Saving Water in the CIP Process in the
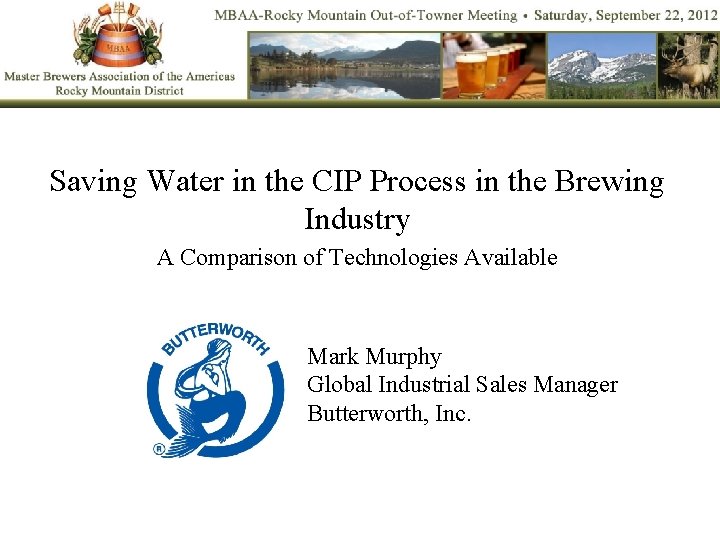
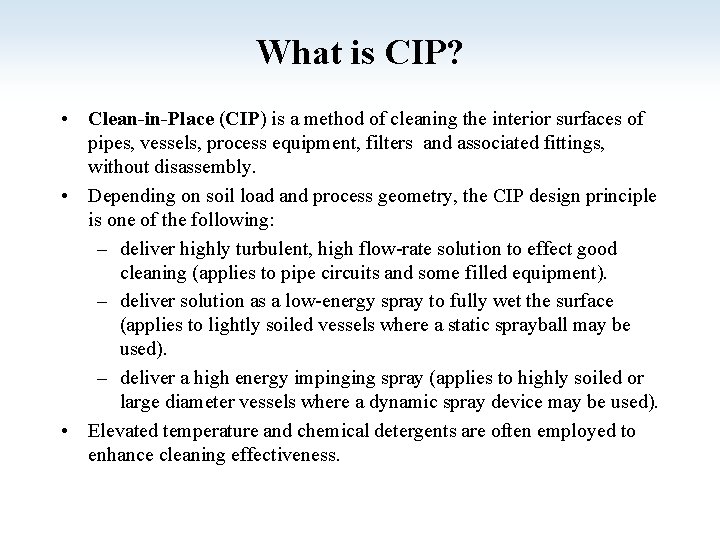
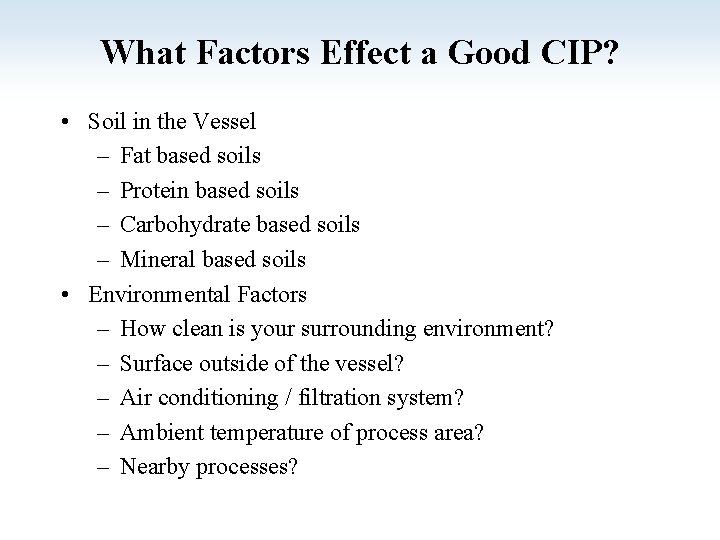
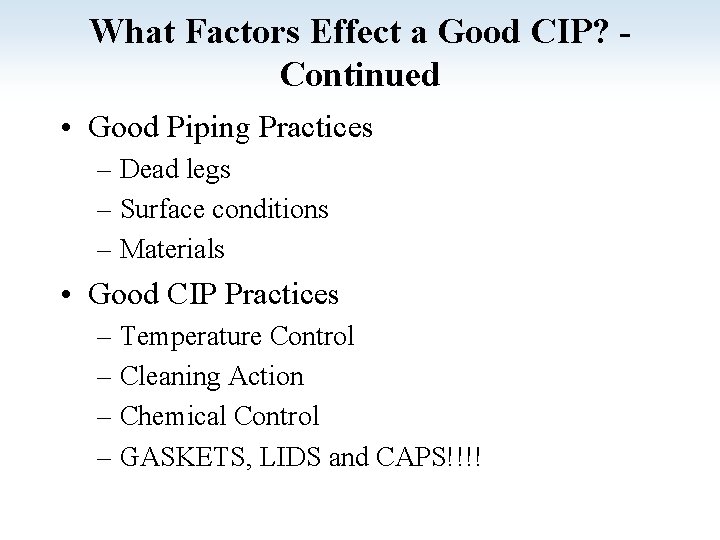
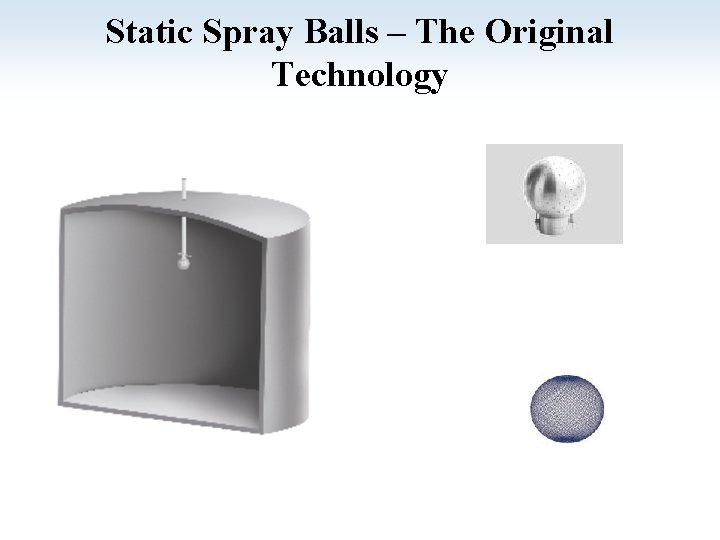
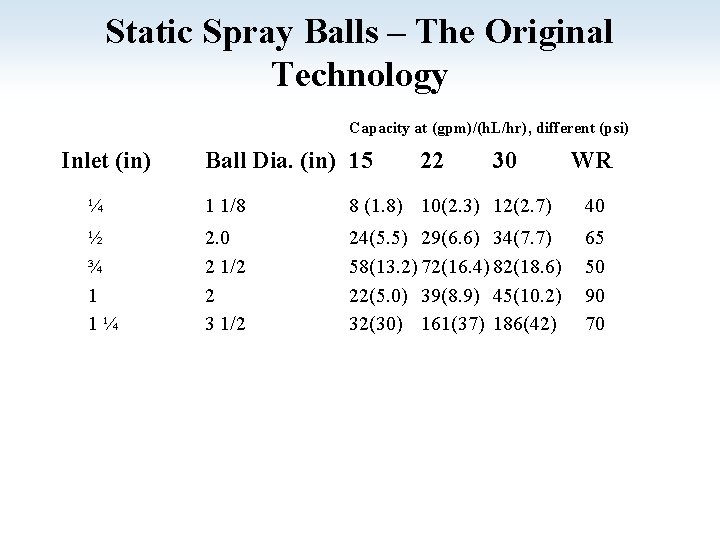

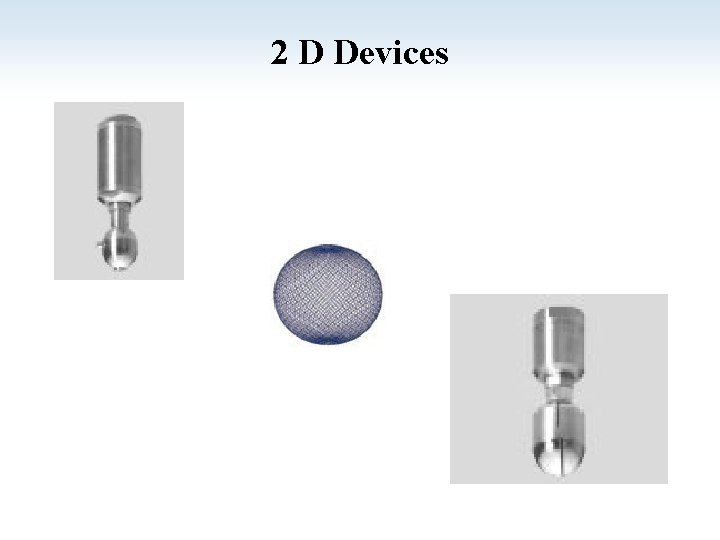


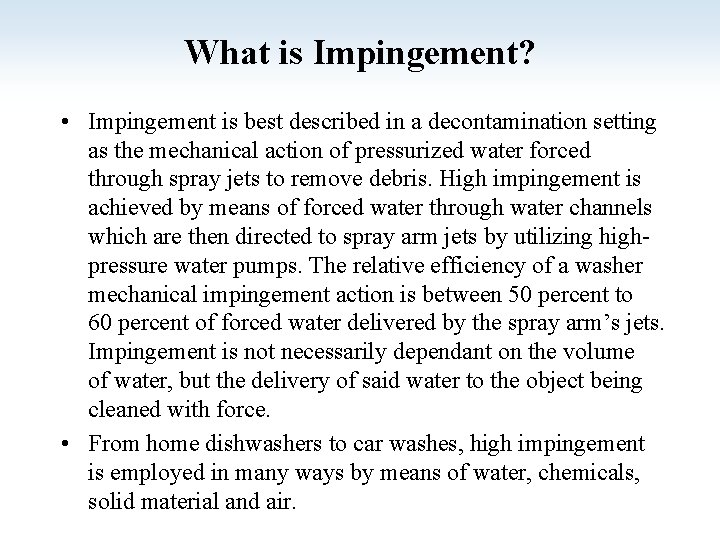
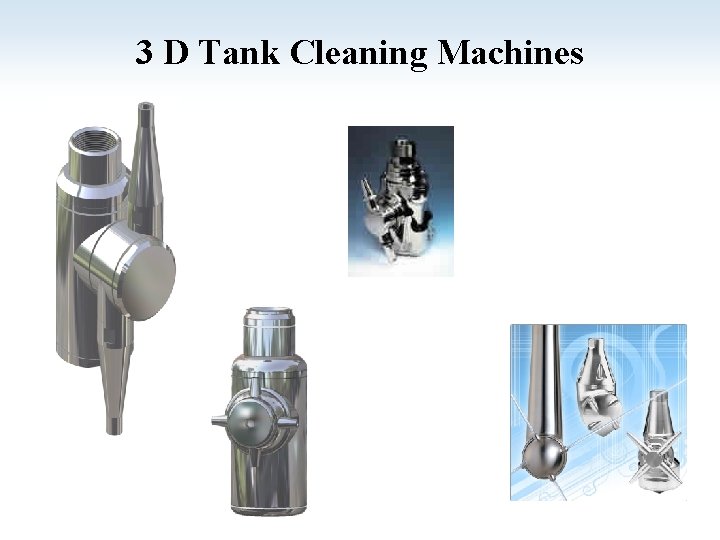
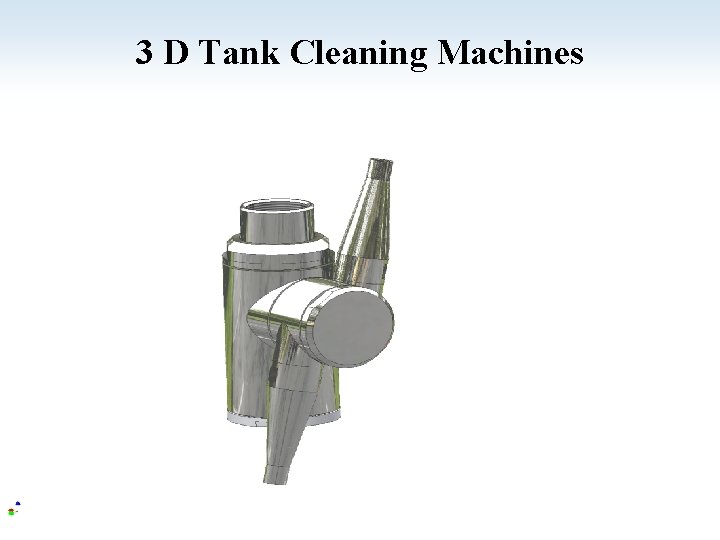
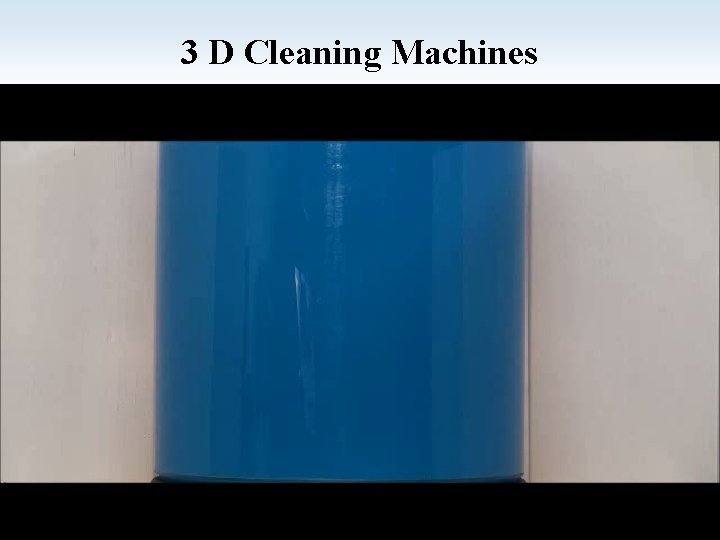
