PrecastPrestressed Industrial Structures Design Specifications and Applications This
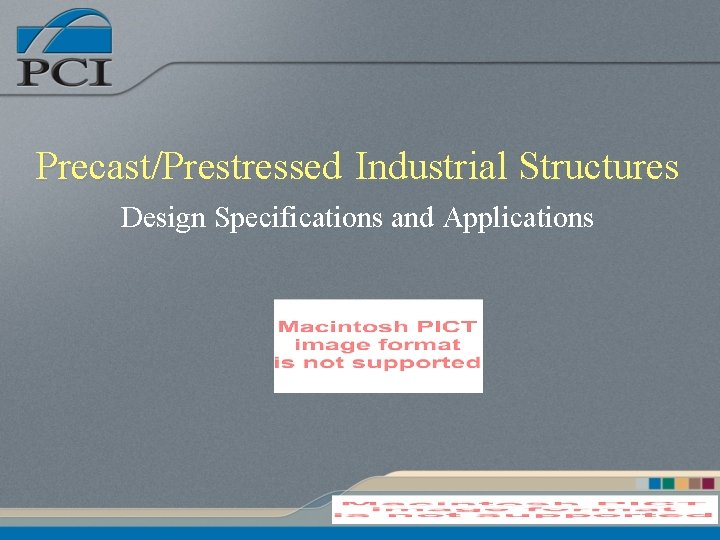
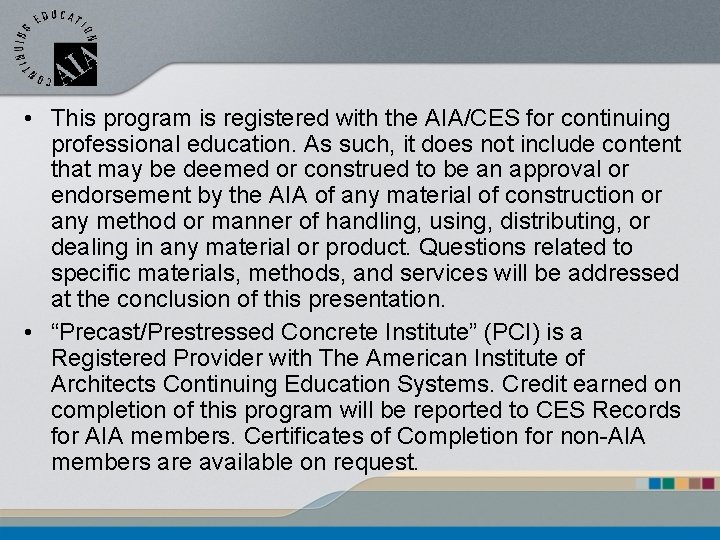
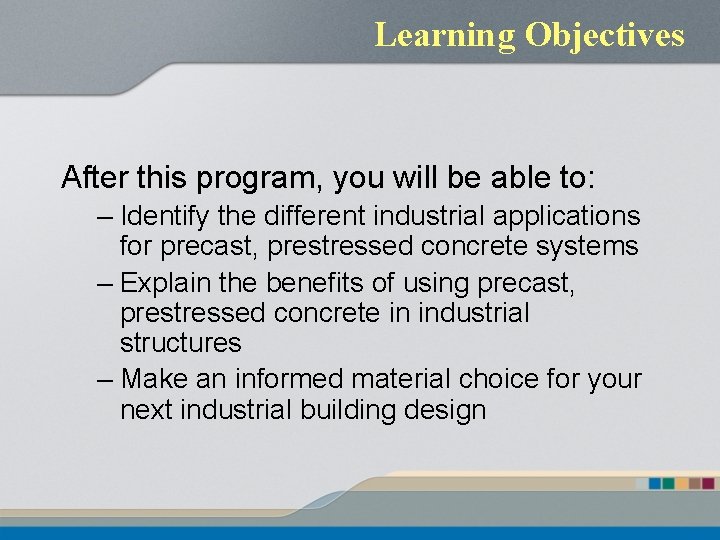
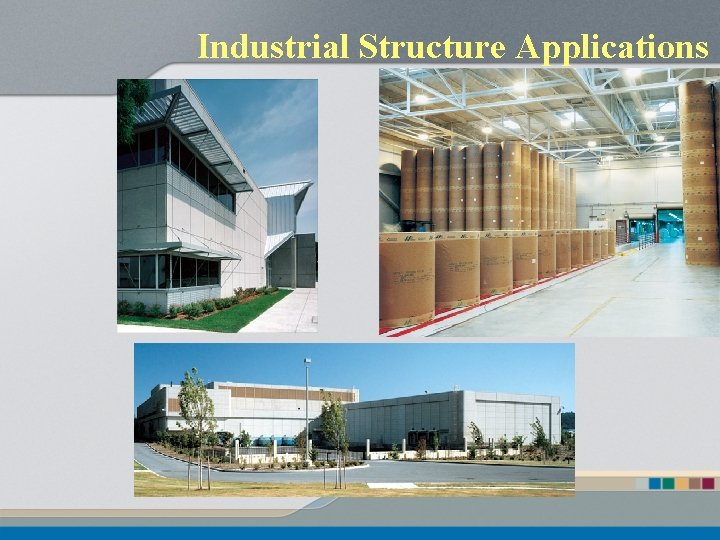
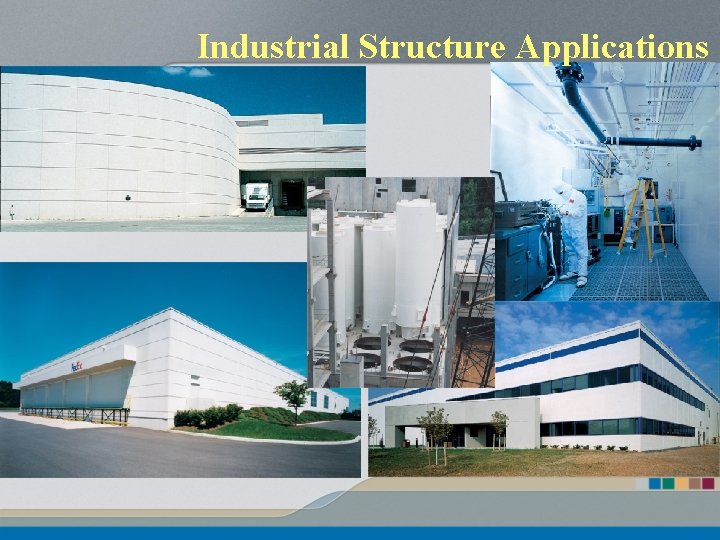
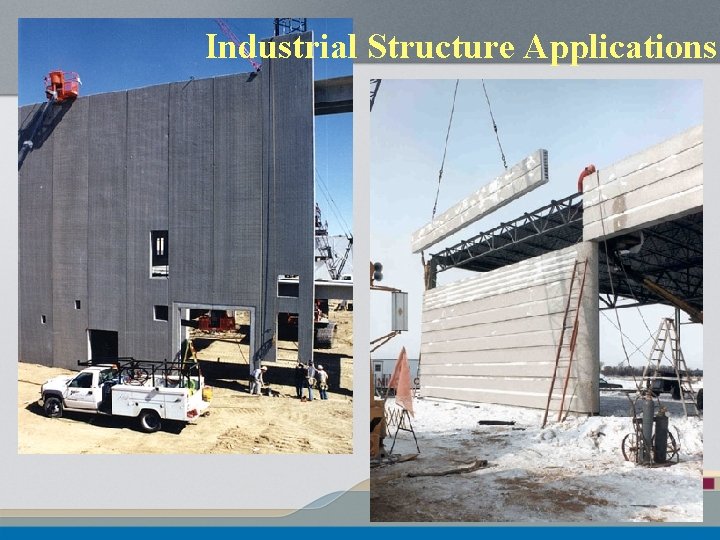

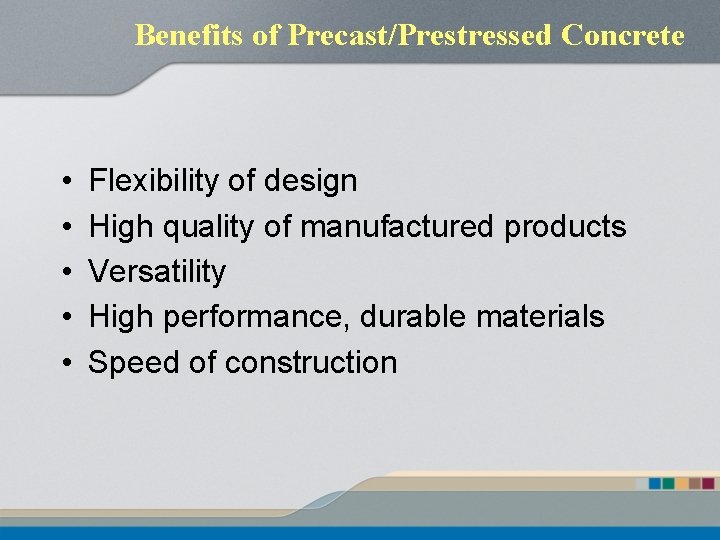
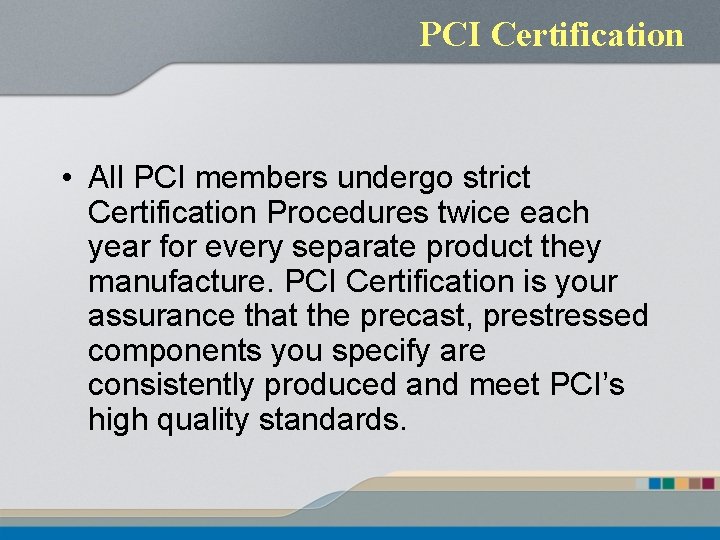
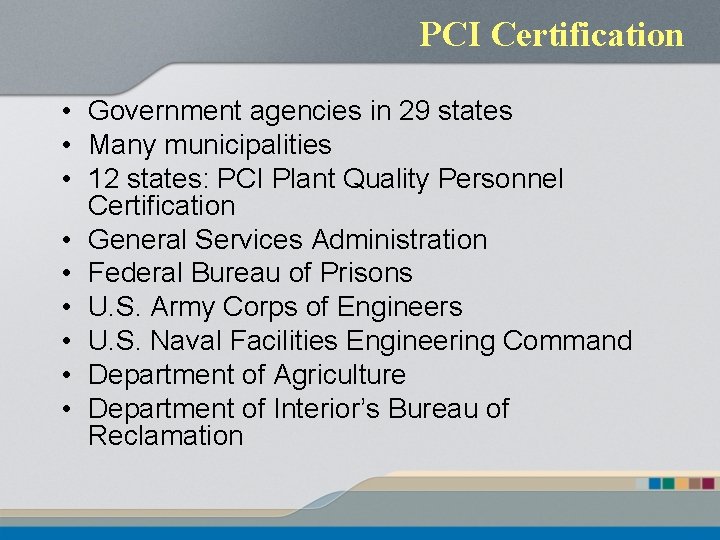
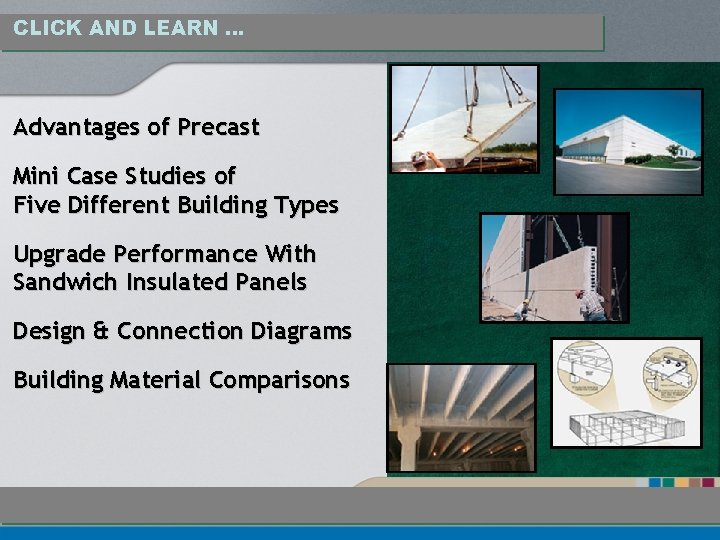
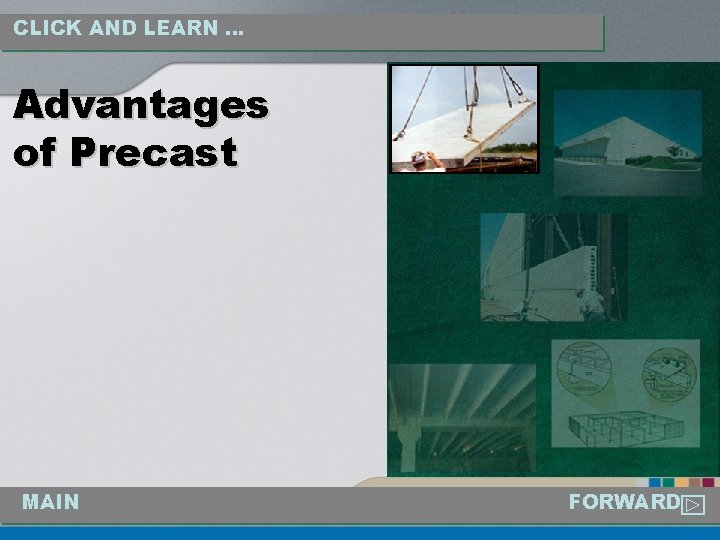
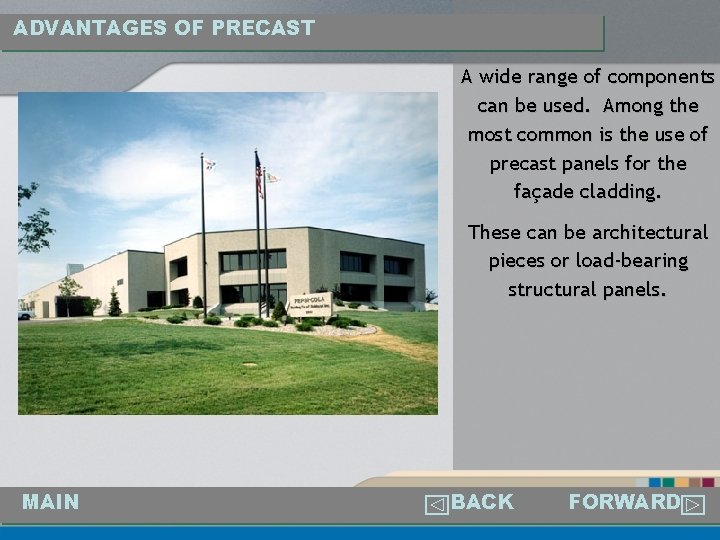
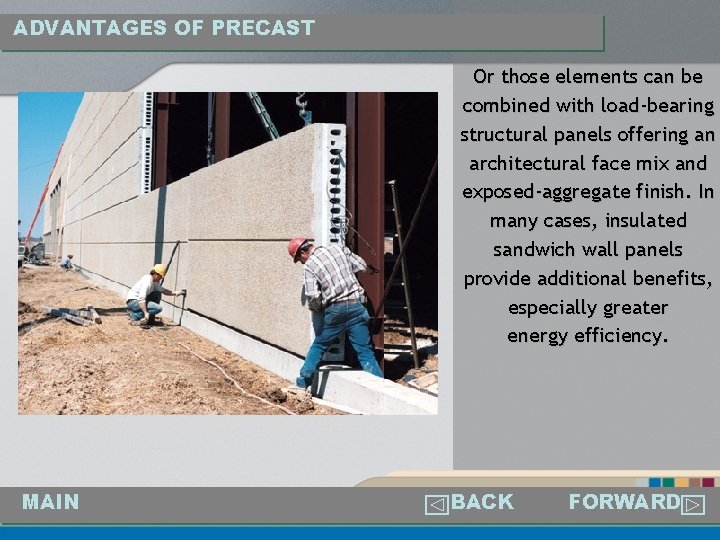
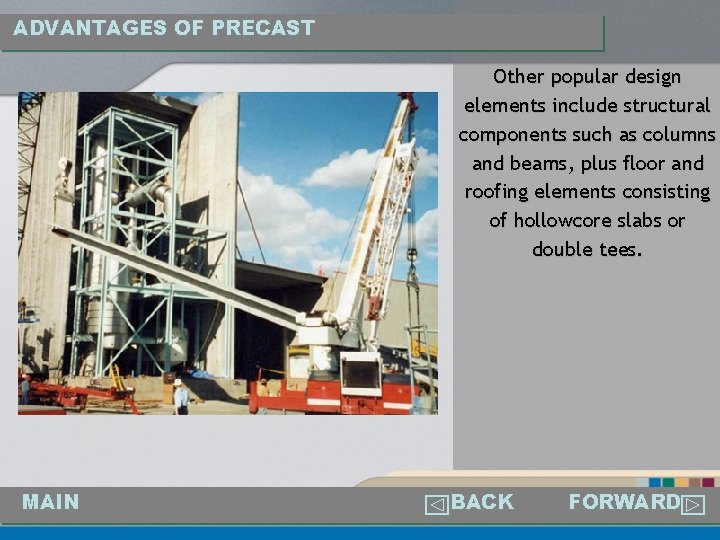
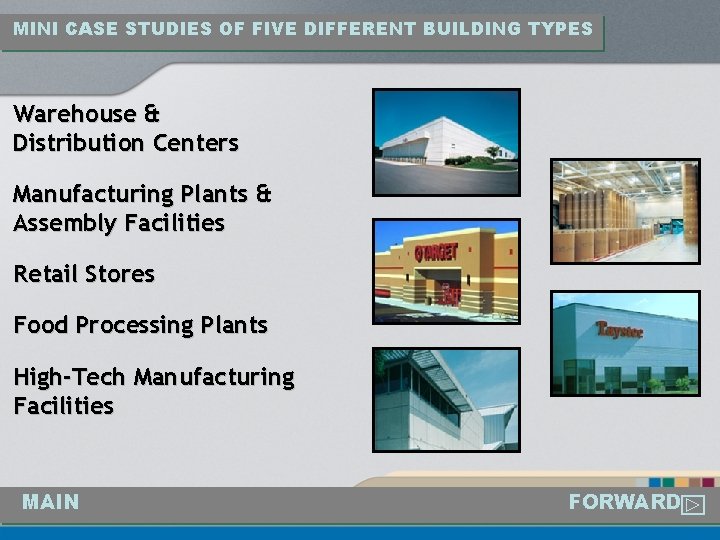
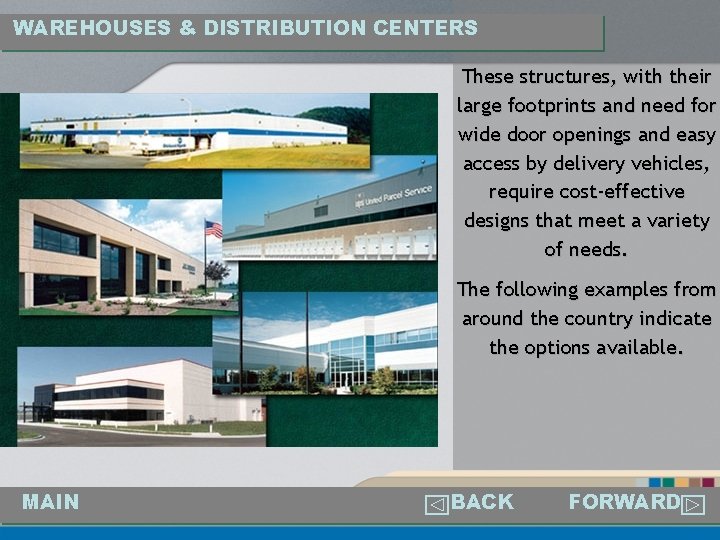
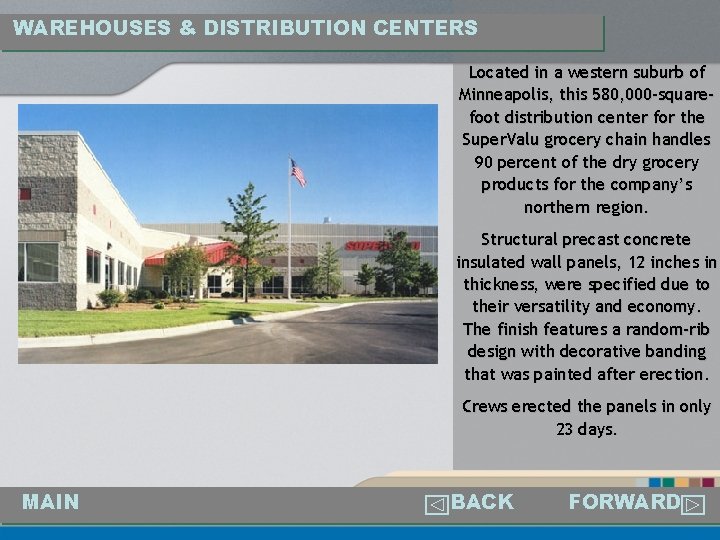
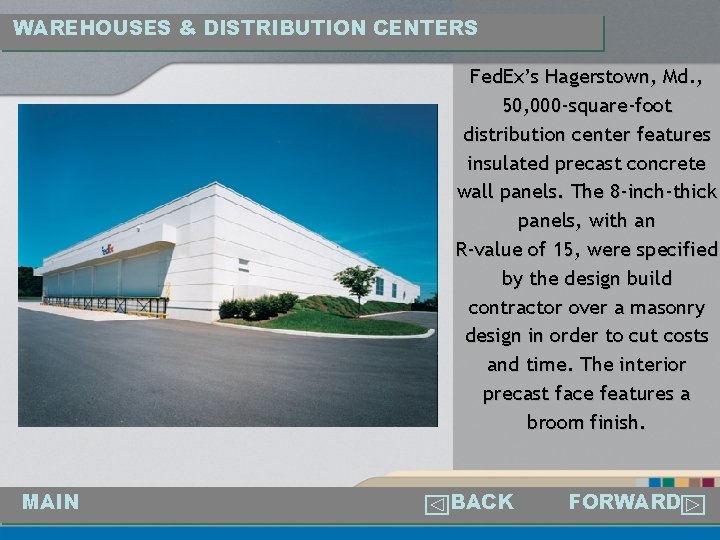
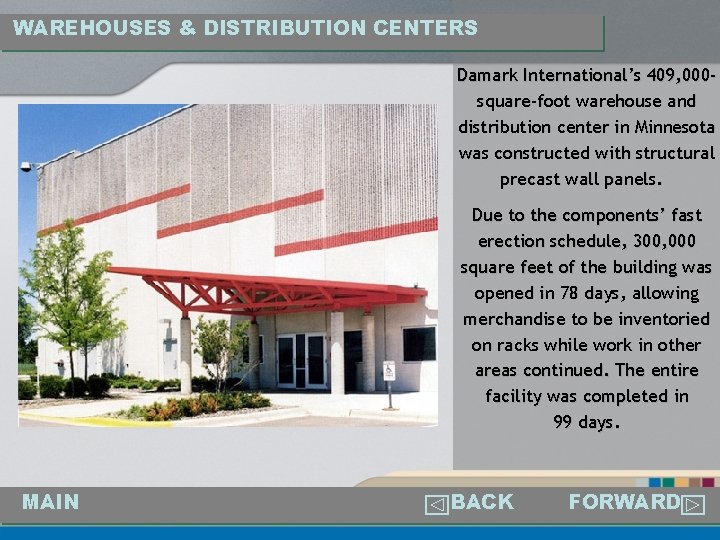
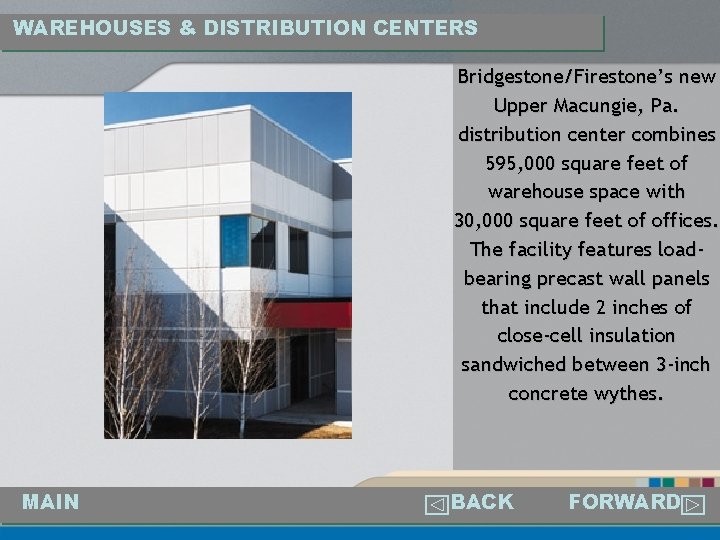
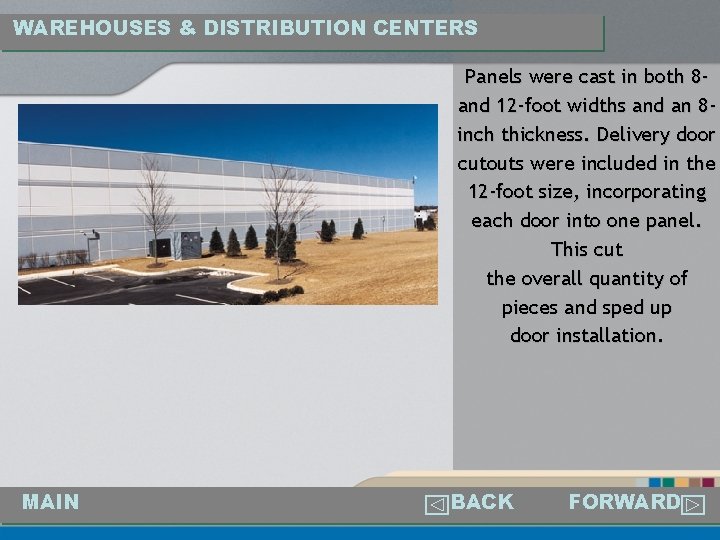
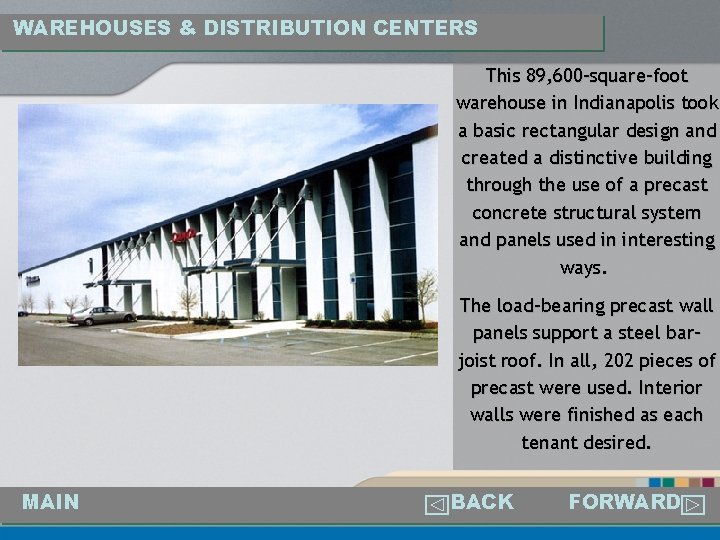
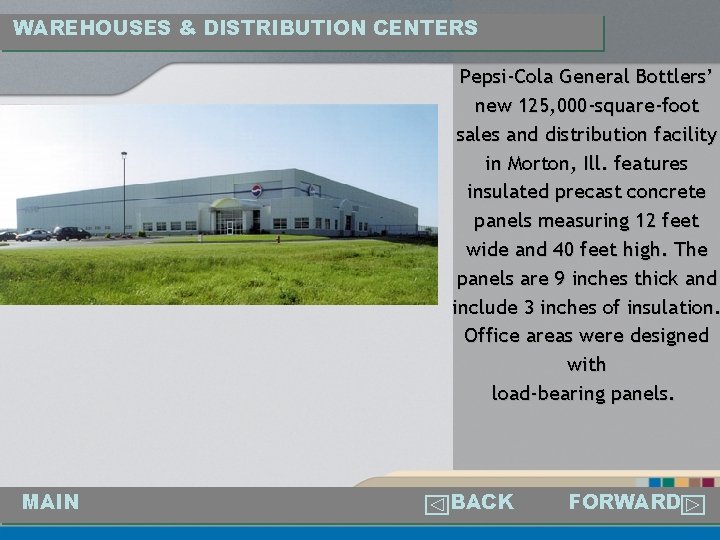
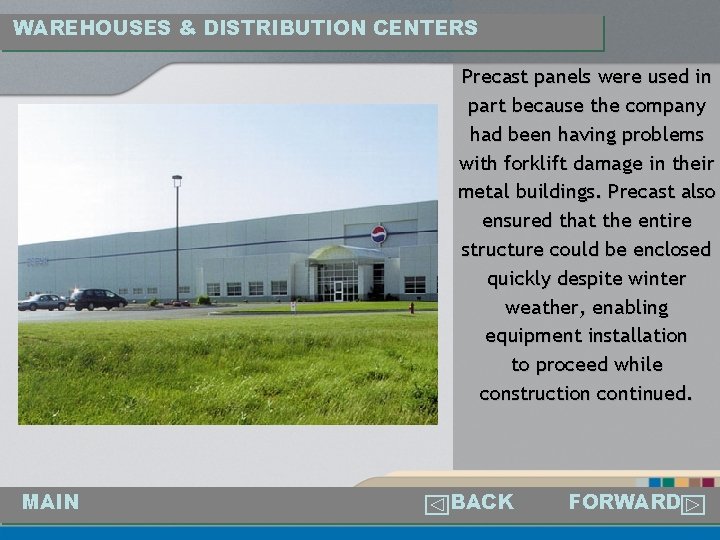
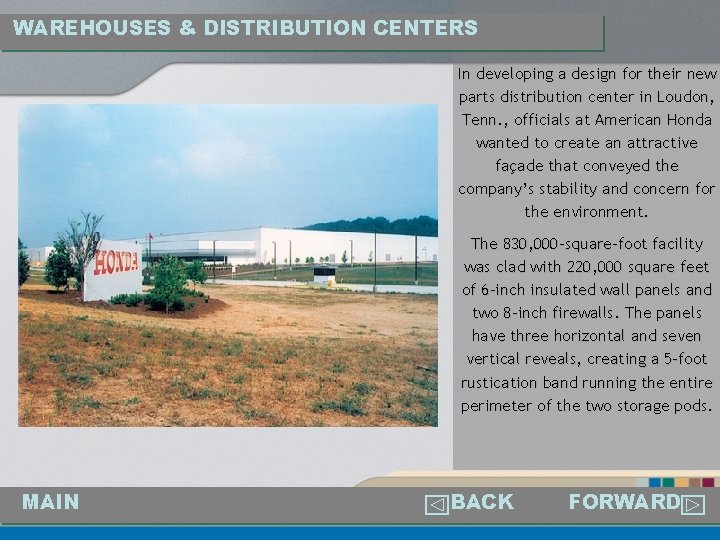
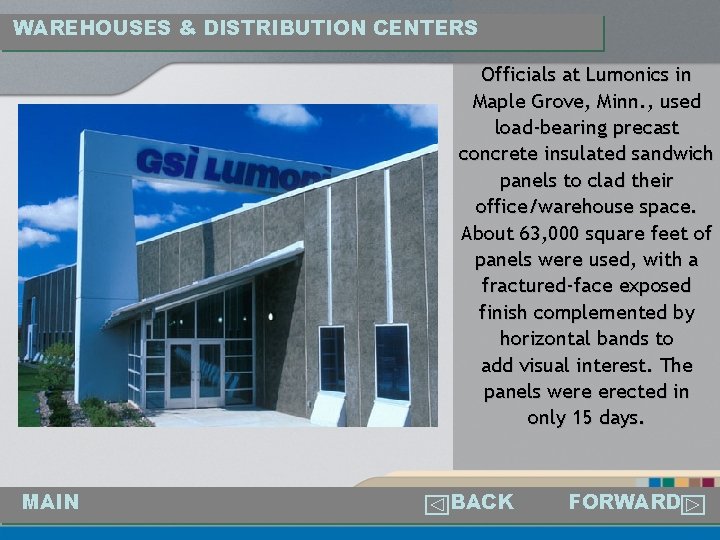
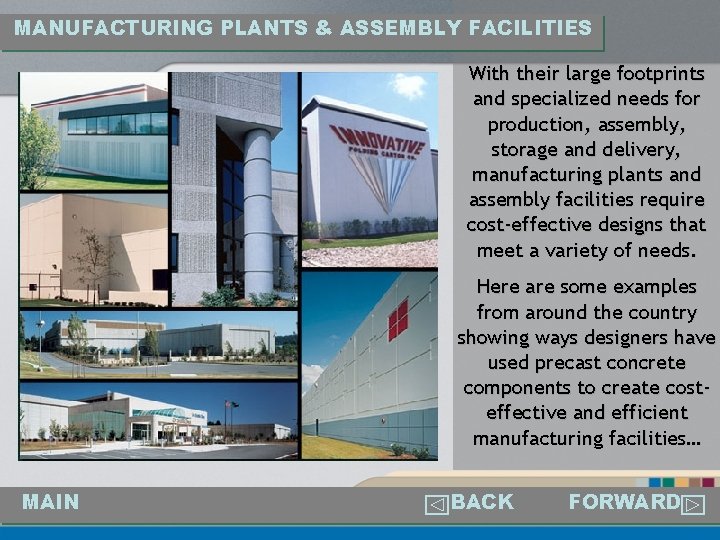
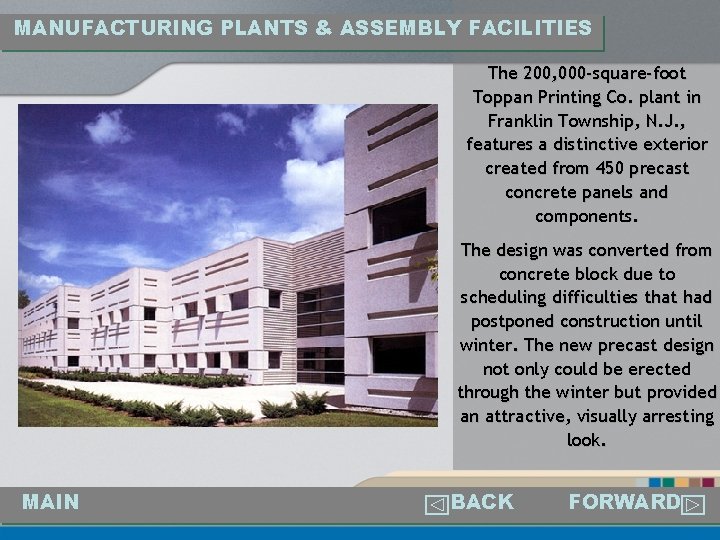

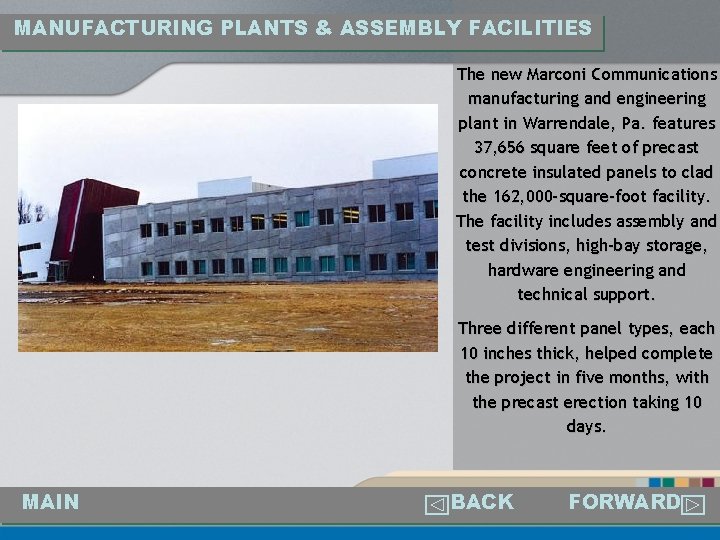
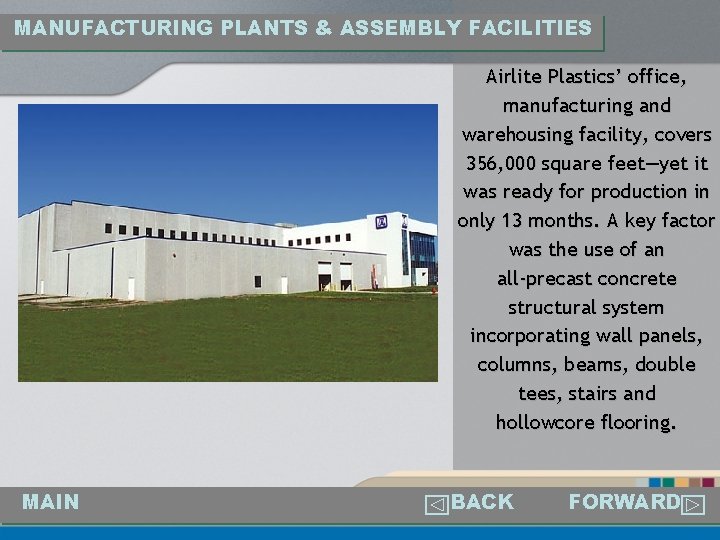
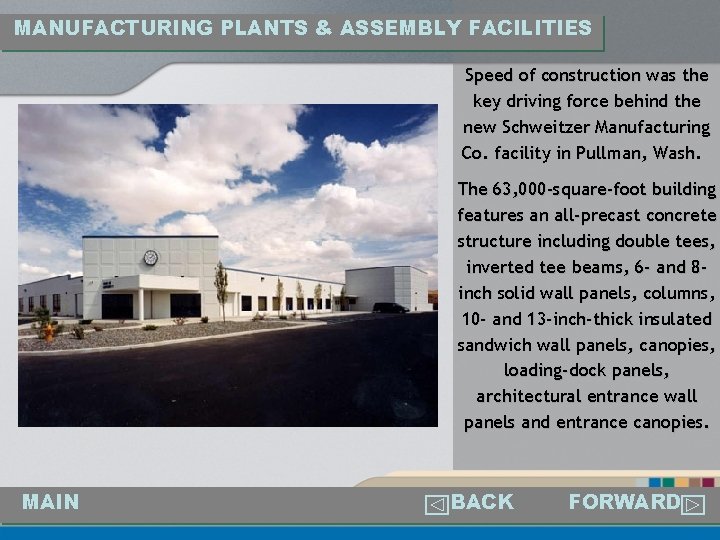
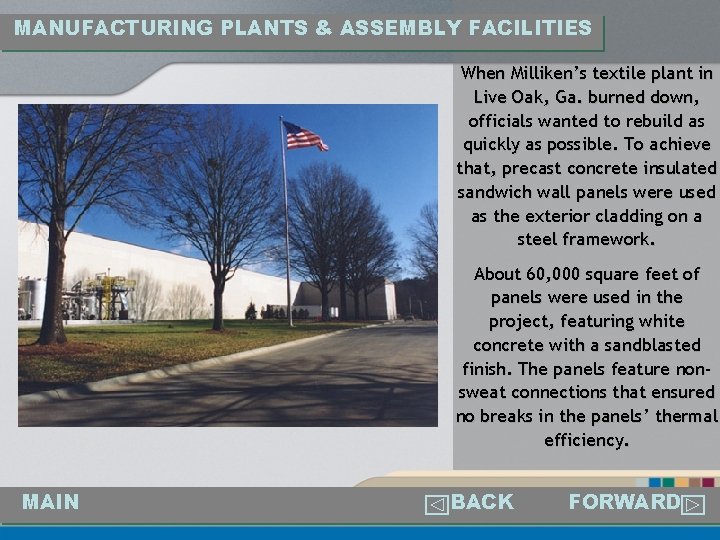
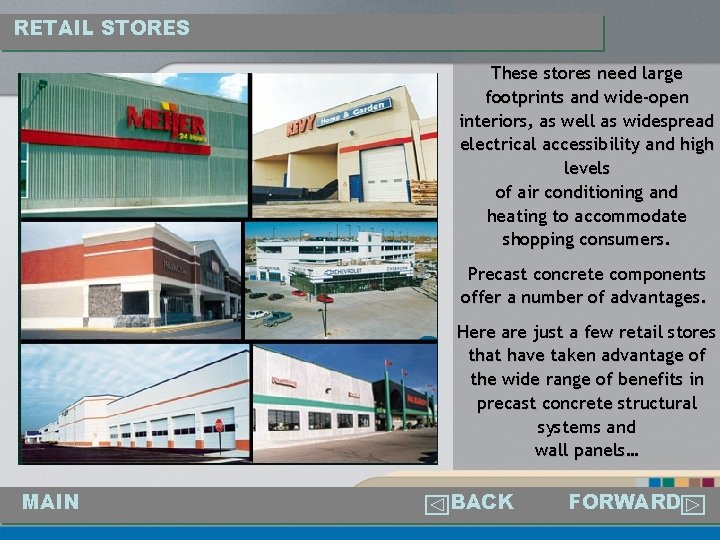
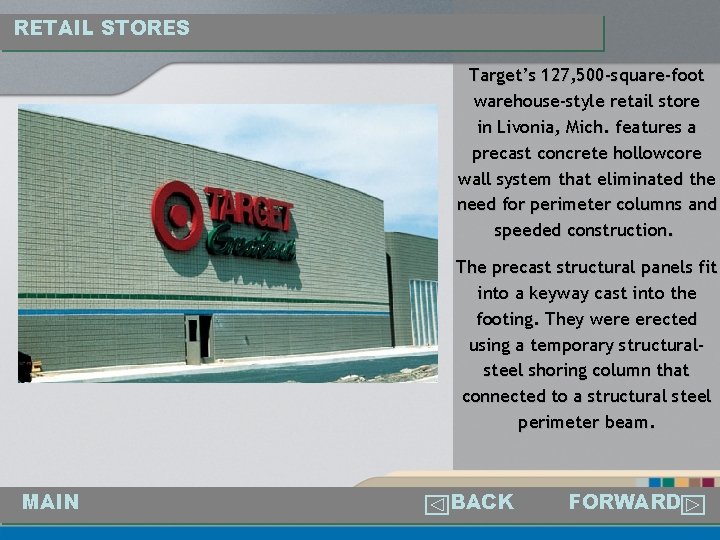
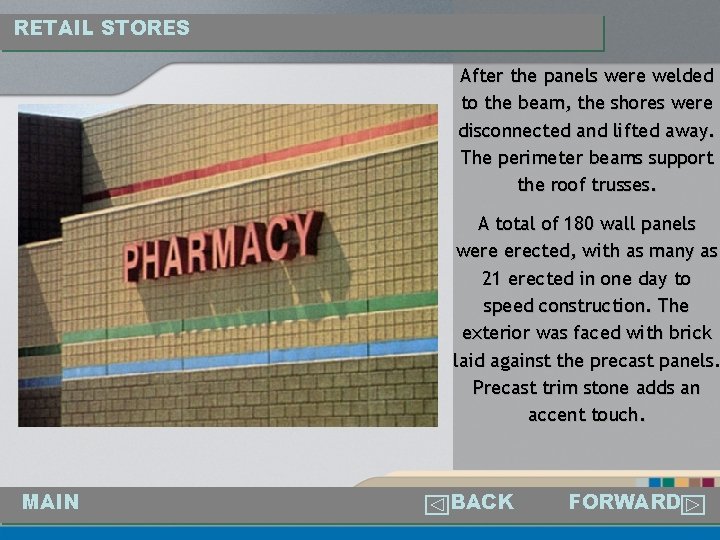
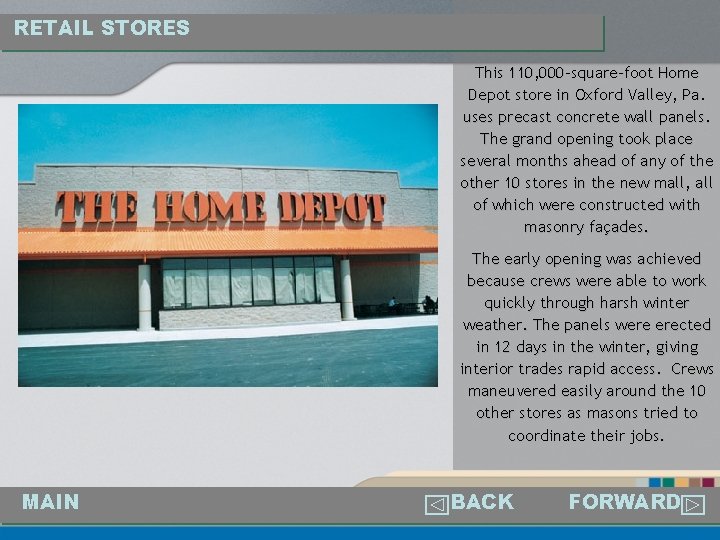
