CIP Training Series CIP Flow Friction and Pump
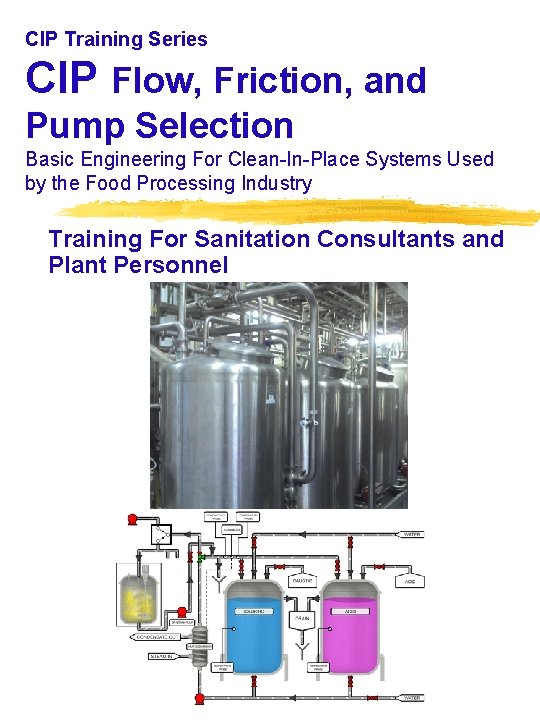
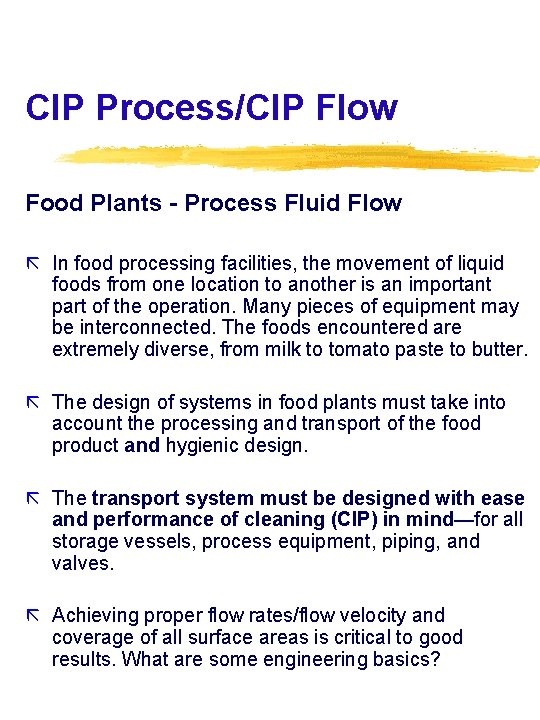
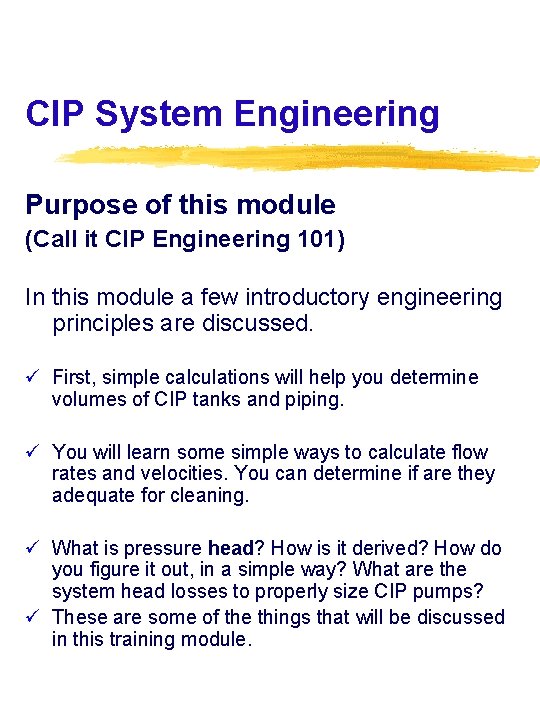
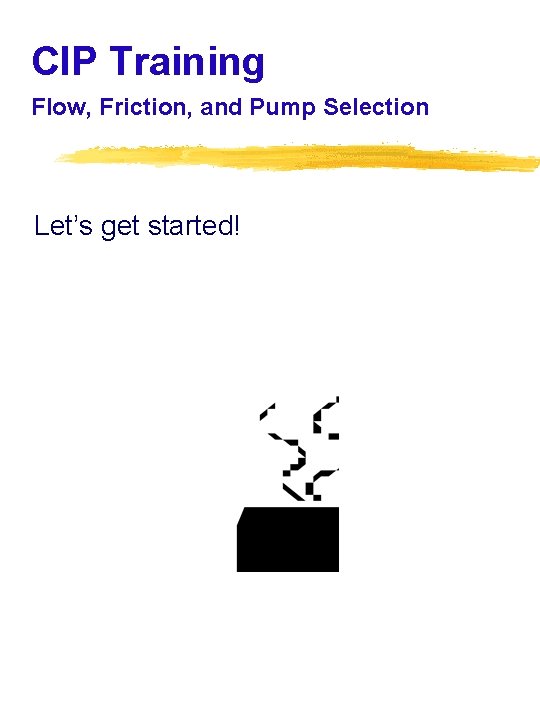
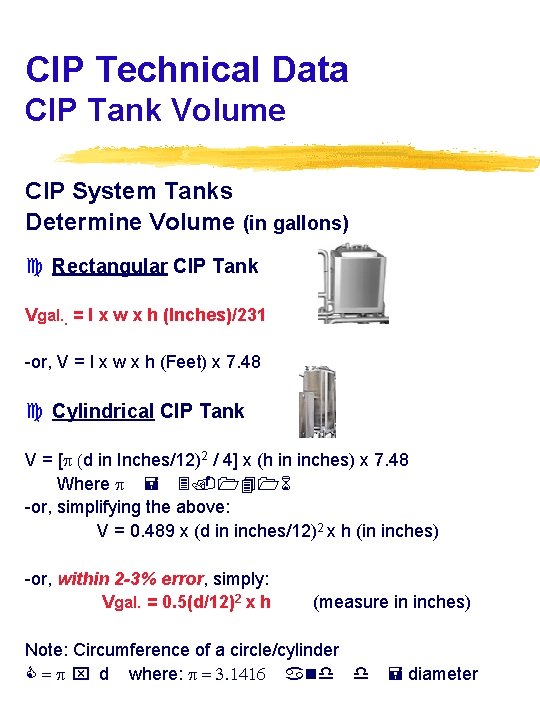
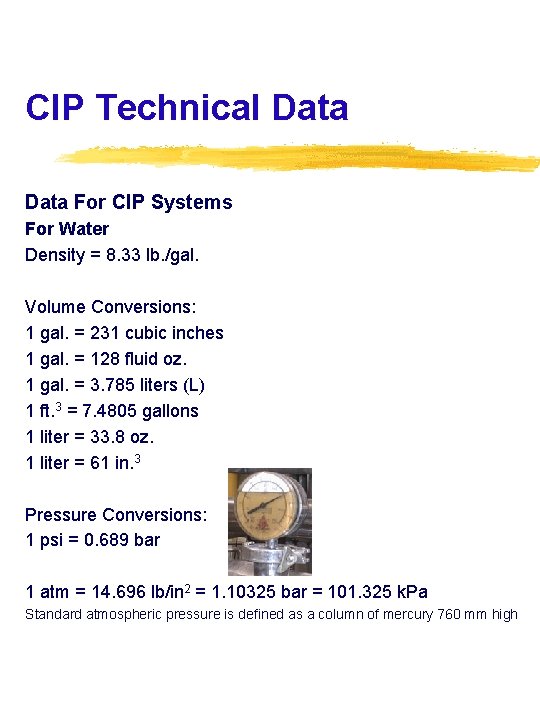
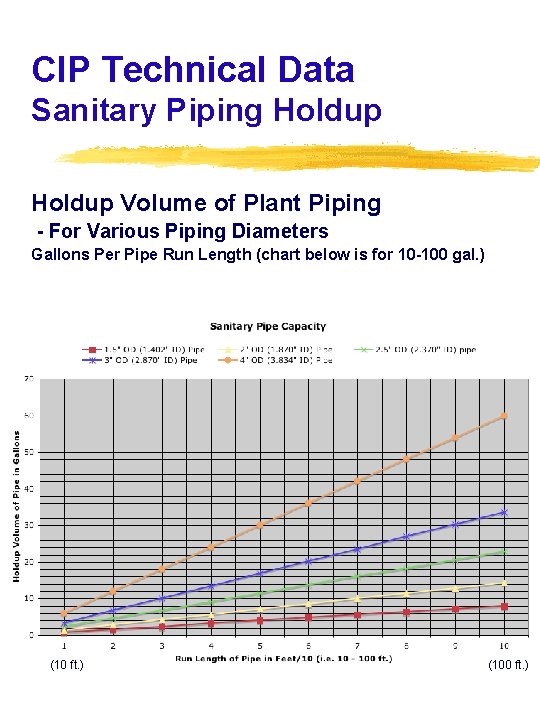
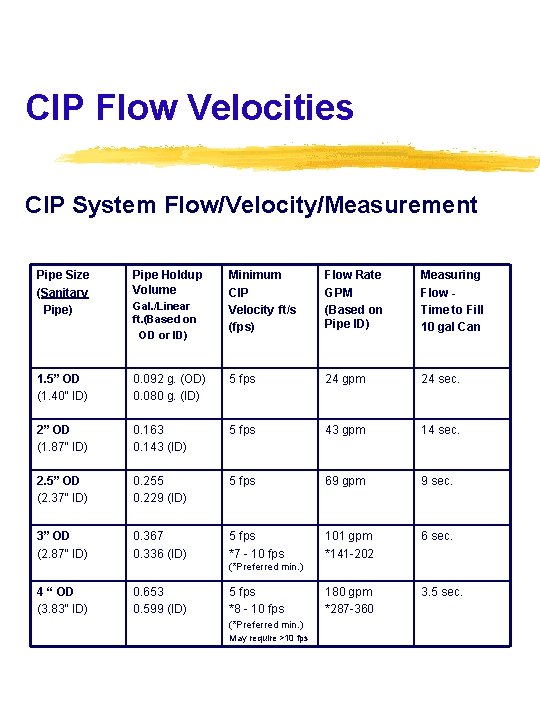
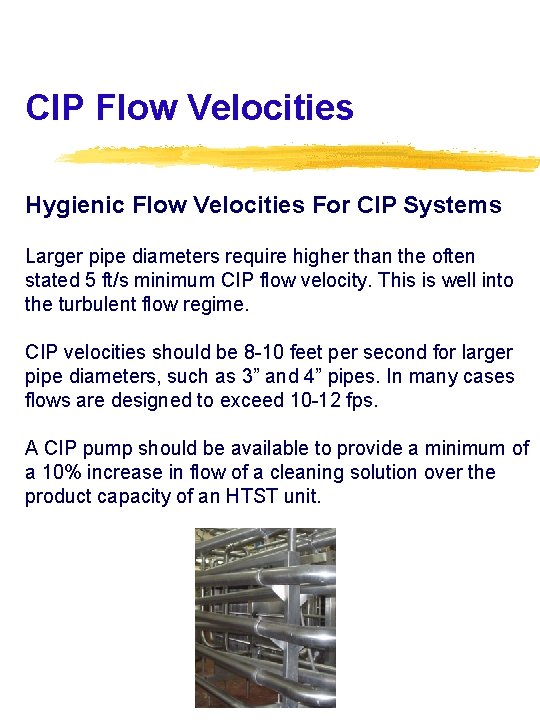
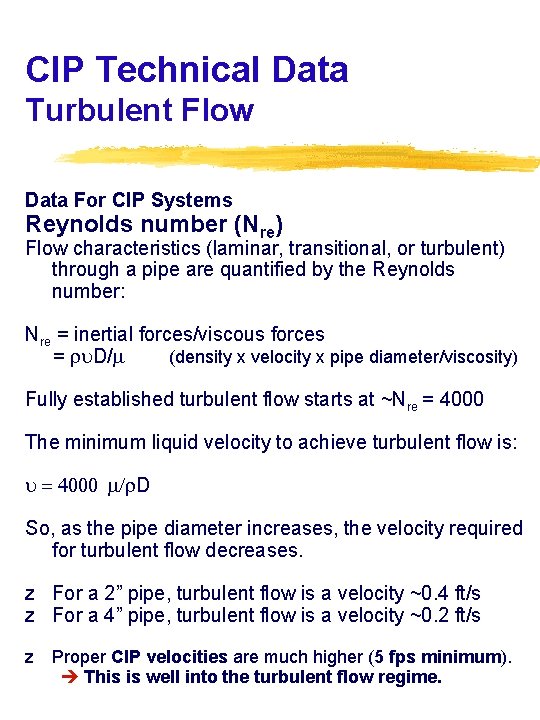
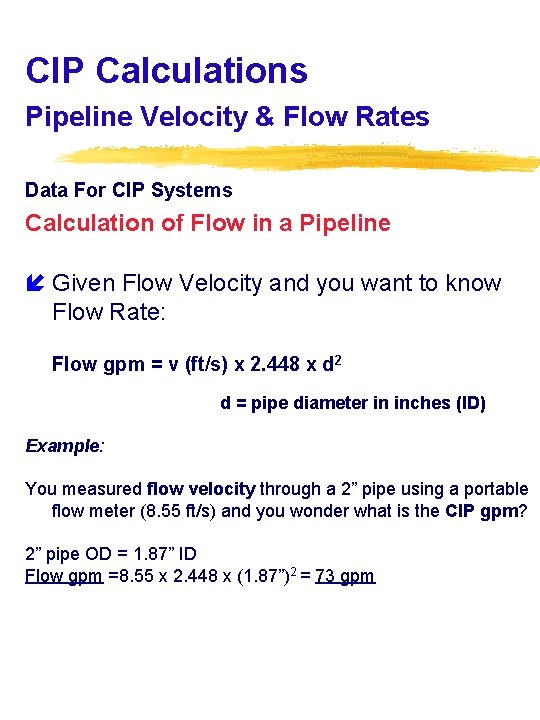
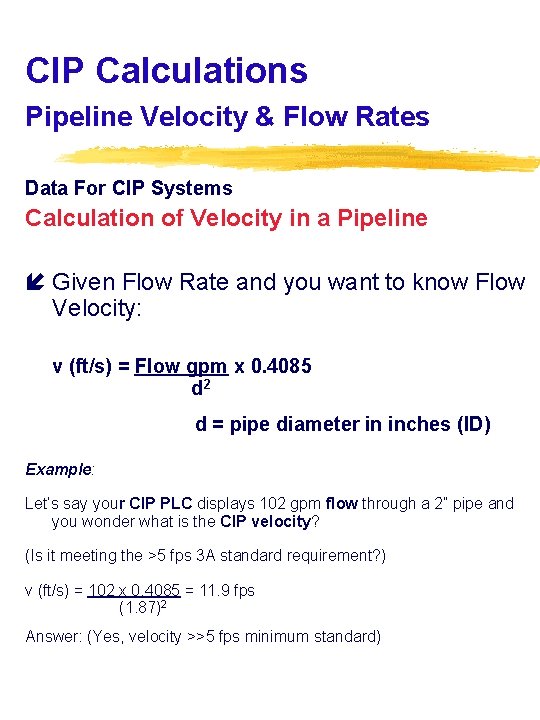
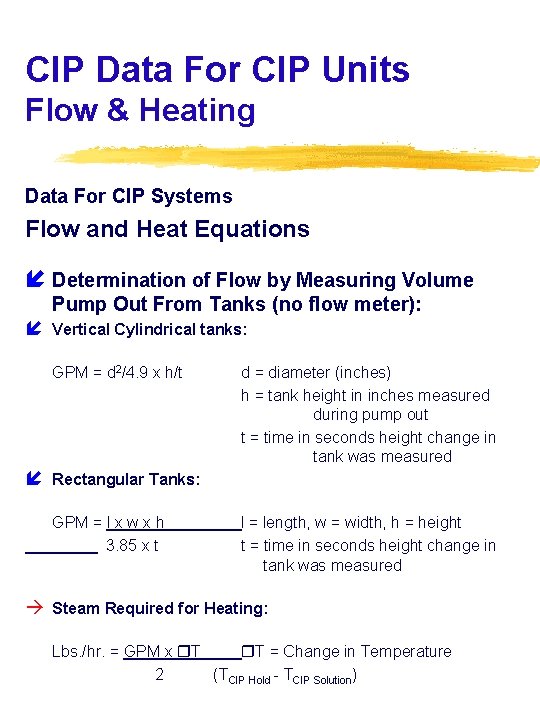
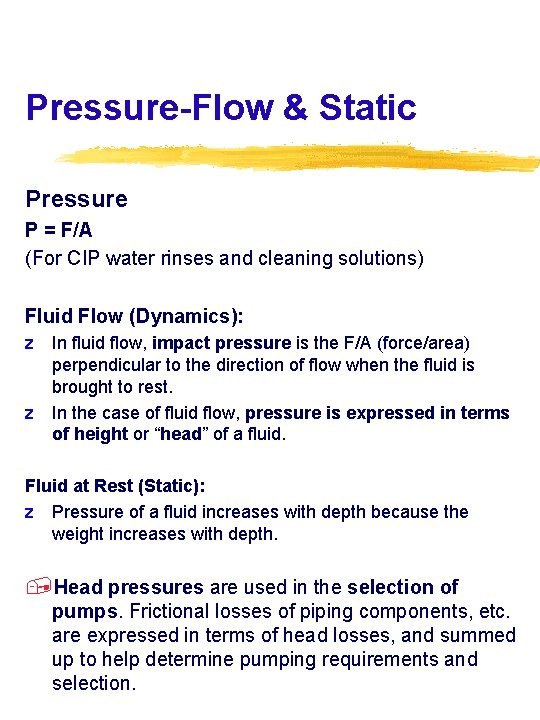
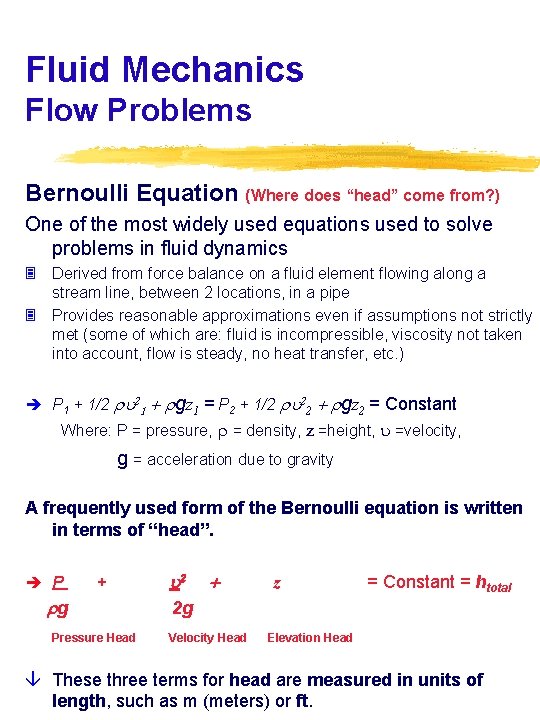
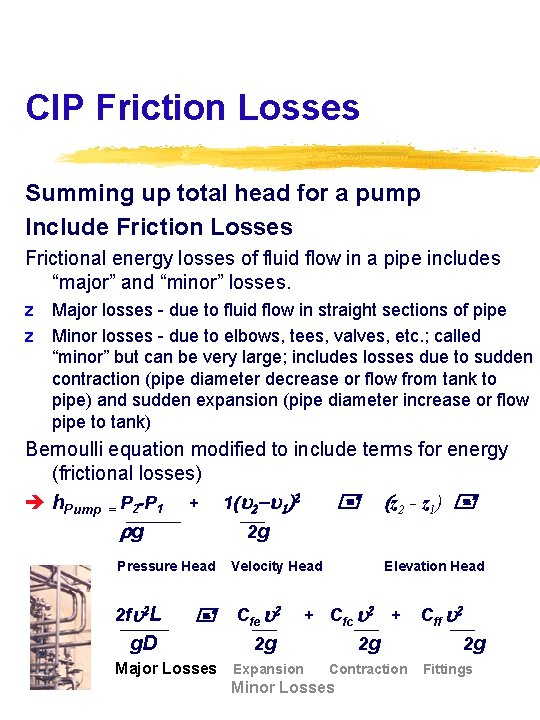
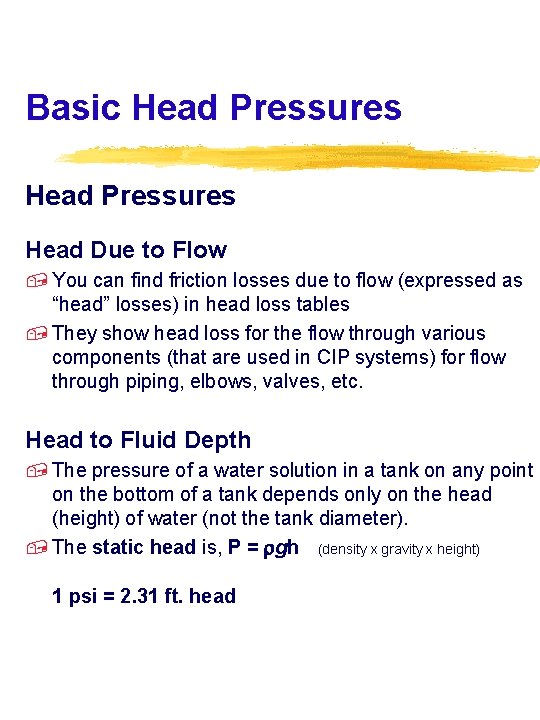
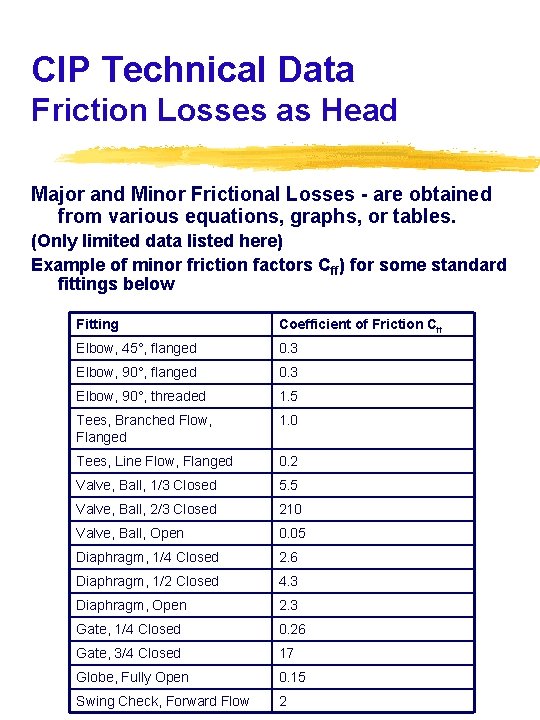
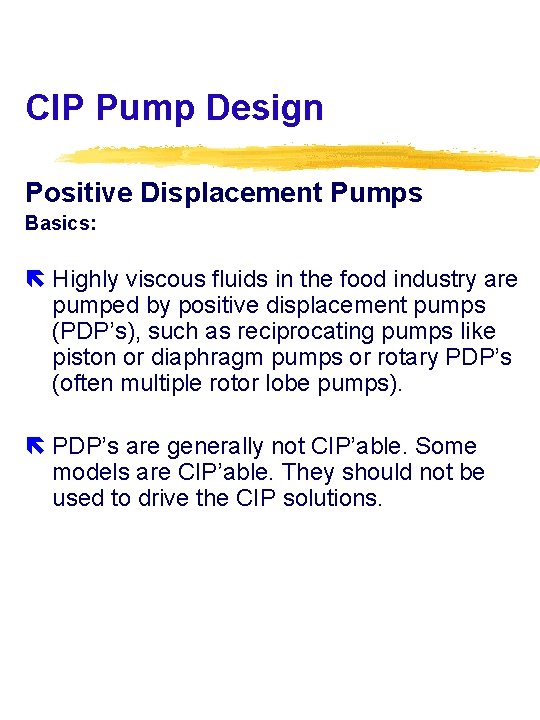
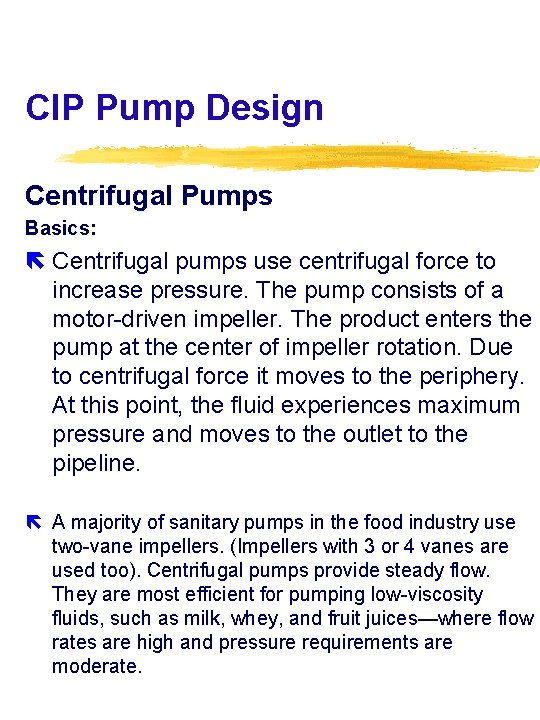
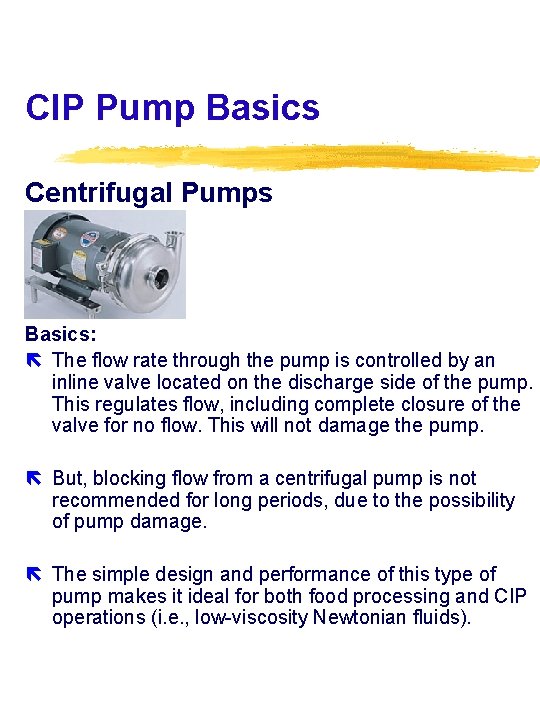
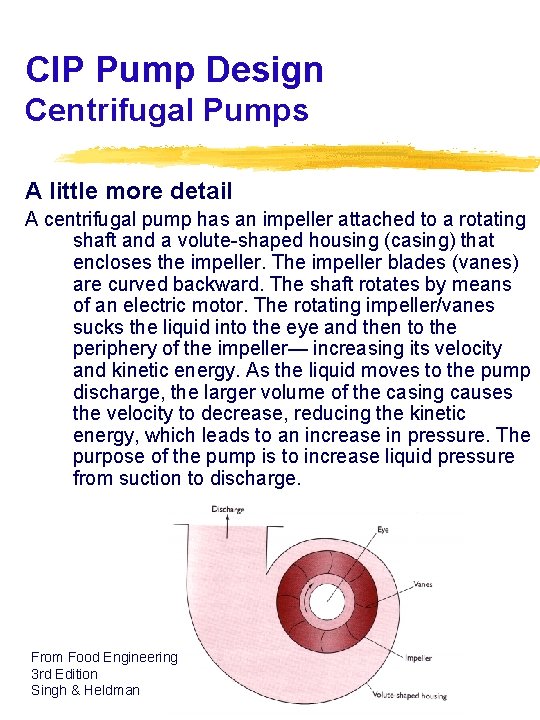
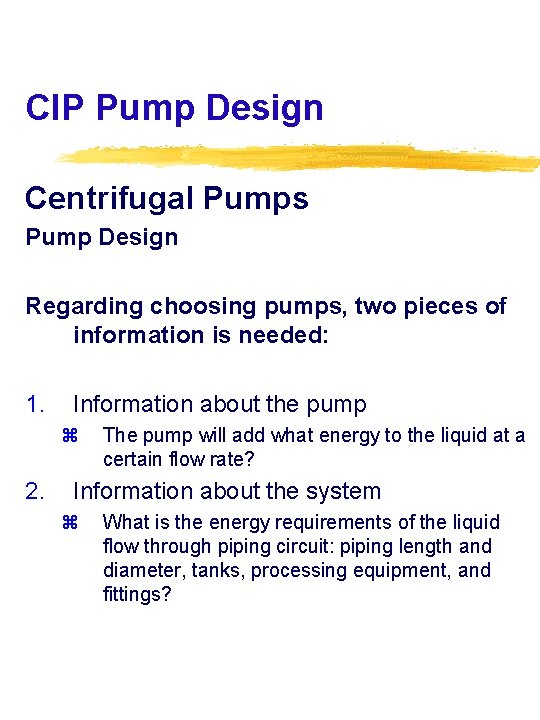
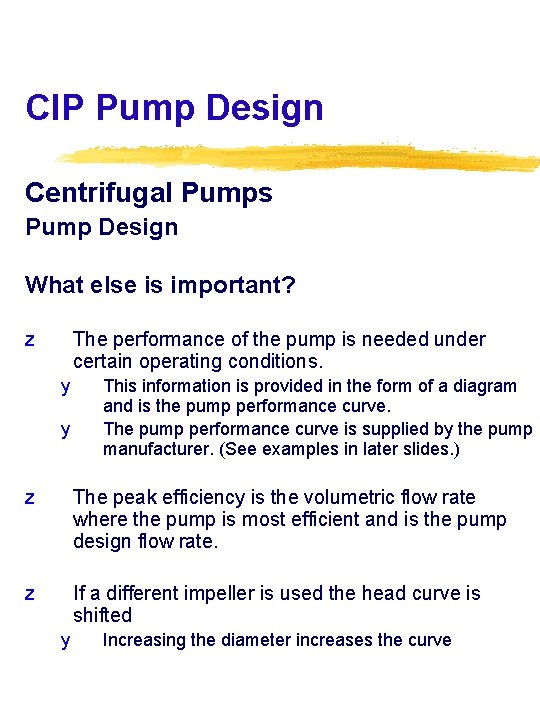
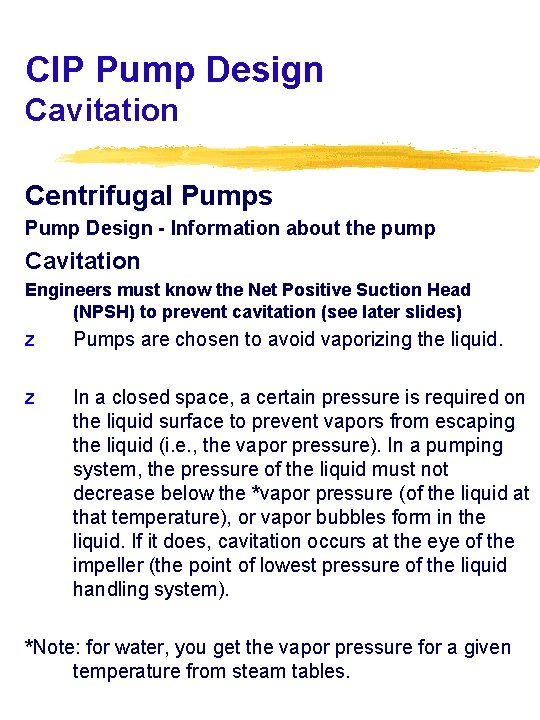
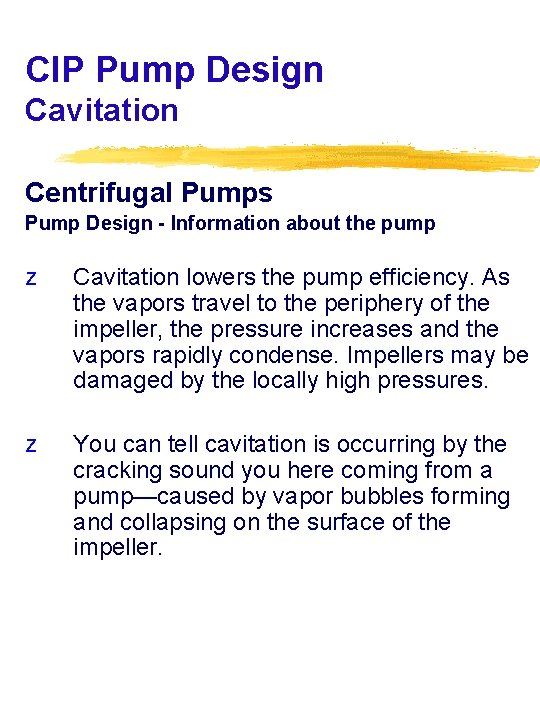
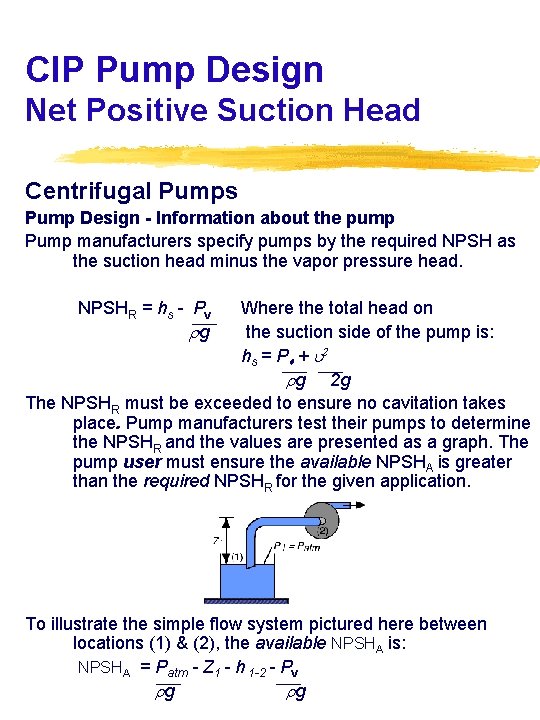
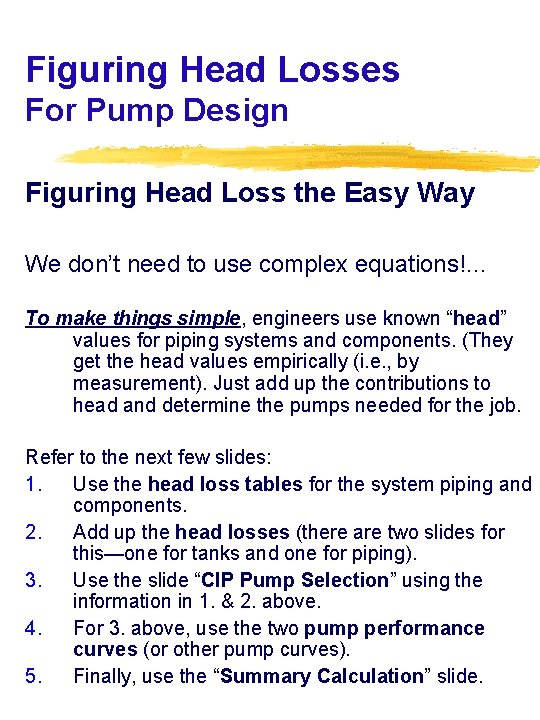
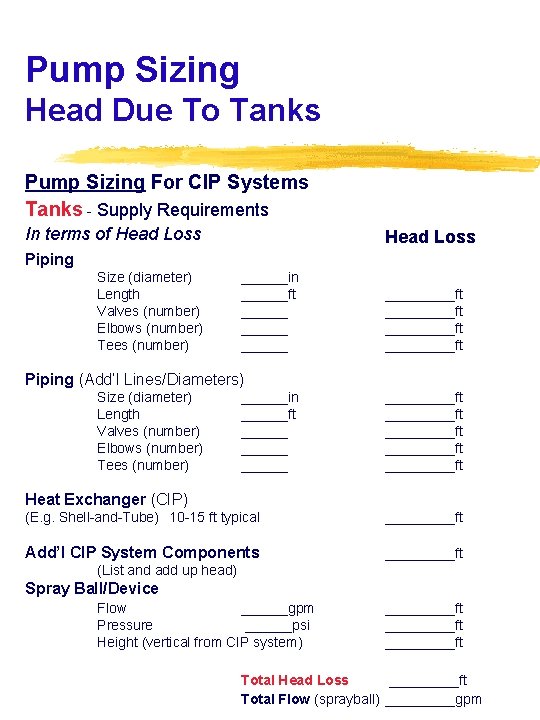
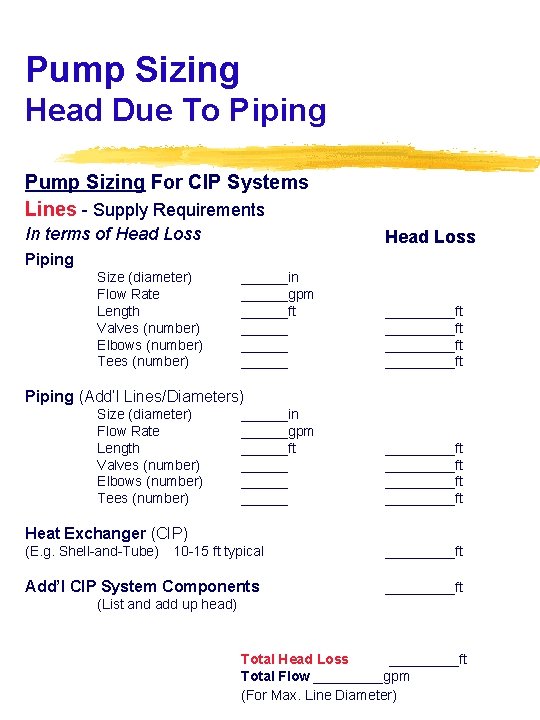
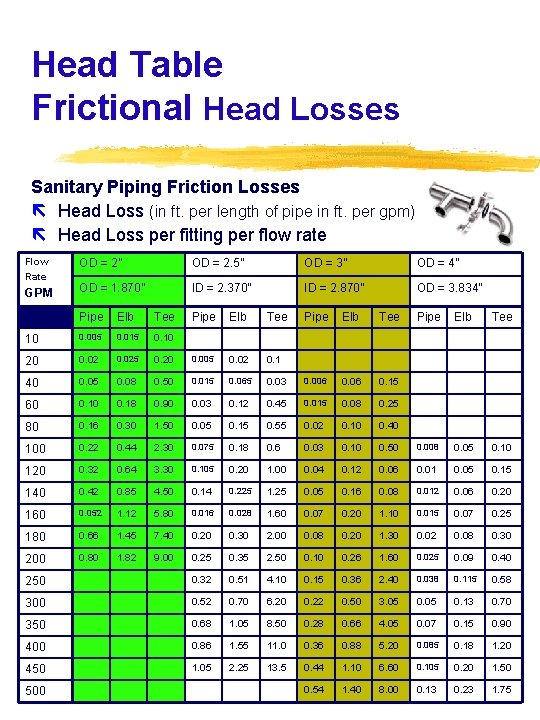
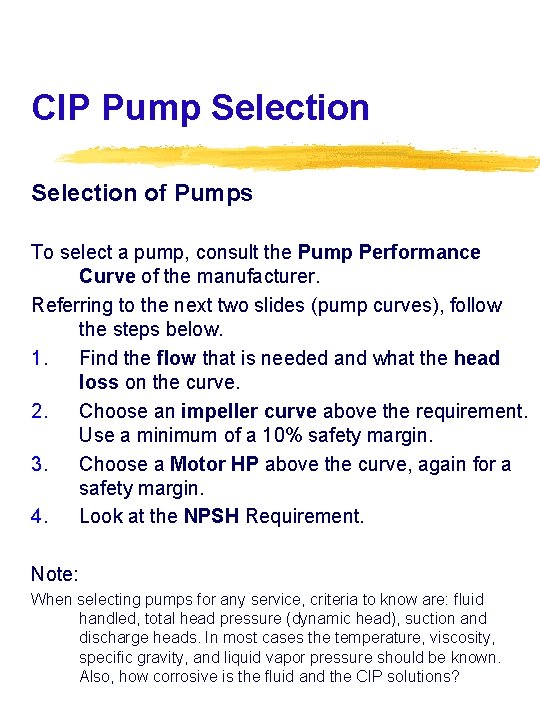
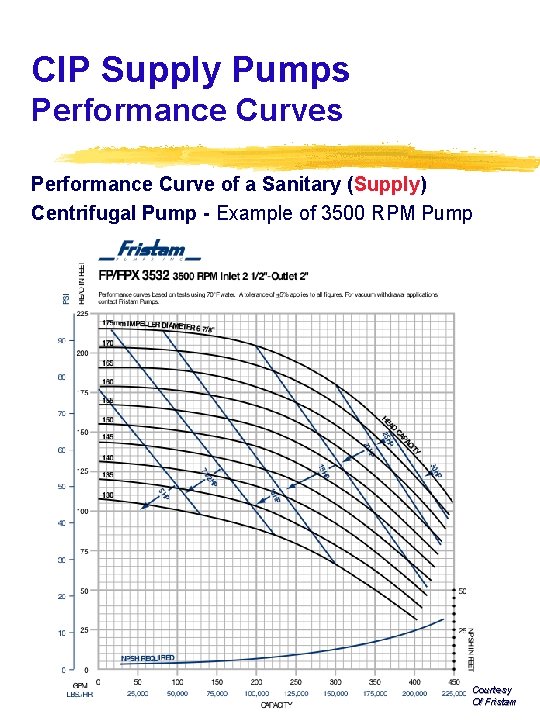
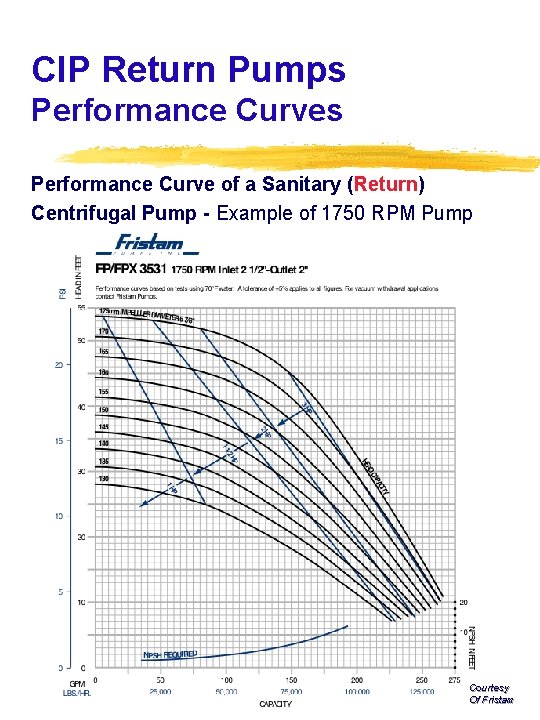
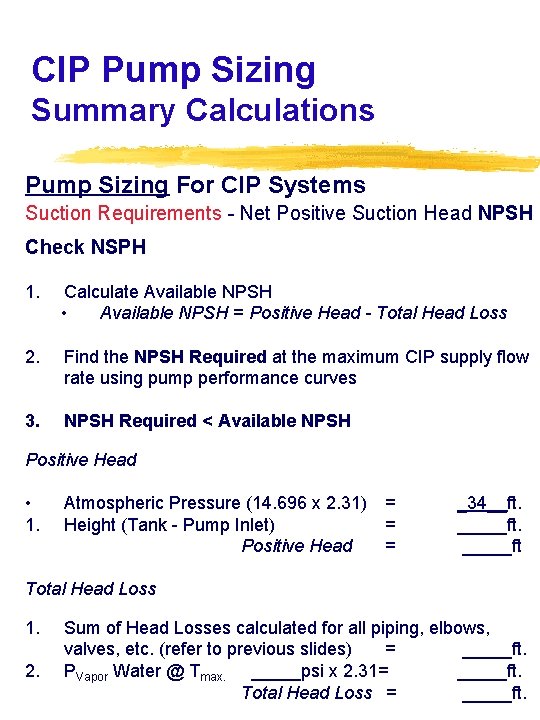
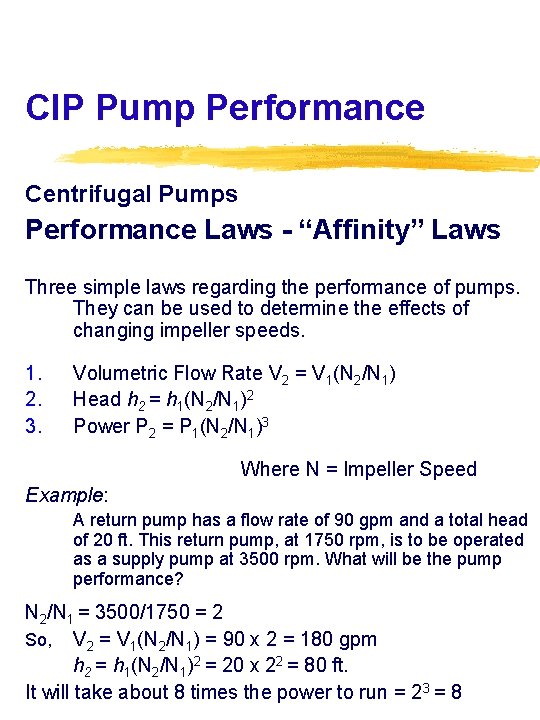

- Slides: 37
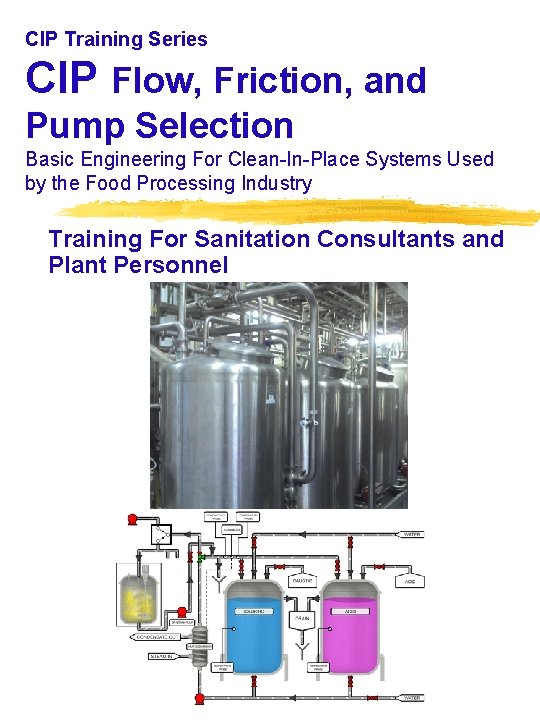
CIP Training Series CIP Flow, Friction, and Pump Selection Basic Engineering For Clean-In-Place Systems Used by the Food Processing Industry Training For Sanitation Consultants and Plant Personnel
