Part Design The Part Design application is used
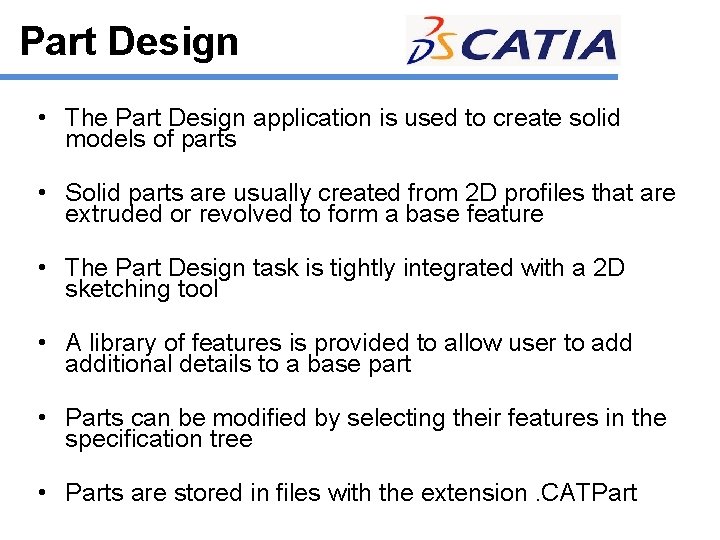
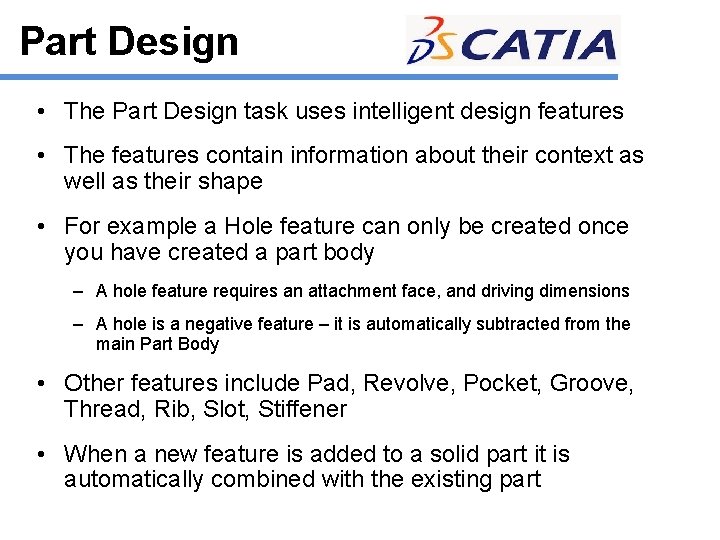
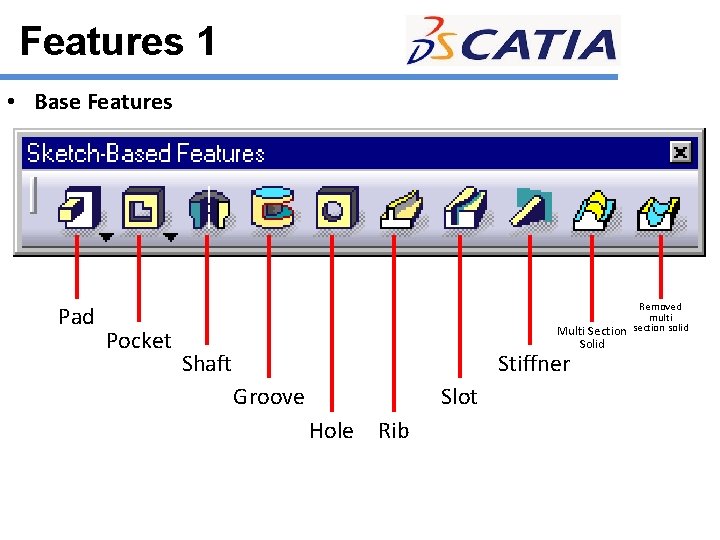
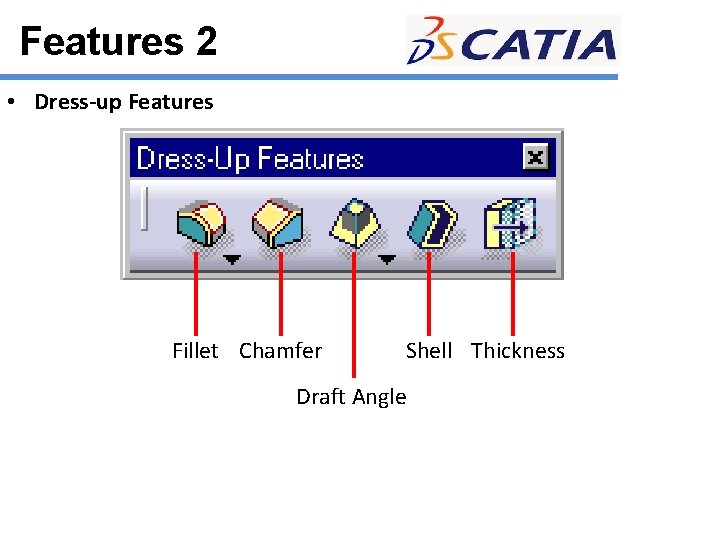
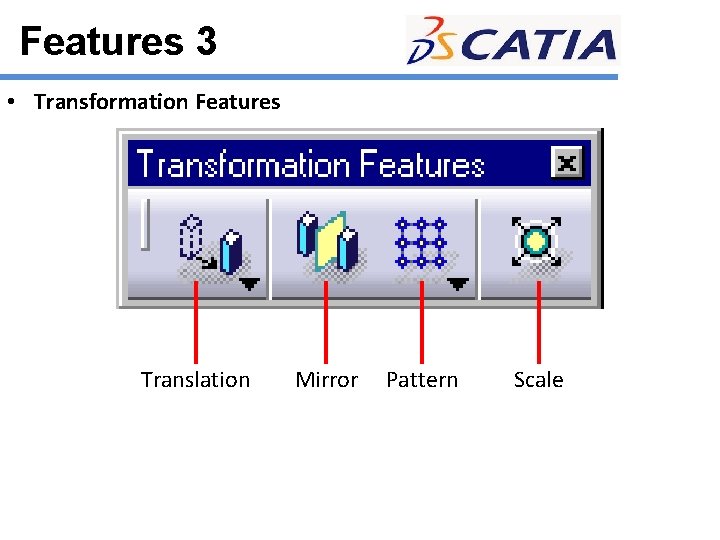
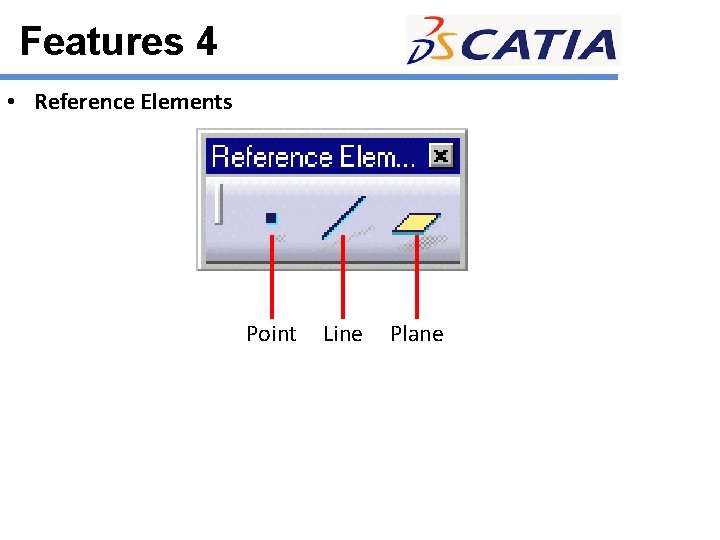
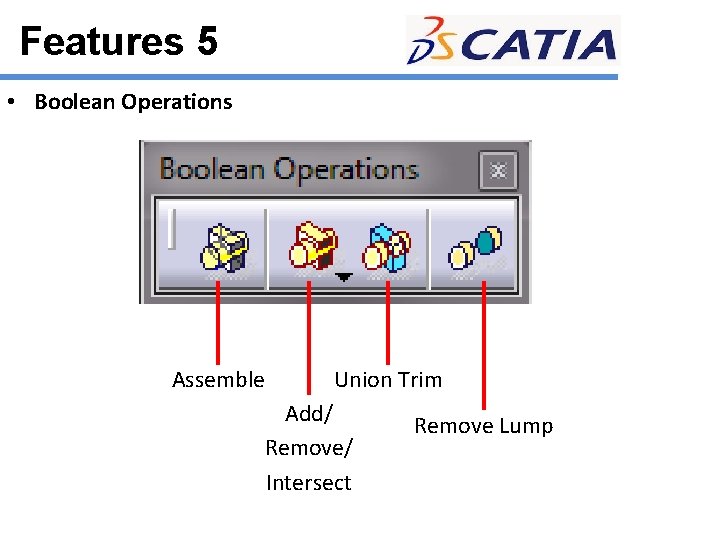
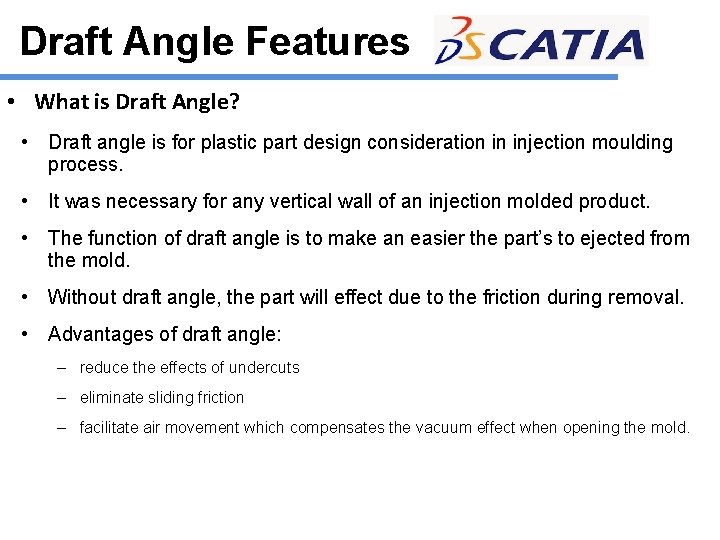
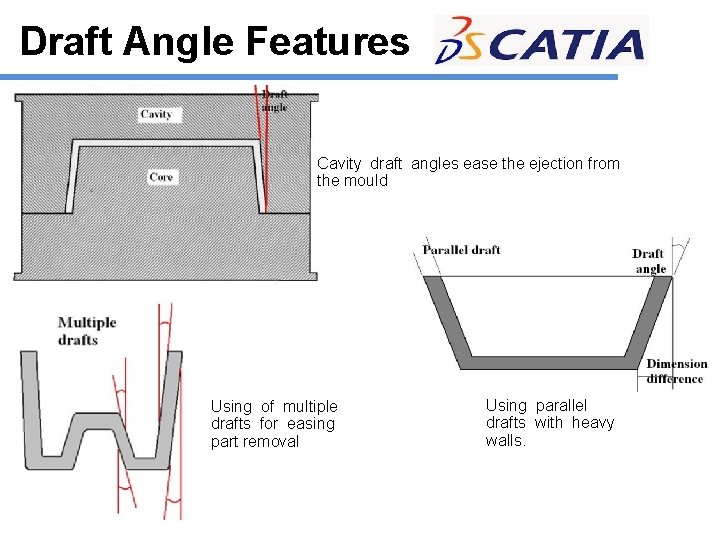
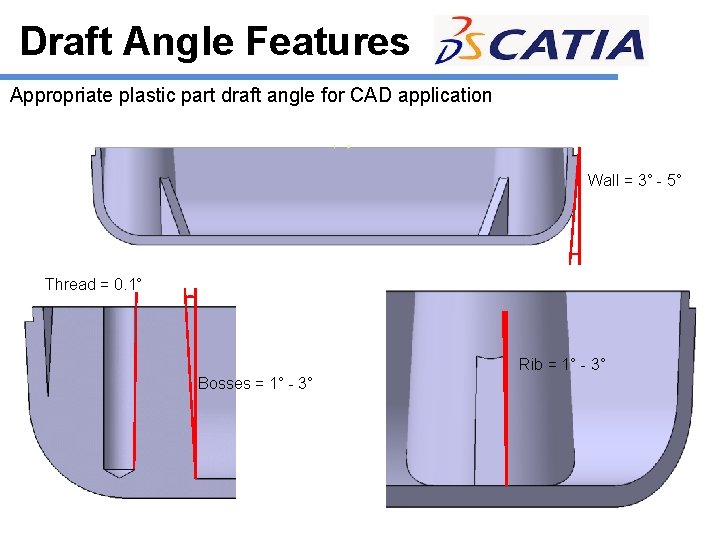
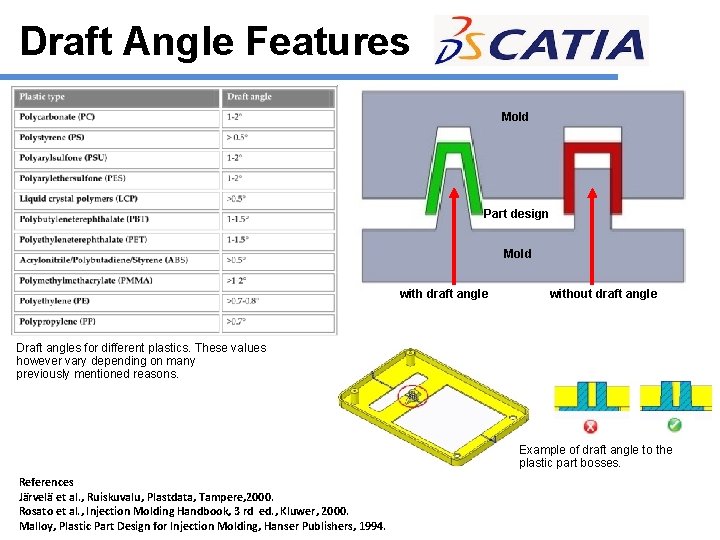
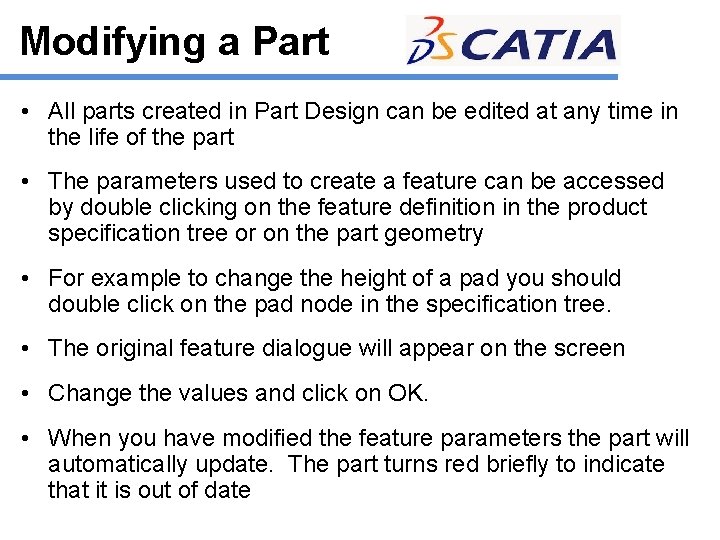
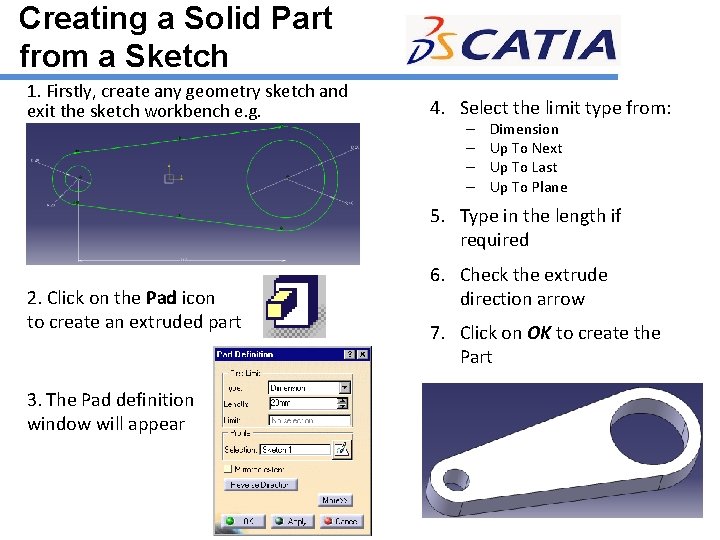
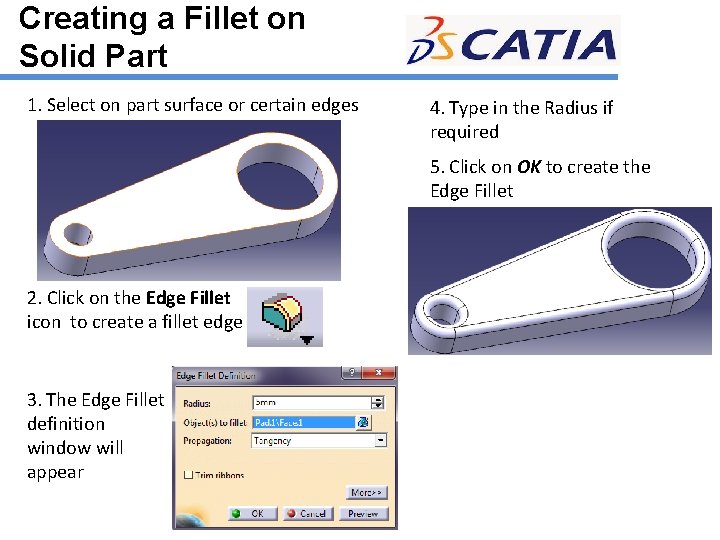
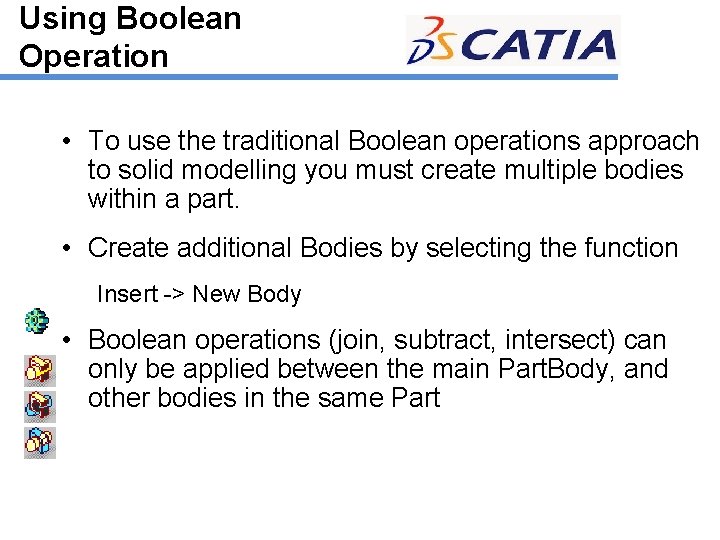