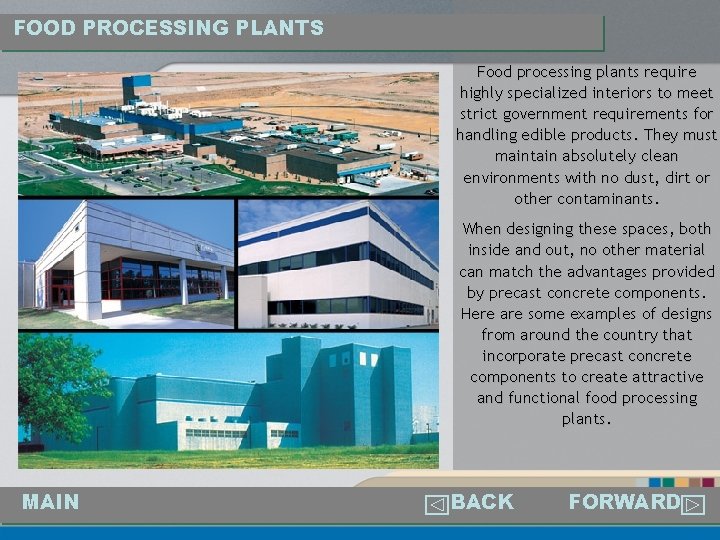
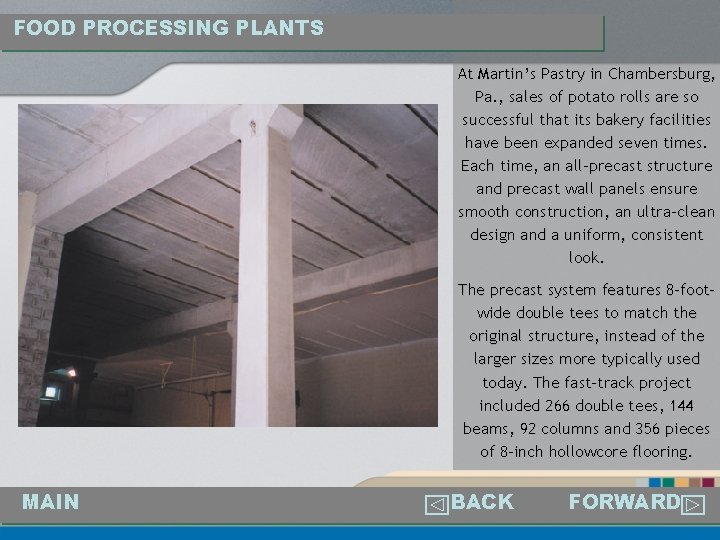
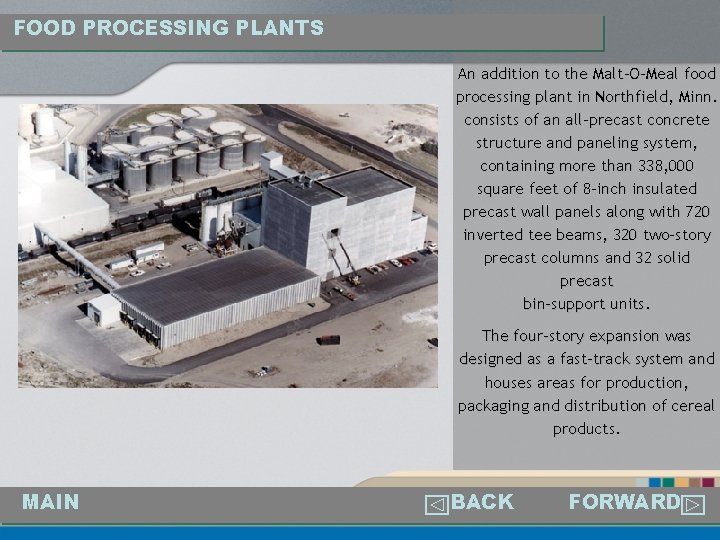
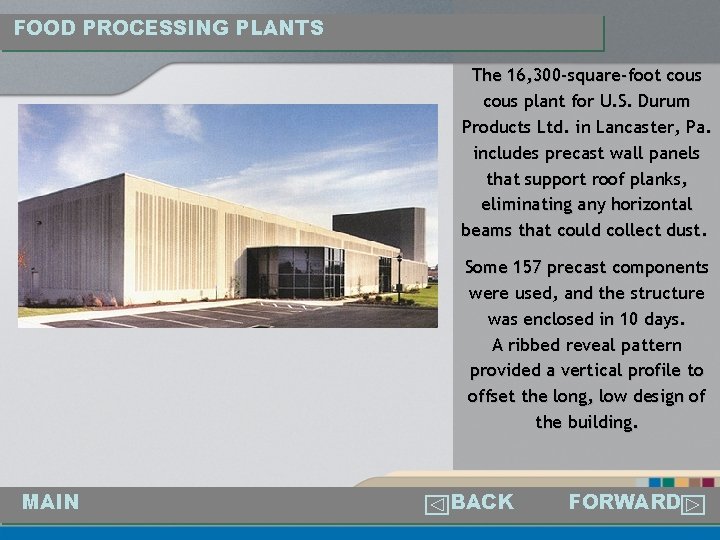
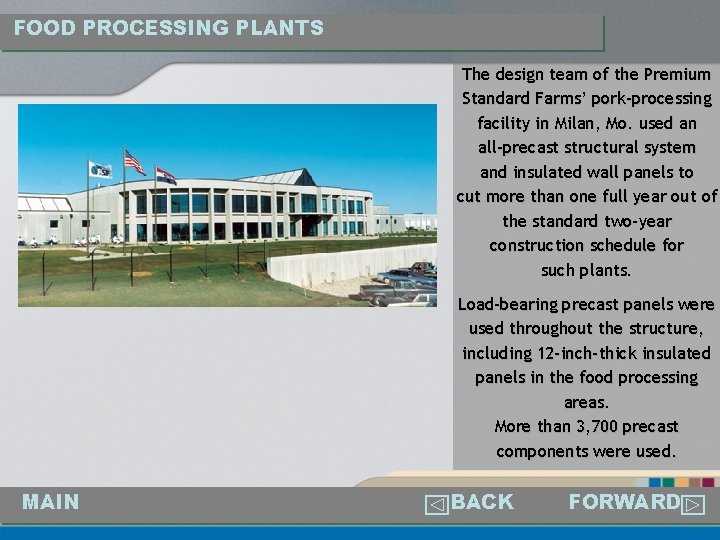
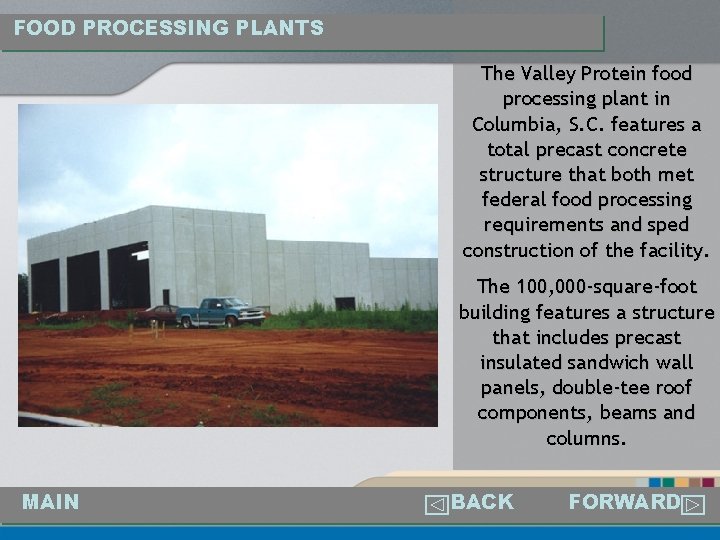
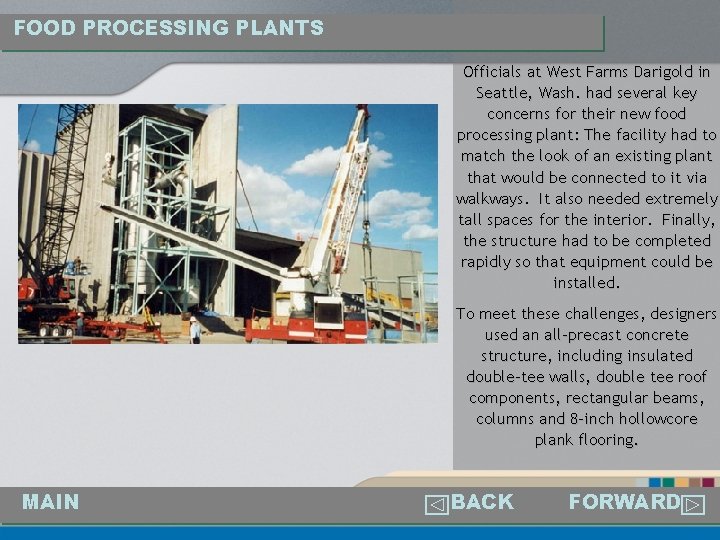
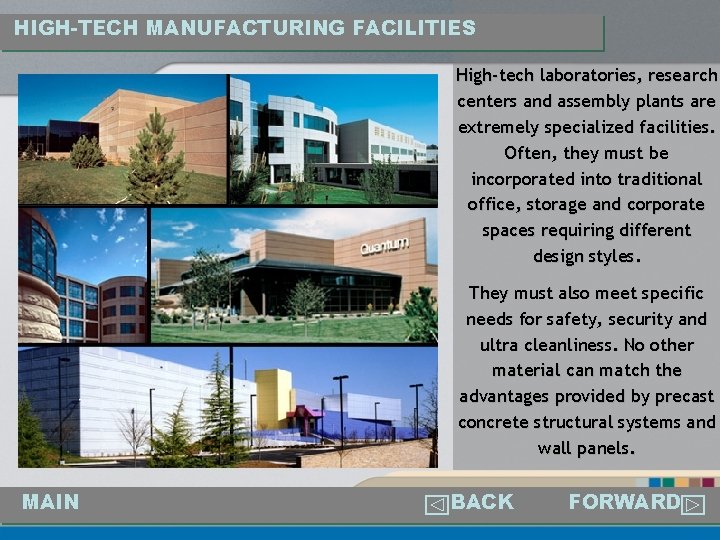
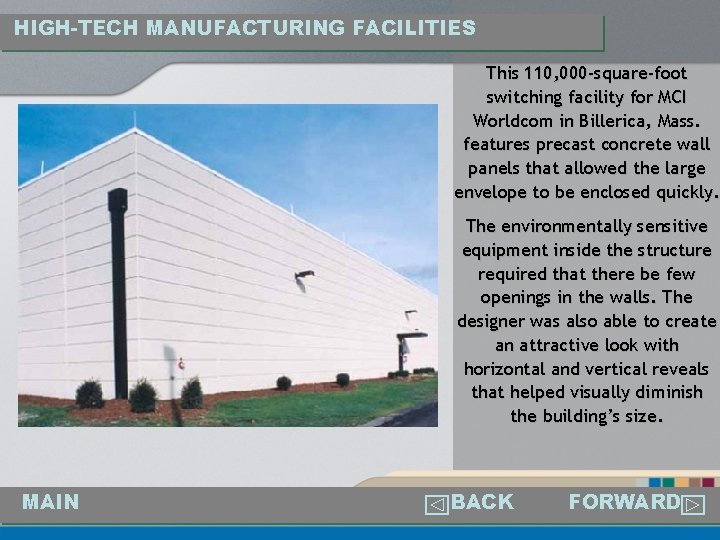
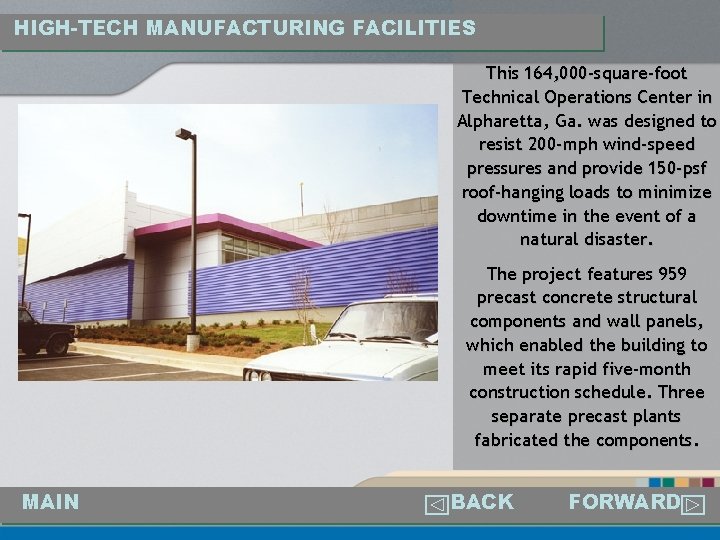
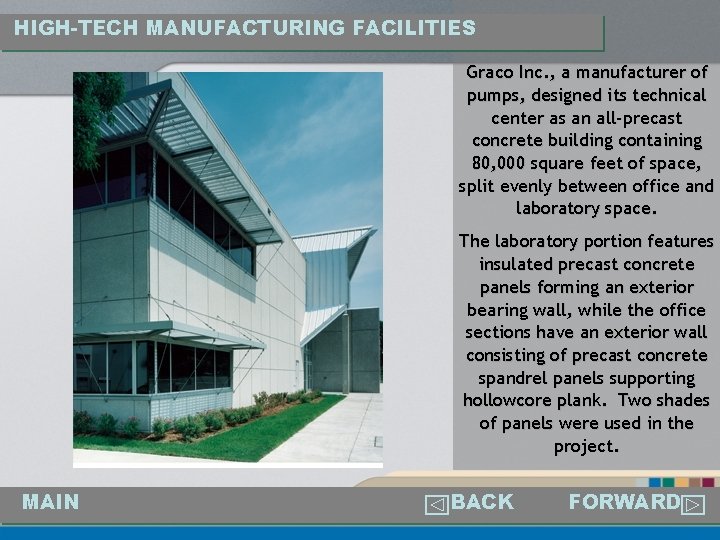
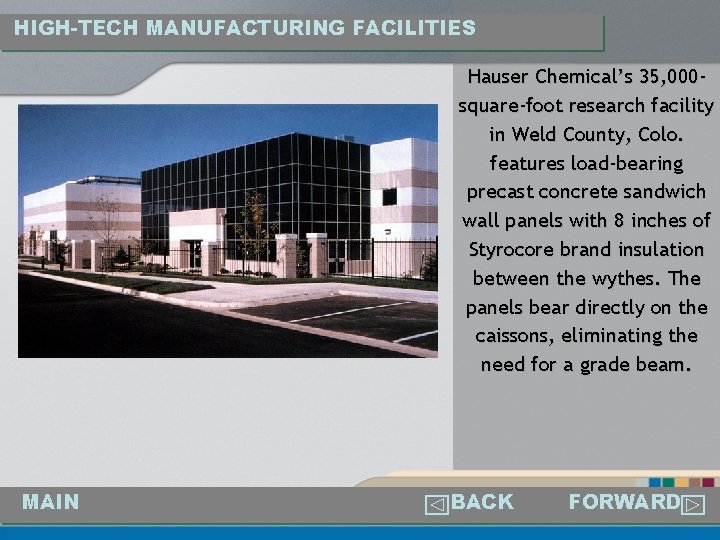
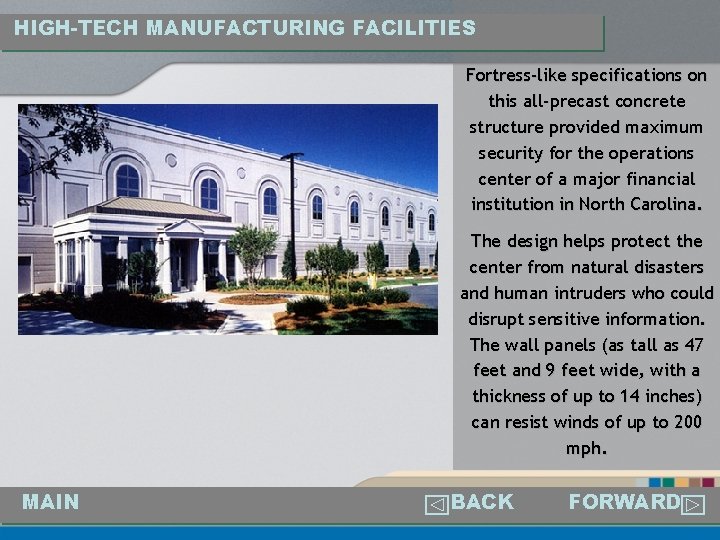
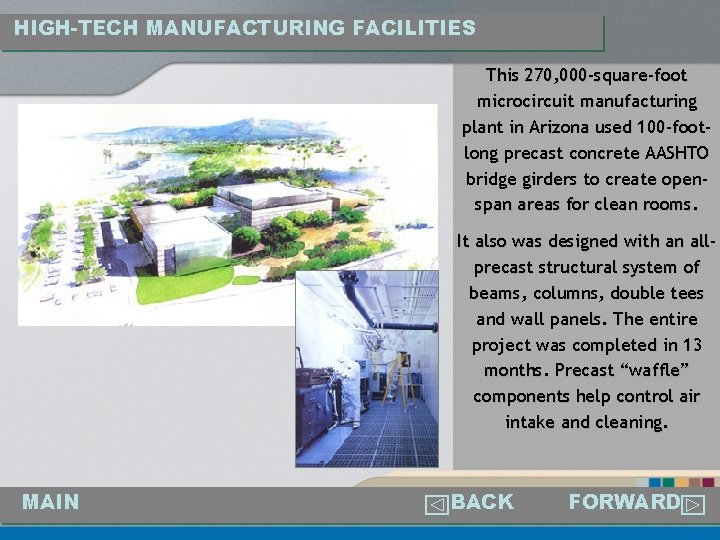
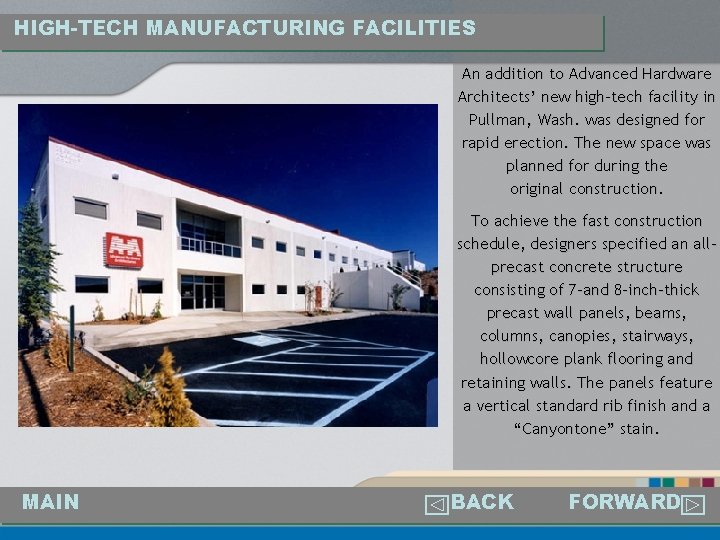
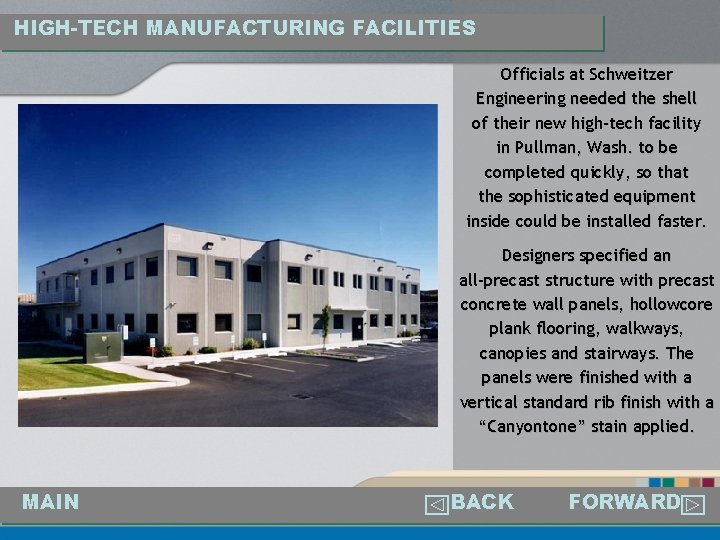
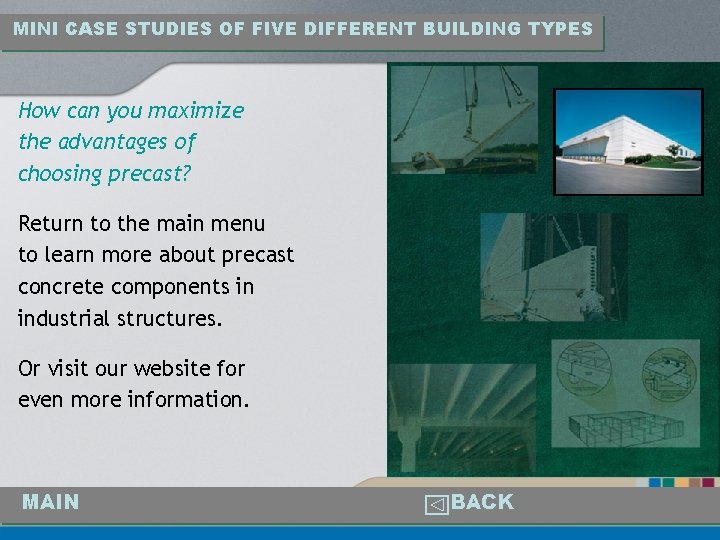
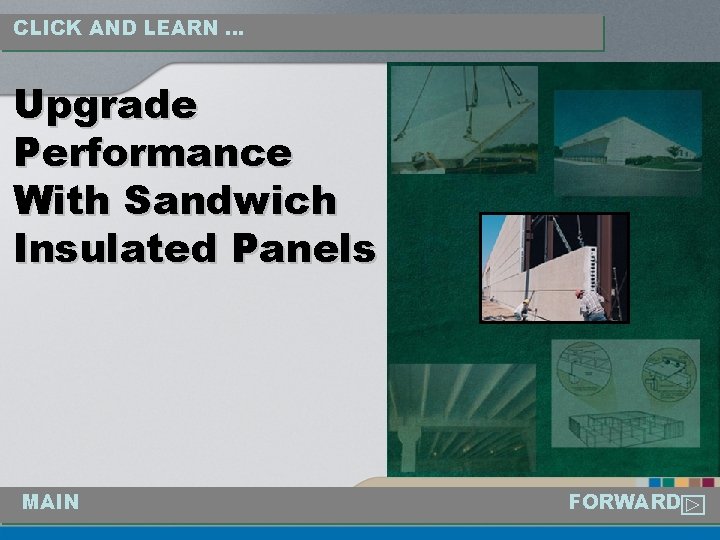
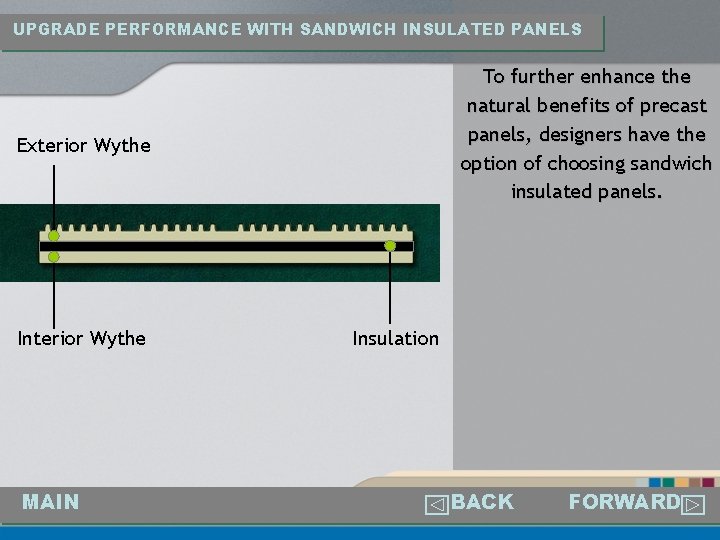
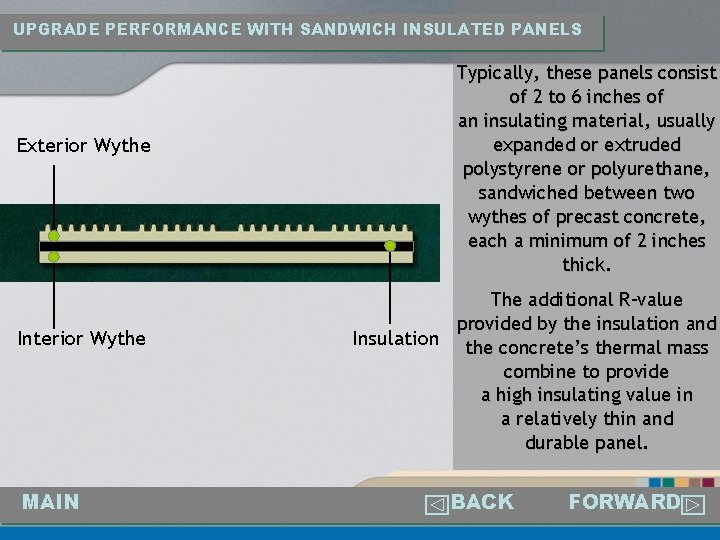
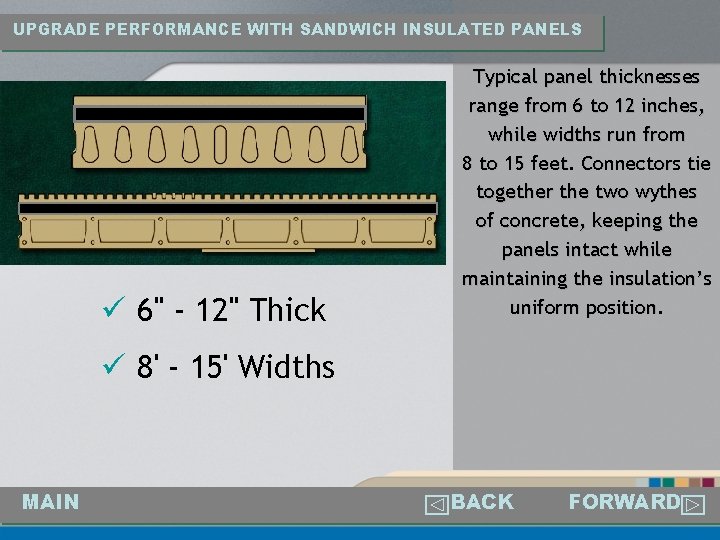
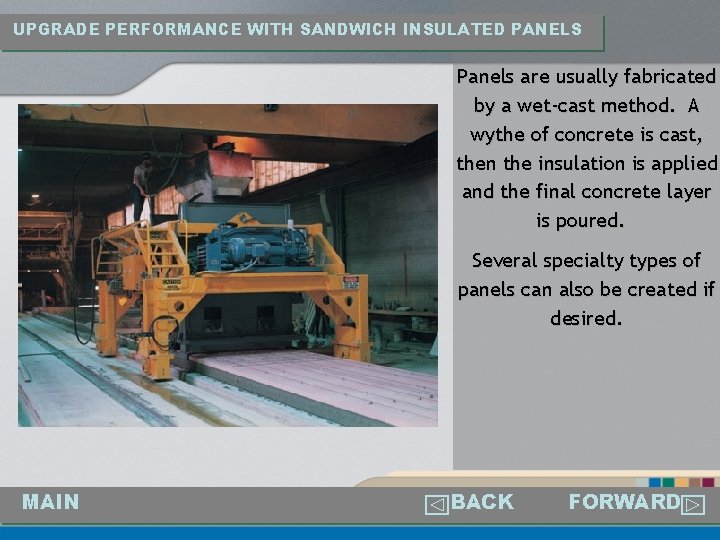
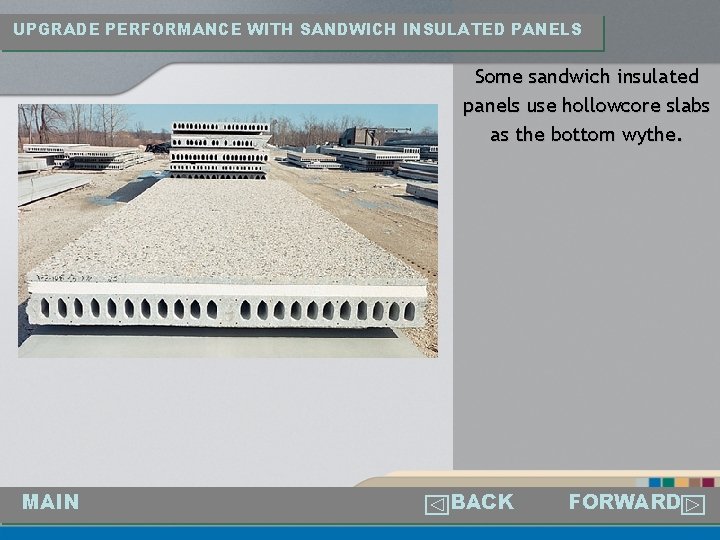
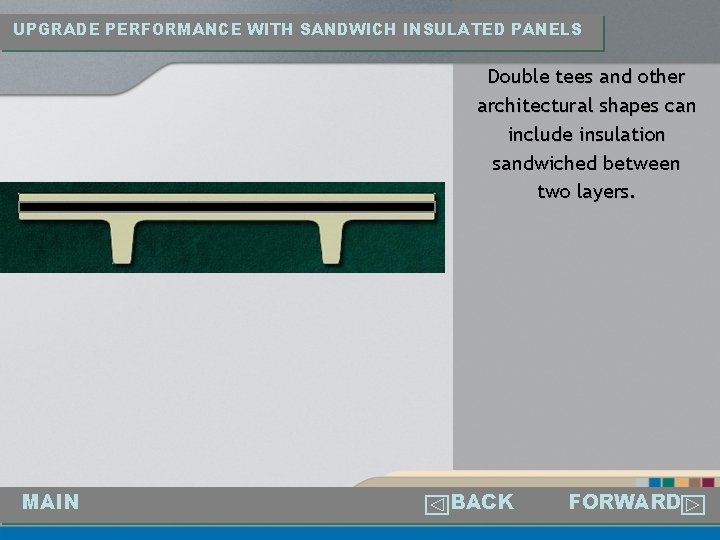
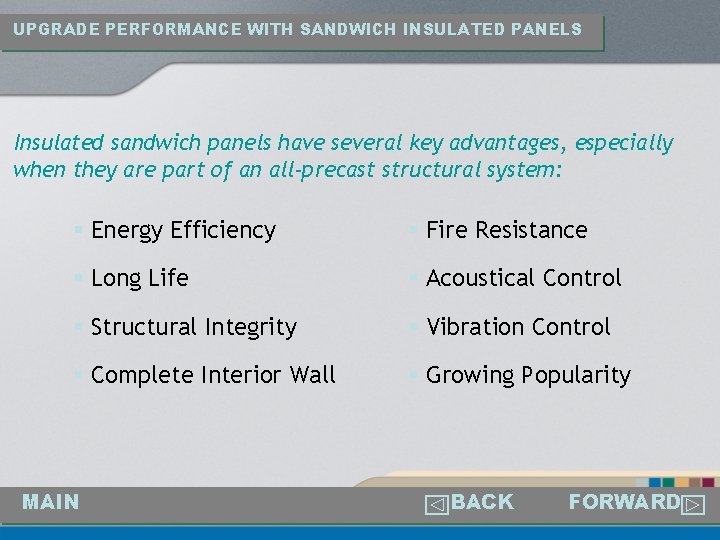
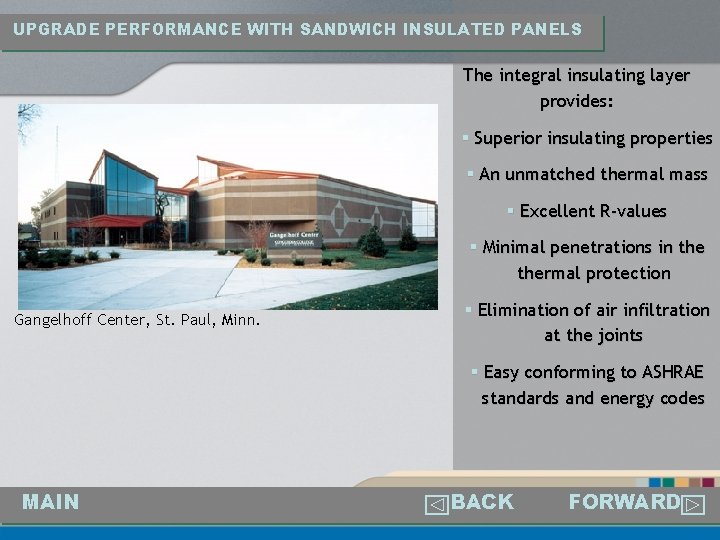
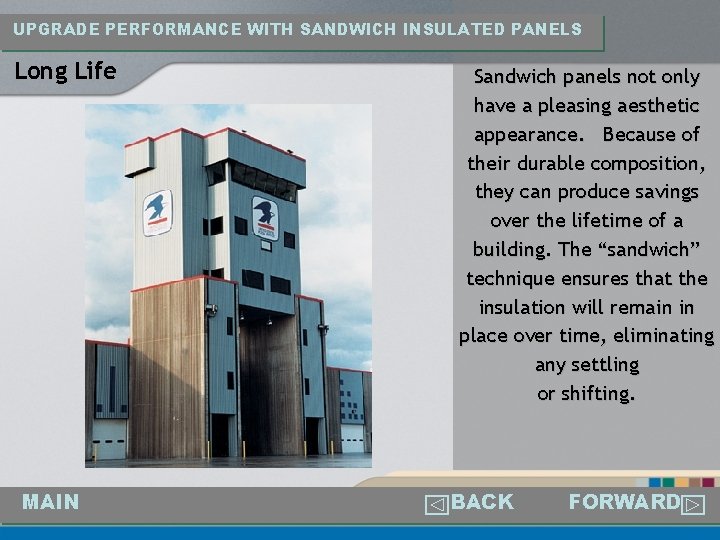
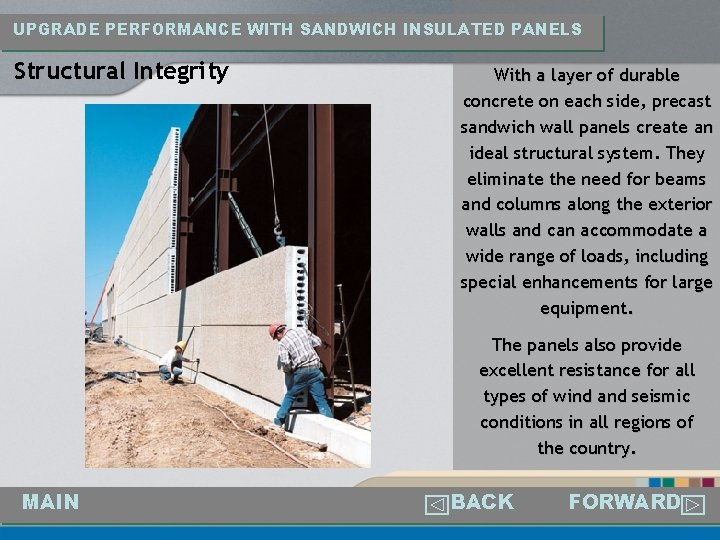
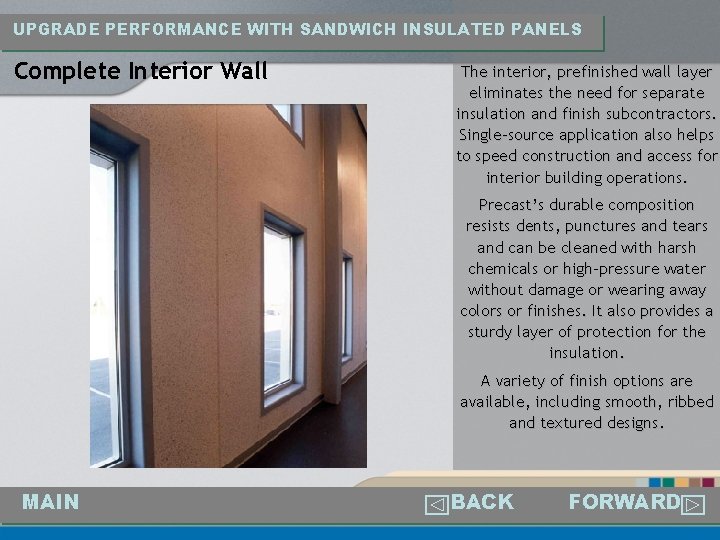
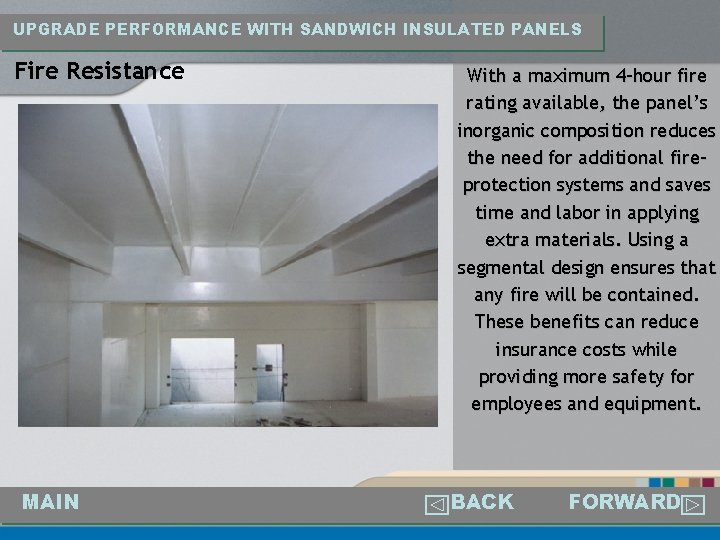
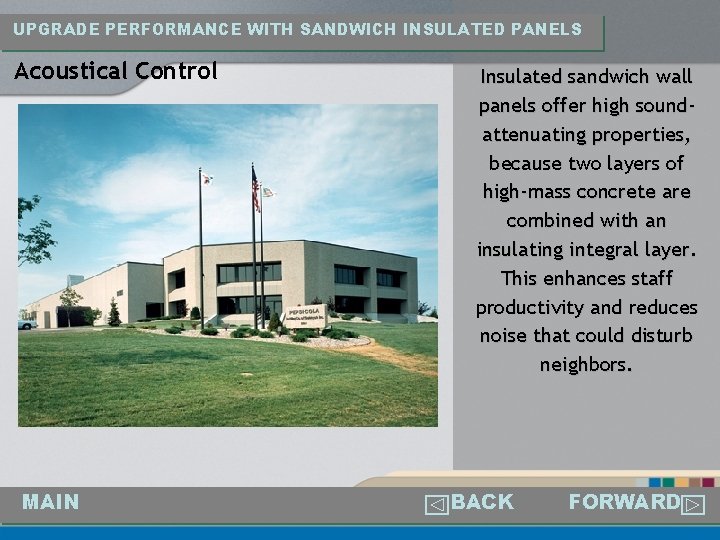
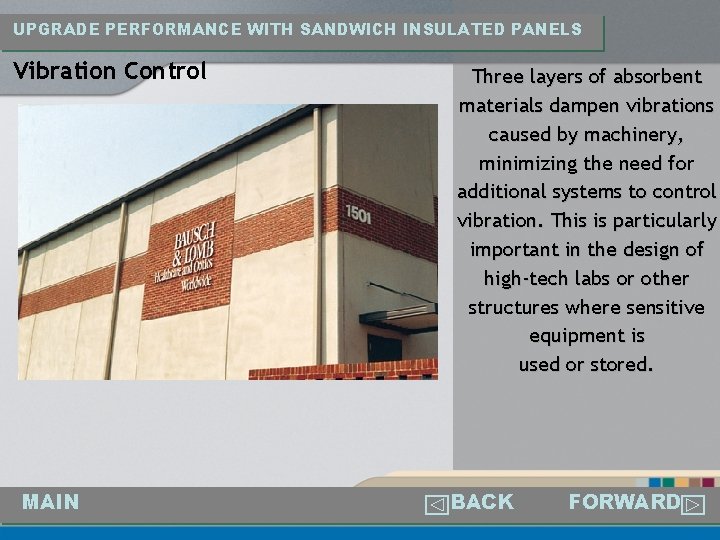
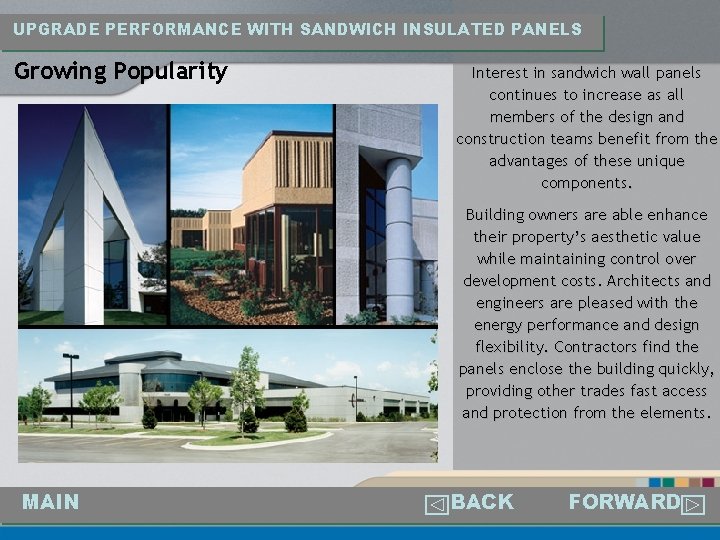
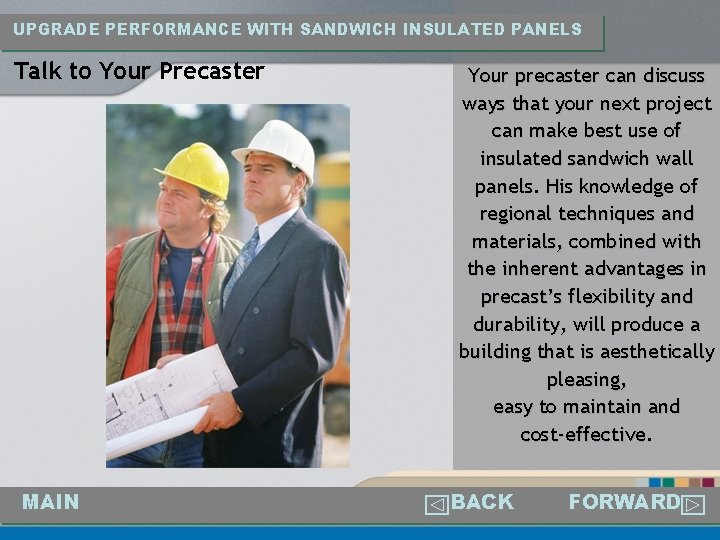
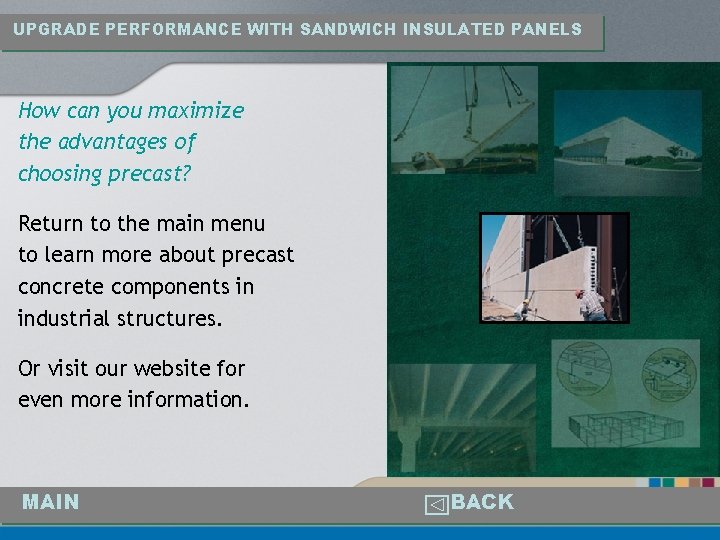
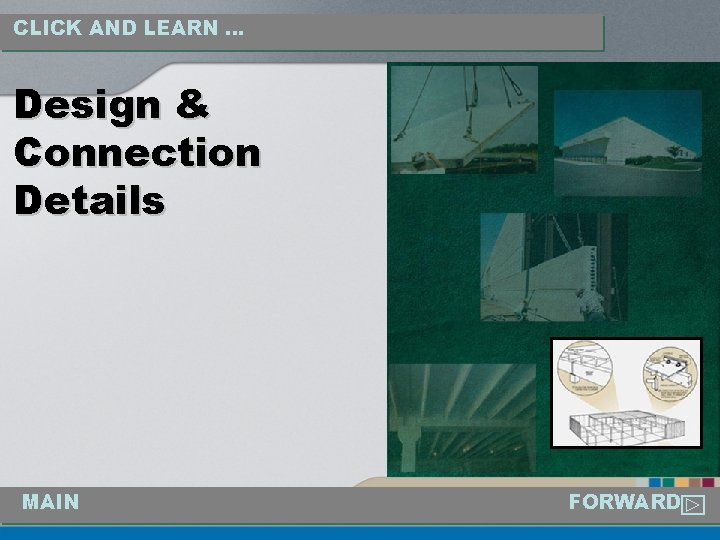
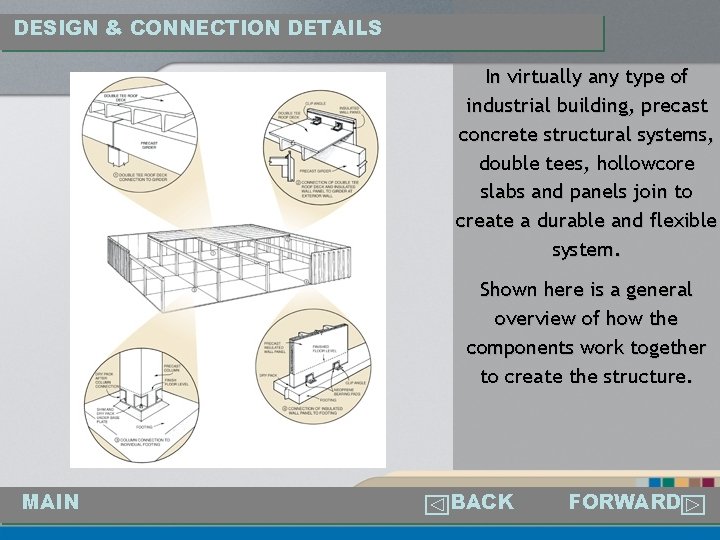
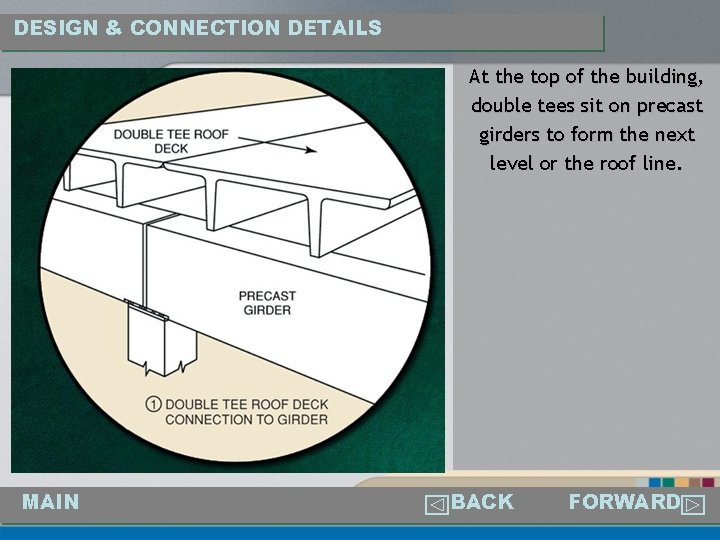
