PLANT DESIGN PROJECT DESIGN OF STYRENE PRODUCTION PLANT
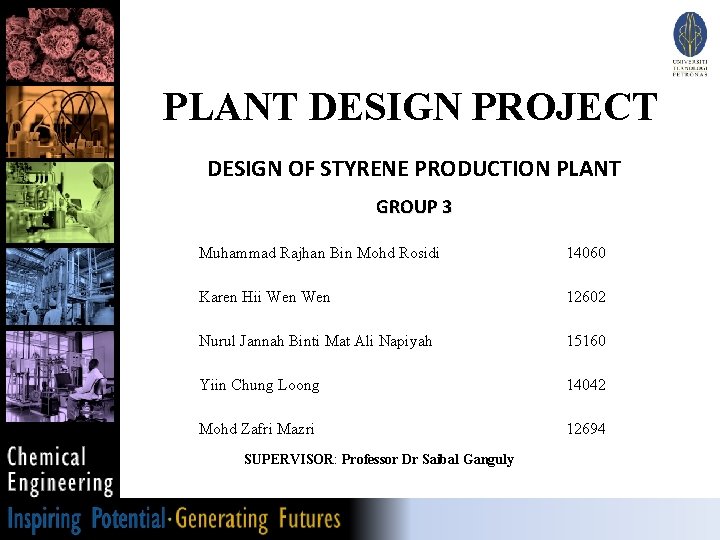
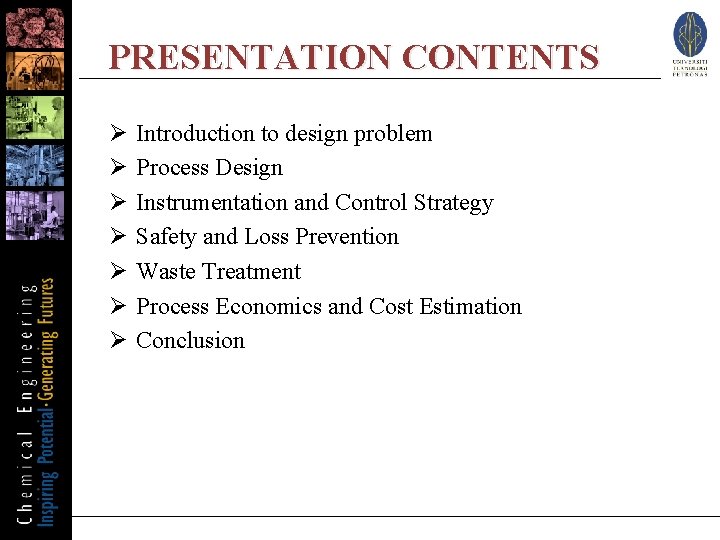
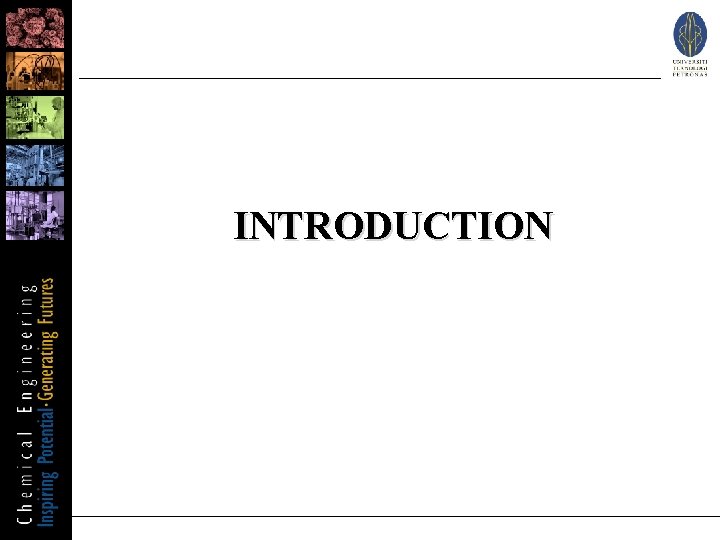
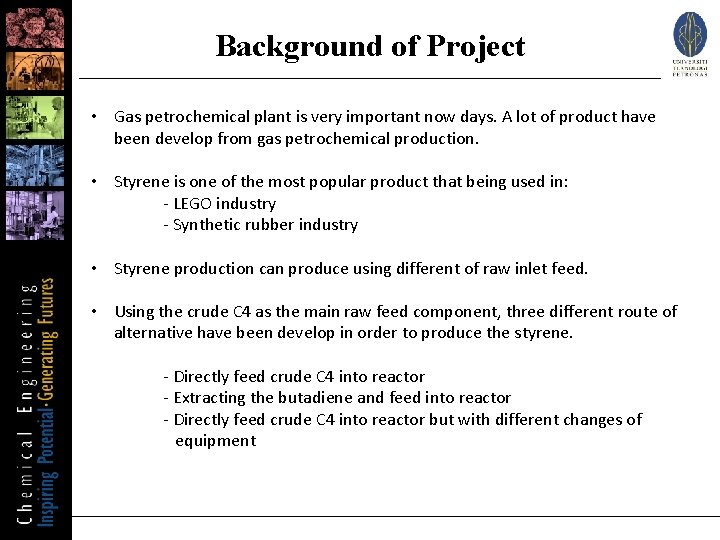
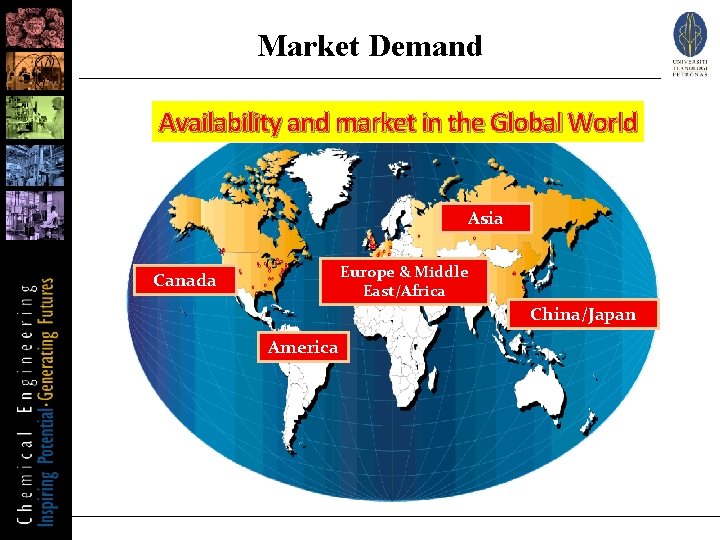
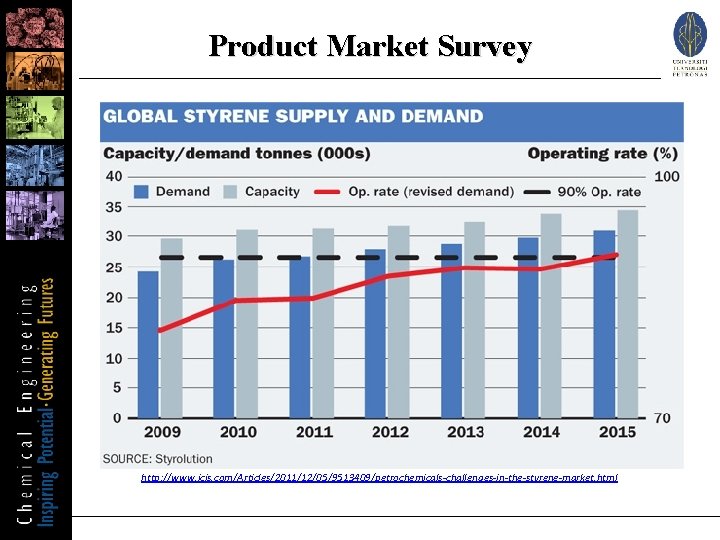
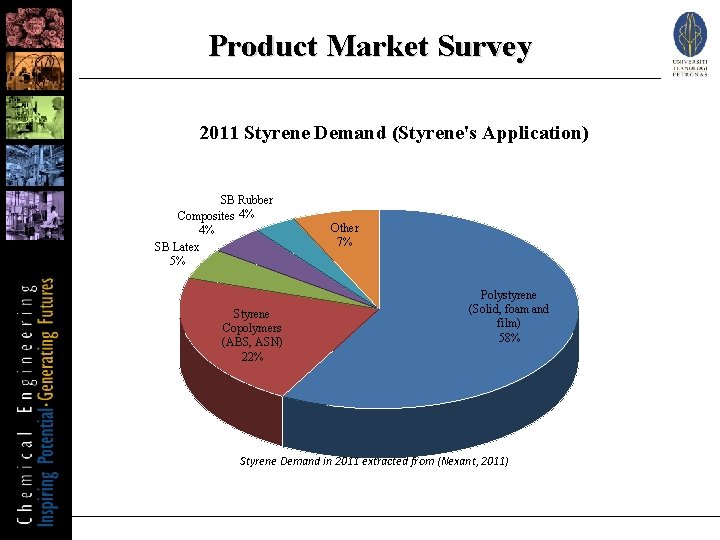
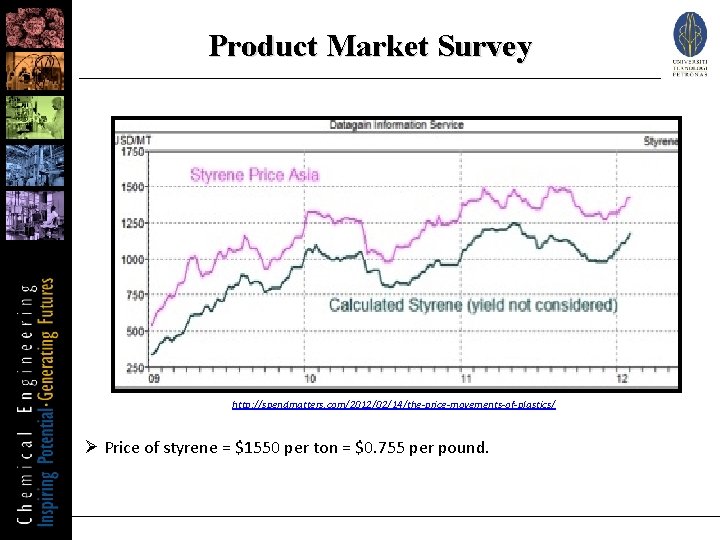
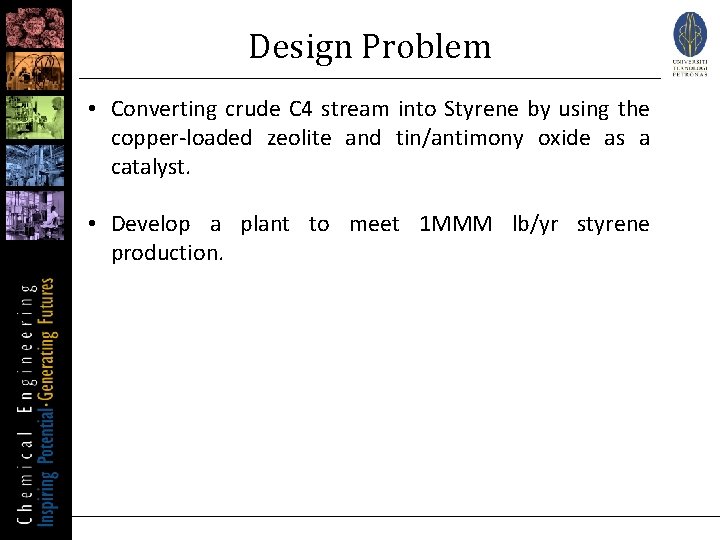
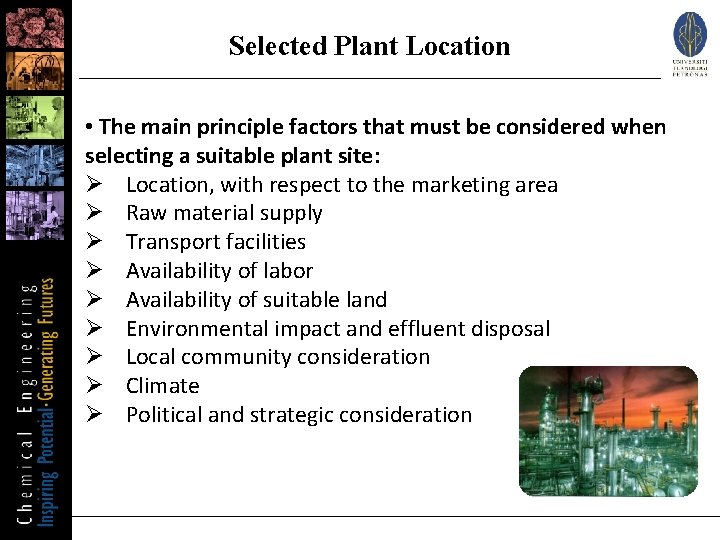
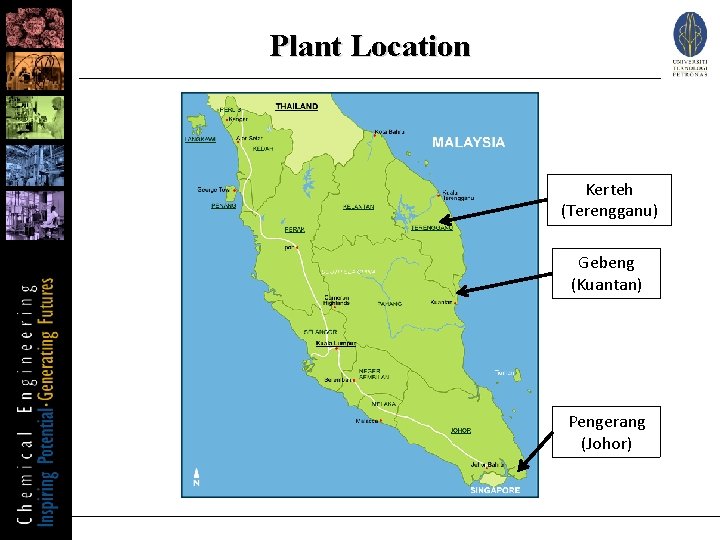
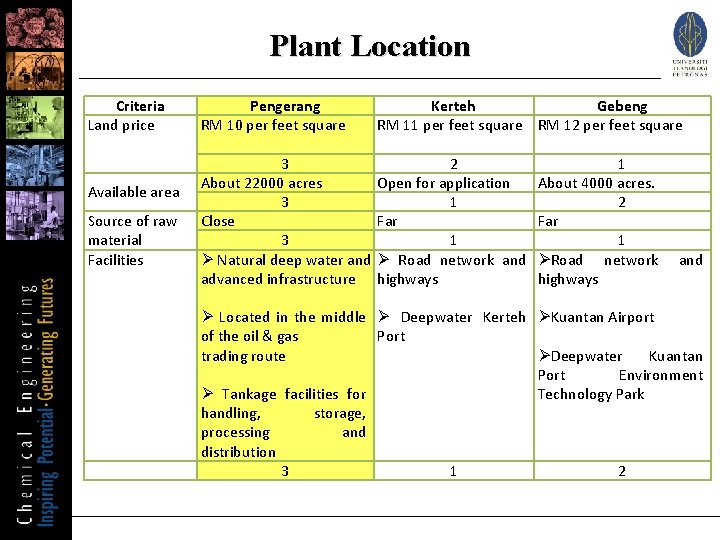
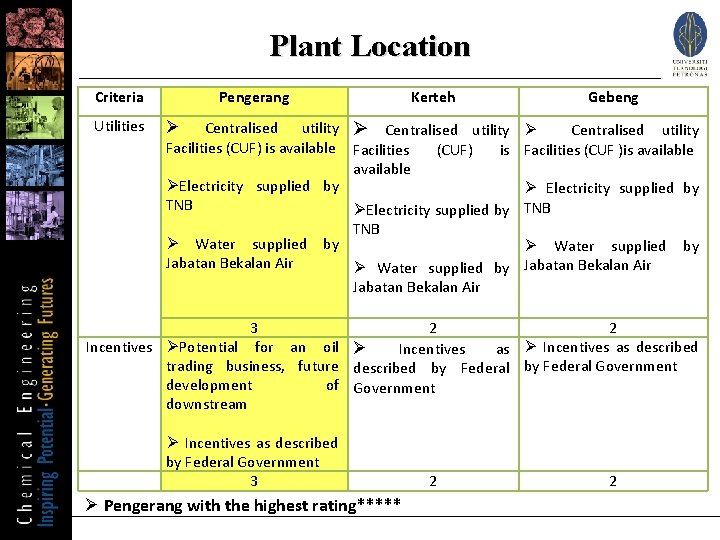
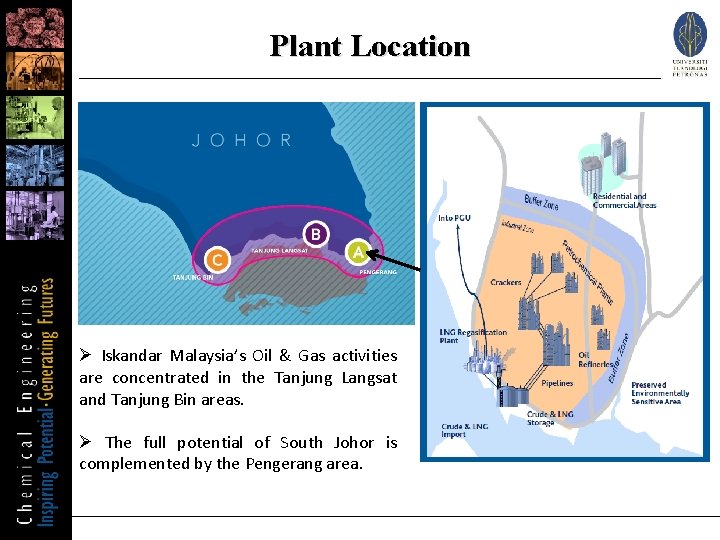
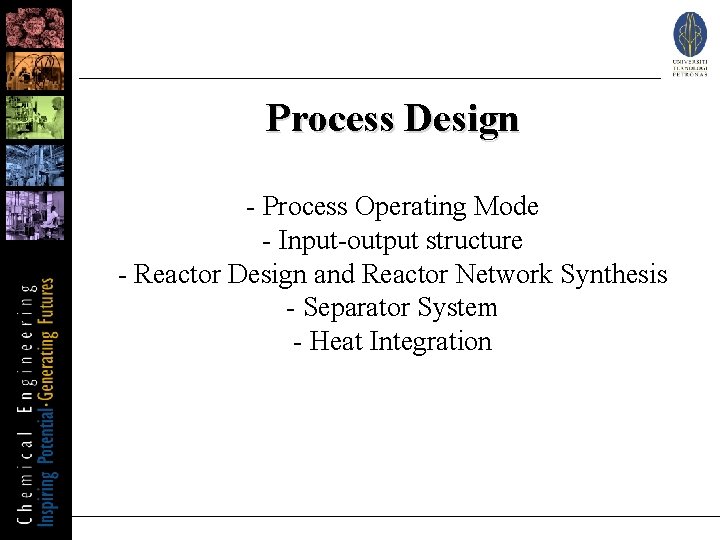
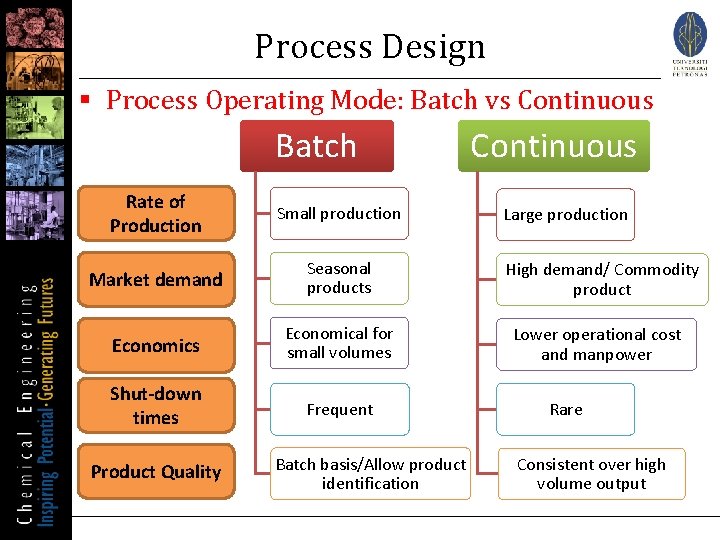
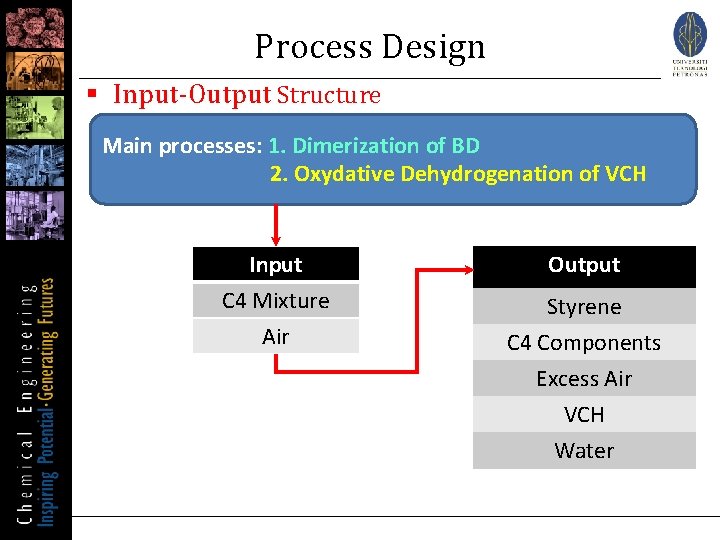
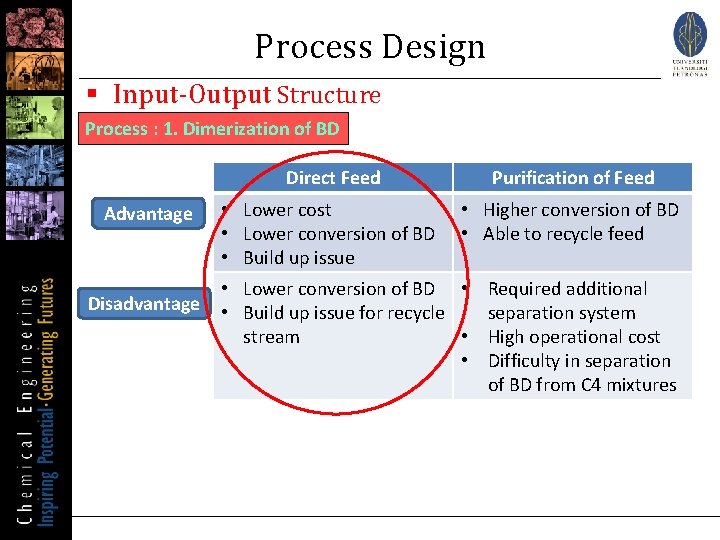
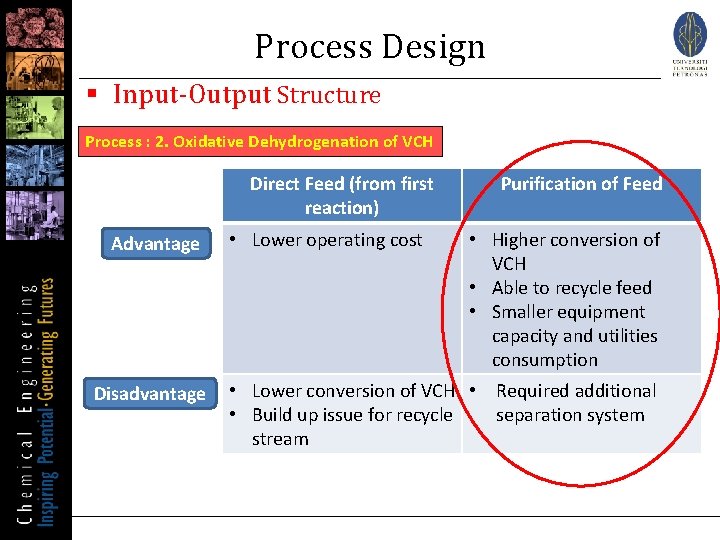
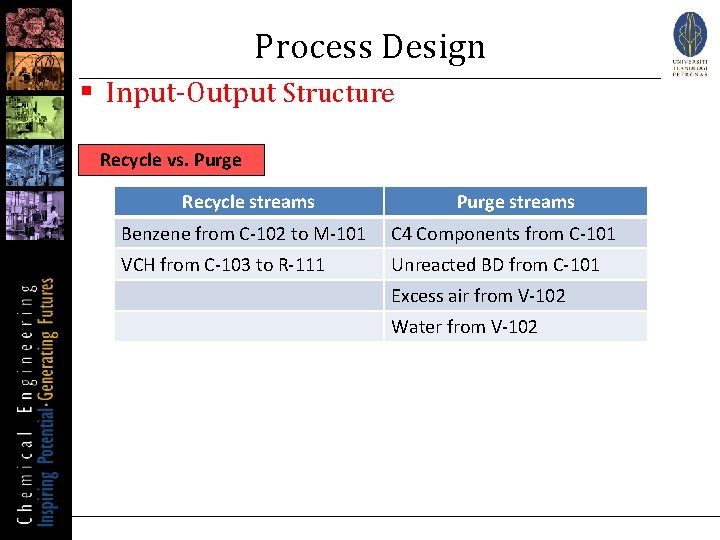
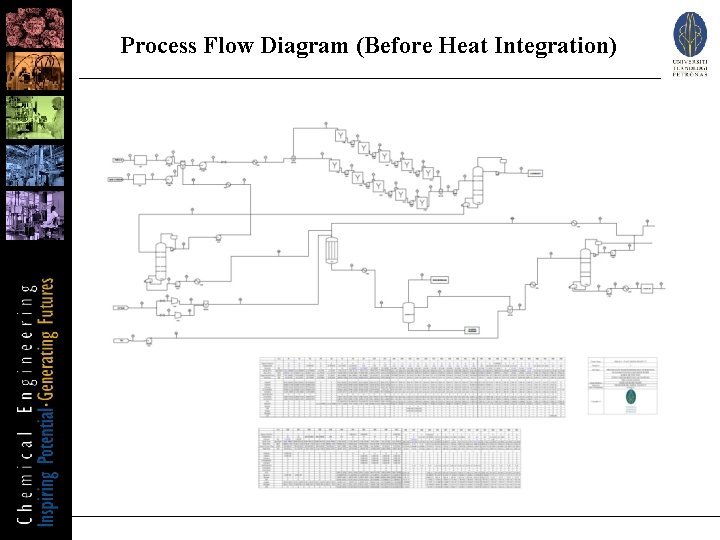

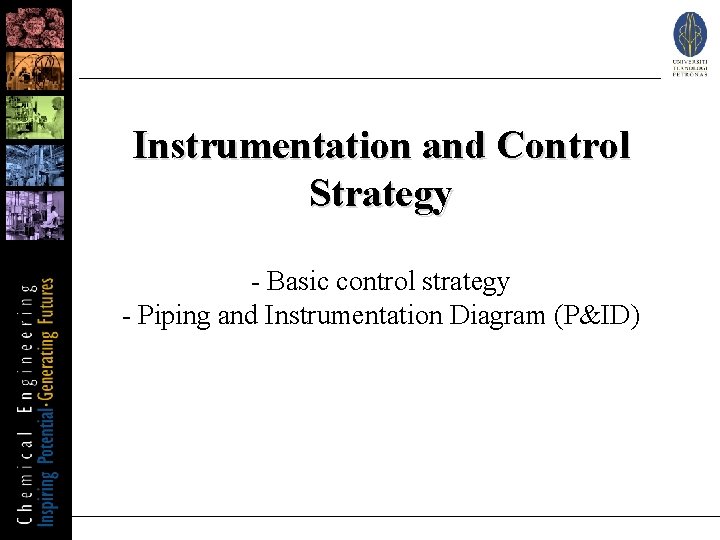
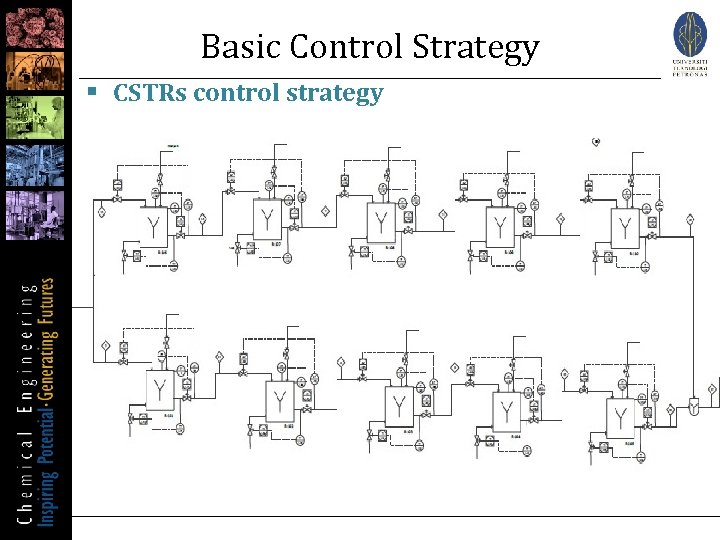
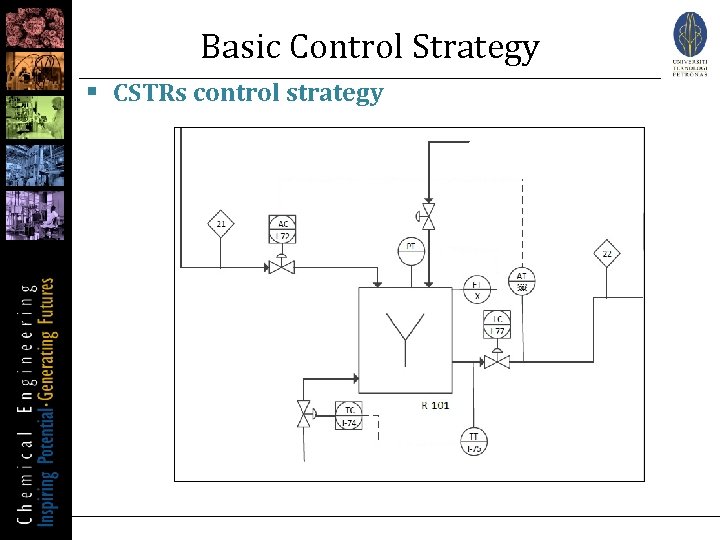
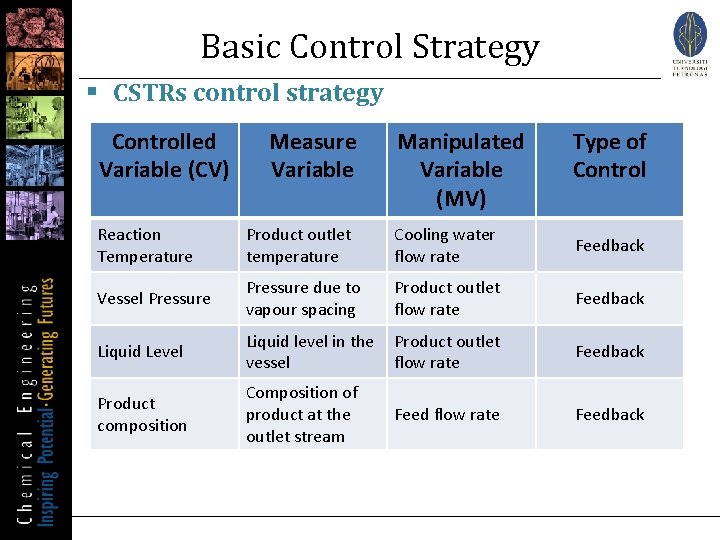
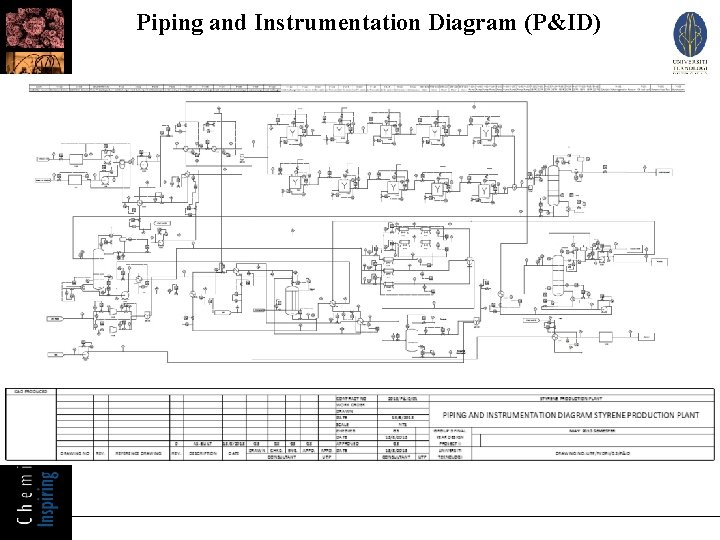
