DESIGN AND ANALYSIS OF CONNECTING ROD WITH DIFFERENT
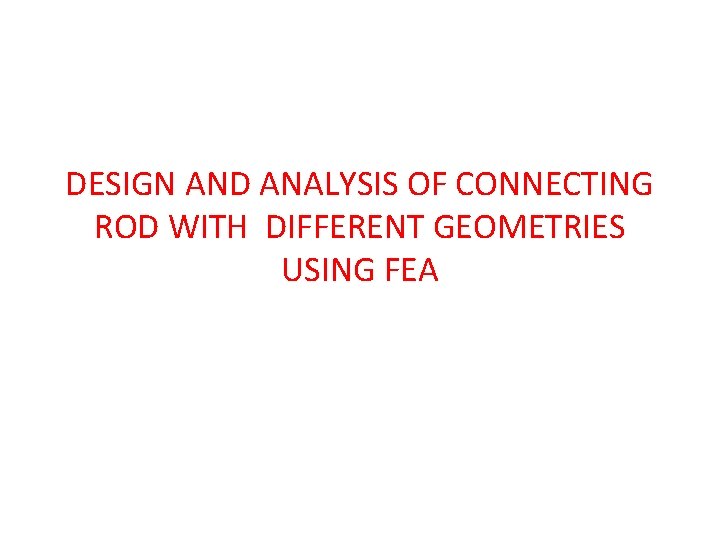
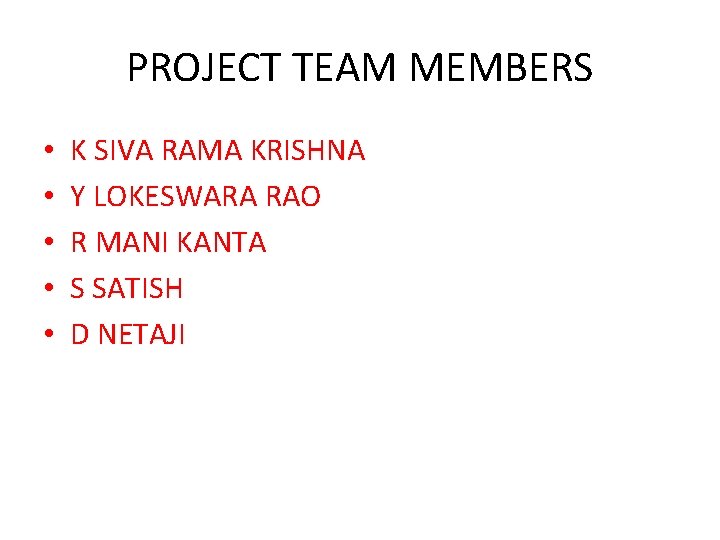
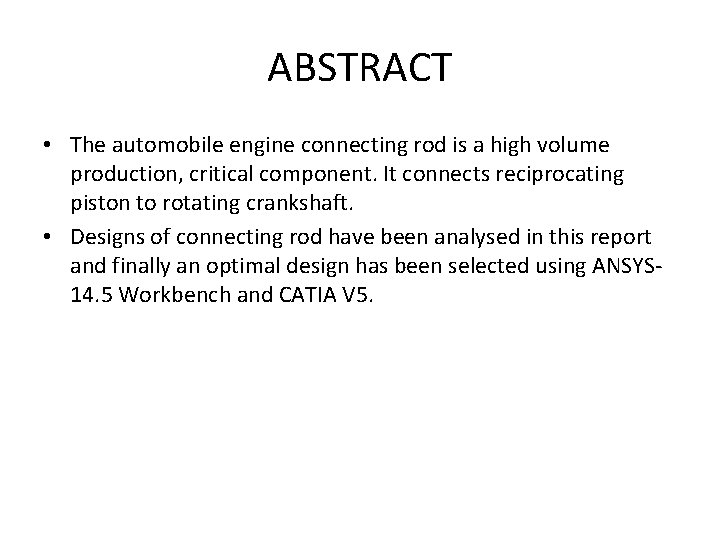
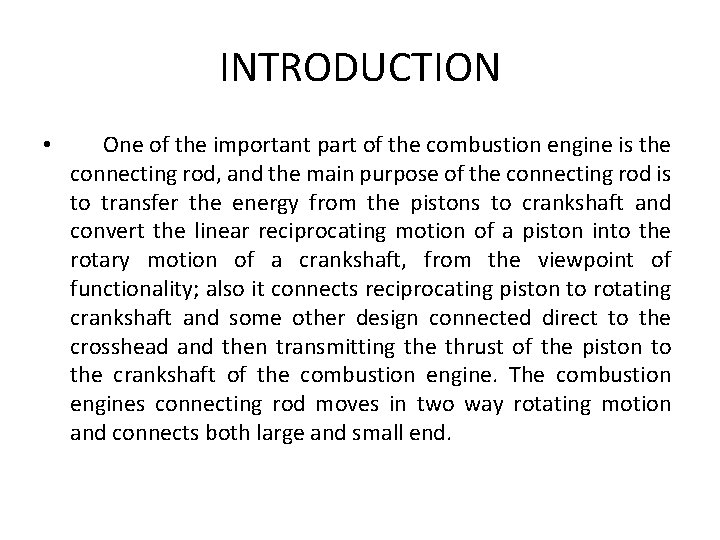

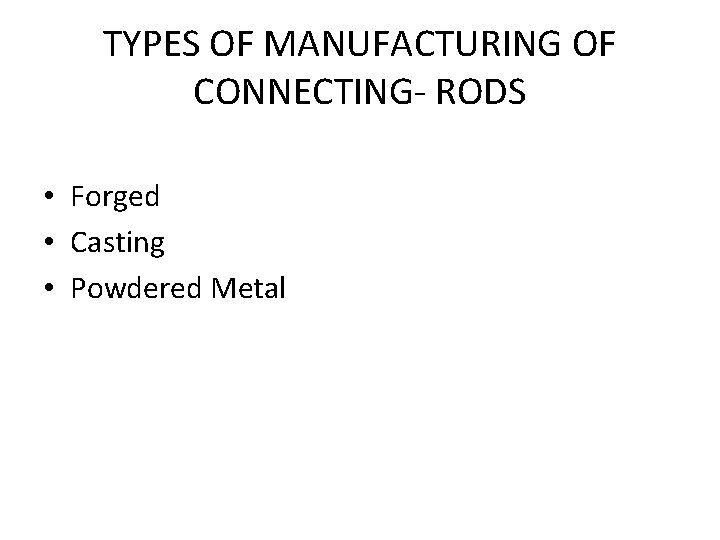
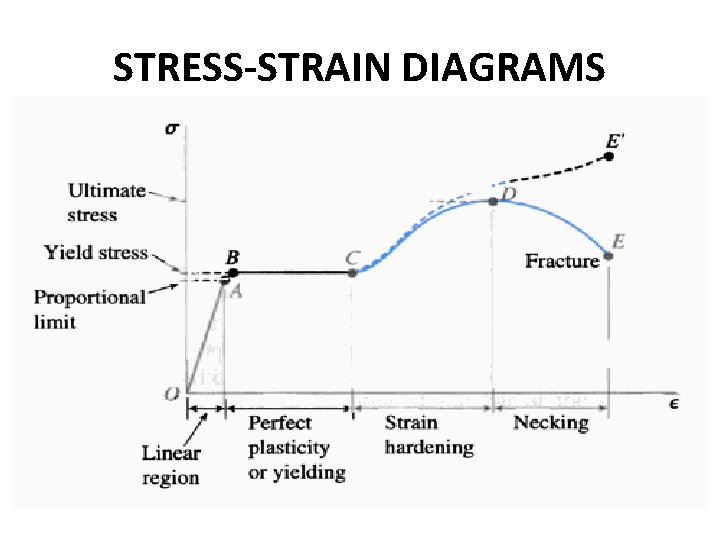
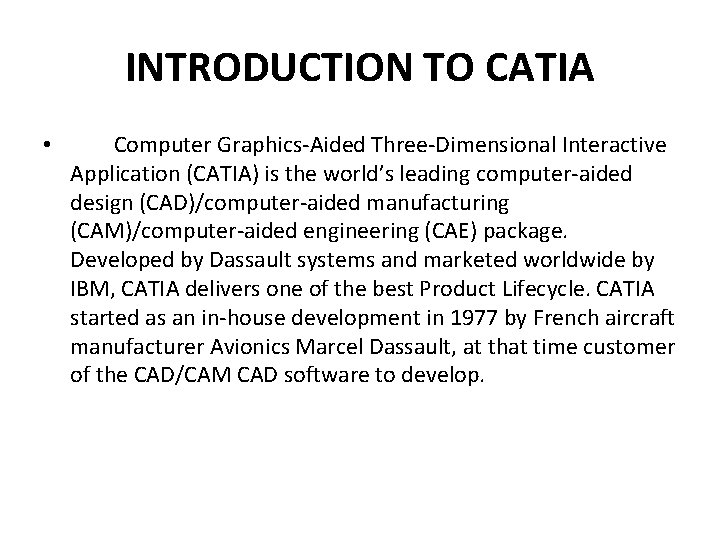
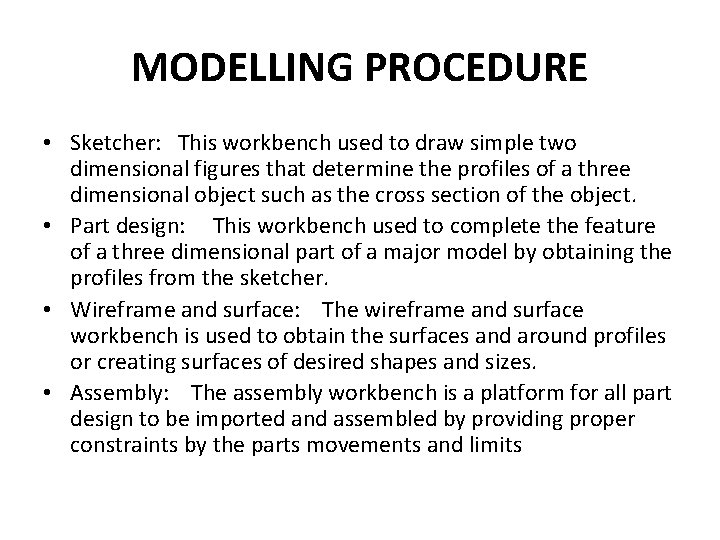
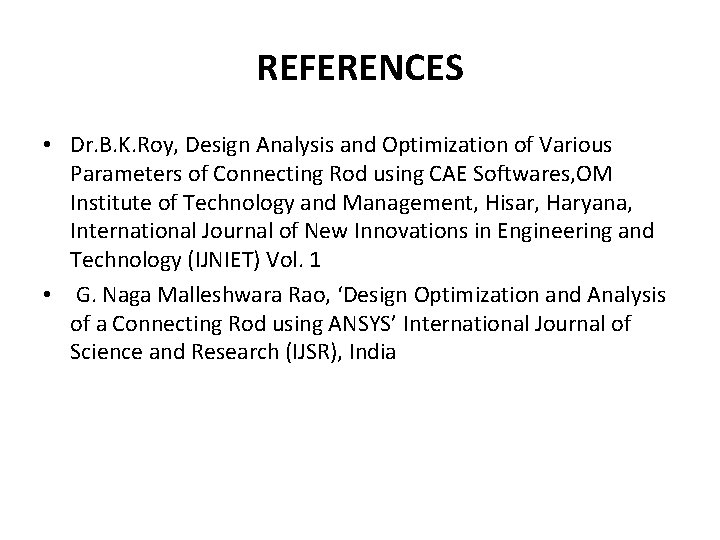
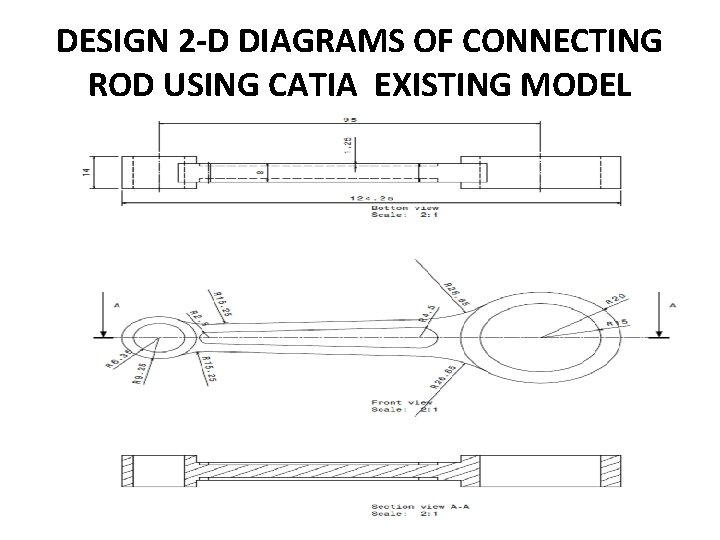
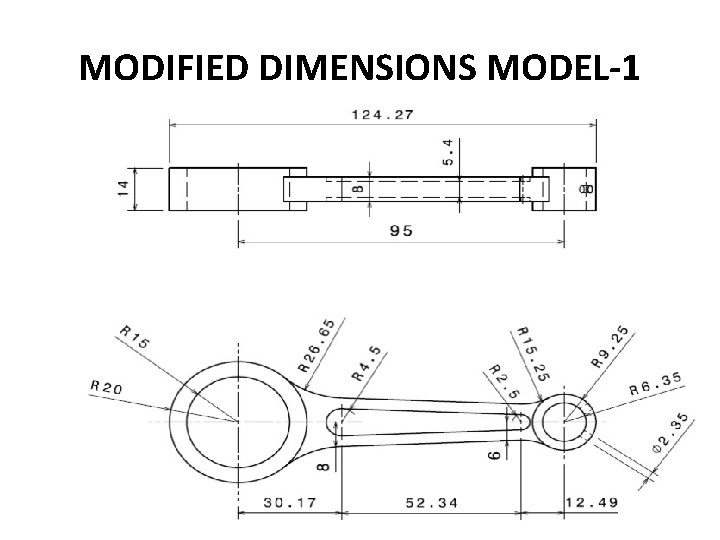
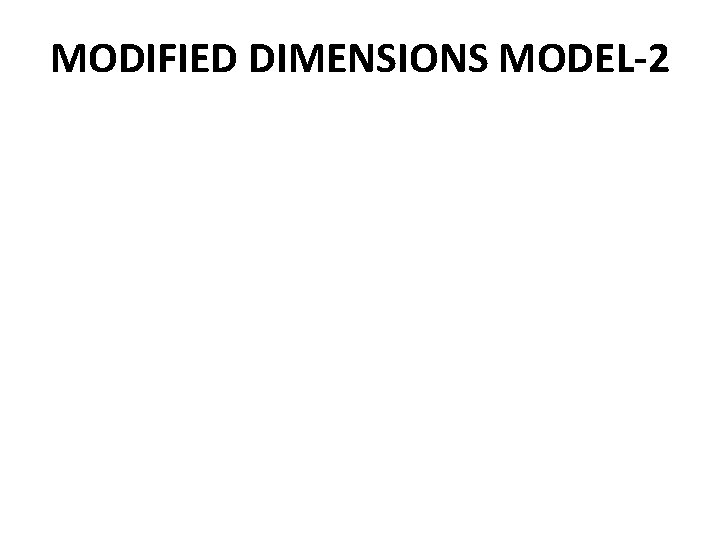
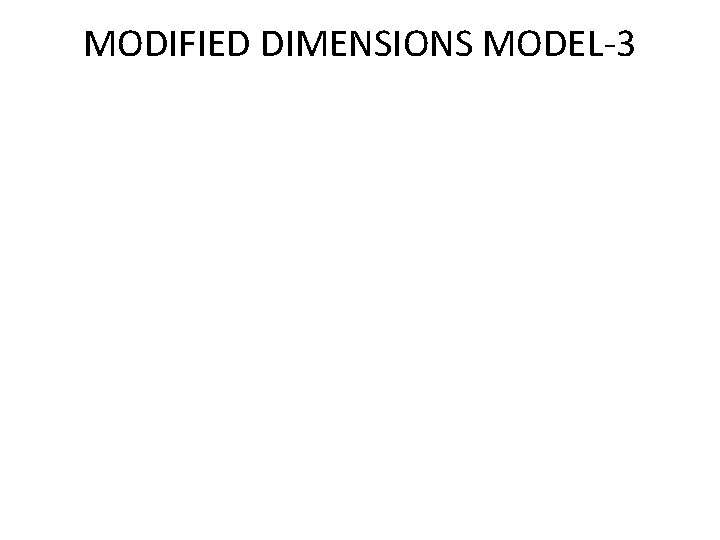