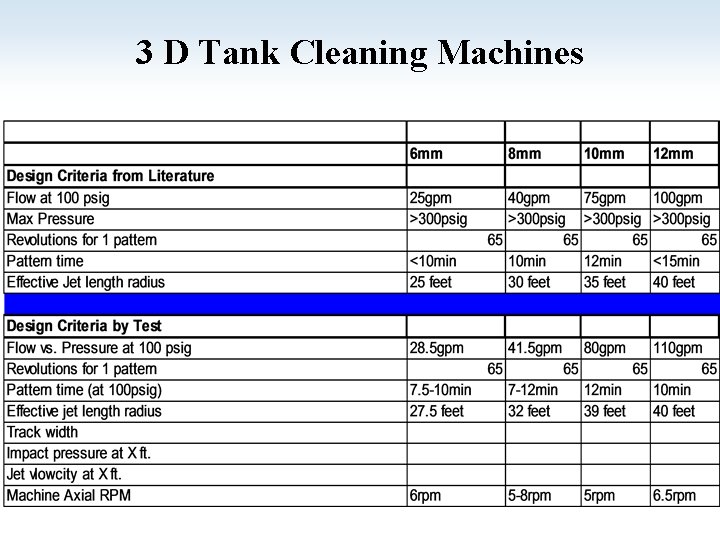
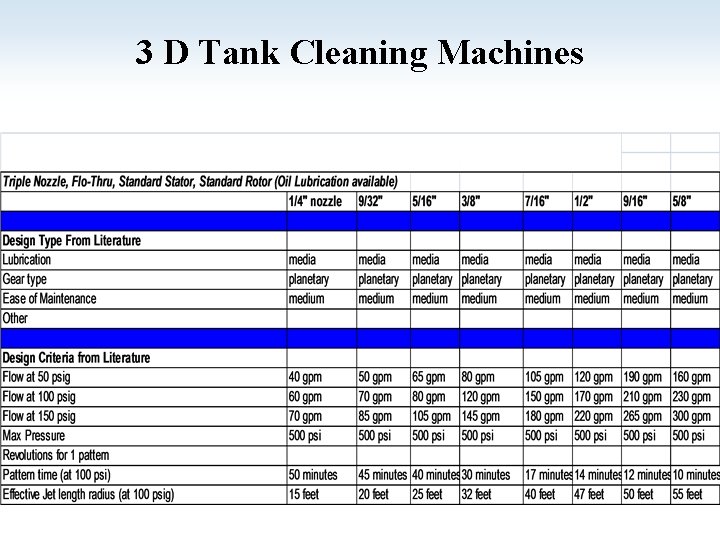
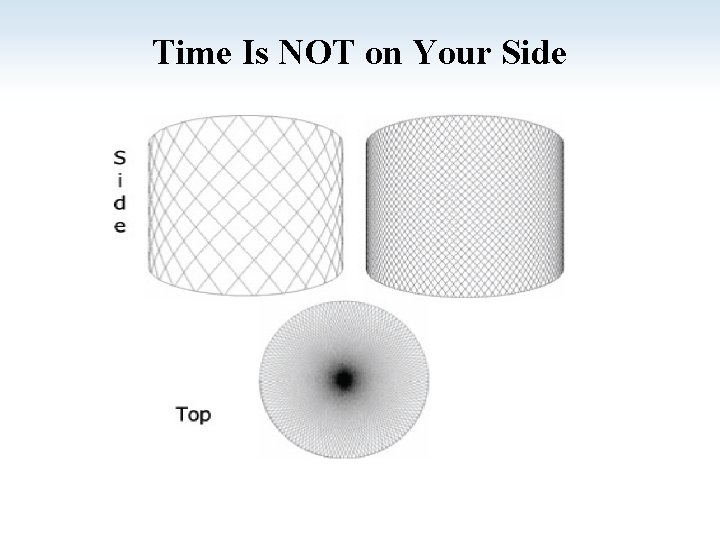
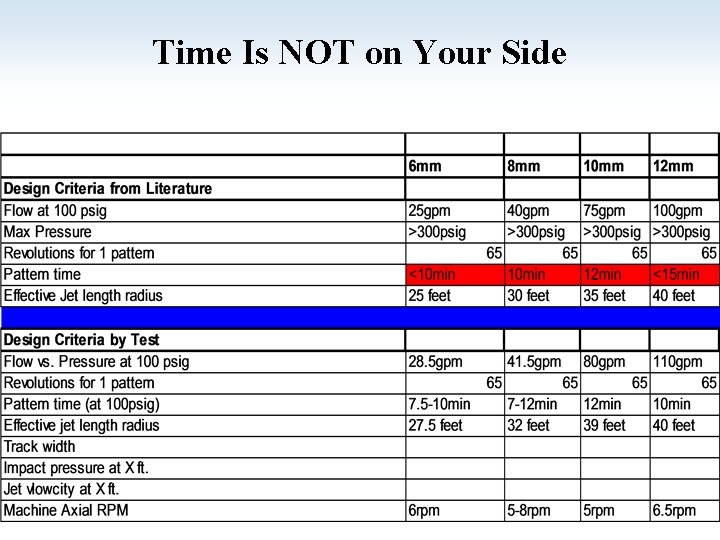
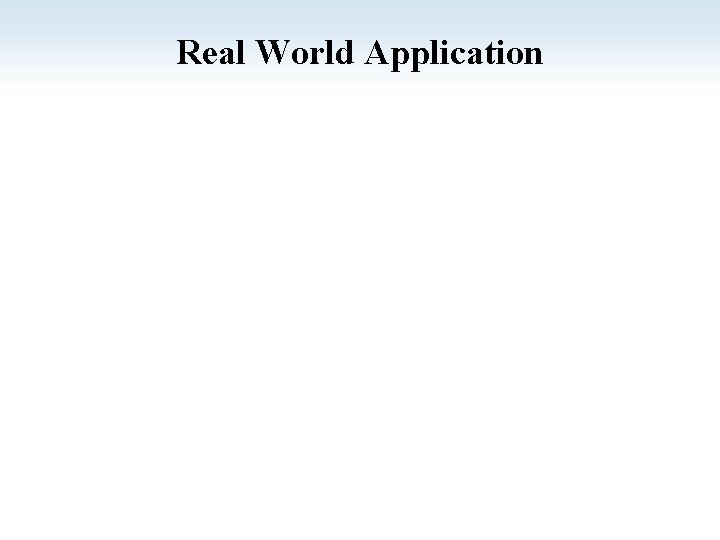
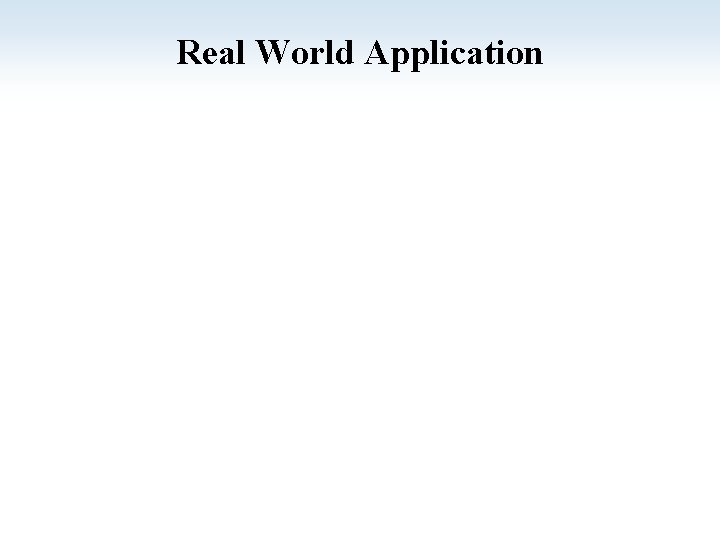
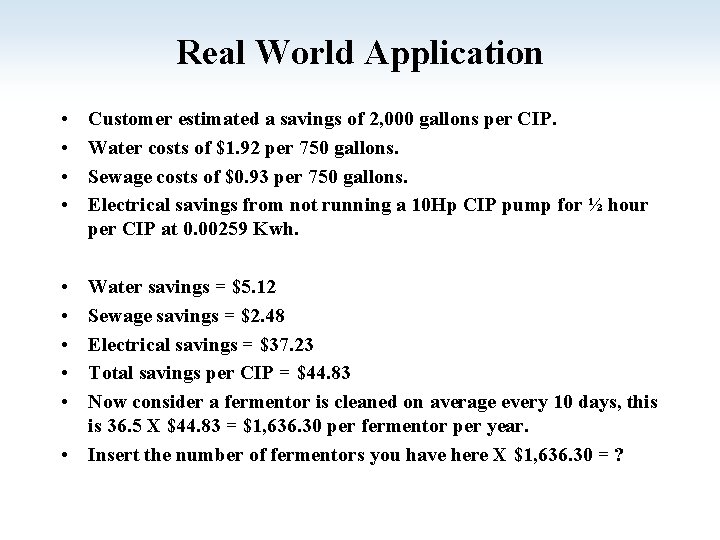
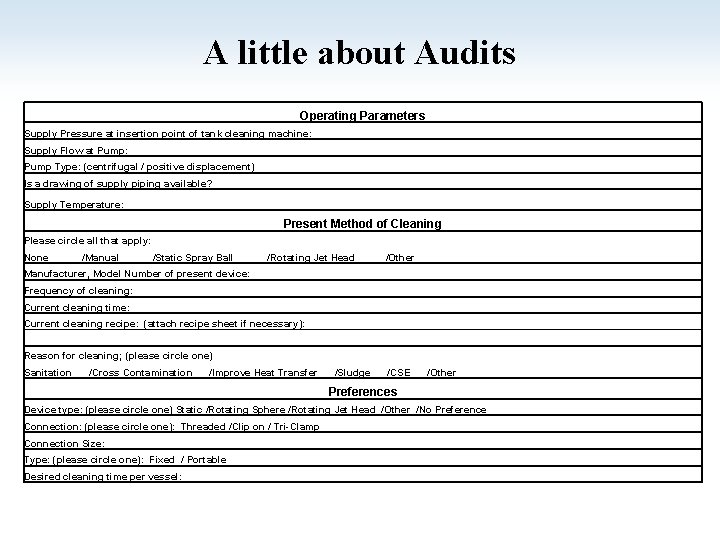
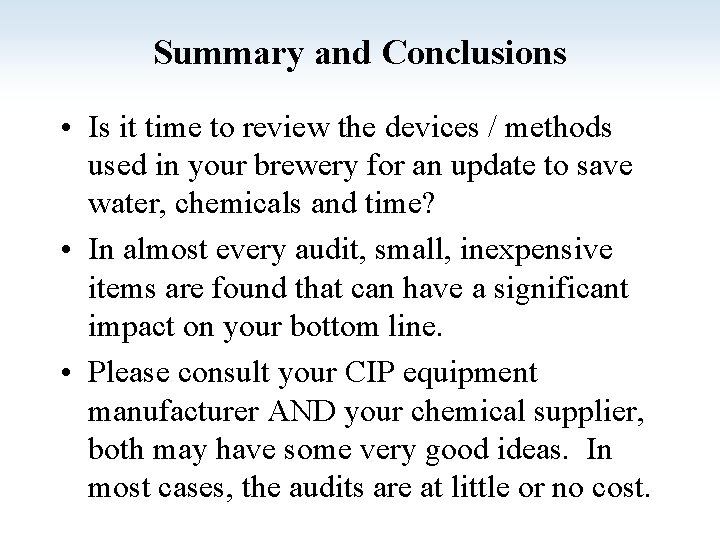
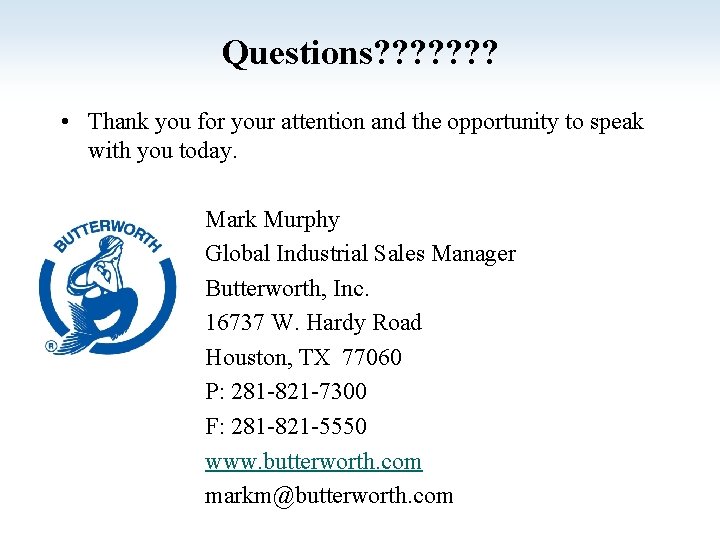
- Slides: 24
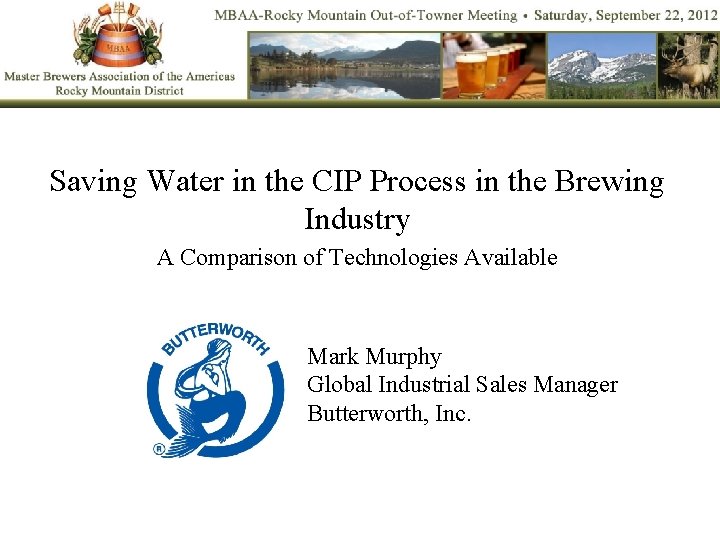