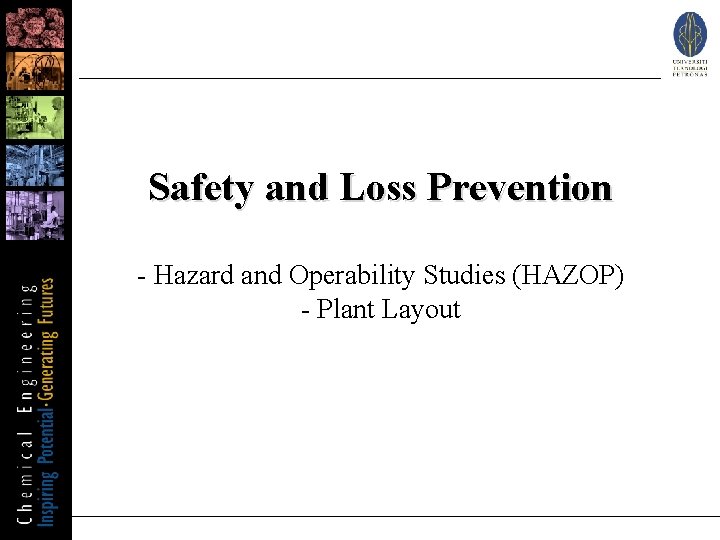
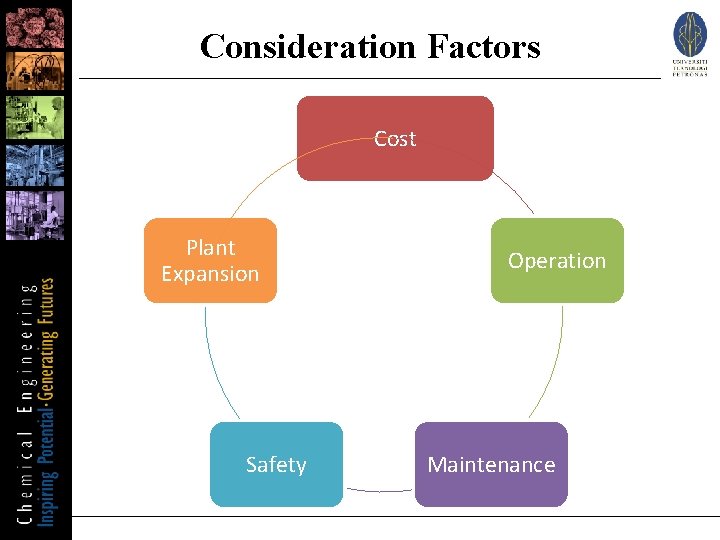
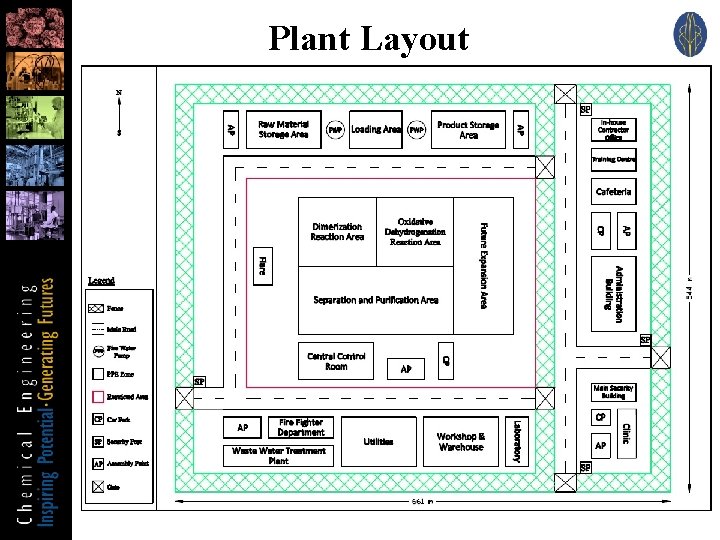
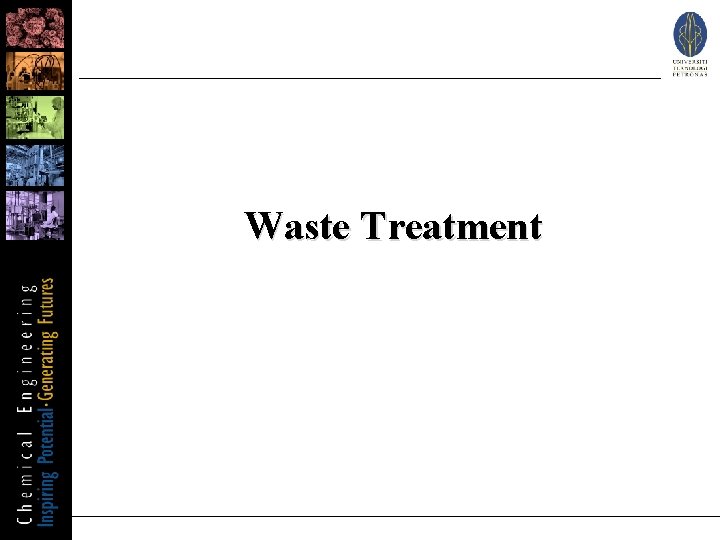
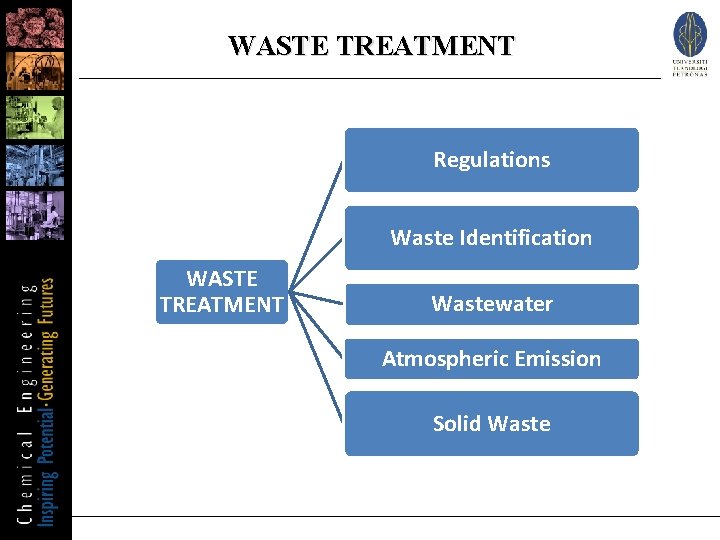
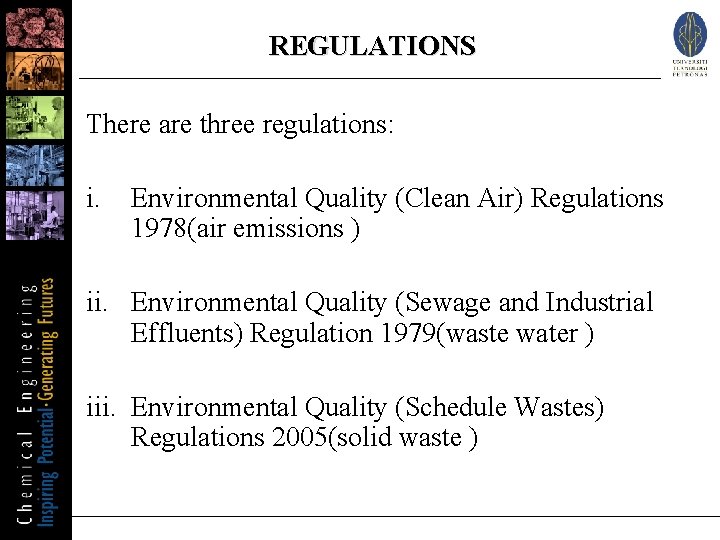
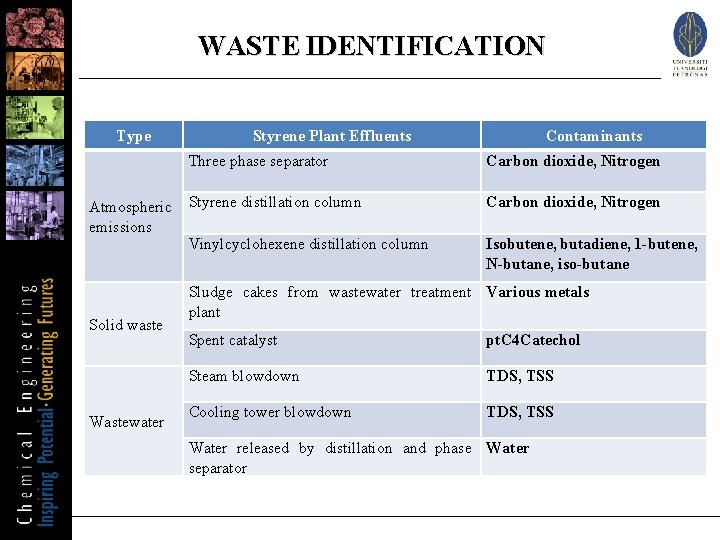
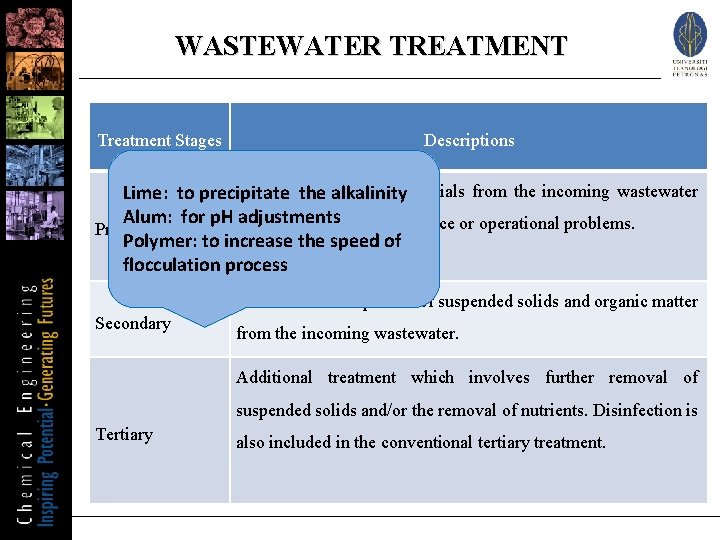

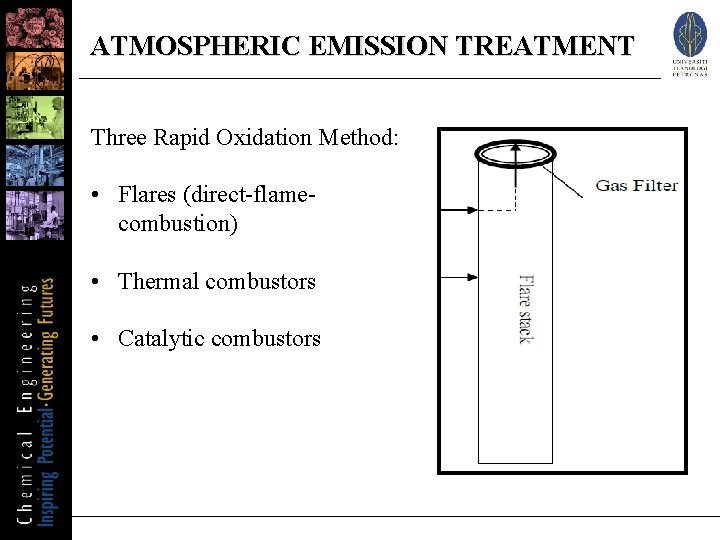
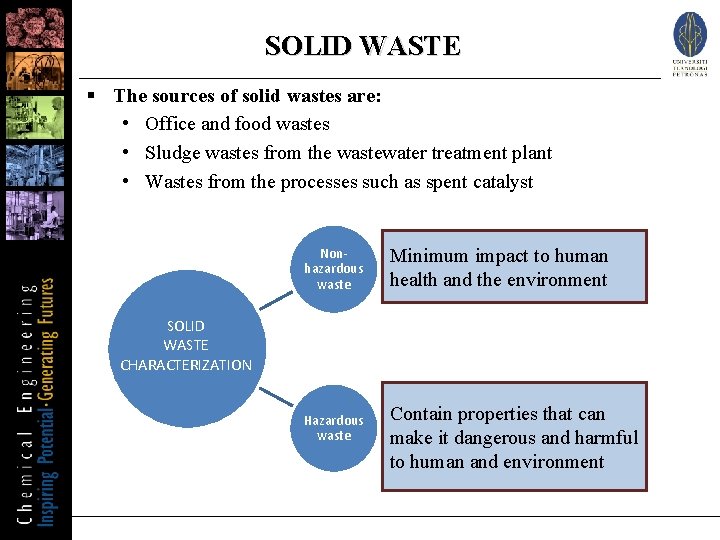
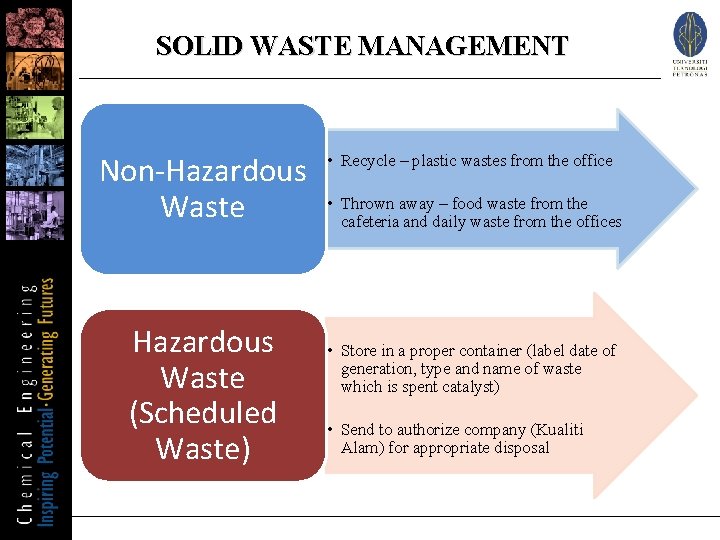
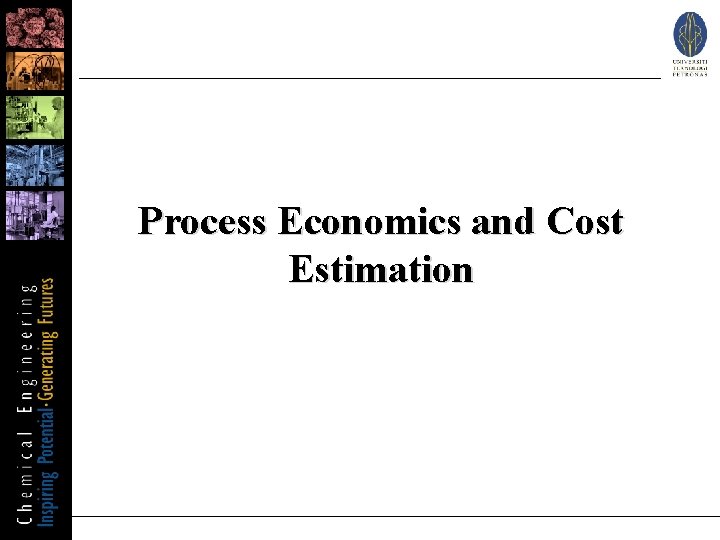
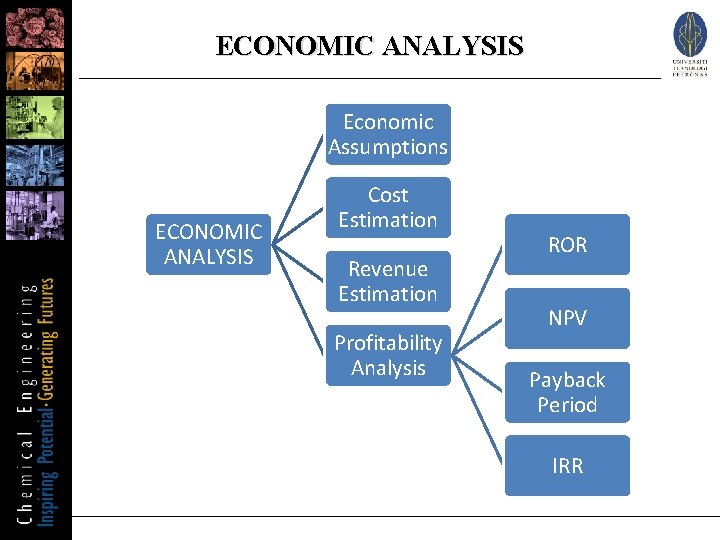
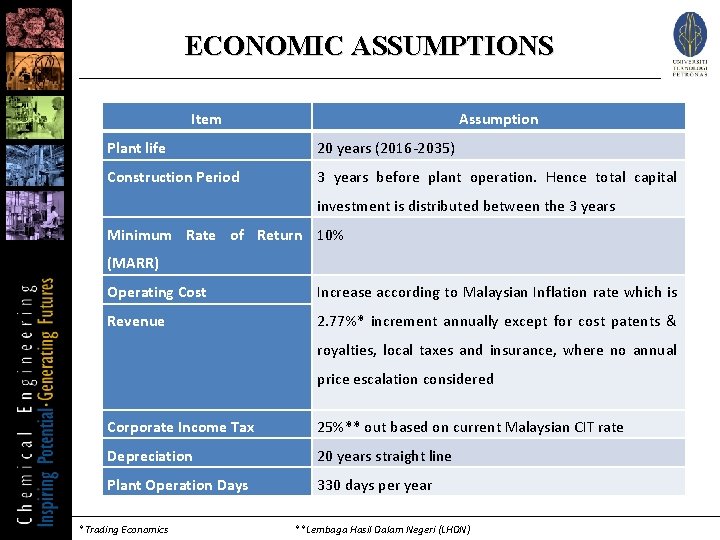
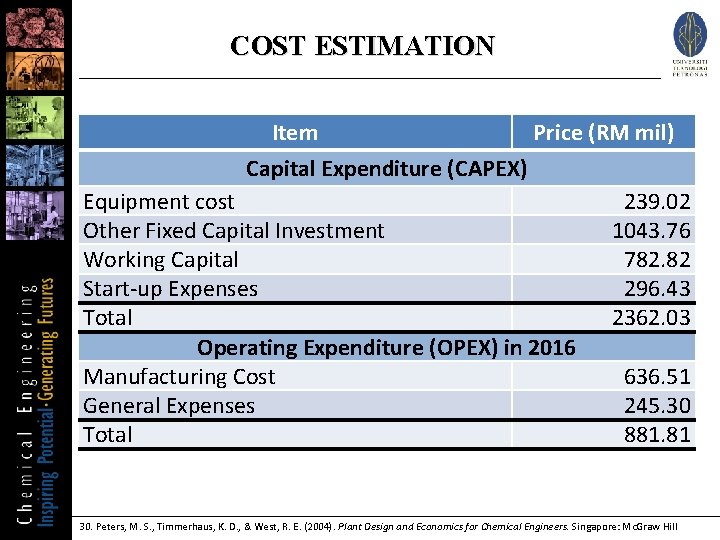
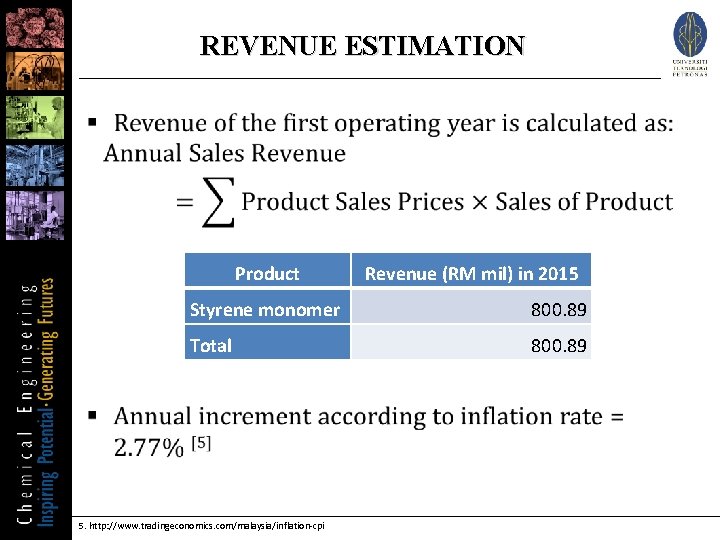
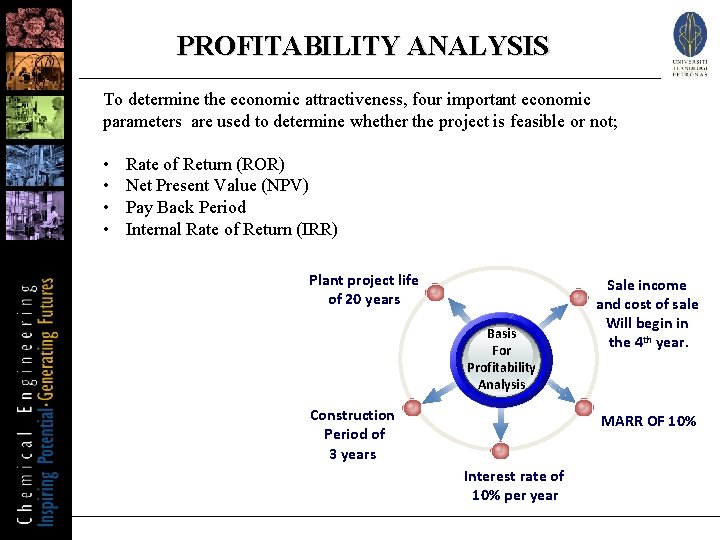
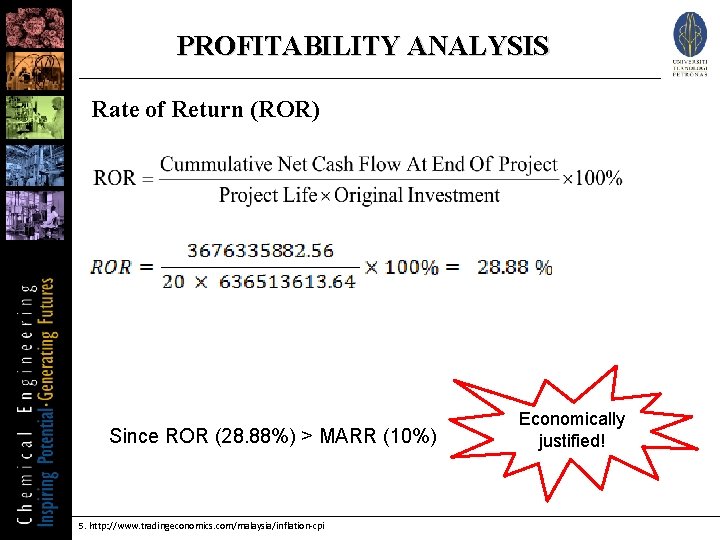
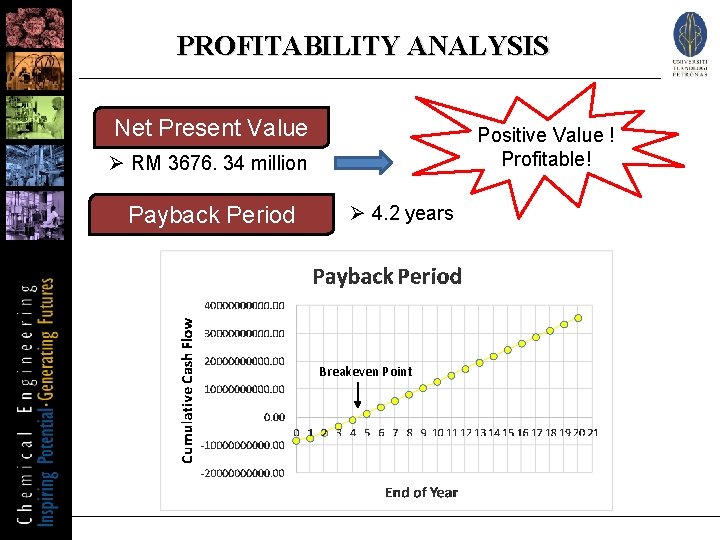
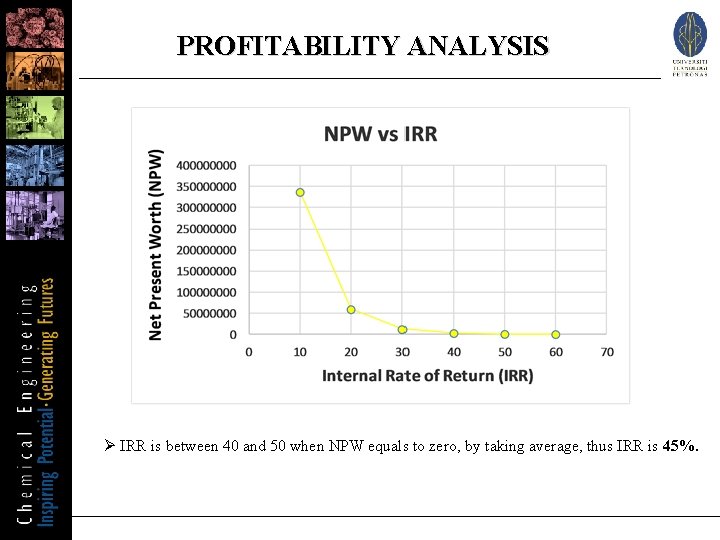
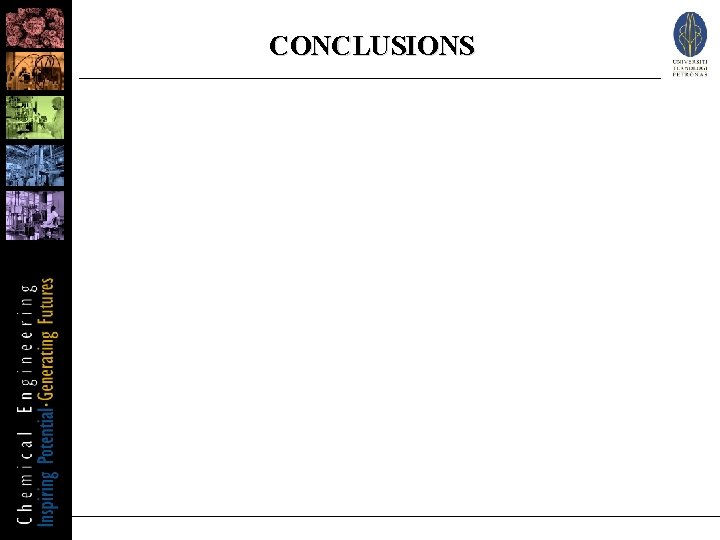
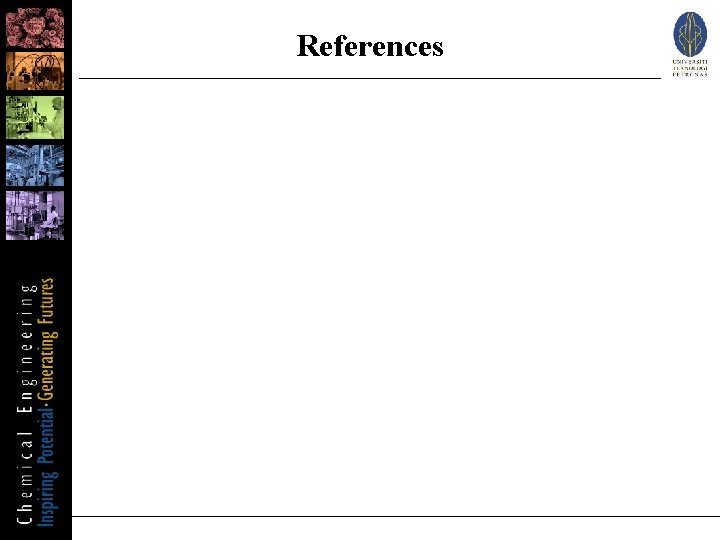
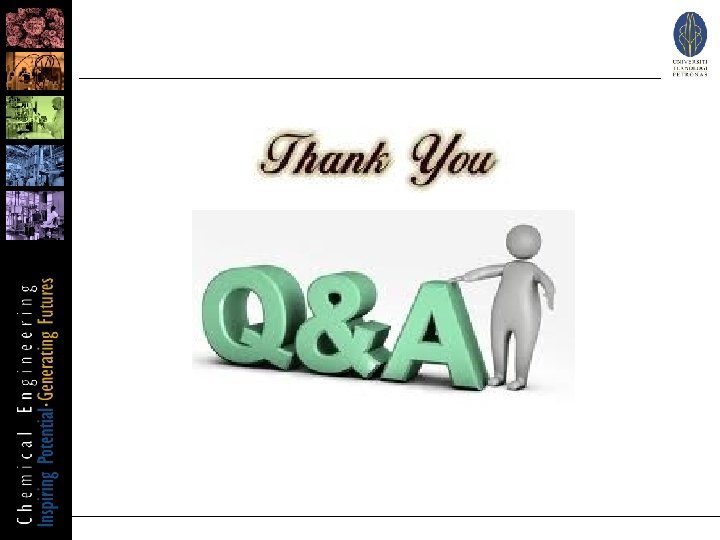
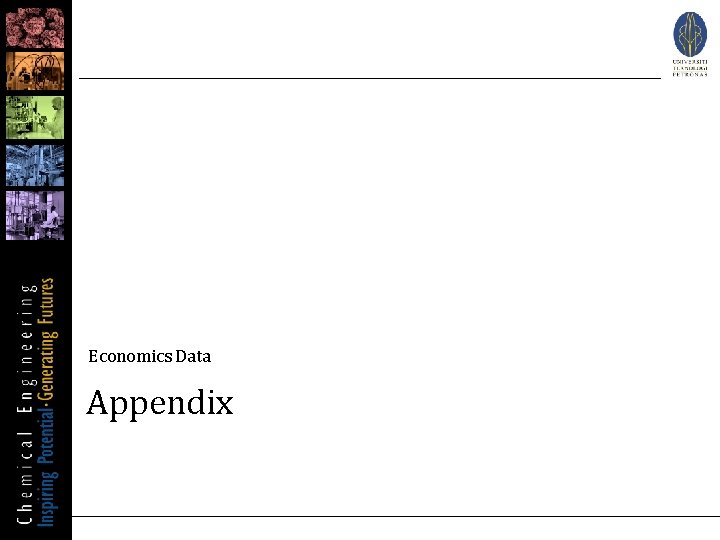
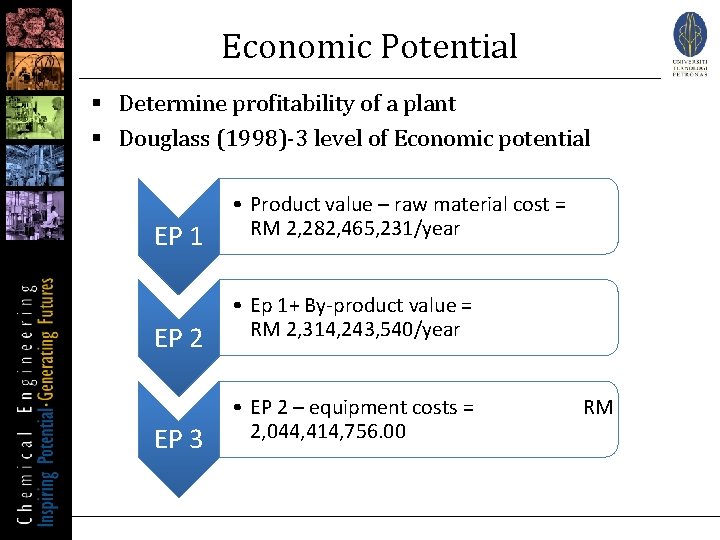
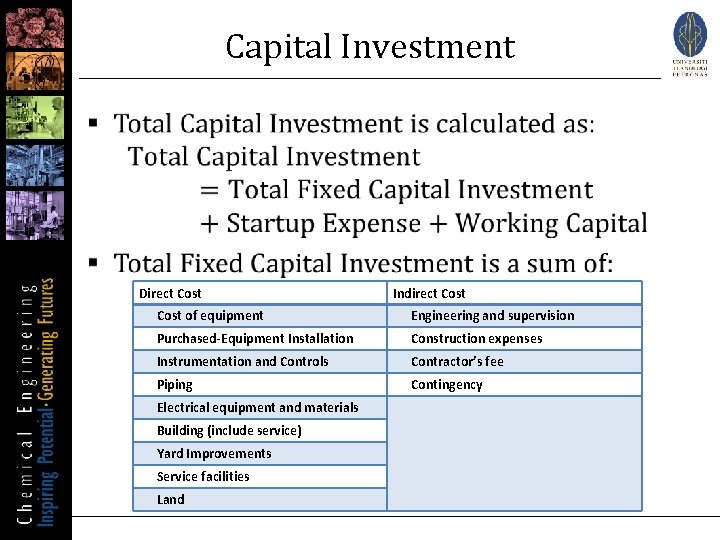
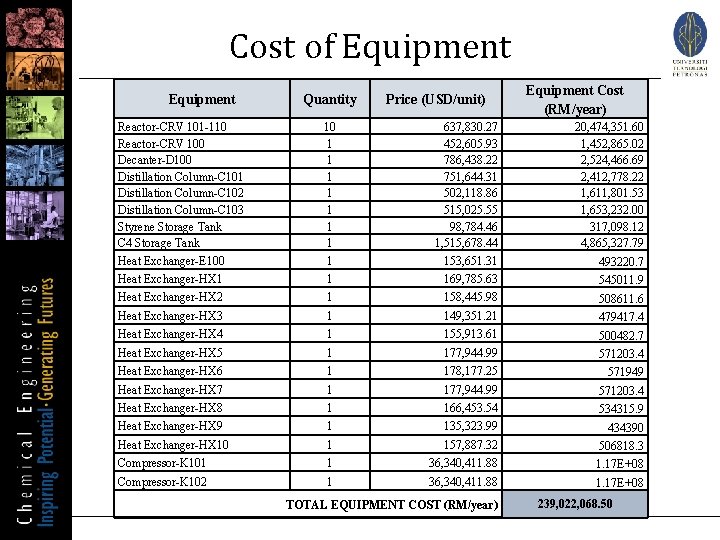