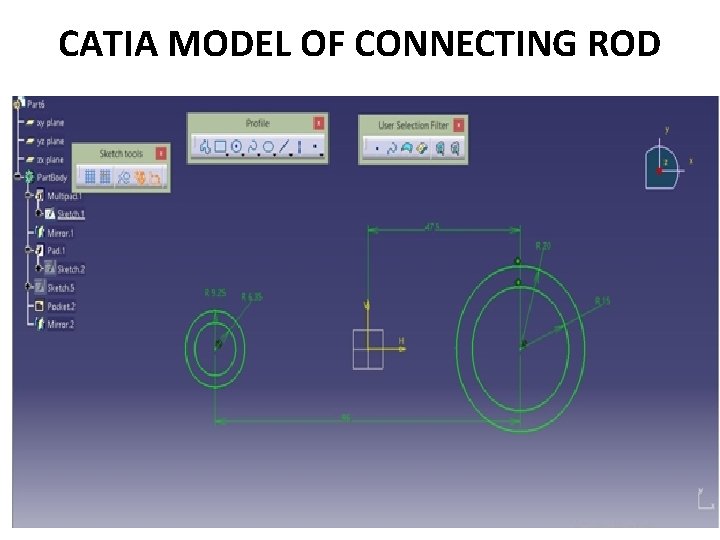
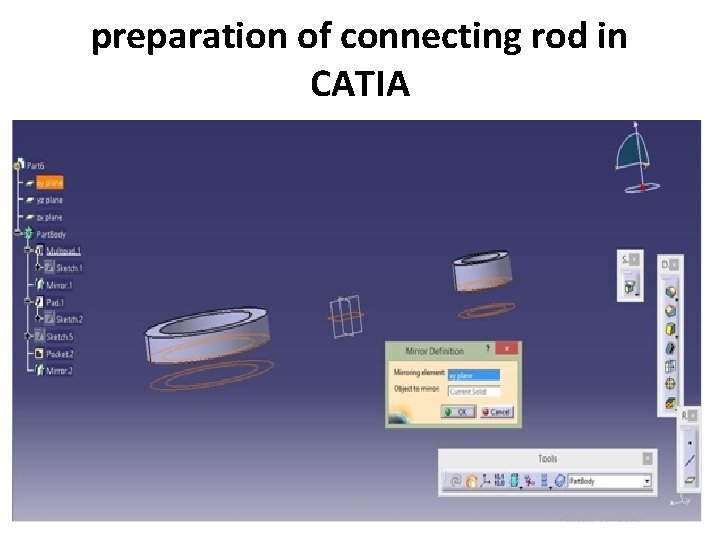
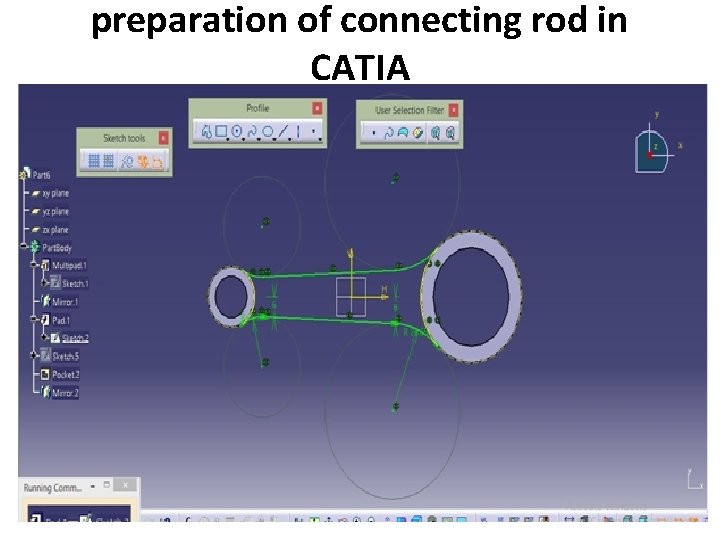
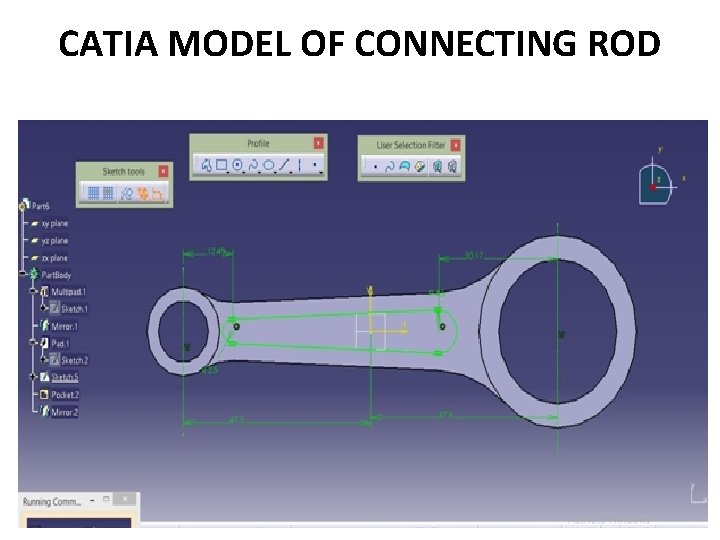
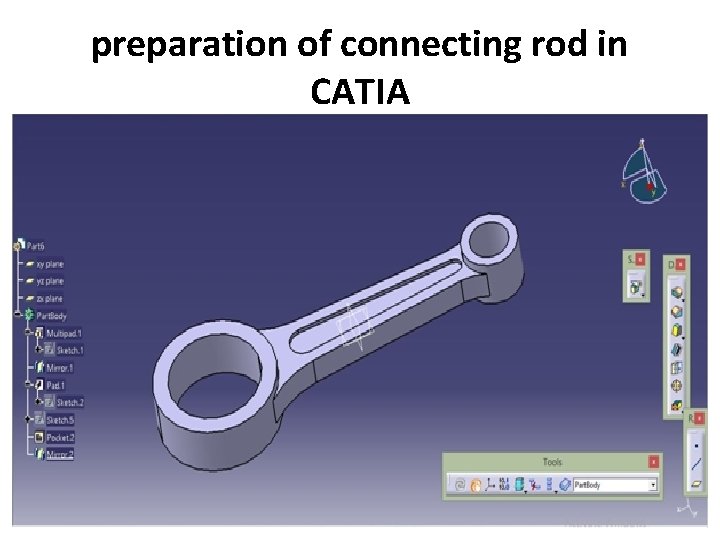
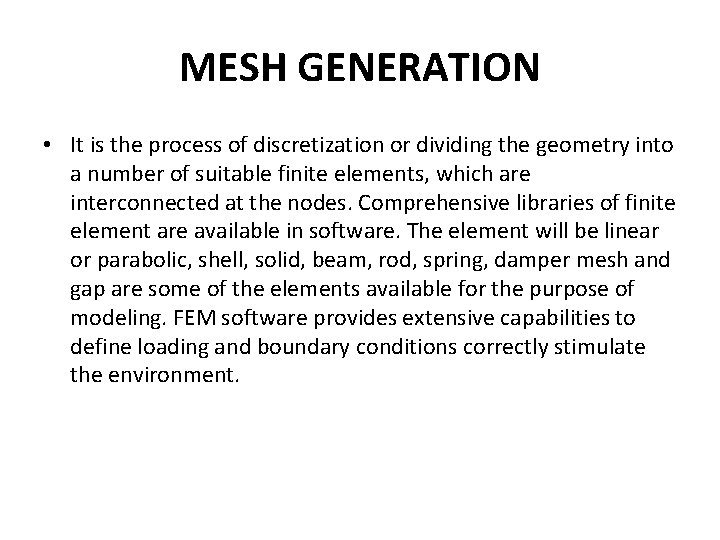
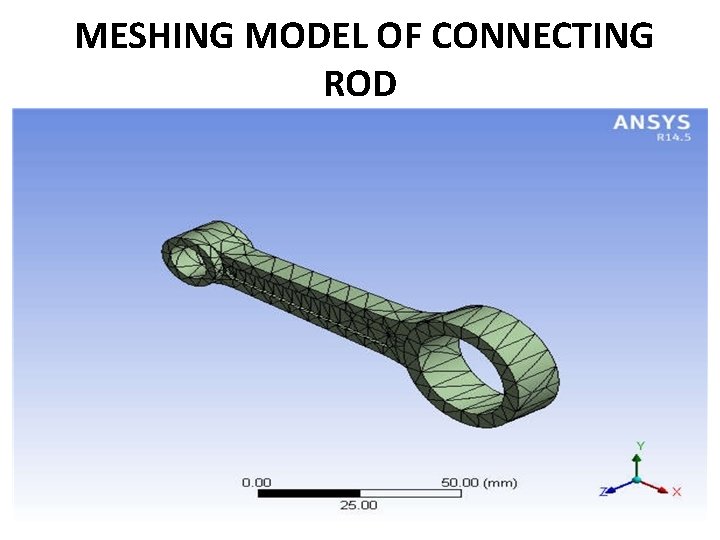
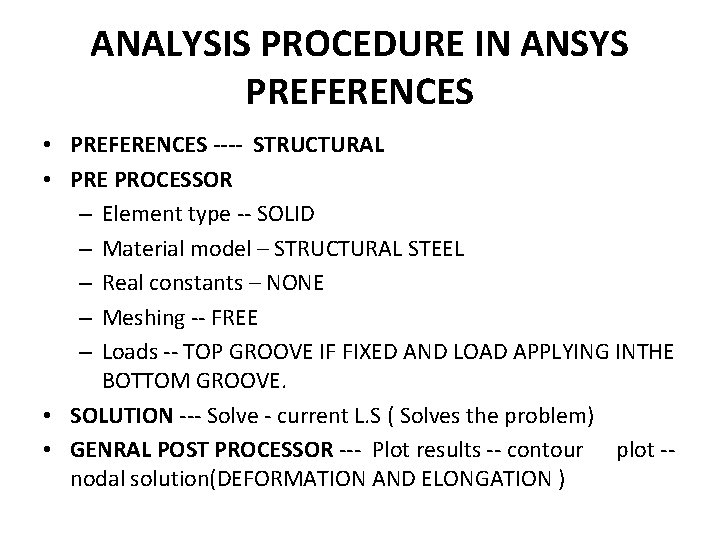
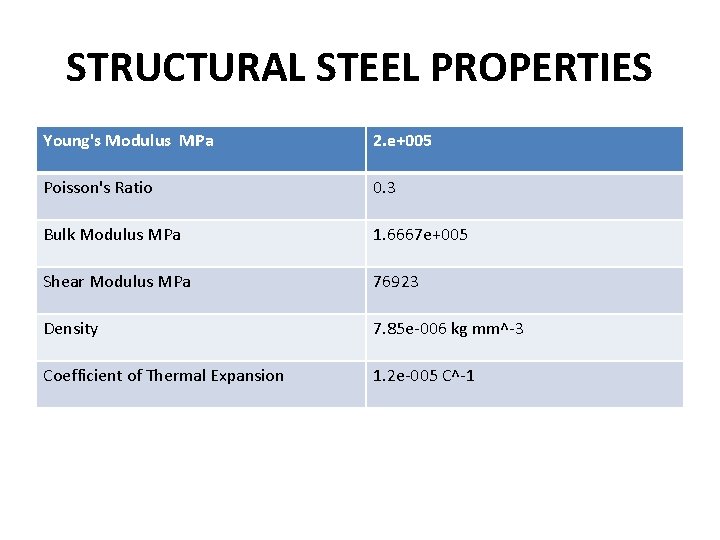
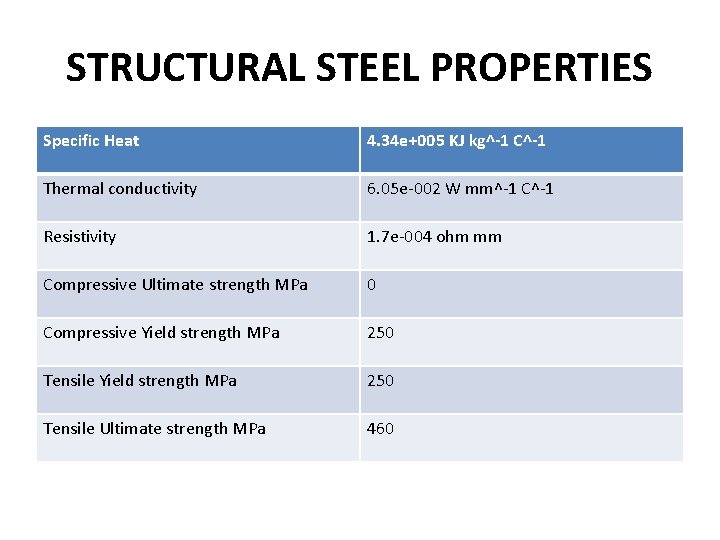
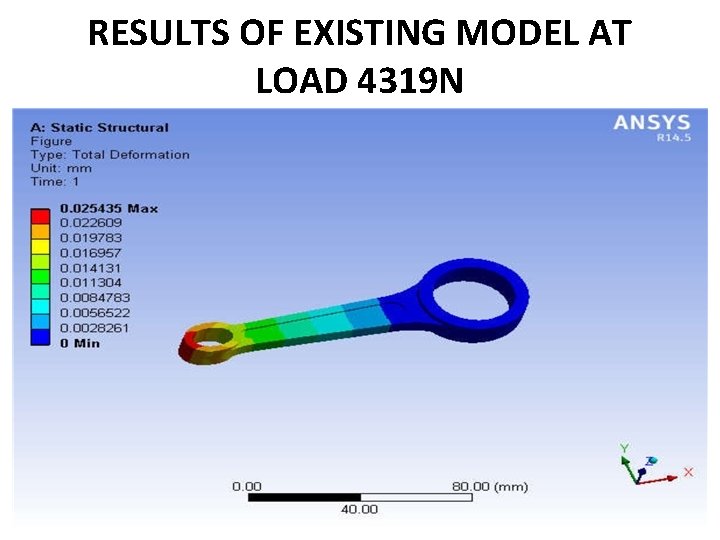
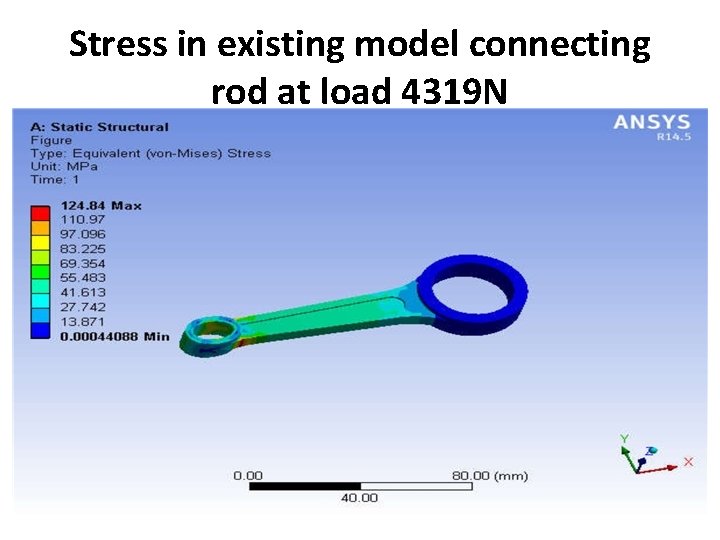

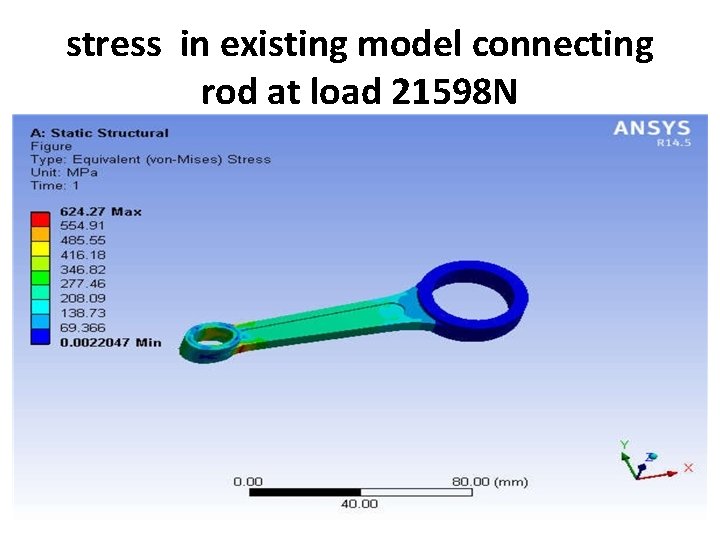
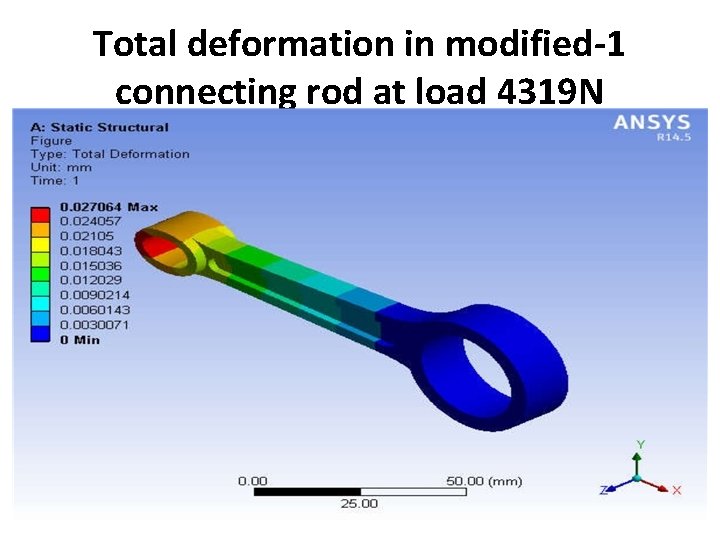
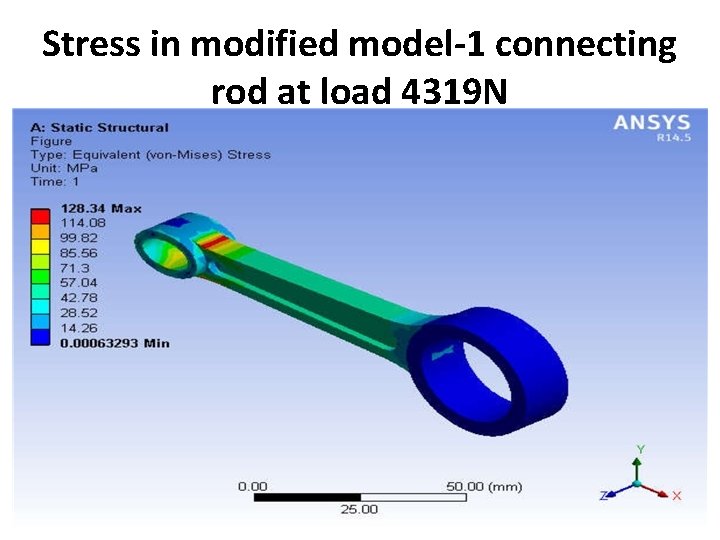