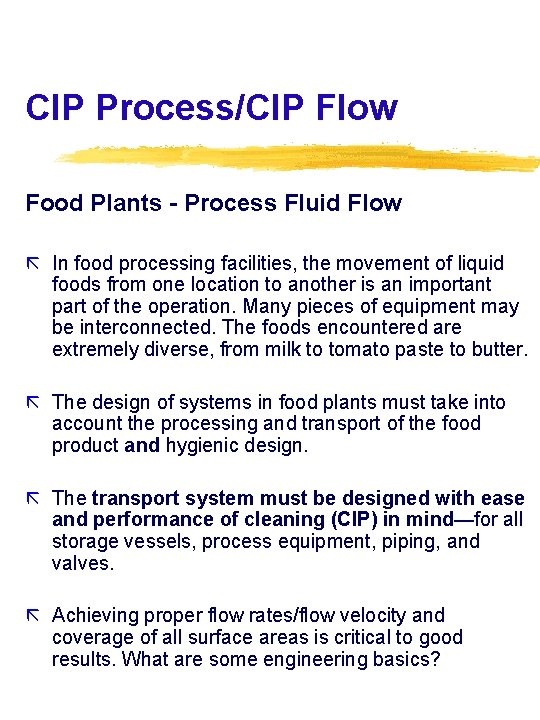
CIP Process/CIP Flow Food Plants - Process Fluid Flow In food processing facilities, the movement of liquid foods from one location to another is an important part of the operation. Many pieces of equipment may be interconnected. The foods encountered are extremely diverse, from milk to tomato paste to butter. The design of systems in food plants must take into account the processing and transport of the food product and hygienic design. The transport system must be designed with ease and performance of cleaning (CIP) in mind—for all storage vessels, process equipment, piping, and valves. Achieving proper flow rates/flow velocity and coverage of all surface areas is critical to good results. What are some engineering basics?
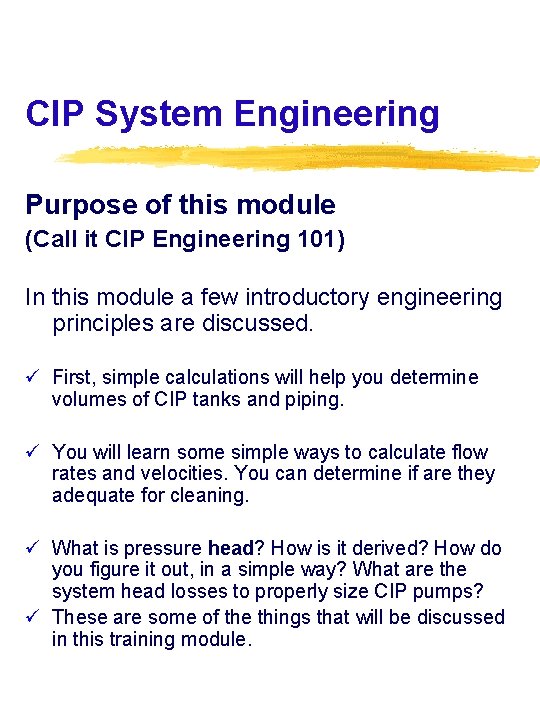
CIP System Engineering Purpose of this module (Call it CIP Engineering 101) In this module a few introductory engineering principles are discussed. ü First, simple calculations will help you determine volumes of CIP tanks and piping. ü You will learn some simple ways to calculate flow rates and velocities. You can determine if are they adequate for cleaning. ü What is pressure head? How is it derived? How do you figure it out, in a simple way? What are the system head losses to properly size CIP pumps? ü These are some of the things that will be discussed in this training module.
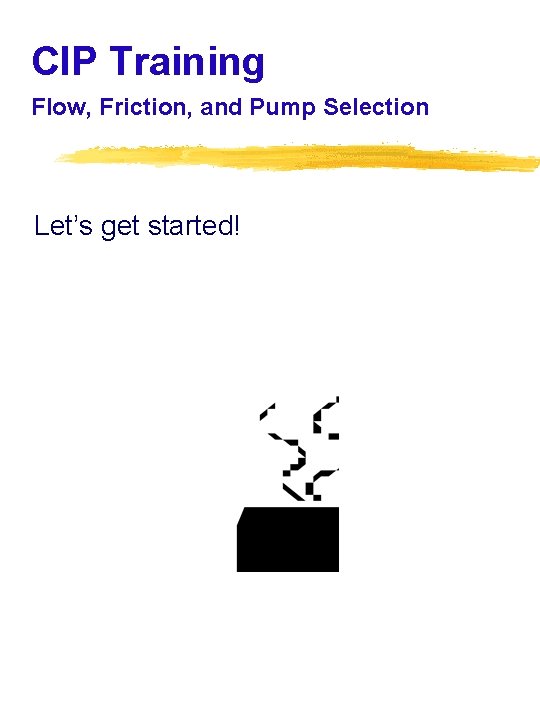
CIP Training Flow, Friction, and Pump Selection Let’s get started!
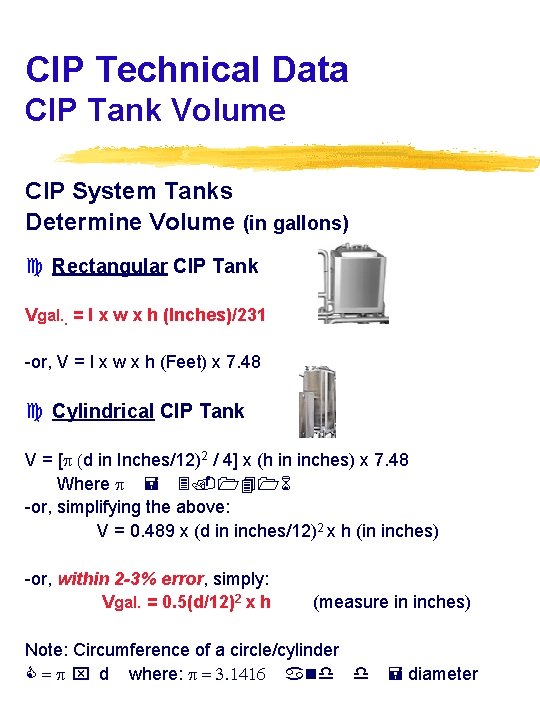