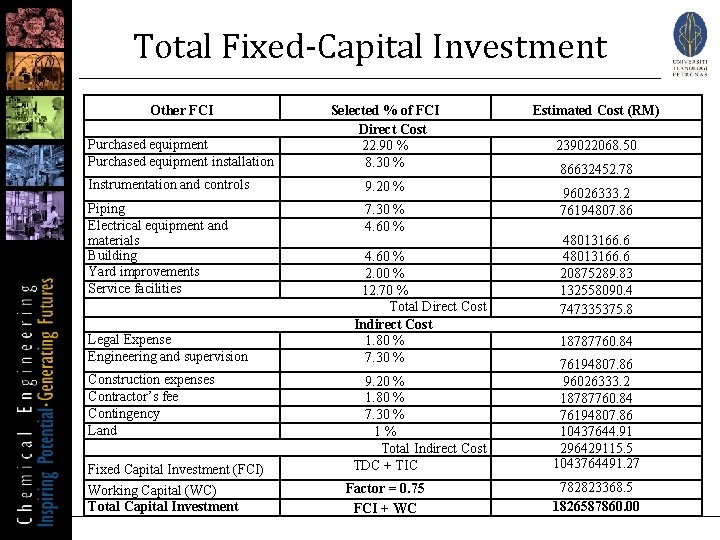
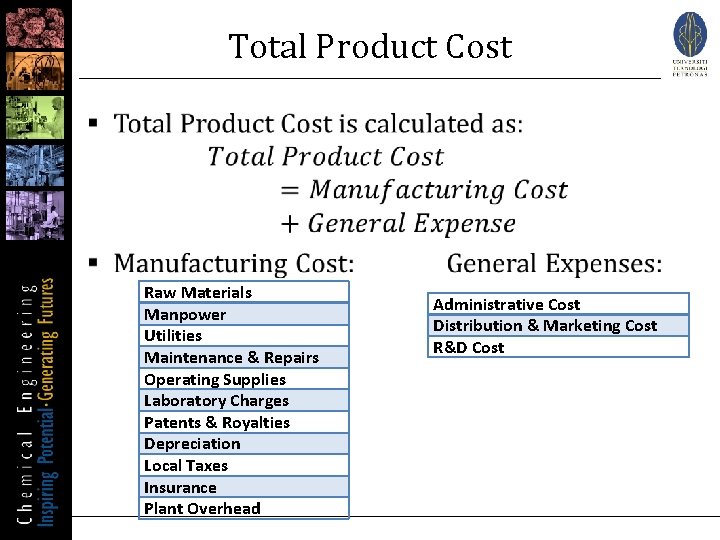
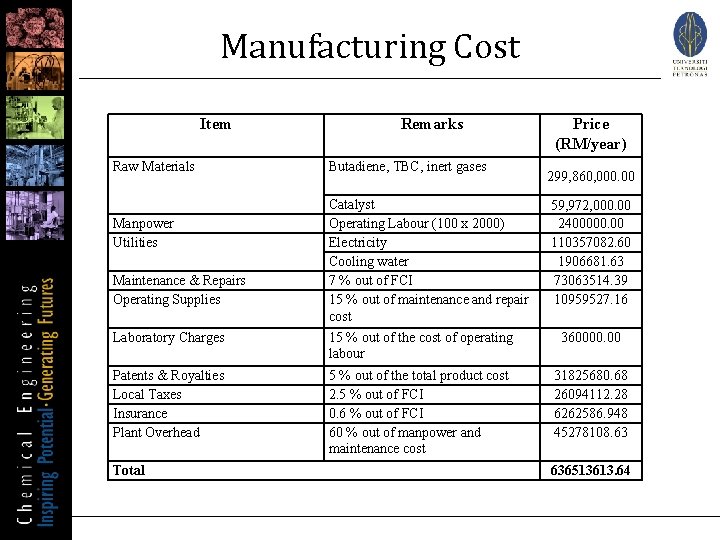
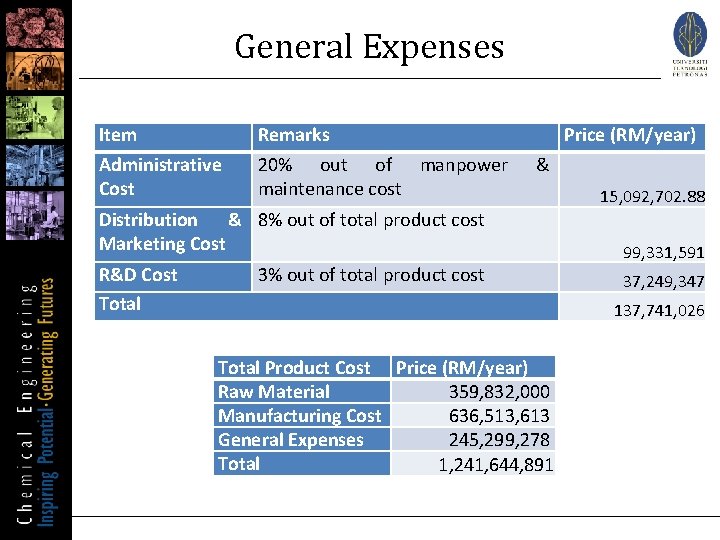
- Slides: 59
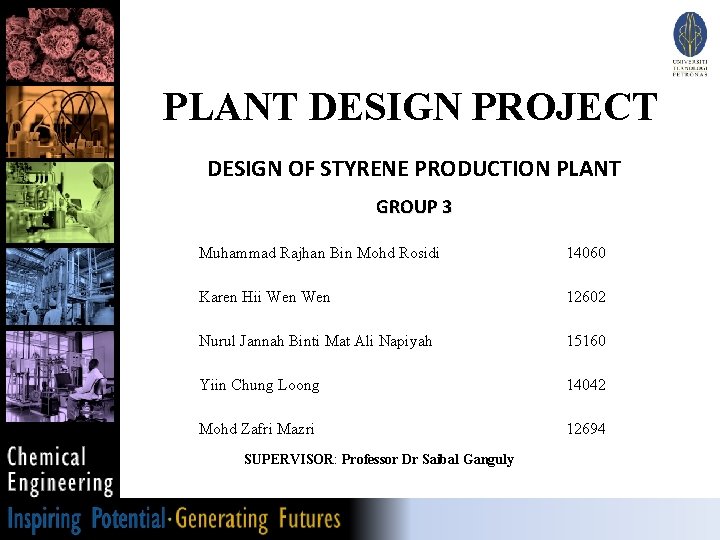
PLANT DESIGN PROJECT DESIGN OF STYRENE PRODUCTION PLANT GROUP 3 Muhammad Rajhan Bin Mohd Rosidi 14060 Karen Hii Wen 12602 Nurul Jannah Binti Mat Ali Napiyah 15160 Yiin Chung Loong 14042 Mohd Zafri Mazri 12694 SUPERVISOR: Professor Dr Saibal Ganguly
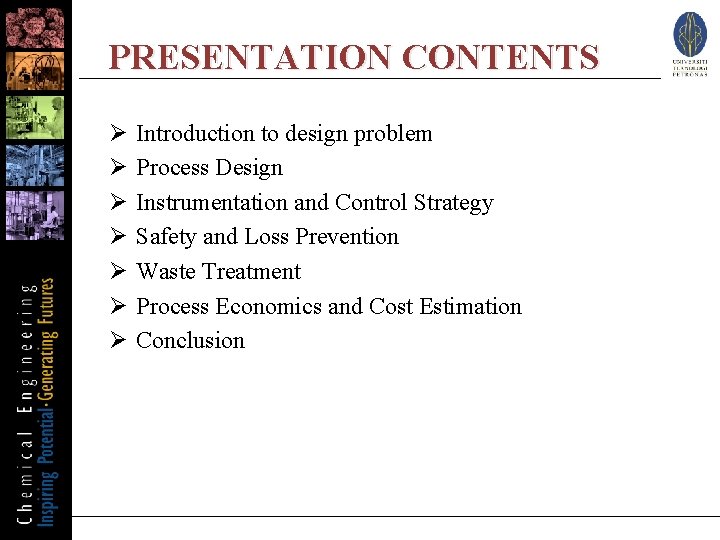
PRESENTATION CONTENTS Ø Ø Ø Ø Introduction to design problem Process Design Instrumentation and Control Strategy Safety and Loss Prevention Waste Treatment Process Economics and Cost Estimation Conclusion
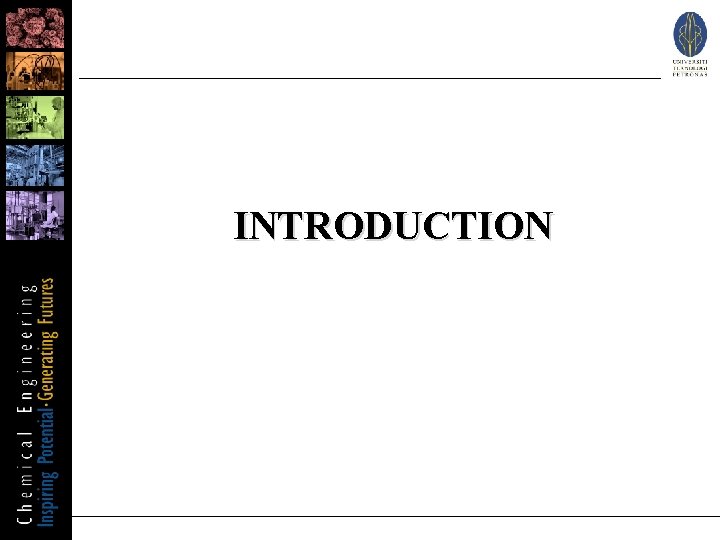
INTRODUCTION
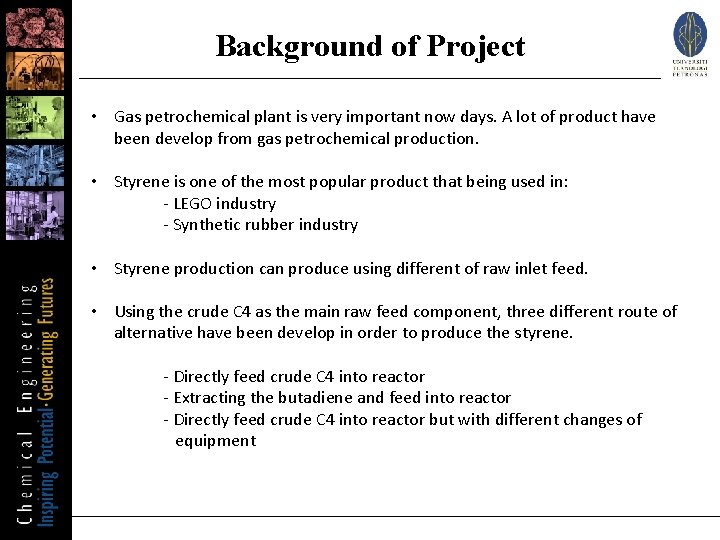
Background of Project • Gas petrochemical plant is very important now days. A lot of product have been develop from gas petrochemical production. • Styrene is one of the most popular product that being used in: - LEGO industry - Synthetic rubber industry • Styrene production can produce using different of raw