Saving Water in the CIP Process in the Brewing Industry A Comparison of Technologies Available Mark Murphy Global Industrial Sales Manager Butterworth, Inc.
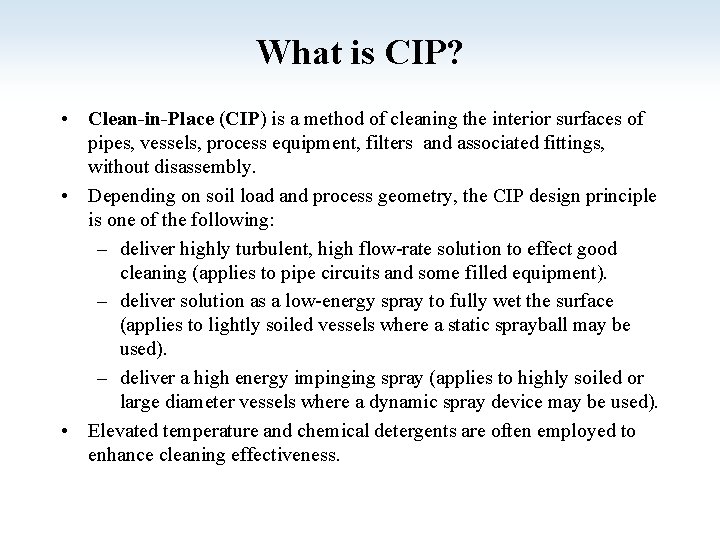
What is CIP? • Clean-in-Place (CIP) is a method of cleaning the interior surfaces of pipes, vessels, process equipment, filters and associated fittings, without disassembly. • Depending on soil load and process geometry, the CIP design principle is one of the following: – deliver highly turbulent, high flow-rate solution to effect good cleaning (applies to pipe circuits and some filled equipment). – deliver solution as a low-energy spray to fully wet the surface (applies to lightly soiled vessels where a static sprayball may be used). – deliver a high energy impinging spray (applies to highly soiled or large diameter vessels where a dynamic spray device may be used). • Elevated temperature and chemical detergents are often employed to enhance cleaning effectiveness.