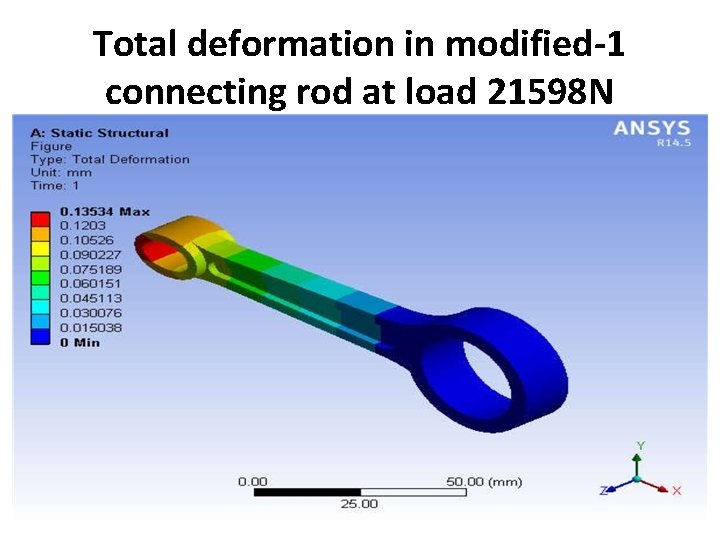

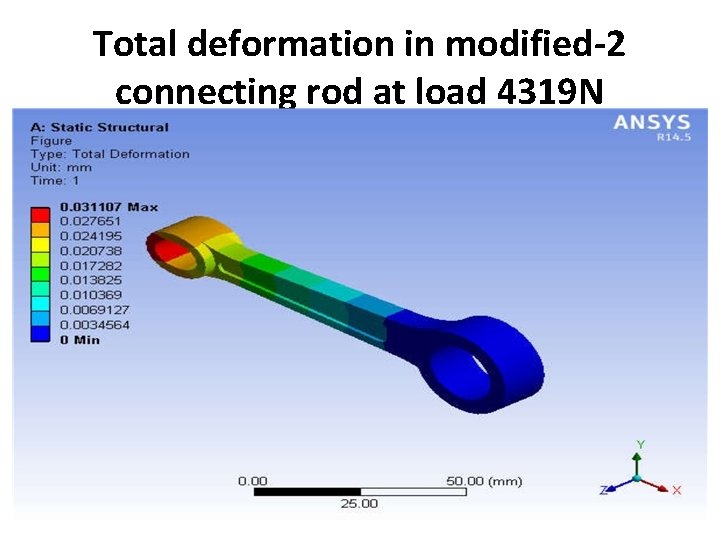
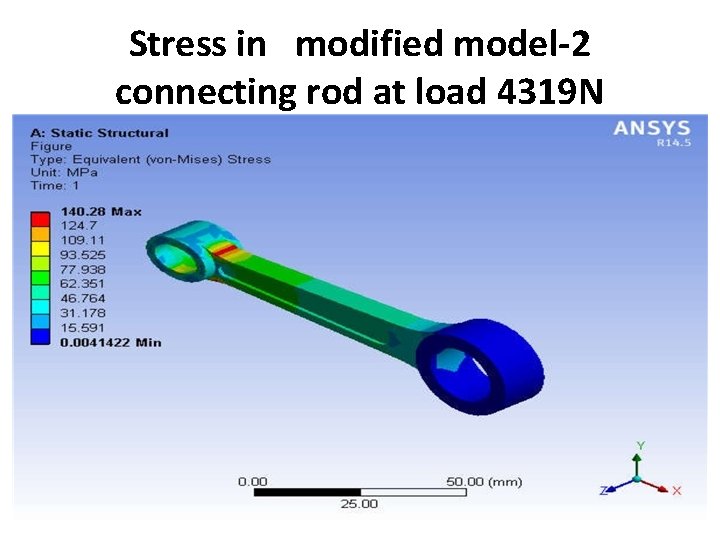
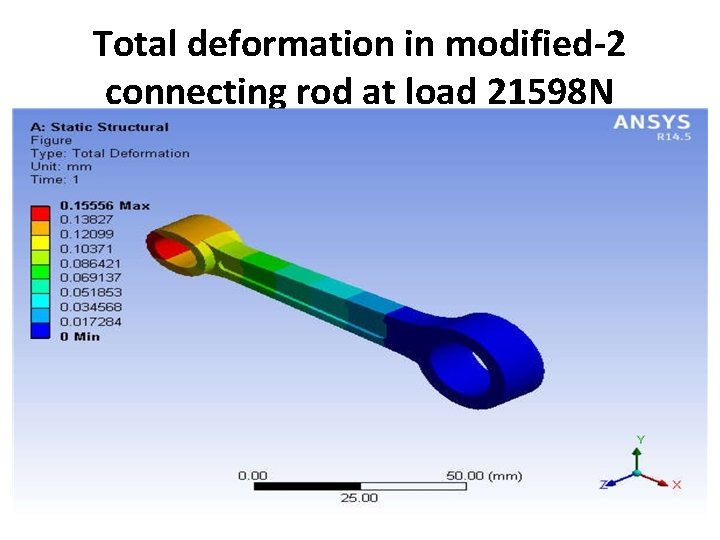
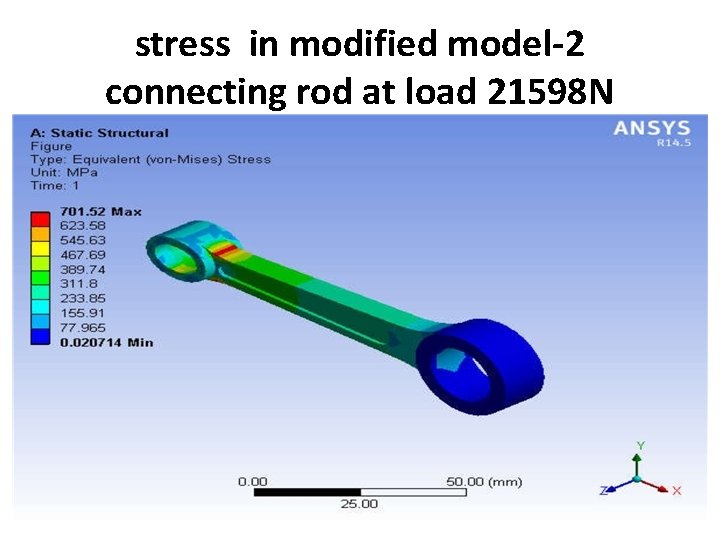
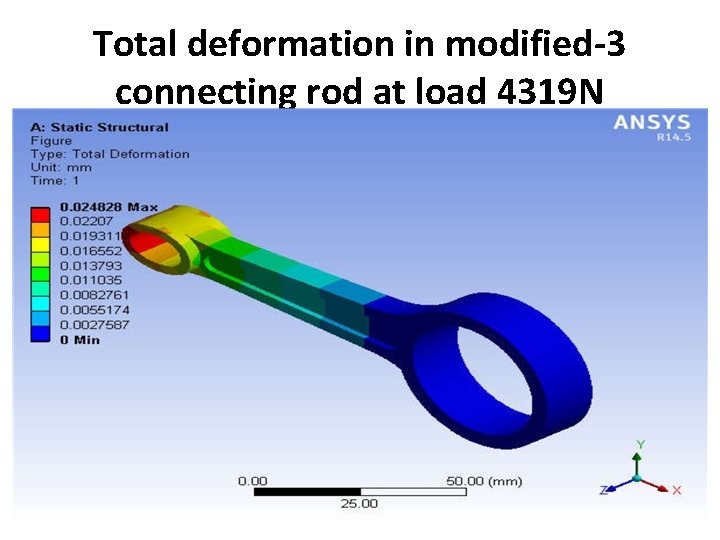
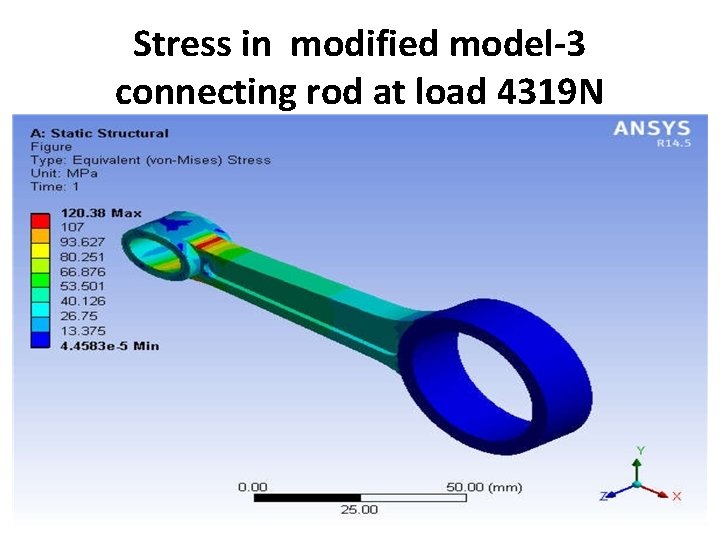
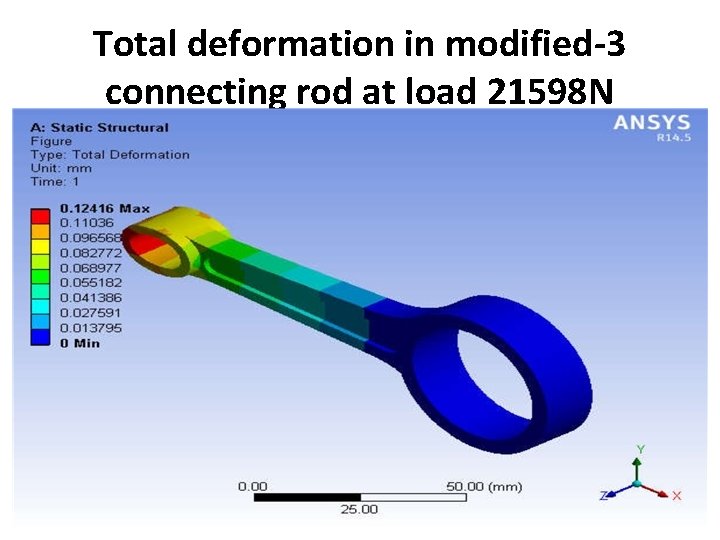
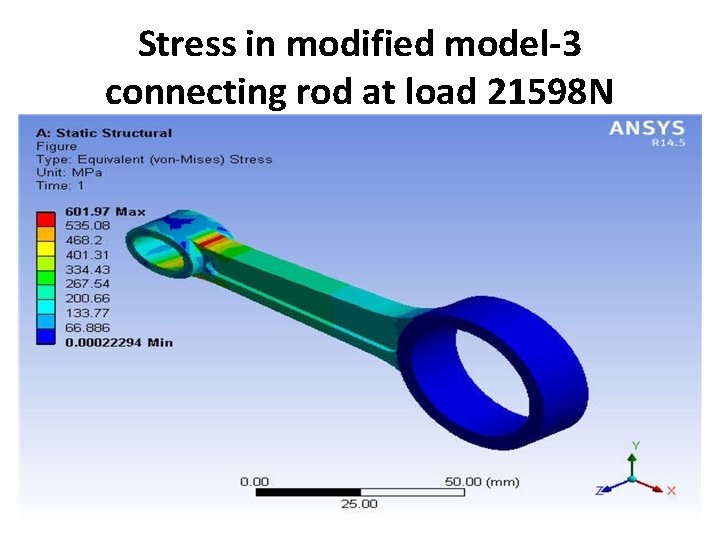
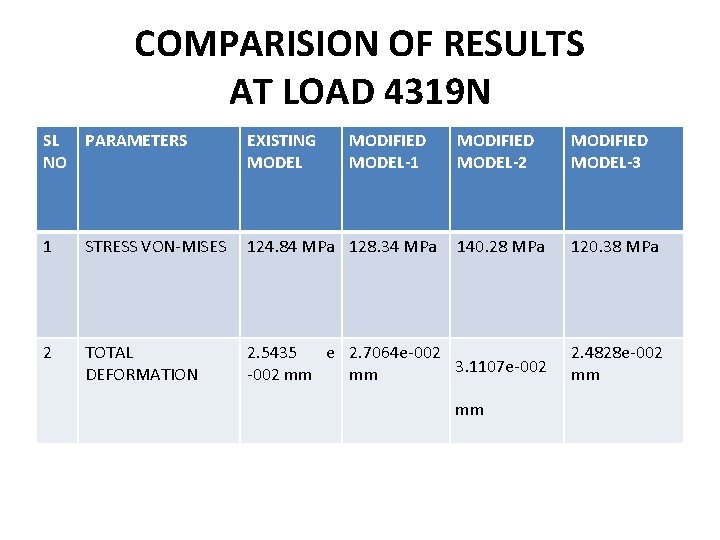
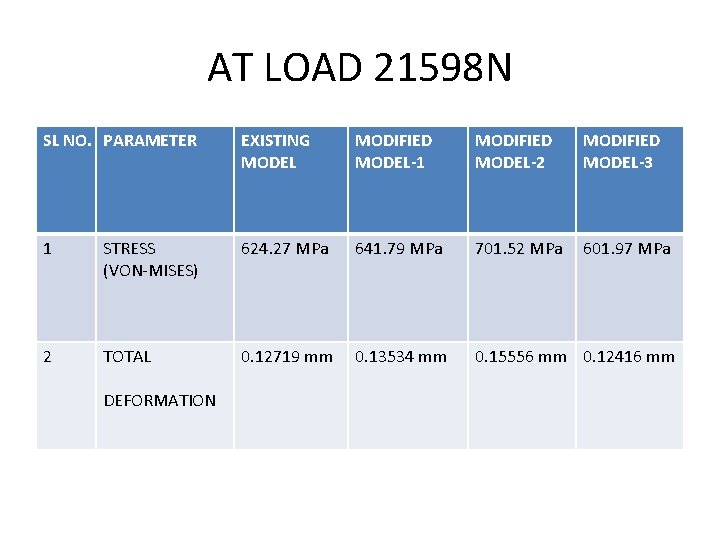
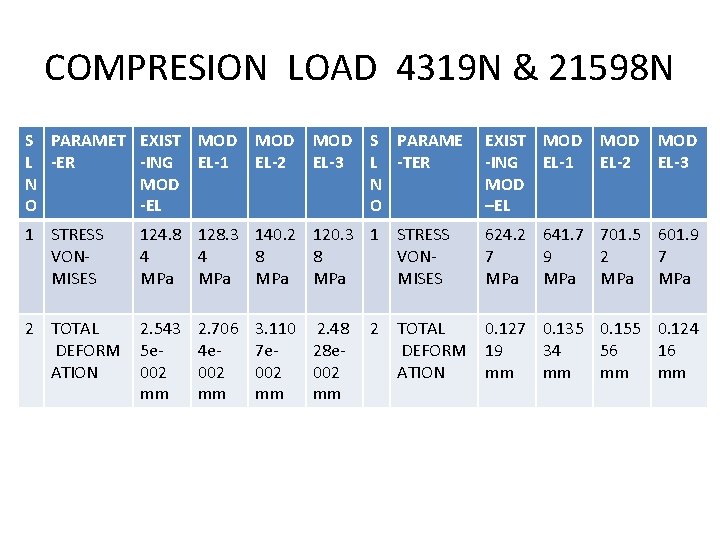
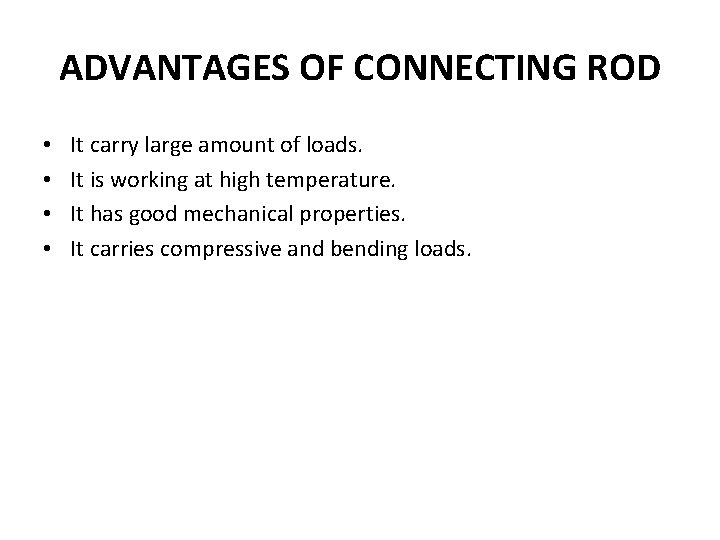
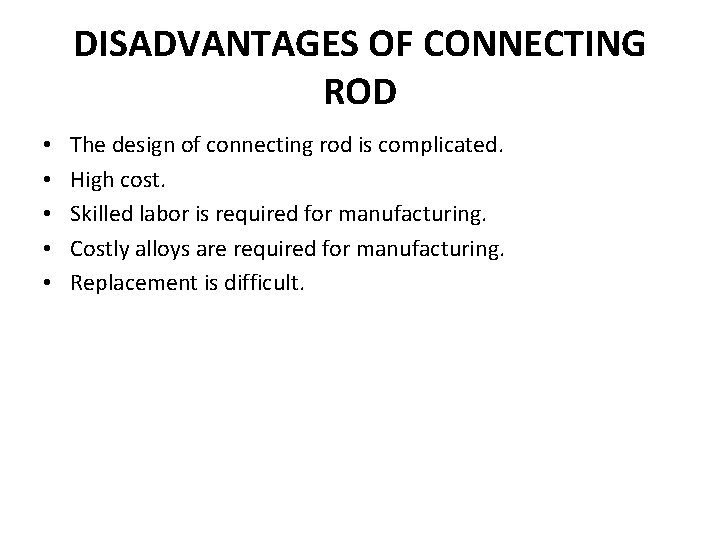
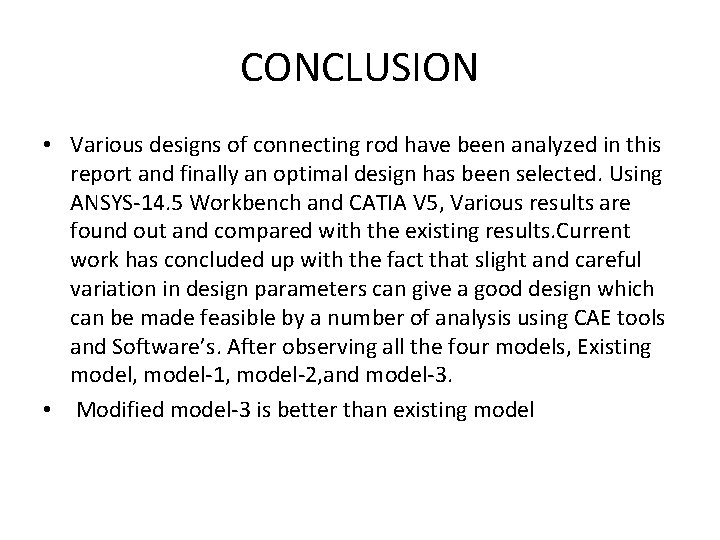