inlet feed. • Using the crude C 4 as the main raw feed component, three different route of alternative have been develop in order to produce the styrene. - Directly feed crude C 4 into reactor - Extracting the butadiene and feed into reactor - Directly feed crude C 4 into reactor but with different changes of equipment
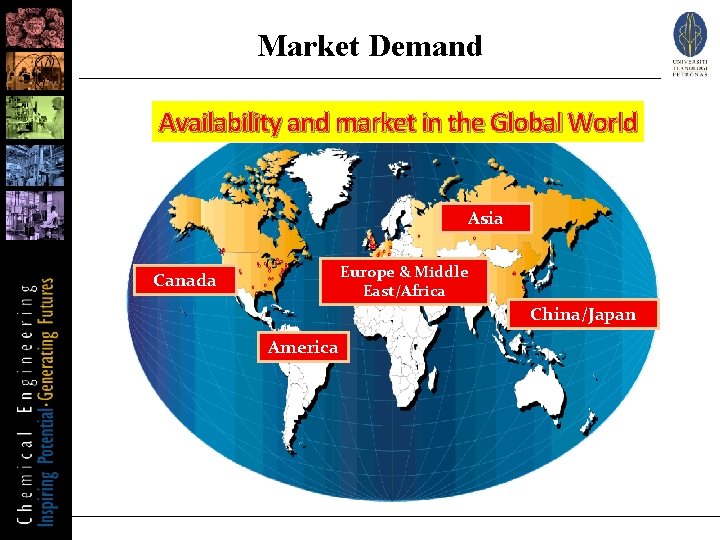
Market Demand Availability and market in the Global World Asia Europe & Middle East/Africa Canada China/Japan America
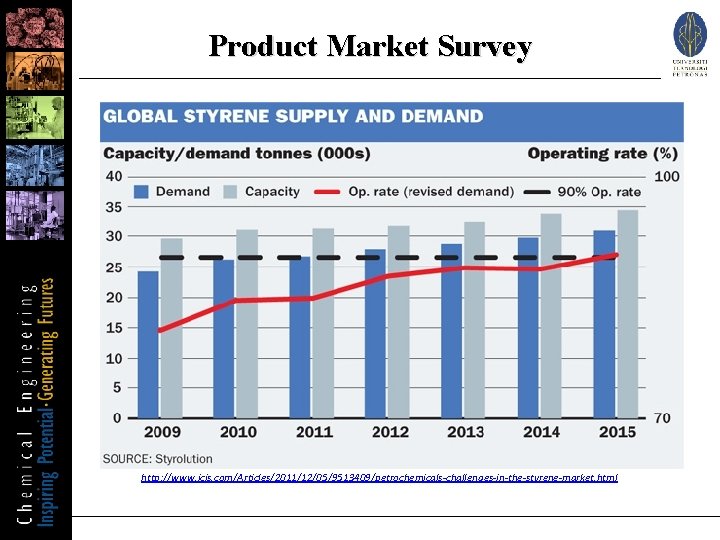
Product Market Survey http: //www. icis. com/Articles/2011/12/05/9513409/petrochemicals-challenges-in-the-styrene-market. html
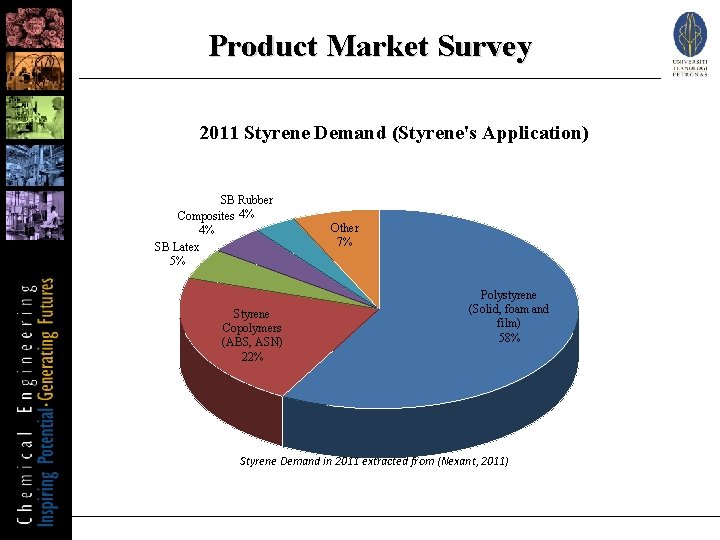
Product Market Survey 2011 Styrene Demand (Styrene's Application) SB Rubber Composites 4% 4% SB Latex 5% Styrene Copolymers (ABS, ASN) 22% Other 7% Polystyrene (Solid, foam and film) 58% Styrene Demand in 2011 extracted from (Nexant, 2011)
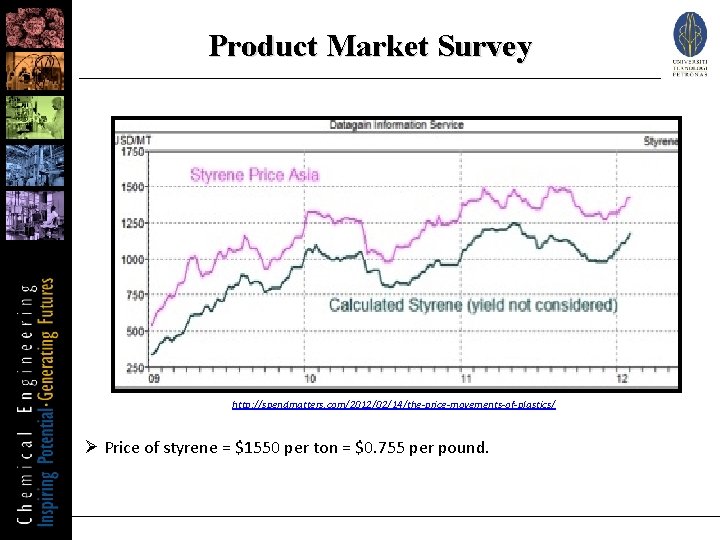
Product Market Survey http: //spendmatters. com/2012/02/14/the-price-movements-of-plastics/ Ø Price of styrene = $1550 per ton = $0. 755 per pound.
