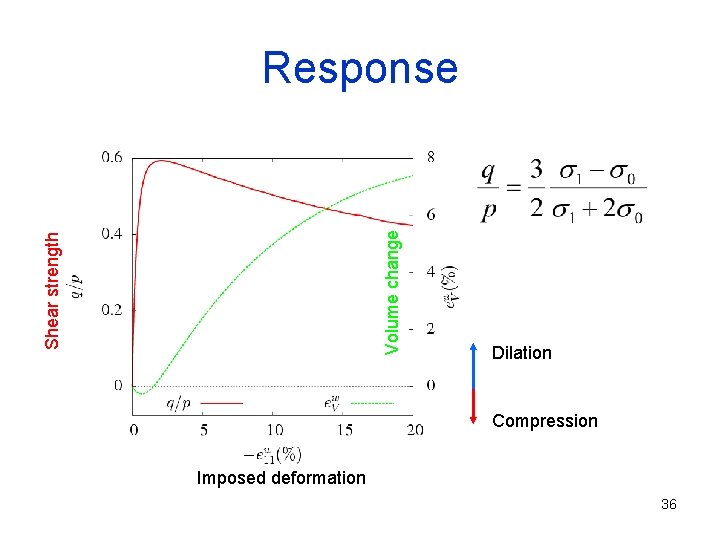
Shear strength Volume change Response Dilation Compression Imposed deformation 36
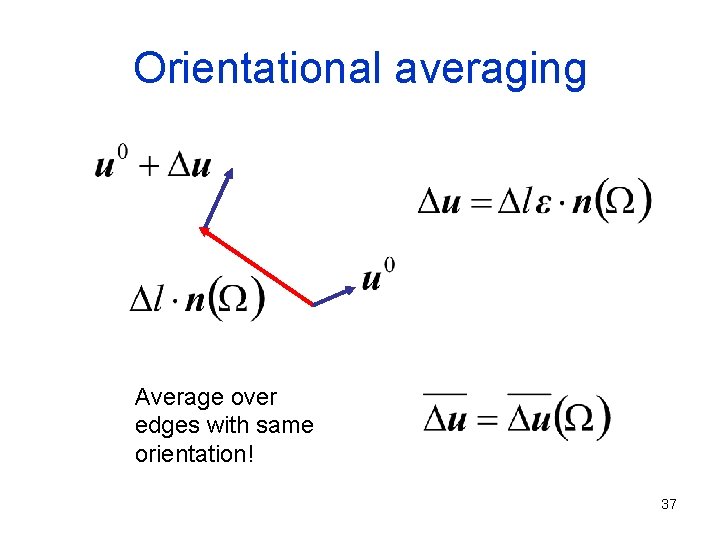
Orientational averaging Average over edges with same orientation! 37
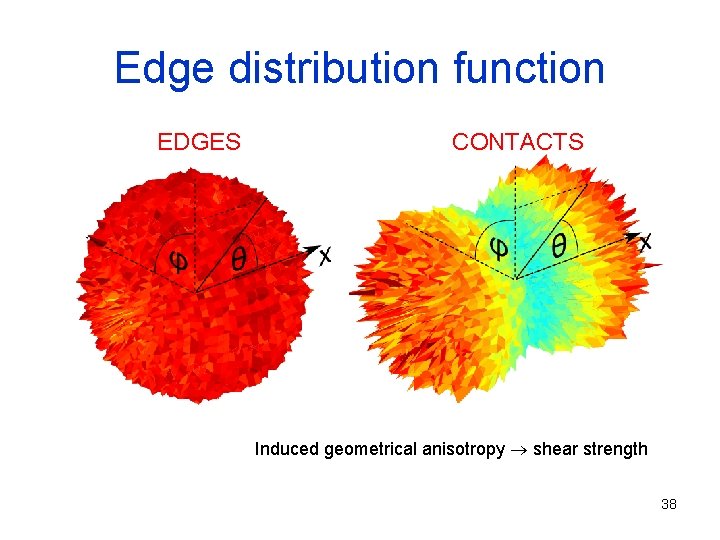
Edge distribution function EDGES CONTACTS Induced geometrical anisotropy ® shear strength 38
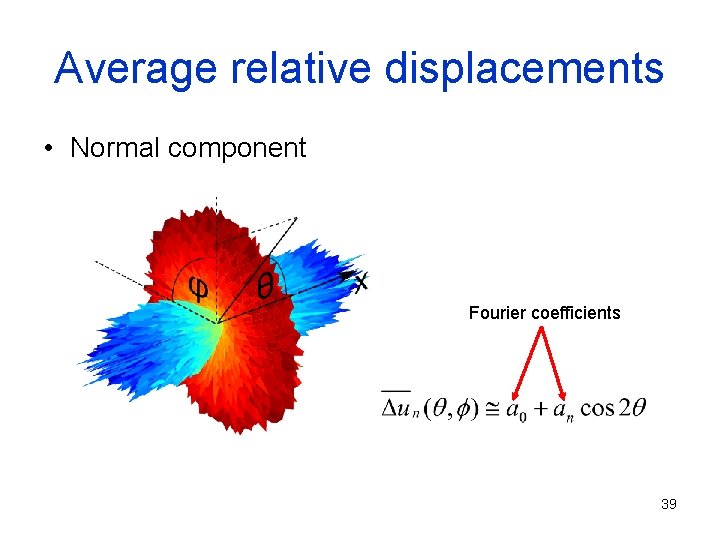
Average relative displacements • Normal component Fourier coefficients 39
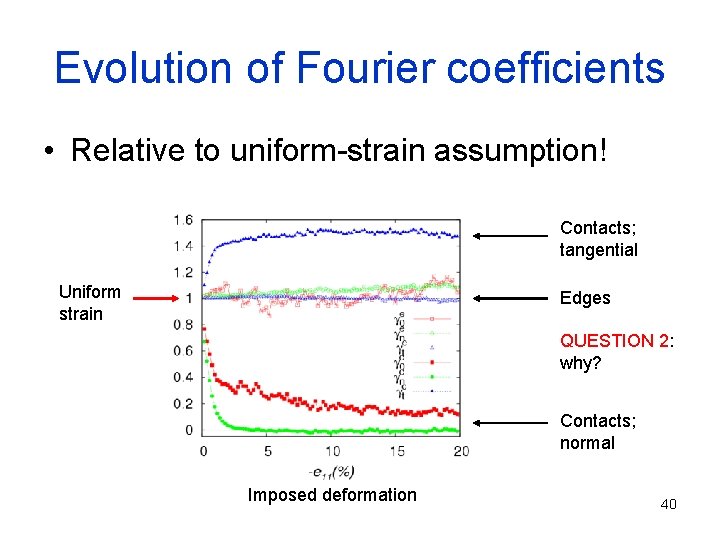
Evolution of Fourier coefficients • Relative to uniform-strain assumption! Contacts; tangential Uniform strain Edges QUESTION 2: why? Contacts; normal Imposed deformation 40
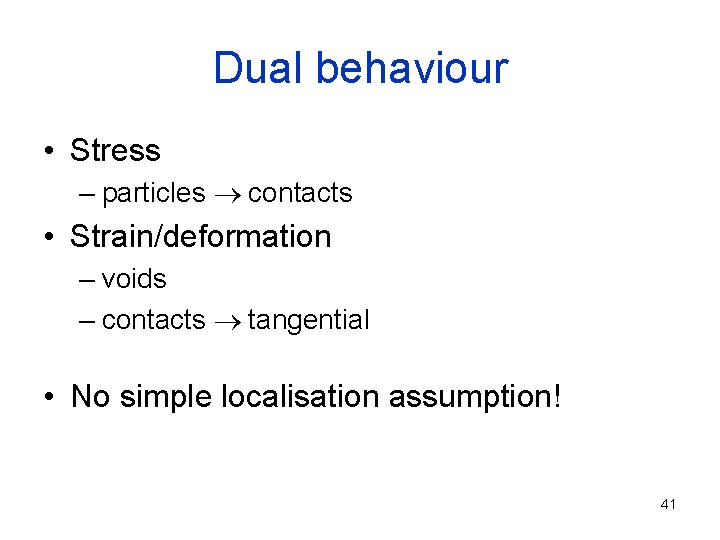