- Slides: 46
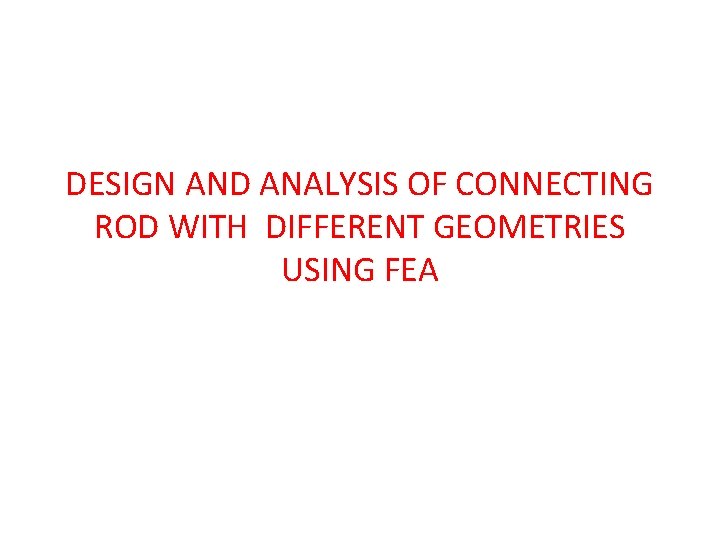
DESIGN AND ANALYSIS OF CONNECTING ROD WITH DIFFERENT GEOMETRIES USING FEA
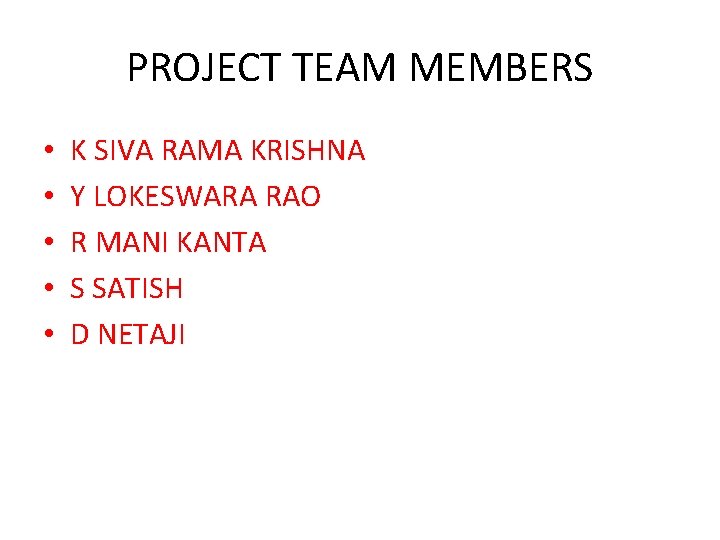
PROJECT TEAM MEMBERS • • • K SIVA RAMA KRISHNA Y LOKESWARA RAO R MANI KANTA S SATISH D NETAJI
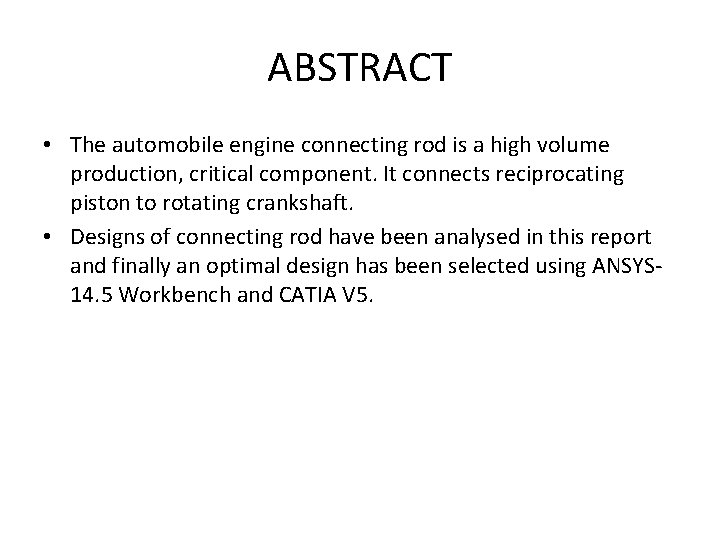
ABSTRACT • The automobile engine connecting rod is a high volume production, critical component. It connects reciprocating piston to rotating crankshaft. • Designs of connecting rod have been analysed in this report and finally an optimal design has been selected using ANSYS 14. 5 Workbench and CATIA V 5.