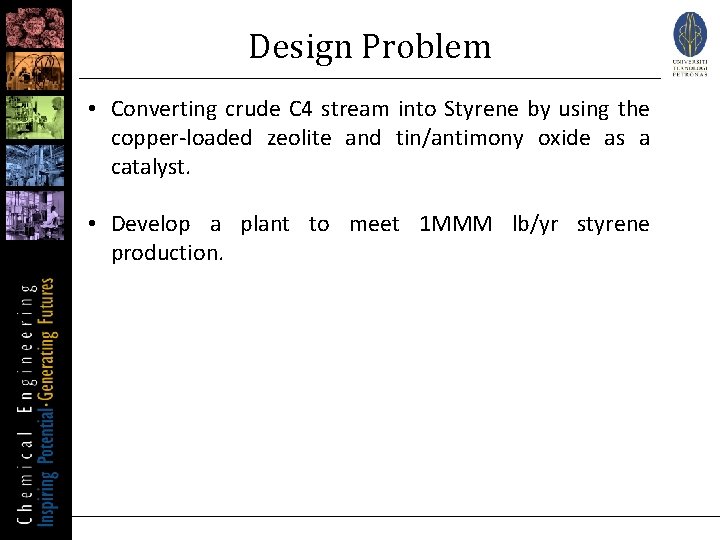
Design Problem • Converting crude C 4 stream into Styrene by using the copper-loaded zeolite and tin/antimony oxide as a catalyst. • Develop a plant to meet 1 MMM lb/yr styrene production.
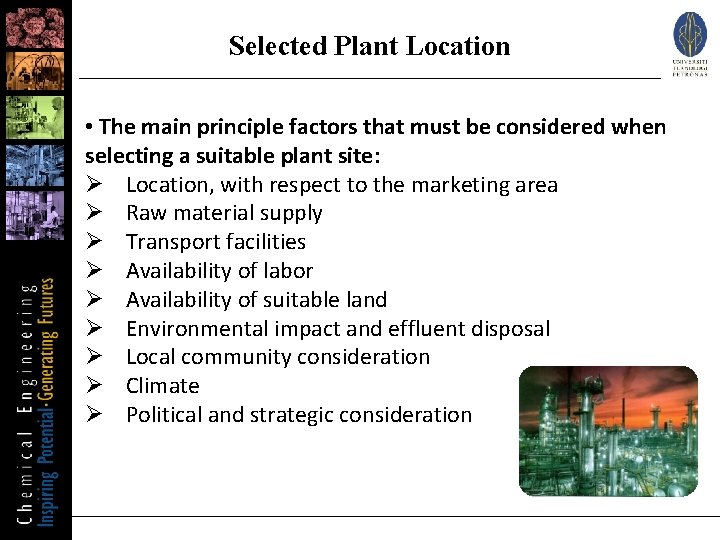
Selected Plant Location • The main principle factors that must be considered when selecting a suitable plant site: Ø Location, with respect to the marketing area Ø Raw material supply Ø Transport facilities Ø Availability of labor Ø Availability of suitable land Ø Environmental impact and effluent disposal Ø Local community consideration Ø Climate Ø Political and strategic consideration
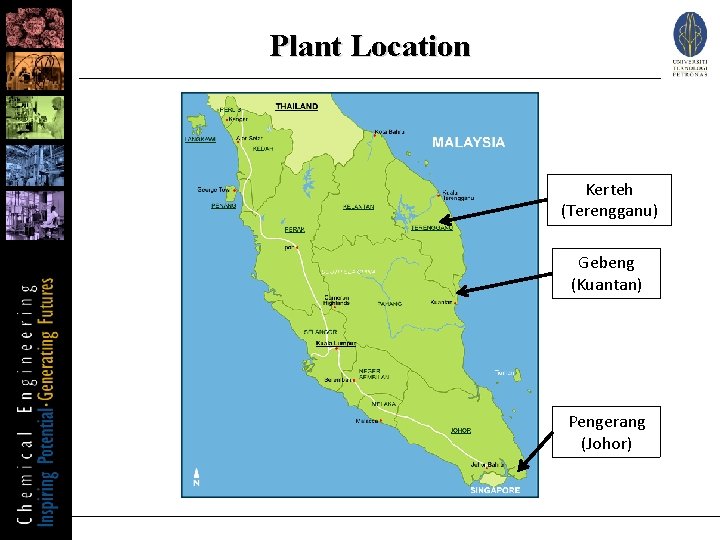
Plant Location Kerteh (Terengganu) Gebeng (Kuantan) Pengerang (Johor)
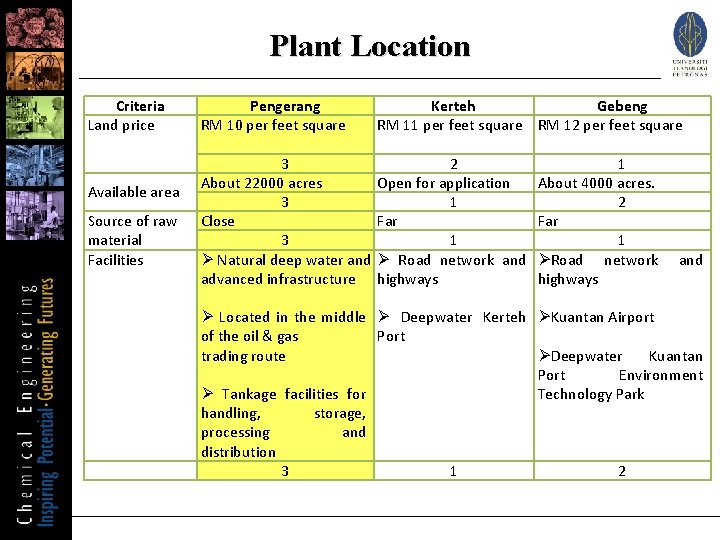
Plant Location Criteria Land price Available area Source of raw material Facilities Pengerang RM 10 per feet square Kerteh Gebeng RM 11 per feet square RM 12 per feet square 3 About 22000 acres 3 Close 3 Ø Natural deep water and advanced infrastructure 2 Open for application 1 Far 1 Ø Road network and highways 1 About 4000 acres. 2 Far 1 ØRoad network highways and Ø Located in the middle Ø Deepwater Kerteh ØKuantan Airport of the oil & gas Port trading route ØDeepwater Kuantan Port Environment Ø Tankage facilities for Technology Park handling, storage, processing and distribution 3 1 2
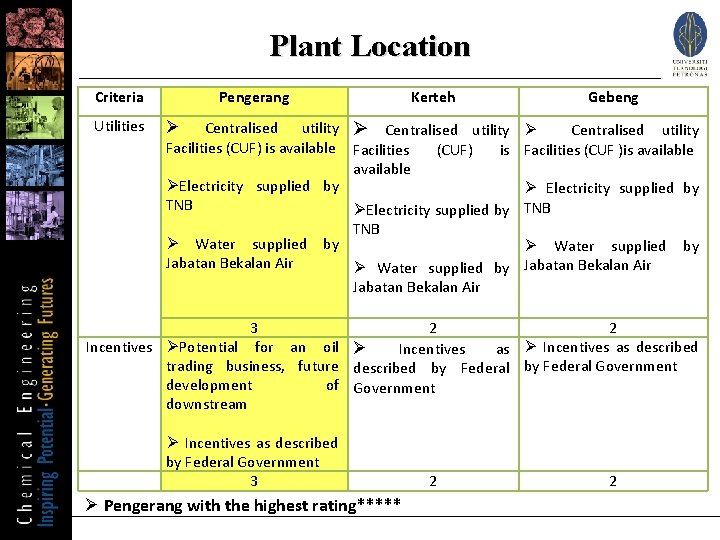
Plant Location Criteria Utilities Pengerang Kerteh Ø Centralised utility Facilities (CUF) is available ØElectricity supplied by TNB Ø Water supplied by Jabatan Bekalan Air Gebeng Ø Centralised utility Facilities (CUF )is available Ø Electricity supplied by TNB Ø Water supplied Jabatan Bekalan Air by 3 2 2 Incentives ØPotential for an oil Ø Incentives as described trading business, future described by Federal Government development of Government downstream Ø Incentives as described by Federal Government 3 Ø Pengerang with the highest rating***** 2 2
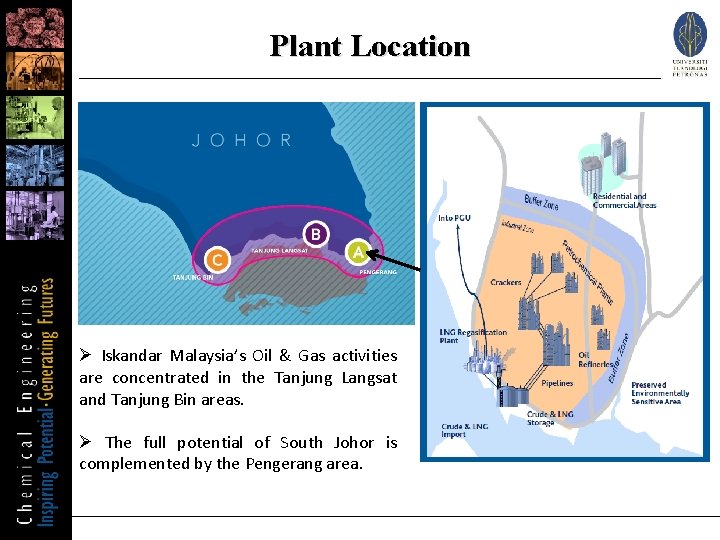
Plant Location Ø Iskandar Malaysia’s Oil & Gas activities are concentrated in the Tanjung Langsat and Tanjung Bin areas. Ø The full potential of South Johor is complemented by the Pengerang area.
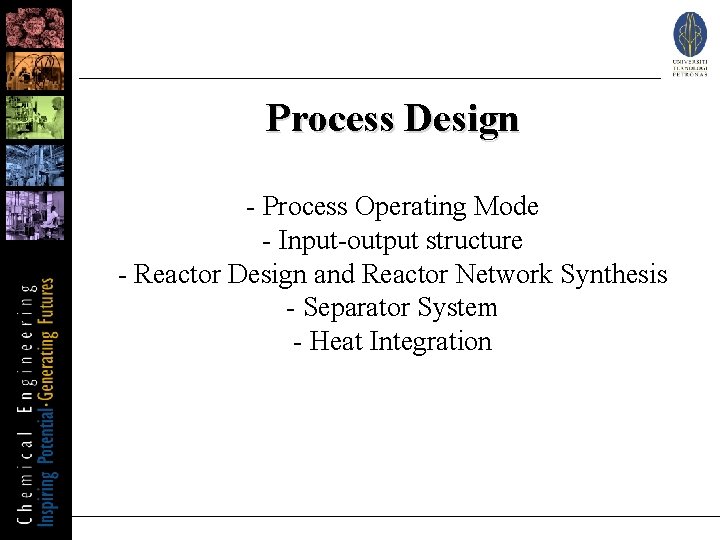
Process Design - Process Operating Mode - Input-output structure - Reactor Design and Reactor Network Synthesis - Separator System - Heat Integration
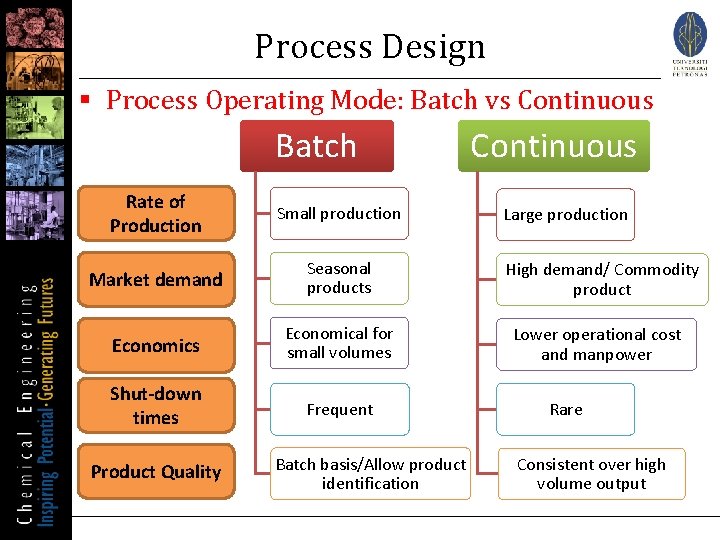
Process Design § Process Operating Mode: Batch vs Continuous Batch Rate of Production Small production Market demand Seasonal products Economical for small volumes Shut-down times Frequent Product Quality Batch basis/Allow product identification Continuous Large production High demand/ Commodity product Lower operational cost and manpower Rare Consistent over high volume output
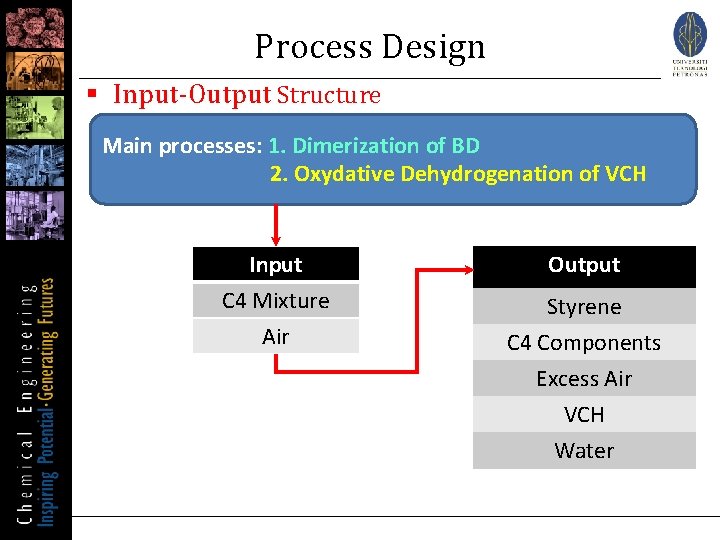
Process Design § Input-Output Structure Main processes: 1. Dimerization of BD 2. Oxydative Dehydrogenation of VCH Input C 4 Mixture Air Output Styrene C 4 Components Excess Air VCH Water
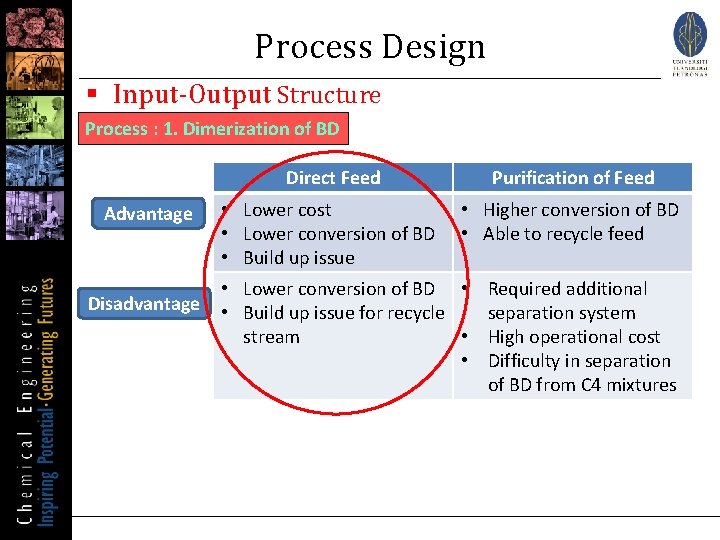
Process Design § Input-Output Structure Process : 1. Dimerization of BD Advantage Direct Feed Purification of Feed • Lower cost • Lower conversion of BD • Build up issue • Higher conversion of BD • Able to recycle feed • Lower conversion of BD • Required additional Disadvantage • Build up issue for recycle separation system stream • High operational cost • Difficulty in separation of BD from C 4 mixtures
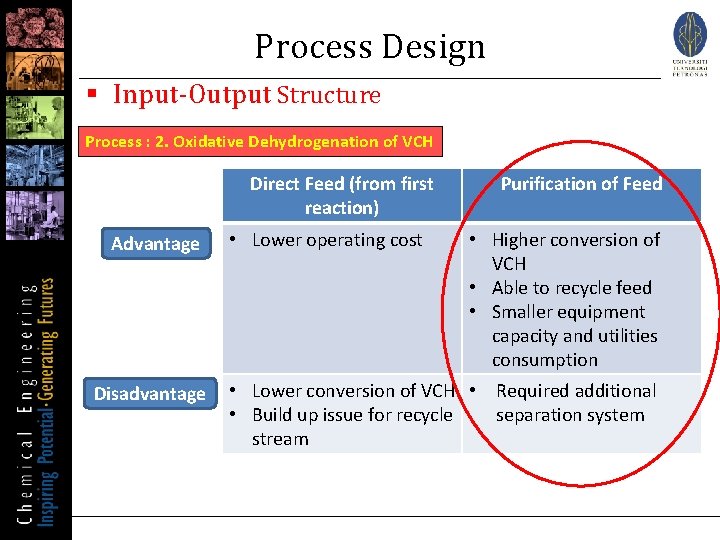