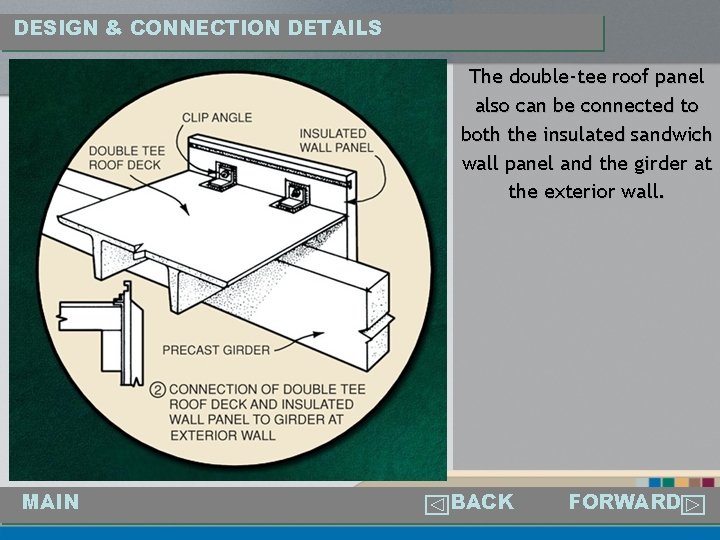
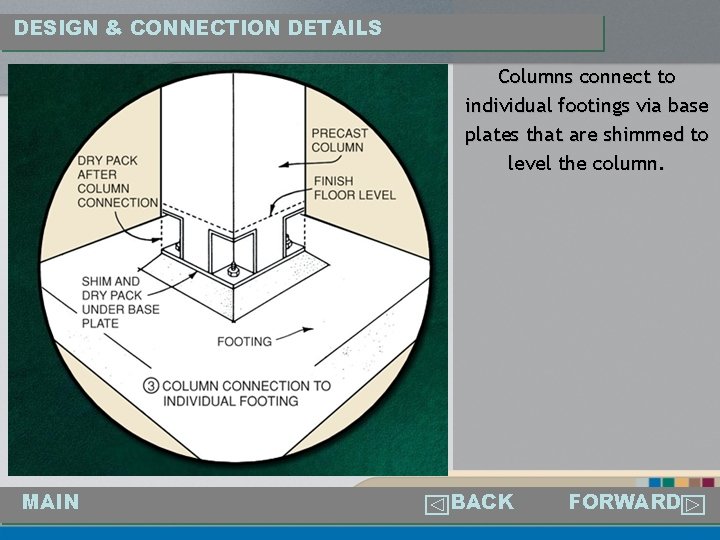
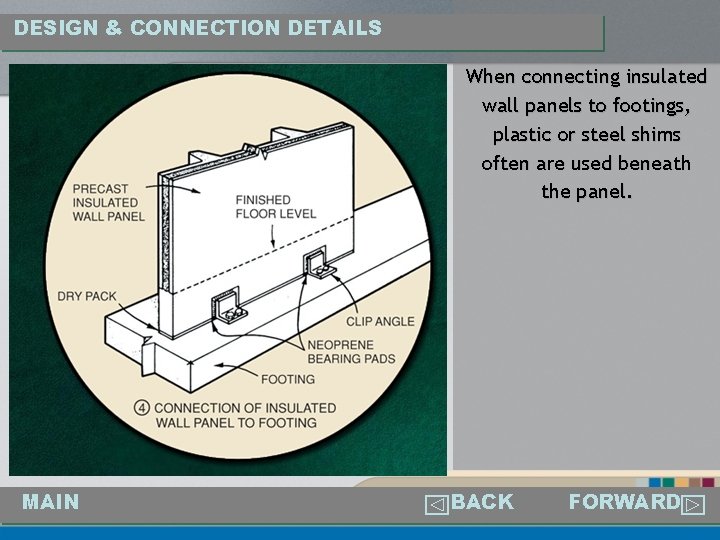
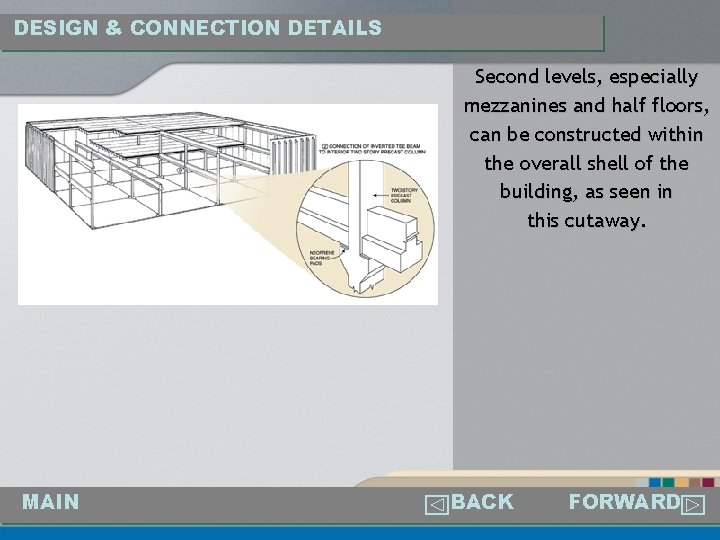
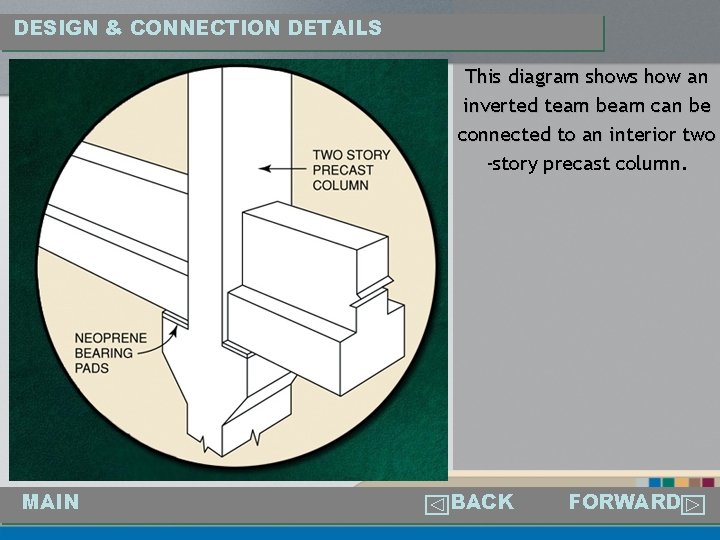
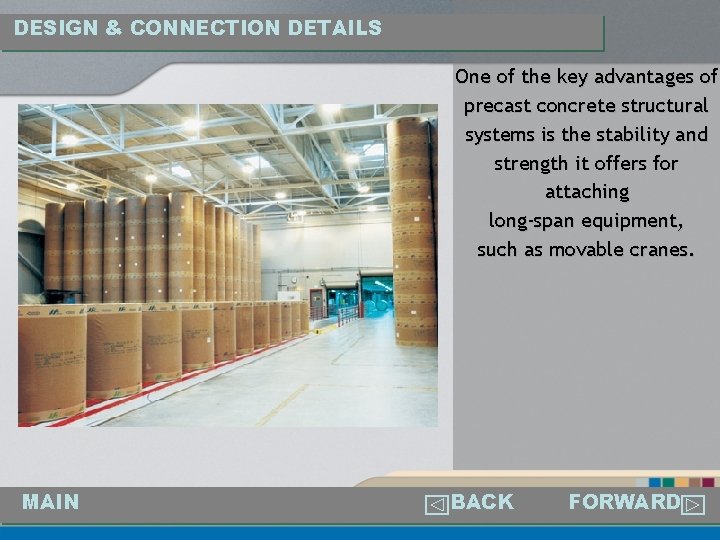
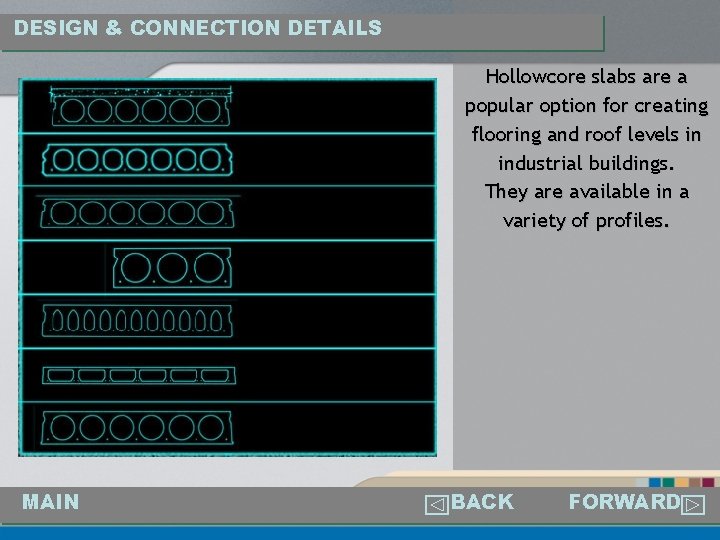
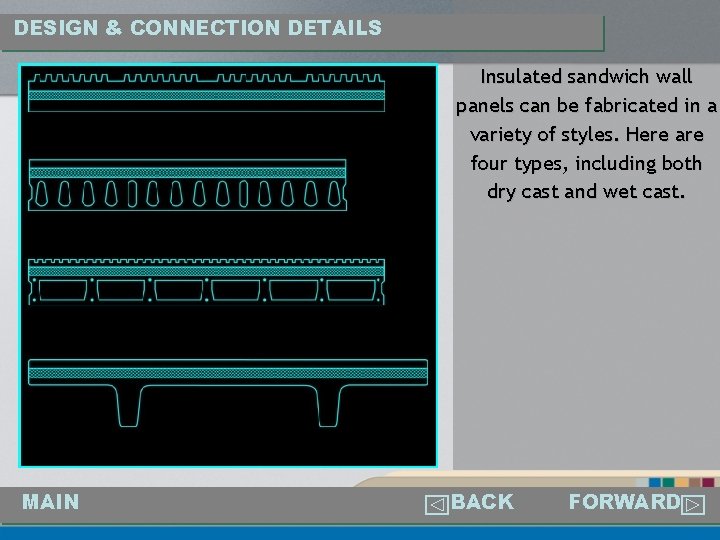
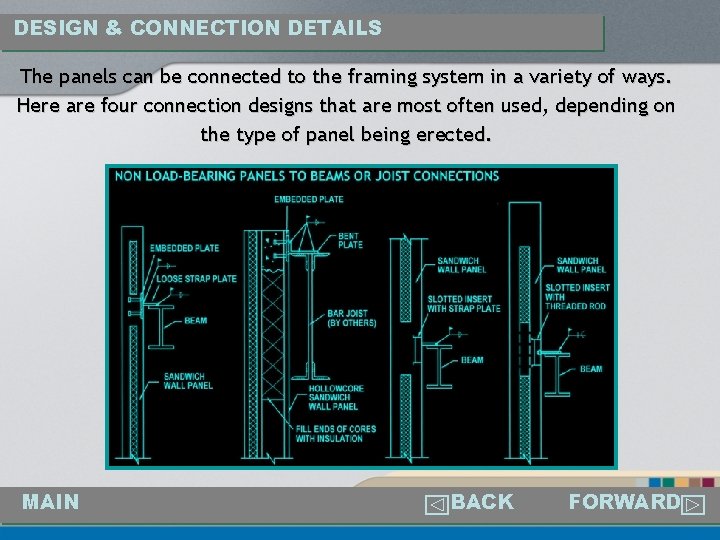
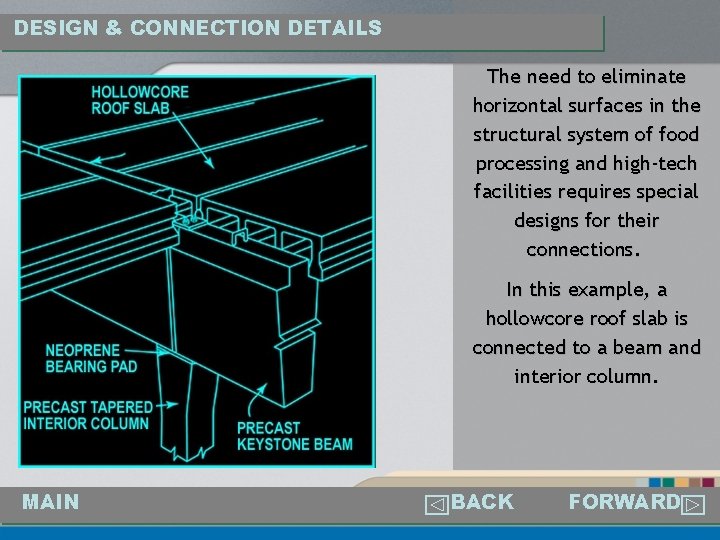
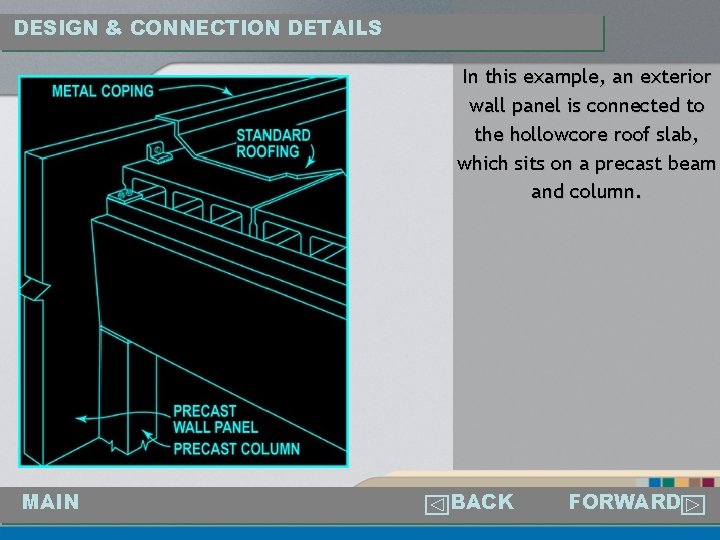
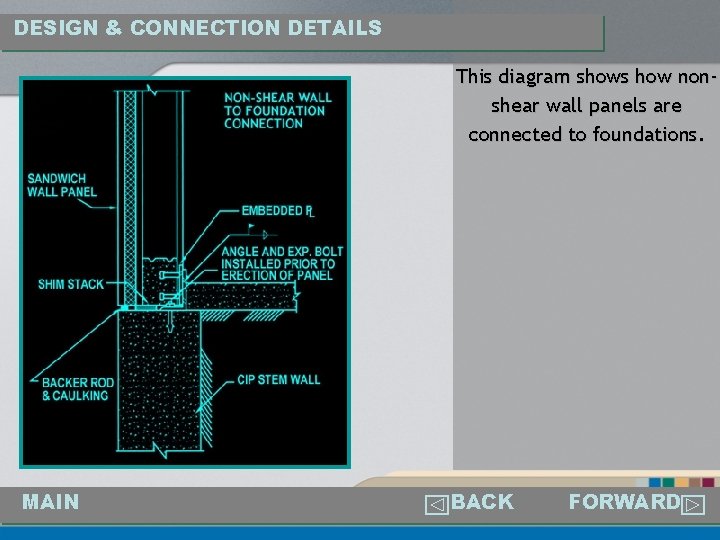
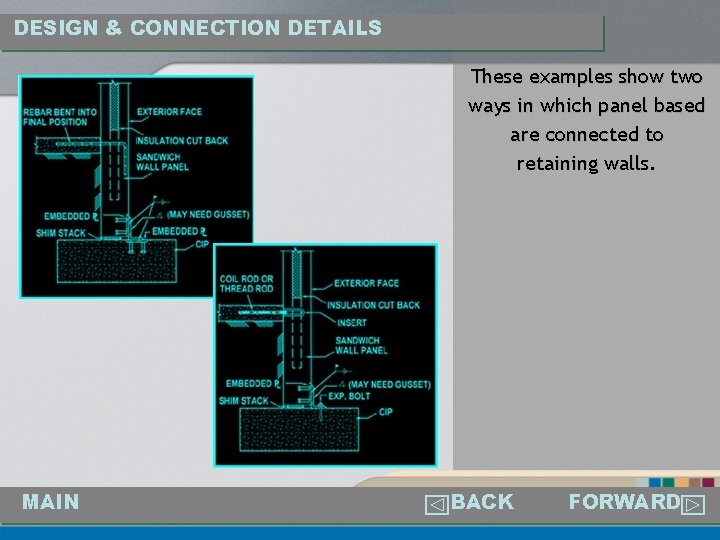
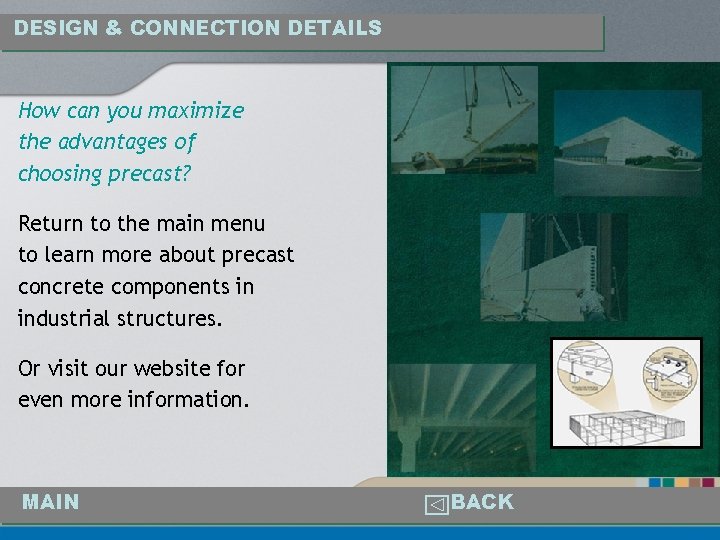
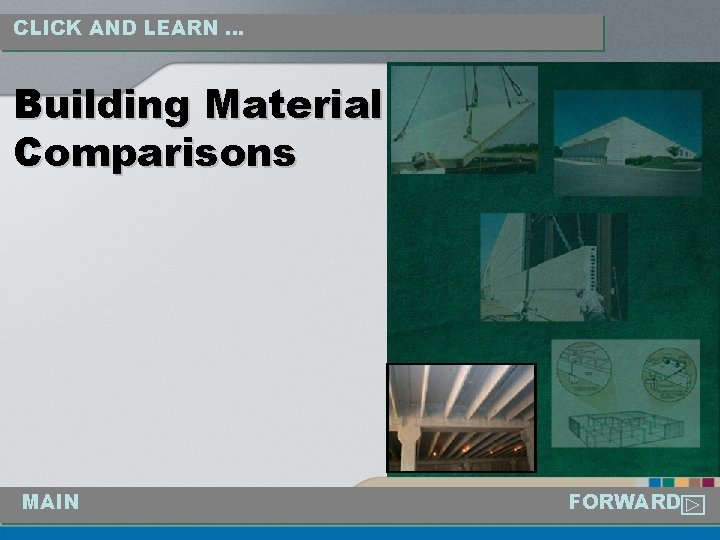
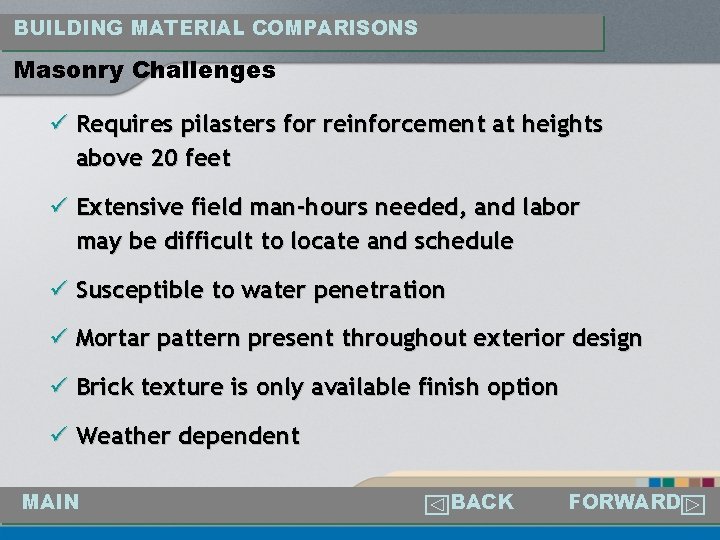
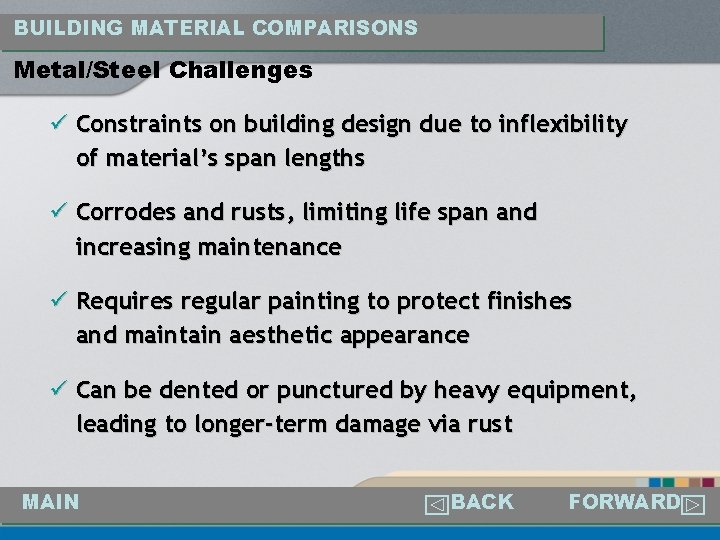
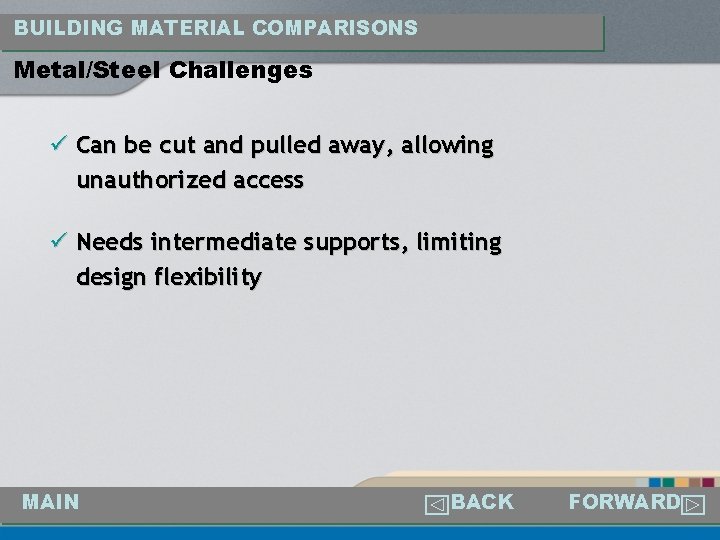
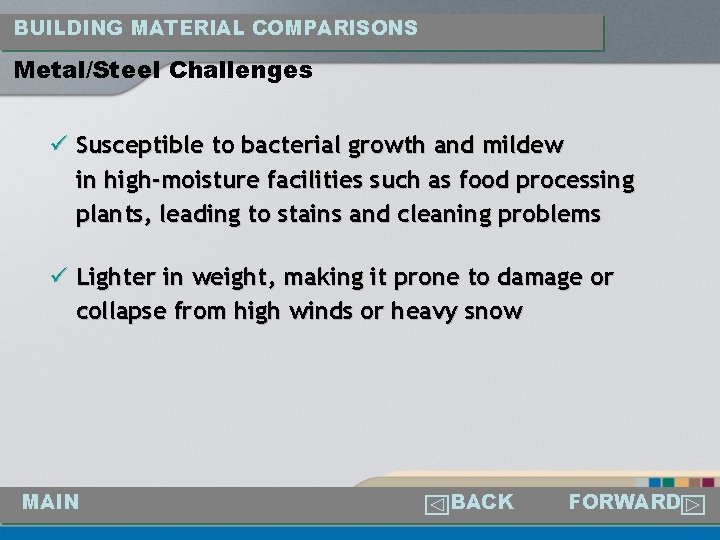
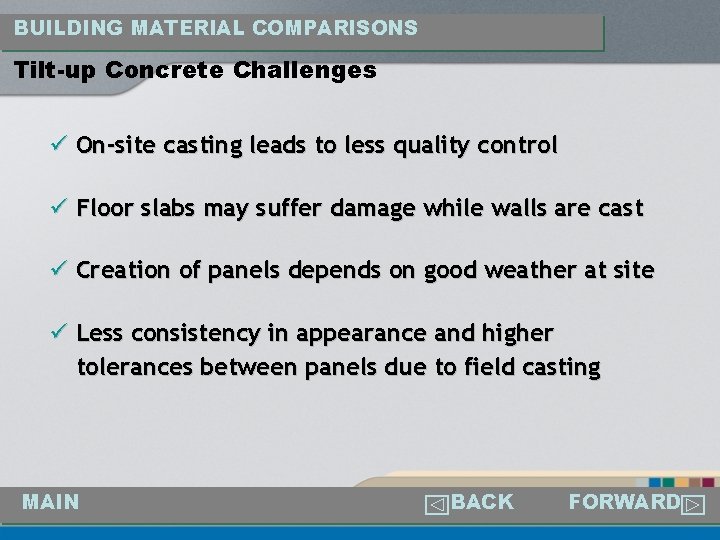
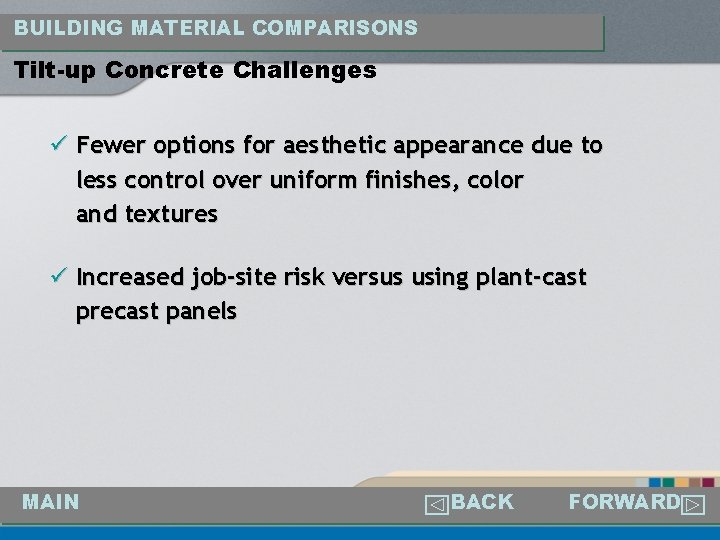
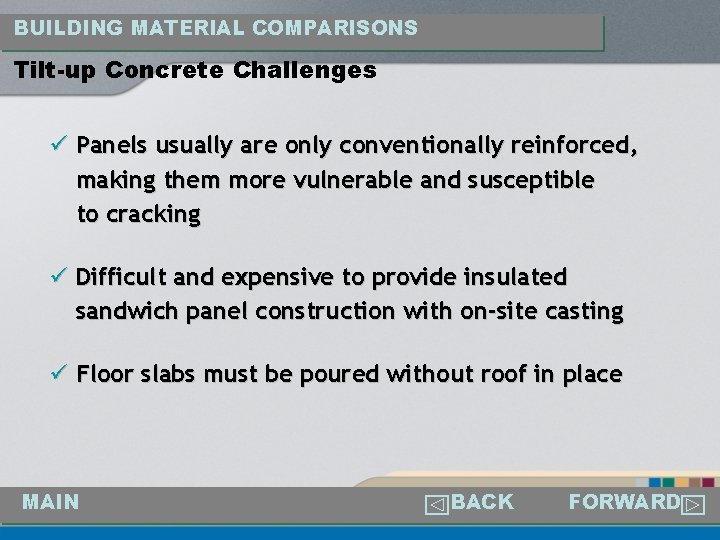
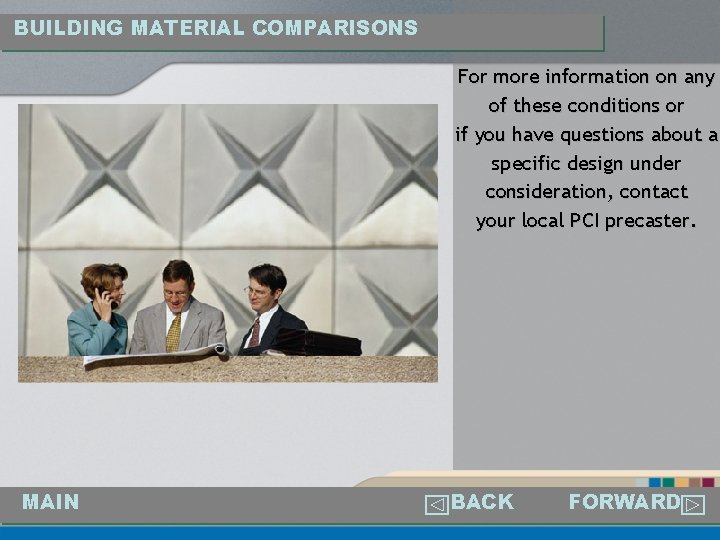
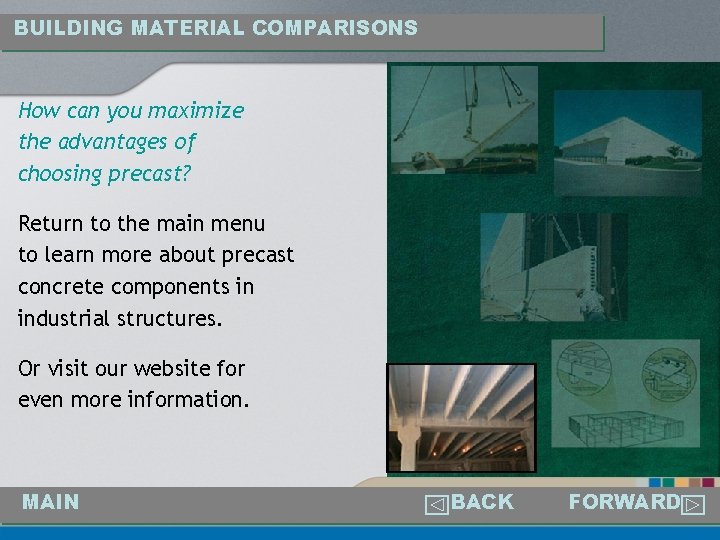
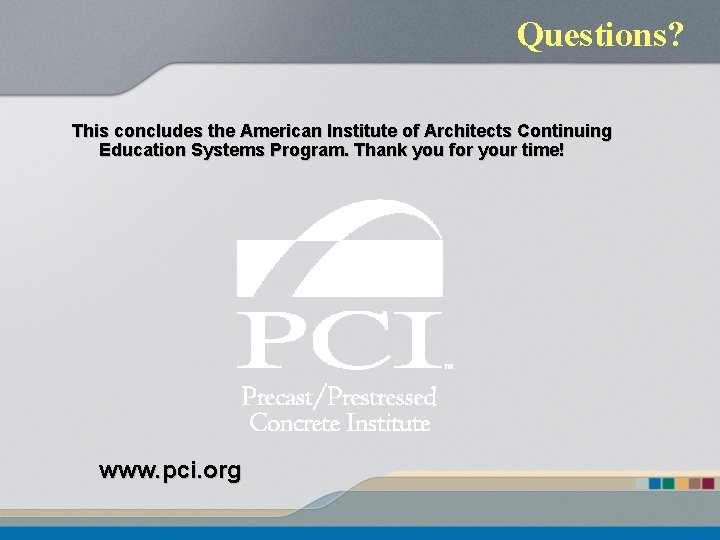
- Slides: 101
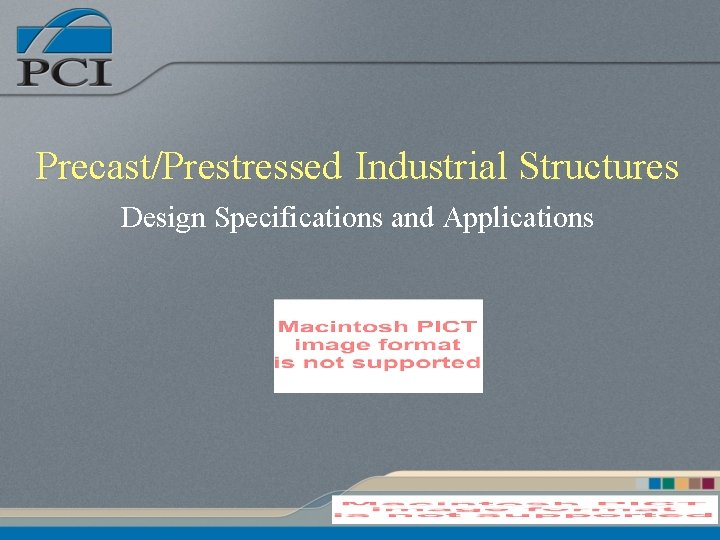
Precast/Prestressed Industrial Structures Design Specifications and Applications
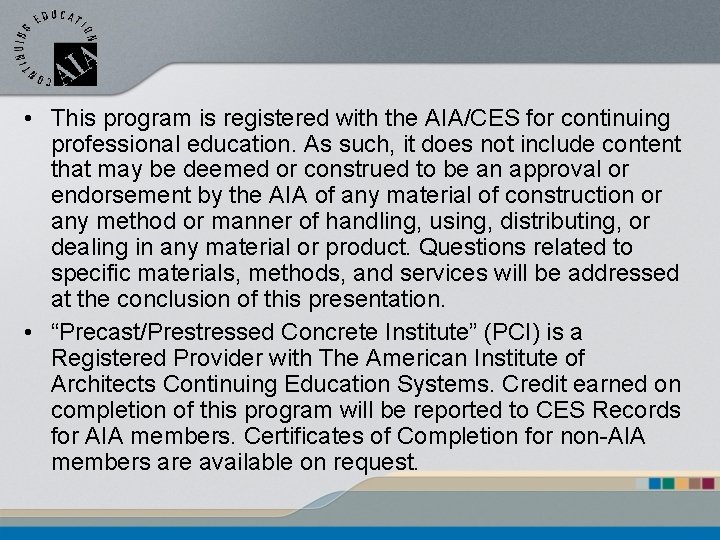
• This program is registered with the AIA/CES for continuing professional education. As such, it does not include content that may be deemed or construed to be an approval or endorsement by the AIA of any material of construction or any method or manner of handling, using, distributing, or dealing in any material or product. Questions related to specific