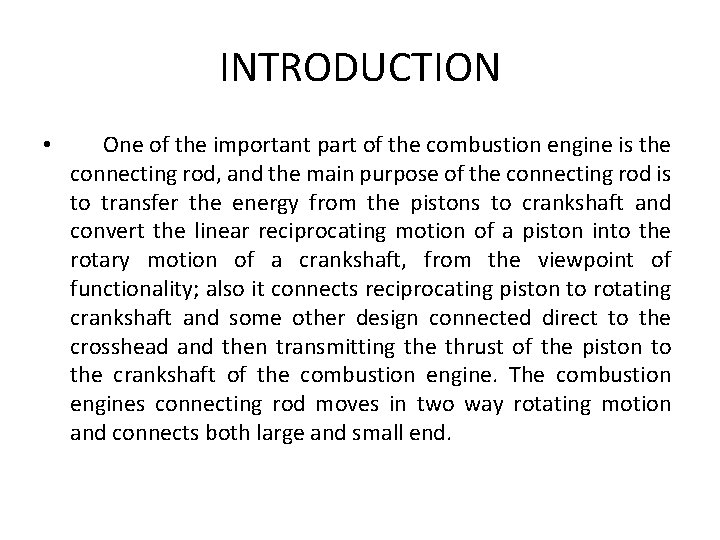
INTRODUCTION • One of the important part of the combustion engine is the connecting rod, and the main purpose of the connecting rod is to transfer the energy from the pistons to crankshaft and convert the linear reciprocating motion of a piston into the rotary motion of a crankshaft, from the viewpoint of functionality; also it connects reciprocating piston to rotating crankshaft and some other design connected direct to the crosshead and then transmitting the thrust of the piston to the crankshaft of the combustion engine. The combustion engines connecting rod moves in two way rotating motion and connects both large and small end.

PARTS AND COMPONENTS OF CONNECTING ROD
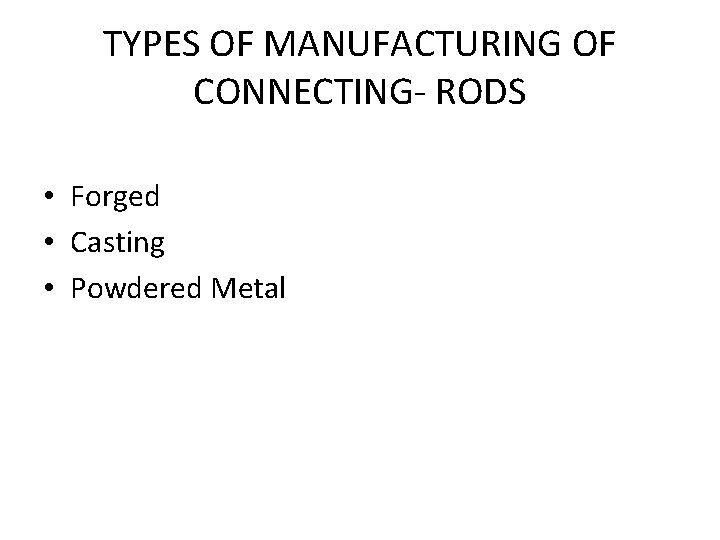
TYPES OF MANUFACTURING OF CONNECTING- RODS • Forged • Casting • Powdered Metal
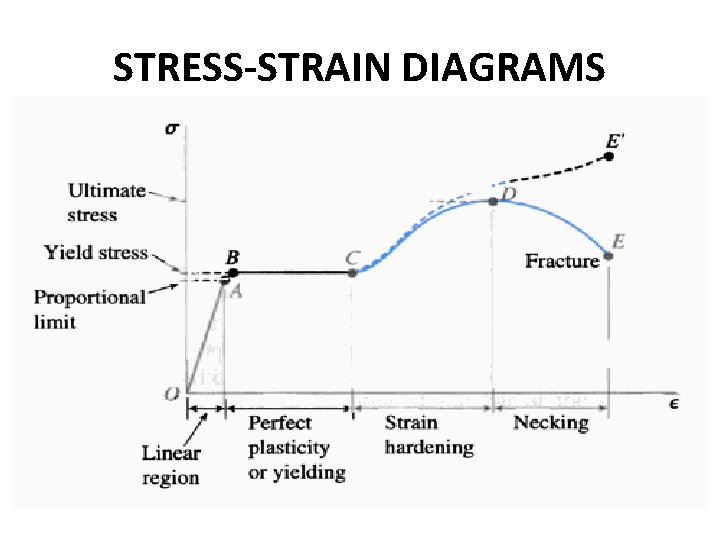
STRESS-STRAIN DIAGRAMS
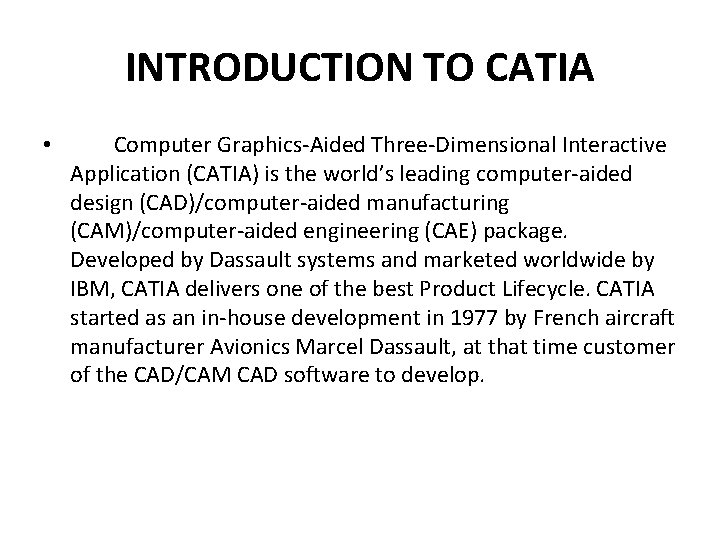
INTRODUCTION TO CATIA • Computer Graphics-Aided Three-Dimensional Interactive Application (CATIA) is the world’s leading computer-aided design (CAD)/computer-aided manufacturing (CAM)/computer-aided engineering (CAE) package. Developed by Dassault systems and marketed worldwide by IBM, CATIA delivers one of the best Product Lifecycle. CATIA started as an in-house development in 1977 by French aircraft manufacturer Avionics Marcel Dassault, at that time customer of the CAD/CAM CAD software to develop.
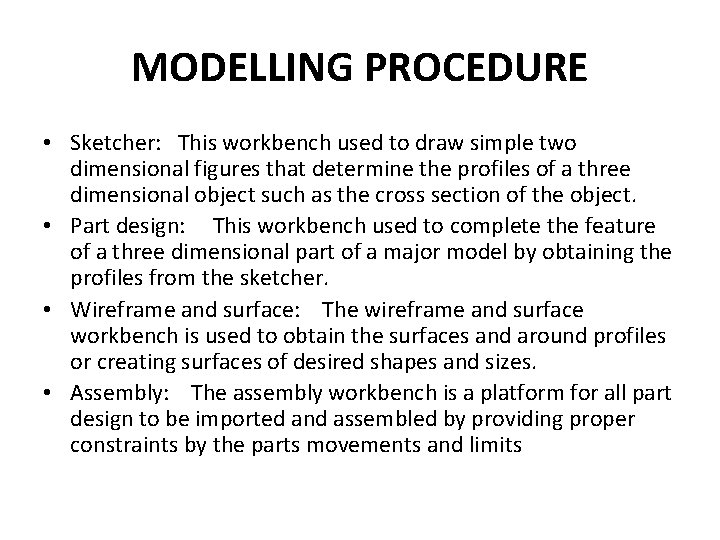
MODELLING PROCEDURE • Sketcher: This workbench used to draw simple two dimensional figures that determine the profiles of a three dimensional object such as the cross section of the object. • Part design: This workbench used to complete the feature of a three dimensional part of a major model by obtaining the profiles from the sketcher. • Wireframe and surface: The wireframe and surface workbench is used to obtain the surfaces and around profiles or creating surfaces of desired shapes and sizes. • Assembly: The assembly workbench is a platform for all part design to be imported and assembled by providing proper constraints by the parts movements and limits
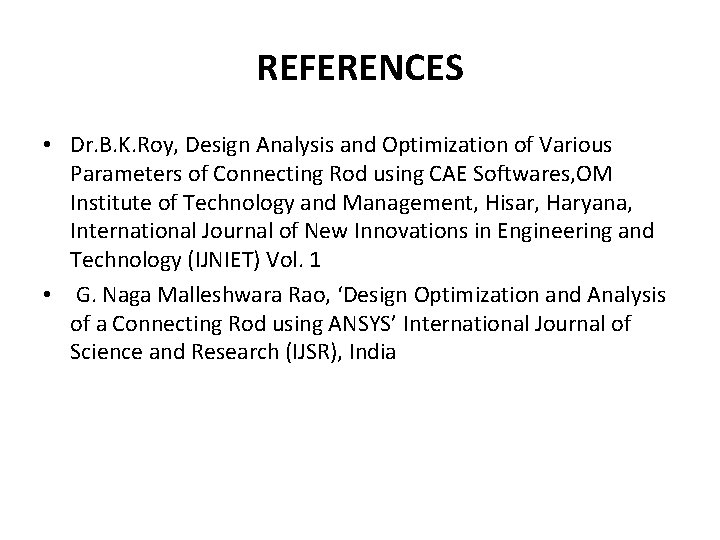
REFERENCES • Dr. B. K. Roy, Design Analysis and Optimization of Various Parameters of Connecting Rod using CAE Softwares, OM Institute of Technology and Management, Hisar, Haryana, International Journal of New Innovations in Engineering and Technology (IJNIET) Vol. 1 • G. Naga Malleshwara Rao, ‘Design Optimization and Analysis of a Connecting Rod using ANSYS’ International Journal of Science and Research (IJSR), India