CIP Technical Data CIP Tank Volume CIP System Tanks Determine Volume (in gallons) c Rectangular CIP Tank Vgal. . = l x w x h (Inches)/231 -or, V = l x w x h (Feet) x 7. 48 c Cylindrical CIP Tank V = [ d in Inches/12)2 / 4] x (h in inches) x 7. 48 Where -or, simplifying the above: V = 0. 489 x (d in inches/12)2 x h (in inches) -or, within 2 -3% error, simply: Vgal. = 0. 5(d/12)2 x h (measure in inches) Note: Circumference of a circle/cylinder d where: diameter
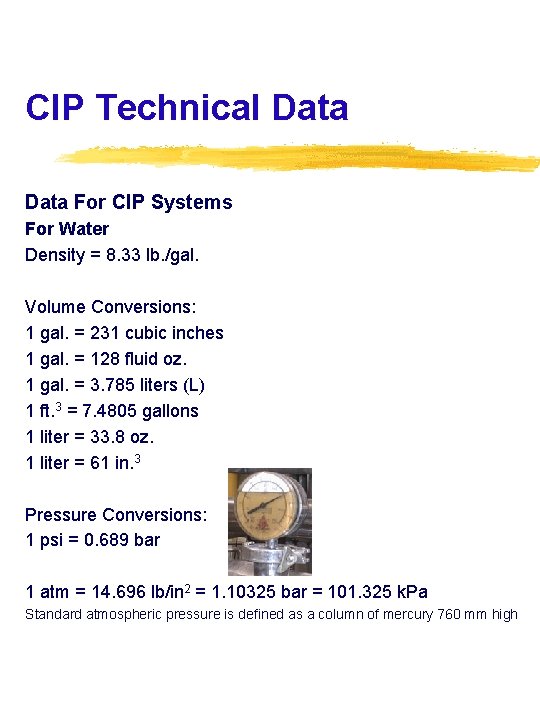
CIP Technical Data For CIP Systems For Water Density = 8. 33 lb. /gal. Volume Conversions: 1 gal. = 231 cubic inches 1 gal. = 128 fluid oz. 1 gal. = 3. 785 liters (L) 1 ft. 3 = 7. 4805 gallons 1 liter = 33. 8 oz. 1 liter = 61 in. 3 Pressure Conversions: 1 psi = 0. 689 bar 1 atm = 14. 696 lb/in 2 = 1. 10325 bar = 101. 325 k. Pa Standard atmospheric pressure is defined as a column of mercury 760 mm high
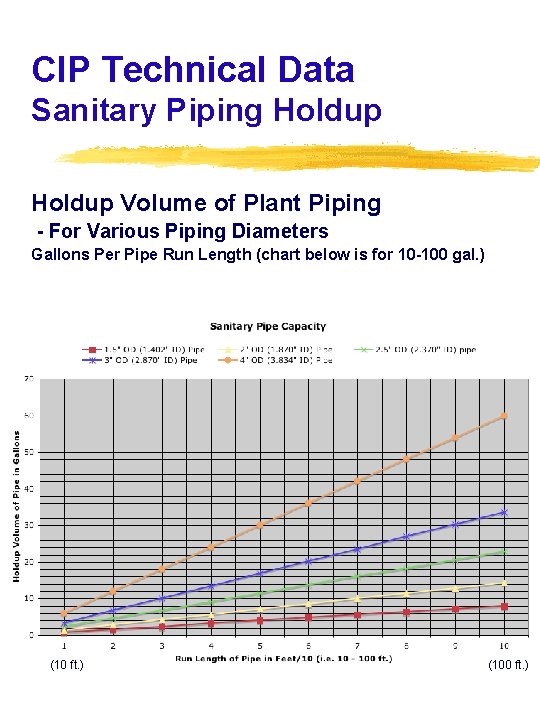
CIP Technical Data Sanitary Piping Holdup Volume of Plant Piping - For Various Piping Diameters Gallons Per Pipe Run Length (chart below is for 10 -100 gal. ) (10 ft. ) (100 ft. )
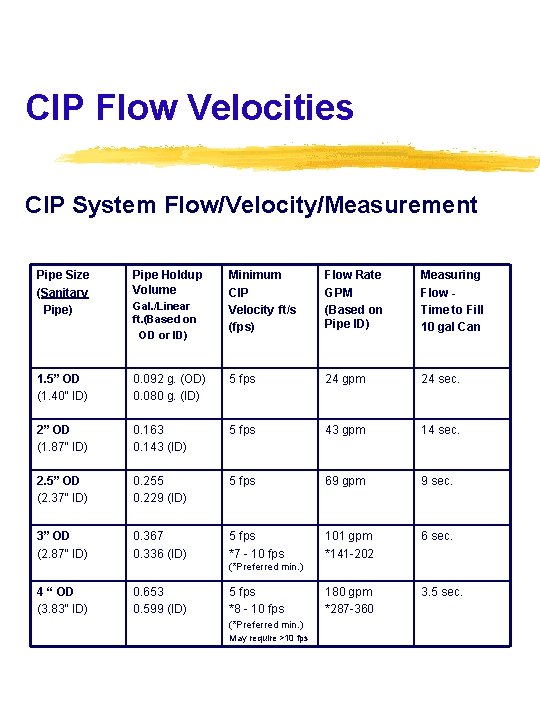
CIP Flow Velocities CIP System Flow/Velocity/Measurement Pipe Size (Sanitary Pipe) Pipe Holdup Volume Minimum CIP Velocity ft/s (fps) Flow Rate GPM (Based on Pipe ID) Measuring Flow Time to Fill 10 gal Can 1. 5” OD (1. 40” ID) 0. 092 g. (OD) 0. 080 g. (ID) 5 fps 24 gpm 24 sec. 2” OD (1. 87” ID) 0. 163 0. 143 (ID) 5 fps 43 gpm 14 sec. 2. 5” OD (2. 37” ID) 0. 255 0. 229 (ID) 5 fps 69 gpm 9 sec. 3” OD (2. 87” ID) 0. 367 0. 336 (ID) 5 fps *7 - 10 fps 101 gpm *141 -202 6 sec. 180 gpm *287 -360 3. 5 sec. Gal. /Linear ft. (Based on OD or ID) (*Preferred min. ) 4 “ OD (3. 83” ID) 0. 653 0. 599 (ID) 5 fps *8 - 10 fps (*Preferred min. ) May require >10 fps
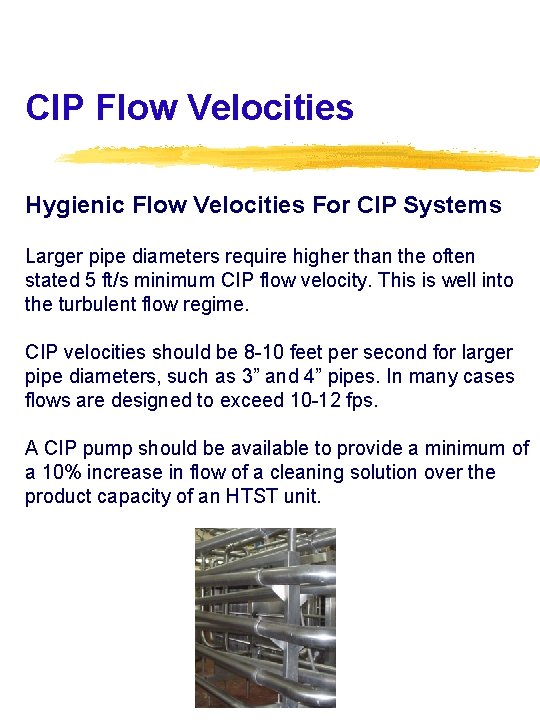