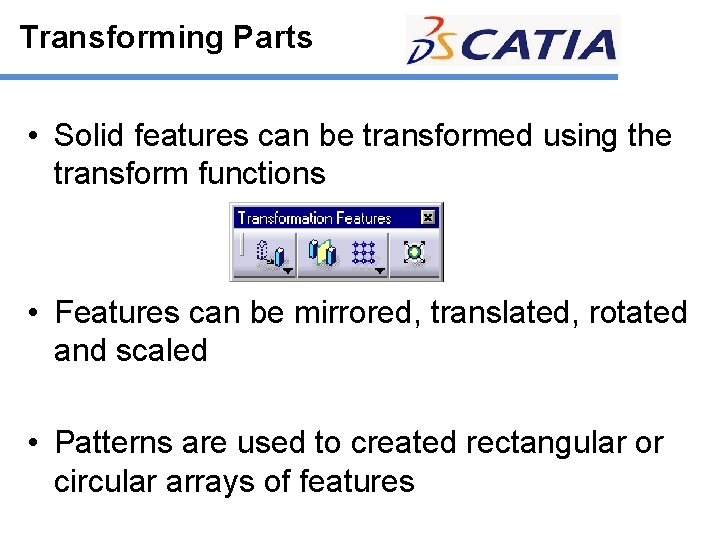
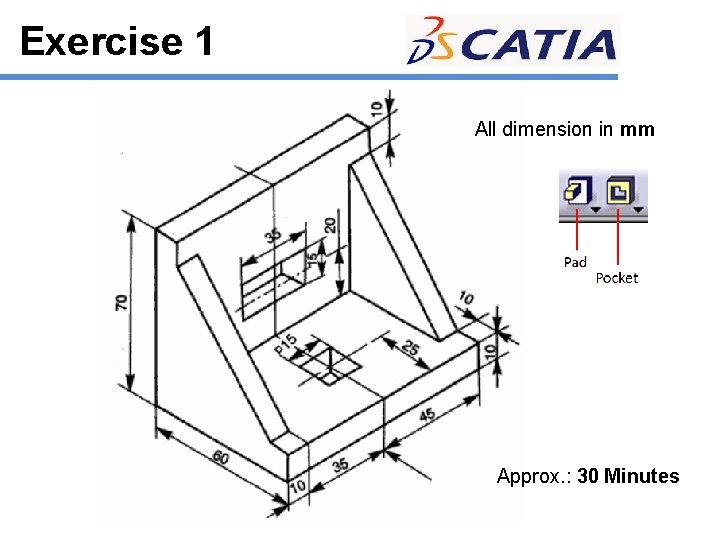
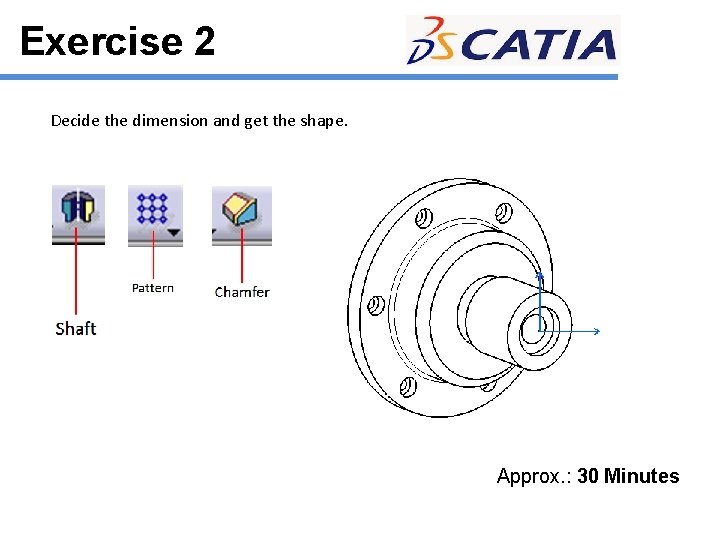
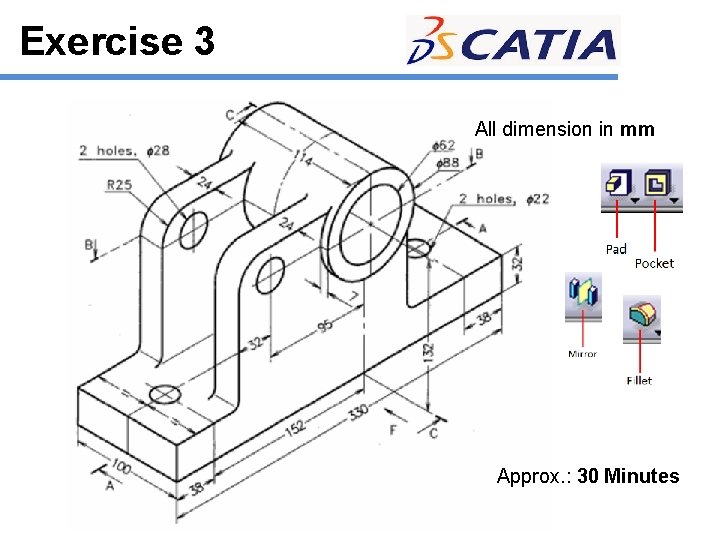
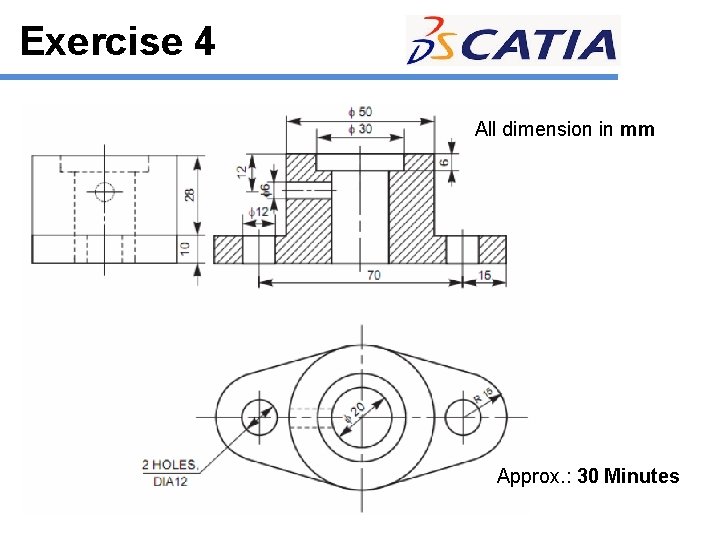

- Slides: 21
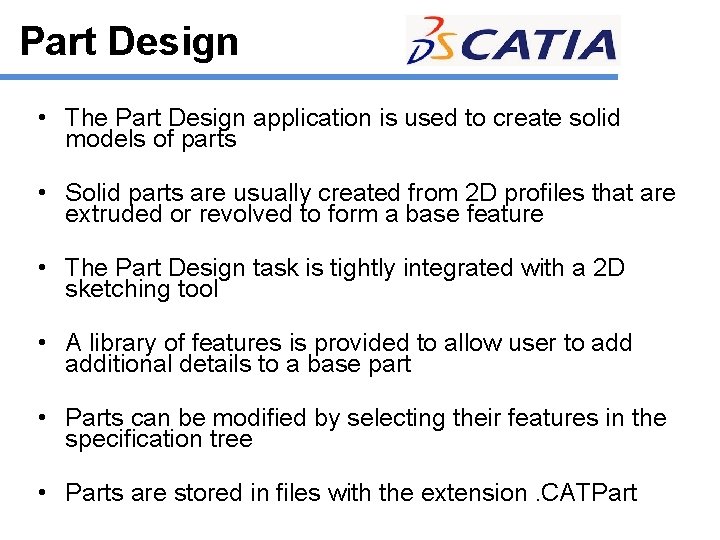
Part Design • The Part Design application is used to create solid models of parts • Solid parts are usually created from 2 D profiles that are extruded or revolved to form a base feature • The Part Design task is tightly integrated with a 2 D sketching tool • A library of features is provided to allow user to additional details to a base part • Parts can be modified by selecting their features in the specification tree • Parts are stored in files with the extension. CATPart