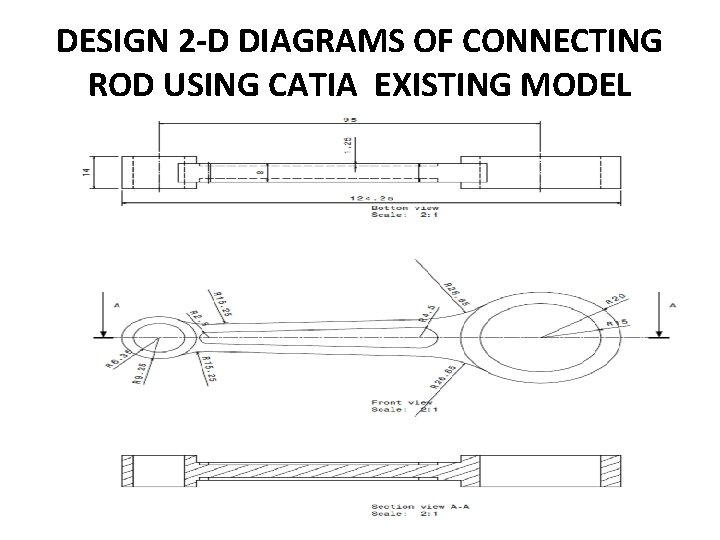
DESIGN 2 -D DIAGRAMS OF CONNECTING ROD USING CATIA EXISTING MODEL
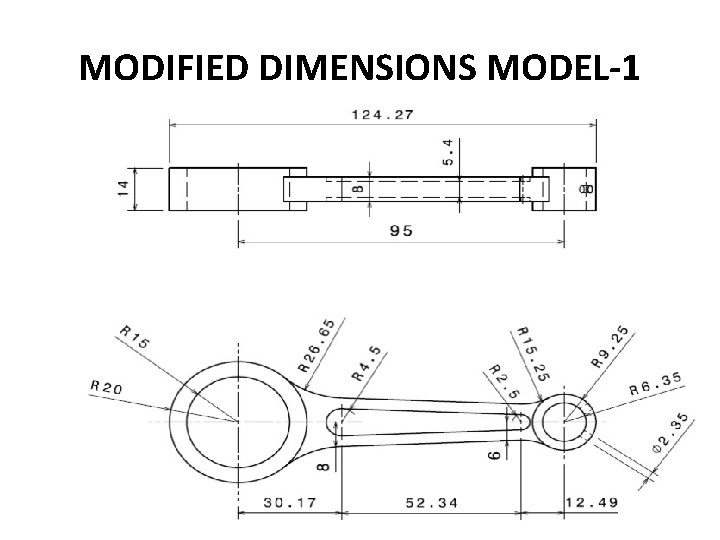
MODIFIED DIMENSIONS MODEL-1
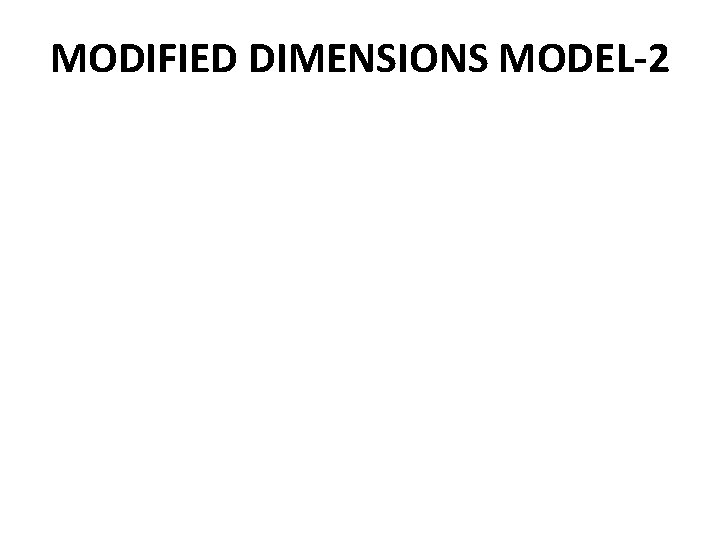
MODIFIED DIMENSIONS MODEL-2
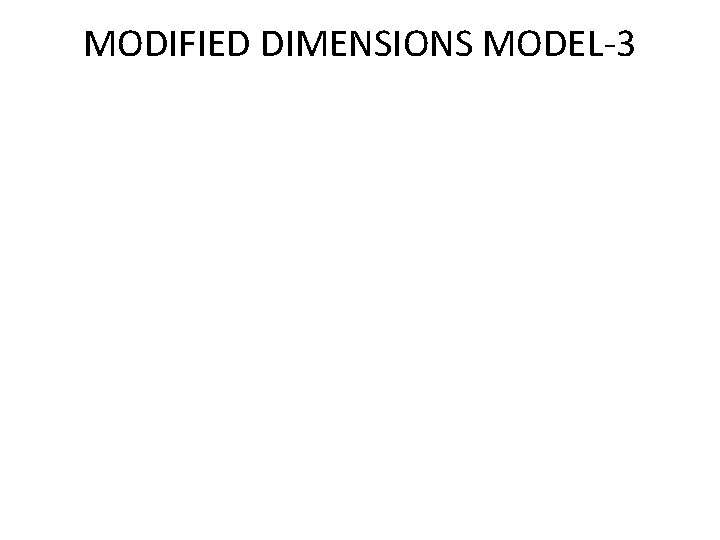
MODIFIED DIMENSIONS MODEL-3
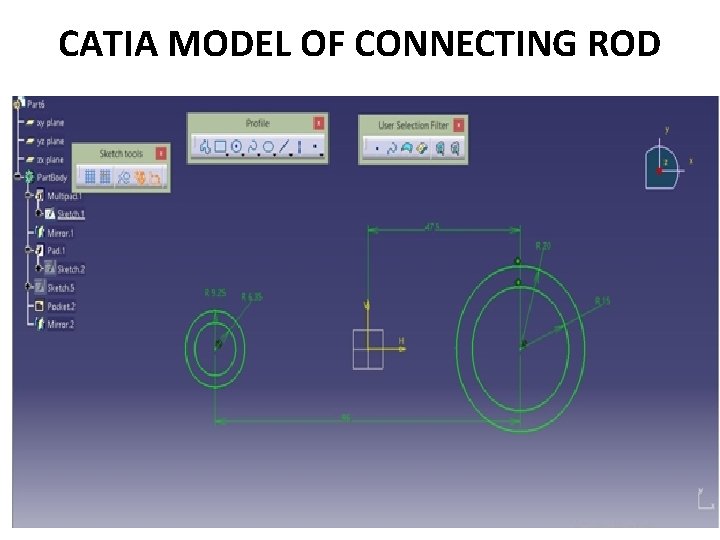
CATIA MODEL OF CONNECTING ROD
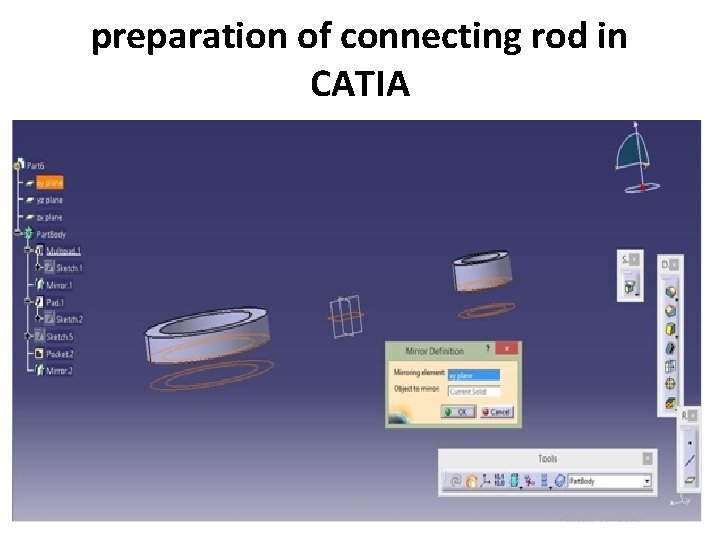
preparation of connecting rod in CATIA
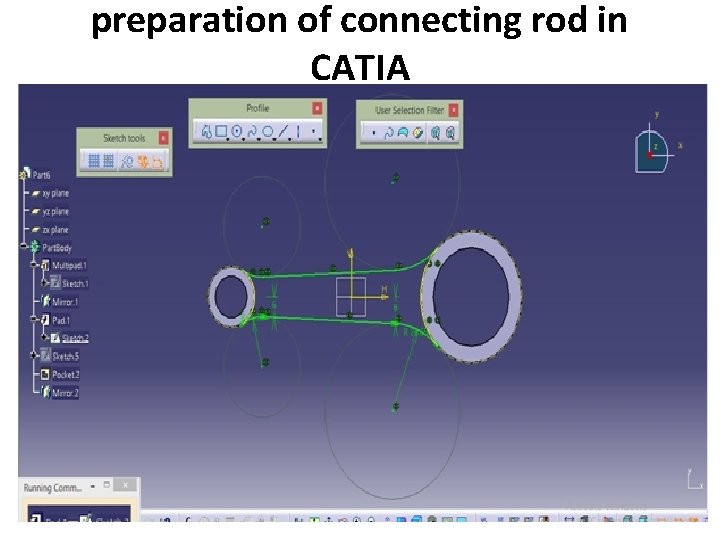
preparation of connecting rod in CATIA
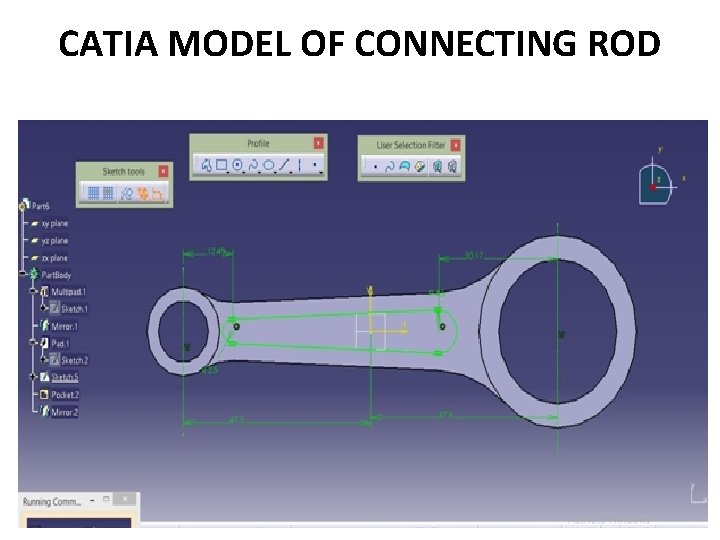
CATIA MODEL OF CONNECTING ROD
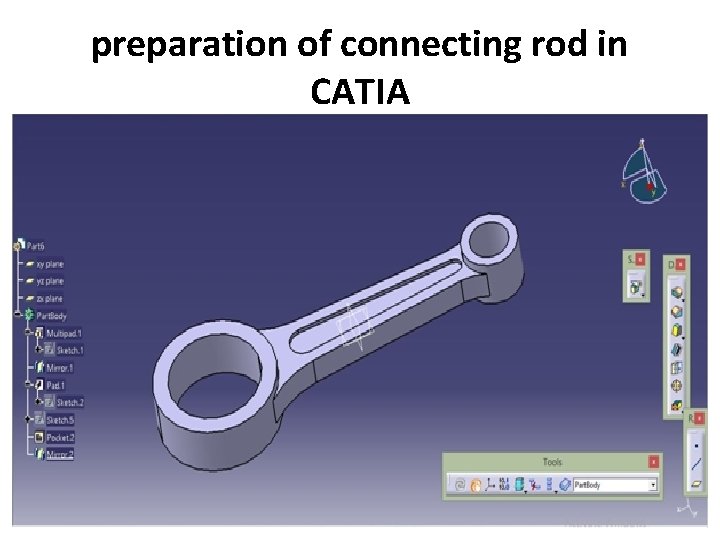
preparation of connecting rod in CATIA
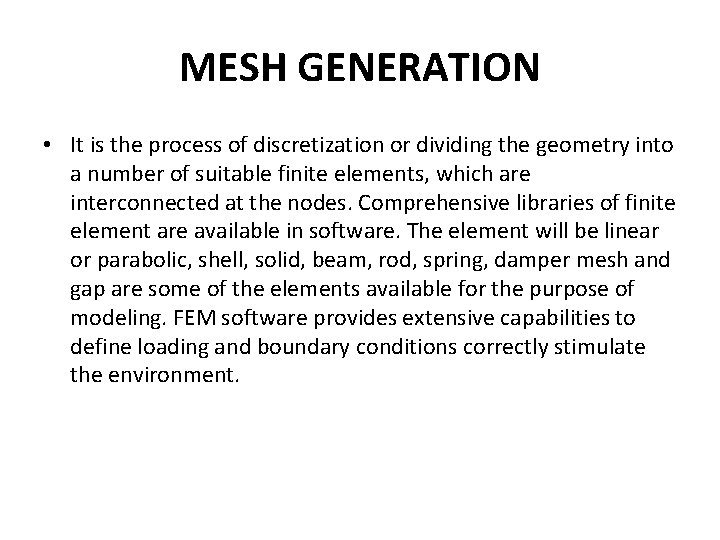
MESH GENERATION • It is the process of discretization or dividing the geometry into a number of suitable finite elements, which are interconnected at the nodes. Comprehensive libraries of finite element are available in software. The element will be linear or parabolic, shell, solid, beam, rod, spring, damper mesh and gap are some of the elements available for the purpose of modeling. FEM software provides extensive capabilities to define loading and boundary conditions correctly stimulate the environment.
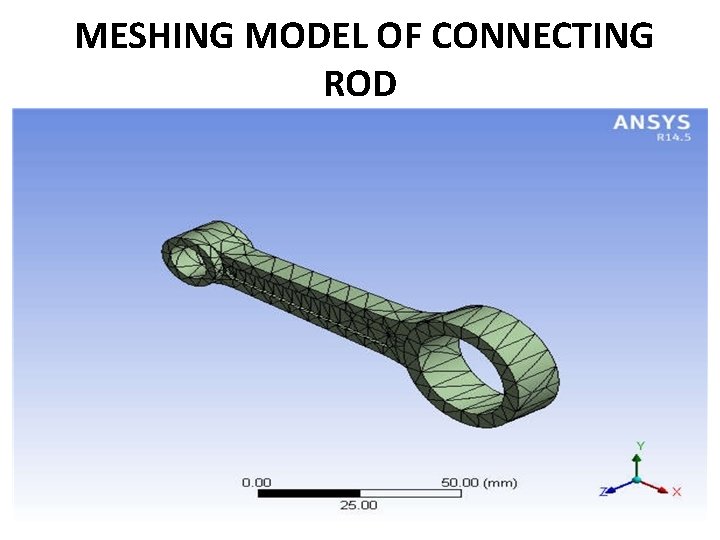
MESHING MODEL OF CONNECTING ROD
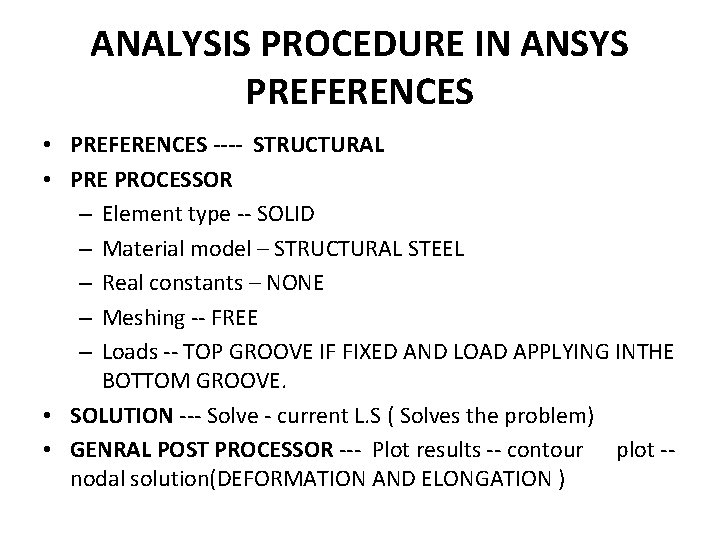
ANALYSIS PROCEDURE IN ANSYS PREFERENCES • PREFERENCES ---- STRUCTURAL • PRE PROCESSOR – Element type -- SOLID – Material model – STRUCTURAL STEEL – Real constants – NONE – Meshing -- FREE – Loads -- TOP GROOVE IF FIXED AND LOAD APPLYING INTHE BOTTOM GROOVE. • SOLUTION --- Solve - current L. S ( Solves the problem) • GENRAL POST PROCESSOR --- Plot results -- contour plot -- nodal solution(DEFORMATION AND ELONGATION )
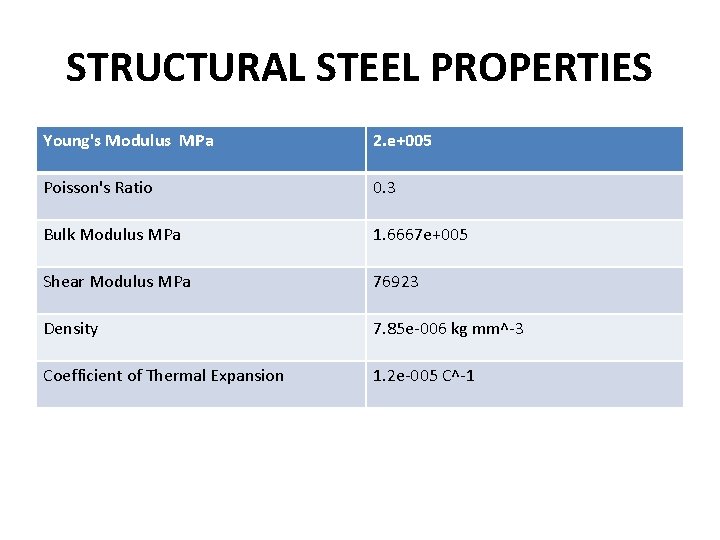
STRUCTURAL STEEL PROPERTIES Young's Modulus MPa 2. e+005 Poisson's Ratio 0. 3 Bulk Modulus MPa 1. 6667 e+005 Shear Modulus MPa 76923 Density 7. 85 e-006 kg mm^-3 Coefficient of Thermal Expansion 1. 2 e-005 C^-1
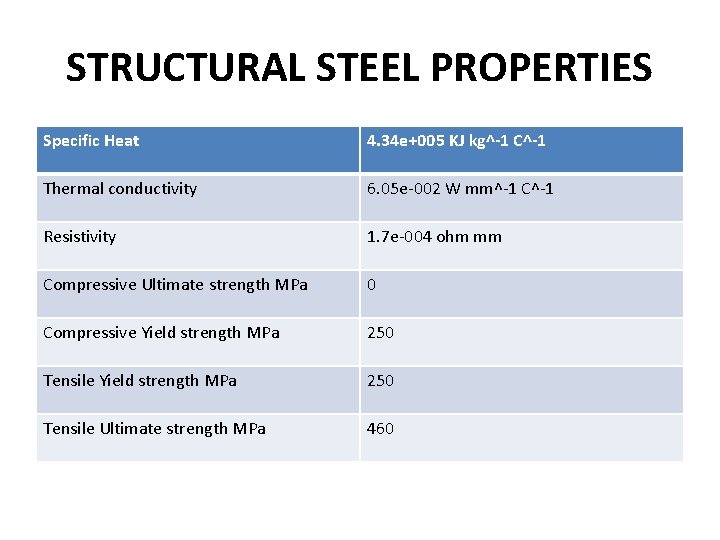
STRUCTURAL STEEL PROPERTIES Specific Heat 4. 34 e+005 KJ kg^-1 C^-1 Thermal conductivity 6. 05 e-002 W mm^-1 C^-1 Resistivity 1. 7 e-004 ohm mm Compressive Ultimate strength MPa 0 Compressive Yield strength MPa 250 Tensile Ultimate strength MPa 460
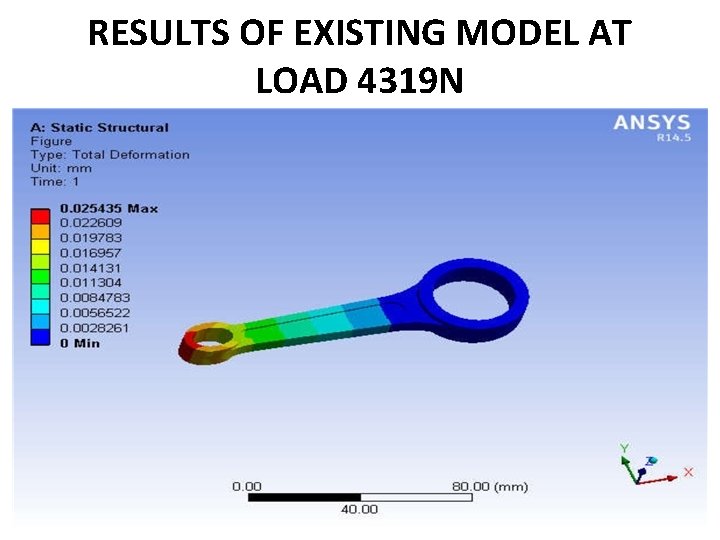
RESULTS OF EXISTING MODEL AT LOAD 4319 N
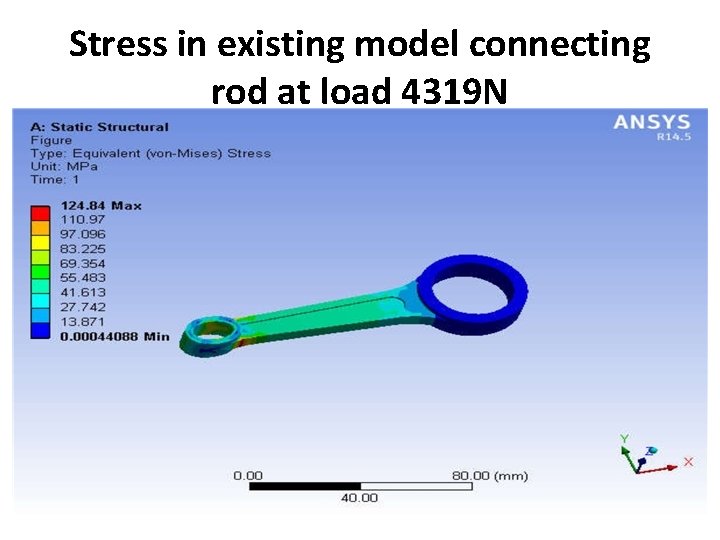
Stress in existing model connecting rod at load 4319 N

Total deformation in existing model connecting rod at load 21598 N