CIP Flow Velocities Hygienic Flow Velocities For CIP Systems Larger pipe diameters require higher than the often stated 5 ft/s minimum CIP flow velocity. This is well into the turbulent flow regime. CIP velocities should be 8 -10 feet per second for larger pipe diameters, such as 3” and 4” pipes. In many cases flows are designed to exceed 10 -12 fps. A CIP pump should be available to provide a minimum of a 10% increase in flow of a cleaning solution over the product capacity of an HTST unit.
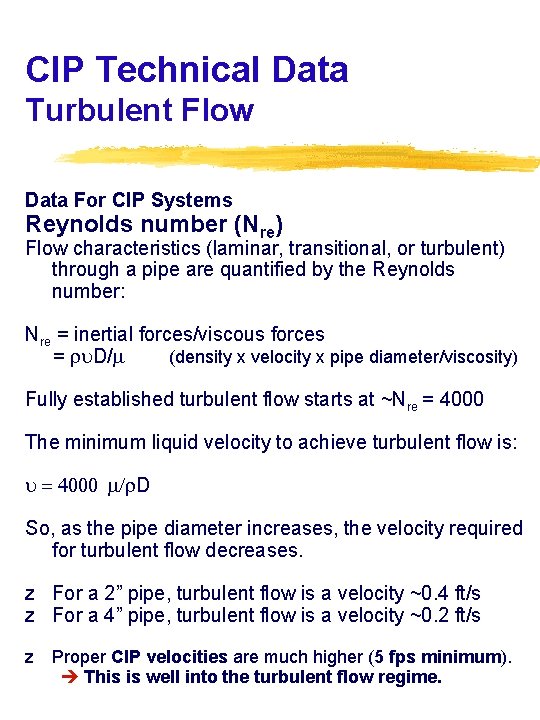
CIP Technical Data Turbulent Flow Data For CIP Systems Reynolds number (Nre) Flow characteristics (laminar, transitional, or turbulent) through a pipe are quantified by the Reynolds number: Nre = inertial forces/viscous forces = D/ (density x velocity x pipe diameter/viscosity) Fully established turbulent flow starts at ~Nre = 4000 The minimum liquid velocity to achieve turbulent flow is: D So, as the pipe diameter increases, the velocity required for turbulent flow decreases. z For a 2” pipe, turbulent flow is a velocity ~0. 4 ft/s z For a 4” pipe, turbulent flow is a velocity ~0. 2 ft/s z Proper CIP velocities are much higher (5 fps minimum). This is well into the turbulent flow regime.
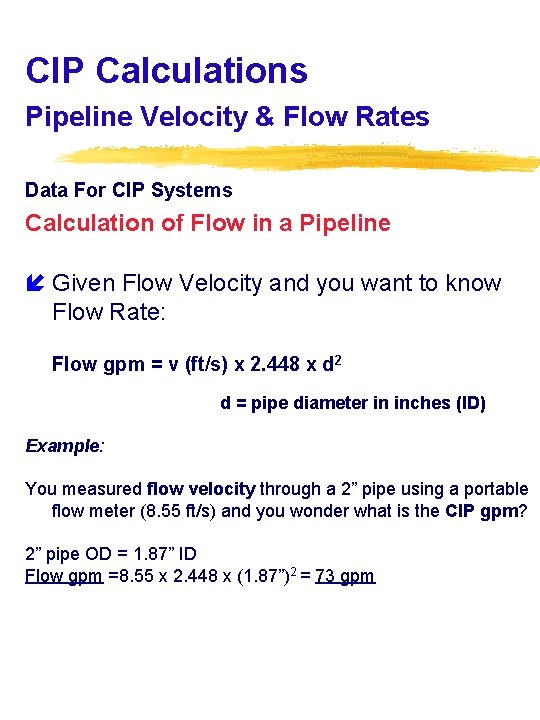
CIP Calculations Pipeline Velocity & Flow Rates Data For CIP Systems Calculation of Flow in a Pipeline Given Flow Velocity and you want to know Flow Rate: Flow gpm = v (ft/s) x 2. 448 x d 2 d = pipe diameter in inches (ID) Example: You measured flow velocity through a 2” pipe using a portable flow meter (8. 55 ft/s) and you wonder what is the CIP gpm? 2” pipe OD = 1. 87” ID Flow gpm =8. 55 x 2. 448 x (1. 87”)2 = 73 gpm
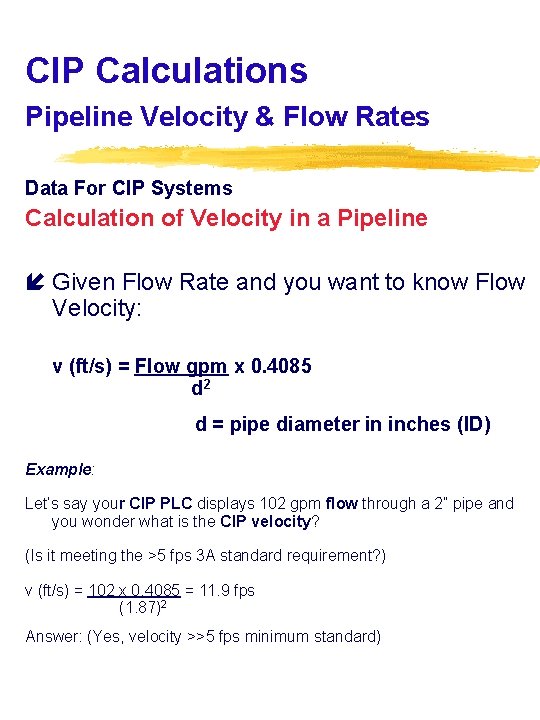