Process Design § Input-Output Structure Process : 2. Oxidative Dehydrogenation of VCH Direct Feed (from first reaction) Advantage Disadvantage • Lower operating cost Purification of Feed • Higher conversion of VCH • Able to recycle feed • Smaller equipment capacity and utilities consumption • Lower conversion of VCH • Required additional • Build up issue for recycle separation system stream
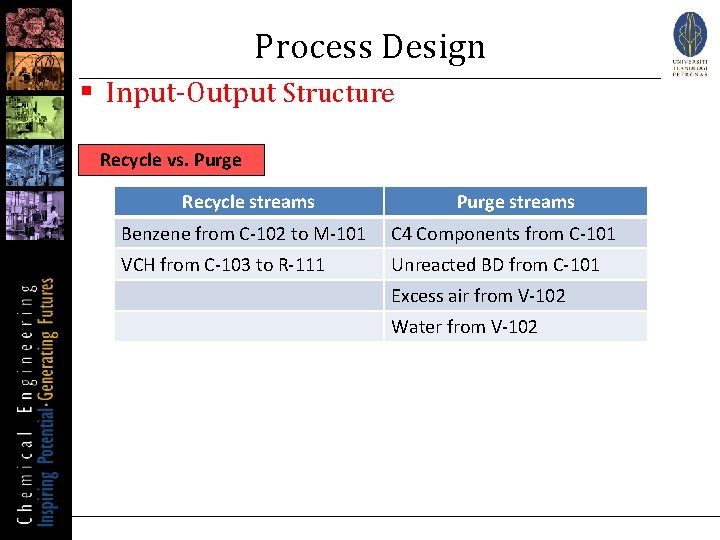
Process Design § Input-Output Structure Recycle vs. Purge Recycle streams Purge streams Benzene from C-102 to M-101 C 4 Components from C-101 VCH from C-103 to R-111 Unreacted BD from C-101 Excess air from V-102 Water from V-102
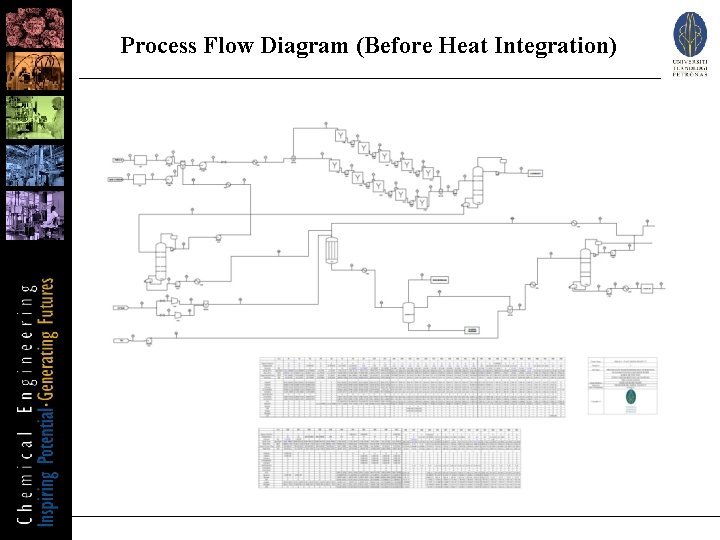
Process Flow Diagram (Before Heat Integration)

Process Flow Diagram (Before Heat Integration)
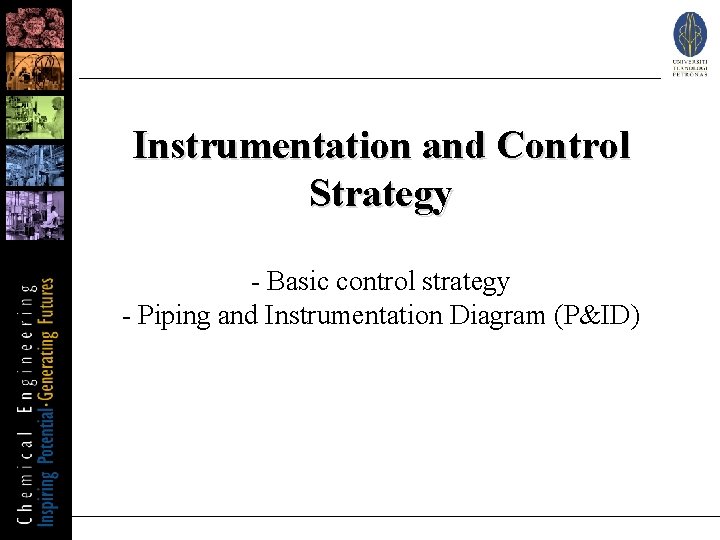
Instrumentation and Control Strategy - Basic control strategy - Piping and Instrumentation Diagram (P&ID)
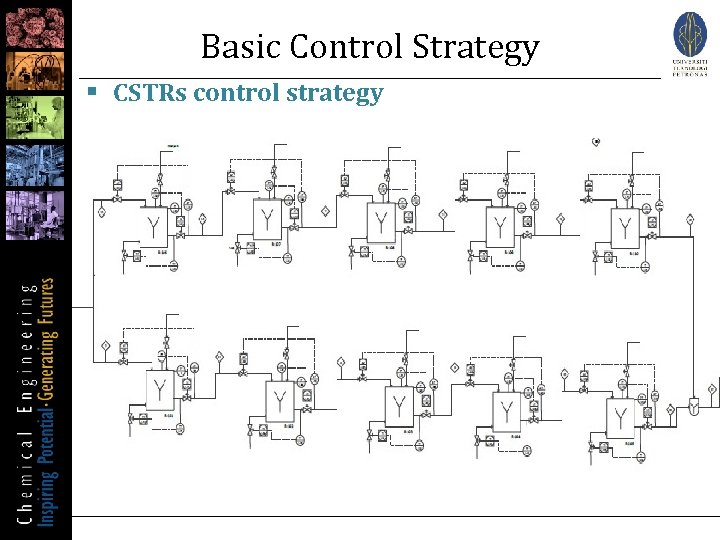
Basic Control Strategy § CSTRs control strategy
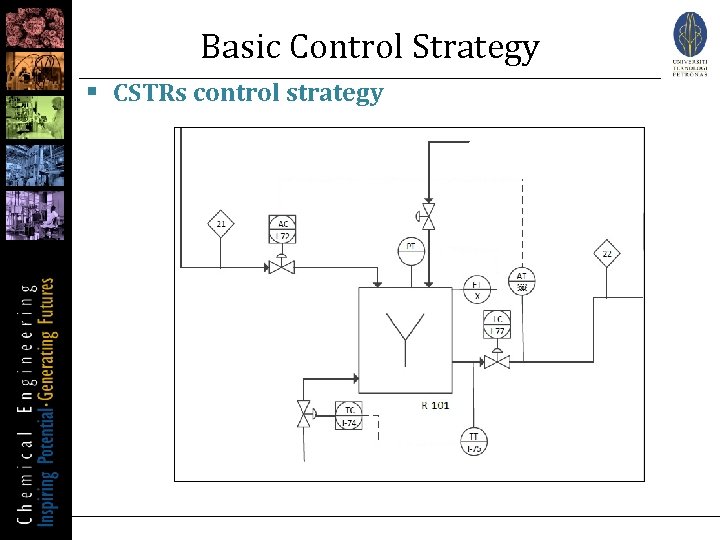
Basic Control Strategy § CSTRs control strategy
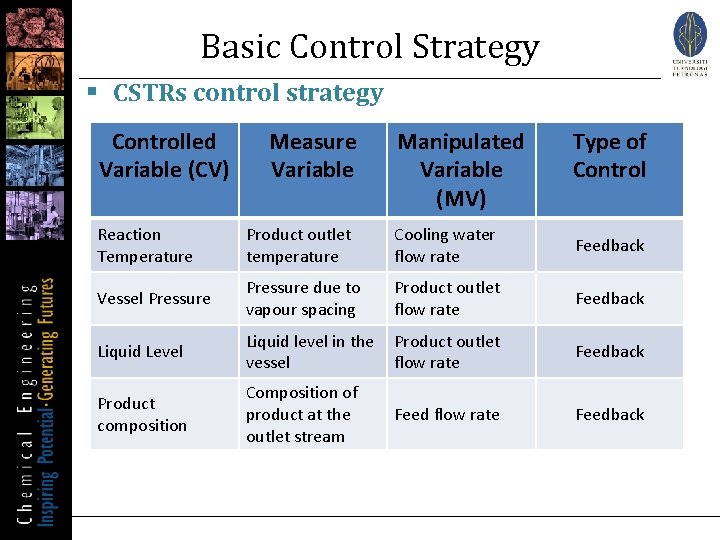
Basic Control Strategy § CSTRs control strategy Controlled Variable (CV) Measure Variable Manipulated Variable (MV) Type of Control Reaction Temperature Product outlet temperature Cooling water flow rate Feedback Vessel Pressure due to vapour spacing Product outlet flow rate Feedback Liquid Level Liquid level in the vessel Product outlet flow rate Feedback Product composition Composition of product at the outlet stream Feed flow rate Feedback
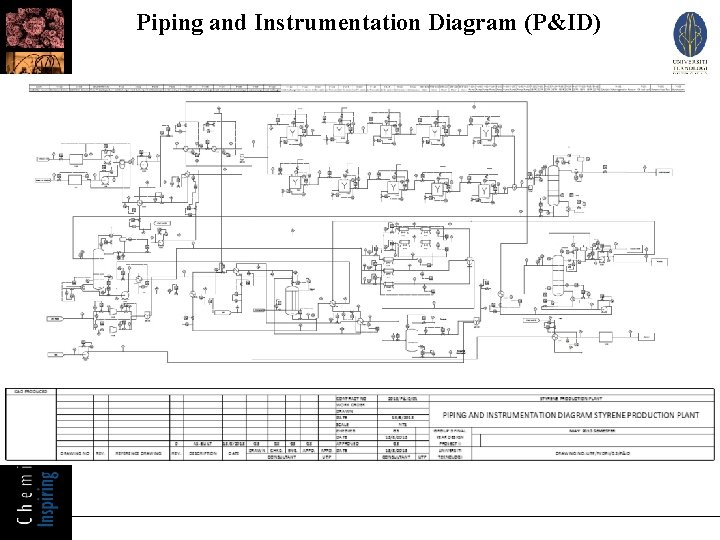
Piping and Instrumentation Diagram (P&ID)
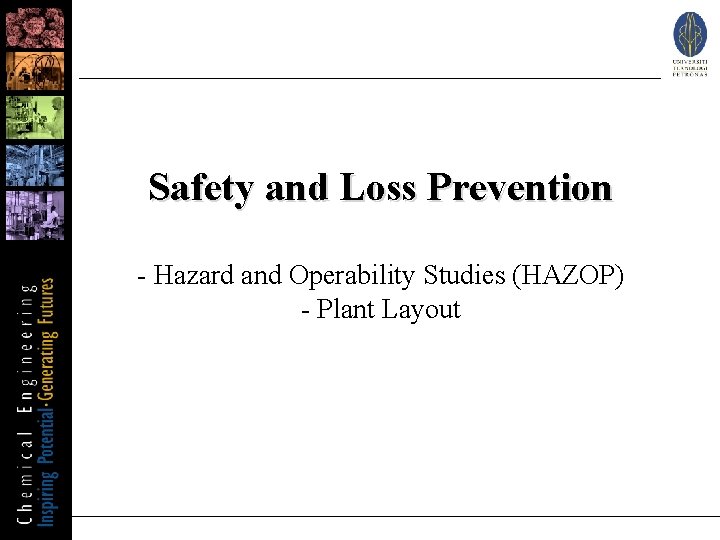
Safety and Loss Prevention - Hazard and Operability Studies (HAZOP) - Plant Layout
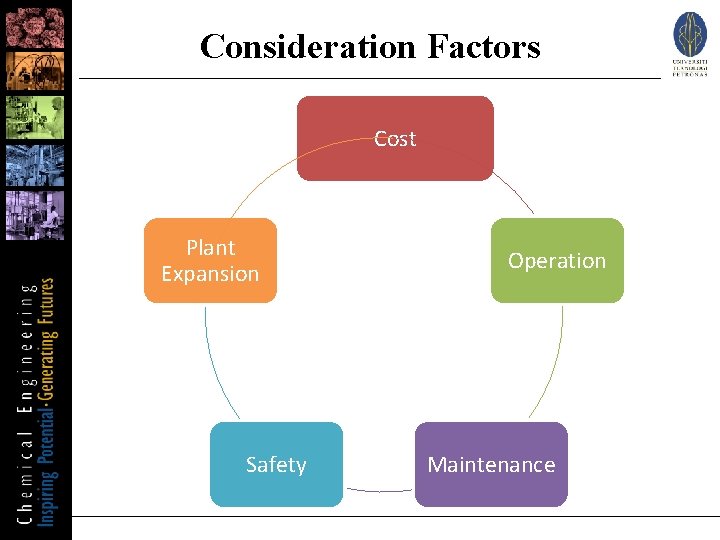
Consideration Factors Cost Plant Expansion Safety Operation Maintenance
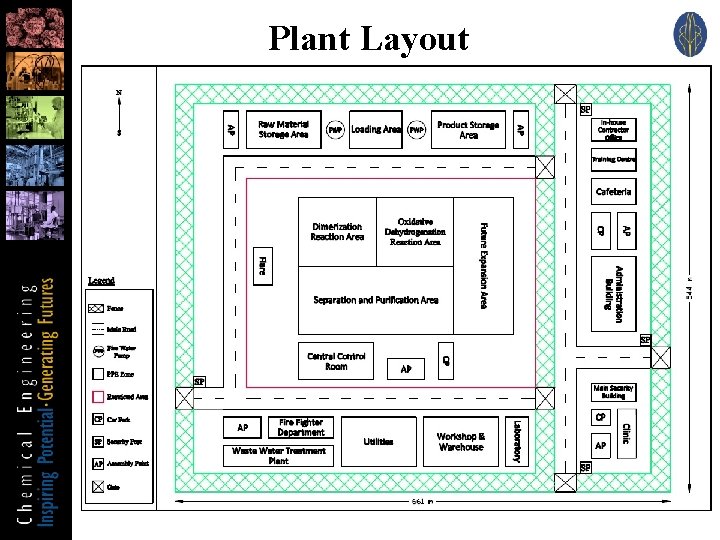
Plant Layout
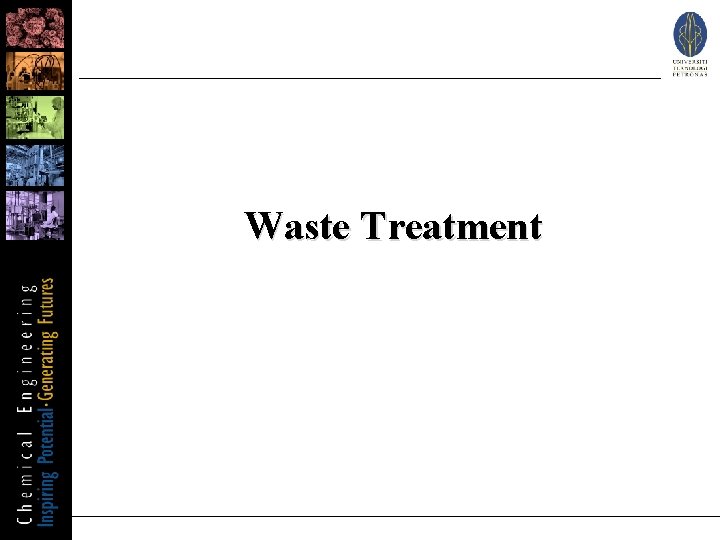
Waste Treatment
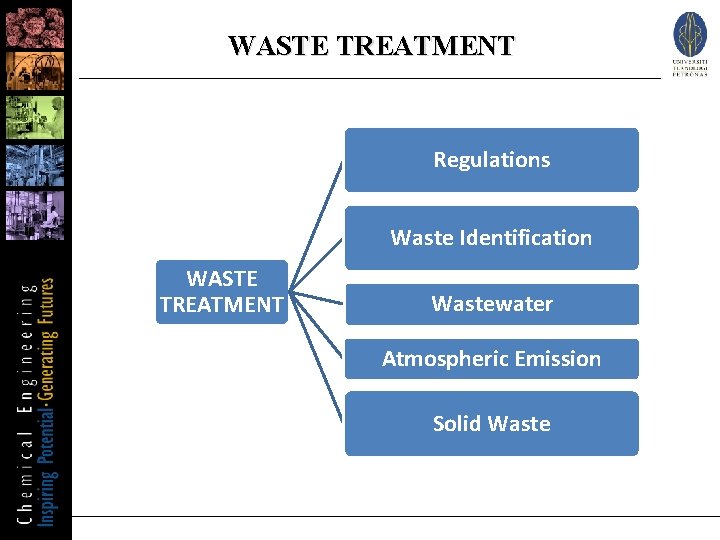
WASTE TREATMENT Regulations Waste Identification WASTE TREATMENT Wastewater Atmospheric Emission Solid Waste
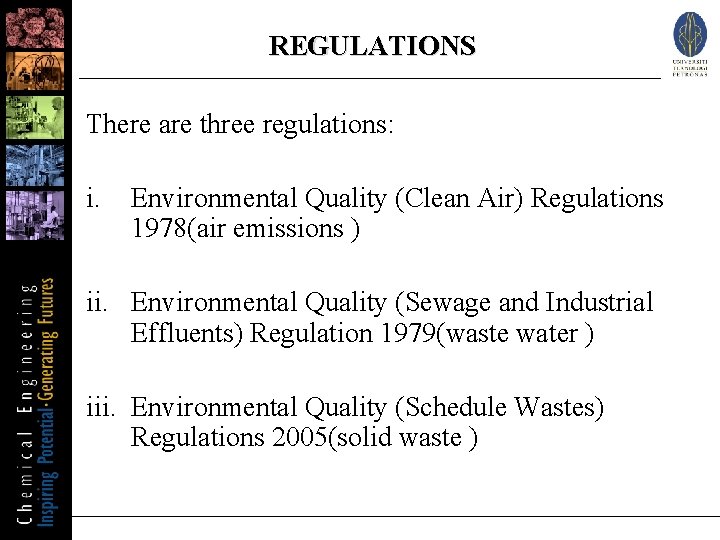
REGULATIONS There are three regulations: i. Environmental Quality (Clean Air) Regulations 1978(air emissions ) ii. Environmental Quality (Sewage and Industrial Effluents) Regulation 1979(waste water ) iii. Environmental Quality (Schedule Wastes) Regulations 2005(solid waste )
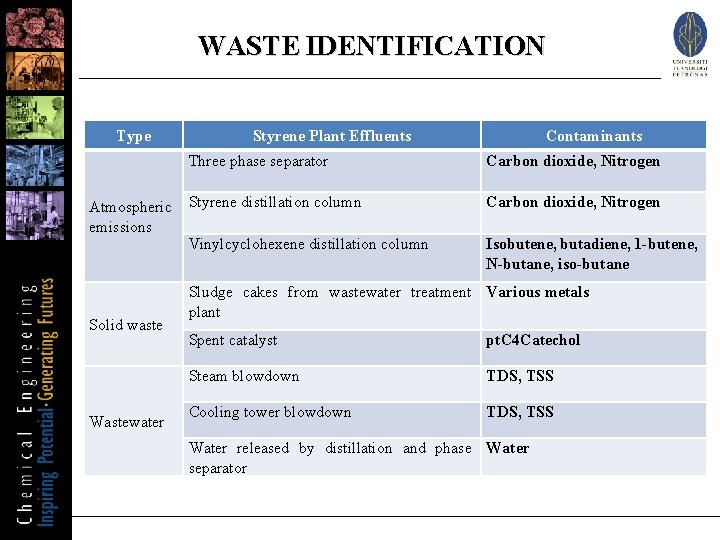
WASTE IDENTIFICATION Type Atmospheric emissions Solid waste Wastewater Styrene Plant Effluents Contaminants Three phase separator Carbon dioxide, Nitrogen Styrene distillation column Carbon dioxide, Nitrogen Vinylcyclohexene distillation column Isobutene, butadiene, 1 -butene, N-butane, iso-butane Sludge cakes from wastewater treatment Various metals plant Spent catalyst pt. C 4 Catechol Steam blowdown TDS, TSS Cooling tower blowdown TDS, TSS Water released by distillation and phase Water separator
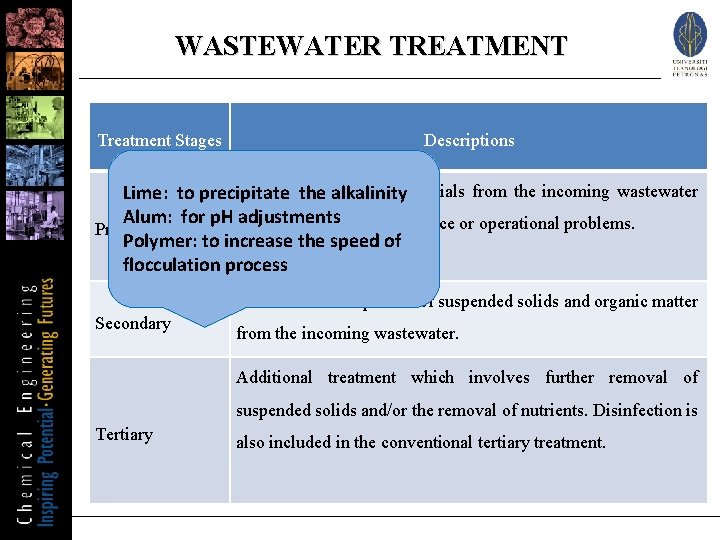
WASTEWATER TREATMENT Treatment Stages Descriptions The removal of solid materials from the incoming wastewater Lime: to precipitate the alkalinity Alum: for p. H which adjustments may cause maintenance or operational problems. Primary Polymer: to increase the speed of flocculation process The removal of a portion of suspended solids and organic matter Secondary from the incoming wastewater. Additional treatment which involves further removal of suspended solids and/or the removal of nutrients. Disinfection is Tertiary also included in the conventional tertiary treatment.