materials, methods, and services will be addressed at the conclusion of this presentation. • “Precast/Prestressed Concrete Institute” (PCI) is a Registered Provider with The American Institute of Architects Continuing Education Systems. Credit earned on completion of this program will be reported to CES Records for AIA members. Certificates of Completion for non-AIA members are available on request.
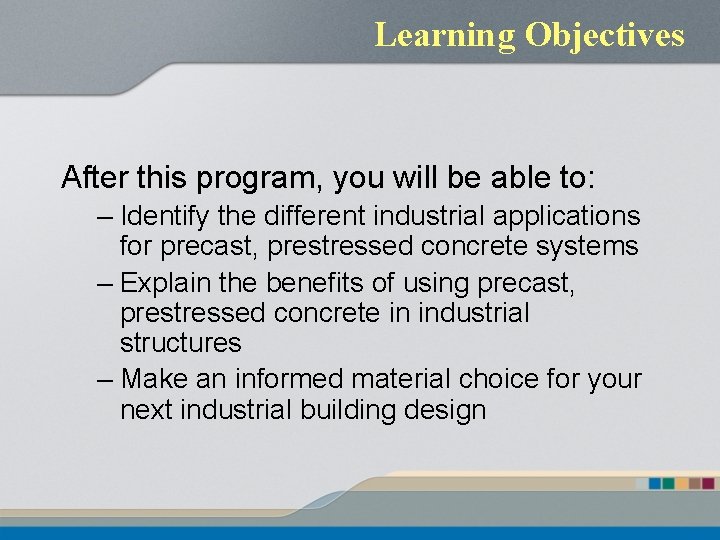
Learning Objectives After this program, you will be able to: – Identify the different industrial applications for precast, prestressed concrete systems – Explain the benefits of using precast, prestressed concrete in industrial structures – Make an informed material choice for your next industrial building design
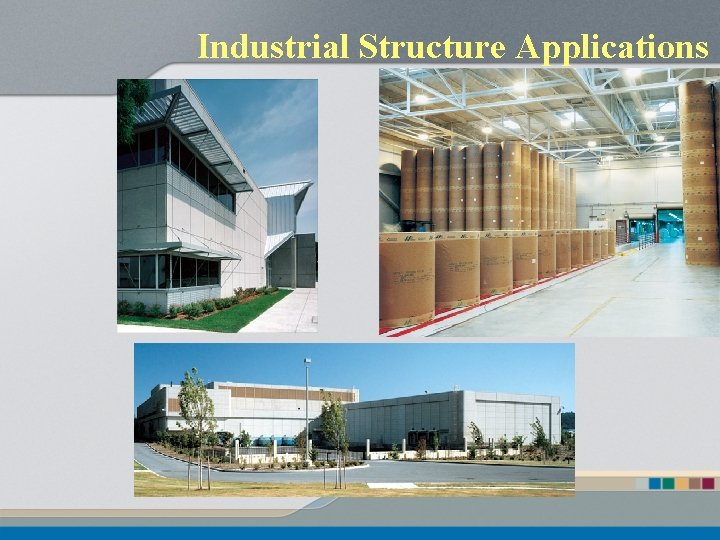
Industrial Structure Applications
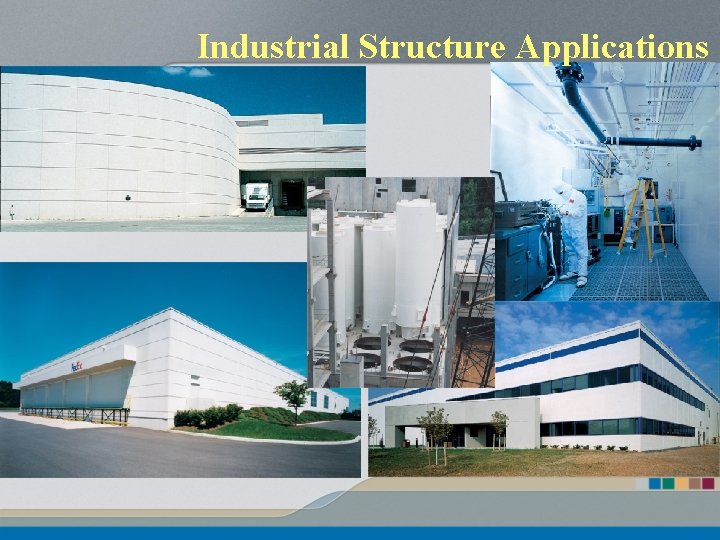
Industrial Structure Applications
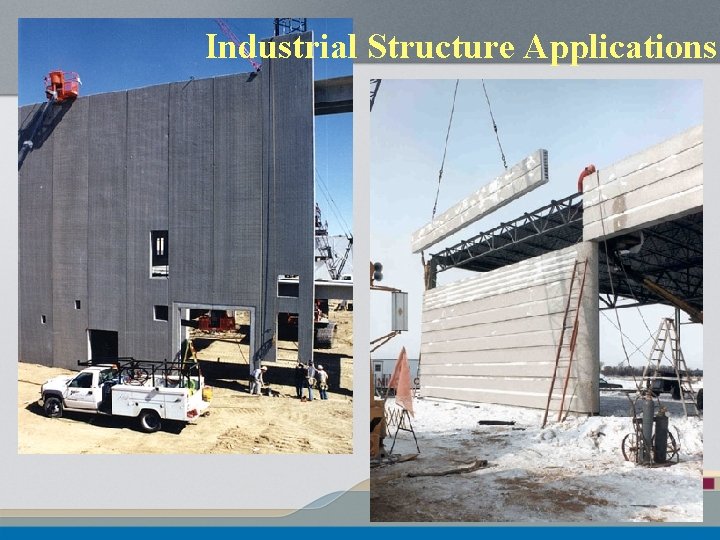
Industrial Structure Applications

Industrial Structure Applications
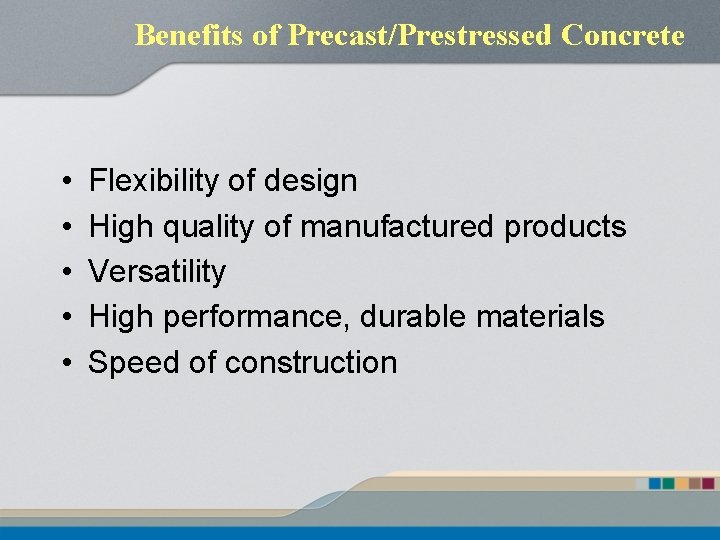
Benefits of Precast/Prestressed Concrete • • • Flexibility of design High quality of manufactured products Versatility High performance, durable materials Speed of construction
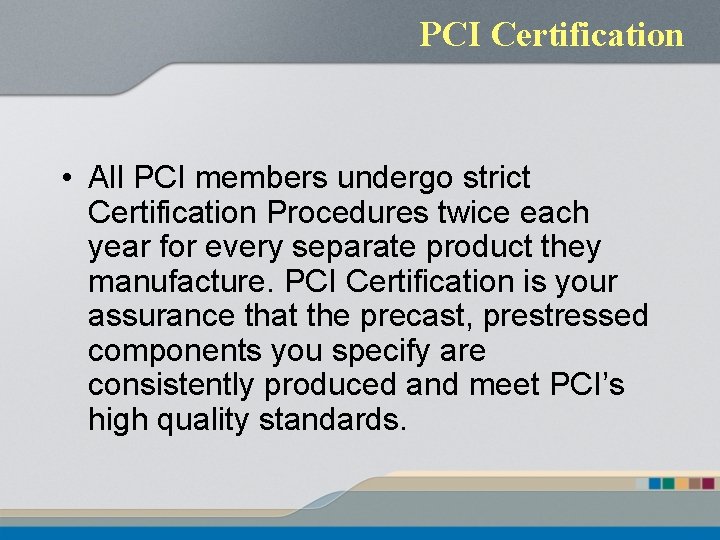
PCI Certification • All PCI members undergo strict Certification Procedures twice each year for every separate product they manufacture. PCI Certification is your assurance that the precast, prestressed components you specify are consistently produced and meet PCI’s high quality standards.