CIP Calculations Pipeline Velocity & Flow Rates Data For CIP Systems Calculation of Velocity in a Pipeline Given Flow Rate and you want to know Flow Velocity: v (ft/s) = Flow gpm x 0. 4085 d 2 d = pipe diameter in inches (ID) Example: Let’s say your CIP PLC displays 102 gpm flow through a 2” pipe and you wonder what is the CIP velocity? (Is it meeting the >5 fps 3 A standard requirement? ) v (ft/s) = 102 x 0. 4085 = 11. 9 fps (1. 87)2 Answer: (Yes, velocity >>5 fps minimum standard)
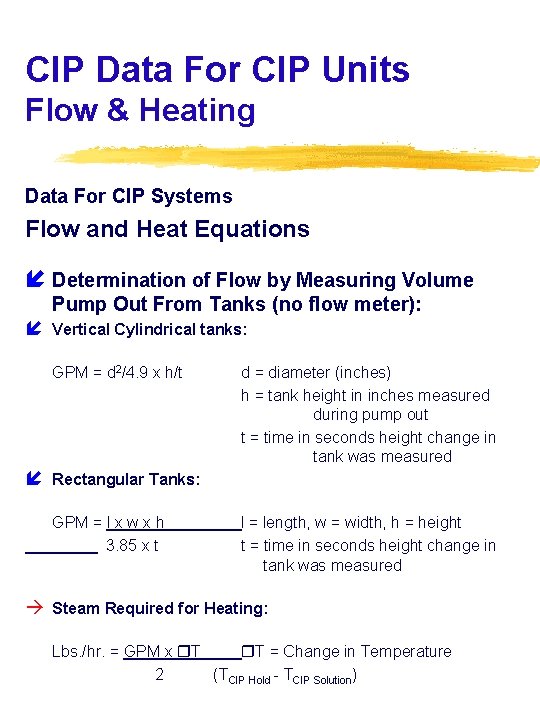
CIP Data For CIP Units Flow & Heating Data For CIP Systems Flow and Heat Equations Determination of Flow by Measuring Volume Pump Out From Tanks (no flow meter): Vertical Cylindrical tanks: GPM = d 2/4. 9 x h/t d = diameter (inches) h = tank height in inches measured during pump out t = time in seconds height change in tank was measured Rectangular Tanks: GPM = l x w x h 3. 85 x t l = length, w = width, h = height t = time in seconds height change in tank was measured Steam Required for Heating: Lbs. /hr. = GPM x r. T = Change in Temperature 2 (TCIP Hold - TCIP Solution)
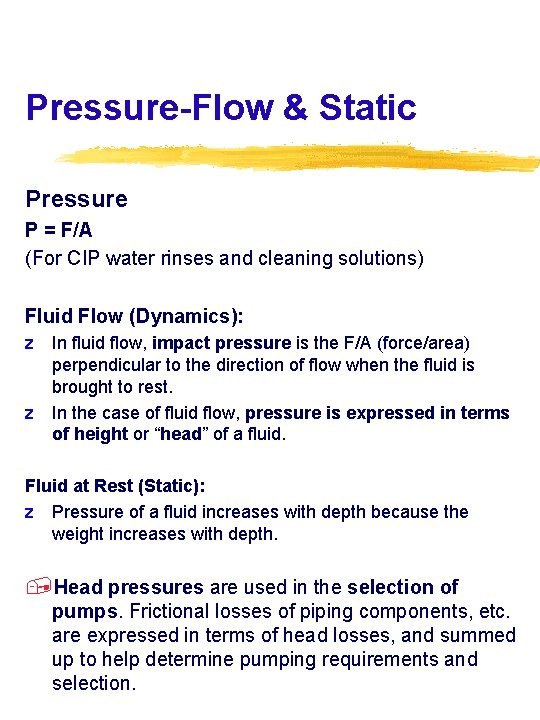
Pressure-Flow & Static Pressure P = F/A (For CIP water rinses and cleaning solutions) Fluid Flow (Dynamics): z In fluid flow, impact pressure is the F/A (force/area) perpendicular to the direction of flow when the fluid is brought to rest. z In the case of fluid flow, pressure is expressed in terms of height or “head” of a fluid. Fluid at Rest (Static): z Pressure of a fluid increases with depth because the weight increases with depth. , Head pressures are used in the selection of pumps. Frictional losses of piping components, etc. are expressed in terms of head losses, and summed up to help determine pumping requirements and selection.