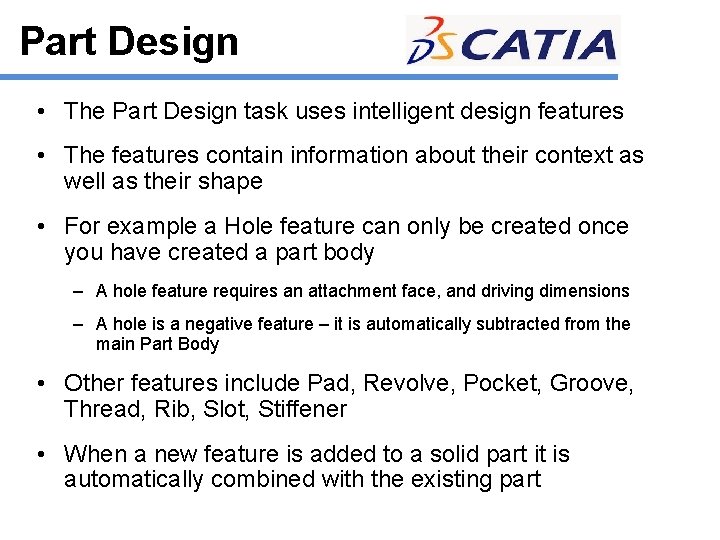
Part Design • The Part Design task uses intelligent design features • The features contain information about their context as well as their shape • For example a Hole feature can only be created once you have created a part body – A hole feature requires an attachment face, and driving dimensions – A hole is a negative feature – it is automatically subtracted from the main Part Body • Other features include Pad, Revolve, Pocket, Groove, Thread, Rib, Slot, Stiffener • When a new feature is added to a solid part it is automatically combined with the existing part
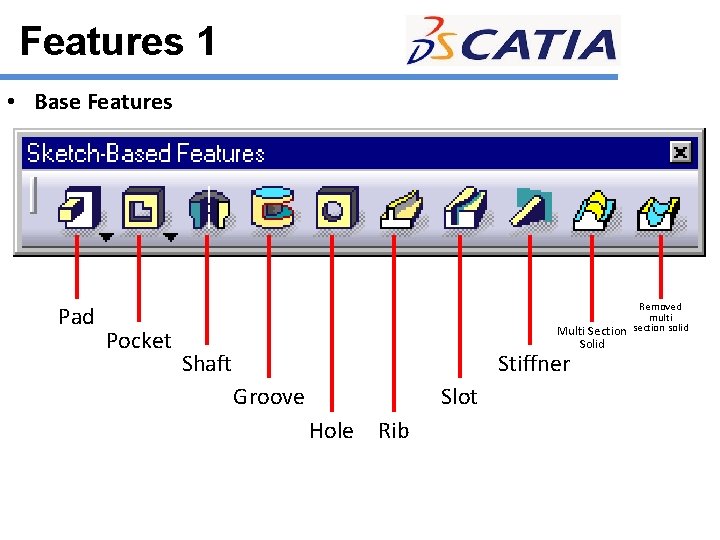