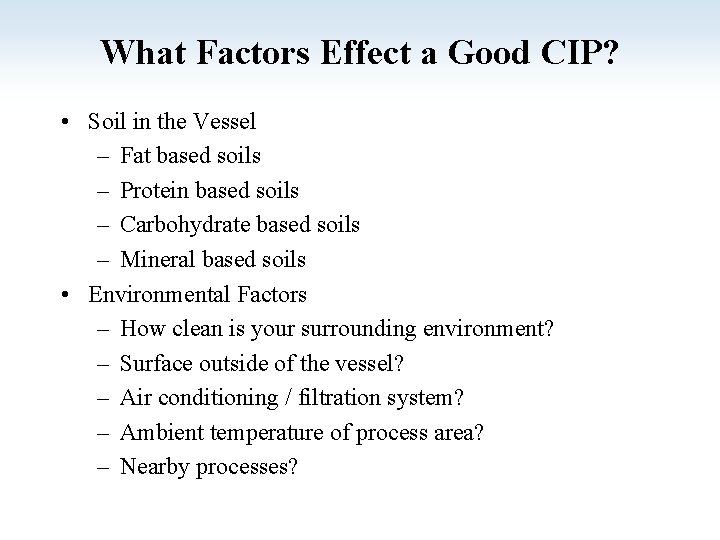
What Factors Effect a Good CIP? • Soil in the Vessel – Fat based soils – Protein based soils – Carbohydrate based soils – Mineral based soils • Environmental Factors – How clean is your surrounding environment? – Surface outside of the vessel? – Air conditioning / filtration system? – Ambient temperature of process area? – Nearby processes?
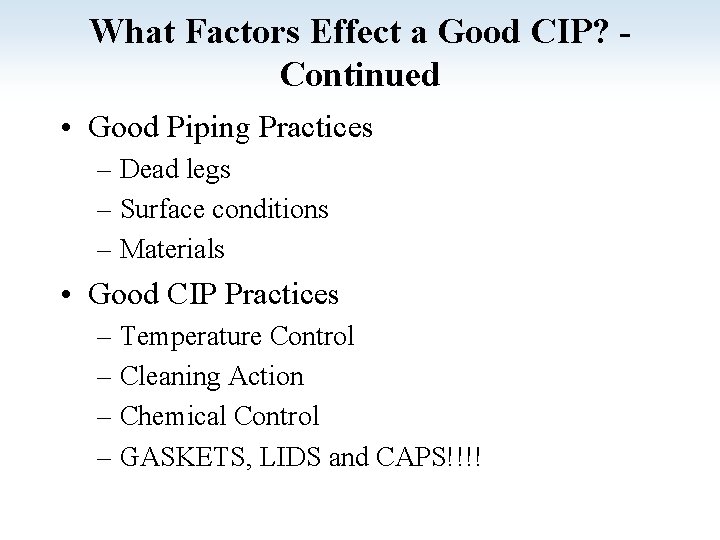
What Factors Effect a Good CIP? Continued • Good Piping Practices – Dead legs – Surface conditions – Materials • Good CIP Practices – Temperature Control – Cleaning Action – Chemical Control – GASKETS, LIDS and CAPS!!!!
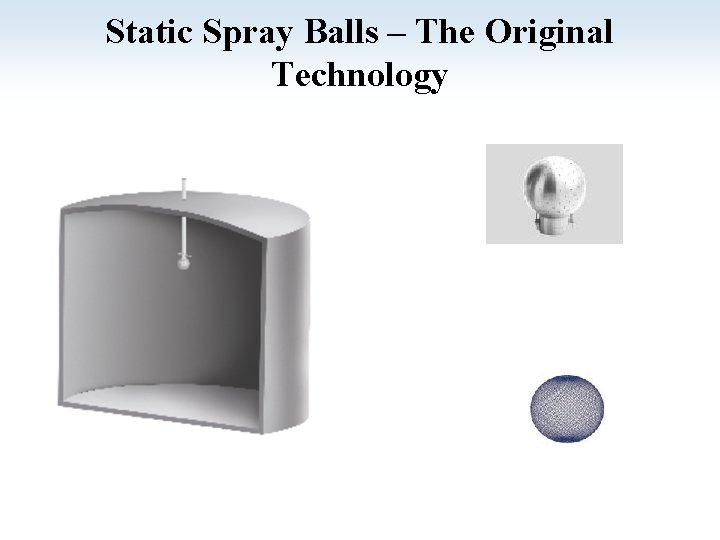
Static Spray Balls – The Original Technology
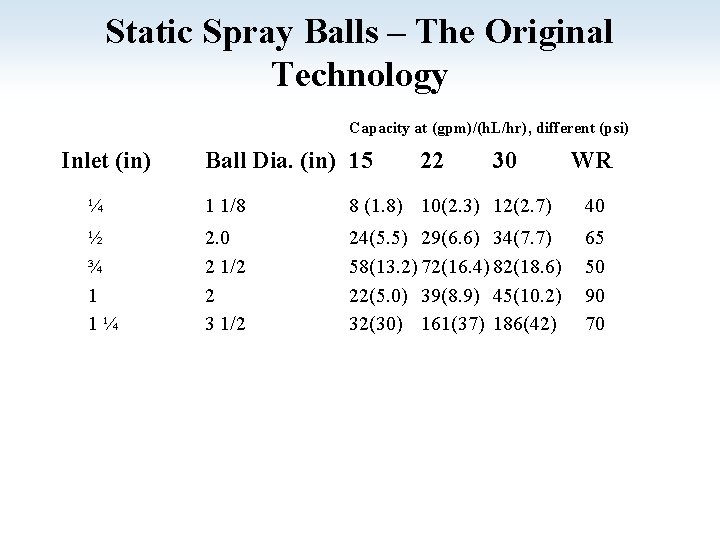
Static Spray Balls – The Original Technology Capacity at (gpm)/(h. L/hr), different (psi) Inlet (in) Ball Dia. (in) 15 22 30 WR ¼ 1 1/8 8 (1. 8) 10(2. 3) 12(2. 7) 40 ½ ¾ 1 1¼ 2. 0 2 1/2 2 3 1/2 24(5. 5) 29(6. 6) 34(7. 7) 58(13. 2) 72(16. 4) 82(18. 6) 22(5. 0) 39(8. 9) 45(10. 2) 32(30) 161(37) 186(42) 65 50 90 70