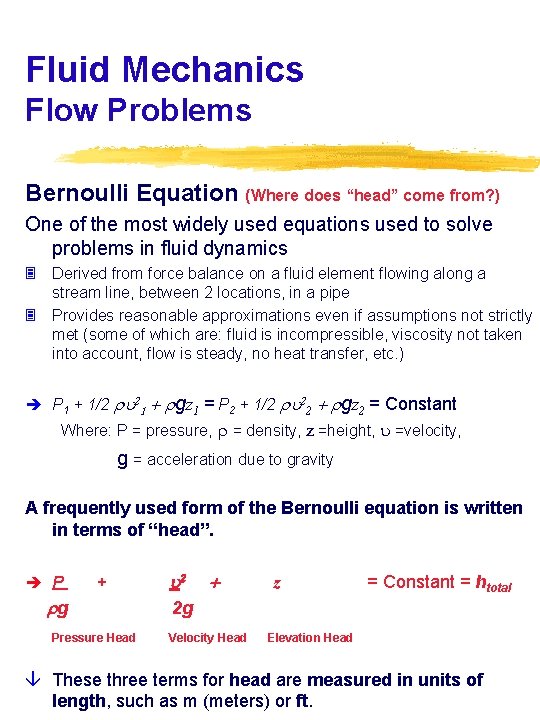
Fluid Mechanics Flow Problems Bernoulli Equation (Where does “head” come from? ) One of the most widely used equations used to solve problems in fluid dynamics Derived from force balance on a fluid element flowing along a stream line, between 2 locations, in a pipe Provides reasonable approximations even if assumptions not strictly met (some of which are: fluid is incompressible, viscosity not taken into account, flow is steady, no heat transfer, etc. ) P 1 + 1/2 gz 1 = P 2 + 1/2 2 gz 2 = Constant Where: P = pressure, = density, z =height, =velocity, g = acceleration due to gravity A frequently used form of the Bernoulli equation is written in terms of “head”. P + g Pressure Head z = Constant = htotal 2 g Velocity Head Elevation Head These three terms for head are measured in units of length, such as m (meters) or ft.
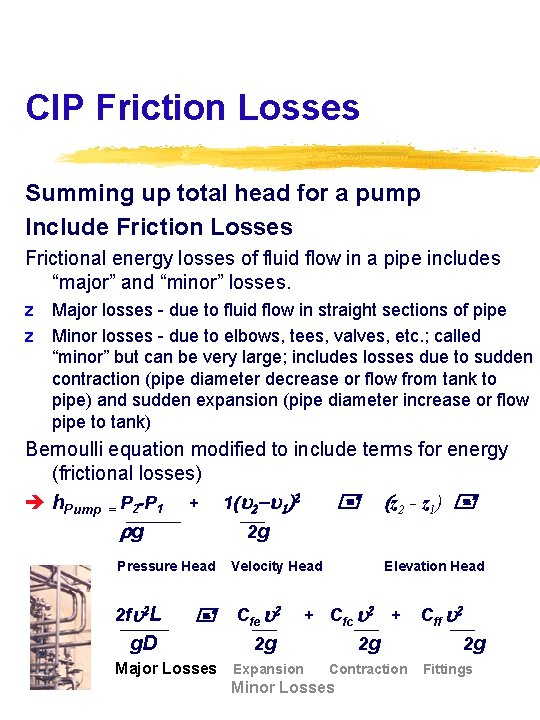
CIP Friction Losses Summing up total head for a pump Include Friction Losses Frictional energy losses of fluid flow in a pipe includes “major” and “minor” losses. z Major losses - due to fluid flow in straight sections of pipe z Minor losses - due to elbows, tees, valves, etc. ; called “minor” but can be very large; includes losses due to sudden contraction (pipe diameter decrease or flow from tank to pipe) and sudden expansion (pipe diameter increase or flow pipe to tank) Bernoulli equation modified to include terms for energy (frictional losses) h. Pump = P 2 -P 1 + 1( z 2 - z 1) g 2 g Pressure Head 2 f L Velocity Head Elevation Head Cfe + Cfc + Cff g. D 2 g 2 g 2 g Major Losses Expansion Contraction Fittings Minor Losses
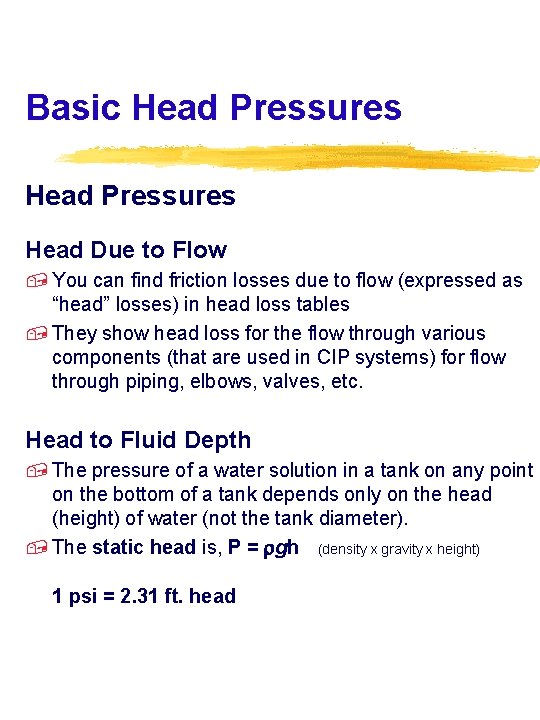
Basic Head Pressures Head Due to Flow , You can find friction losses due to flow (expressed as “head” losses) in head loss tables , They show head loss for the flow through various components (that are used in CIP systems) for flow through piping, elbows, valves, etc. Head to Fluid Depth , The pressure of a water solution in a tank on any point on the bottom of a tank depends only on the head (height) of water (not the tank diameter). , The static head is, P = gh (density x gravity x height) 1 psi = 2. 31 ft. head
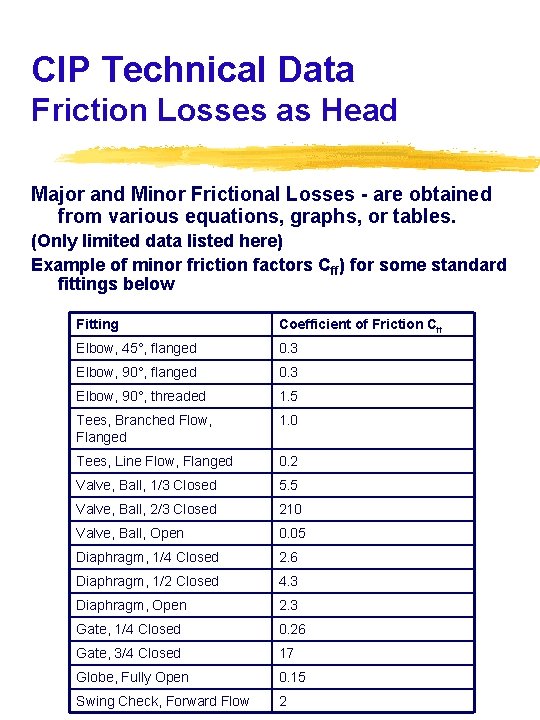
CIP Technical Data Friction Losses as Head Major and Minor Frictional Losses - are obtained from various equations, graphs, or tables. (Only limited data listed here) Example of minor friction factors Cff) for some standard fittings below Fitting Coefficient of Friction Cff Elbow, 45°, flanged 0. 3 Elbow, 90°, threaded 1. 5 Tees, Branched Flow, Flanged 1. 0 Tees, Line Flow, Flanged 0. 2 Valve, Ball, 1/3 Closed 5. 5 Valve, Ball, 2/3 Closed 210 Valve, Ball, Open 0. 05 Diaphragm, 1/4 Closed 2. 6 Diaphragm, 1/2 Closed 4. 3 Diaphragm, Open 2. 3 Gate, 1/4 Closed 0. 26 Gate, 3/4 Closed 17 Globe, Fully Open 0. 15 Swing Check, Forward Flow 2
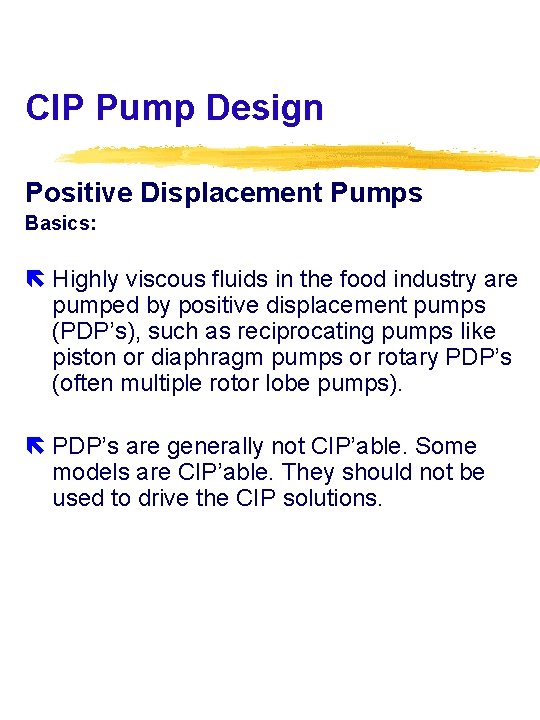
CIP Pump Design Positive Displacement Pumps Basics: Highly viscous fluids in the food industry are pumped by positive displacement pumps (PDP’s), such as reciprocating pumps like piston or diaphragm pumps or rotary PDP’s (often multiple rotor lobe pumps). PDP’s are generally not CIP’able. Some models are CIP’able. They should not be used to drive the CIP solutions.
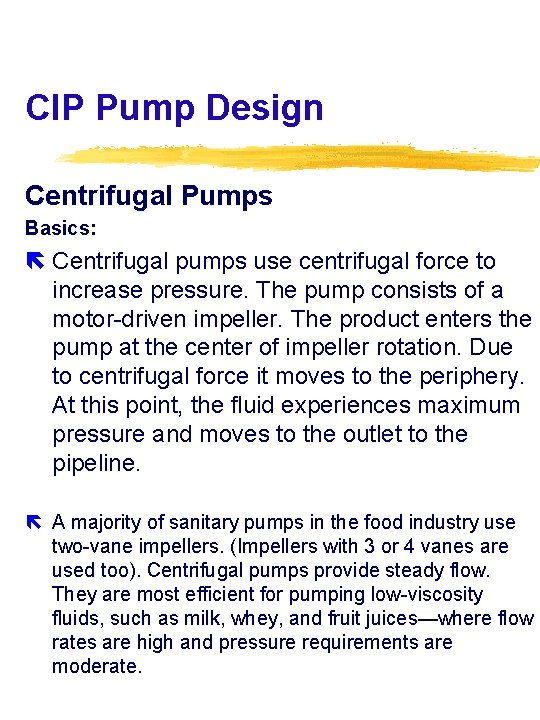
CIP Pump Design Centrifugal Pumps Basics: Centrifugal pumps use centrifugal force to increase pressure. The pump consists of a motor-driven impeller. The product enters the pump at the center of impeller rotation. Due to centrifugal force it moves to the periphery. At this point, the fluid experiences maximum pressure and moves to the outlet to the pipeline. A majority of sanitary pumps in the food industry use two-vane impellers. (Impellers with 3 or 4 vanes are used too). Centrifugal pumps provide steady flow. They are most efficient for pumping low-viscosity fluids, such as milk, whey, and fruit juices—where flow rates are high and pressure requirements are moderate.
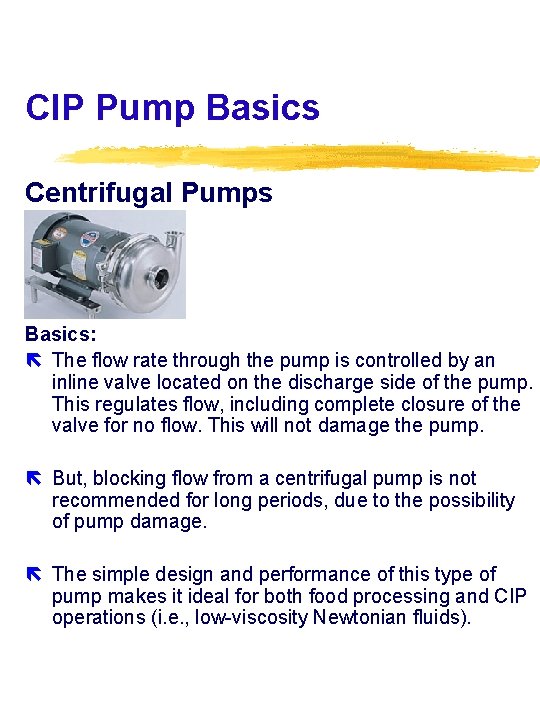
CIP Pump Basics Centrifugal Pumps Basics: The flow rate through the pump is controlled by an inline valve located on the discharge side of the pump. This regulates flow, including complete closure of the valve for no flow. This will not damage the pump. But, blocking flow from a centrifugal pump is not recommended for long periods, due to the possibility of pump damage. The simple design and performance of this type of pump makes it ideal for both food processing and CIP operations (i. e. , low-viscosity Newtonian fluids).