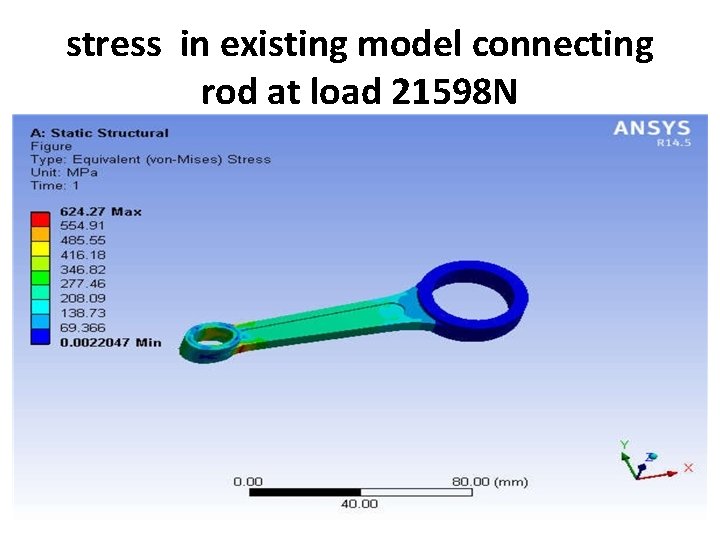
stress in existing model connecting rod at load 21598 N
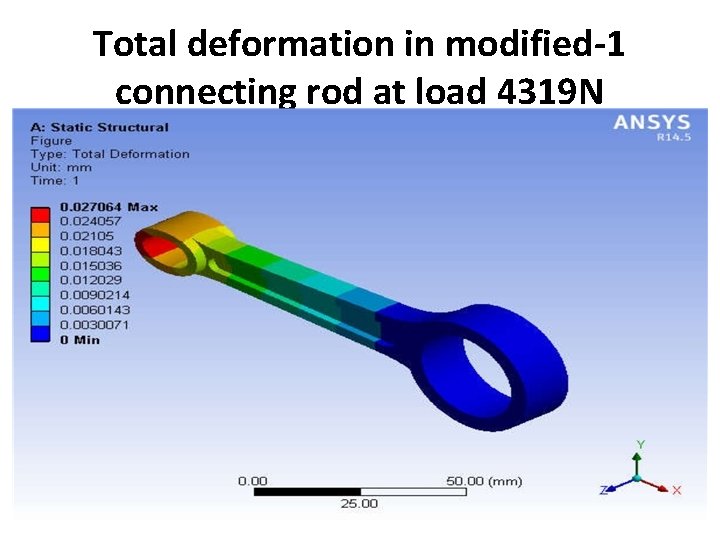
Total deformation in modified-1 connecting rod at load 4319 N
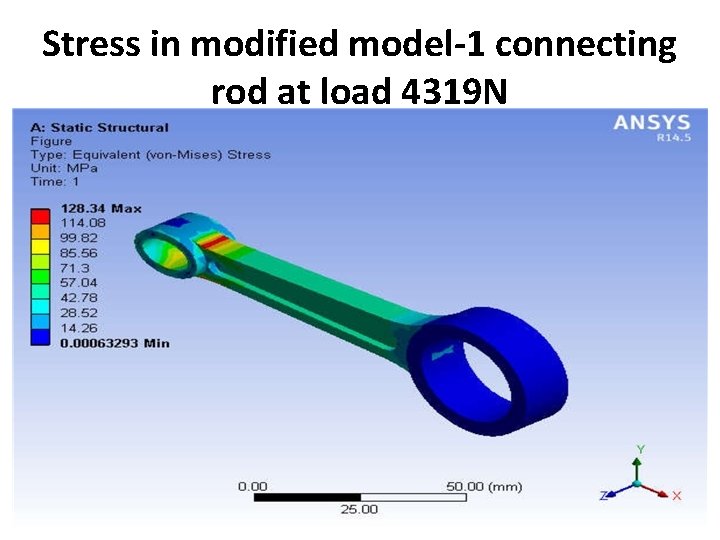
Stress in modified model-1 connecting rod at load 4319 N
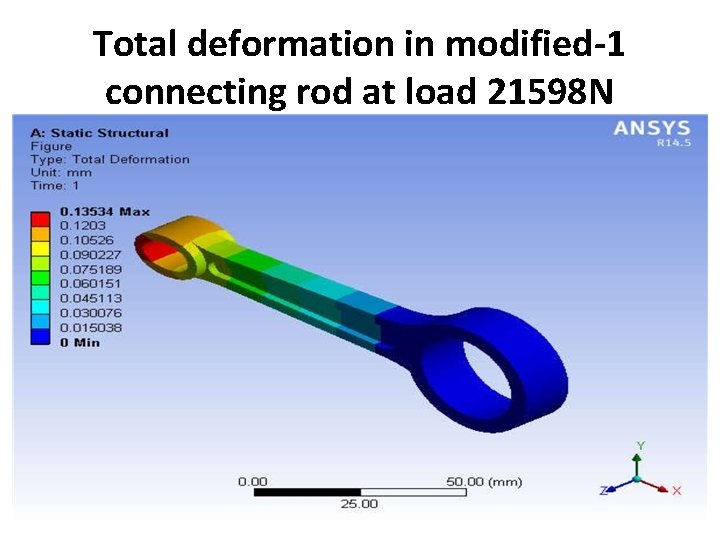
Total deformation in modified-1 connecting rod at load 21598 N

Stress in modified model-1 connecting rod at load 21598 N
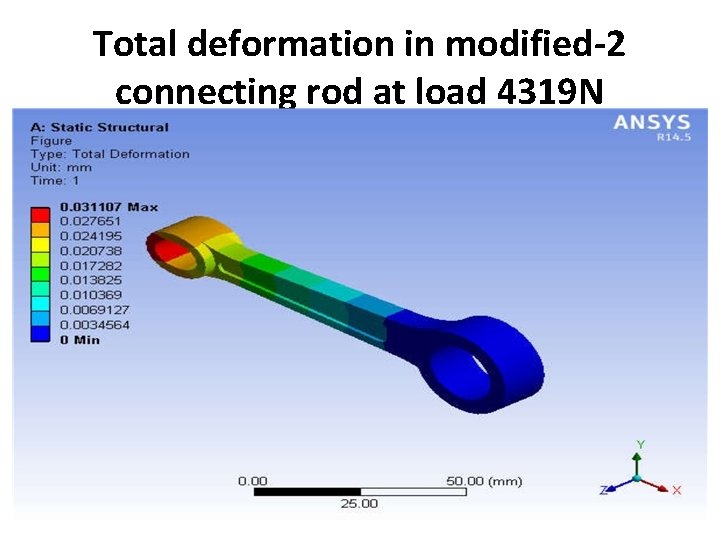
Total deformation in modified-2 connecting rod at load 4319 N
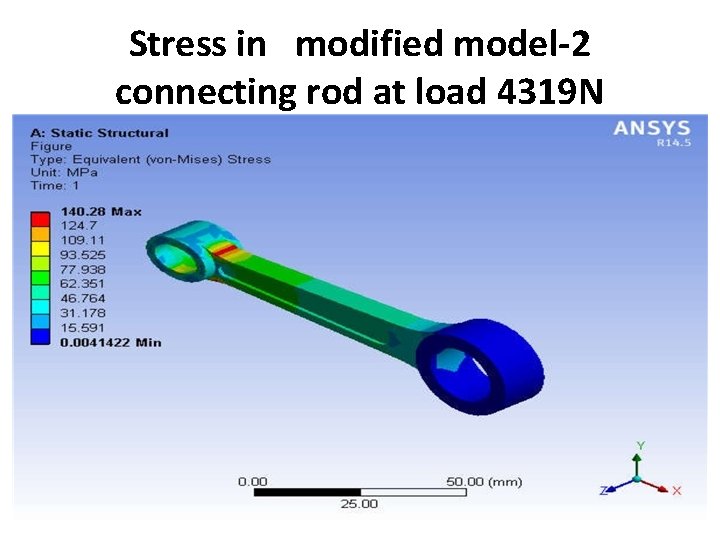
Stress in modified model-2 connecting rod at load 4319 N
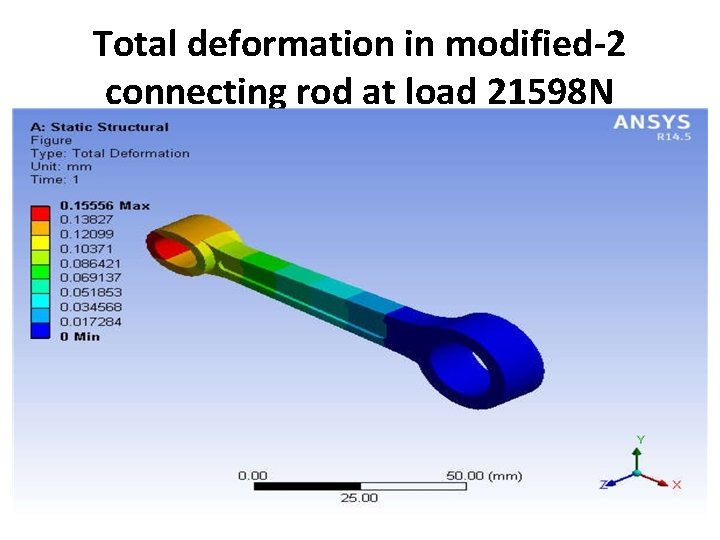
Total deformation in modified-2 connecting rod at load 21598 N
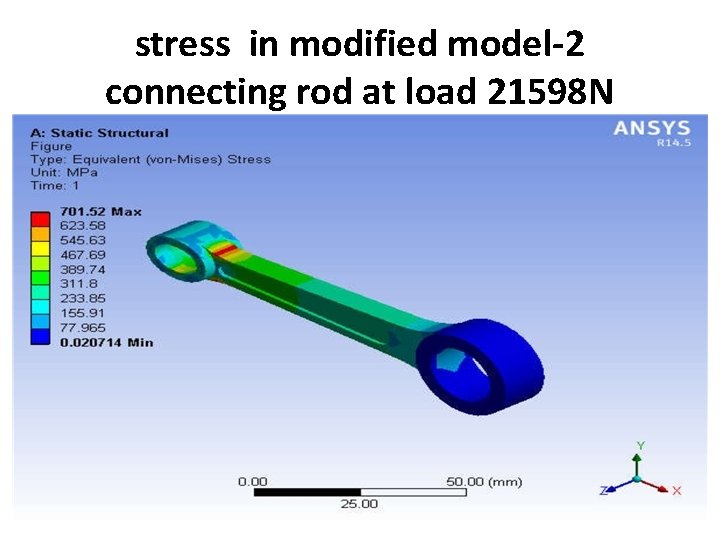
stress in modified model-2 connecting rod at load 21598 N
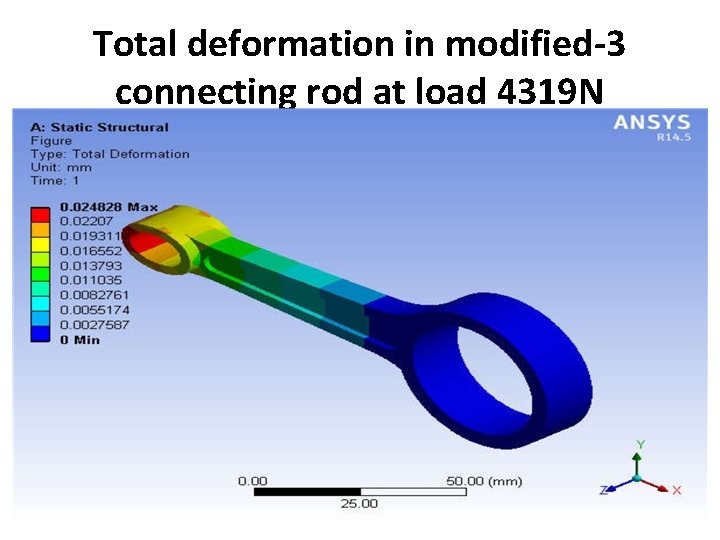
Total deformation in modified-3 connecting rod at load 4319 N
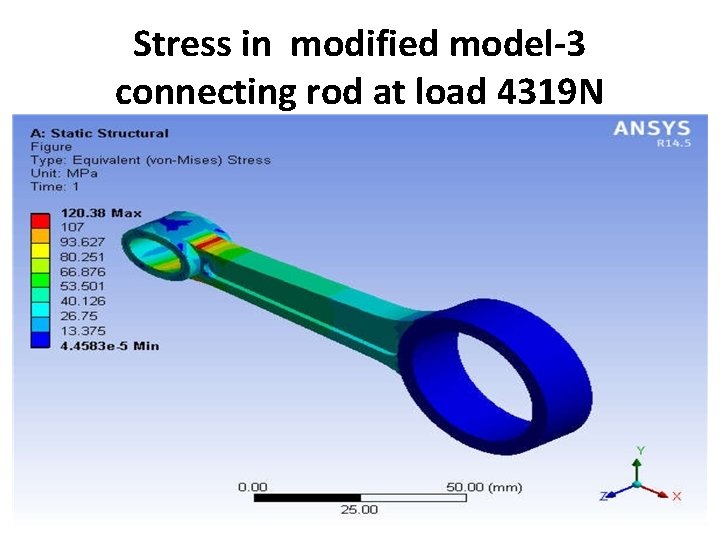
Stress in modified model-3 connecting rod at load 4319 N
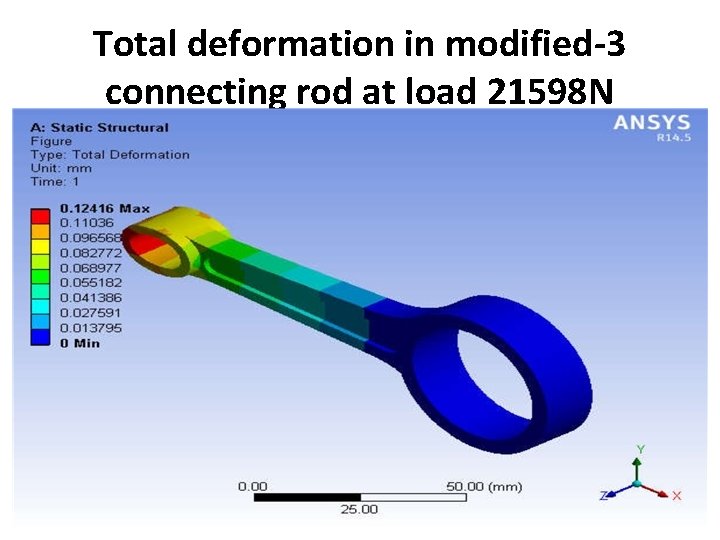
Total deformation in modified-3 connecting rod at load 21598 N
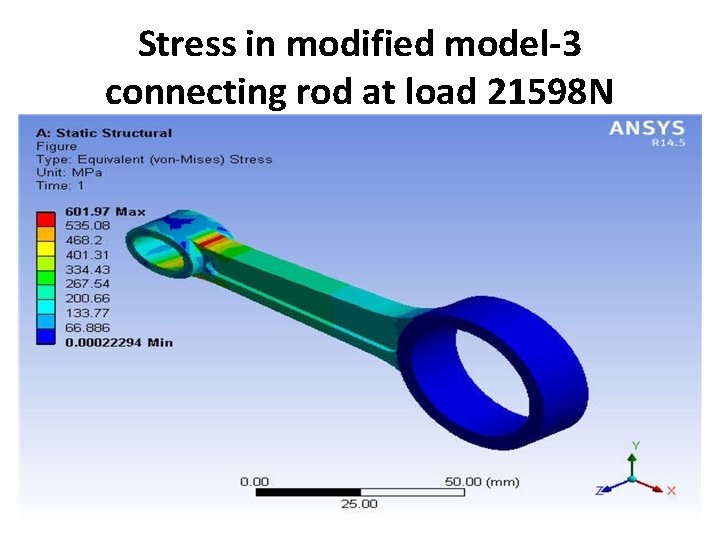
Stress in modified model-3 connecting rod at load 21598 N
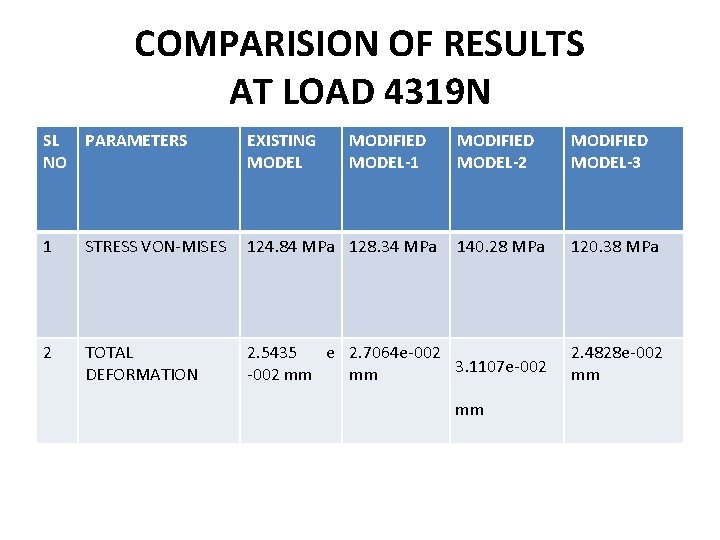
COMPARISION OF RESULTS AT LOAD 4319 N SL PARAMETERS NO EXISTING MODEL MODIFIED MODEL-1 MODIFIED MODEL-2 MODIFIED MODEL-3 1 STRESS VON-MISES 124. 84 MPa 128. 34 MPa 140. 28 MPa 120. 38 MPa 2 TOTAL DEFORMATION 2. 5435 e 2. 7064 e-002 3. 1107 e-002 mm mm mm 2. 4828 e-002 mm
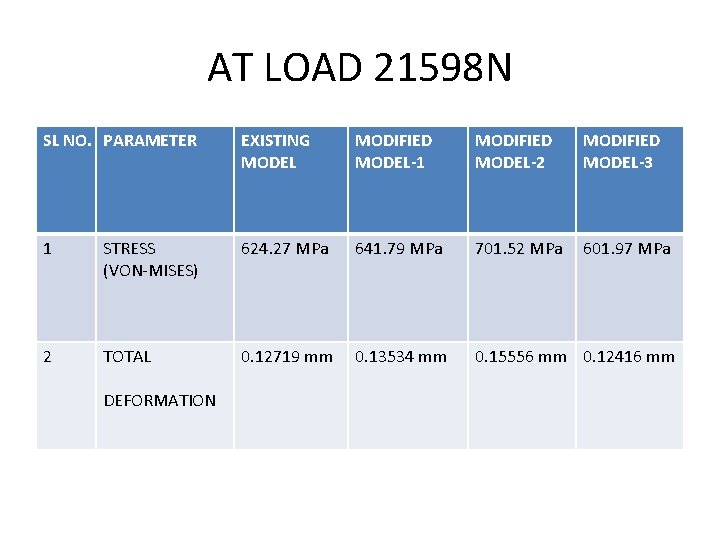
AT LOAD 21598 N SL NO. PARAMETER EXISTING MODEL MODIFIED MODEL-1 MODIFIED MODEL-2 MODIFIED MODEL-3 1 STRESS (VON-MISES) 624. 27 MPa 641. 79 MPa 701. 52 MPa 601. 97 MPa 2 TOTAL DEFORMATION 0. 12719 mm 0. 13534 mm 0. 15556 mm 0. 12416 mm
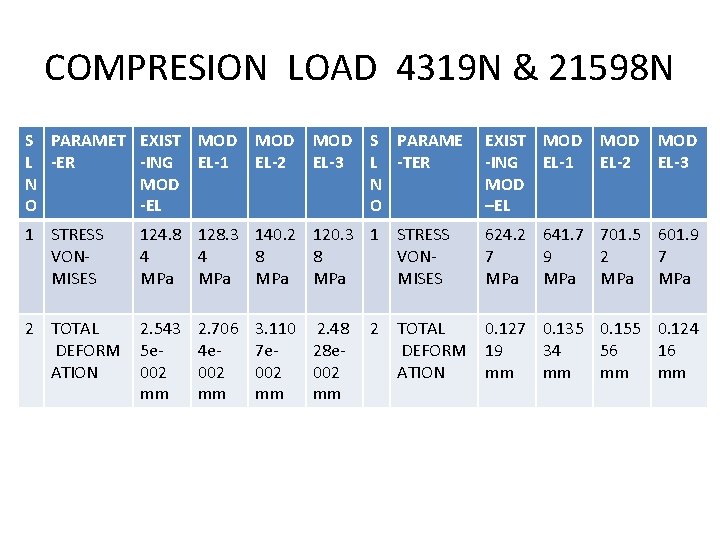
COMPRESION LOAD 4319 N & 21598 N S PARAMET EXIST MOD L -ER -ING EL-1 N MOD O -EL MOD EL-2 MOD EL-3 S PARAME L -TER N O EXIST MOD -ING EL-1 MOD –EL MOD EL-2 MOD EL-3 1 STRESS VONMISES 124. 8 128. 3 140. 2 120. 3 1 STRESS 4 4 8 8 VONMPa MPa MISES 624. 2 641. 7 701. 5 601. 9 7 9 2 7 MPa MPa 2 TOTAL DEFORM ATION 2. 543 5 e 002 mm 0. 127 0. 135 0. 155 0. 124 19 34 56 16 mm mm 2. 706 4 e 002 mm 3. 110 7 e 002 mm 2. 48 28 e 002 mm 2 TOTAL DEFORM ATION
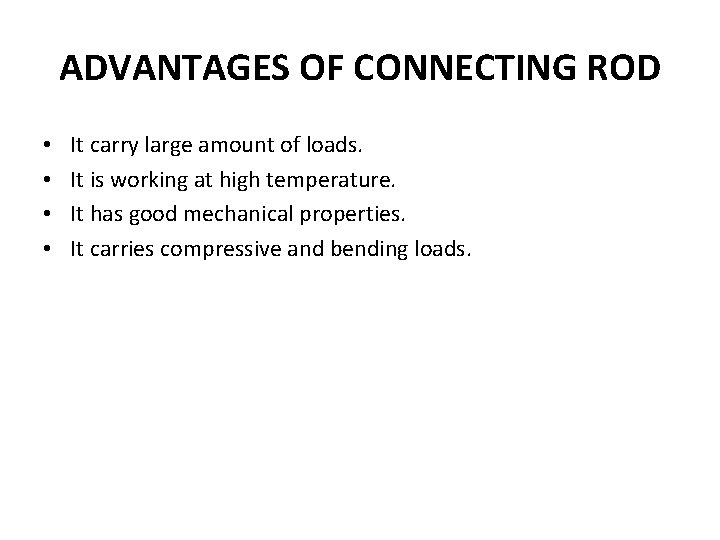
ADVANTAGES OF CONNECTING ROD • • It carry large amount of loads. It is working at high temperature. It has good mechanical properties. It carries compressive and bending loads.