Dual behaviour • Stress – particles ® contacts • Strain/deformation – voids – contacts ® tangential • No simple localisation assumption! 41
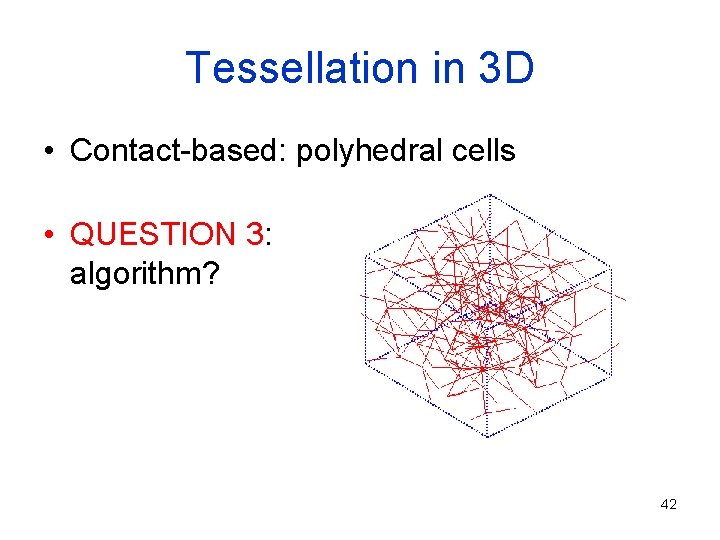
Tessellation in 3 D • Contact-based: polyhedral cells • QUESTION 3: algorithm? 42
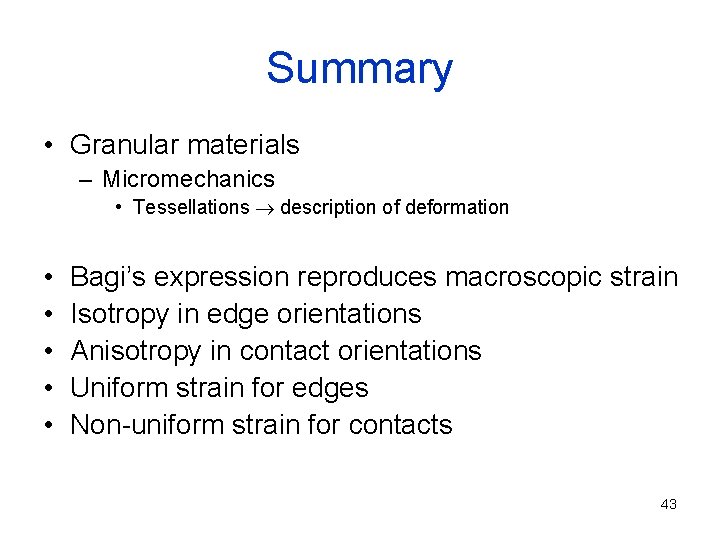
Summary • Granular materials – Micromechanics • Tessellations ® description of deformation • • • Bagi’s expression reproduces macroscopic strain Isotropy in edge orientations Anisotropy in contact orientations Uniform strain for edges Non-uniform strain for contacts 43
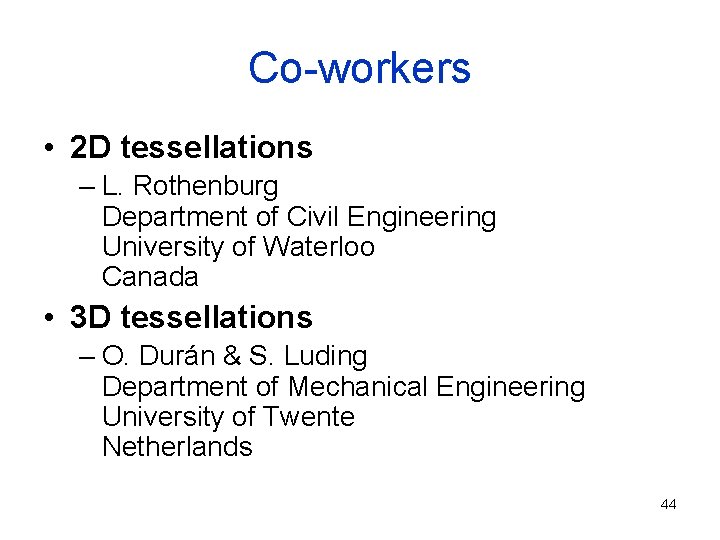