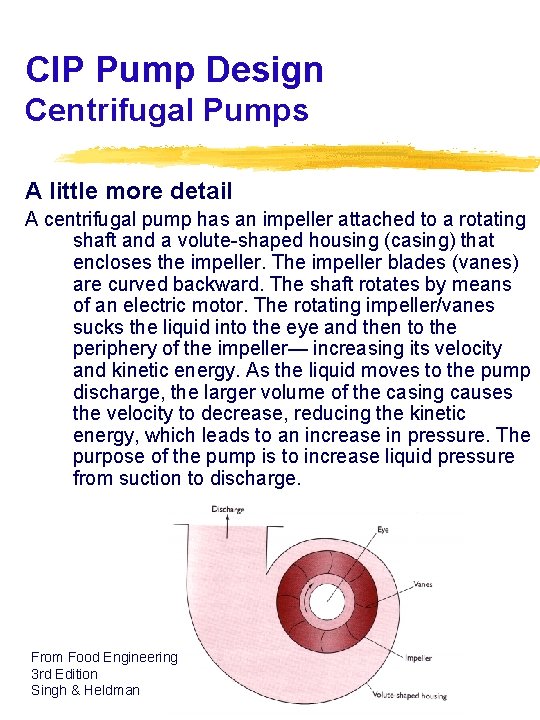
CIP Pump Design Centrifugal Pumps A little more detail A centrifugal pump has an impeller attached to a rotating shaft and a volute-shaped housing (casing) that encloses the impeller. The impeller blades (vanes) are curved backward. The shaft rotates by means of an electric motor. The rotating impeller/vanes sucks the liquid into the eye and then to the periphery of the impeller— increasing its velocity and kinetic energy. As the liquid moves to the pump discharge, the larger volume of the casing causes the velocity to decrease, reducing the kinetic energy, which leads to an increase in pressure. The purpose of the pump is to increase liquid pressure from suction to discharge. From Food Engineering 3 rd Edition Singh & Heldman
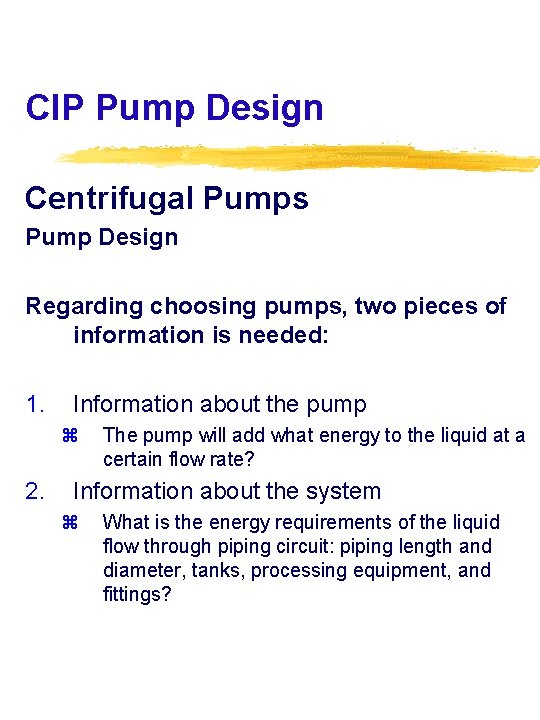
CIP Pump Design Centrifugal Pumps Pump Design Regarding choosing pumps, two pieces of information is needed: 1. Information about the pump z 2. The pump will add what energy to the liquid at a certain flow rate? Information about the system z What is the energy requirements of the liquid flow through piping circuit: piping length and diameter, tanks, processing equipment, and fittings?
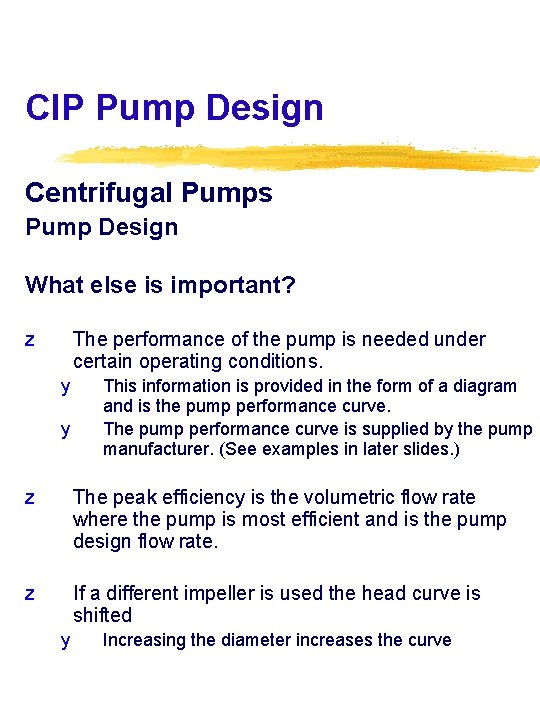
CIP Pump Design Centrifugal Pumps Pump Design What else is important? z The performance of the pump is needed under certain operating conditions. y y This information is provided in the form of a diagram and is the pump performance curve. The pump performance curve is supplied by the pump manufacturer. (See examples in later slides. ) z The peak efficiency is the volumetric flow rate where the pump is most efficient and is the pump design flow rate. z If a different impeller is used the head curve is shifted y Increasing the diameter increases the curve
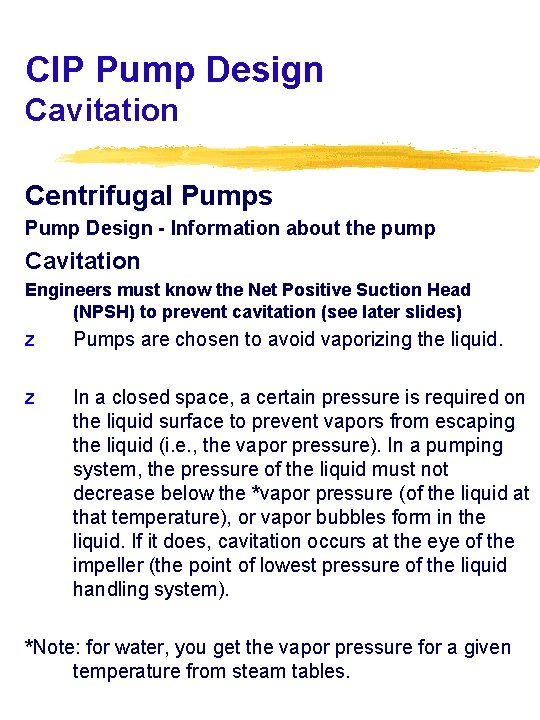
CIP Pump Design Cavitation Centrifugal Pumps Pump Design - Information about the pump Cavitation Engineers must know the Net Positive Suction Head (NPSH) to prevent cavitation (see later slides) z Pumps are chosen to avoid vaporizing the liquid. z In a closed space, a certain pressure is required on the liquid surface to prevent vapors from escaping the liquid (i. e. , the vapor pressure). In a pumping system, the pressure of the liquid must not decrease below the *vapor pressure (of the liquid at that temperature), or vapor bubbles form in the liquid. If it does, cavitation occurs at the eye of the impeller (the point of lowest pressure of the liquid handling system). *Note: for water, you get the vapor pressure for a given temperature from steam tables.
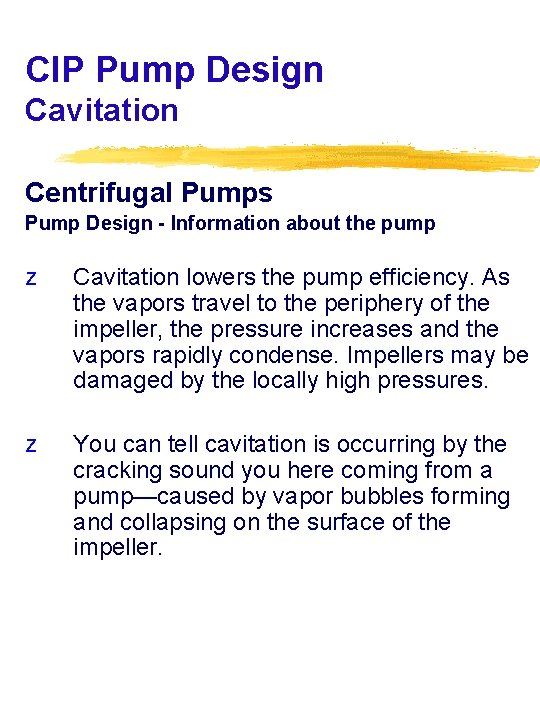
CIP Pump Design Cavitation Centrifugal Pumps Pump Design - Information about the pump z Cavitation lowers the pump efficiency. As the vapors travel to the periphery of the impeller, the pressure increases and the vapors rapidly condense. Impellers may be damaged by the locally high pressures. z You can tell cavitation is occurring by the cracking sound you here coming from a pump—caused by vapor bubbles forming and collapsing on the surface of the impeller.
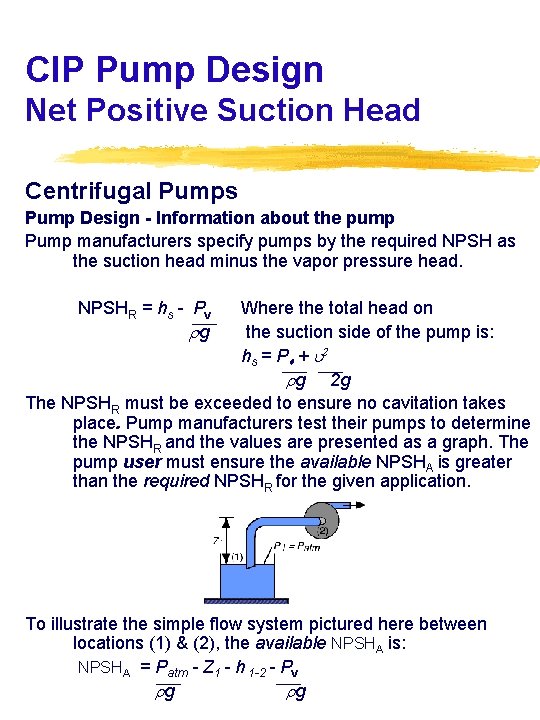
CIP Pump Design Net Positive Suction Head Centrifugal Pumps Pump Design - Information about the pump Pump manufacturers specify pumps by the required NPSH as the suction head minus the vapor pressure head. NPSHR = hs - Pv g Where the total head on the suction side of the pump is: hs = P + g 2 g The NPSHR must be exceeded to ensure no cavitation takes place. Pump manufacturers test their pumps to determine the NPSHR and the values are presented as a graph. The pump user must ensure the available NPSHA is greater than the required NPSHR for the given application. To illustrate the simple flow system pictured here between locations (1) & (2), the available NPSHA is: NPSHA = Patm - Z 1 - h 1 -2 - Pv g g
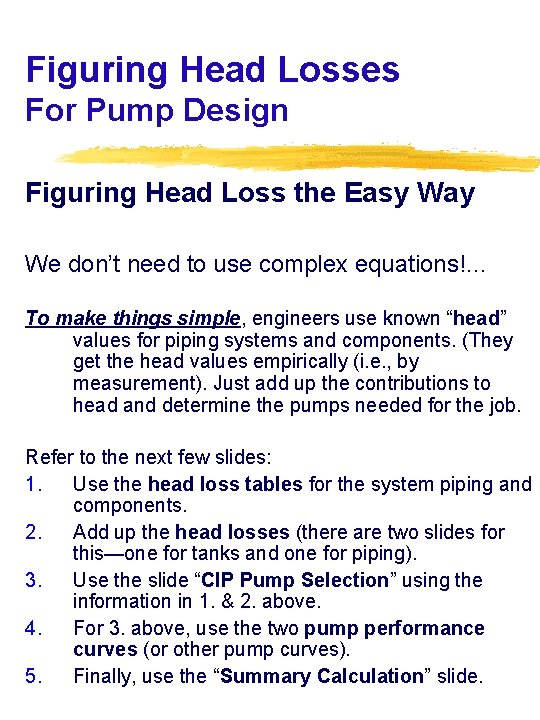
Figuring Head Losses For Pump Design Figuring Head Loss the Easy Way We don’t need to use complex equations!… To make things simple, engineers use known “head” values for piping systems and components. (They get the head values empirically (i. e. , by measurement). Just add up the contributions to head and determine the pumps needed for the job. Refer to the next few slides: 1. Use the head loss tables for the system piping and components. 2. Add up the head losses (there are two slides for this—one for tanks and one for piping). 3. Use the slide “CIP Pump Selection” using the information in 1. & 2. above. 4. For 3. above, use the two pump performance curves (or other pump curves). 5. Finally, use the “Summary Calculation” slide.