Features 1 • Base Features Pad Pocket Removed multi Multi Section solid Shaft Stiffner Groove Slot Hole Rib Solid
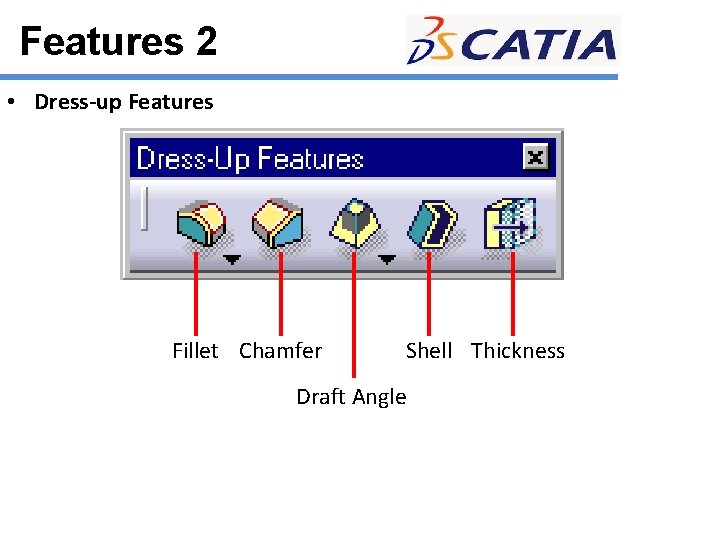
Features 2 • Dress-up Features Fillet Chamfer Shell Thickness Draft Angle
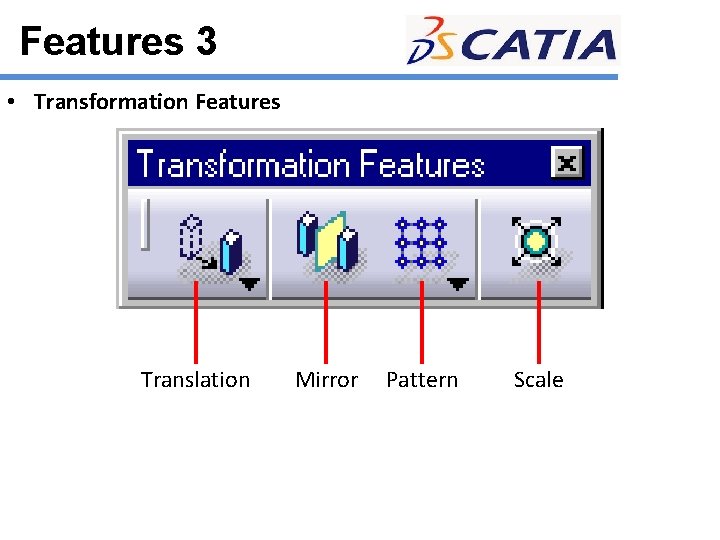
Features 3 • Transformation Features Translation Mirror Pattern Scale
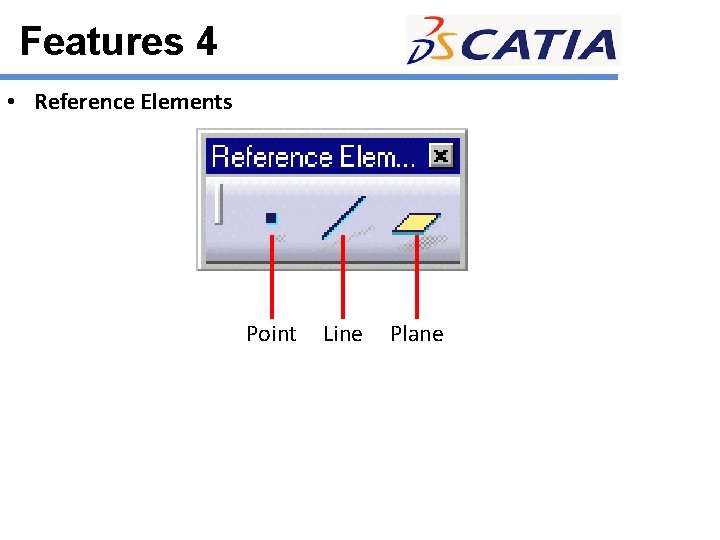
Features 4 • Reference Elements Point Line Plane
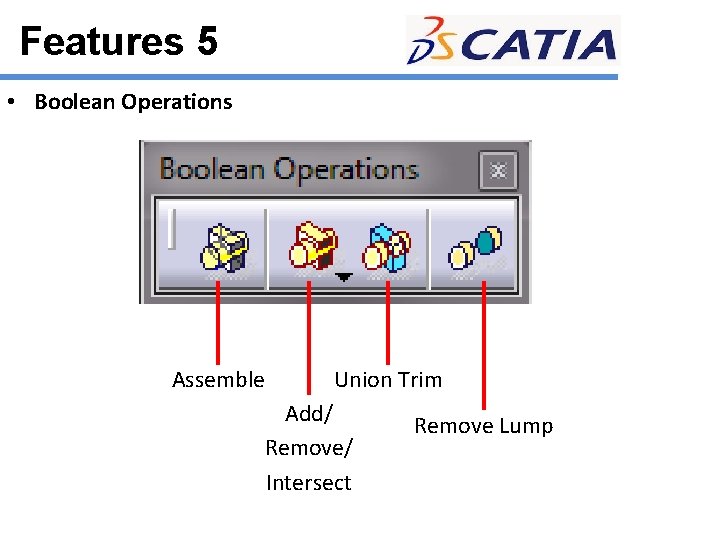
Features 5 • Boolean Operations Assemble Union Trim Add/ Remove/ Intersect Remove Lump
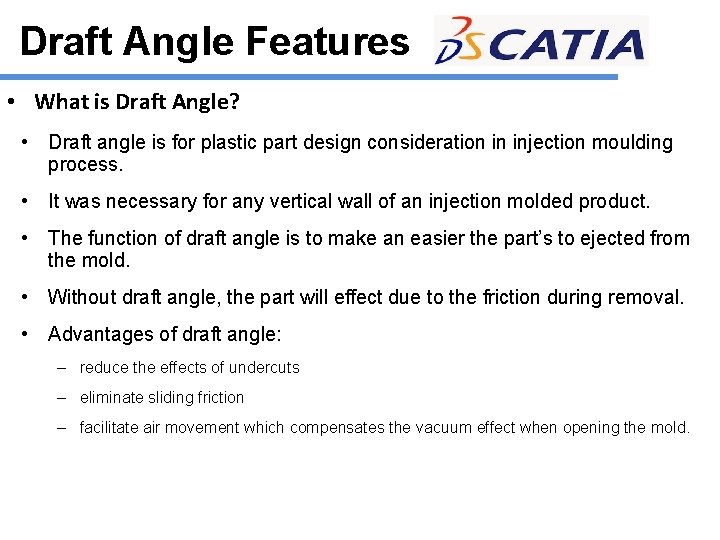