Static Spray Ball
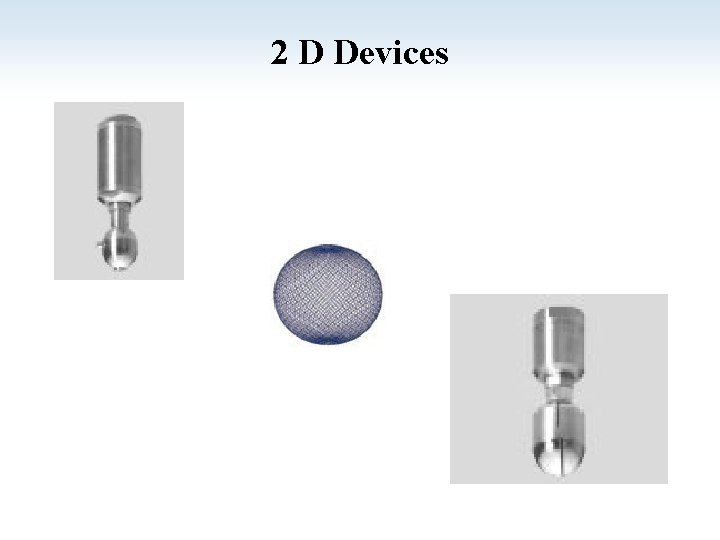
2 D Devices

2 D Devices

2 Dimensional Devices
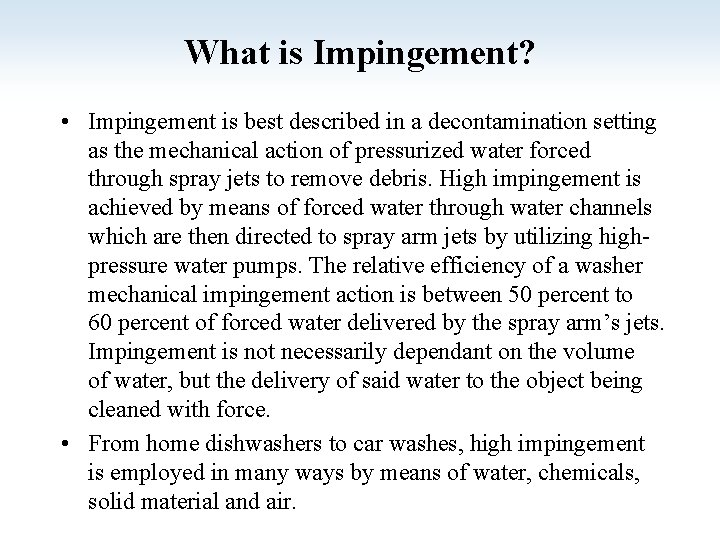
What is Impingement? • Impingement is best described in a decontamination setting as the mechanical action of pressurized water forced through spray jets to remove debris. High impingement is achieved by means of forced water through water channels which are then directed to spray arm jets by utilizing highpressure water pumps. The relative efficiency of a washer mechanical impingement action is between 50 percent to 60 percent of forced water delivered by the spray arm’s jets. Impingement is not necessarily dependant on the volume of water, but the delivery of said water to the object being cleaned with force. • From home dishwashers to car washes, high impingement is employed in many ways by means of water, chemicals, solid material and air.
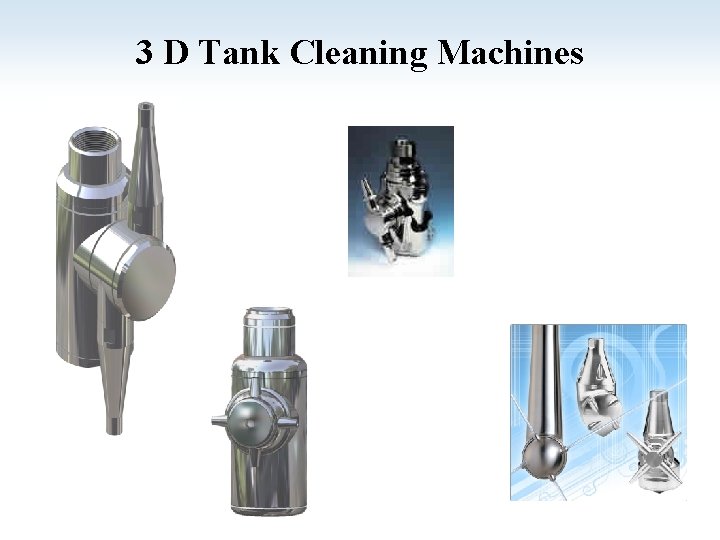
3 D Tank Cleaning Machines
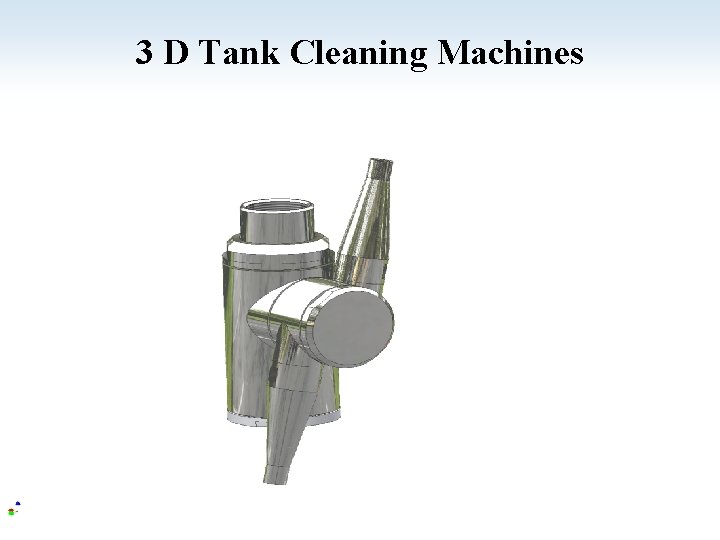
3 D Tank Cleaning Machines