WASTEWATER TREATMENT
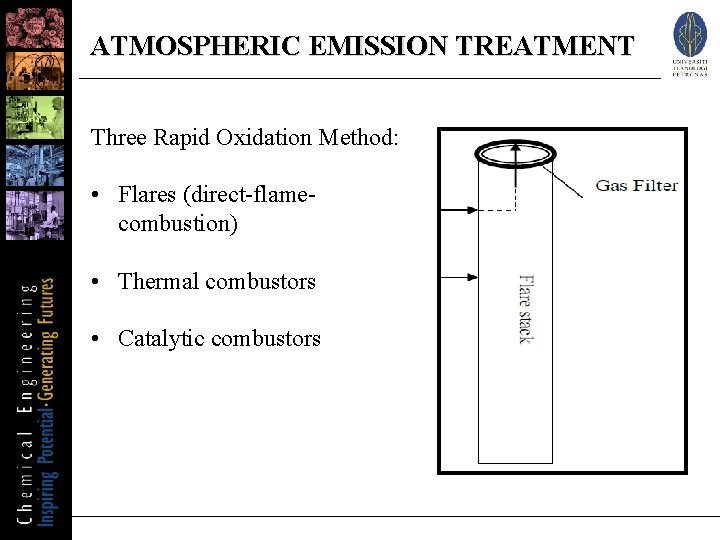
ATMOSPHERIC EMISSION TREATMENT Three Rapid Oxidation Method: • Flares (direct-flamecombustion) • Thermal combustors • Catalytic combustors
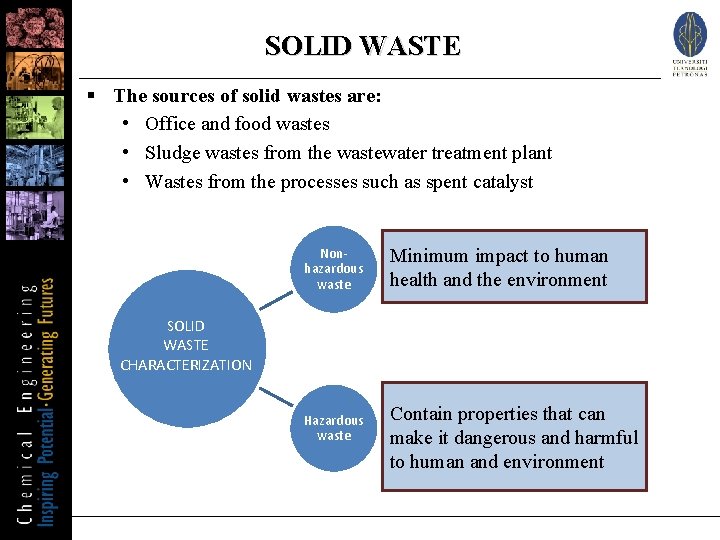
SOLID WASTE § The sources of solid wastes are: • Office and food wastes • Sludge wastes from the wastewater treatment plant • Wastes from the processes such as spent catalyst Nonhazardous waste Minimum impact to human health and the environment SOLID WASTE CHARACTERIZATION Hazardous waste Contain properties that can make it dangerous and harmful to human and environment
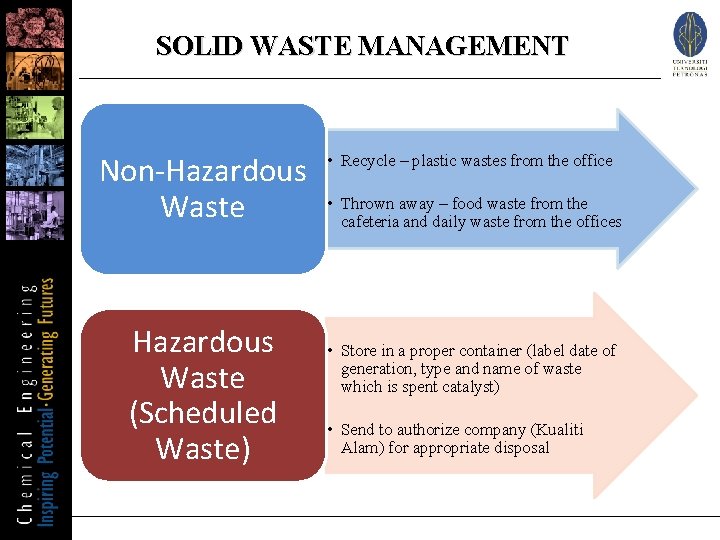
SOLID WASTE MANAGEMENT Non-Hazardous Waste (Scheduled Waste) • Recycle – plastic wastes from the office • Thrown away – food waste from the cafeteria and daily waste from the offices • Store in a proper container (label date of generation, type and name of waste which is spent catalyst) • Send to authorize company (Kualiti Alam) for appropriate disposal
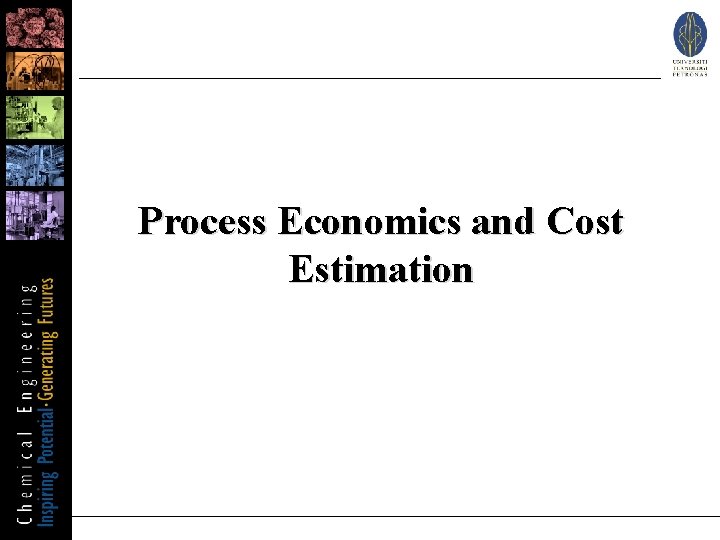
Process Economics and Cost Estimation
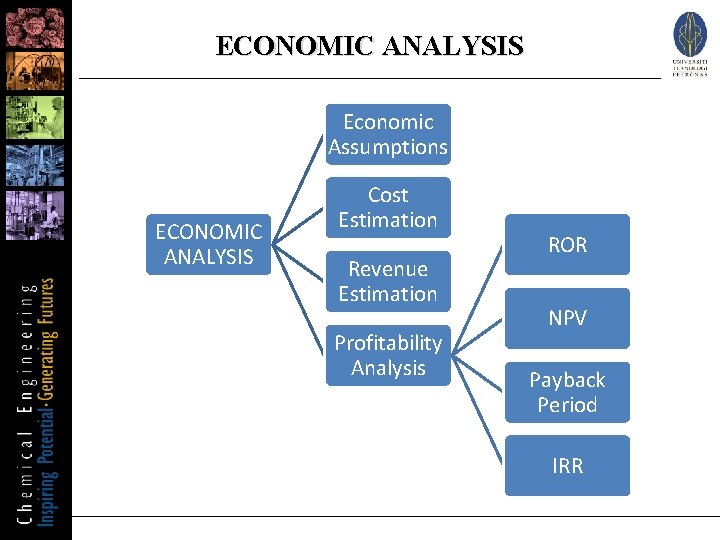
ECONOMIC ANALYSIS Economic Assumptions ECONOMIC ANALYSIS Cost Estimation Revenue Estimation Profitability Analysis ROR NPV Payback Period IRR
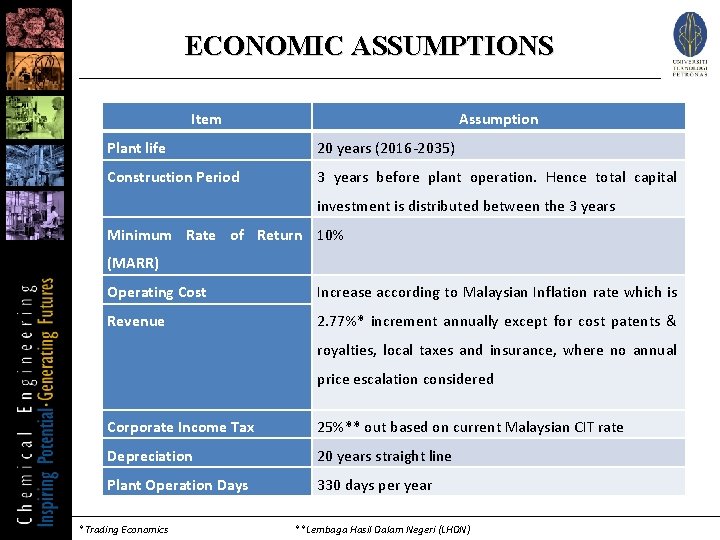
ECONOMIC ASSUMPTIONS Item Assumption Plant life 20 years (2016 -2035) Construction Period 3 years before plant operation. Hence total capital investment is distributed between the 3 years Minimum Rate of Return 10% (MARR) Operating Cost Increase according to Malaysian Inflation rate which is Revenue 2. 77%* increment annually except for cost patents & royalties, local taxes and insurance, where no annual price escalation considered Corporate Income Tax 25%** out based on current Malaysian CIT rate Depreciation 20 years straight line Plant Operation Days 330 days per year *Trading Economics **Lembaga Hasil Dalam Negeri (LHDN)
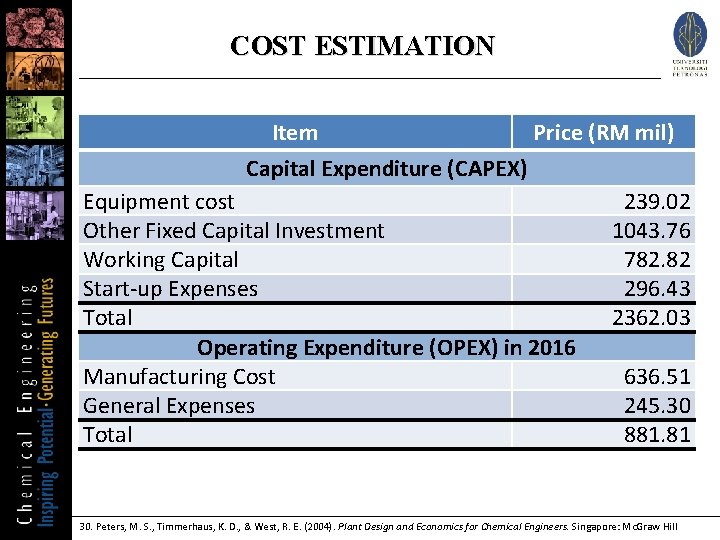
COST ESTIMATION Item Price (RM mil) Capital Expenditure (CAPEX) Equipment cost 239. 02 Other Fixed Capital Investment 1043. 76 Working Capital 782. 82 Start-up Expenses 296. 43 Total 2362. 03 Operating Expenditure (OPEX) in 2016 Manufacturing Cost 636. 51 General Expenses 245. 30 Total 881. 81 30. Peters, M. S. , Timmerhaus, K. D. , & West, R. E. (2004). Plant Design and Economics for Chemical Engineers. Singapore: Mc. Graw Hill
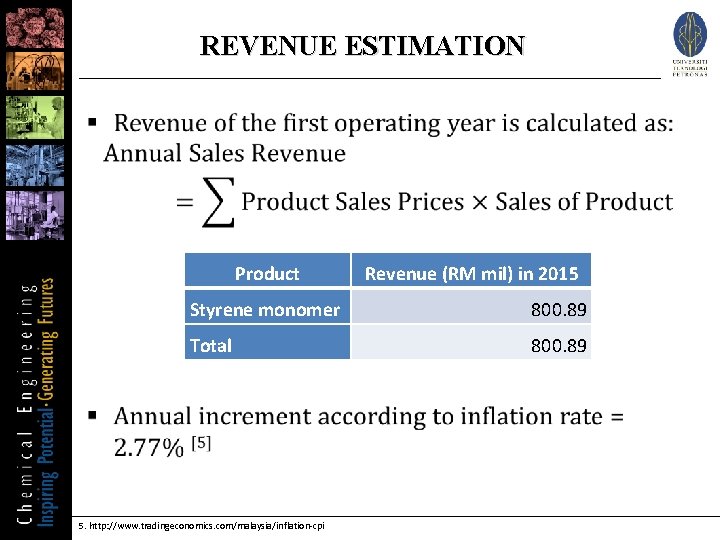
REVENUE ESTIMATION § Product Revenue (RM mil) in 2015 Styrene monomer 800. 89 Total 800. 89 5. http: //www. tradingeconomics. com/malaysia/inflation-cpi
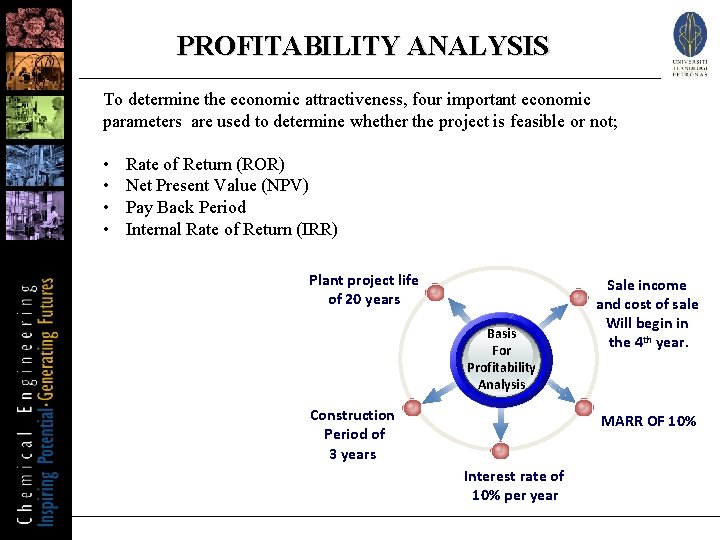
PROFITABILITY ANALYSIS To determine the economic attractiveness, four important economic parameters are used to determine whether the project is feasible or not; • • Rate of Return (ROR) Net Present Value (NPV) Pay Back Period Internal Rate of Return (IRR) Plant project life of 20 years Basis For Profitability Analysis Construction Period of 3 years Sale income and cost of sale Will begin in the 4 th year. MARR OF 10% Interest rate of 10% per year
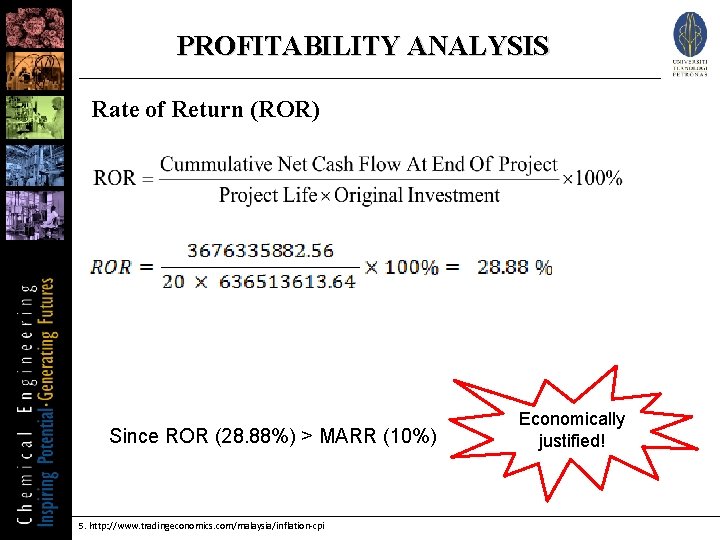
PROFITABILITY ANALYSIS Rate of Return (ROR) Since ROR (28. 88%) > MARR (10%) 5. http: //www. tradingeconomics. com/malaysia/inflation-cpi Economically justified!
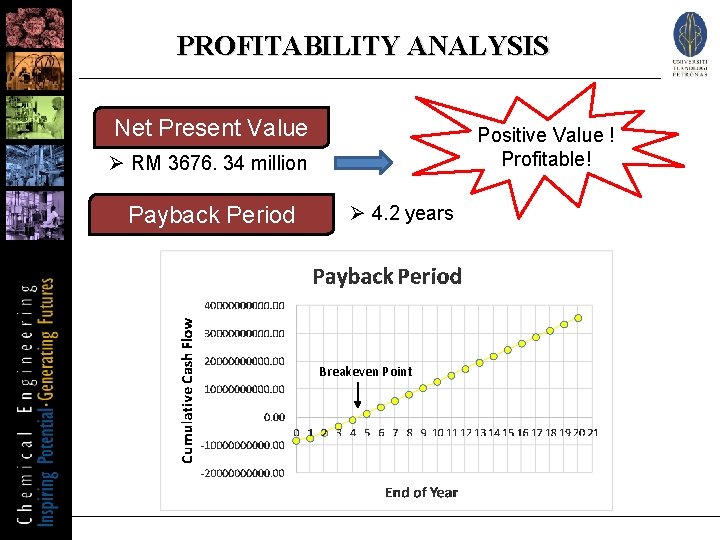
PROFITABILITY ANALYSIS Net Present Value Positive Value ! Profitable! Ø RM 3676. 34 million Payback Period Ø 4. 2 years Breakeven Point
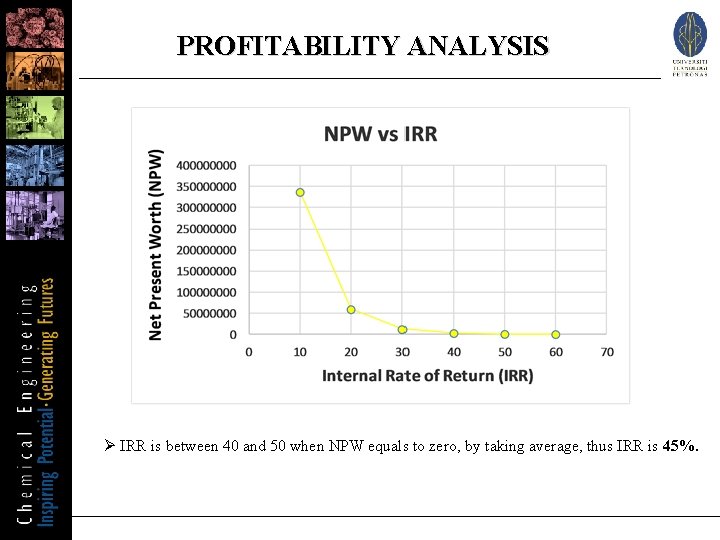
PROFITABILITY ANALYSIS Ø IRR is between 40 and 50 when NPW equals to zero, by taking average, thus IRR is 45%.