Draft Angle Features • What is Draft Angle? • Draft angle is for plastic part design consideration in injection moulding process. • It was necessary for any vertical wall of an injection molded product. • The function of draft angle is to make an easier the part’s to ejected from the mold. • Without draft angle, the part will effect due to the friction during removal. • Advantages of draft angle: – reduce the effects of undercuts – eliminate sliding friction – facilitate air movement which compensates the vacuum effect when opening the mold.
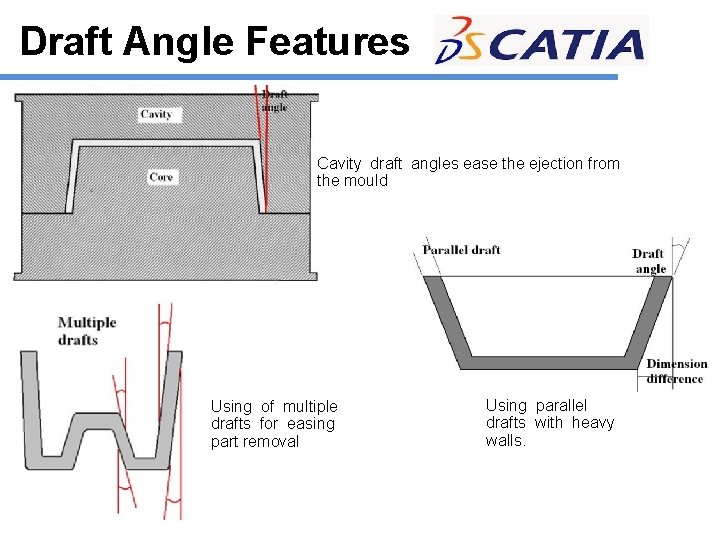
Draft Angle Features Cavity draft angles ease the ejection from the mould Using of multiple drafts for easing part removal Using parallel drafts with heavy walls.