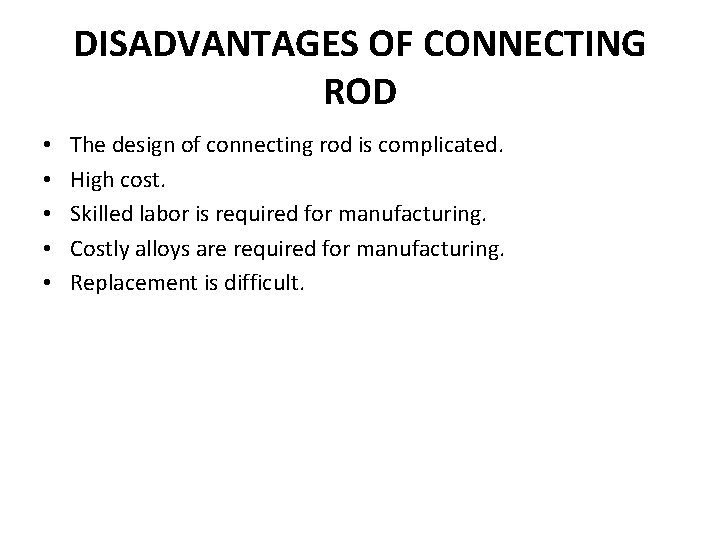
DISADVANTAGES OF CONNECTING ROD • • • The design of connecting rod is complicated. High cost. Skilled labor is required for manufacturing. Costly alloys are required for manufacturing. Replacement is difficult.
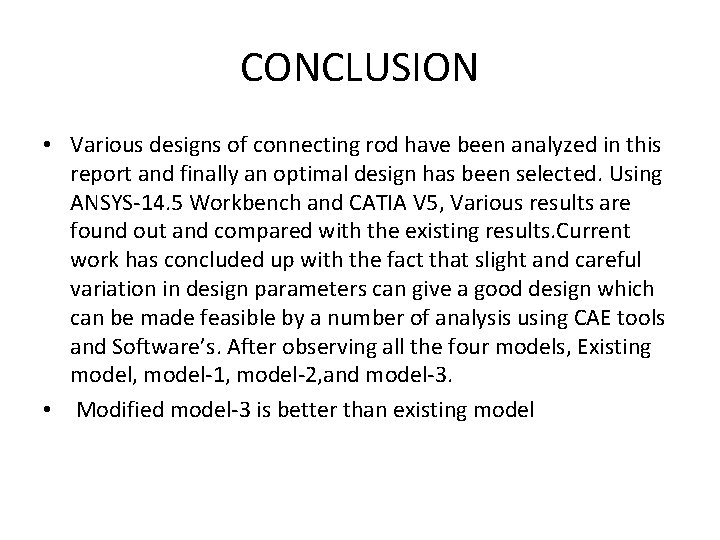
CONCLUSION • Various designs of connecting rod have been analyzed in this report and finally an optimal design has been selected. Using ANSYS-14. 5 Workbench and CATIA V 5, Various results are found out and compared with the existing results. Current work has concluded up with the fact that slight and careful variation in design parameters can give a good design which can be made feasible by a number of analysis using CAE tools and Software’s. After observing all the four models, Existing model, model-1, model-2, and model-3. • Modified model-3 is better than existing model
Connecting rod
Srednji rod primjeri
Fork and blade connecting rods
Marine ot desing
Input design and output design
What is the connecting stalk
Connectives that express cause and effect
Connecting a verbal description to table and graph
Pistons rings and connecting rods
The cleft connecting the nose and mouth to the larynx
Name the transversal connecting 1 and 5
User interface design in system analysis and design
Dialogue design in system analysis and design
What is structured analysis
Fact analysis in system analysis and design
System analysis and design project proposal example
Why do different polymers have different properties
Flame test principle
Sound will travel at different speeds in different mediums.
Sound will travel at different speeds in different mediums.
Cultural relarivism
Different angle different story
Different faces different places song
Different materials have different
No two people
Argumenterande tal struktur
Temporal isolation
Line connecting points of equal temperature
Hook background information thesis statement example
Connecting the concepts angiosperm reproductive structures
Creativity is just connecting things
Connecting families bath
Connecting the concepts sexual reproduction
Connecting the concepts aquatic biomes
Bus backbone and star backbone
Connecting the concepts sexual reproduction
Connecting the concepts evolution
Human domain and kingdom
Connecting the concepts macroevolution
Transversal connecting angles
A repeater is a connecting device that operates in the
Lysosome picture in animal cell
Connecting hemispheres world history
Pythagorean theorem
Connecting families bath
A repeater is a connecting device that operates in the
Connecting the concepts exploring life