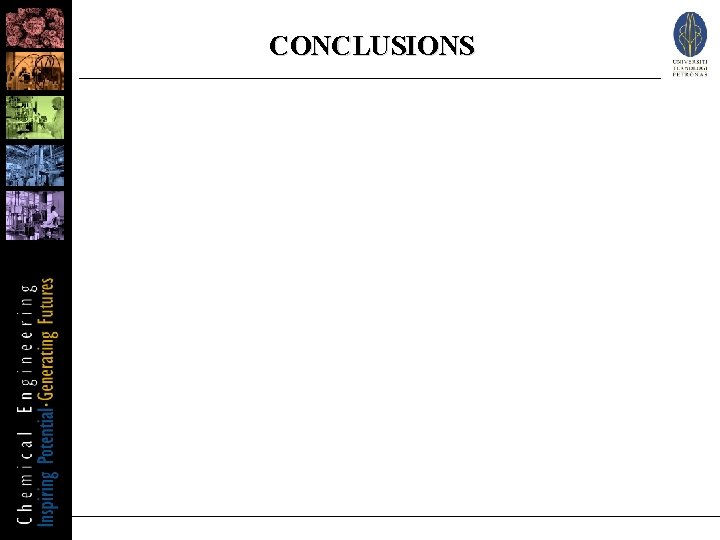
CONCLUSIONS
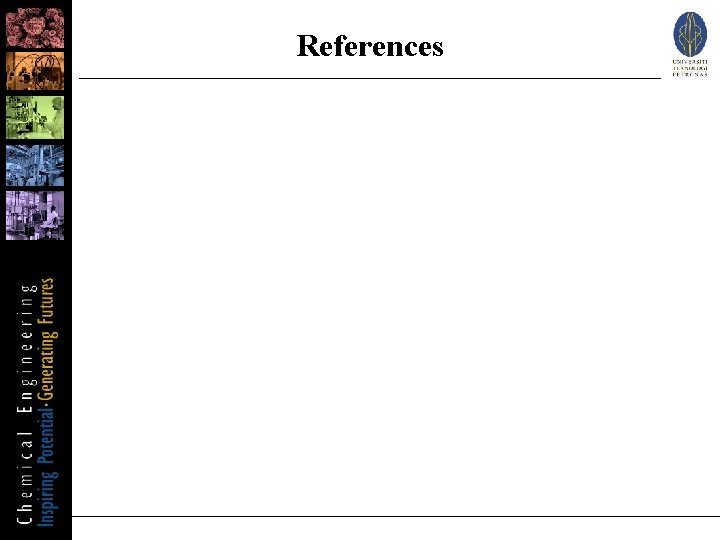
References
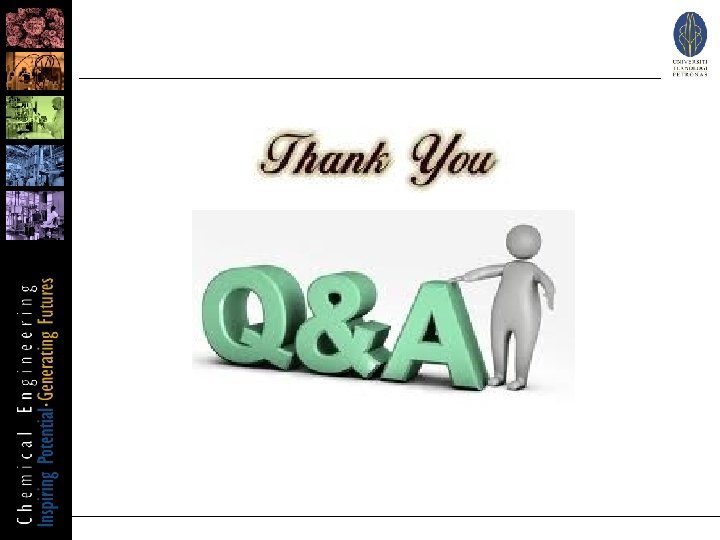
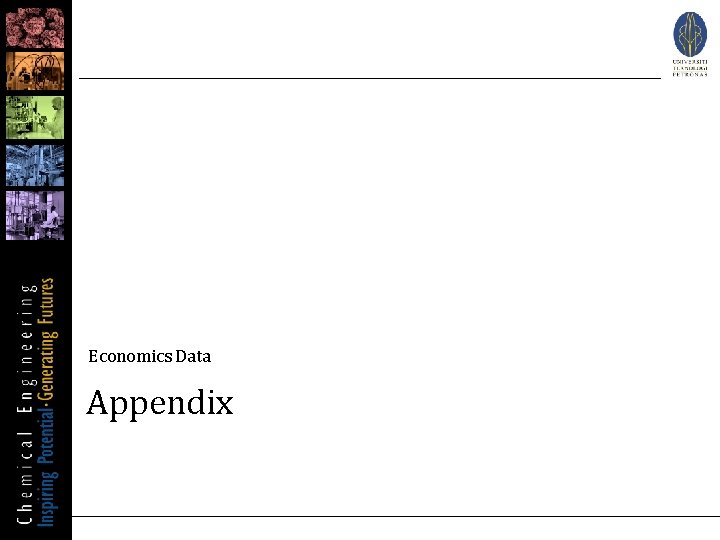
Economics Data Appendix
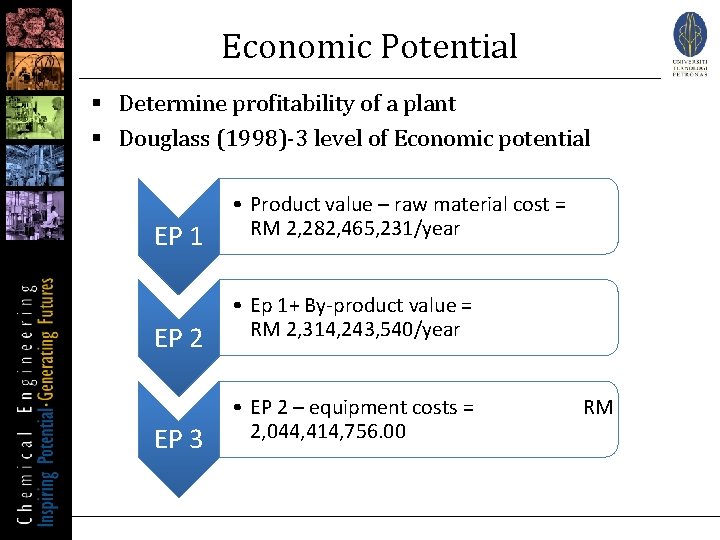
Economic Potential § Determine profitability of a plant § Douglass (1998)-3 level of Economic potential EP 1 EP 2 EP 3 • Product value – raw material cost = RM 2, 282, 465, 231/year • Ep 1+ By-product value = RM 2, 314, 243, 540/year • EP 2 – equipment costs = 2, 044, 414, 756. 00 RM
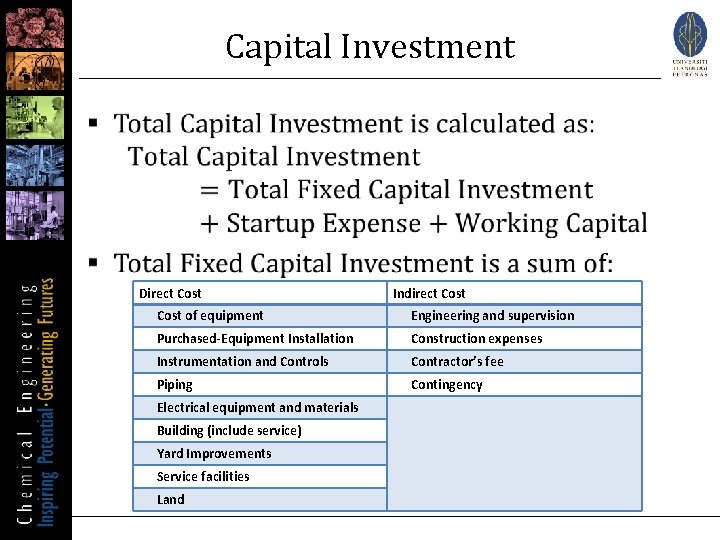
Capital Investment § Direct Cost Indirect Cost of equipment Engineering and supervision Purchased-Equipment Installation Construction expenses Instrumentation and Controls Contractor’s fee Piping Contingency Electrical equipment and materials Building (include service) Yard Improvements Service facilities Land
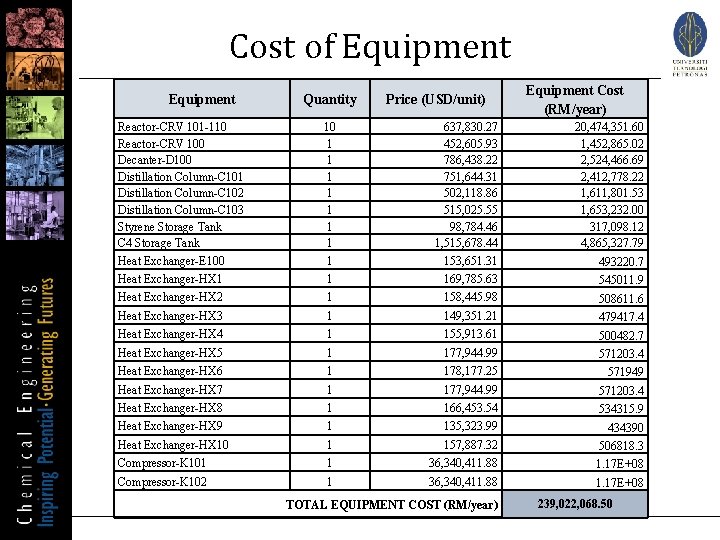
Cost of Equipment Quantity Price (USD/unit) Equipment Cost (RM/year) Reactor-CRV 101 -110 Reactor-CRV 100 Decanter-D 100 Distillation Column-C 101 Distillation Column-C 102 Distillation Column-C 103 Styrene Storage Tank C 4 Storage Tank Heat Exchanger-E 100 10 1 1 1 1 637, 830. 27 452, 605. 93 786, 438. 22 751, 644. 31 502, 118. 86 515, 025. 55 98, 784. 46 1, 515, 678. 44 153, 651. 31 20, 474, 351. 60 1, 452, 865. 02 2, 524, 466. 69 2, 412, 778. 22 1, 611, 801. 53 1, 653, 232. 00 317, 098. 12 4, 865, 327. 79 Heat Exchanger-HX 1 1 169, 785. 63 545011. 9 Heat Exchanger-HX 2 1 158, 445. 98 508611. 6 Heat Exchanger-HX 3 1 149, 351. 21 479417. 4 Heat Exchanger-HX 4 1 155, 913. 61 500482. 7 Heat Exchanger-HX 5 1 177, 944. 99 571203. 4 Heat Exchanger-HX 6 1 178, 177. 25 571949 Heat Exchanger-HX 7 1 177, 944. 99 571203. 4 Heat Exchanger-HX 8 1 166, 453. 54 534315. 9 Heat Exchanger-HX 9 1 135, 323. 99 434390 Heat Exchanger-HX 10 1 157, 887. 32 506818. 3 Compressor-K 101 1 36, 340, 411. 88 1. 17 E+08 Compressor-K 102 1 36, 340, 411. 88 1. 17 E+08 TOTAL EQUIPMENT COST (RM/year) 493220. 7 239, 022, 068. 50
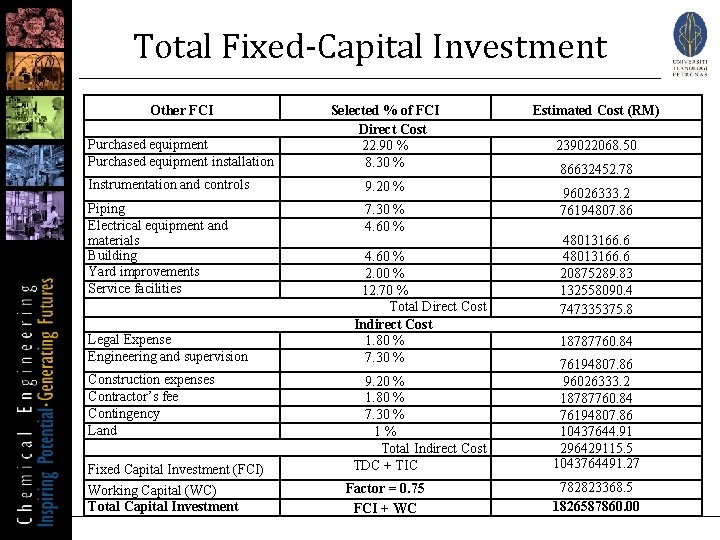
Total Fixed-Capital Investment Other FCI Purchased equipment installation Selected % of FCI Direct Cost 22. 90 % 8. 30 % Instrumentation and controls 9. 20 % Piping Electrical equipment and materials Building Yard improvements Service facilities 7. 30 % 4. 60 % Legal Expense Engineering and supervision Construction expenses Contractor’s fee Contingency Land Fixed Capital Investment (FCI) Working Capital (WC) Total Capital Investment 4. 60 % 2. 00 % 12. 70 % Total Direct Cost Indirect Cost 1. 80 % 7. 30 % 9. 20 % 1. 80 % 7. 30 % 1% Total Indirect Cost TDC + TIC Factor = 0. 75 FCI + WC Estimated Cost (RM) 239022068. 50 86632452. 78 96026333. 2 76194807. 86 48013166. 6 20875289. 83 132558090. 4 747335375. 8 18787760. 84 76194807. 86 96026333. 2 18787760. 84 76194807. 86 10437644. 91 296429115. 5 1043764491. 27 782823368. 5 1826587860. 00
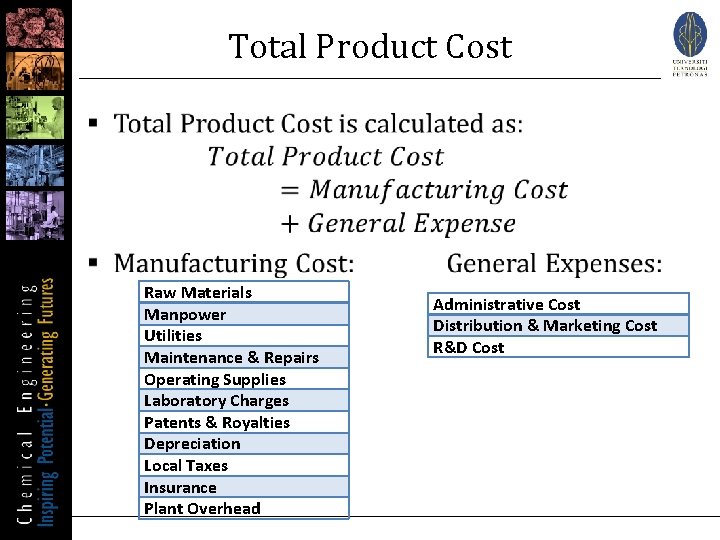
Total Product Cost § Raw Materials Manpower Utilities Maintenance & Repairs Operating Supplies Laboratory Charges Patents & Royalties Depreciation Local Taxes Insurance Plant Overhead Administrative Cost Distribution & Marketing Cost R&D Cost
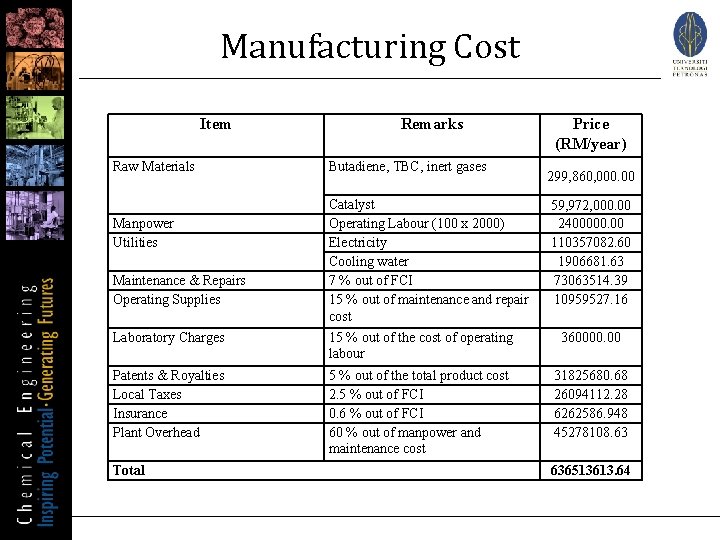
Manufacturing Cost Item Raw Materials Manpower Utilities Maintenance & Repairs Operating Supplies Remarks Butadiene, TBC, inert gases Catalyst Operating Labour (100 x 2000) Electricity Cooling water 7 % out of FCI 15 % out of maintenance and repair cost Price (RM/year) 299, 860, 000. 00 59, 972, 000. 00 2400000. 00 110357082. 60 1906681. 63 73063514. 39 10959527. 16 Laboratory Charges 15 % out of the cost of operating labour 360000. 00 Patents & Royalties Local Taxes Insurance Plant Overhead 5 % out of the total product cost 2. 5 % out of FCI 0. 6 % out of FCI 60 % out of manpower and maintenance cost 31825680. 68 26094112. 28 6262586. 948 45278108. 63 Total 636513613. 64
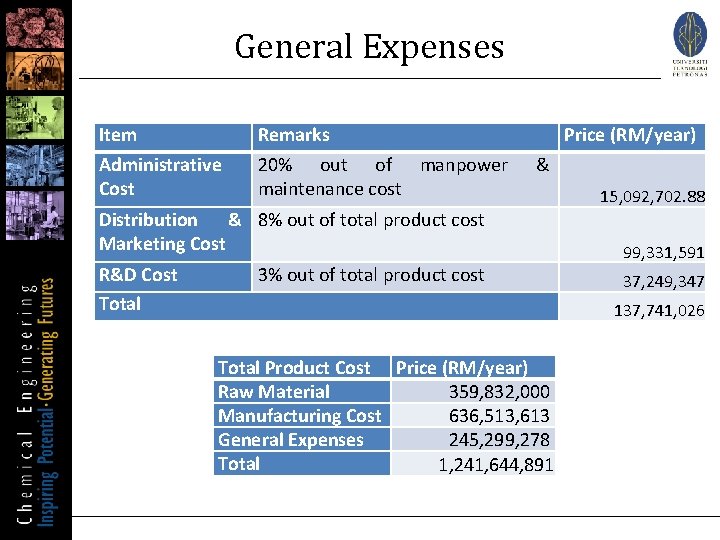
General Expenses Item Administrative Cost Remarks 20% out of manpower maintenance cost Price (RM/year) & Distribution & 8% out of total product cost Marketing Cost R&D Cost Total 3% out of total product cost 15, 092, 702. 88 99, 331, 591 37, 249, 347 137, 741, 026 Total Product Cost Price (RM/year) Raw Material 359, 832, 000 Manufacturing Cost 636, 513, 613 General Expenses 245, 299, 278 Total 1, 241, 644, 891
Multimedia content production adalah
Properties of polystyrene
Styrene uses
Styrene monomer
The empirical formula of styrene is ch
Explain the objectives of plant layout
Nitric acid production plant
Introduction in plant breeding
Plant breeding for disease resistance
Plant introduction in plant breeding
Tronsmo plant pathology and plant diseases download
Tronsmo plant pathology and plant diseases download
Albugo eye
Process selection operations management
Photosynthesis poster ideas
Valuation of plant machinery and equipment
Plant tissue culture ppt
The role of project management in achieving project success
Example of background of the project
Process discriminants in software project management
Project cost duration graph
Modern project management began with what project
Project evaluation in software project management
Introduction for project
When conducting post project audits
Project indicator enables a software project manager to
Microsoft project agile project management
Project proposal methodology example
Type n terminations
Biotechnology plant design
Seafood plant design
Bioprocess plant design
Gmp plant design
Plant layout design rules
Modular plant design
Symbol name
Project design in research
Glider fuselage design
Connecting rod
Reactor design project
Project selection in system analysis and design
Food truck design project
Project design là gì
Empatisera
Project title design
Project management in system analysis and design
Crm project plan
Technical feasibility example
Atr room
Idp project for civil engineering
Roller coaster design project
It analysis design and project management
Design project title
Pltw design brief example
Hazop
Idp project
Project design background
Simple design for project
Topic design for project
Anatomy of magazine cover