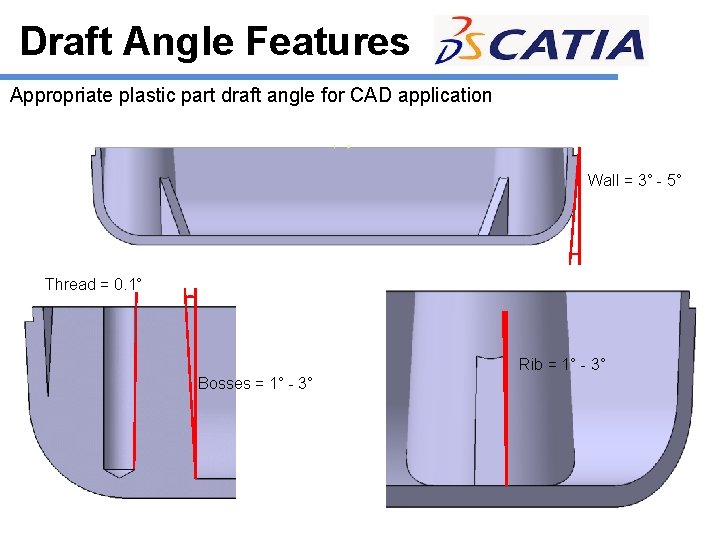
Draft Angle Features Appropriate plastic part draft angle for CAD application Wall = 3° - 5° Thread = 0. 1° Rib = 1° - 3° Bosses = 1° - 3°
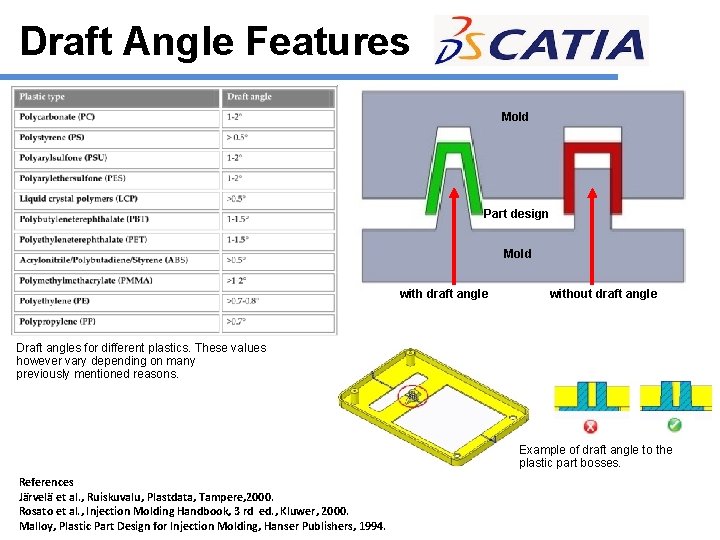
Draft Angle Features Mold Part design Mold with draft angle without draft angle Draft angles for different plastics. These values however vary depending on many previously mentioned reasons. Example of draft angle to the plastic part bosses. References Järvelä et al. , Ruiskuvalu, Plastdata, Tampere, 2000. Rosato et al. , Injection Molding Handbook, 3 rd ed. , Kluwer, 2000. Malloy, Plastic Part Design for Injection Molding, Hanser Publishers, 1994.