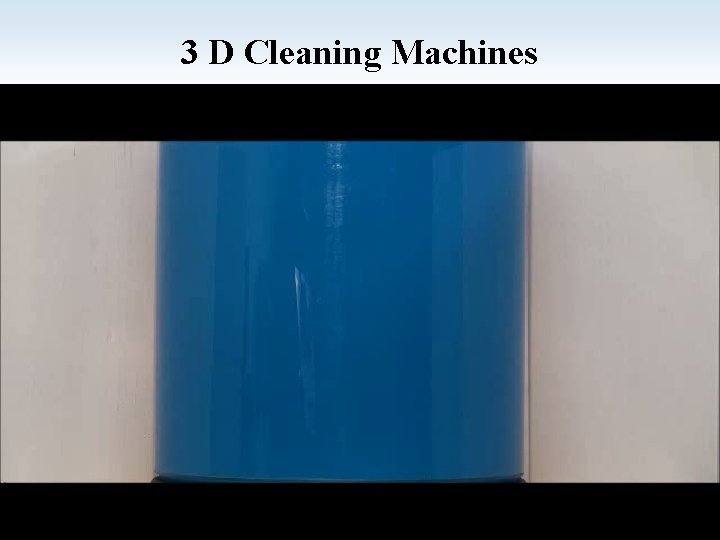
3 D Cleaning Machines
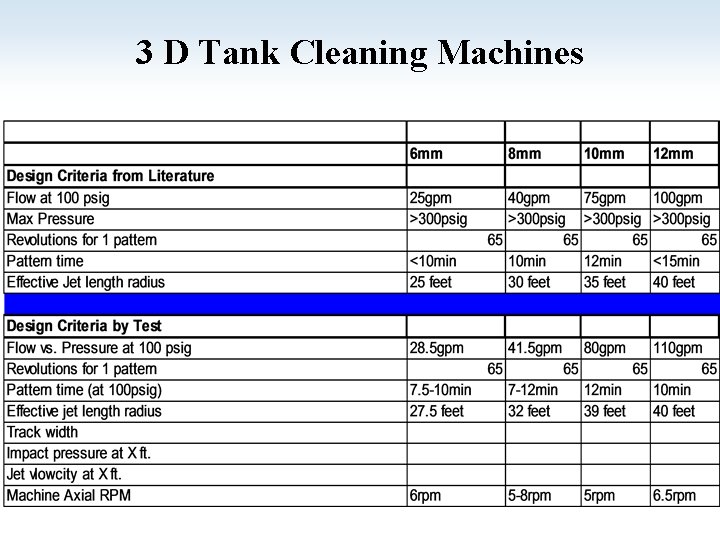
3 D Tank Cleaning Machines
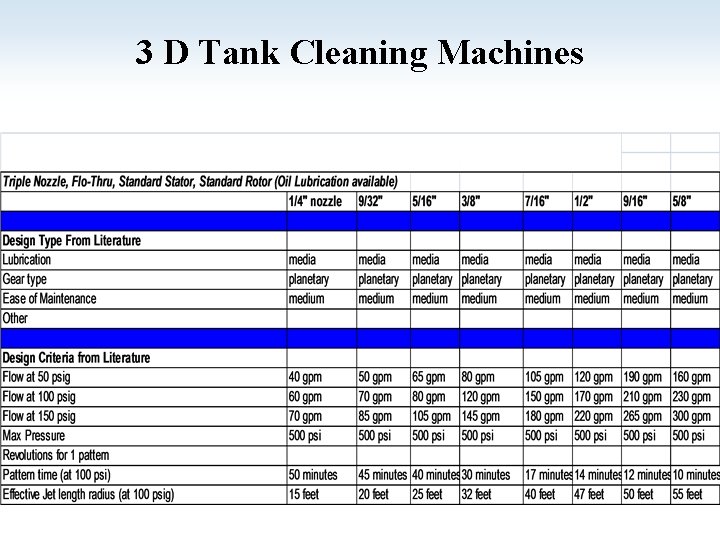
3 D Tank Cleaning Machines
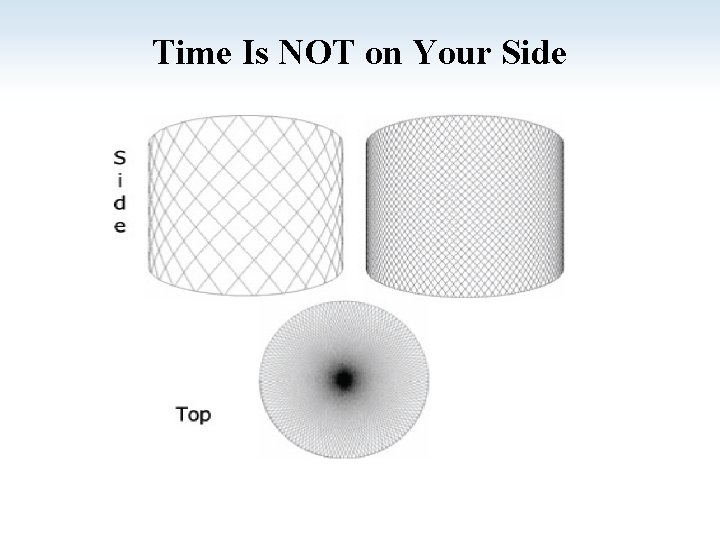
Time Is NOT on Your Side
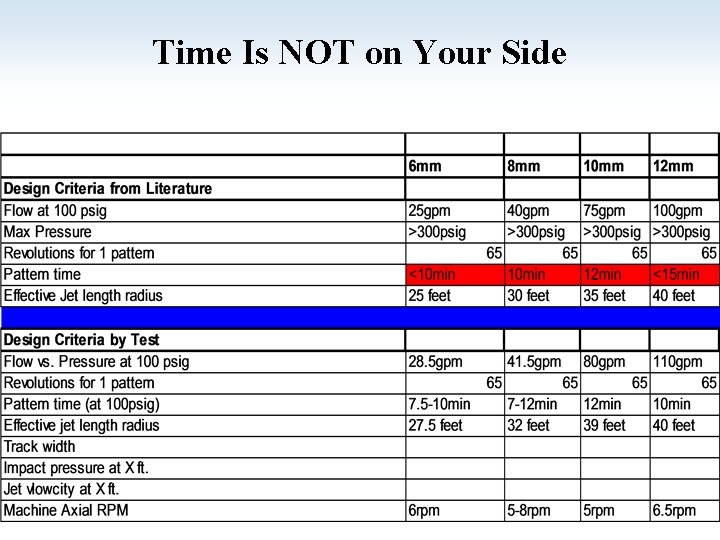
Time Is NOT on Your Side
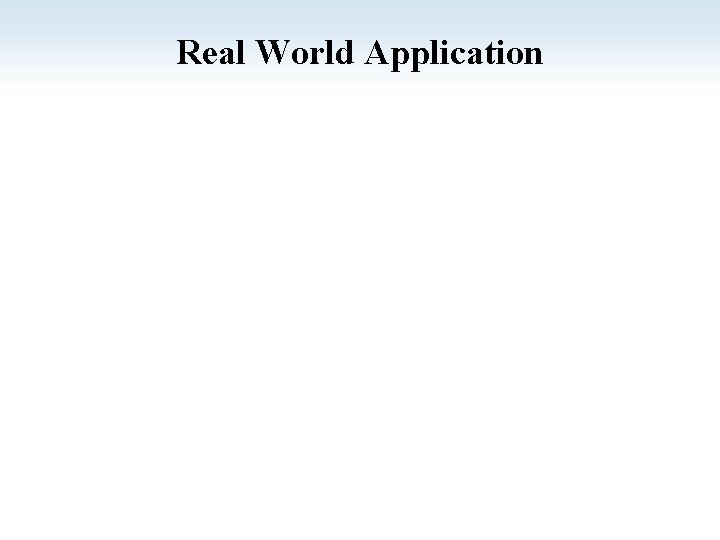
Real World Application
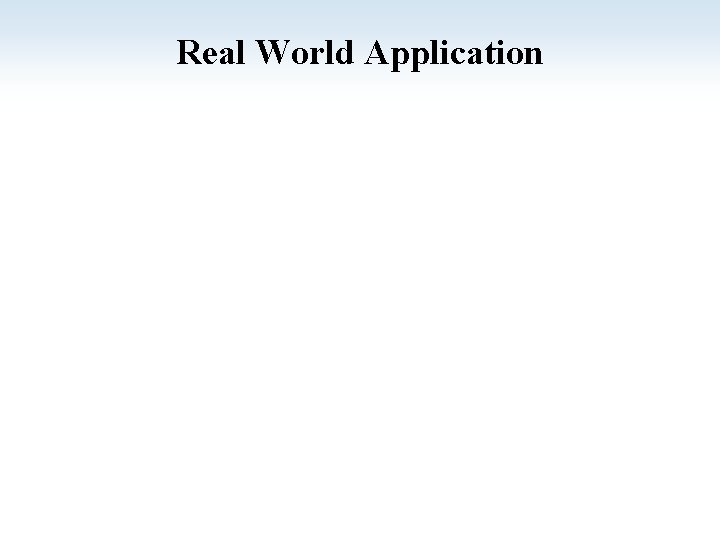
Real World Application
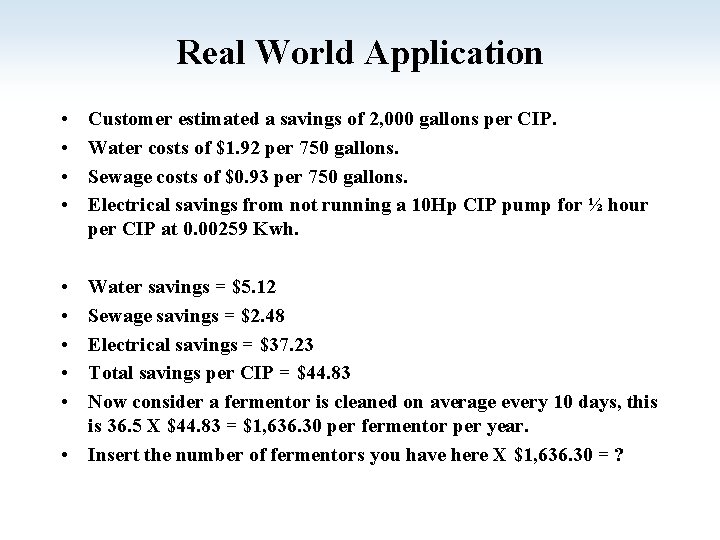
Real World Application • • • Customer estimated a savings of 2, 000 gallons per CIP. Water costs of $1. 92 per 750 gallons. Sewage costs of $0. 93 per 750 gallons. Electrical savings from not running a 10 Hp CIP pump for ½ hour per CIP at 0. 00259 Kwh. Water savings = $5. 12 Sewage savings = $2. 48 Electrical savings = $37. 23 Total savings per CIP = $44. 83 Now consider a fermentor is cleaned on average every 10 days, this is 36. 5 X $44. 83 = $1, 636. 30 per fermentor per year. • Insert the number of fermentors you have here X $1, 636. 30 = ?