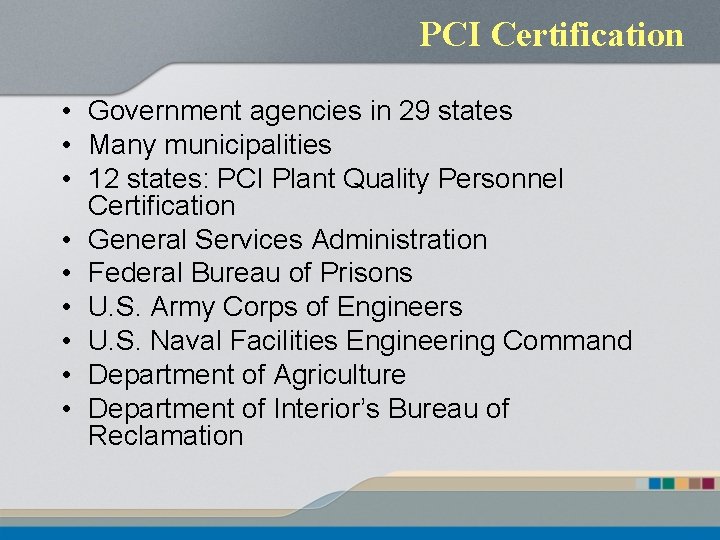
PCI Certification • Government agencies in 29 states • Many municipalities • 12 states: PCI Plant Quality Personnel Certification • General Services Administration • Federal Bureau of Prisons • U. S. Army Corps of Engineers • U. S. Naval Facilities Engineering Command • Department of Agriculture • Department of Interior’s Bureau of Reclamation
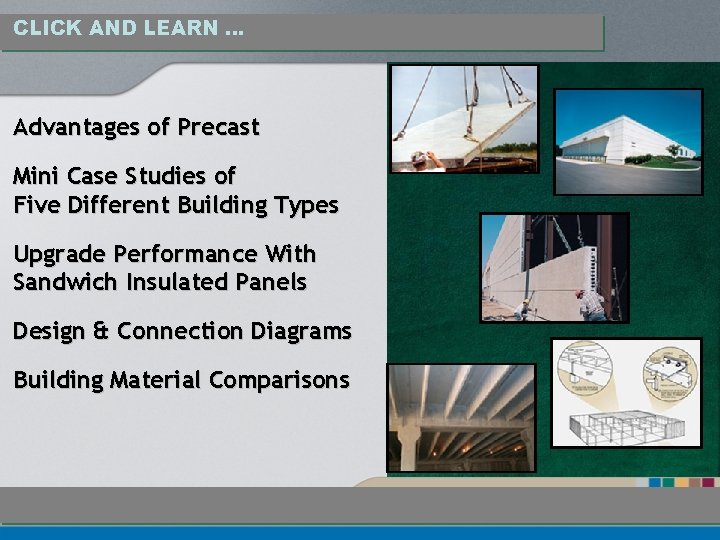
CLICK AND LEARN … Advantages of Precast Mini Case Studies of Five Different Building Types Upgrade Performance With Sandwich Insulated Panels Design & Connection Diagrams Building Material Comparisons
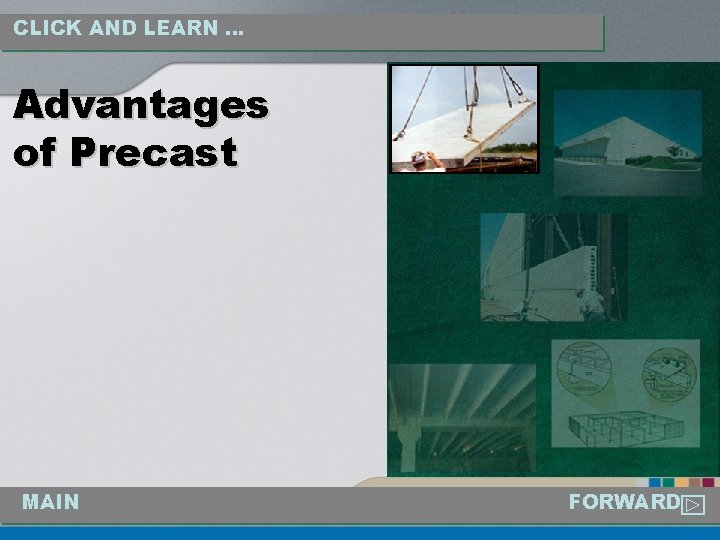
CLICK AND LEARN … Advantages of Precast MAIN FORWARD
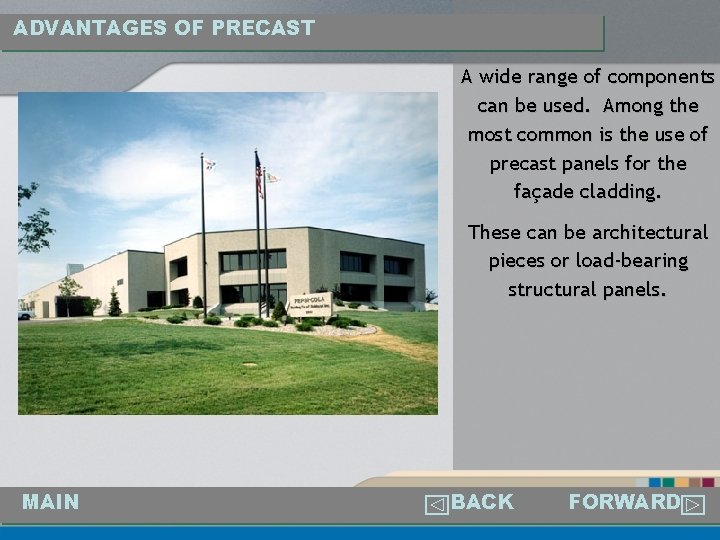
ADVANTAGES OF PRECAST A wide range of components can be used. Among the most common is the use of precast panels for the façade cladding. These can be architectural pieces or load-bearing structural panels. MAIN BACK FORWARD
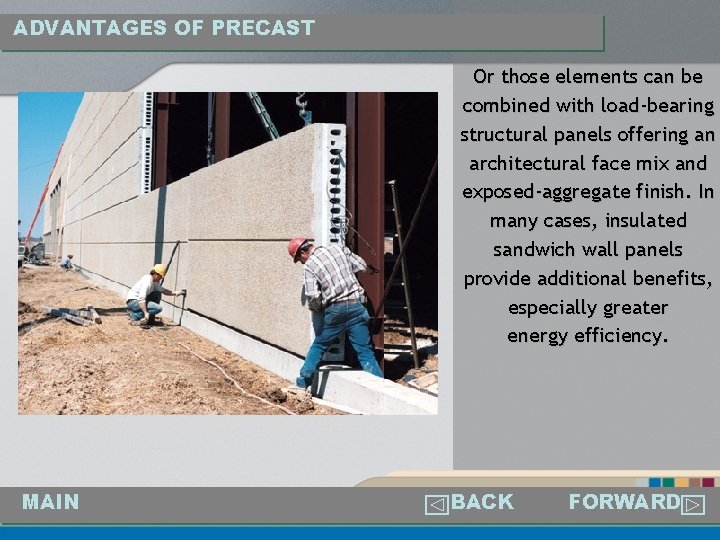
ADVANTAGES OF PRECAST Or those elements can be combined with load-bearing structural panels offering an architectural face mix and exposed-aggregate finish. In many cases, insulated sandwich wall panels provide additional benefits, especially greater energy efficiency. MAIN BACK FORWARD
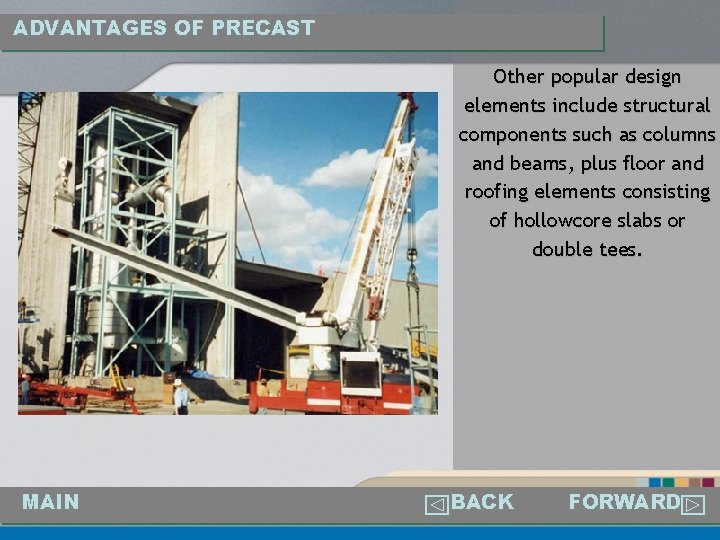
ADVANTAGES OF PRECAST Other popular design elements include structural components such as columns and beams, plus floor and roofing elements consisting of hollowcore slabs or double tees. MAIN BACK FORWARD
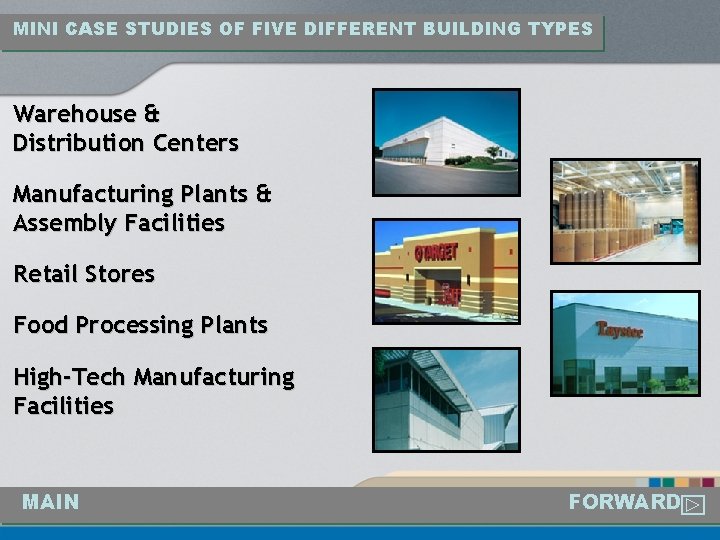
MINI CASE STUDIES OF FIVE DIFFERENT BUILDING TYPES Warehouse & Distribution Centers Manufacturing Plants & Assembly Facilities Retail Stores Food Processing Plants High-Tech Manufacturing Facilities MAIN FORWARD
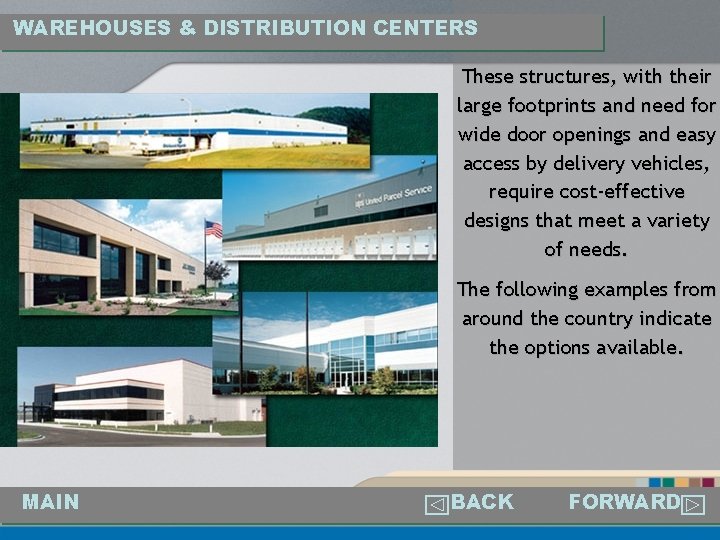
WAREHOUSES & DISTRIBUTION CENTERS These structures, with their large footprints and need for wide door openings and easy access by delivery vehicles, require cost-effective designs that meet a variety of needs. The following examples from around the country indicate the options available. MAIN BACK FORWARD
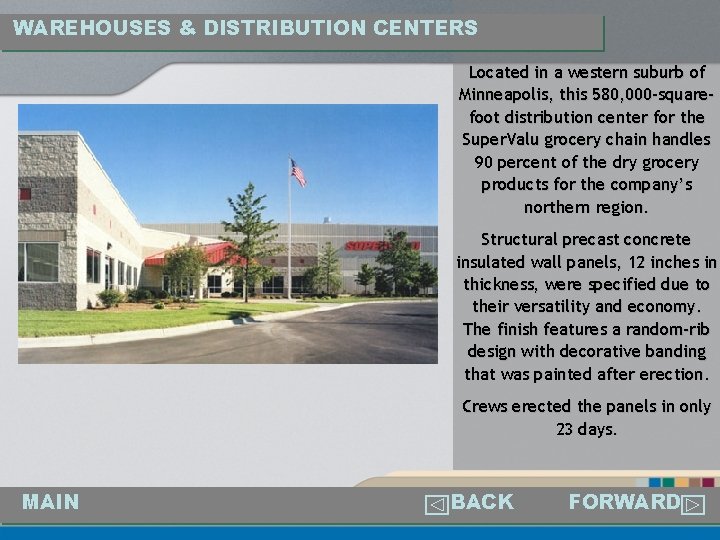
WAREHOUSES & DISTRIBUTION CENTERS Located in a western suburb of Minneapolis, this 580, 000 -squarefoot distribution center for the Super. Valu grocery chain handles 90 percent of the dry grocery products for the company’s northern region. Structural precast concrete insulated wall panels, 12 inches in thickness, were specified due to their versatility and economy. The finish features a random-rib design with decorative banding that was painted after erection. Crews erected the panels in only 23 days. MAIN BACK FORWARD
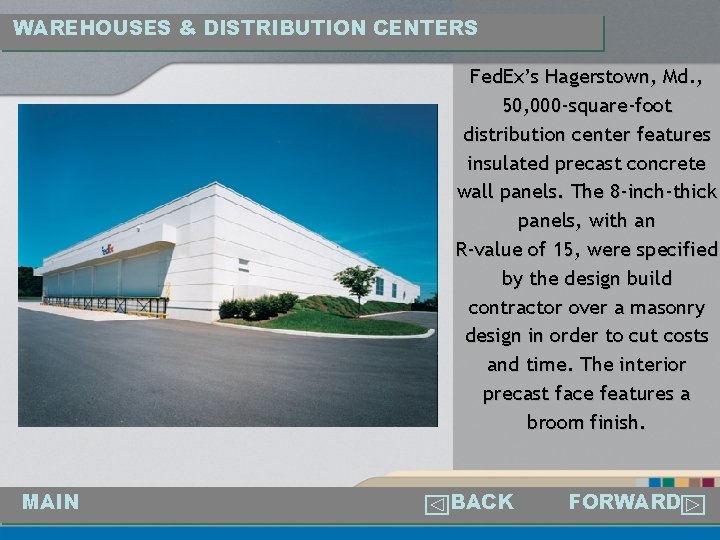
WAREHOUSES & DISTRIBUTION CENTERS Fed. Ex’s Hagerstown, Md. , 50, 000 -square-foot distribution center features insulated precast concrete wall panels. The 8 -inch-thick panels, with an R-value of 15, were specified by the design build contractor over a masonry design in order to cut costs and time. The interior precast face features a broom finish. MAIN BACK FORWARD
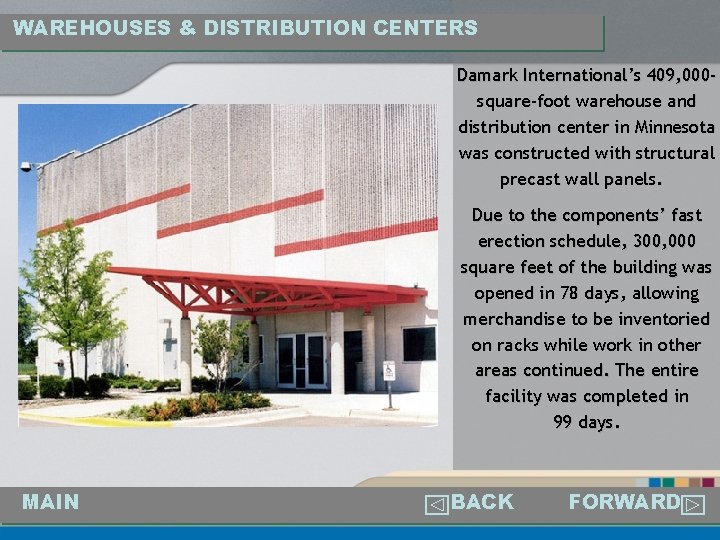
WAREHOUSES & DISTRIBUTION CENTERS Damark International’s 409, 000 square-foot warehouse and distribution center in Minnesota was constructed with structural precast wall panels. Due to the components’ fast erection schedule, 300, 000 square feet of the building was opened in 78 days, allowing merchandise to be inventoried on racks while work in other areas continued. The entire facility was completed in 99 days. MAIN BACK FORWARD
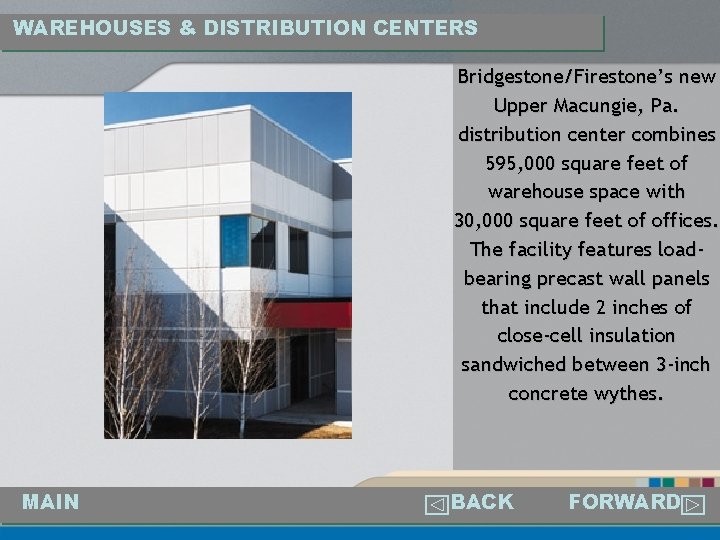
WAREHOUSES & DISTRIBUTION CENTERS Bridgestone/Firestone’s new Upper Macungie, Pa. distribution center combines 595, 000 square feet of warehouse space with 30, 000 square feet of offices. The facility features loadbearing precast wall panels that include 2 inches of close-cell insulation sandwiched between 3 -inch concrete wythes. MAIN BACK FORWARD
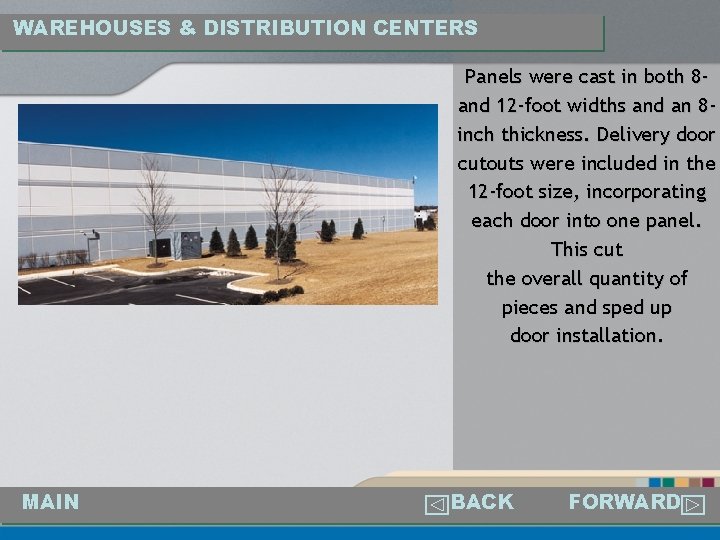
WAREHOUSES & DISTRIBUTION CENTERS Panels were cast in both 8 and 12 -foot widths and an 8 inch thickness. Delivery door cutouts were included in the 12 -foot size, incorporating each door into one panel. This cut the overall quantity of pieces and sped up door installation. MAIN BACK FORWARD
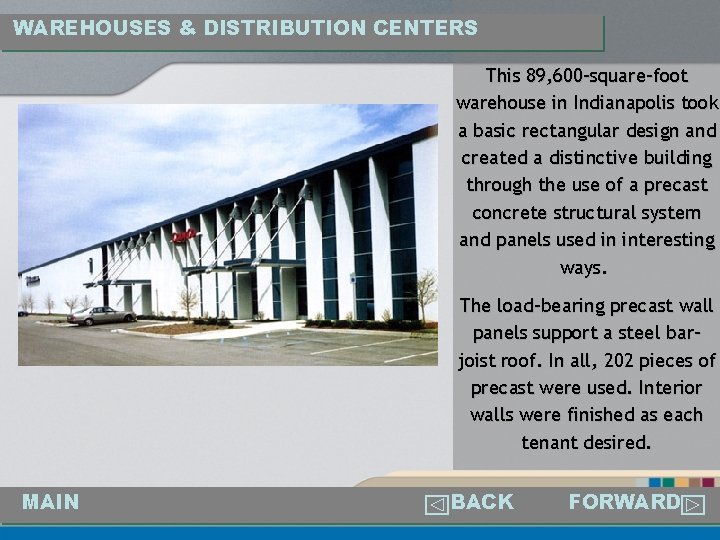
WAREHOUSES & DISTRIBUTION CENTERS This 89, 600 -square-foot warehouse in Indianapolis took a basic rectangular design and created a distinctive building through the use of a precast concrete structural system and panels used in interesting ways. The load-bearing precast wall panels support a steel barjoist roof. In all, 202 pieces of precast were used. Interior walls were finished as each tenant desired. MAIN BACK FORWARD
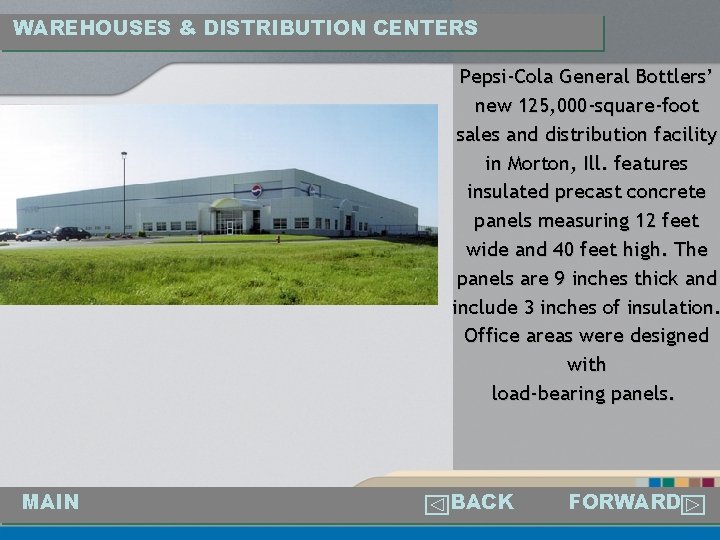
WAREHOUSES & DISTRIBUTION CENTERS Pepsi-Cola General Bottlers’ new 125, 000 -square-foot sales and distribution facility in Morton, Ill. features insulated precast concrete panels measuring 12 feet wide and 40 feet high. The panels are 9 inches thick and include 3 inches of insulation. Office areas were designed with load-bearing panels. MAIN BACK FORWARD
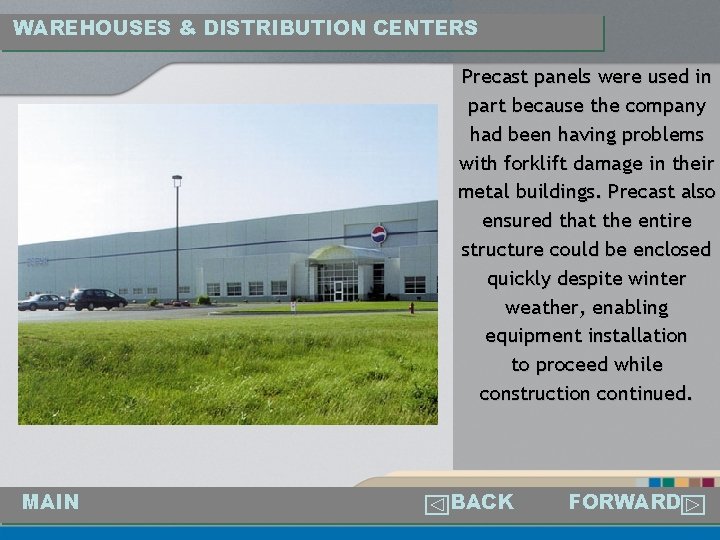
WAREHOUSES & DISTRIBUTION CENTERS Precast panels were used in part because the company had been having problems with forklift damage in their metal buildings. Precast also ensured that the entire structure could be enclosed quickly despite winter weather, enabling equipment installation to proceed while construction continued. MAIN BACK FORWARD
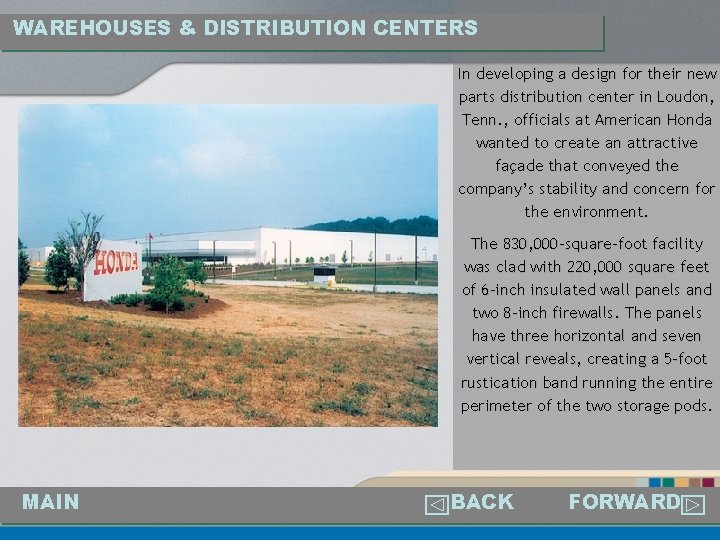
WAREHOUSES & DISTRIBUTION CENTERS In developing a design for their new parts distribution center in Loudon, Tenn. , officials at American Honda wanted to create an attractive façade that conveyed the company’s stability and concern for the environment. The 830, 000 -square-foot facility was clad with 220, 000 square feet of 6 -inch insulated wall panels and two 8 -inch firewalls. The panels have three horizontal and seven vertical reveals, creating a 5 -foot rustication band running the entire perimeter of the two storage pods. MAIN BACK FORWARD
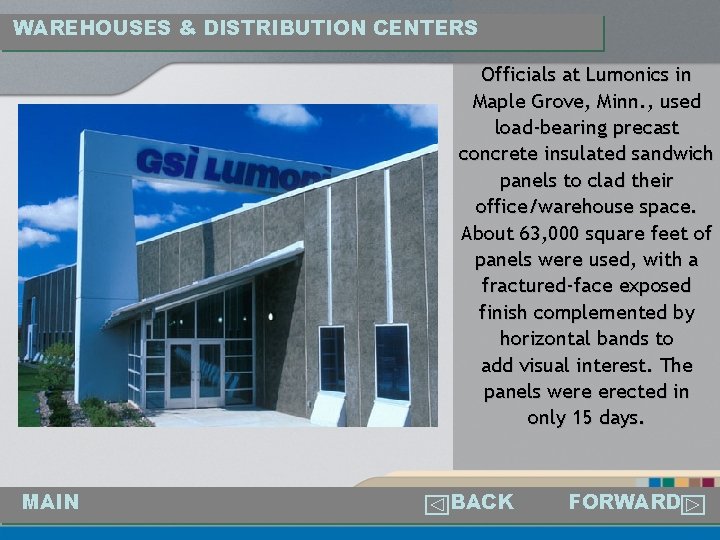
WAREHOUSES & DISTRIBUTION CENTERS Officials at Lumonics in Maple Grove, Minn. , used load-bearing precast concrete insulated sandwich panels to clad their office/warehouse space. About 63, 000 square feet of panels were used, with a fractured-face exposed finish complemented by horizontal bands to add visual interest. The panels were erected in only 15 days. MAIN BACK FORWARD
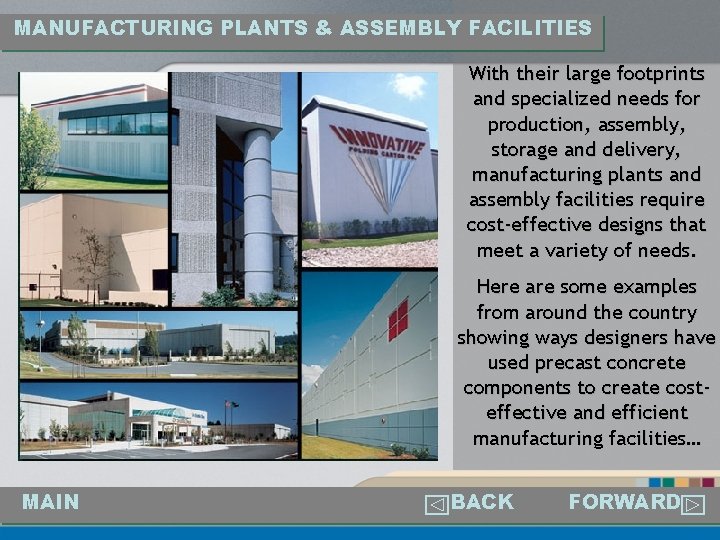
MANUFACTURING PLANTS & ASSEMBLY FACILITIES With their large footprints and specialized needs for production, assembly, storage and delivery, manufacturing plants and assembly facilities require cost-effective designs that meet a variety of needs. Here are some examples from around the country showing ways designers have used precast concrete components to create costeffective and efficient manufacturing facilities… MAIN BACK FORWARD
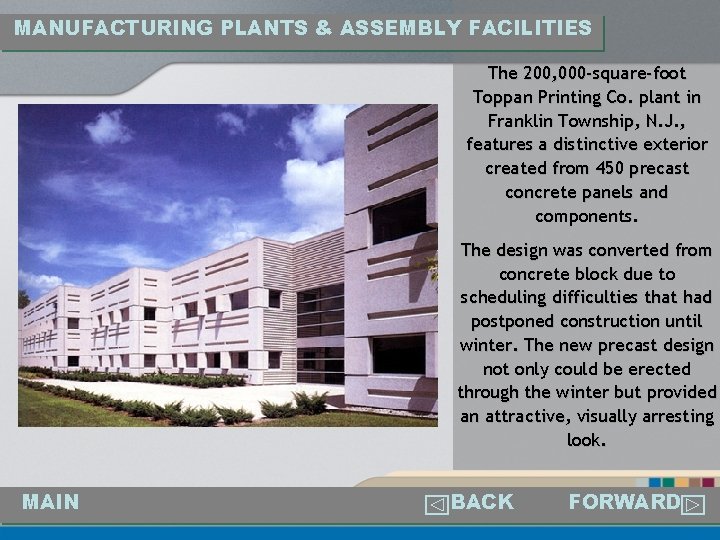
MANUFACTURING PLANTS & ASSEMBLY FACILITIES The 200, 000 -square-foot Toppan Printing Co. plant in Franklin Township, N. J. , features a distinctive exterior created from 450 precast concrete panels and components. The design was converted from concrete block due to scheduling difficulties that had postponed construction until winter. The new precast design not only could be erected through the winter but provided an attractive, visually arresting look. MAIN BACK FORWARD

MANUFACTURING PLANTS & ASSEMBLY FACILITIES The precast concrete architectural panels used to clad the Phillips Communications manufacturing facility in Lancaster, Pa. were cast in two colors and three finishes. The design complements the adjacent brick office building, which features precast accents, while allowing the structure to blend with the surrounding neighborhood. MAIN BACK FORWARD
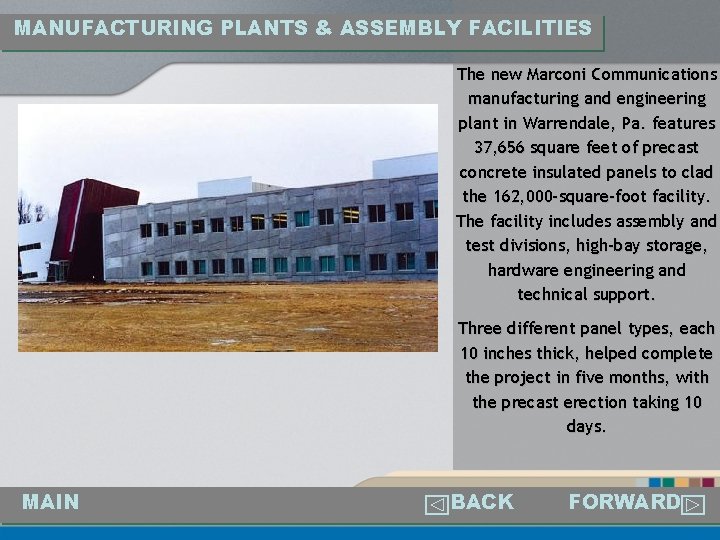
MANUFACTURING PLANTS & ASSEMBLY FACILITIES The new Marconi Communications manufacturing and engineering plant in Warrendale, Pa. features 37, 656 square feet of precast concrete insulated panels to clad the 162, 000 -square-foot facility. The facility includes assembly and test divisions, high-bay storage, hardware engineering and technical support. Three different panel types, each 10 inches thick, helped complete the project in five months, with the precast erection taking 10 days. MAIN BACK FORWARD
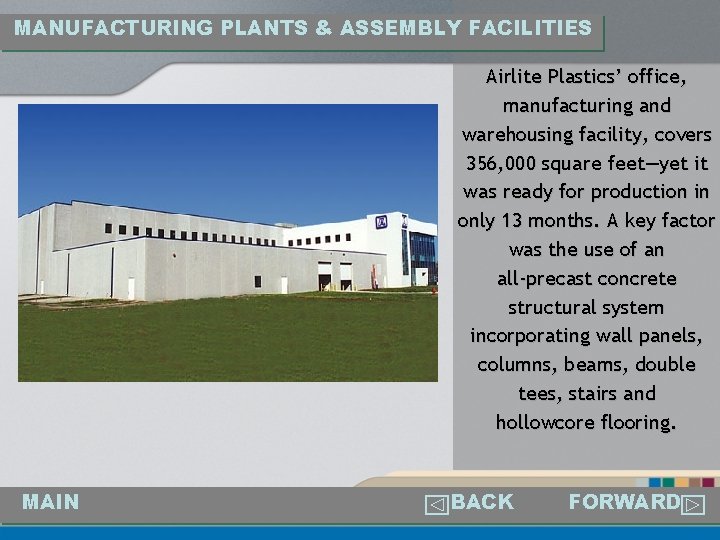
MANUFACTURING PLANTS & ASSEMBLY FACILITIES Airlite Plastics’ office, manufacturing and warehousing facility, covers 356, 000 square feet—yet it was ready for production in only 13 months. A key factor was the use of an all-precast concrete structural system incorporating wall panels, columns, beams, double tees, stairs and hollowcore flooring. MAIN BACK FORWARD
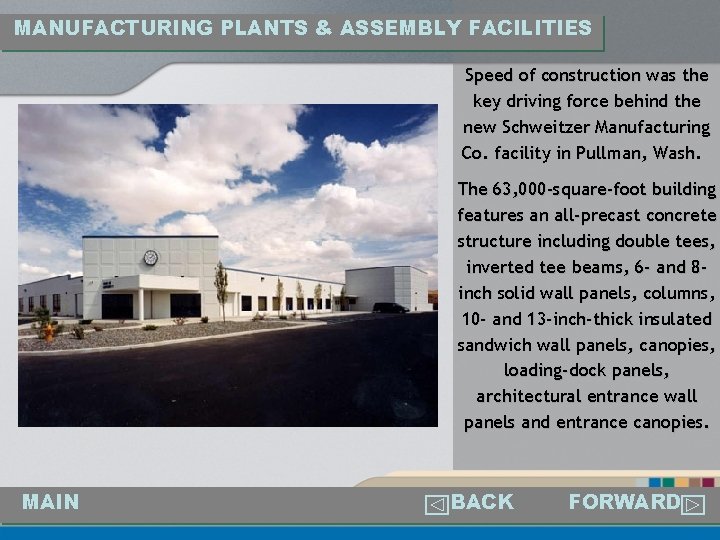
MANUFACTURING PLANTS & ASSEMBLY FACILITIES Speed of construction was the key driving force behind the new Schweitzer Manufacturing Co. facility in Pullman, Wash. The 63, 000 -square-foot building features an all-precast concrete structure including double tees, inverted tee beams, 6 - and 8 inch solid wall panels, columns, 10 - and 13 -inch-thick insulated sandwich wall panels, canopies, loading-dock panels, architectural entrance wall panels and entrance canopies. MAIN BACK FORWARD
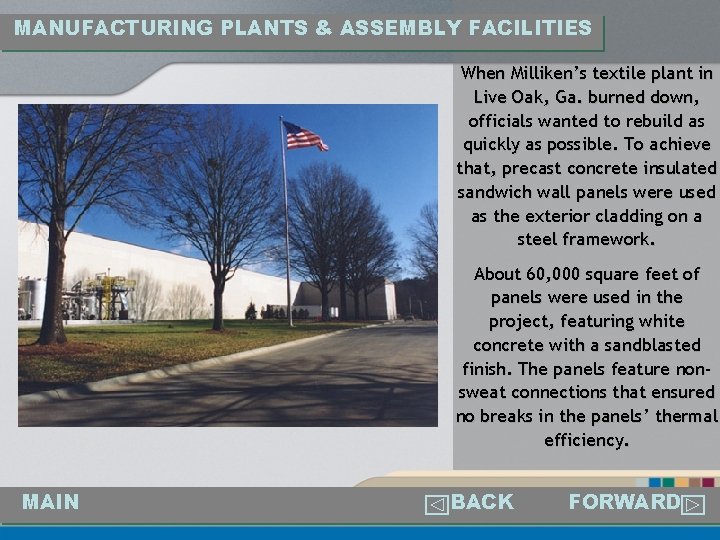