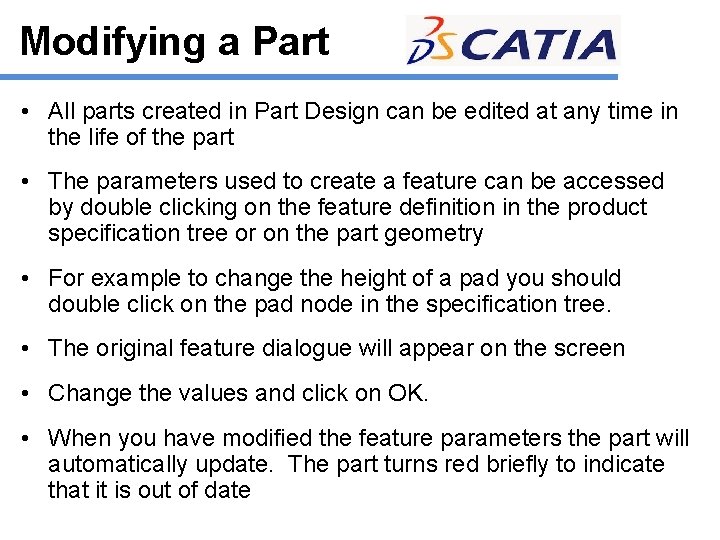
Modifying a Part • All parts created in Part Design can be edited at any time in the life of the part • The parameters used to create a feature can be accessed by double clicking on the feature definition in the product specification tree or on the part geometry • For example to change the height of a pad you should double click on the pad node in the specification tree. • The original feature dialogue will appear on the screen • Change the values and click on OK. • When you have modified the feature parameters the part will automatically update. The part turns red briefly to indicate that it is out of date
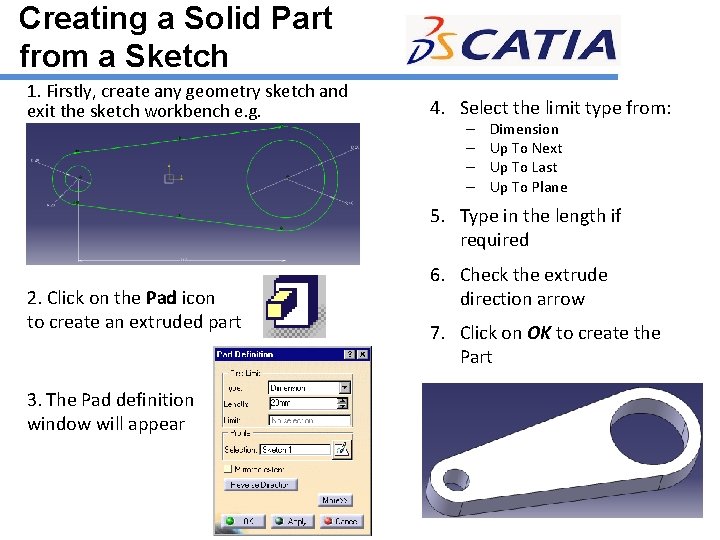
Creating a Solid Part from a Sketch 1. Firstly, create any geometry sketch and exit the sketch workbench e. g. 4. Select the limit type from: – – Dimension Up To Next Up To Last Up To Plane 5. Type in the length if required 2. Click on the Pad icon to create an extruded part 3. The Pad definition window will appear 6. Check the extrude direction arrow 7. Click on OK to create the Part
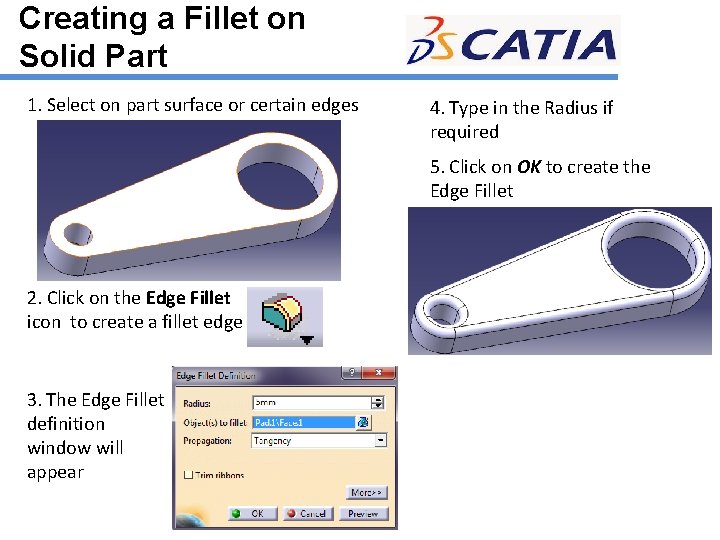
Creating a Fillet on Solid Part 1. Select on part surface or certain edges 4. Type in the Radius if required 5. Click on OK to create the Edge Fillet 2. Click on the Edge Fillet icon to create a fillet edge 3. The Edge Fillet definition window will appear
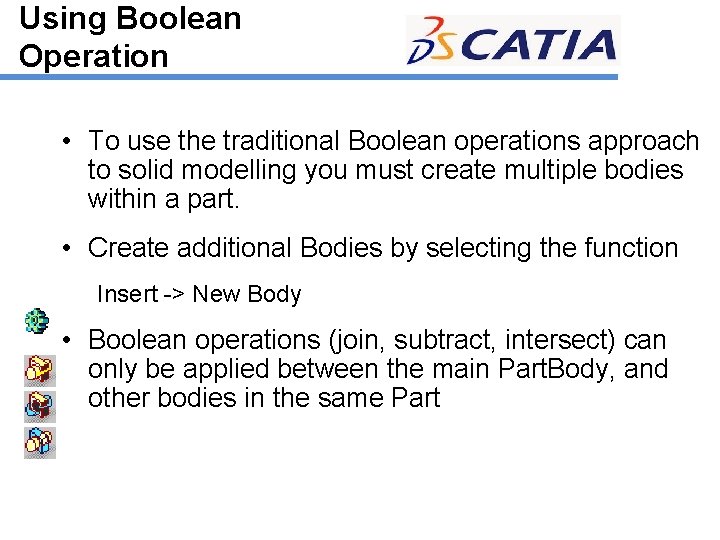