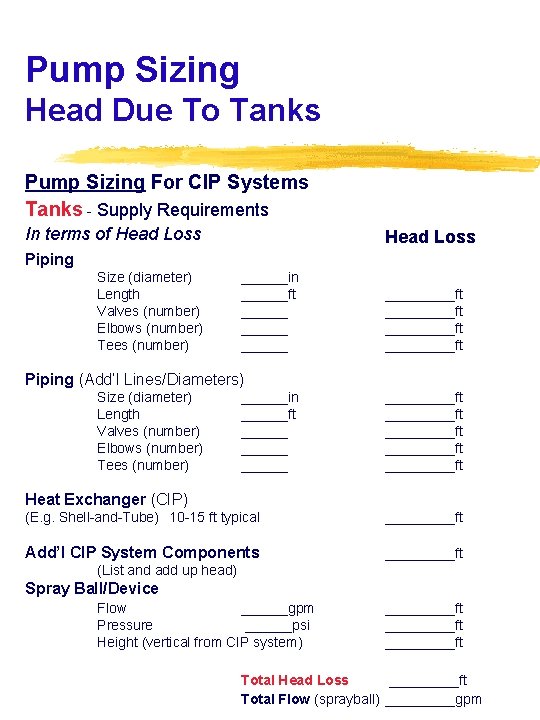
Pump Sizing Head Due To Tanks Pump Sizing For CIP Systems Tanks - Supply Requirements In terms of Head Loss Piping Size (diameter) Length Valves (number) Elbows (number) Tees (number) ______in ______ft _________ft _________ft Piping (Add’l Lines/Diameters) Size (diameter) Length Valves (number) Elbows (number) Tees (number) ______in ______ft _________ft _________ft Heat Exchanger (CIP) (E. g. Shell-and-Tube) 10 -15 ft typical _____ft Add’l CIP System Components _____ft (List and add up head) Spray Ball/Device Flow ______gpm Pressure ______psi Height (vertical from CIP system) _________ft Total Head Loss _____ft Total Flow (sprayball) _____gpm
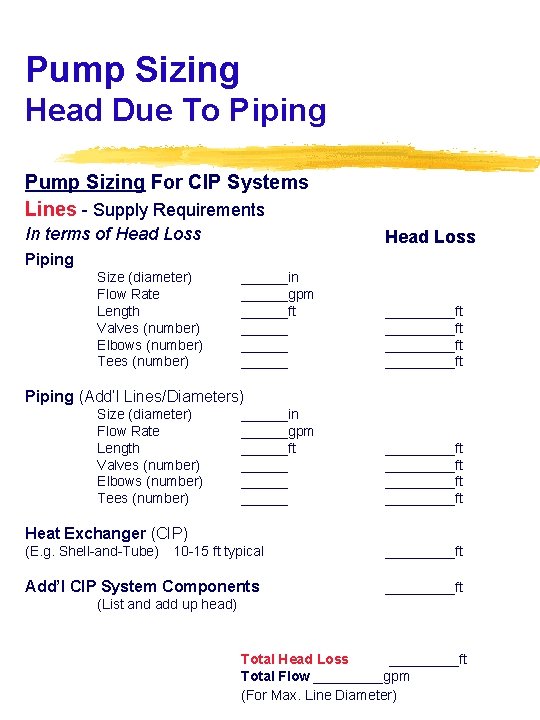
Pump Sizing Head Due To Piping Pump Sizing For CIP Systems Lines - Supply Requirements In terms of Head Loss Piping Size (diameter) Flow Rate Length Valves (number) Elbows (number) Tees (number) ______in ______gpm ______ft _________ft _________ft Piping (Add’l Lines/Diameters) Size (diameter) Flow Rate Length Valves (number) Elbows (number) Tees (number) ______in ______gpm ______ft _________ft _________ft Heat Exchanger (CIP) (E. g. Shell-and-Tube) 10 -15 ft typical Add’l CIP System Components _________ft (List and add up head) Total Head Loss _____ft Total Flow _____gpm (For Max. Line Diameter)
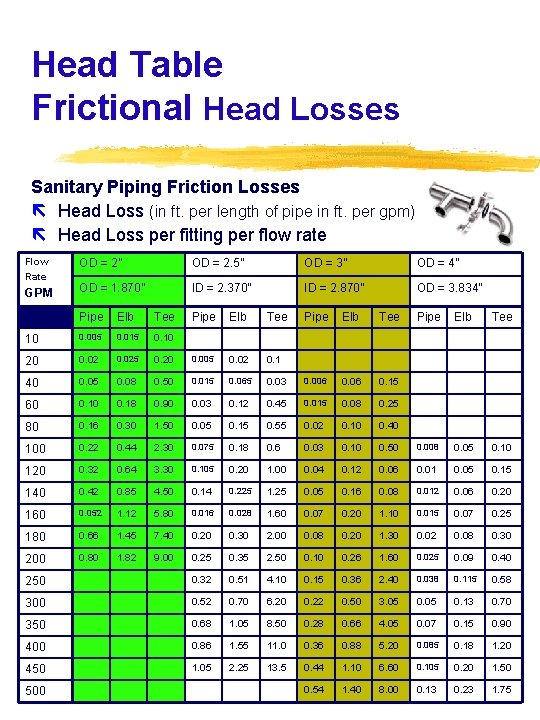
Head Table Frictional Head Losses Sanitary Piping Friction Losses Head Loss (in ft. per length of pipe in ft. per gpm) Head Loss per fitting per flow rate Flow Rate GPM OD = 2” OD = 2. 5” OD = 3” OD = 4” OD = 1. 870” ID = 2. 370” ID = 2. 870” OD = 3. 834” Pipe Elb Tee 10 0. 005 0. 015 0. 10 20 0. 025 0. 20 0. 005 0. 02 0. 1 40 0. 05 0. 08 0. 50 0. 015 0. 065 0. 03 0. 006 0. 15 60 0. 18 0. 90 0. 03 0. 12 0. 45 0. 015 0. 08 0. 25 80 0. 16 0. 30 1. 50 0. 05 0. 15 0. 55 0. 02 0. 10 0. 40 100 0. 22 0. 44 2. 30 0. 075 0. 18 0. 6 0. 03 0. 10 0. 50 0. 008 0. 05 0. 10 120 0. 32 0. 64 3. 30 0. 105 0. 20 1. 00 0. 04 0. 12 0. 06 0. 01 0. 05 0. 15 140 0. 42 0. 85 4. 50 0. 14 0. 225 1. 25 0. 05 0. 16 0. 08 0. 012 0. 06 0. 20 160 0. 052 1. 12 5. 80 0. 016 0. 028 1. 60 0. 07 0. 20 1. 10 0. 015 0. 07 0. 25 180 0. 66 1. 45 7. 40 0. 20 0. 30 2. 00 0. 08 0. 20 1. 30 0. 02 0. 08 0. 30 200 0. 80 1. 82 9. 00 0. 25 0. 35 2. 50 0. 10 0. 26 1. 60 0. 025 0. 09 0. 40 250 0. 32 0. 51 4. 10 0. 15 0. 36 2. 40 0. 038 0. 115 0. 58 300 0. 52 0. 70 6. 20 0. 22 0. 50 3. 05 0. 13 0. 70 350 0. 68 1. 05 8. 50 0. 28 0. 66 4. 05 0. 07 0. 15 0. 90 400 0. 86 1. 55 11. 0 0. 36 0. 88 5. 20 0. 085 0. 18 1. 20 450 1. 05 2. 25 13. 5 0. 44 1. 10 6. 60 0. 105 0. 20 1. 50 0. 54 1. 40 8. 00 0. 13 0. 23 1. 75 500
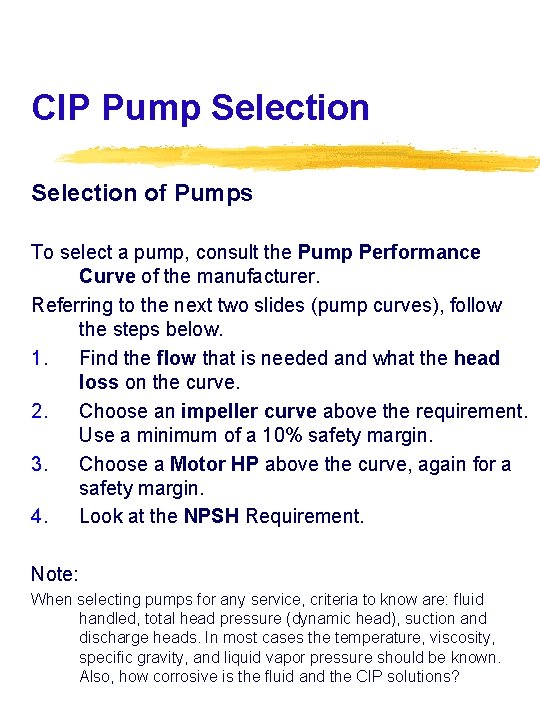
CIP Pump Selection of Pumps To select a pump, consult the Pump Performance Curve of the manufacturer. Referring to the next two slides (pump curves), follow the steps below. 1. Find the flow that is needed and what the head loss on the curve. 2. Choose an impeller curve above the requirement. Use a minimum of a 10% safety margin. 3. Choose a Motor HP above the curve, again for a safety margin. 4. Look at the NPSH Requirement. Note: When selecting pumps for any service, criteria to know are: fluid handled, total head pressure (dynamic head), suction and discharge heads. In most cases the temperature, viscosity, specific gravity, and liquid vapor pressure should be known. Also, how corrosive is the fluid and the CIP solutions?
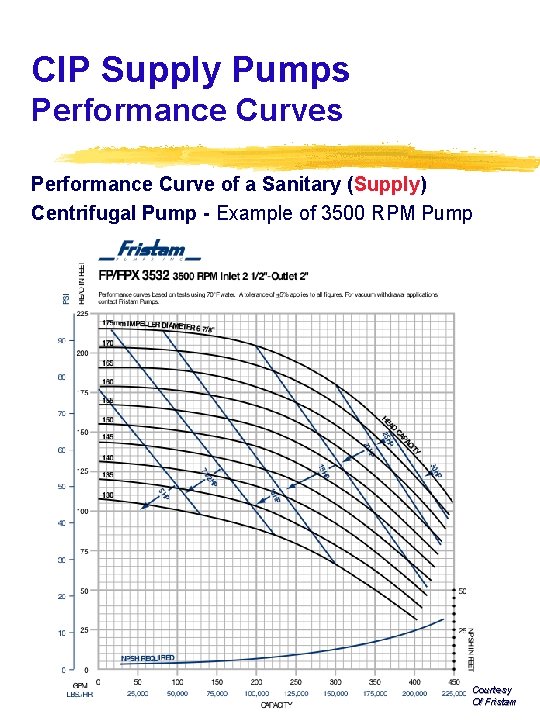
CIP Supply Pumps Performance Curve of a Sanitary (Supply) Centrifugal Pump - Example of 3500 RPM Pump Courtesy Of Fristam
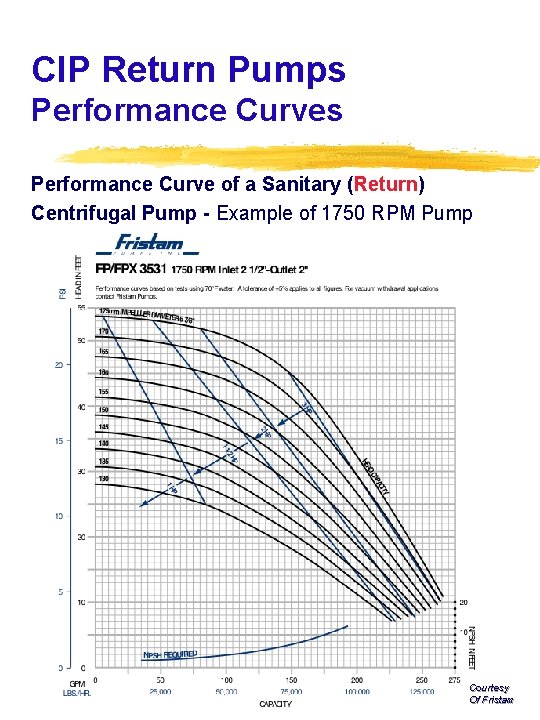
CIP Return Pumps Performance Curve of a Sanitary (Return) Centrifugal Pump - Example of 1750 RPM Pump Courtesy Of Fristam
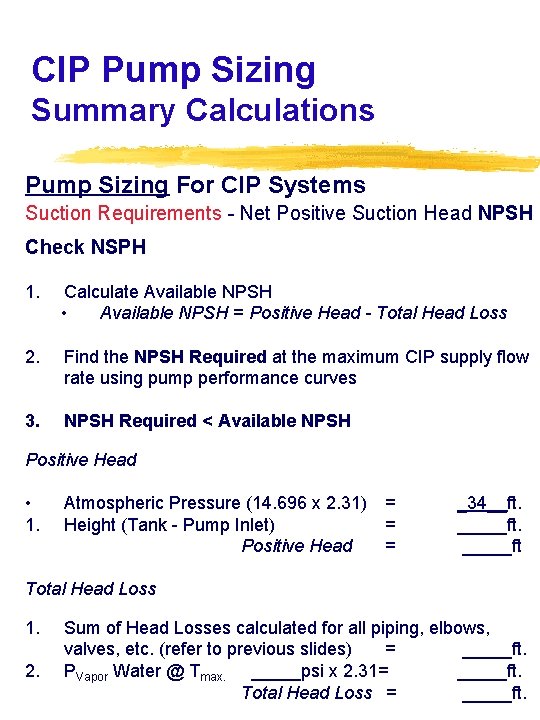
CIP Pump Sizing Summary Calculations Pump Sizing For CIP Systems Suction Requirements - Net Positive Suction Head NPSH Check NSPH 1. Calculate Available NPSH • Available NPSH = Positive Head - Total Head Loss 2. Find the NPSH Required at the maximum CIP supply flow rate using pump performance curves 3. NPSH Required < Available NPSH Positive Head • 1. Atmospheric Pressure (14. 696 x 2. 31) Height (Tank - Pump Inlet) Positive Head = = = _34__ft. _____ft Total Head Loss 1. 2. Sum of Head Losses calculated for all piping, elbows, valves, etc. (refer to previous slides) = _____ft. PVapor Water @ Tmax. _____psi x 2. 31= _____ft. Total Head Loss = _____ft.
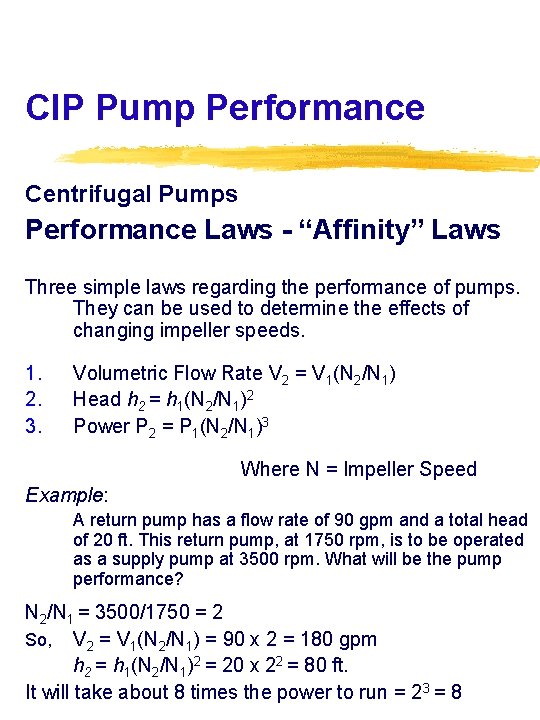
CIP Pump Performance Centrifugal Pumps Performance Laws - “Affinity” Laws Three simple laws regarding the performance of pumps. They can be used to determine the effects of changing impeller speeds. 1. 2. 3. Volumetric Flow Rate V 2 = V 1(N 2/N 1) Head h 2 = h 1(N 2/N 1)2 Power P 2 = P 1(N 2/N 1)3 Where N = Impeller Speed Example: A return pump has a flow rate of 90 gpm and a total head of 20 ft. This return pump, at 1750 rpm, is to be operated as a supply pump at 3500 rpm. What will be the pump performance? N 2/N 1 = 3500/1750 = 2 So, V 2 = V 1(N 2/N 1) = 90 x 2 = 180 gpm h 2 = h 1(N 2/N 1)2 = 20 x 22 = 80 ft. It will take about 8 times the power to run = 23 = 8

CIP Training Flow, Friction, and Pump Selection Thank you for your time! Questions?
Jill is climbing. where does she need high friction
Classify reciprocating pump
Difference between external and internal gear pump
Screw pump vs gear pump
Reynolds number equation
Reynold number in pipe
Reynolds number for pipe flow
Flow in closed conduits
Friction factor for laminar flow
Quattromix
Radial flow pumps
Radial flow centrifugal pump
Fundamentals of fluid mechanics
Radial flow centrifugal pump
Radial flow centrifugal pump
Series aiding and series opposing
Centrifugal pump training
Maclaurin series vs taylor series
Balmer series lyman series
Taylor series of composite functions
Maclaurin polynomial
Ibm p series server
Series series feedback amplifier
Sum of infinite series
Transform flow and transaction flow in software engineering
Data flow structure
Rotational flow means
Internal flow examples
Control flow and data flow computers
Explain turbulent flow
Cash flow series
Nerc cip v4
How to use less water in cip
Rc cip
Paritet cfr
Kurt forster
Cip continuous improvement program
Cognitive information processing pyramid