MANUFACTURING PLANTS & ASSEMBLY FACILITIES When Milliken’s textile plant in Live Oak, Ga. burned down, officials wanted to rebuild as quickly as possible. To achieve that, precast concrete insulated sandwich wall panels were used as the exterior cladding on a steel framework. About 60, 000 square feet of panels were used in the project, featuring white concrete with a sandblasted finish. The panels feature nonsweat connections that ensured no breaks in the panels’ thermal efficiency. MAIN BACK FORWARD
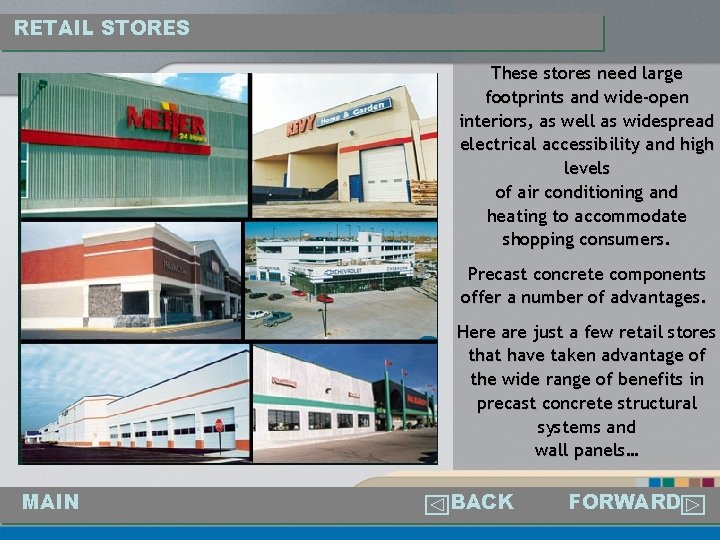
RETAIL STORES These stores need large footprints and wide-open interiors, as well as widespread electrical accessibility and high levels of air conditioning and heating to accommodate shopping consumers. Precast concrete components offer a number of advantages. Here are just a few retail stores that have taken advantage of the wide range of benefits in precast concrete structural systems and wall panels… MAIN BACK FORWARD
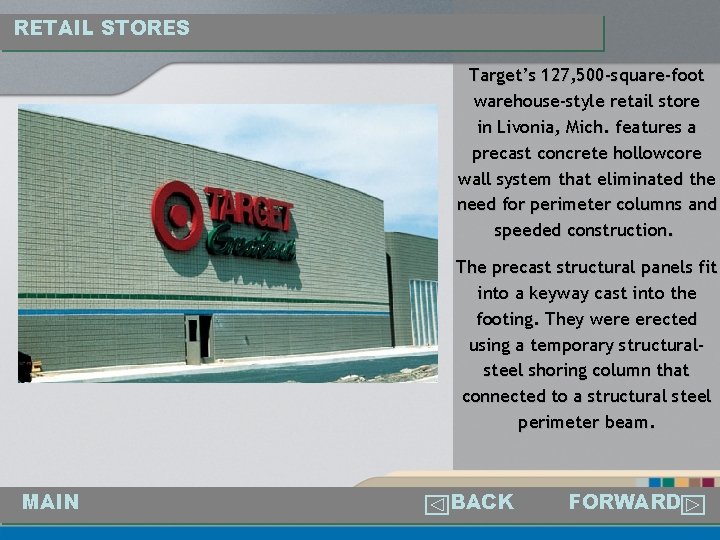
RETAIL STORES Target’s 127, 500 -square-foot warehouse-style retail store in Livonia, Mich. features a precast concrete hollowcore wall system that eliminated the need for perimeter columns and speeded construction. The precast structural panels fit into a keyway cast into the footing. They were erected using a temporary structuralsteel shoring column that connected to a structural steel perimeter beam. MAIN BACK FORWARD
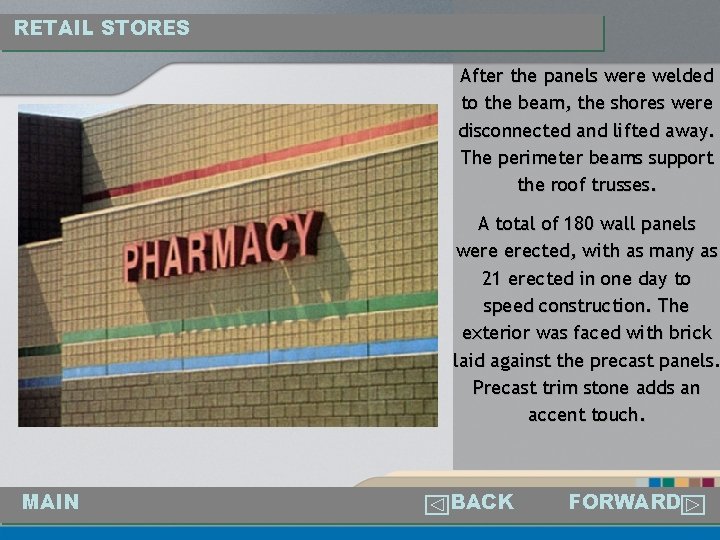
RETAIL STORES After the panels were welded to the beam, the shores were disconnected and lifted away. The perimeter beams support the roof trusses. A total of 180 wall panels were erected, with as many as 21 erected in one day to speed construction. The exterior was faced with brick laid against the precast panels. Precast trim stone adds an accent touch. MAIN BACK FORWARD
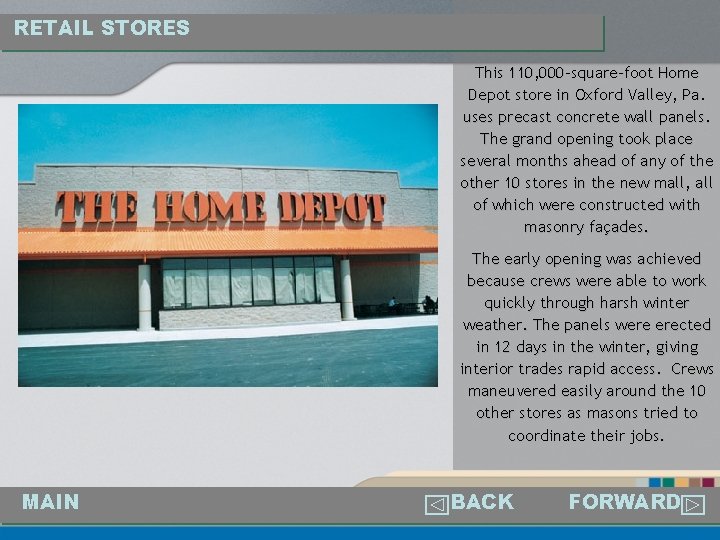
RETAIL STORES This 110, 000 -square-foot Home Depot store in Oxford Valley, Pa. uses precast concrete wall panels. The grand opening took place several months ahead of any of the other 10 stores in the new mall, all of which were constructed with masonry façades. The early opening was achieved because crews were able to work quickly through harsh winter weather. The panels were erected in 12 days in the winter, giving interior trades rapid access. Crews maneuvered easily around the 10 other stores as masons tried to coordinate their jobs. MAIN BACK FORWARD
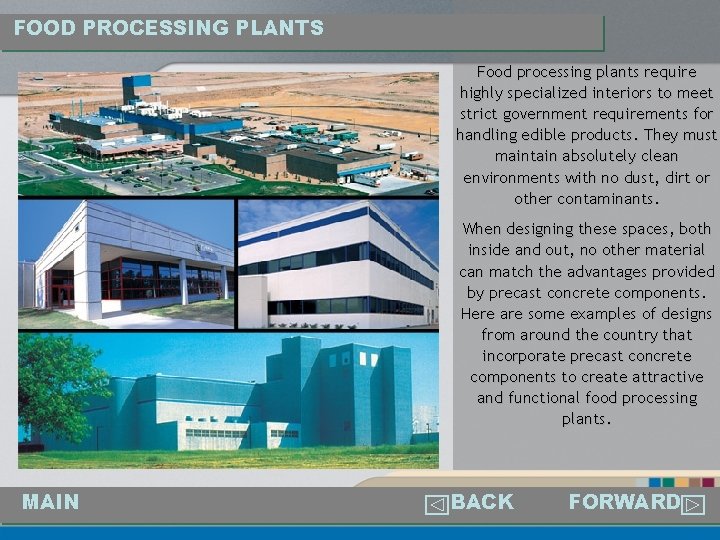
FOOD PROCESSING PLANTS Food processing plants require highly specialized interiors to meet strict government requirements for handling edible products. They must maintain absolutely clean environments with no dust, dirt or other contaminants. When designing these spaces, both inside and out, no other material can match the advantages provided by precast concrete components. Here are some examples of designs from around the country that incorporate precast concrete components to create attractive and functional food processing plants. MAIN BACK FORWARD
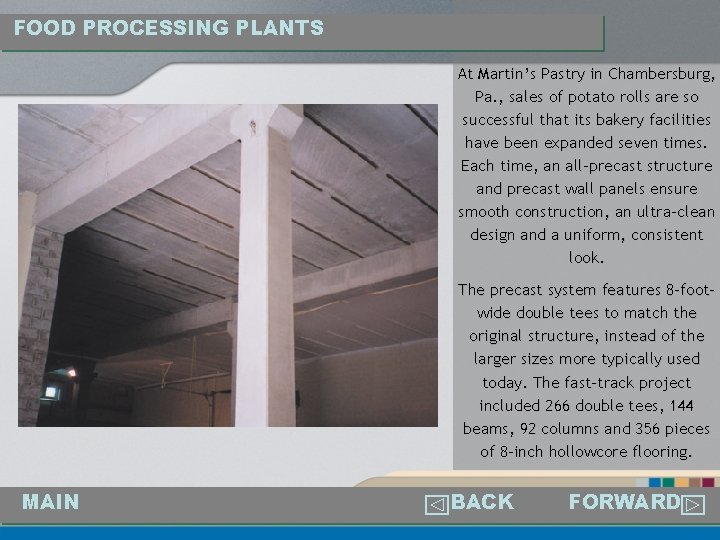
FOOD PROCESSING PLANTS At Martin’s Pastry in Chambersburg, Pa. , sales of potato rolls are so successful that its bakery facilities have been expanded seven times. Each time, an all-precast structure and precast wall panels ensure smooth construction, an ultra-clean design and a uniform, consistent look. The precast system features 8 -footwide double tees to match the original structure, instead of the larger sizes more typically used today. The fast-track project included 266 double tees, 144 beams, 92 columns and 356 pieces of 8 -inch hollowcore flooring. MAIN BACK FORWARD
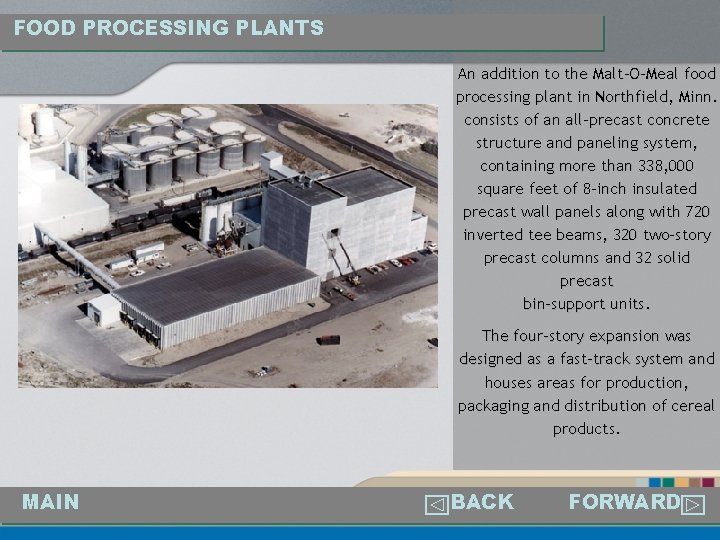
FOOD PROCESSING PLANTS An addition to the Malt-O-Meal food processing plant in Northfield, Minn. consists of an all-precast concrete structure and paneling system, containing more than 338, 000 square feet of 8 -inch insulated precast wall panels along with 720 inverted tee beams, 320 two-story precast columns and 32 solid precast bin-support units. The four-story expansion was designed as a fast-track system and houses areas for production, packaging and distribution of cereal products. MAIN BACK FORWARD
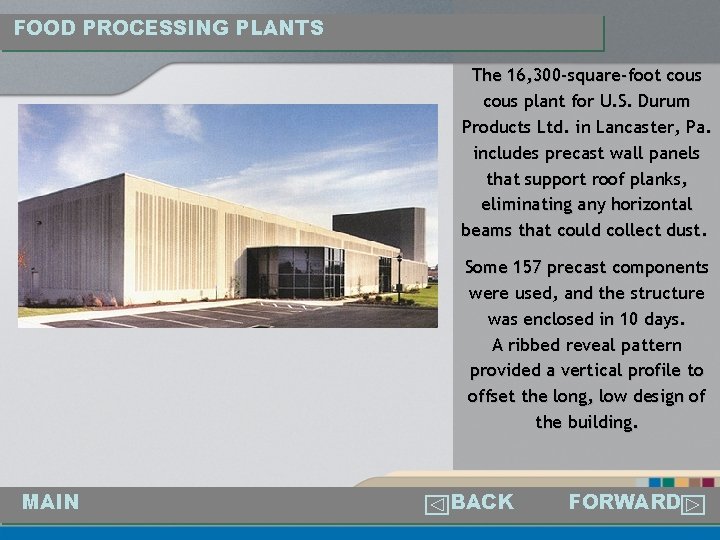
FOOD PROCESSING PLANTS The 16, 300 -square-foot cous plant for U. S. Durum Products Ltd. in Lancaster, Pa. includes precast wall panels that support roof planks, eliminating any horizontal beams that could collect dust. Some 157 precast components were used, and the structure was enclosed in 10 days. A ribbed reveal pattern provided a vertical profile to offset the long, low design of the building. MAIN BACK FORWARD
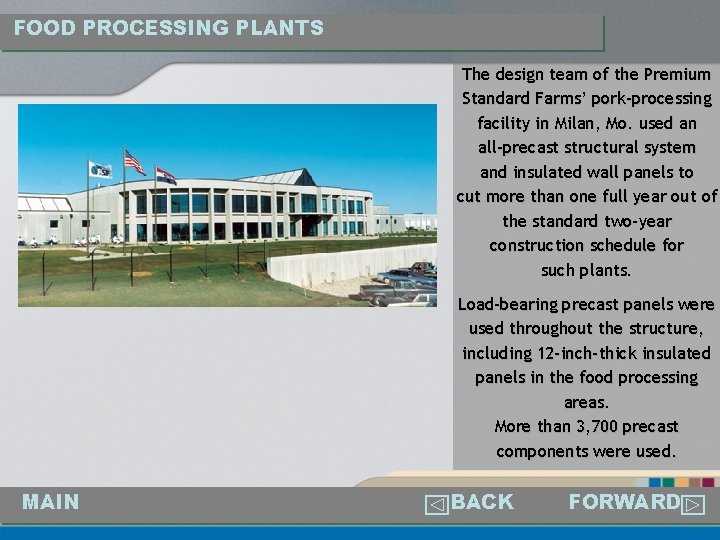
FOOD PROCESSING PLANTS The design team of the Premium Standard Farms’ pork-processing facility in Milan, Mo. used an all-precast structural system and insulated wall panels to cut more than one full year out of the standard two-year construction schedule for such plants. Load-bearing precast panels were used throughout the structure, including 12 -inch-thick insulated panels in the food processing areas. More than 3, 700 precast components were used. MAIN BACK FORWARD
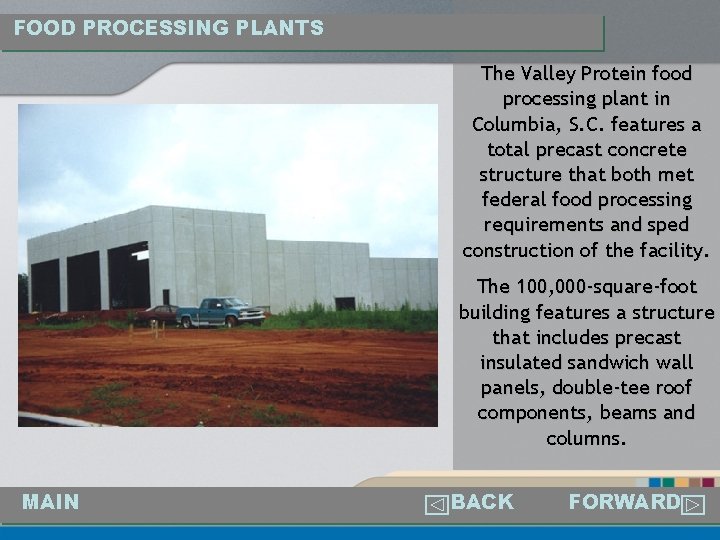
FOOD PROCESSING PLANTS The Valley Protein food processing plant in Columbia, S. C. features a total precast concrete structure that both met federal food processing requirements and sped construction of the facility. The 100, 000 -square-foot building features a structure that includes precast insulated sandwich wall panels, double-tee roof components, beams and columns. MAIN BACK FORWARD
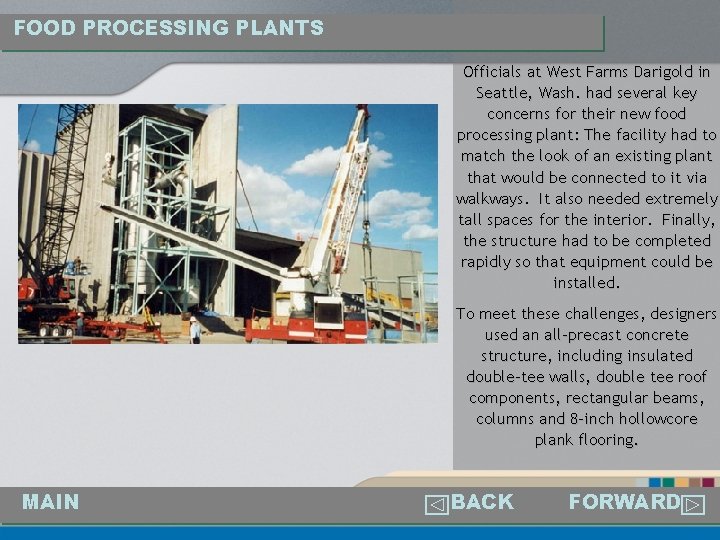
FOOD PROCESSING PLANTS Officials at West Farms Darigold in Seattle, Wash. had several key concerns for their new food processing plant: The facility had to match the look of an existing plant that would be connected to it via walkways. It also needed extremely tall spaces for the interior. Finally, the structure had to be completed rapidly so that equipment could be installed. To meet these challenges, designers used an all-precast concrete structure, including insulated double-tee walls, double tee roof components, rectangular beams, columns and 8 -inch hollowcore plank flooring. MAIN BACK FORWARD
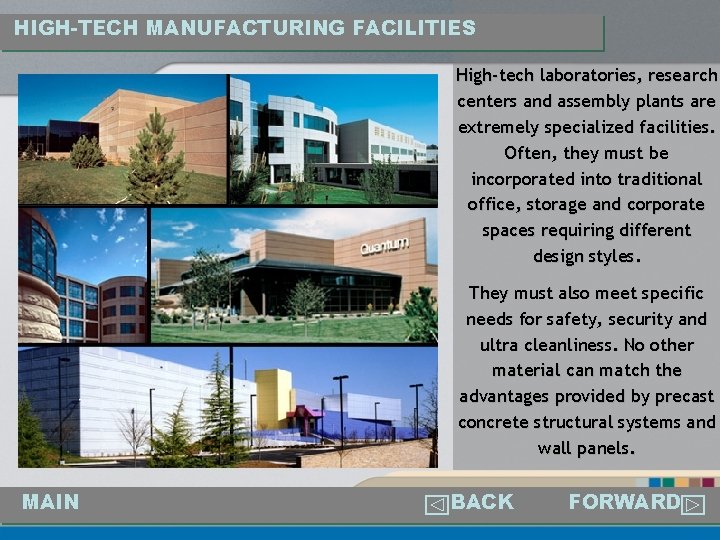
HIGH-TECH MANUFACTURING FACILITIES High-tech laboratories, research centers and assembly plants are extremely specialized facilities. Often, they must be incorporated into traditional office, storage and corporate spaces requiring different design styles. They must also meet specific needs for safety, security and ultra cleanliness. No other material can match the advantages provided by precast concrete structural systems and wall panels. MAIN BACK FORWARD
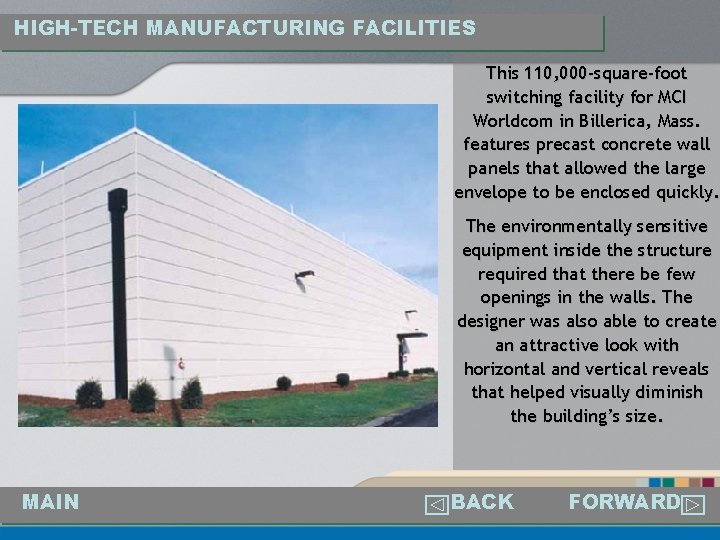
HIGH-TECH MANUFACTURING FACILITIES This 110, 000 -square-foot switching facility for MCI Worldcom in Billerica, Mass. features precast concrete wall panels that allowed the large envelope to be enclosed quickly. The environmentally sensitive equipment inside the structure required that there be few openings in the walls. The designer was also able to create an attractive look with horizontal and vertical reveals that helped visually diminish the building’s size. MAIN BACK FORWARD
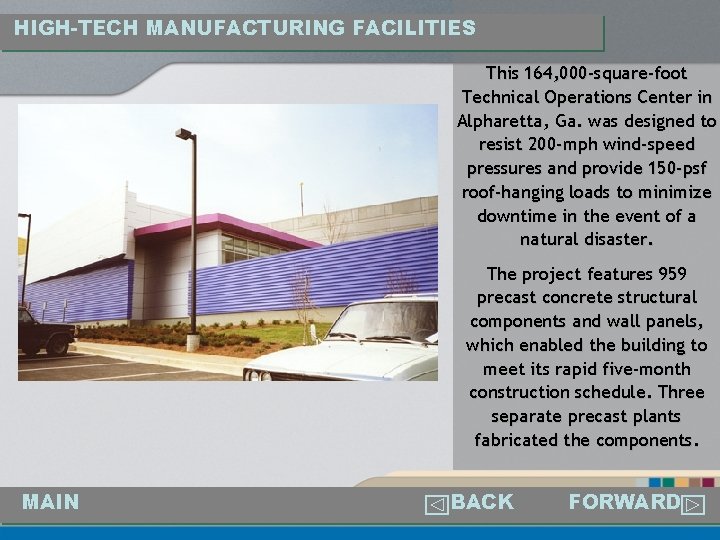
HIGH-TECH MANUFACTURING FACILITIES This 164, 000 -square-foot Technical Operations Center in Alpharetta, Ga. was designed to resist 200 -mph wind-speed pressures and provide 150 -psf roof-hanging loads to minimize downtime in the event of a natural disaster. The project features 959 precast concrete structural components and wall panels, which enabled the building to meet its rapid five-month construction schedule. Three separate precast plants fabricated the components. MAIN BACK FORWARD
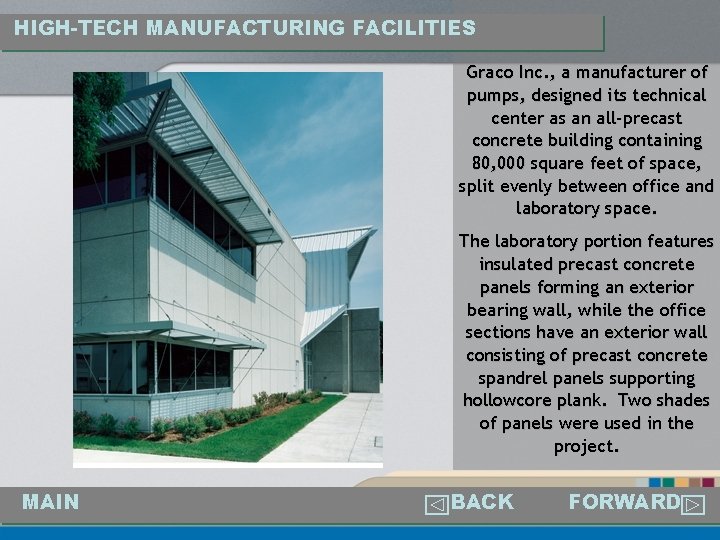
HIGH-TECH MANUFACTURING FACILITIES Graco Inc. , a manufacturer of pumps, designed its technical center as an all-precast concrete building containing 80, 000 square feet of space, split evenly between office and laboratory space. The laboratory portion features insulated precast concrete panels forming an exterior bearing wall, while the office sections have an exterior wall consisting of precast concrete spandrel panels supporting hollowcore plank. Two shades of panels were used in the project. MAIN BACK FORWARD
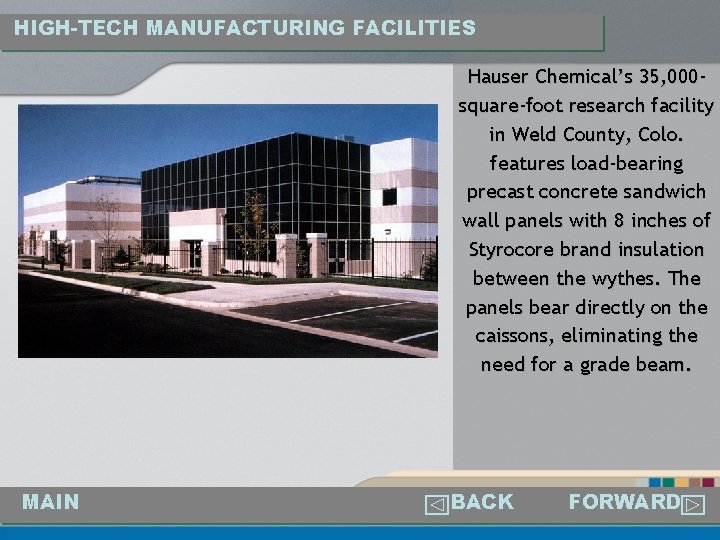
HIGH-TECH MANUFACTURING FACILITIES Hauser Chemical’s 35, 000 square-foot research facility in Weld County, Colo. features load-bearing precast concrete sandwich wall panels with 8 inches of Styrocore brand insulation between the wythes. The panels bear directly on the caissons, eliminating the need for a grade beam. MAIN BACK FORWARD
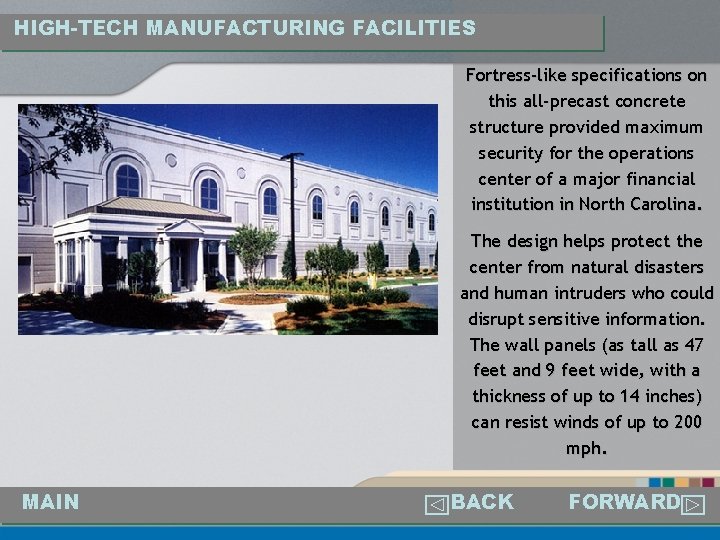
HIGH-TECH MANUFACTURING FACILITIES Fortress-like specifications on this all-precast concrete structure provided maximum security for the operations center of a major financial institution in North Carolina. The design helps protect the center from natural disasters and human intruders who could disrupt sensitive information. The wall panels (as tall as 47 feet and 9 feet wide, with a thickness of up to 14 inches) can resist winds of up to 200 mph. MAIN BACK FORWARD
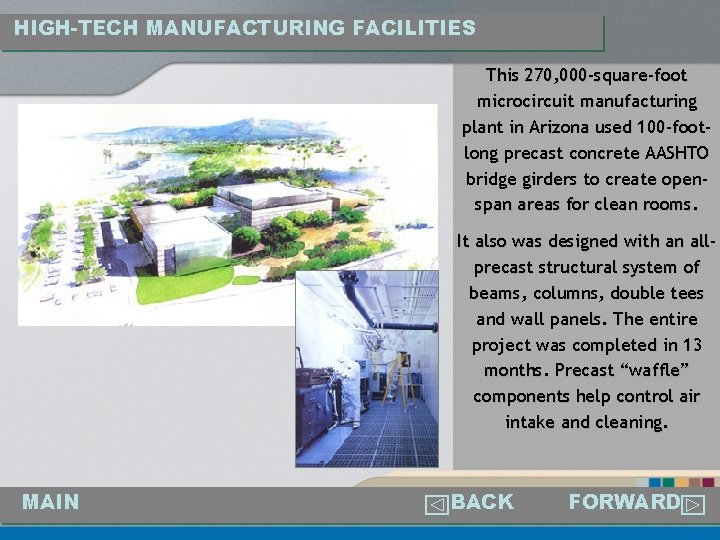
HIGH-TECH MANUFACTURING FACILITIES This 270, 000 -square-foot microcircuit manufacturing plant in Arizona used 100 -footlong precast concrete AASHTO bridge girders to create openspan areas for clean rooms. It also was designed with an allprecast structural system of beams, columns, double tees and wall panels. The entire project was completed in 13 months. Precast “waffle” components help control air intake and cleaning. MAIN BACK FORWARD