Using Boolean Operation • To use the traditional Boolean operations approach to solid modelling you must create multiple bodies within a part. • Create additional Bodies by selecting the function Insert -> New Body • Boolean operations (join, subtract, intersect) can only be applied between the main Part. Body, and other bodies in the same Part
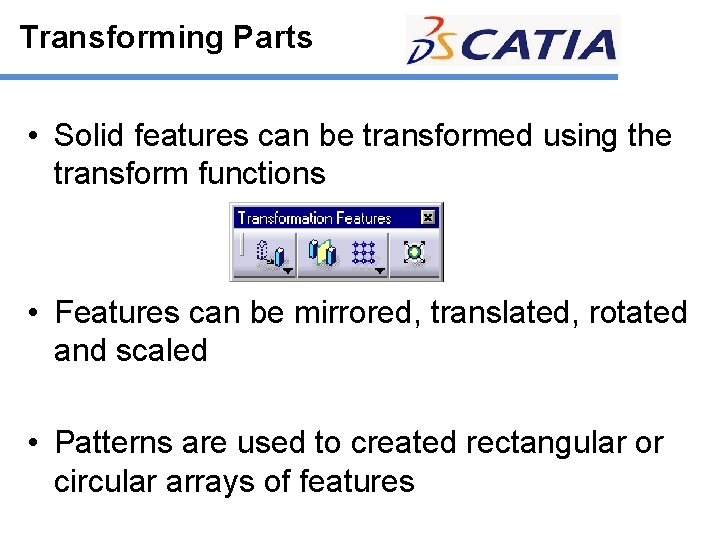
Transforming Parts • Solid features can be transformed using the transform functions • Features can be mirrored, translated, rotated and scaled • Patterns are used to created rectangular or circular arrays of features
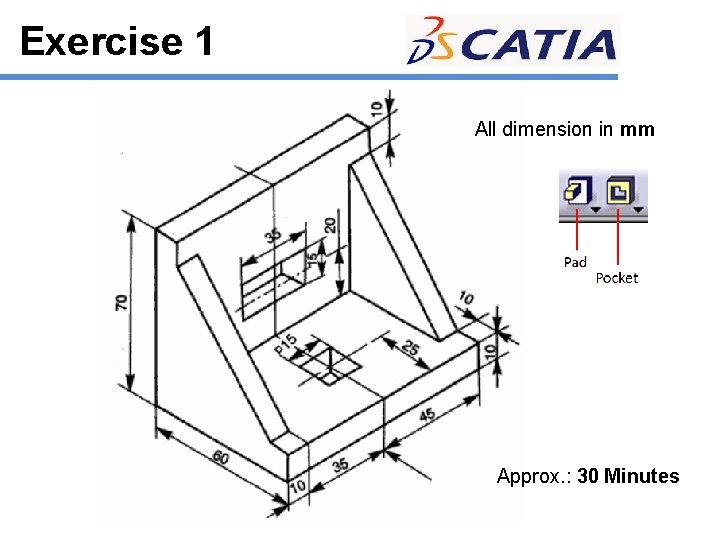
Exercise 1 All dimension in mm Approx. : 30 Minutes
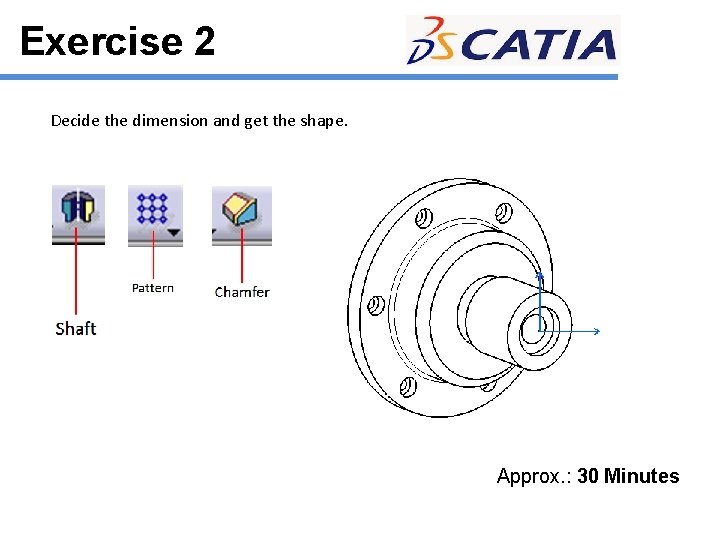
Exercise 2 Decide the dimension and get the shape. Approx. : 30 Minutes
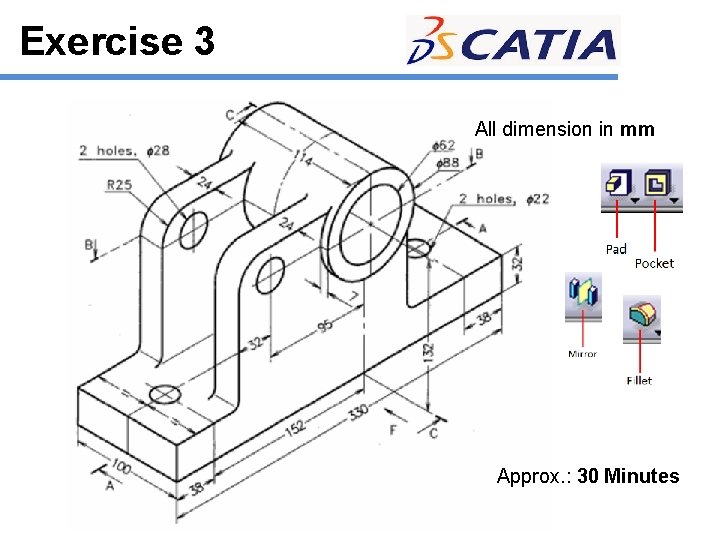
Exercise 3 All dimension in mm Approx. : 30 Minutes
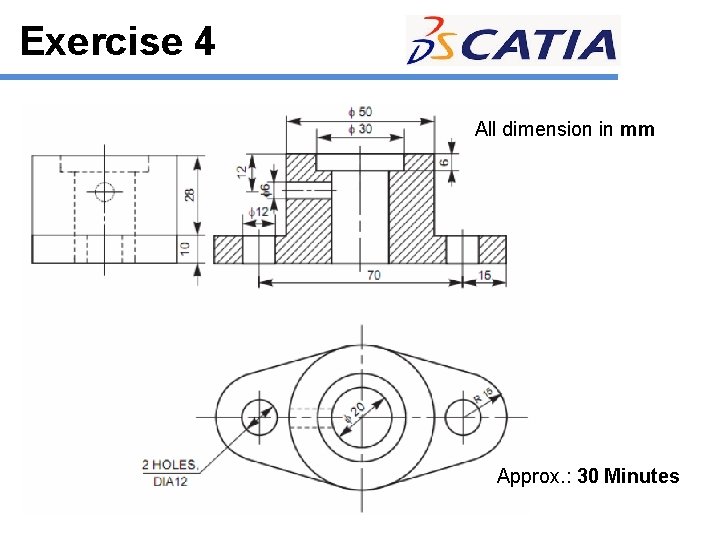
Exercise 4 All dimension in mm Approx. : 30 Minutes

Exercise 5 All dimension in mm Approx. : 30 Minutes
Hình ảnh bộ gõ cơ thể búng tay
Slidetodoc
Bổ thể
Tỉ lệ cơ thể trẻ em
Gấu đi như thế nào
Tư thế worm breton
Chúa yêu trần thế alleluia
Các môn thể thao bắt đầu bằng tiếng nhảy
Thế nào là hệ số cao nhất
Các châu lục và đại dương trên thế giới
Công của trọng lực
Trời xanh đây là của chúng ta thể thơ
Mật thư tọa độ 5x5
Phép trừ bù
Phản ứng thế ankan
Các châu lục và đại dương trên thế giới
Thơ thất ngôn tứ tuyệt đường luật
Quá trình desamine hóa có thể tạo ra
Một số thể thơ truyền thống
Cái miệng nó xinh thế chỉ nói điều hay thôi
Vẽ hình chiếu vuông góc của vật thể sau
Biện pháp chống mỏi cơ