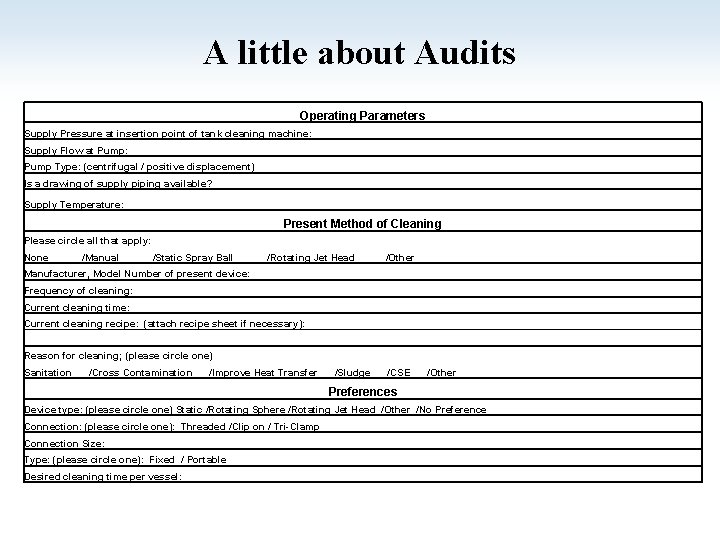
A little about Audits Operating Parameters Supply Pressure at insertion point of tank cleaning machine: Supply Flow at Pump: Pump Type: (centrifugal / positive displacement) Is a drawing of supply piping available? Supply Temperature: Present Method of Cleaning Please circle all that apply: None /Manual /Static Spray Ball /Rotating Jet Head /Other Manufacturer, Model Number of present device: Frequency of cleaning: Current cleaning time: Current cleaning recipe: (attach recipe sheet if necessary): Reason for cleaning; (please circle one) Sanitation /Cross Contamination /Improve Heat Transfer /Sludge /CSE /Other Preferences Device type: (please circle one) Static /Rotating Sphere /Rotating Jet Head /Other /No Preference Connection: (please circle one): Threaded /Clip on / Tri-Clamp Connection Size: Type: (please circle one): Fixed / Portable Desired cleaning time per vessel:
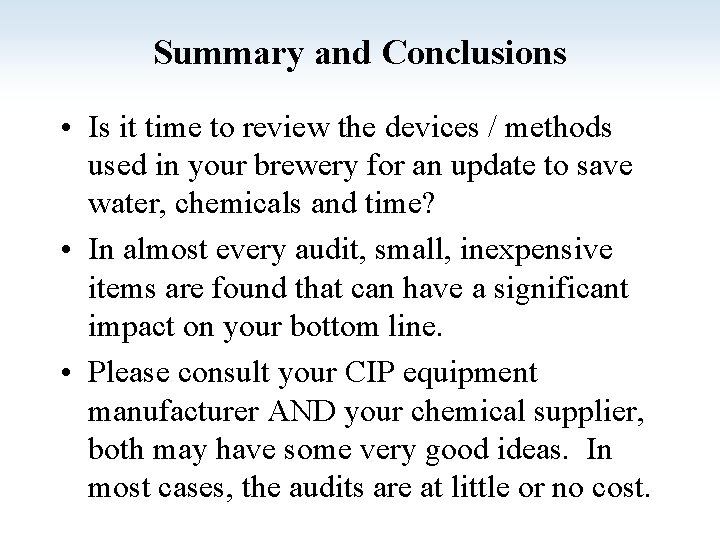
Summary and Conclusions • Is it time to review the devices / methods used in your brewery for an update to save water, chemicals and time? • In almost every audit, small, inexpensive items are found that can have a significant impact on your bottom line. • Please consult your CIP equipment manufacturer AND your chemical supplier, both may have some very good ideas. In most cases, the audits are at little or no cost.
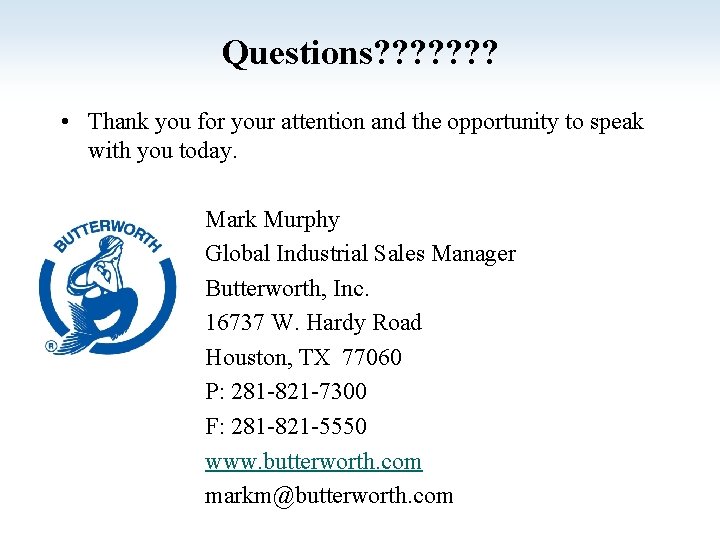
Questions? ? ? ? • Thank you for your attention and the opportunity to speak with you today. Mark Murphy Global Industrial Sales Manager Butterworth, Inc. 16737 W. Hardy Road Houston, TX 77060 P: 281 -821 -7300 F: 281 -821 -5550 www. butterworth. com markm@butterworth. com
Water and water and water water
How to use less water in cip
What is nerc cip
Rc cip
Dap paritet
Kurt forster
Cip continuous improvement program
Cip theory career development
Cognitive information processing theory
Cognitive information processing theory career
Nerc cip webinar
Cip modellen
Ansep cip
Rc cip
Abgangsgruppe
Cip lean manufacturing
Cip 002-009
Contactos sexo galicia
Cip database
Cip lagny
Cena cip
Cip sakana
Fixed asset cip
Cip chips
Cataloging in publication