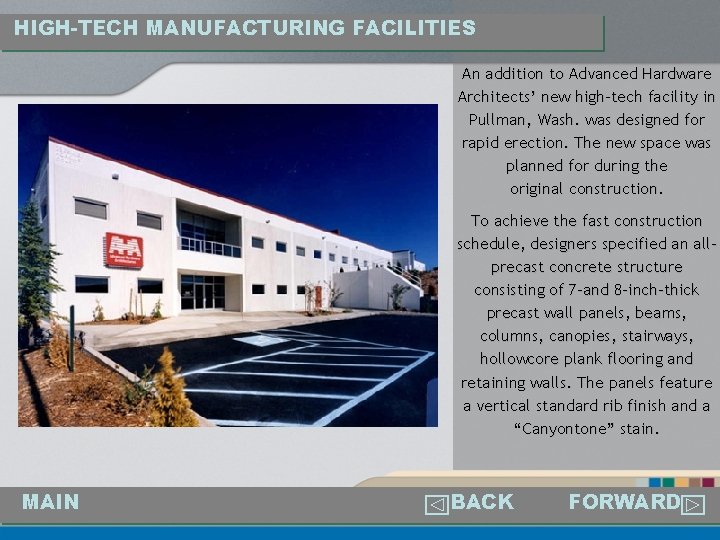
HIGH-TECH MANUFACTURING FACILITIES An addition to Advanced Hardware Architects’ new high-tech facility in Pullman, Wash. was designed for rapid erection. The new space was planned for during the original construction. To achieve the fast construction schedule, designers specified an allprecast concrete structure consisting of 7 -and 8 -inch-thick precast wall panels, beams, columns, canopies, stairways, hollowcore plank flooring and retaining walls. The panels feature a vertical standard rib finish and a “Canyontone” stain. MAIN BACK FORWARD
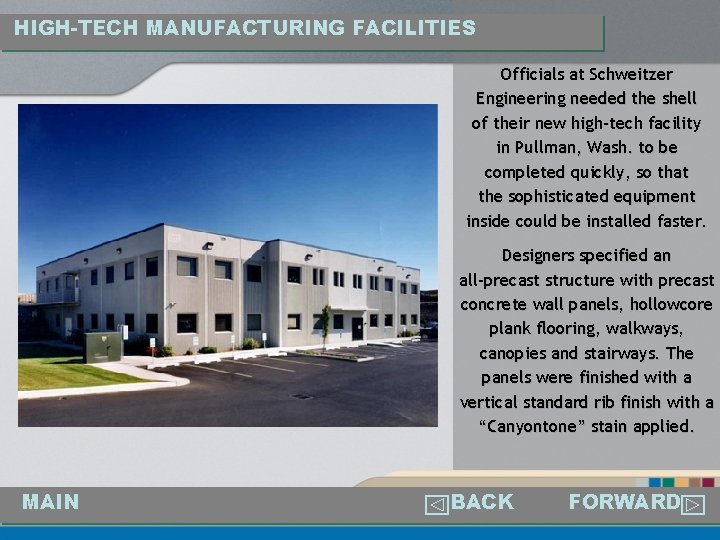
HIGH-TECH MANUFACTURING FACILITIES Officials at Schweitzer Engineering needed the shell of their new high-tech facility in Pullman, Wash. to be completed quickly, so that the sophisticated equipment inside could be installed faster. Designers specified an all-precast structure with precast concrete wall panels, hollowcore plank flooring, walkways, canopies and stairways. The panels were finished with a vertical standard rib finish with a “Canyontone” stain applied. MAIN BACK FORWARD
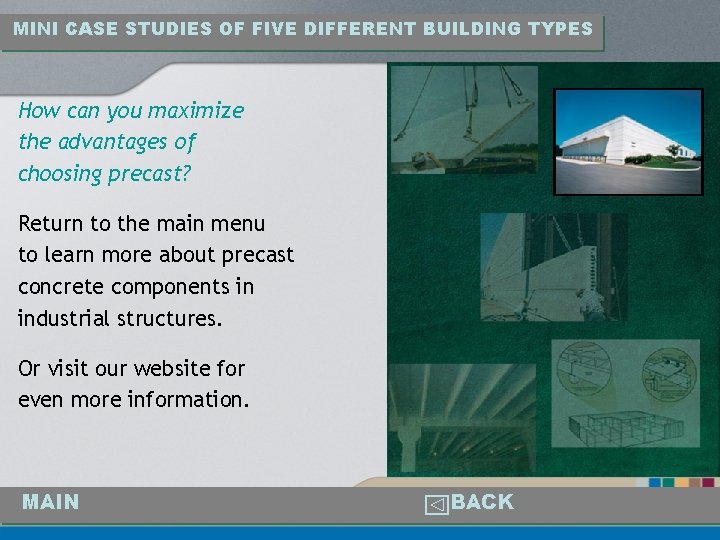
MINI CASE STUDIES OF FIVE DIFFERENT BUILDING TYPES How can you maximize the advantages of choosing precast? Return to the main menu to learn more about precast concrete components in industrial structures. Or visit our website for even more information. MAIN BACK
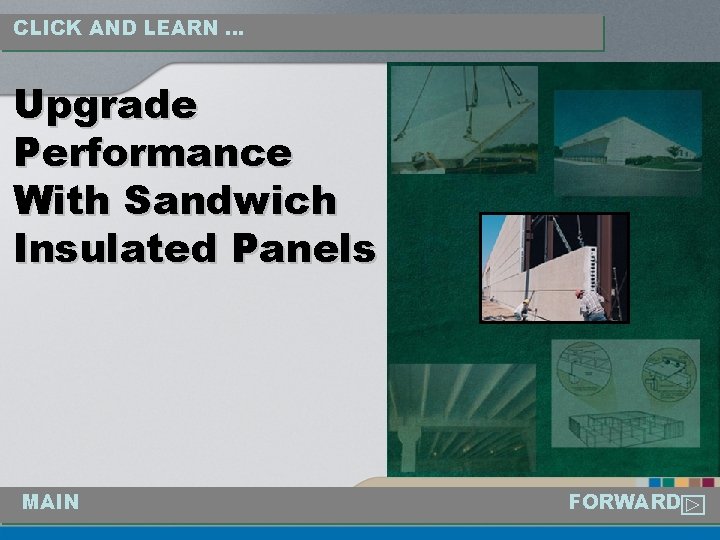
CLICK AND LEARN … Upgrade Performance With Sandwich Insulated Panels MAIN FORWARD
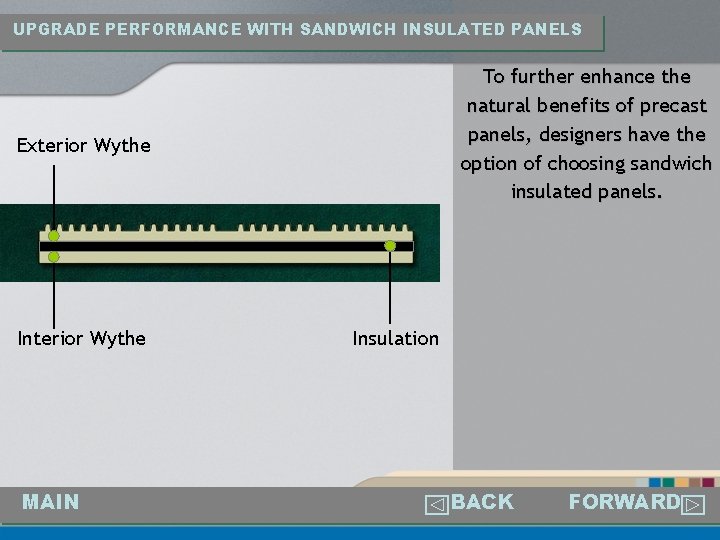
UPGRADE PERFORMANCE WITH SANDWICH INSULATED PANELS To further enhance the natural benefits of precast panels, designers have the option of choosing sandwich insulated panels. Exterior Wythe Interior Wythe MAIN Insulation BACK FORWARD
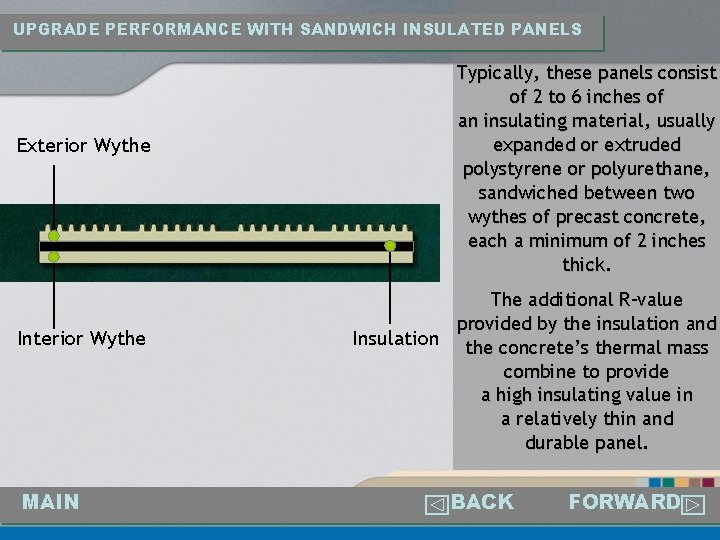
UPGRADE PERFORMANCE WITH SANDWICH INSULATED PANELS Exterior Wythe Interior Wythe MAIN Typically, these panels consist of 2 to 6 inches of an insulating material, usually expanded or extruded polystyrene or polyurethane, sandwiched between two wythes of precast concrete, each a minimum of 2 inches thick. The additional R-value provided by the insulation and Insulation the concrete’s thermal mass combine to provide a high insulating value in a relatively thin and durable panel. BACK FORWARD
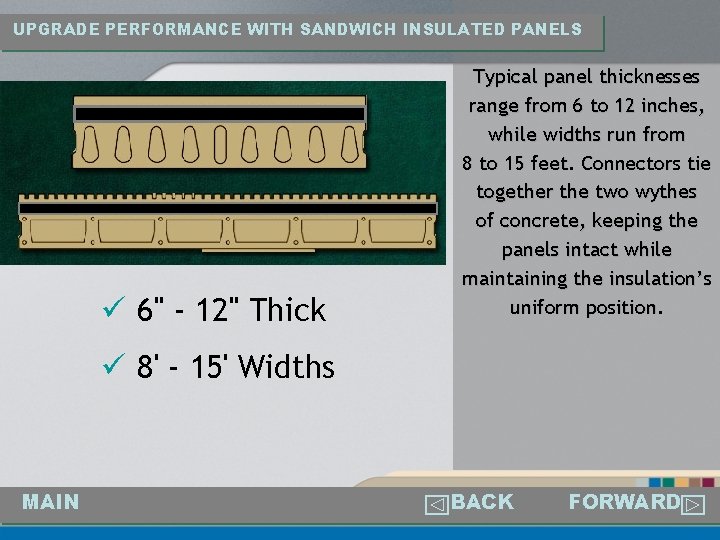
UPGRADE PERFORMANCE WITH SANDWICH INSULATED PANELS ü 6" - 12" Thick Typical panel thicknesses range from 6 to 12 inches, while widths run from 8 to 15 feet. Connectors tie together the two wythes of concrete, keeping the panels intact while maintaining the insulation’s uniform position. ü 8' - 15' Widths MAIN BACK FORWARD
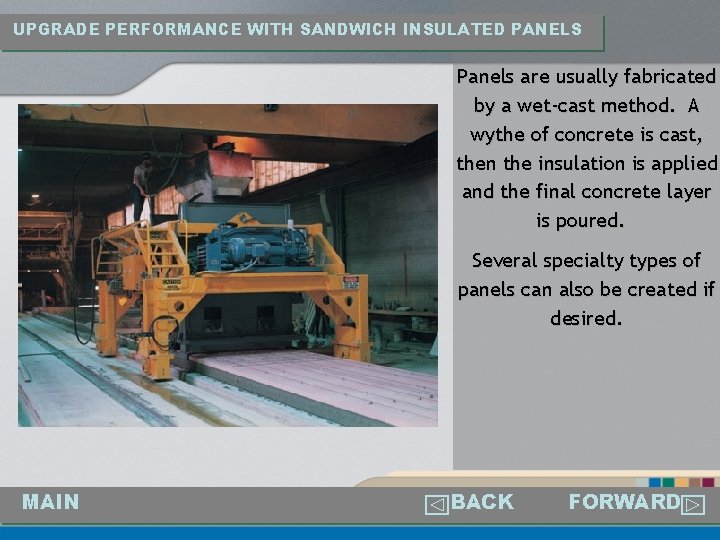
UPGRADE PERFORMANCE WITH SANDWICH INSULATED PANELS Panels are usually fabricated by a wet-cast method. A wythe of concrete is cast, then the insulation is applied and the final concrete layer is poured. Several specialty types of panels can also be created if desired. MAIN BACK FORWARD
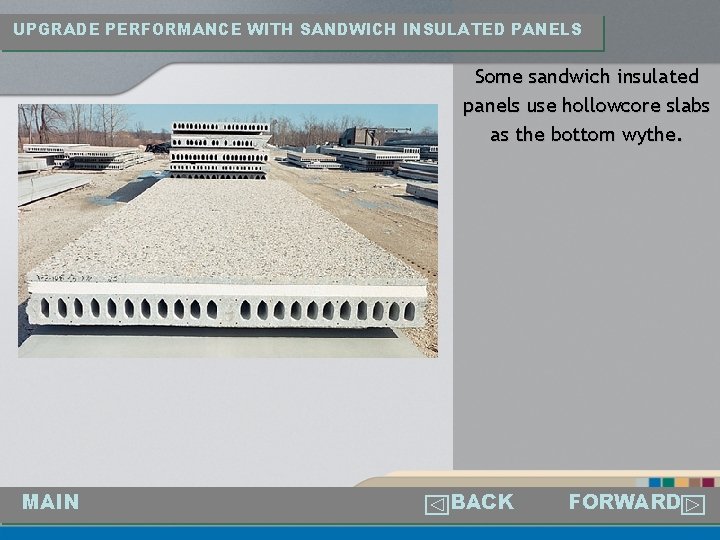
UPGRADE PERFORMANCE WITH SANDWICH INSULATED PANELS Some sandwich insulated panels use hollowcore slabs as the bottom wythe. MAIN BACK FORWARD
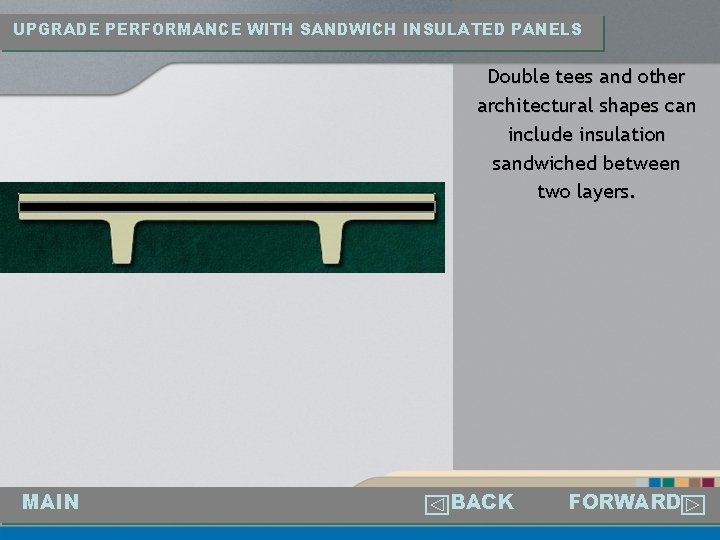
UPGRADE PERFORMANCE WITH SANDWICH INSULATED PANELS Double tees and other architectural shapes can include insulation sandwiched between two layers. MAIN BACK FORWARD
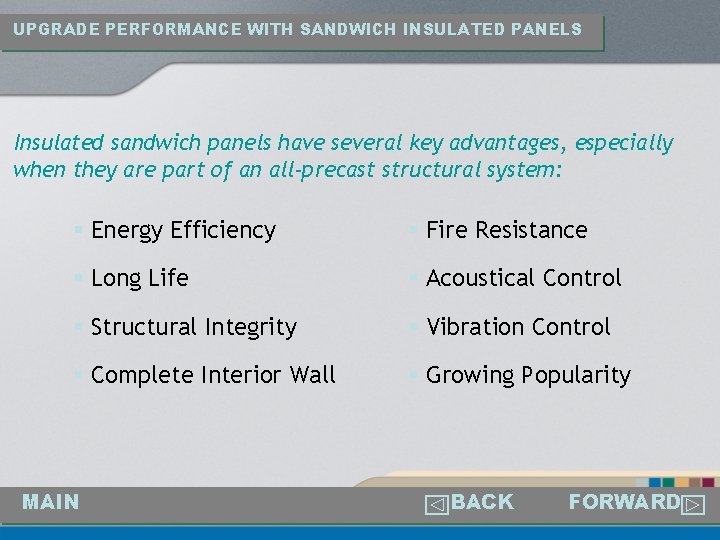
UPGRADE PERFORMANCE WITH SANDWICH INSULATED PANELS Insulated sandwich panels have several key advantages, especially when they are part of an all-precast structural system: § Energy Efficiency § Fire Resistance § Long Life § Acoustical Control § Structural Integrity § Vibration Control § Complete Interior Wall § Growing Popularity MAIN BACK FORWARD
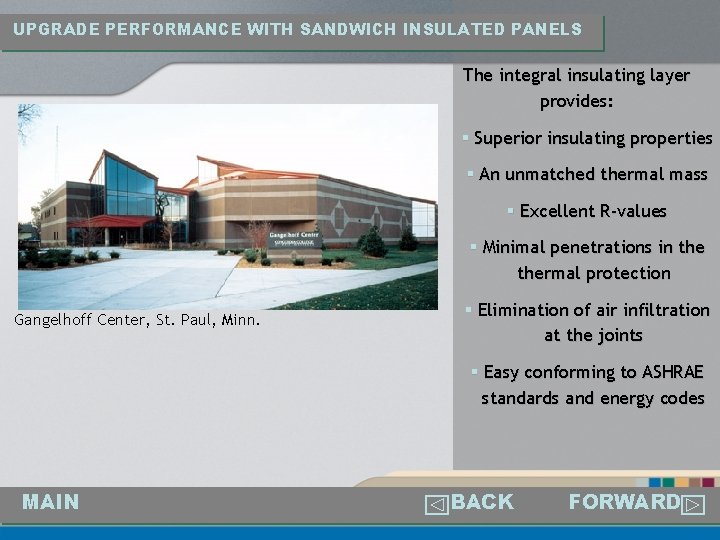
UPGRADE PERFORMANCE WITH SANDWICH INSULATED PANELS The integral insulating layer provides: § Superior insulating properties § An unmatched thermal mass § Excellent R-values § Minimal penetrations in thermal protection Gangelhoff Center, St. Paul, Minn. § Elimination of air infiltration at the joints § Easy conforming to ASHRAE standards and energy codes MAIN BACK FORWARD
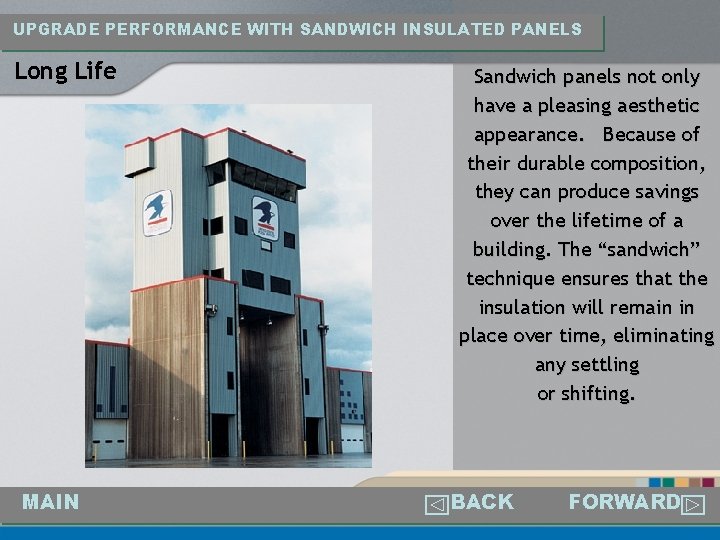
UPGRADE PERFORMANCE WITH SANDWICH INSULATED PANELS Long Life Sandwich panels not only have a pleasing aesthetic appearance. Because of their durable composition, they can produce savings over the lifetime of a building. The “sandwich” technique ensures that the insulation will remain in place over time, eliminating any settling or shifting. MAIN BACK FORWARD
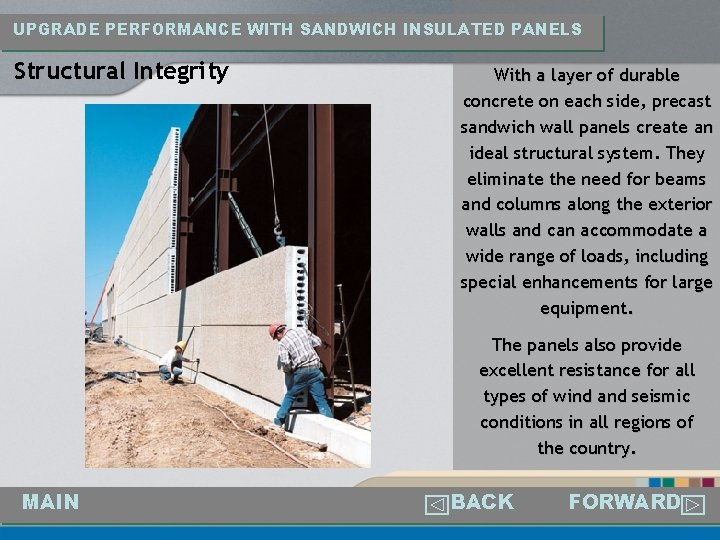
UPGRADE PERFORMANCE WITH SANDWICH INSULATED PANELS Structural Integrity With a layer of durable concrete on each side, precast sandwich wall panels create an ideal structural system. They eliminate the need for beams and columns along the exterior walls and can accommodate a wide range of loads, including special enhancements for large equipment. The panels also provide excellent resistance for all types of wind and seismic conditions in all regions of the country. MAIN BACK FORWARD
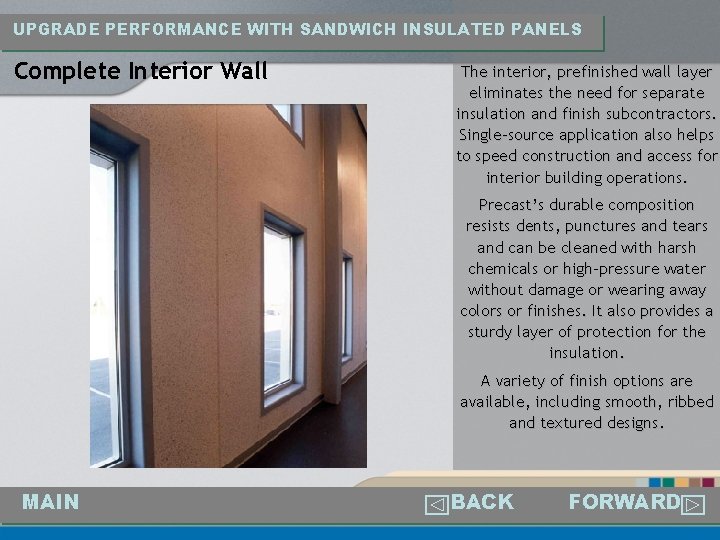
UPGRADE PERFORMANCE WITH SANDWICH INSULATED PANELS Complete Interior Wall The interior, prefinished wall layer eliminates the need for separate insulation and finish subcontractors. Single-source application also helps to speed construction and access for interior building operations. Precast’s durable composition resists dents, punctures and tears and can be cleaned with harsh chemicals or high-pressure water without damage or wearing away colors or finishes. It also provides a sturdy layer of protection for the insulation. A variety of finish options are available, including smooth, ribbed and textured designs. MAIN BACK FORWARD
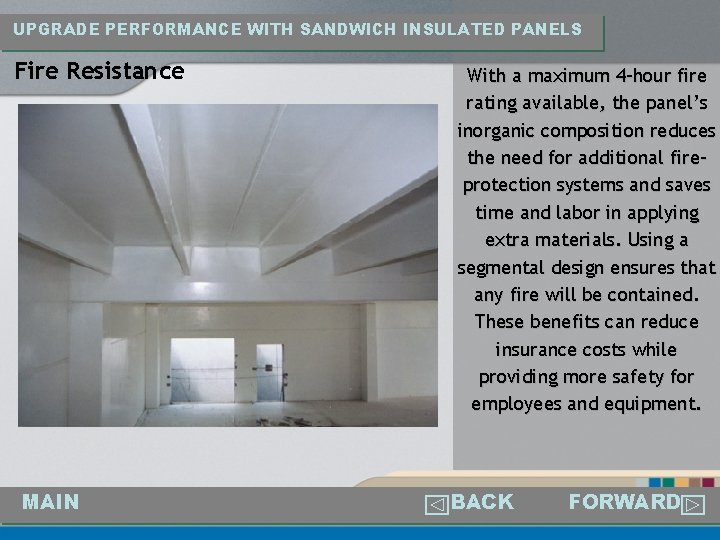
UPGRADE PERFORMANCE WITH SANDWICH INSULATED PANELS Fire Resistance MAIN With a maximum 4 -hour fire rating available, the panel’s inorganic composition reduces the need for additional fireprotection systems and saves time and labor in applying extra materials. Using a segmental design ensures that any fire will be contained. These benefits can reduce insurance costs while providing more safety for employees and equipment. BACK FORWARD
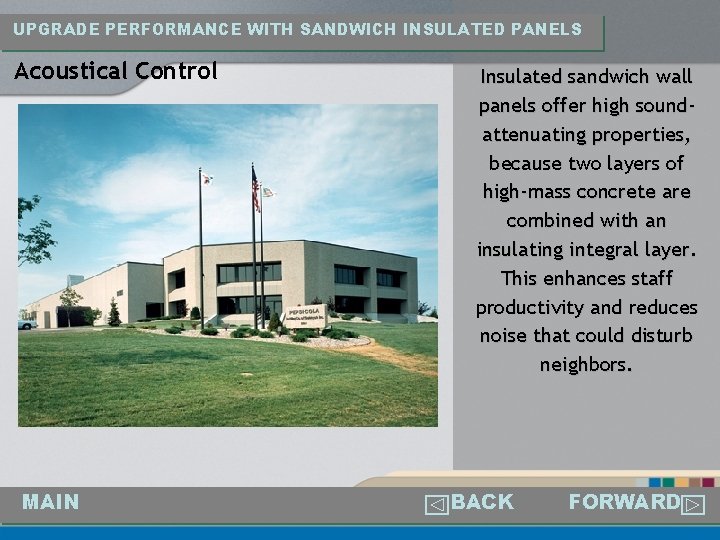
UPGRADE PERFORMANCE WITH SANDWICH INSULATED PANELS Acoustical Control MAIN Insulated sandwich wall panels offer high soundattenuating properties, because two layers of high-mass concrete are combined with an insulating integral layer. This enhances staff productivity and reduces noise that could disturb neighbors. BACK FORWARD
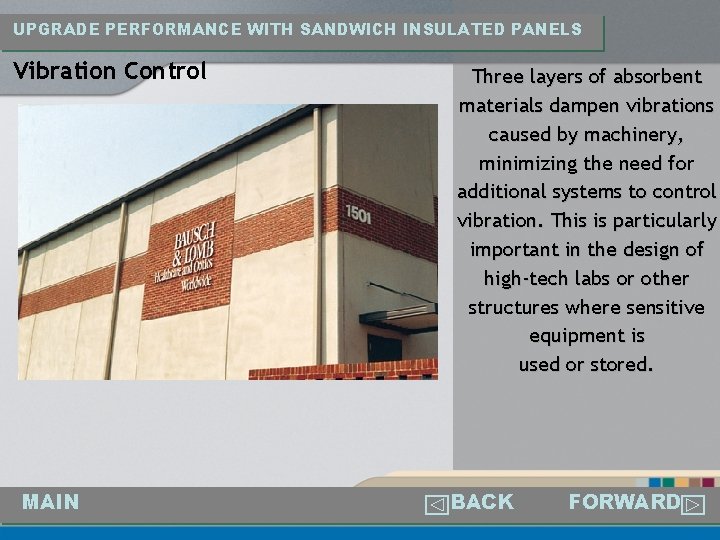
UPGRADE PERFORMANCE WITH SANDWICH INSULATED PANELS Vibration Control MAIN Three layers of absorbent materials dampen vibrations caused by machinery, minimizing the need for additional systems to control vibration. This is particularly important in the design of high-tech labs or other structures where sensitive equipment is used or stored. BACK FORWARD
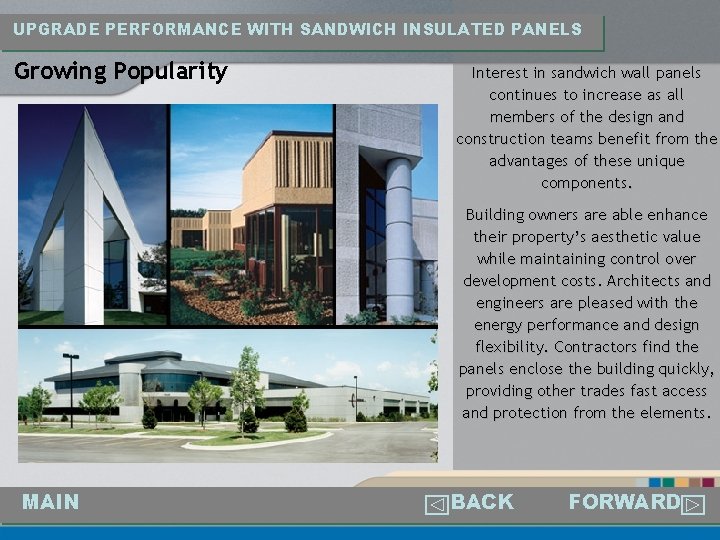
UPGRADE PERFORMANCE WITH SANDWICH INSULATED PANELS Growing Popularity Interest in sandwich wall panels continues to increase as all members of the design and construction teams benefit from the advantages of these unique components. Building owners are able enhance their property’s aesthetic value while maintaining control over development costs. Architects and engineers are pleased with the energy performance and design flexibility. Contractors find the panels enclose the building quickly, providing other trades fast access and protection from the elements. MAIN BACK FORWARD
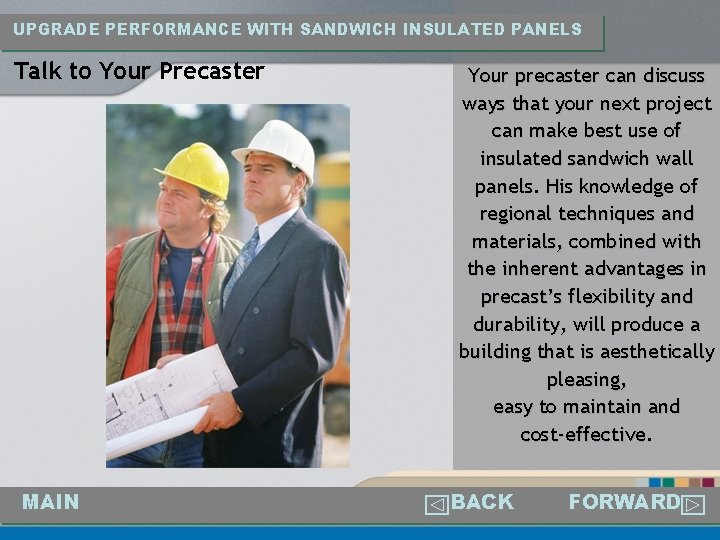
UPGRADE PERFORMANCE WITH SANDWICH INSULATED PANELS Talk to Your Precaster MAIN Your precaster can discuss ways that your next project can make best use of insulated sandwich wall panels. His knowledge of regional techniques and materials, combined with the inherent advantages in precast’s flexibility and durability, will produce a building that is aesthetically pleasing, easy to maintain and cost-effective. BACK FORWARD
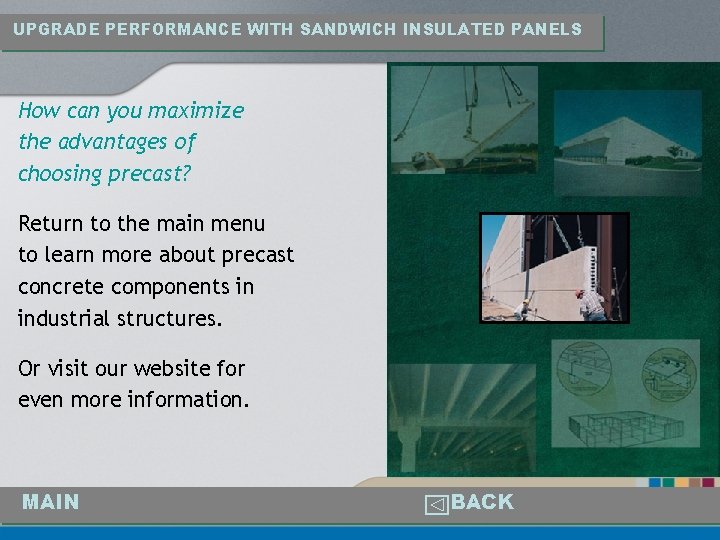
UPGRADE PERFORMANCE WITH SANDWICH INSULATED PANELS How can you maximize the advantages of choosing precast? Return to the main menu to learn more about precast concrete components in industrial structures. Or visit our website for even more information. MAIN BACK
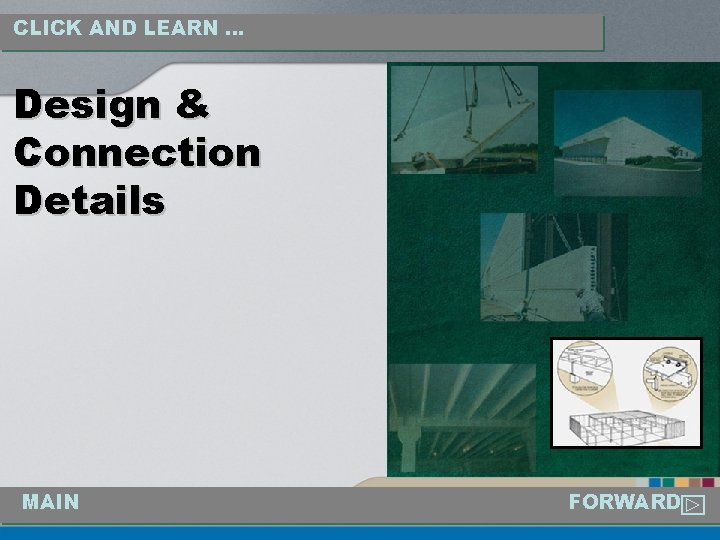
CLICK AND LEARN … Design & Connection Details MAIN FORWARD
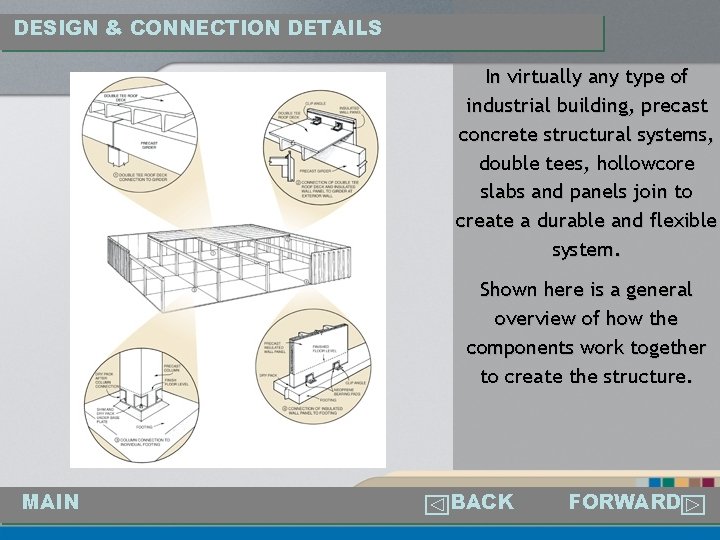
DESIGN & CONNECTION DETAILS In virtually any type of industrial building, precast concrete structural systems, double tees, hollowcore slabs and panels join to create a durable and flexible system. Shown here is a general overview of how the components work together to create the structure. MAIN BACK FORWARD
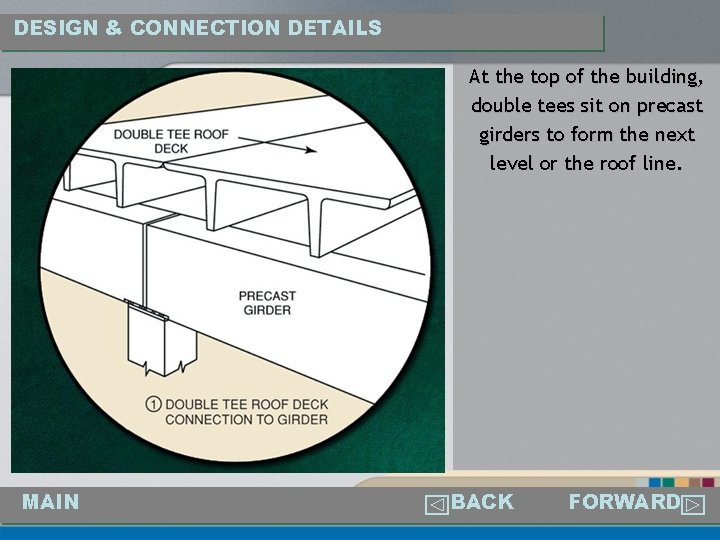
DESIGN & CONNECTION DETAILS At the top of the building, double tees sit on precast girders to form the next level or the roof line. MAIN BACK FORWARD
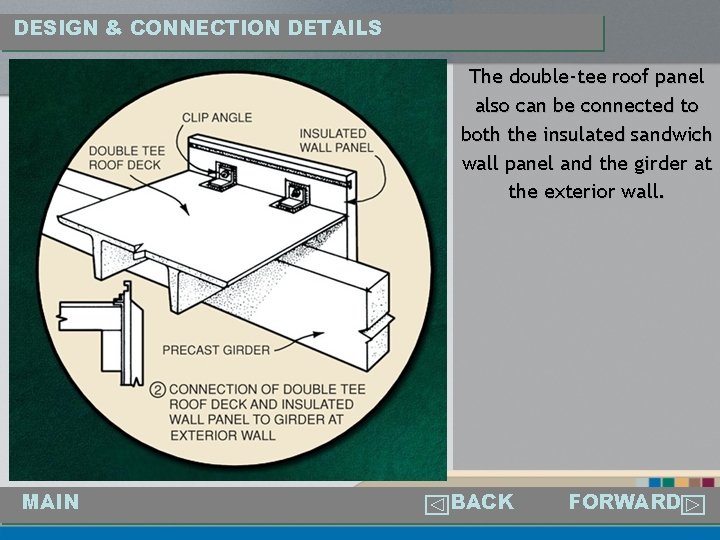
DESIGN & CONNECTION DETAILS The double-tee roof panel also can be connected to both the insulated sandwich wall panel and the girder at the exterior wall. MAIN BACK FORWARD
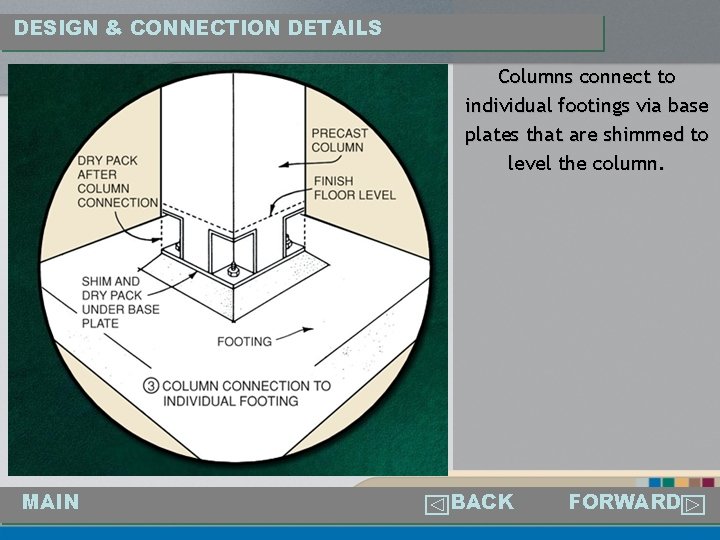