Co-workers • 2 D tessellations – L. Rothenburg Department of Civil Engineering University of Waterloo Canada • 3 D tessellations – O. Durán & S. Luding Department of Mechanical Engineering University of Twente Netherlands 44
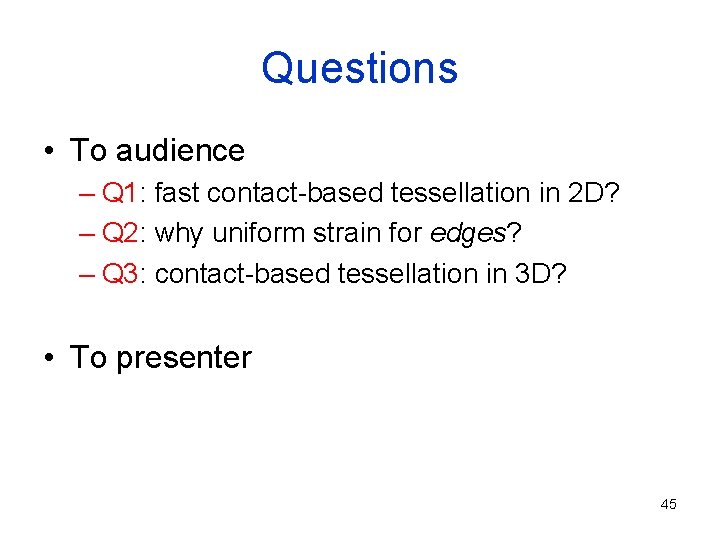
Questions • To audience – Q 1: fast contact-based tessellation in 2 D? – Q 2: why uniform strain for edges? – Q 3: contact-based tessellation in 3 D? • To presenter 45
Niels kruyt
Types of tessellations
How to name a tessellation
Father of tessellation
Escher ghosts
Examples of tessellations in nature
Agranular and granular leukocytes
Agranular and granular leukocytes
Wbc cast
Estructura angular del suelo
Granular bed filter
Tomes granular layer
Contraction porosity denture
Examples of granules drugs
Quantization error formula
Burke plummer equation
Pure data granular
Mekanika tanah 1
High endothelial venules
Megacariocito granular
Porosity in denture base resins
Bentuk struktur tanah
Slit diaphragm
Pulse code modulation
Granular synthesis
Eacademics.iitd
Natural materials
Useful and harmful materials at home examples
Man made map
Differentiate adopting materials and adapting materials
Materials department
Four basic needs of material management
Materials department
Direct materials budget with multiple materials
Niels kooijman
Kriminallitteratur særemne
Niels veldman
Niels provos
Neil bohr contribution to atomic theory
Hendrik abel
Niels bohr (1913)
Modelo atomico actual creador
Niels bohr 1913
Gambar model atom niels bohr
Julius thomsens plads 6
Niels fuglsang phd