DESIGN & CONNECTION DETAILS Columns connect to individual footings via base plates that are shimmed to level the column. MAIN BACK FORWARD
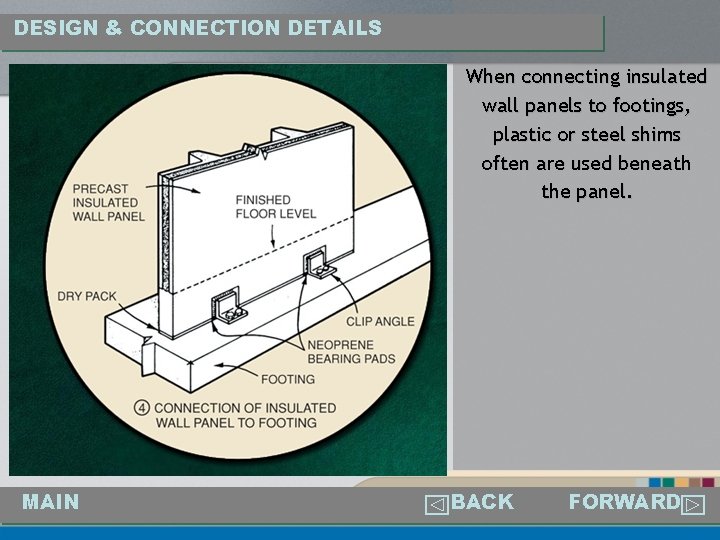
DESIGN & CONNECTION DETAILS When connecting insulated wall panels to footings, plastic or steel shims often are used beneath the panel. MAIN BACK FORWARD
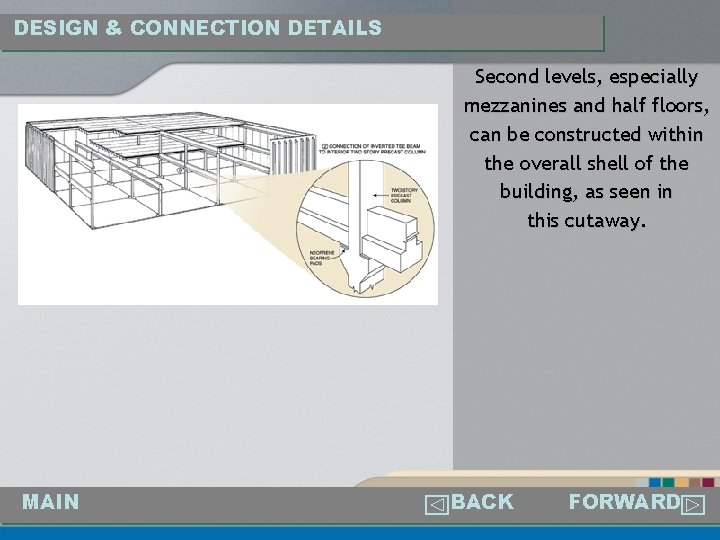
DESIGN & CONNECTION DETAILS Second levels, especially mezzanines and half floors, can be constructed within the overall shell of the building, as seen in this cutaway. MAIN BACK FORWARD
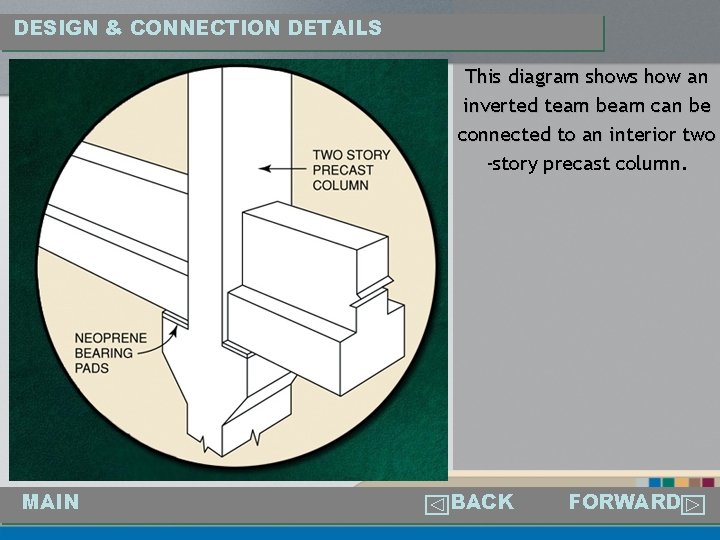
DESIGN & CONNECTION DETAILS This diagram shows how an inverted team beam can be connected to an interior two -story precast column. MAIN BACK FORWARD
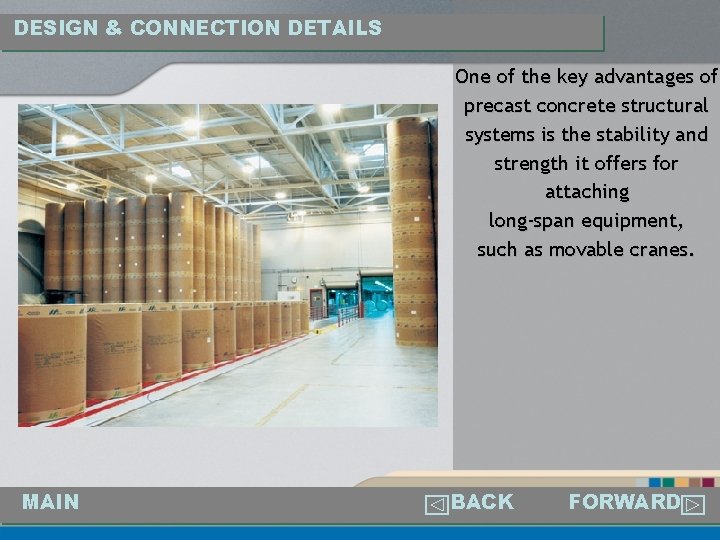
DESIGN & CONNECTION DETAILS One of the key advantages of precast concrete structural systems is the stability and strength it offers for attaching long-span equipment, such as movable cranes. MAIN BACK FORWARD
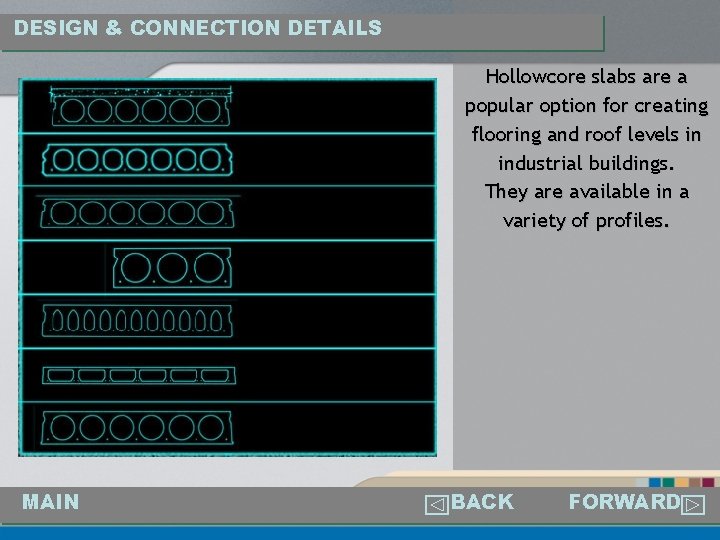
DESIGN & CONNECTION DETAILS Duracore Dynaspan Elematic Hollowcore slabs are a popular option for creating flooring and roof levels in industrial buildings. They are available in a variety of profiles. Flexicore Spancrete Span. Deck Ultra-Span MAIN BACK FORWARD
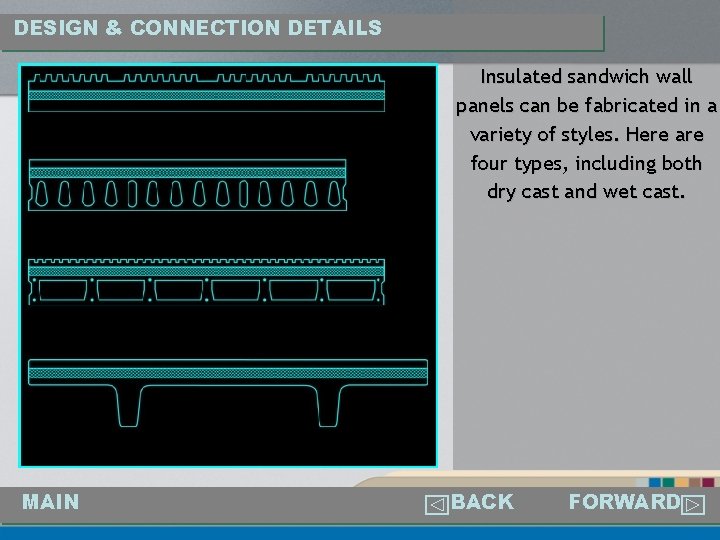
DESIGN & CONNECTION DETAILS COREWALL PANEL Insulated sandwich wall panels can be fabricated in a variety of styles. Here are four types, including both dry cast and wet cast. SPANCRETE WALL PANEL SPANDECK WALL PANEL INSULATED DOUBLE TEE MAIN BACK FORWARD
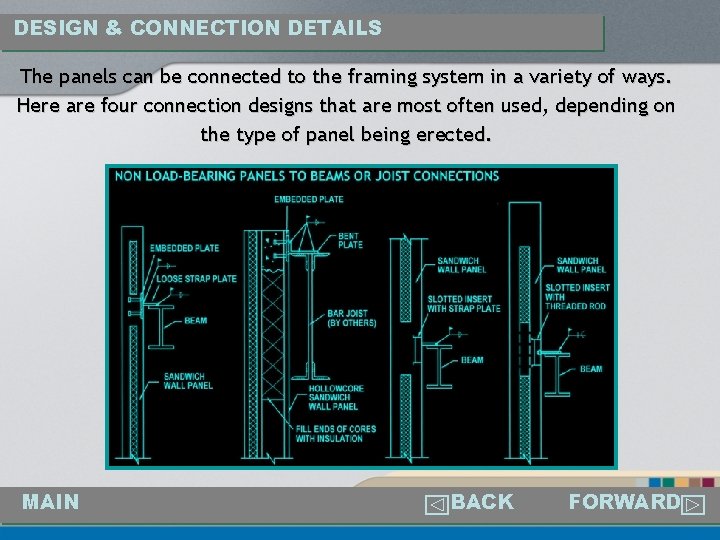
DESIGN & CONNECTION DETAILS The panels can be connected to the framing system in a variety of ways. Here are four connection designs that are most often used, depending on the type of panel being erected. MAIN BACK FORWARD
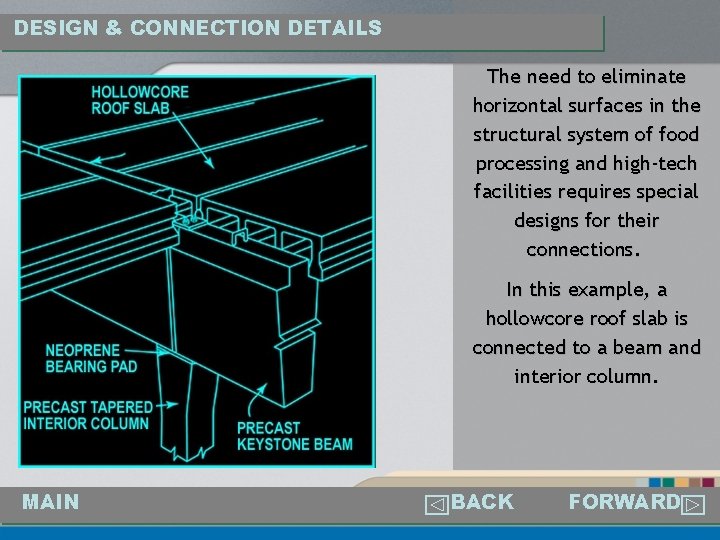
DESIGN & CONNECTION DETAILS The need to eliminate horizontal surfaces in the structural system of food processing and high-tech facilities requires special designs for their connections. In this example, a hollowcore roof slab is connected to a beam and interior column. MAIN BACK FORWARD
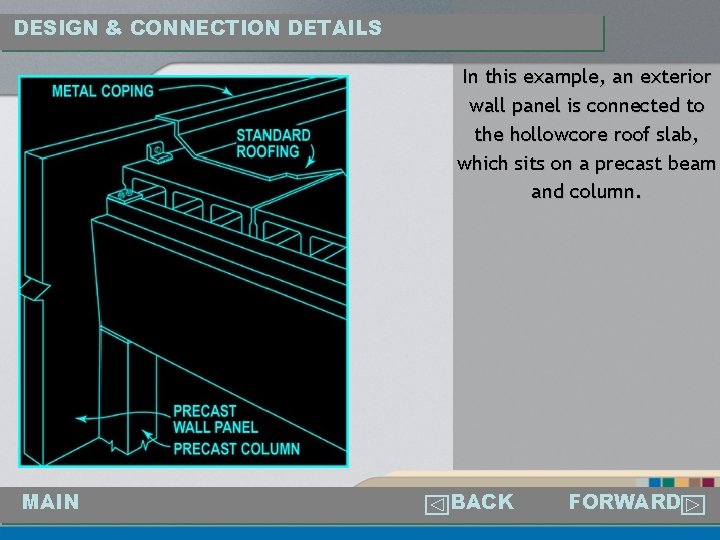
DESIGN & CONNECTION DETAILS In this example, an exterior wall panel is connected to the hollowcore roof slab, which sits on a precast beam and column. MAIN BACK FORWARD
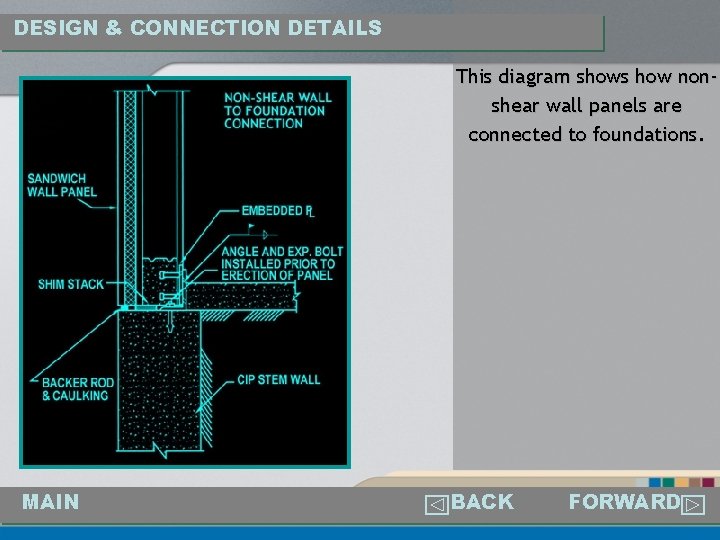
DESIGN & CONNECTION DETAILS This diagram shows how nonshear wall panels are connected to foundations. MAIN BACK FORWARD
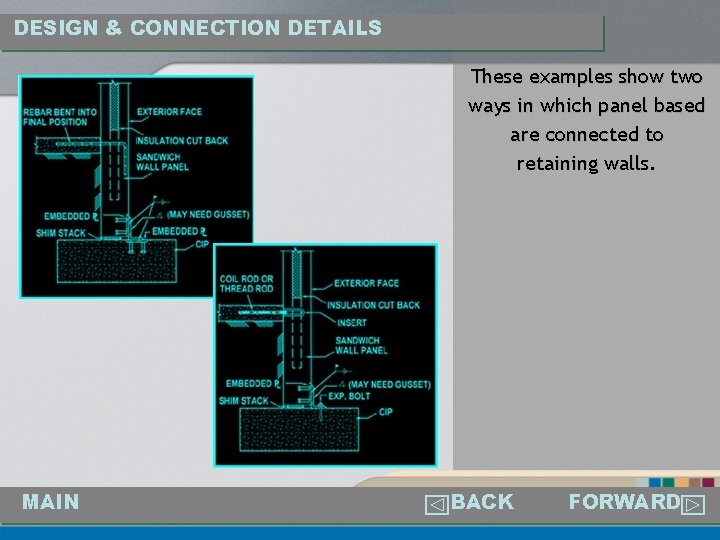
DESIGN & CONNECTION DETAILS These examples show two ways in which panel based are connected to retaining walls. MAIN BACK FORWARD
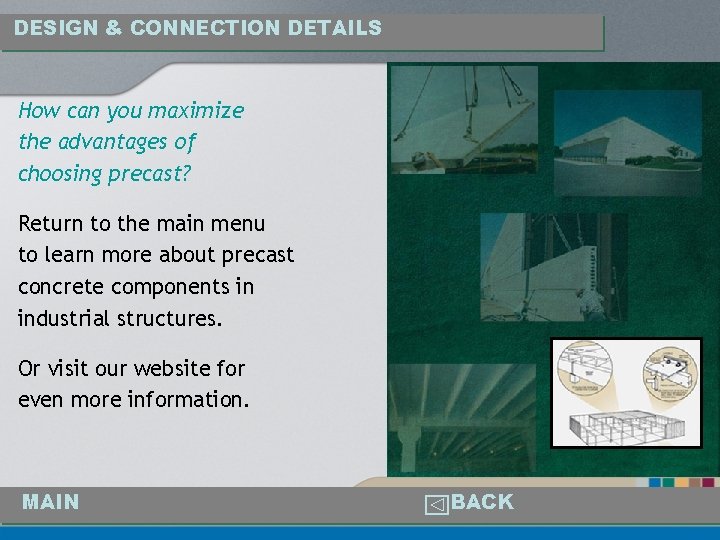
DESIGN & CONNECTION DETAILS How can you maximize the advantages of choosing precast? Return to the main menu to learn more about precast concrete components in industrial structures. Or visit our website for even more information. MAIN BACK
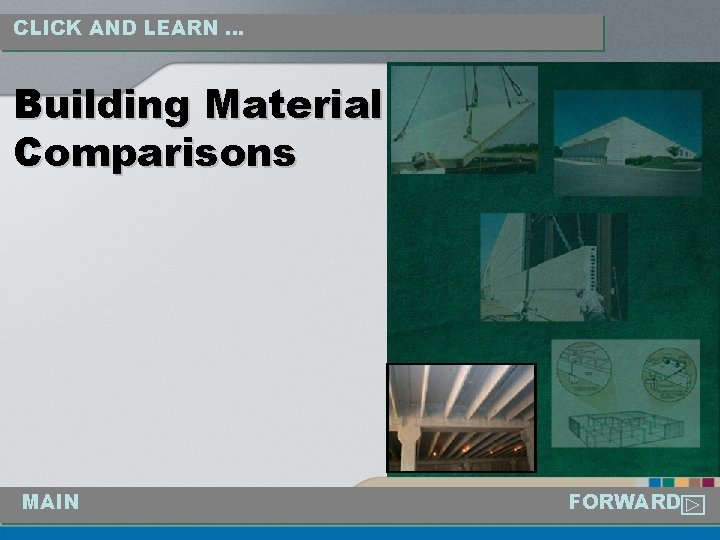
CLICK AND LEARN … Building Material Comparisons MAIN FORWARD
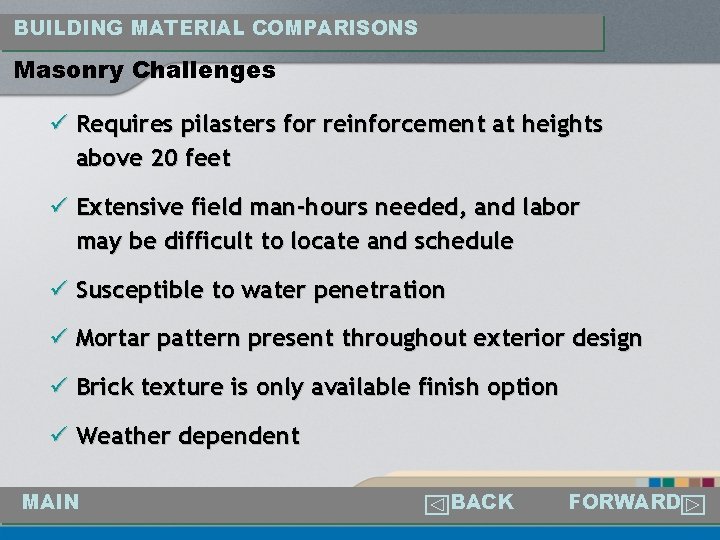
BUILDING MATERIAL COMPARISONS Masonry Challenges ü Requires pilasters for reinforcement at heights above 20 feet ü Extensive field man-hours needed, and labor may be difficult to locate and schedule ü Susceptible to water penetration ü Mortar pattern present throughout exterior design ü Brick texture is only available finish option ü Weather dependent MAIN BACK FORWARD
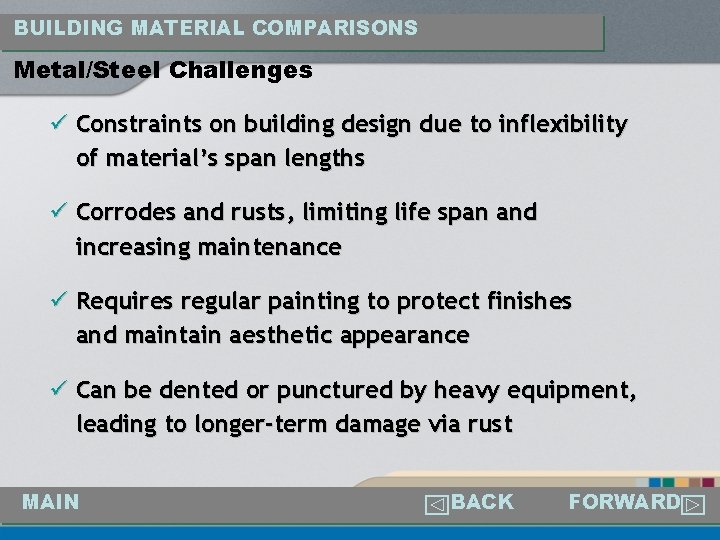
BUILDING MATERIAL COMPARISONS Metal/Steel Challenges ü Constraints on building design due to inflexibility of material’s span lengths ü Corrodes and rusts, limiting life span and increasing maintenance ü Requires regular painting to protect finishes and maintain aesthetic appearance ü Can be dented or punctured by heavy equipment, leading to longer-term damage via rust MAIN BACK FORWARD
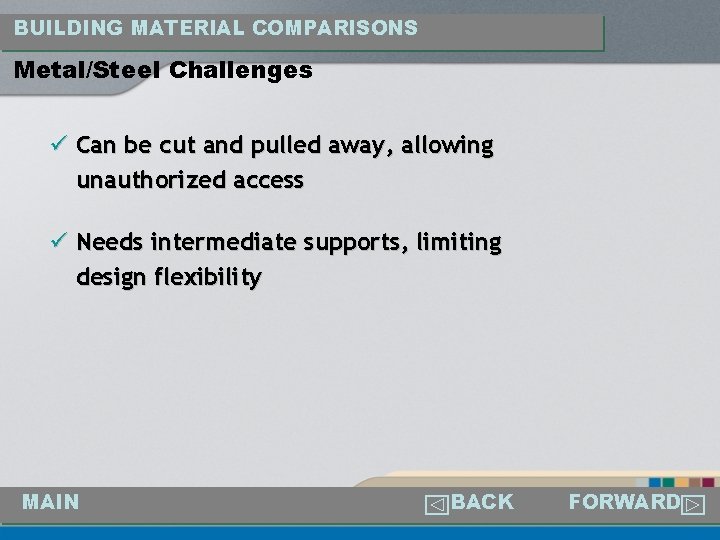
BUILDING MATERIAL COMPARISONS Metal/Steel Challenges ü Can be cut and pulled away, allowing unauthorized access ü Needs intermediate supports, limiting design flexibility MAIN BACK FORWARD
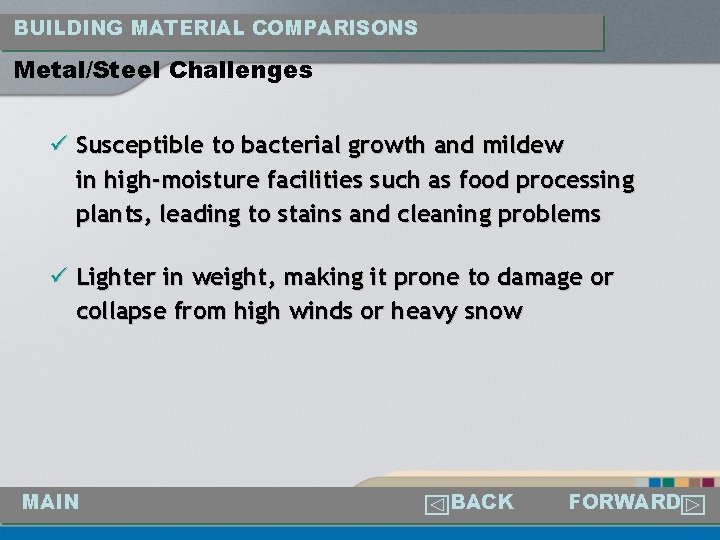
BUILDING MATERIAL COMPARISONS Metal/Steel Challenges ü Susceptible to bacterial growth and mildew in high-moisture facilities such as food processing plants, leading to stains and cleaning problems ü Lighter in weight, making it prone to damage or collapse from high winds or heavy snow MAIN BACK FORWARD
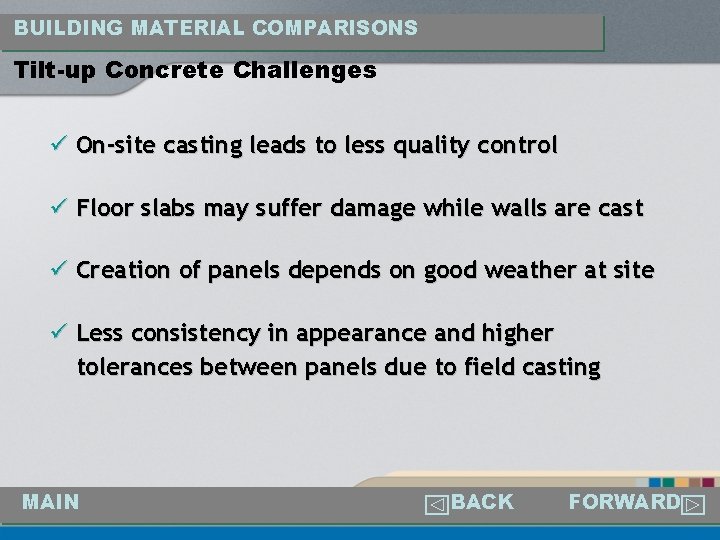
BUILDING MATERIAL COMPARISONS Tilt-up Concrete Challenges ü On-site casting leads to less quality control ü Floor slabs may suffer damage while walls are cast ü Creation of panels depends on good weather at site ü Less consistency in appearance and higher tolerances between panels due to field casting MAIN BACK FORWARD
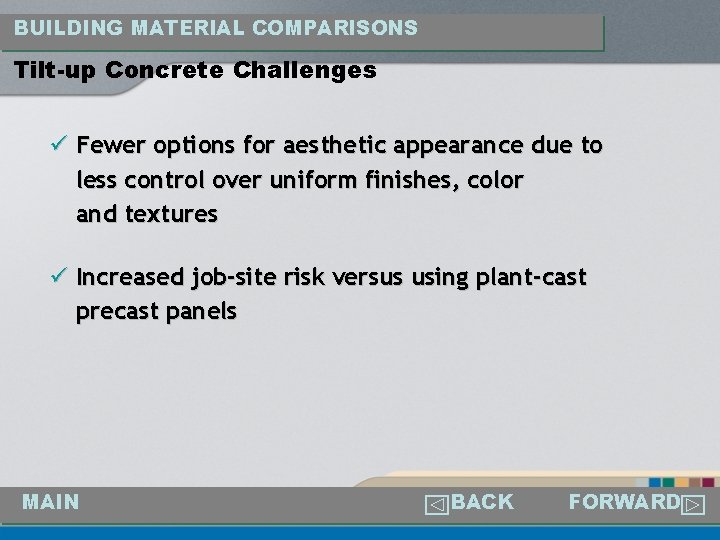
BUILDING MATERIAL COMPARISONS Tilt-up Concrete Challenges ü Fewer options for aesthetic appearance due to less control over uniform finishes, color and textures ü Increased job-site risk versus using plant-cast precast panels MAIN BACK FORWARD
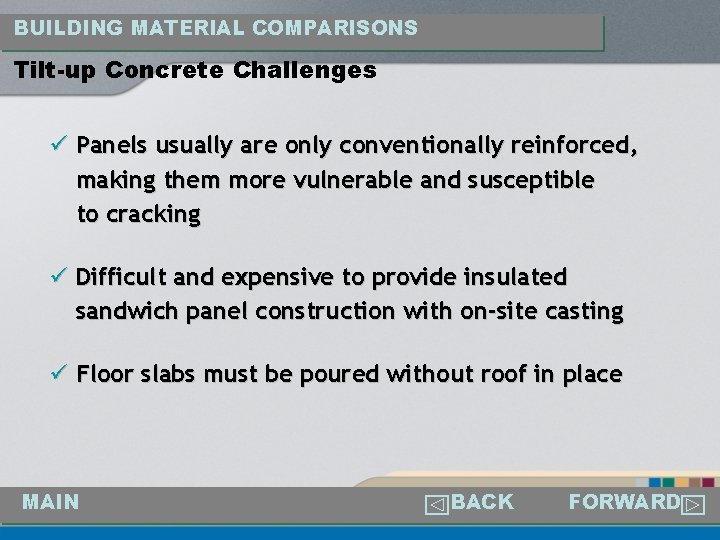
BUILDING MATERIAL COMPARISONS Tilt-up Concrete Challenges ü Panels usually are only conventionally reinforced, making them more vulnerable and susceptible to cracking ü Difficult and expensive to provide insulated sandwich panel construction with on-site casting ü Floor slabs must be poured without roof in place MAIN BACK FORWARD
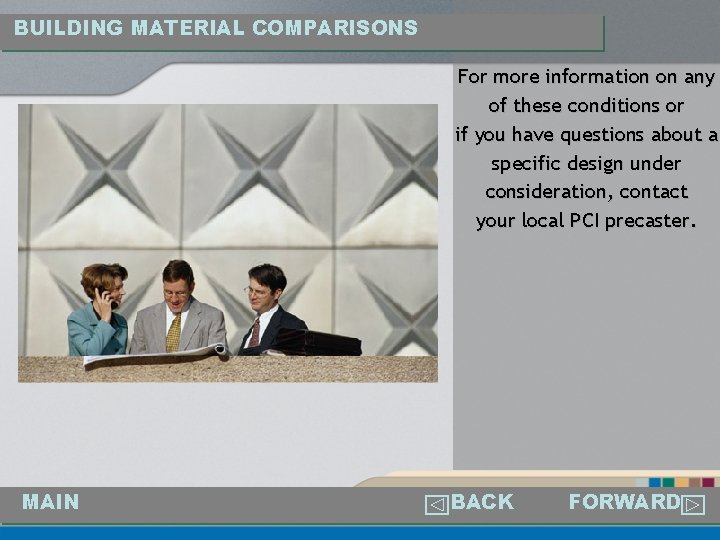
BUILDING MATERIAL COMPARISONS For more information on any of these conditions or if you have questions about a specific design under consideration, contact your local PCI precaster. MAIN BACK FORWARD
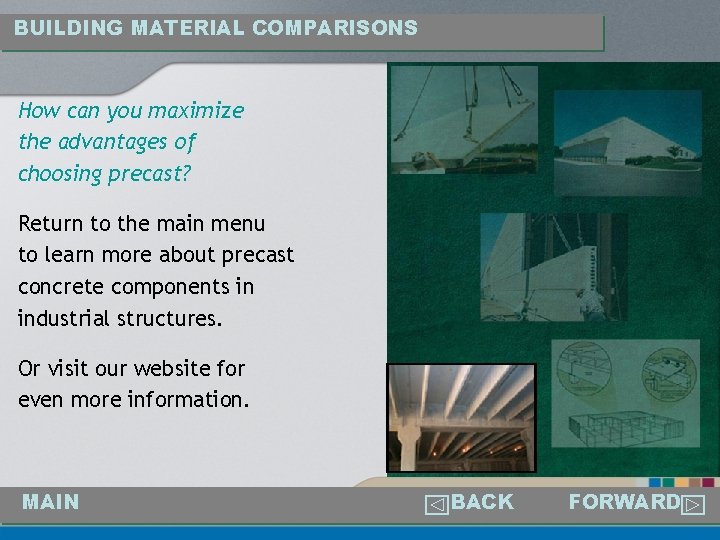
BUILDING MATERIAL COMPARISONS How can you maximize the advantages of choosing precast? Return to the main menu to learn more about precast concrete components in industrial structures. Or visit our website for even more information. MAIN BACK FORWARD
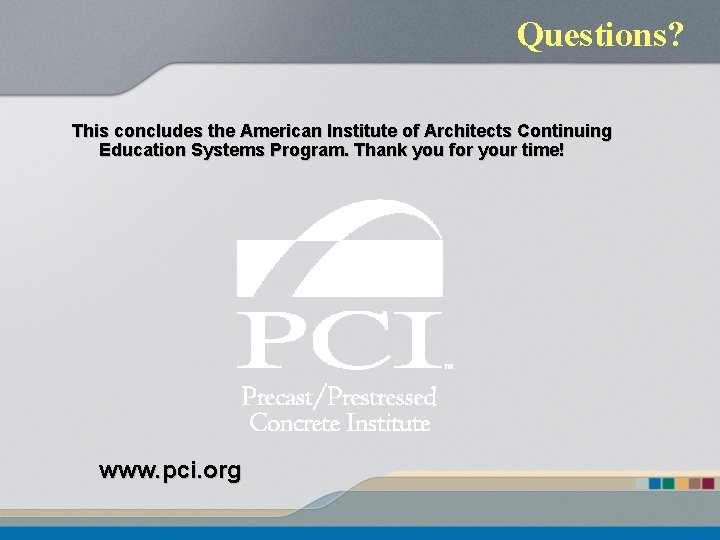
Questions? This concludes the American Institute of Architects Continuing Education Systems Program. Thank you for your time! www. pci. org
How are the whale flipper and the human arm different
Food design process
Application of distillation in food processing
Industrial applications of robots
Xml constraints
Comparison of ideal and practical op-amp
Process specifications and structured decisions
Opponent process theory vs trichromatic theory
Drawing up test specifications
Mla format specifications
Tdot standard specifications
Apwa standards
What is domain requirements in software engineering
Software requirements definition
Form-based specifications
Application specifications
Ball can seam specs
Table of specifications example
Nao robot specifications
Boxn wagon dimensions
Geofoam tiered seating
Tdot standard specifications
Steel roof truss drawing
Is engineers designers
Direct motion specification in computer graphics
Spot welding symbol
Jayco sterling 2010 brochure
Use case specifications
Iot platforms design methodology
Roller chain specifications
Matt looney
Typical primary coil resistance specifications
Edifact specifications
Process specification diagram
A goal of producing process specifications is to:
Amba specification
Raw material quality control
Tdot standard specifications
Implies objective listing of the job title tasks duties
Enni ethernet
Chlorine tank car
Medical equipment technical specifications
Parts of table of specification
Vce english study design 2023
Car specifications explained
Inspire data specification
Inspire data specifications
Ispme
Unit step response
Spring pageable
Scratch-dig
Atlantic systems guild
Reflected ceiling plan specifications
Pdo specifications
Fluke 789 simulate
Raspberry pi 3 model b specifications pdf
Bloom's taxonomy table of specification
A goal of producing process specifications is to:
Structured english in system analysis and design
Annual investment income report
International guidelines for industrial parks
Design of seismic-resistant steel building structures
Design of seismic-resistant steel building structures
Advanced design of steel structures notes
Tension members
Organizational design traditional structures
Evaluation orders for sdd's in compiler design
Applications of sdd in compiler design
Industrial design ipr
Industrial design organization
Art deco industrial design
Industrial ventilation system design
Industrial exhaust hood design
Industrial technology design
Industrial design
Local exhaust ventilation definition
"mw industrial design"
What is input output design
Networks and graphs: circuits, paths, and graph structures
Application of heat transfer
Fuzzy sets and fuzzy logic theory and applications
A decorative design or pattern
Structural and decorative design
Split range
User interface design in system analysis and design
Bad designs examples
Dialogue design in system analysis and design
While loops and if-else structures
Virtualization
Hardware and control structures
Homologous or analogous
Nims mac group
Natural frame structures
Structure and mechanism
How do coordination structures help organize
Unit 15 plant structures and taxonomy
Advantages of statically determinate structures
Data structures and algorithms iit bombay
How to draw bohr model of atom
Parallel structure rhetorical device
Statically determinate and indeterminate structures
Designing pay levels mix and pay structures